Direct Design Olander vs Heger Margarita Takou Josh
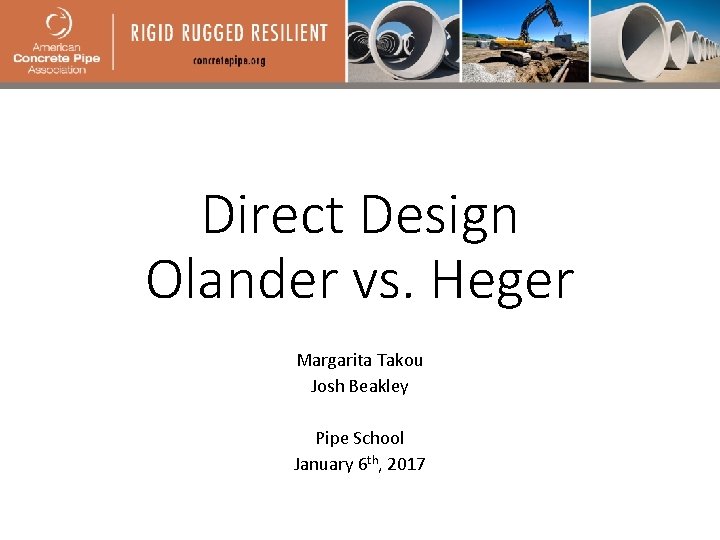
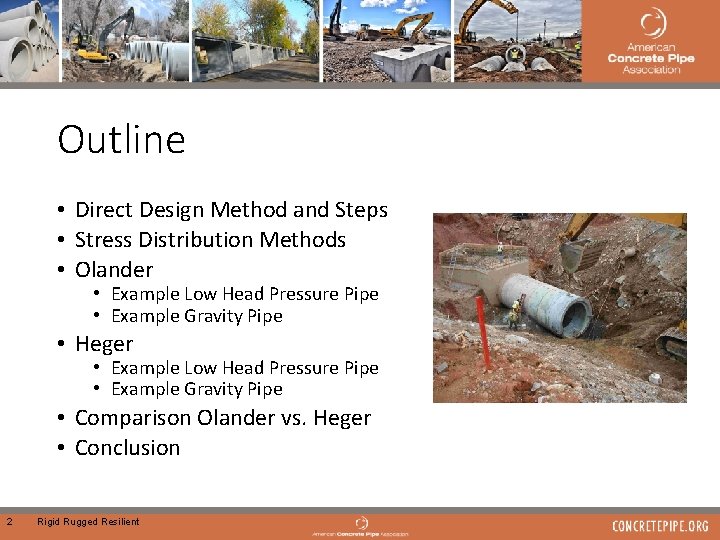
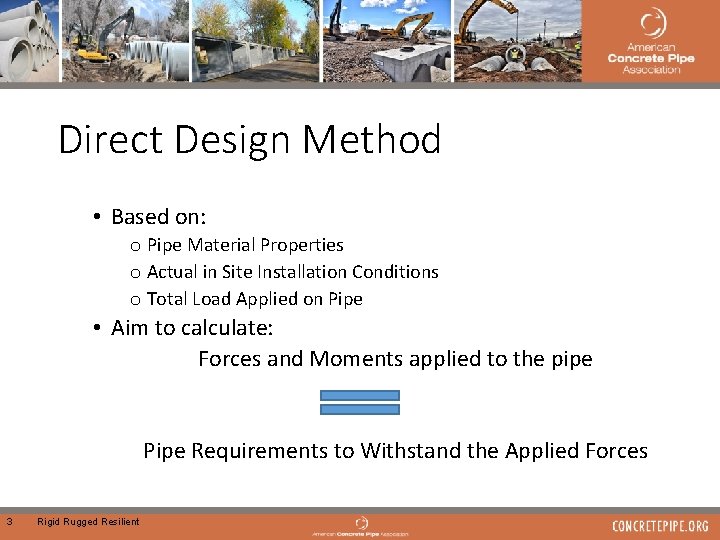
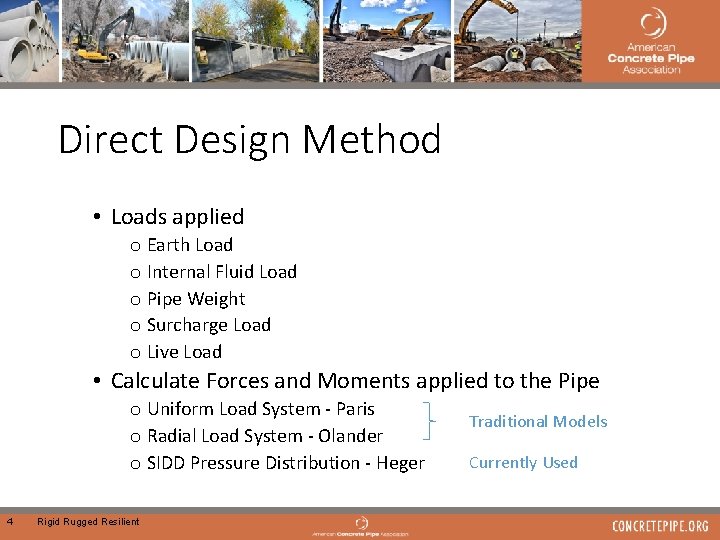
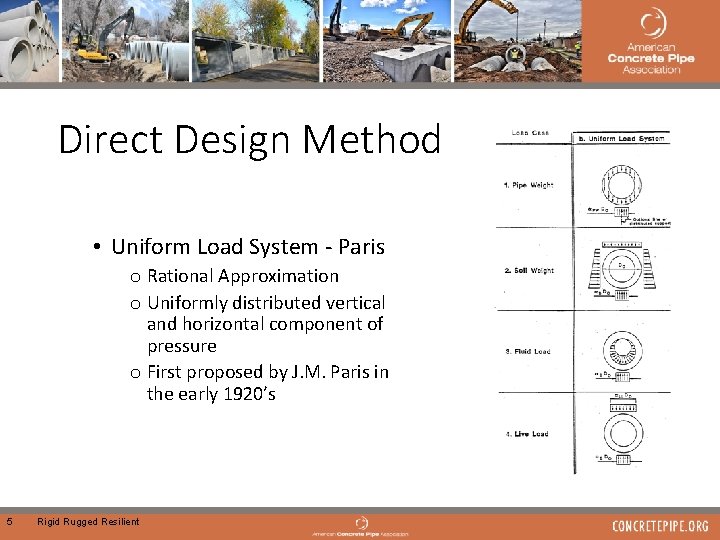
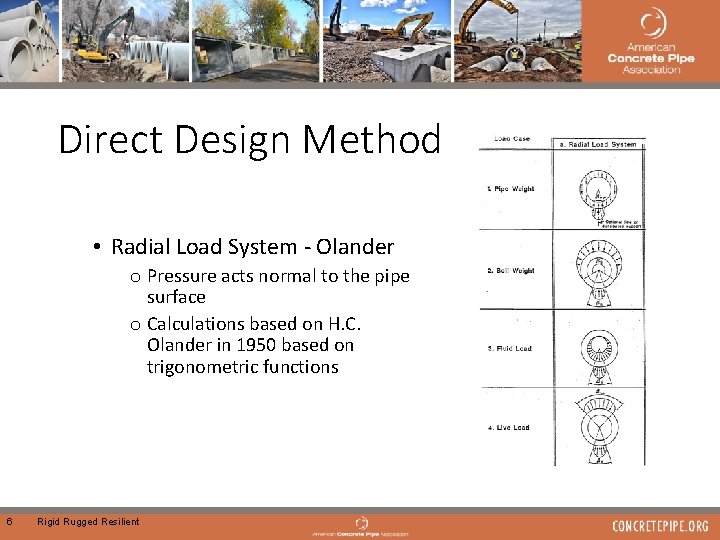
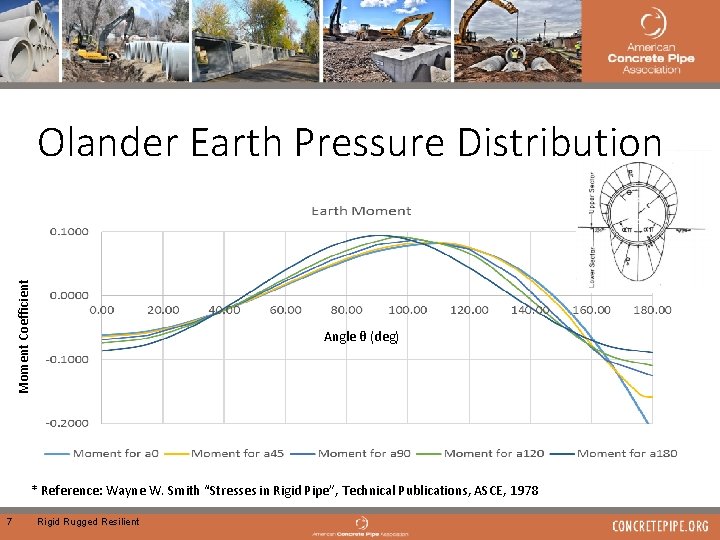
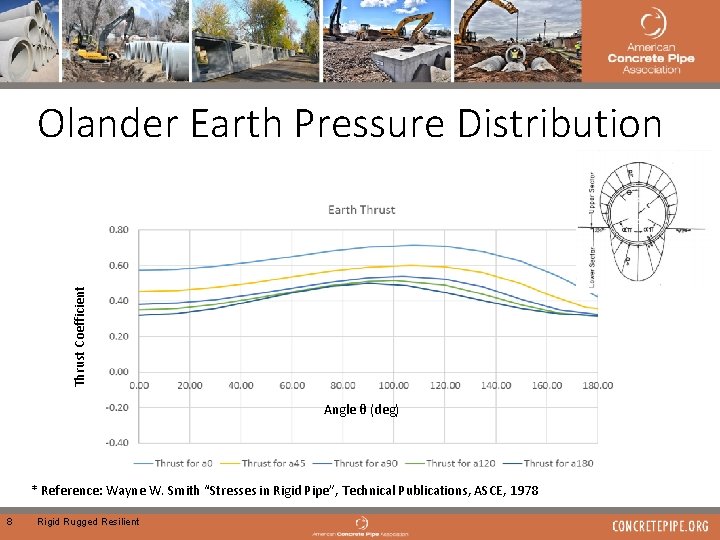
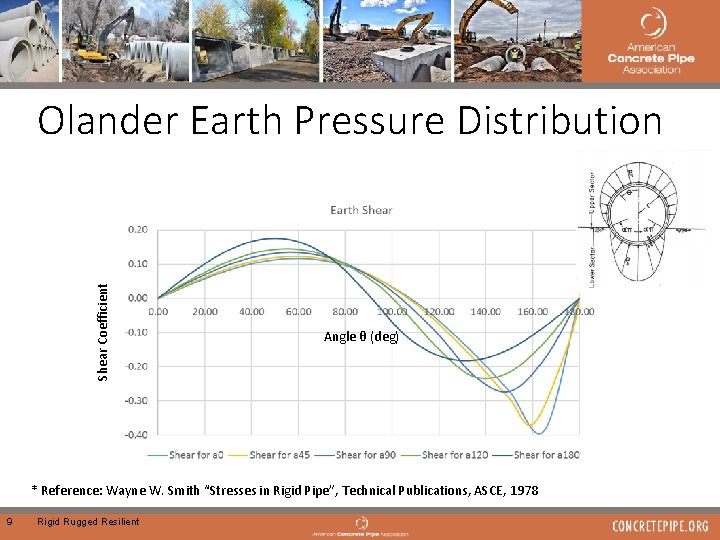
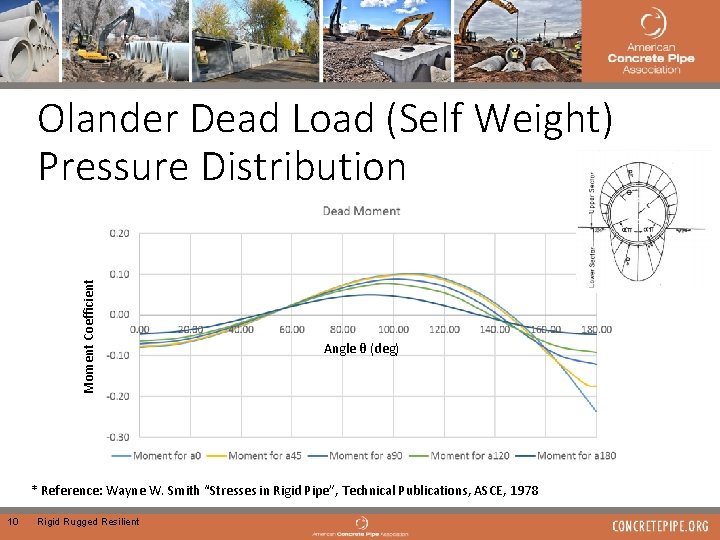
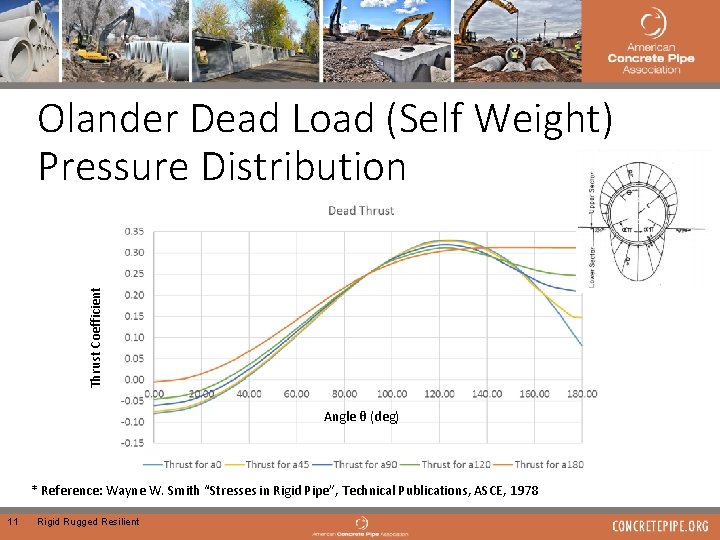
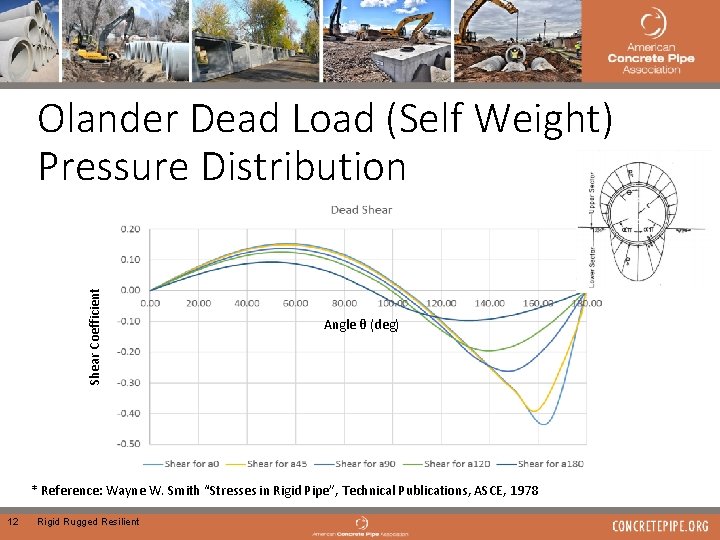
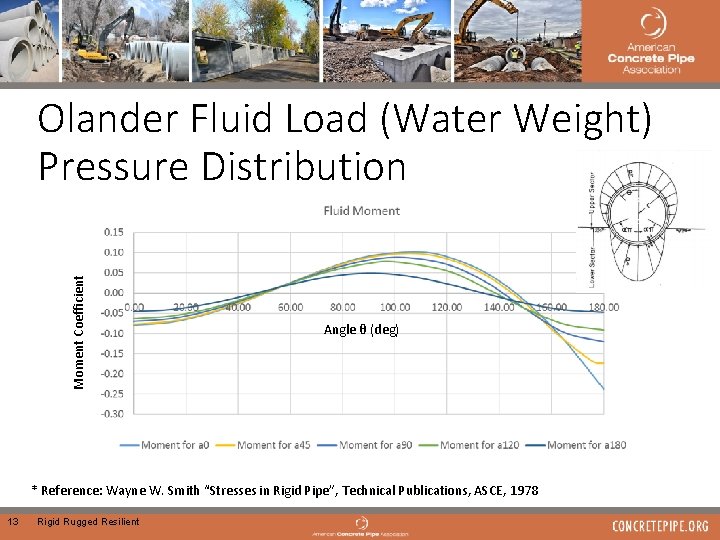
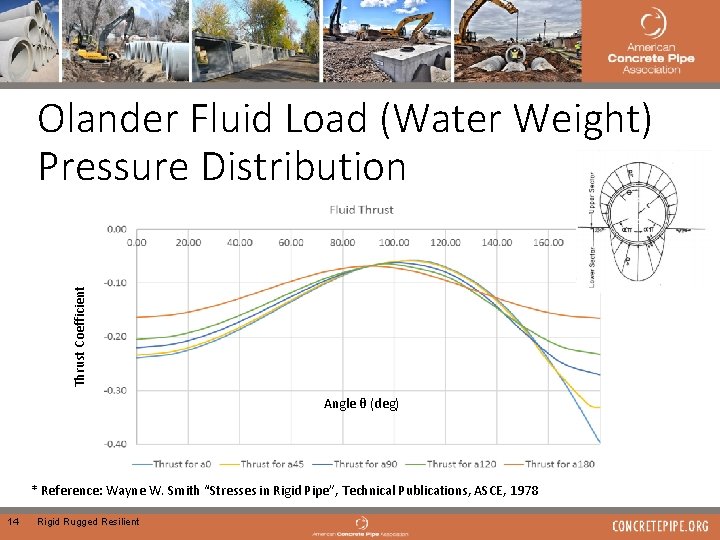
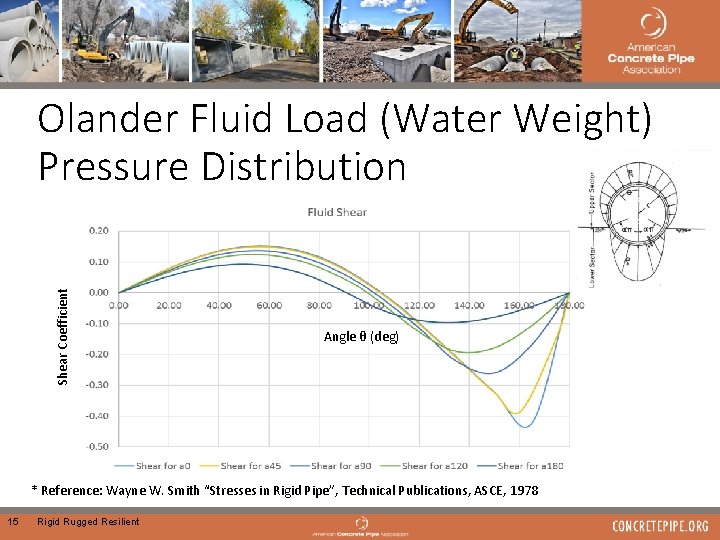
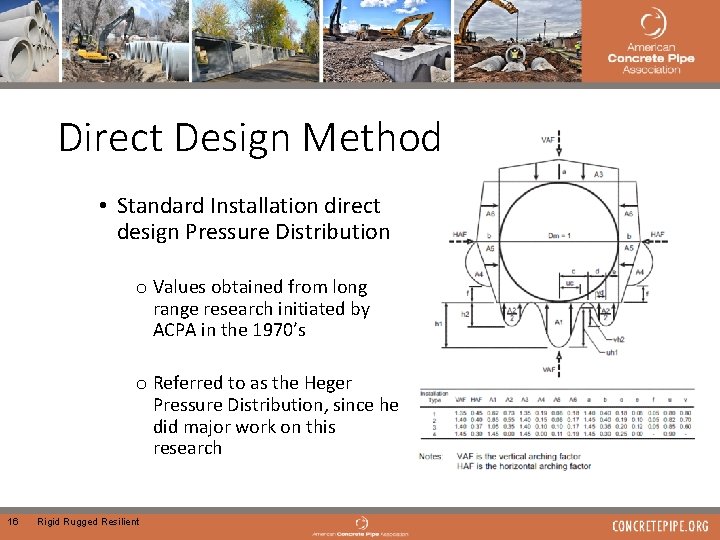
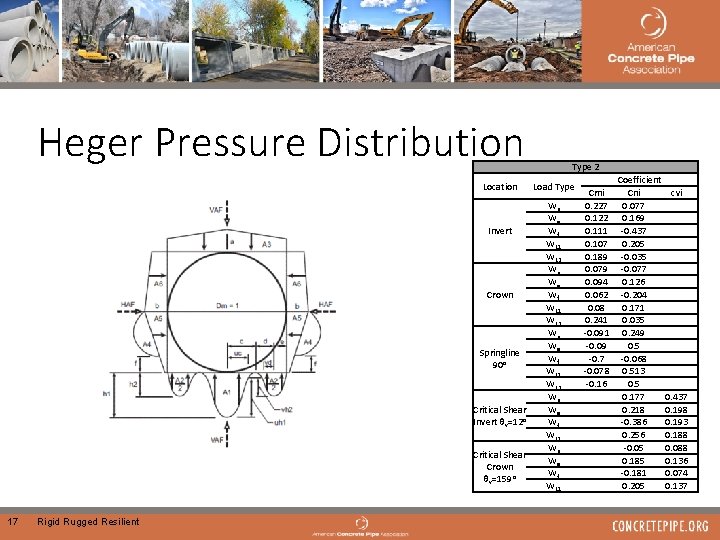
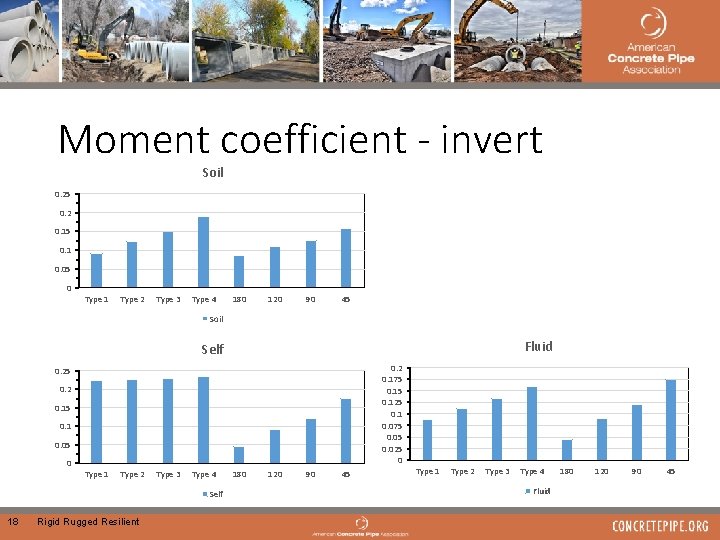
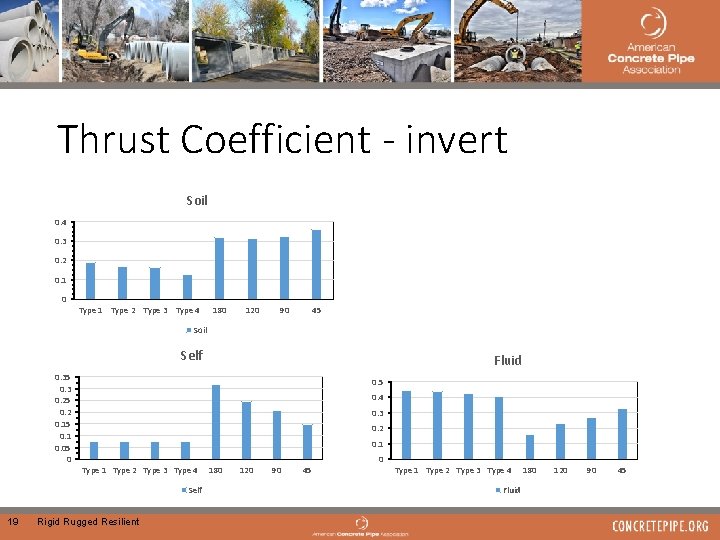
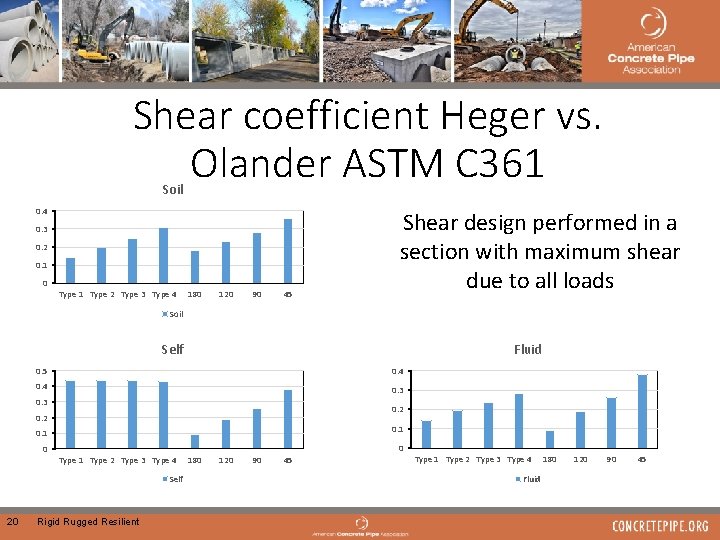
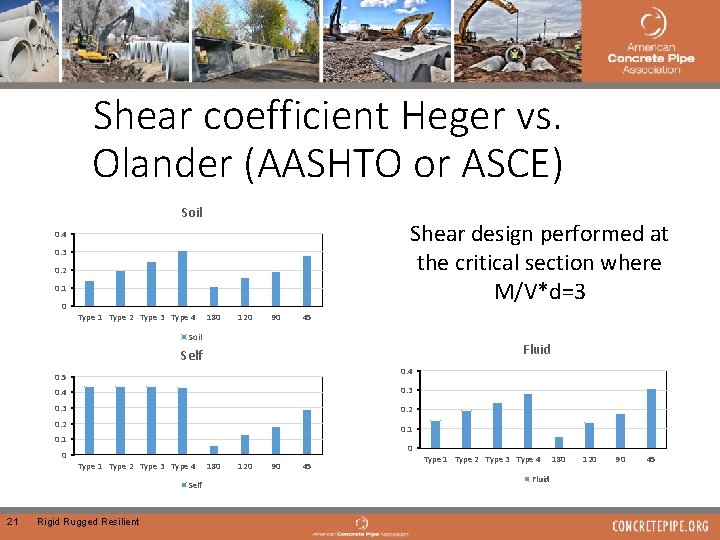
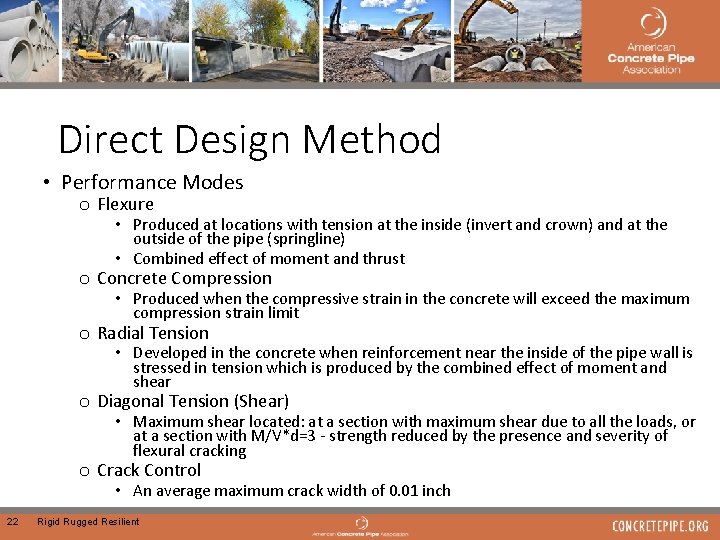
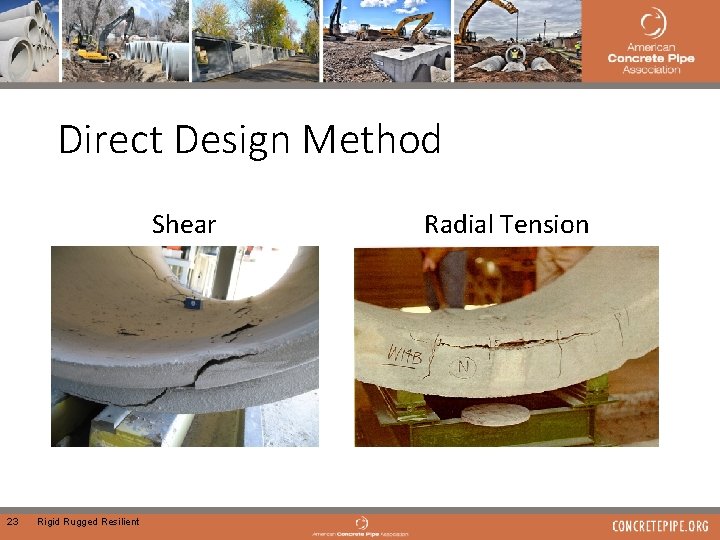
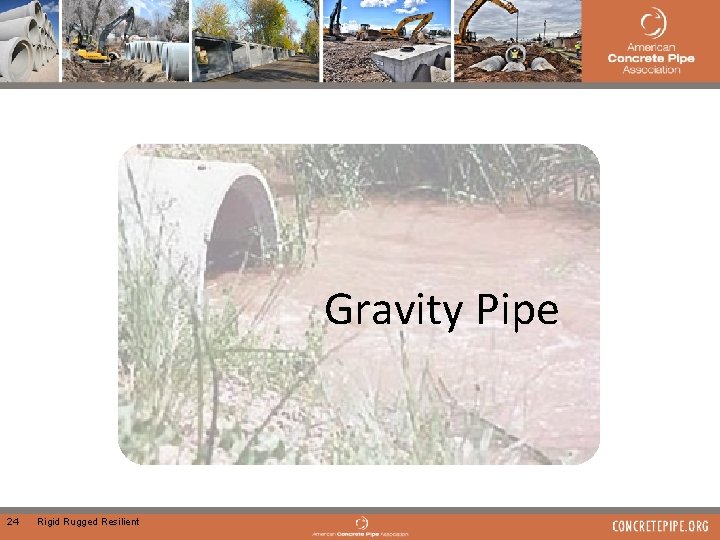
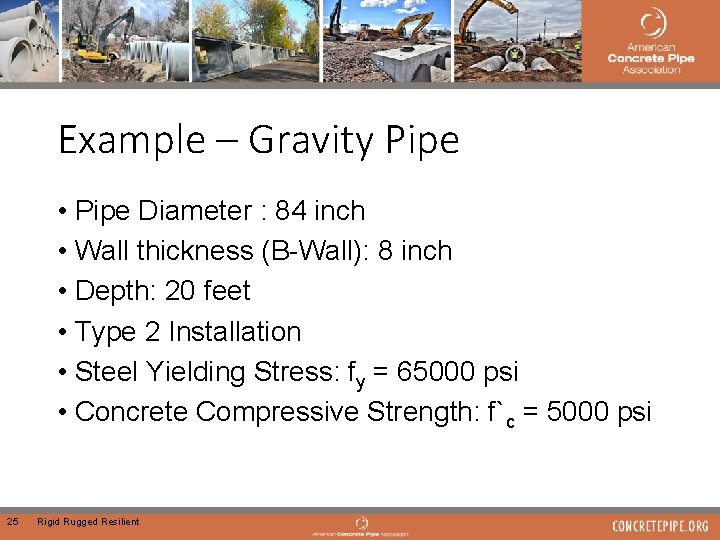
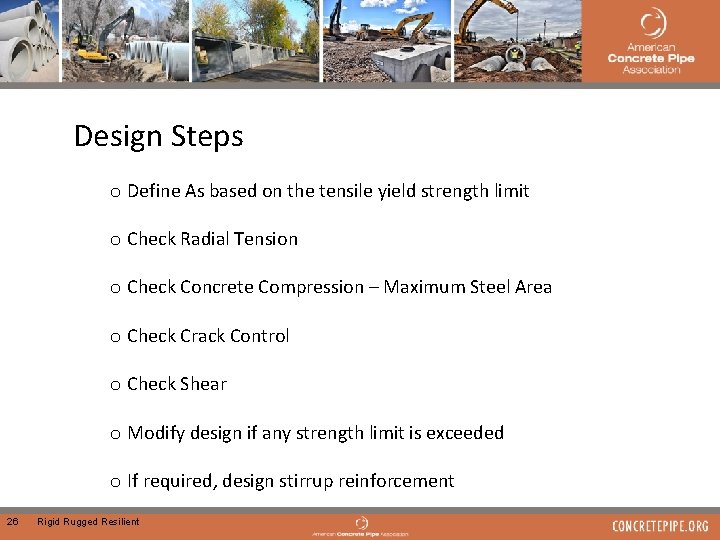
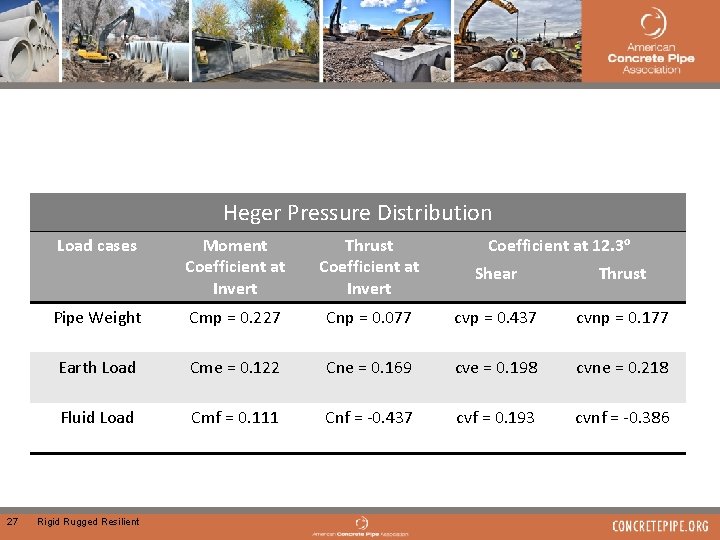
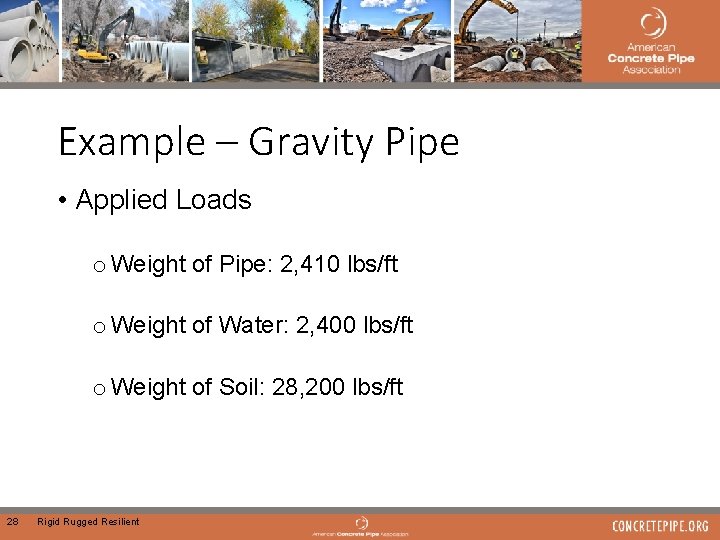
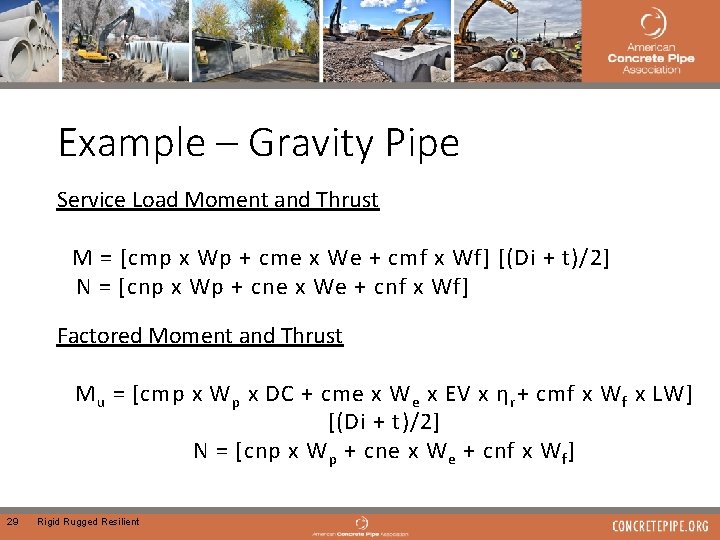
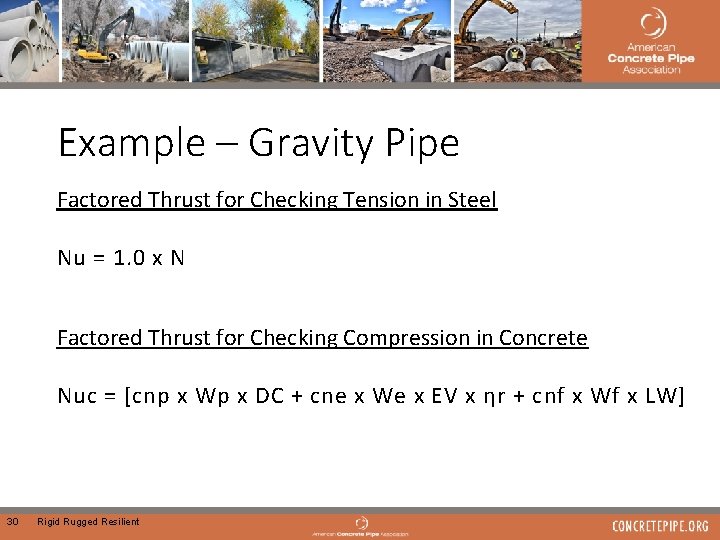
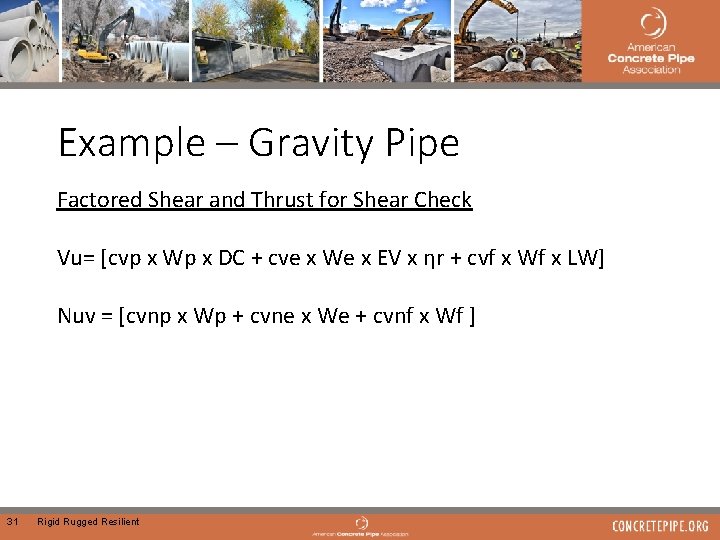
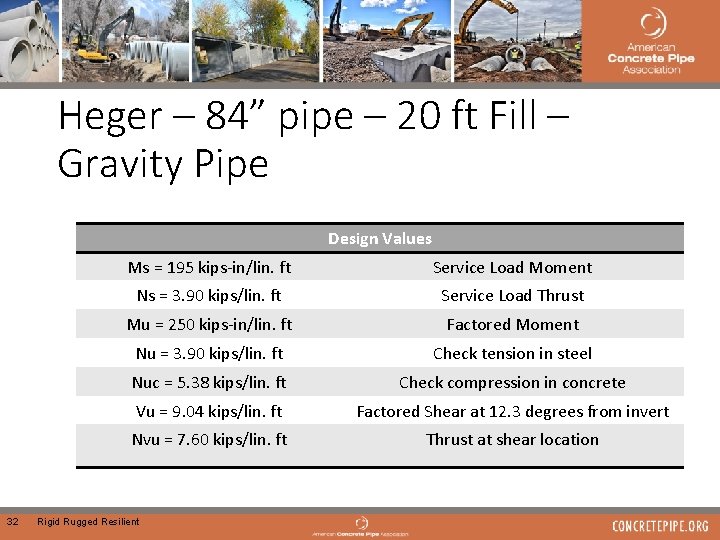
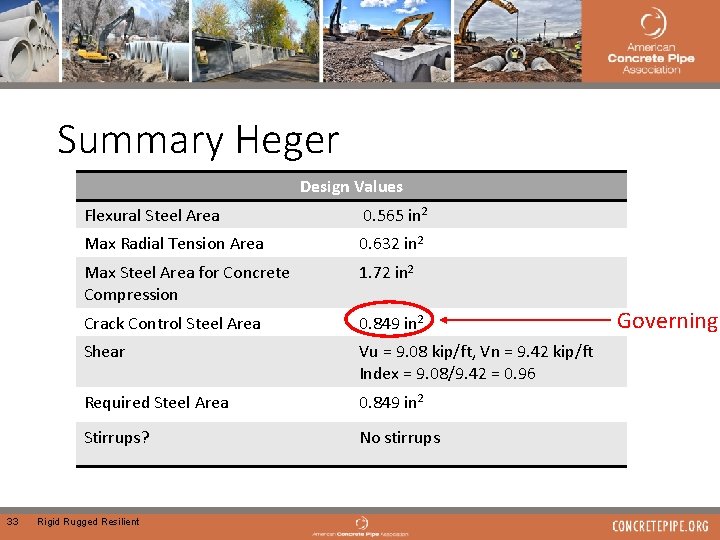
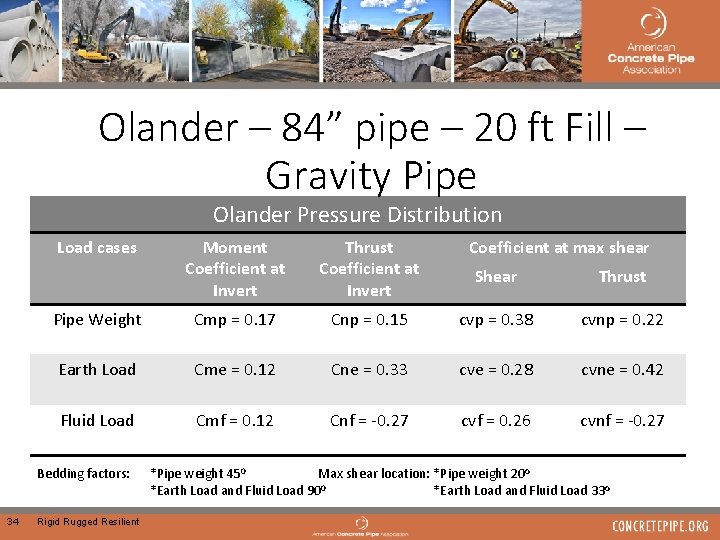
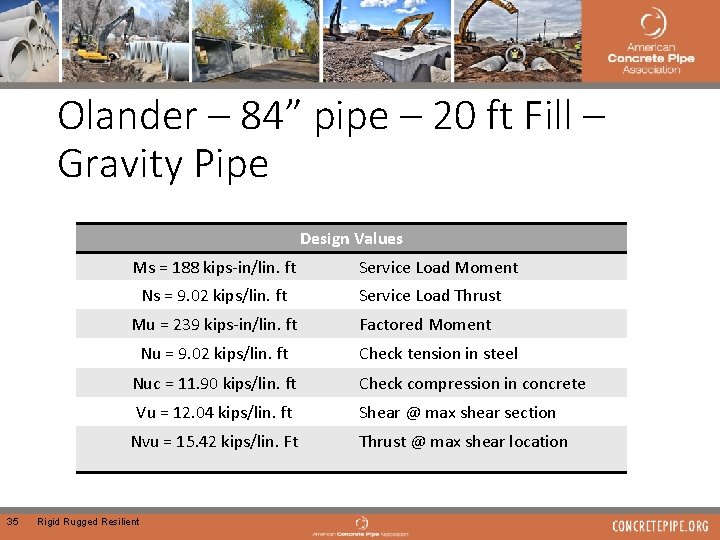
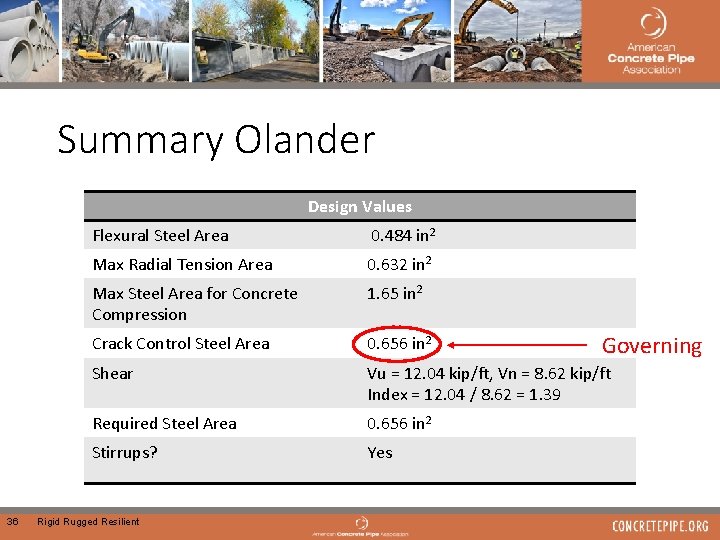
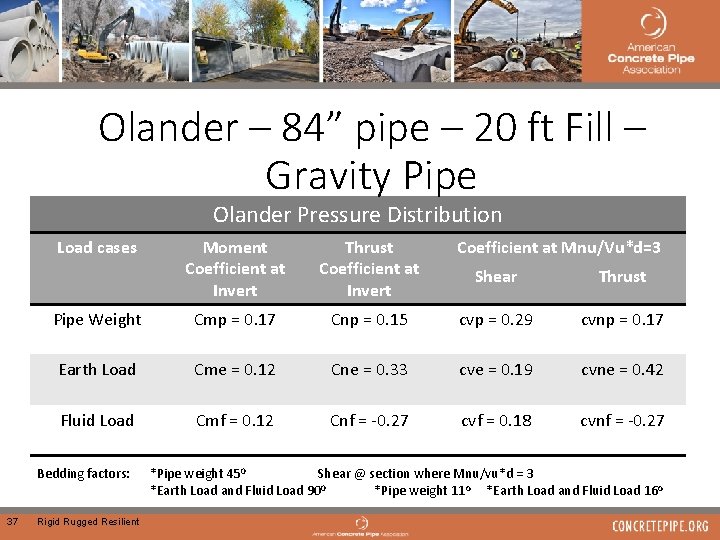
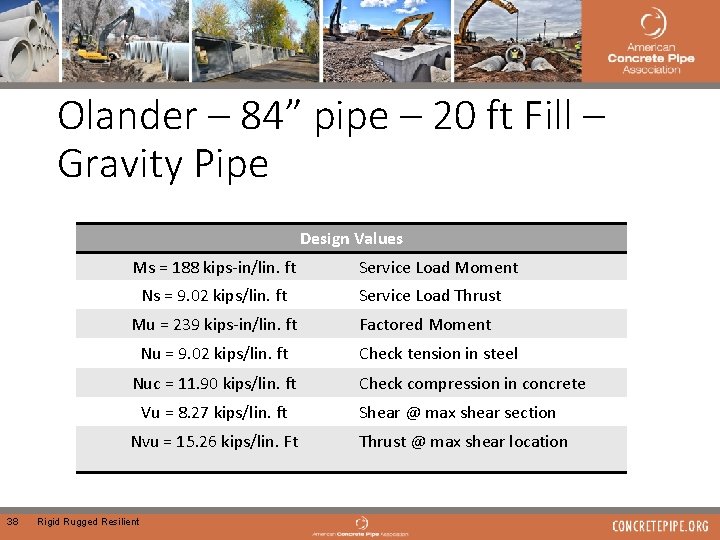
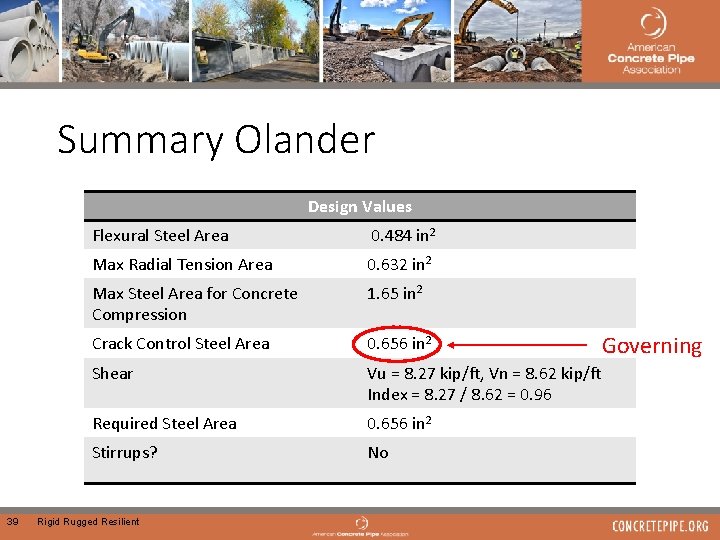
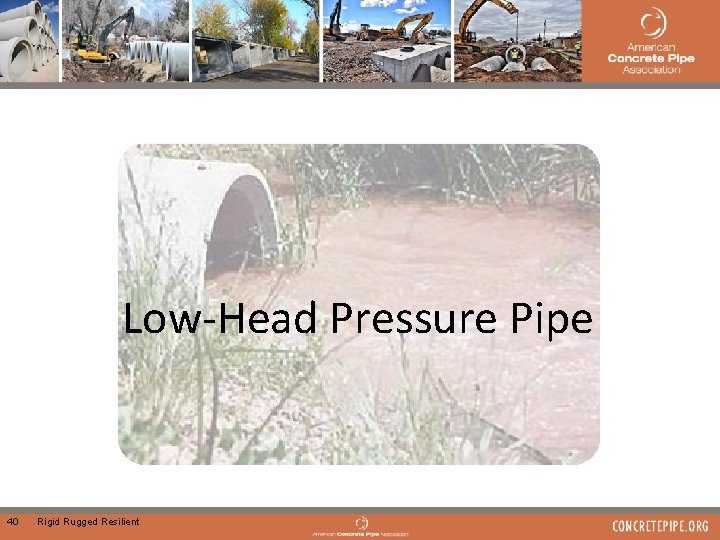
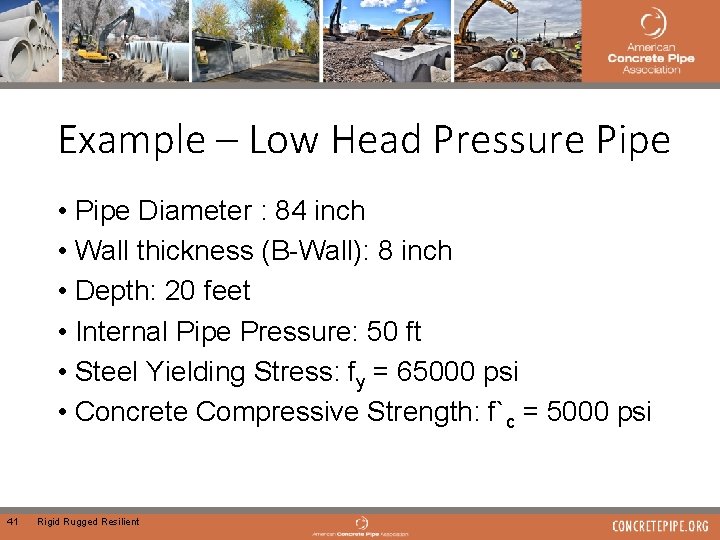
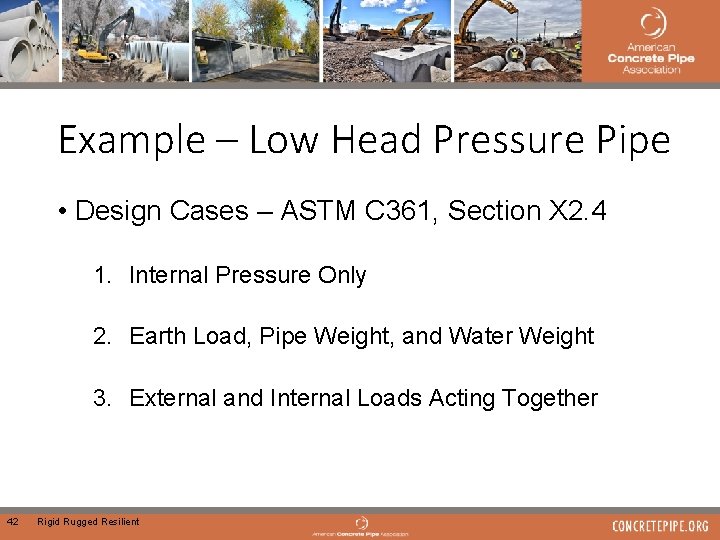
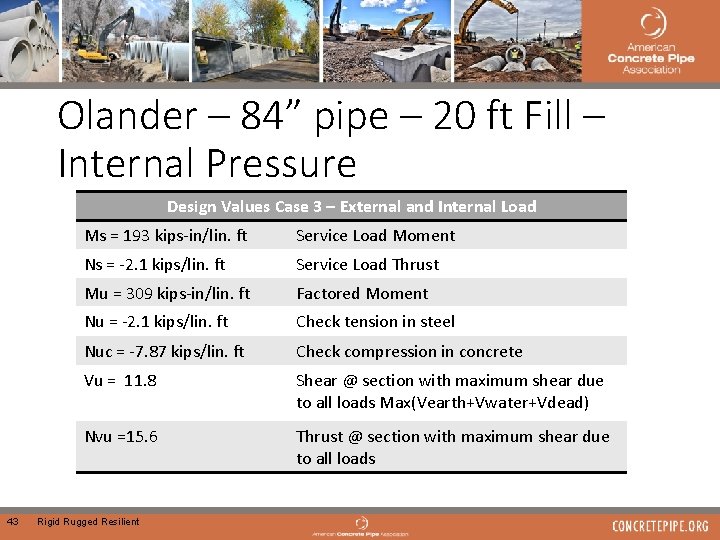
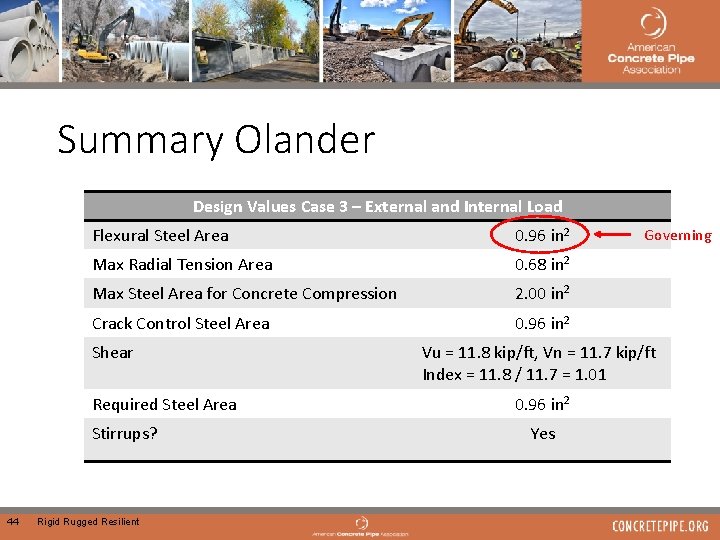
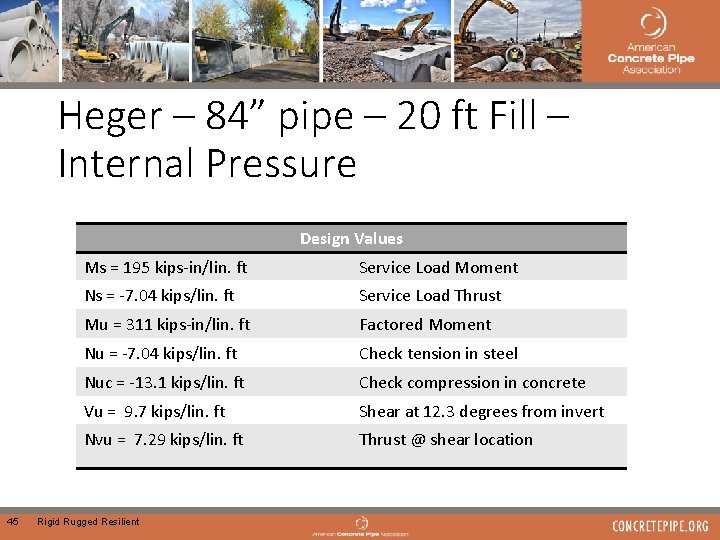
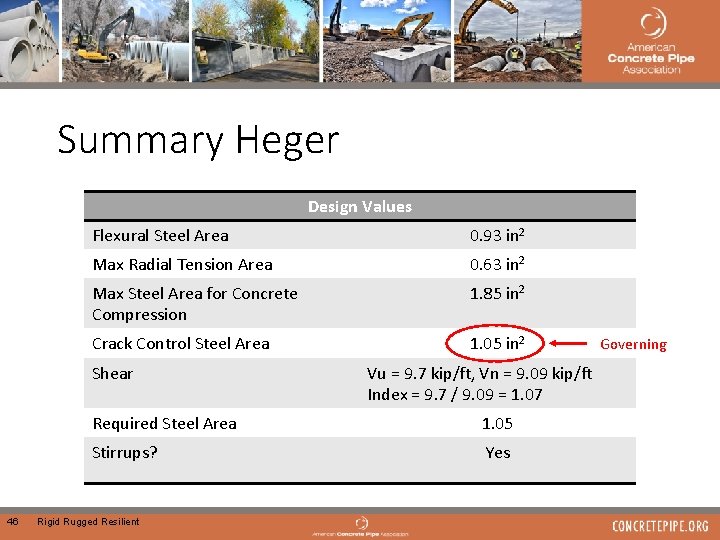
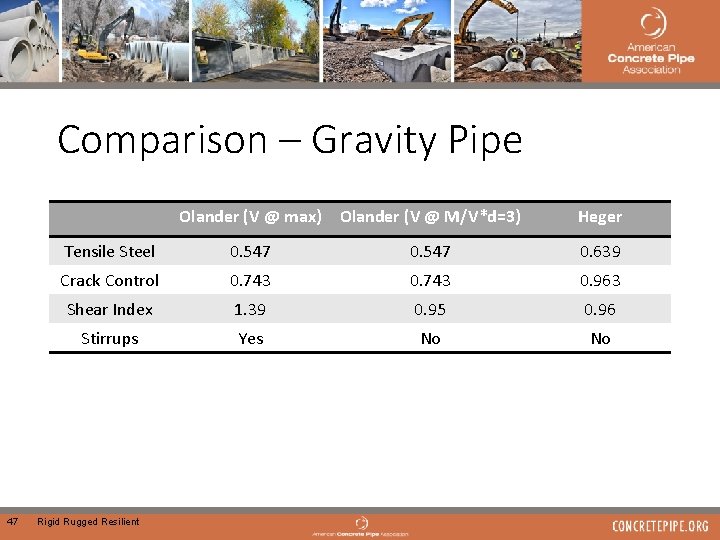
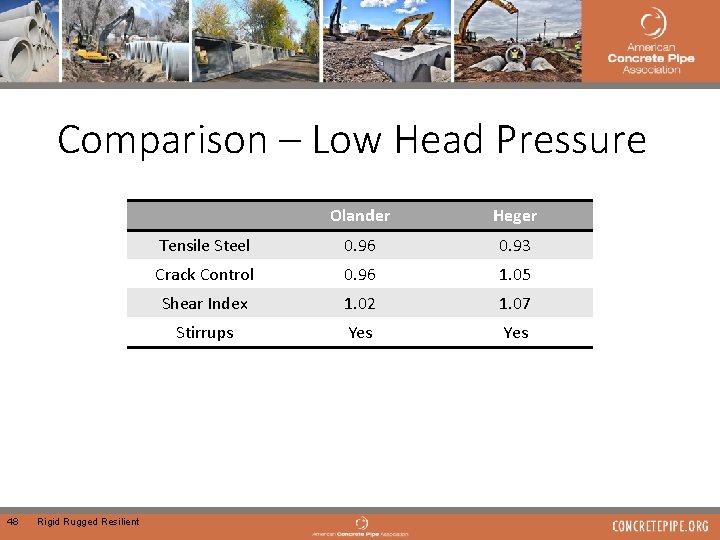
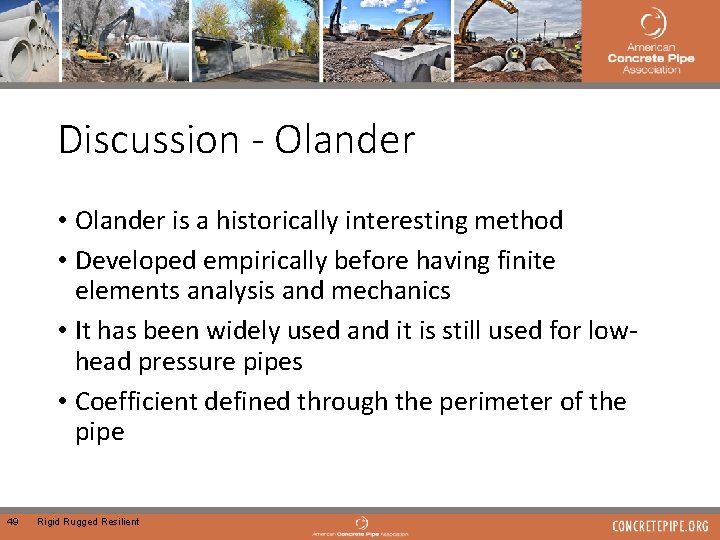
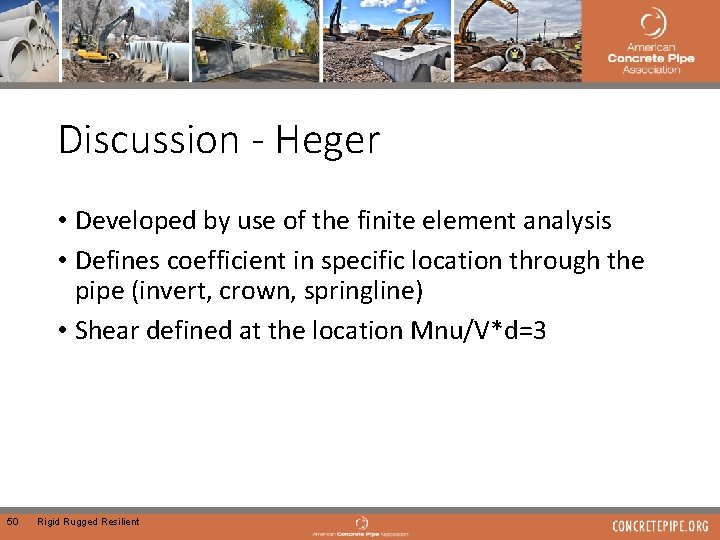
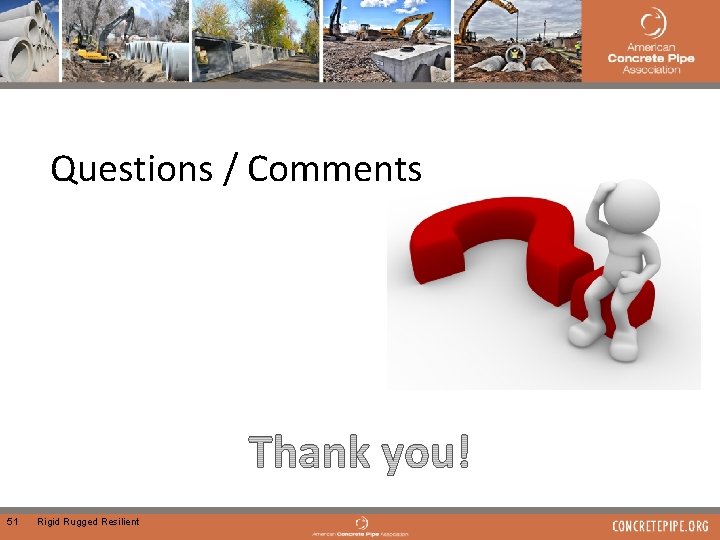
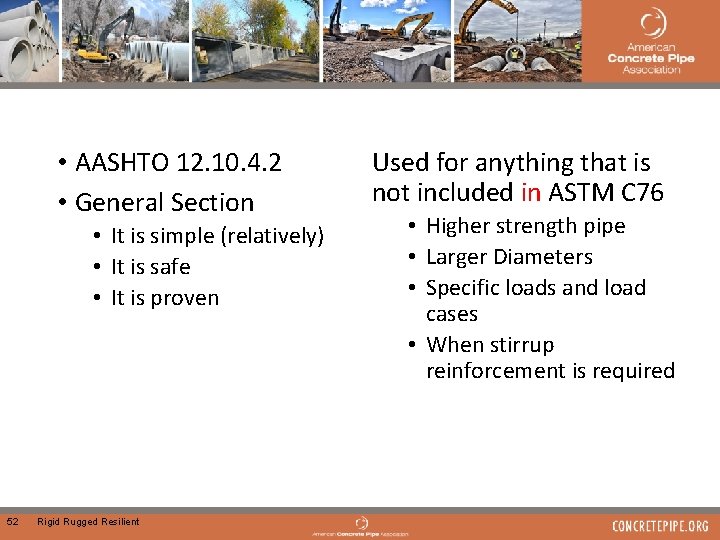
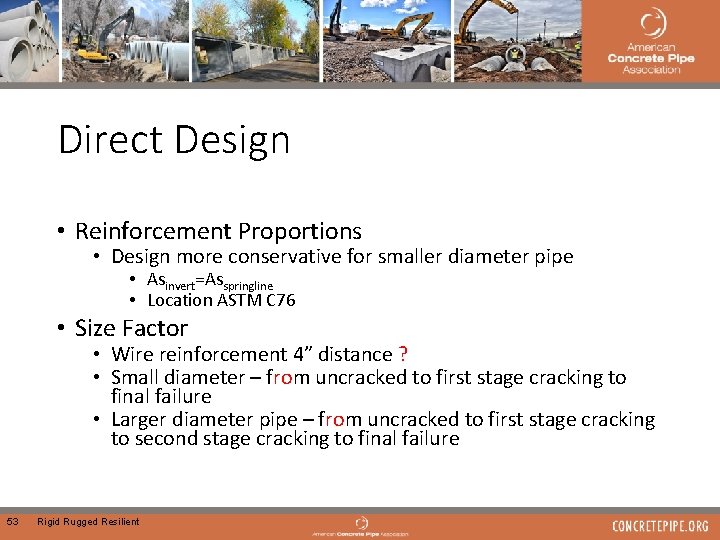
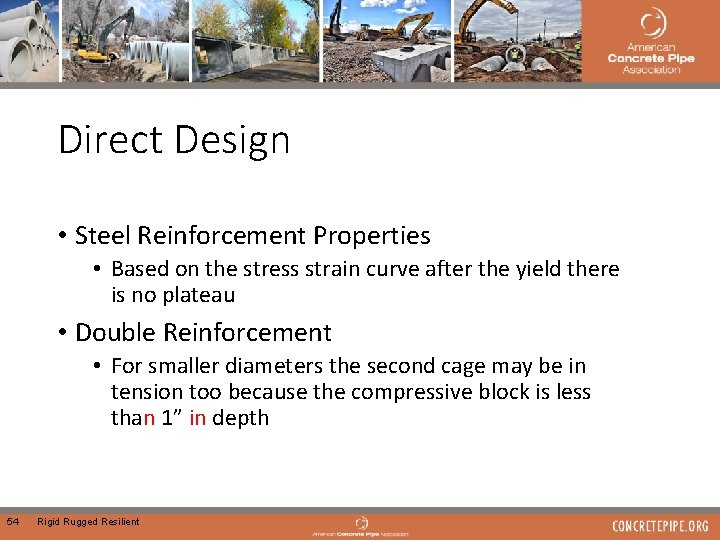
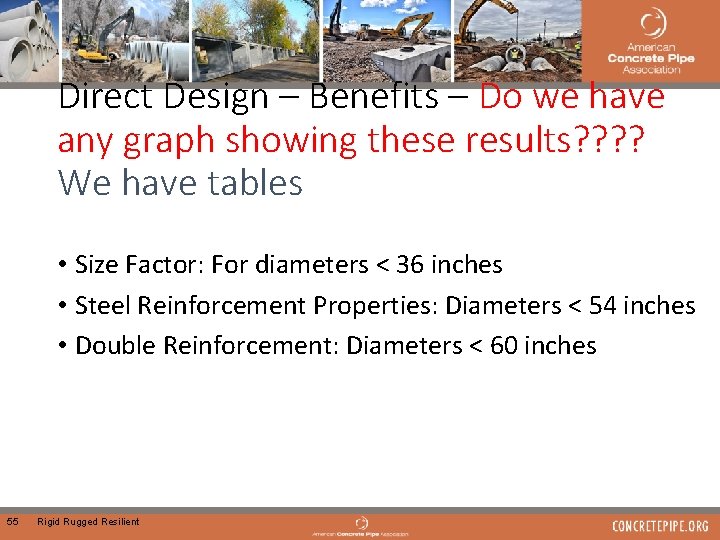
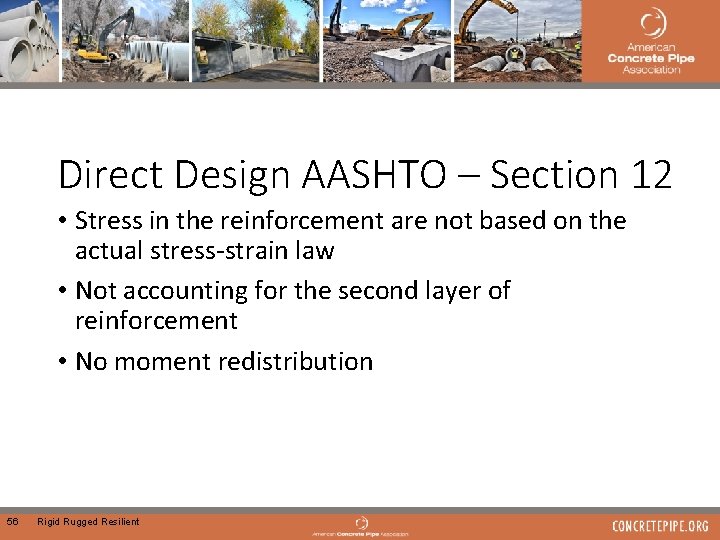
- Slides: 56
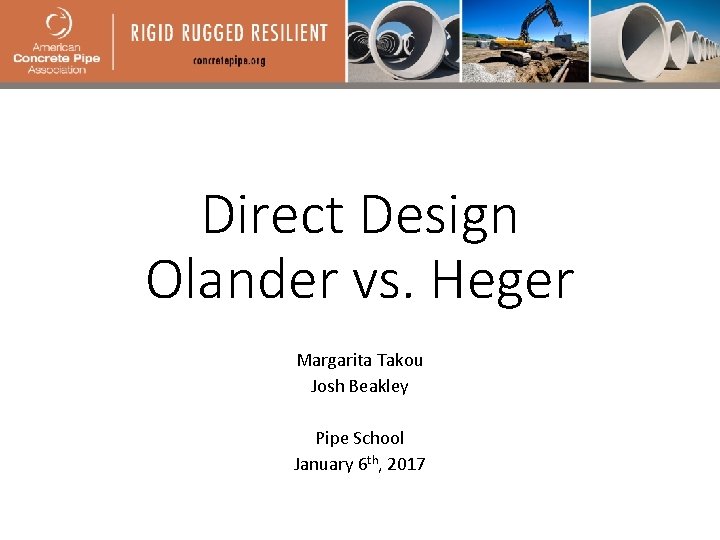
Direct Design Olander vs. Heger Margarita Takou Josh Beakley Pipe School January 6 th, 2017
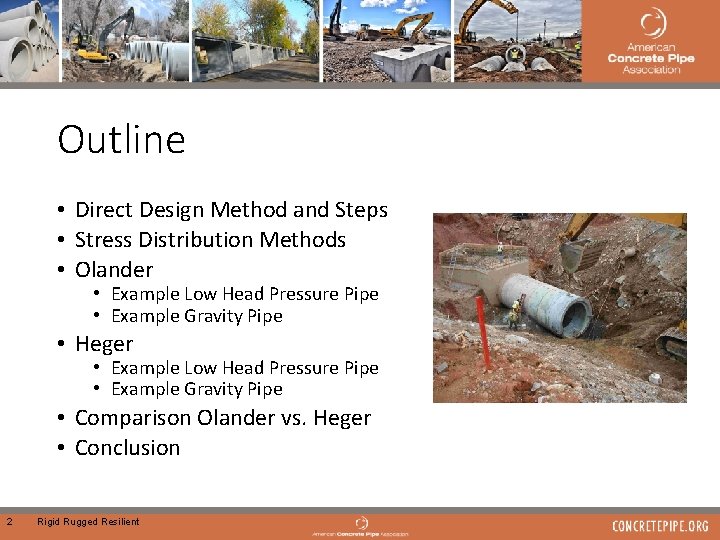
Outline • Direct Design Method and Steps • Stress Distribution Methods • Olander • Example Low Head Pressure Pipe • Example Gravity Pipe • Heger • Example Low Head Pressure Pipe • Example Gravity Pipe • Comparison Olander vs. Heger • Conclusion 2 Rigid Rugged Resilient
