Automating the In Circuit Test in Your Factory
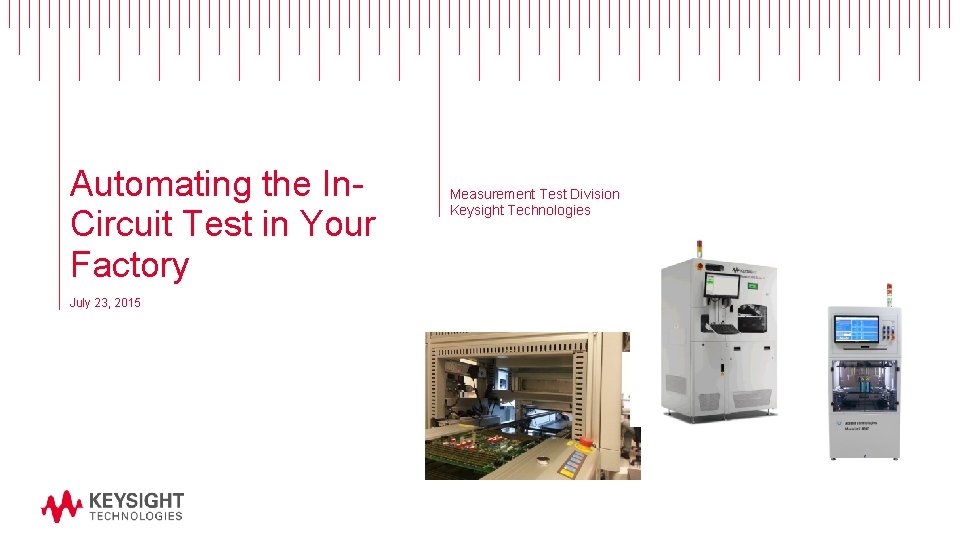
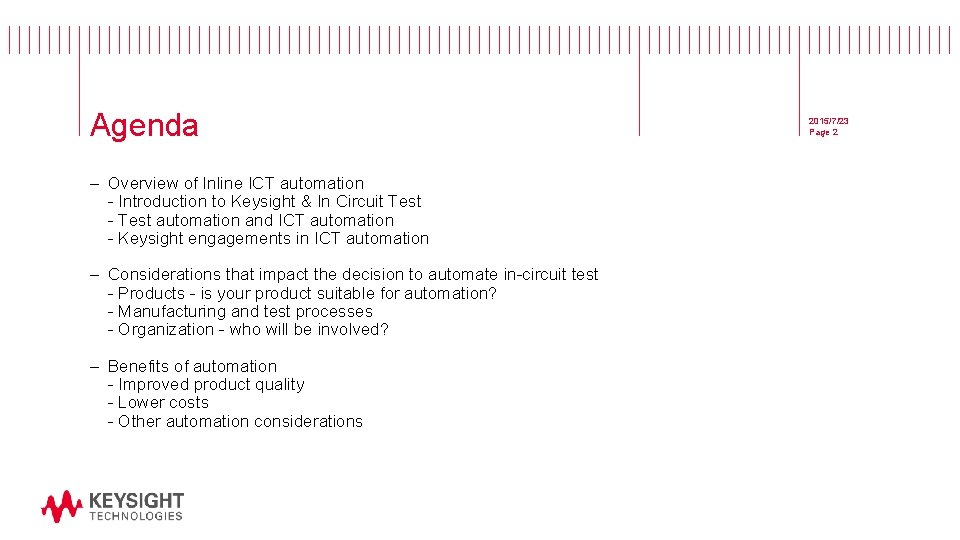

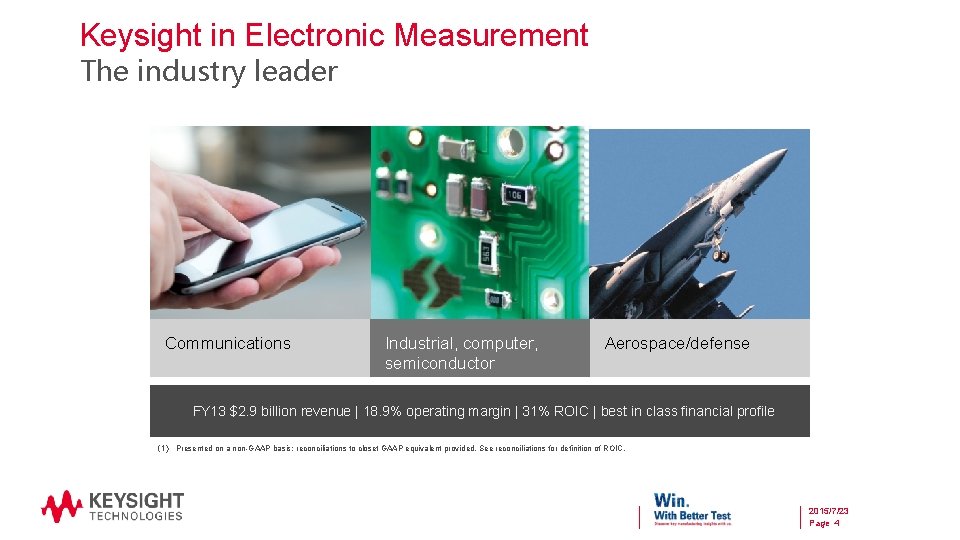
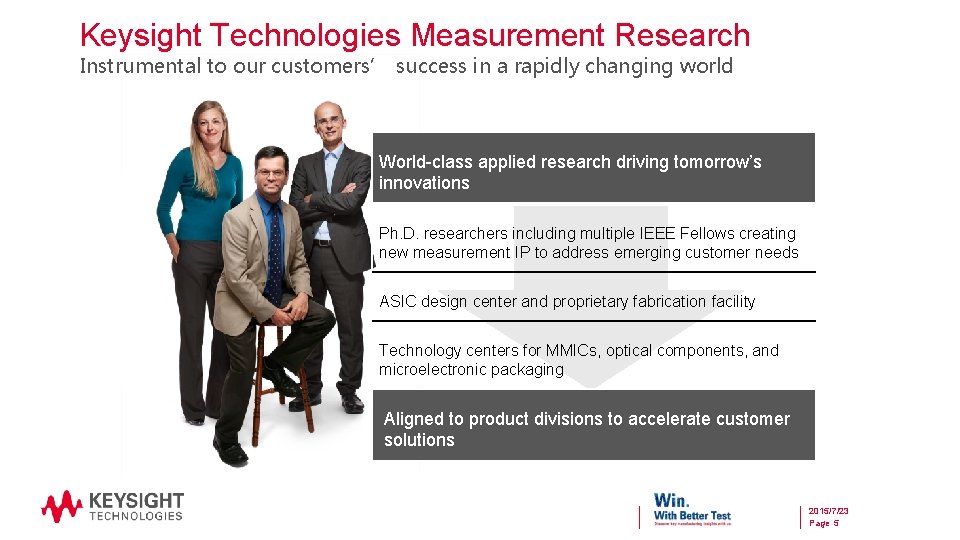
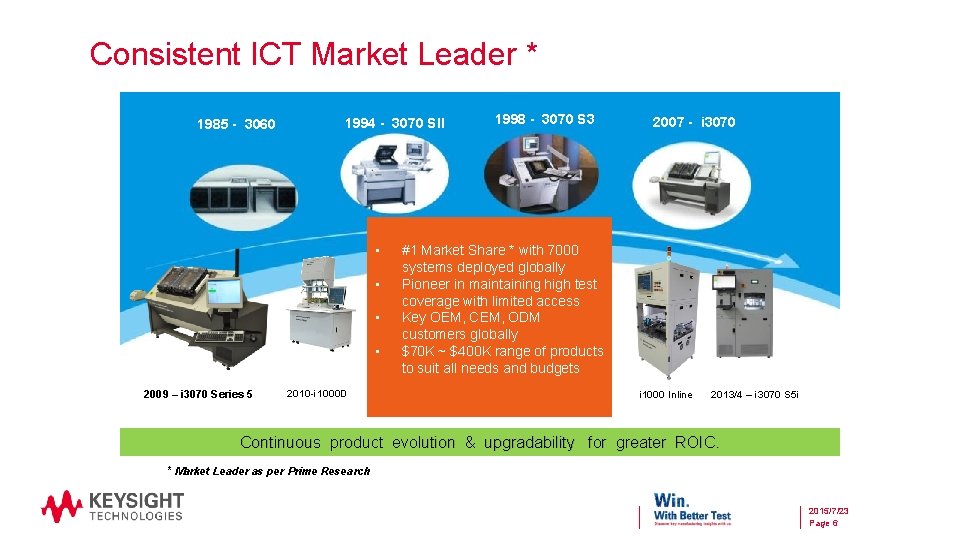
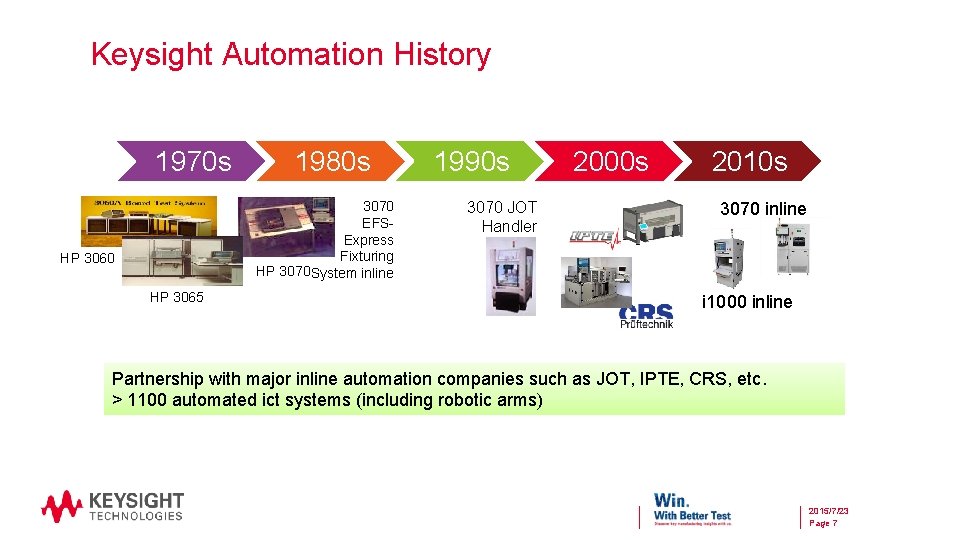
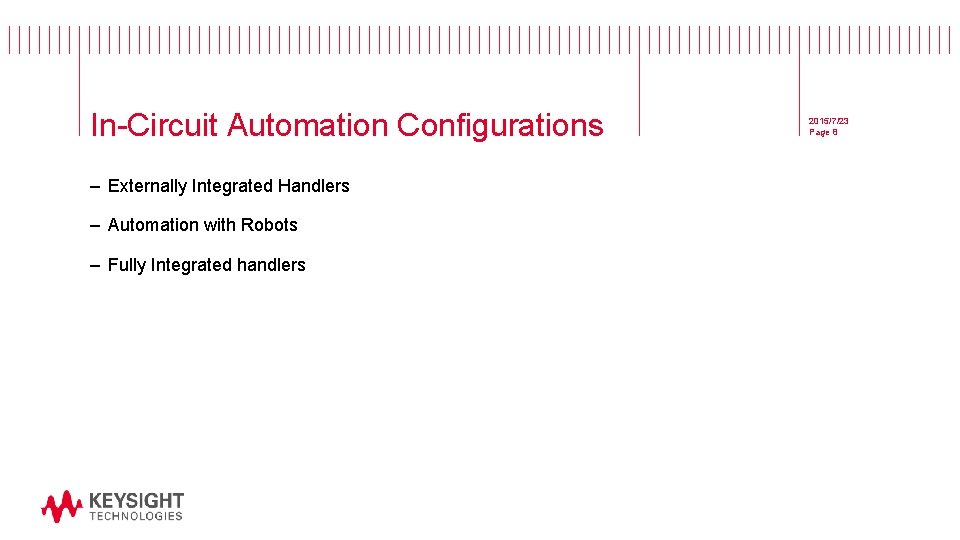
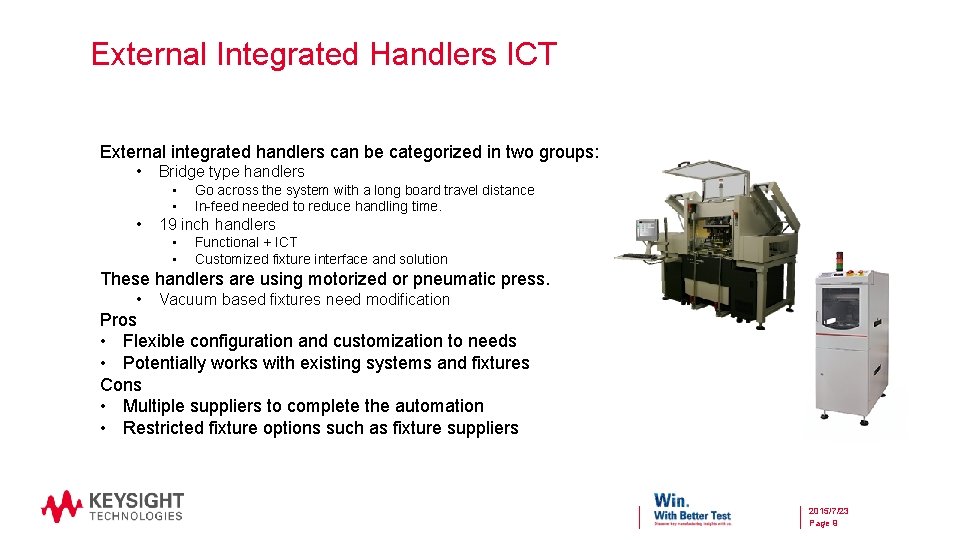
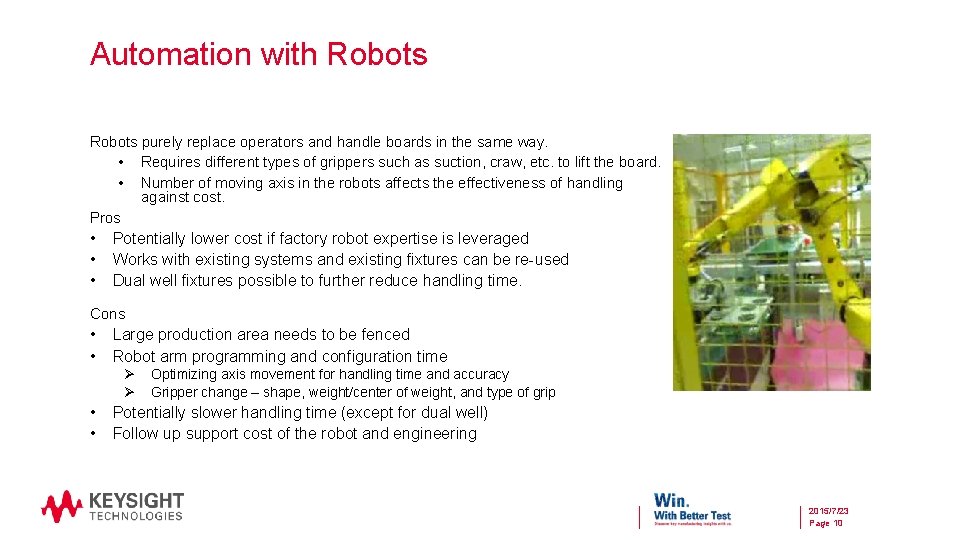
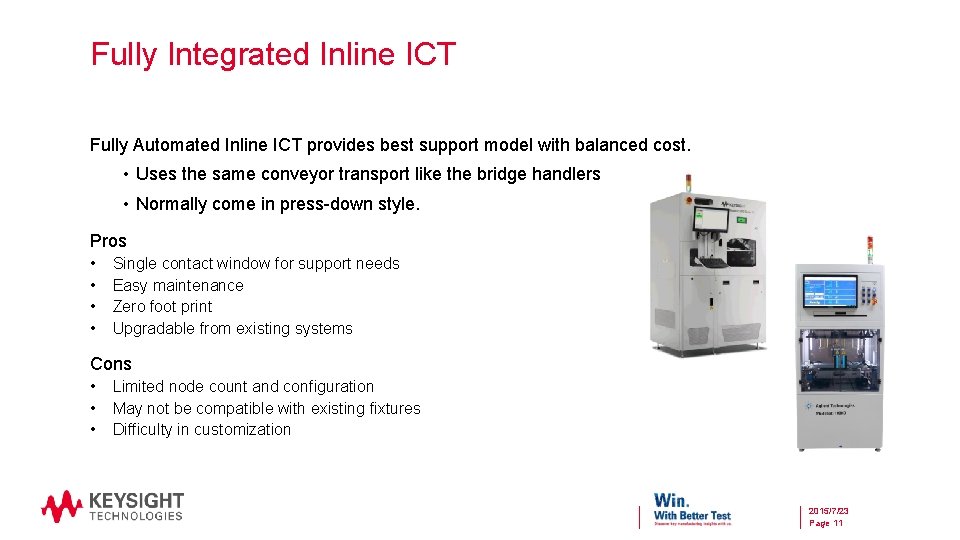
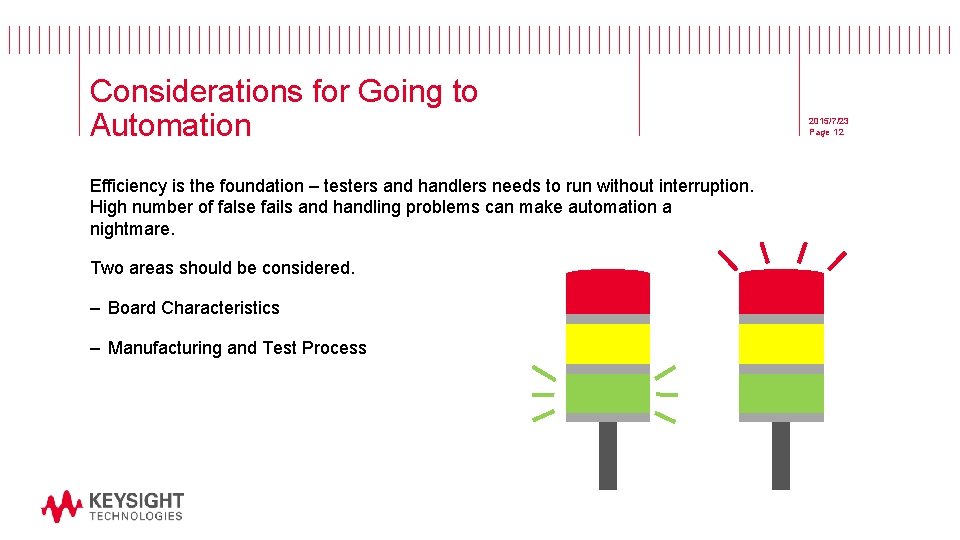
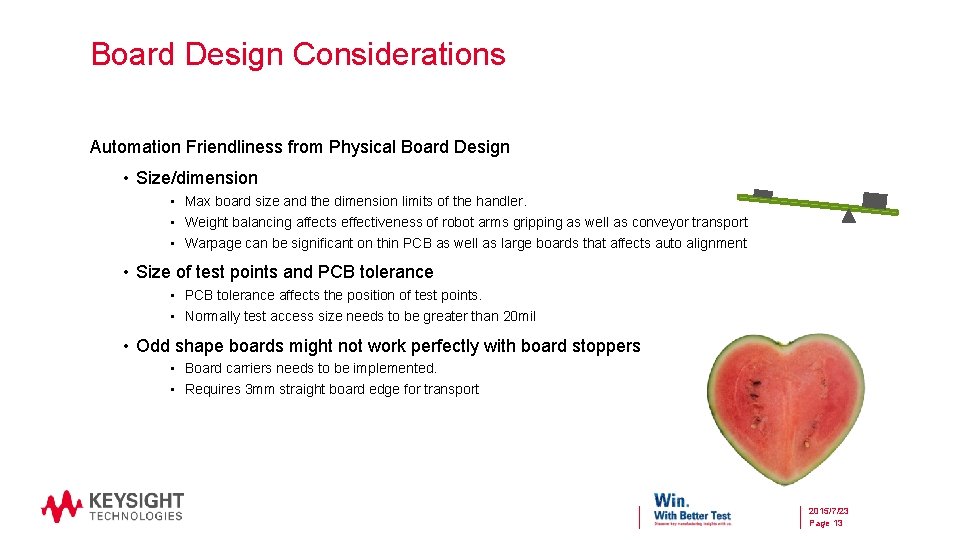
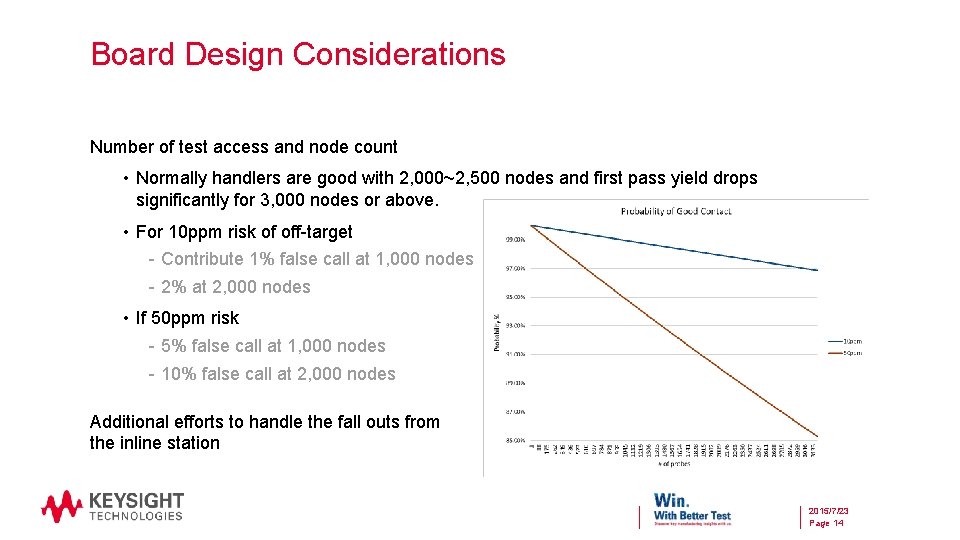

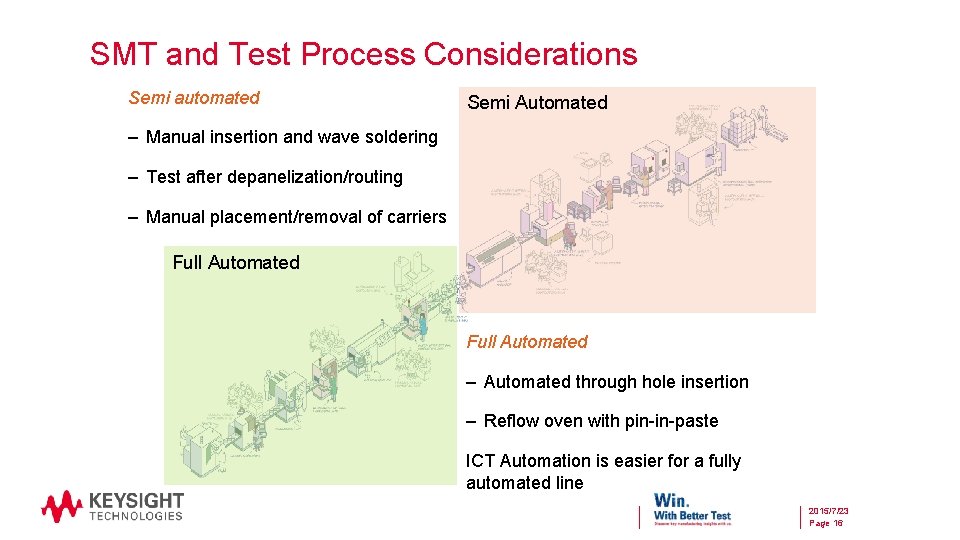
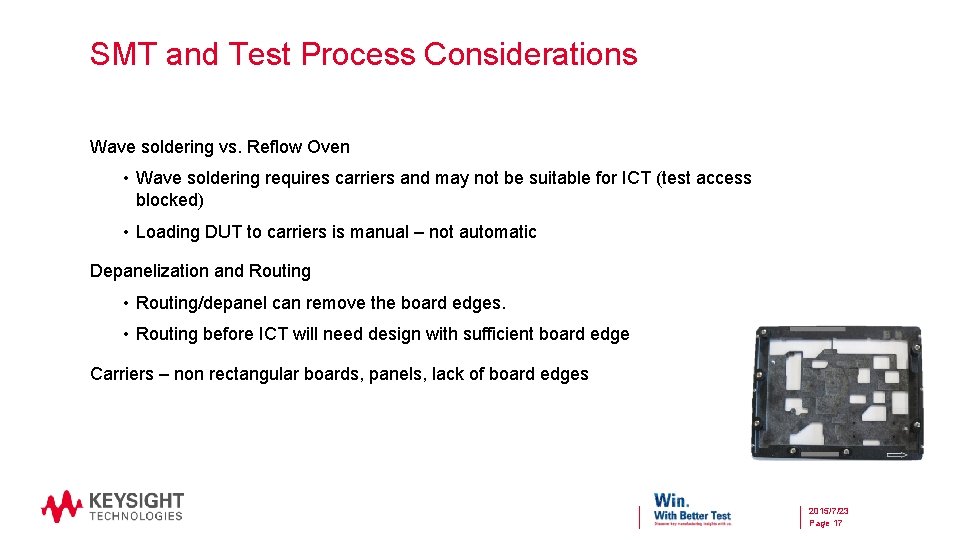
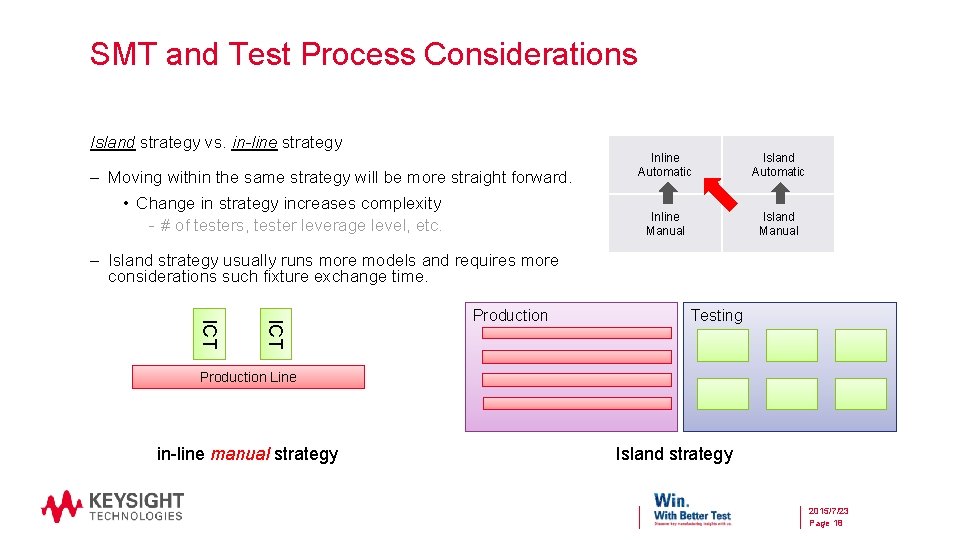
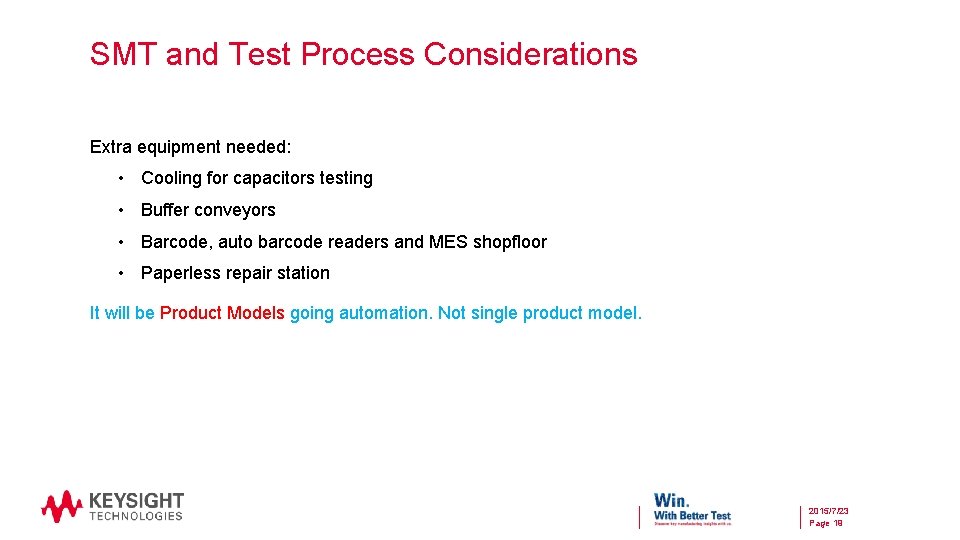
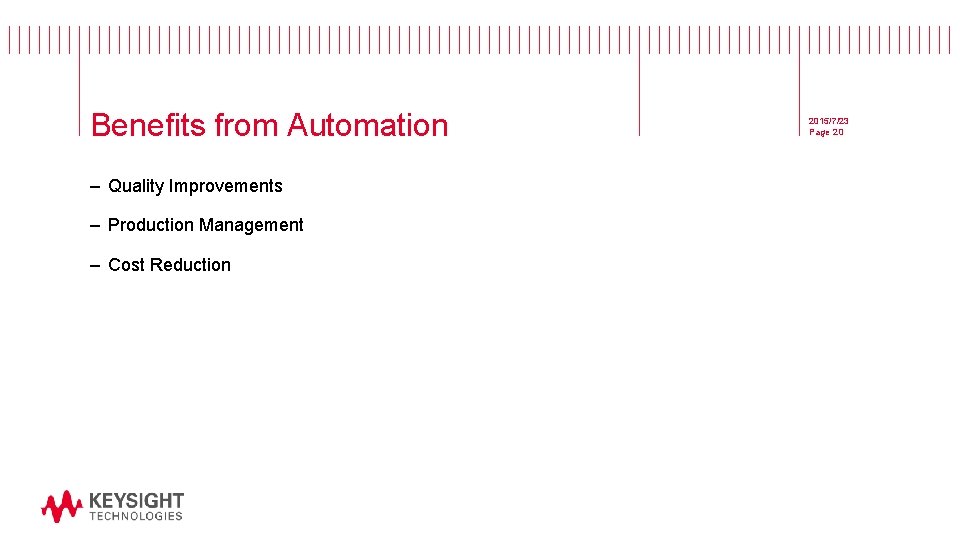
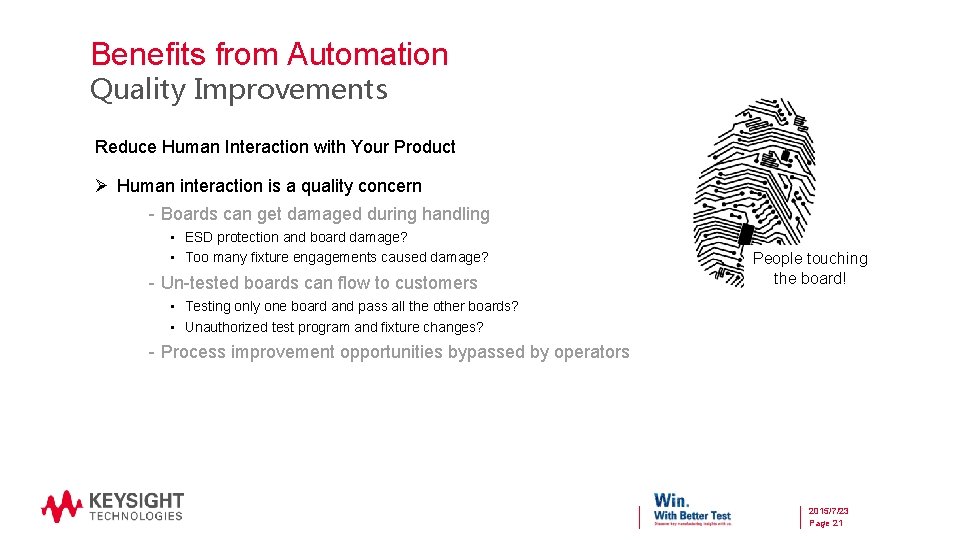
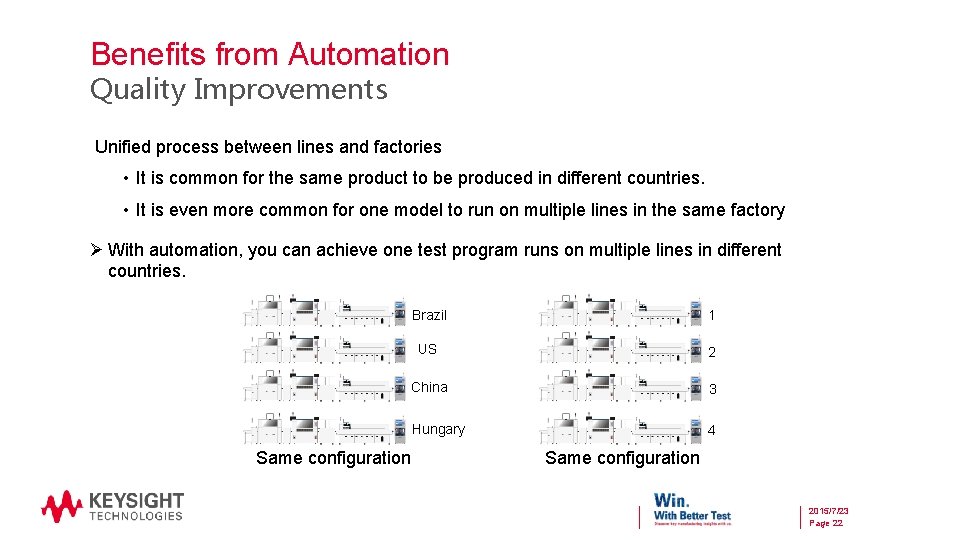
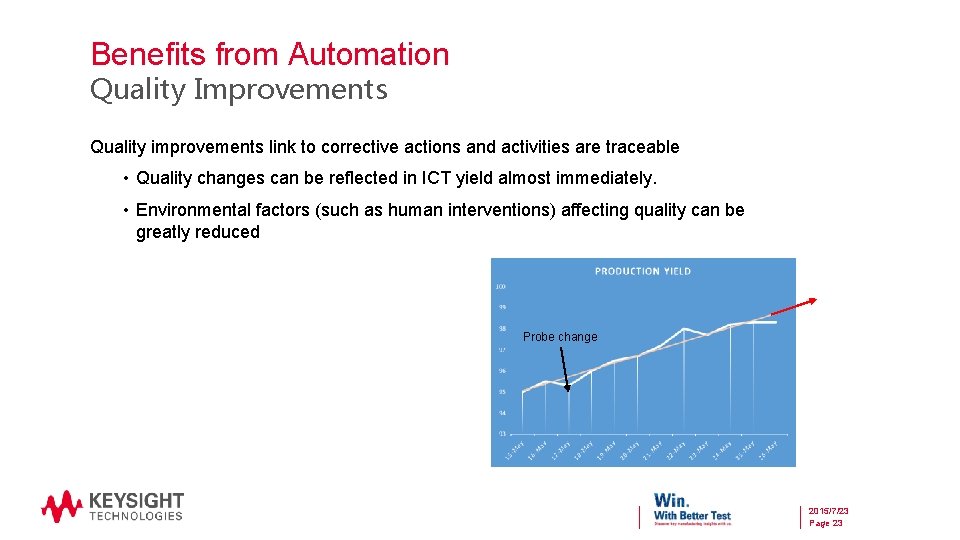

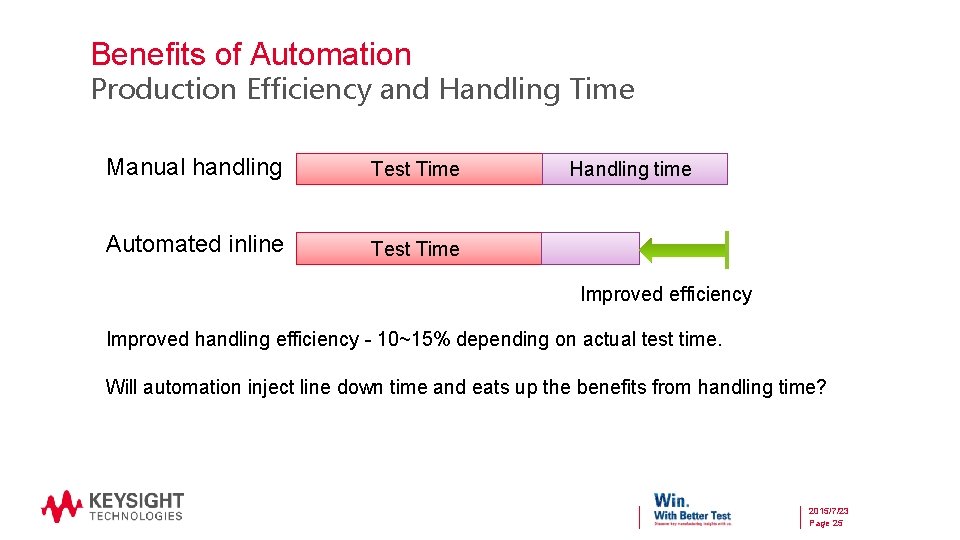
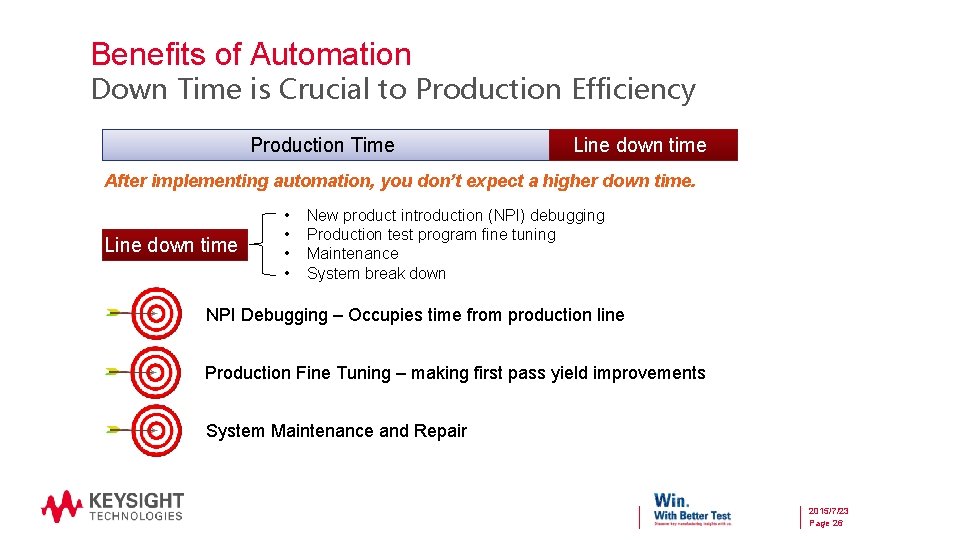
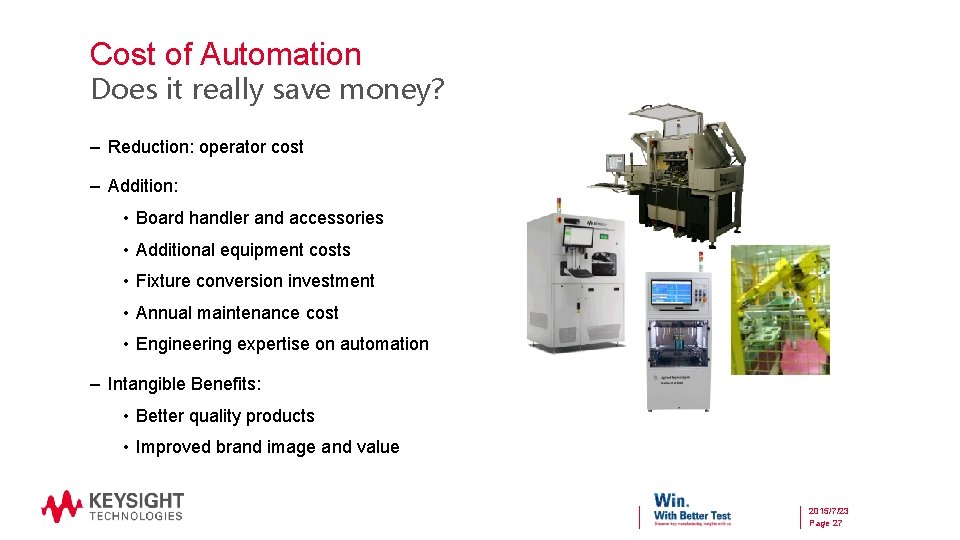
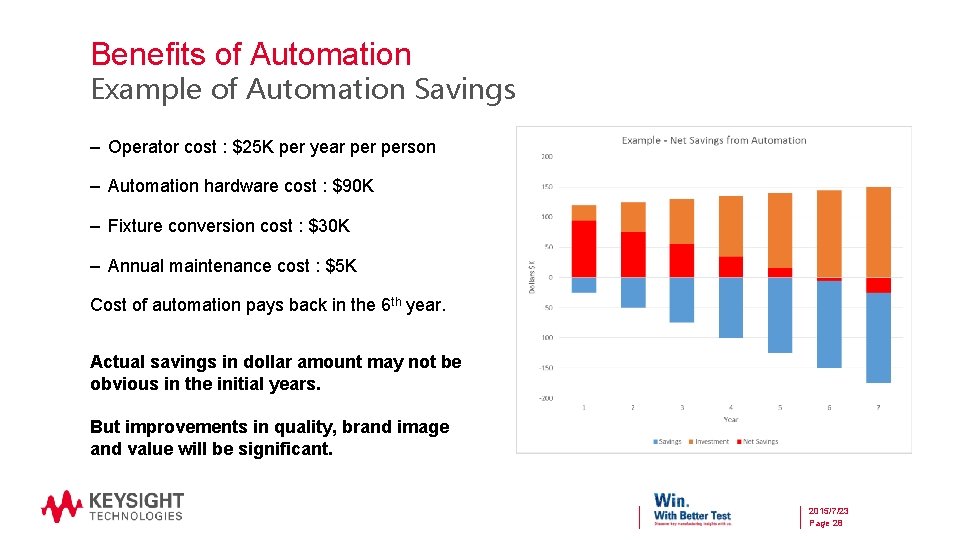
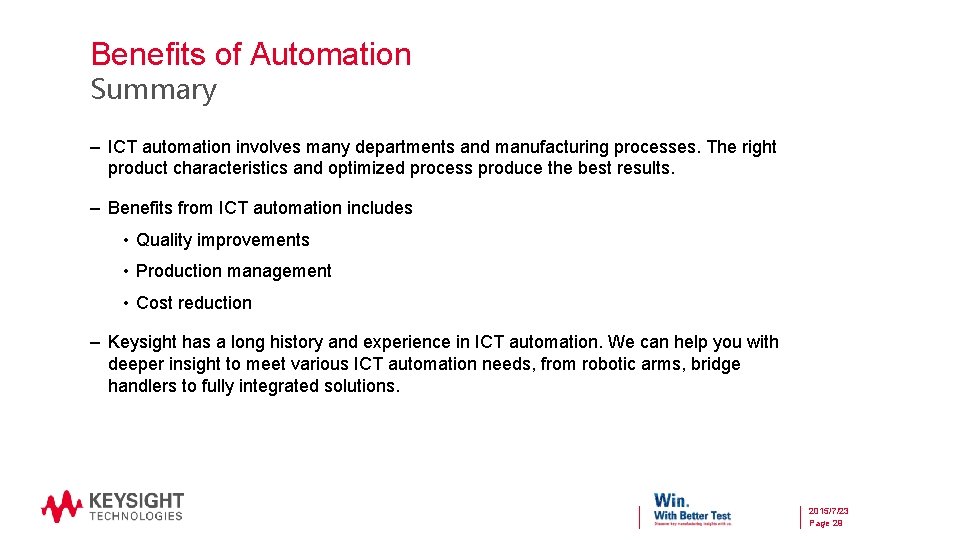
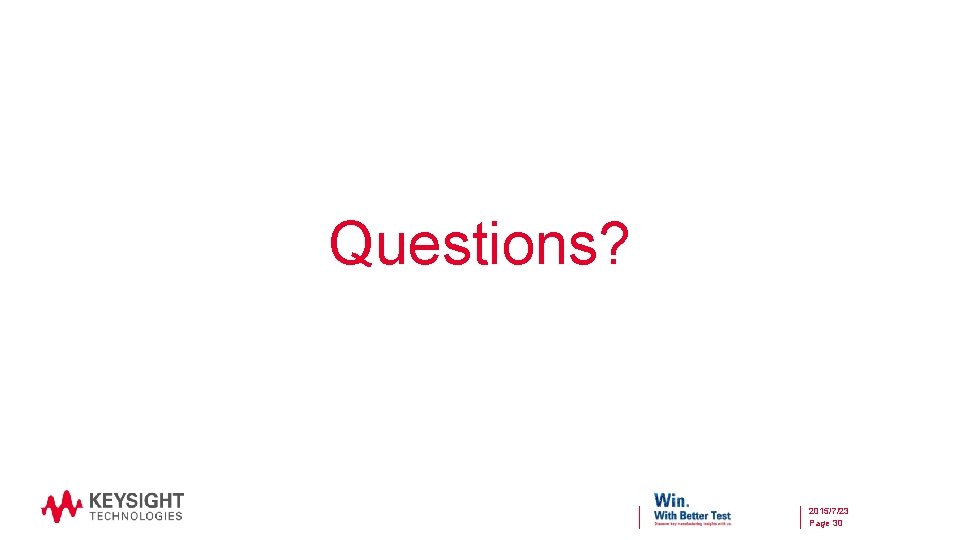
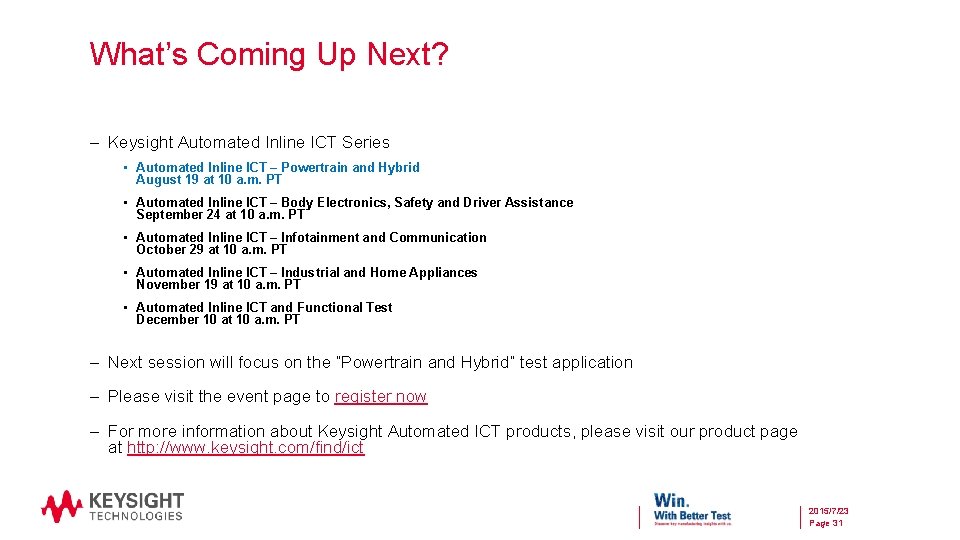
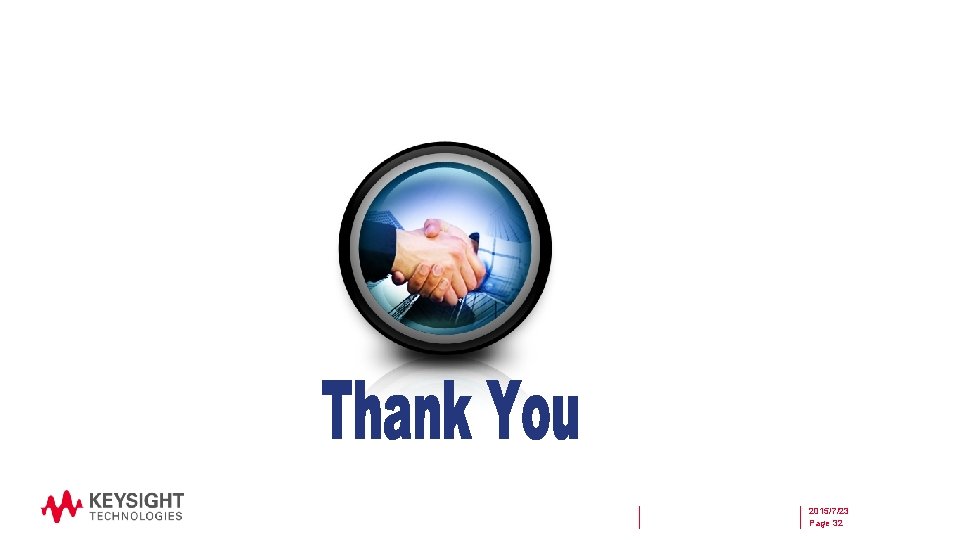
- Slides: 32
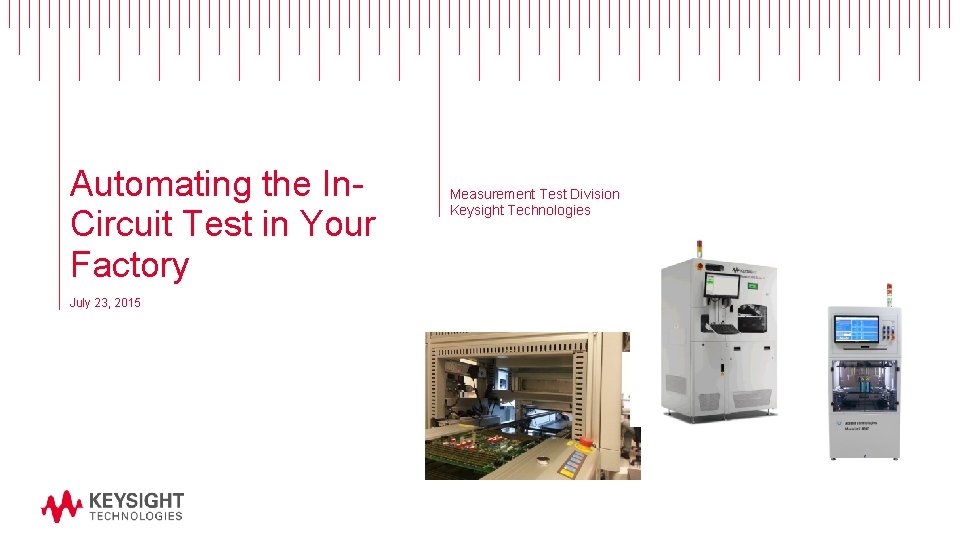
Automating the In. Circuit Test in Your Factory July 23, 2015 Measurement Test Division Keysight Technologies
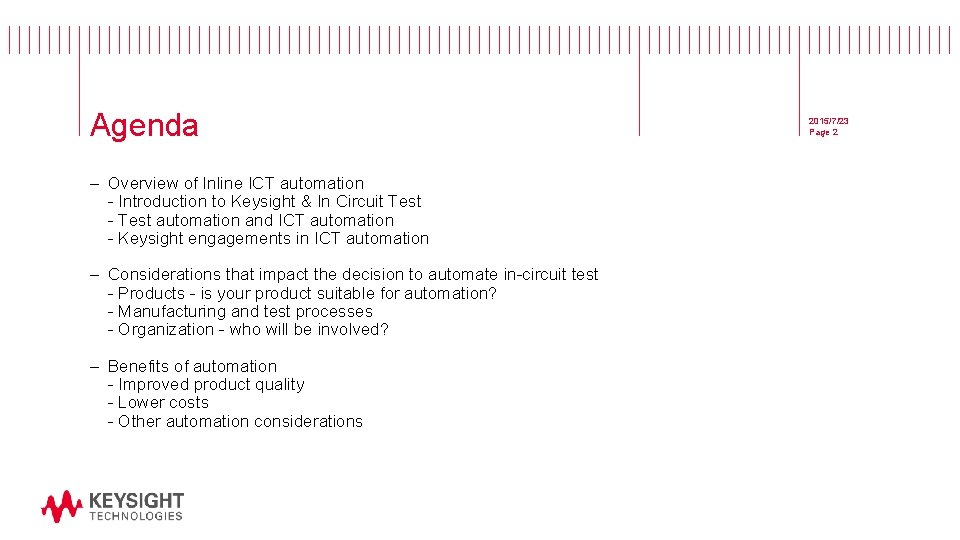
Agenda – Overview of Inline ICT automation - Introduction to Keysight & In Circuit Test - Test automation and ICT automation - Keysight engagements in ICT automation – Considerations that impact the decision to automate in-circuit test - Products - is your product suitable for automation? - Manufacturing and test processes - Organization - who will be involved? – Benefits of automation - Improved product quality - Lower costs - Other automation considerations 2015/7/23 Page 2

