FEA Model of Collaring Mockup Michal Holko at
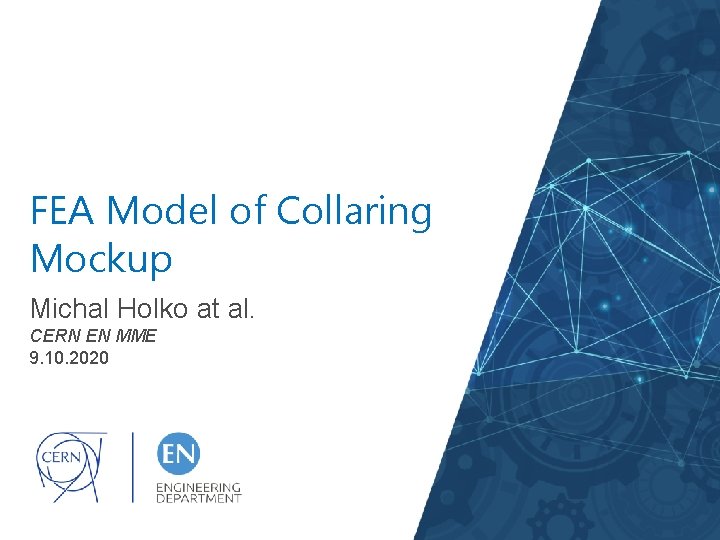
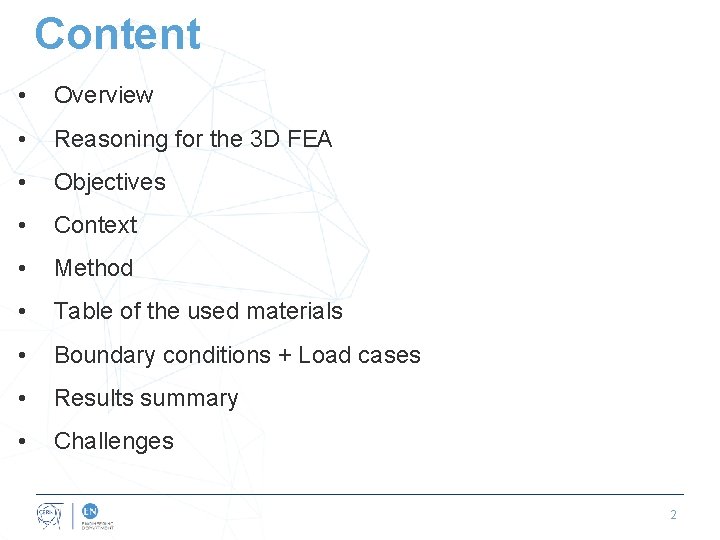
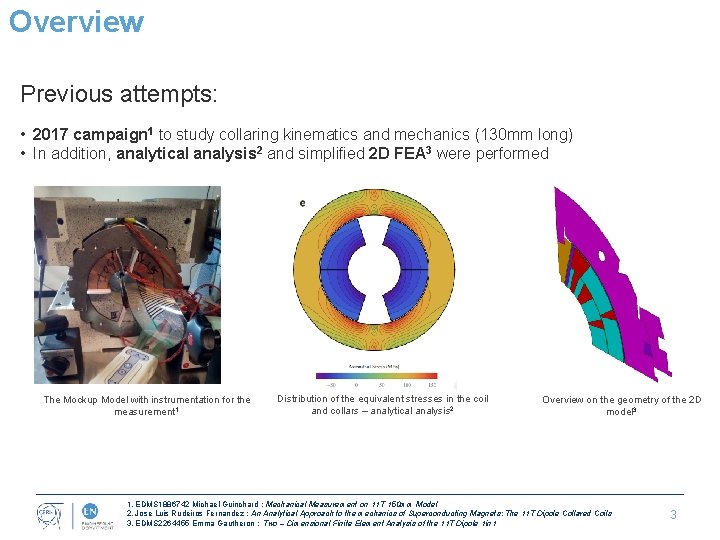
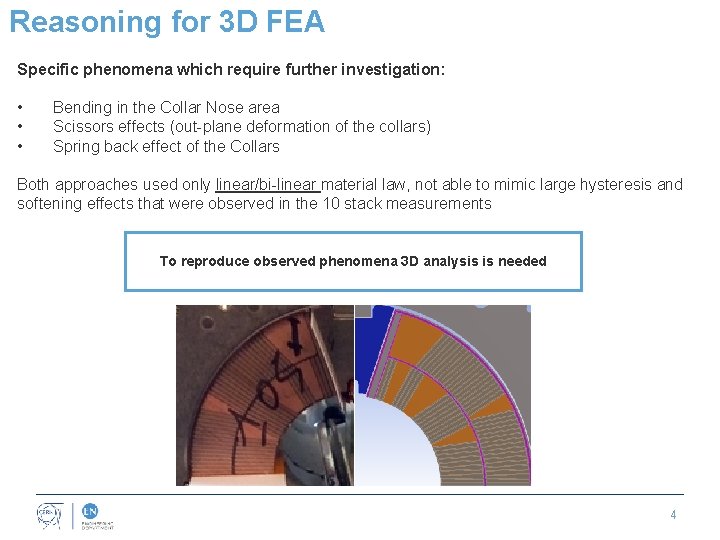
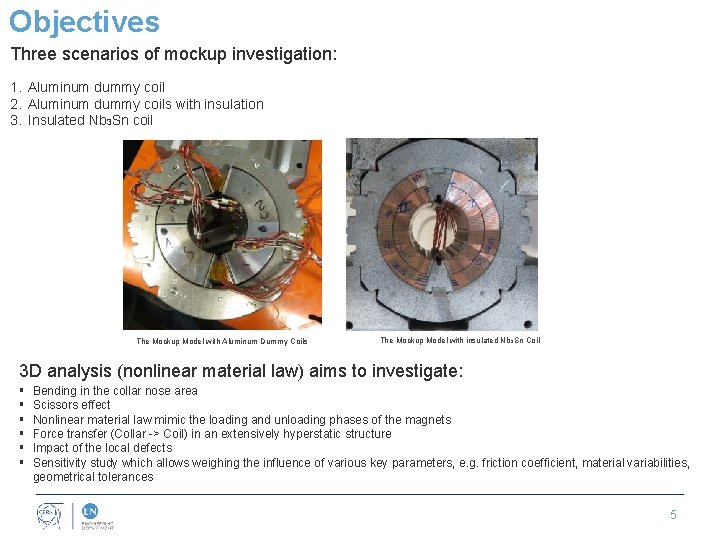
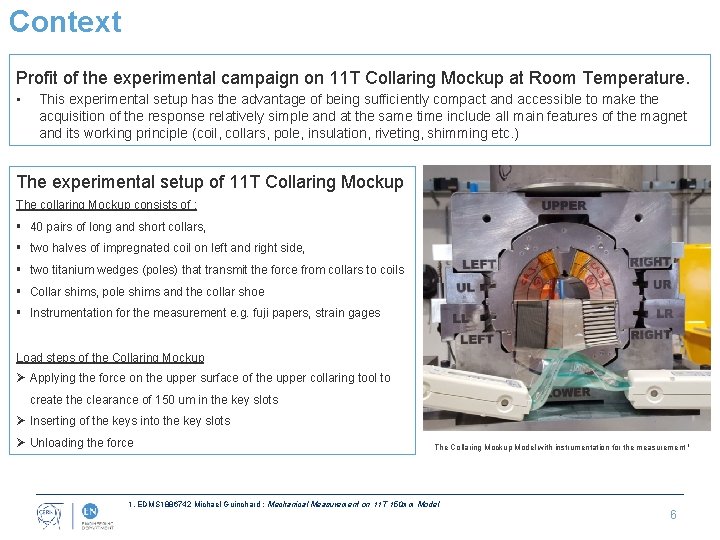
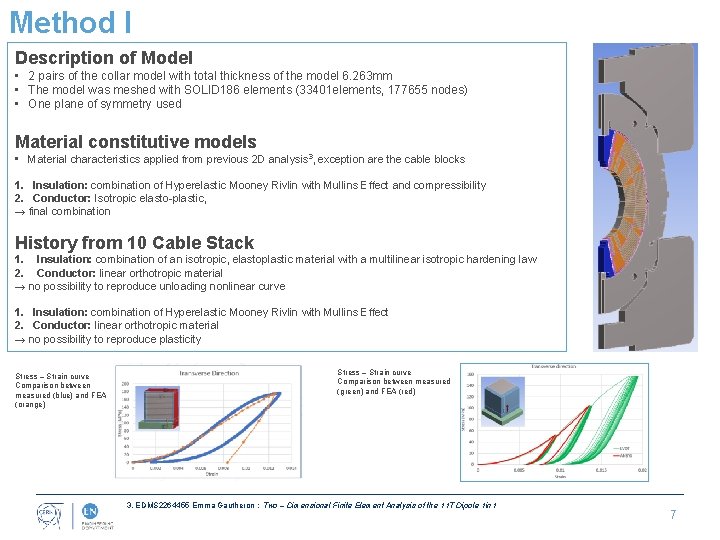
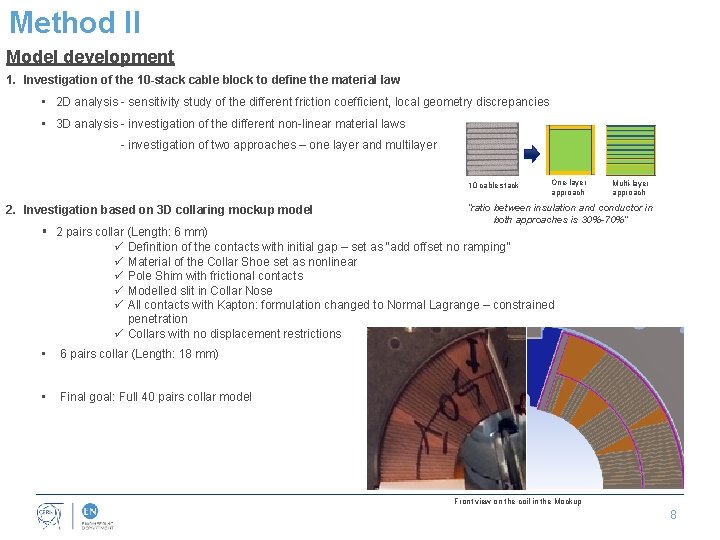
![Material Definition E [GPa] POISSON YIELD [MPa] TANGENT [MPa] PARAMETERS SOURCE 304 L 193 Material Definition E [GPa] POISSON YIELD [MPa] TANGENT [MPa] PARAMETERS SOURCE 304 L 193](https://slidetodoc.com/presentation_image_h/2b2597867473798f74f263d719b93fa7/image-9.jpg)
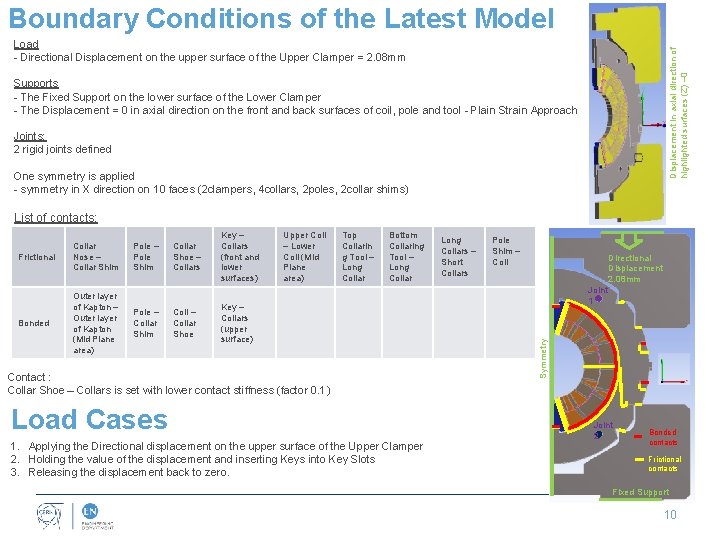
![Results Summary Load Case Max Loading Force (6. 263 mm) [N] Max Loading Force Results Summary Load Case Max Loading Force (6. 263 mm) [N] Max Loading Force](https://slidetodoc.com/presentation_image_h/2b2597867473798f74f263d719b93fa7/image-11.jpg)
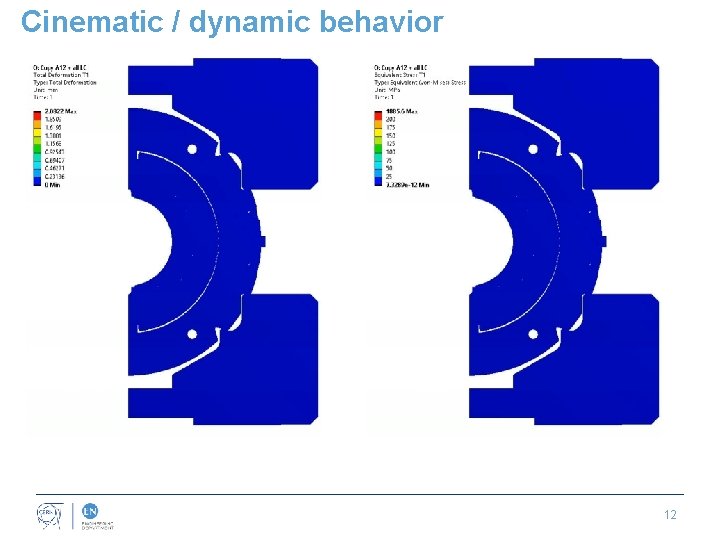
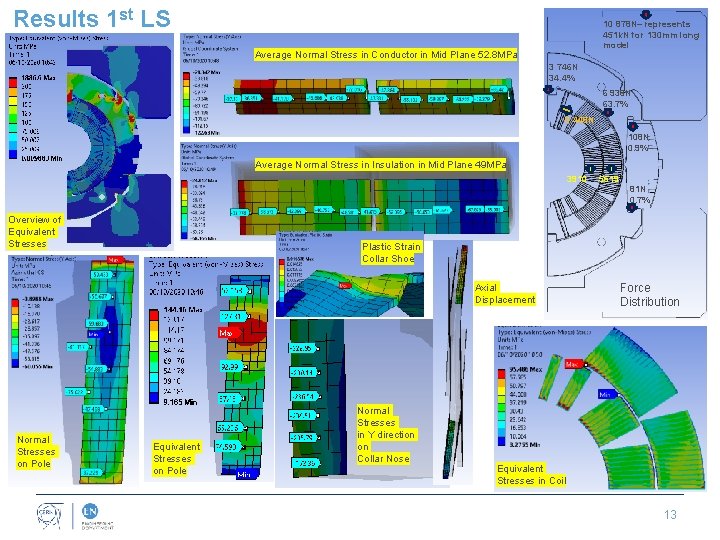
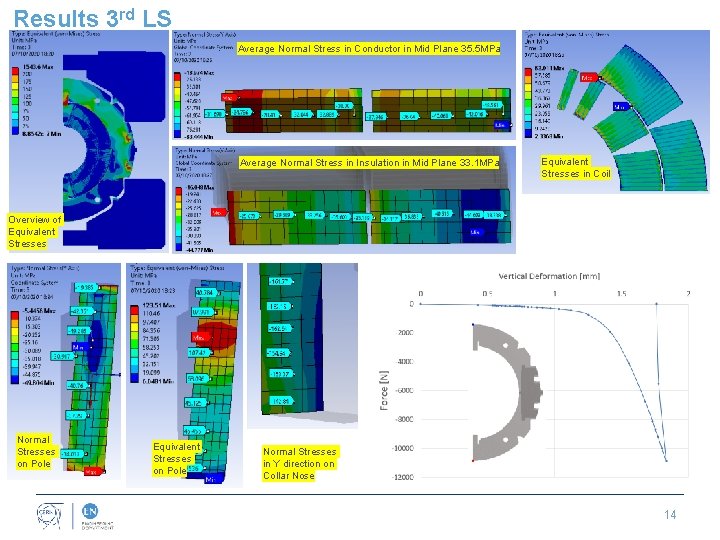
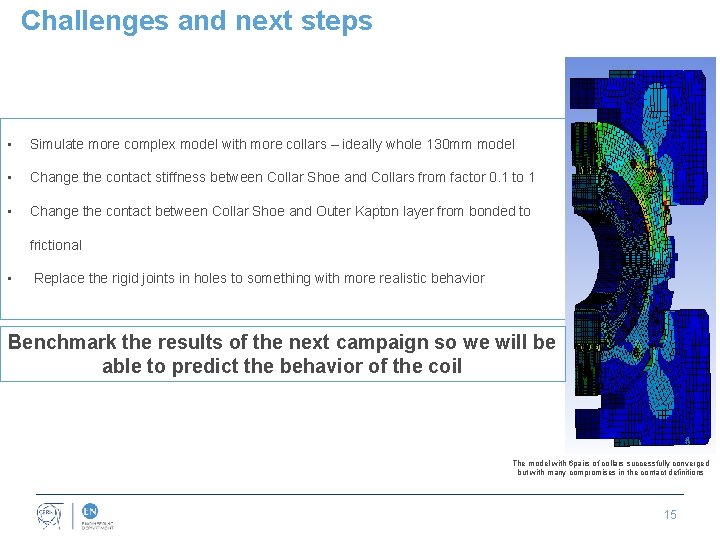
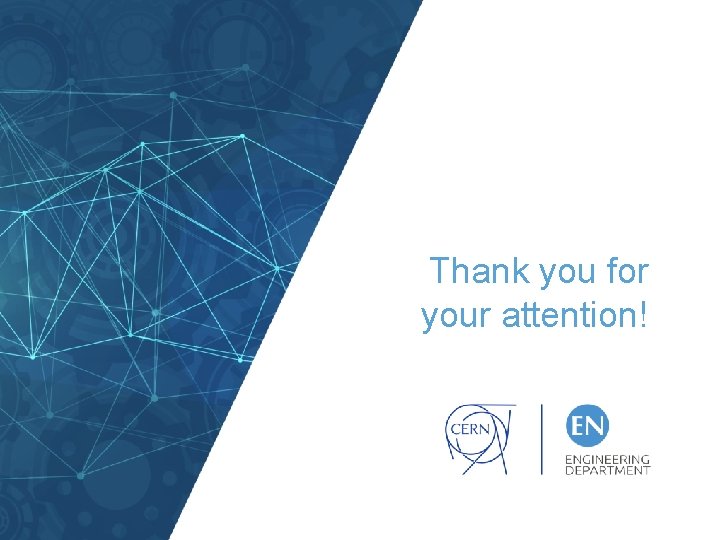
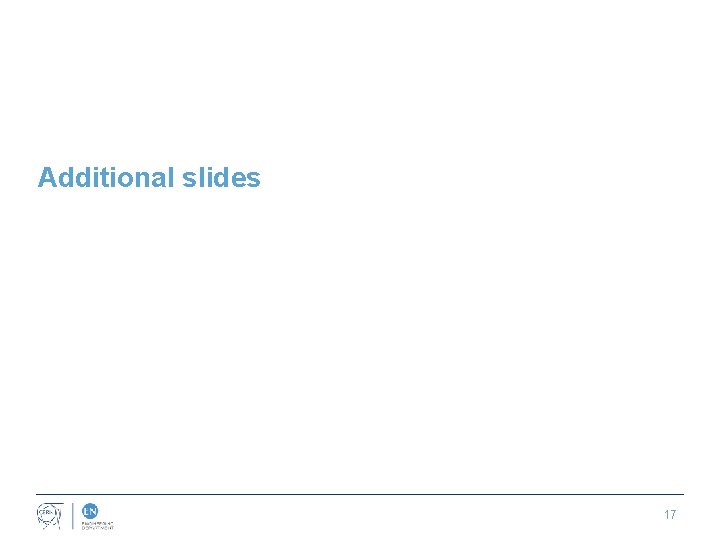
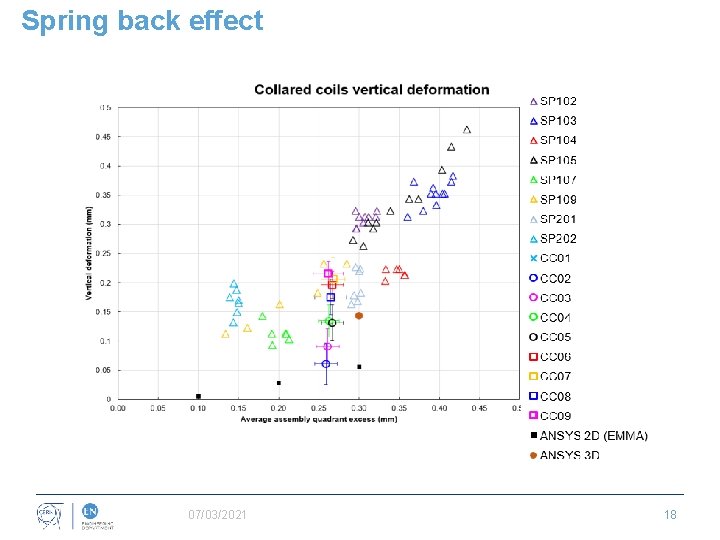
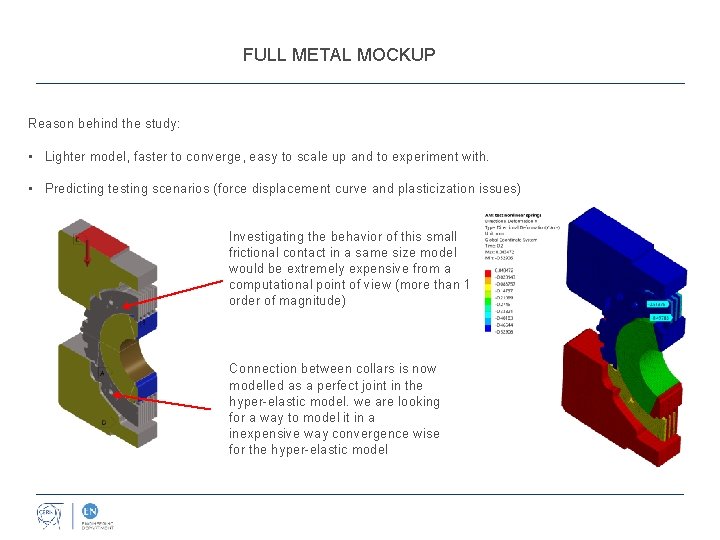
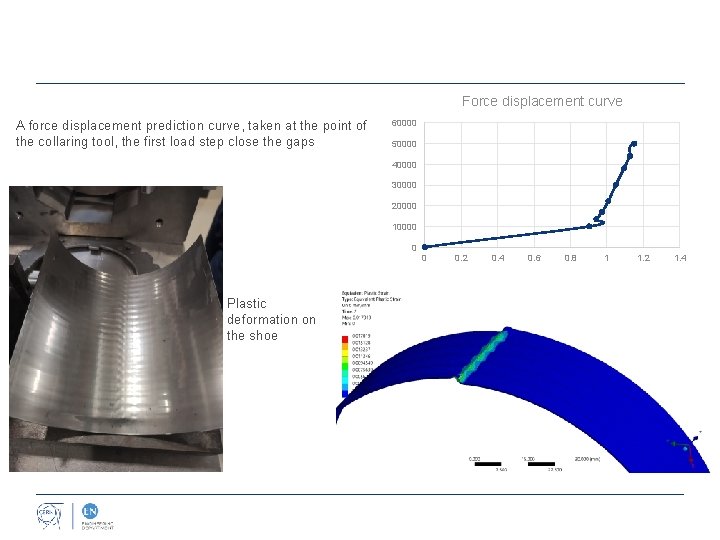
- Slides: 20
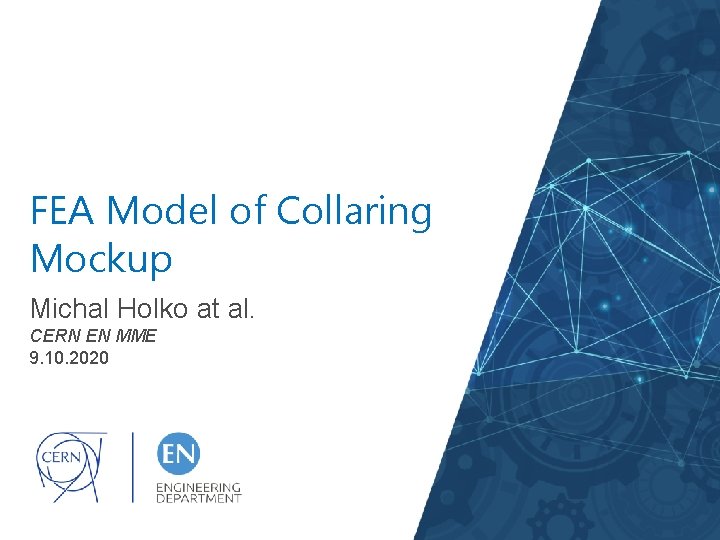
FEA Model of Collaring Mockup Michal Holko at al. CERN EN MME 9. 10. 2020
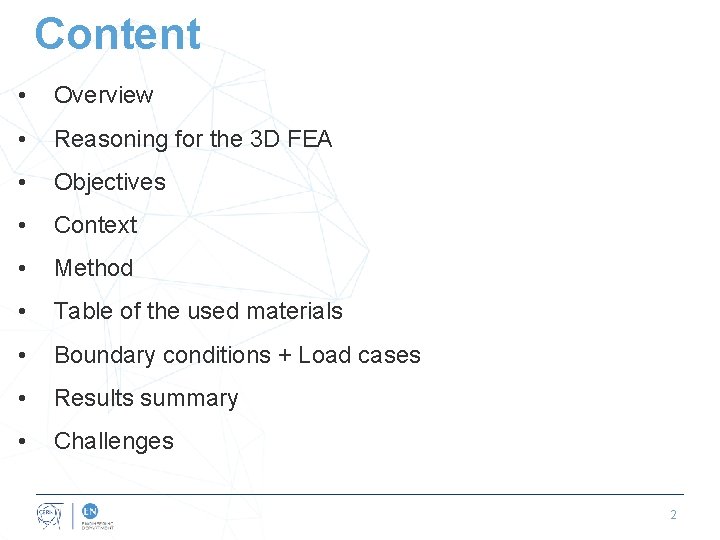
Content • Overview • Reasoning for the 3 D FEA • Objectives • Context • Method • Table of the used materials • Boundary conditions + Load cases • Results summary • Challenges 2
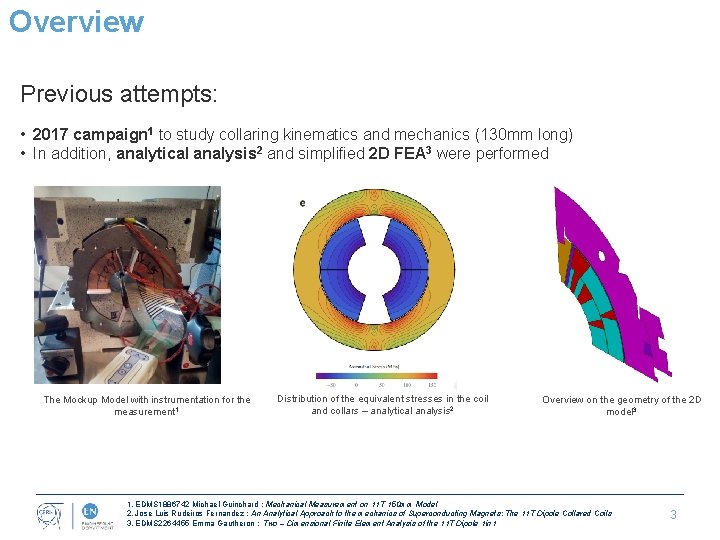
