Extrusion Injection Moulding Resin Transfer Moulding John Summerscales
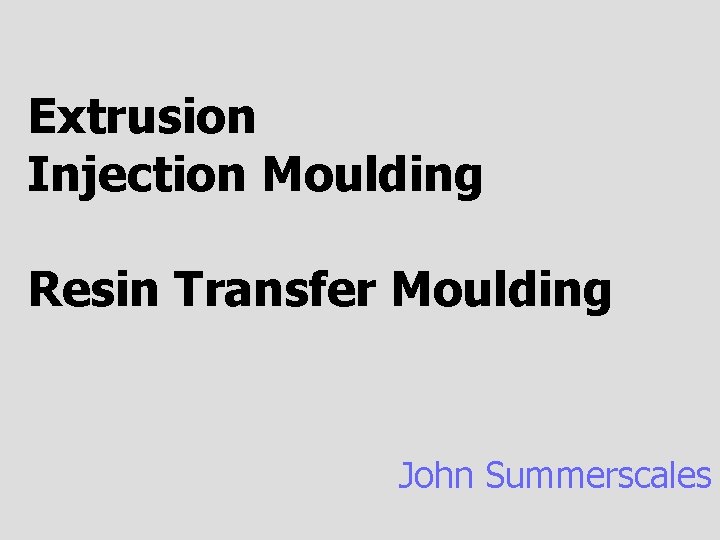
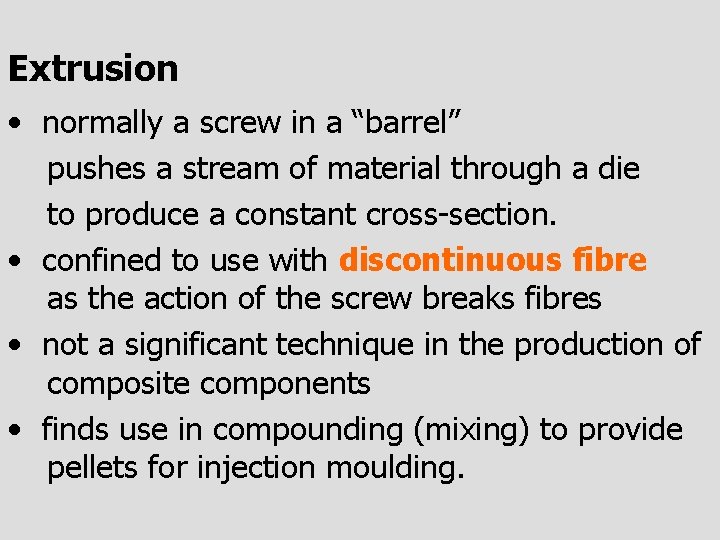
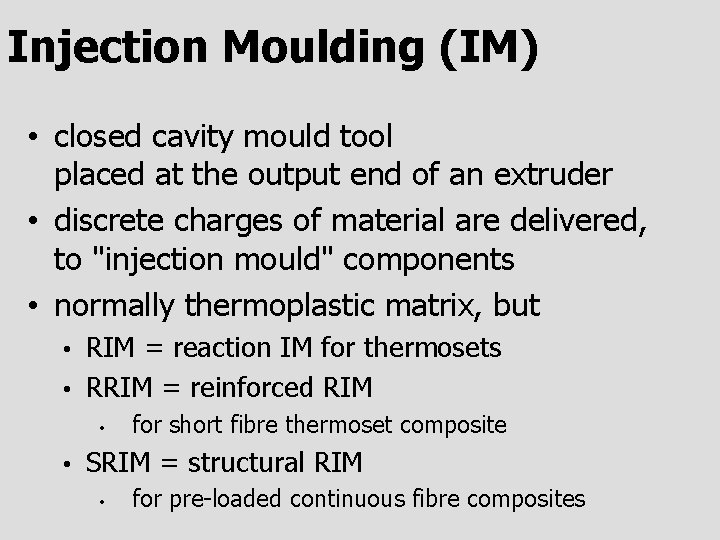
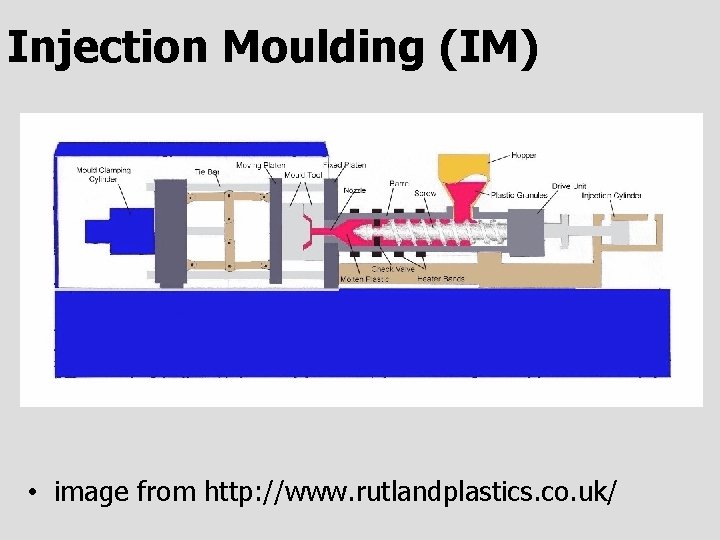
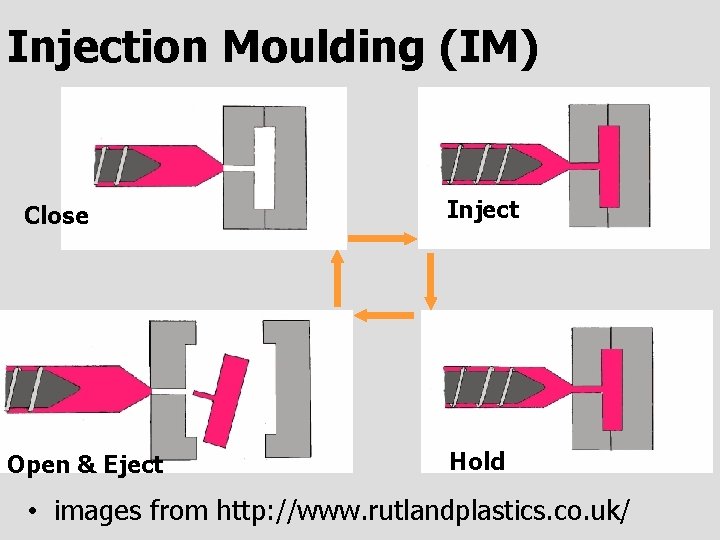
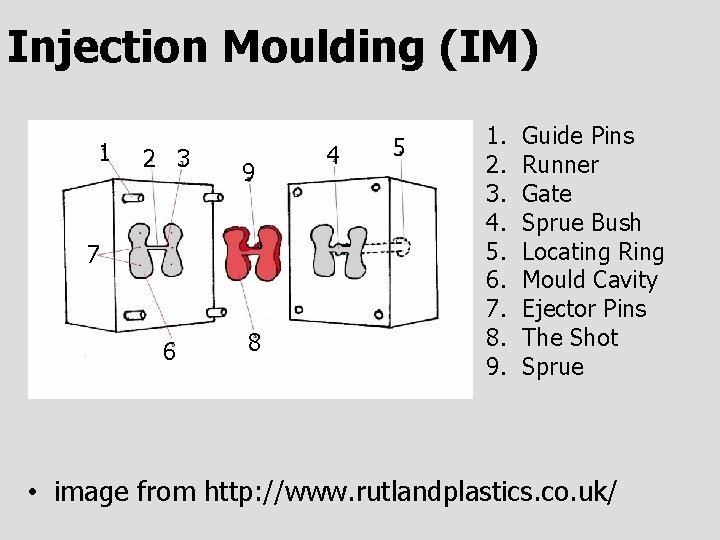
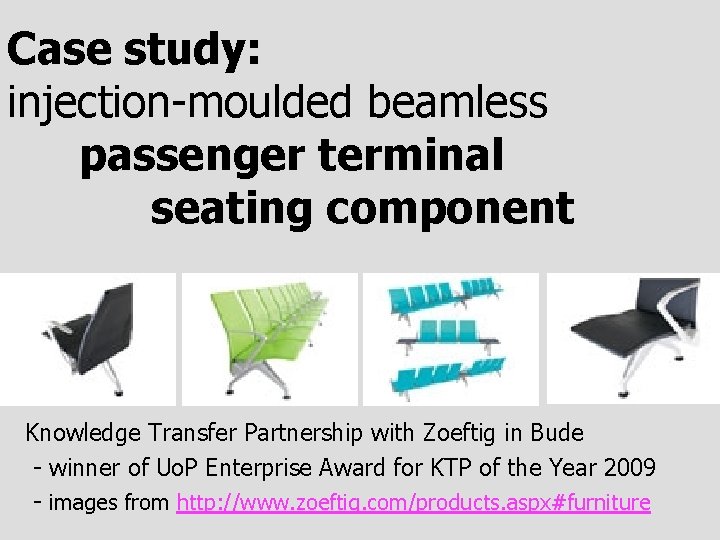
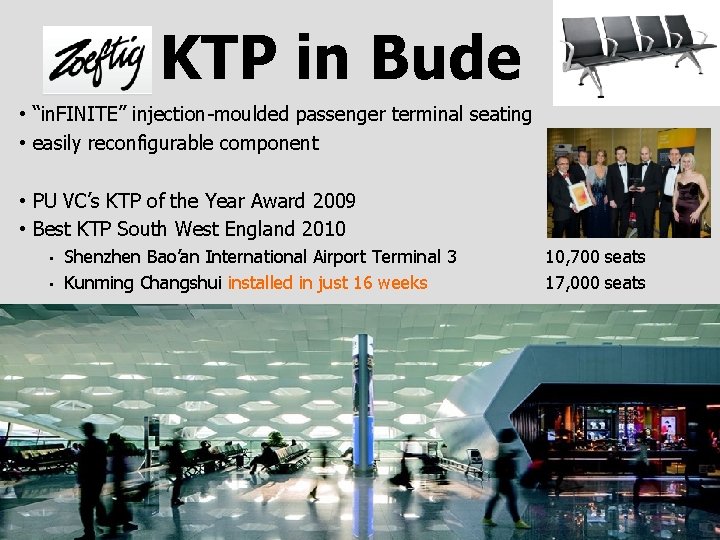

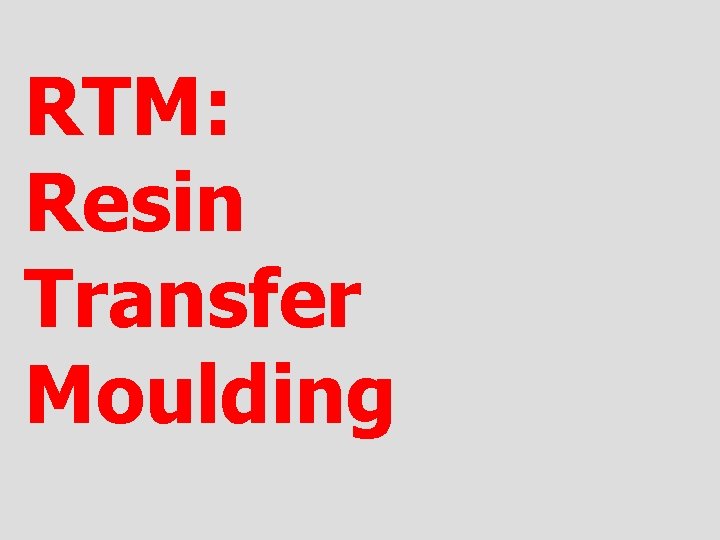