A Brief History of Keysight 1939– 1998: Hewlett-Packard years A company founded on electronic measurement innovation 1999– 2013: Agilent Technologies years Spun off from HP, Agilent became the World’s Premier Measurement Company. In September 2013, it announced the spinoff of its electronic measurement business 2014: Keysight begins operations November 1, Keysight is an independent company focused 100% on the electronic measurement industry We believe in “Firsts” Bill Hewlett and Dave Packard’s original vision launched Silicon Valley and shaped our passion for “firsts” 75 years ago. Today we are committed to provide a new generation of “firsts” – software-oriented solutions – that create value for our investors and valued insights for our customers. 2015/7/23 Page 3
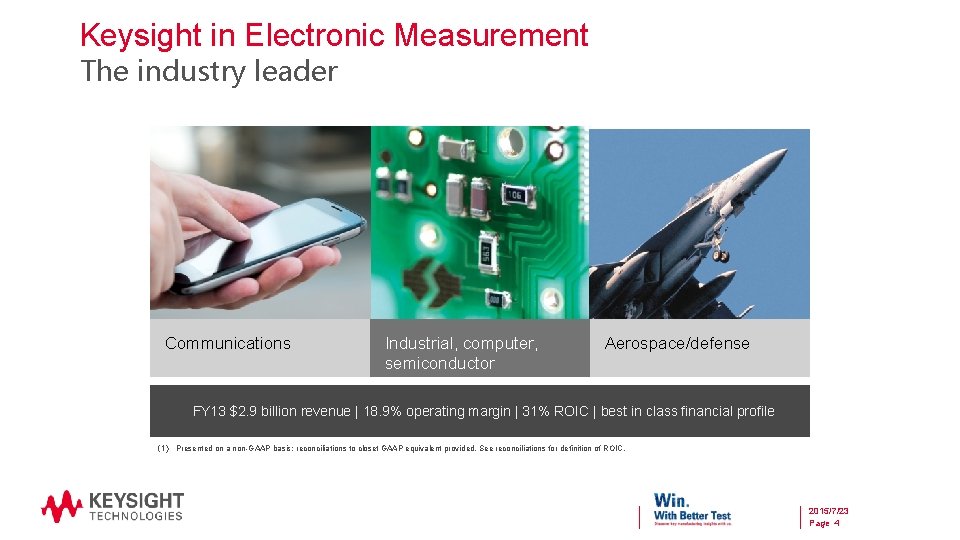
Keysight in Electronic Measurement The industry leader Communications Industrial, computer, semiconductor Aerospace/defense FY 13 $2. 9 billion revenue | 18. 9% operating margin | 31% ROIC | best in class financial profile (1) Presented on a non-GAAP basis; reconciliations to closet GAAP equivalent provided. See reconciliations for definition of ROIC. 2015/7/23 Page 4
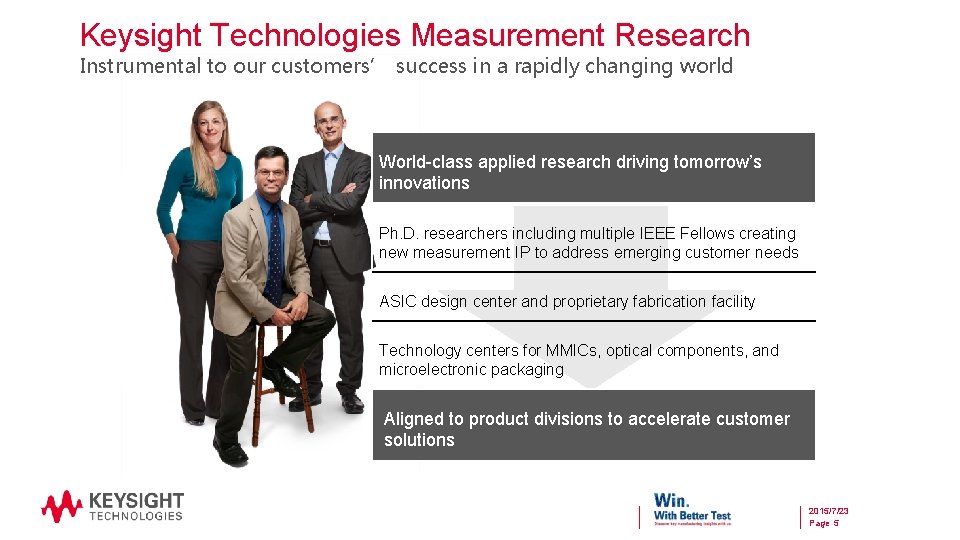
Keysight Technologies Measurement Research Instrumental to our customers’ success in a rapidly changing world World-class applied research driving tomorrow’s innovations Ph. D. researchers including multiple IEEE Fellows creating new measurement IP to address emerging customer needs ASIC design center and proprietary fabrication facility Technology centers for MMICs, optical components, and microelectronic packaging Aligned to product divisions to accelerate customer solutions 2015/7/23 Page 5
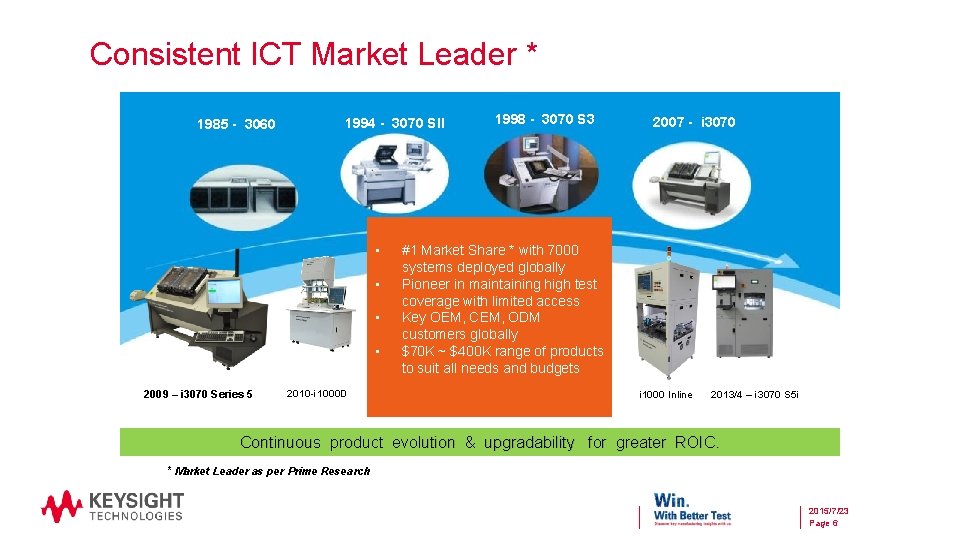
Consistent ICT Market Leader * 1985 - 3060 1994 - 3070 SII • • 2009 – i 3070 Series 5 2010 -i 1000 D 1998 - 3070 S 3 2007 - i 3070 #1 Market Share * with 7000 systems deployed globally Pioneer in maintaining high test coverage with limited access Key OEM, CEM, ODM customers globally $70 K ~ $400 K range of products to suit all needs and budgets 2012 – i 3070 HNC 2013 – i 3070 E 9901 EL i 1000 Inline 2013/4 – i 3070 S 5 i Continuous product evolution & upgradability for greater ROIC. * Market Leader as per Prime Research 2015/7/23 Page 6
