Electrical Discharge Machining EDM Dr L S Raju
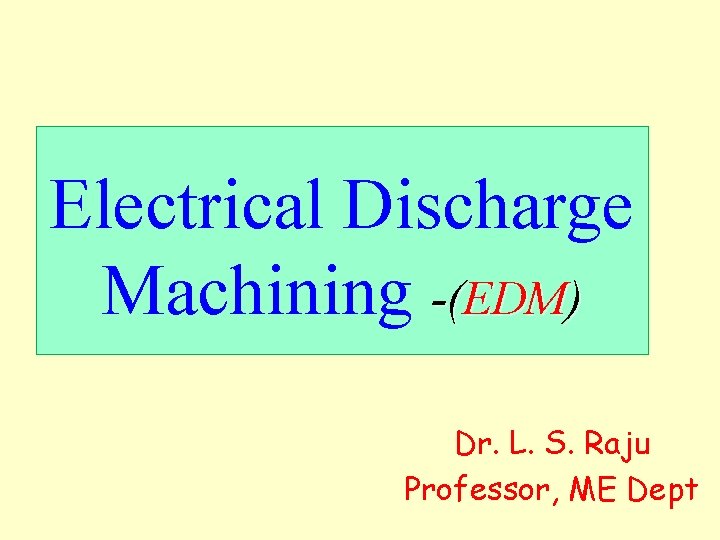
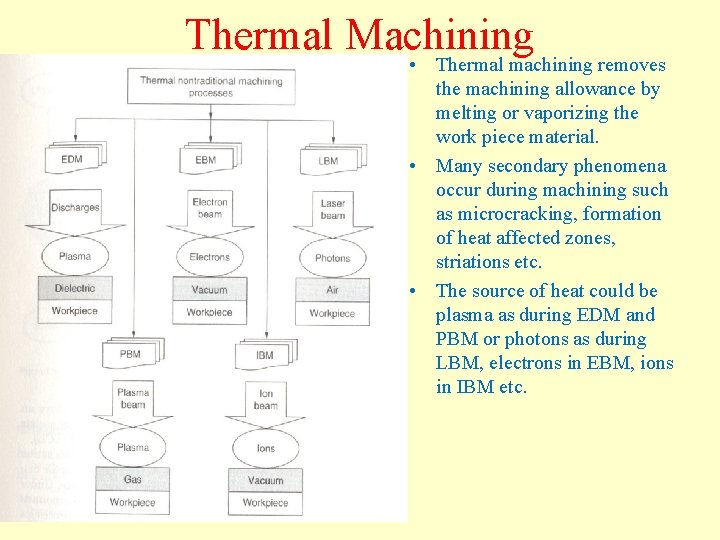
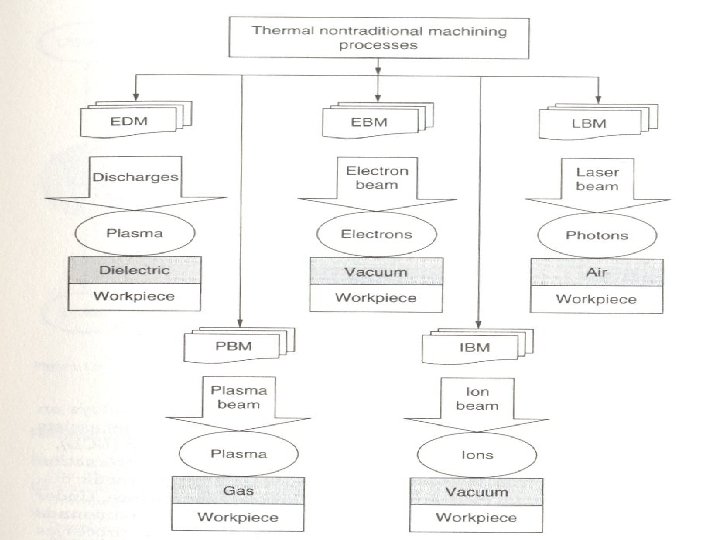
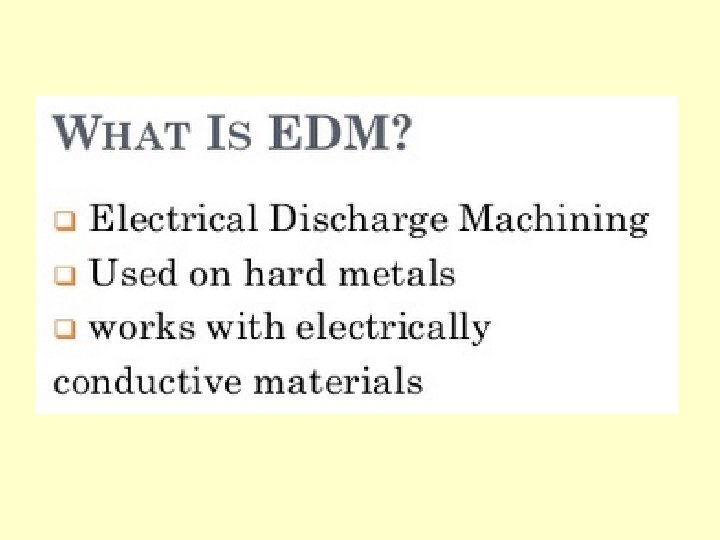
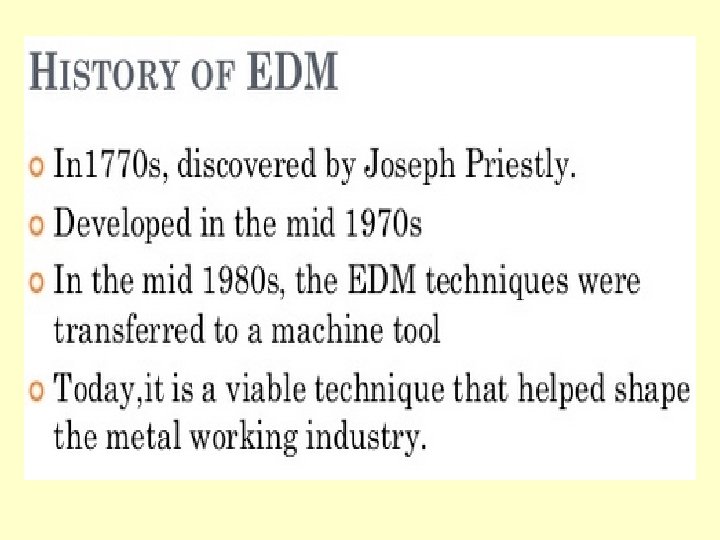
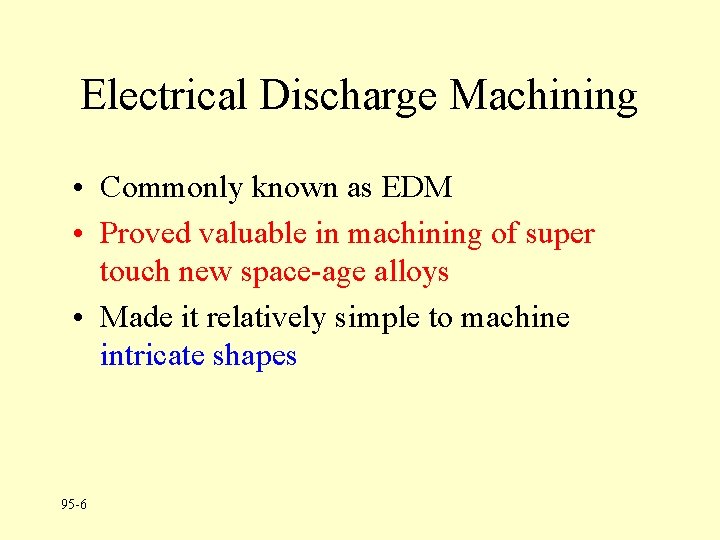
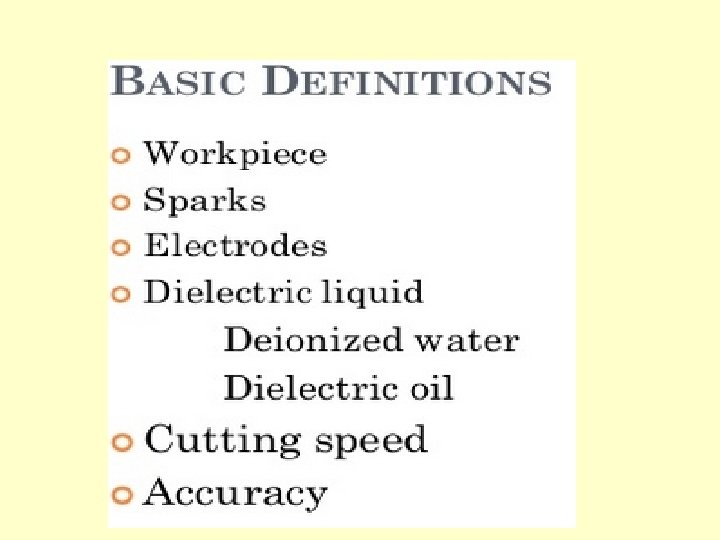
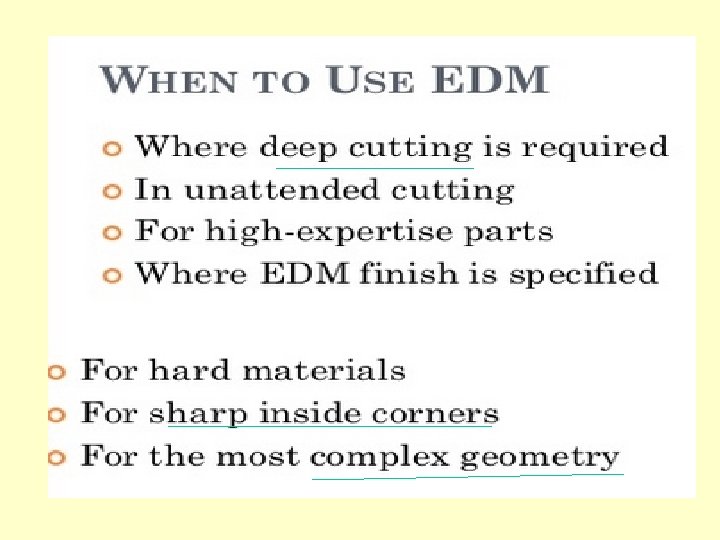
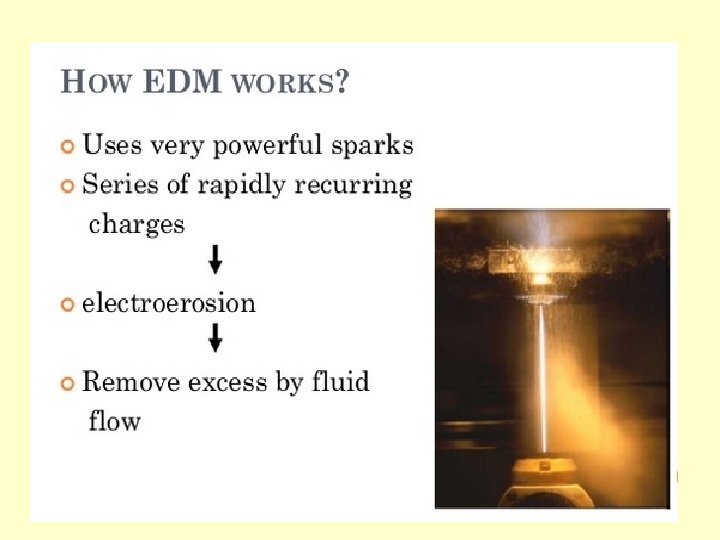
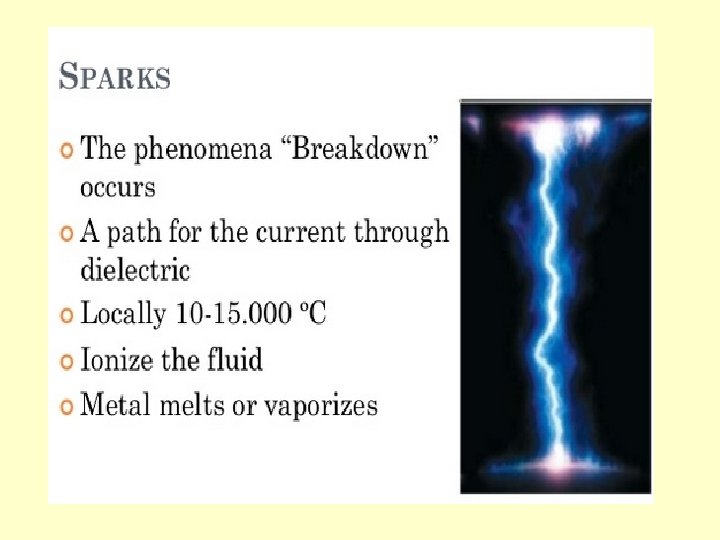
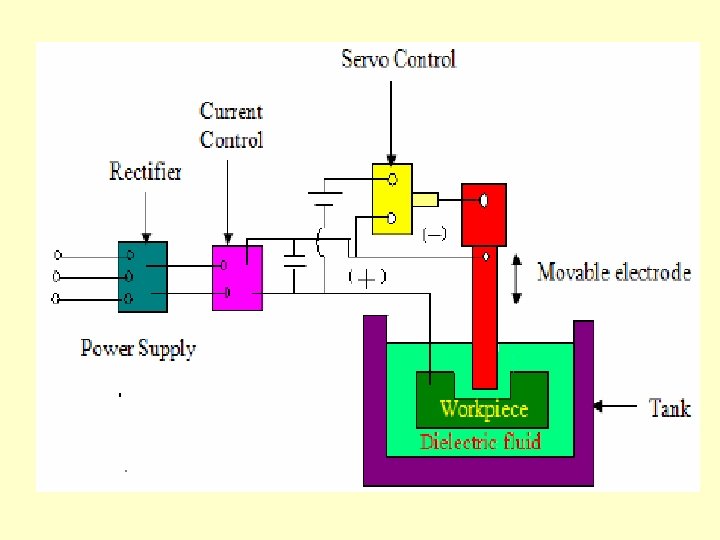
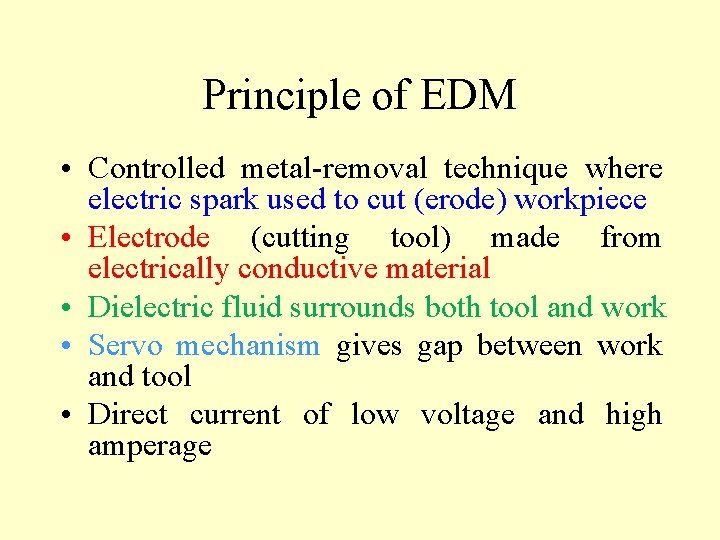
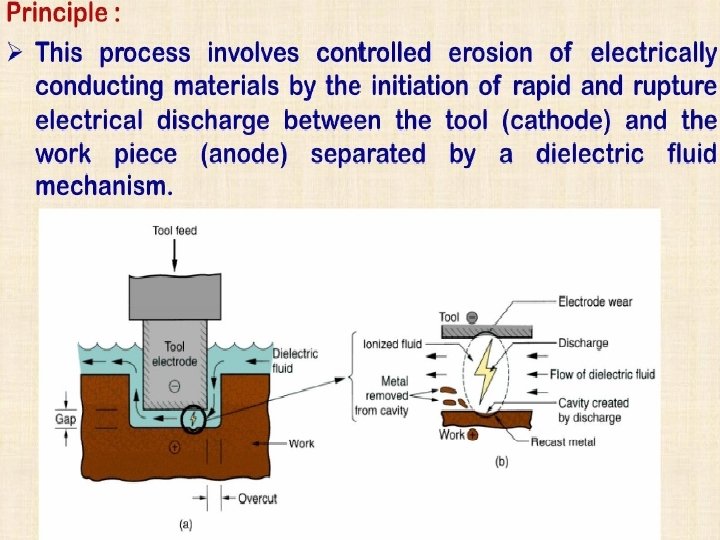
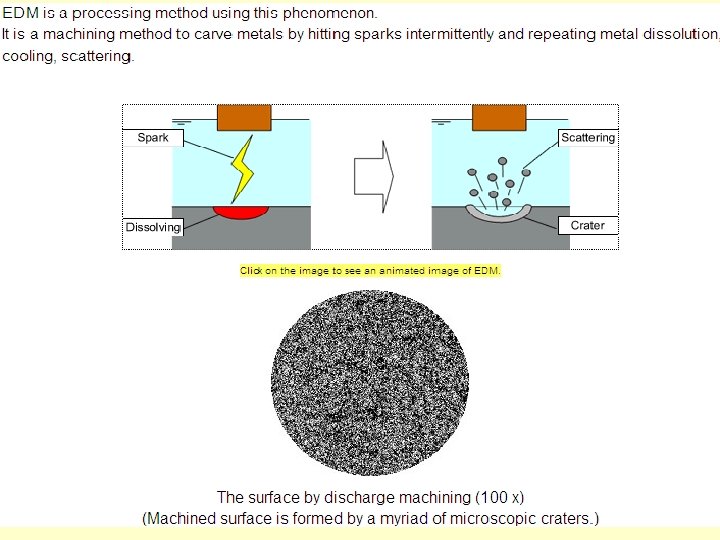
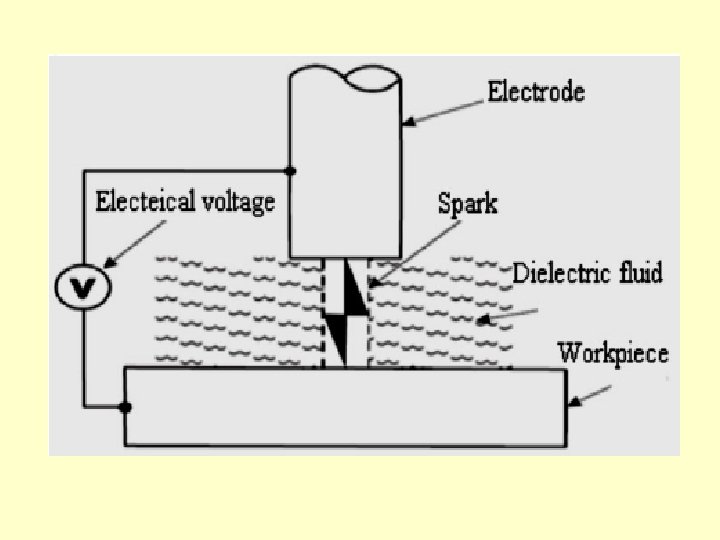