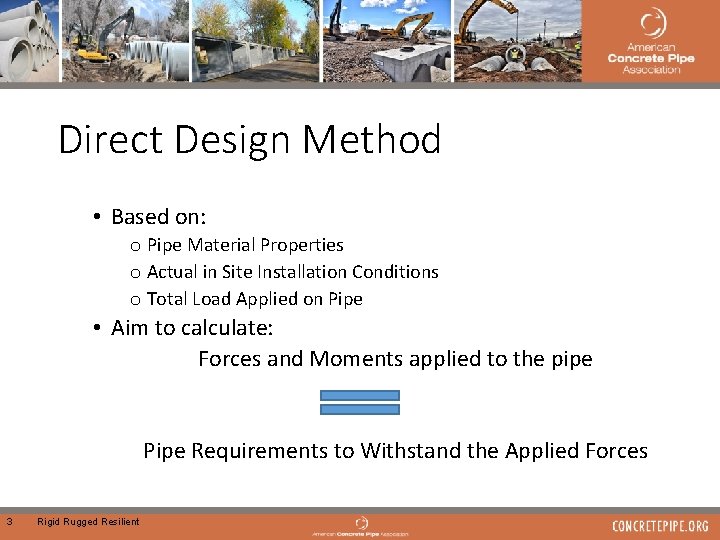
Direct Design Method • Based on: o Pipe Material Properties o Actual in Site Installation Conditions o Total Load Applied on Pipe • Aim to calculate: Forces and Moments applied to the pipe Pipe Requirements to Withstand the Applied Forces 3 Rigid Rugged Resilient
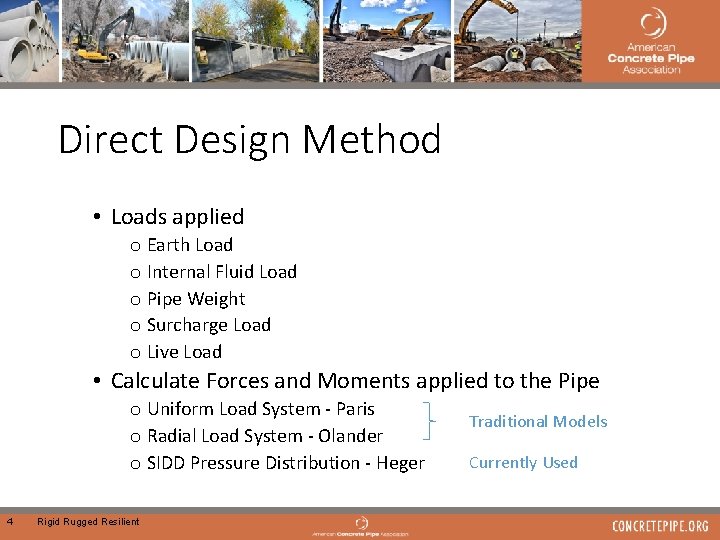
Direct Design Method • Loads applied o Earth Load o Internal Fluid Load o Pipe Weight o Surcharge Load o Live Load • Calculate Forces and Moments applied to the Pipe o Uniform Load System - Paris o Radial Load System - Olander o SIDD Pressure Distribution - Heger 4 Rigid Rugged Resilient Traditional Models Currently Used
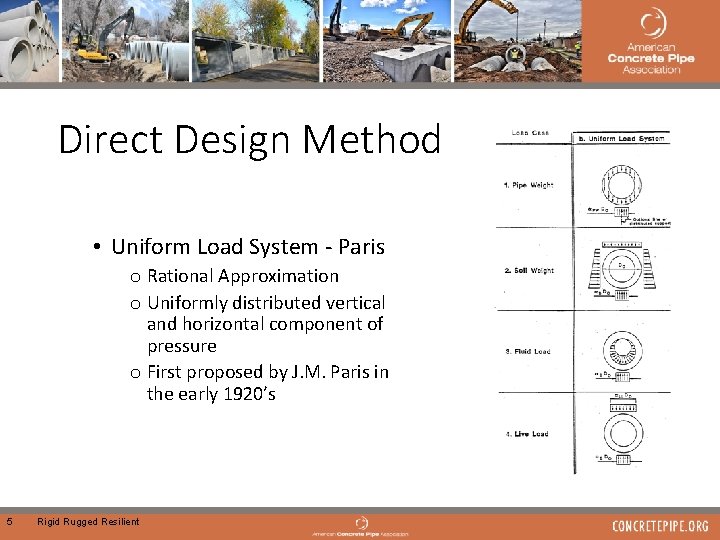
Direct Design Method • Uniform Load System - Paris o Rational Approximation o Uniformly distributed vertical and horizontal component of pressure o First proposed by J. M. Paris in the early 1920’s 5 Rigid Rugged Resilient
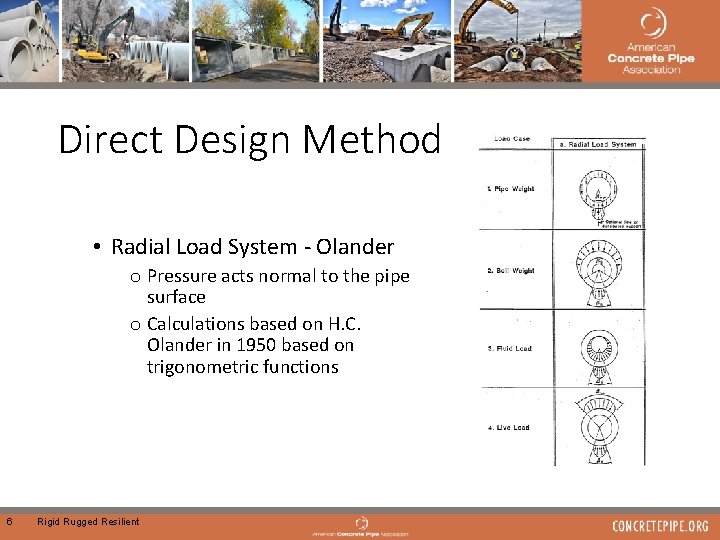
Direct Design Method • Radial Load System - Olander o Pressure acts normal to the pipe surface o Calculations based on H. C. Olander in 1950 based on trigonometric functions 6 Rigid Rugged Resilient
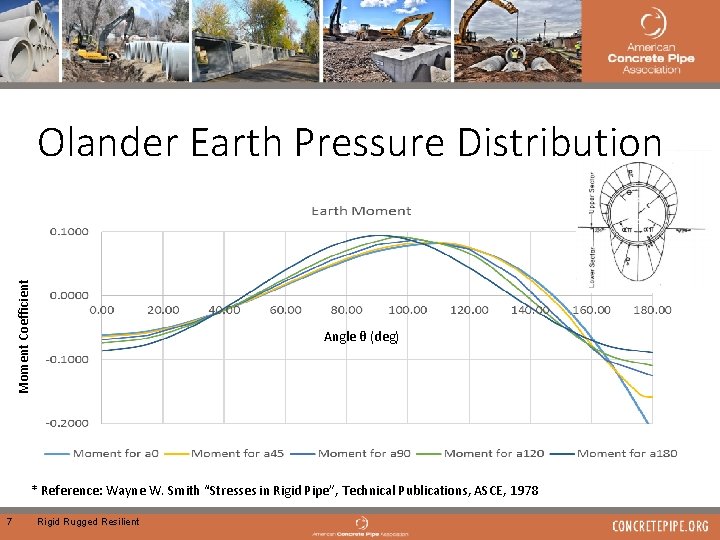
Moment Coefficient Olander Earth Pressure Distribution Angle θ (deg) * Reference: Wayne W. Smith “Stresses in Rigid Pipe”, Technical Publications, ASCE, 1978 7 Rigid Rugged Resilient
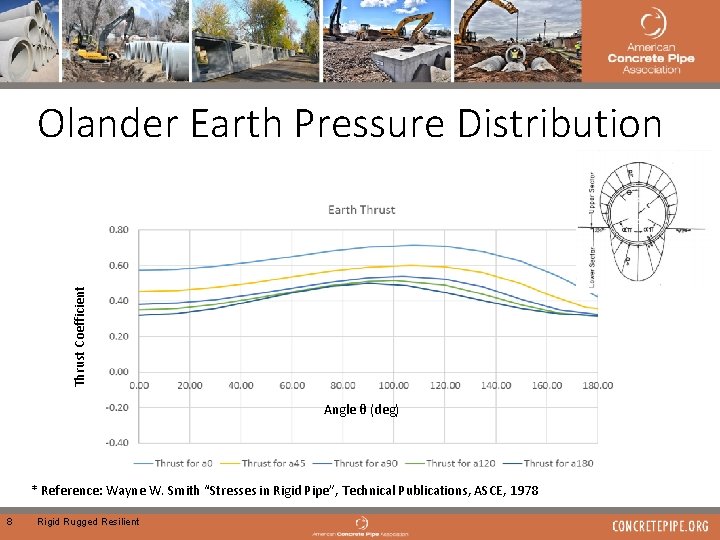
Thrust Coefficient Olander Earth Pressure Distribution Angle θ (deg) * Reference: Wayne W. Smith “Stresses in Rigid Pipe”, Technical Publications, ASCE, 1978 8 Rigid Rugged Resilient
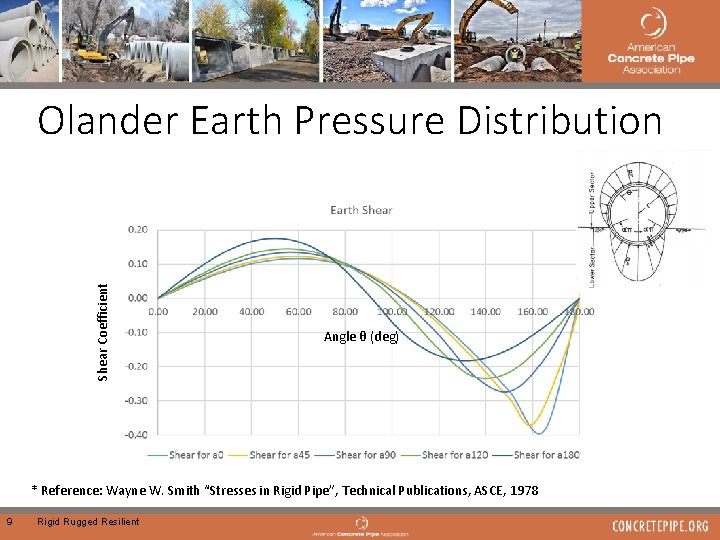
Shear Coefficient Olander Earth Pressure Distribution Angle θ (deg) * Reference: Wayne W. Smith “Stresses in Rigid Pipe”, Technical Publications, ASCE, 1978 9 Rigid Rugged Resilient
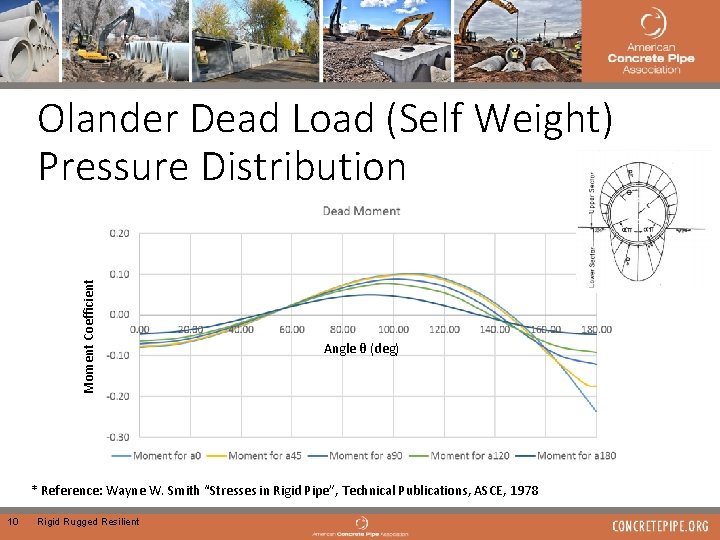
Moment Coefficient Olander Dead Load (Self Weight) Pressure Distribution Angle θ (deg) * Reference: Wayne W. Smith “Stresses in Rigid Pipe”, Technical Publications, ASCE, 1978 10 Rigid Rugged Resilient
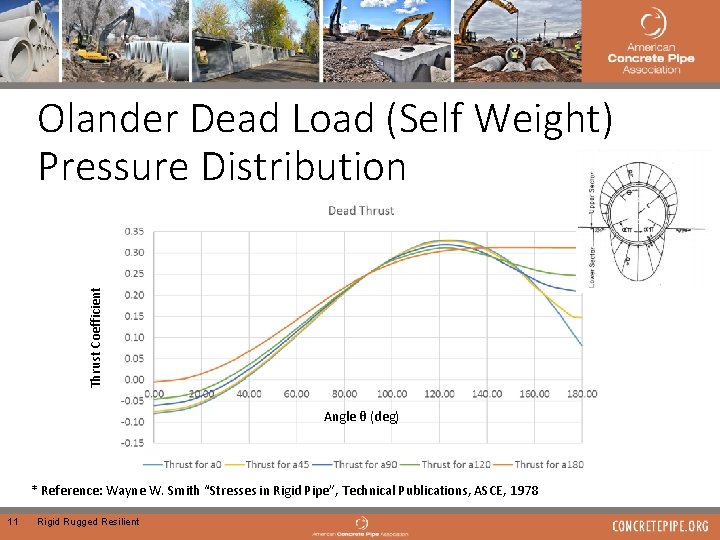
Thrust Coefficient Olander Dead Load (Self Weight) Pressure Distribution Angle θ (deg) * Reference: Wayne W. Smith “Stresses in Rigid Pipe”, Technical Publications, ASCE, 1978 11 Rigid Rugged Resilient
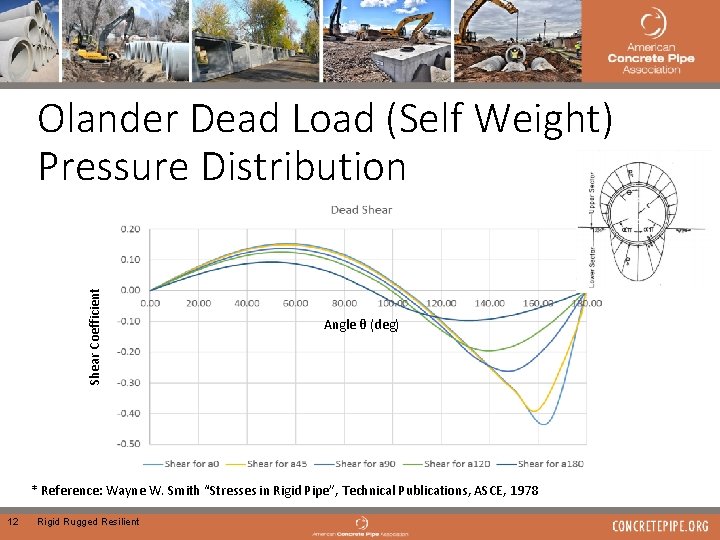
Shear Coefficient Olander Dead Load (Self Weight) Pressure Distribution Angle θ (deg) * Reference: Wayne W. Smith “Stresses in Rigid Pipe”, Technical Publications, ASCE, 1978 12 Rigid Rugged Resilient
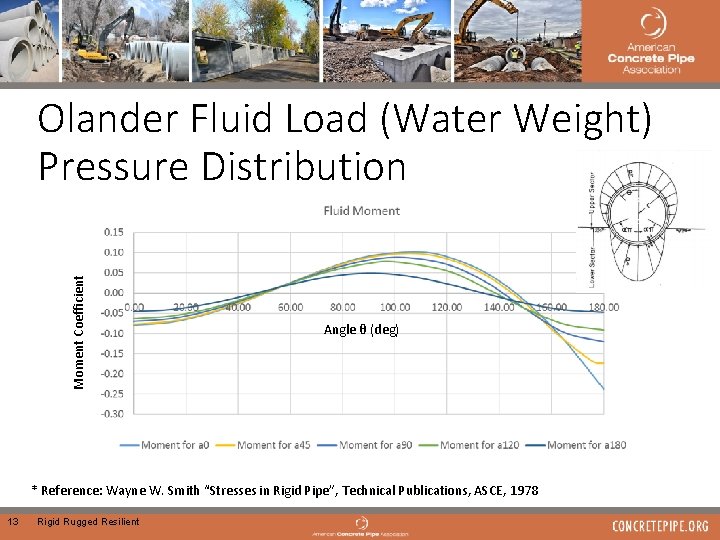