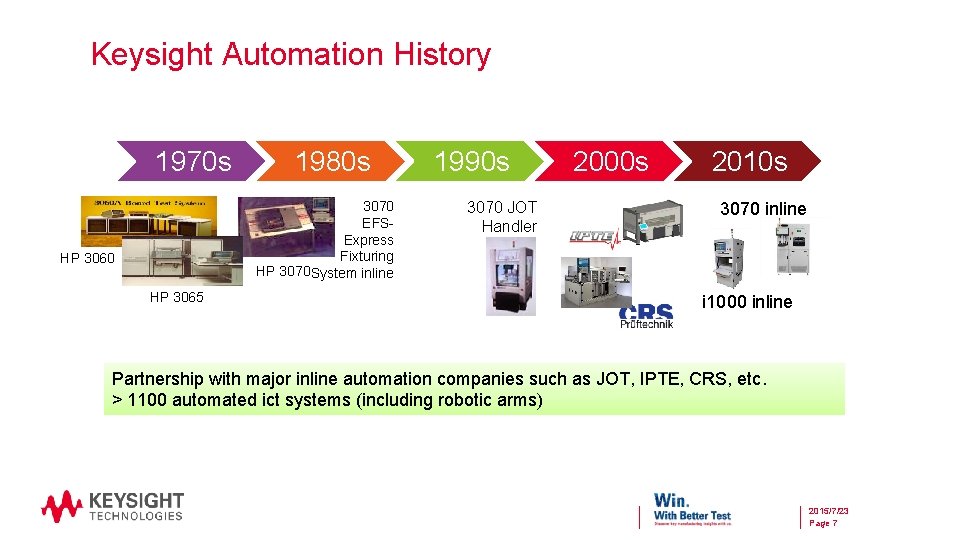
Keysight Automation History 1970 s 1980 s 3070 EFSExpress Fixturing HP 3070 System inline HP 3060 HP 3065 1990 s 3070 JOT Handler 2000 s 2010 s 3070 inline i 1000 inline Partnership with major inline automation companies such as JOT, IPTE, CRS, etc. > 1100 automated ict systems (including robotic arms) 2015/7/23 Page 7
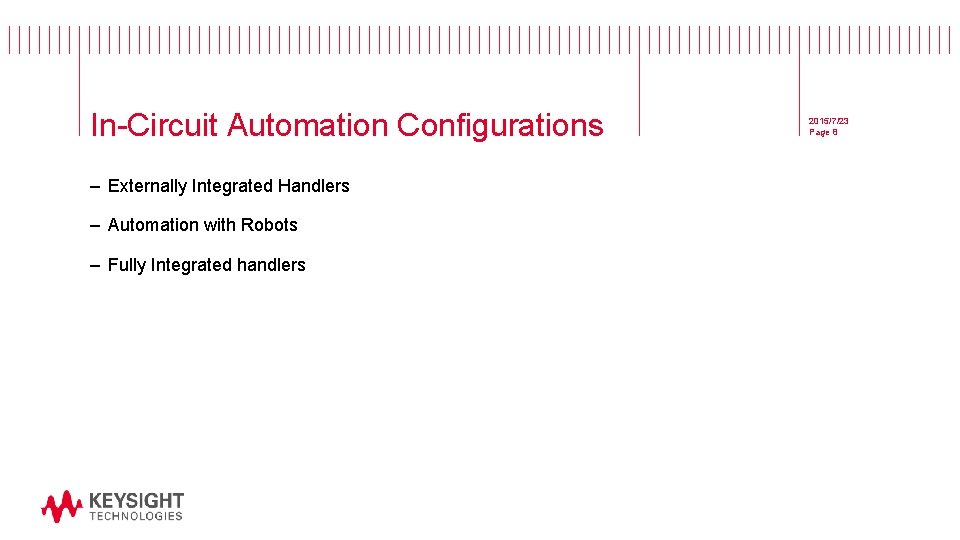
In-Circuit Automation Configurations – Externally Integrated Handlers – Automation with Robots – Fully Integrated handlers 2015/7/23 Page 8
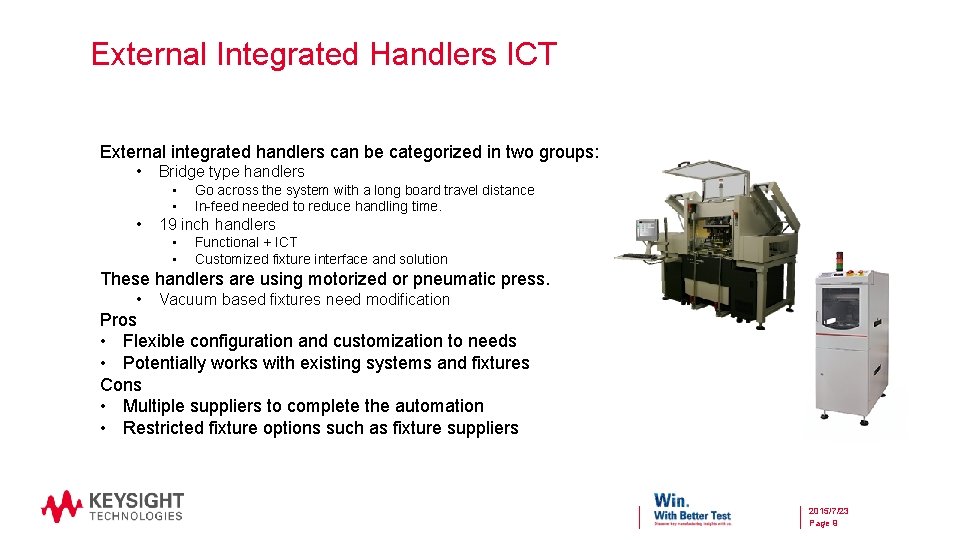
External Integrated Handlers ICT External integrated handlers can be categorized in two groups: • Bridge type handlers • • • Go across the system with a long board travel distance In-feed needed to reduce handling time. 19 inch handlers • • Functional + ICT Customized fixture interface and solution These handlers are using motorized or pneumatic press. • Vacuum based fixtures need modification Pros • Flexible configuration and customization to needs • Potentially works with existing systems and fixtures Cons • Multiple suppliers to complete the automation • Restricted fixture options such as fixture suppliers 2015/7/23 Page 9
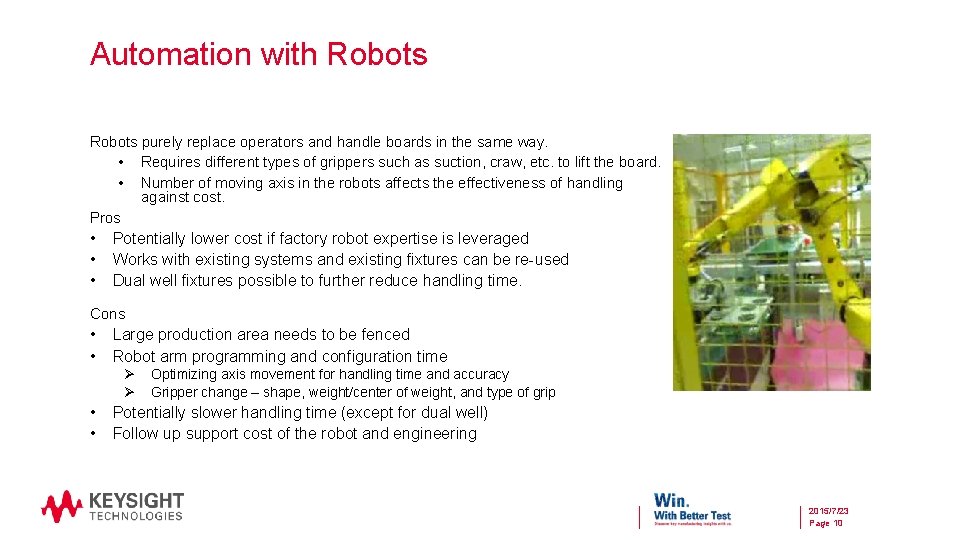
Automation with Robots purely replace operators and handle boards in the same way. • Requires different types of grippers such as suction, craw, etc. to lift the board. • Number of moving axis in the robots affects the effectiveness of handling against cost. Pros • • • Potentially lower cost if factory robot expertise is leveraged Works with existing systems and existing fixtures can be re-used Dual well fixtures possible to further reduce handling time. Cons • • Large production area needs to be fenced Robot arm programming and configuration time Ø Ø • • Optimizing axis movement for handling time and accuracy Gripper change – shape, weight/center of weight, and type of grip Potentially slower handling time (except for dual well) Follow up support cost of the robot and engineering 2015/7/23 Page 10
