ETCulvert Design and Rating of Precast Culverts ACPA
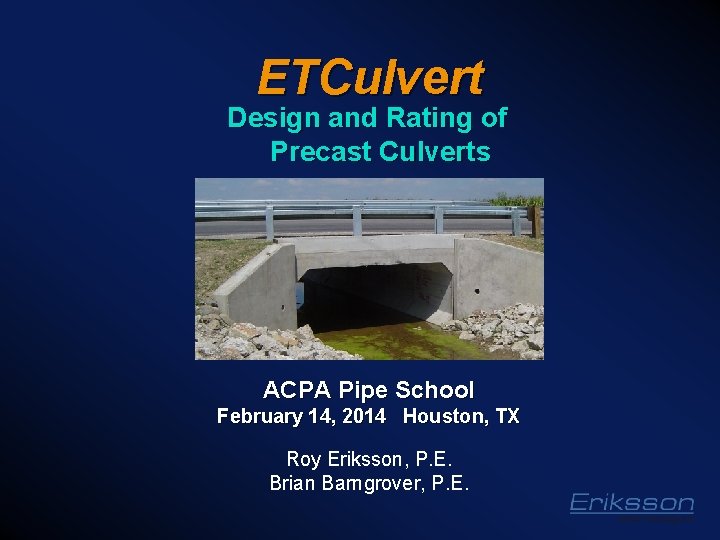
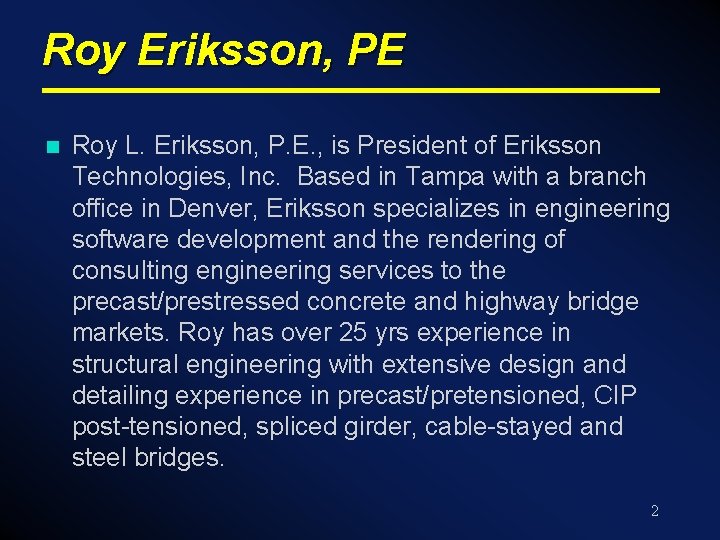
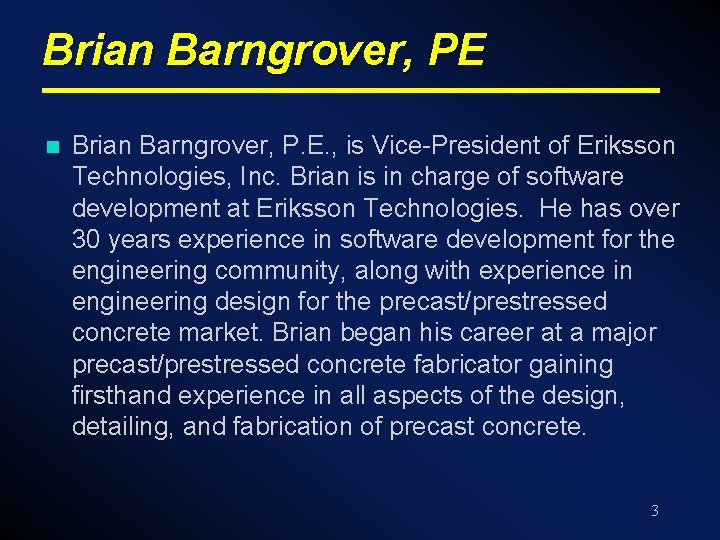
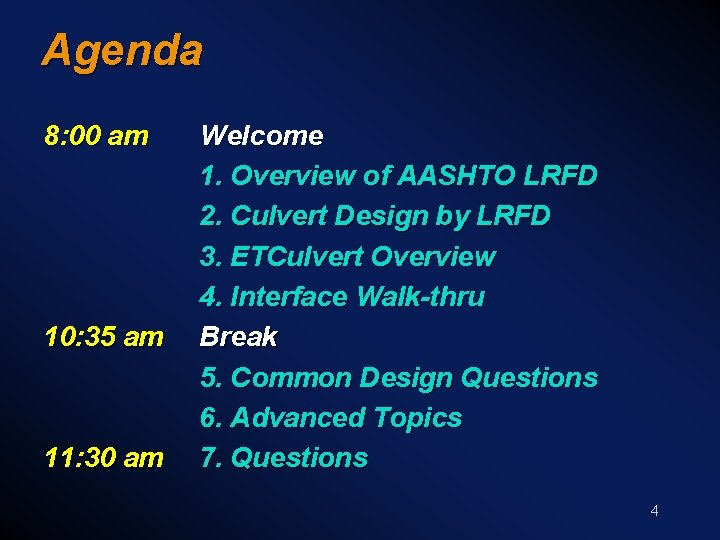
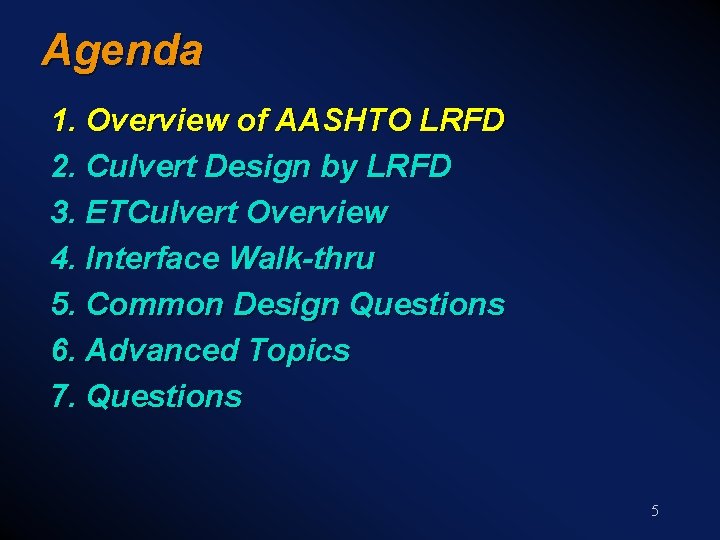
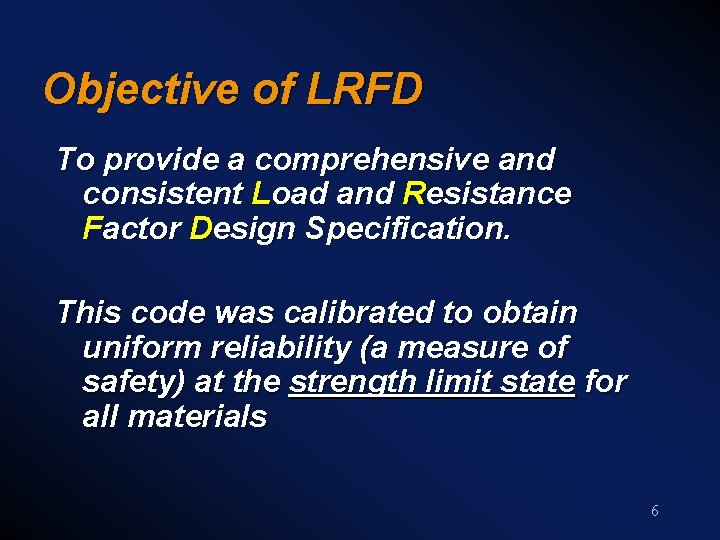
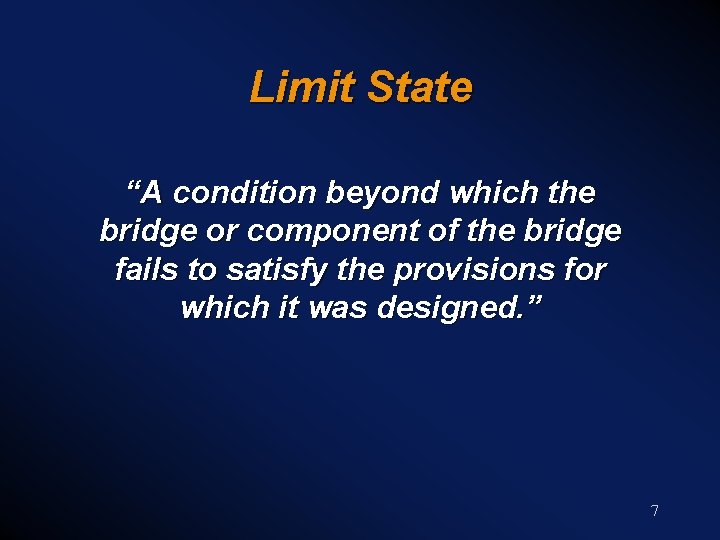
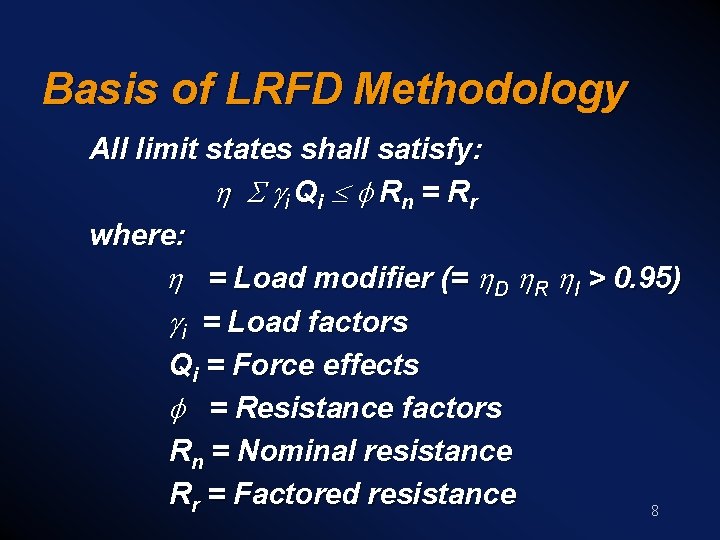
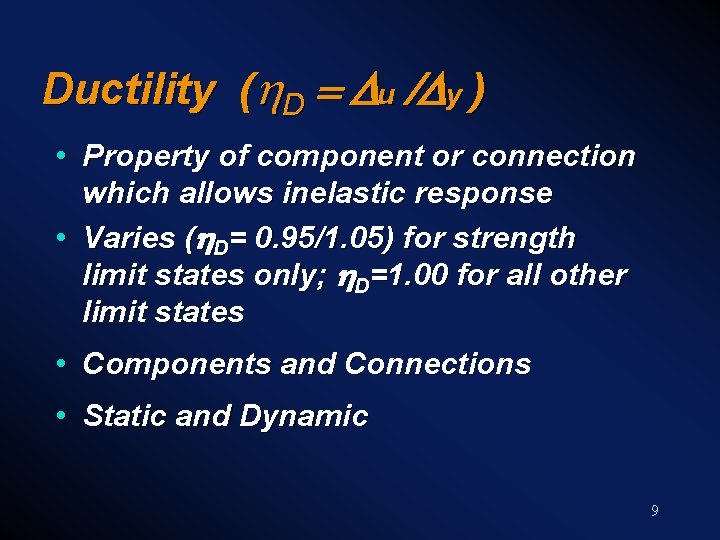
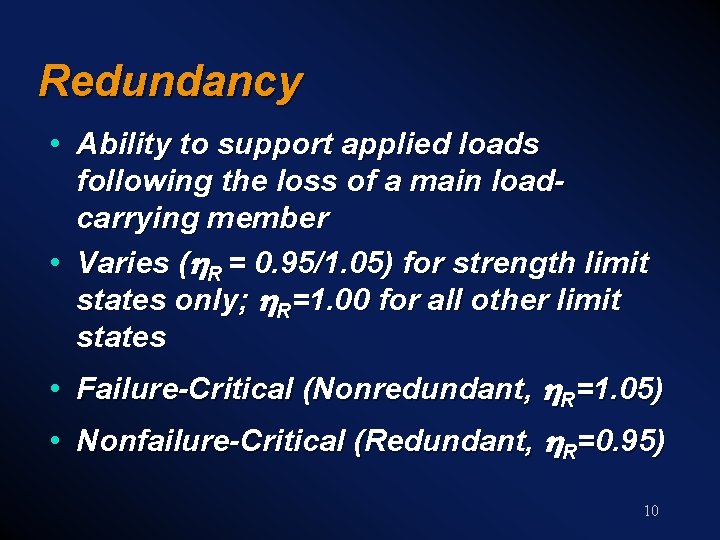
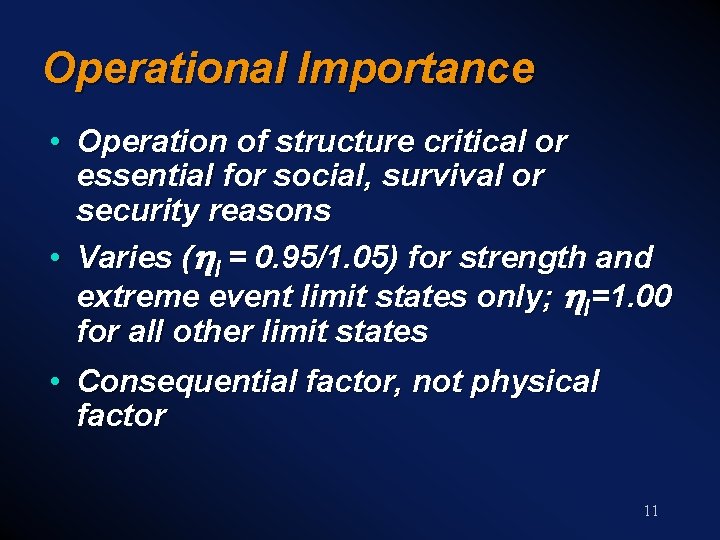

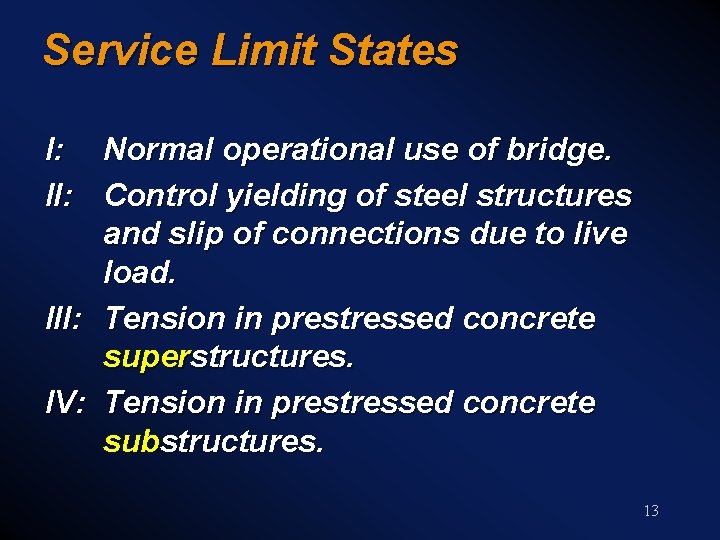
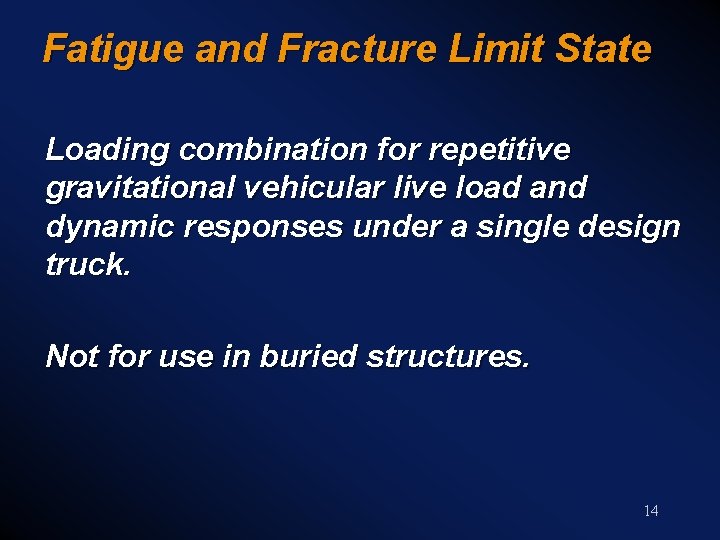
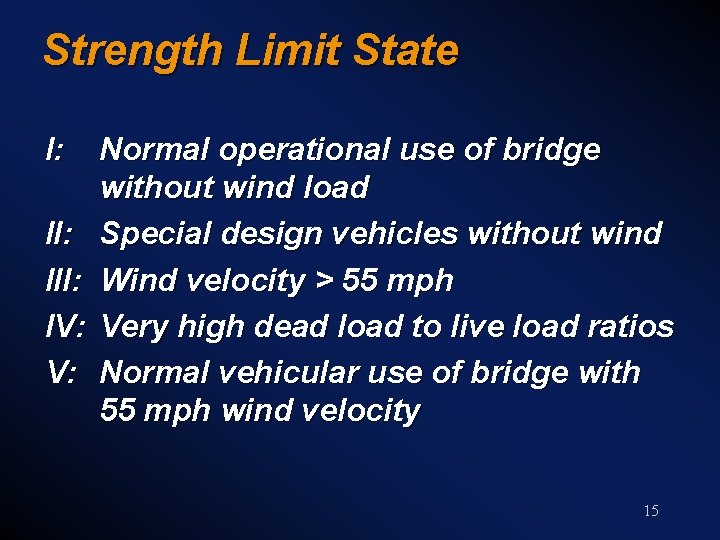
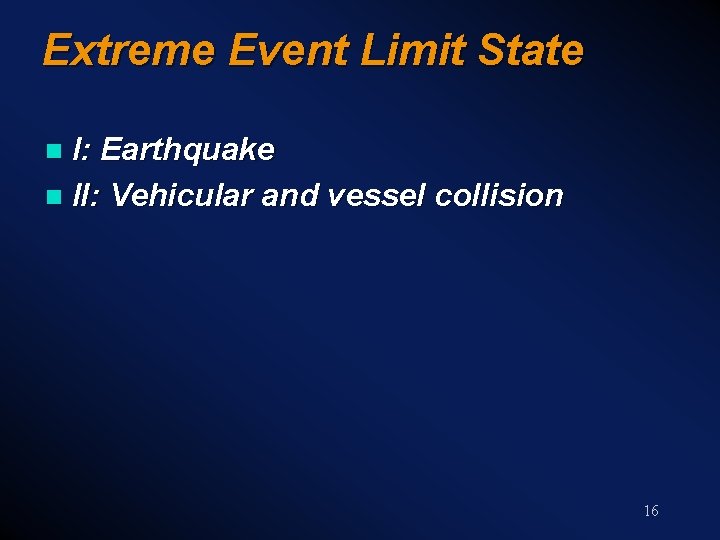
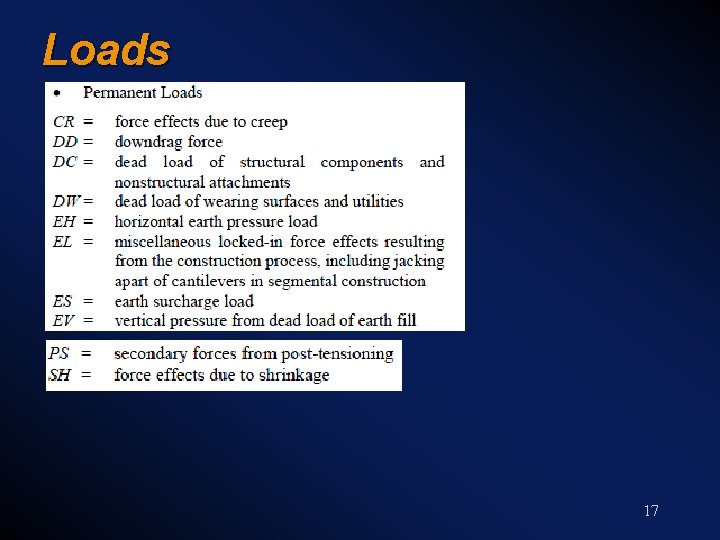
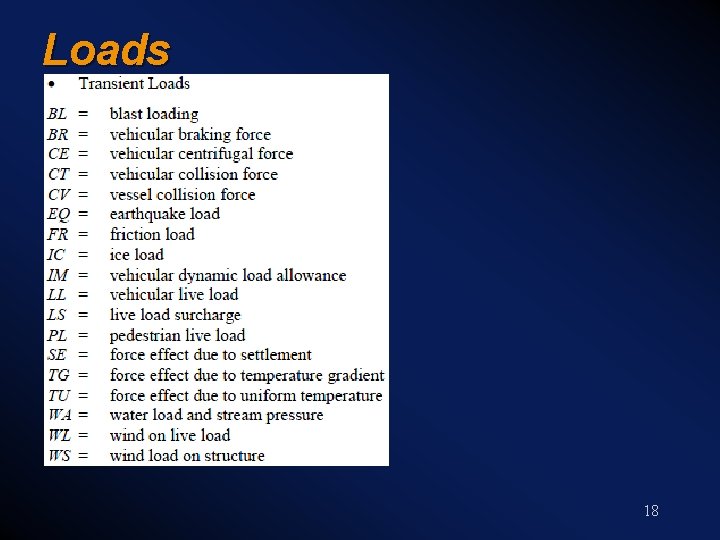
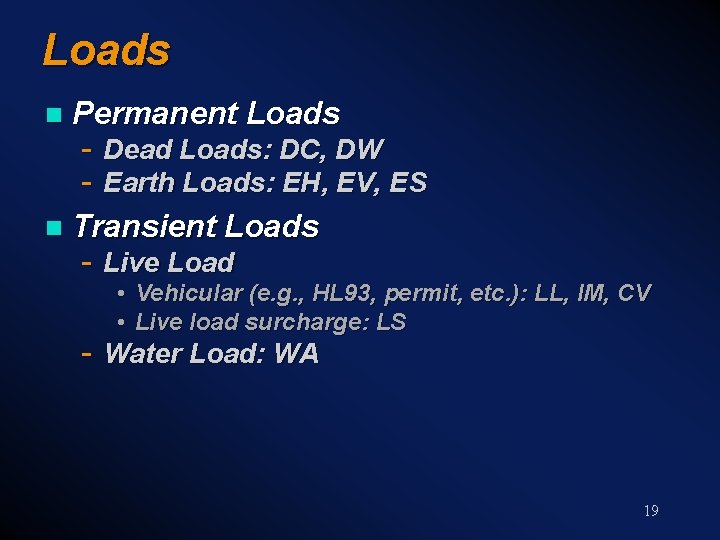
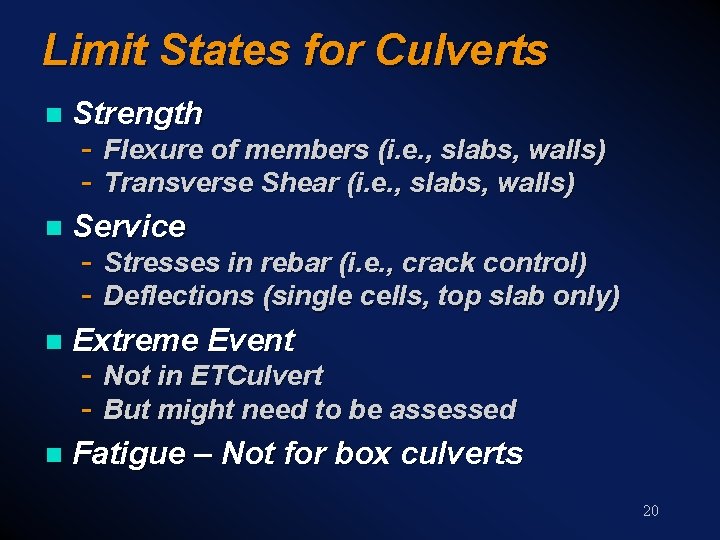