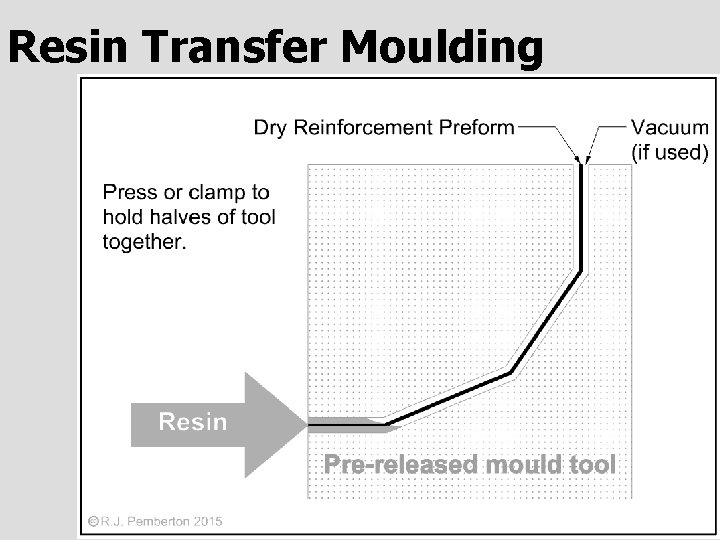
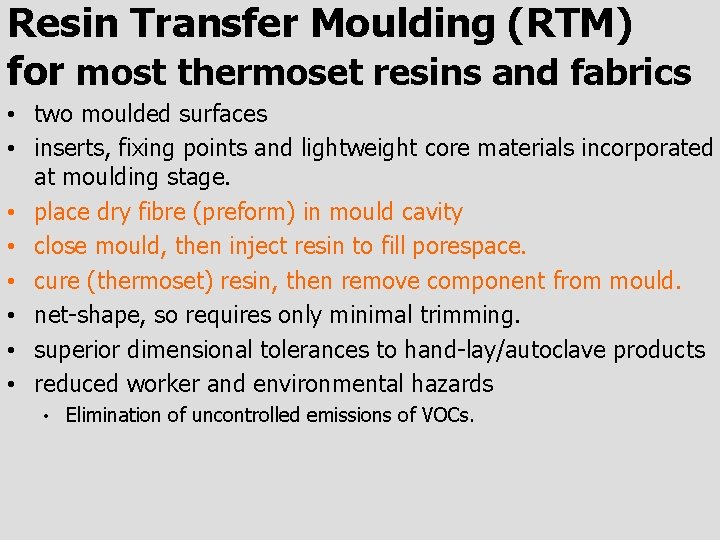
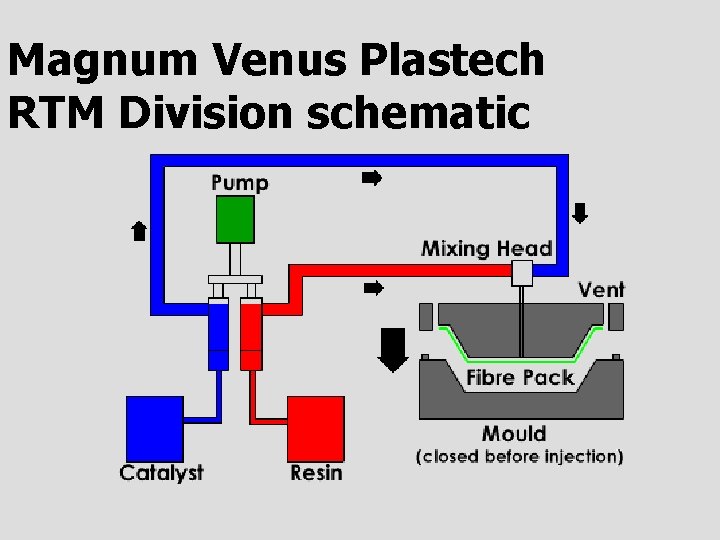
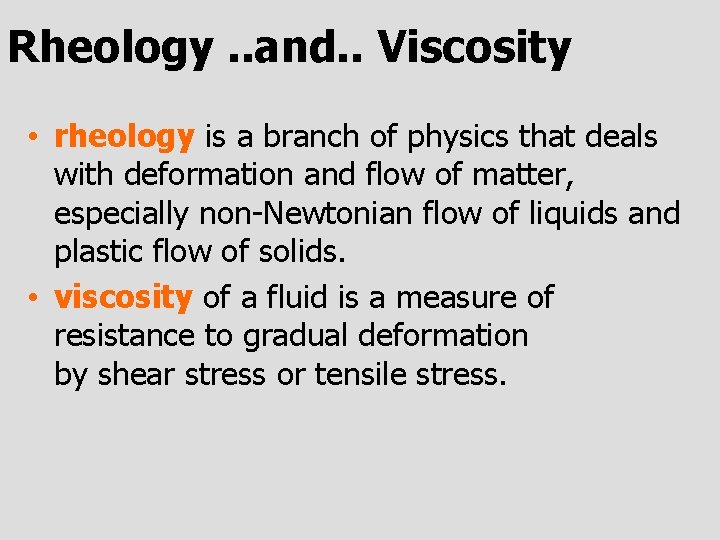
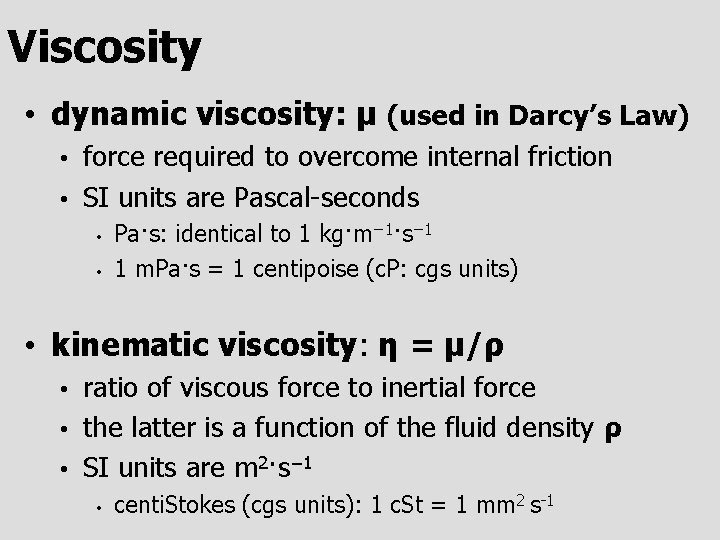
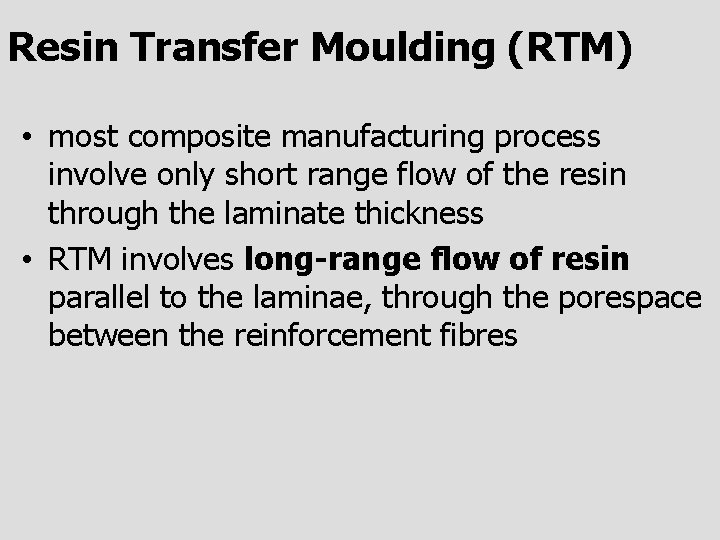
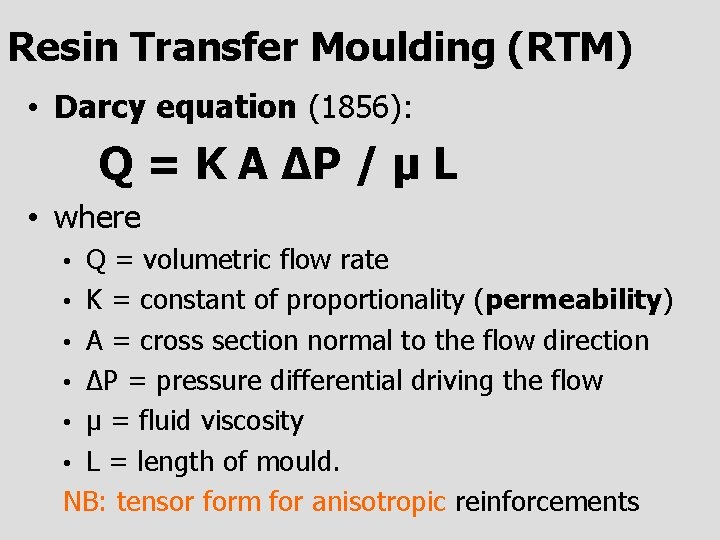
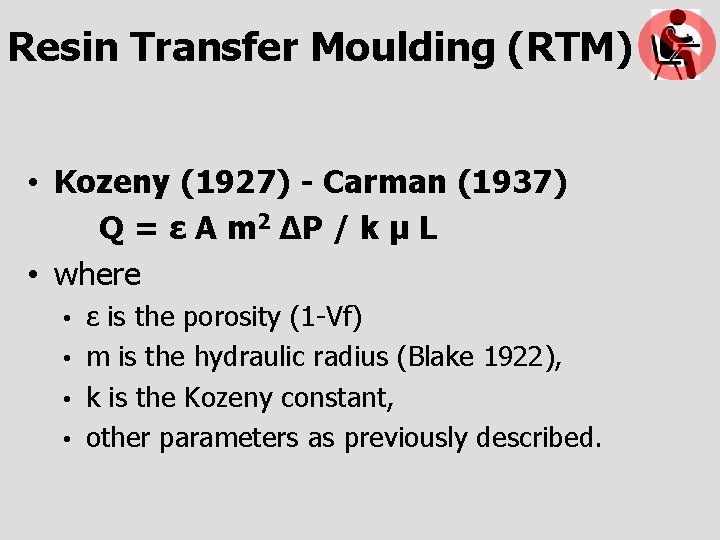
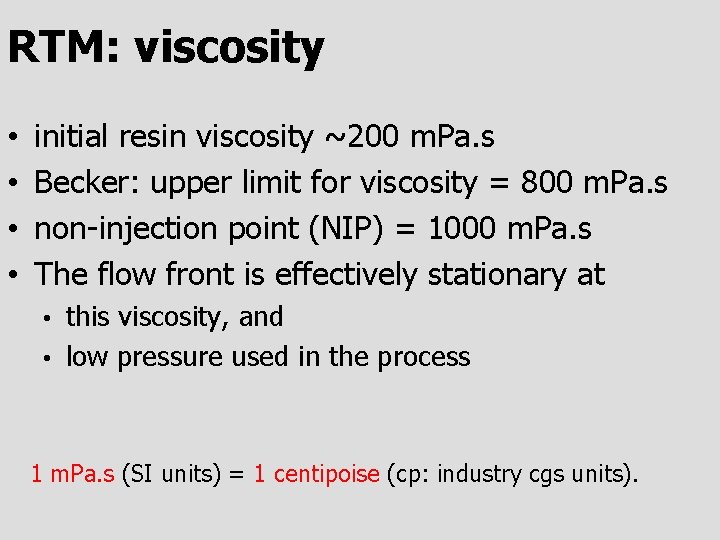
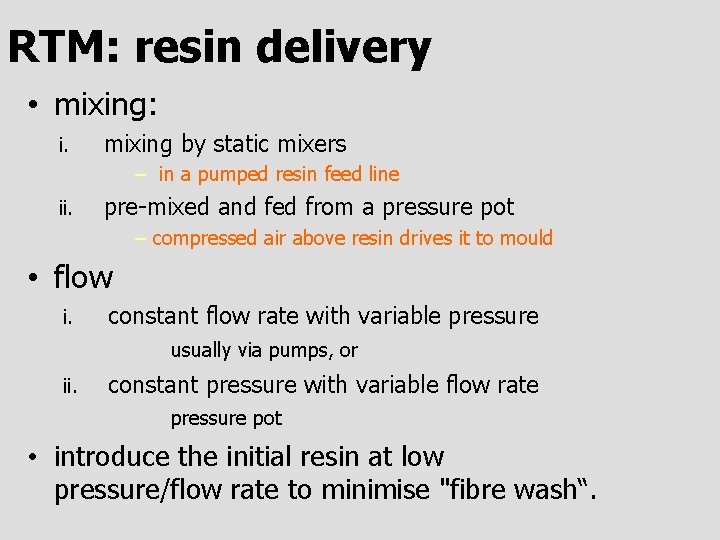
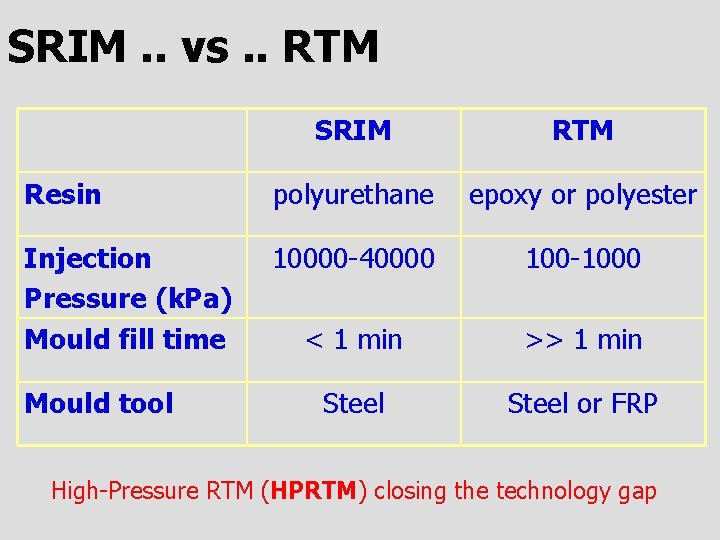
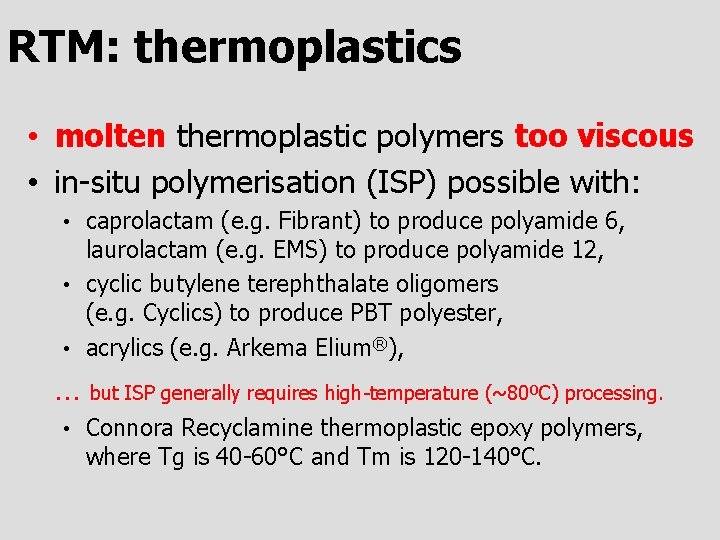