Moment Coefficient Olander Fluid Load (Water Weight) Pressure Distribution Angle θ (deg) * Reference: Wayne W. Smith “Stresses in Rigid Pipe”, Technical Publications, ASCE, 1978 13 Rigid Rugged Resilient
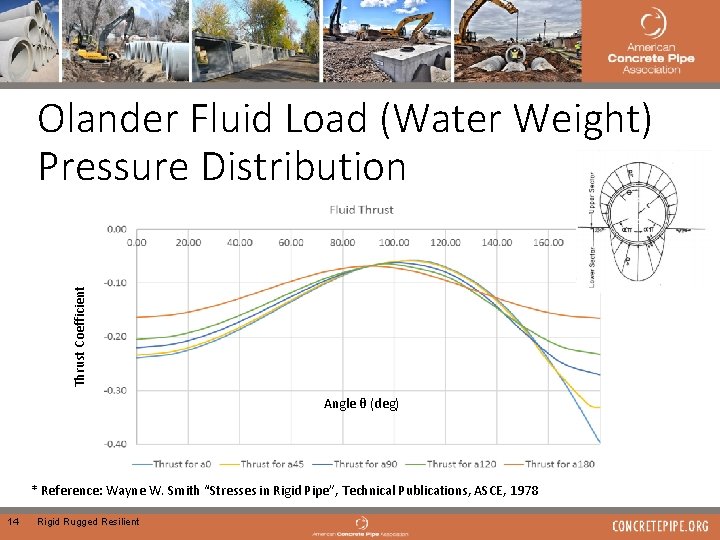
Thrust Coefficient Olander Fluid Load (Water Weight) Pressure Distribution Angle θ (deg) * Reference: Wayne W. Smith “Stresses in Rigid Pipe”, Technical Publications, ASCE, 1978 14 Rigid Rugged Resilient
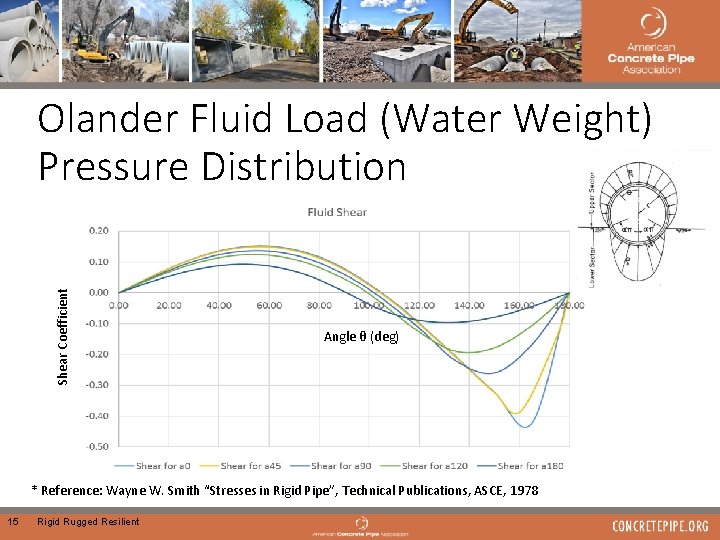
Shear Coefficient Olander Fluid Load (Water Weight) Pressure Distribution Angle θ (deg) * Reference: Wayne W. Smith “Stresses in Rigid Pipe”, Technical Publications, ASCE, 1978 15 Rigid Rugged Resilient
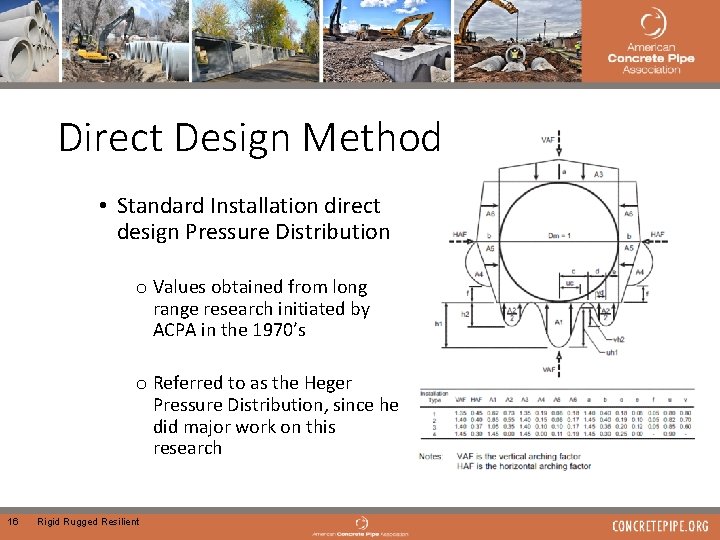
Direct Design Method • Standard Installation direct design Pressure Distribution o Values obtained from long range research initiated by ACPA in the 1970’s o Referred to as the Heger Pressure Distribution, since he did major work on this research 16 Rigid Rugged Resilient
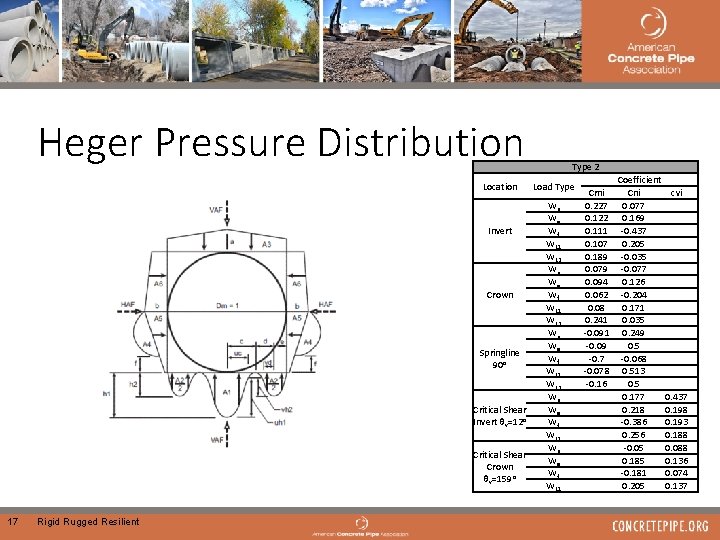
Heger Pressure Distribution Location Invert Crown Springline 90 o Critical Shear Invert θv=12 o Critical Shear Crown θv=159 o 17 Rigid Rugged Resilient Type 2 Load Type Wp We Wf WL 1 WL 2 Wp We Wf WL 1 Cmi 0. 227 0. 122 0. 111 0. 107 0. 189 0. 079 0. 094 0. 062 0. 08 0. 241 -0. 09 -0. 7 -0. 078 -0. 16 Coefficient Cni 0. 077 0. 169 -0. 437 0. 205 -0. 035 -0. 077 0. 126 -0. 204 0. 171 0. 035 0. 249 0. 5 -0. 068 0. 513 0. 5 0. 177 0. 218 -0. 386 0. 256 -0. 05 0. 185 -0. 181 0. 205 cvi 0. 437 0. 198 0. 193 0. 188 0. 088 0. 136 0. 074 0. 137
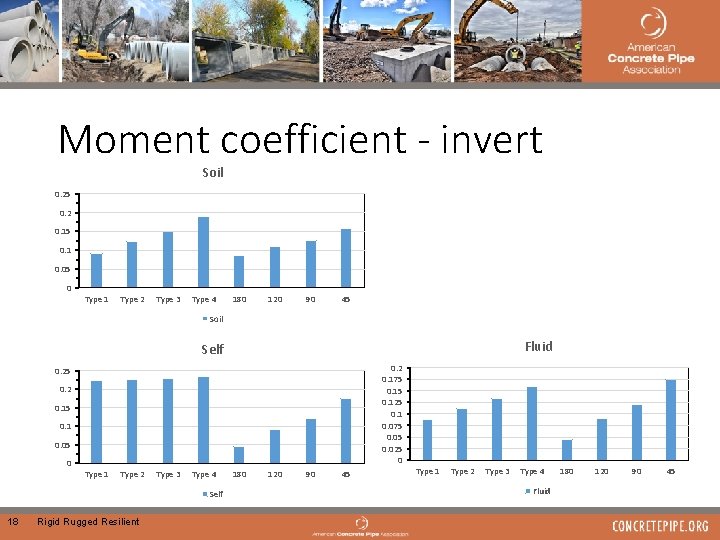
Moment coefficient - invert Soil 0. 25 0. 2 0. 15 0. 1 0. 05 0 Type 1 Type 2 Type 3 Type 4 180 120 90 45 Soil Fluid Self 0. 2 0. 175 0. 125 0. 1 0. 075 0. 025 0 0. 25 0. 2 0. 15 0. 1 0. 05 0 Type 1 Type 2 Type 3 Type 4 Self 18 Rigid Rugged Resilient 180 120 90 45 Type 1 Type 2 Type 3 Type 4 Fluid 180 120 90 45
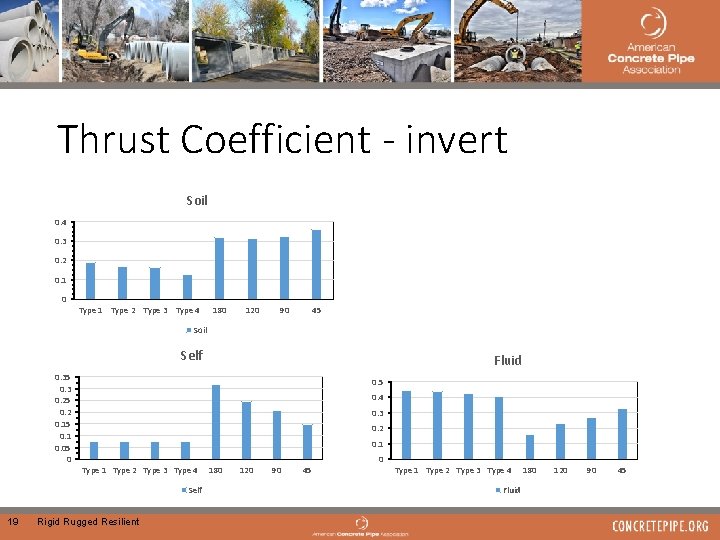
Thrust Coefficient - invert Soil 0. 4 0. 3 0. 2 0. 1 0 Type 1 Type 2 Type 3 Type 4 180 120 90 45 Soil Self 0. 35 0. 3 0. 25 0. 2 0. 15 0. 1 0. 05 0 0. 5 0. 4 0. 3 0. 2 0. 1 0 Type 1 Type 2 Type 3 Type 4 Self 19 Fluid Rigid Rugged Resilient 180 120 90 45 Type 1 Type 2 Type 3 Type 4 Fluid 180 120 90 45
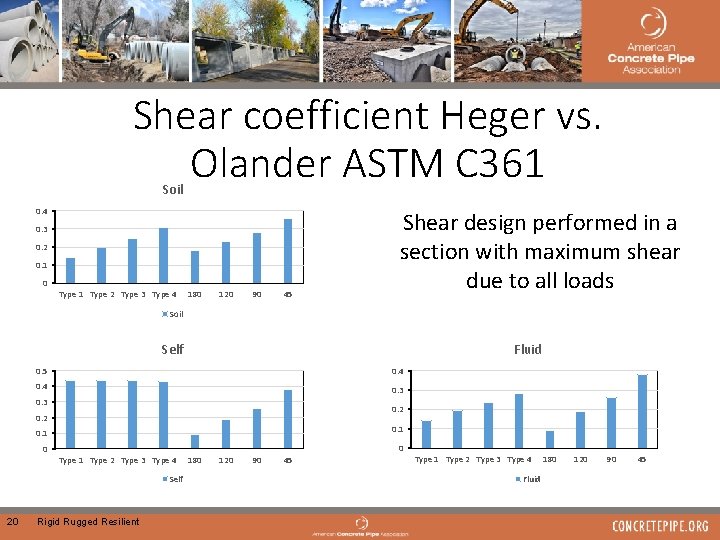
Shear coefficient Heger vs. Olander ASTM C 361 Soil 0. 4 0. 3 0. 2 0. 1 0 Type 1 Type 2 Type 3 Type 4 180 120 90 45 Shear design performed in a section with maximum shear due to all loads Soil Self Fluid 0. 5 0. 4 0. 3 0. 2 0. 1 0 0 Type 1 Type 2 Type 3 Type 4 Self 20 Rigid Rugged Resilient 180 120 90 45 Type 1 Type 2 Type 3 Type 4 Fluid 180 120 90 45
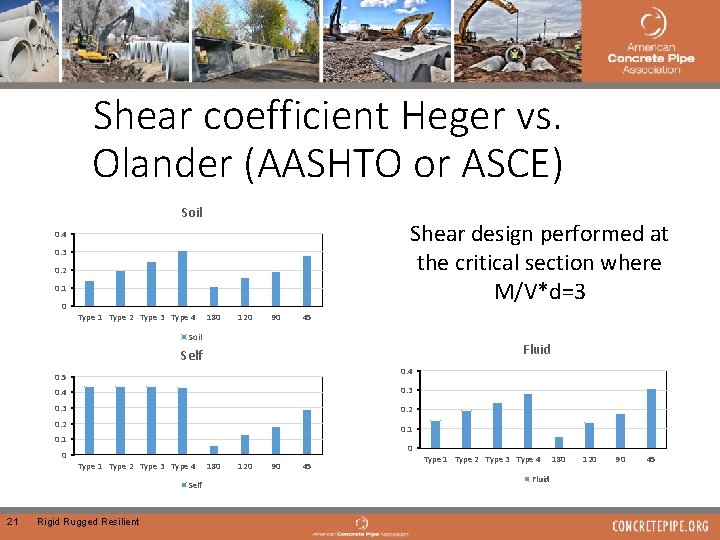
