Main Changes to Canada GAP Food Safety Manuals
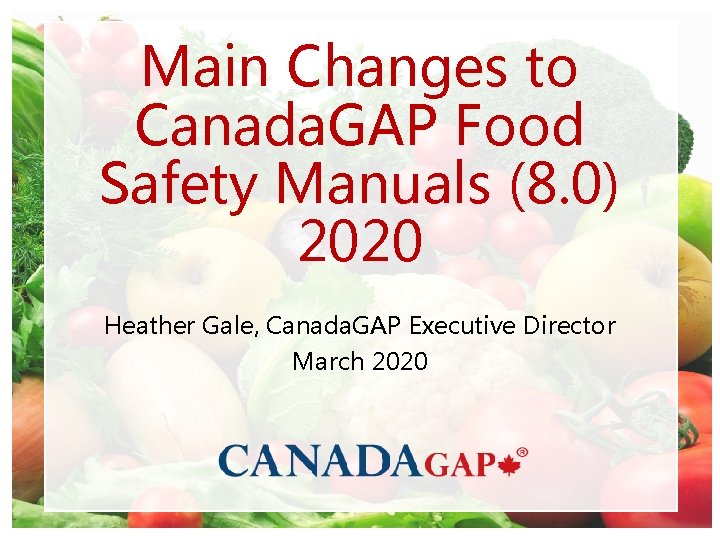
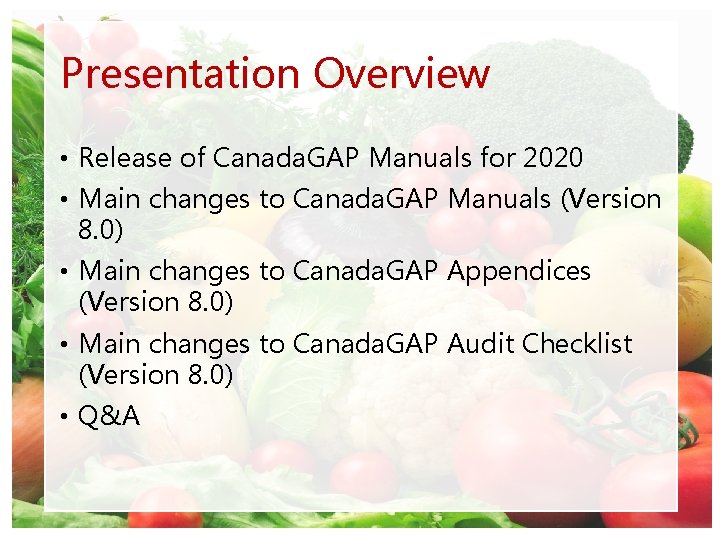
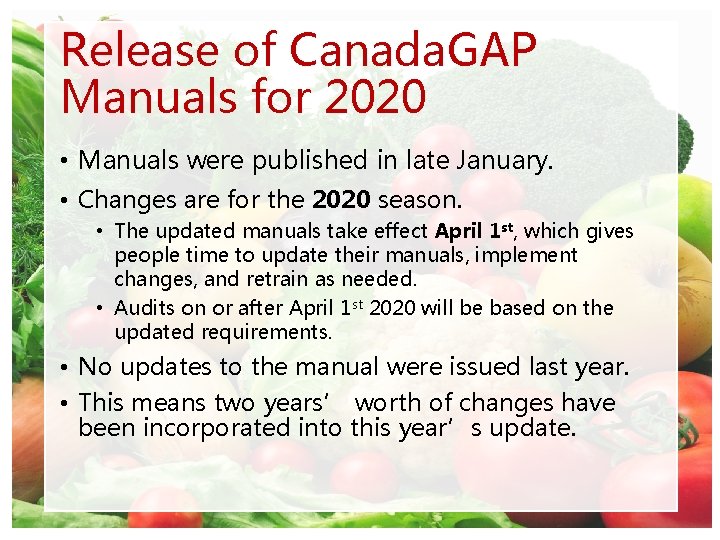
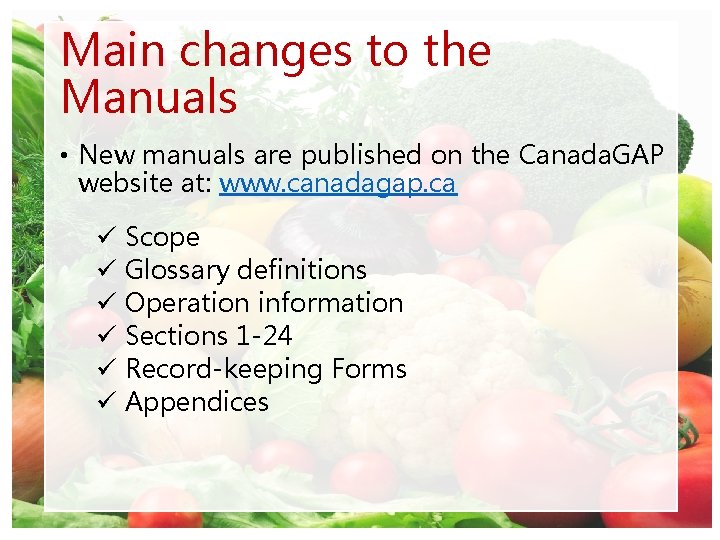
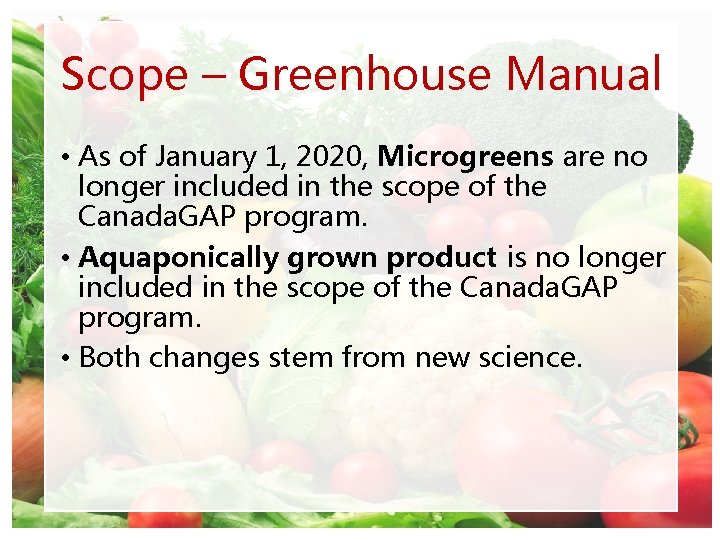
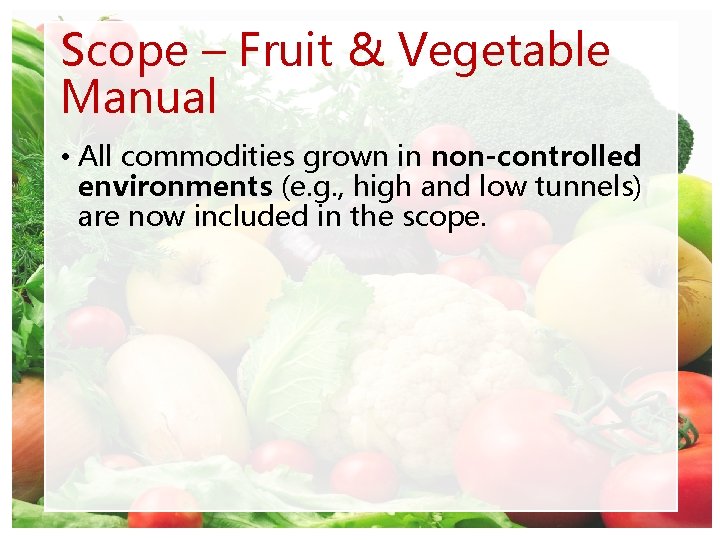
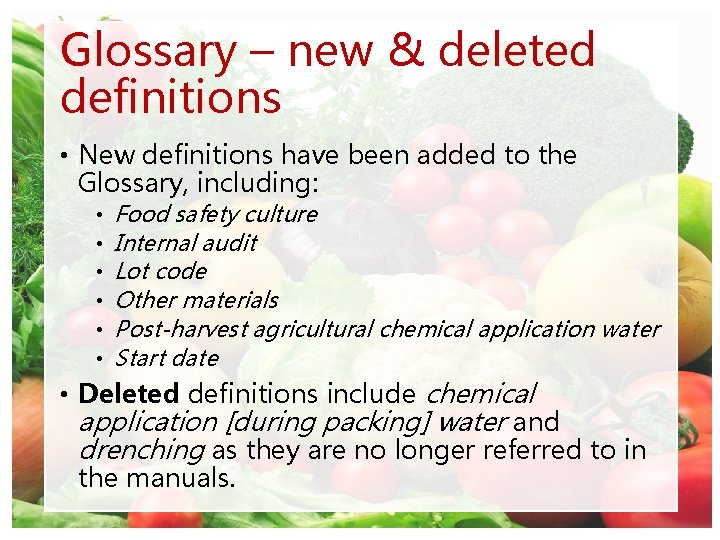
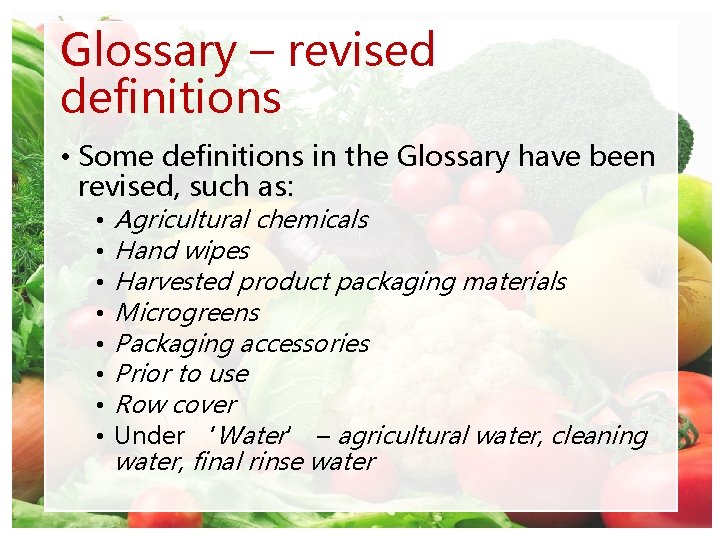
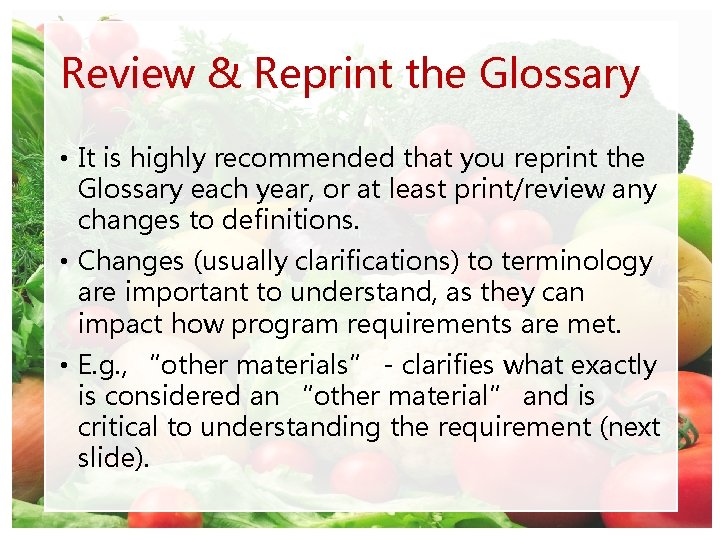
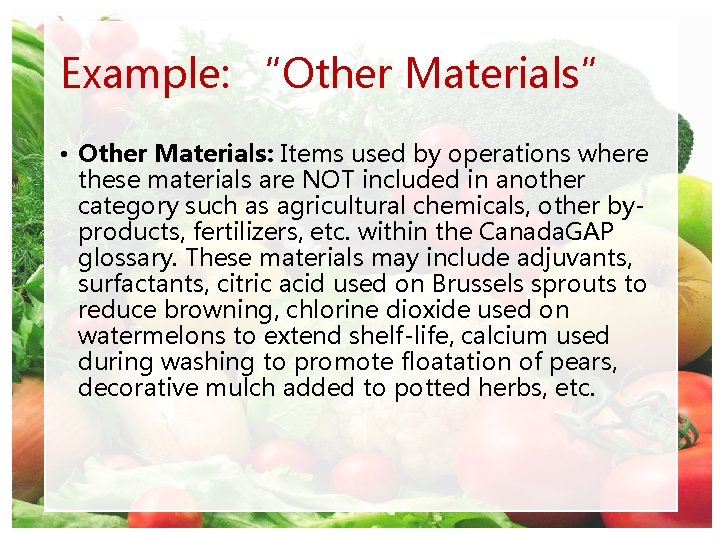
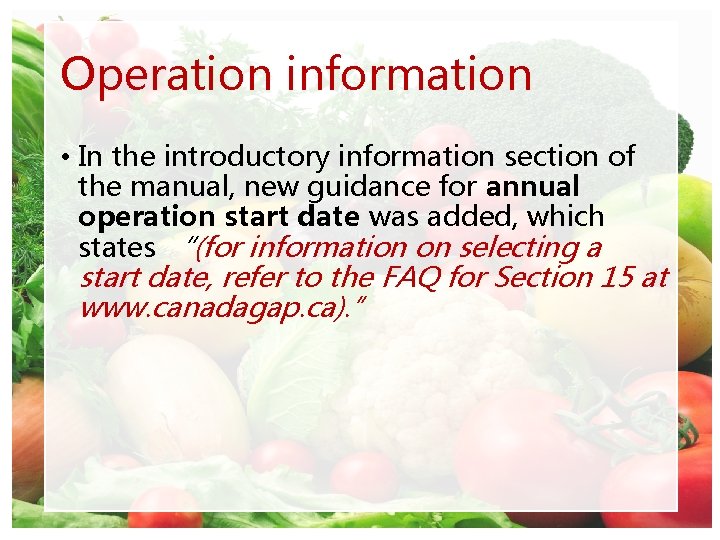
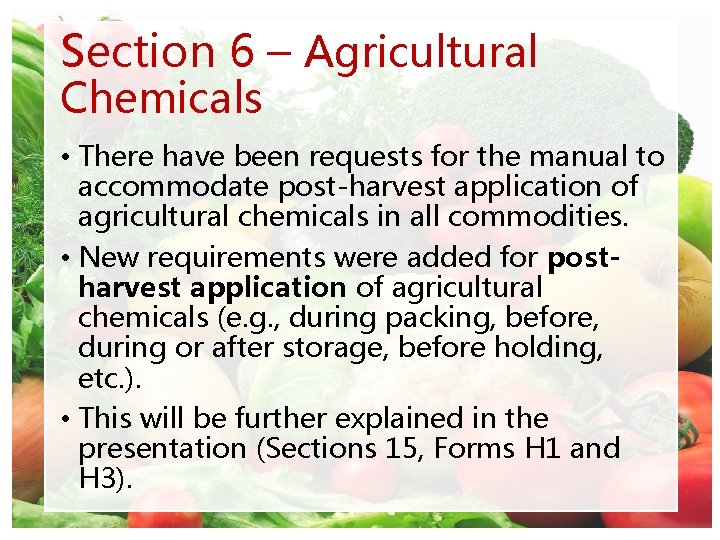
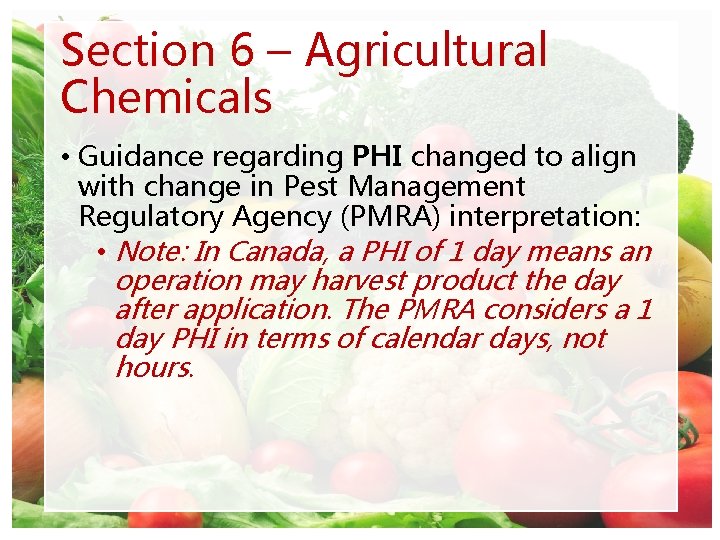
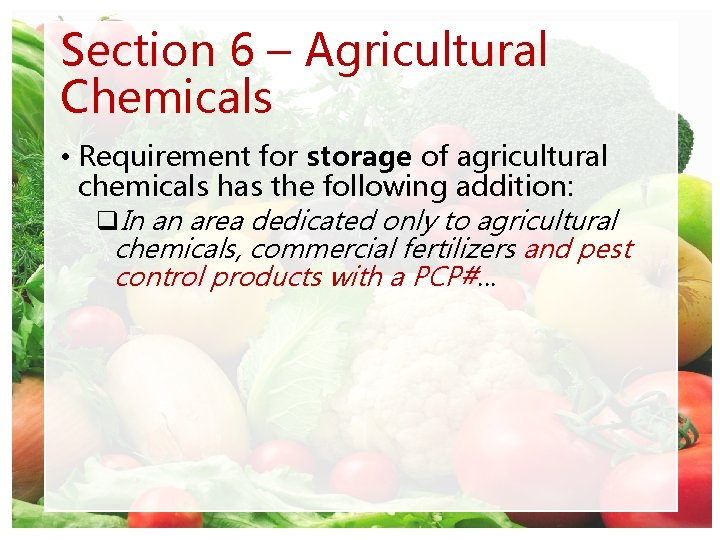
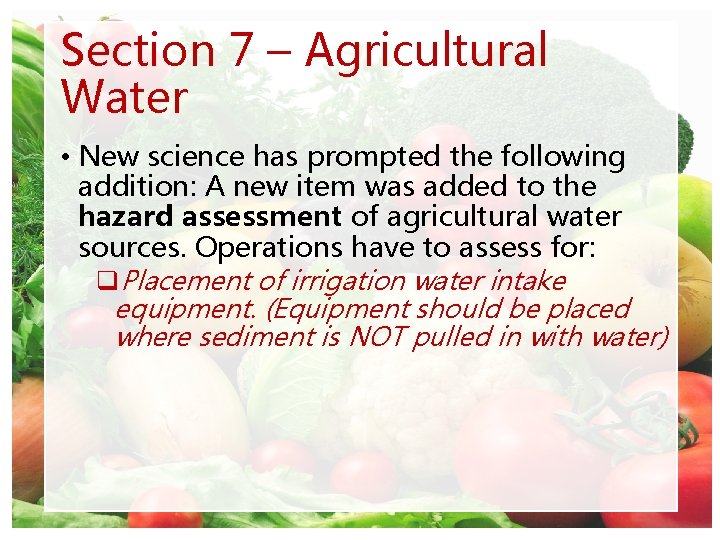
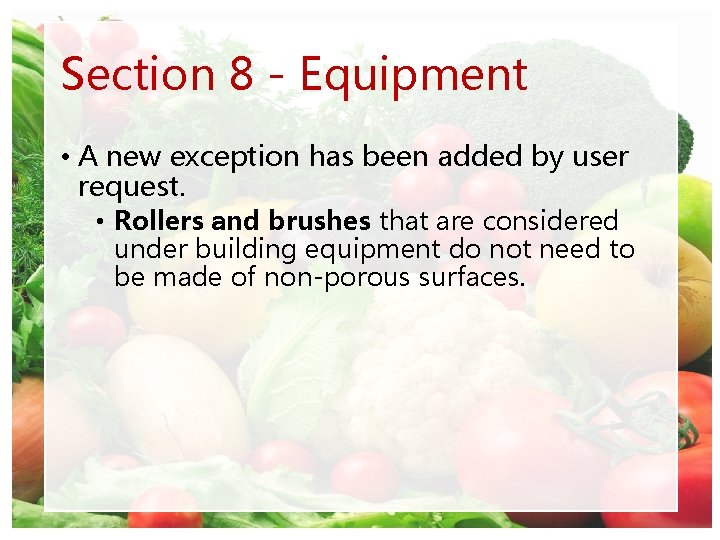
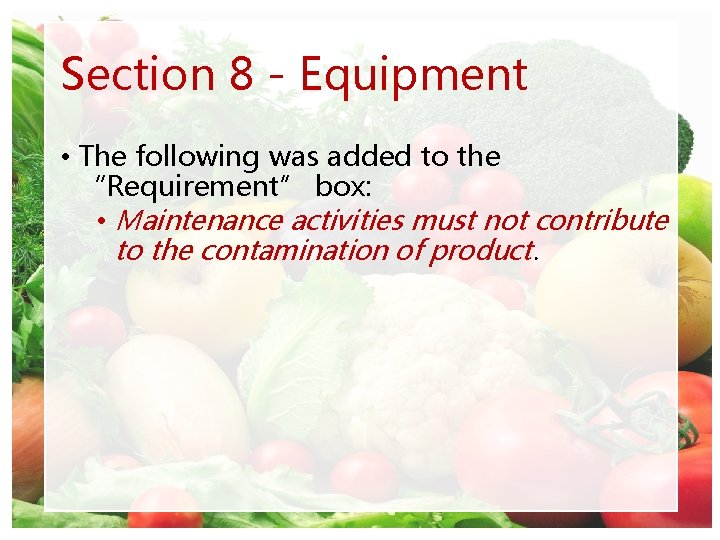
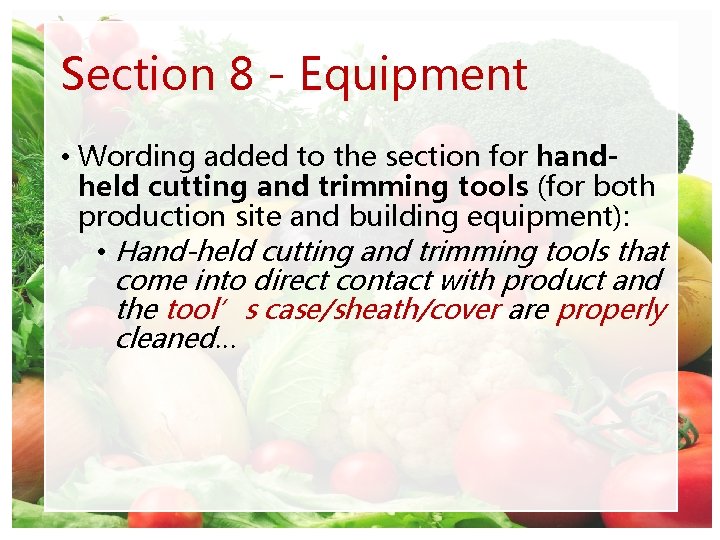
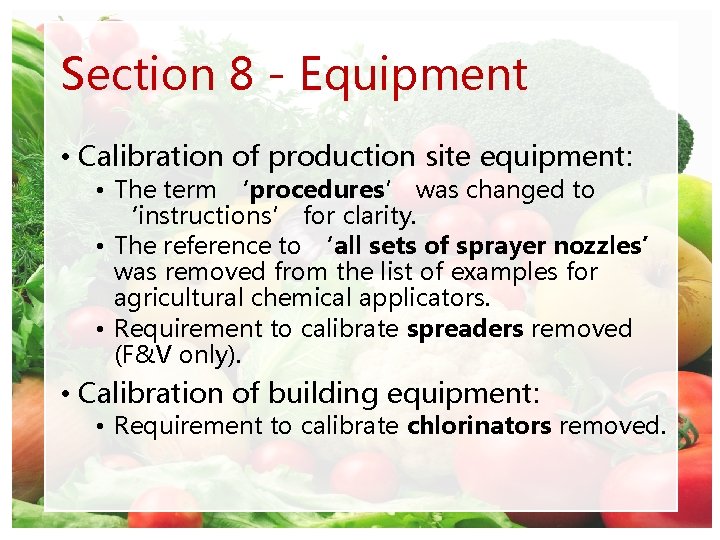
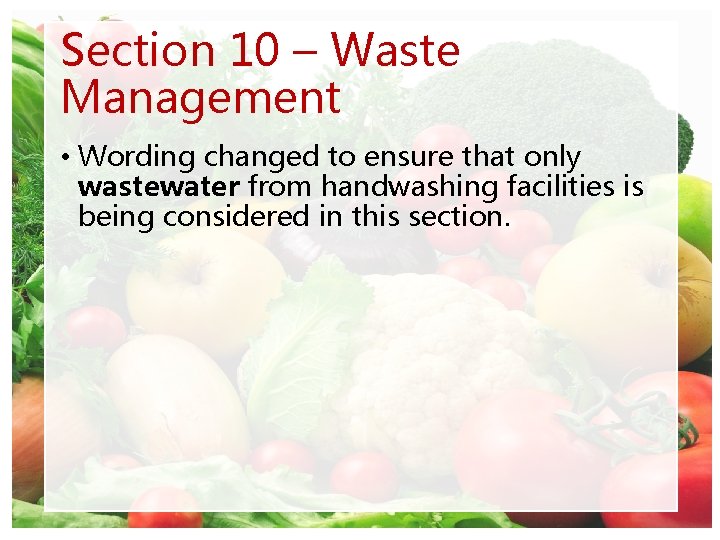
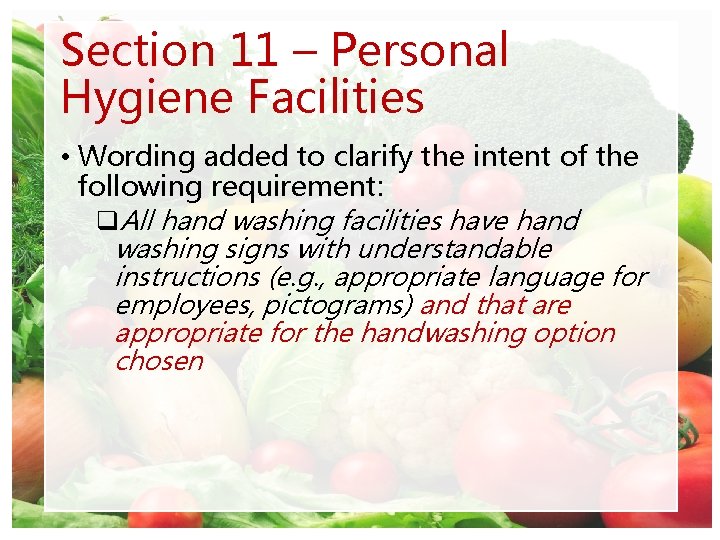
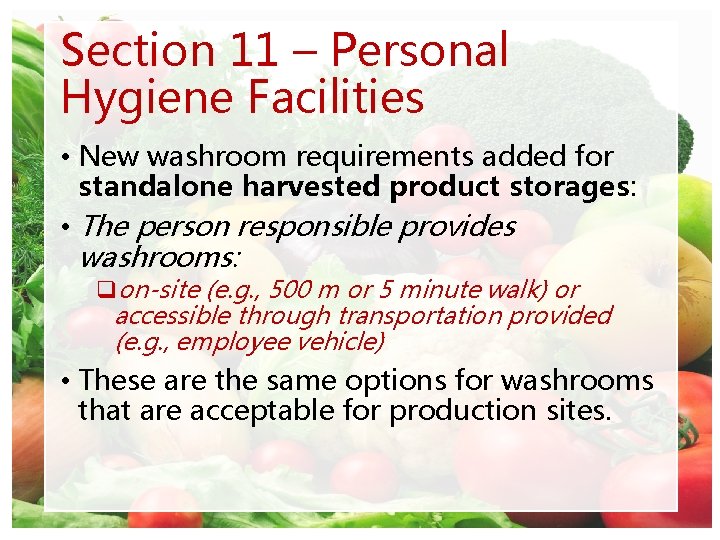
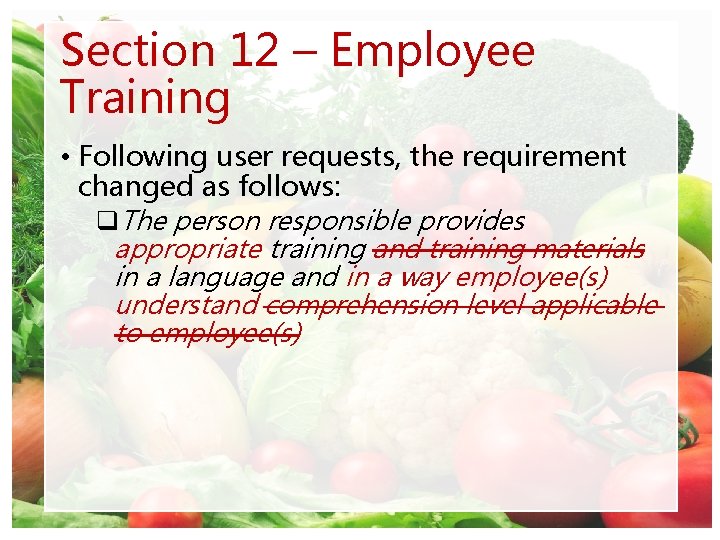
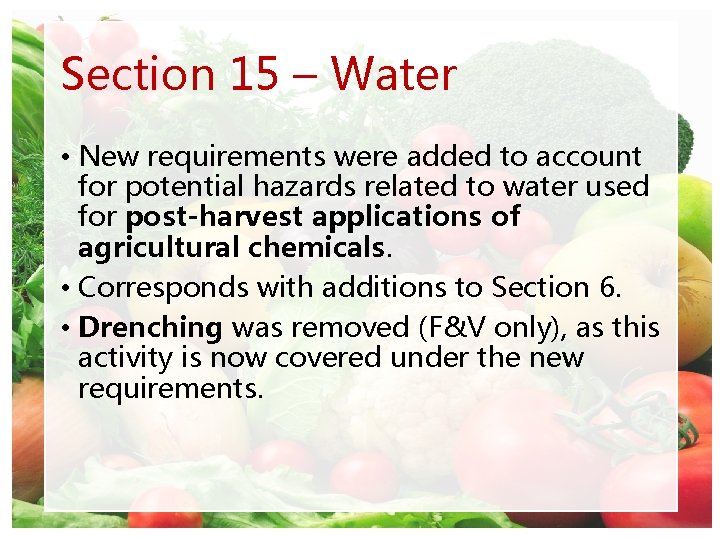
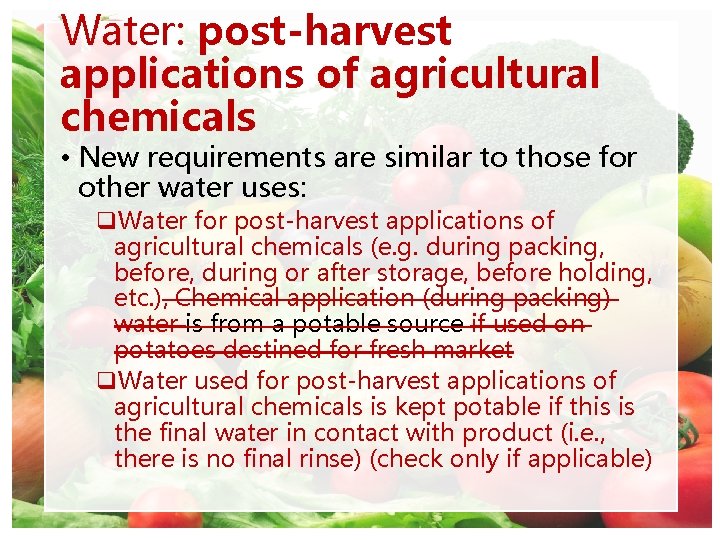
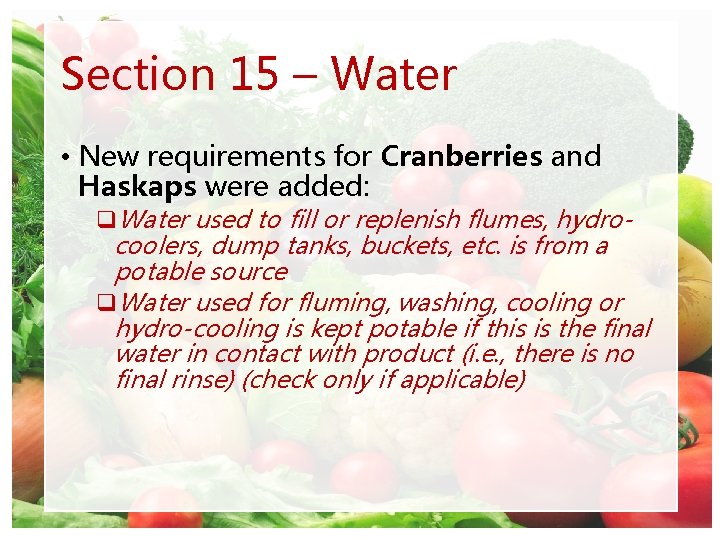
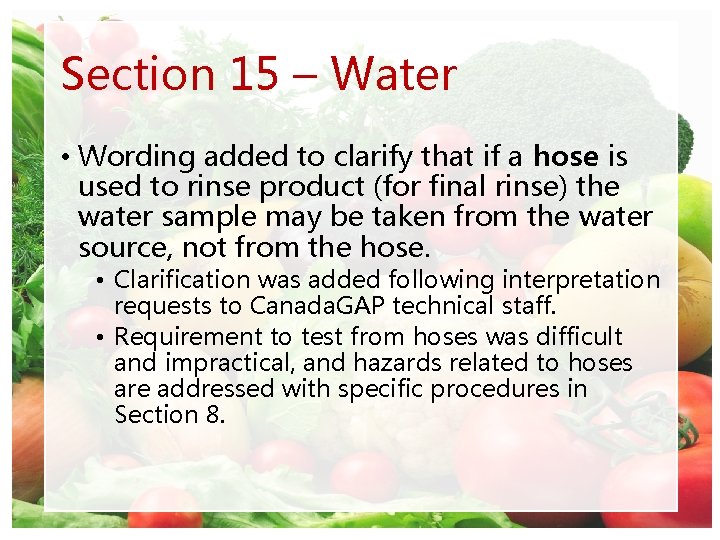
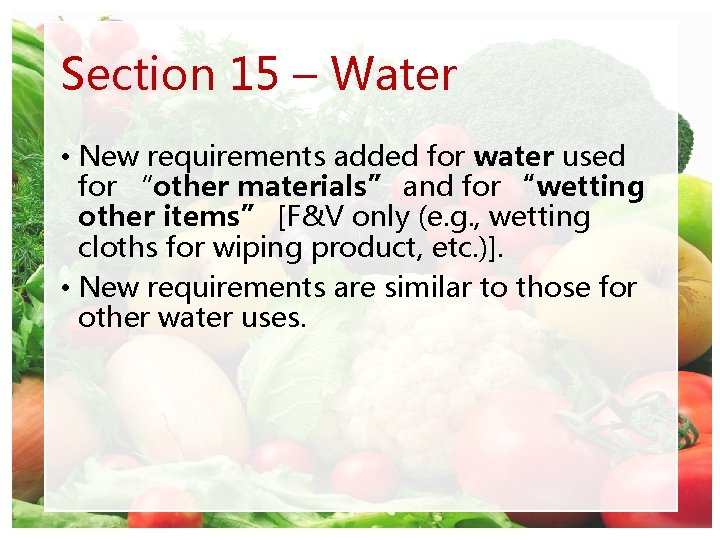
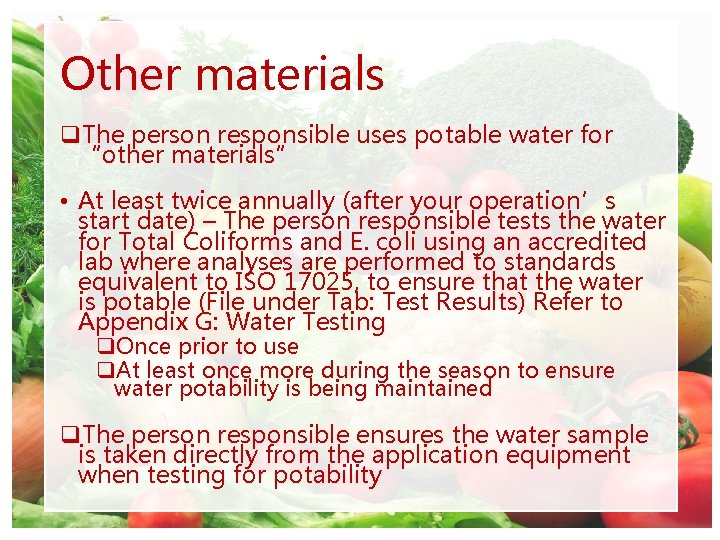
