Production and Operation mangement Definition Production It implies
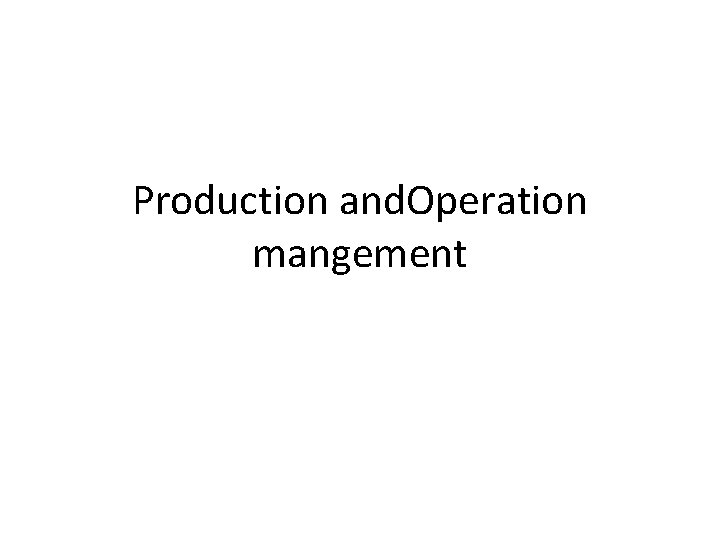

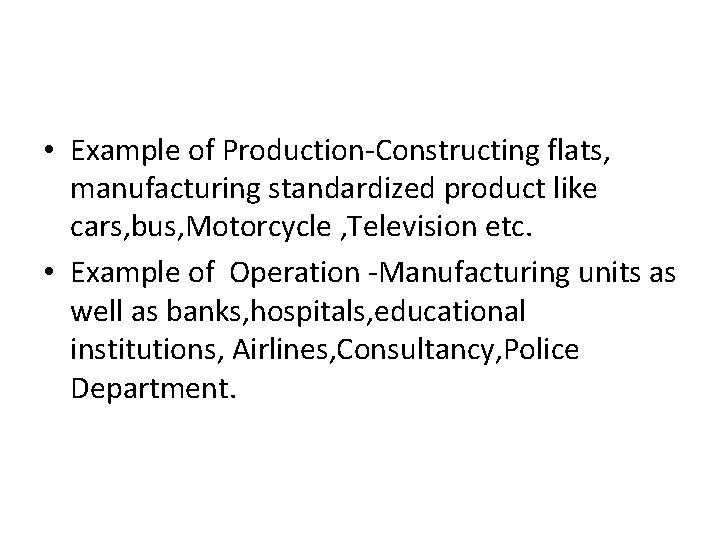
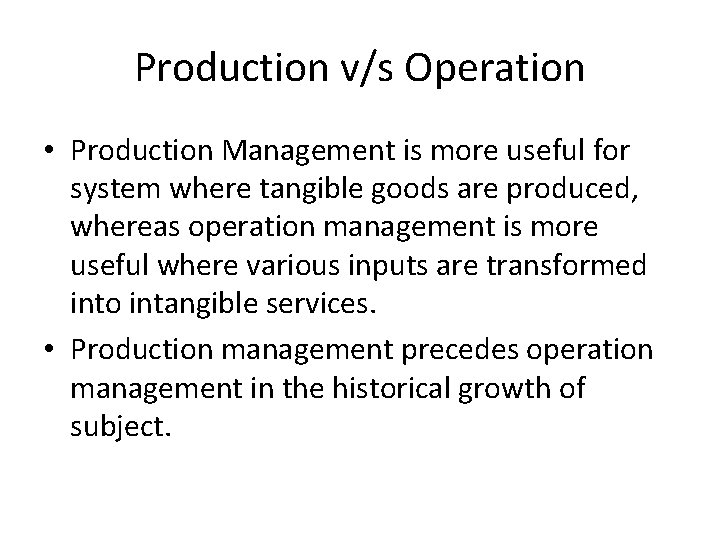
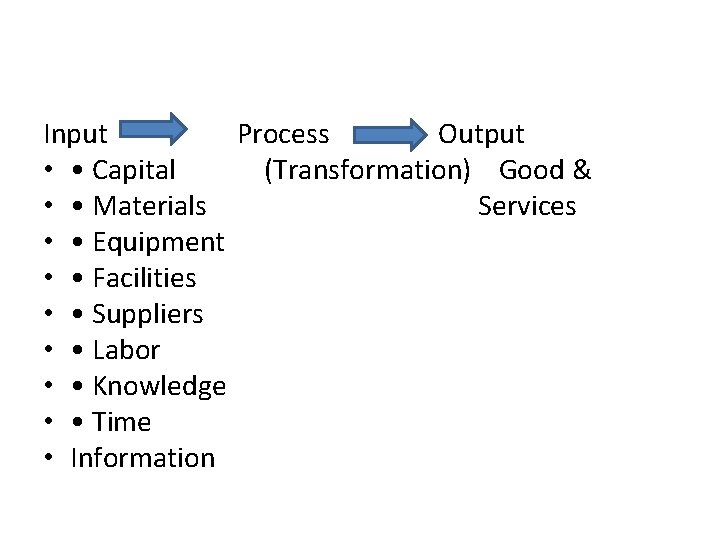
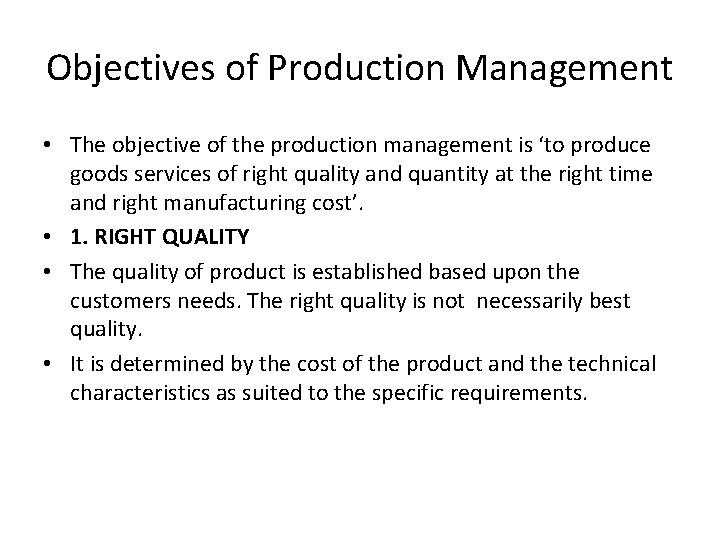
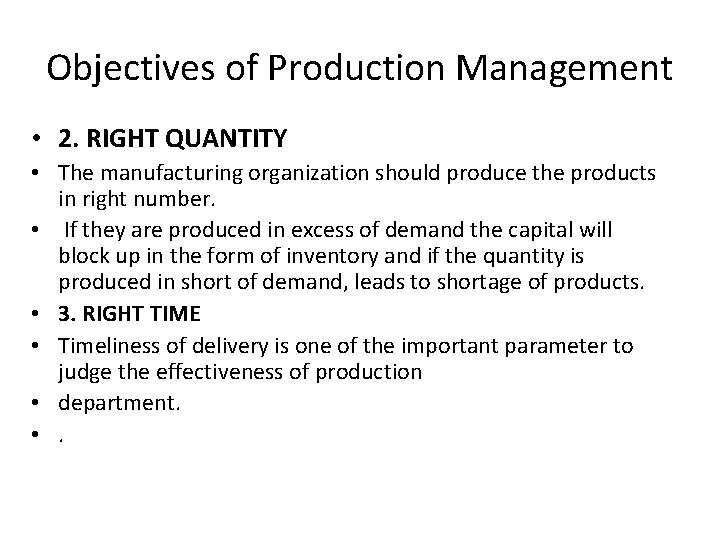
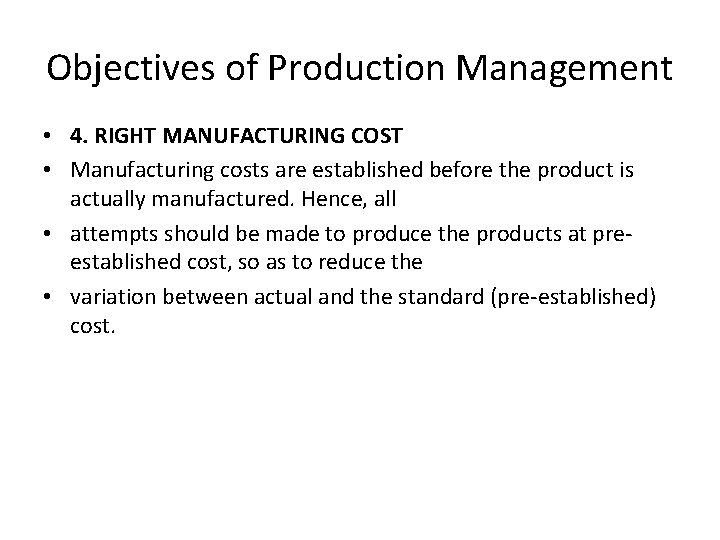
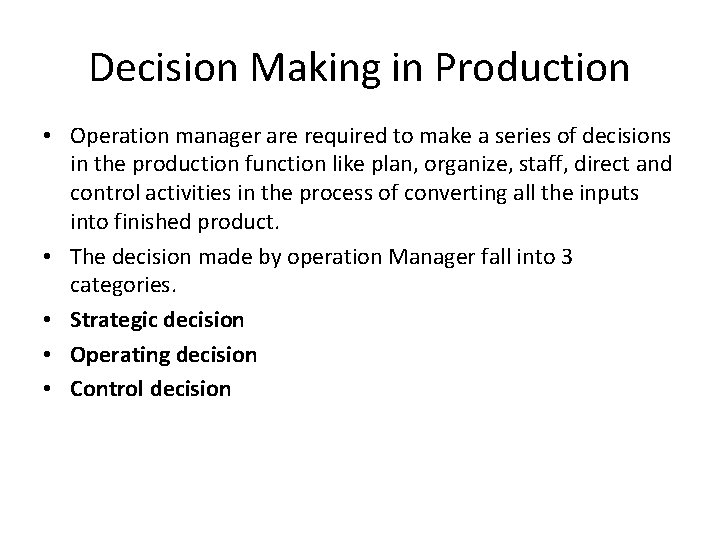
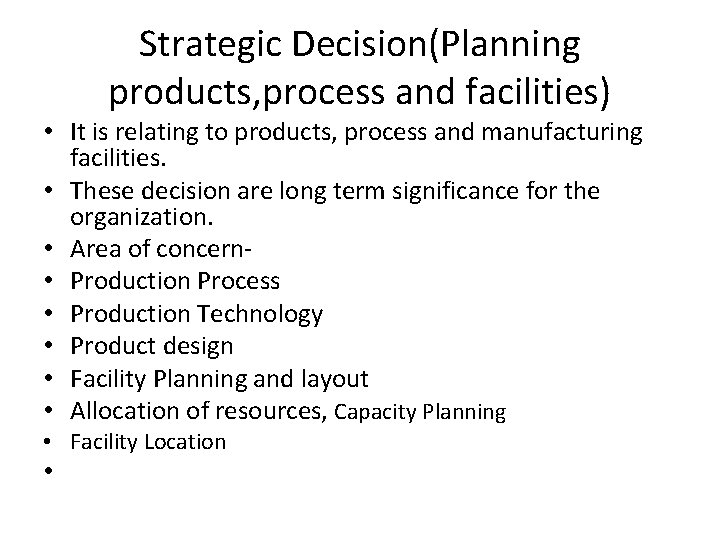
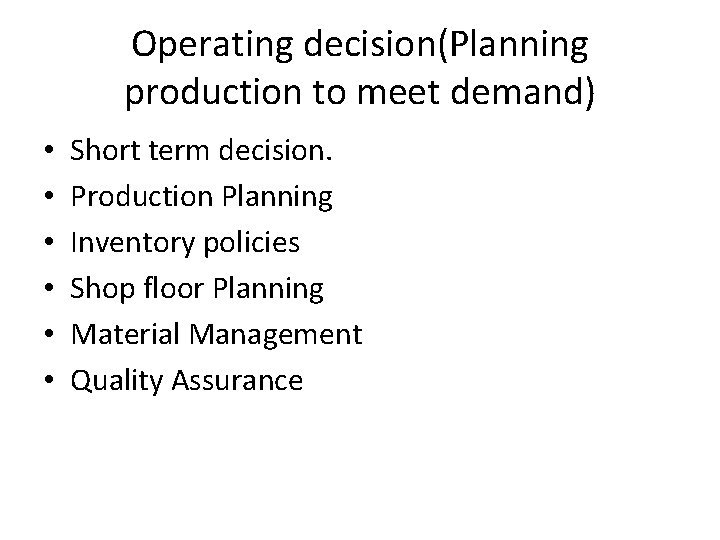
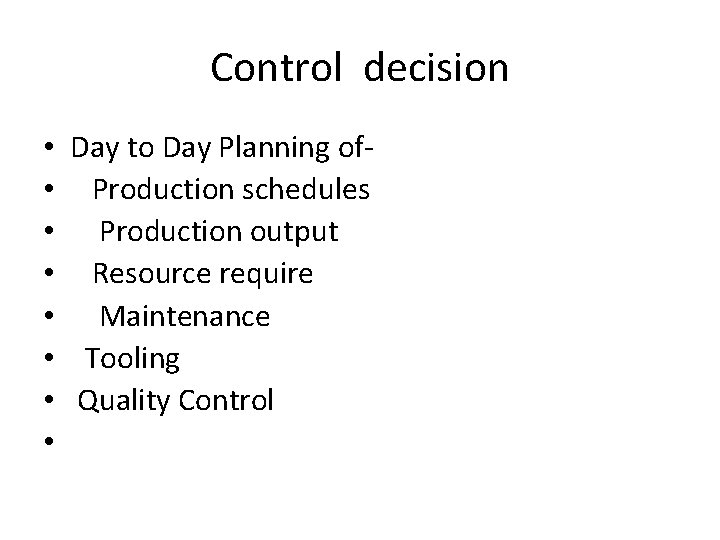
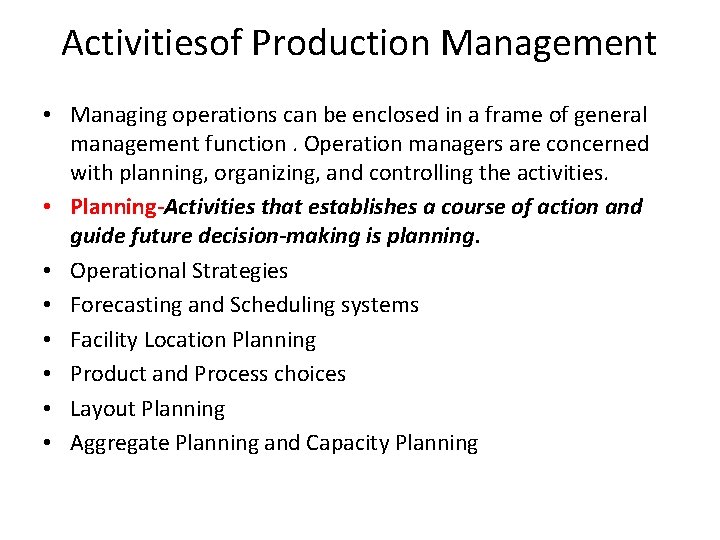
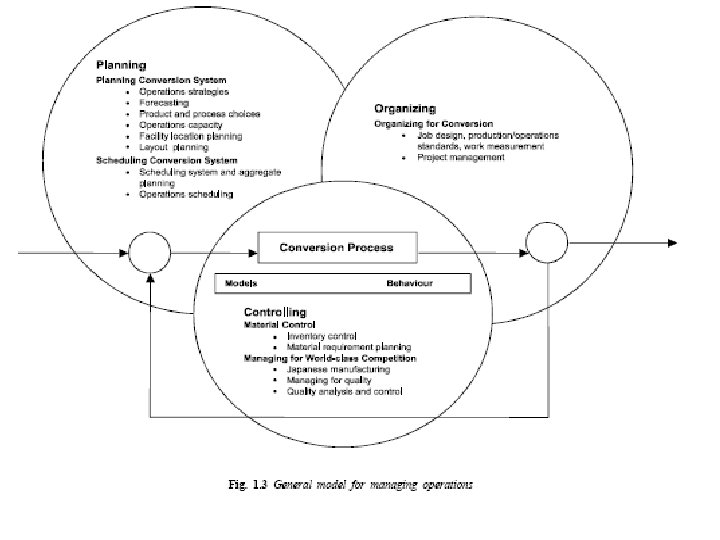
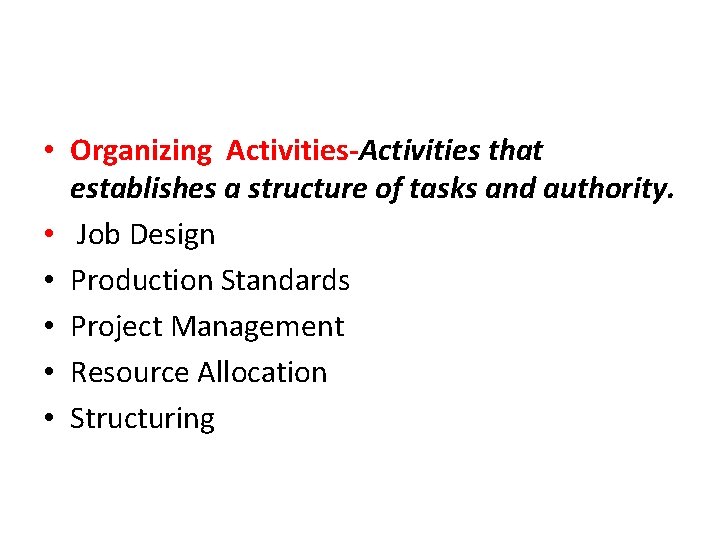
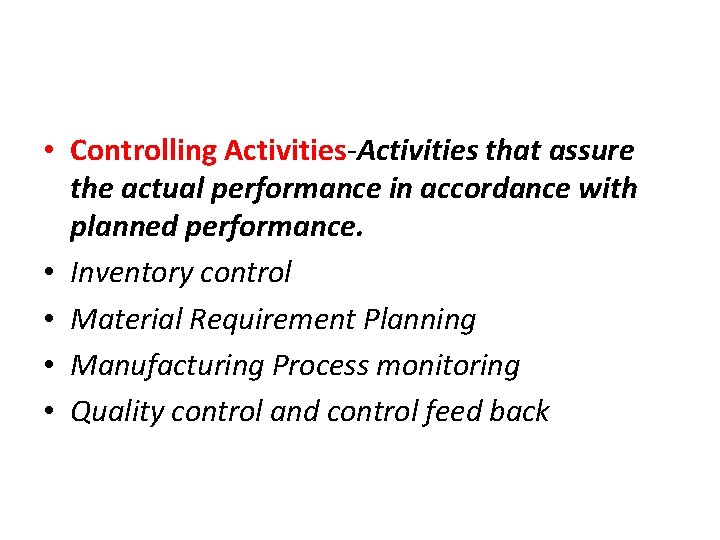
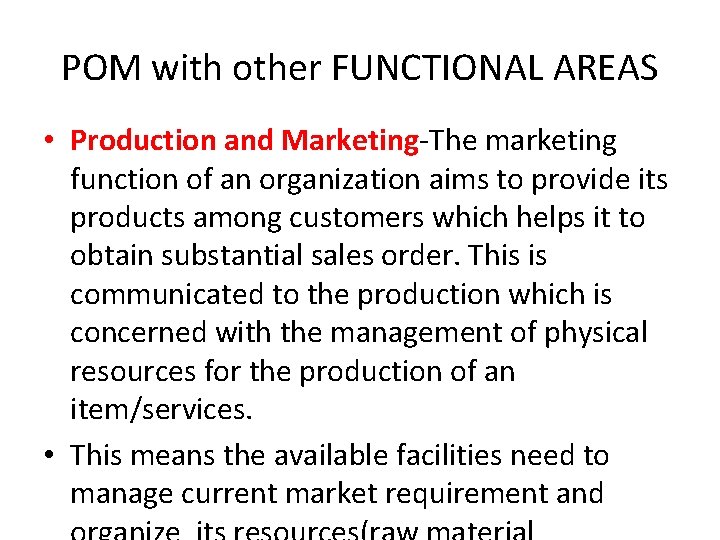
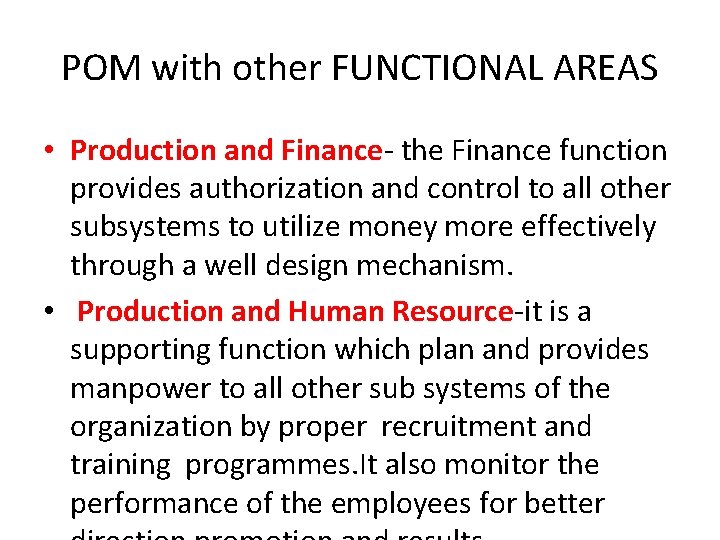
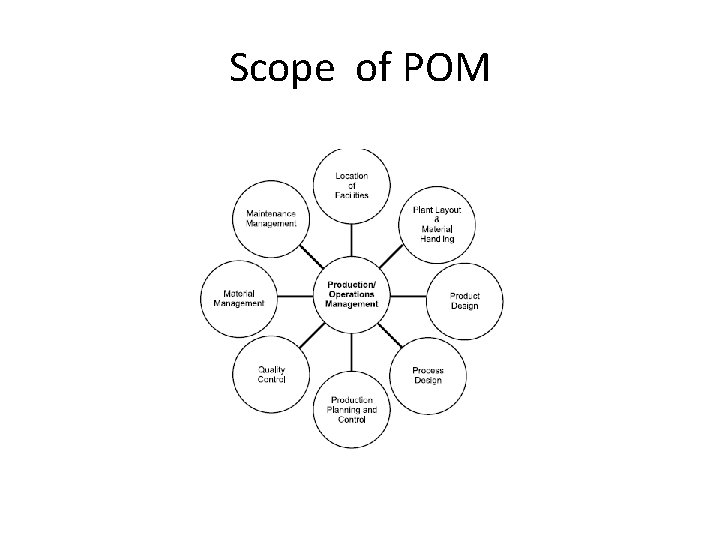
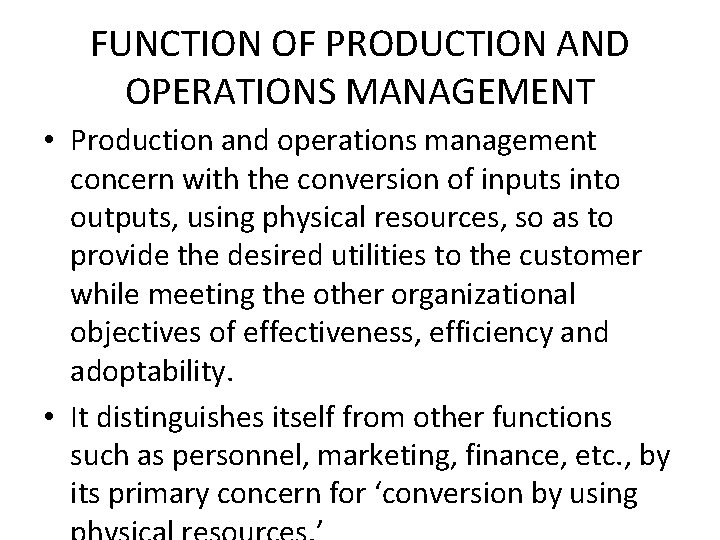
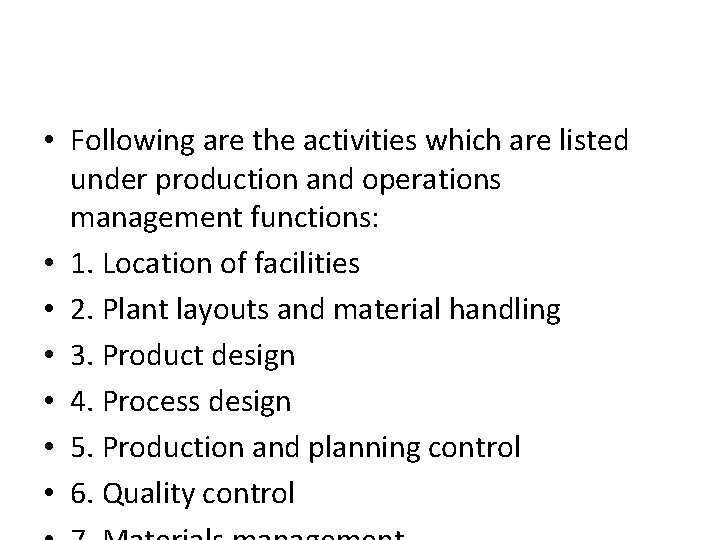
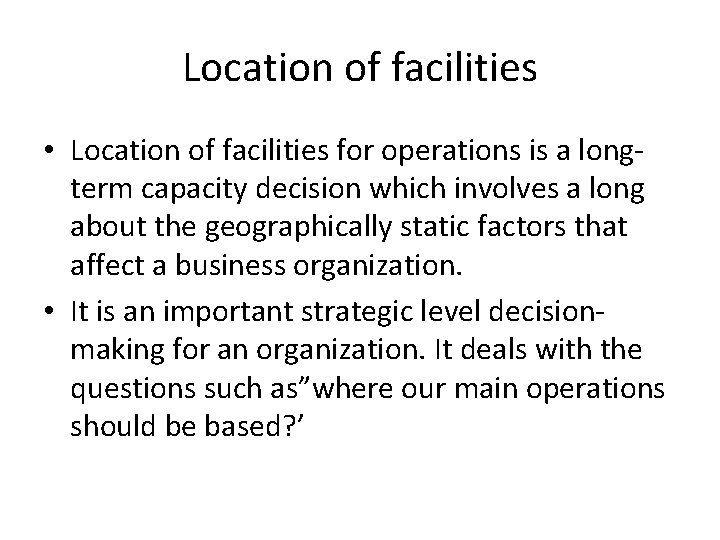
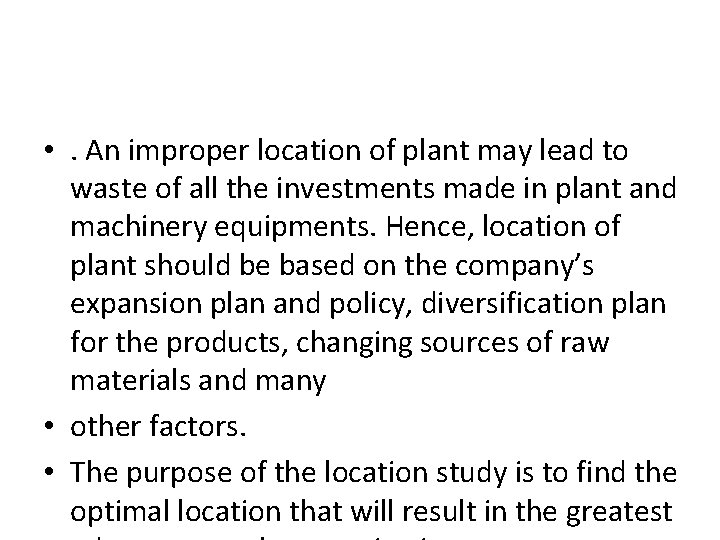

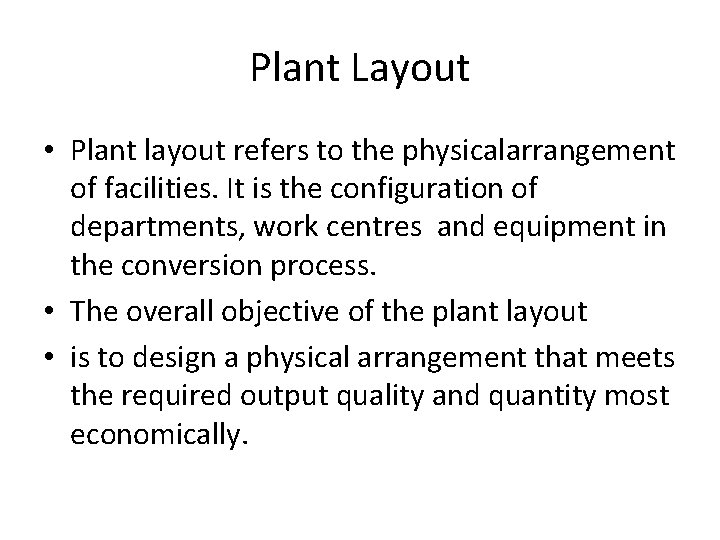
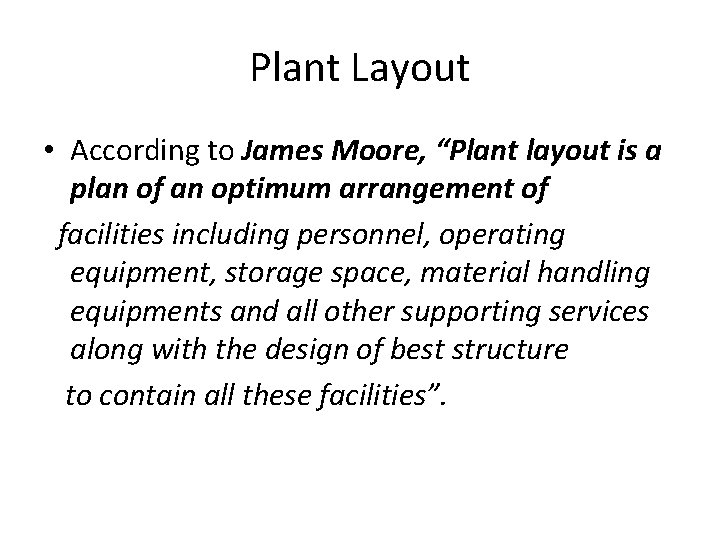
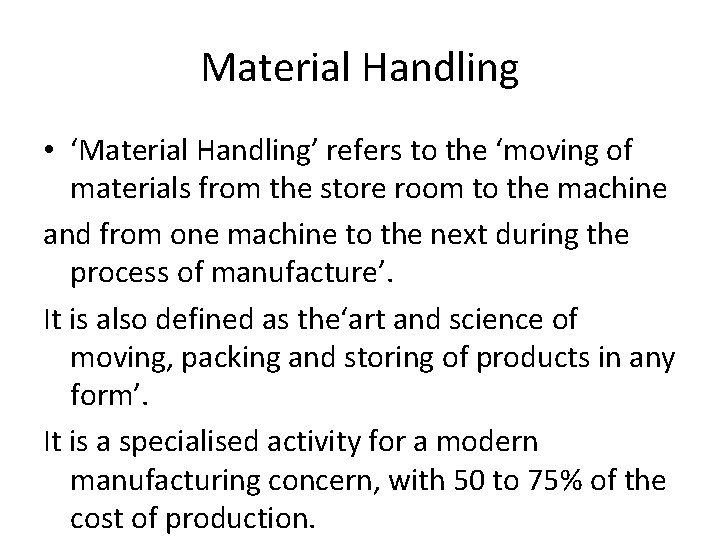
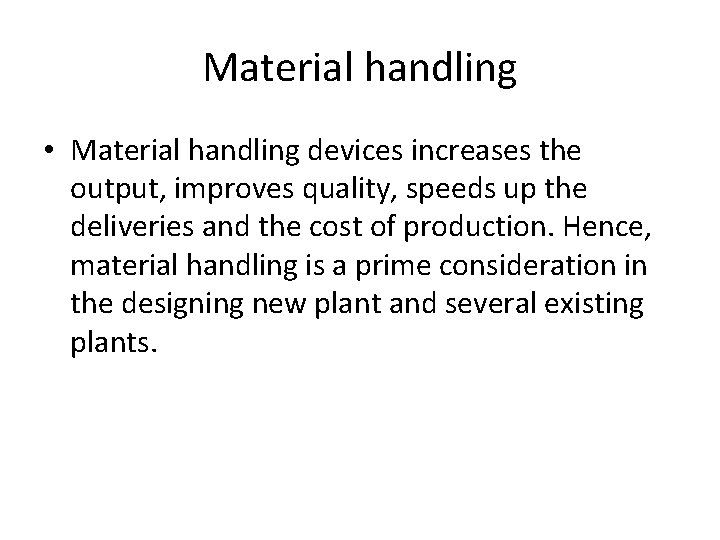
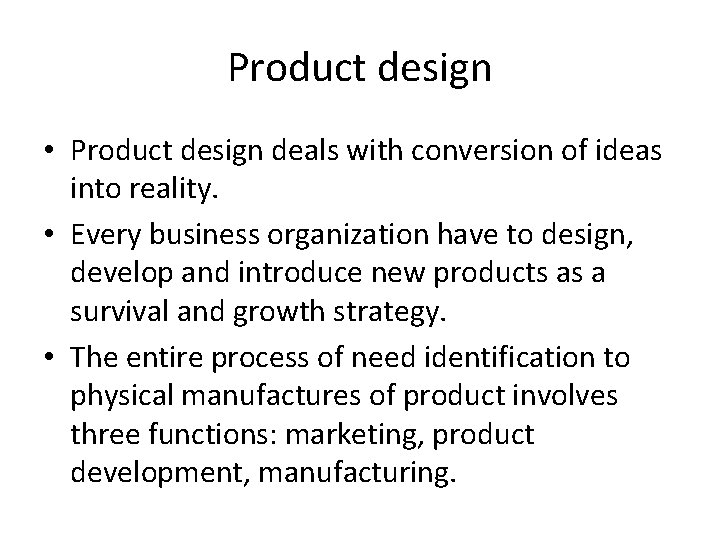

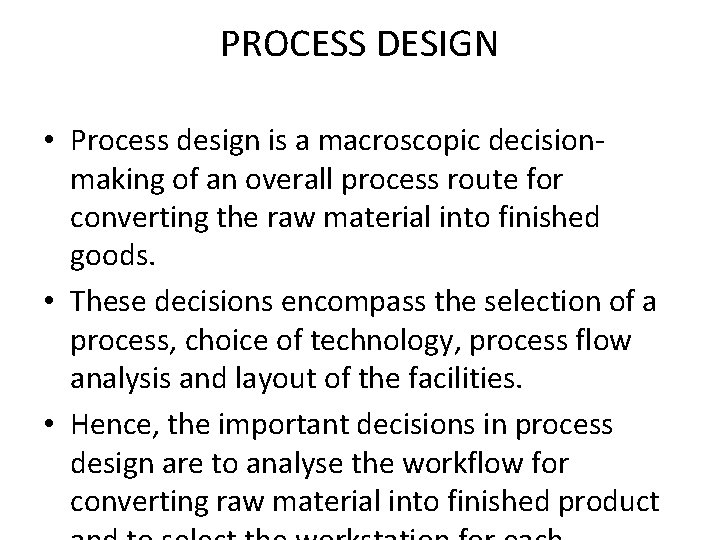
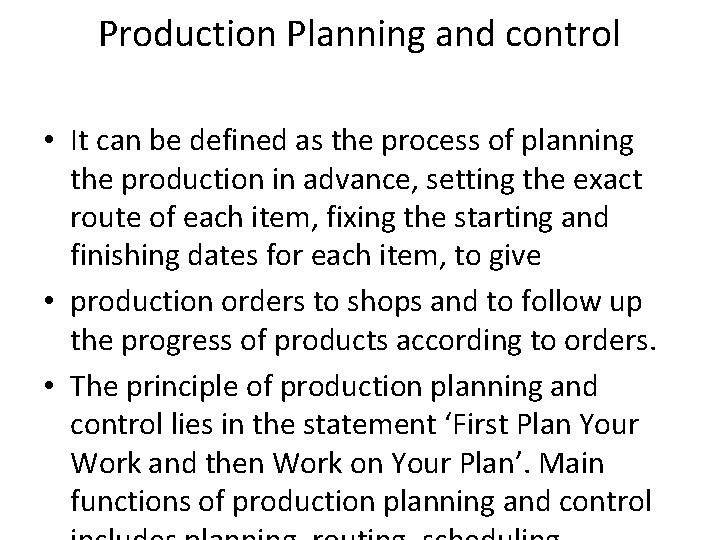
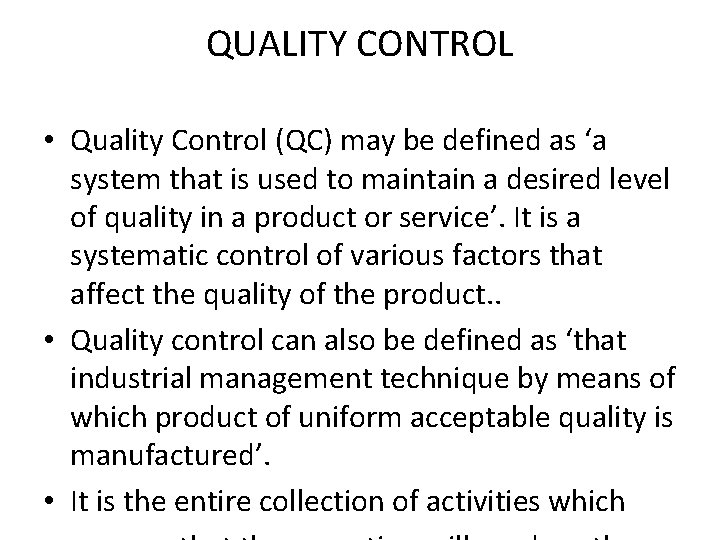
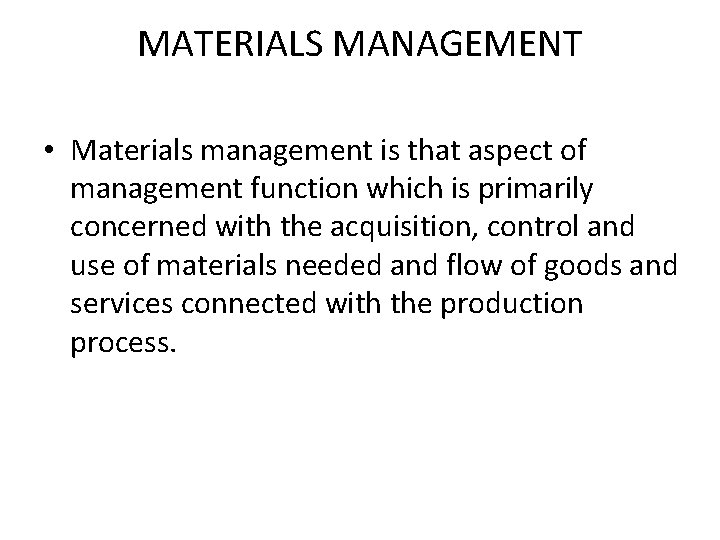
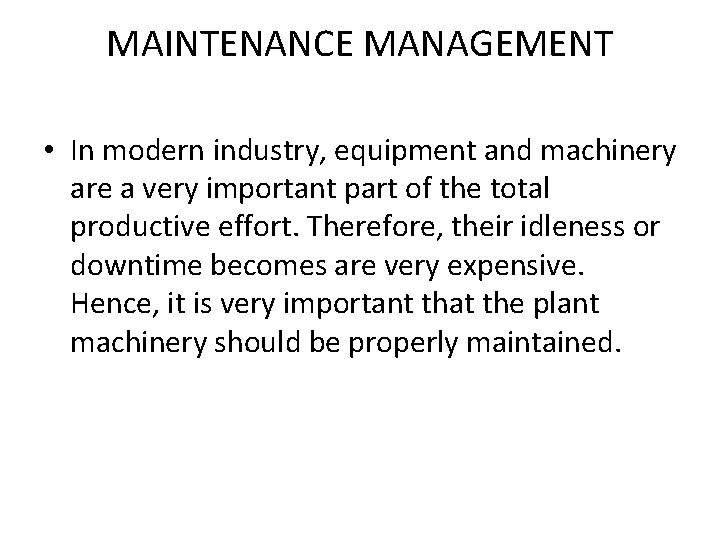
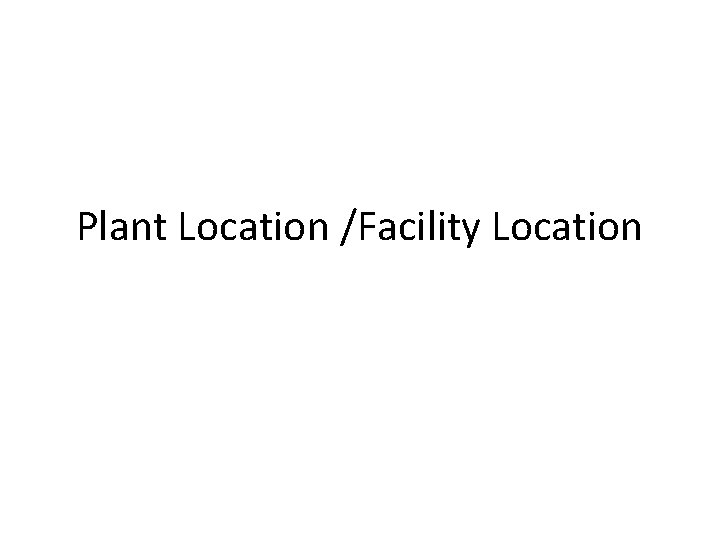
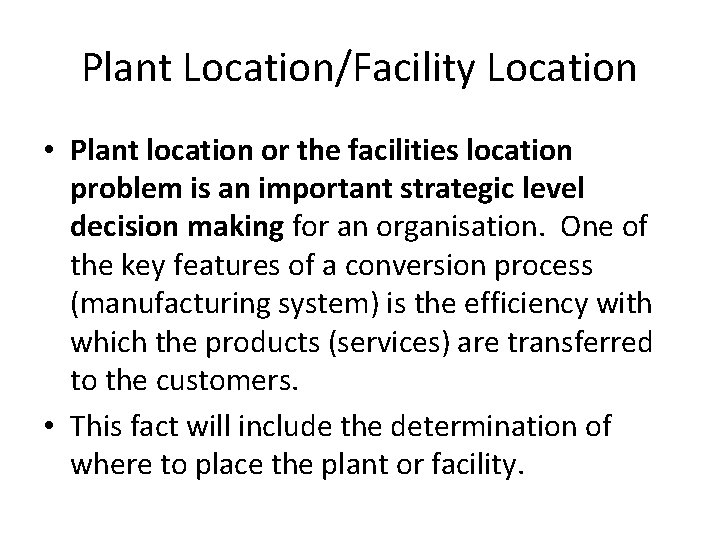
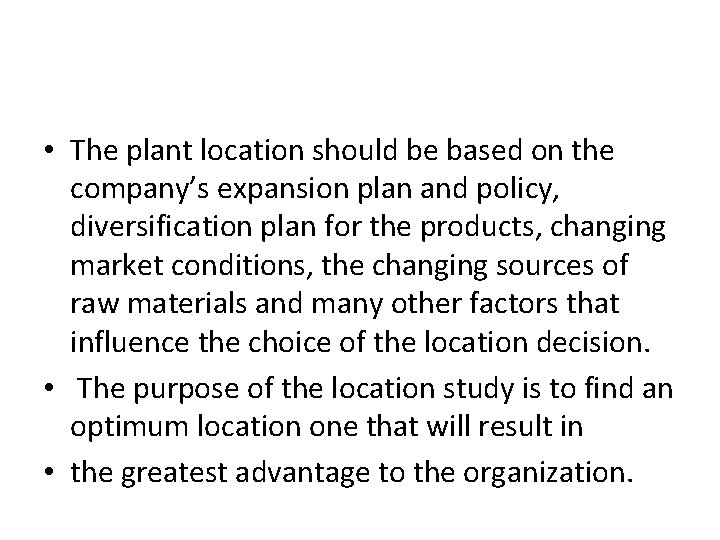
