Production Operation Management The Field of Operation Management
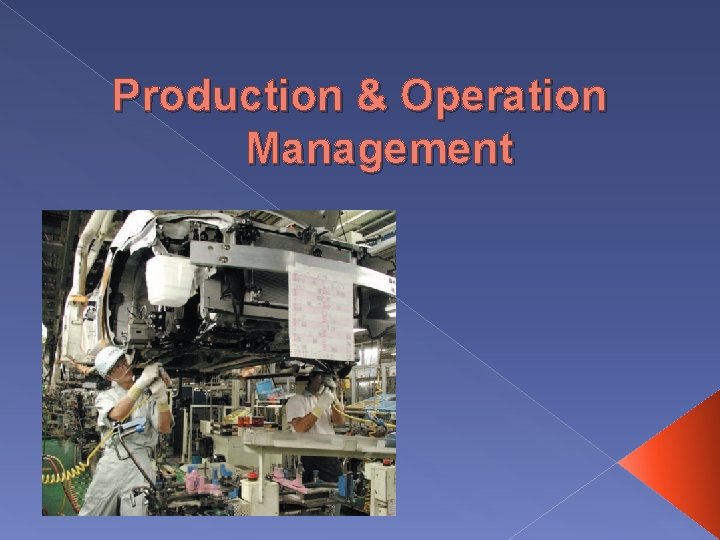
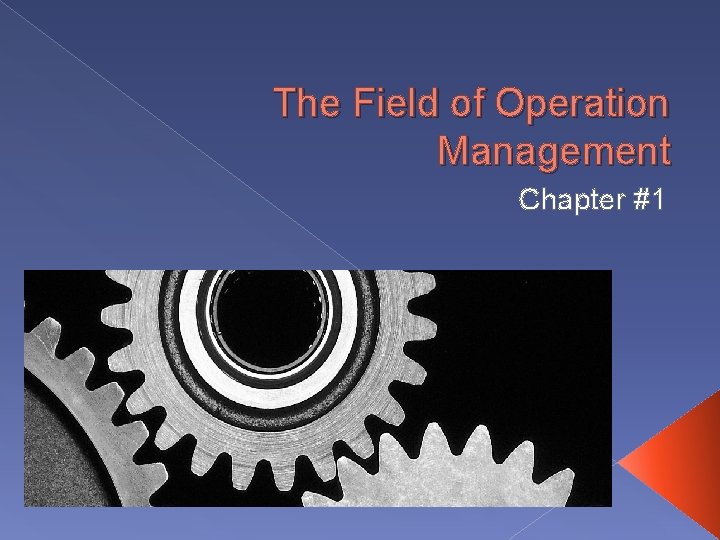
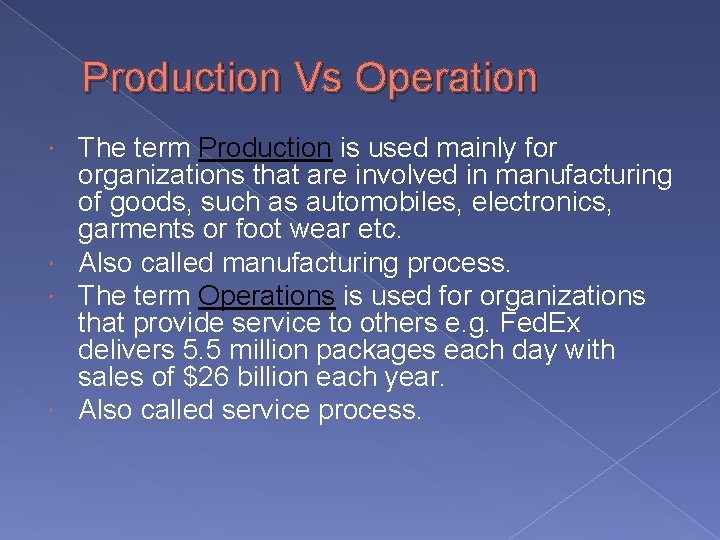
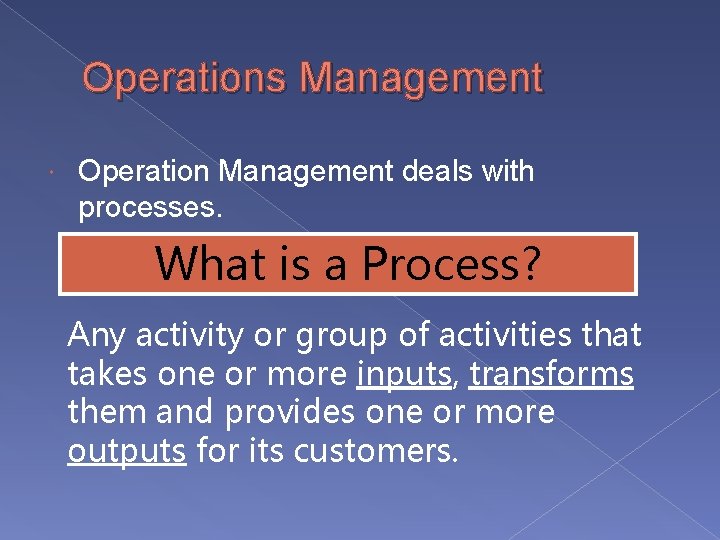
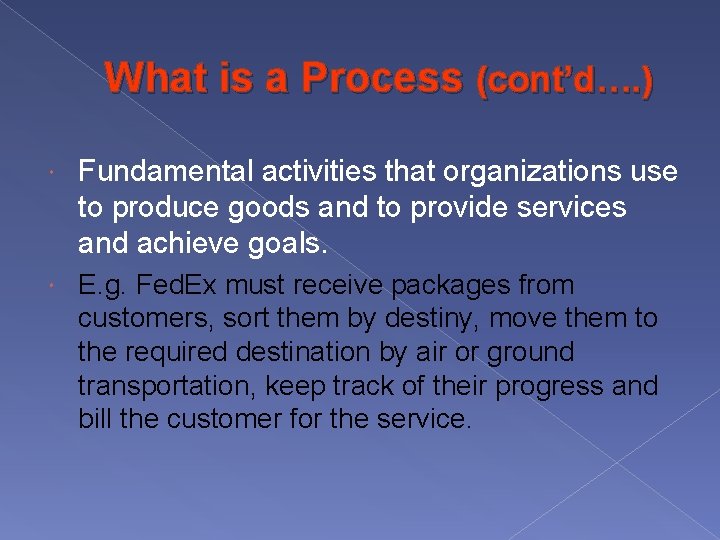
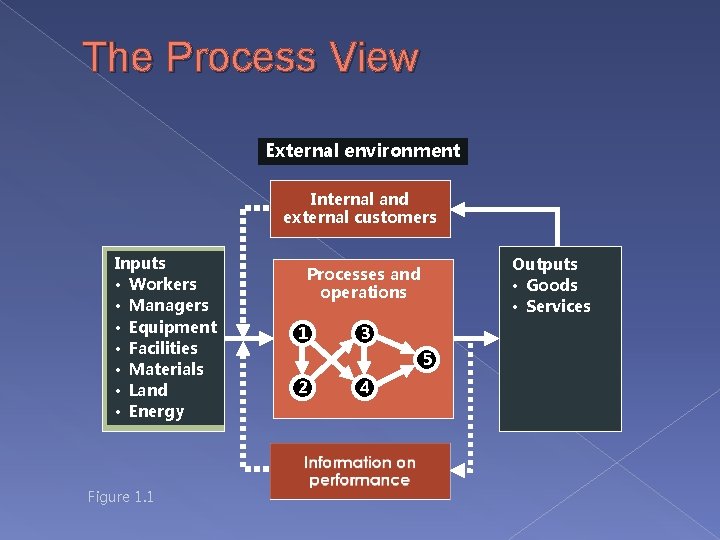
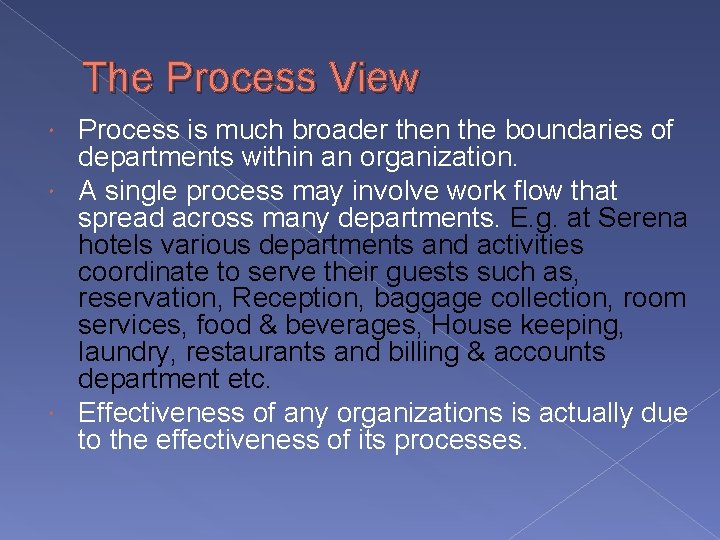
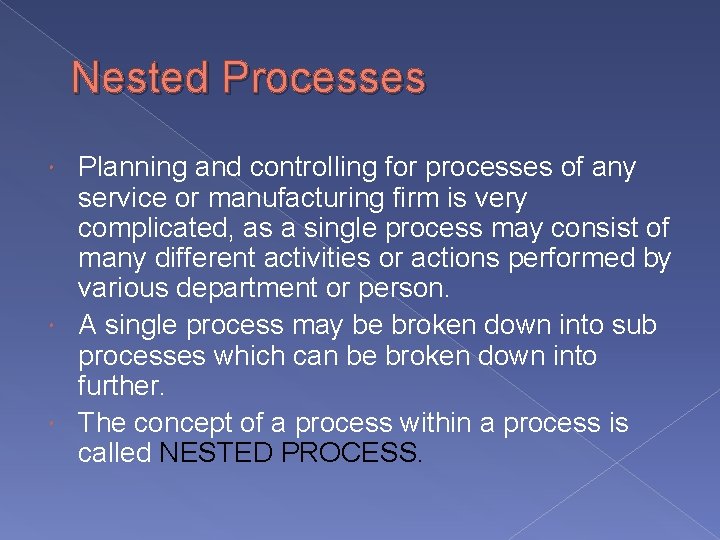
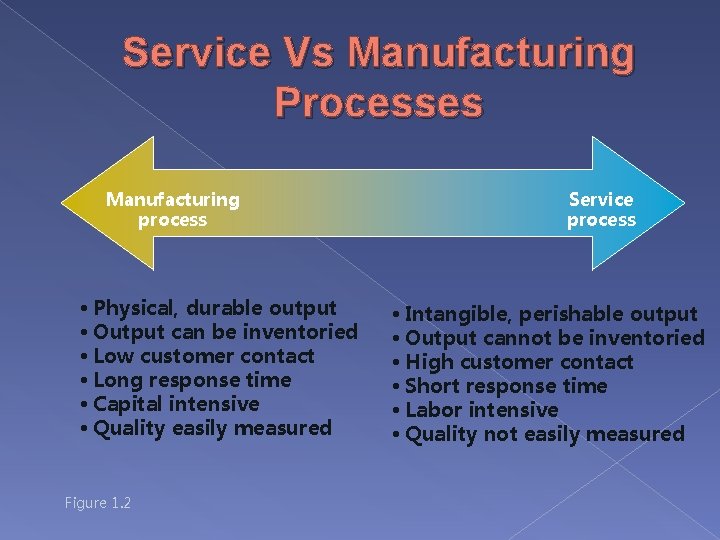
