2 Dry etching Outline Terminology Wet Etching Dry
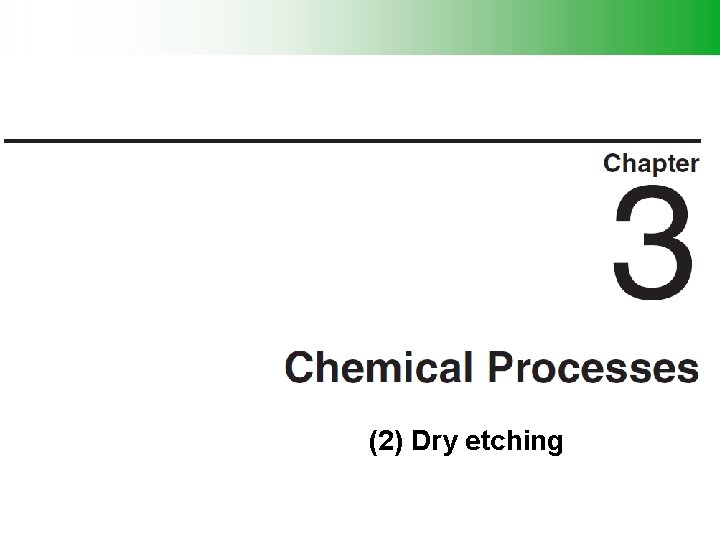
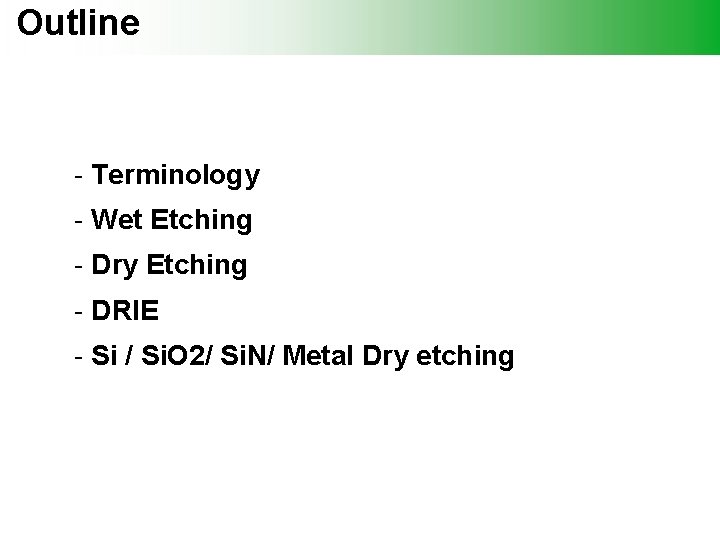
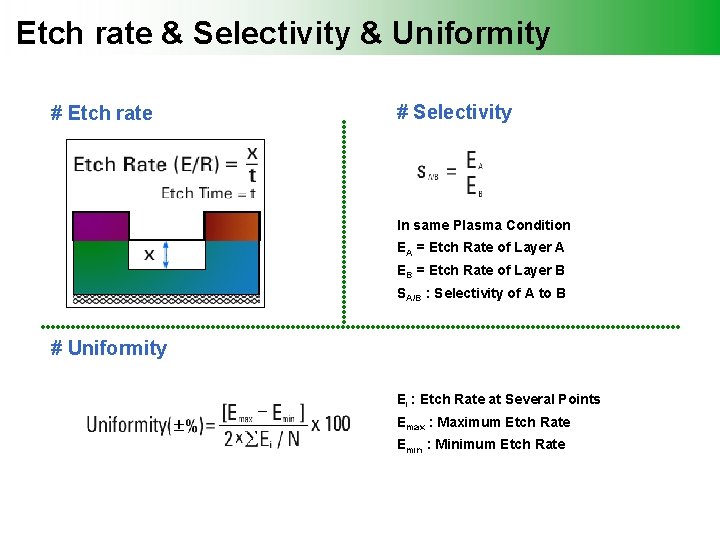
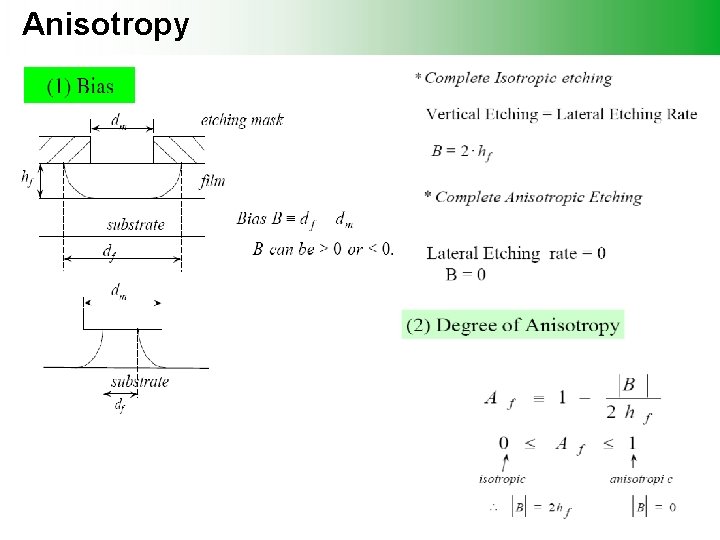
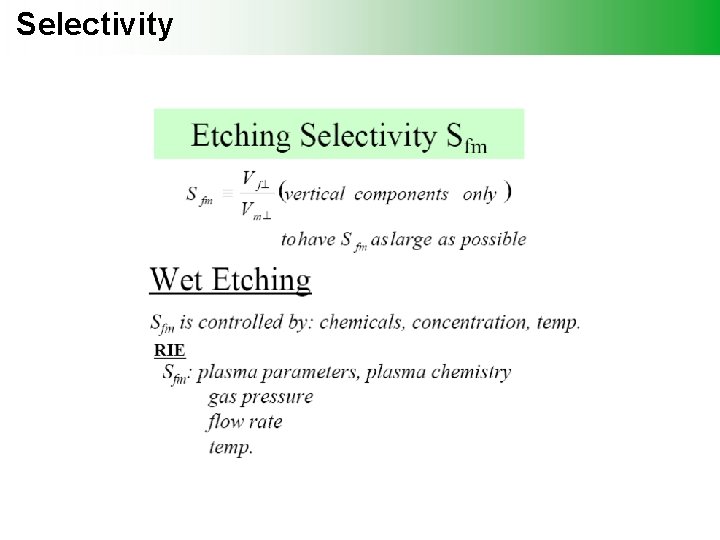
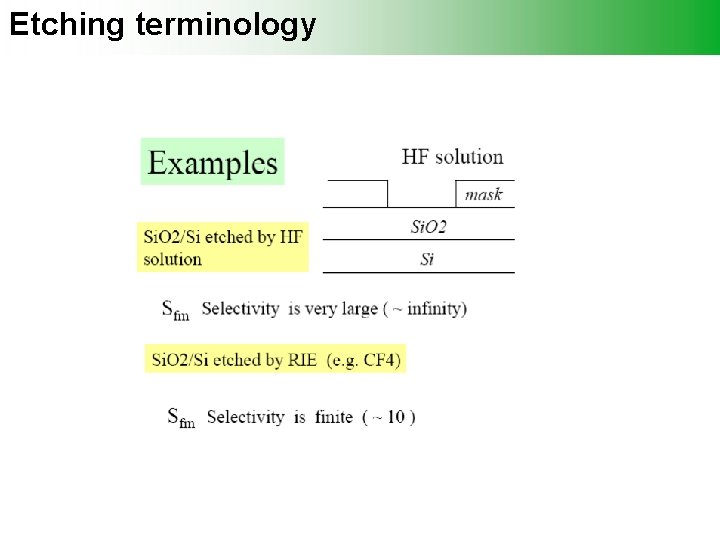
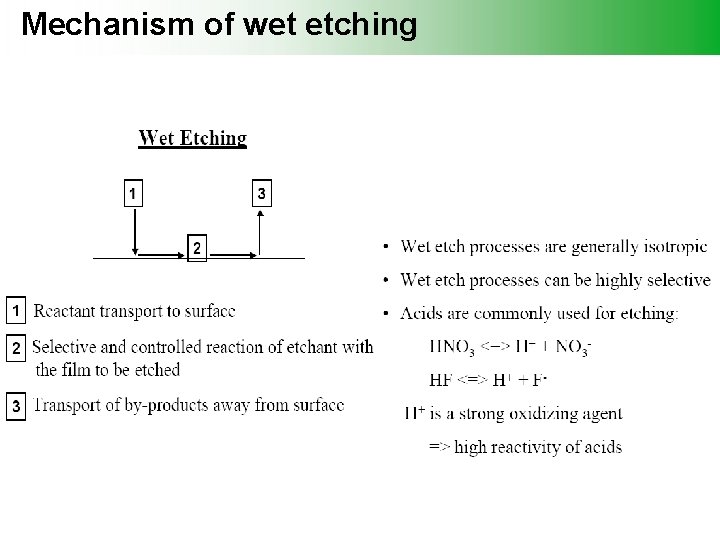
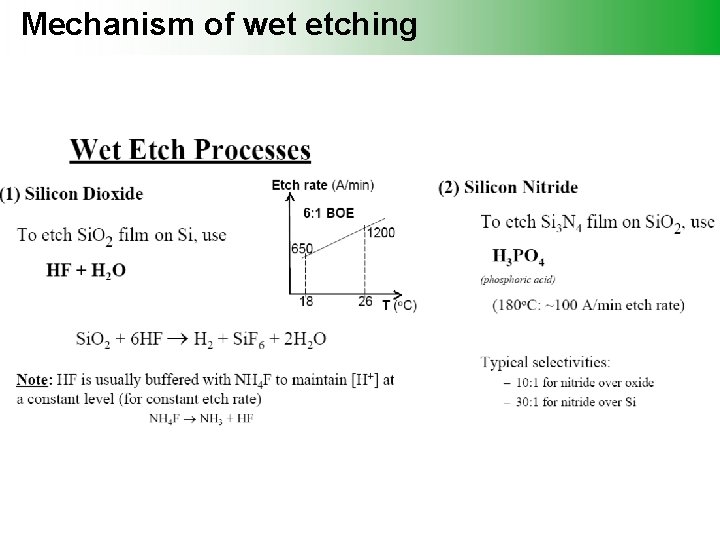
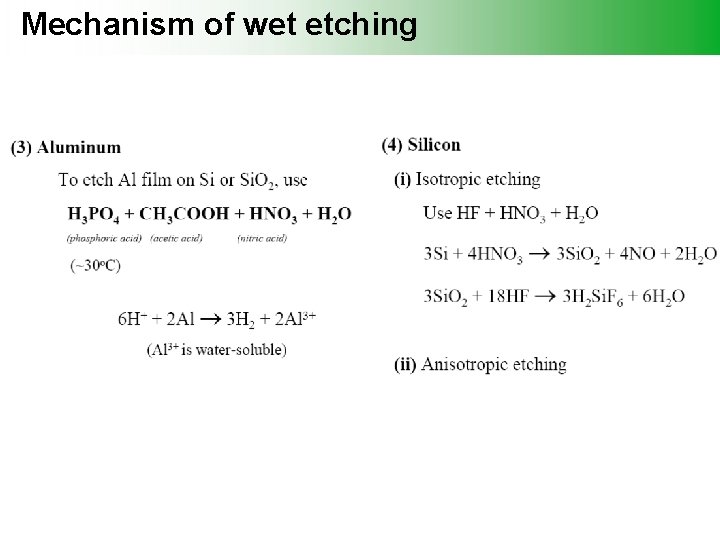
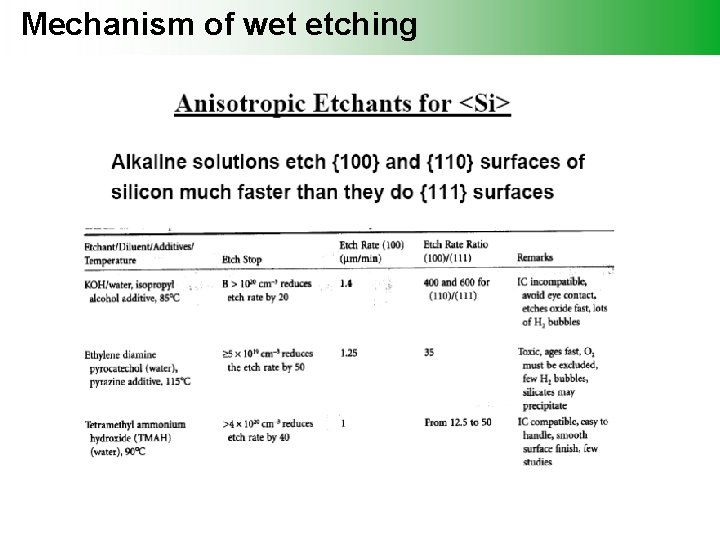
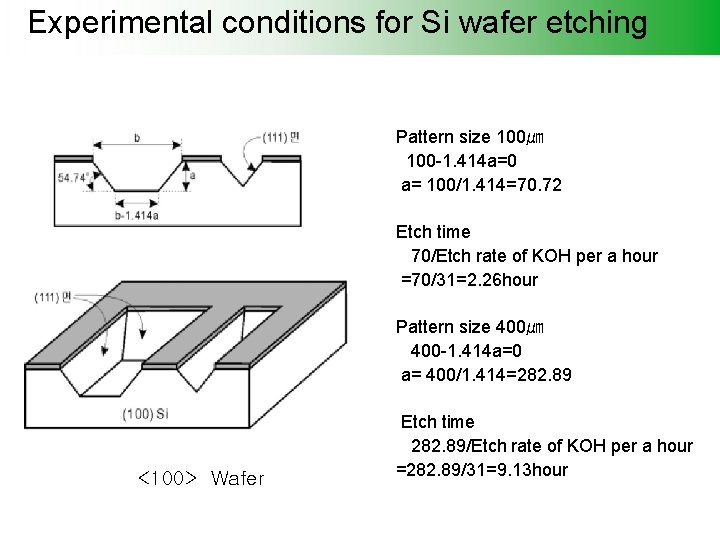