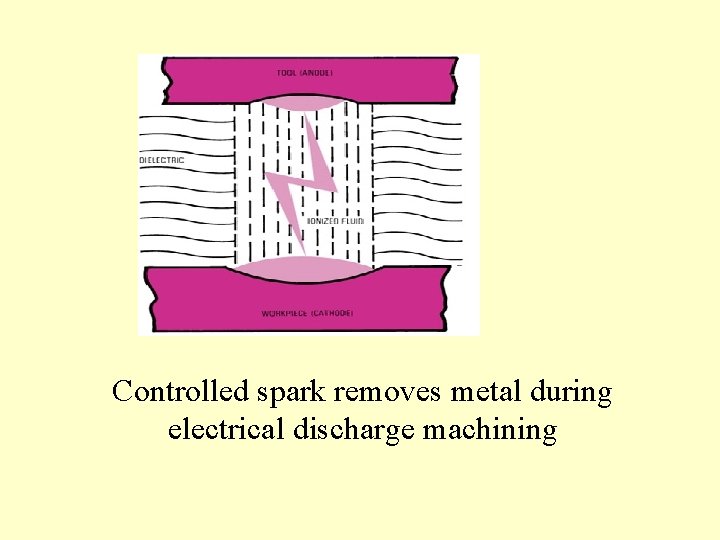
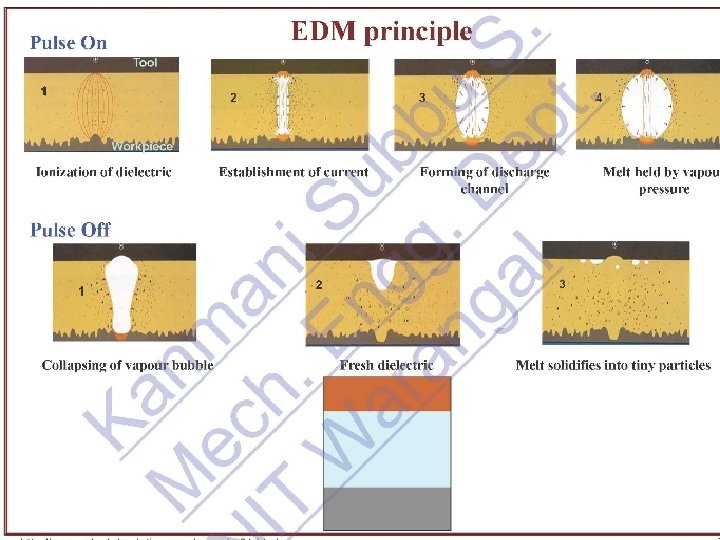
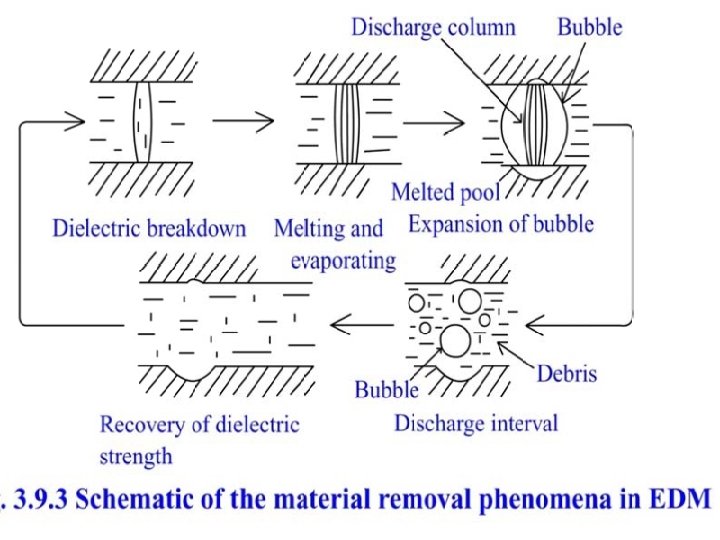
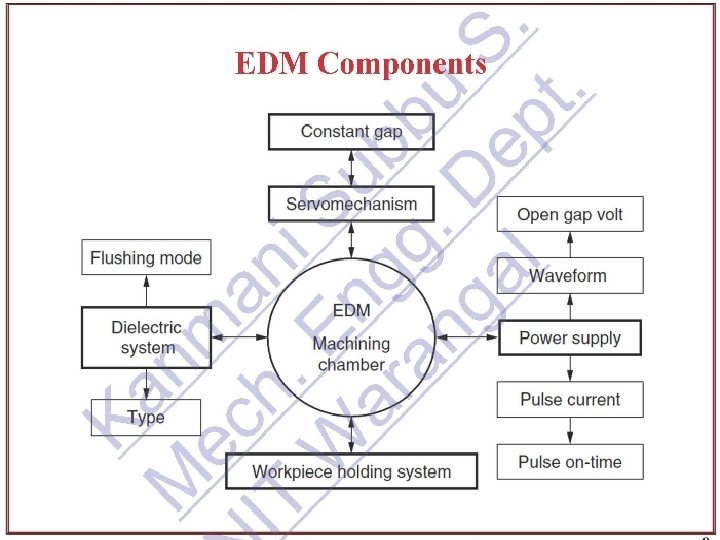
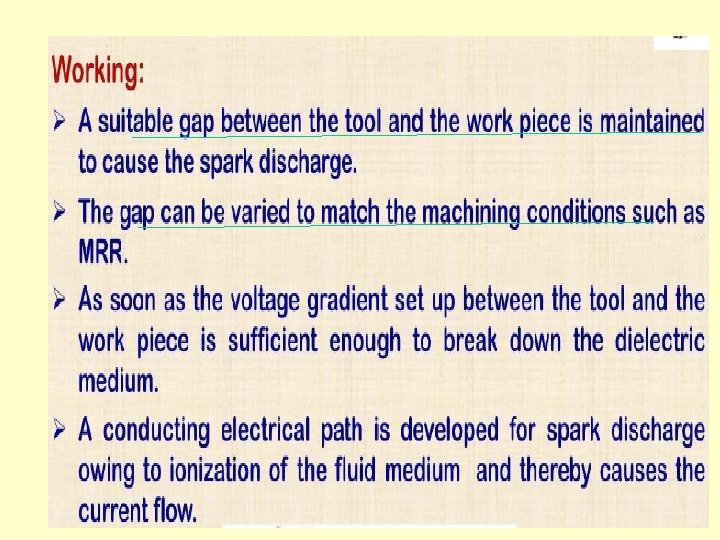
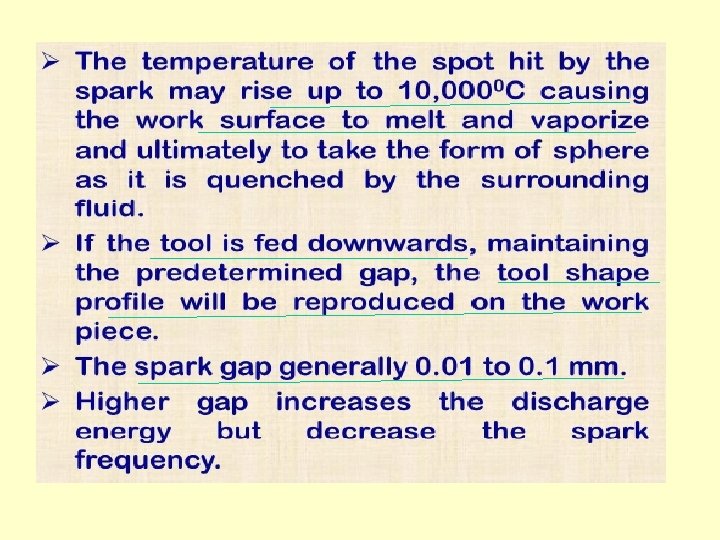
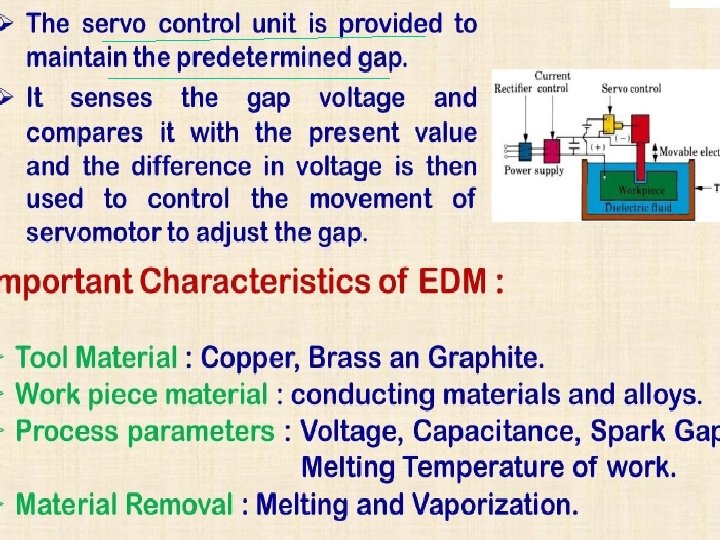
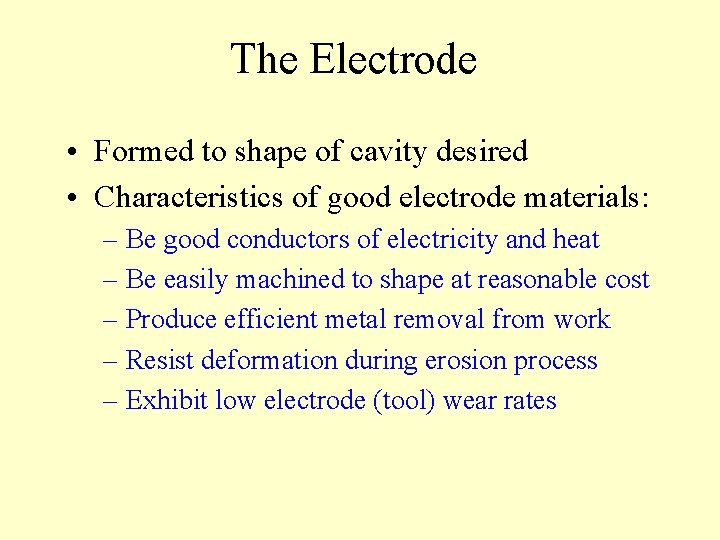
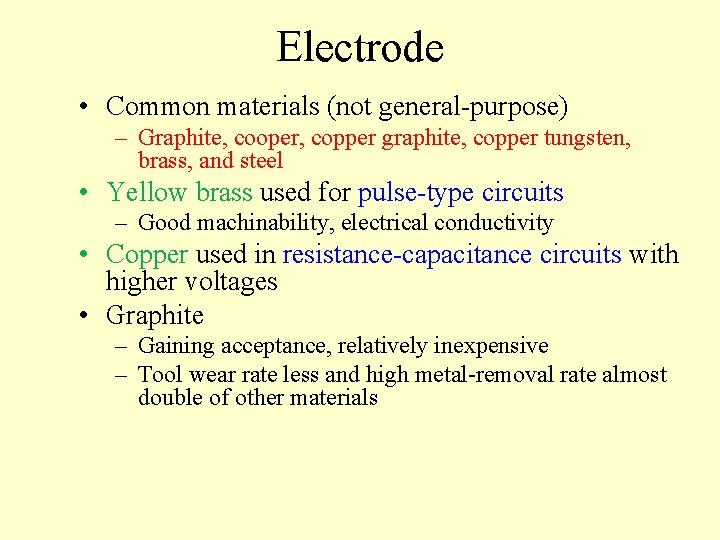
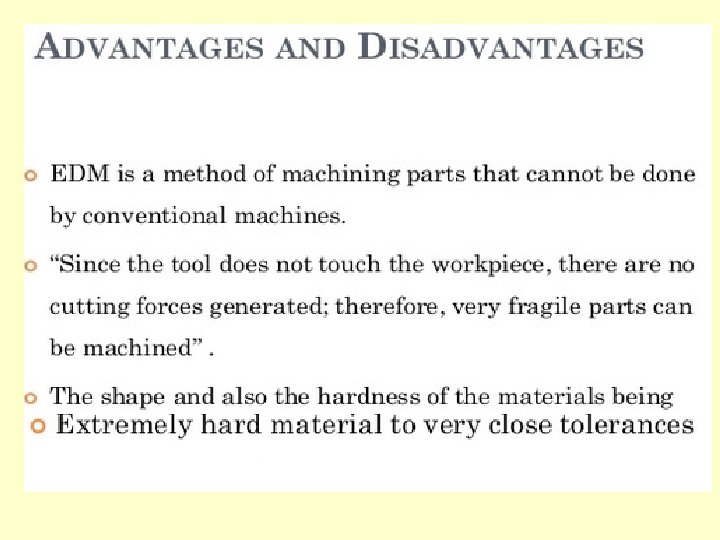
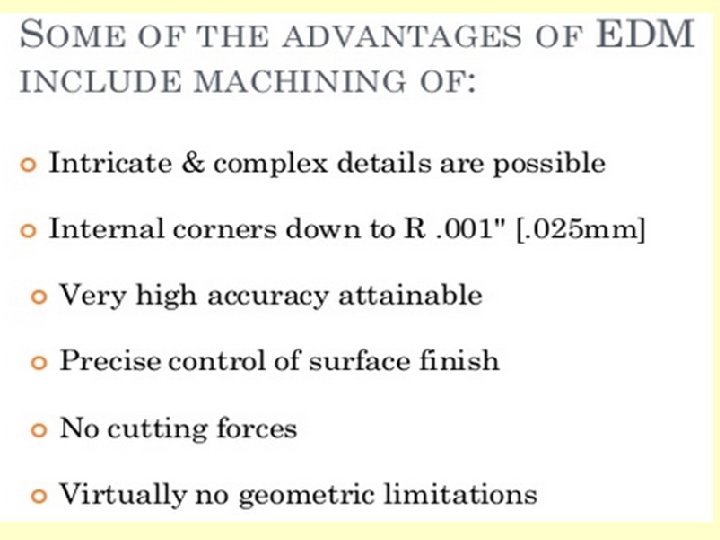
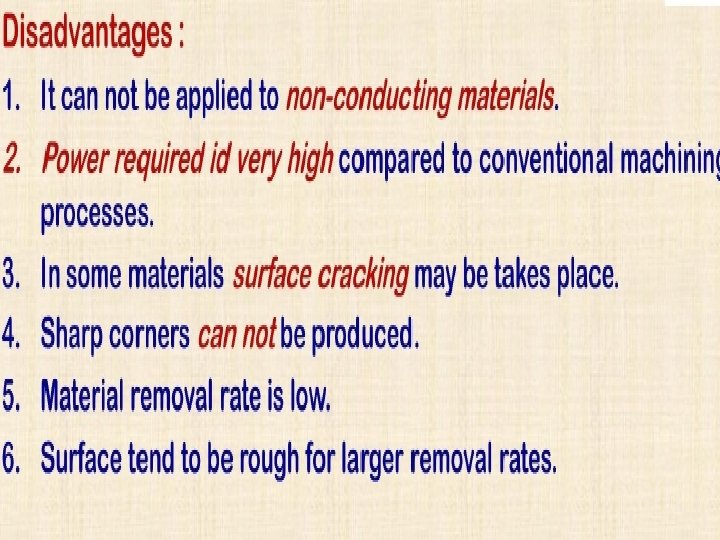

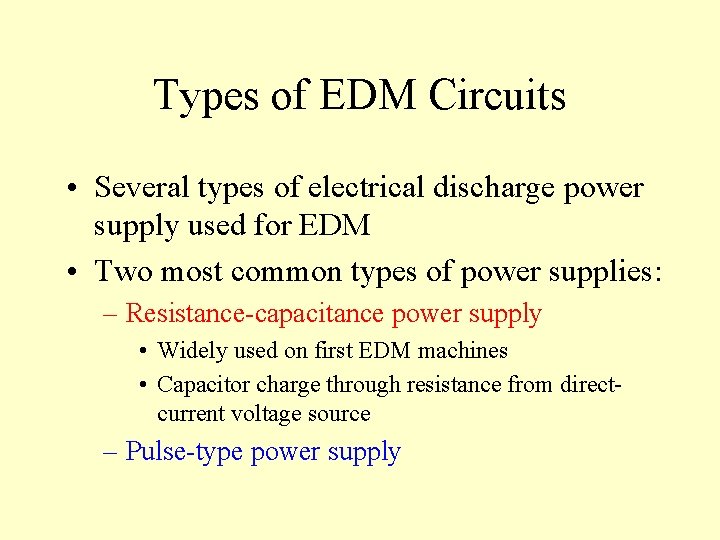
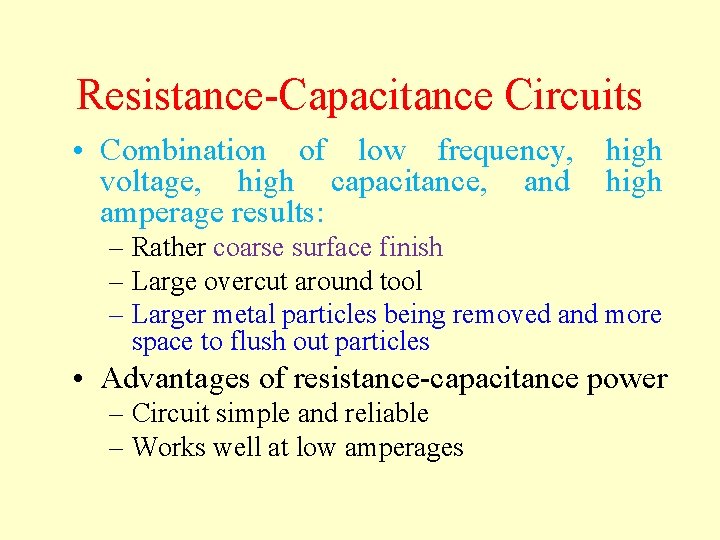
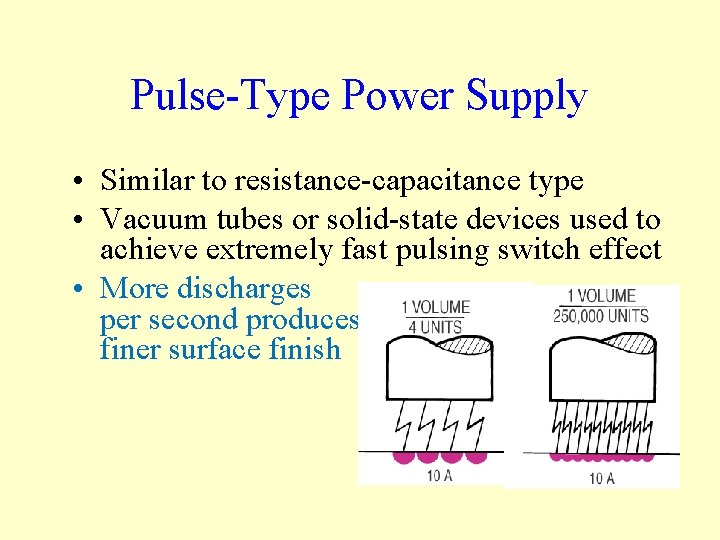
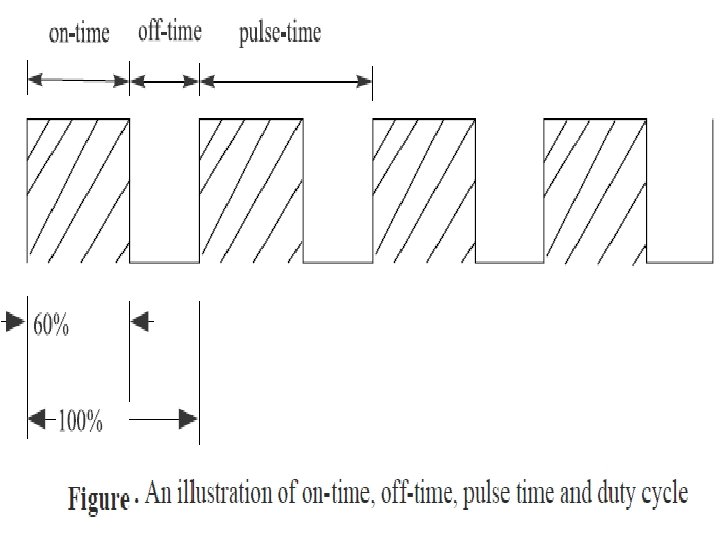