Shear coefficient Heger vs. Olander (AASHTO or ASCE) Soil Shear design performed at the critical section where M/V*d=3 0. 4 0. 3 0. 2 0. 1 0 Type 1 Type 2 Type 3 Type 4 180 120 90 45 Soil Fluid Self 0. 4 0. 5 0. 4 0. 3 0. 2 0. 1 0 0 Type 1 Type 2 Type 3 Type 4 Self 21 Rigid Rugged Resilient 180 120 90 45 Type 1 Type 2 Type 3 Type 4 Fluid 180 120 90 45
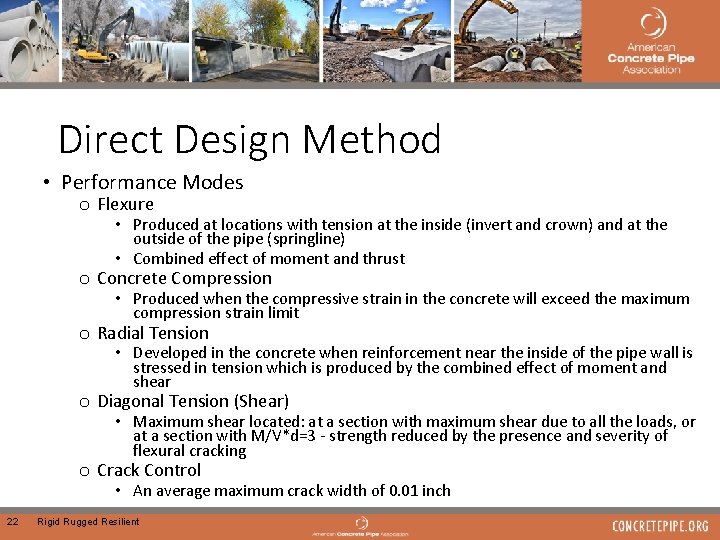
Direct Design Method • Performance Modes o Flexure • Produced at locations with tension at the inside (invert and crown) and at the outside of the pipe (springline) • Combined effect of moment and thrust o Concrete Compression • Produced when the compressive strain in the concrete will exceed the maximum compression strain limit o Radial Tension • Developed in the concrete when reinforcement near the inside of the pipe wall is stressed in tension which is produced by the combined effect of moment and shear o Diagonal Tension (Shear) • Maximum shear located: at a section with maximum shear due to all the loads, or at a section with M/V*d=3 - strength reduced by the presence and severity of flexural cracking o Crack Control • An average maximum crack width of 0. 01 inch 22 Rigid Rugged Resilient
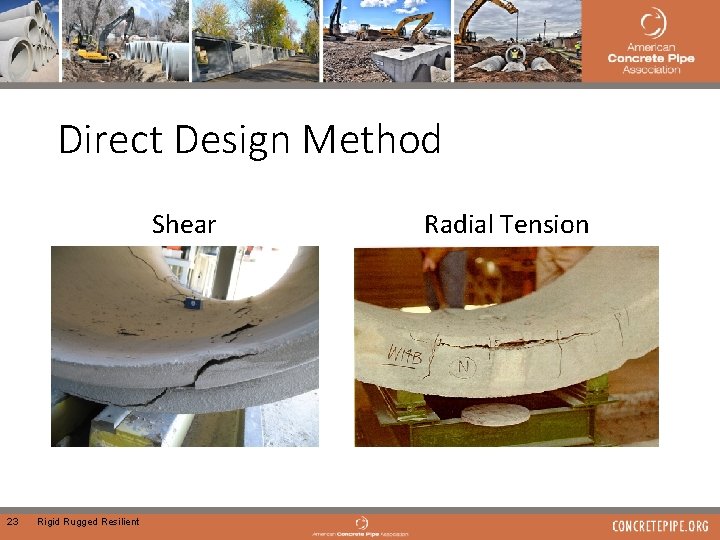
Direct Design Method Shear 23 Rigid Rugged Resilient Radial Tension
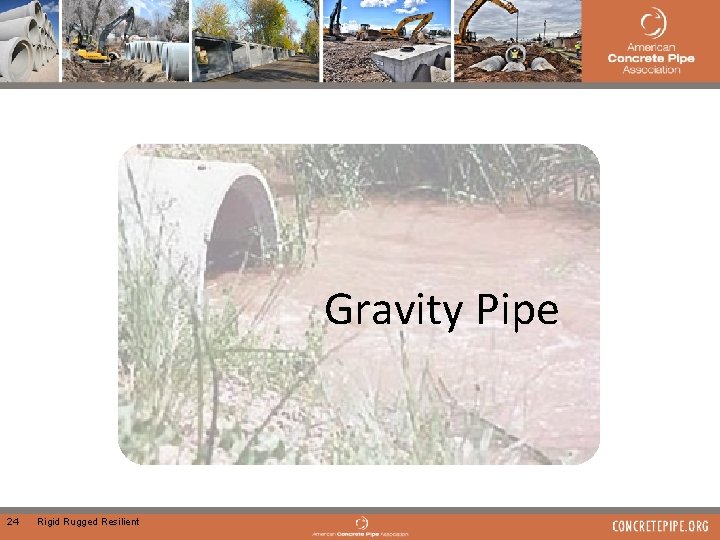
Gravity Pipe 24 Rigid Rugged Resilient
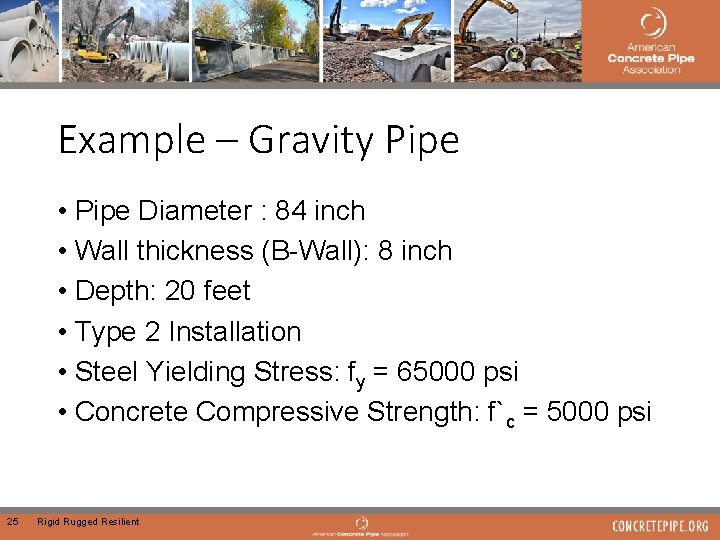
Example – Gravity Pipe • Pipe Diameter : 84 inch • Wall thickness (B-Wall): 8 inch • Depth: 20 feet • Type 2 Installation • Steel Yielding Stress: fy = 65000 psi • Concrete Compressive Strength: f`c = 5000 psi 25 Rigid Rugged Resilient
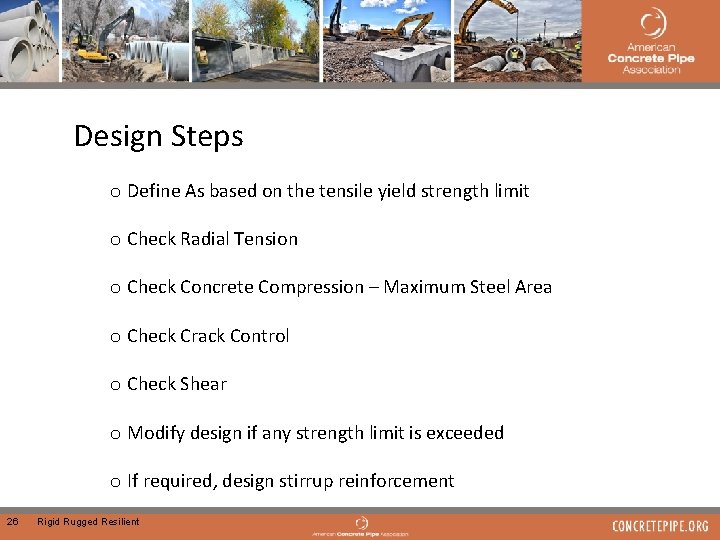
Design Steps o Define As based on the tensile yield strength limit o Check Radial Tension o Check Concrete Compression – Maximum Steel Area o Check Crack Control o Check Shear o Modify design if any strength limit is exceeded o If required, design stirrup reinforcement 26 Rigid Rugged Resilient
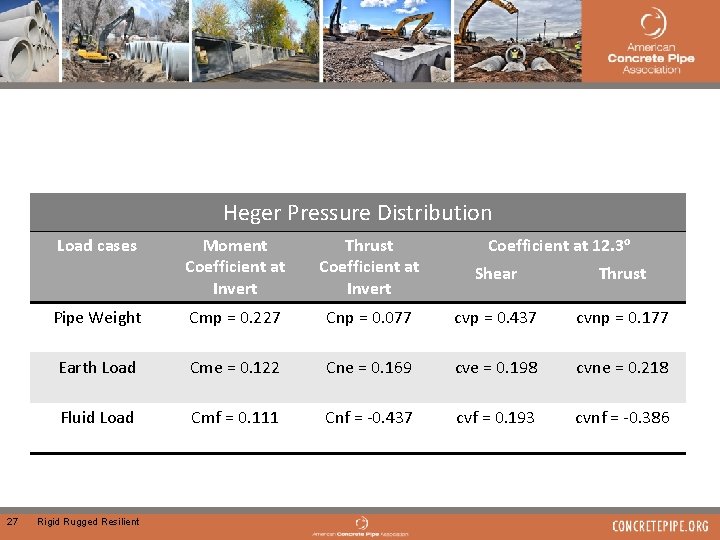
Heger Pressure Distribution Load cases 27 Moment Coefficient at Invert Thrust Coefficient at Invert Shear Thrust Pipe Weight Cmp = 0. 227 Cnp = 0. 077 cvp = 0. 437 cvnp = 0. 177 Earth Load Cme = 0. 122 Cne = 0. 169 cve = 0. 198 cvne = 0. 218 Fluid Load Cmf = 0. 111 Cnf = -0. 437 cvf = 0. 193 cvnf = -0. 386 Rigid Rugged Resilient Coefficient at 12. 3 o
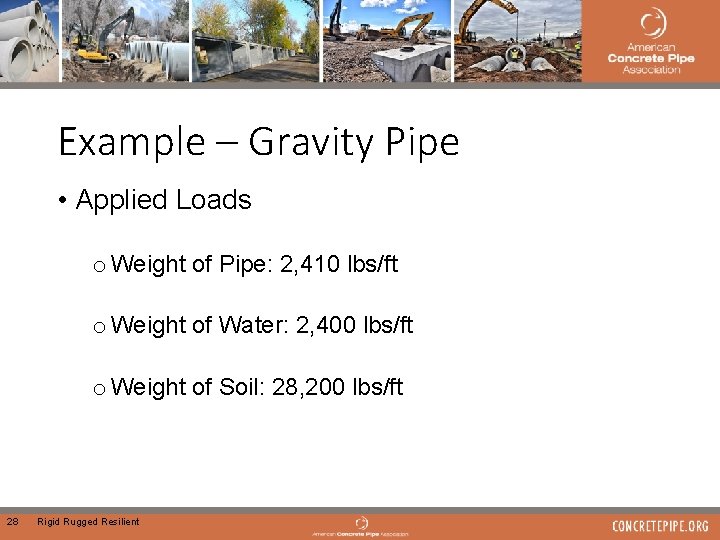
Example – Gravity Pipe • Applied Loads o Weight of Pipe: 2, 410 lbs/ft o Weight of Water: 2, 400 lbs/ft o Weight of Soil: 28, 200 lbs/ft 28 Rigid Rugged Resilient
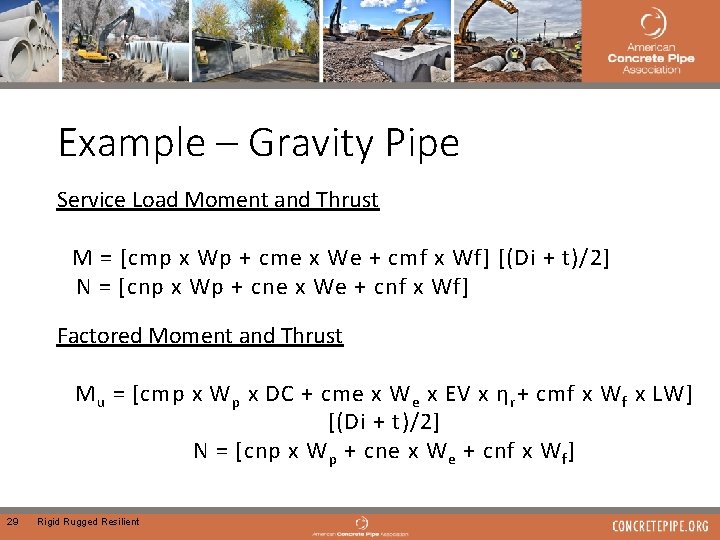