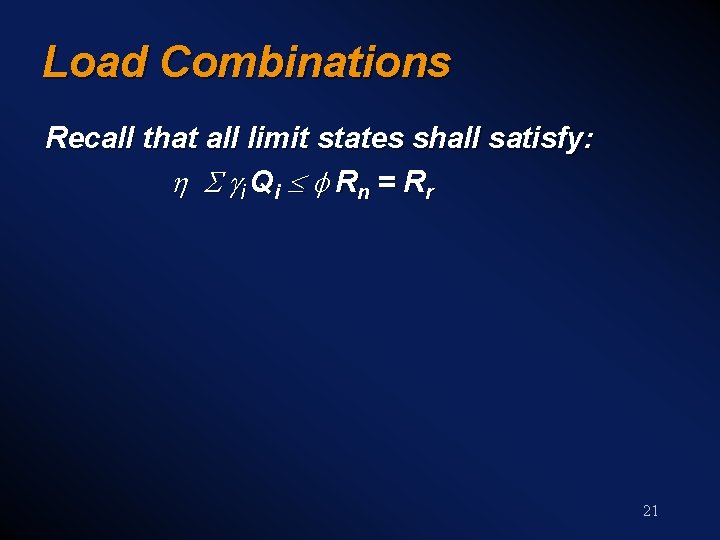
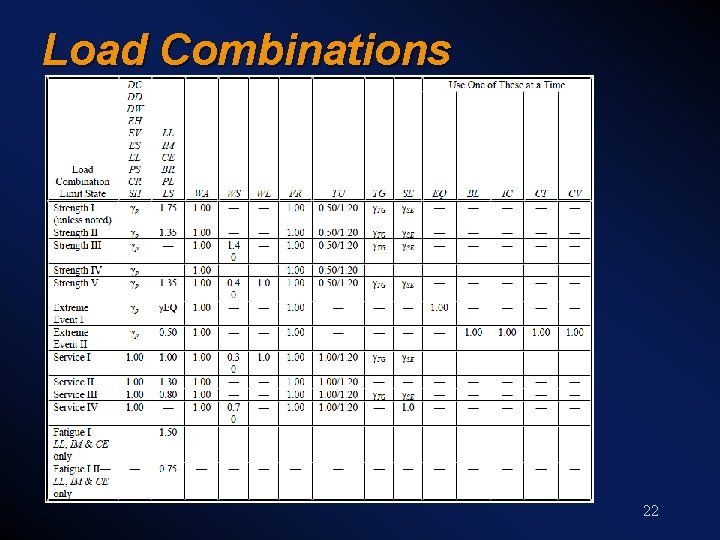
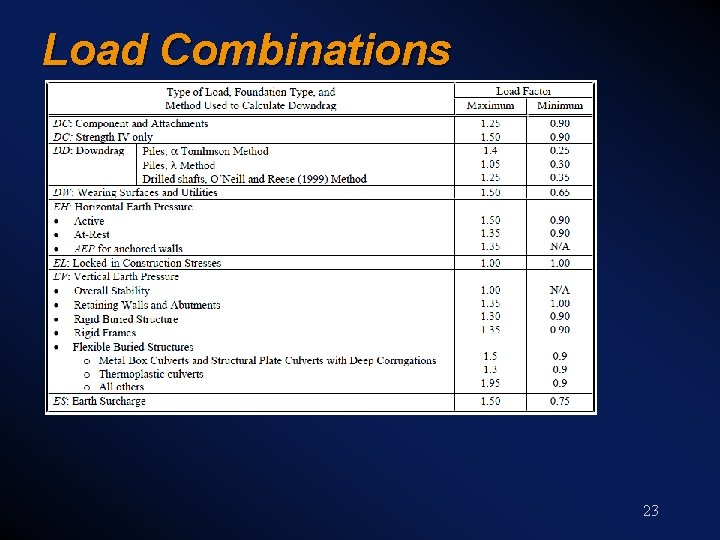
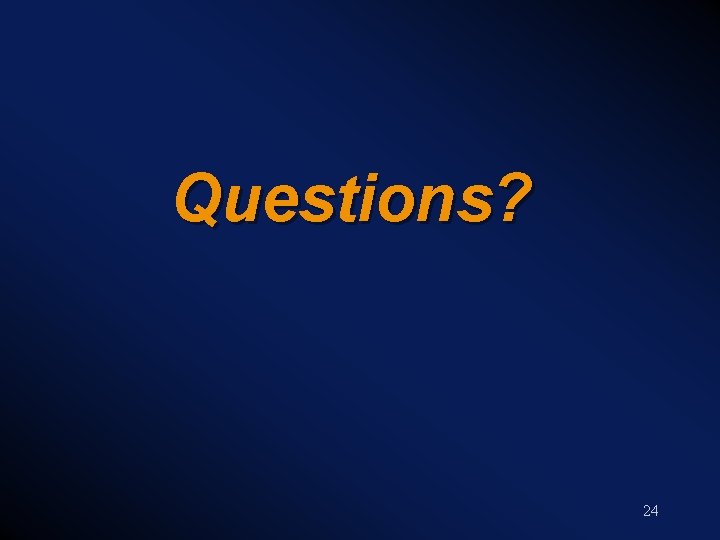
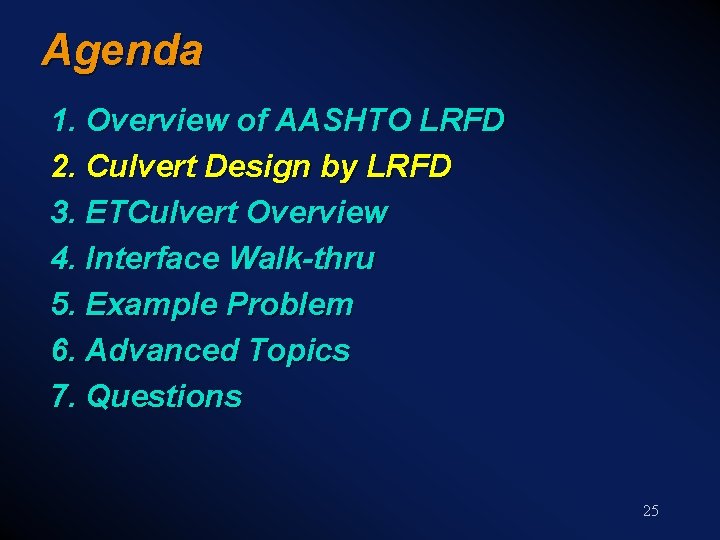
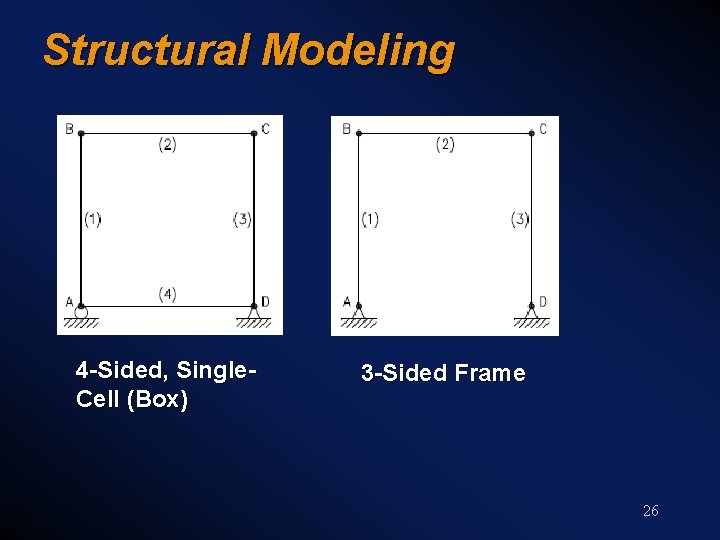
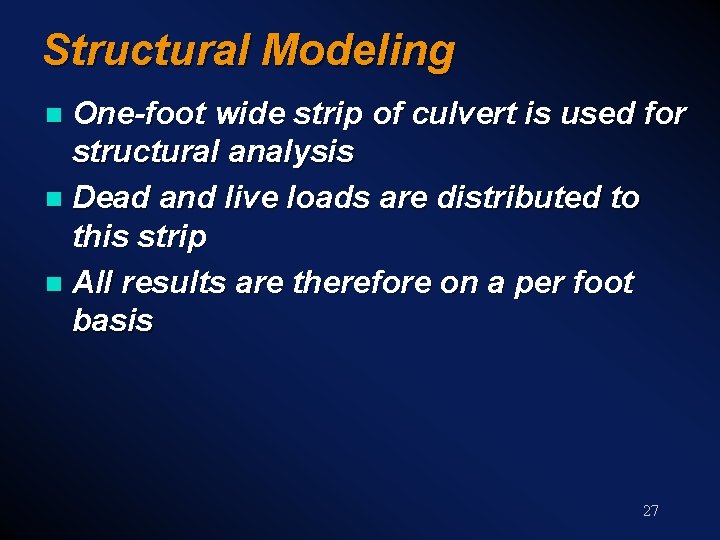
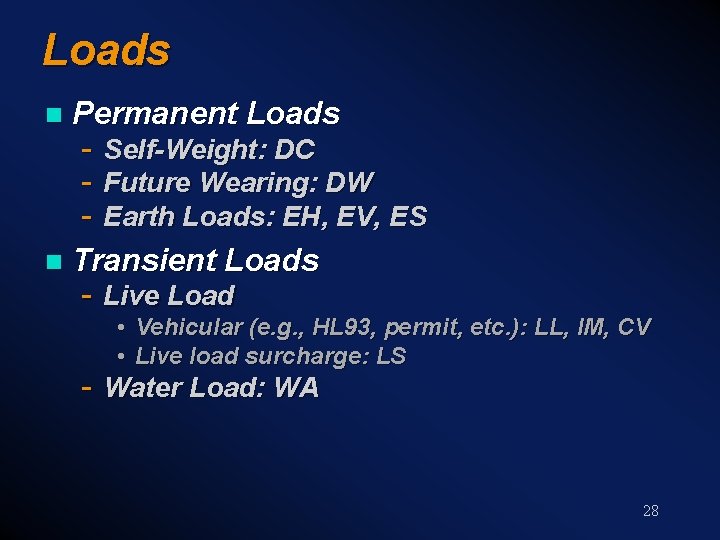
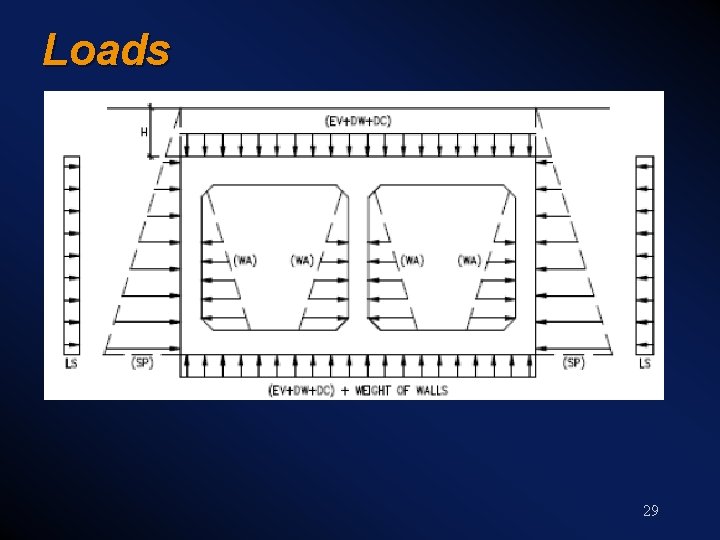
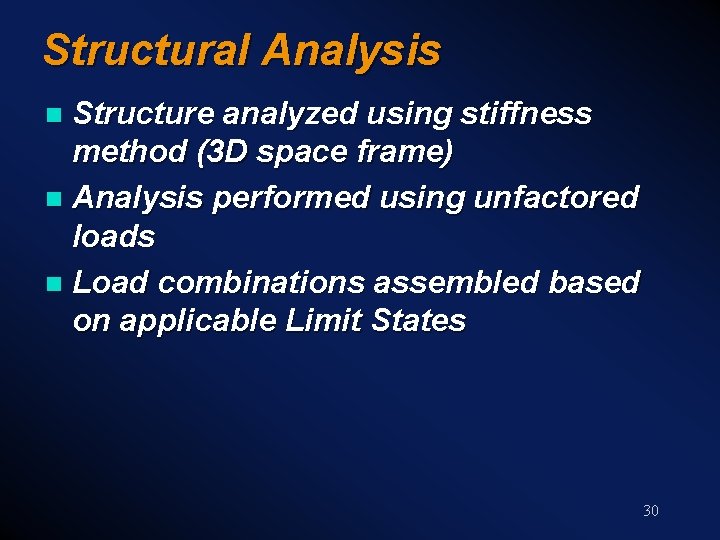
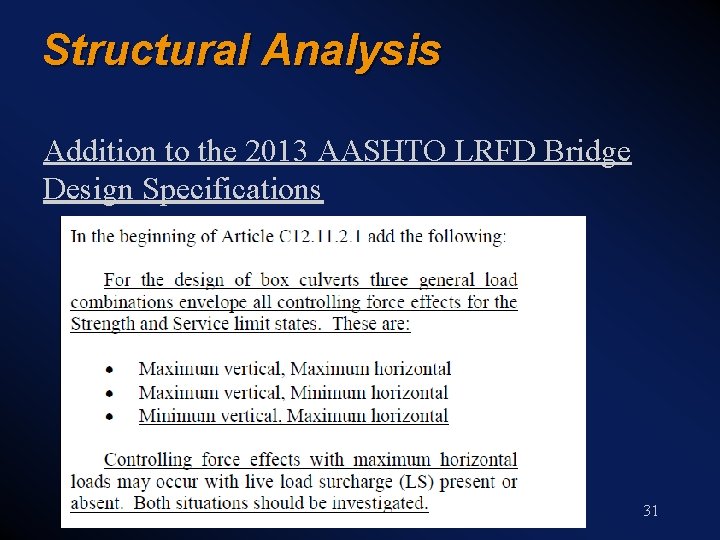

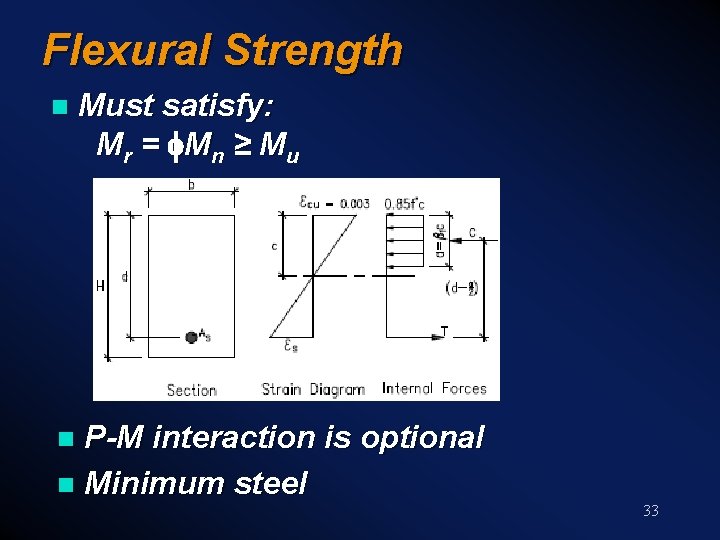
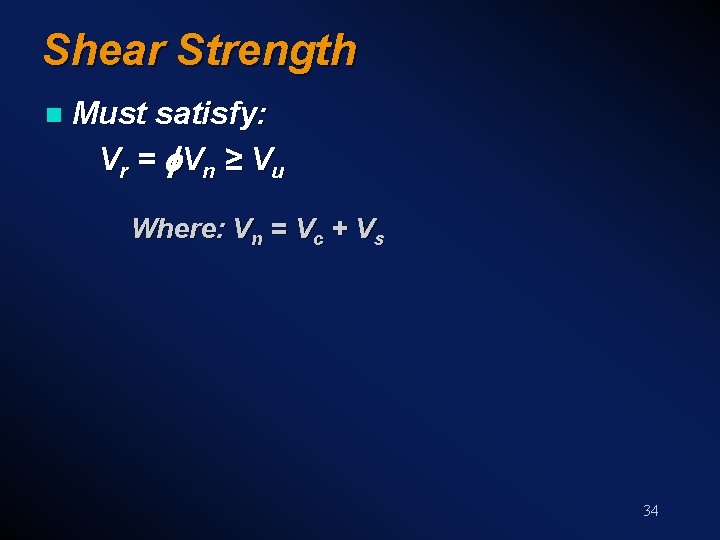
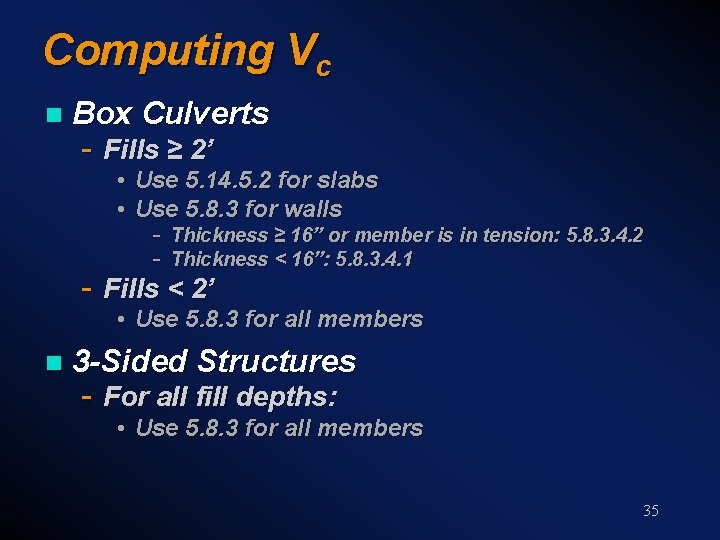
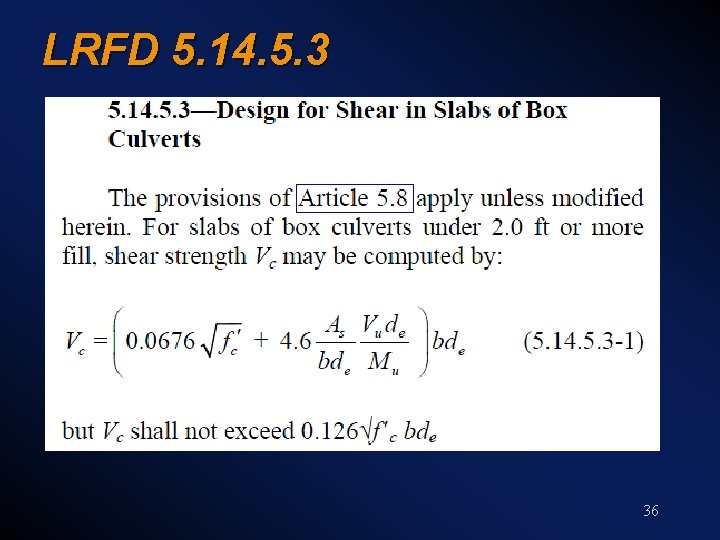
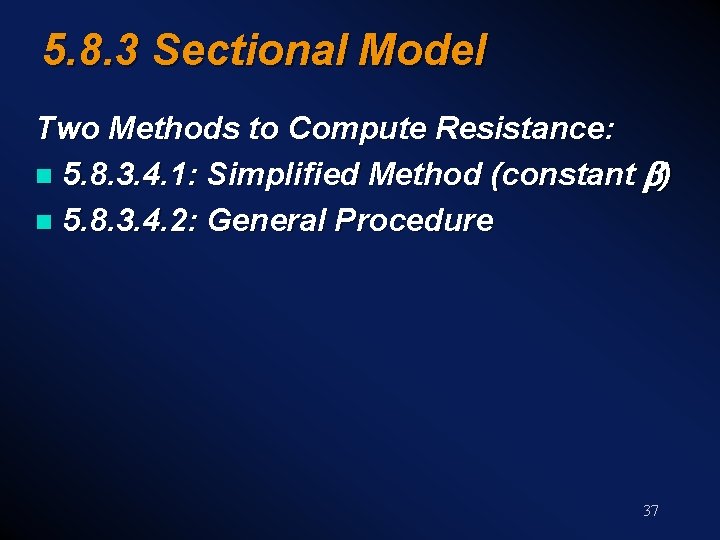
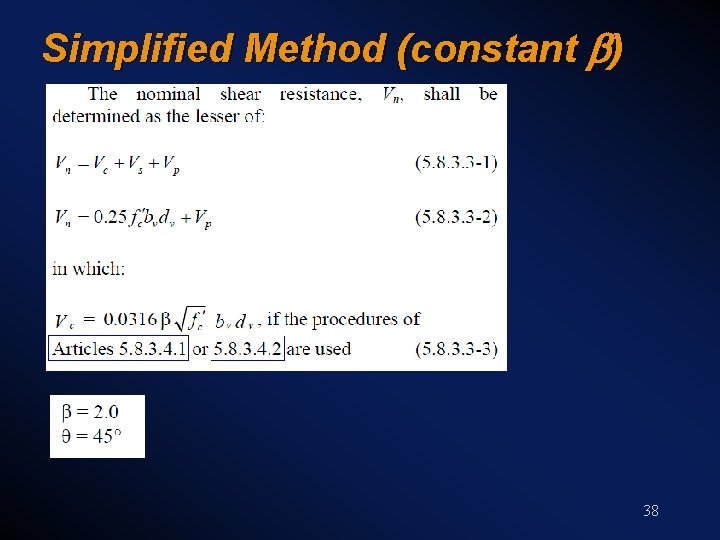
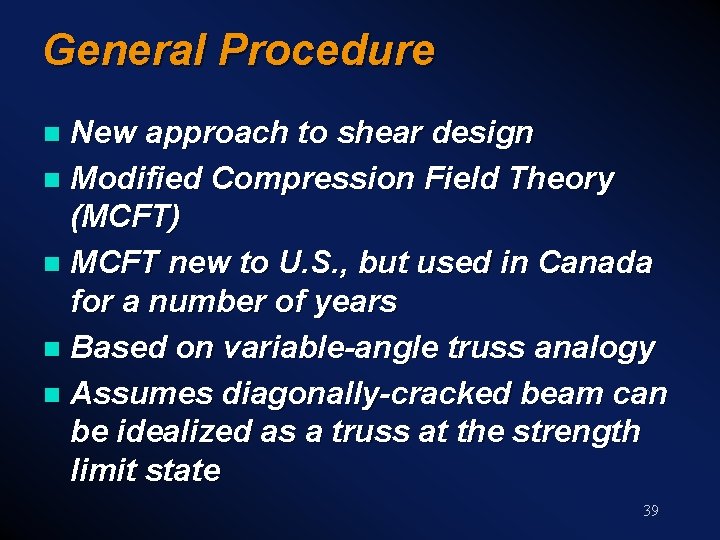
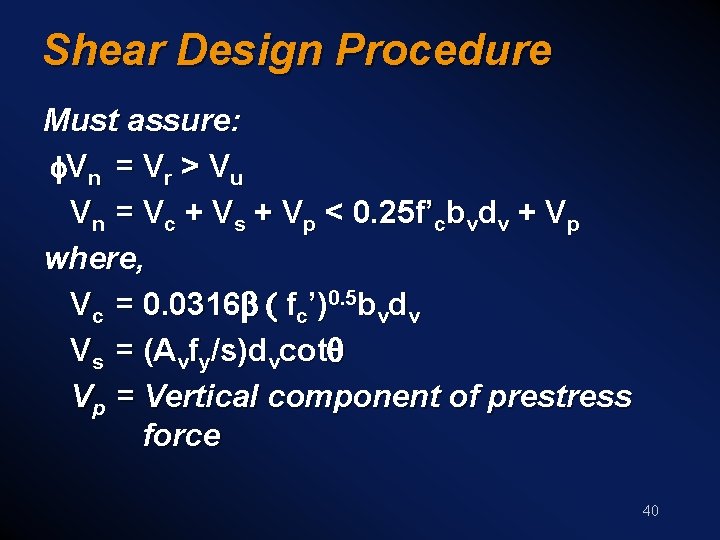
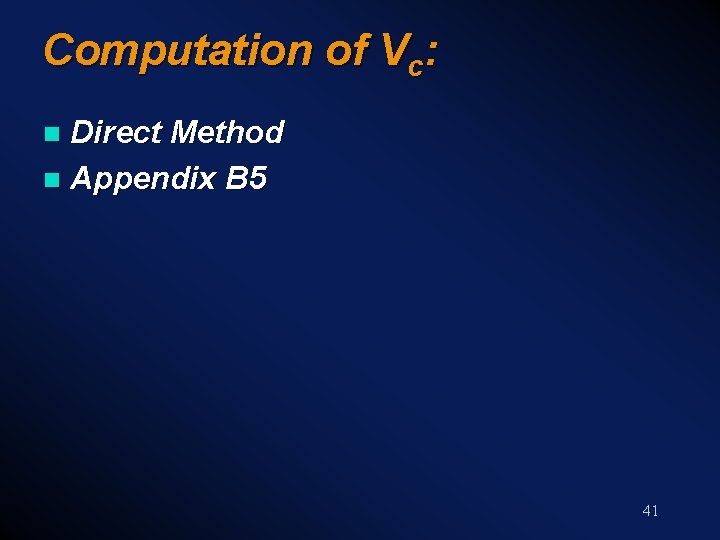
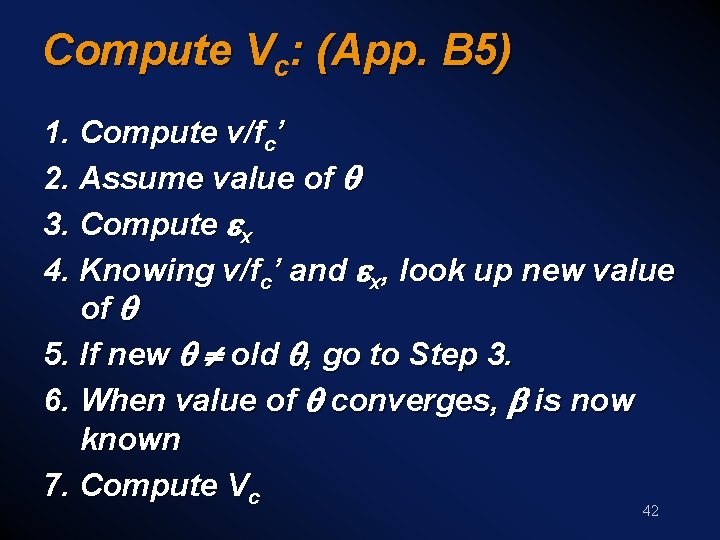

