FE Analysis of Collaring Mockup Michal Holko at
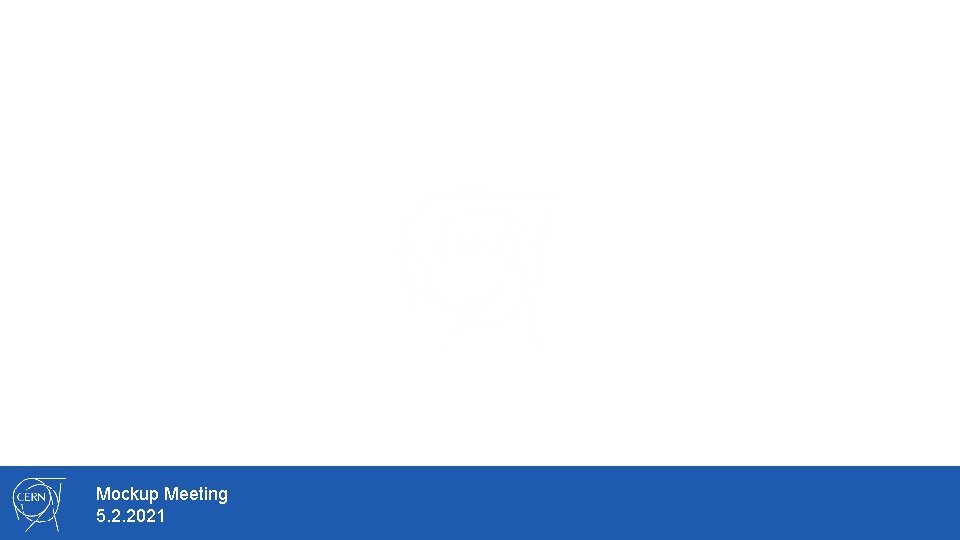
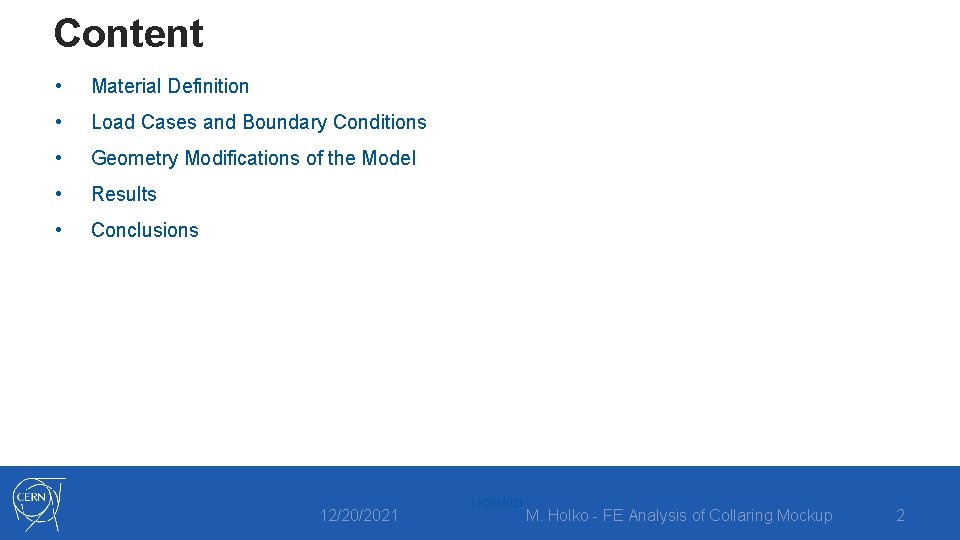
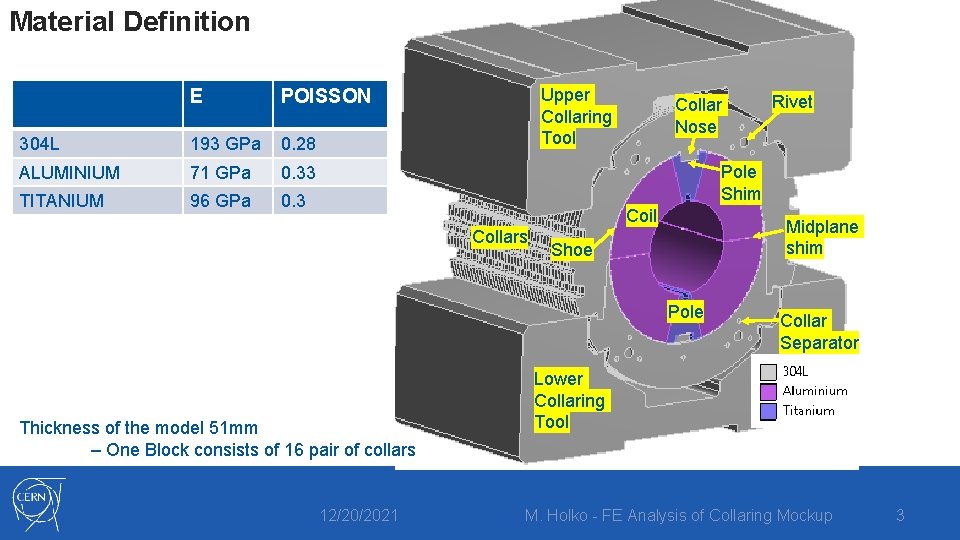
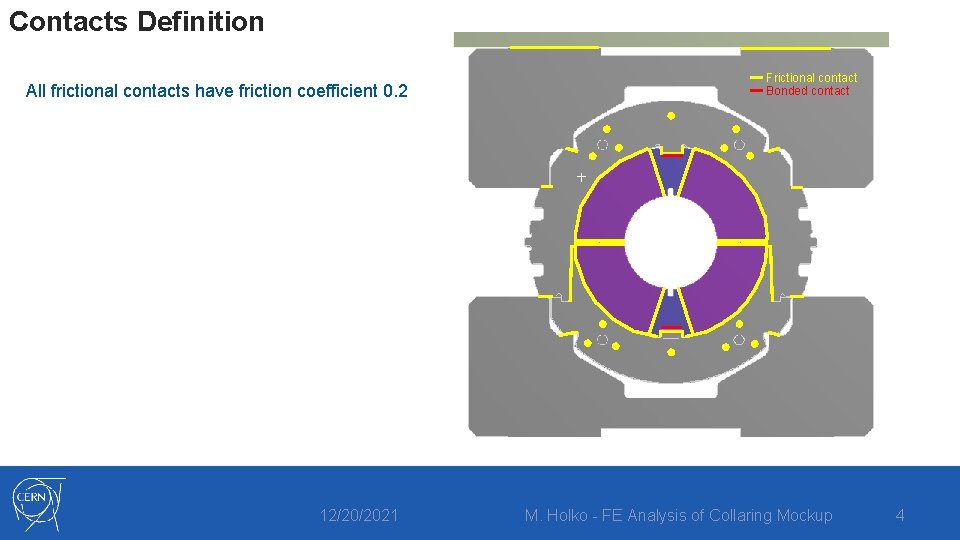
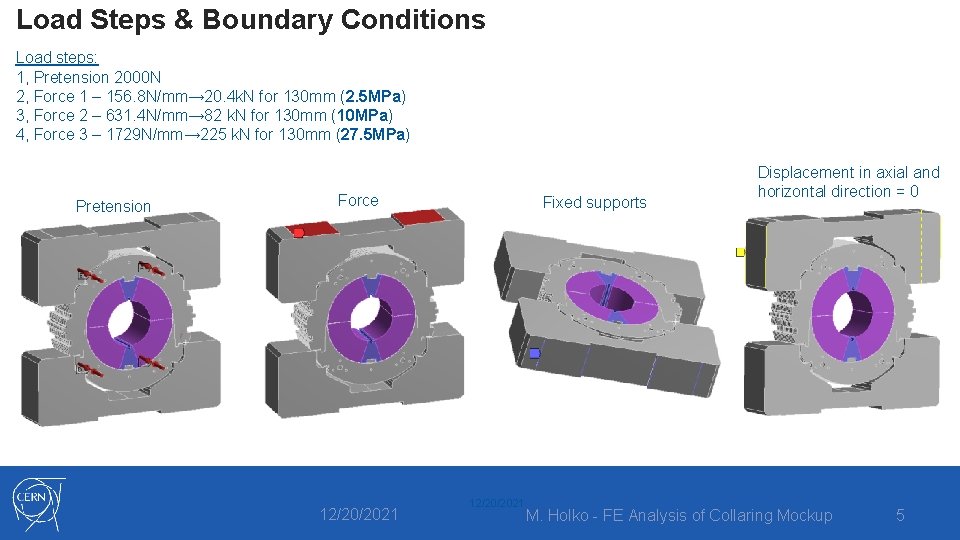
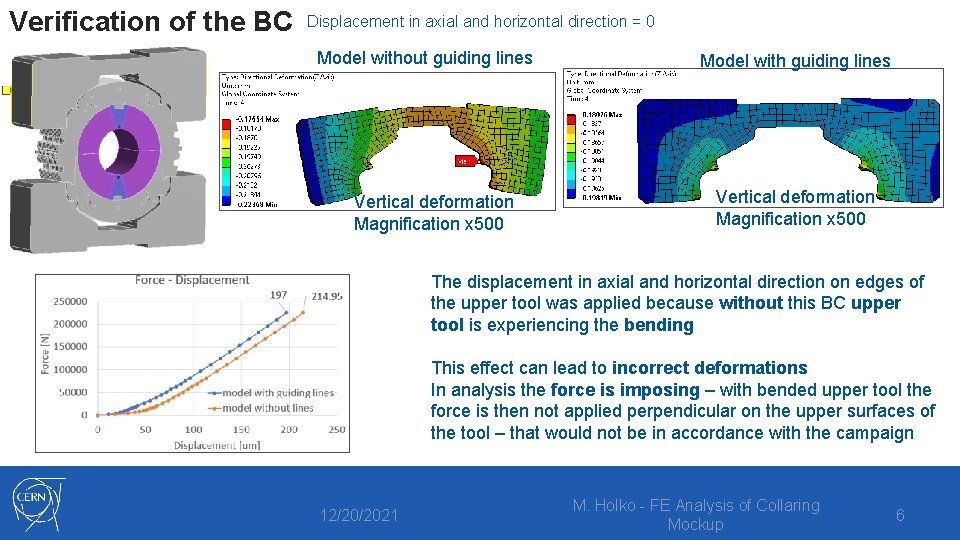
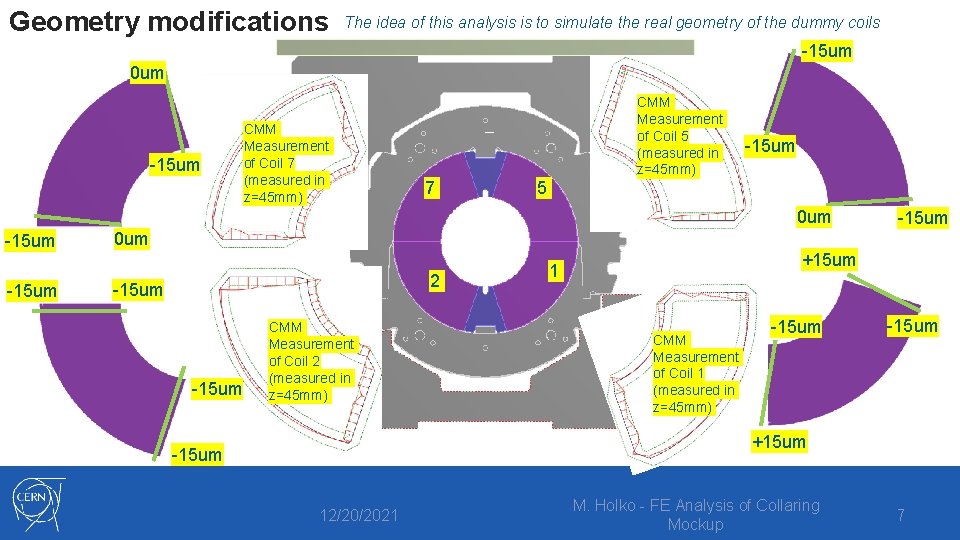
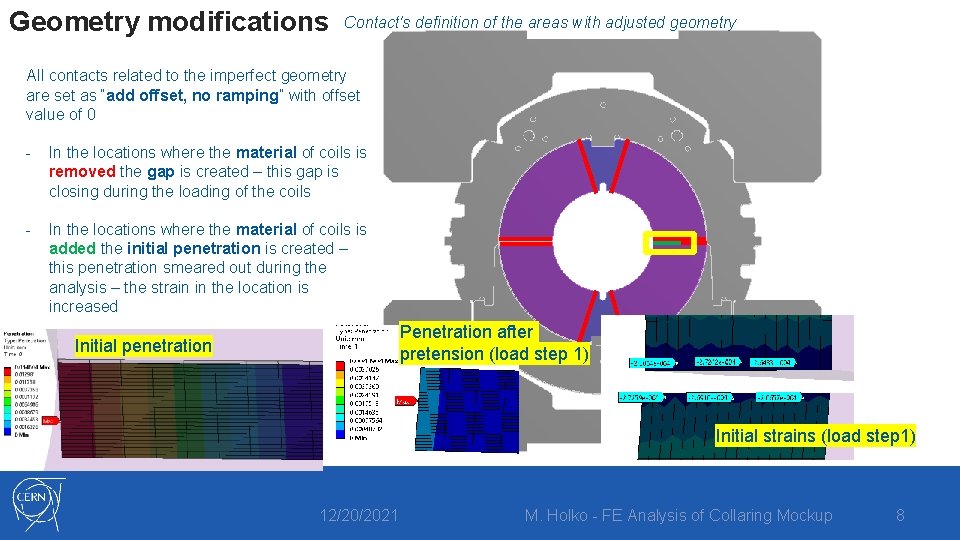
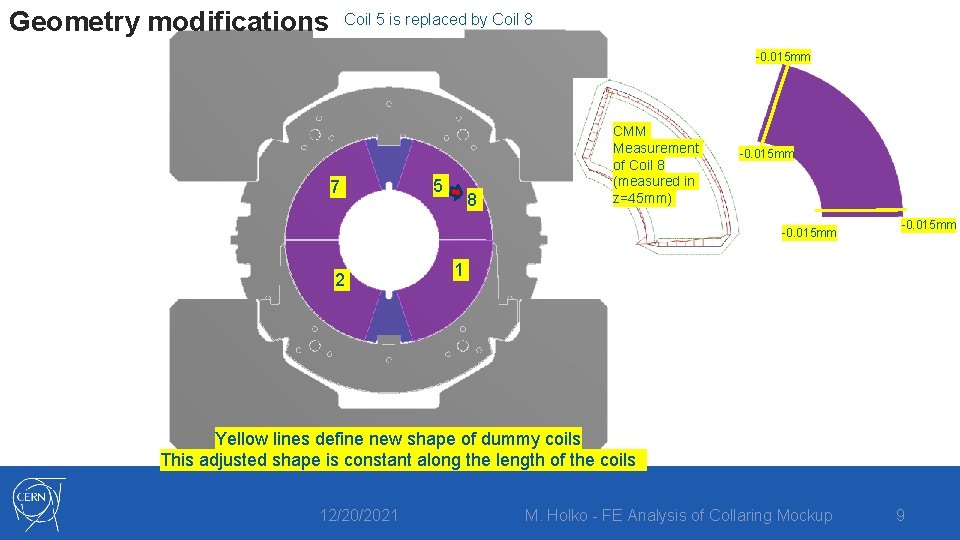
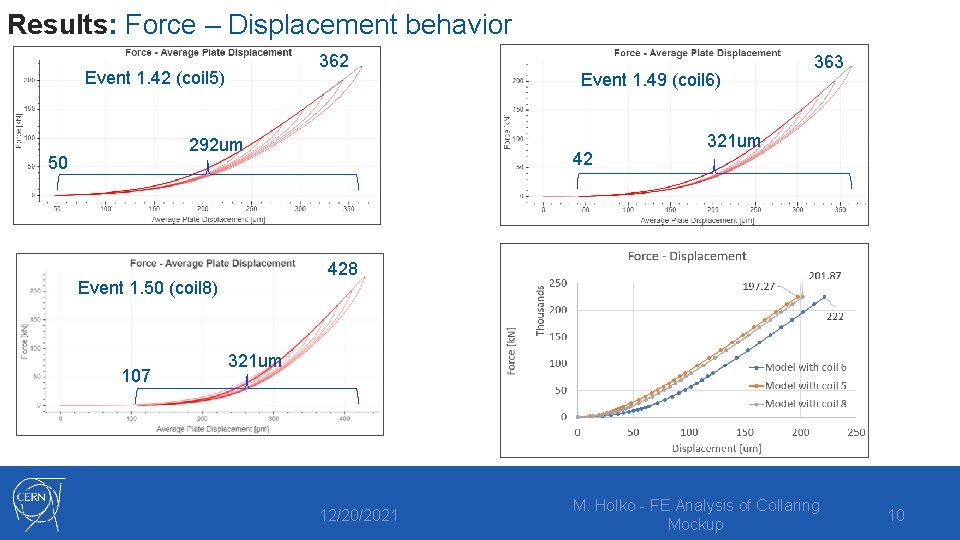
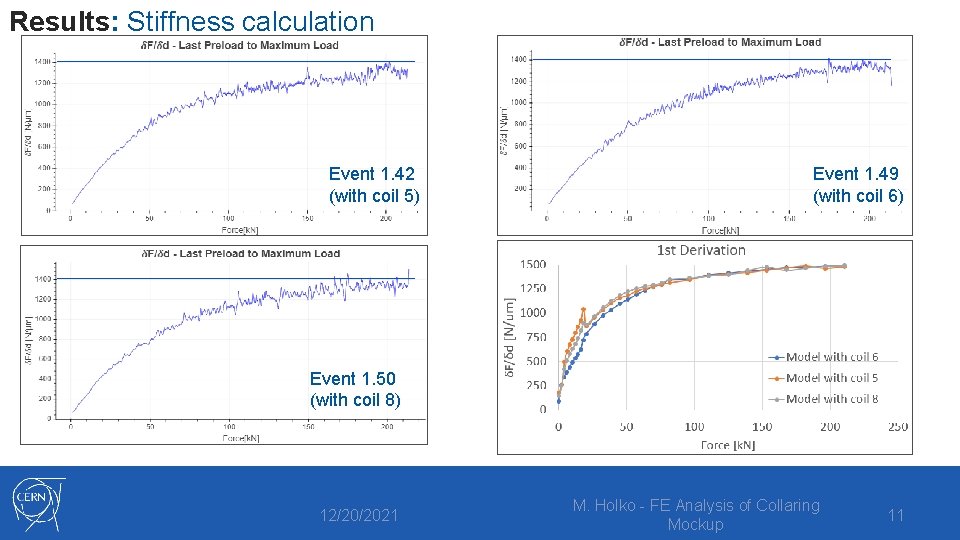
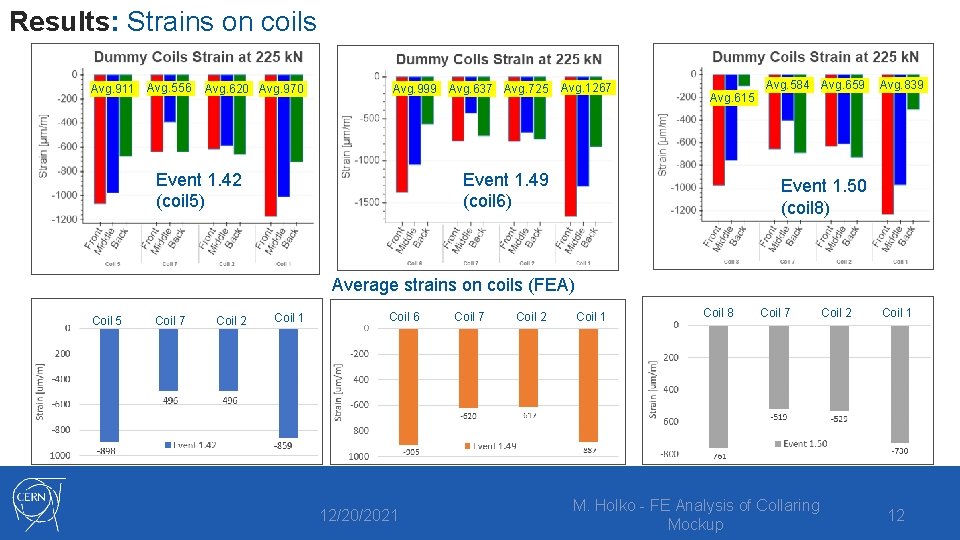
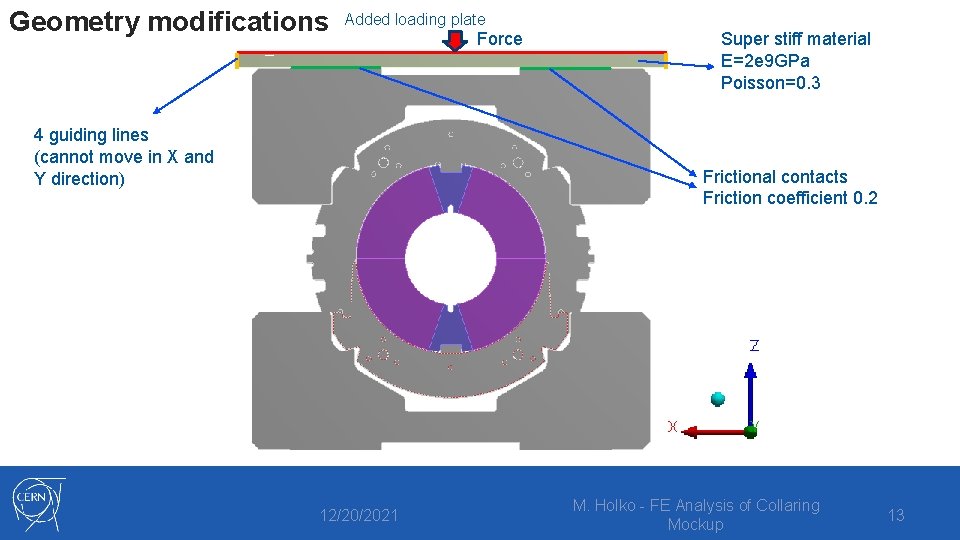
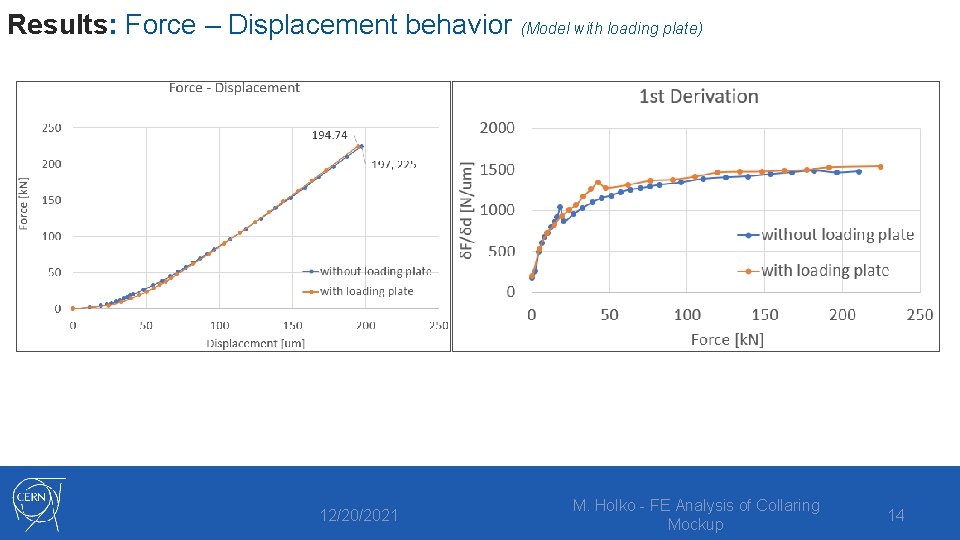
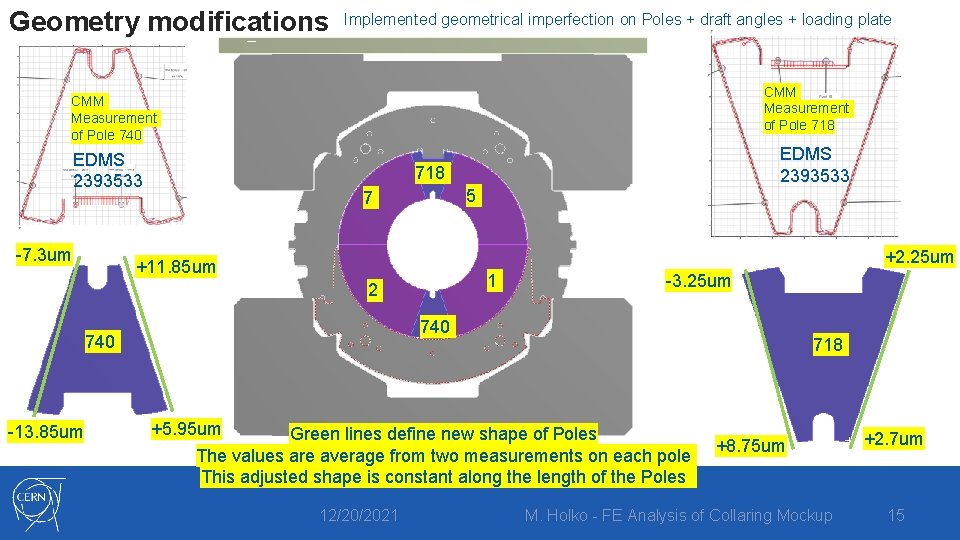
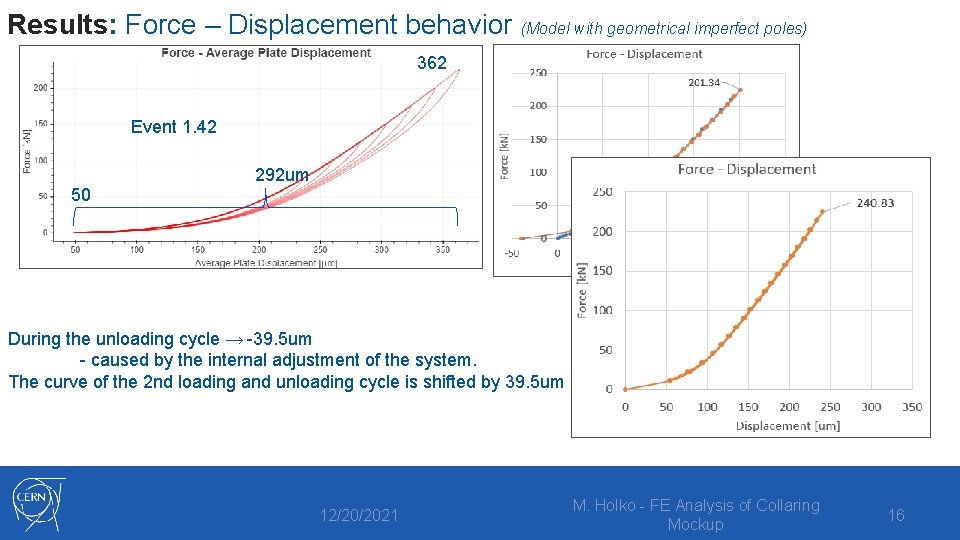
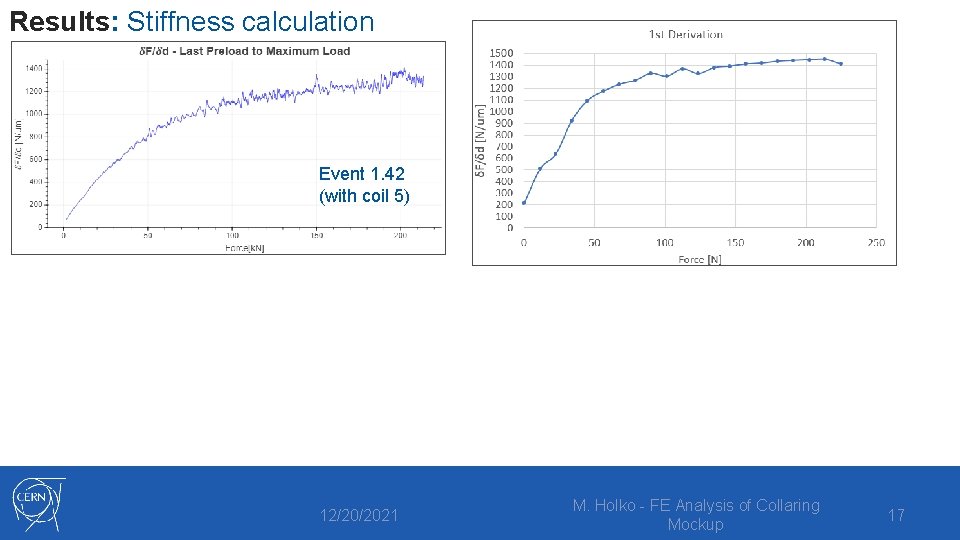
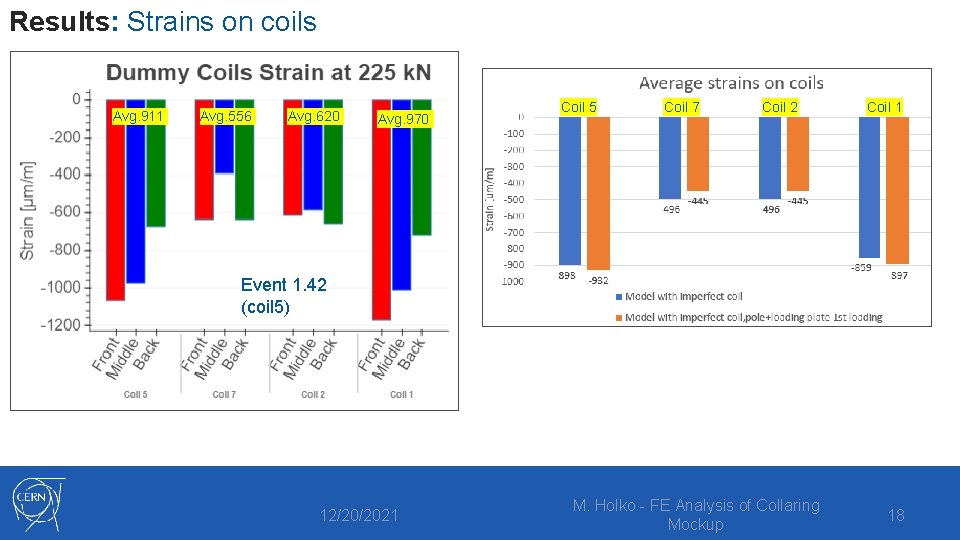
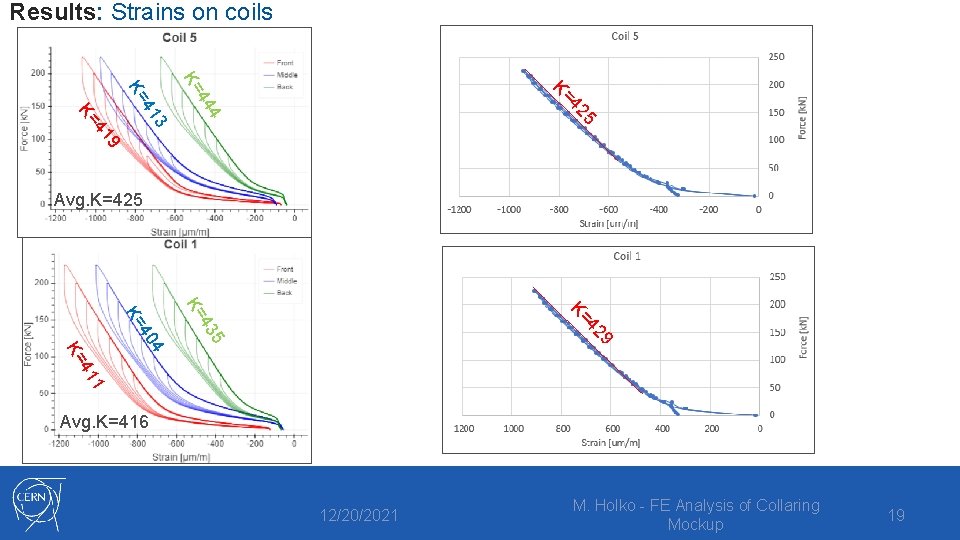
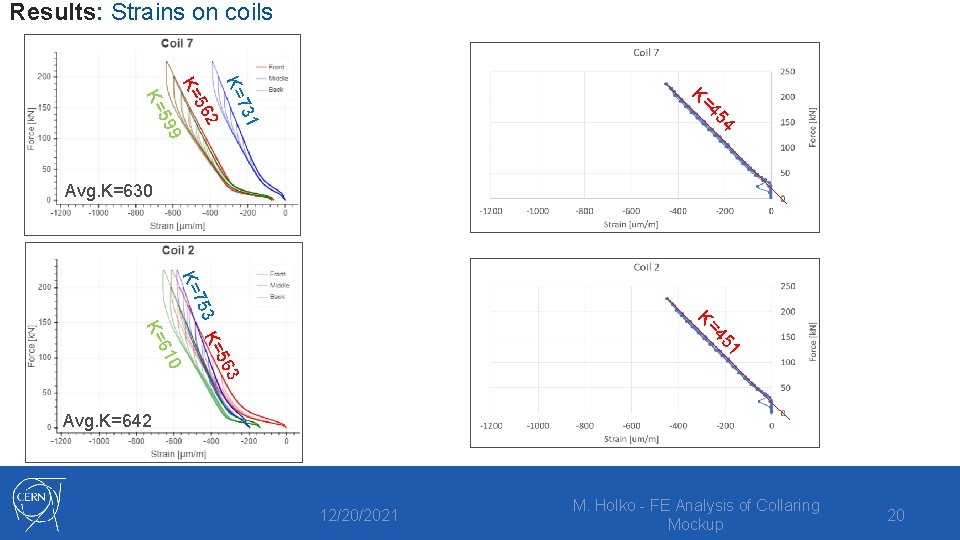
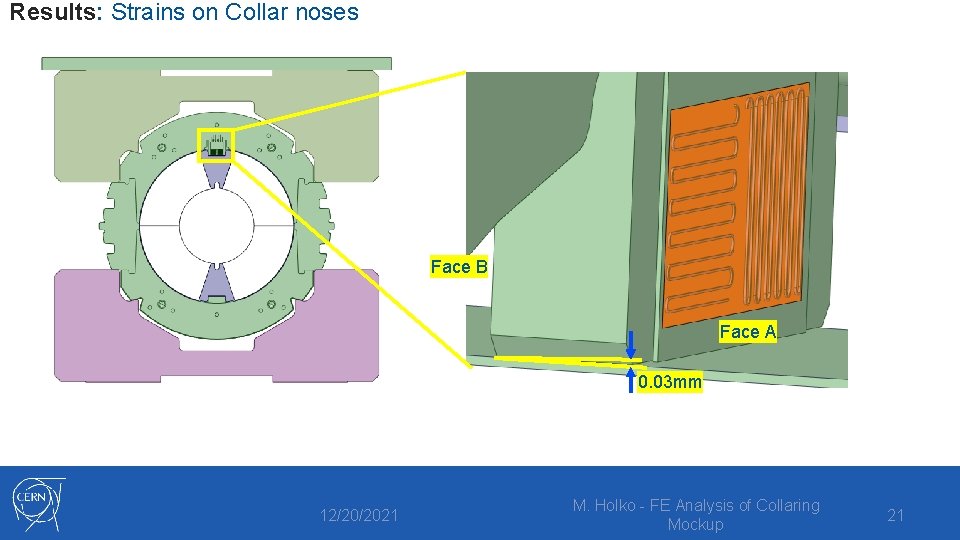
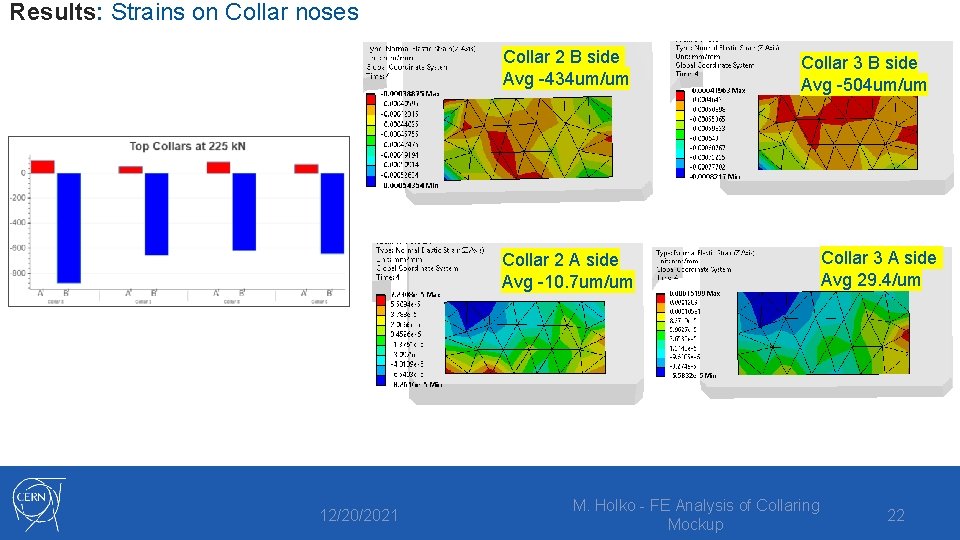
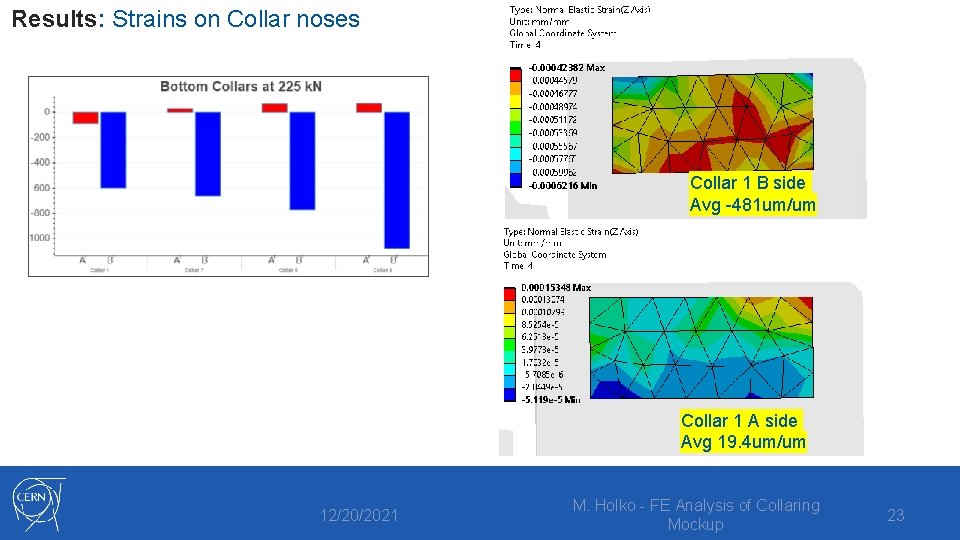
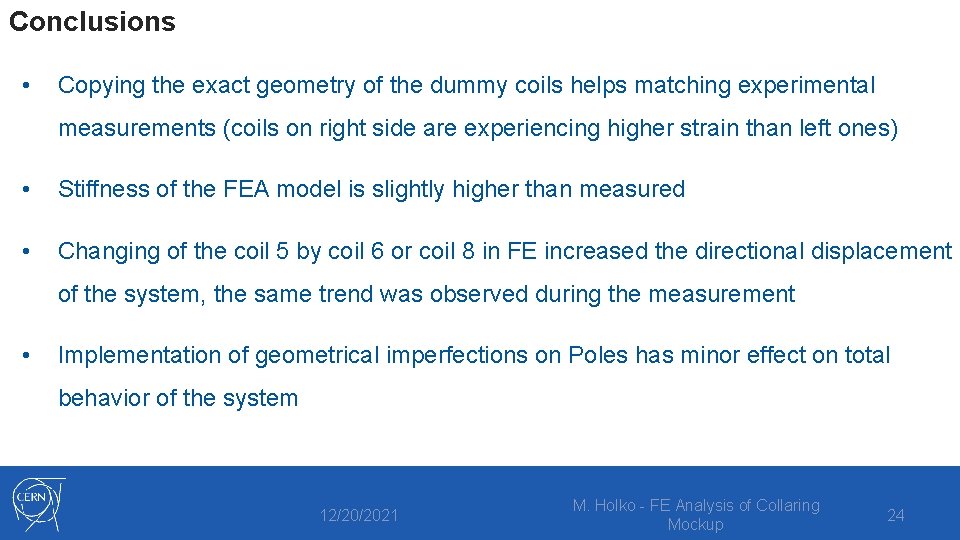
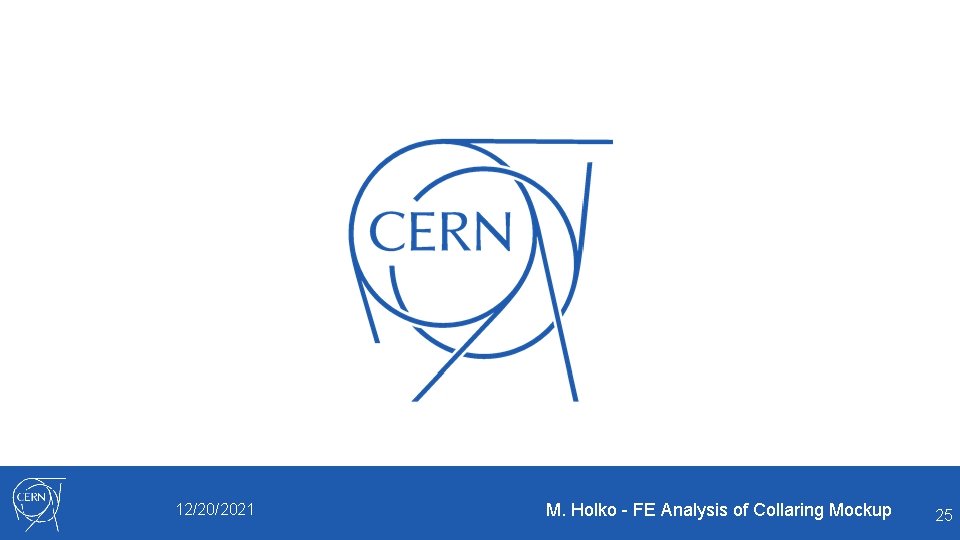
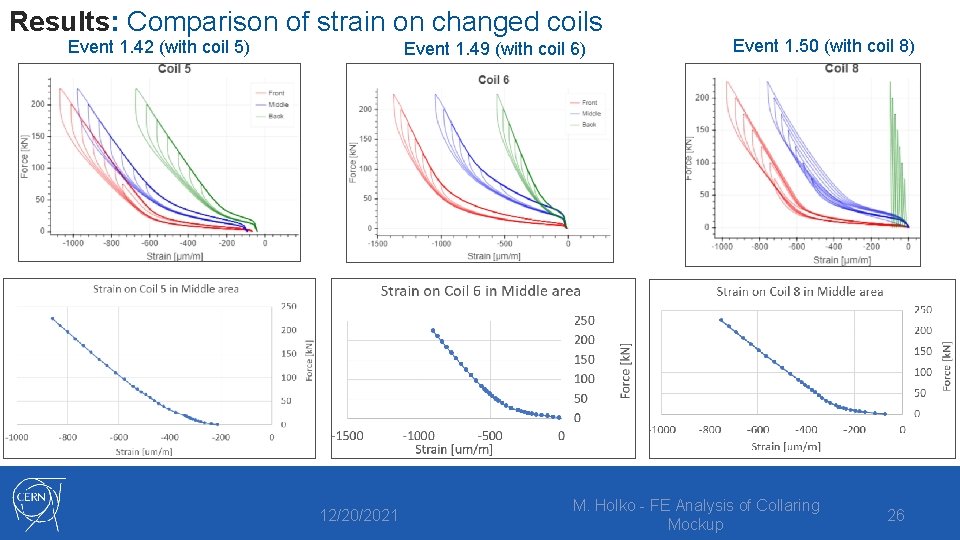
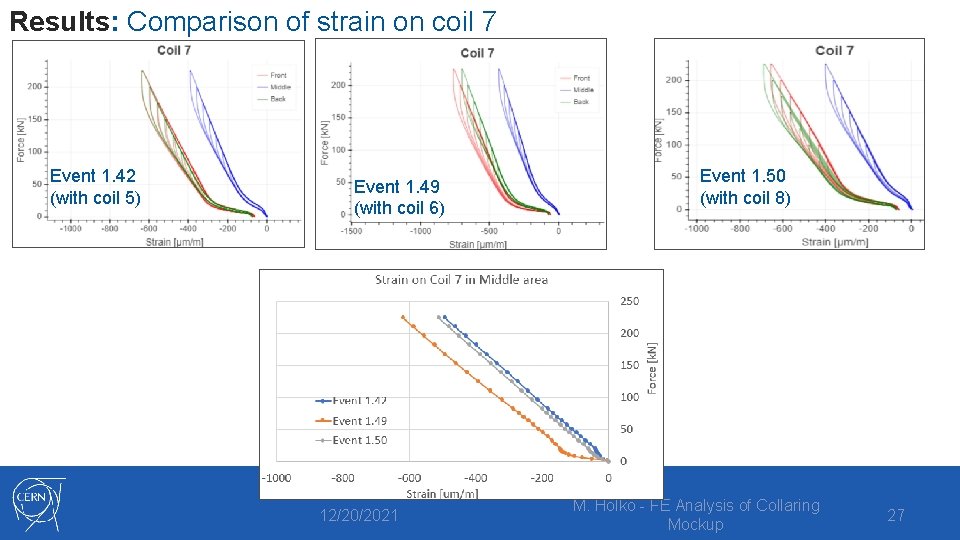
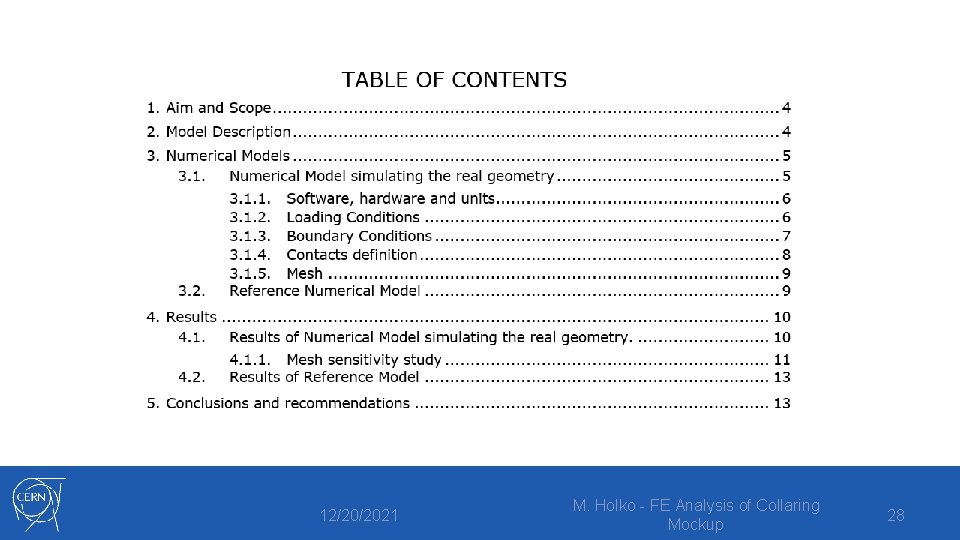
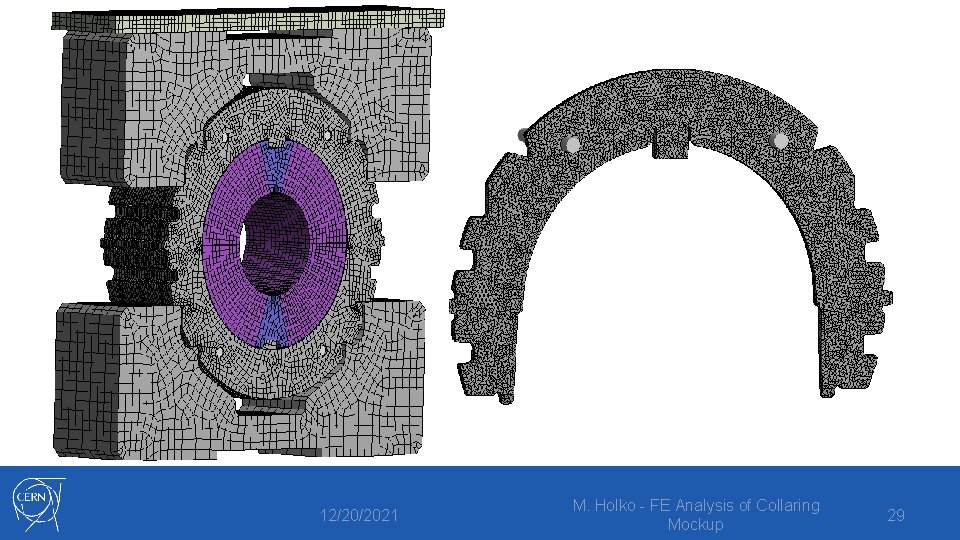
- Slides: 29
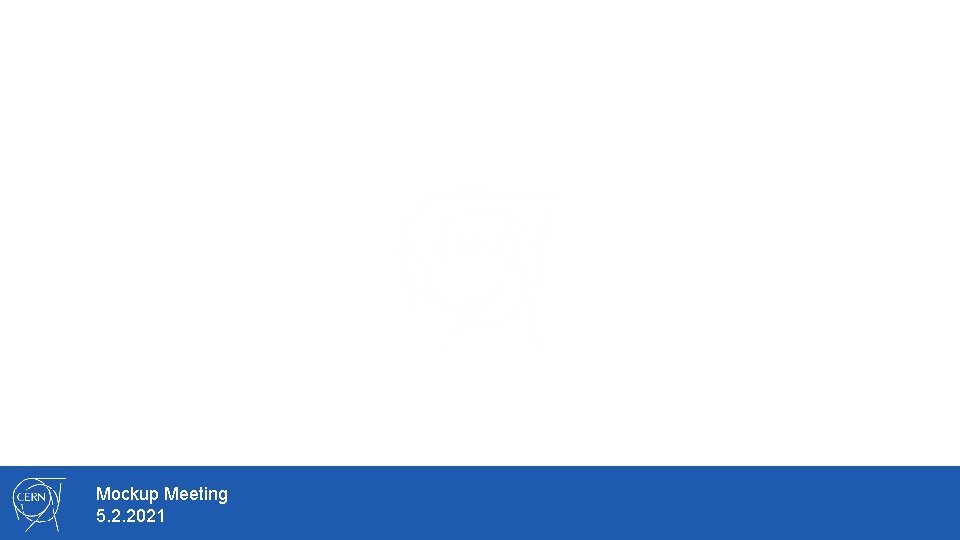
