Materials of Electrochemical Equipment Their degradation and Corrosion
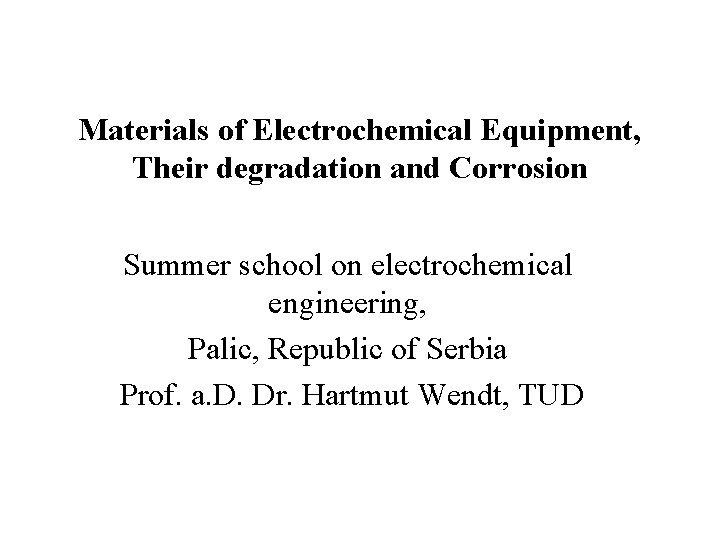
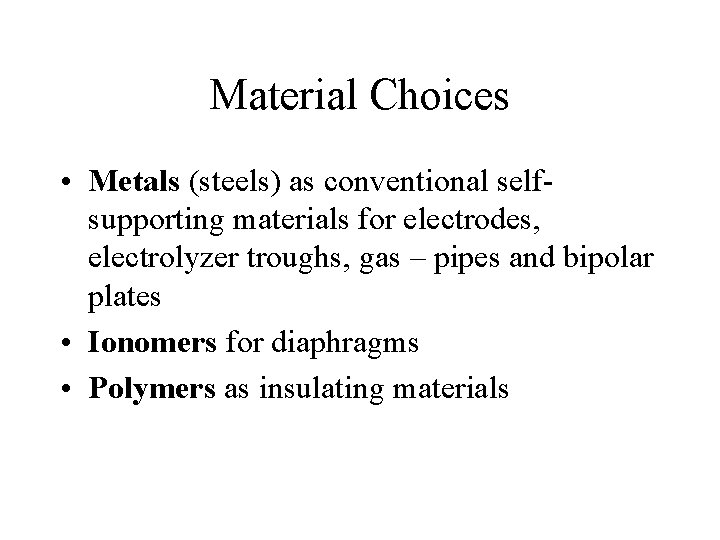
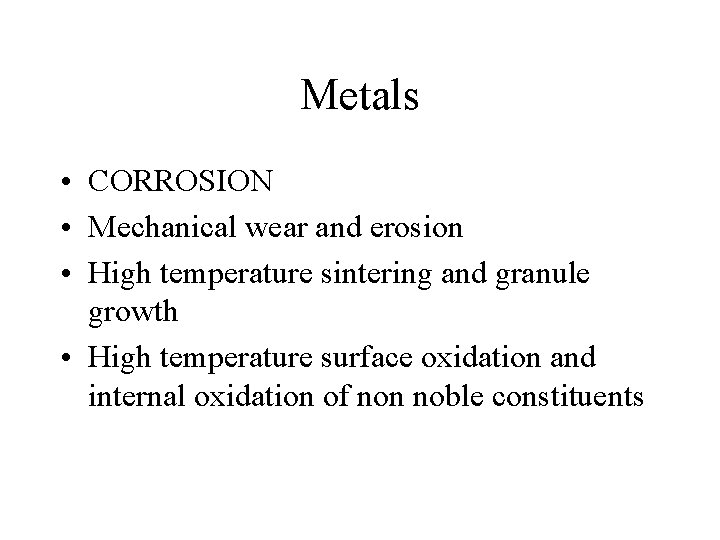
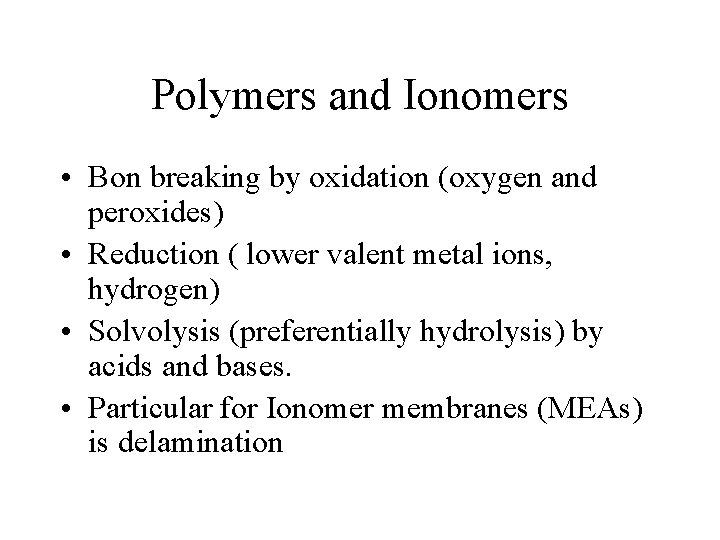
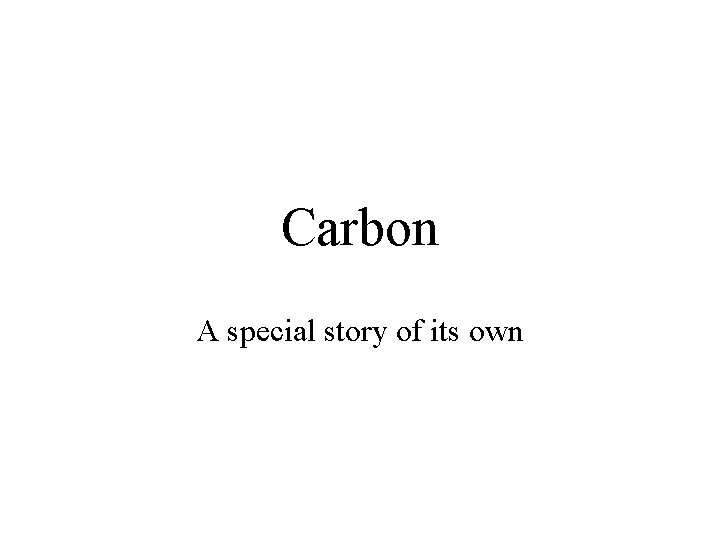
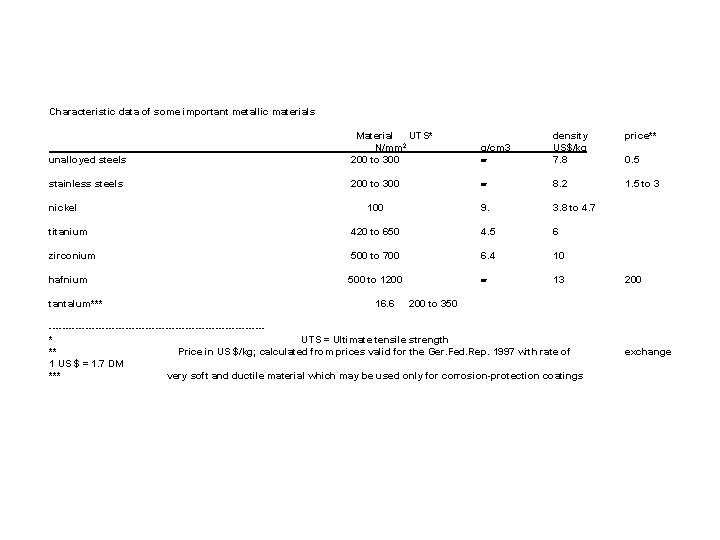
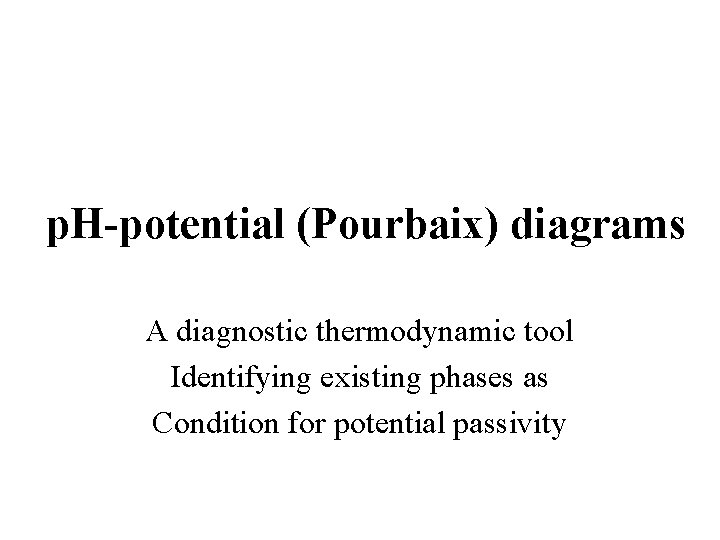

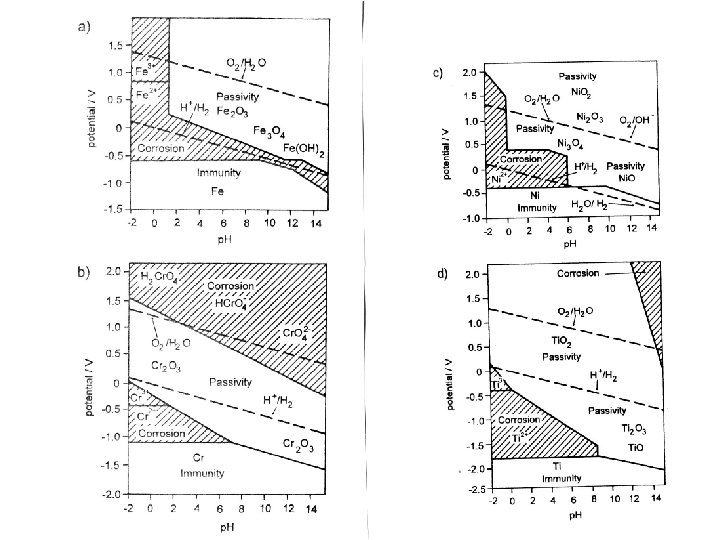
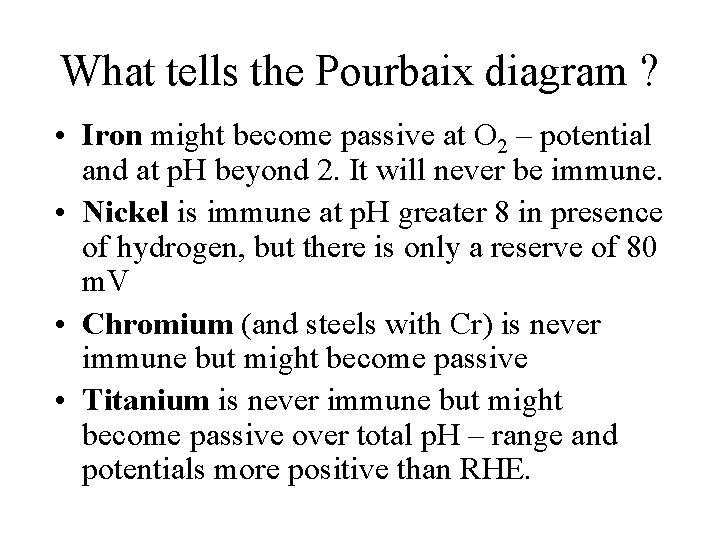
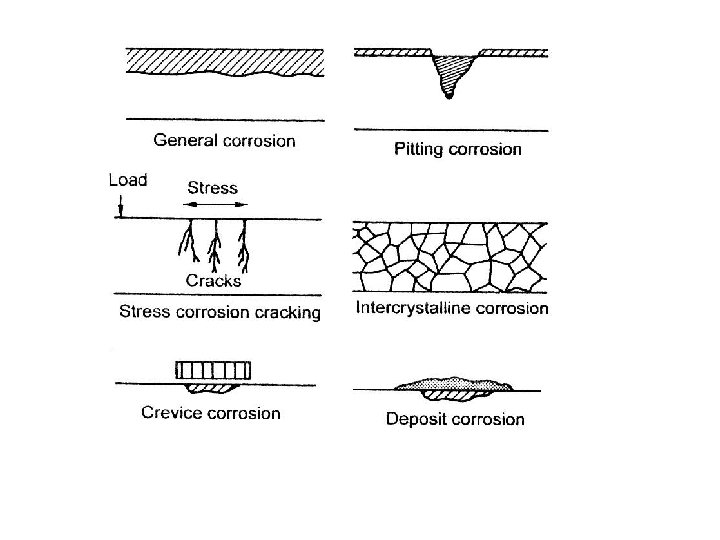
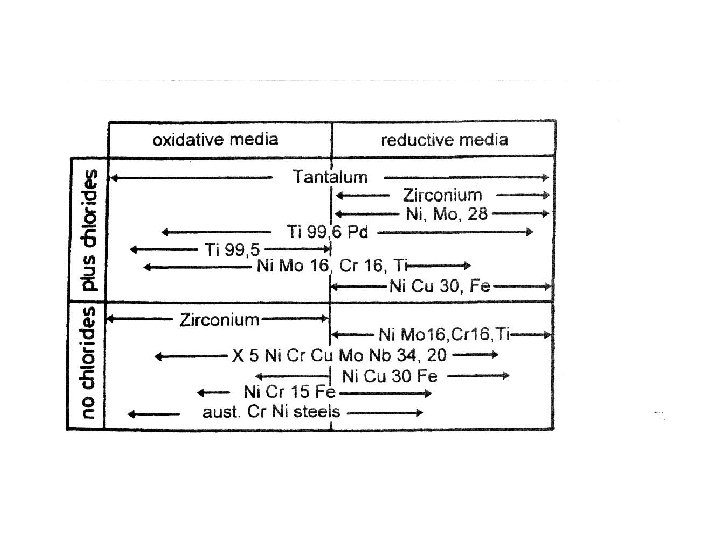
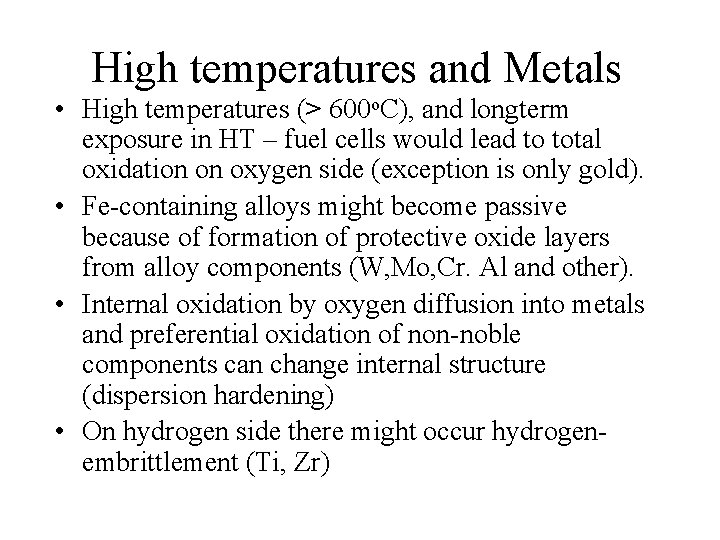
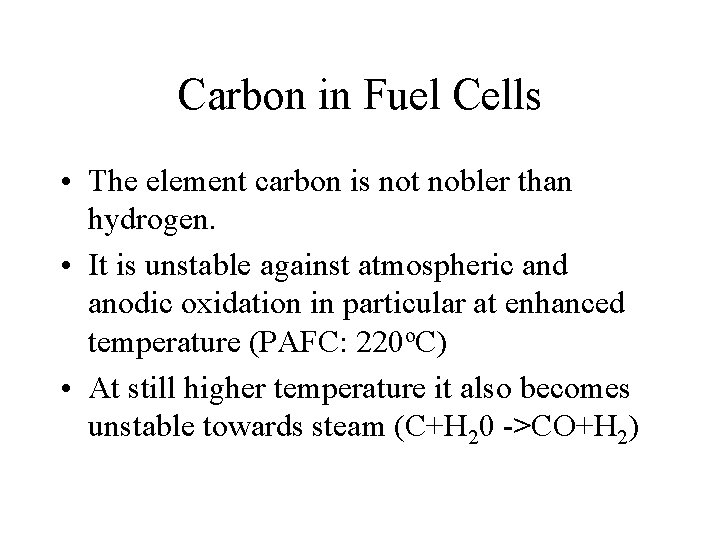
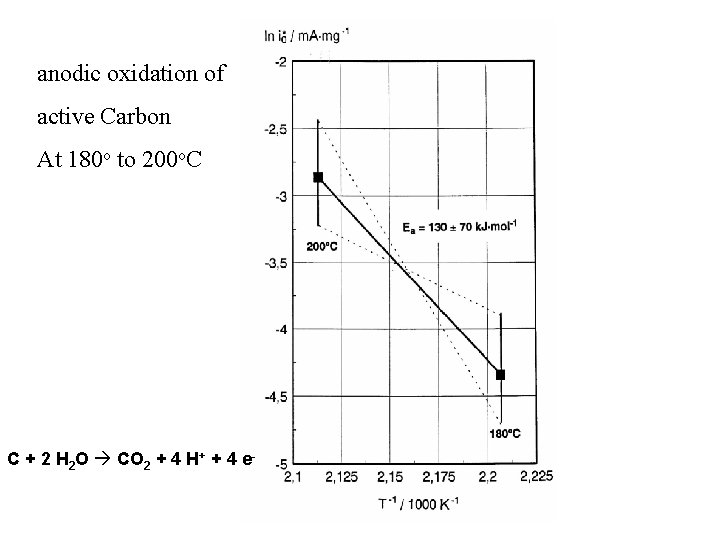
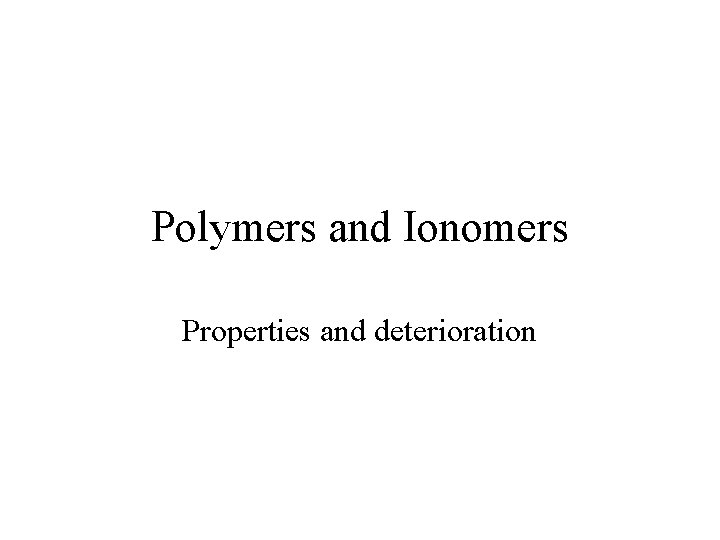