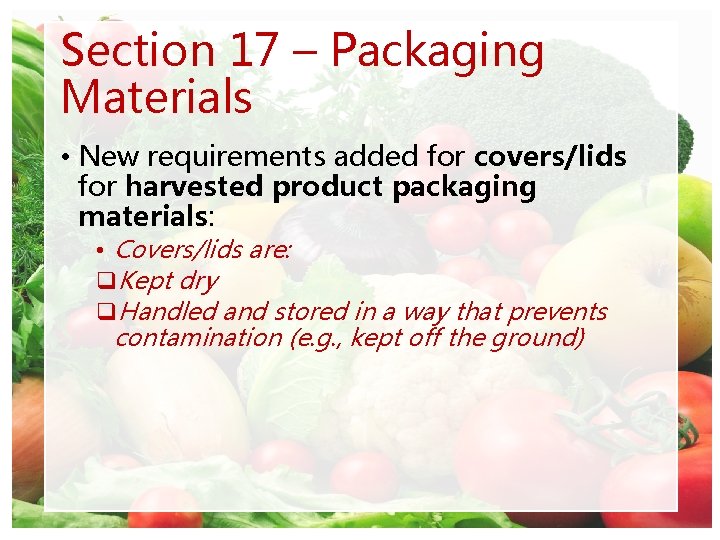
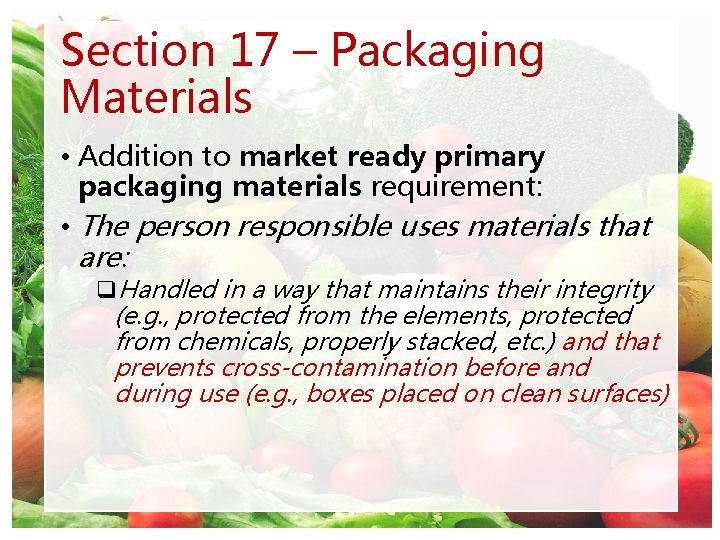
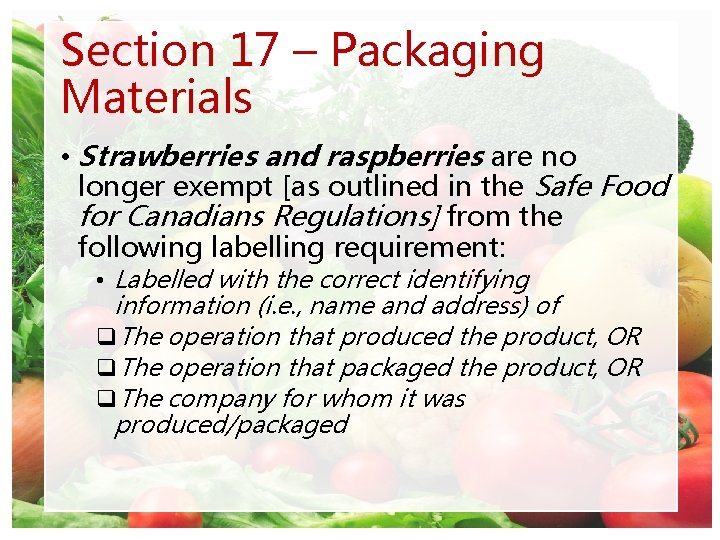
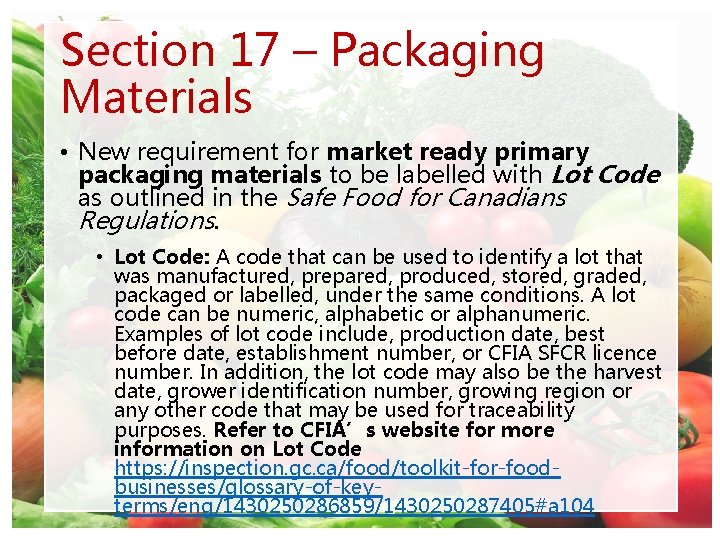
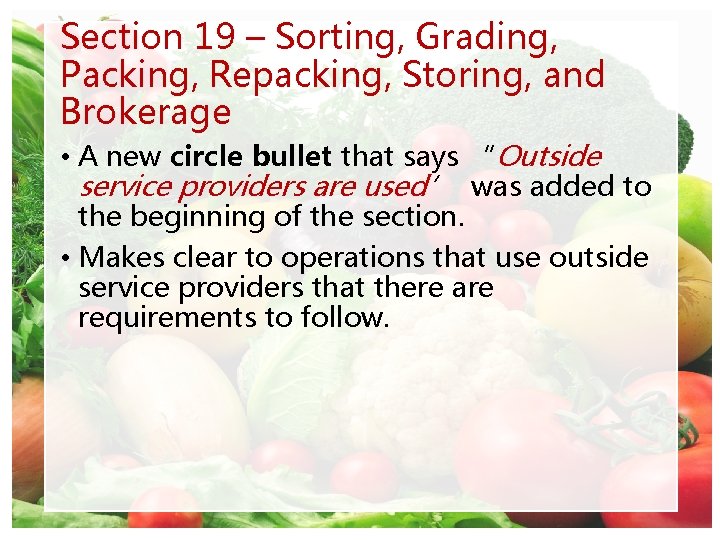
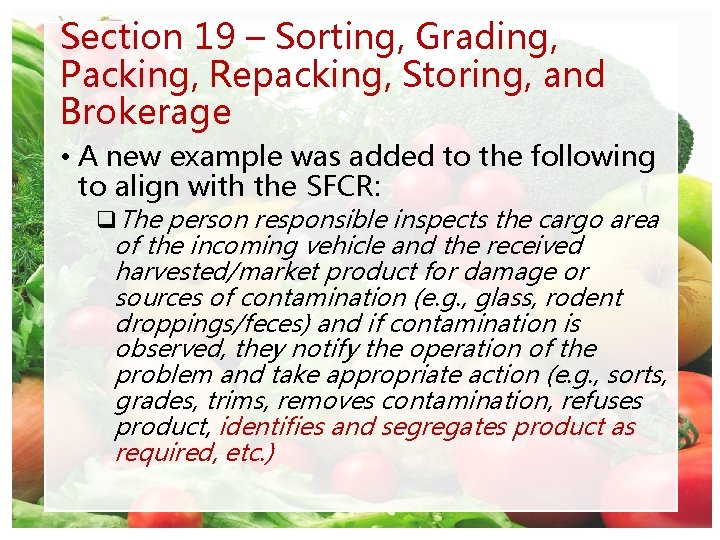
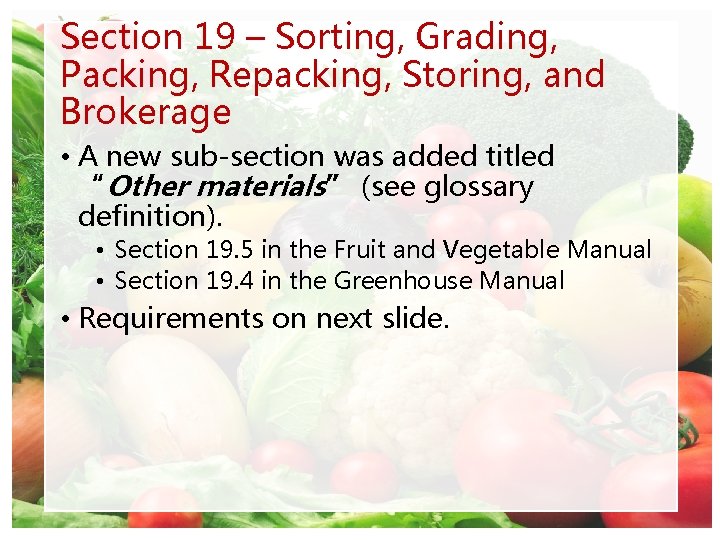
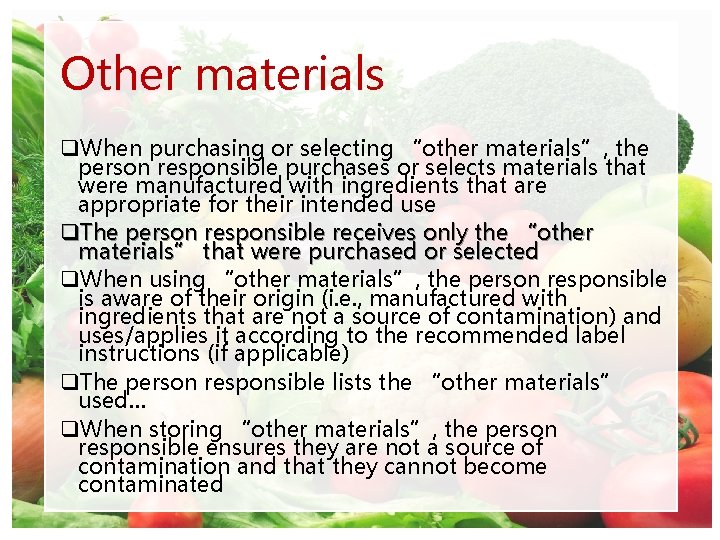
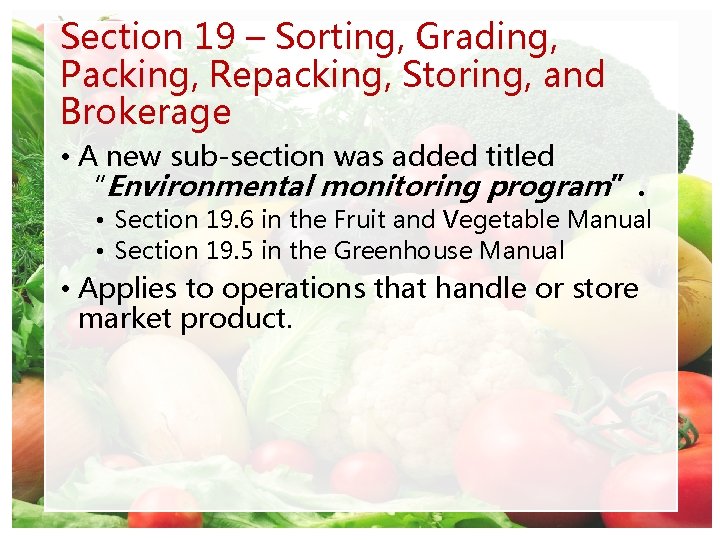
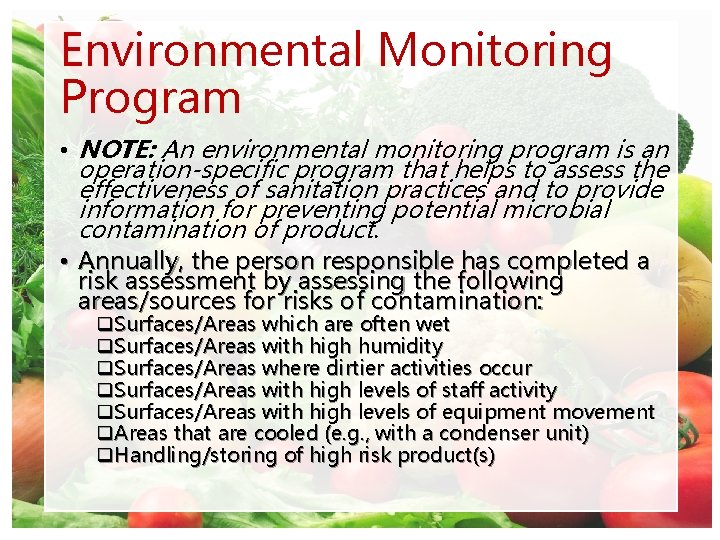
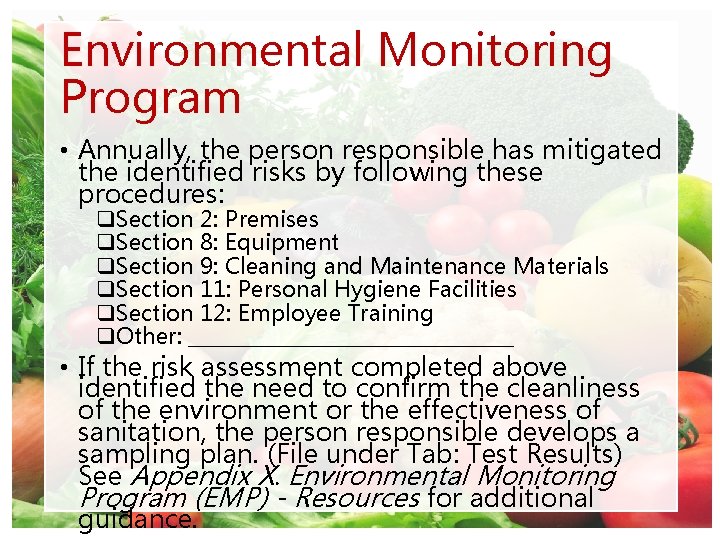
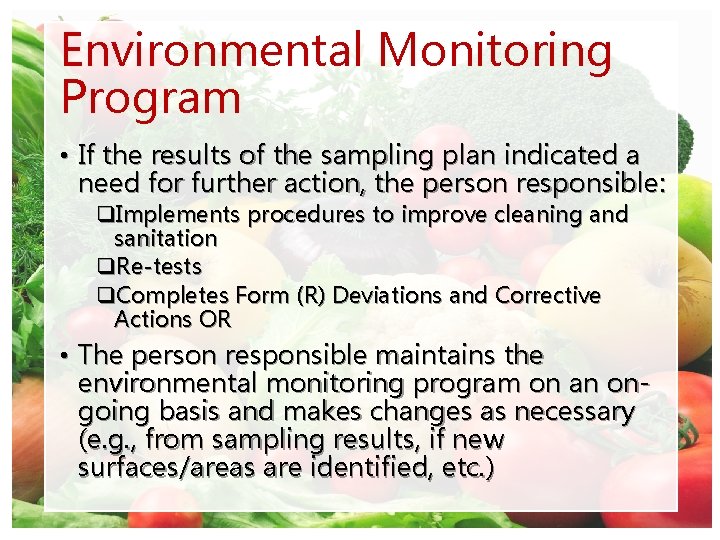
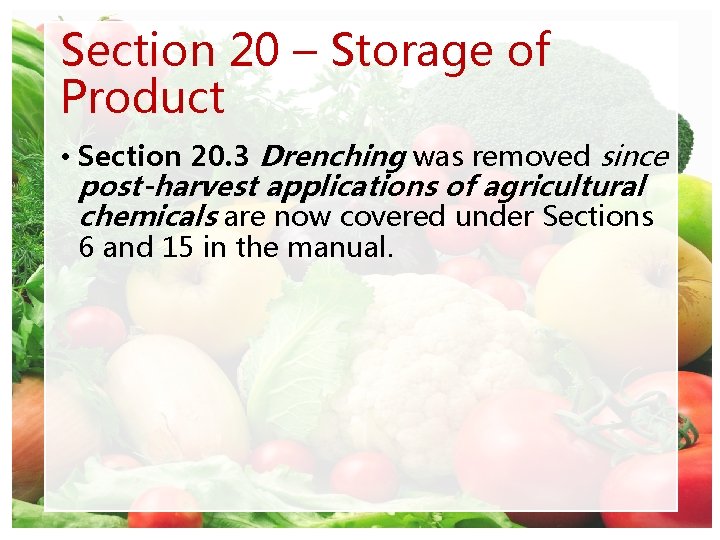
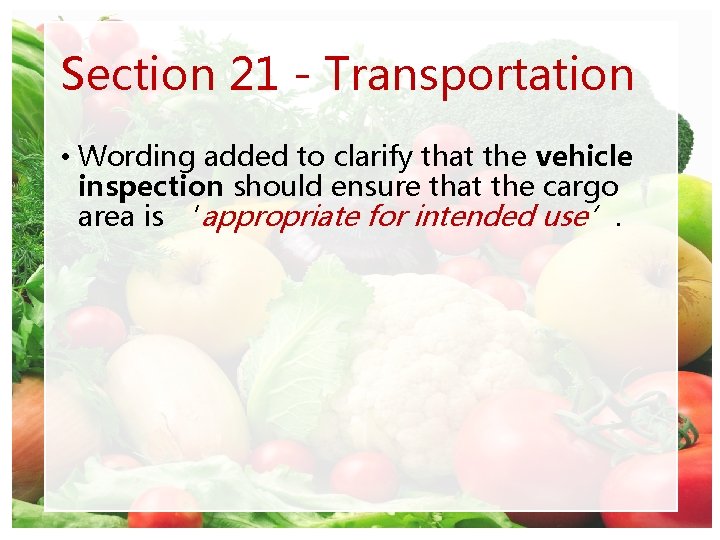
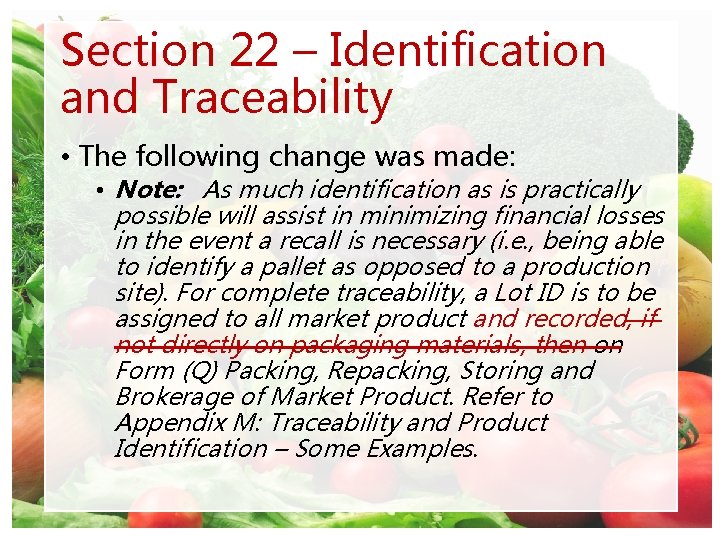
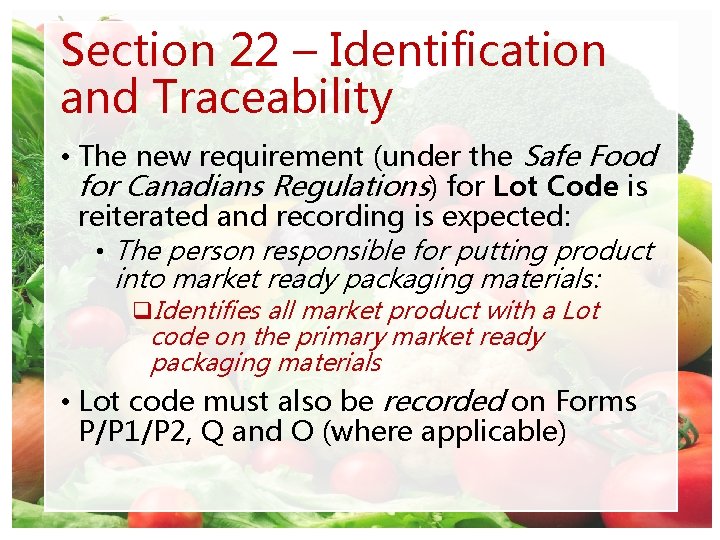
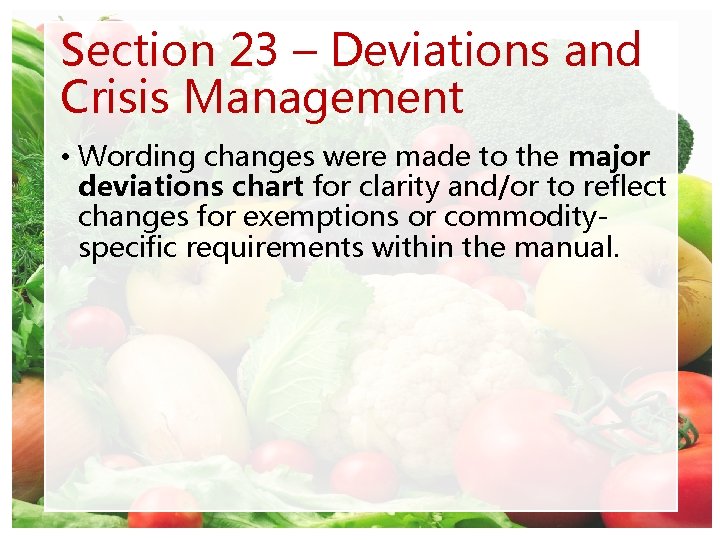
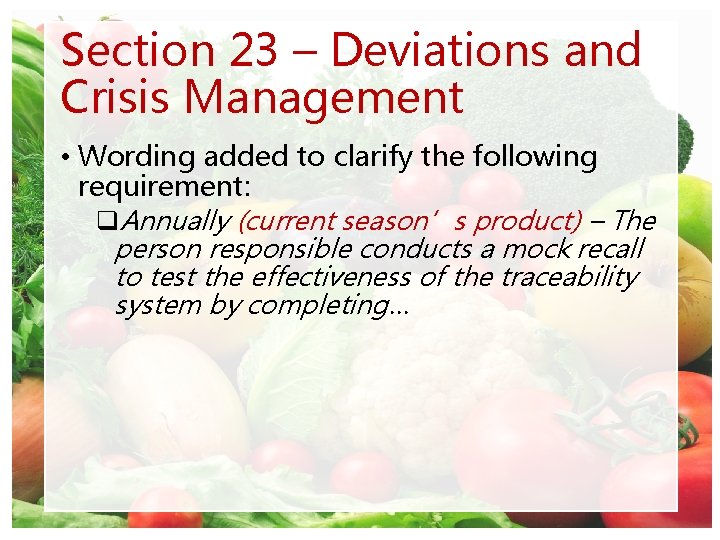
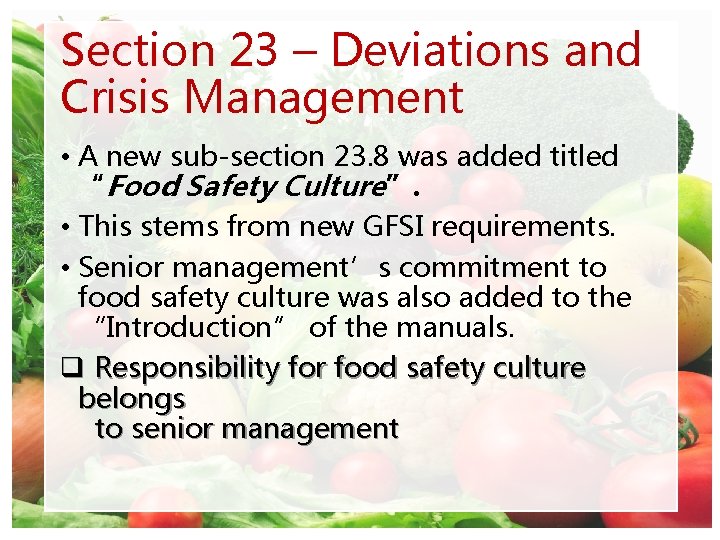
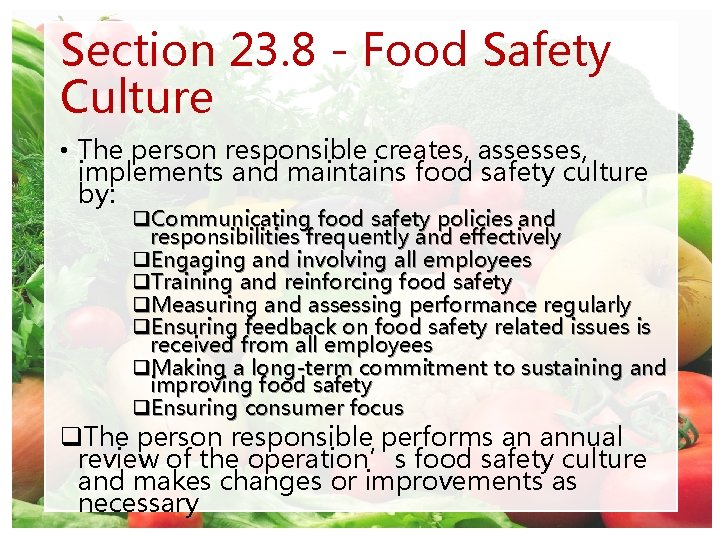
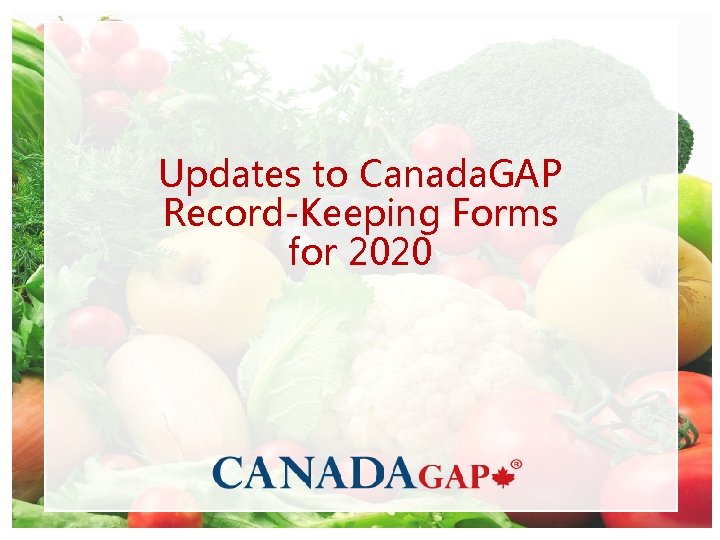
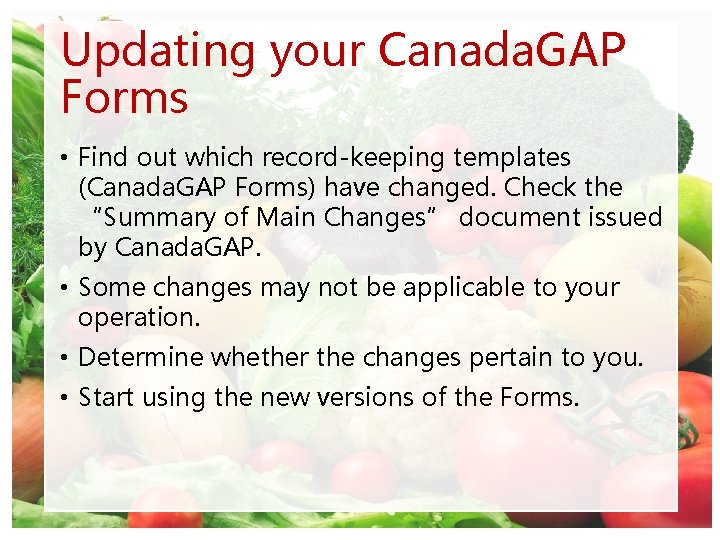
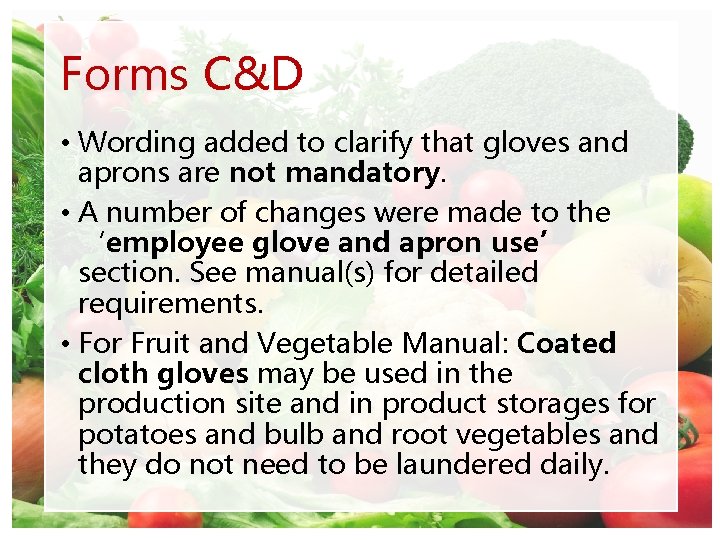
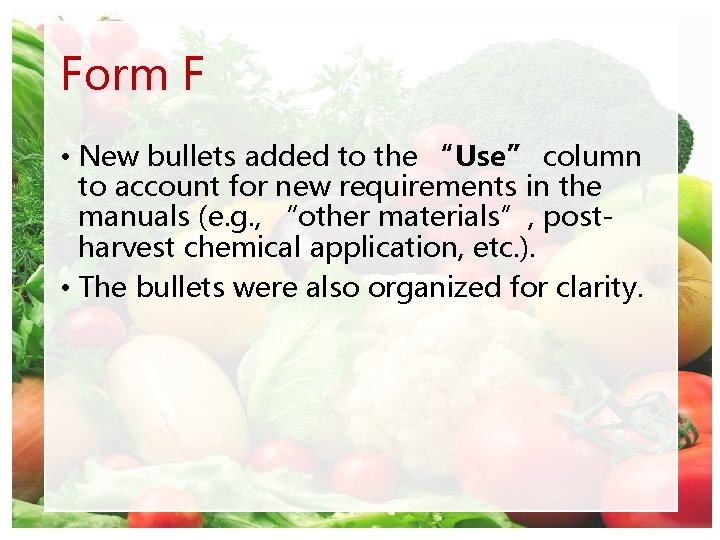
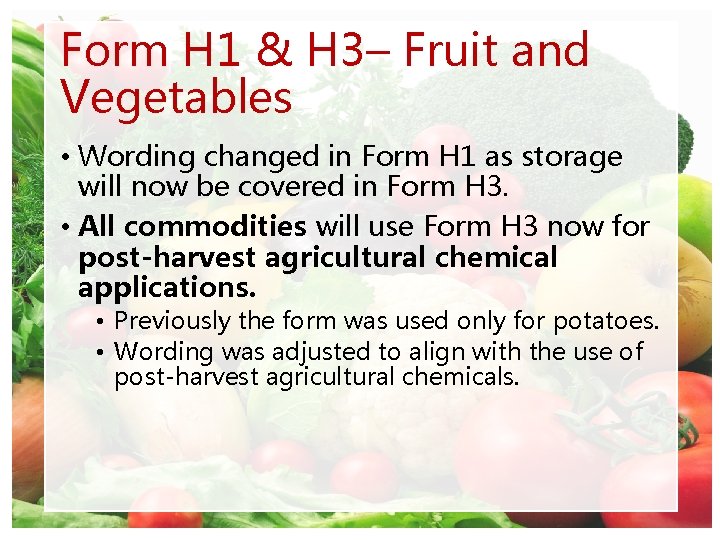
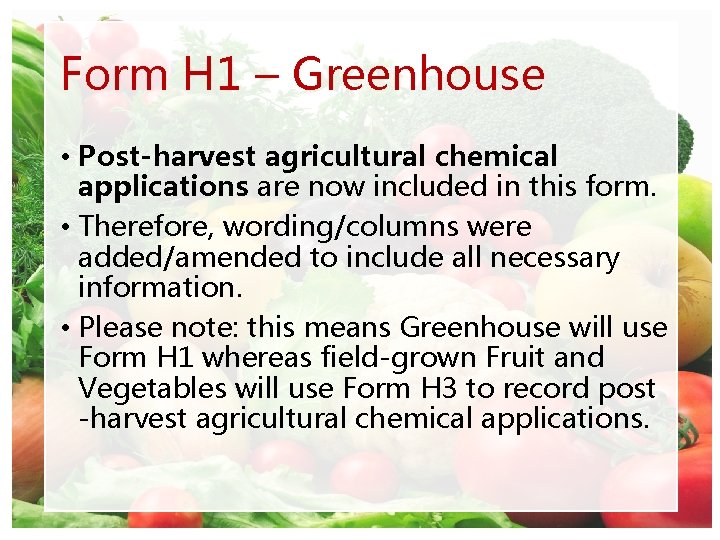
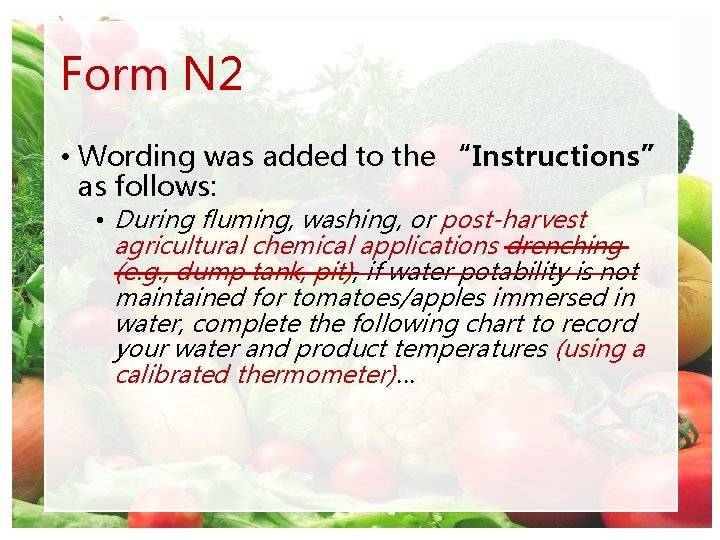
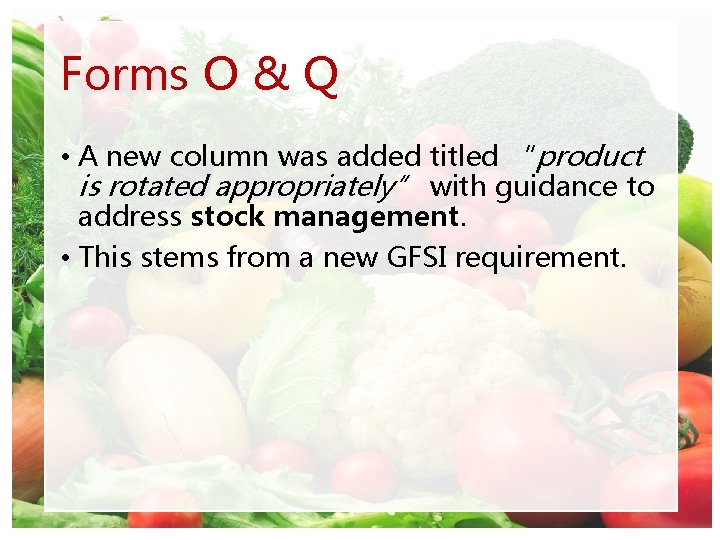
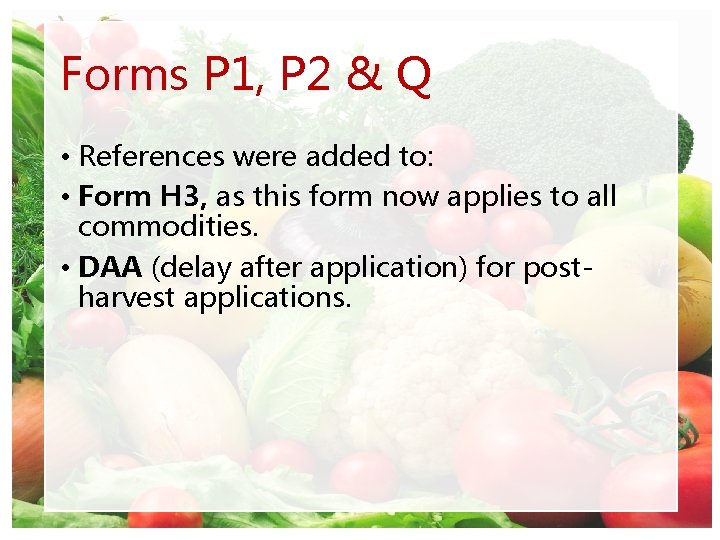
