FE Analysis of Collaring Mockup Michal Holko at
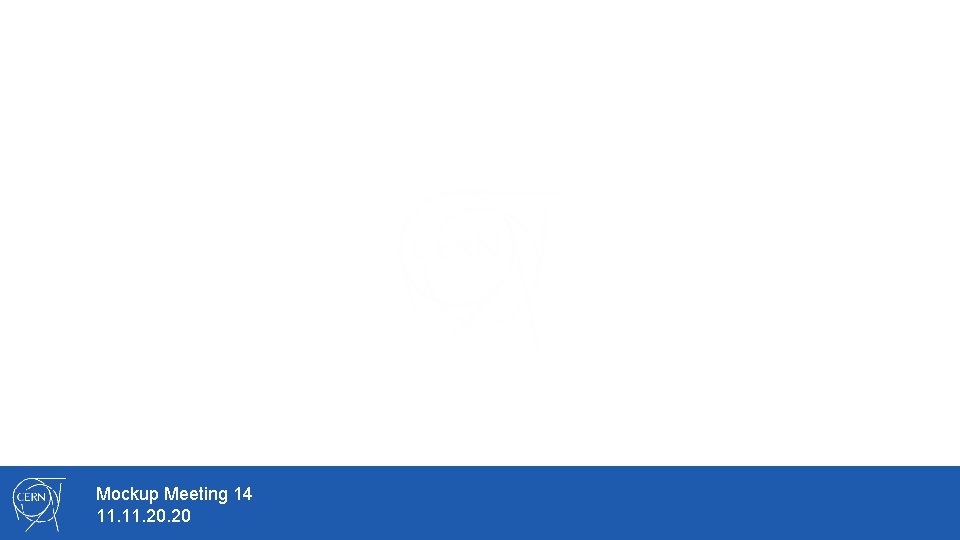
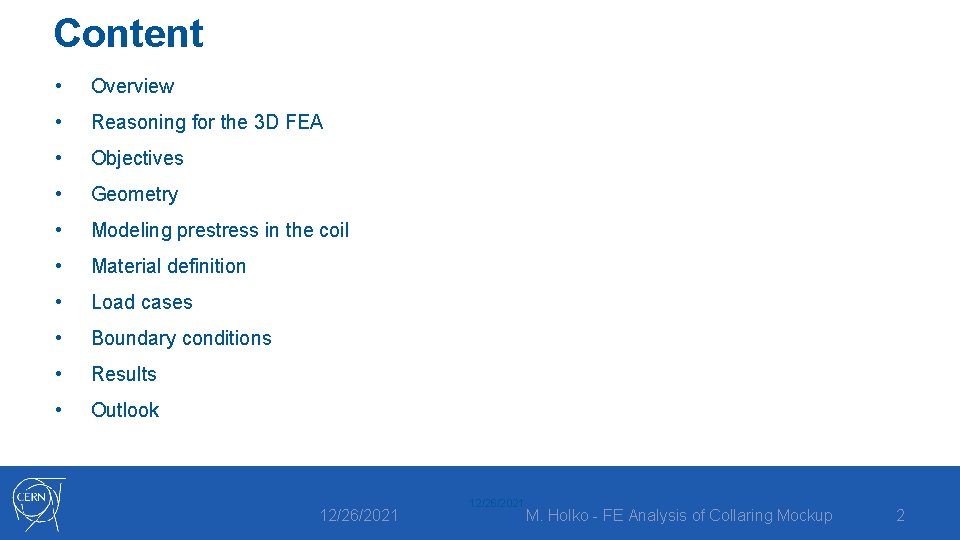
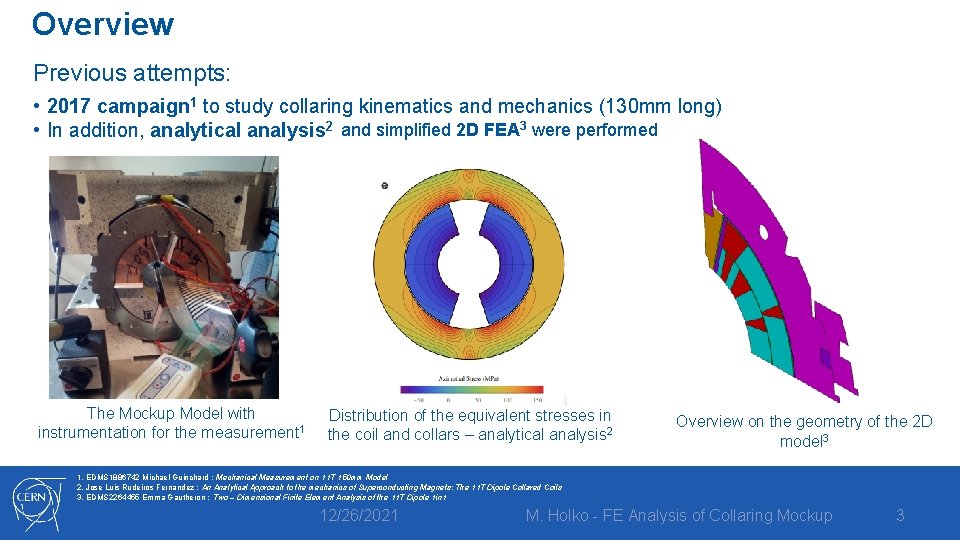
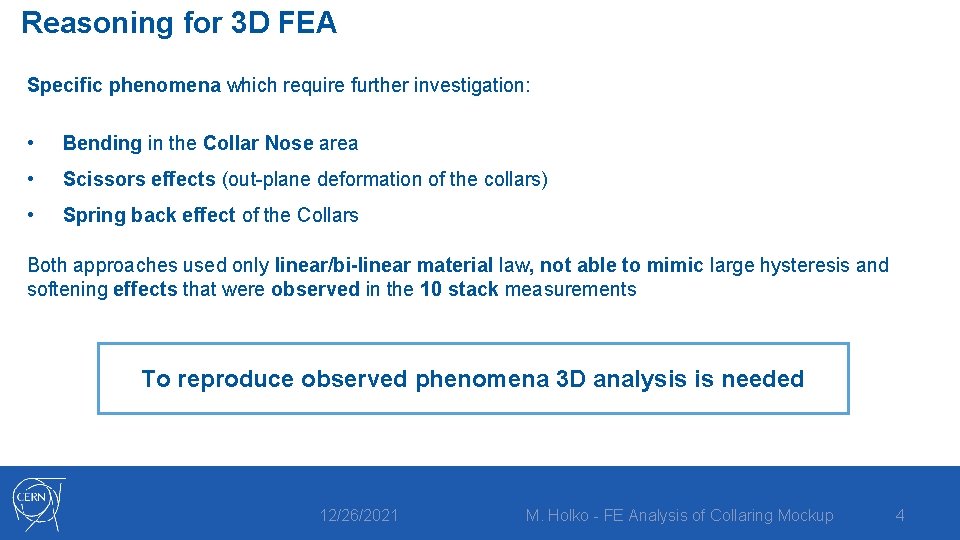
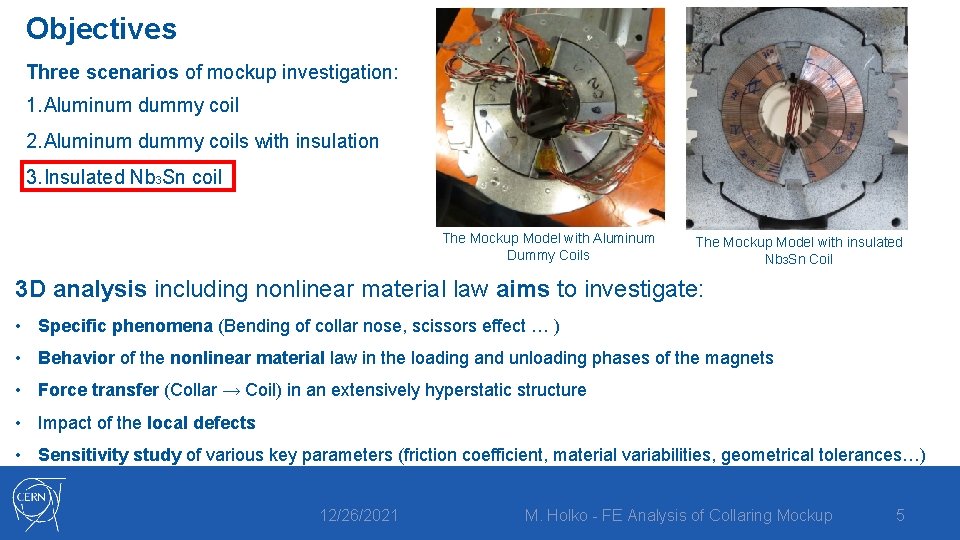
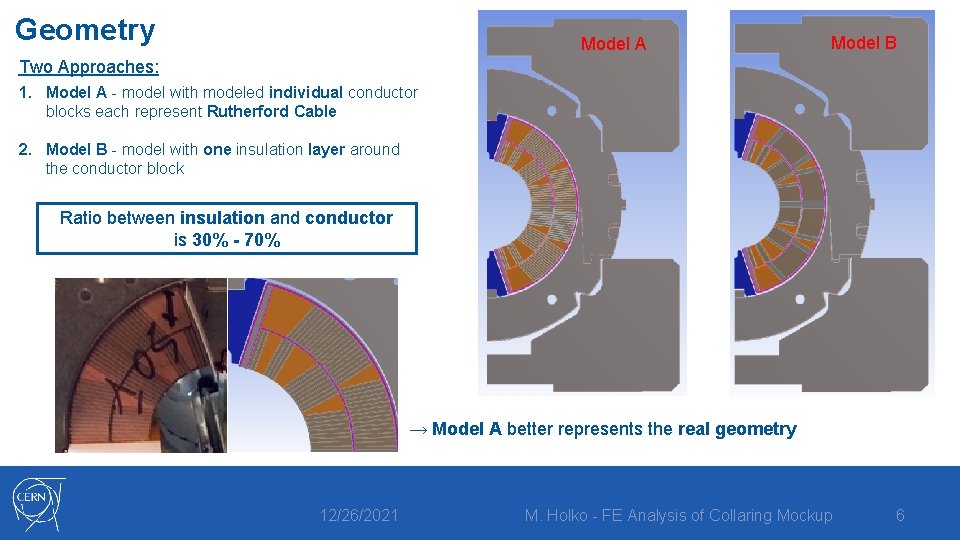
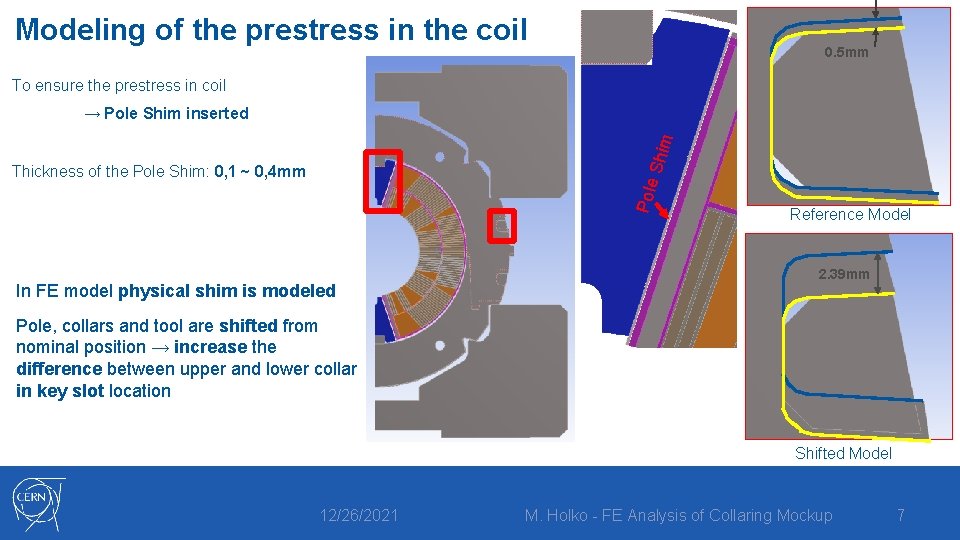
![Material Definition E [GPa] POISSON YIELD [MPa] TANGENT [MPa] PARAMETERS SOURCE 304 L 193 Material Definition E [GPa] POISSON YIELD [MPa] TANGENT [MPa] PARAMETERS SOURCE 304 L 193](https://slidetodoc.com/presentation_image_h2/310b8ea423e9076eb66c963584e60b30/image-8.jpg)
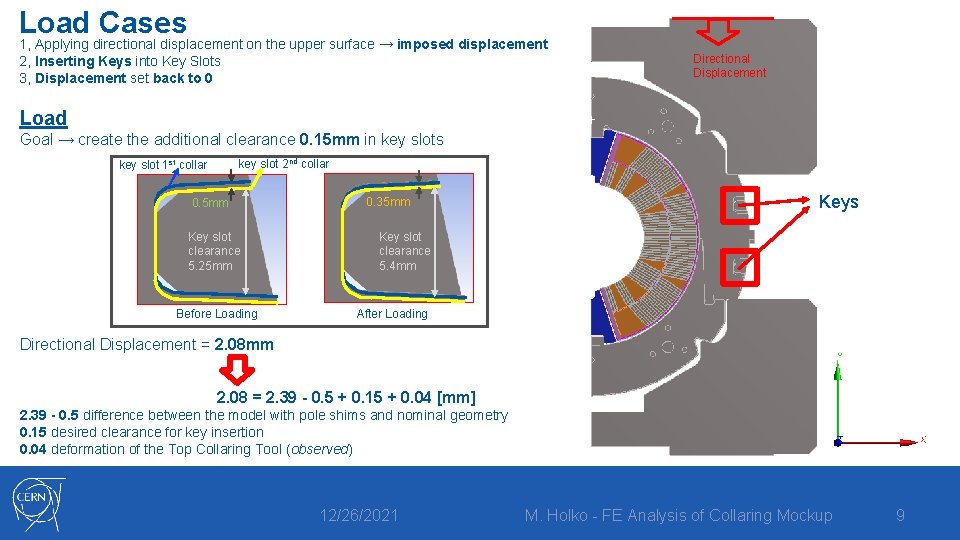
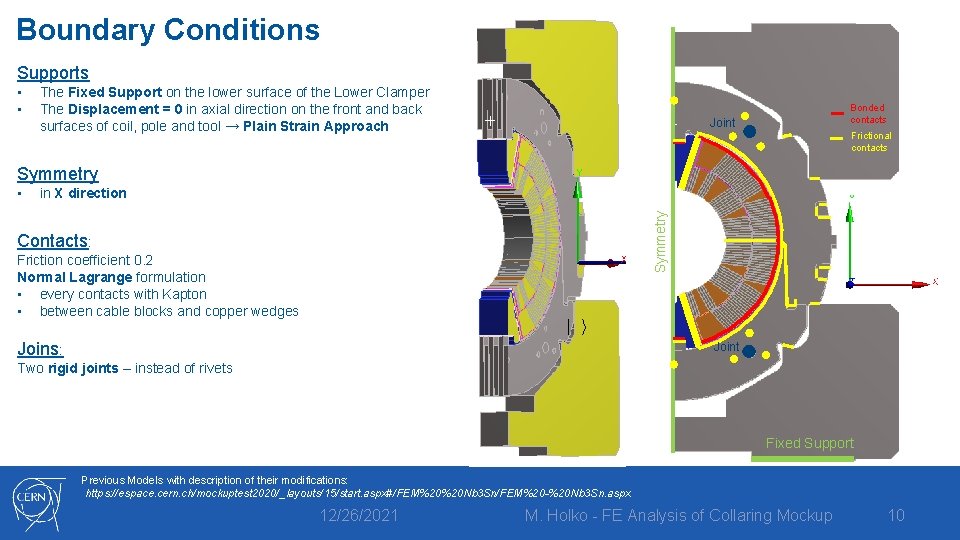
![Results Force from Collar Nose to Pole (25. 8%) [N] 46 180 N– represents Results Force from Collar Nose to Pole (25. 8%) [N] 46 180 N– represents](https://slidetodoc.com/presentation_image_h2/310b8ea423e9076eb66c963584e60b30/image-11.jpg)
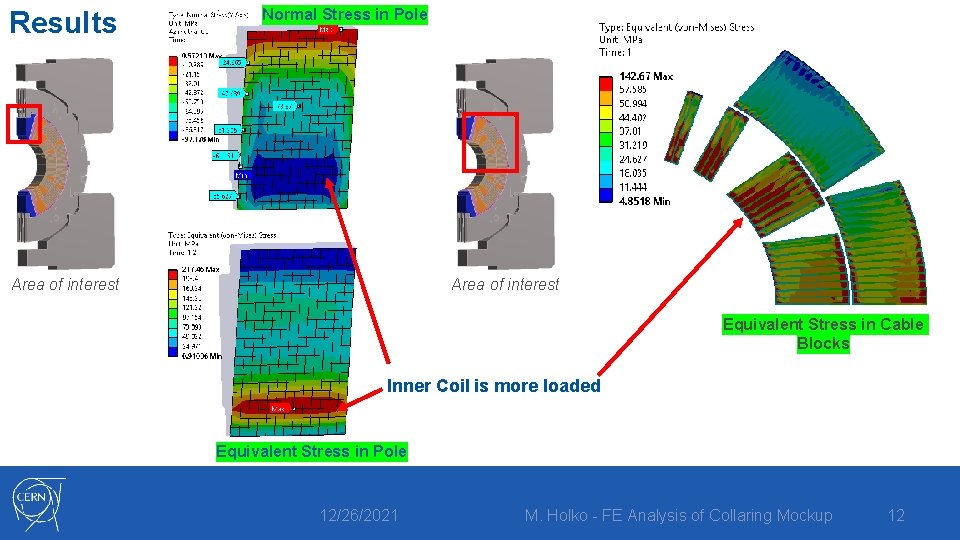
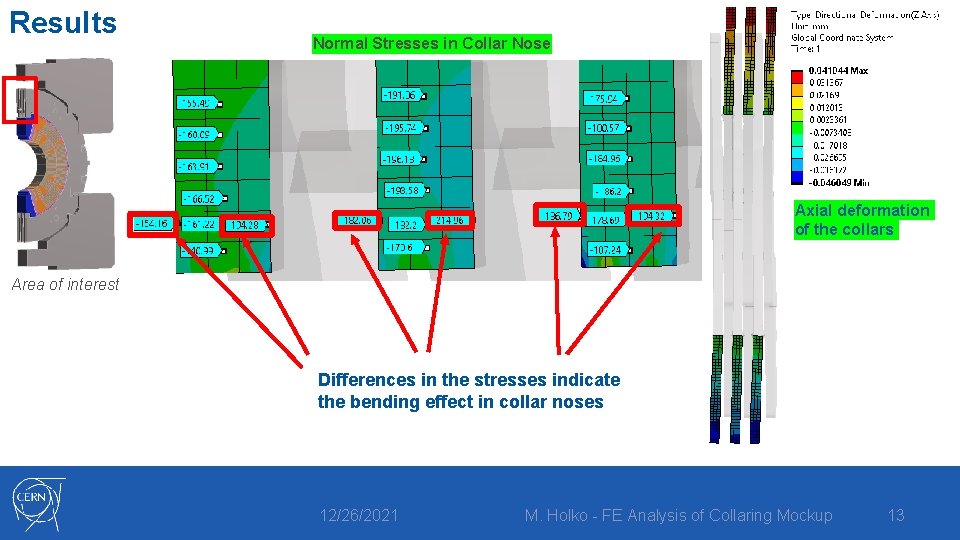
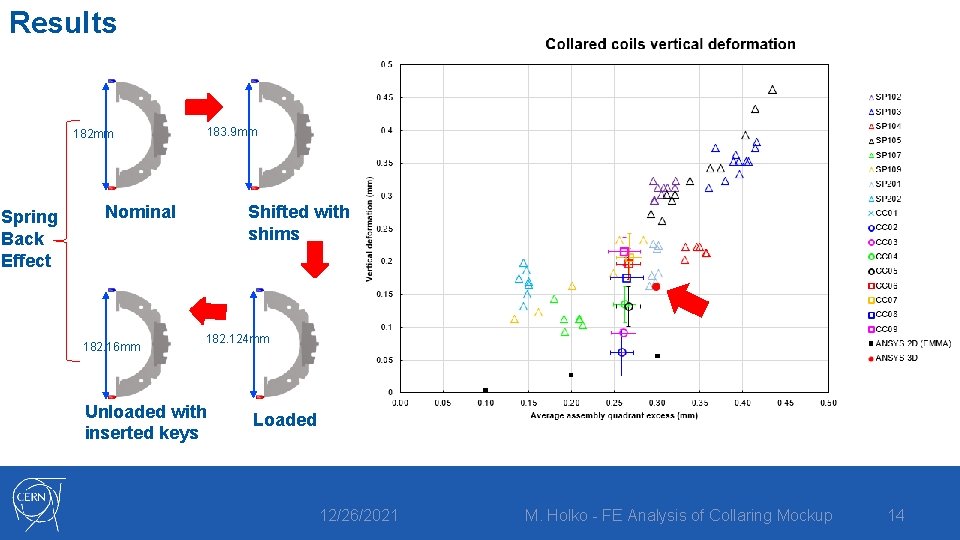
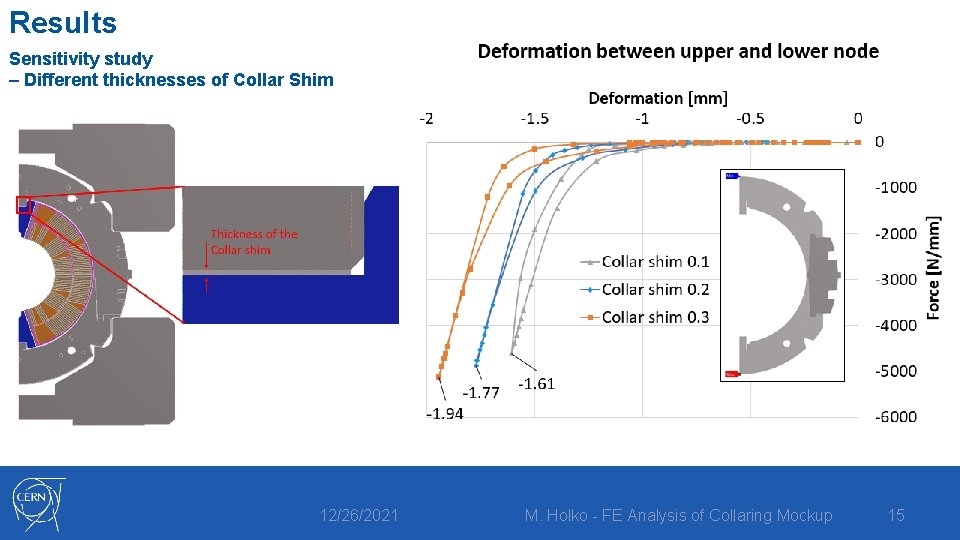
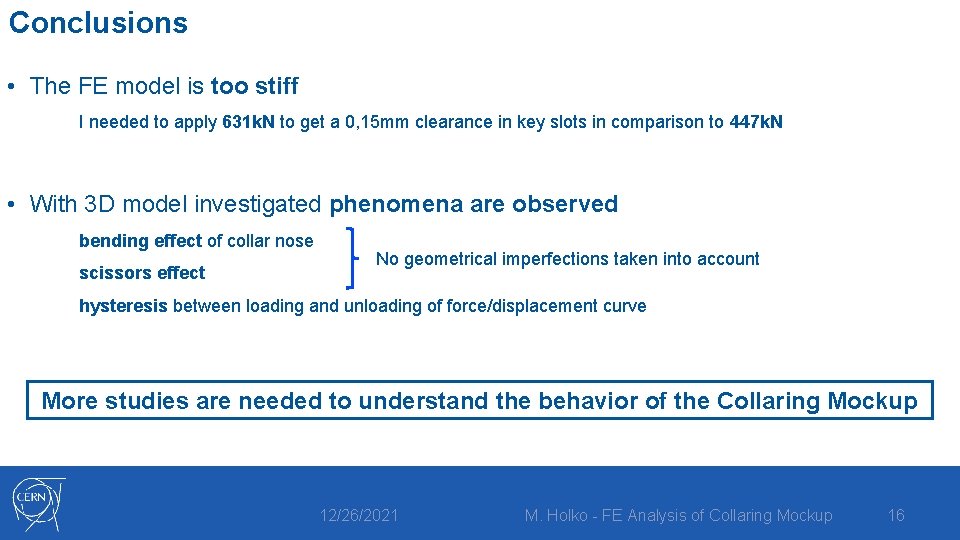
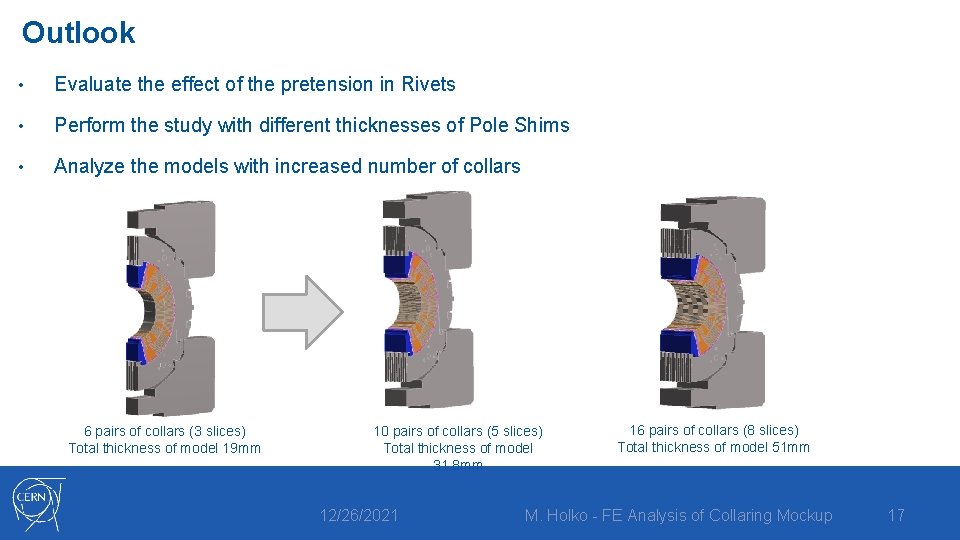
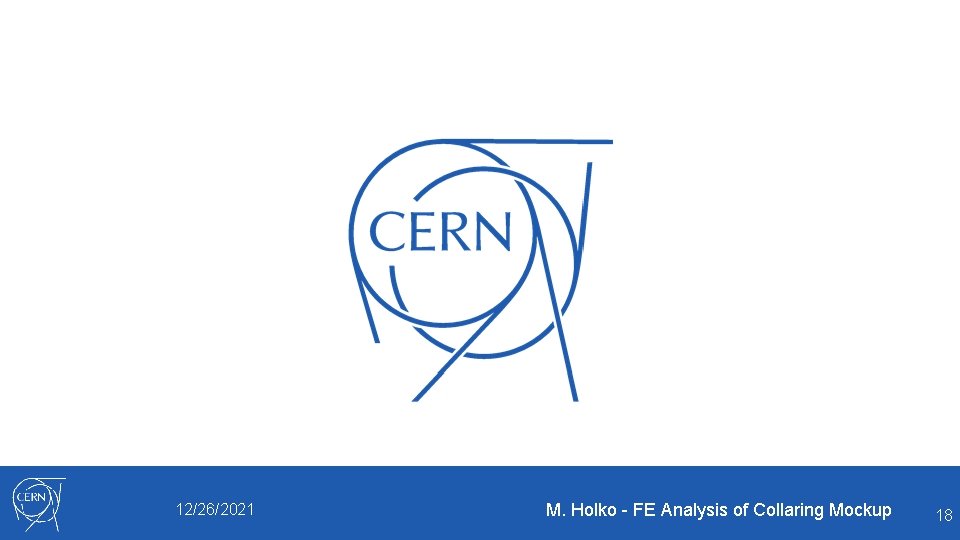
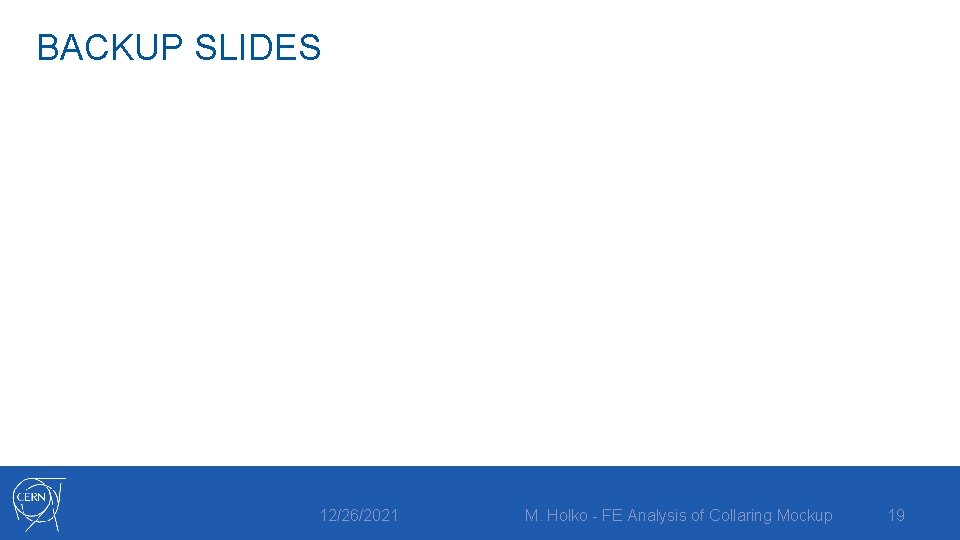
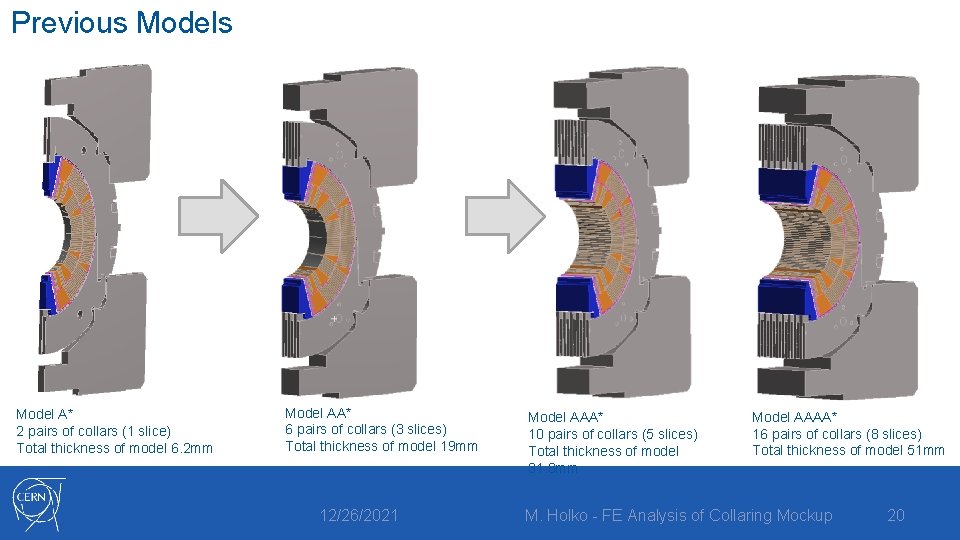
![Previous Models Modification Max Loading Force [N/mm] Max Loading Force (130 mm) [k. N] Previous Models Modification Max Loading Force [N/mm] Max Loading Force (130 mm) [k. N]](https://slidetodoc.com/presentation_image_h2/310b8ea423e9076eb66c963584e60b30/image-21.jpg)
![Previous Models Modification Max Loading Force [N/mm] Max Loading Force (130 mm) [k. N] Previous Models Modification Max Loading Force [N/mm] Max Loading Force (130 mm) [k. N]](https://slidetodoc.com/presentation_image_h2/310b8ea423e9076eb66c963584e60b30/image-22.jpg)