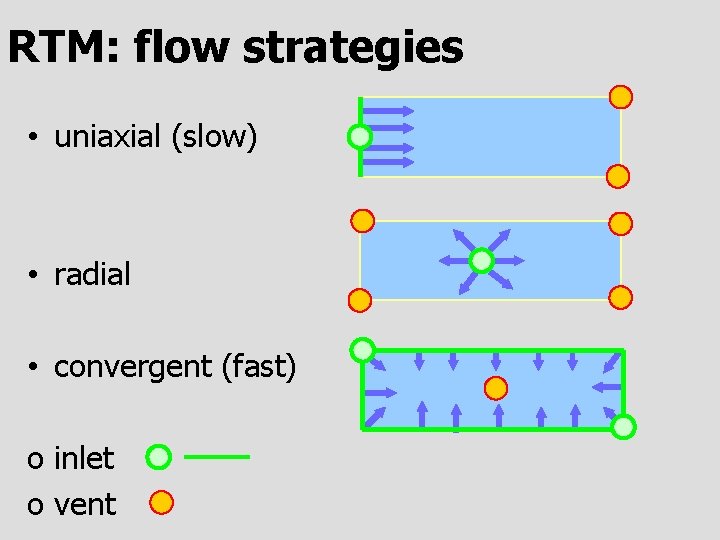

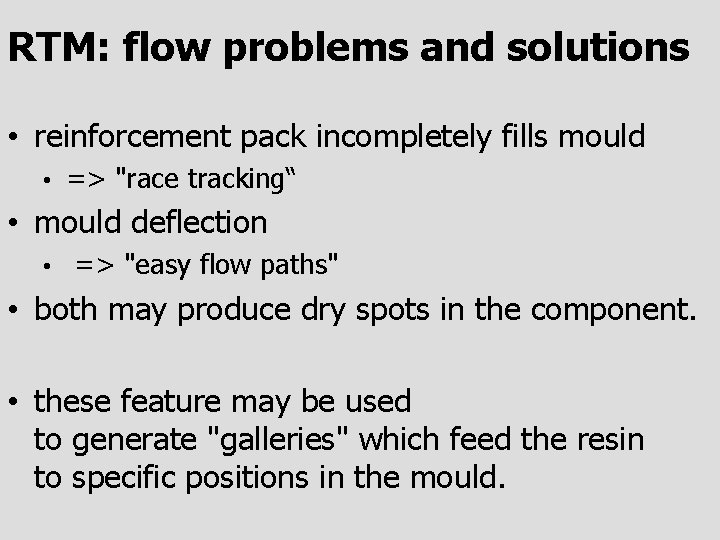
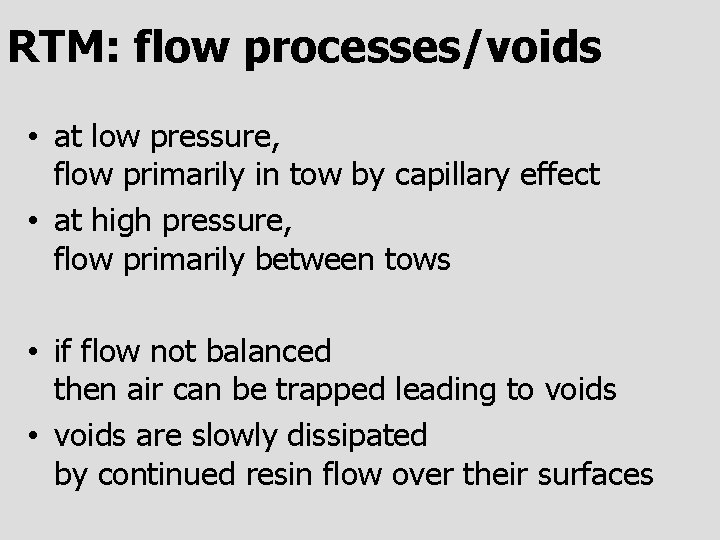
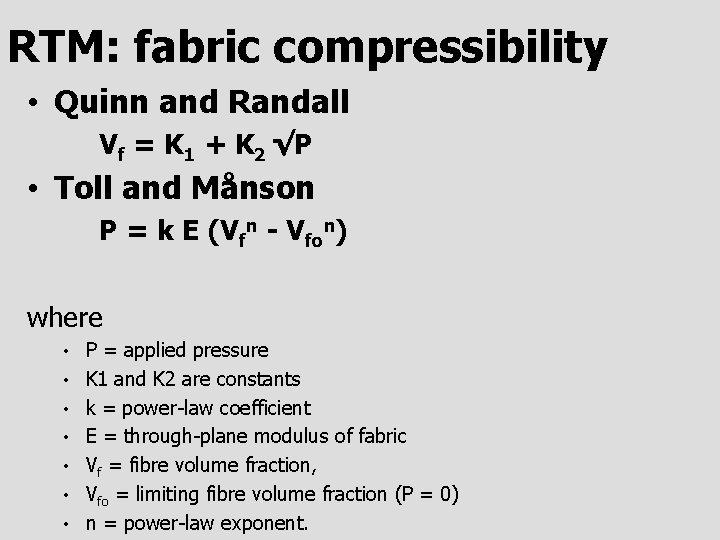
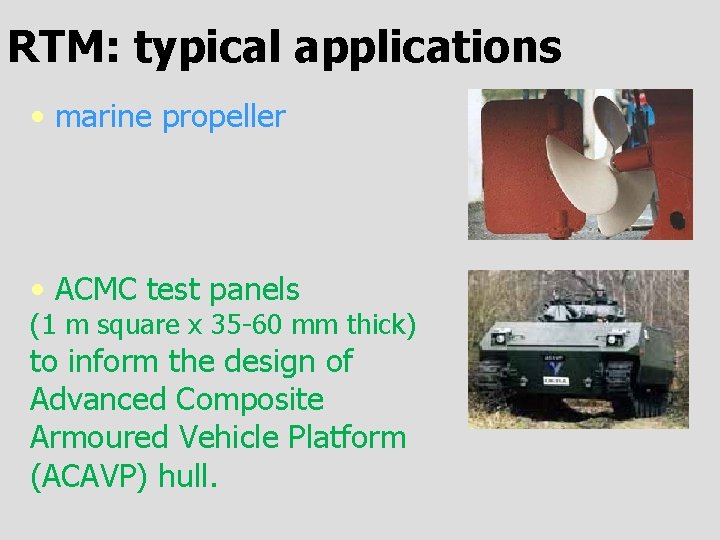
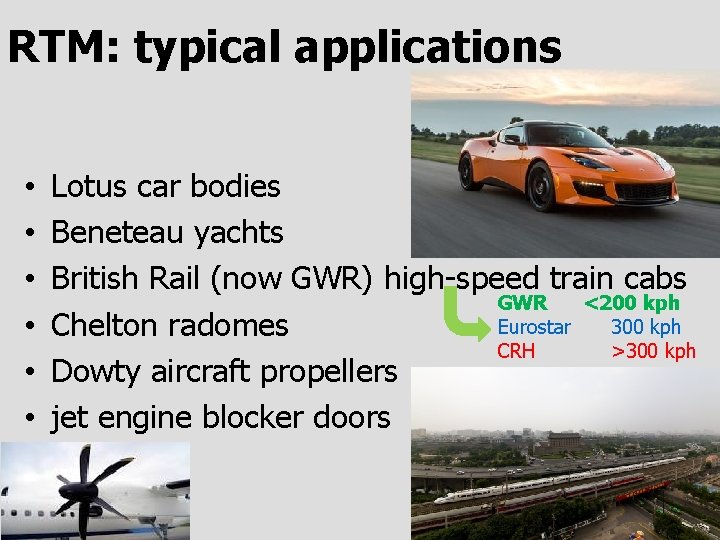
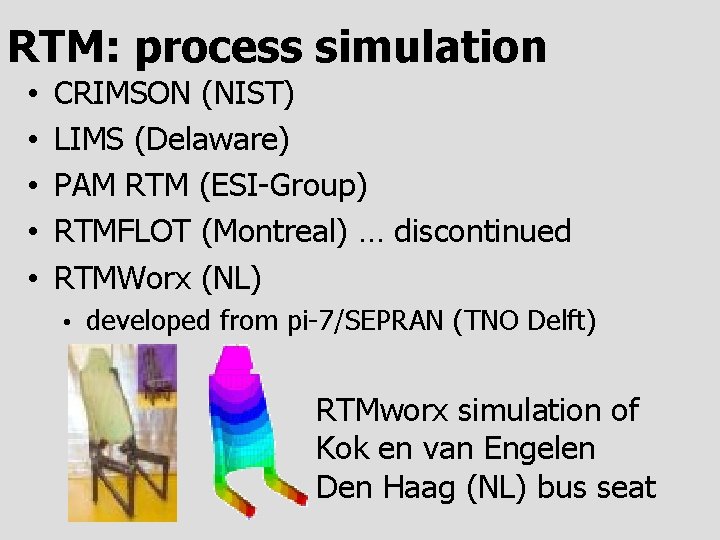
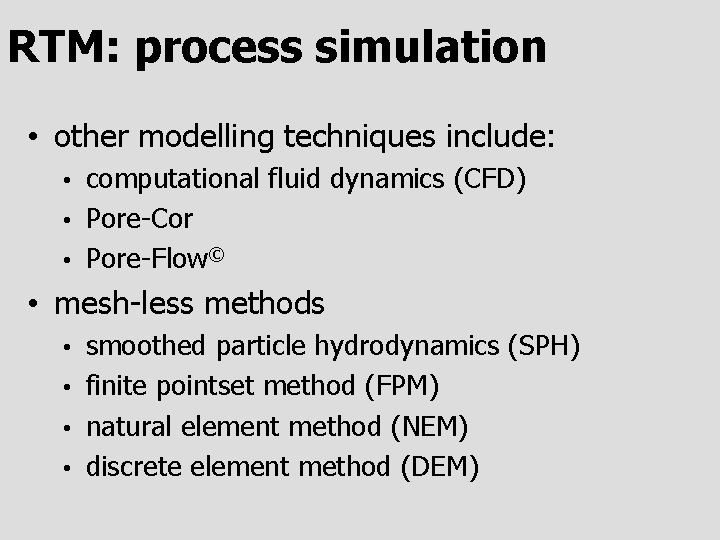
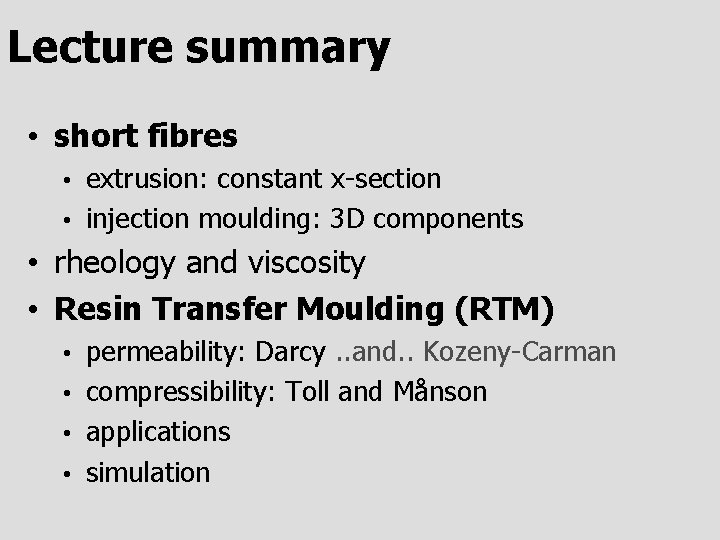
- Slides: 32
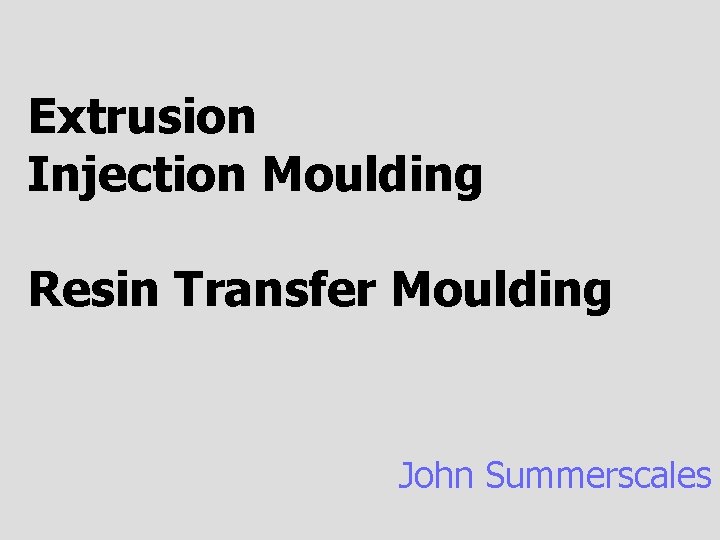