FE Analysis of Collaring Mockup Michal Holko at al. CERN EN MME Mockup Meeting 5. 2. 2021
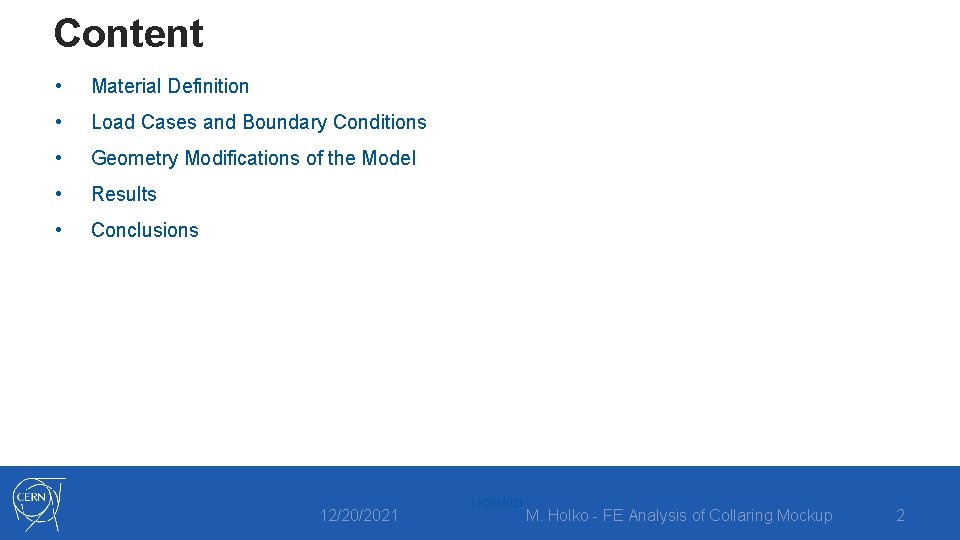
Content • Material Definition • Load Cases and Boundary Conditions • Geometry Modifications of the Model • Results • Conclusions 12/20/2021 M. Holko - FE Analysis of Collaring Mockup 2
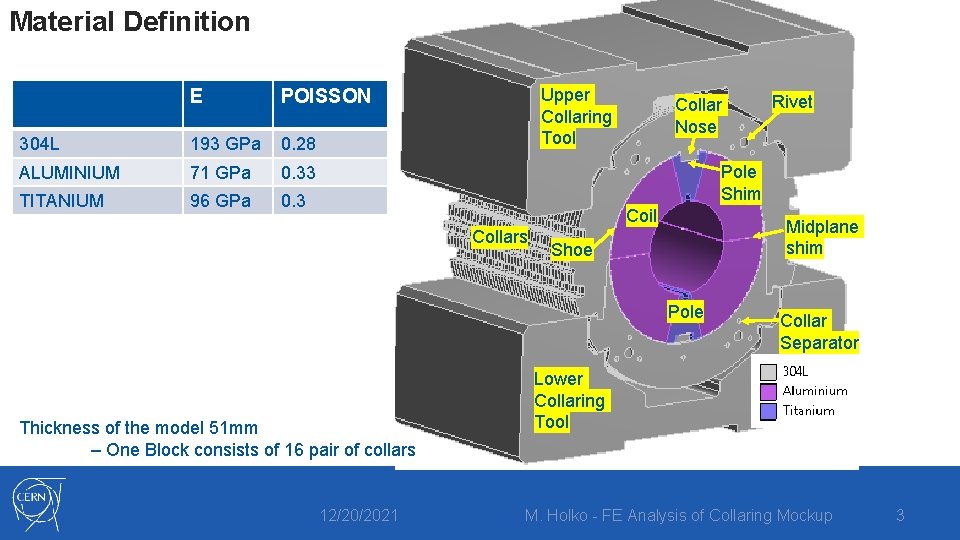
Material Definition E POISSON 304 L 193 GPa 0. 28 ALUMINIUM 71 GPa 0. 33 TITANIUM 96 GPa 0. 3 Upper Collaring Tool Collar Nose Rivet Pole Shim Coil Collars Midplane shim Shoe Pole Thickness of the model 51 mm – One Block consists of 16 pair of collars 12/20/2021 Collar Separator Lower Collaring Tool M. Holko - FE Analysis of Collaring Mockup 3
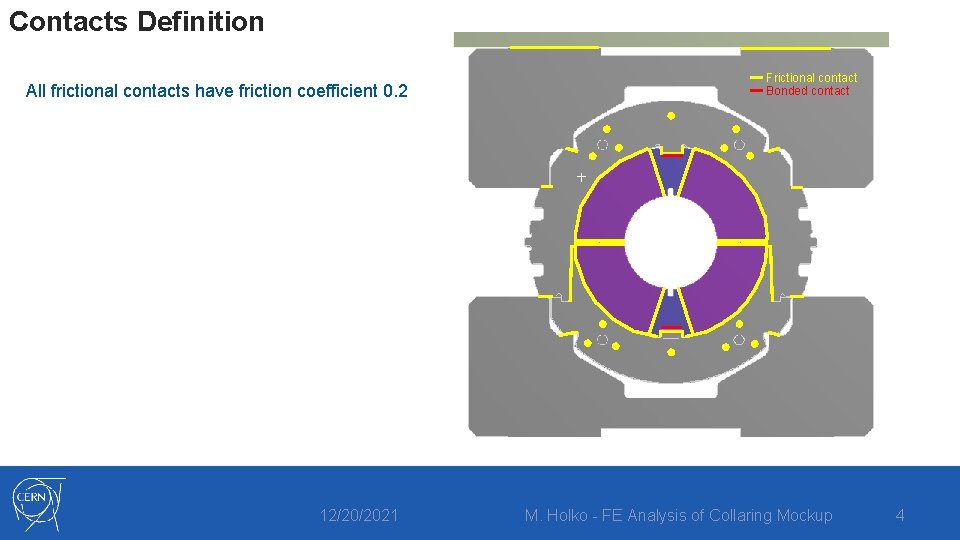
Contacts Definition All frictional contacts have friction coefficient 0. 2 12/20/2021 Frictional contact Bonded contact M. Holko - FE Analysis of Collaring Mockup 4
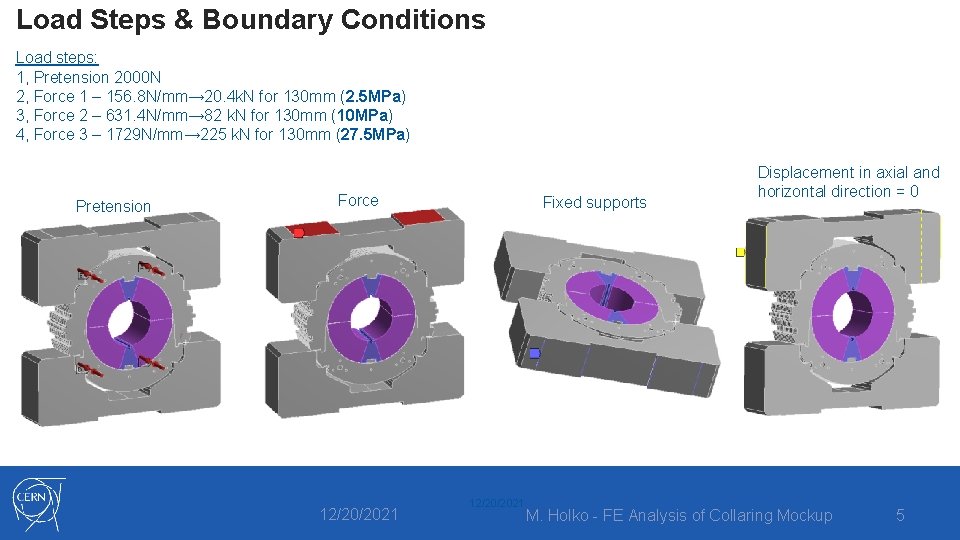
Load Steps & Boundary Conditions Load steps: 1, Pretension 2000 N 2, Force 1 – 156. 8 N/mm→ 20. 4 k. N for 130 mm (2. 5 MPa) 3, Force 2 – 631. 4 N/mm→ 82 k. N for 130 mm (10 MPa) 4, Force 3 – 1729 N/mm→ 225 k. N for 130 mm (27. 5 MPa) Pretension Force 12/20/2021 Fixed supports 12/20/2021 Displacement in axial and horizontal direction = 0 M. Holko - FE Analysis of Collaring Mockup 5