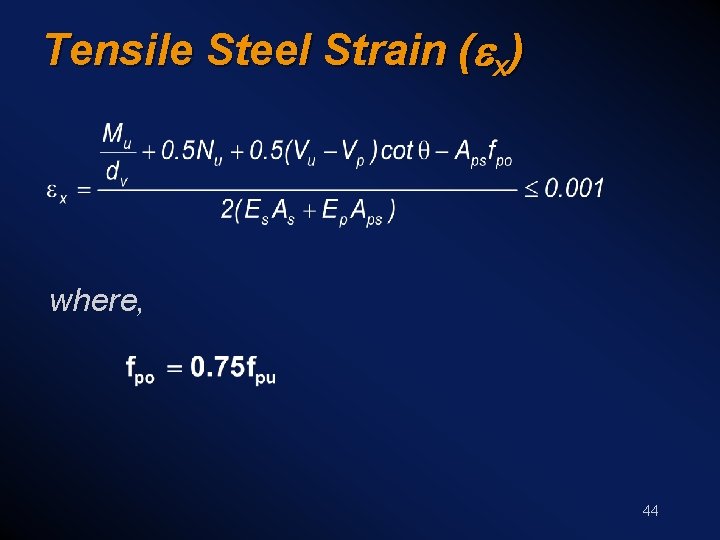
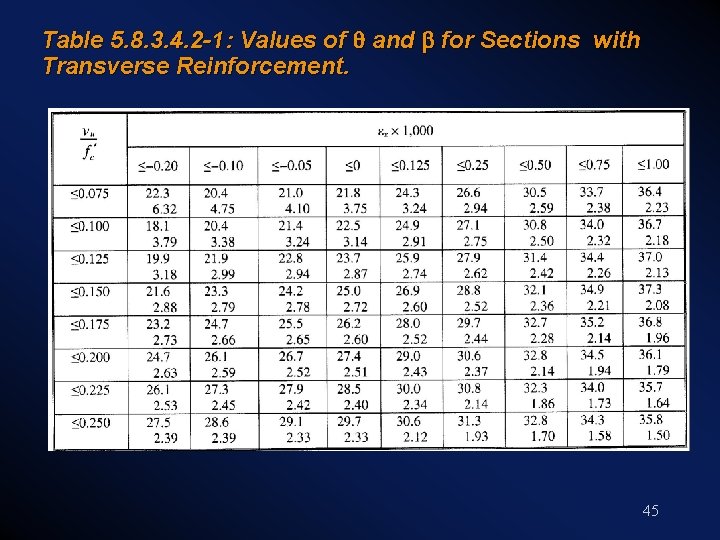
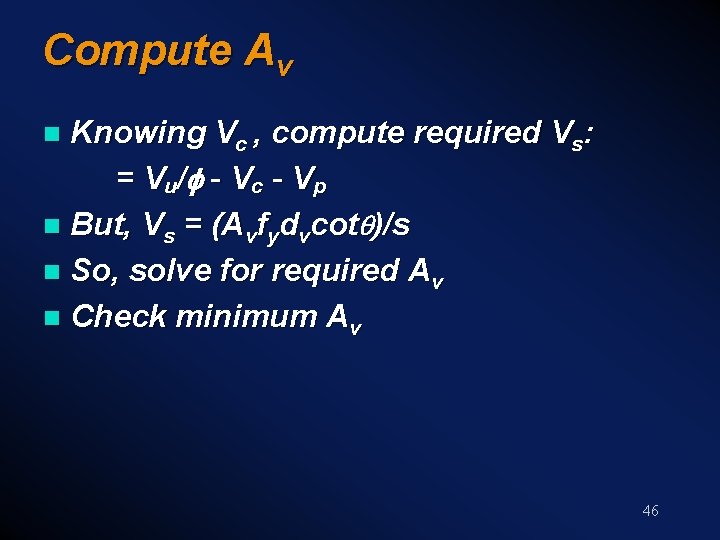
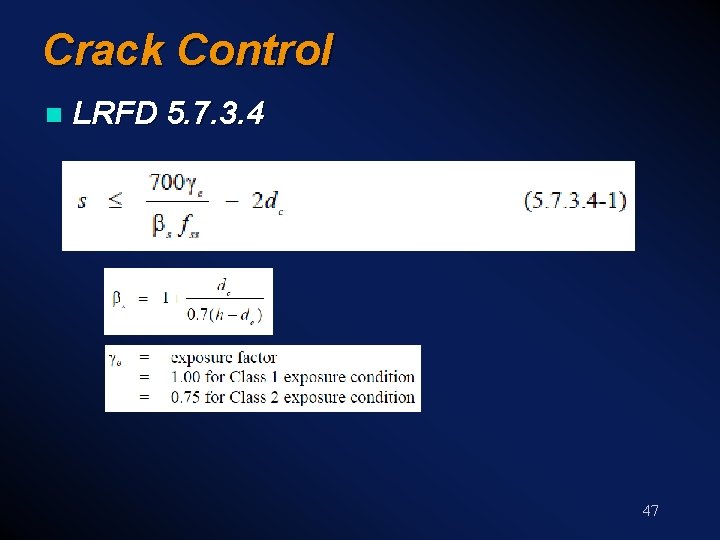
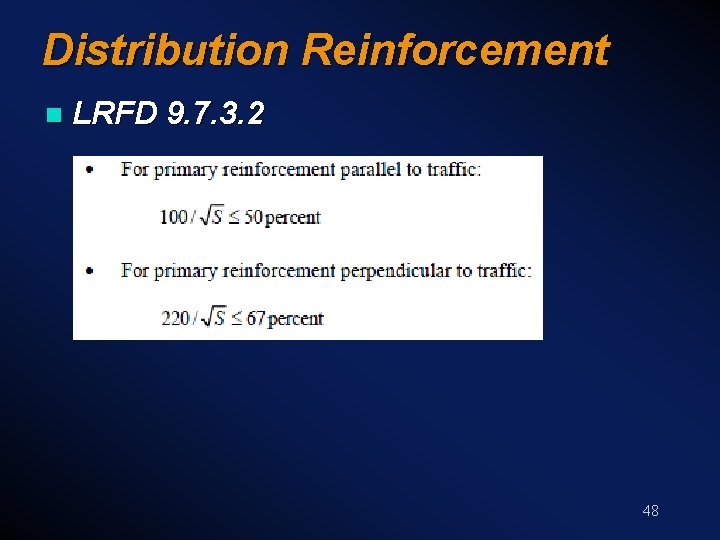
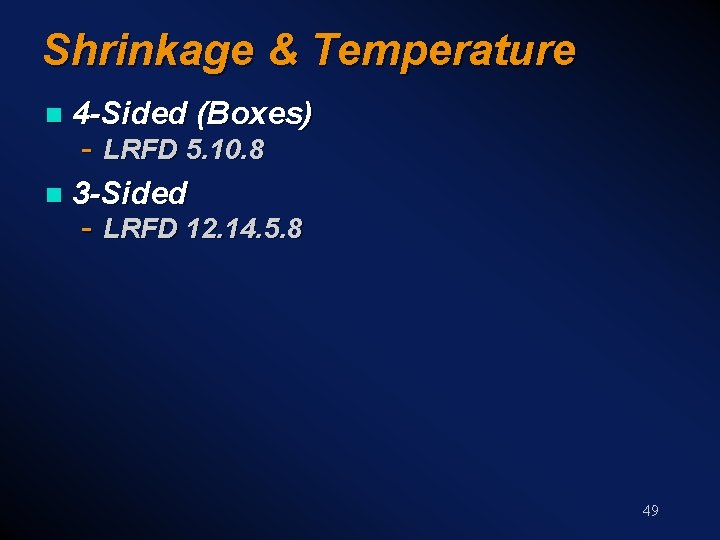
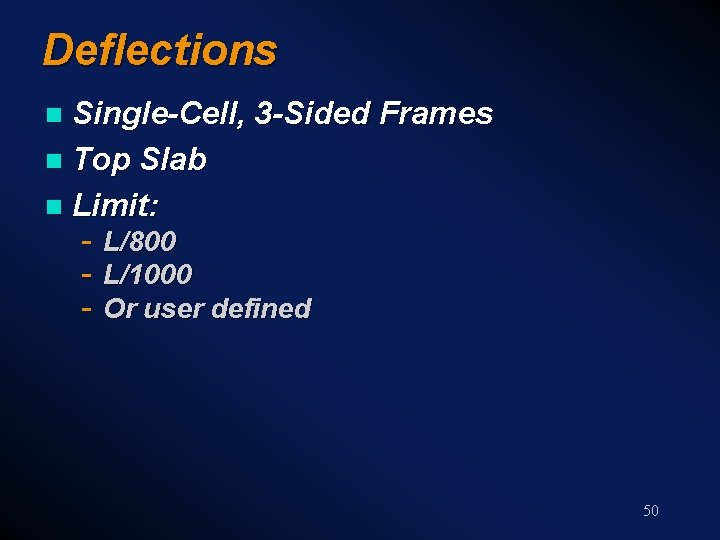
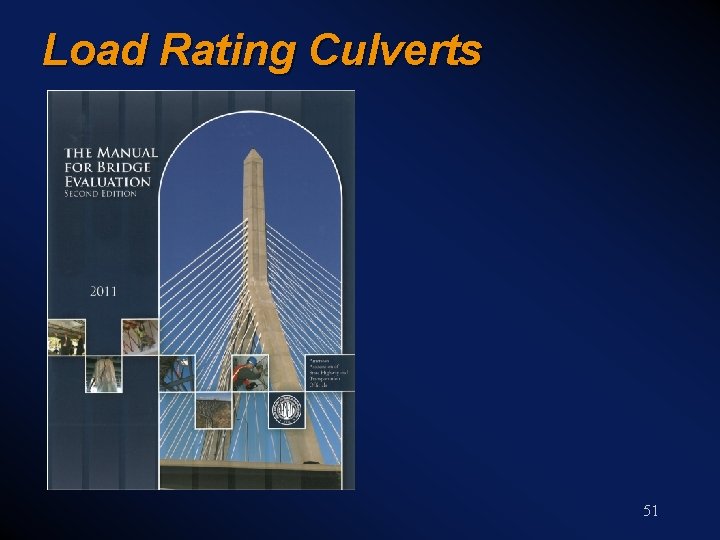
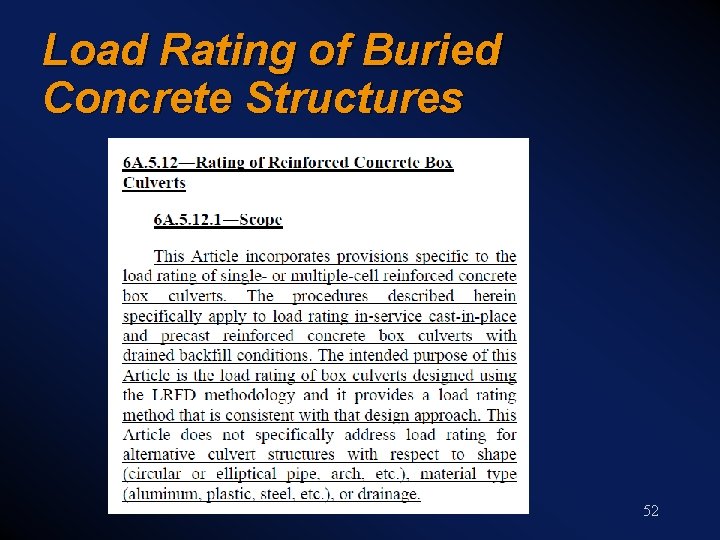
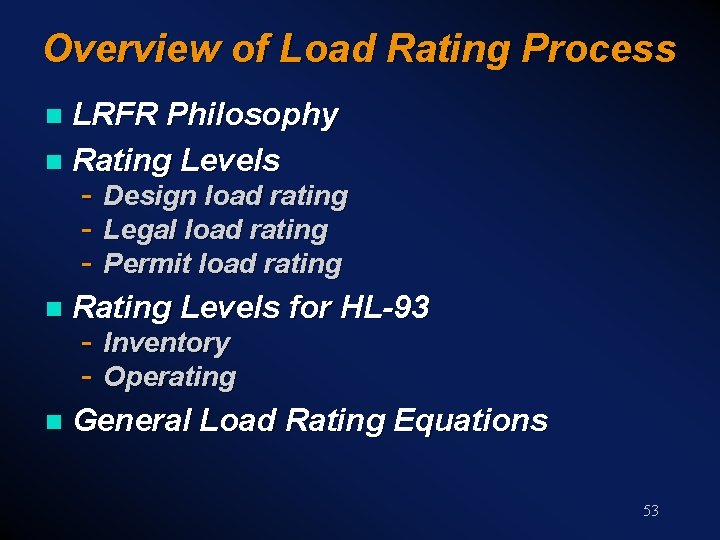
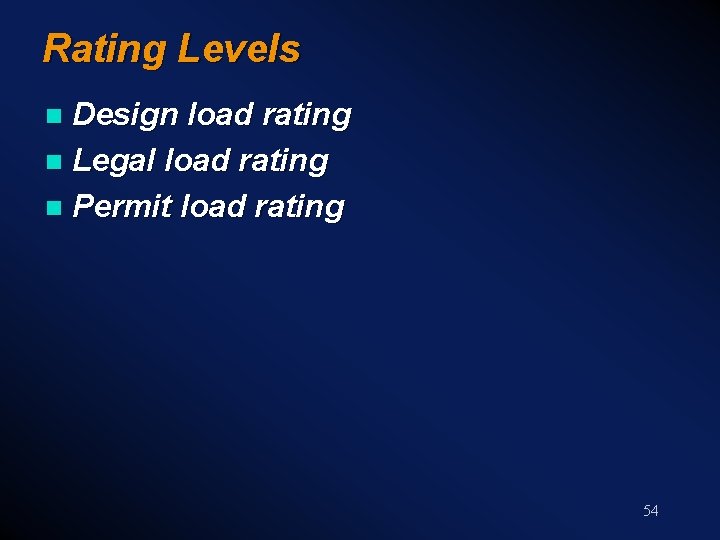
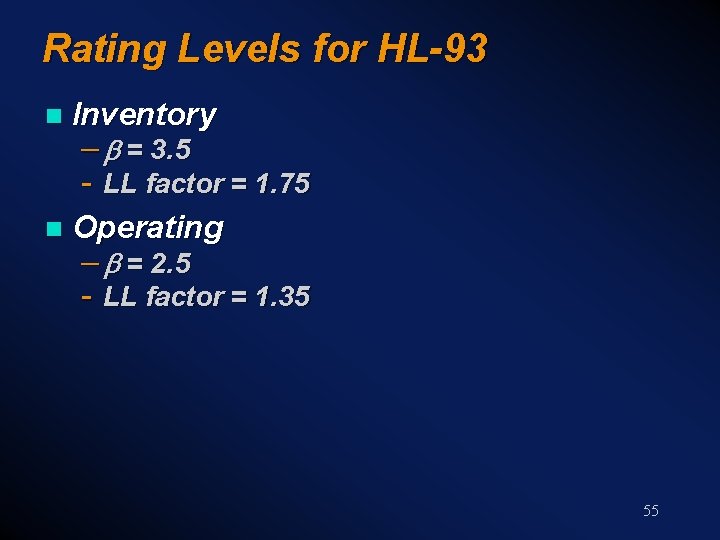
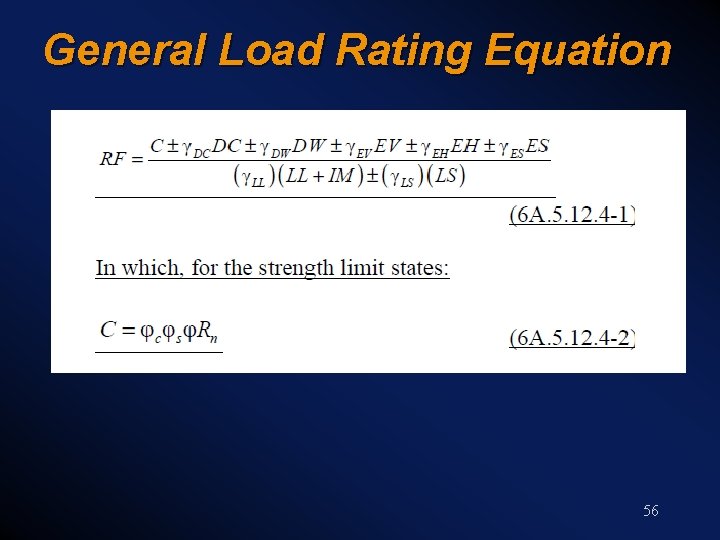
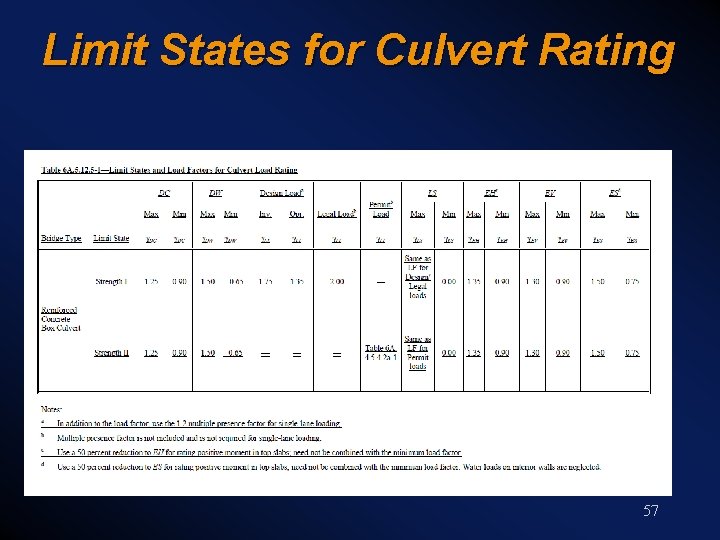
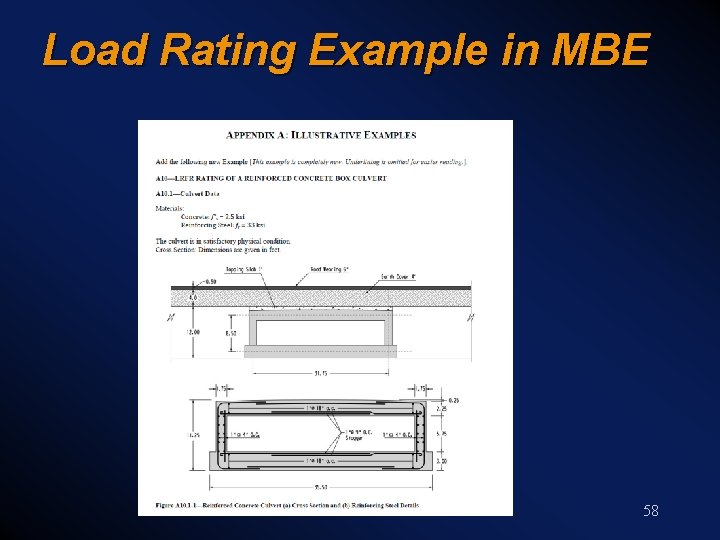
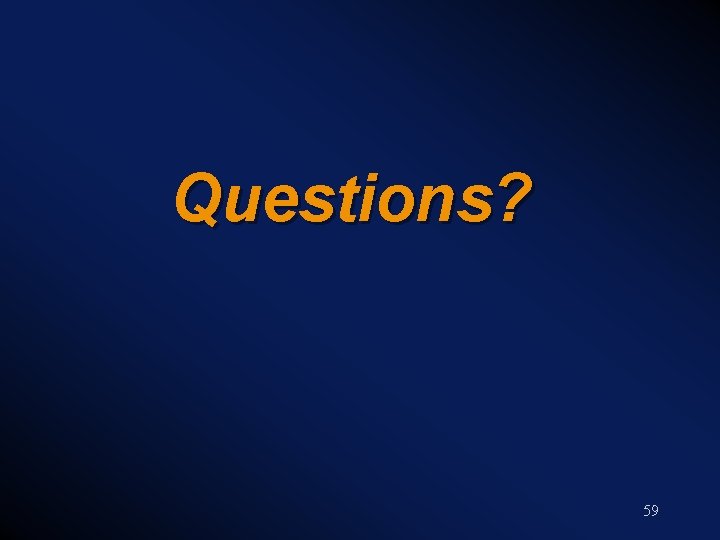
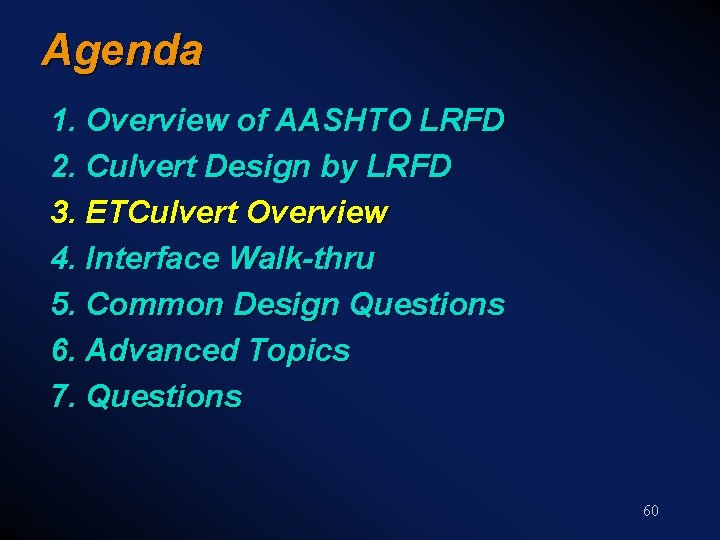
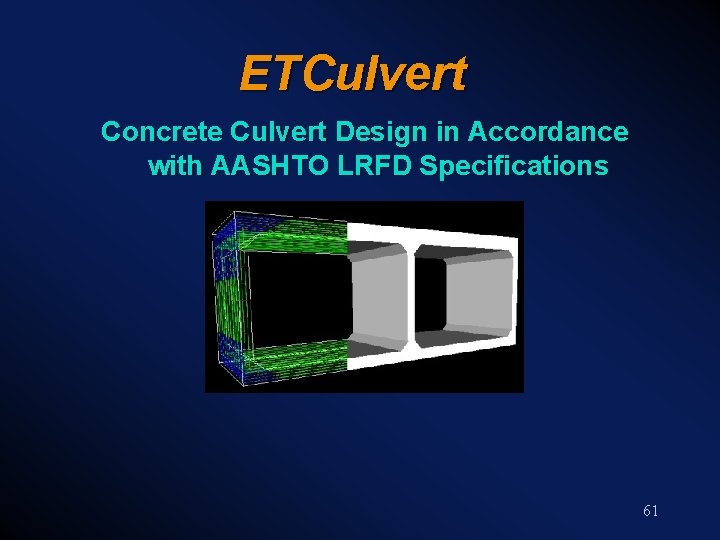
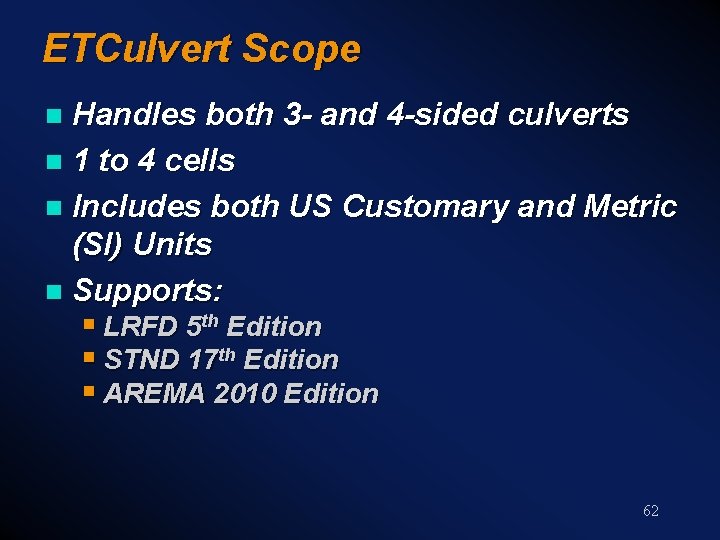
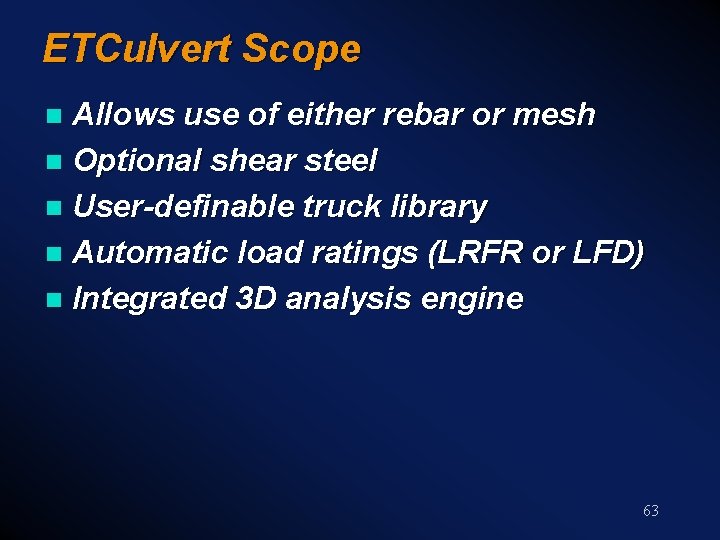
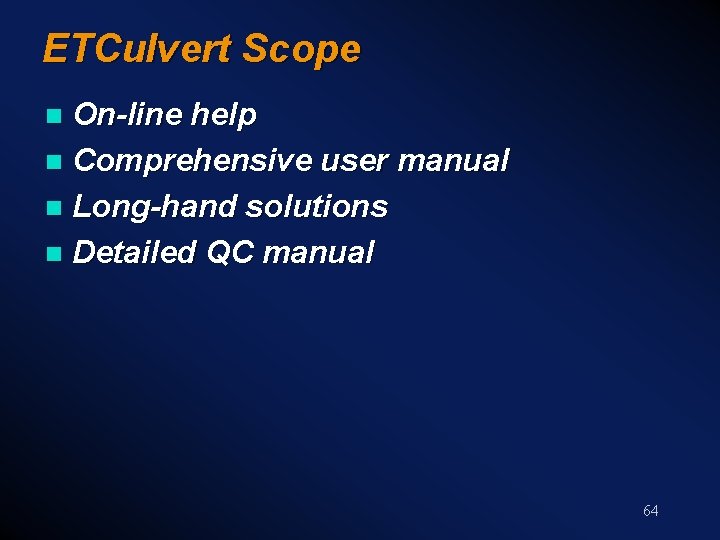
