SprayApplied Asphalt Seals 2001 Asphalt Institute Pavement Preservation
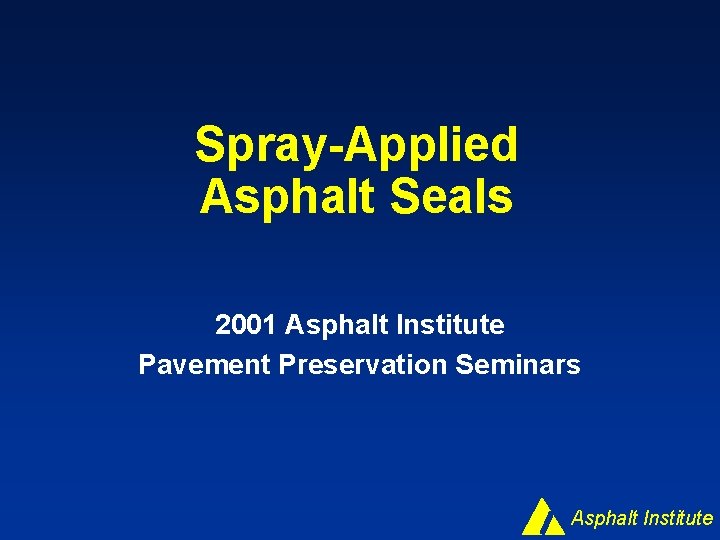
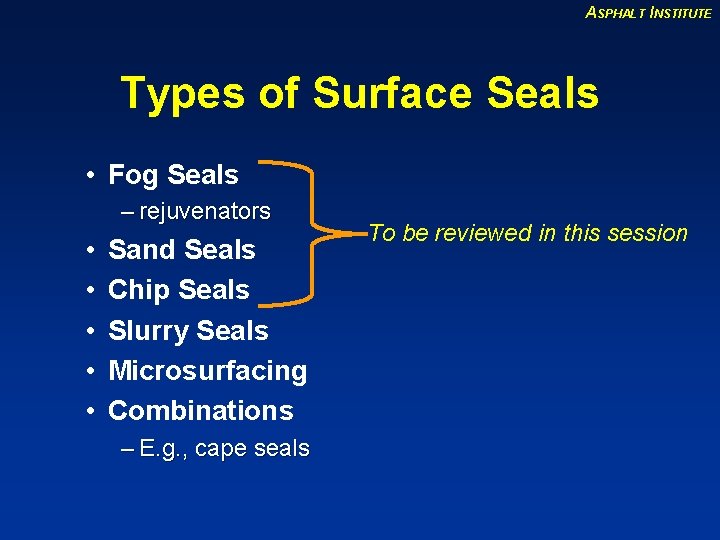
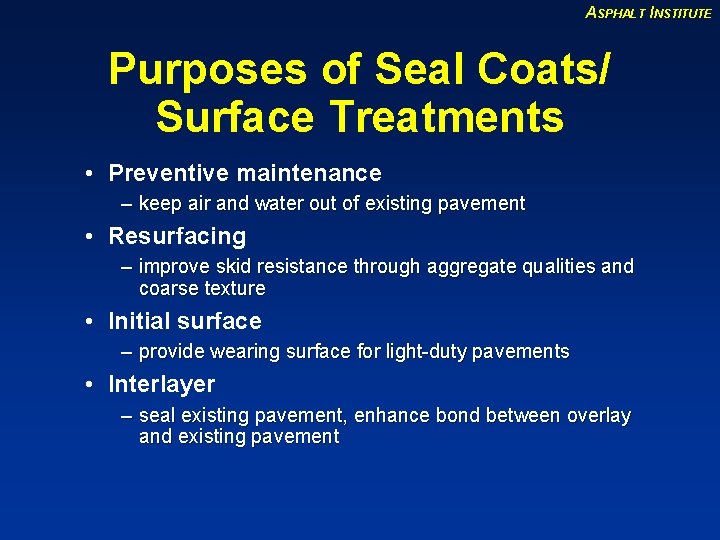
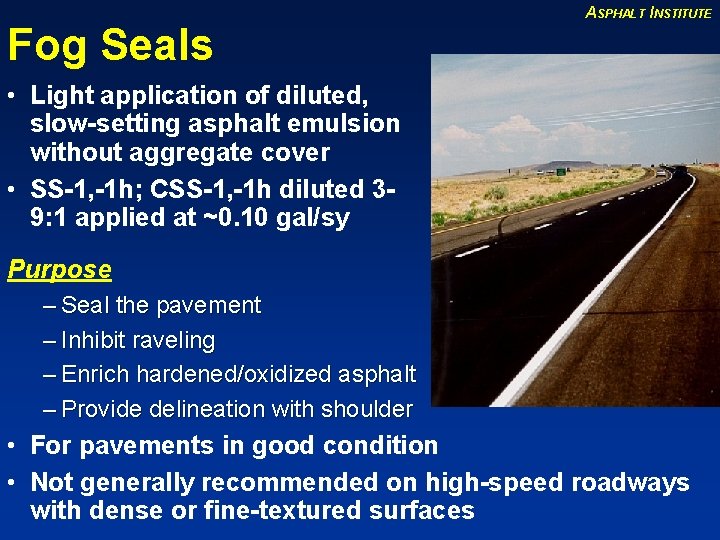
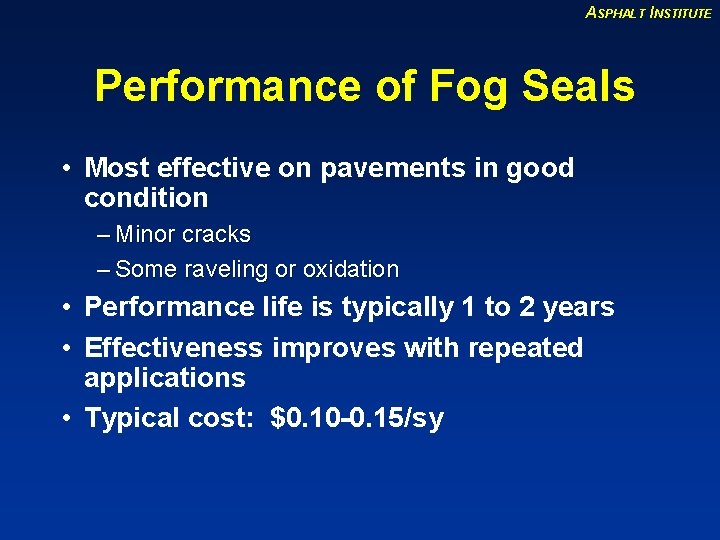
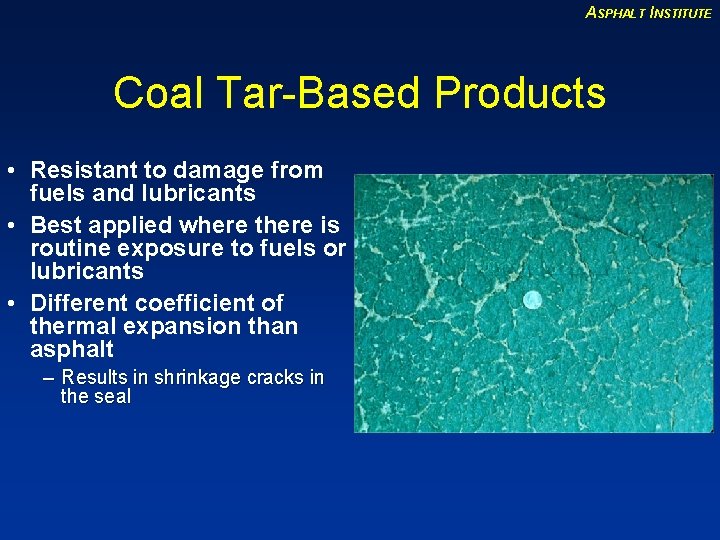
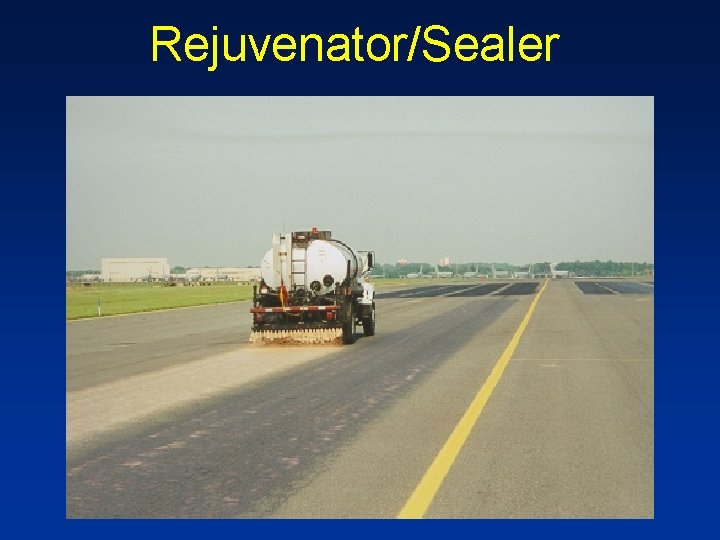
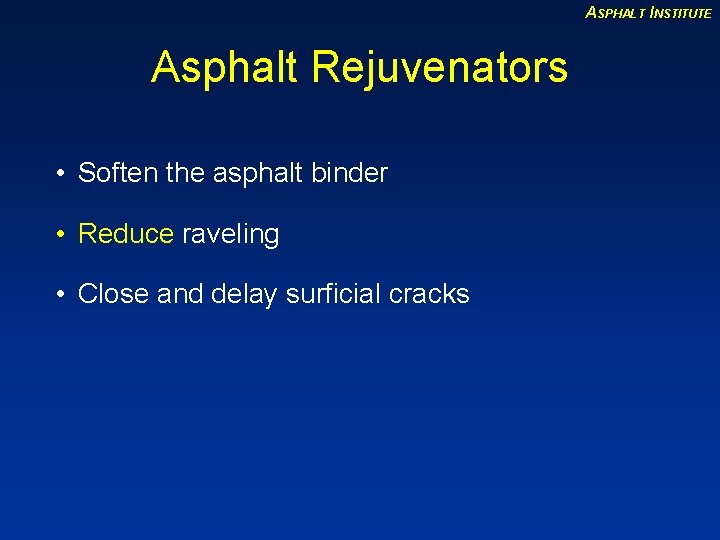
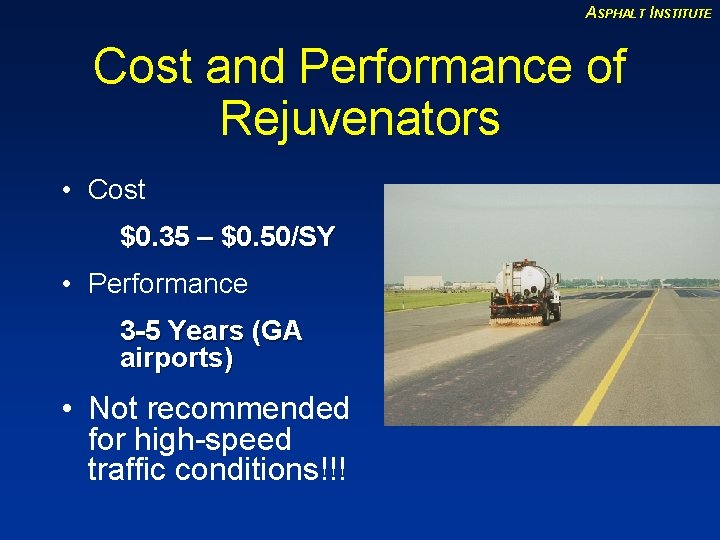
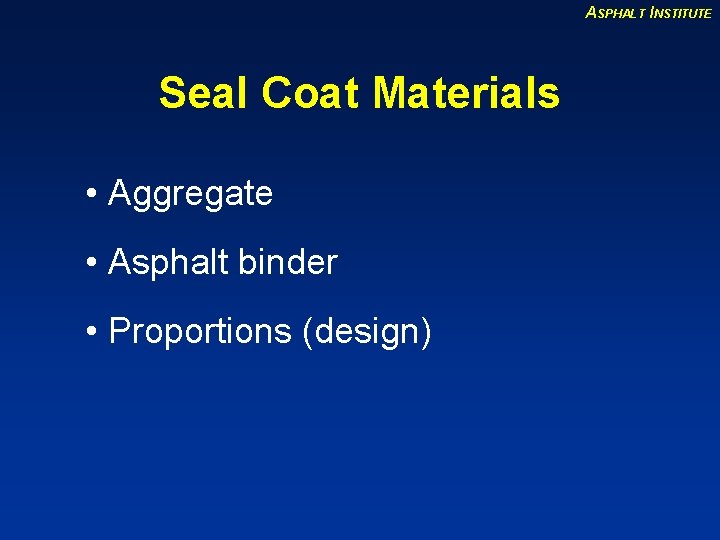
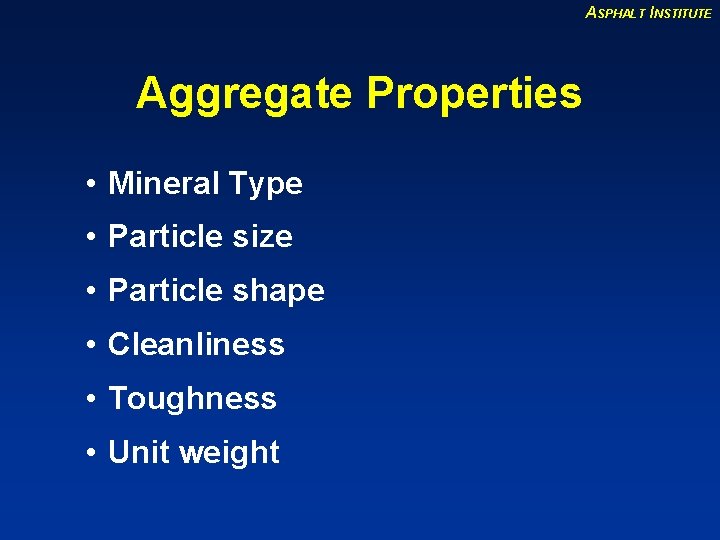
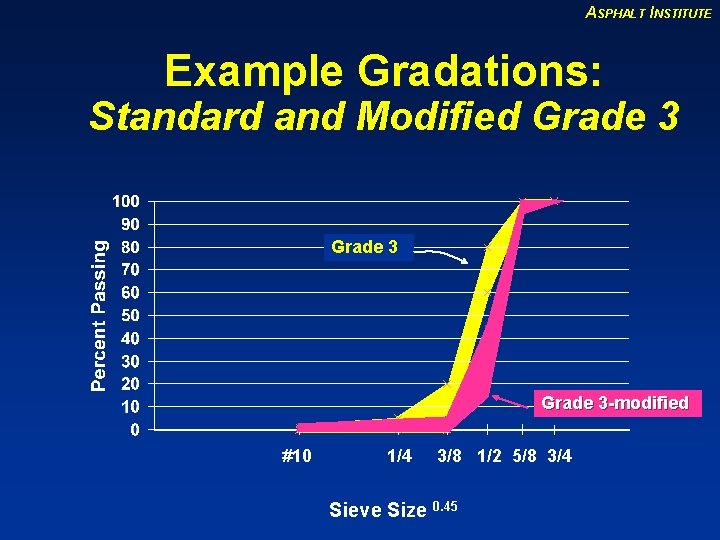
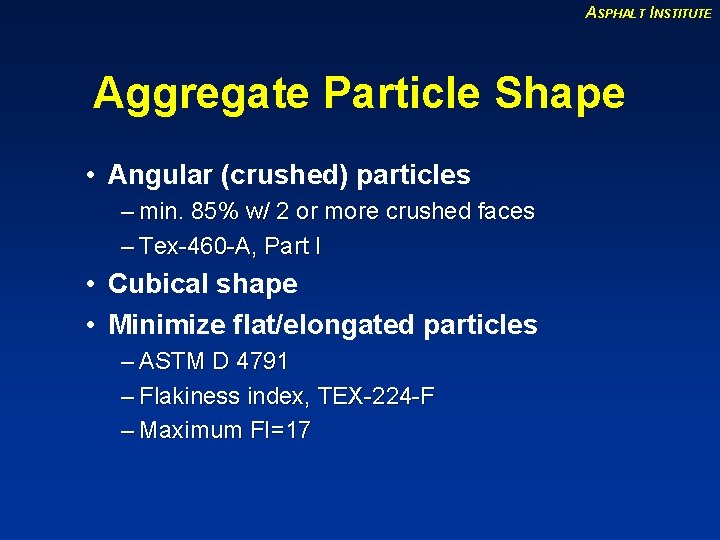
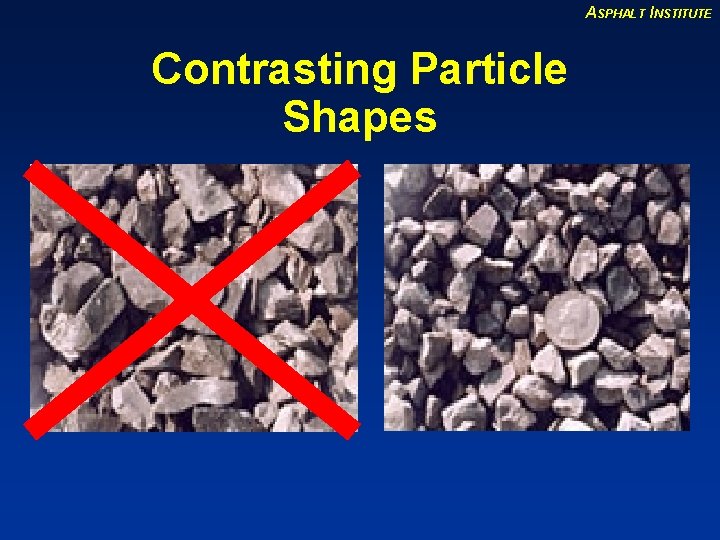
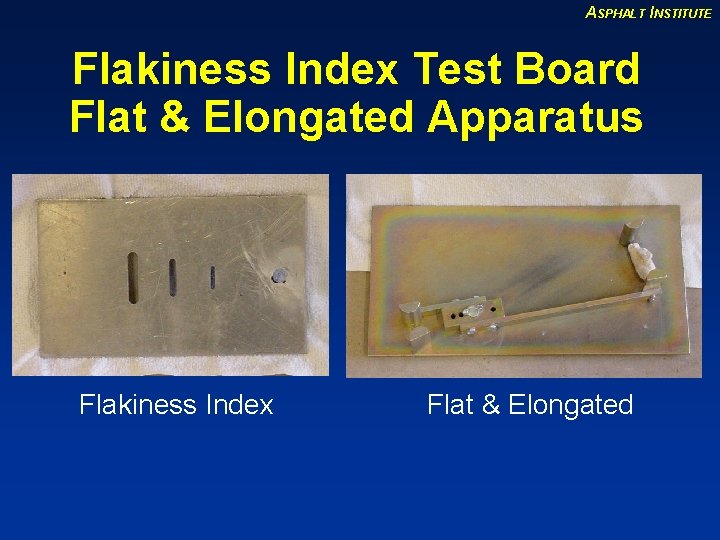
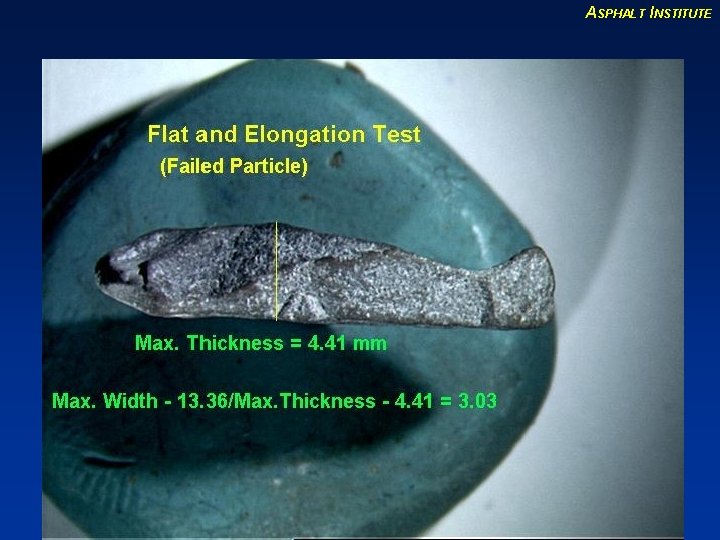
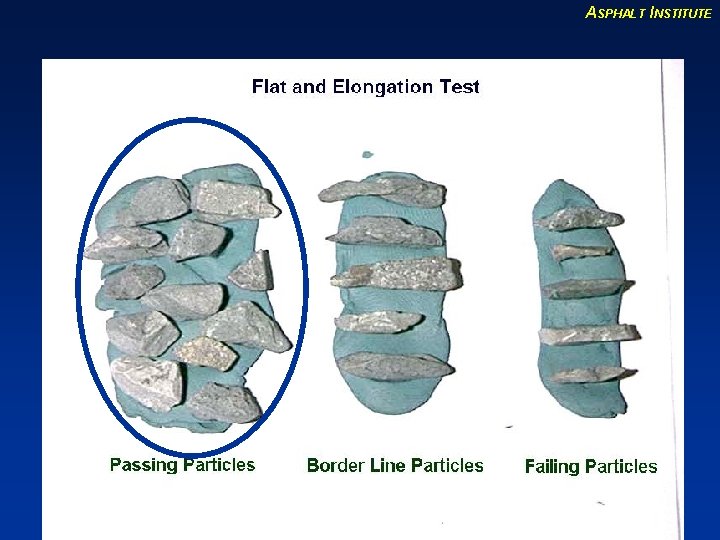
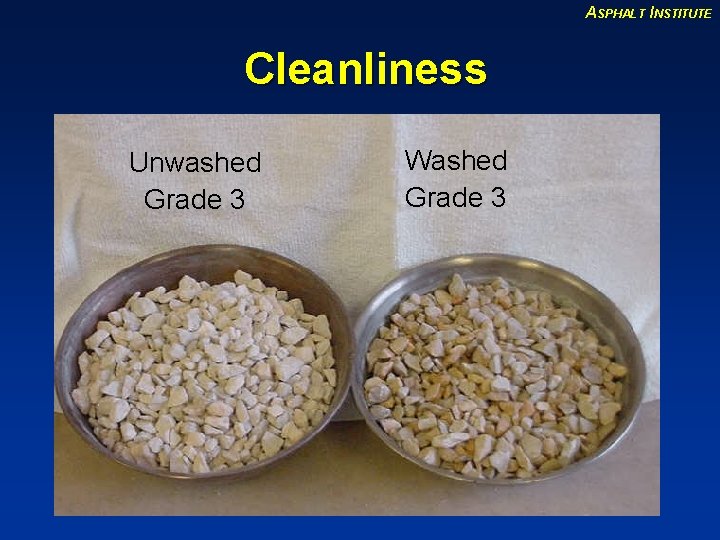
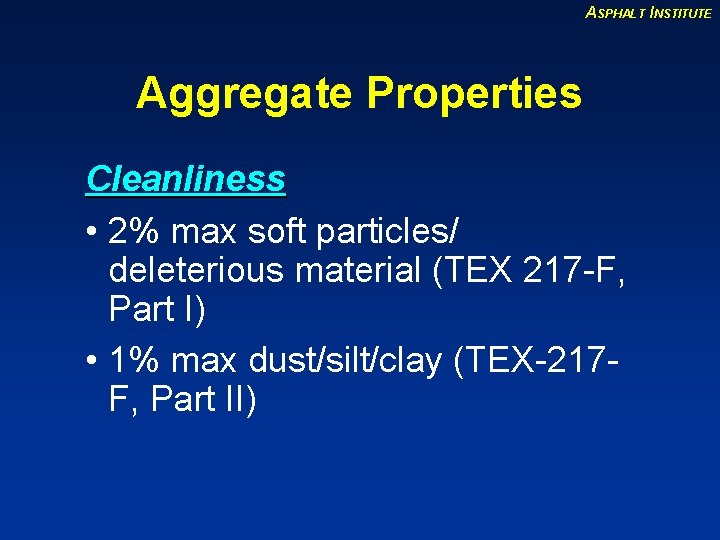
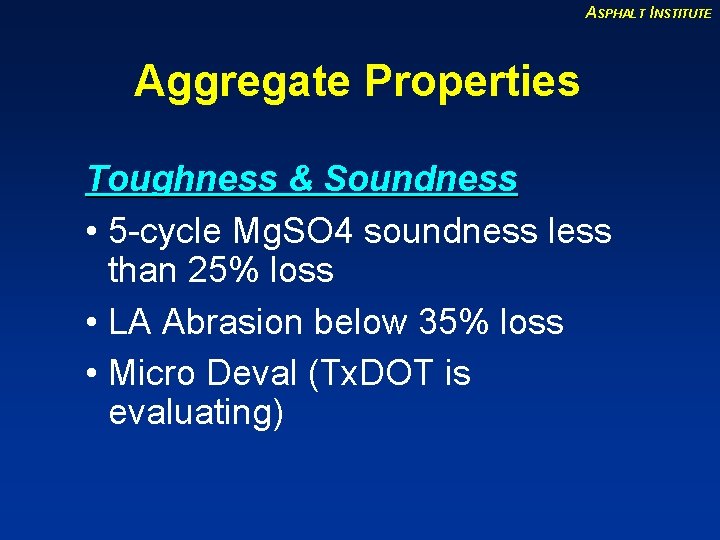
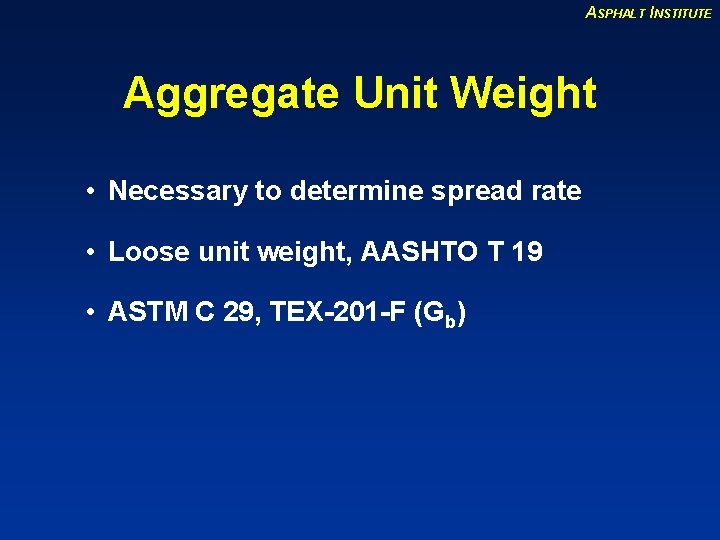
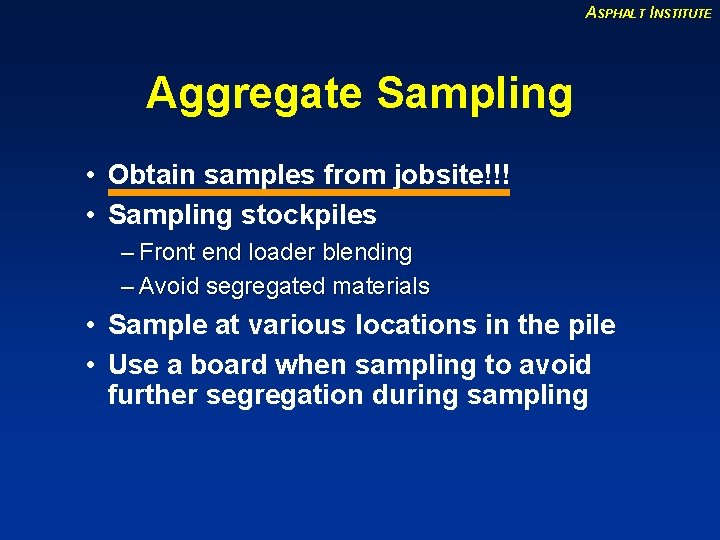
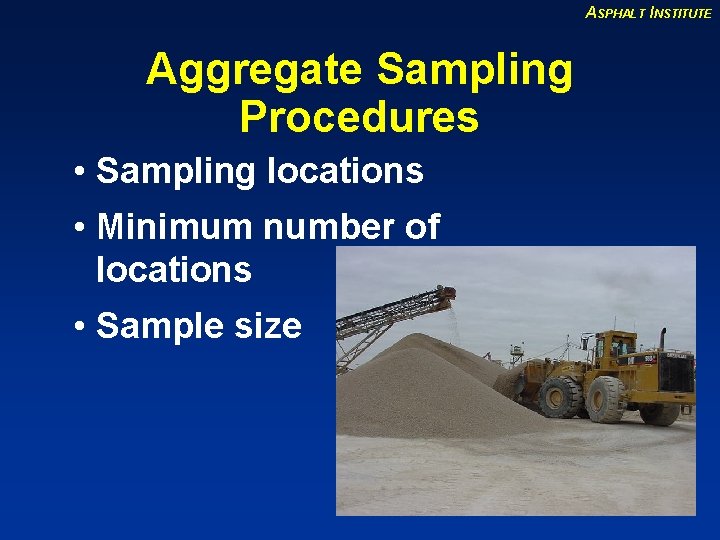
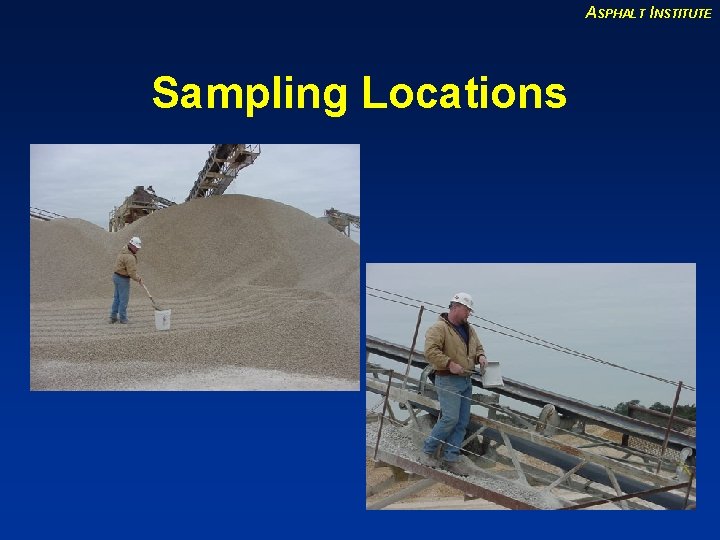
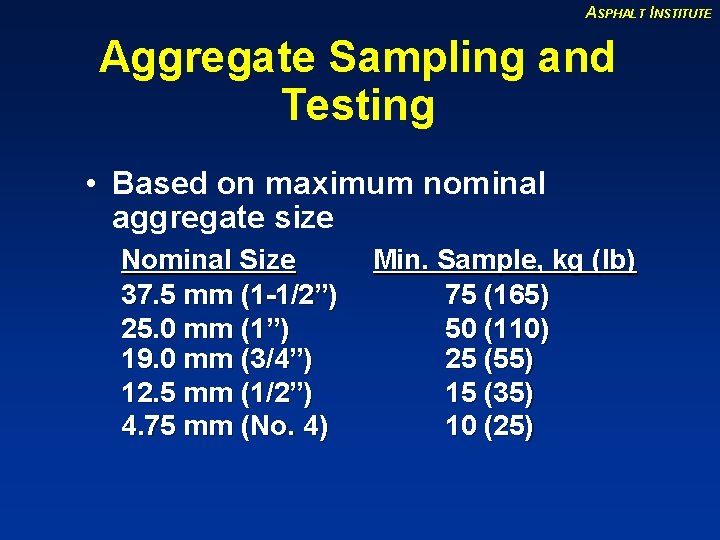
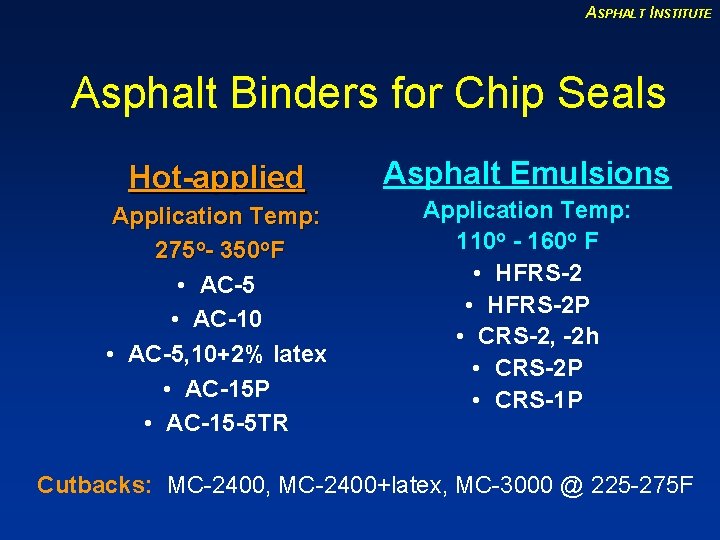
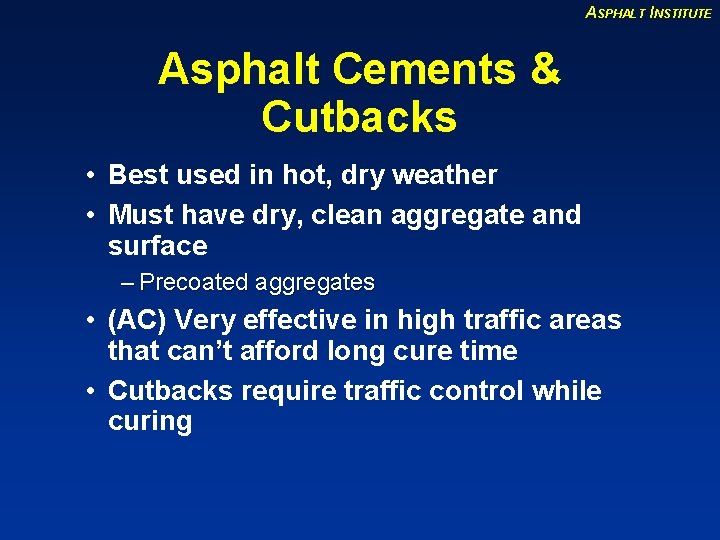
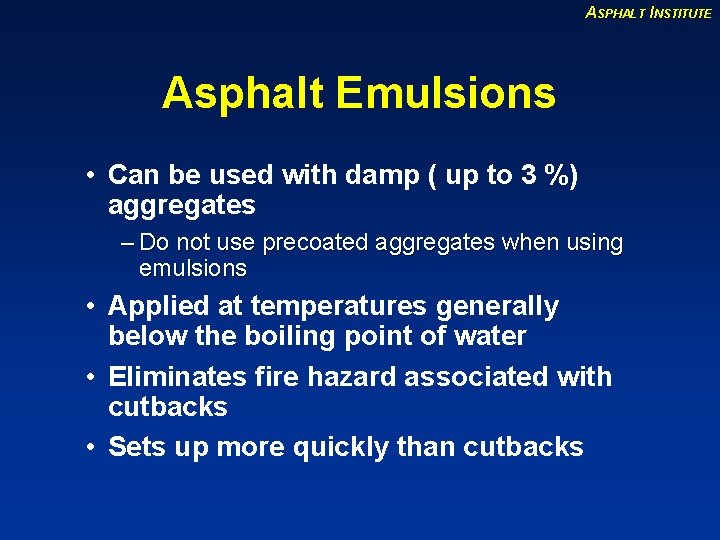
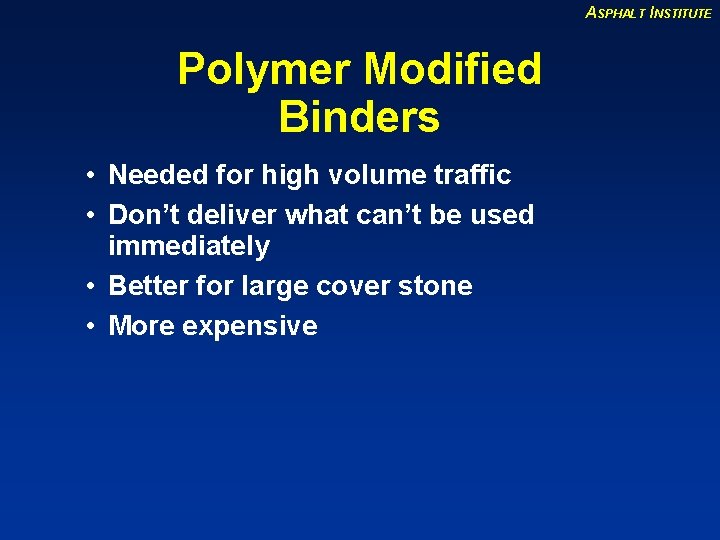
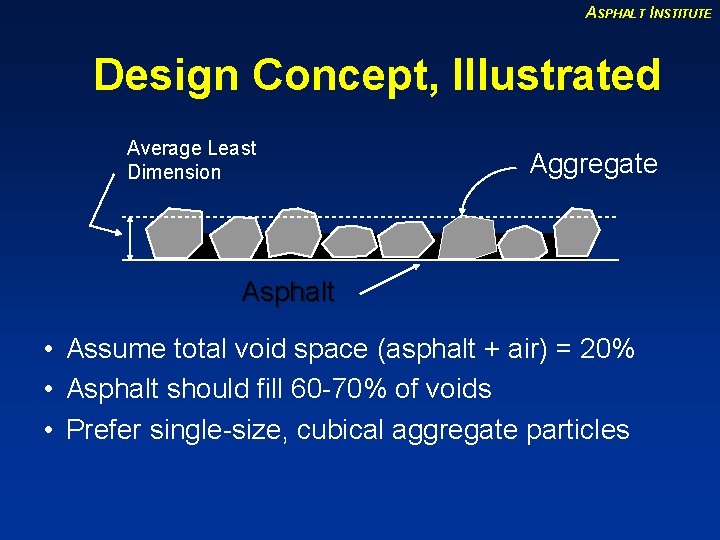
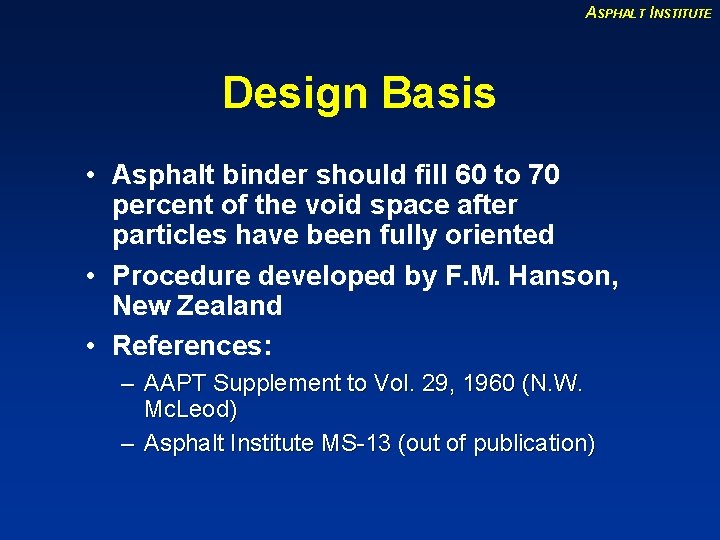
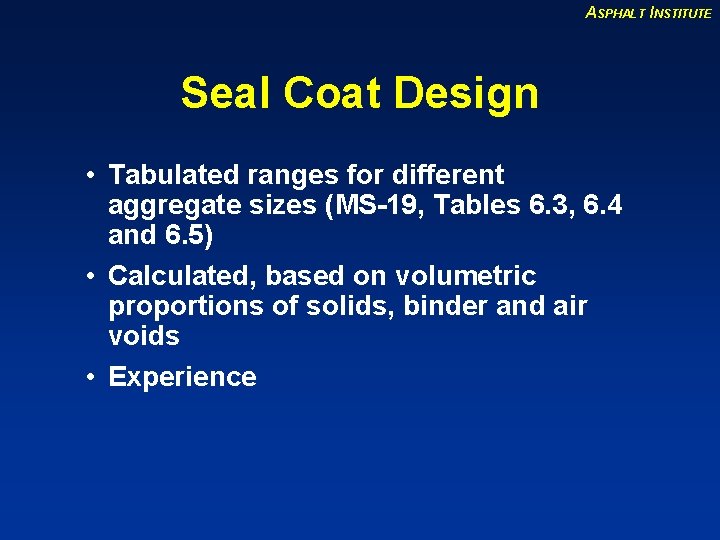