- Slides: 22
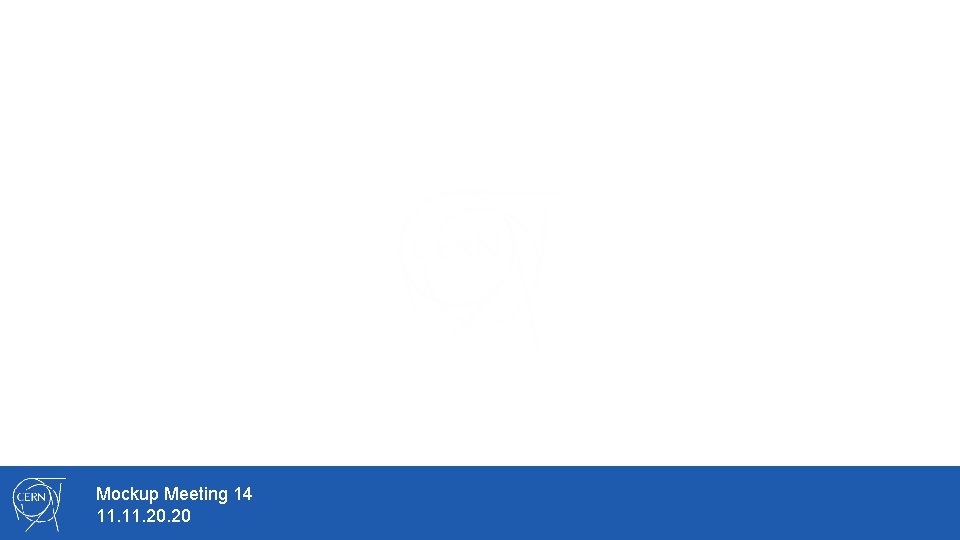
FE Analysis of Collaring Mockup Michal Holko at al. CERN EN MME Mockup Meeting 14 11. 20. 20
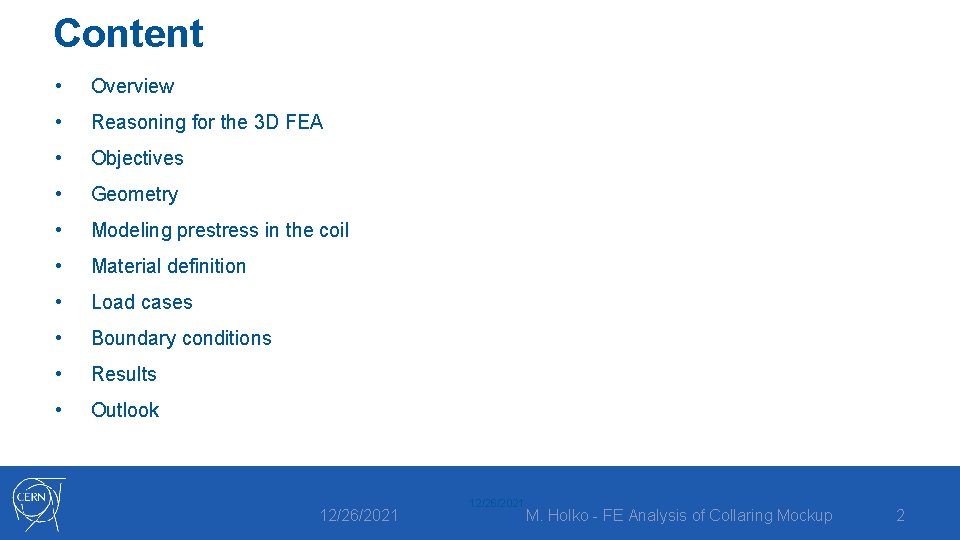
Content • Overview • Reasoning for the 3 D FEA • Objectives • Geometry • Modeling prestress in the coil • Material definition • Load cases • Boundary conditions • Results • Outlook 12/26/2021 M. Holko - FE Analysis of Collaring Mockup 2
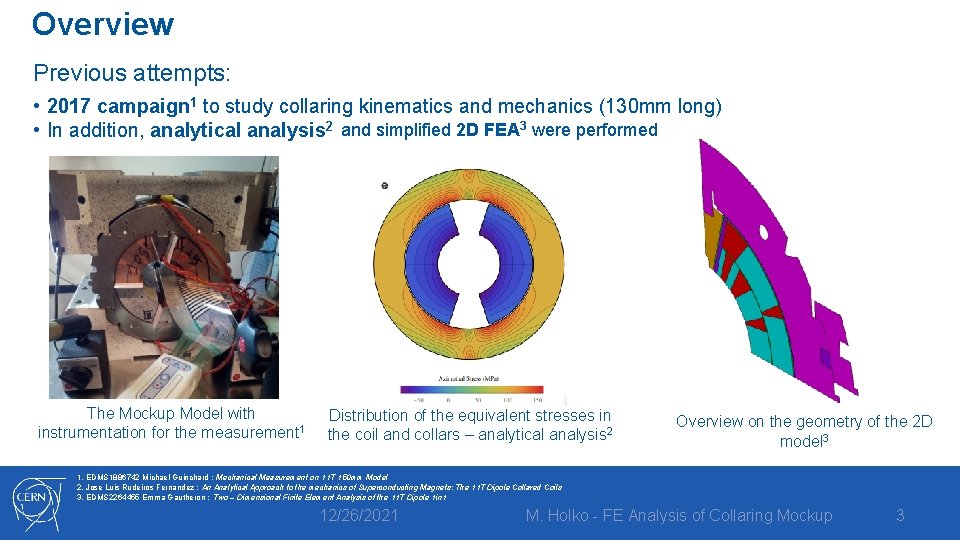
Overview Previous attempts: • 2017 campaign 1 to study collaring kinematics and mechanics (130 mm long) • In addition, analytical analysis 2 and simplified 2 D FEA 3 were performed The Mockup Model with instrumentation for the measurement 1 Distribution of the equivalent stresses in the coil and collars – analytical analysis 2 Overview on the geometry of the 2 D model 3 1, EDMS 1886742 Michael Guinchard : Mechanical Measurement on 11 T 150 mm Model 2, Jose Luis Rudeiros Fernandez : An Analytical Approach to the mechanics of Superconducting Magnets: The 11 T Dipole Collared Coils 3, EDMS 2264455 Emma Gautheron : Two – Dimensional Finite Element Analysis of the 11 T Dipole 1 in 1 12/26/2021 M. Holko - FE Analysis of Collaring Mockup 3
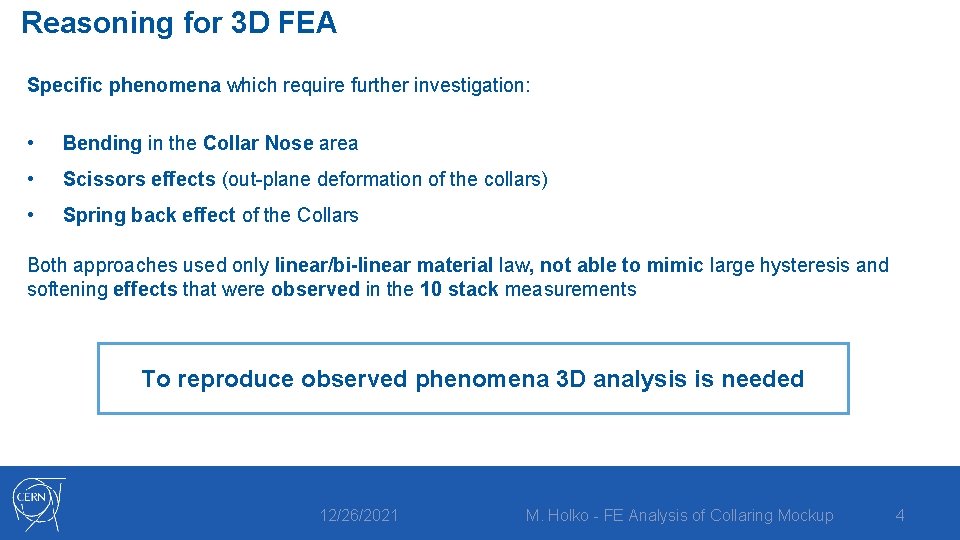
Reasoning for 3 D FEA Specific phenomena which require further investigation: • Bending in the Collar Nose area • Scissors effects (out-plane deformation of the collars) • Spring back effect of the Collars Both approaches used only linear/bi-linear material law, not able to mimic large hysteresis and softening effects that were observed in the 10 stack measurements To reproduce observed phenomena 3 D analysis is needed 12/26/2021 M. Holko - FE Analysis of Collaring Mockup 4
