Celltrack MIU 01 Machine Interface Unit 01 MIU
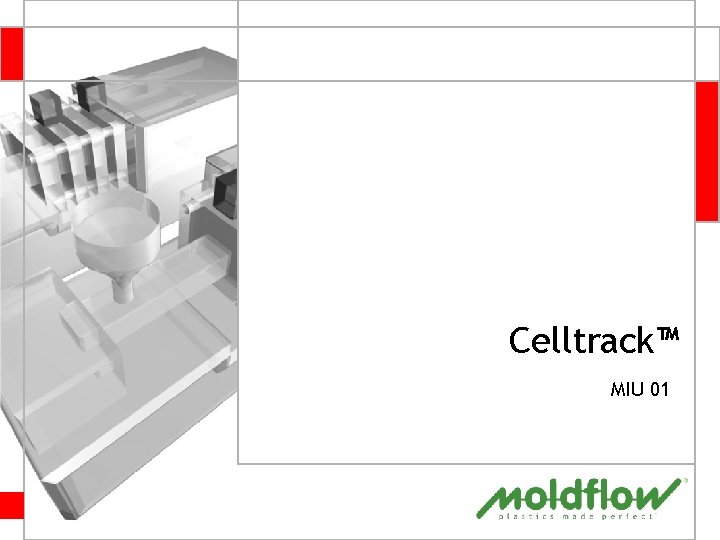
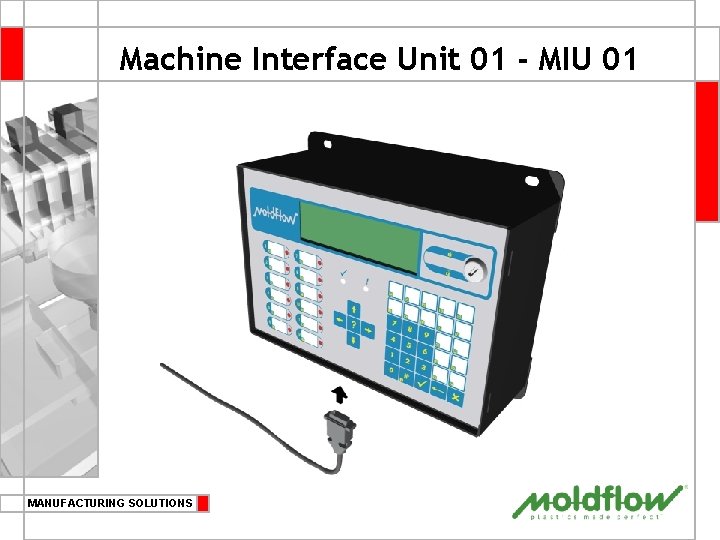
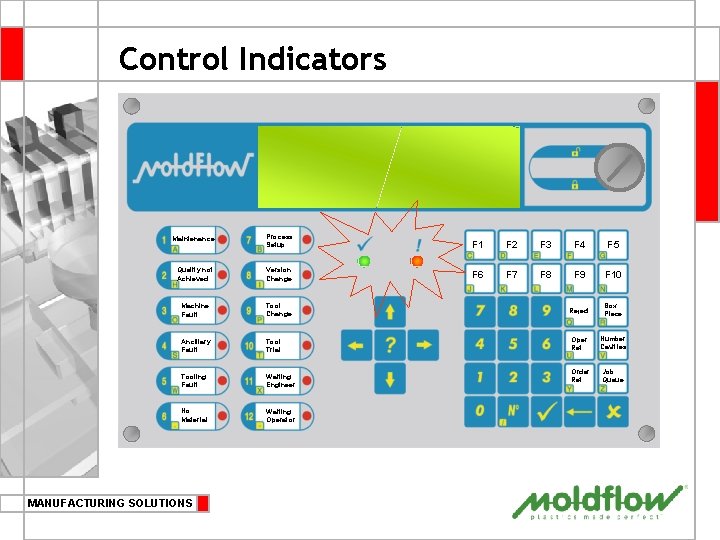
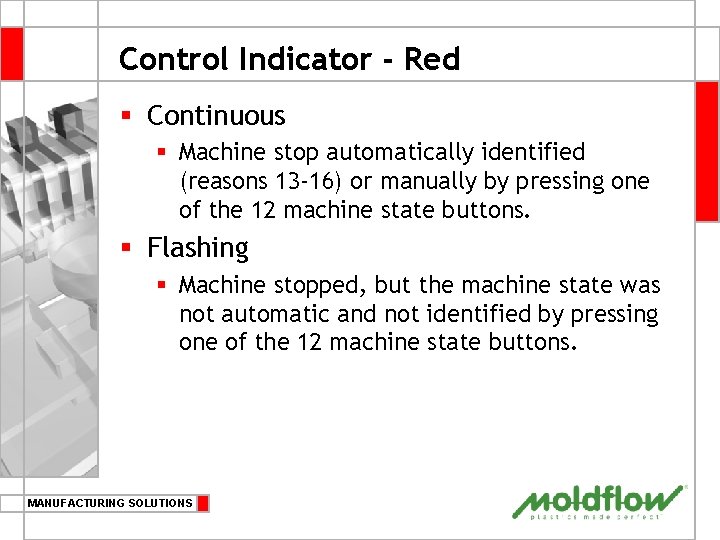

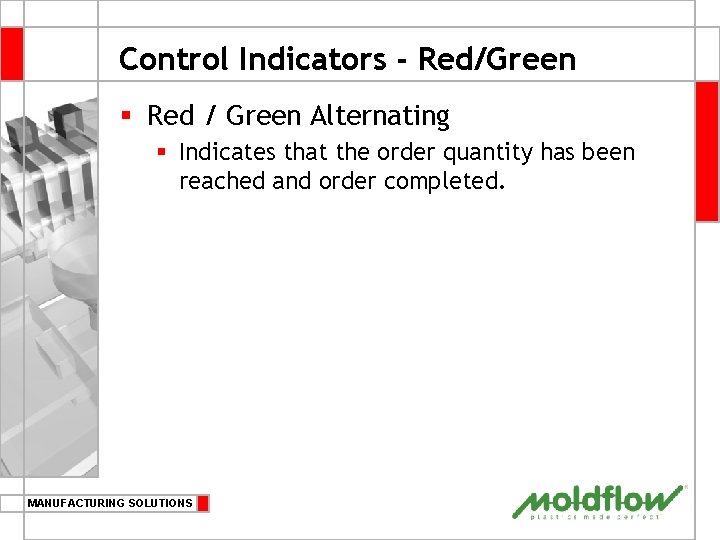
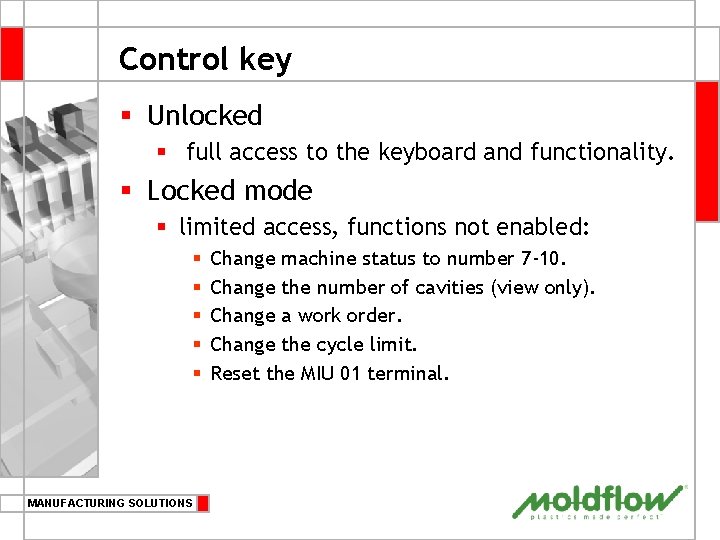
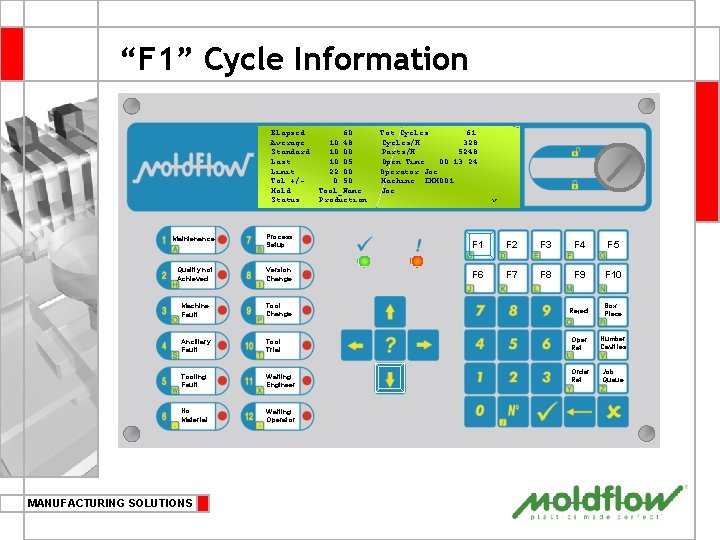
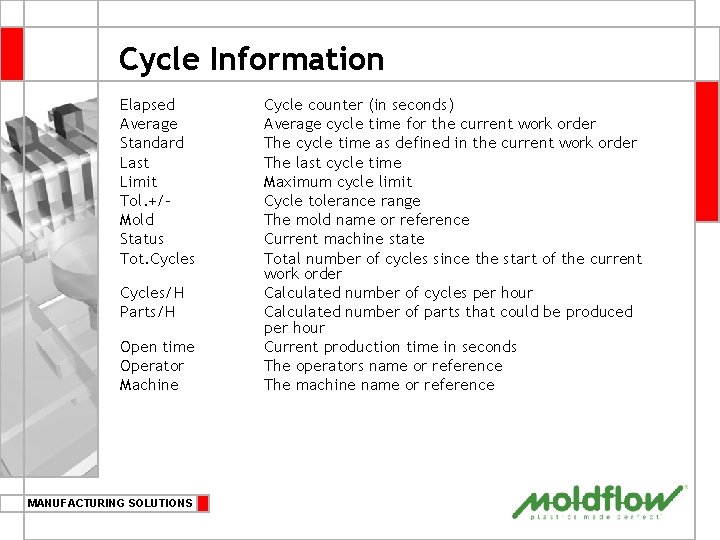
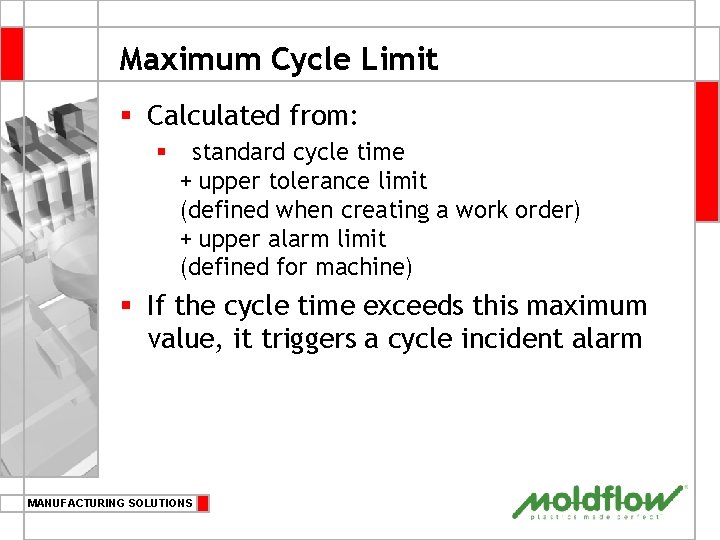
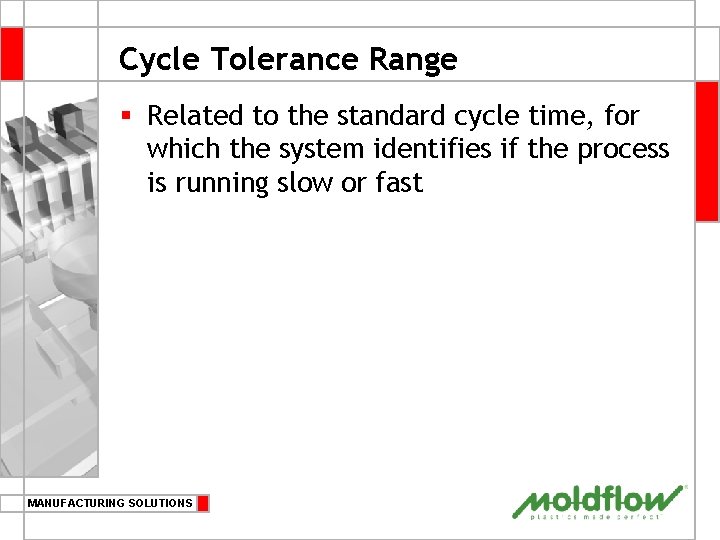
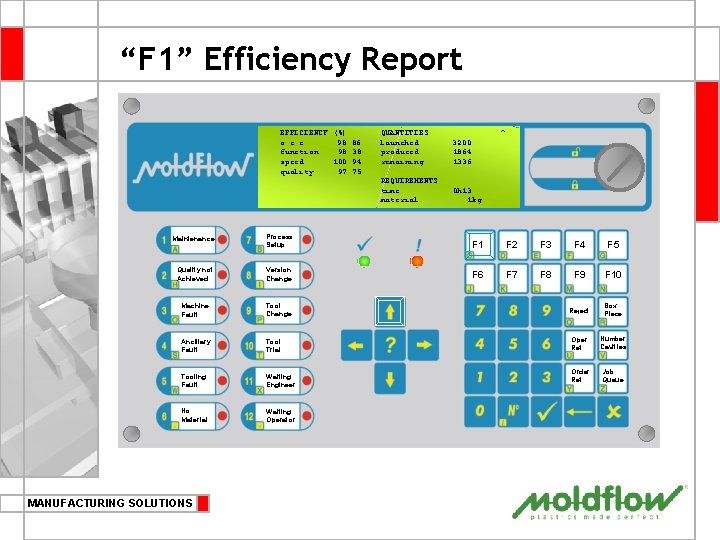
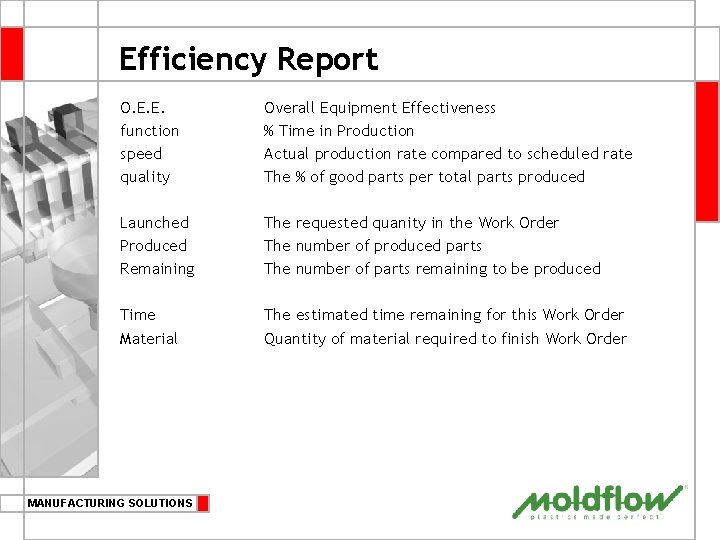
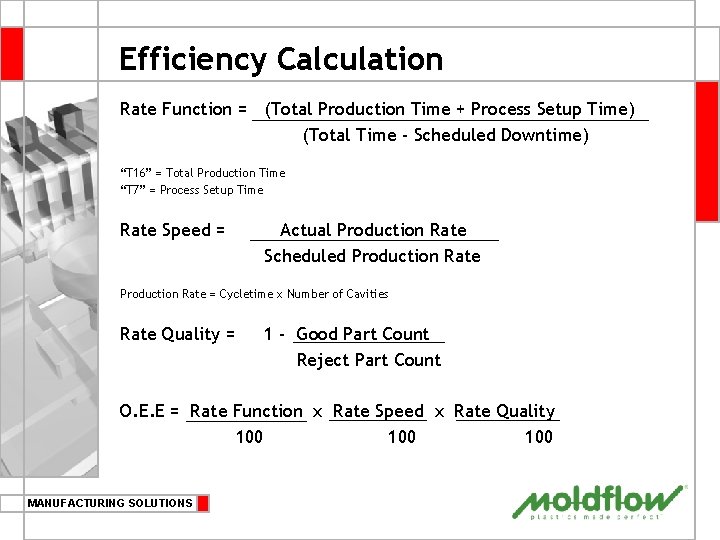
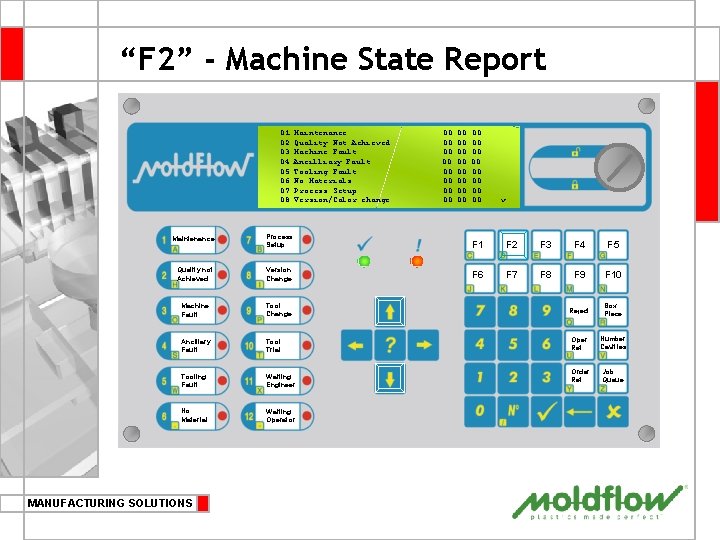
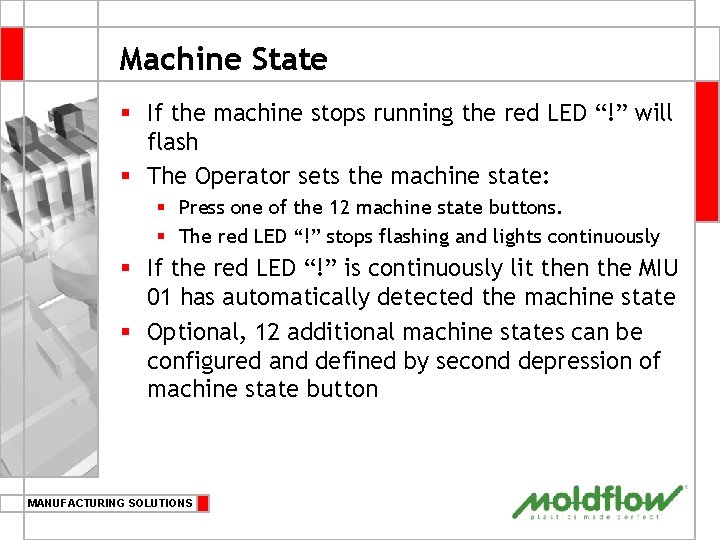
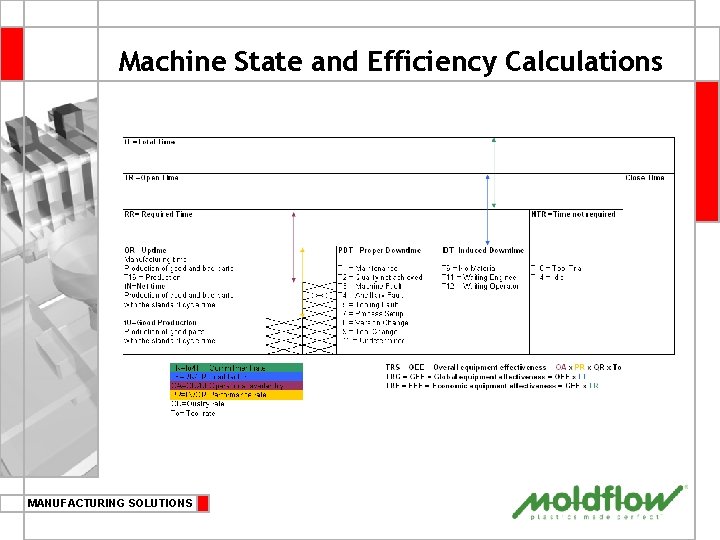
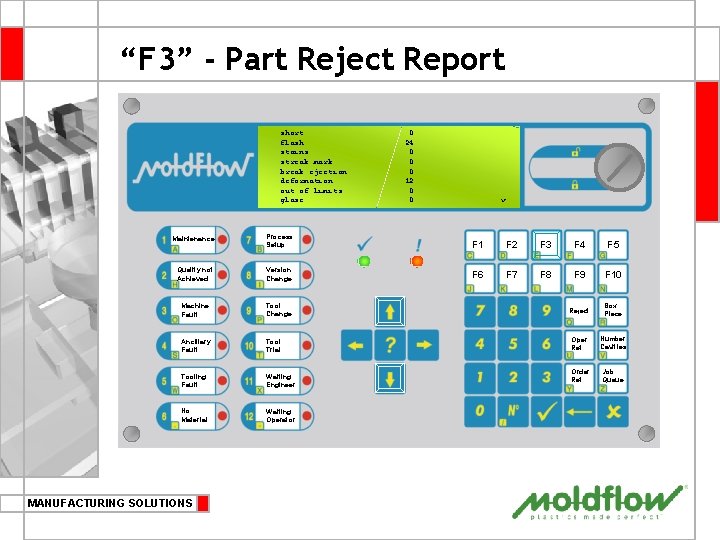
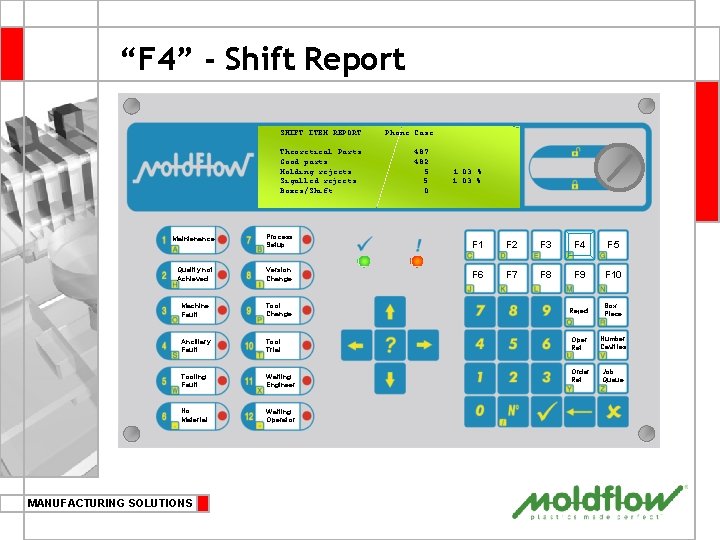
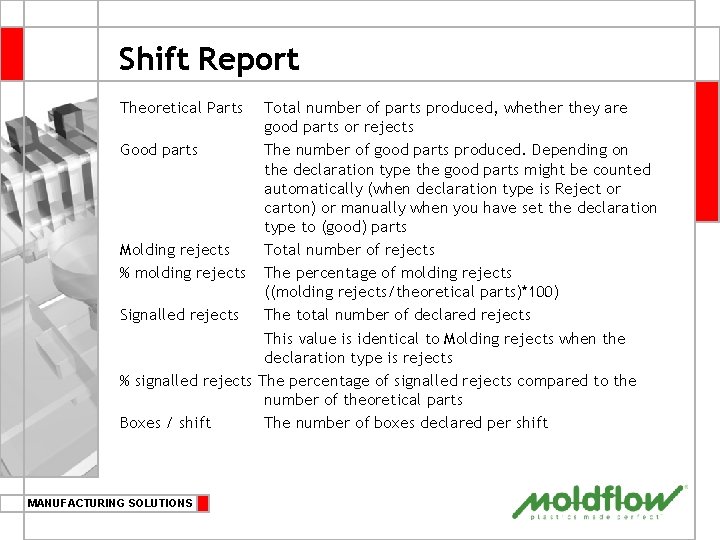
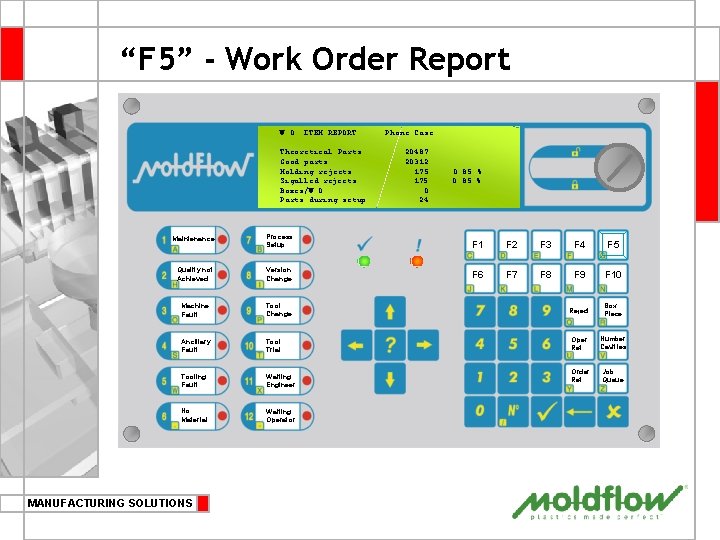