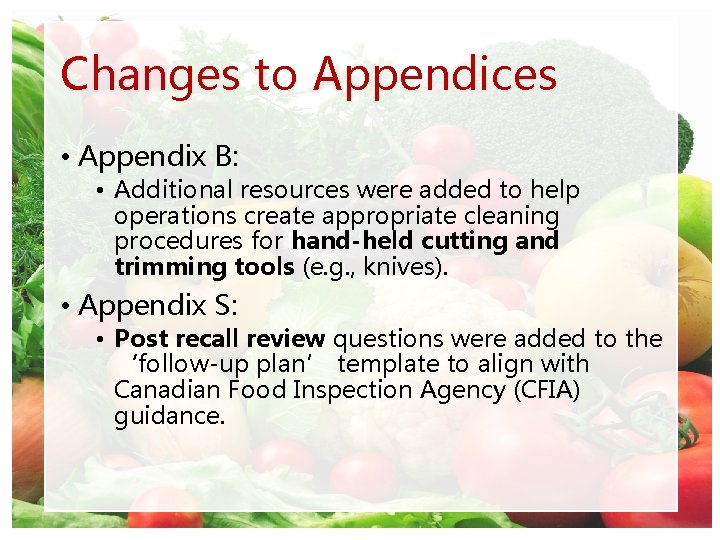
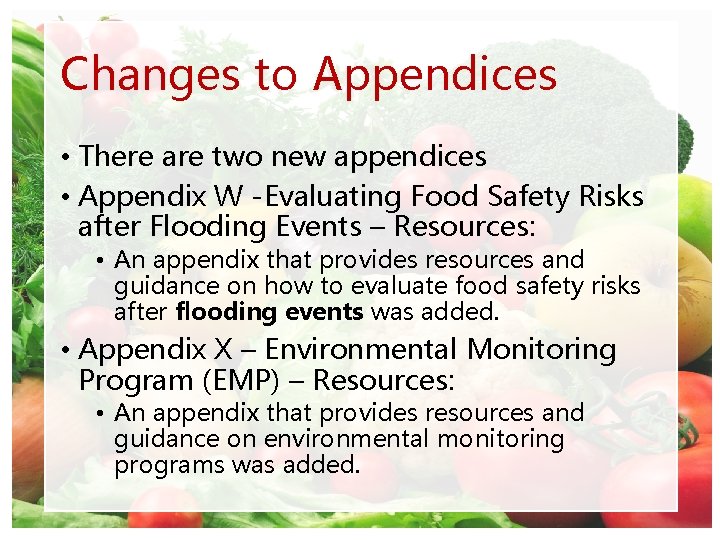
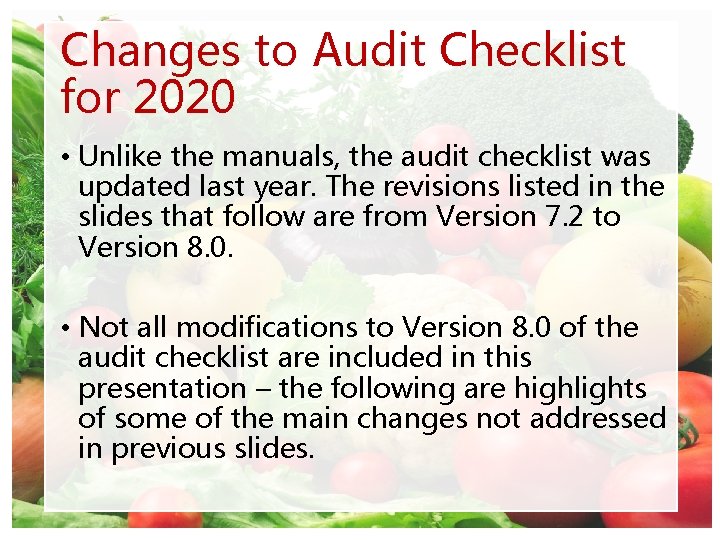
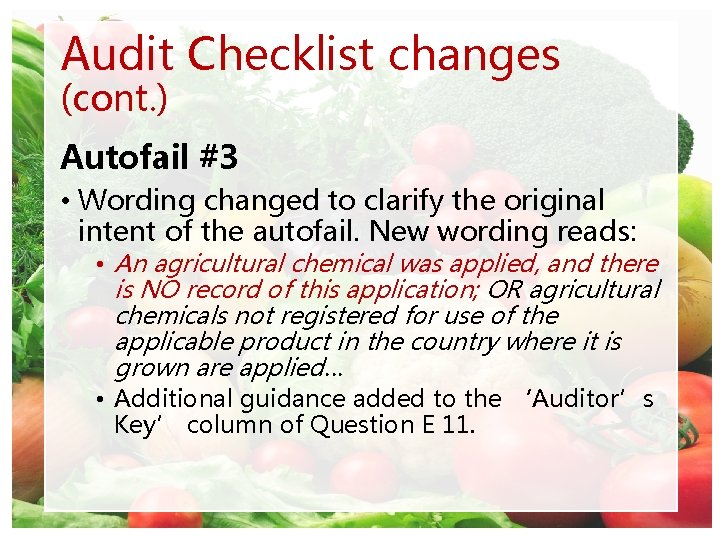
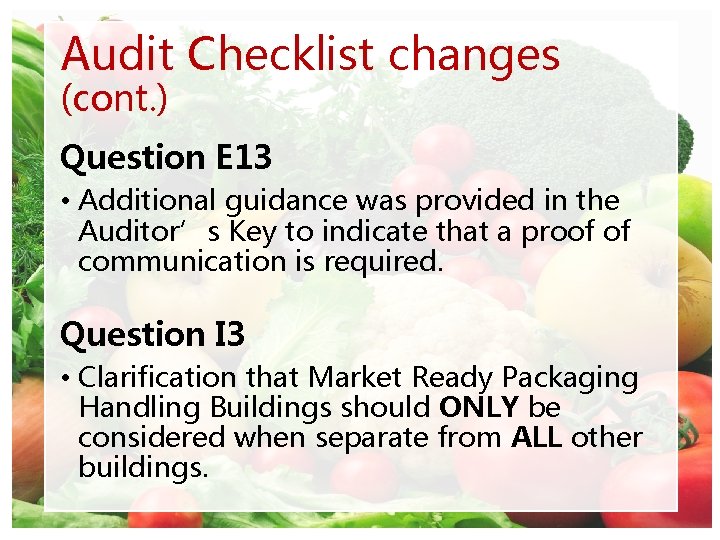
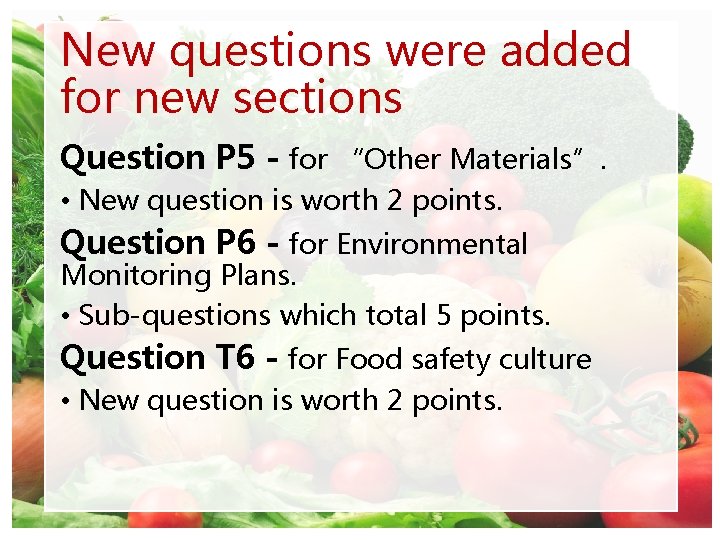
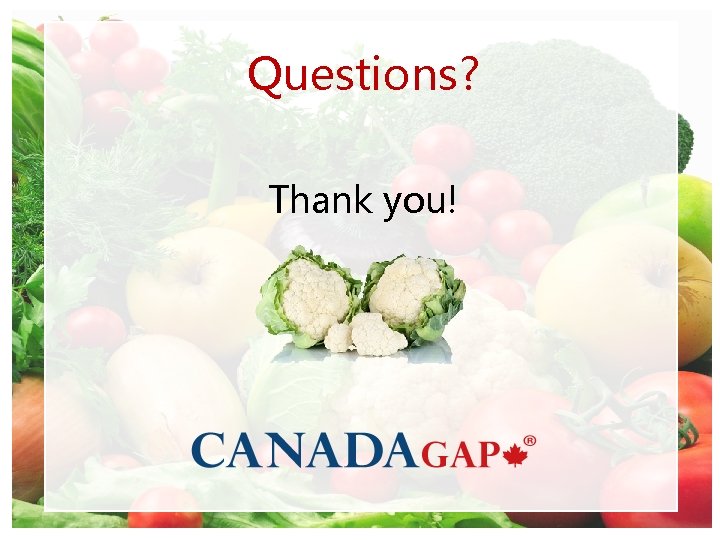
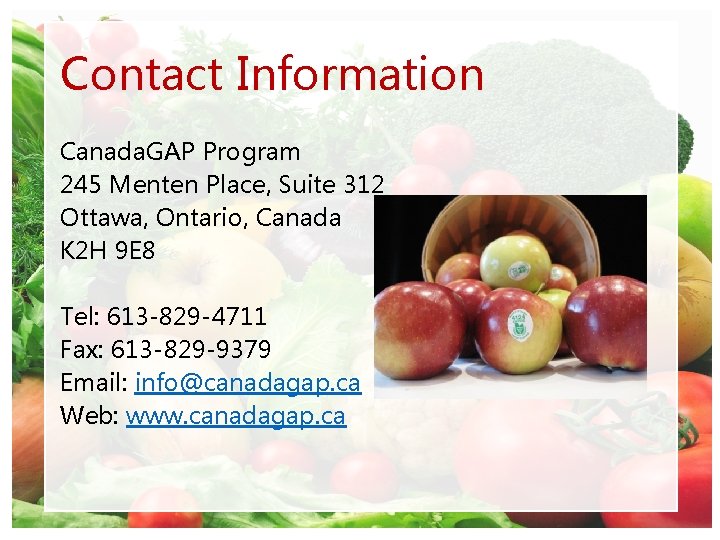
- Slides: 66
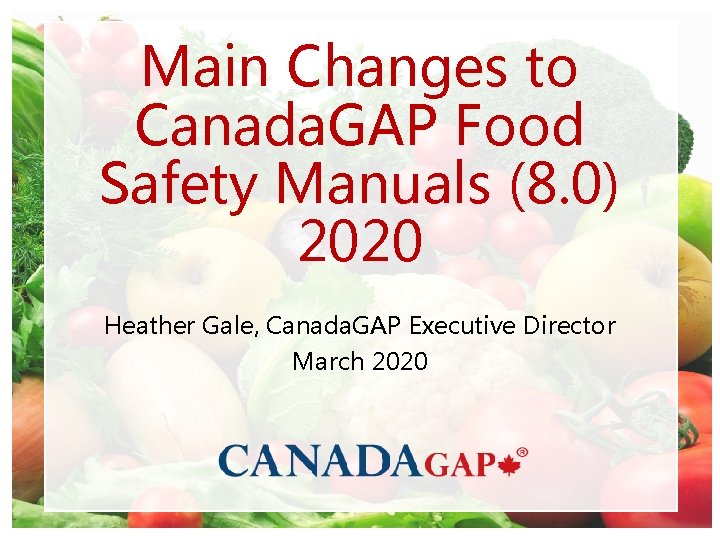
Main Changes to Canada. GAP Food Safety Manuals (8. 0) 2020 Heather Gale, Canada. GAP Executive Director March 2020
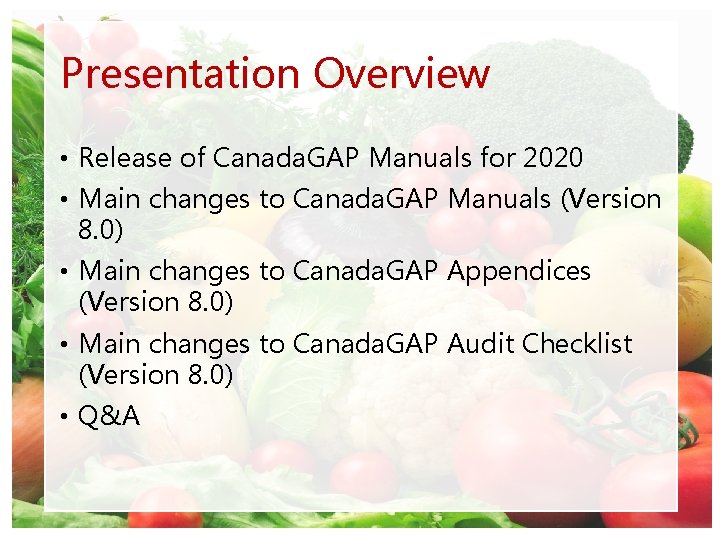
Presentation Overview • Release of Canada. GAP Manuals for 2020 • Main changes to Canada. GAP Manuals (Version 8. 0) • Main changes to Canada. GAP Appendices (Version 8. 0) • Main changes to Canada. GAP Audit Checklist (Version 8. 0) • Q&A
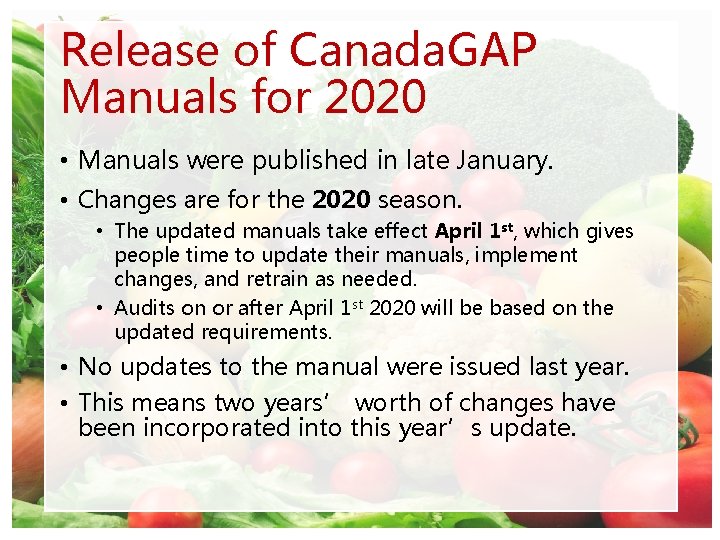
Release of Canada. GAP Manuals for 2020 • Manuals were published in late January. • Changes are for the 2020 season. • The updated manuals take effect April 1 st, which gives people time to update their manuals, implement changes, and retrain as needed. • Audits on or after April 1 st 2020 will be based on the updated requirements. • No updates to the manual were issued last year. • This means two years’ worth of changes have been incorporated into this year’s update.
