IN PROCESS QUALITY CONTROL In process quality control
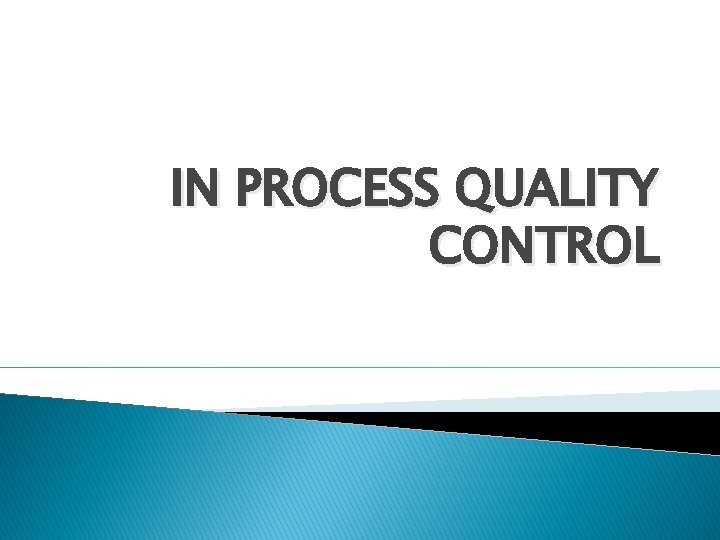
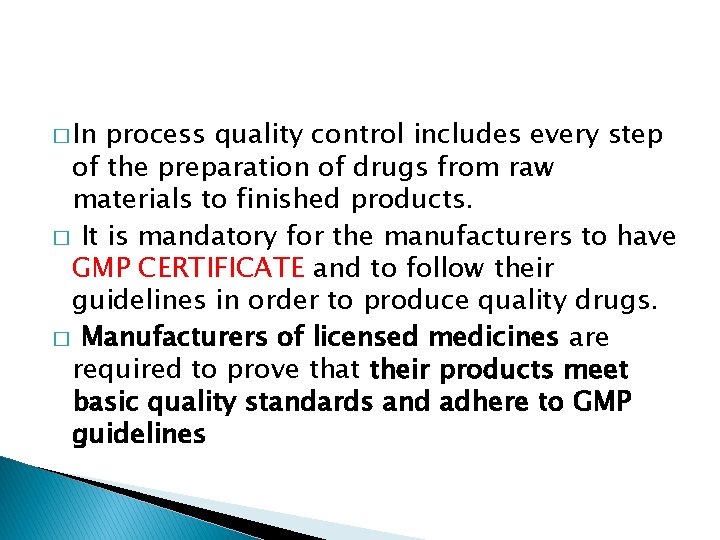
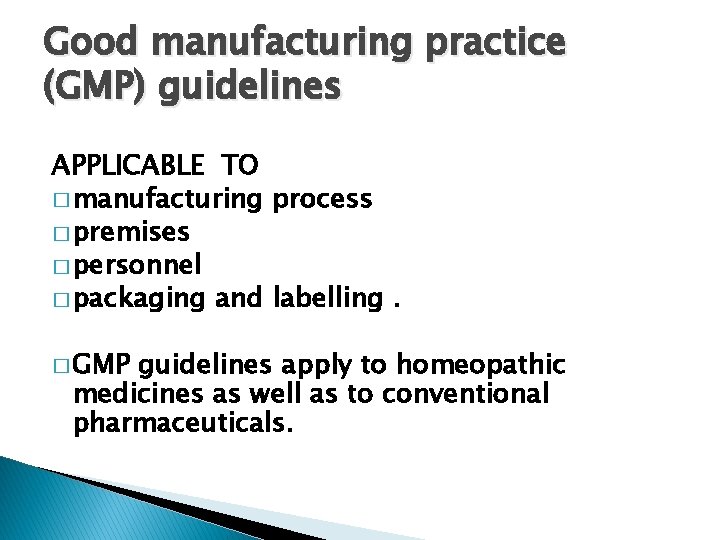
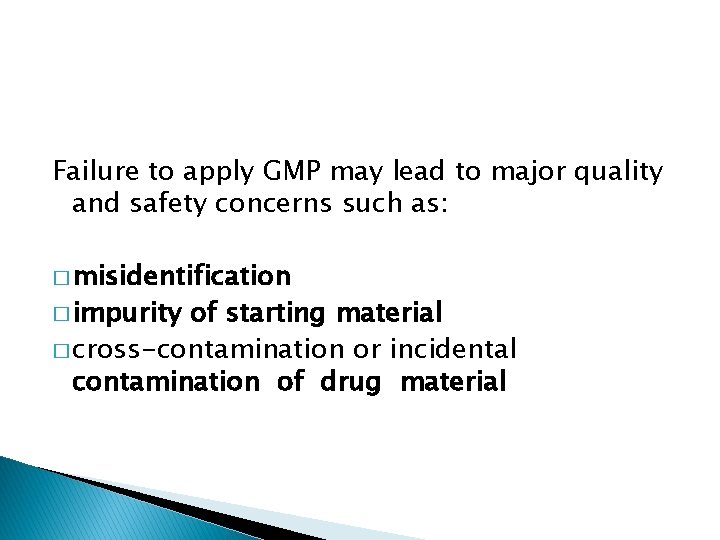
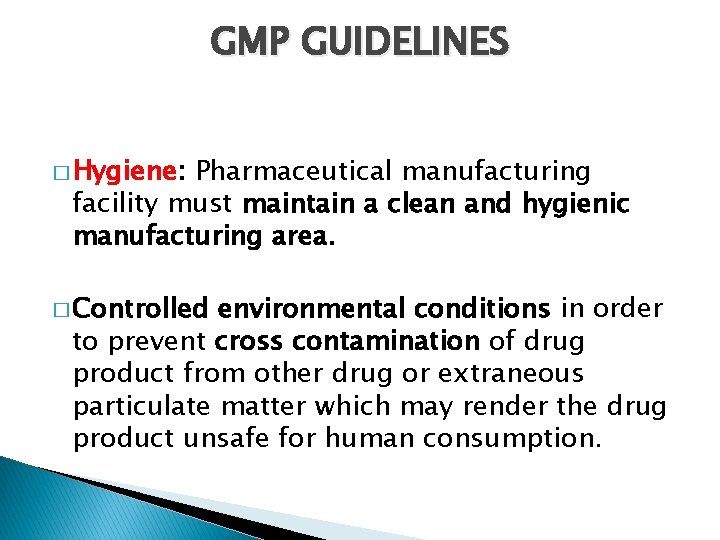
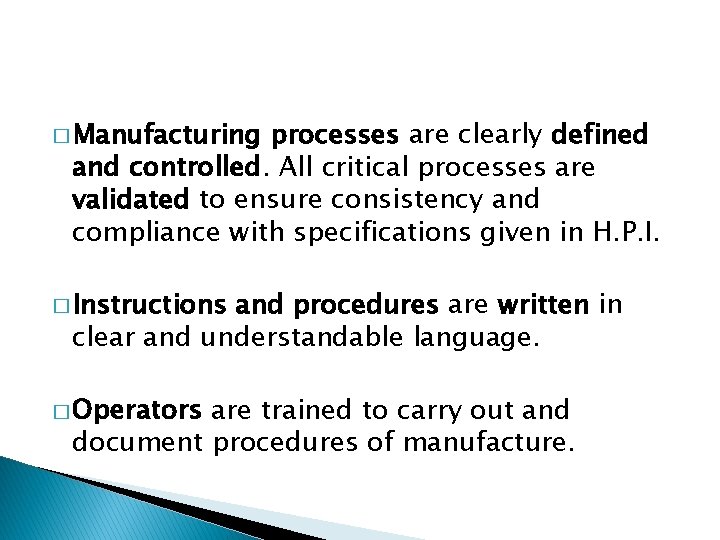
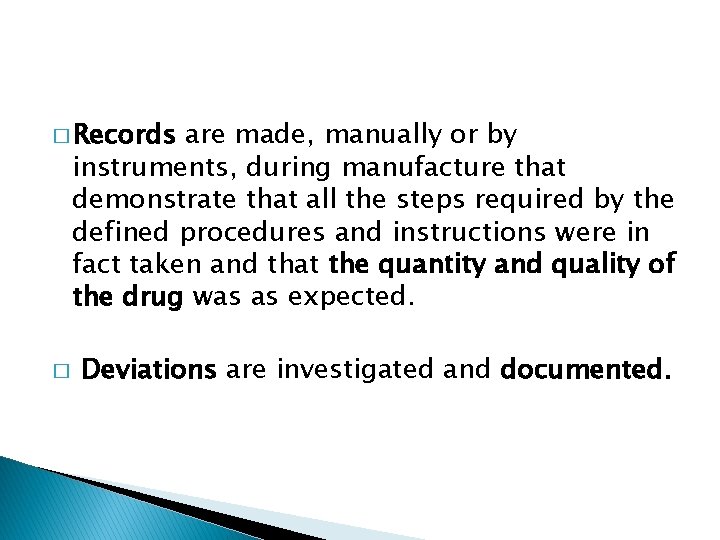
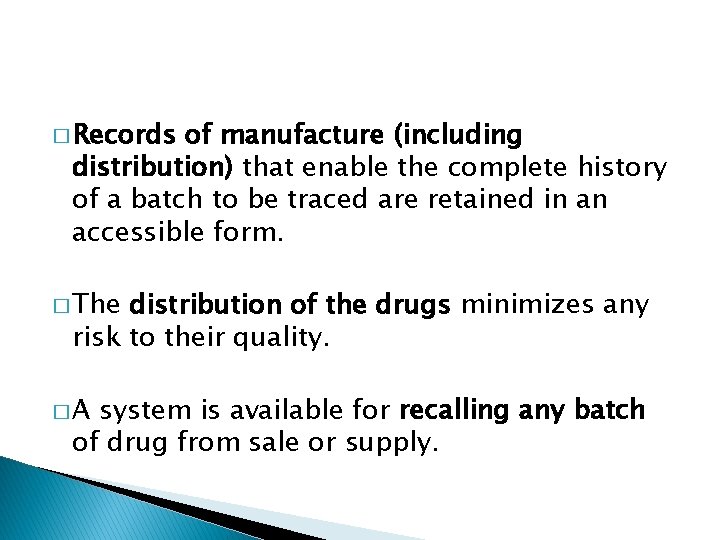
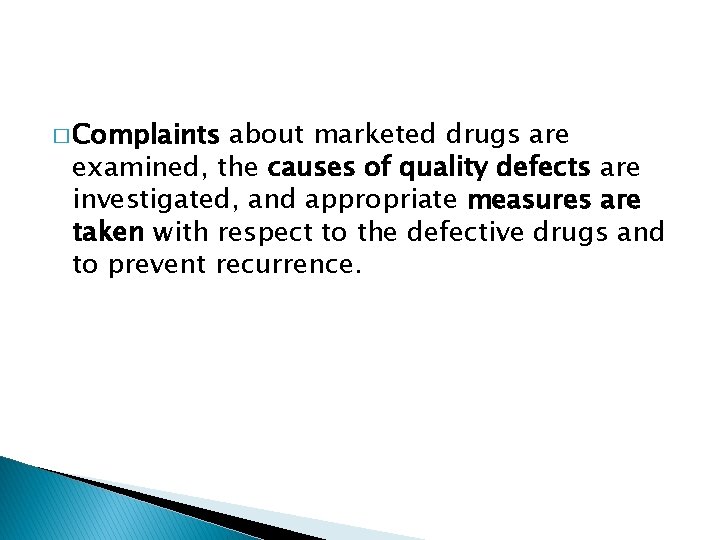