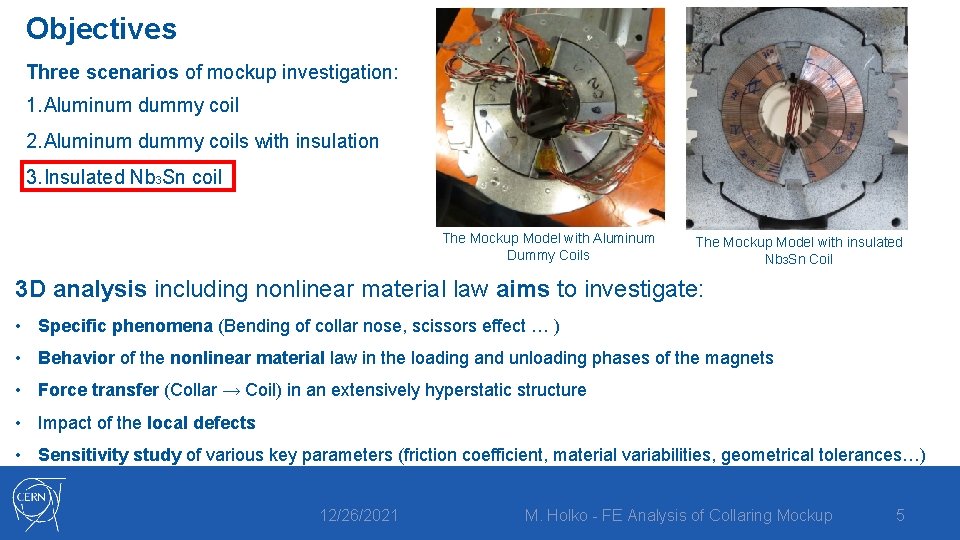
Objectives Three scenarios of mockup investigation: 1. Aluminum dummy coil 2. Aluminum dummy coils with insulation 3. Insulated Nb 3 Sn coil The Mockup Model with Aluminum Dummy Coils The Mockup Model with insulated Nb 3 Sn Coil 3 D analysis including nonlinear material law aims to investigate: • Specific phenomena (Bending of collar nose, scissors effect … ) • Behavior of the nonlinear material law in the loading and unloading phases of the magnets • Force transfer (Collar → Coil) in an extensively hyperstatic structure • Impact of the local defects • Sensitivity study of various key parameters (friction coefficient, material variabilities, geometrical tolerances…) 12/26/2021 M. Holko - FE Analysis of Collaring Mockup 5
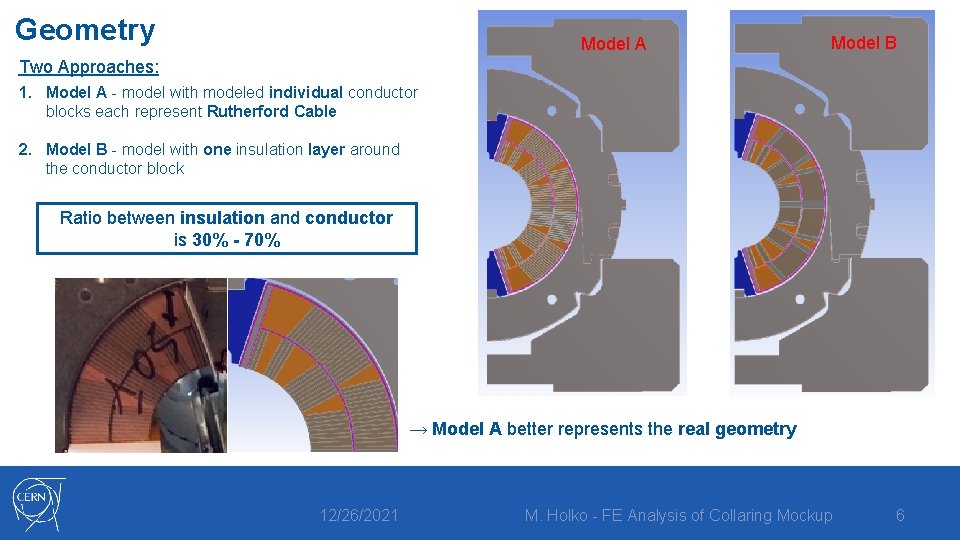
Geometry Model A Model B Two Approaches: 1. Model A - model with modeled individual conductor blocks each represent Rutherford Cable 2. Model B - model with one insulation layer around the conductor block Ratio between insulation and conductor is 30% - 70% → Model A better represents the real geometry 12/26/2021 M. Holko - FE Analysis of Collaring Mockup 6
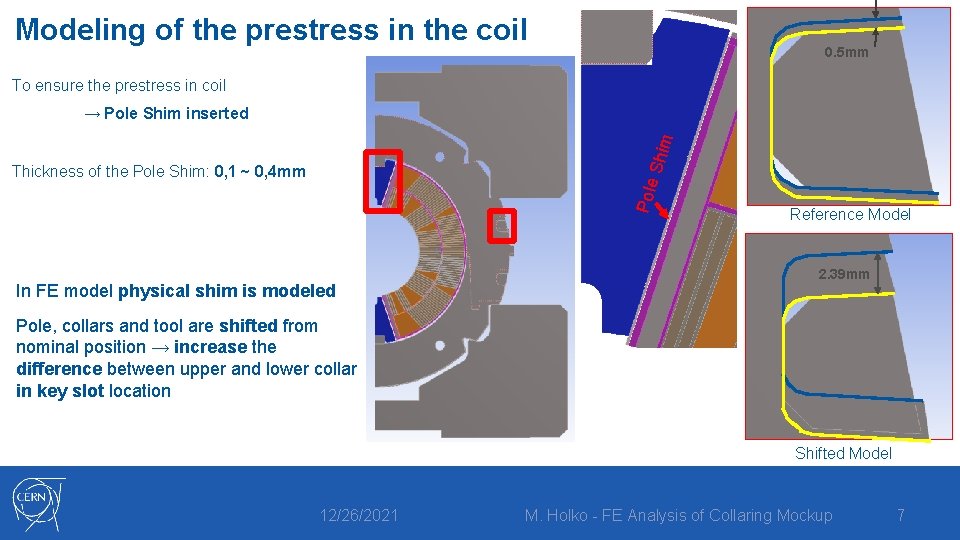
Modeling of the prestress in the coil 0. 5 mm To ensure the prestress in coil Shim → Pole Shim inserted Pole Thickness of the Pole Shim: 0, 1 ~ 0, 4 mm In FE model physical shim is modeled Reference Model 2. 39 mm Pole, collars and tool are shifted from nominal position → increase the difference between upper and lower collar in key slot location Shifted Model 12/26/2021 M. Holko - FE Analysis of Collaring Mockup 7
![Material Definition E GPa POISSON YIELD MPa TANGENT MPa PARAMETERS SOURCE 304 L 193 Material Definition E [GPa] POISSON YIELD [MPa] TANGENT [MPa] PARAMETERS SOURCE 304 L 193](https://slidetodoc.com/presentation_image_h2/310b8ea423e9076eb66c963584e60b30/image-8.jpg)