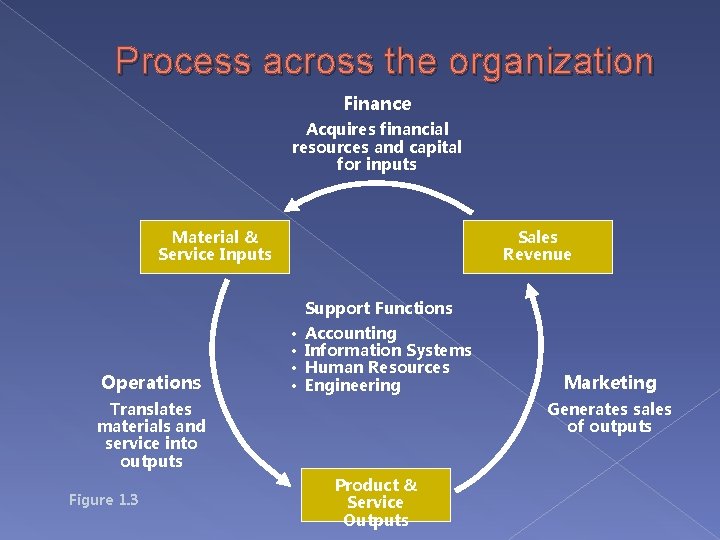
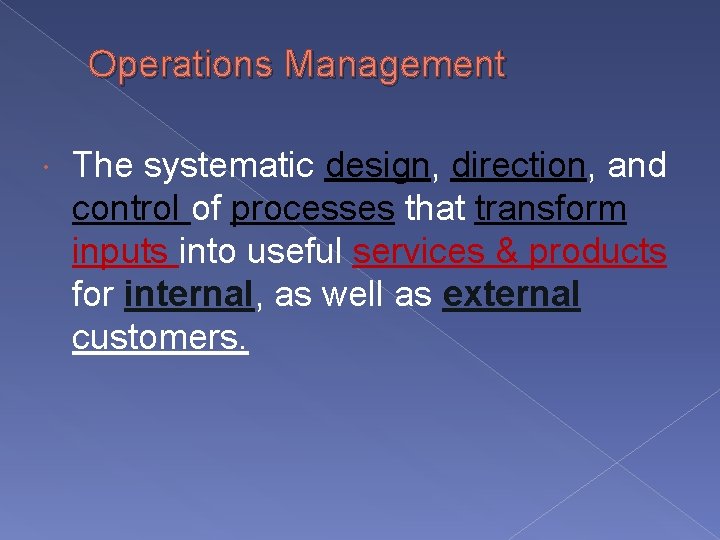
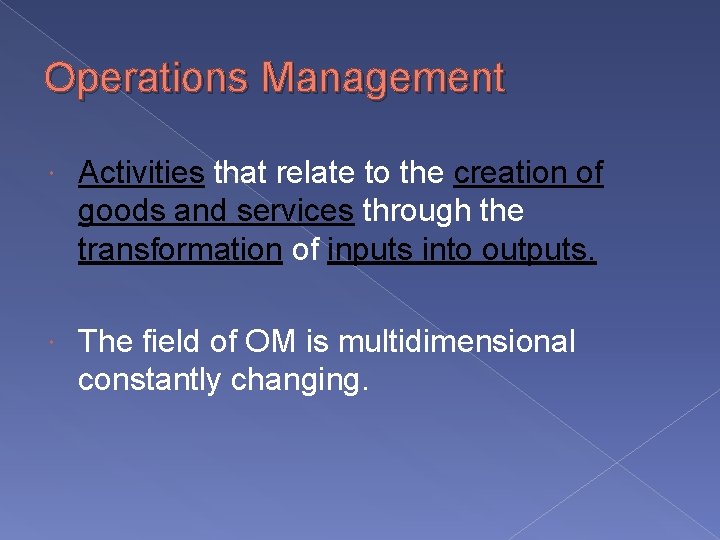
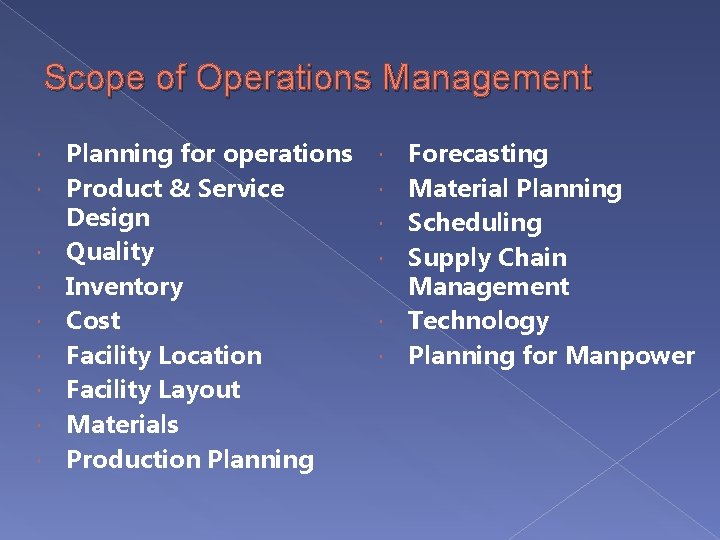
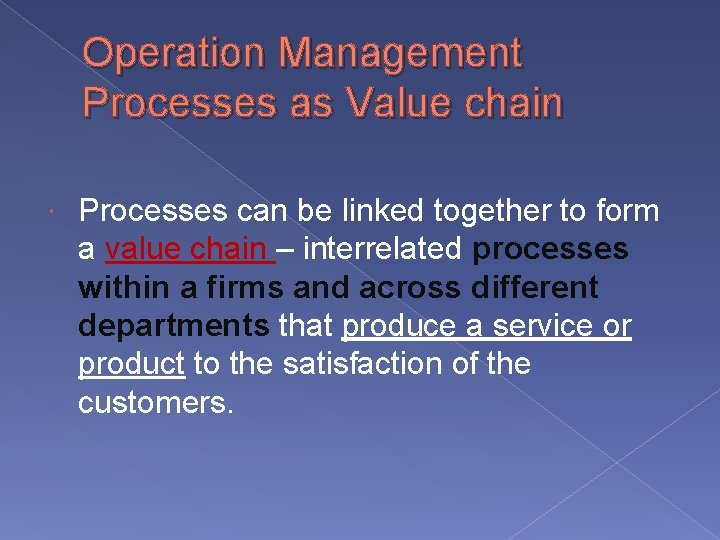
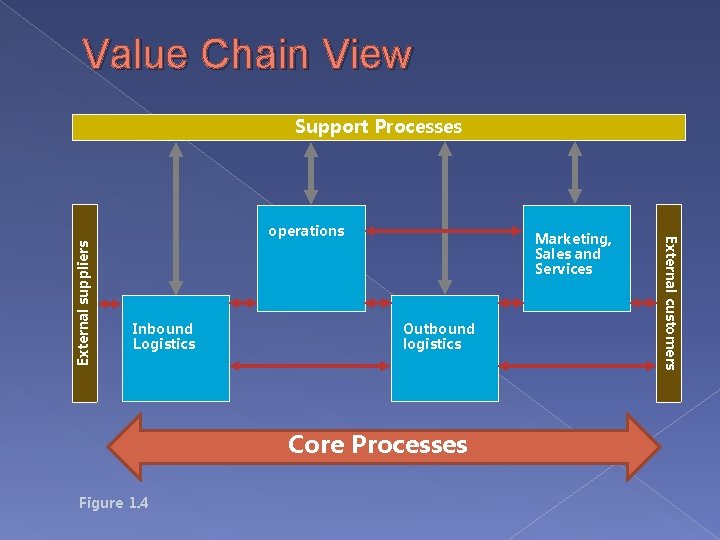
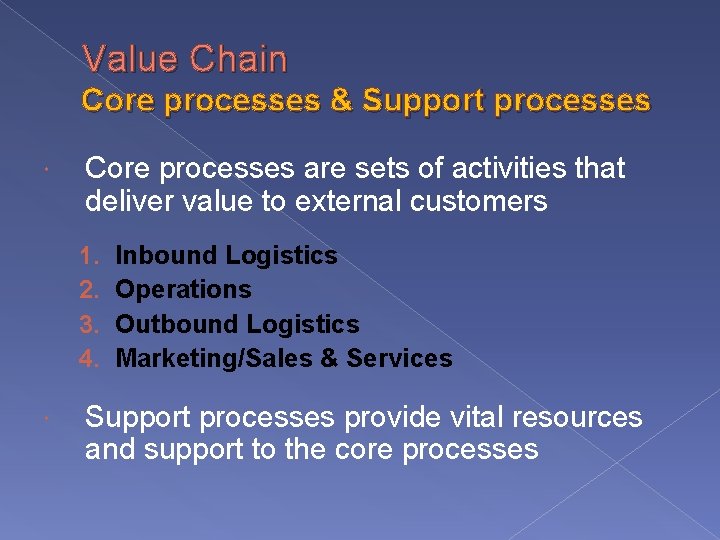
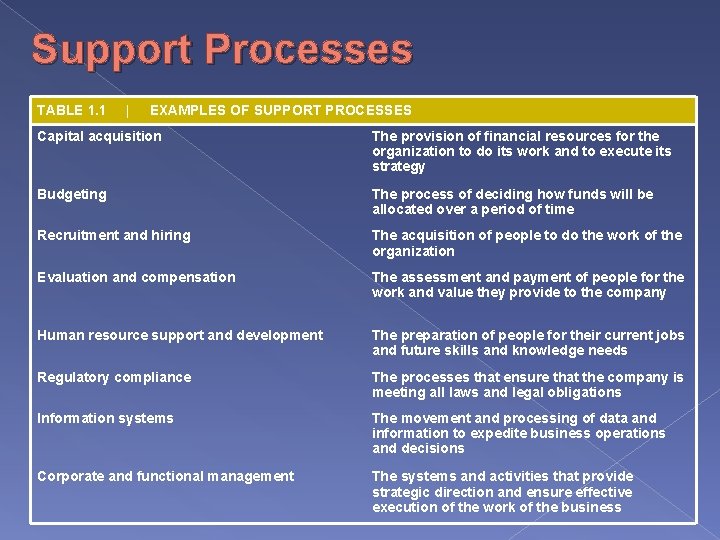
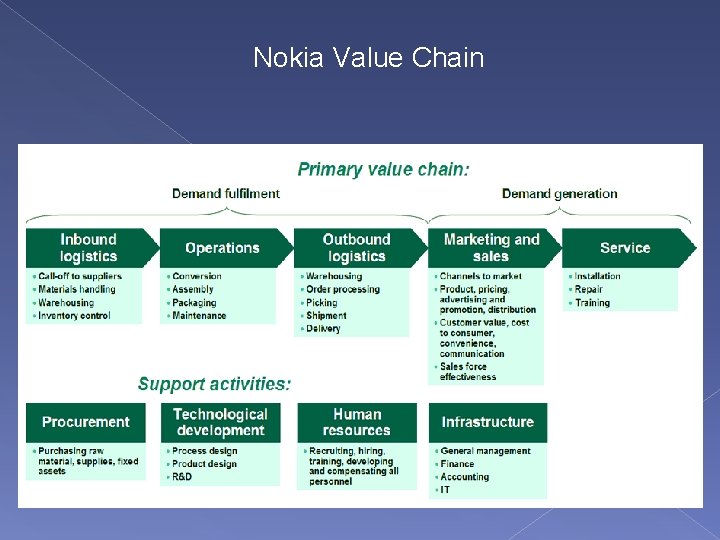
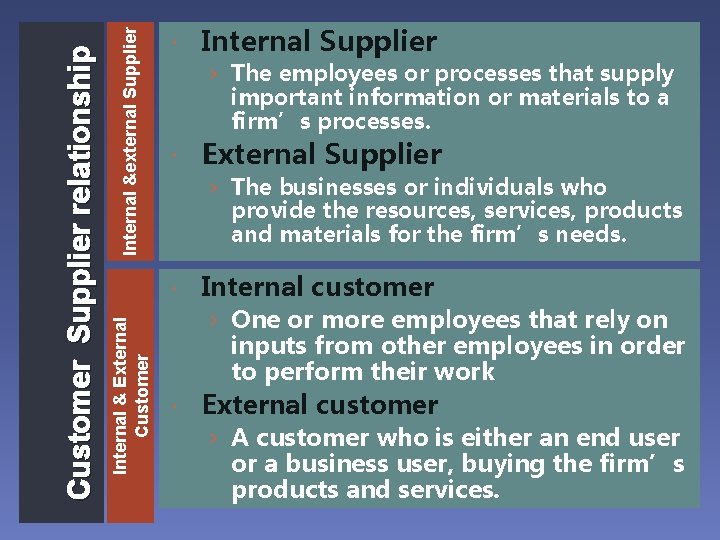
