Etching and Cleaning remove contaminated layers Etching remove
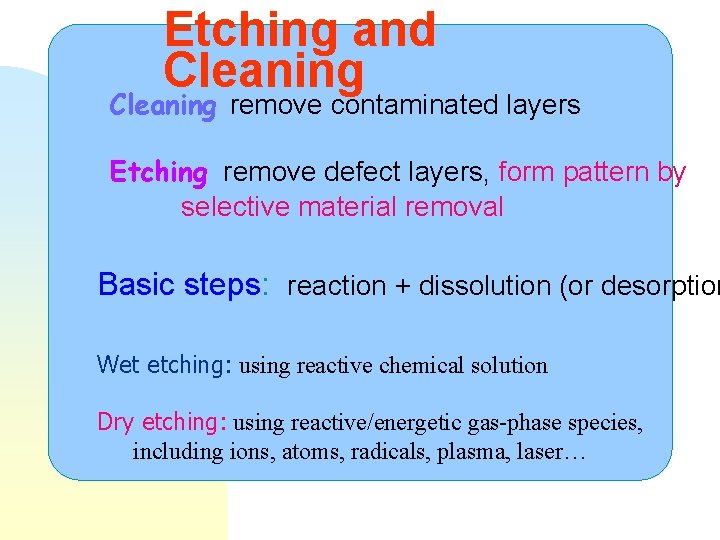
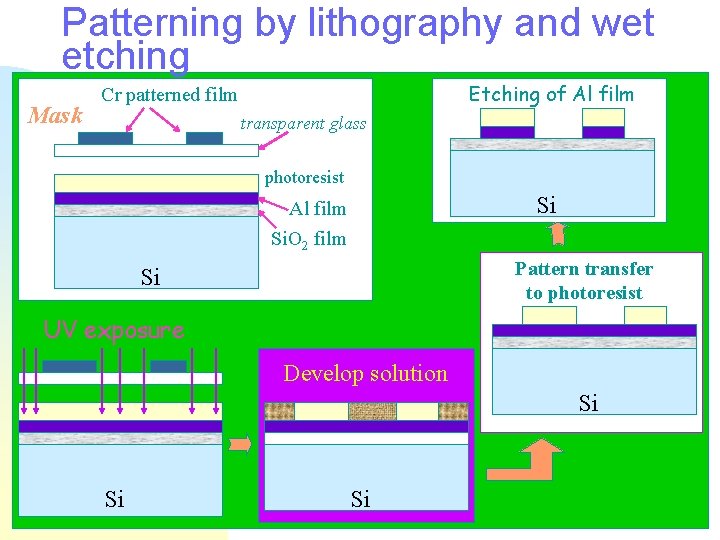
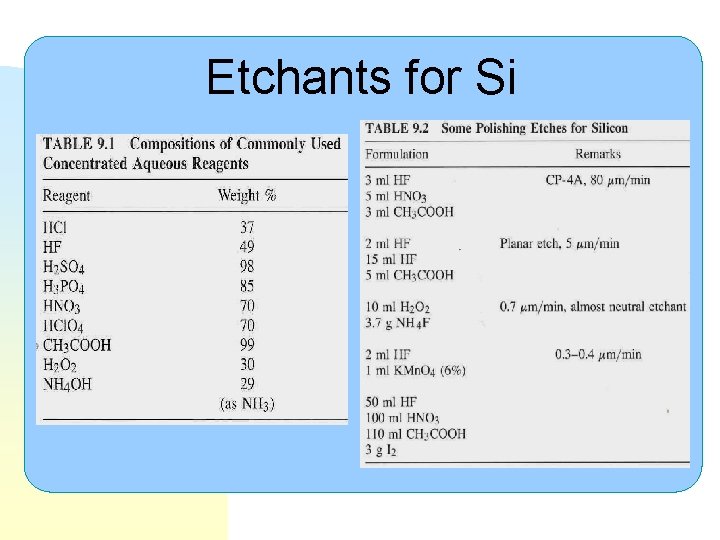
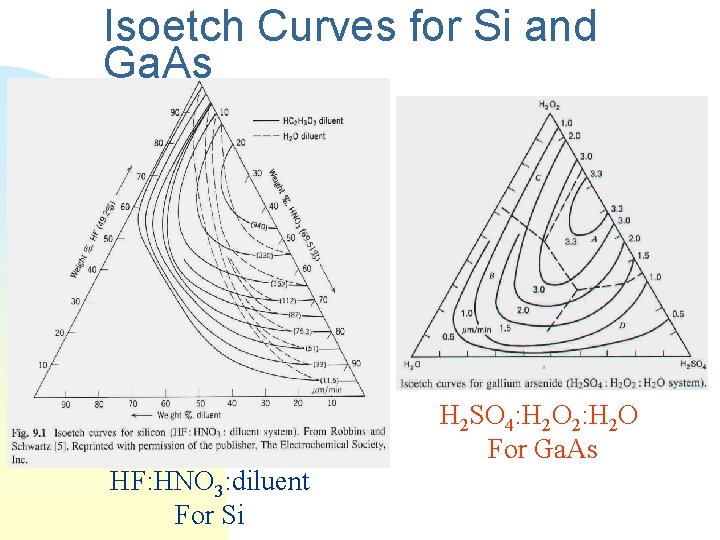
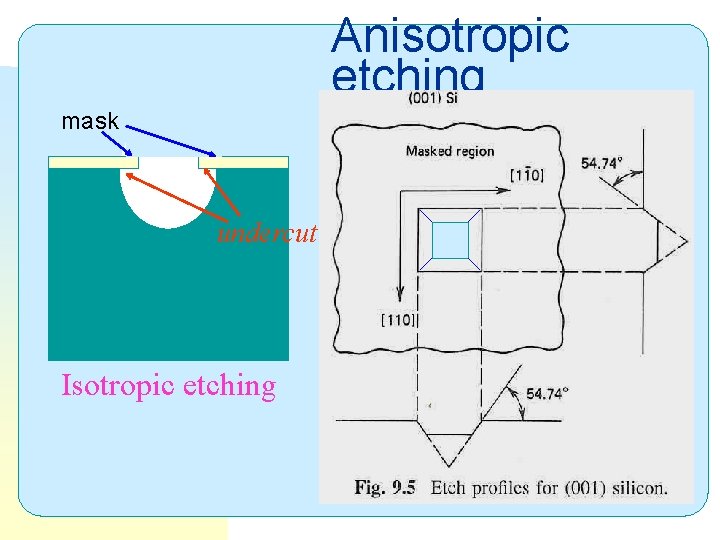
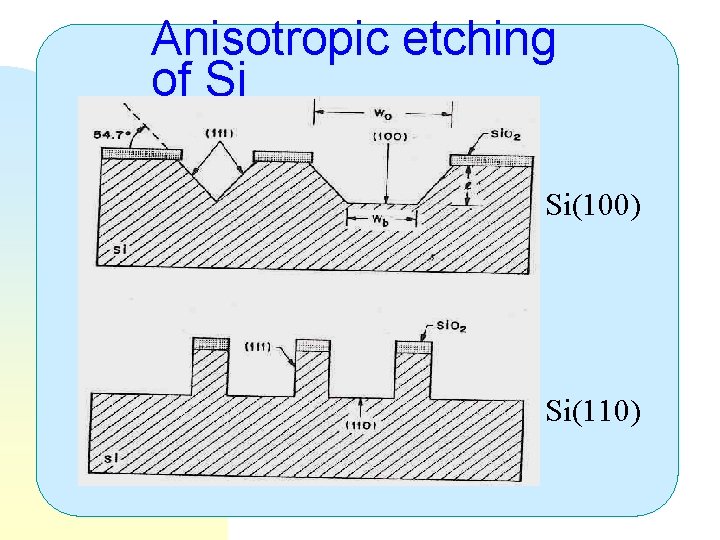
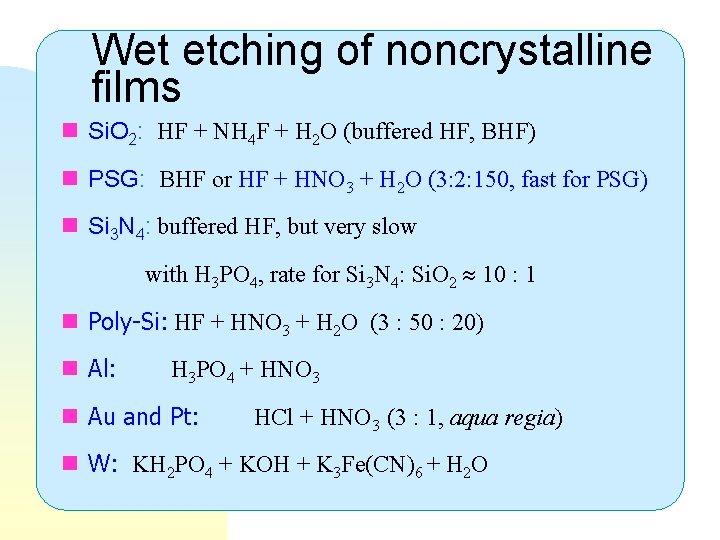
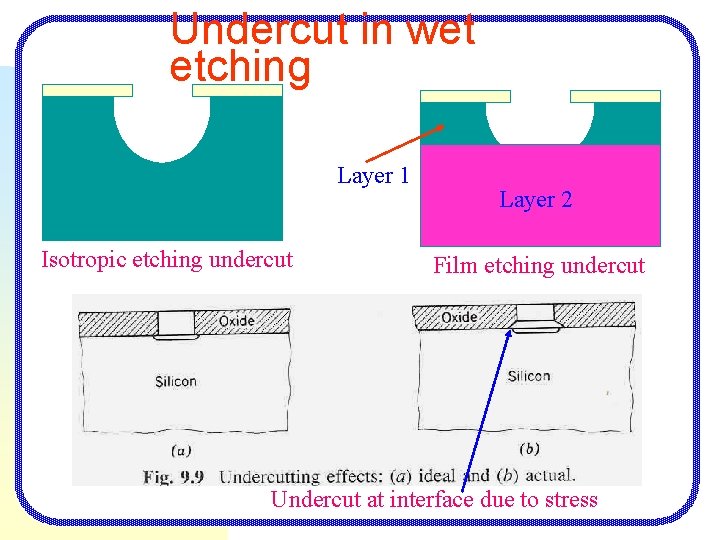
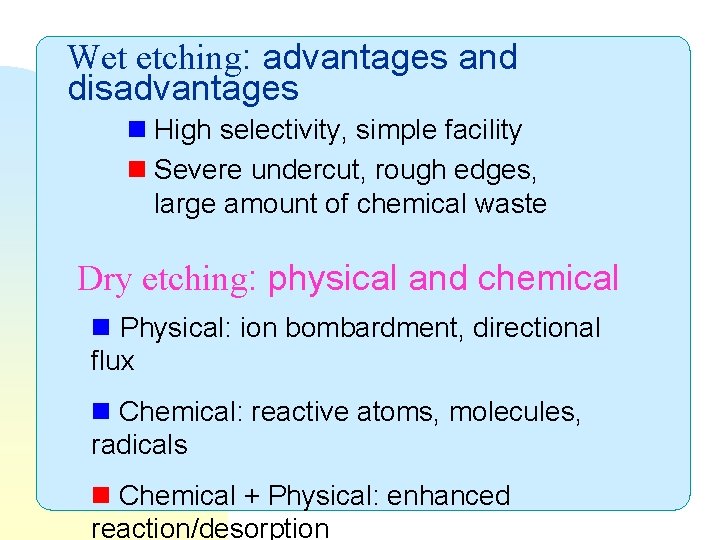
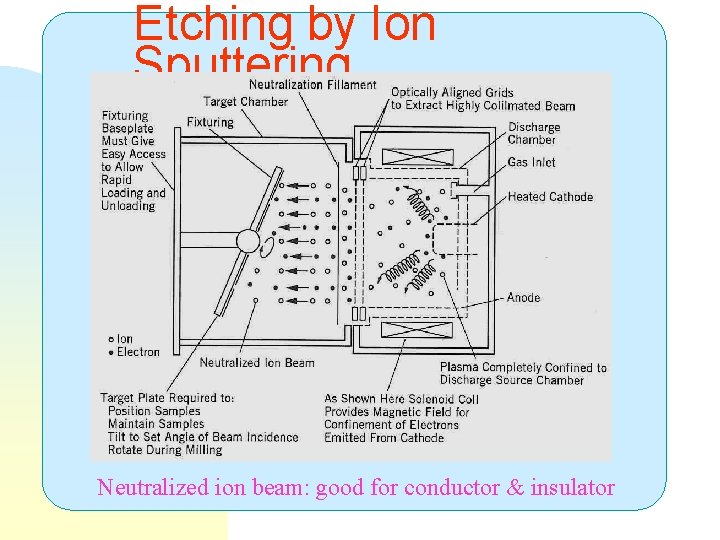
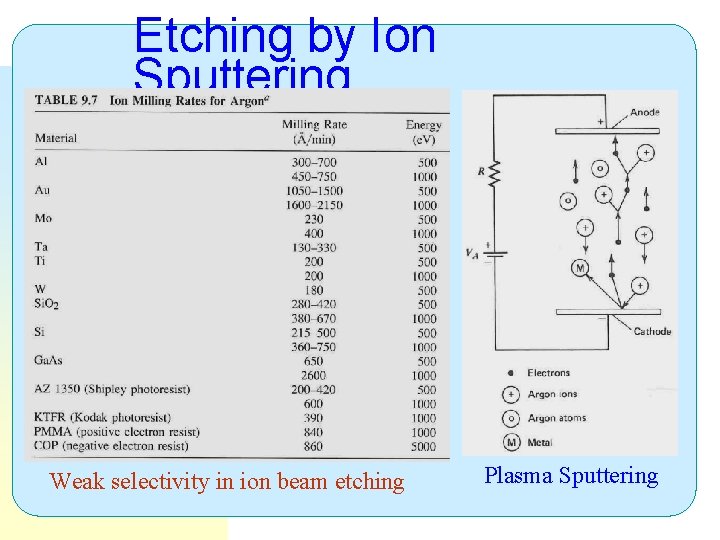
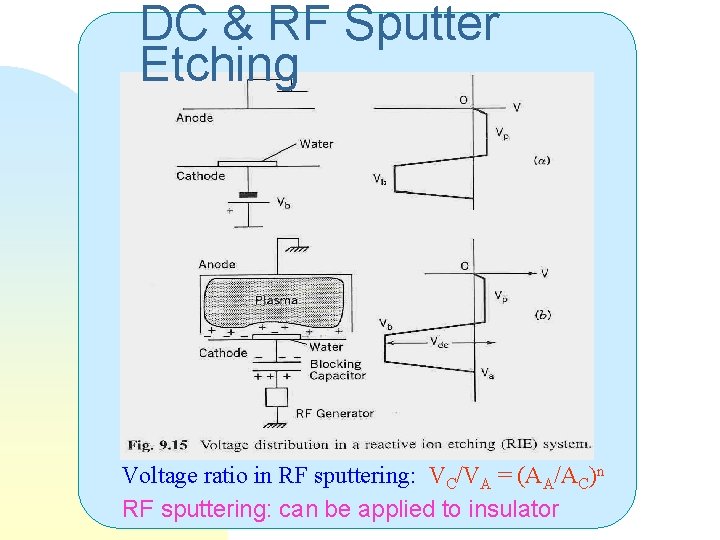