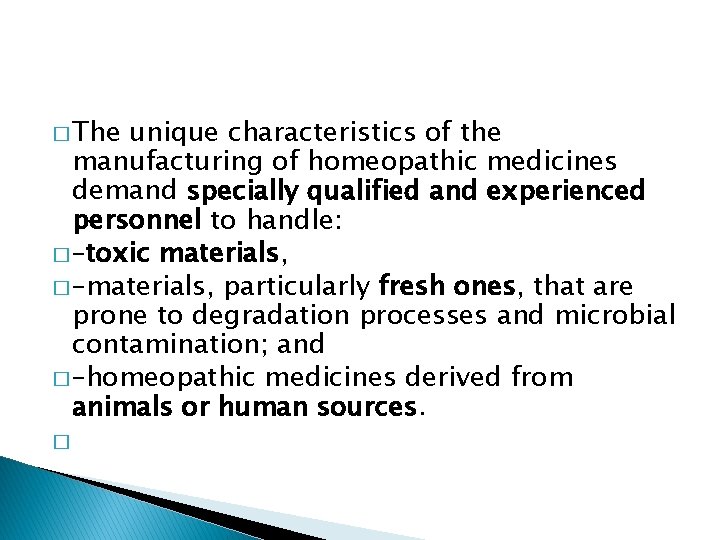
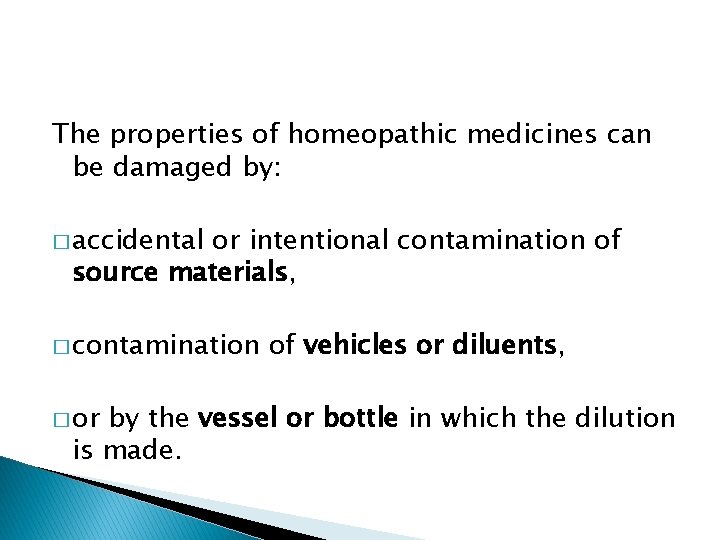
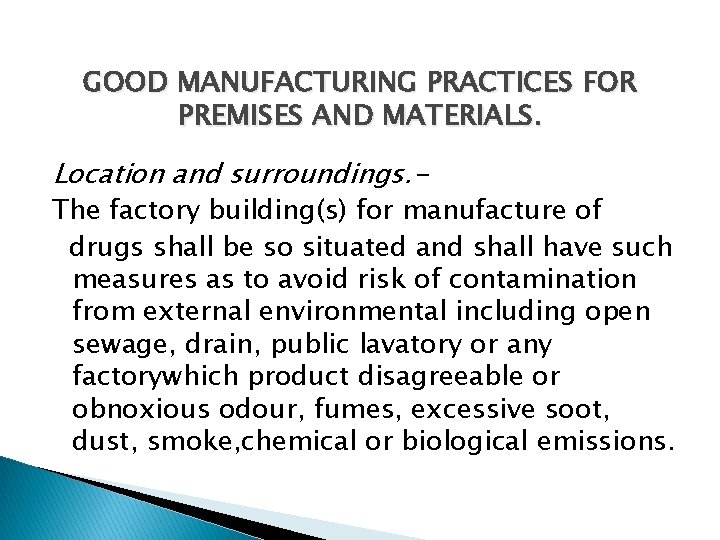
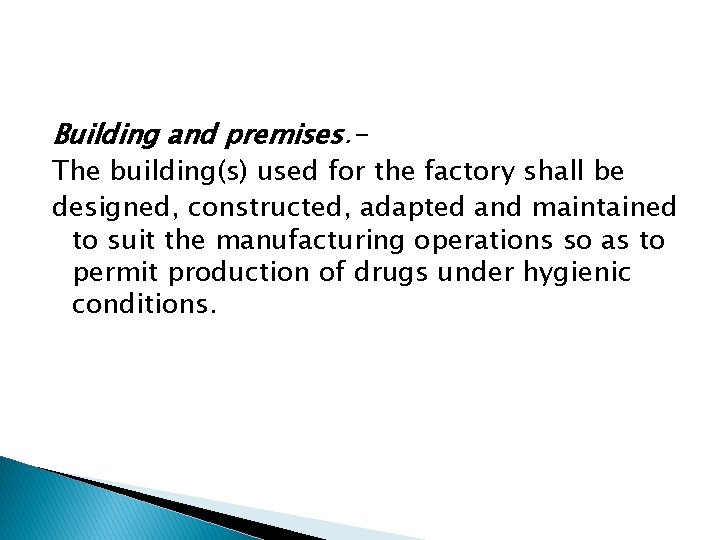
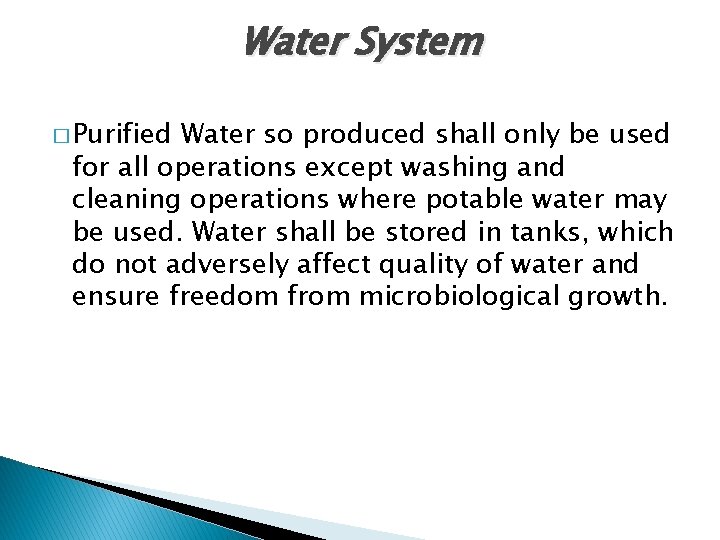
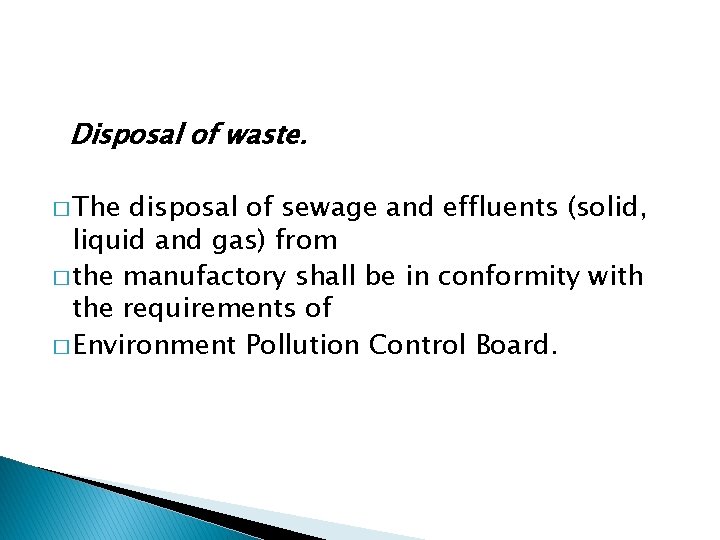
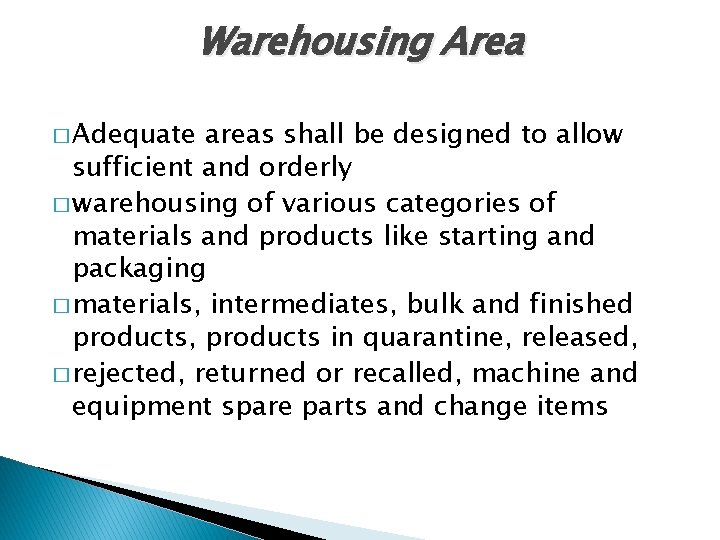
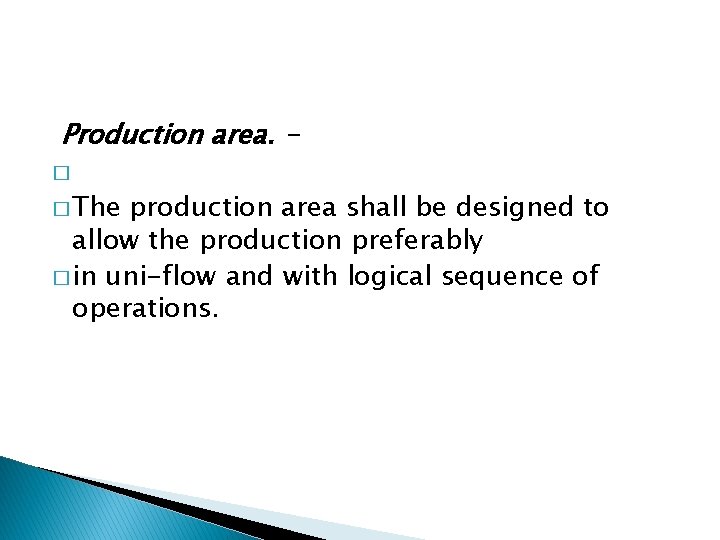
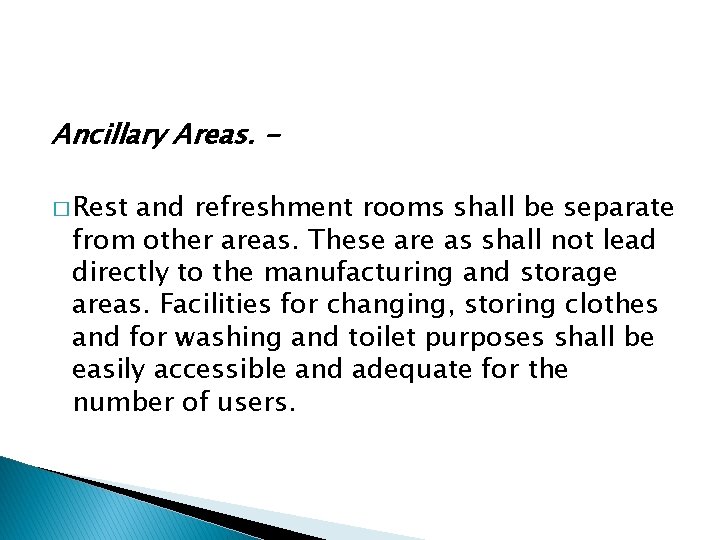
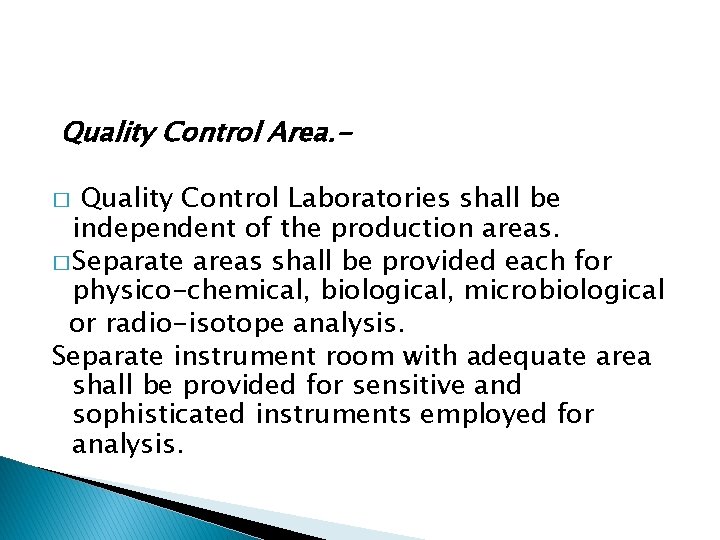
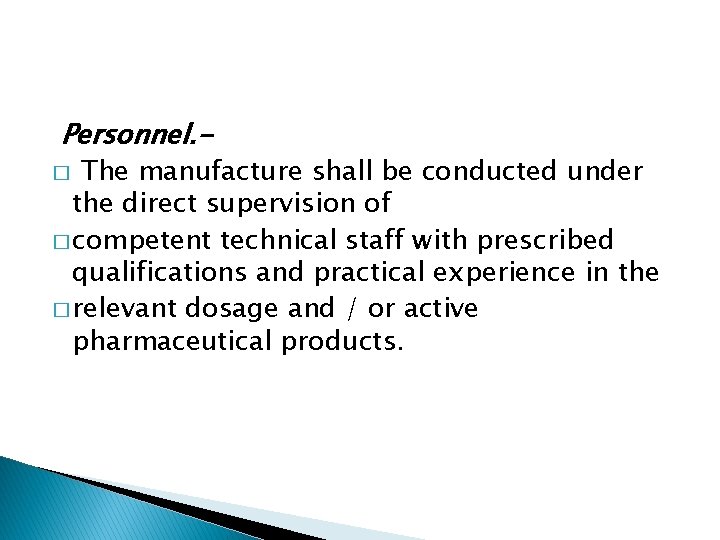