Overview Previous attempts: • 2017 campaign 1 to study collaring kinematics and mechanics (130 mm long) • In addition, analytical analysis 2 and simplified 2 D FEA 3 were performed The Mockup Model with instrumentation for the measurement 1 Distribution of the equivalent stresses in the coil and collars – analytical analysis 2 Overview on the geometry of the 2 D model 3 1, EDMS 1886742 Michael Guinchard : Mechanical Measurement on 11 T 150 mm Model 2, Jose Luis Rudeiros Fernandez : An Analytical Approach to the mechanics of Superconducting Magnets: The 11 T Dipole Collared Coils 3, EDMS 2264455 Emma Gautheron : Two – Dimensional Finite Element Analysis of the 11 T Dipole 1 in 1 3
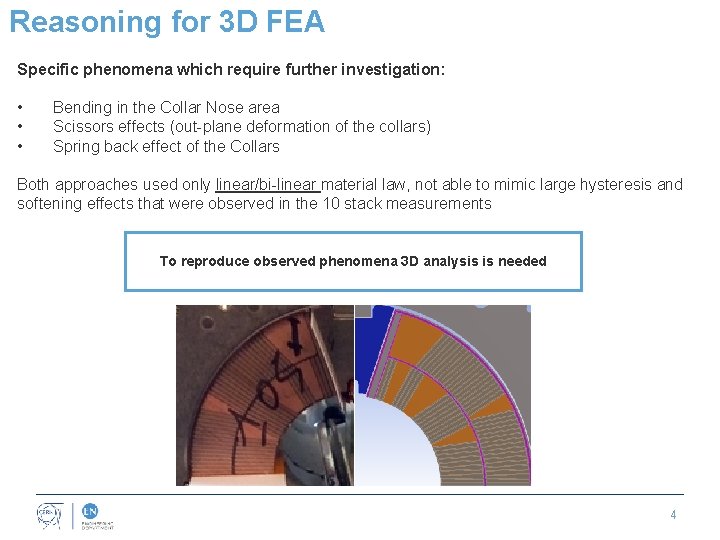
Reasoning for 3 D FEA Specific phenomena which require further investigation: • • • Bending in the Collar Nose area Scissors effects (out-plane deformation of the collars) Spring back effect of the Collars Both approaches used only linear/bi-linear material law, not able to mimic large hysteresis and softening effects that were observed in the 10 stack measurements To reproduce observed phenomena 3 D analysis is needed 4
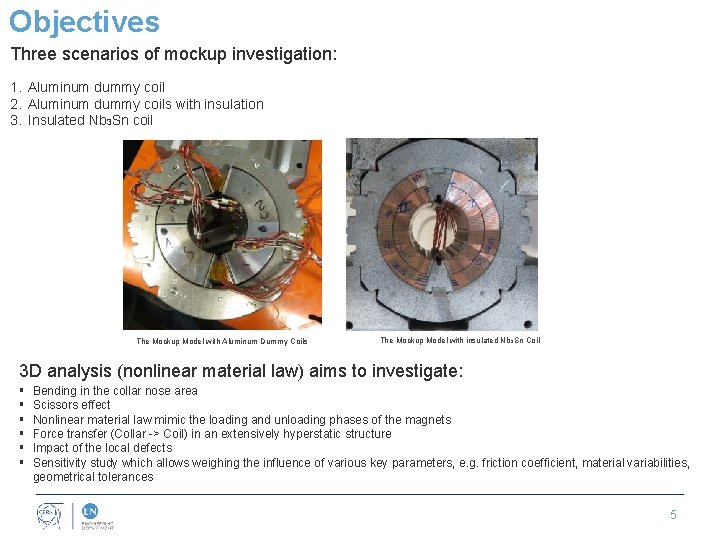
Objectives Three scenarios of mockup investigation: 1. Aluminum dummy coil 2. Aluminum dummy coils with insulation 3. Insulated Nb 3 Sn coil The Mockup Model with Aluminum Dummy Coils The Mockup Model with insulated Nb 3 Sn Coil 3 D analysis (nonlinear material law) aims to investigate: § § § Bending in the collar nose area Scissors effect Nonlinear material law mimic the loading and unloading phases of the magnets Force transfer (Collar -> Coil) in an extensively hyperstatic structure Impact of the local defects Sensitivity study which allows weighing the influence of various key parameters, e. g. friction coefficient, material variabilities, geometrical tolerances 5