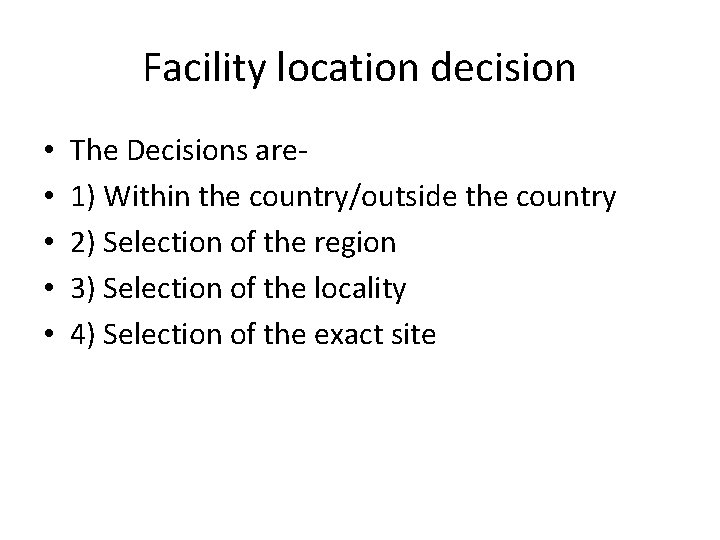
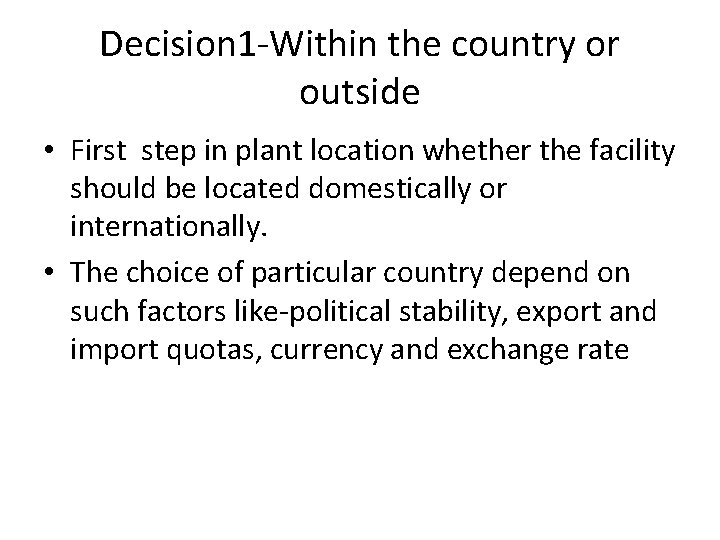
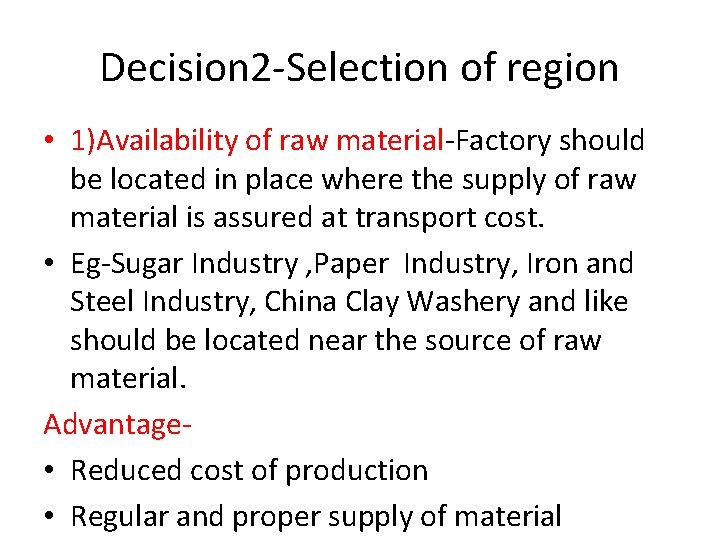
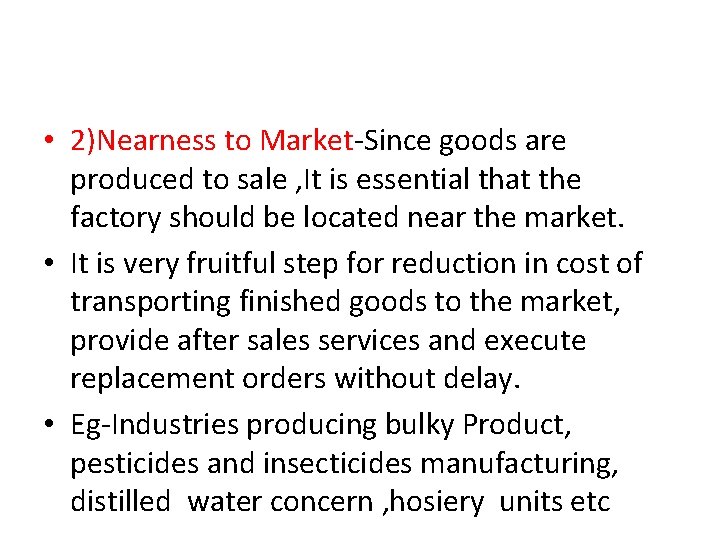
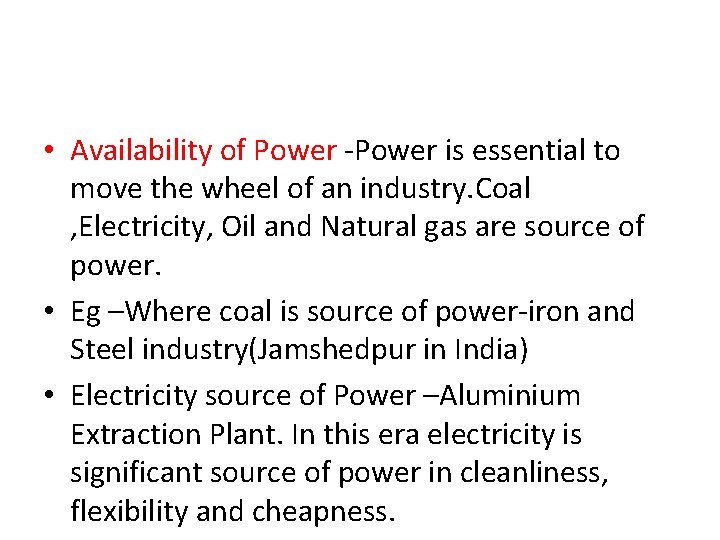
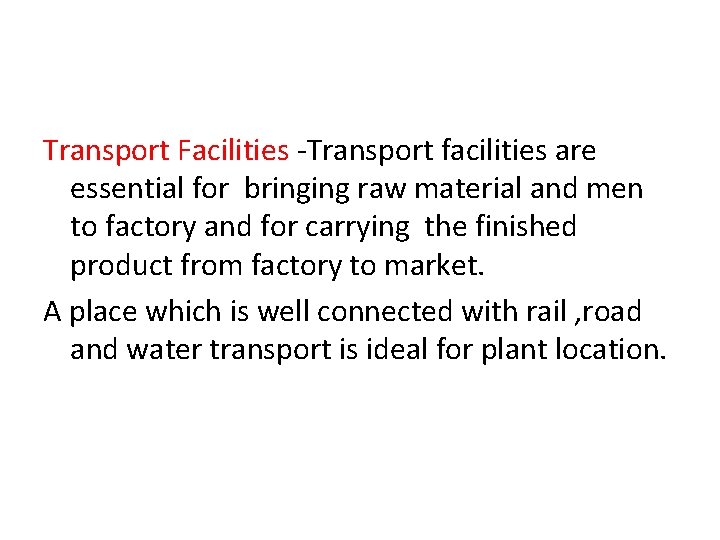
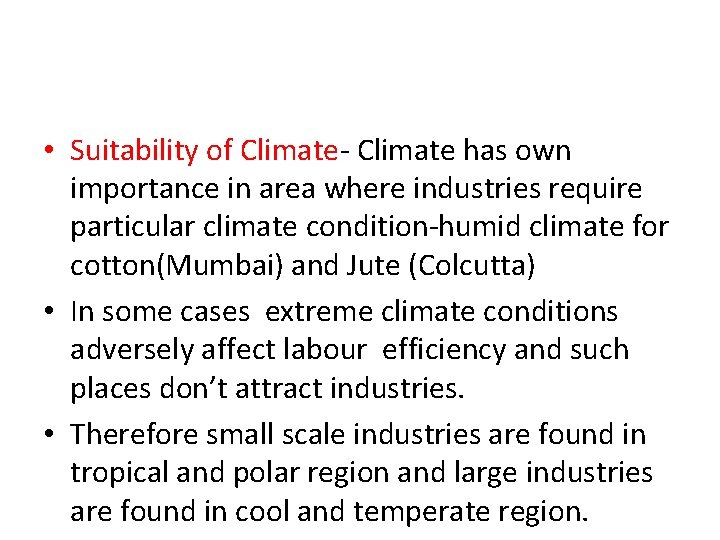
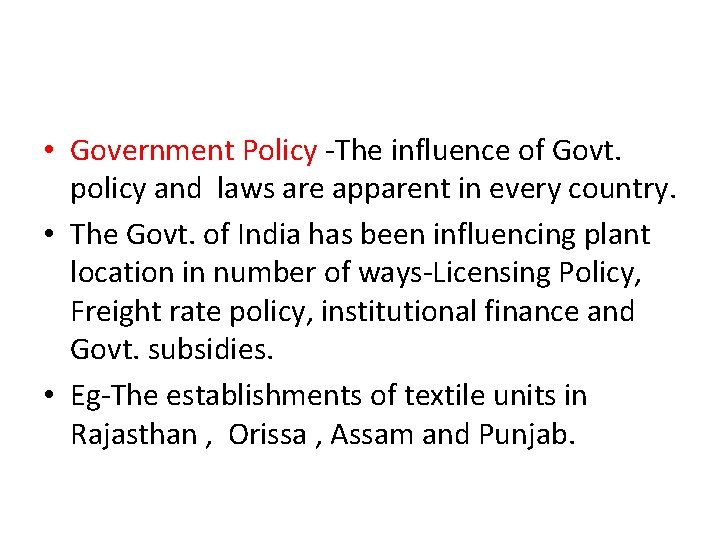
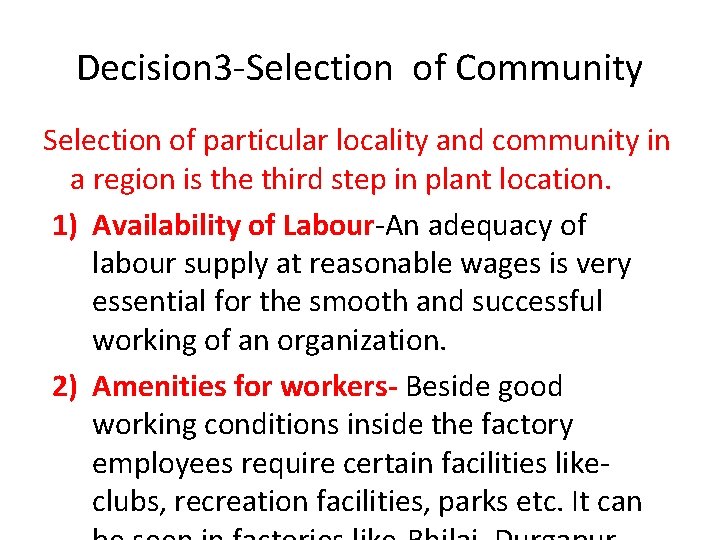
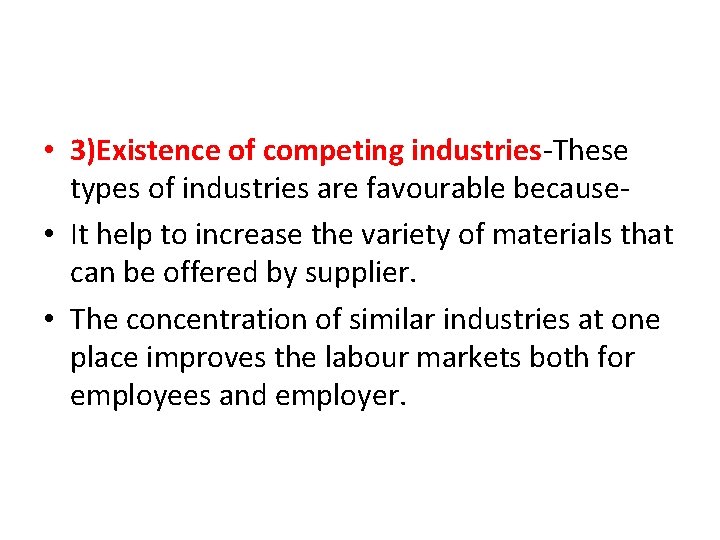
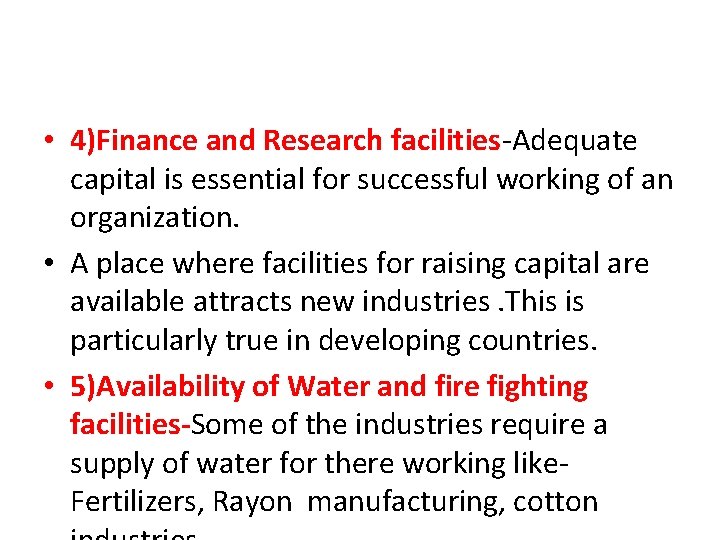
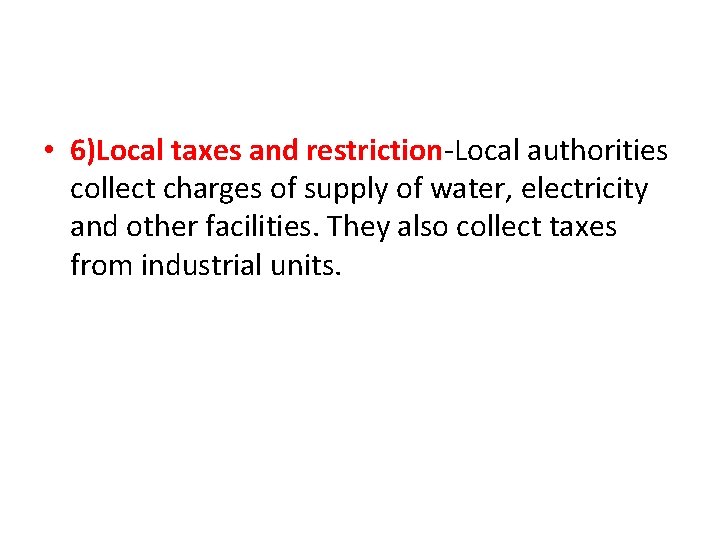
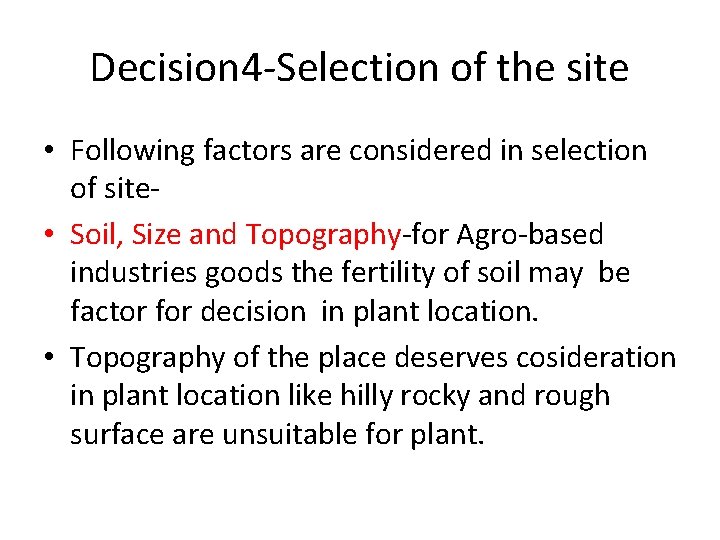
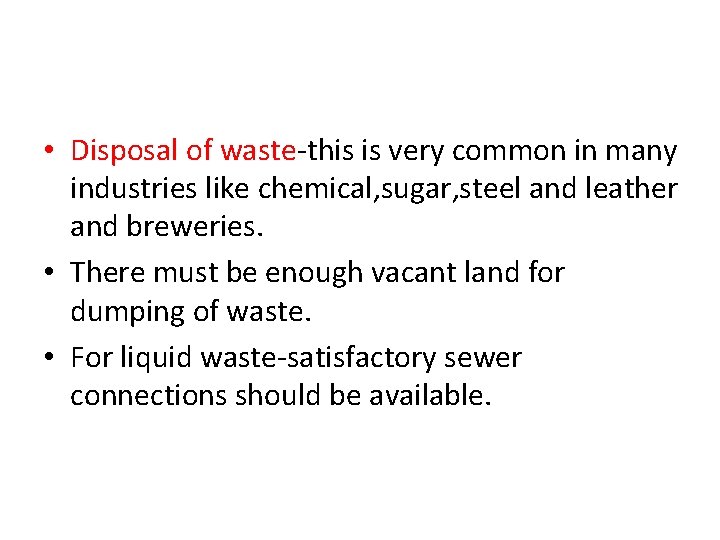
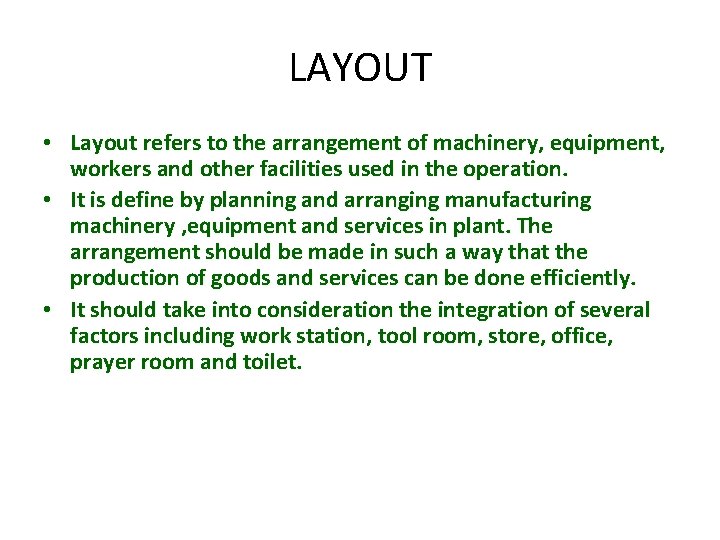
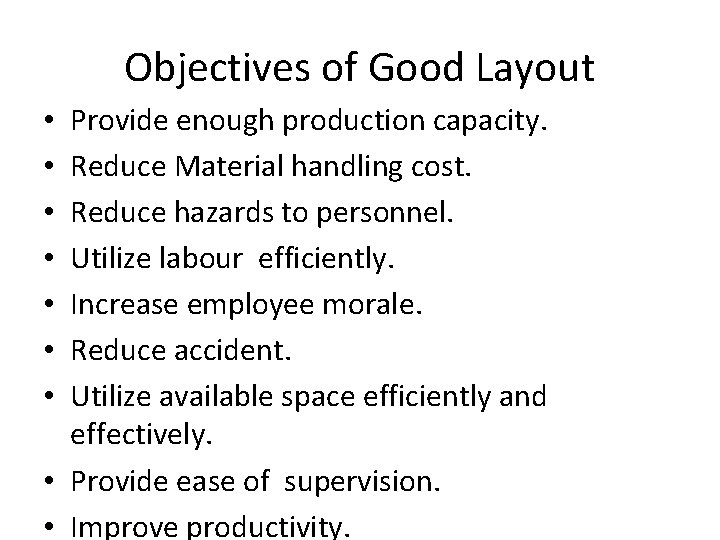
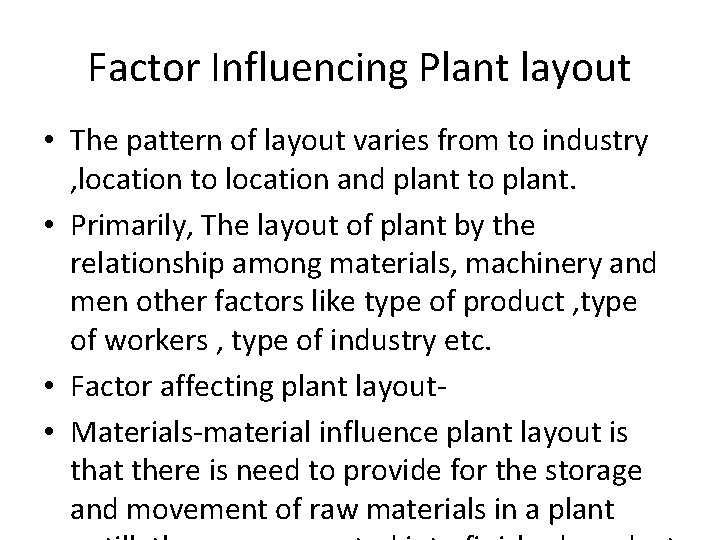
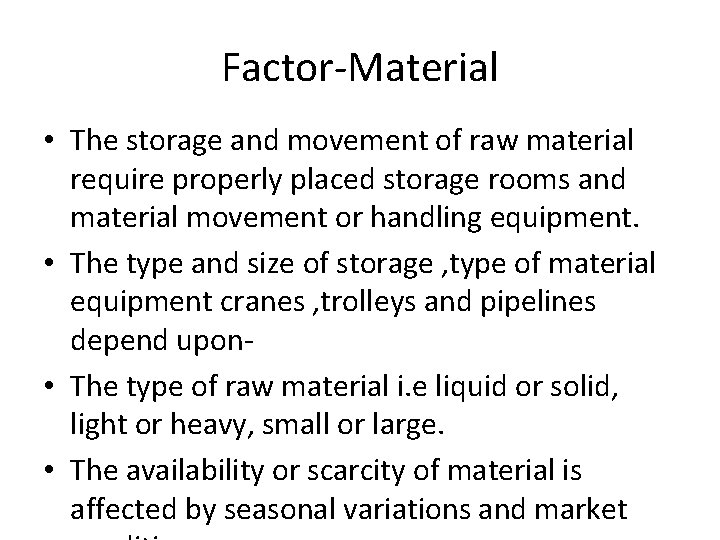
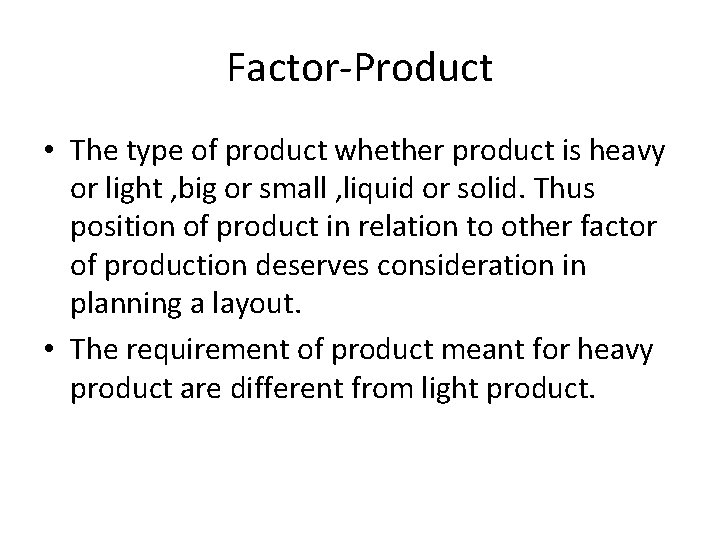
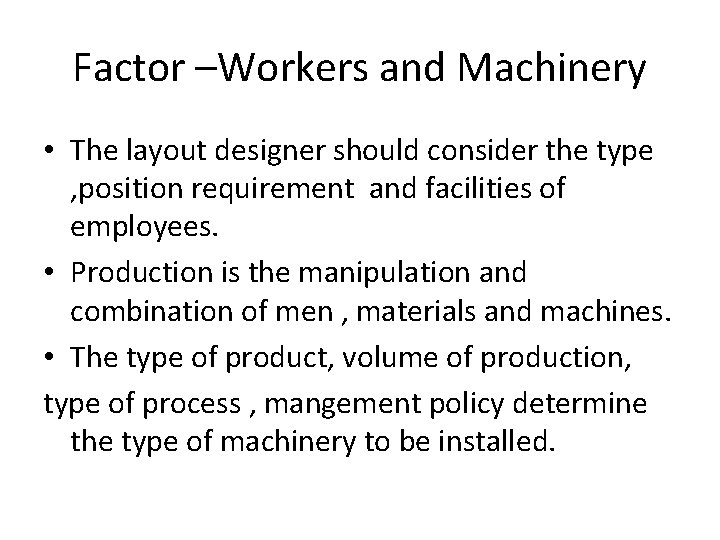
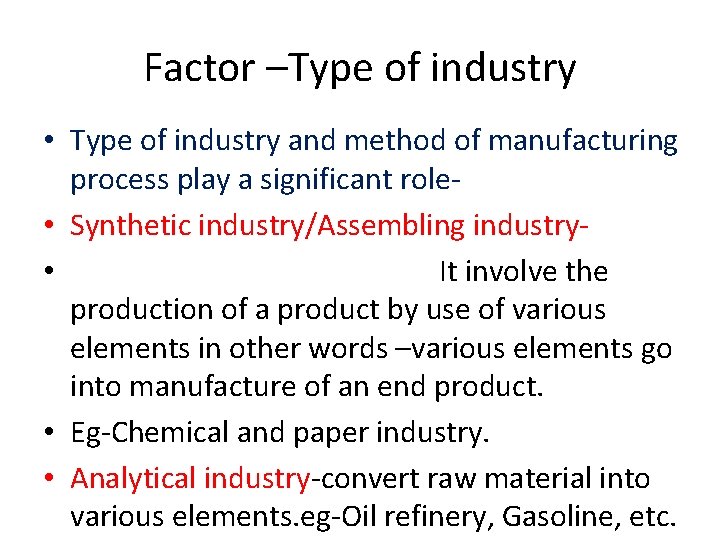
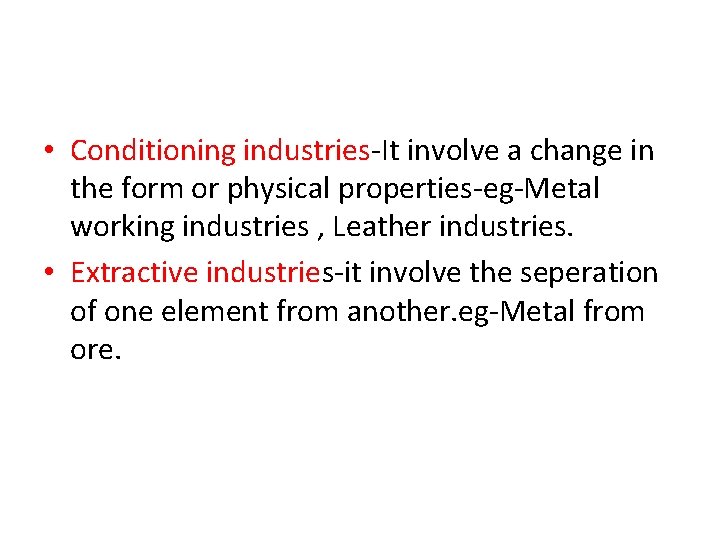
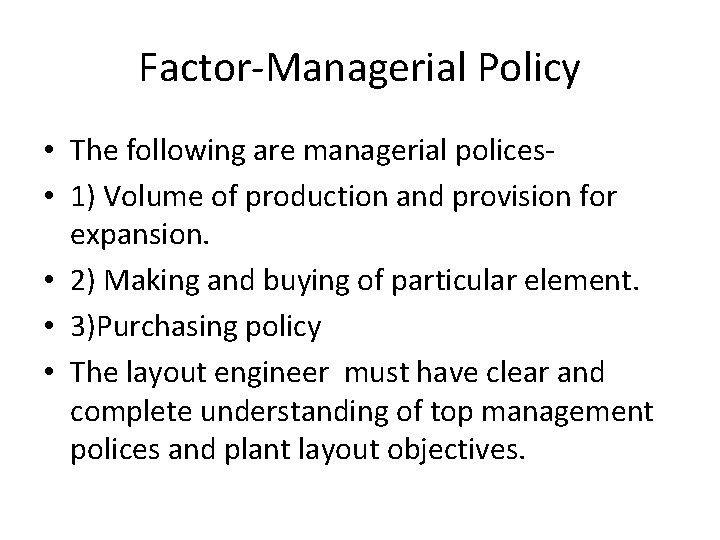
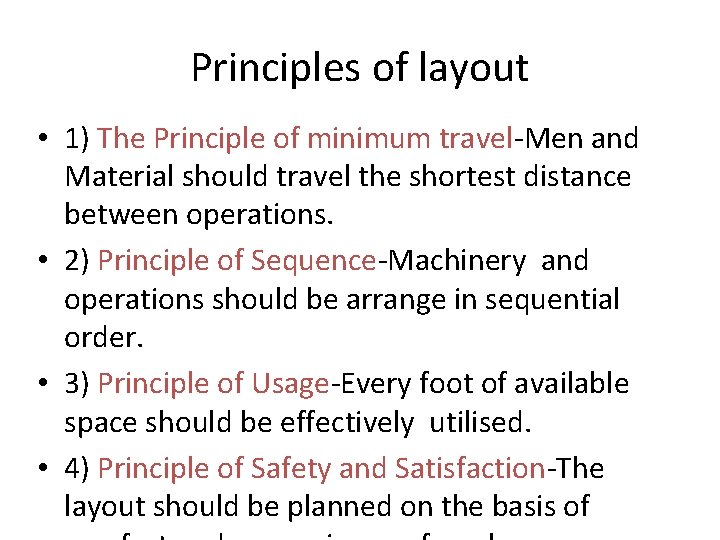
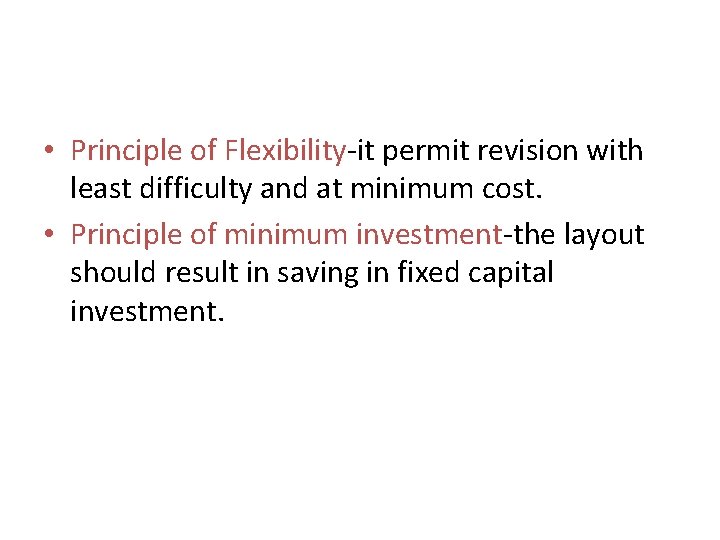
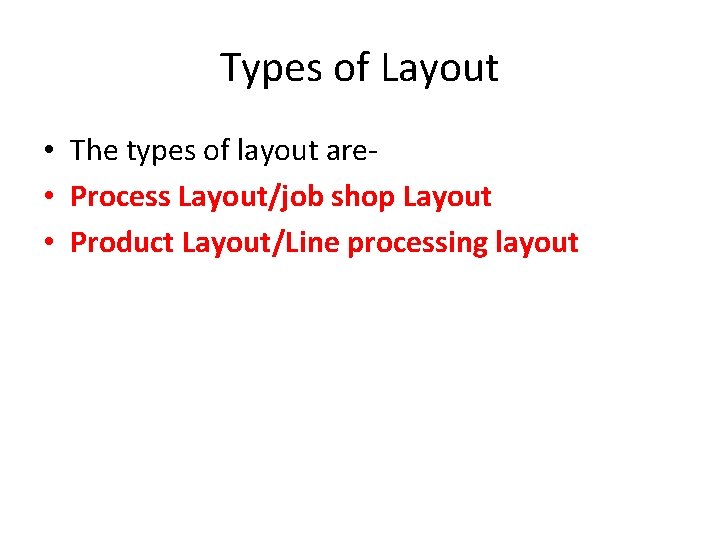
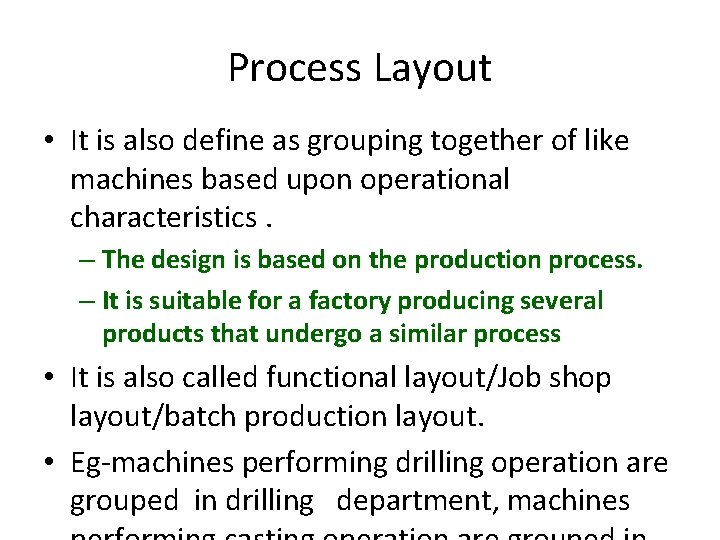
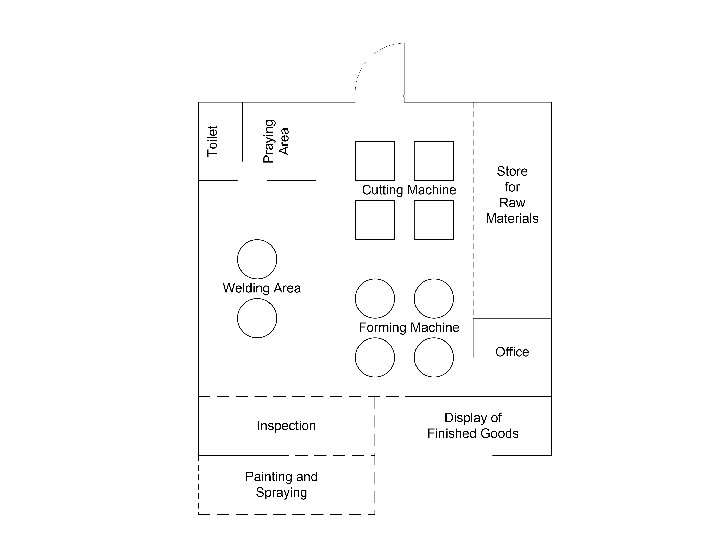
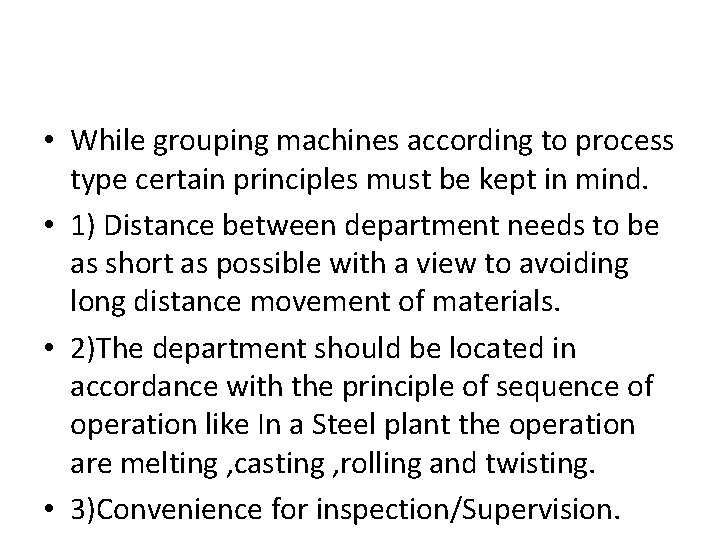
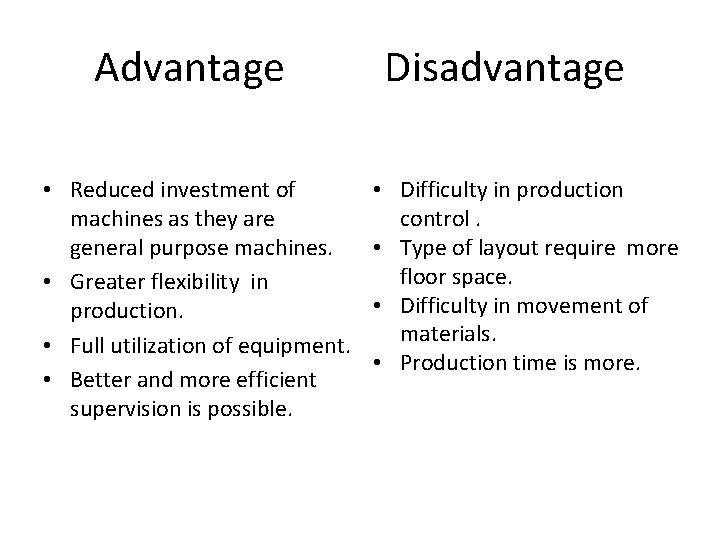
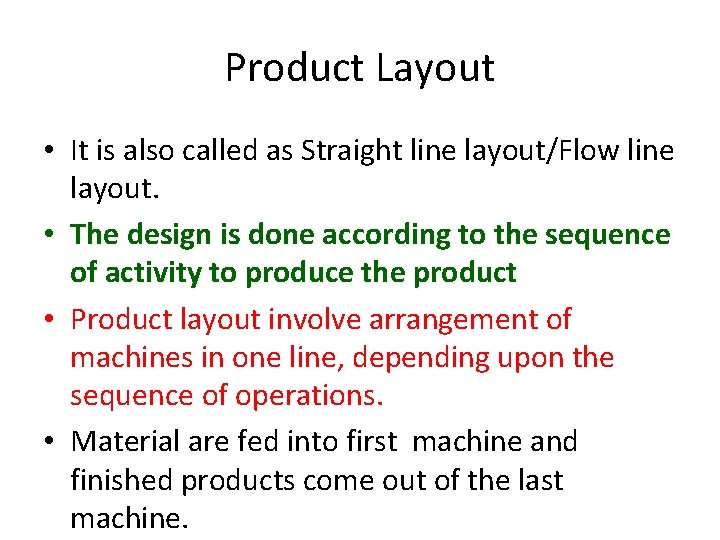
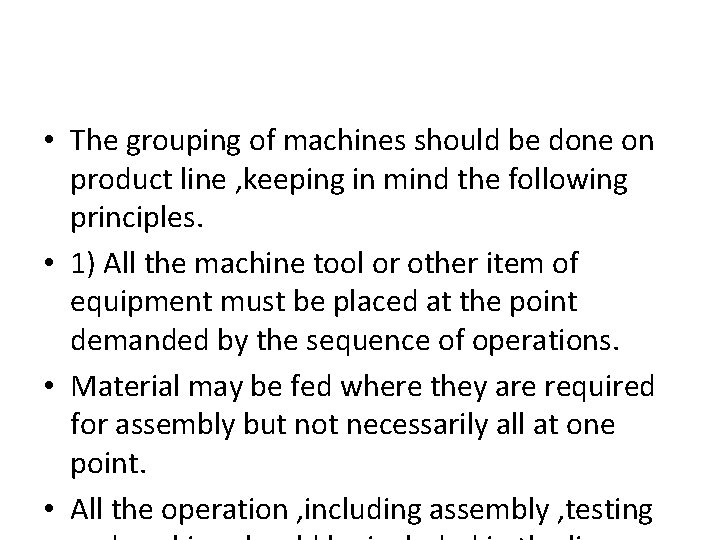
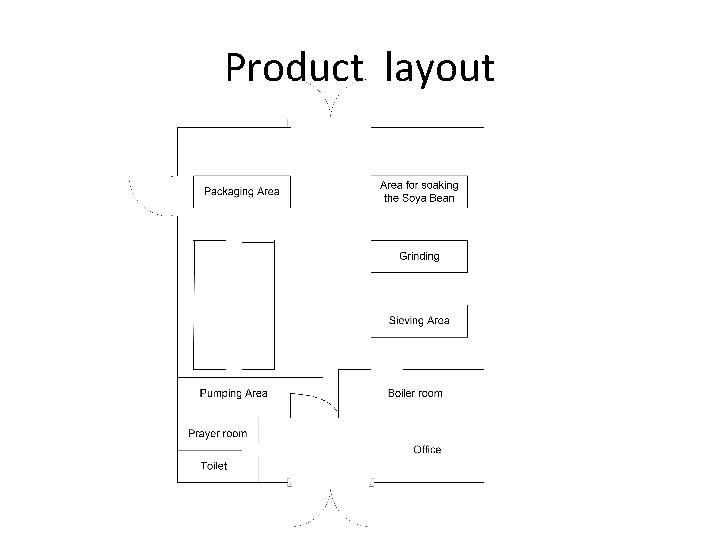
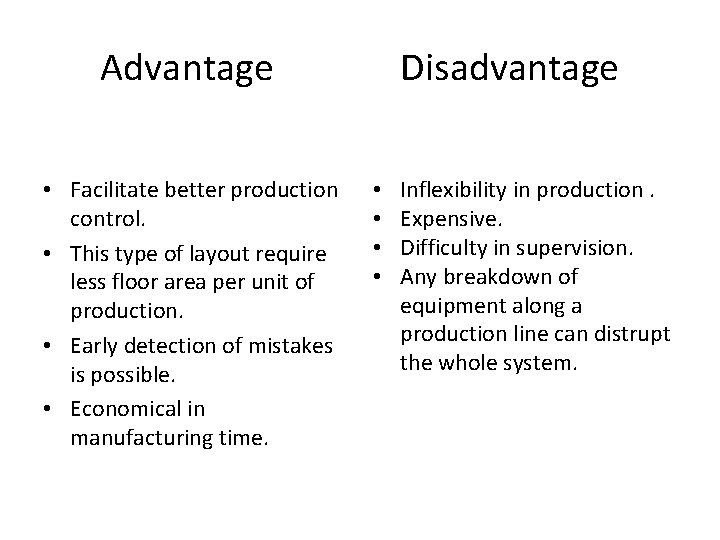
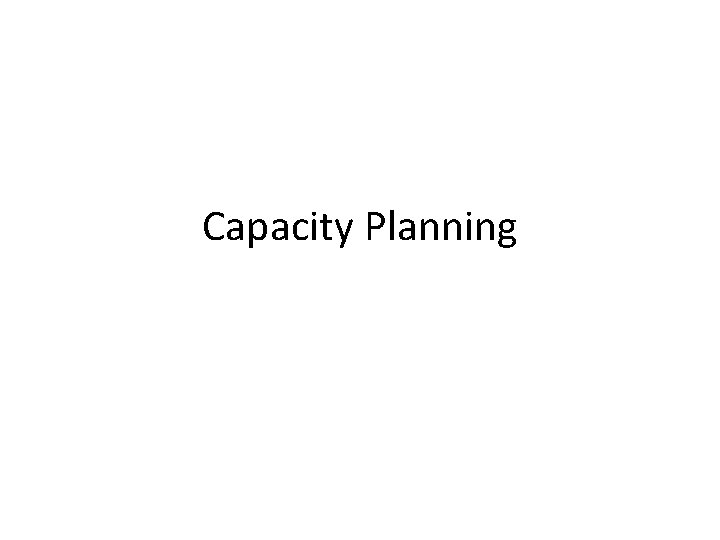
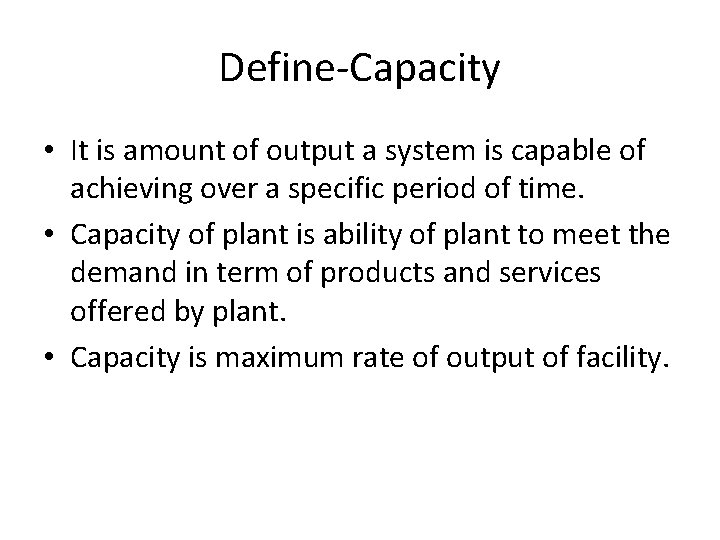
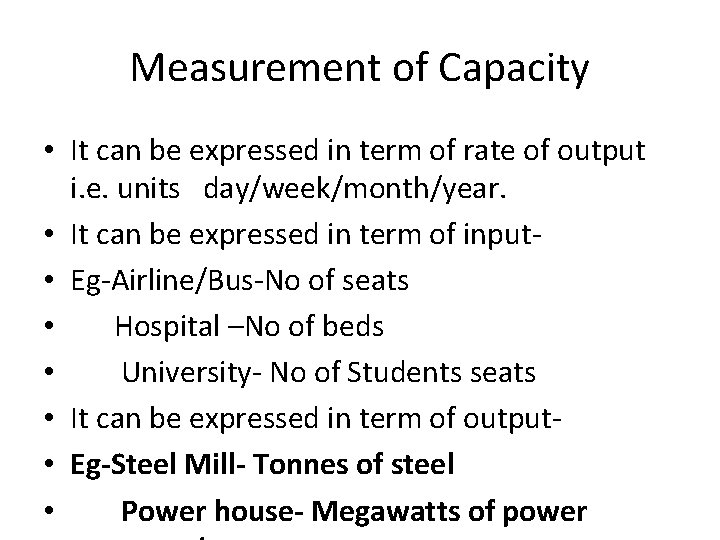