Material Definition E [GPa] POISSON YIELD [MPa] TANGENT [MPa] PARAMETERS SOURCE 304 L 193 0. 28 x x x 304 L Non-Linear 193 0. 28 250 1000 x From previous 2 D analysis of Emma Gautheron et al. 3 304 L Non-Linear COLLARS 193 0. 28 415 1000 x COPPER 93 0. 3 x x x KAPTON 2. 5 0. 3 x x x TITANIUM 130 0. 3 x x x ~3. 5 ~0. 35 x x C 10=216. 9 MPa C 01=366. 4 MPa D 1=0. 000514 R=1. 01 M=1 e-07 MPa B=0. 25 70 0. 3 18000 x INSULATION Hyperelastic Material Law (Mooney-Rivlin) +compressibility +Mullins Effect CONDUCTOR Assumption from the investigation of 10 stack 3, EDMS 2264455 Emma Gautheron : Two – Dimensional Finite Element Analysis of the 11 T Dipole 1 in 1 12/26/2021 M. Holko - FE Analysis of Collaring Mockup 8
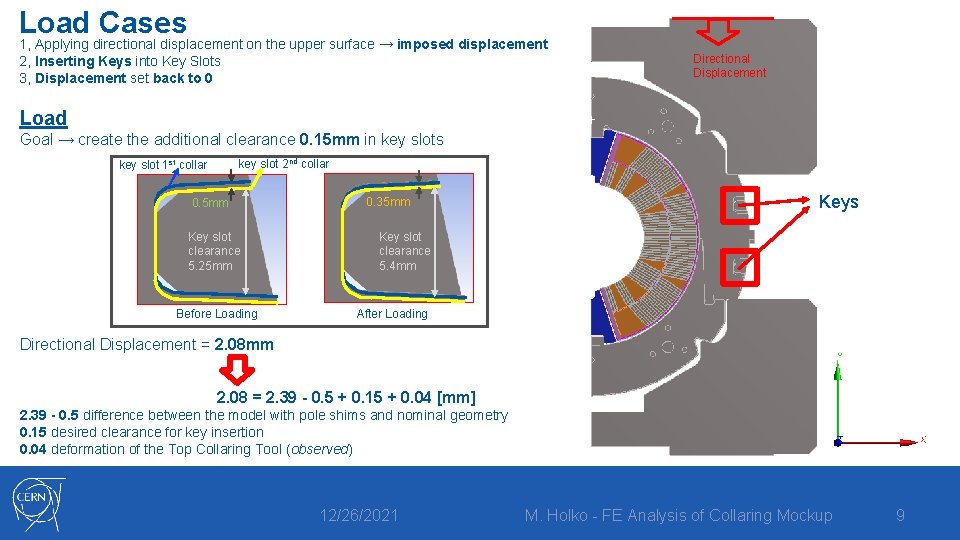
Load Cases 1, Applying directional displacement on the upper surface → imposed displacement 2, Inserting Keys into Key Slots 3, Displacement set back to 0 Directional Displacement Load Goal → create the additional clearance 0. 15 mm in key slots key slot 2 nd collar key slot 1 st collar 0. 5 mm Key slot clearance 5. 25 mm Before Loading 0. 35 mm Keys Key slot clearance 5. 4 mm After Loading Directional Displacement = 2. 08 mm 2. 08 = 2. 39 - 0. 5 + 0. 15 + 0. 04 [mm] 2. 39 - 0. 5 difference between the model with pole shims and nominal geometry 0. 15 desired clearance for key insertion 0. 04 deformation of the Top Collaring Tool (observed) 12/26/2021 M. Holko - FE Analysis of Collaring Mockup 9
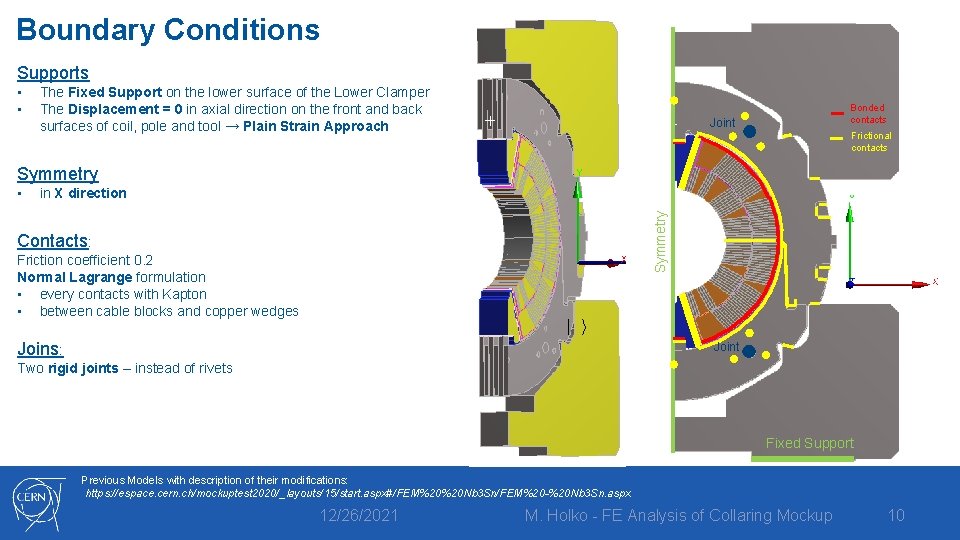