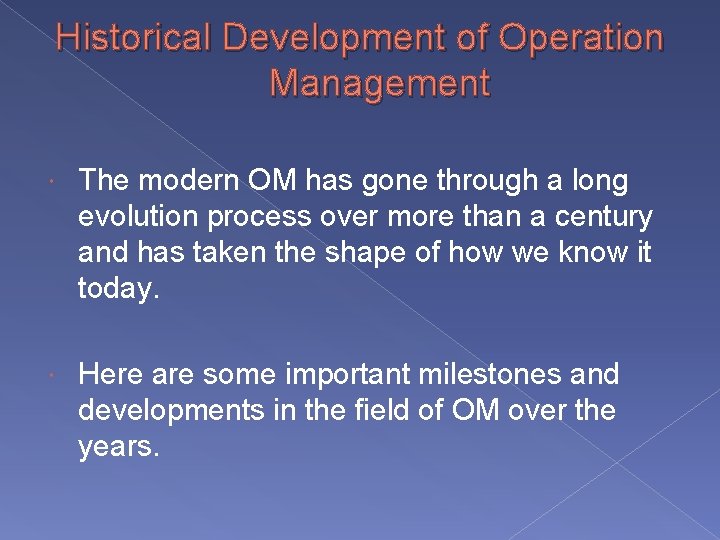
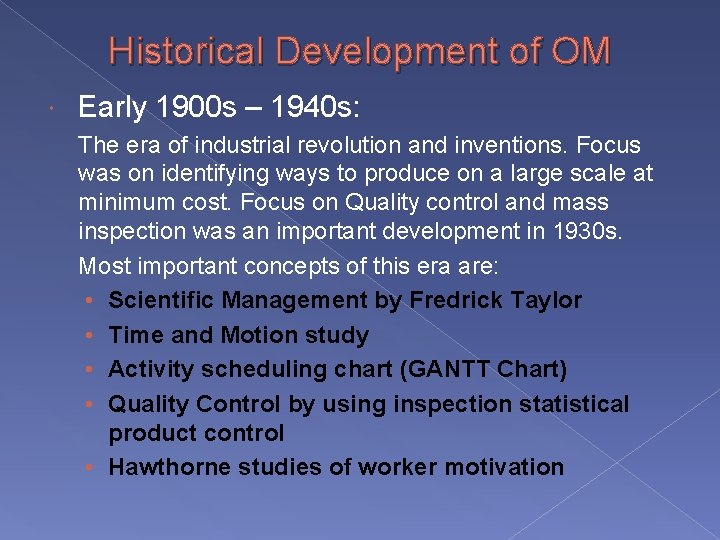
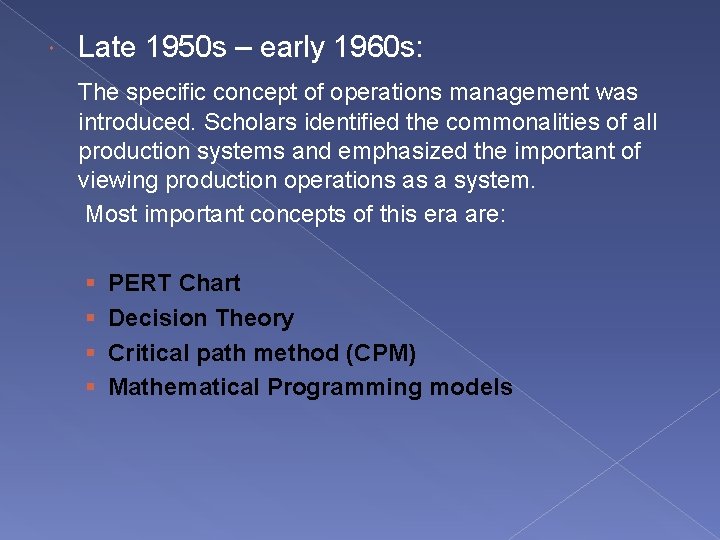
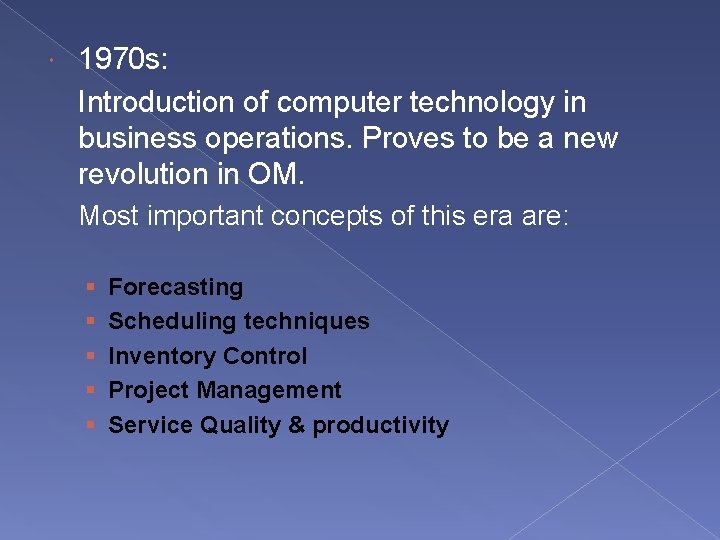
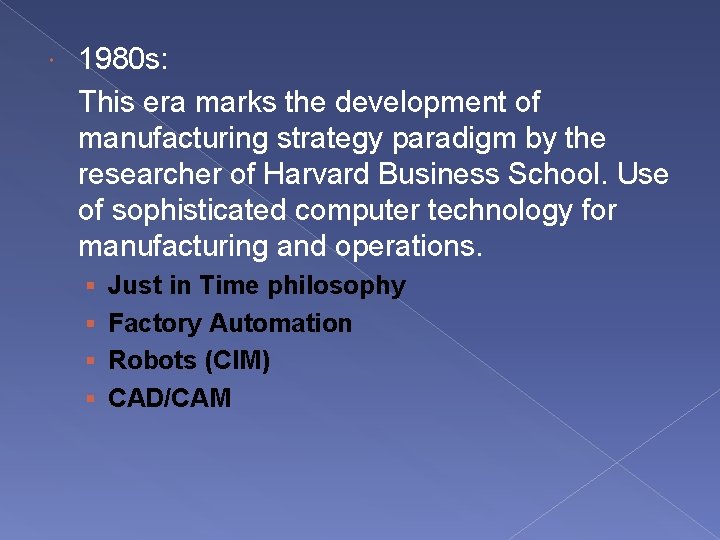
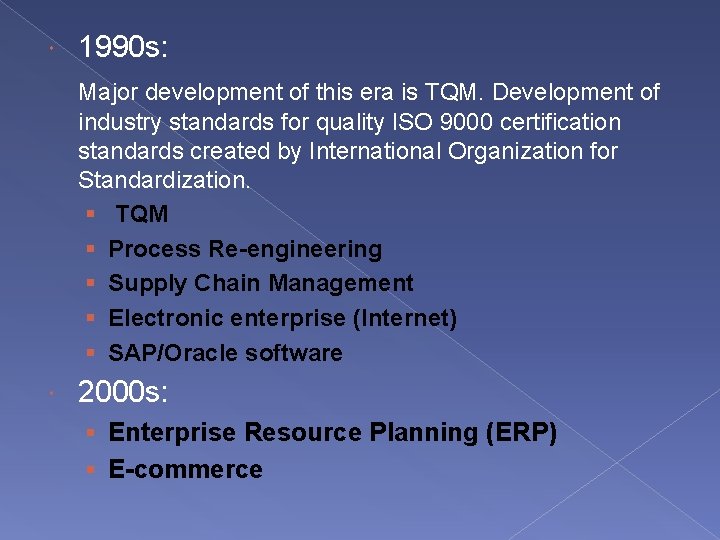
- Slides: 25
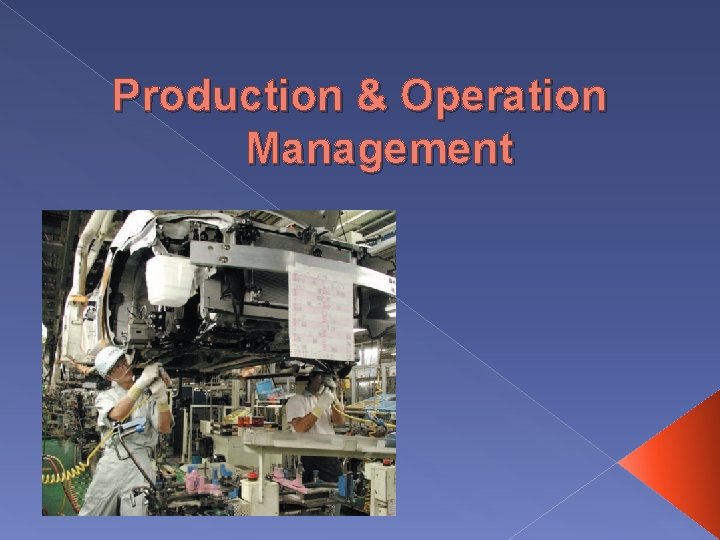
Production & Operation Management
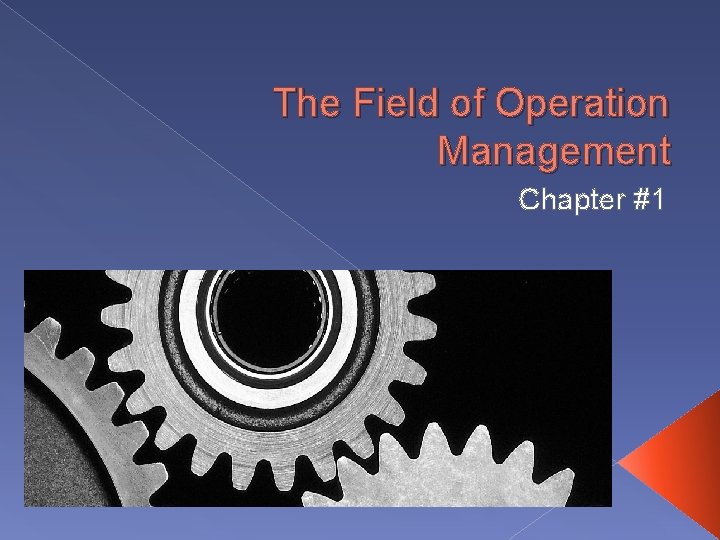
The Field of Operation Management Chapter #1
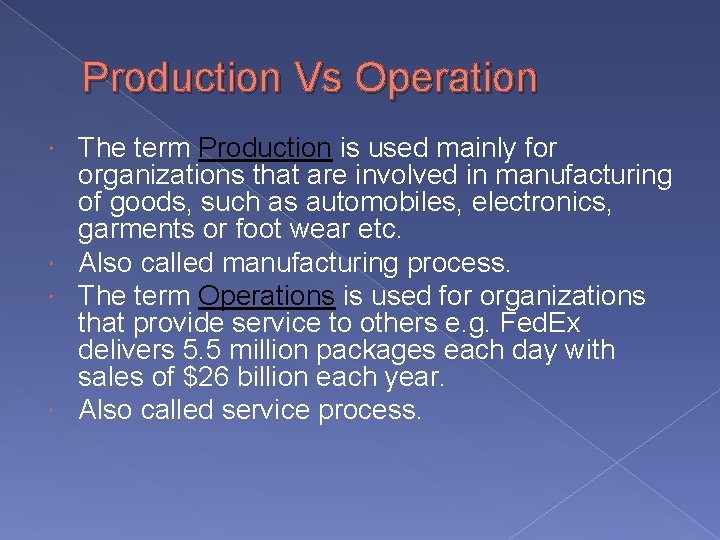
Production Vs Operation The term Production is used mainly for organizations that are involved in manufacturing of goods, such as automobiles, electronics, garments or foot wear etc. Also called manufacturing process. The term Operations is used for organizations that provide service to others e. g. Fed. Ex delivers 5. 5 million packages each day with sales of $26 billion each year. Also called service process.