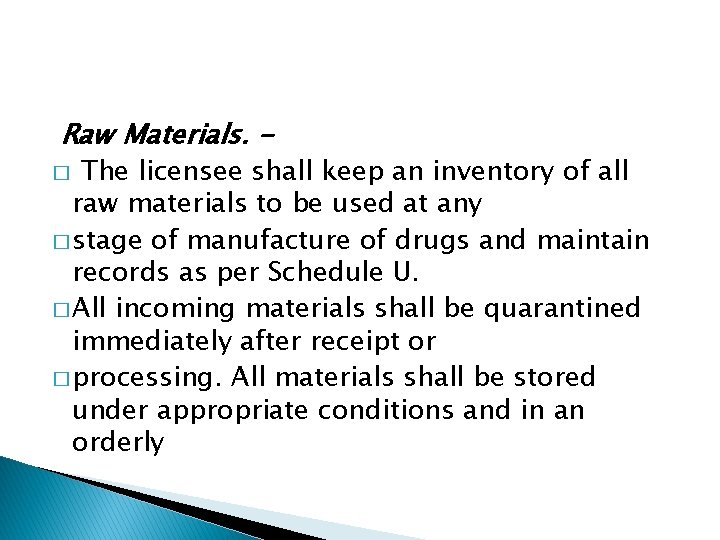
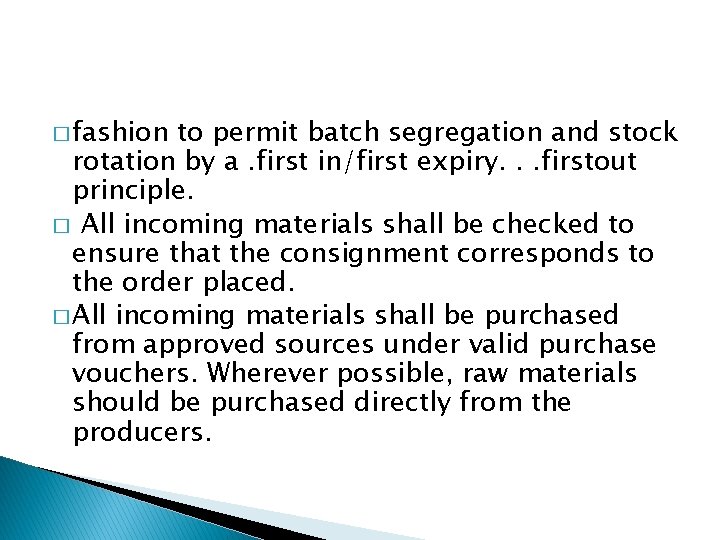
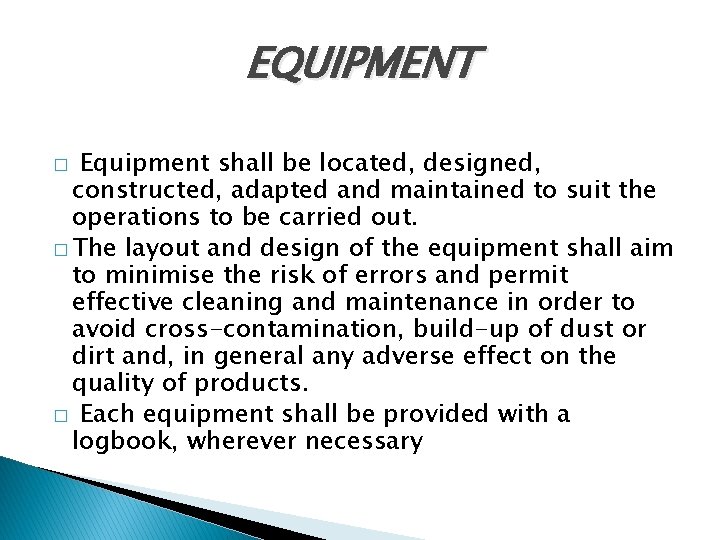
- Slides: 23
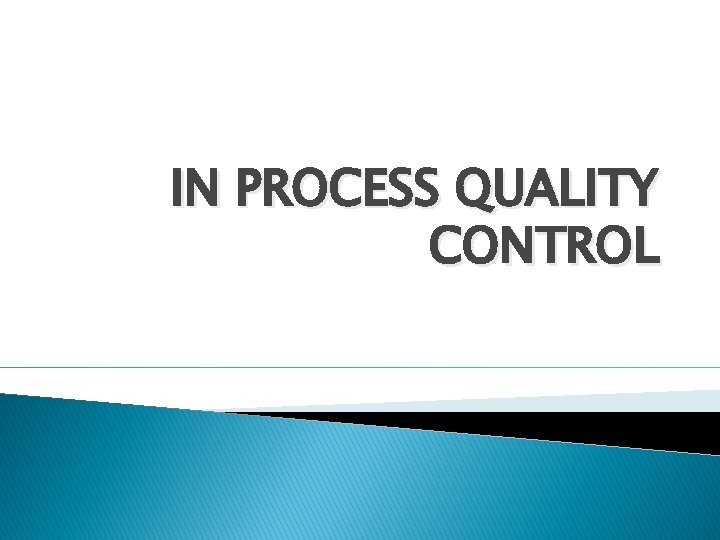
IN PROCESS QUALITY CONTROL
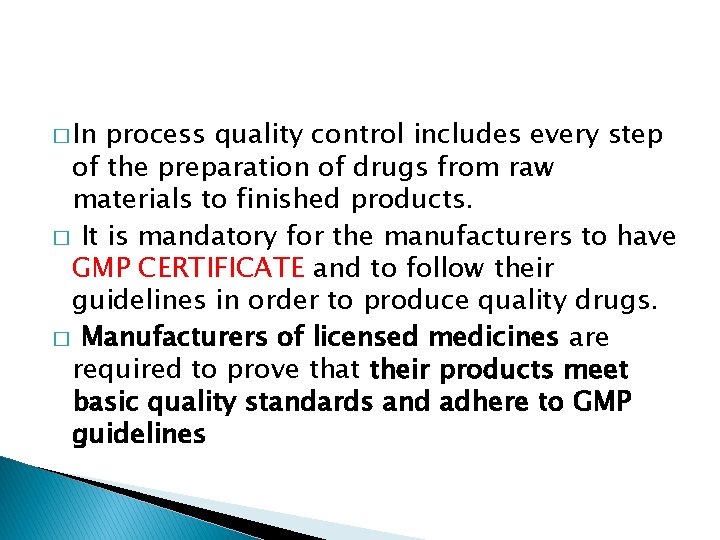
� In process quality control includes every step of the preparation of drugs from raw materials to finished products. � It is mandatory for the manufacturers to have GMP CERTIFICATE and to follow their guidelines