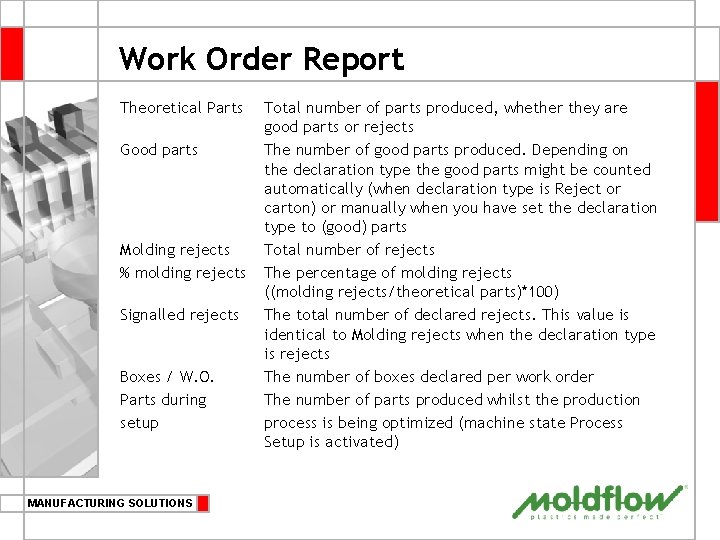
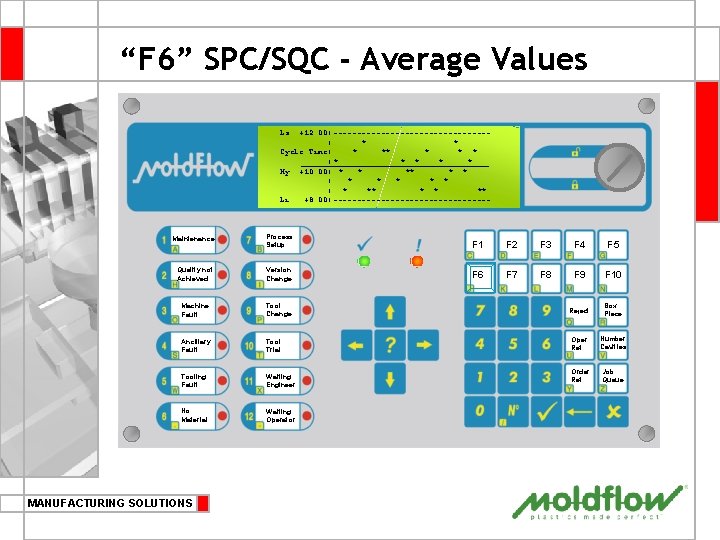
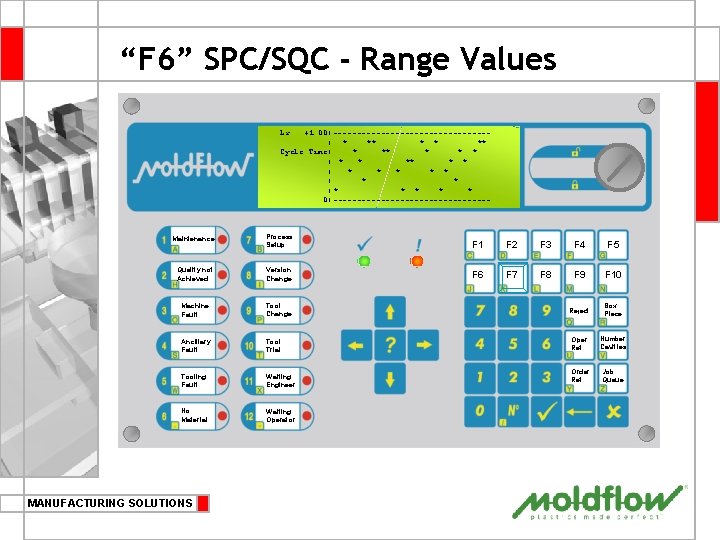
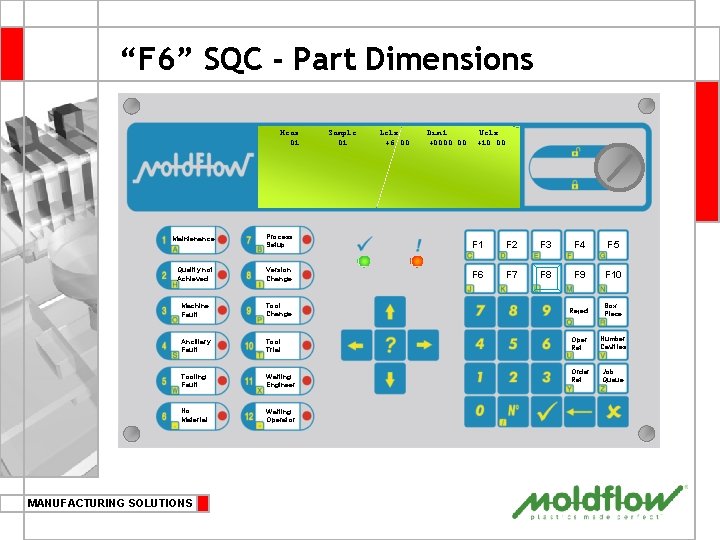
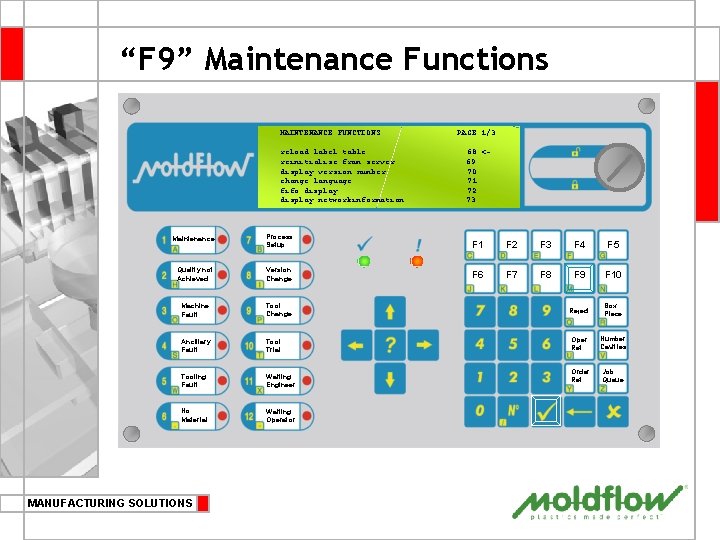
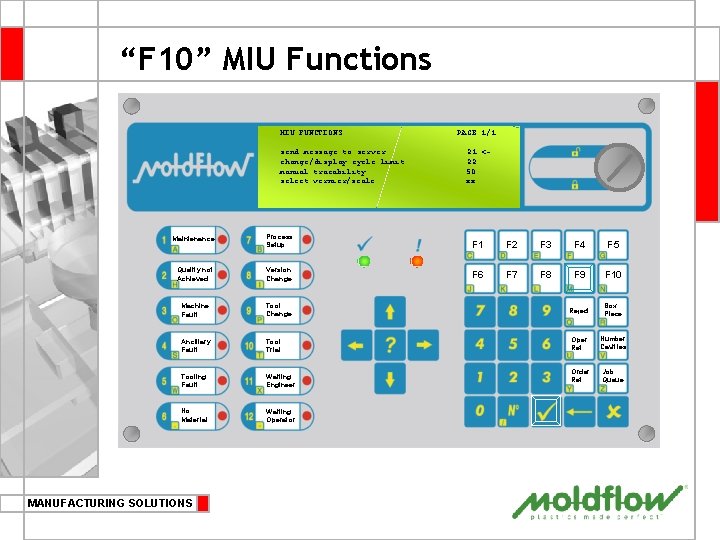
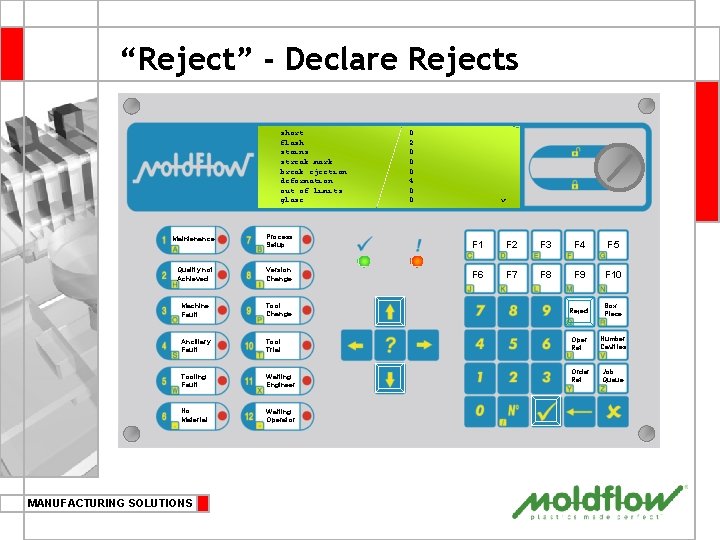
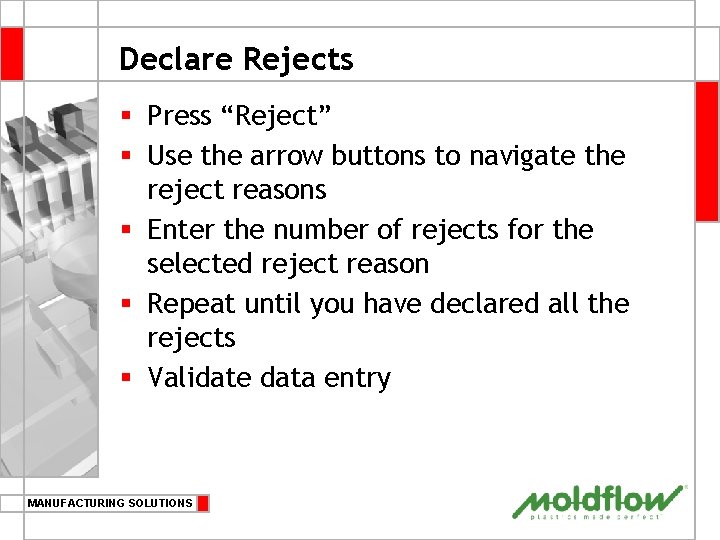
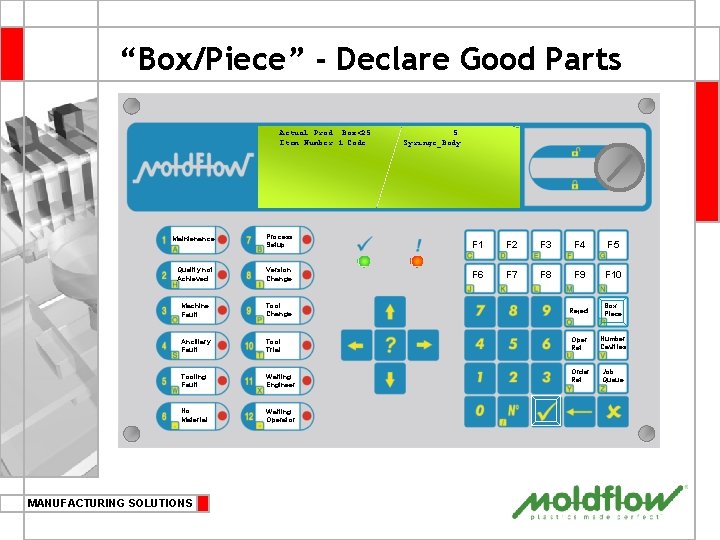
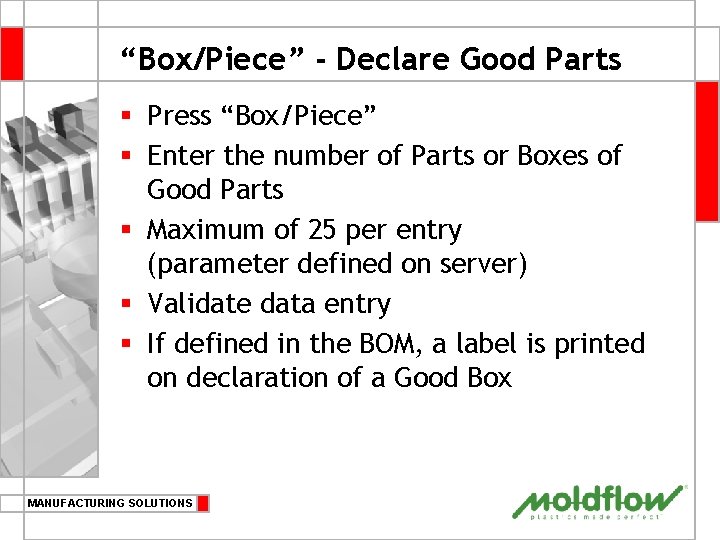
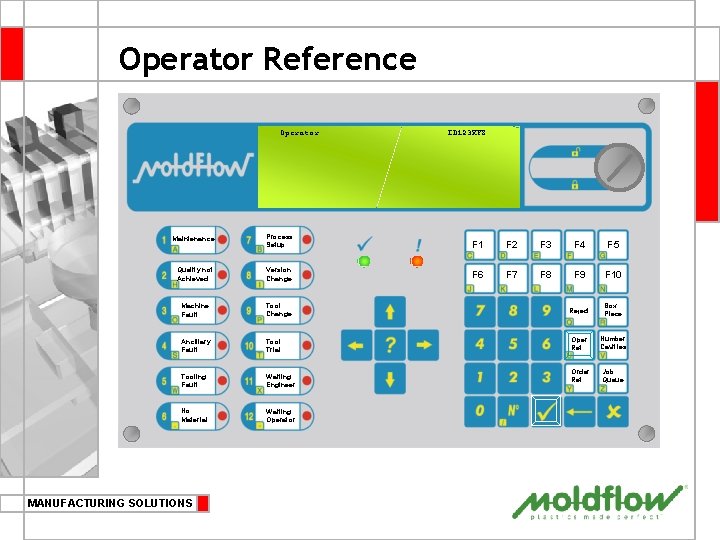
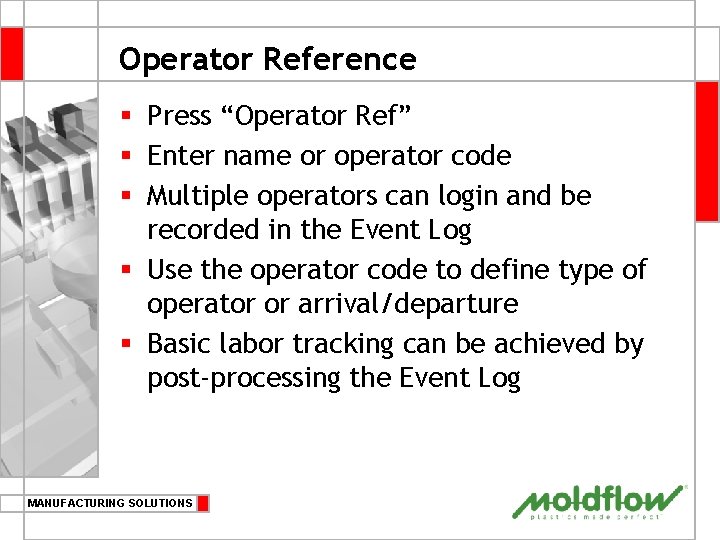
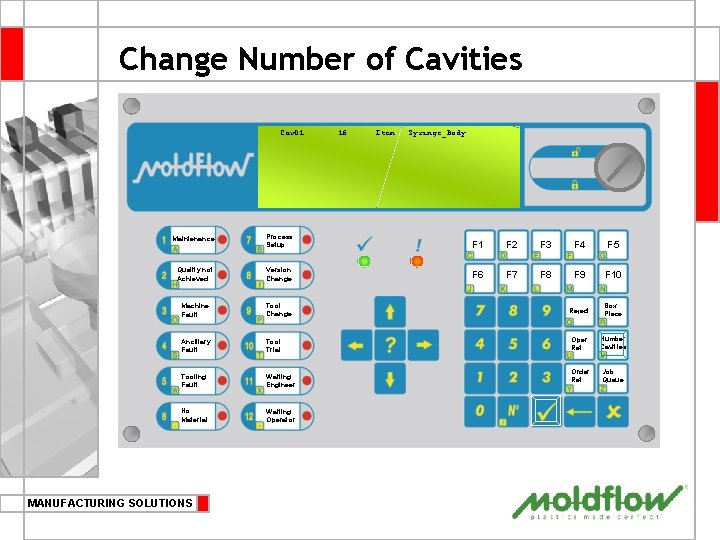
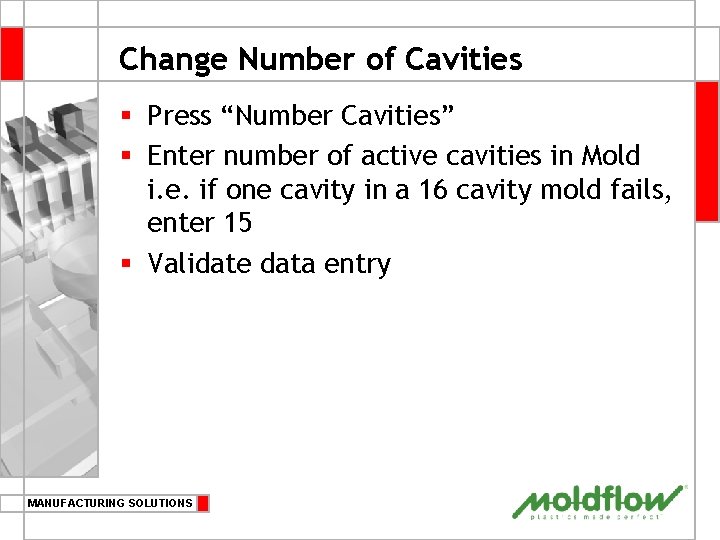
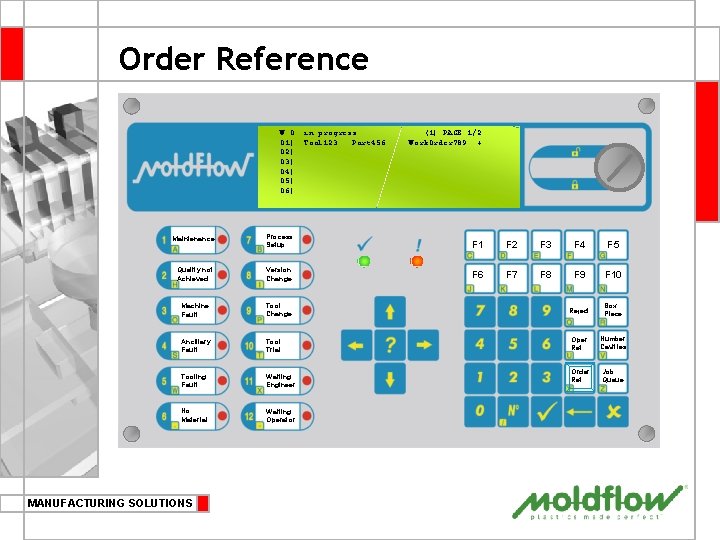
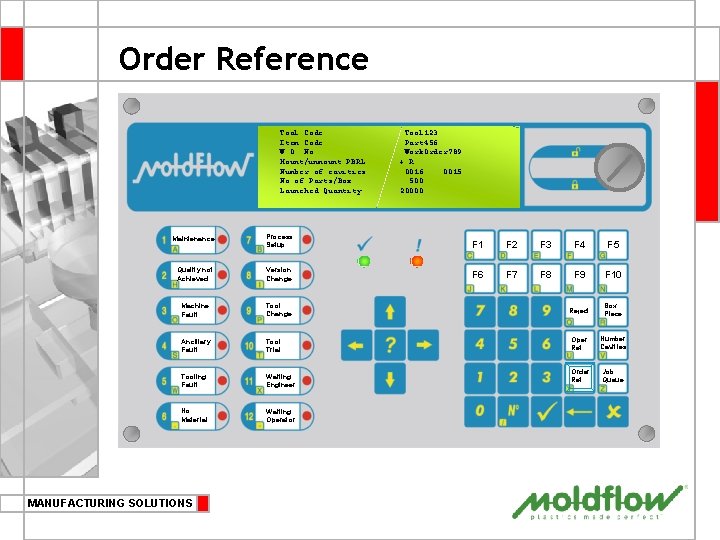
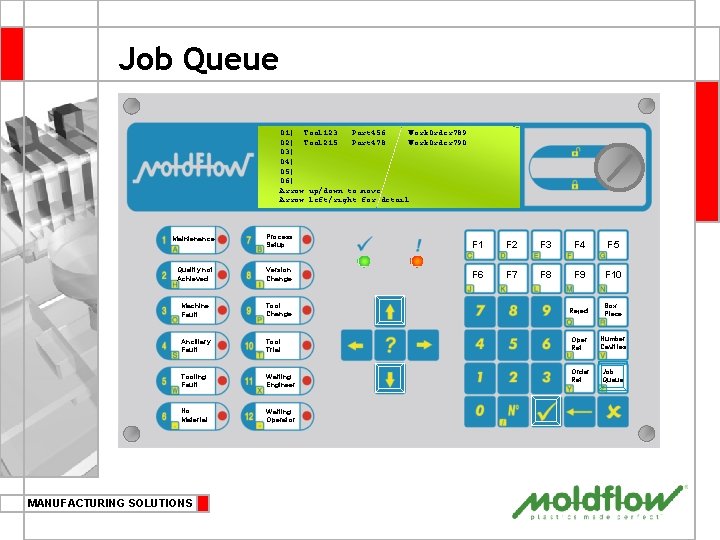
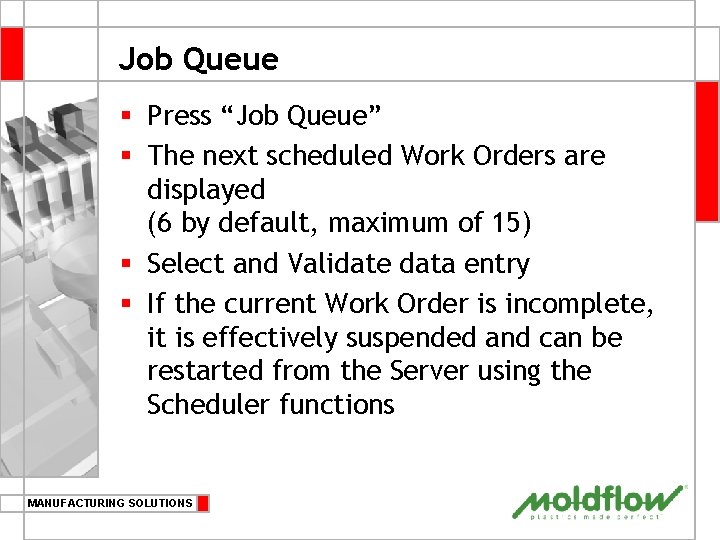
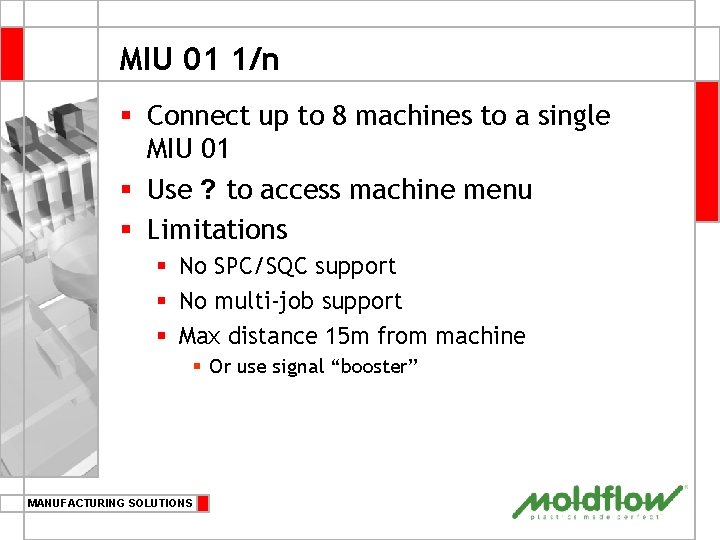
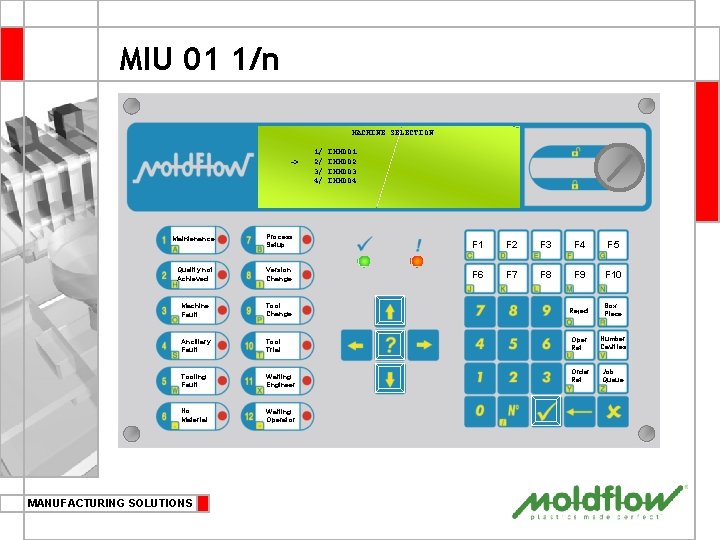
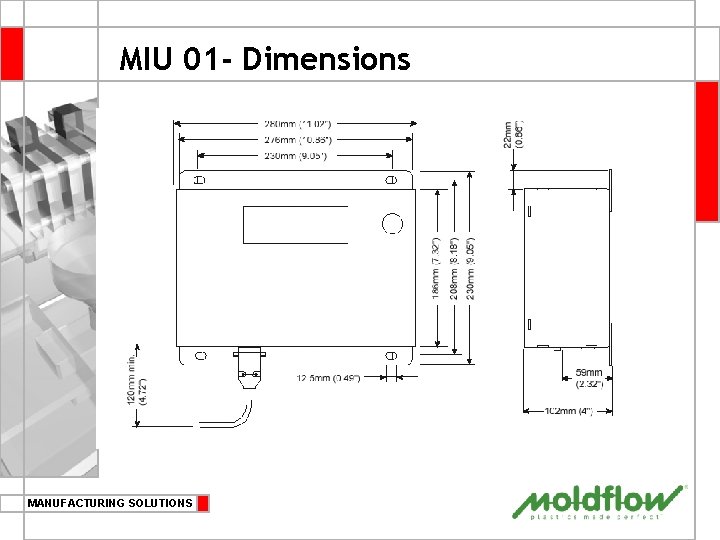
