DRYVIT OUTSULATION Methods of application 1 General hints
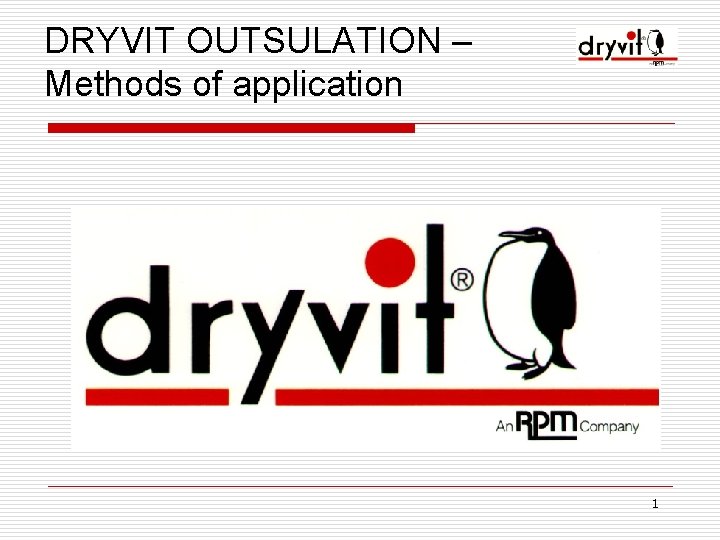
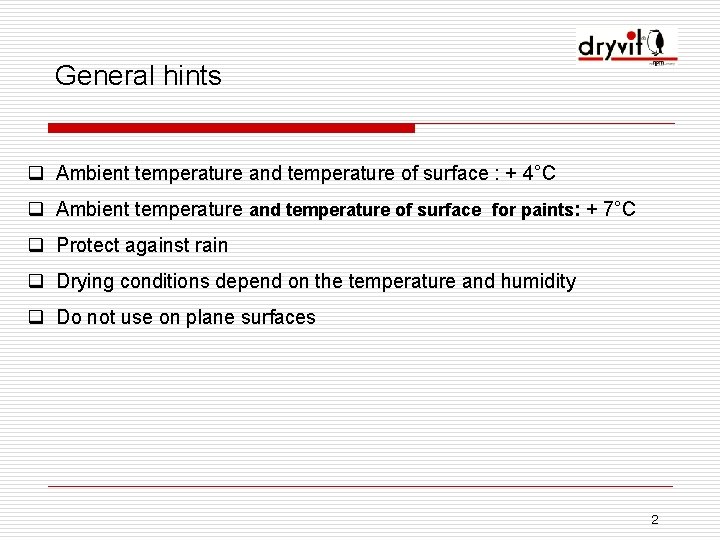
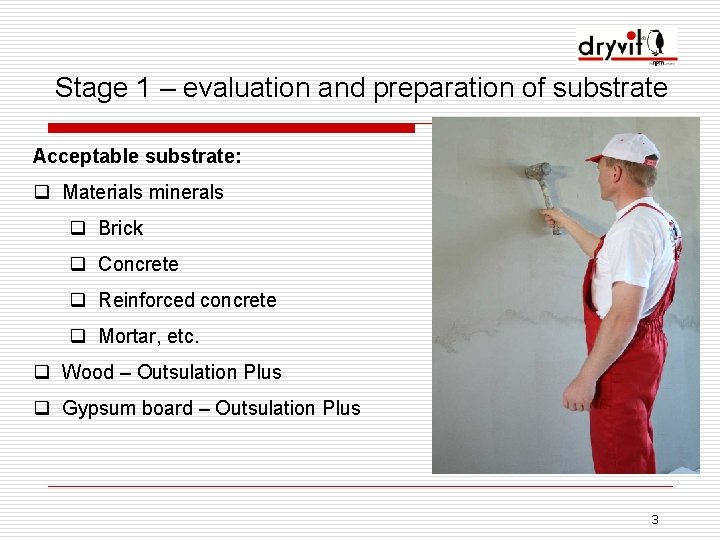
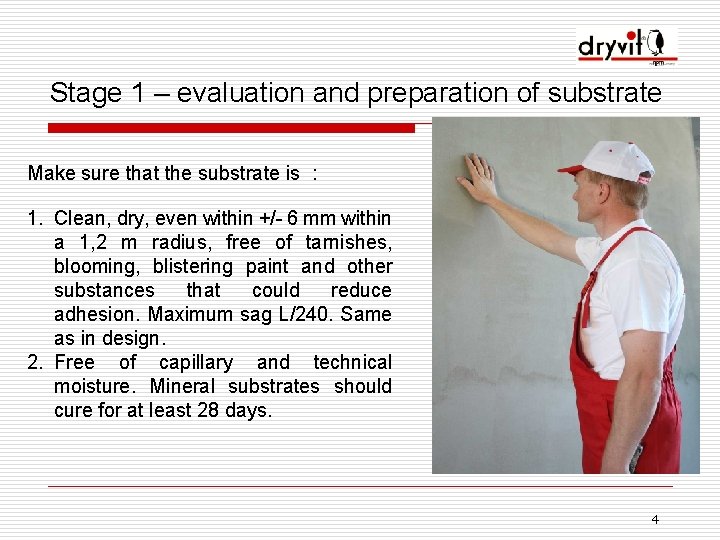

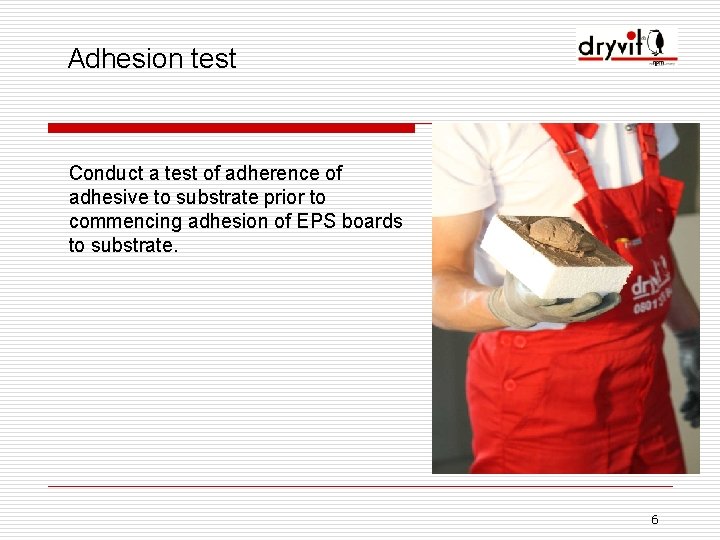
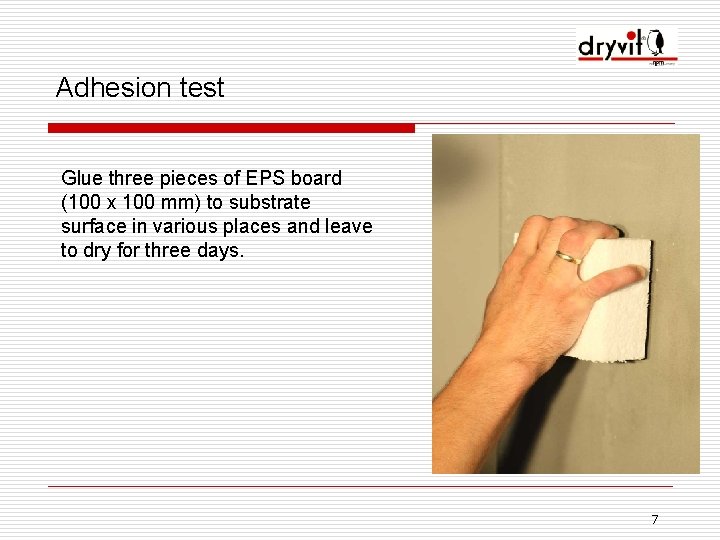
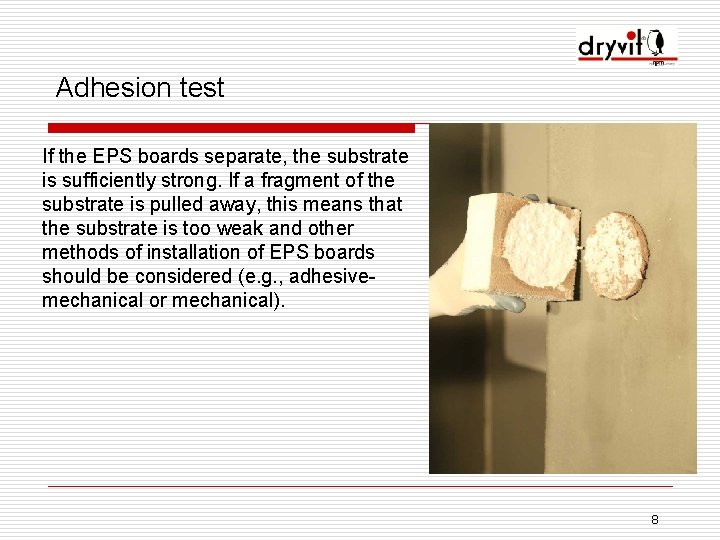
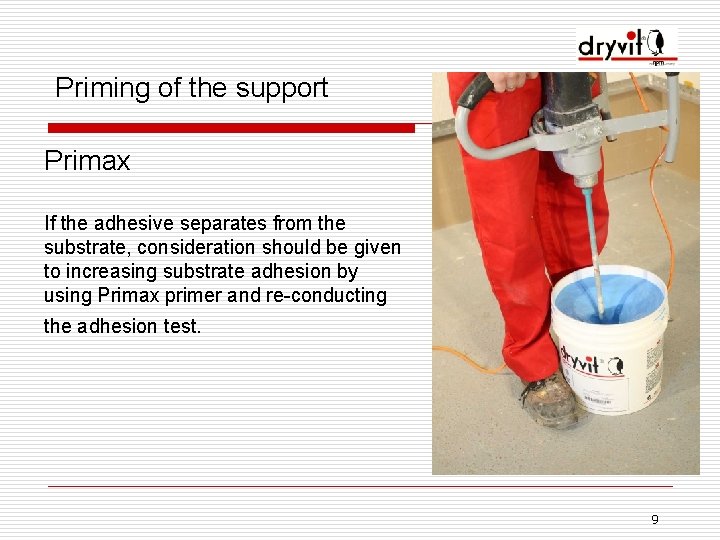

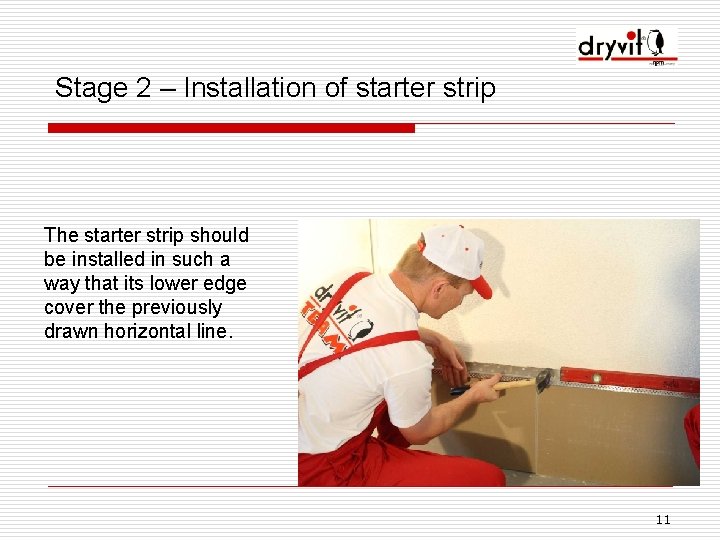
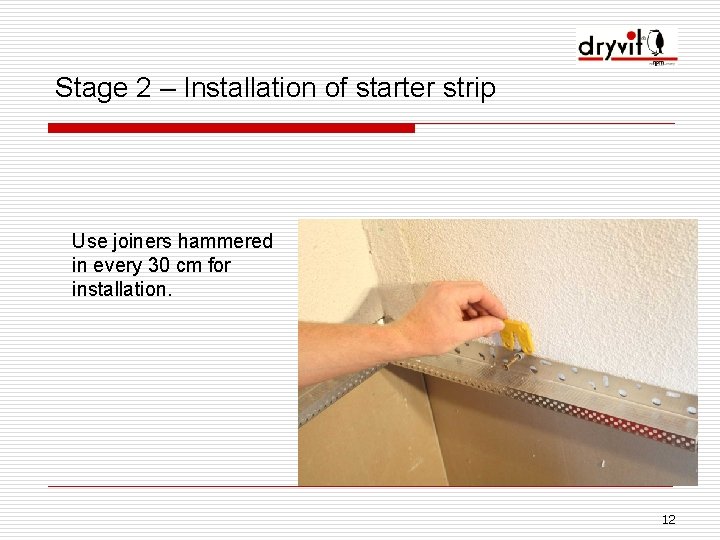
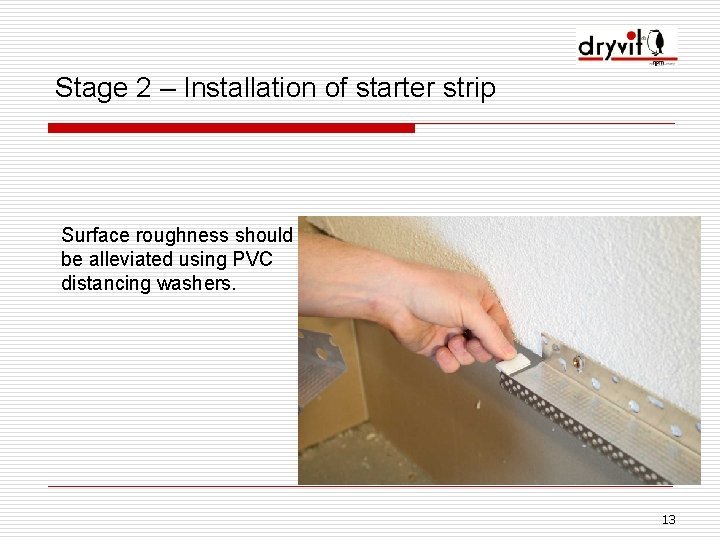
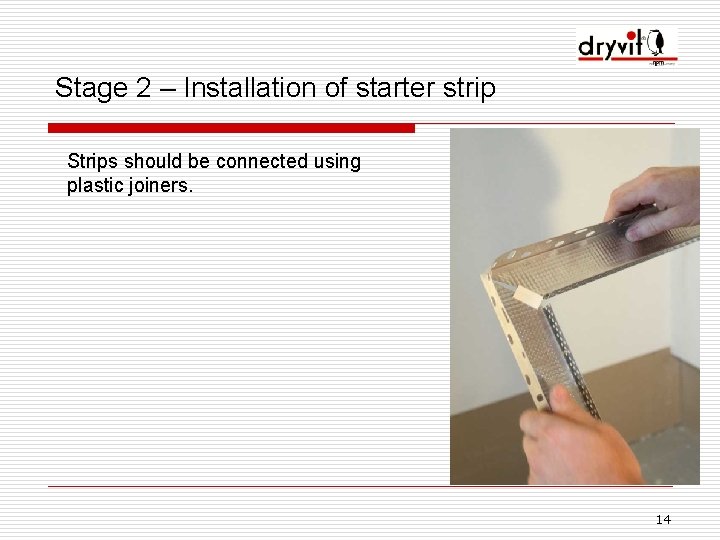
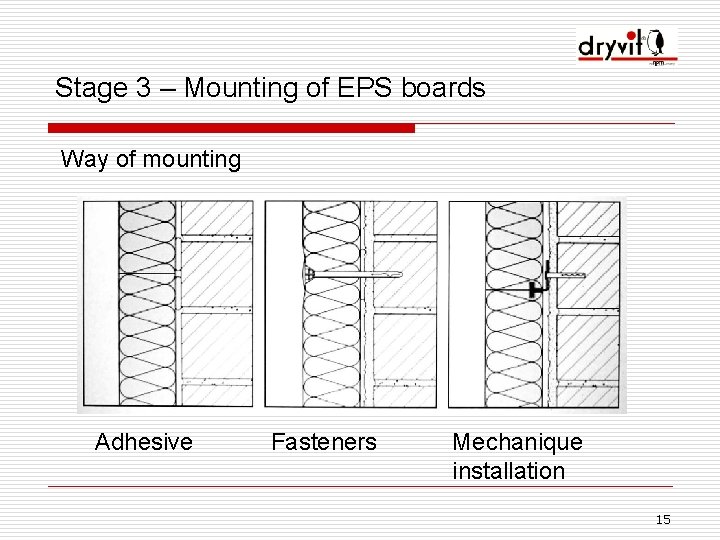
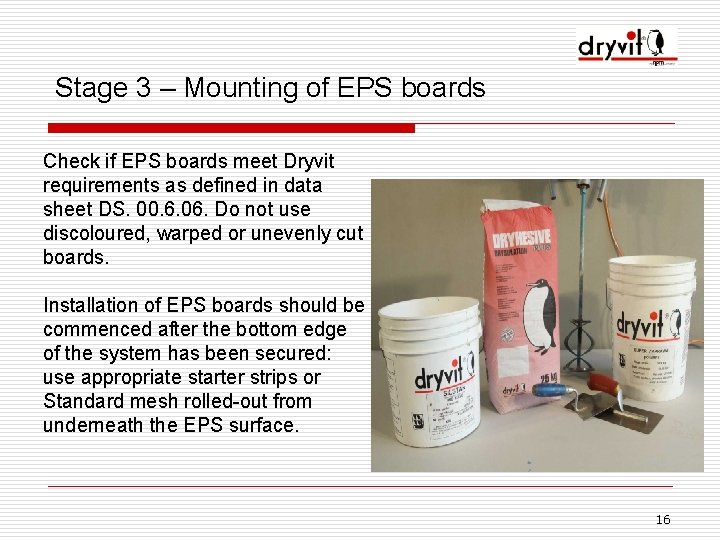
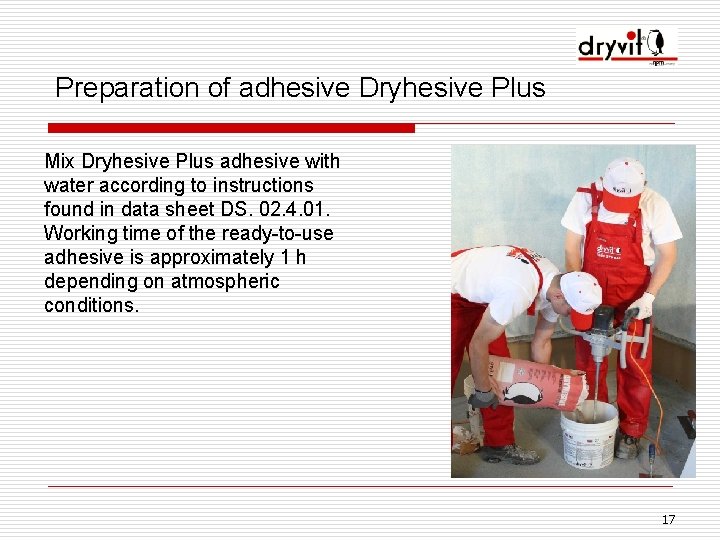
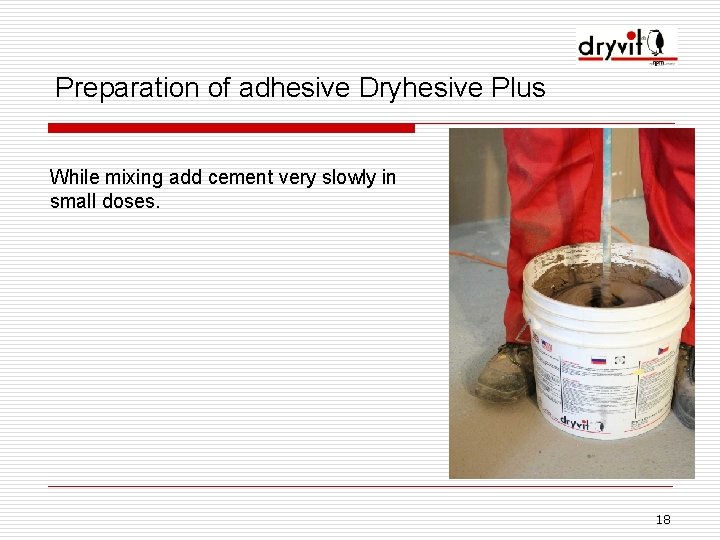
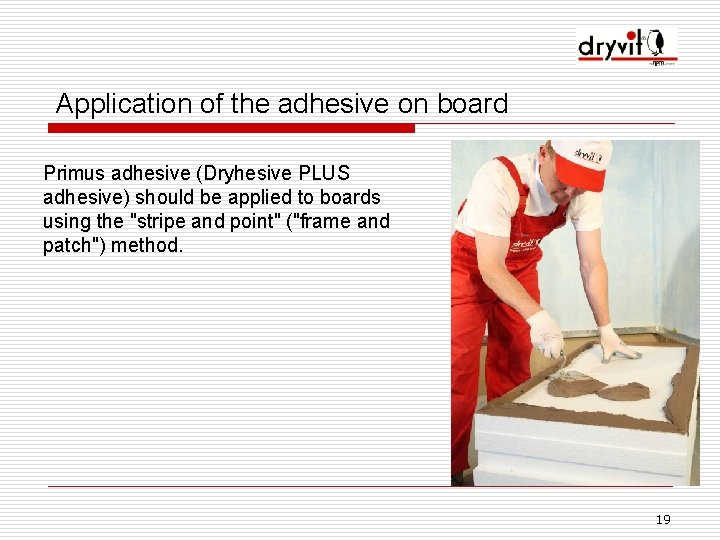
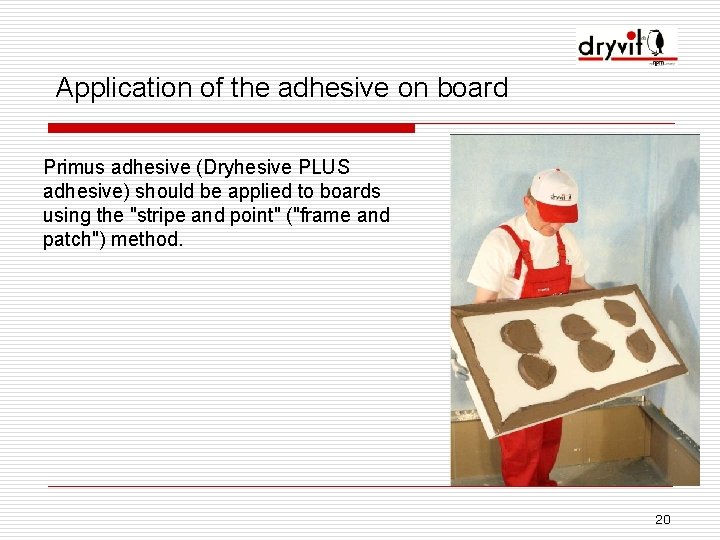
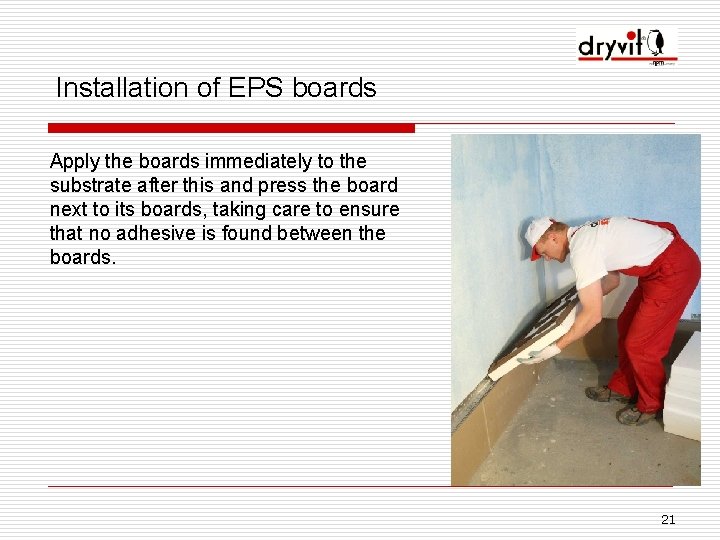
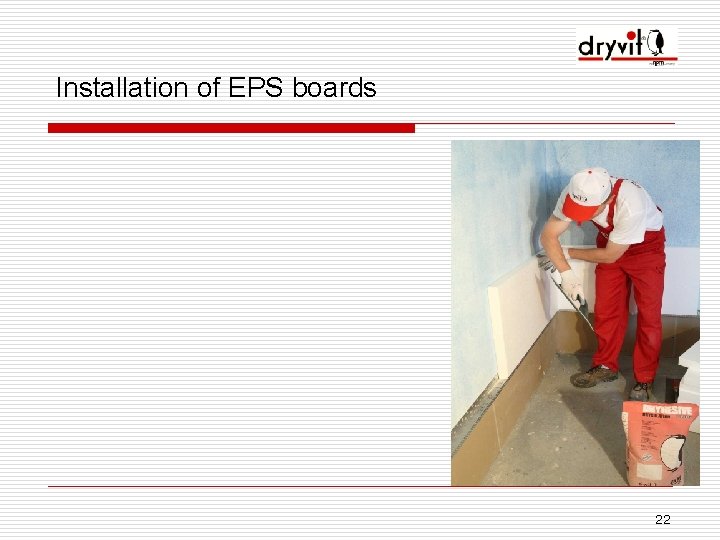
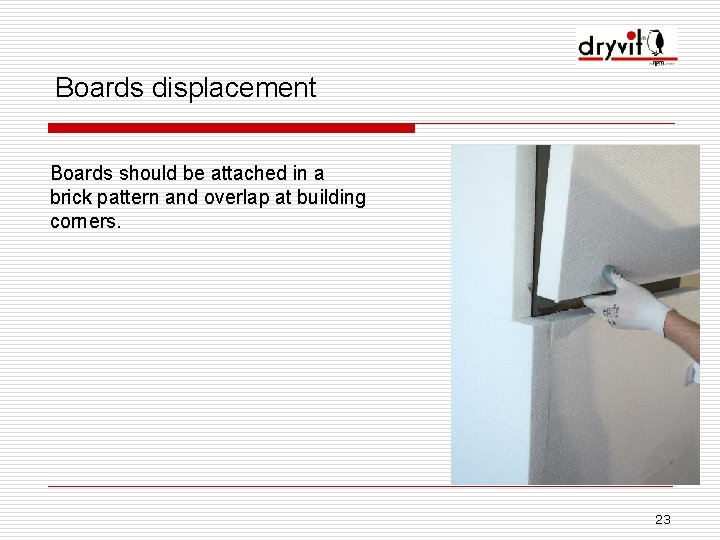
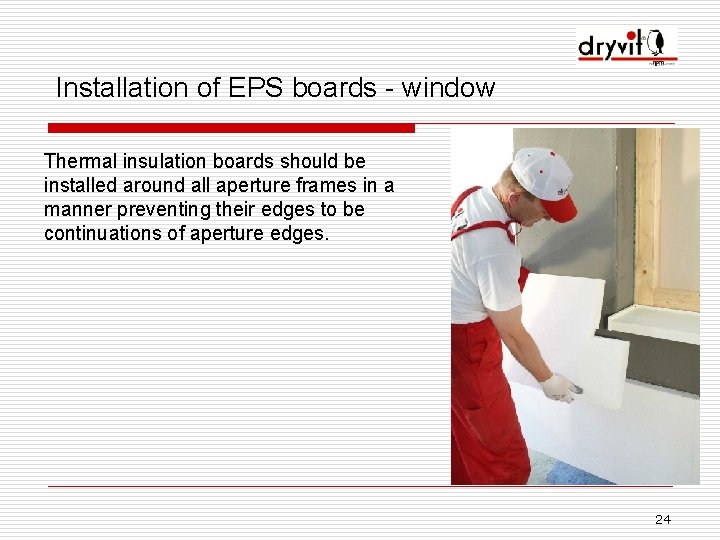
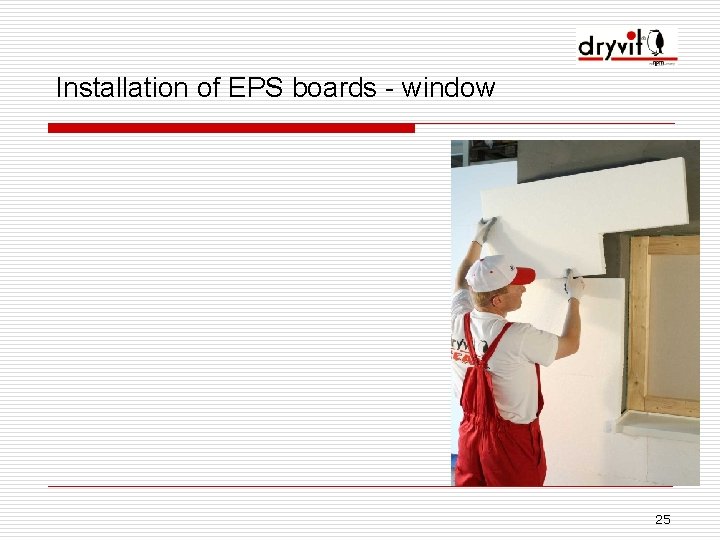
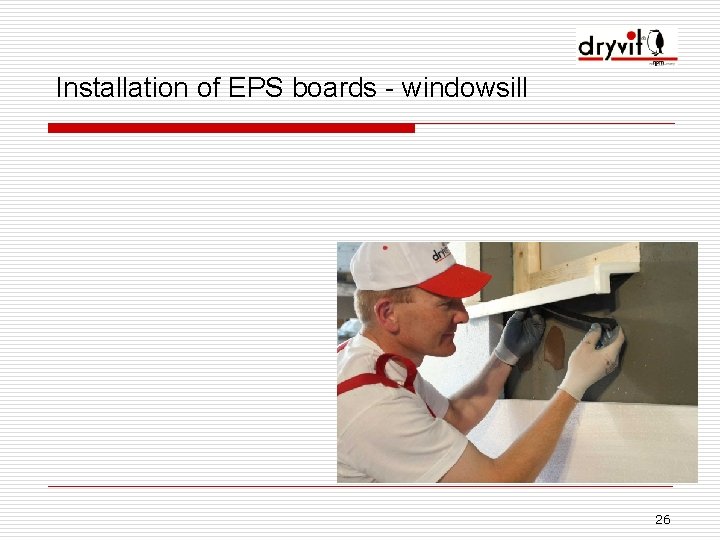
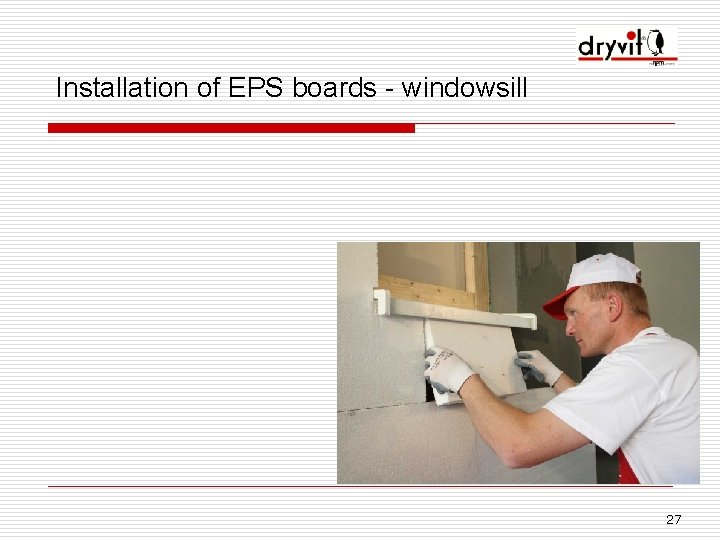
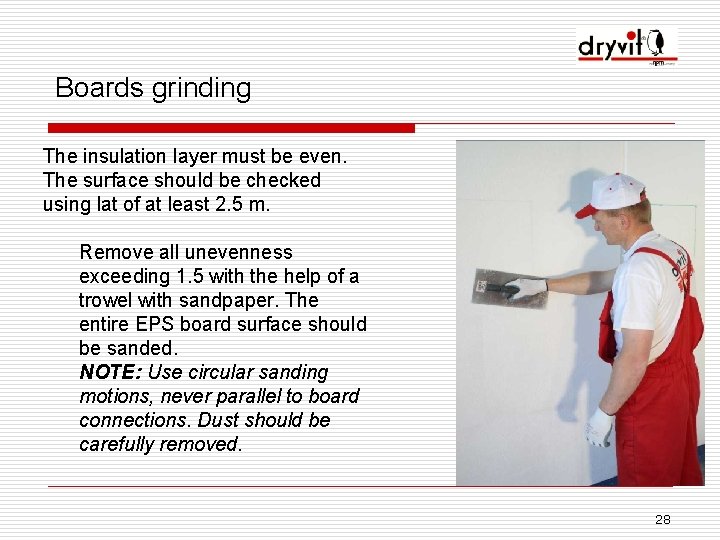
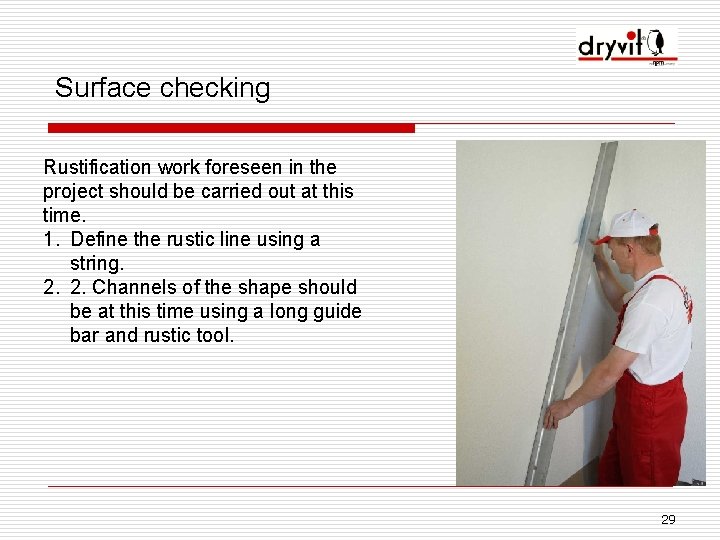
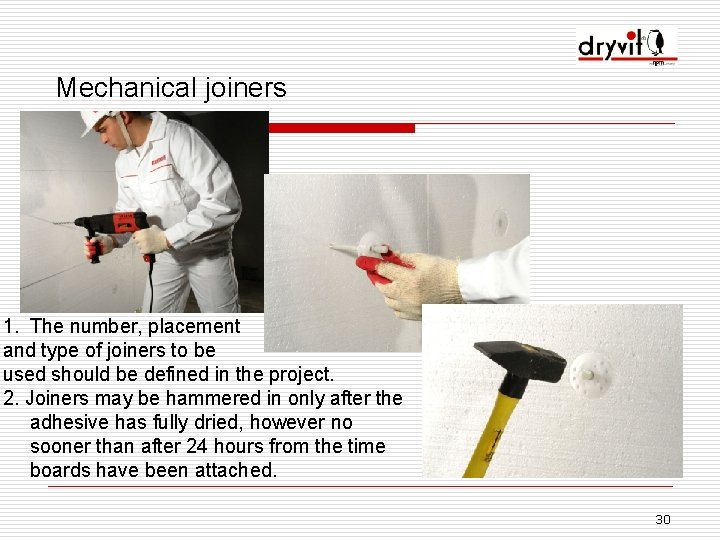
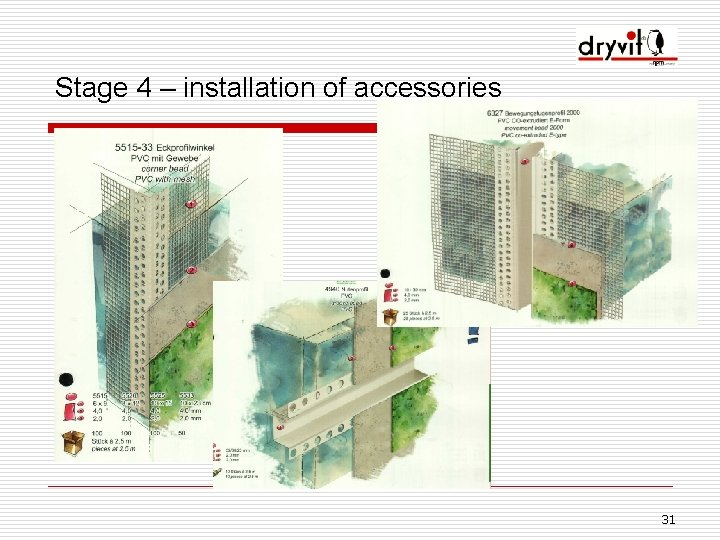
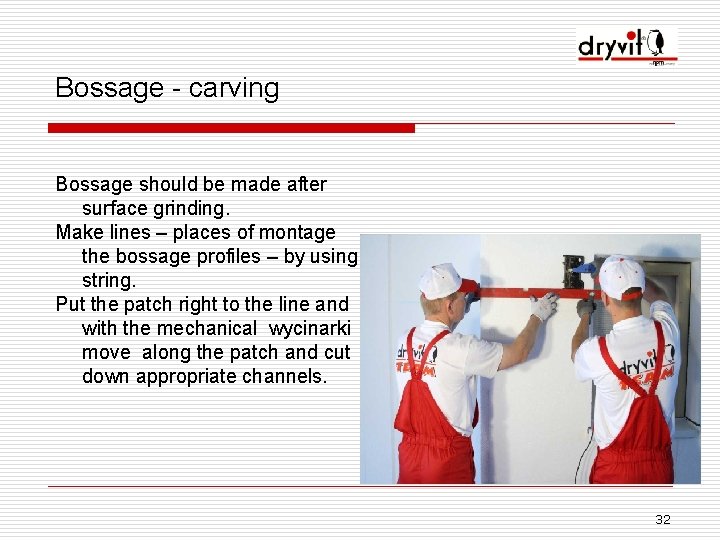
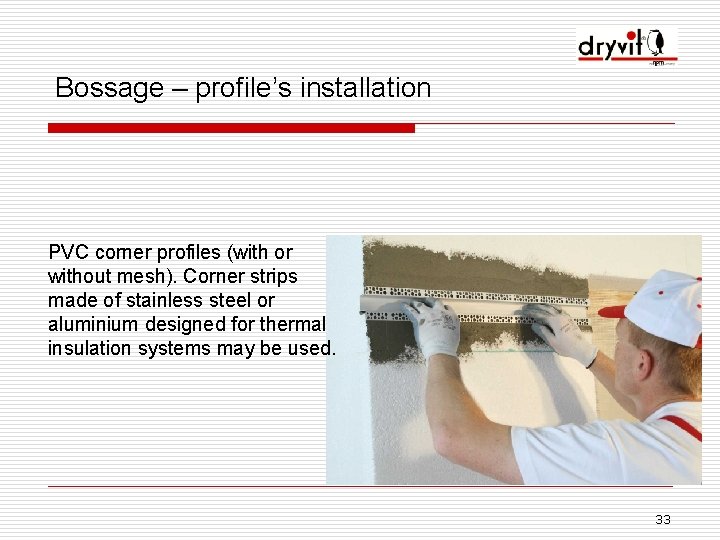
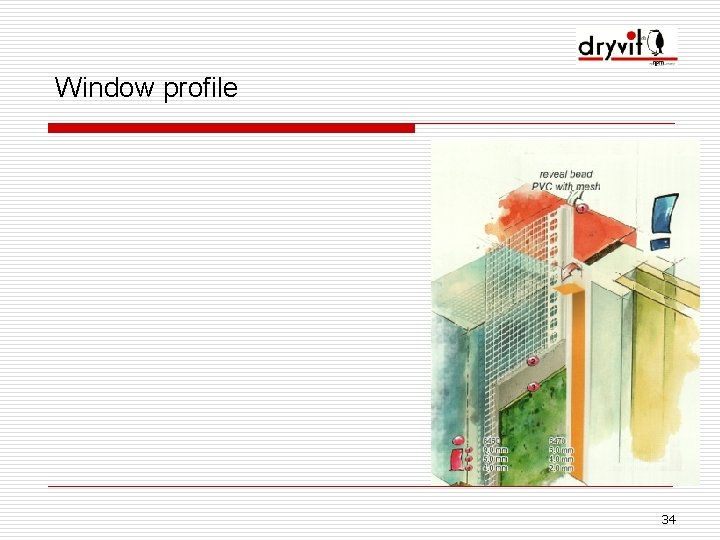
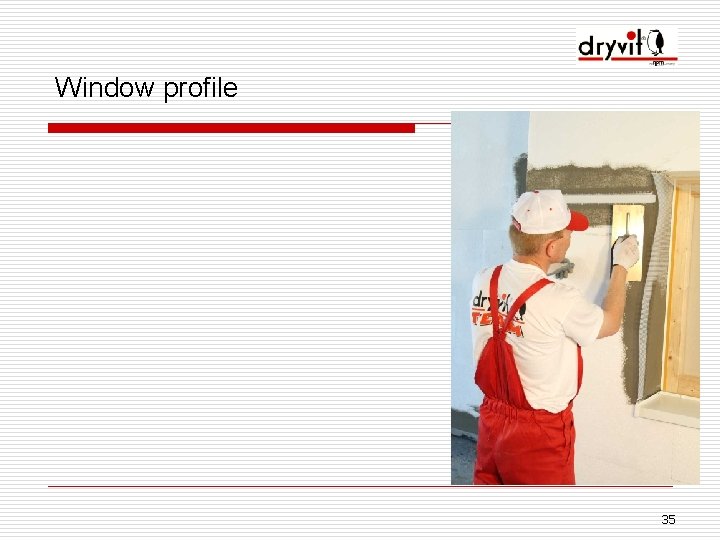
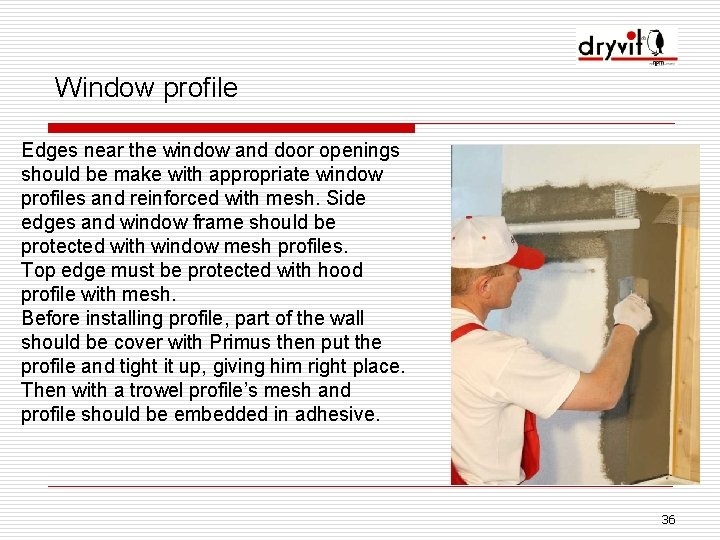
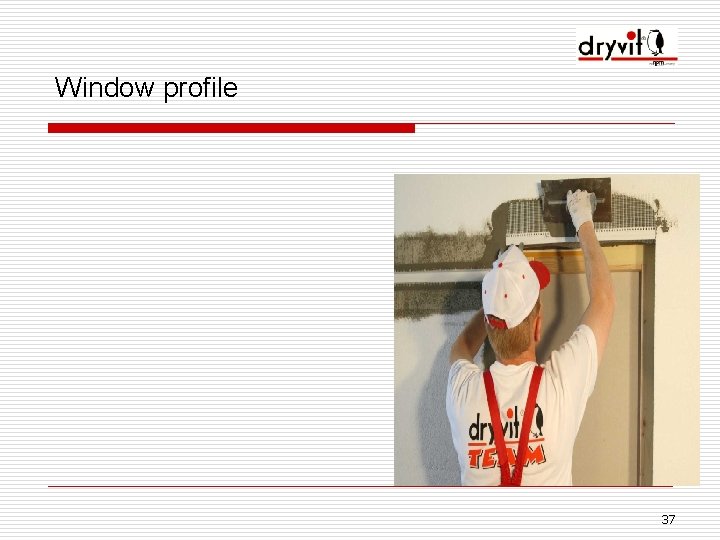
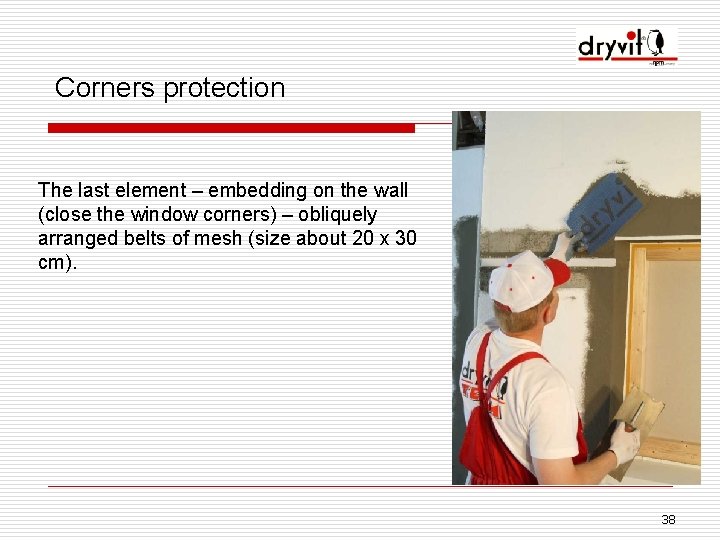
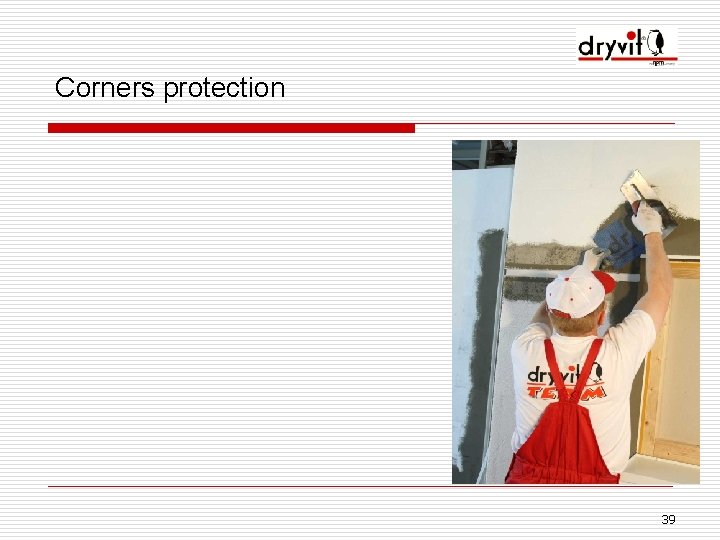
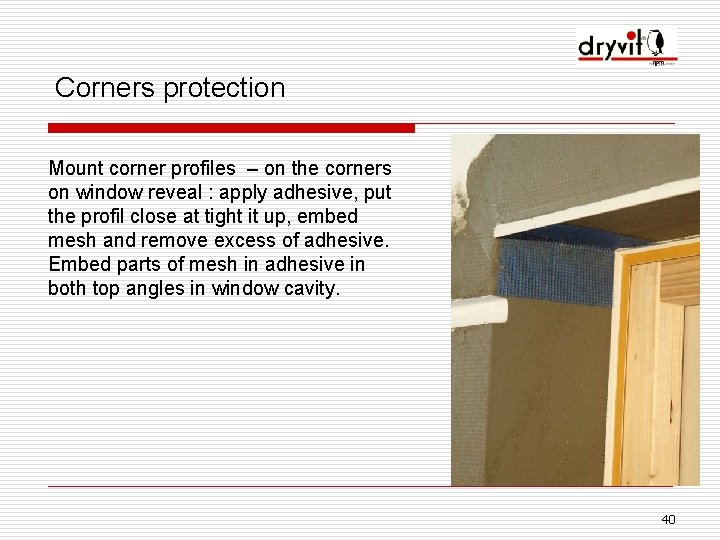
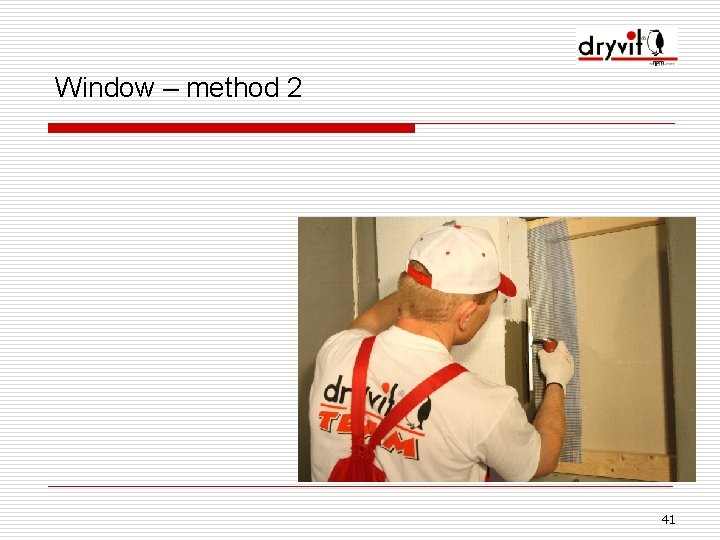
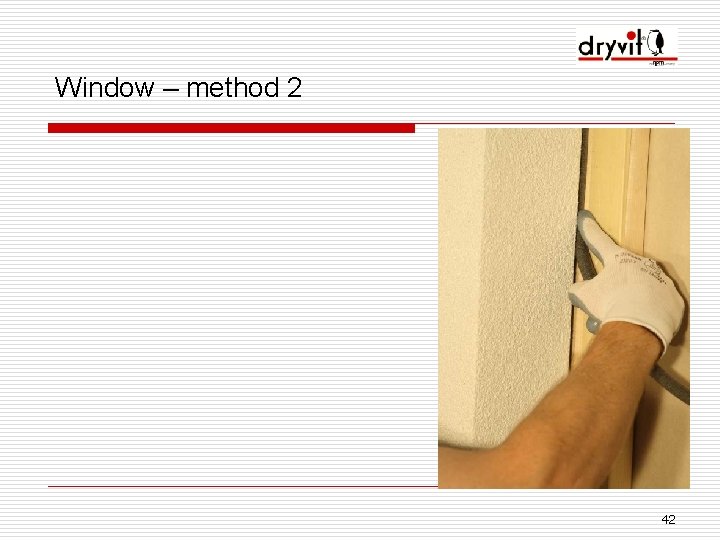
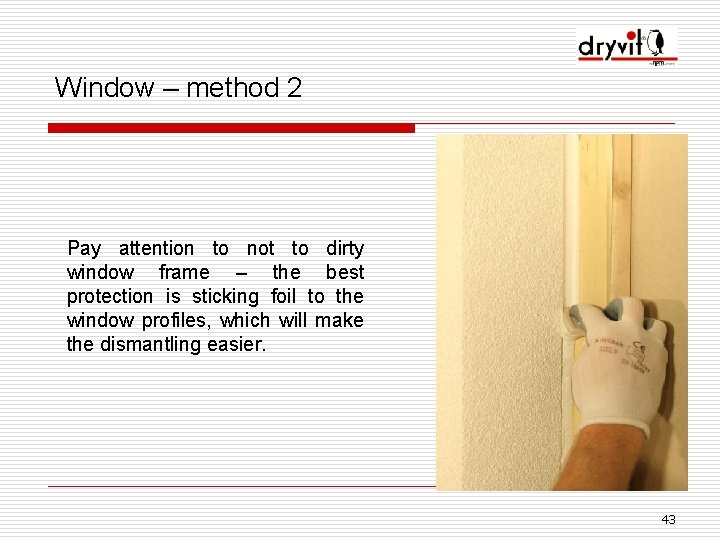
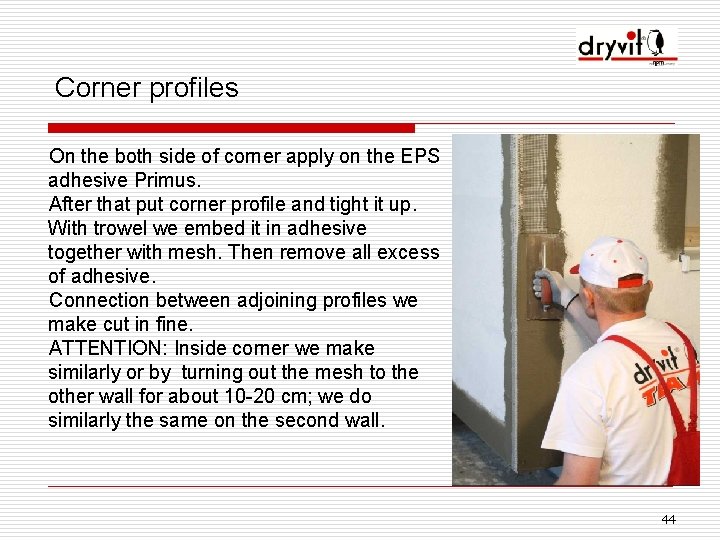
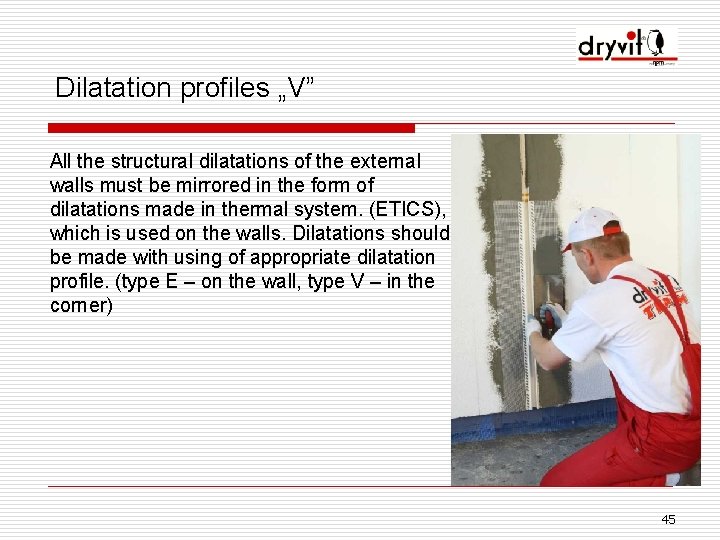
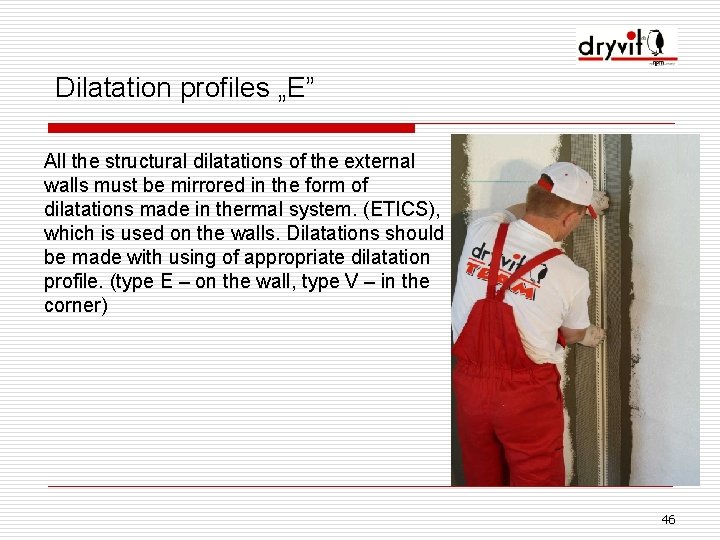
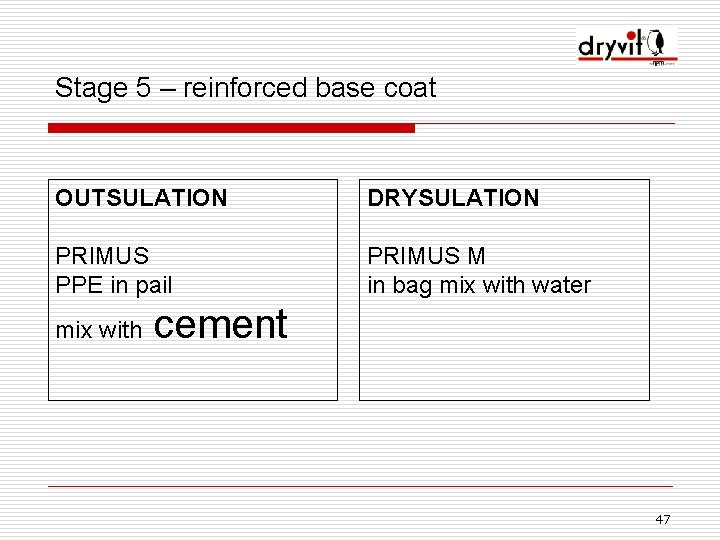
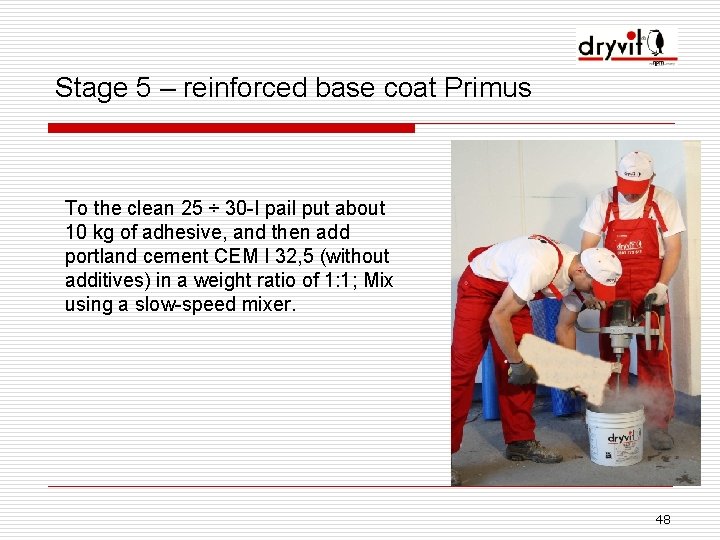
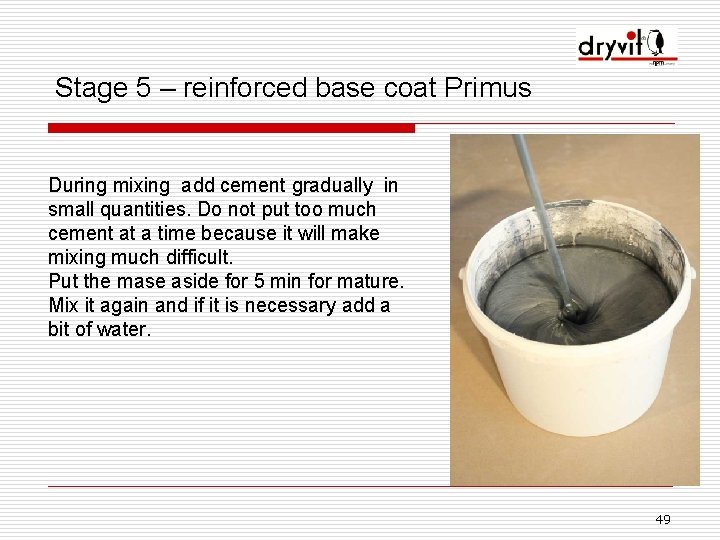
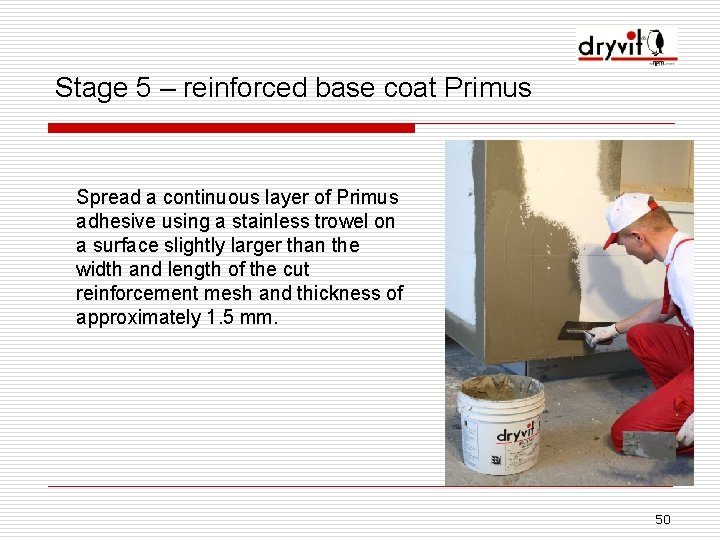
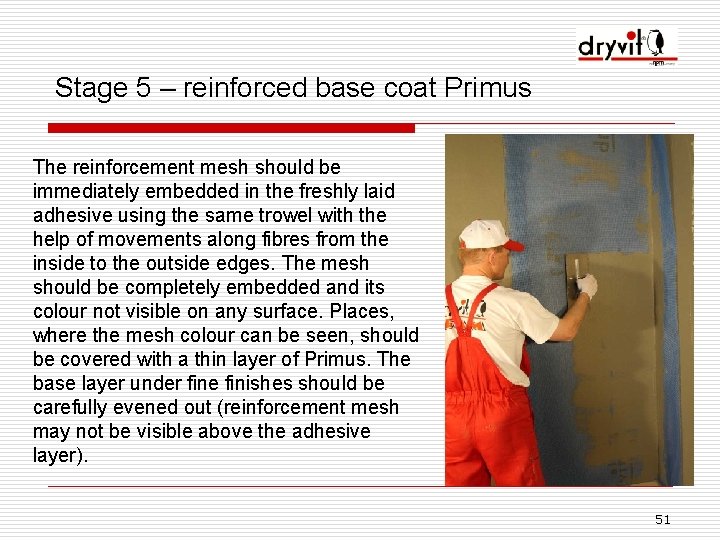
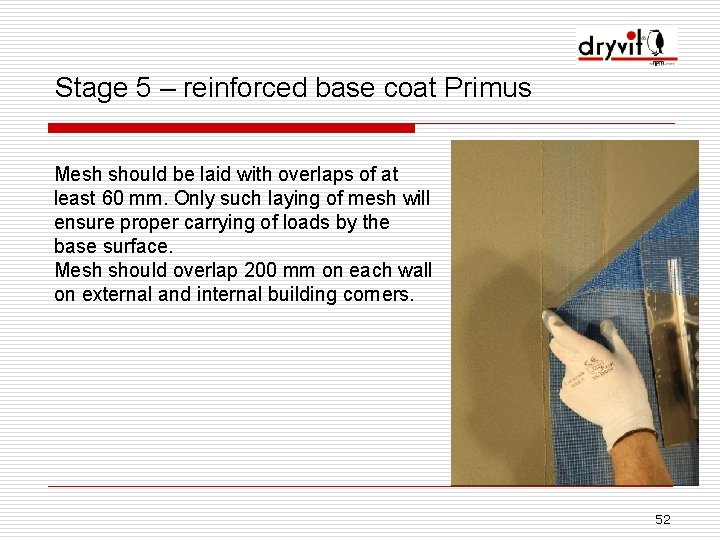
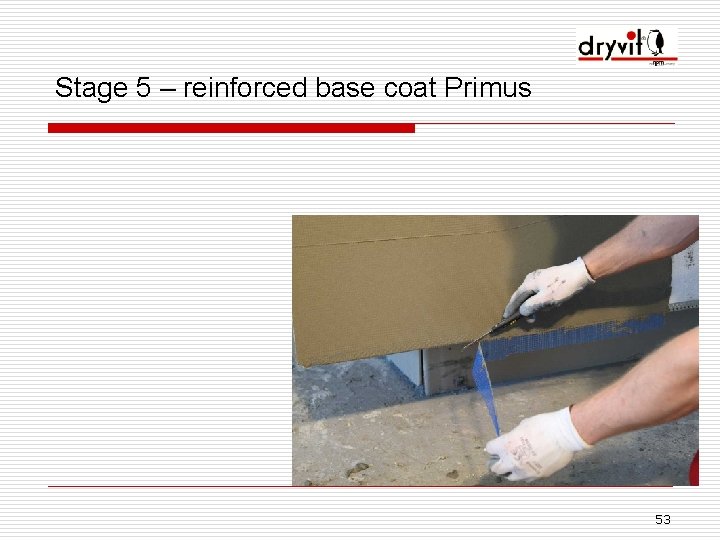
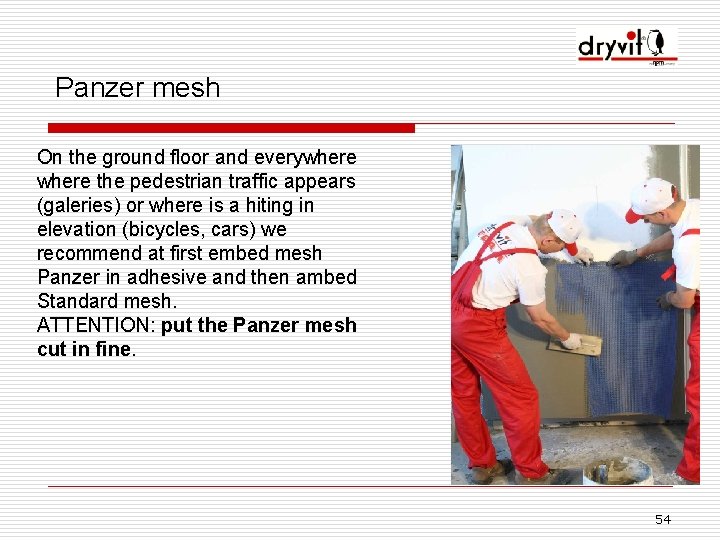
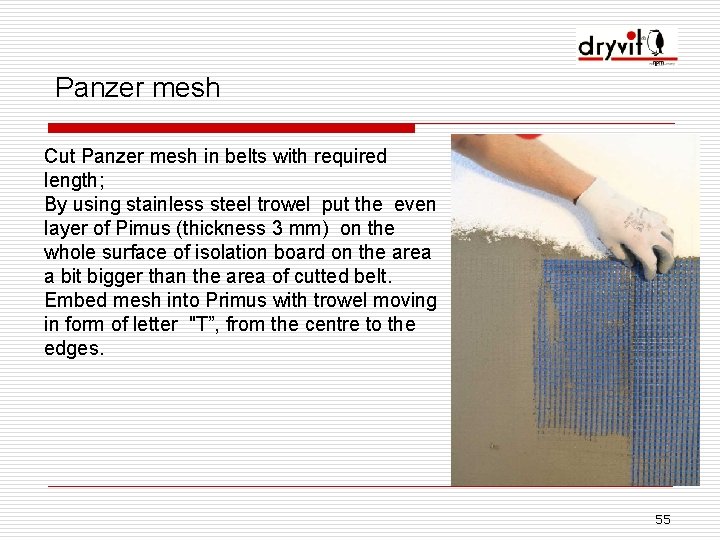
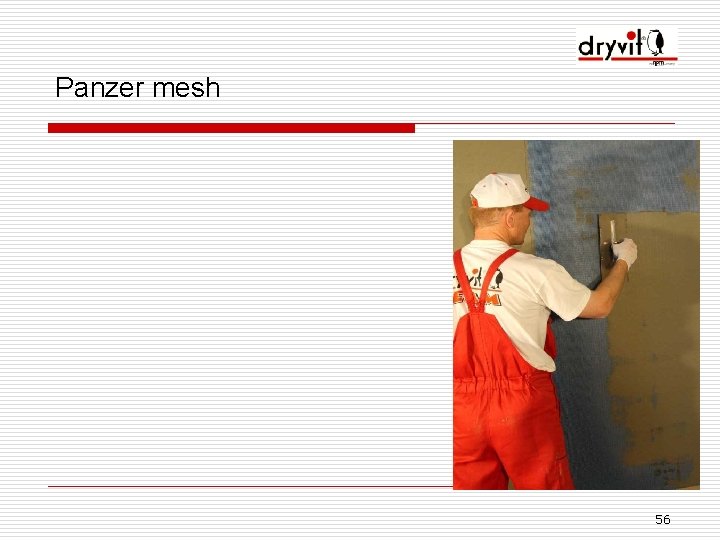
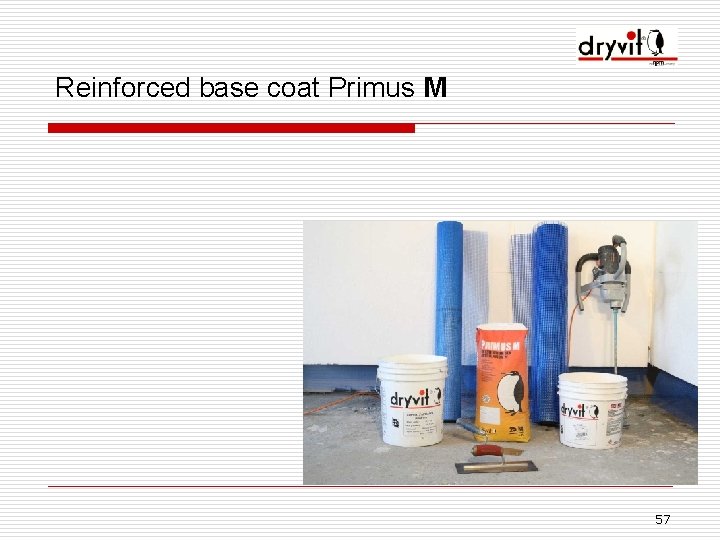
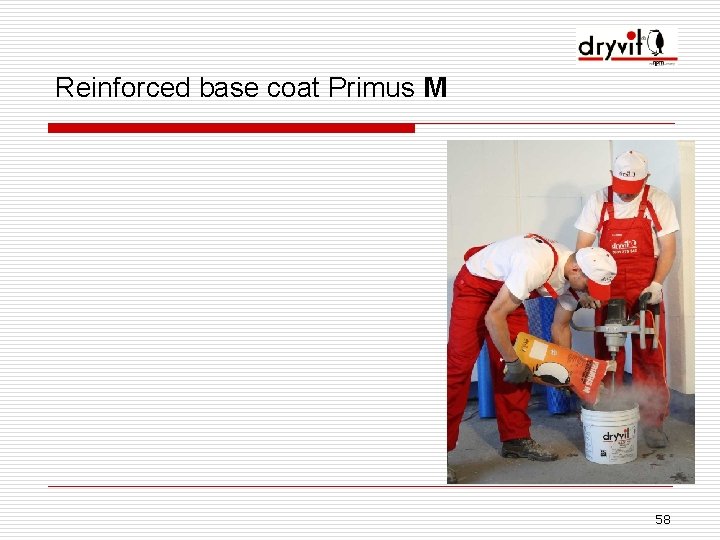
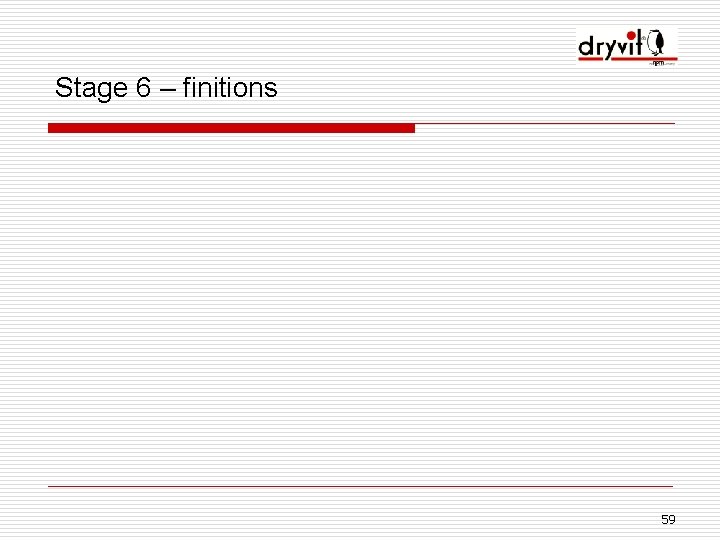
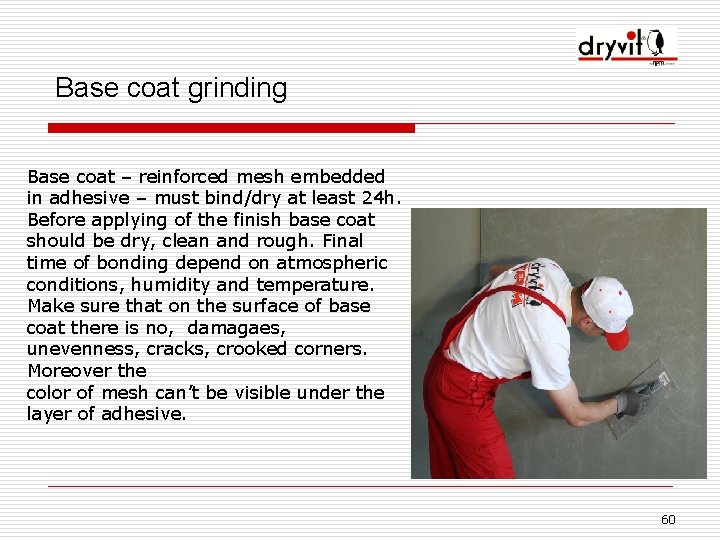
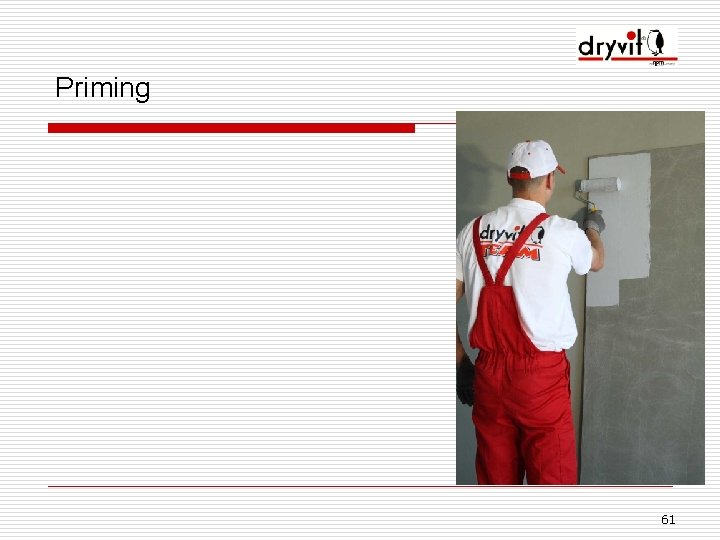
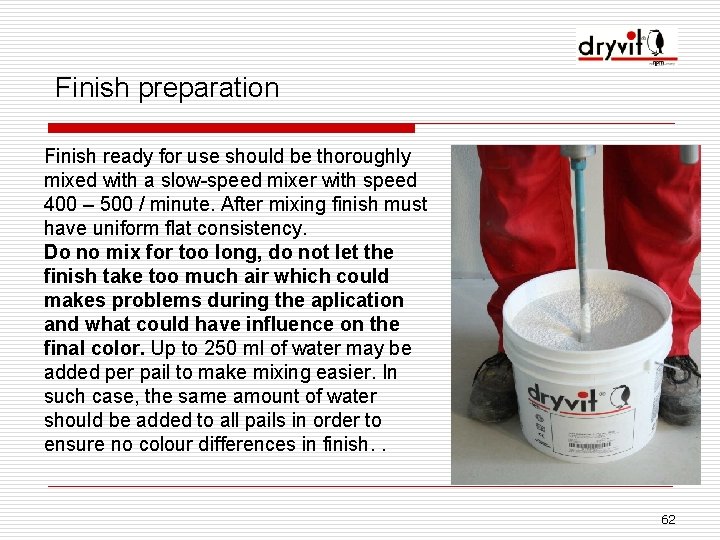
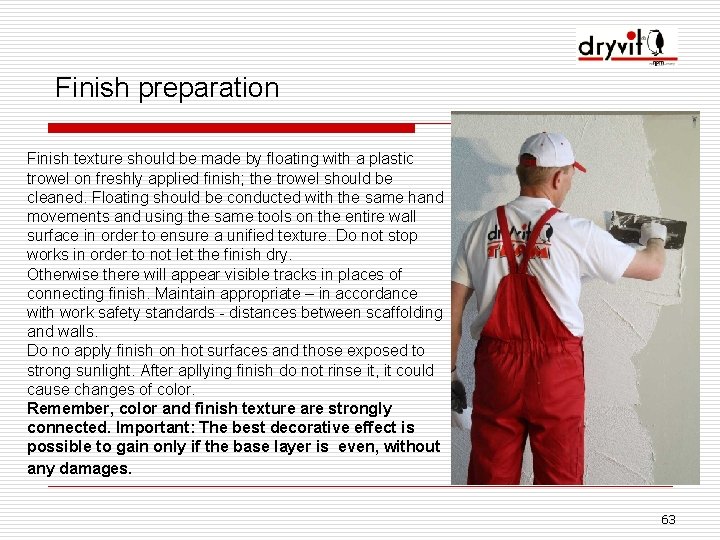
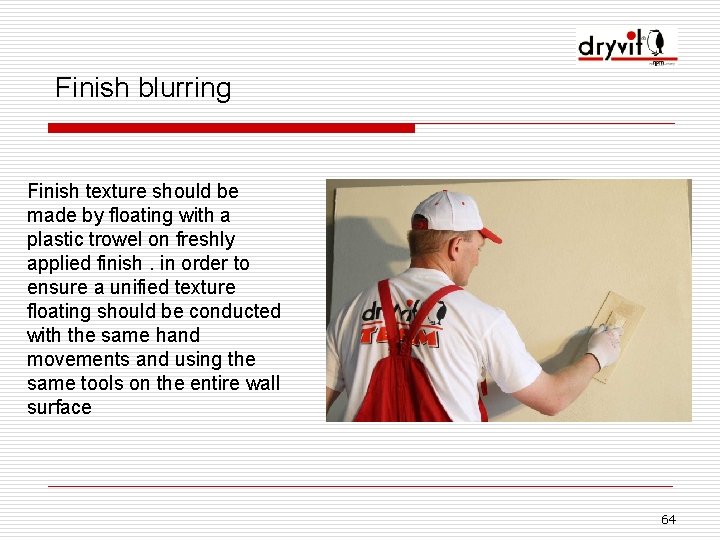
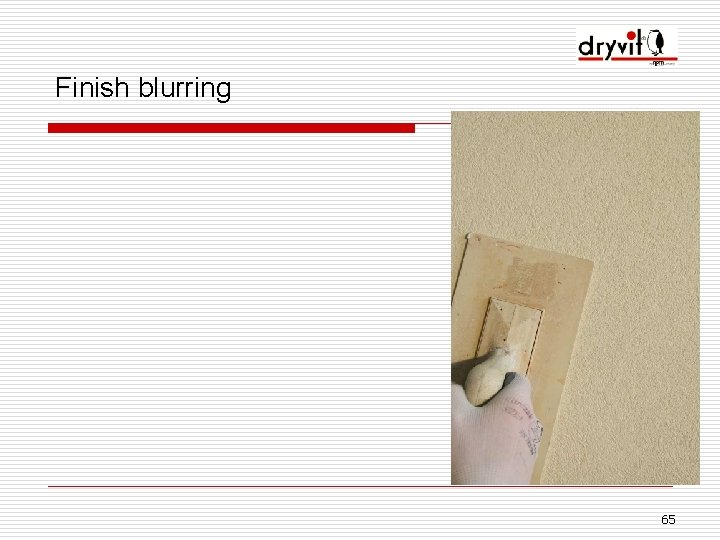
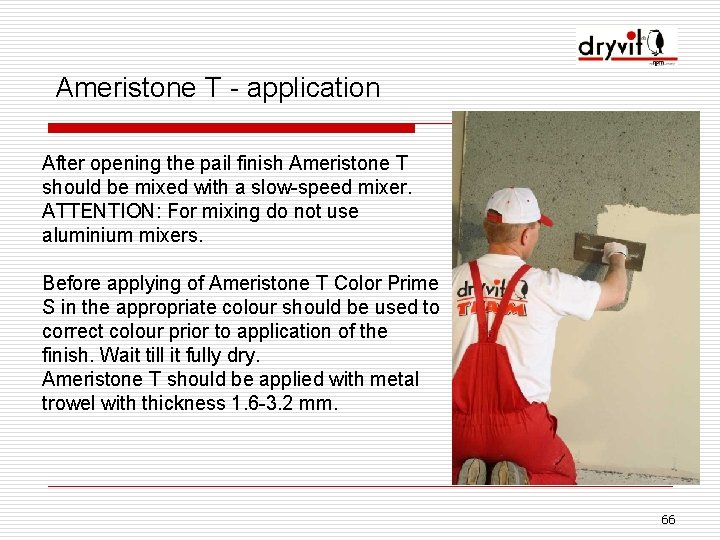
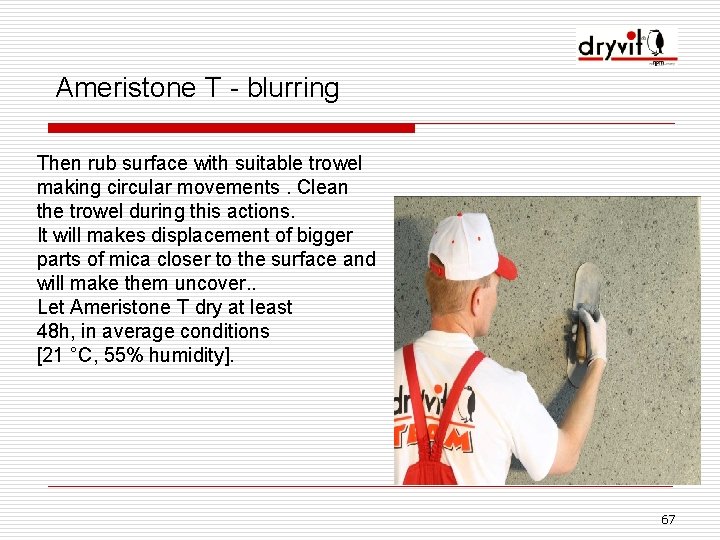
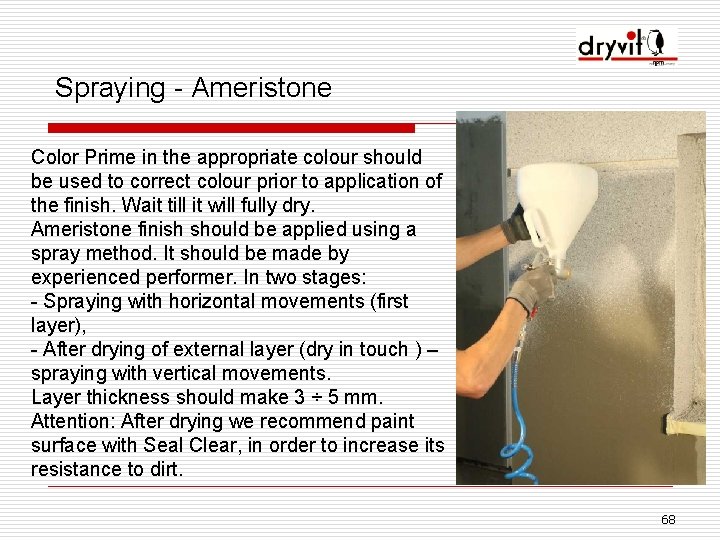
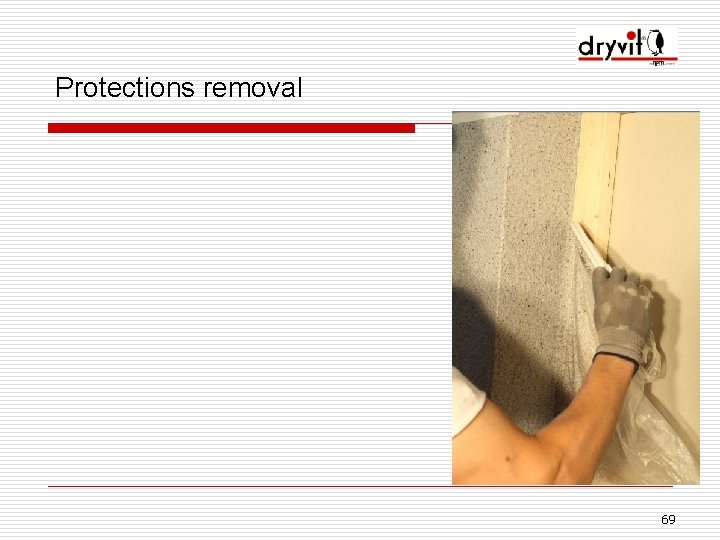
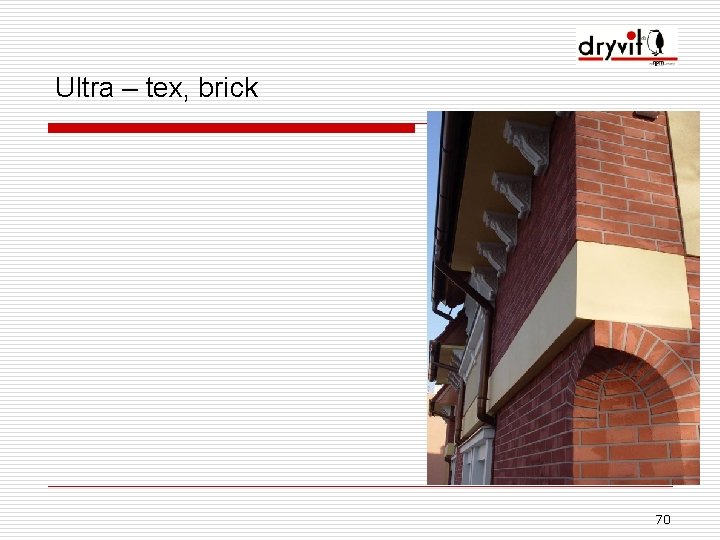
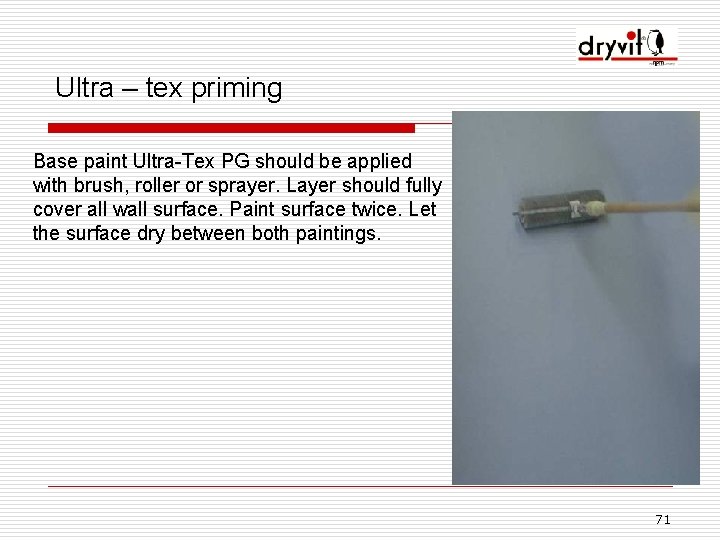