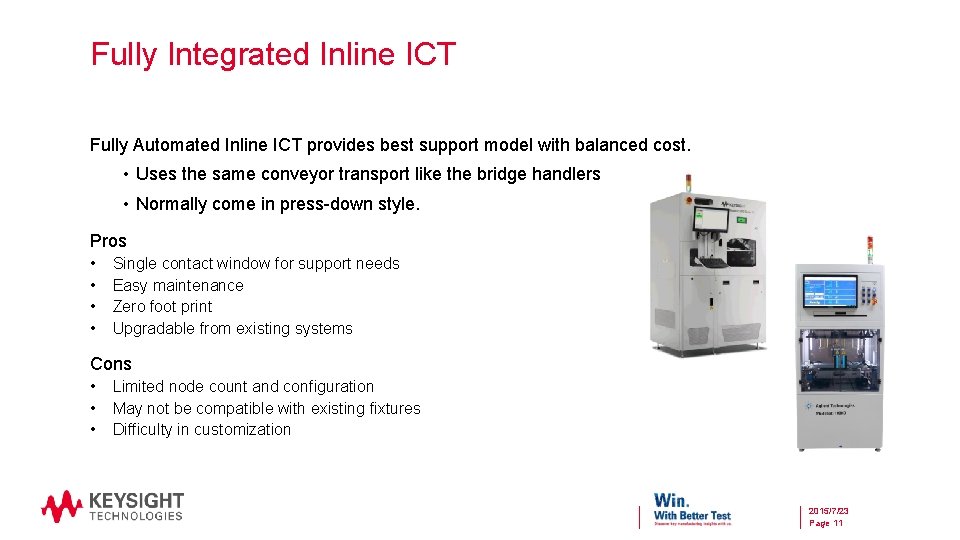
Fully Integrated Inline ICT Fully Automated Inline ICT provides best support model with balanced cost. • Uses the same conveyor transport like the bridge handlers • Normally come in press-down style. Pros • • Single contact window for support needs Easy maintenance Zero foot print Upgradable from existing systems Cons • • • Limited node count and configuration May not be compatible with existing fixtures Difficulty in customization 2015/7/23 Page 11
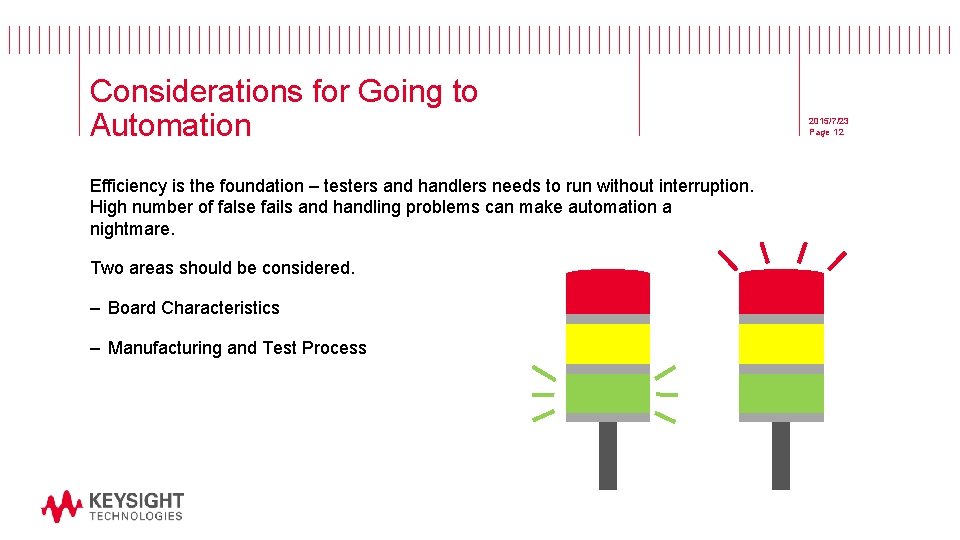
Considerations for Going to Automation Efficiency is the foundation – testers and handlers needs to run without interruption. High number of false fails and handling problems can make automation a nightmare. Two areas should be considered. – Board Characteristics – Manufacturing and Test Process 2015/7/23 Page 12
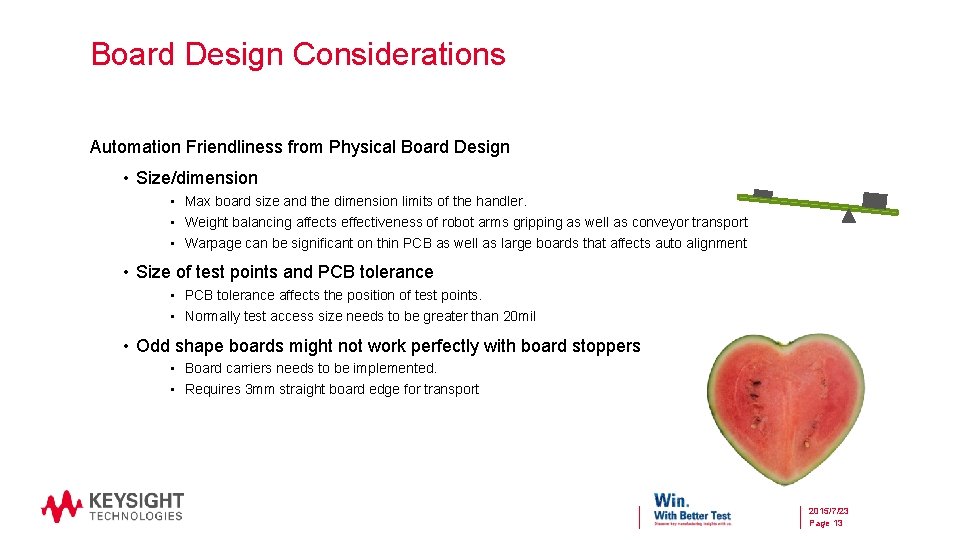
Board Design Considerations Automation Friendliness from Physical Board Design • Size/dimension • Max board size and the dimension limits of the handler. • Weight balancing affects effectiveness of robot arms gripping as well as conveyor transport • Warpage can be significant on thin PCB as well as large boards that affects auto alignment • Size of test points and PCB tolerance • PCB tolerance affects the position of test points. • Normally test access size needs to be greater than 20 mil • Odd shape boards might not work perfectly with board stoppers • Board carriers needs to be implemented. • Requires 3 mm straight board edge for transport 2015/7/23 Page 13
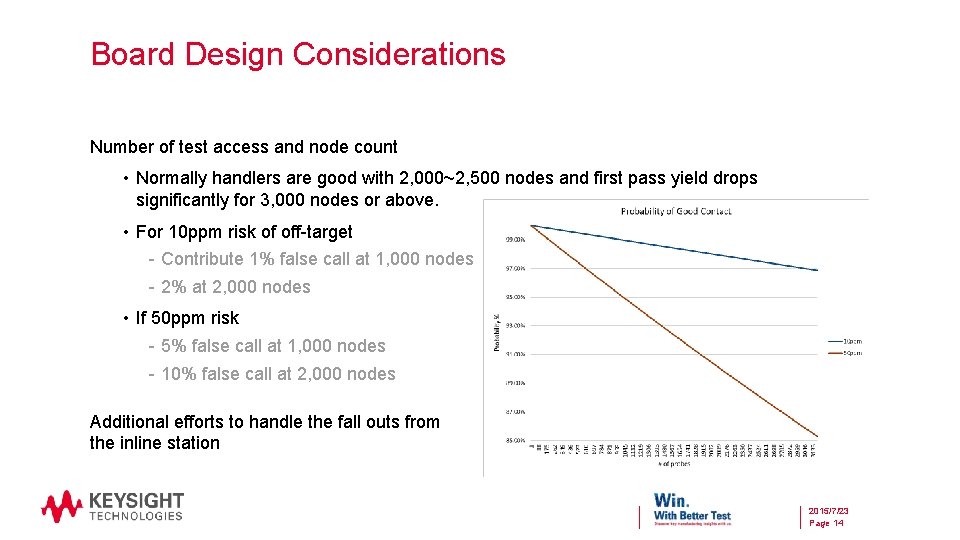
Board Design Considerations Number of test access and node count • Normally handlers are good with 2, 000~2, 500 nodes and first pass yield drops significantly for 3, 000 nodes or above. • For 10 ppm risk of off-target - Contribute 1% false call at 1, 000 nodes - 2% at 2, 000 nodes • If 50 ppm risk - 5% false call at 1, 000 nodes - 10% false call at 2, 000 nodes Additional efforts to handle the fall outs from the inline station 2015/7/23 Page 14