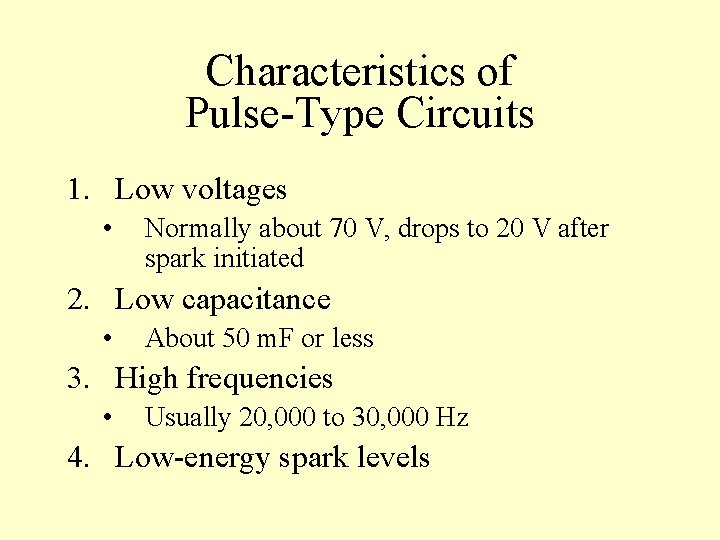
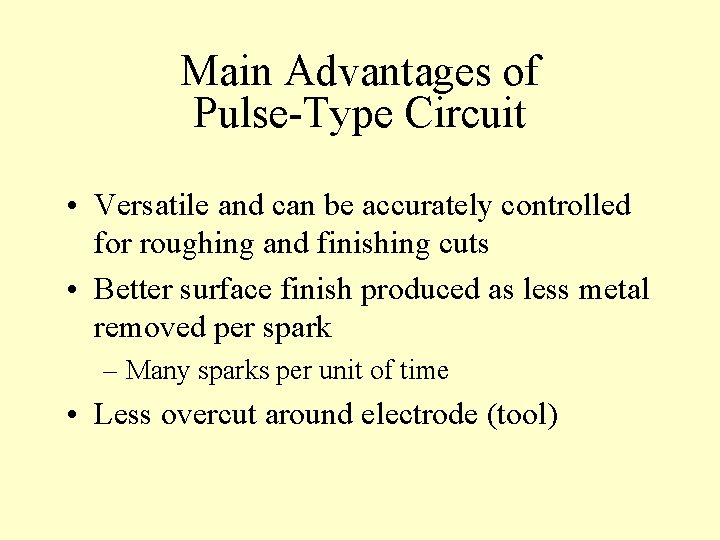
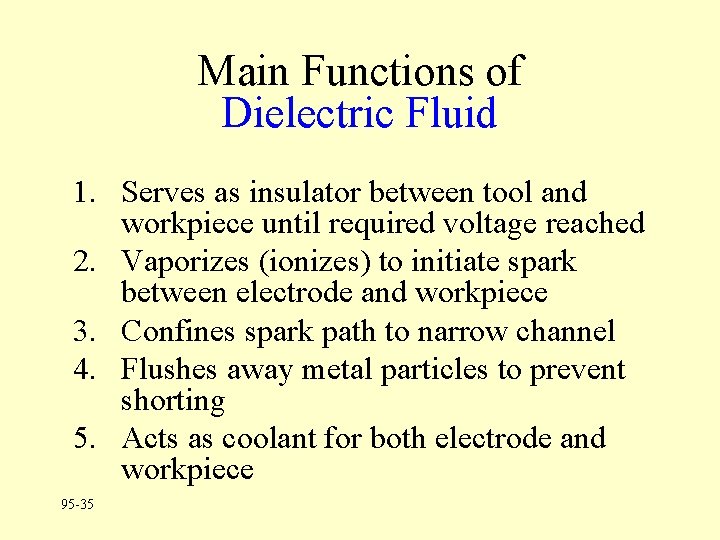
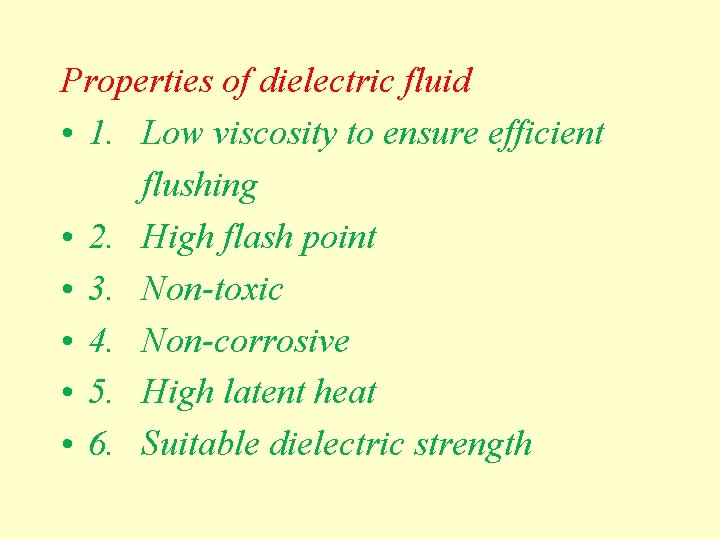
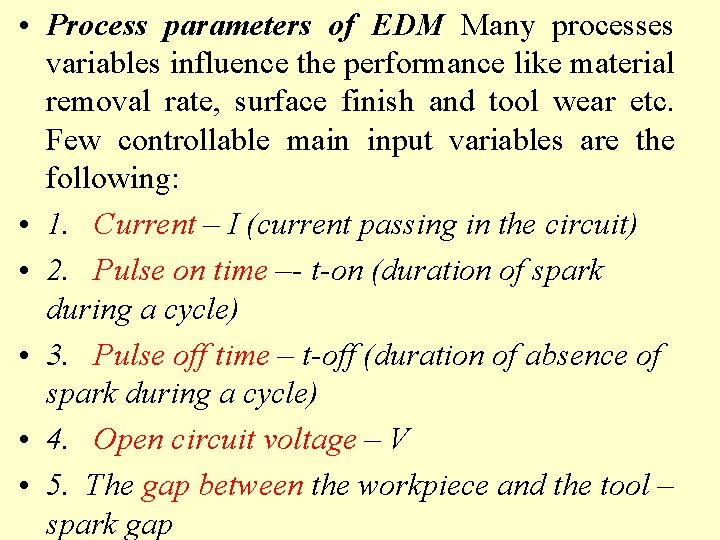
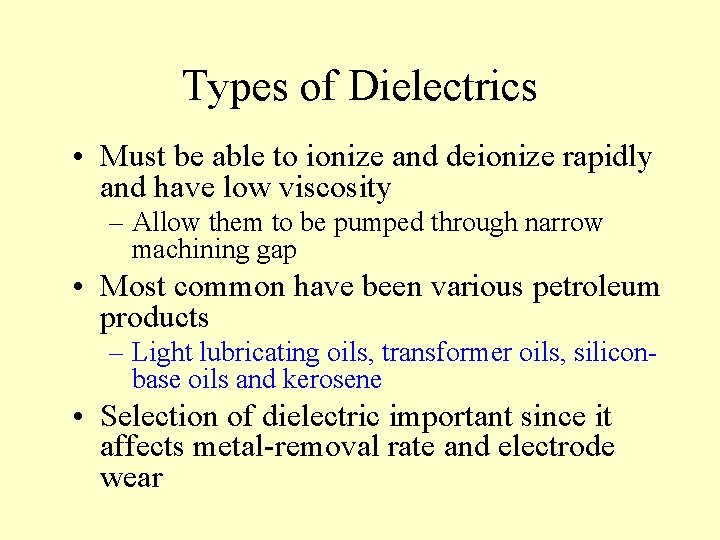
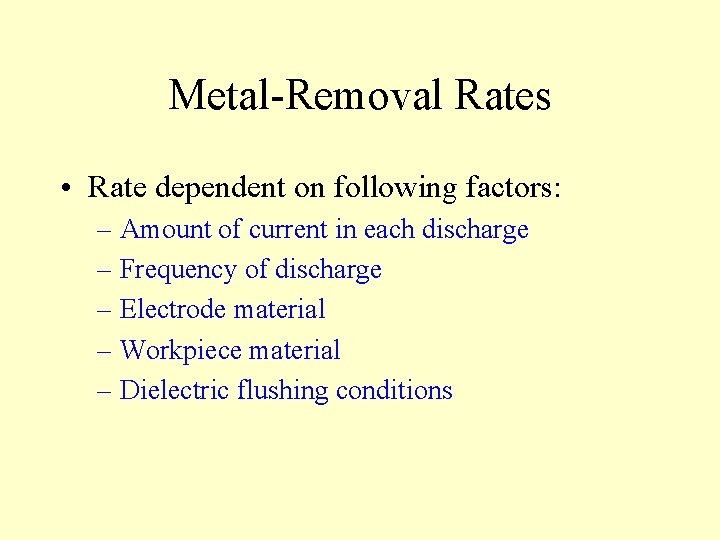

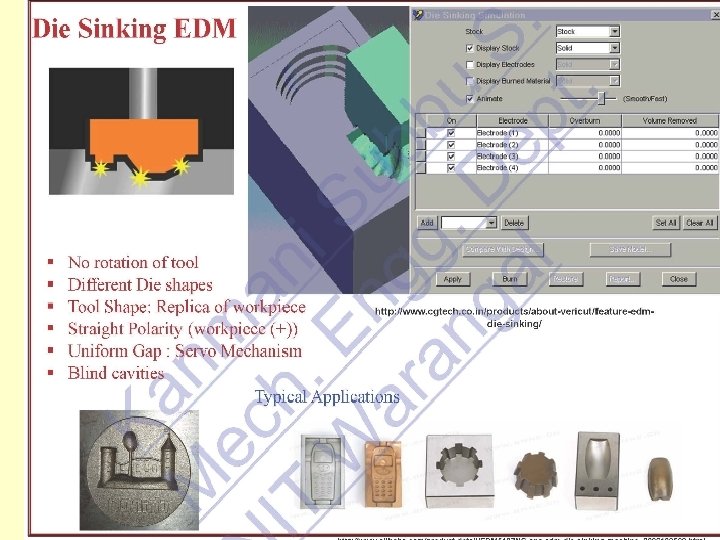
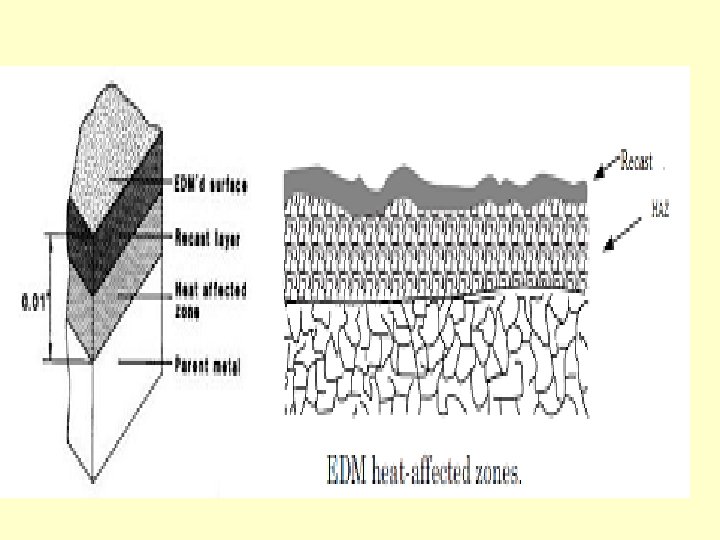
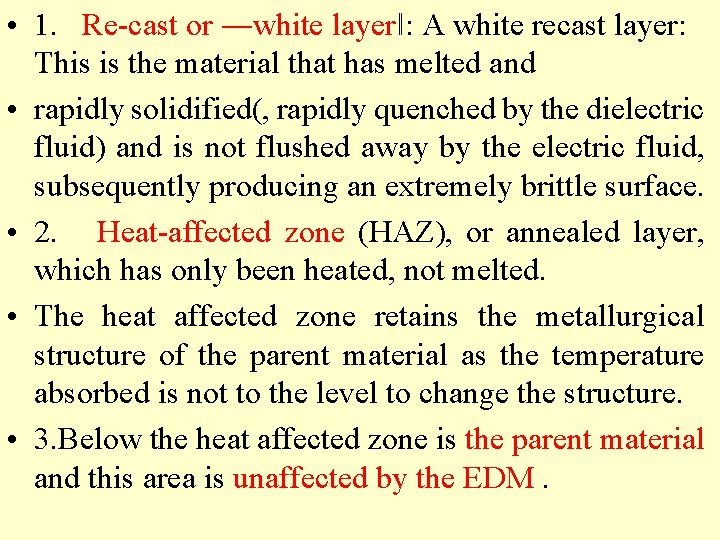
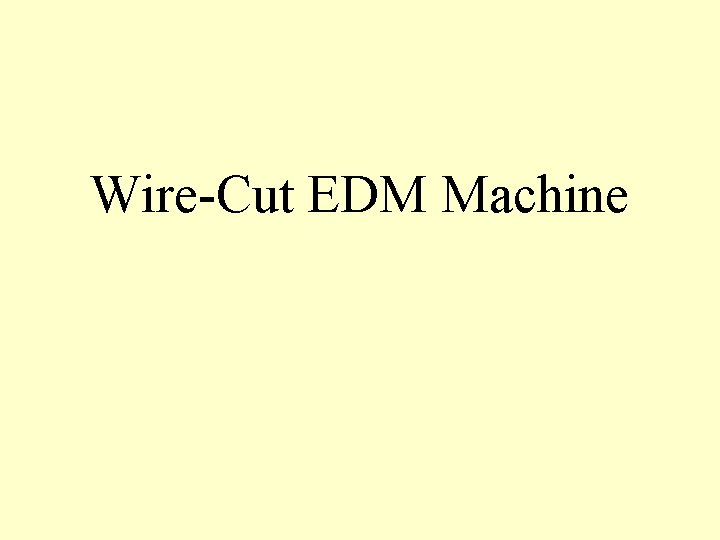
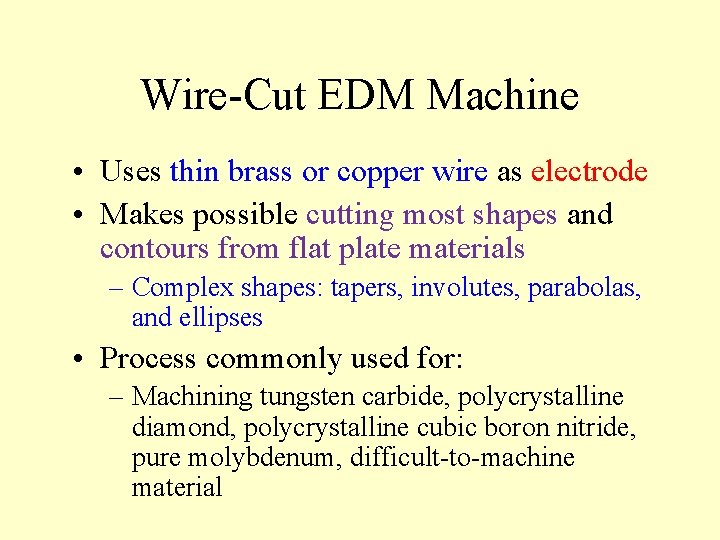
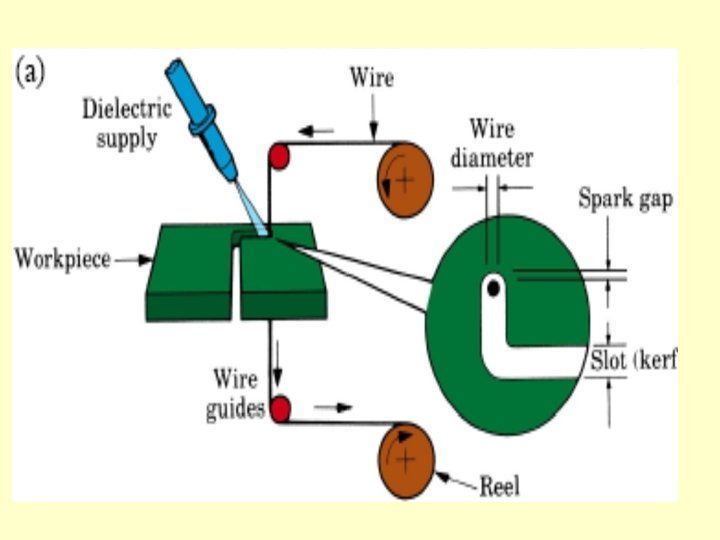
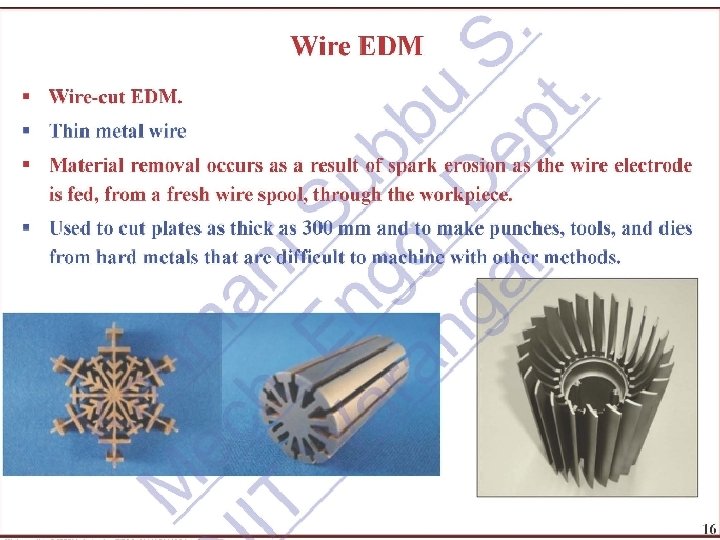
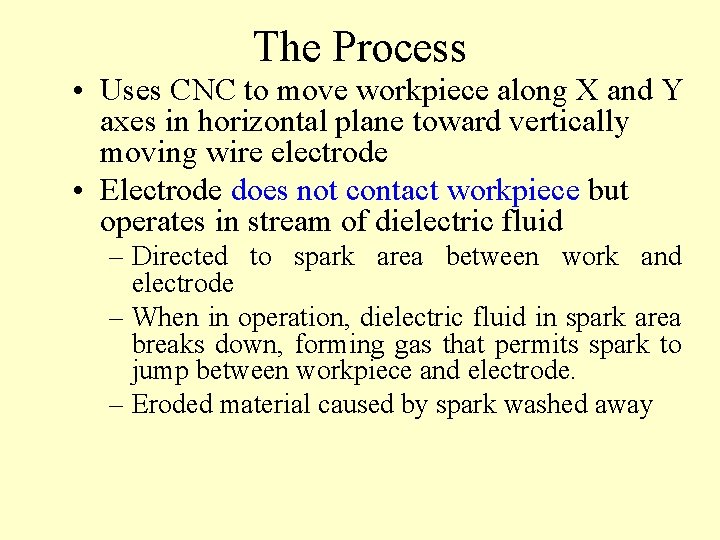
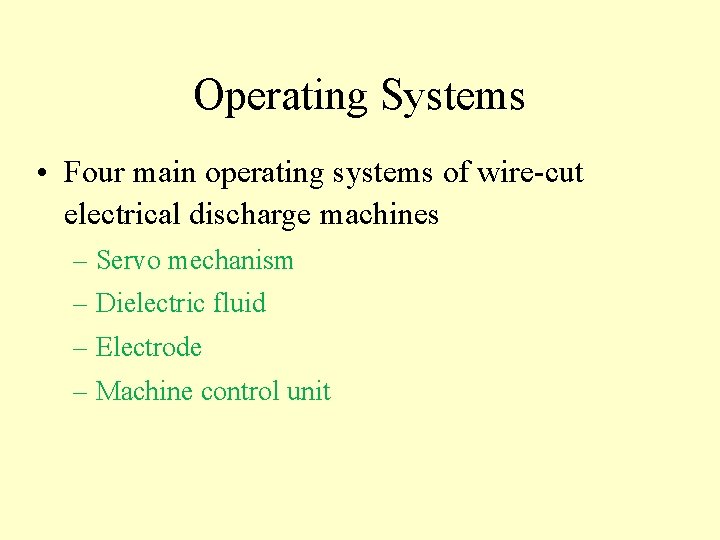