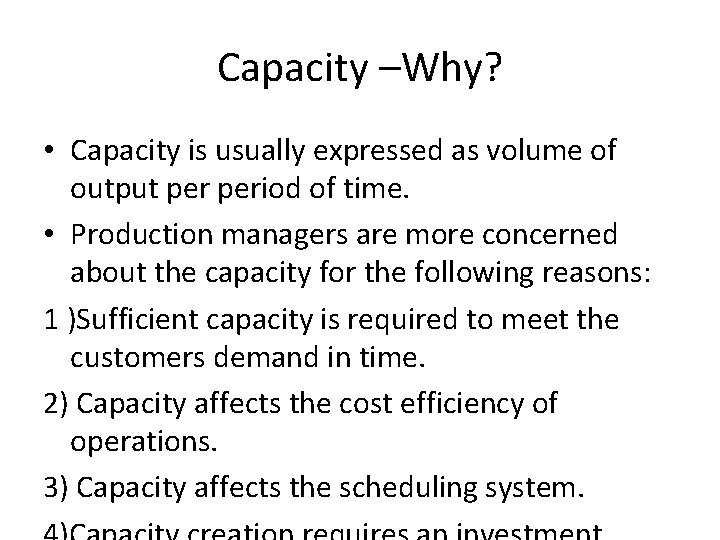
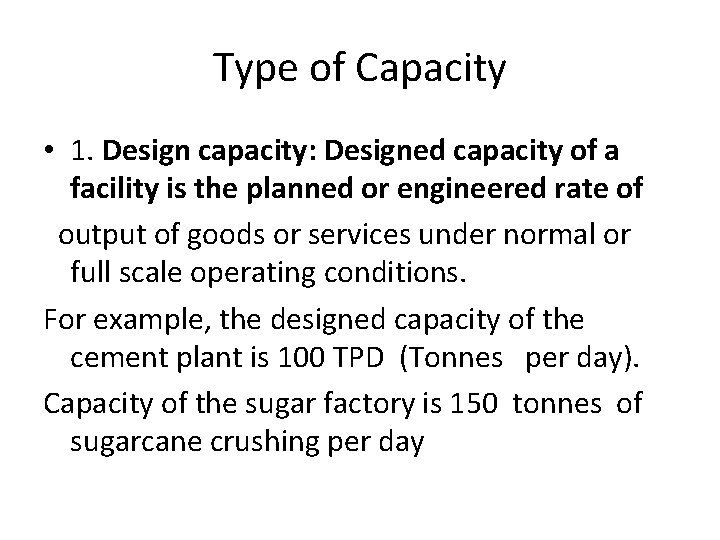
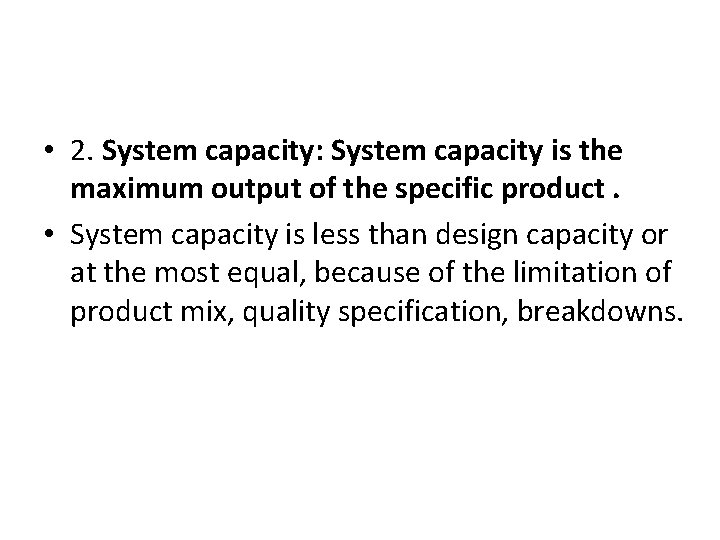
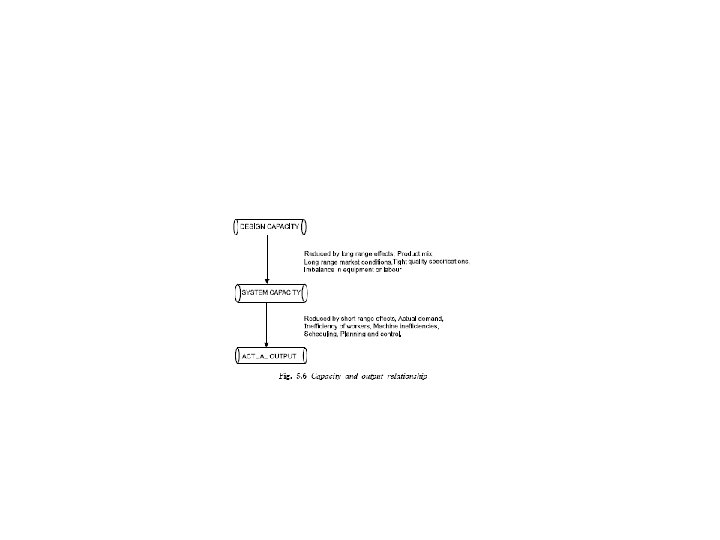
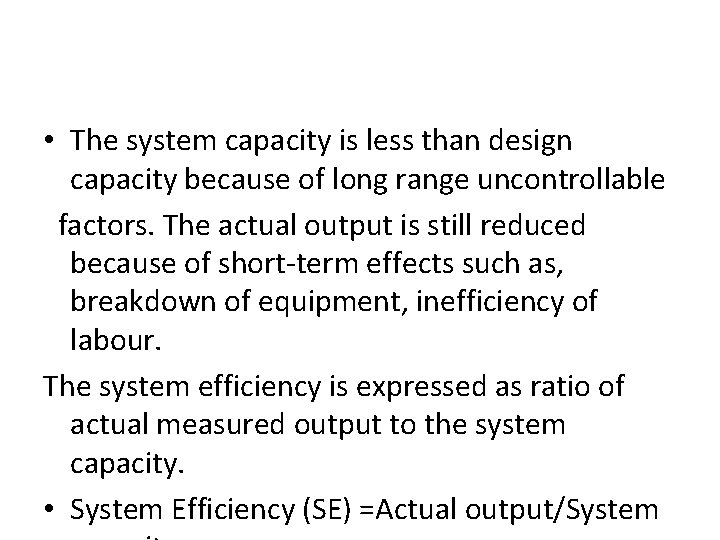
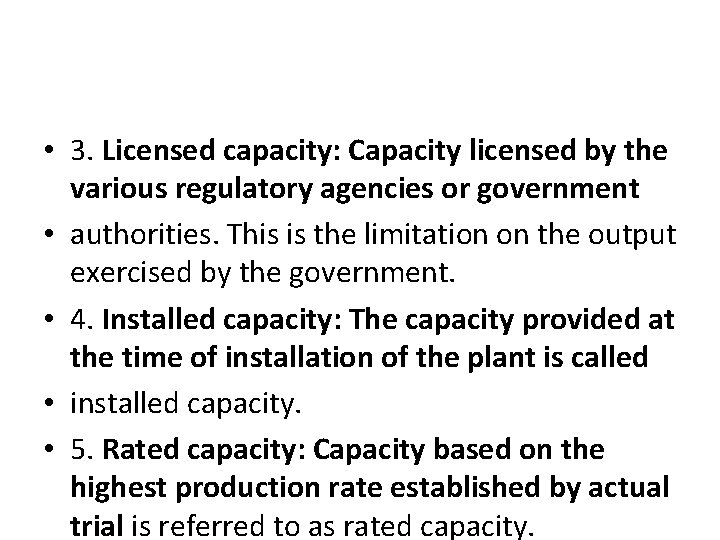
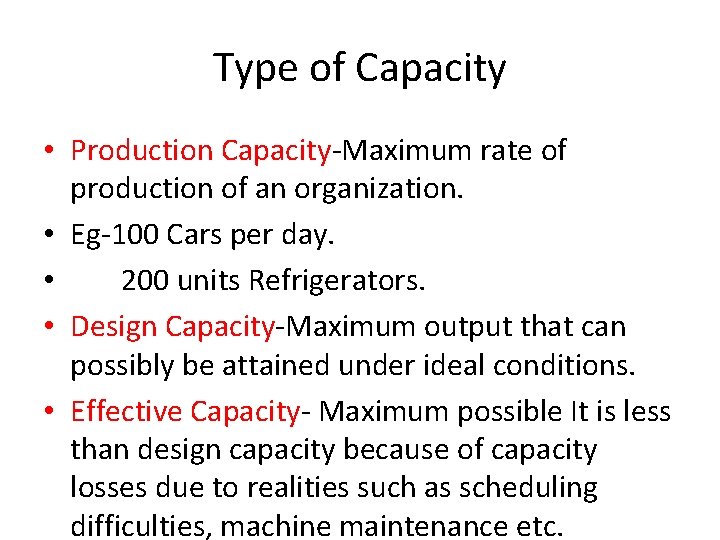
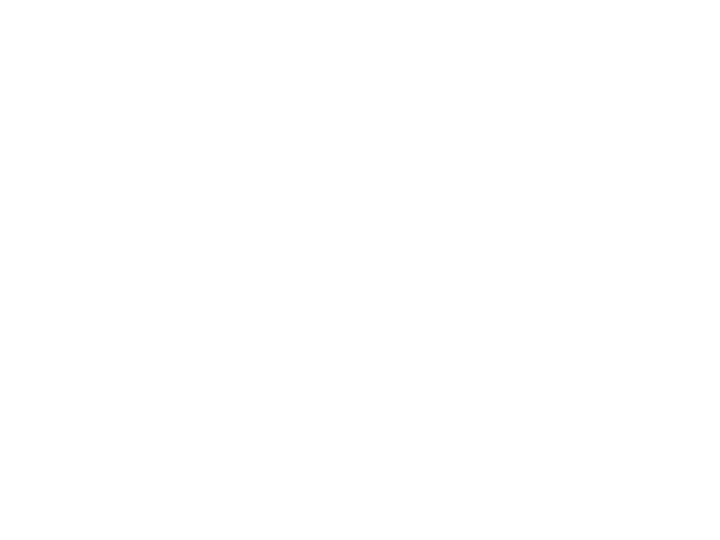
- Slides: 83
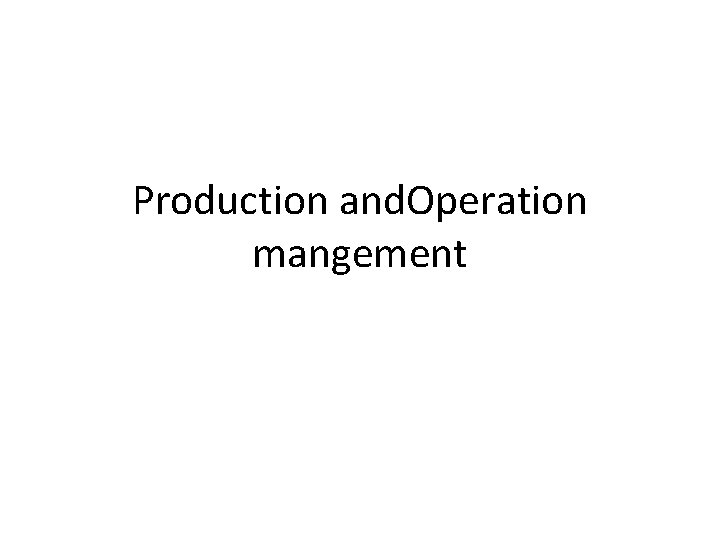
Production and. Operation mangement

Definition • Production : -It implies the creation of goods and services to satisfy the need /wants. • A process of transforming input (raw material ) into output(finished product) may be called as production/Operation management. • The set of interrelated management activities which are involved in manufacturing certain product is called as production management and providing services is called as operations management.
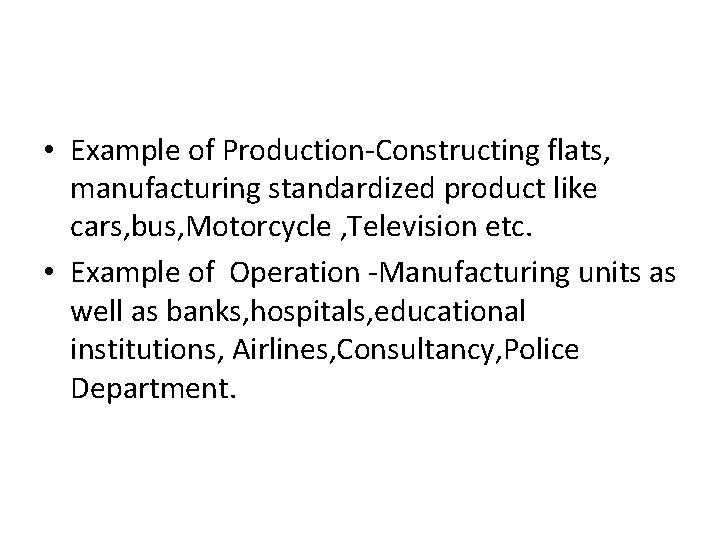
• Example of Production-Constructing flats, manufacturing standardized product like cars, bus, Motorcycle , Television etc. • Example of Operation -Manufacturing units as well as banks, hospitals, educational institutions, Airlines, Consultancy, Police Department.
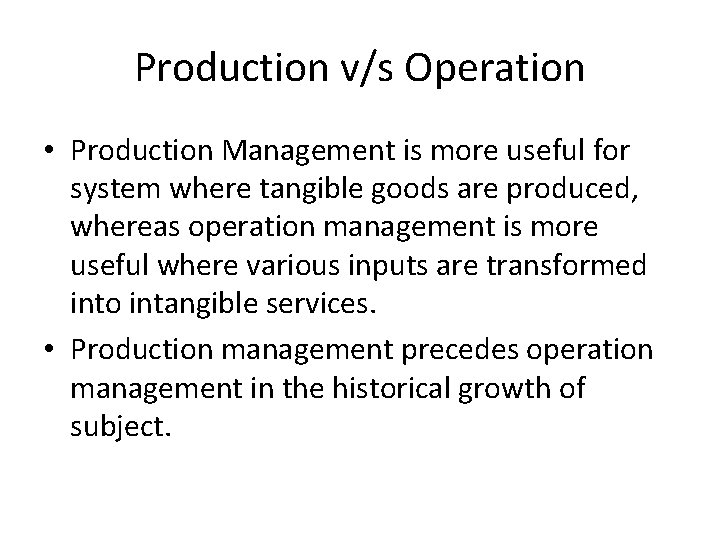
Production v/s Operation • Production Management is more useful for system where tangible goods are produced, whereas operation management is more useful where various inputs are transformed into intangible services. • Production management precedes operation management in the historical growth of subject.
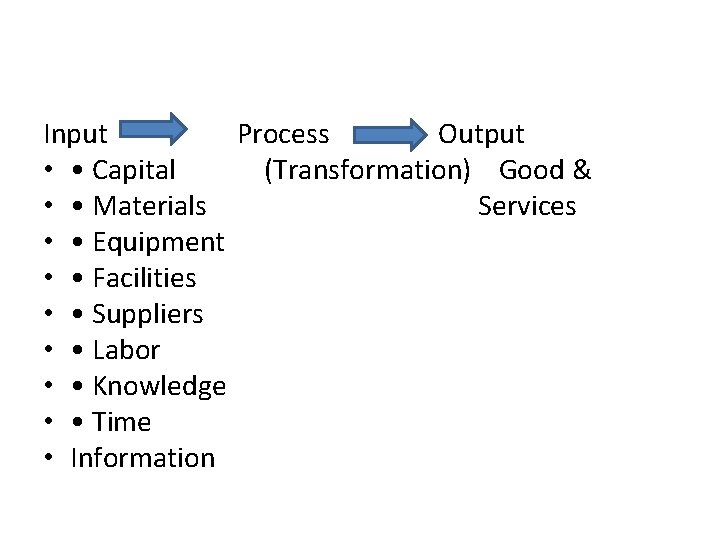