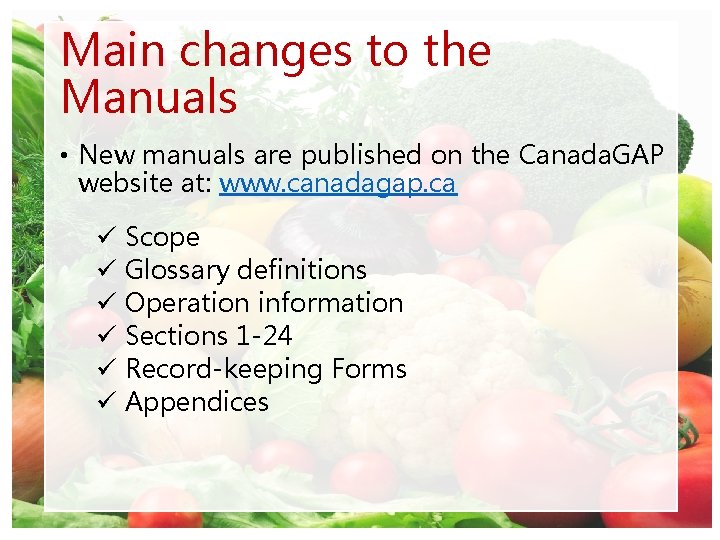
Main changes to the Manuals • New manuals are published on the Canada. GAP website at: www. canadagap. ca ü Scope ü Glossary definitions ü Operation information ü Sections 1 -24 ü Record-keeping Forms ü Appendices
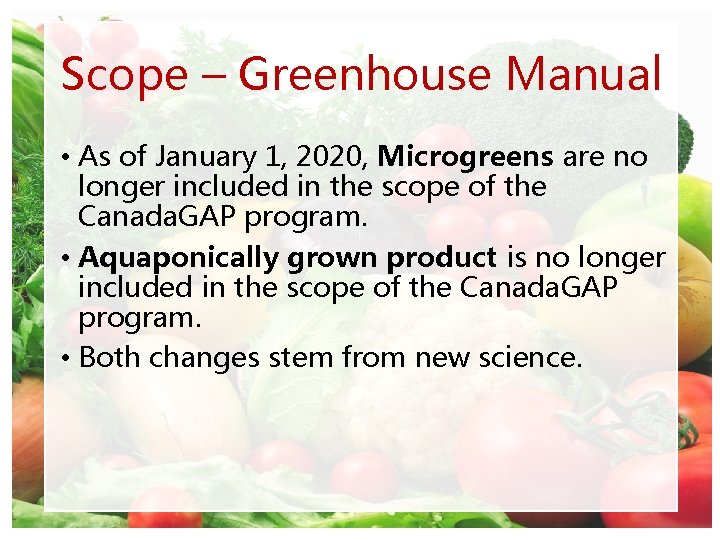
Scope – Greenhouse Manual • As of January 1, 2020, Microgreens are no longer included in the scope of the Canada. GAP program. • Aquaponically grown product is no longer included in the scope of the Canada. GAP program. • Both changes stem from new science.
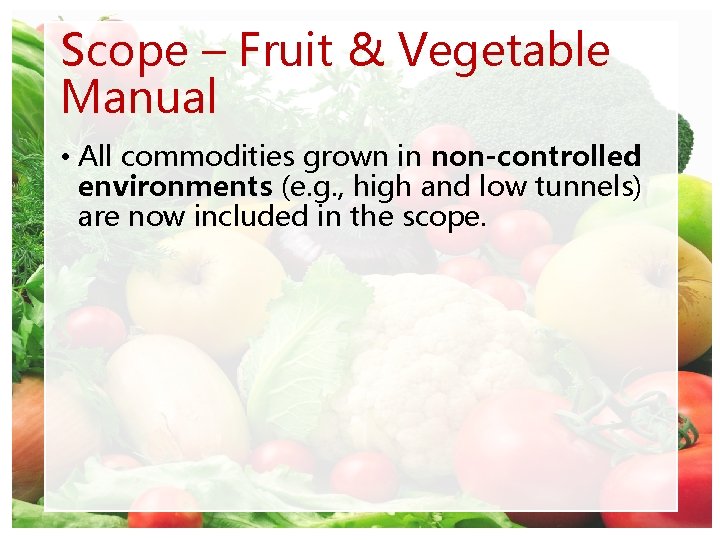
Scope – Fruit & Vegetable Manual • All commodities grown in non-controlled environments (e. g. , high and low tunnels) are now included in the scope.
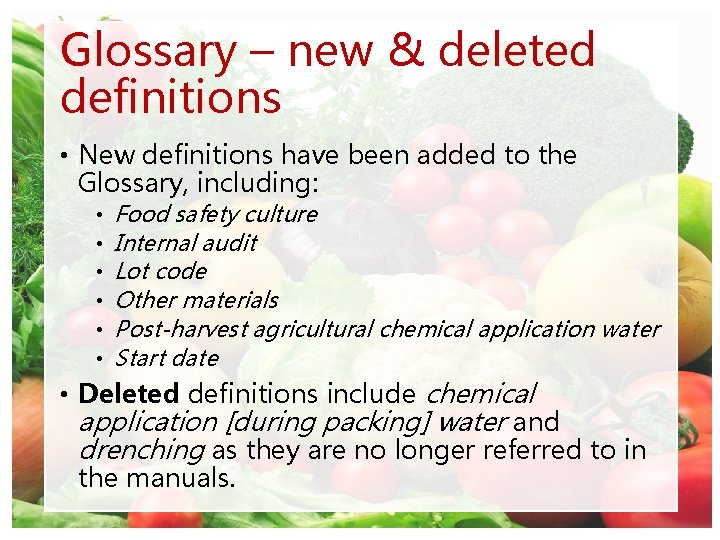
Glossary – new & deleted definitions • New definitions have been added to the Glossary, including: • • • Food safety culture Internal audit Lot code Other materials Post-harvest agricultural chemical application water Start date • Deleted definitions include chemical application [during packing] water and drenching as they are no longer referred to in the manuals.