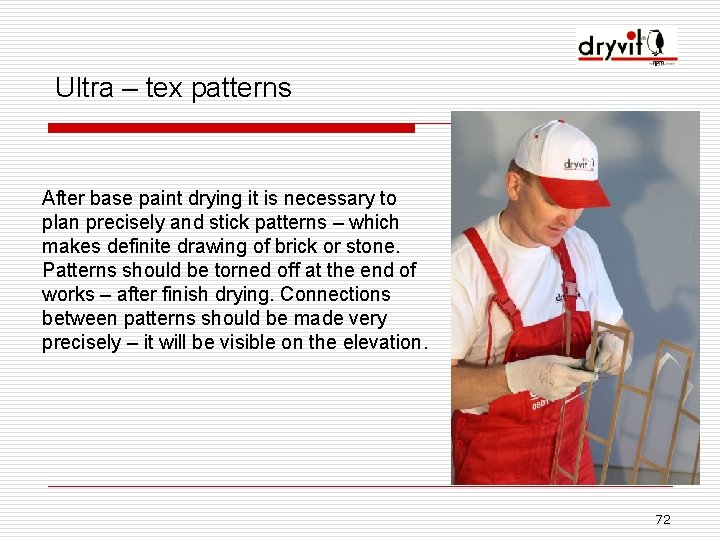
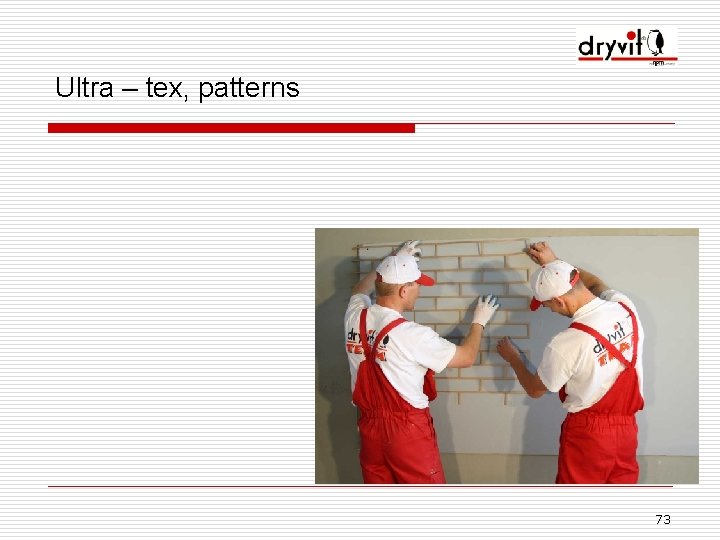
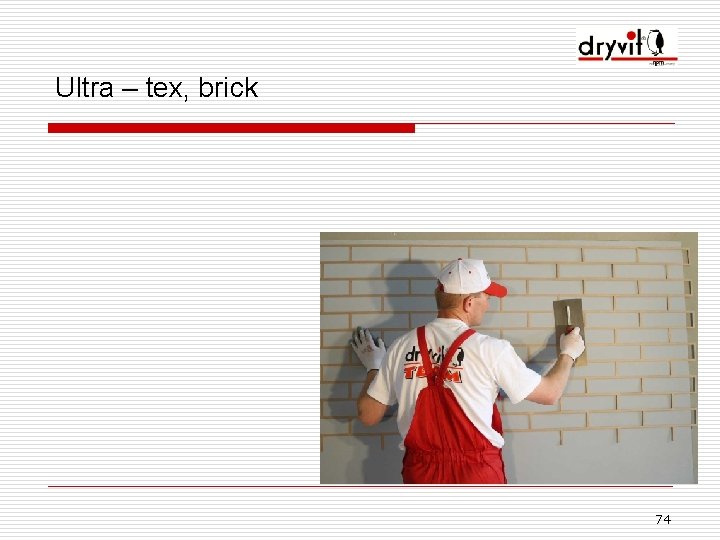
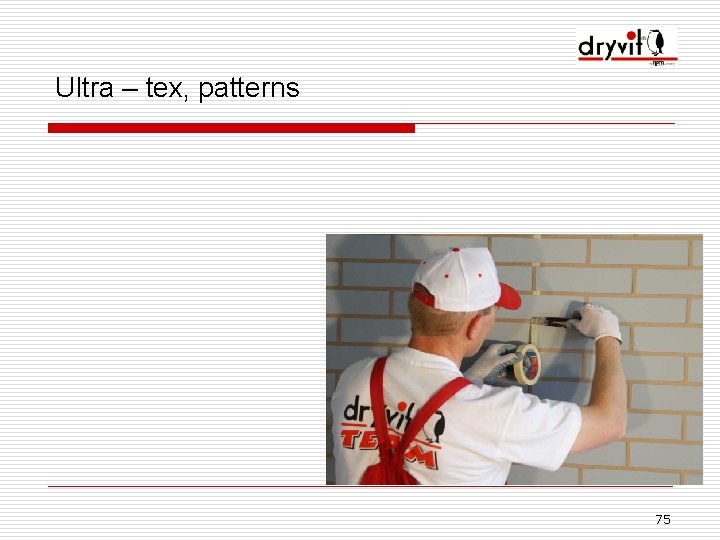
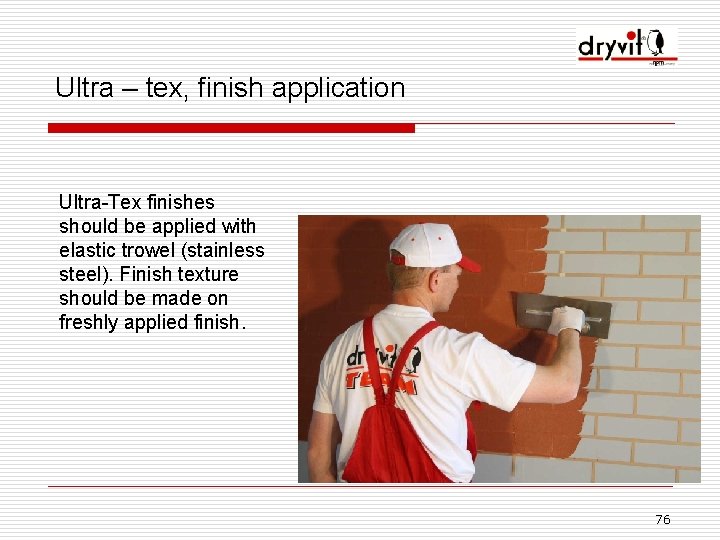
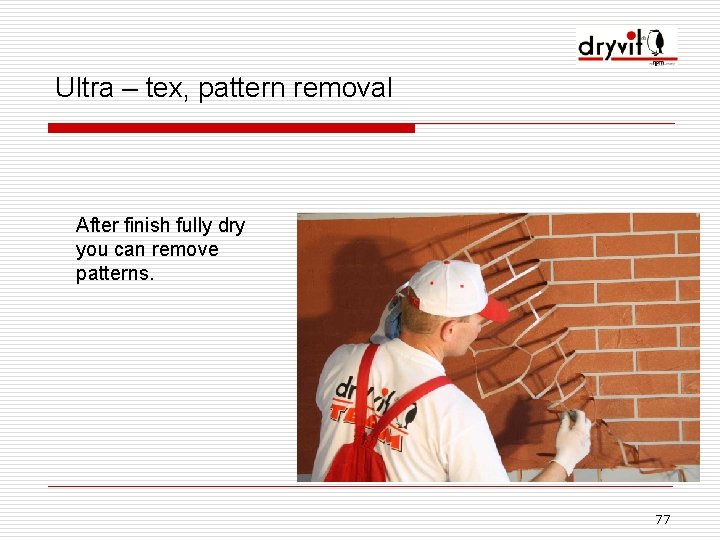
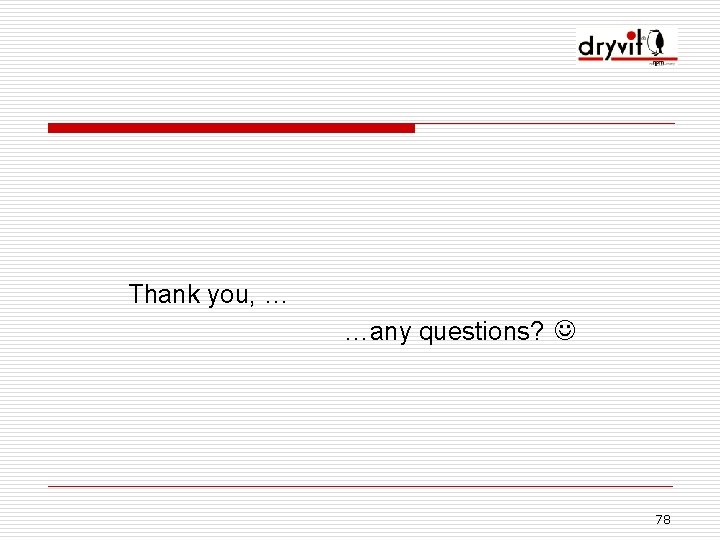
- Slides: 78
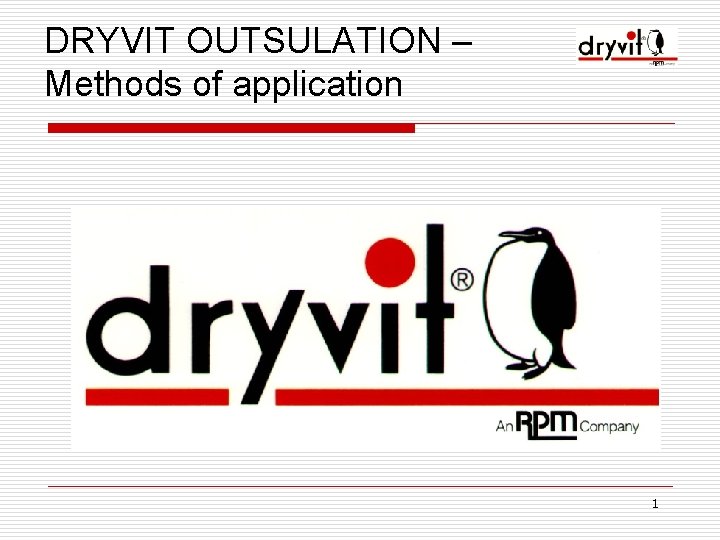
DRYVIT OUTSULATION – Methods of application 1
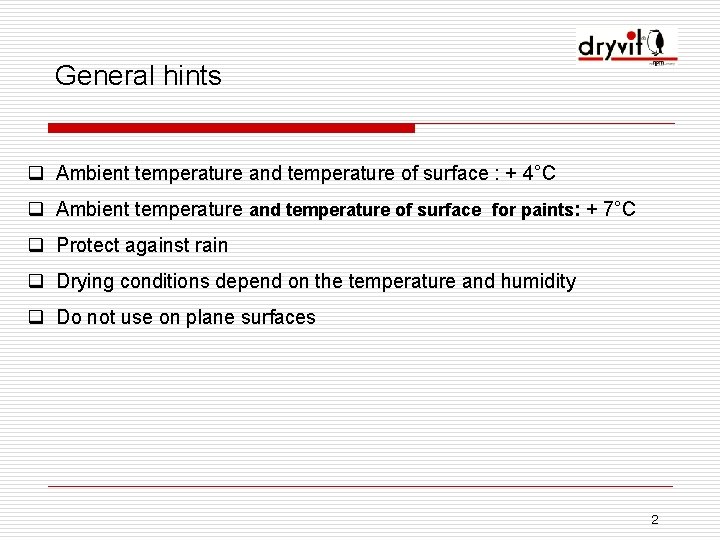
General hints q Ambient temperature and temperature of surface : + 4°C q Ambient temperature and temperature of surface for paints: + 7°C q Protect against rain q Drying conditions depend on the temperature and humidity q Do not use on plane surfaces 2
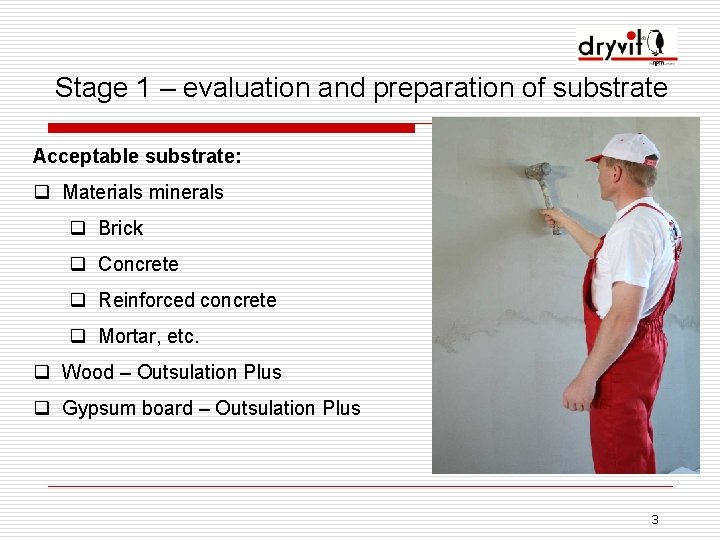
Stage 1 – evaluation and preparation of substrate Acceptable substrate: q Materials minerals q Brick q Concrete q Reinforced concrete q Mortar, etc. q Wood – Outsulation Plus q Gypsum board – Outsulation Plus 3
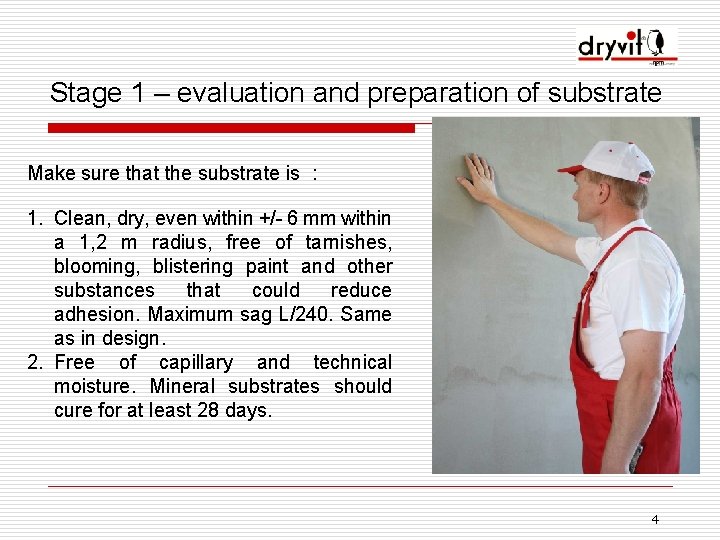
Stage 1 – evaluation and preparation of substrate Make sure that the substrate is : 1. Clean, dry, even within +/- 6 mm within a 1, 2 m radius, free of tarnishes, blooming, blistering paint and other substances that could reduce adhesion. Maximum sag L/240. Same as in design. 2. Free of capillary and technical moisture. Mineral substrates should cure for at least 28 days. 4

Stage 1 – evaluation and preparation of substrate 5
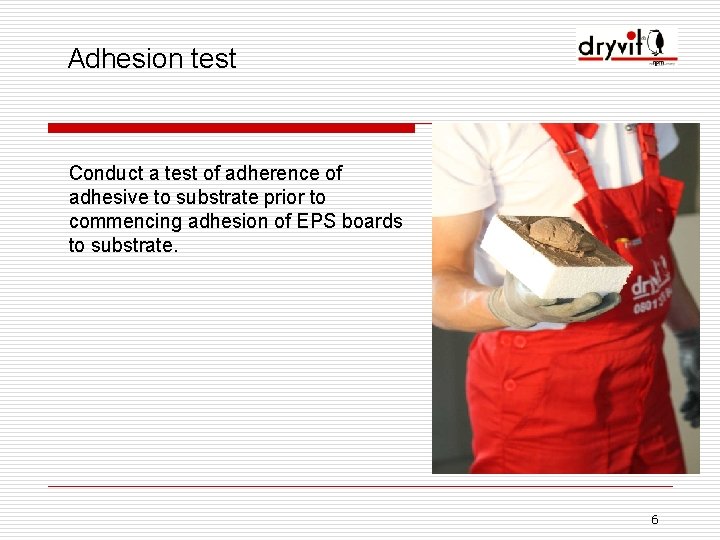
Adhesion test Conduct a test of adherence of adhesive to substrate prior to commencing adhesion of EPS boards to substrate. 6
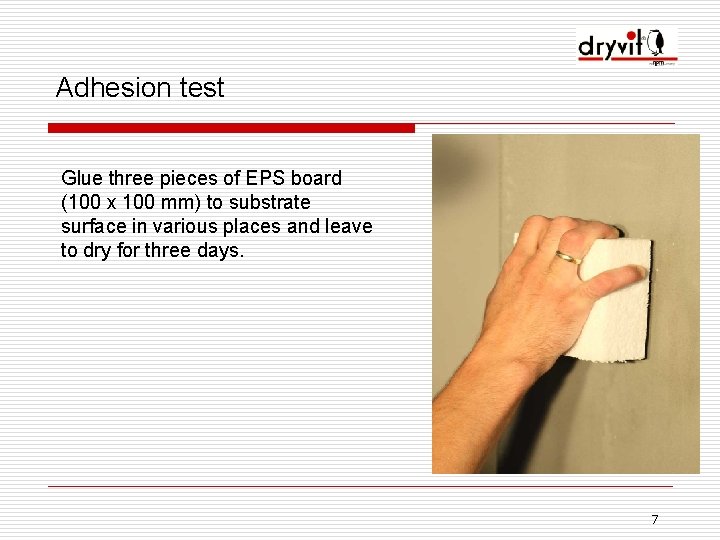
Adhesion test Glue three pieces of EPS board (100 x 100 mm) to substrate surface in various places and leave to dry for three days. 7
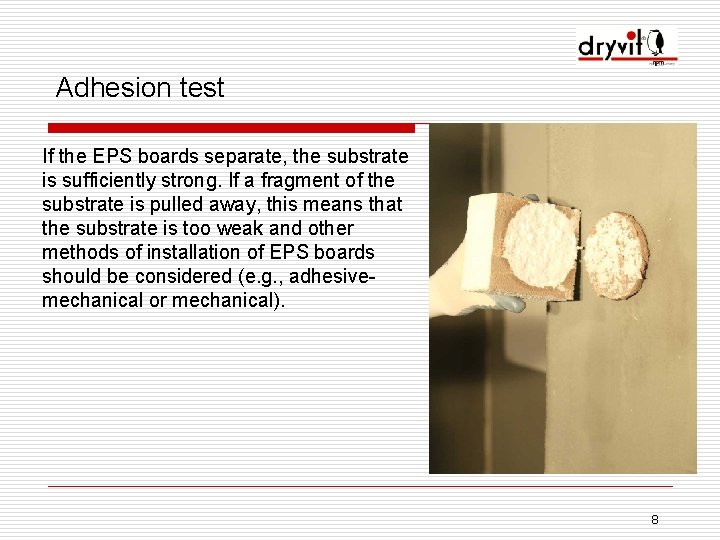
Adhesion test If the EPS boards separate, the substrate is sufficiently strong. If a fragment of the substrate is pulled away, this means that the substrate is too weak and other methods of installation of EPS boards should be considered (e. g. , adhesivemechanical or mechanical). 8
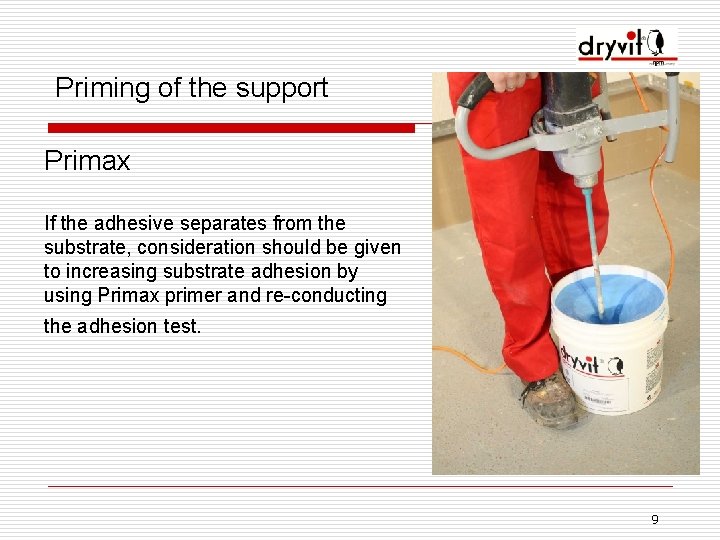
Priming of the support Primax If the adhesive separates from the substrate, consideration should be given to increasing substrate adhesion by using Primax primer and re-conducting the adhesion test. 9

Priming of the support Strongsil If a thin layer of substrate is pulled away, the substrate should be primed using Strongsil and the test conducted again. 10
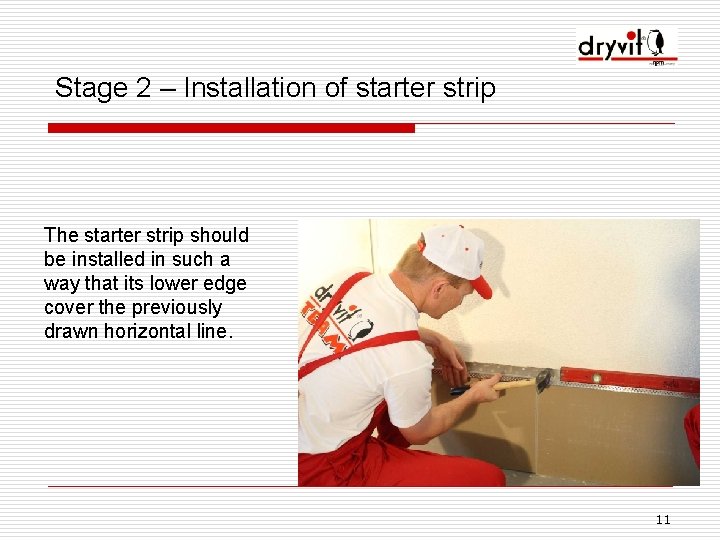
Stage 2 – Installation of starter strip The starter strip should be installed in such a way that its lower edge cover the previously drawn horizontal line. 11
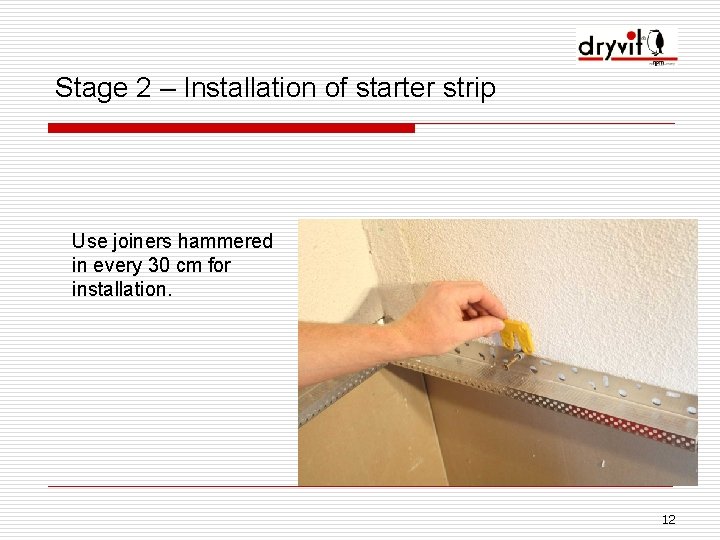
Stage 2 – Installation of starter strip Use joiners hammered in every 30 cm for installation. 12
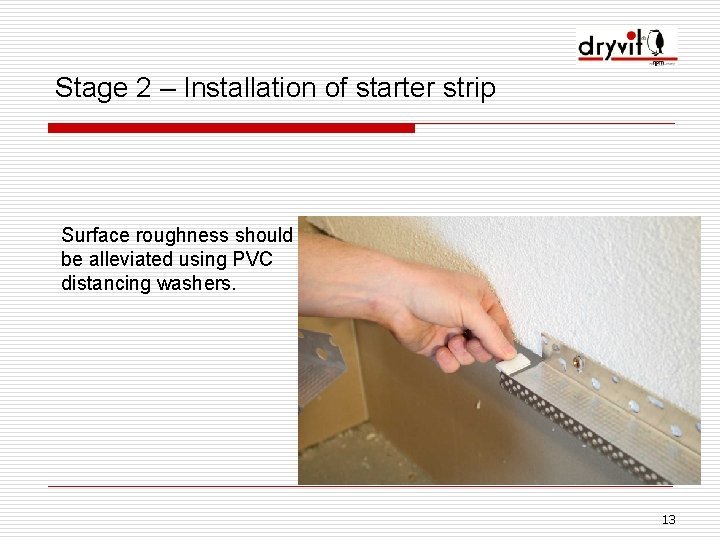