Boundary Conditions Supports • • The Fixed Support on the lower surface of the Lower Clamper The Displacement = 0 in axial direction on the front and back surfaces of coil, pole and tool → Plain Strain Approach Bonded contacts Joint Frictional contacts Symmetry in X direction Symmetry • Contacts: Friction coefficient 0. 2 Normal Lagrange formulation • every contacts with Kapton • between cable blocks and copper wedges Joins: Joint Two rigid joints – instead of rivets Fixed Support Previous Models with description of their modifications: https: //espace. cern. ch/mockuptest 2020/_layouts/15/start. aspx#/FEM%20%20 Nb 3 Sn/FEM%20 -%20 Nb 3 Sn. aspx 12/26/2021 M. Holko - FE Analysis of Collaring Mockup 10
![Results Force from Collar Nose to Pole 25 8 N 46 180 N represents Results Force from Collar Nose to Pole (25. 8%) [N] 46 180 N– represents](https://slidetodoc.com/presentation_image_h2/310b8ea423e9076eb66c963584e60b30/image-11.jpg)
Results Force from Collar Nose to Pole (25. 8%) [N] 46 180 N– represents 631 k. N for 130 mm long model Main Findings of the Latest Model: Model AA 3 (12 collars): Collar Nose - Pole o The stiffness of the model has increased – max force for increasing the clearance in key slots is 631 k. N o Ratio between Collar Nose Force and Shoe Force is 26: 73 Collar to Shoe Short Collar to Long Collar 37 725 1 st 2 nd 3 rd 4330 N(9. 4%) 3790(8. 2%) 3785(8. 2%) Force from Collar to Shoe (73. 3%) [N] Long Short 1 st 7623 (16. 5%) 4408 (9. 5%) 2 nd 8118 (17. 6%) 3047 (6. 7%) 3 rd 8442 (18. 3%) 2176 (4. 7%) 17 557 24 315 Long Collar to Short Collar o Inner coil is more loaded 3 rd 2 nd 1 st o Visible bending effect on the Collar Nose o Average Normal stresses in Midplane 72 MPa 12/26/2021 Force Distribution M. Holko - FE Analysis of Collaring Mockup 11
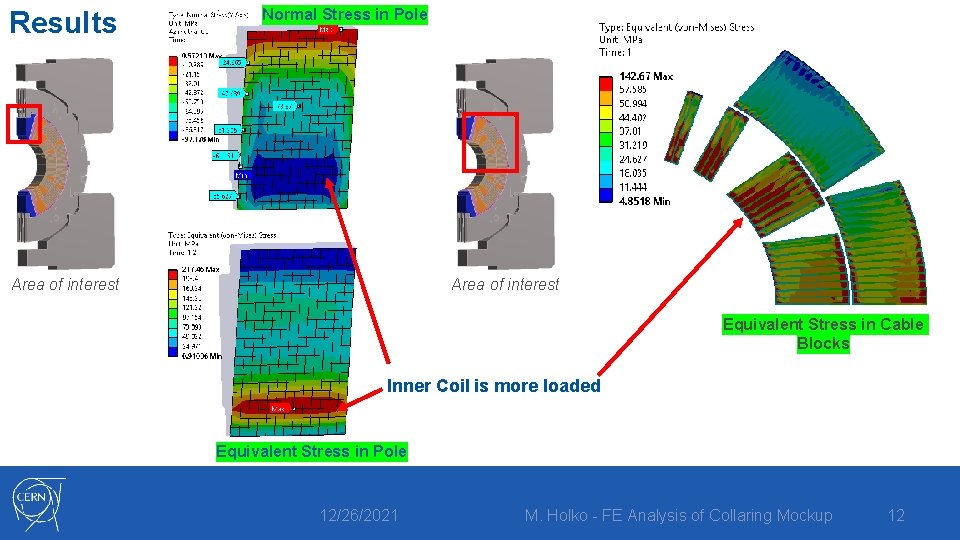