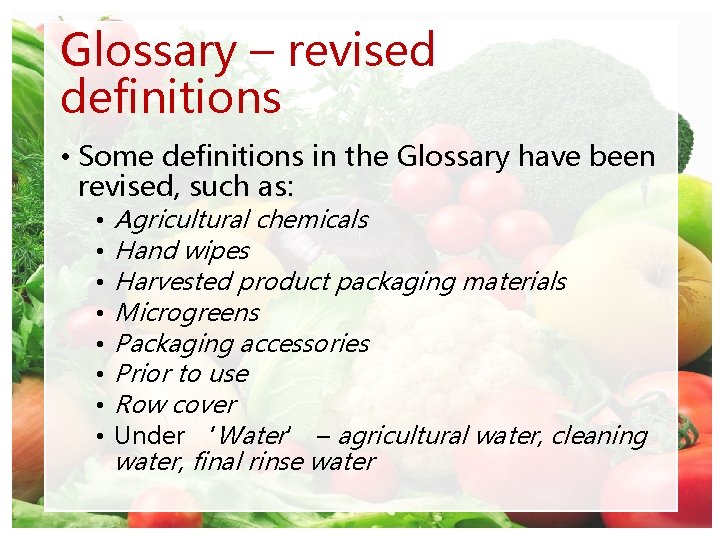
Glossary – revised definitions • Some definitions in the Glossary have been revised, such as: • • Agricultural chemicals Hand wipes Harvested product packaging materials Microgreens Packaging accessories Prior to use Row cover Under ‘Water’ – agricultural water, cleaning water, final rinse water
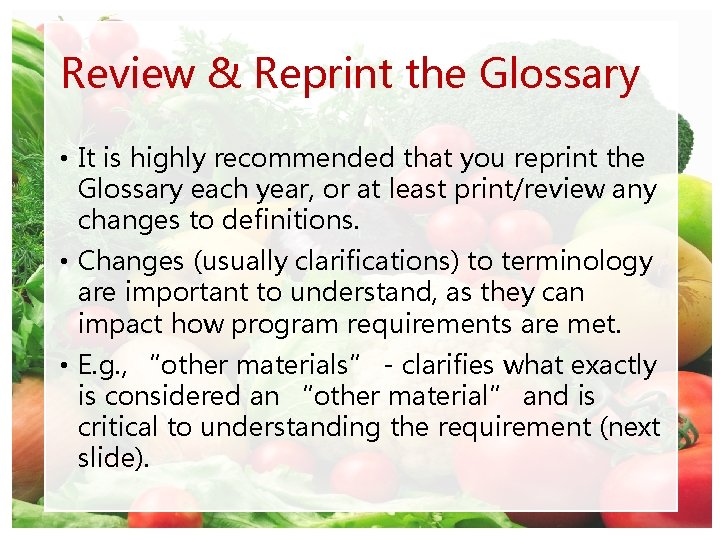
Review & Reprint the Glossary • It is highly recommended that you reprint the Glossary each year, or at least print/review any changes to definitions. • Changes (usually clarifications) to terminology are important to understand, as they can impact how program requirements are met. • E. g. , “other materials” - clarifies what exactly is considered an “other material” and is critical to understanding the requirement (next slide).
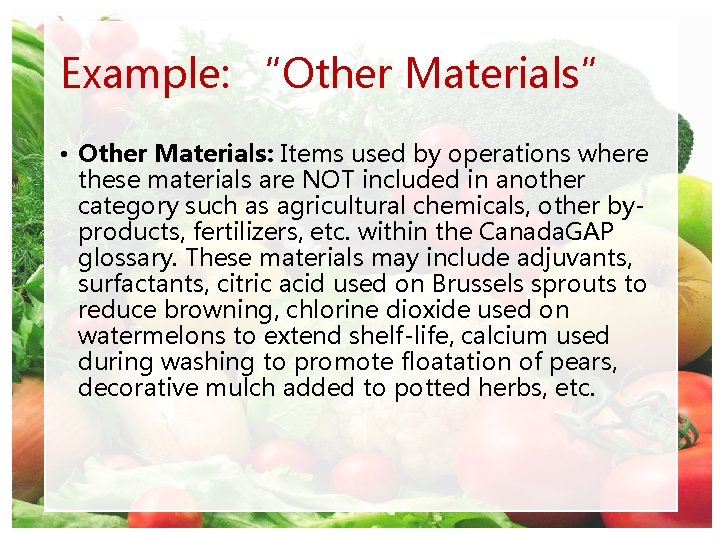
Example: “Other Materials” • Other Materials: Items used by operations where these materials are NOT included in another category such as agricultural chemicals, other byproducts, fertilizers, etc. within the Canada. GAP glossary. These materials may include adjuvants, surfactants, citric acid used on Brussels sprouts to reduce browning, chlorine dioxide used on watermelons to extend shelf-life, calcium used during washing to promote floatation of pears, decorative mulch added to potted herbs, etc.
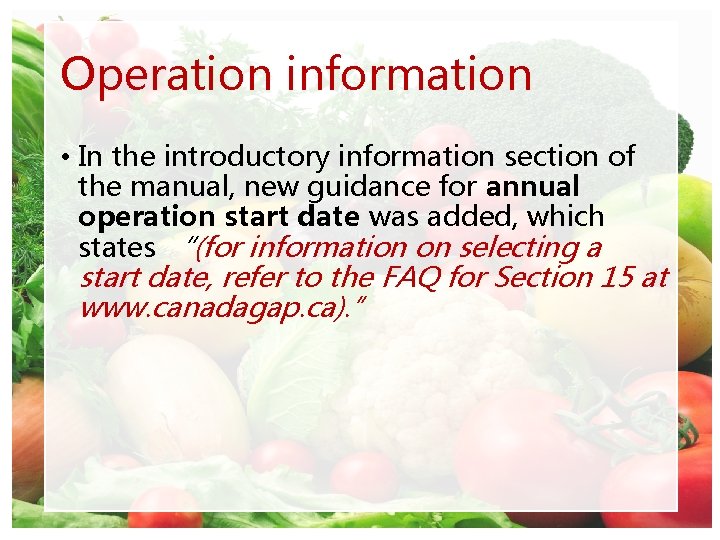
Operation information • In the introductory information section of the manual, new guidance for annual operation start date was added, which states “(for information on selecting a start date, refer to the FAQ for Section 15 at www. canadagap. ca). ”
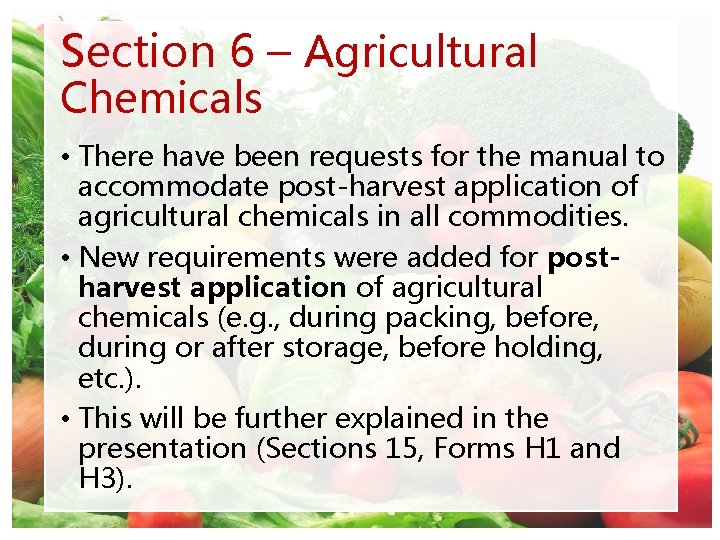
Section 6 – Agricultural Chemicals • There have been requests for the manual to accommodate post-harvest application of agricultural chemicals in all commodities. • New requirements were added for postharvest application of agricultural chemicals (e. g. , during packing, before, during or after storage, before holding, etc. ). • This will be further explained in the presentation (Sections 15, Forms H 1 and H 3).
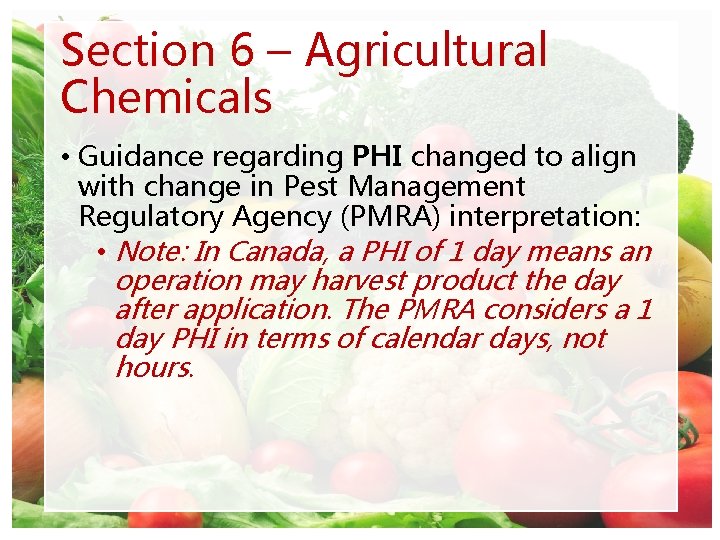
Section 6 – Agricultural Chemicals • Guidance regarding PHI changed to align with change in Pest Management Regulatory Agency (PMRA) interpretation: • Note: In Canada, a PHI of 1 day means an operation may harvest product the day after application. The PMRA considers a 1 day PHI in terms of calendar days, not hours.
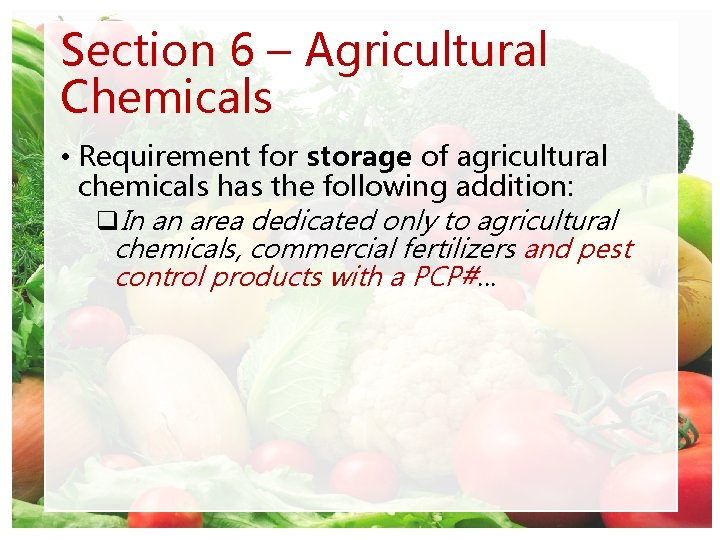
Section 6 – Agricultural Chemicals • Requirement for storage of agricultural chemicals has the following addition: q. In an area dedicated only to agricultural chemicals, commercial fertilizers and pest control products with a PCP#. . .
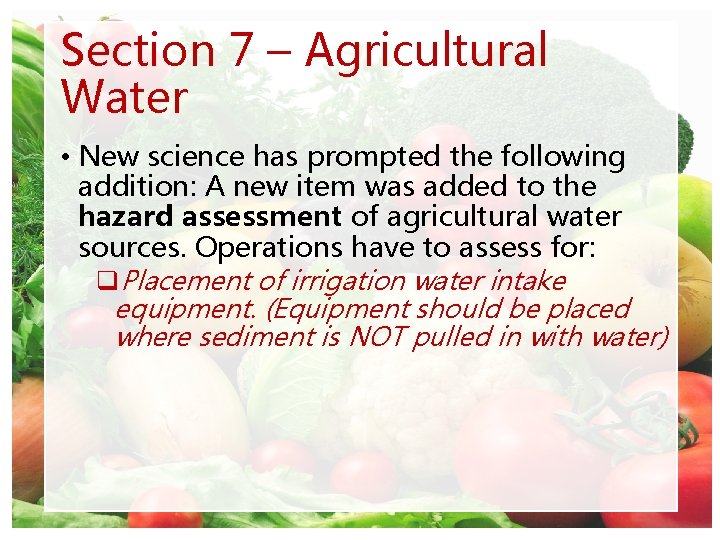
Section 7 – Agricultural Water • New science has prompted the following addition: A new item was added to the hazard assessment of agricultural water sources. Operations have to assess for: q. Placement of irrigation water intake equipment. (Equipment should be placed where sediment is NOT pulled in with water)
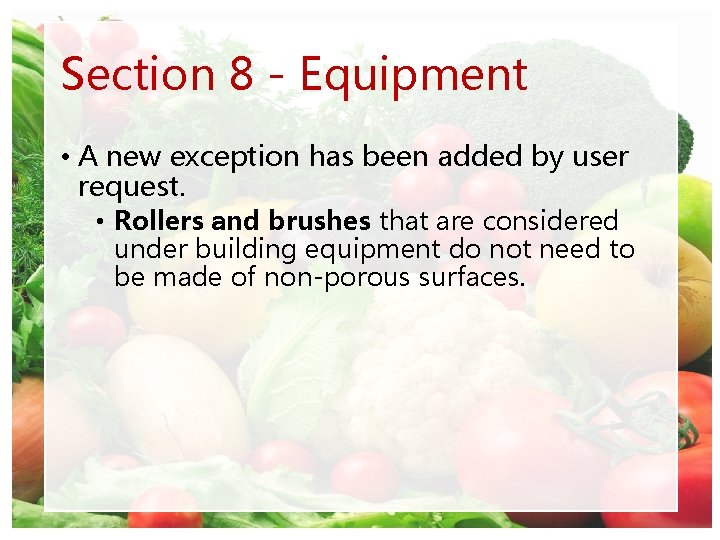
Section 8 - Equipment • A new exception has been added by user request. • Rollers and brushes that are considered under building equipment do not need to be made of non-porous surfaces.
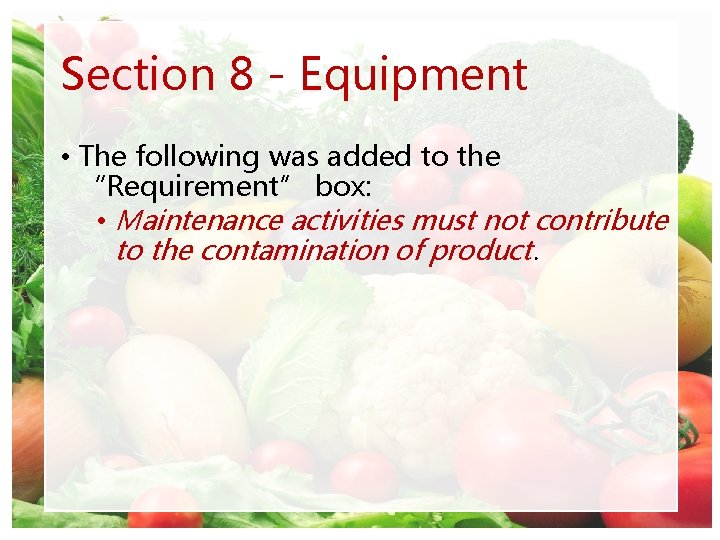
Section 8 - Equipment • The following was added to the “Requirement” box: • Maintenance activities must not contribute to the contamination of product.
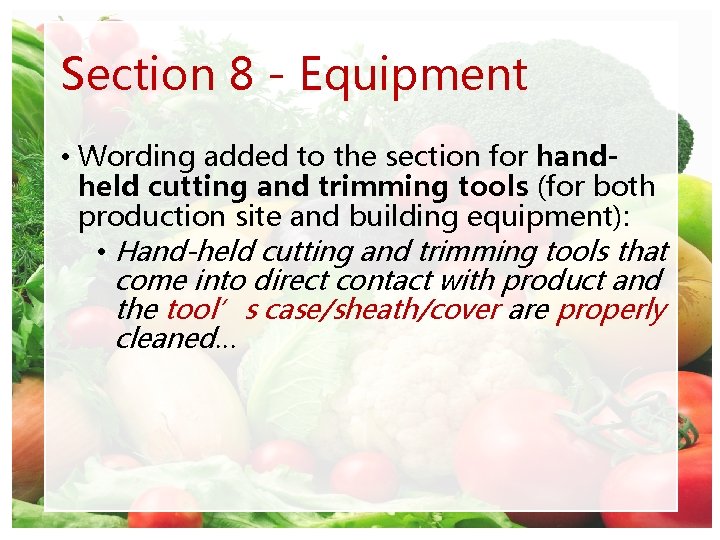
Section 8 - Equipment • Wording added to the section for handheld cutting and trimming tools (for both production site and building equipment): • Hand-held cutting and trimming tools that come into direct contact with product and the tool’s case/sheath/cover are properly cleaned…
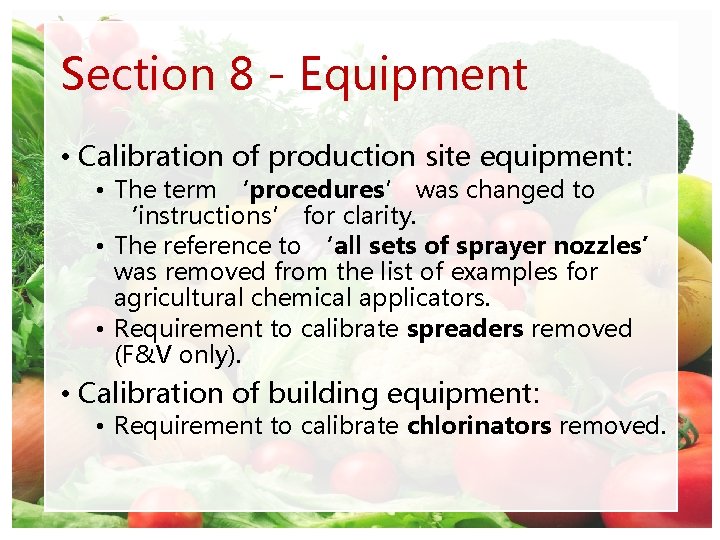
Section 8 - Equipment • Calibration of production site equipment: • The term ‘procedures’ was changed to ‘instructions’ for clarity. • The reference to ‘all sets of sprayer nozzles’ was removed from the list of examples for agricultural chemical applicators. • Requirement to calibrate spreaders removed (F&V only). • Calibration of building equipment: • Requirement to calibrate chlorinators removed.
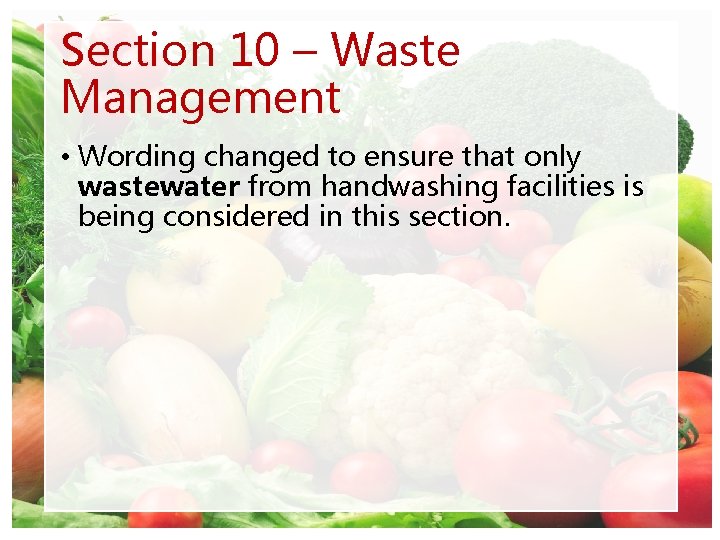
Section 10 – Waste Management • Wording changed to ensure that only wastewater from handwashing facilities is being considered in this section.
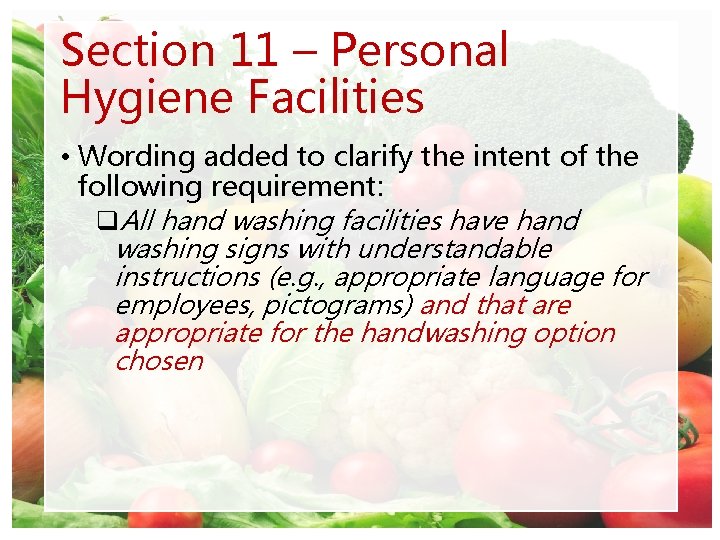
Section 11 – Personal Hygiene Facilities • Wording added to clarify the intent of the following requirement: q. All hand washing facilities have hand washing signs with understandable instructions (e. g. , appropriate language for employees, pictograms) and that are appropriate for the handwashing option chosen
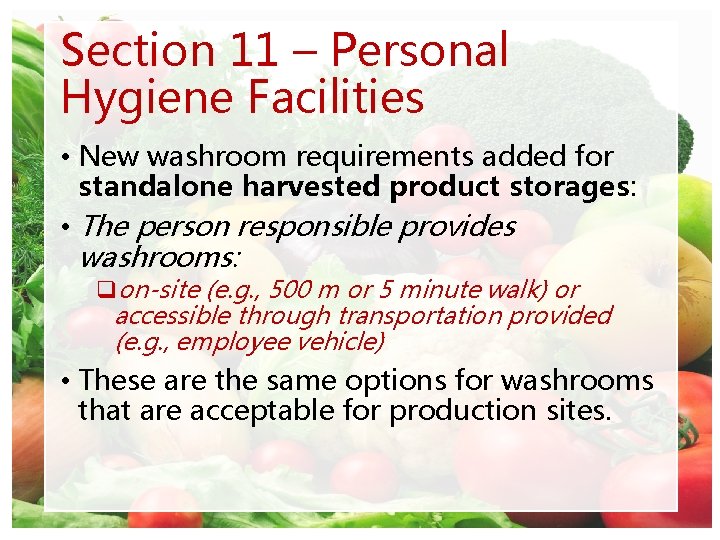
Section 11 – Personal Hygiene Facilities • New washroom requirements added for standalone harvested product storages: • The person responsible provides washrooms: qon-site (e. g. , 500 m or 5 minute walk) or accessible through transportation provided (e. g. , employee vehicle) • These are the same options for washrooms that are acceptable for production sites.
