WORK STUDY SOME DEFINITIONS Work Study is the
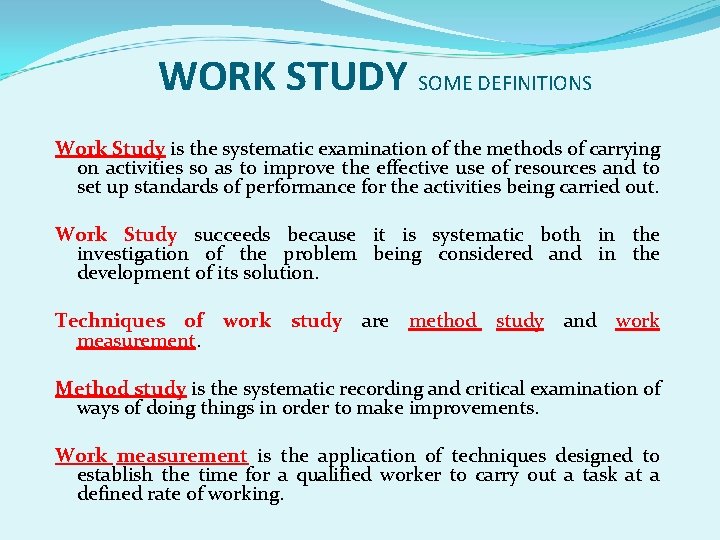
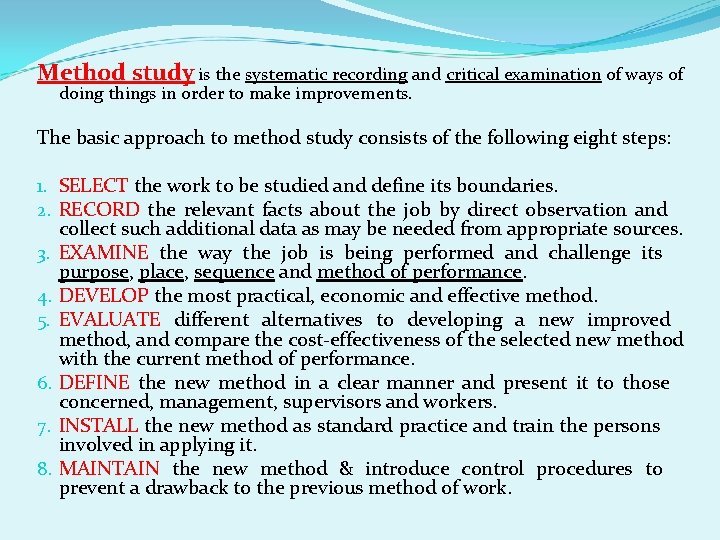
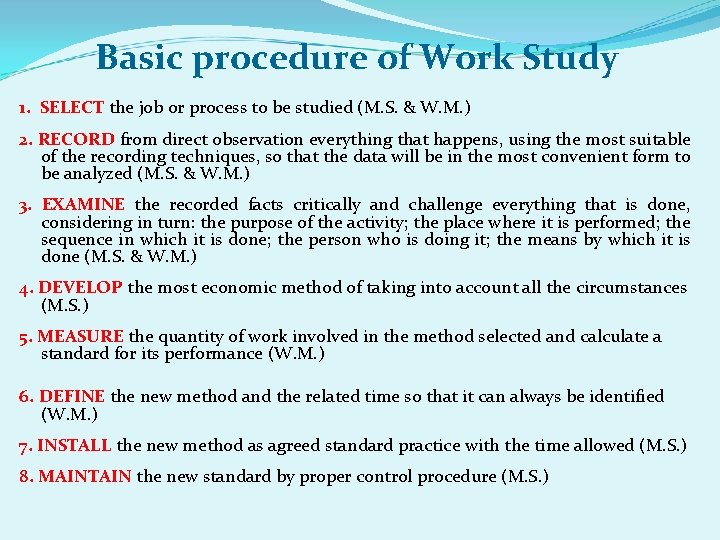
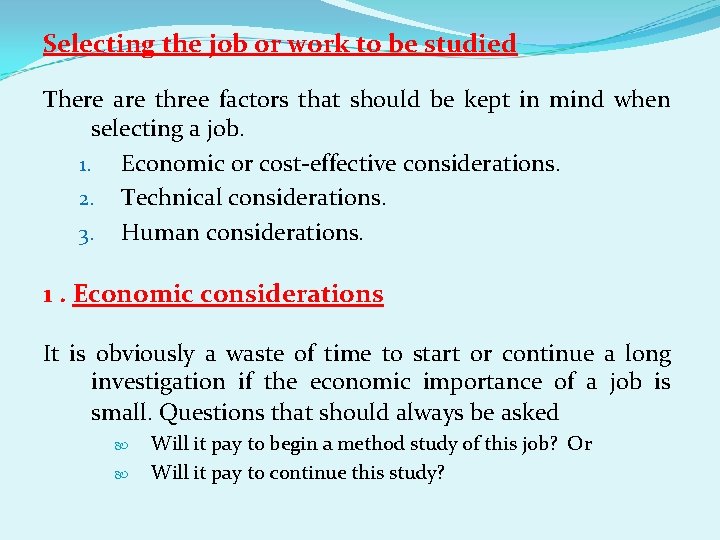
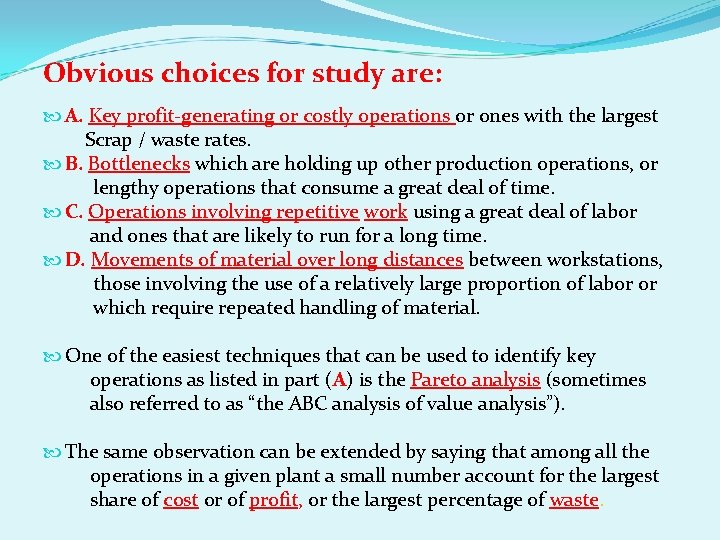
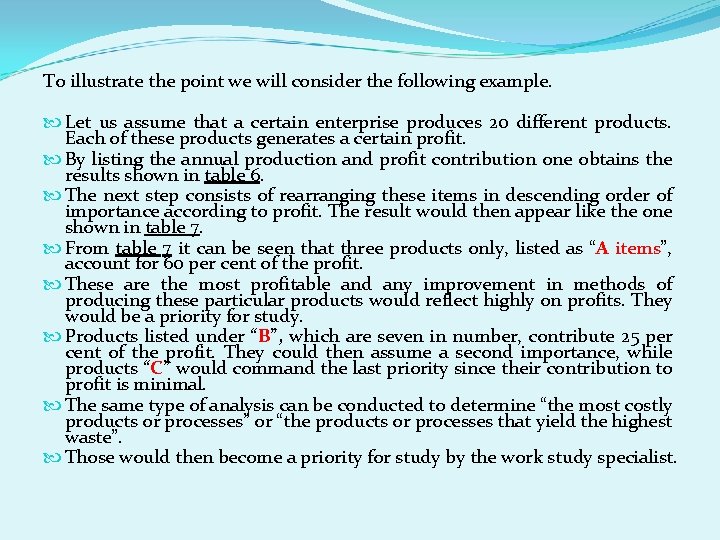
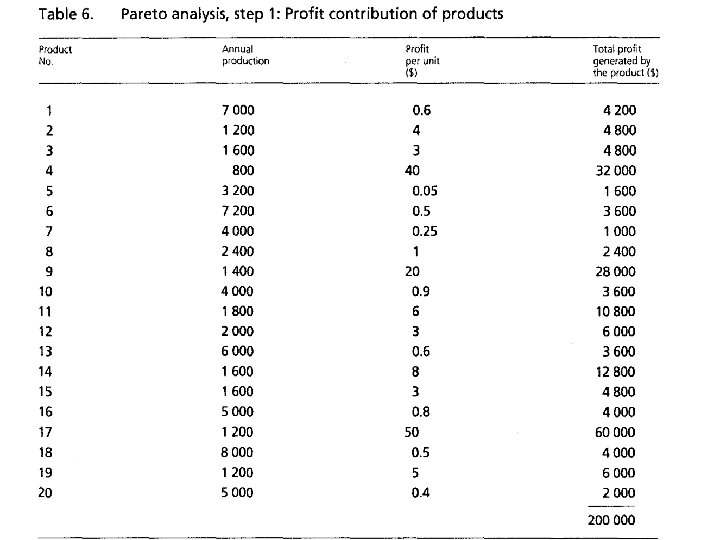
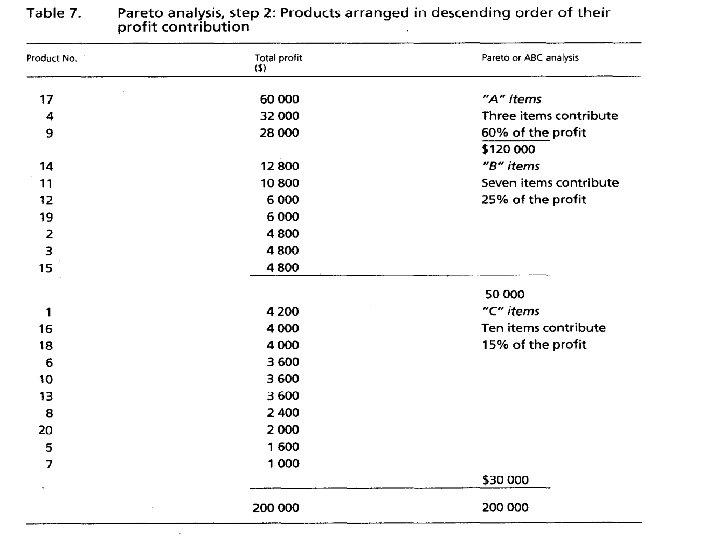
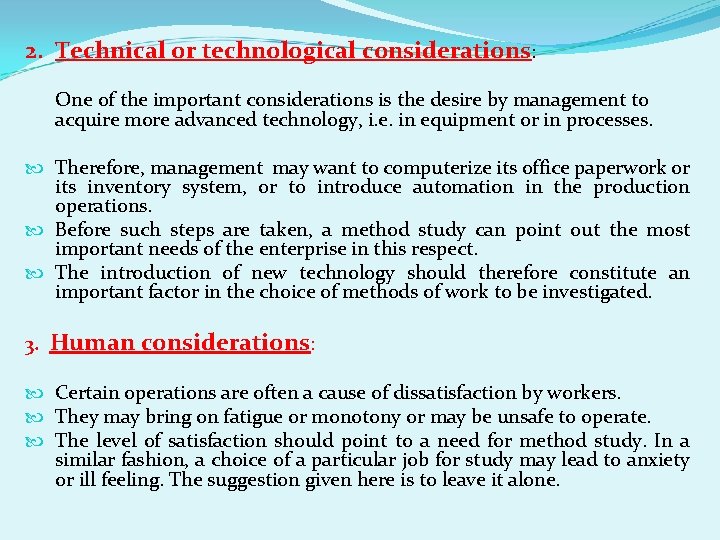
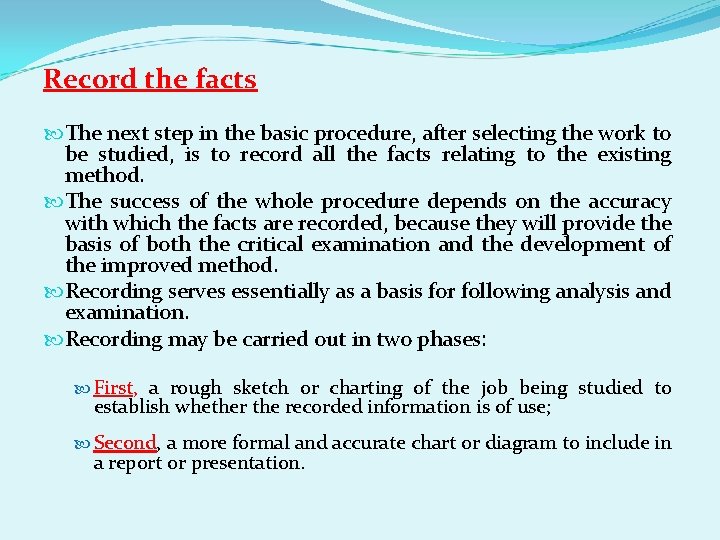
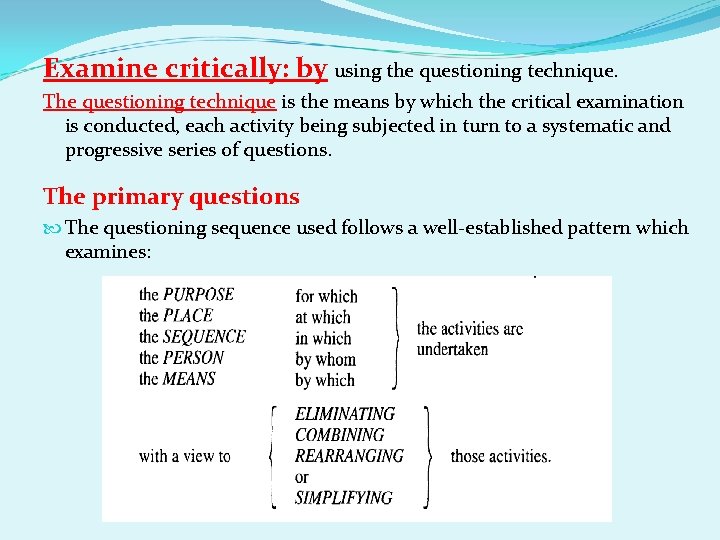
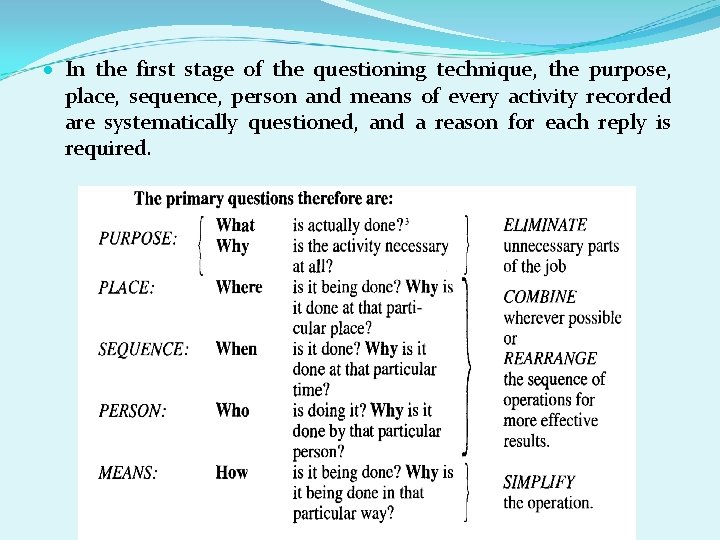
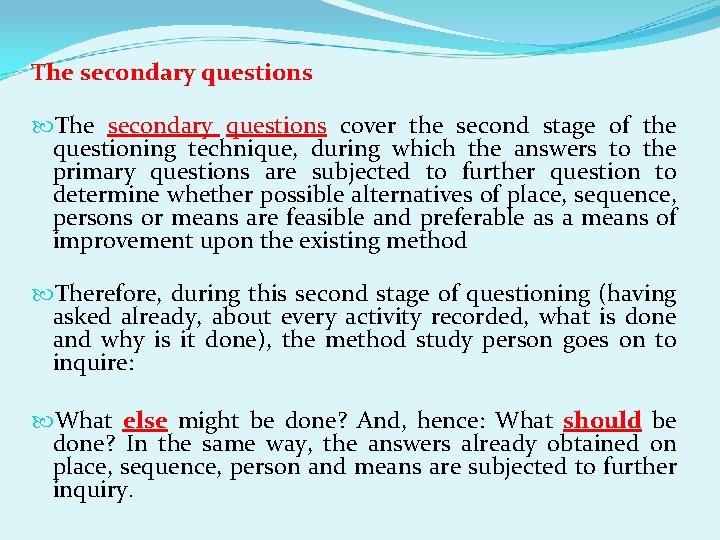
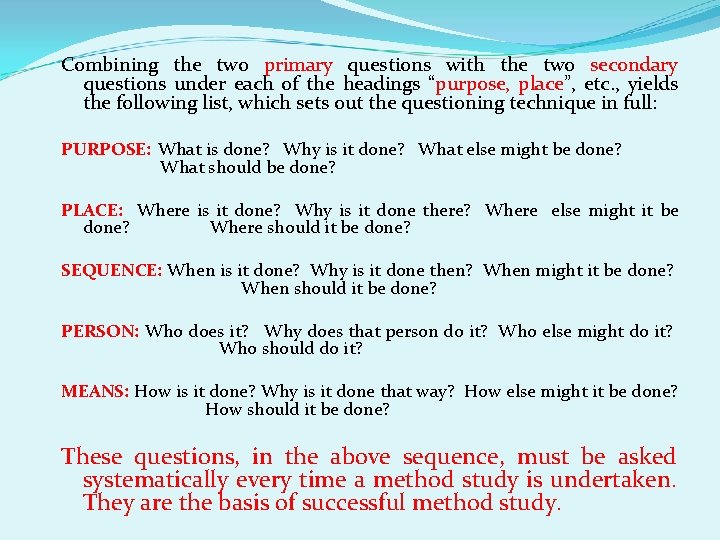
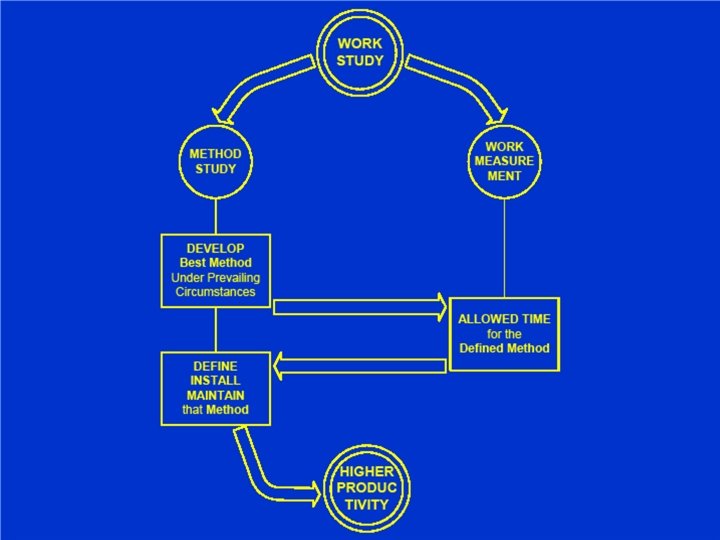
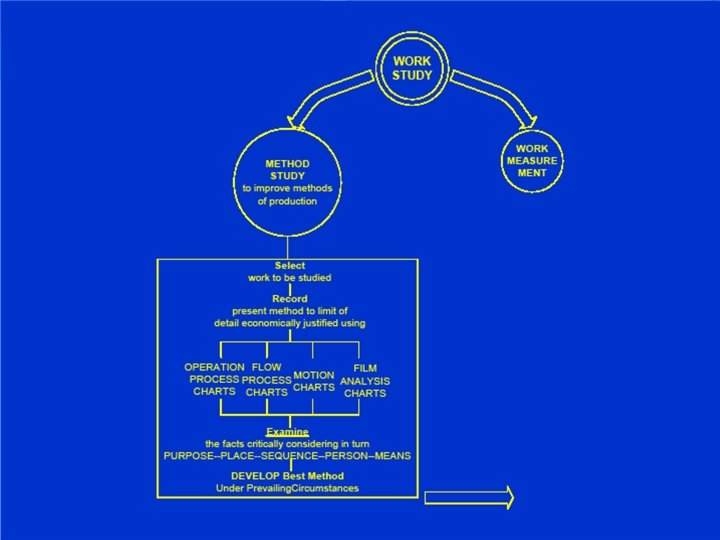
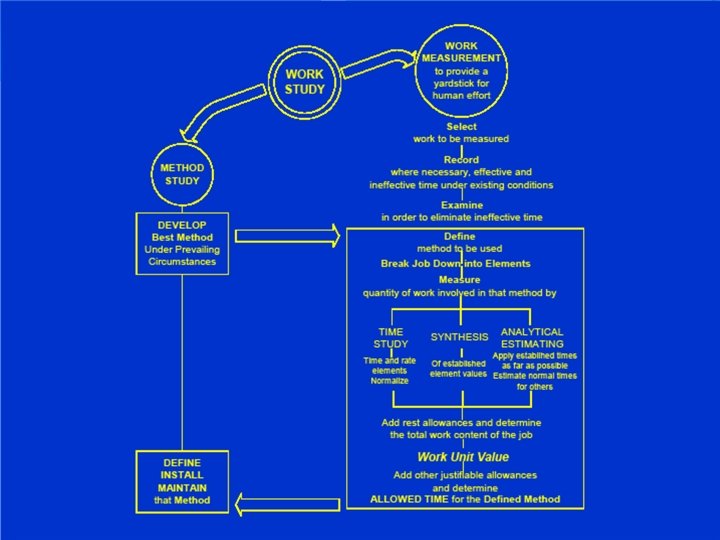