Results Normal Stress in Pole Area of interest Equivalent Stress in Cable Blocks Inner Coil is more loaded Equivalent Stress in Pole 12/26/2021 M. Holko - FE Analysis of Collaring Mockup 12
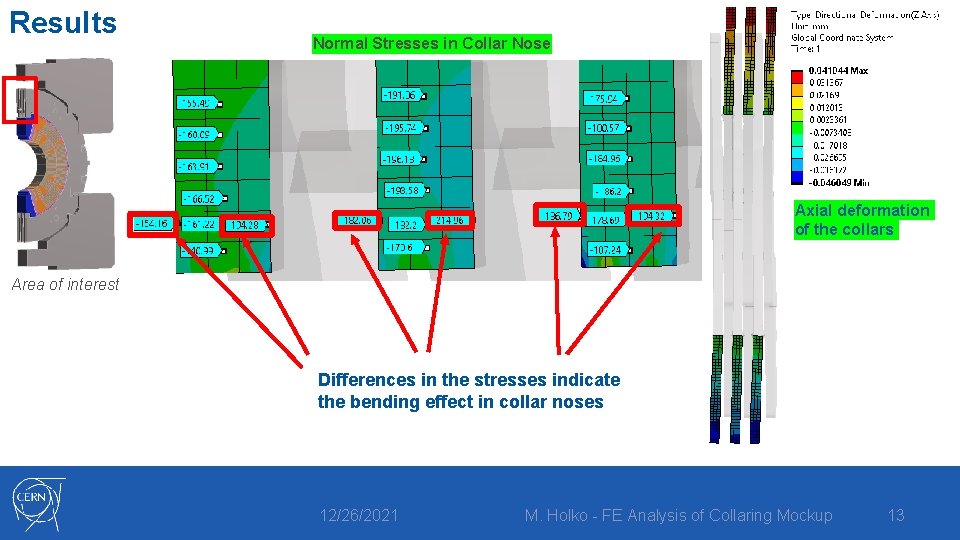
Results Normal Stresses in Collar Nose Axial deformation of the collars Area of interest Differences in the stresses indicate the bending effect in collar noses 12/26/2021 M. Holko - FE Analysis of Collaring Mockup 13
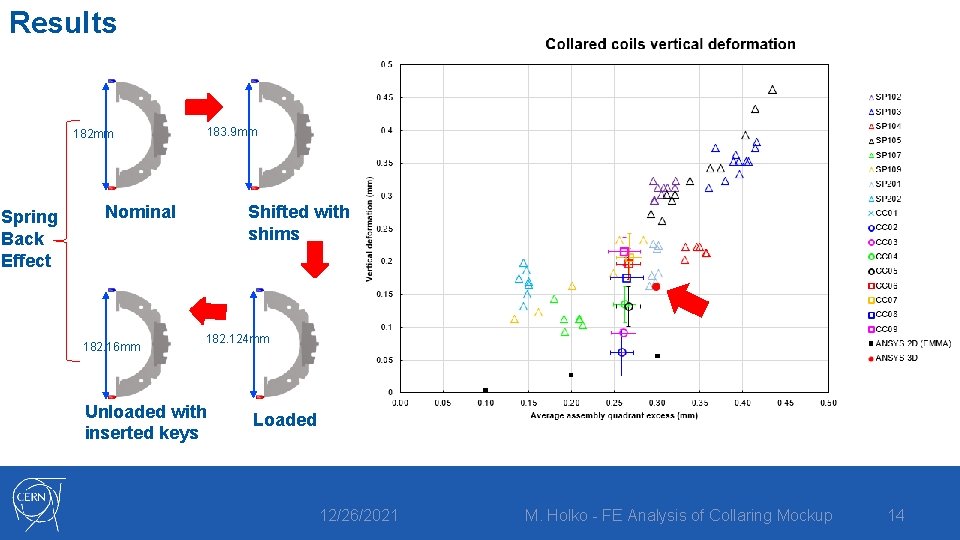
Results 182 mm Spring Back Effect 183. 9 mm Nominal 182. 16 mm Shifted with shims 182. 124 mm Unloaded with inserted keys Loaded 12/26/2021 M. Holko - FE Analysis of Collaring Mockup 14
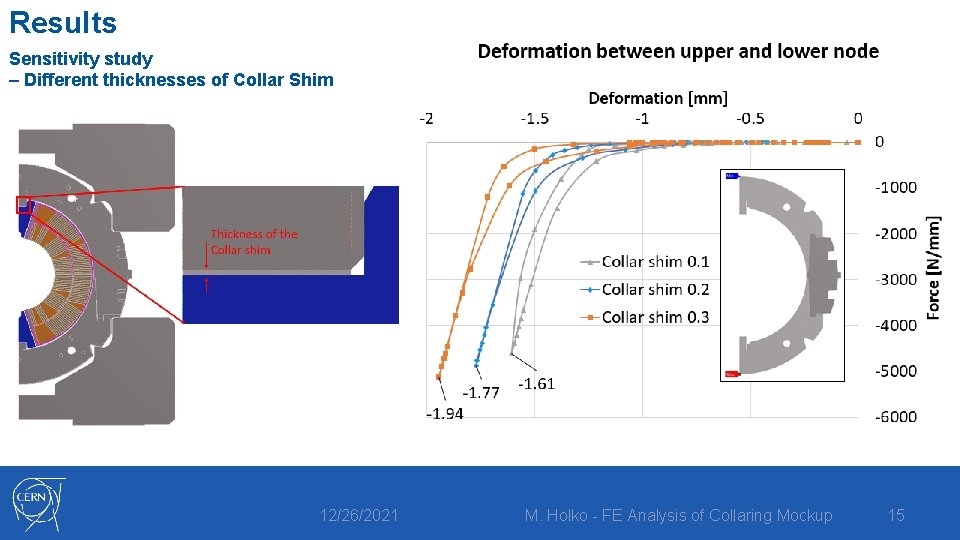
Results Sensitivity study – Different thicknesses of Collar Shim 12/26/2021 M. Holko - FE Analysis of Collaring Mockup 15
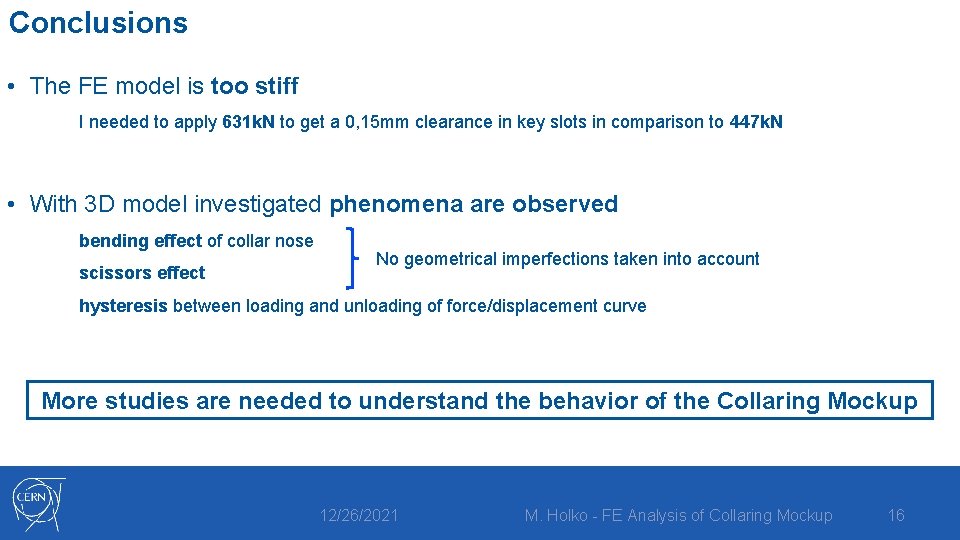
Conclusions • The FE model is too stiff I needed to apply 631 k. N to get a 0, 15 mm clearance in key slots in comparison to 447 k. N • With 3 D model investigated phenomena are observed bending effect of collar nose scissors effect No geometrical imperfections taken into account hysteresis between loading and unloading of force/displacement curve More studies are needed to understand the behavior of the Collaring Mockup 12/26/2021 M. Holko - FE Analysis of Collaring Mockup 16
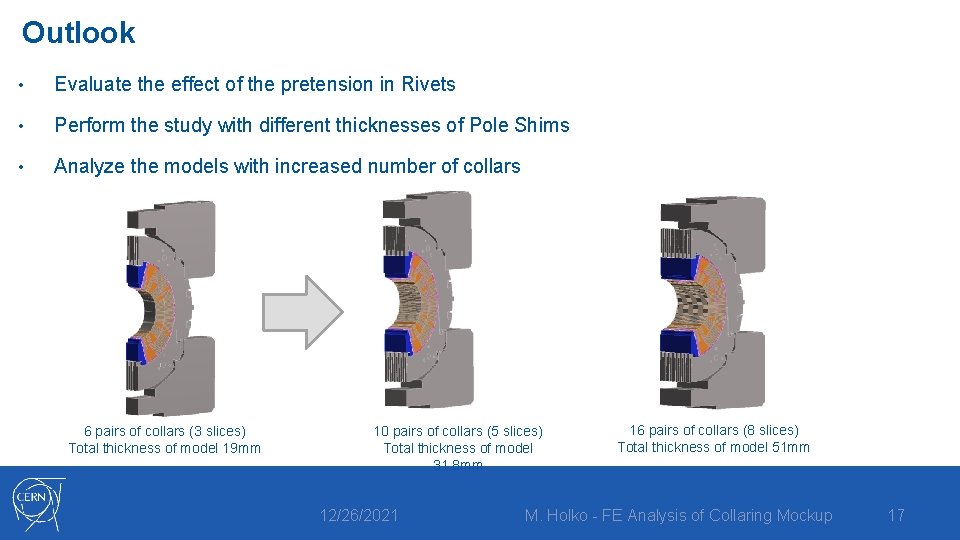
Outlook • Evaluate the effect of the pretension in Rivets • Perform the study with different thicknesses of Pole Shims • Analyze the models with increased number of collars 6 pairs of collars (3 slices) Total thickness of model 19 mm 10 pairs of collars (5 slices) Total thickness of model 31. 8 mm 12/26/2021 16 pairs of collars (8 slices) Total thickness of model 51 mm M. Holko - FE Analysis of Collaring Mockup 17
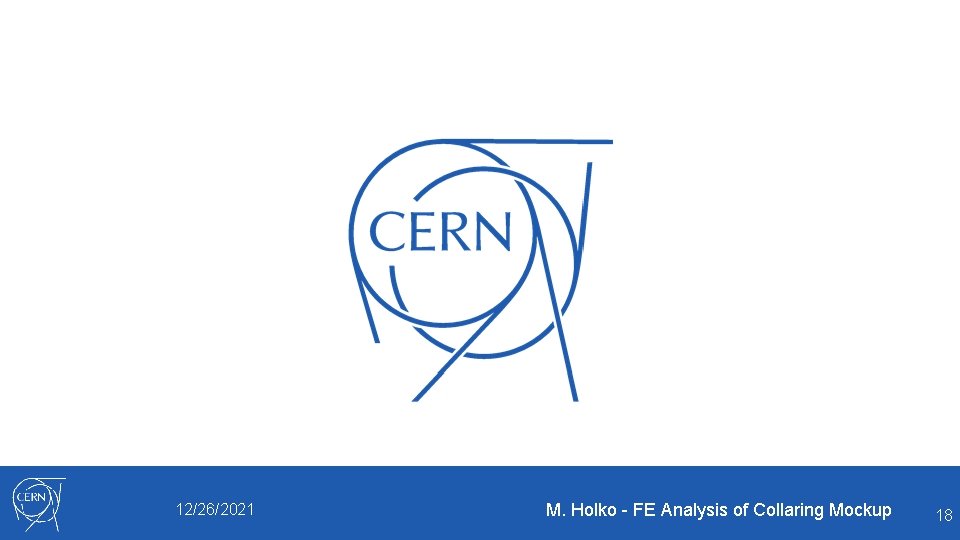