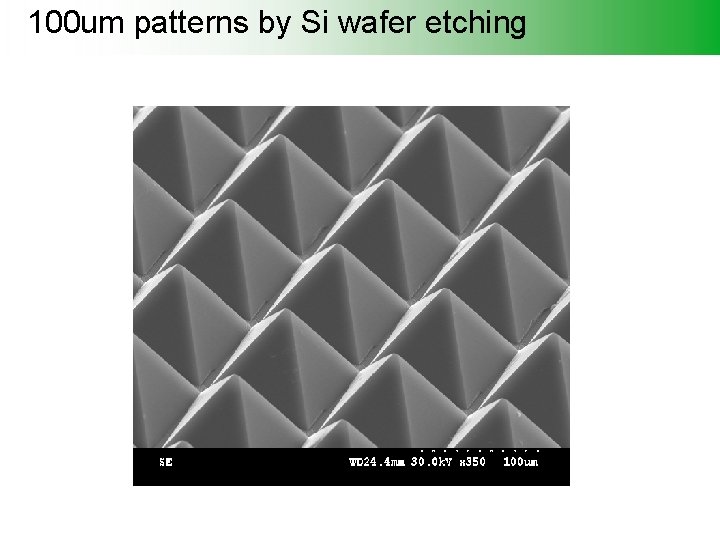
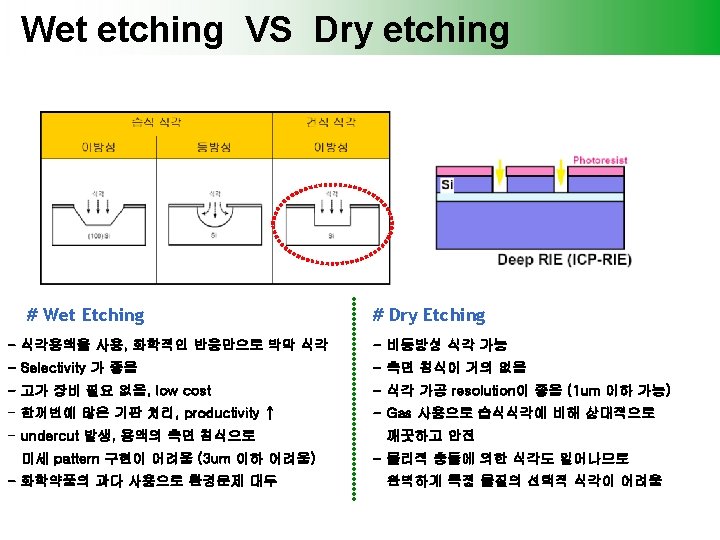
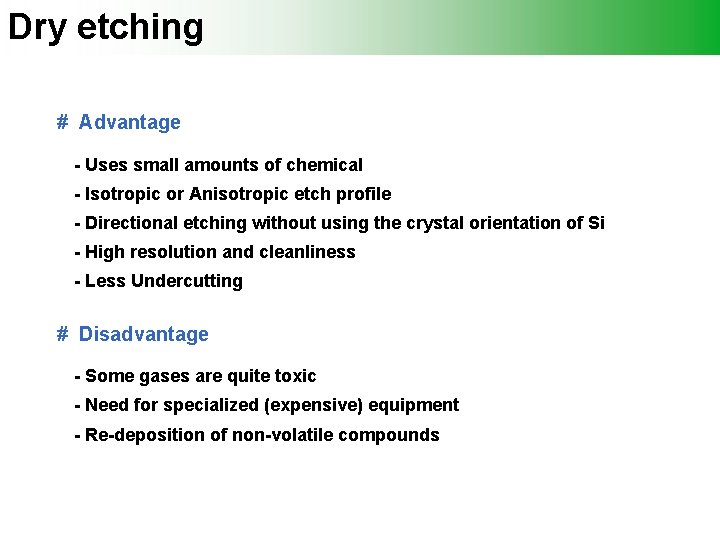
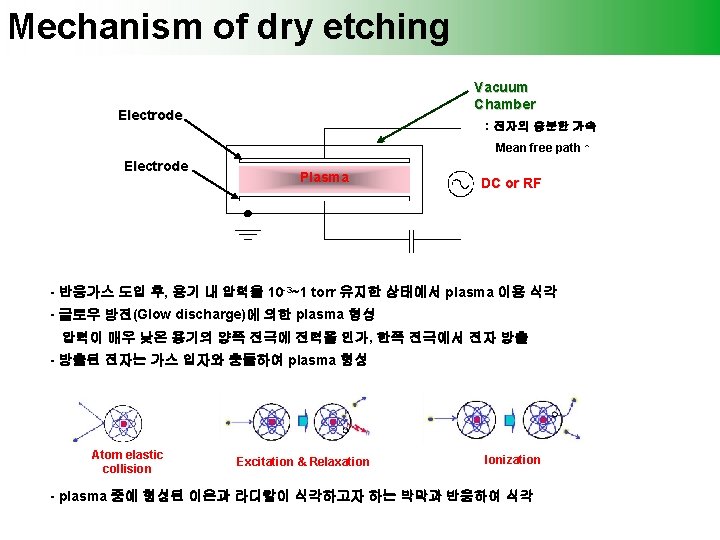
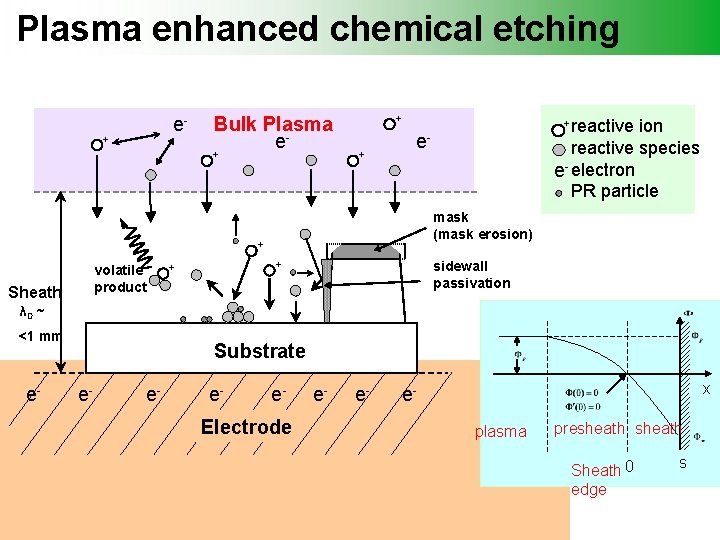
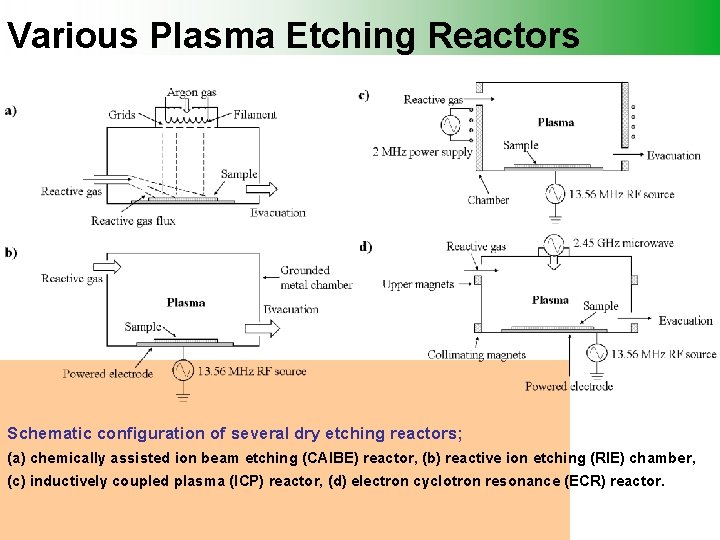
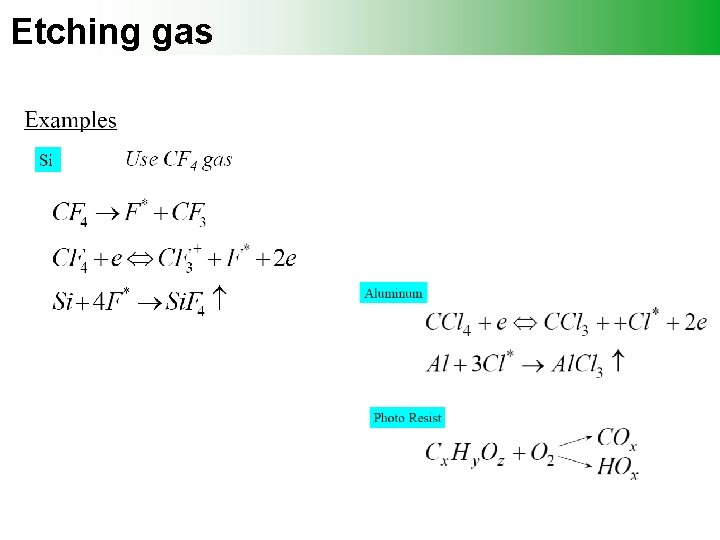
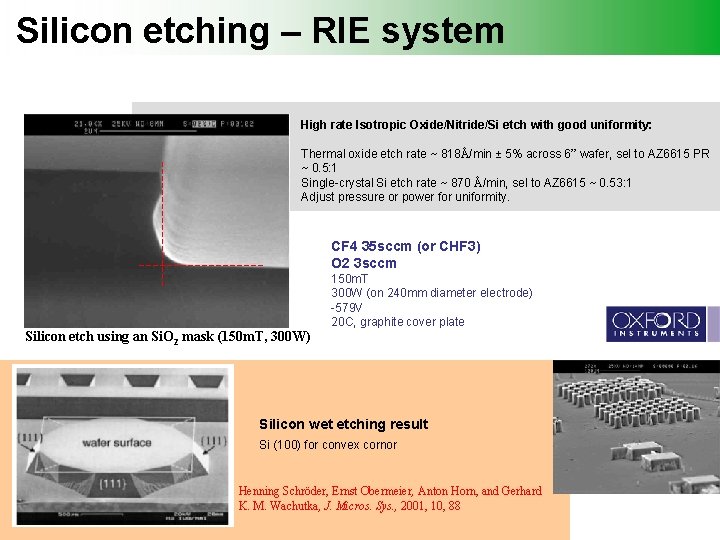
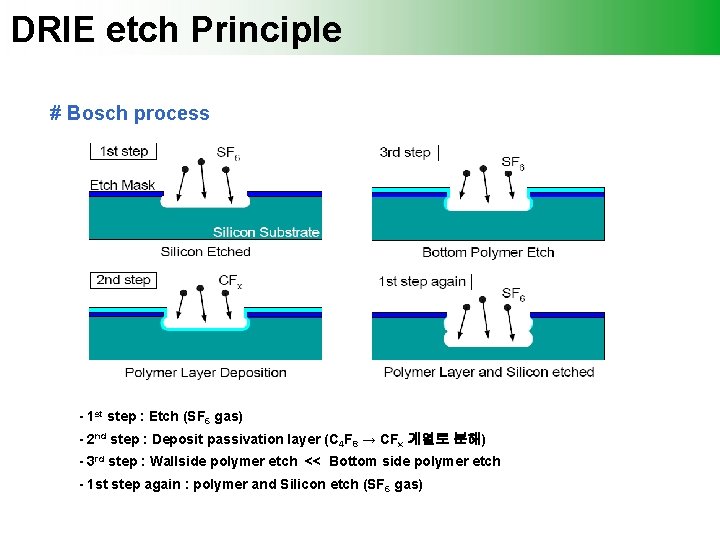
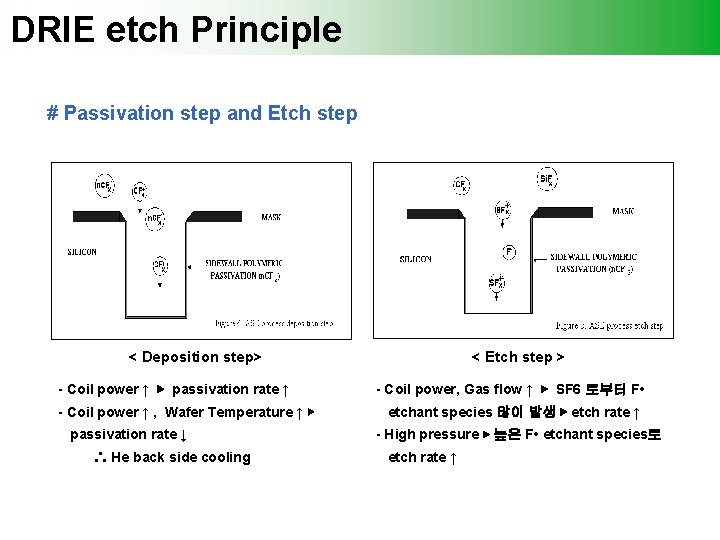
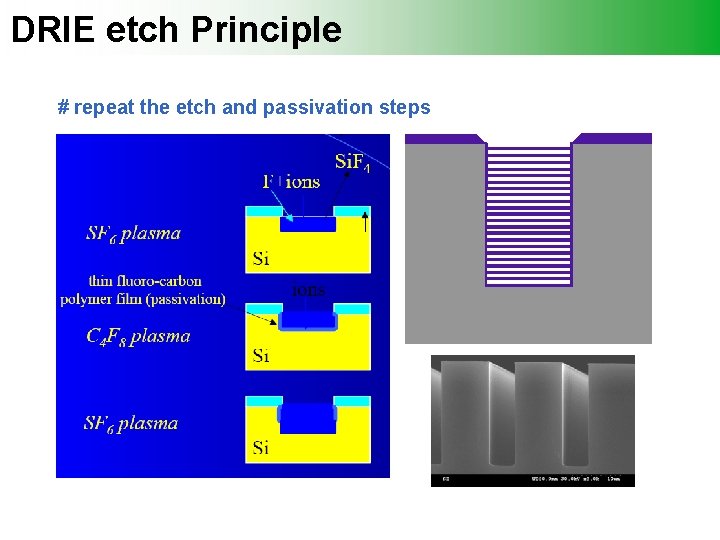
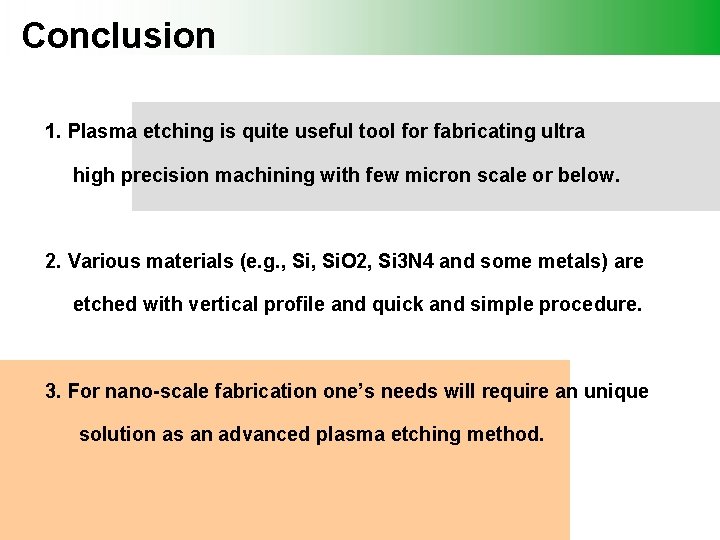