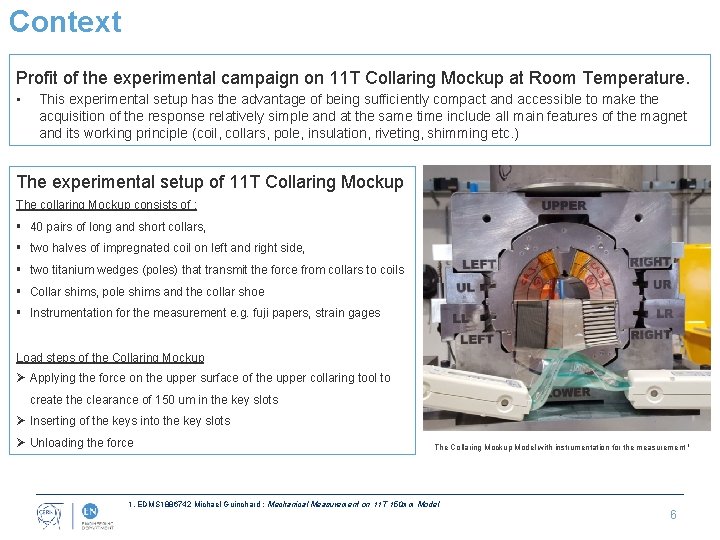
Context Profit of the experimental campaign on 11 T Collaring Mockup at Room Temperature. • This experimental setup has the advantage of being sufficiently compact and accessible to make the acquisition of the response relatively simple and at the same time include all main features of the magnet and its working principle (coil, collars, pole, insulation, riveting, shimming etc. ) The experimental setup of 11 T Collaring Mockup The collaring Mockup consists of : § 40 pairs of long and short collars, § two halves of impregnated coil on left and right side, § two titanium wedges (poles) that transmit the force from collars to coils § Collar shims, pole shims and the collar shoe § Instrumentation for the measurement e. g. fuji papers, strain gages Load steps of the Collaring Mockup Ø Applying the force on the upper surface of the upper collaring tool to create the clearance of 150 um in the key slots Ø Inserting of the keys into the key slots Ø Unloading the force The Collaring Mockup Model with instrumentation for the measurement 1 1, EDMS 1886742 Michael Guinchard : Mechanical Measurement on 11 T 150 mm Model 6
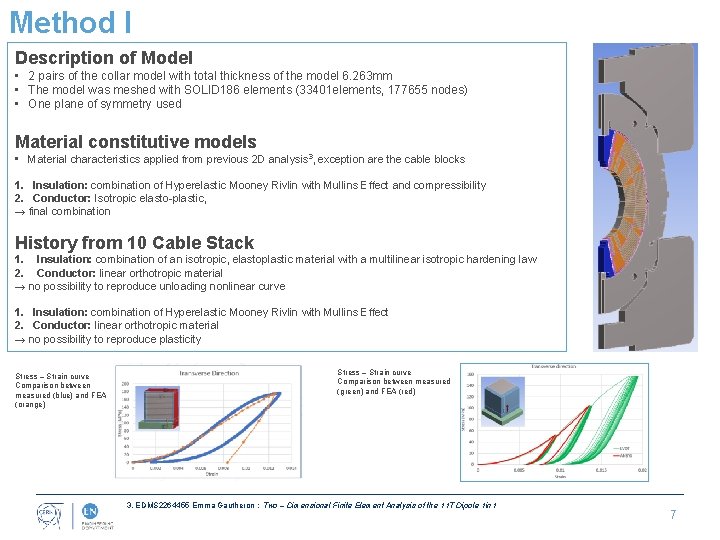
Method I Description of Model • 2 pairs of the collar model with total thickness of the model 6. 263 mm • The model was meshed with SOLID 186 elements (33401 elements, 177655 nodes) • One plane of symmetry used Material constitutive models • Material characteristics applied from previous 2 D analysis 3, exception are the cable blocks 1. Insulation: combination of Hyperelastic Mooney Rivlin with Mullins Effect and compressibility 2. Conductor: Isotropic elasto-plastic, → final combination