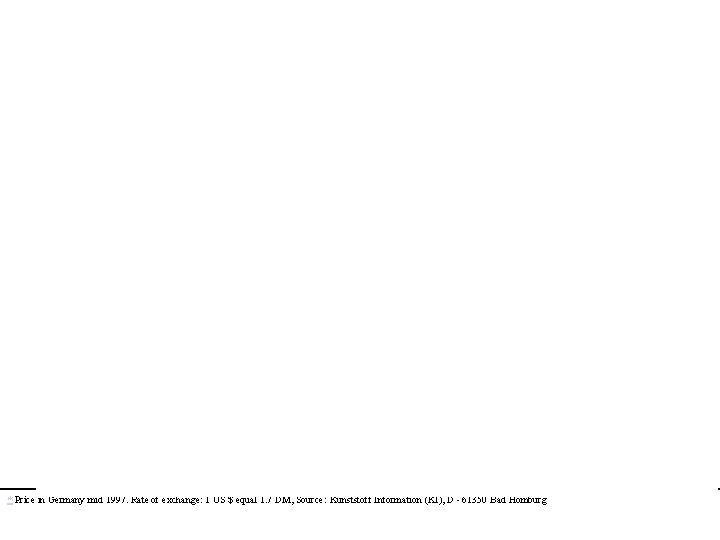
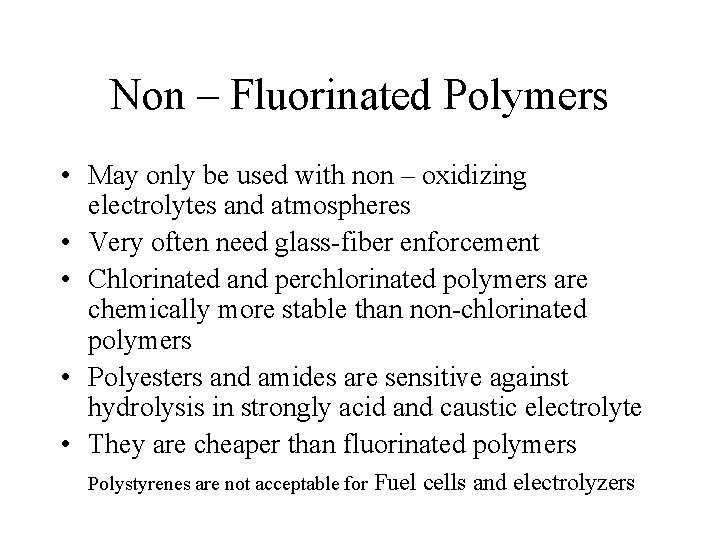
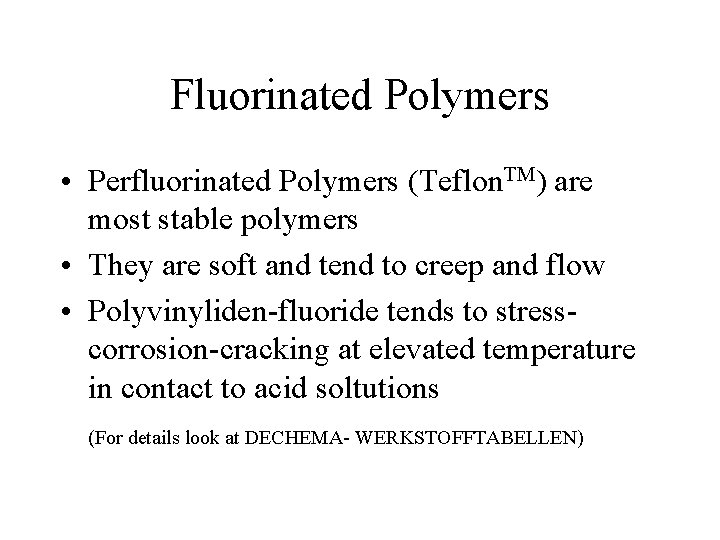
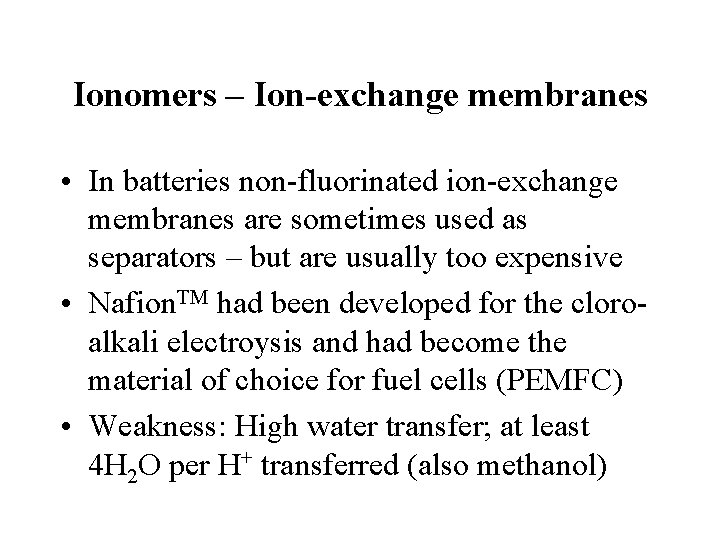
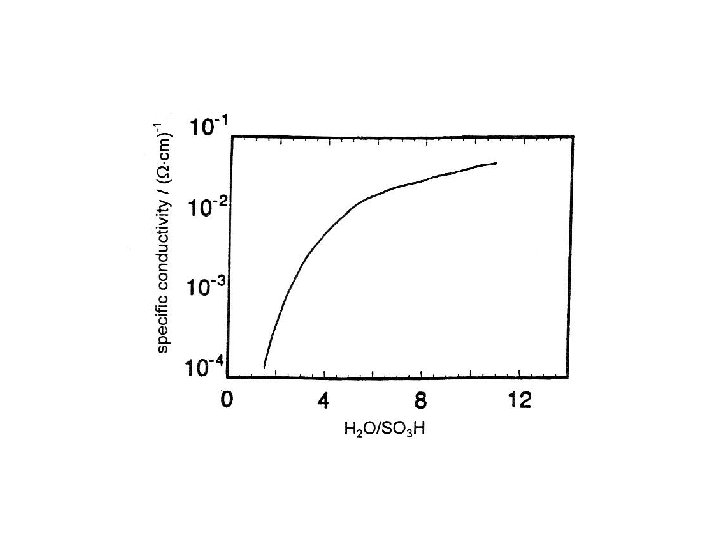
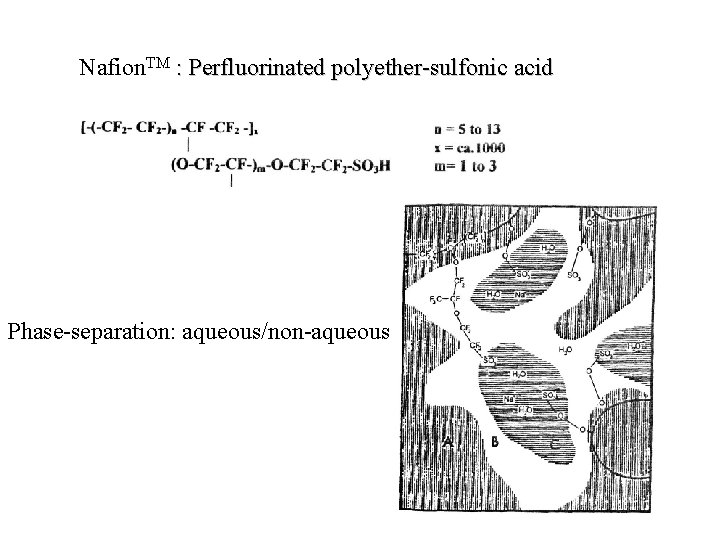
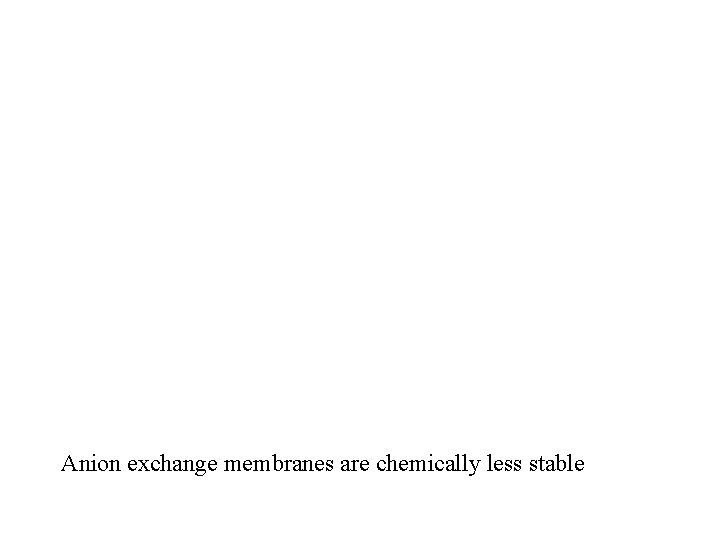
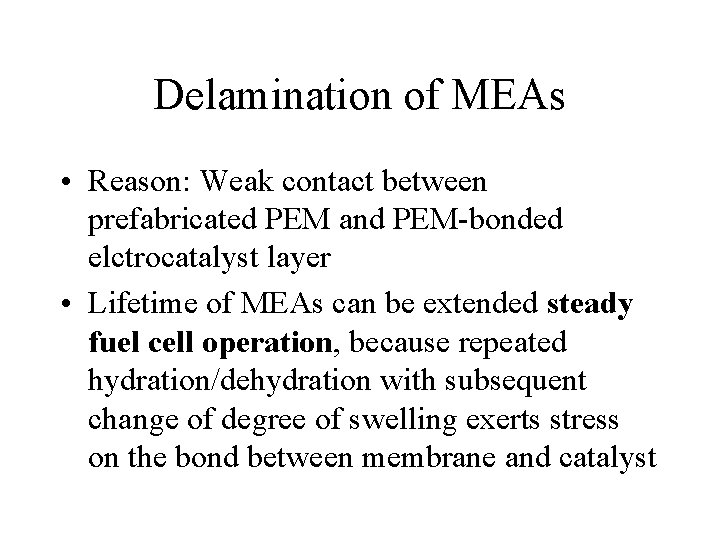
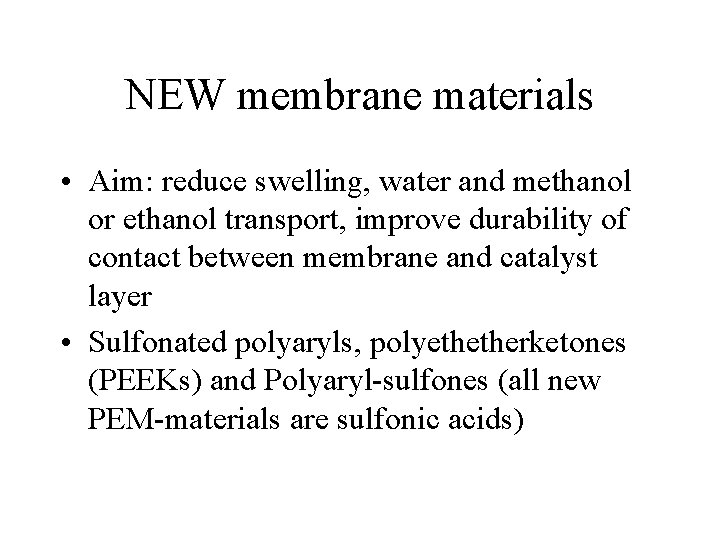
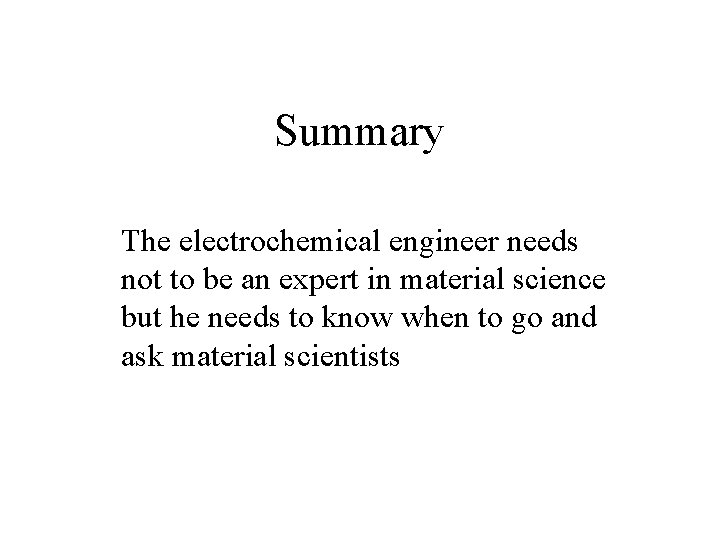
- Slides: 26
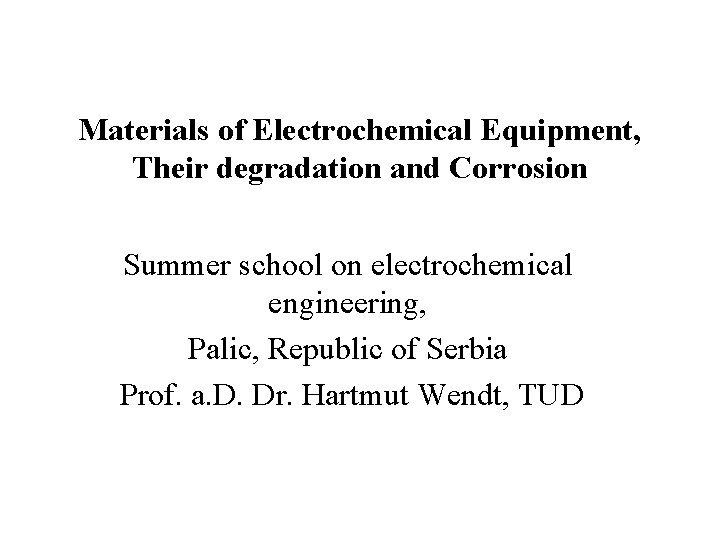
Materials of Electrochemical Equipment, Their degradation and Corrosion Summer school on electrochemical engineering, Palic, Republic of Serbia Prof. a. D. Dr. Hartmut Wendt, TUD
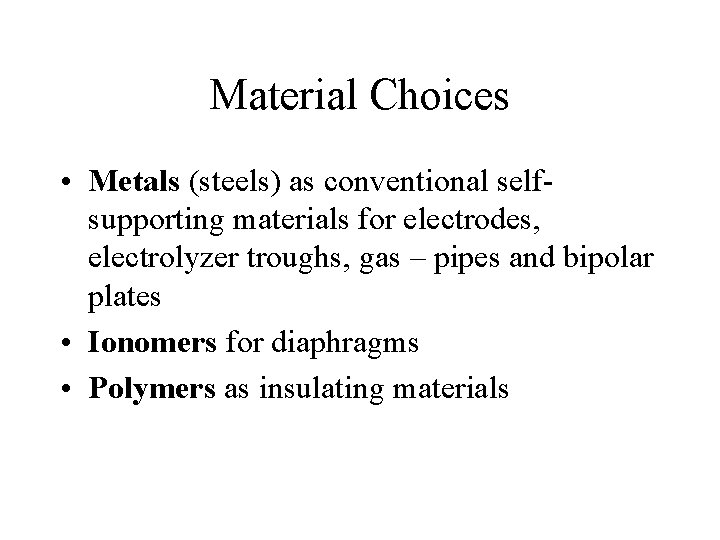