Board Design Considerations – Single side vs. double side • Topside and bottom side probing alignment makes testing double side boards more difficult. – Panelization • Panelized board normally increase the efficiency • Some parallel testing can be performed to further improve output. – Component height - especially tall components on both sides of the DUT. • Topside is normally not an issue – as high as 100 mm • Bottom side normally is 25 mm as IPC standard. 40 mm R C • Flow direction considerations 60 mm? 2015/7/23 Page 15
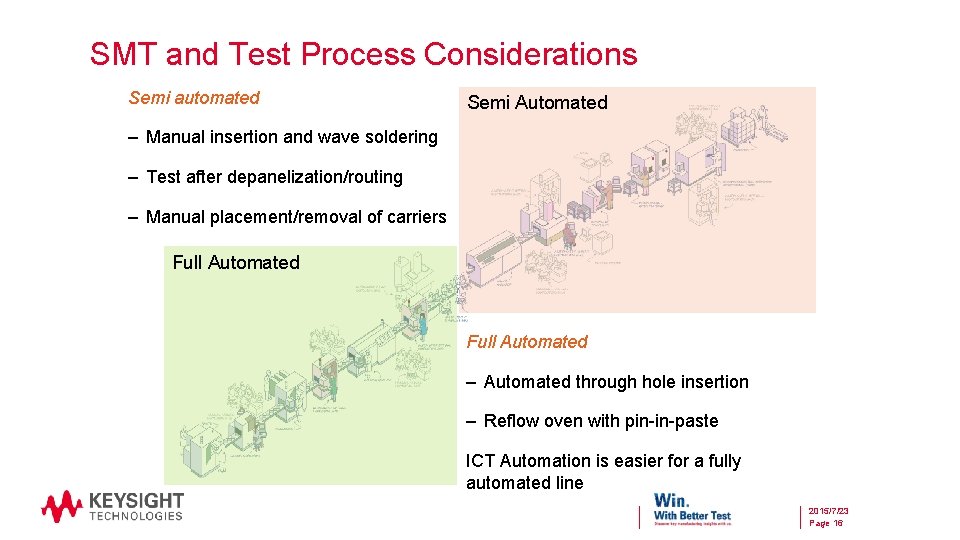
SMT and Test Process Considerations Semi automated Semi Automated – Manual insertion and wave soldering – Test after depanelization/routing – Manual placement/removal of carriers Full Automated – Automated through hole insertion – Reflow oven with pin-in-paste ICT Automation is easier for a fully automated line 2015/7/23 Page 16
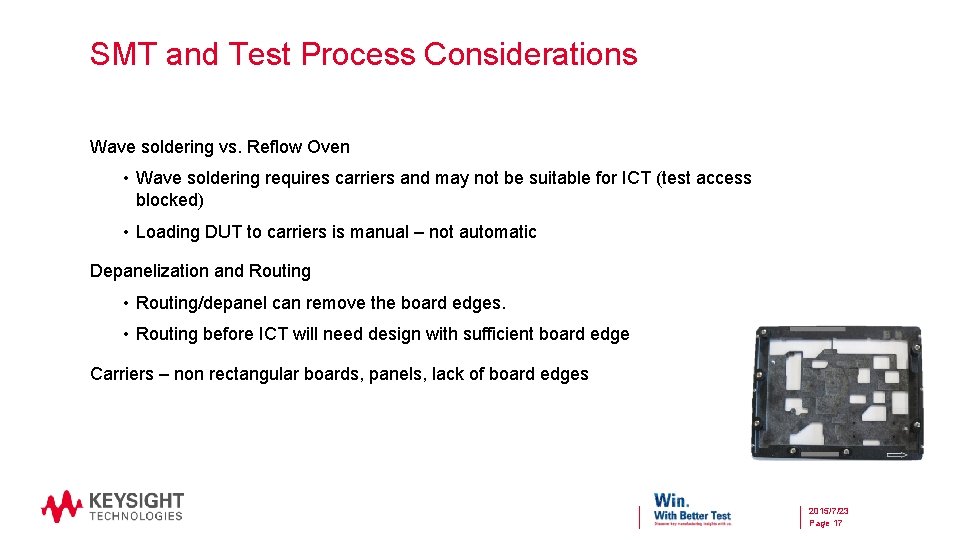
SMT and Test Process Considerations Wave soldering vs. Reflow Oven • Wave soldering requires carriers and may not be suitable for ICT (test access blocked) • Loading DUT to carriers is manual – not automatic Depanelization and Routing • Routing/depanel can remove the board edges. • Routing before ICT will need design with sufficient board edge Carriers – non rectangular boards, panels, lack of board edges 2015/7/23 Page 17
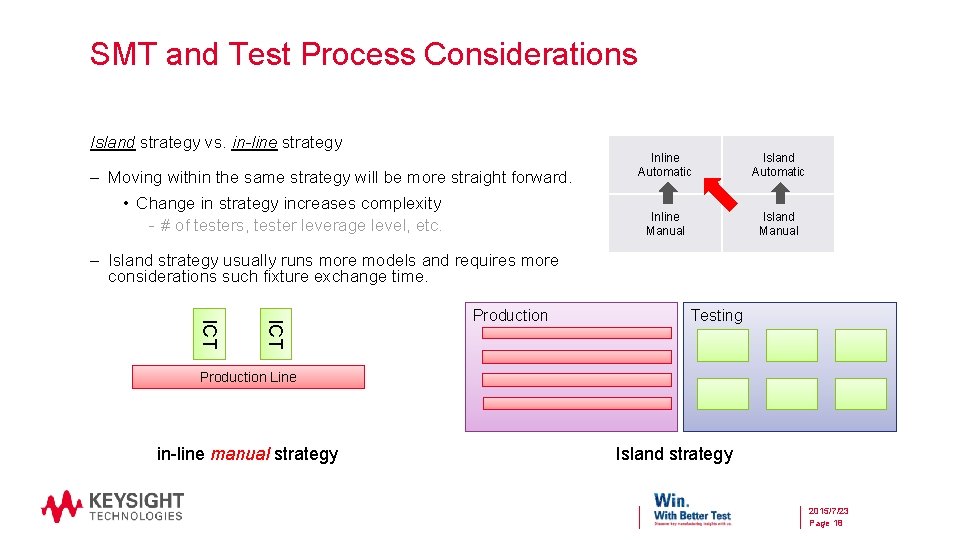
SMT and Test Process Considerations Island strategy vs. in-line strategy – Moving within the same strategy will be more straight forward. • Change in strategy increases complexity - # of testers, tester leverage level, etc. Inline Automatic Island Automatic Inline Manual Island Manual – Island strategy usually runs more models and requires more considerations such fixture exchange time. ICT Production Testing Production Line in-line manual strategy Island strategy 2015/7/23 Page 18
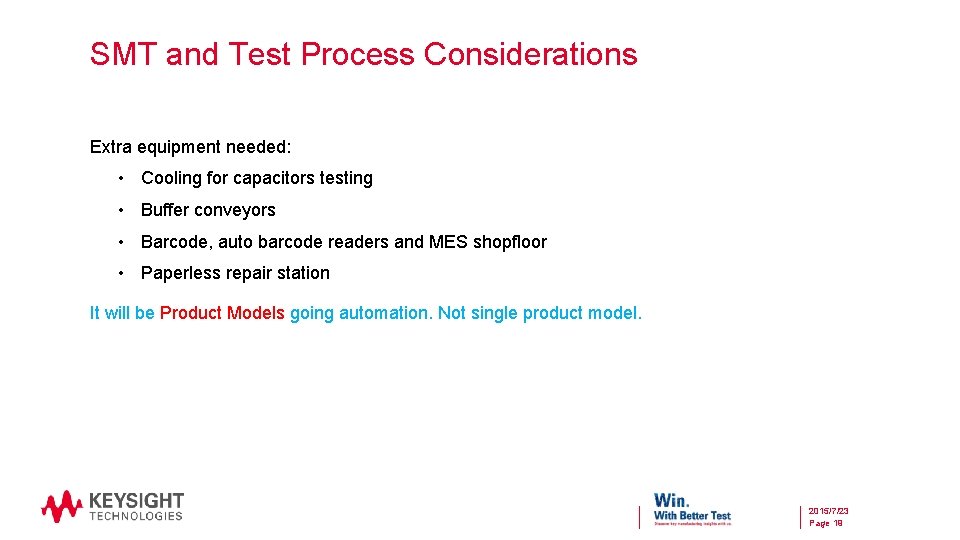