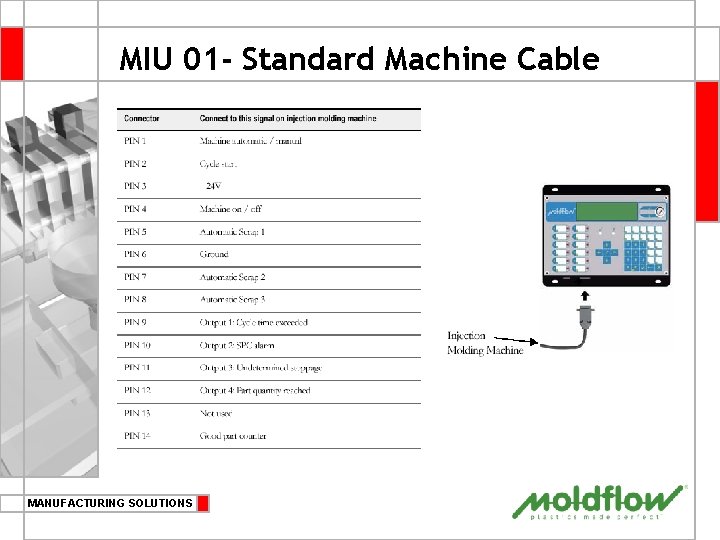
- Slides: 43
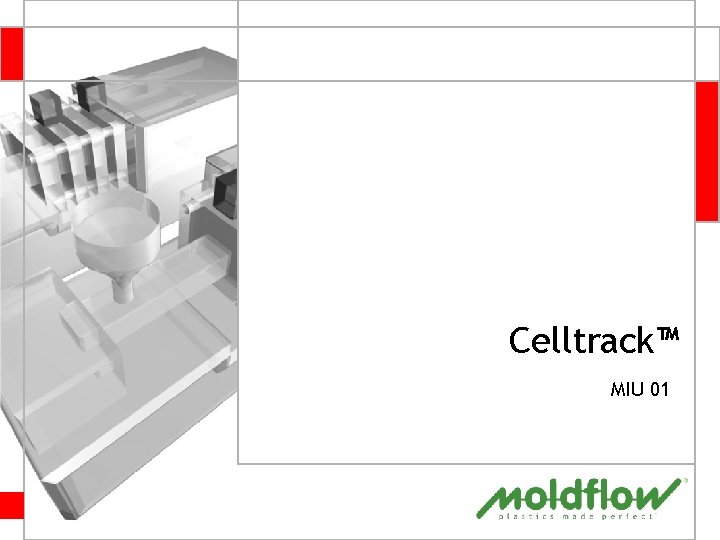
Celltrack™ MIU 01
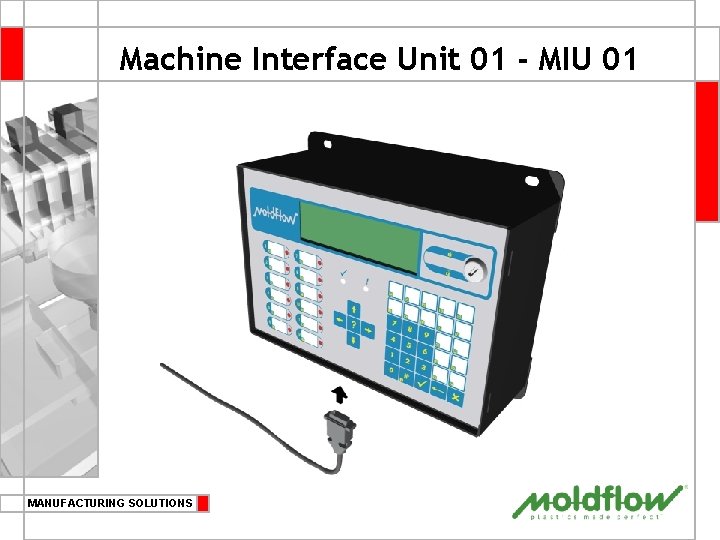
Machine Interface Unit 01 - MIU 01 MANUFACTURING SOLUTIONS
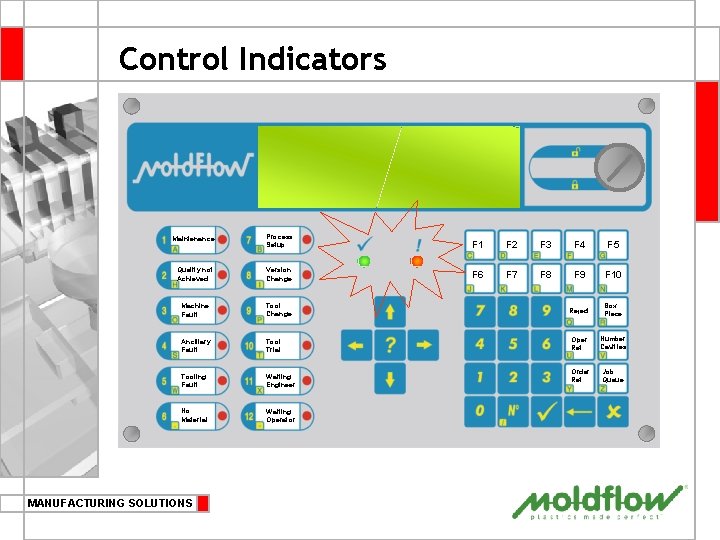
Control Indicators Maintenance Process Setup F 1 F 2 F 3 F 4 F 5 Quality not Achieved Version Change F 6 F 7 F 8 F 9 F 10 Machine Fault Tool Change Reject Box Piece Anciliary Fault Tool Trial Oper. Ref. Number Cavities Tooling Fault Waiting Engineer Order Ref. Job Queue No Material Waiting Operator MANUFACTURING SOLUTIONS
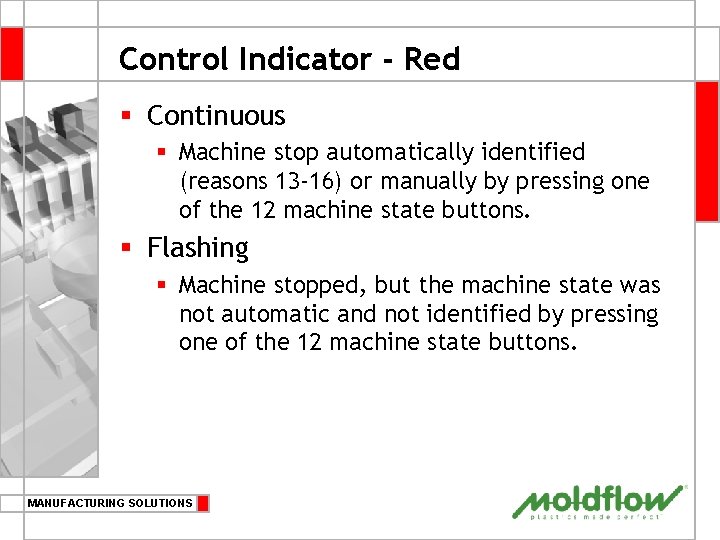
Control Indicator - Red § Continuous § Machine stop automatically identified (reasons 13 -16) or manually by pressing one of the 12 machine state buttons. § Flashing § Machine stopped, but the machine state was not automatic and not identified by pressing one of the 12 machine state buttons. MANUFACTURING SOLUTIONS