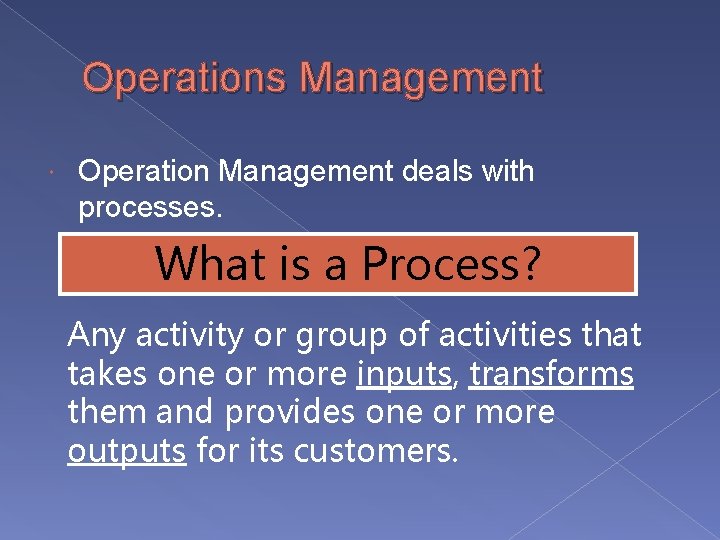
Operations Management Operation Management deals with processes. What is a Process? Any activity or group of activities that takes one or more inputs, transforms them and provides one or more outputs for its customers.
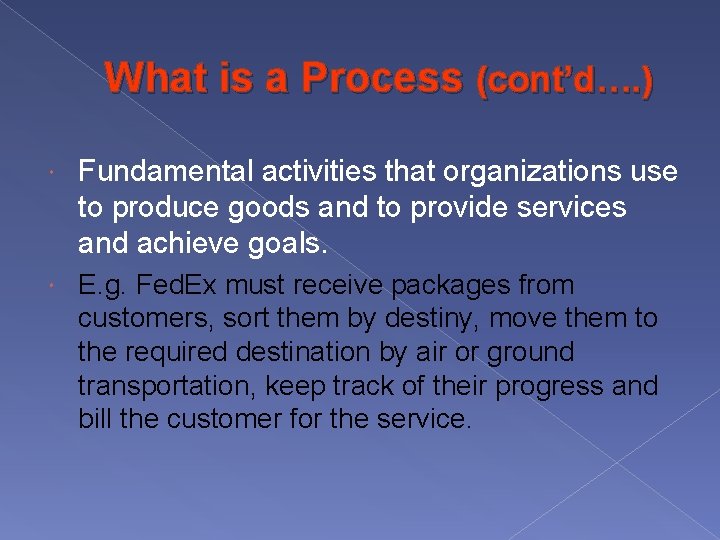
What is a Process (cont’d…. ) Fundamental activities that organizations use to produce goods and to provide services and achieve goals. E. g. Fed. Ex must receive packages from customers, sort them by destiny, move them to the required destination by air or ground transportation, keep track of their progress and bill the customer for the service.
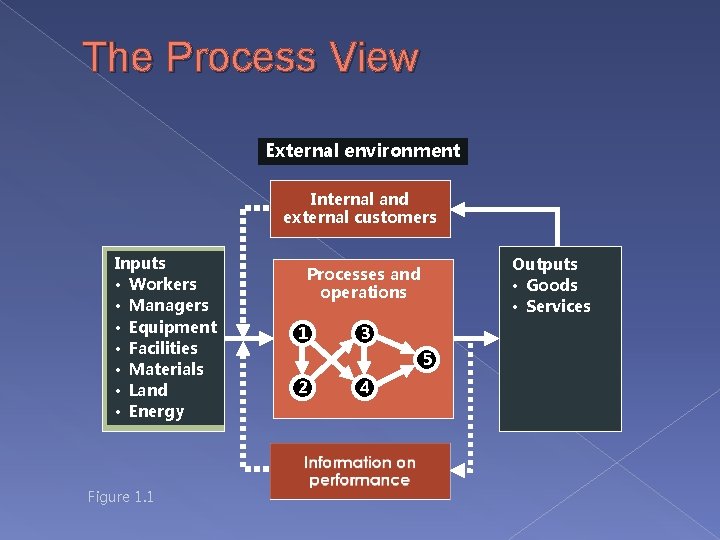
The Process View External environment Internal and external customers Inputs • Workers • Managers • Equipment • Facilities • Materials • Land • Energy Figure 1. 1 Outputs • Goods • Services Processes and operations 1 3 5 2 4
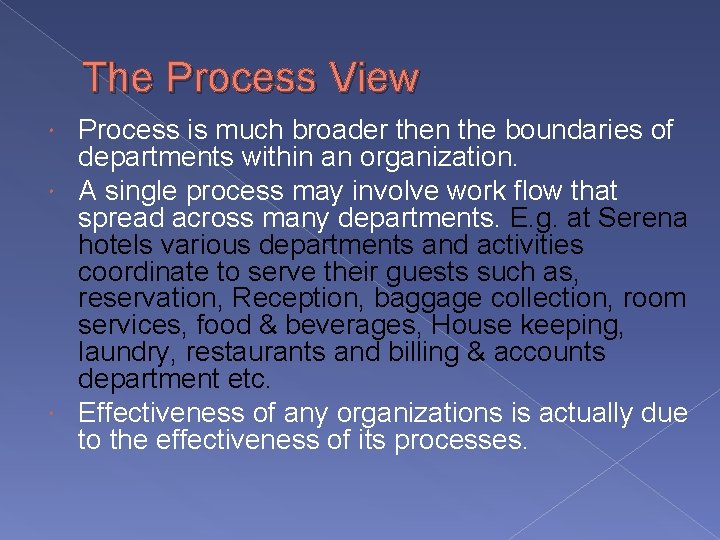
The Process View Process is much broader then the boundaries of departments within an organization. A single process may involve work flow that spread across many departments. E. g. at Serena hotels various departments and activities coordinate to serve their guests such as, reservation, Reception, baggage collection, room services, food & beverages, House keeping, laundry, restaurants and billing & accounts department etc. Effectiveness of any organizations is actually due to the effectiveness of its processes.
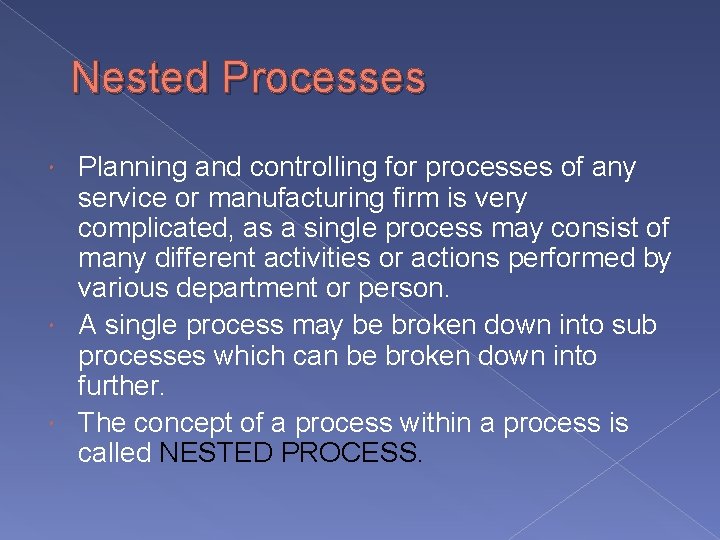
Nested Processes Planning and controlling for processes of any service or manufacturing firm is very complicated, as a single process may consist of many different activities or actions performed by various department or person. A single process may be broken down into sub processes which can be broken down into further. The concept of a process within a process is called NESTED PROCESS.