- Slides: 23
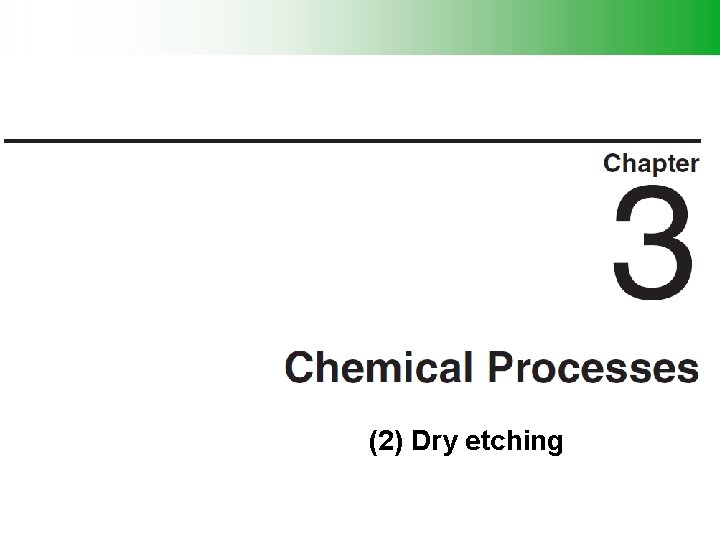
(2) Dry etching
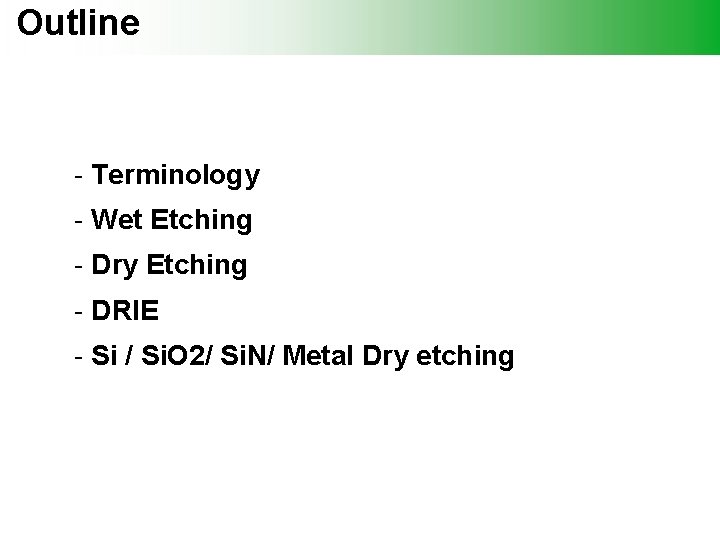
Outline - Terminology - Wet Etching - Dry Etching - DRIE - Si / Si. O 2/ Si. N/ Metal Dry etching
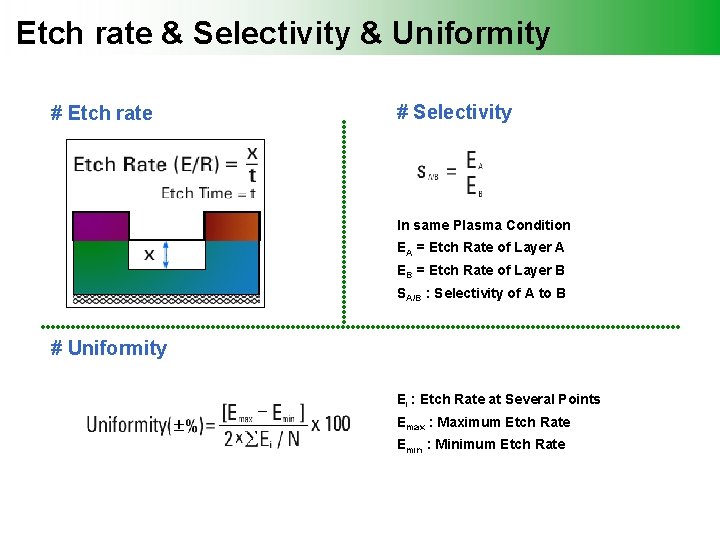
Etch rate & Selectivity & Uniformity # Etch rate # Selectivity In same Plasma Condition EA = Etch Rate of Layer A EB = Etch Rate of Layer B SA/B : Selectivity of A to B # Uniformity Ei : Etch Rate at Several Points Emax : Maximum Etch Rate Emin : Minimum Etch Rate