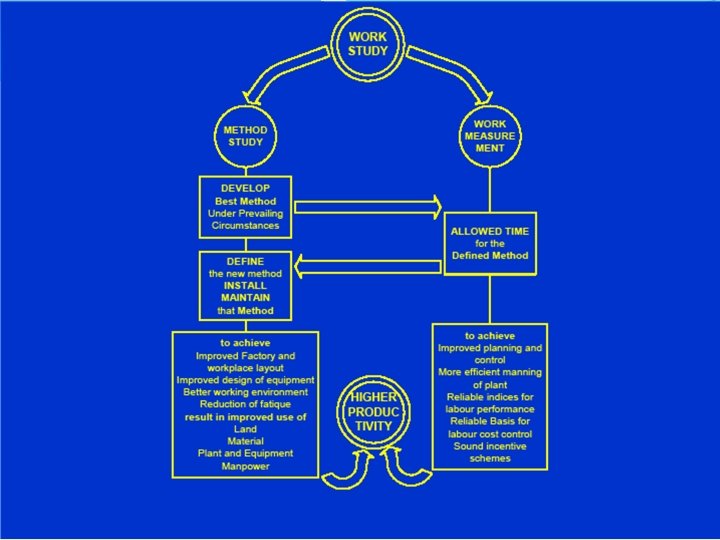
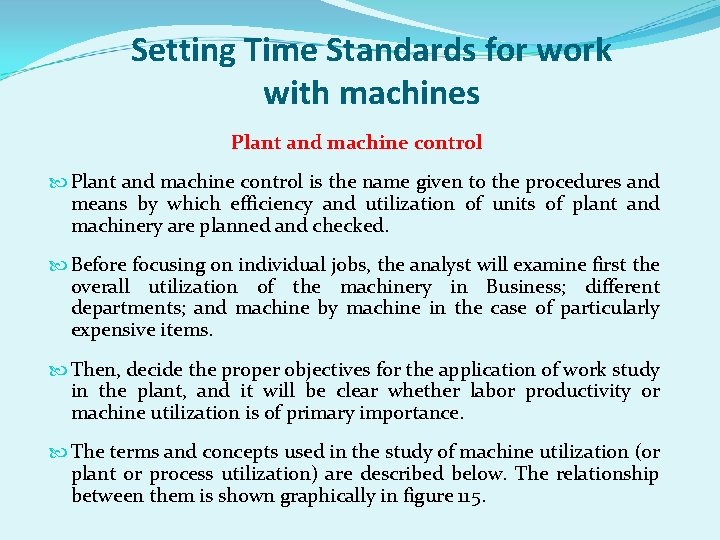
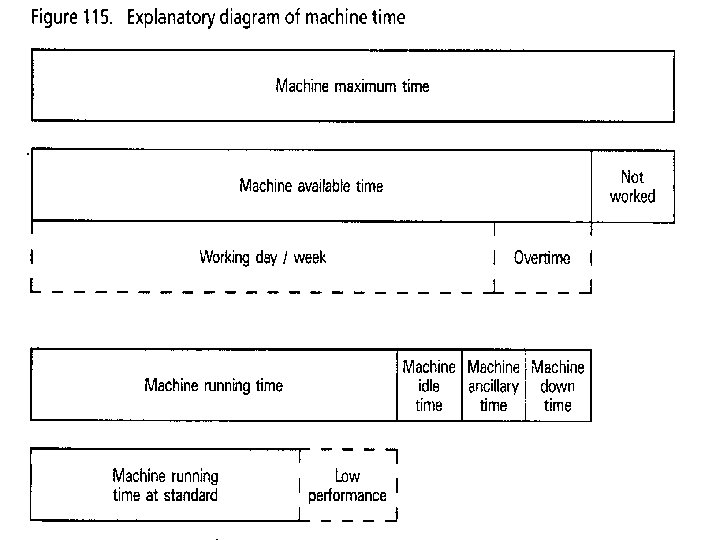
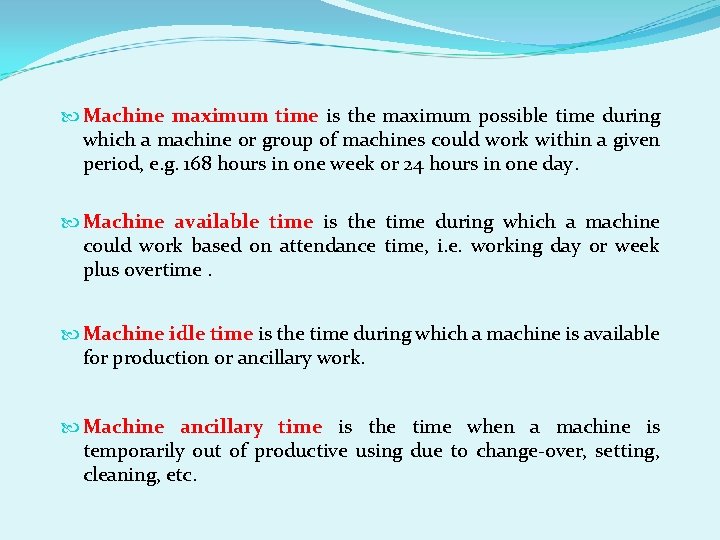
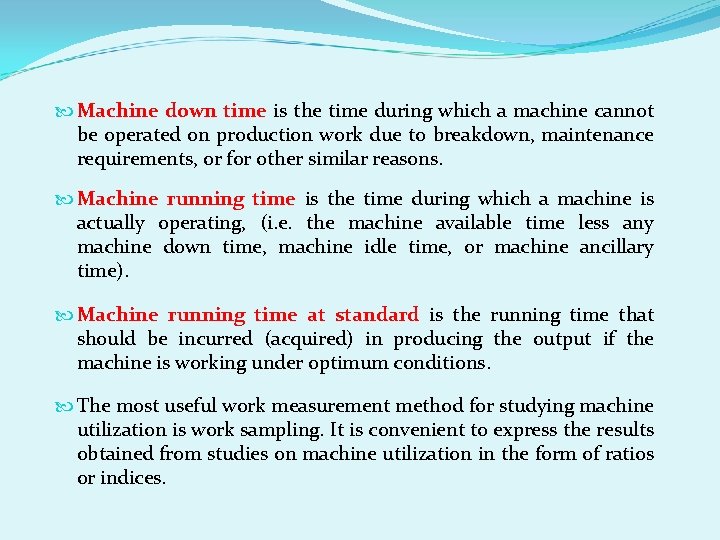

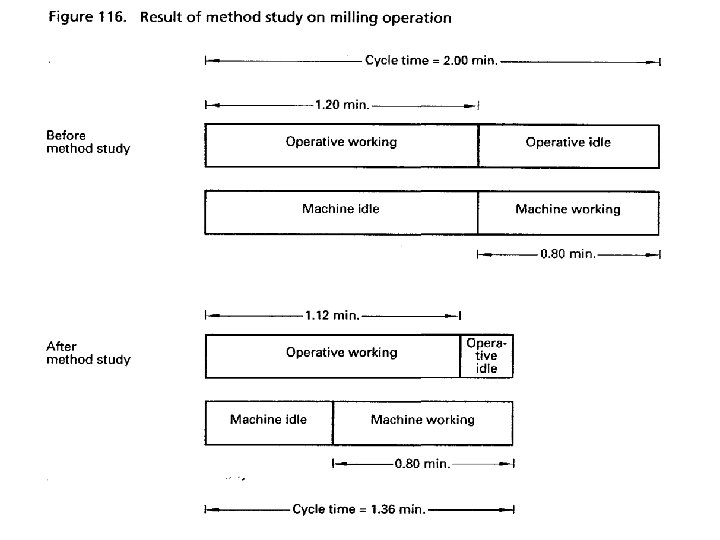

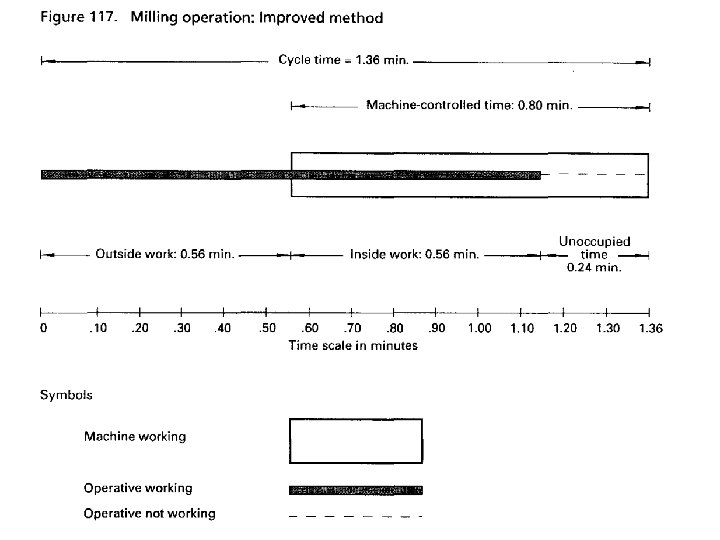
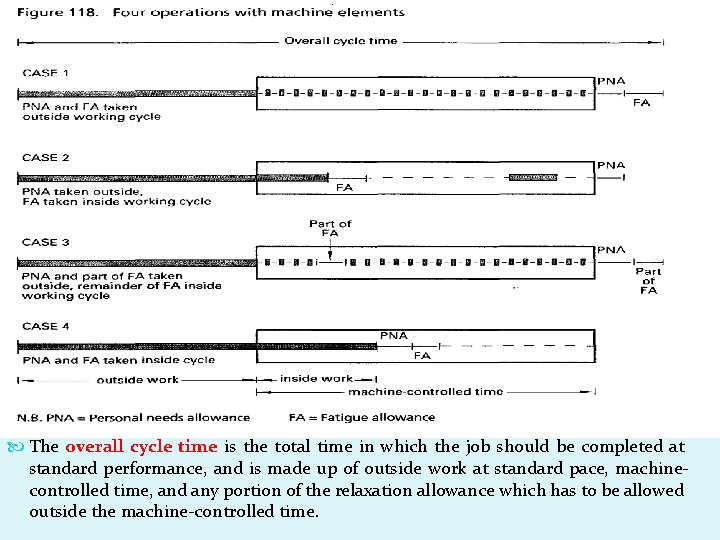
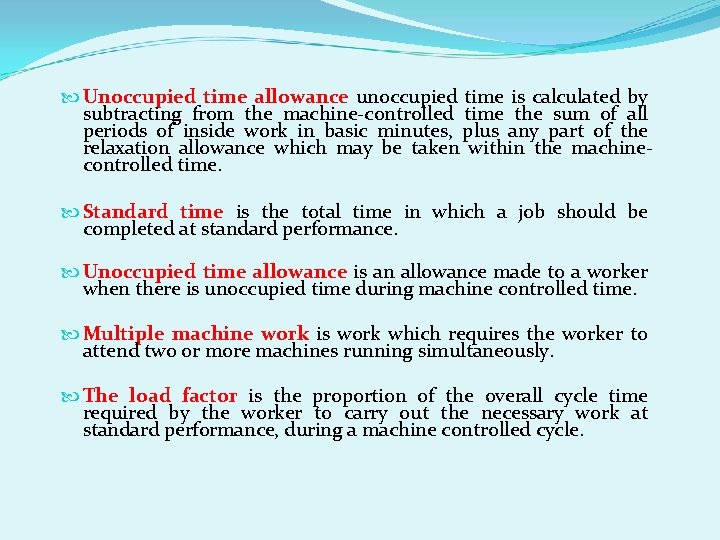
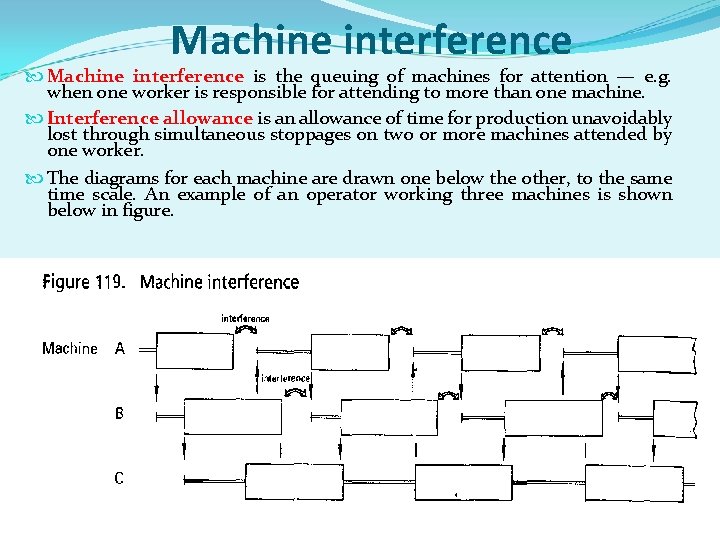
- Slides: 29
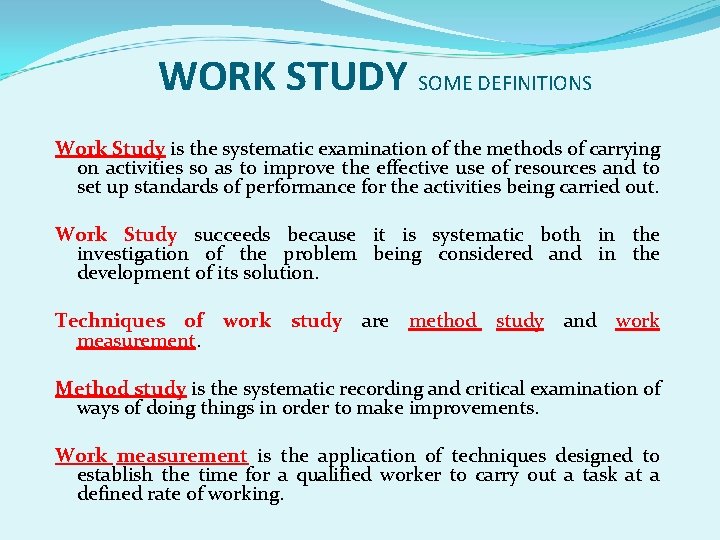
WORK STUDY SOME DEFINITIONS Work Study is the systematic examination of the methods of carrying on activities so as to improve the effective use of resources and to set up standards of performance for the activities being carried out. Work Study succeeds because it is systematic both in the investigation of