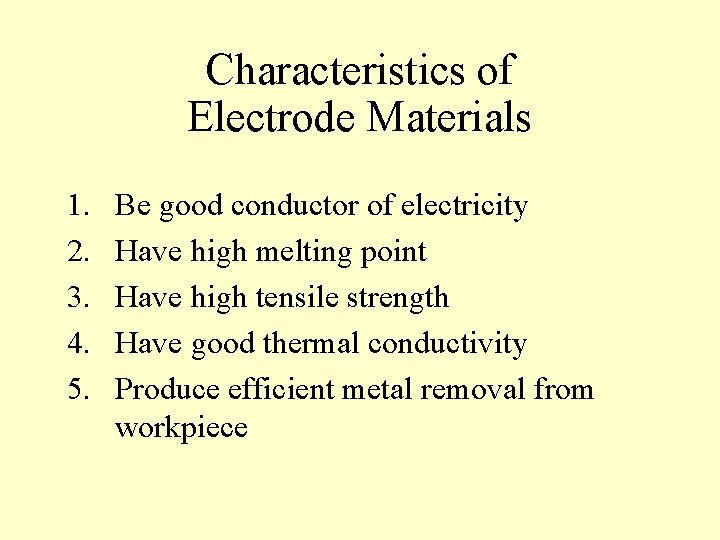
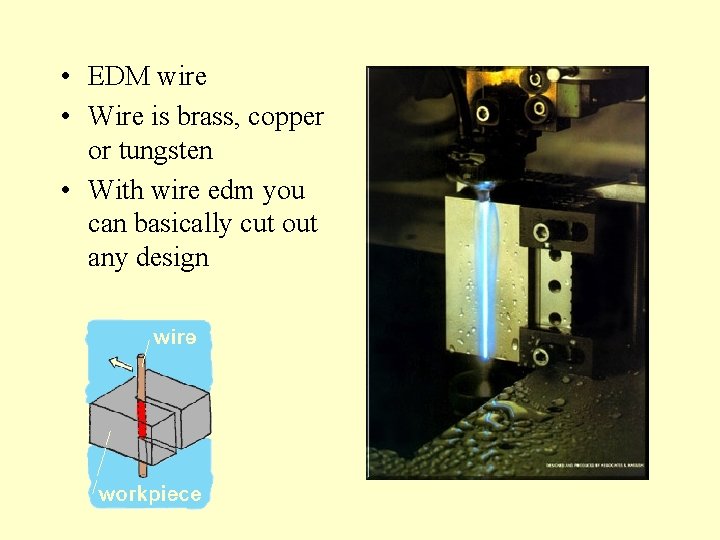
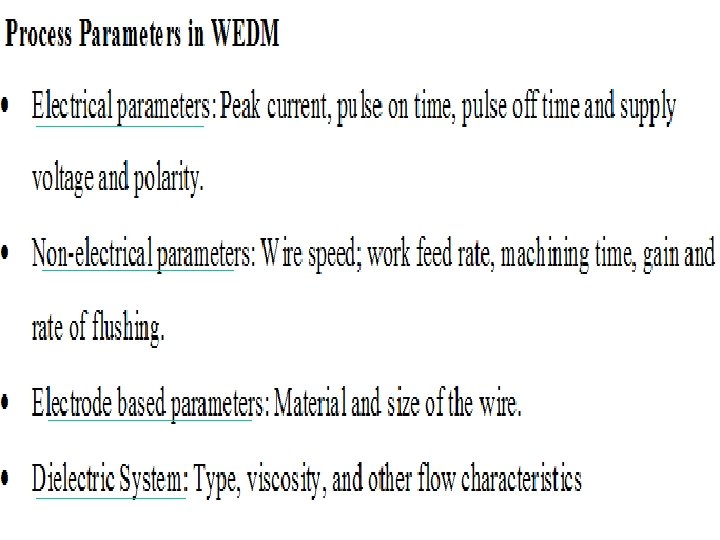
- Slides: 52
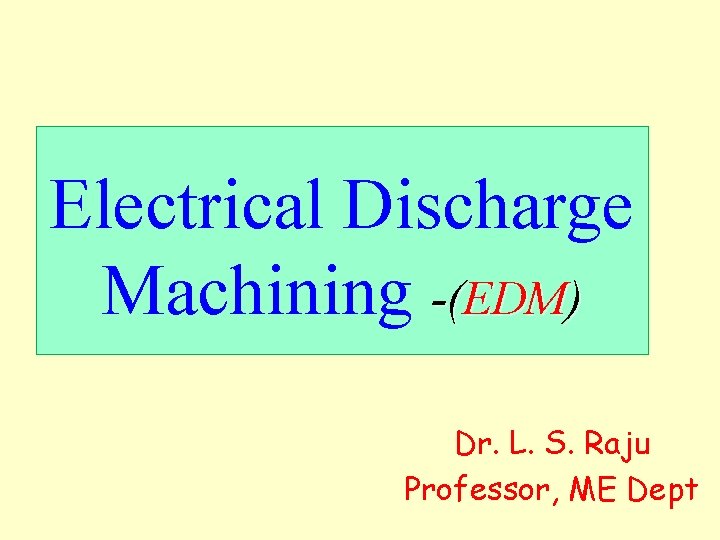
Electrical Discharge Machining -(EDM) Dr. L. S. Raju Professor, ME Dept
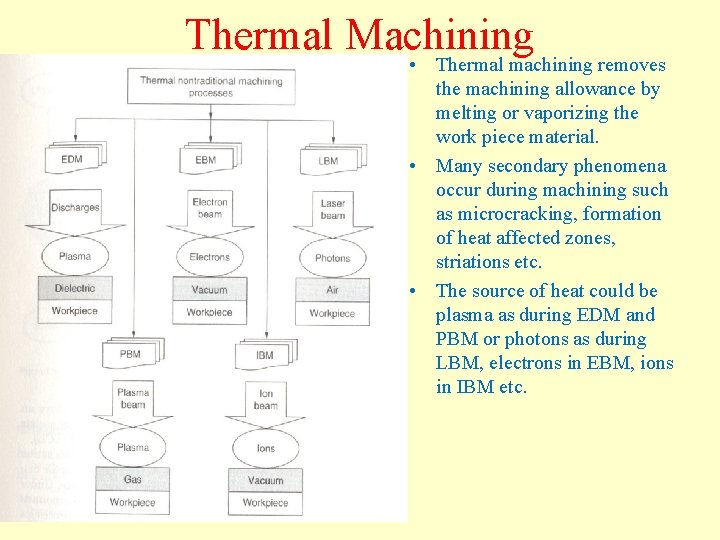
Thermal Machining • Thermal machining removes the machining allowance by melting or vaporizing the work piece material. • Many secondary phenomena occur during machining such as microcracking, formation of heat affected zones, striations etc. • The source of heat could be plasma as during EDM and PBM or photons as during LBM, electrons in EBM, ions in IBM etc.