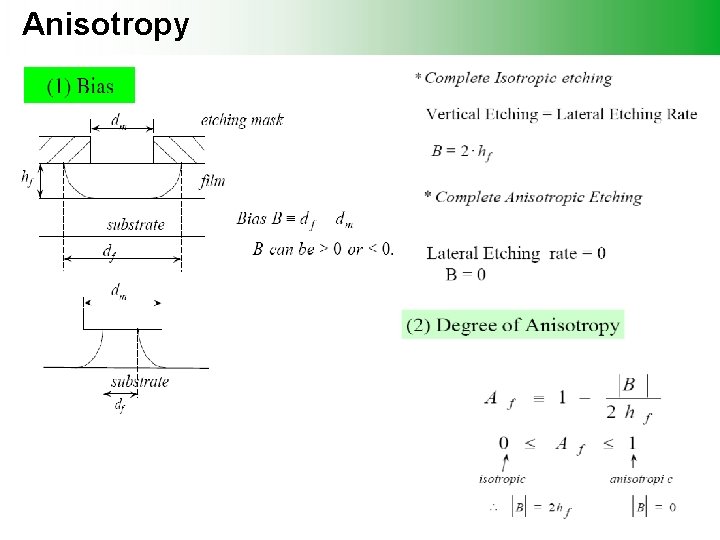
Anisotropy
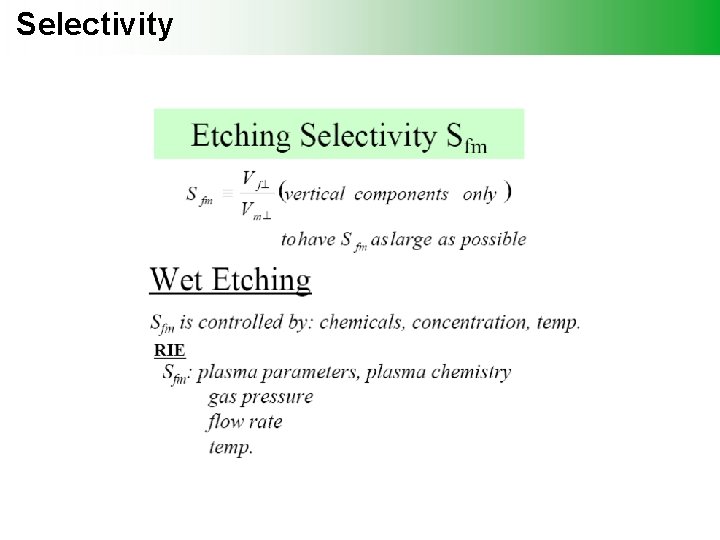
Selectivity
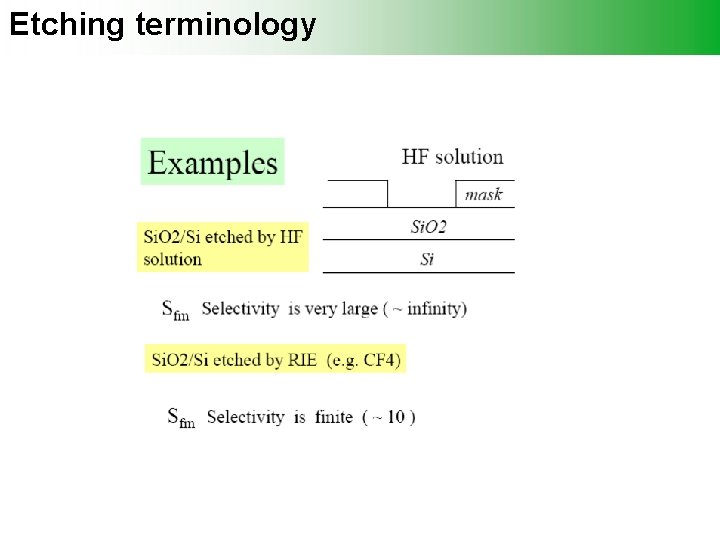
Etching terminology
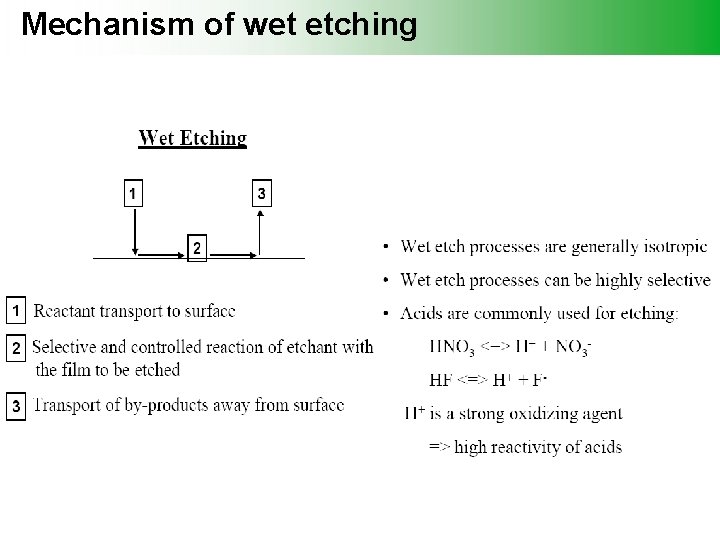
Mechanism of wet etching
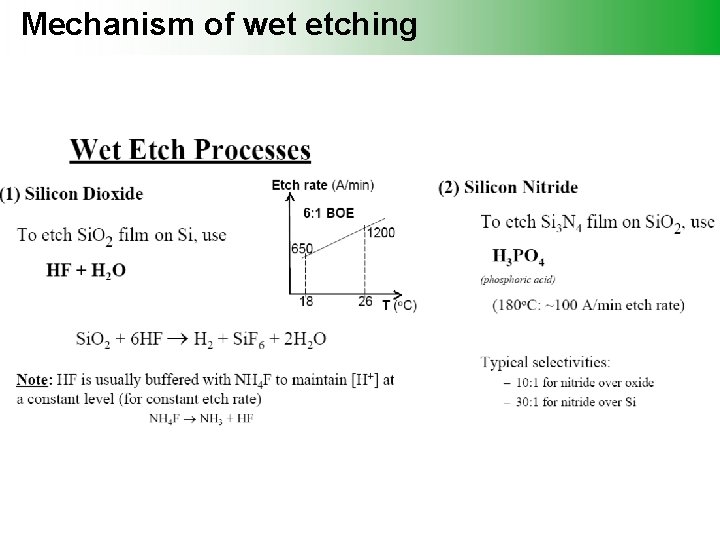
Mechanism of wet etching
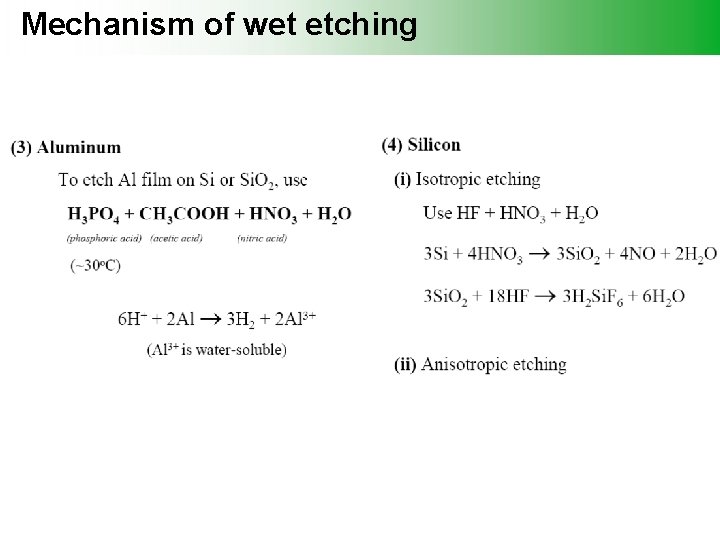
Mechanism of wet etching
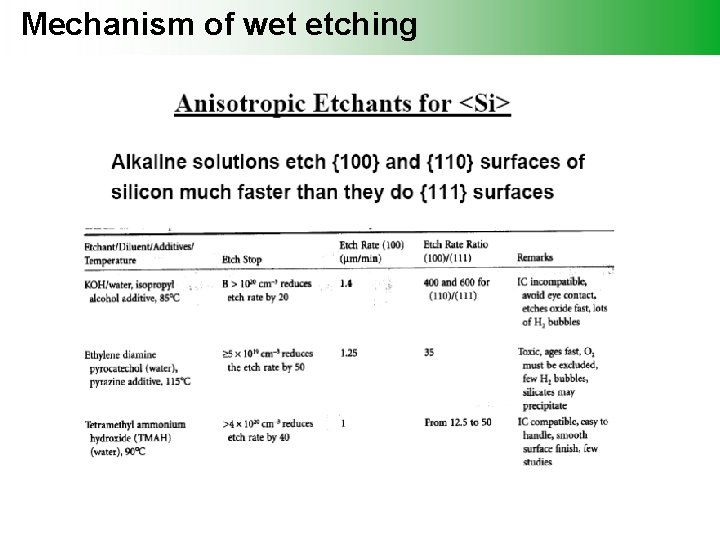
Mechanism of wet etching
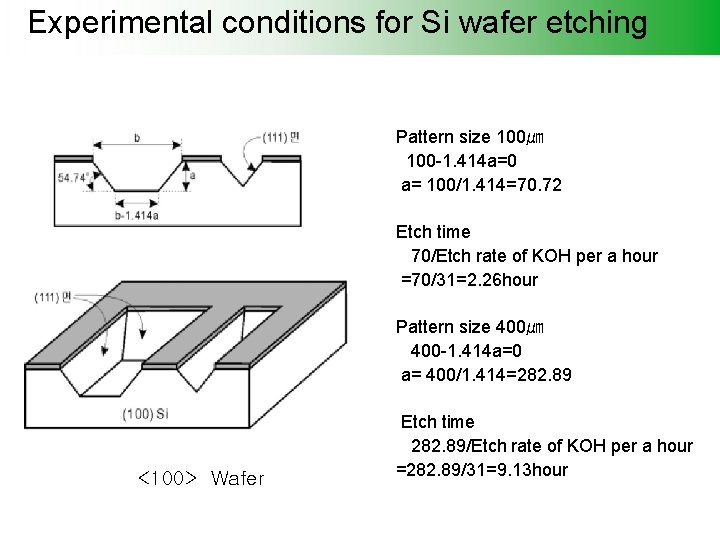