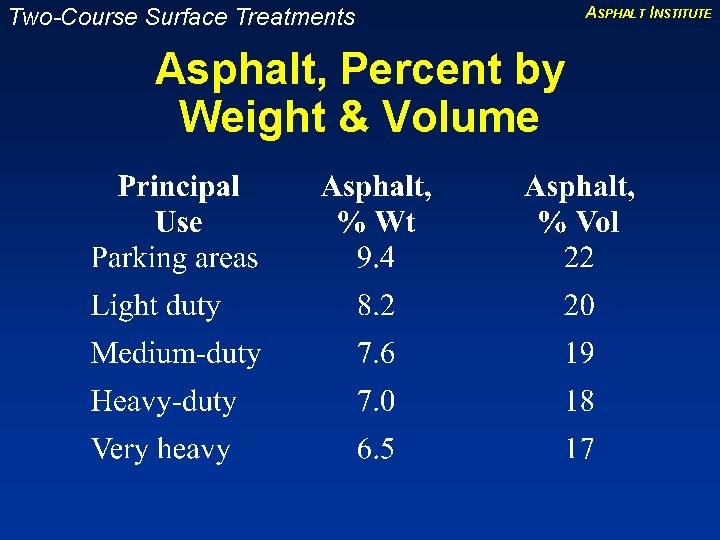
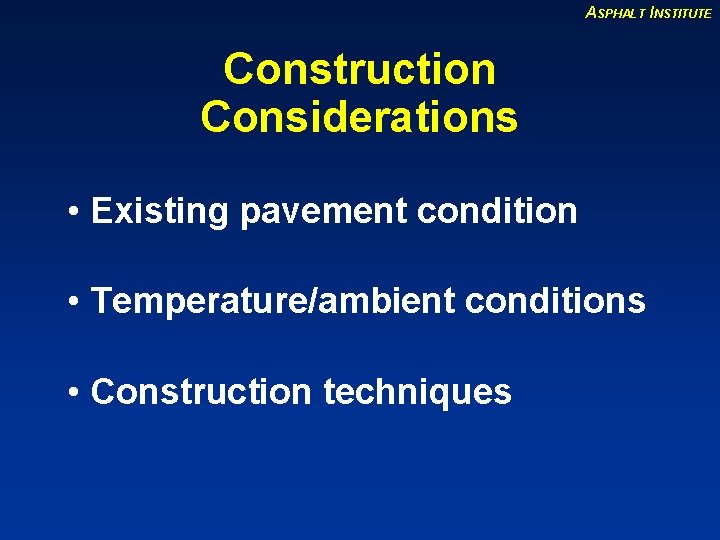
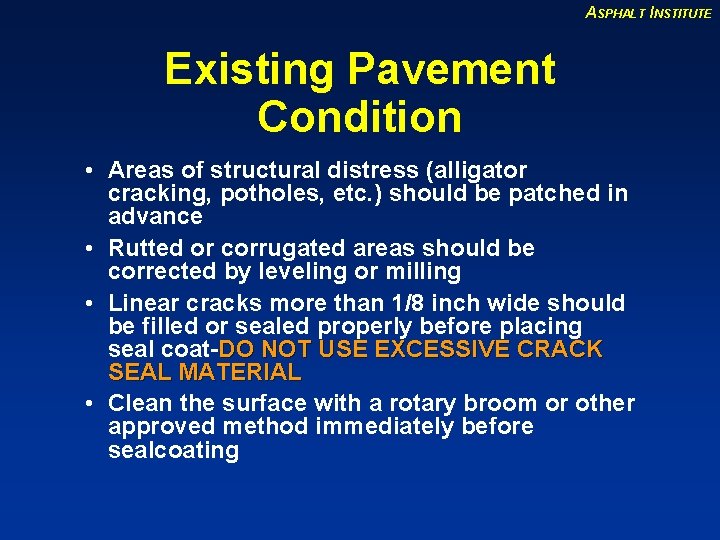
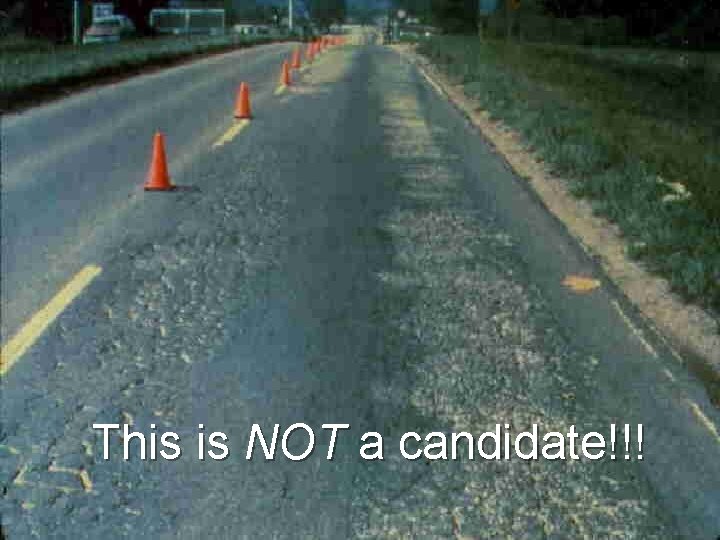
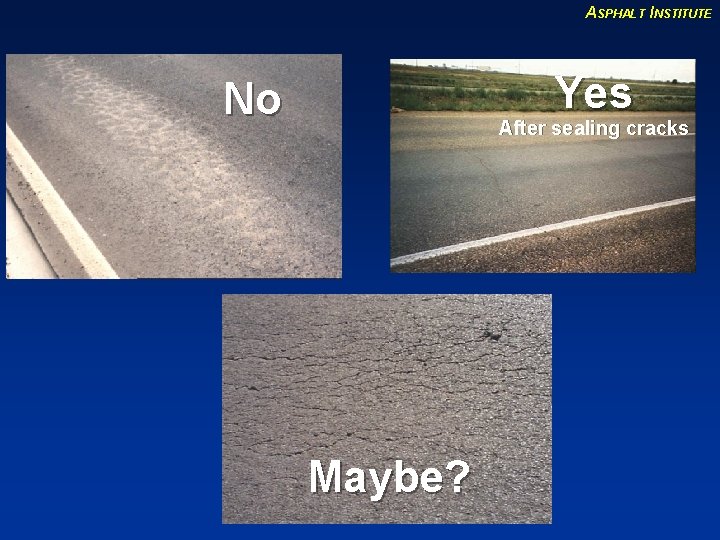
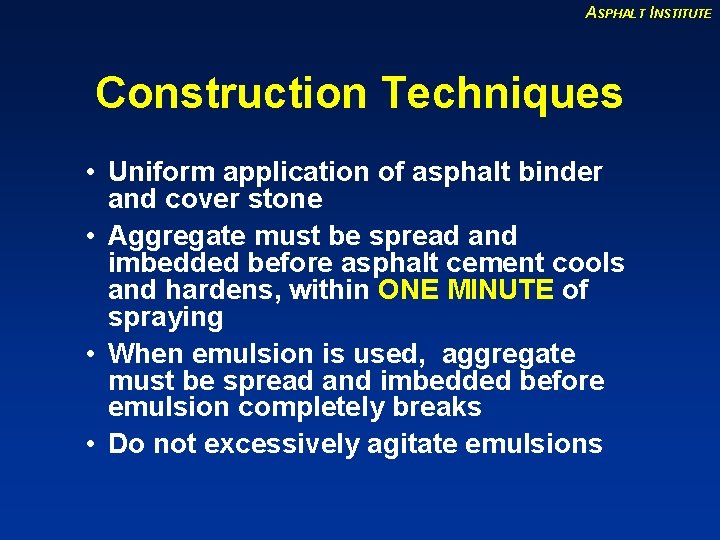

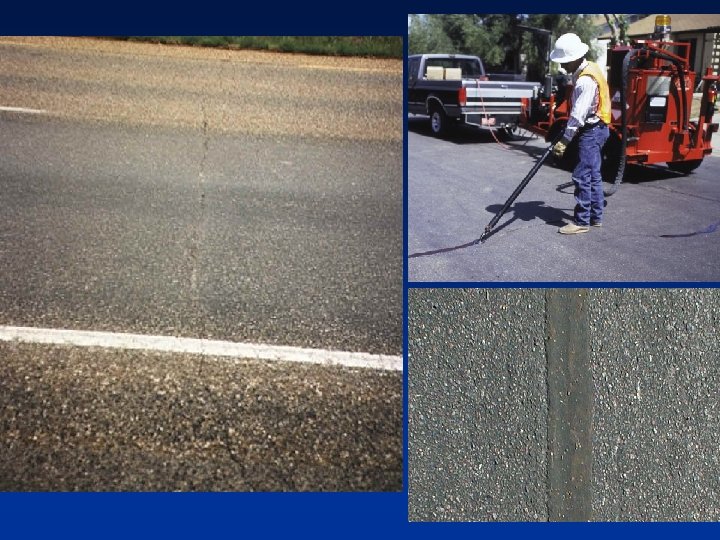

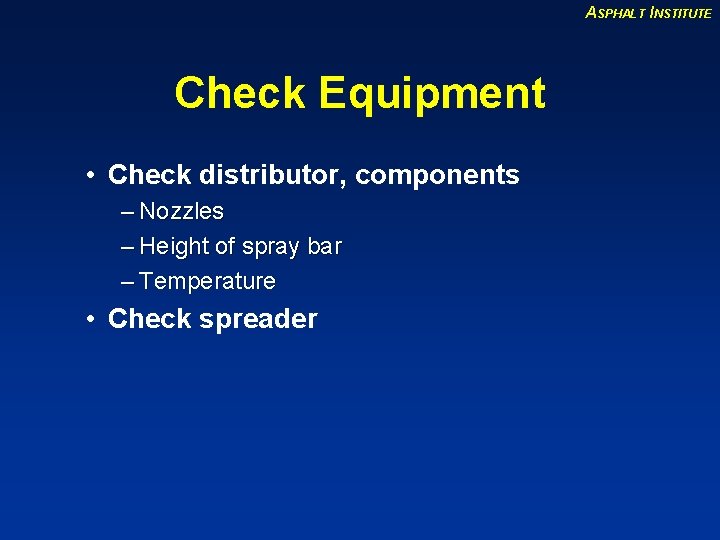
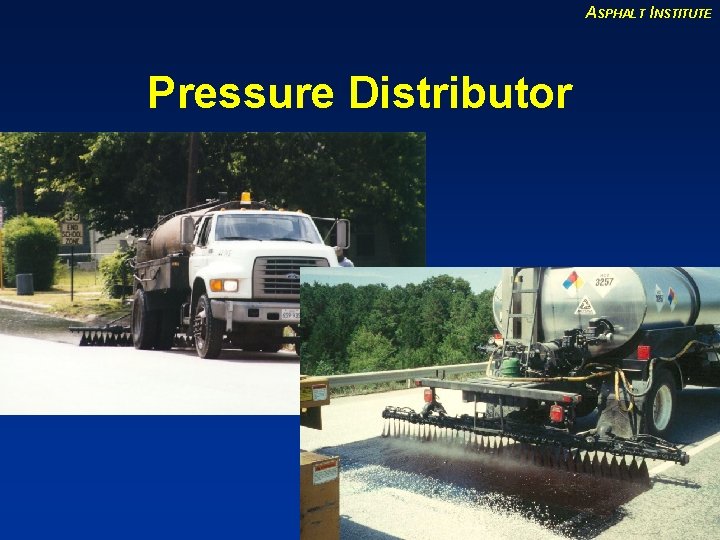
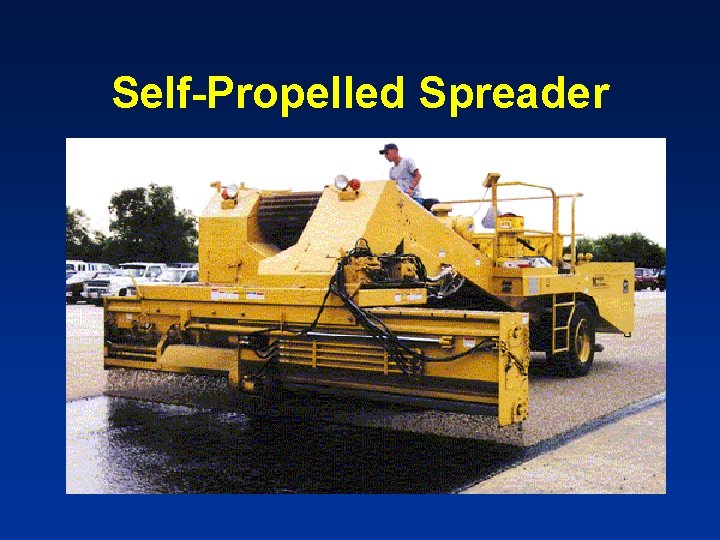

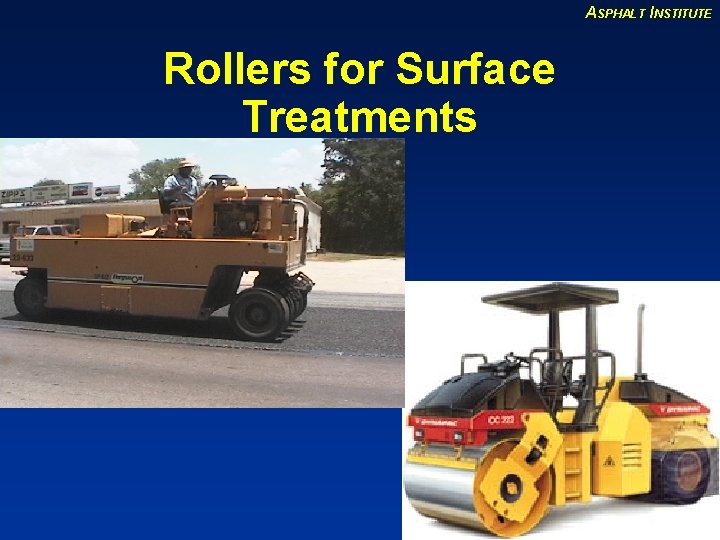
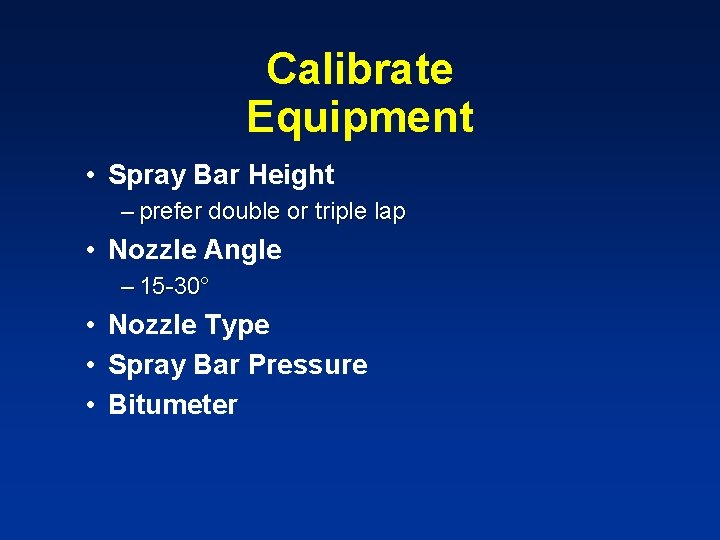
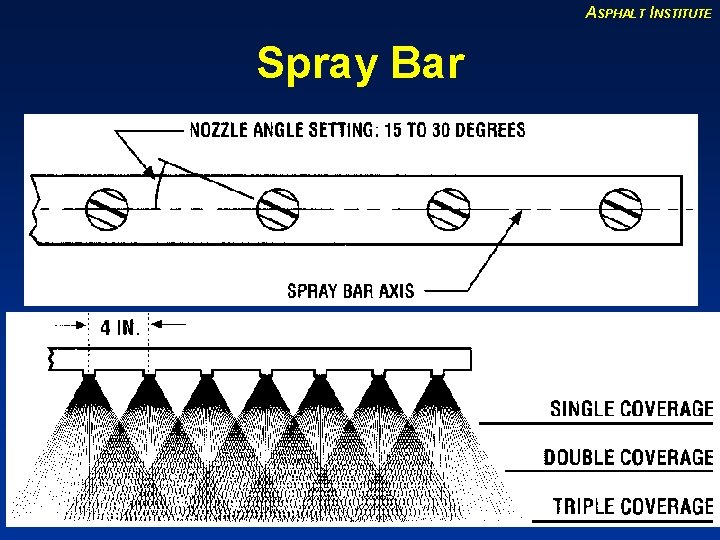
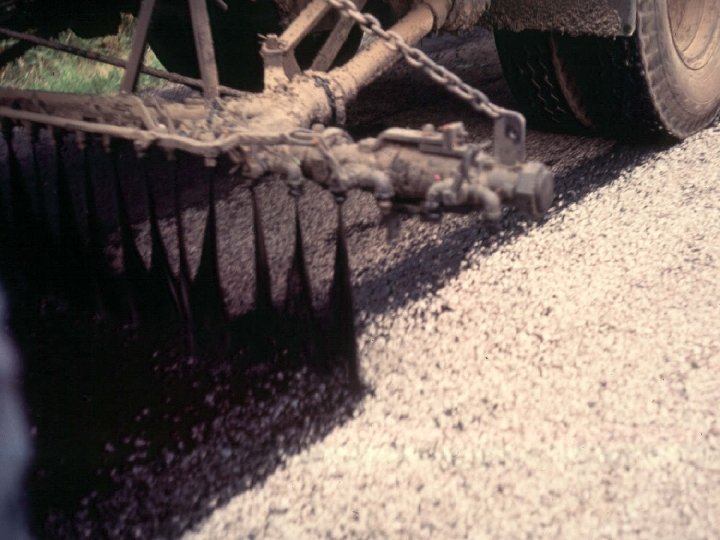
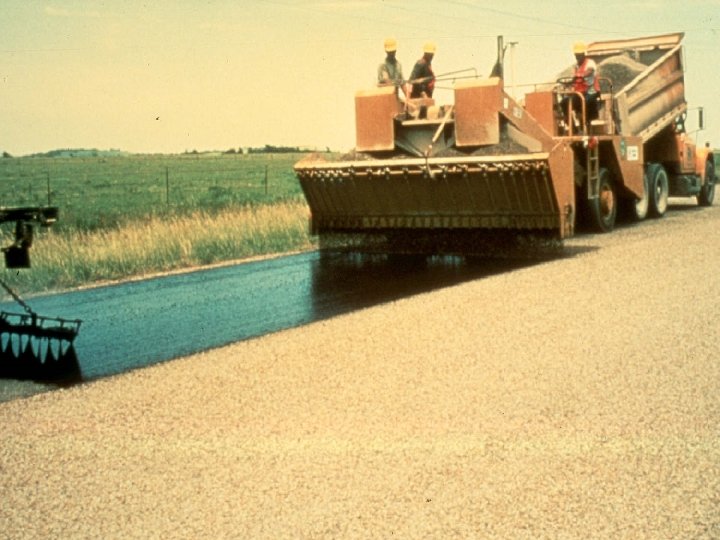
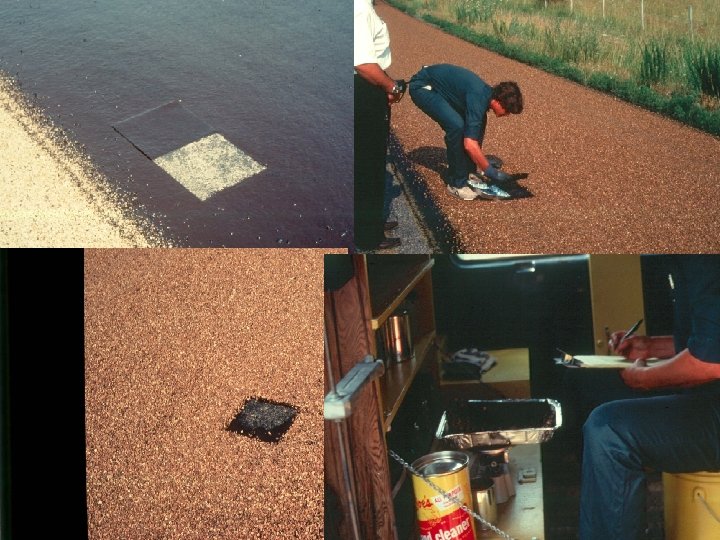
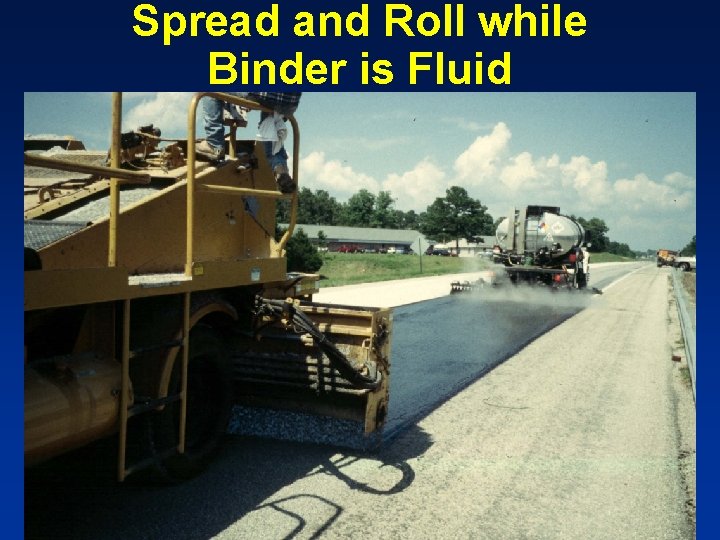
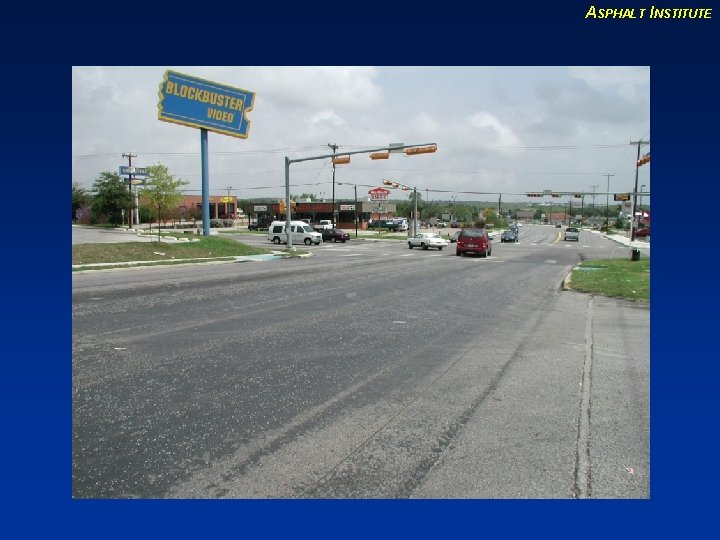
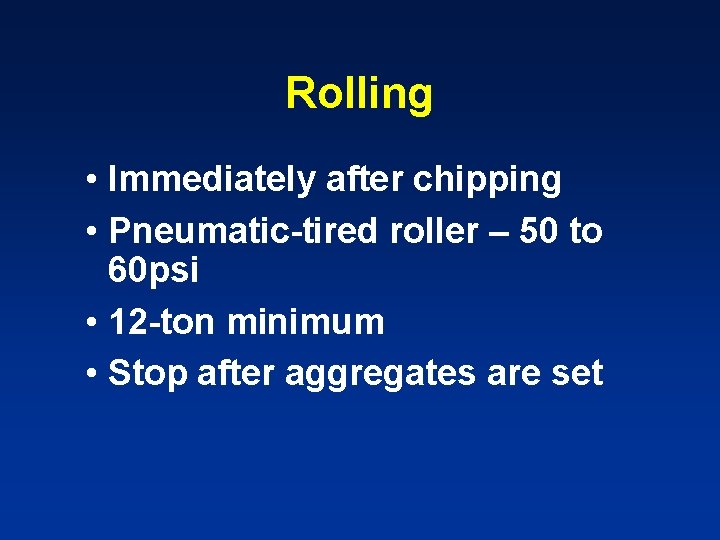
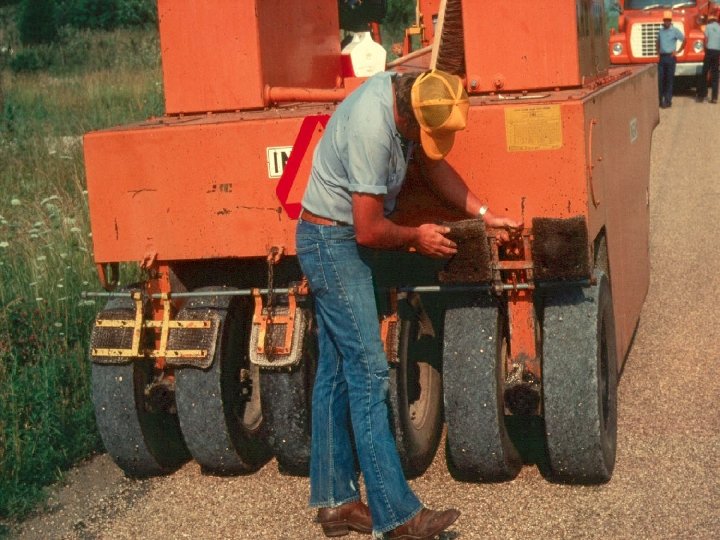
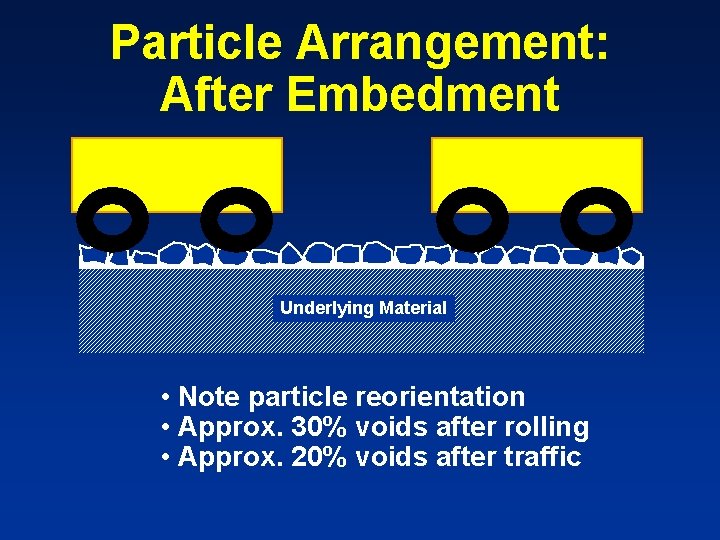
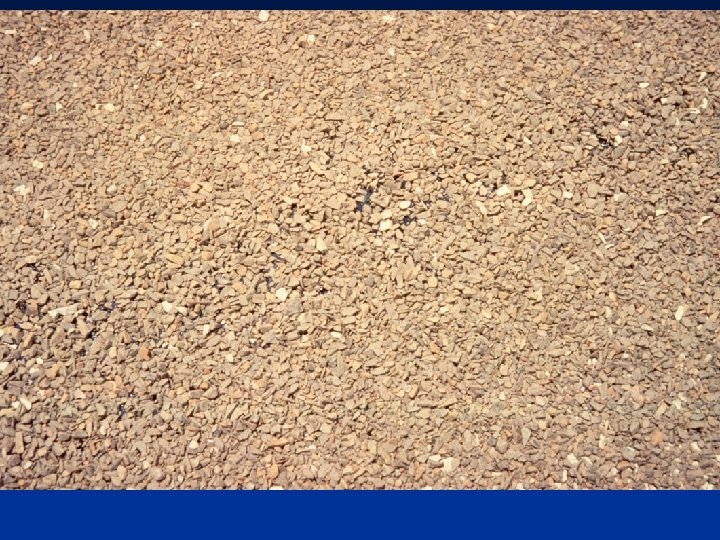
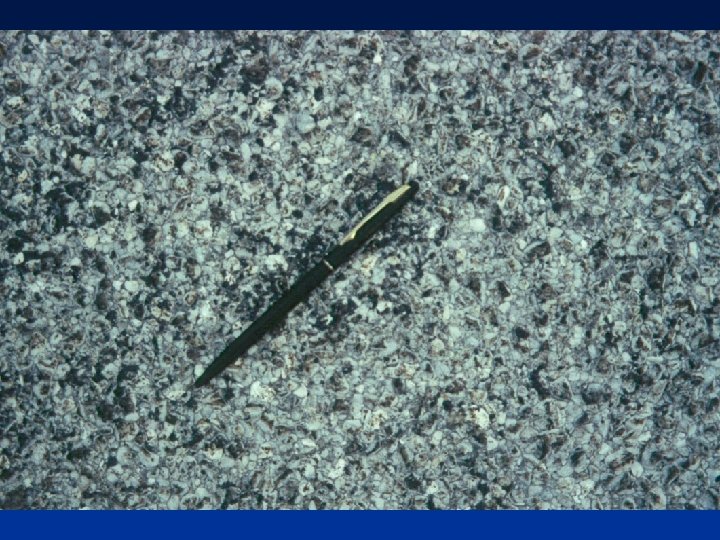
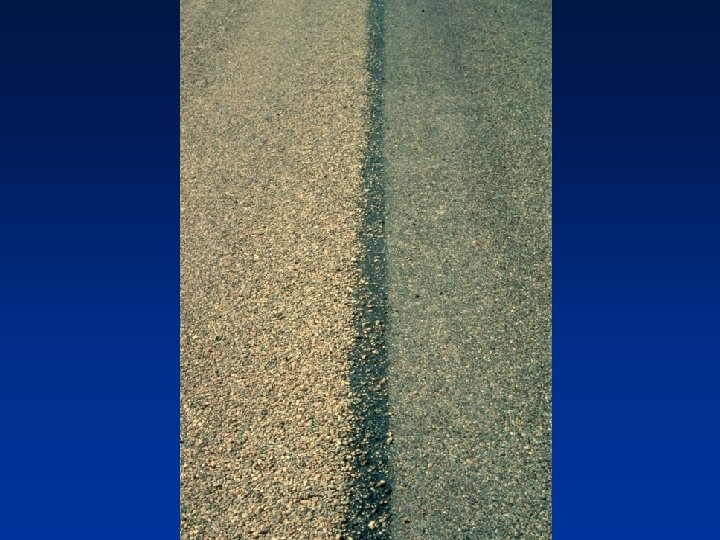
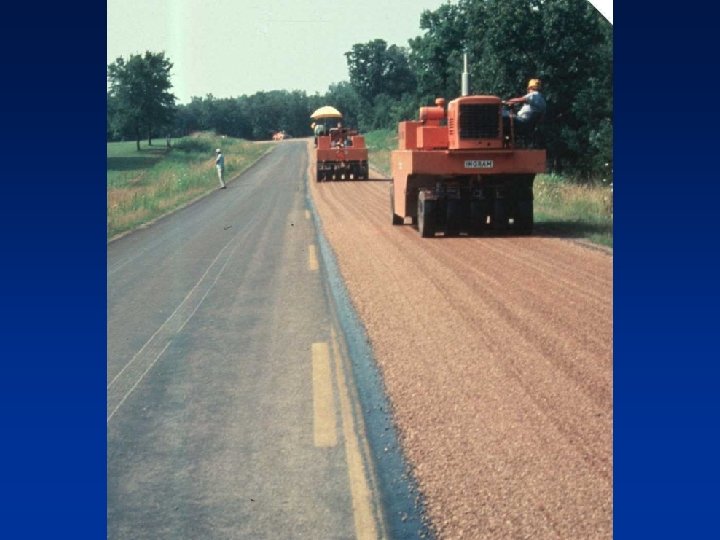
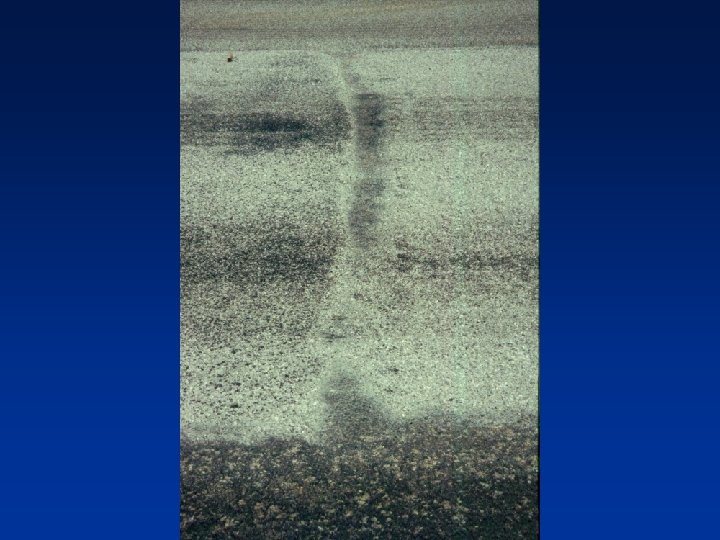
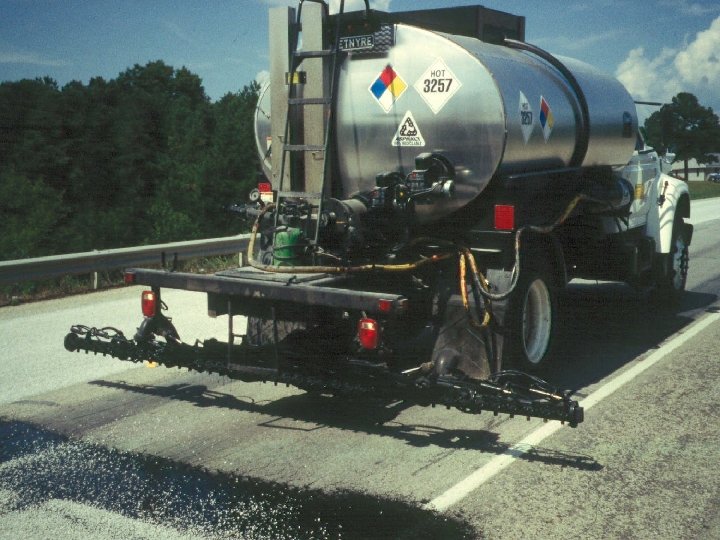
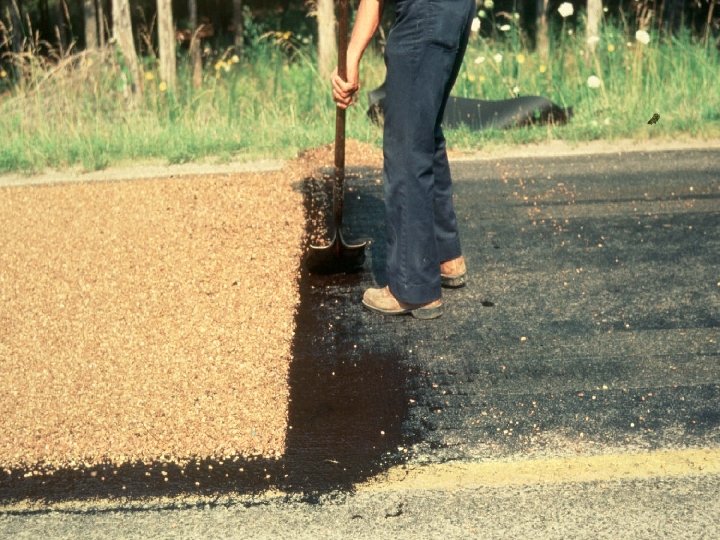
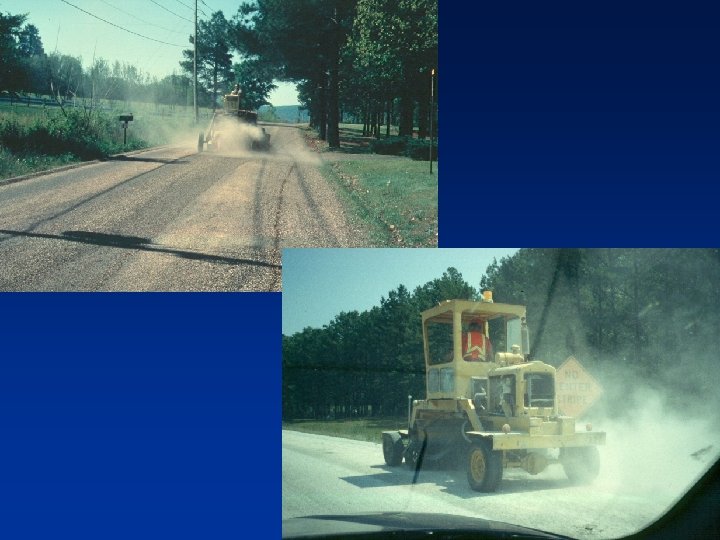
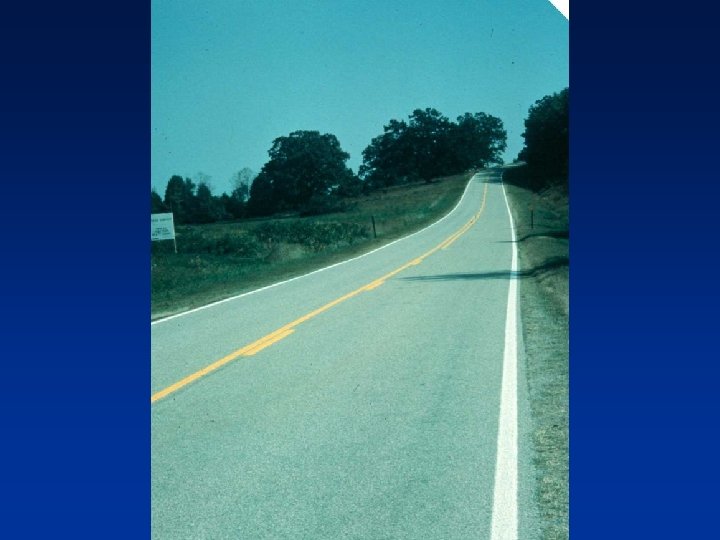
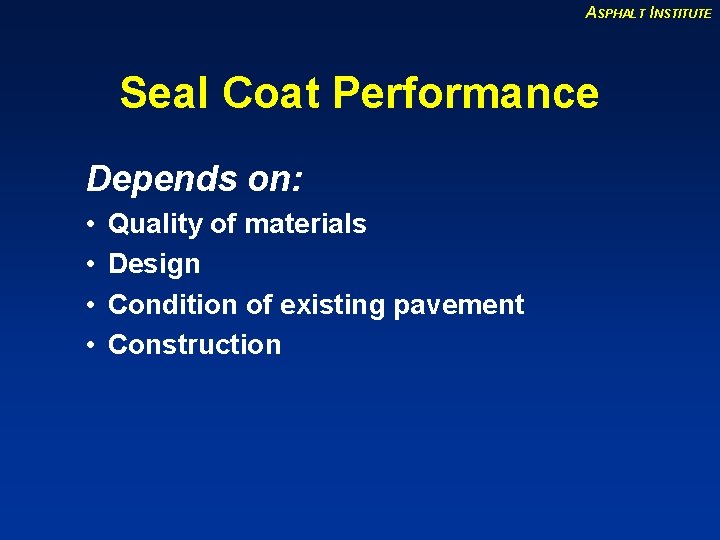
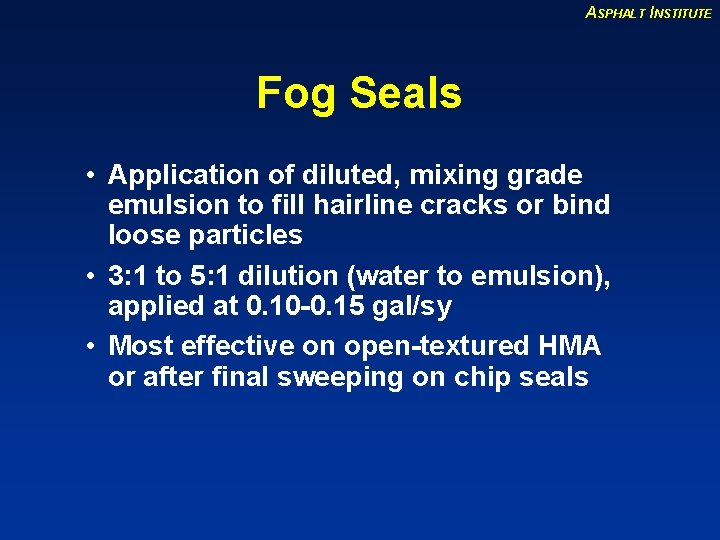
- Slides: 68
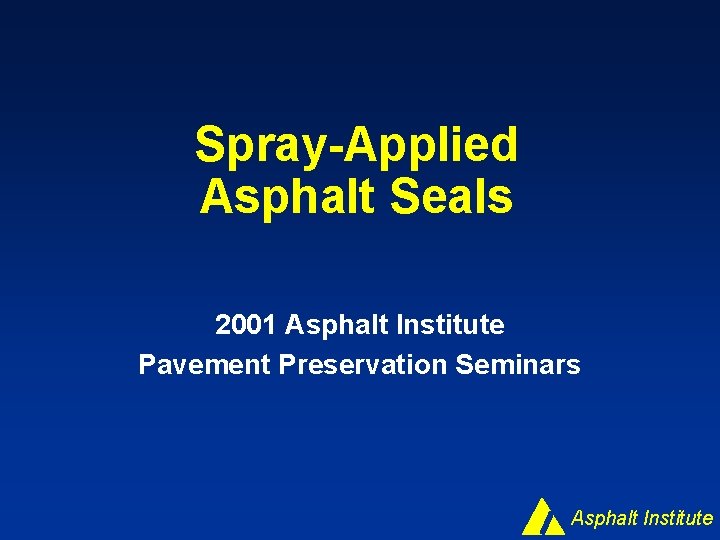