in order to produce quality drugs. � Manufacturers of licensed medicines are required to prove that their products meet basic quality standards and adhere to GMP guidelines
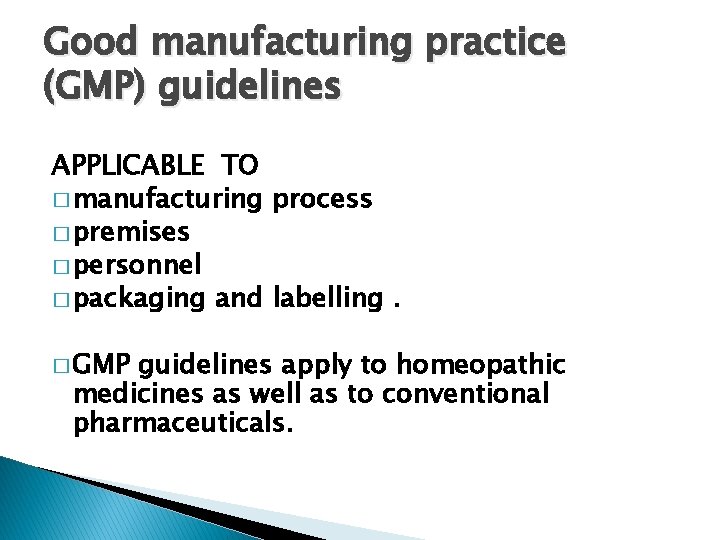
Good manufacturing practice (GMP) guidelines APPLICABLE TO � manufacturing process � premises � personnel � packaging and labelling. � GMP guidelines apply to homeopathic medicines as well as to conventional pharmaceuticals.