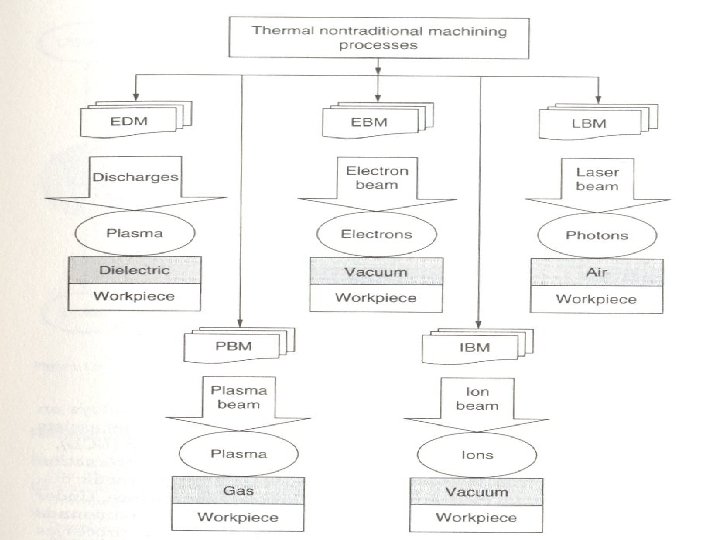
Continue… • Thermal Method The material is removed due to controlled, localized heating of the work piece. It result into material removal by melting and evaporation. The source of heat generation in such cases can be widely different. 1. Electric Discharge Machining (EDM). 2. Plasma Arc Machining (PAM). 3. Electron Beam Machining (EBM) 4. Laser Beam Machining (LBM)
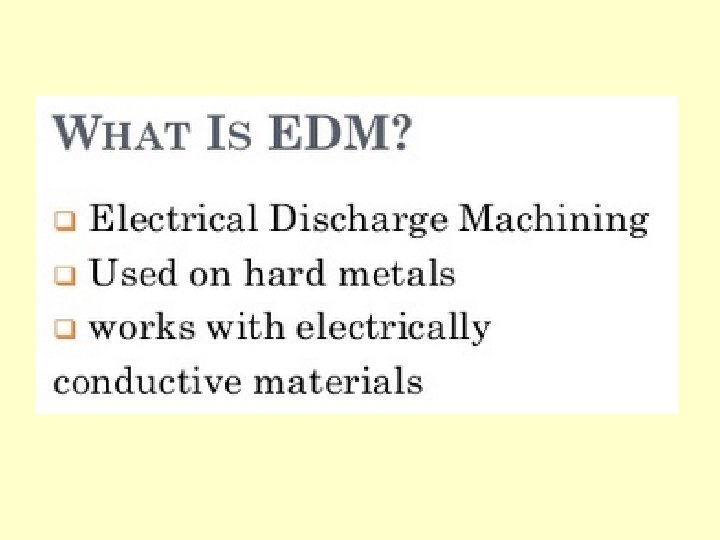
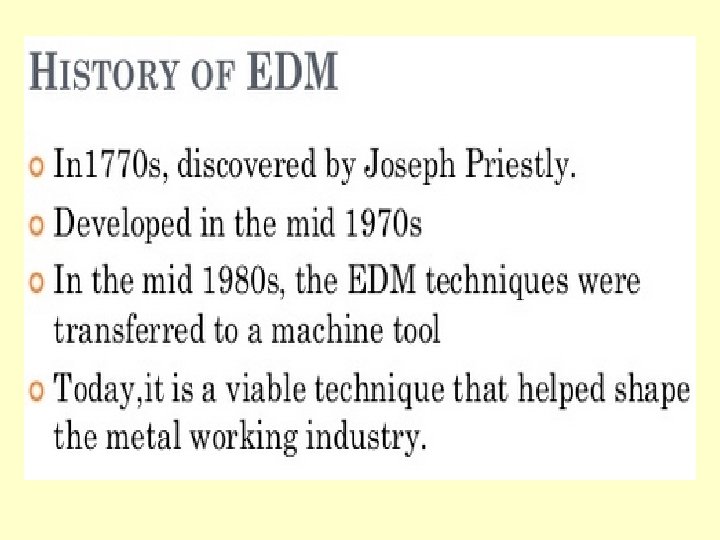
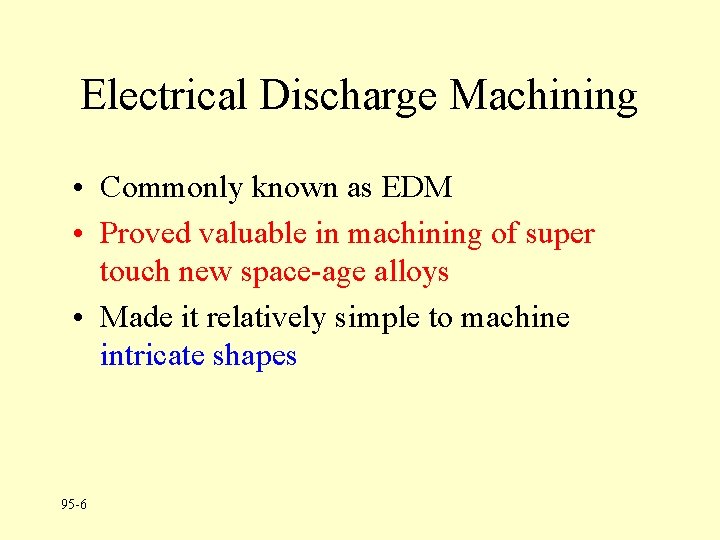
Electrical Discharge Machining • Commonly known as EDM • Proved valuable in machining of super touch new space-age alloys • Made it relatively simple to machine intricate shapes 95 -6
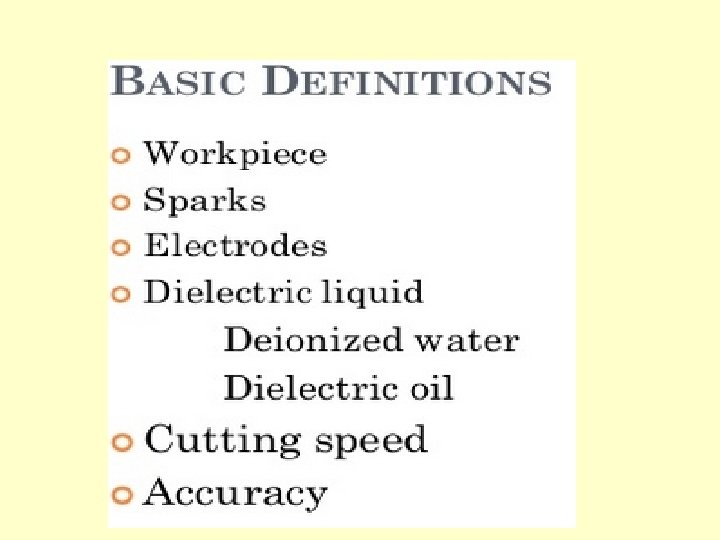
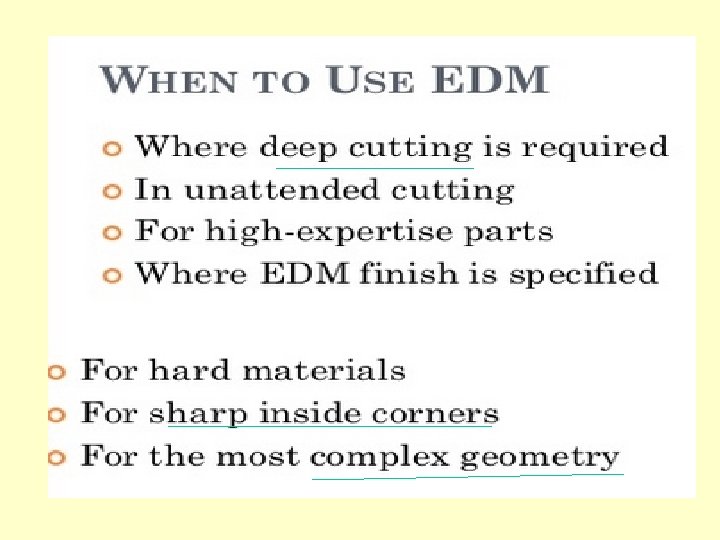
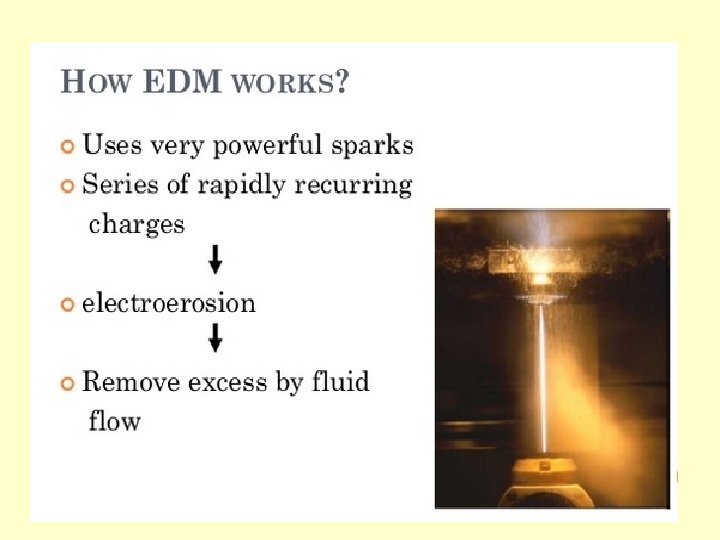
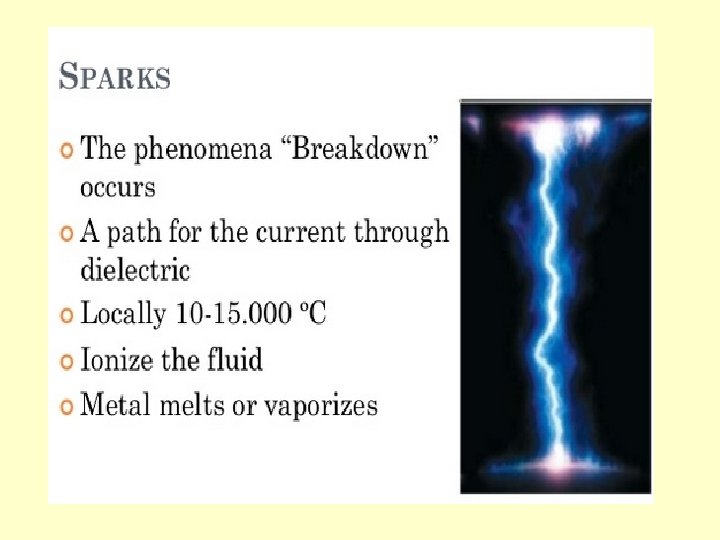
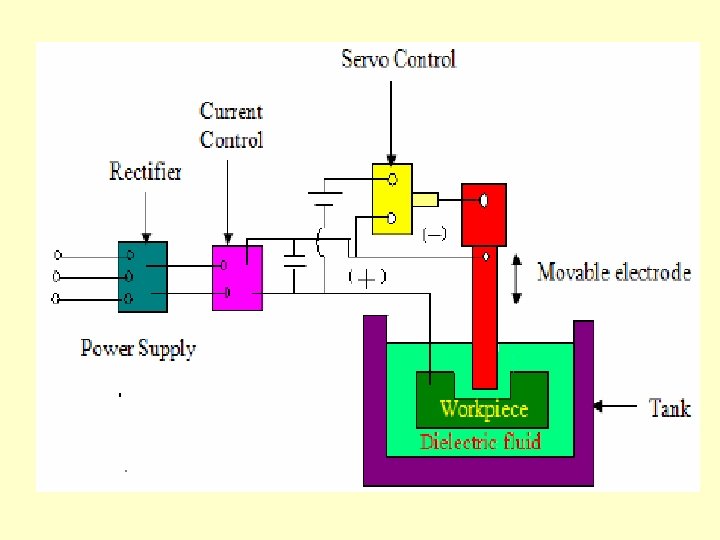
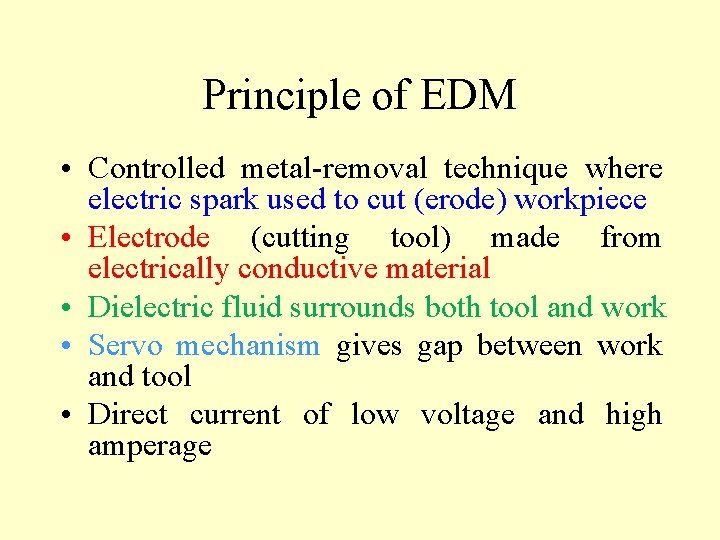
Principle of EDM • Controlled metal-removal technique where electric spark used to cut (erode) workpiece • Electrode (cutting tool) made from electrically conductive material • Dielectric fluid surrounds both tool and work • Servo mechanism gives gap between work and tool • Direct current of low voltage and high amperage
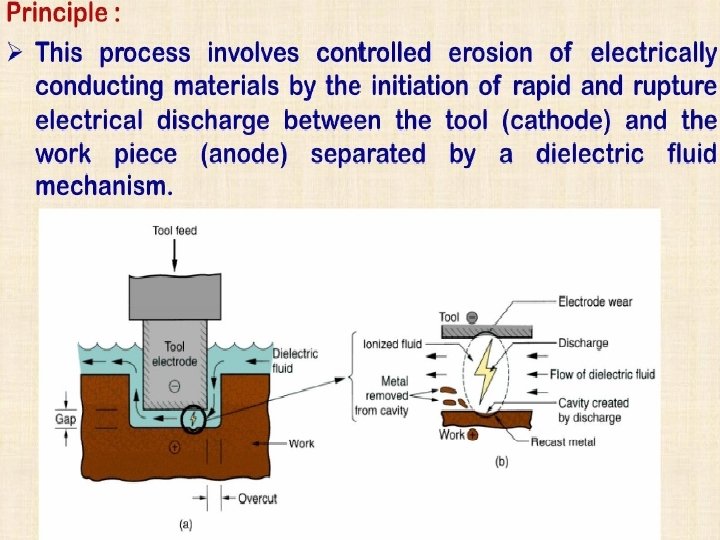
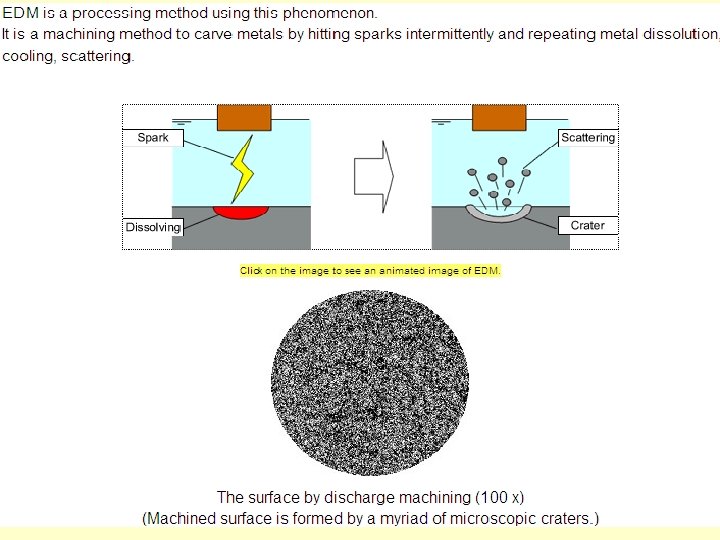
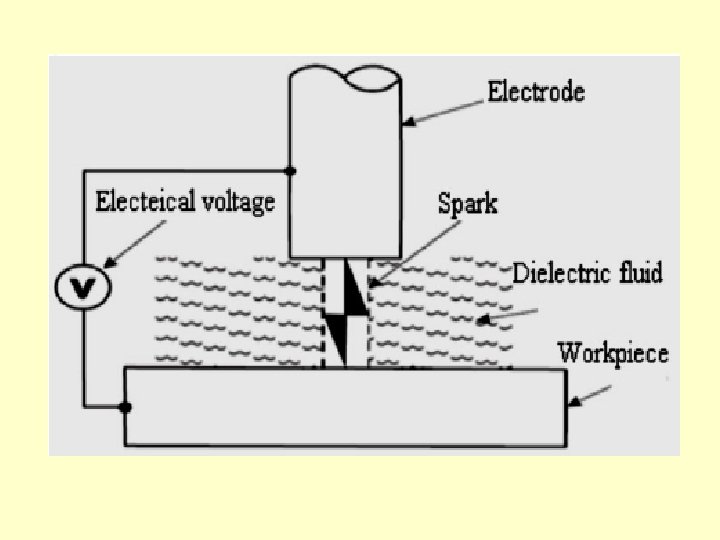
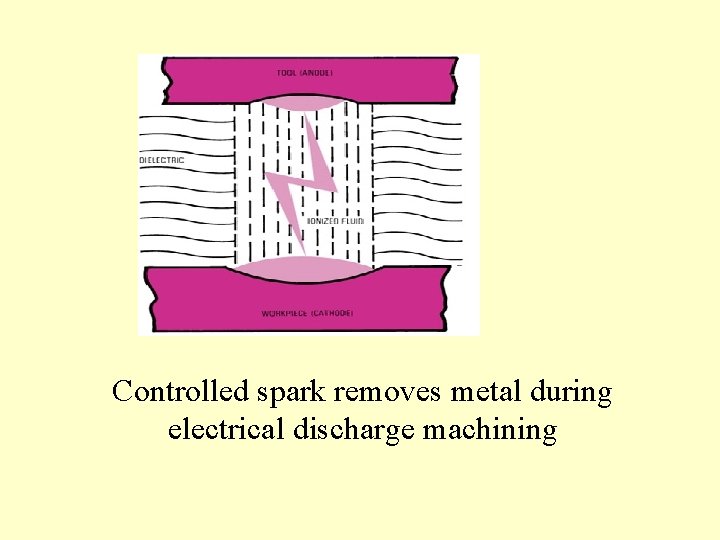
Controlled spark removes metal during electrical discharge machining
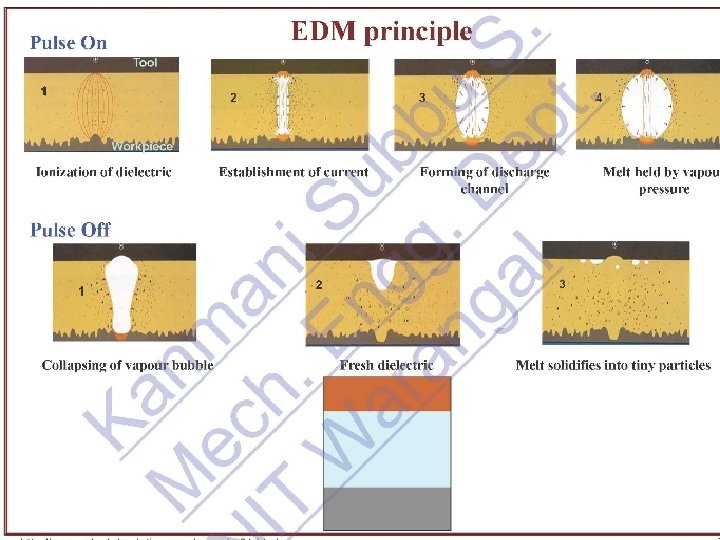
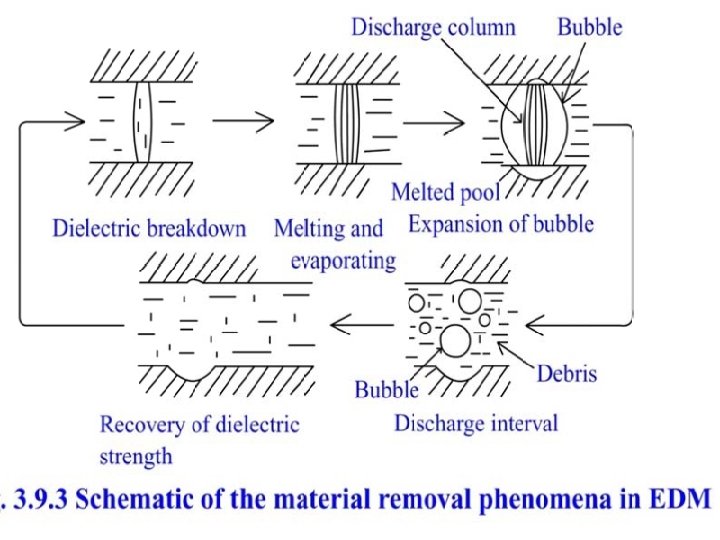
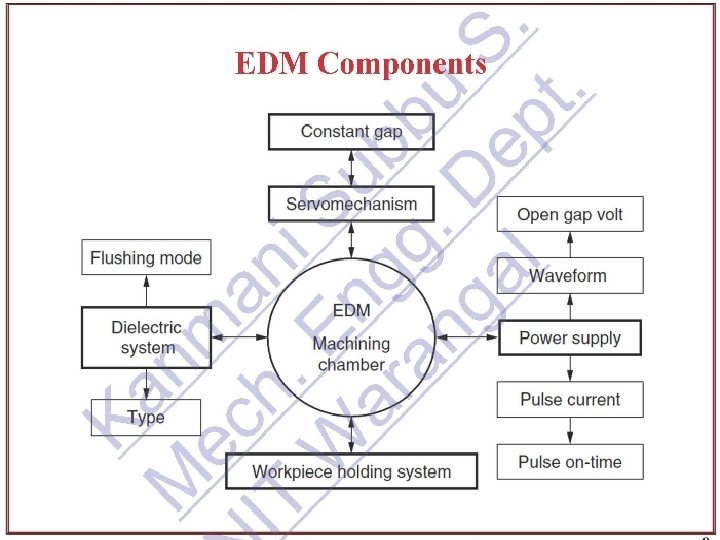
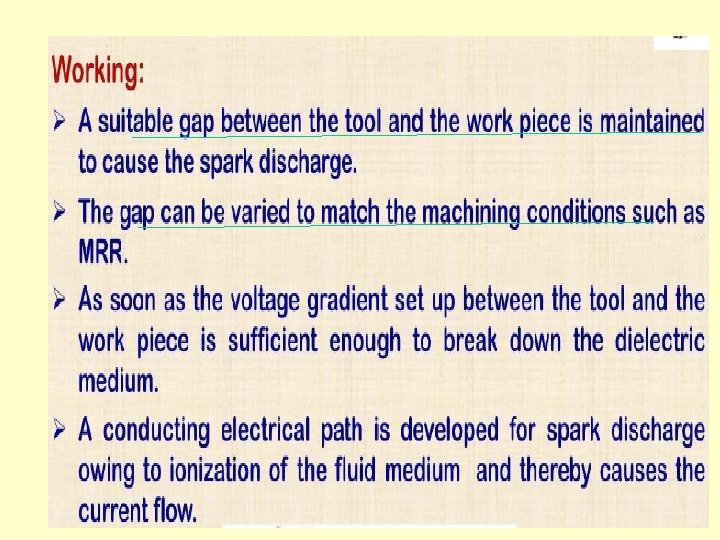
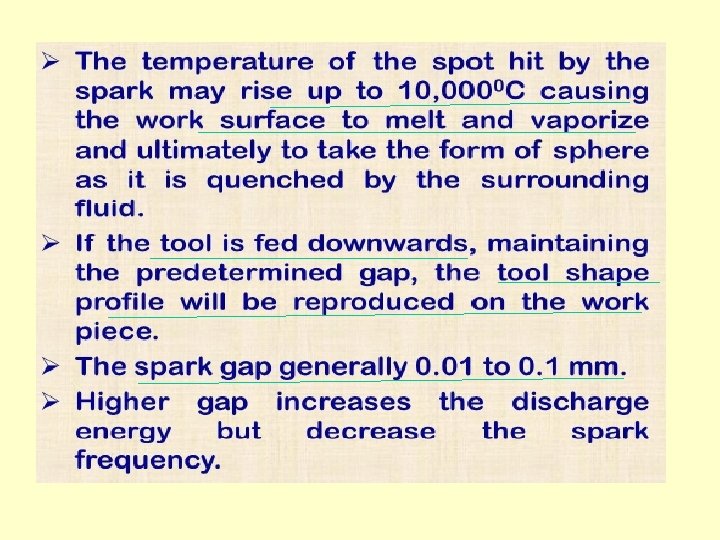
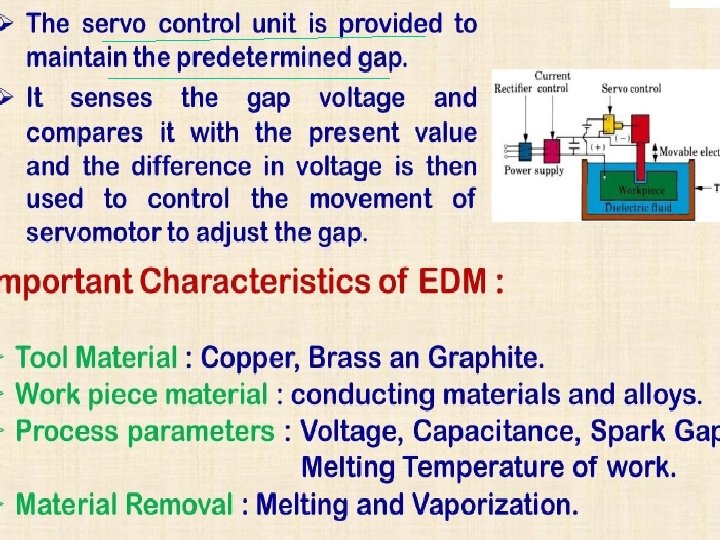
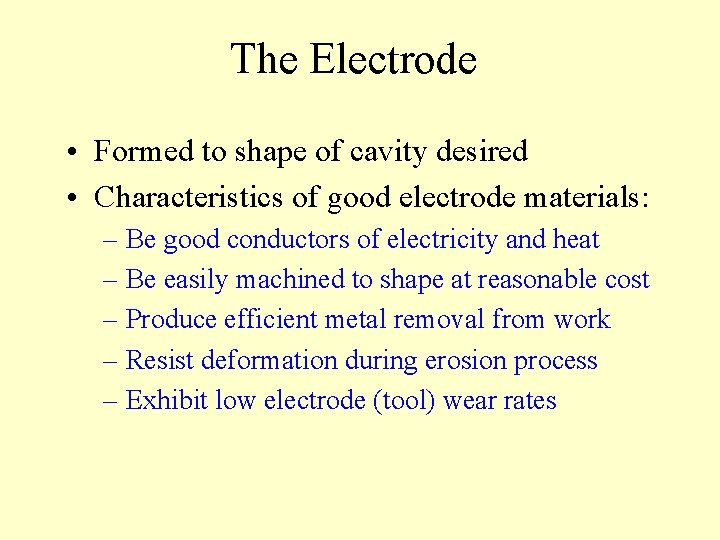
The Electrode • Formed to shape of cavity desired • Characteristics of good electrode materials: – Be good conductors of electricity and heat – Be easily machined to shape at reasonable cost – Produce efficient metal removal from work – Resist deformation during erosion process – Exhibit low electrode (tool) wear rates
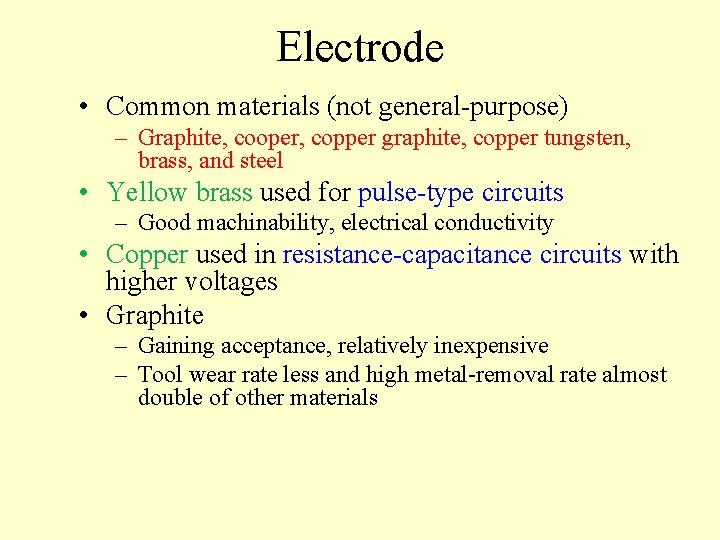