Input Process Output • • Capital (Transformation) Good & • • Materials Services • • Equipment • • Facilities • • Suppliers • • Labor • • Knowledge • • Time • Information
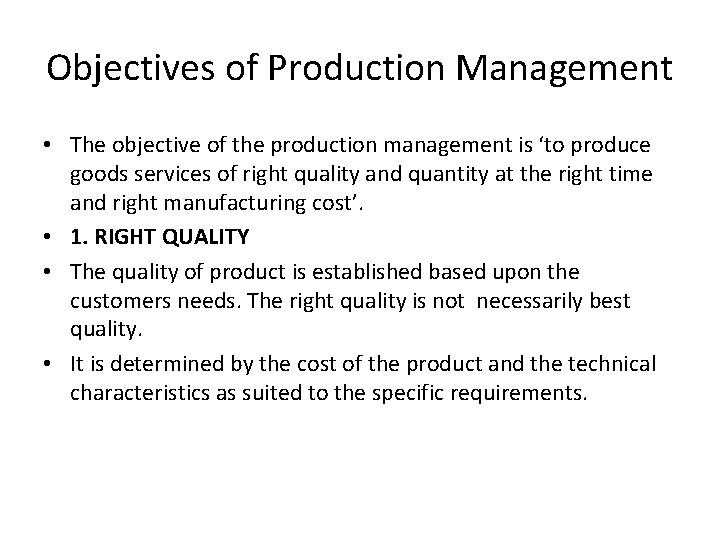
Objectives of Production Management • The objective of the production management is ‘to produce goods services of right quality and quantity at the right time and right manufacturing cost’. • 1. RIGHT QUALITY • The quality of product is established based upon the customers needs. The right quality is not necessarily best quality. • It is determined by the cost of the product and the technical characteristics as suited to the specific requirements.
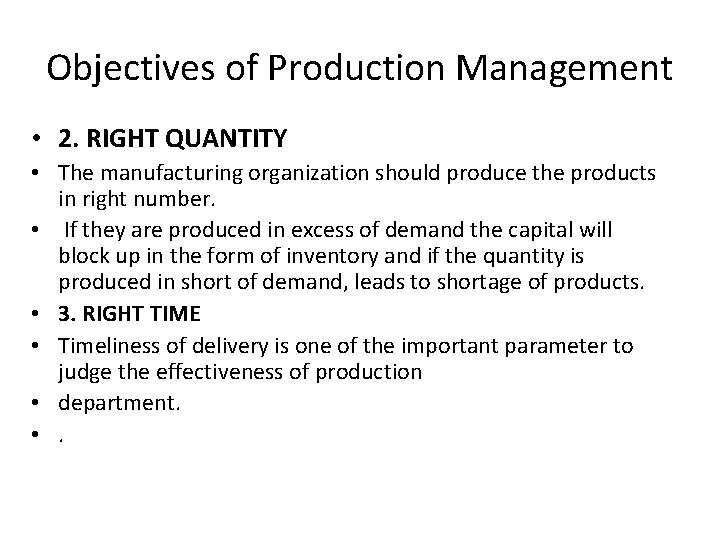
Objectives of Production Management • 2. RIGHT QUANTITY • The manufacturing organization should produce the products in right number. • If they are produced in excess of demand the capital will block up in the form of inventory and if the quantity is produced in short of demand, leads to shortage of products. • 3. RIGHT TIME • Timeliness of delivery is one of the important parameter to judge the effectiveness of production • department. • .
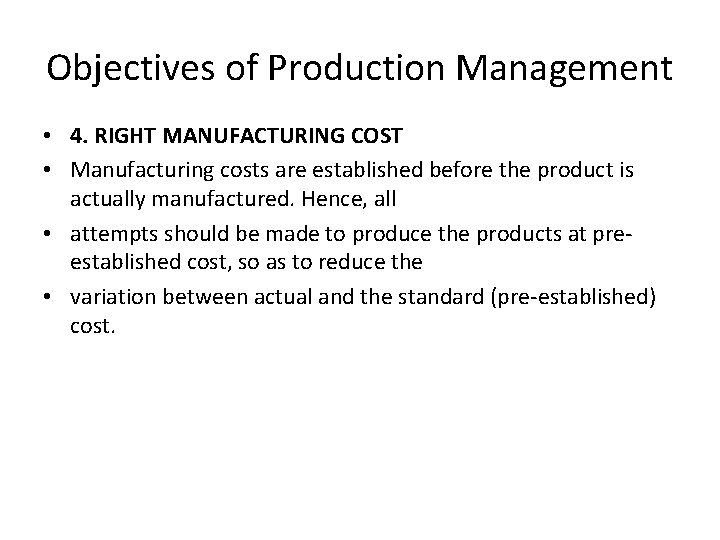
Objectives of Production Management • 4. RIGHT MANUFACTURING COST • Manufacturing costs are established before the product is actually manufactured. Hence, all • attempts should be made to produce the products at preestablished cost, so as to reduce the • variation between actual and the standard (pre-established) cost.