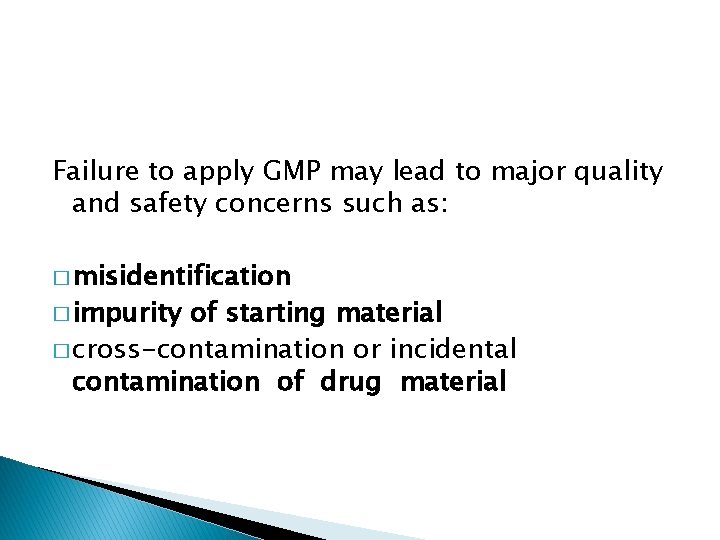
Failure to apply GMP may lead to major quality and safety concerns such as: � misidentification � impurity of starting material � cross-contamination or incidental contamination of drug material
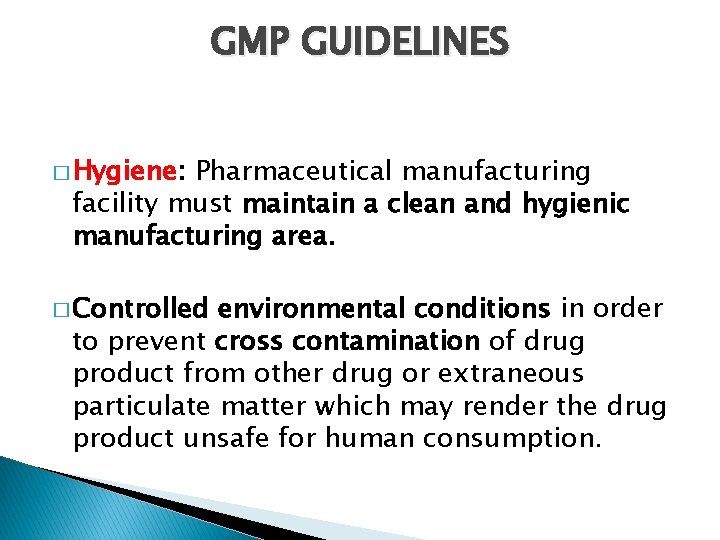
GMP GUIDELINES � Hygiene: Pharmaceutical manufacturing facility must maintain a clean and hygienic manufacturing area. � Controlled environmental conditions in order to prevent cross contamination of drug product from other drug or extraneous particulate matter which may render the drug product unsafe for human consumption.
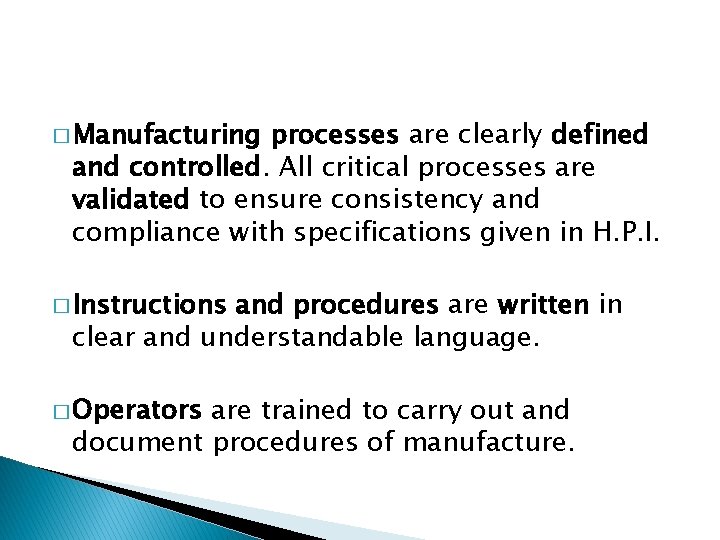
� Manufacturing processes are clearly defined and controlled. All critical processes are validated to ensure consistency and compliance with specifications given in H. P. I. � Instructions and procedures are written in clear and understandable language. � Operators are trained to carry out and document procedures of manufacture.
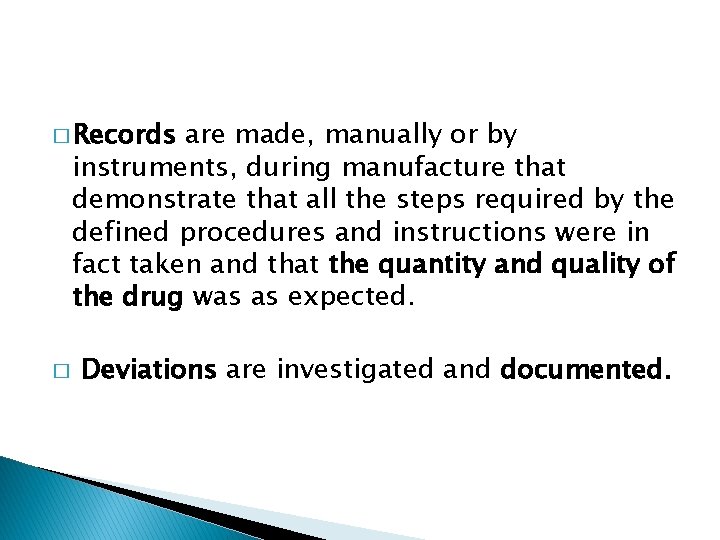
� Records are made, manually or by instruments, during manufacture that demonstrate that all the steps required by the defined procedures and instructions were in fact taken and that the quantity and quality of the drug was as expected. � Deviations are investigated and documented.