Example – Gravity Pipe Service Load Moment and Thrust M = [cmp x Wp + cme x We + cmf x Wf] [(Di + t)/2] N = [cnp x Wp + cne x We + cnf x Wf] Factored Moment and Thrust M u = [cmp x W p x DC + cme x W e x EV x η r + cmf x W f x LW] [(Di + t)/2] N = [cnp x W p + cne x W e + cnf x W f ] 29 Rigid Rugged Resilient
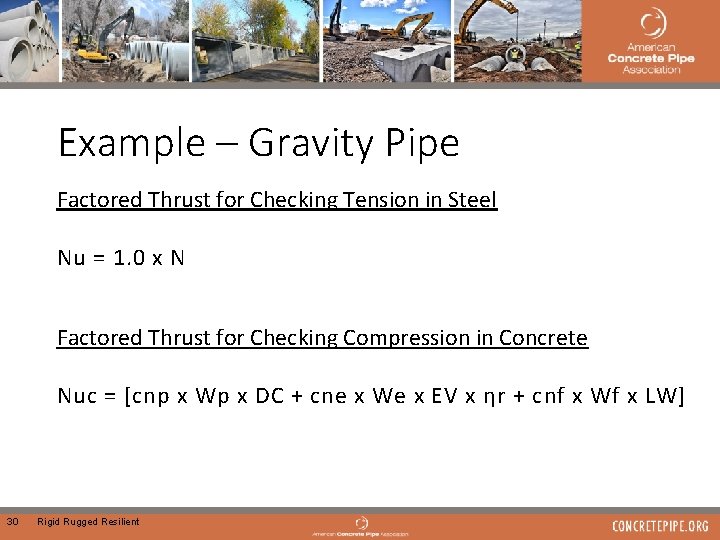
Example – Gravity Pipe Factored Thrust for Checking Tension in Steel Nu = 1. 0 x N Factored Thrust for Checking Compression in Concrete Nuc = [cnp x Wp x DC + cne x We x EV x ηr + cnf x Wf x LW] 30 Rigid Rugged Resilient
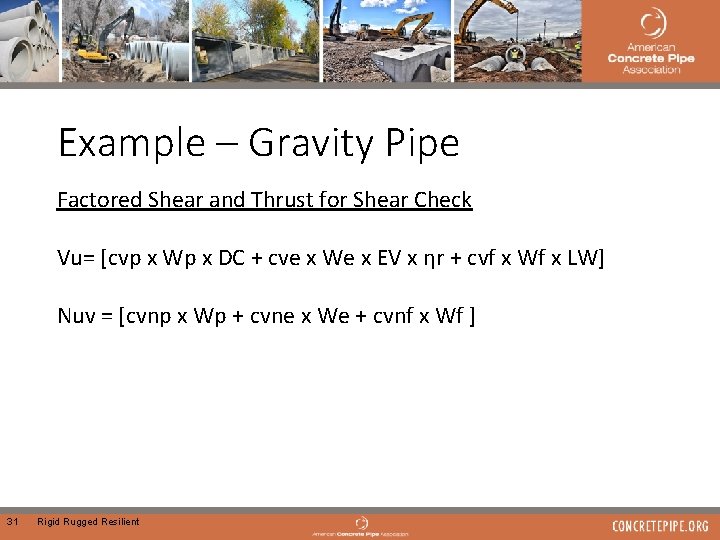
Example – Gravity Pipe Factored Shear and Thrust for Shear Check Vu= [cvp x Wp x DC + cve x We x EV x ηr + cvf x Wf x LW] Nuv = [cvnp x Wp + cvne x We + cvnf x Wf ] 31 Rigid Rugged Resilient
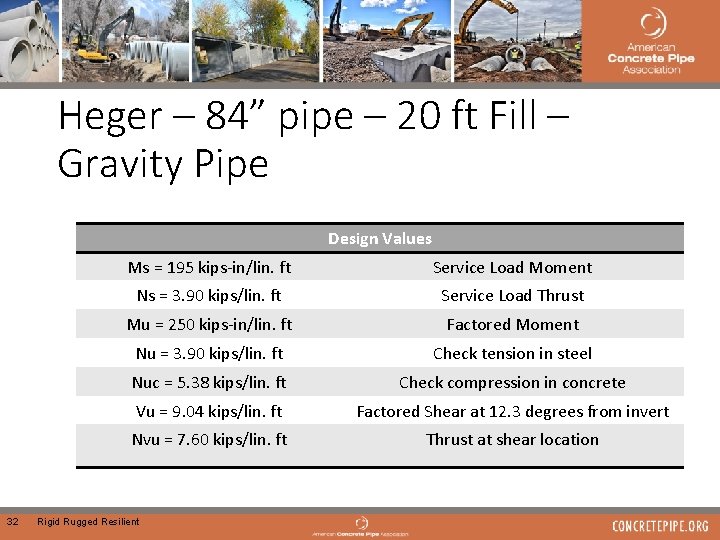
Heger – 84” pipe – 20 ft Fill – Gravity Pipe Design Values 32 Ms = 195 kips-in/lin. ft Service Load Moment Ns = 3. 90 kips/lin. ft Service Load Thrust Mu = 250 kips-in/lin. ft Factored Moment Nu = 3. 90 kips/lin. ft Check tension in steel Nuc = 5. 38 kips/lin. ft Check compression in concrete Vu = 9. 04 kips/lin. ft Factored Shear at 12. 3 degrees from invert Nvu = 7. 60 kips/lin. ft Thrust at shear location Rigid Rugged Resilient
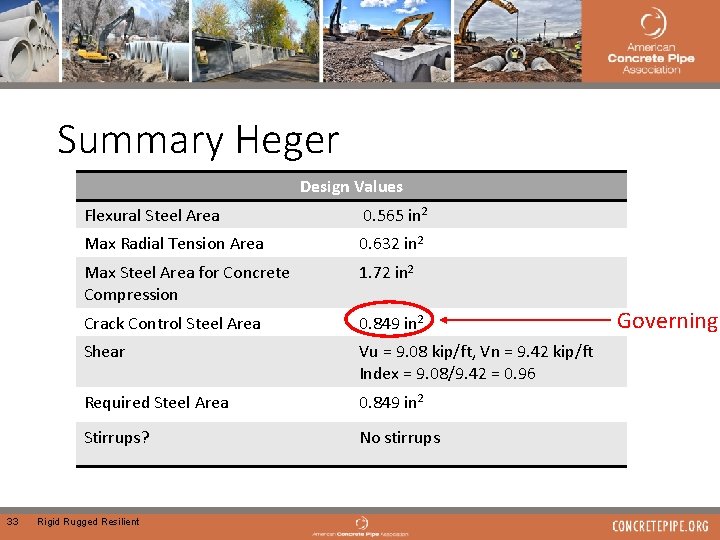
Summary Heger Design Values 33 Flexural Steel Area 0. 565 in 2 Max Radial Tension Area 0. 632 in 2 Max Steel Area for Concrete Compression 1. 72 in 2 Crack Control Steel Area 0. 849 in 2 Shear Vu = 9. 08 kip/ft, Vn = 9. 42 kip/ft Index = 9. 08/9. 42 = 0. 96 Required Steel Area 0. 849 in 2 Stirrups? No stirrups Rigid Rugged Resilient Governing
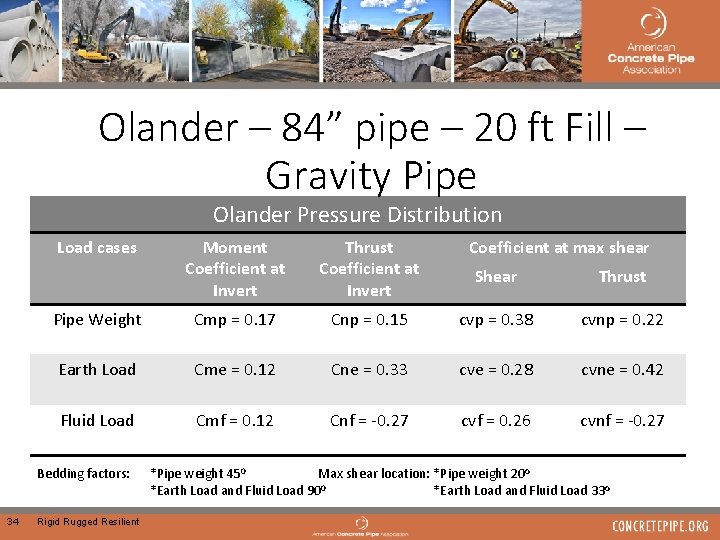
Olander – 84” pipe – 20 ft Fill – Gravity Pipe Olander Pressure Distribution Load cases Moment Coefficient at Invert Thrust Coefficient at Invert Pipe Weight Cmp = 0. 17 Earth Load Fluid Load Bedding factors: 34 Rigid Rugged Resilient Coefficient at max shear Shear Thrust Cnp = 0. 15 cvp = 0. 38 cvnp = 0. 22 Cme = 0. 12 Cne = 0. 33 cve = 0. 28 cvne = 0. 42 Cmf = 0. 12 Cnf = -0. 27 cvf = 0. 26 cvnf = -0. 27 *Pipe weight 450 Max shear location: *Pipe weight 20 o *Earth Load and Fluid Load 900 *Earth Load and Fluid Load 33 o
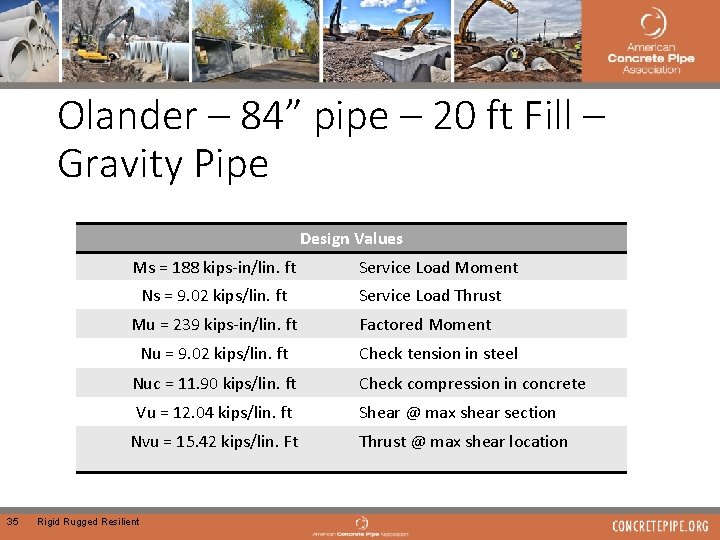
Olander – 84” pipe – 20 ft Fill – Gravity Pipe Design Values Ms = 188 kips-in/lin. ft Ns = 9. 02 kips/lin. ft Service Load Thrust Mu = 239 kips-in/lin. ft Factored Moment Nu = 9. 02 kips/lin. ft Check tension in steel Nuc = 11. 90 kips/lin. ft Check compression in concrete Vu = 12. 04 kips/lin. ft Shear @ max shear section Nvu = 15. 42 kips/lin. Ft 35 Service Load Moment Rigid Rugged Resilient Thrust @ max shear location
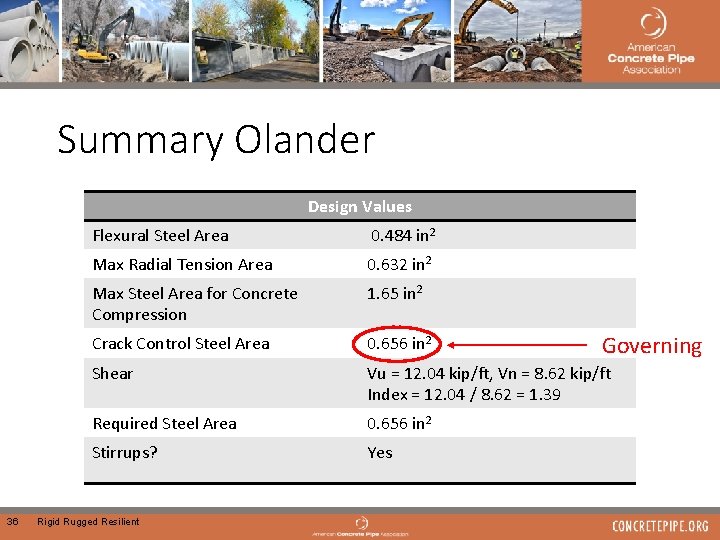