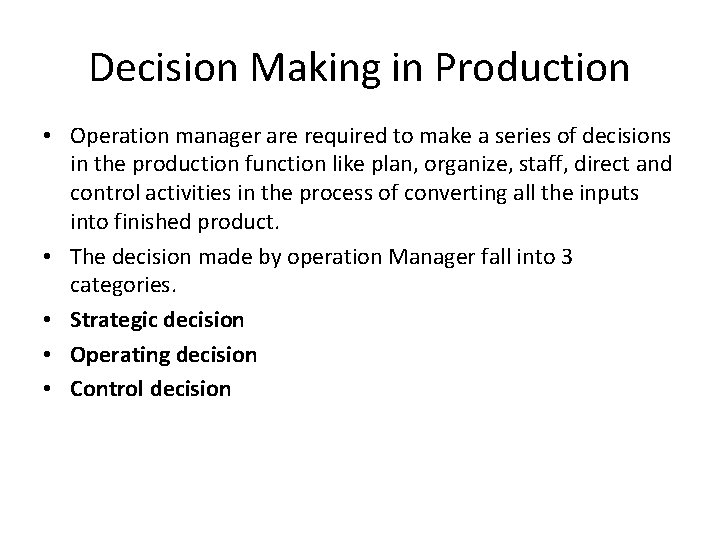
Decision Making in Production • Operation manager are required to make a series of decisions in the production function like plan, organize, staff, direct and control activities in the process of converting all the inputs into finished product. • The decision made by operation Manager fall into 3 categories. • Strategic decision • Operating decision • Control decision
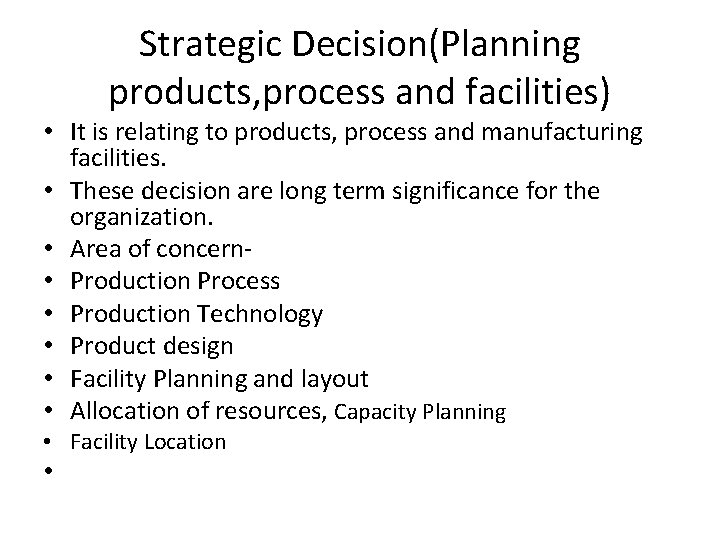
Strategic Decision(Planning products, process and facilities) • It is relating to products, process and manufacturing facilities. • These decision are long term significance for the organization. • Area of concern • Production Process • Production Technology • Product design • Facility Planning and layout • Allocation of resources, Capacity Planning • Facility Location •
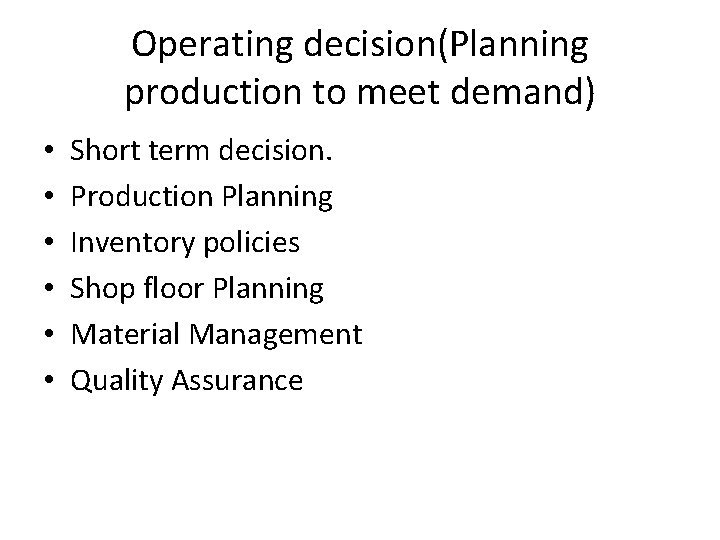
Operating decision(Planning production to meet demand) • • • Short term decision. Production Planning Inventory policies Shop floor Planning Material Management Quality Assurance
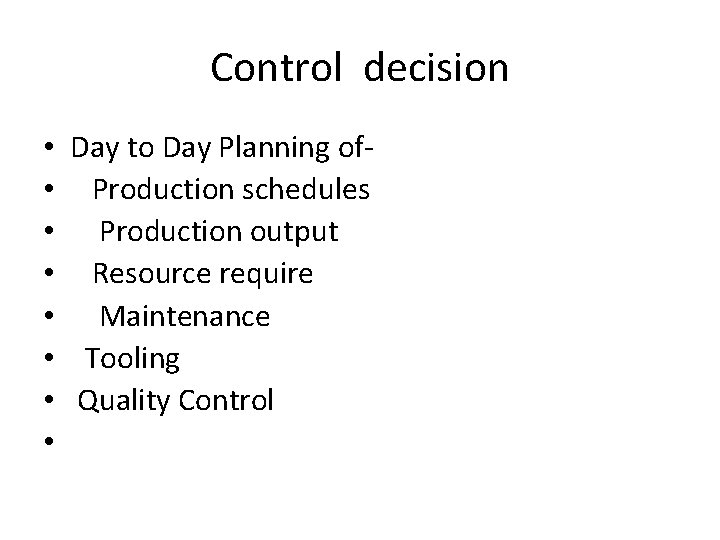
Control decision • Day to Day Planning of • Production schedules • Production output • Resource require • Maintenance • Tooling • Quality Control •
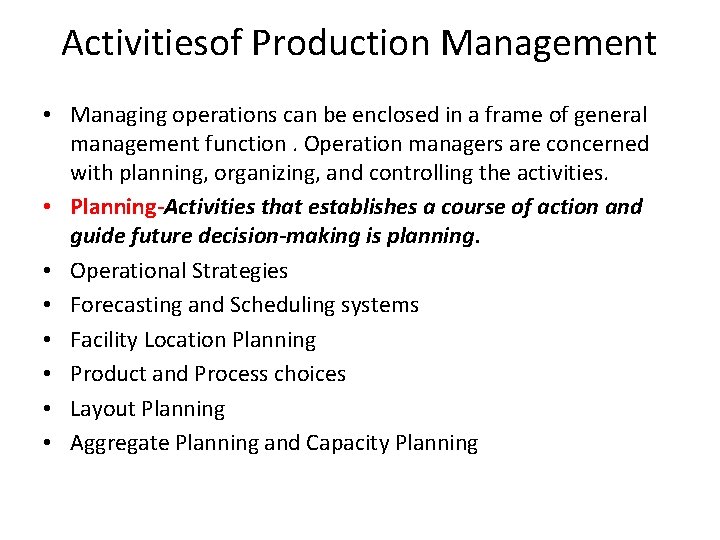
Activitiesof Production Management • Managing operations can be enclosed in a frame of general management function. Operation managers are concerned with planning, organizing, and controlling the activities. • Planning-Activities that establishes a course of action and guide future decision-making is planning. • Operational Strategies • Forecasting and Scheduling systems • Facility Location Planning • Product and Process choices • Layout Planning • Aggregate Planning and Capacity Planning
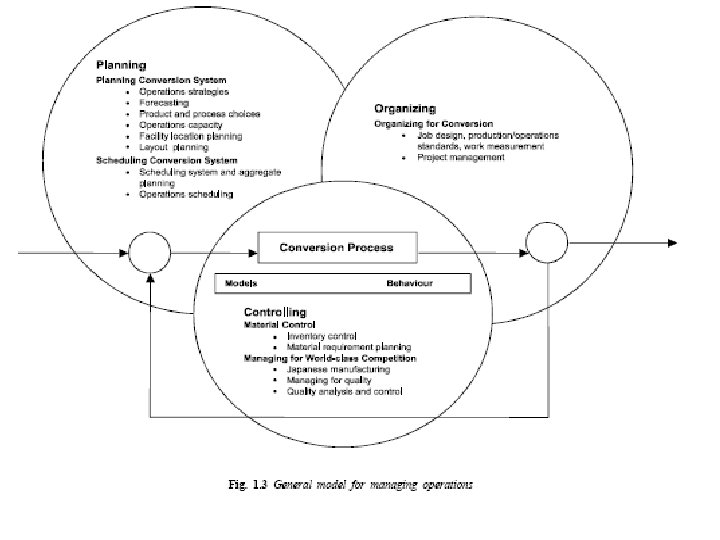
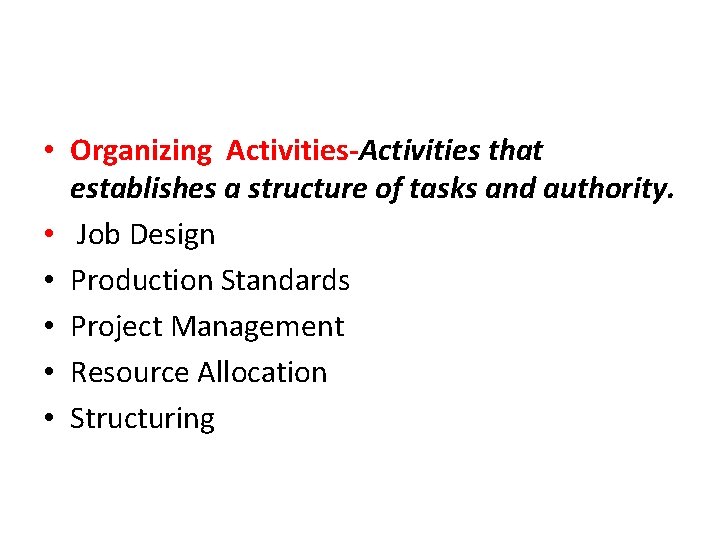
• Organizing Activities-Activities that establishes a structure of tasks and authority. • Job Design • Production Standards • Project Management • Resource Allocation • Structuring
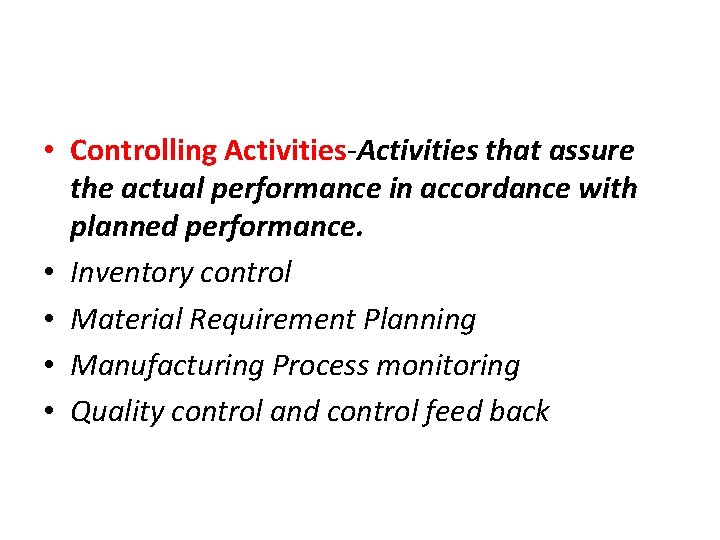
• Controlling Activities-Activities that assure the actual performance in accordance with planned performance. • Inventory control • Material Requirement Planning • Manufacturing Process monitoring • Quality control and control feed back
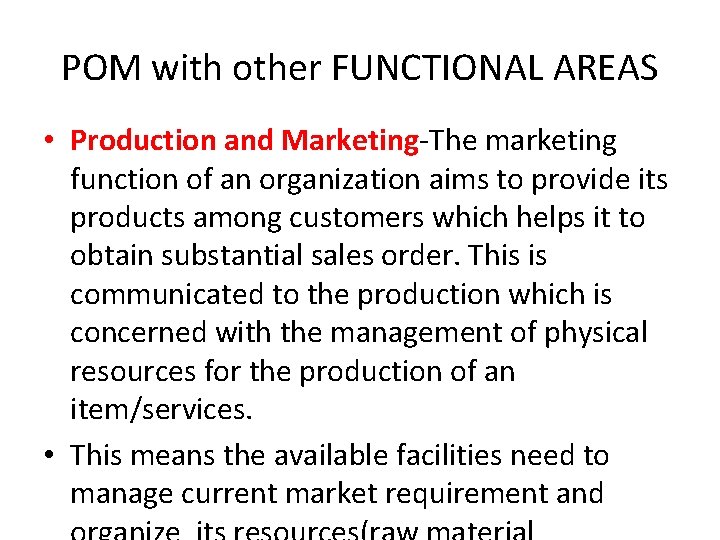
POM with other FUNCTIONAL AREAS • Production and Marketing-The marketing function of an organization aims to provide its products among customers which helps it to obtain substantial sales order. This is communicated to the production which is concerned with the management of physical resources for the production of an item/services. • This means the available facilities need to manage current market requirement and
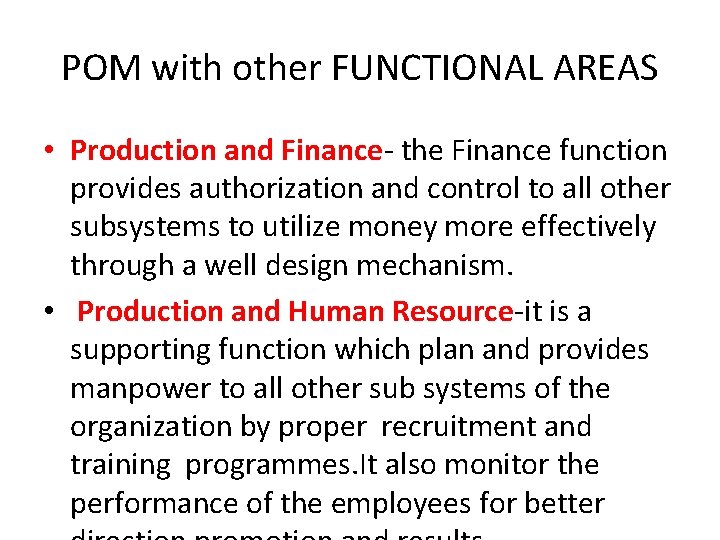
POM with other FUNCTIONAL AREAS • Production and Finance- the Finance function provides authorization and control to all other subsystems to utilize money more effectively through a well design mechanism. • Production and Human Resource-it is a supporting function which plan and provides manpower to all other sub systems of the organization by proper recruitment and training programmes. It also monitor the performance of the employees for better
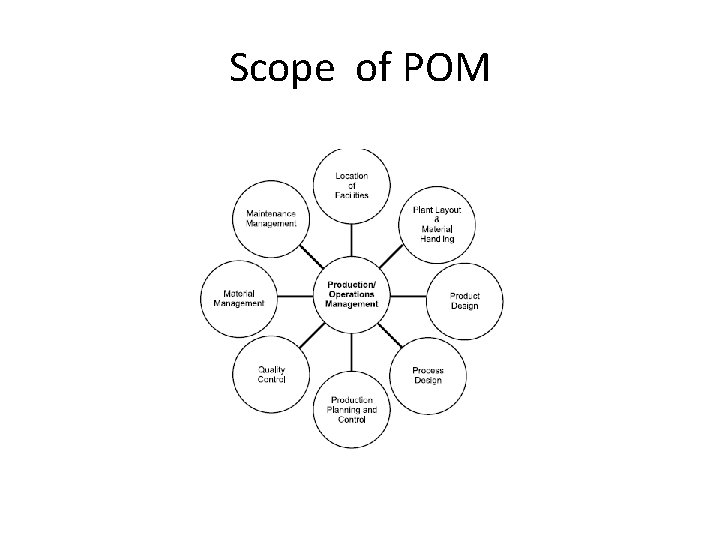
Scope of POM
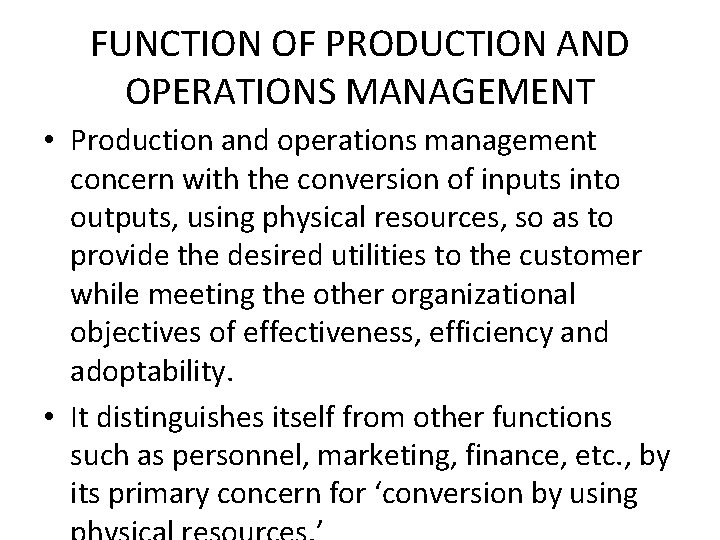
FUNCTION OF PRODUCTION AND OPERATIONS MANAGEMENT • Production and operations management concern with the conversion of inputs into outputs, using physical resources, so as to provide the desired utilities to the customer while meeting the other organizational objectives of effectiveness, efficiency and adoptability. • It distinguishes itself from other functions such as personnel, marketing, finance, etc. , by its primary concern for ‘conversion by using
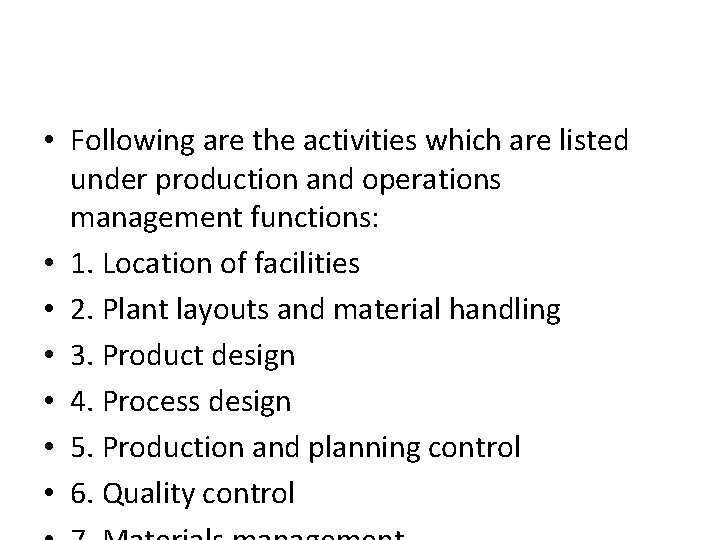
• Following are the activities which are listed under production and operations management functions: • 1. Location of facilities • 2. Plant layouts and material handling • 3. Product design • 4. Process design • 5. Production and planning control • 6. Quality control
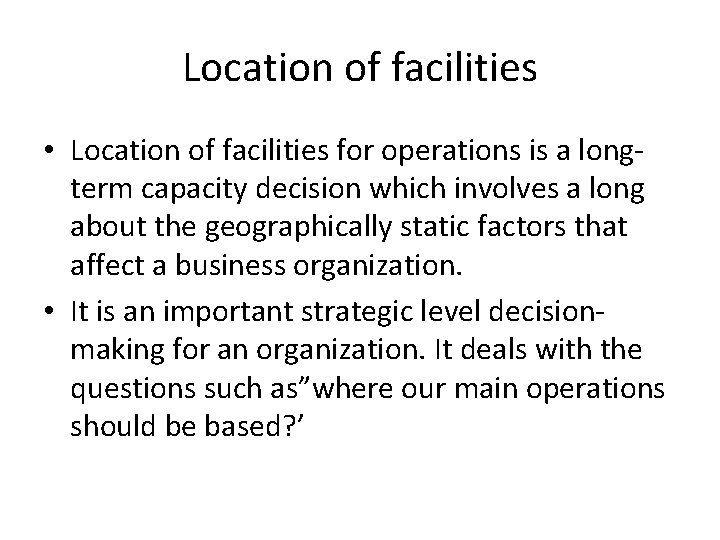
Location of facilities • Location of facilities for operations is a longterm capacity decision which involves a long about the geographically static factors that affect a business organization. • It is an important strategic level decisionmaking for an organization. It deals with the questions such as”where our main operations should be based? ’
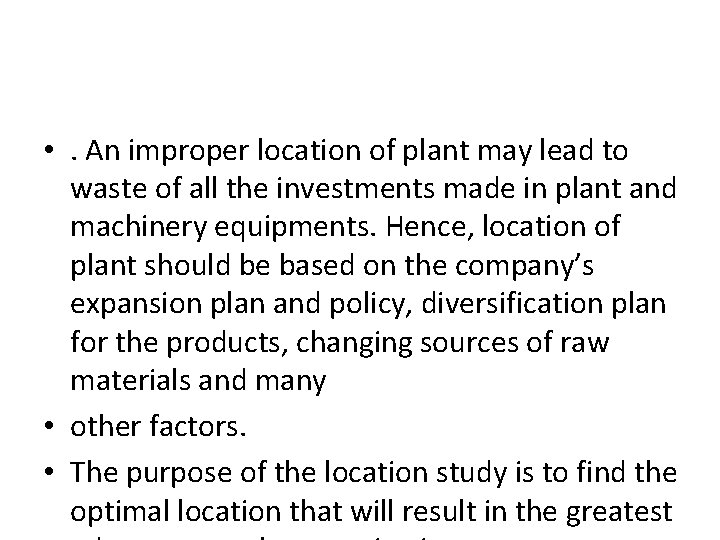
• . An improper location of plant may lead to waste of all the investments made in plant and machinery equipments. Hence, location of plant should be based on the company’s expansion plan and policy, diversification plan for the products, changing sources of raw materials and many • other factors. • The purpose of the location study is to find the optimal location that will result in the greatest

Facility location/Plant location • Plant location or the facilities location problem is an important strategic level decision making for an organisation. • This fact will include the determination of where to place the plant or facility. • The selection of location is a key-decision as large investment is made in building plant and machinery. • The purpose of the location study is to find an optimum location one that will result in
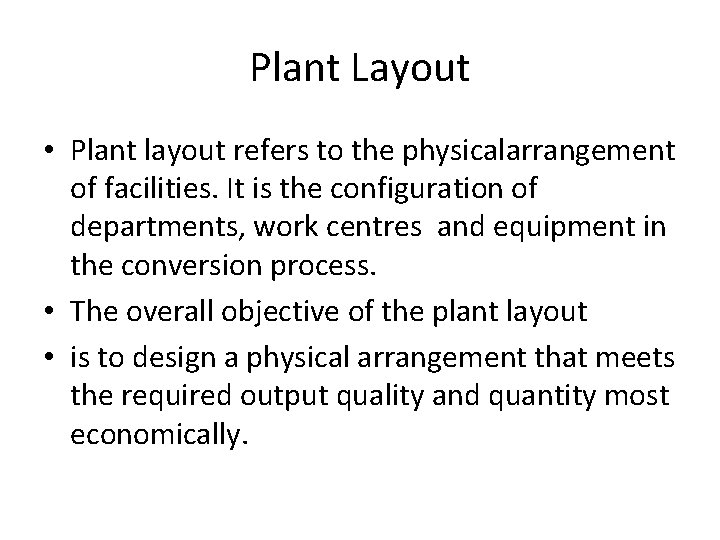
Plant Layout • Plant layout refers to the physicalarrangement of facilities. It is the configuration of departments, work centres and equipment in the conversion process. • The overall objective of the plant layout • is to design a physical arrangement that meets the required output quality and quantity most economically.
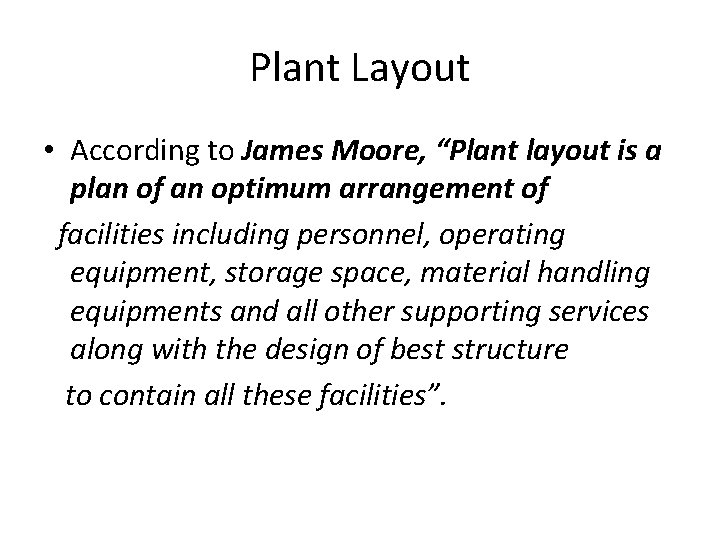
Plant Layout • According to James Moore, “Plant layout is a plan of an optimum arrangement of facilities including personnel, operating equipment, storage space, material handling equipments and all other supporting services along with the design of best structure to contain all these facilities”.
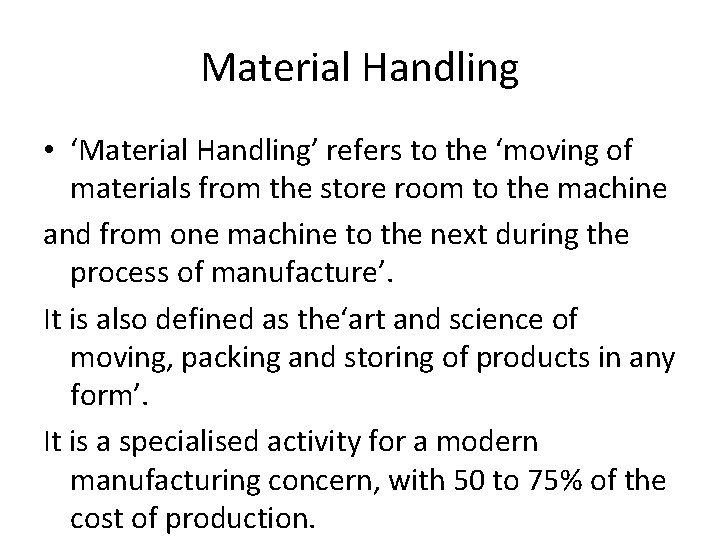
Material Handling • ‘Material Handling’ refers to the ‘moving of materials from the store room to the machine and from one machine to the next during the process of manufacture’. It is also defined as the‘art and science of moving, packing and storing of products in any form’. It is a specialised activity for a modern manufacturing concern, with 50 to 75% of the cost of production.