History from 10 Cable Stack 1. Insulation: combination of an isotropic, elastoplastic material with a multilinear isotropic hardening law 2. Conductor: linear orthotropic material → no possibility to reproduce unloading nonlinear curve 1. Insulation: combination of Hyperelastic Mooney Rivlin with Mullins Effect 2. Conductor: linear orthotropic material → no possibility to reproduce plasticity Stress – Strain curve Comparison between measured (blue) and FEA (orange) Stress – Strain curve Comparison between measured (green) and FEA (red) 3, EDMS 2264455 Emma Gautheron : Two – Dimensional Finite Element Analysis of the 11 T Dipole 1 in 1 7
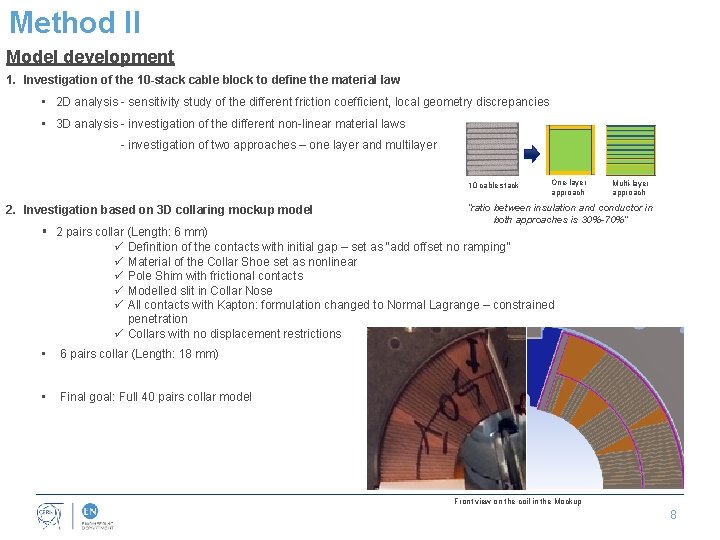
Method II Model development 1. Investigation of the 10 -stack cable block to define the material law • 2 D analysis - sensitivity study of the different friction coefficient, local geometry discrepancies • 3 D analysis - investigation of the different non-linear material laws - investigation of two approaches – one layer and multilayer 10 cable stack 2. Investigation based on 3 D collaring mockup model One-layer approach Multi-layer approach “ratio between insulation and conductor in both approaches is 30%-70%” § 2 pairs collar (Length: 6 mm) ü Definition of the contacts with initial gap – set as “add offset no ramping” ü Material of the Collar Shoe set as nonlinear ü Pole Shim with frictional contacts ü Modelled slit in Collar Nose ü All contacts with Kapton: formulation changed to Normal Lagrange – constrained penetration ü Collars with no displacement restrictions • 6 pairs collar (Length: 18 mm) • Final goal: Full 40 pairs collar model Front view on the coil in the Mockup 8
