MultiState Advanced Manufacturing Consortium RELEASE DATE 10212015 VERSION
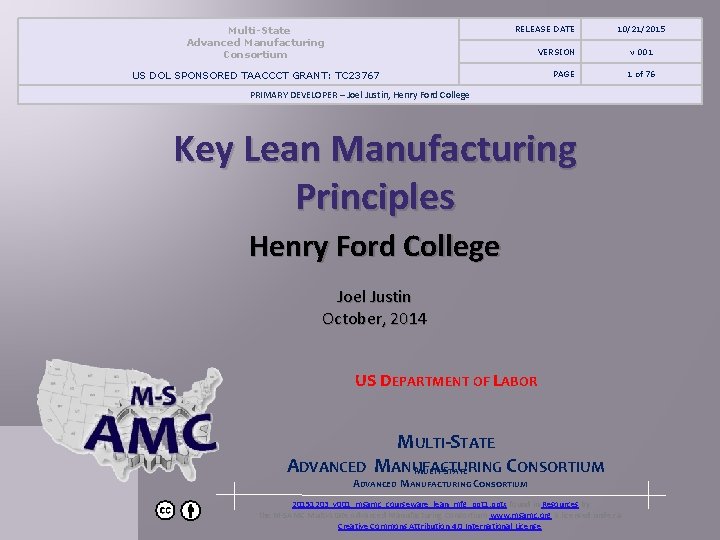
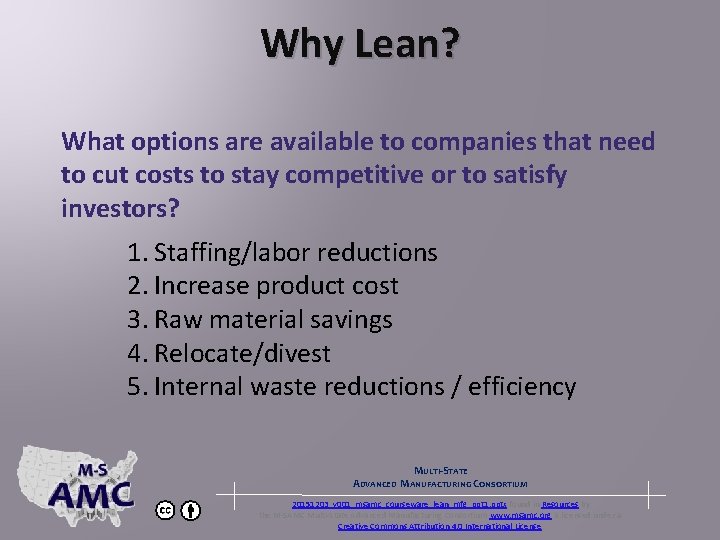
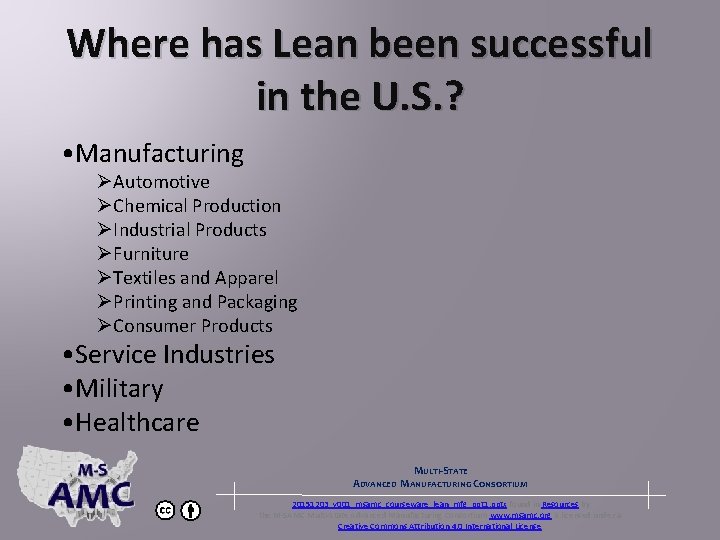
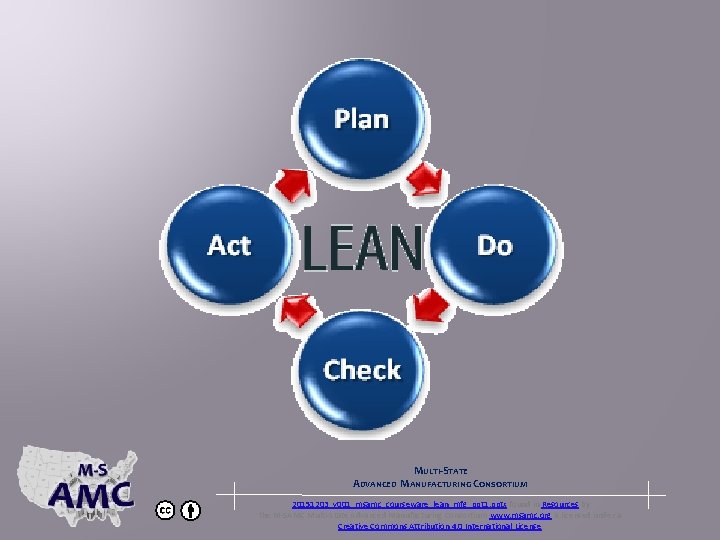
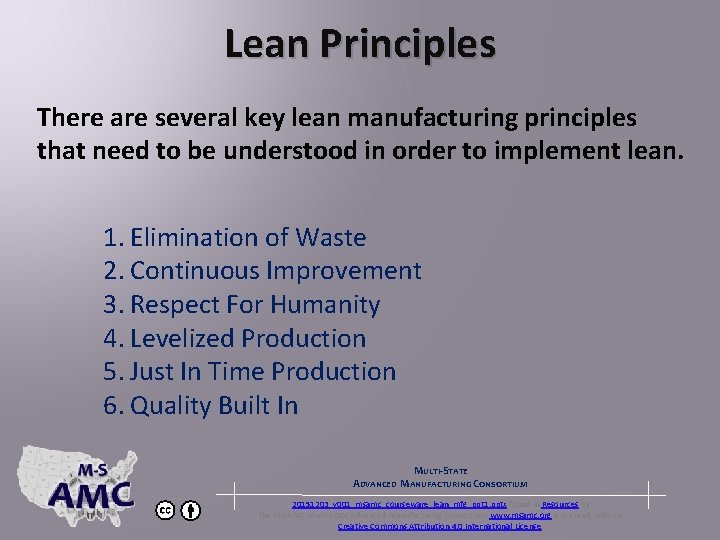
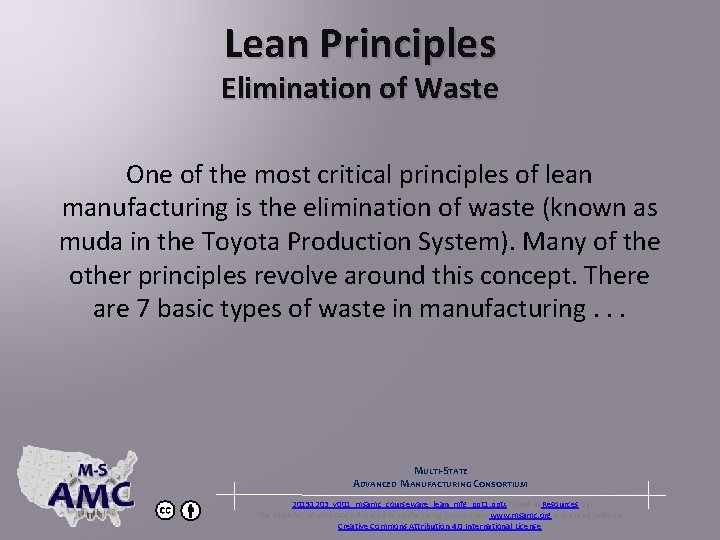
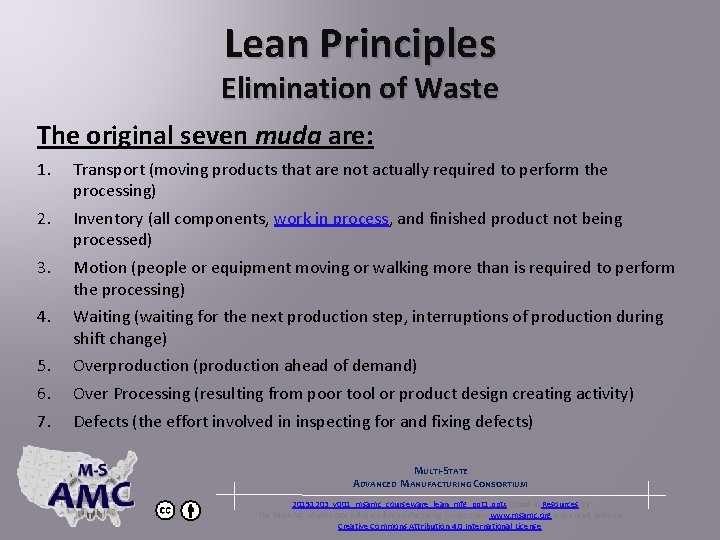

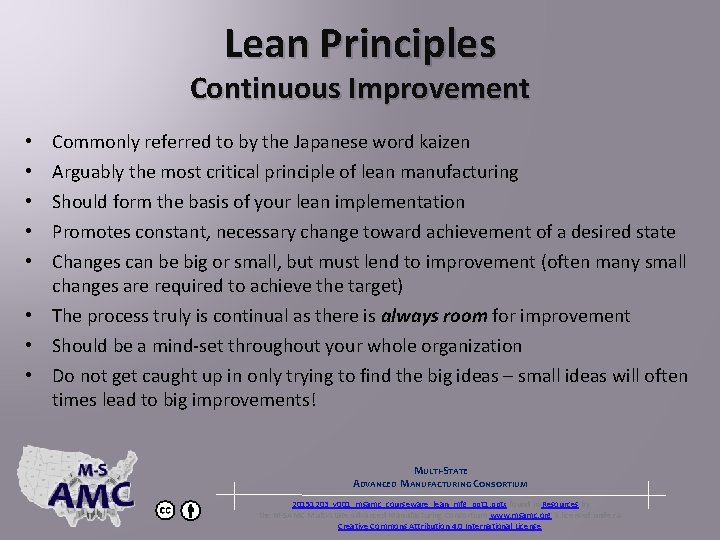
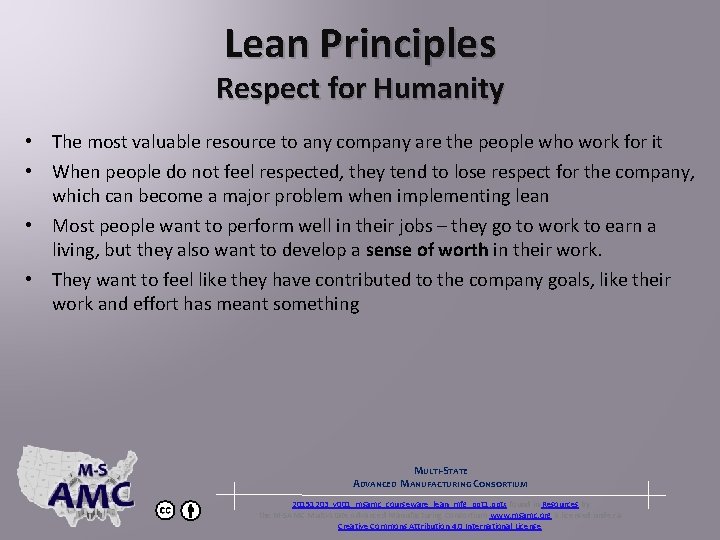
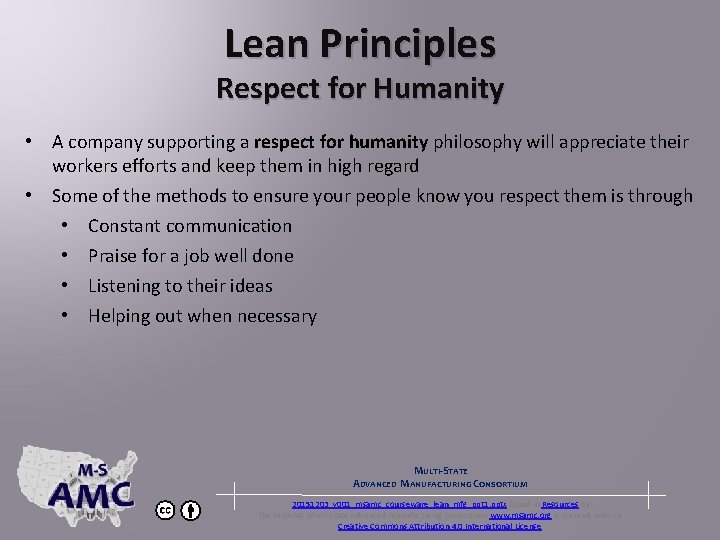
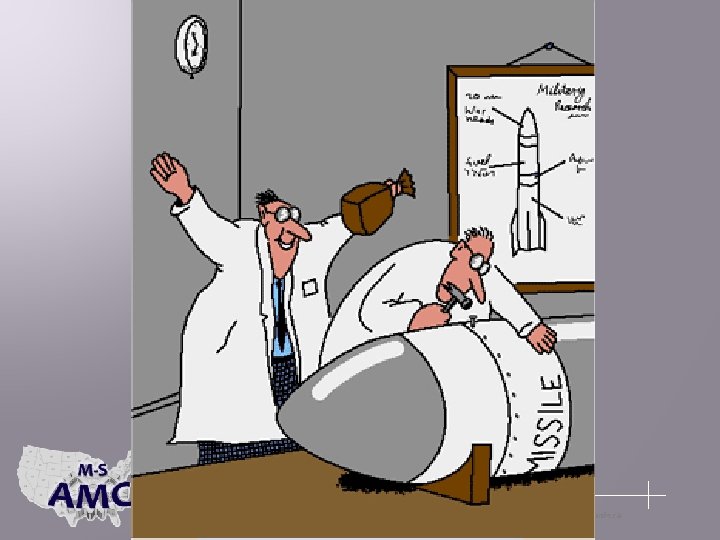
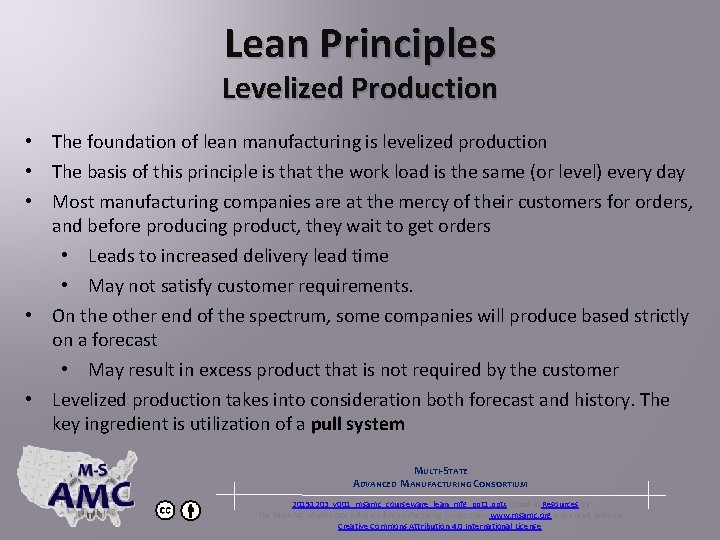
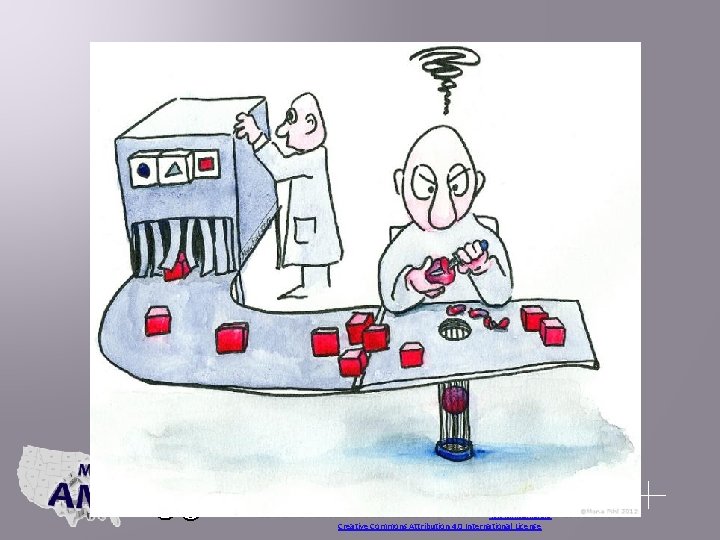
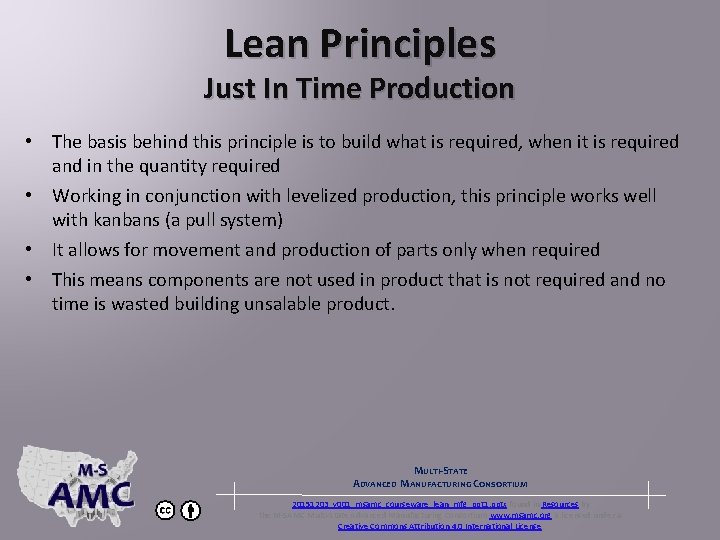
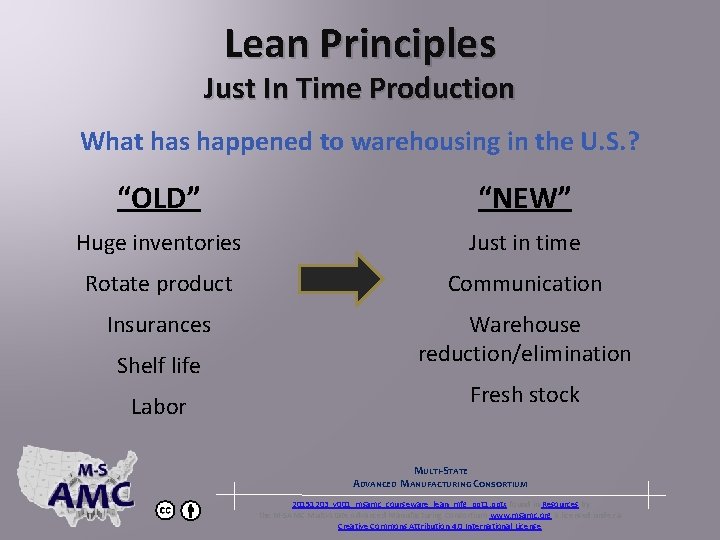
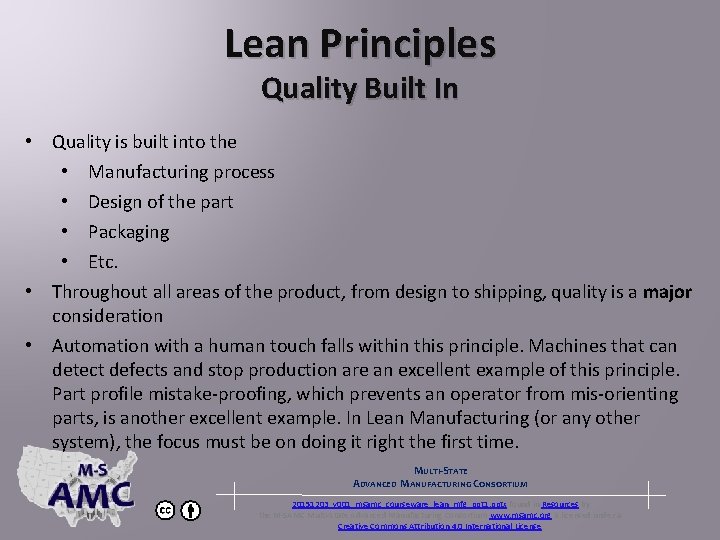
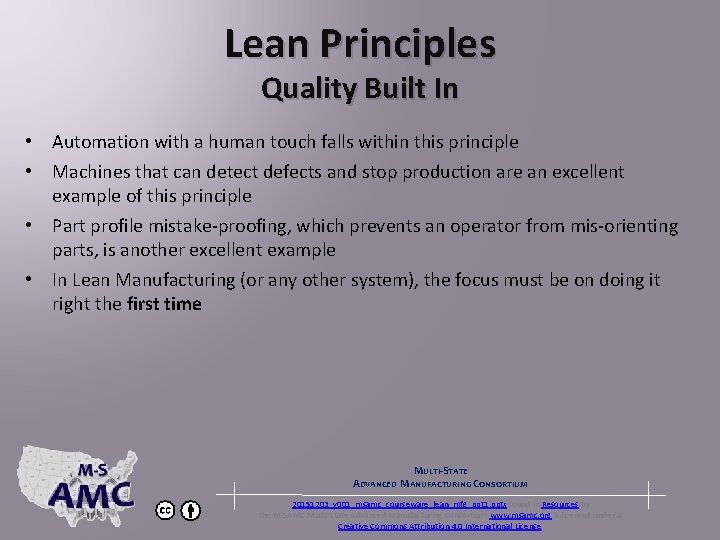
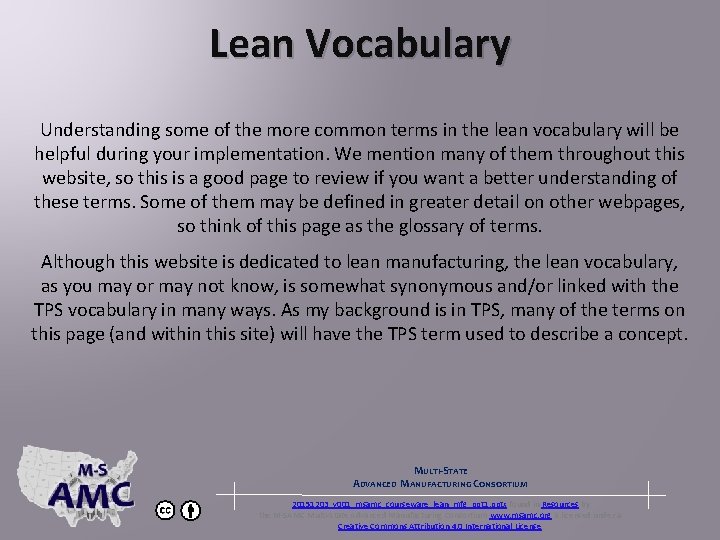
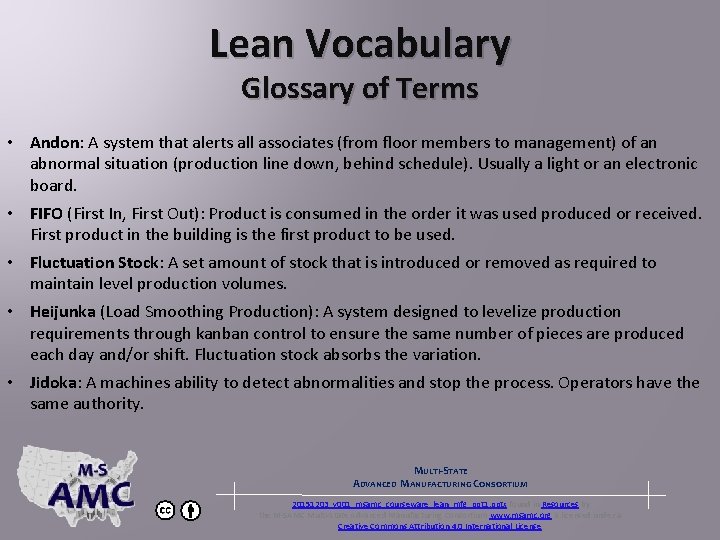
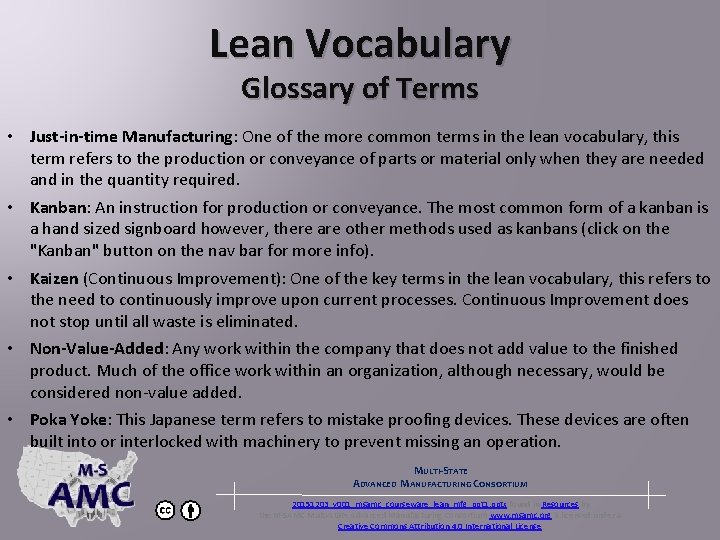
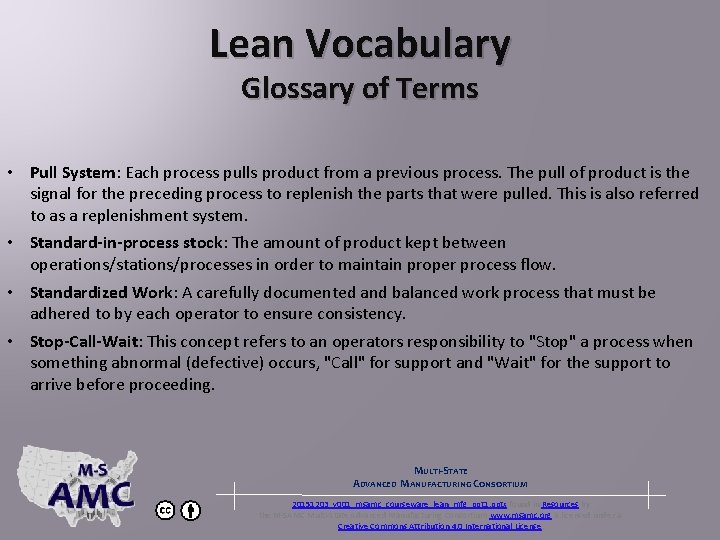
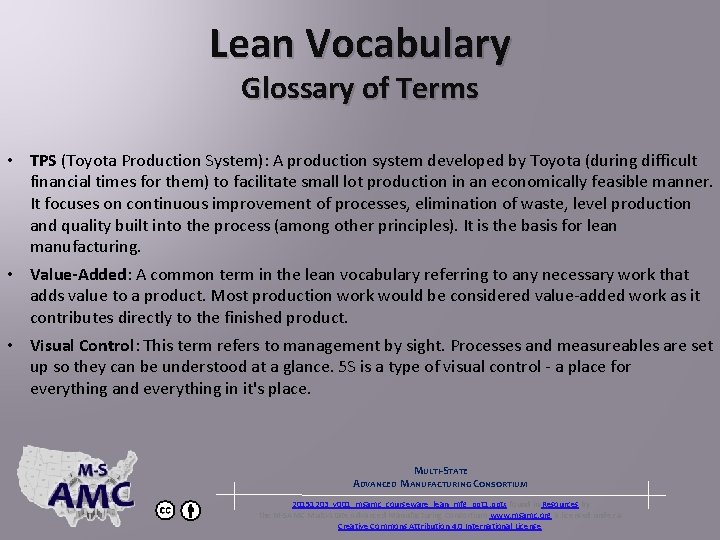
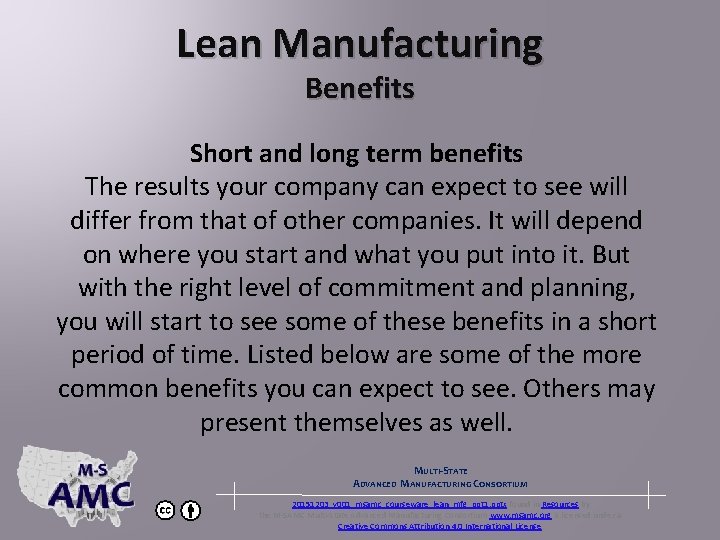
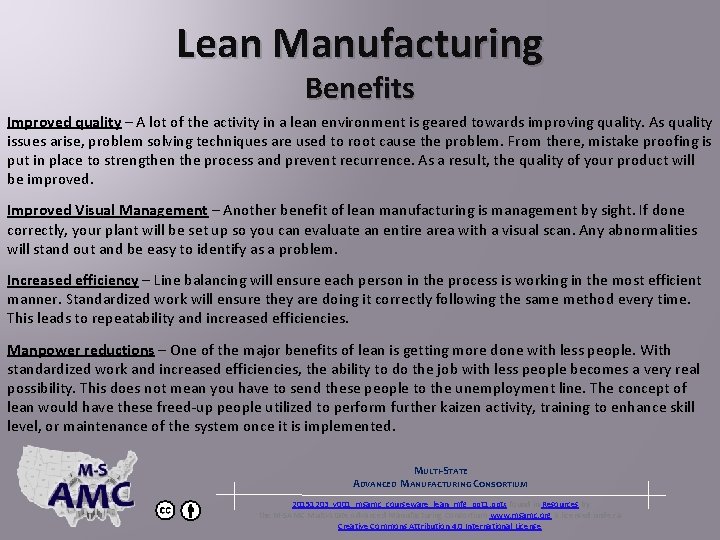
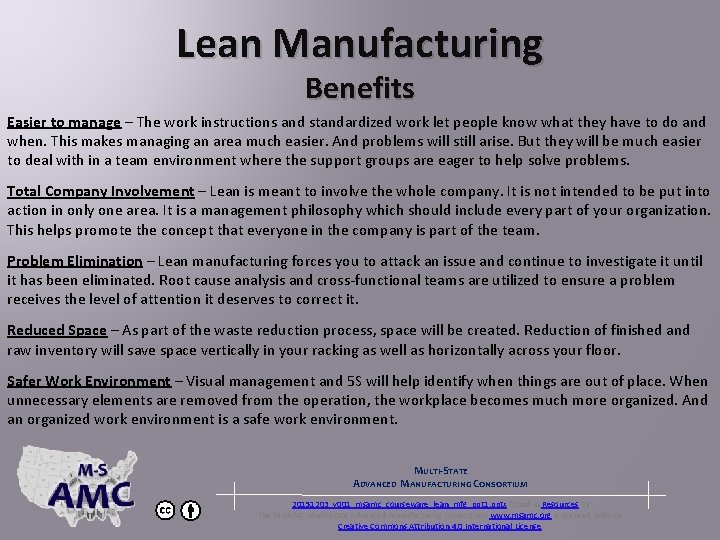
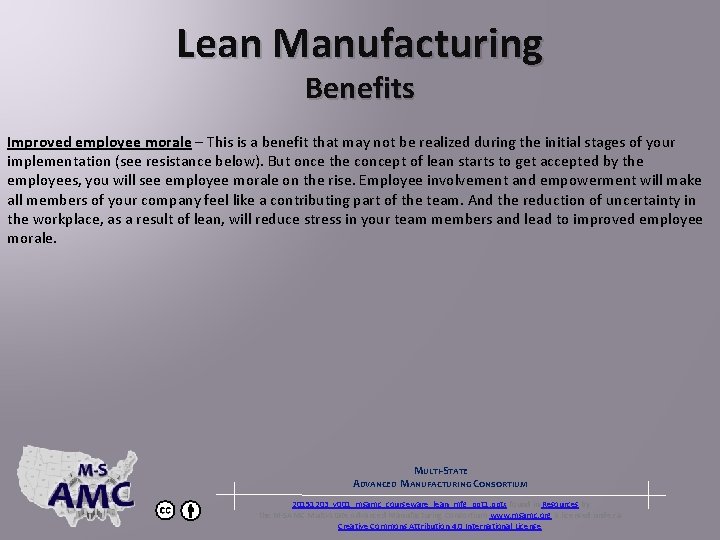
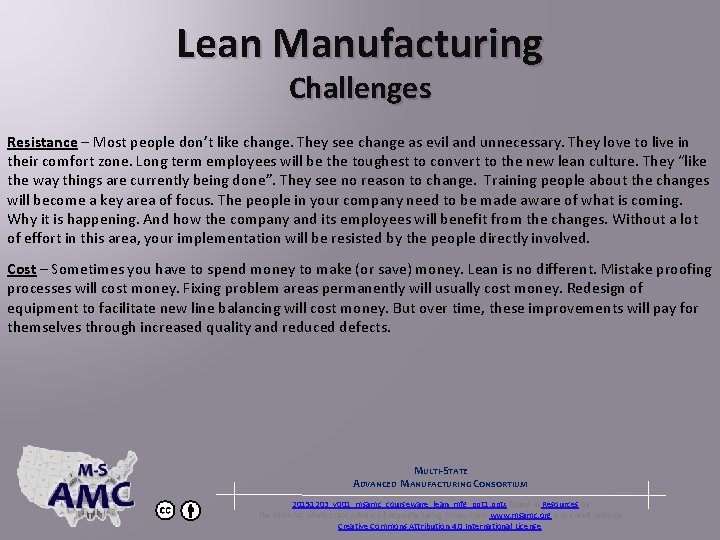
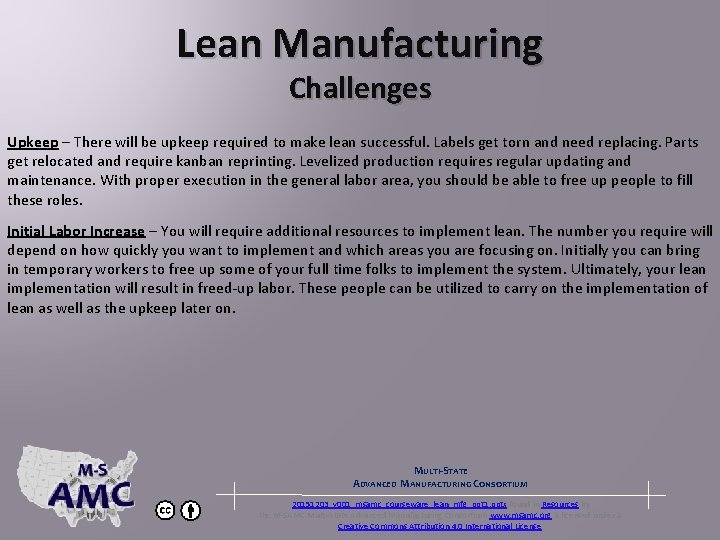
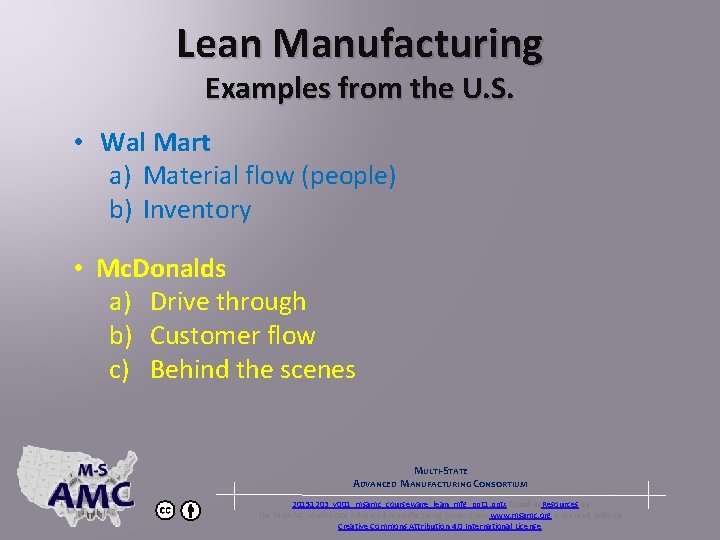
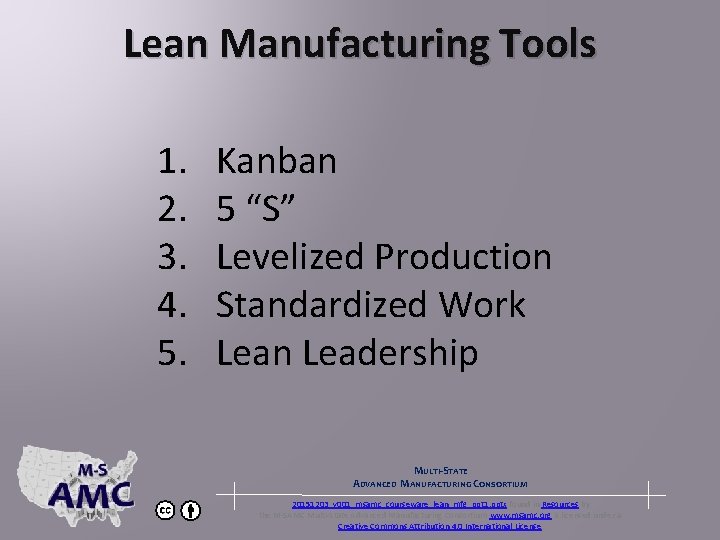
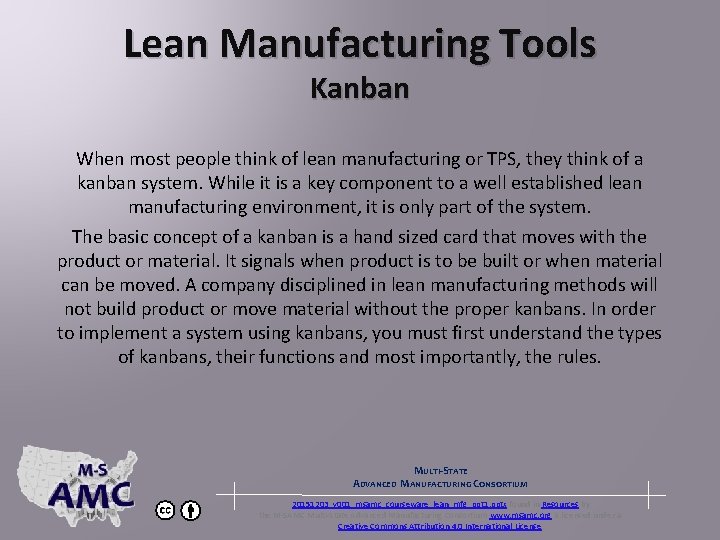
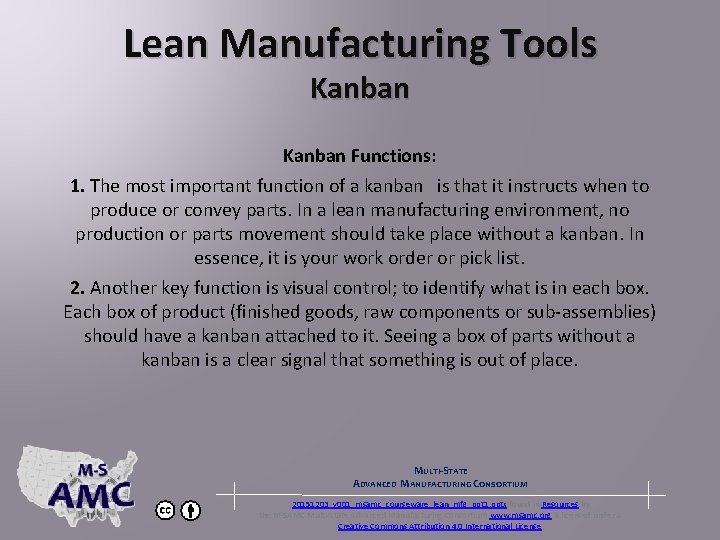
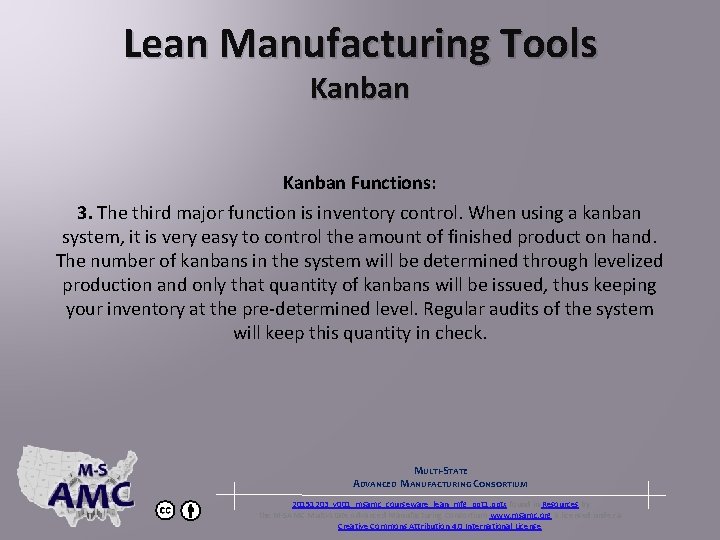