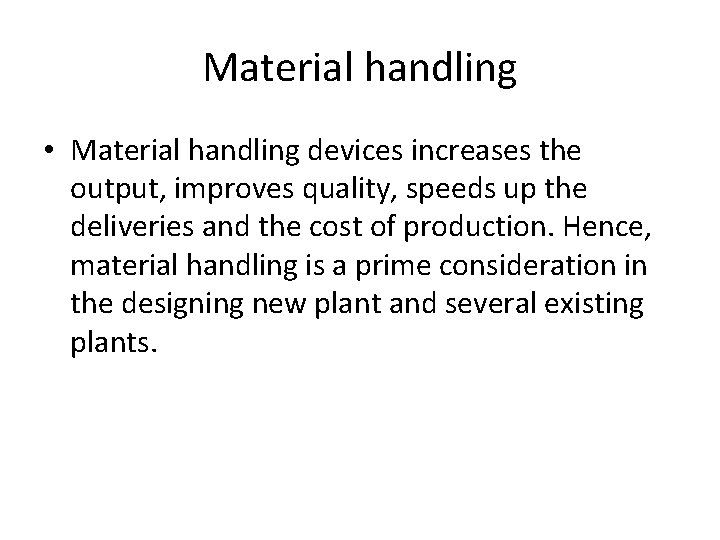
Material handling • Material handling devices increases the output, improves quality, speeds up the deliveries and the cost of production. Hence, material handling is a prime consideration in the designing new plant and several existing plants.
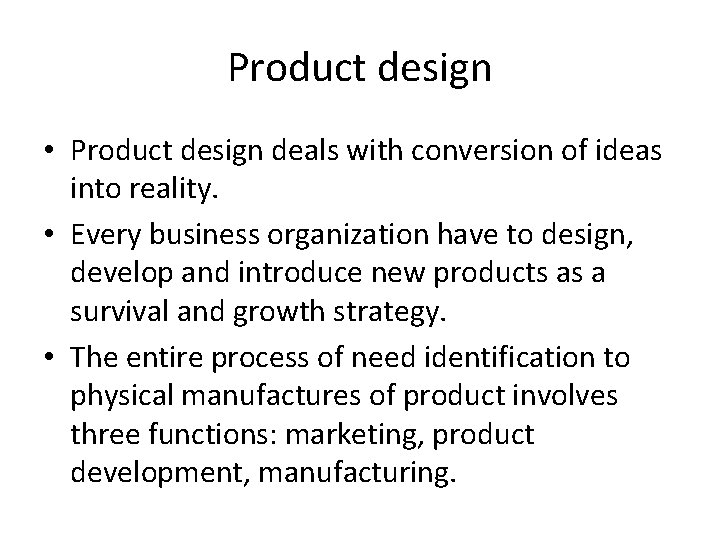
Product design • Product design deals with conversion of ideas into reality. • Every business organization have to design, develop and introduce new products as a survival and growth strategy. • The entire process of need identification to physical manufactures of product involves three functions: marketing, product development, manufacturing.

Product design • Product development translates the needs of customers given by marketing into technical specifications and designing the various features into the product to these specifications.
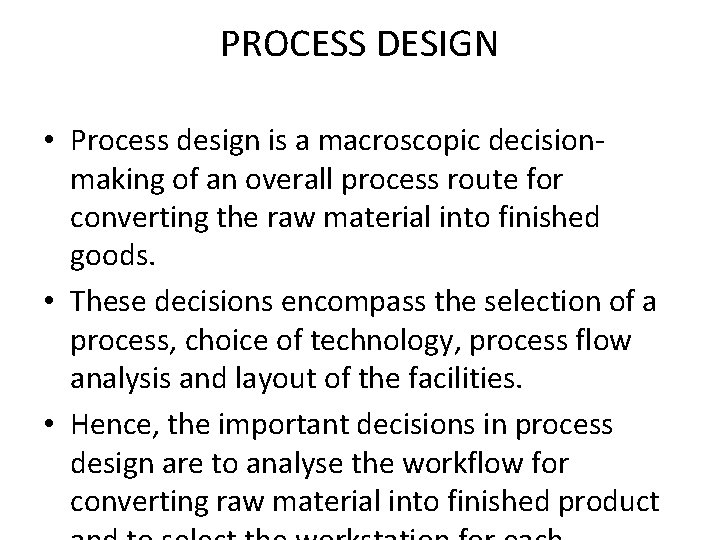
PROCESS DESIGN • Process design is a macroscopic decisionmaking of an overall process route for converting the raw material into finished goods. • These decisions encompass the selection of a process, choice of technology, process flow analysis and layout of the facilities. • Hence, the important decisions in process design are to analyse the workflow for converting raw material into finished product
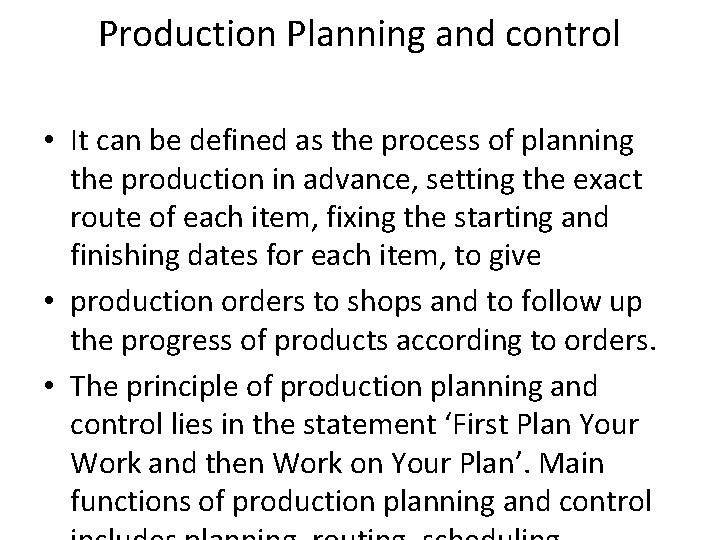
Production Planning and control • It can be defined as the process of planning the production in advance, setting the exact route of each item, fixing the starting and finishing dates for each item, to give • production orders to shops and to follow up the progress of products according to orders. • The principle of production planning and control lies in the statement ‘First Plan Your Work and then Work on Your Plan’. Main functions of production planning and control
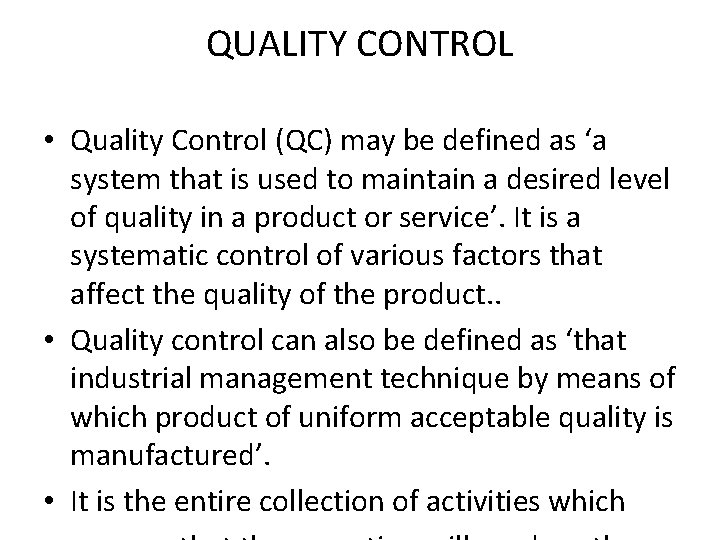
QUALITY CONTROL • Quality Control (QC) may be defined as ‘a system that is used to maintain a desired level of quality in a product or service’. It is a systematic control of various factors that affect the quality of the product. . • Quality control can also be defined as ‘that industrial management technique by means of which product of uniform acceptable quality is manufactured’. • It is the entire collection of activities which
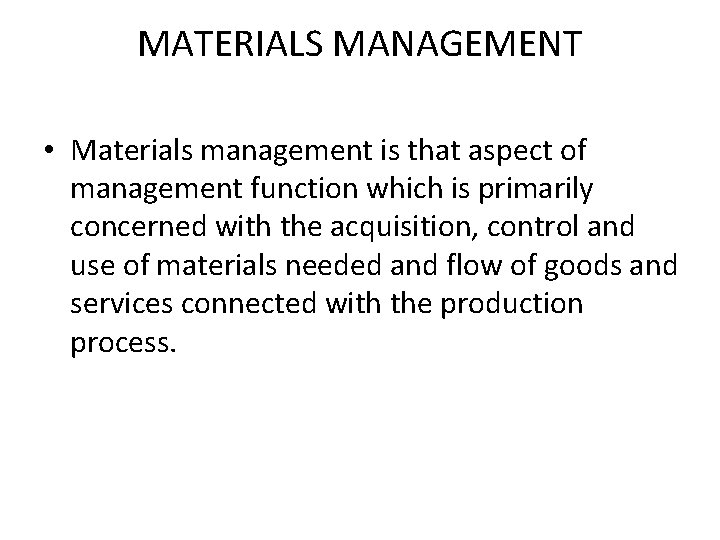
MATERIALS MANAGEMENT • Materials management is that aspect of management function which is primarily concerned with the acquisition, control and use of materials needed and flow of goods and services connected with the production process.
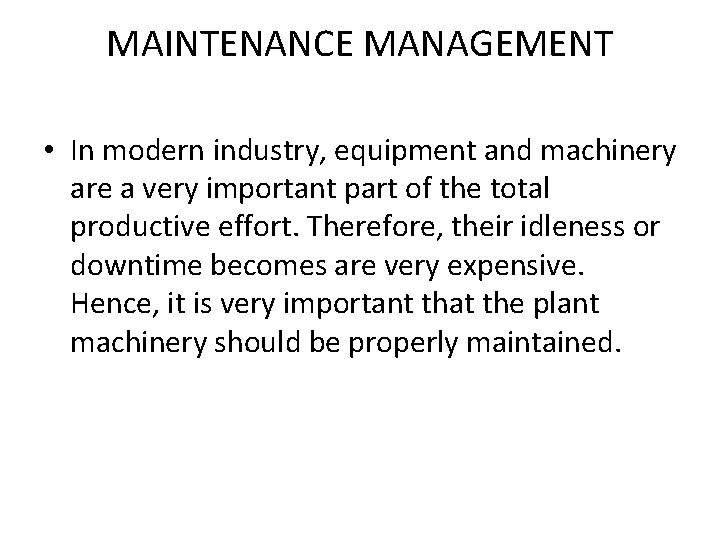
MAINTENANCE MANAGEMENT • In modern industry, equipment and machinery are a very important part of the total productive effort. Therefore, their idleness or downtime becomes are very expensive. Hence, it is very important that the plant machinery should be properly maintained.
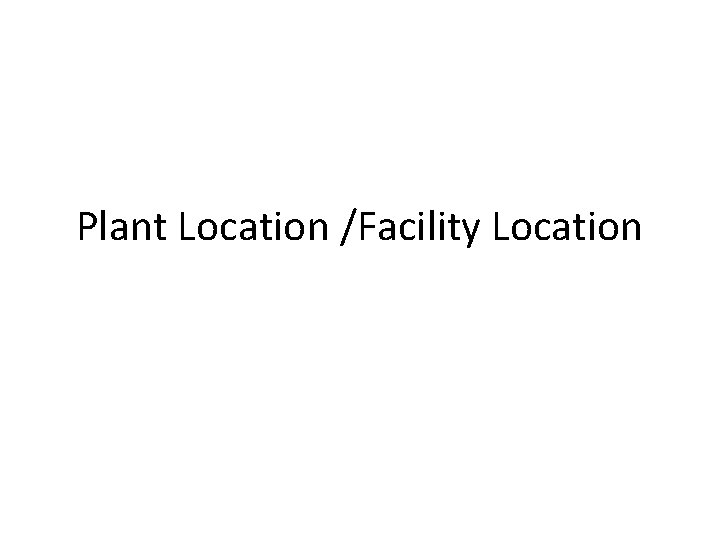
Plant Location /Facility Location
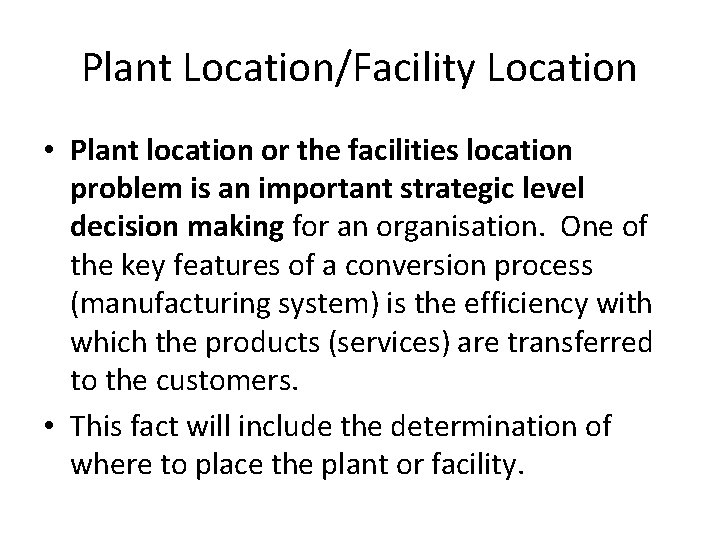
Plant Location/Facility Location • Plant location or the facilities location problem is an important strategic level decision making for an organisation. One of the key features of a conversion process (manufacturing system) is the efficiency with which the products (services) are transferred to the customers. • This fact will include the determination of where to place the plant or facility.
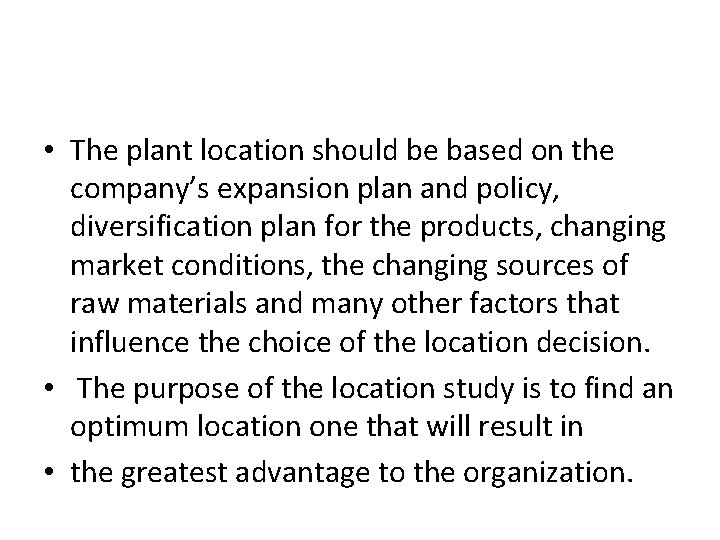
• The plant location should be based on the company’s expansion plan and policy, diversification plan for the products, changing market conditions, the changing sources of raw materials and many other factors that influence the choice of the location decision. • The purpose of the location study is to find an optimum location one that will result in • the greatest advantage to the organization.
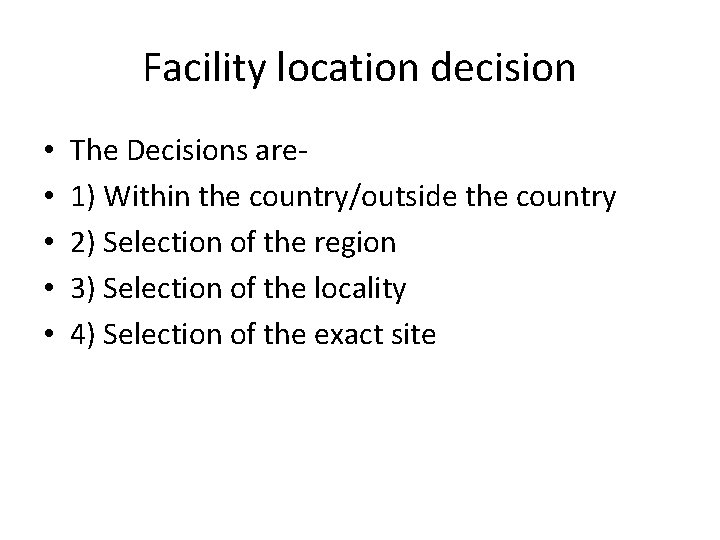
Facility location decision • • • The Decisions are 1) Within the country/outside the country 2) Selection of the region 3) Selection of the locality 4) Selection of the exact site
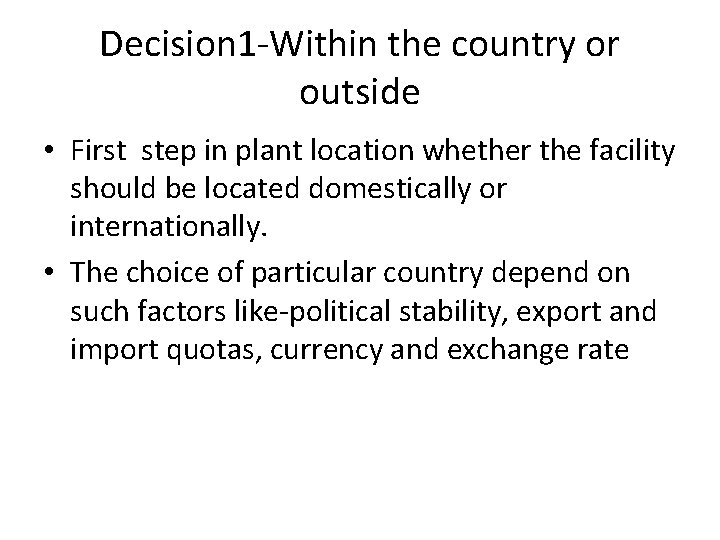
Decision 1 -Within the country or outside • First step in plant location whether the facility should be located domestically or internationally. • The choice of particular country depend on such factors like-political stability, export and import quotas, currency and exchange rate
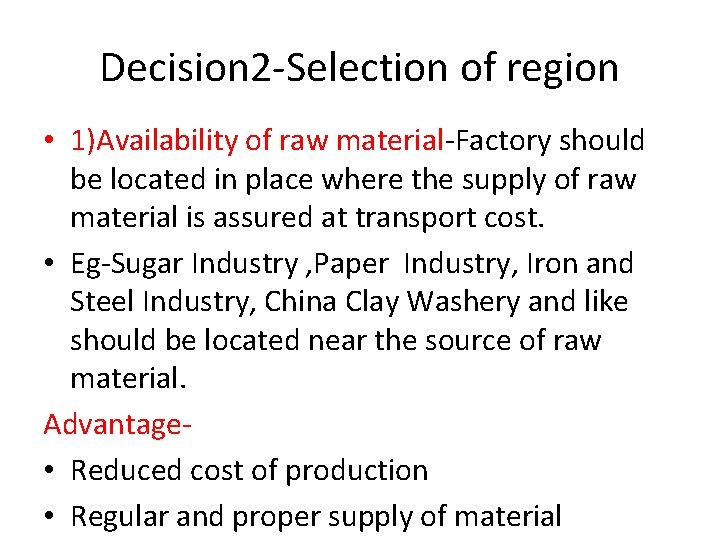
Decision 2 -Selection of region • 1)Availability of raw material-Factory should be located in place where the supply of raw material is assured at transport cost. • Eg-Sugar Industry , Paper Industry, Iron and Steel Industry, China Clay Washery and like should be located near the source of raw material. Advantage • Reduced cost of production • Regular and proper supply of material
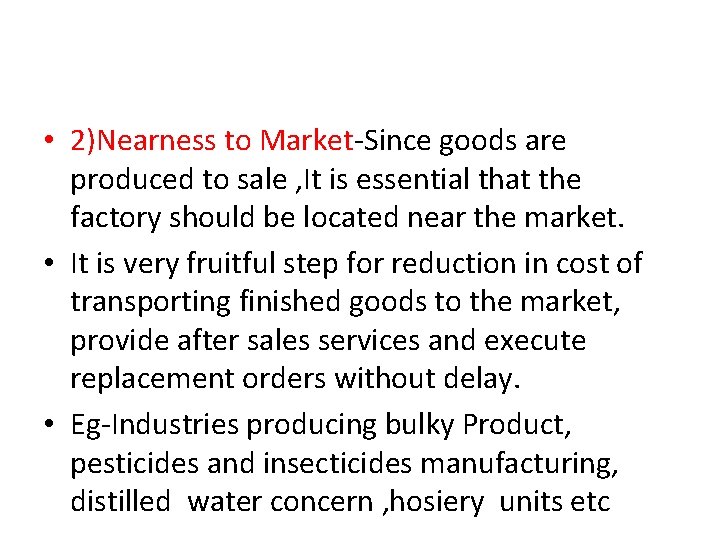
• 2)Nearness to Market-Since goods are produced to sale , It is essential that the factory should be located near the market. • It is very fruitful step for reduction in cost of transporting finished goods to the market, provide after sales services and execute replacement orders without delay. • Eg-Industries producing bulky Product, pesticides and insecticides manufacturing, distilled water concern , hosiery units etc
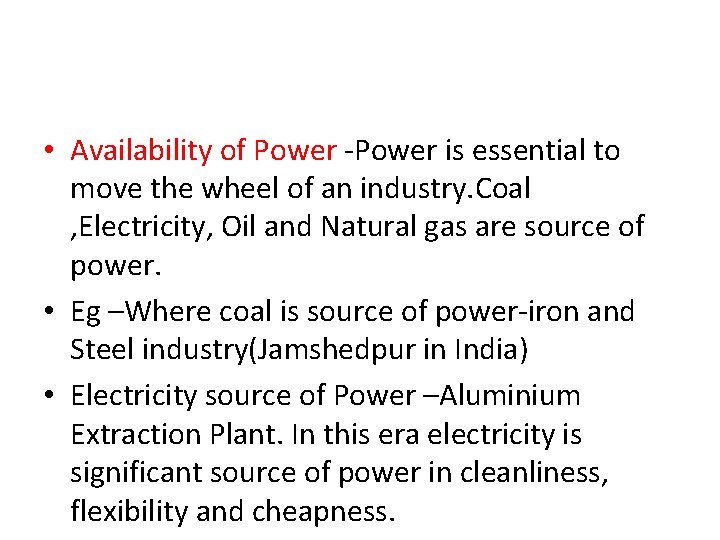
• Availability of Power -Power is essential to move the wheel of an industry. Coal , Electricity, Oil and Natural gas are source of power. • Eg –Where coal is source of power-iron and Steel industry(Jamshedpur in India) • Electricity source of Power –Aluminium Extraction Plant. In this era electricity is significant source of power in cleanliness, flexibility and cheapness.
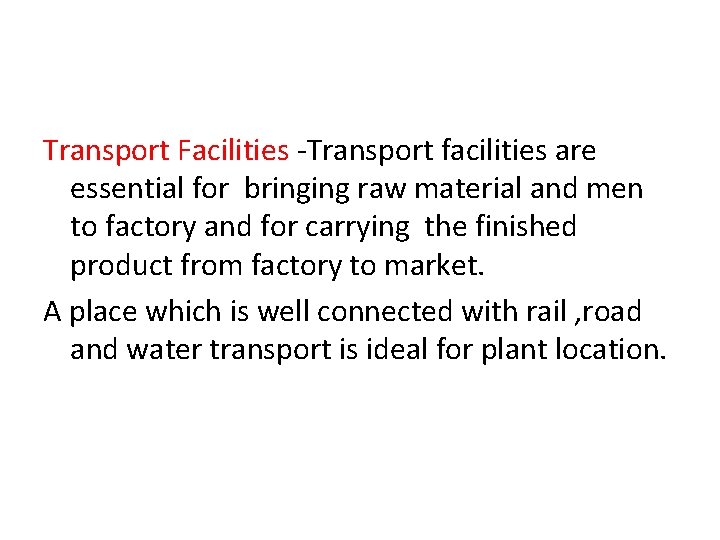
Transport Facilities -Transport facilities are essential for bringing raw material and men to factory and for carrying the finished product from factory to market. A place which is well connected with rail , road and water transport is ideal for plant location.
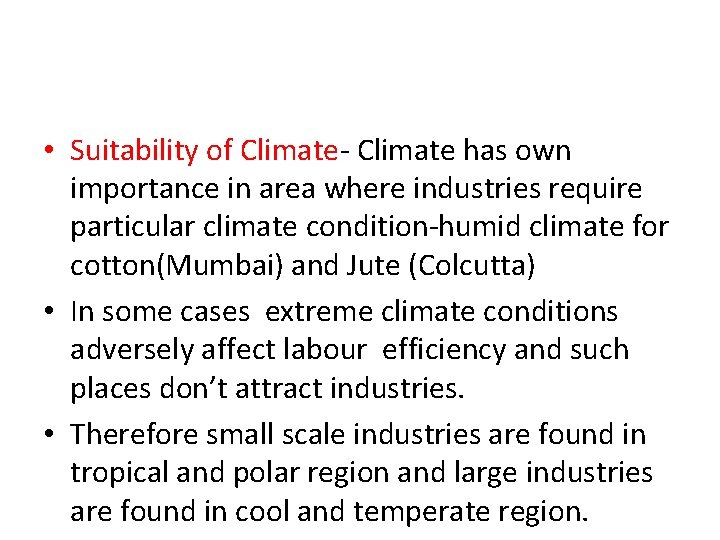
• Suitability of Climate- Climate has own importance in area where industries require particular climate condition-humid climate for cotton(Mumbai) and Jute (Colcutta) • In some cases extreme climate conditions adversely affect labour efficiency and such places don’t attract industries. • Therefore small scale industries are found in tropical and polar region and large industries are found in cool and temperate region.
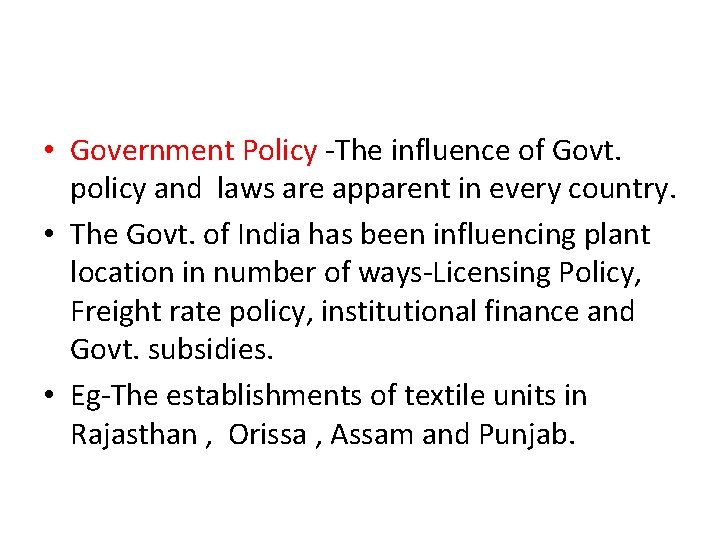
• Government Policy -The influence of Govt. policy and laws are apparent in every country. • The Govt. of India has been influencing plant location in number of ways-Licensing Policy, Freight rate policy, institutional finance and Govt. subsidies. • Eg-The establishments of textile units in Rajasthan , Orissa , Assam and Punjab.