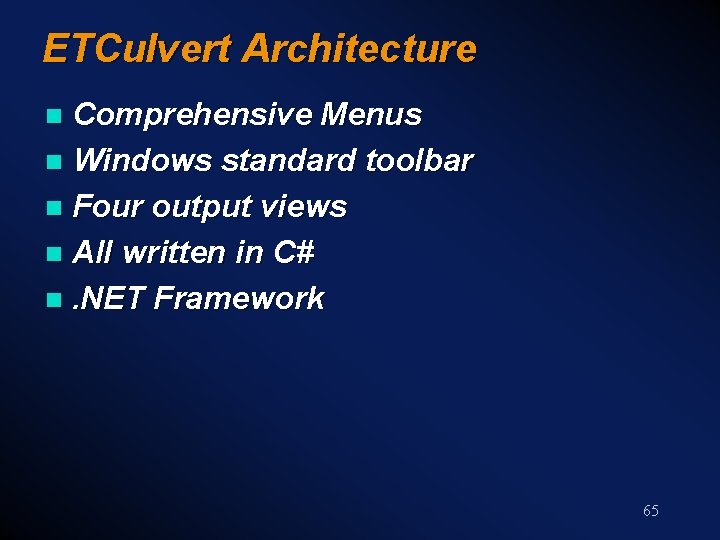
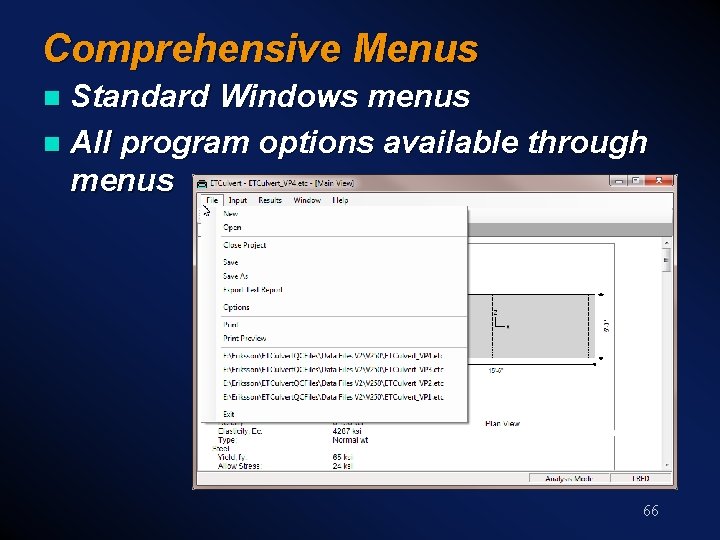
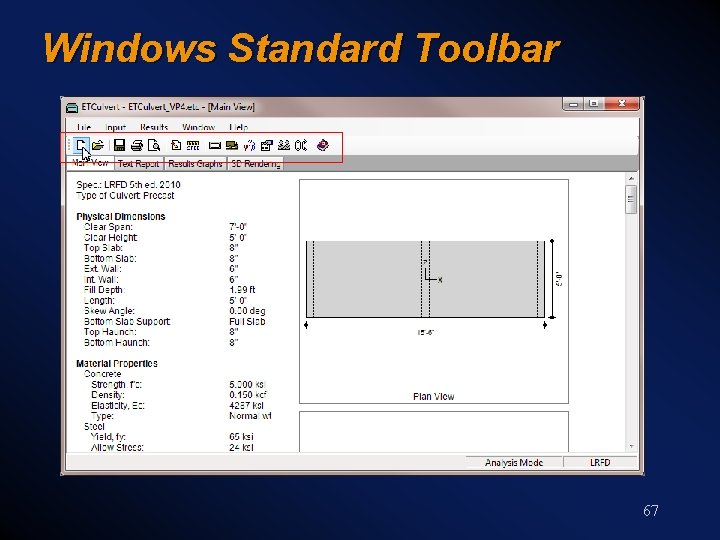
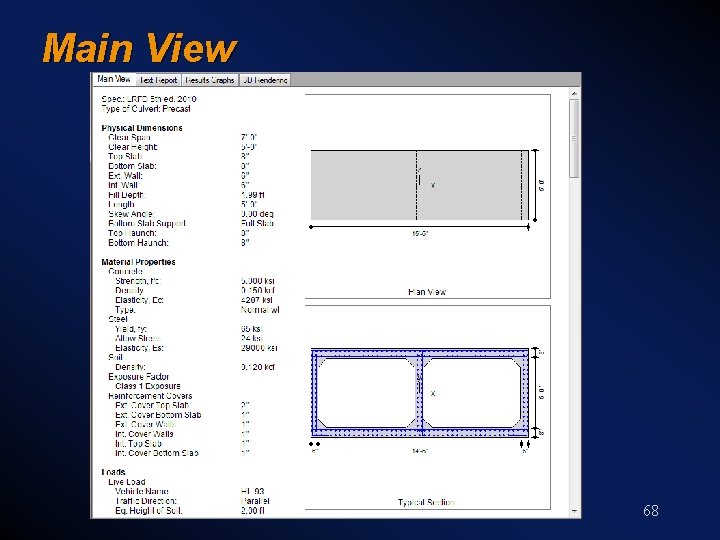
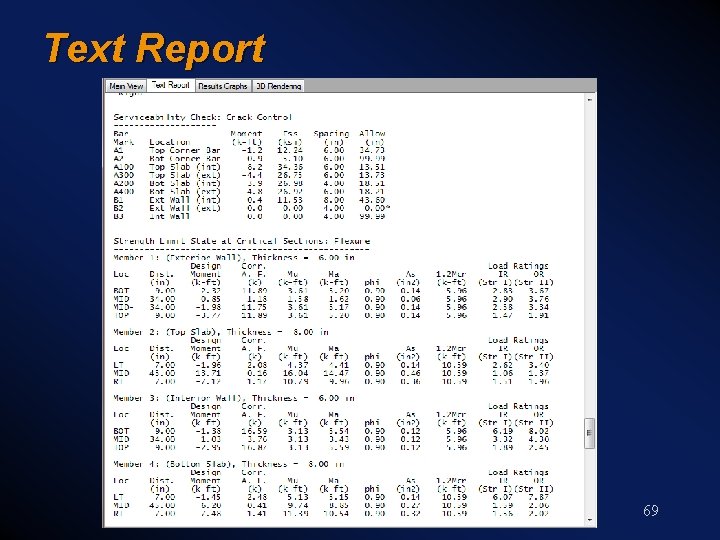
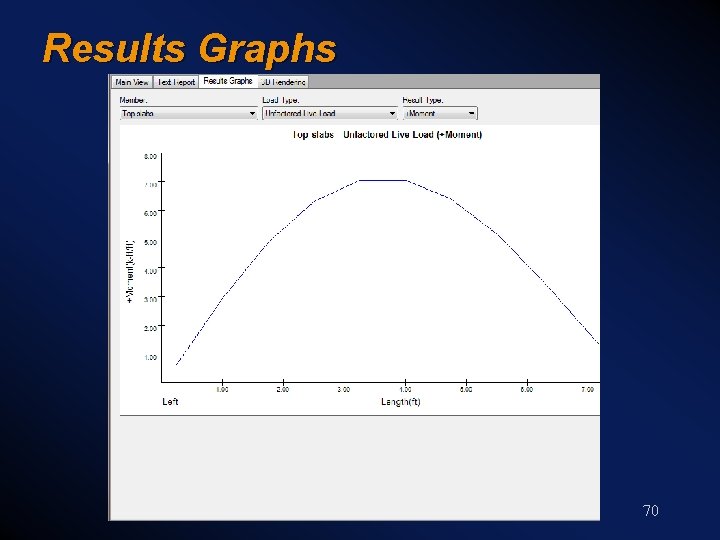
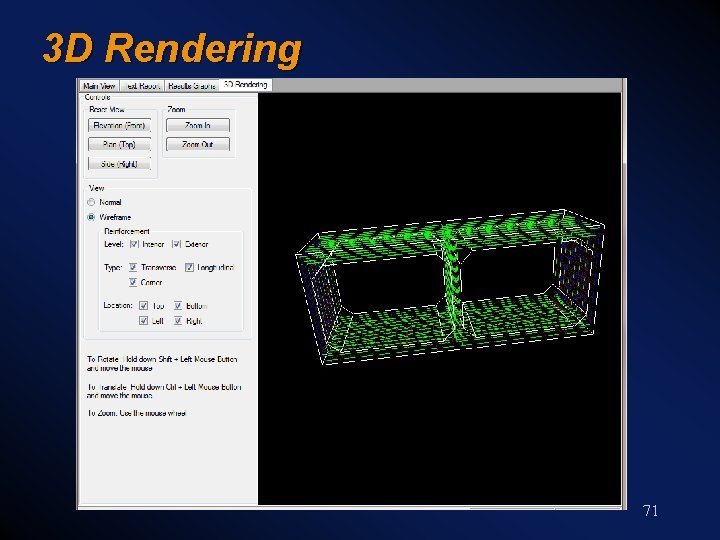
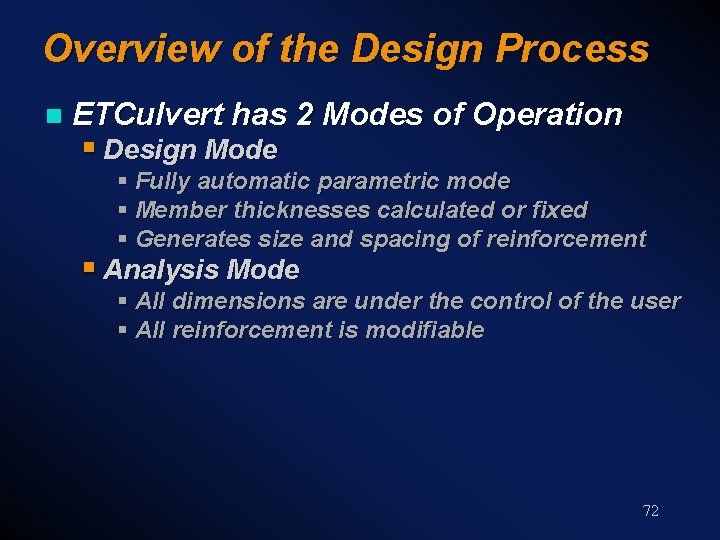
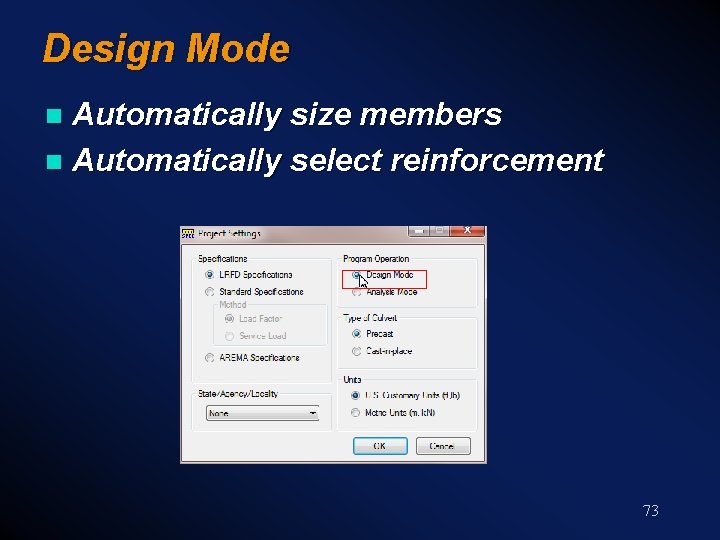
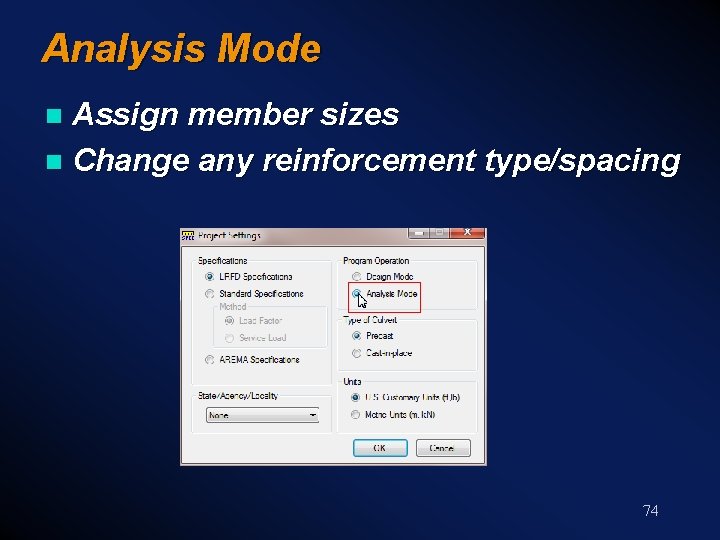
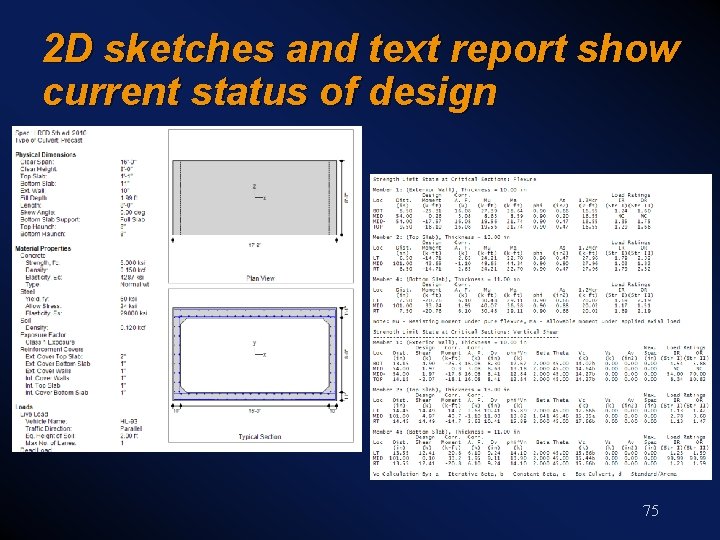
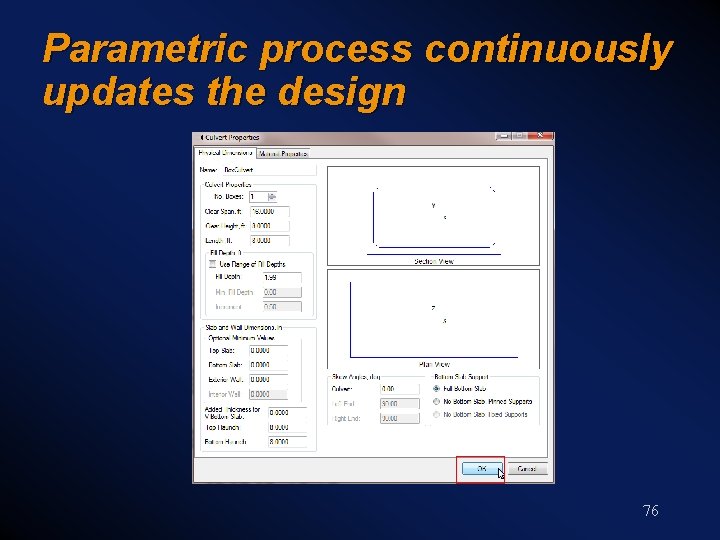
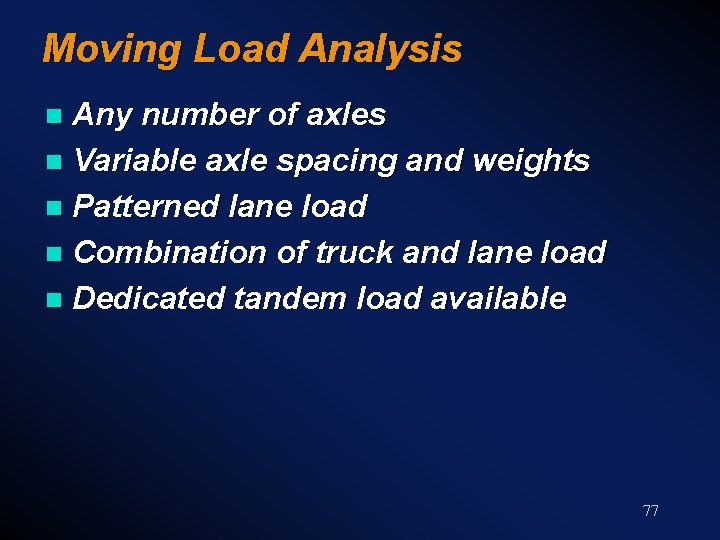
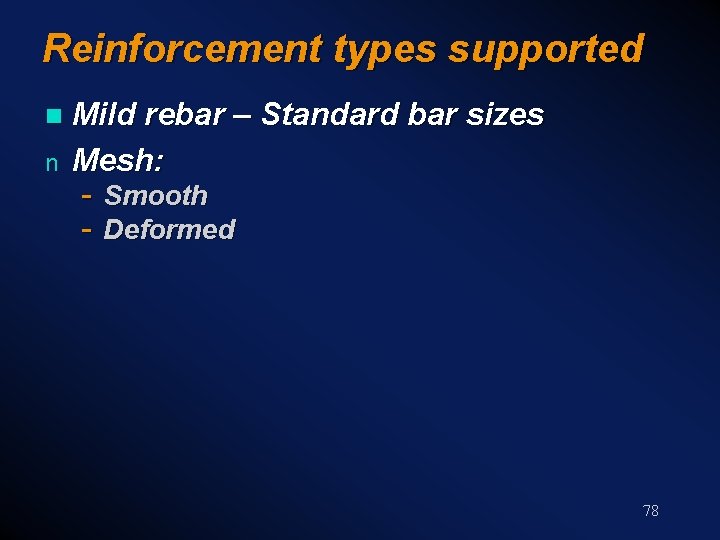
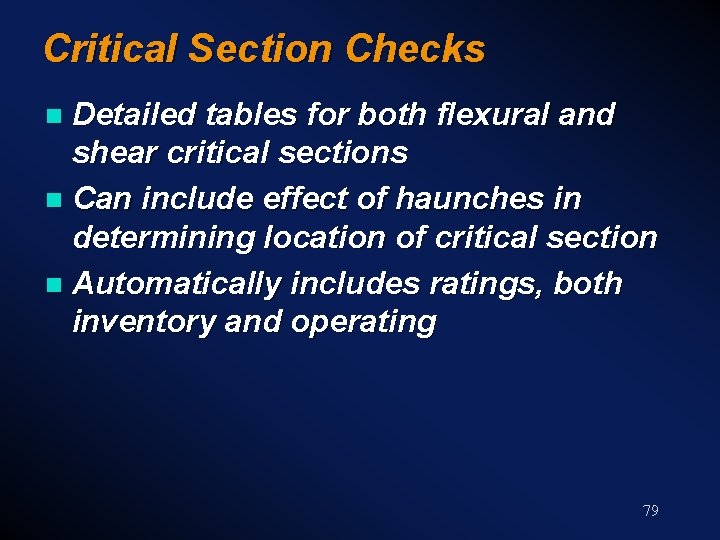
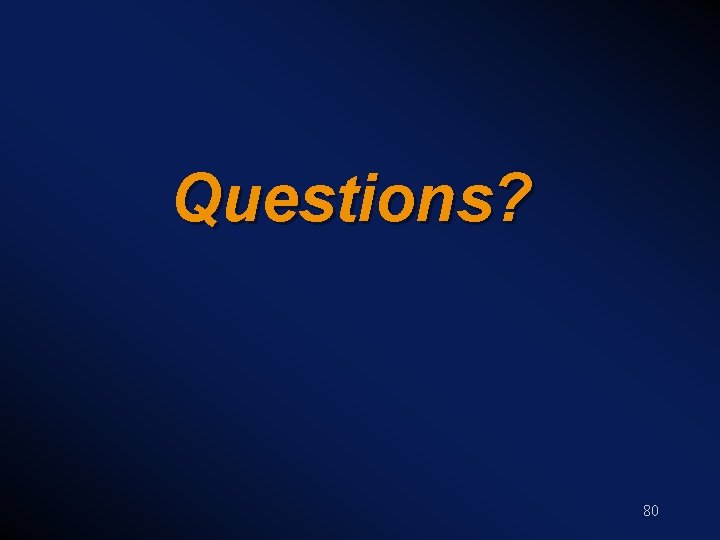
- Slides: 80
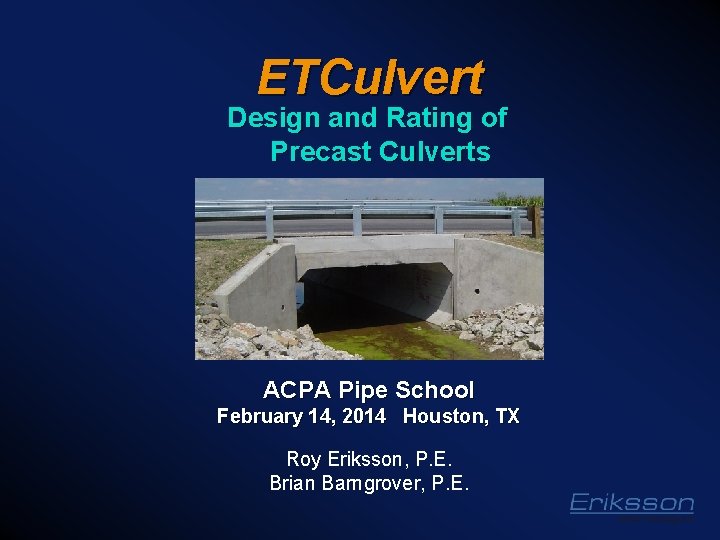
ETCulvert Design and Rating of Precast Culverts ACPA Pipe School February 14, 2014 Houston, TX Roy Eriksson, P. E. Brian Barngrover, P. E.
