Introductions Lean knowledge or experience No prior experience
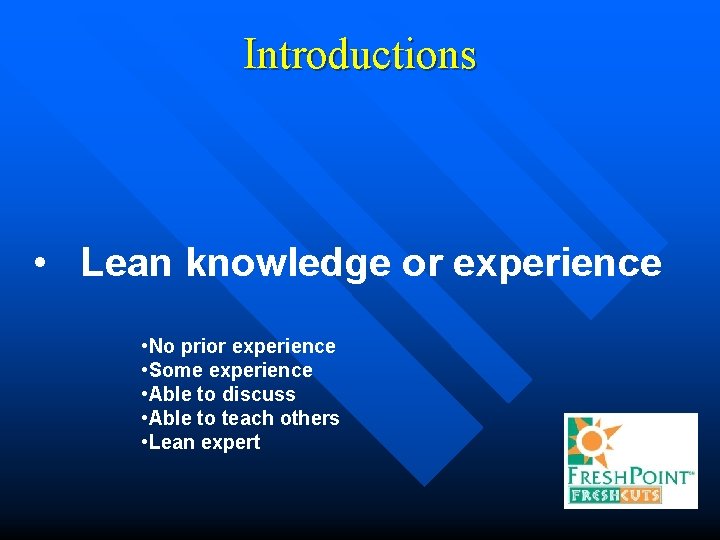
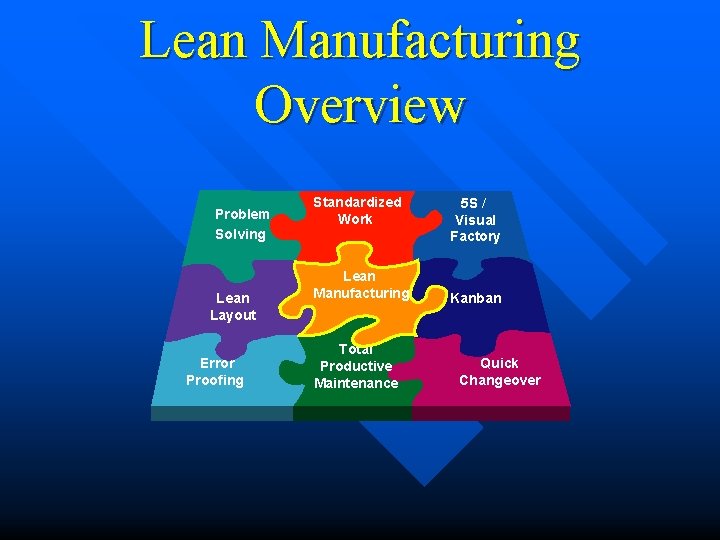
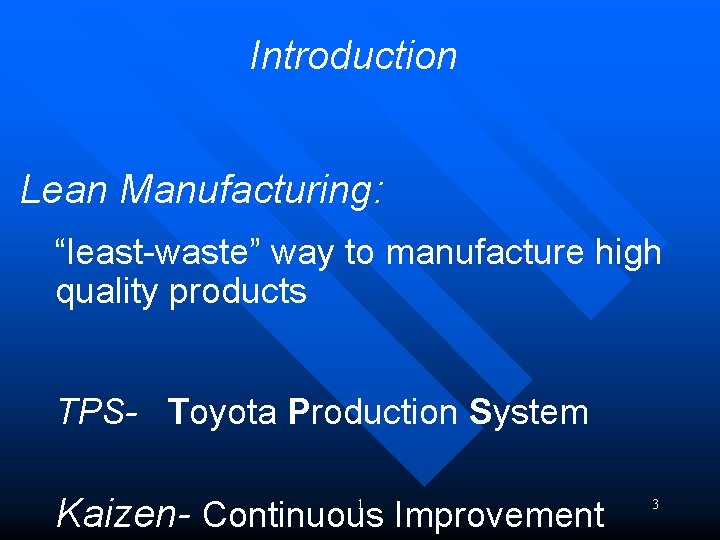
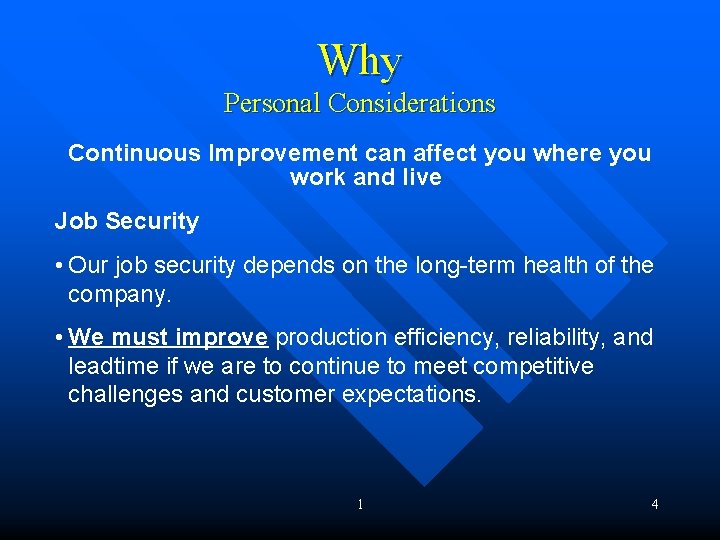
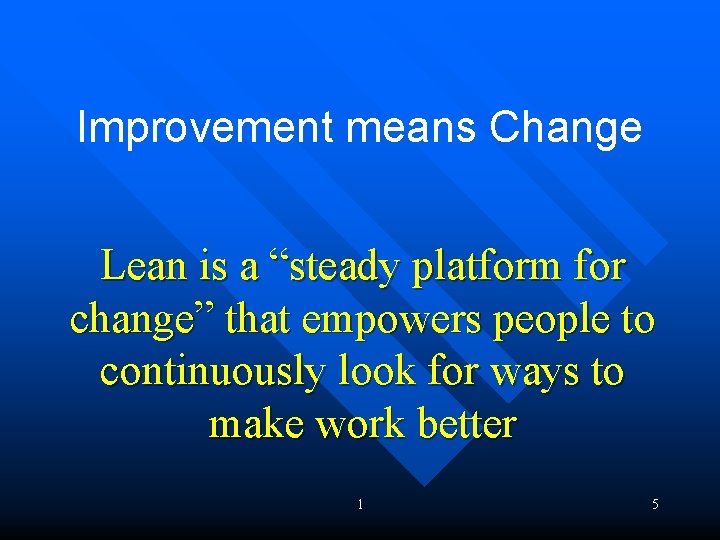
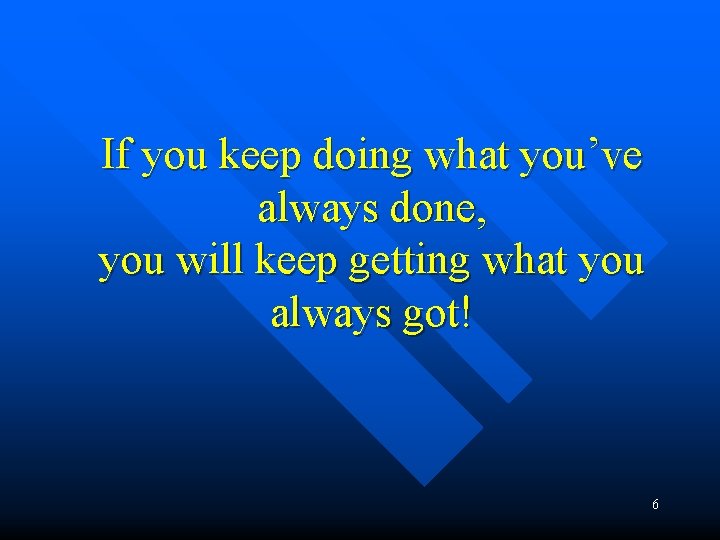
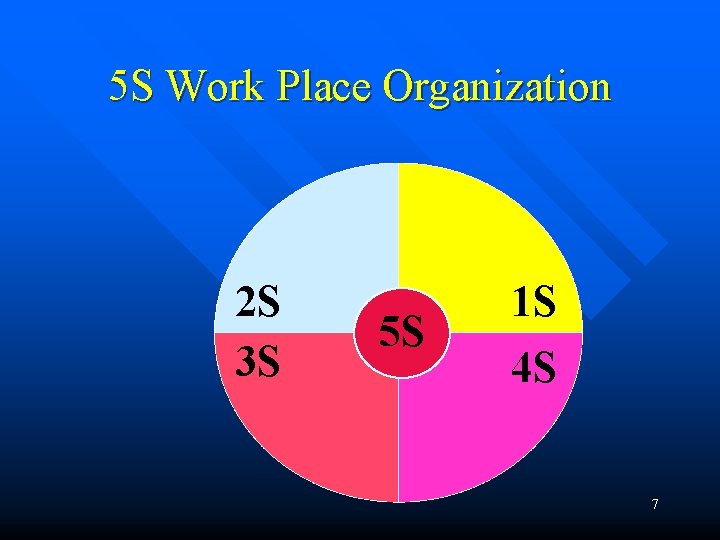
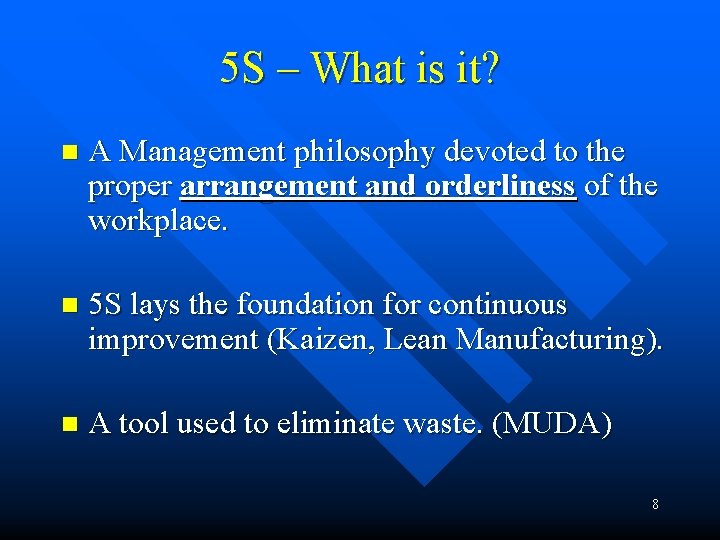
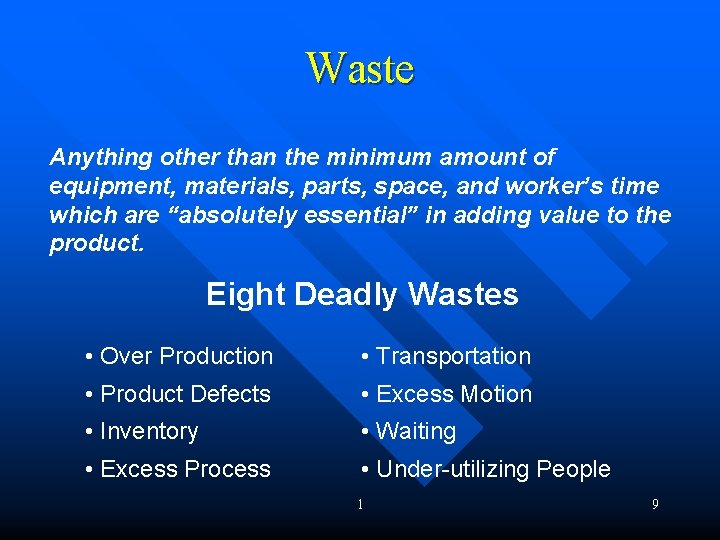
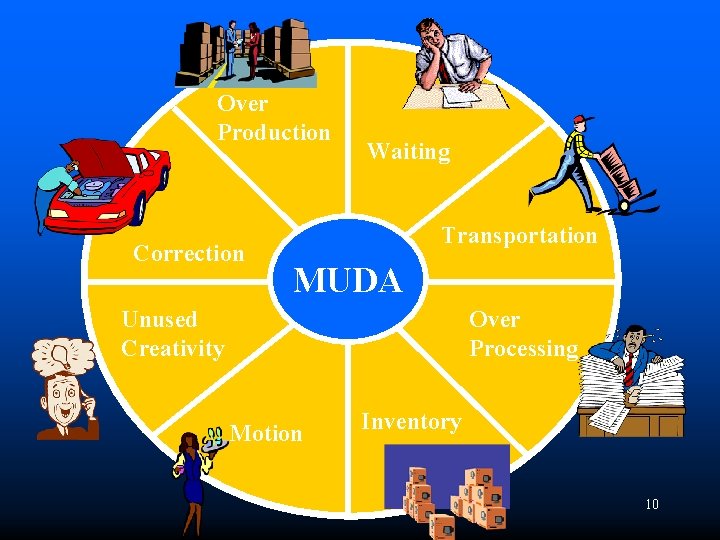
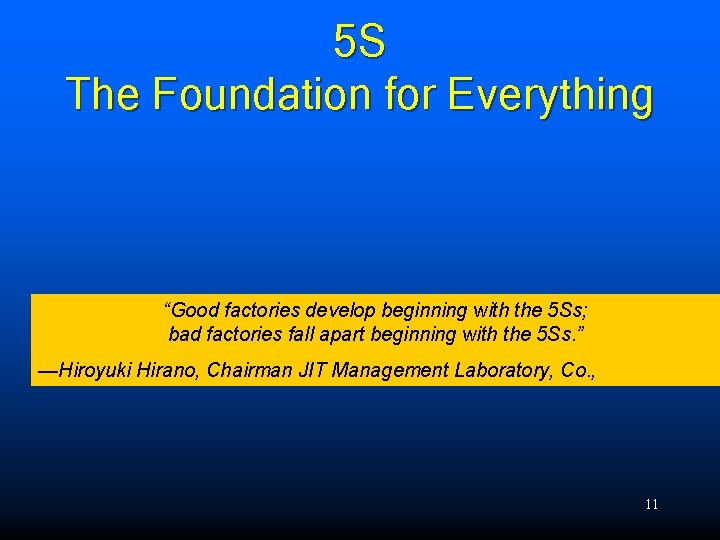
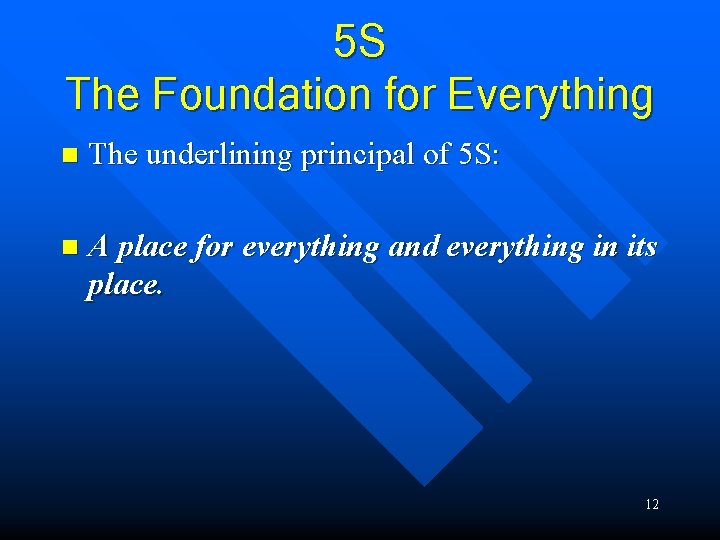
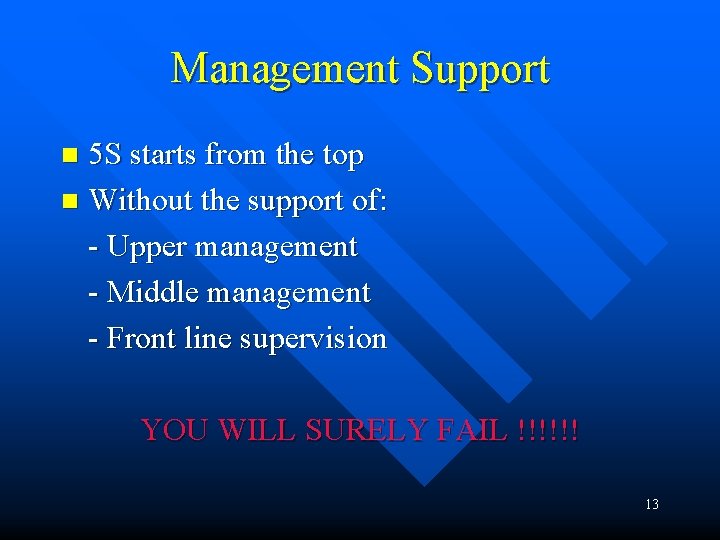
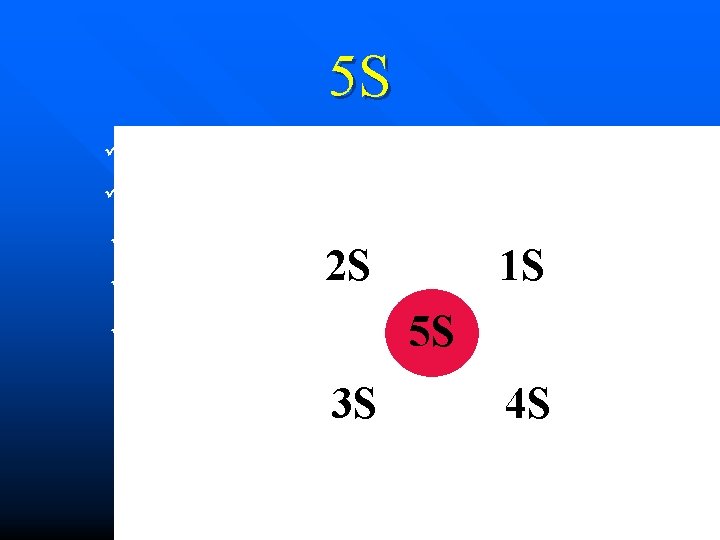
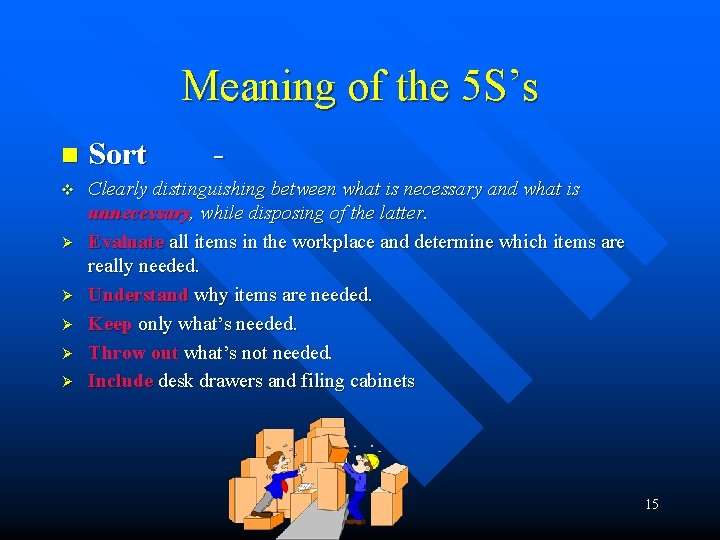
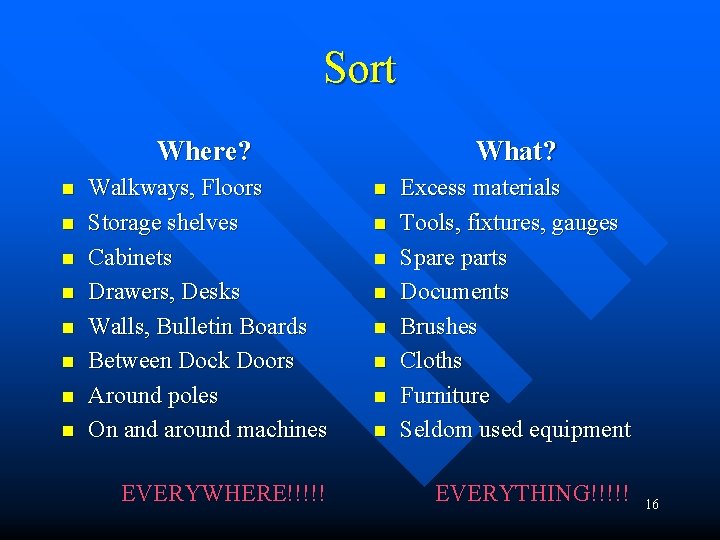
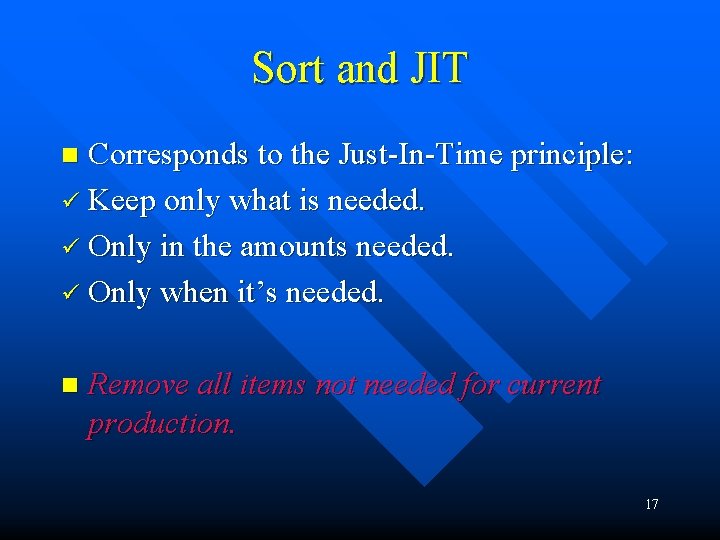
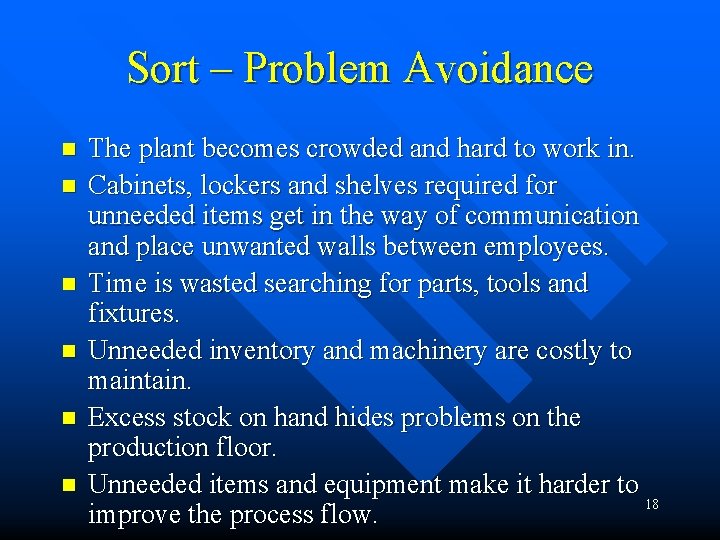
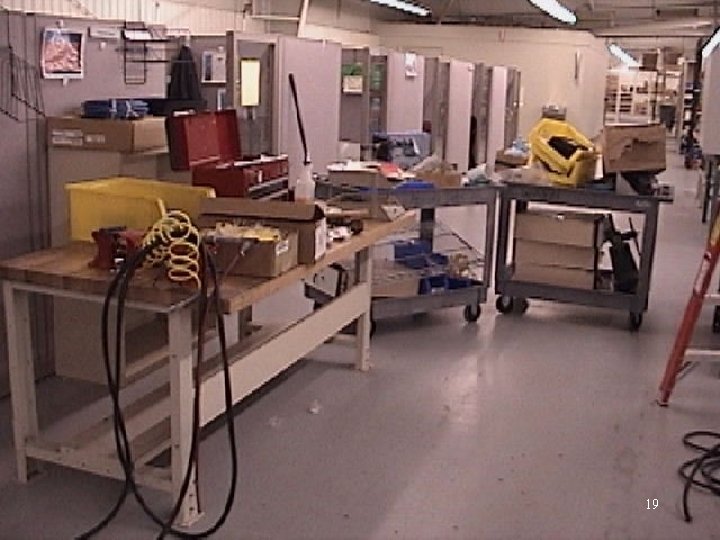
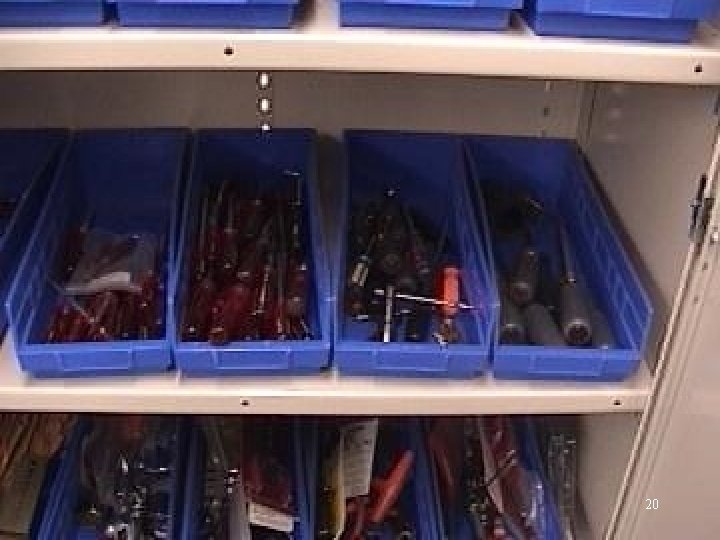
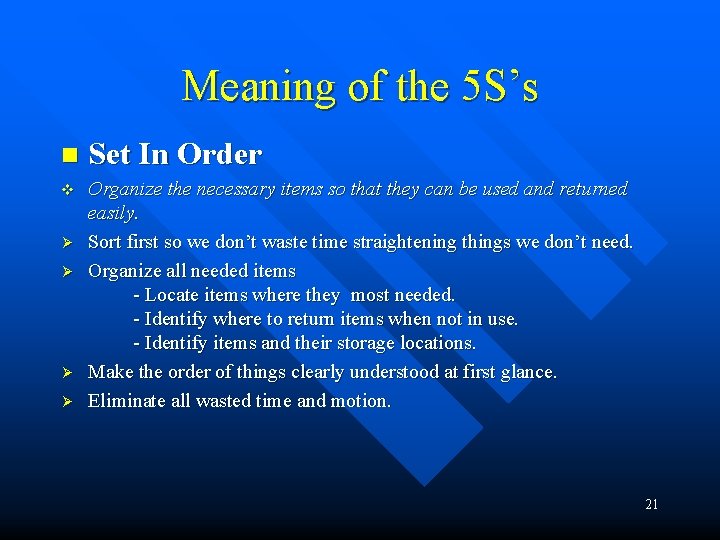
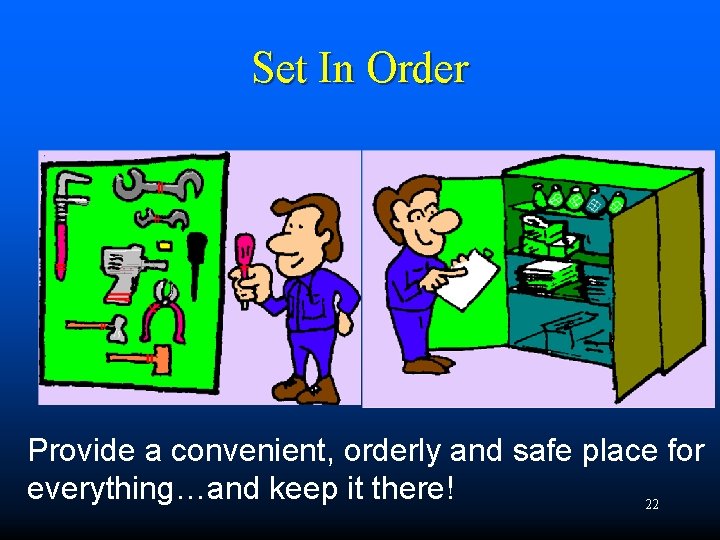
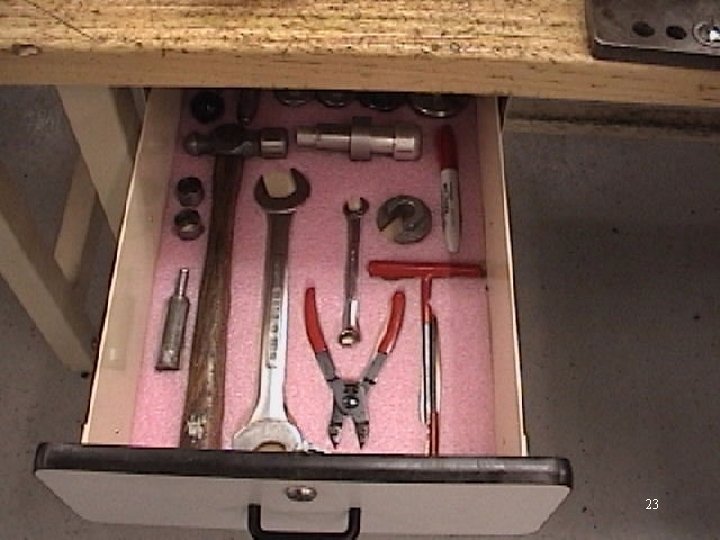
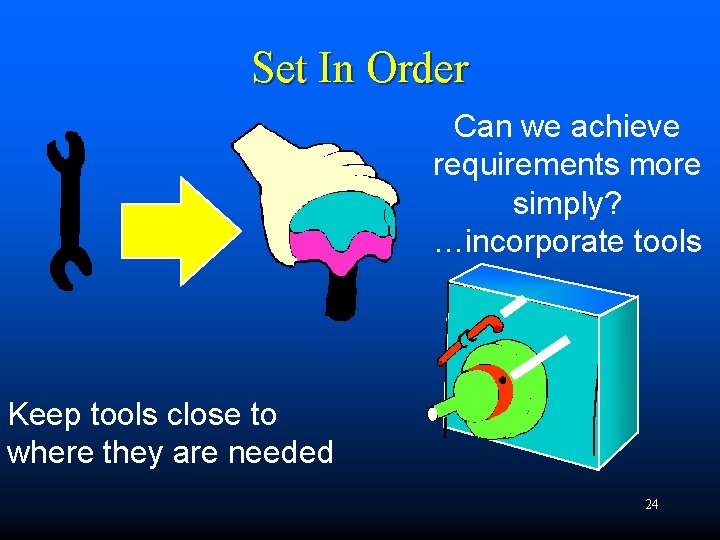
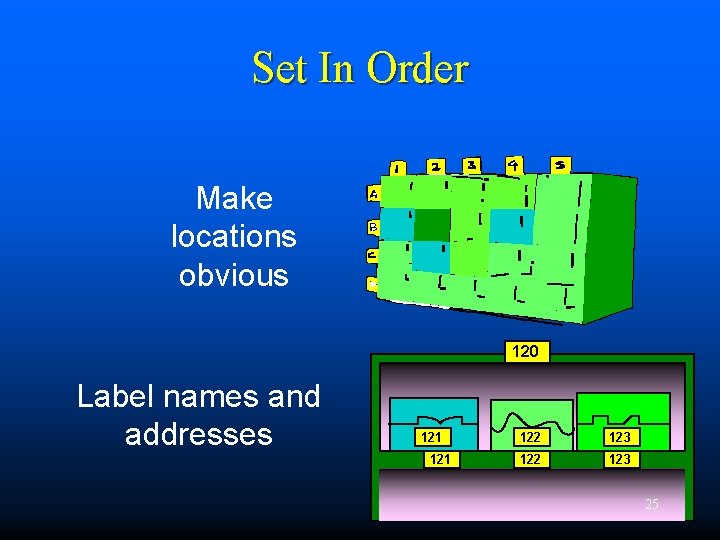
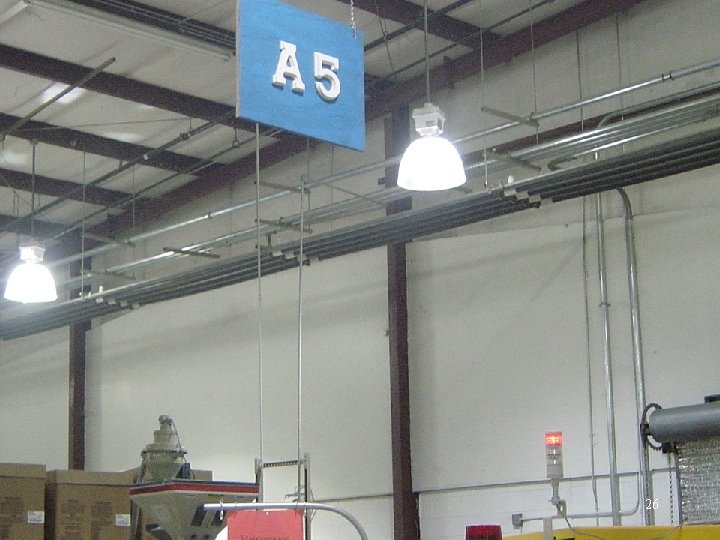
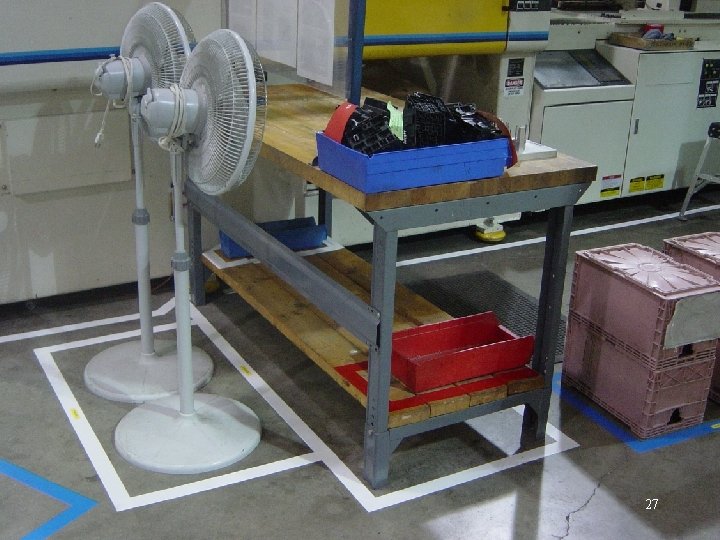
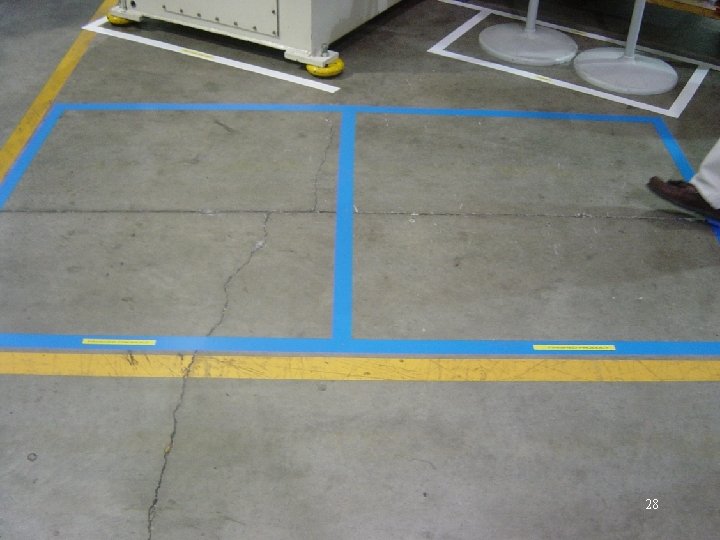
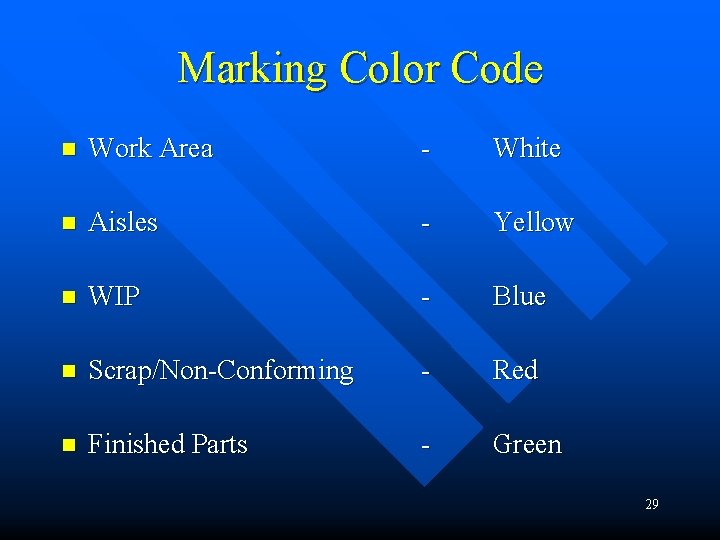
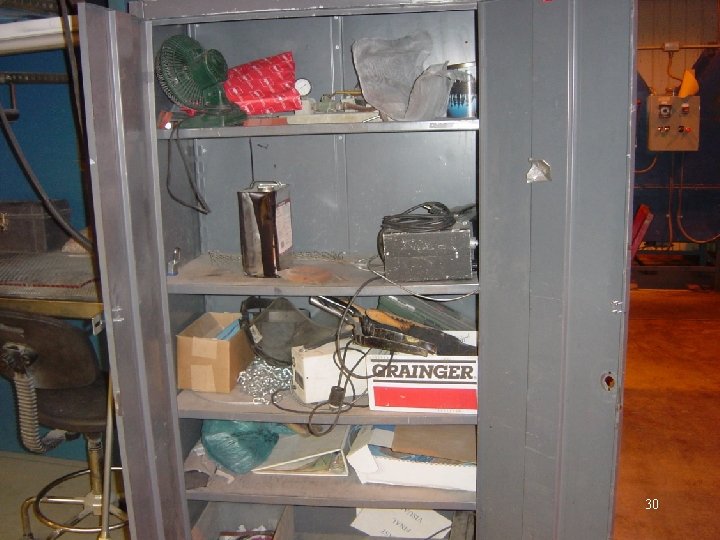
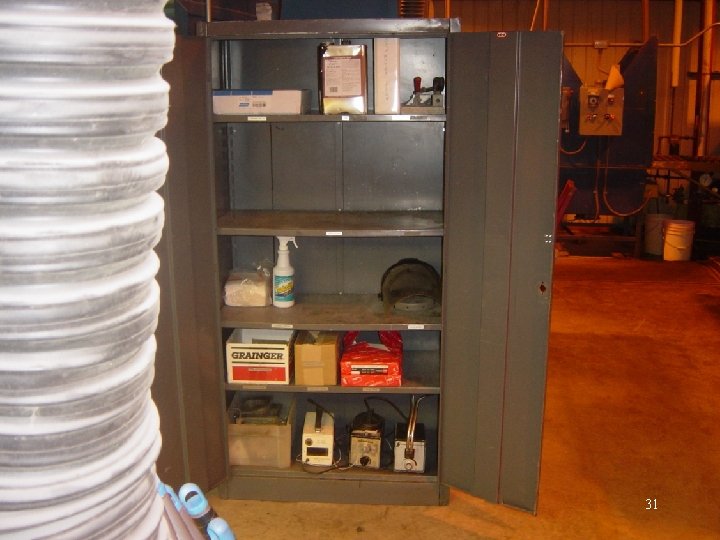
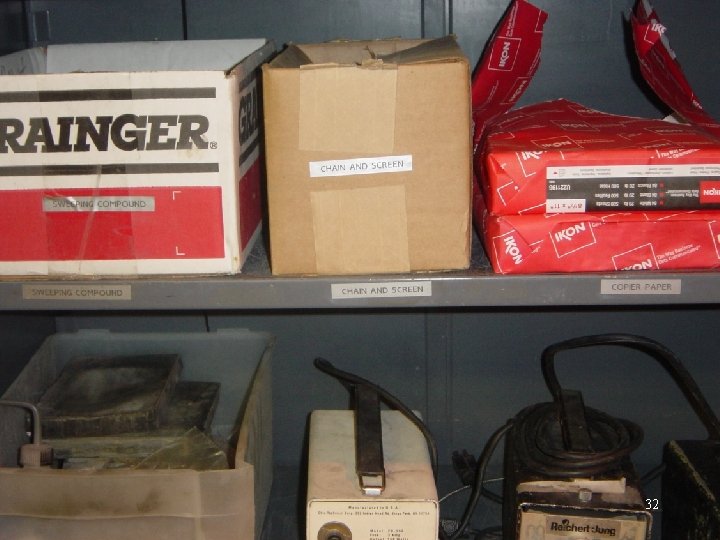