![Material Definition E GPa POISSON YIELD MPa TANGENT MPa PARAMETERS SOURCE 304 L 193 Material Definition E [GPa] POISSON YIELD [MPa] TANGENT [MPa] PARAMETERS SOURCE 304 L 193](https://slidetodoc.com/presentation_image_h/2b2597867473798f74f263d719b93fa7/image-9.jpg)
Material Definition E [GPa] POISSON YIELD [MPa] TANGENT [MPa] PARAMETERS SOURCE 304 L 193 0. 28 X X x 304 L Non-Linear 193 0. 28 250 1000 x From previous 2 D analysis of Emma Gautheron et al. 3 193 0. 28 415 1000 x COPPER 93 0. 3 x x x KAPTON 2. 5 0. 3 x x x TITANIUM 130 0. 3 x x x ~3. 5 ~0. 35 x x C 10=216. 9 MPa C 01=366. 4 MPa D 1=0. 000514 R=1. 05 M=1 MPa B=0. 3 70 0. 3 18000 x 304 L Non-Linear COLLARS INSULATION Hyperelastic Material Law (Mooney-Rivlin) +Mullins Effect + compressibility CONDUCTOR 304 L NON-LINEAR Collar Shim Pole Shim Collaring Tool Top Collaring Tool Bottom Loading Plate Keys, Collar Shoe 304 L NON-LINEAR COLLAR COPPER KAPTON TITANIUM Long Collars Short Collars Copper Wedges Inter Layer Outer Layer between Loading Plate and Shim Layer between Loading Plate and Coil Poles Assumption from the investigation of 10 stack INSULATION HYPERELASTIC + MULLINS EFFECT CONDUCTOR ISOTROPIC ELASTICITY Insulation Parts of Cable Blocks Conductor Part of Cable Blocks 3, EDMS 2264455 Emma Gautheron : Two – Dimensional Finite Element Analysis of the 11 T Dipole 1 in 1 9
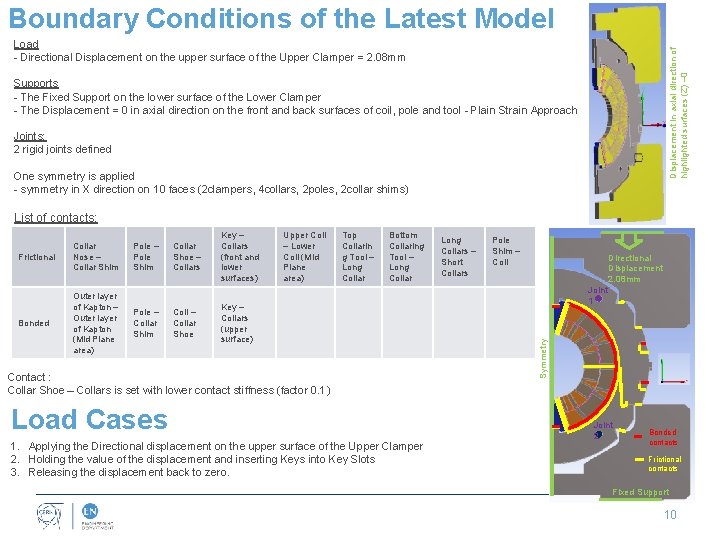
Boundary Conditions of the Latest Model Displacement in axial direction of highlighted surfaces (Z) =0 Load - Directional Displacement on the upper surface of the Upper Clamper = 2. 