Control Indicator - Green § Continuous § Machine is in production and cycle time is within defined limits. § Flashing slowly § Cycle time is above maximum limit. § Flashing quickly § Cycle time is below minimum limit. MANUFACTURING SOLUTIONS
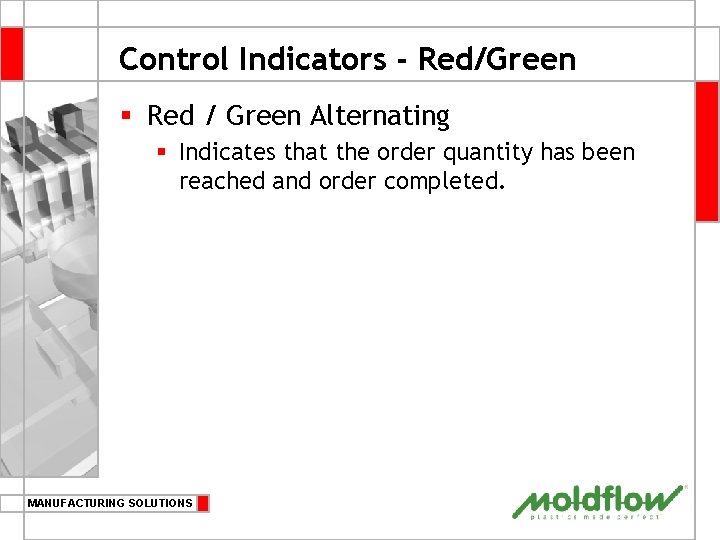
Control Indicators - Red/Green § Red / Green Alternating § Indicates that the order quantity has been reached and order completed. MANUFACTURING SOLUTIONS
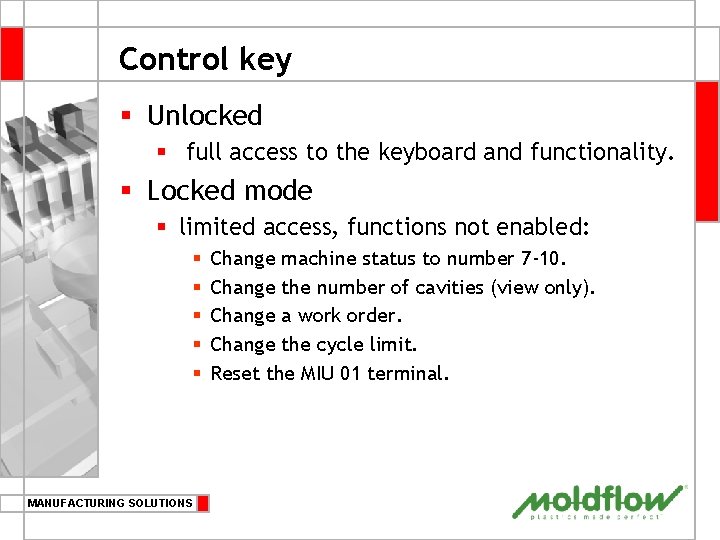
Control key § Unlocked § full access to the keyboard and functionality. § Locked mode § limited access, functions not enabled: § § § MANUFACTURING SOLUTIONS Change machine status to number 7 -10. Change the number of cavities (view only). Change a work order. Change the cycle limit. Reset the MIU 01 terminal.