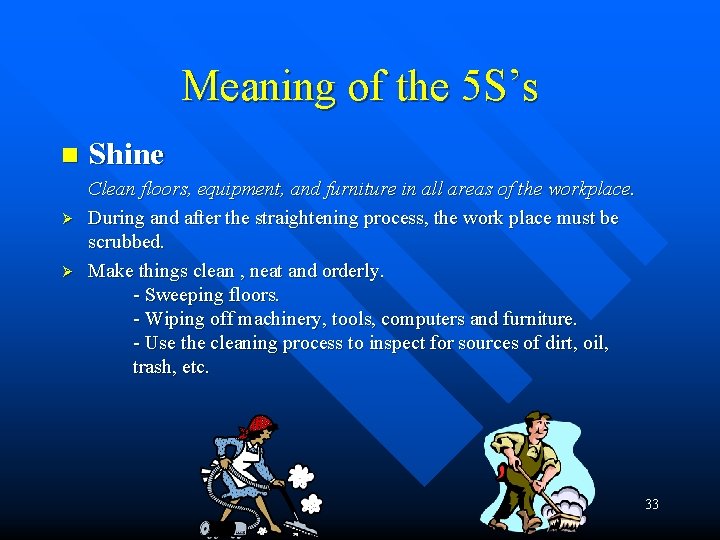
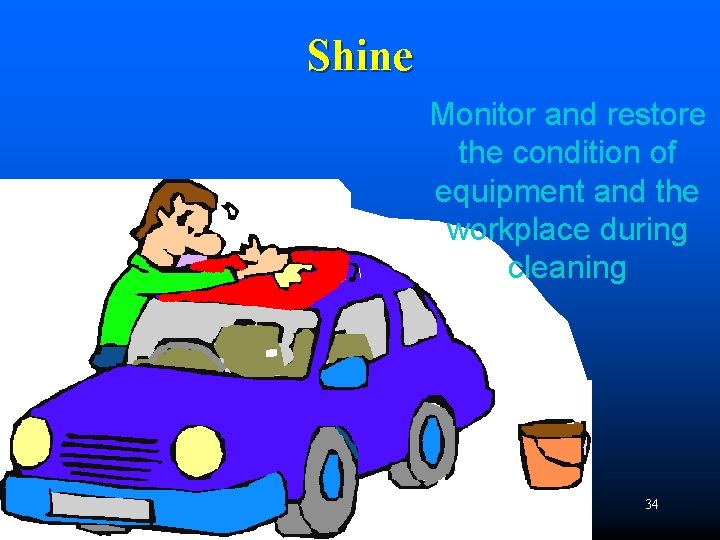
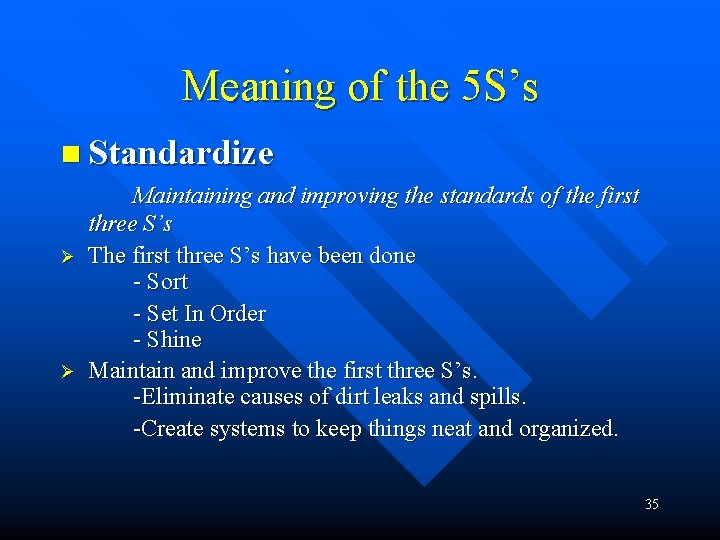
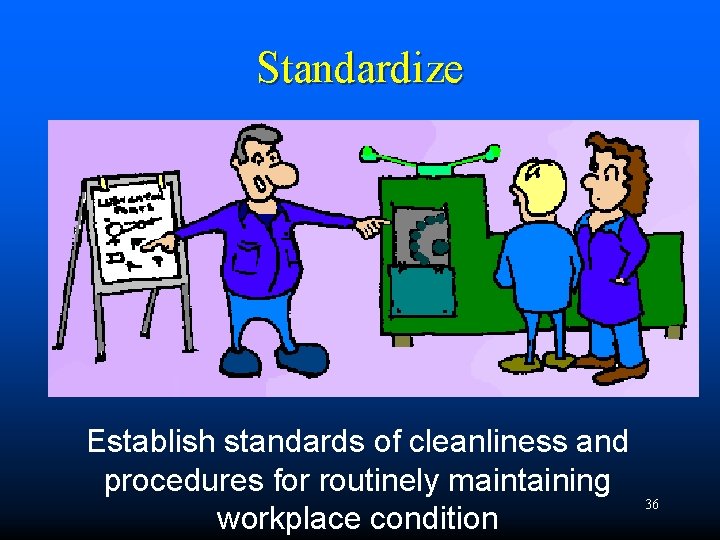
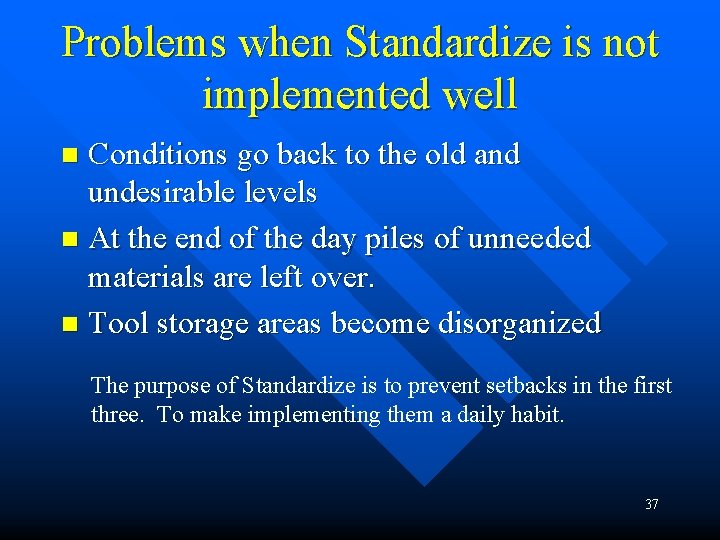
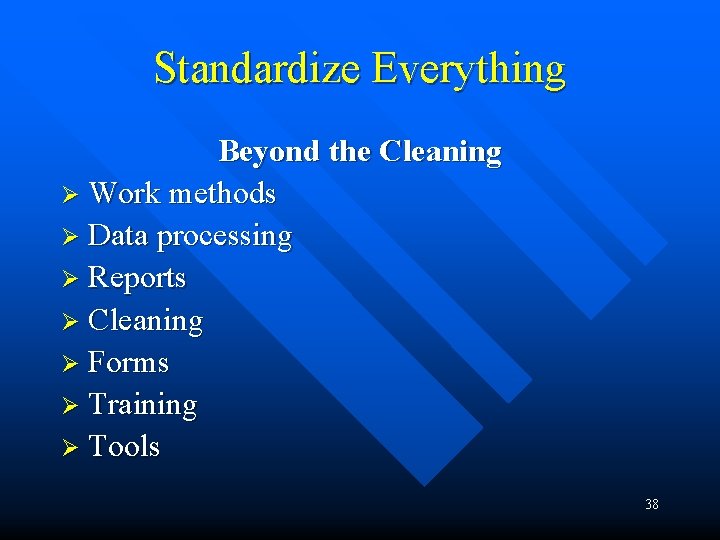
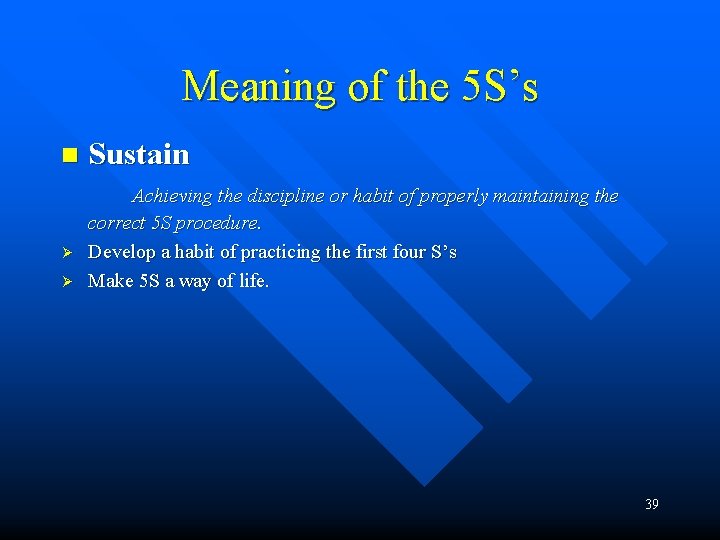
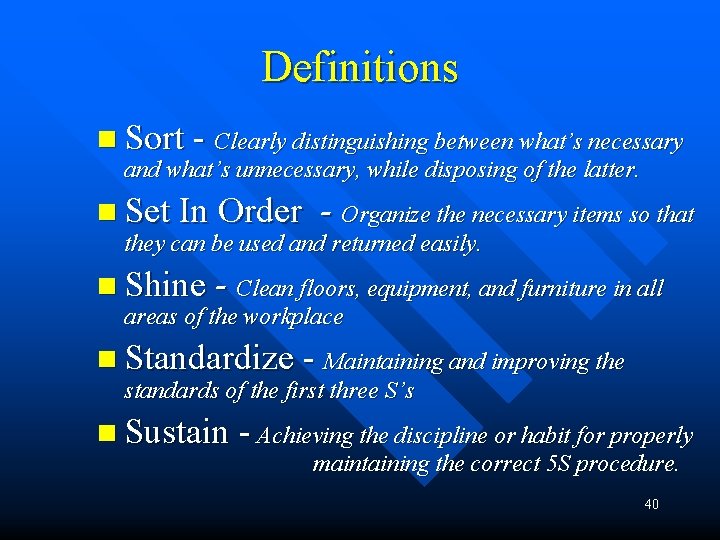
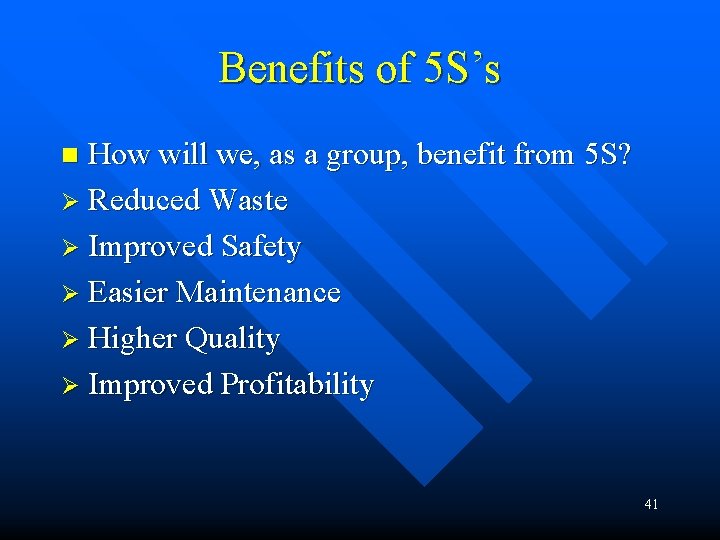
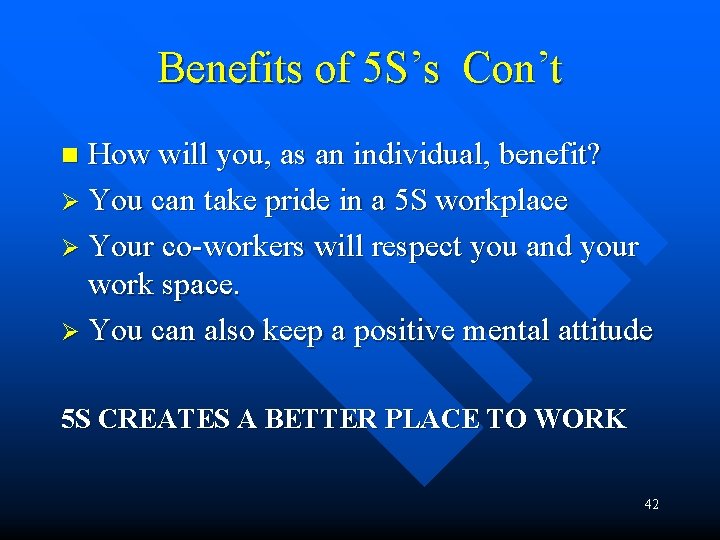
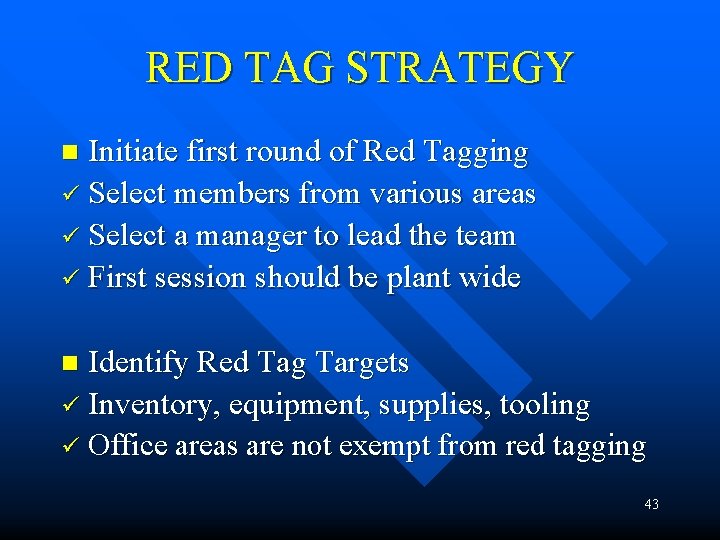

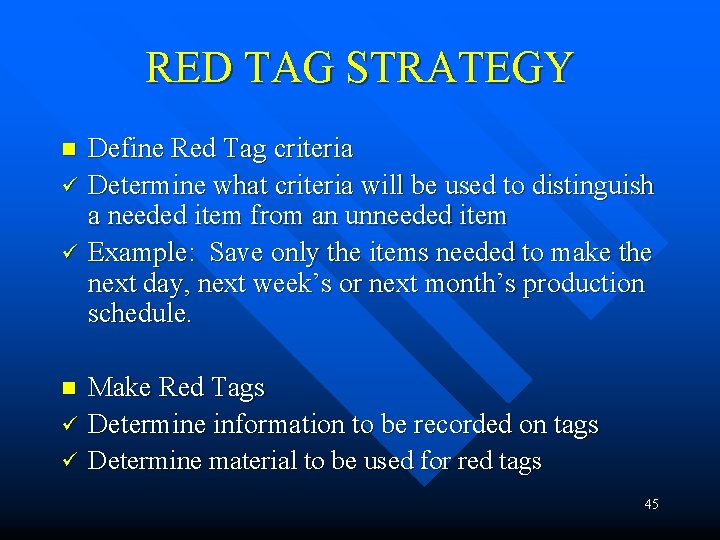
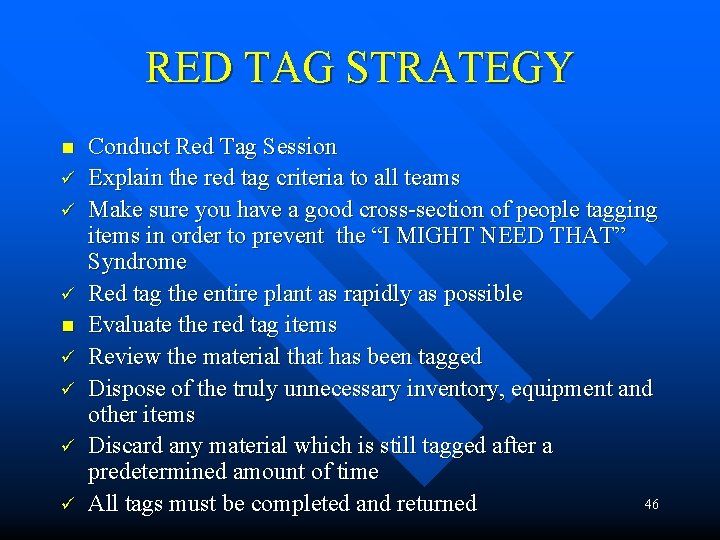
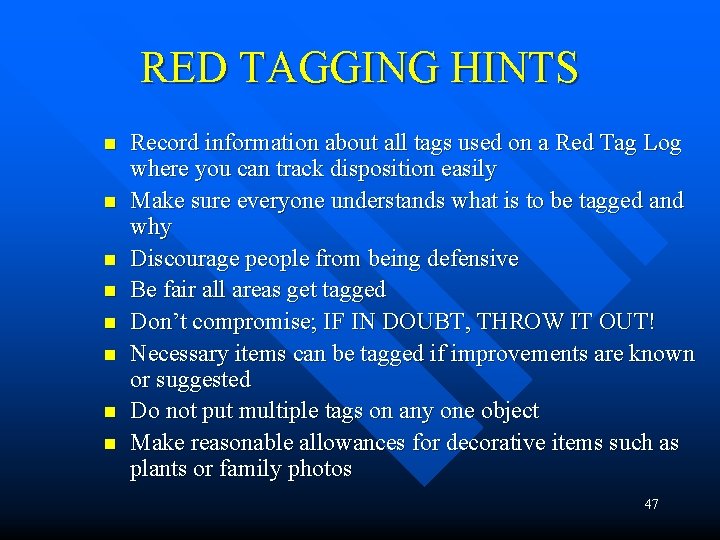
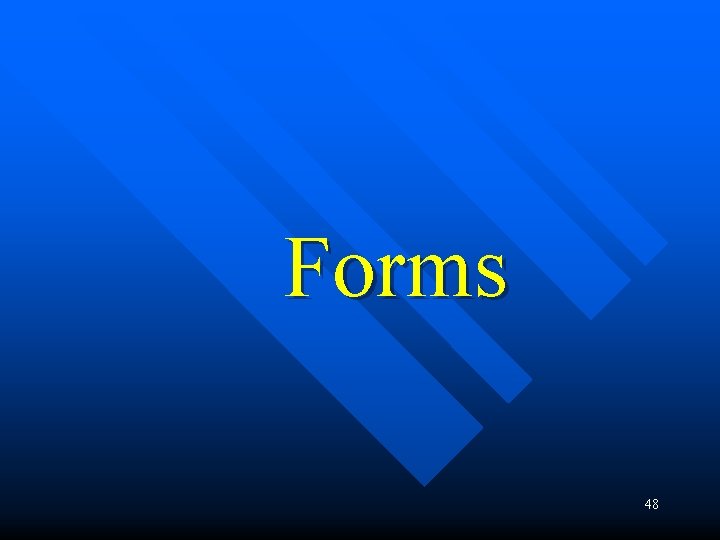
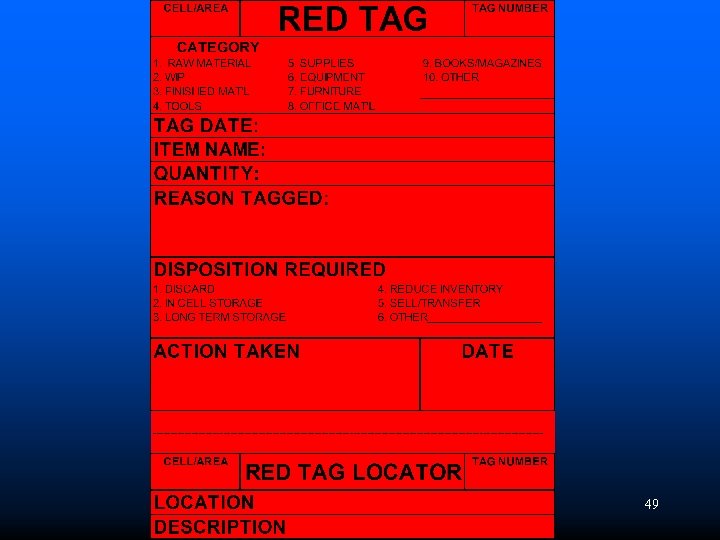
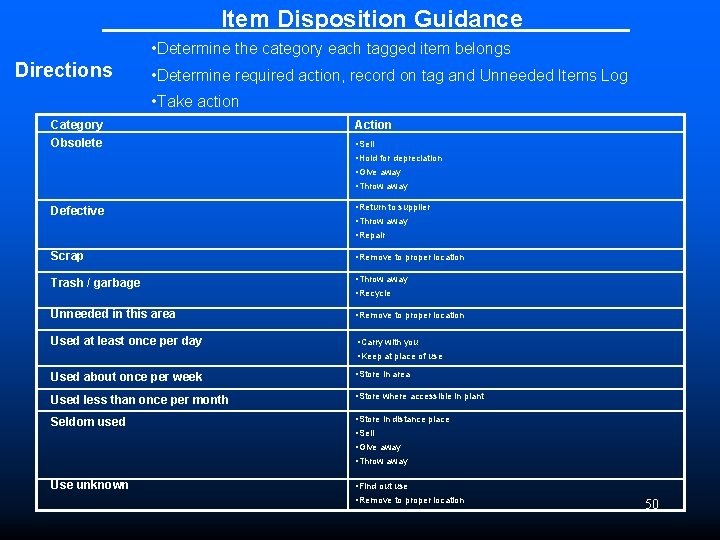

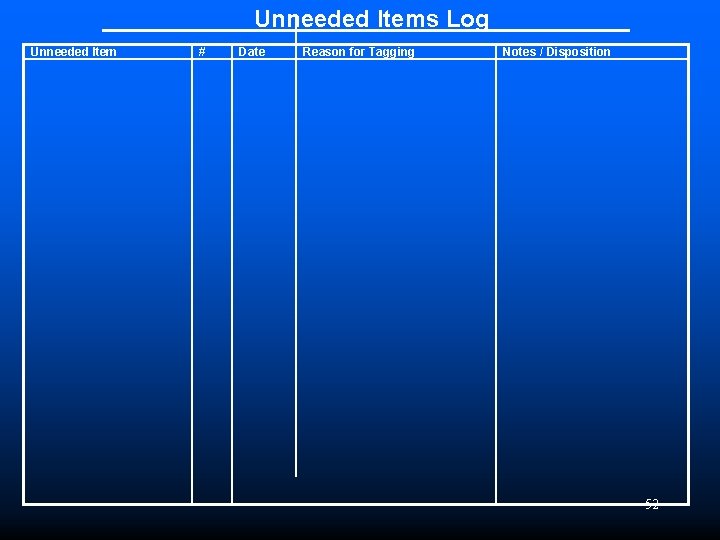
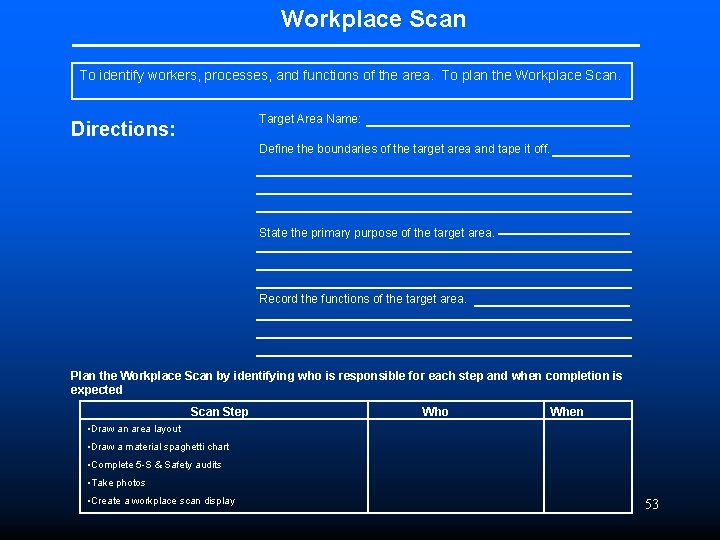
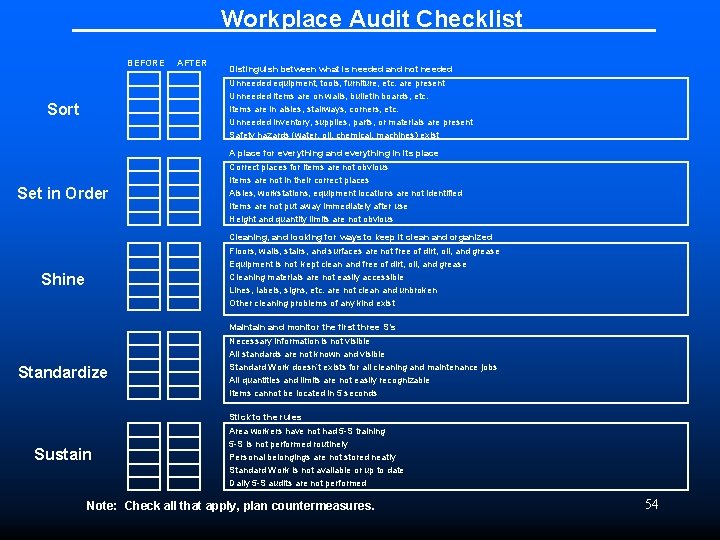
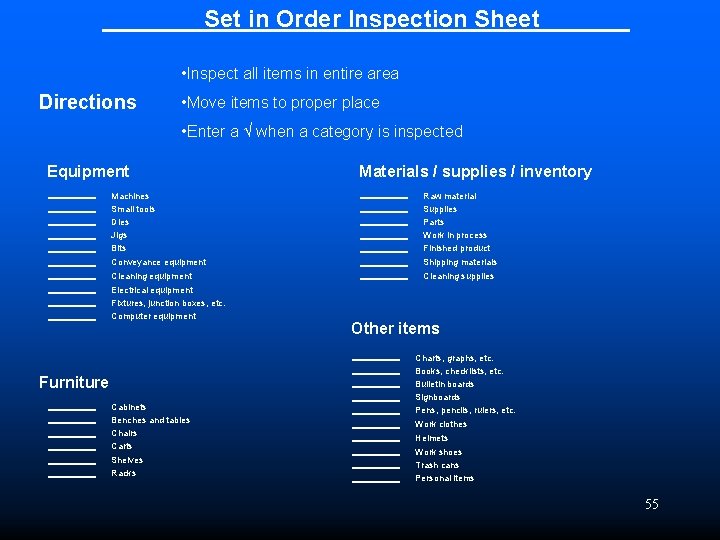
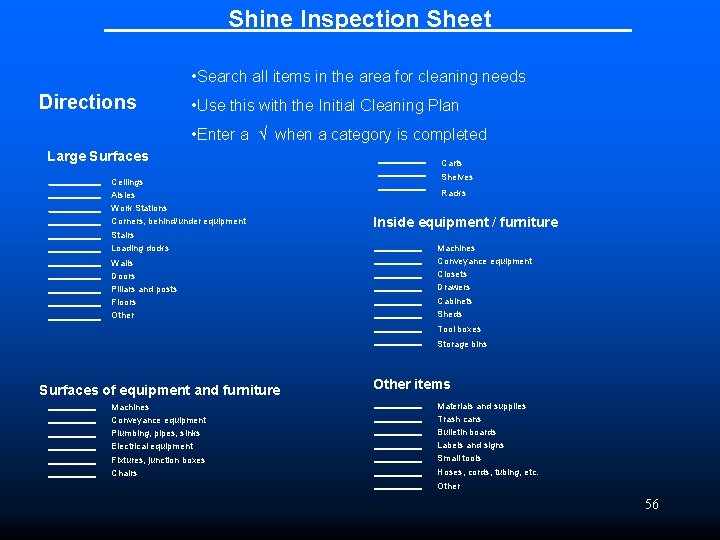

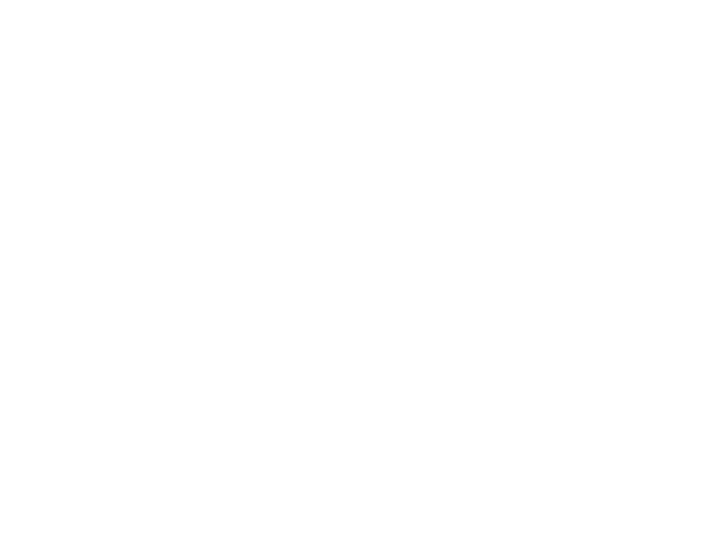
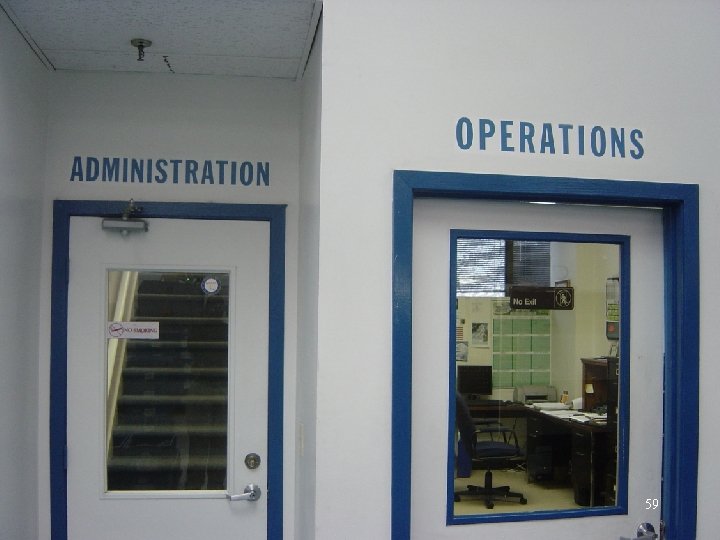
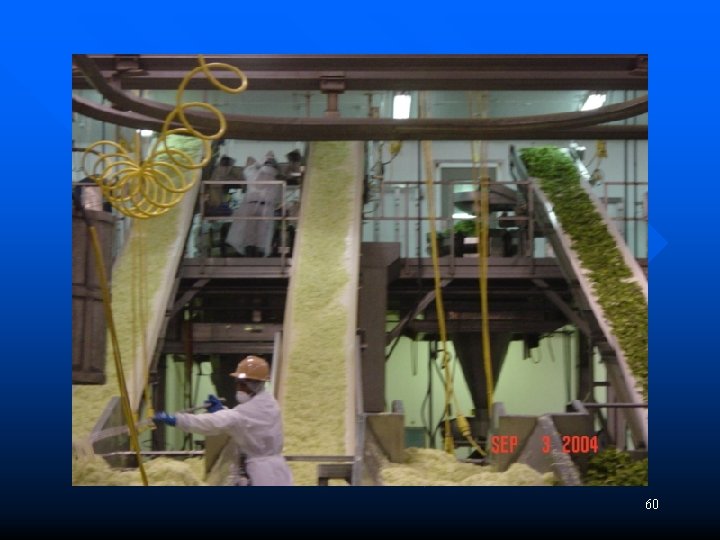
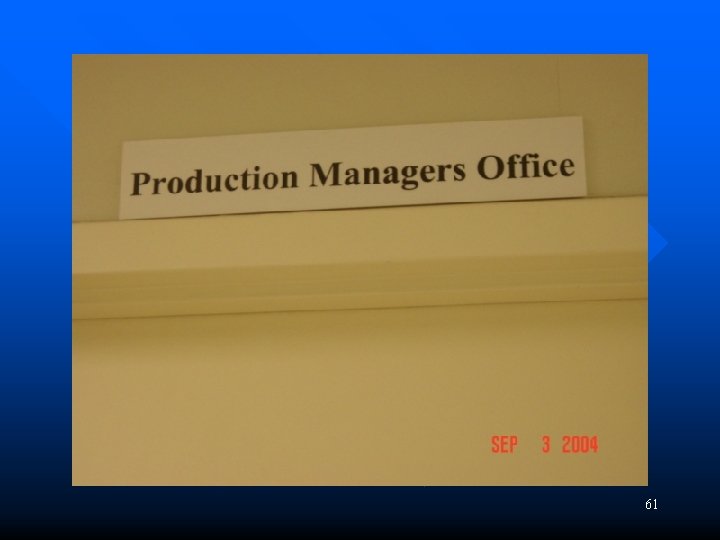
- Slides: 61
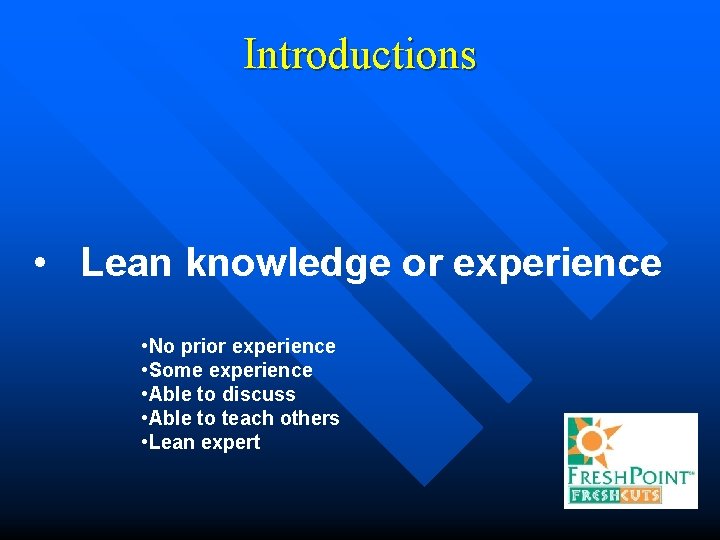
Introductions • Lean knowledge or experience • No prior experience • Some experience • Able to discuss • Able to teach others • Lean expert
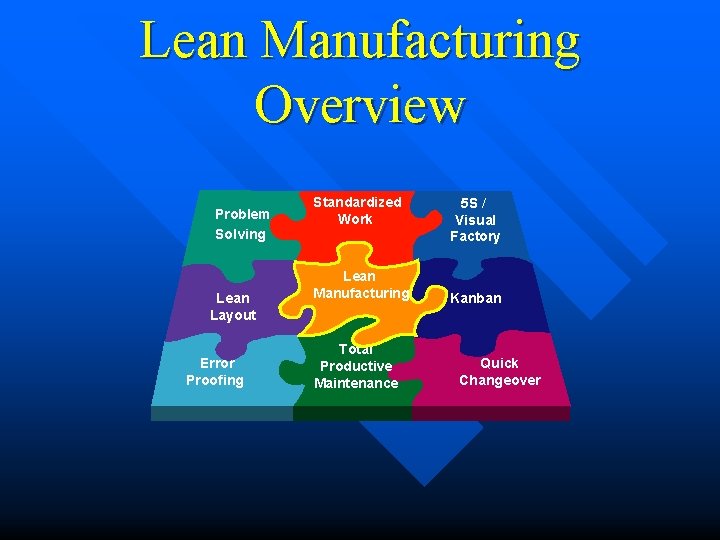