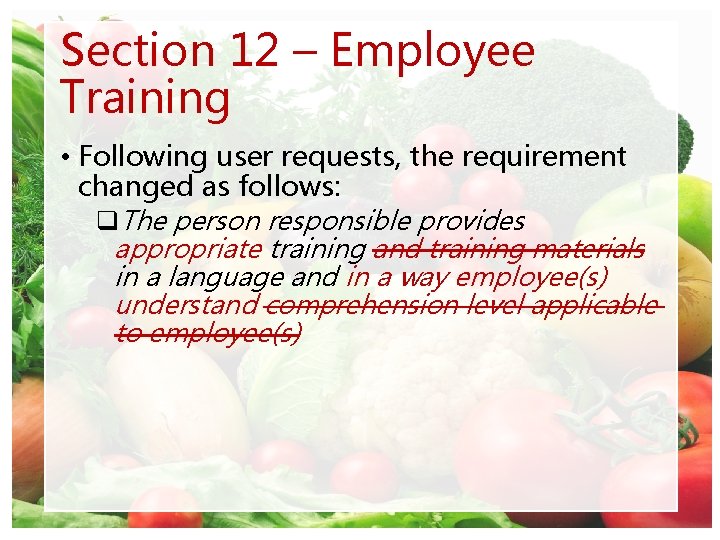
Section 12 – Employee Training • Following user requests, the requirement changed as follows: q. The person responsible provides appropriate training and training materials in a language and in a way employee(s) understand comprehension level applicable to employee(s)
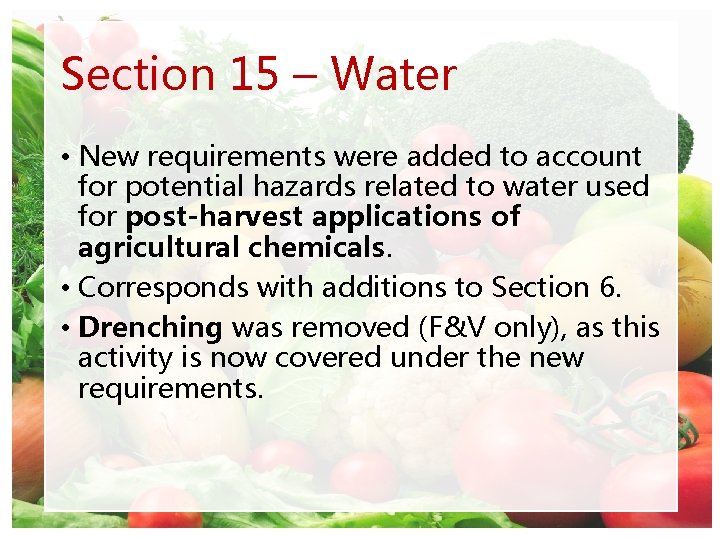
Section 15 – Water • New requirements were added to account for potential hazards related to water used for post-harvest applications of agricultural chemicals. • Corresponds with additions to Section 6. • Drenching was removed (F&V only), as this activity is now covered under the new requirements.
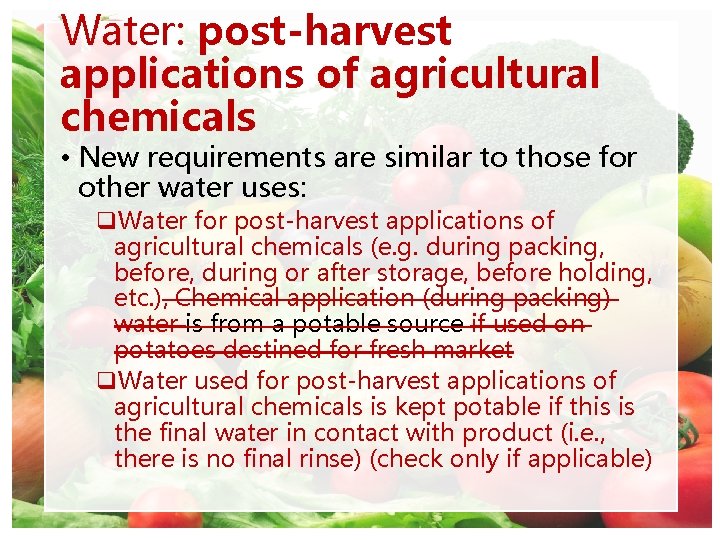
Water: post-harvest applications of agricultural chemicals • New requirements are similar to those for other water uses: q. Water for post-harvest applications of agricultural chemicals (e. g. during packing, before, during or after storage, before holding, etc. ), Chemical application (during packing) water is from a potable source if used on potatoes destined for fresh market q. Water used for post-harvest applications of agricultural chemicals is kept potable if this is the final water in contact with product (i. e. , there is no final rinse) (check only if applicable)
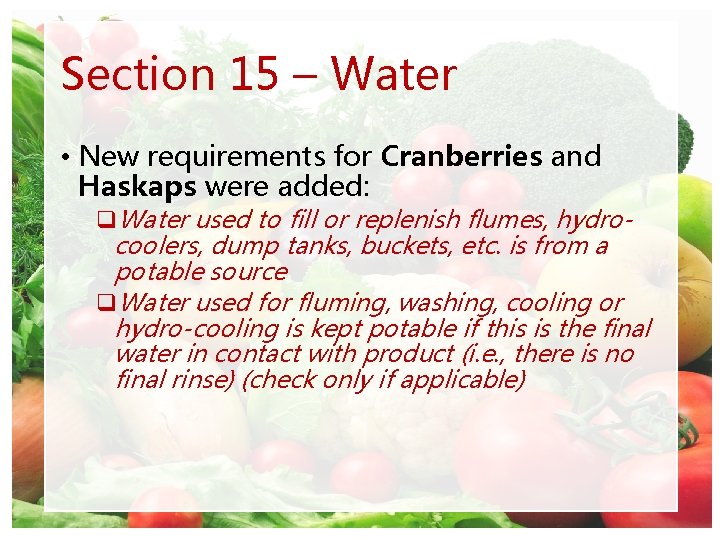
Section 15 – Water • New requirements for Cranberries and Haskaps were added: q. Water used to fill or replenish flumes, hydrocoolers, dump tanks, buckets, etc. is from a potable source q. Water used for fluming, washing, cooling or hydro-cooling is kept potable if this is the final water in contact with product (i. e. , there is no final rinse) (check only if applicable)
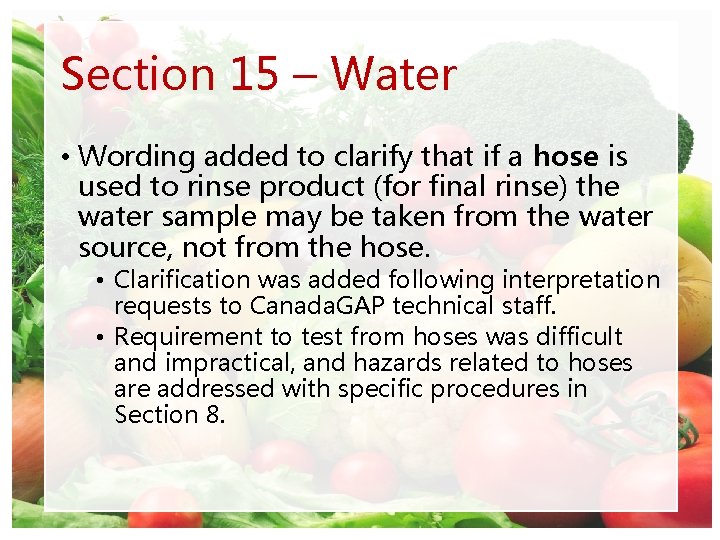
Section 15 – Water • Wording added to clarify that if a hose is used to rinse product (for final rinse) the water sample may be taken from the water source, not from the hose. • Clarification was added following interpretation requests to Canada. GAP technical staff. • Requirement to test from hoses was difficult and impractical, and hazards related to hoses are addressed with specific procedures in Section 8.
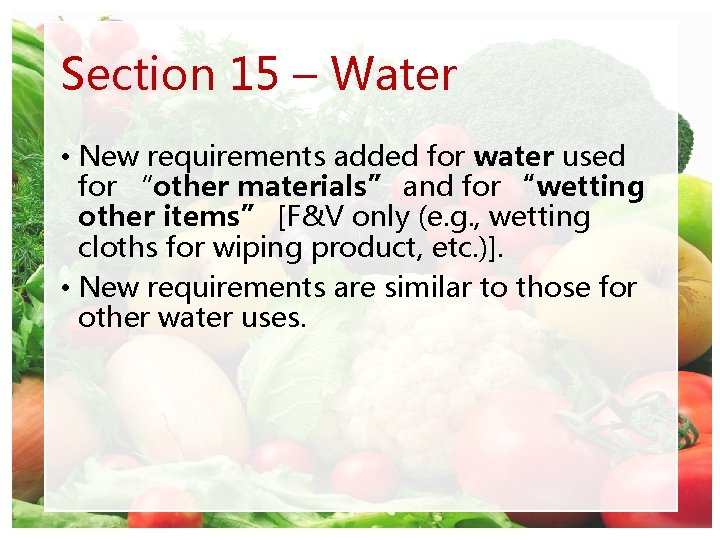
Section 15 – Water • New requirements added for water used for “other materials” and for “wetting other items” [F&V only (e. g. , wetting cloths for wiping product, etc. )]. • New requirements are similar to those for other water uses.
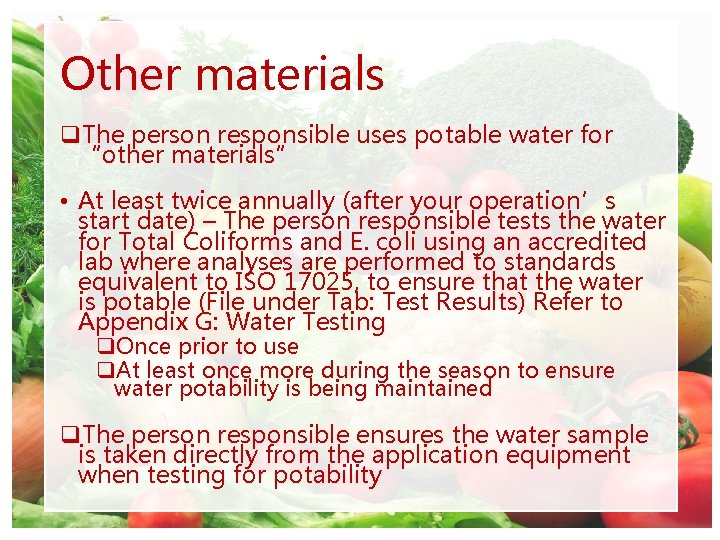
Other materials q. The person responsible uses potable water for “other materials” • At least twice annually (after your operation’s start date) – The person responsible tests the water for Total Coliforms and E. coli using an accredited lab where analyses are performed to standards equivalent to ISO 17025, to ensure that the water is potable (File under Tab: Test Results) Refer to Appendix G: Water Testing q. Once prior to use q. At least once more during the season to ensure water potability is being maintained q. The person responsible ensures the water sample is taken directly from the application equipment when testing for potability
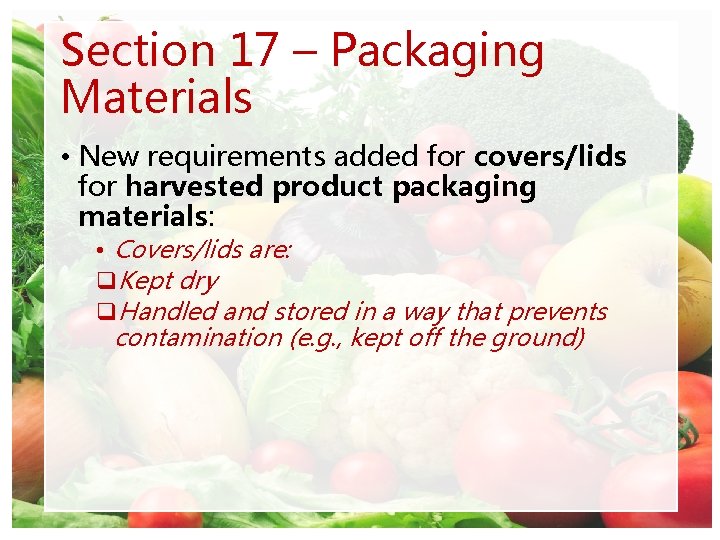
Section 17 – Packaging Materials • New requirements added for covers/lids for harvested product packaging materials: • Covers/lids are: q. Kept dry q. Handled and stored in a way that prevents contamination (e. g. , kept off the ground)
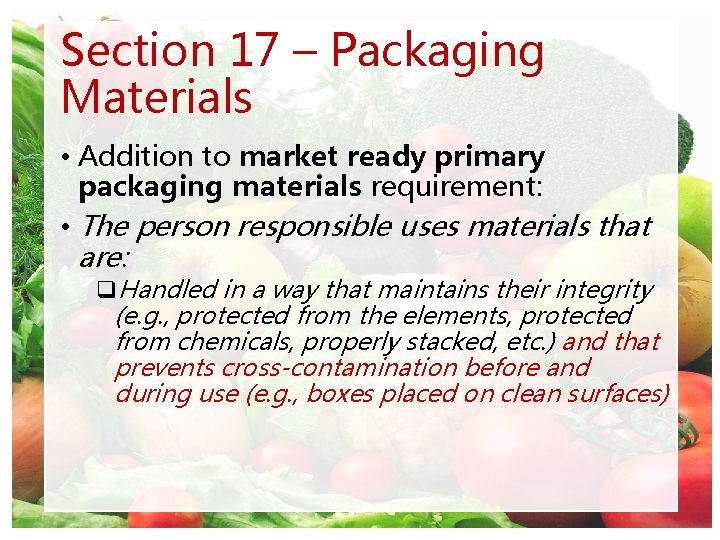
Section 17 – Packaging Materials • Addition to market ready primary packaging materials requirement: • The person responsible uses materials that are: q. Handled in a way that maintains their integrity (e. g. , protected from the elements, protected from chemicals, properly stacked, etc. ) and that prevents cross-contamination before and during use (e. g. , boxes placed on clean surfaces)
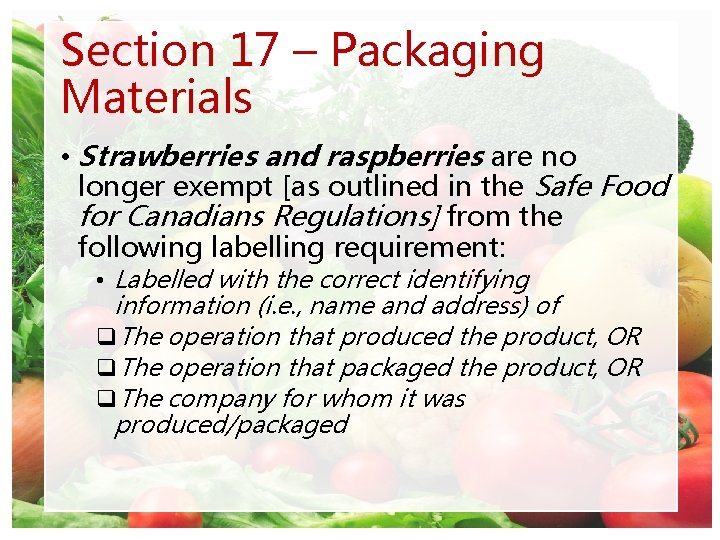
Section 17 – Packaging Materials • Strawberries and raspberries are no longer exempt [as outlined in the Safe Food for Canadians Regulations] from the following labelling requirement: • Labelled with the correct identifying information (i. e. , name and address) of q. The operation that produced the product, OR q. The operation that packaged the product, OR q. The company for whom it was produced/packaged
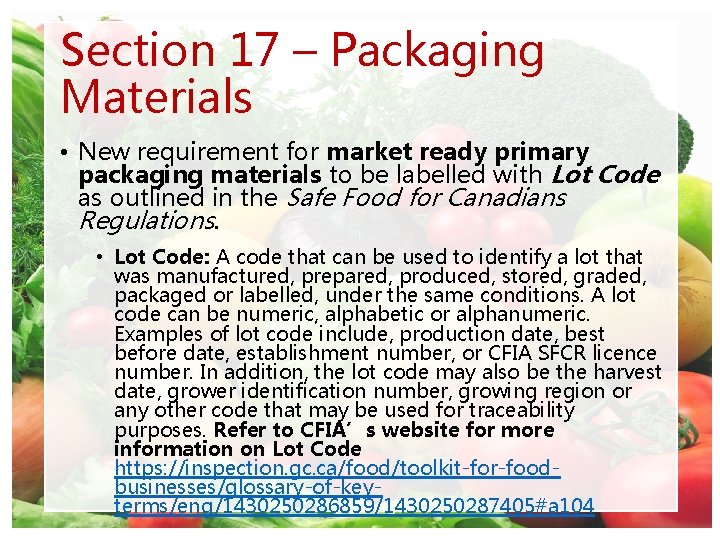
Section 17 – Packaging Materials • New requirement for market ready primary packaging materials to be labelled with Lot Code as outlined in the Safe Food for Canadians Regulations. • Lot Code: A code that can be used to identify a lot that was manufactured, prepared, produced, stored, graded, packaged or labelled, under the same conditions. A lot code can be numeric, alphabetic or alphanumeric. Examples of lot code include, production date, best before date, establishment number, or CFIA SFCR licence number. In addition, the lot code may also be the harvest date, grower identification number, growing region or any other code that may be used for traceability purposes. Refer to CFIA’s website for more information on Lot Code https: //inspection. gc. ca/food/toolkit-for-foodbusinesses/glossary-of-keyterms/eng/1430250286859/1430250287405#a 104
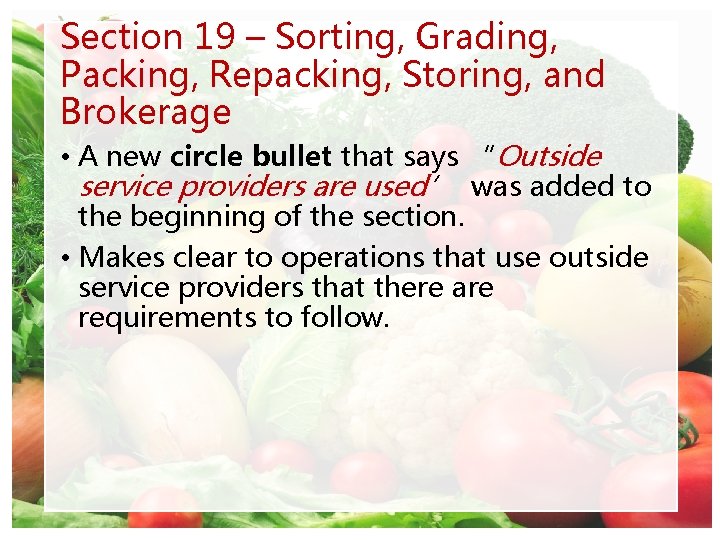
Section 19 – Sorting, Grading, Packing, Repacking, Storing, and Brokerage • A new circle bullet that says “Outside service providers are used’ was added to the beginning of the section. • Makes clear to operations that use outside service providers that there are requirements to follow.
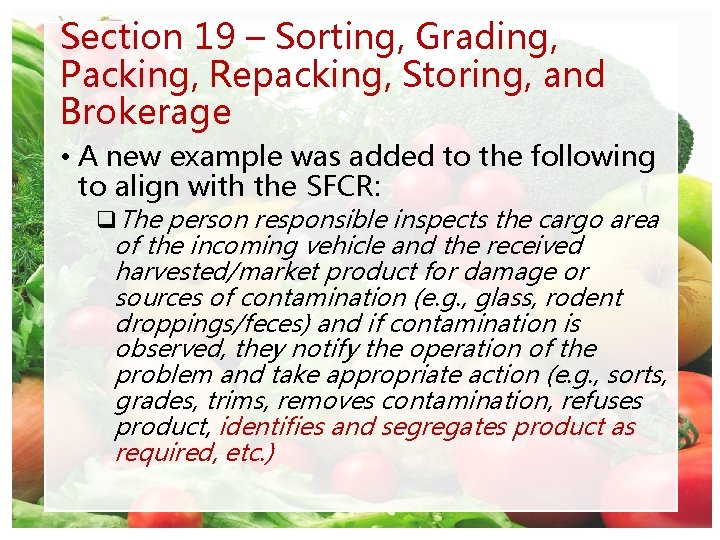
Section 19 – Sorting, Grading, Packing, Repacking, Storing, and Brokerage • A new example was added to the following to align with the SFCR: q. The person responsible inspects the cargo area of the incoming vehicle and the received harvested/market product for damage or sources of contamination (e. g. , glass, rodent droppings/feces) and if contamination is observed, they notify the operation of the problem and take appropriate action (e. g. , sorts, grades, trims, removes contamination, refuses product, identifies and segregates product as required, etc. )
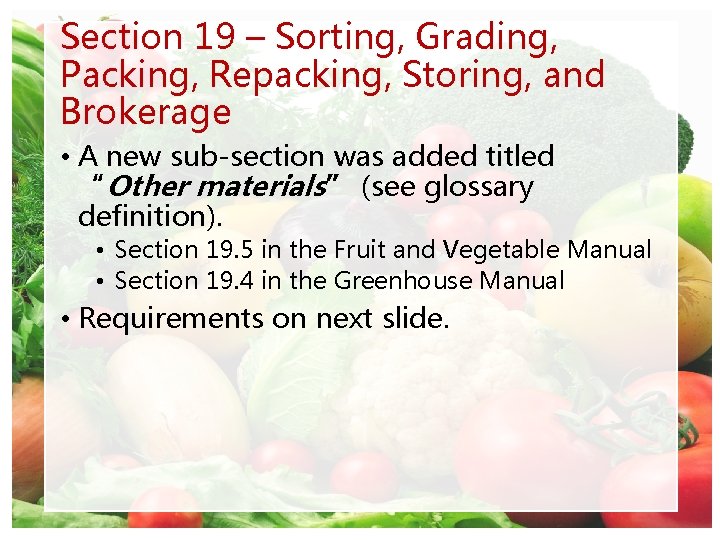
Section 19 – Sorting, Grading, Packing, Repacking, Storing, and Brokerage • A new sub-section was added titled “Other materials” (see glossary definition). • Section 19. 5 in the Fruit and Vegetable Manual • Section 19. 4 in the Greenhouse Manual • Requirements on next slide.