Spray-Applied Asphalt Seals 2001 Asphalt Institute Pavement Preservation Seminars Asphalt Institute
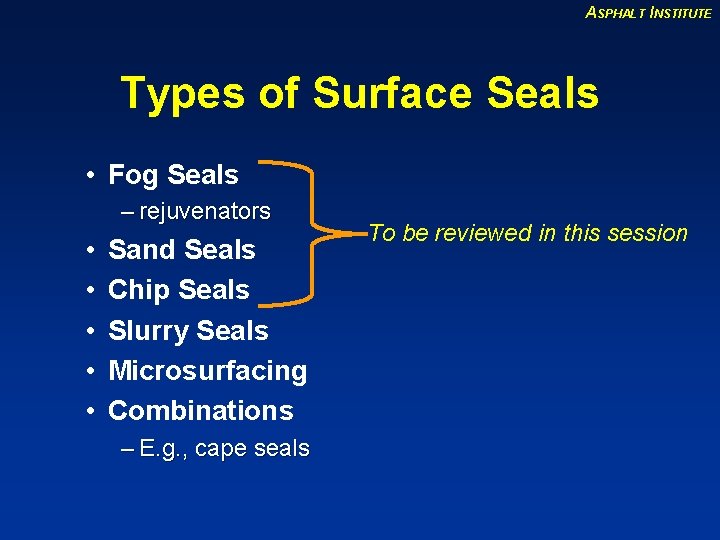
ASPHALT INSTITUTE Types of Surface Seals • Fog Seals – rejuvenators • • • Sand Seals Chip Seals Slurry Seals Microsurfacing Combinations – E. g. , cape seals To be reviewed in this session
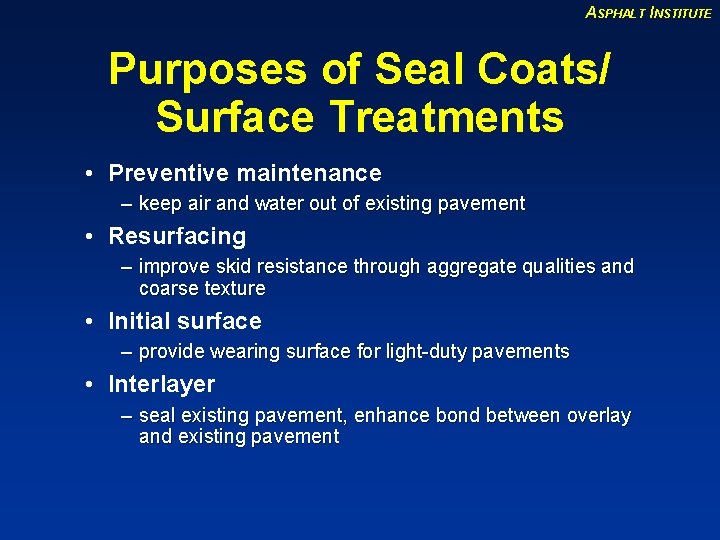
ASPHALT INSTITUTE Purposes of Seal Coats/ Surface Treatments • Preventive maintenance – keep air and water out of existing pavement • Resurfacing – improve skid resistance through aggregate qualities and coarse texture • Initial surface – provide wearing surface for light-duty pavements • Interlayer – seal existing pavement, enhance bond between overlay and existing pavement
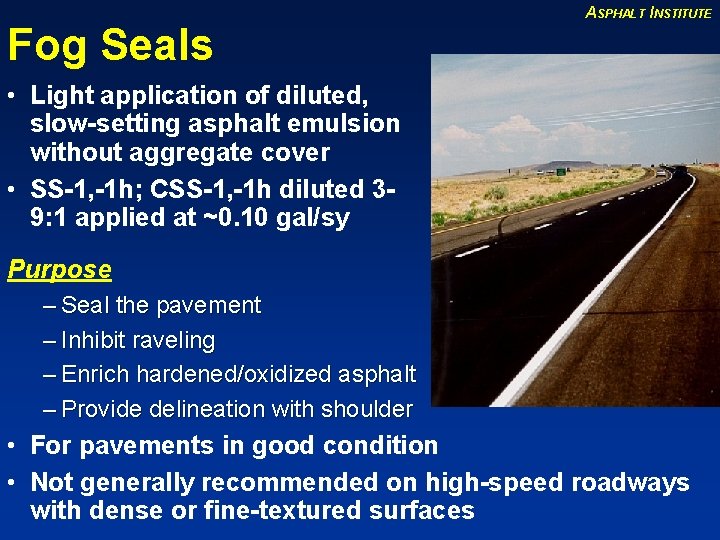
Fog Seals ASPHALT INSTITUTE • Light application of diluted, slow-setting asphalt emulsion without aggregate cover • SS-1, -1 h; CSS-1, -1 h diluted 39: 1 applied at ~0. 10 gal/sy Purpose – Seal the pavement – Inhibit raveling – Enrich hardened/oxidized asphalt – Provide delineation with shoulder • For pavements in good condition • Not generally recommended on high-speed roadways with dense or fine-textured surfaces
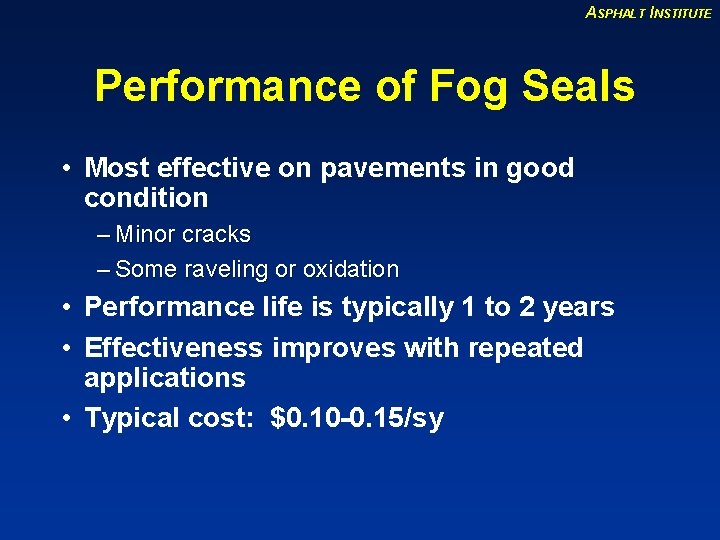
ASPHALT INSTITUTE Performance of Fog Seals • Most effective on pavements in good condition – Minor cracks – Some raveling or oxidation • Performance life is typically 1 to 2 years • Effectiveness improves with repeated applications • Typical cost: $0. 10 -0. 15/sy