Lean Manufacturing Overview Problem Solving Lean Layout Error Proofing Standardized Work Lean Manufacturing Total Productive Maintenance 5 S / Visual Factory Kanban Quick Changeover
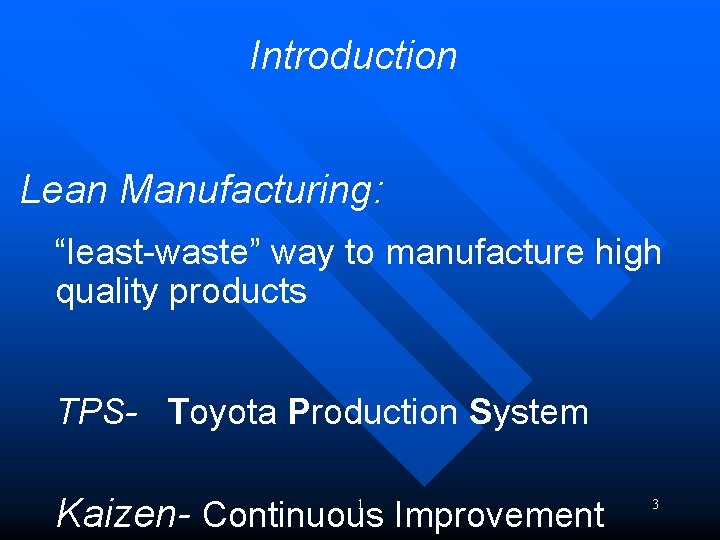
Introduction Lean Manufacturing: “least-waste” way to manufacture high quality products TPS- Toyota Production System Kaizen- Continuous Improvement 1 3
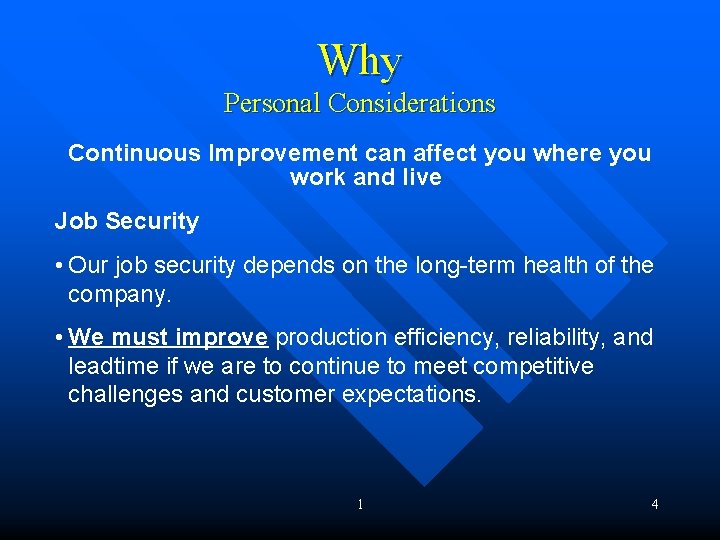
Why Personal Considerations Continuous Improvement can affect you where you work and live Job Security • Our job security depends on the long-term health of the company. • We must improve production efficiency, reliability, and leadtime if we are to continue to meet competitive challenges and customer expectations. 1 4
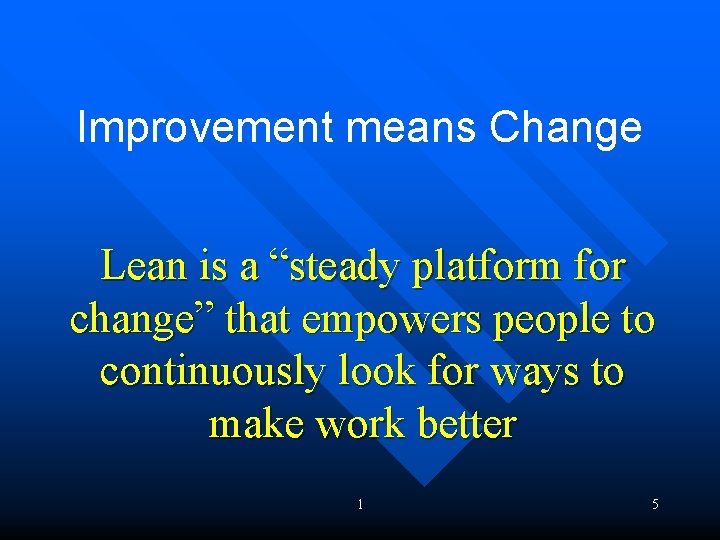
Improvement means Change Lean is a “steady platform for change” that empowers people to continuously look for ways to make work better 1 5
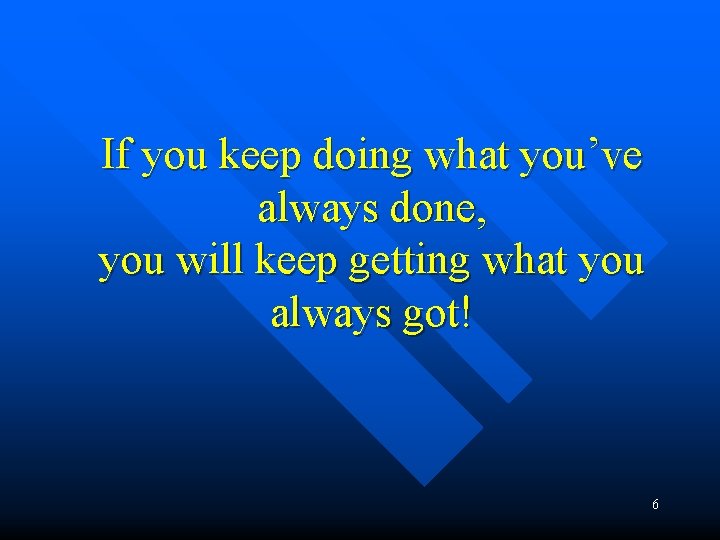
If you keep doing what you’ve always done, you will keep getting what you always got! 6
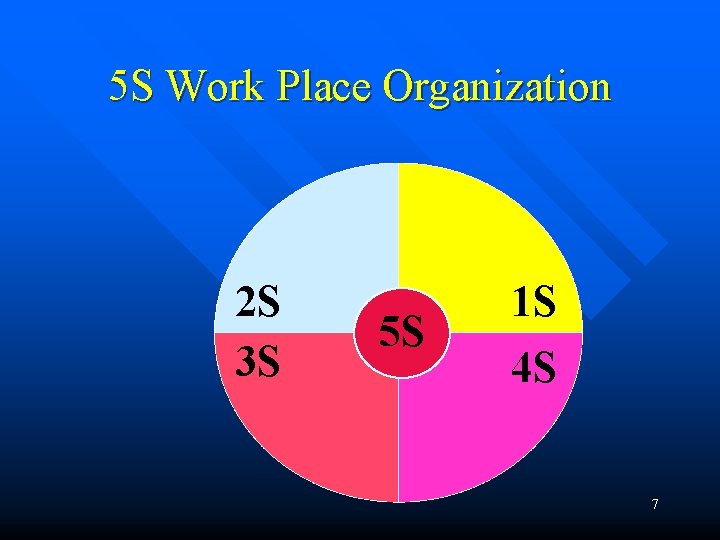
5 S Work Place Organization 2 S 3 S 5 S 1 S 4 S 7
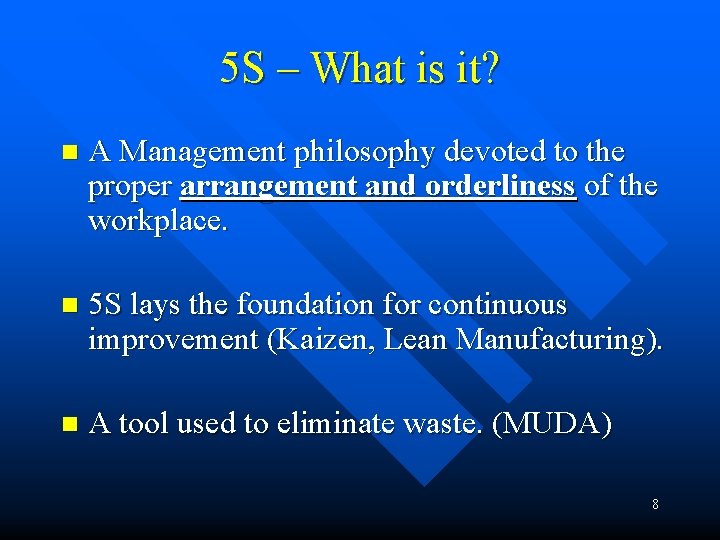
5 S – What is it? n A Management philosophy devoted to the proper arrangement and orderliness of the workplace. n 5 S lays the foundation for continuous improvement (Kaizen, Lean Manufacturing). n A tool used to eliminate waste. (MUDA) 8