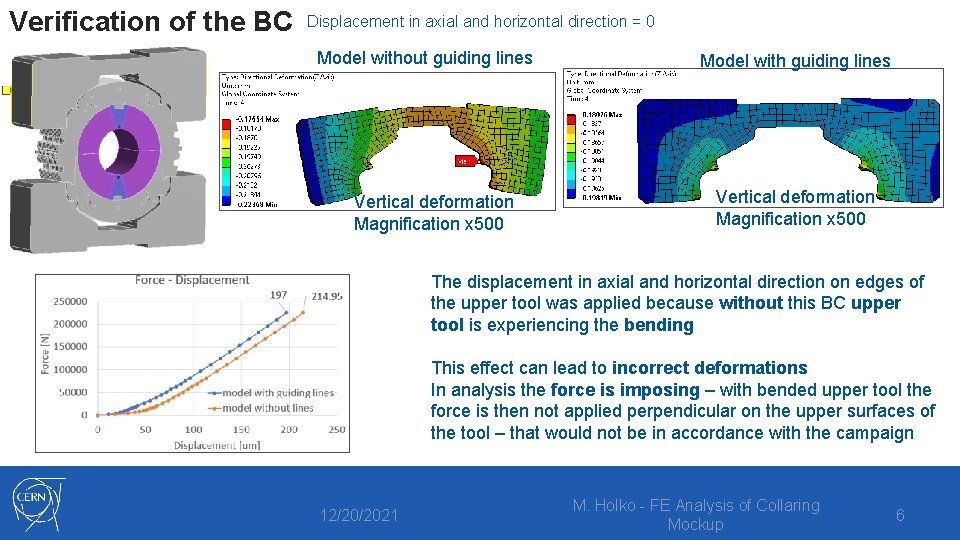
Verification of the BC Displacement in axial and horizontal direction = 0 Model without guiding lines Vertical deformation Magnification x 500 Model with guiding lines Vertical deformation Magnification x 500 The displacement in axial and horizontal direction on edges of the upper tool was applied because without this BC upper tool is experiencing the bending This effect can lead to incorrect deformations In analysis the force is imposing – with bended upper tool the force is then not applied perpendicular on the upper surfaces of the tool – that would not be in accordance with the campaign 12/20/2021 M. Holko - FE Analysis of Collaring Mockup 6
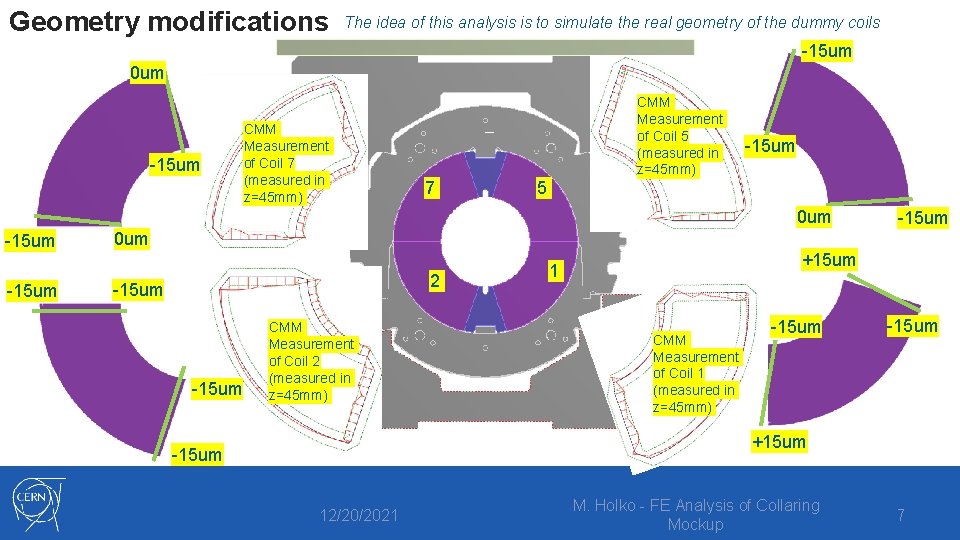
Geometry modifications The idea of this analysis is to simulate the real geometry of the dummy coils -15 um 0 um -15 um CMM Measurement of Coil 7 (measured in z=45 mm) CMM Measurement of Coil 5 (measured in z=45 mm) 7 -15 um 5 0 um -15 um 0 um 2 -15 um CMM Measurement of Coil 2 (measured in z=45 mm) +15 um 1 CMM Measurement of Coil 1 (measured in z=45 mm) -15 um +15 um -15 um 12/20/2021 M. Holko - FE Analysis of Collaring Mockup 7
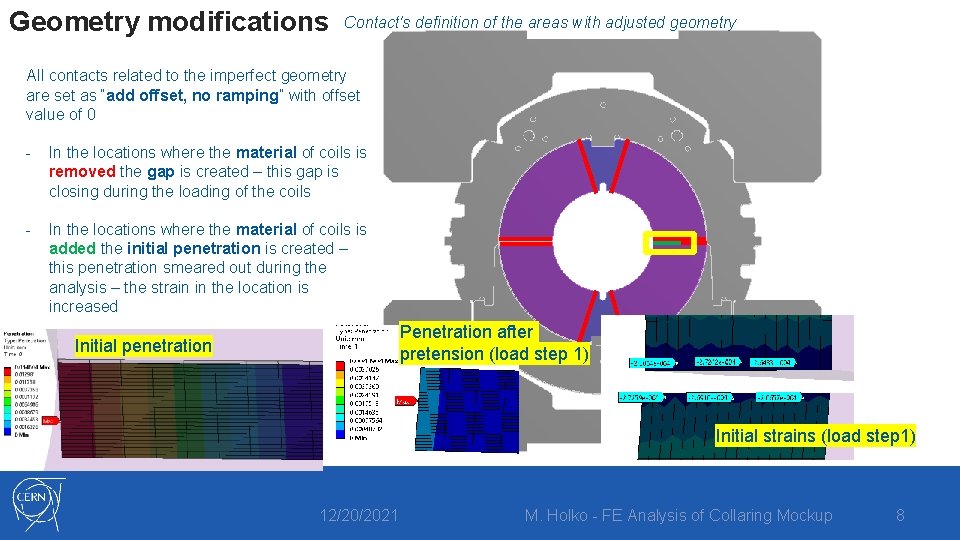