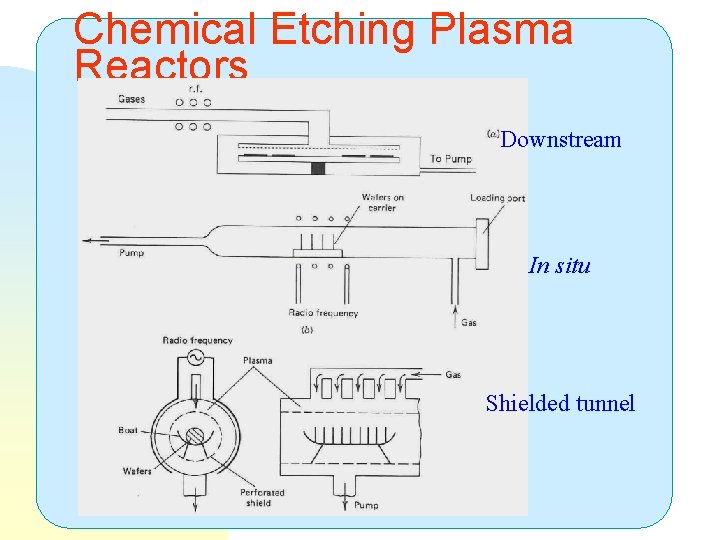
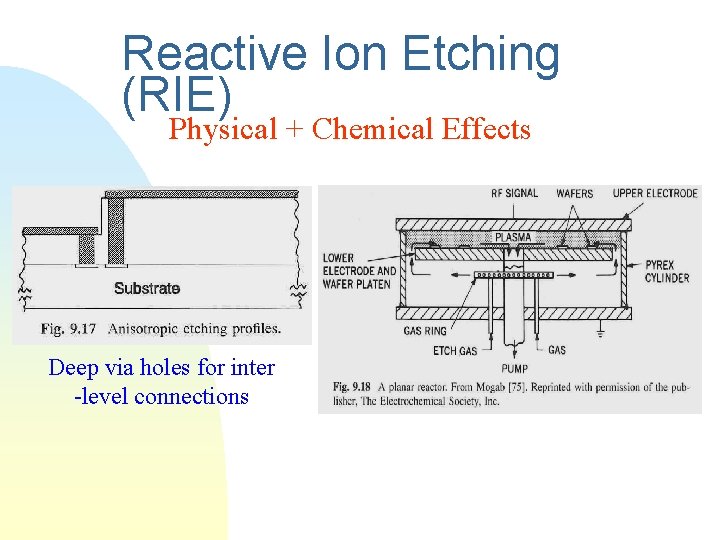
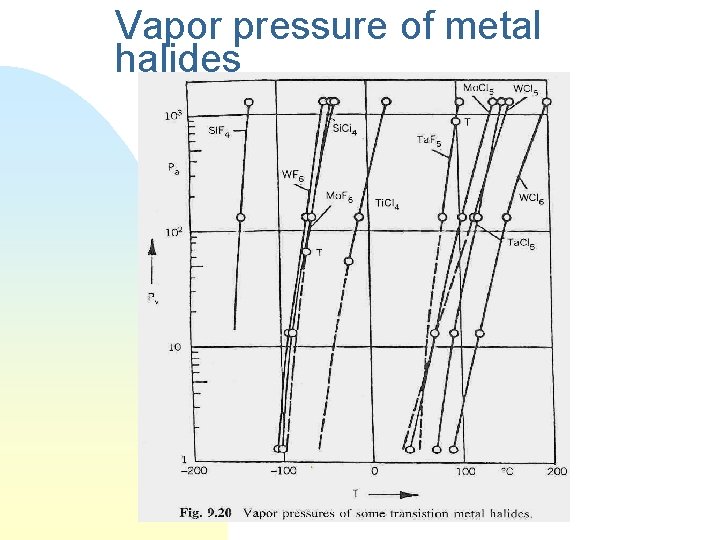
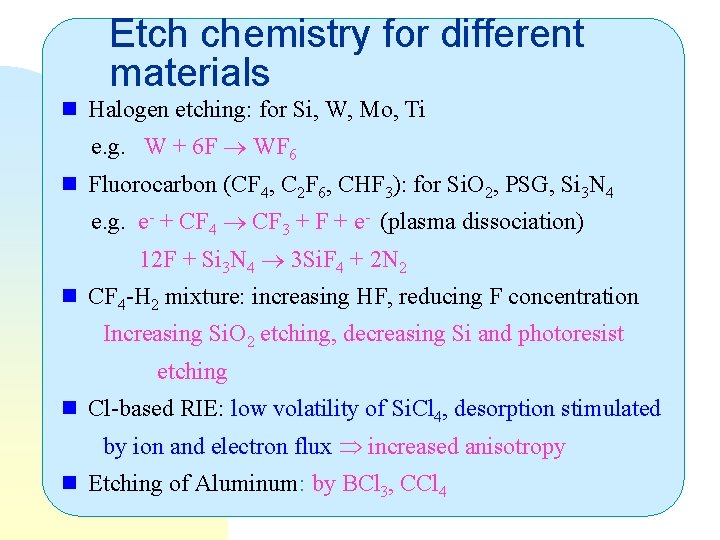
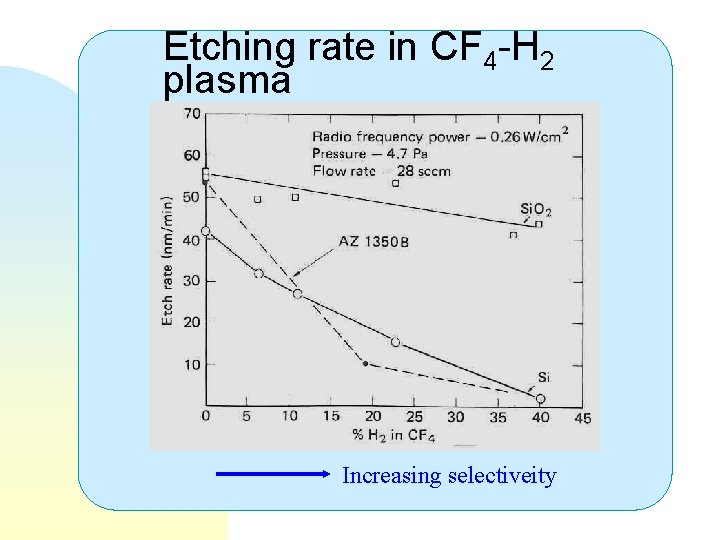
- Slides: 17
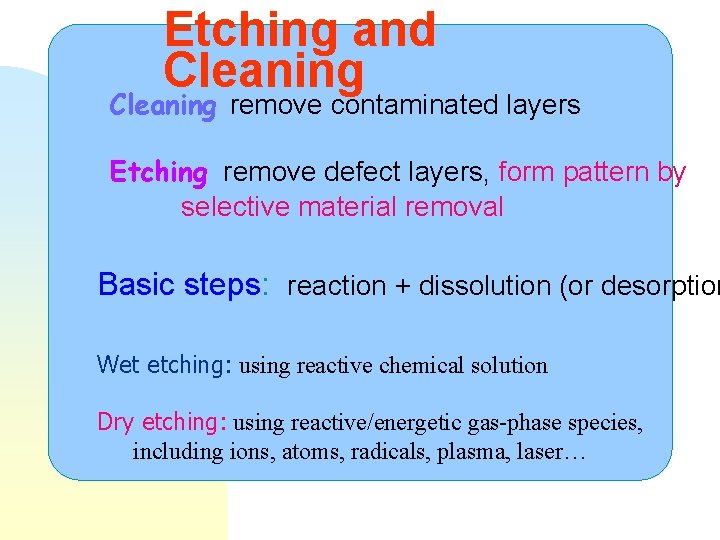
Etching and Cleaning remove contaminated layers Etching remove defect layers, form pattern by selective material removal Basic steps: reaction + dissolution (or desorption Wet etching: using reactive chemical solution Dry etching: using reactive/energetic gas-phase species, including ions, atoms, radicals, plasma, laser…