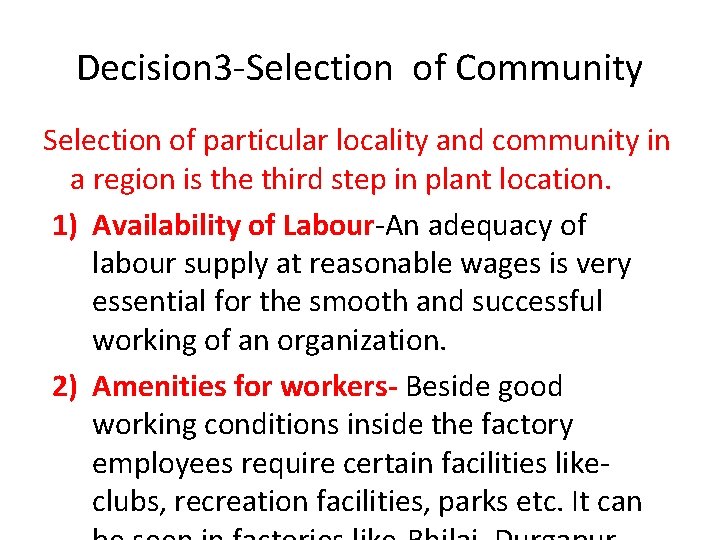
Decision 3 -Selection of Community Selection of particular locality and community in a region is the third step in plant location. 1) Availability of Labour-An adequacy of labour supply at reasonable wages is very essential for the smooth and successful working of an organization. 2) Amenities for workers- Beside good working conditions inside the factory employees require certain facilities likeclubs, recreation facilities, parks etc. It can
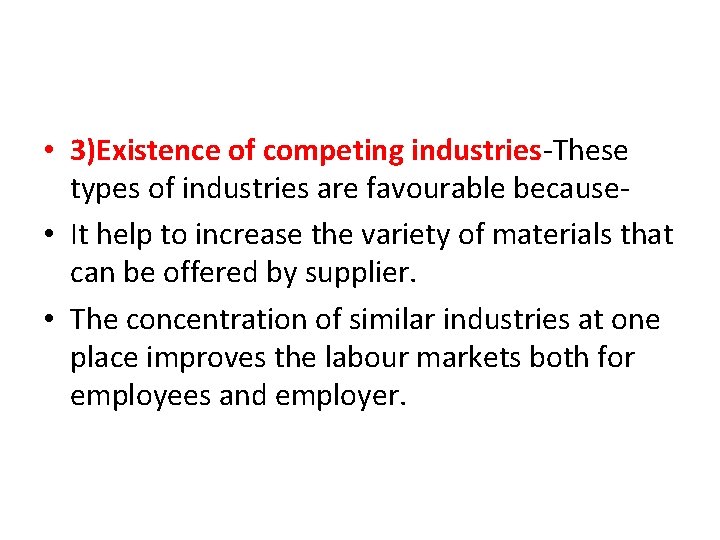
• 3)Existence of competing industries-These types of industries are favourable because • It help to increase the variety of materials that can be offered by supplier. • The concentration of similar industries at one place improves the labour markets both for employees and employer.
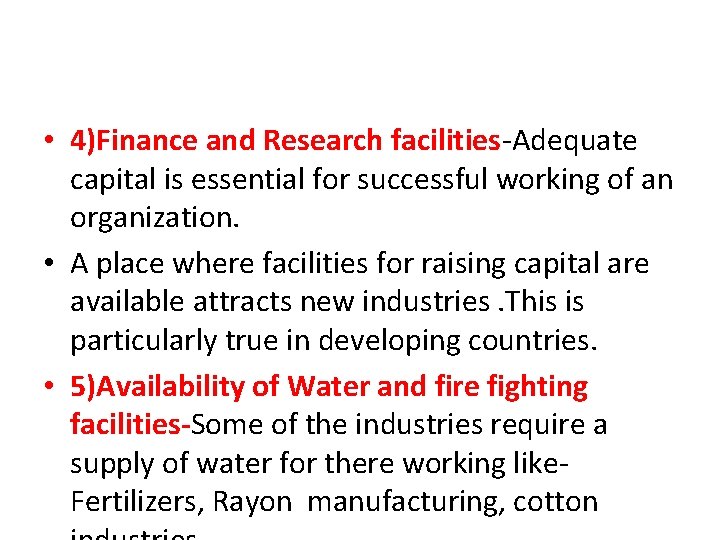
• 4)Finance and Research facilities-Adequate capital is essential for successful working of an organization. • A place where facilities for raising capital are available attracts new industries. This is particularly true in developing countries. • 5)Availability of Water and fire fighting facilities-Some of the industries require a supply of water for there working like. Fertilizers, Rayon manufacturing, cotton
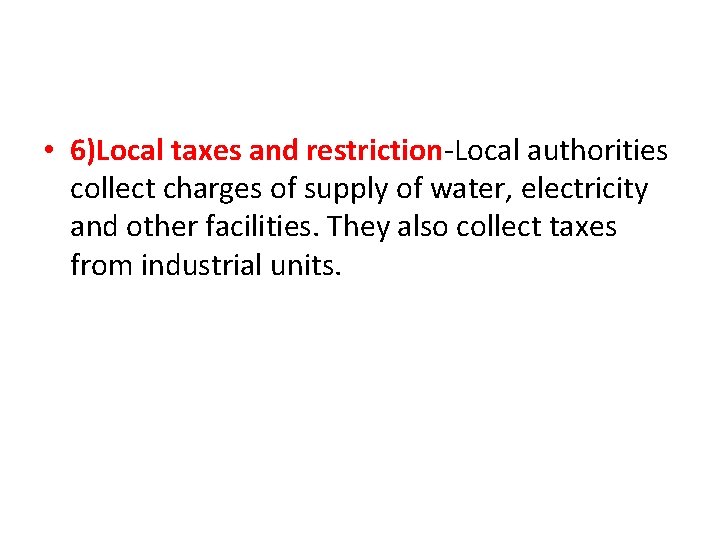
• 6)Local taxes and restriction-Local authorities collect charges of supply of water, electricity and other facilities. They also collect taxes from industrial units.
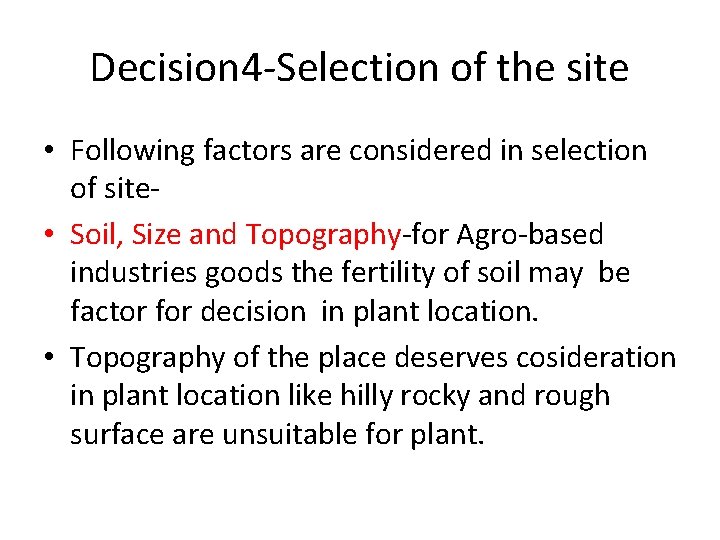
Decision 4 -Selection of the site • Following factors are considered in selection of site • Soil, Size and Topography-for Agro-based industries goods the fertility of soil may be factor for decision in plant location. • Topography of the place deserves cosideration in plant location like hilly rocky and rough surface are unsuitable for plant.
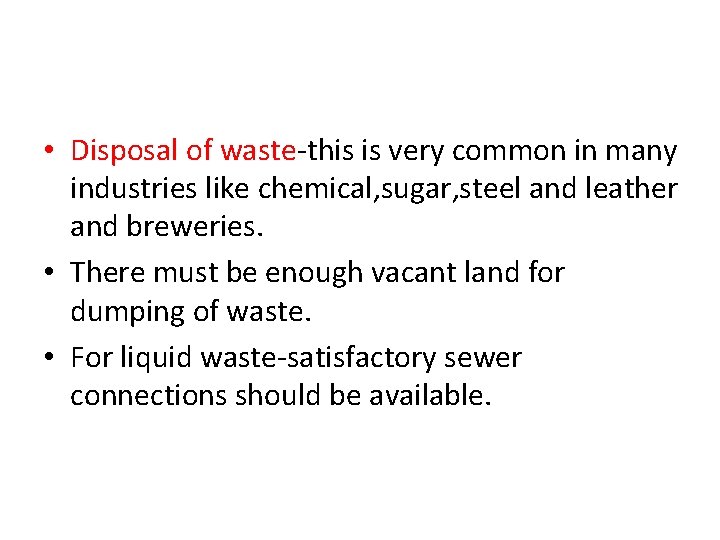
• Disposal of waste-this is very common in many industries like chemical, sugar, steel and leather and breweries. • There must be enough vacant land for dumping of waste. • For liquid waste-satisfactory sewer connections should be available.
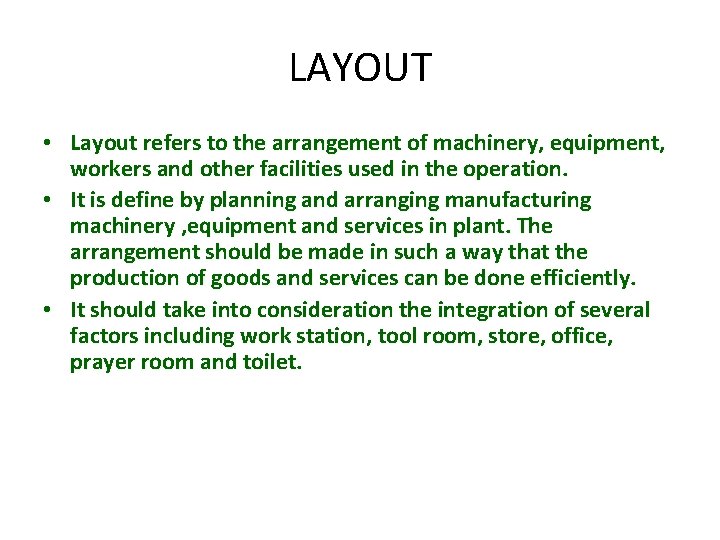
LAYOUT • Layout refers to the arrangement of machinery, equipment, workers and other facilities used in the operation. • It is define by planning and arranging manufacturing machinery , equipment and services in plant. The arrangement should be made in such a way that the production of goods and services can be done efficiently. • It should take into consideration the integration of several factors including work station, tool room, store, office, prayer room and toilet.
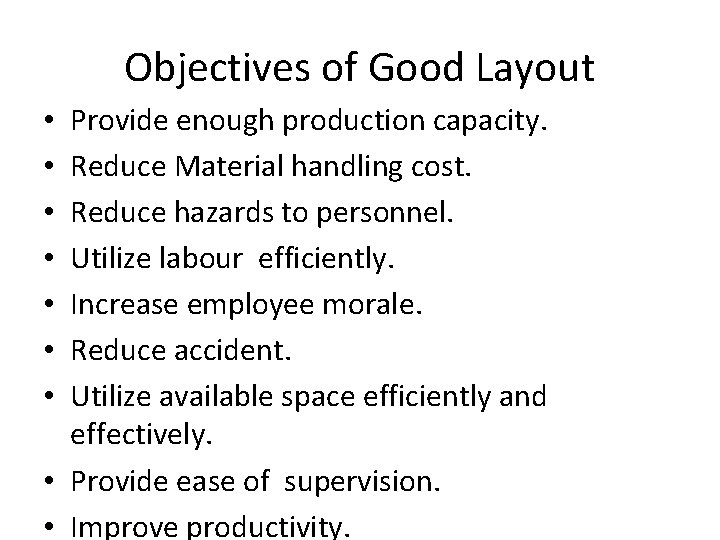
Objectives of Good Layout Provide enough production capacity. Reduce Material handling cost. Reduce hazards to personnel. Utilize labour efficiently. Increase employee morale. Reduce accident. Utilize available space efficiently and effectively. • Provide ease of supervision. • Improve productivity. • •
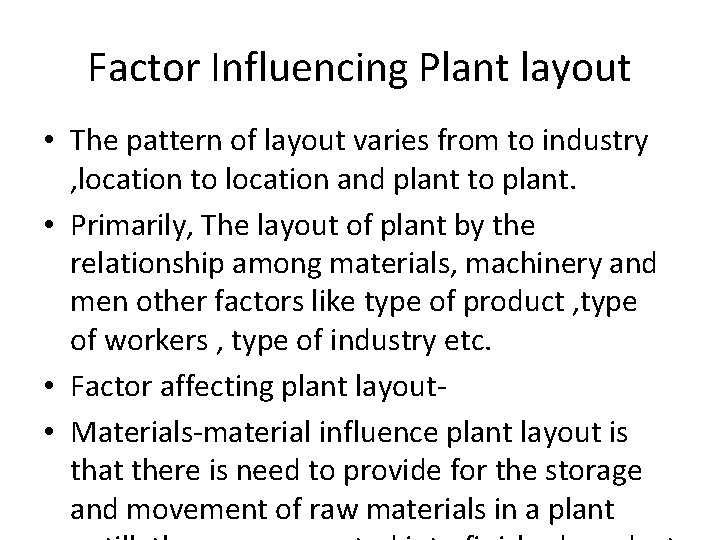
Factor Influencing Plant layout • The pattern of layout varies from to industry , location to location and plant to plant. • Primarily, The layout of plant by the relationship among materials, machinery and men other factors like type of product , type of workers , type of industry etc. • Factor affecting plant layout • Materials-material influence plant layout is that there is need to provide for the storage and movement of raw materials in a plant
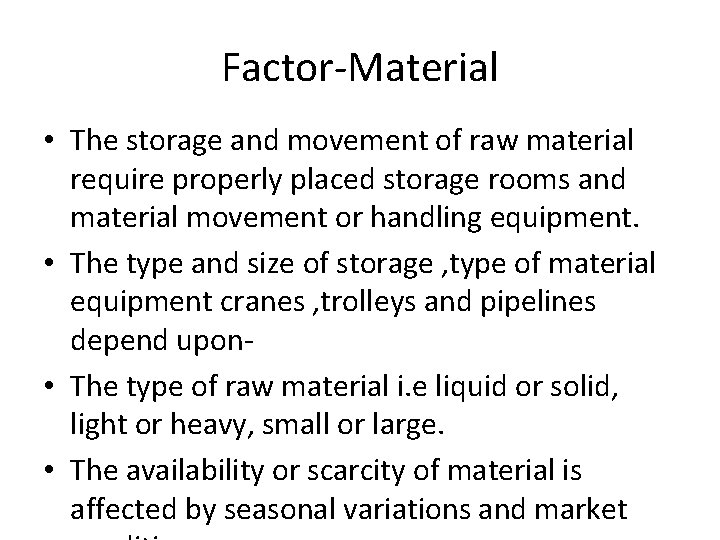
Factor-Material • The storage and movement of raw material require properly placed storage rooms and material movement or handling equipment. • The type and size of storage , type of material equipment cranes , trolleys and pipelines depend upon • The type of raw material i. e liquid or solid, light or heavy, small or large. • The availability or scarcity of material is affected by seasonal variations and market
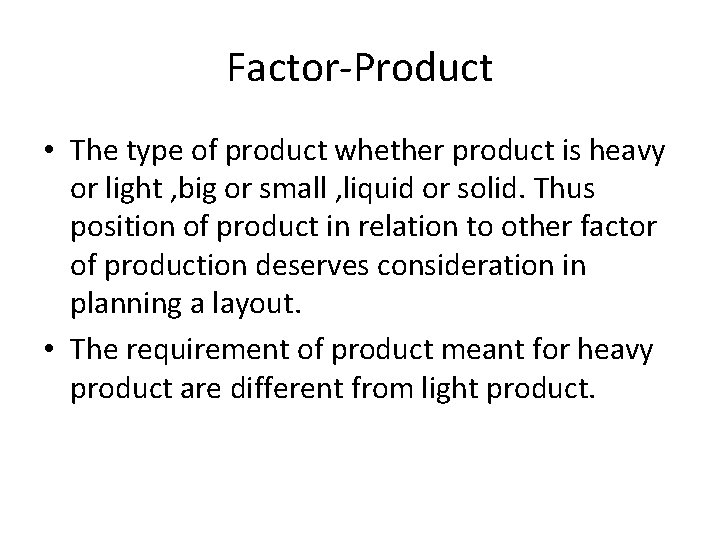
Factor-Product • The type of product whether product is heavy or light , big or small , liquid or solid. Thus position of product in relation to other factor of production deserves consideration in planning a layout. • The requirement of product meant for heavy product are different from light product.
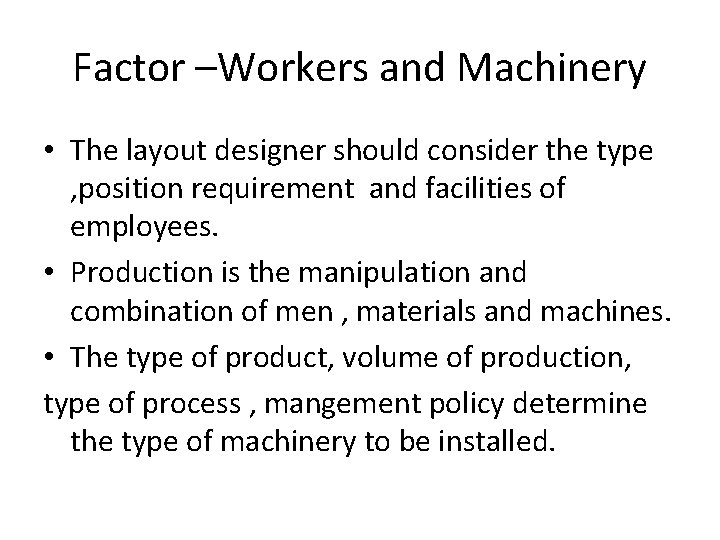
Factor –Workers and Machinery • The layout designer should consider the type , position requirement and facilities of employees. • Production is the manipulation and combination of men , materials and machines. • The type of product, volume of production, type of process , mangement policy determine the type of machinery to be installed.
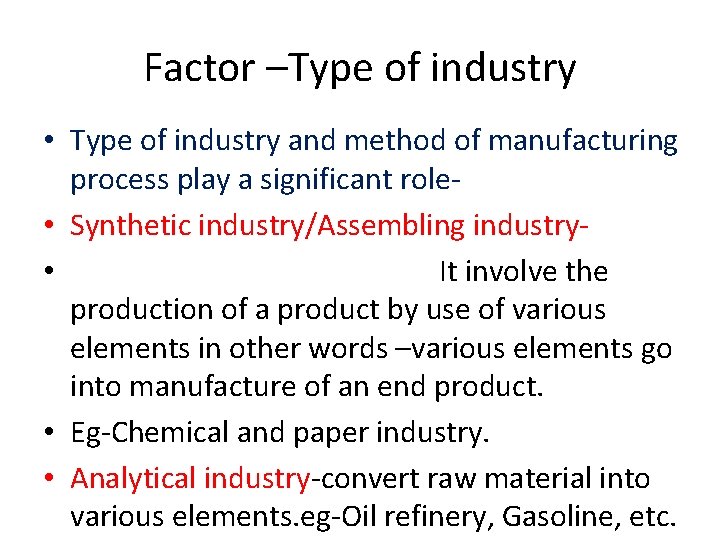
Factor –Type of industry • Type of industry and method of manufacturing process play a significant role • Synthetic industry/Assembling industry • It involve the production of a product by use of various elements in other words –various elements go into manufacture of an end product. • Eg-Chemical and paper industry. • Analytical industry-convert raw material into various elements. eg-Oil refinery, Gasoline, etc.
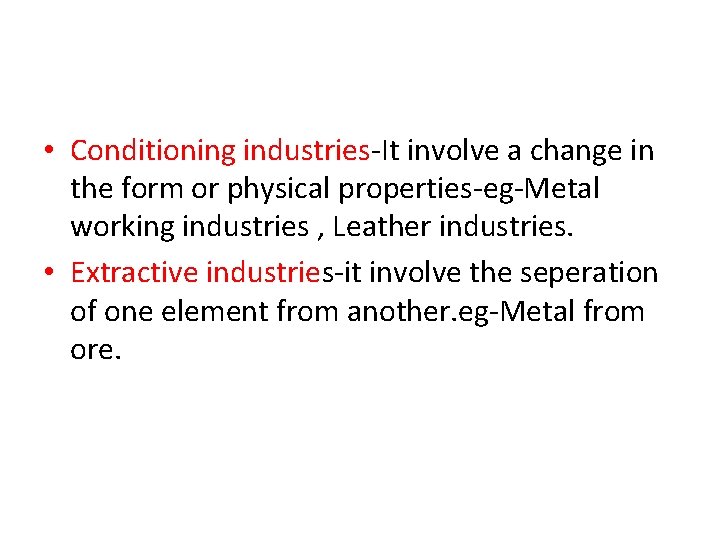
• Conditioning industries-It involve a change in the form or physical properties-eg-Metal working industries , Leather industries. • Extractive industries-it involve the seperation of one element from another. eg-Metal from ore.
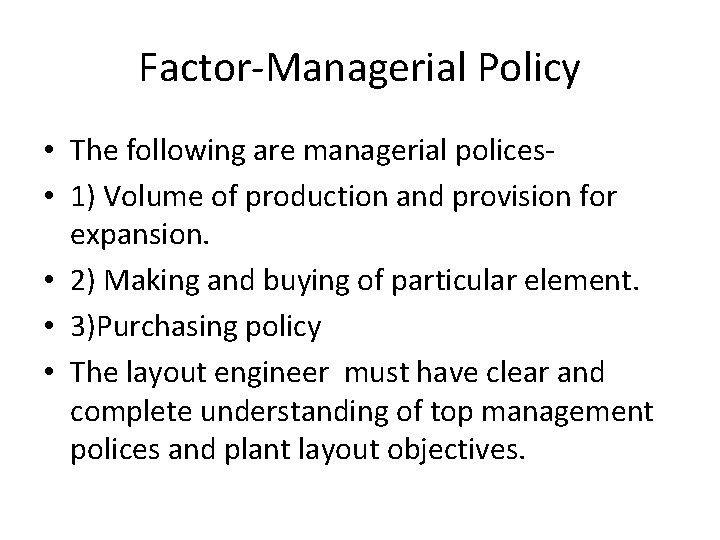
Factor-Managerial Policy • The following are managerial polices • 1) Volume of production and provision for expansion. • 2) Making and buying of particular element. • 3)Purchasing policy • The layout engineer must have clear and complete understanding of top management polices and plant layout objectives.
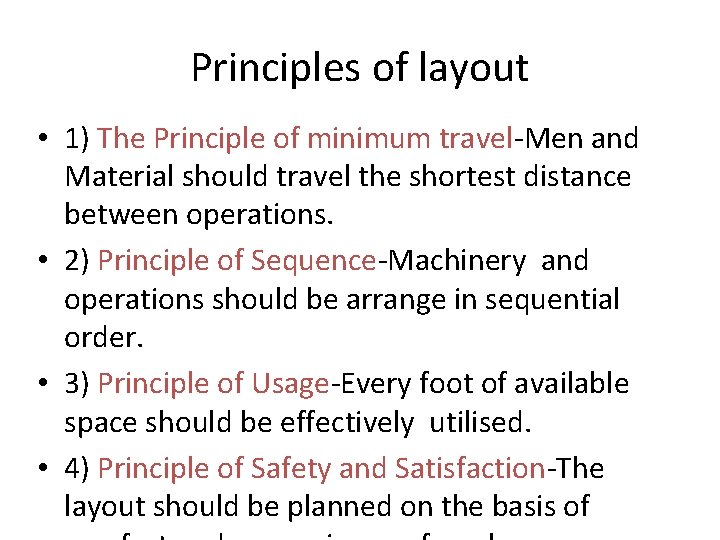
Principles of layout • 1) The Principle of minimum travel-Men and Material should travel the shortest distance between operations. • 2) Principle of Sequence-Machinery and operations should be arrange in sequential order. • 3) Principle of Usage-Every foot of available space should be effectively utilised. • 4) Principle of Safety and Satisfaction-The layout should be planned on the basis of
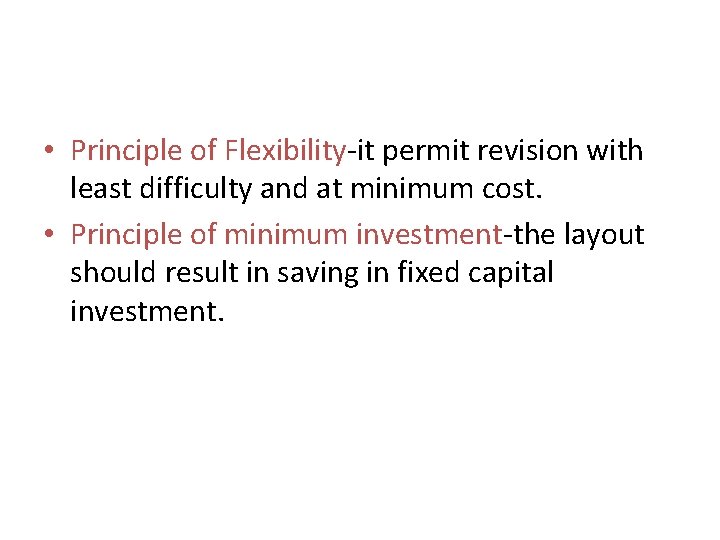
• Principle of Flexibility-it permit revision with least difficulty and at minimum cost. • Principle of minimum investment-the layout should result in saving in fixed capital investment.
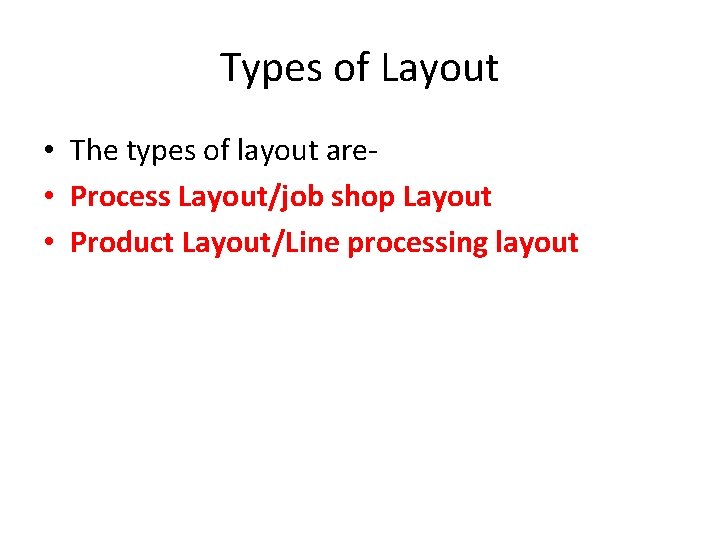
Types of Layout • The types of layout are • Process Layout/job shop Layout • Product Layout/Line processing layout
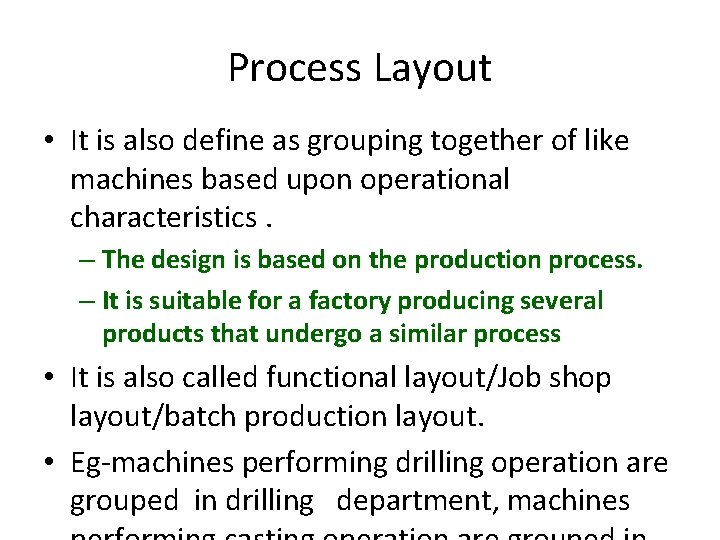
Process Layout • It is also define as grouping together of like machines based upon operational characteristics. – The design is based on the production process. – It is suitable for a factory producing several products that undergo a similar process • It is also called functional layout/Job shop layout/batch production layout. • Eg-machines performing drilling operation are grouped in drilling department, machines
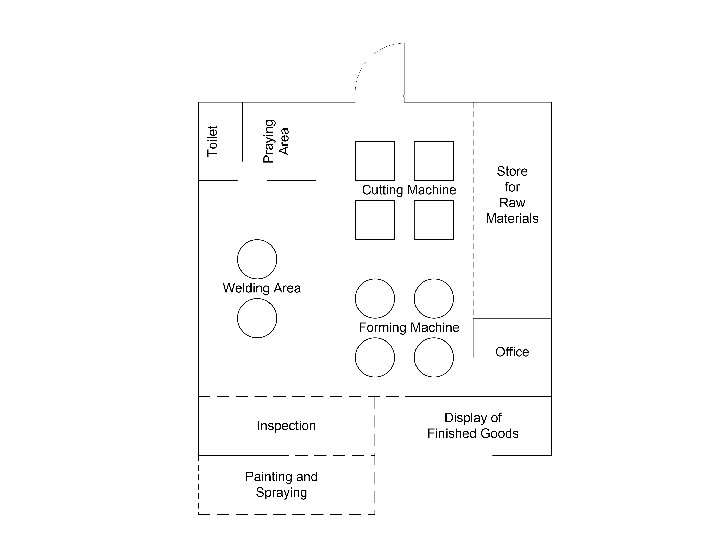
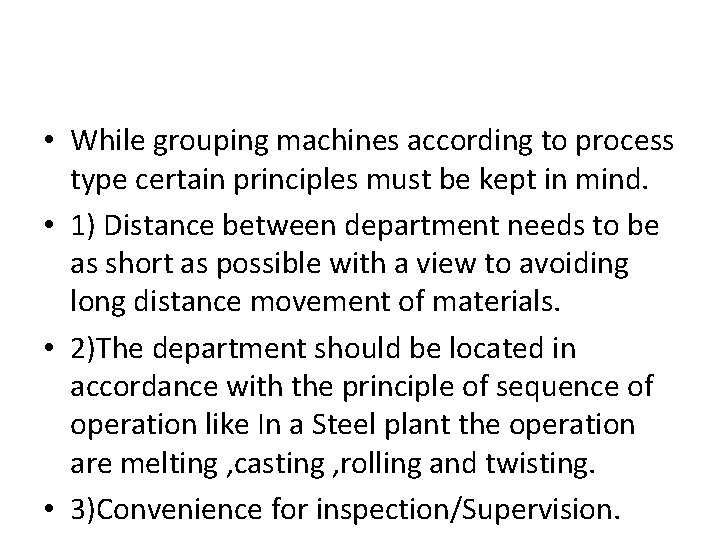
• While grouping machines according to process type certain principles must be kept in mind. • 1) Distance between department needs to be as short as possible with a view to avoiding long distance movement of materials. • 2)The department should be located in accordance with the principle of sequence of operation like In a Steel plant the operation are melting , casting , rolling and twisting. • 3)Convenience for inspection/Supervision.