Stage 2 – Installation of starter strip Surface roughness should be alleviated using PVC distancing washers. 13
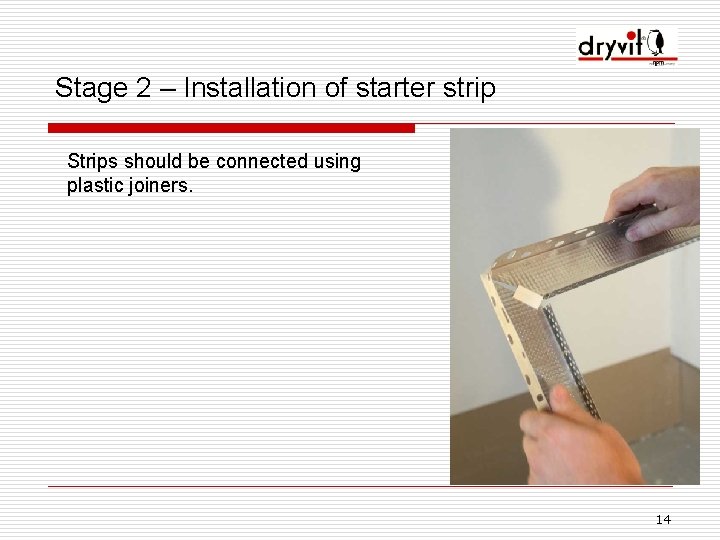
Stage 2 – Installation of starter strip Strips should be connected using plastic joiners. 14
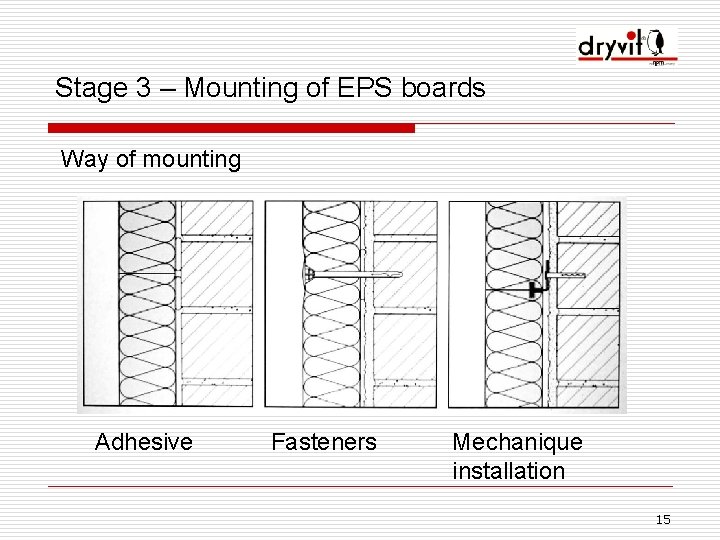
Stage 3 – Mounting of EPS boards Way of mounting Adhesive Fasteners Mechanique installation 15
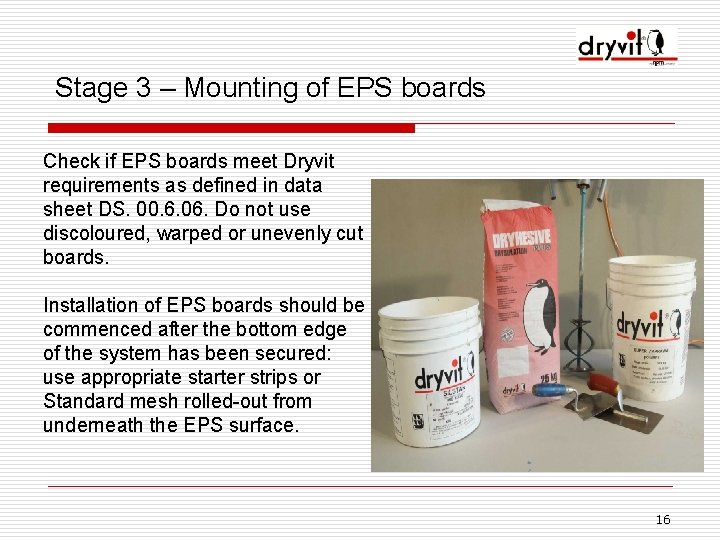
Stage 3 – Mounting of EPS boards Check if EPS boards meet Dryvit requirements as defined in data sheet DS. 00. 6. 06. Do not use discoloured, warped or unevenly cut boards. Installation of EPS boards should be commenced after the bottom edge of the system has been secured: use appropriate starter strips or Standard mesh rolled-out from underneath the EPS surface. 16
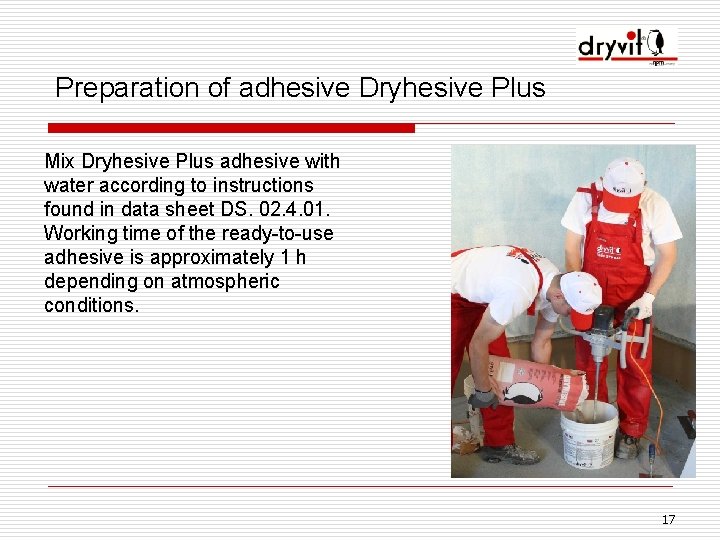
Preparation of adhesive Dryhesive Plus Mix Dryhesive Plus adhesive with water according to instructions found in data sheet DS. 02. 4. 01. Working time of the ready-to-use adhesive is approximately 1 h depending on atmospheric conditions. 17
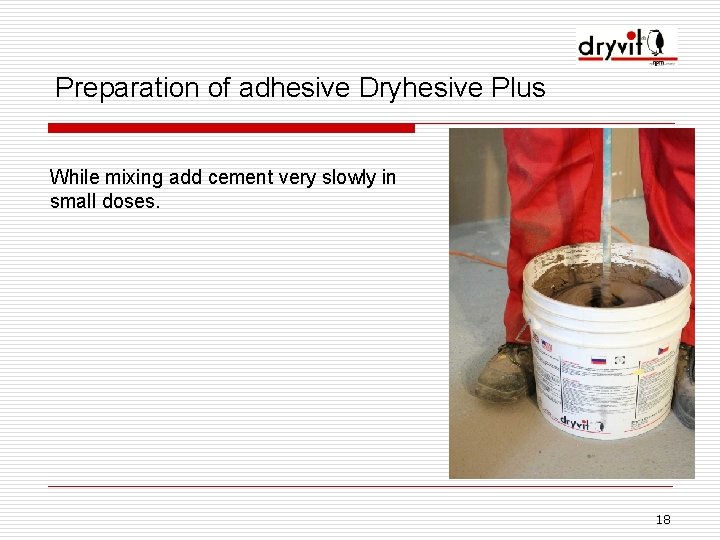
Preparation of adhesive Dryhesive Plus While mixing add cement very slowly in small doses. 18
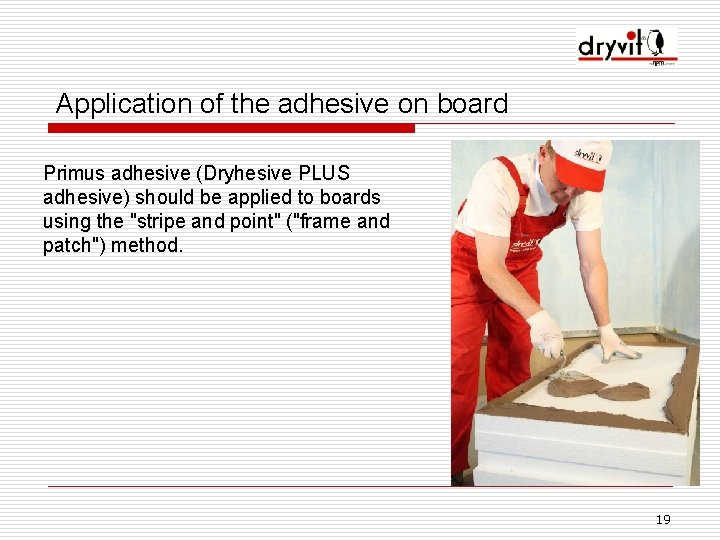
Application of the adhesive on board Primus adhesive (Dryhesive PLUS adhesive) should be applied to boards using the "stripe and point" ("frame and patch") method. 19
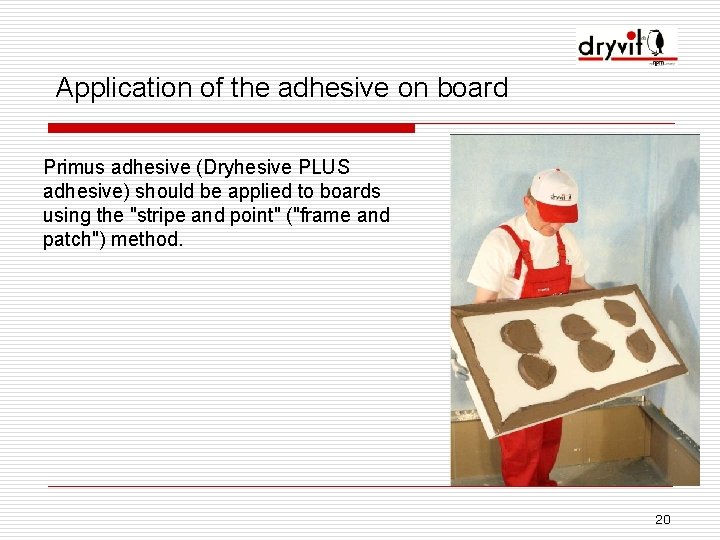
Application of the adhesive on board Primus adhesive (Dryhesive PLUS adhesive) should be applied to boards using the "stripe and point" ("frame and patch") method. 20
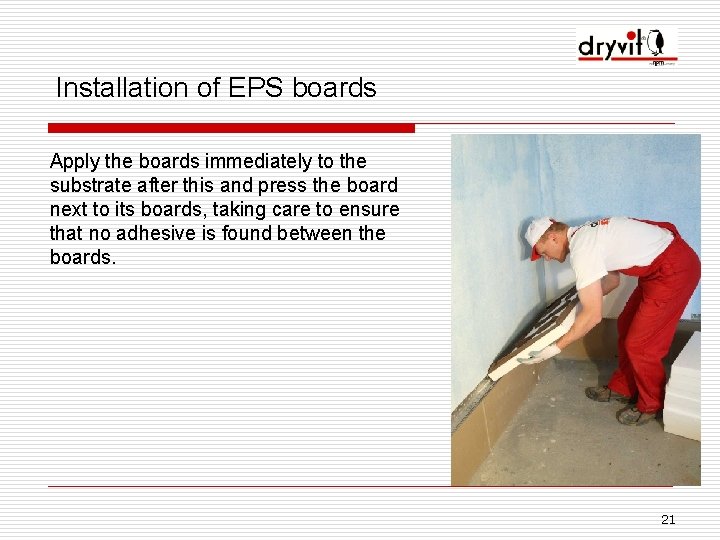
Installation of EPS boards Apply the boards immediately to the substrate after this and press the board next to its boards, taking care to ensure that no adhesive is found between the boards. 21
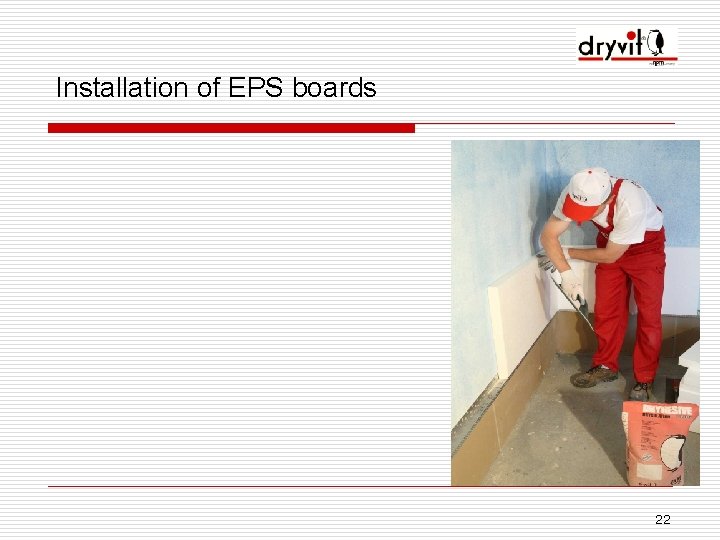
Installation of EPS boards 22
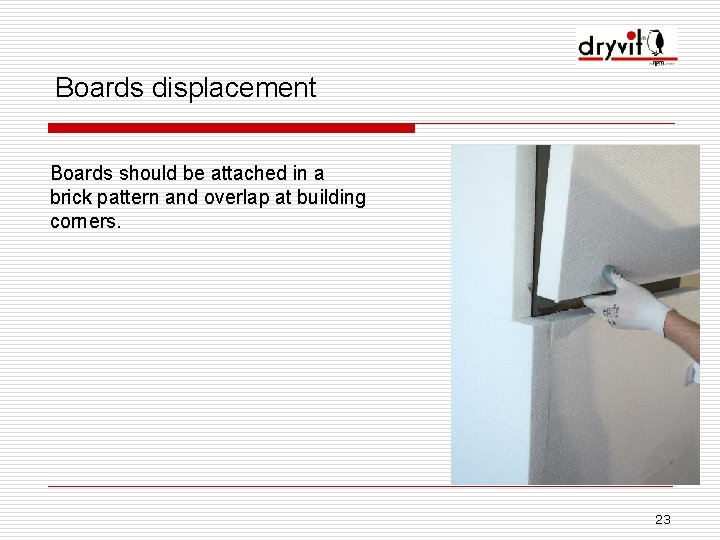
Boards displacement Boards should be attached in a brick pattern and overlap at building corners. 23
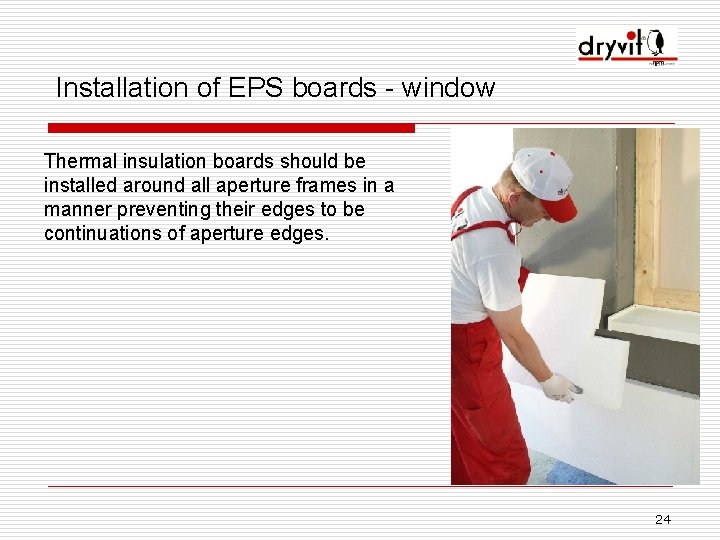
Installation of EPS boards - window Thermal insulation boards should be installed around all aperture frames in a manner preventing their edges to be continuations of aperture edges. 24
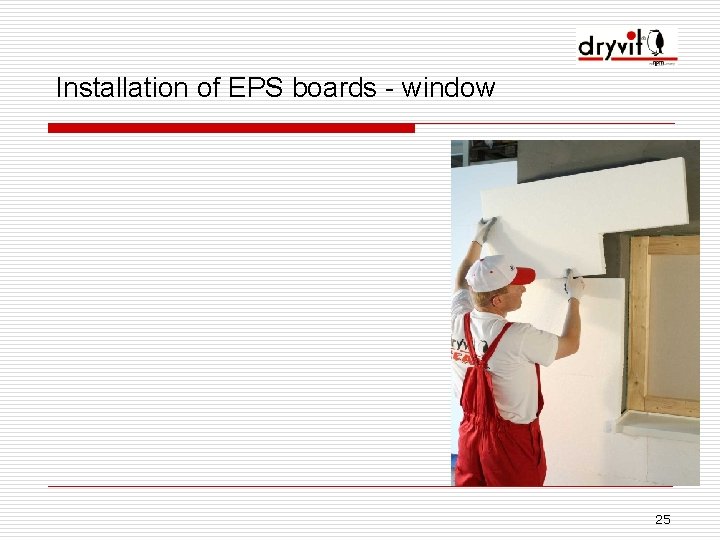
Installation of EPS boards - window 25
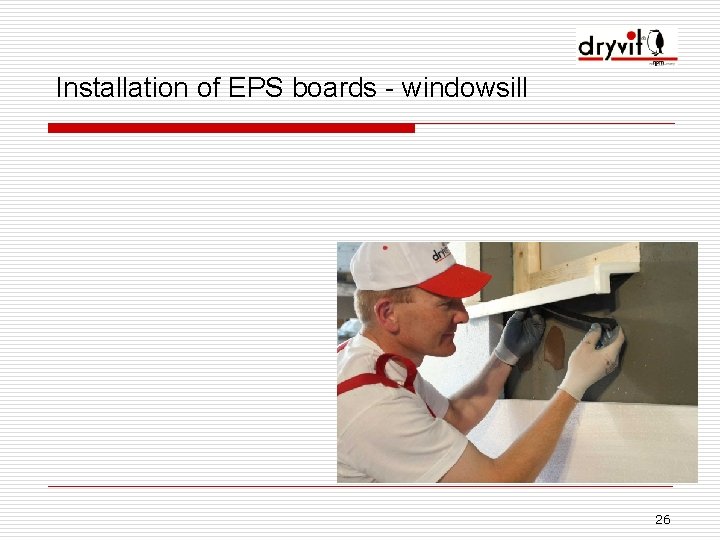
Installation of EPS boards - windowsill 26
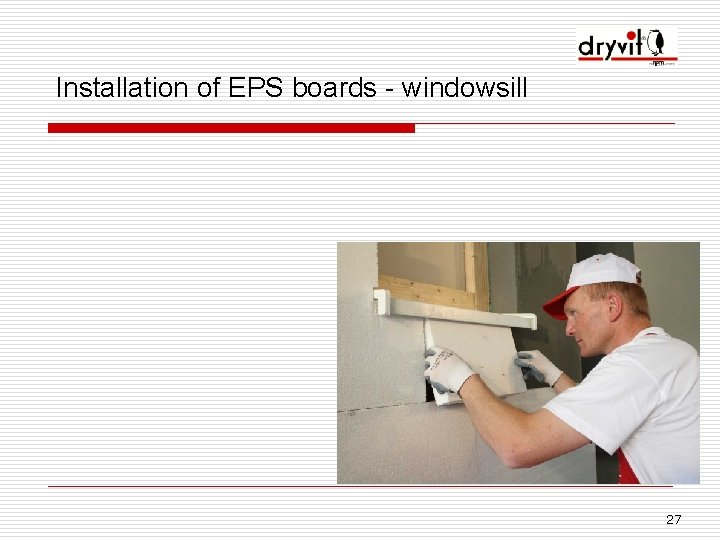
Installation of EPS boards - windowsill 27
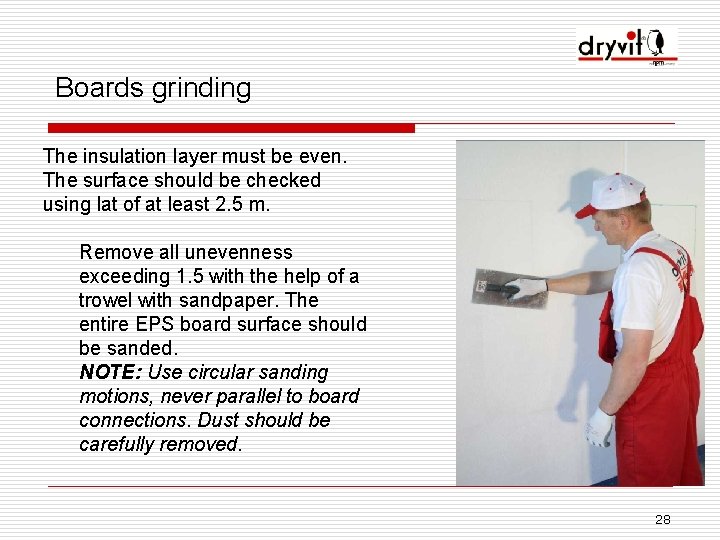
Boards grinding The insulation layer must be even. The surface should be checked using lat of at least 2. 5 m. Remove all unevenness exceeding 1. 5 with the help of a trowel with sandpaper. The entire EPS board surface should be sanded. NOTE: Use circular sanding motions, never parallel to board connections. Dust should be carefully removed. 28