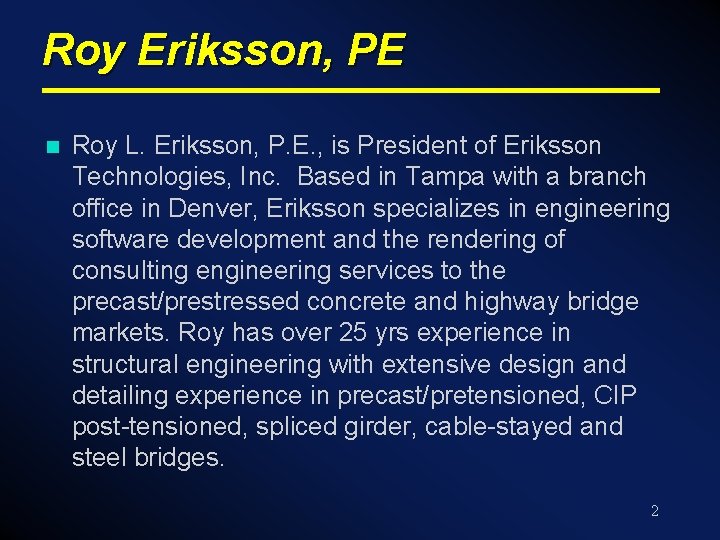
Roy Eriksson, PE n Roy L. Eriksson, P. E. , is President of Eriksson Technologies, Inc. Based in Tampa with a branch office in Denver, Eriksson specializes in engineering software development and the rendering of consulting engineering services to the precast/prestressed concrete and highway bridge markets. Roy has over 25 yrs experience in structural engineering with extensive design and detailing experience in precast/pretensioned, CIP post-tensioned, spliced girder, cable-stayed and steel bridges. 2
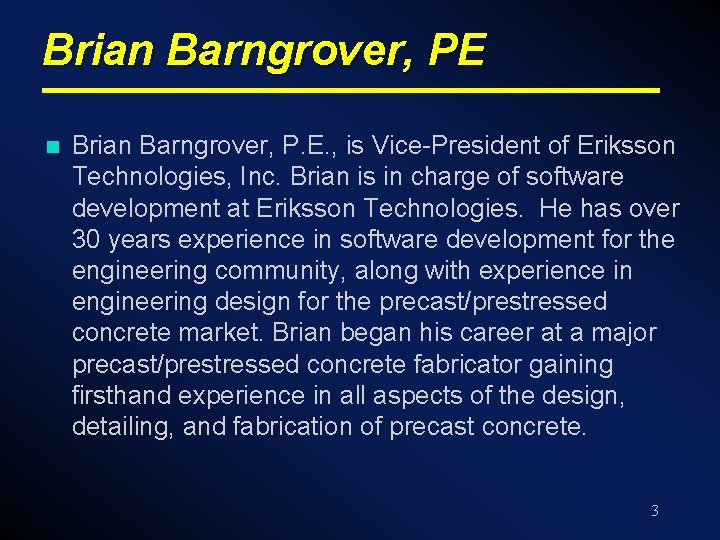
Brian Barngrover, PE n Brian Barngrover, P. E. , is Vice-President of Eriksson Technologies, Inc. Brian is in charge of software development at Eriksson Technologies. He has over 30 years experience in software development for the engineering community, along with experience in engineering design for the precast/prestressed concrete market. Brian began his career at a major precast/prestressed concrete fabricator gaining firsthand experience in all aspects of the design, detailing, and fabrication of precast concrete. 3
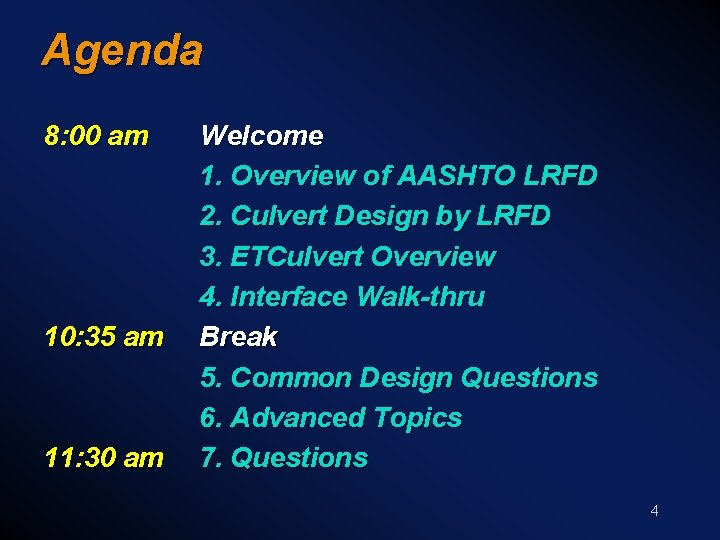
Agenda 8: 00 am 10: 35 am 11: 30 am Welcome 1. Overview of AASHTO LRFD 2. Culvert Design by LRFD 3. ETCulvert Overview 4. Interface Walk-thru Break 5. Common Design Questions 6. Advanced Topics 7. Questions 4
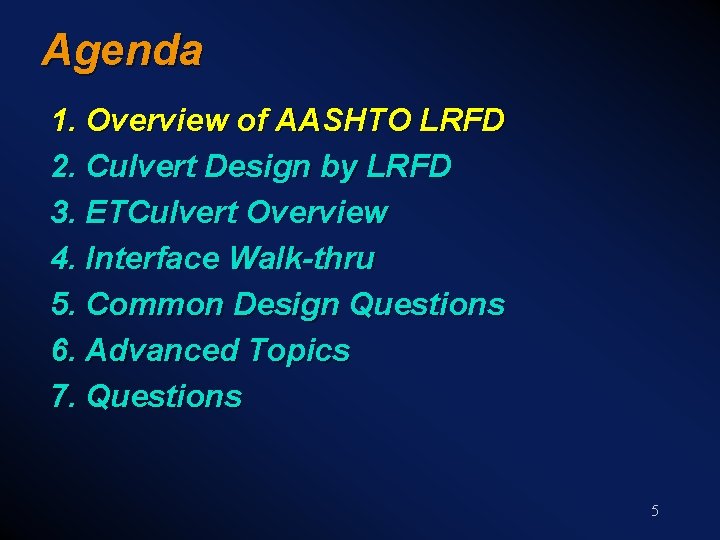
Agenda 1. Overview of AASHTO LRFD 2. Culvert Design by LRFD 3. ETCulvert Overview 4. Interface Walk-thru 5. Common Design Questions 6. Advanced Topics 7. Questions 5
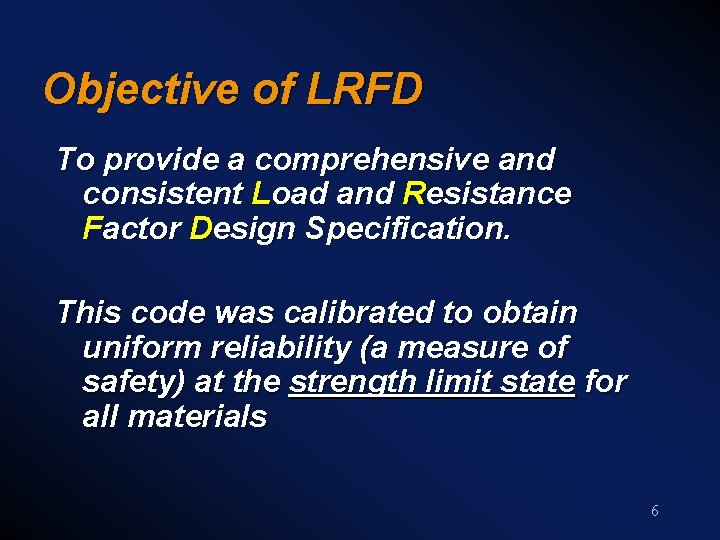
Objective of LRFD To provide a comprehensive and consistent Load and Resistance Factor Design Specification. This code was calibrated to obtain uniform reliability (a measure of safety) at the strength limit state for all materials 6
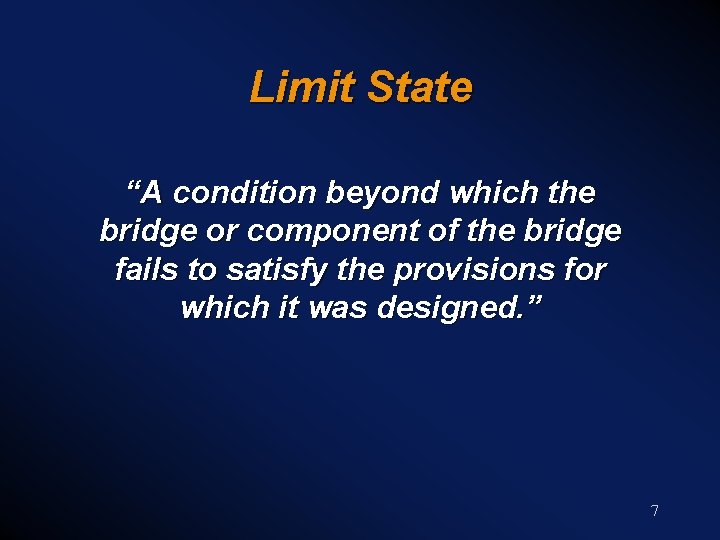
Limit State “A condition beyond which the bridge or component of the bridge fails to satisfy the provisions for which it was designed. ” 7
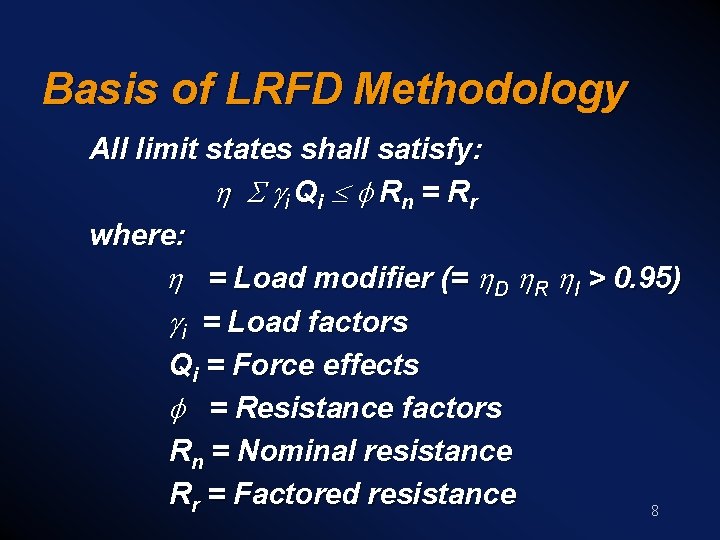
Basis of LRFD Methodology All limit states shall satisfy: h S g i Q i £ f Rn = R r where: h = Load modifier (= h. D h. R h. I > 0. 95) gi = Load factors Qi = Force effects f = Resistance factors Rn = Nominal resistance Rr = Factored resistance 8
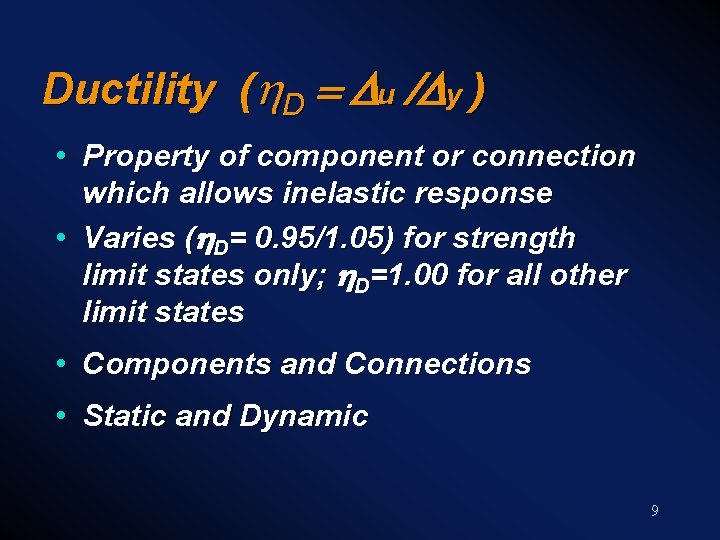
Ductility (h. D = Du /Dy ) • Property of component or connection which allows inelastic response • Varies (h. D= 0. 95/1. 05) for strength limit states only; h. D=1. 00 for all other limit states • Components and Connections • Static and Dynamic 9
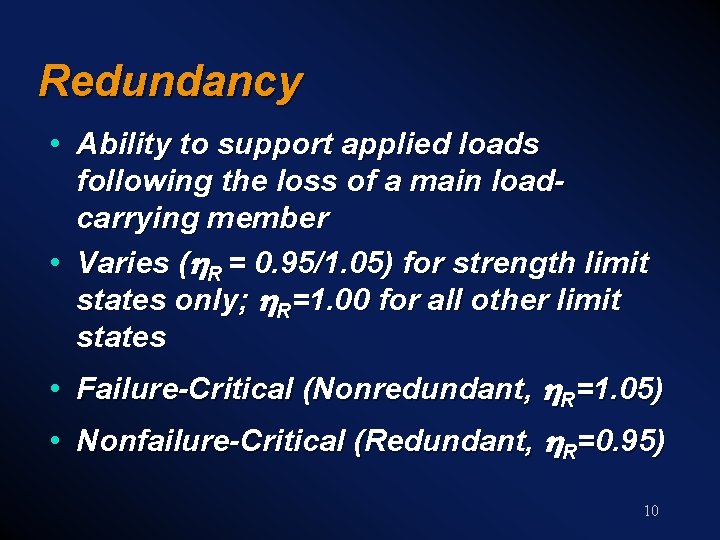
Redundancy • Ability to support applied loads following the loss of a main loadcarrying member • Varies (h. R = 0. 95/1. 05) for strength limit states only; h. R=1. 00 for all other limit states • Failure-Critical (Nonredundant, h. R=1. 05) • Nonfailure-Critical (Redundant, h. R=0. 95) 10
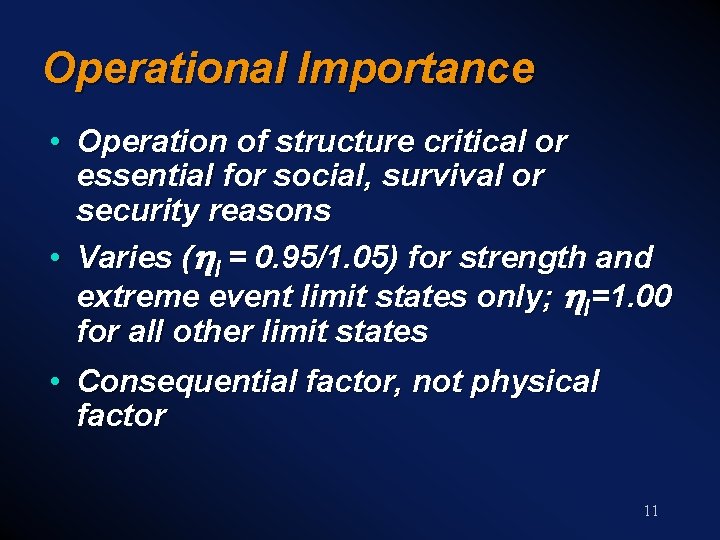
Operational Importance • Operation of structure critical or essential for social, survival or security reasons • Varies (h. I = 0. 95/1. 05) for strength and extreme event limit states only; h. I=1. 00 for all other limit states • Consequential factor, not physical factor 11

Limit States Service: Stress, deformation, and cracking n Fatigue and Fracture: Limit cracking n Strength: Strength and stability n Extreme Event: Period of return greater n than life of structure (e. g. , crash barrier) 12
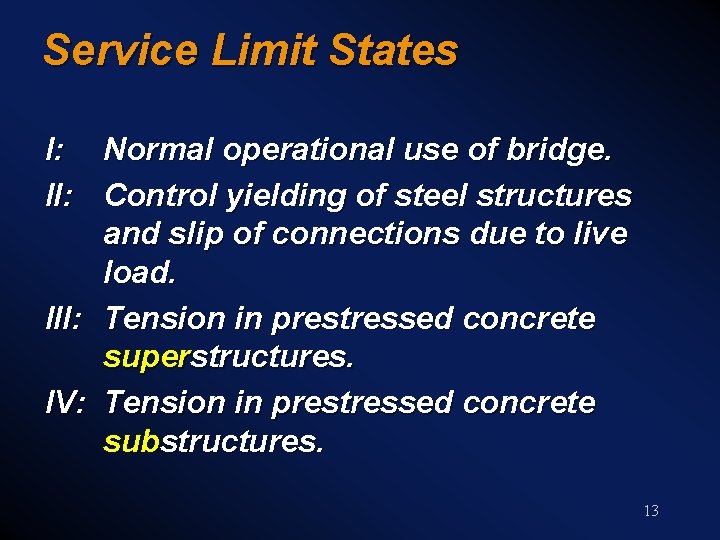
Service Limit States I: Normal operational use of bridge. II: Control yielding of steel structures and slip of connections due to live load. III: Tension in prestressed concrete superstructures. IV: Tension in prestressed concrete substructures. 13
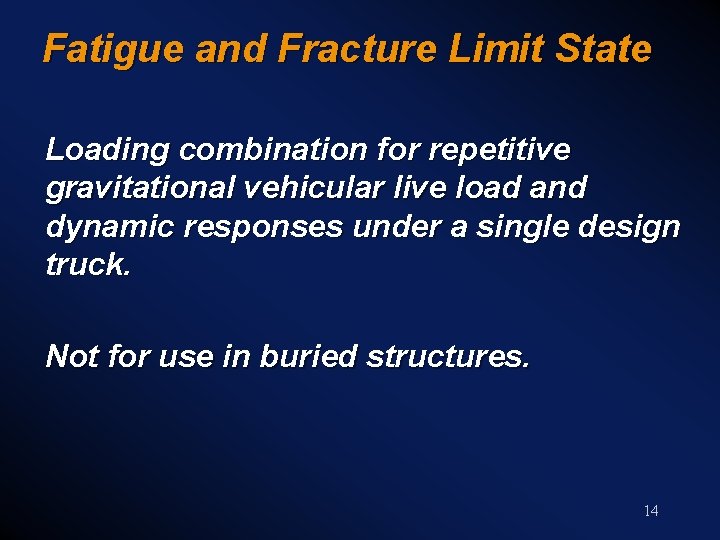
Fatigue and Fracture Limit State Loading combination for repetitive gravitational vehicular live load and dynamic responses under a single design truck. Not for use in buried structures. 14