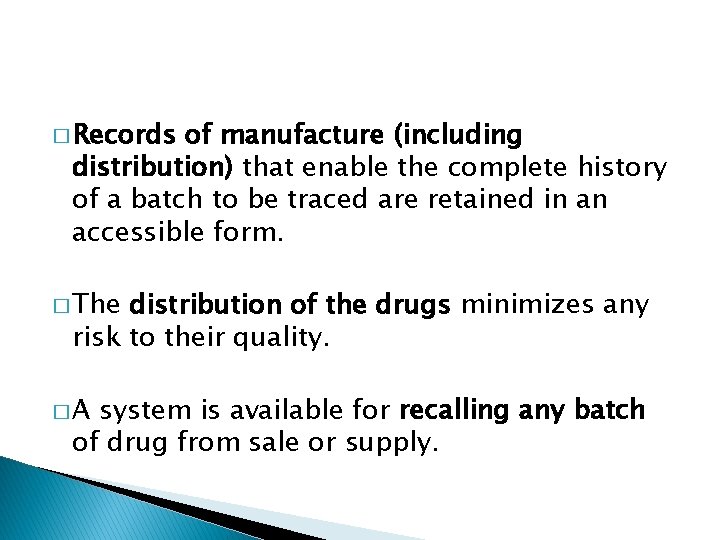
� Records of manufacture (including distribution) that enable the complete history of a batch to be traced are retained in an accessible form. � The distribution of the drugs minimizes any risk to their quality. �A system is available for recalling any batch of drug from sale or supply.
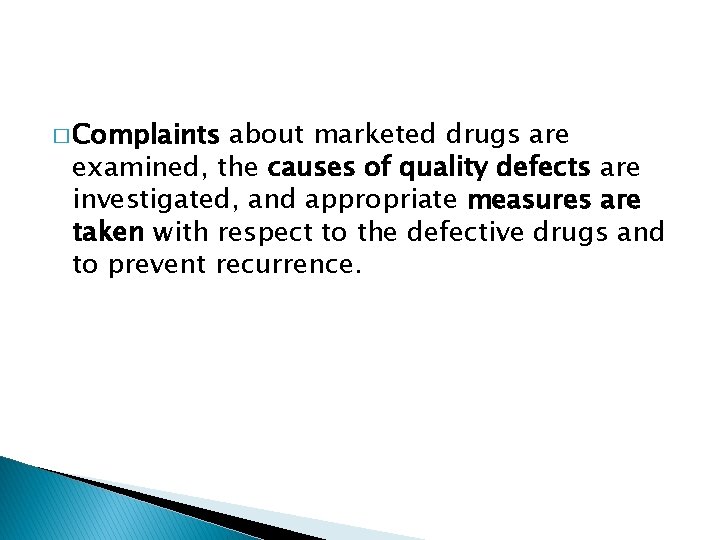
� Complaints about marketed drugs are examined, the causes of quality defects are investigated, and appropriate measures are taken with respect to the defective drugs and to prevent recurrence.
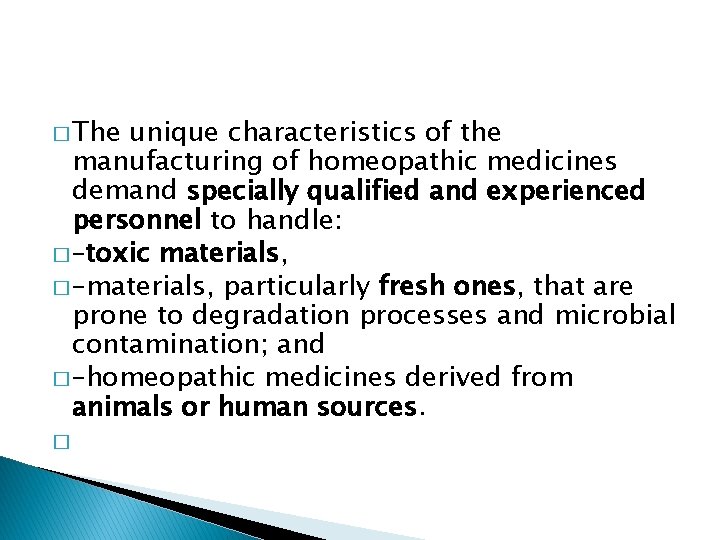
� The unique characteristics of the manufacturing of homeopathic medicines demand specially qualified and experienced personnel to handle: � –toxic materials, � –materials, particularly fresh ones, that are prone to degradation processes and microbial contamination; and � –homeopathic medicines derived from animals or human sources. �
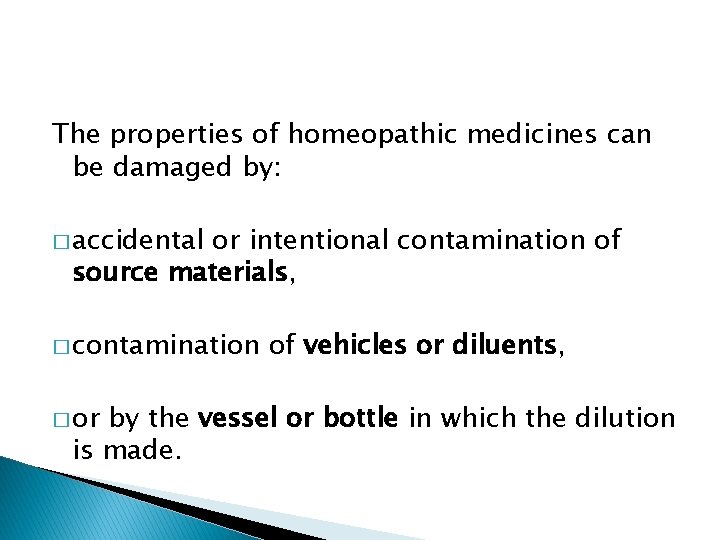
The properties of homeopathic medicines can be damaged by: � accidental or intentional contamination of source materials, � contamination � or of vehicles or diluents, by the vessel or bottle in which the dilution is made.
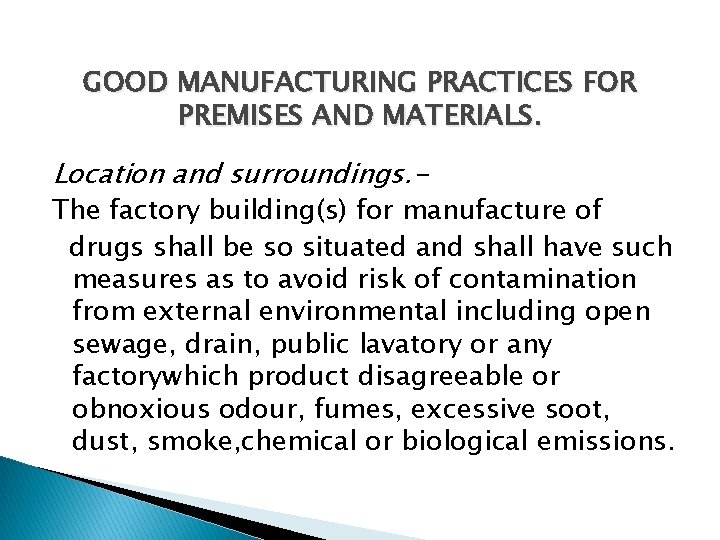
GOOD MANUFACTURING PRACTICES FOR PREMISES AND MATERIALS. Location and surroundings. - The factory building(s) for manufacture of drugs shall be so situated and shall have such measures as to avoid risk of contamination from external environmental including open sewage, drain, public lavatory or any factorywhich product disagreeable or obnoxious odour, fumes, excessive soot, dust, smoke, chemical or biological emissions.
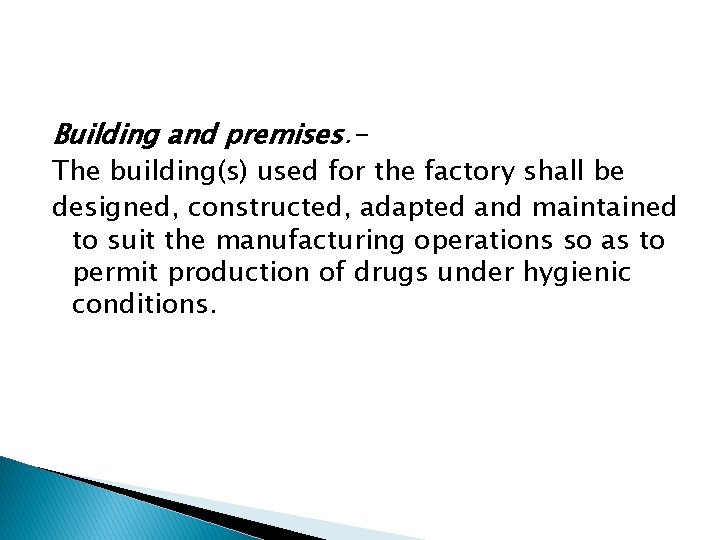
Building and premises. - The building(s) used for the factory shall be designed, constructed, adapted and maintained to suit the manufacturing operations so as to permit production of drugs under hygienic conditions.