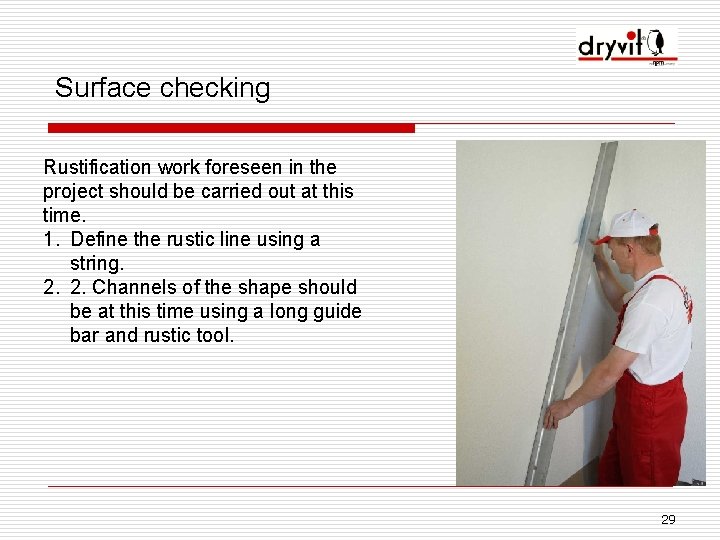
Surface checking Rustification work foreseen in the project should be carried out at this time. 1. Define the rustic line using a string. 2. 2. Channels of the shape should be at this time using a long guide bar and rustic tool. 29
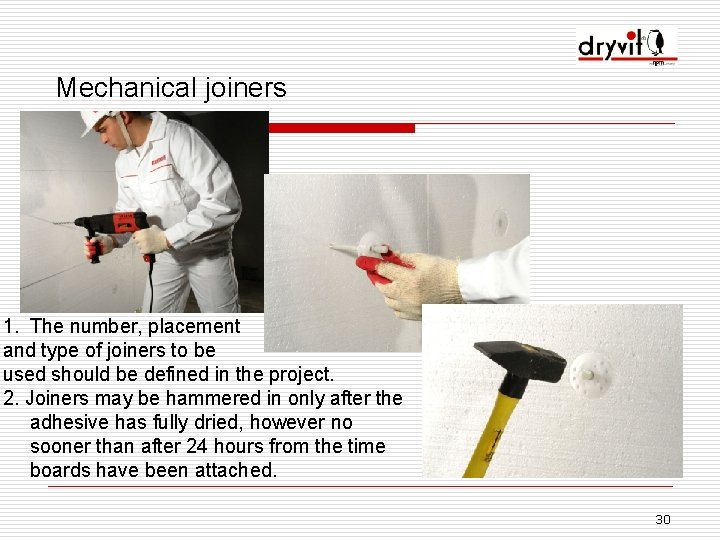
Mechanical joiners 1. The number, placement and type of joiners to be used should be defined in the project. 2. Joiners may be hammered in only after the adhesive has fully dried, however no sooner than after 24 hours from the time boards have been attached. 30
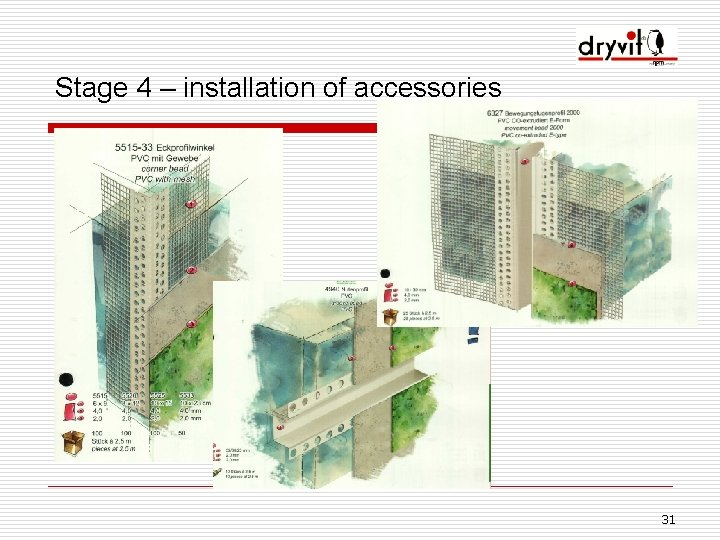
Stage 4 – installation of accessories 31
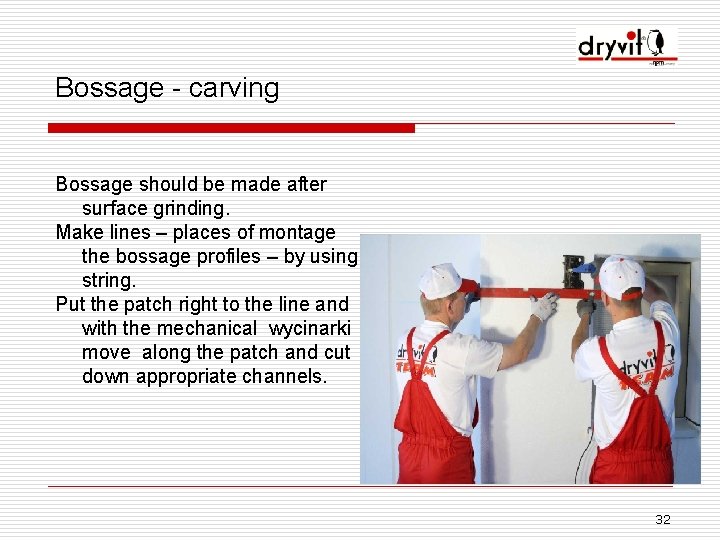
Bossage - carving Bossage should be made after surface grinding. Make lines – places of montage the bossage profiles – by using string. Put the patch right to the line and with the mechanical wycinarki move along the patch and cut down appropriate channels. 32
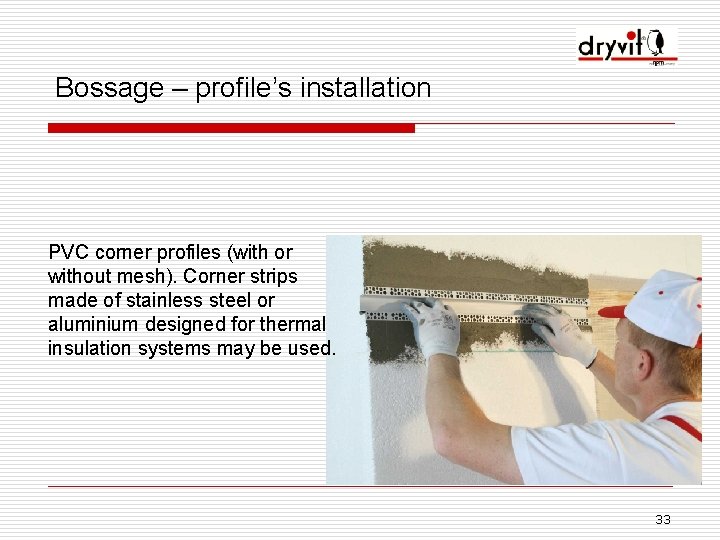
Bossage – profile’s installation PVC corner profiles (with or without mesh). Corner strips made of stainless steel or aluminium designed for thermal insulation systems may be used. 33
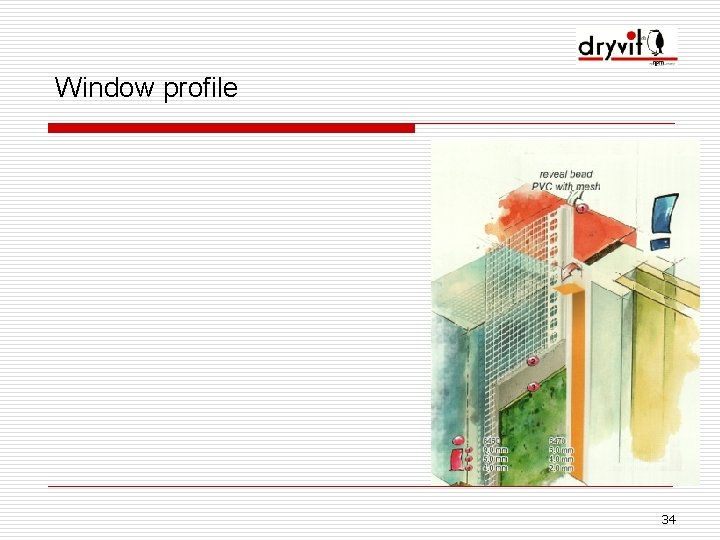
Window profile 34
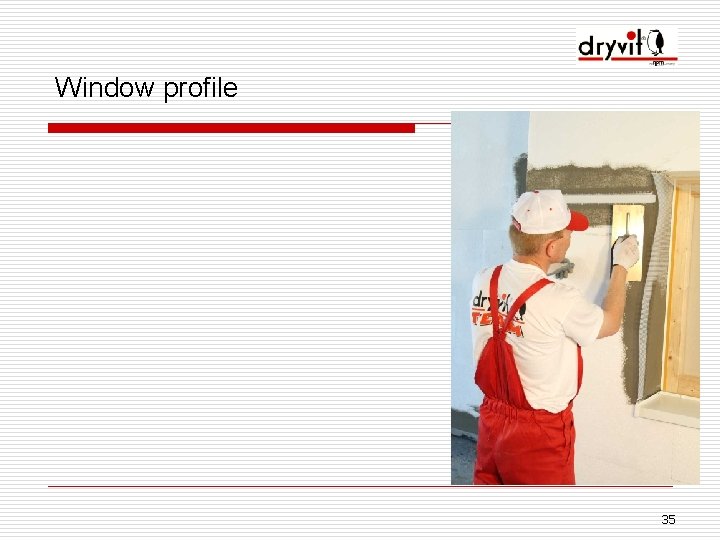
Window profile 35
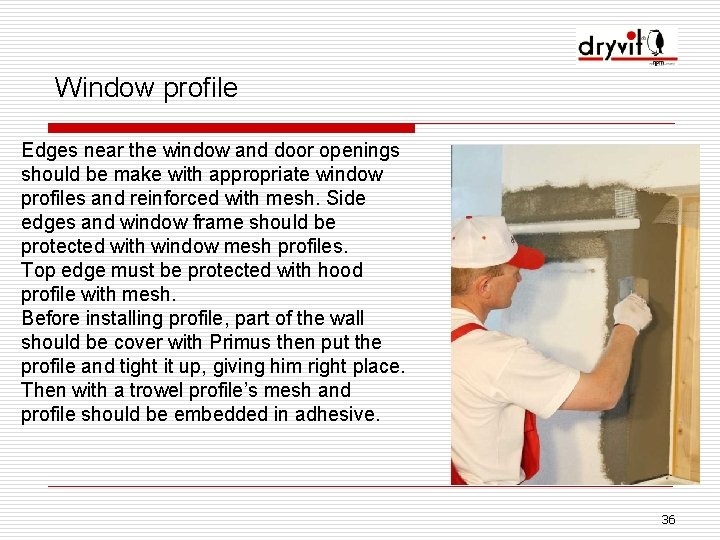
Window profile Edges near the window and door openings should be make with appropriate window profiles and reinforced with mesh. Side edges and window frame should be protected with window mesh profiles. Top edge must be protected with hood profile with mesh. Before installing profile, part of the wall should be cover with Primus then put the profile and tight it up, giving him right place. Then with a trowel profile’s mesh and profile should be embedded in adhesive. 36
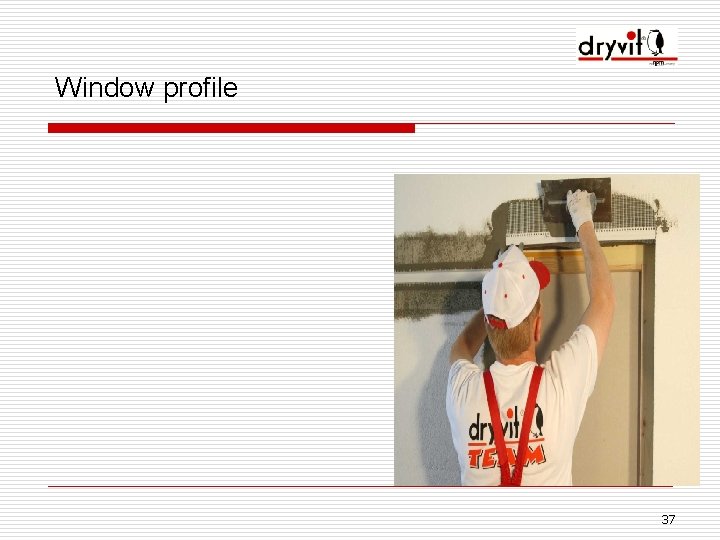
Window profile 37
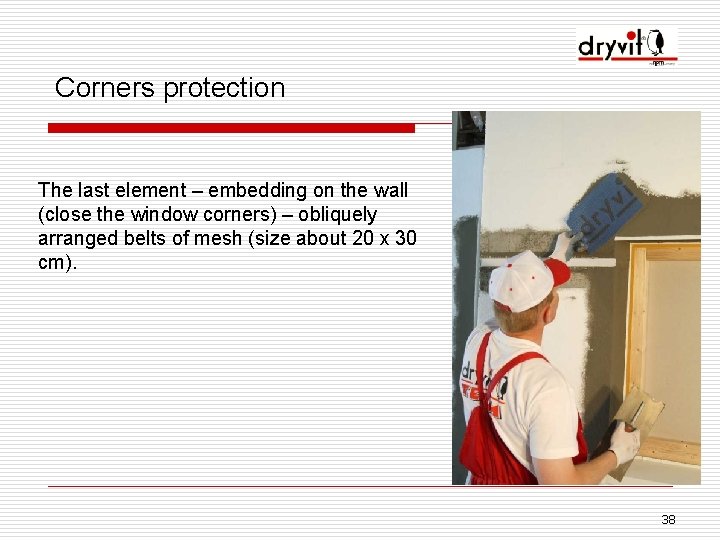
Corners protection The last element – embedding on the wall (close the window corners) – obliquely arranged belts of mesh (size about 20 x 30 cm). 38
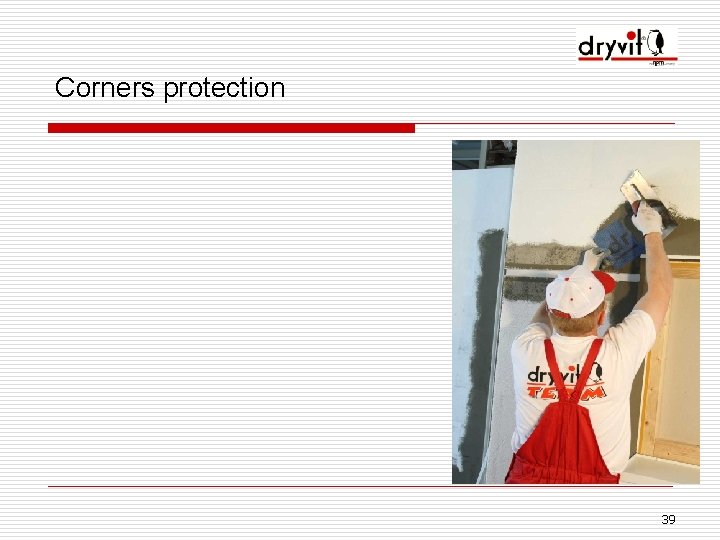
Corners protection 39
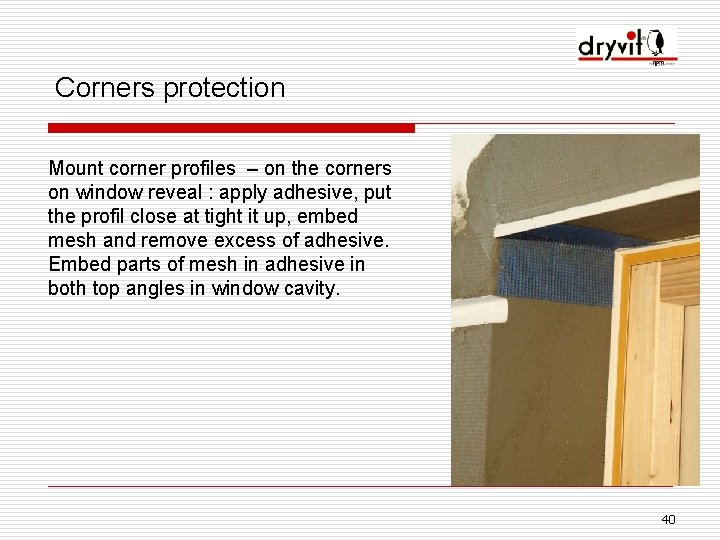
Corners protection Mount corner profiles – on the corners on window reveal : apply adhesive, put the profil close at tight it up, embed mesh and remove excess of adhesive. Embed parts of mesh in adhesive in both top angles in window cavity. 40
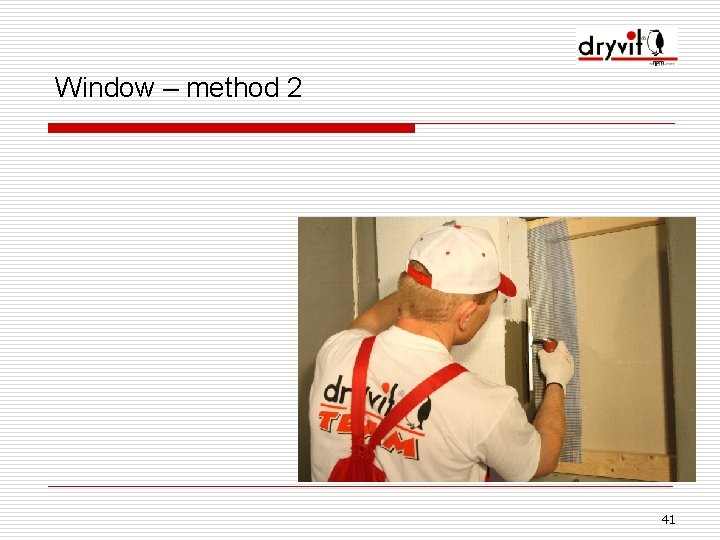
Window – method 2 41
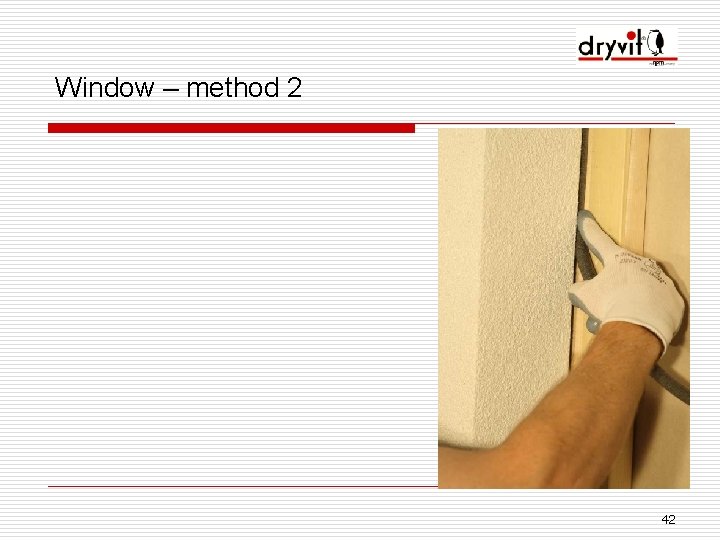
Window – method 2 42
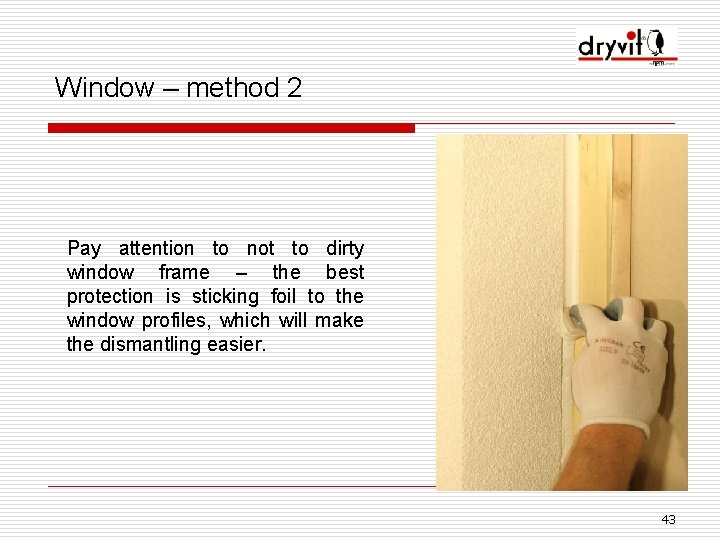
Window – method 2 Pay attention to not to dirty window frame – the best protection is sticking foil to the window profiles, which will make the dismantling easier. 43
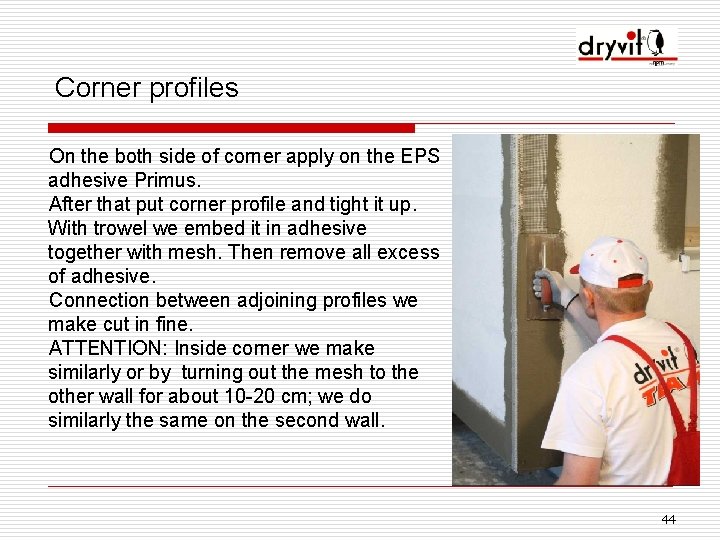