Material Choices • Metals (steels) as conventional selfsupporting materials for electrodes, electrolyzer troughs, gas – pipes and bipolar plates • Ionomers for diaphragms • Polymers as insulating materials
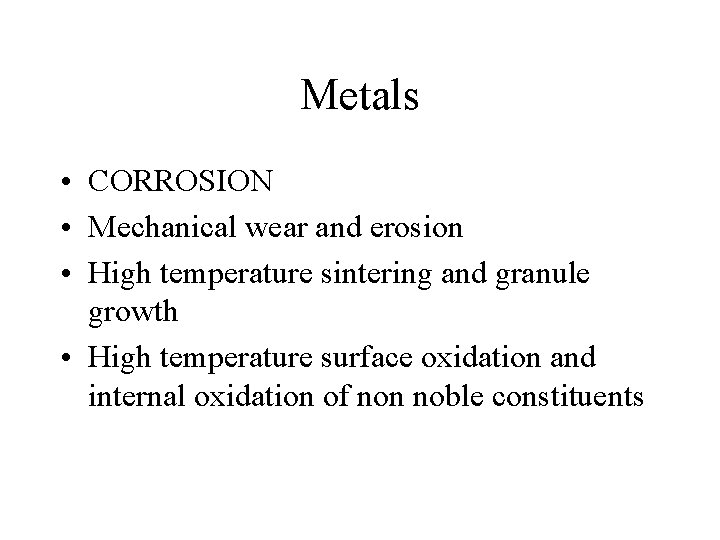
Metals • CORROSION • Mechanical wear and erosion • High temperature sintering and granule growth • High temperature surface oxidation and internal oxidation of non noble constituents
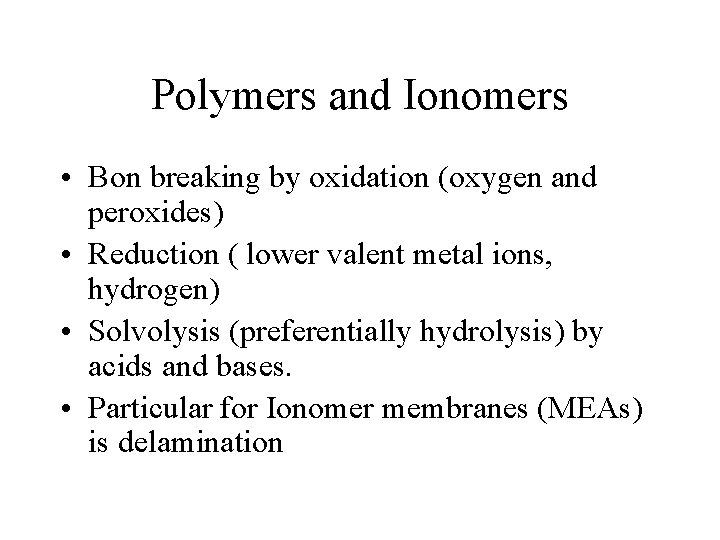
Polymers and Ionomers • Bon breaking by oxidation (oxygen and peroxides) • Reduction ( lower valent metal ions, hydrogen) • Solvolysis (preferentially hydrolysis) by acids and bases. • Particular for Ionomer membranes (MEAs) is delamination