the problem being considered and in the development of its solution. Techniques of work study are method study and work measurement. Method study is the systematic recording and critical examination of ways of doing things in order to make improvements. Work measurement is the application of techniques designed to establish the time for a qualified worker to carry out a task at a defined rate of working.
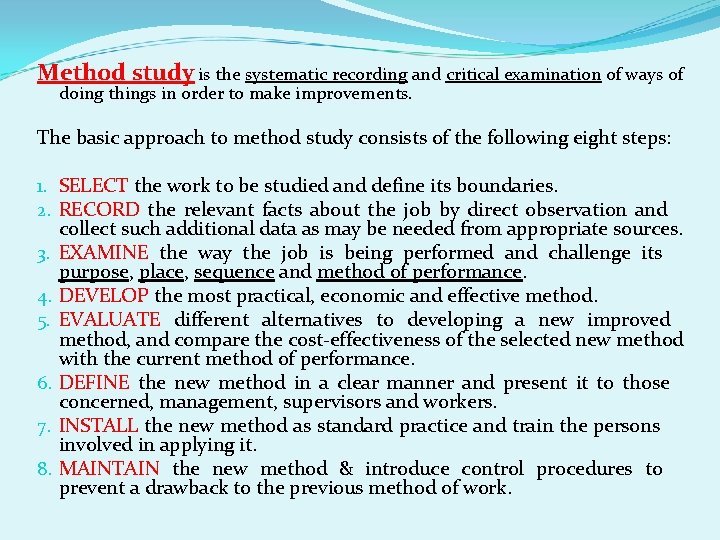
Method study is the systematic recording and critical examination of ways of doing things in order to make improvements. The basic approach to method study consists of the following eight steps: 1. SELECT the work to be studied and define its boundaries. 2. RECORD the relevant facts about the job by direct observation and collect such additional data as may be needed from appropriate sources. 3. EXAMINE the way the job is being performed and challenge its purpose, place, sequence and method of performance. 4. DEVELOP the most practical, economic and effective method. 5. EVALUATE different alternatives to developing a new improved method, and compare the cost-effectiveness of the selected new method with the current method of performance. 6. DEFINE the new method in a clear manner and present it to those concerned, management, supervisors and workers. 7. INSTALL the new method as standard practice and train the persons involved in applying it. 8. MAINTAIN the new method & introduce control procedures to prevent a drawback to the previous method of work.