Summary Olander Design Values 36 Flexural Steel Area 0. 484 in 2 Max Radial Tension Area 0. 632 in 2 Max Steel Area for Concrete Compression 1. 65 in 2 Crack Control Steel Area 0. 656 in 2 Shear Vu = 12. 04 kip/ft, Vn = 8. 62 kip/ft Index = 12. 04 / 8. 62 = 1. 39 Required Steel Area 0. 656 in 2 Stirrups? Yes Rigid Rugged Resilient Governing
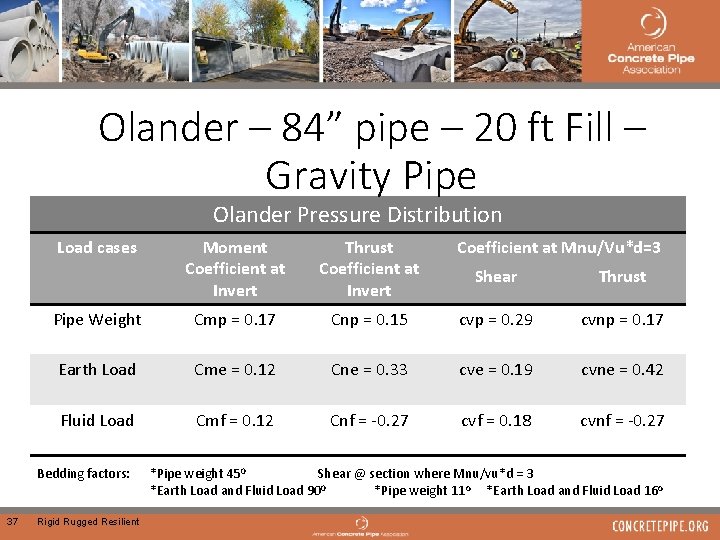
Olander – 84” pipe – 20 ft Fill – Gravity Pipe Olander Pressure Distribution Load cases Moment Coefficient at Invert Thrust Coefficient at Invert Pipe Weight Cmp = 0. 17 Earth Load Fluid Load Bedding factors: 37 Rigid Rugged Resilient Coefficient at Mnu/Vu*d=3 Shear Thrust Cnp = 0. 15 cvp = 0. 29 cvnp = 0. 17 Cme = 0. 12 Cne = 0. 33 cve = 0. 19 cvne = 0. 42 Cmf = 0. 12 Cnf = -0. 27 cvf = 0. 18 cvnf = -0. 27 *Pipe weight 450 Shear @ section where Mnu/vu*d = 3 *Earth Load and Fluid Load 900 *Pipe weight 11 o *Earth Load and Fluid Load 16 o
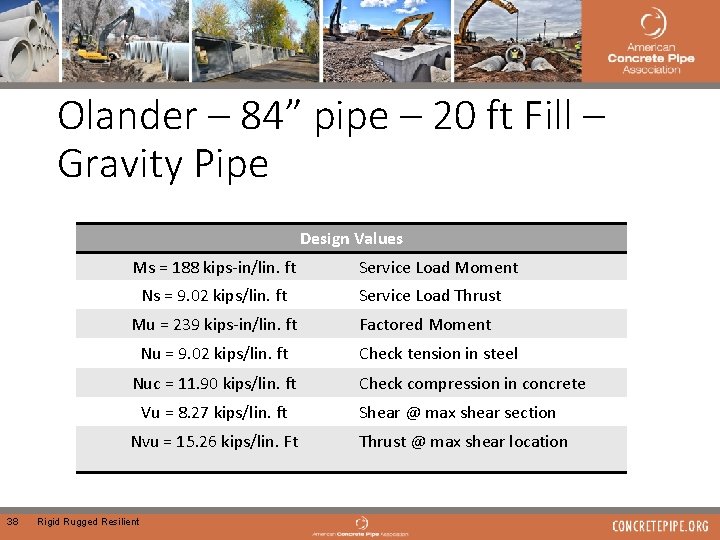
Olander – 84” pipe – 20 ft Fill – Gravity Pipe Design Values Ms = 188 kips-in/lin. ft Ns = 9. 02 kips/lin. ft Service Load Thrust Mu = 239 kips-in/lin. ft Factored Moment Nu = 9. 02 kips/lin. ft Nuc = 11. 90 kips/lin. ft Vu = 8. 27 kips/lin. ft Nvu = 15. 26 kips/lin. Ft 38 Service Load Moment Rigid Rugged Resilient Check tension in steel Check compression in concrete Shear @ max shear section Thrust @ max shear location
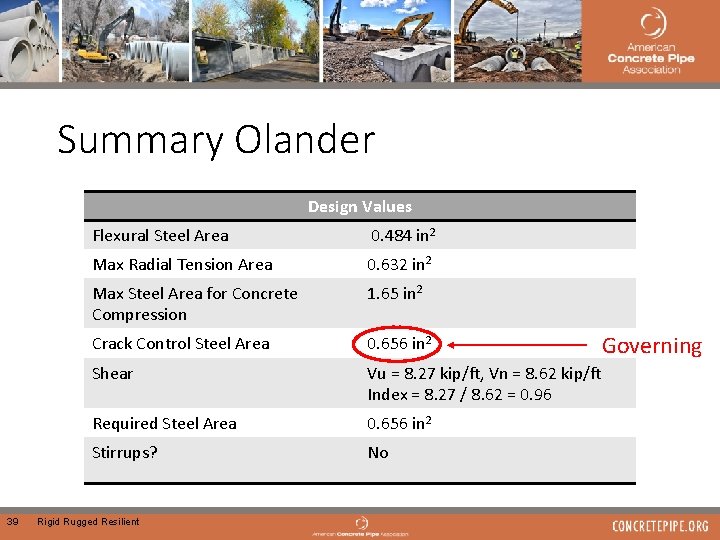
Summary Olander Design Values 39 Flexural Steel Area 0. 484 in 2 Max Radial Tension Area 0. 632 in 2 Max Steel Area for Concrete Compression 1. 65 in 2 Crack Control Steel Area 0. 656 in 2 Shear Vu = 8. 27 kip/ft, Vn = 8. 62 kip/ft Index = 8. 27 / 8. 62 = 0. 96 Required Steel Area 0. 656 in 2 Stirrups? No Rigid Rugged Resilient Governing
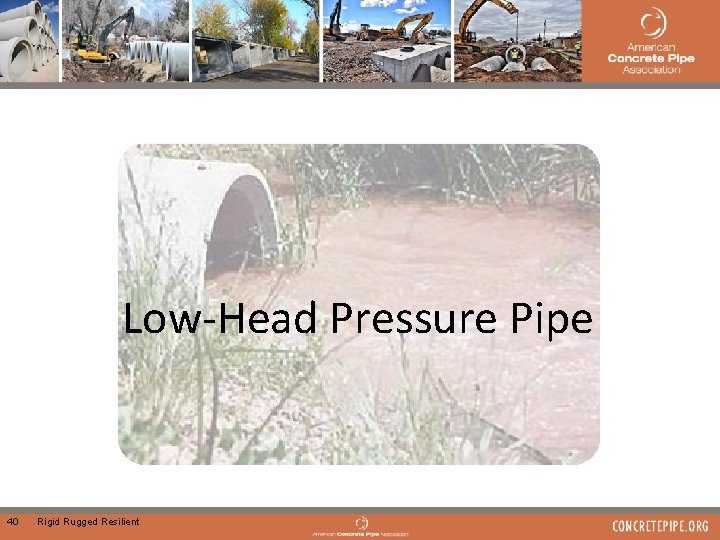
Low-Head Pressure Pipe 40 Rigid Rugged Resilient
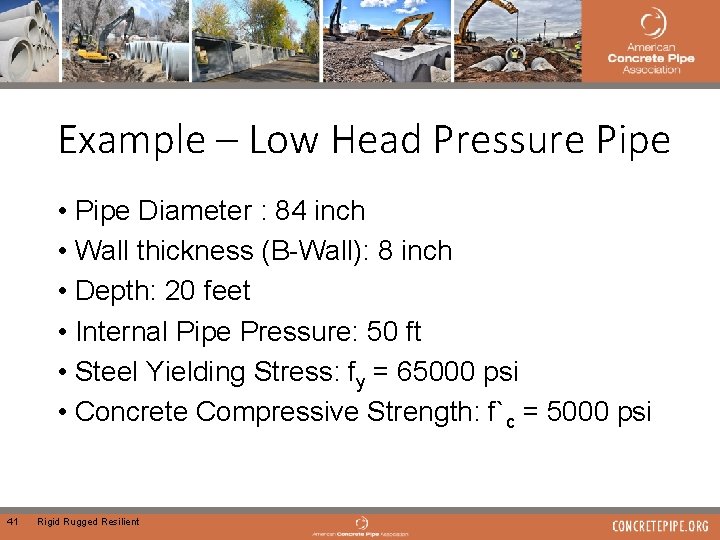
Example – Low Head Pressure Pipe • Pipe Diameter : 84 inch • Wall thickness (B-Wall): 8 inch • Depth: 20 feet • Internal Pipe Pressure: 50 ft • Steel Yielding Stress: fy = 65000 psi • Concrete Compressive Strength: f`c = 5000 psi 41 Rigid Rugged Resilient
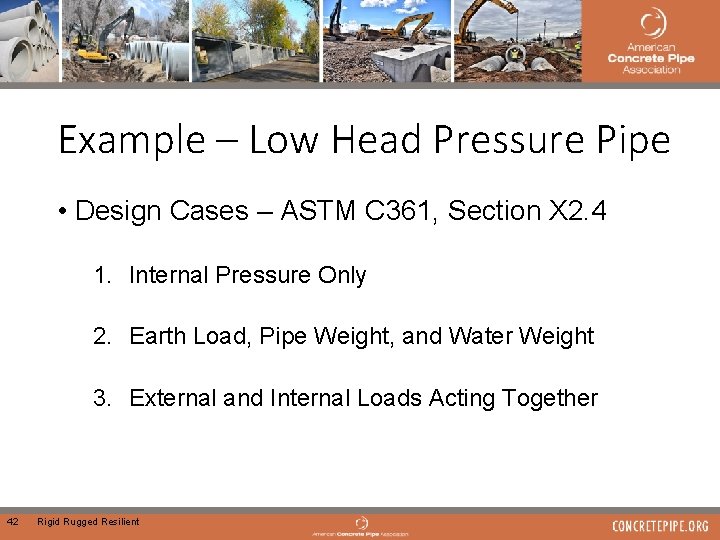
Example – Low Head Pressure Pipe • Design Cases – ASTM C 361, Section X 2. 4 1. Internal Pressure Only 2. Earth Load, Pipe Weight, and Water Weight 3. External and Internal Loads Acting Together 42 Rigid Rugged Resilient
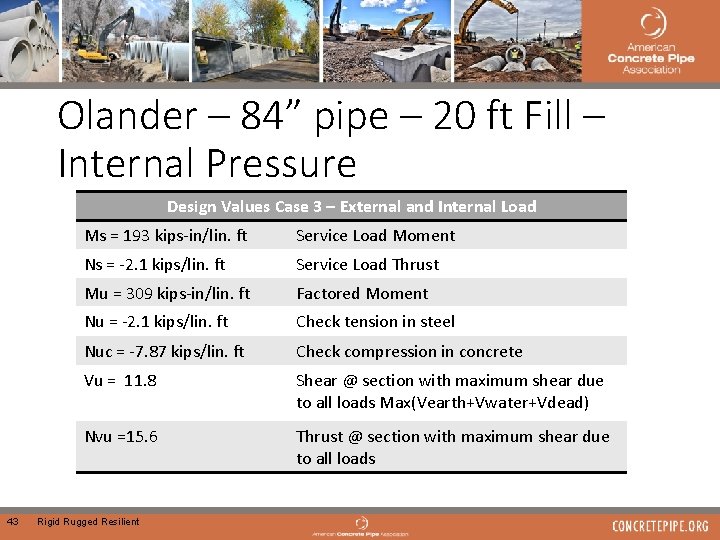
Olander – 84” pipe – 20 ft Fill – Internal Pressure Design Values Case 3 – External and Internal Load 43 Ms = 193 kips-in/lin. ft Service Load Moment Ns = -2. 1 kips/lin. ft Service Load Thrust Mu = 309 kips-in/lin. ft Factored Moment Nu = -2. 1 kips/lin. ft Check tension in steel Nuc = -7. 87 kips/lin. ft Check compression in concrete Vu = 11. 8 Shear @ section with maximum shear due to all loads Max(Vearth+Vwater+Vdead) Nvu =15. 6 Thrust @ section with maximum shear due to all loads Rigid Rugged Resilient