Corner profiles On the both side of corner apply on the EPS adhesive Primus. After that put corner profile and tight it up. With trowel we embed it in adhesive together with mesh. Then remove all excess of adhesive. Connection between adjoining profiles we make cut in fine. ATTENTION: Inside corner we make similarly or by turning out the mesh to the other wall for about 10 -20 cm; we do similarly the same on the second wall. 44
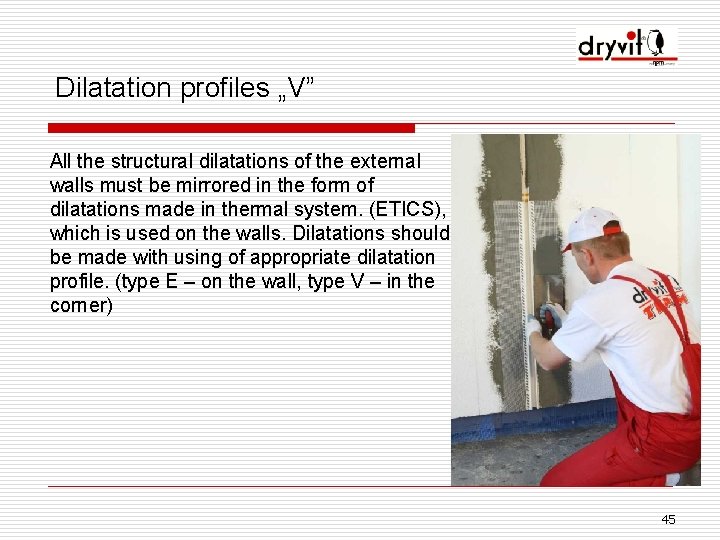
Dilatation profiles „V” All the structural dilatations of the external walls must be mirrored in the form of dilatations made in thermal system. (ETICS), which is used on the walls. Dilatations should be made with using of appropriate dilatation profile. (type E – on the wall, type V – in the corner) 45
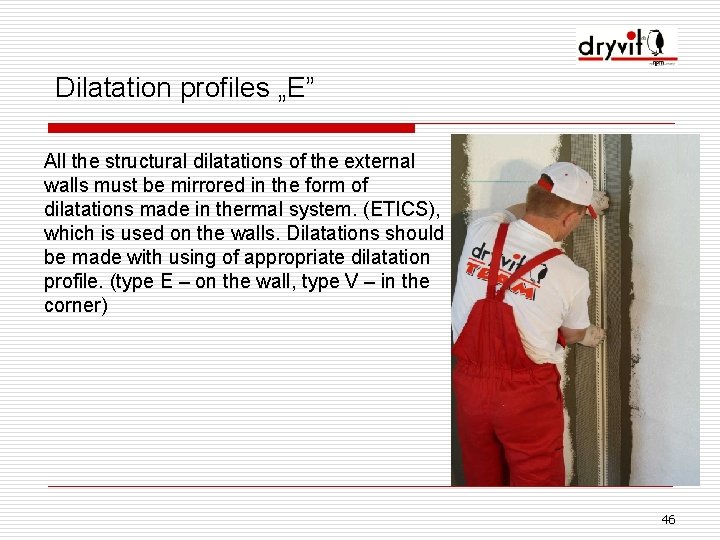
Dilatation profiles „E” All the structural dilatations of the external walls must be mirrored in the form of dilatations made in thermal system. (ETICS), which is used on the walls. Dilatations should be made with using of appropriate dilatation profile. (type E – on the wall, type V – in the corner) 46
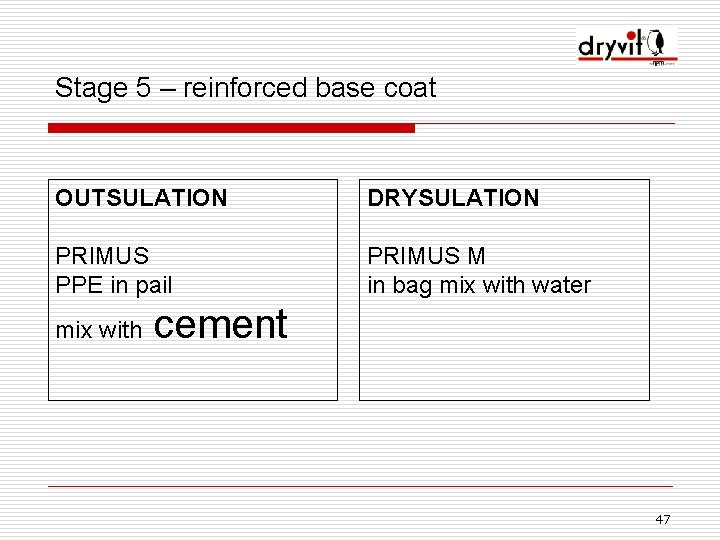
Stage 5 – reinforced base coat OUTSULATION DRYSULATION PRIMUS PPE in pail PRIMUS M in bag mix with water mix with cement 47
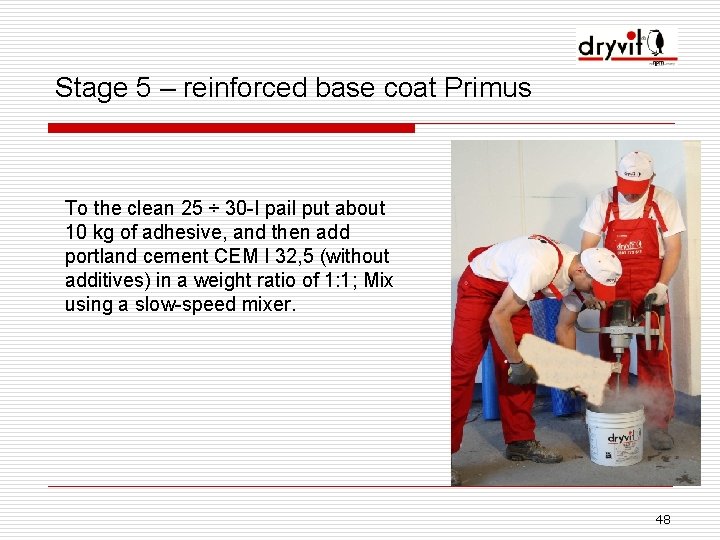
Stage 5 – reinforced base coat Primus To the clean 25 ÷ 30 -I pail put about 10 kg of adhesive, and then add portland cement CEM I 32, 5 (without additives) in a weight ratio of 1: 1; Mix using a slow-speed mixer. 48
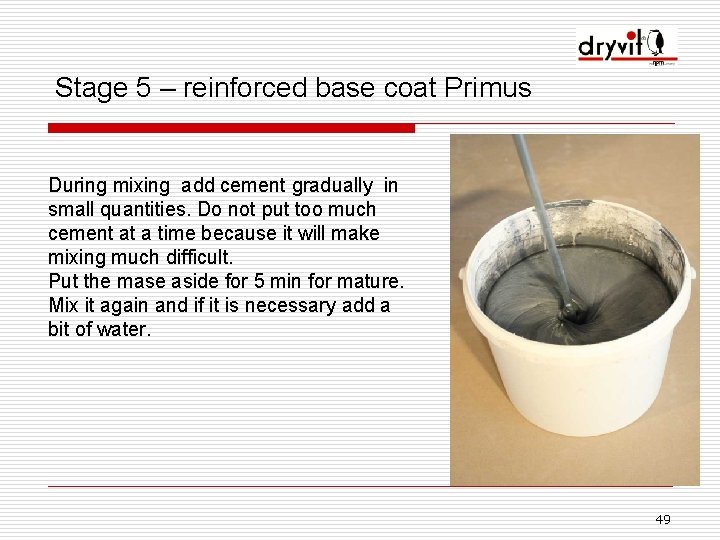
Stage 5 – reinforced base coat Primus During mixing add cement gradually in small quantities. Do not put too much cement at a time because it will make mixing much difficult. Put the mase aside for 5 min for mature. Mix it again and if it is necessary add a bit of water. 49
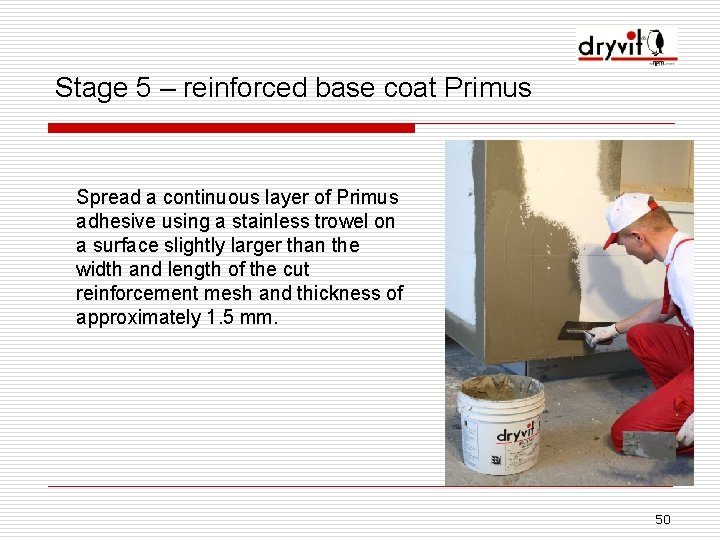
Stage 5 – reinforced base coat Primus Spread a continuous layer of Primus adhesive using a stainless trowel on a surface slightly larger than the width and length of the cut reinforcement mesh and thickness of approximately 1. 5 mm. 50
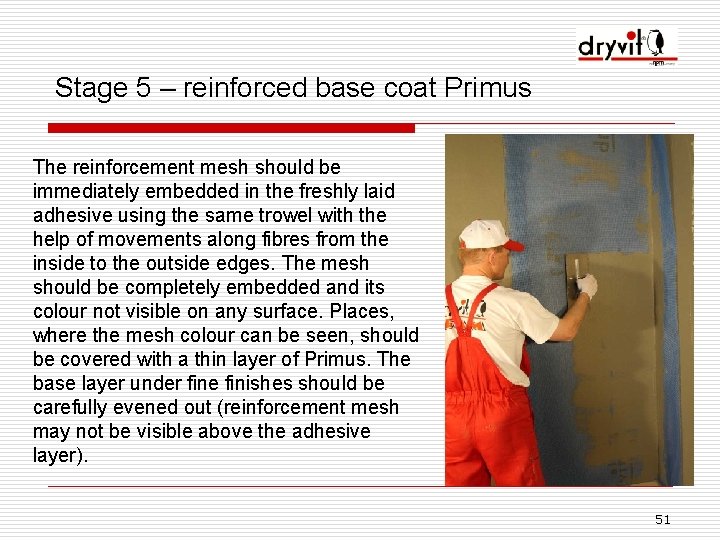
Stage 5 – reinforced base coat Primus The reinforcement mesh should be immediately embedded in the freshly laid adhesive using the same trowel with the help of movements along fibres from the inside to the outside edges. The mesh should be completely embedded and its colour not visible on any surface. Places, where the mesh colour can be seen, should be covered with a thin layer of Primus. The base layer under fine finishes should be carefully evened out (reinforcement mesh may not be visible above the adhesive layer). 51
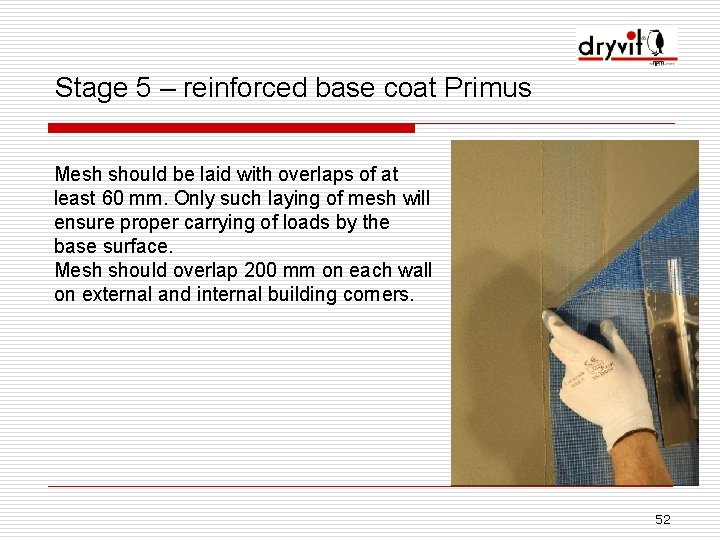
Stage 5 – reinforced base coat Primus Mesh should be laid with overlaps of at least 60 mm. Only such laying of mesh will ensure proper carrying of loads by the base surface. Mesh should overlap 200 mm on each wall on external and internal building corners. 52