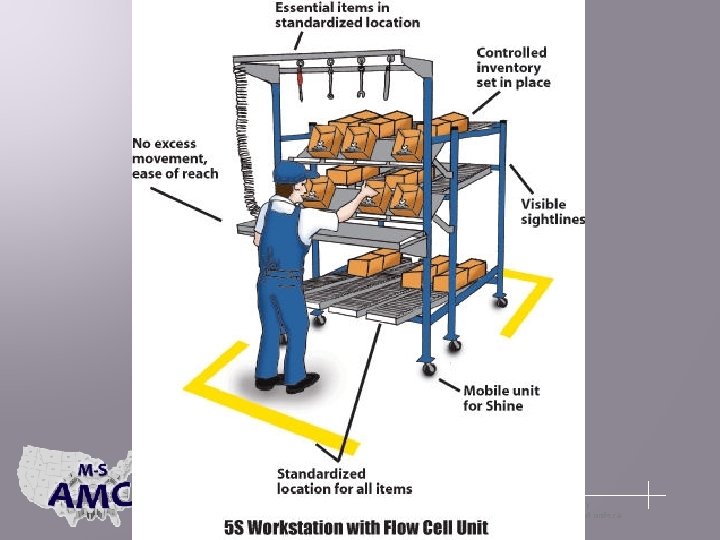
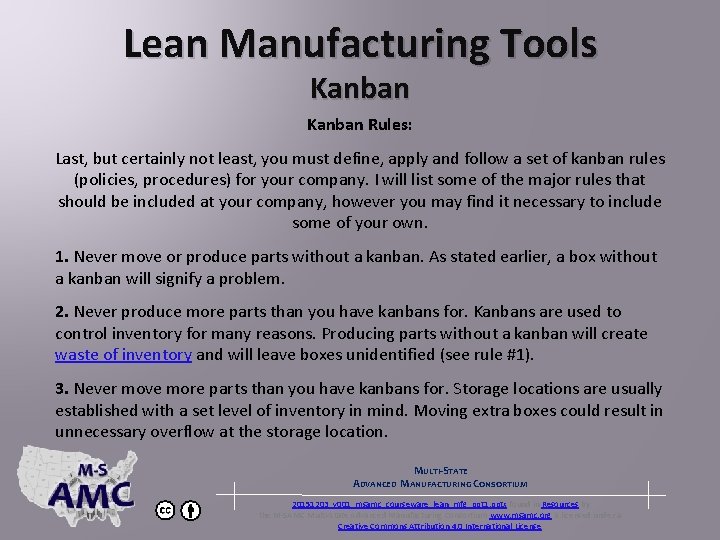
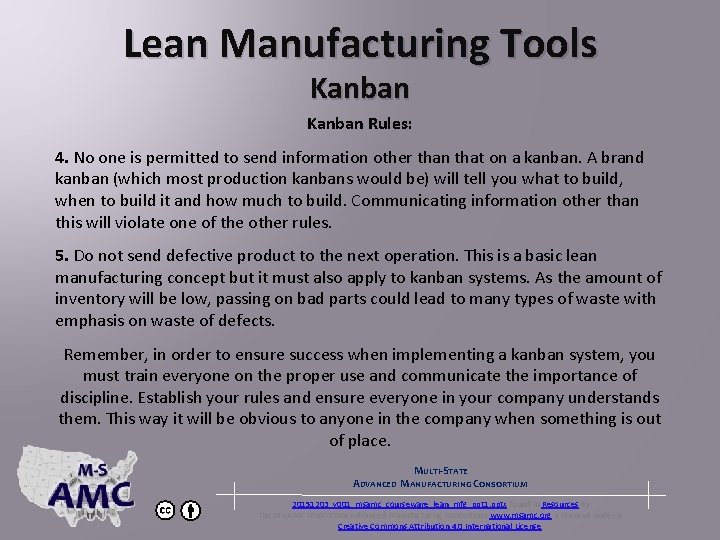

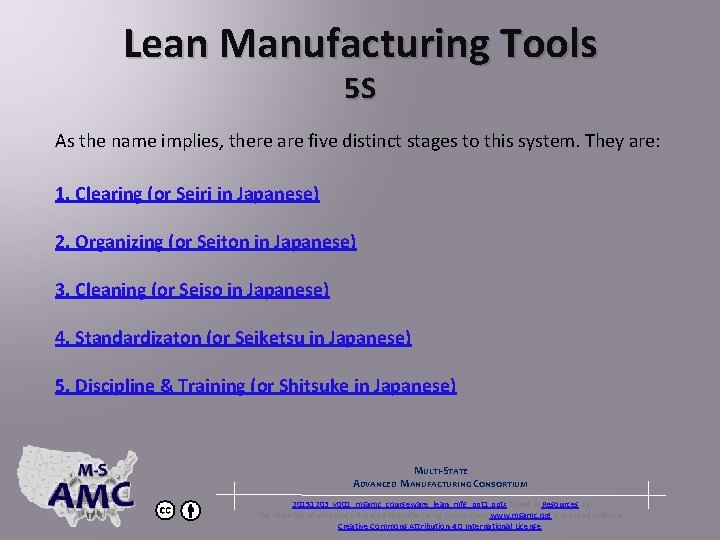
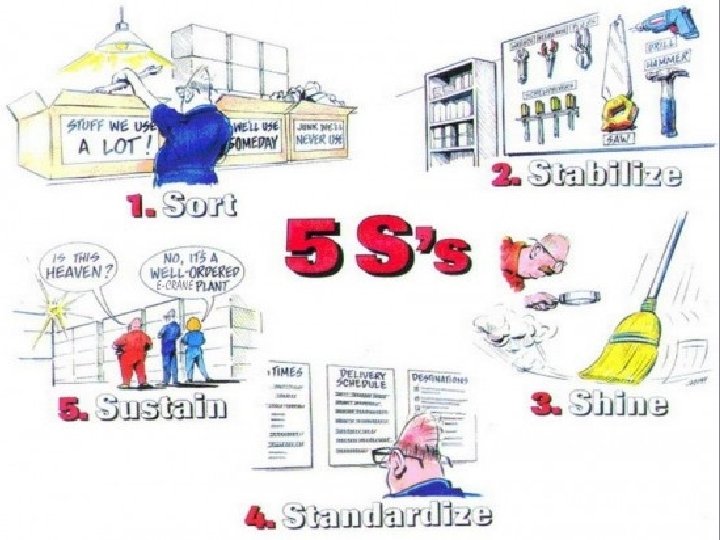
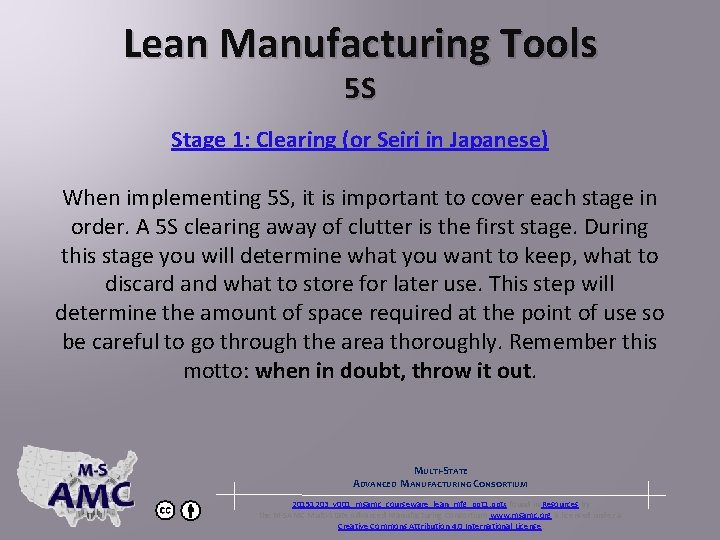
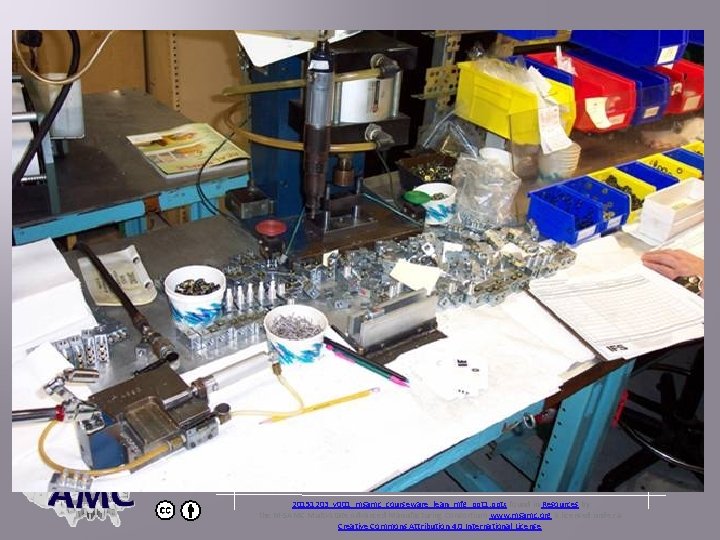
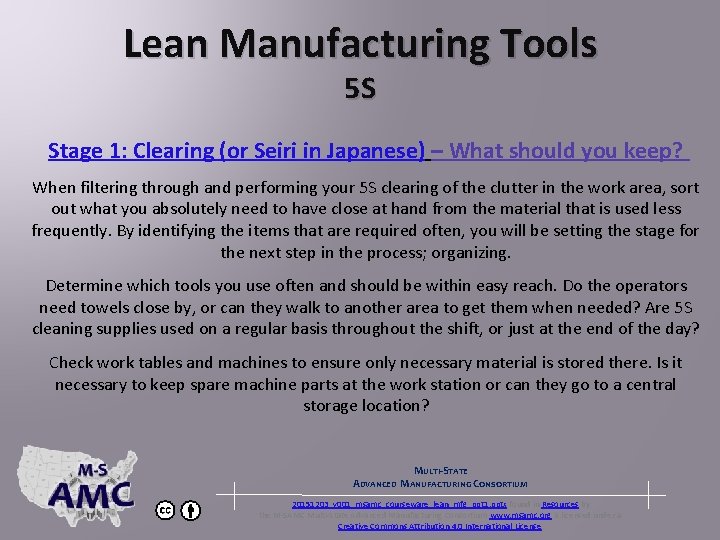
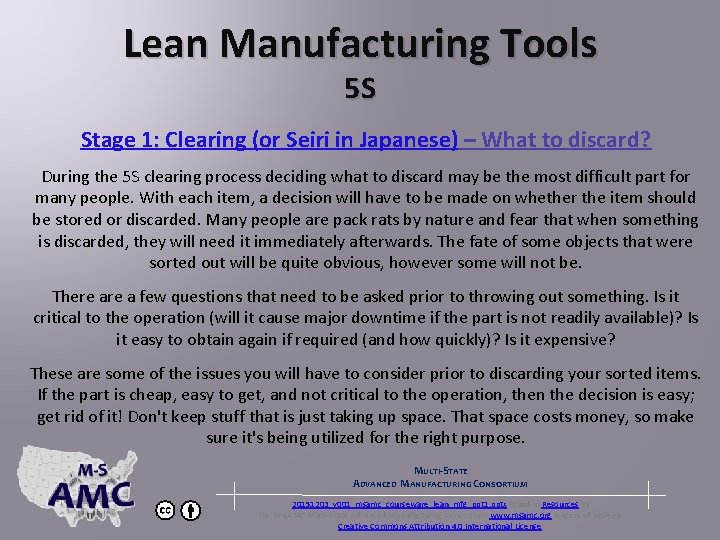
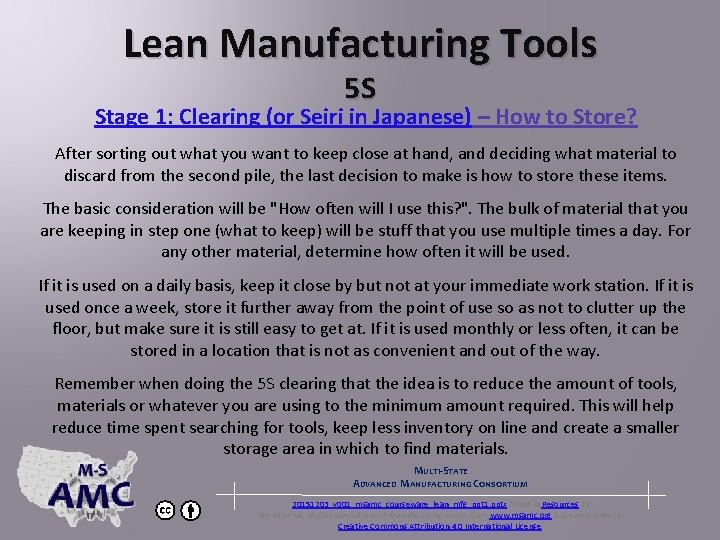

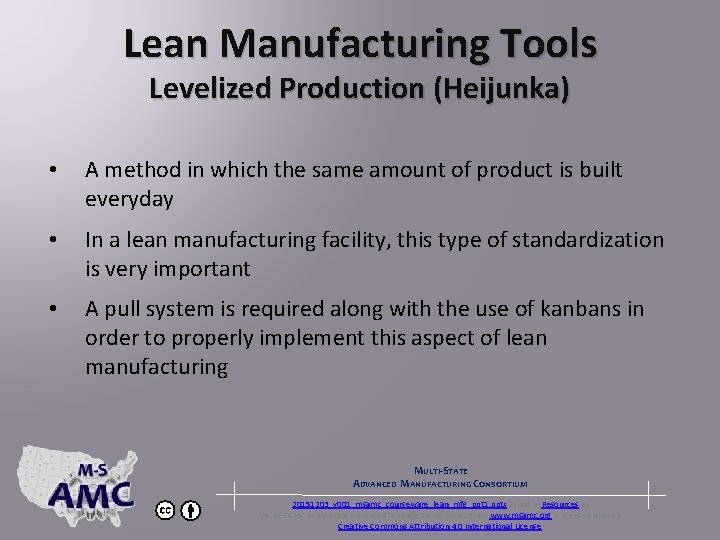
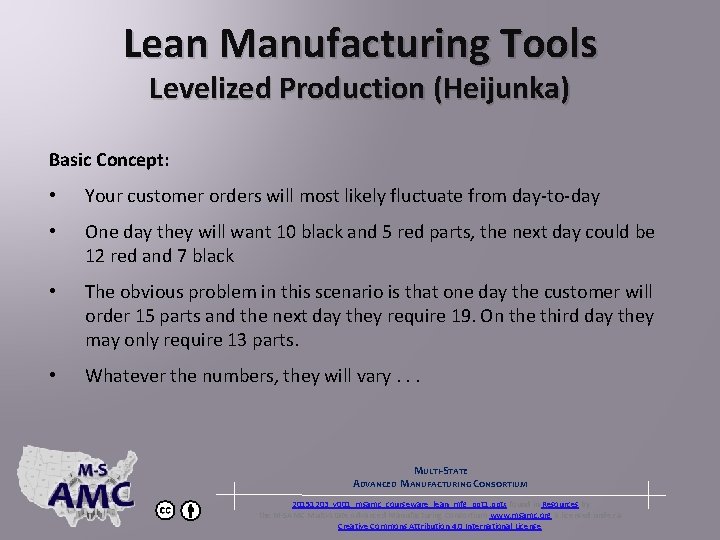
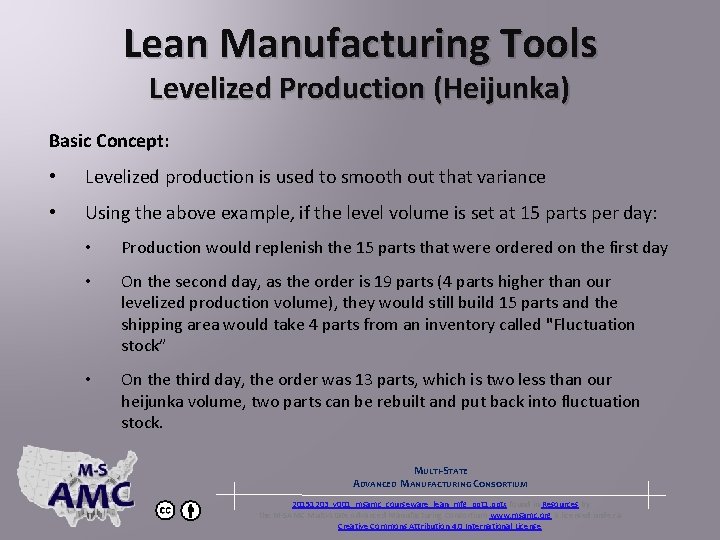
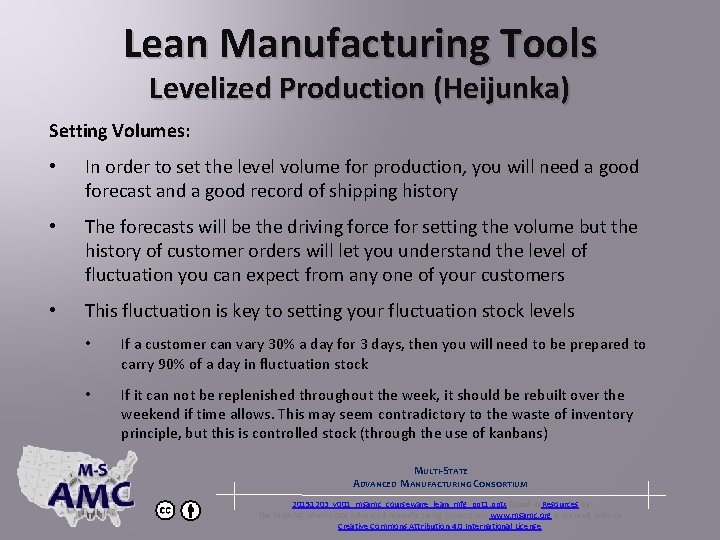
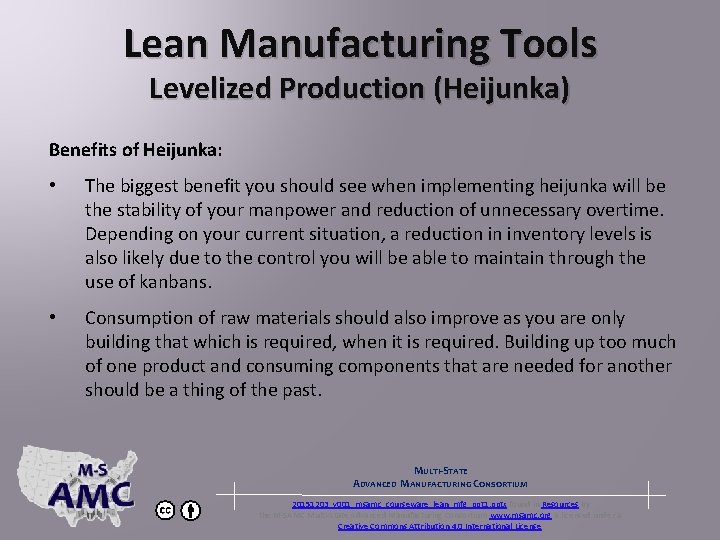
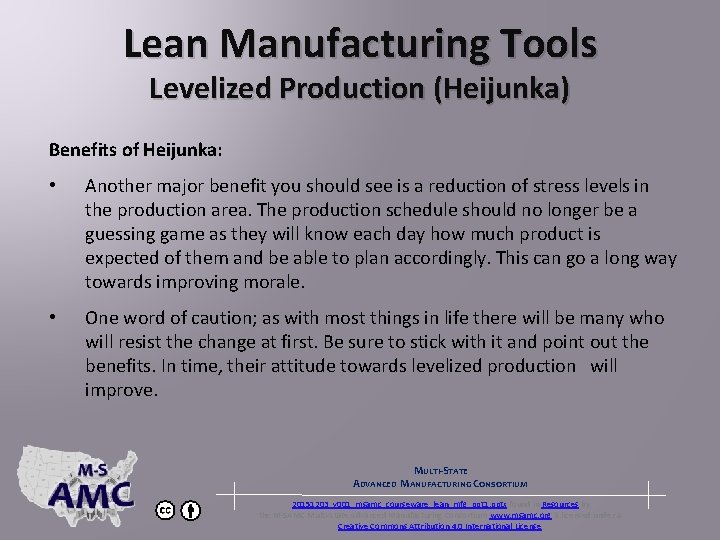
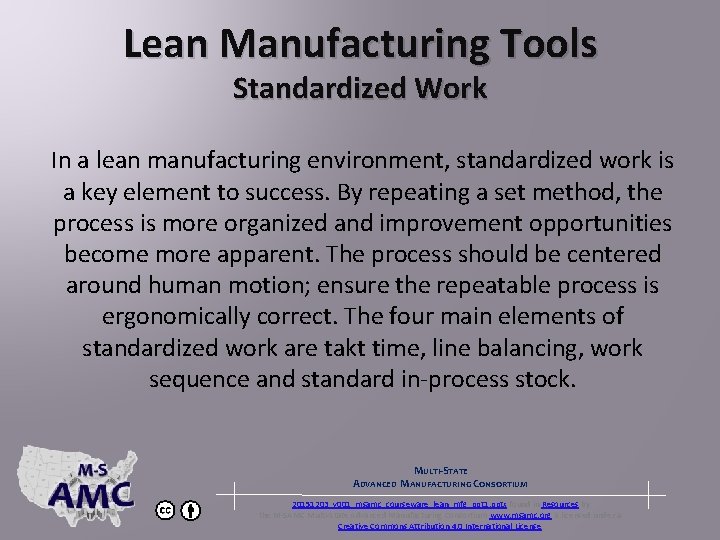
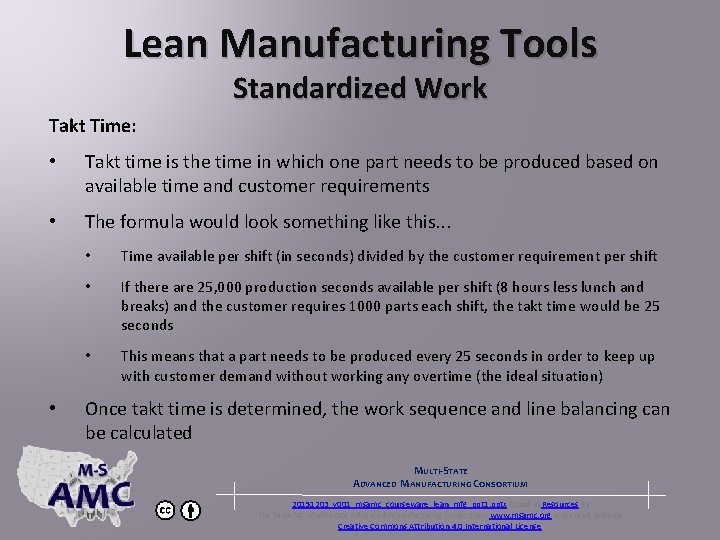
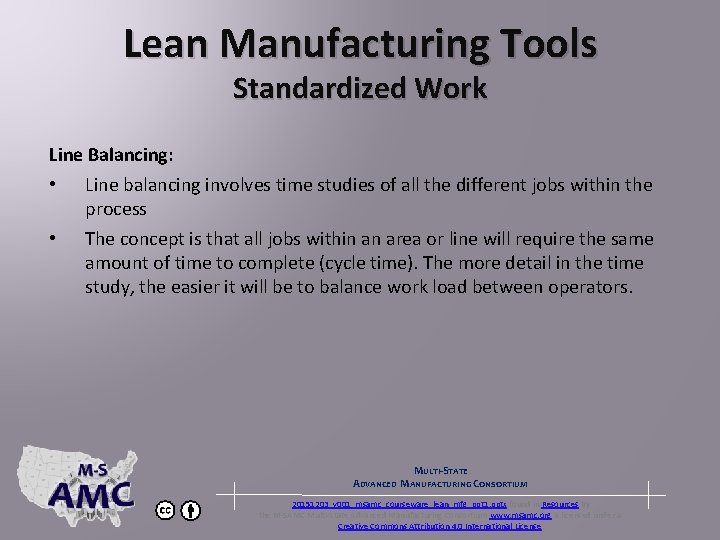
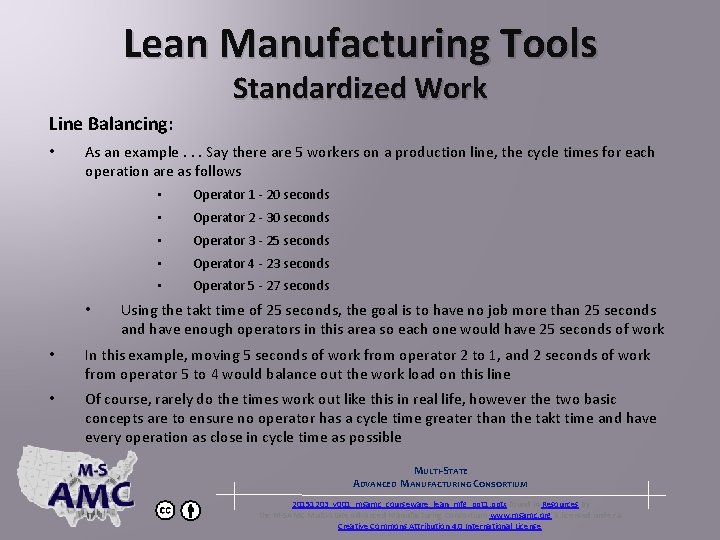
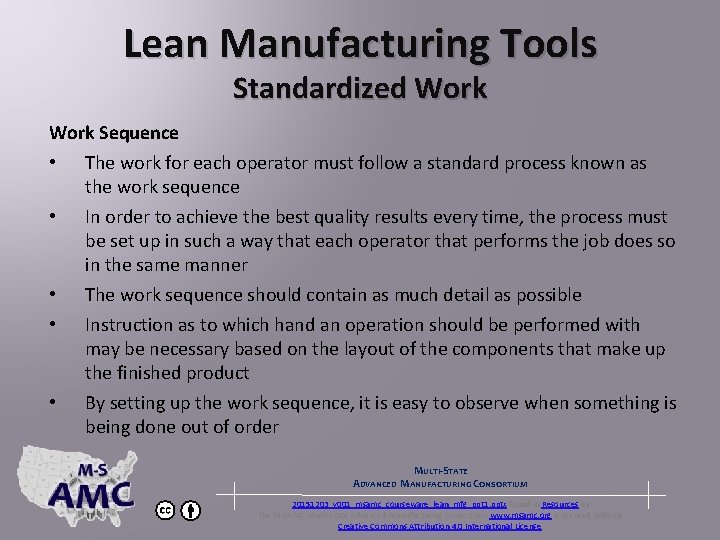
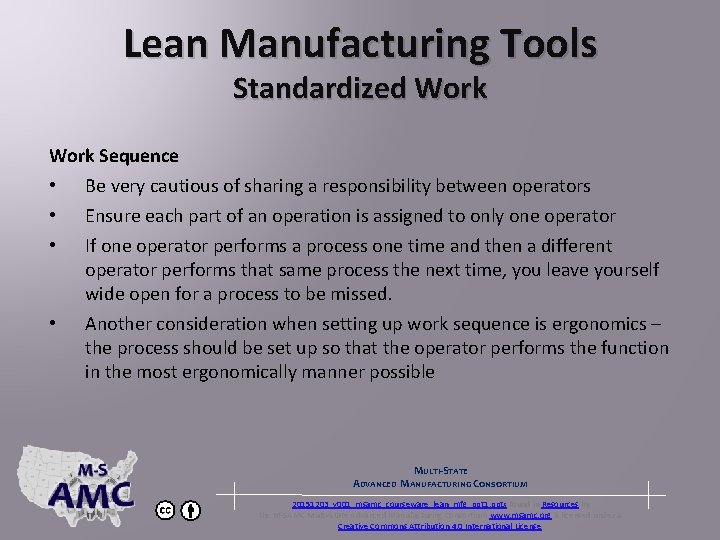
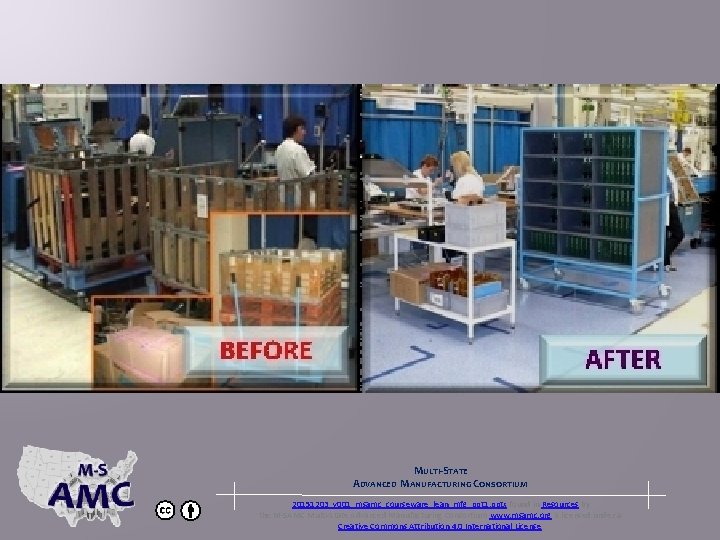
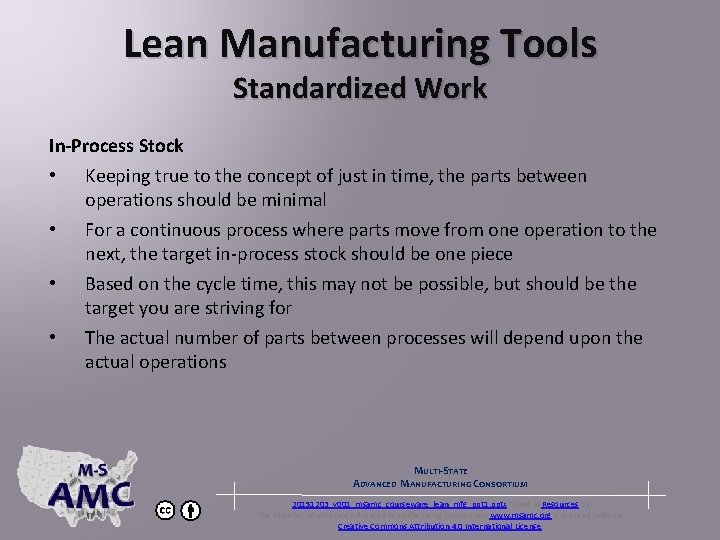
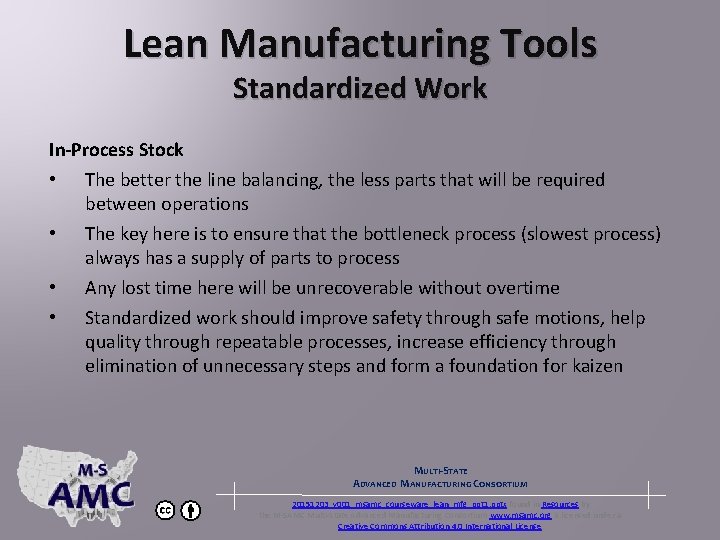
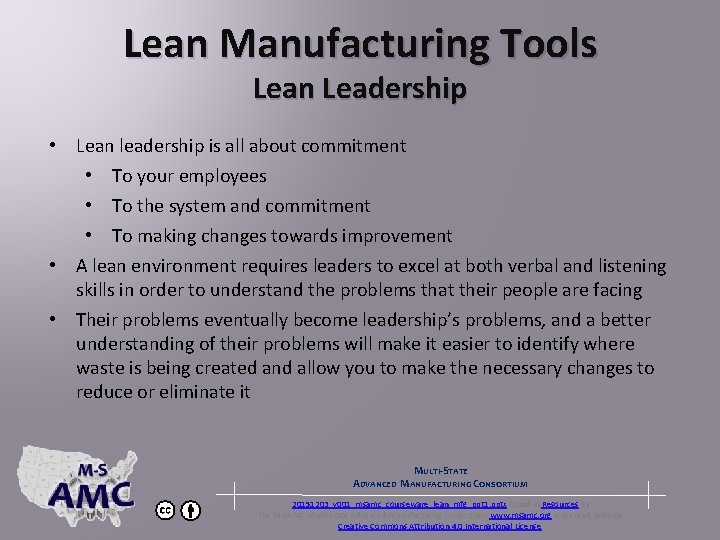
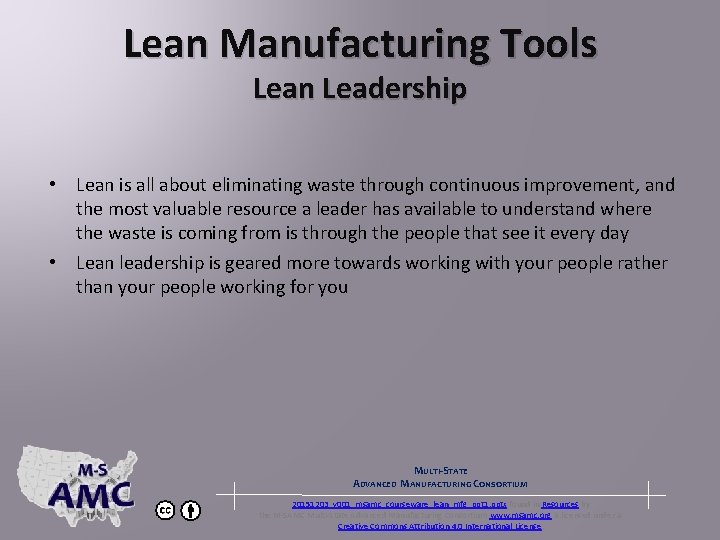
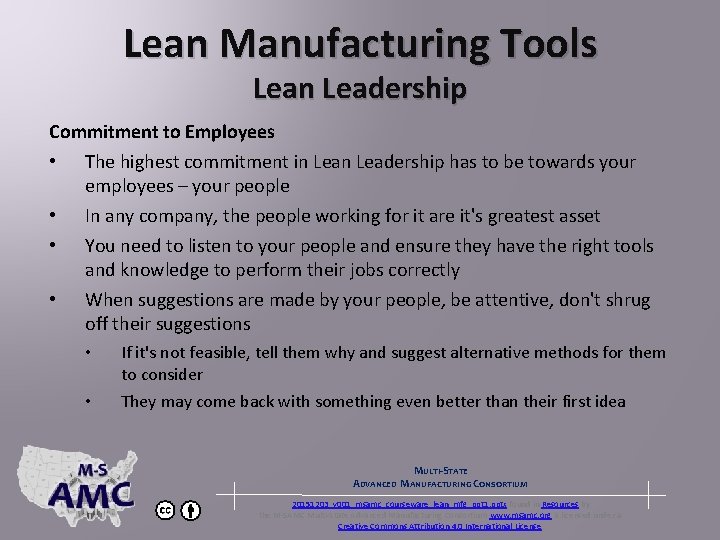
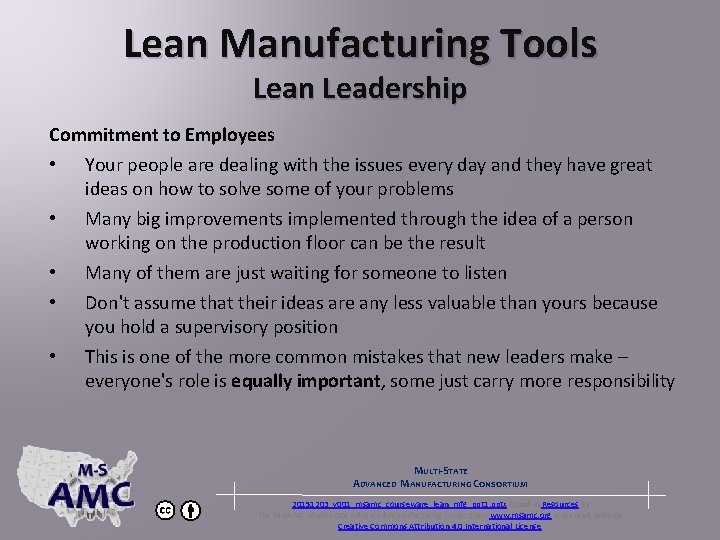
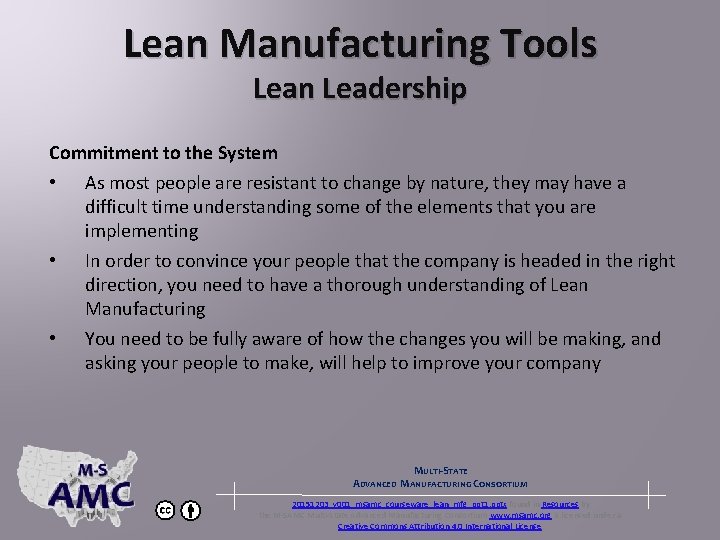
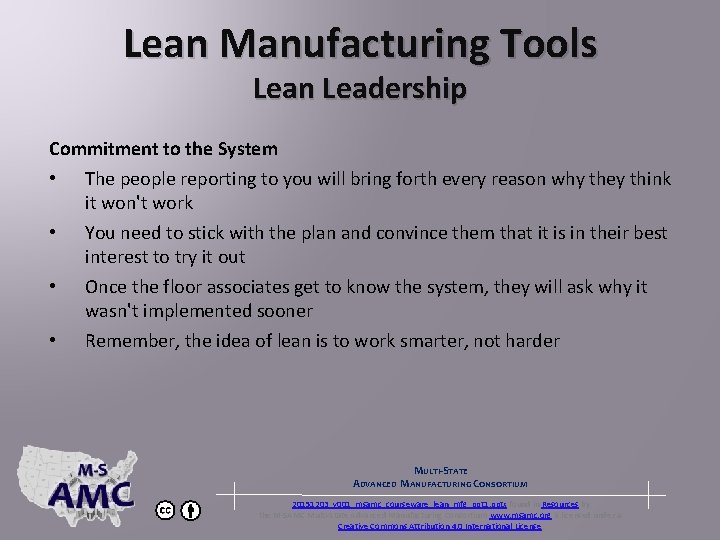
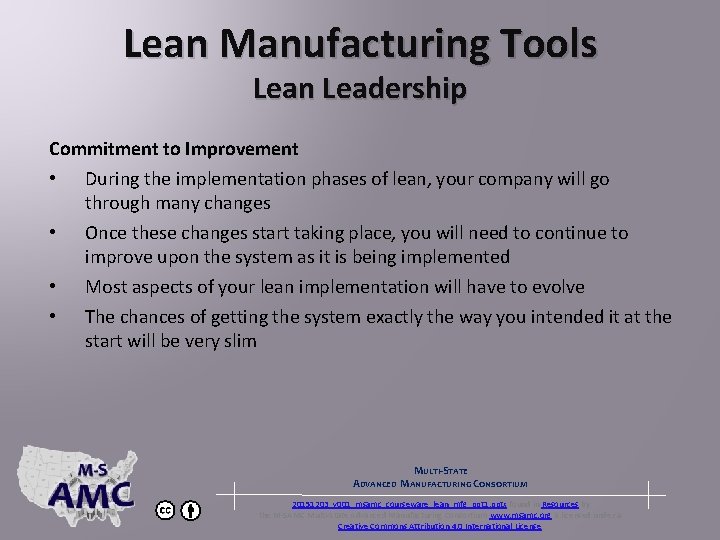
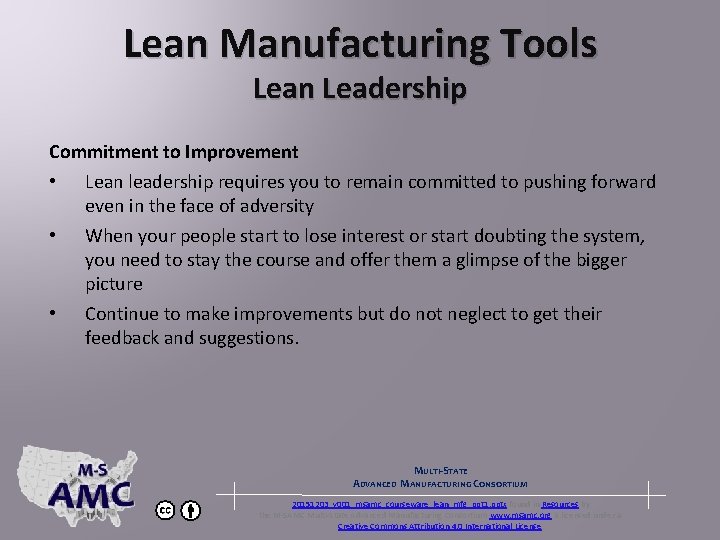
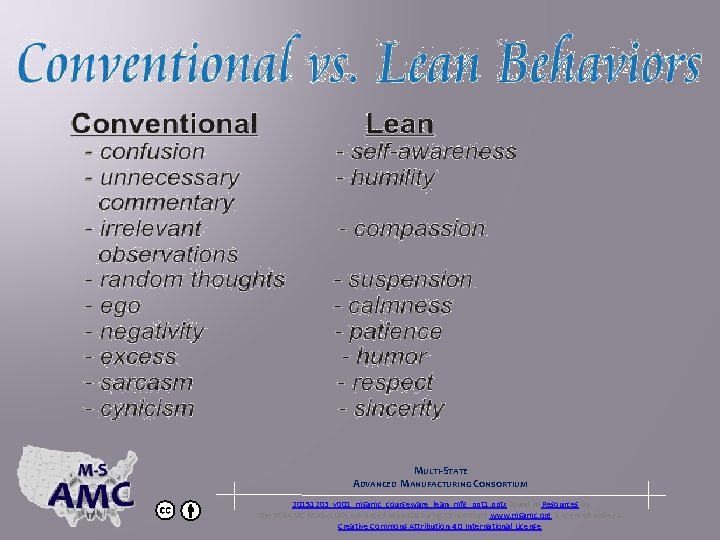