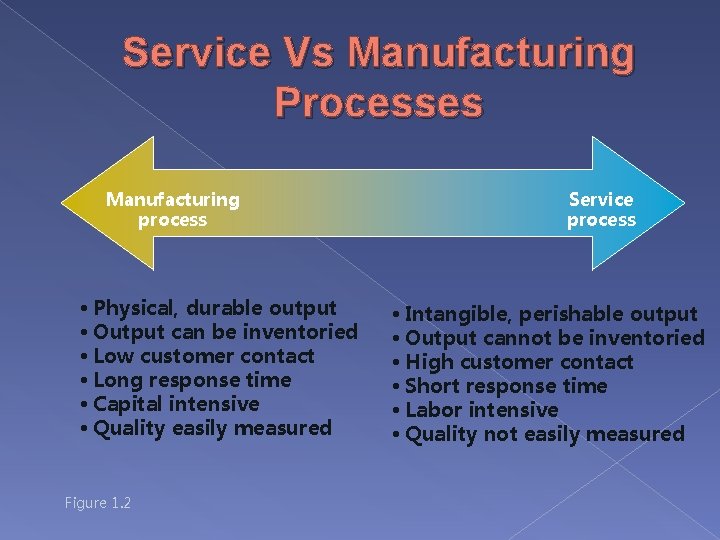
Service Vs Manufacturing Processes Manufacturing process • Physical, durable output • Output can be inventoried • Low customer contact • Long response time • Capital intensive • Quality easily measured Figure 1. 2 Service process • Intangible, perishable output • Output cannot be inventoried • High customer contact • Short response time • Labor intensive • Quality not easily measured
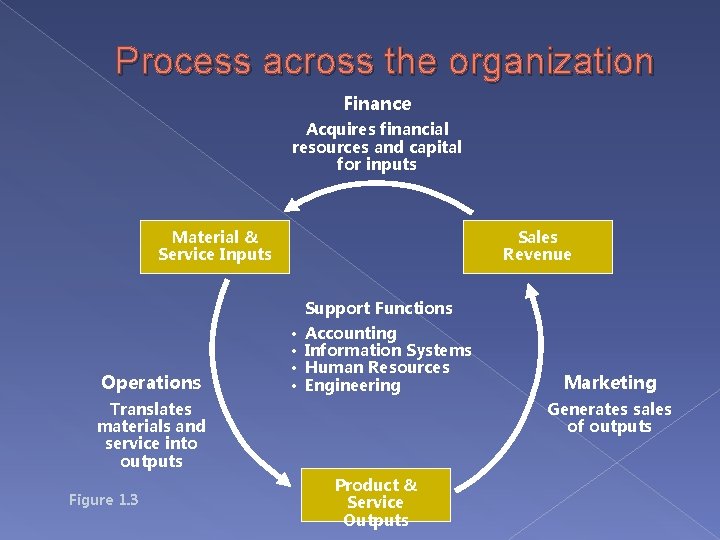
Process across the organization Finance Acquires financial resources and capital for inputs Material & Service Inputs Sales Revenue Support Functions Operations • • Accounting Information Systems Human Resources Engineering Translates materials and service into outputs Figure 1. 3 Marketing Generates sales of outputs Product & Service Outputs
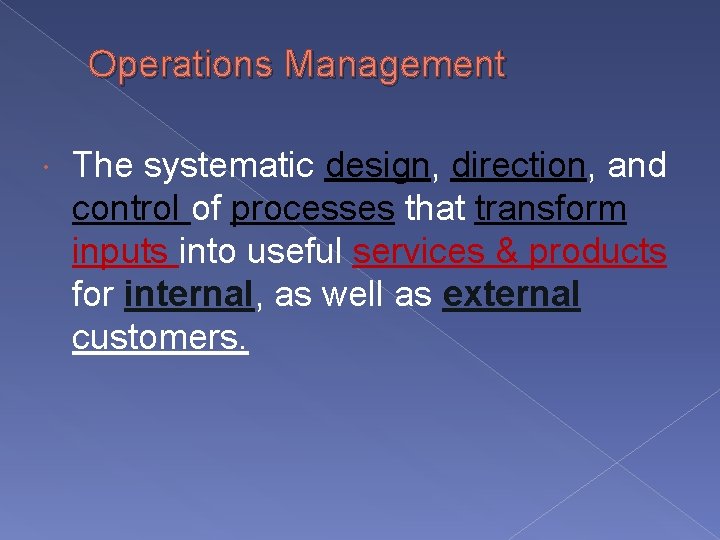
Operations Management The systematic design, direction, and control of processes that transform inputs into useful services & products for internal, as well as external customers.
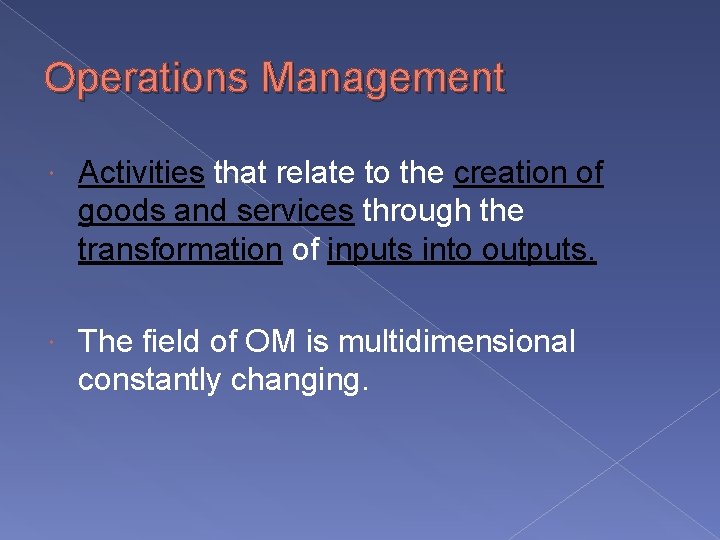
Operations Management Activities that relate to the creation of goods and services through the transformation of inputs into outputs. The field of OM is multidimensional constantly changing.
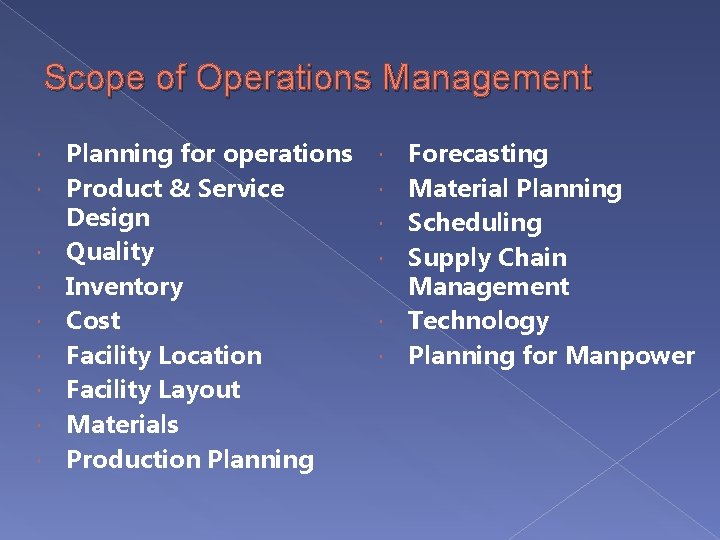
Scope of Operations Management Planning for operations Product & Service Design Quality Inventory Cost Facility Location Facility Layout Materials Production Planning Forecasting Material Planning Scheduling Supply Chain Management Technology Planning for Manpower
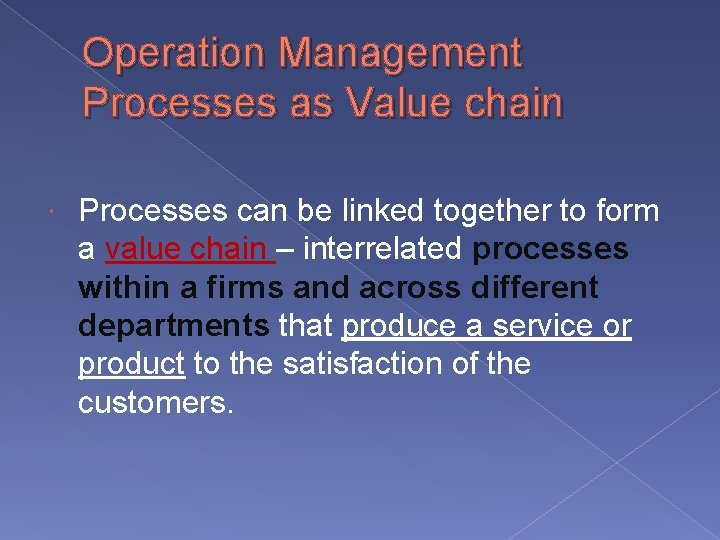
Operation Management Processes as Value chain Processes can be linked together to form a value chain – interrelated processes within a firms and across different departments that produce a service or product to the satisfaction of the customers.