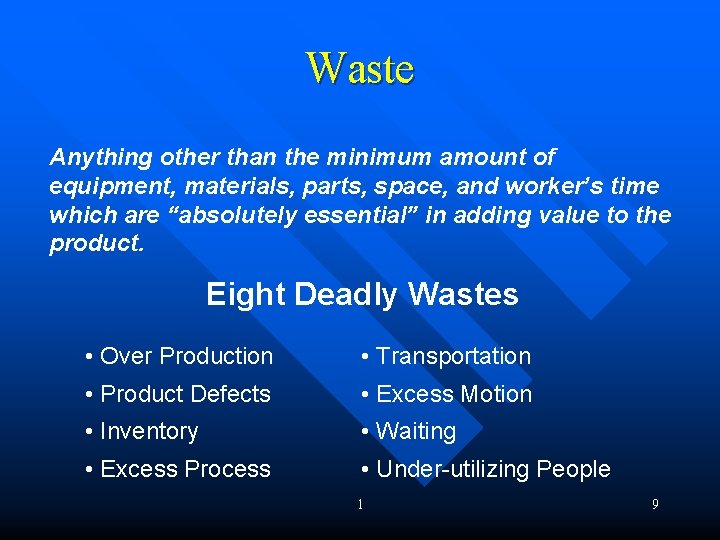
Waste Anything other than the minimum amount of equipment, materials, parts, space, and worker’s time which are “absolutely essential” in adding value to the product. Eight Deadly Wastes • Over Production • Transportation • Product Defects • Excess Motion • Inventory • Waiting • Excess Process • Under-utilizing People 1 9
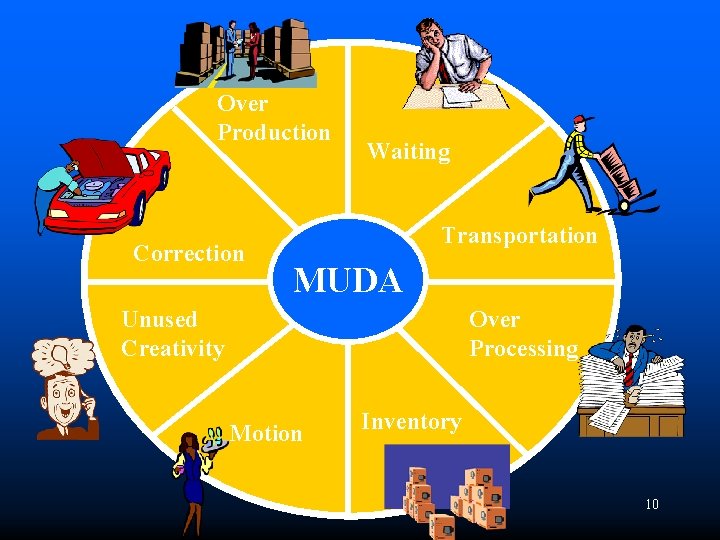
Over Production Correction Waiting Transportation MUDA Unused Creativity Over Processing Motion Inventory 10
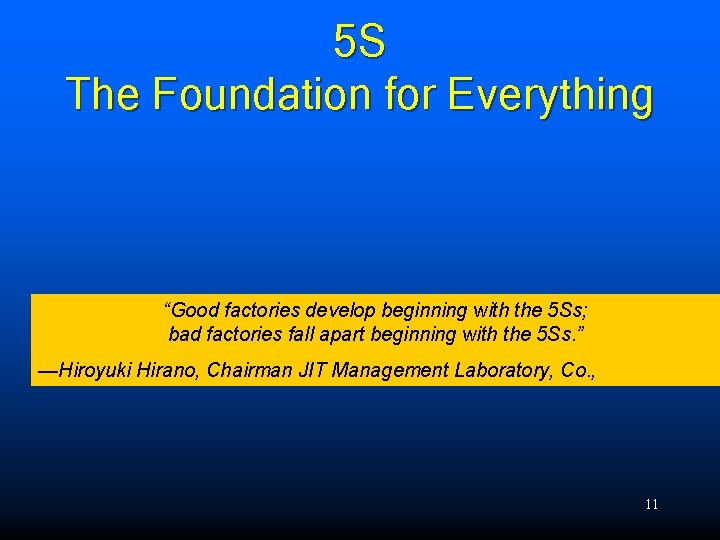
5 S The Foundation for Everything “Good factories develop beginning with the 5 Ss; bad factories fall apart beginning with the 5 Ss. ” —Hiroyuki Hirano, Chairman JIT Management Laboratory, Co. , 11
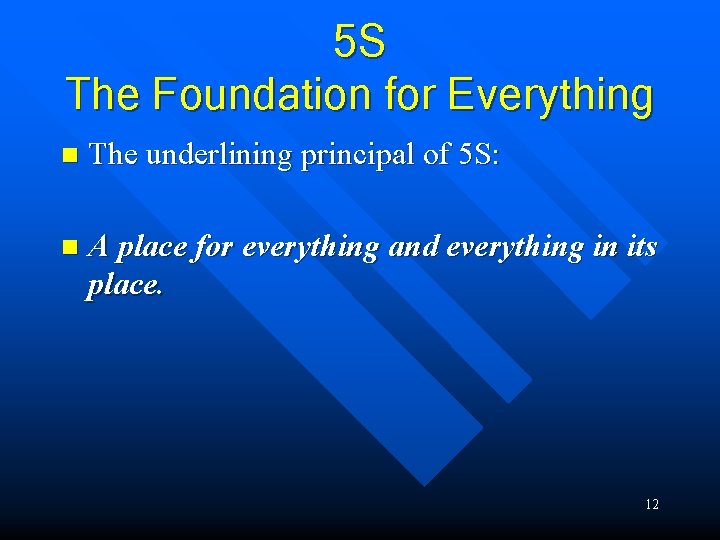
5 S The Foundation for Everything n The underlining principal of 5 S: n A place for everything and everything in its place. 12
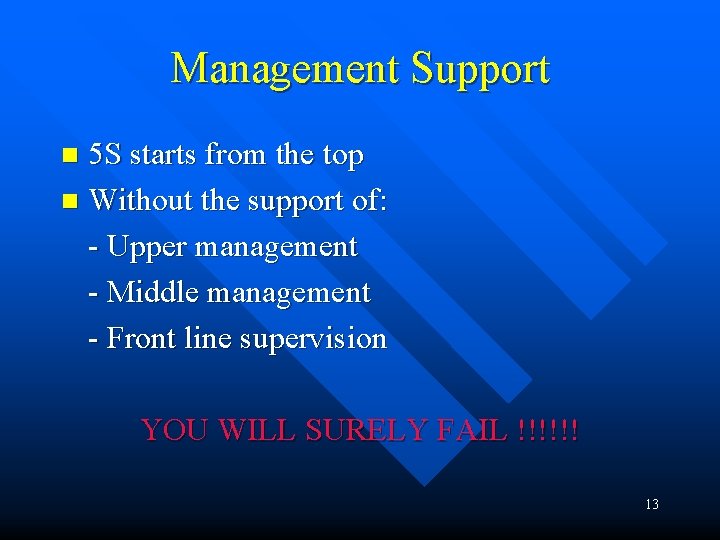
Management Support 5 S starts from the top n Without the support of: - Upper management - Middle management - Front line supervision n YOU WILL SURELY FAIL !!!!!! 13
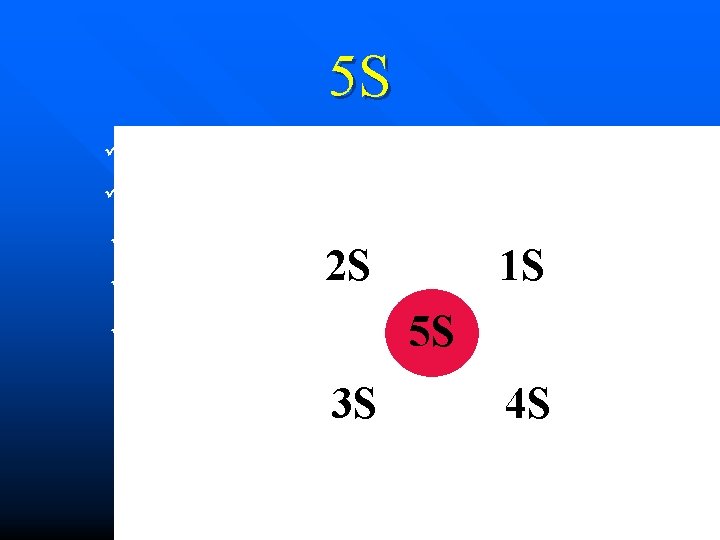
5 S üSort üSet In Order üShine üStandardize 2 S 1 S 5 S üSustain 3 S 4 S 14
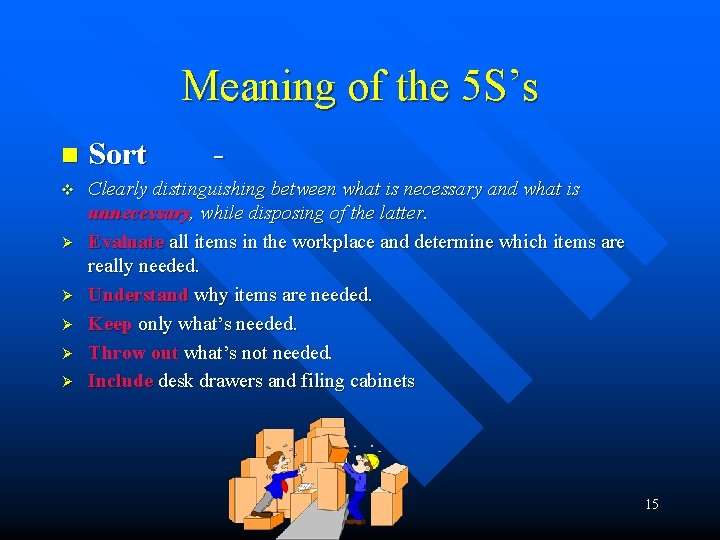