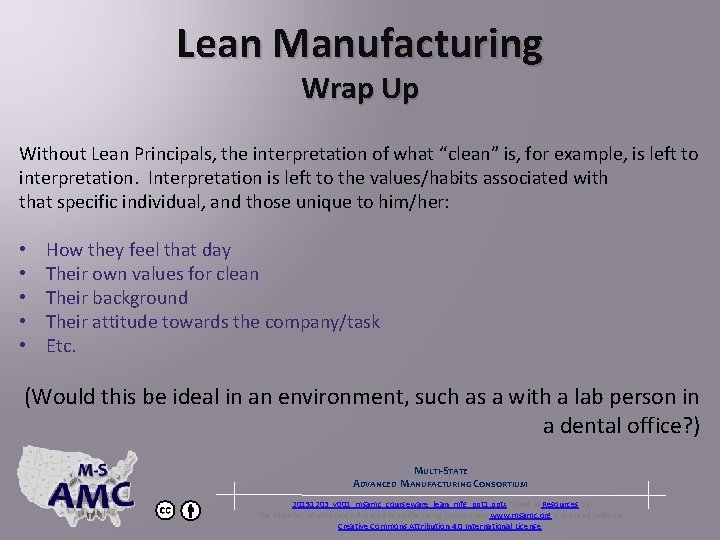
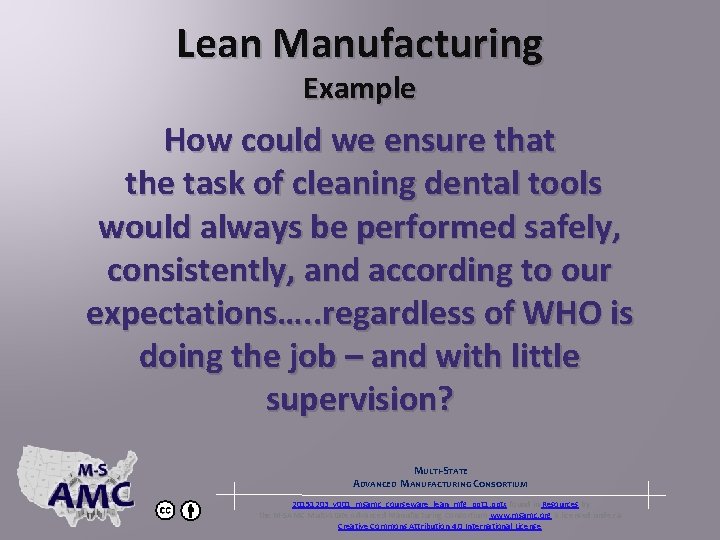
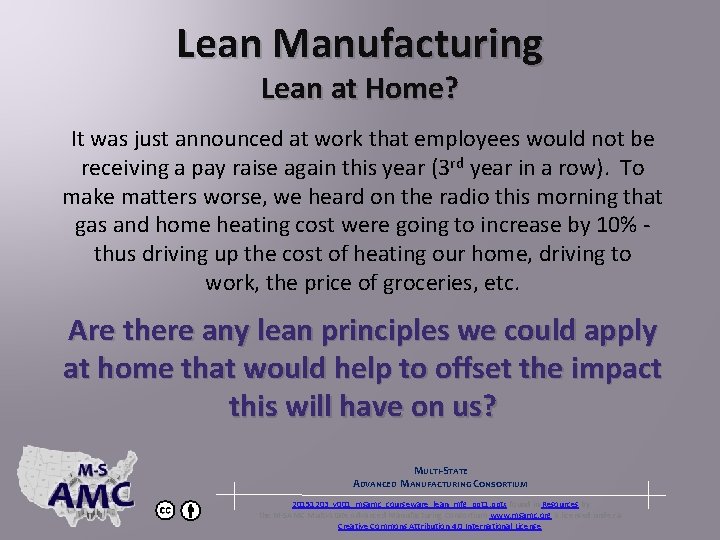
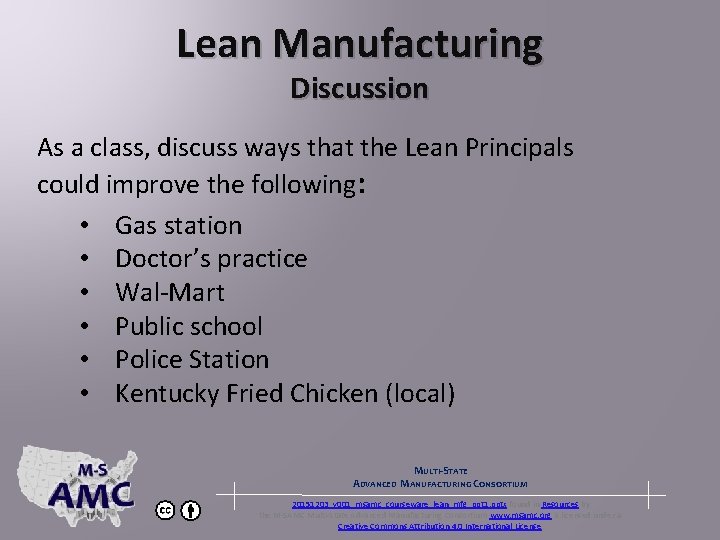
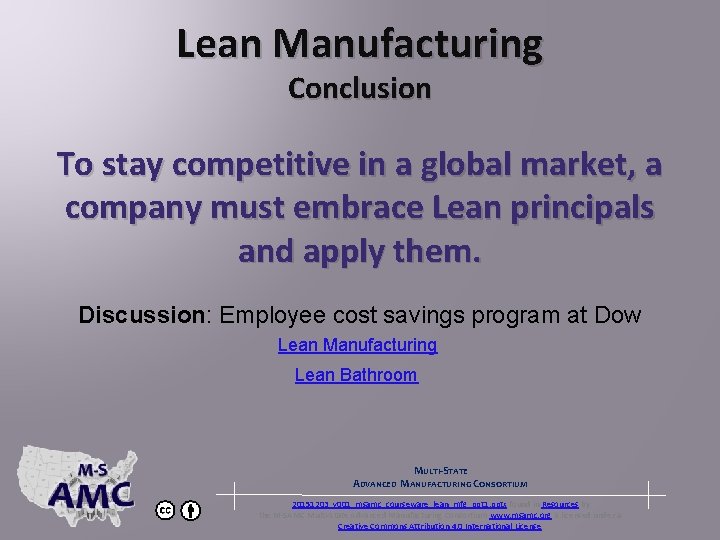
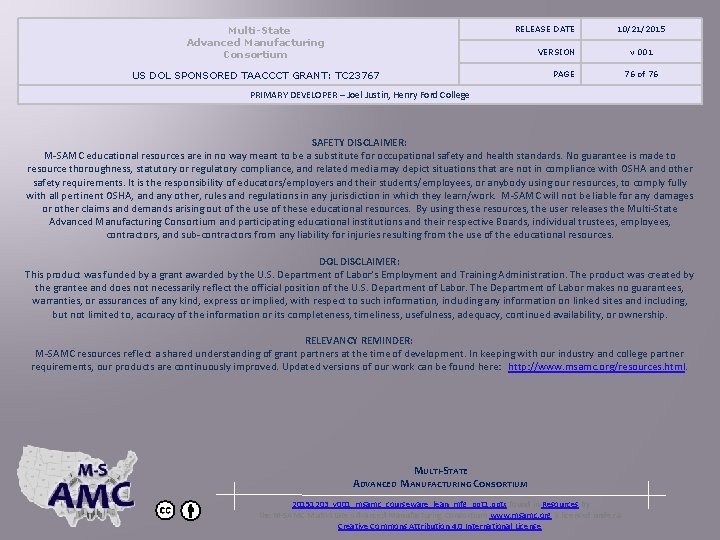
- Slides: 76
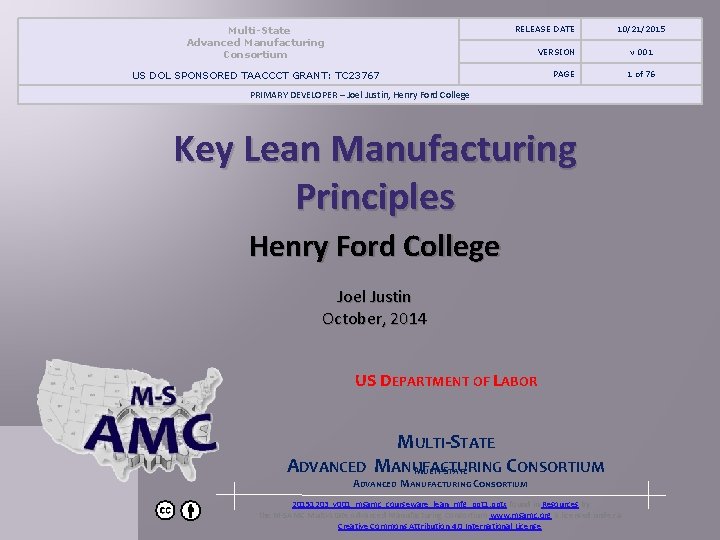
Multi-State Advanced Manufacturing Consortium RELEASE DATE 10/21/2015 VERSION PAGE US DOL SPONSORED TAACCCT GRANT: TC 23767 PRIMARY DEVELOPER – Joel Justin, Henry Ford College Key Lean Manufacturing Principles Henry Ford College Joel Justin October, 2014 US DEPARTMENT OF LABOR MULTI-STATE ADVANCED MANUFACTURING CONSORTIUM 20151203_v 001_msamc_courseware_lean_mfg_ppt 1. pptx found in Resources by the M-SAMC Multi-State Advanced Manufacturing Consortium www. msamc. org is licensed under a Creative Commons Attribution 4. 0 International License. v 001 1 of 76
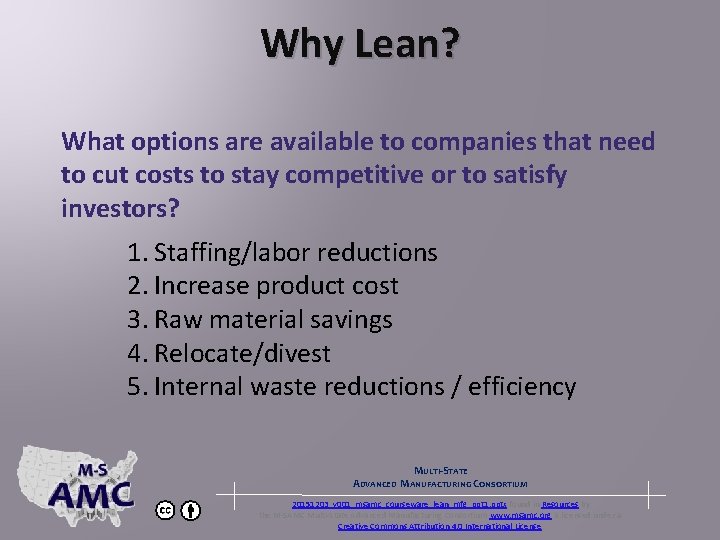
Why Lean? What options are available to companies that need to cut costs to stay competitive or to satisfy investors? 1. Staffing/labor reductions 2. Increase product cost 3. Raw material savings 4. Relocate/divest 5. Internal waste reductions / efficiency MULTI-STATE ADVANCED MANUFACTURING CONSORTIUM 20151203_v 001_msamc_courseware_lean_mfg_ppt 1. pptx found in Resources by the M-SAMC Multi-State Advanced Manufacturing Consortium www. msamc. org is licensed under a Creative Commons Attribution 4. 0 International License.