Experimental conditions for Si wafer etching Pattern size 100㎛ 100 -1. 414 a=0 a= 100/1. 414=70. 72 Etch time 70/Etch rate of KOH per a hour =70/31=2. 26 hour Pattern size 400㎛ 400 -1. 414 a=0 a= 400/1. 414=282. 89 <100> Wafer Etch time 282. 89/Etch rate of KOH per a hour =282. 89/31=9. 13 hour
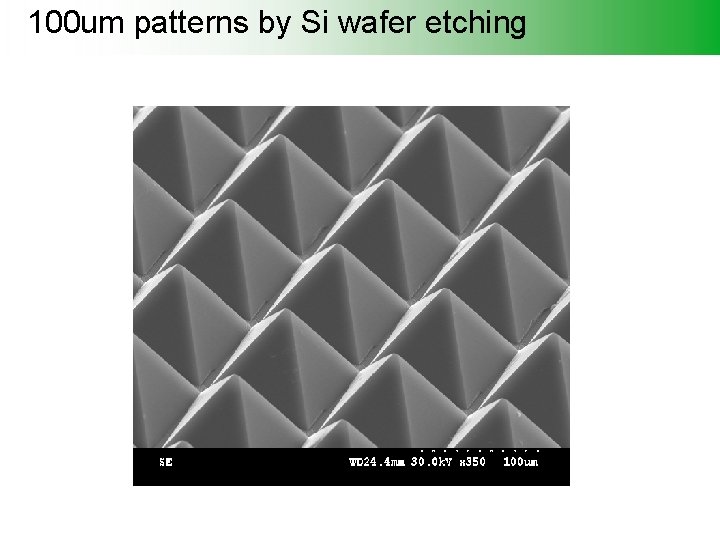
100 um patterns by Si wafer etching
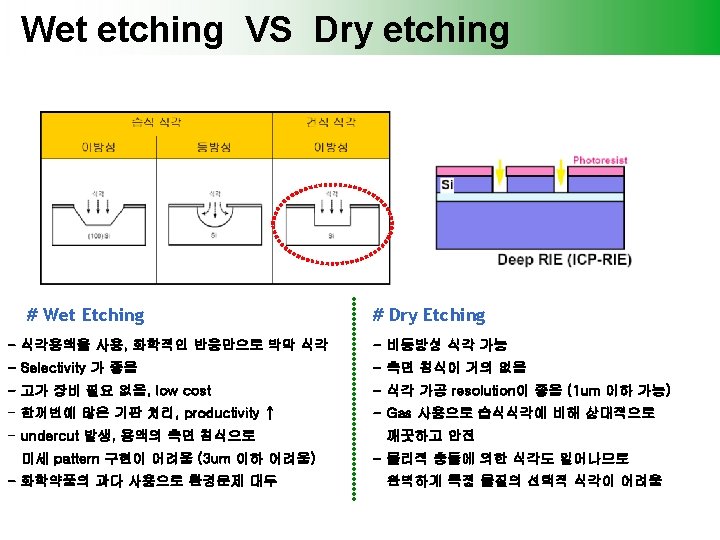
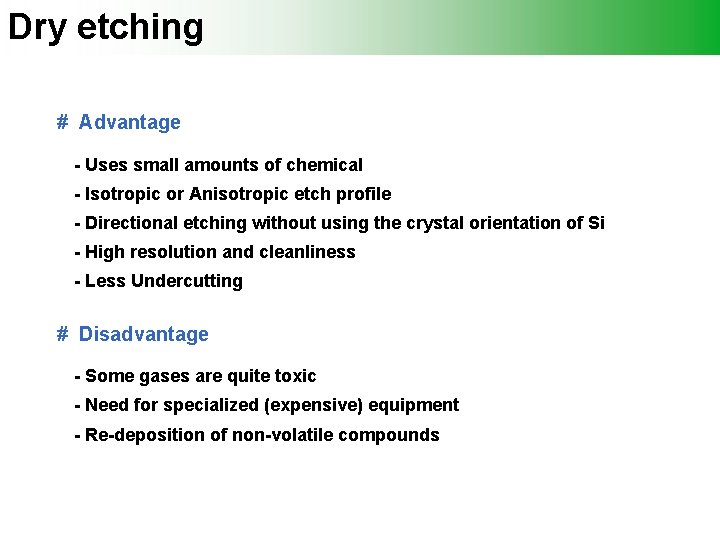