SMT and Test Process Considerations Extra equipment needed: • Cooling for capacitors testing • Buffer conveyors • Barcode, auto barcode readers and MES shopfloor • Paperless repair station It will be Product Models going automation. Not single product model. 2015/7/23 Page 19
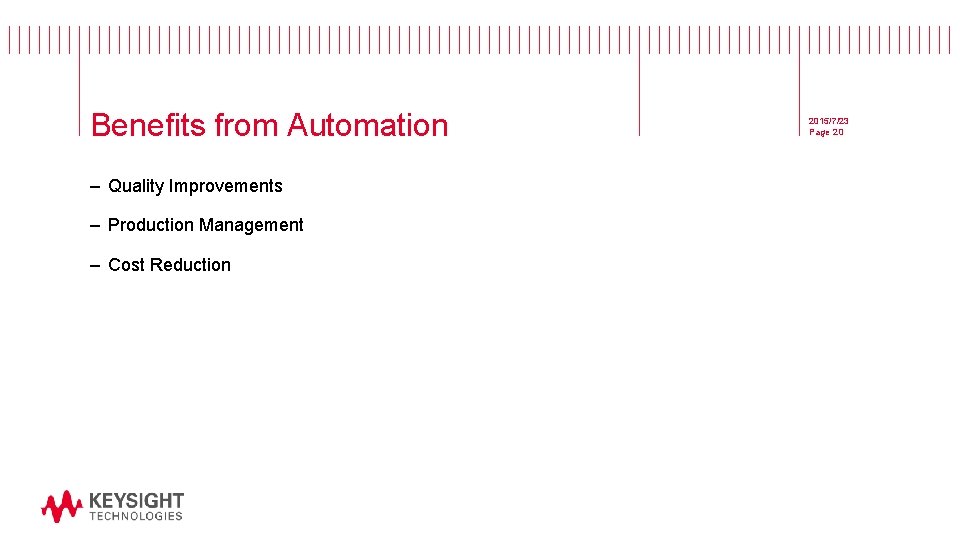
Benefits from Automation – Quality Improvements – Production Management – Cost Reduction 2015/7/23 Page 20
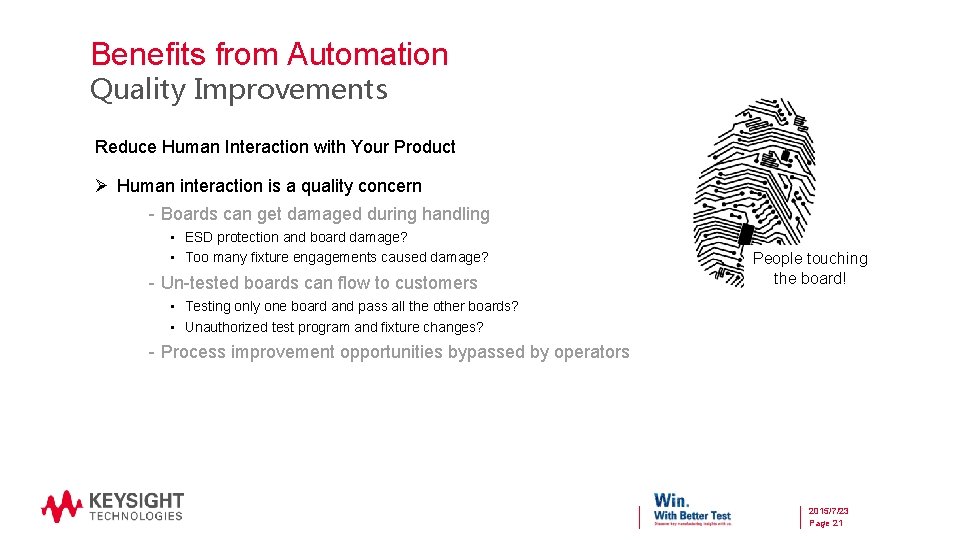
Benefits from Automation Quality Improvements Reduce Human Interaction with Your Product Ø Human interaction is a quality concern - Boards can get damaged during handling • ESD protection and board damage? • Too many fixture engagements caused damage? - Un-tested boards can flow to customers People touching the board! • Testing only one board and pass all the other boards? • Unauthorized test program and fixture changes? - Process improvement opportunities bypassed by operators 2015/7/23 Page 21
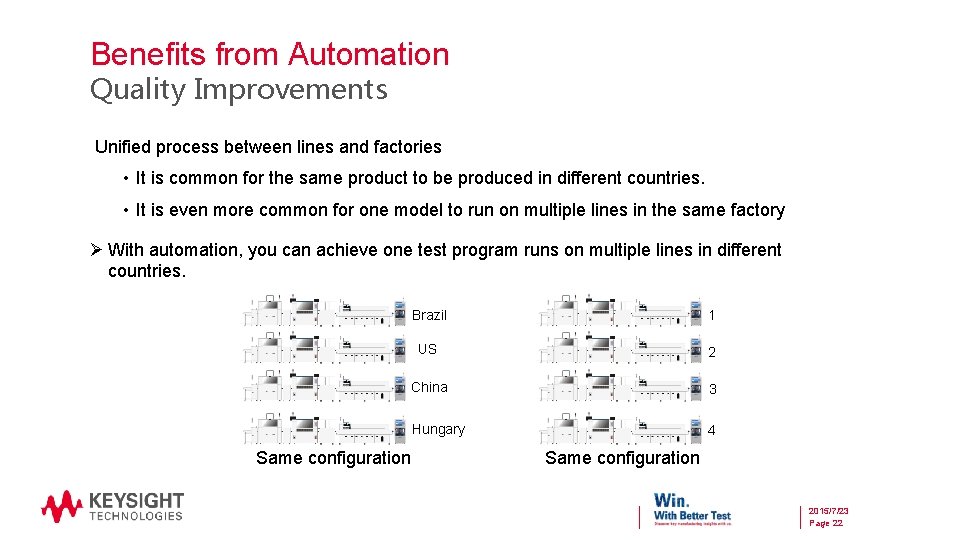
Benefits from Automation Quality Improvements Unified process between lines and factories • It is common for the same product to be produced in different countries. • It is even more common for one model to run on multiple lines in the same factory Ø With automation, you can achieve one test program runs on multiple lines in different countries. Same configuration Brazil 1 US 2 China 3 Hungary 4 Same configuration 2015/7/23 Page 22
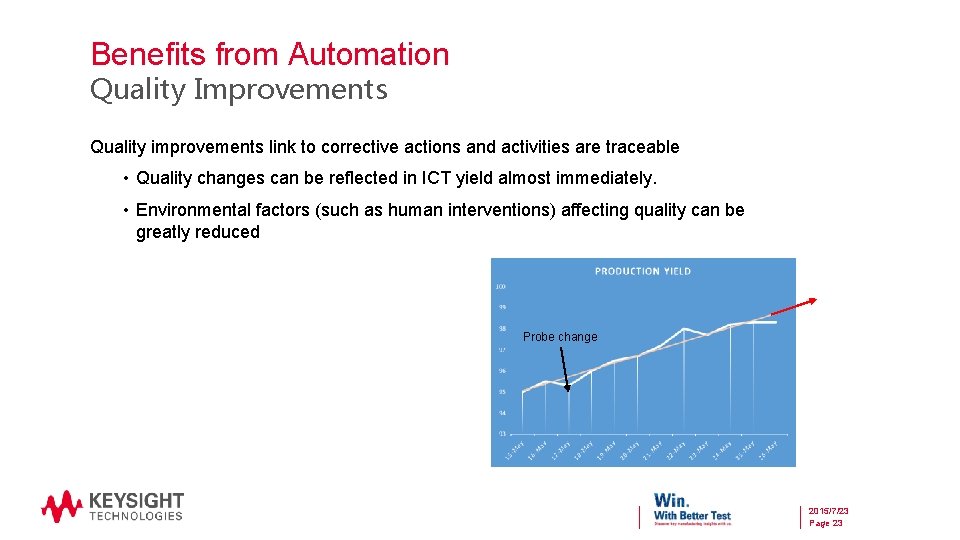
Benefits from Automation Quality Improvements Quality improvements link to corrective actions and activities are traceable • Quality changes can be reflected in ICT yield almost immediately. • Environmental factors (such as human interventions) affecting quality can be greatly reduced Probe change 2015/7/23 Page 23

Benefits from Automation Production Management • Output Volume – stable and predictable shipments - No more baskets of un-tested boards Two shifts • Remove labor variations – cost and experience - Temporary operators, shift changes • More output per line – better efficiency 2015/7/23 Page 24
