Slag Valorisation Symposium 01 05 April 2019 Thermodynamics
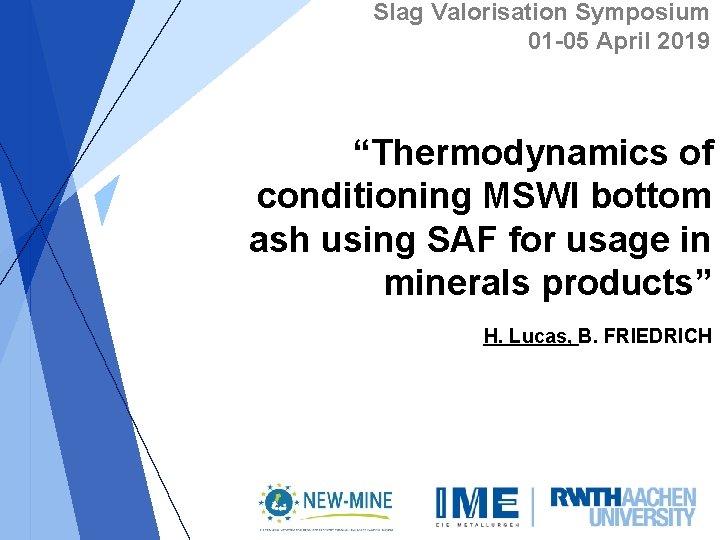
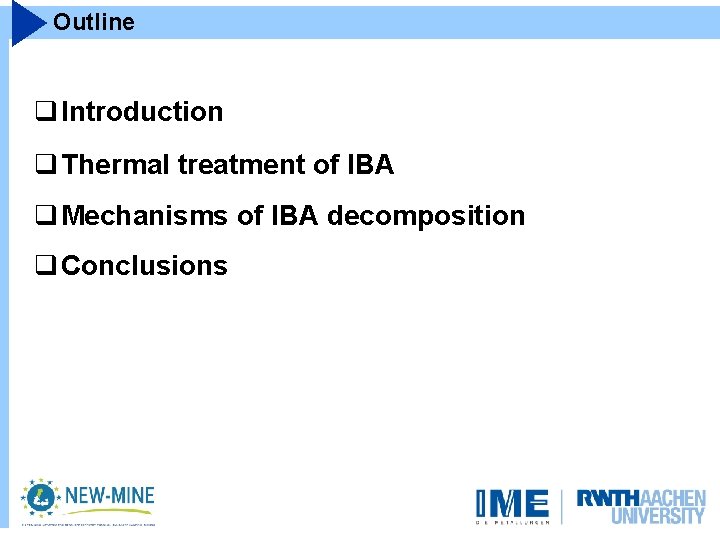
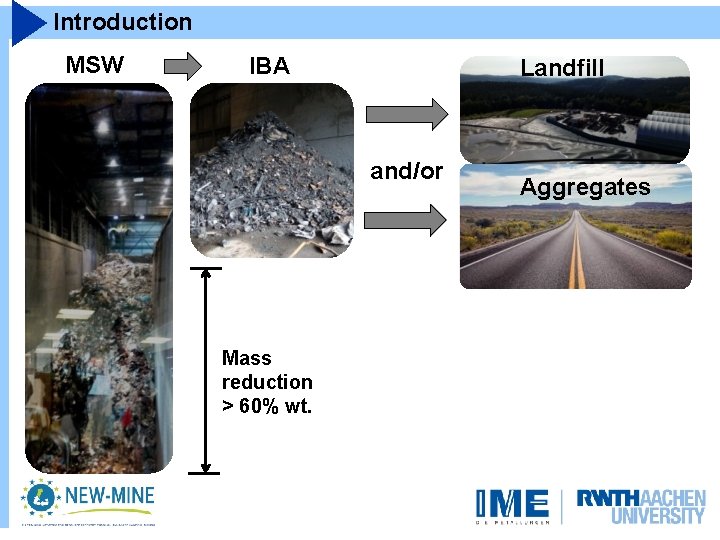
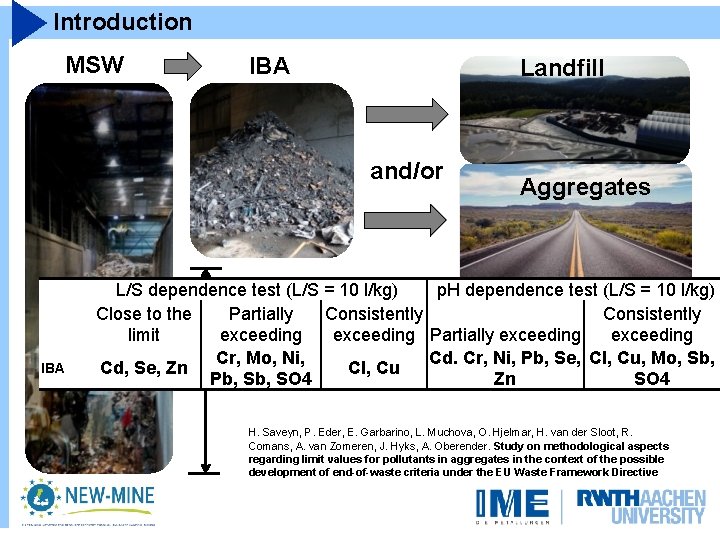
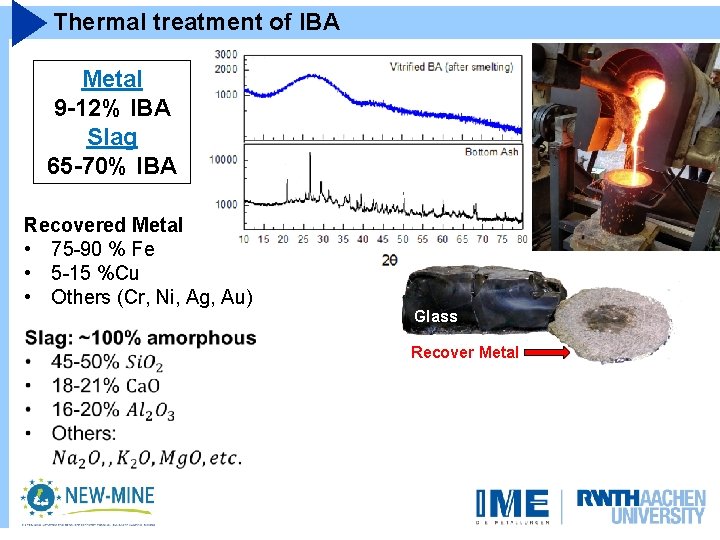
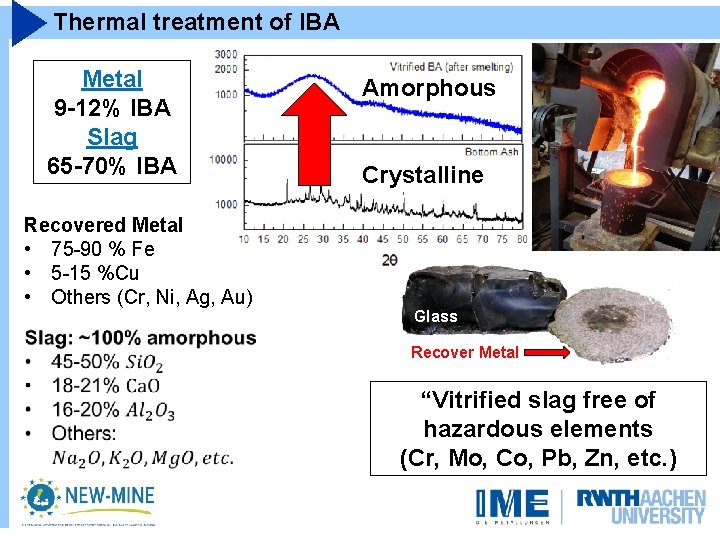
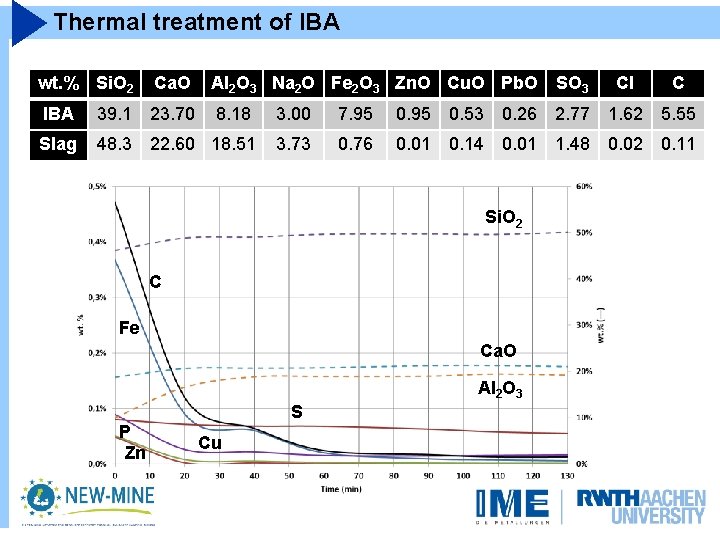
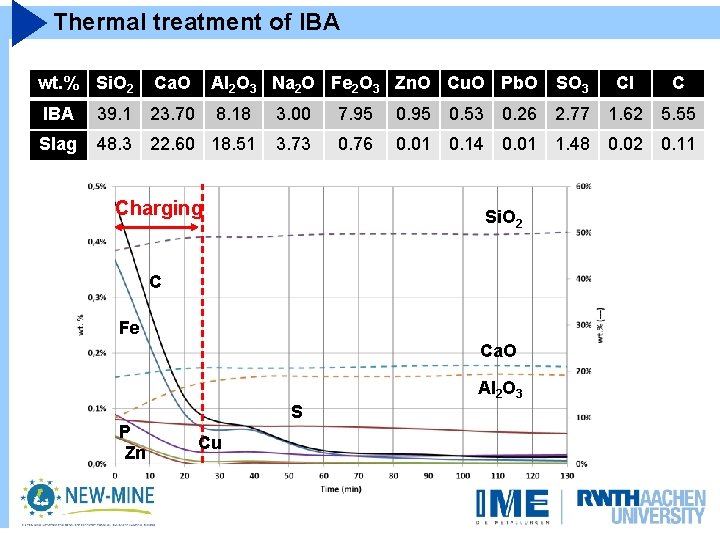
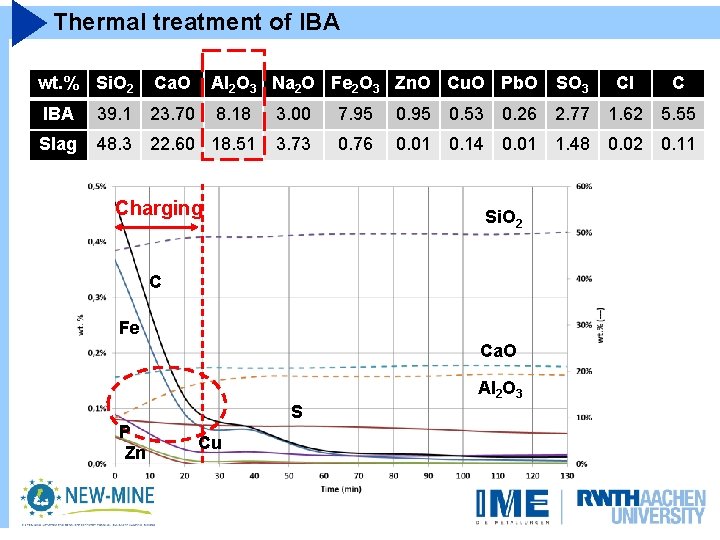
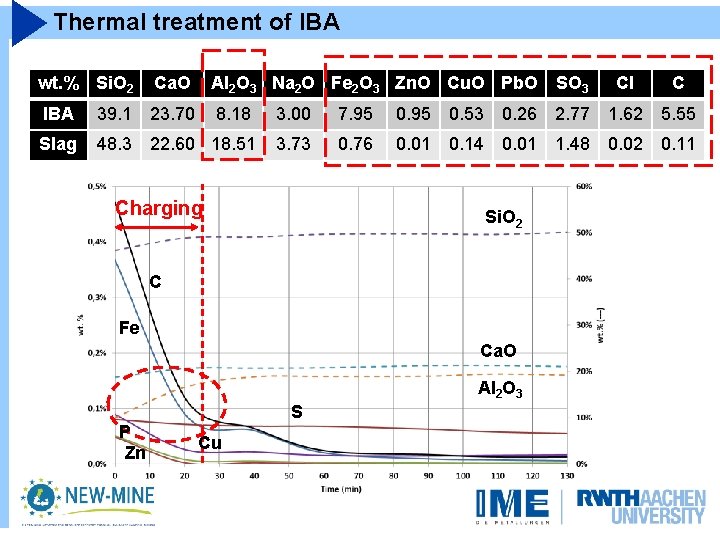
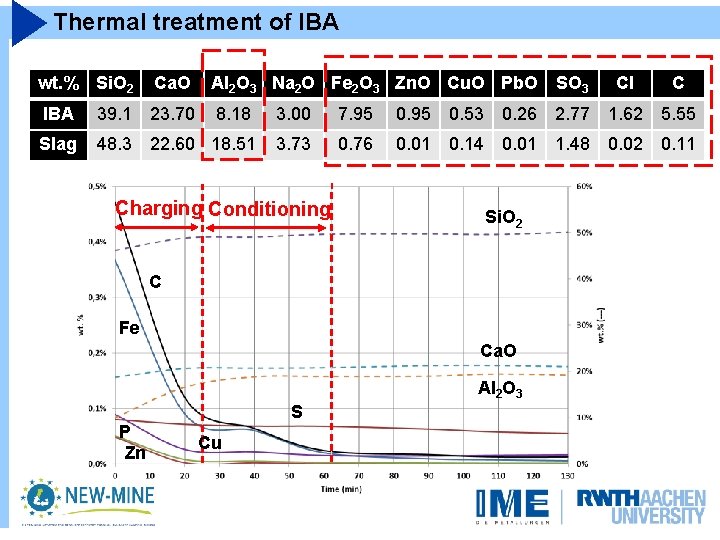

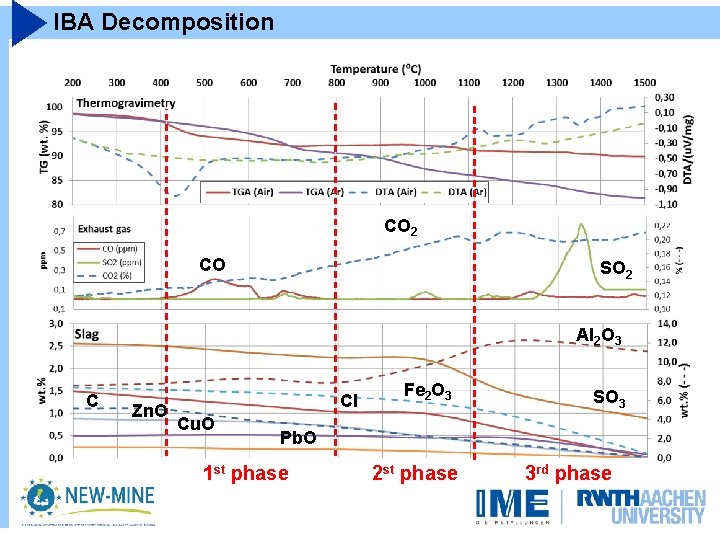
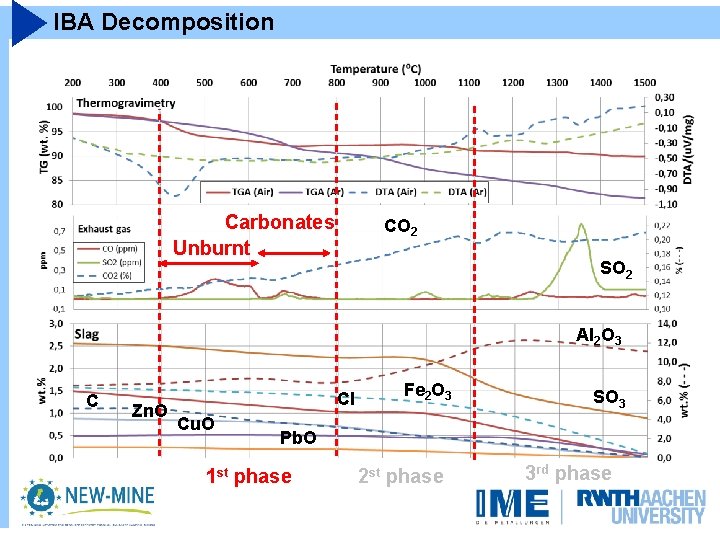
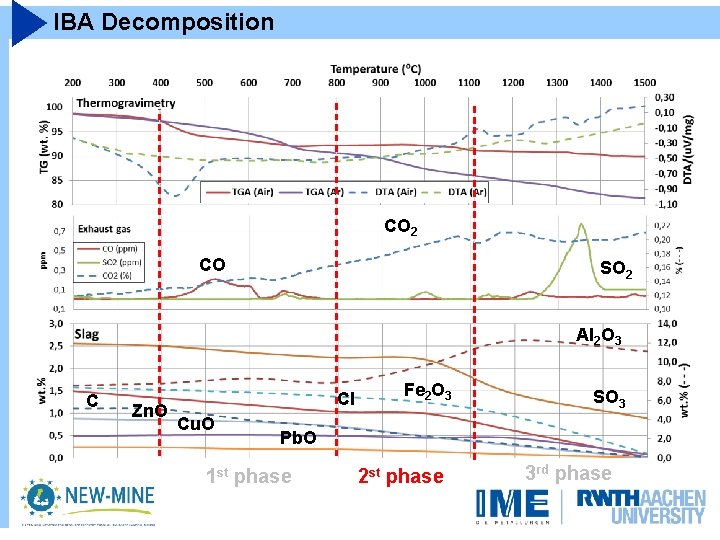
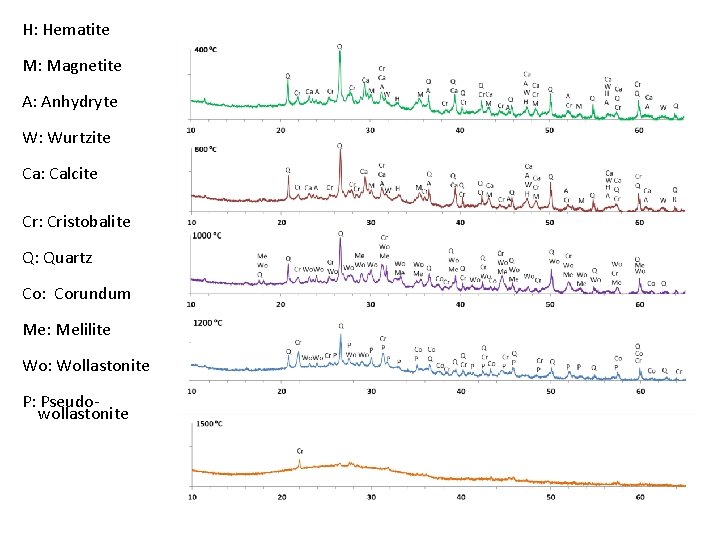

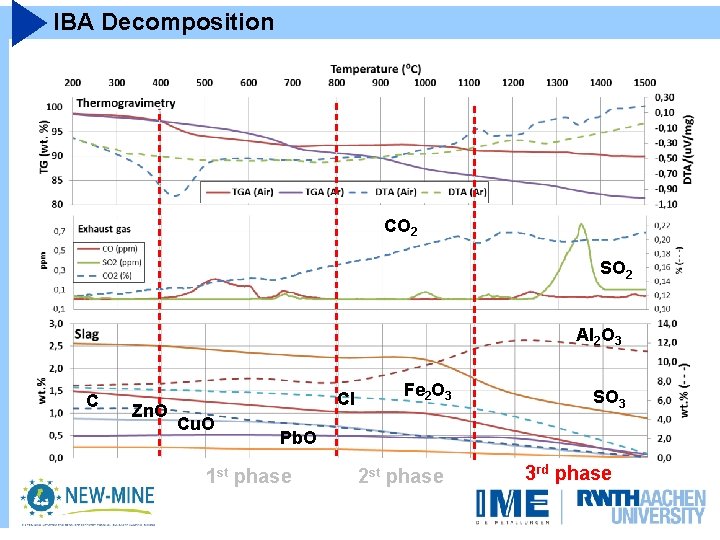
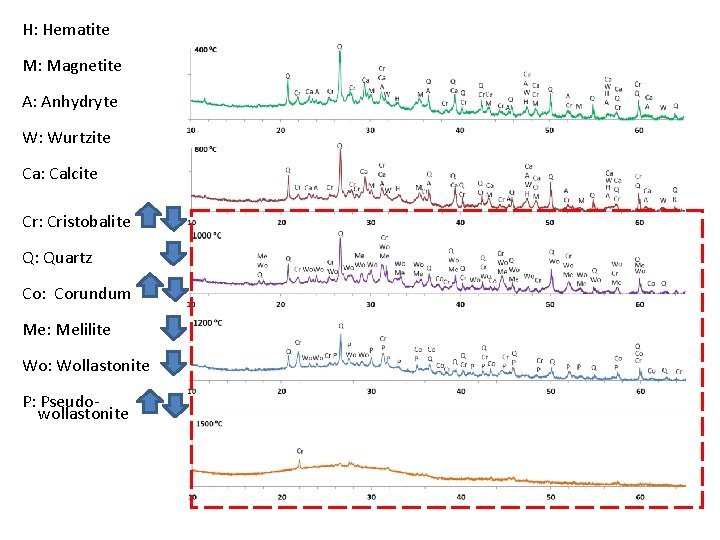
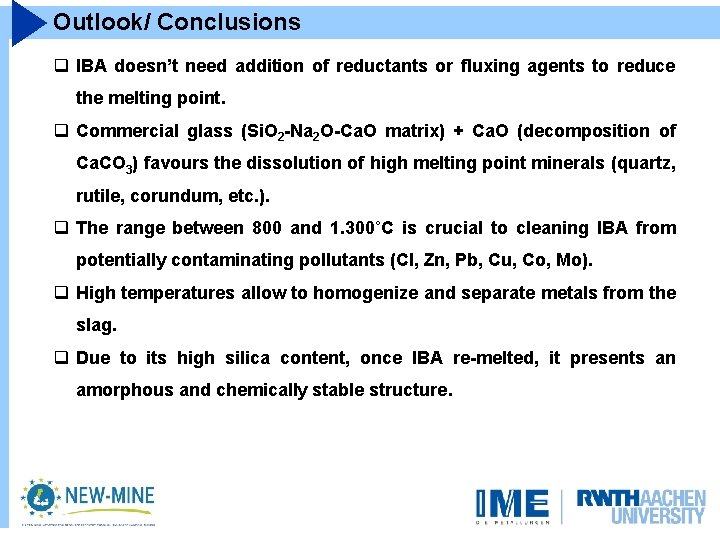
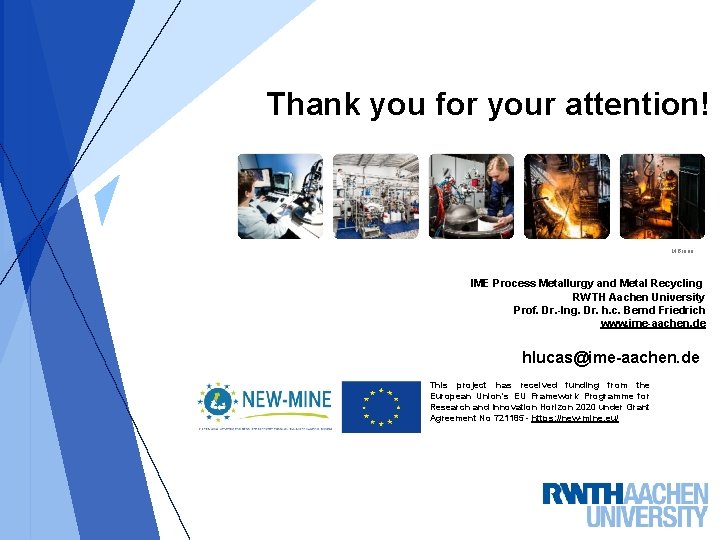
- Slides: 21