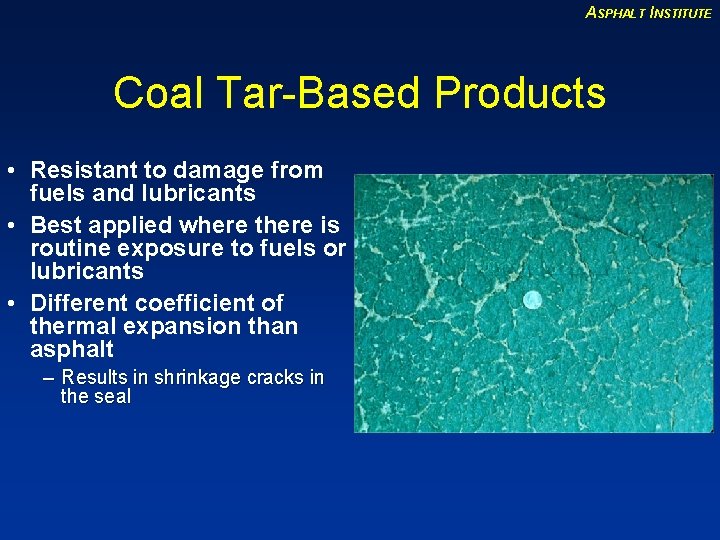
ASPHALT INSTITUTE Coal Tar-Based Products • Resistant to damage from fuels and lubricants • Best applied where there is routine exposure to fuels or lubricants • Different coefficient of thermal expansion than asphalt – Results in shrinkage cracks in the seal
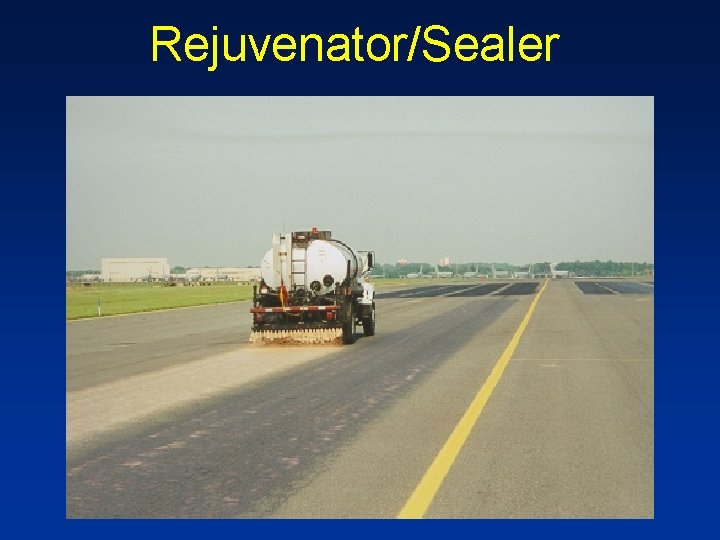
Rejuvenator/Sealer
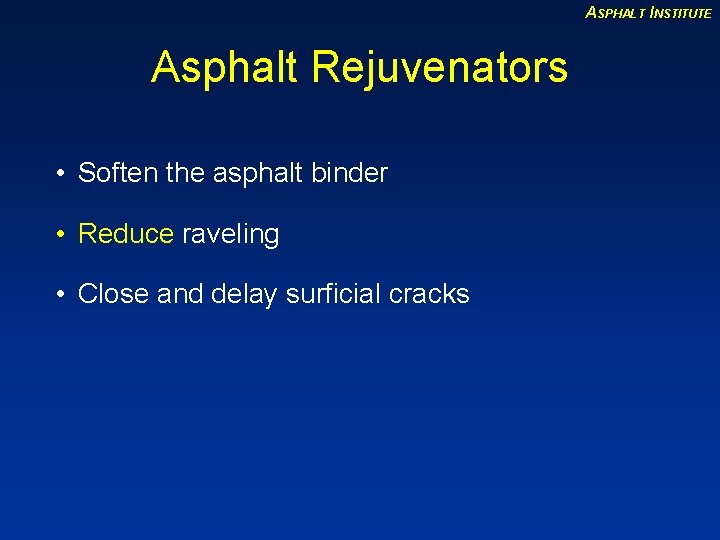
ASPHALT INSTITUTE Asphalt Rejuvenators • Soften the asphalt binder • Reduce raveling • Close and delay surficial cracks
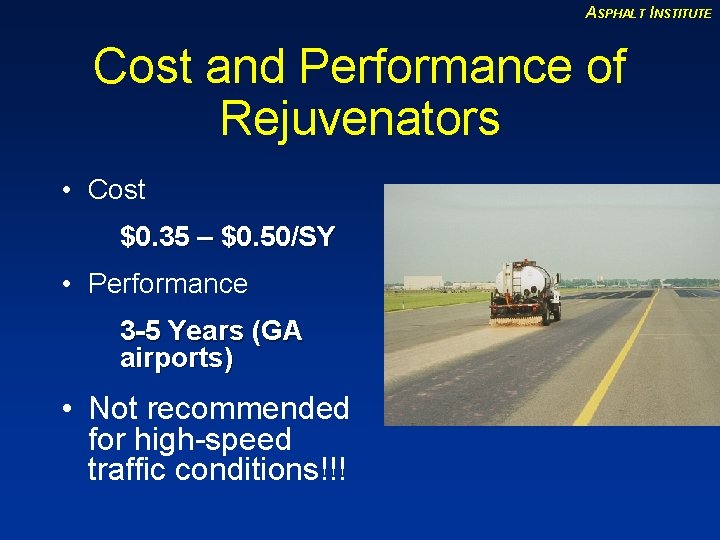
ASPHALT INSTITUTE Cost and Performance of Rejuvenators • Cost $0. 35 – $0. 50/SY • Performance 3 -5 Years (GA airports) • Not recommended for high-speed traffic conditions!!!
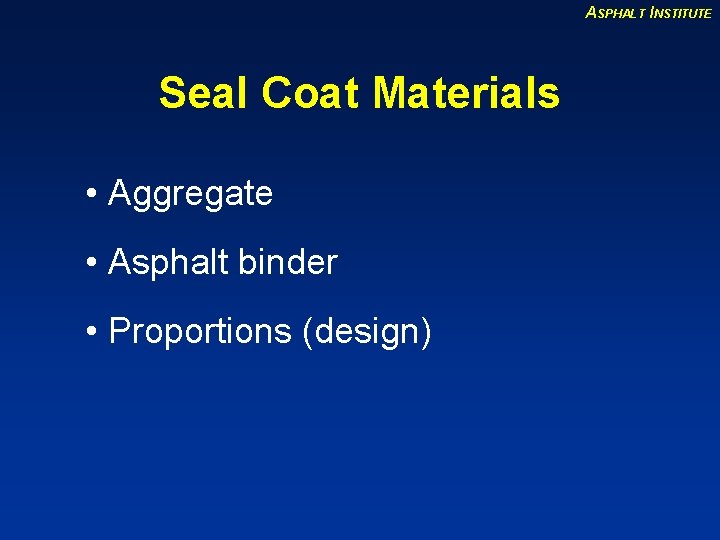
ASPHALT INSTITUTE Seal Coat Materials • Aggregate • Asphalt binder • Proportions (design)
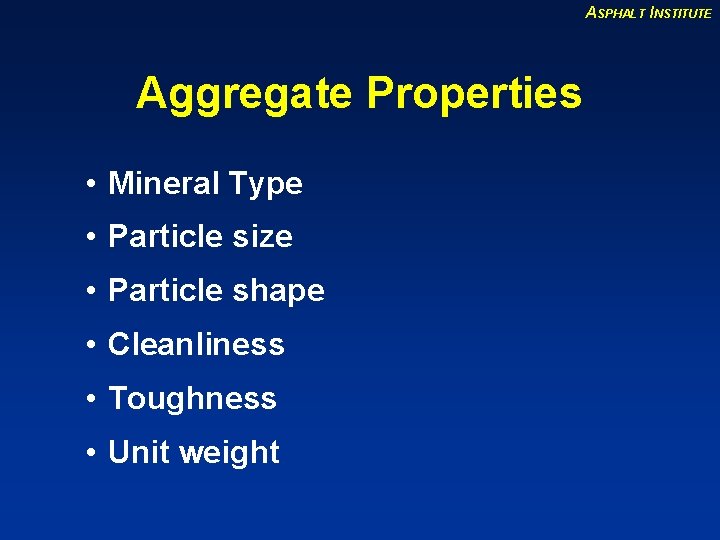
ASPHALT INSTITUTE Aggregate Properties • Mineral Type • Particle size • Particle shape • Cleanliness • Toughness • Unit weight
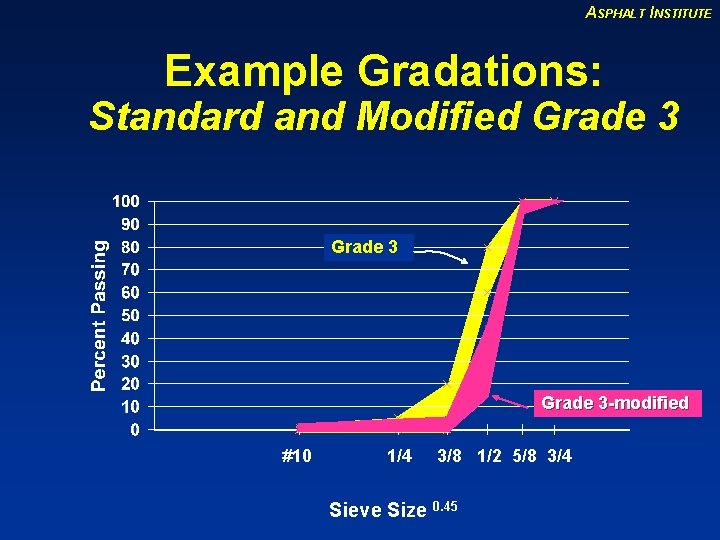
ASPHALT INSTITUTE Example Gradations: Standard and Modified Grade 3 -modified #10 1/4 3/8 1/2 5/8 3/4 Sieve Size 0. 45
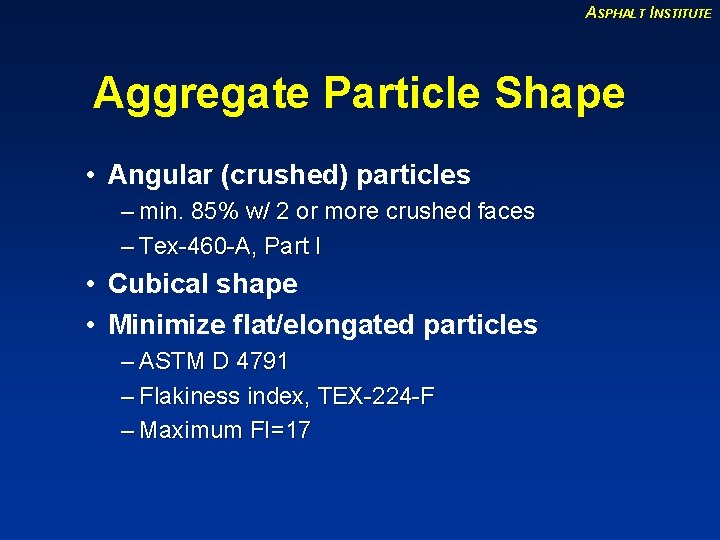