Meaning of the 5 S’s n Sort v Clearly distinguishing between what is necessary and what is unnecessary, while disposing of the latter. Evaluate all items in the workplace and determine which items are really needed. Understand why items are needed. Keep only what’s needed. Throw out what’s not needed. Include desk drawers and filing cabinets Ø Ø Ø - 15
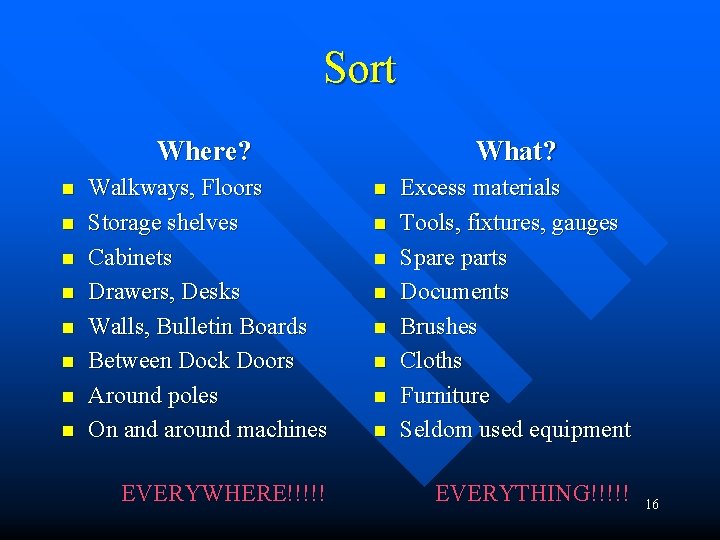
Sort Where? n n n n Walkways, Floors Storage shelves Cabinets Drawers, Desks Walls, Bulletin Boards Between Dock Doors Around poles On and around machines EVERYWHERE!!!!! What? n n n n Excess materials Tools, fixtures, gauges Spare parts Documents Brushes Cloths Furniture Seldom used equipment EVERYTHING!!!!! 16
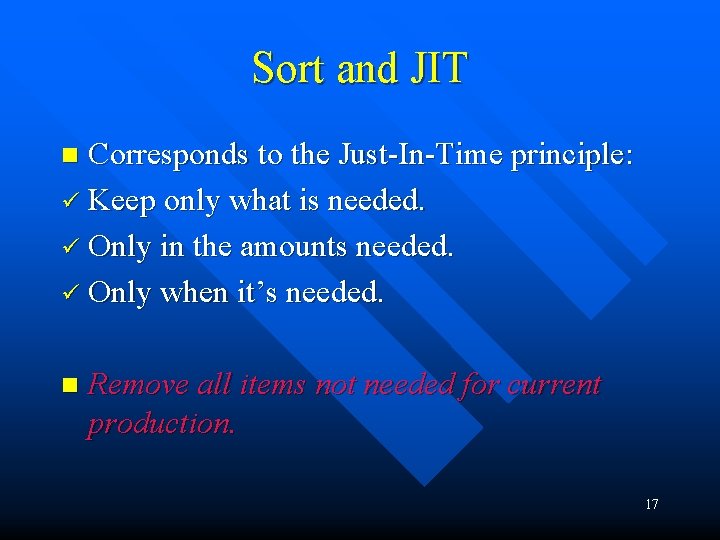
Sort and JIT Corresponds to the Just-In-Time principle: ü Keep only what is needed. ü Only in the amounts needed. ü Only when it’s needed. n n Remove all items not needed for current production. 17
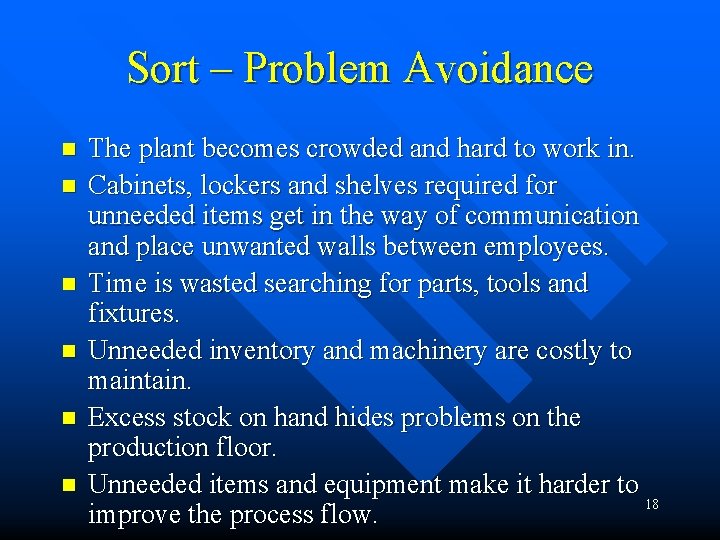
Sort – Problem Avoidance n n n The plant becomes crowded and hard to work in. Cabinets, lockers and shelves required for unneeded items get in the way of communication and place unwanted walls between employees. Time is wasted searching for parts, tools and fixtures. Unneeded inventory and machinery are costly to maintain. Excess stock on hand hides problems on the production floor. Unneeded items and equipment make it harder to 18 improve the process flow.