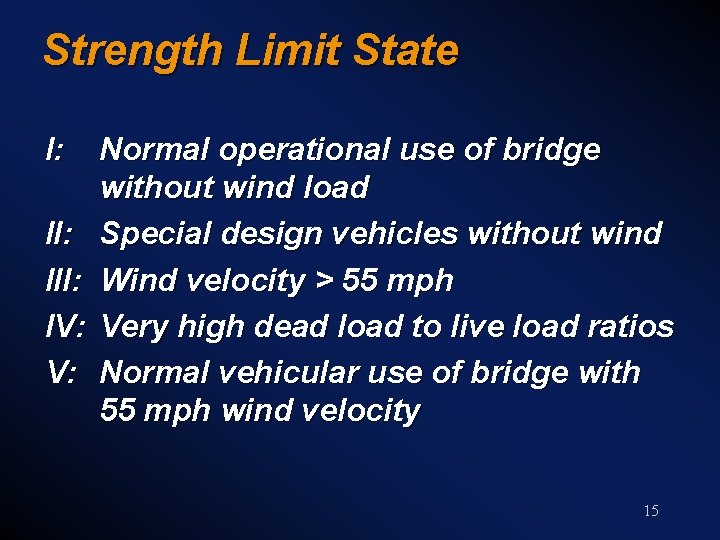
Strength Limit State I: III: IV: V: Normal operational use of bridge without wind load Special design vehicles without wind Wind velocity > 55 mph Very high dead load to live load ratios Normal vehicular use of bridge with 55 mph wind velocity 15
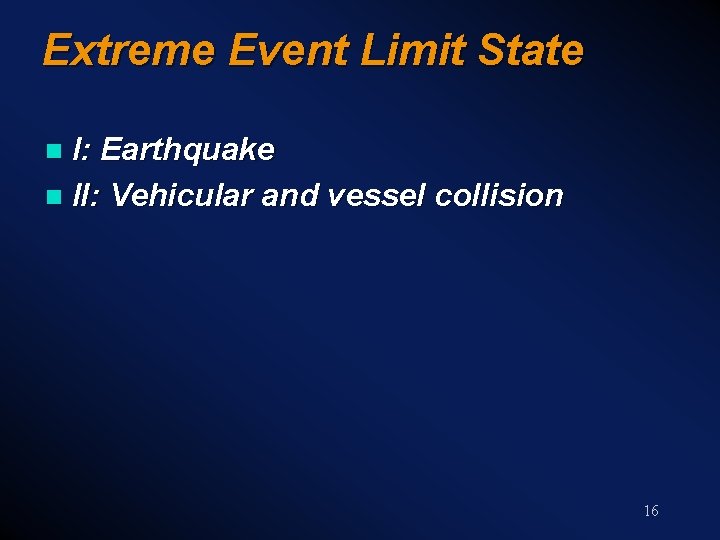
Extreme Event Limit State I: Earthquake n II: Vehicular and vessel collision n 16
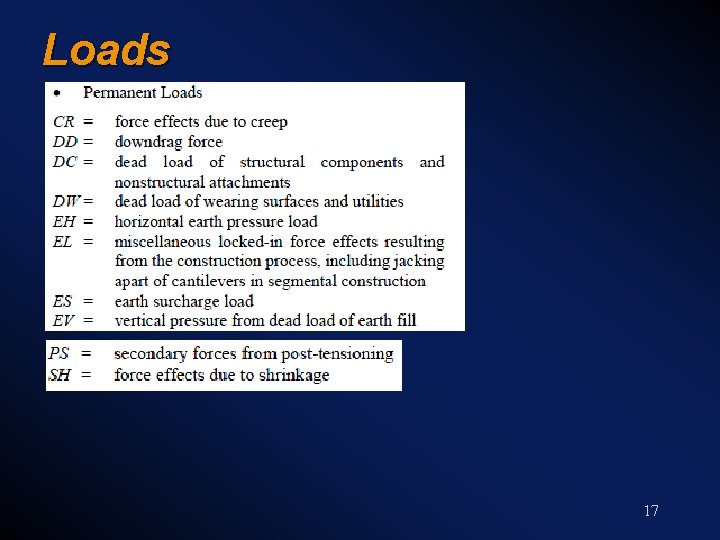
Loads 17
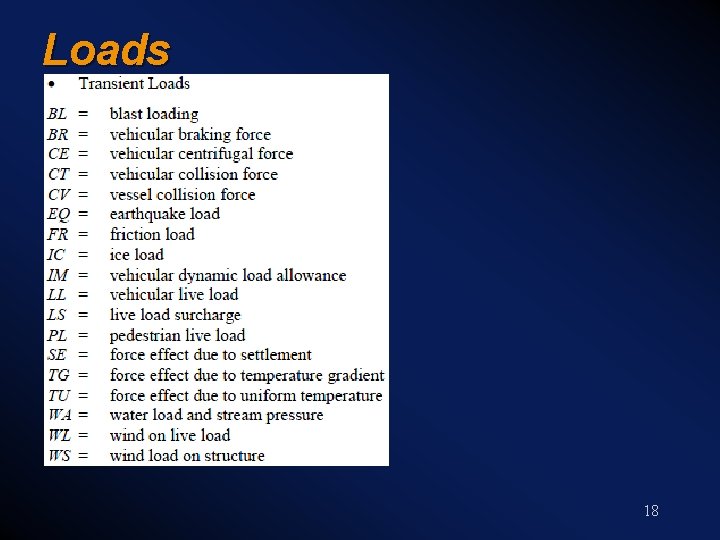
Loads 18
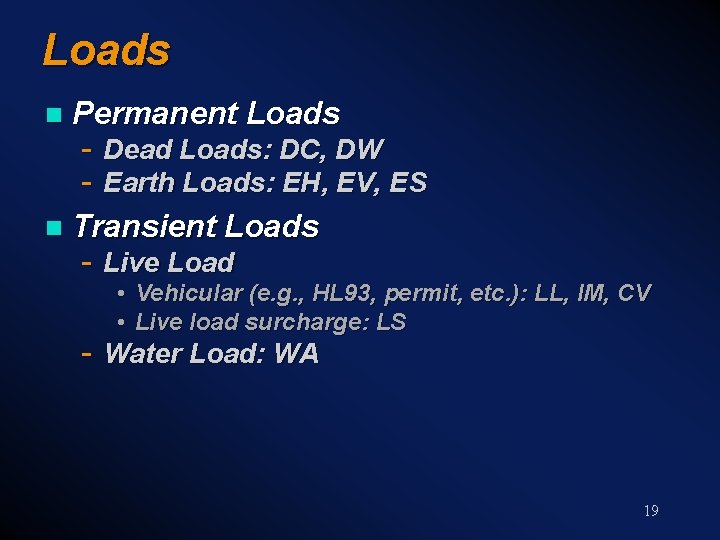
Loads n Permanent Loads n Transient Loads - Dead Loads: DC, DW - Earth Loads: EH, EV, ES - Live Load • Vehicular (e. g. , HL 93, permit, etc. ): LL, IM, CV • Live load surcharge: LS - Water Load: WA 19
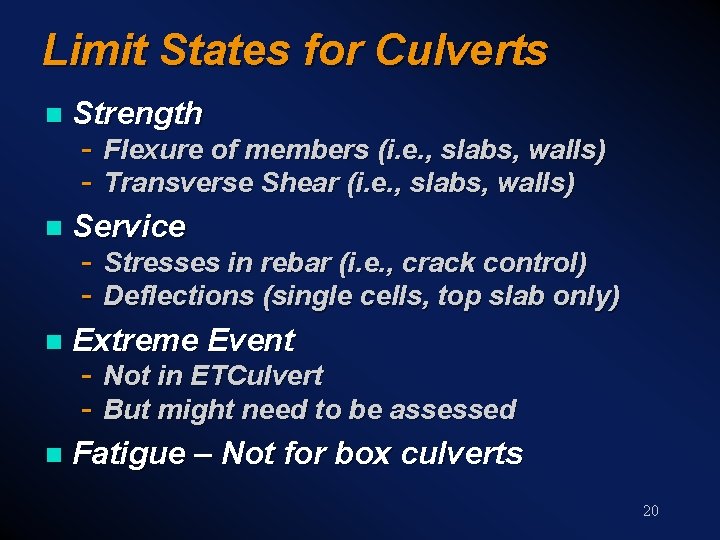
Limit States for Culverts n Strength n Service n Extreme Event n Fatigue – Not for box culverts - Flexure of members (i. e. , slabs, walls) - Transverse Shear (i. e. , slabs, walls) - Stresses in rebar (i. e. , crack control) - Deflections (single cells, top slab only) - Not in ETCulvert - But might need to be assessed 20
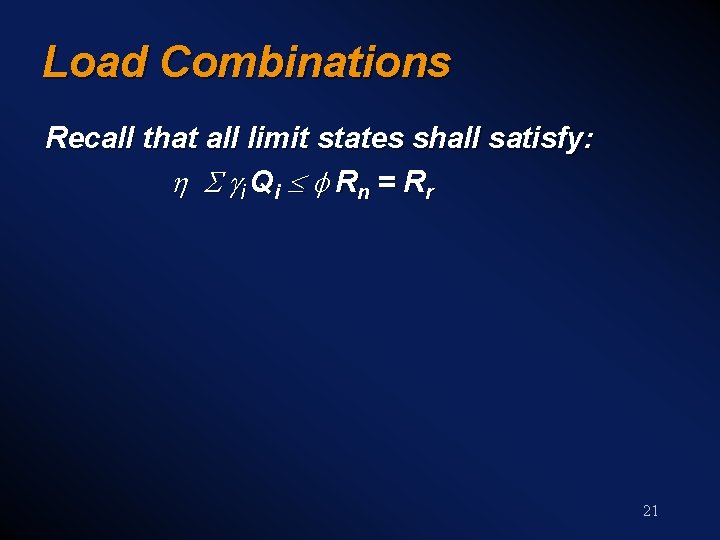
Load Combinations Recall that all limit states shall satisfy: h S g i Q i £ f Rn = R r 21
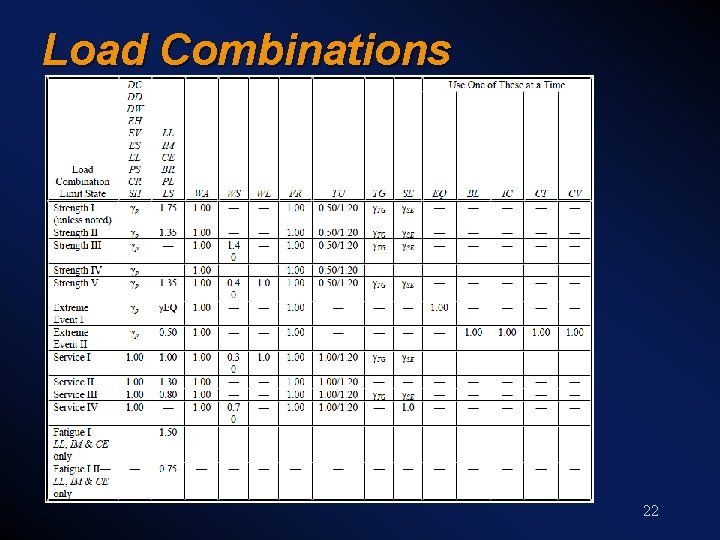
Load Combinations 22
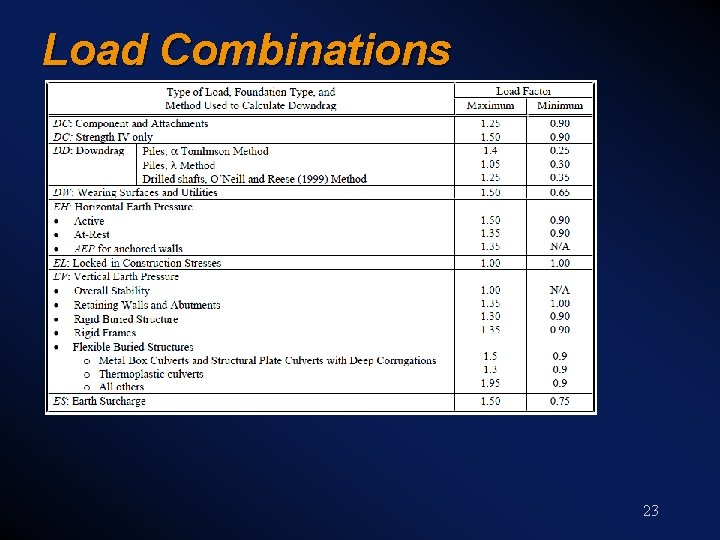
Load Combinations 23
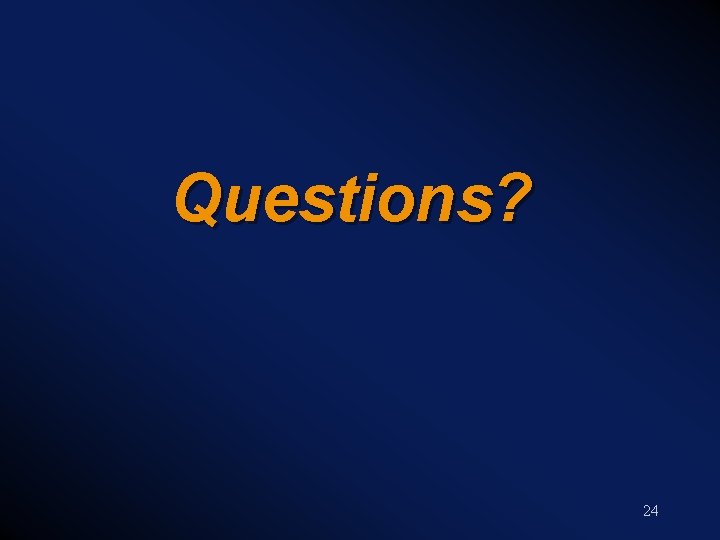
Questions? 24
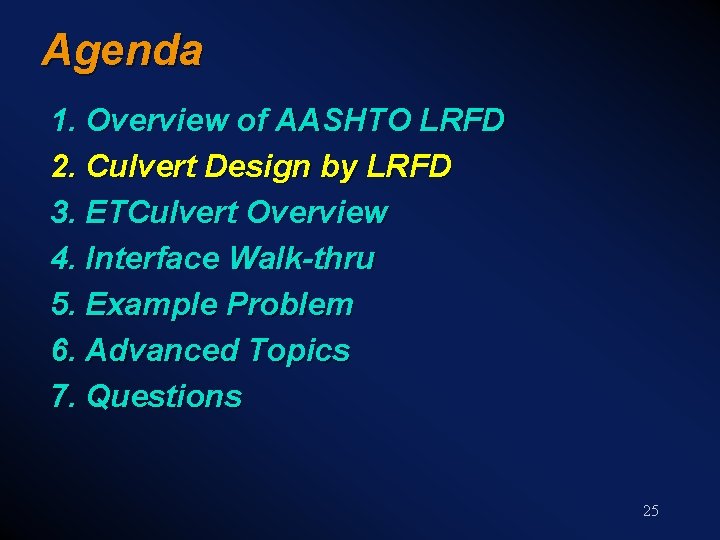
Agenda 1. Overview of AASHTO LRFD 2. Culvert Design by LRFD 3. ETCulvert Overview 4. Interface Walk-thru 5. Example Problem 6. Advanced Topics 7. Questions 25
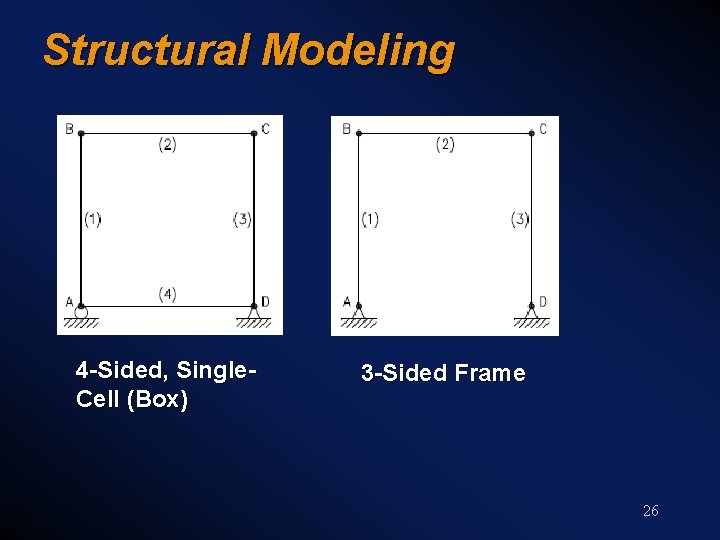
Structural Modeling 4 -Sided, Single. Cell (Box) 3 -Sided Frame 26
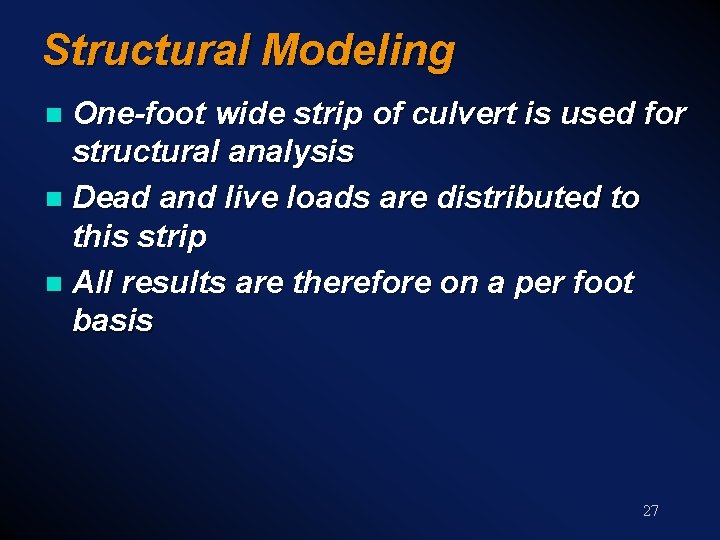
Structural Modeling One-foot wide strip of culvert is used for structural analysis n Dead and live loads are distributed to this strip n All results are therefore on a per foot basis n 27
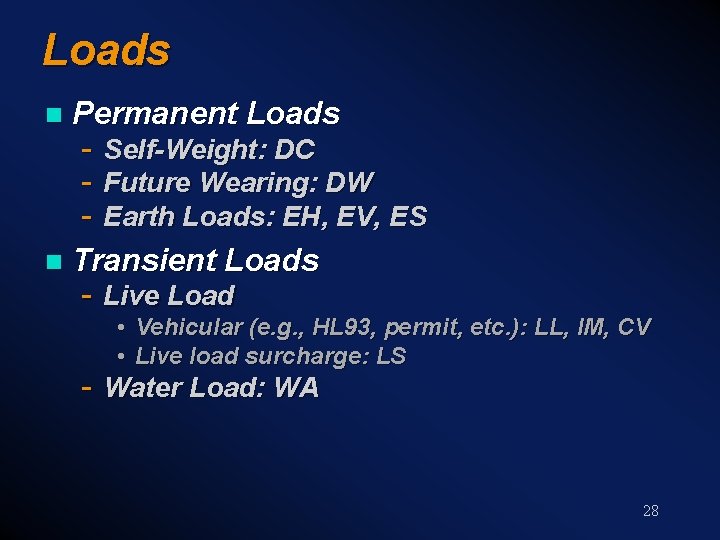
Loads n Permanent Loads n Transient Loads - Self-Weight: DC - Future Wearing: DW - Earth Loads: EH, EV, ES - Live Load • • Vehicular (e. g. , HL 93, permit, etc. ): LL, IM, CV Live load surcharge: LS - Water Load: WA 28
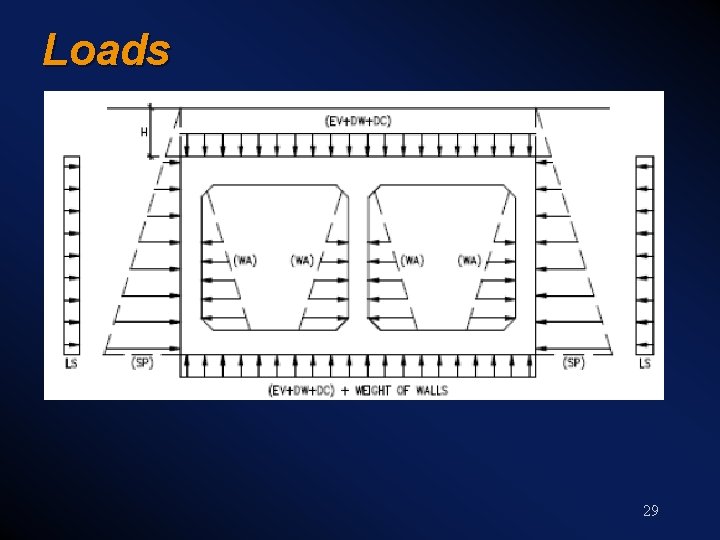
Loads 29
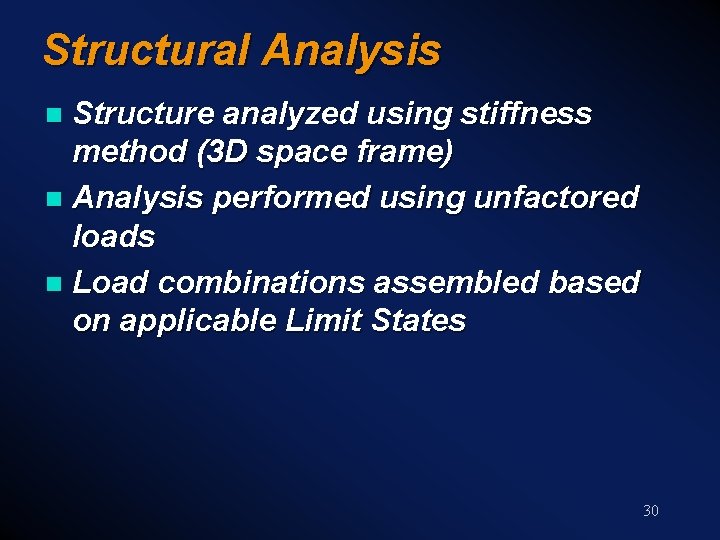
Structural Analysis Structure analyzed using stiffness method (3 D space frame) n Analysis performed using unfactored loads n Load combinations assembled based on applicable Limit States n 30
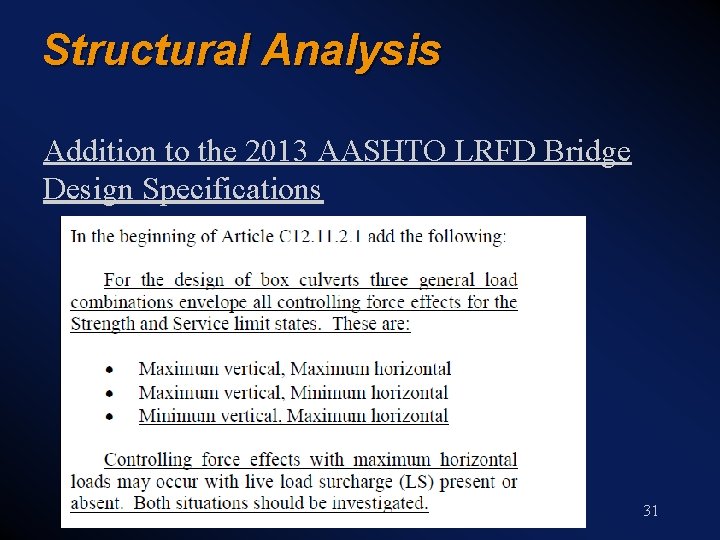
Structural Analysis Addition to the 2013 AASHTO LRFD Bridge Design Specifications 31

Must Assess/Check: Flexure n Shear n Stresses in Rebar n Deflections n 32
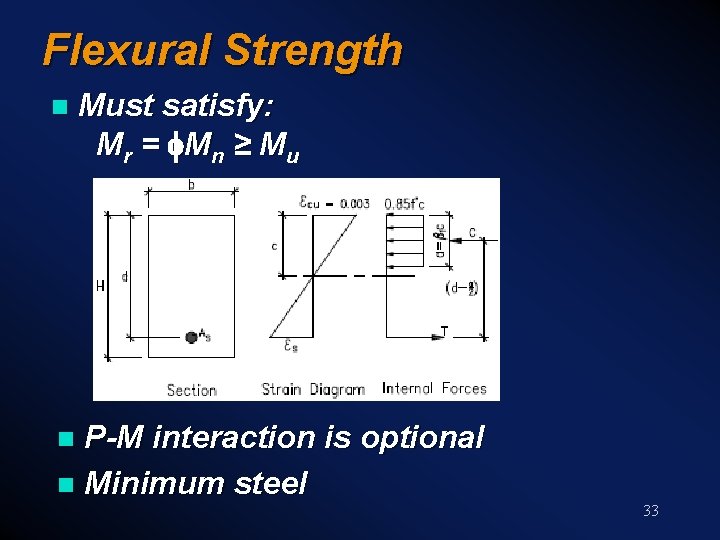
Flexural Strength n Must satisfy: M r = Mn ≥ M u P-M interaction is optional n Minimum steel n 33
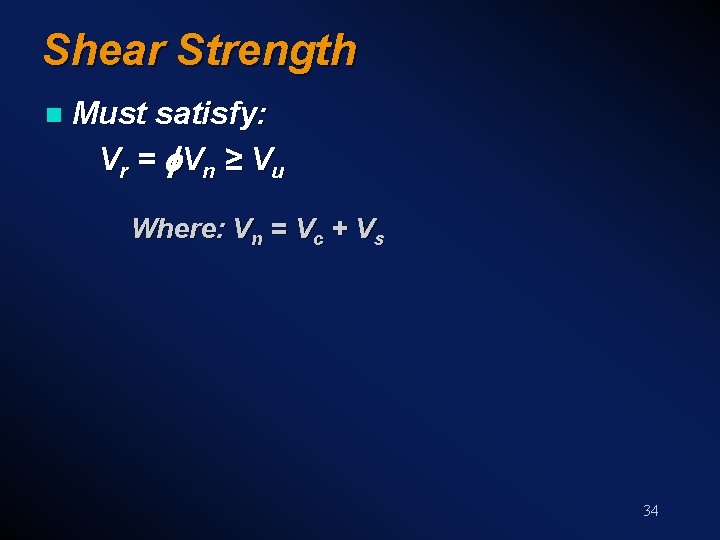
Shear Strength n Must satisfy: V r = Vn ≥ V u Where: Vn = Vc + Vs 34
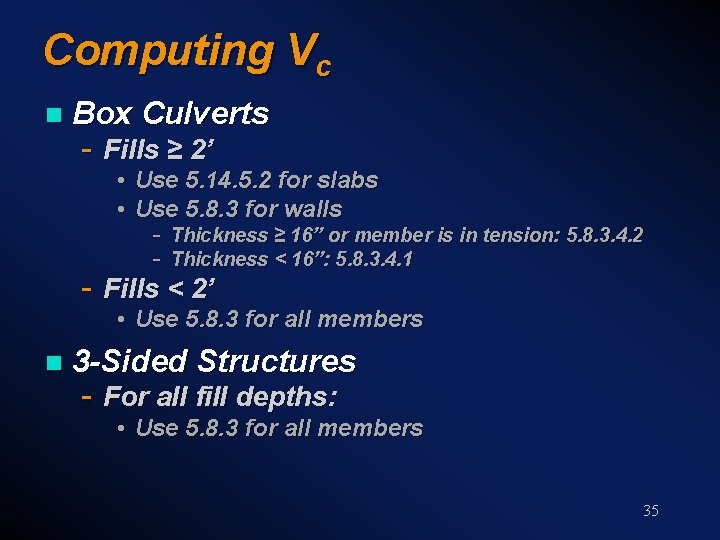
Computing Vc n Box Culverts - Fills ≥ 2’ • Use 5. 14. 5. 2 for slabs • Use 5. 8. 3 for walls - Thickness ≥ 16” or member is in tension: 5. 8. 3. 4. 2 - Thickness < 16”: 5. 8. 3. 4. 1 - Fills < 2’ • Use 5. 8. 3 for all members n 3 -Sided Structures - For all fill depths: • Use 5. 8. 3 for all members 35
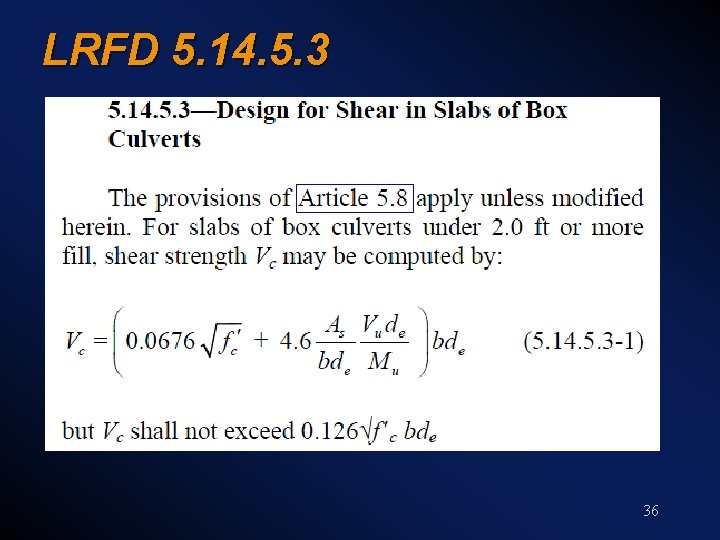
LRFD 5. 14. 5. 3 36
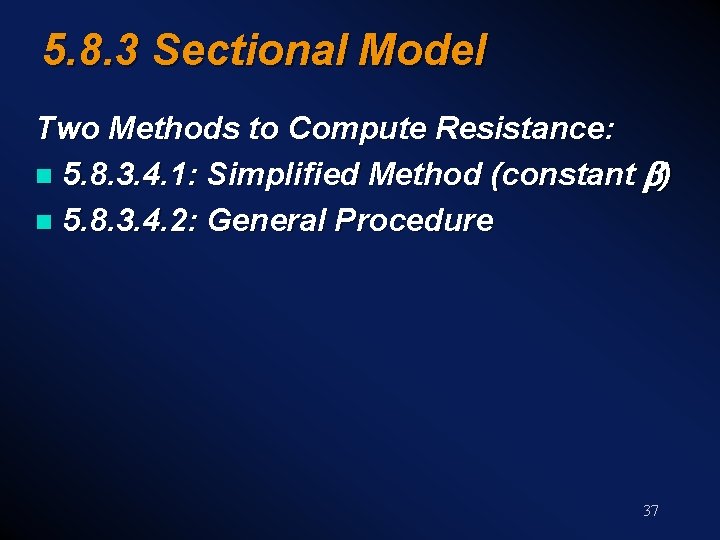
5. 8. 3 Sectional Model Two Methods to Compute Resistance: n 5. 8. 3. 4. 1: Simplified Method (constant b) n 5. 8. 3. 4. 2: General Procedure 37
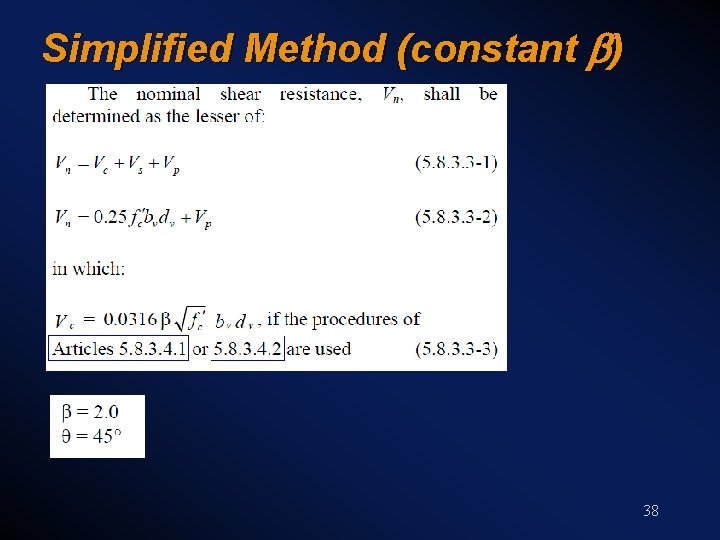
Simplified Method (constant b) 38
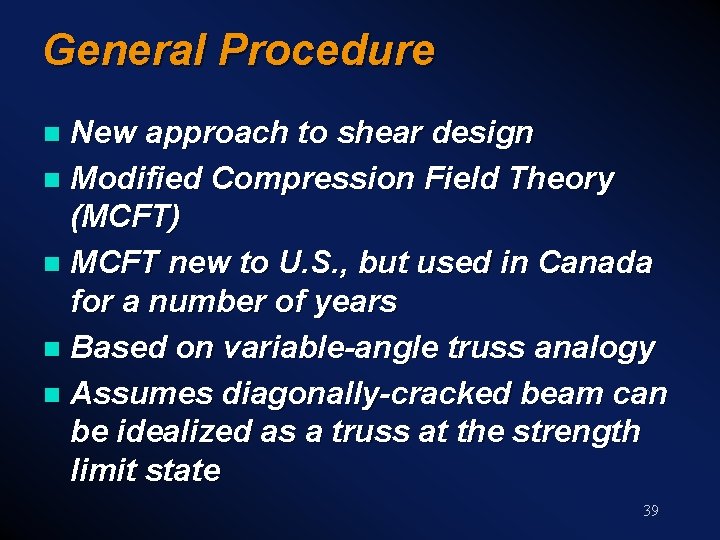
General Procedure New approach to shear design n Modified Compression Field Theory (MCFT) n MCFT new to U. S. , but used in Canada for a number of years n Based on variable-angle truss analogy n Assumes diagonally-cracked beam can be idealized as a truss at the strength limit state n 39