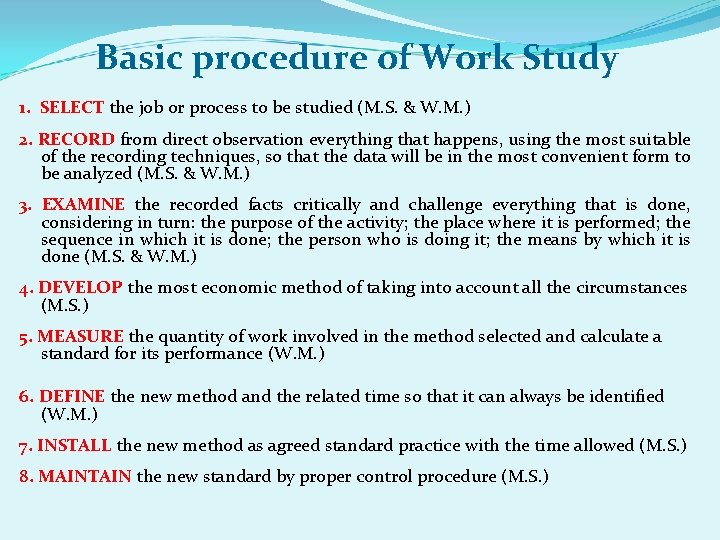
Basic procedure of Work Study 1. SELECT the job or process to be studied (M. S. & W. M. ) 2. RECORD from direct observation everything that happens, using the most suitable of the recording techniques, so that the data will be in the most convenient form to be analyzed (M. S. & W. M. ) 3. EXAMINE the recorded facts critically and challenge everything that is done, considering in turn: the purpose of the activity; the place where it is performed; the sequence in which it is done; the person who is doing it; the means by which it is done (M. S. & W. M. ) 4. DEVELOP the most economic method of taking into account all the circumstances (M. S. ) 5. MEASURE the quantity of work involved in the method selected and calculate a standard for its performance (W. M. ) 6. DEFINE the new method and the related time so that it can always be identified (W. M. ) 7. INSTALL the new method as agreed standard practice with the time allowed (M. S. ) 8. MAINTAIN the new standard by proper control procedure (M. S. )
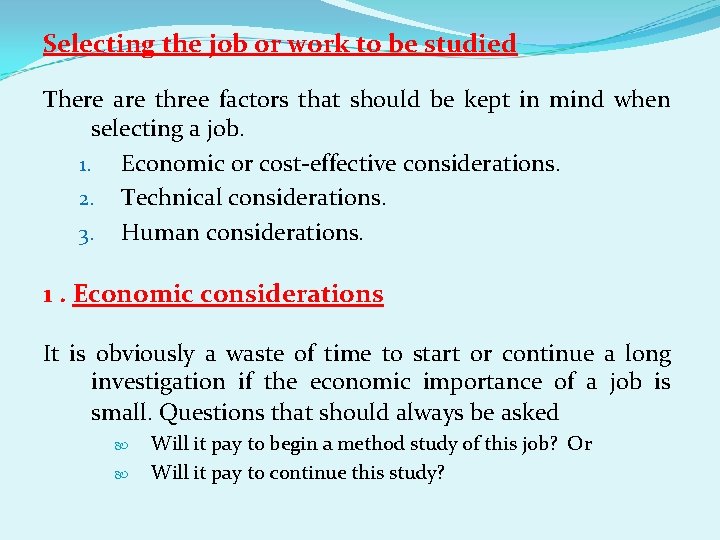
Selecting the job or work to be studied There are three factors that should be kept in mind when selecting a job. 1. Economic or cost-effective considerations. 2. Technical considerations. 3. Human considerations. 1. Economic considerations It is obviously a waste of time to start or continue a long investigation if the economic importance of a job is small. Questions that should always be asked Will it pay to begin a method study of this job? Or Will it pay to continue this study?
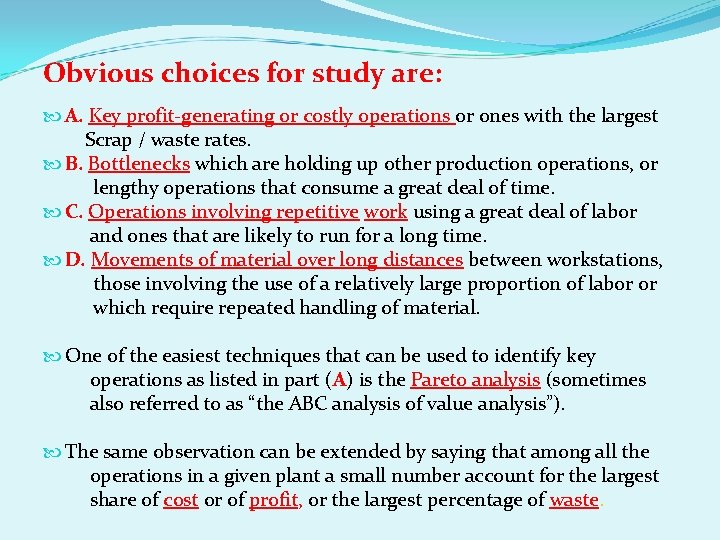
Obvious choices for study are: A. Key profit-generating or costly operations or ones with the largest Scrap / waste rates. B. Bottlenecks which are holding up other production operations, or lengthy operations that consume a great deal of time. C. Operations involving repetitive work using a great deal of labor and ones that are likely to run for a long time. D. Movements of material over long distances between workstations, those involving the use of a relatively large proportion of labor or which require repeated handling of material. One of the easiest techniques that can be used to identify key operations as listed in part (A) is the Pareto analysis (sometimes also referred to as “the ABC analysis of value analysis”). The same observation can be extended by saying that among all the operations in a given plant a small number account for the largest share of cost or of profit, or the largest percentage of waste.
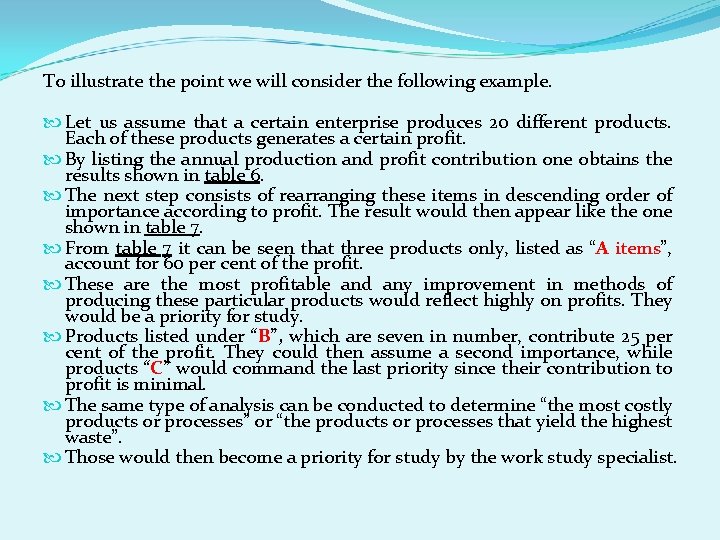
To illustrate the point we will consider the following example. Let us assume that a certain enterprise produces 20 different products. Each of these products generates a certain profit. By listing the annual production and profit contribution one obtains the results shown in table 6. The next step consists of rearranging these items in descending order of importance according to profit. The result would then appear like the one shown in table 7. From table 7 it can be seen that three products only, listed as “A items”, account for 60 per cent of the profit. These are the most profitable and any improvement in methods of producing these particular products would reflect highly on profits. They would be a priority for study. Products listed under “B”, which are seven in number, contribute 25 per cent of the profit. They could then assume a second importance, while products “C” would command the last priority since their contribution to profit is minimal. The same type of analysis can be conducted to determine “the most costly products or processes” or “the products or processes that yield the highest waste”. Those would then become a priority for study by the work study specialist.
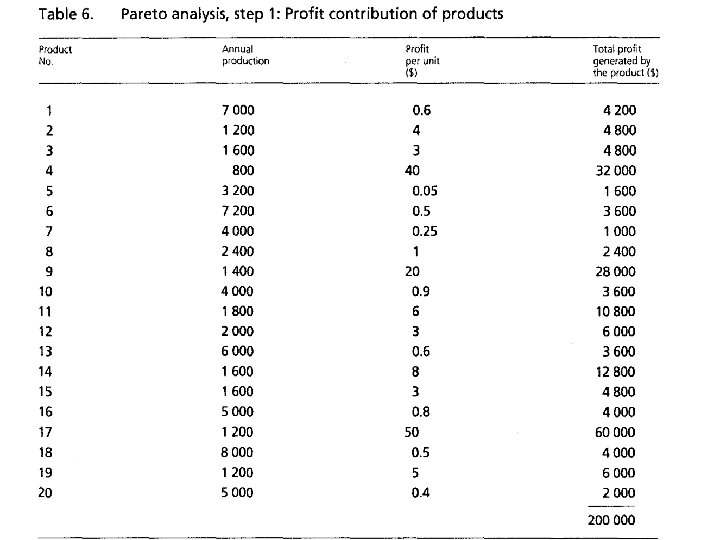
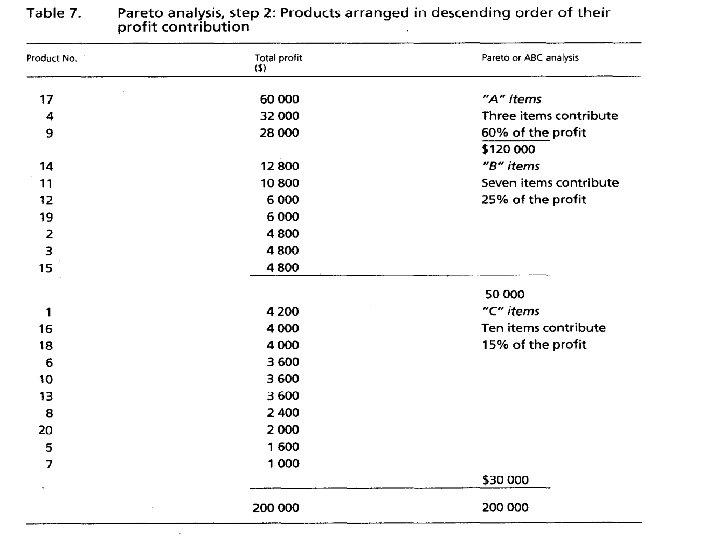
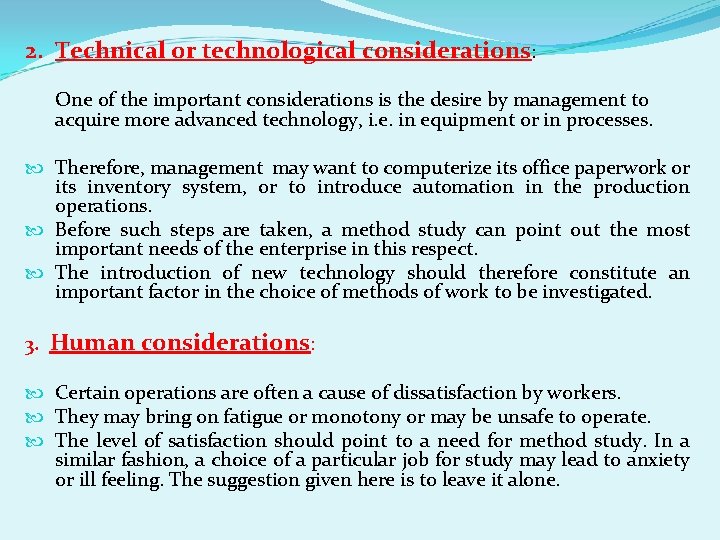
2. Technical or technological considerations: One of the important considerations is the desire by management to acquire more advanced technology, i. e. in equipment or in processes. Therefore, management may want to computerize its office paperwork or its inventory system, or to introduce automation in the production operations. Before such steps are taken, a method study can point out the most important needs of the enterprise in this respect. The introduction of new technology should therefore constitute an important factor in the choice of methods of work to be investigated. 3. Human considerations: Certain operations are often a cause of dissatisfaction by workers. They may bring on fatigue or monotony or may be unsafe to operate. The level of satisfaction should point to a need for method study. In a similar fashion, a choice of a particular job for study may lead to anxiety or ill feeling. The suggestion given here is to leave it alone.