Thank you for your attention 12/26/2021 M. Holko - FE Analysis of Collaring Mockup 18
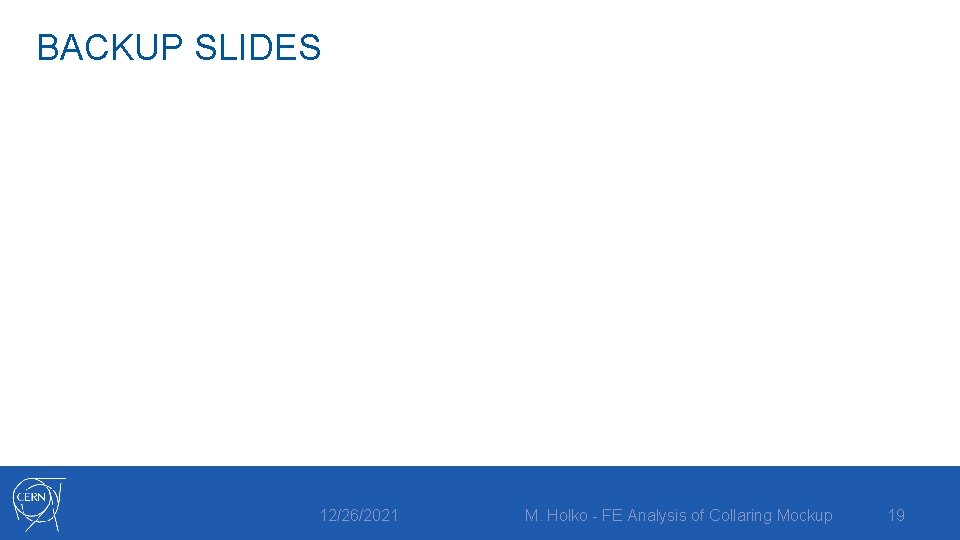
BACKUP SLIDES 12/26/2021 M. Holko - FE Analysis of Collaring Mockup 19
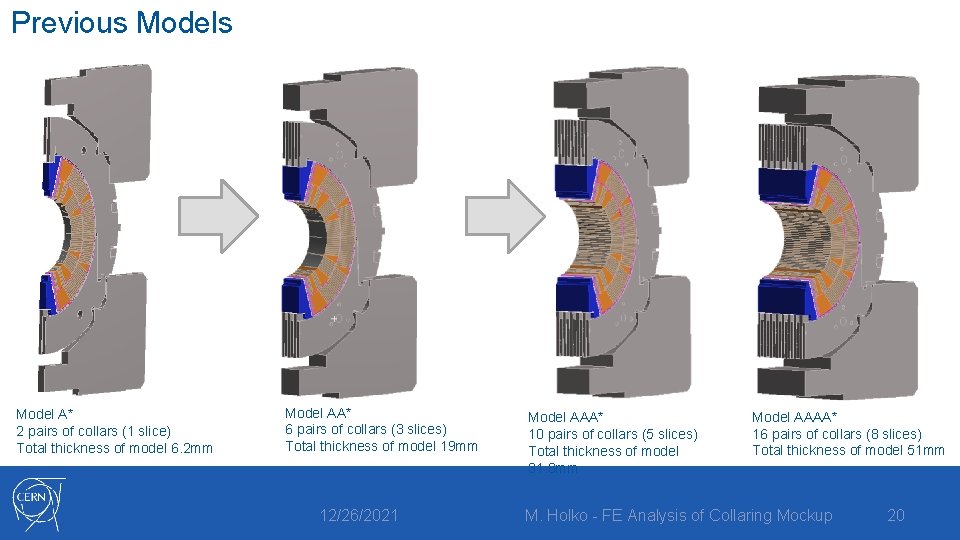
Previous Model A* 2 pairs of collars (1 slice) Total thickness of model 6. 2 mm Model AA* 6 pairs of collars (3 slices) Total thickness of model 19 mm 12/26/2021 Model AAA* 10 pairs of collars (5 slices) Total thickness of model 31. 8 mm Model AAAA* 16 pairs of collars (8 slices) Total thickness of model 51 mm M. Holko - FE Analysis of Collaring Mockup 20
![Previous Models Modification Max Loading Force Nmm Max Loading Force 130 mm k N Previous Models Modification Max Loading Force [N/mm] Max Loading Force (130 mm) [k. N]](https://slidetodoc.com/presentation_image_h2/310b8ea423e9076eb66c963584e60b30/image-21.jpg)
Previous Models Modification Max Loading Force [N/mm] Max Loading Force (130 mm) [k. N] Collar Nose Normal Stress [MPa] Mid Plane Avg. Normal Stress in Insulation [MPa] Model A Reference model 4090 532 145 40. 1 Model A 1 Slit in collar nose area 3910 508 156 39. 9 Model A 2 Changed bonded contacts to frictional (between tool and collars 3855 501 90. 5 38 Model A 3 + Changed the contact definition between collars from “adjust to touch” to “add offset no ramping” 3251 422. 6 128 35 Model A 4 + Slit in the Collar Nose area 3612 470 179 39. 4 Model A 5 + Collar Shoe nonlinear 3452 448 157 45 Model A 6 + No contact between shim and shoe 3289 427 145 42. 7 Model A 7 + Frictional contact between shoe and Kapton 3156 410 154 40. 5 Model A 8 + Contact stiffness factor set to 1 in the contact between collars + Bonded shoe to Kapton (back) 3310 430 154 43 Model A 9 + Change “adjusted to touch” to “add Offset, no ramping” – the contact between collars 2662 346 144 36 Model A 10 + All contacts with Kapton: formulation changed to Normal Lagrange 3462 450 181 47. 