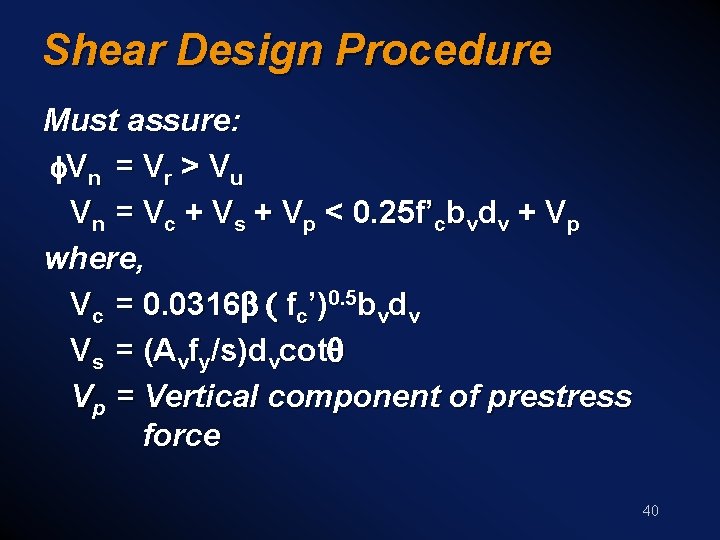
Shear Design Procedure Must assure: Vn = V r > V u Vn = Vc + Vs + Vp < 0. 25 f’cbvdv + Vp where, Vc = 0. 0316 b ( fc’)0. 5 bvdv Vs = (Avfy/s)dvcotq Vp = Vertical component of prestress force 40
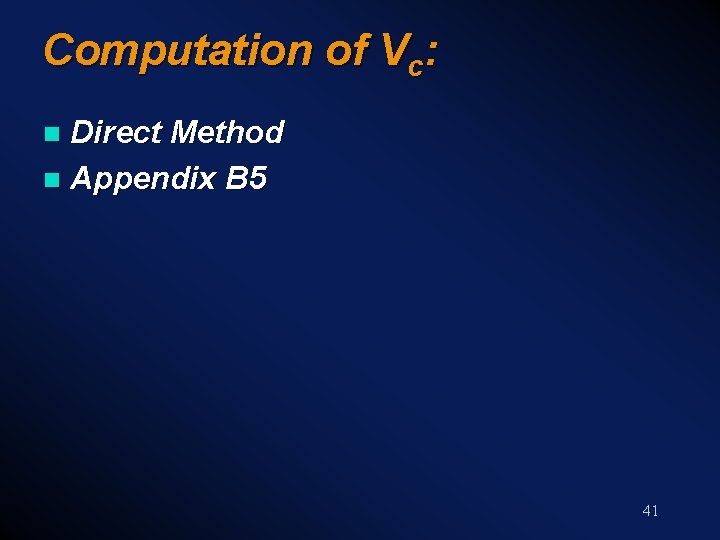
Computation of Vc: Direct Method n Appendix B 5 n 41
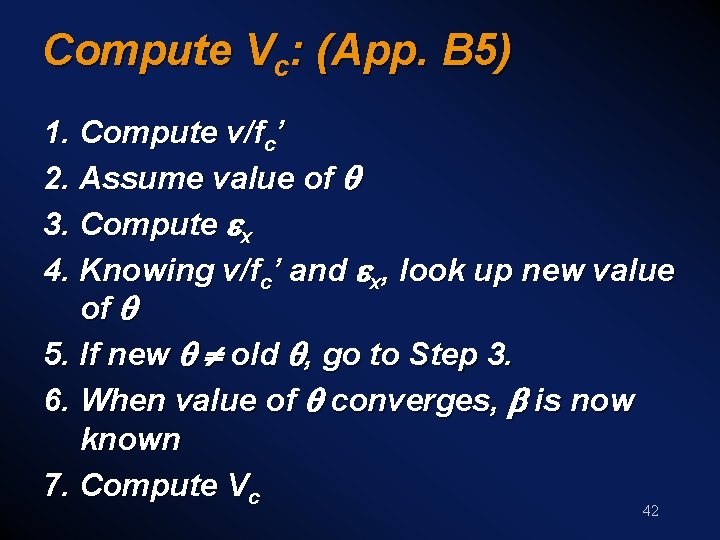
Compute Vc: (App. B 5) 1. Compute v/fc’ 2. Assume value of q 3. Compute ex 4. Knowing v/fc’ and ex, look up new value of q 5. If new q ¹ old q, go to Step 3. 6. When value of q converges, b is now known 7. Compute Vc 42

Concrete Shear Stress (v) Shear stress on the concrete is computed by: 43
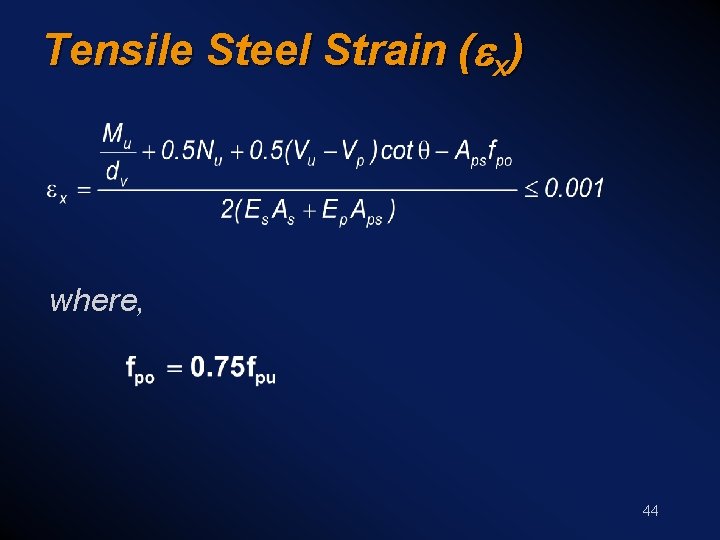
Tensile Steel Strain (ex) where, 44
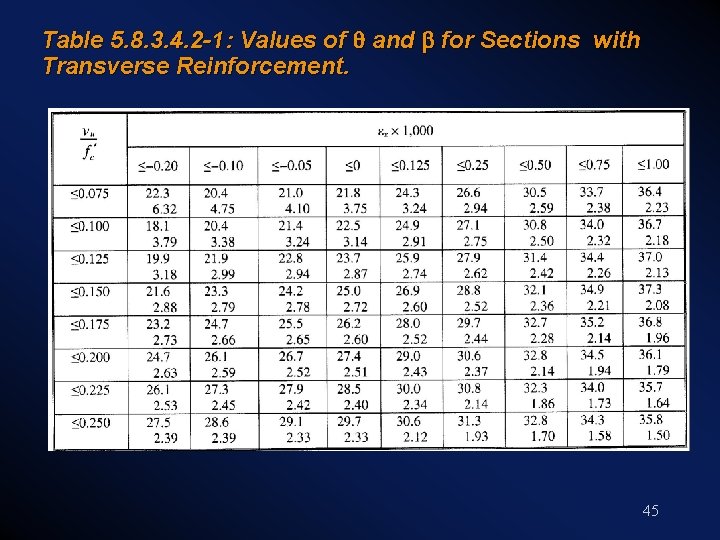
Table 5. 8. 3. 4. 2 -1: Values of q and b for Sections with Transverse Reinforcement. 45
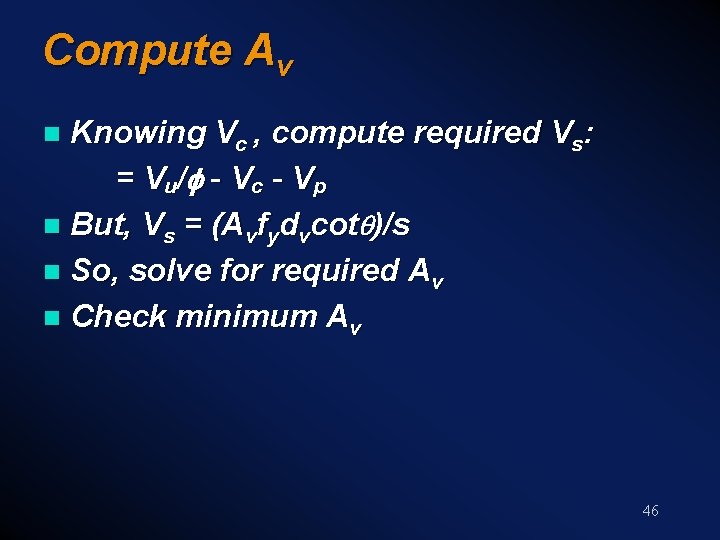
Compute Av Knowing Vc , compute required Vs: = V u/ - V c - V p n But, Vs = (Avfydvcotq)/s n So, solve for required Av n Check minimum Av n 46
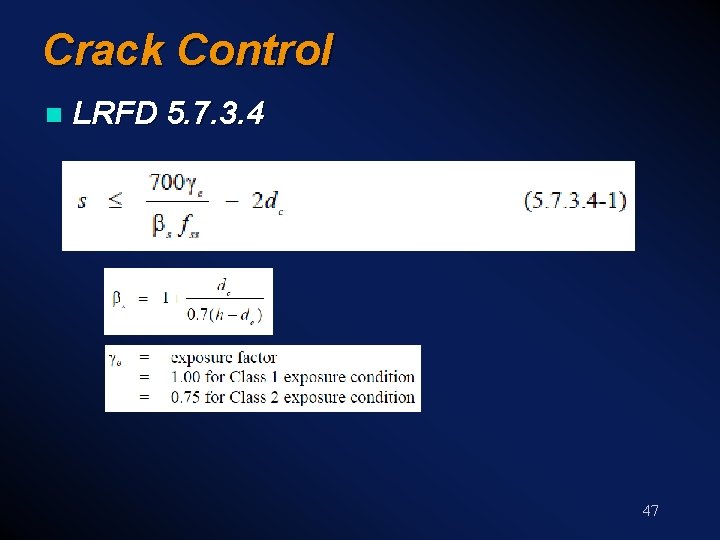
Crack Control n LRFD 5. 7. 3. 4 47
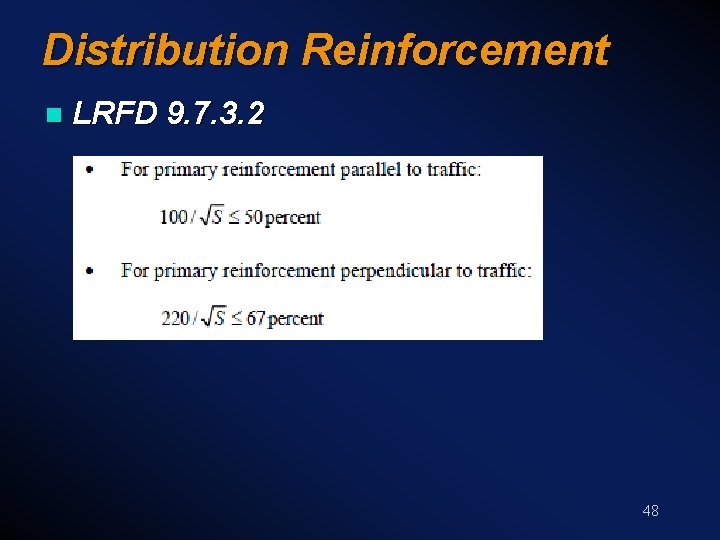
Distribution Reinforcement n LRFD 9. 7. 3. 2 48
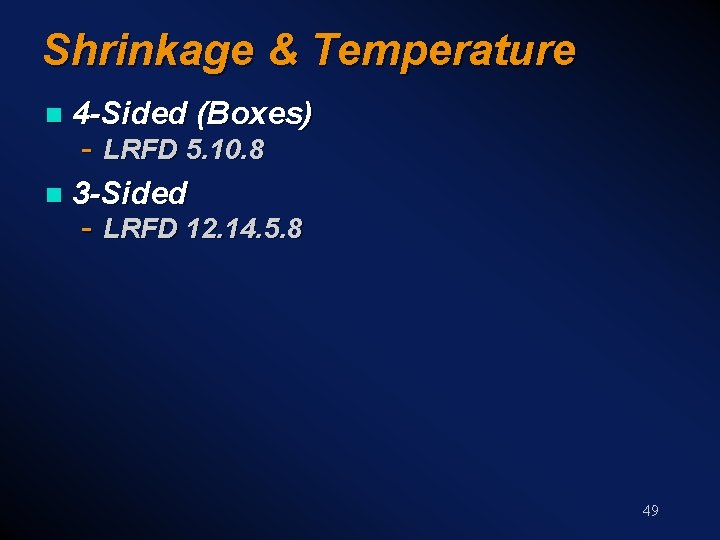
Shrinkage & Temperature n 4 -Sided (Boxes) n 3 -Sided - LRFD 5. 10. 8 - LRFD 12. 14. 5. 8 49
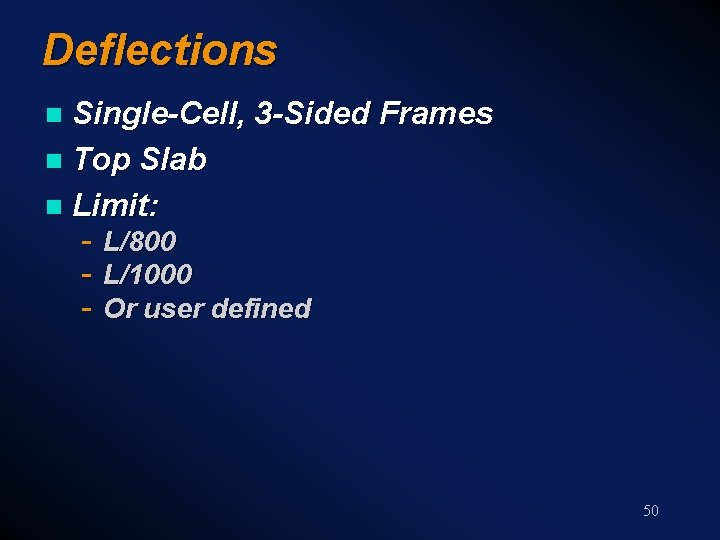
Deflections Single-Cell, 3 -Sided Frames n Top Slab n Limit: n - L/800 - L/1000 - Or user defined 50
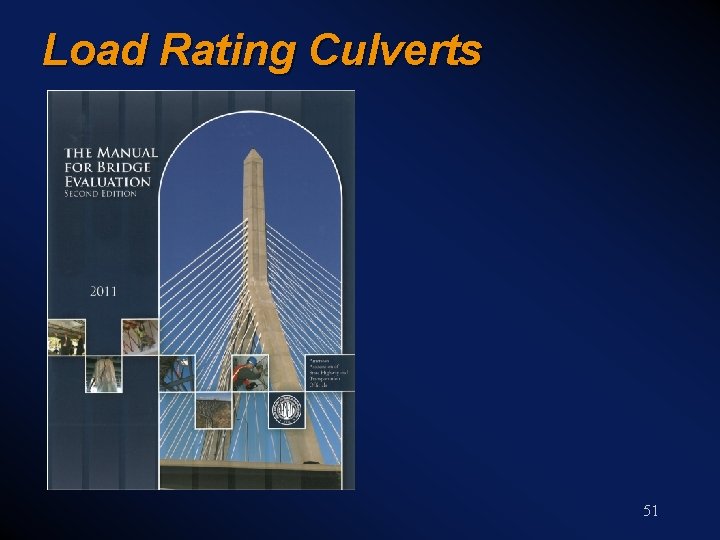
Load Rating Culverts 51
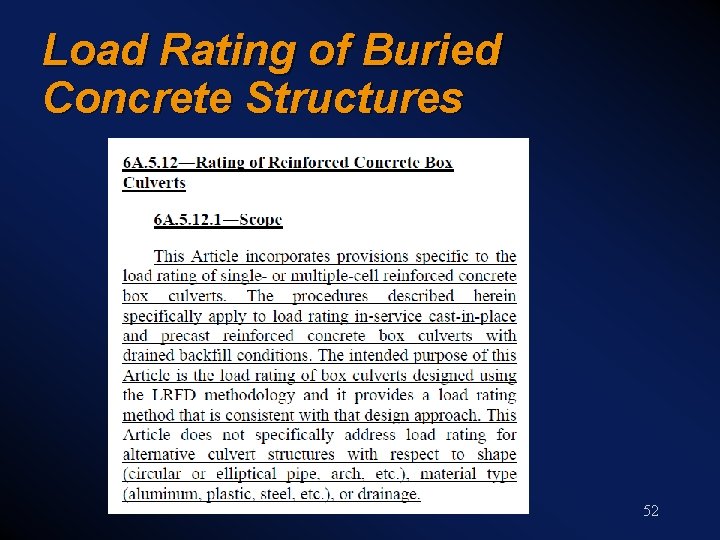
Load Rating of Buried Concrete Structures 52
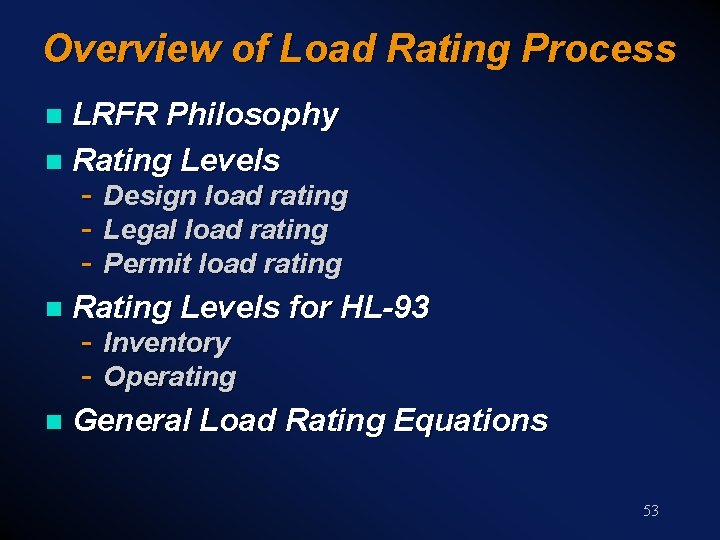
Overview of Load Rating Process LRFR Philosophy n Rating Levels n - Design load rating - Legal load rating - Permit load rating n Rating Levels for HL-93 n General Load Rating Equations - Inventory - Operating 53
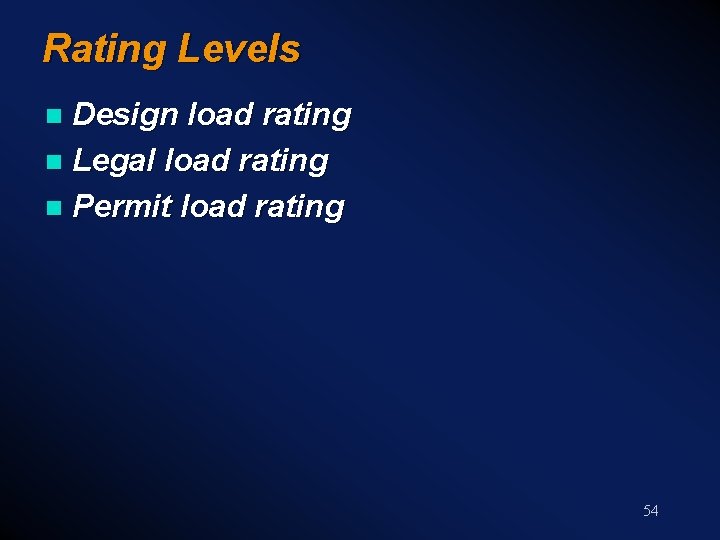
Rating Levels Design load rating n Legal load rating n Permit load rating n 54
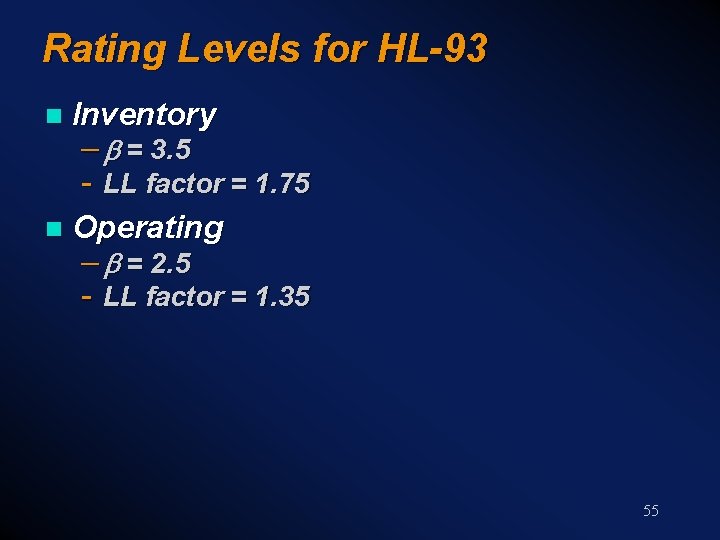
Rating Levels for HL-93 n Inventory n Operating - b = 3. 5 - LL factor = 1. 75 - b = 2. 5 - LL factor = 1. 35 55
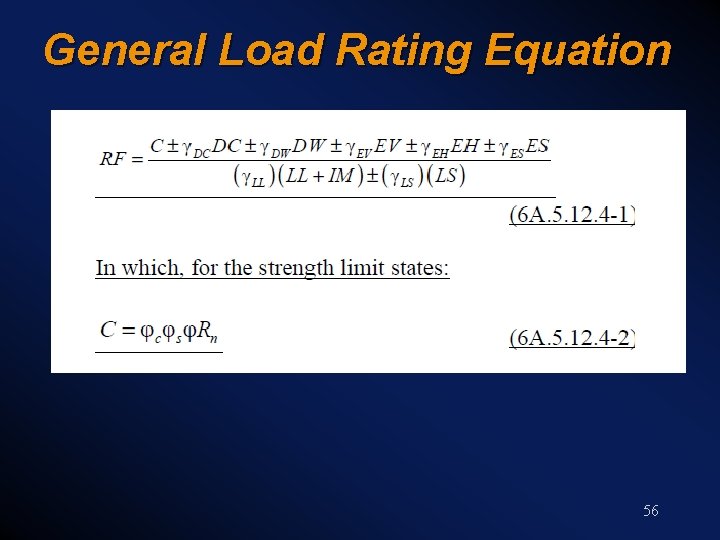
General Load Rating Equation 56
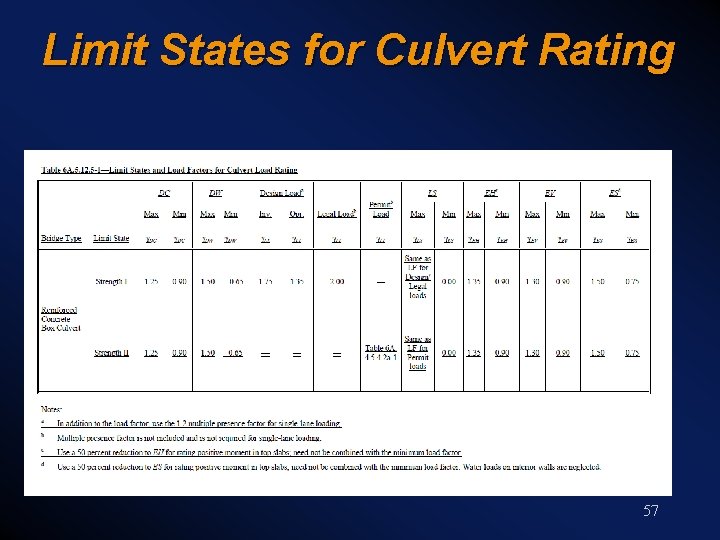
Limit States for Culvert Rating 57
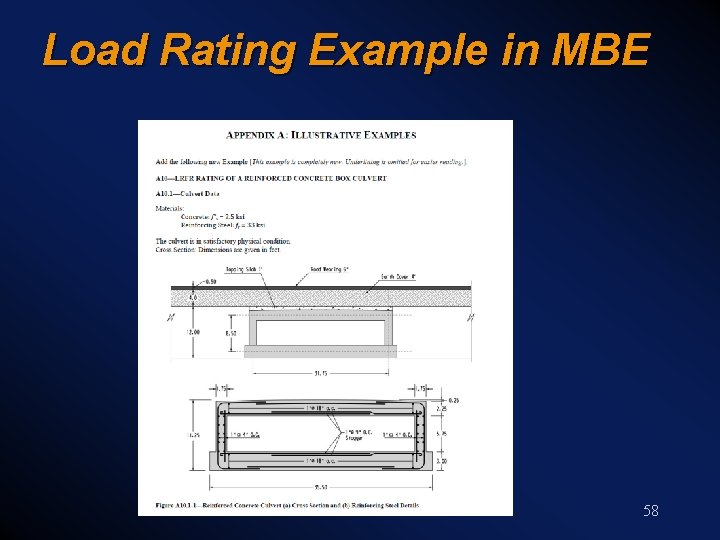
Load Rating Example in MBE 58
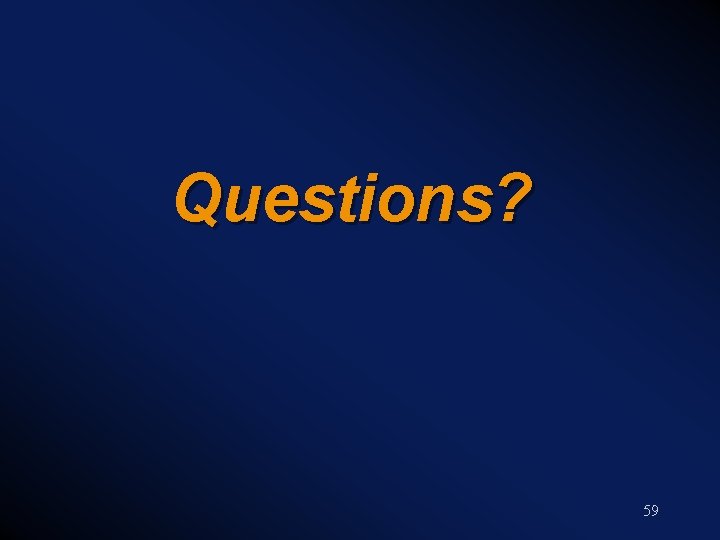
Questions? 59
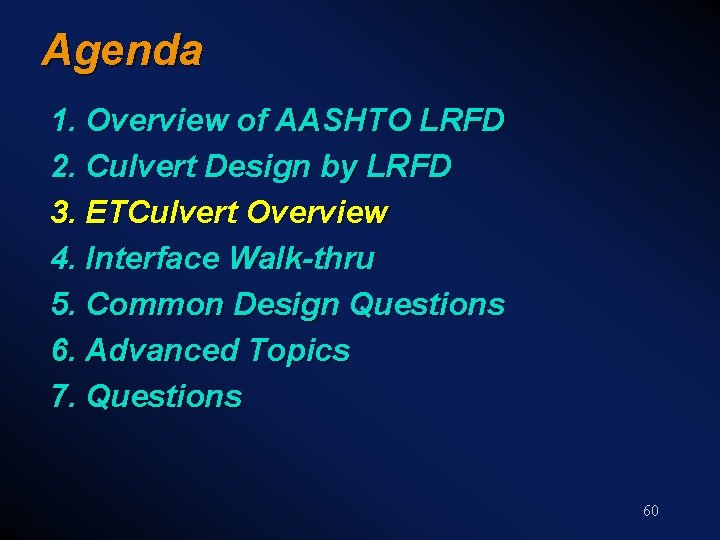
Agenda 1. Overview of AASHTO LRFD 2. Culvert Design by LRFD 3. ETCulvert Overview 4. Interface Walk-thru 5. Common Design Questions 6. Advanced Topics 7. Questions 60
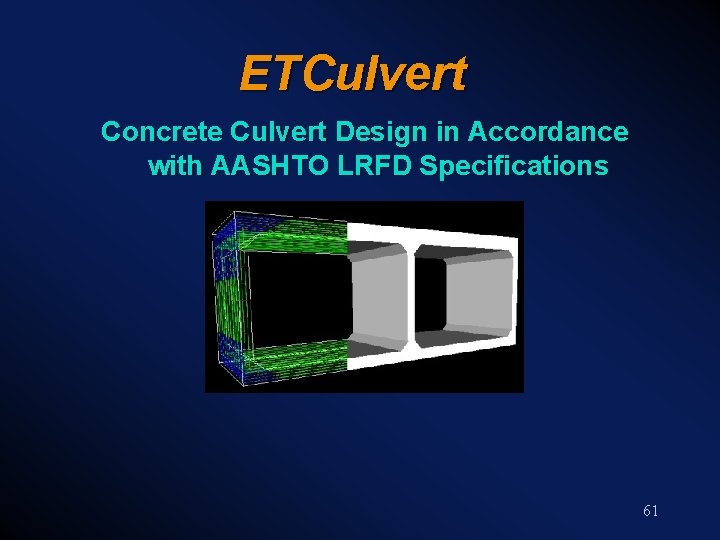
ETCulvert Concrete Culvert Design in Accordance with AASHTO LRFD Specifications 61
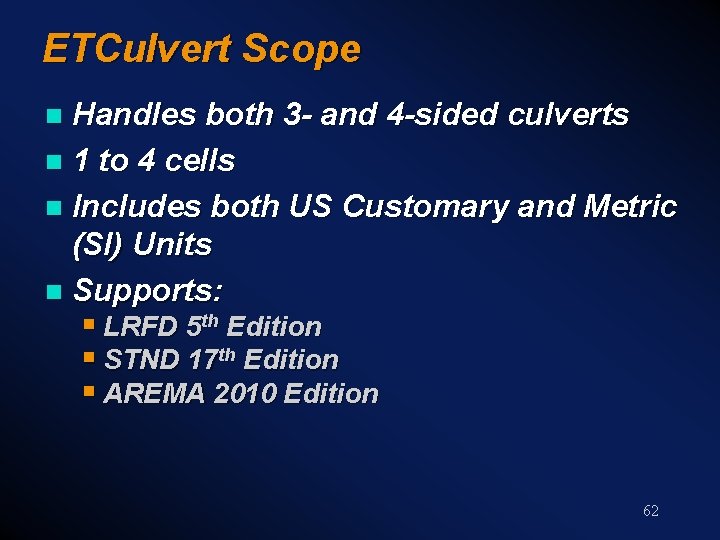
ETCulvert Scope Handles both 3 - and 4 -sided culverts n 1 to 4 cells n Includes both US Customary and Metric (SI) Units n Supports: n § LRFD 5 th Edition § STND 17 th Edition § AREMA 2010 Edition 62
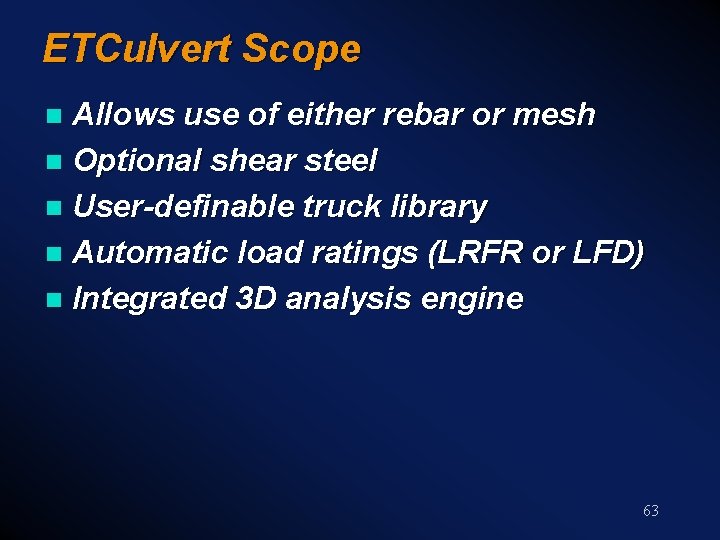
ETCulvert Scope Allows use of either rebar or mesh n Optional shear steel n User-definable truck library n Automatic load ratings (LRFR or LFD) n Integrated 3 D analysis engine n 63
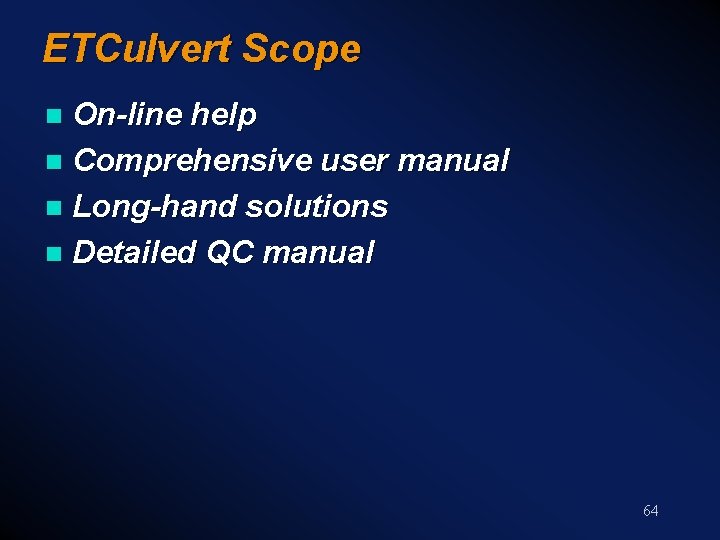
ETCulvert Scope On-line help n Comprehensive user manual n Long-hand solutions n Detailed QC manual n 64
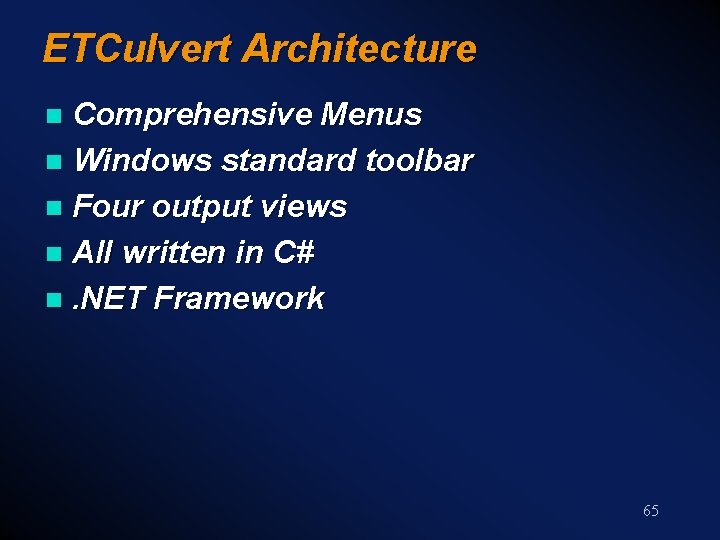
ETCulvert Architecture Comprehensive Menus n Windows standard toolbar n Four output views n All written in C# n. NET Framework n 65
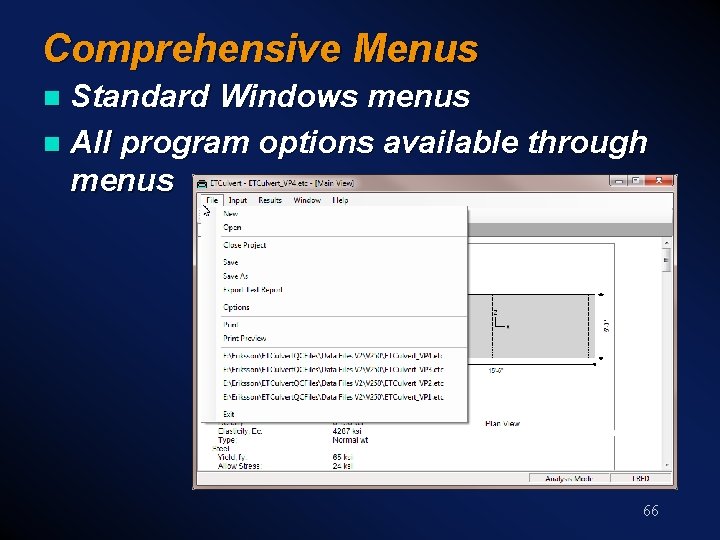
Comprehensive Menus Standard Windows menus n All program options available through menus n 66
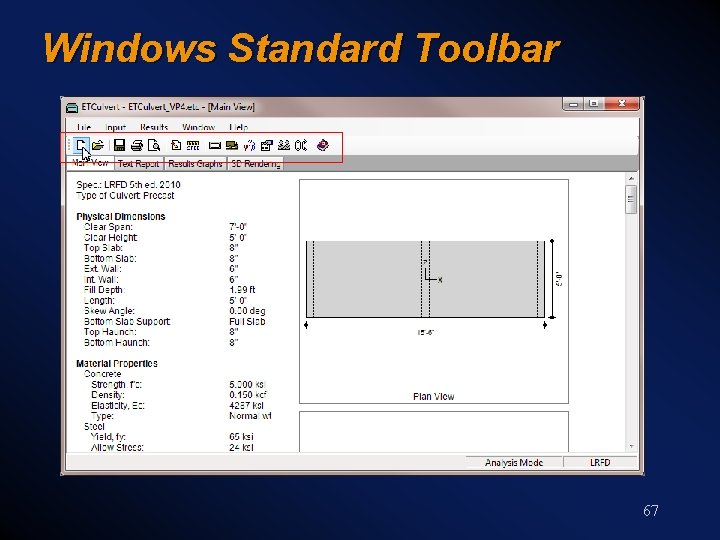
Windows Standard Toolbar 67