Geometry modifications Contact's definition of the areas with adjusted geometry All contacts related to the imperfect geometry are set as “add offset, no ramping” with offset value of 0 - In the locations where the material of coils is removed the gap is created – this gap is closing during the loading of the coils - In the locations where the material of coils is added the initial penetration is created – this penetration smeared out during the analysis – the strain in the location is increased Penetration after pretension (load step 1) Initial penetration Initial strains (load step 1) 12/20/2021 M. Holko - FE Analysis of Collaring Mockup 8
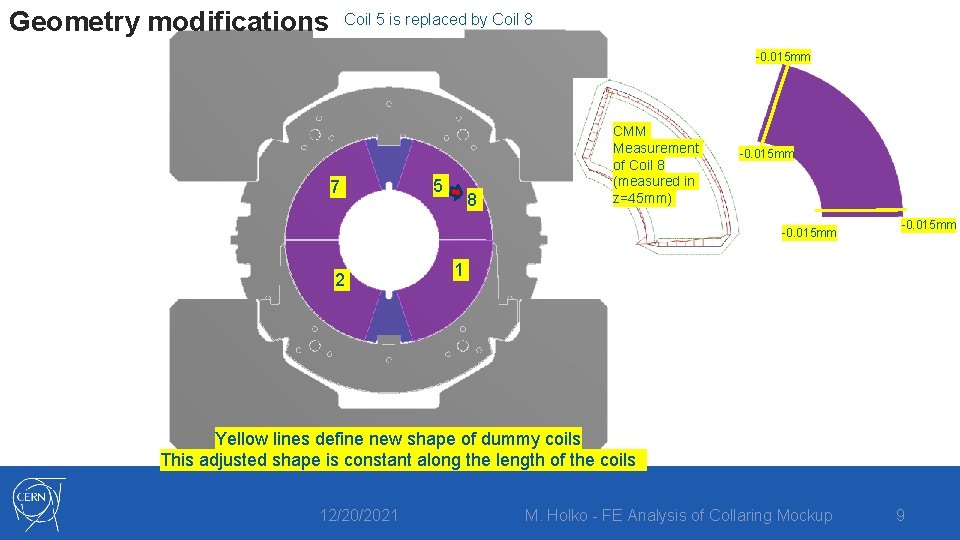
Geometry modifications Coil 5 is replaced by Coil 8 -0. 015 mm 7 5 8 CMM Measurement of Coil 8 (measured in z=45 mm) -0. 015 mm 2 -0. 015 mm 1 Yellow lines define new shape of dummy coils This adjusted shape is constant along the length of the coils 12/20/2021 M. Holko - FE Analysis of Collaring Mockup 9
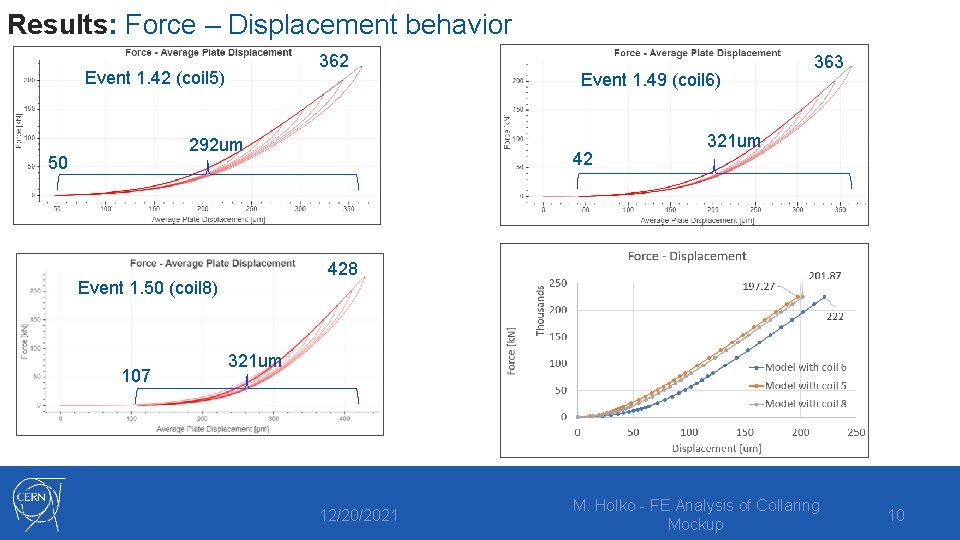
Results: Force – Displacement behavior 362 Event 1. 42 (coil 5) 292 um 50 42 321 um 428 Event 1. 50 (coil 8) 107 Event 1. 49 (coil 6) 363 321 um 12/20/2021 M. Holko - FE Analysis of Collaring Mockup 10
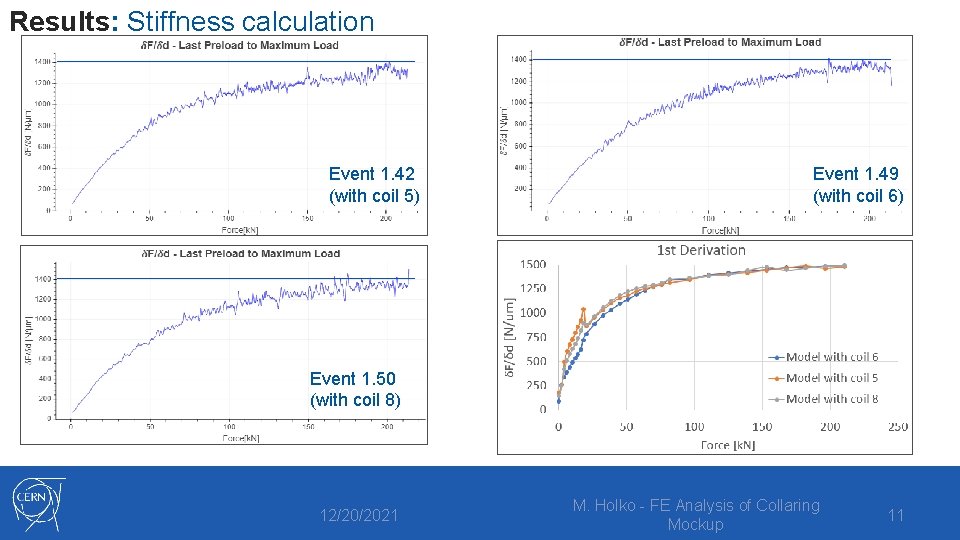