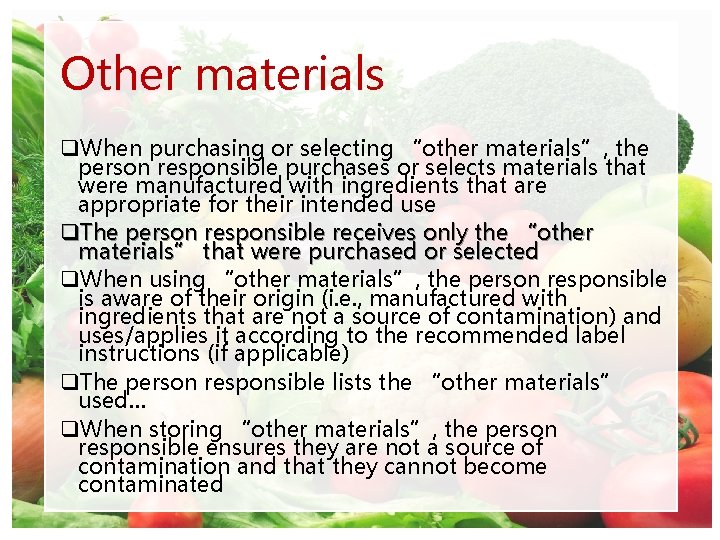
Other materials q. When purchasing or selecting “other materials”, the person responsible purchases or selects materials that were manufactured with ingredients that are appropriate for their intended use q. The person responsible receives only the “other materials” that were purchased or selected q. When using “other materials”, the person responsible is aware of their origin (i. e. , manufactured with ingredients that are not a source of contamination) and uses/applies it according to the recommended label instructions (if applicable) q. The person responsible lists the “other materials” used… q. When storing “other materials”, the person responsible ensures they are not a source of contamination and that they cannot become contaminated
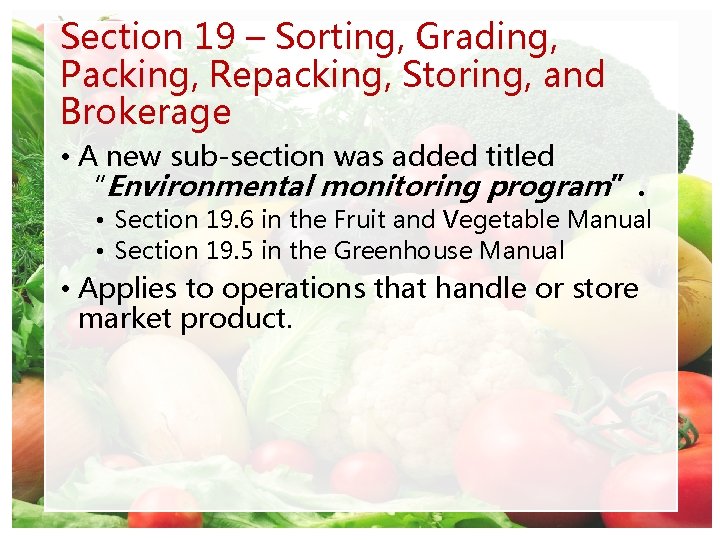
Section 19 – Sorting, Grading, Packing, Repacking, Storing, and Brokerage • A new sub-section was added titled “Environmental monitoring program”. • Section 19. 6 in the Fruit and Vegetable Manual • Section 19. 5 in the Greenhouse Manual • Applies to operations that handle or store market product.
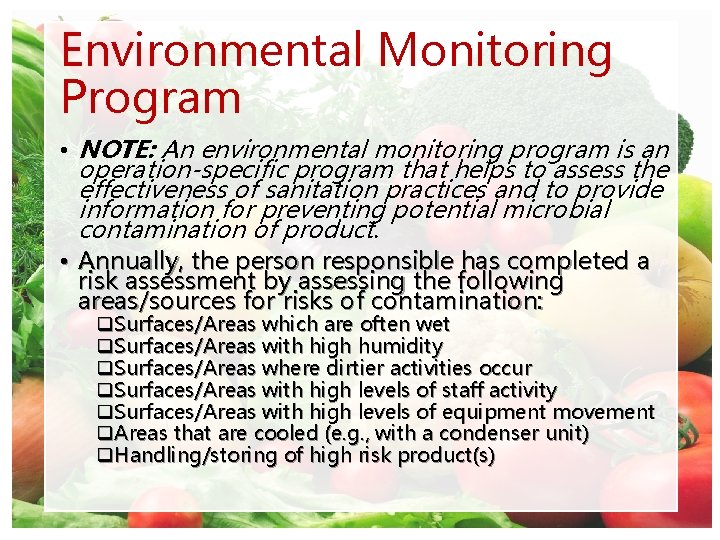
Environmental Monitoring Program • NOTE: An environmental monitoring program is an operation-specific program that helps to assess the effectiveness of sanitation practices and to provide information for preventing potential microbial contamination of product. • Annually, the person responsible has completed a risk assessment by assessing the following areas/sources for risks of contamination: q. Surfaces/Areas which are often wet q. Surfaces/Areas with high humidity q. Surfaces/Areas where dirtier activities occur q. Surfaces/Areas with high levels of staff activity q. Surfaces/Areas with high levels of equipment movement q. Areas that are cooled (e. g. , with a condenser unit) q. Handling/storing of high risk product(s)
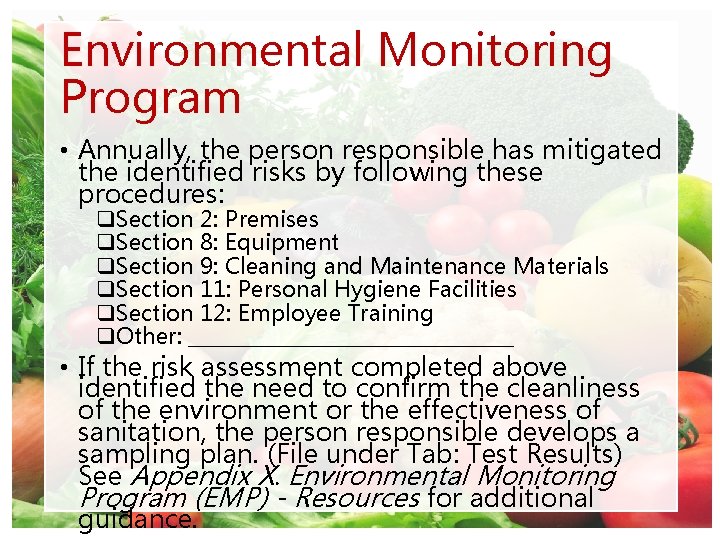
Environmental Monitoring Program • Annually, the person responsible has mitigated the identified risks by following these procedures: q. Section 2: Premises q. Section 8: Equipment q. Section 9: Cleaning and Maintenance Materials q. Section 11: Personal Hygiene Facilities q. Section 12: Employee Training q. Other: _________________ • If the risk assessment completed above identified the need to confirm the cleanliness of the environment or the effectiveness of sanitation, the person responsible develops a sampling plan. (File under Tab: Test Results) See Appendix X. Environmental Monitoring Program (EMP) - Resources for additional guidance.
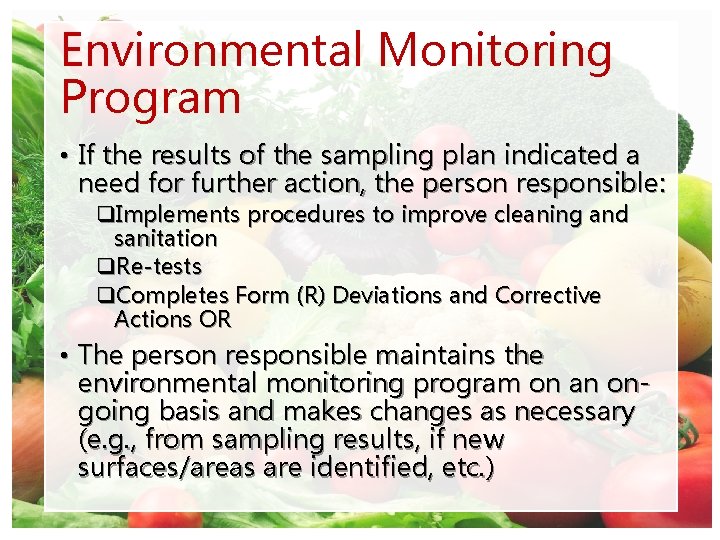
Environmental Monitoring Program • If the results of the sampling plan indicated a need for further action, the person responsible: q. Implements procedures to improve cleaning and sanitation q. Re-tests q. Completes Form (R) Deviations and Corrective Actions OR • The person responsible maintains the environmental monitoring program on an ongoing basis and makes changes as necessary (e. g. , from sampling results, if new surfaces/areas are identified, etc. )
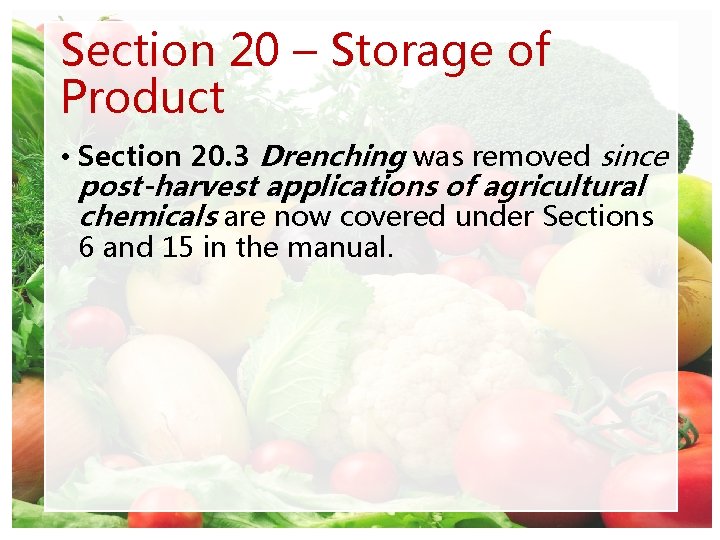
Section 20 – Storage of Product • Section 20. 3 Drenching was removed since post-harvest applications of agricultural chemicals are now covered under Sections 6 and 15 in the manual.
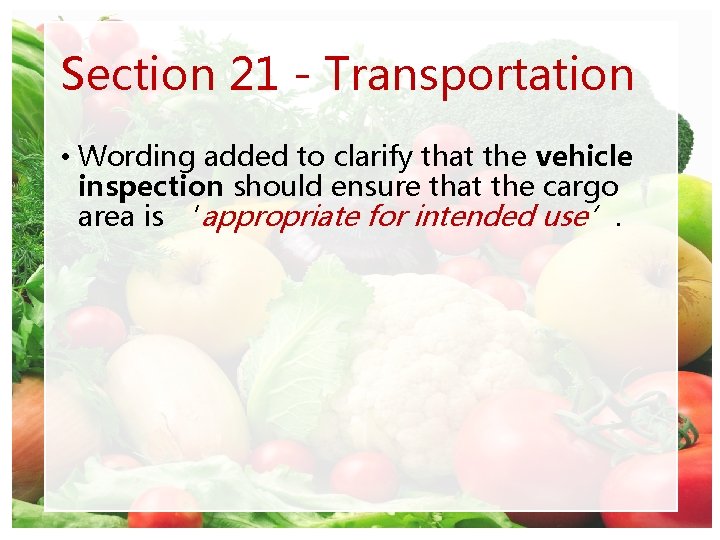
Section 21 - Transportation • Wording added to clarify that the vehicle inspection should ensure that the cargo area is ‘appropriate for intended use’.
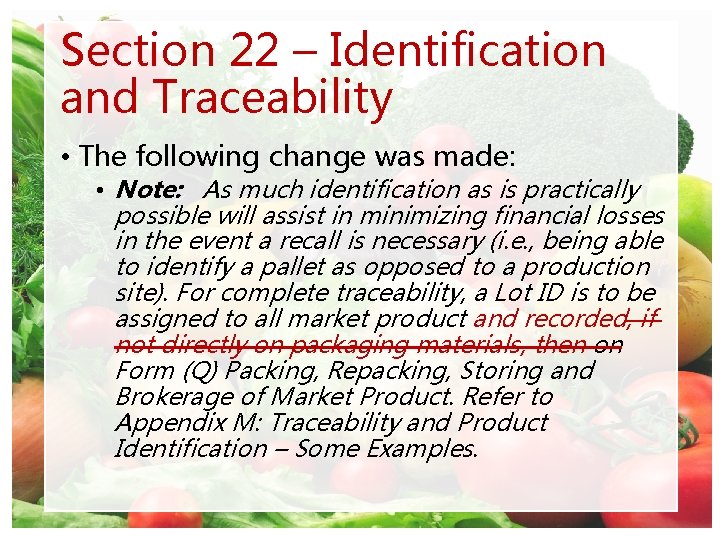
Section 22 – Identification and Traceability • The following change was made: • Note: As much identification as is practically possible will assist in minimizing financial losses in the event a recall is necessary (i. e. , being able to identify a pallet as opposed to a production site). For complete traceability, a Lot ID is to be assigned to all market product and recorded, if not directly on packaging materials, then on Form (Q) Packing, Repacking, Storing and Brokerage of Market Product. Refer to Appendix M: Traceability and Product Identification – Some Examples.
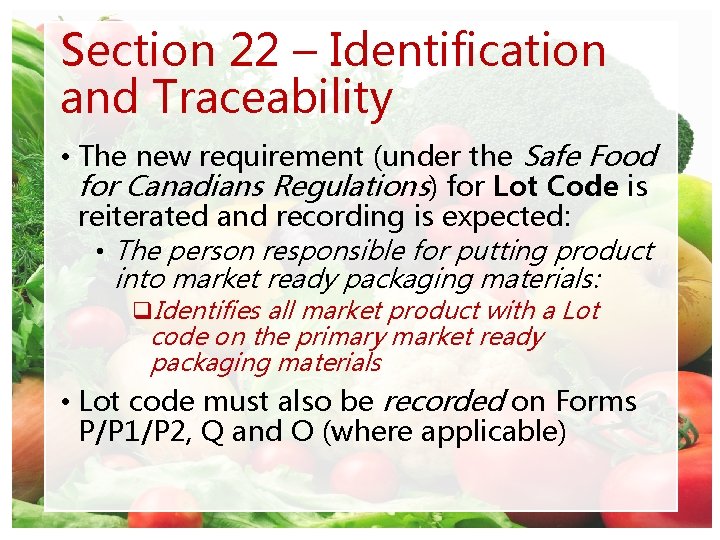
Section 22 – Identification and Traceability • The new requirement (under the Safe Food for Canadians Regulations) for Lot Code is reiterated and recording is expected: • The person responsible for putting product into market ready packaging materials: q. Identifies all market product with a Lot code on the primary market ready packaging materials • Lot code must also be recorded on Forms P/P 1/P 2, Q and O (where applicable)
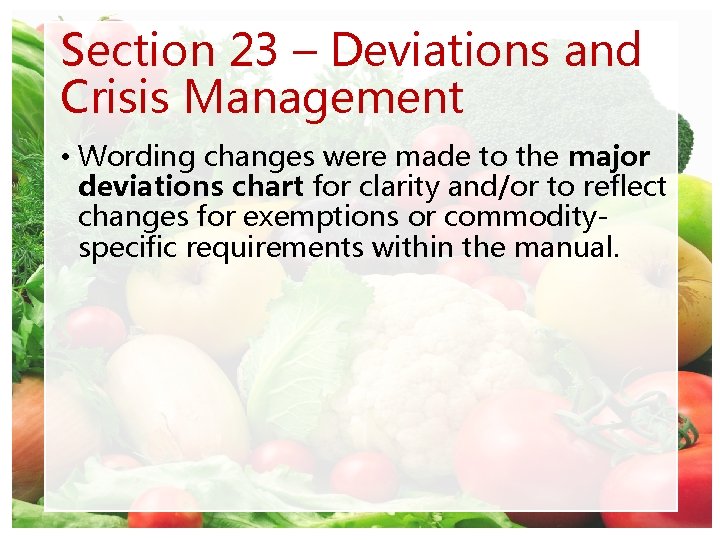
Section 23 – Deviations and Crisis Management • Wording changes were made to the major deviations chart for clarity and/or to reflect changes for exemptions or commodityspecific requirements within the manual.
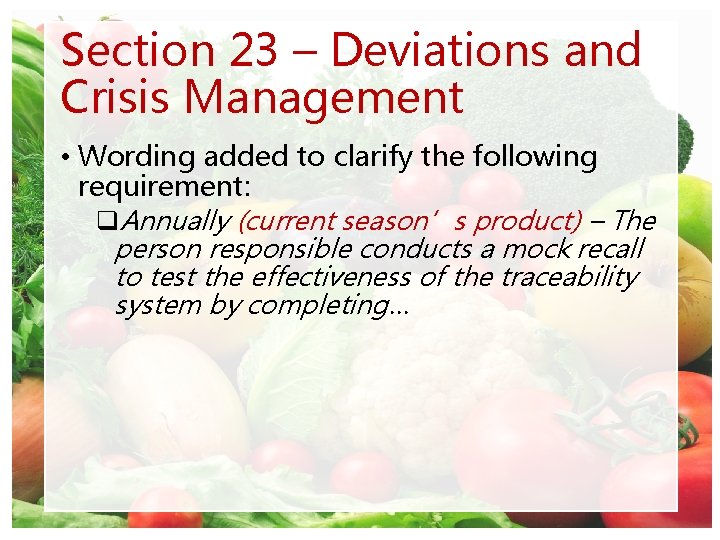
Section 23 – Deviations and Crisis Management • Wording added to clarify the following requirement: q. Annually (current season’s product) – The person responsible conducts a mock recall to test the effectiveness of the traceability system by completing…
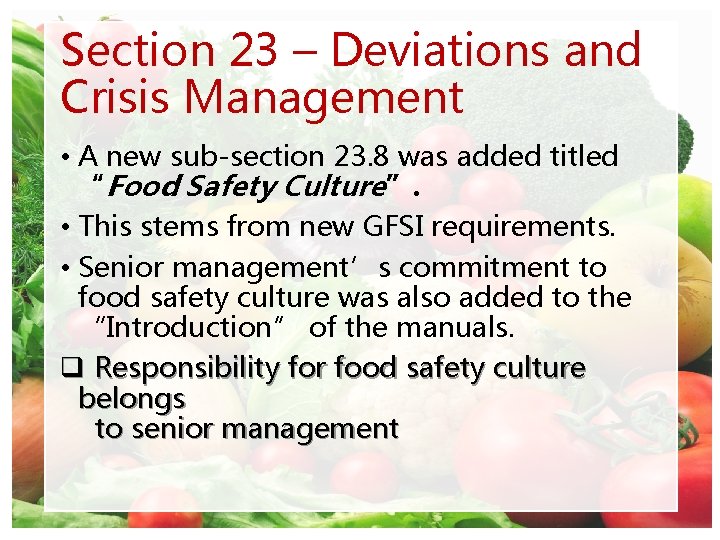
Section 23 – Deviations and Crisis Management • A new sub-section 23. 8 was added titled “Food Safety Culture”. • This stems from new GFSI requirements. • Senior management’s commitment to food safety culture was also added to the “Introduction” of the manuals. q Responsibility for food safety culture belongs to senior management
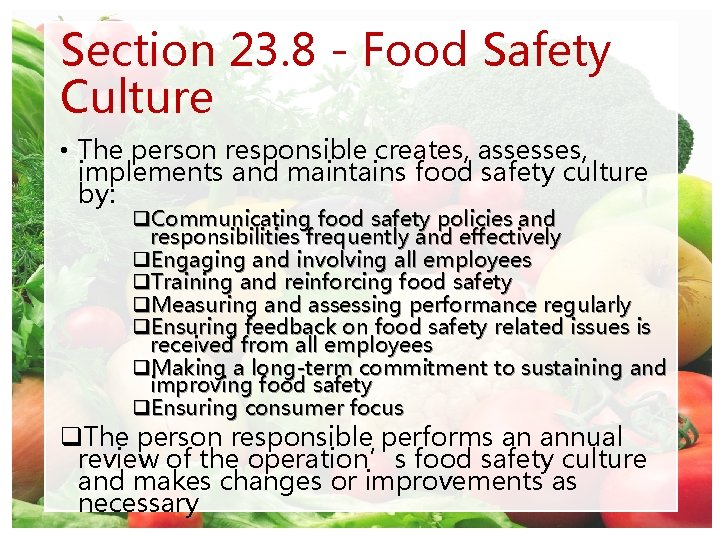
Section 23. 8 - Food Safety Culture • The person responsible creates, assesses, implements and maintains food safety culture by: q. Communicating food safety policies and responsibilities frequently and effectively q. Engaging and involving all employees q. Training and reinforcing food safety q. Measuring and assessing performance regularly q. Ensuring feedback on food safety related issues is received from all employees q. Making a long-term commitment to sustaining and improving food safety q. Ensuring consumer focus q. The person responsible performs an annual review of the operation’s food safety culture and makes changes or improvements as necessary
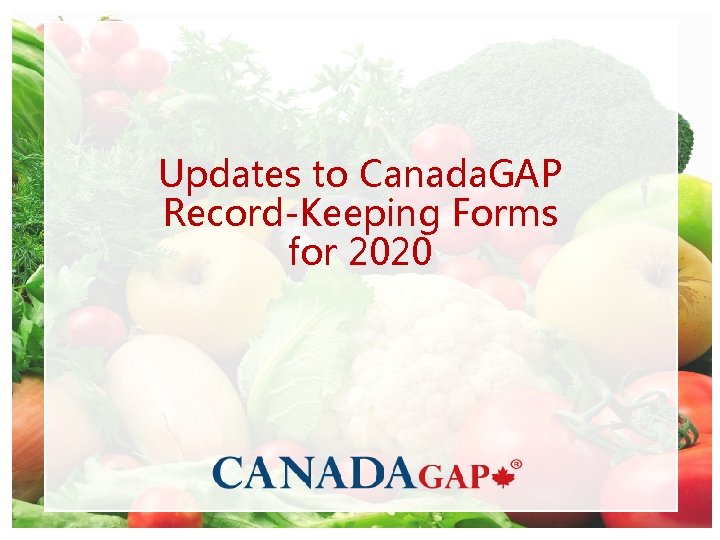
Updates to Canada. GAP Record-Keeping Forms for 2020
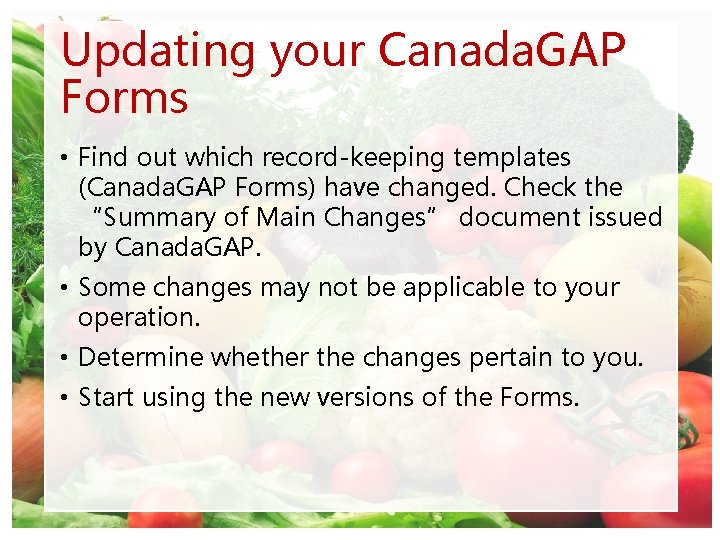
Updating your Canada. GAP Forms • Find out which record-keeping templates (Canada. GAP Forms) have changed. Check the “Summary of Main Changes” document issued by Canada. GAP. • Some changes may not be applicable to your operation. • Determine whether the changes pertain to you. • Start using the new versions of the Forms.
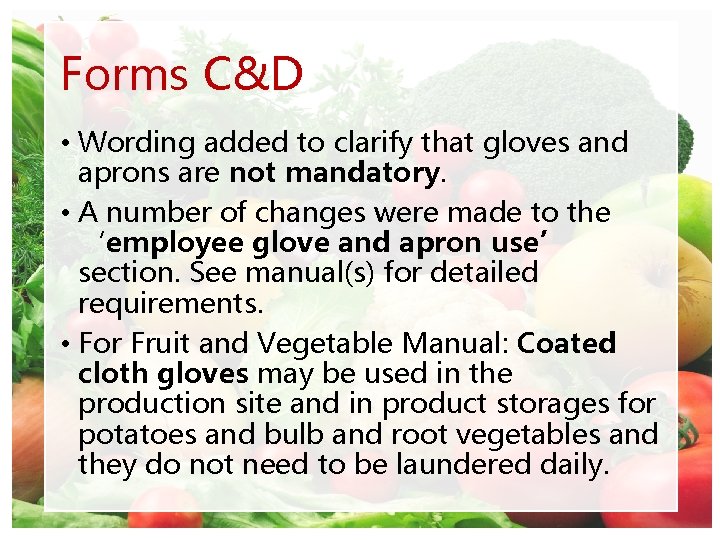
Forms C&D • Wording added to clarify that gloves and aprons are not mandatory. • A number of changes were made to the ‘employee glove and apron use’ section. See manual(s) for detailed requirements. • For Fruit and Vegetable Manual: Coated cloth gloves may be used in the production site and in product storages for potatoes and bulb and root vegetables and they do not need to be laundered daily.