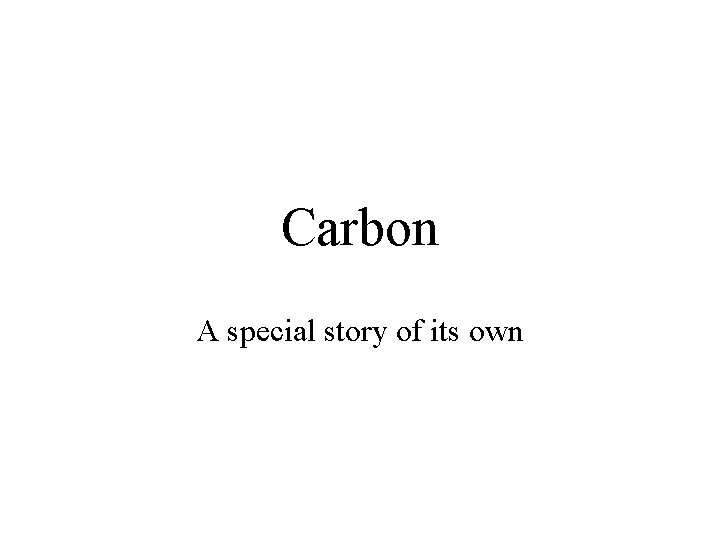
Carbon A special story of its own
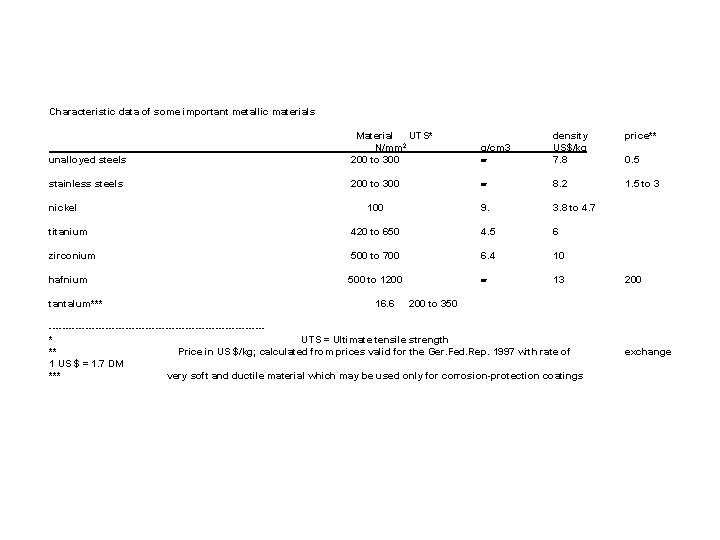
Characteristic data of some important metallic materials g/cm 3 density US$/kg 7. 8 price** unalloyed steels Material UTS* N/mm 2 200 to 300 stainless steels 200 to 300 8. 2 1. 5 to 3 100 9. 3. 8 to 4. 7 titanium 420 to 650 4. 5 6 zirconium 500 to 700 6. 4 10 hafnium 500 to 1200 13 nickel tantalum*** 16. 6 0. 5 200 to 350 --------------------------------* UTS = Ultimate tensile strength ** Price in US $/kg; calculated from prices valid for the Ger. Fed. Rep. 1997 with rate of 1 US $ = 1. 7 DM *** very soft and ductile material which may be used only for corrosion-protection coatings exchange