ASPHALT INSTITUTE Aggregate Particle Shape • Angular (crushed) particles – min. 85% w/ 2 or more crushed faces – Tex-460 -A, Part I • Cubical shape • Minimize flat/elongated particles – ASTM D 4791 – Flakiness index, TEX-224 -F – Maximum FI=17
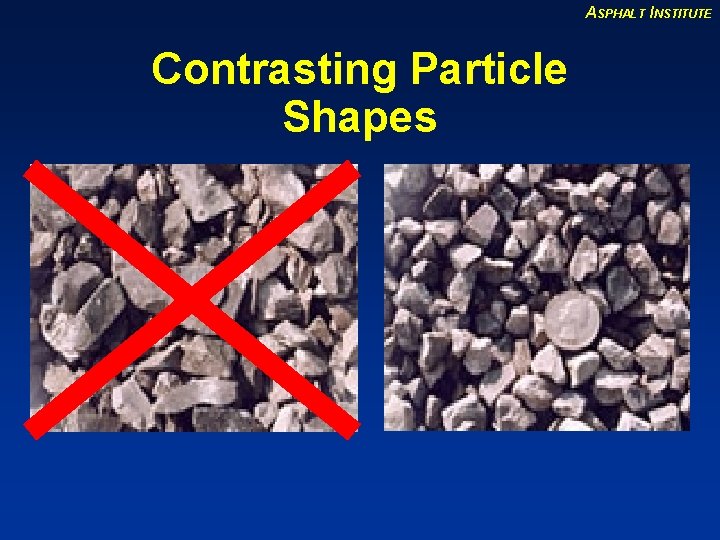
ASPHALT INSTITUTE Contrasting Particle Shapes
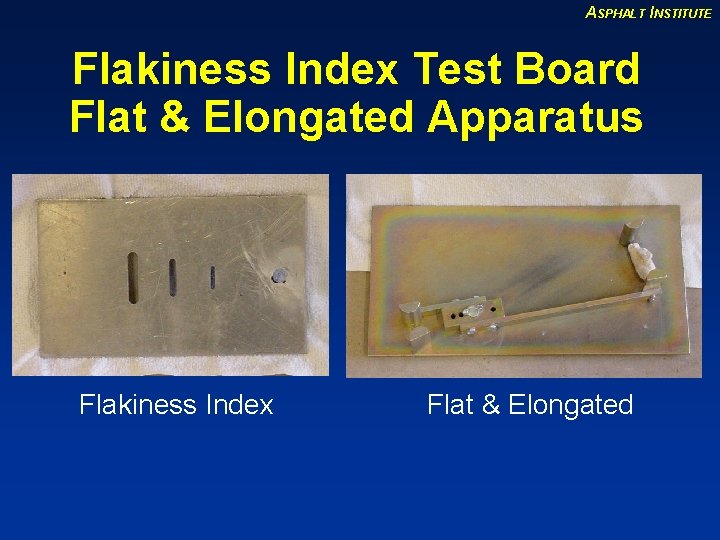
ASPHALT INSTITUTE Flakiness Index Test Board Flat & Elongated Apparatus Flakiness Index Flat & Elongated
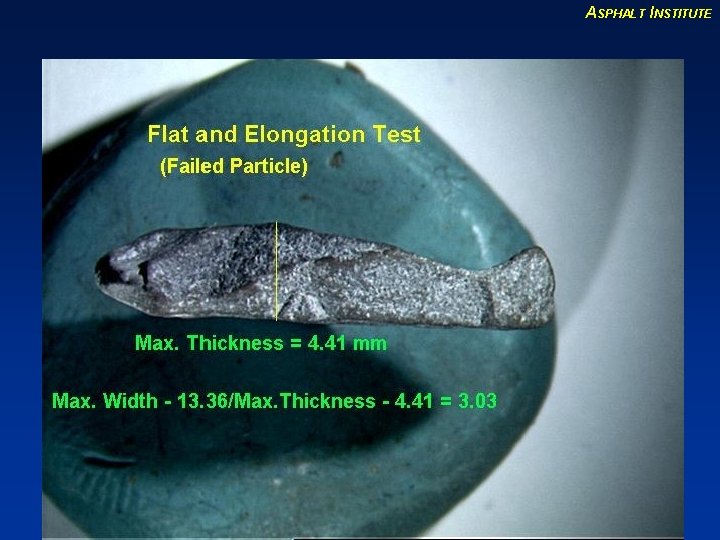
ASPHALT INSTITUTE
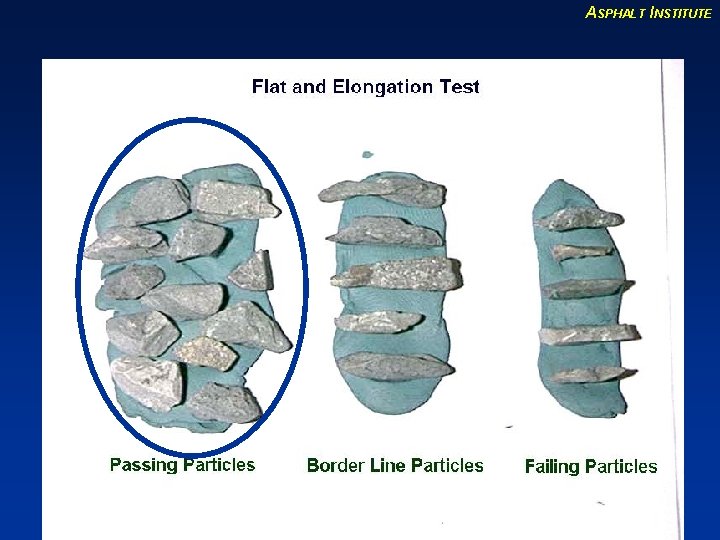
ASPHALT INSTITUTE
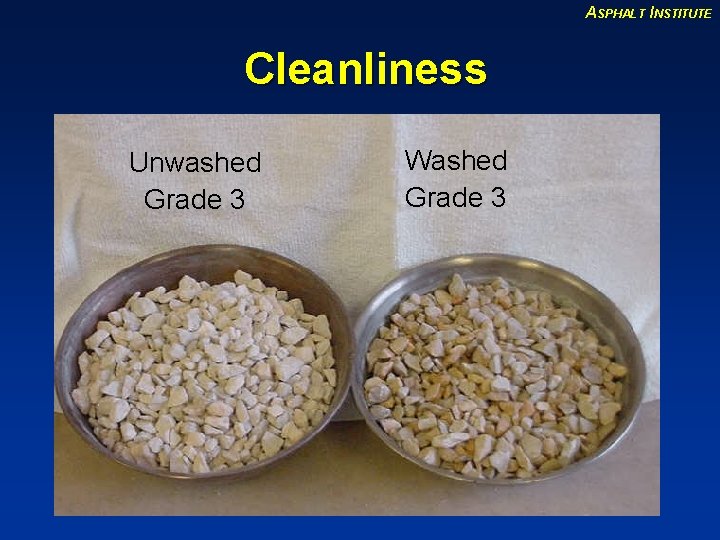
ASPHALT INSTITUTE Cleanliness Unwashed Grade 3 Washed Grade 3
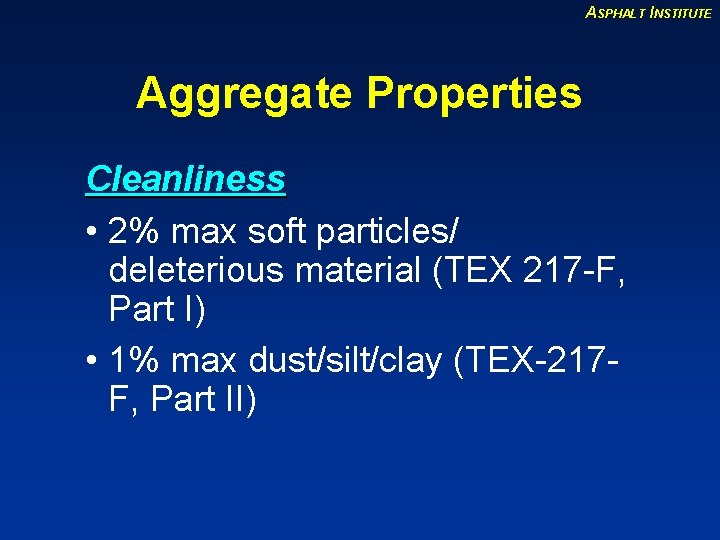
ASPHALT INSTITUTE Aggregate Properties Cleanliness • 2% max soft particles/ deleterious material (TEX 217 -F, Part I) • 1% max dust/silt/clay (TEX-217 F, Part II)
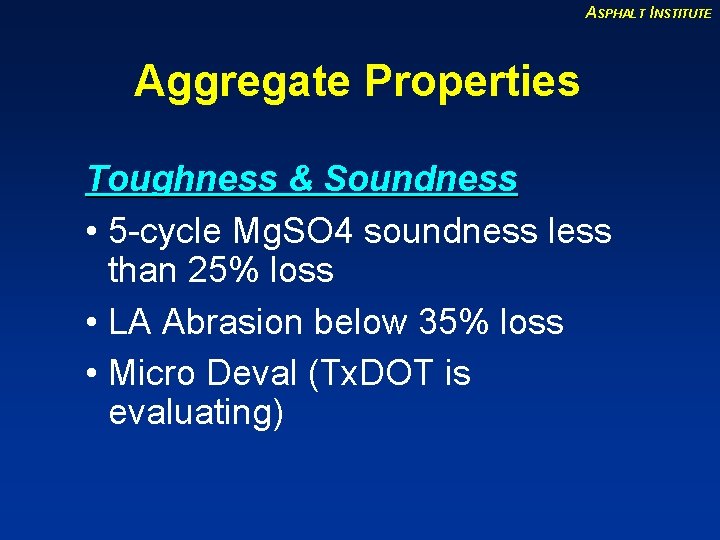
ASPHALT INSTITUTE Aggregate Properties Toughness & Soundness • 5 -cycle Mg. SO 4 soundness less than 25% loss • LA Abrasion below 35% loss • Micro Deval (Tx. DOT is evaluating)
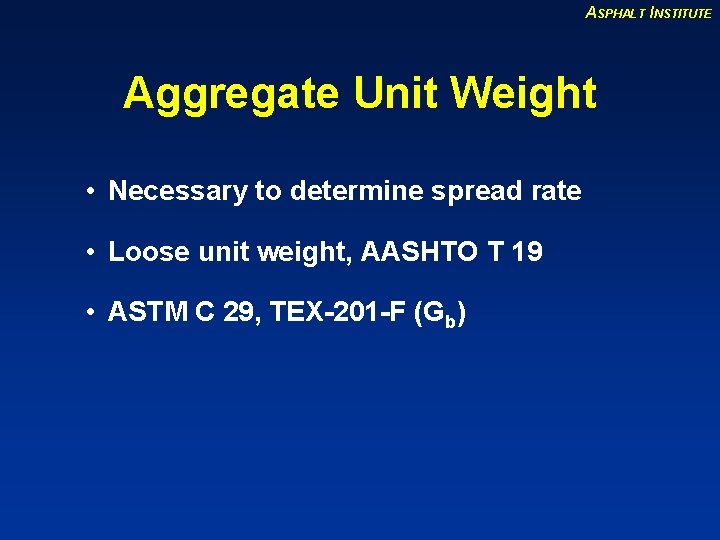
ASPHALT INSTITUTE Aggregate Unit Weight • Necessary to determine spread rate • Loose unit weight, AASHTO T 19 • ASTM C 29, TEX-201 -F (Gb)
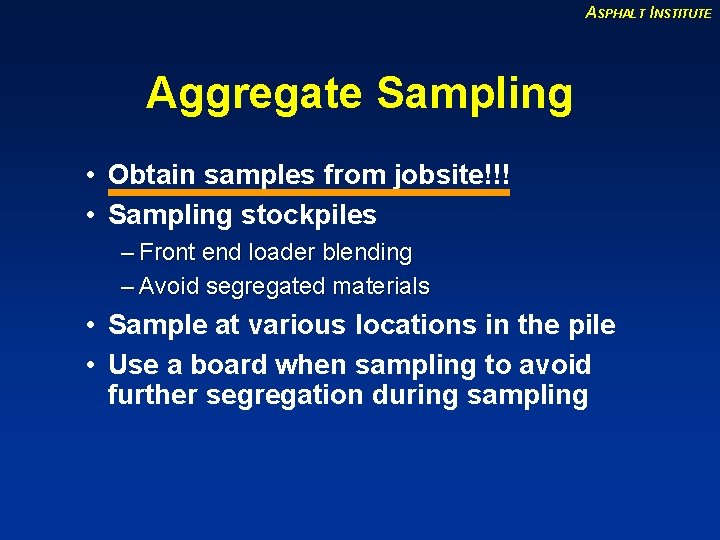