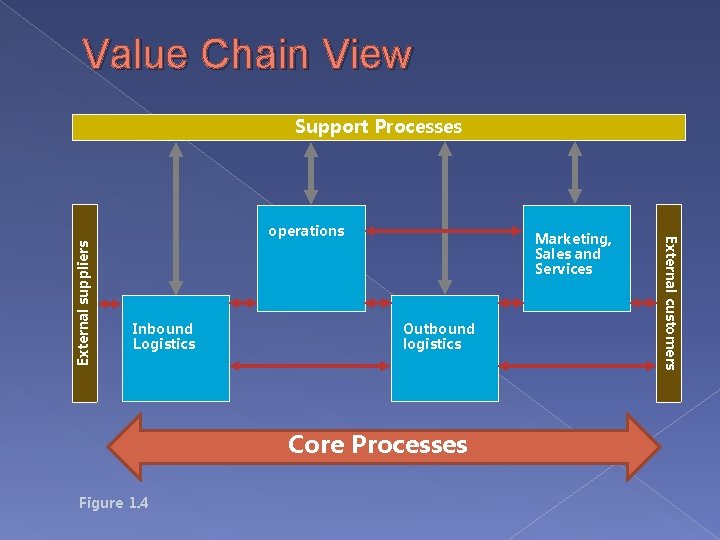
Value Chain View Support Processes External suppliers Inbound Logistics Marketing, Sales and Services Outbound logistics Core Processes Figure 1. 4 External customers operations
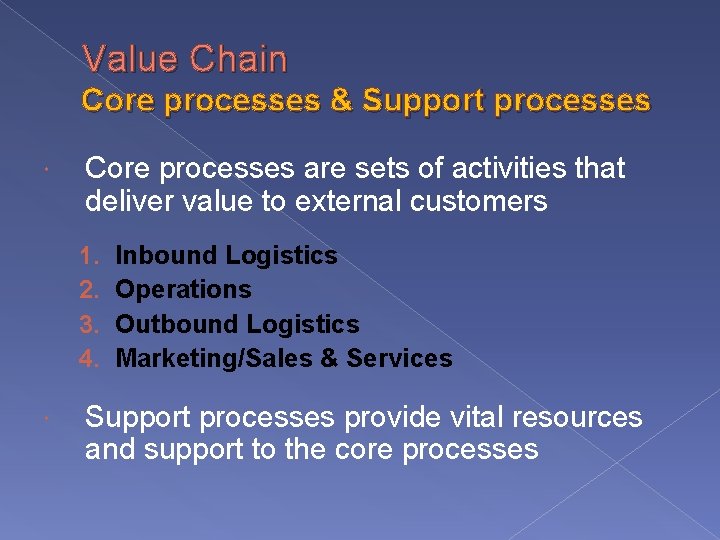
Value Chain Core processes & Support processes Core processes are sets of activities that deliver value to external customers 1. 2. 3. 4. Inbound Logistics Operations Outbound Logistics Marketing/Sales & Services Support processes provide vital resources and support to the core processes
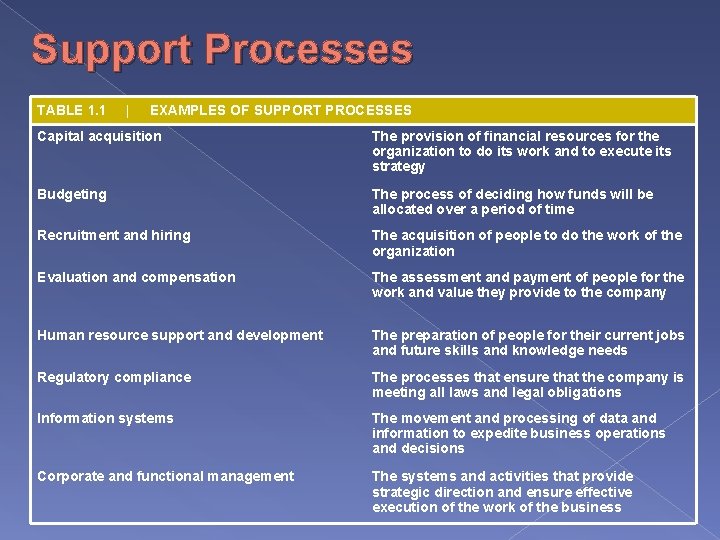
Support Processes TABLE 1. 1 | EXAMPLES OF SUPPORT PROCESSES Capital acquisition The provision of financial resources for the organization to do its work and to execute its strategy Budgeting The process of deciding how funds will be allocated over a period of time Recruitment and hiring The acquisition of people to do the work of the organization Evaluation and compensation The assessment and payment of people for the work and value they provide to the company Human resource support and development The preparation of people for their current jobs and future skills and knowledge needs Regulatory compliance The processes that ensure that the company is meeting all laws and legal obligations Information systems The movement and processing of data and information to expedite business operations and decisions Corporate and functional management The systems and activities that provide strategic direction and ensure effective execution of the work of the business
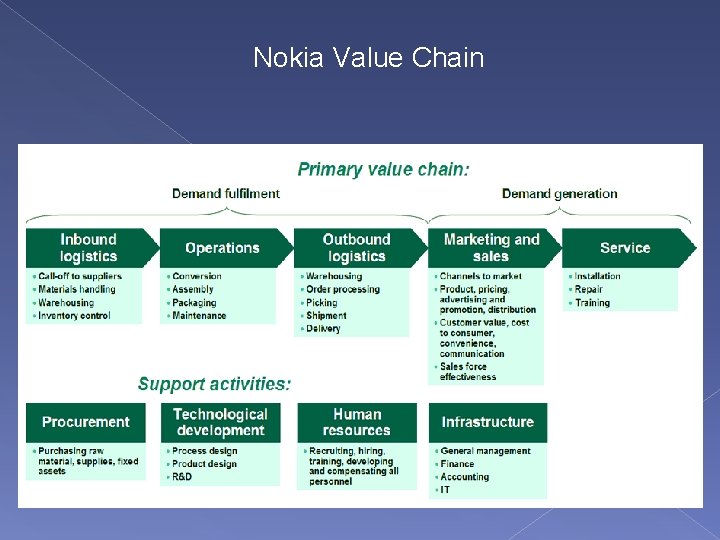
Nokia Value Chain
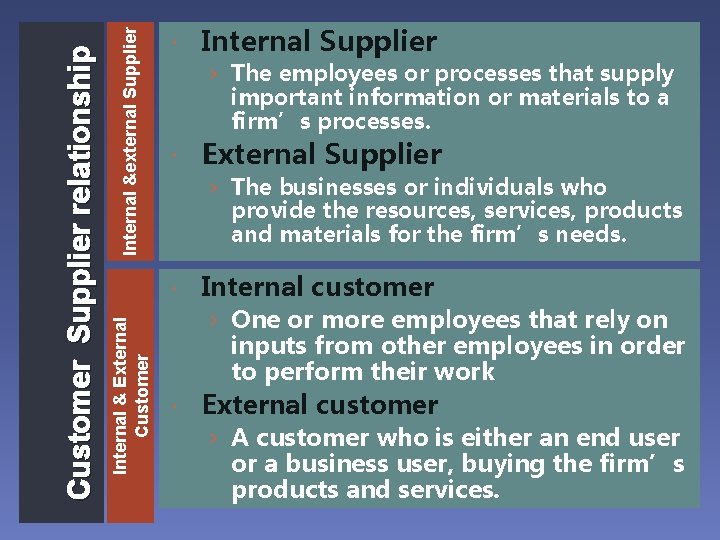
Internal &external Supplier Internal Supplier › The employees or processes that supply important information or materials to a firm’s processes. External Supplier › The businesses or individuals who provide the resources, services, products and materials for the firm’s needs. Internal & External Customer Supplier relationship Internal customer › One or more employees that rely on inputs from other employees in order to perform their work External customer › A customer who is either an end user or a business user, buying the firm’s products and services.
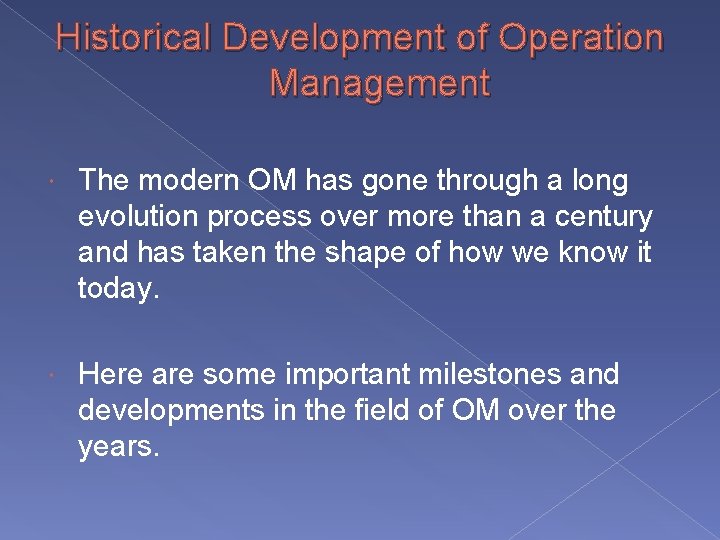
Historical Development of Operation Management The modern OM has gone through a long evolution process over more than a century and has taken the shape of how we know it today. Here are some important milestones and developments in the field of OM over the years.