08 mm Supports - The Fixed Support on the lower surface of the Lower Clamper - The Displacement = 0 in axial direction on the front and back surfaces of coil, pole and tool - Plain Strain Approach Joints: 2 rigid joints defined One symmetry is applied - symmetry in X direction on 10 faces (2 clampers, 4 collars, 2 poles, 2 collar shims) List of contacts: Bonded Outer layer of Kapton – Outer layer of Kapton (Mid Plane area) Pole – Pole Shim Pole – Collar Shim Collar Shoe – Collars Coil – Collar Shoe Key – Collars (front and lower surfaces) Upper Coil – Lower Coil (Mid Plane area) Top Collarin g Tool – Long Collar Bottom Collaring Tool – Long Collar Key – Collars (upper surface) Contact : Collar Shoe – Collars is set with lower contact stiffness (factor 0. 1) Load Cases 1. Applying the Directional displacement on the upper surface of the Upper Clamper 2. Holding the value of the displacement and inserting Keys into Key Slots 3. Releasing the displacement back to zero. Long Collars – Short Collars Pole Shim – Coil Directional Displacement 2. 08 mm Joint 1 Symmetry Frictional Collar Nose – Collar Shim Joint 2 Bonded contacts Frictional contacts Fixed Support 10
![Results Summary Load Case Max Loading Force 6 263 mm N Max Loading Force Results Summary Load Case Max Loading Force (6. 263 mm) [N] Max Loading Force](https://slidetodoc.com/presentation_image_h/2b2597867473798f74f263d719b93fa7/image-11.jpg)
Results Summary Load Case Max Loading Force (6. 263 mm) [N] Max Loading Force (130 mm) [k. N] Collar Nose Normal Stress [MPa] Pole Normal Stress (max) [MPa] Pole Equivalent Stress (max) [MPa] Mid Plane Avg. Normal Stress in Insulation [MPa] Mid Plane Avg. Normal Stress in Conductor [MPa] 1 st Load Case 10878 451 230 60 144 49 52. 8 3 rd Load Case - - 155 49. 8 123 33. 1 35. 5 Vertical deformation of the Collars after unloading : 0. 143 mm Horizontal deformation of the Collars after unloading : 0. 037 mm Measured data (max. values): Loading Force : 447 k. N Stress on Collar Nose (1 st LC): 134 MPa Stress on Collar Nose (2 nd LC): 82 MPa Stress on Pole (1 st LC): 75 MPa Stress on Pole (2 nd LC): 50 MPa Stress in midplane : 144 MPa 11