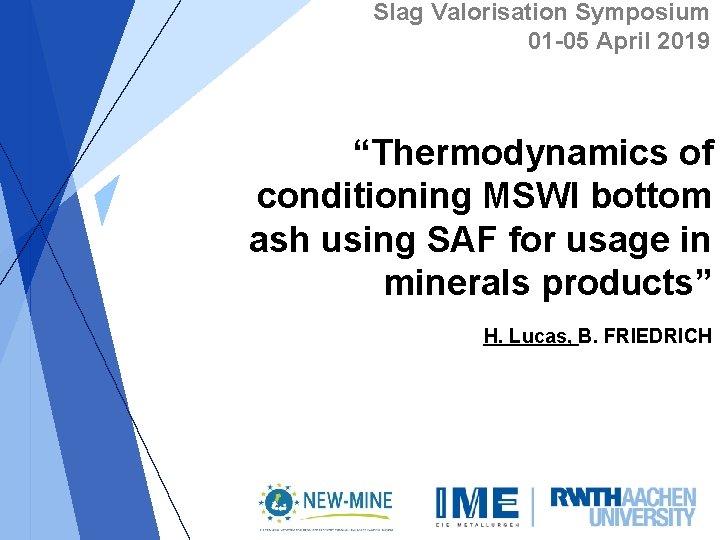
Slag Valorisation Symposium 01 -05 April 2019 “Thermodynamics of conditioning MSWI bottom ash using SAF for usage in minerals products” H. Lucas, B. FRIEDRICH
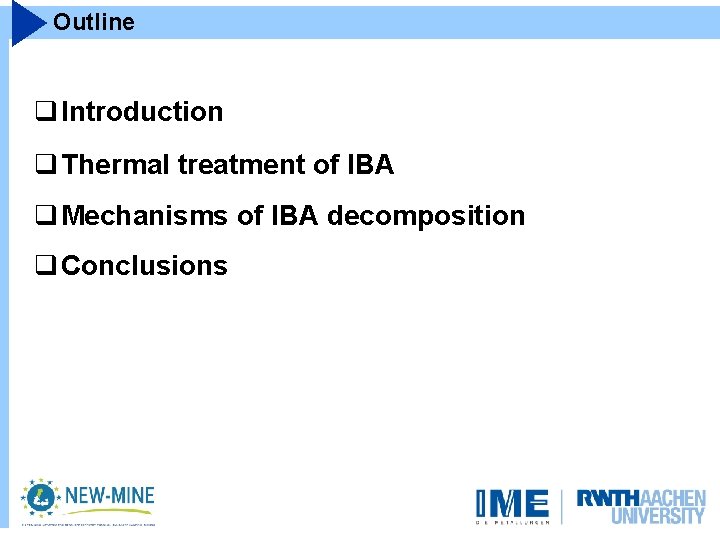
Outline q Introduction q Thermal treatment of IBA q Mechanisms of IBA decomposition q Conclusions
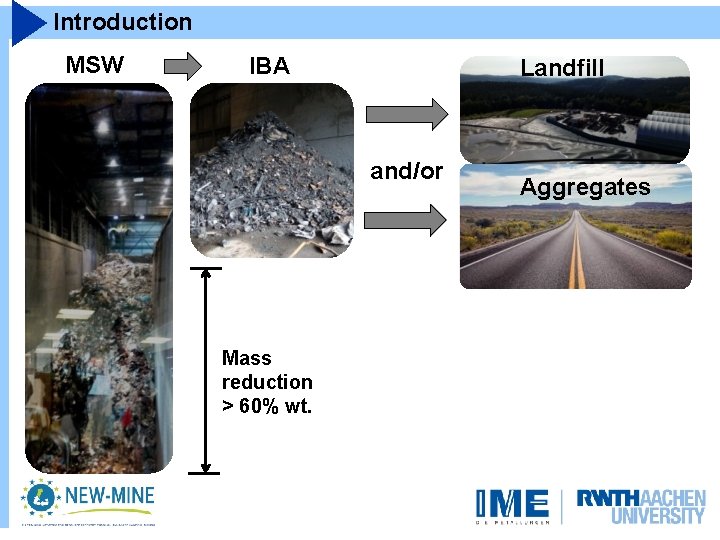
Introduction MSW IBA Landfill and/or Mass reduction > 60% wt. Aggregates
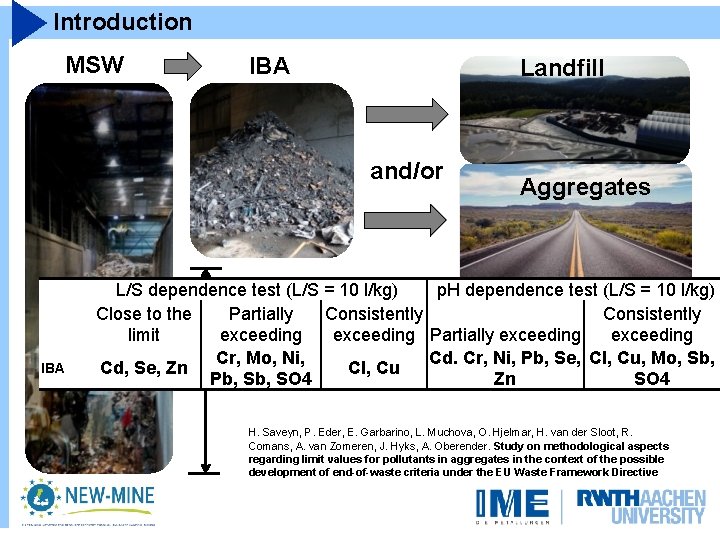
Introduction MSW IBA Landfill and/or IBA Aggregates L/S dependence test (L/S = 10 l/kg) p. H dependence test (L/S = 10 l/kg) Close to the Partially Consistently limit exceeding Partially exceeding Cr, Mo, reduction Ni, Mass > 60%Cd. wt. Cr, Ni, Pb, Se, Cl, Cu, Mo, Sb, Cd, Se, Zn Cl, Cu Pb, SO 4 Zn SO 4 H. Saveyn, P. Eder, E. Garbarino, L. Muchova, O. Hjelmar, H. van der Sloot, R. Comans, A. van