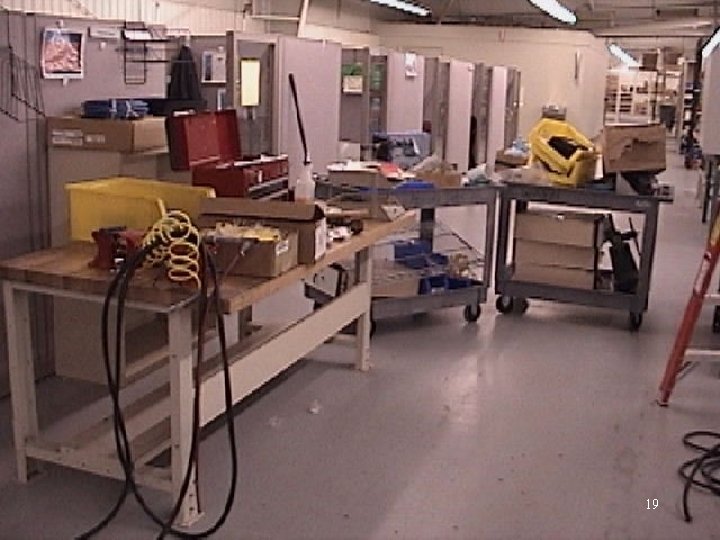
Sort 19
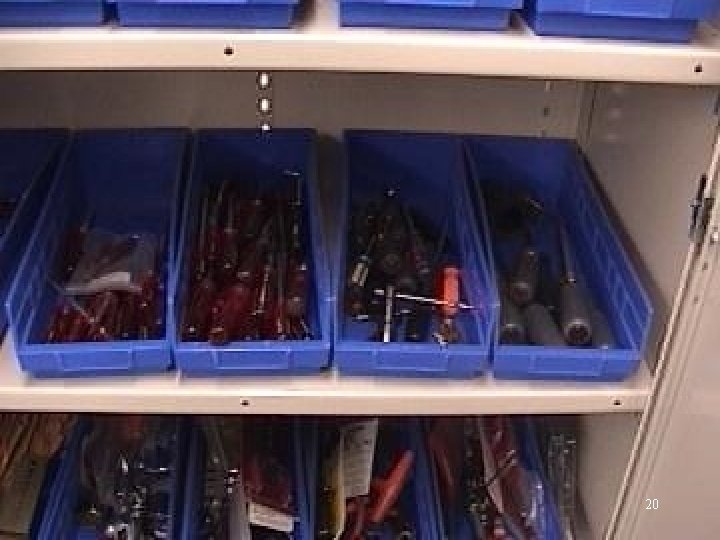
Sort 20
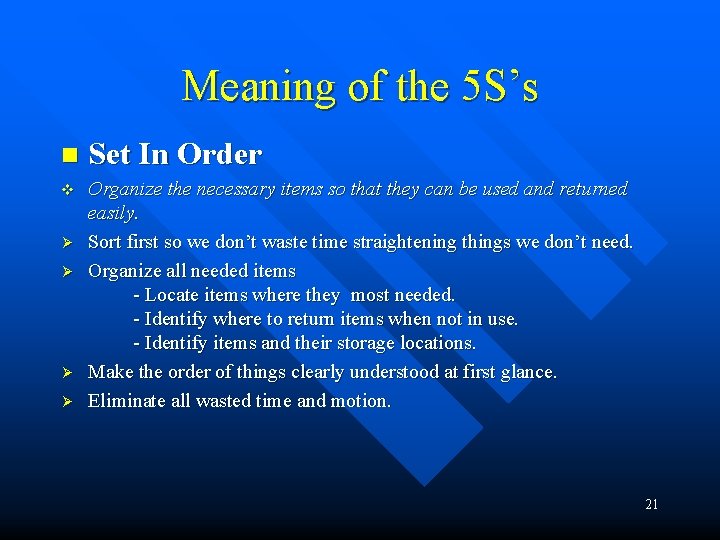
Meaning of the 5 S’s n Set In Order v Organize the necessary items so that they can be used and returned easily. Sort first so we don’t waste time straightening things we don’t need. Organize all needed items - Locate items where they most needed. - Identify where to return items when not in use. - Identify items and their storage locations. Make the order of things clearly understood at first glance. Eliminate all wasted time and motion. Ø Ø 21
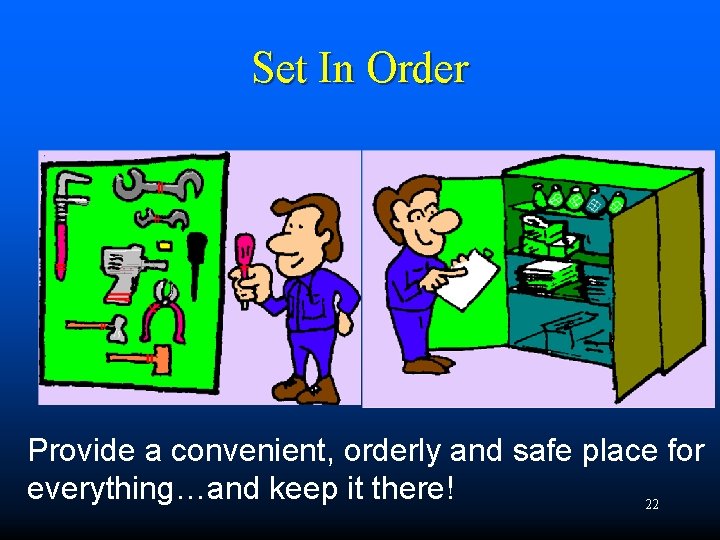
Set In Order Provide a convenient, orderly and safe place for everything…and keep it there! 22
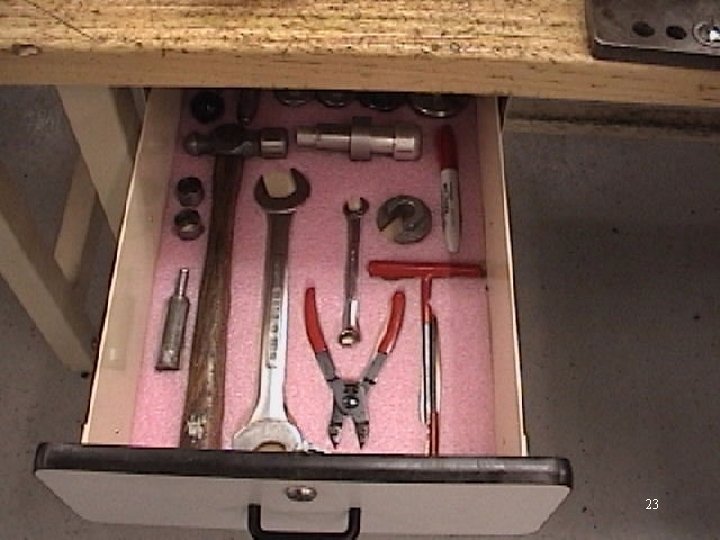
Set In Order 23
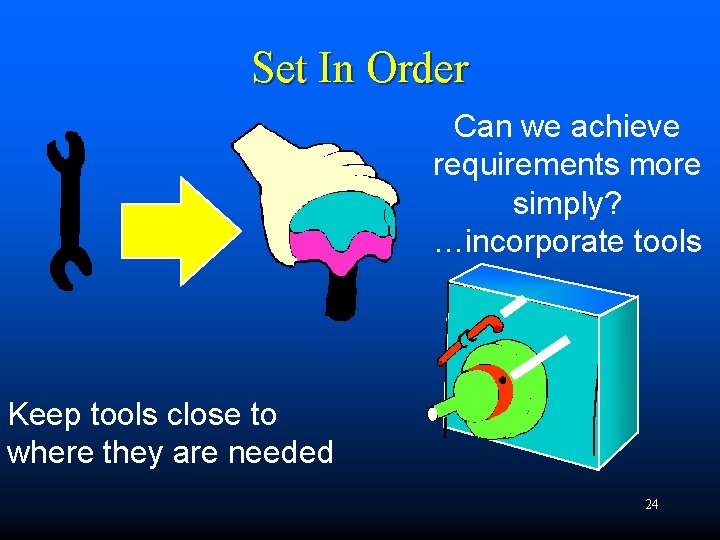
Set In Order Can we achieve requirements more simply? …incorporate tools Keep tools close to where they are needed 24
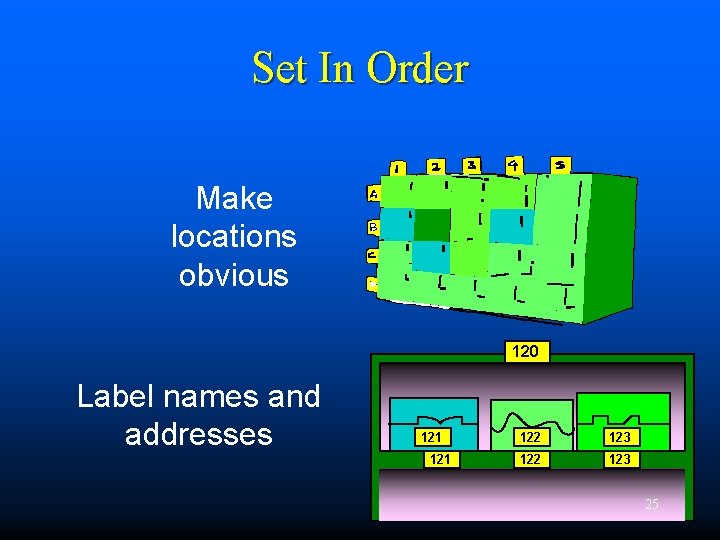
Set In Order Make locations obvious 120 Label names and addresses 121 122 123 25
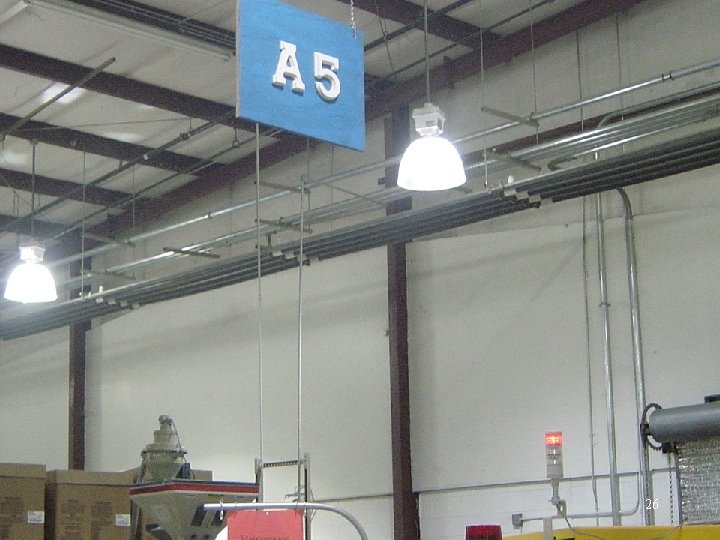
26
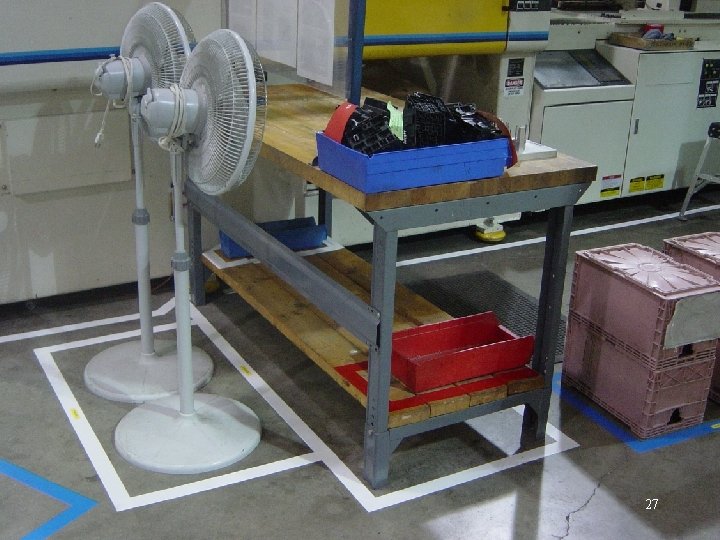
27
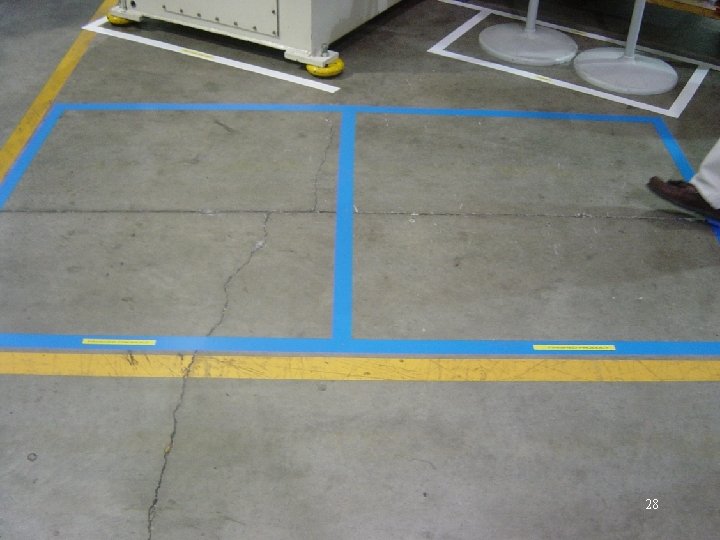
28
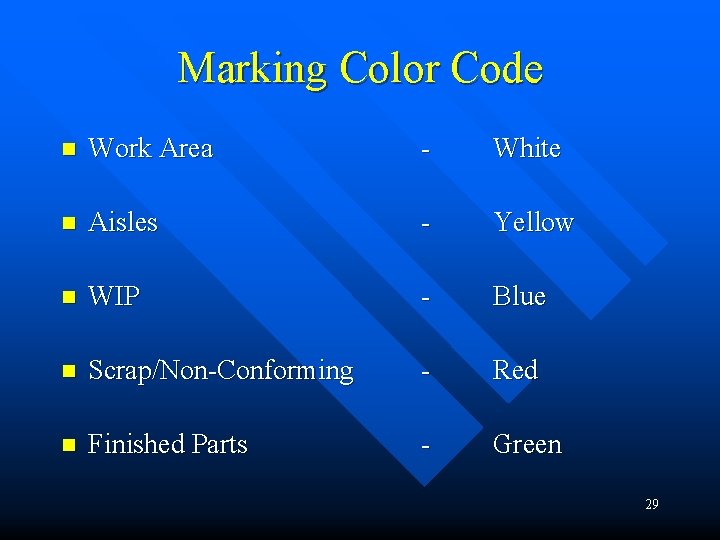
Marking Color Code n Work Area - White n Aisles - Yellow n WIP - Blue n Scrap/Non-Conforming - Red n Finished Parts - Green 29
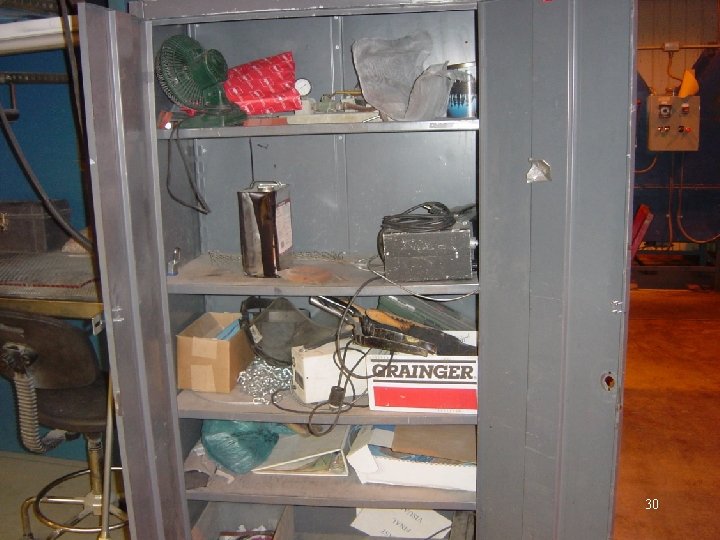
30
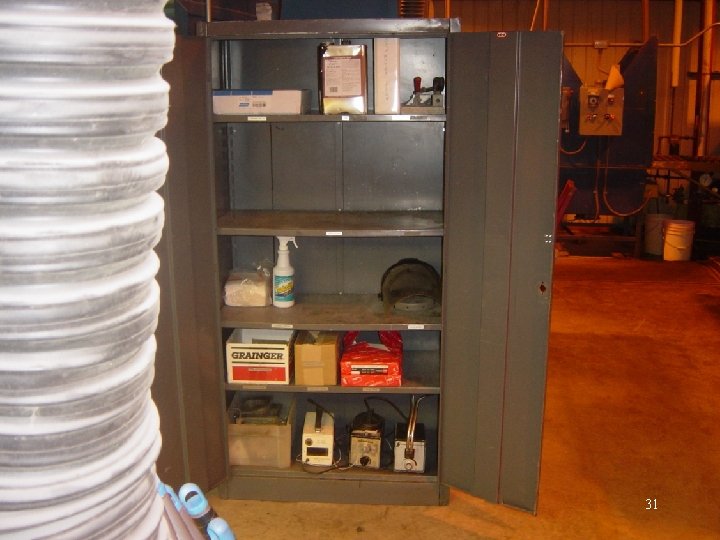
31
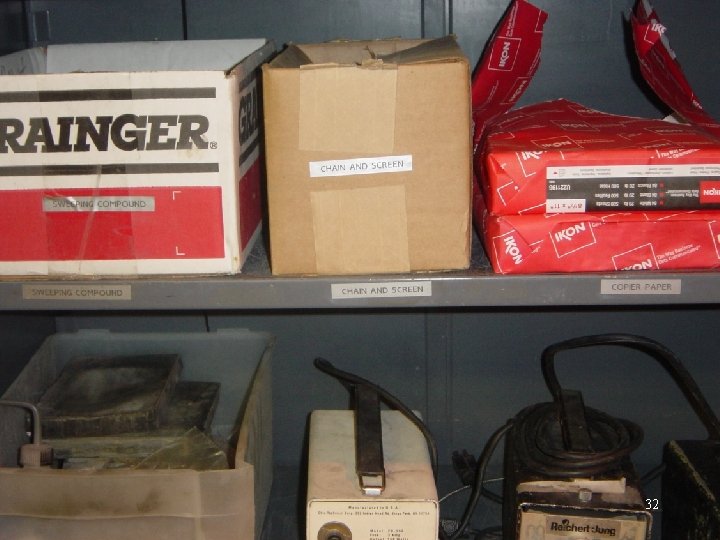
32
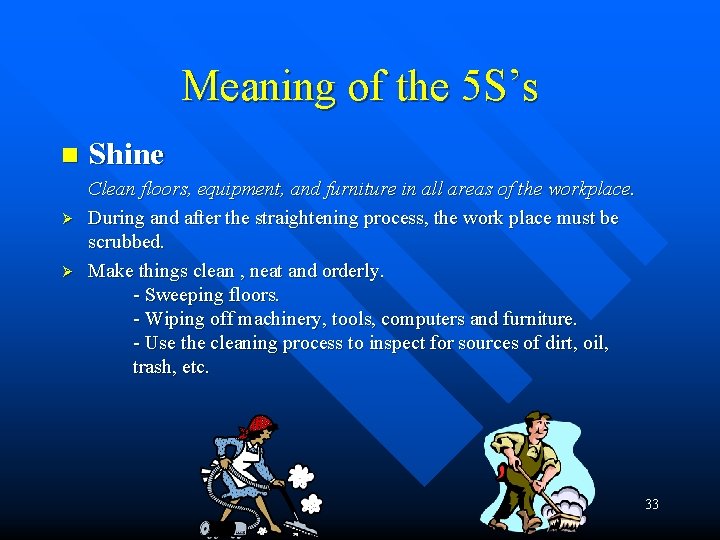
Meaning of the 5 S’s n Ø Ø Shine Clean floors, equipment, and furniture in all areas of the workplace. During and after the straightening process, the work place must be scrubbed. Make things clean , neat and orderly. - Sweeping floors. - Wiping off machinery, tools, computers and furniture. - Use the cleaning process to inspect for sources of dirt, oil, trash, etc. 33
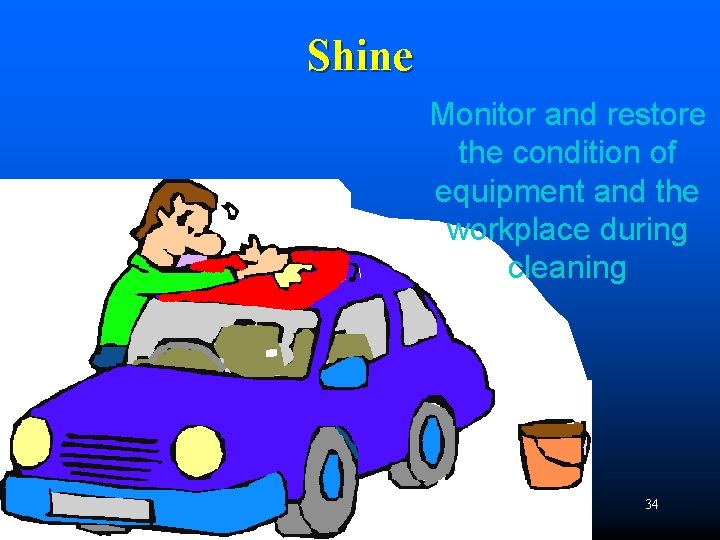
Shine Monitor and restore the condition of equipment and the workplace during cleaning 34
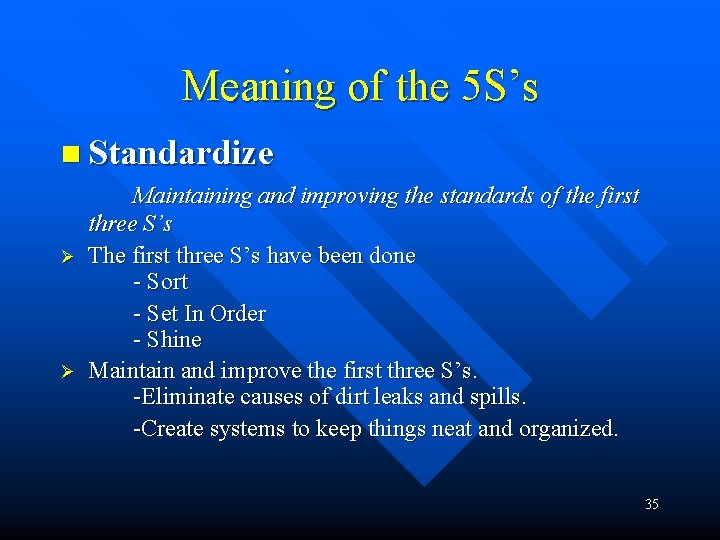
Meaning of the 5 S’s n Standardize Ø Ø Maintaining and improving the standards of the first three S’s The first three S’s have been done - Sort - Set In Order - Shine Maintain and improve the first three S’s. -Eliminate causes of dirt leaks and spills. -Create systems to keep things neat and organized. 35
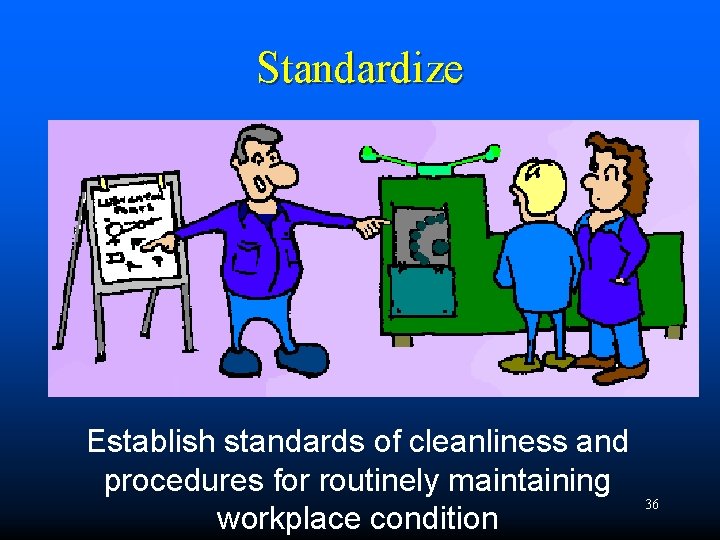
Standardize Establish standards of cleanliness and procedures for routinely maintaining workplace condition 36
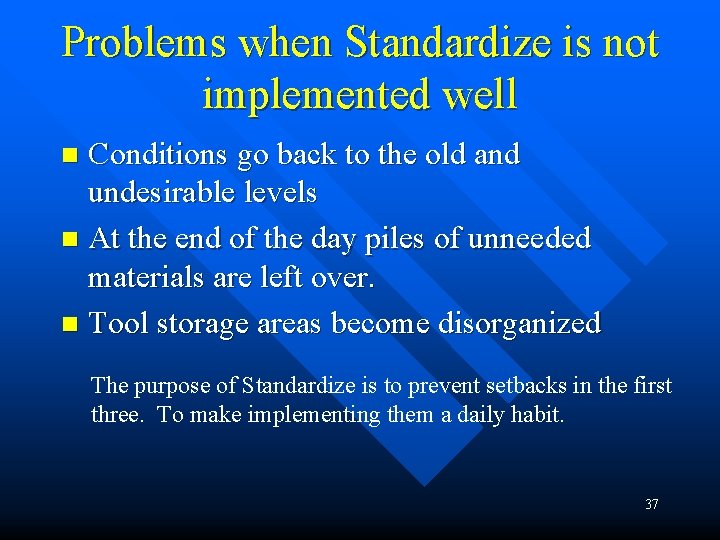
Problems when Standardize is not implemented well Conditions go back to the old and undesirable levels n At the end of the day piles of unneeded materials are left over. n Tool storage areas become disorganized n The purpose of Standardize is to prevent setbacks in the first three. To make implementing them a daily habit. 37
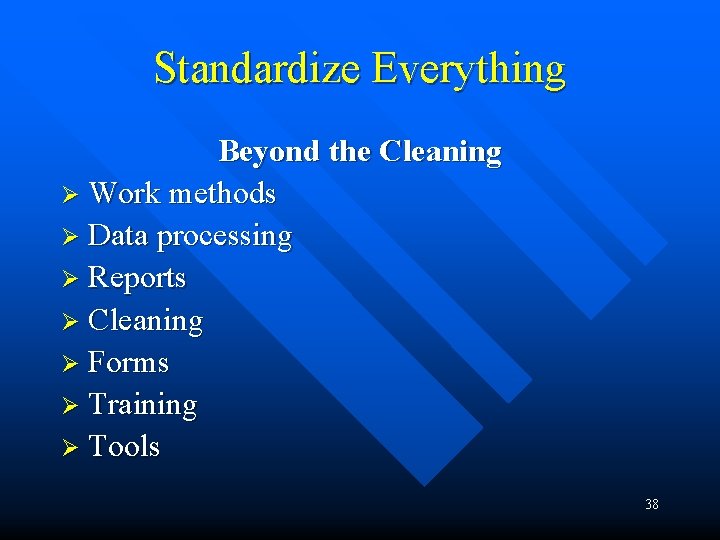
Standardize Everything Beyond the Cleaning Ø Work methods Ø Data processing Ø Reports Ø Cleaning Ø Forms Ø Training Ø Tools 38
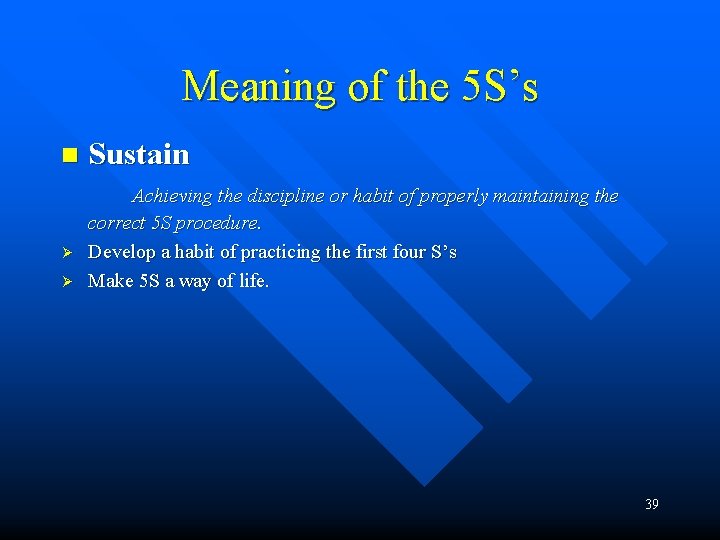
Meaning of the 5 S’s n Ø Ø Sustain Achieving the discipline or habit of properly maintaining the correct 5 S procedure. Develop a habit of practicing the first four S’s Make 5 S a way of life. 39
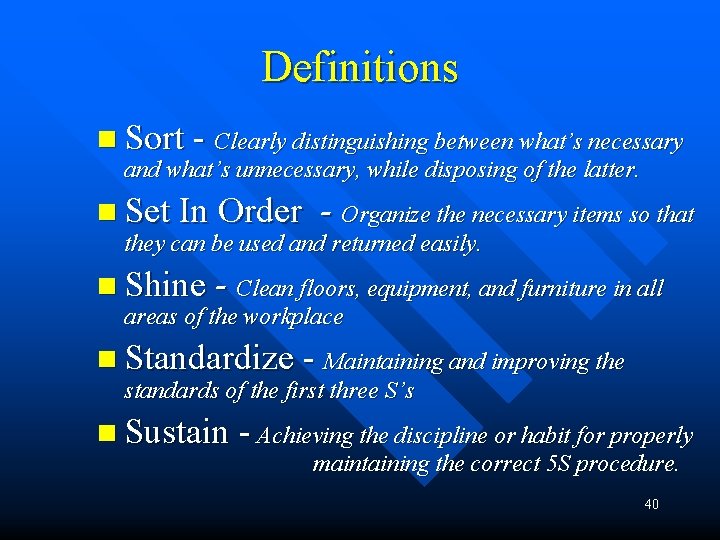
Definitions n Sort - Clearly distinguishing between what’s necessary and what’s unnecessary, while disposing of the latter. n Set In Order - Organize the necessary items so that they can be used and returned easily. n Shine - Clean floors, equipment, and furniture in all areas of the workplace n Standardize - Maintaining and improving the standards of the first three S’s n Sustain - Achieving the discipline or habit for properly maintaining the correct 5 S procedure. 40
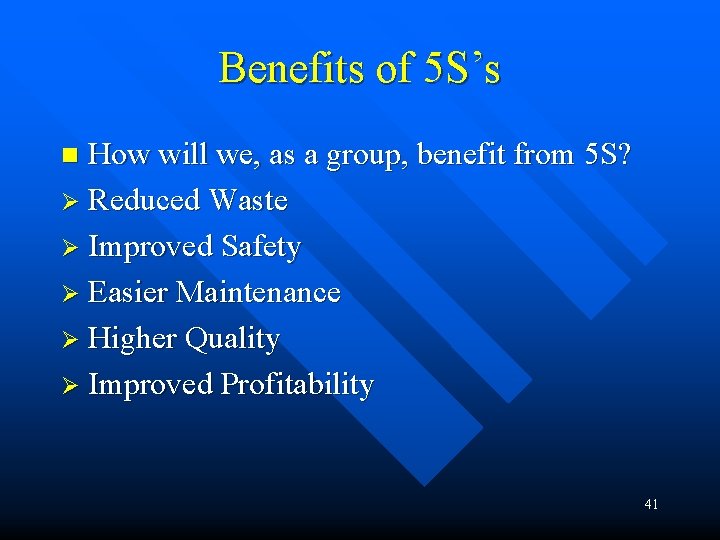
Benefits of 5 S’s How will we, as a group, benefit from 5 S? Ø Reduced Waste Ø Improved Safety Ø Easier Maintenance Ø Higher Quality Ø Improved Profitability n 41
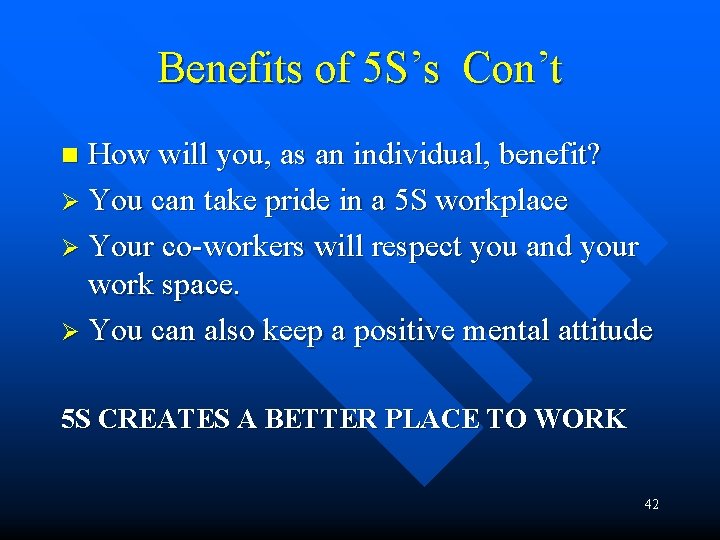
Benefits of 5 S’s Con’t How will you, as an individual, benefit? Ø You can take pride in a 5 S workplace Ø Your co-workers will respect you and your work space. Ø You can also keep a positive mental attitude n 5 S CREATES A BETTER PLACE TO WORK 42
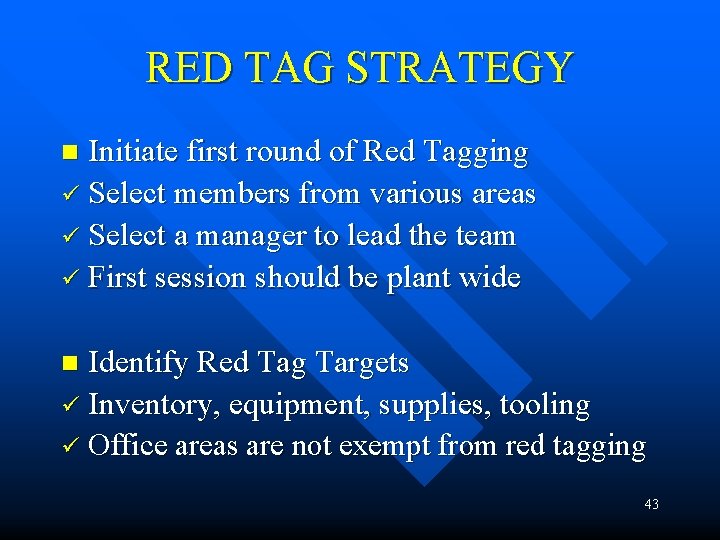
RED TAG STRATEGY Initiate first round of Red Tagging ü Select members from various areas ü Select a manager to lead the team ü First session should be plant wide n Identify Red Tag Targets ü Inventory, equipment, supplies, tooling ü Office areas are not exempt from red tagging n 43