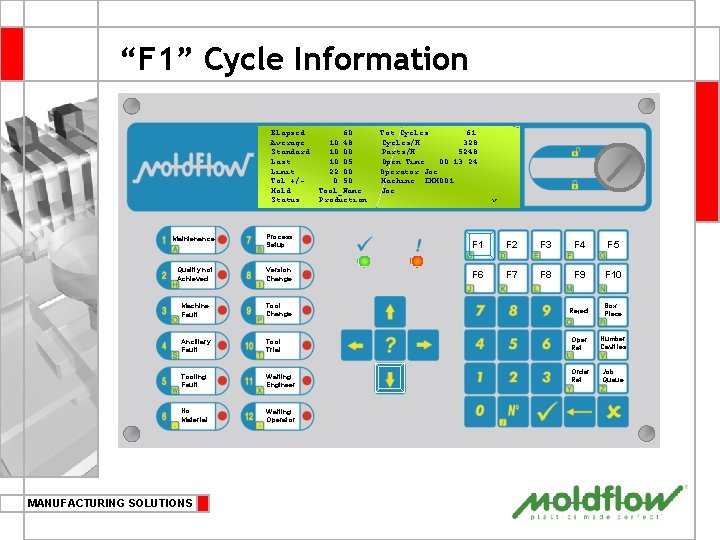
“F 1” Cycle Information Elapsed Average Standard Last Limit Tol +/Mold Status : . 60 : 10. 48 : 10. 00 : 10. 05 : 22. 00 : 0. 50 : Tool_Name : Production Tot. Cycles : 61 Cycles/H : 328 Parts/H : 5248 Open Time : 00: 13: 24 Operator: Joe Machine : IMM 001 Joe v Maintenance Process Setup F 1 F 2 F 3 F 4 F 5 Quality not Achieved Version Change F 6 F 7 F 8 F 9 F 10 Machine Fault Tool Change Reject Box Piece Anciliary Fault Tool Trial Oper. Ref. Number Cavities Tooling Fault Waiting Engineer Order Ref. Job Queue No Material Waiting Operator MANUFACTURING SOLUTIONS
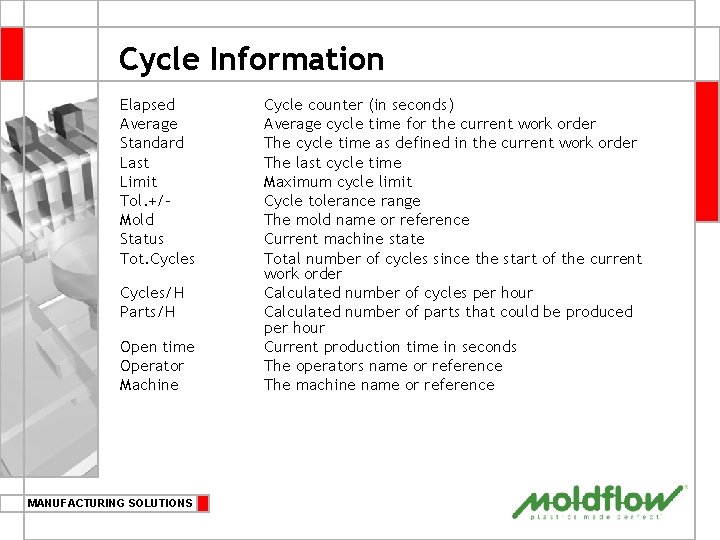
Cycle Information Elapsed Average Standard Last Limit Tol. +/Mold Status Tot. Cycles/H Parts/H Open time Operator Machine MANUFACTURING SOLUTIONS Cycle counter (in seconds) Average cycle time for the current work order The cycle time as defined in the current work order The last cycle time Maximum cycle limit Cycle tolerance range The mold name or reference Current machine state Total number of cycles since the start of the current work order Calculated number of cycles per hour Calculated number of parts that could be produced per hour Current production time in seconds The operators name or reference The machine name or reference
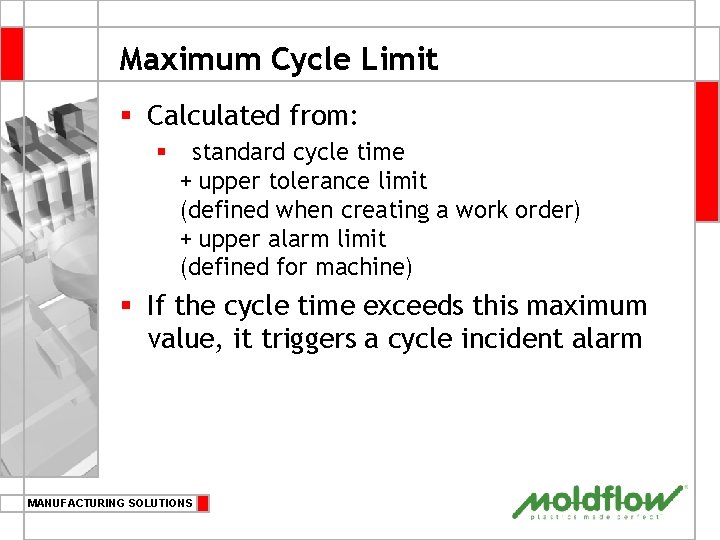
Maximum Cycle Limit § Calculated from: § standard cycle time + upper tolerance limit (defined when creating a work order) + upper alarm limit (defined for machine) § If the cycle time exceeds this maximum value, it triggers a cycle incident alarm MANUFACTURING SOLUTIONS
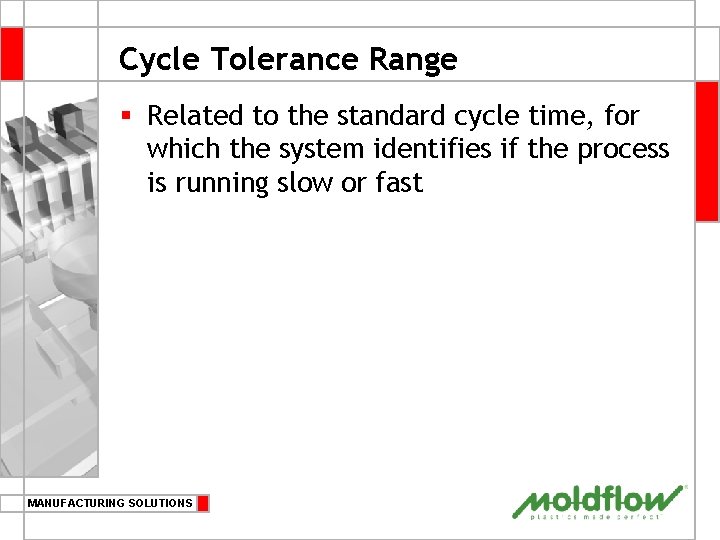
Cycle Tolerance Range § Related to the standard cycle time, for which the system identifies if the process is running slow or fast MANUFACTURING SOLUTIONS
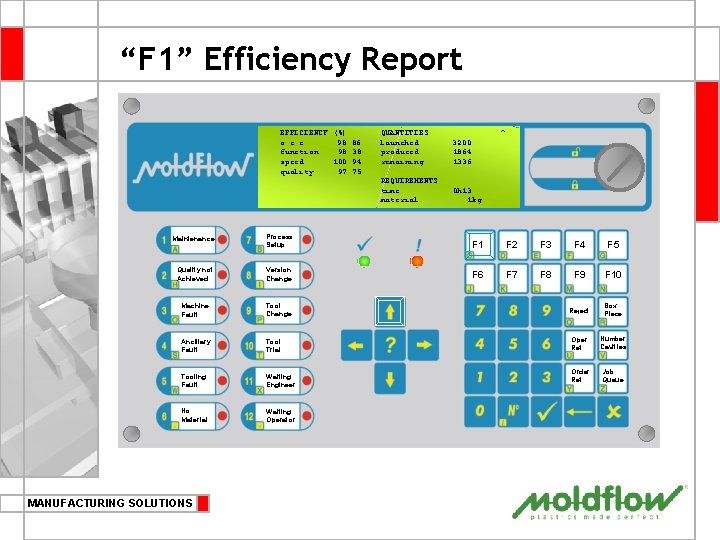
“F 1” Efficiency Report EFFICIENCY (%) o. e. e. : 98. 86 function: 98. 38 speed : 100. 94 quality : 97. 75 QUANTITIES launched : produced : remaining : 3200 1864 1336 ^ REQUIREMENTS time : material : 0 h 13 1 kg Maintenance Process Setup F 1 F 2 F 3 F 4 F 5 Quality not Achieved Version Change F 6 F 7 F 8 F 9 F 10 Machine Fault Tool Change Reject Box Piece Anciliary Fault Tool Trial Oper. Ref. Number Cavities Tooling Fault Waiting Engineer Order Ref. Job Queue No Material Waiting Operator MANUFACTURING SOLUTIONS
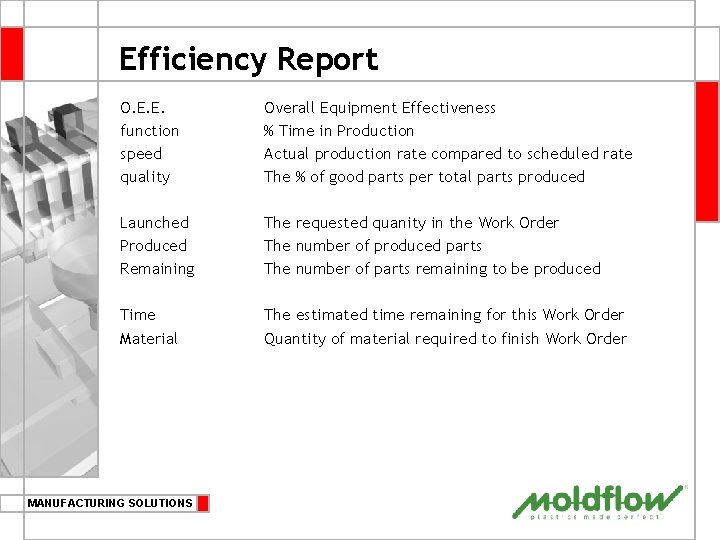
Efficiency Report O. E. E. function speed quality Overall Equipment Effectiveness % Time in Production Actual production rate compared to scheduled rate The % of good parts per total parts produced Launched Produced Remaining The requested quanity in the Work Order The number of produced parts The number of parts remaining to be produced Time Material The estimated time remaining for this Work Order Quantity of material required to finish Work Order MANUFACTURING SOLUTIONS
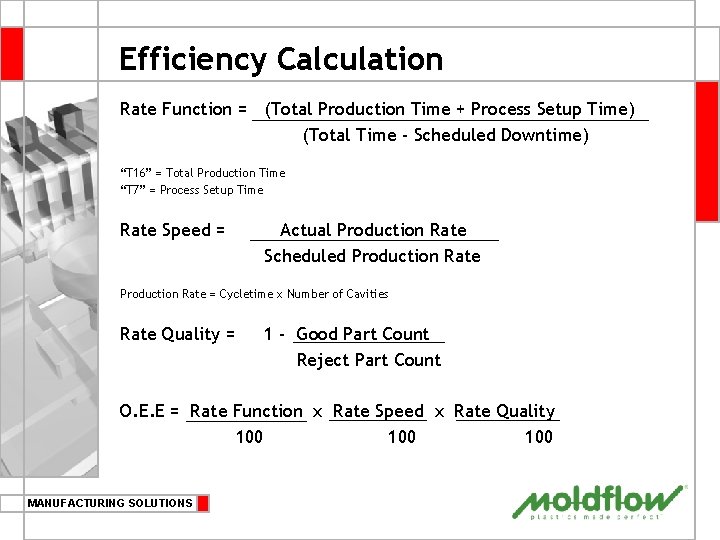
Efficiency Calculation Rate Function = (Total Production Time + Process Setup Time) (Total Time - Scheduled Downtime) “T 16” = Total Production Time “T 7” = Process Setup Time Rate Speed = Actual Production Rate Scheduled Production Rate = Cycletime x Number of Cavities Rate Quality = 1 - Good Part Count Reject Part Count O. E. E = Rate Function x Rate Speed x Rate Quality 100 100 MANUFACTURING SOLUTIONS
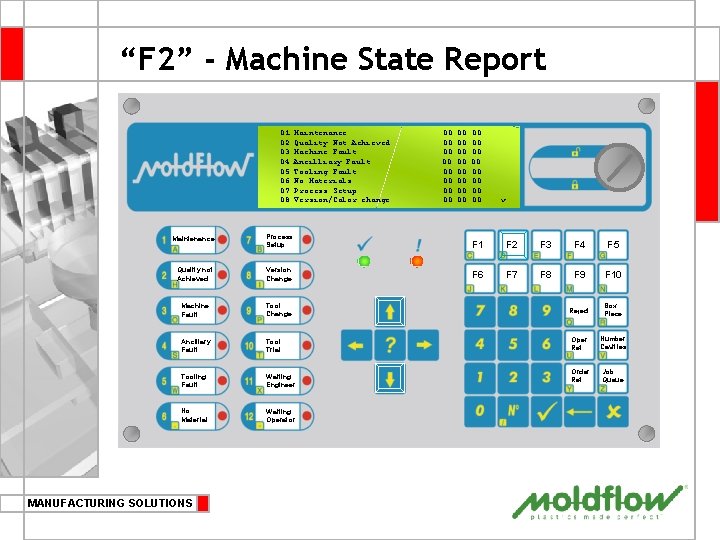
“F 2” - Machine State Report 01 02 03 04 05 06 07 08 Maintenance Quality Not Achieved Machine Fault Ancilliary Fault Tooling Fault No Materials Process Setup Version/Color change 00: 00: 00 00: 00: 00 v Maintenance Process Setup F 1 F 2 F 3 F 4 F 5 Quality not Achieved Version Change F 6 F 7 F 8 F 9 F 10 Machine Fault Tool Change Reject Box Piece Anciliary Fault Tool Trial Oper. Ref. Number Cavities Tooling Fault Waiting Engineer Order Ref. Job Queue No Material Waiting Operator MANUFACTURING SOLUTIONS
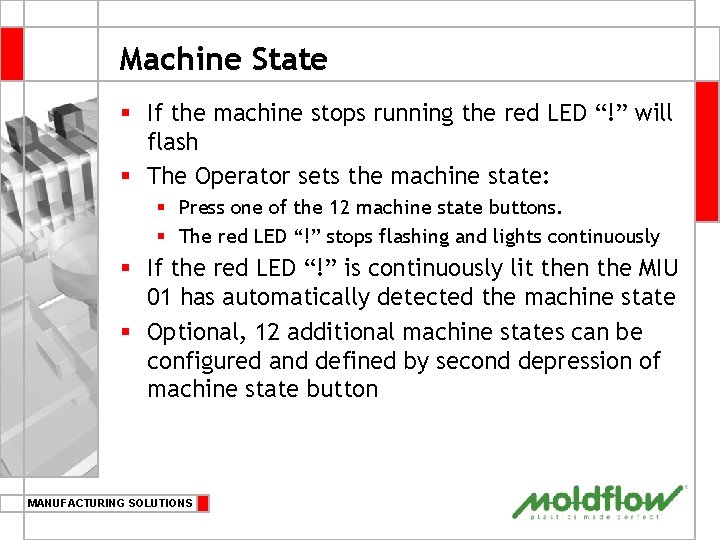
Machine State § If the machine stops running the red LED “!” will flash § The Operator sets the machine state: § Press one of the 12 machine state buttons. § The red LED “!” stops flashing and lights continuously § If the red LED “!” is continuously lit then the MIU 01 has automatically detected the machine state § Optional, 12 additional machine states can be configured and defined by second depression of machine state button MANUFACTURING SOLUTIONS