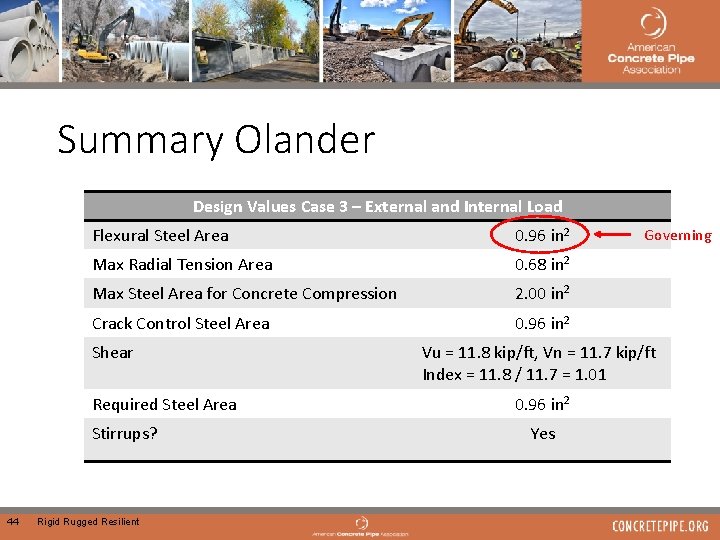
Summary Olander Design Values Case 3 – External and Internal Load Flexural Steel Area 0. 96 in 2 Max Radial Tension Area 0. 68 in 2 Max Steel Area for Concrete Compression 2. 00 in 2 Crack Control Steel Area 0. 96 in 2 Shear Required Steel Area Stirrups? 44 Rigid Rugged Resilient Governing Vu = 11. 8 kip/ft, Vn = 11. 7 kip/ft Index = 11. 8 / 11. 7 = 1. 01 0. 96 in 2 Yes
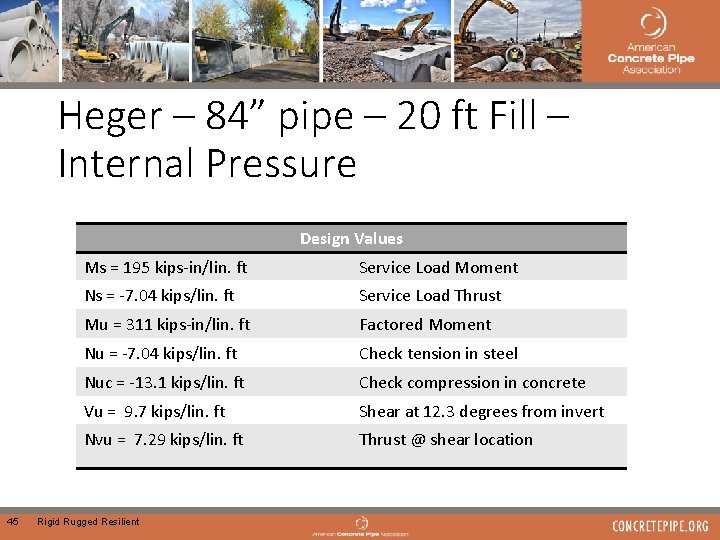
Heger – 84” pipe – 20 ft Fill – Internal Pressure Design Values 45 Ms = 195 kips-in/lin. ft Service Load Moment Ns = -7. 04 kips/lin. ft Service Load Thrust Mu = 311 kips-in/lin. ft Factored Moment Nu = -7. 04 kips/lin. ft Check tension in steel Nuc = -13. 1 kips/lin. ft Check compression in concrete Vu = 9. 7 kips/lin. ft Shear at 12. 3 degrees from invert Nvu = 7. 29 kips/lin. ft Thrust @ shear location Rigid Rugged Resilient
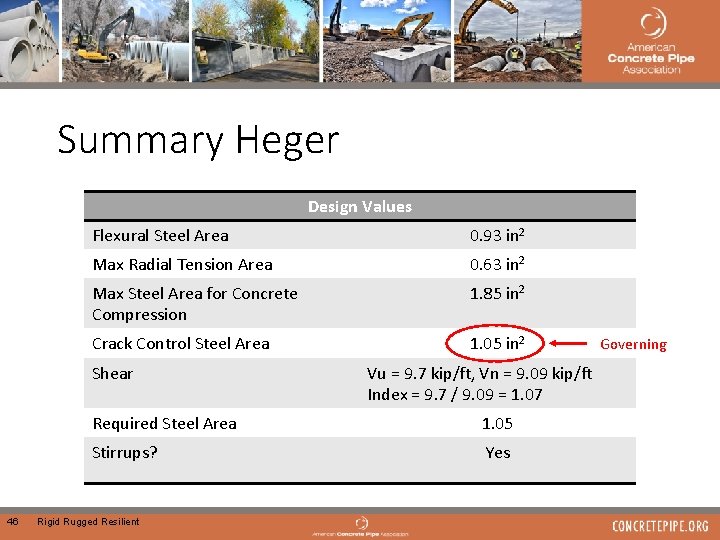
Summary Heger Design Values Flexural Steel Area 0. 93 in 2 Max Radial Tension Area 0. 63 in 2 Max Steel Area for Concrete Compression 1. 85 in 2 Crack Control Steel Area 1. 05 in 2 Shear 46 Vu = 9. 7 kip/ft, Vn = 9. 09 kip/ft Index = 9. 7 / 9. 09 = 1. 07 Required Steel Area 1. 05 Stirrups? Yes Rigid Rugged Resilient Governing
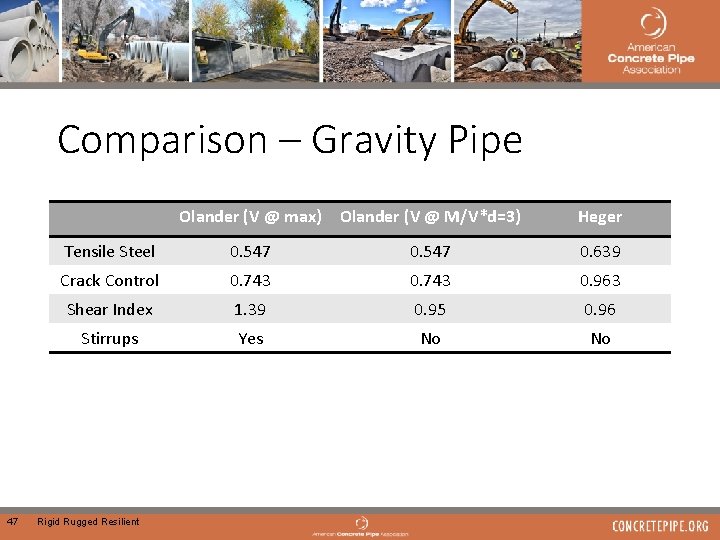
Comparison – Gravity Pipe 47 Olander (V @ max) Olander (V @ M/V*d=3) Heger Tensile Steel 0. 547 0. 639 Crack Control 0. 743 0. 963 Shear Index 1. 39 0. 95 0. 96 Stirrups Yes No No Rigid Rugged Resilient
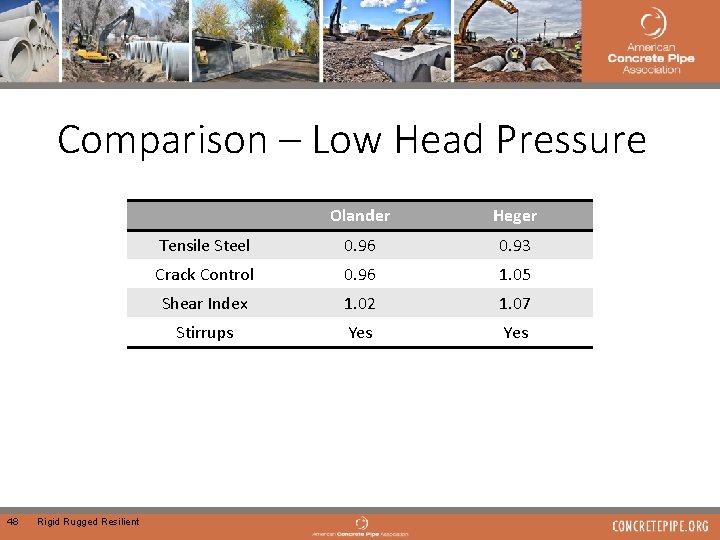
Comparison – Low Head Pressure 48 Rigid Rugged Resilient Olander Heger Tensile Steel 0. 96 0. 93 Crack Control 0. 96 1. 05 Shear Index 1. 02 1. 07 Stirrups Yes
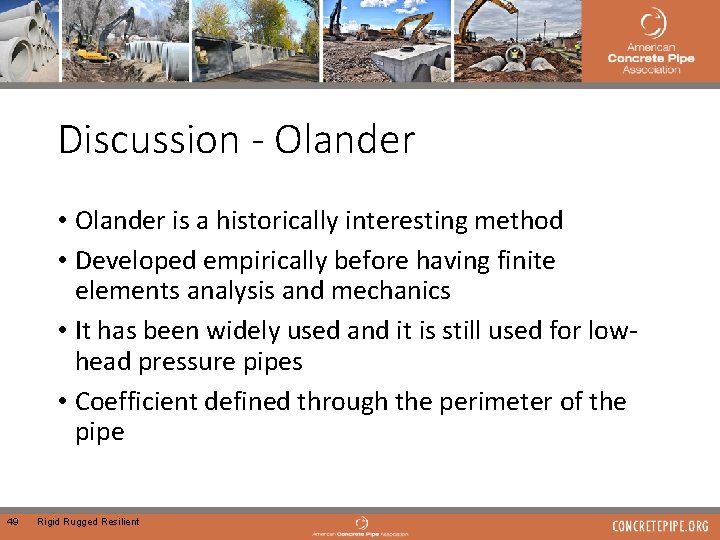
Discussion - Olander • Olander is a historically interesting method • Developed empirically before having finite elements analysis and mechanics • It has been widely used and it is still used for lowhead pressure pipes • Coefficient defined through the perimeter of the pipe 49 Rigid Rugged Resilient
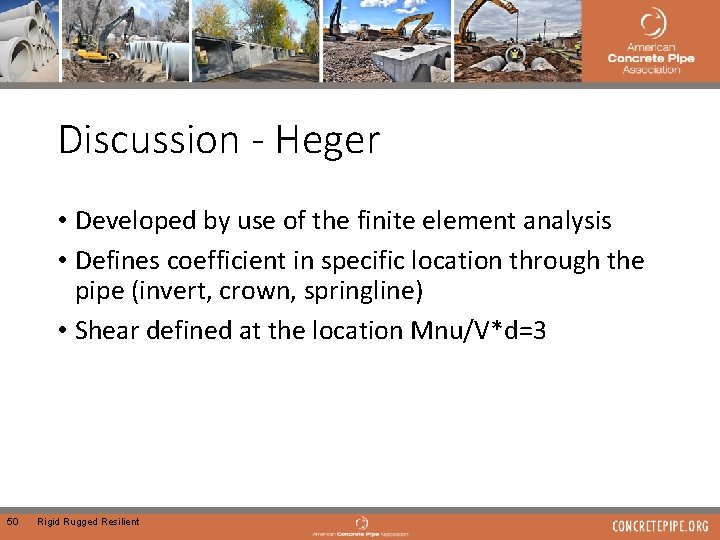
Discussion - Heger • Developed by use of the finite element analysis • Defines coefficient in specific location through the pipe (invert, crown, springline) • Shear defined at the location Mnu/V*d=3 50 Rigid Rugged Resilient
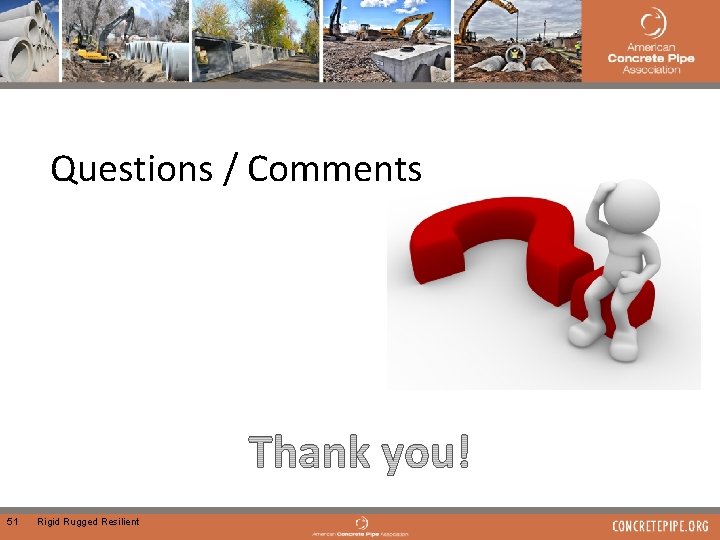
Questions / Comments 51 Rigid Rugged Resilient
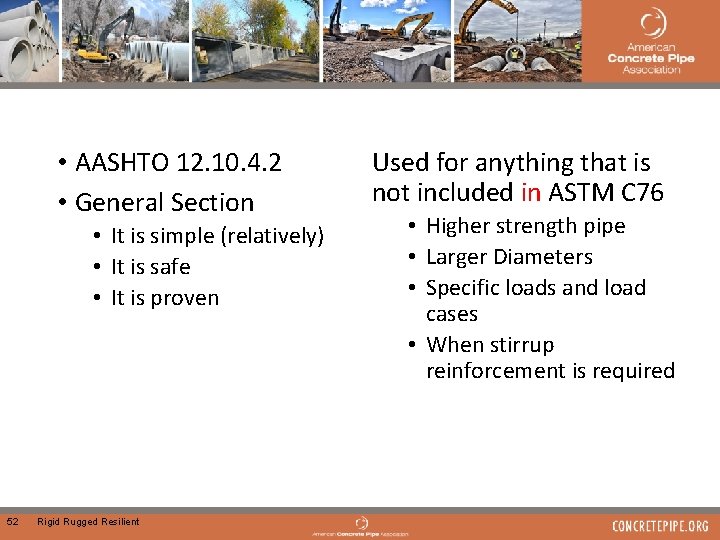