Zomeren, J. Hyks, A. Oberender. Study on methodological aspects regarding limit values for pollutants in aggregates in the context of the possible development of end-of-waste criteria under the EU Waste Framework Directive
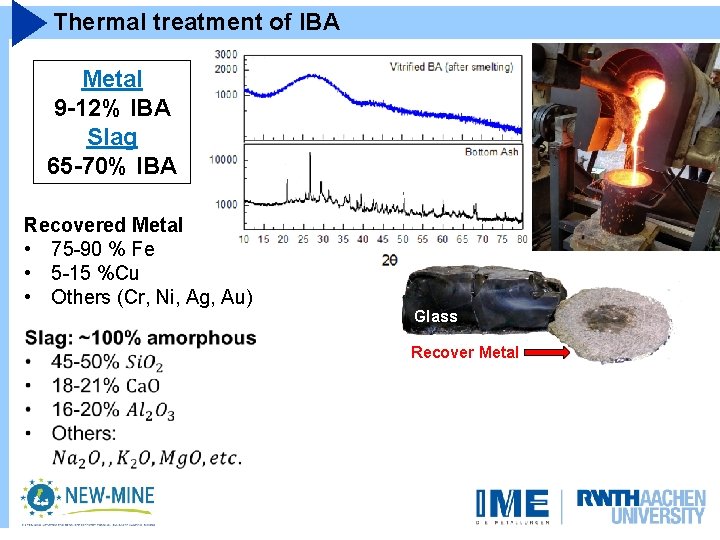
Thermal treatment of IBA Metal 9 -12% IBA Slag 65 -70% IBA Recovered Metal • 75 -90 % Fe • 5 -15 %Cu • Others (Cr, Ni, Ag, Au) Glass Recover Metal
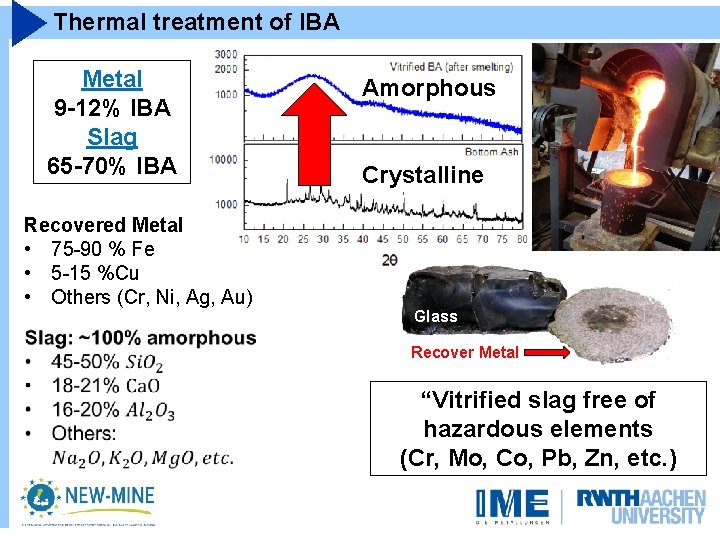
Thermal treatment of IBA Metal 9 -12% IBA Slag 65 -70% IBA Recovered Metal • 75 -90 % Fe • 5 -15 %Cu • Others (Cr, Ni, Ag, Au) Amorphous Crystalline Glass Recover Metal “Vitrified slag free of hazardous elements (Cr, Mo, Co, Pb, Zn, etc. )
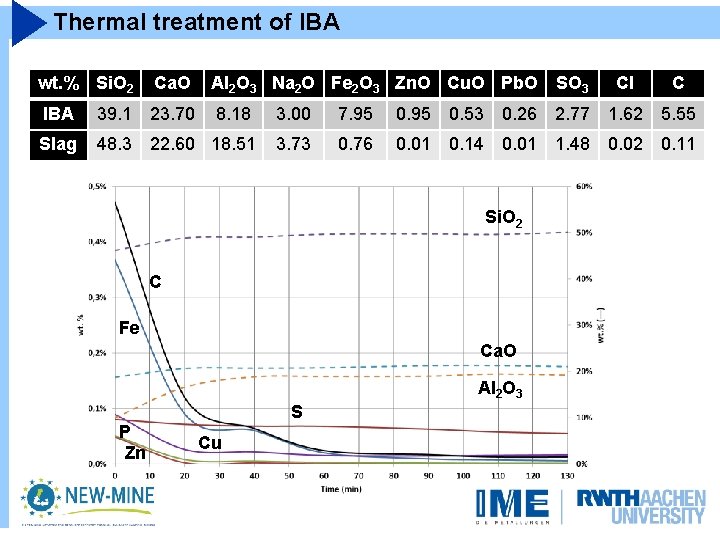