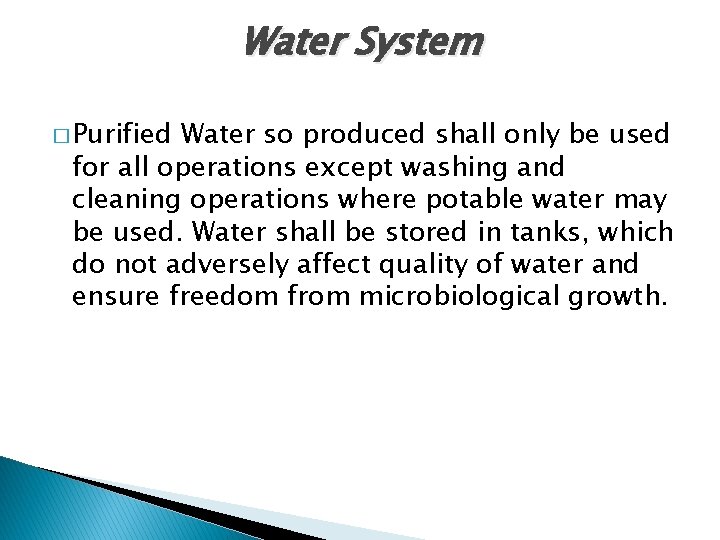
Water System � Purified Water so produced shall only be used for all operations except washing and cleaning operations where potable water may be used. Water shall be stored in tanks, which do not adversely affect quality of water and ensure freedom from microbiological growth.
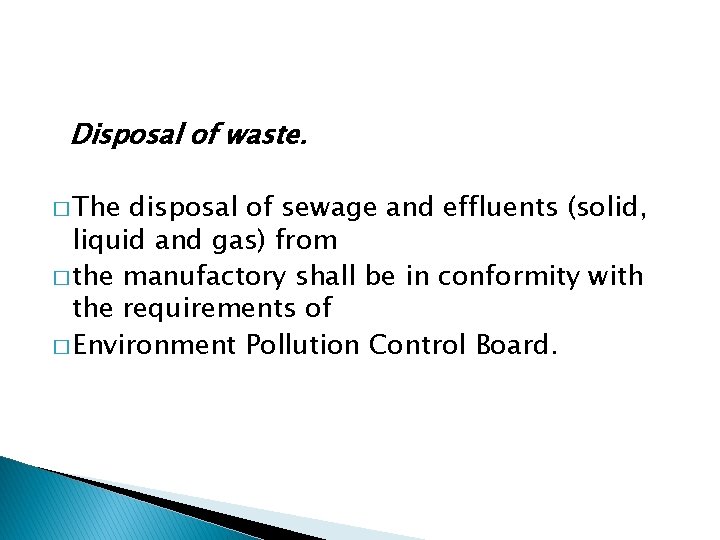
Disposal of waste. � The disposal of sewage and effluents (solid, liquid and gas) from � the manufactory shall be in conformity with the requirements of � Environment Pollution Control Board.
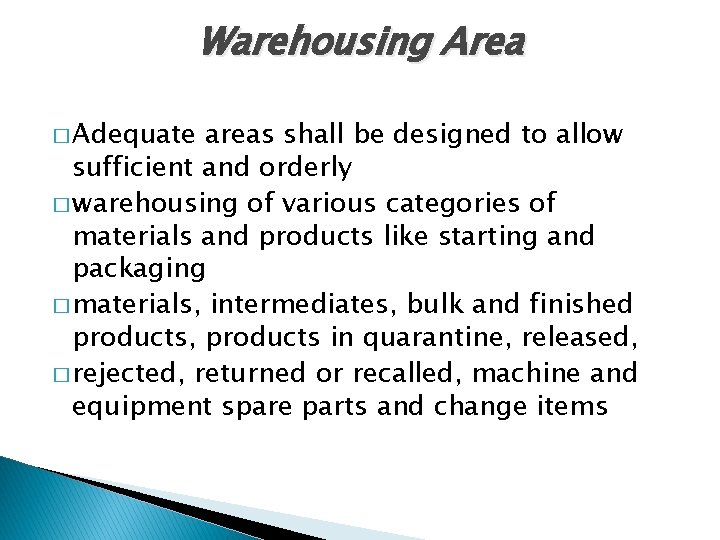
Warehousing Area � Adequate areas shall be designed to allow sufficient and orderly � warehousing of various categories of materials and products like starting and packaging � materials, intermediates, bulk and finished products, products in quarantine, released, � rejected, returned or recalled, machine and equipment spare parts and change items
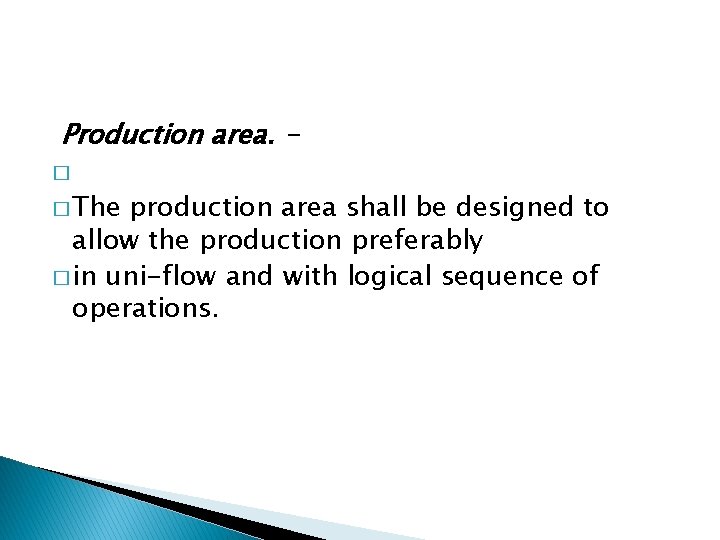
Production area. � � The production area shall be designed to allow the production preferably � in uni-flow and with logical sequence of operations.
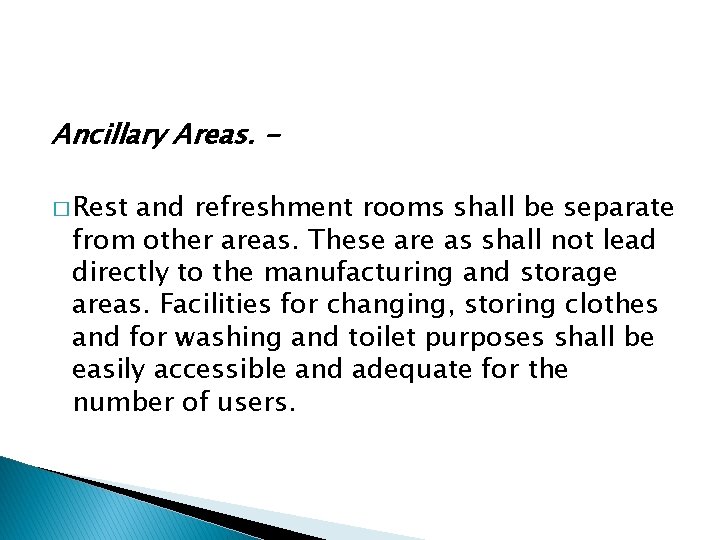
Ancillary Areas. � Rest and refreshment rooms shall be separate from other areas. These are as shall not lead directly to the manufacturing and storage areas. Facilities for changing, storing clothes and for washing and toilet purposes shall be easily accessible and adequate for the number of users.