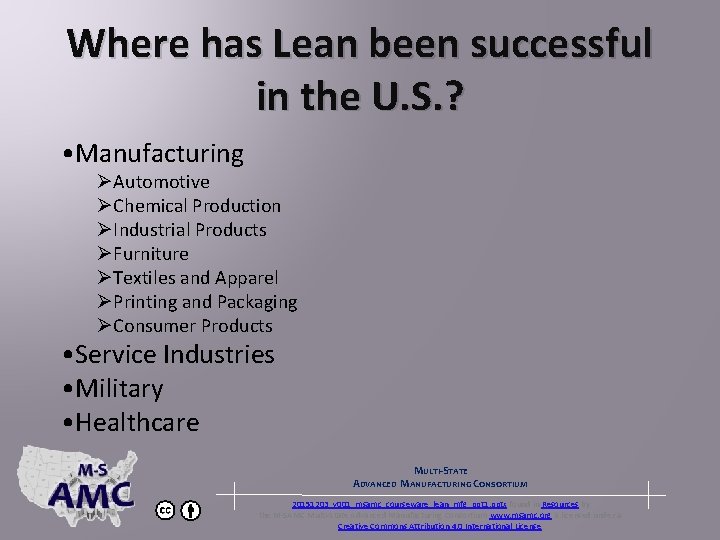
Where has Lean been successful in the U. S. ? • Manufacturing ØAutomotive ØChemical Production ØIndustrial Products ØFurniture ØTextiles and Apparel ØPrinting and Packaging ØConsumer Products • Service Industries • Military • Healthcare MULTI-STATE ADVANCED MANUFACTURING CONSORTIUM 20151203_v 001_msamc_courseware_lean_mfg_ppt 1. pptx found in Resources by the M-SAMC Multi-State Advanced Manufacturing Consortium www. msamc. org is licensed under a Creative Commons Attribution 4. 0 International License.
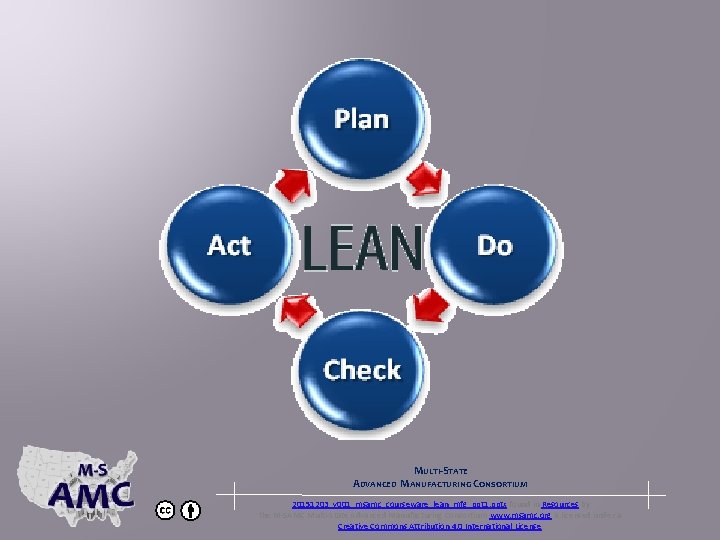
MULTI-STATE ADVANCED MANUFACTURING CONSORTIUM 20151203_v 001_msamc_courseware_lean_mfg_ppt 1. pptx found in Resources by the M-SAMC Multi-State Advanced Manufacturing Consortium www. msamc. org is licensed under a Creative Commons Attribution 4. 0 International License.
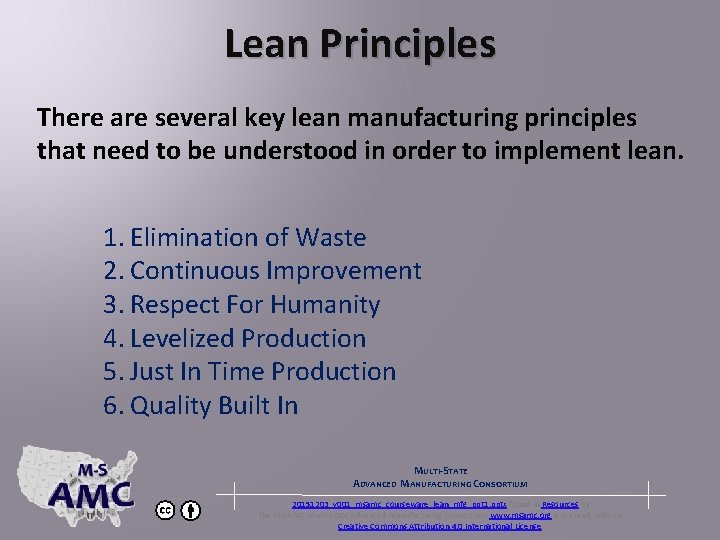
Lean Principles There are several key lean manufacturing principles that need to be understood in order to implement lean. 1. Elimination of Waste 2. Continuous Improvement 3. Respect For Humanity 4. Levelized Production 5. Just In Time Production 6. Quality Built In MULTI-STATE ADVANCED MANUFACTURING CONSORTIUM 20151203_v 001_msamc_courseware_lean_mfg_ppt 1. pptx found in Resources by the M-SAMC Multi-State Advanced Manufacturing Consortium www. msamc. org is licensed under a Creative Commons Attribution 4. 0 International License.
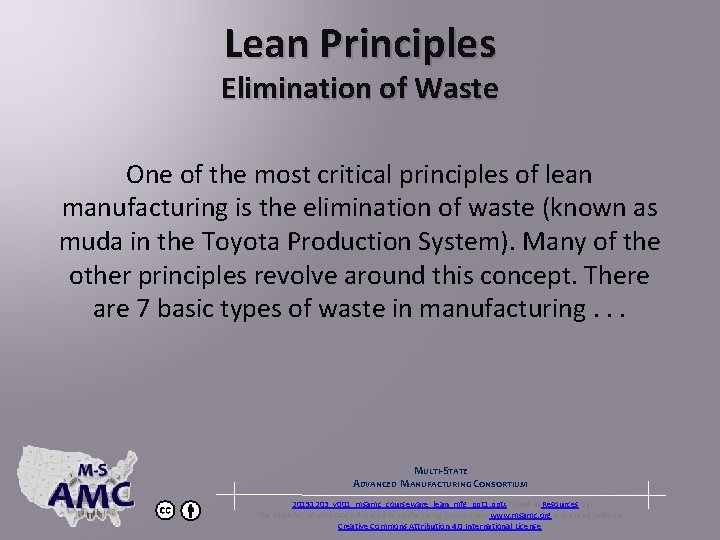
Lean Principles Elimination of Waste One of the most critical principles of lean manufacturing is the elimination of waste (known as muda in the Toyota Production System). Many of the other principles revolve around this concept. There are 7 basic types of waste in manufacturing. . . MULTI-STATE ADVANCED MANUFACTURING CONSORTIUM 20151203_v 001_msamc_courseware_lean_mfg_ppt 1. pptx found in Resources by the M-SAMC Multi-State Advanced Manufacturing Consortium www. msamc. org is licensed under a Creative Commons Attribution 4. 0 International License.
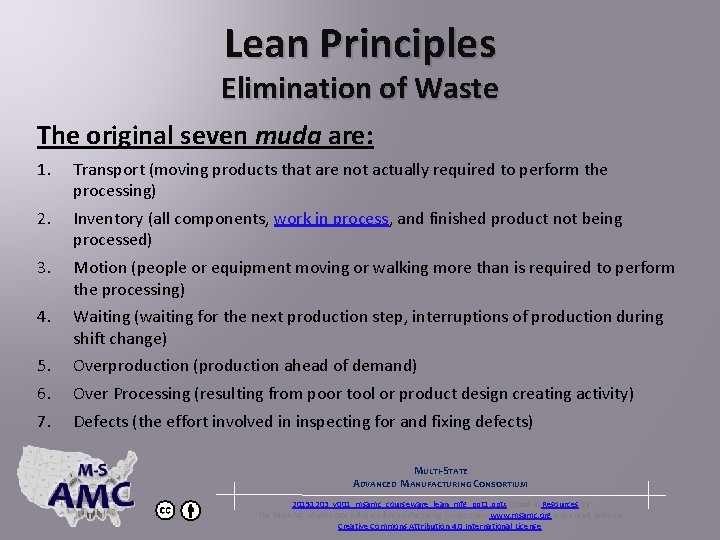
Lean Principles Elimination of Waste The original seven muda are: 1. Transport (moving products that are not actually required to perform the processing) 2. Inventory (all components, work in process, and finished product not being processed) 3. Motion (people or equipment moving or walking more than is required to perform the processing) 4. Waiting (waiting for the next production step, interruptions of production during shift change) 5. 6. 7. Overproduction (production ahead of demand) Over Processing (resulting from poor tool or product design creating activity) Defects (the effort involved in inspecting for and fixing defects) MULTI-STATE ADVANCED MANUFACTURING CONSORTIUM 20151203_v 001_msamc_courseware_lean_mfg_ppt 1. pptx found in Resources by the M-SAMC Multi-State Advanced Manufacturing Consortium www. msamc. org is licensed under a Creative Commons Attribution 4. 0 International License.

Lean Principles Elimination of Waste Overproduction Bad Quality Inventory The Seven Wastes Operator Motion Transport Idle Time Processing MULTI-STATE ADVANCED MANUFACTURING CONSORTIUM 20151203_v 001_msamc_courseware_lean_mfg_ppt 1. pptx found in Resources by the M-SAMC Multi-State Advanced Manufacturing Consortium www. msamc. org is licensed under a Creative Commons Attribution 4. 0 International License.
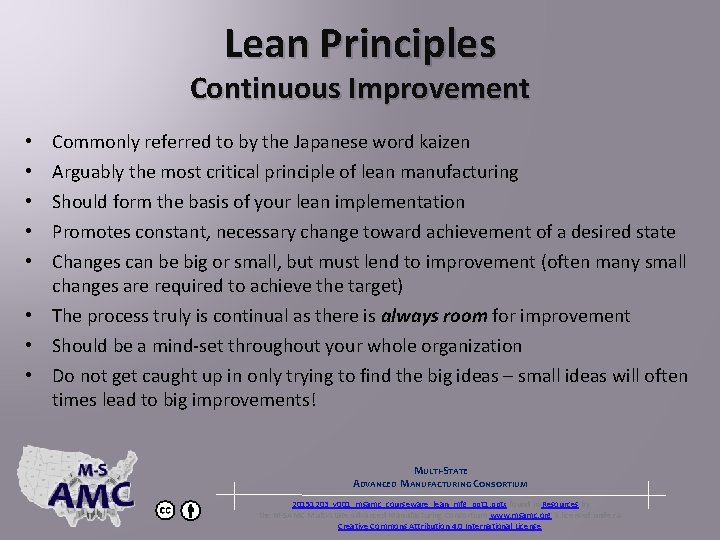
Lean Principles Continuous Improvement • • • Commonly referred to by the Japanese word kaizen Arguably the most critical principle of lean manufacturing Should form the basis of your lean implementation Promotes constant, necessary change toward achievement of a desired state Changes can be big or small, but must lend to improvement (often many small changes are required to achieve the target) • The process truly is continual as there is always room for improvement • Should be a mind-set throughout your whole organization • Do not get caught up in only trying to find the big ideas – small ideas will often times lead to big improvements! MULTI-STATE ADVANCED MANUFACTURING CONSORTIUM 20151203_v 001_msamc_courseware_lean_mfg_ppt 1. pptx found in Resources by the M-SAMC Multi-State Advanced Manufacturing Consortium www. msamc. org is licensed under a Creative Commons Attribution 4. 0 International License.
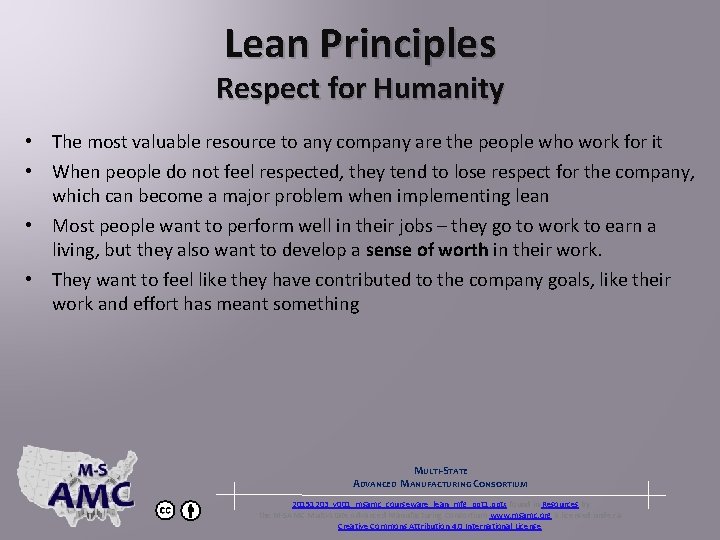
Lean Principles Respect for Humanity • The most valuable resource to any company are the people who work for it • When people do not feel respected, they tend to lose respect for the company, which can become a major problem when implementing lean • Most people want to perform well in their jobs – they go to work to earn a living, but they also want to develop a sense of worth in their work. • They want to feel like they have contributed to the company goals, like their work and effort has meant something MULTI-STATE ADVANCED MANUFACTURING CONSORTIUM 20151203_v 001_msamc_courseware_lean_mfg_ppt 1. pptx found in Resources by the M-SAMC Multi-State Advanced Manufacturing Consortium www. msamc. org is licensed under a Creative Commons Attribution 4. 0 International License.
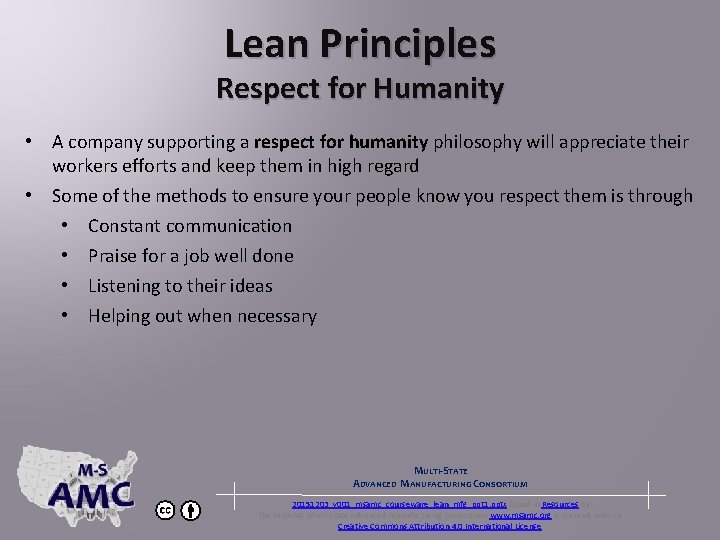
Lean Principles Respect for Humanity • A company supporting a respect for humanity philosophy will appreciate their workers efforts and keep them in high regard • Some of the methods to ensure your people know you respect them is through • Constant communication • Praise for a job well done • Listening to their ideas • Helping out when necessary MULTI-STATE ADVANCED MANUFACTURING CONSORTIUM 20151203_v 001_msamc_courseware_lean_mfg_ppt 1. pptx found in Resources by the M-SAMC Multi-State Advanced Manufacturing Consortium www. msamc. org is licensed under a Creative Commons Attribution 4. 0 International License.
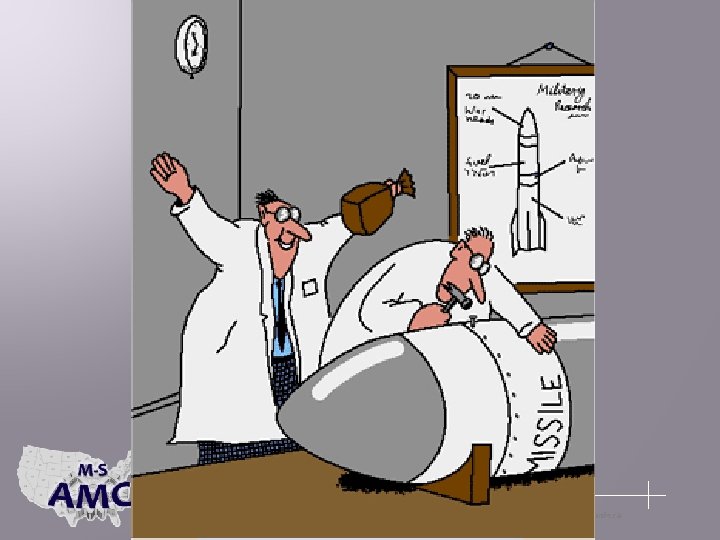
MULTI-STATE ADVANCED MANUFACTURING CONSORTIUM 20151203_v 001_msamc_courseware_lean_mfg_ppt 1. pptx found in Resources by the M-SAMC Multi-State Advanced Manufacturing Consortium www. msamc. org is licensed under a Creative Commons Attribution 4. 0 International License.
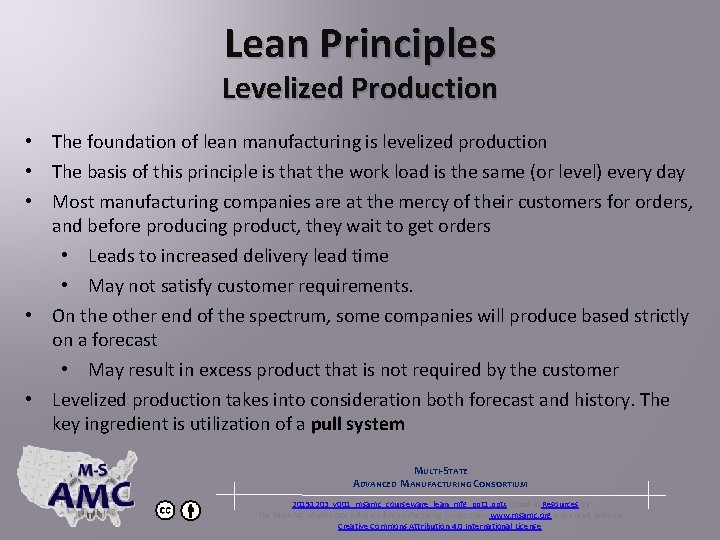
Lean Principles Levelized Production • The foundation of lean manufacturing is levelized production • The basis of this principle is that the work load is the same (or level) every day • Most manufacturing companies are at the mercy of their customers for orders, and before producing product, they wait to get orders • Leads to increased delivery lead time • May not satisfy customer requirements. • On the other end of the spectrum, some companies will produce based strictly on a forecast • May result in excess product that is not required by the customer • Levelized production takes into consideration both forecast and history. The key ingredient is utilization of a pull system MULTI-STATE ADVANCED MANUFACTURING CONSORTIUM 20151203_v 001_msamc_courseware_lean_mfg_ppt 1. pptx found in Resources by the M-SAMC Multi-State Advanced Manufacturing Consortium www. msamc. org is licensed under a Creative Commons Attribution 4. 0 International License.
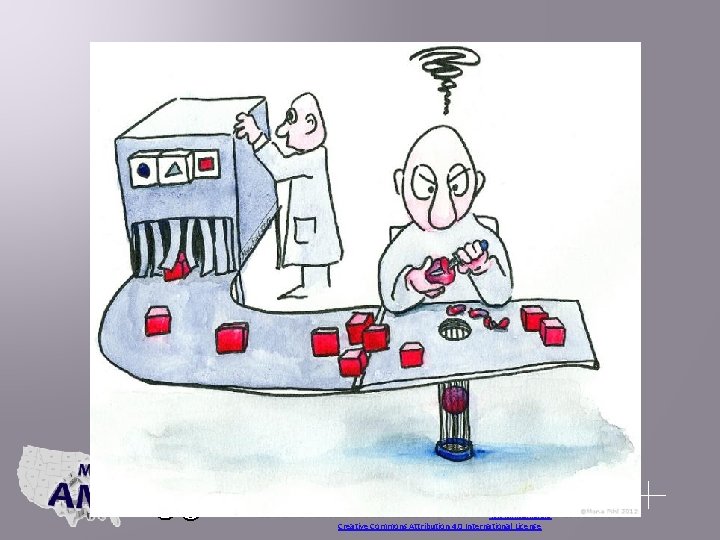
MULTI-STATE ADVANCED MANUFACTURING CONSORTIUM 20151203_v 001_msamc_courseware_lean_mfg_ppt 1. pptx found in Resources by the M-SAMC Multi-State Advanced Manufacturing Consortium www. msamc. org is licensed under a Creative Commons Attribution 4. 0 International License.
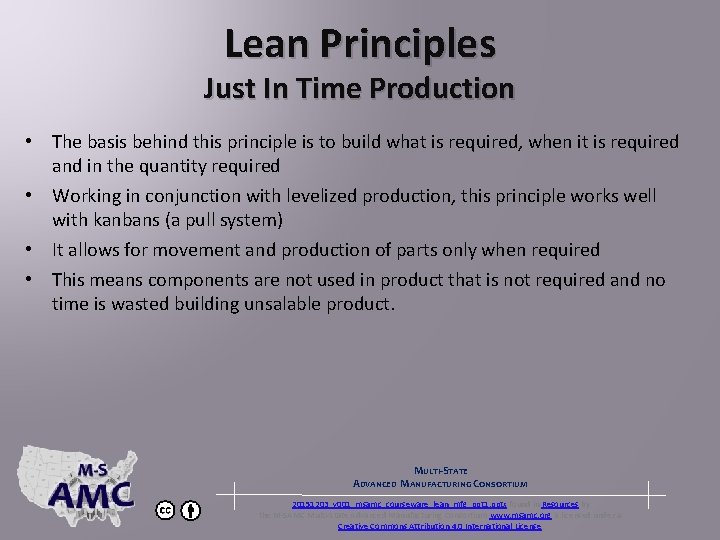
Lean Principles Just In Time Production • The basis behind this principle is to build what is required, when it is required and in the quantity required • Working in conjunction with levelized production, this principle works well with kanbans (a pull system) • It allows for movement and production of parts only when required • This means components are not used in product that is not required and no time is wasted building unsalable product. MULTI-STATE ADVANCED MANUFACTURING CONSORTIUM 20151203_v 001_msamc_courseware_lean_mfg_ppt 1. pptx found in Resources by the M-SAMC Multi-State Advanced Manufacturing Consortium www. msamc. org is licensed under a Creative Commons Attribution 4. 0 International License.
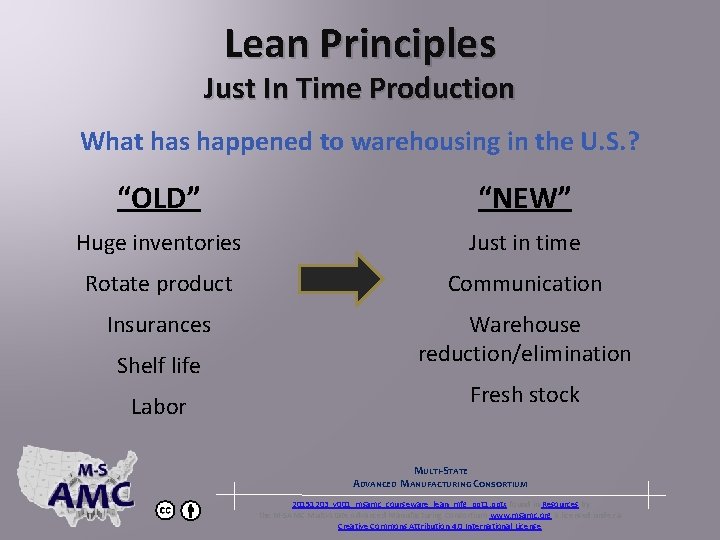
Lean Principles Just In Time Production What has happened to warehousing in the U. S. ? “OLD” “NEW” Huge inventories Just in time Rotate product Communication Insurances Warehouse reduction/elimination Shelf life Labor Fresh stock MULTI-STATE ADVANCED MANUFACTURING CONSORTIUM 20151203_v 001_msamc_courseware_lean_mfg_ppt 1. pptx found in Resources by the M-SAMC Multi-State Advanced Manufacturing Consortium www. msamc. org is licensed under a Creative Commons Attribution 4. 0 International License.