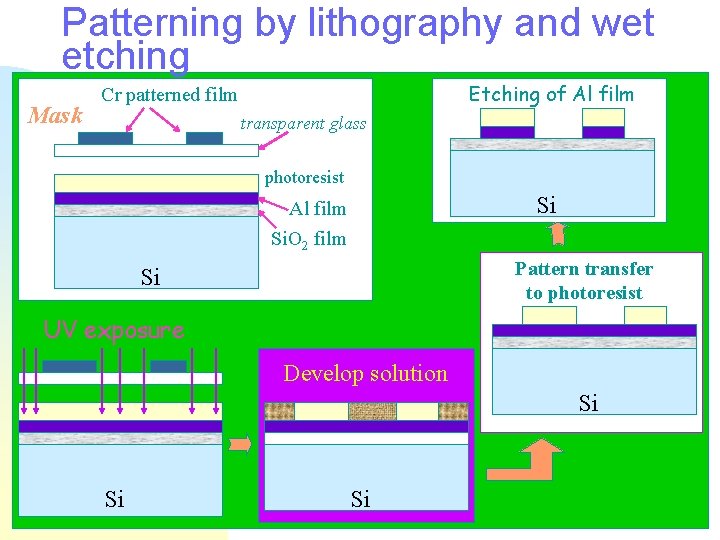
Patterning by lithography and wet etching Mask Etching of Al film Cr patterned film transparent glass photoresist Si Al film Si. O 2 film Pattern transfer to photoresist Si UV exposure Develop solution Si Si Si
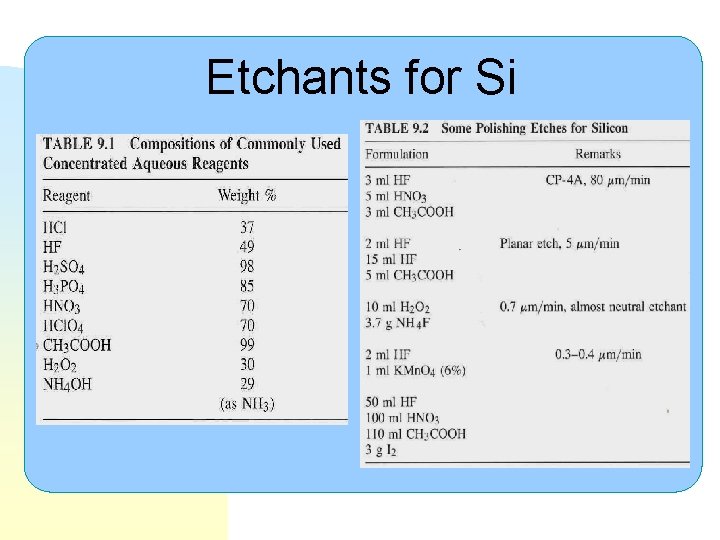
Etchants for Si
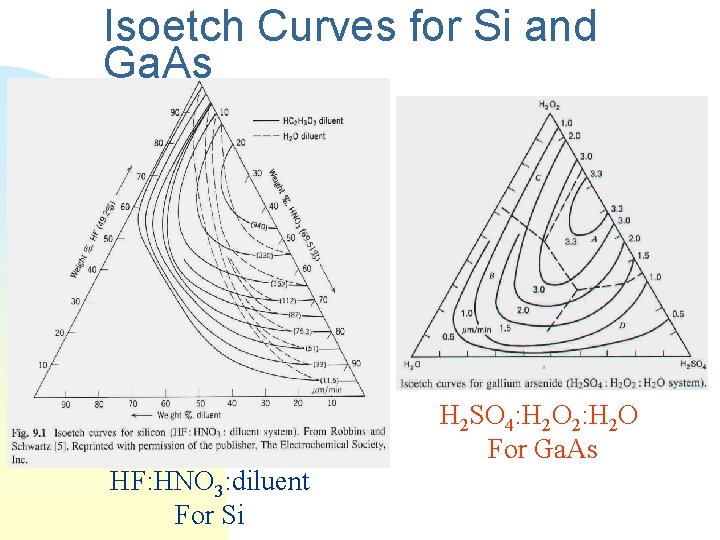
Isoetch Curves for Si and Ga. As H 2 SO 4: H 2 O 2: H 2 O For Ga. As HF: HNO 3: diluent For Si
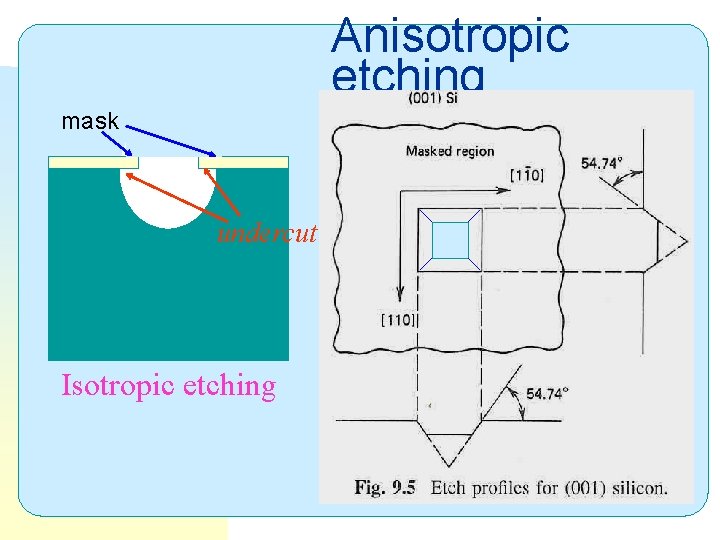
Anisotropic etching mask undercut Isotropic etching
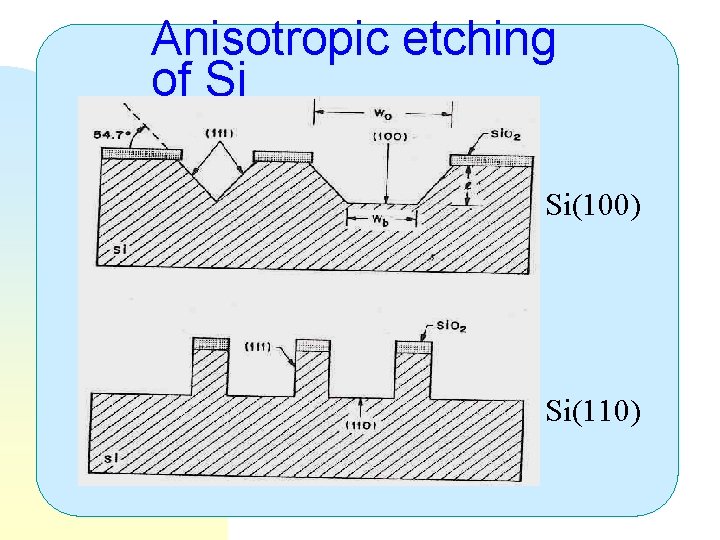