• AASHTO 12. 10. 4. 2 • General Section • It is simple (relatively) • It is safe • It is proven 52 Rigid Rugged Resilient Used for anything that is not included in ASTM C 76 • Higher strength pipe • Larger Diameters • Specific loads and load cases • When stirrup reinforcement is required
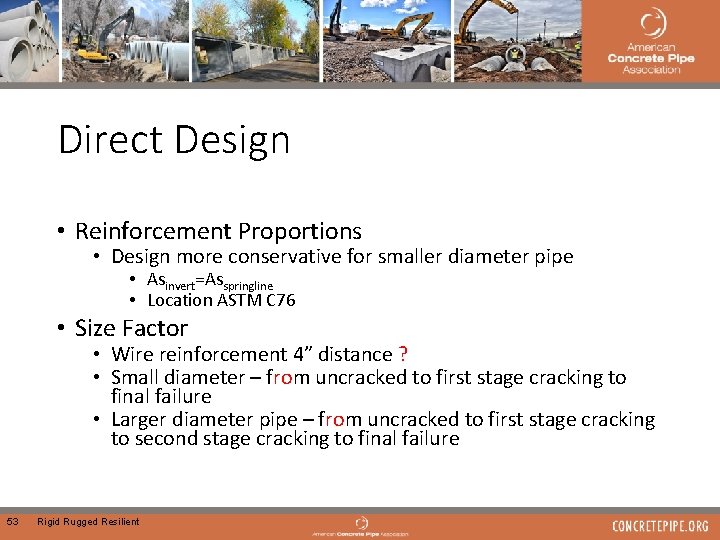
Direct Design • Reinforcement Proportions • Design more conservative for smaller diameter pipe • Asinvert=Asspringline • Location ASTM C 76 • Size Factor • Wire reinforcement 4” distance ? • Small diameter – from uncracked to first stage cracking to final failure • Larger diameter pipe – from uncracked to first stage cracking to second stage cracking to final failure 53 Rigid Rugged Resilient
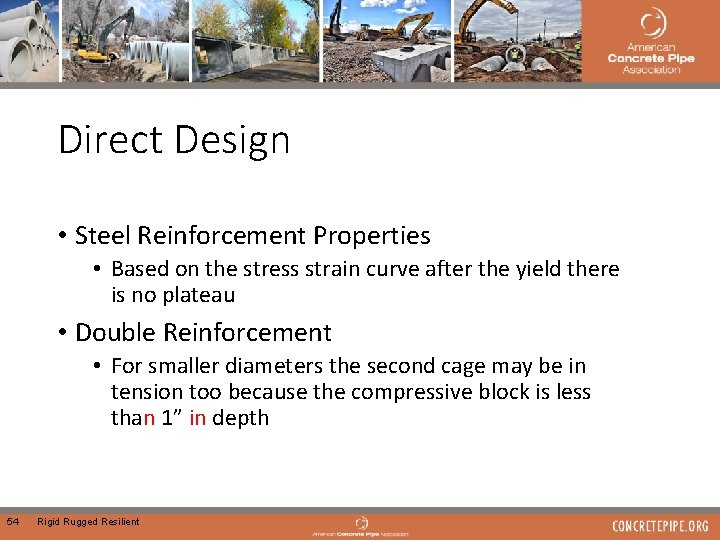
Direct Design • Steel Reinforcement Properties • Based on the stress strain curve after the yield there is no plateau • Double Reinforcement • For smaller diameters the second cage may be in tension too because the compressive block is less than 1” in depth 54 Rigid Rugged Resilient
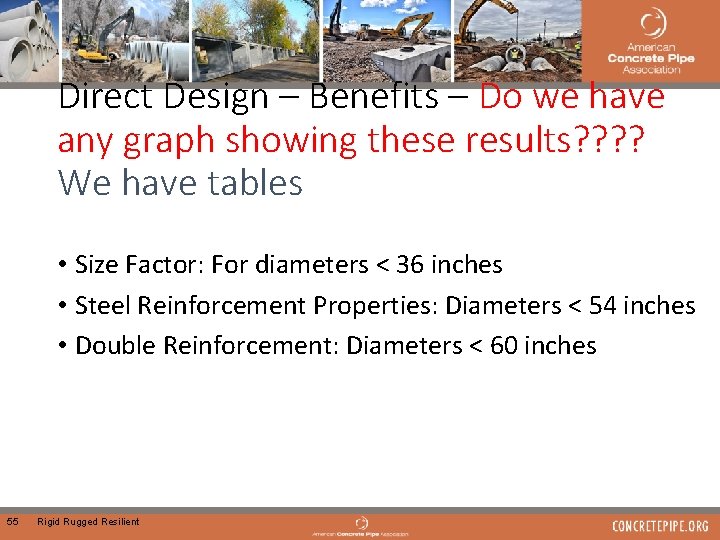
Direct Design – Benefits – Do we have any graph showing these results? ? We have tables • Size Factor: For diameters < 36 inches • Steel Reinforcement Properties: Diameters < 54 inches • Double Reinforcement: Diameters < 60 inches 55 Rigid Rugged Resilient
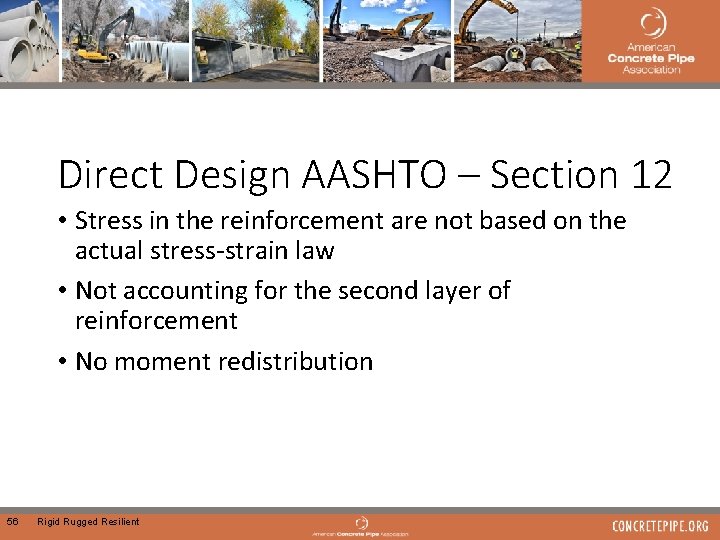
Direct Design AASHTO – Section 12 • Stress in the reinforcement are not based on the actual stress-strain law • Not accounting for the second layer of reinforcement • No moment redistribution 56 Rigid Rugged Resilient
Margarita takou
Bacson hoabinh
Jens heger
Dra margarita villar
Margarita porete frases
Bulgakov meister ja margarita
La camisa de margarita
Dra margarita villar
Vrste kitova
Margarita alonso ramos
Juan bosco domenica bossone
Margarita gomez acevedo
Latin america quiz
Ana luz esquinas murillo
Margarita todorova
Ricardo palma la camisa de margarita
Carcel de san antonio margarita
Como se llama
Ies margarita de fuenmayor
Margarita salas arroyo de la encomienda
Margarita de piria
Mihail afanaszjevics bulgakov elena s. bulgakova
Milka tesla marica kosanović
Trabajo social unpsjb
El enamorado y el otro preguntas y respuestas
Impresora de rueda de margarita
Margarita safonova
Margarita pirovska
Dr margarita alonso
M bulgakov
Detaistina
Margarita palacios sierra
Miss margarita
Pca clearly explained
Josh davis pimco
Josh farley
Josh portman
Josh brownlow
Josh tenenbaum mit
Just like josh gibson
Josh dempsey shooting
Dr josh wright
Josh duarte pottery
Josh garrison indiana
Josh laxton
Josh bachynski
Josh christianson
Josh lieberman agent
Josh ellithorpe
Josh barron medication error
Joshua phillips maddie clifton
Parker rodenbaugh
Sue harker
Josh gluckman
Josh benaloh
Joshua probert
Josh davies work ethic