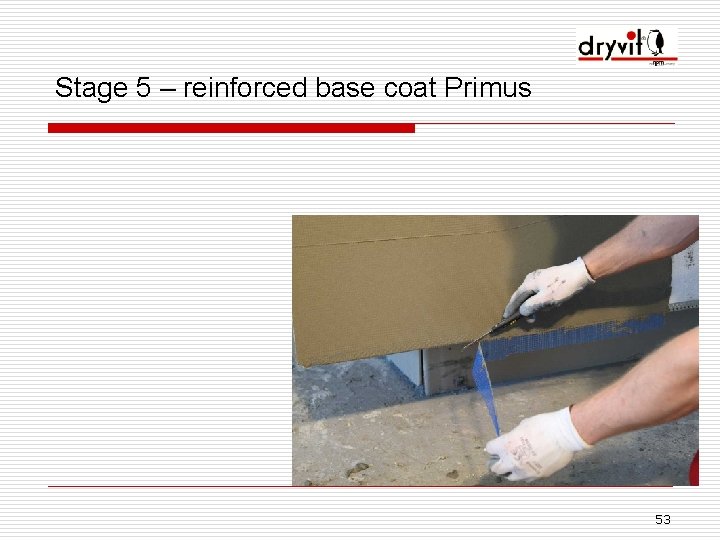
Stage 5 – reinforced base coat Primus 53
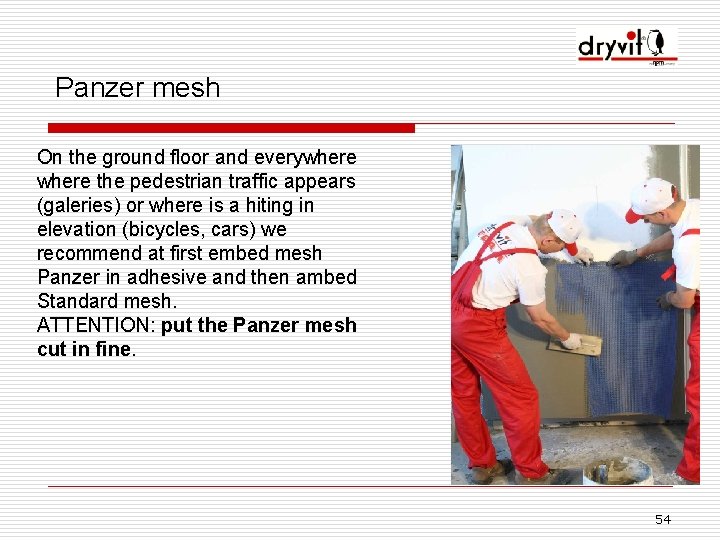
Panzer mesh On the ground floor and everywhere the pedestrian traffic appears (galeries) or where is a hiting in elevation (bicycles, cars) we recommend at first embed mesh Panzer in adhesive and then ambed Standard mesh. ATTENTION: put the Panzer mesh cut in fine. 54
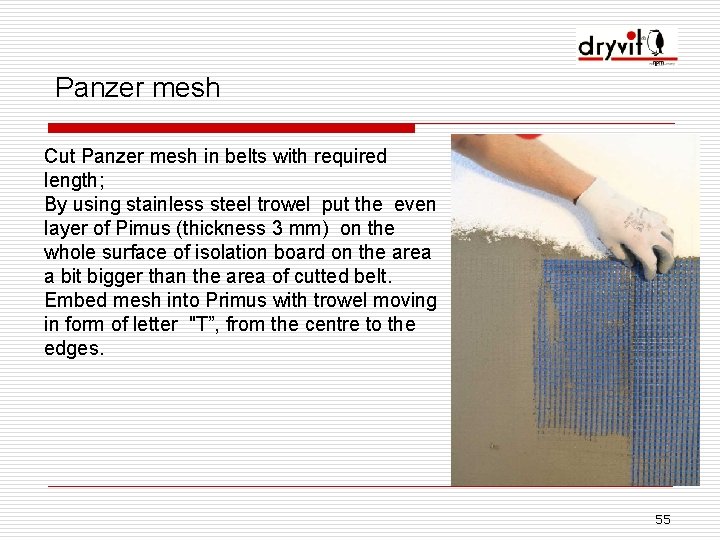
Panzer mesh Cut Panzer mesh in belts with required length; By using stainless steel trowel put the even layer of Pimus (thickness 3 mm) on the whole surface of isolation board on the area a bit bigger than the area of cutted belt. Embed mesh into Primus with trowel moving in form of letter "T”, from the centre to the edges. 55
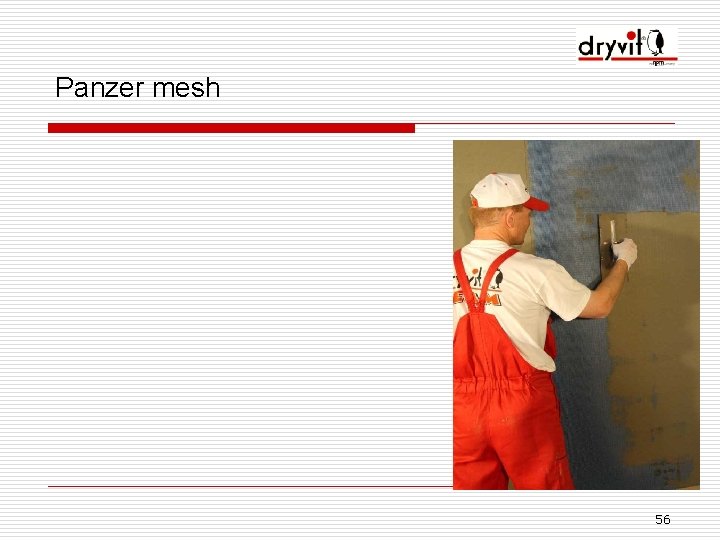
Panzer mesh 56
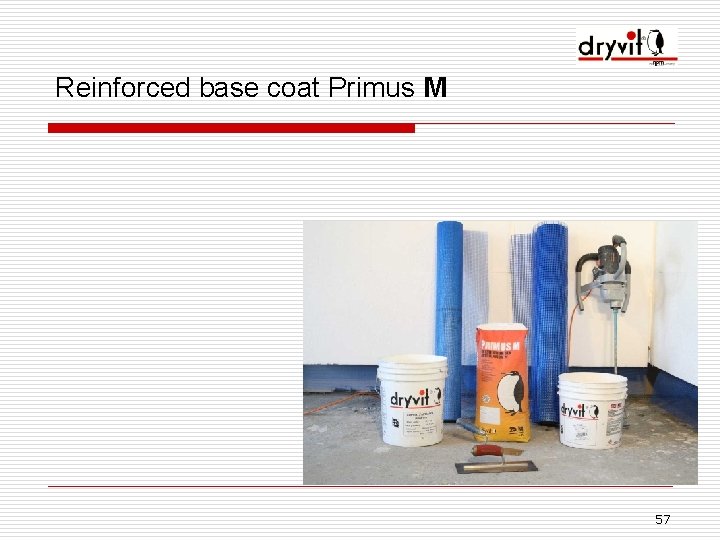
Reinforced base coat Primus M 57
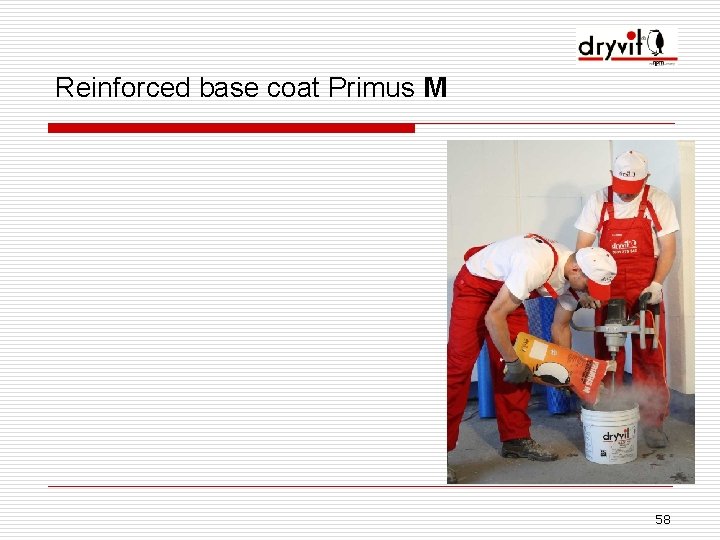
Reinforced base coat Primus M 58
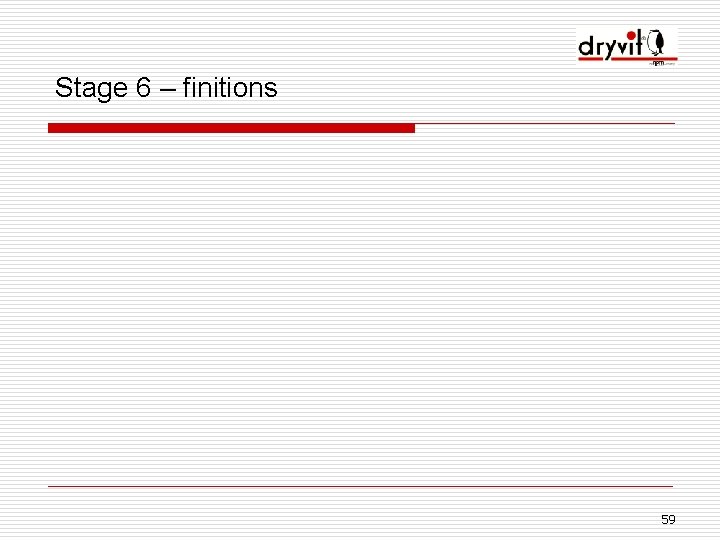
Stage 6 – finitions 59
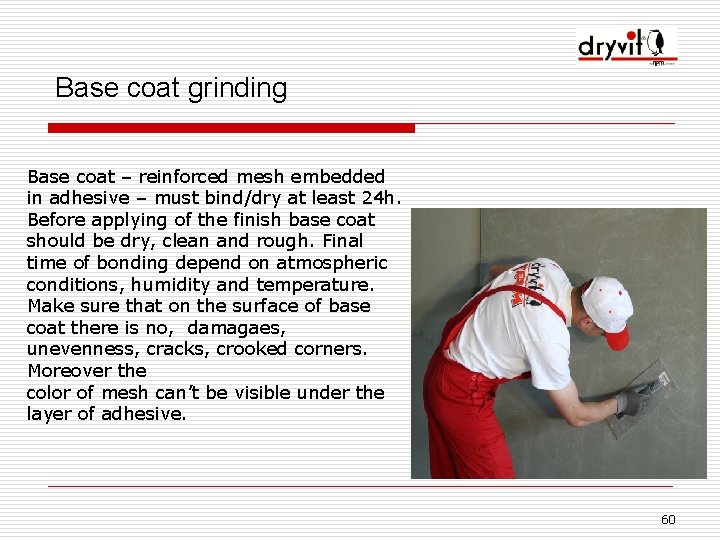
Base coat grinding Base coat – reinforced mesh embedded in adhesive – must bind/dry at least 24 h. Before applying of the finish base coat should be dry, clean and rough. Final time of bonding depend on atmospheric conditions, humidity and temperature. Make sure that on the surface of base coat there is no, damagaes, unevenness, cracks, crooked corners. Moreover the color of mesh can’t be visible under the layer of adhesive. 60
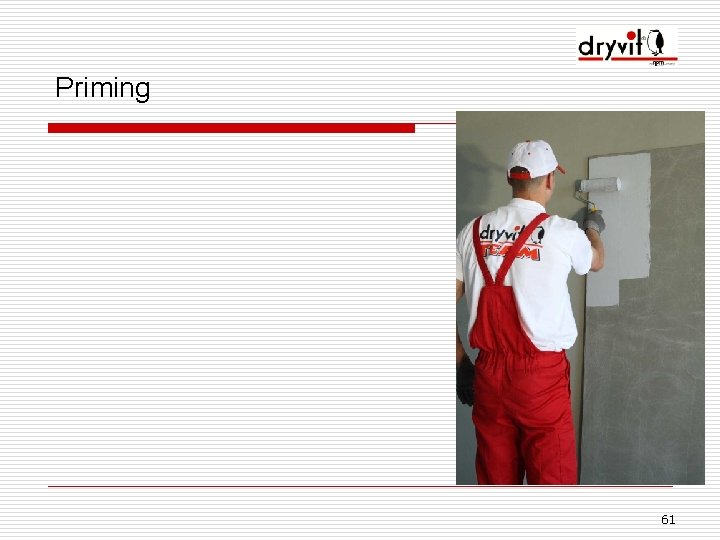
Priming 61
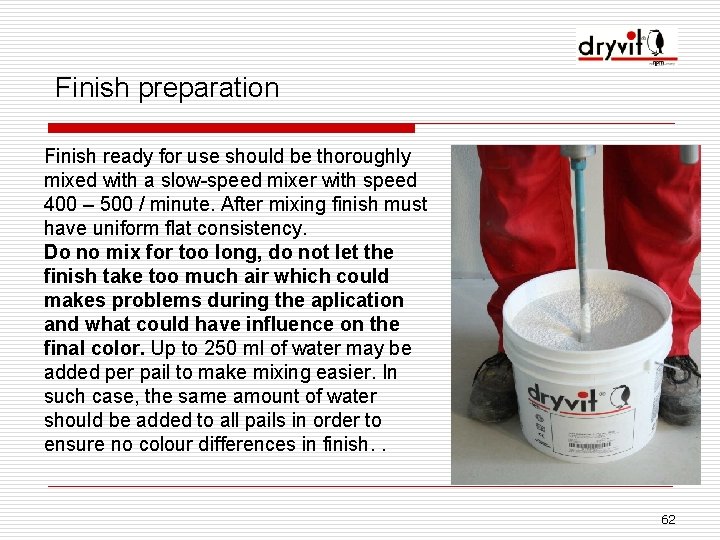
Finish preparation Finish ready for use should be thoroughly mixed with a slow-speed mixer with speed 400 – 500 / minute. After mixing finish must have uniform flat consistency. Do no mix for too long, do not let the finish take too much air which could makes problems during the aplication and what could have influence on the final color. Up to 250 ml of water may be added per pail to make mixing easier. In such case, the same amount of water should be added to all pails in order to ensure no colour differences in finish. . 62
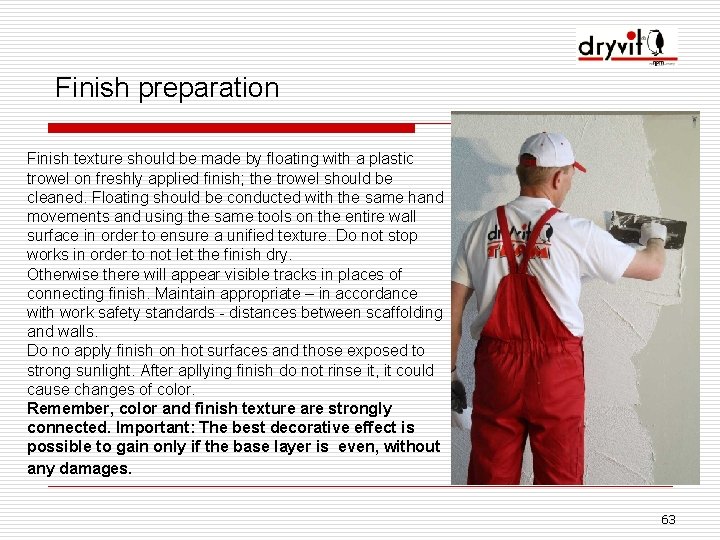
Finish preparation Finish texture should be made by floating with a plastic trowel on freshly applied finish; the trowel should be cleaned. Floating should be conducted with the same hand movements and using the same tools on the entire wall surface in order to ensure a unified texture. Do not stop works in order to not let the finish dry. Otherwise there will appear visible tracks in places of connecting finish. Maintain appropriate – in accordance with work safety standards - distances between scaffolding and walls. Do no apply finish on hot surfaces and those exposed to strong sunlight. After apllying finish do not rinse it, it could cause changes of color. Remember, color and finish texture are strongly connected. Important: The best decorative effect is possible to gain only if the base layer is even, without any damages. 63