Extrusion Injection Moulding Resin Transfer Moulding John Summerscales
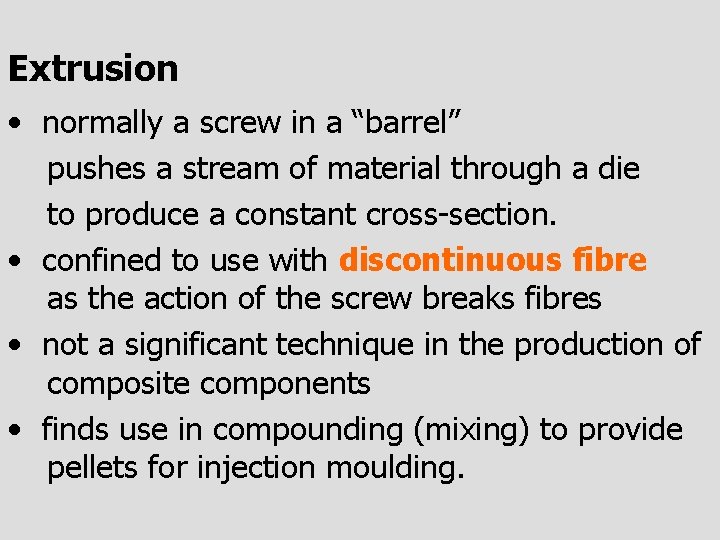
Extrusion • normally a screw in a “barrel” pushes a stream of material through a die to produce a constant cross-section. • confined to use with discontinuous fibre as the action of the screw breaks fibres • not a significant technique in the production of composite components • finds use in compounding (mixing) to provide pellets for injection moulding.