Dry etching # Advantage - Uses small amounts of chemical - Isotropic or Anisotropic etch profile - Directional etching without using the crystal orientation of Si - High resolution and cleanliness - Less Undercutting # Disadvantage - Some gases are quite toxic - Need for specialized (expensive) equipment - Re-deposition of non-volatile compounds
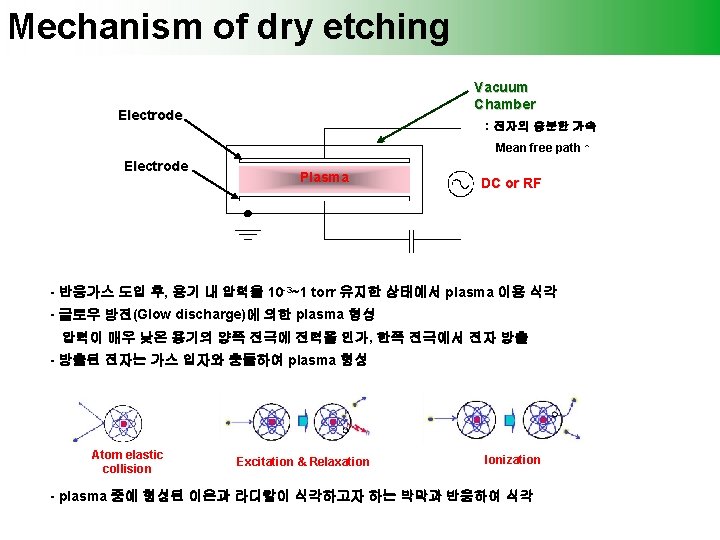
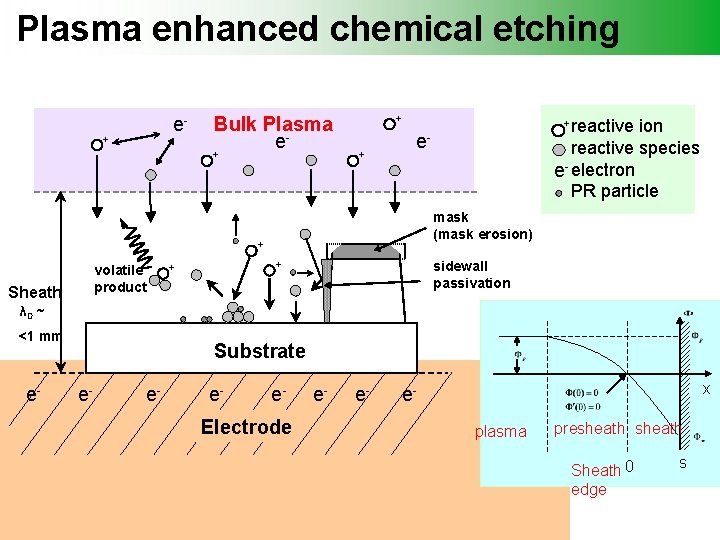
Plasma enhanced chemical etching e- + Bulk Plasma e- + + + e- mask (mask erosion) + volatile product