ASPHALT INSTITUTE Aggregate Sampling • Obtain samples from jobsite!!! • Sampling stockpiles – Front end loader blending – Avoid segregated materials • Sample at various locations in the pile • Use a board when sampling to avoid further segregation during sampling
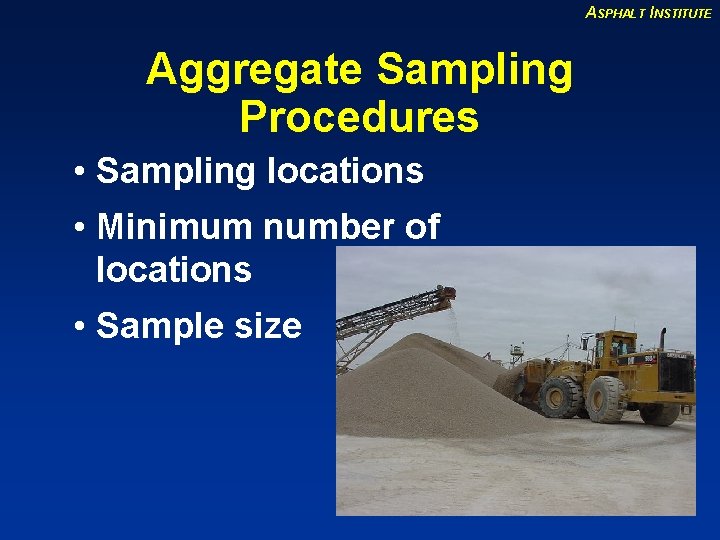
ASPHALT INSTITUTE Aggregate Sampling Procedures • Sampling locations • Minimum number of locations • Sample size
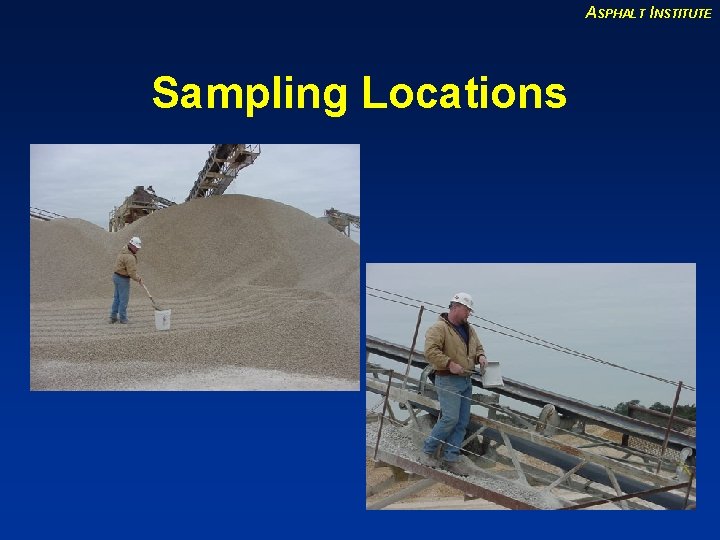
ASPHALT INSTITUTE Sampling Locations
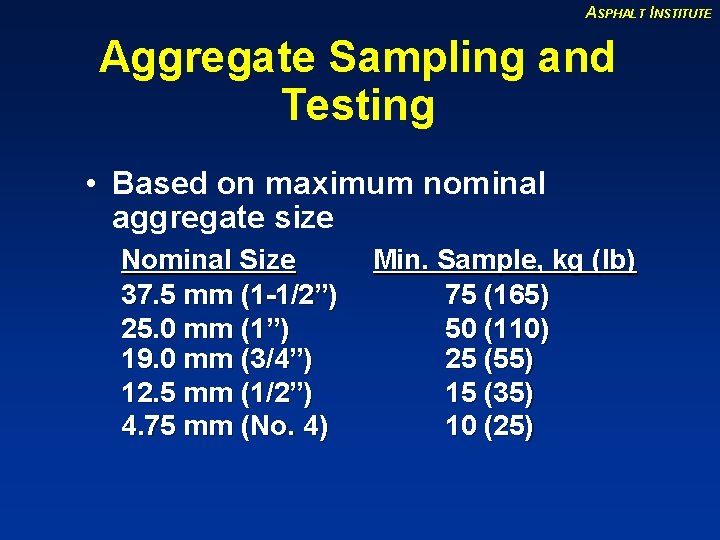
ASPHALT INSTITUTE Aggregate Sampling and Testing • Based on maximum nominal aggregate size Nominal Size 37. 5 mm (1 -1/2”) 25. 0 mm (1”) 19. 0 mm (3/4”) 12. 5 mm (1/2”) 4. 75 mm (No. 4) Min. Sample, kg (lb) 75 (165) 50 (110) 25 (55) 15 (35) 10 (25)
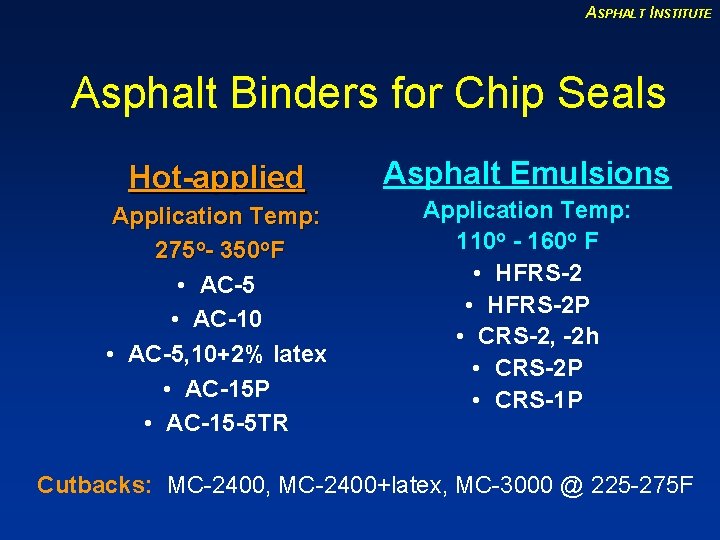
ASPHALT INSTITUTE Asphalt Binders for Chip Seals Hot-applied Asphalt Emulsions Application Temp: 275 o- 350 o. F • AC-5 • AC-10 • AC-5, 10+2% latex • AC-15 P • AC-15 -5 TR Application Temp: 110 o - 160 o F • HFRS-2 P • CRS-2, -2 h • CRS-2 P • CRS-1 P Cutbacks: MC-2400, MC-2400+latex, MC-3000 @ 225 -275 F
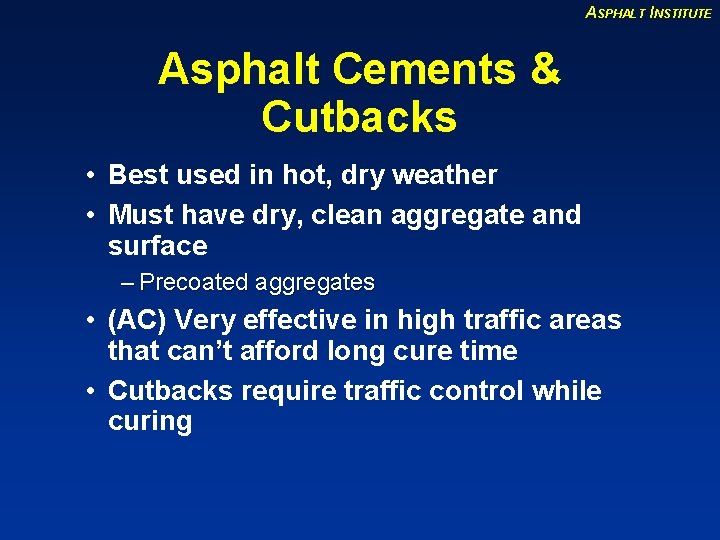
ASPHALT INSTITUTE Asphalt Cements & Cutbacks • Best used in hot, dry weather • Must have dry, clean aggregate and surface – Precoated aggregates • (AC) Very effective in high traffic areas that can’t afford long cure time • Cutbacks require traffic control while curing