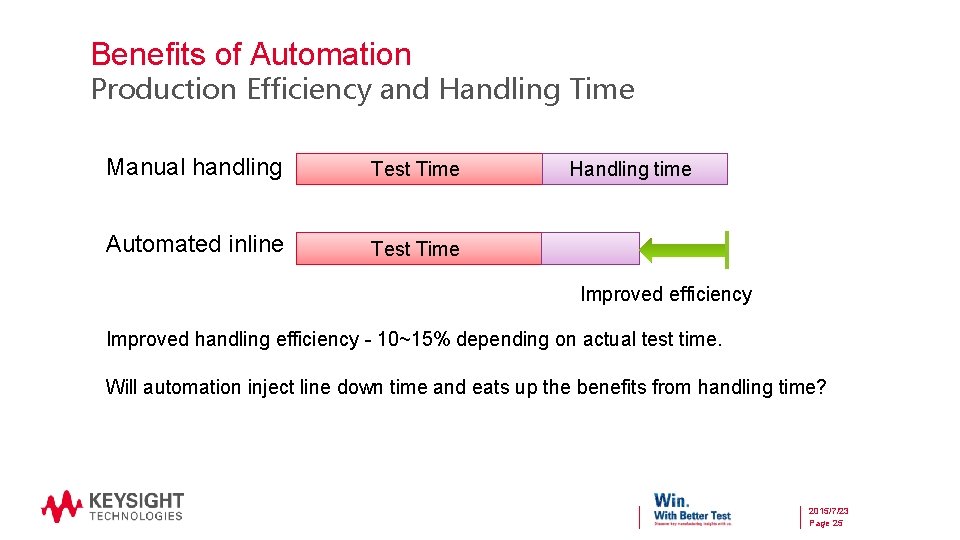
Benefits of Automation Production Efficiency and Handling Time Manual handling Test Time Automated inline Test Time Handling time Improved efficiency Improved handling efficiency - 10~15% depending on actual test time. Will automation inject line down time and eats up the benefits from handling time? 2015/7/23 Page 25
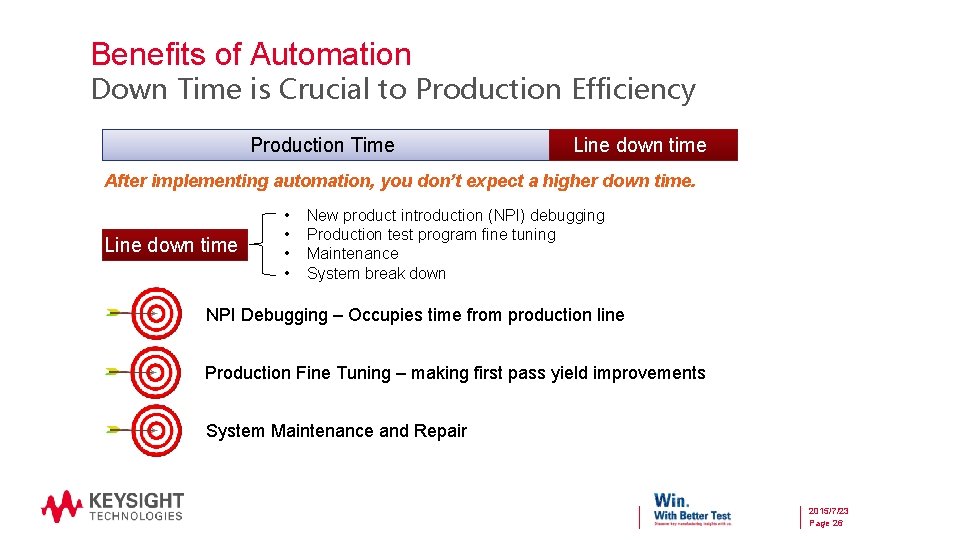
Benefits of Automation Down Time is Crucial to Production Efficiency Production Time Line down time After implementing automation, you don’t expect a higher down time. Line down time • • New product introduction (NPI) debugging Production test program fine tuning Maintenance System break down NPI Debugging – Occupies time from production line Production Fine Tuning – making first pass yield improvements System Maintenance and Repair 2015/7/23 Page 26
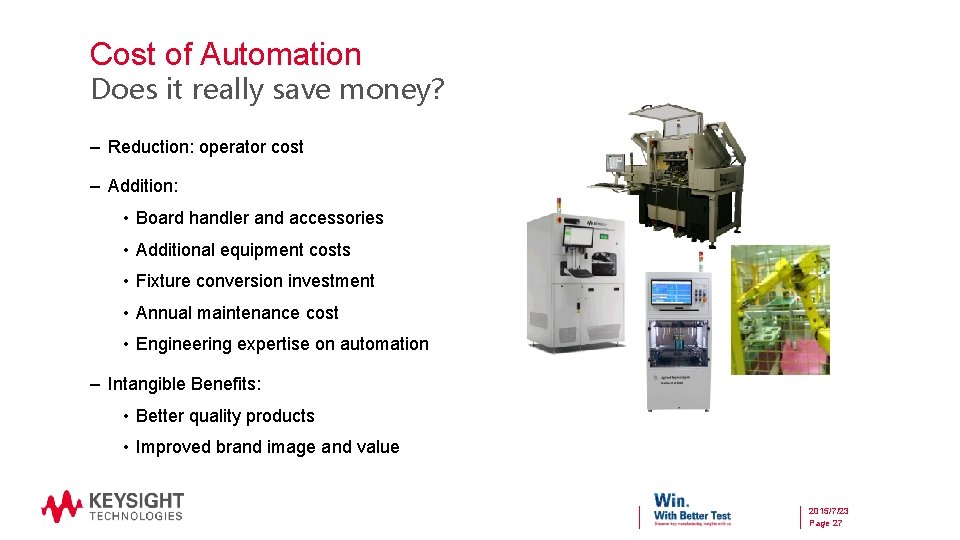
Cost of Automation Does it really save money? – Reduction: operator cost – Addition: • Board handler and accessories • Additional equipment costs • Fixture conversion investment • Annual maintenance cost • Engineering expertise on automation – Intangible Benefits: • Better quality products • Improved brand image and value 2015/7/23 Page 27
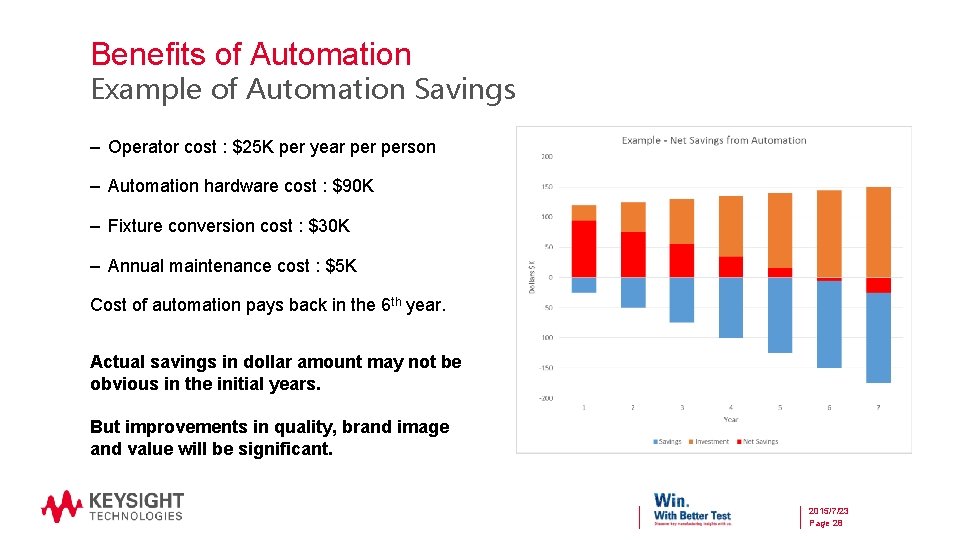
Benefits of Automation Example of Automation Savings – Operator cost : $25 K per year person – Automation hardware cost : $90 K – Fixture conversion cost : $30 K – Annual maintenance cost : $5 K Cost of automation pays back in the 6 th year. Actual savings in dollar amount may not be obvious in the initial years. But improvements in quality, brand image and value will be significant. 2015/7/23 Page 28
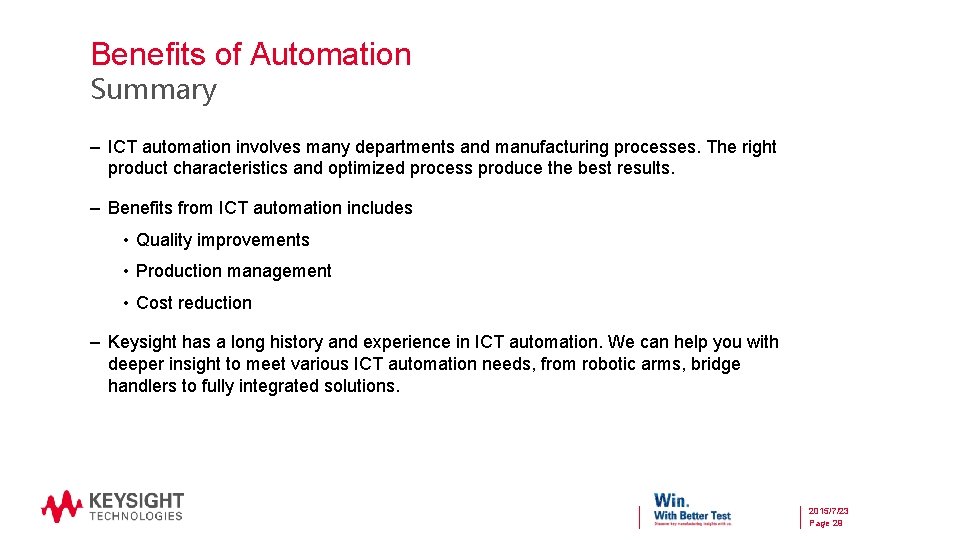
Benefits of Automation Summary – ICT automation involves many departments and manufacturing processes. The right product characteristics and optimized process produce the best results. – Benefits from ICT automation includes • Quality improvements • Production management • Cost reduction – Keysight has a long history and experience in ICT automation. We can help you with deeper insight to meet various ICT automation needs, from robotic arms, bridge handlers to fully integrated solutions. 2015/7/23 Page 29