Results: Stiffness calculation Event 1. 42 (with coil 5) Event 1. 49 (with coil 6) Event 1. 50 (with coil 8) 12/20/2021 M. Holko - FE Analysis of Collaring Mockup 11
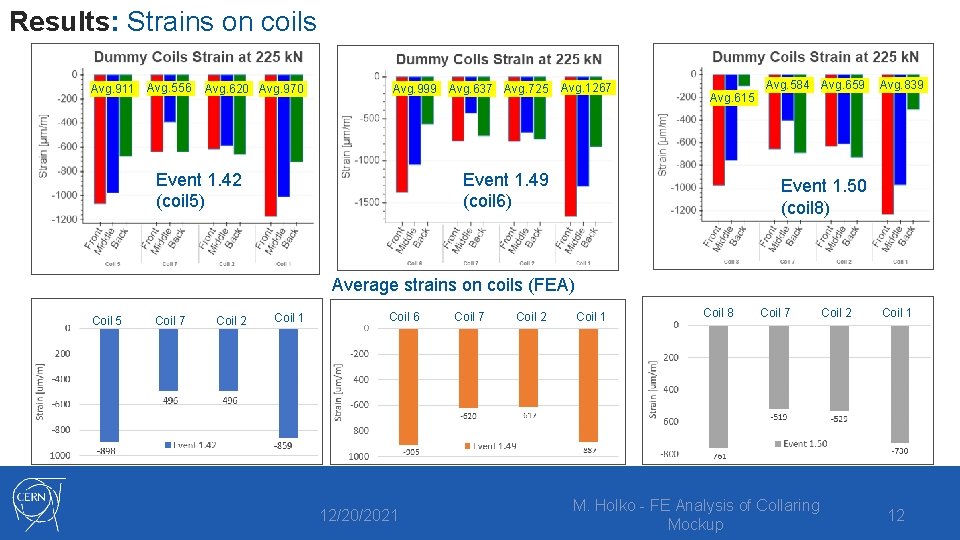
Results: Strains on coils Avg. 911 Avg. 556 Avg. 620 Avg. 970 Avg. 999 Avg. 637 Avg. 725 Event 1. 42 (coil 5) Avg. 1267 Avg. 615 Event 1. 49 (coil 6) Avg. 584 Avg. 659 Avg. 839 Event 1. 50 (coil 8) Average strains on coils (FEA) Coil 5 Coil 7 Coil 2 Coil 1 Coil 6 12/20/2021 Coil 7 Coil 2 Coil 1 Coil 8 Coil 7 M. Holko - FE Analysis of Collaring Mockup Coil 2 Coil 1 12
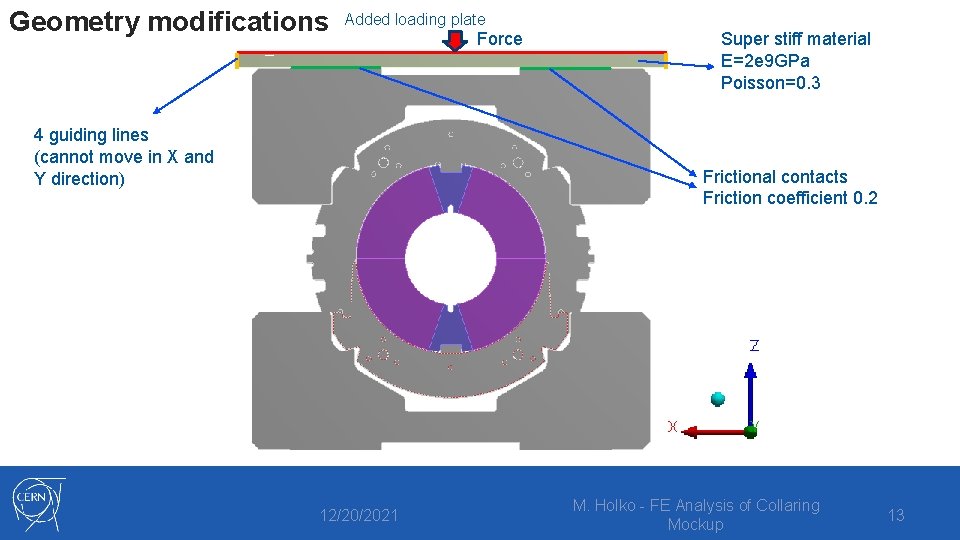
Geometry modifications Added loading plate 4 guiding lines (cannot move in X and Y direction) Force Super stiff material E=2 e 9 GPa Poisson=0. 3 Frictional contacts Friction coefficient 0. 2 12/20/2021 M. Holko - FE Analysis of Collaring Mockup 13
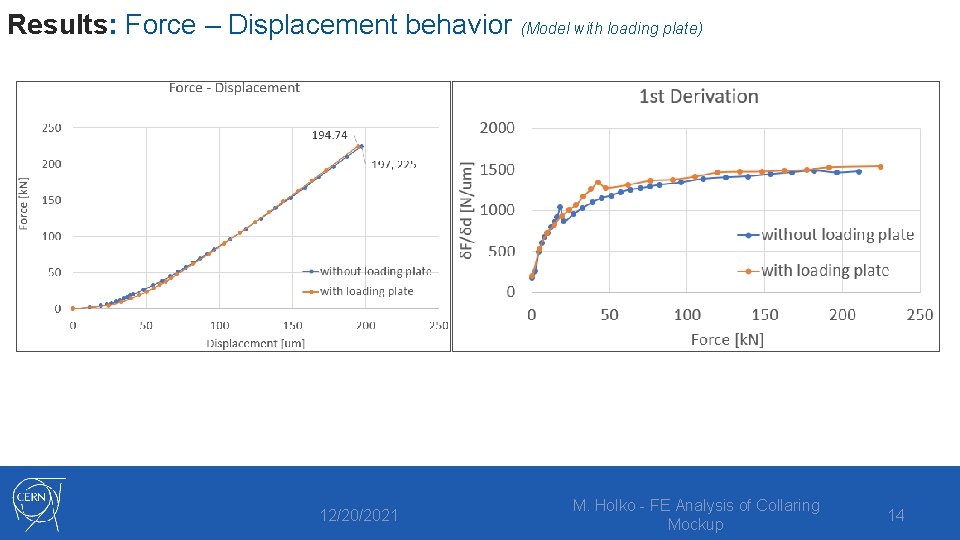
Results: Force – Displacement behavior (Model with loading plate) 12/20/2021 M. Holko - FE Analysis of Collaring Mockup 14
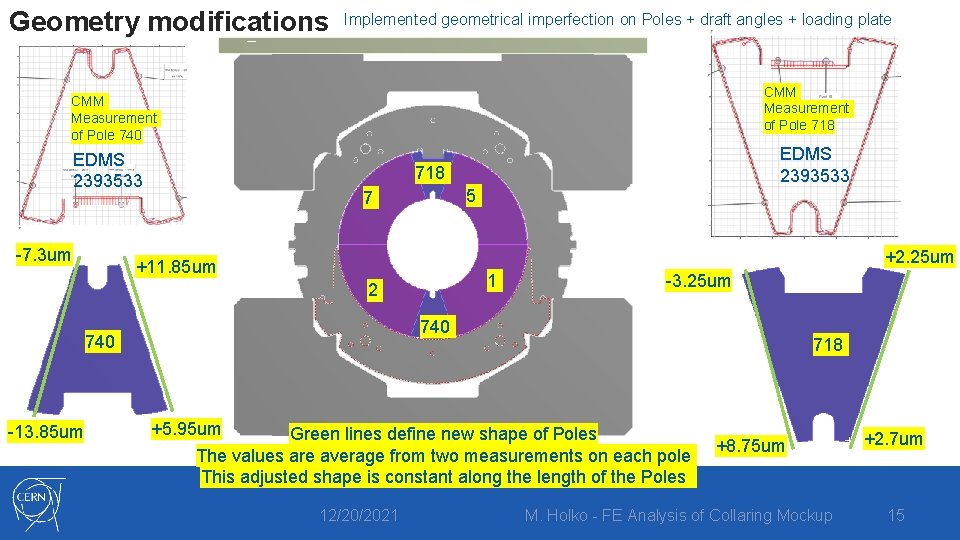
Geometry modifications Implemented geometrical imperfection on Poles + draft angles + loading plate CMM Measurement of Pole 718 CMM Measurement of Pole 740 EDMS 2393533 -7. 3 um 718 5 7 +2. 25 um +11. 85 um 1 2 -3. 25 um 740 -13. 