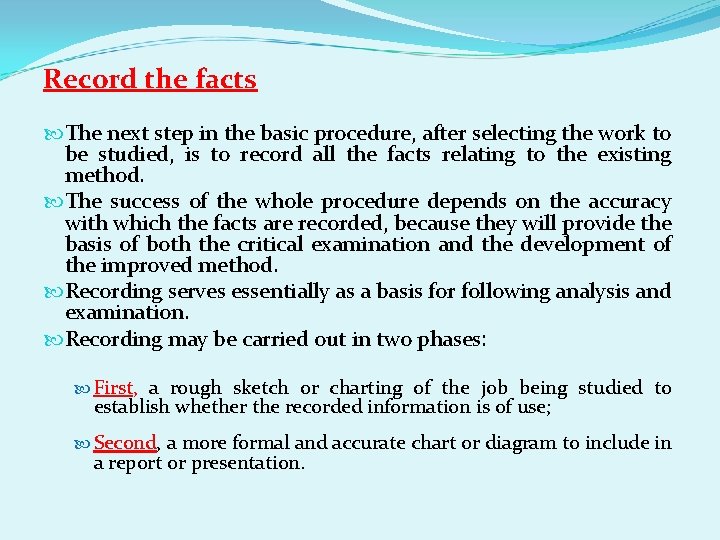
Record the facts The next step in the basic procedure, after selecting the work to be studied, is to record all the facts relating to the existing method. The success of the whole procedure depends on the accuracy with which the facts are recorded, because they will provide the basis of both the critical examination and the development of the improved method. Recording serves essentially as a basis for following analysis and examination. Recording may be carried out in two phases: First, a rough sketch or charting of the job being studied to establish whether the recorded information is of use; Second, a more formal and accurate chart or diagram to include in a report or presentation.
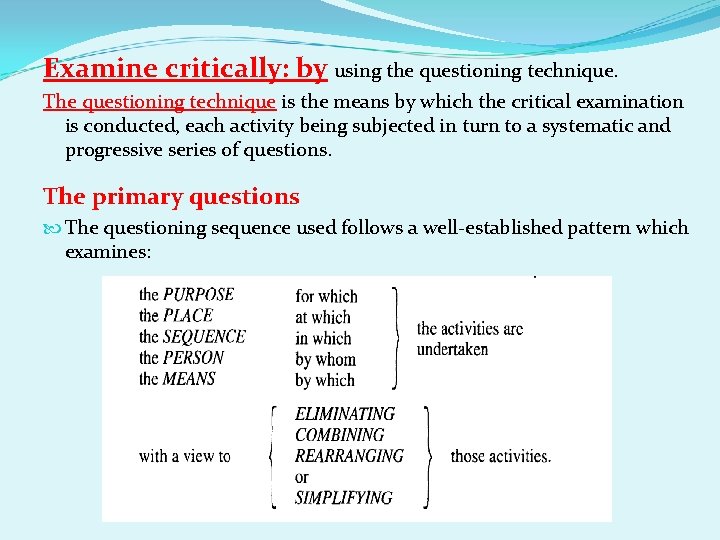
Examine critically: by using the questioning technique. The questioning technique is the means by which the critical examination is conducted, each activity being subjected in turn to a systematic and progressive series of questions. The primary questions The questioning sequence used follows a well-established pattern which examines:
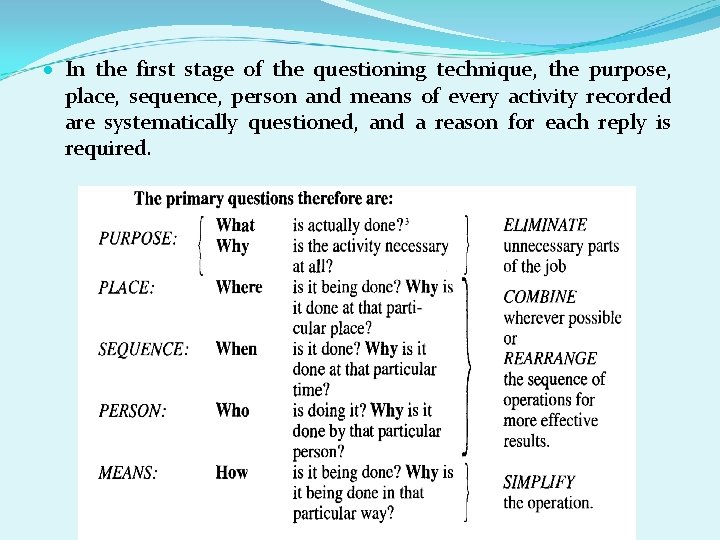
In the first stage of the questioning technique, the purpose, place, sequence, person and means of every activity recorded are systematically questioned, and a reason for each reply is required.
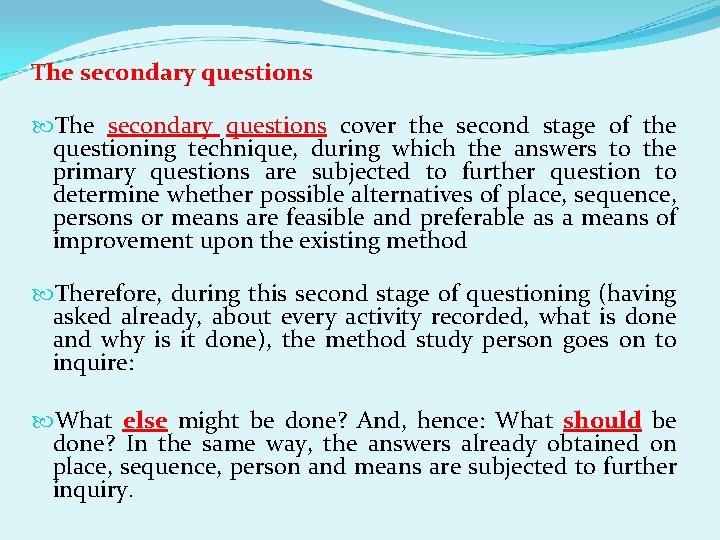
The secondary questions cover the second stage of the questioning technique, during which the answers to the primary questions are subjected to further question to determine whether possible alternatives of place, sequence, persons or means are feasible and preferable as a means of improvement upon the existing method Therefore, during this second stage of questioning (having asked already, about every activity recorded, what is done and why is it done), the method study person goes on to inquire: What else might be done? And, hence: What should be done? In the same way, the answers already obtained on place, sequence, person and means are subjected to further inquiry.
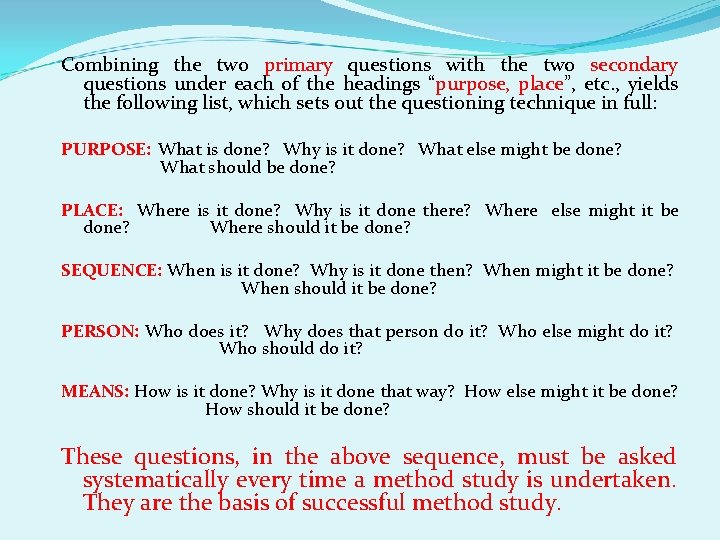
Combining the two primary questions with the two secondary questions under each of the headings “purpose, place”, etc. , yields the following list, which sets out the questioning technique in full: PURPOSE: What is done? Why is it done? What else might be done? What should be done? PLACE: Where is it done? Why is it done there? Where else might it be done? Where should it be done? SEQUENCE: When is it done? Why is it done then? When might it be done? When should it be done? PERSON: Who does it? Why does that person do it? Who else might do it? Who should do it? MEANS: How is it done? Why is it done that way? How else might it be done? How should it be done? These questions, in the above sequence, must be asked systematically every time a method study is undertaken. They are the basis of successful method study.