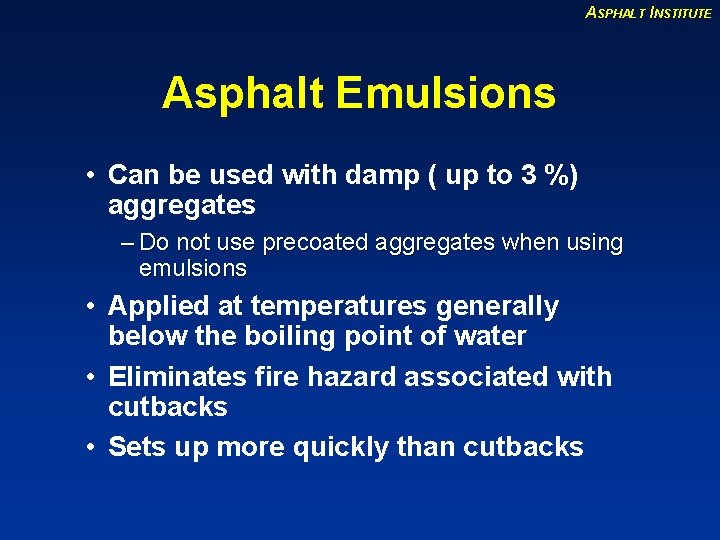
ASPHALT INSTITUTE Asphalt Emulsions • Can be used with damp ( up to 3 %) aggregates – Do not use precoated aggregates when using emulsions • Applied at temperatures generally below the boiling point of water • Eliminates fire hazard associated with cutbacks • Sets up more quickly than cutbacks
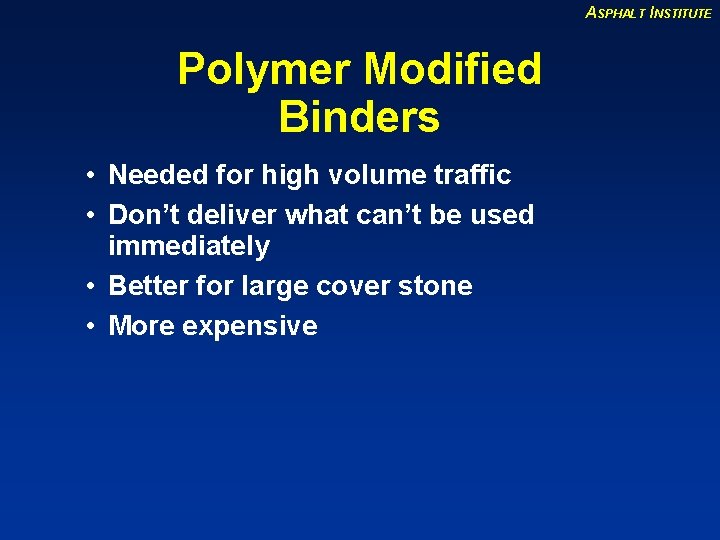
ASPHALT INSTITUTE Polymer Modified Binders • Needed for high volume traffic • Don’t deliver what can’t be used immediately • Better for large cover stone • More expensive
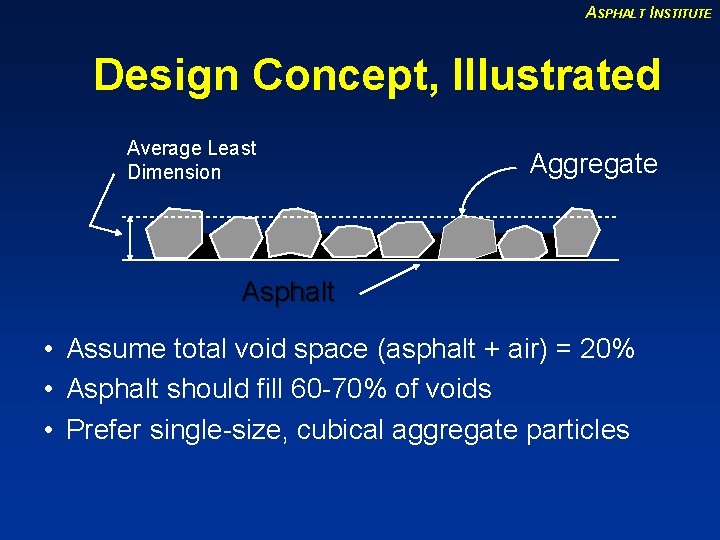
ASPHALT INSTITUTE Design Concept, Illustrated Average Least Dimension Aggregate Asphalt • Assume total void space (asphalt + air) = 20% • Asphalt should fill 60 -70% of voids • Prefer single-size, cubical aggregate particles
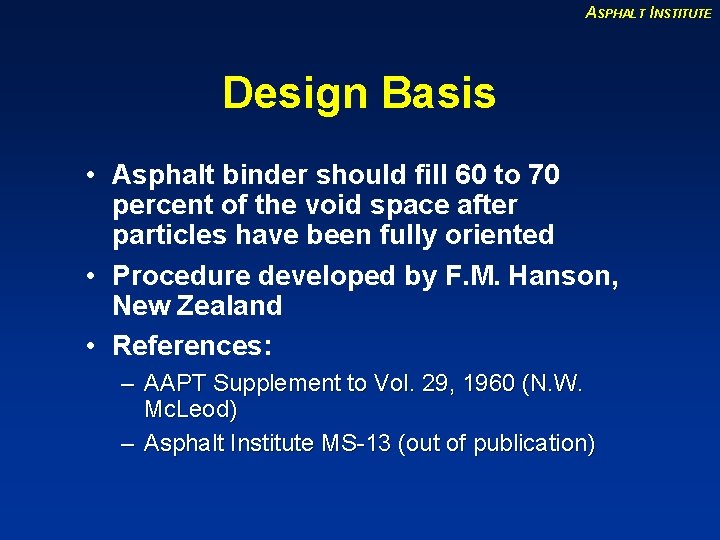
ASPHALT INSTITUTE Design Basis • Asphalt binder should fill 60 to 70 percent of the void space after particles have been fully oriented • Procedure developed by F. M. Hanson, New Zealand • References: – AAPT Supplement to Vol. 29, 1960 (N. W. Mc. Leod) – Asphalt Institute MS-13 (out of publication)
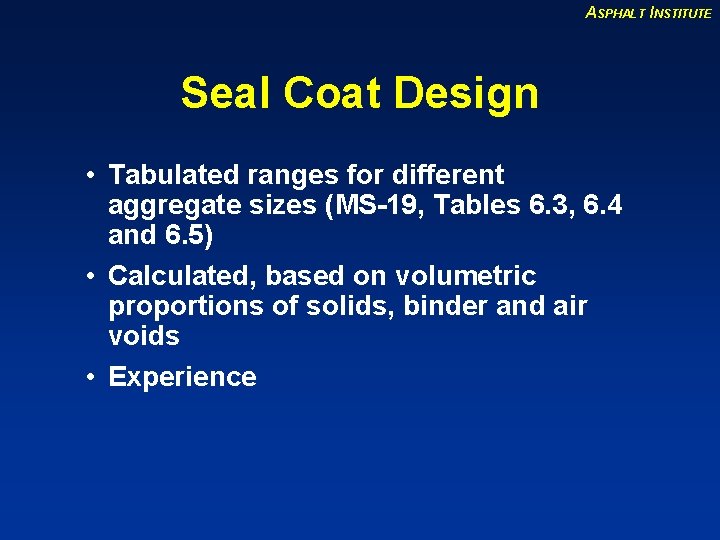
ASPHALT INSTITUTE Seal Coat Design • Tabulated ranges for different aggregate sizes (MS-19, Tables 6. 3, 6. 4 and 6. 5) • Calculated, based on volumetric proportions of solids, binder and air voids • Experience