Anisotropic etching of Si Si(100) Si(110)
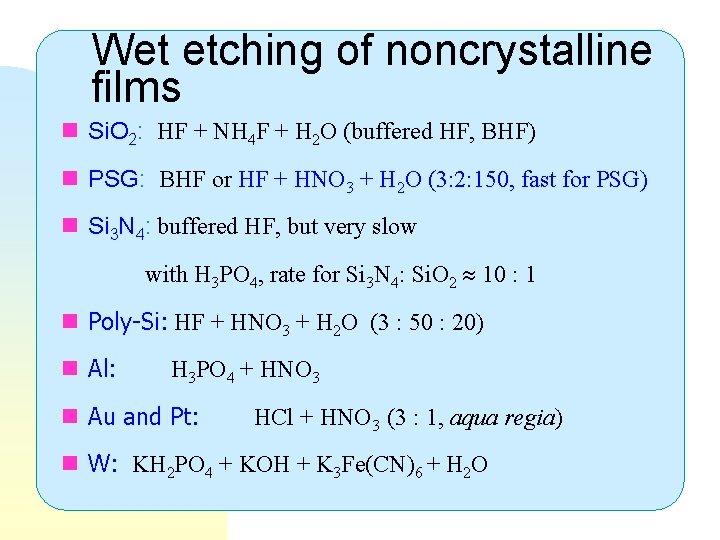
Wet etching of noncrystalline films n Si. O 2: HF + NH 4 F + H 2 O (buffered HF, BHF) n PSG: BHF or HF + HNO 3 + H 2 O (3: 2: 150, fast for PSG) n Si 3 N 4: buffered HF, but very slow with H 3 PO 4, rate for Si 3 N 4: Si. O 2 10 : 1 n Poly-Si: HF + HNO 3 + H 2 O (3 : 50 : 20) n Al: H 3 PO 4 + HNO 3 n Au and Pt: HCl + HNO 3 (3 : 1, aqua regia) n W: KH 2 PO 4 + KOH + K 3 Fe(CN)6 + H 2 O
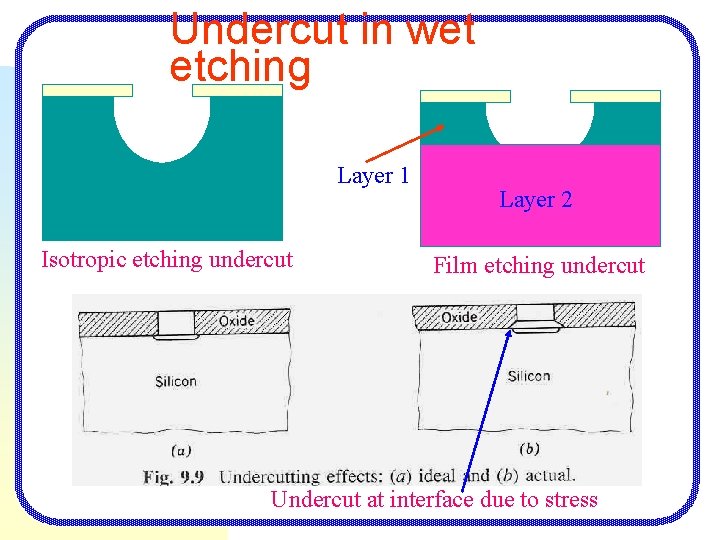
Undercut in wet etching Layer 1 Isotropic etching undercut Layer 2 Film etching undercut Undercut at interface due to stress