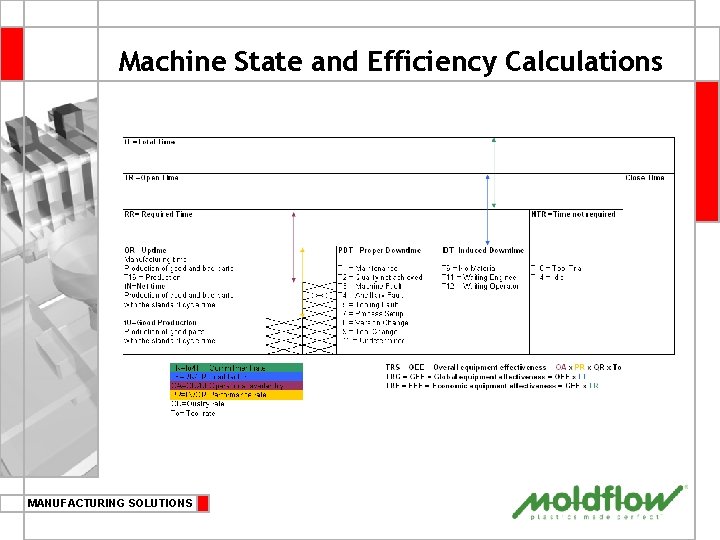
Machine State and Efficiency Calculations MANUFACTURING SOLUTIONS
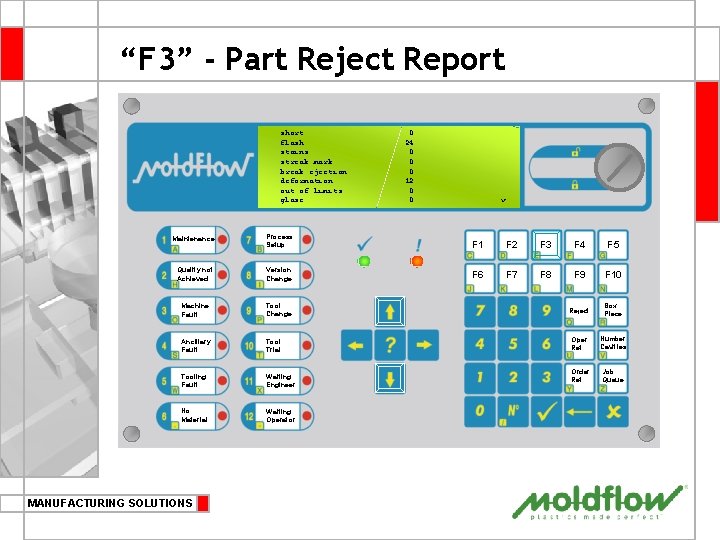
“F 3” - Part Reject Report short flash stains streak mark break ejection deformation out of limits glaze : : : : 0 24 0 0 0 12 0 0 v Maintenance Process Setup F 1 F 2 F 3 F 4 F 5 Quality not Achieved Version Change F 6 F 7 F 8 F 9 F 10 Machine Fault Tool Change Reject Box Piece Anciliary Fault Tool Trial Oper. Ref. Number Cavities Tooling Fault Waiting Engineer Order Ref. Job Queue No Material Waiting Operator MANUFACTURING SOLUTIONS
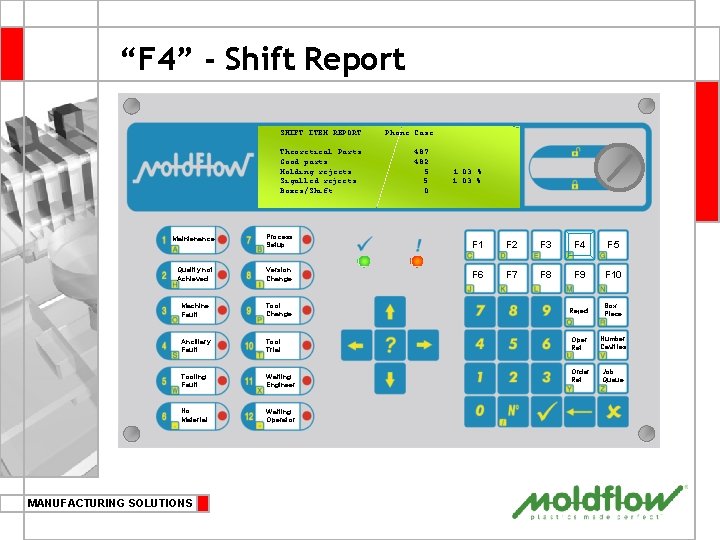
“F 4” - Shift Report SHIFT ITEM REPORT : Phone Case Theoretical Parts Good parts Molding rejects Sigalled rejects Boxes/Shift : : : 487 482 5 5 0 1. 03 % Maintenance Process Setup F 1 F 2 F 3 F 4 F 5 Quality not Achieved Version Change F 6 F 7 F 8 F 9 F 10 Machine Fault Tool Change Reject Box Piece Anciliary Fault Tool Trial Oper. Ref. Number Cavities Tooling Fault Waiting Engineer Order Ref. Job Queue No Material Waiting Operator MANUFACTURING SOLUTIONS
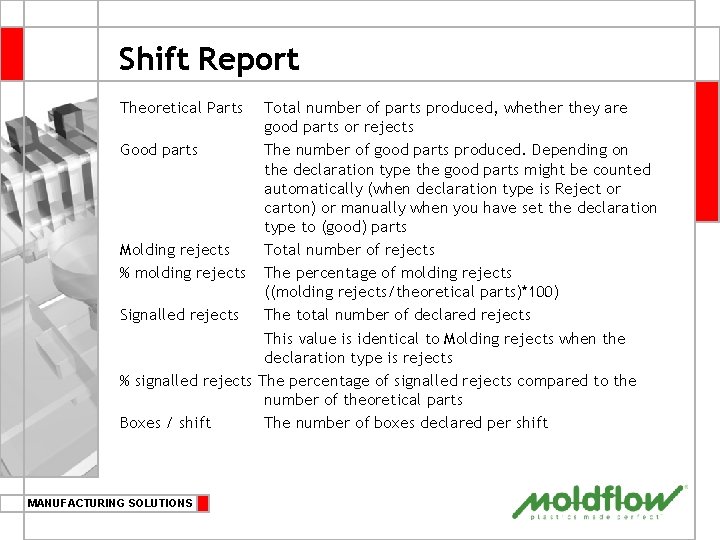
Shift Report Theoretical Parts Total number of parts produced, whether they are good parts or rejects Good parts The number of good parts produced. Depending on the declaration type the good parts might be counted automatically (when declaration type is Reject or carton) or manually when you have set the declaration type to (good) parts Molding rejects Total number of rejects % molding rejects The percentage of molding rejects ((molding rejects/theoretical parts)*100) Signalled rejects The total number of declared rejects This value is identical to Molding rejects when the declaration type is rejects % signalled rejects The percentage of signalled rejects compared to the number of theoretical parts Boxes / shift The number of boxes declared per shift MANUFACTURING SOLUTIONS
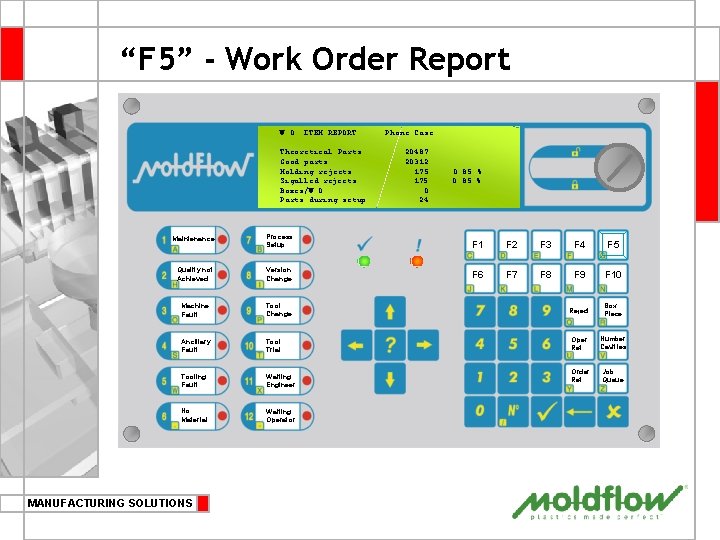
“F 5” - Work Order Report W. O. ITEM REPORT : Phone Case Theoretical Parts Good parts Molding rejects Sigalled rejects Boxes/W. O. Parts during setup : : : 20487 20312 175 0 24 0. 85 % Maintenance Process Setup F 1 F 2 F 3 F 4 F 5 Quality not Achieved Version Change F 6 F 7 F 8 F 9 F 10 Machine Fault Tool Change Reject Box Piece Anciliary Fault Tool Trial Oper. Ref. Number Cavities Tooling Fault Waiting Engineer Order Ref. Job Queue No Material Waiting Operator MANUFACTURING SOLUTIONS
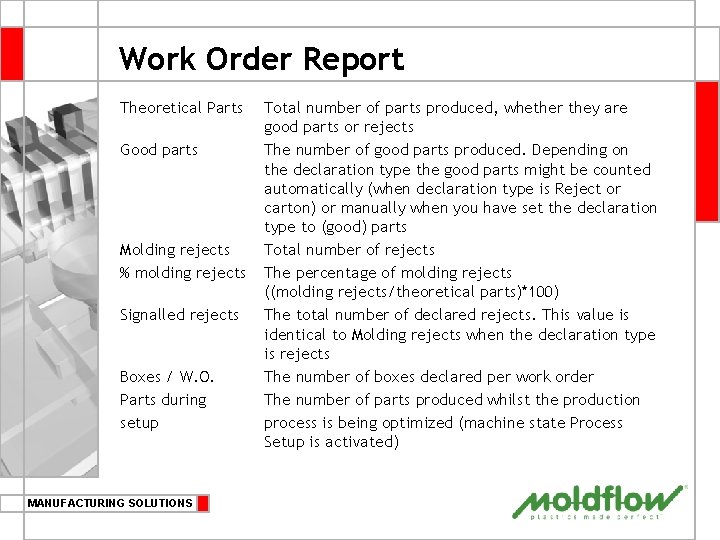
Work Order Report Theoretical Parts Good parts Molding rejects % molding rejects Signalled rejects Boxes / W. O. Parts during setup MANUFACTURING SOLUTIONS Total number of parts produced, whether they are good parts or rejects The number of good parts produced. Depending on the declaration type the good parts might be counted automatically (when declaration type is Reject or carton) or manually when you have set the declaration type to (good) parts Total number of rejects The percentage of molding rejects ((molding rejects/theoretical parts)*100) The total number of declared rejects. This value is identical to Molding rejects when the declaration type is rejects The number of boxes declared per work order The number of parts produced whilst the production process is being optimized (machine state Process Setup is activated)
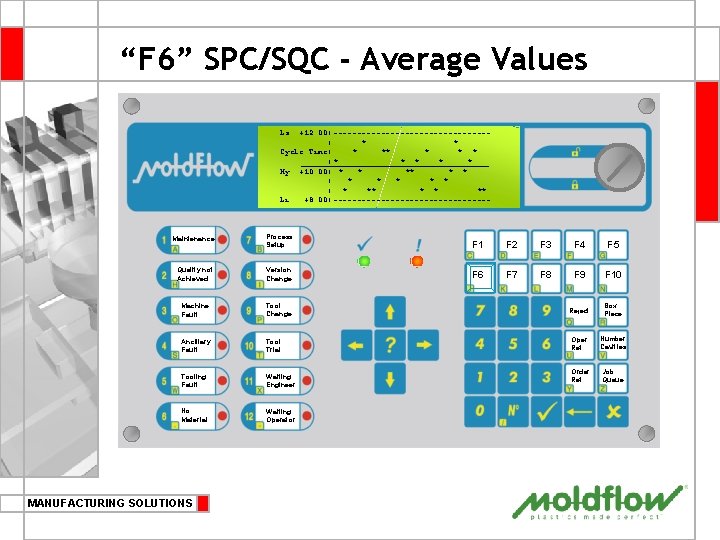
“F 6” SPC/SQC - Average Values Ls +12. 00|----------------| * * Cycle Time| * ** * |* * * My +10. 00| * * * | * ** * * ** Li +8. 00|----------------- Maintenance Process Setup F 1 F 2 F 3 F 4 F 5 Quality not Achieved Version Change F 6 F 7 F 8 F 9 F 10 Machine Fault Tool Change Reject Box Piece Anciliary Fault Tool Trial Oper. Ref. Number Cavities Tooling Fault Waiting Engineer Order Ref. Job Queue No Material Waiting Operator MANUFACTURING SOLUTIONS
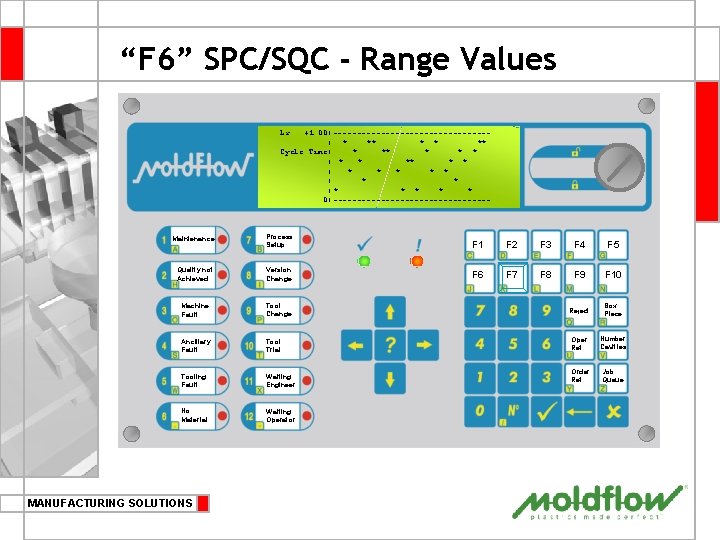