Sheath sidewall passivation + + reactive ion reactive species e- electron PR particle + λD ~ <1 mm e- Substrate e- e- Electrode e- e- x eplasma presheath Sheath 0 edge s
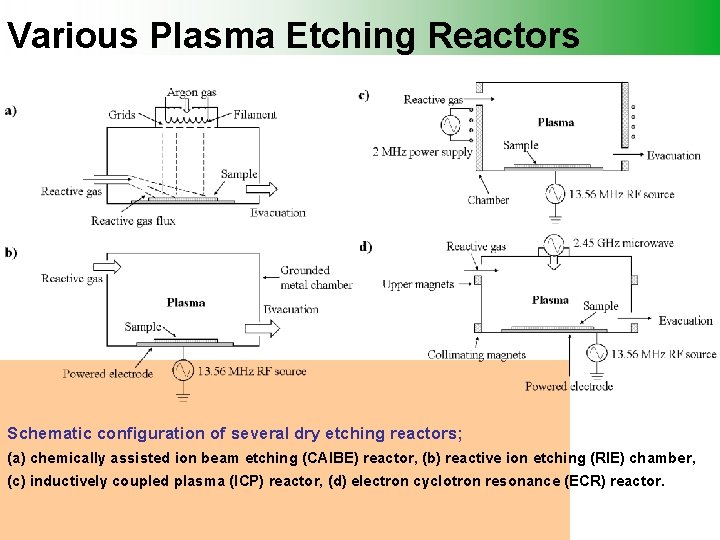
Various Plasma Etching Reactors Schematic configuration of several dry etching reactors; (a) chemically assisted ion beam etching (CAIBE) reactor, (b) reactive ion etching (RIE) chamber, (c) inductively coupled plasma (ICP) reactor, (d) electron cyclotron resonance (ECR) reactor.