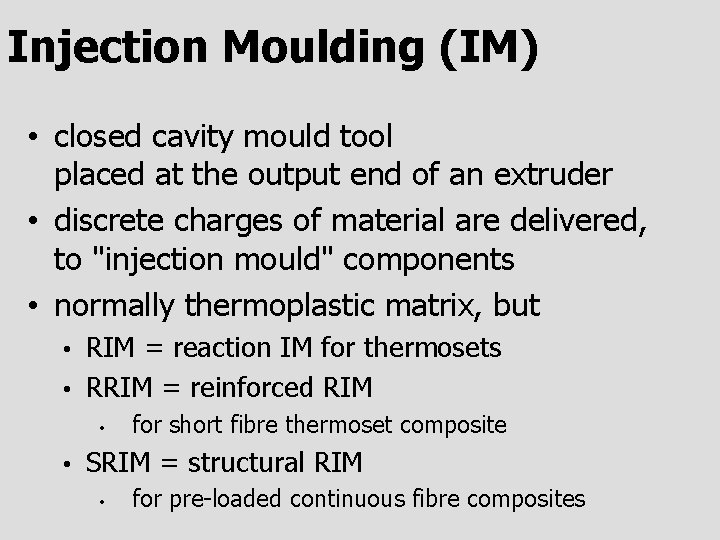
Injection Moulding (IM) • closed cavity mould tool placed at the output end of an extruder • discrete charges of material are delivered, to "injection mould" components • normally thermoplastic matrix, but RIM = reaction IM for thermosets • RRIM = reinforced RIM • • • for short fibre thermoset composite SRIM = structural RIM • for pre-loaded continuous fibre composites
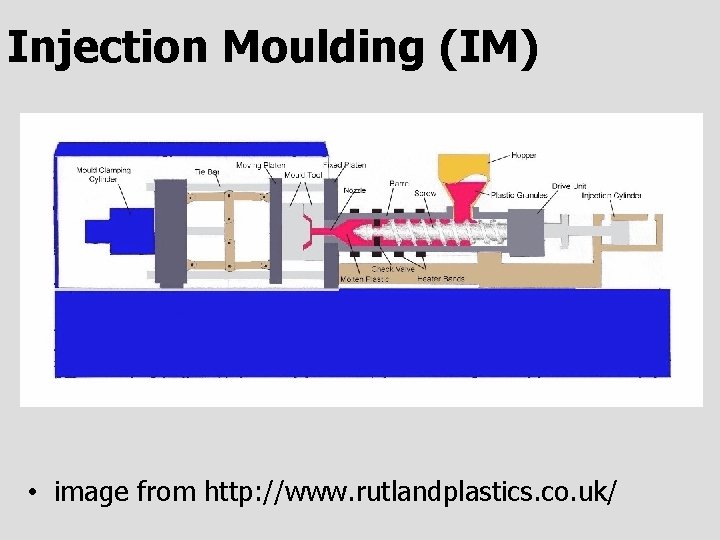
Injection Moulding (IM) • image from http: //www. rutlandplastics. co. uk/
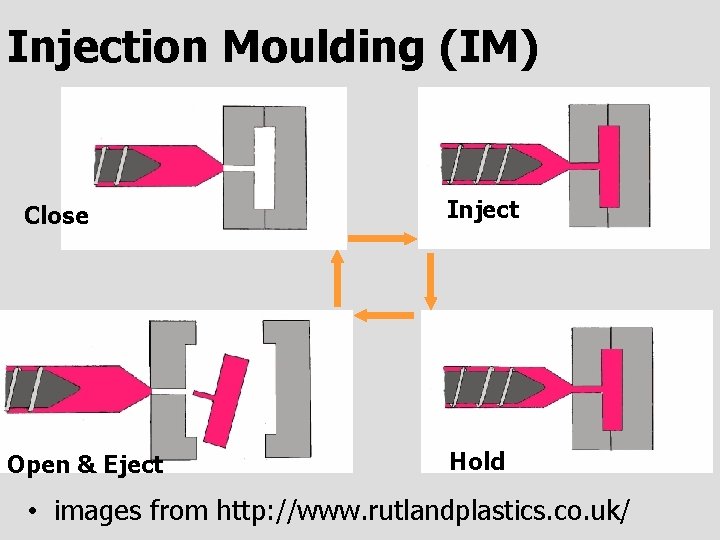
Injection Moulding (IM) Close Open & Eject Inject Hold • images from http: //www. rutlandplastics. co. uk/
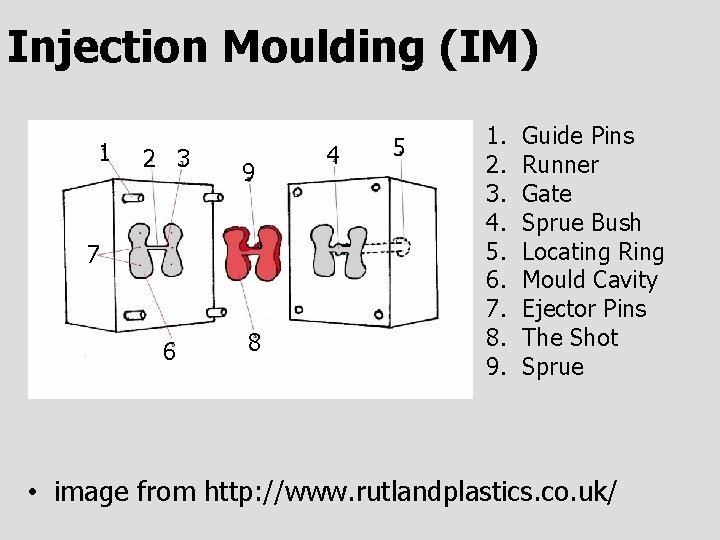
Injection Moulding (IM) 1 2 3 9 7 6 8 4 5 1. 2. 3. 4. 5. 6. 7. 8. 9. Guide Pins Runner Gate Sprue Bush Locating Ring Mould Cavity Ejector Pins The Shot Sprue • image from http: //www. rutlandplastics. co. uk/
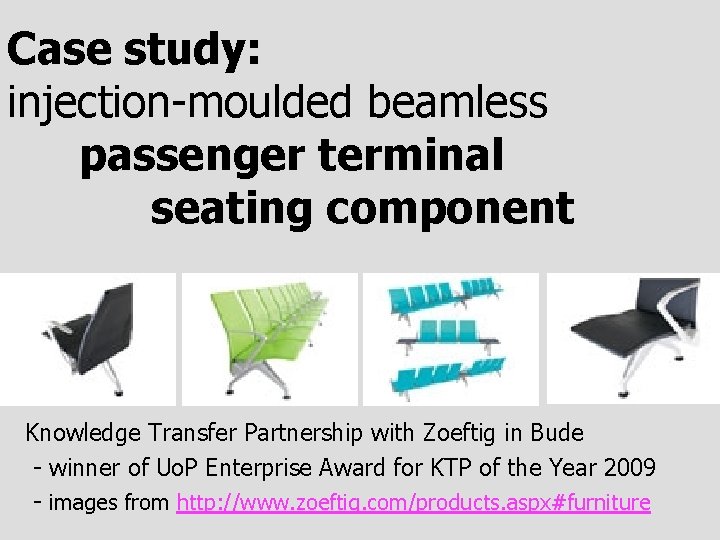
Case study: injection-moulded beamless passenger terminal seating component Knowledge Transfer Partnership with Zoeftig in Bude - winner of Uo. P Enterprise Award for KTP of the Year 2009 - images from http: //www. zoeftig. com/products. aspx#furniture
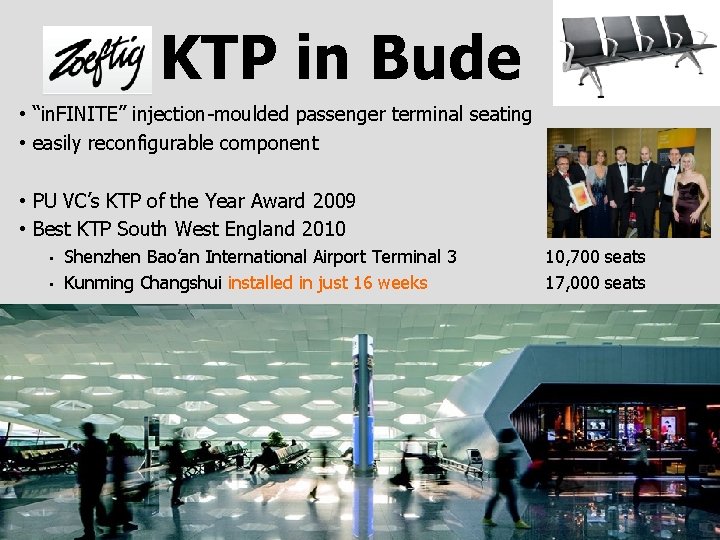
KTP in Bude • “in. FINITE” injection-moulded passenger terminal seating • easily reconfigurable component • PU VC’s KTP of the Year Award 2009 • Best KTP South West England 2010 • • Shenzhen Bao’an International Airport Terminal 3 Kunming Changshui installed in just 16 weeks 10, 700 seats 17, 000 seats

Shear controlled technologies • Wolfson Centre for Materials Processing developed Shear Controlled Technologies to improve orientation in short fibre composites SCOREX: shear controlled orientation in extrusion • SCORIM: s’c’o’ in injection moulding • Images from http: //www. brunel. ac. uk/about/acad/wolfson/cmp/technology • << SCOREX • SCORIM >>
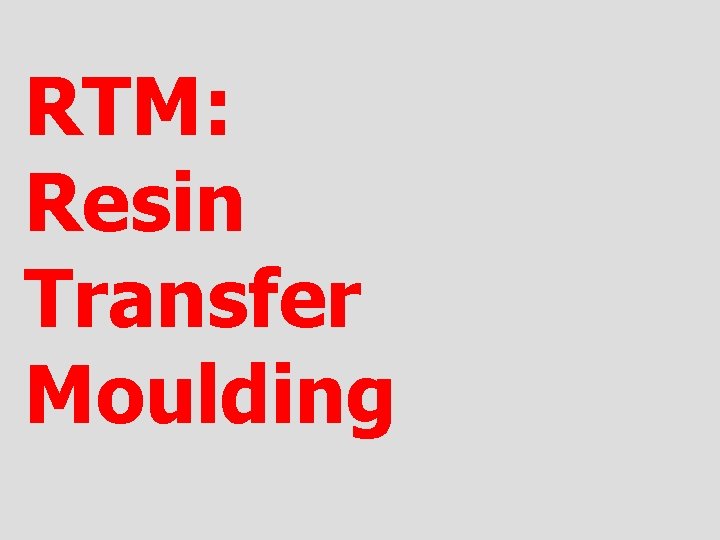
RTM: Resin Transfer Moulding
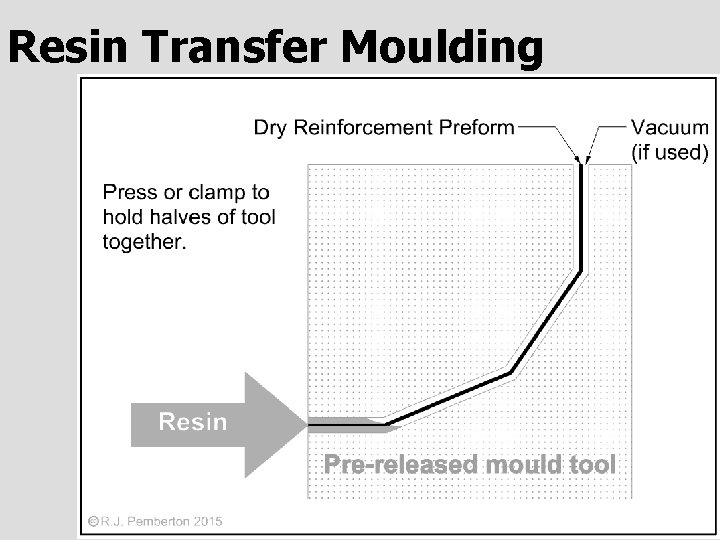
Resin Transfer Moulding
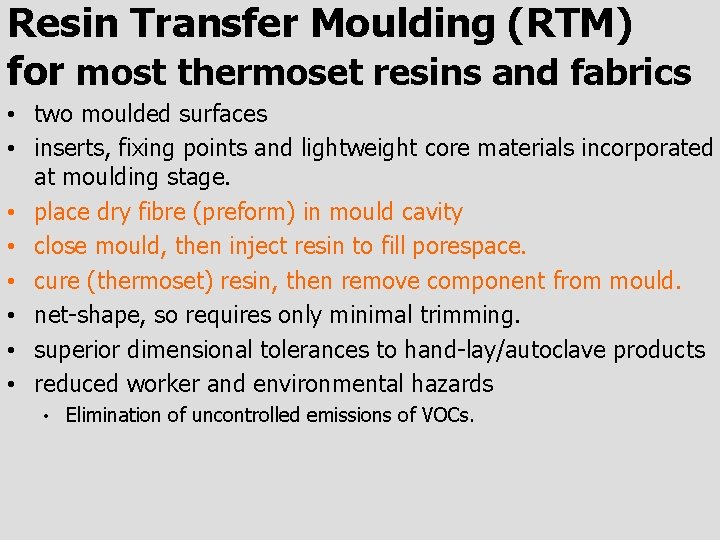
Resin Transfer Moulding (RTM) for most thermoset resins and fabrics • two moulded surfaces • inserts, fixing points and lightweight core materials incorporated at moulding stage. • place dry fibre (preform) in mould cavity • close mould, then inject resin to fill porespace. • cure (thermoset) resin, then remove component from mould. • net-shape, so requires only minimal trimming. • superior dimensional tolerances to hand-lay/autoclave products • reduced worker and environmental hazards • Elimination of uncontrolled emissions of VOCs.