85 um EDMS 2393533 718 +5. 95 um Green lines define new shape of Poles The values are average from two measurements on each pole This adjusted shape is constant along the length of the Poles 12/20/2021 +8. 75 um M. Holko - FE Analysis of Collaring Mockup +2. 7 um 15
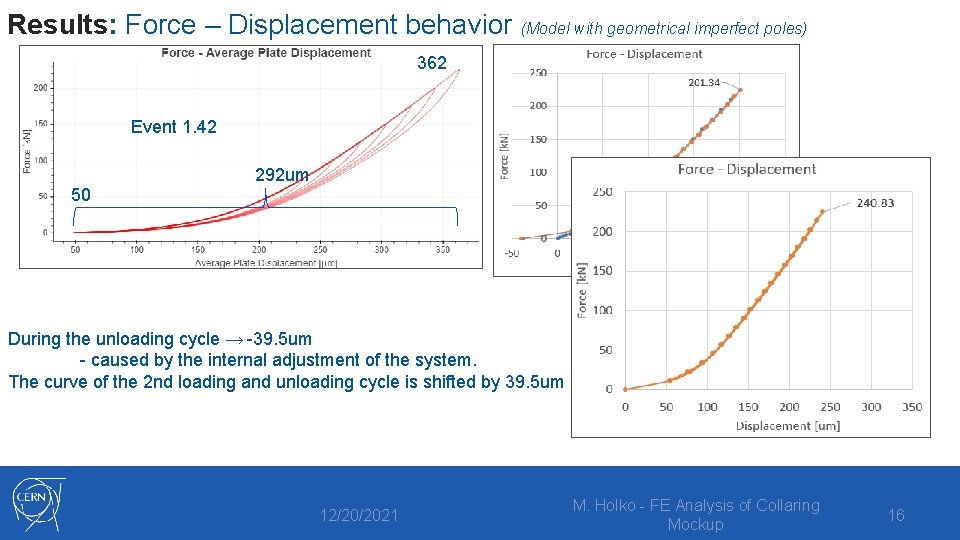
Results: Force – Displacement behavior (Model with geometrical imperfect poles) 362 Event 1. 42 50 292 um During the unloading cycle → -39. 5 um - caused by the internal adjustment of the system. The curve of the 2 nd loading and unloading cycle is shifted by 39. 5 um 12/20/2021 M. Holko - FE Analysis of Collaring Mockup 16
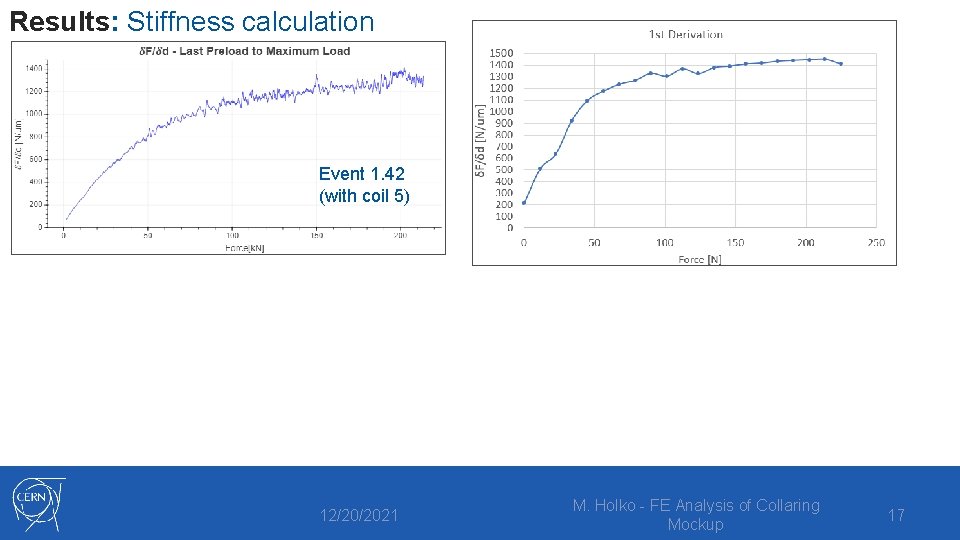
Results: Stiffness calculation Event 1. 42 (with coil 5) 12/20/2021 M. Holko - FE Analysis of Collaring Mockup 17
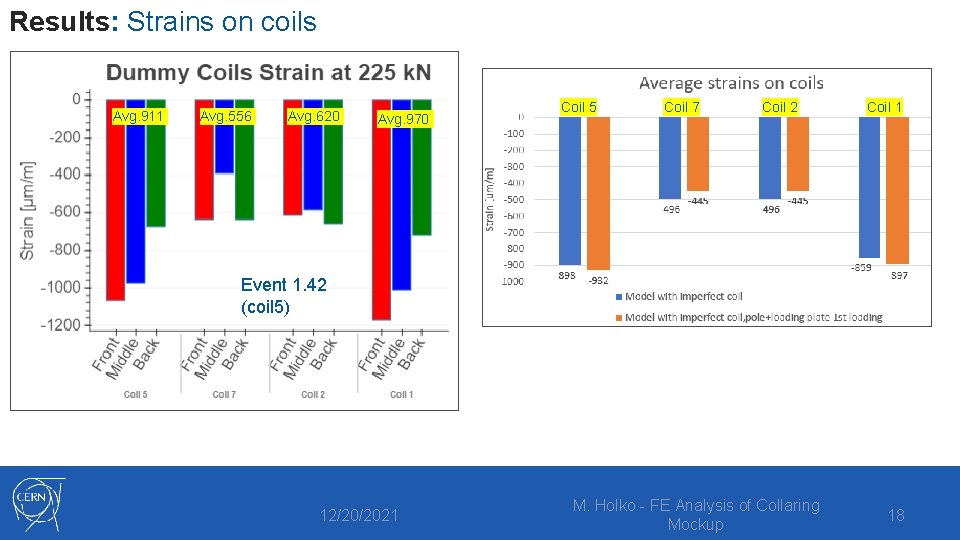
Results: Strains on coils Avg. 911 Avg. 556 Avg. 620 Avg. 970 Coil 5 Coil 7 Coil 2 Coil 1 Event 1. 42 (coil 5) 12/20/2021 M. Holko - FE Analysis of Collaring Mockup 18
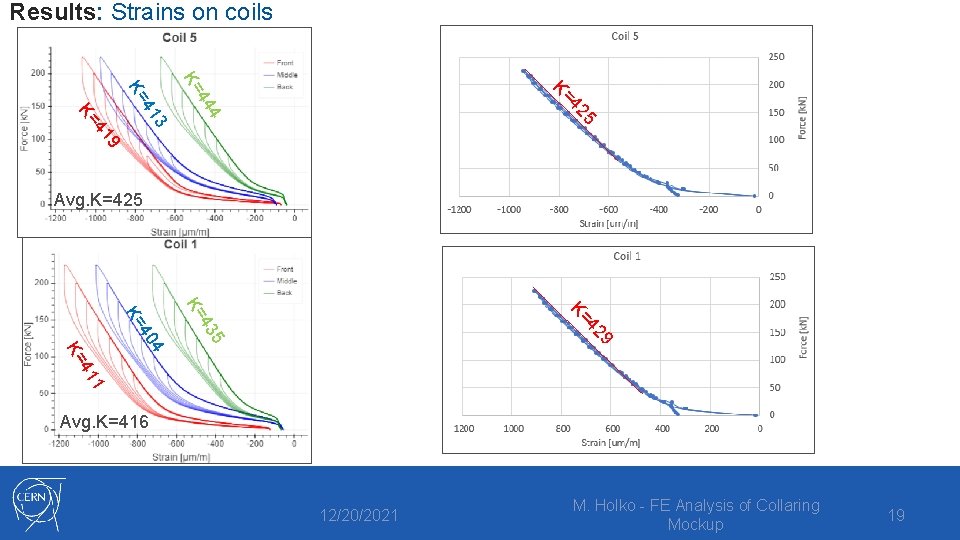
Results: Strains on coils 42 5 13 4 44 K= K= 41 K= 9 Avg. K=425 9 5 43 42 K= K= 4 40 K= 1 41 K= Avg. K=416 12/20/2021 M. Holko - FE Analysis of Collaring Mockup 19
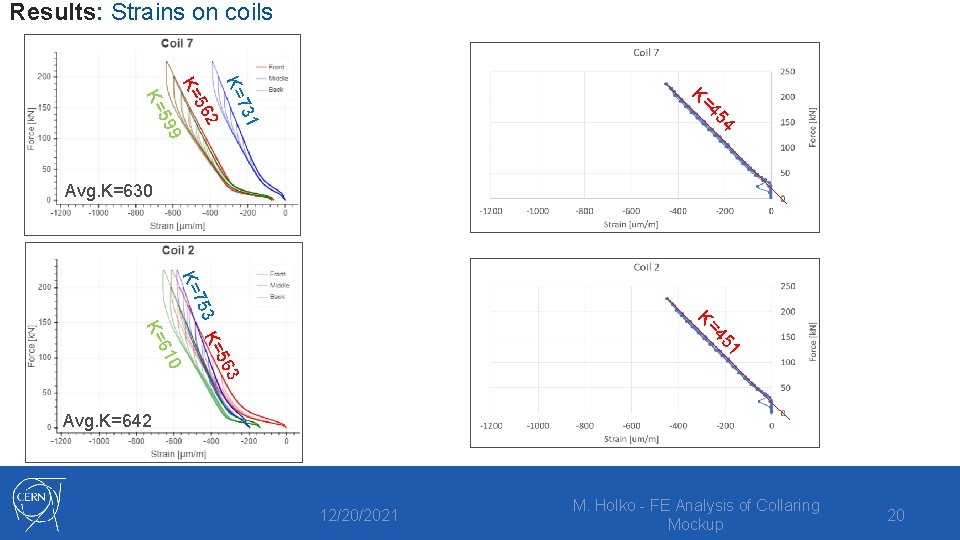