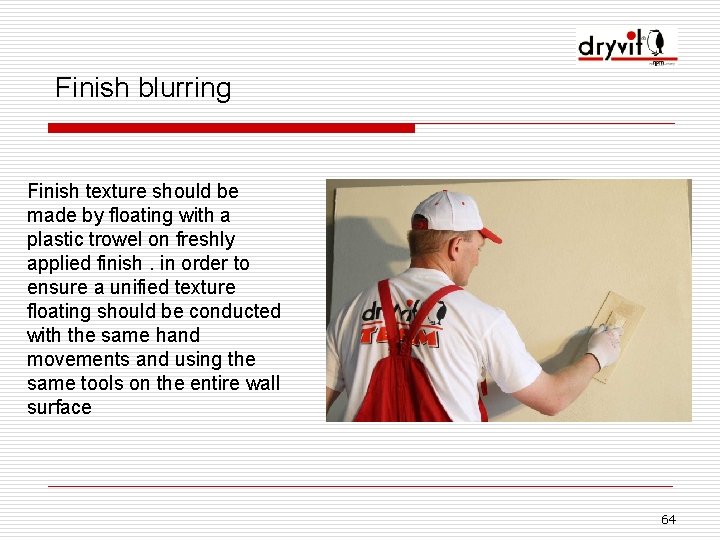
Finish blurring Finish texture should be made by floating with a plastic trowel on freshly applied finish. in order to ensure a unified texture floating should be conducted with the same hand movements and using the same tools on the entire wall surface 64
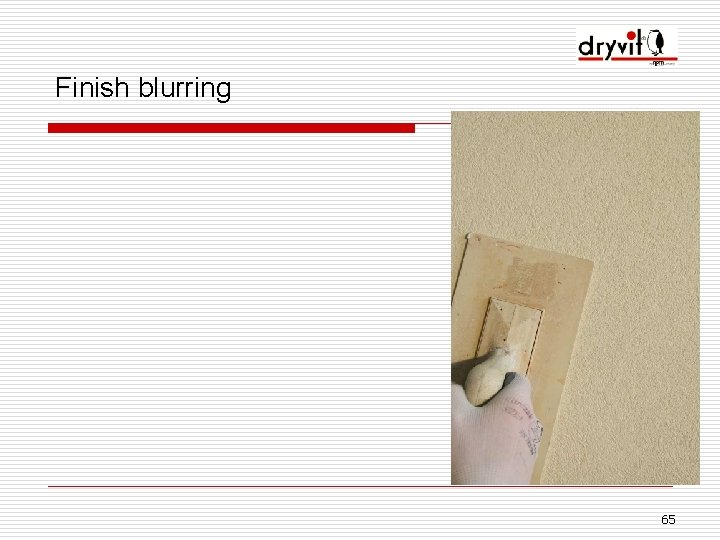
Finish blurring 65
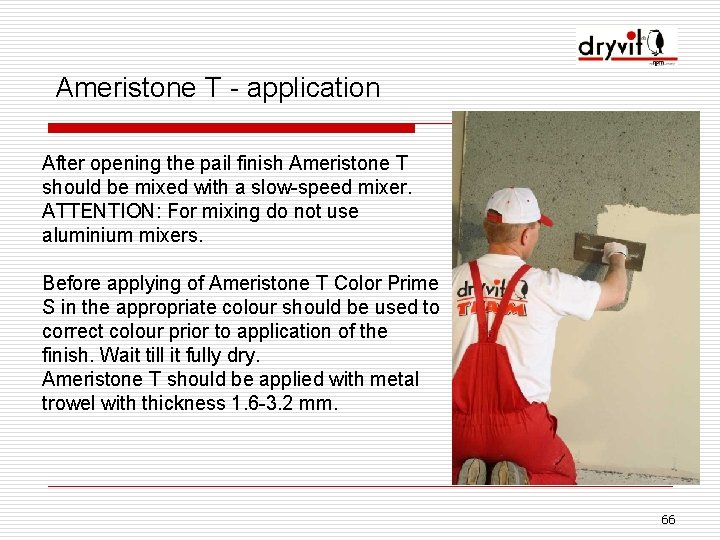
Ameristone T - application After opening the pail finish Ameristone T should be mixed with a slow-speed mixer. ATTENTION: For mixing do not use aluminium mixers. Before applying of Ameristone T Color Prime S in the appropriate colour should be used to correct colour prior to application of the finish. Wait till it fully dry. Ameristone T should be applied with metal trowel with thickness 1. 6 -3. 2 mm. 66
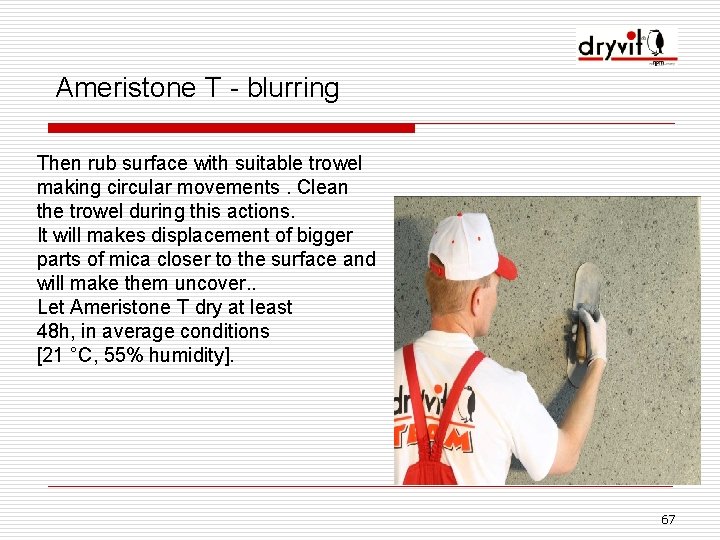
Ameristone T - blurring Then rub surface with suitable trowel making circular movements. Clean the trowel during this actions. It will makes displacement of bigger parts of mica closer to the surface and will make them uncover. . Let Ameristone T dry at least 48 h, in average conditions [21 °C, 55% humidity]. 67
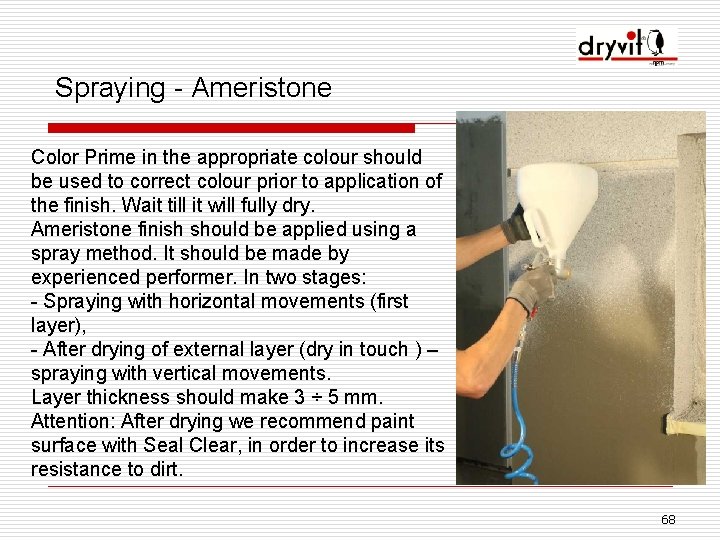
Spraying - Ameristone Color Prime in the appropriate colour should be used to correct colour prior to application of the finish. Wait till it will fully dry. Ameristone finish should be applied using a spray method. It should be made by experienced performer. In two stages: - Spraying with horizontal movements (first layer), - After drying of external layer (dry in touch ) – spraying with vertical movements. Layer thickness should make 3 ÷ 5 mm. Attention: After drying we recommend paint surface with Seal Clear, in order to increase its resistance to dirt. 68
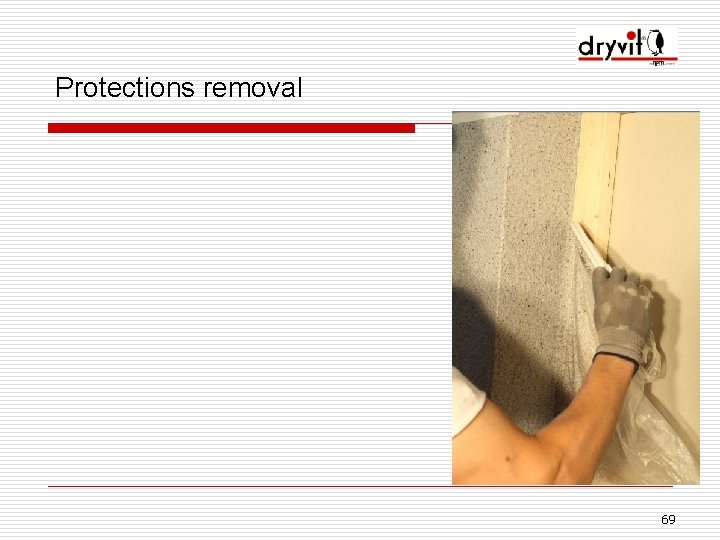
Protections removal 69
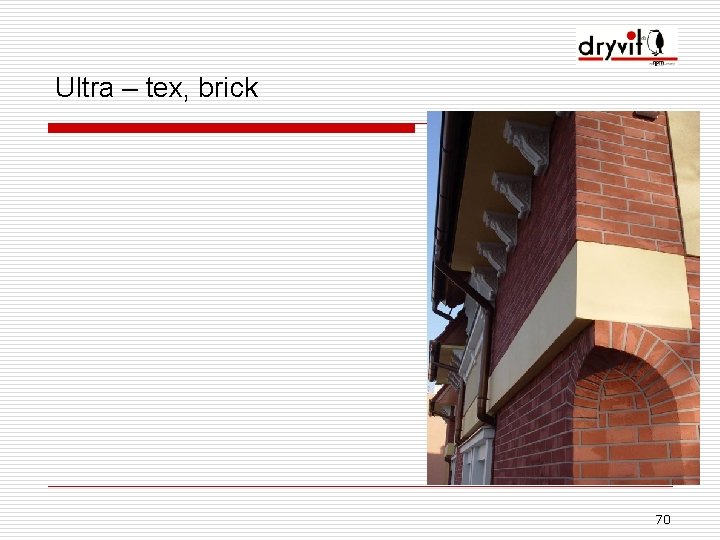
Ultra – tex, brick 70
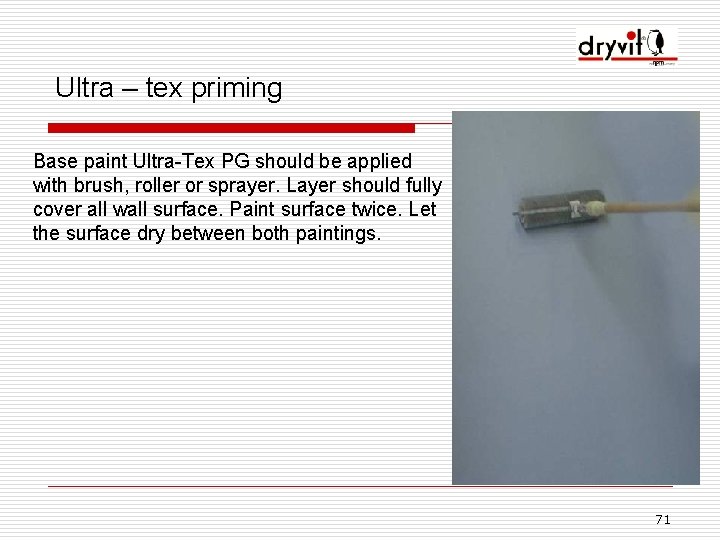
Ultra – tex priming Base paint Ultra-Tex PG should be applied with brush, roller or sprayer. Layer should fully cover all wall surface. Paint surface twice. Let the surface dry between both paintings. 71
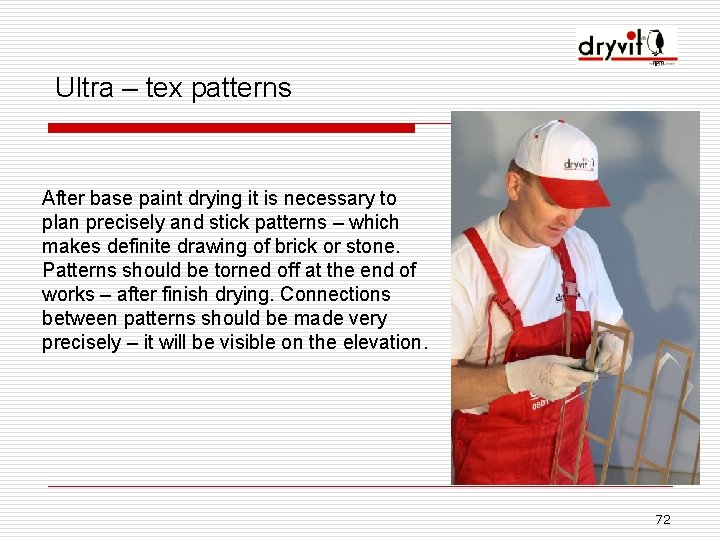
Ultra – tex patterns After base paint drying it is necessary to plan precisely and stick patterns – which makes definite drawing of brick or stone. Patterns should be torned off at the end of works – after finish drying. Connections between patterns should be made very precisely – it will be visible on the elevation. 72
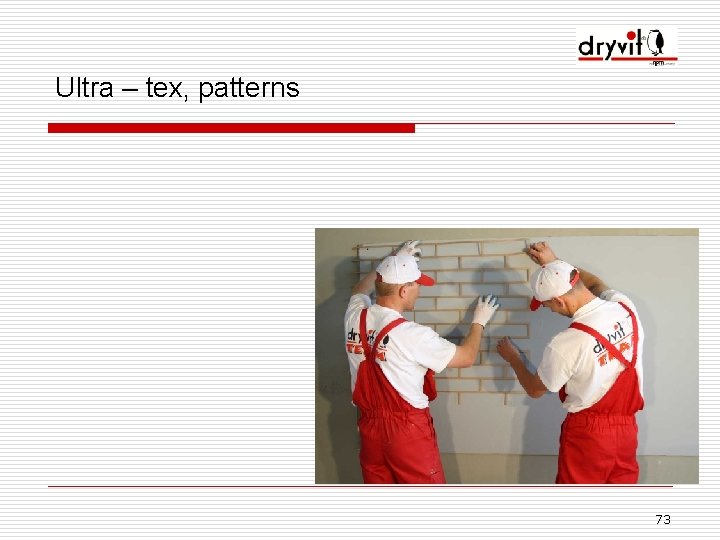
Ultra – tex, patterns 73
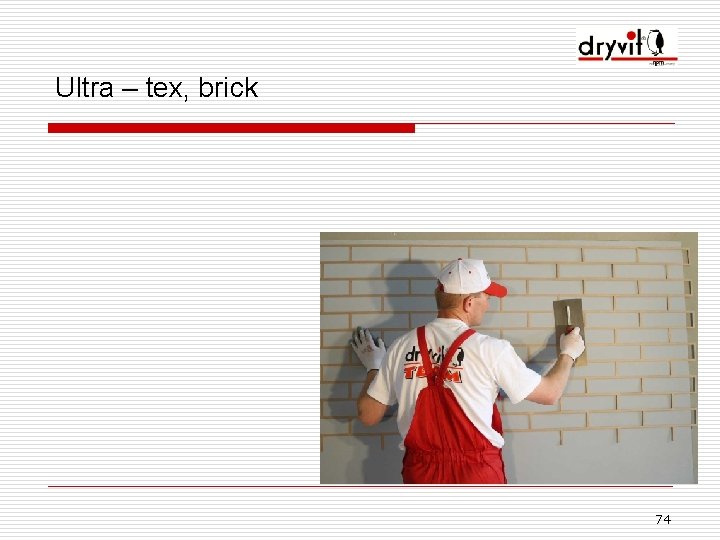
Ultra – tex, brick 74