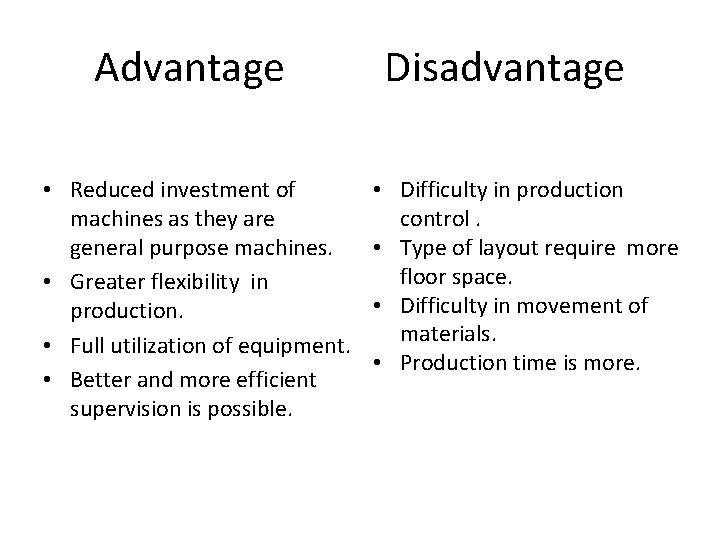
Advantage • Reduced investment of machines as they are general purpose machines. • Greater flexibility in production. • Full utilization of equipment. • Better and more efficient supervision is possible. Disadvantage • Difficulty in production control. • Type of layout require more floor space. • Difficulty in movement of materials. • Production time is more.
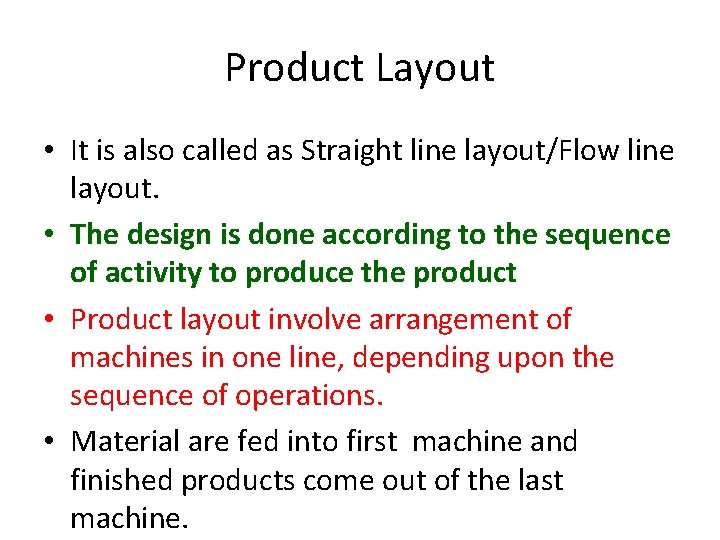
Product Layout • It is also called as Straight line layout/Flow line layout. • The design is done according to the sequence of activity to produce the product • Product layout involve arrangement of machines in one line, depending upon the sequence of operations. • Material are fed into first machine and finished products come out of the last machine.
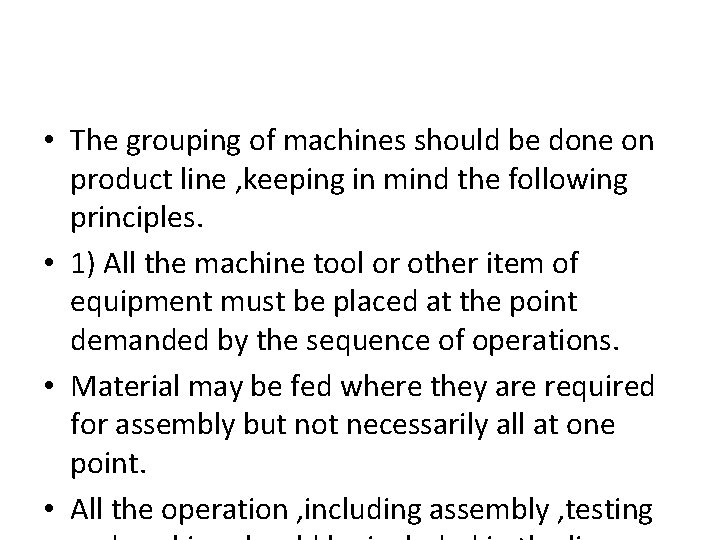
• The grouping of machines should be done on product line , keeping in mind the following principles. • 1) All the machine tool or other item of equipment must be placed at the point demanded by the sequence of operations. • Material may be fed where they are required for assembly but not necessarily all at one point. • All the operation , including assembly , testing
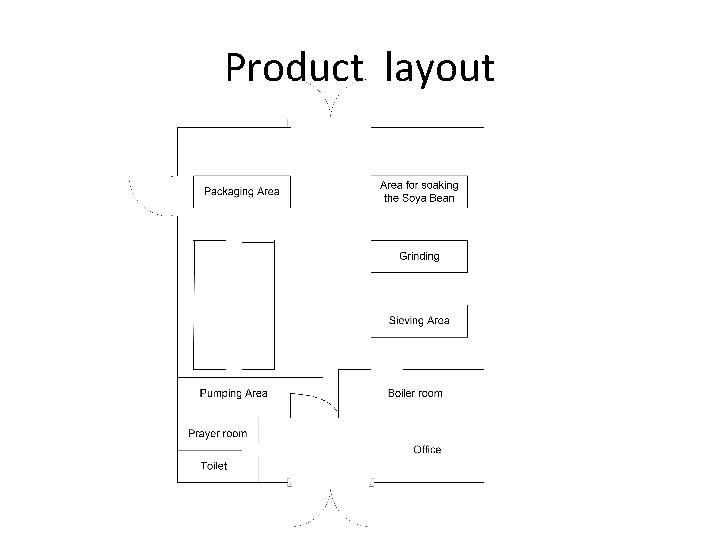
Product layout
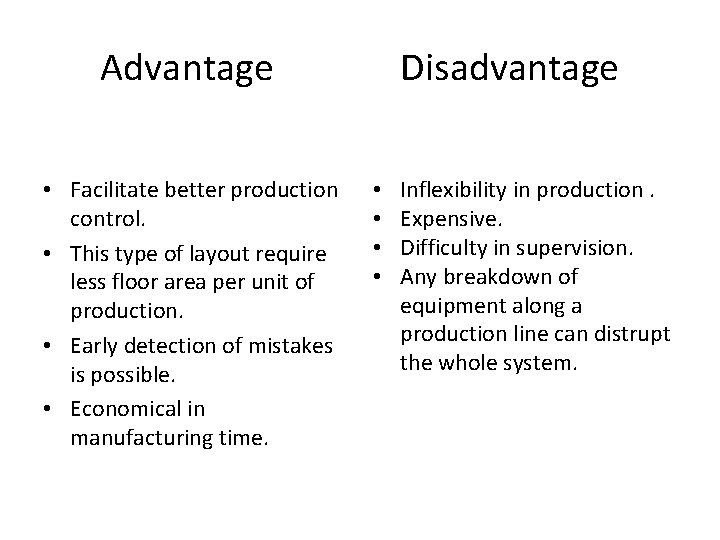
Advantage • Facilitate better production control. • This type of layout require less floor area per unit of production. • Early detection of mistakes is possible. • Economical in manufacturing time. Disadvantage • • Inflexibility in production. Expensive. Difficulty in supervision. Any breakdown of equipment along a production line can distrupt the whole system.
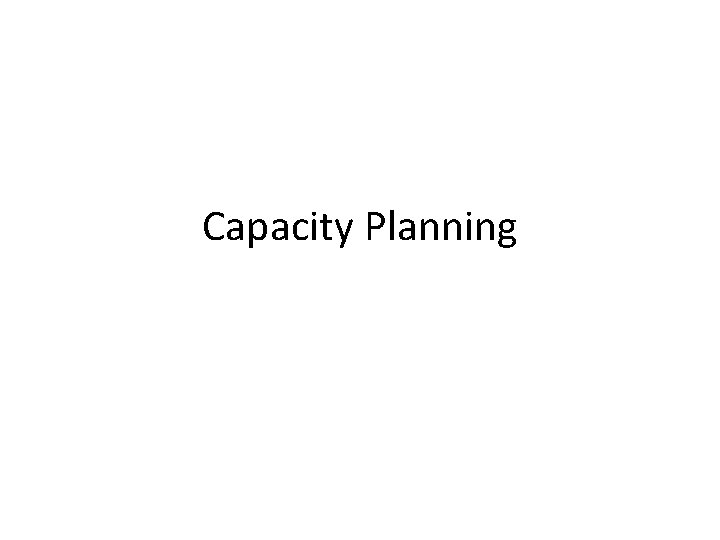
Capacity Planning
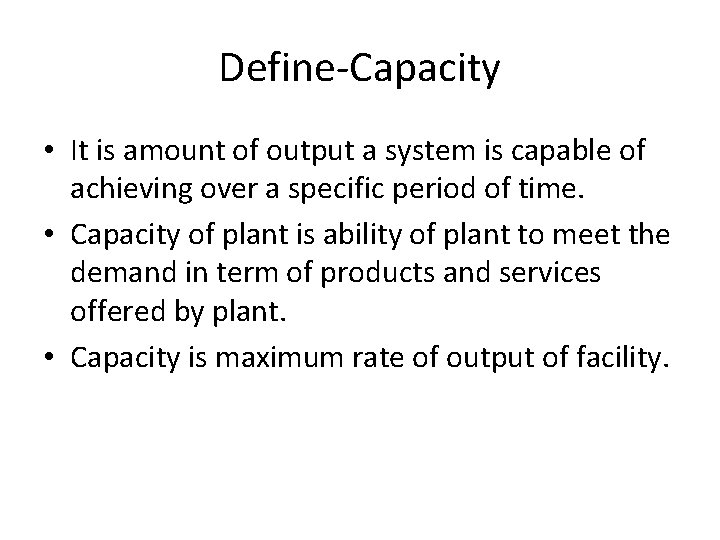
Define-Capacity • It is amount of output a system is capable of achieving over a specific period of time. • Capacity of plant is ability of plant to meet the demand in term of products and services offered by plant. • Capacity is maximum rate of output of facility.
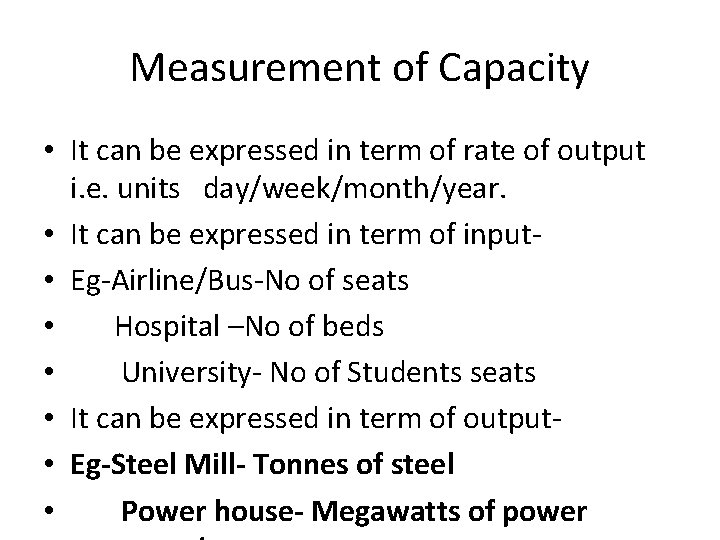
Measurement of Capacity • It can be expressed in term of rate of output i. e. units day/week/month/year. • It can be expressed in term of input • Eg-Airline/Bus-No of seats • Hospital –No of beds • University- No of Students seats • It can be expressed in term of output • Eg-Steel Mill- Tonnes of steel • Power house- Megawatts of power
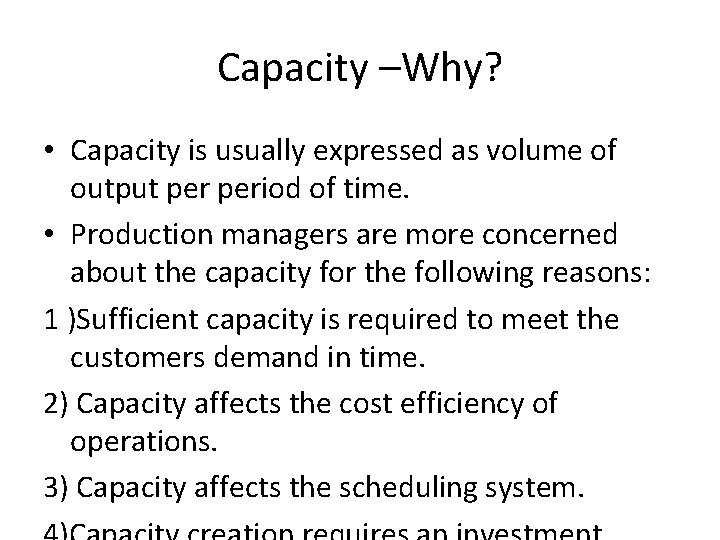
Capacity –Why? • Capacity is usually expressed as volume of output period of time. • Production managers are more concerned about the capacity for the following reasons: 1 )Sufficient capacity is required to meet the customers demand in time. 2) Capacity affects the cost efficiency of operations. 3) Capacity affects the scheduling system.
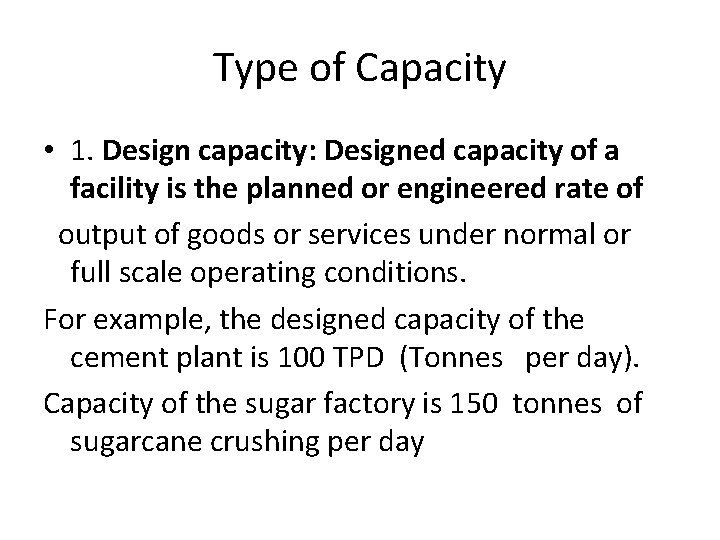
Type of Capacity • 1. Design capacity: Designed capacity of a facility is the planned or engineered rate of output of goods or services under normal or full scale operating conditions. For example, the designed capacity of the cement plant is 100 TPD (Tonnes per day). Capacity of the sugar factory is 150 tonnes of sugarcane crushing per day
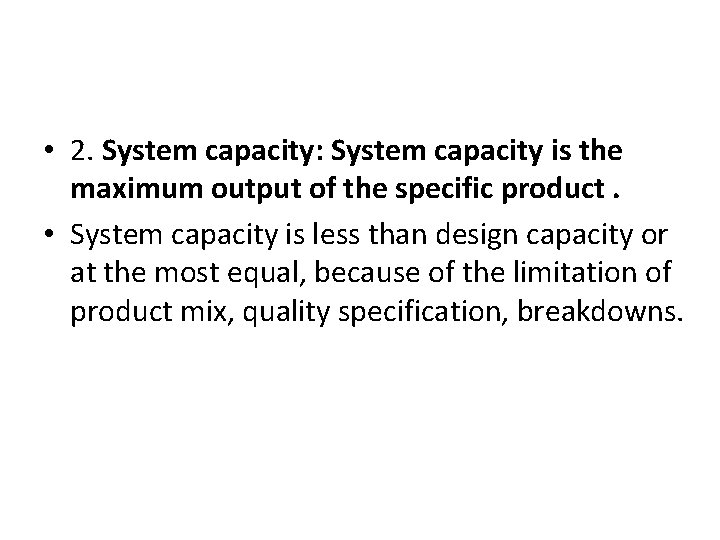
• 2. System capacity: System capacity is the maximum output of the specific product. • System capacity is less than design capacity or at the most equal, because of the limitation of product mix, quality specification, breakdowns.
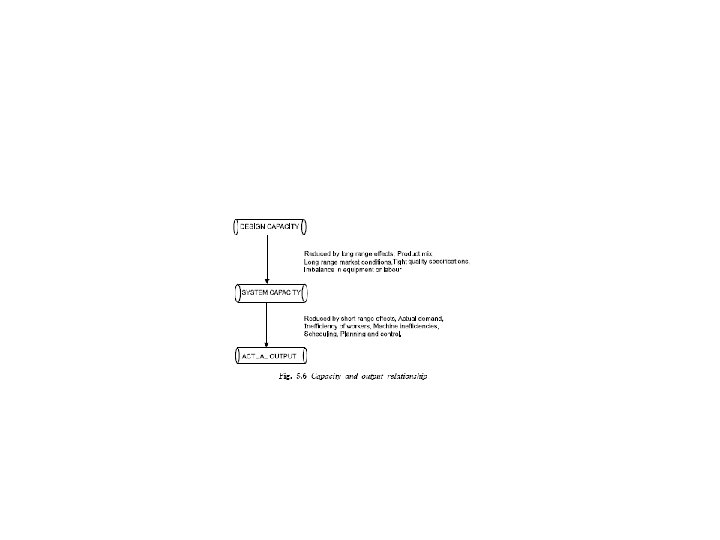
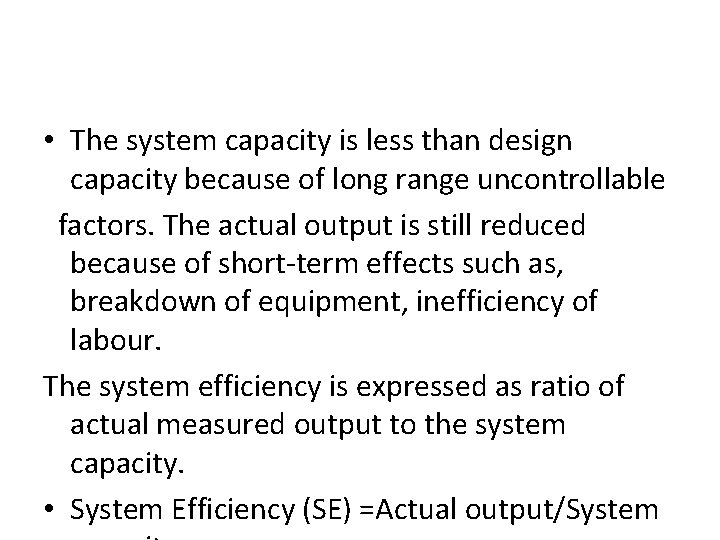
• The system capacity is less than design capacity because of long range uncontrollable factors. The actual output is still reduced because of short-term effects such as, breakdown of equipment, inefficiency of labour. The system efficiency is expressed as ratio of actual measured output to the system capacity. • System Efficiency (SE) =Actual output/System
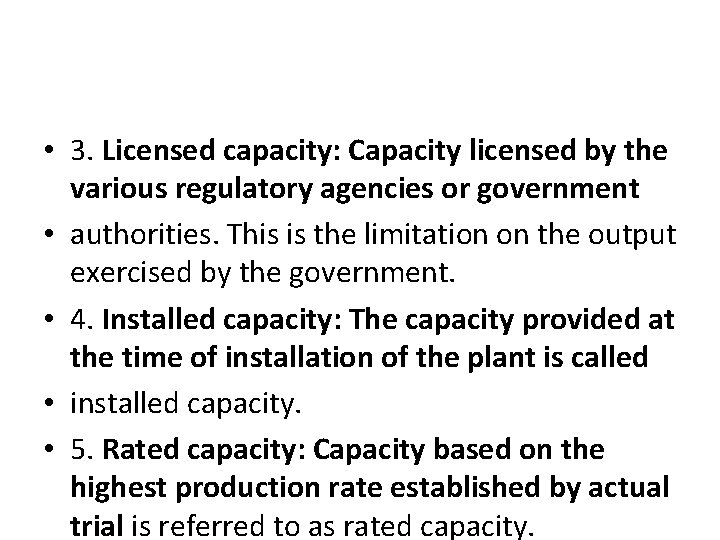
• 3. Licensed capacity: Capacity licensed by the various regulatory agencies or government • authorities. This is the limitation on the output exercised by the government. • 4. Installed capacity: The capacity provided at the time of installation of the plant is called • installed capacity. • 5. Rated capacity: Capacity based on the highest production rate established by actual trial is referred to as rated capacity.
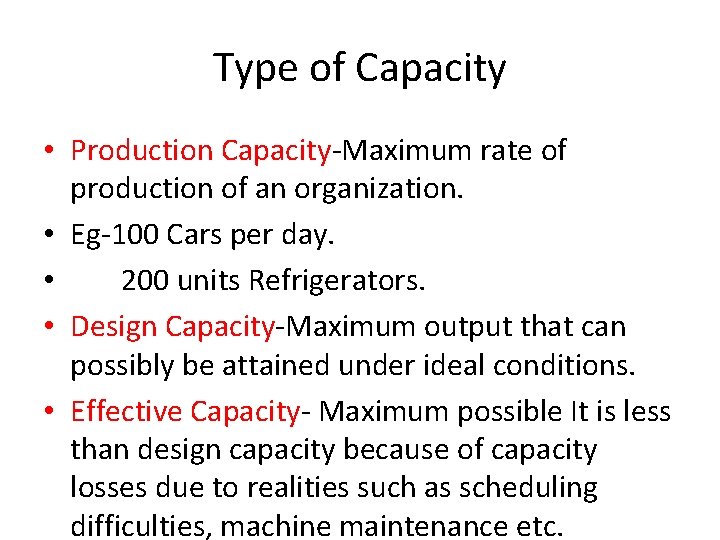
Type of Capacity • Production Capacity-Maximum rate of production of an organization. • Eg-100 Cars per day. • 200 units Refrigerators. • Design Capacity-Maximum output that can possibly be attained under ideal conditions. • Effective Capacity- Maximum possible It is less than design capacity because of capacity losses due to realities such as scheduling difficulties, machine maintenance etc.
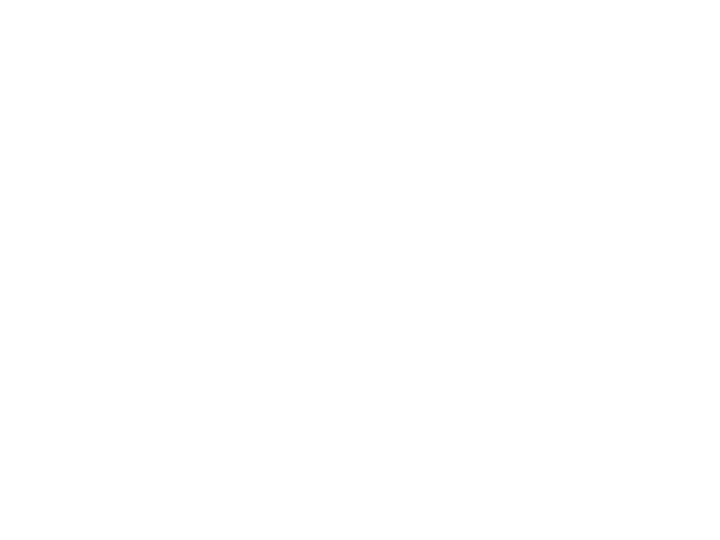
Define production
Jelaskan proses pembuatan multimedia content production
Money mangement international
Human resource mangement
What are the 5 stages of the service lifecycle
What is stress mangement
Project mangement institute
Difference between rm and crm
Sales mangement
Sales mangement
Sales mangement
Project mangement security
Demand forecasting in operations management
Forecasting in operations management
Implies in propositional logic
Job specifications definition
Tense logic
Components of mathematical system
When is something conditionally convergent
Reflexive axiom
Consideration
7 c's of effective communication
What is this picture
Uniform circular motion lab
Absolute continuity implies uniform continuity
The derivative and the tangent line problem
The first condition of equilibrium implies that: phy101
Segment partition formula
Who implies something?
5 examples of proposition
Logical connectives
Management implies
Andrew jackson found his greatest support among
Symptoms of overtrading
Operation definition in research
Binary operation means
What is tending operations
Split brain operation subcortex definition psychology
Closed loop obstruction examples
Simple distillation definition
What is production planning and control
Production and productivity definition
Production and productivity definition
Batch production advantages and disadvantages
Vc vs datagram
Leica total station setup and operation
Linux operation and administration chapter 8
Sales and operations planning sap
Operation and maintenance of dairy plant
Productivity definition in operations management
Sr latch truth table
Lesson 6 - composition of linear functions
Boolean expression
Types of undercover assignment
And operation
System design implementation and operation
Types of food and beverage service operation
And operation
Location planning in operations management
Location planning and analysis summary
Operation torch map
Small signal model fet
Mosfet structure and operation
Operation and productivity chapter 1
Front office manager roles and responsibilities
A splice in a welding cable should never be any closer than
Partnership formation and operation
Multimode operation in os
Iffco boiler
Partnership formation and operation
Mbbr operation and maintenance manual
Pengertian food and beverage product
Fundamentals of food and beverage service operation
Partnership formation and operation
Bsbsmb405
Headroom camera shot
Operation planning
Introduction to inventory management
Unit process and unit operation
Difference between unit process and unit operation
Apollo guidance computer manual
Perform the indicated operation. (see objectives 1 and 2.)
Characteristics of limited partnership
One off production meaning