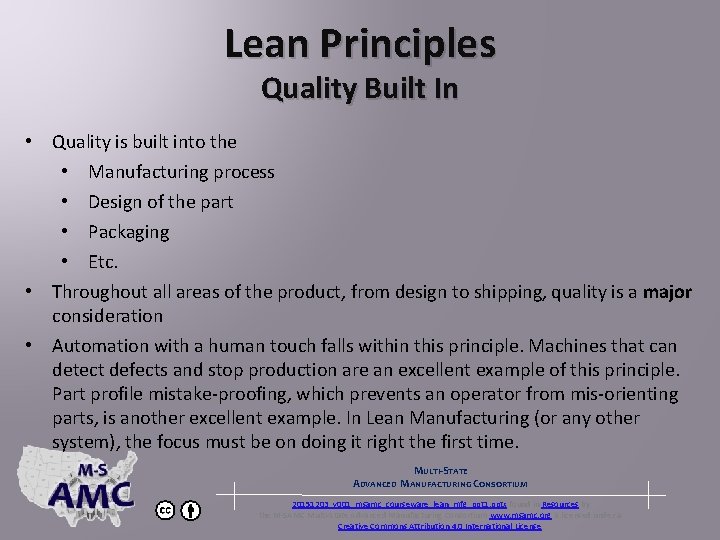
Lean Principles Quality Built In • Quality is built into the • Manufacturing process • Design of the part • Packaging • Etc. • Throughout all areas of the product, from design to shipping, quality is a major consideration • Automation with a human touch falls within this principle. Machines that can detect defects and stop production are an excellent example of this principle. Part profile mistake-proofing, which prevents an operator from mis-orienting parts, is another excellent example. In Lean Manufacturing (or any other system), the focus must be on doing it right the first time. MULTI-STATE ADVANCED MANUFACTURING CONSORTIUM 20151203_v 001_msamc_courseware_lean_mfg_ppt 1. pptx found in Resources by the M-SAMC Multi-State Advanced Manufacturing Consortium www. msamc. org is licensed under a Creative Commons Attribution 4. 0 International License.
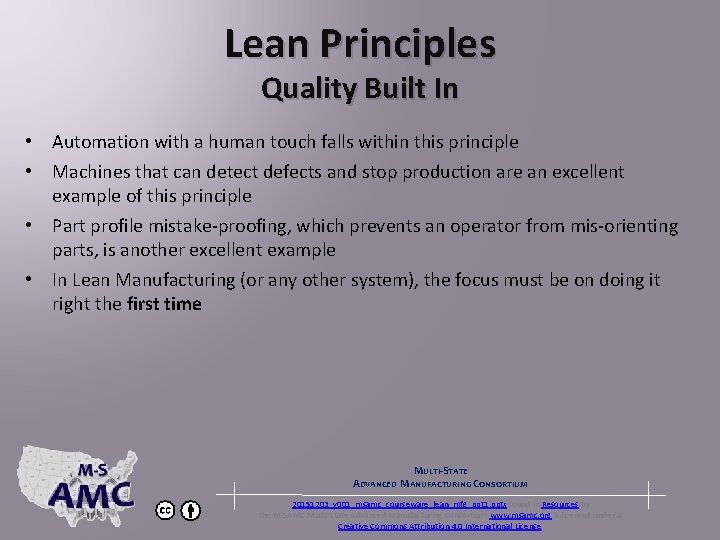
Lean Principles Quality Built In • Automation with a human touch falls within this principle • Machines that can detect defects and stop production are an excellent example of this principle • Part profile mistake-proofing, which prevents an operator from mis-orienting parts, is another excellent example • In Lean Manufacturing (or any other system), the focus must be on doing it right the first time MULTI-STATE ADVANCED MANUFACTURING CONSORTIUM 20151203_v 001_msamc_courseware_lean_mfg_ppt 1. pptx found in Resources by the M-SAMC Multi-State Advanced Manufacturing Consortium www. msamc. org is licensed under a Creative Commons Attribution 4. 0 International License.
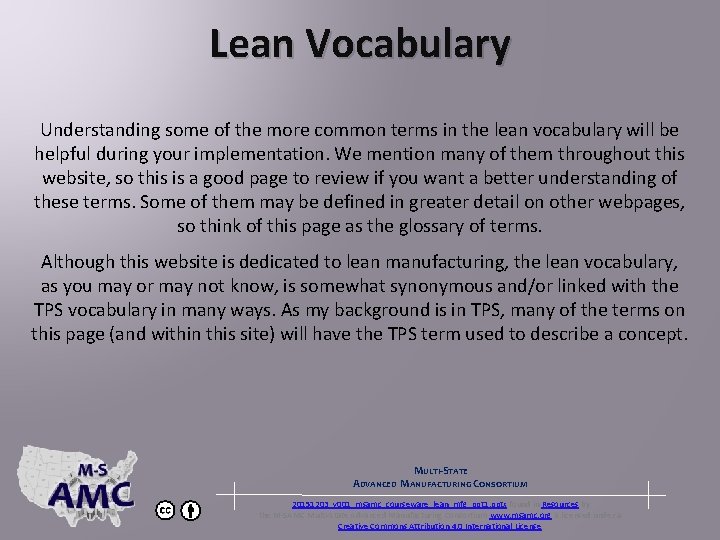
Lean Vocabulary Understanding some of the more common terms in the lean vocabulary will be helpful during your implementation. We mention many of them throughout this website, so this is a good page to review if you want a better understanding of these terms. Some of them may be defined in greater detail on other webpages, so think of this page as the glossary of terms. Although this website is dedicated to lean manufacturing, the lean vocabulary, as you may or may not know, is somewhat synonymous and/or linked with the TPS vocabulary in many ways. As my background is in TPS, many of the terms on this page (and within this site) will have the TPS term used to describe a concept. MULTI-STATE ADVANCED MANUFACTURING CONSORTIUM 20151203_v 001_msamc_courseware_lean_mfg_ppt 1. pptx found in Resources by the M-SAMC Multi-State Advanced Manufacturing Consortium www. msamc. org is licensed under a Creative Commons Attribution 4. 0 International License.
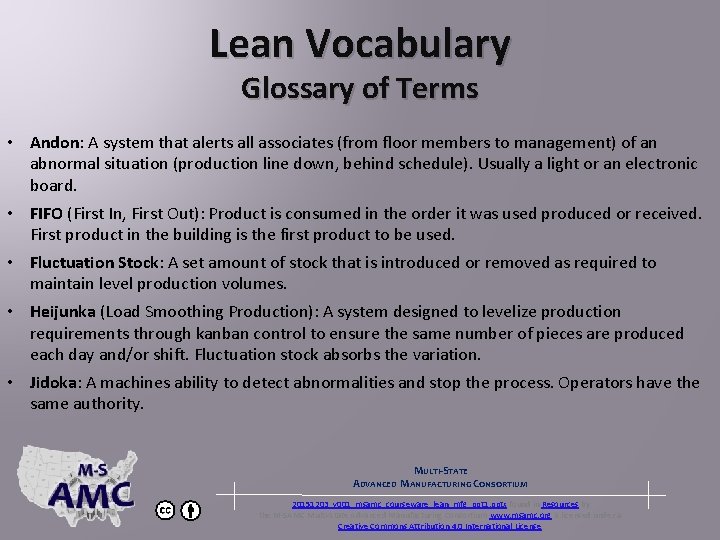
Lean Vocabulary Glossary of Terms • Andon: A system that alerts all associates (from floor members to management) of an abnormal situation (production line down, behind schedule). Usually a light or an electronic board. • FIFO (First In, First Out): Product is consumed in the order it was used produced or received. First product in the building is the first product to be used. • Fluctuation Stock: A set amount of stock that is introduced or removed as required to maintain level production volumes. • Heijunka (Load Smoothing Production): A system designed to levelize production requirements through kanban control to ensure the same number of pieces are produced each day and/or shift. Fluctuation stock absorbs the variation. • Jidoka: A machines ability to detect abnormalities and stop the process. Operators have the same authority. MULTI-STATE ADVANCED MANUFACTURING CONSORTIUM 20151203_v 001_msamc_courseware_lean_mfg_ppt 1. pptx found in Resources by the M-SAMC Multi-State Advanced Manufacturing Consortium www. msamc. org is licensed under a Creative Commons Attribution 4. 0 International License.
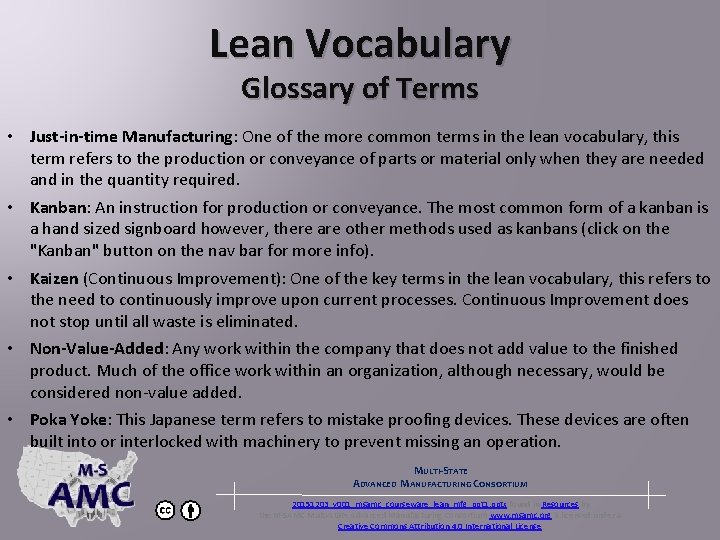
Lean Vocabulary Glossary of Terms • Just-in-time Manufacturing: One of the more common terms in the lean vocabulary, this term refers to the production or conveyance of parts or material only when they are needed and in the quantity required. • Kanban: An instruction for production or conveyance. The most common form of a kanban is a hand sized signboard however, there are other methods used as kanbans (click on the "Kanban" button on the nav bar for more info). • Kaizen (Continuous Improvement): One of the key terms in the lean vocabulary, this refers to the need to continuously improve upon current processes. Continuous Improvement does not stop until all waste is eliminated. • Non-Value-Added: Any work within the company that does not add value to the finished product. Much of the office work within an organization, although necessary, would be considered non-value added. • Poka Yoke: This Japanese term refers to mistake proofing devices. These devices are often built into or interlocked with machinery to prevent missing an operation. MULTI-STATE ADVANCED MANUFACTURING CONSORTIUM 20151203_v 001_msamc_courseware_lean_mfg_ppt 1. pptx found in Resources by the M-SAMC Multi-State Advanced Manufacturing Consortium www. msamc. org is licensed under a Creative Commons Attribution 4. 0 International License.
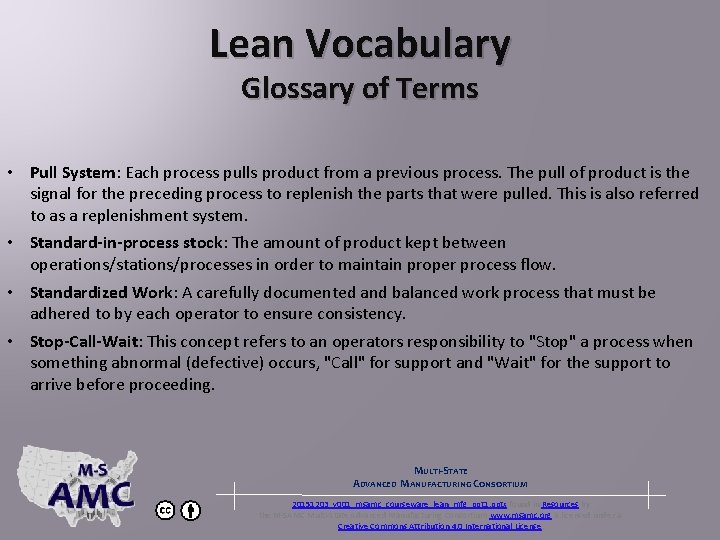
Lean Vocabulary Glossary of Terms • Pull System: Each process pulls product from a previous process. The pull of product is the signal for the preceding process to replenish the parts that were pulled. This is also referred to as a replenishment system. • Standard-in-process stock: The amount of product kept between operations/stations/processes in order to maintain proper process flow. • Standardized Work: A carefully documented and balanced work process that must be adhered to by each operator to ensure consistency. • Stop-Call-Wait: This concept refers to an operators responsibility to "Stop" a process when something abnormal (defective) occurs, "Call" for support and "Wait" for the support to arrive before proceeding. MULTI-STATE ADVANCED MANUFACTURING CONSORTIUM 20151203_v 001_msamc_courseware_lean_mfg_ppt 1. pptx found in Resources by the M-SAMC Multi-State Advanced Manufacturing Consortium www. msamc. org is licensed under a Creative Commons Attribution 4. 0 International License.
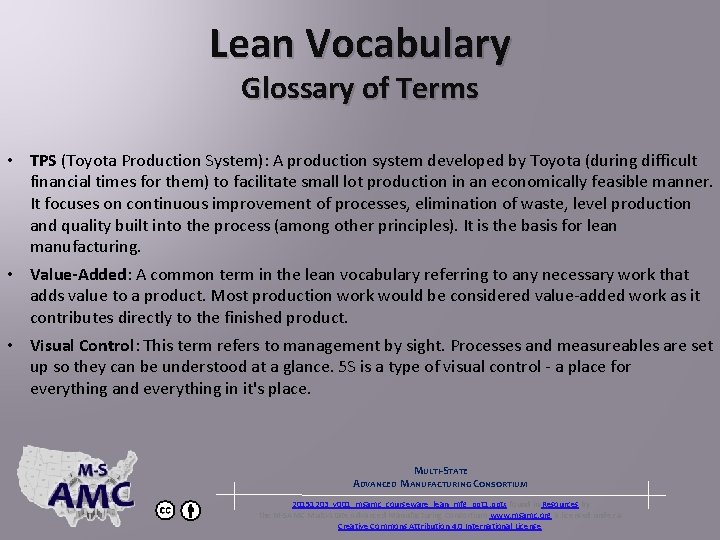
Lean Vocabulary Glossary of Terms • TPS (Toyota Production System): A production system developed by Toyota (during difficult financial times for them) to facilitate small lot production in an economically feasible manner. It focuses on continuous improvement of processes, elimination of waste, level production and quality built into the process (among other principles). It is the basis for lean manufacturing. • Value-Added: A common term in the lean vocabulary referring to any necessary work that adds value to a product. Most production work would be considered value-added work as it contributes directly to the finished product. • Visual Control: This term refers to management by sight. Processes and measureables are set up so they can be understood at a glance. 5 S is a type of visual control - a place for everything and everything in it's place. MULTI-STATE ADVANCED MANUFACTURING CONSORTIUM 20151203_v 001_msamc_courseware_lean_mfg_ppt 1. pptx found in Resources by the M-SAMC Multi-State Advanced Manufacturing Consortium www. msamc. org is licensed under a Creative Commons Attribution 4. 0 International License.
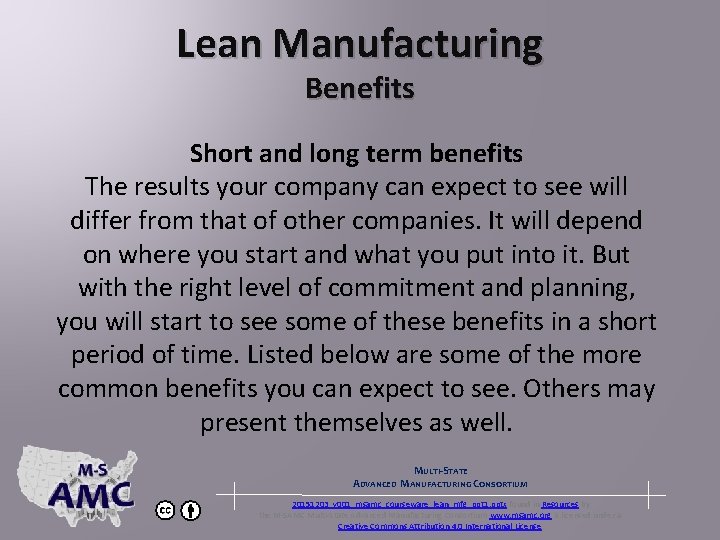
Lean Manufacturing Benefits Short and long term benefits The results your company can expect to see will differ from that of other companies. It will depend on where you start and what you put into it. But with the right level of commitment and planning, you will start to see some of these benefits in a short period of time. Listed below are some of the more common benefits you can expect to see. Others may present themselves as well. MULTI-STATE ADVANCED MANUFACTURING CONSORTIUM 20151203_v 001_msamc_courseware_lean_mfg_ppt 1. pptx found in Resources by the M-SAMC Multi-State Advanced Manufacturing Consortium www. msamc. org is licensed under a Creative Commons Attribution 4. 0 International License.
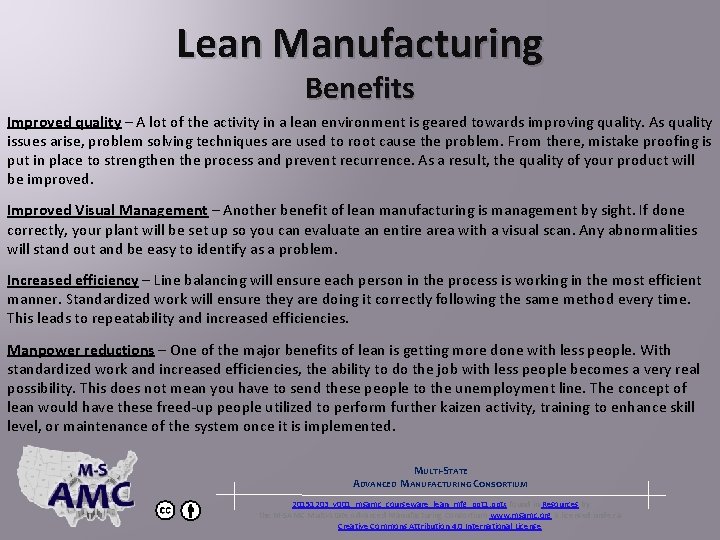
Lean Manufacturing Benefits Improved quality – A lot of the activity in a lean environment is geared towards improving quality. As quality issues arise, problem solving techniques are used to root cause the problem. From there, mistake proofing is put in place to strengthen the process and prevent recurrence. As a result, the quality of your product will be improved. Improved Visual Management – Another benefit of lean manufacturing is management by sight. If done correctly, your plant will be set up so you can evaluate an entire area with a visual scan. Any abnormalities will stand out and be easy to identify as a problem. Increased efficiency – Line balancing will ensure each person in the process is working in the most efficient manner. Standardized work will ensure they are doing it correctly following the same method every time. This leads to repeatability and increased efficiencies. Manpower reductions – One of the major benefits of lean is getting more done with less people. With standardized work and increased efficiencies, the ability to do the job with less people becomes a very real possibility. This does not mean you have to send these people to the unemployment line. The concept of lean would have these freed-up people utilized to perform further kaizen activity, training to enhance skill level, or maintenance of the system once it is implemented. MULTI-STATE ADVANCED MANUFACTURING CONSORTIUM 20151203_v 001_msamc_courseware_lean_mfg_ppt 1. pptx found in Resources by the M-SAMC Multi-State Advanced Manufacturing Consortium www. msamc. org is licensed under a Creative Commons Attribution 4. 0 International License.
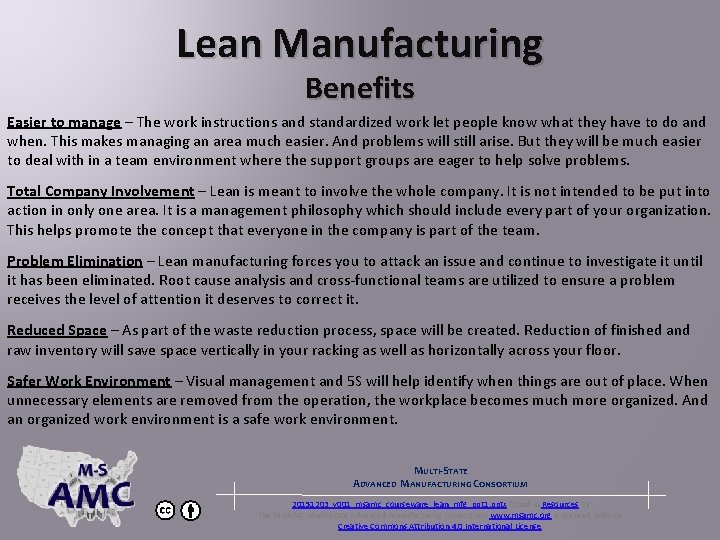
Lean Manufacturing Benefits Easier to manage – The work instructions and standardized work let people know what they have to do and when. This makes managing an area much easier. And problems will still arise. But they will be much easier to deal with in a team environment where the support groups are eager to help solve problems. Total Company Involvement – Lean is meant to involve the whole company. It is not intended to be put into action in only one area. It is a management philosophy which should include every part of your organization. This helps promote the concept that everyone in the company is part of the team. Problem Elimination – Lean manufacturing forces you to attack an issue and continue to investigate it until it has been eliminated. Root cause analysis and cross-functional teams are utilized to ensure a problem receives the level of attention it deserves to correct it. Reduced Space – As part of the waste reduction process, space will be created. Reduction of finished and raw inventory will save space vertically in your racking as well as horizontally across your floor. Safer Work Environment – Visual management and 5 S will help identify when things are out of place. When unnecessary elements are removed from the operation, the workplace becomes much more organized. And an organized work environment is a safe work environment. MULTI-STATE ADVANCED MANUFACTURING CONSORTIUM 20151203_v 001_msamc_courseware_lean_mfg_ppt 1. pptx found in Resources by the M-SAMC Multi-State Advanced Manufacturing Consortium www. msamc. org is licensed under a Creative Commons Attribution 4. 0 International License.
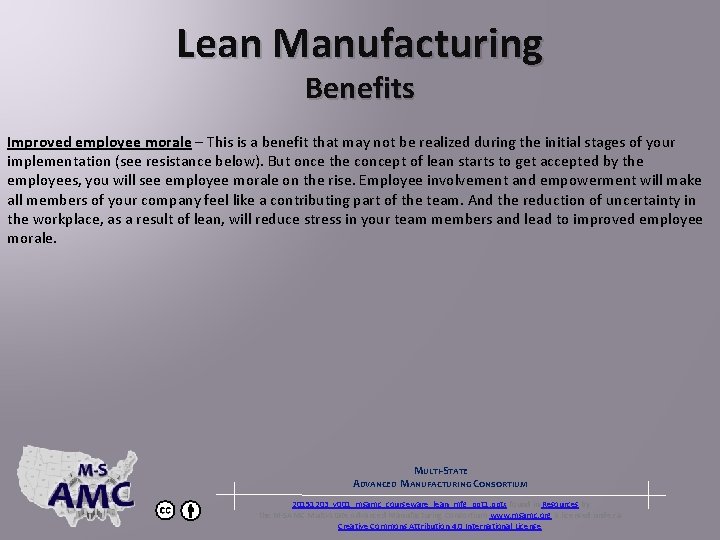
Lean Manufacturing Benefits Improved employee morale – This is a benefit that may not be realized during the initial stages of your implementation (see resistance below). But once the concept of lean starts to get accepted by the employees, you will see employee morale on the rise. Employee involvement and empowerment will make all members of your company feel like a contributing part of the team. And the reduction of uncertainty in the workplace, as a result of lean, will reduce stress in your team members and lead to improved employee morale. MULTI-STATE ADVANCED MANUFACTURING CONSORTIUM 20151203_v 001_msamc_courseware_lean_mfg_ppt 1. pptx found in Resources by the M-SAMC Multi-State Advanced Manufacturing Consortium www. msamc. org is licensed under a Creative Commons Attribution 4. 0 International License.
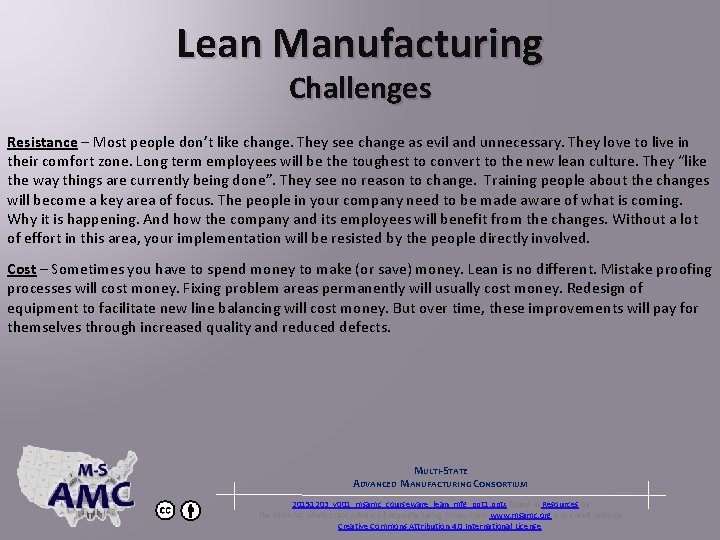
Lean Manufacturing Challenges Resistance – Most people don’t like change. They see change as evil and unnecessary. They love to live in their comfort zone. Long term employees will be the toughest to convert to the new lean culture. They “like the way things are currently being done”. They see no reason to change. Training people about the changes will become a key area of focus. The people in your company need to be made aware of what is coming. Why it is happening. And how the company and its employees will benefit from the changes. Without a lot of effort in this area, your implementation will be resisted by the people directly involved. Cost – Sometimes you have to spend money to make (or save) money. Lean is no different. Mistake proofing processes will cost money. Fixing problem areas permanently will usually cost money. Redesign of equipment to facilitate new line balancing will cost money. But over time, these improvements will pay for themselves through increased quality and reduced defects. MULTI-STATE ADVANCED MANUFACTURING CONSORTIUM 20151203_v 001_msamc_courseware_lean_mfg_ppt 1. pptx found in Resources by the M-SAMC Multi-State Advanced Manufacturing Consortium www. msamc. org is licensed under a Creative Commons Attribution 4. 0 International License.
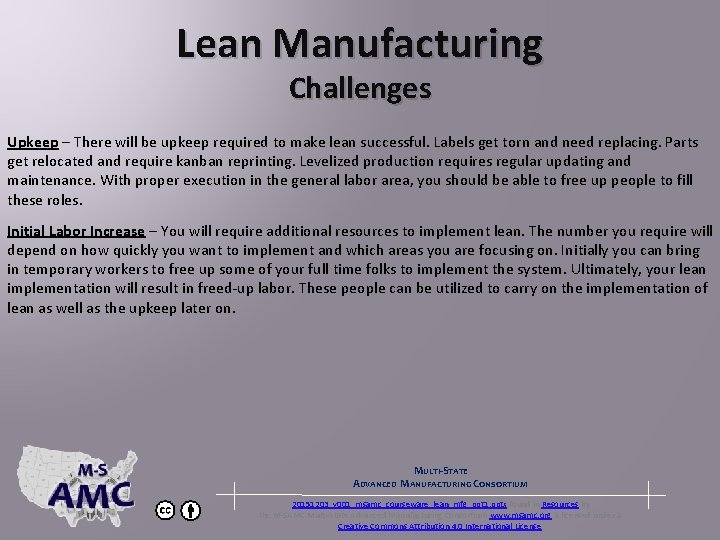
Lean Manufacturing Challenges Upkeep – There will be upkeep required to make lean successful. Labels get torn and need replacing. Parts get relocated and require kanban reprinting. Levelized production requires regular updating and maintenance. With proper execution in the general labor area, you should be able to free up people to fill these roles. Initial Labor Increase – You will require additional resources to implement lean. The number you require will depend on how quickly you want to implement and which areas you are focusing on. Initially you can bring in temporary workers to free up some of your full time folks to implement the system. Ultimately, your lean implementation will result in freed-up labor. These people can be utilized to carry on the implementation of lean as well as the upkeep later on. MULTI-STATE ADVANCED MANUFACTURING CONSORTIUM 20151203_v 001_msamc_courseware_lean_mfg_ppt 1. pptx found in Resources by the M-SAMC Multi-State Advanced Manufacturing Consortium www. msamc. org is licensed under a Creative Commons Attribution 4. 0 International License.
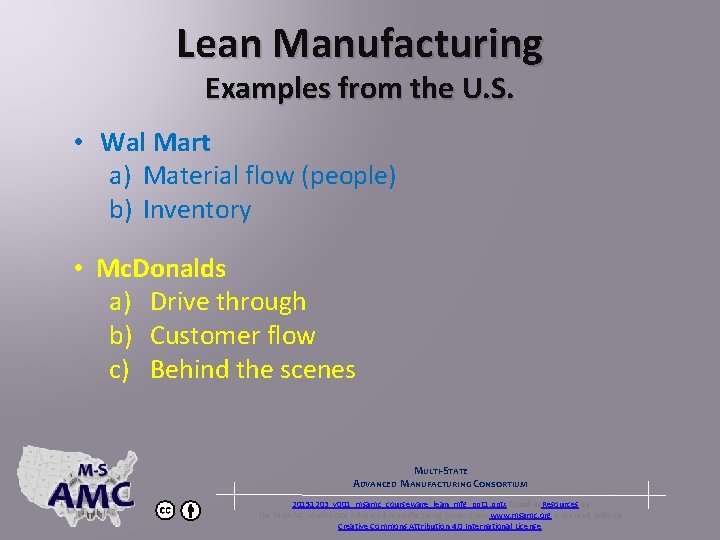
Lean Manufacturing Examples from the U. S. • Wal Mart a) Material flow (people) b) Inventory • Mc. Donalds a) Drive through b) Customer flow c) Behind the scenes MULTI-STATE ADVANCED MANUFACTURING CONSORTIUM 20151203_v 001_msamc_courseware_lean_mfg_ppt 1. pptx found in Resources by the M-SAMC Multi-State Advanced Manufacturing Consortium www. msamc. org is licensed under a Creative Commons Attribution 4. 0 International License.