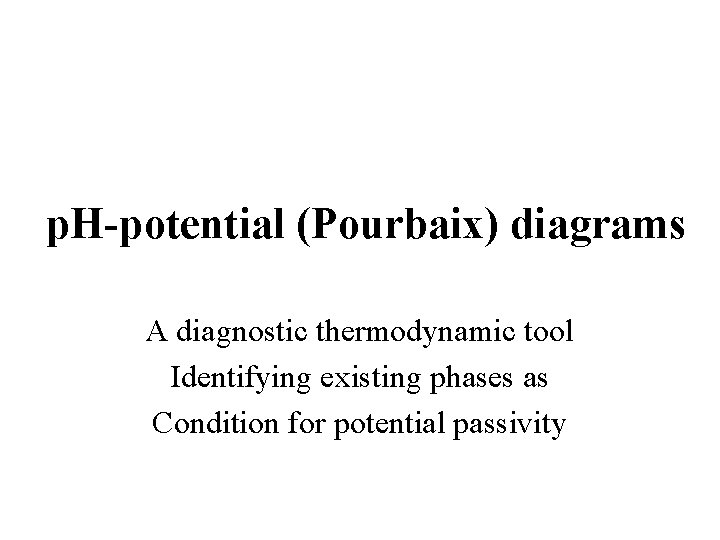
p. H-potential (Pourbaix) diagrams A diagnostic thermodynamic tool Identifying existing phases as Condition for potential passivity

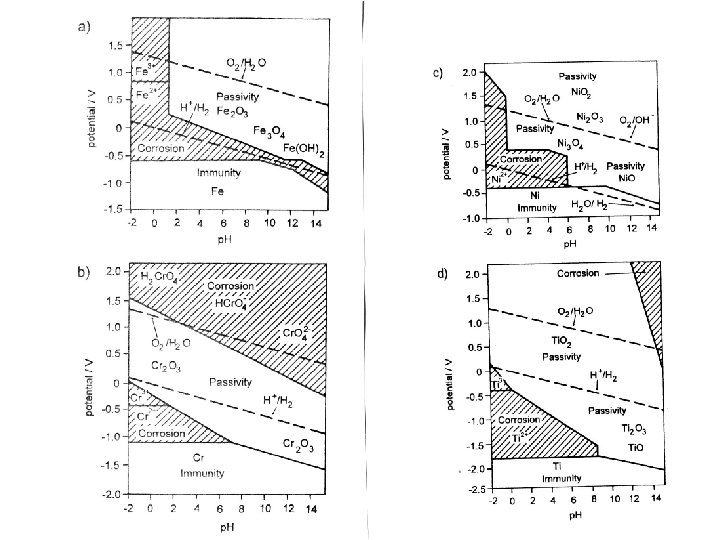
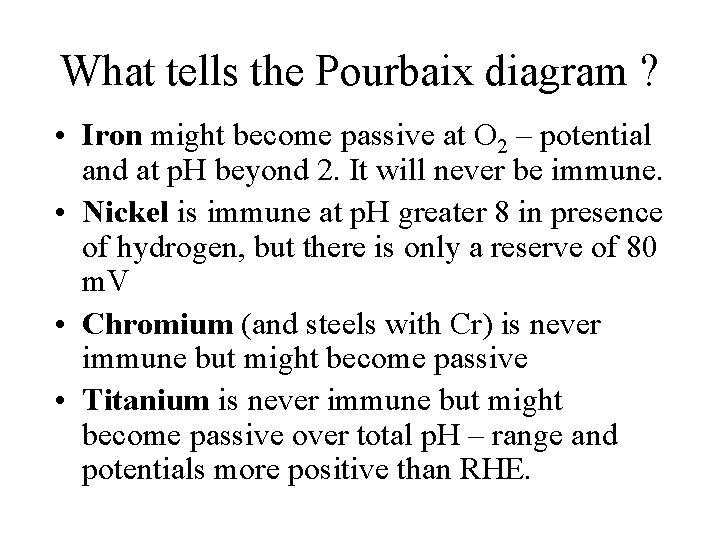
What tells the Pourbaix diagram ? • Iron might become passive at O 2 – potential and at p. H beyond 2. It will never be immune. • Nickel is immune at p. H greater 8 in presence of hydrogen, but there is only a reserve of 80 m. V • Chromium (and steels with Cr) is never immune but might become passive • Titanium is never immune but might become passive over total p. H – range and potentials more positive than RHE.