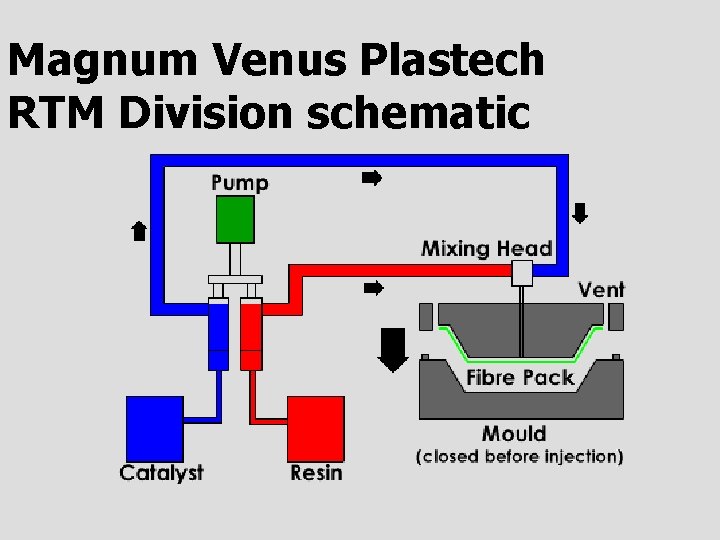
Magnum Venus Plastech RTM Division schematic
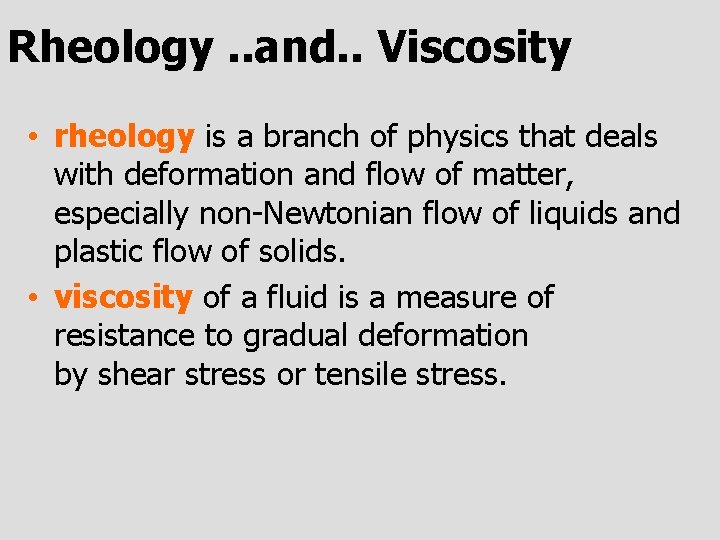
Rheology. . and. . Viscosity • rheology is a branch of physics that deals with deformation and flow of matter, especially non-Newtonian flow of liquids and plastic flow of solids. • viscosity of a fluid is a measure of resistance to gradual deformation by shear stress or tensile stress.
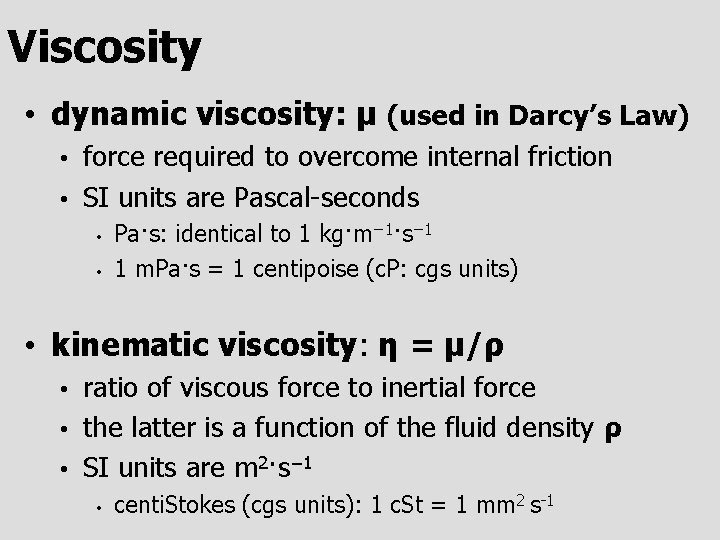
Viscosity • dynamic viscosity: μ (used in Darcy’s Law) force required to overcome internal friction • SI units are Pascal-seconds • • • Pa·s: identical to 1 kg·m− 1·s− 1 1 m. Pa·s = 1 centipoise (c. P: cgs units) • kinematic viscosity: η = μ/ρ ratio of viscous force to inertial force • the latter is a function of the fluid density ρ • SI units are m 2·s− 1 • • centi. Stokes (cgs units): 1 c. St = 1 mm 2 s-1
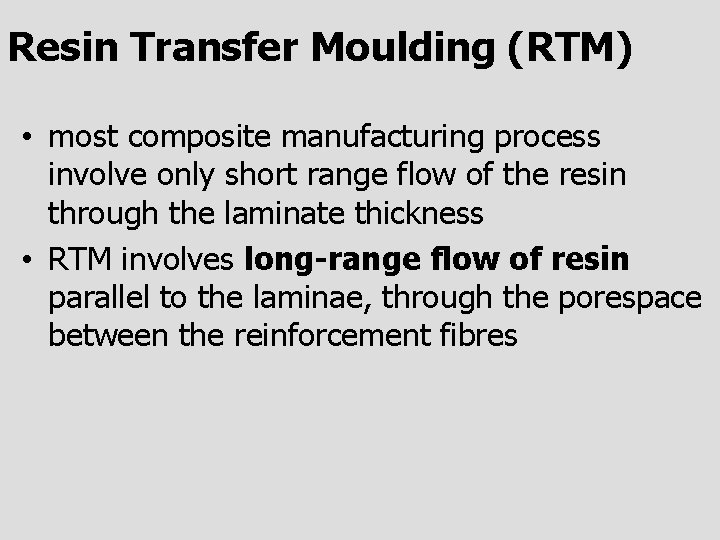
Resin Transfer Moulding (RTM) • most composite manufacturing process involve only short range flow of the resin through the laminate thickness • RTM involves long-range flow of resin parallel to the laminae, through the porespace between the reinforcement fibres
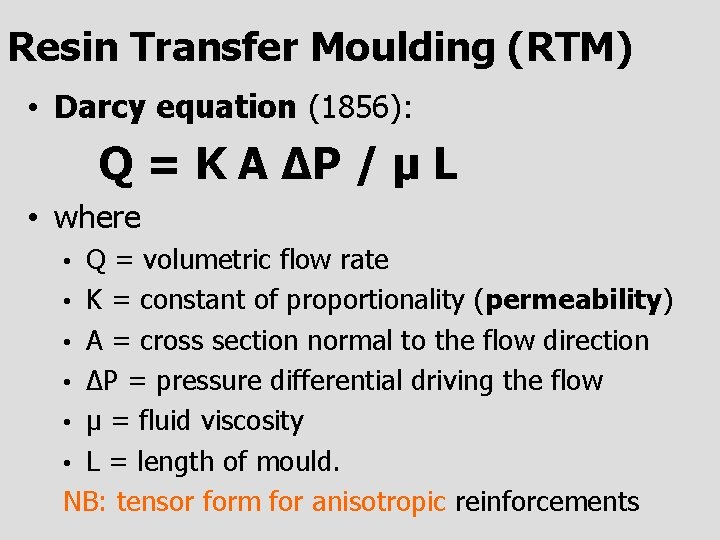
Resin Transfer Moulding (RTM) • Darcy equation (1856): Q = K A ΔP / μ L • where Q = volumetric flow rate • K = constant of proportionality (permeability) • A = cross section normal to the flow direction • ΔP = pressure differential driving the flow • μ = fluid viscosity • L = length of mould. NB: tensor form for anisotropic reinforcements •
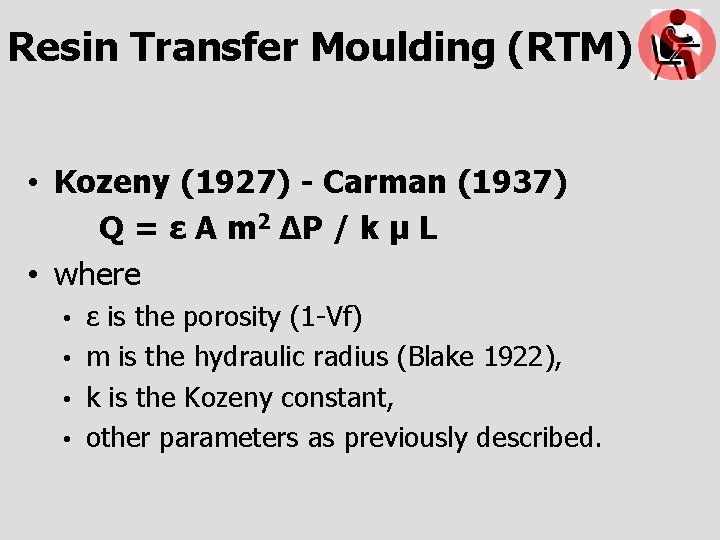
Resin Transfer Moulding (RTM) • Kozeny (1927) - Carman (1937) Q = ε A m 2 ΔP / k μ L • where ε is the porosity (1 -Vf) • m is the hydraulic radius (Blake 1922), • k is the Kozeny constant, • other parameters as previously described. •
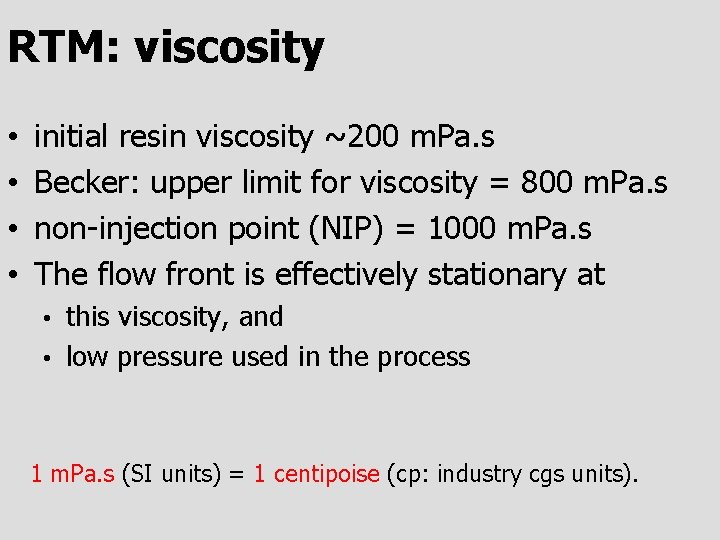
RTM: viscosity • • initial resin viscosity ~200 m. Pa. s Becker: upper limit for viscosity = 800 m. Pa. s non-injection point (NIP) = 1000 m. Pa. s The flow front is effectively stationary at this viscosity, and • low pressure used in the process • 1 m. Pa. s (SI units) = 1 centipoise (cp: industry cgs units).