“F 6” SPC/SQC - Range Values Lr +1. 00|----------------| * ** * * ** Cycle Time| * ** * | * * * |* * * 0|----------------- Maintenance Process Setup F 1 F 2 F 3 F 4 F 5 Quality not Achieved Version Change F 6 F 7 F 8 F 9 F 10 Machine Fault Tool Change Reject Box Piece Anciliary Fault Tool Trial Oper. Ref. Number Cavities Tooling Fault Waiting Engineer Order Ref. Job Queue No Material Waiting Operator MANUFACTURING SOLUTIONS
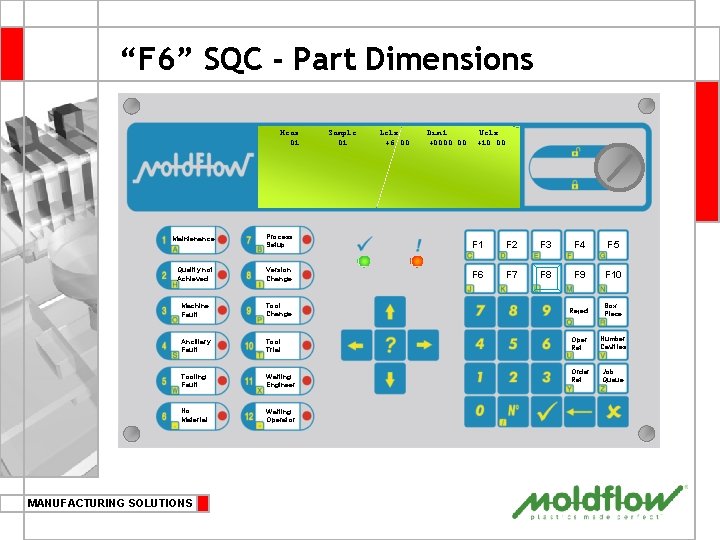
“F 6” SQC - Part Dimensions Meas. 01 Sample 01 Lclx +6. 00 Dim 1 +0000. 00 Uclx +10. 00 Maintenance Process Setup F 1 F 2 F 3 F 4 F 5 Quality not Achieved Version Change F 6 F 7 F 8 F 9 F 10 Machine Fault Tool Change Reject Box Piece Anciliary Fault Tool Trial Oper. Ref. Number Cavities Tooling Fault Waiting Engineer Order Ref. Job Queue No Material Waiting Operator MANUFACTURING SOLUTIONS
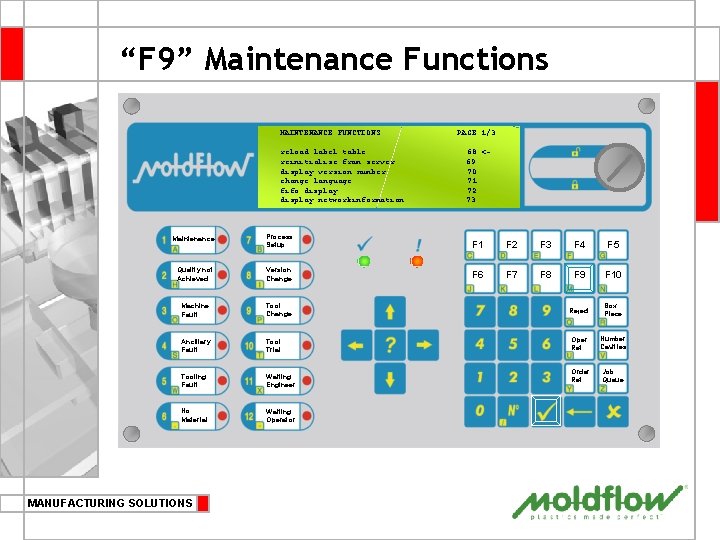
“F 9” Maintenance Functions MAINTENANCE FUNCTIONS reload label table reinitialise from server display version number change language fifo display networkinformation PAGE 1/3 68 <69 70 71 72 73 Maintenance Process Setup F 1 F 2 F 3 F 4 F 5 Quality not Achieved Version Change F 6 F 7 F 8 F 9 F 10 Machine Fault Tool Change Reject Box Piece Anciliary Fault Tool Trial Oper. Ref. Number Cavities Tooling Fault Waiting Engineer Order Ref. Job Queue No Material Waiting Operator MANUFACTURING SOLUTIONS
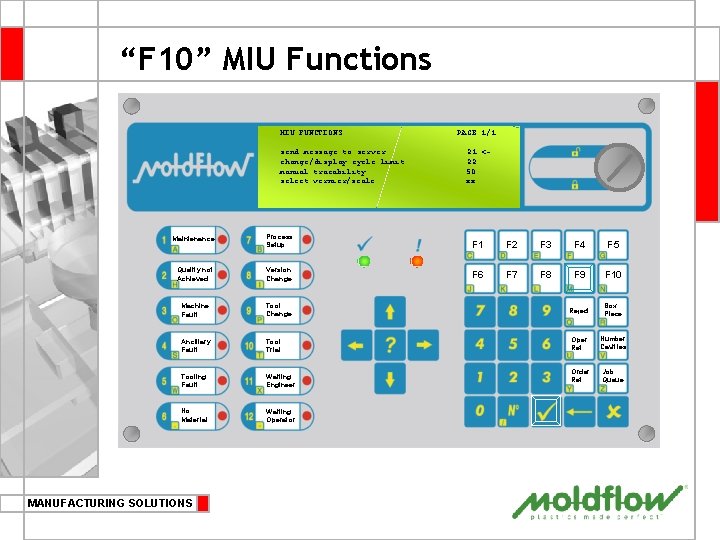
“F 10” MIU Functions MIU FUNCTIONS send message to server change/display cycle limit manual tracability select vernier/scale PAGE 1/1 21 <22 50 xx Maintenance Process Setup F 1 F 2 F 3 F 4 F 5 Quality not Achieved Version Change F 6 F 7 F 8 F 9 F 10 Machine Fault Tool Change Reject Box Piece Anciliary Fault Tool Trial Oper. Ref. Number Cavities Tooling Fault Waiting Engineer Order Ref. Job Queue No Material Waiting Operator MANUFACTURING SOLUTIONS
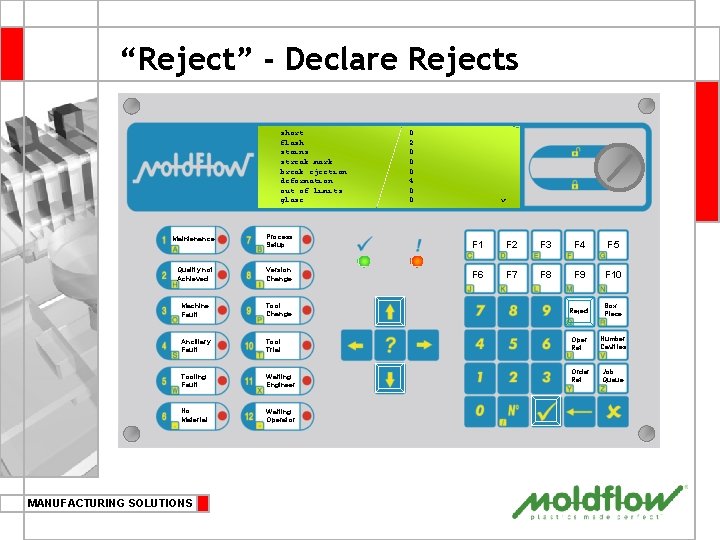
“Reject” - Declare Rejects short flash stains streak mark break ejection deformation out of limits glaze : : : : 0 2 0 0 0 4 0 0 v Maintenance Process Setup F 1 F 2 F 3 F 4 F 5 Quality not Achieved Version Change F 6 F 7 F 8 F 9 F 10 Machine Fault Tool Change Reject Box Piece Anciliary Fault Tool Trial Oper. Ref. Number Cavities Tooling Fault Waiting Engineer Order Ref. Job Queue No Material Waiting Operator MANUFACTURING SOLUTIONS
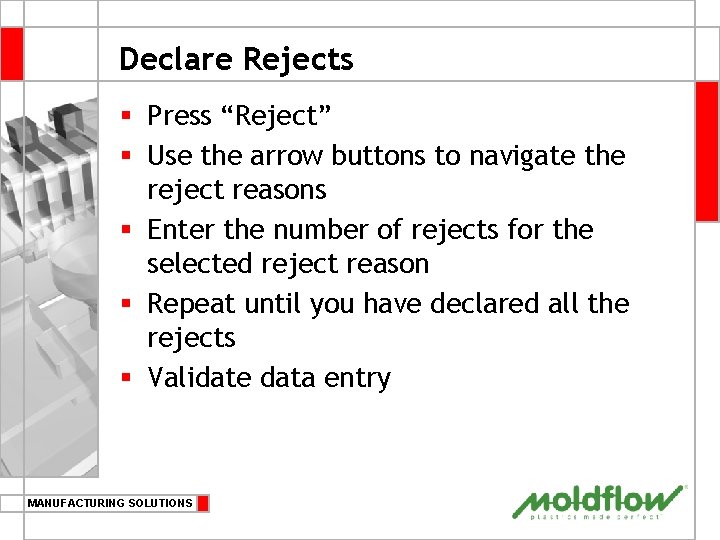
Declare Rejects § Press “Reject” § Use the arrow buttons to navigate the reject reasons § Enter the number of rejects for the selected reject reason § Repeat until you have declared all the rejects § Validate data entry MANUFACTURING SOLUTIONS
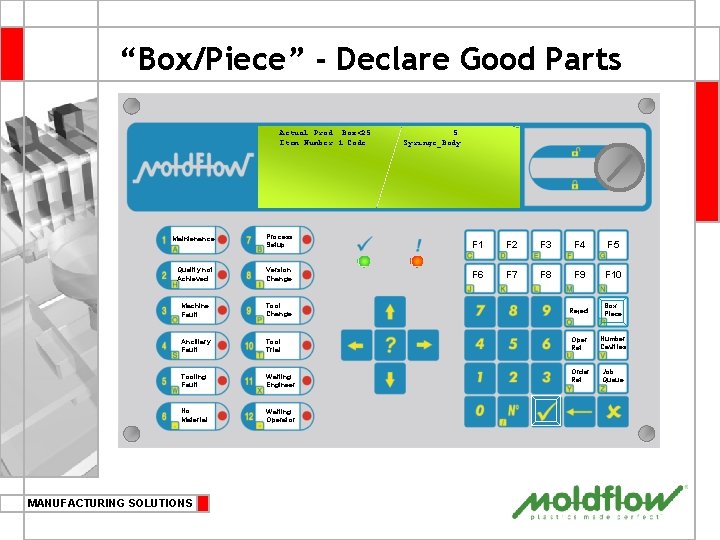
“Box/Piece” - Declare Good Parts Actual Prod. Box<25 Item Number 1 Code : 5 : Syringe_Body Maintenance Process Setup F 1 F 2 F 3 F 4 F 5 Quality not Achieved Version Change F 6 F 7 F 8 F 9 F 10 Machine Fault Tool Change Reject Box Piece Anciliary Fault Tool Trial Oper. Ref. Number Cavities Tooling Fault Waiting Engineer Order Ref. Job Queue No Material Waiting Operator MANUFACTURING SOLUTIONS
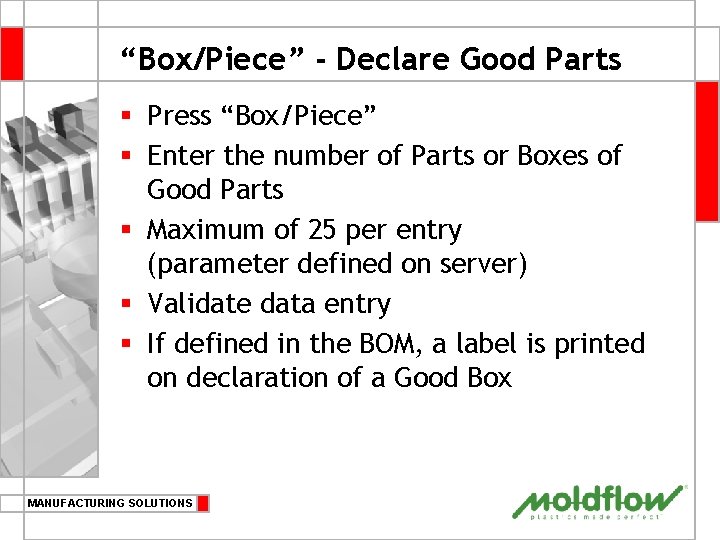
“Box/Piece” - Declare Good Parts § Press “Box/Piece” § Enter the number of Parts or Boxes of Good Parts § Maximum of 25 per entry (parameter defined on server) § Validate data entry § If defined in the BOM, a label is printed on declaration of a Good Box MANUFACTURING SOLUTIONS
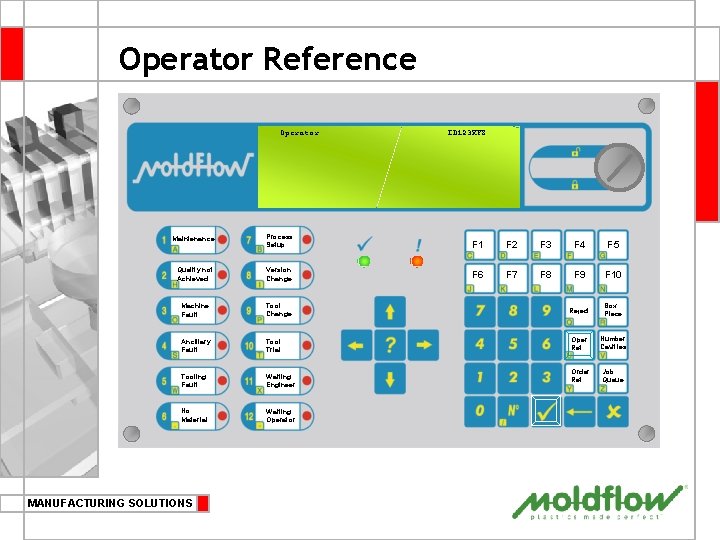
Operator Reference Operator : ID 123 XYZ Maintenance Process Setup F 1 F 2 F 3 F 4 F 5 Quality not Achieved Version Change F 6 F 7 F 8 F 9 F 10 Machine Fault Tool Change Reject Box Piece Anciliary Fault Tool Trial Oper. Ref. Number Cavities Tooling Fault Waiting Engineer Order Ref. Job Queue No Material Waiting Operator MANUFACTURING SOLUTIONS
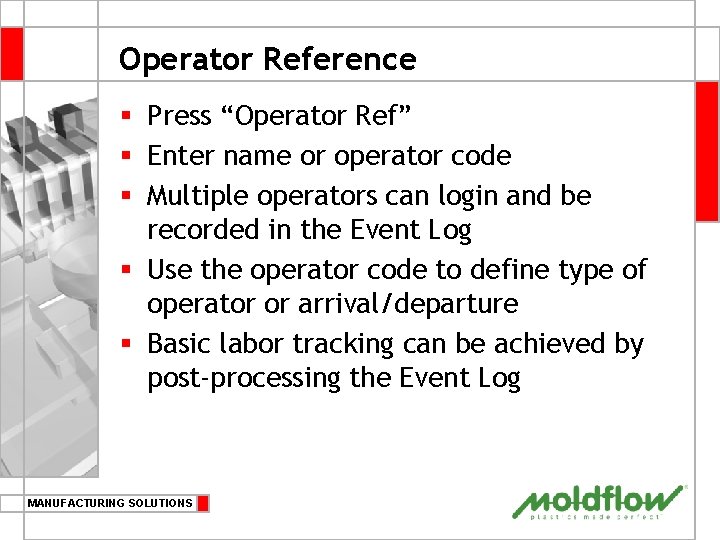
Operator Reference § Press “Operator Ref” § Enter name or operator code § Multiple operators can login and be recorded in the Event Log § Use the operator code to define type of operator or arrival/departure § Basic labor tracking can be achieved by post-processing the Event Log MANUFACTURING SOLUTIONS
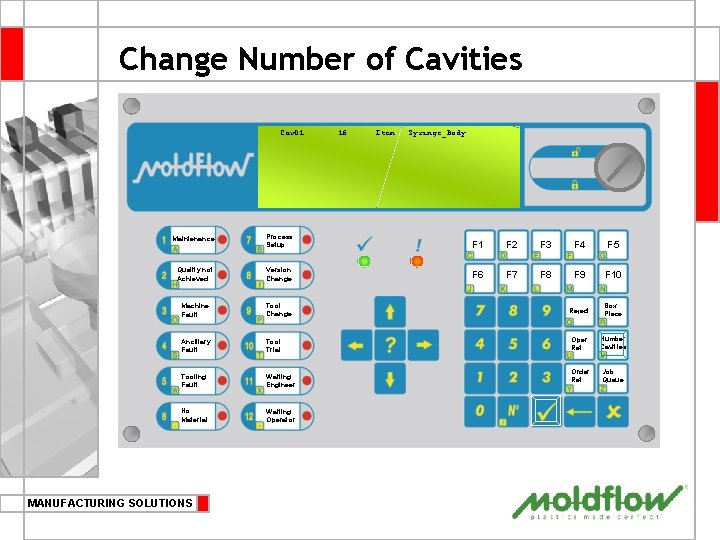
Change Number of Cavities Cav 01: 16 Item: Syringe_Body Maintenance Process Setup F 1 F 2 F 3 F 4 F 5 Quality not Achieved Version Change F 6 F 7 F 8 F 9 F 10 Machine Fault Tool Change Reject Box Piece Anciliary Fault Tool Trial Oper. Ref. Number Cavities Tooling Fault Waiting Engineer Order Ref. Job Queue No Material Waiting Operator MANUFACTURING SOLUTIONS