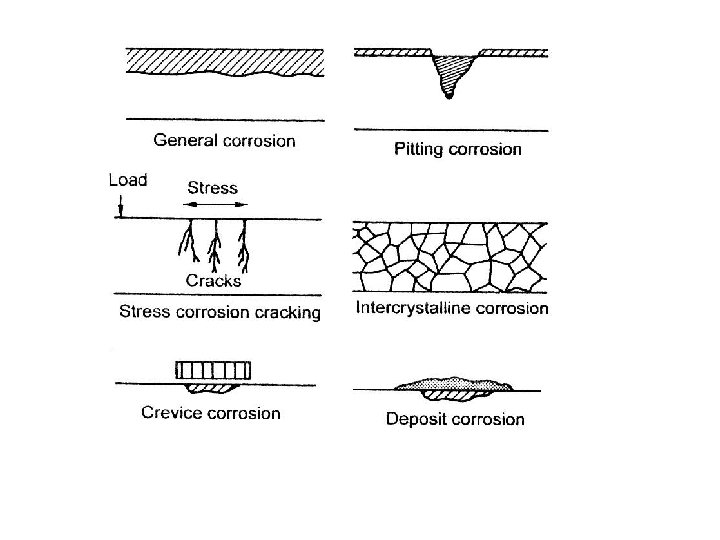
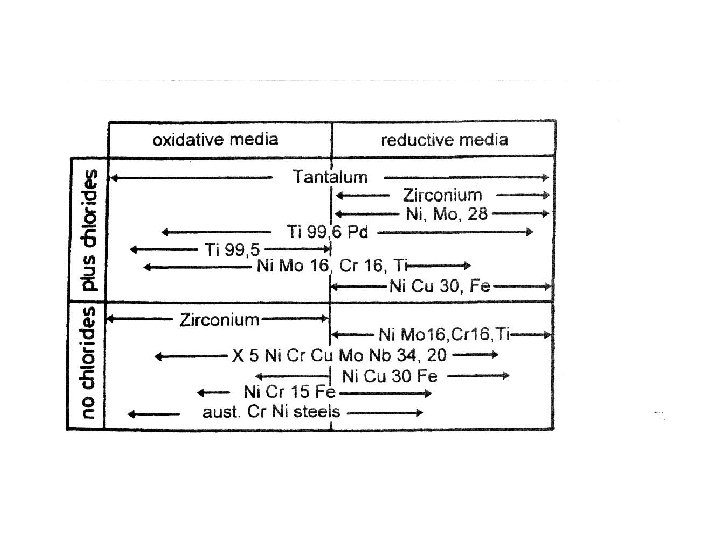
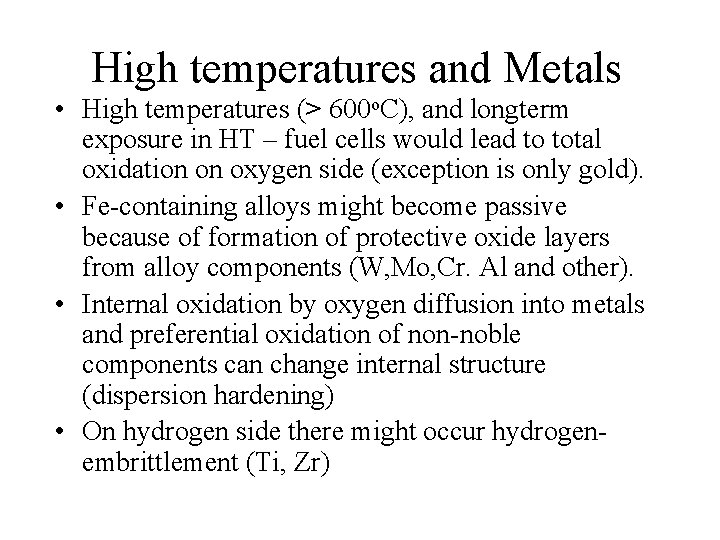
High temperatures and Metals • High temperatures (> 600 o. C), and longterm exposure in HT – fuel cells would lead to total oxidation on oxygen side (exception is only gold). • Fe-containing alloys might become passive because of formation of protective oxide layers from alloy components (W, Mo, Cr. Al and other). • Internal oxidation by oxygen diffusion into metals and preferential oxidation of non-noble components can change internal structure (dispersion hardening) • On hydrogen side there might occur hydrogenembrittlement (Ti, Zr)
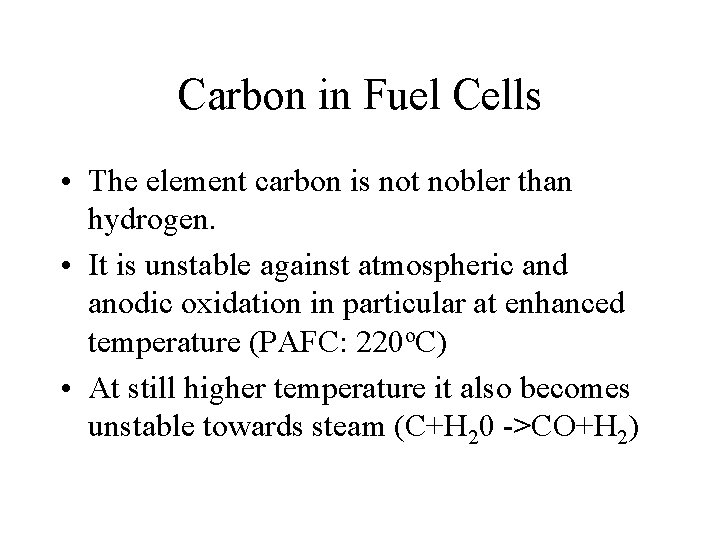
Carbon in Fuel Cells • The element carbon is not nobler than hydrogen. • It is unstable against atmospheric and anodic oxidation in particular at enhanced temperature (PAFC: 220 o. C) • At still higher temperature it also becomes unstable towards steam (C+H 20 ->CO+H 2)
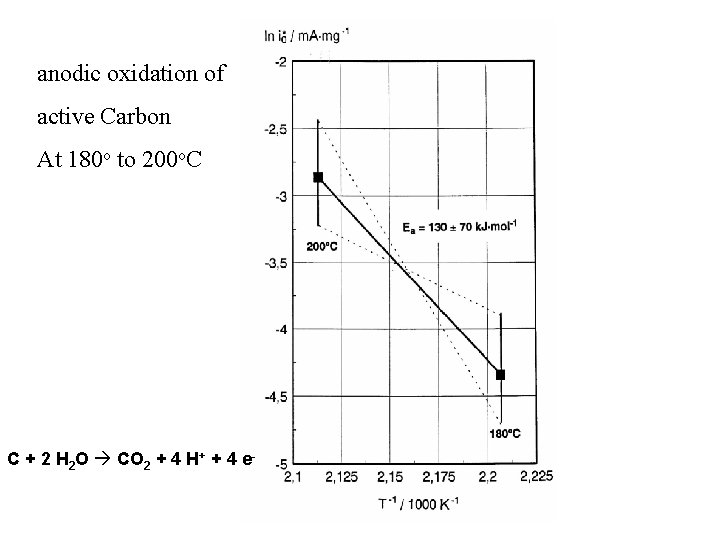
anodic oxidation of active Carbon At 180 o to 200 o. C C + 2 H 2 O CO 2 + 4 H+ + 4 e-
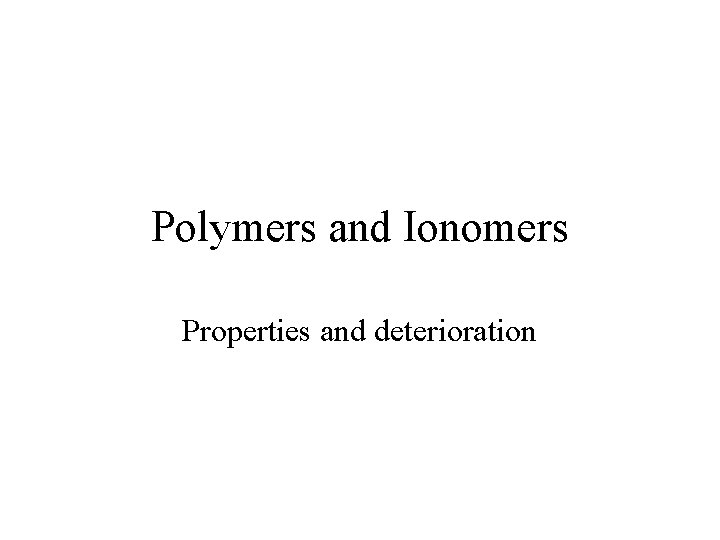
Polymers and Ionomers Properties and deterioration
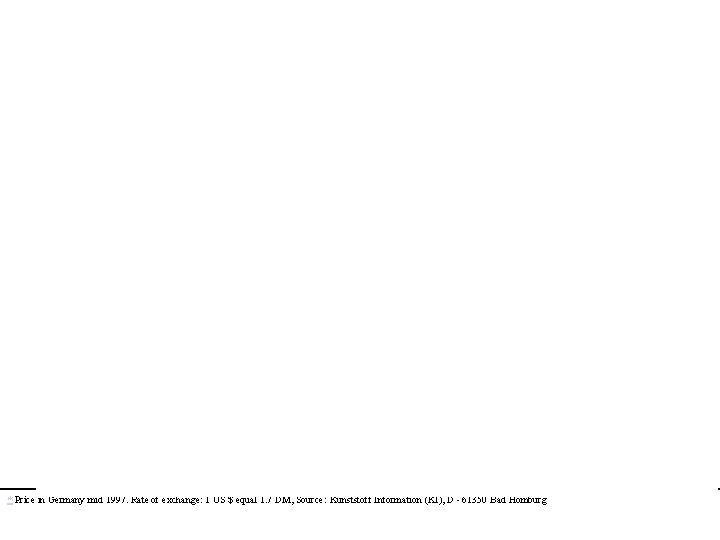
* Price in Germany mid 1997. Rate of exchange: 1 US $ equal 1. 7 DM, Source: Kunststoff Information (KI), D - 61350 Bad Homburg
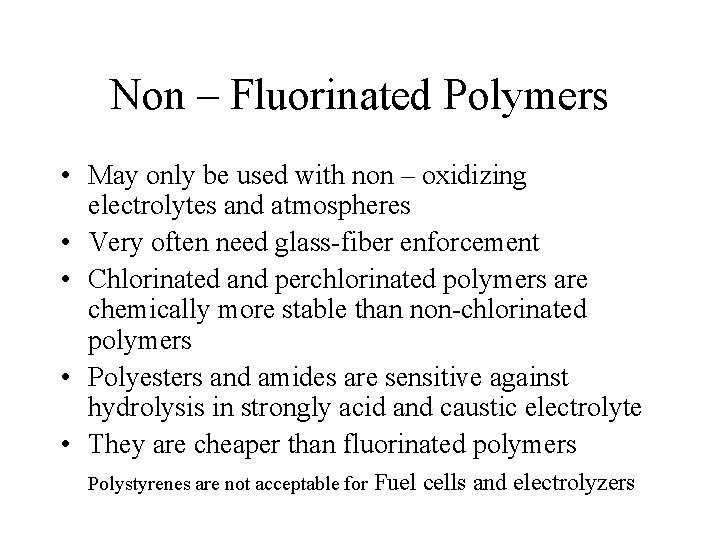