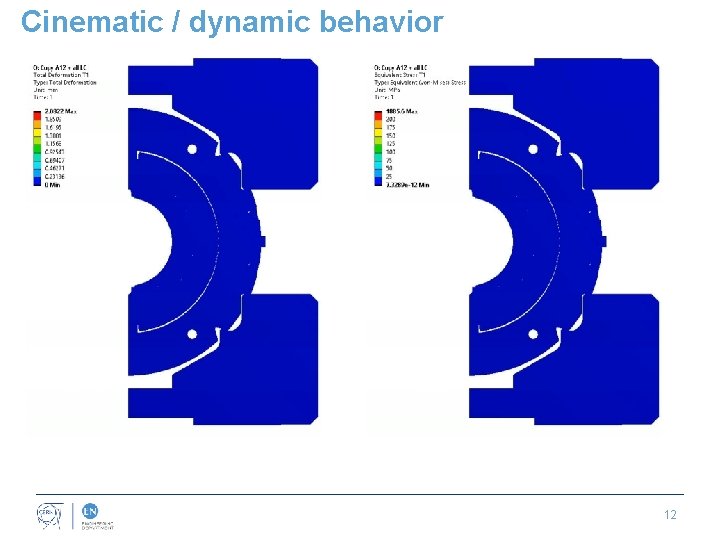
Cinematic / dynamic behavior 12
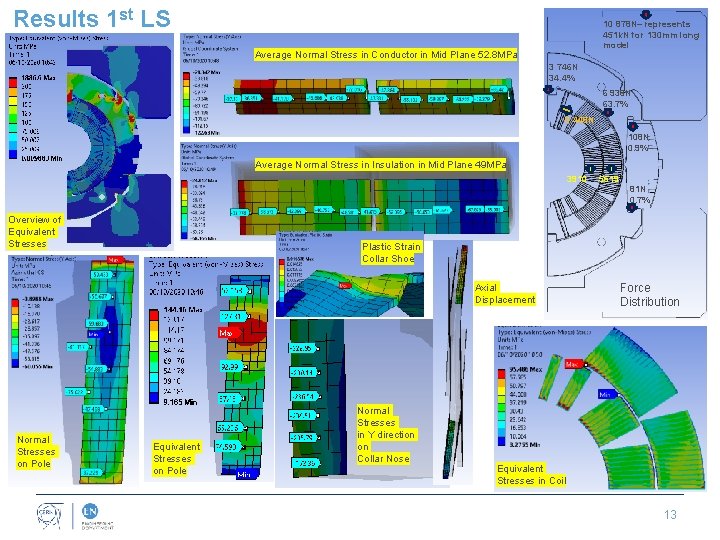
Results 1 st LS 10 878 N– represents 451 k. N for 130 mm long model Average Normal Stress in Conductor in Mid Plane 52. 8 MPa 3 746 N 34. 4% 6 938 N 63. 7% 8 448 N 108 N 0. 9% Average Normal Stress in Insulation in Mid Plane 49 MPa 3910 5519 81 N 0. 7% Overview of Equivalent Stresses Plastic Strain Collar Shoe Axial Displacement Normal Stresses on Pole Equivalent Stresses on Pole Normal Stresses in Y direction on Collar Nose Force Distribution Equivalent Stresses in Coil 13
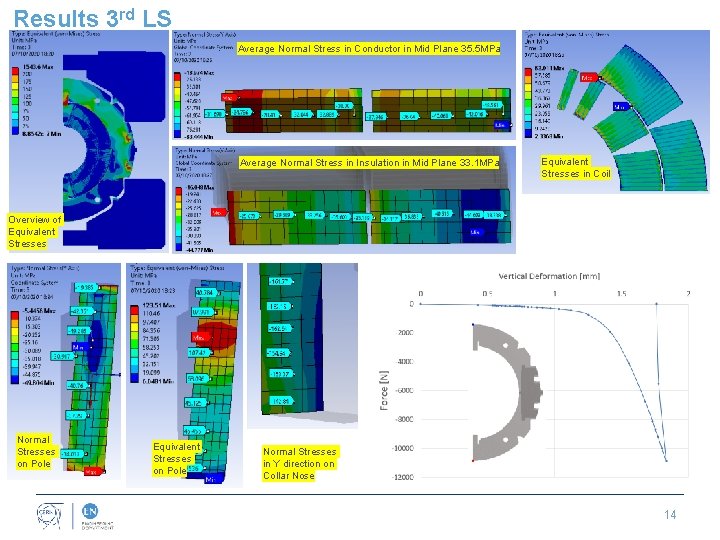
Results 3 rd LS Average Normal Stress in Conductor in Mid Plane 35. 5 MPa Average Normal Stress in Insulation in Mid Plane 33. 1 MPa Equivalent Stresses in Coil Overview of Equivalent Stresses Normal Stresses on Pole Equivalent Stresses on Pole Normal Stresses in Y direction on Collar Nose 14
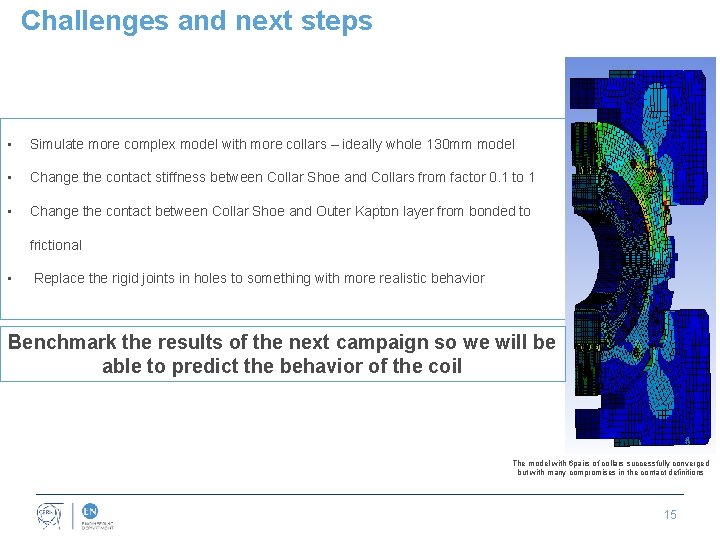
Challenges and next steps • Simulate more complex model with more collars – ideally whole 130 mm model • Change the contact stiffness between Collar Shoe and Collars from factor 0. 1 to 1 • Change the contact between Collar Shoe and Outer Kapton layer from bonded to frictional • Replace the rigid joints in holes to something with more realistic behavior Benchmark the results of the next campaign so we will be able to predict the behavior of the coil The model with 6 pairs of collars successfully converged but with many compromises in the contact definitions 15
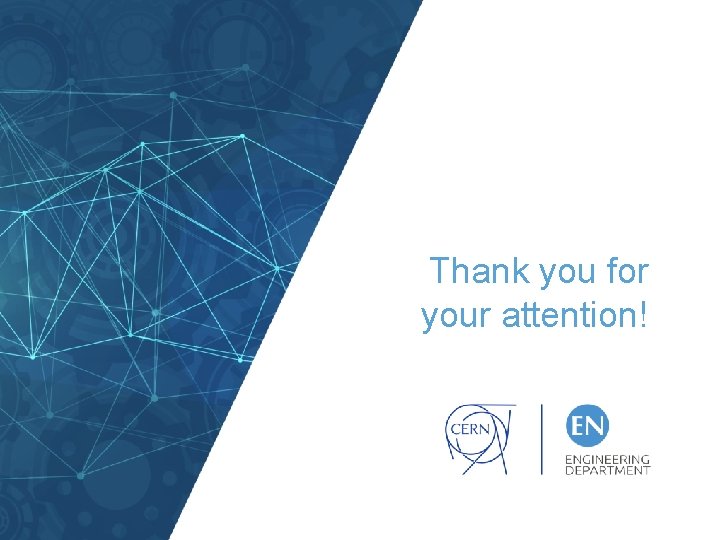
Thank you for your attention!