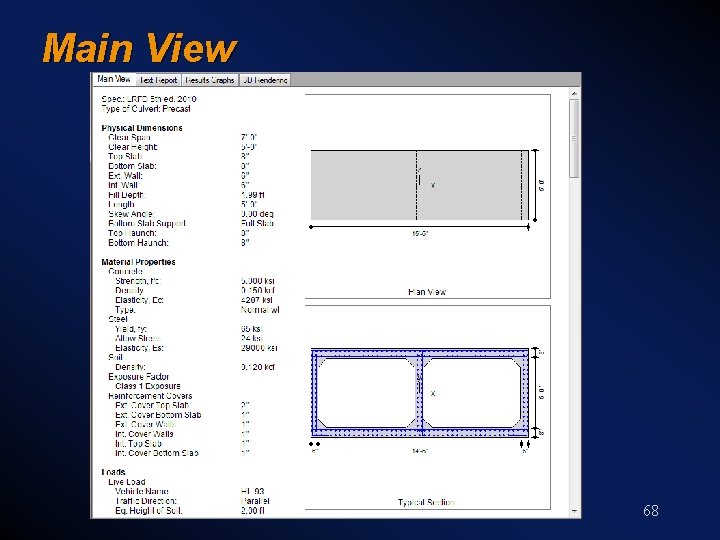
Main View 68
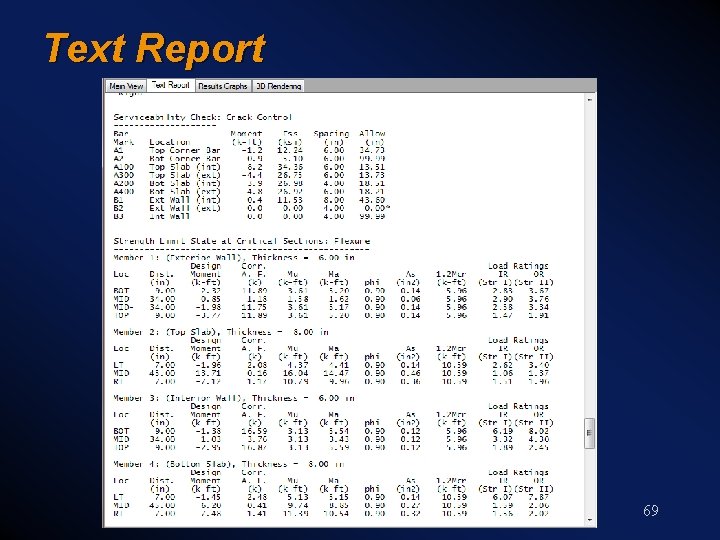
Text Report 69
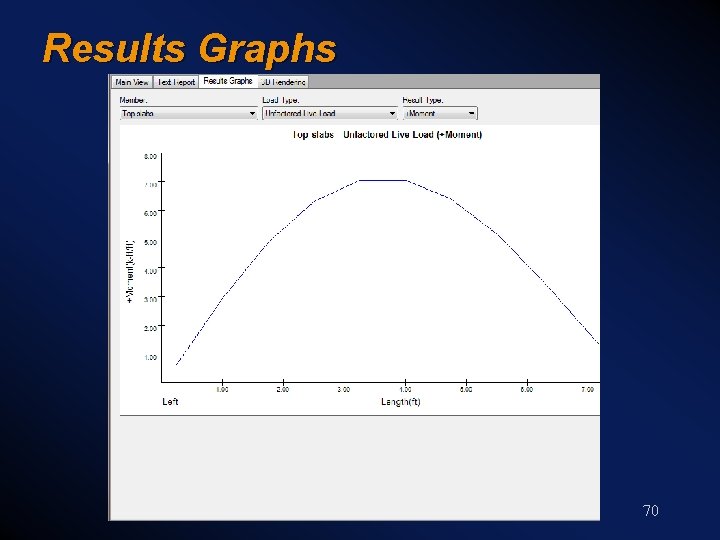
Results Graphs 70
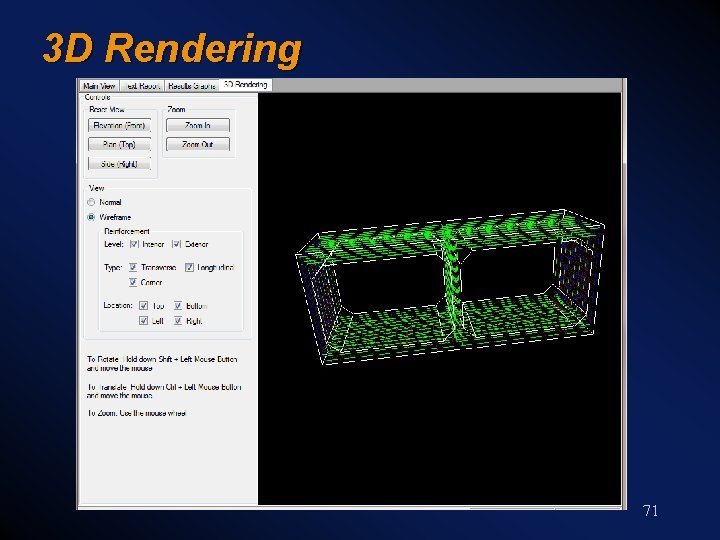
3 D Rendering 71
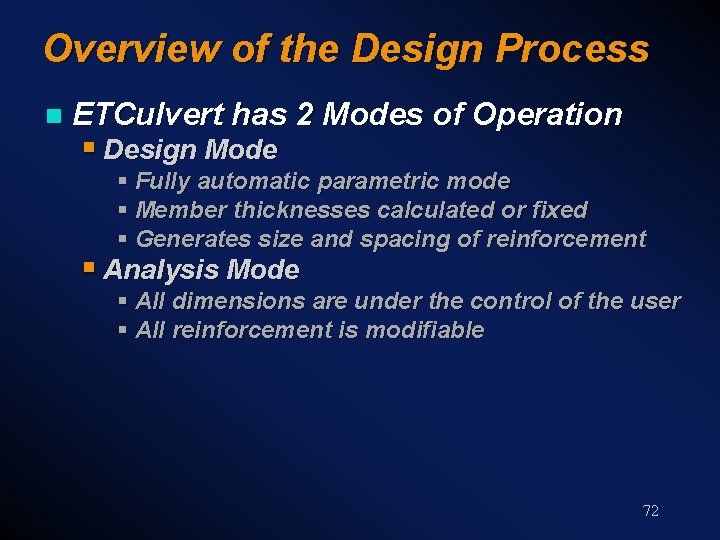
Overview of the Design Process n ETCulvert has 2 Modes of Operation § Design Mode § Fully automatic parametric mode § Member thicknesses calculated or fixed § Generates size and spacing of reinforcement § Analysis Mode § All dimensions are under the control of the user § All reinforcement is modifiable 72
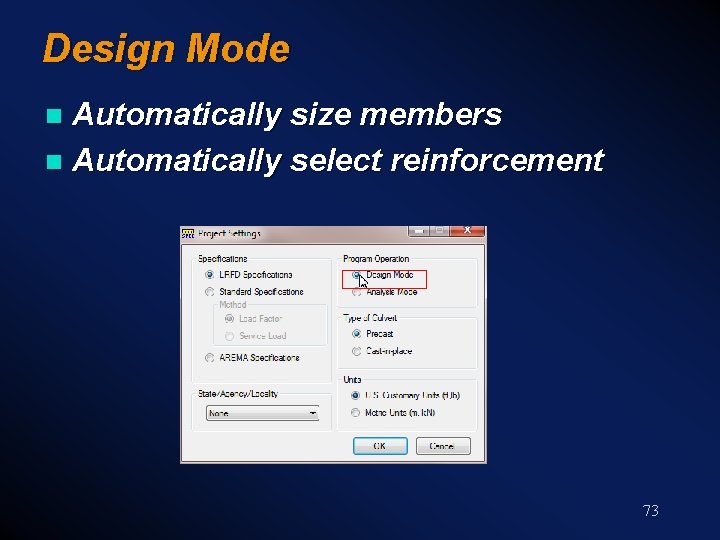
Design Mode Automatically size members n Automatically select reinforcement n 73
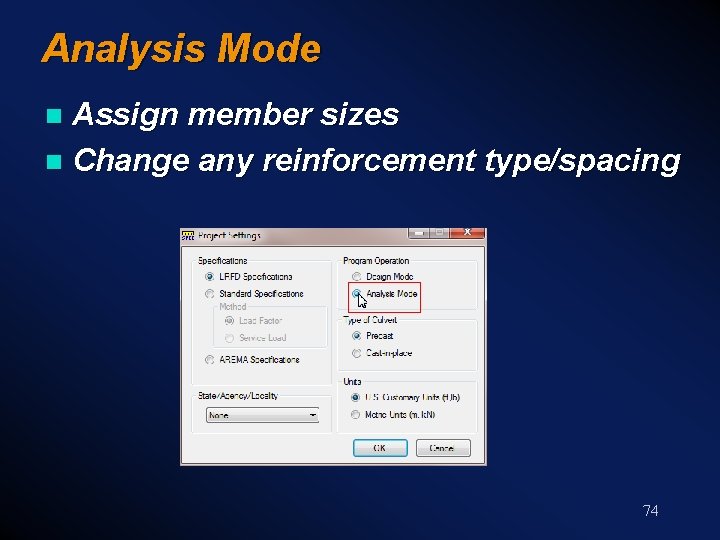
Analysis Mode Assign member sizes n Change any reinforcement type/spacing n 74
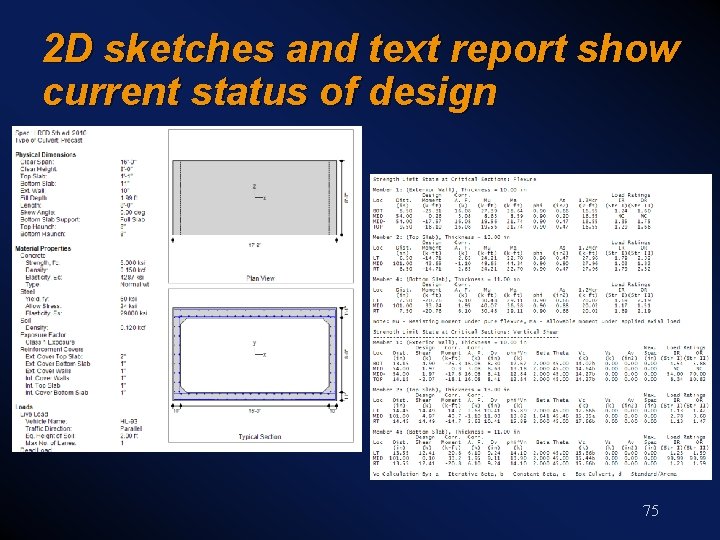
2 D sketches and text report show current status of design 75
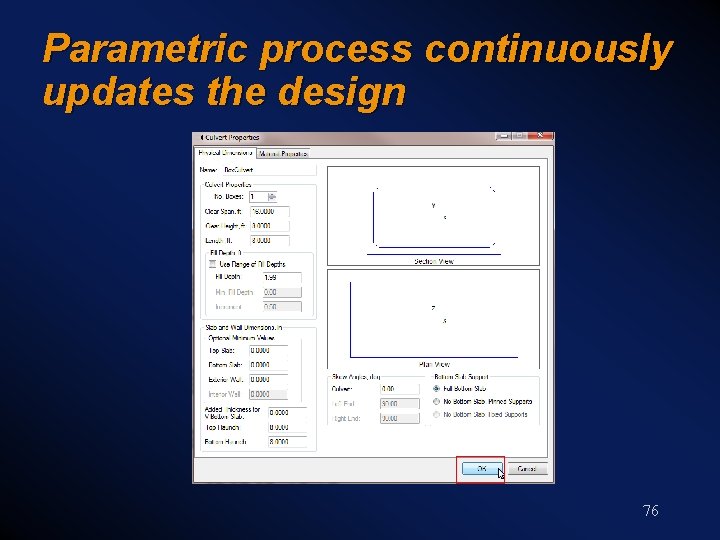
Parametric process continuously updates the design 76
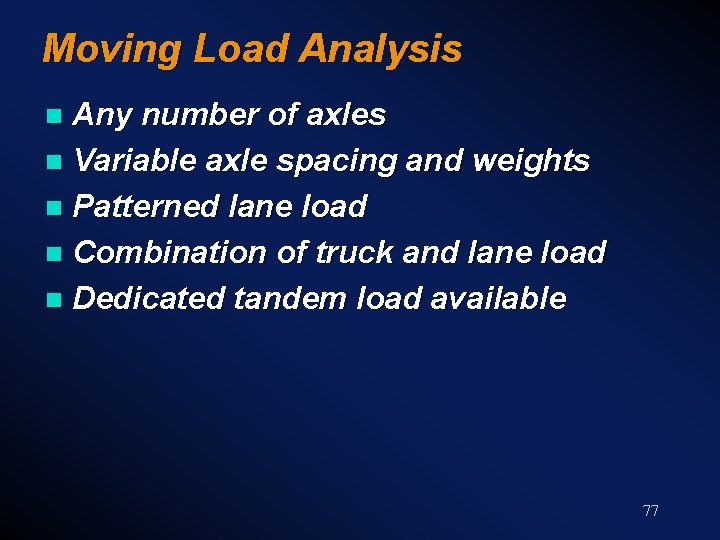
Moving Load Analysis Any number of axles n Variable axle spacing and weights n Patterned lane load n Combination of truck and lane load n Dedicated tandem load available n 77
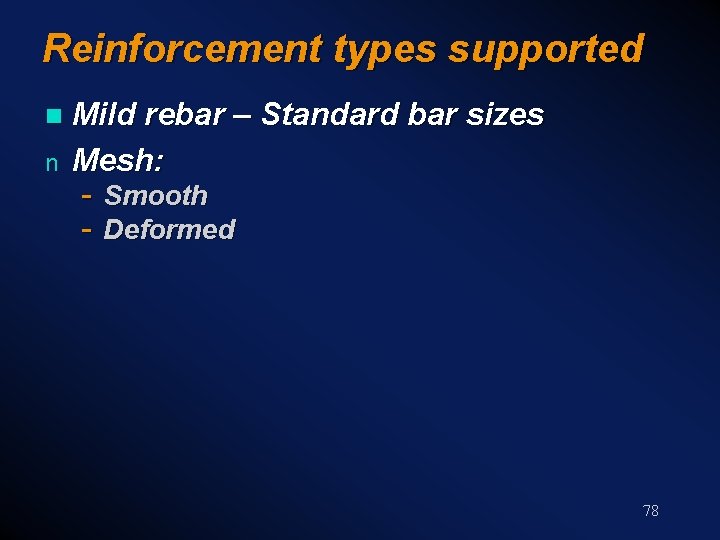
Reinforcement types supported n n Mild rebar – Standard bar sizes Mesh: - Smooth - Deformed 78
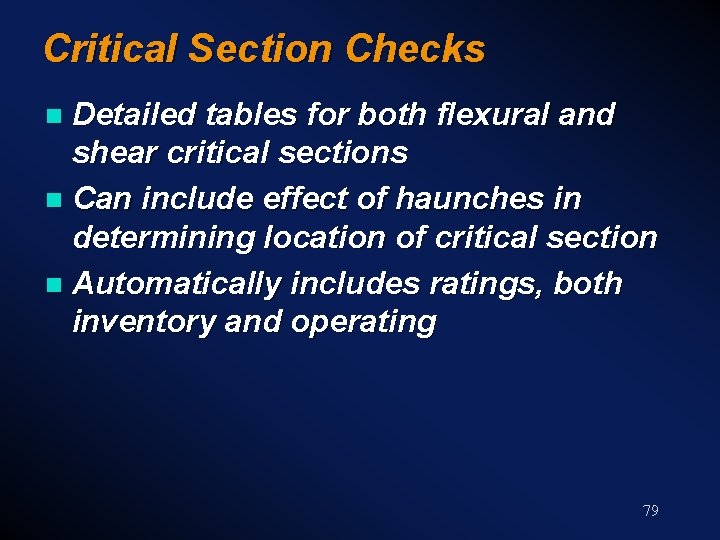
Critical Section Checks Detailed tables for both flexural and shear critical sections n Can include effect of haunches in determining location of critical section n Automatically includes ratings, both inventory and operating n 79
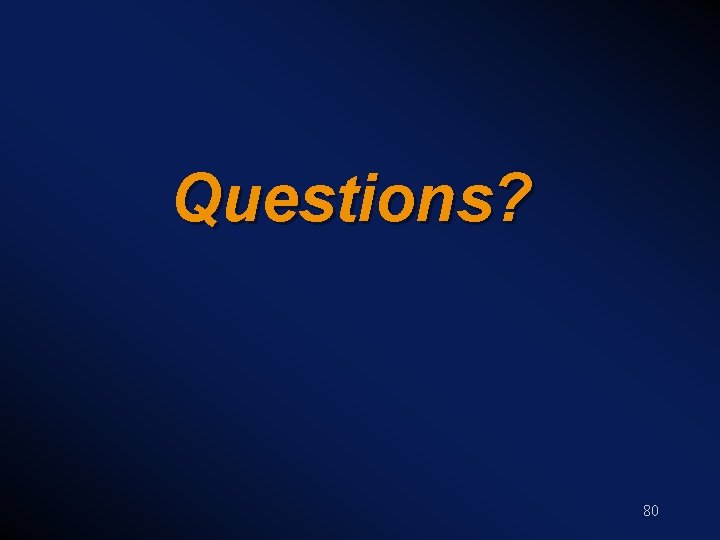
Questions? 80
Hec-ras deck roadway data editor
Etculvert
Acpa land acknowledgement
Protocole acpa
Riset rating dan non rating
Precast concrete utility vaults
"precast pipe"
Hollow core slab connection details
Admixtures
Concrete veneer panels
Parapet wall construction detail
Precast concrete toilet structures
Precast concrete brisbane
Precast sound wall
Osha concrete and masonry construction
Precast
Precast aerated concrete
M&m precast
Precast roof nd
Precast concrete dog leg staircases
Vendor rating advantages and disadvantages
Interconnect billing solution
Rating scales and rubrics
Pilot testing in performance management
Nqs assessment
Emotional rating scale
What is form in system analysis and design
Grid controlled x ray tube
Sil rating table
Workday performance rating scale
Ama impairment rating chart
Value questions examples
5 point scale examples
Learning space rating system
Ama impairment rating chart
Supports intensity scale rating key
Texas assessment.gov/telpastrainingcenter
Individual performance contract rating (ipcr) form
Ssis-rs
Summated rating
Ska rating
Synthetic rating cost of debt
Heathrow elementary school
Predictive prioritization
Va ptsd rating scale pdf
Graphic rating scale example
Graphic rating scale
A 540 degree appraisal involves evaluation by
Forced distribution method
Bars rating scale
Palin parent rating scale
Behaviorally anchored rating scale
Credit rating scale
Gross rating points
Contoh skala penilaian grafis
Latent aspect rating analysis
Latent aspect rating analysis
Jenis skala psikologi
Fire suppression rating schedule
Example of semantic differential scale
Graphic rating scale method
Esrb rating font
Which rating star is given by griha for points 71-80
Graphic rating scale method
Layout planning and design
Fuse rating
Presentation rating scale
Ip rating scale
Schedule 40 pressure rating
Tanner staging male
Direct behavior ratings
Credit rating spread table
Credit rating
Computer organization & architecture: themes and variations
Wright's classification of behaviour
A rating error occurs
Behaviorally anchored rating scale
Palin parent rating scale
Evaluation of sales force
Performance levels
Disadvantages of bell curve in performance appraisal