Thermal treatment of IBA wt. % Si. O 2 Ca. O Al 2 O 3 Na 2 O Fe 2 O 3 Zn. O Cu. O Pb. O SO 3 Cl C IBA 39. 1 23. 70 8. 18 3. 00 7. 95 0. 53 0. 26 2. 77 1. 62 5. 55 Slag 48. 3 22. 60 18. 51 3. 73 0. 76 0. 01 0. 14 0. 01 1. 48 0. 02 0. 11 Si. O 2 C Fe Ca. O Al 2 O 3 P Zn S Cu
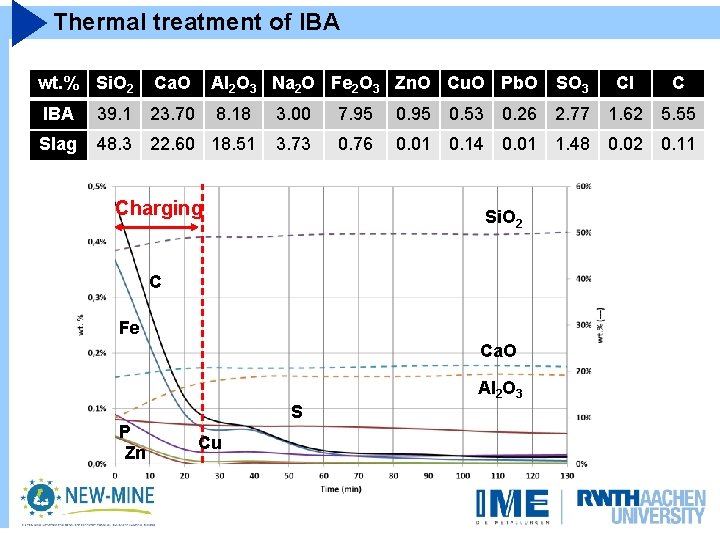
Thermal treatment of IBA wt. % Si. O 2 Ca. O Al 2 O 3 Na 2 O Fe 2 O 3 Zn. O Cu. O Pb. O SO 3 Cl C IBA 39. 1 23. 70 8. 18 3. 00 7. 95 0. 53 0. 26 2. 77 1. 62 5. 55 Slag 48. 3 22. 60 18. 51 3. 73 0. 76 0. 01 0. 14 0. 01 1. 48 0. 02 0. 11 Charging Si. O 2 C Fe Ca. O Al 2 O 3 P Zn S Cu
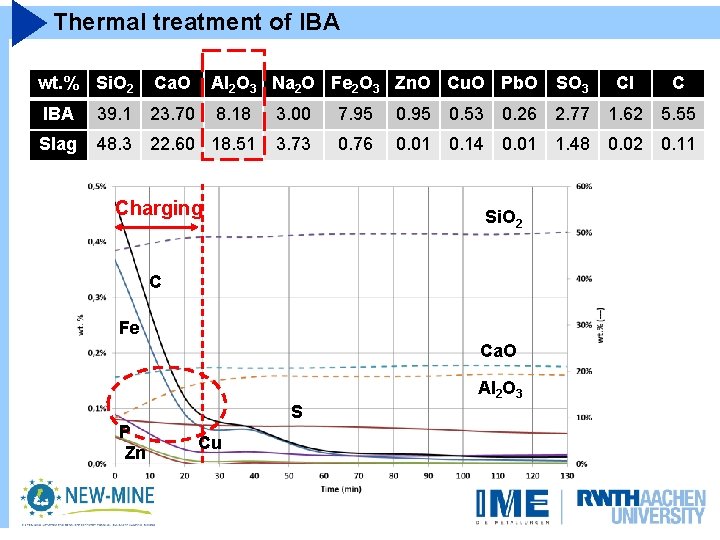
Thermal treatment of IBA wt. % Si. O 2 Ca. O Al 2 O 3 Na 2 O Fe 2 O 3 Zn. O Cu. O Pb. O SO 3 Cl C IBA 39. 1 23. 70 8. 18 3. 00 7. 95 0. 53 0. 26 2. 77 1. 62 5. 55 Slag 48. 3 22. 60 18. 51 3. 73 0. 76 0. 01 0. 14 0. 01 1. 48 0. 02 0. 11 Charging Si. O 2 C Fe Ca. O Al 2 O 3 P Zn S Cu
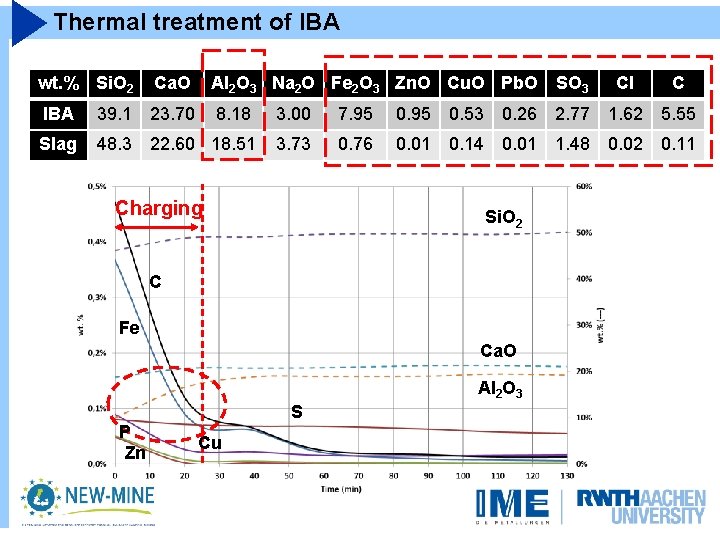