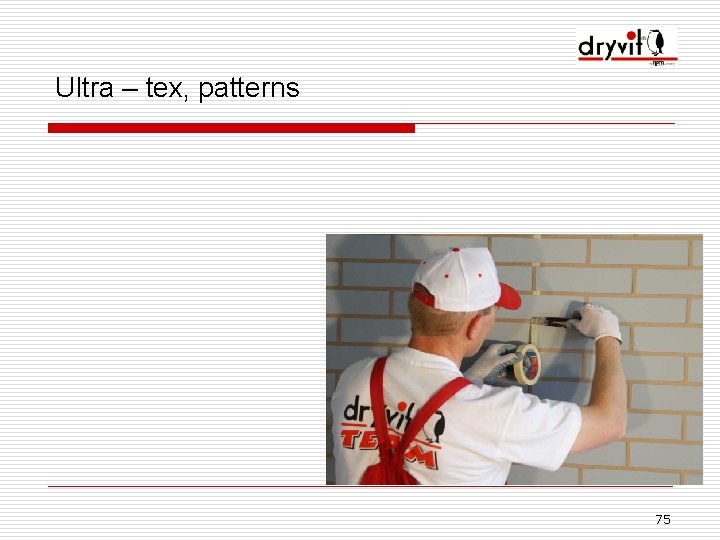
Ultra – tex, patterns 75
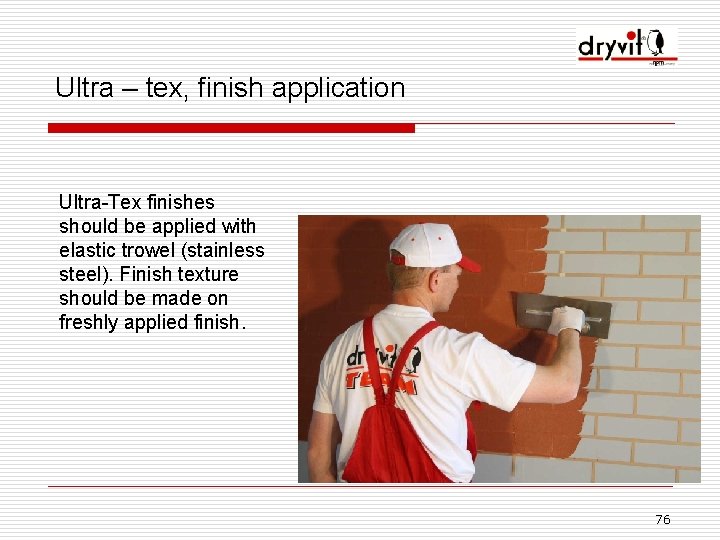
Ultra – tex, finish application Ultra-Tex finishes should be applied with elastic trowel (stainless steel). Finish texture should be made on freshly applied finish. 76
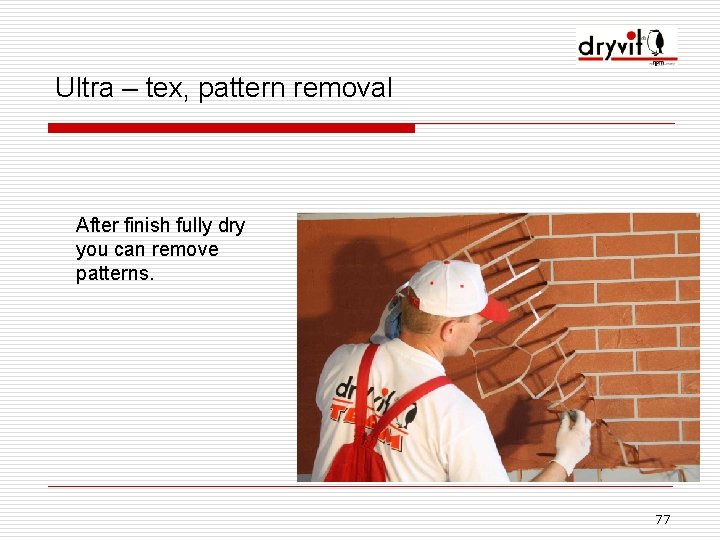
Ultra – tex, pattern removal After finish fully dry you can remove patterns. 77
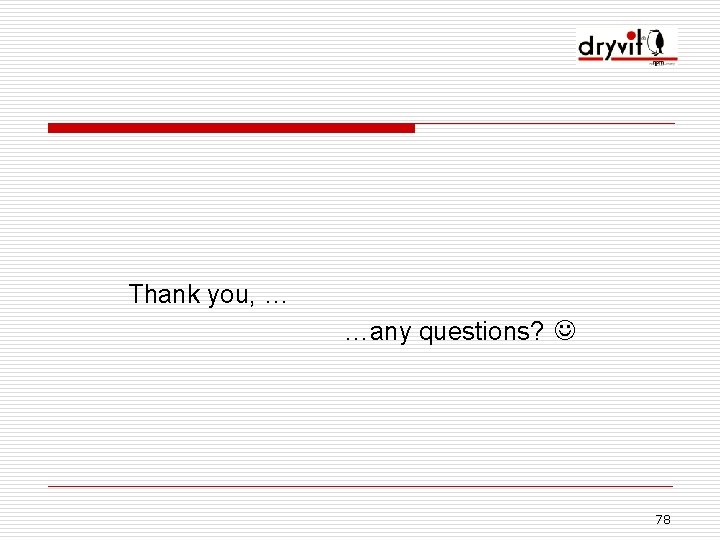
Thank you, … …any questions? 78
Panzermesh
Fabrication of wax pattern
Topology aware hints
Hints yrsel
Label the breast using the hints provided
Write 2 sentences by using expressing purpose
Guess the country by hints
When an author gives hints or clues
Agonal rhythm asystole strip
Story writing with hints
Oracle plan de ejecucion
Gsp focus areas
When an author gives hints or clues
Study guide questions for fahrenheit 451
Olle hints
Shape hints merupakan jenis animasi untuk mengatur
Dnslint
Analytical verbs
Word scramble hints
Foreshadowing in little red riding hood
What is the alphabet of lines
General controls vs application controls
Etsu scholarship office
Diferencia entre gran plano general y plano general
Where did general lee surrender to general grant?
Integrating quotes into an essay
Wood joining methods
Destructive and nondestructive testing of welds
Schaeffer's formula in kg
How to calculate warehouse space
Vertical jaw relation at rest
Vendor rating methods
U vegetable
Principle of god pod method
Goodwill valuation methods
Innovative methods of teaching english language
Using risk to balance agile and plan driven methods
Procurement plan
Alan bryman social research methods
What is translation loss
Transfer pricing methods with examples
Traditional method of fish preservation
How can ngt be used for requirements determination?
Methods of thrust augmentation
Combination cooking methods
What are the four acceptable methods for thawing food?
Formal amendment definition
Ck metrics
A method of characterization is
Black acting methods
Junit testing private methods
Teaching learning material
A thousand teachers a thousand methods reflection
Characteristics of good teaching methods
Fact analysis in system analysis and design
Energy methods in structural analysis
Stripping methods
Grade 12 accounting inventory valuation
Mechanical methods of sterilization
Principle of autoclave
Bmi504
Staining methods
Oil spill containment methods
What is separation
Two shading techniques
Seamless quote integration
Quota sampling in qualitative research
Dry salting method
Sampling methods psychology
Research method notes
Method of social psychology
Research methods in developmental psychology
What is dimensions in research
Research design example
Define the term recruitment
Advantages and disadvantages of boundary fill algorithm
Rank aggregation methods for the web
Public relations research methods
What is field methods in psychology