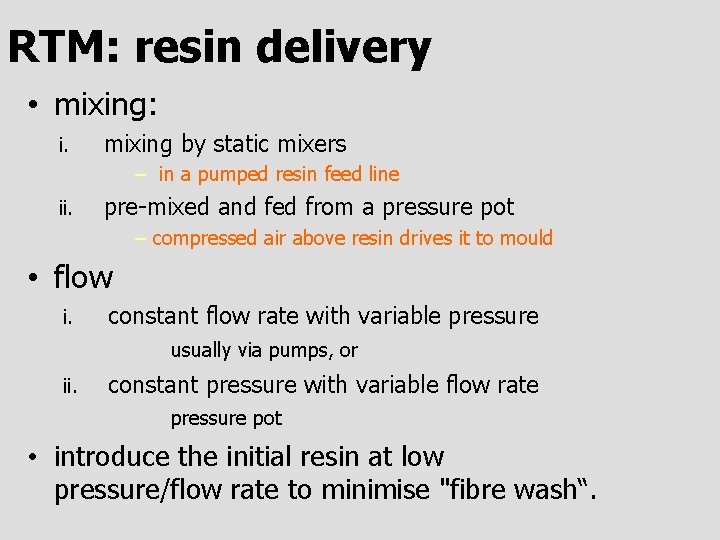
RTM: resin delivery • mixing: i. mixing by static mixers – in a pumped resin feed line ii. pre-mixed and fed from a pressure pot – compressed air above resin drives it to mould • flow i. constant flow rate with variable pressure usually via pumps, or ii. constant pressure with variable flow rate pressure pot • introduce the initial resin at low pressure/flow rate to minimise "fibre wash“.
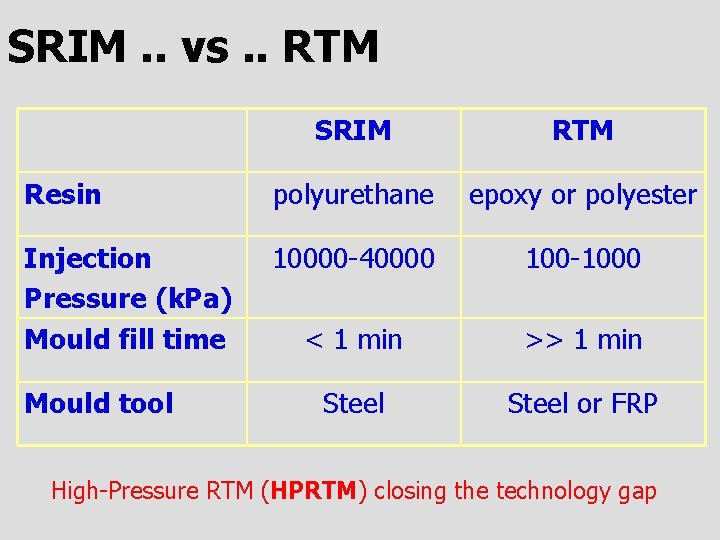
SRIM. . vs. . RTM SRIM RTM Resin polyurethane epoxy or polyester Injection Pressure (k. Pa) Mould fill time 10000 -40000 100 -1000 < 1 min >> 1 min Steel or FRP Mould tool High-Pressure RTM (HPRTM) closing the technology gap
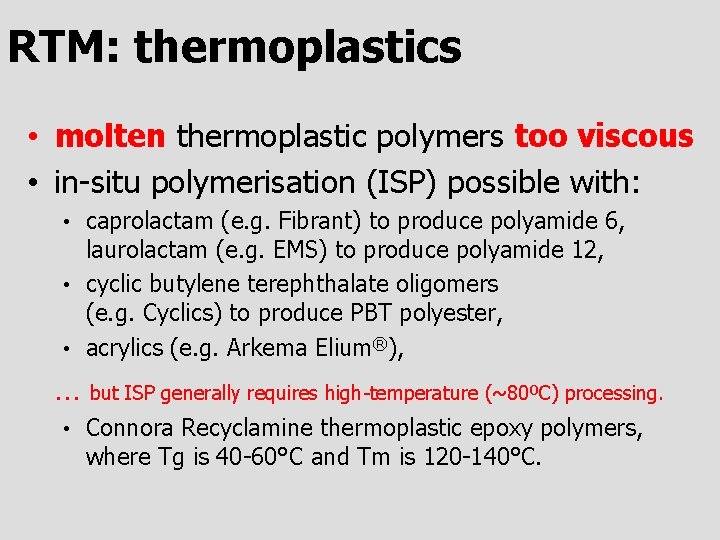
RTM: thermoplastics • molten thermoplastic polymers too viscous • in-situ polymerisation (ISP) possible with: caprolactam (e. g. Fibrant) to produce polyamide 6, laurolactam (e. g. EMS) to produce polyamide 12, • cyclic butylene terephthalate oligomers (e. g. Cyclics) to produce PBT polyester, • acrylics (e. g. Arkema Elium®), • … but ISP generally requires high-temperature (~80ºC) processing. • Connora Recyclamine thermoplastic epoxy polymers, where Tg is 40 -60°C and Tm is 120 -140°C.
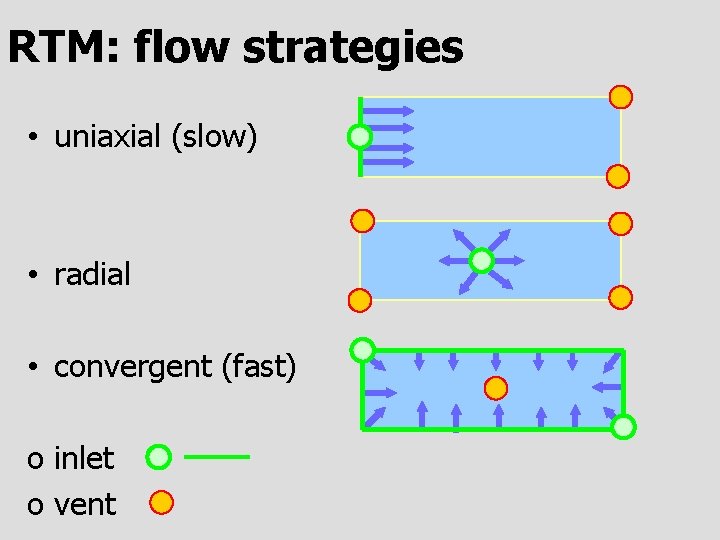
RTM: flow strategies • uniaxial (slow) • radial • convergent (fast) o inlet o vent

RTM: mould tools • positive pressure: the mould edges may “leak” resin • reinforcement may be placed over the seals to provide a path for air to escape • • vacuum: requires the tool has vacuum integrity • no air ingress paths through the tool • some vacuum systems use peripheral channel at higher vacuum than the cavity to clamp the mould halves together. • pressure driven flow + vacuum for low void content •
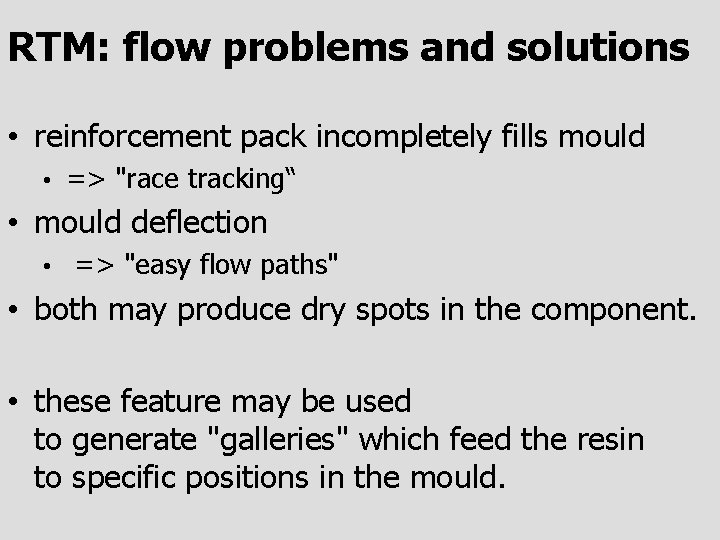
RTM: flow problems and solutions • reinforcement pack incompletely fills mould • => "race tracking“ • mould deflection • => "easy flow paths" • both may produce dry spots in the component. • these feature may be used to generate "galleries" which feed the resin to specific positions in the mould.