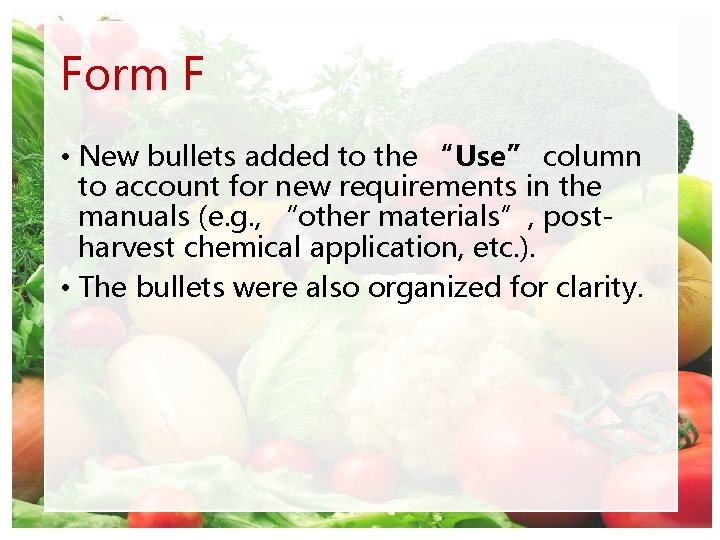
Form F • New bullets added to the “Use” column to account for new requirements in the manuals (e. g. , “other materials”, postharvest chemical application, etc. ). • The bullets were also organized for clarity.
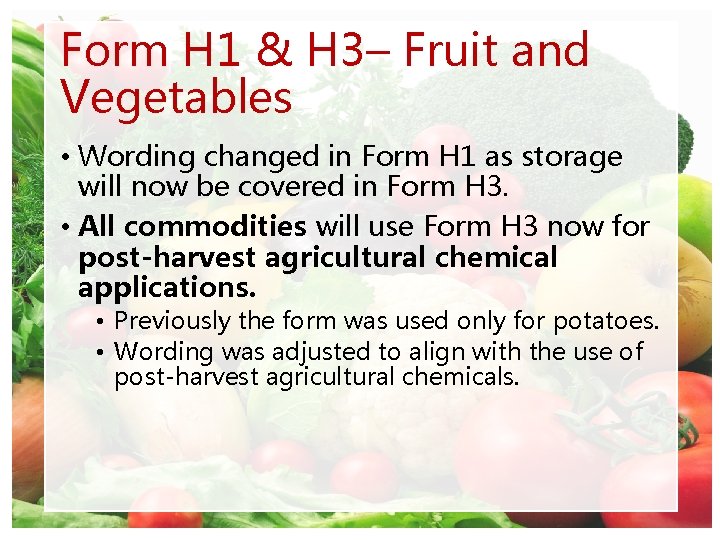
Form H 1 & H 3– Fruit and Vegetables • Wording changed in Form H 1 as storage will now be covered in Form H 3. • All commodities will use Form H 3 now for post-harvest agricultural chemical applications. • Previously the form was used only for potatoes. • Wording was adjusted to align with the use of post-harvest agricultural chemicals.
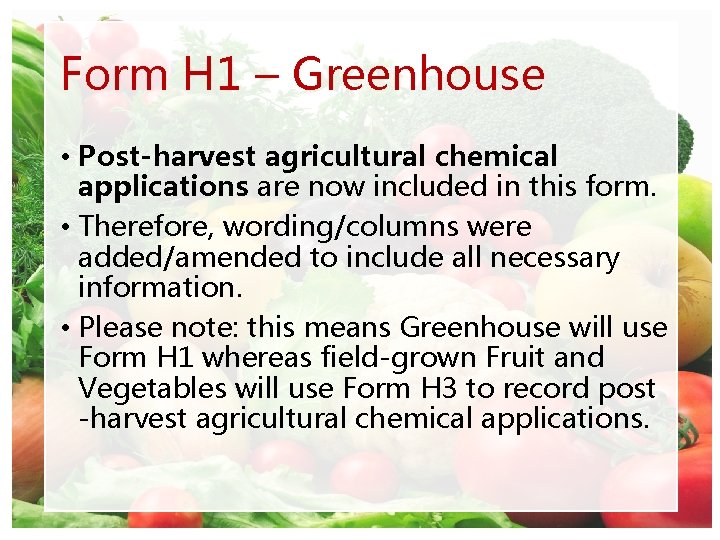
Form H 1 – Greenhouse • Post-harvest agricultural chemical applications are now included in this form. • Therefore, wording/columns were added/amended to include all necessary information. • Please note: this means Greenhouse will use Form H 1 whereas field-grown Fruit and Vegetables will use Form H 3 to record post -harvest agricultural chemical applications.
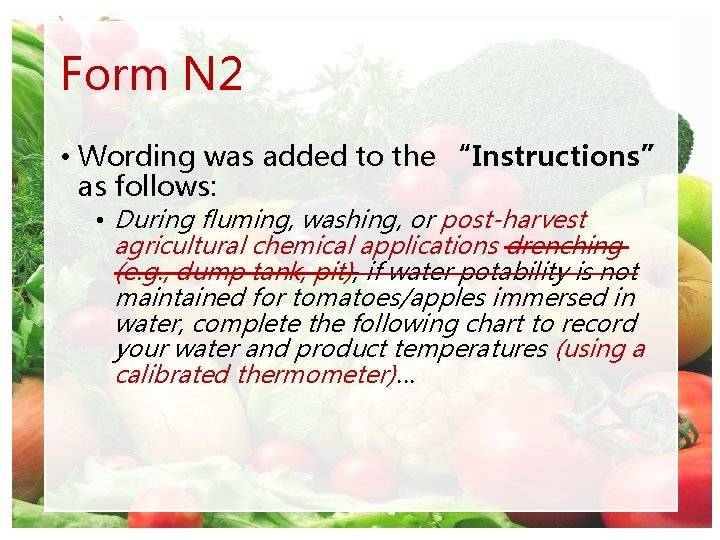
Form N 2 • Wording was added to the “Instructions” as follows: • During fluming, washing, or post-harvest agricultural chemical applications drenching (e. g. , dump tank, pit), if water potability is not maintained for tomatoes/apples immersed in water, complete the following chart to record your water and product temperatures (using a calibrated thermometer)…
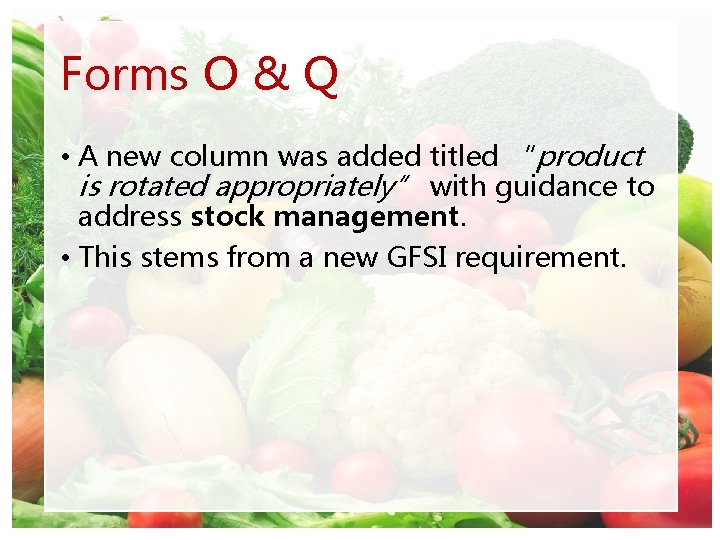
Forms O & Q • A new column was added titled “product is rotated appropriately” with guidance to address stock management. • This stems from a new GFSI requirement.
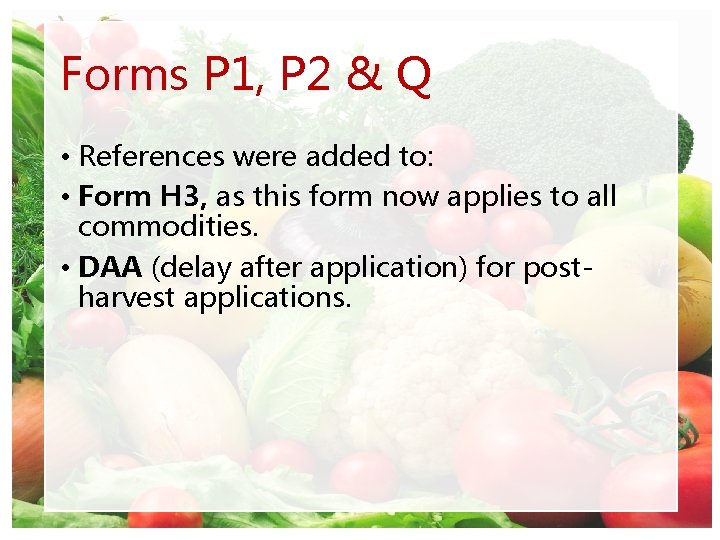
Forms P 1, P 2 & Q • References were added to: • Form H 3, as this form now applies to all commodities. • DAA (delay after application) for postharvest applications.
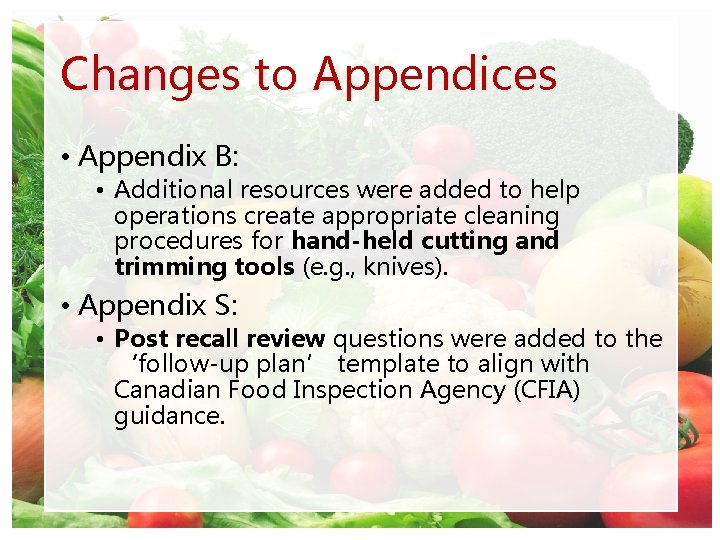
Changes to Appendices • Appendix B: • Additional resources were added to help operations create appropriate cleaning procedures for hand-held cutting and trimming tools (e. g. , knives). • Appendix S: • Post recall review questions were added to the ‘follow-up plan’ template to align with Canadian Food Inspection Agency (CFIA) guidance.
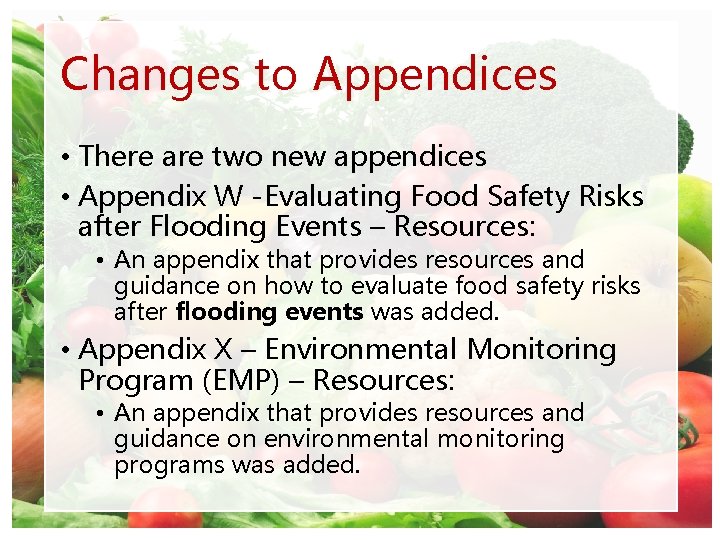
Changes to Appendices • There are two new appendices • Appendix W -Evaluating Food Safety Risks after Flooding Events – Resources: • An appendix that provides resources and guidance on how to evaluate food safety risks after flooding events was added. • Appendix X – Environmental Monitoring Program (EMP) – Resources: • An appendix that provides resources and guidance on environmental monitoring programs was added.
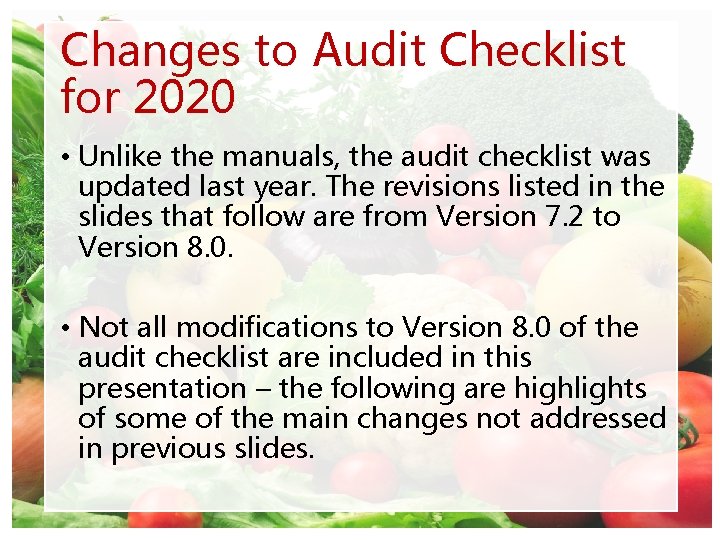
Changes to Audit Checklist for 2020 • Unlike the manuals, the audit checklist was updated last year. The revisions listed in the slides that follow are from Version 7. 2 to Version 8. 0. • Not all modifications to Version 8. 0 of the audit checklist are included in this presentation – the following are highlights of some of the main changes not addressed in previous slides.
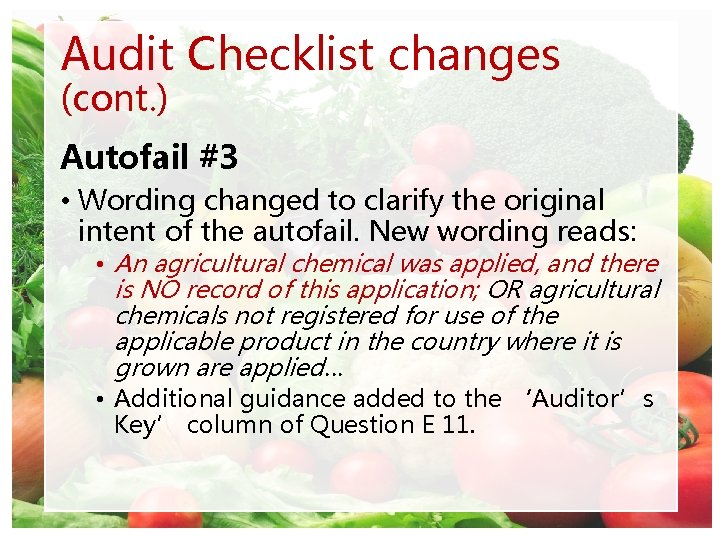
Audit Checklist changes (cont. ) Autofail #3 • Wording changed to clarify the original intent of the autofail. New wording reads: • An agricultural chemical was applied, and there is NO record of this application; OR agricultural chemicals not registered for use of the applicable product in the country where it is grown are applied… • Additional guidance added to the ‘Auditor’s Key’ column of Question E 11.
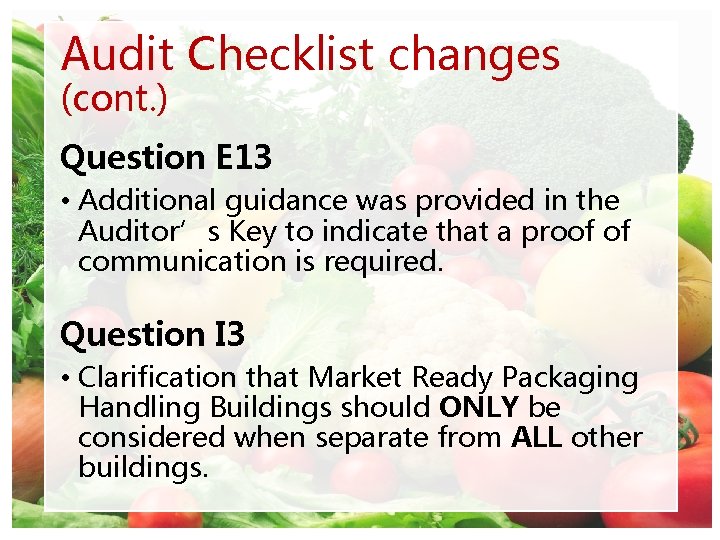
Audit Checklist changes (cont. ) Question E 13 • Additional guidance was provided in the Auditor’s Key to indicate that a proof of communication is required. Question I 3 • Clarification that Market Ready Packaging Handling Buildings should ONLY be considered when separate from ALL other buildings.
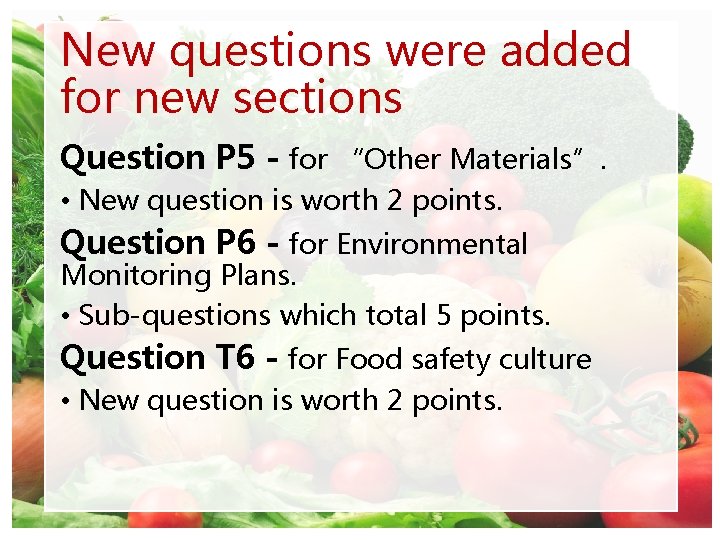
New questions were added for new sections Question P 5 - for “Other Materials”. • New question is worth 2 points. Question P 6 - for Environmental Monitoring Plans. • Sub-questions which total 5 points. Question T 6 - for Food safety culture • New question is worth 2 points.
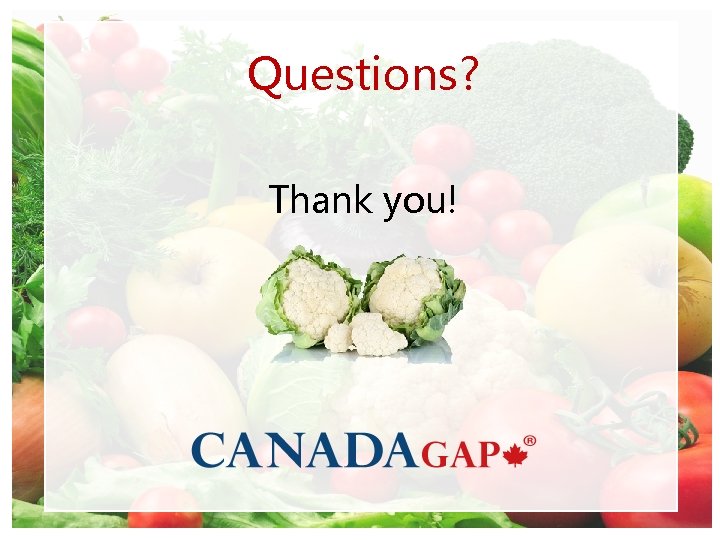
Questions? Thank you!
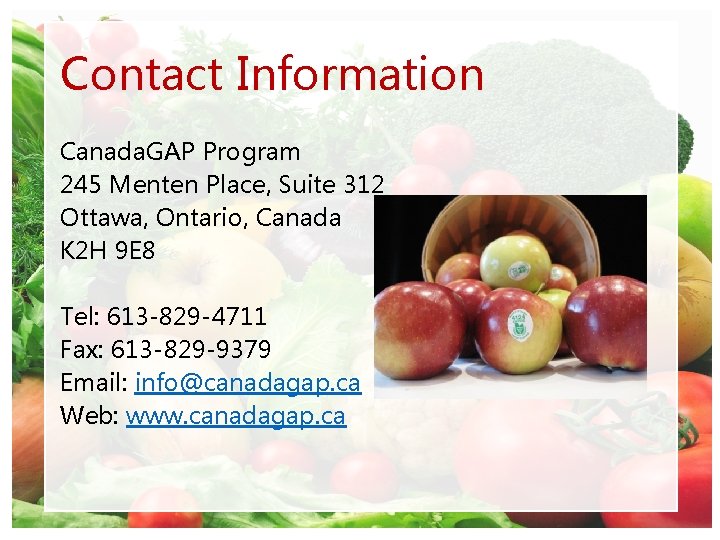
Contact Information Canada. GAP Program 245 Menten Place, Suite 312 Ottawa, Ontario, Canada K 2 H 9 E 8 Tel: 613 -829 -4711 Fax: 613 -829 -9379 Email: info@canadagap. ca Web: www. canadagap. ca
Canada gap forms
Electronic service manuals
Ca idms manuals
Ev 7300
Toastmasters successful club series
Nieco broiler burger king
Codes and manuals
Elizabeth mulroney
Physical change example
Food safety food security
Bir necha ergash gapli qo'shma gap
A_______ bridges the specification gap between two pls.
Unit 2 food food food
Grazing food chain diagram
Motor vehicle safety regulations
Transport canada safety management system
Historical changes to food availability in australia
Food test chart
Eer formula
Food recalls canada
Present expressing future
Tell more about the main idea
Void main int main
Four shades function for the encs
Safety care 2 person stability hold
Process safety vs personal safety
Ind safety report
Basic safety construction site safety orientation
Construction site safety orientation
Main sources of food
Main sources of food
Main source of food
Foodinsight.org
Savvy food safety
Test strips for food safety
Reinstated food handler
Safe plates module 2
Food safety management system template
Food safety training in dubai
Lesson 4 nutrition labels and food safety
Questions and answers for food safety
Define food safety
Safe stand for in food
Food safety standards
Chocolate food safety
Food safety regulations and standards
Chapter 10: nutrition for health lesson 1 answer key
Chapter 10 lesson 4 nutrition labels and food safety
Tcs in food safety
Canadian supply chain food safety coalition
Tcs food
4 c's of food safety
Module 1 introduction to food safety
Sitxfsa001a
Implement food safety procedures
Incidental additives examples
Food safety controls
Hot holding temperature in dubai
Food safety controls
Chapter 19 food safety and storage
Fs22000
Virginia department of agriculture food safety
Time as a public health control example
Prp food safety
Food safety from farm to table
Data driven food safety
Food safety assurance