Thermal treatment of IBA wt. % Si. O 2 Ca. O Al 2 O 3 Na 2 O Fe 2 O 3 Zn. O Cu. O Pb. O SO 3 Cl C IBA 39. 1 23. 70 8. 18 3. 00 7. 95 0. 53 0. 26 2. 77 1. 62 5. 55 Slag 48. 3 22. 60 18. 51 3. 73 0. 76 0. 01 0. 14 0. 01 1. 48 0. 02 0. 11 Charging Si. O 2 C Fe Ca. O Al 2 O 3 P Zn S Cu
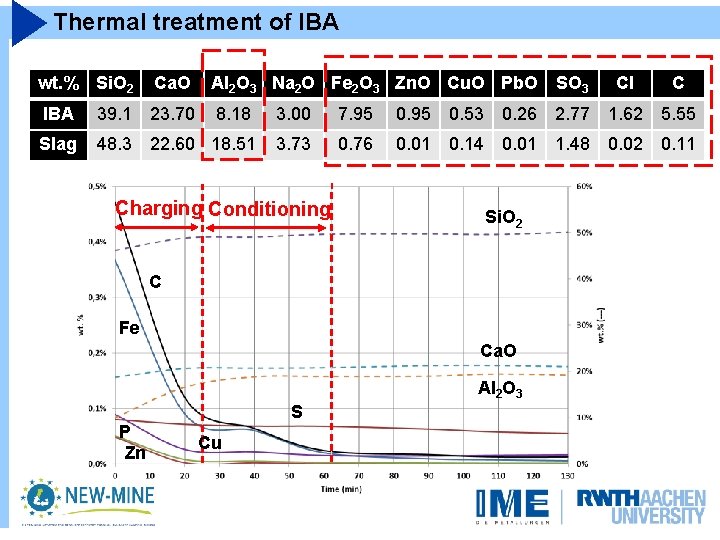
Thermal treatment of IBA wt. % Si. O 2 Ca. O Al 2 O 3 Na 2 O Fe 2 O 3 Zn. O Cu. O Pb. O SO 3 Cl C IBA 39. 1 23. 70 8. 18 3. 00 7. 95 0. 53 0. 26 2. 77 1. 62 5. 55 Slag 48. 3 22. 60 18. 51 3. 73 0. 76 0. 01 0. 14 0. 01 1. 48 0. 02 0. 11 Charging Conditioning Si. O 2 C Fe Ca. O Al 2 O 3 P Zn S Cu

IBA Decomposition CO 2 CO SO 2 Al 2 O 3 C Zn. O Cl Cu. O Pb. O Fe 2 O 3 SO 3
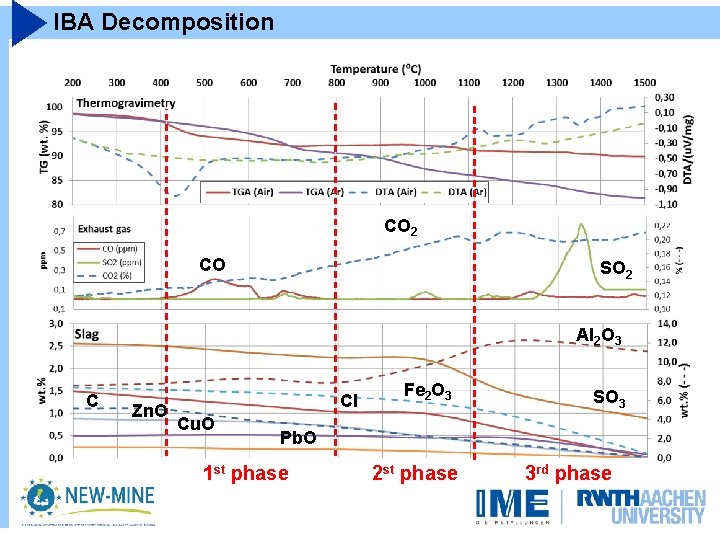
IBA Decomposition CO 2 CO SO 2 Al 2 O 3 C Zn. O Cl Cu. O Fe 2 O 3 SO 3 Pb. O 1 st phase 2 st phase 3 rd phase
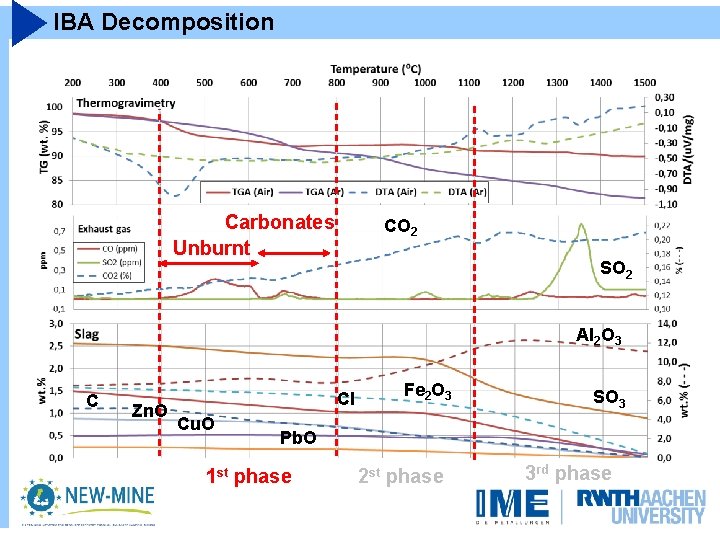