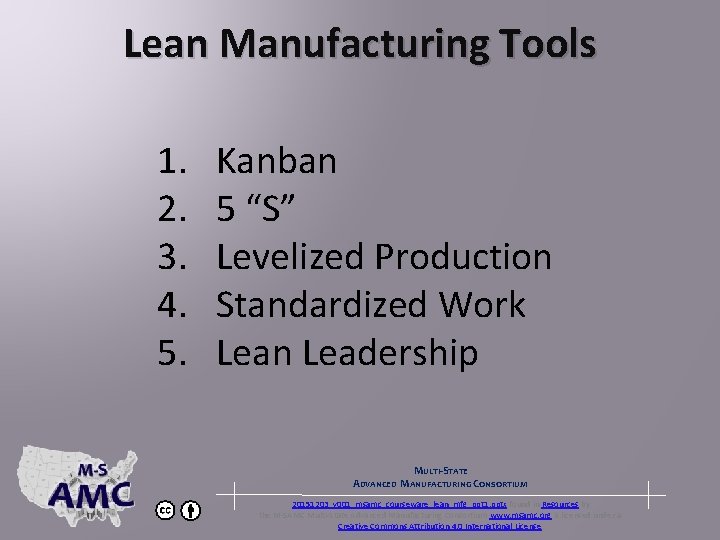
Lean Manufacturing Tools 1. 2. 3. 4. 5. Kanban 5 “S” Levelized Production Standardized Work Lean Leadership MULTI-STATE ADVANCED MANUFACTURING CONSORTIUM 20151203_v 001_msamc_courseware_lean_mfg_ppt 1. pptx found in Resources by the M-SAMC Multi-State Advanced Manufacturing Consortium www. msamc. org is licensed under a Creative Commons Attribution 4. 0 International License.
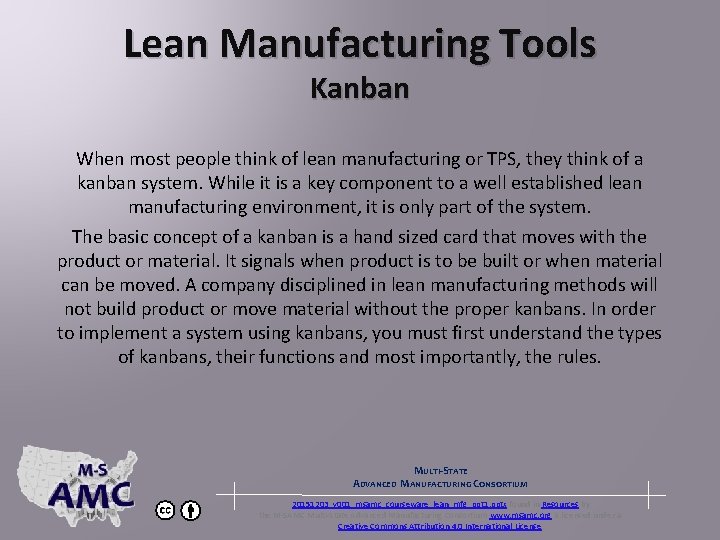
Lean Manufacturing Tools Kanban When most people think of lean manufacturing or TPS, they think of a kanban system. While it is a key component to a well established lean manufacturing environment, it is only part of the system. The basic concept of a kanban is a hand sized card that moves with the product or material. It signals when product is to be built or when material can be moved. A company disciplined in lean manufacturing methods will not build product or move material without the proper kanbans. In order to implement a system using kanbans, you must first understand the types of kanbans, their functions and most importantly, the rules. MULTI-STATE ADVANCED MANUFACTURING CONSORTIUM 20151203_v 001_msamc_courseware_lean_mfg_ppt 1. pptx found in Resources by the M-SAMC Multi-State Advanced Manufacturing Consortium www. msamc. org is licensed under a Creative Commons Attribution 4. 0 International License.
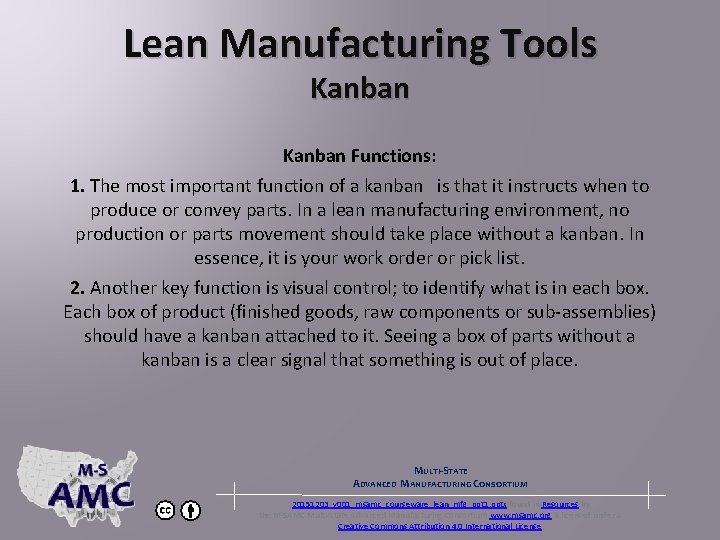
Lean Manufacturing Tools Kanban Functions: 1. The most important function of a kanban is that it instructs when to produce or convey parts. In a lean manufacturing environment, no production or parts movement should take place without a kanban. In essence, it is your work order or pick list. 2. Another key function is visual control; to identify what is in each box. Each box of product (finished goods, raw components or sub-assemblies) should have a kanban attached to it. Seeing a box of parts without a kanban is a clear signal that something is out of place. MULTI-STATE ADVANCED MANUFACTURING CONSORTIUM 20151203_v 001_msamc_courseware_lean_mfg_ppt 1. pptx found in Resources by the M-SAMC Multi-State Advanced Manufacturing Consortium www. msamc. org is licensed under a Creative Commons Attribution 4. 0 International License.
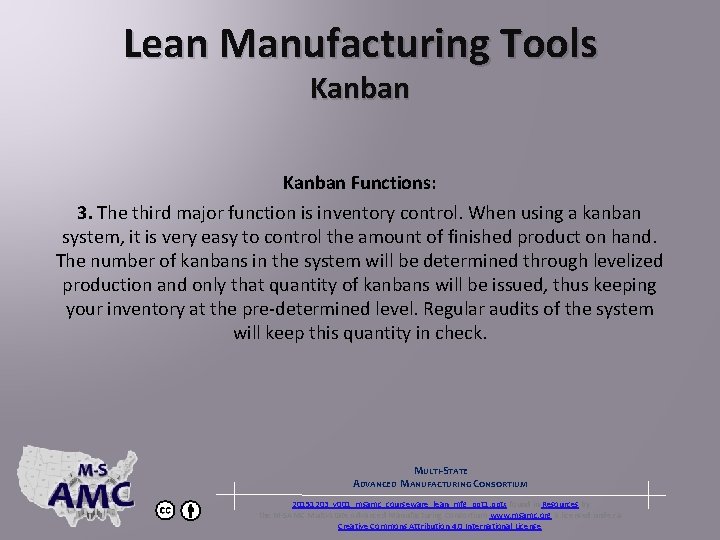
Lean Manufacturing Tools Kanban Functions: 3. The third major function is inventory control. When using a kanban system, it is very easy to control the amount of finished product on hand. The number of kanbans in the system will be determined through levelized production and only that quantity of kanbans will be issued, thus keeping your inventory at the pre-determined level. Regular audits of the system will keep this quantity in check. MULTI-STATE ADVANCED MANUFACTURING CONSORTIUM 20151203_v 001_msamc_courseware_lean_mfg_ppt 1. pptx found in Resources by the M-SAMC Multi-State Advanced Manufacturing Consortium www. msamc. org is licensed under a Creative Commons Attribution 4. 0 International License.
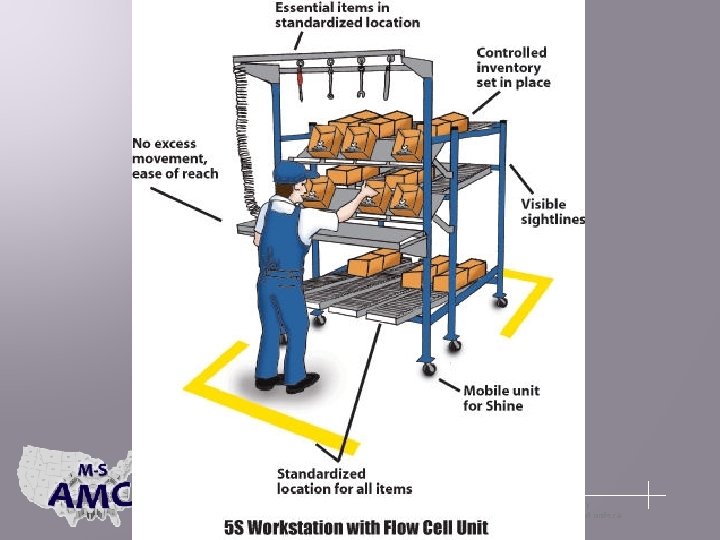
MULTI-STATE ADVANCED MANUFACTURING CONSORTIUM 20151203_v 001_msamc_courseware_lean_mfg_ppt 1. pptx found in Resources by the M-SAMC Multi-State Advanced Manufacturing Consortium www. msamc. org is licensed under a Creative Commons Attribution 4. 0 International License.
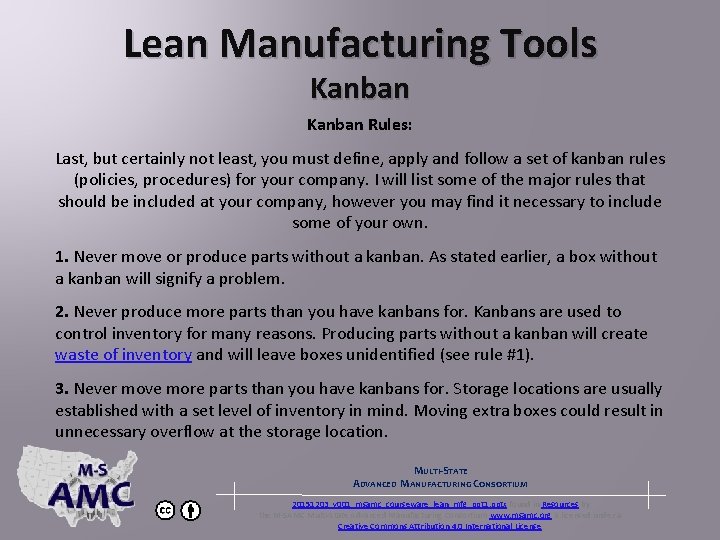
Lean Manufacturing Tools Kanban Rules: Last, but certainly not least, you must define, apply and follow a set of kanban rules (policies, procedures) for your company. I will list some of the major rules that should be included at your company, however you may find it necessary to include some of your own. 1. Never move or produce parts without a kanban. As stated earlier, a box without a kanban will signify a problem. 2. Never produce more parts than you have kanbans for. Kanbans are used to control inventory for many reasons. Producing parts without a kanban will create waste of inventory and will leave boxes unidentified (see rule #1). 3. Never move more parts than you have kanbans for. Storage locations are usually established with a set level of inventory in mind. Moving extra boxes could result in unnecessary overflow at the storage location. MULTI-STATE ADVANCED MANUFACTURING CONSORTIUM 20151203_v 001_msamc_courseware_lean_mfg_ppt 1. pptx found in Resources by the M-SAMC Multi-State Advanced Manufacturing Consortium www. msamc. org is licensed under a Creative Commons Attribution 4. 0 International License.
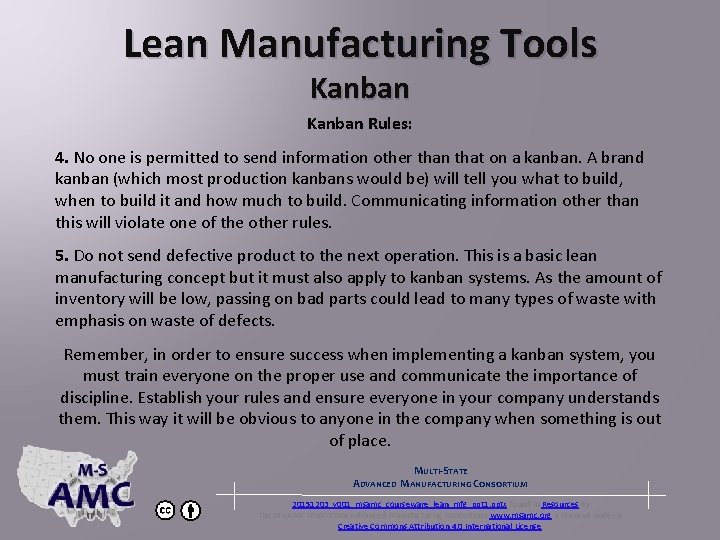
Lean Manufacturing Tools Kanban Rules: 4. No one is permitted to send information other than that on a kanban. A brand kanban (which most production kanbans would be) will tell you what to build, when to build it and how much to build. Communicating information other than this will violate one of the other rules. 5. Do not send defective product to the next operation. This is a basic lean manufacturing concept but it must also apply to kanban systems. As the amount of inventory will be low, passing on bad parts could lead to many types of waste with emphasis on waste of defects. Remember, in order to ensure success when implementing a kanban system, you must train everyone on the proper use and communicate the importance of discipline. Establish your rules and ensure everyone in your company understands them. This way it will be obvious to anyone in the company when something is out of place. MULTI-STATE ADVANCED MANUFACTURING CONSORTIUM 20151203_v 001_msamc_courseware_lean_mfg_ppt 1. pptx found in Resources by the M-SAMC Multi-State Advanced Manufacturing Consortium www. msamc. org is licensed under a Creative Commons Attribution 4. 0 International License.

Lean Manufacturing Tools 5 S In any factory, office or retail environment, 5 S can play such a big part towards improving your company. It is an absolute necessity in any lean manufacturing facility. You should gain improvements in quality, productivity, safety, efficiency and morale once you implement. It has been referred to by different names in North America, however it holds the same basic concept; a place for everything and everything in it's place. It is a system designed to make your job easier, through organization, when done correctly. MULTI-STATE ADVANCED MANUFACTURING CONSORTIUM 20151203_v 001_msamc_courseware_lean_mfg_ppt 1. pptx found in Resources by the M-SAMC Multi-State Advanced Manufacturing Consortium www. msamc. org is licensed under a Creative Commons Attribution 4. 0 International License.
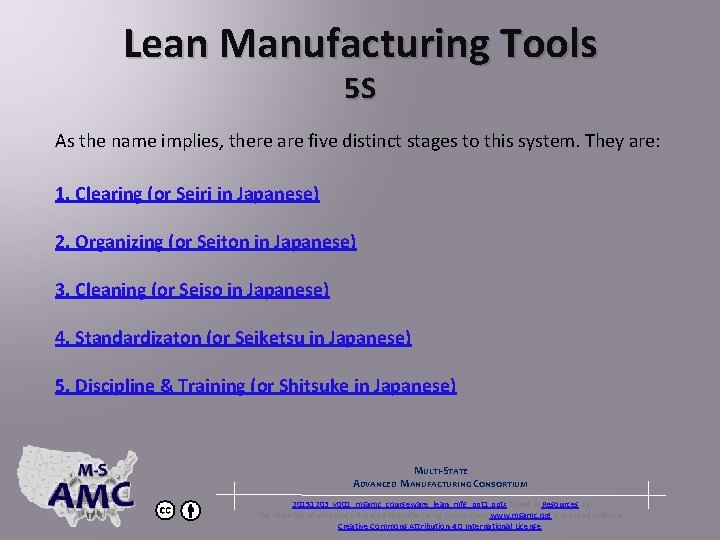
Lean Manufacturing Tools 5 S As the name implies, there are five distinct stages to this system. They are: 1. Clearing (or Seiri in Japanese) 2. Organizing (or Seiton in Japanese) 3. Cleaning (or Seiso in Japanese) 4. Standardizaton (or Seiketsu in Japanese) 5. Discipline & Training (or Shitsuke in Japanese) MULTI-STATE ADVANCED MANUFACTURING CONSORTIUM 20151203_v 001_msamc_courseware_lean_mfg_ppt 1. pptx found in Resources by the M-SAMC Multi-State Advanced Manufacturing Consortium www. msamc. org is licensed under a Creative Commons Attribution 4. 0 International License.
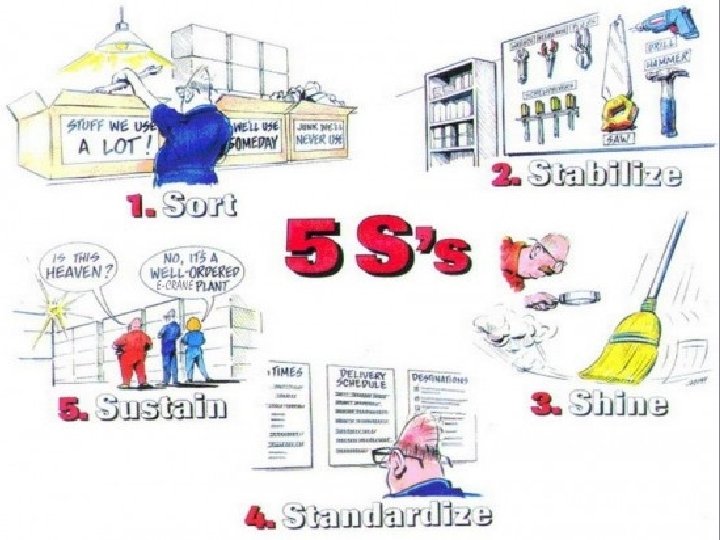
MULTI-STATE ADVANCED MANUFACTURING CONSORTIUM 20151203_v 001_msamc_courseware_lean_mfg_ppt 1. pptx found in Resources by the M-SAMC Multi-State Advanced Manufacturing Consortium www. msamc. org is licensed under a Creative Commons Attribution 4. 0 International License.
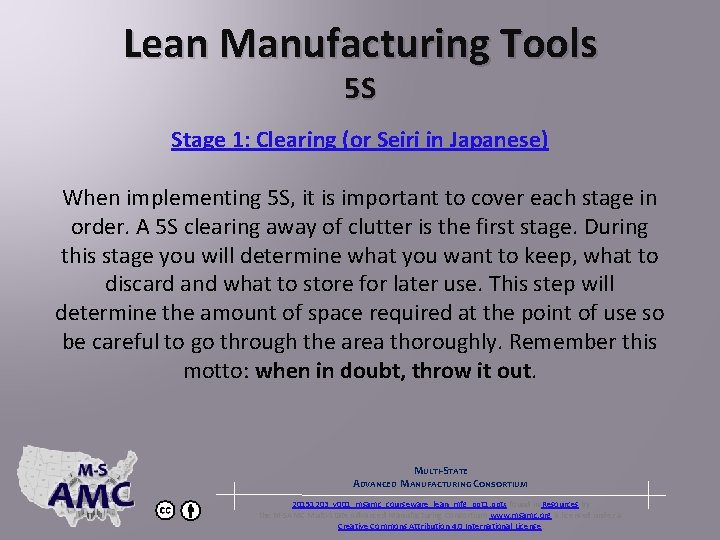
Lean Manufacturing Tools 5 S Stage 1: Clearing (or Seiri in Japanese) When implementing 5 S, it is important to cover each stage in order. A 5 S clearing away of clutter is the first stage. During this stage you will determine what you want to keep, what to discard and what to store for later use. This step will determine the amount of space required at the point of use so be careful to go through the area thoroughly. Remember this motto: when in doubt, throw it out. MULTI-STATE ADVANCED MANUFACTURING CONSORTIUM 20151203_v 001_msamc_courseware_lean_mfg_ppt 1. pptx found in Resources by the M-SAMC Multi-State Advanced Manufacturing Consortium www. msamc. org is licensed under a Creative Commons Attribution 4. 0 International License.
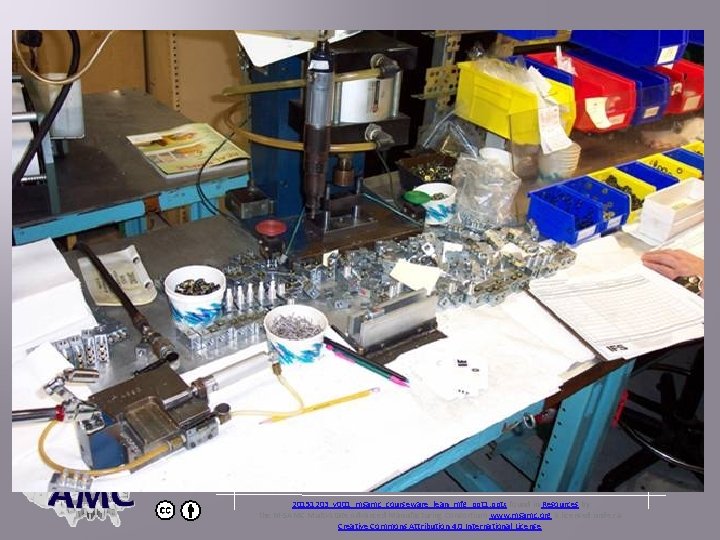
MULTI-STATE ADVANCED MANUFACTURING CONSORTIUM 20151203_v 001_msamc_courseware_lean_mfg_ppt 1. pptx found in Resources by the M-SAMC Multi-State Advanced Manufacturing Consortium www. msamc. org is licensed under a Creative Commons Attribution 4. 0 International License.
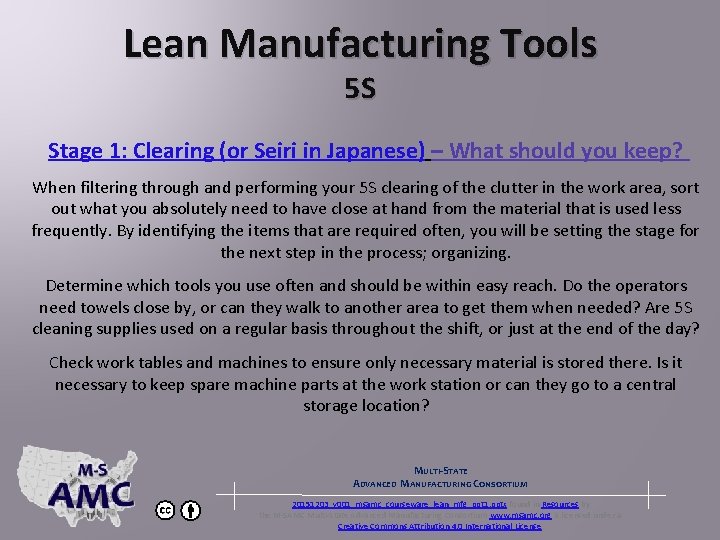
Lean Manufacturing Tools 5 S Stage 1: Clearing (or Seiri in Japanese) – What should you keep? When filtering through and performing your 5 S clearing of the clutter in the work area, sort out what you absolutely need to have close at hand from the material that is used less frequently. By identifying the items that are required often, you will be setting the stage for the next step in the process; organizing. Determine which tools you use often and should be within easy reach. Do the operators need towels close by, or can they walk to another area to get them when needed? Are 5 S cleaning supplies used on a regular basis throughout the shift, or just at the end of the day? Check work tables and machines to ensure only necessary material is stored there. Is it necessary to keep spare machine parts at the work station or can they go to a central storage location? MULTI-STATE ADVANCED MANUFACTURING CONSORTIUM 20151203_v 001_msamc_courseware_lean_mfg_ppt 1. pptx found in Resources by the M-SAMC Multi-State Advanced Manufacturing Consortium www. msamc. org is licensed under a Creative Commons Attribution 4. 0 International License.
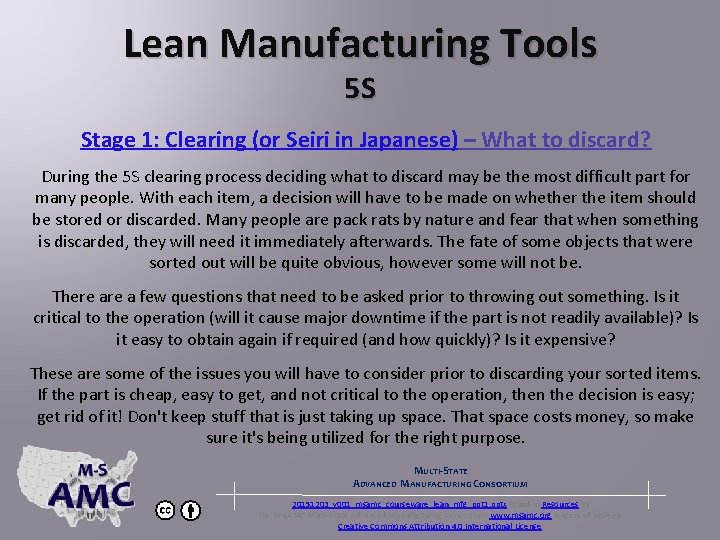
Lean Manufacturing Tools 5 S Stage 1: Clearing (or Seiri in Japanese) – What to discard? During the 5 S clearing process deciding what to discard may be the most difficult part for many people. With each item, a decision will have to be made on whether the item should be stored or discarded. Many people are pack rats by nature and fear that when something is discarded, they will need it immediately afterwards. The fate of some objects that were sorted out will be quite obvious, however some will not be. There a few questions that need to be asked prior to throwing out something. Is it critical to the operation (will it cause major downtime if the part is not readily available)? Is it easy to obtain again if required (and how quickly)? Is it expensive? These are some of the issues you will have to consider prior to discarding your sorted items. If the part is cheap, easy to get, and not critical to the operation, then the decision is easy; get rid of it! Don't keep stuff that is just taking up space. That space costs money, so make sure it's being utilized for the right purpose. MULTI-STATE ADVANCED MANUFACTURING CONSORTIUM 20151203_v 001_msamc_courseware_lean_mfg_ppt 1. pptx found in Resources by the M-SAMC Multi-State Advanced Manufacturing Consortium www. msamc. org is licensed under a Creative Commons Attribution 4. 0 International License.
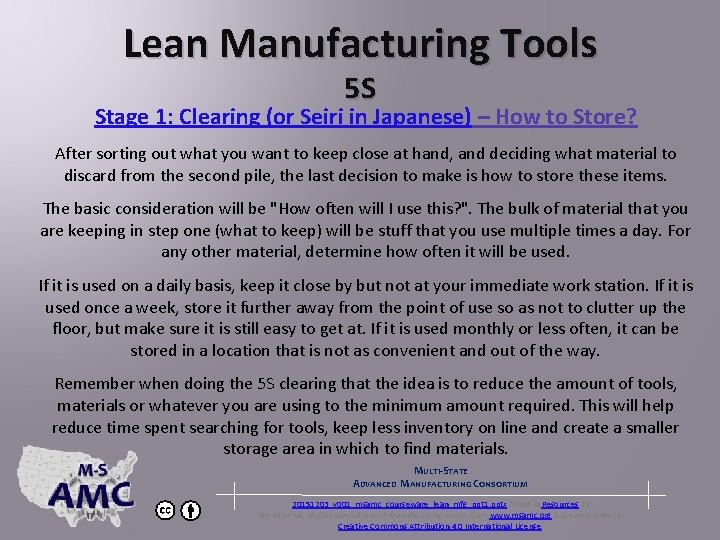
Lean Manufacturing Tools 5 S Stage 1: Clearing (or Seiri in Japanese) – How to Store? After sorting out what you want to keep close at hand, and deciding what material to discard from the second pile, the last decision to make is how to store these items. The basic consideration will be "How often will I use this? ". The bulk of material that you are keeping in step one (what to keep) will be stuff that you use multiple times a day. For any other material, determine how often it will be used. If it is used on a daily basis, keep it close by but not at your immediate work station. If it is used once a week, store it further away from the point of use so as not to clutter up the floor, but make sure it is still easy to get at. If it is used monthly or less often, it can be stored in a location that is not as convenient and out of the way. Remember when doing the 5 S clearing that the idea is to reduce the amount of tools, materials or whatever you are using to the minimum amount required. This will help reduce time spent searching for tools, keep less inventory on line and create a smaller storage area in which to find materials. MULTI-STATE ADVANCED MANUFACTURING CONSORTIUM 20151203_v 001_msamc_courseware_lean_mfg_ppt 1. pptx found in Resources by the M-SAMC Multi-State Advanced Manufacturing Consortium www. msamc. org is licensed under a Creative Commons Attribution 4. 0 International License.

Lean Manufacturing Tools 5 S Visual Controls are simple signals that provide an immediate understanding of a situation or condition. They are efficient, self regulating, and worker managed. Examples include: • • Pictures, diagrams Color coded dies, tools, pallets Lines on the floor to delineate storage areas, walkways, work areas, etc. Improved lighting MULTI-STATE ADVANCED MANUFACTURING CONSORTIUM 20151203_v 001_msamc_courseware_lean_mfg_ppt 1. pptx found in Resources by the M-SAMC Multi-State Advanced Manufacturing Consortium www. msamc. org is licensed under a Creative Commons Attribution 4. 0 International License.