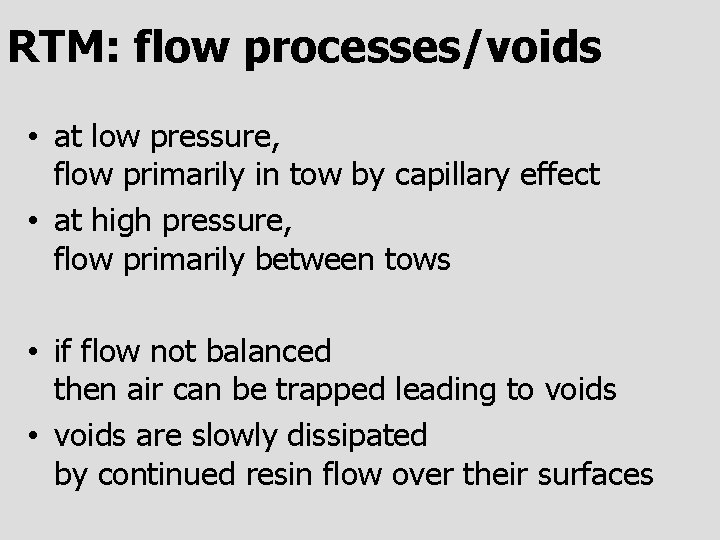
RTM: flow processes/voids • at low pressure, flow primarily in tow by capillary effect • at high pressure, flow primarily between tows • if flow not balanced then air can be trapped leading to voids • voids are slowly dissipated by continued resin flow over their surfaces
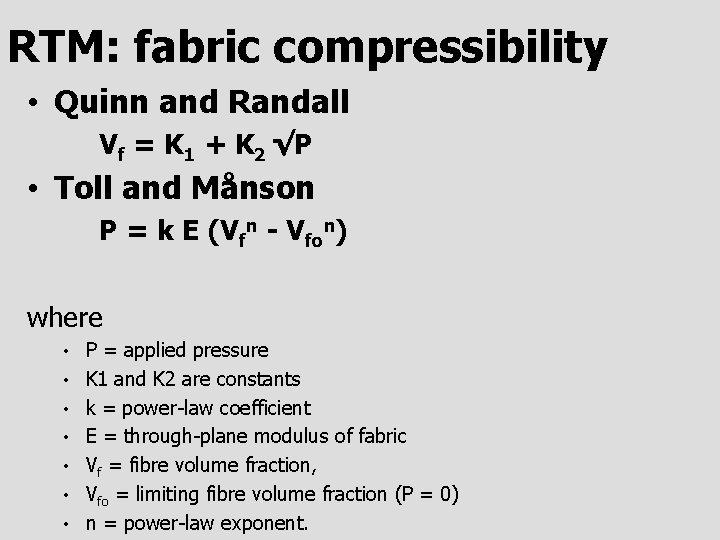
RTM: fabric compressibility • Quinn and Randall Vf = K 1 + K 2 √P • Toll and Månson P = k E (Vfn - Vfon) where • • P = applied pressure K 1 and K 2 are constants k = power-law coefficient E = through-plane modulus of fabric Vf = fibre volume fraction, Vfo = limiting fibre volume fraction (P = 0) n = power-law exponent.
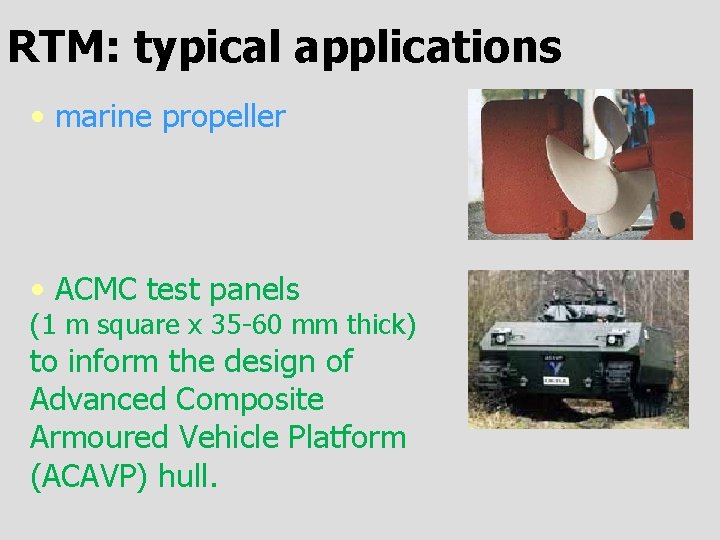
RTM: typical applications • marine propeller • ACMC test panels (1 m square x 35 -60 mm thick) to inform the design of Advanced Composite Armoured Vehicle Platform (ACAVP) hull.
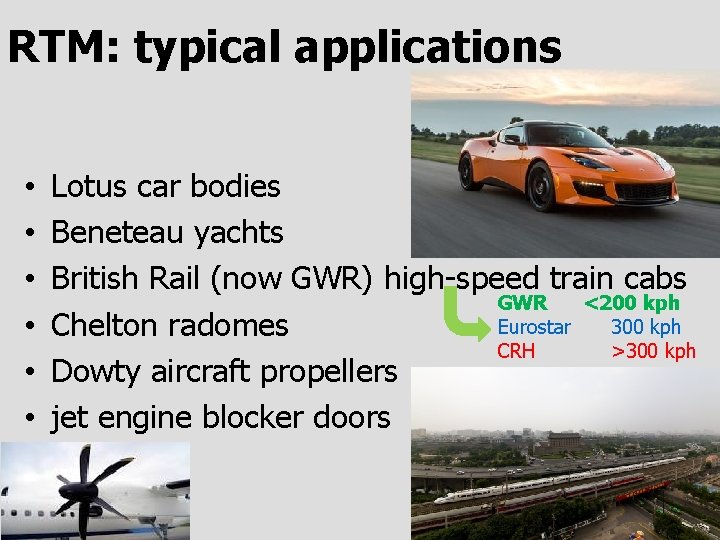
RTM: typical applications • • • Lotus car bodies Beneteau yachts British Rail (now GWR) high-speed train cabs GWR <200 kph Eurostar 300 kph Chelton radomes CRH >300 kph Dowty aircraft propellers jet engine blocker doors
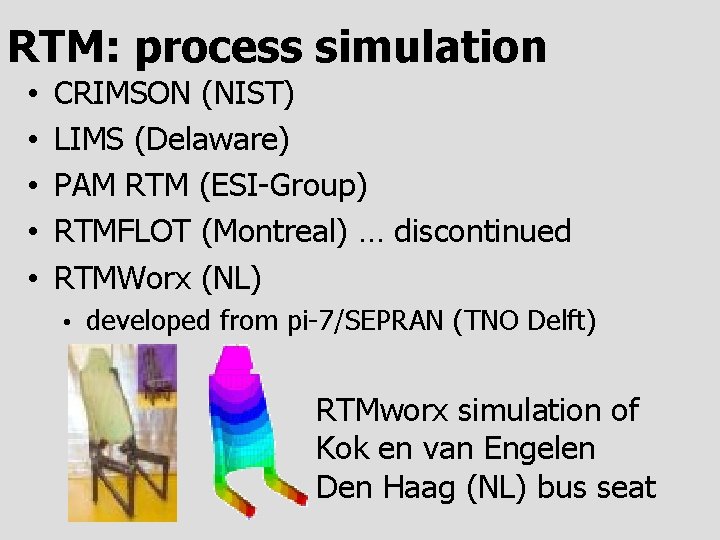
RTM: process simulation • • • CRIMSON (NIST) LIMS (Delaware) PAM RTM (ESI-Group) RTMFLOT (Montreal) … discontinued RTMWorx (NL) • developed from pi-7/SEPRAN (TNO Delft) RTMworx simulation of Kok en van Engelen Den Haag (NL) bus seat
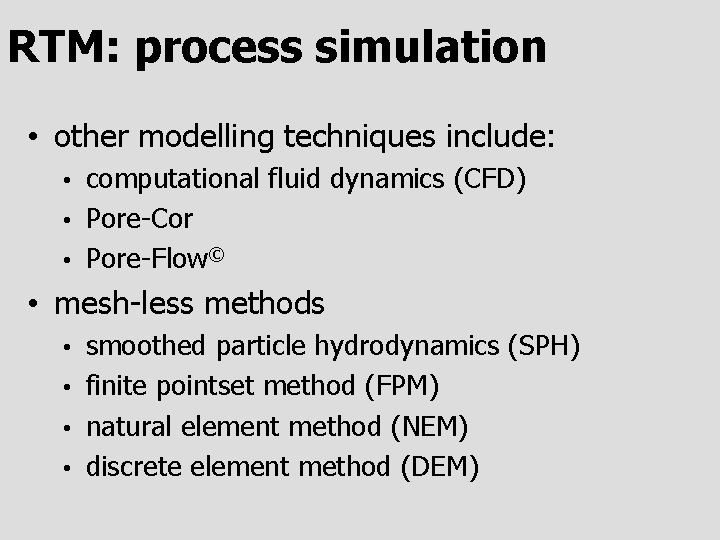
RTM: process simulation • other modelling techniques include: computational fluid dynamics (CFD) • Pore-Cor • Pore-Flow© • • mesh-less methods smoothed particle hydrodynamics (SPH) • finite pointset method (FPM) • natural element method (NEM) • discrete element method (DEM) •
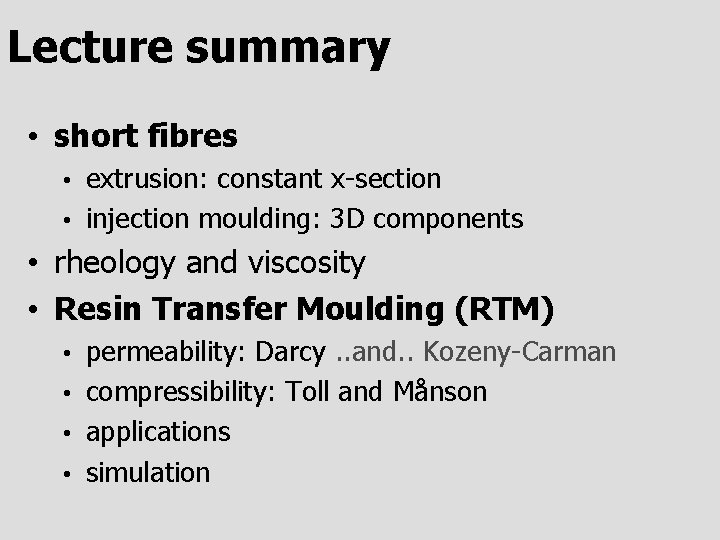
Lecture summary • short fibres extrusion: constant x-section • injection moulding: 3 D components • • rheology and viscosity • Resin Transfer Moulding (RTM) permeability: Darcy. . and. . Kozeny-Carman • compressibility: Toll and Månson • applications • simulation •
Resin transfer molding
Sqrtm - same-qualified resin transfer moulding
John summerscales
John summerscales
John summerscales
Micro milli nano
Kelly tyson
John summerscales
Injection blow moulding advantages and disadvantages
Z type sprue puller
Health and safety injection moulding
Delamination injection molding
Compression and transfer moulding
Moldflow plastic insight
Advantages of injection moulding
Blow molding advantages and disadvantages
Multi colour injection moulding process
Purchasing flashing injection moulding
Gas injection technology
"plastic welding"
"plastic injection moulding"
"plastic welding"
Magnesium stent
Multi-layers co-extrusion feedblock
Light resin transfer molding
Resin transfer molding
Compression molded
A disturbance in a field that carries energy
Rink amide resin cleavage
Resin based composite
Vacuum infusion london
Resin application server monitoring
Flexera resin