IBA Decomposition Carbonates Unburnt CO 2 SO 2 Al 2 O 3 C Zn. O Cl Cu. O Fe 2 O 3 SO 3 Pb. O 1 st phase 2 st phase 3 rd phase
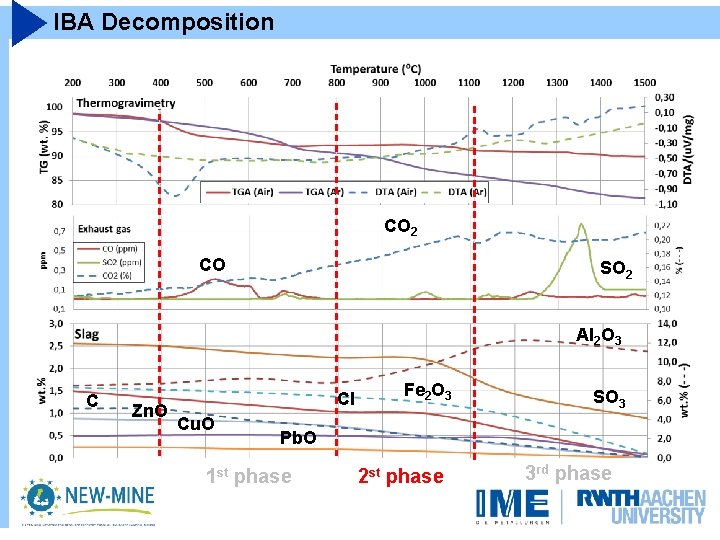
IBA Decomposition CO 2 CO SO 2 Al 2 O 3 C Zn. O Cl Cu. O Fe 2 O 3 SO 3 Pb. O 1 st phase 2 st phase 3 rd phase
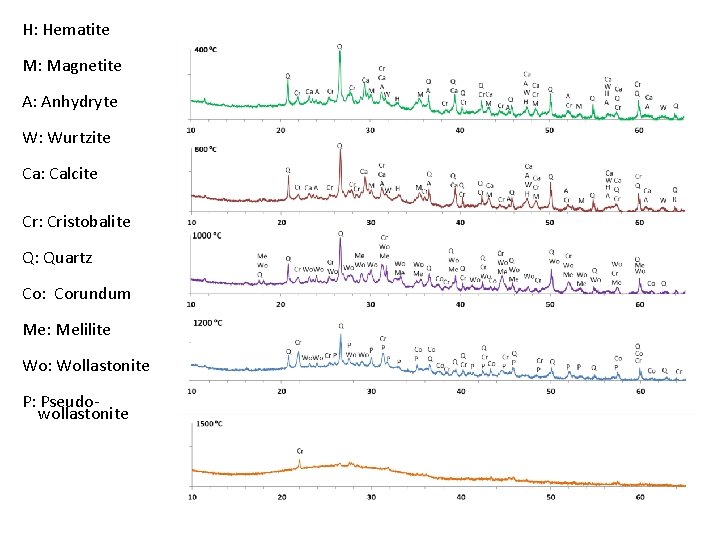
H: Hematite M: Magnetite A: Anhydryte W: Wurtzite Ca: Calcite Cr: Cristobalite Q: Quartz Co: Corundum Me: Melilite Wo: Wollastonite P: Pseudowollastonite

H: Hematite M: Magnetite A: Anhydryte W: Wurtzite Ca: Calcite Cr: Cristobalite Q: Quartz Co: Corundum Me: Melilite Wo: Wollastonite P: Pseudowollastonite
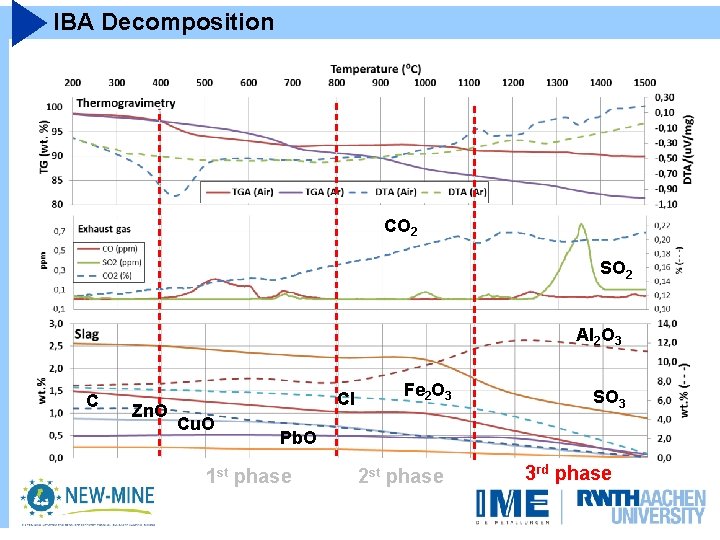
IBA Decomposition CO 2 SO 2 Al 2 O 3 C Zn. O Cl Cu. O Fe 2 O 3 SO 3 Pb. O 1 st phase 2 st phase 3 rd phase
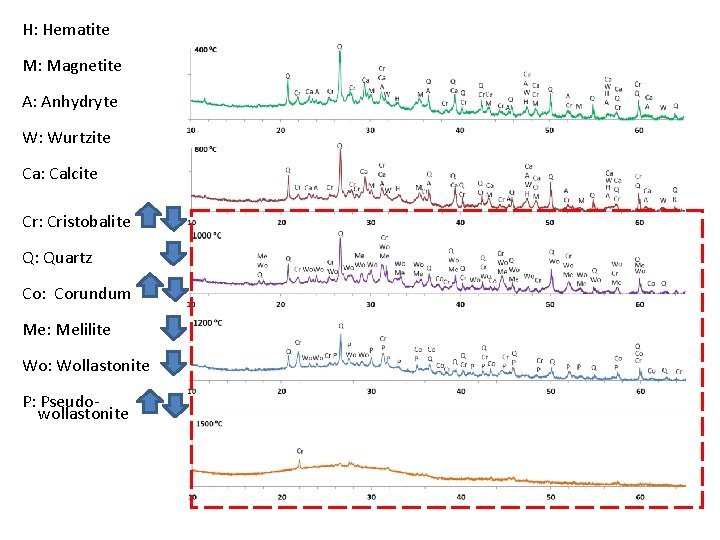