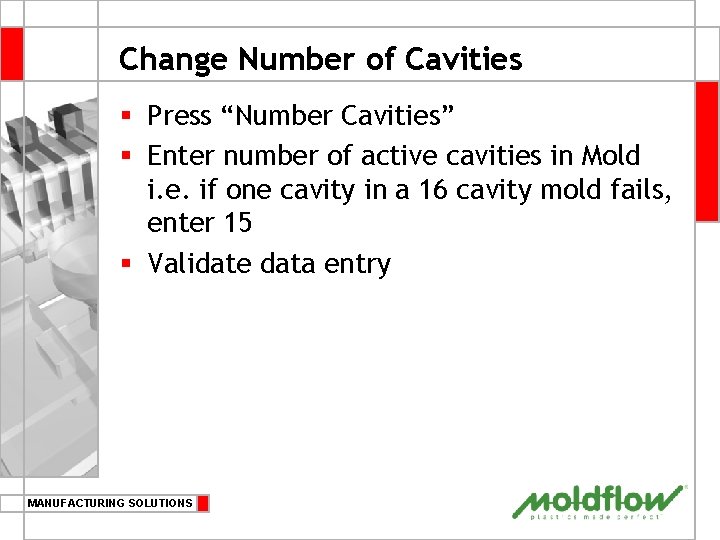
Change Number of Cavities § Press “Number Cavities” § Enter number of active cavities in Mold i. e. if one cavity in a 16 cavity mold fails, enter 15 § Validate data entry MANUFACTURING SOLUTIONS
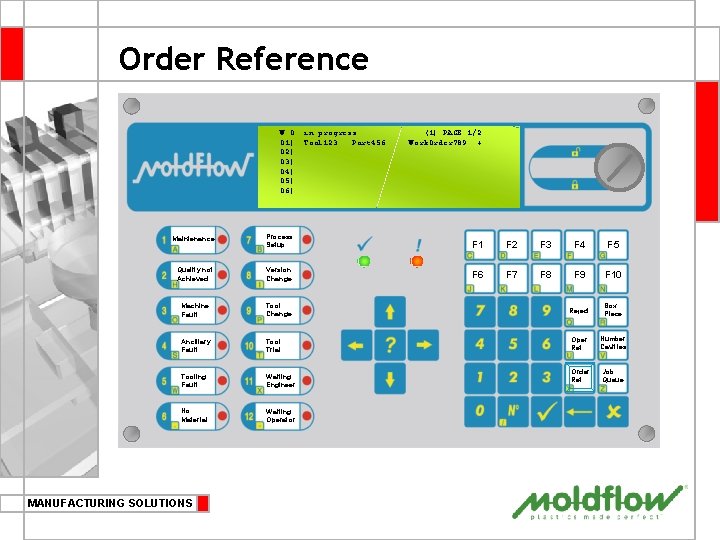
Order Reference W. O. in progress 01) Tool 123 Part 456 02) 03) 04) 05) 06) (1) PAGE 1/2 Work. Order 789 + Maintenance Process Setup F 1 F 2 F 3 F 4 F 5 Quality not Achieved Version Change F 6 F 7 F 8 F 9 F 10 Machine Fault Tool Change Reject Box Piece Anciliary Fault Tool Trial Oper. Ref. Number Cavities Tooling Fault Waiting Engineer Order Ref. Job Queue No Material Waiting Operator MANUFACTURING SOLUTIONS
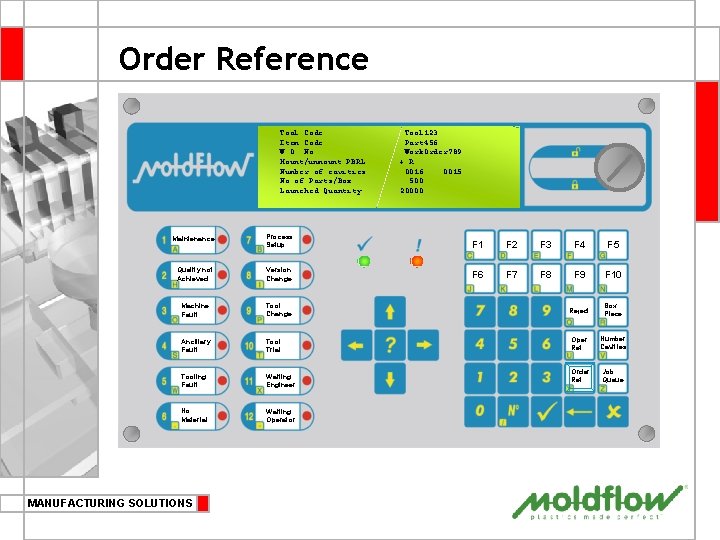
Order Reference Tool Code Item Code W. O. No Mount/unmount PBRL Number of cavities No of Parts/Box Launched Quantity : Tool 123 : Part 456 : Work. Order 789 : + R : 0016 0015 : 500 : 20000 Maintenance Process Setup F 1 F 2 F 3 F 4 F 5 Quality not Achieved Version Change F 6 F 7 F 8 F 9 F 10 Machine Fault Tool Change Reject Box Piece Anciliary Fault Tool Trial Oper. Ref. Number Cavities Tooling Fault Waiting Engineer Order Ref. Job Queue No Material Waiting Operator MANUFACTURING SOLUTIONS
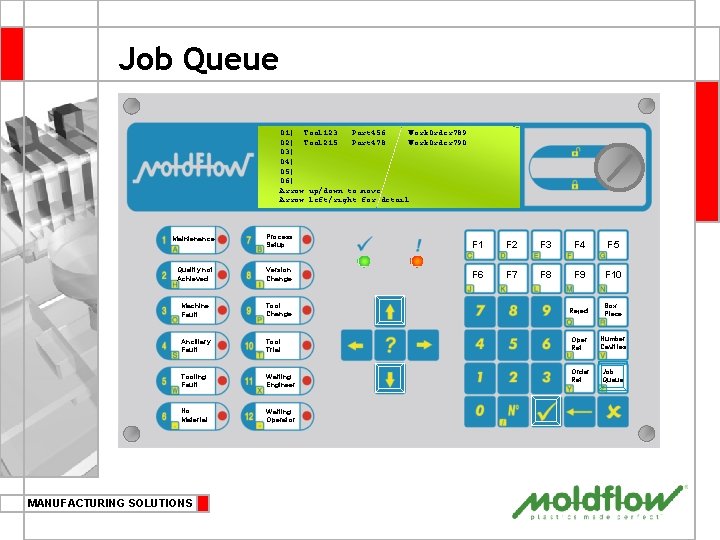
Job Queue 01) Tool 123 Part 456 Work. Order 789 02) Tool 215 Part 478 Work. Order 790 03) 04) 05) 06) Arrow up/down to move Arrow left/right for detail Maintenance Process Setup F 1 F 2 F 3 F 4 F 5 Quality not Achieved Version Change F 6 F 7 F 8 F 9 F 10 Machine Fault Tool Change Reject Box Piece Anciliary Fault Tool Trial Oper. Ref. Number Cavities Tooling Fault Waiting Engineer Order Ref. Job Queue No Material Waiting Operator MANUFACTURING SOLUTIONS
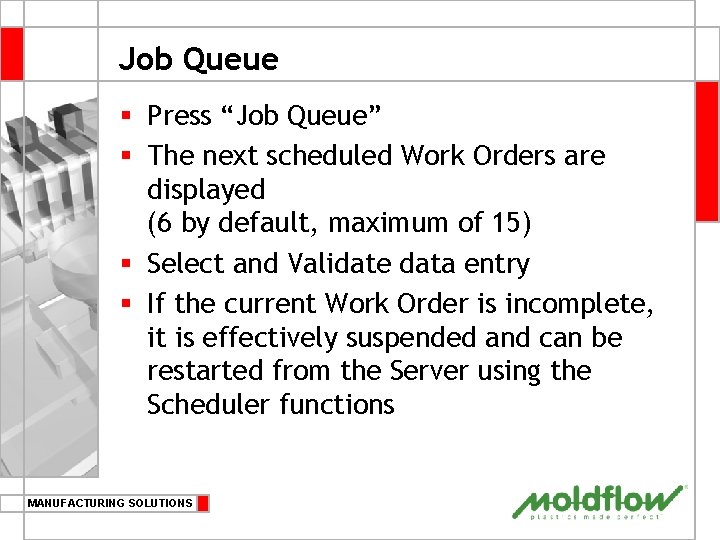
Job Queue § Press “Job Queue” § The next scheduled Work Orders are displayed (6 by default, maximum of 15) § Select and Validate data entry § If the current Work Order is incomplete, it is effectively suspended and can be restarted from the Server using the Scheduler functions MANUFACTURING SOLUTIONS
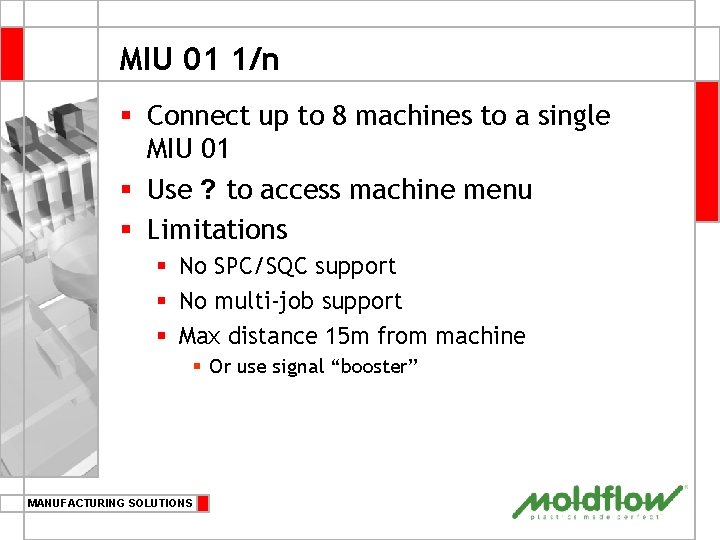
MIU 01 1/n § Connect up to 8 machines to a single MIU 01 § Use ? to access machine menu § Limitations § No SPC/SQC support § No multi-job support § Max distance 15 m from machine § Or use signal “booster” MANUFACTURING SOLUTIONS
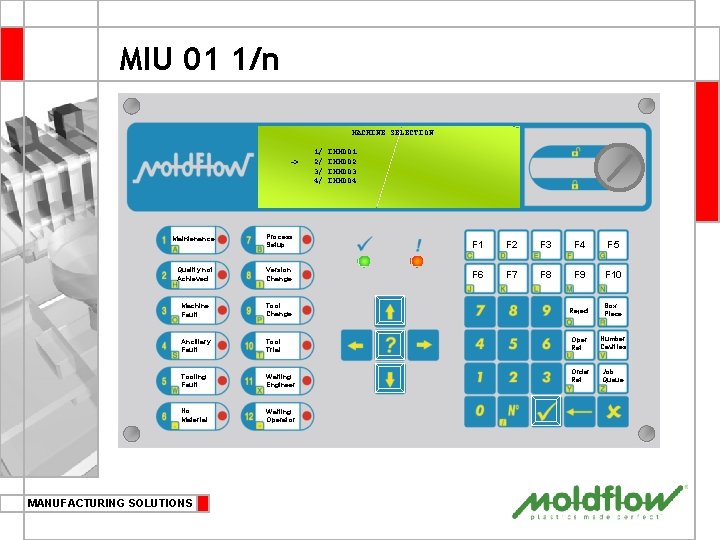
MIU 01 1/n MACHINE SELECTION -> 1/ 2/ 3/ 4/ IMM 001 IMM 002 IMM 003 IMM 004 Maintenance Process Setup F 1 F 2 F 3 F 4 F 5 Quality not Achieved Version Change F 6 F 7 F 8 F 9 F 10 Machine Fault Tool Change Reject Box Piece Anciliary Fault Tool Trial Oper. Ref. Number Cavities Tooling Fault Waiting Engineer Order Ref. Job Queue No Material Waiting Operator MANUFACTURING SOLUTIONS
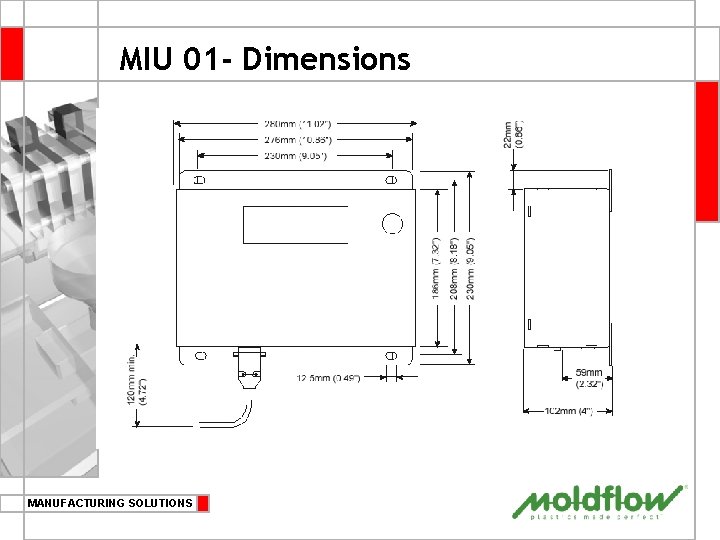
MIU 01 - Dimensions MANUFACTURING SOLUTIONS
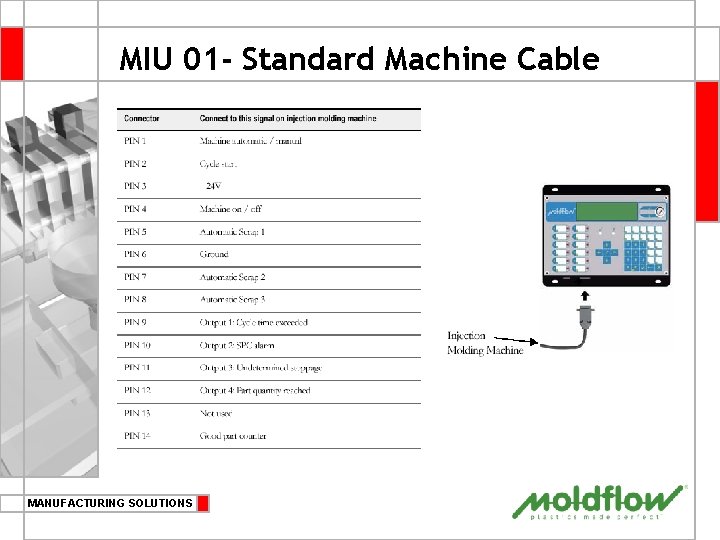
MIU 01 - Standard Machine Cable MANUFACTURING SOLUTIONS
Yorkhill minor injuries
Liceul miu satu mare
Miu shiromani
Miu shiromani
Miu shiromani
Mattec miu
Miu
Miu
Dr miu nicolae
Interface in java
Fluidity in hci
Industrial interfaces
An interface
Human machine interface
Unit 6 review questions
Hydraulic interface units
Finite state machine vending machine example
Mealy moore
Moore machine
Chapter 10 energy, work and simple machines answer key
Suatu lembaga yang
Hyp opp adj triangle
Si units mass
Unit test unit test review algebra 2
Perhitungan unit cost rekam medis
Unit process and unit operation
What is unit operation and unit process
Kerangka konseptual akuntansi pemerintahan
Somnoware device interface
Yahoo user interface library (yui)
What is xul
Interface list wireshark
Idoe tide portal
Web service interface
Cash register interface
Graphical user interface testing
Komponen user interface
Interface structure design
Interface design diagram
Guidelines for data entry screen design
User interface design cycle
The importance of user interface
User interface design steps in software engineering
User interface analysis and design