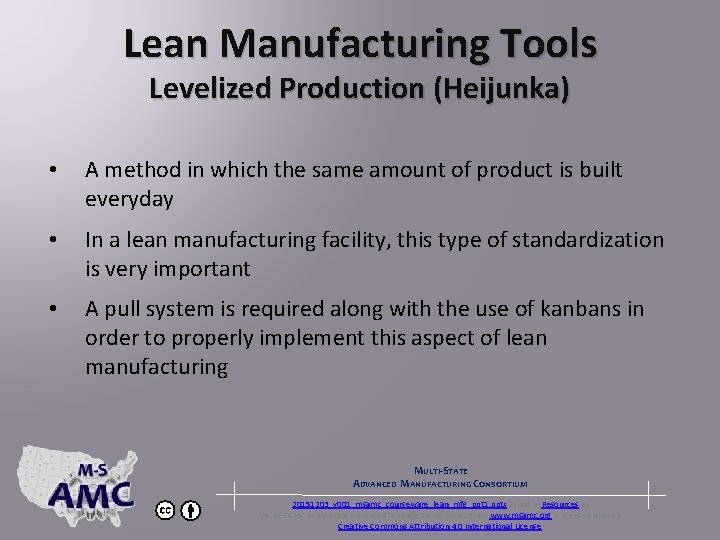
Lean Manufacturing Tools Levelized Production (Heijunka) • A method in which the same amount of product is built everyday • In a lean manufacturing facility, this type of standardization is very important • A pull system is required along with the use of kanbans in order to properly implement this aspect of lean manufacturing. MULTI-STATE ADVANCED MANUFACTURING CONSORTIUM 20151203_v 001_msamc_courseware_lean_mfg_ppt 1. pptx found in Resources by the M-SAMC Multi-State Advanced Manufacturing Consortium www. msamc. org is licensed under a Creative Commons Attribution 4. 0 International License.
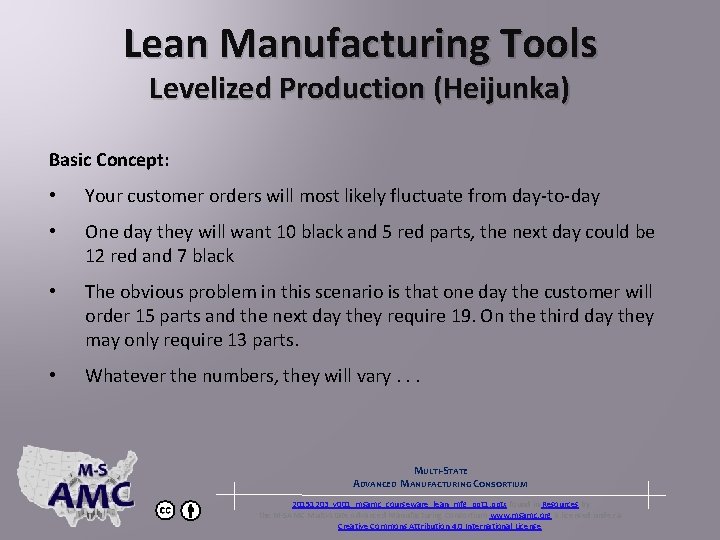
Lean Manufacturing Tools Levelized Production (Heijunka) Basic Concept: • Your customer orders will most likely fluctuate from day-to-day • One day they will want 10 black and 5 red parts, the next day could be 12 red and 7 black • The obvious problem in this scenario is that one day the customer will order 15 parts and the next day they require 19. On the third day they may only require 13 parts. • Whatever the numbers, they will vary. . . MULTI-STATE ADVANCED MANUFACTURING CONSORTIUM 20151203_v 001_msamc_courseware_lean_mfg_ppt 1. pptx found in Resources by the M-SAMC Multi-State Advanced Manufacturing Consortium www. msamc. org is licensed under a Creative Commons Attribution 4. 0 International License.
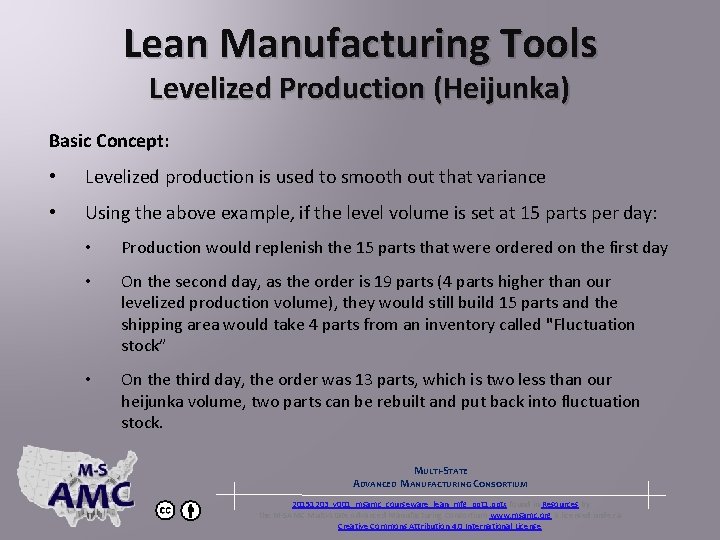
Lean Manufacturing Tools Levelized Production (Heijunka) Basic Concept: • Levelized production is used to smooth out that variance • Using the above example, if the level volume is set at 15 parts per day: • Production would replenish the 15 parts that were ordered on the first day • On the second day, as the order is 19 parts (4 parts higher than our levelized production volume), they would still build 15 parts and the shipping area would take 4 parts from an inventory called "Fluctuation stock” • On the third day, the order was 13 parts, which is two less than our heijunka volume, two parts can be rebuilt and put back into fluctuation stock. MULTI-STATE ADVANCED MANUFACTURING CONSORTIUM 20151203_v 001_msamc_courseware_lean_mfg_ppt 1. pptx found in Resources by the M-SAMC Multi-State Advanced Manufacturing Consortium www. msamc. org is licensed under a Creative Commons Attribution 4. 0 International License.
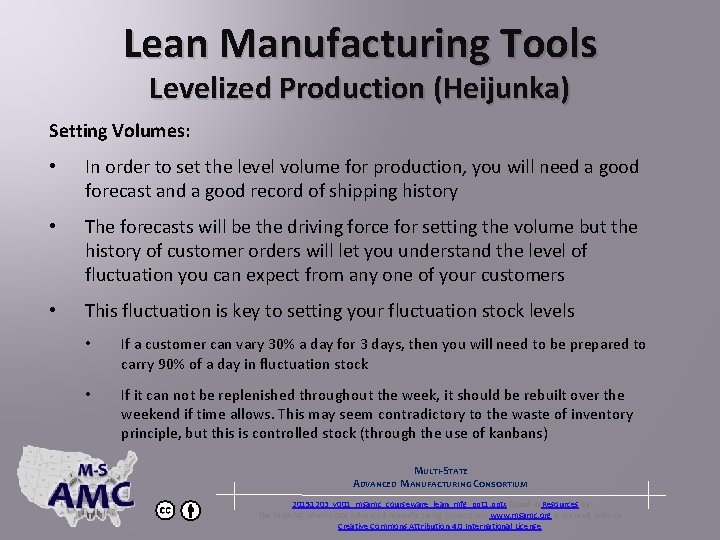
Lean Manufacturing Tools Levelized Production (Heijunka) Setting Volumes: • In order to set the level volume for production, you will need a good forecast and a good record of shipping history • The forecasts will be the driving force for setting the volume but the history of customer orders will let you understand the level of fluctuation you can expect from any one of your customers • This fluctuation is key to setting your fluctuation stock levels • If a customer can vary 30% a day for 3 days, then you will need to be prepared to carry 90% of a day in fluctuation stock • If it can not be replenished throughout the week, it should be rebuilt over the weekend if time allows. This may seem contradictory to the waste of inventory principle, but this is controlled stock (through the use of kanbans) MULTI-STATE ADVANCED MANUFACTURING CONSORTIUM 20151203_v 001_msamc_courseware_lean_mfg_ppt 1. pptx found in Resources by the M-SAMC Multi-State Advanced Manufacturing Consortium www. msamc. org is licensed under a Creative Commons Attribution 4. 0 International License.
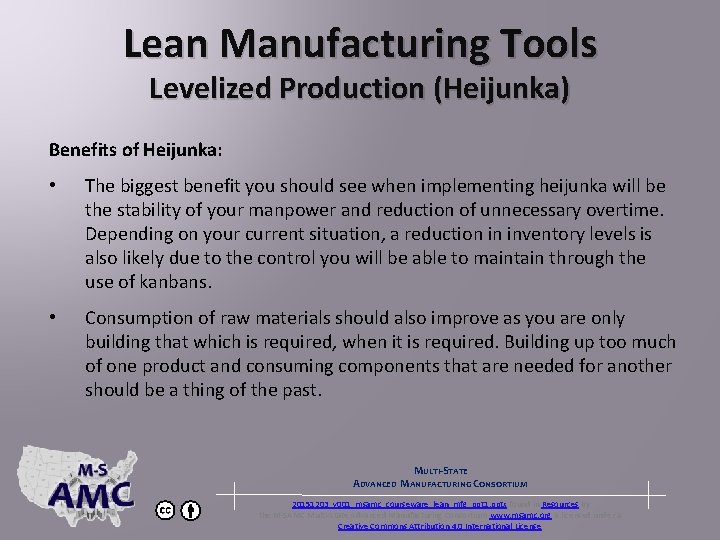
Lean Manufacturing Tools Levelized Production (Heijunka) Benefits of Heijunka: • The biggest benefit you should see when implementing heijunka will be the stability of your manpower and reduction of unnecessary overtime. Depending on your current situation, a reduction in inventory levels is also likely due to the control you will be able to maintain through the use of kanbans. • Consumption of raw materials should also improve as you are only building that which is required, when it is required. Building up too much of one product and consuming components that are needed for another should be a thing of the past. MULTI-STATE ADVANCED MANUFACTURING CONSORTIUM 20151203_v 001_msamc_courseware_lean_mfg_ppt 1. pptx found in Resources by the M-SAMC Multi-State Advanced Manufacturing Consortium www. msamc. org is licensed under a Creative Commons Attribution 4. 0 International License.
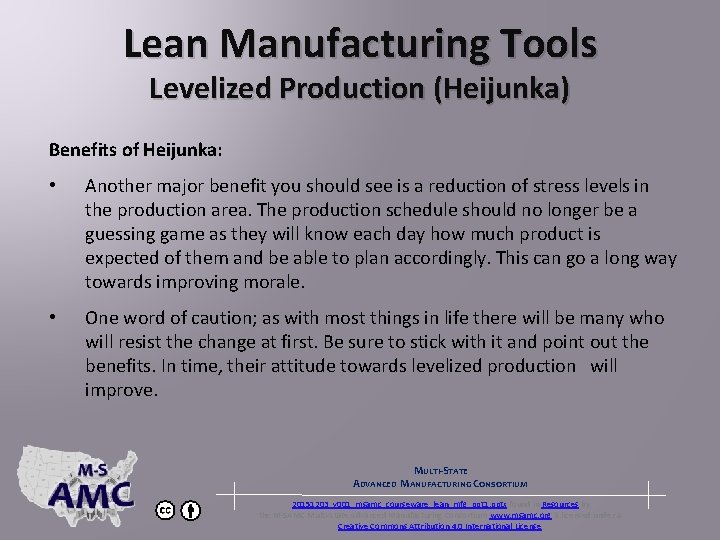
Lean Manufacturing Tools Levelized Production (Heijunka) Benefits of Heijunka: • Another major benefit you should see is a reduction of stress levels in the production area. The production schedule should no longer be a guessing game as they will know each day how much product is expected of them and be able to plan accordingly. This can go a long way towards improving morale. • One word of caution; as with most things in life there will be many who will resist the change at first. Be sure to stick with it and point out the benefits. In time, their attitude towards levelized production will improve. MULTI-STATE ADVANCED MANUFACTURING CONSORTIUM 20151203_v 001_msamc_courseware_lean_mfg_ppt 1. pptx found in Resources by the M-SAMC Multi-State Advanced Manufacturing Consortium www. msamc. org is licensed under a Creative Commons Attribution 4. 0 International License.
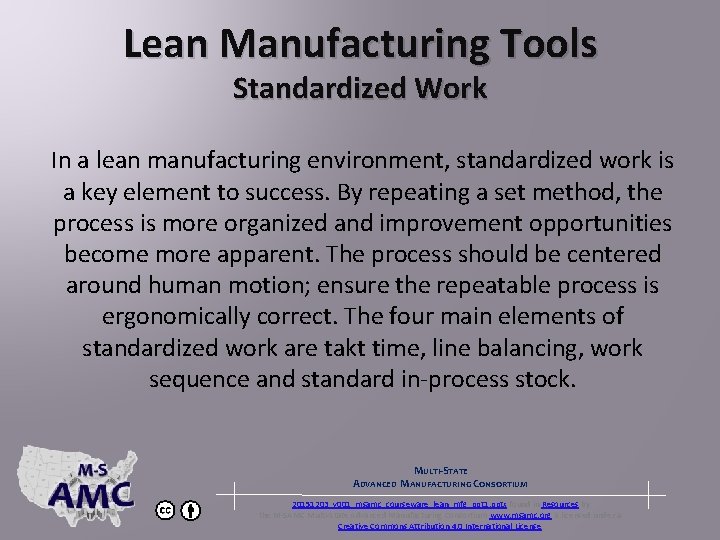
Lean Manufacturing Tools Standardized Work In a lean manufacturing environment, standardized work is a key element to success. By repeating a set method, the process is more organized and improvement opportunities become more apparent. The process should be centered around human motion; ensure the repeatable process is ergonomically correct. The four main elements of standardized work are takt time, line balancing, work sequence and standard in-process stock. MULTI-STATE ADVANCED MANUFACTURING CONSORTIUM 20151203_v 001_msamc_courseware_lean_mfg_ppt 1. pptx found in Resources by the M-SAMC Multi-State Advanced Manufacturing Consortium www. msamc. org is licensed under a Creative Commons Attribution 4. 0 International License.
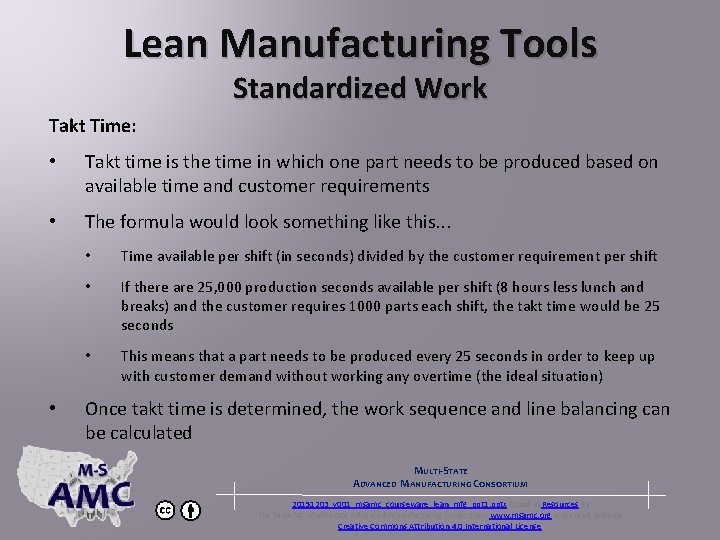
Lean Manufacturing Tools Standardized Work Takt Time: • Takt time is the time in which one part needs to be produced based on available time and customer requirements • The formula would look something like this. . . • • Time available per shift (in seconds) divided by the customer requirement per shift • If there are 25, 000 production seconds available per shift (8 hours less lunch and breaks) and the customer requires 1000 parts each shift, the takt time would be 25 seconds • This means that a part needs to be produced every 25 seconds in order to keep up with customer demand without working any overtime (the ideal situation) Once takt time is determined, the work sequence and line balancing can be calculated MULTI-STATE ADVANCED MANUFACTURING CONSORTIUM 20151203_v 001_msamc_courseware_lean_mfg_ppt 1. pptx found in Resources by the M-SAMC Multi-State Advanced Manufacturing Consortium www. msamc. org is licensed under a Creative Commons Attribution 4. 0 International License.
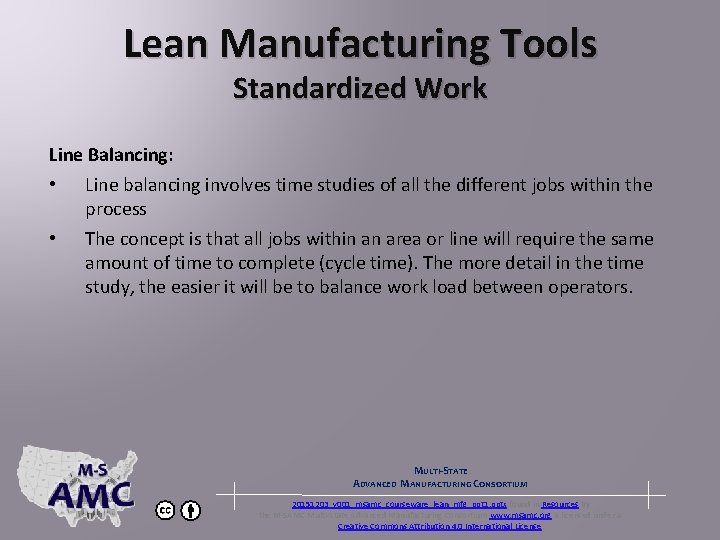
Lean Manufacturing Tools Standardized Work Line Balancing: • • Line balancing involves time studies of all the different jobs within the process The concept is that all jobs within an area or line will require the same amount of time to complete (cycle time). The more detail in the time study, the easier it will be to balance work load between operators. MULTI-STATE ADVANCED MANUFACTURING CONSORTIUM 20151203_v 001_msamc_courseware_lean_mfg_ppt 1. pptx found in Resources by the M-SAMC Multi-State Advanced Manufacturing Consortium www. msamc. org is licensed under a Creative Commons Attribution 4. 0 International License.
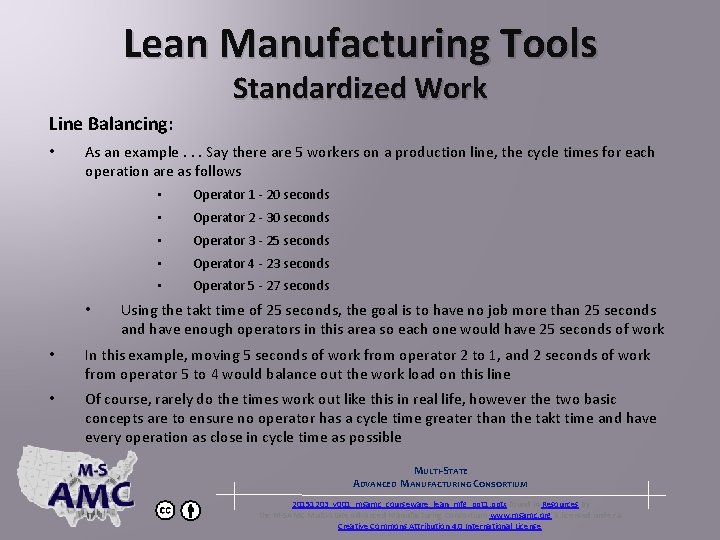
Lean Manufacturing Tools Standardized Work Line Balancing: • As an example. . . Say there are 5 workers on a production line, the cycle times for each operation are as follows • • Operator 1 - 20 seconds • Operator 2 - 30 seconds • Operator 3 - 25 seconds • Operator 4 - 23 seconds • Operator 5 - 27 seconds Using the takt time of 25 seconds, the goal is to have no job more than 25 seconds and have enough operators in this area so each one would have 25 seconds of work • In this example, moving 5 seconds of work from operator 2 to 1, and 2 seconds of work from operator 5 to 4 would balance out the work load on this line • Of course, rarely do the times work out like this in real life, however the two basic concepts are to ensure no operator has a cycle time greater than the takt time and have every operation as close in cycle time as possible MULTI-STATE ADVANCED MANUFACTURING CONSORTIUM 20151203_v 001_msamc_courseware_lean_mfg_ppt 1. pptx found in Resources by the M-SAMC Multi-State Advanced Manufacturing Consortium www. msamc. org is licensed under a Creative Commons Attribution 4. 0 International License.
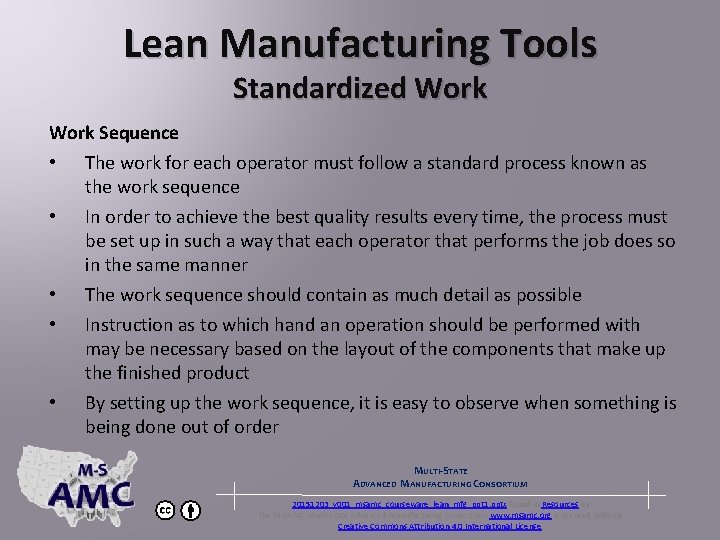
Lean Manufacturing Tools Standardized Work Sequence • • • The work for each operator must follow a standard process known as the work sequence In order to achieve the best quality results every time, the process must be set up in such a way that each operator that performs the job does so in the same manner The work sequence should contain as much detail as possible Instruction as to which hand an operation should be performed with may be necessary based on the layout of the components that make up the finished product By setting up the work sequence, it is easy to observe when something is being done out of order MULTI-STATE ADVANCED MANUFACTURING CONSORTIUM 20151203_v 001_msamc_courseware_lean_mfg_ppt 1. pptx found in Resources by the M-SAMC Multi-State Advanced Manufacturing Consortium www. msamc. org is licensed under a Creative Commons Attribution 4. 0 International License.
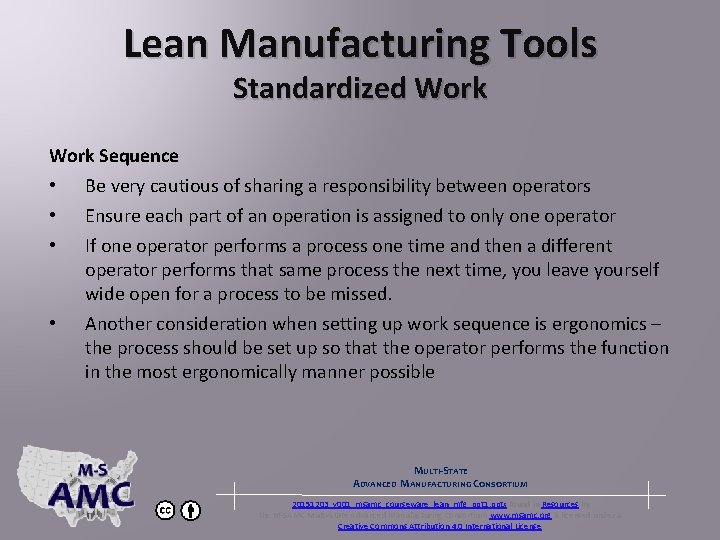
Lean Manufacturing Tools Standardized Work Sequence • • Be very cautious of sharing a responsibility between operators Ensure each part of an operation is assigned to only one operator If one operator performs a process one time and then a different operator performs that same process the next time, you leave yourself wide open for a process to be missed. Another consideration when setting up work sequence is ergonomics – the process should be set up so that the operator performs the function in the most ergonomically manner possible MULTI-STATE ADVANCED MANUFACTURING CONSORTIUM 20151203_v 001_msamc_courseware_lean_mfg_ppt 1. pptx found in Resources by the M-SAMC Multi-State Advanced Manufacturing Consortium www. msamc. org is licensed under a Creative Commons Attribution 4. 0 International License.
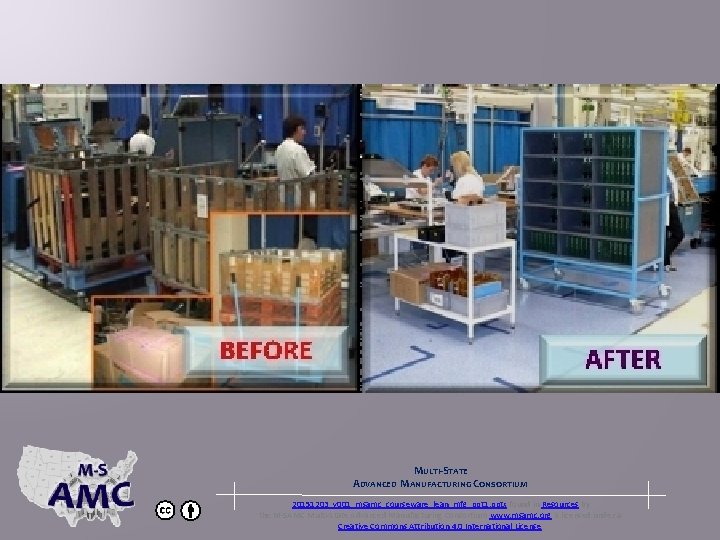
MULTI-STATE ADVANCED MANUFACTURING CONSORTIUM 20151203_v 001_msamc_courseware_lean_mfg_ppt 1. pptx found in Resources by the M-SAMC Multi-State Advanced Manufacturing Consortium www. msamc. org is licensed under a Creative Commons Attribution 4. 0 International License.
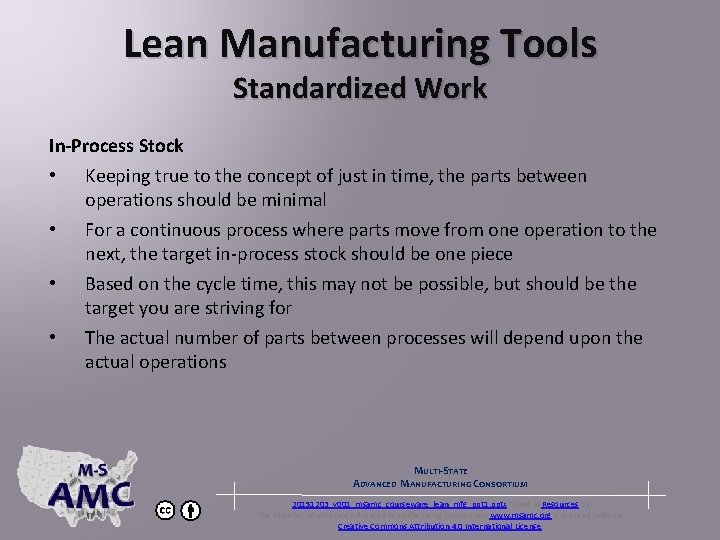
Lean Manufacturing Tools Standardized Work In-Process Stock • • Keeping true to the concept of just in time, the parts between operations should be minimal For a continuous process where parts move from one operation to the next, the target in-process stock should be one piece Based on the cycle time, this may not be possible, but should be the target you are striving for The actual number of parts between processes will depend upon the actual operations MULTI-STATE ADVANCED MANUFACTURING CONSORTIUM 20151203_v 001_msamc_courseware_lean_mfg_ppt 1. pptx found in Resources by the M-SAMC Multi-State Advanced Manufacturing Consortium www. msamc. org is licensed under a Creative Commons Attribution 4. 0 International License.
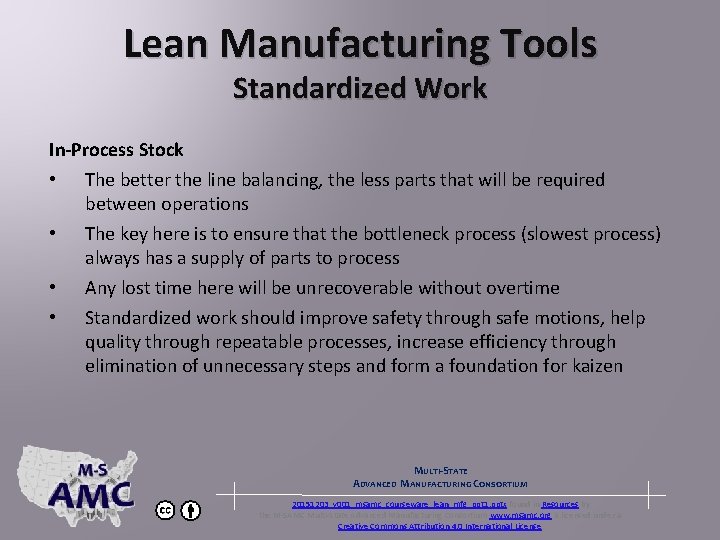
Lean Manufacturing Tools Standardized Work In-Process Stock • • The better the line balancing, the less parts that will be required between operations The key here is to ensure that the bottleneck process (slowest process) always has a supply of parts to process Any lost time here will be unrecoverable without overtime Standardized work should improve safety through safe motions, help quality through repeatable processes, increase efficiency through elimination of unnecessary steps and form a foundation for kaizen MULTI-STATE ADVANCED MANUFACTURING CONSORTIUM 20151203_v 001_msamc_courseware_lean_mfg_ppt 1. pptx found in Resources by the M-SAMC Multi-State Advanced Manufacturing Consortium www. msamc. org is licensed under a Creative Commons Attribution 4. 0 International License.
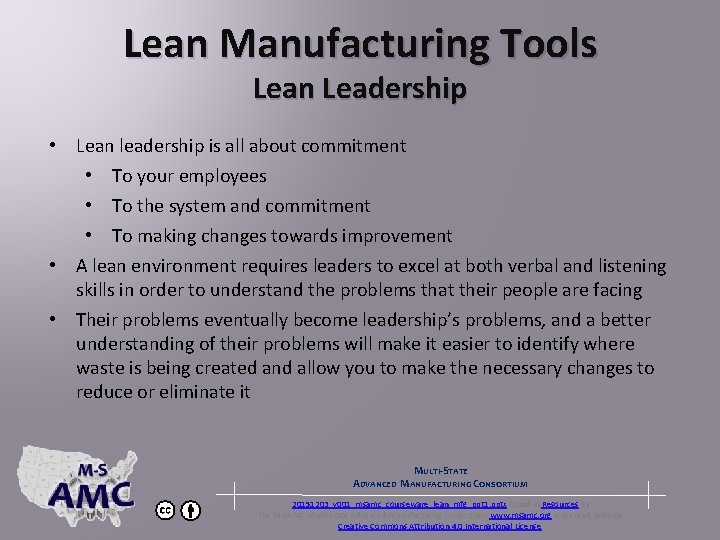
Lean Manufacturing Tools Lean Leadership • Lean leadership is all about commitment • To your employees • To the system and commitment • To making changes towards improvement • A lean environment requires leaders to excel at both verbal and listening skills in order to understand the problems that their people are facing • Their problems eventually become leadership’s problems, and a better understanding of their problems will make it easier to identify where waste is being created and allow you to make the necessary changes to reduce or eliminate it MULTI-STATE ADVANCED MANUFACTURING CONSORTIUM 20151203_v 001_msamc_courseware_lean_mfg_ppt 1. pptx found in Resources by the M-SAMC Multi-State Advanced Manufacturing Consortium www. msamc. org is licensed under a Creative Commons Attribution 4. 0 International License.