H: Hematite M: Magnetite A: Anhydryte W: Wurtzite Ca: Calcite Cr: Cristobalite Q: Quartz Co: Corundum Me: Melilite Wo: Wollastonite P: Pseudowollastonite
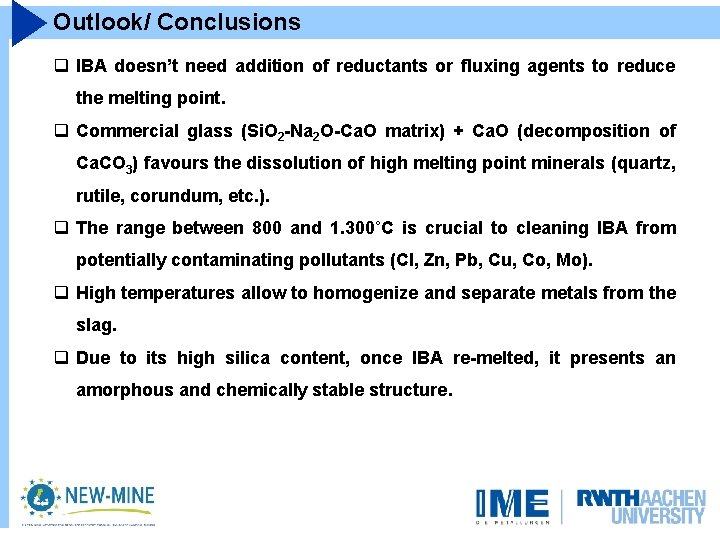
Outlook/ Conclusions q IBA doesn’t need addition of reductants or fluxing agents to reduce the melting point. q Commercial glass (Si. O 2 -Na 2 O-Ca. O matrix) + Ca. O (decomposition of Ca. CO 3) favours the dissolution of high melting point minerals (quartz, rutile, corundum, etc. ). q The range between 800 and 1. 300˚C is crucial to cleaning IBA from potentially contaminating pollutants (Cl, Zn, Pb, Cu, Co, Mo). q High temperatures allow to homogenize and separate metals from the slag. q Due to its high silica content, once IBA re-melted, it presents an amorphous and chemically stable structure.
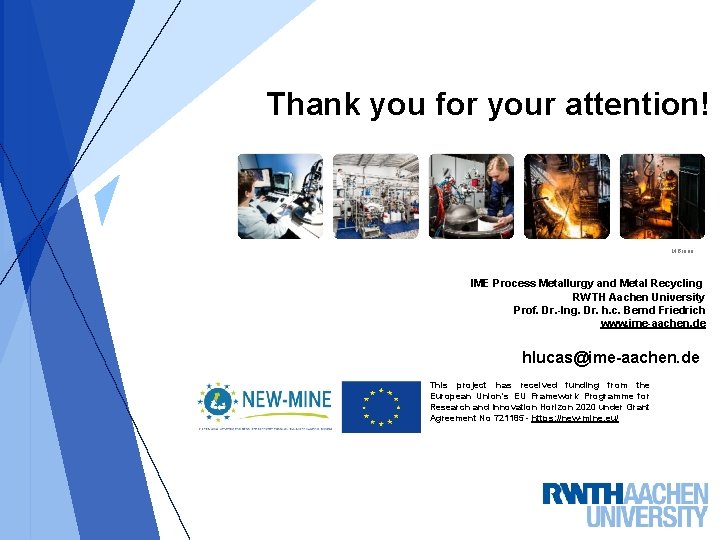
Thank you for your attention! M. Braun IME Process Metallurgy and Metal Recycling RWTH Aachen University Prof. Dr. -Ing. Dr. h. c. Bernd Friedrich www. ime-aachen. de hlucas@ime-aachen. de This project has received funding from the European Union's EU Framework Programme for Research and Innovation Horizon 2020 under Grant Agreement No 721185 - https: //new-mine. eu/
Slag valorisation symposium 2021
Valorisation
Methode de valorisation des stock
Valorisation des terres
Calcul du cmpc
Master biologie et valorisation des plantes
Slag bij hastings
Orkes instrumente
Root concavity weld defect
Electrode holder preventive maintenance
Slum as big as doom literary devices
Steam steam generator slag
Slag om verdun
Meaning:symposium
Title iii symposium
Geo virtual symposium
Acm symposium on cloud computing
Banking analytics symposium
Shock and vibration symposium
Ny metro asc symposium new york
You couldnt have
International perforating symposium