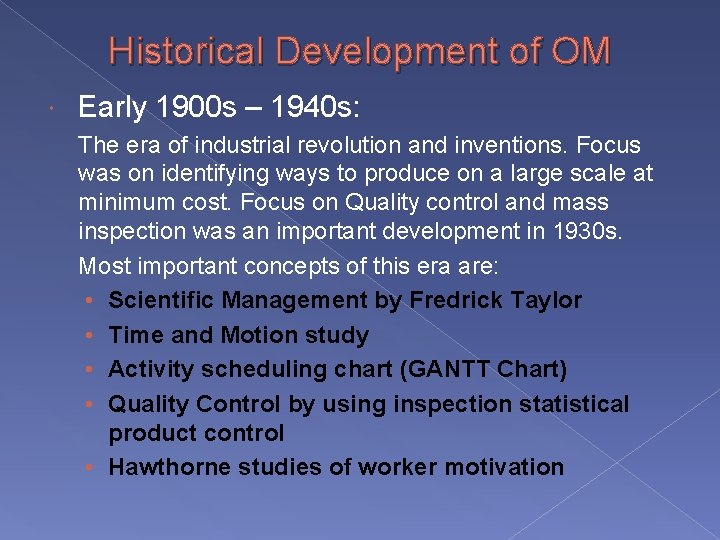
Historical Development of OM Early 1900 s – 1940 s: The era of industrial revolution and inventions. Focus was on identifying ways to produce on a large scale at minimum cost. Focus on Quality control and mass inspection was an important development in 1930 s. Most important concepts of this era are: • Scientific Management by Fredrick Taylor • Time and Motion study • Activity scheduling chart (GANTT Chart) • Quality Control by using inspection statistical product control • Hawthorne studies of worker motivation
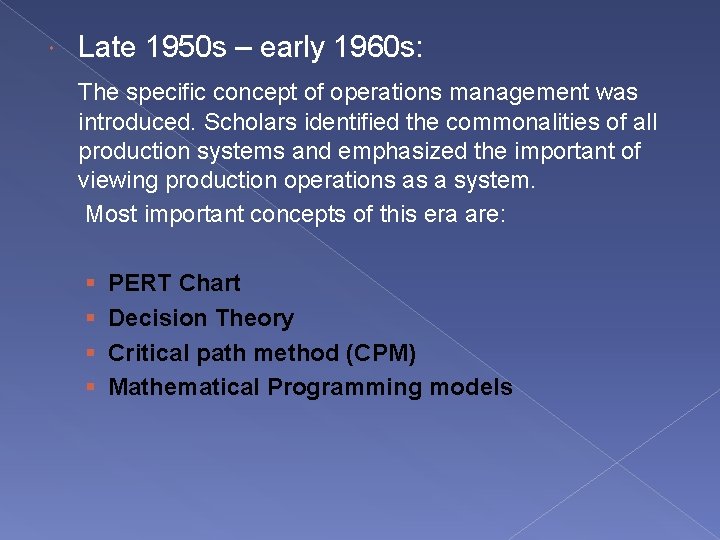
Late 1950 s – early 1960 s: The specific concept of operations management was introduced. Scholars identified the commonalities of all production systems and emphasized the important of viewing production operations as a system. Most important concepts of this era are: § § PERT Chart Decision Theory Critical path method (CPM) Mathematical Programming models
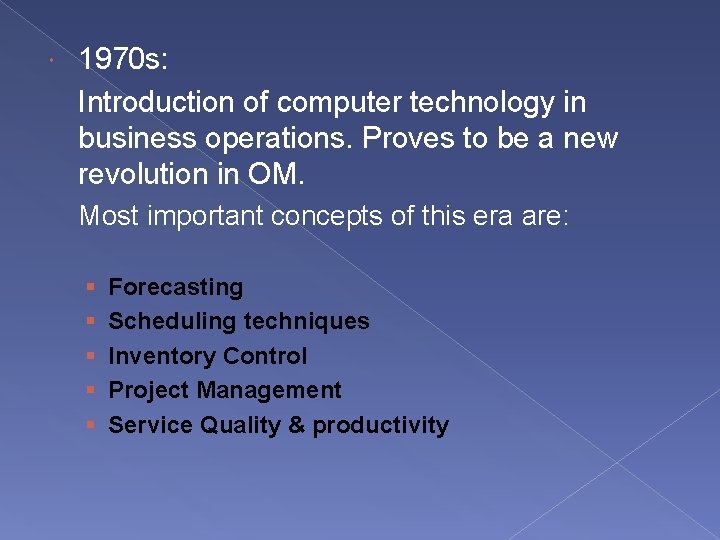
1970 s: Introduction of computer technology in business operations. Proves to be a new revolution in OM. Most important concepts of this era are: § § § Forecasting Scheduling techniques Inventory Control Project Management Service Quality & productivity
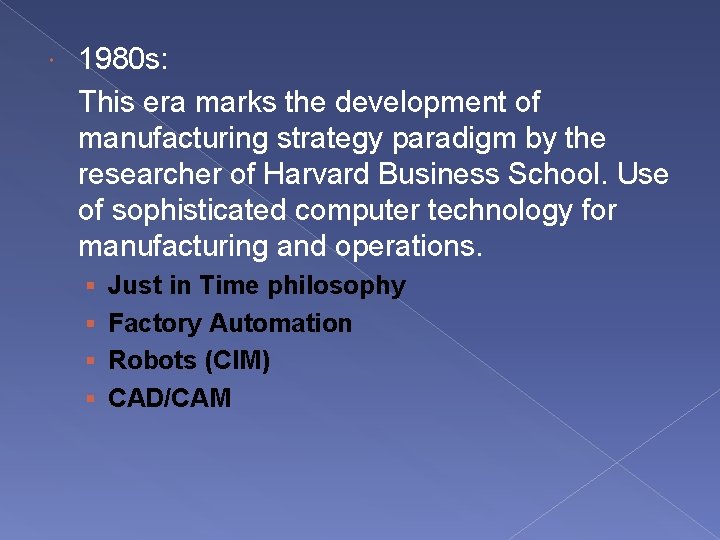
1980 s: This era marks the development of manufacturing strategy paradigm by the researcher of Harvard Business School. Use of sophisticated computer technology for manufacturing and operations. § § Just in Time philosophy Factory Automation Robots (CIM) CAD/CAM
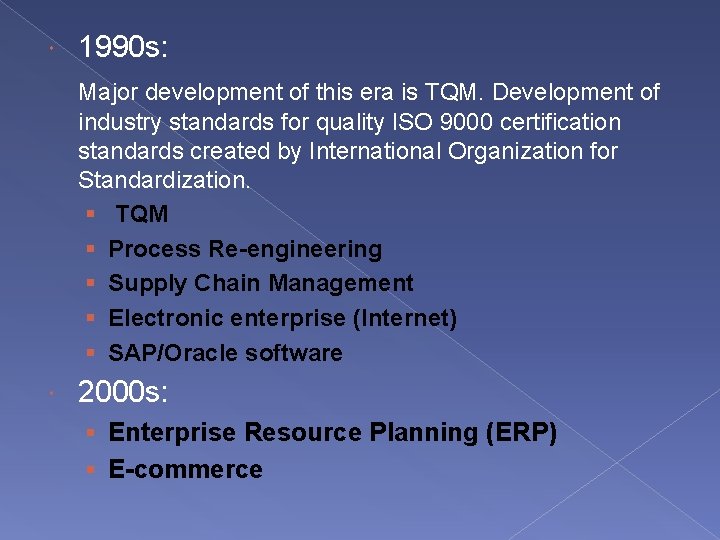
1990 s: Major development of this era is TQM. Development of industry standards for quality ISO 9000 certification standards created by International Organization for Standardization. § TQM § Process Re-engineering § Supply Chain Management § Electronic enterprise (Internet) § SAP/Oracle software 2000 s: § Enterprise Resource Planning (ERP) § E-commerce
Pre production production post production
Forecasting production operation management
Forecasting methods operations management
Electronic news gathering and electronic field production
21lwuy8i6hw -site:youtube.com
Individual differences factors
Field dependent vs field independent
Electric field and magnetic field difference
E field h field
Database field types and field properties
Field dependent definition
Magnetic field
Hát kết hợp bộ gõ cơ thể
Bổ thể
Tỉ lệ cơ thể trẻ em
Gấu đi như thế nào
Glasgow thang điểm
Alleluia hat len nguoi oi
Môn thể thao bắt đầu bằng từ chạy
Thế nào là hệ số cao nhất
Các châu lục và đại dương trên thế giới
Công của trọng lực
Trời xanh đây là của chúng ta thể thơ
Mật thư anh em như thể tay chân
Phép trừ bù