Non – Fluorinated Polymers • May only be used with non – oxidizing electrolytes and atmospheres • Very often need glass-fiber enforcement • Chlorinated and perchlorinated polymers are chemically more stable than non-chlorinated polymers • Polyesters and amides are sensitive against hydrolysis in strongly acid and caustic electrolyte • They are cheaper than fluorinated polymers Polystyrenes are not acceptable for Fuel cells and electrolyzers
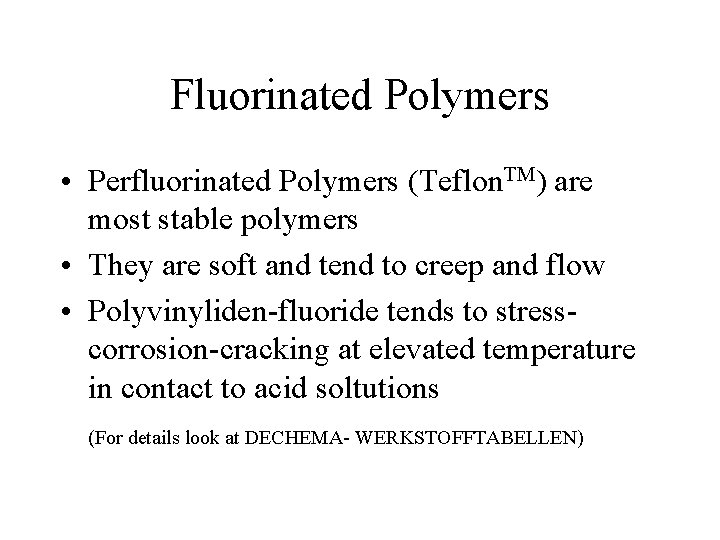
Fluorinated Polymers • Perfluorinated Polymers (Teflon. TM) are most stable polymers • They are soft and tend to creep and flow • Polyvinyliden-fluoride tends to stresscorrosion-cracking at elevated temperature in contact to acid soltutions (For details look at DECHEMA- WERKSTOFFTABELLEN)
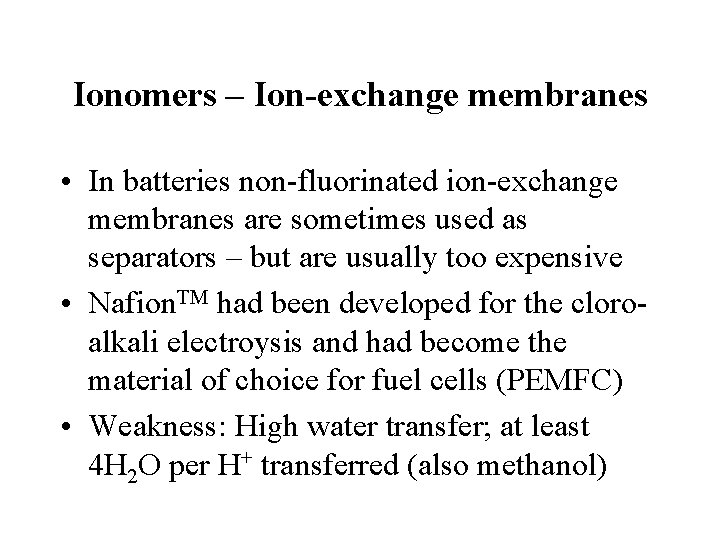
Ionomers – Ion-exchange membranes • In batteries non-fluorinated ion-exchange membranes are sometimes used as separators – but are usually too expensive • Nafion. TM had been developed for the cloroalkali electroysis and had become the material of choice for fuel cells (PEMFC) • Weakness: High water transfer; at least 4 H 2 O per H+ transferred (also methanol)
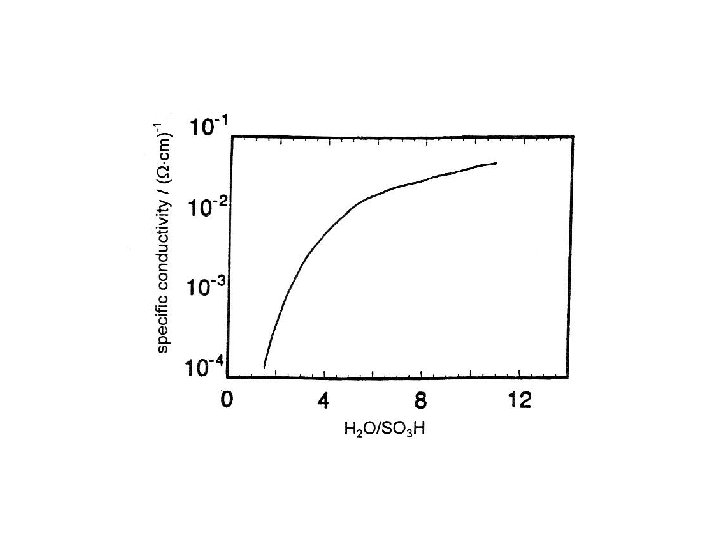
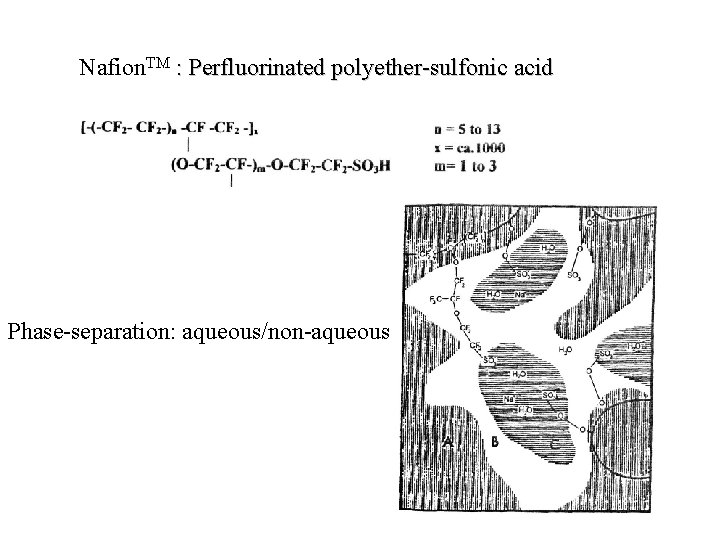
Nafion. TM : Perfluorinated polyether-sulfonic acid Phase-separation: aqueous/non-aqueous
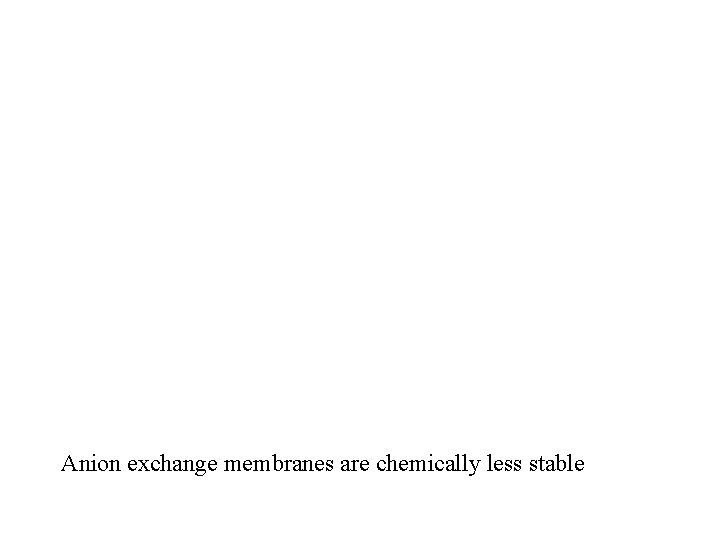
Anion exchange membranes are chemically less stable
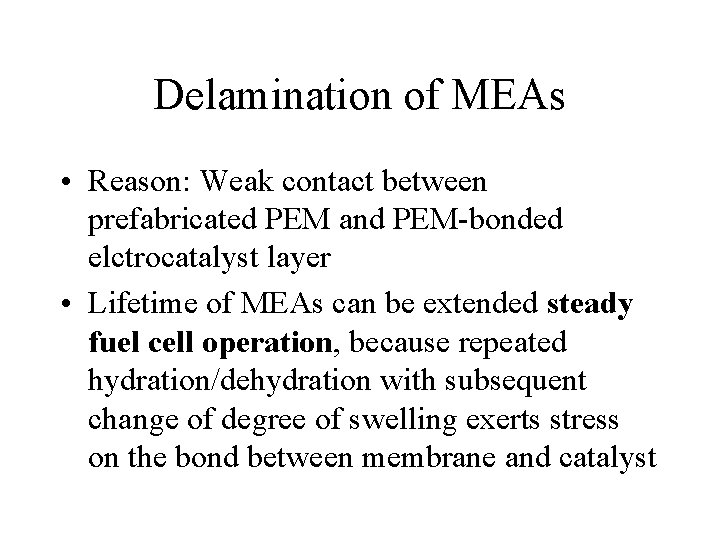