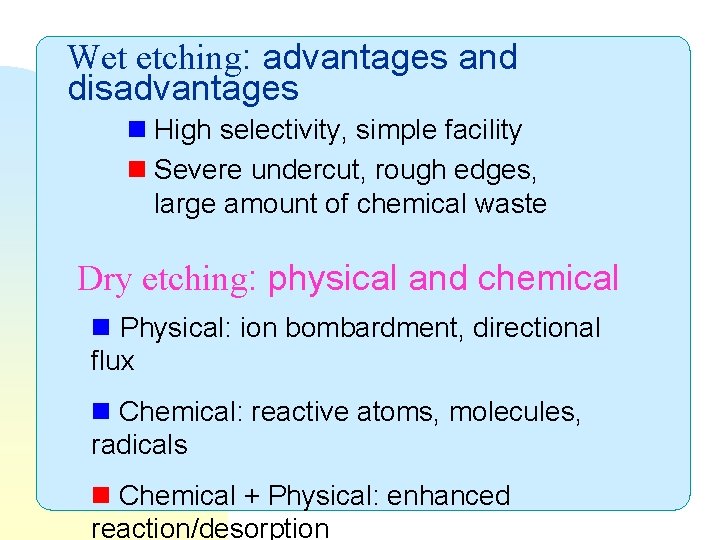
Wet etching: advantages and disadvantages n High selectivity, simple facility n Severe undercut, rough edges, large amount of chemical waste Dry etching: physical and chemical n Physical: ion bombardment, directional flux n Chemical: reactive atoms, molecules, radicals n Chemical + Physical: enhanced reaction/desorption
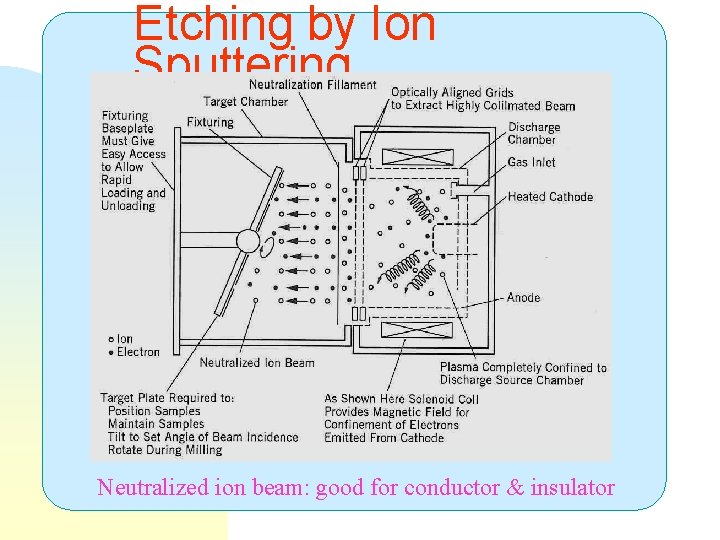
Etching by Ion Sputtering Neutralized ion beam: good for conductor & insulator
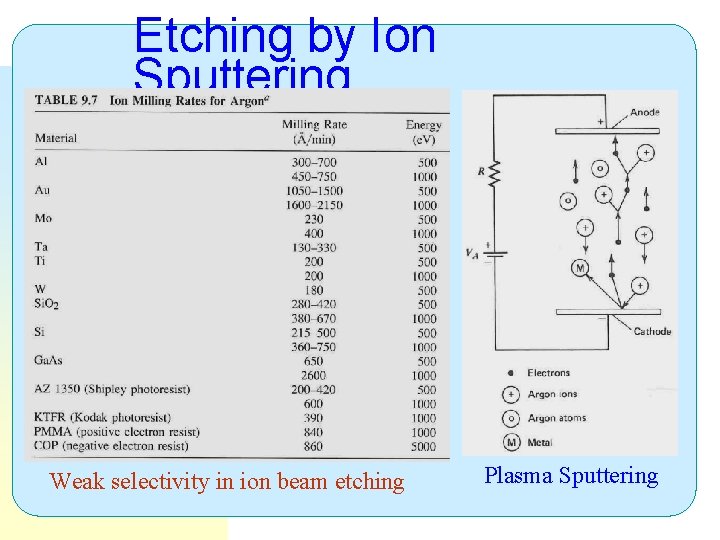