RED TAG STRATEGY Hillman B. S. A. ARMSTRONG Sopwith Ltd. . Re d. L ab Ite el m_ No __ __. __ Qu __ an __ __ tity __ _ __ Lo __ __ ca __ tio __ __ n __ _ Da __ __ te_ __ __ _ Cl _ __ __ ea _ __ ran _ ce Pu D ate __ rpos __ __ ___ e__ __ __ __ __ __ __ _ __ 44
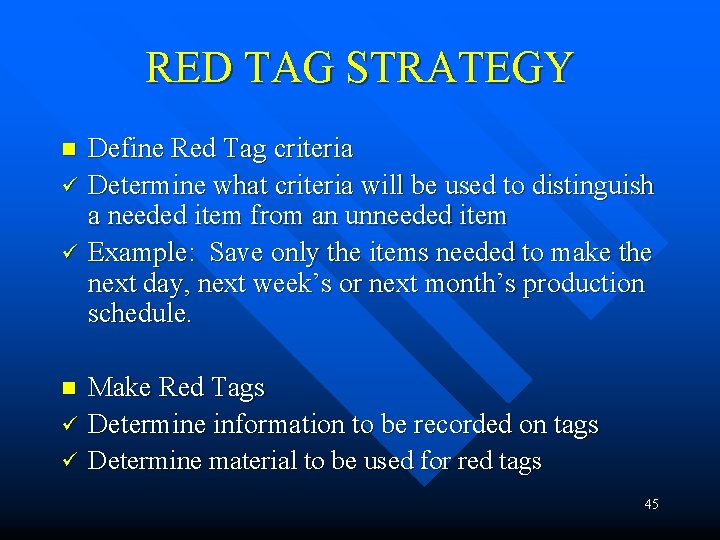
RED TAG STRATEGY n ü ü Define Red Tag criteria Determine what criteria will be used to distinguish a needed item from an unneeded item Example: Save only the items needed to make the next day, next week’s or next month’s production schedule. Make Red Tags Determine information to be recorded on tags Determine material to be used for red tags 45
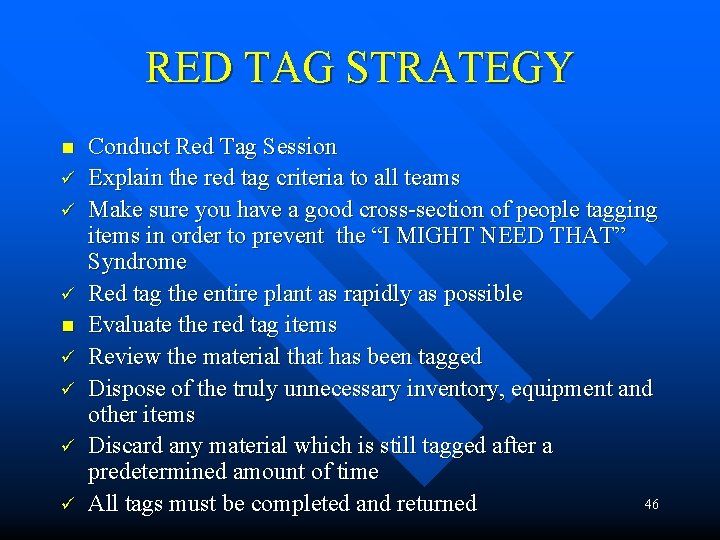
RED TAG STRATEGY n ü ü ü ü Conduct Red Tag Session Explain the red tag criteria to all teams Make sure you have a good cross-section of people tagging items in order to prevent the “I MIGHT NEED THAT” Syndrome Red tag the entire plant as rapidly as possible Evaluate the red tag items Review the material that has been tagged Dispose of the truly unnecessary inventory, equipment and other items Discard any material which is still tagged after a predetermined amount of time 46 All tags must be completed and returned
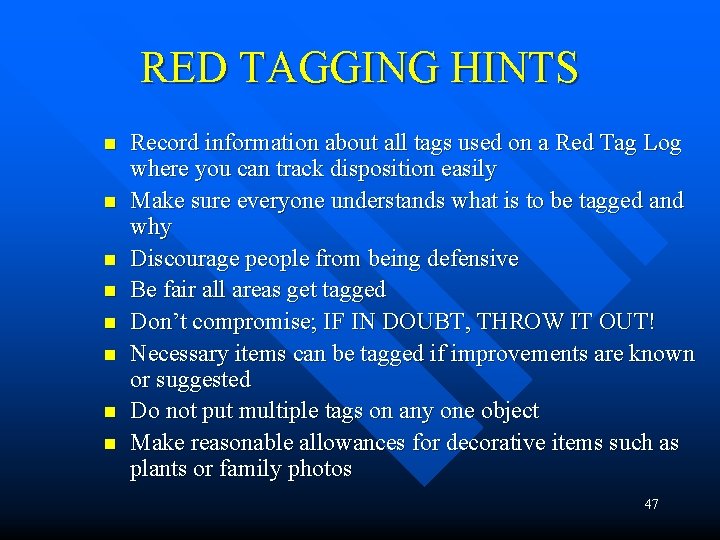
RED TAGGING HINTS n n n n Record information about all tags used on a Red Tag Log where you can track disposition easily Make sure everyone understands what is to be tagged and why Discourage people from being defensive Be fair all areas get tagged Don’t compromise; IF IN DOUBT, THROW IT OUT! Necessary items can be tagged if improvements are known or suggested Do not put multiple tags on any one object Make reasonable allowances for decorative items such as plants or family photos 47
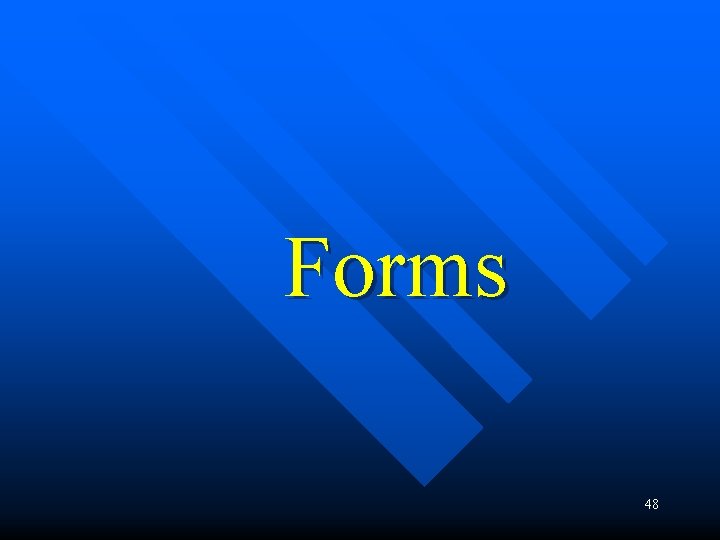
Forms 48
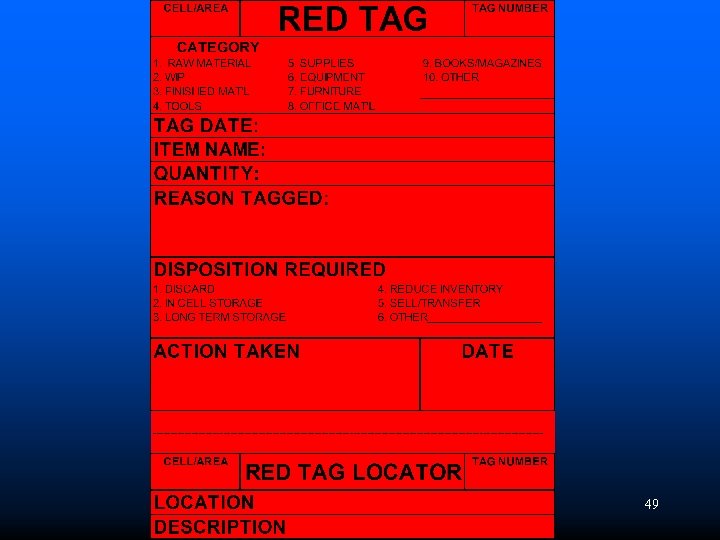
49
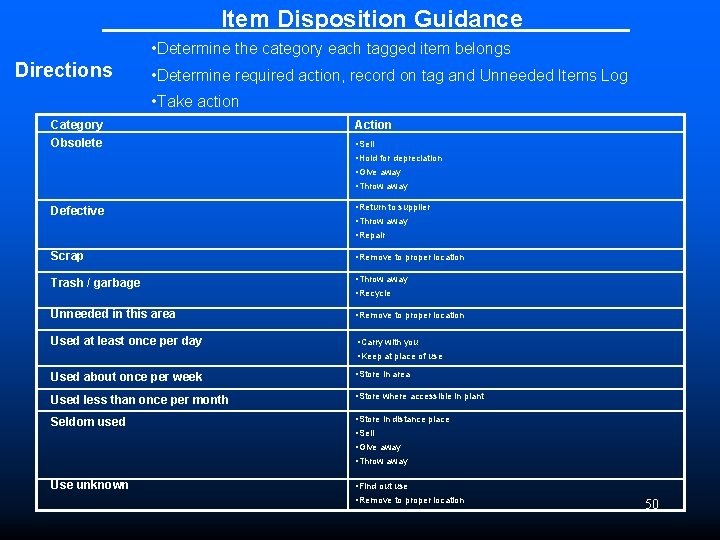
Item Disposition Guidance • Determine the category each tagged item belongs Directions • Determine required action, record on tag and Unneeded Items Log • Take action Category Action Obsolete • Sell • Hold for depreciation • Give away • Throw away Defective • Return to supplier • Throw away • Repair Scrap • Remove to proper location Trash / garbage • Throw away • Recycle Unneeded in this area • Remove to proper location Used at least once per day • Carry with you • Keep at place of use Used about once per week • Store in area Used less than once per month • Store where accessible in plant Seldom used • Store in distance place • Sell • Give away • Throw away Use unknown • Find out use • Remove to proper location 50

Red Tag Checklist • Examine all items in each category Directions • Red tag every item that may not be needed • Enter a Ö when a category is inspected Search these spaces Floors Aisles Operation areas Work Stations Corners, behind/under equipment Stairs Small rooms Offices Loading docks Inside cabinets and drawers Look for unneeded equipment Machines Small tools Dies Jigs Bits Conveyance equipment Plumbing, pipes, etc. Electrical equipment Wire, fixtures, junction boxes Look for unneeded furniture Cabinets Benches and tables Chairs Carts Other Search these storage places Shelves Racks Closets Sheds Other storage areas Search the walls, boards, etc. Items hung on walls Bulletin boards Signboards Other Look for unneeded material / supplies Raw materials Supplies Parts Work in process Finished products Shipping materials Look for other unneeded items Work clothes Helmets Work shoes Trash cans Other 51
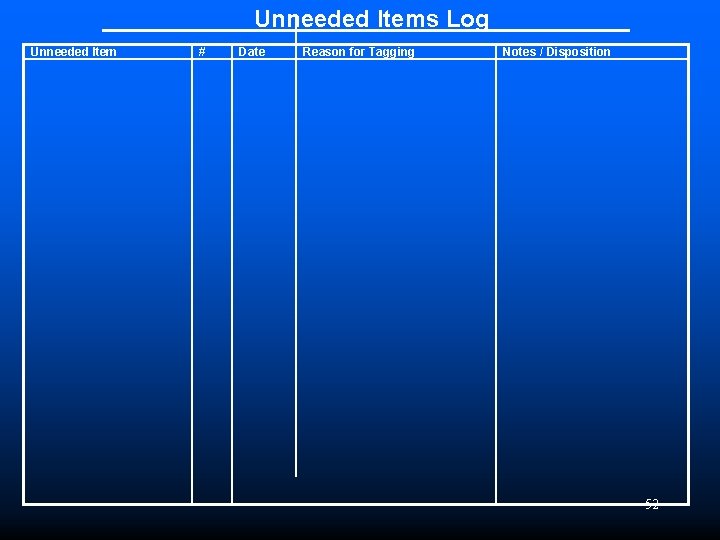
Unneeded Items Log Unneeded Item # Date Reason for Tagging Notes / Disposition 52
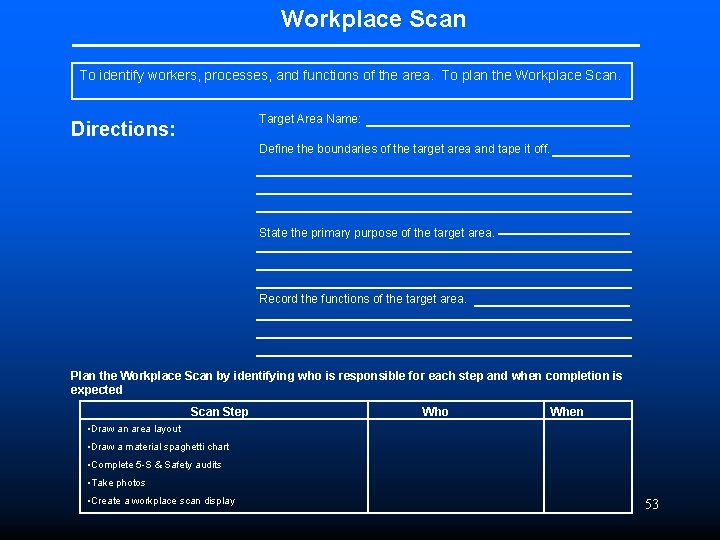
Workplace Scan To identify workers, processes, and functions of the area. To plan the Workplace Scan. Target Area Name: Directions: Define the boundaries of the target area and tape it off. State the primary purpose of the target area. Record the functions of the target area. Plan the Workplace Scan by identifying who is responsible for each step and when completion is expected Scan Step Who When • Draw an area layout • Draw a material spaghetti chart • Complete 5 -S & Safety audits • Take photos • Create a workplace scan display 53
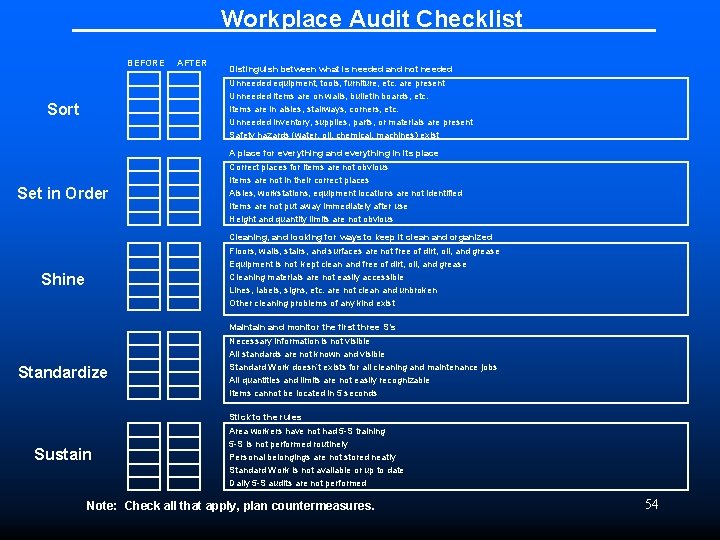