Delamination of MEAs • Reason: Weak contact between prefabricated PEM and PEM-bonded elctrocatalyst layer • Lifetime of MEAs can be extended steady fuel cell operation, because repeated hydration/dehydration with subsequent change of degree of swelling exerts stress on the bond between membrane and catalyst
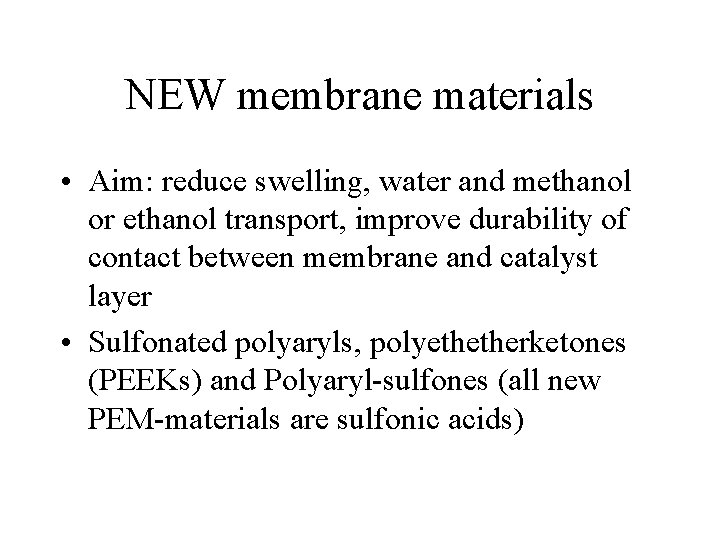
NEW membrane materials • Aim: reduce swelling, water and methanol or ethanol transport, improve durability of contact between membrane and catalyst layer • Sulfonated polyaryls, polyethetherketones (PEEKs) and Polyaryl-sulfones (all new PEM-materials are sulfonic acids)
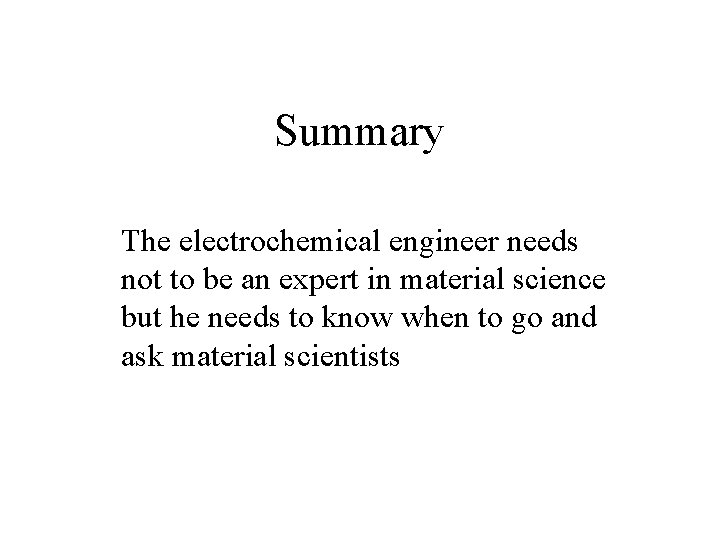
Summary The electrochemical engineer needs not to be an expert in material science but he needs to know when to go and ask material scientists
Galvanic corrosion
Mechanism of wet corrosion
Types of electrochemical corrosion
Dry corrosion and wet corrosion
Difference between wet corrosion and dry corrosion
Flow of anions and cations in an electrochemical cell
Chemical machining applications
Estimation of degradation function
Purification table
Prdp biochemistry
Mechanical degradation
Metabolismn
How environmental degradation occurs
Noise
Light induced degradation
Edman degradation
Purification yield calculation
Conclusion of environmental degradation
How environmental degradation occurs
Land degradation definition
Fructose 1 6 bisphosphatase
Jurawatt
Abnormal degradation of disaccharides
Edman degradation
Tag degradation
Glycogen degradation
Linear position invariant degradation