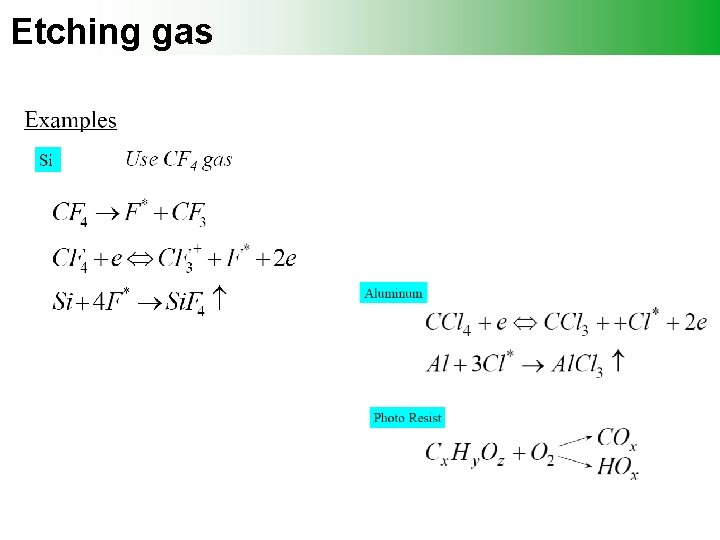
Etching gas
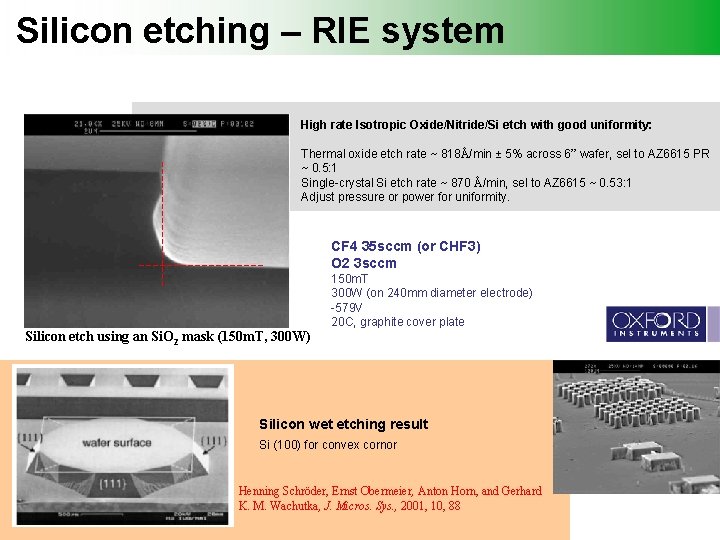
Silicon etching – RIE system High rate Isotropic Oxide/Nitride/Si etch with good uniformity: Thermal oxide etch rate ~ 818Å/min ± 5% across 6” wafer, sel to AZ 6615 PR ~ 0. 5: 1 Single-crystal Si etch rate ~ 870 Å/min, sel to AZ 6615 ~ 0. 53: 1 Adjust pressure or power for uniformity. CF 4 35 sccm (or CHF 3) O 2 3 sccm 150 m. T 300 W (on 240 mm diameter electrode) -579 V 20 C, graphite cover plate Silicon etch using an Si. O 2 mask (150 m. T, 300 W) Silicon wet etching result Si (100) for convex cornor Henning Schröder, Ernst Obermeier, Anton Horn, and Gerhard K. M. Wachutka, J. Micros. Sys. , 2001, 10, 88
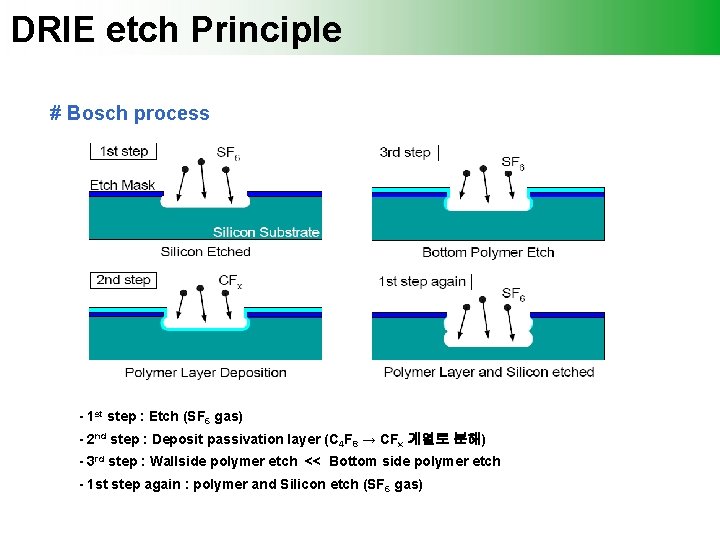
DRIE etch Principle # Bosch process - 1 st step : Etch (SF 6 gas) - 2 nd step : Deposit passivation layer (C 4 F 8 → CFx 계열로 분해) - 3 rd step : Wallside polymer etch << Bottom side polymer etch - 1 st step again : polymer and Silicon etch (SF 6 gas)
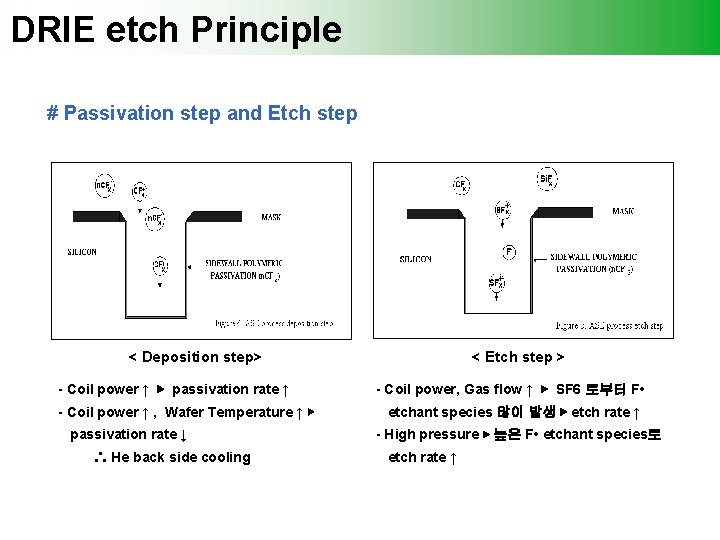
DRIE etch Principle # Passivation step and Etch step < Deposition step> - Coil power ↑ ▶ passivation rate ↑ - Coil power ↑ , Wafer Temperature ↑ ▶ passivation rate ↓ ∴ He back side cooling < Etch step > - Coil power, Gas flow ↑ ▶ SF 6 로부터 F • etchant species 많이 발생 ▶ etch rate ↑ - High pressure ▶ 높은 F • etchant species로 etch rate ↑
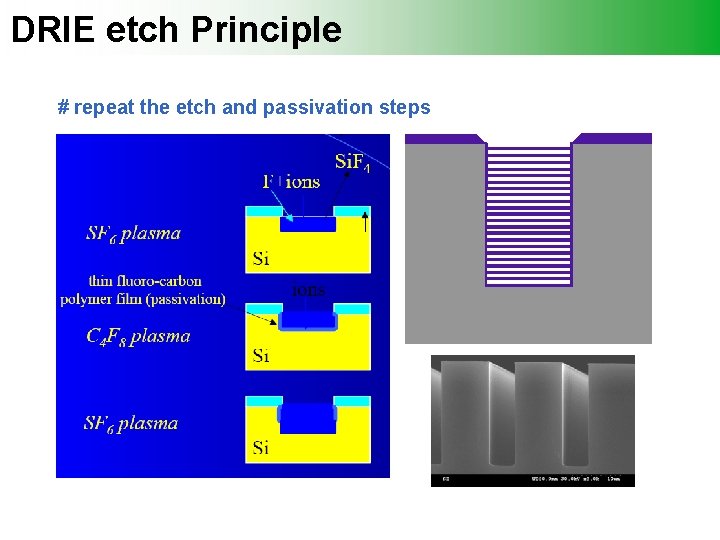
DRIE etch Principle # repeat the etch and passivation steps
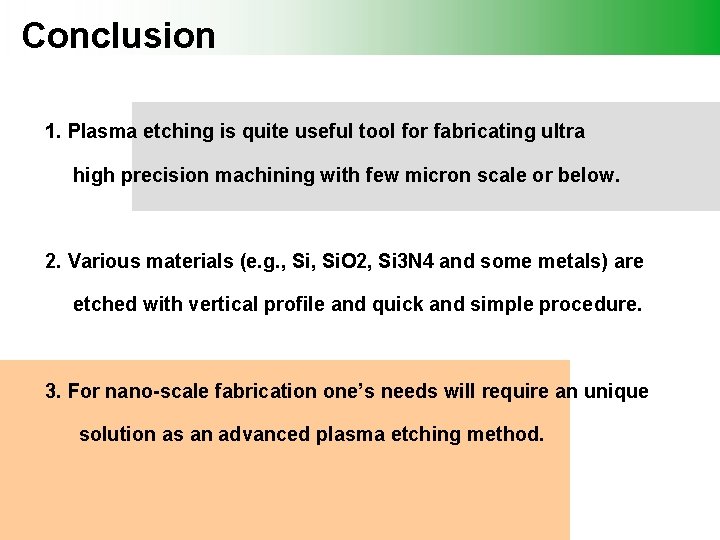
Conclusion 1. Plasma etching is quite useful tool for fabricating ultra high precision machining with few micron scale or below. 2. Various materials (e. g. , Si. O 2, Si 3 N 4 and some metals) are etched with vertical profile and quick and simple procedure. 3. For nano-scale fabrication one’s needs will require an unique solution as an advanced plasma etching method.
Wet etching vs dry etching
Anisotropy
Wet wet wet
Wet etching
Dry and wet adiabatic lapse rate
Emulsion definition pharmacy
Superadded putrefaction meaning
Use in wet and dry land preparation
Dry cell vs wet cell
Tropical wet and dry locations
Salting fish
Diagram of wet bundh
Slugging in industrial pharmacy
Intracellular accumulation
Continental method of emulsion
Chest tube placement
Wet or electrochemical corrosion
Bonding agents
Auxiliary emulsifying agents
Differentiate between dry corrosion and wet corrosion
Types of gypsum products
Dry gum method of emulsion is also known as (
Wet bonding vs dry bonding
Enamel composition