Electrode • Common materials (not general-purpose) – Graphite, cooper, copper graphite, copper tungsten, brass, and steel • Yellow brass used for pulse-type circuits – Good machinability, electrical conductivity • Copper used in resistance-capacitance circuits with higher voltages • Graphite – Gaining acceptance, relatively inexpensive – Tool wear rate less and high metal-removal rate almost double of other materials
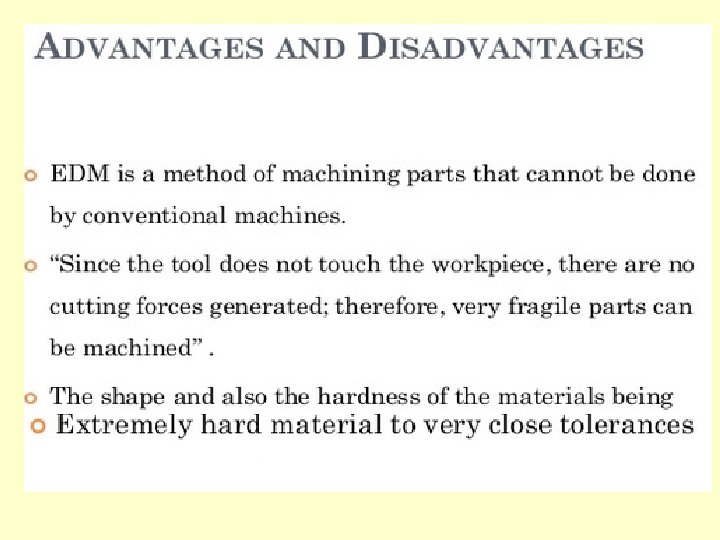
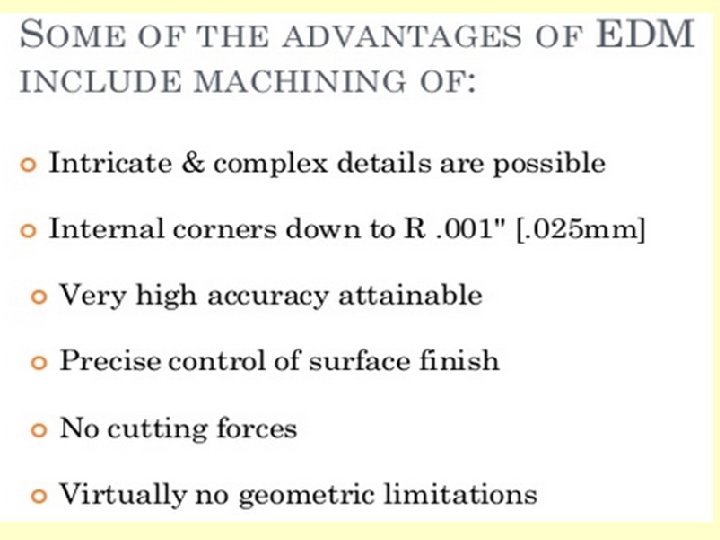
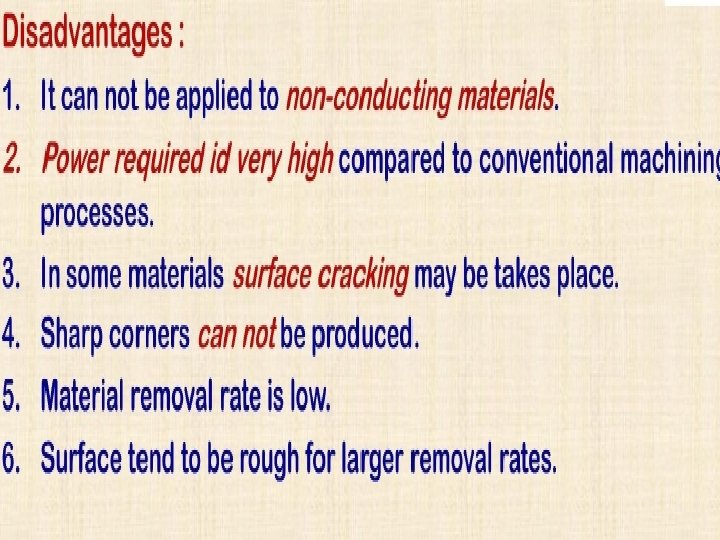

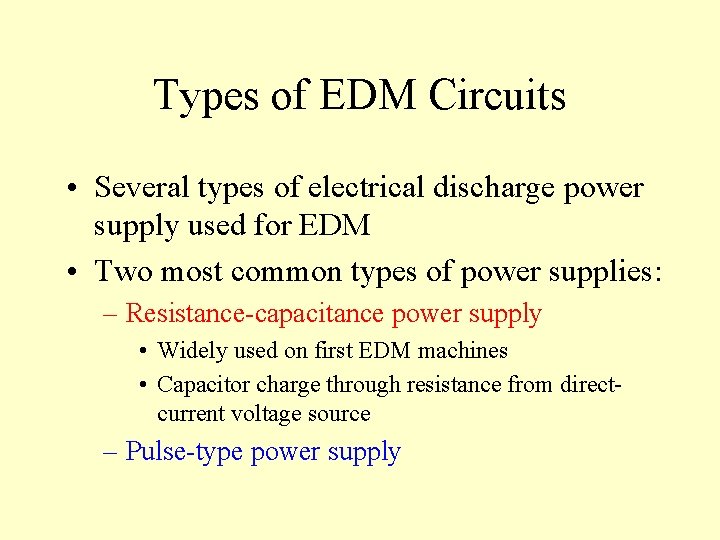
Types of EDM Circuits • Several types of electrical discharge power supply used for EDM • Two most common types of power supplies: – Resistance-capacitance power supply • Widely used on first EDM machines • Capacitor charge through resistance from directcurrent voltage source – Pulse-type power supply
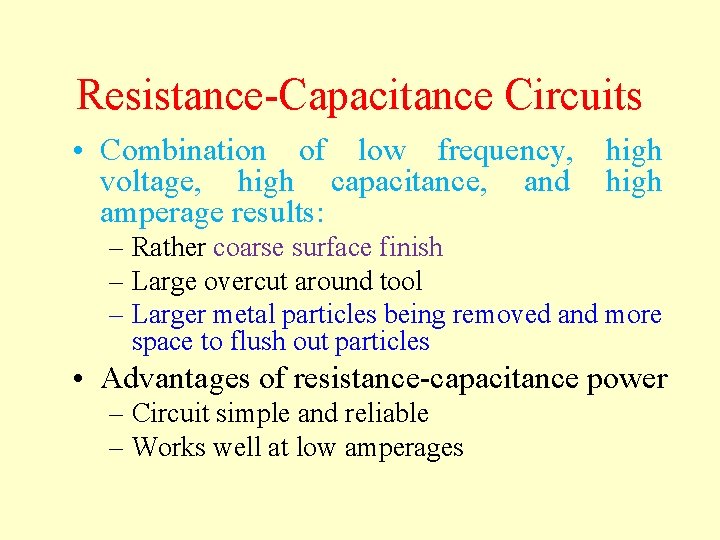
Resistance-Capacitance Circuits • Combination of low frequency, high voltage, high capacitance, and high amperage results: – Rather coarse surface finish – Large overcut around tool – Larger metal particles being removed and more space to flush out particles • Advantages of resistance-capacitance power – Circuit simple and reliable – Works well at low amperages
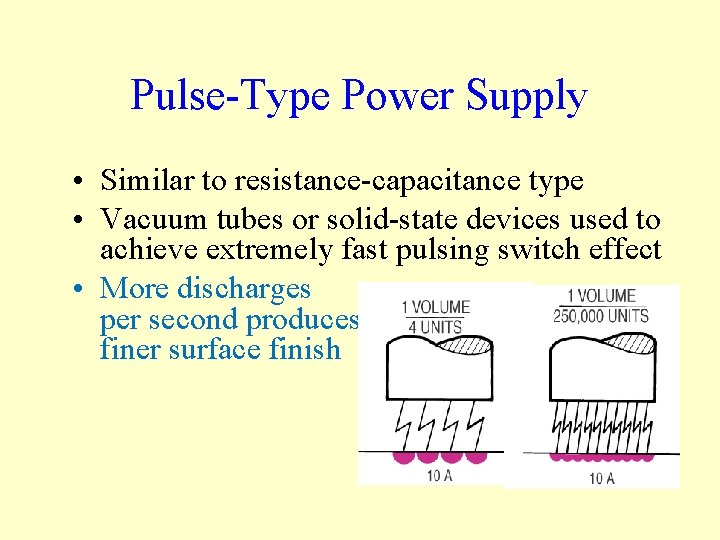
Pulse-Type Power Supply • Similar to resistance-capacitance type • Vacuum tubes or solid-state devices used to achieve extremely fast pulsing switch effect • More discharges per second produces finer surface finish
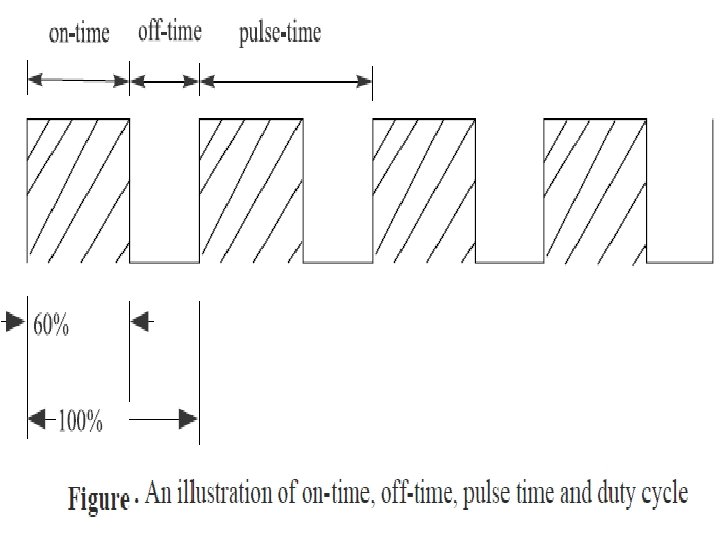
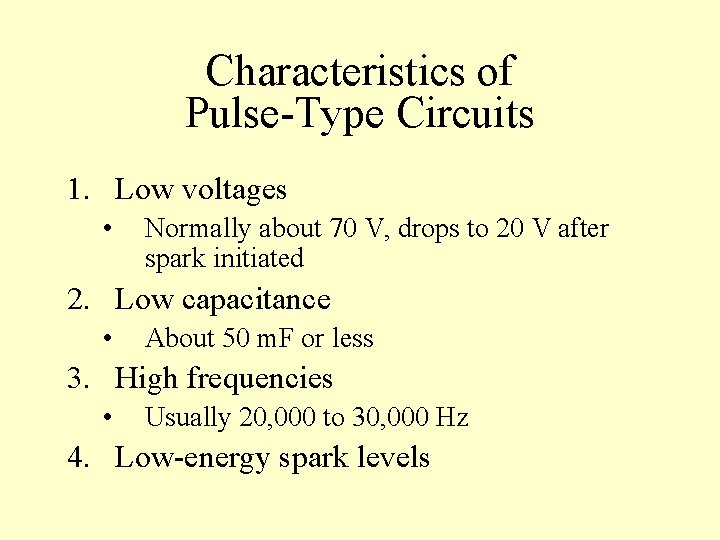
Characteristics of Pulse-Type Circuits 1. Low voltages • Normally about 70 V, drops to 20 V after spark initiated 2. Low capacitance • About 50 m. F or less 3. High frequencies • Usually 20, 000 to 30, 000 Hz 4. Low-energy spark levels
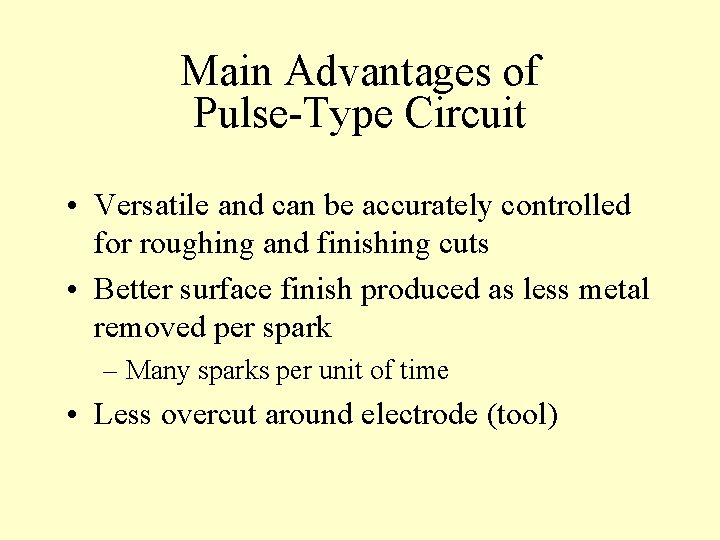
Main Advantages of Pulse-Type Circuit • Versatile and can be accurately controlled for roughing and finishing cuts • Better surface finish produced as less metal removed per spark – Many sparks per unit of time • Less overcut around electrode (tool)
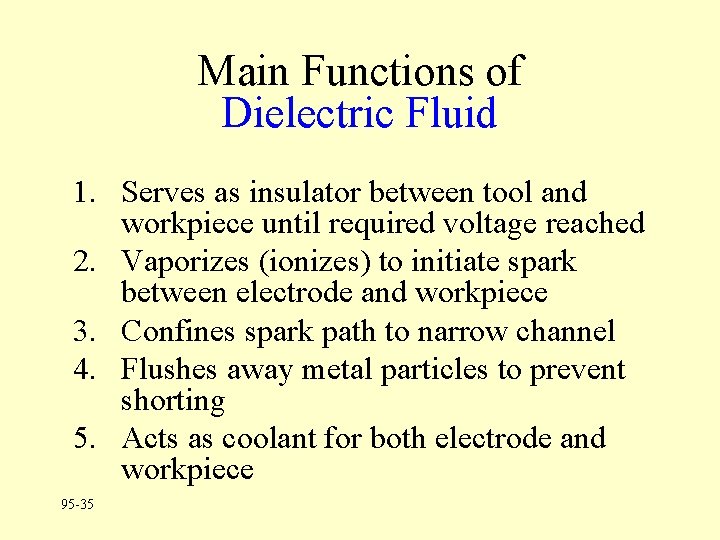
Main Functions of Dielectric Fluid 1. Serves as insulator between tool and workpiece until required voltage reached 2. Vaporizes (ionizes) to initiate spark between electrode and workpiece 3. Confines spark path to narrow channel 4. Flushes away metal particles to prevent shorting 5. Acts as coolant for both electrode and workpiece 95 -35