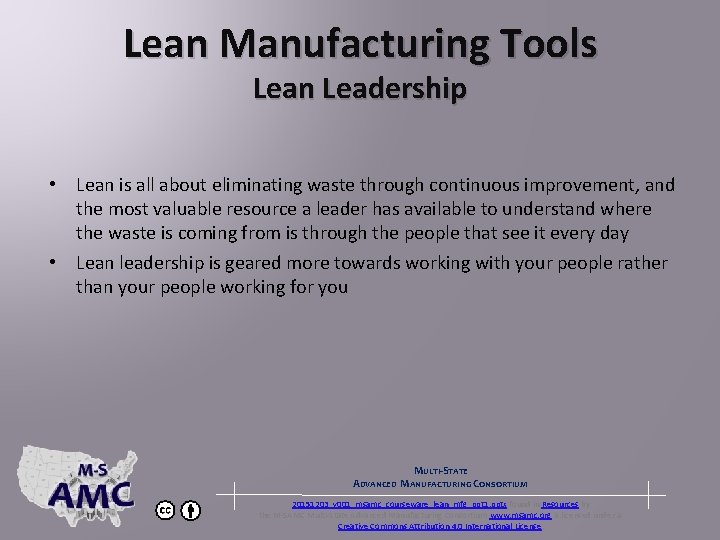
Lean Manufacturing Tools Lean Leadership • Lean is all about eliminating waste through continuous improvement, and the most valuable resource a leader has available to understand where the waste is coming from is through the people that see it every day • Lean leadership is geared more towards working with your people rather than your people working for you MULTI-STATE ADVANCED MANUFACTURING CONSORTIUM 20151203_v 001_msamc_courseware_lean_mfg_ppt 1. pptx found in Resources by the M-SAMC Multi-State Advanced Manufacturing Consortium www. msamc. org is licensed under a Creative Commons Attribution 4. 0 International License.
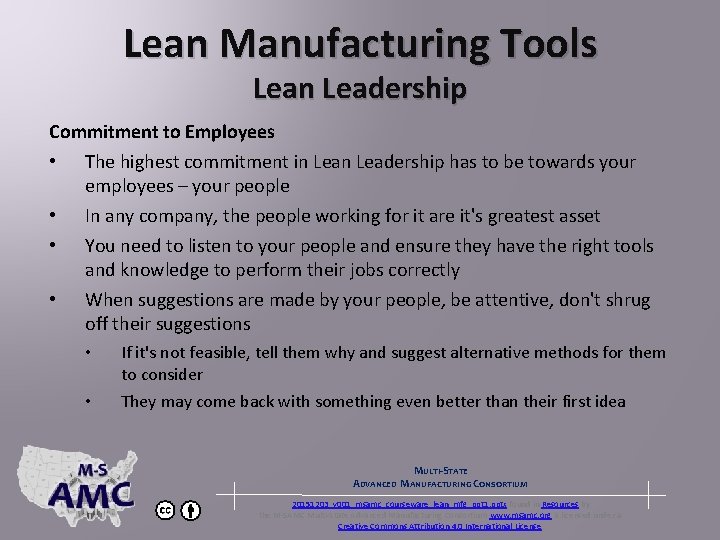
Lean Manufacturing Tools Lean Leadership Commitment to Employees • • The highest commitment in Leadership has to be towards your employees – your people In any company, the people working for it are it's greatest asset You need to listen to your people and ensure they have the right tools and knowledge to perform their jobs correctly When suggestions are made by your people, be attentive, don't shrug off their suggestions • If it's not feasible, tell them why and suggest alternative methods for them to consider • They may come back with something even better than their first idea MULTI-STATE ADVANCED MANUFACTURING CONSORTIUM 20151203_v 001_msamc_courseware_lean_mfg_ppt 1. pptx found in Resources by the M-SAMC Multi-State Advanced Manufacturing Consortium www. msamc. org is licensed under a Creative Commons Attribution 4. 0 International License.
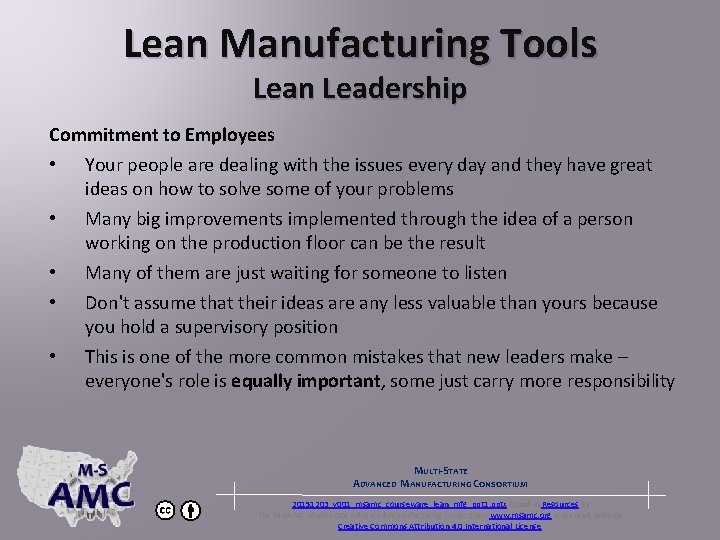
Lean Manufacturing Tools Lean Leadership Commitment to Employees • • • Your people are dealing with the issues every day and they have great ideas on how to solve some of your problems Many big improvements implemented through the idea of a person working on the production floor can be the result Many of them are just waiting for someone to listen Don't assume that their ideas are any less valuable than yours because you hold a supervisory position This is one of the more common mistakes that new leaders make – everyone's role is equally important, some just carry more responsibility MULTI-STATE ADVANCED MANUFACTURING CONSORTIUM 20151203_v 001_msamc_courseware_lean_mfg_ppt 1. pptx found in Resources by the M-SAMC Multi-State Advanced Manufacturing Consortium www. msamc. org is licensed under a Creative Commons Attribution 4. 0 International License.
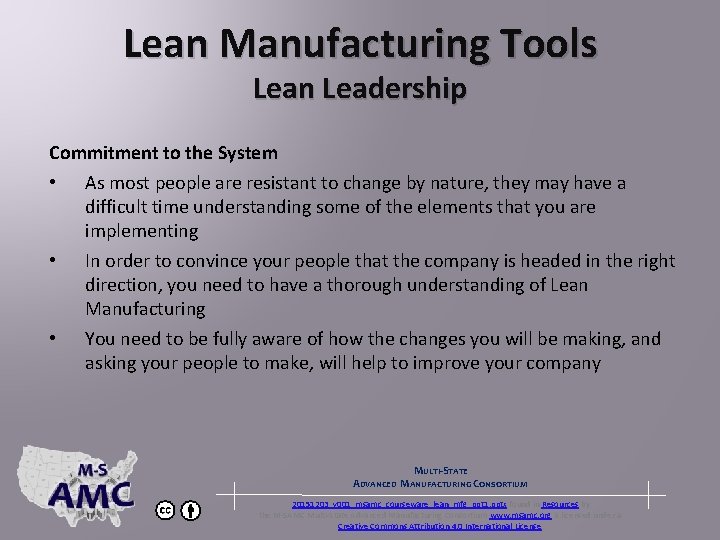
Lean Manufacturing Tools Lean Leadership Commitment to the System • • • As most people are resistant to change by nature, they may have a difficult time understanding some of the elements that you are implementing In order to convince your people that the company is headed in the right direction, you need to have a thorough understanding of Lean Manufacturing You need to be fully aware of how the changes you will be making, and asking your people to make, will help to improve your company MULTI-STATE ADVANCED MANUFACTURING CONSORTIUM 20151203_v 001_msamc_courseware_lean_mfg_ppt 1. pptx found in Resources by the M-SAMC Multi-State Advanced Manufacturing Consortium www. msamc. org is licensed under a Creative Commons Attribution 4. 0 International License.
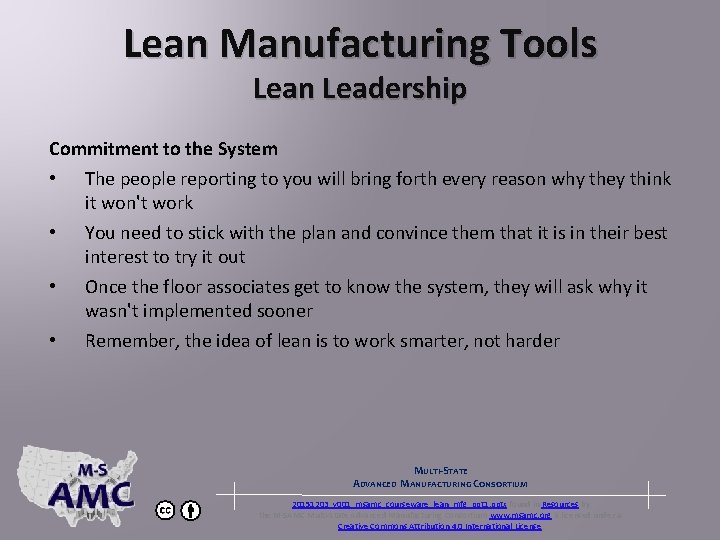
Lean Manufacturing Tools Lean Leadership Commitment to the System • • The people reporting to you will bring forth every reason why they think it won't work You need to stick with the plan and convince them that it is in their best interest to try it out Once the floor associates get to know the system, they will ask why it wasn't implemented sooner Remember, the idea of lean is to work smarter, not harder MULTI-STATE ADVANCED MANUFACTURING CONSORTIUM 20151203_v 001_msamc_courseware_lean_mfg_ppt 1. pptx found in Resources by the M-SAMC Multi-State Advanced Manufacturing Consortium www. msamc. org is licensed under a Creative Commons Attribution 4. 0 International License.
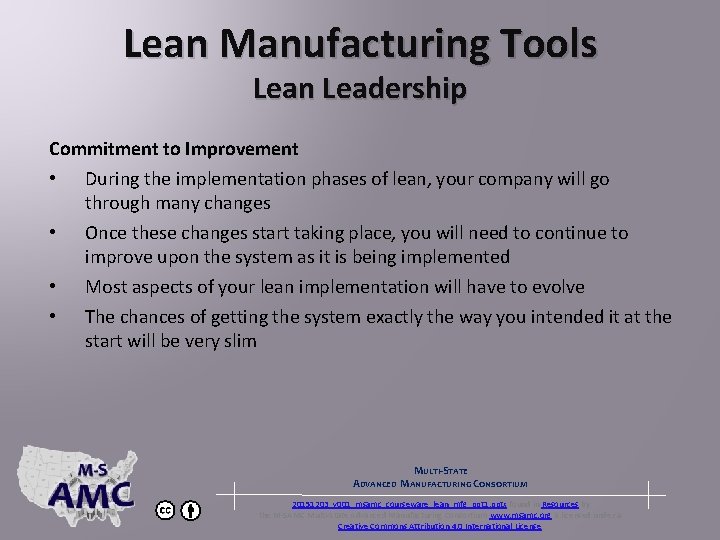
Lean Manufacturing Tools Lean Leadership Commitment to Improvement • • During the implementation phases of lean, your company will go through many changes Once these changes start taking place, you will need to continue to improve upon the system as it is being implemented Most aspects of your lean implementation will have to evolve The chances of getting the system exactly the way you intended it at the start will be very slim MULTI-STATE ADVANCED MANUFACTURING CONSORTIUM 20151203_v 001_msamc_courseware_lean_mfg_ppt 1. pptx found in Resources by the M-SAMC Multi-State Advanced Manufacturing Consortium www. msamc. org is licensed under a Creative Commons Attribution 4. 0 International License.
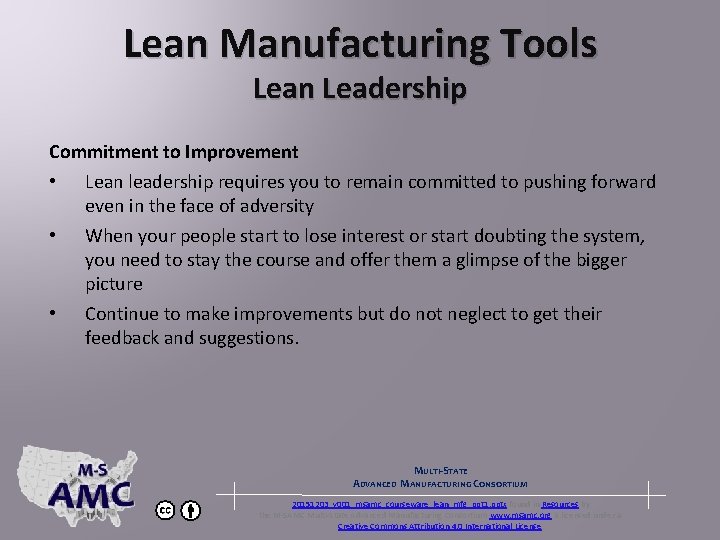
Lean Manufacturing Tools Lean Leadership Commitment to Improvement • • • Lean leadership requires you to remain committed to pushing forward even in the face of adversity When your people start to lose interest or start doubting the system, you need to stay the course and offer them a glimpse of the bigger picture Continue to make improvements but do not neglect to get their feedback and suggestions. MULTI-STATE ADVANCED MANUFACTURING CONSORTIUM 20151203_v 001_msamc_courseware_lean_mfg_ppt 1. pptx found in Resources by the M-SAMC Multi-State Advanced Manufacturing Consortium www. msamc. org is licensed under a Creative Commons Attribution 4. 0 International License.
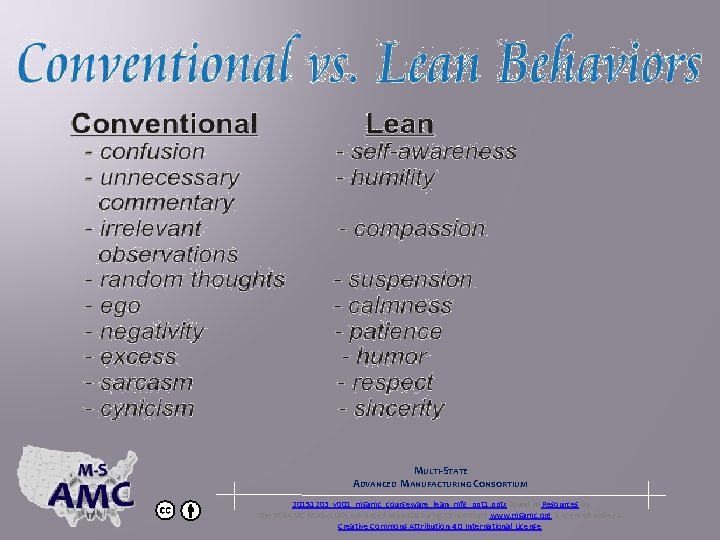
MULTI-STATE ADVANCED MANUFACTURING CONSORTIUM 20151203_v 001_msamc_courseware_lean_mfg_ppt 1. pptx found in Resources by the M-SAMC Multi-State Advanced Manufacturing Consortium www. msamc. org is licensed under a Creative Commons Attribution 4. 0 International License.
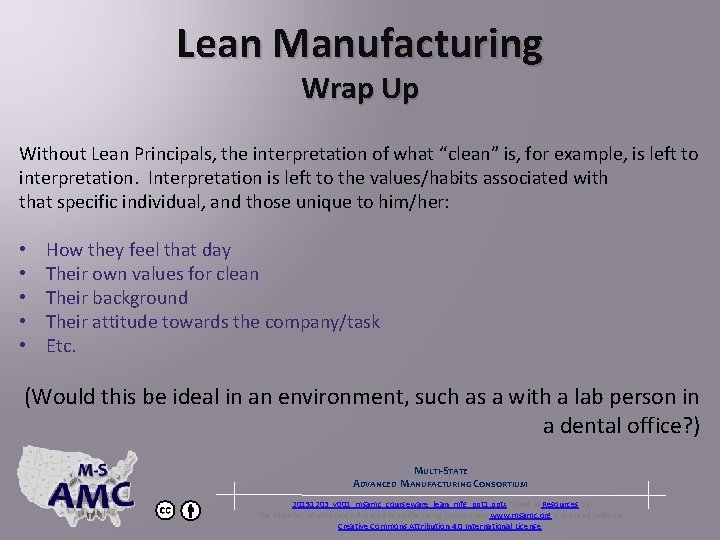
Lean Manufacturing Wrap Up Without Lean Principals, the interpretation of what “clean” is, for example, is left to interpretation. Interpretation is left to the values/habits associated with that specific individual, and those unique to him/her: • • • How they feel that day Their own values for clean Their background Their attitude towards the company/task Etc. (Would this be ideal in an environment, such as a with a lab person in a dental office? ) MULTI-STATE ADVANCED MANUFACTURING CONSORTIUM 20151203_v 001_msamc_courseware_lean_mfg_ppt 1. pptx found in Resources by the M-SAMC Multi-State Advanced Manufacturing Consortium www. msamc. org is licensed under a Creative Commons Attribution 4. 0 International License.
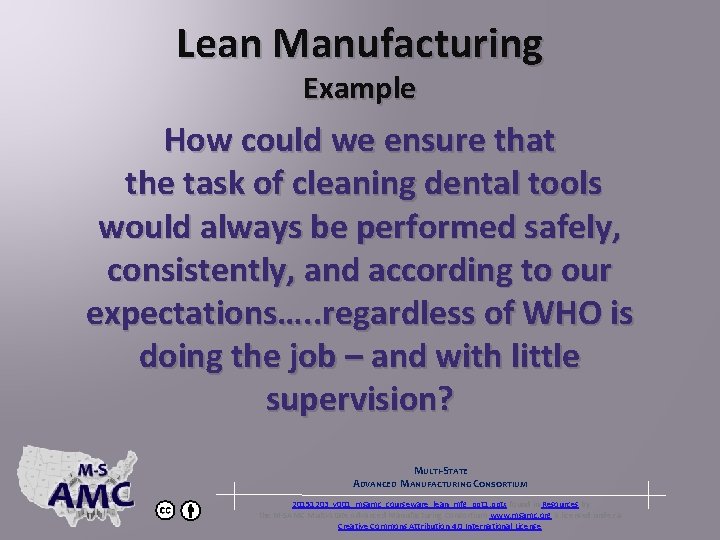
Lean Manufacturing Example How could we ensure that the task of cleaning dental tools would always be performed safely, consistently, and according to our expectations…. . regardless of WHO is doing the job – and with little supervision? MULTI-STATE ADVANCED MANUFACTURING CONSORTIUM 20151203_v 001_msamc_courseware_lean_mfg_ppt 1. pptx found in Resources by the M-SAMC Multi-State Advanced Manufacturing Consortium www. msamc. org is licensed under a Creative Commons Attribution 4. 0 International License.
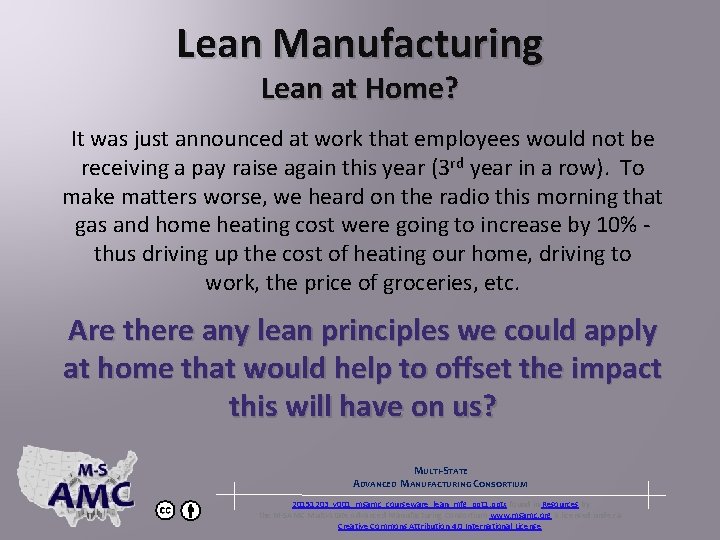
Lean Manufacturing Lean at Home? It was just announced at work that employees would not be receiving a pay raise again this year (3 rd year in a row). To make matters worse, we heard on the radio this morning that gas and home heating cost were going to increase by 10% - thus driving up the cost of heating our home, driving to work, the price of groceries, etc. Are there any lean principles we could apply at home that would help to offset the impact this will have on us? MULTI-STATE ADVANCED MANUFACTURING CONSORTIUM 20151203_v 001_msamc_courseware_lean_mfg_ppt 1. pptx found in Resources by the M-SAMC Multi-State Advanced Manufacturing Consortium www. msamc. org is licensed under a Creative Commons Attribution 4. 0 International License.
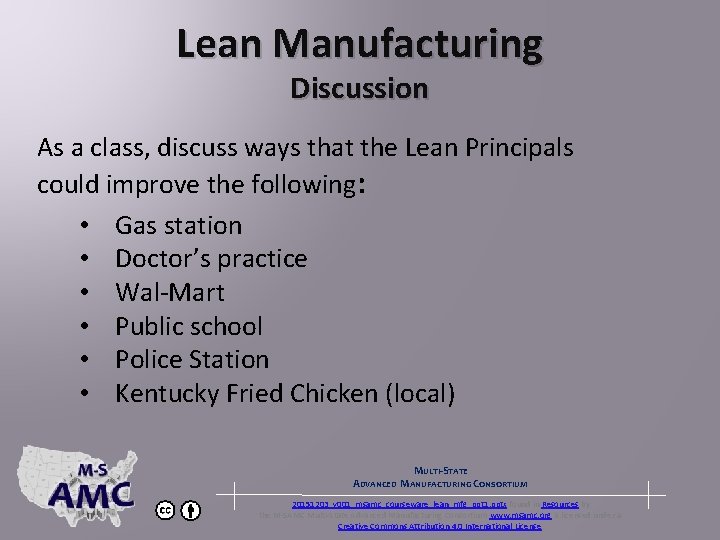
Lean Manufacturing Discussion As a class, discuss ways that the Lean Principals could improve the following: • Gas station • Doctor’s practice • Wal-Mart • Public school • Police Station • Kentucky Fried Chicken (local) MULTI-STATE ADVANCED MANUFACTURING CONSORTIUM 20151203_v 001_msamc_courseware_lean_mfg_ppt 1. pptx found in Resources by the M-SAMC Multi-State Advanced Manufacturing Consortium www. msamc. org is licensed under a Creative Commons Attribution 4. 0 International License.
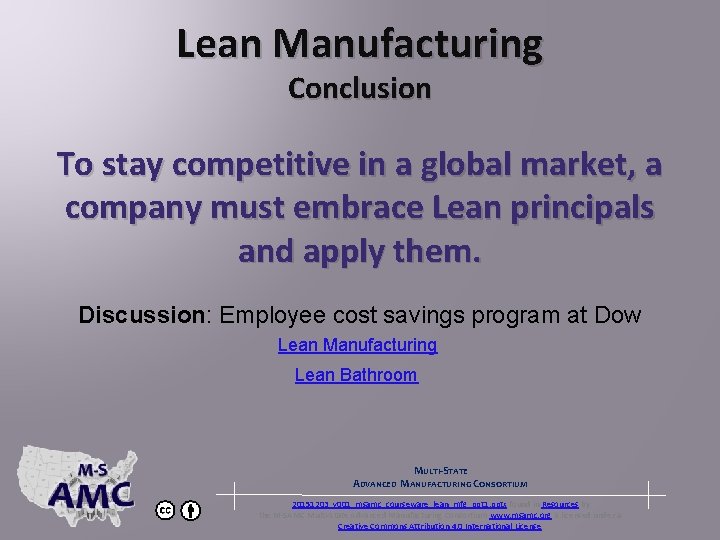
Lean Manufacturing Conclusion To stay competitive in a global market, a company must embrace Lean principals and apply them. Discussion: Employee cost savings program at Dow Lean Manufacturing Lean Bathroom MULTI-STATE ADVANCED MANUFACTURING CONSORTIUM 20151203_v 001_msamc_courseware_lean_mfg_ppt 1. pptx found in Resources by the M-SAMC Multi-State Advanced Manufacturing Consortium www. msamc. org is licensed under a Creative Commons Attribution 4. 0 International License.
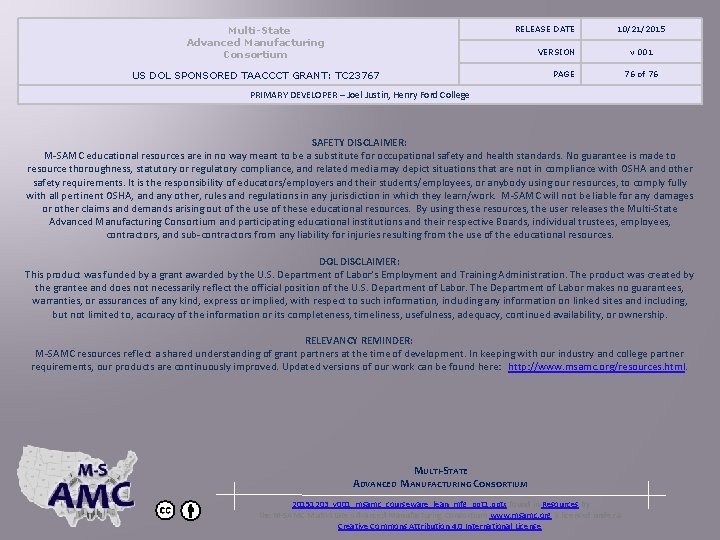
Multi-State Advanced Manufacturing Consortium RELEASE DATE 10/21/2015 VERSION US DOL SPONSORED TAACCCT GRANT: TC 23767 PAGE v 001 76 of 76 PRIMARY DEVELOPER – Joel Justin, Henry Ford College SAFETY DISCLAIMER: M-SAMC educational resources are in no way meant to be a substitute for occupational safety and health standards. No guarantee is made to resource thoroughness, statutory or regulatory compliance, and related media may depict situations that are not in compliance with OSHA and other safety requirements. It is the responsibility of educators/employers and their students/employees, or anybody using our resources, to comply fully with all pertinent OSHA, and any other, rules and regulations in any jurisdiction in which they learn/work. M-SAMC will not be liable for any damages or other claims and demands arising out of the use of these educational resources. By using these resources, the user releases the Multi-State Advanced Manufacturing Consortium and participating educational institutions and their respective Boards, individual trustees, employees, contractors, and sub-contractors from any liability for injuries resulting from the use of the educational resources. DOL DISCLAIMER: This product was funded by a grant awarded by the U. S. Department of Labor’s Employment and Training Administration. The product was created by the grantee and does not necessarily reflect the official position of the U. S. Department of Labor. The Department of Labor makes no guarantees, warranties, or assurances of any kind, express or implied, with respect to such information, including any information on linked sites and including, but not limited to, accuracy of the information or its completeness, timeliness, usefulness, adequacy, continued availability, or ownership. RELEVANCY REMINDER: M-SAMC resources reflect a shared understanding of grant partners at the time of development. In keeping with our industry and college partner requirements, our products are continuously improved. Updated versions of our work can be found here: http: //www. msamc. org/resources. html. MULTI-STATE ADVANCED MANUFACTURING CONSORTIUM 20151203_v 001_msamc_courseware_lean_mfg_ppt 1. pptx found in Resources by the M-SAMC Multi-State Advanced Manufacturing Consortium www. msamc. org is licensed under a Creative Commons Attribution 4. 0 International License.
Are the kurds a multistate nation
Arizona multistate service provider election
Nocoderm
Extended release vs sustained release
Sustained release dosage form
Blue team leader release date
Entity framework 7 release date
Ppap release date
Estrutura de uma carta informal
Job vs process costing
Uncontrollable cost example
Manufacturing cost vs non manufacturing cost
Manufacturing cost vs non manufacturing cost
Additive manufacturing vs subtractive manufacturing
Ex dividend record date
Record date for dividend
Advanced manufacturing process
Ct advanced manufacturing
Advanced manufacturing office
Cgm open consortium
Financial services technology consortium
Training officers consortium
Keprecon
New jersey space grant consortium
Maximum range of bluetooth
Africa soil health consortium
Car to car communication consortium
Infrastructure consortium for africa
East central consortium
Wisconsin space grant consortium
Puget sound lidar consortium
Open geospatial consortium standards
Disciplined agile consortium
Pa space grant
San francisco community clinic consortium
Software productivity consortium
Vertical lift consortium
International color consortium
Oregon lidar consortium
Computing community consortium
Spirit consortium
World university consortium
Dangerous goods consortium
Shuhari agile
Lidar consortium
Concord consortium molecular workbench photosynthesis
Irrigation innovation consortium
Pediatric diabetes consortium
Africa soil health consortium
Youth suicide research consortium
Blended learning consortium
Dsdm consortium
New jersey space grant consortium
Ceww health insurance consortium
Mcps middle school magnet consortium
Michigan lean consortium
Safer recruitment consortium
The consortium stationery
National consortium of interpreter education centers
Perlis power plant
Physician consortium for performance improvement
Consortium format
Adr dangerous goods consortium
Virginia microelectronics consortium
Digital dissertation consortium
Learnnowbiz
Uchicago consortium on school research
Physician wellness academic consortium
Gcche
Rise consortium
Massachusetts higher education consortium
Afp consortium
Jason laberge
Argos consortium
First suburbs consortium
Boston library consortium
Michigan lean consortium