8 Model A 11 + Frictional contact between pole shim and coil 3450 448 140. 4 47. 8 Model A 12 + Collars without displacement z=0 3473 451 235. 8 49 A* Previous Models with description of their modifications: https: //espace. cern. ch/mockuptest 2020/_layouts/15/start. aspx#/FEM%20%20 Nb 3 Sn/FEM%20 -%20 Nb 3 Sn. aspx 12/26/2021 M. Holko - FE Analysis of Collaring Mockup 21
![Previous Models Modification Max Loading Force Nmm Max Loading Force 130 mm k N Previous Models Modification Max Loading Force [N/mm] Max Loading Force (130 mm) [k. N]](https://slidetodoc.com/presentation_image_h2/310b8ea423e9076eb66c963584e60b30/image-22.jpg)
Previous Models Modification Max Loading Force [N/mm] Max Loading Force (130 mm) [k. N] Collar Nose Normal Stress [MPa] Mid Plane Avg. Normal Stress in Insulation [MPa] Model AA 1 Same as Model A 12 but with 12 pairs of Collars 3490 453 130 48. 2 Model AA 2 + Normal Lagrange in coil 4854 631 188 69. 7 Model AA 3 - Gap between collars set to 0. 2 (frictional contact between separators and collars) 4861 631 182 71. 6 AA* Previous Models with description of their modifications: https: //espace. cern. ch/mockuptest 2020/_layouts/15/start. aspx#/FEM%20%20 Nb 3 Sn/FEM%20 -%20 Nb 3 Sn. aspx 12/26/2021 M. Holko - FE Analysis of Collaring Mockup 22
Holko logistic
Peter holko
Functional mockup interface
Login page mockup
Address mockup
Menu sistem
Prinsip mockup
Visio sql server
Assembly image
Segregator mockup
Michal cyprian
Michal hammer
Michal lehnert
Michal tkaczyk
Adsl standard
Michal grešlik
Michal kalman vek
Casus nocet domino
Michal drobot
Meniny michala
Michal bick
Fabry disease
Michal kolcun