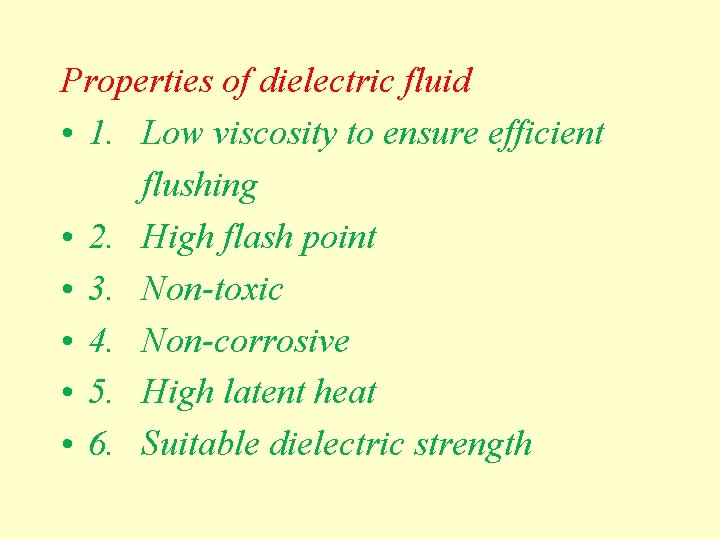
Properties of dielectric fluid • 1. Low viscosity to ensure efficient flushing • 2. High flash point • 3. Non-toxic • 4. Non-corrosive • 5. High latent heat • 6. Suitable dielectric strength
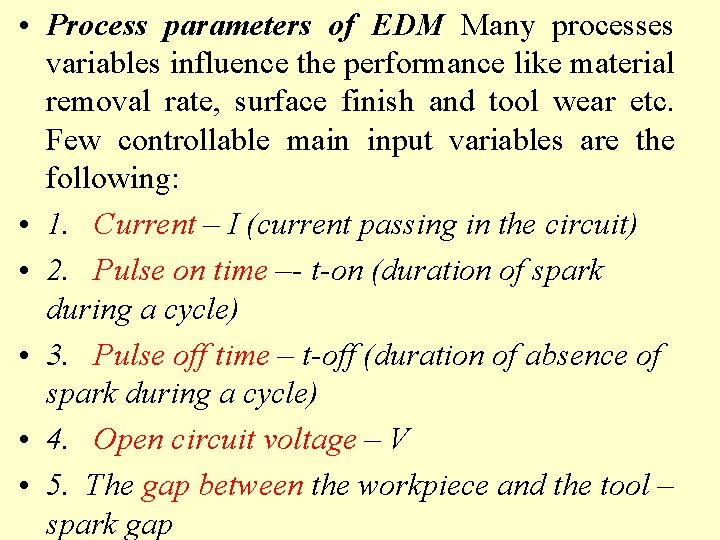
• Process parameters of EDM Many processes variables influence the performance like material removal rate, surface finish and tool wear etc. Few controllable main input variables are the following: • 1. Current – I (current passing in the circuit) • 2. Pulse on time –- t-on (duration of spark during a cycle) • 3. Pulse off time – t-off (duration of absence of spark during a cycle) • 4. Open circuit voltage – V • 5. The gap between the workpiece and the tool – spark gap
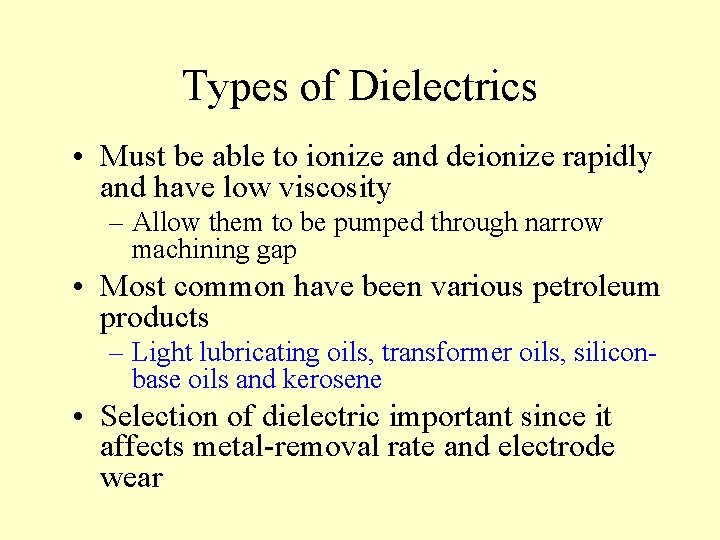
Types of Dielectrics • Must be able to ionize and deionize rapidly and have low viscosity – Allow them to be pumped through narrow machining gap • Most common have been various petroleum products – Light lubricating oils, transformer oils, siliconbase oils and kerosene • Selection of dielectric important since it affects metal-removal rate and electrode wear
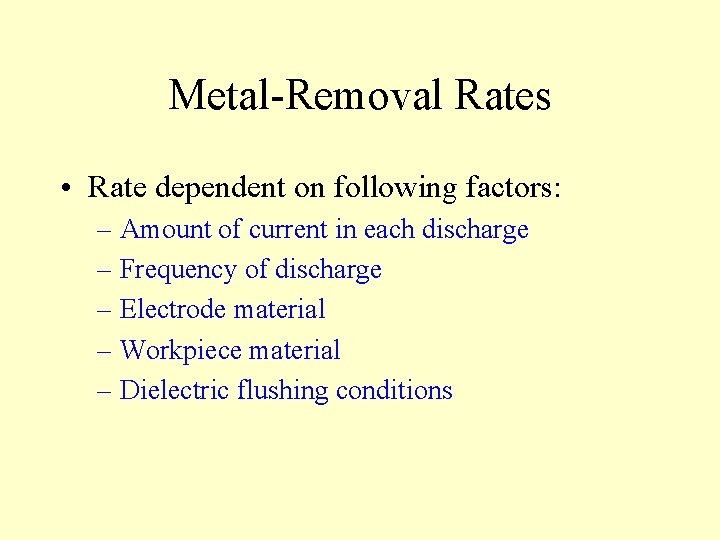
Metal-Removal Rates • Rate dependent on following factors: – Amount of current in each discharge – Frequency of discharge – Electrode material – Workpiece material – Dielectric flushing conditions

Electrode (Tool) Wear • During discharge process, tool subject to wear or erosion • Difficult to hold close tolerances as tool gradually loses its shape during machining operation
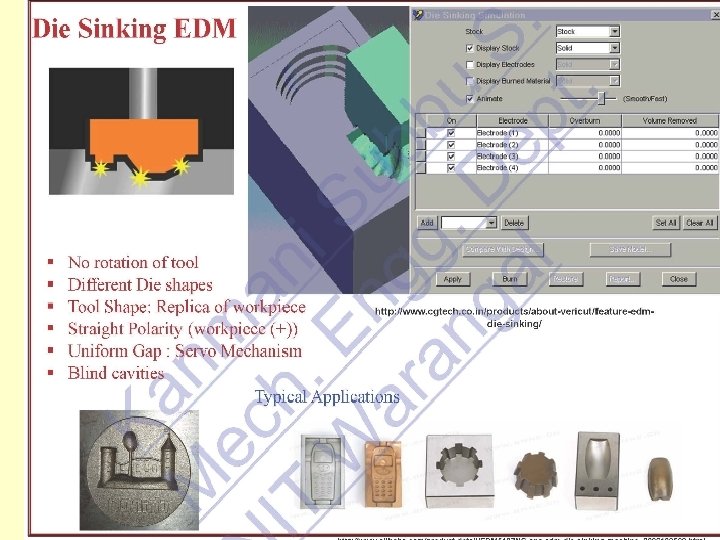
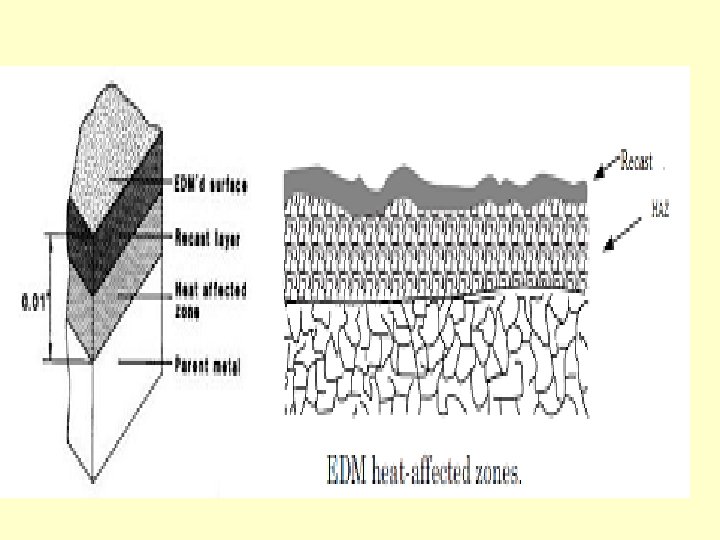
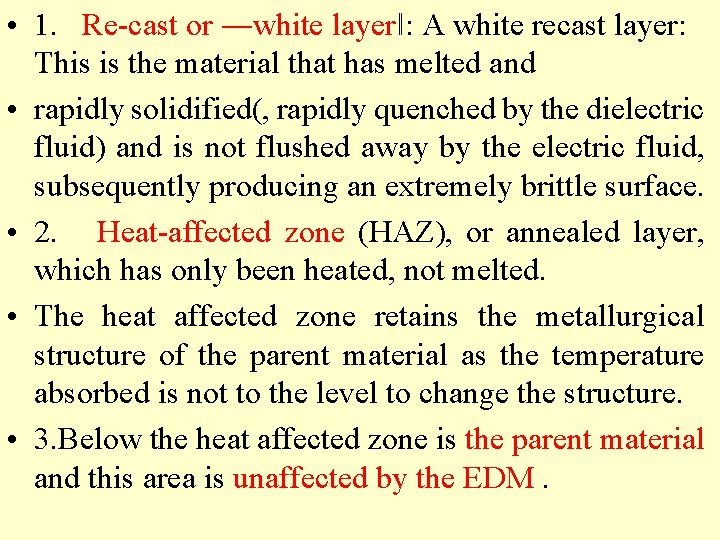
• 1. Re-cast or ―white layer‖: A white recast layer: This is the material that has melted and • rapidly solidified(, rapidly quenched by the dielectric fluid) and is not flushed away by the electric fluid, subsequently producing an extremely brittle surface. • 2. Heat-affected zone (HAZ), or annealed layer, which has only been heated, not melted. • The heat affected zone retains the metallurgical structure of the parent material as the temperature absorbed is not to the level to change the structure. • 3. Below the heat affected zone is the parent material and this area is unaffected by the EDM.