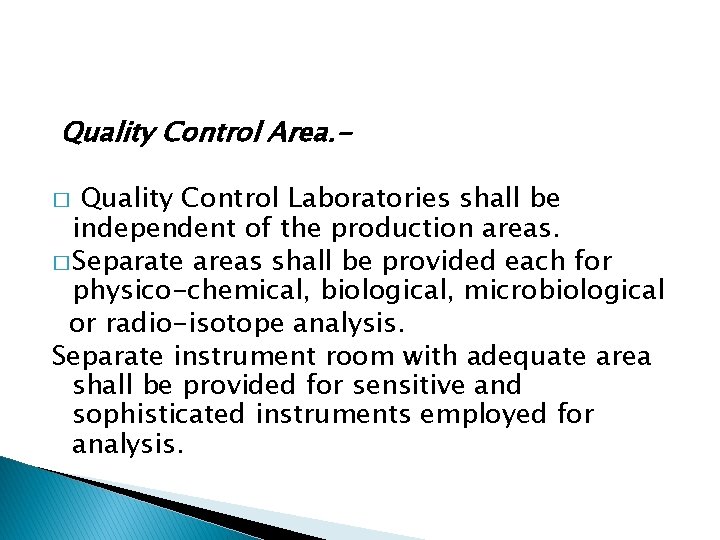
Quality Control Area. Quality Control Laboratories shall be independent of the production areas. � Separate areas shall be provided each for physico-chemical, biological, microbiological or radio-isotope analysis. Separate instrument room with adequate area shall be provided for sensitive and sophisticated instruments employed for analysis. �
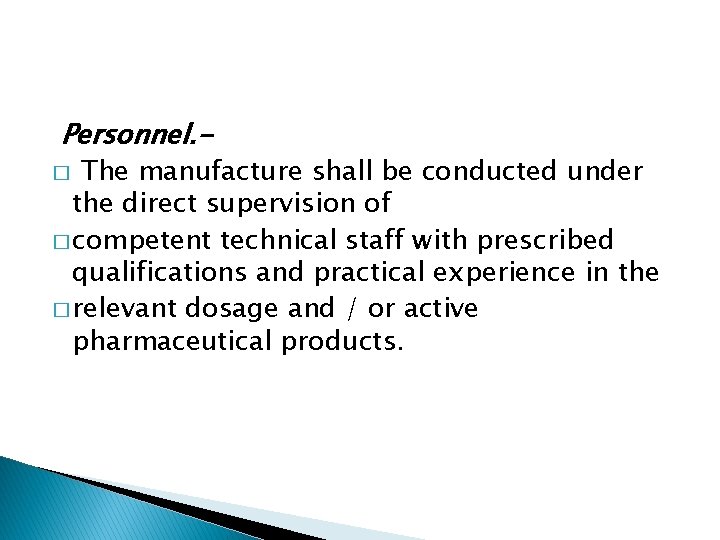
Personnel. - The manufacture shall be conducted under the direct supervision of � competent technical staff with prescribed qualifications and practical experience in the � relevant dosage and / or active pharmaceutical products. �
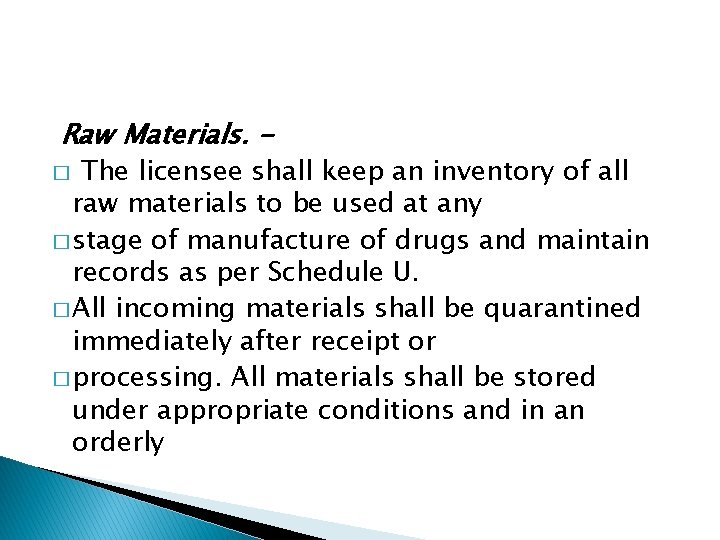
Raw Materials. - The licensee shall keep an inventory of all raw materials to be used at any � stage of manufacture of drugs and maintain records as per Schedule U. � All incoming materials shall be quarantined immediately after receipt or � processing. All materials shall be stored under appropriate conditions and in an orderly �
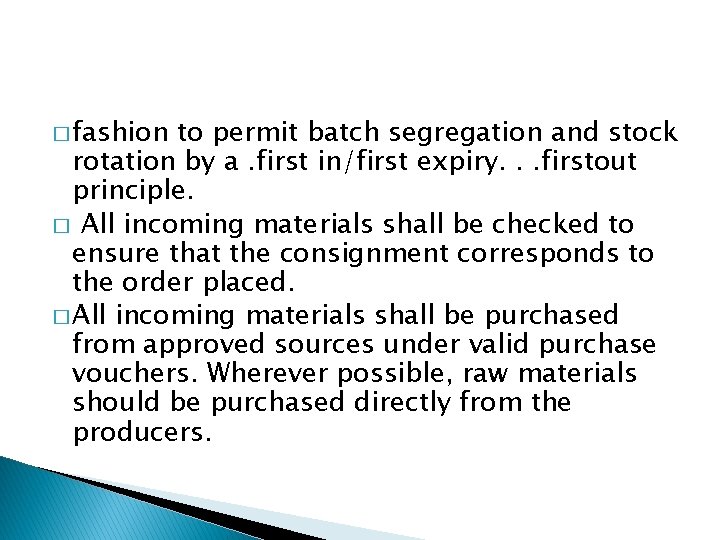
� fashion to permit batch segregation and stock rotation by a. first in/first expiry. . . firstout principle. � All incoming materials shall be checked to ensure that the consignment corresponds to the order placed. � All incoming materials shall be purchased from approved sources under valid purchase vouchers. Wherever possible, raw materials should be purchased directly from the producers.
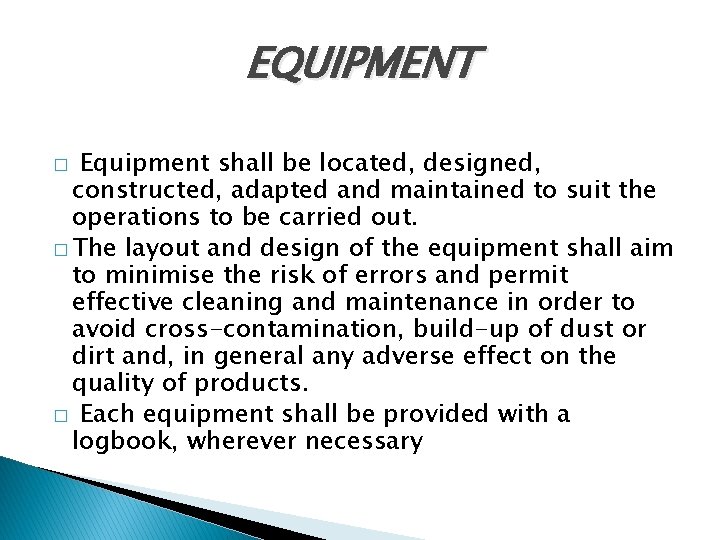
EQUIPMENT Equipment shall be located, designed, constructed, adapted and maintained to suit the operations to be carried out. � The layout and design of the equipment shall aim to minimise the risk of errors and permit effective cleaning and maintenance in order to avoid cross-contamination, build-up of dust or dirt and, in general any adverse effect on the quality of products. � Each equipment shall be provided with a logbook, wherever necessary �
Quality control and quality assurance
Quality control vs quality assurance pmp
Pmp gold plating
Basic concept of quality management
Mbaknol.com
Pengertian total quality management
Product control
Quality assurance model in nursing
Quality improvement vs quality assurance
Which of the gurus would be the father of quality control?
Quality is free: the art of making quality certain
Old quality vs new quality
Ipc quality control
Total quality control tqc
Acceptance sampling procedure
Average run length in quality control
Tqm wheel
Software quality control plan
Quality control log examples
Subway quality control
Seismic quality control
Quality control in business plan
Quality determination
Quality control raw materials