Etching by Ion Sputtering Weak selectivity in ion beam etching Plasma Sputtering
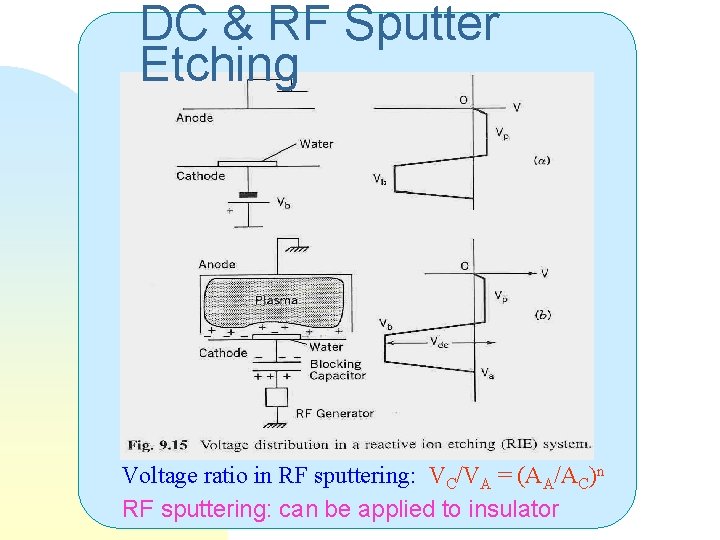
DC & RF Sputter Etching Voltage ratio in RF sputtering: VC/VA = (AA/AC)n RF sputtering: can be applied to insulator
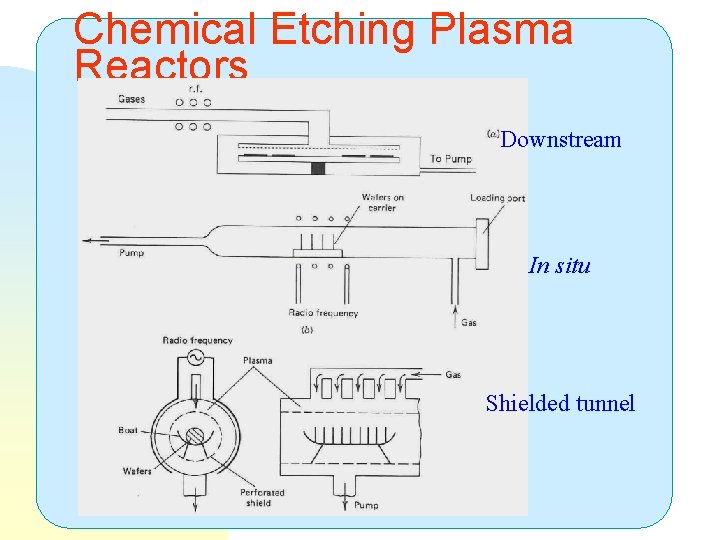
Chemical Etching Plasma Reactors Downstream In situ Shielded tunnel
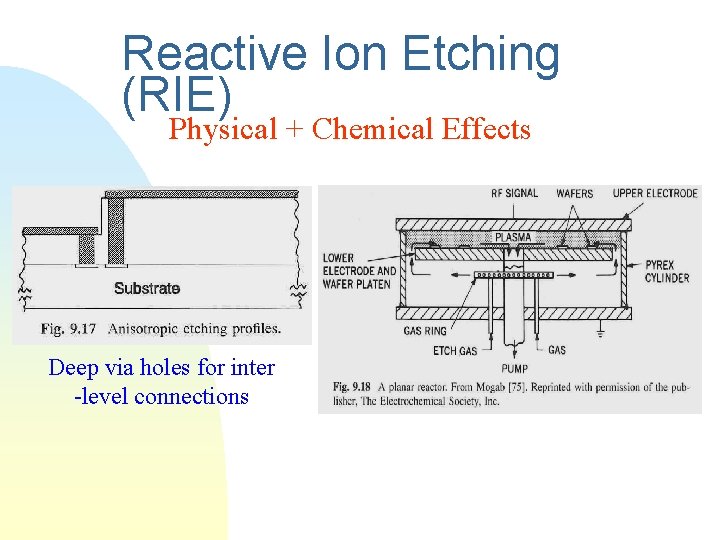
Reactive Ion Etching (RIE) Physical + Chemical Effects Deep via holes for inter -level connections
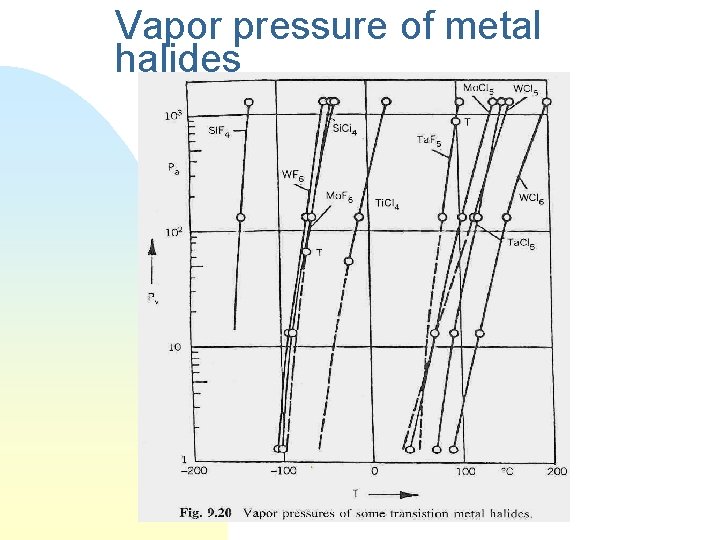
Vapor pressure of metal halides