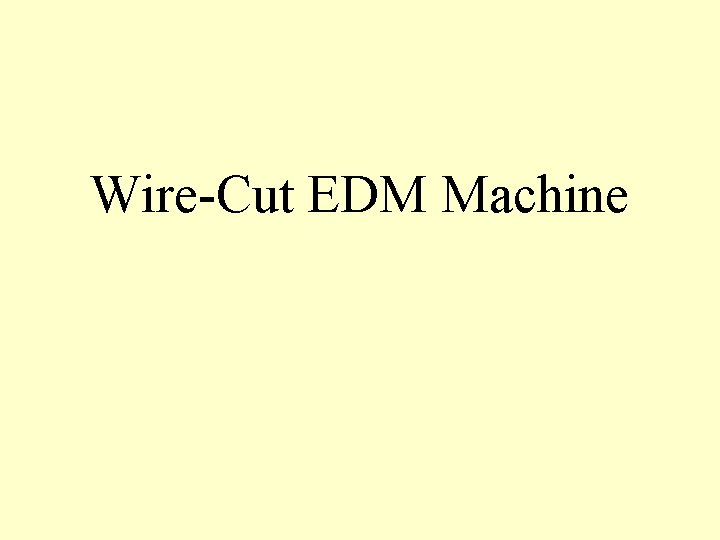
Wire-Cut EDM Machine
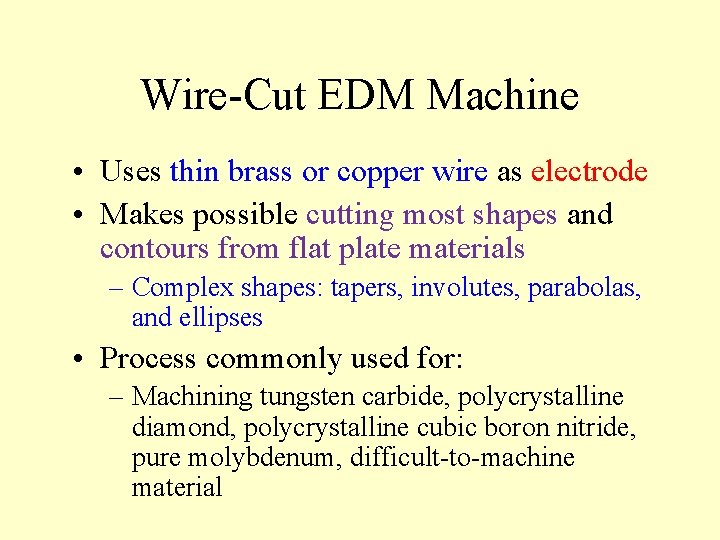
Wire-Cut EDM Machine • Uses thin brass or copper wire as electrode • Makes possible cutting most shapes and contours from flat plate materials – Complex shapes: tapers, involutes, parabolas, and ellipses • Process commonly used for: – Machining tungsten carbide, polycrystalline diamond, polycrystalline cubic boron nitride, pure molybdenum, difficult-to-machine material
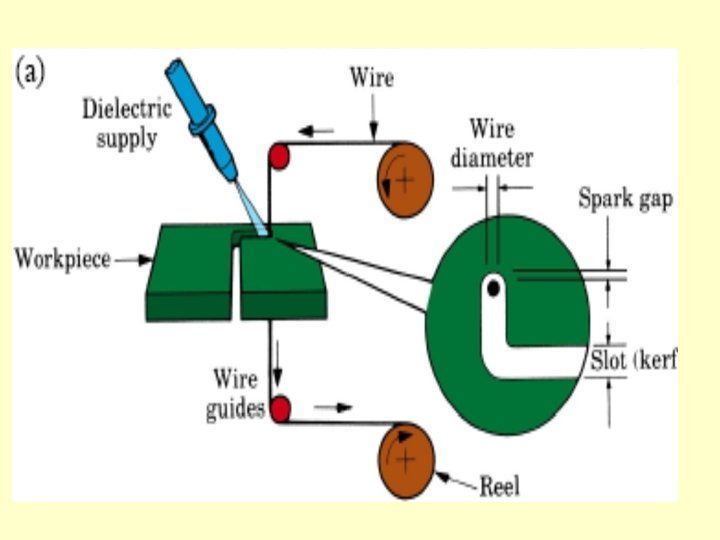
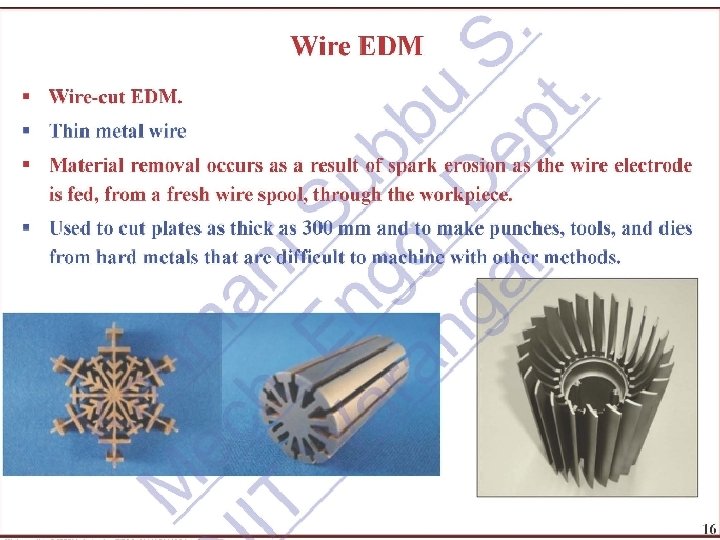
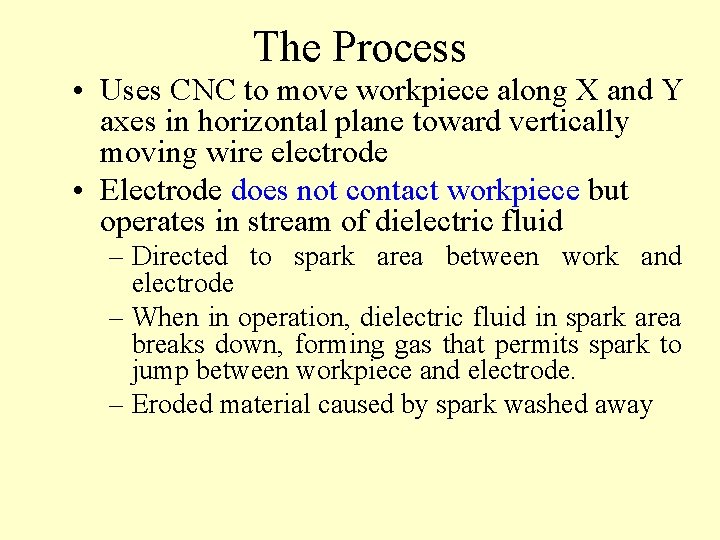
The Process • Uses CNC to move workpiece along X and Y axes in horizontal plane toward vertically moving wire electrode • Electrode does not contact workpiece but operates in stream of dielectric fluid – Directed to spark area between work and electrode – When in operation, dielectric fluid in spark area breaks down, forming gas that permits spark to jump between workpiece and electrode. – Eroded material caused by spark washed away
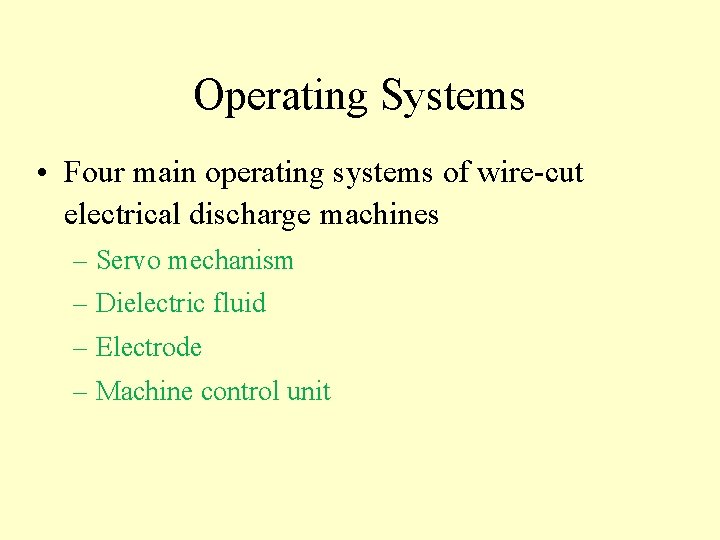
Operating Systems • Four main operating systems of wire-cut electrical discharge machines – Servo mechanism – Dielectric fluid – Electrode – Machine control unit
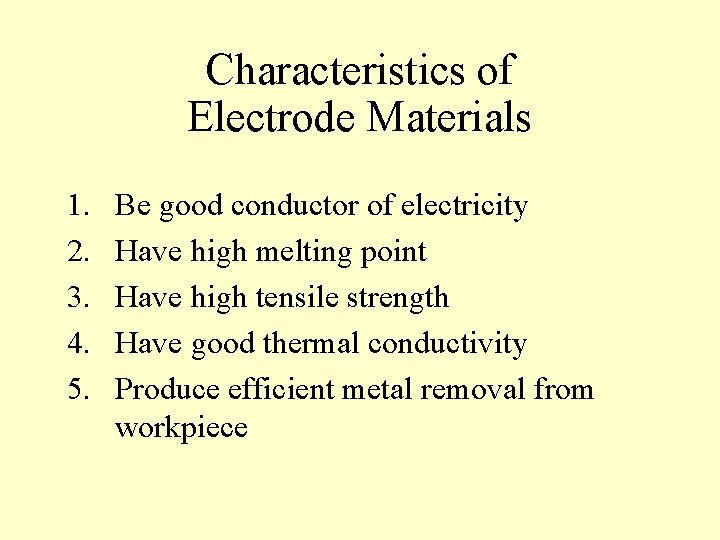
Characteristics of Electrode Materials 1. 2. 3. 4. 5. Be good conductor of electricity Have high melting point Have high tensile strength Have good thermal conductivity Produce efficient metal removal from workpiece
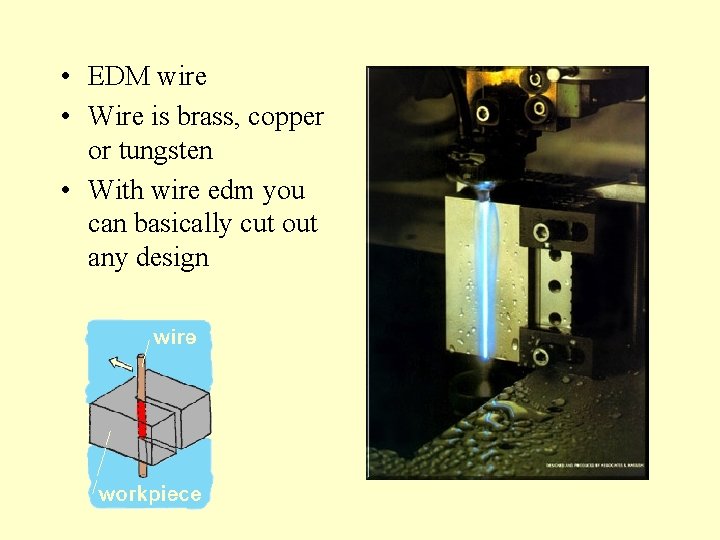
• EDM wire • Wire is brass, copper or tungsten • With wire edm you can basically cut out any design
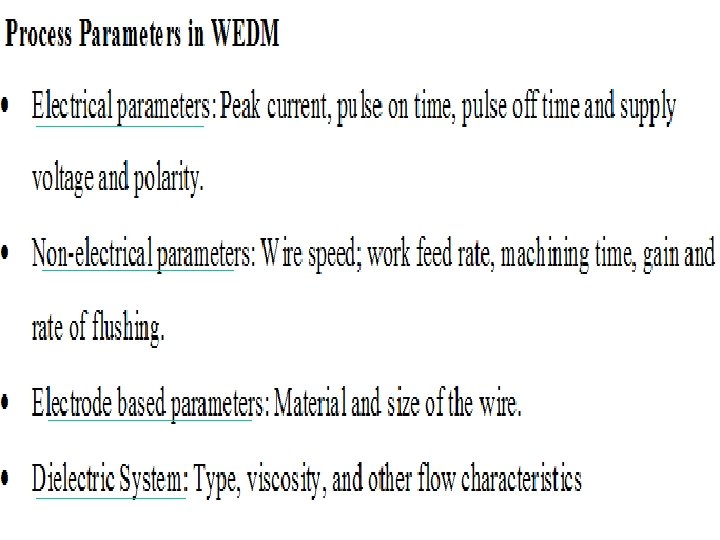
Output dan hasil erkam
Srp electric
Dr deepak raju
Buddyzm założenia
Broad differential meaning
Raju venugopalan
Blastula
Raju balakrishnan
Nara images
Ranga raju vatsavai
Edm services inc
Alur input hasil edm
Disciplina edm
Edm
Edm arc generator schematic
Edm data model
Edm council
Edm wire cut machine
Milling machine
Environmental impact of cnc machining
Primary machining
Machining process
Ultrasonic machining module
Chemical blanking
What is the expected life of the nozzles used in wjm
Laser beam machining
Flexible machining cell
Electron beam cutting
Qualex machining
The gun in ebm is used in mode
Surface finish symbols
Schematic diagram of abrasive jet machining
Characteristics of unconventional machining process
Ajm process
Micro machining processes
Machining operations
Advantages of electrochemical machining
Abrasive machining and finishing operations
Electrochemical machining animation
Classification of modern machining process
Contoh mesin non konvensional
"machining"
Theory of metal machining
High speed machining titanium
Prismatic machining
High speed machining definition
Classification of modern machining process
Machining fundamentals 10th edition
Spc machining
Machining process
"machining"
Electron beam machining diagram
Modular tooling plates