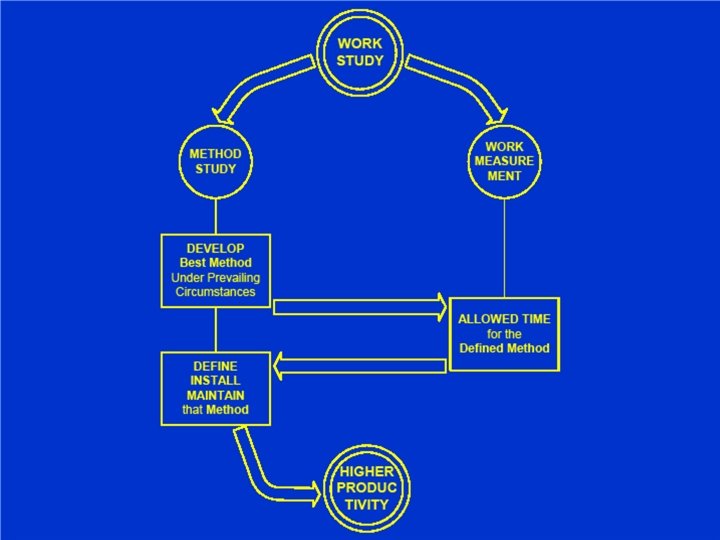
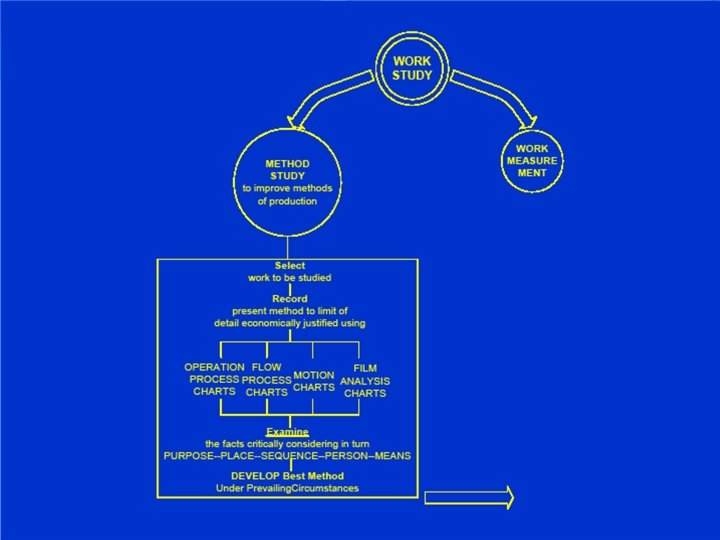
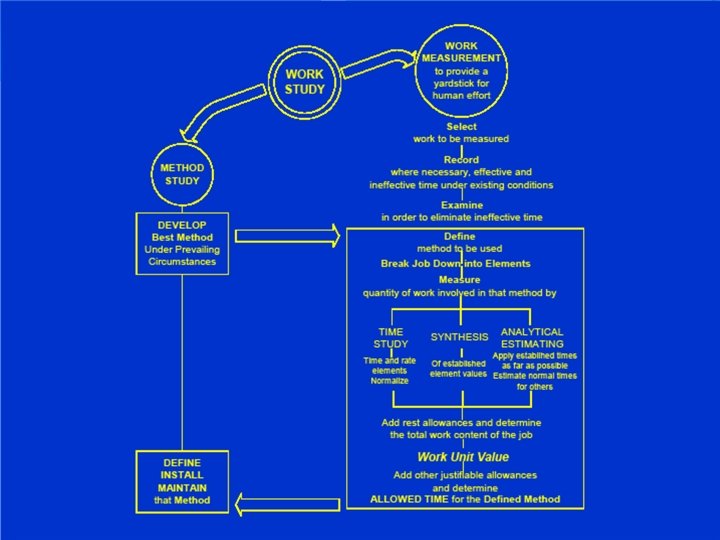
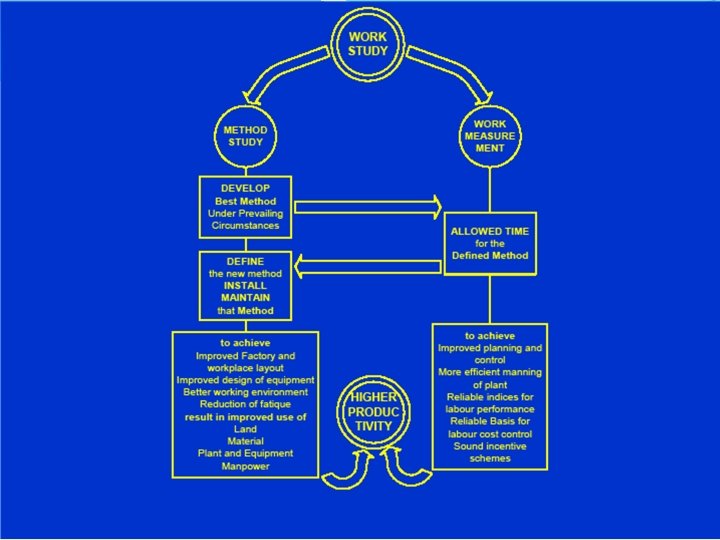
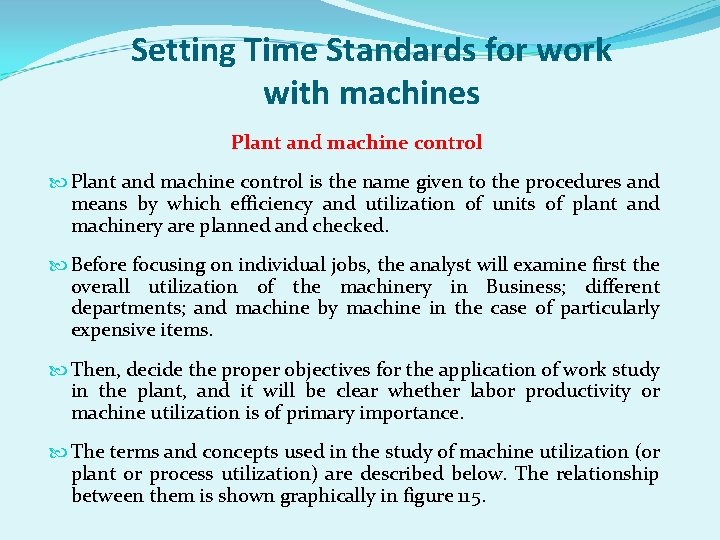
Setting Time Standards for work with machines Plant and machine control is the name given to the procedures and means by which efficiency and utilization of units of plant and machinery are planned and checked. Before focusing on individual jobs, the analyst will examine first the overall utilization of the machinery in Business; different departments; and machine by machine in the case of particularly expensive items. Then, decide the proper objectives for the application of work study in the plant, and it will be clear whether labor productivity or machine utilization is of primary importance. The terms and concepts used in the study of machine utilization (or plant or process utilization) are described below. The relationship between them is shown graphically in figure 115.
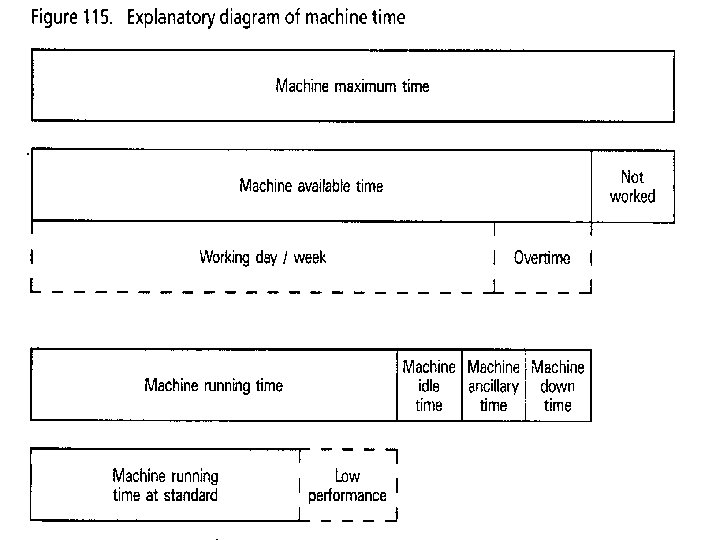
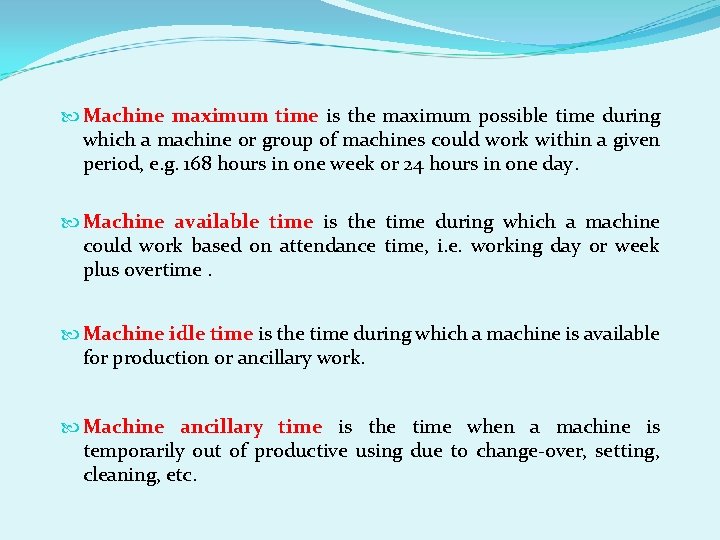
Machine maximum time is the maximum possible time during which a machine or group of machines could work within a given period, e. g. 168 hours in one week or 24 hours in one day. Machine available time is the time during which a machine could work based on attendance time, i. e. working day or week plus overtime. Machine idle time is the time during which a machine is available for production or ancillary work. Machine ancillary time is the time when a machine is temporarily out of productive using due to change-over, setting, cleaning, etc.
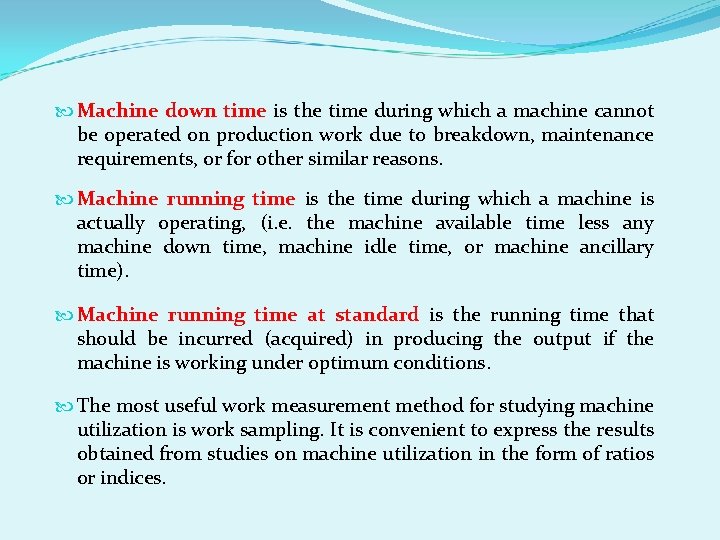
Machine down time is the time during which a machine cannot be operated on production work due to breakdown, maintenance requirements, or for other similar reasons. Machine running time is the time during which a machine is actually operating, (i. e. the machine available time less any machine down time, machine idle time, or machine ancillary time). Machine running time at standard is the running time that should be incurred (acquired) in producing the output if the machine is working under optimum conditions. The most useful work measurement method for studying machine utilization is work sampling. It is convenient to express the results obtained from studies on machine utilization in the form of ratios or indices.