Results: Strains on coils 9 4 45 K= 2 731 K= 56 K= 59 K= Avg. K=630 3 56 K= 1 45 K= 753 K= 0 61 K= Avg. K=642 12/20/2021 M. Holko - FE Analysis of Collaring Mockup 20
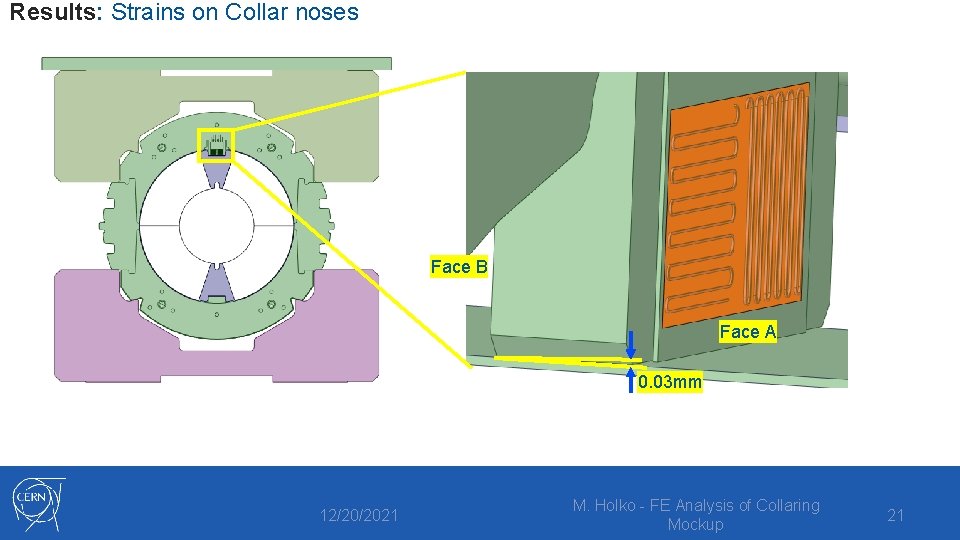
Results: Strains on Collar noses Face B Face A 0. 03 mm 12/20/2021 M. Holko - FE Analysis of Collaring Mockup 21
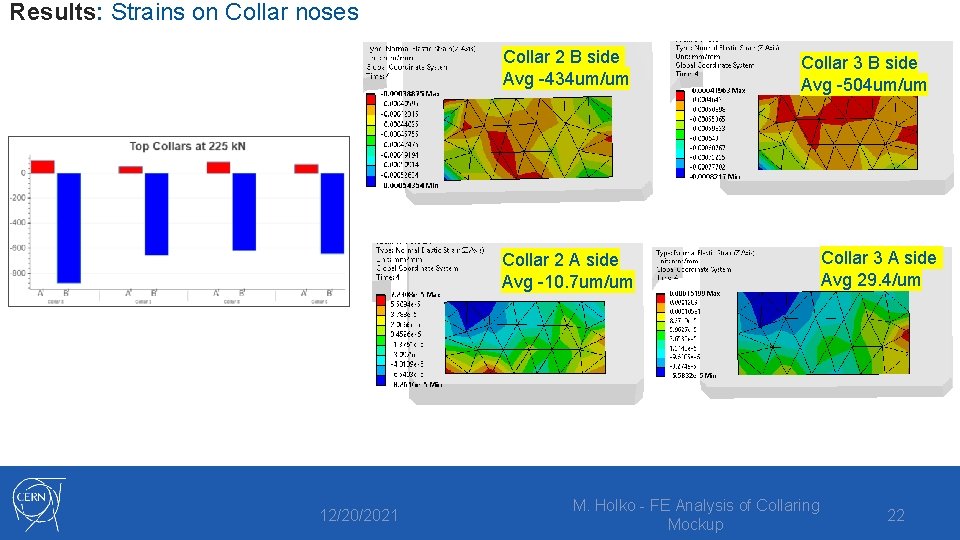
Results: Strains on Collar noses Collar 2 B side Avg -434 um/um Collar 3 B side Avg -504 um/um Collar 3 A side Avg 29. 4/um Collar 2 A side Avg -10. 7 um/um Face A 12/20/2021 M. Holko - FE Analysis of Collaring Mockup 22
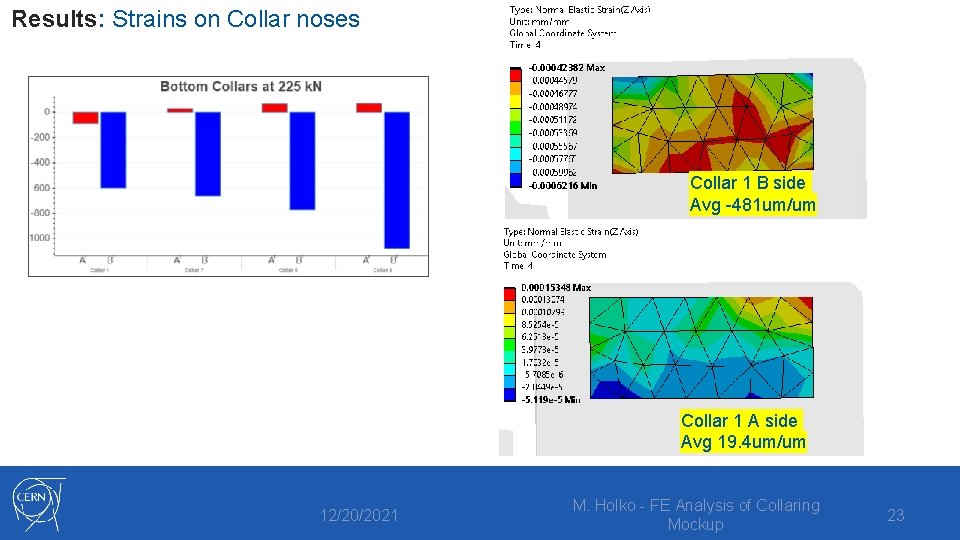
Results: Strains on Collar noses Collar 1 B side Avg -481 um/um Collar 1 A side Avg 19. 4 um/um 12/20/2021 M. Holko - FE Analysis of Collaring Mockup 23
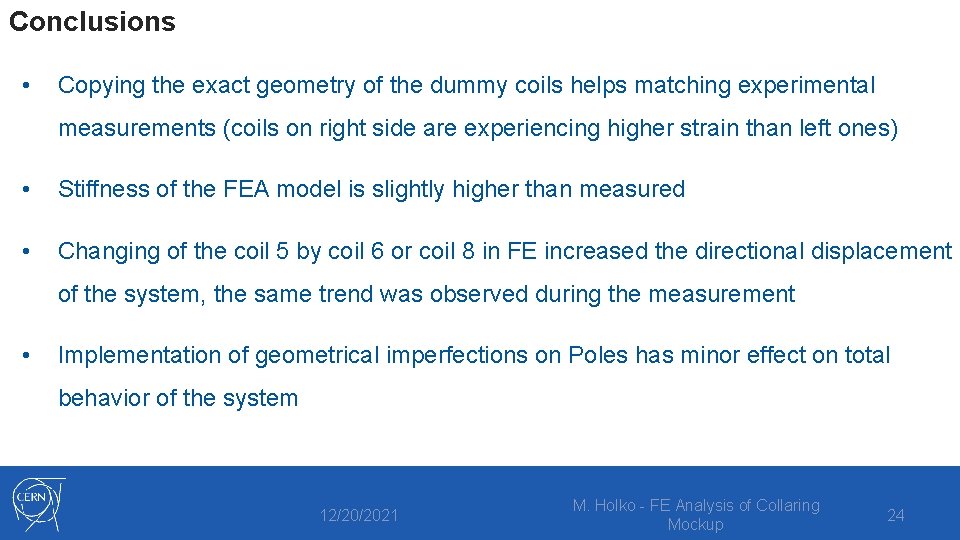
Conclusions • Copying the exact geometry of the dummy coils helps matching experimental measurements (coils on right side are experiencing higher strain than left ones) • Stiffness of the FEA model is slightly higher than measured • Changing of the coil 5 by coil 6 or coil 8 in FE increased the directional displacement of the system, the same trend was observed during the measurement • Implementation of geometrical imperfections on Poles has minor effect on total behavior of the system 12/20/2021 M. Holko - FE Analysis of Collaring Mockup 24