Workplace Audit Checklist BEFORE AFTER Distinguish between what is needed and not needed Unneeded equipment, tools, furniture, etc. are present Unneeded items are on walls, bulletin boards, etc. Items are in aisles, stairways, corners, etc. Unneeded inventory, supplies, parts, or materials are present Safety hazards (water, oil, chemical, machines) exist Sort A place for everything and everything in its place Set in Order Correct places for items are not obvious Items are not in their correct places Aisles, workstations, equipment locations are not identified Items are not put away immediately after use Height and quantity limits are not obvious Cleaning, and looking for ways to keep it clean and organized Floors, walls, stairs, and surfaces are not free of dirt, oil, and grease Equipment is not kept clean and free of dirt, oil, and grease Cleaning materials are not easily accessible Lines, labels, signs, etc. are not clean and unbroken Other cleaning problems of any kind exist Shine Maintain and monitor the first three S’s Standardize Necessary information is not visible All standards are not known and visible Standard Work doesn’t exists for all cleaning and maintenance jobs All quantities and limits are not easily recognizable Items cannot be located in 5 seconds Stick to the rules Sustain Area workers have not had 5 -S training 5 -S is not performed routinely Personal belongings are not stored neatly Standard Work is not available or up to date Daily 5 -S audits are not performed Note: Check all that apply, plan countermeasures. 54
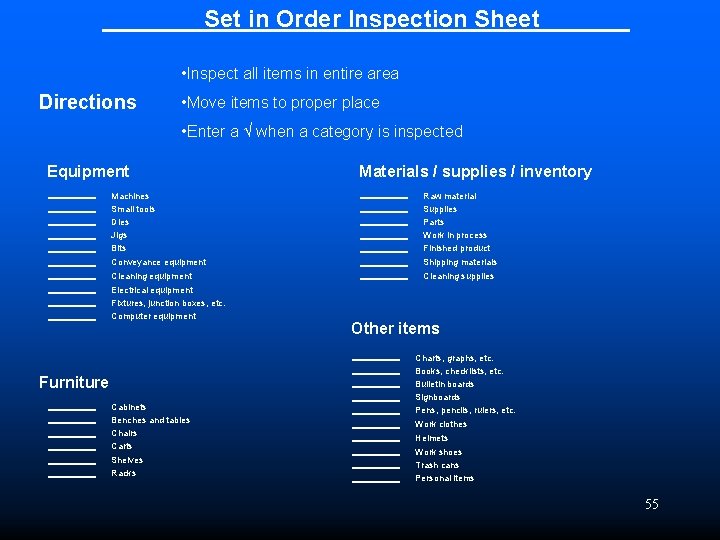
Set in Order Inspection Sheet • Inspect all items in entire area Directions • Move items to proper place • Enter a Ö when a category is inspected Equipment Materials / supplies / inventory Machines Small tools Dies Jigs Raw material Supplies Parts Work in process Bits Conveyance equipment Finished product Shipping materials Cleaning equipment Electrical equipment Fixtures, junction boxes, etc. Computer equipment Cleaning supplies Other items Charts, graphs, etc. Books, checklists, etc. Bulletin boards Signboards Furniture Cabinets Benches and tables Chairs Carts Shelves Racks Pens, pencils, rulers, etc. Work clothes Helmets Work shoes Trash cans Personal items 55
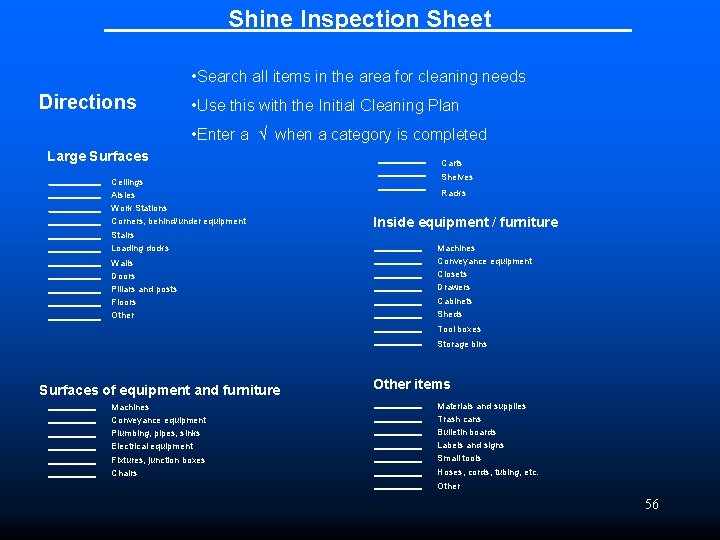
Shine Inspection Sheet • Search all items in the area for cleaning needs Directions • Use this with the Initial Cleaning Plan • Enter a Ö when a category is completed Large Surfaces Ceilings Aisles Work Stations Corners, behind/under equipment Stairs Loading docks Walls Doors Pillars and posts Floors Other Carts Shelves Racks Inside equipment / furniture Machines Conveyance equipment Closets Drawers Cabinets Sheds Tool boxes Storage bins Surfaces of equipment and furniture Other items Machines Conveyance equipment Plumbing, pipes, sinks Electrical equipment Materials and supplies Trash cans Bulletin boards Labels and signs Fixtures, junction boxes Chairs Small tools Hoses, cords, tubing, etc. Other 56

Initial Cleaning Plan Directions • List tasks and complete the columns below Target Area Task Location Who When Materials and Tools Needed 57
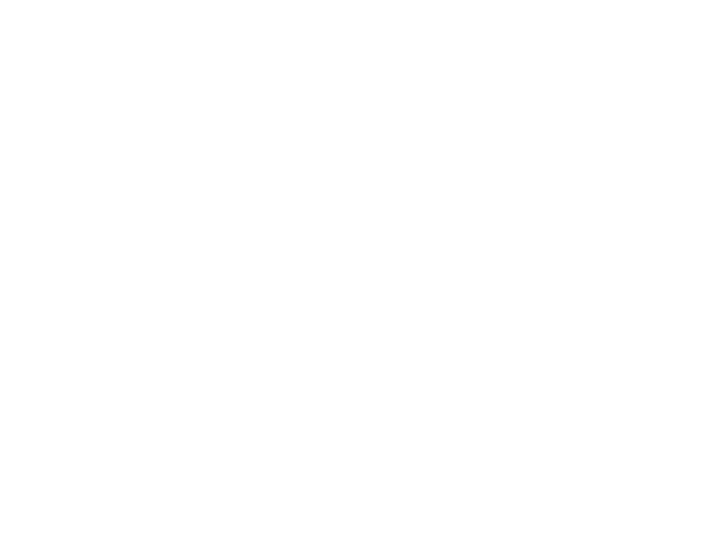
58
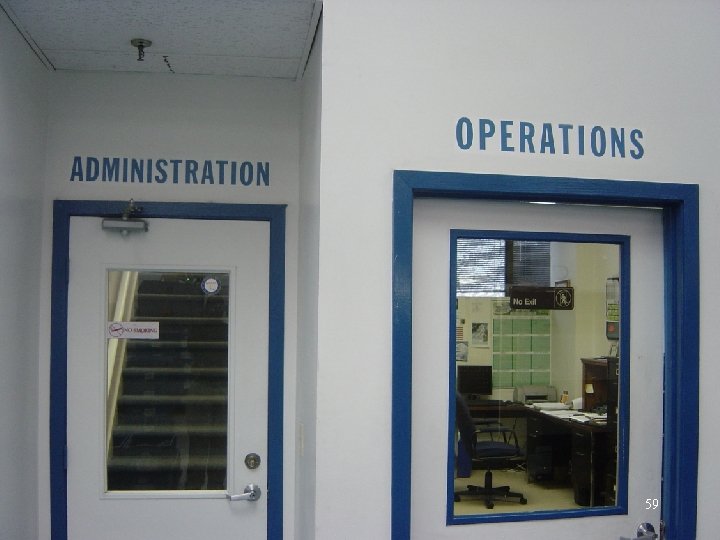
59
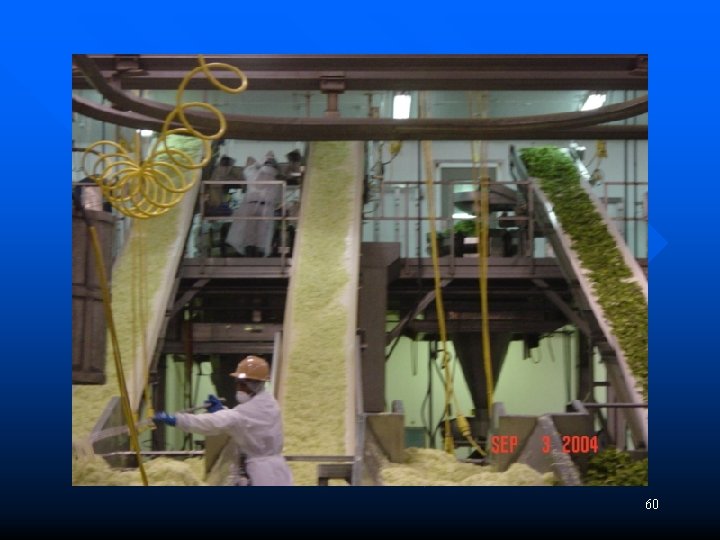
60
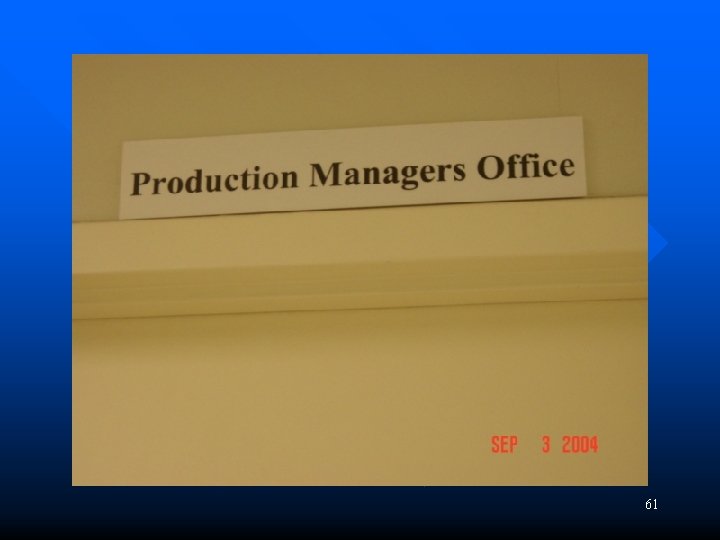
61
Activating prior knowledge examples
Symbolism vs allegory
Prior knowledge survey
Continuity vs discontinuity
Direct and indirect experience examples
Imprinting psychology
Agenda welcome and introductions
German family vocabulary
Agenda welcome and introductions
Introductions by marsha
Business english conversation
British council introductions
Meeting agenda welcome and introductions
Agenda welcome and introductions
Agenda welcome and introductions
Examples of survey introductions
Agenda welcome and introductions
Asl greetings and introductions
Creative introduction examples
Greeting in english conversations
Interesting introductions
Pip conclusion sample
Greetings and introductions lesson plan
Catchy introductions
Meeting agenda welcome and introductions
Attention grabber in an essay
Types of introductions
Persuasive text about scotland
Agenda for parent orientation
Titles for introductions
Introductions clip art
Agenda welcome and introductions
Agenda welcome and introductions
Agenda welcome and introductions
Meeting agenda welcome and introductions
Knowledge comes from experience
Shares research experiences and knowledge
The view that knowledge originates in experience
Knowledge shared is knowledge multiplied meaning
Street knowledge vs book knowledge
Knowledge creation and knowledge architecture
What is shared knowledge
Shared knowledge vs personal knowledge
Contoh shallow knowledge dan deep knowledge
Knowledge shared is knowledge squared meaning
Gertler econ
A priori and a posteriori knowledge
Prior to muhammad’s teachings, arabs were polytheistic.
Prior inconsistent statements
Charlie prior
New york state medicaid prior authorization
Optumlink
Mdwise prior authorization form
Dark channel prior
Uts plt
Free prior and informed consent
Florida cession prior owner of territory
Aberlearn
Cristiane gonzalez prior
Gain more friends isaac
Pre incorporation meaning
Usf colinas de odivelas