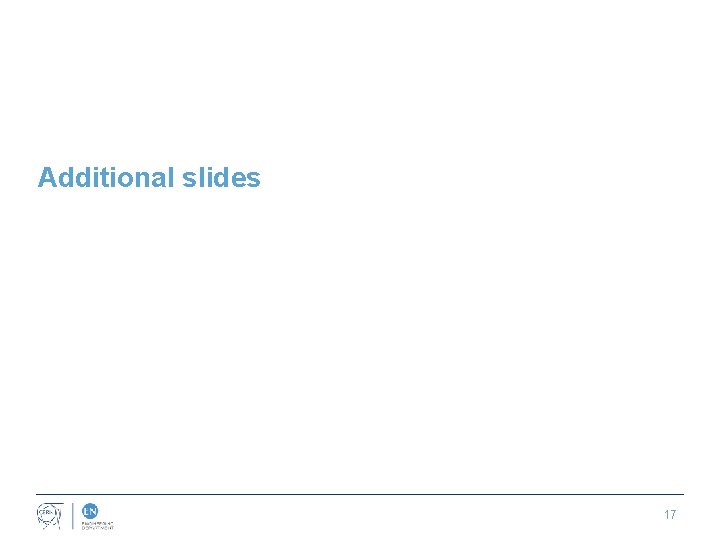
Additional slides 17
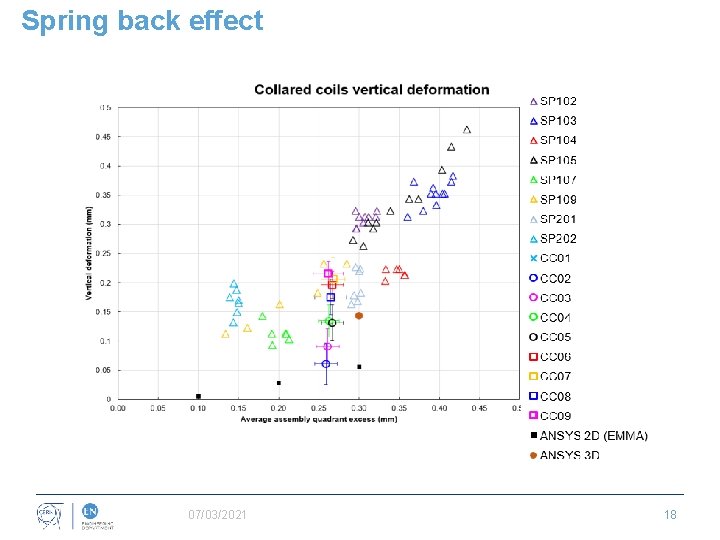
Spring back effect 07/03/2021 18
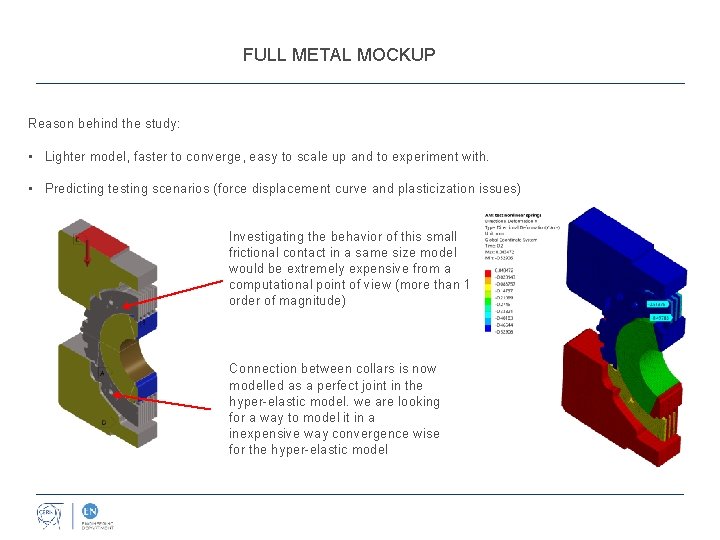
FULL METAL MOCKUP Reason behind the study: • Lighter model, faster to converge, easy to scale up and to experiment with. • Predicting testing scenarios (force displacement curve and plasticization issues) Investigating the behavior of this small frictional contact in a same size model would be extremely expensive from a computational point of view (more than 1 order of magnitude) Connection between collars is now modelled as a perfect joint in the hyper-elastic model. we are looking for a way to model it in a inexpensive way convergence wise for the hyper-elastic model
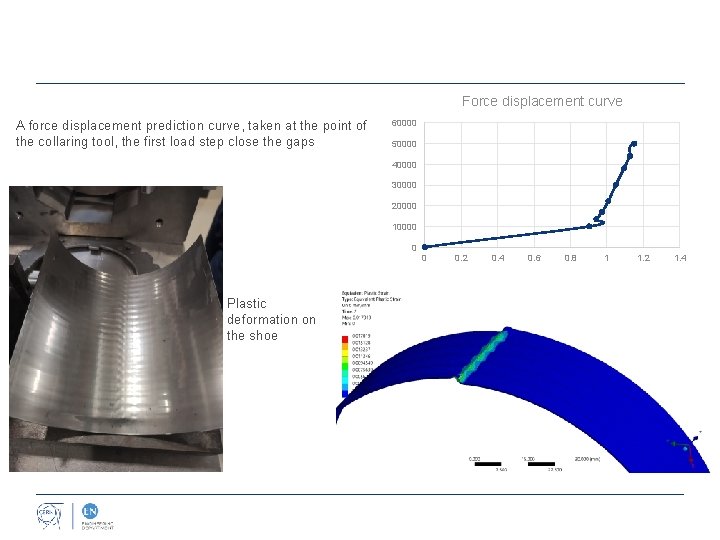
Force displacement curve A force displacement prediction curve, taken at the point of the collaring tool, the first load step close the gaps 60000 50000 40000 30000 20000 10000 0 0 Plastic deformation on the shoe 0. 2 0. 4 0. 6 0. 8 1 1. 2 1. 4
Holko logistic
Peter holko
Functional mock-up interface
Mockup login page
Address mockup
Tahapan membangun menu sistem dan skema navigasi
Prinsip mockup
Pivot diagram visio
Mockup assembly
Segregator mockup
Preguntas del poema la higuera
What is fea
Fea enterprise architecture
La ratona fea y la coneja bonita
Maya fea
Alva myrda
Fea
Internal design review
Introduction to fem
Difference between fea and fem
Fpix