For this purpose three indices are commonly used: Machine utilization index, is the ratio of Machine running time to machine available time. Machine efficiency index, is the ratio of Machine running time at standard to machine running time. Machine effective utilization index, the ratio of Machine running time at standard to machine available time. Machine effective utilization index ratio can be used to provide an indication of the scope for cost reduction that would be available if the machine were operated at full efficiency for the whole of the working time.
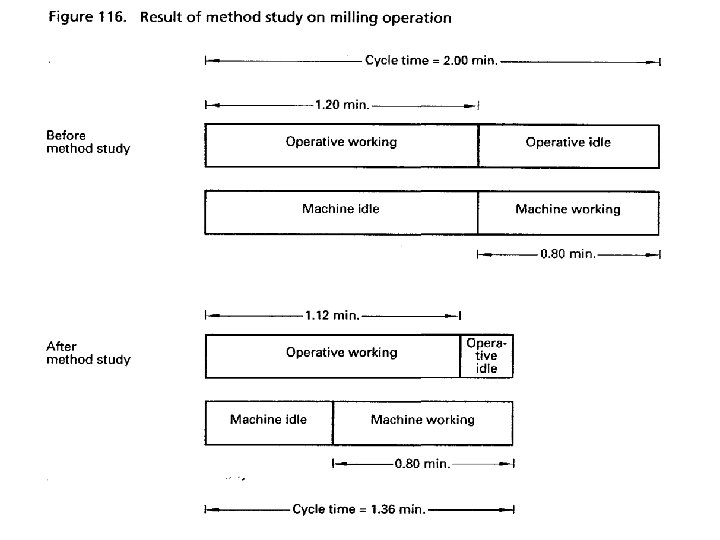

One worker and one machine Machine-controlled time is the time taken to complete that part of the work cycle. It will be seen that the operator carries out part of the manual work while the machine is stopped and part while it is running. These parts are called “outside work” and “inside work” respectively. Outside work comprises elements which must necessarily be performed by a worker outside the machine controlled time Inside work comprises those elements which can be performed by a worker within the machine controlled time. Unoccupied time comprises the periods during machine controlled time when a worker is neither engaged on inside work nor taking authorized rest.
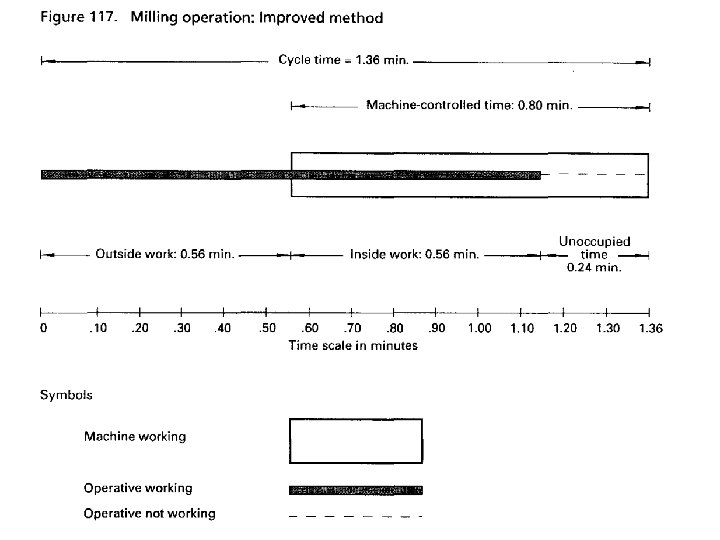
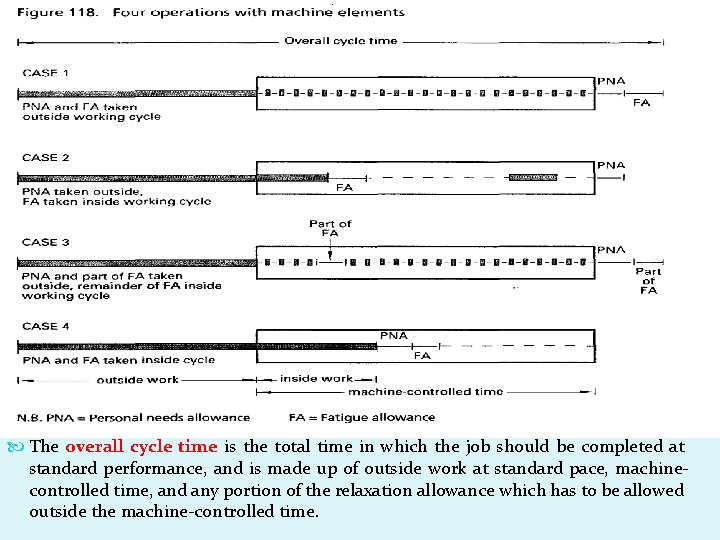
The overall cycle time is the total time in which the job should be completed at standard performance, and is made up of outside work at standard pace, machinecontrolled time, and any portion of the relaxation allowance which has to be allowed outside the machine-controlled time.
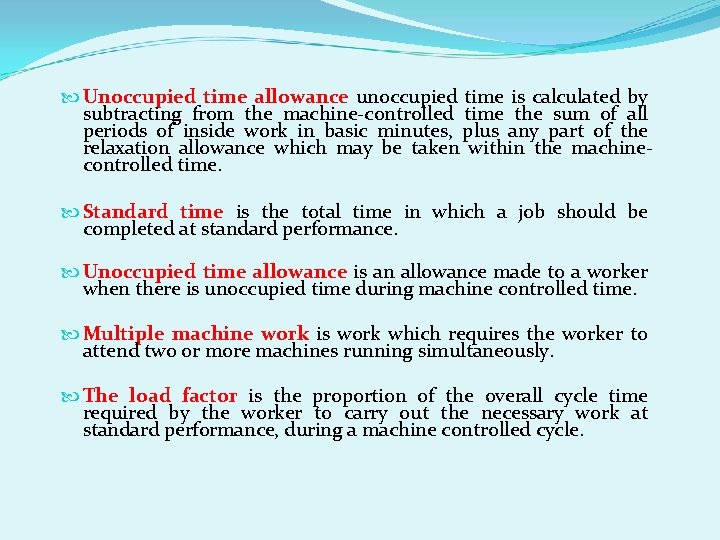
Unoccupied time allowance unoccupied time is calculated by subtracting from the machine-controlled time the sum of all periods of inside work in basic minutes, plus any part of the relaxation allowance which may be taken within the machinecontrolled time. Standard time is the total time in which a job should be completed at standard performance. Unoccupied time allowance is an allowance made to a worker when there is unoccupied time during machine controlled time. Multiple machine work is work which requires the worker to attend two or more machines running simultaneously. The load factor is the proportion of the overall cycle time required by the worker to carry out the necessary work at standard performance, during a machine controlled cycle.
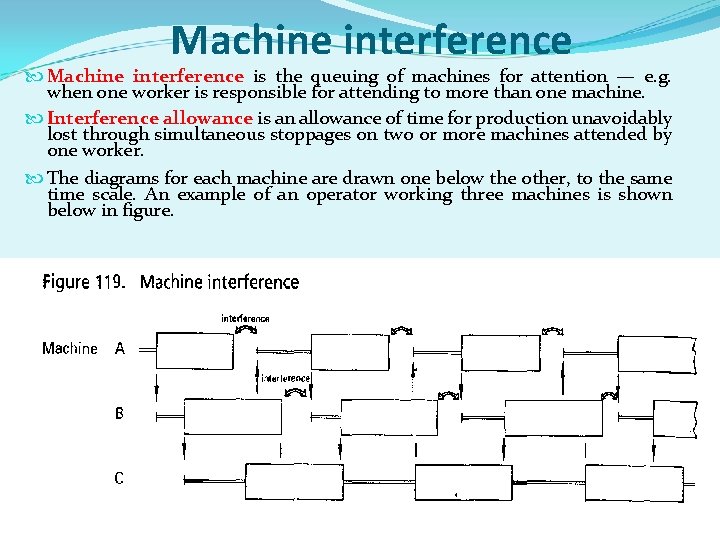
Machine interference is the queuing of machines for attention — e. g. when one worker is responsible for attending to more than one machine. Interference allowance is an allowance of time for production unavoidably lost through simultaneous stoppages on two or more machines attended by one worker. The diagrams for each machine are drawn one below the other, to the same time scale. An example of an operator working three machines is shown below in figure.
The problem of concept drift: definitions and related work
They say it only takes a little faith to move a mountain
They say it only takes a little faith to move a mountain
Cakes is countable or uncountable
What are some contact forces and some noncontact forces
Fire and ice diamante poem
Some say the world will end in fire some say in ice
Some trust in chariots and some in horses song
Work study definition
Hát kết hợp bộ gõ cơ thể
Ng-html
Bổ thể
Tỉ lệ cơ thể trẻ em
Chó sói
Chụp phim tư thế worms-breton
Hát lên người ơi
Môn thể thao bắt đầu bằng từ chạy
Thế nào là hệ số cao nhất
Các châu lục và đại dương trên thế giới
Công thức tính thế năng
Trời xanh đây là của chúng ta thể thơ
Mật thư anh em như thể tay chân
Phép trừ bù
độ dài liên kết
Các châu lục và đại dương trên thế giới
Thơ thất ngôn tứ tuyệt đường luật
Quá trình desamine hóa có thể tạo ra
Một số thể thơ truyền thống
Bàn tay mà dây bẩn
Vẽ hình chiếu vuông góc của vật thể sau