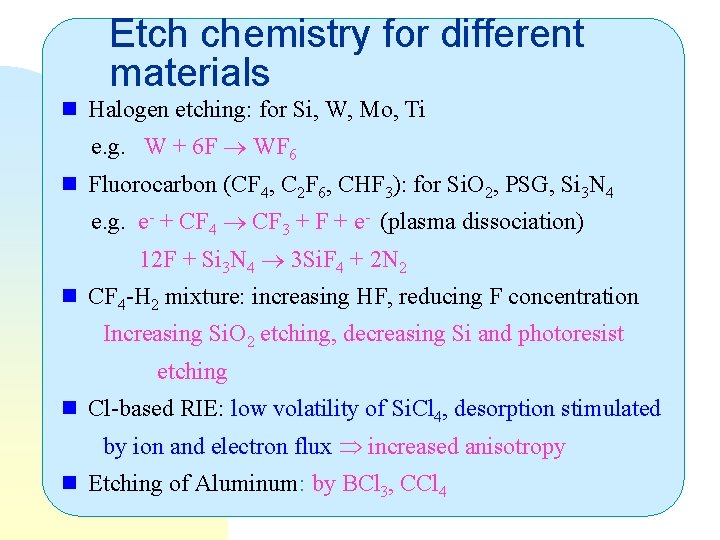
Etch chemistry for different materials n Halogen etching: for Si, W, Mo, Ti e. g. W + 6 F WF 6 n Fluorocarbon (CF 4, C 2 F 6, CHF 3): for Si. O 2, PSG, Si 3 N 4 e. g. e- + CF 4 CF 3 + F + e- (plasma dissociation) 12 F + Si 3 N 4 3 Si. F 4 + 2 N 2 n CF 4 -H 2 mixture: increasing HF, reducing F concentration Increasing Si. O 2 etching, decreasing Si and photoresist etching n Cl-based RIE: low volatility of Si. Cl 4, desorption stimulated by ion and electron flux increased anisotropy n Etching of Aluminum: by BCl 3, CCl 4
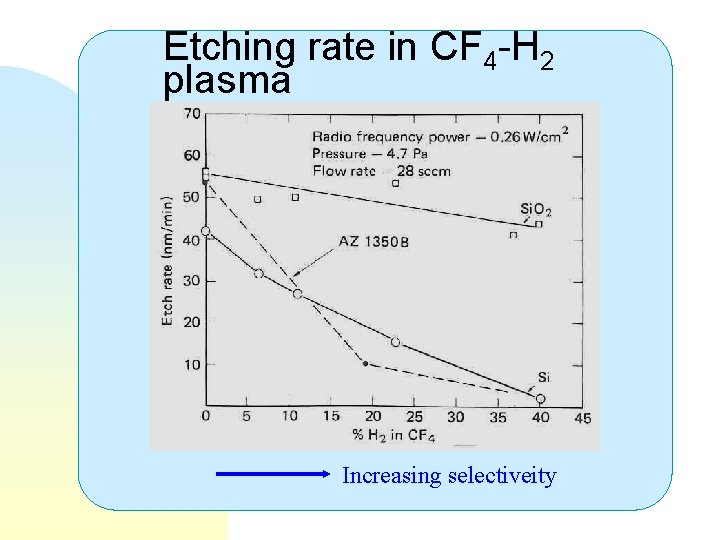
Etching rate in CF 4 -H 2 plasma Increasing selectiveity
Etching definition chemistry
Wet etching vs dry etching
Particle removal wet etch filters
Contaminated wound
To inform the readers/listeners about a newsworthy event
Australian contaminated land consultants association
Waste mangment
Contaminated product insurance
Cervident ss white
What is serial number restoration
Harc etching
Anisotropic vs isotropic etching
What is serial number restoration
What is scratchboard
Chemical etching glass
Bulk material flow enhancement
Electrolytic etching
Harc etch