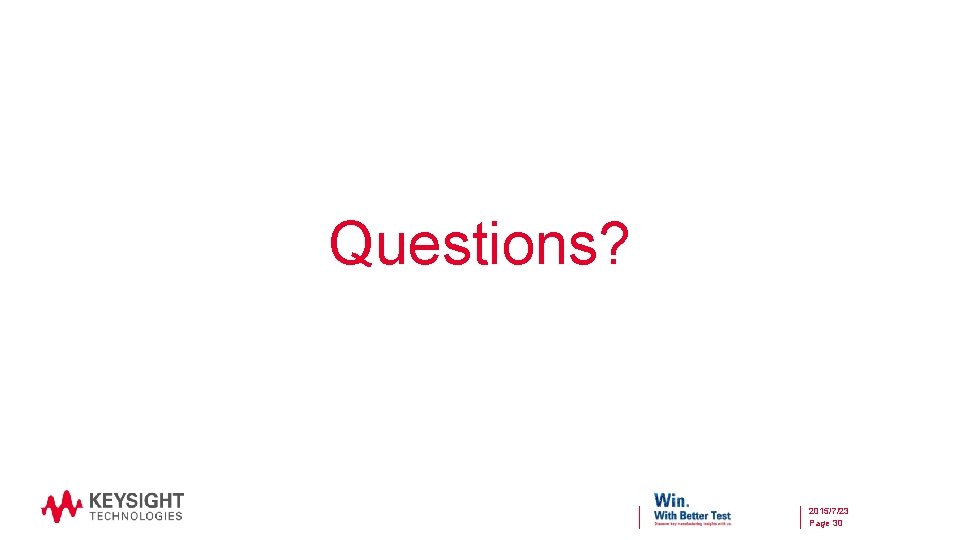
Questions? 2015/7/23 Page 30
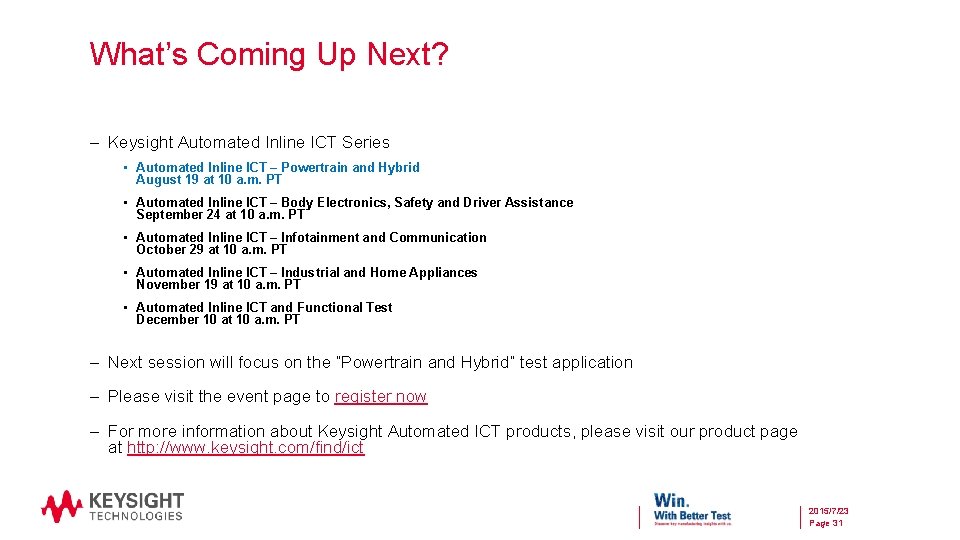
What’s Coming Up Next? – Keysight Automated Inline ICT Series • Automated Inline ICT – Powertrain and Hybrid August 19 at 10 a. m. PT • Automated Inline ICT – Body Electronics, Safety and Driver Assistance September 24 at 10 a. m. PT • Automated Inline ICT – Infotainment and Communication October 29 at 10 a. m. PT • Automated Inline ICT – Industrial and Home Appliances November 19 at 10 a. m. PT • Automated Inline ICT and Functional Test December 10 at 10 a. m. PT – Next session will focus on the “Powertrain and Hybrid” test application – Please visit the event page to register now – For more information about Keysight Automated ICT products, please visit our product page at http: //www. keysight. com/find/ict 2015/7/23 Page 31
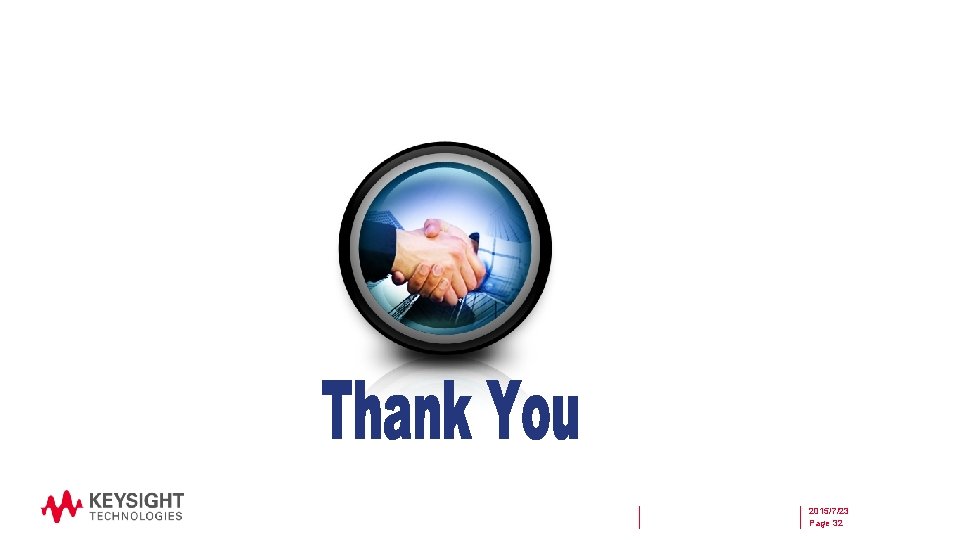
2015/7/23 Page 32
Java factory factory joke
How to automate desktop application using java
Desktop automation python
Python windows automation
Rl circuit charging
Give us your hungry your tired your poor
Parallel vs series circuit
Types of circuit
Parallel circuit circuit construction kit
Parallel vs series
Complete and incomplete circuits with inference
Voltage in series and parallel
Venn diagram of series and parallel circuit
Pulmonary circuit and systemic circuit
What is a parallel circuit in physics
Hình ảnh bộ gõ cơ thể búng tay
Slidetodoc
Bổ thể
Tỉ lệ cơ thể trẻ em
Voi kéo gỗ như thế nào
Tư thế worm breton là gì
Alleluia hat len nguoi oi
Các môn thể thao bắt đầu bằng tiếng đua
Thế nào là hệ số cao nhất
Các châu lục và đại dương trên thế giới
Công của trọng lực
Trời xanh đây là của chúng ta thể thơ
Mật thư tọa độ 5x5
Phép trừ bù
độ dài liên kết
Các châu lục và đại dương trên thế giới
Thơ thất ngôn tứ tuyệt đường luật
Quá trình desamine hóa có thể tạo ra