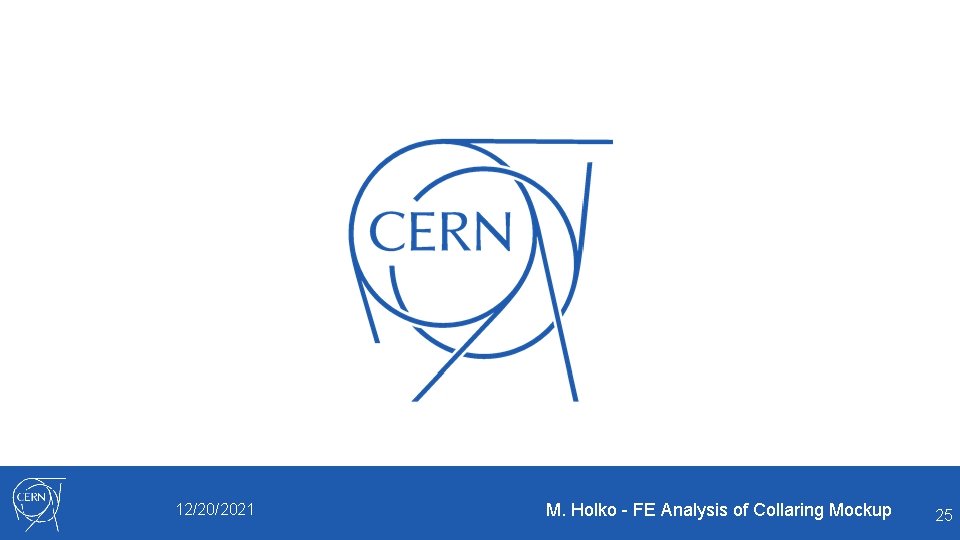
Thank you for your attention 12/20/2021 M. Holko - FE Analysis of Collaring Mockup 25
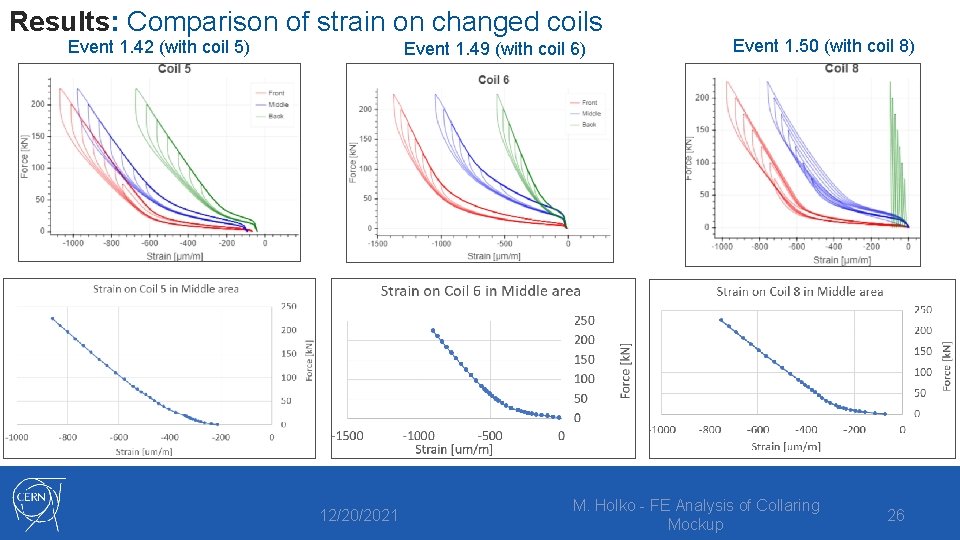
Results: Comparison of strain on changed coils Event 1. 42 (with coil 5) Event 1. 49 (with coil 6) 12/20/2021 Event 1. 50 (with coil 8) M. Holko - FE Analysis of Collaring Mockup 26
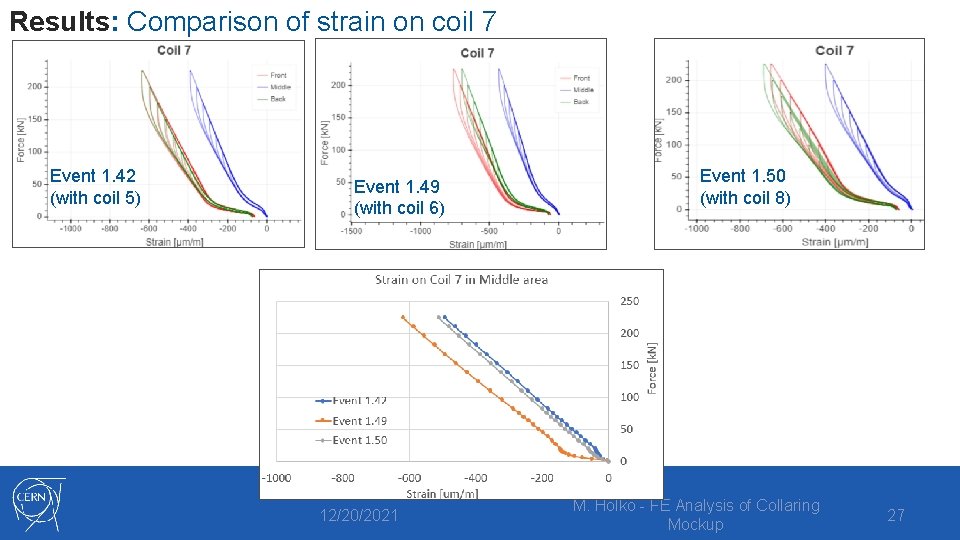
Results: Comparison of strain on coil 7 Event 1. 42 (with coil 5) Event 1. 49 (with coil 6) 12/20/2021 Event 1. 50 (with coil 8) M. Holko - FE Analysis of Collaring Mockup 27
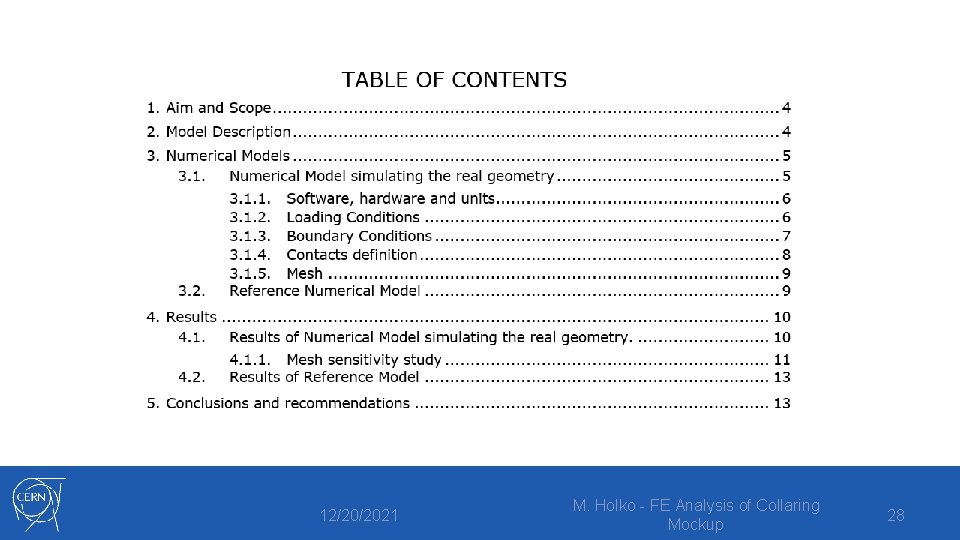
12/20/2021 M. Holko - FE Analysis of Collaring Mockup 28
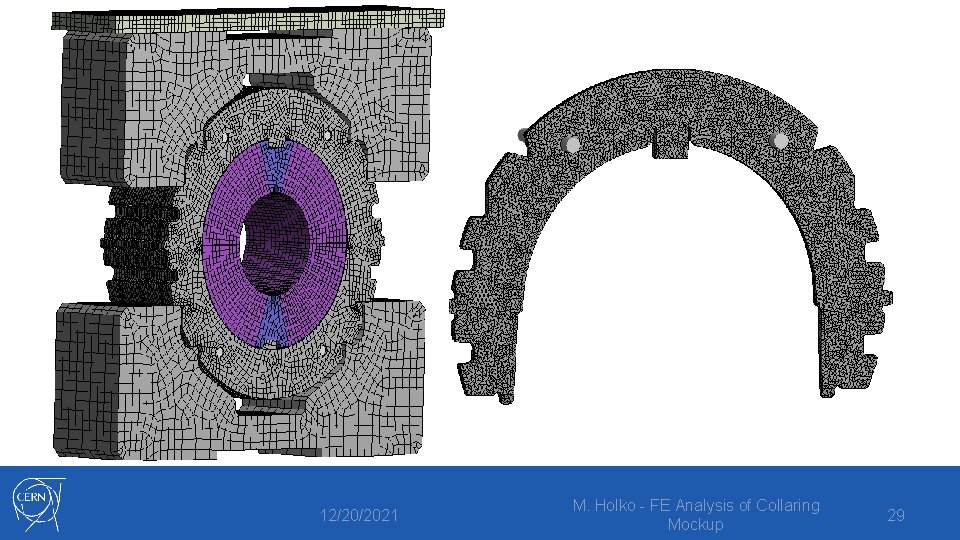
12/20/2021 M. Holko - FE Analysis of Collaring Mockup 29
Holko logistic
Peter holko
Functional mock-up interface
Login page mockup
Address mockup
Menu sistem
Prinsip mockup
Visio sql
Mockup assembly
Segregator mockup
Michal cyprian
Michal hammer
Michal lehnert
Michal tkaczyk
Sigla adsl
Michal grešlik
Michal kalman vek
Periculum est emptoris
Michal drobot
Michal meniny
Michal bick
Fabry disease
Martin kabrhel
Michal shinnar
Inotaj v hadanke
"michal franck"
Skloňování jména iva
Tvary podstatných jmen
Michal tulek
Michal pranostika