ASPHALT INSTITUTE Effect of Changing Variables • Traffic: ADT from 1200 to 300 – Shot rate increases from 0. 32 to 0. 37 gal/sy • Flakiness Index: FI from 0 to 20% – Use ALD instead of M – Spread rate decreases from 22. 4 to 16. 6 lb/sy – Shot rate decreases from 0. 32 to 0. 24 gal/sy • Surface: Smooth, non-porous to slightly raveled-porous – Shot rate increases from 0. 32 to 0. 41 gal/sy
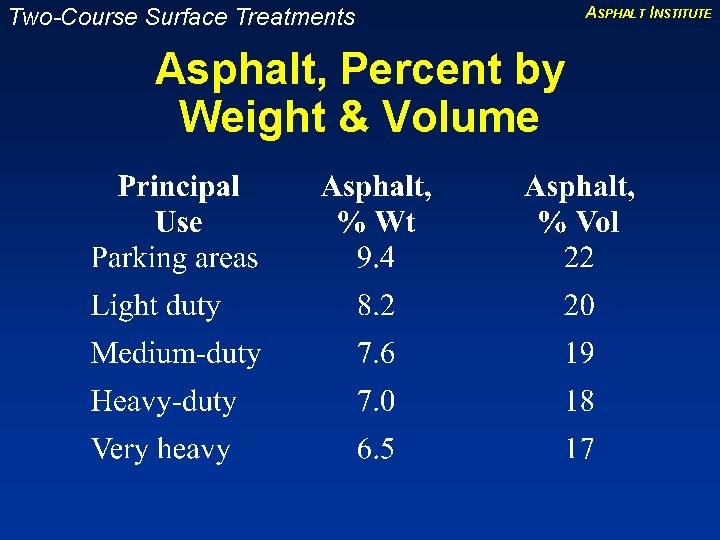
Two-Course Surface Treatments Asphalt, Percent by Weight & Volume ASPHALT INSTITUTE
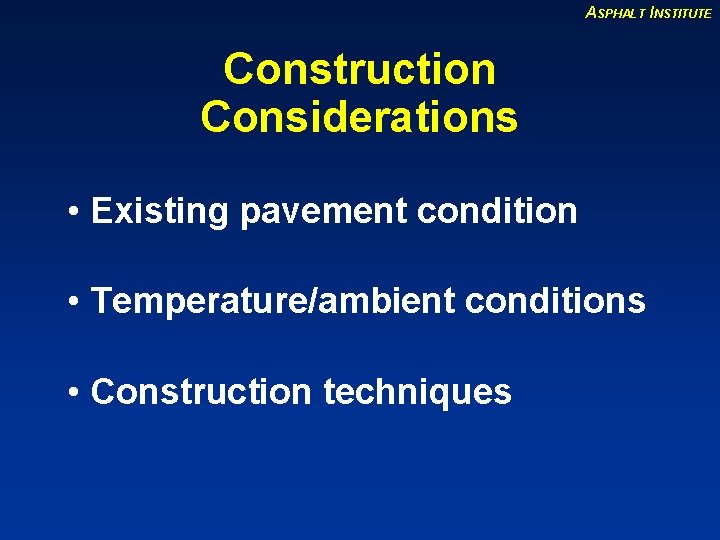
ASPHALT INSTITUTE Construction Considerations • Existing pavement condition • Temperature/ambient conditions • Construction techniques
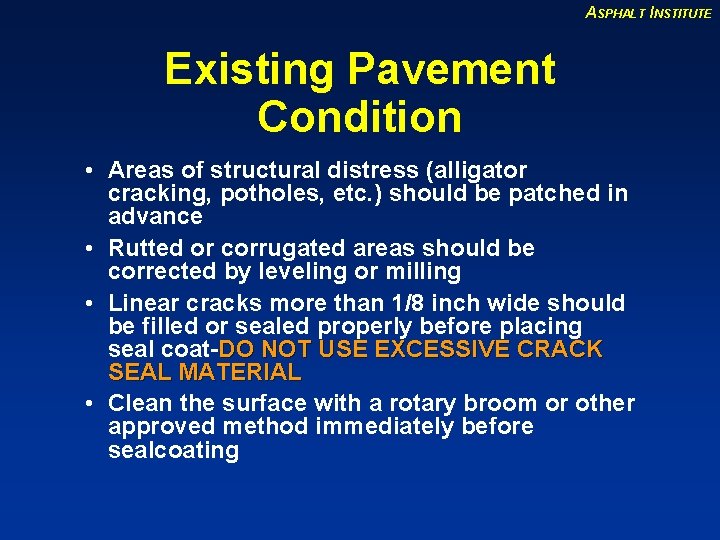
ASPHALT INSTITUTE Existing Pavement Condition • Areas of structural distress (alligator cracking, potholes, etc. ) should be patched in advance • Rutted or corrugated areas should be corrected by leveling or milling • Linear cracks more than 1/8 inch wide should be filled or sealed properly before placing seal coat-DO NOT USE EXCESSIVE CRACK SEAL MATERIAL • Clean the surface with a rotary broom or other approved method immediately before sealcoating
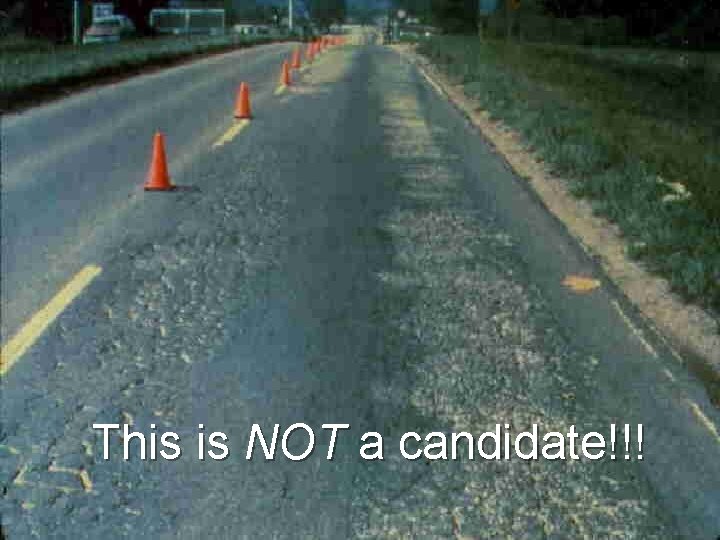
This is NOT a candidate!!!
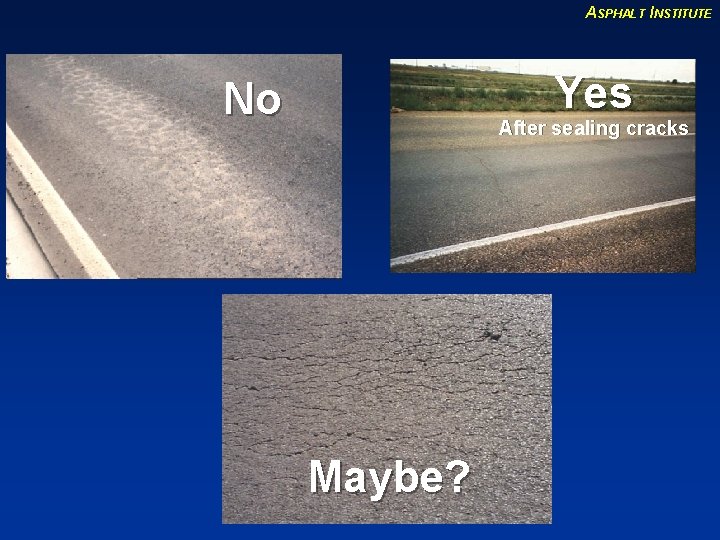
ASPHALT INSTITUTE Yes No After sealing cracks Maybe?
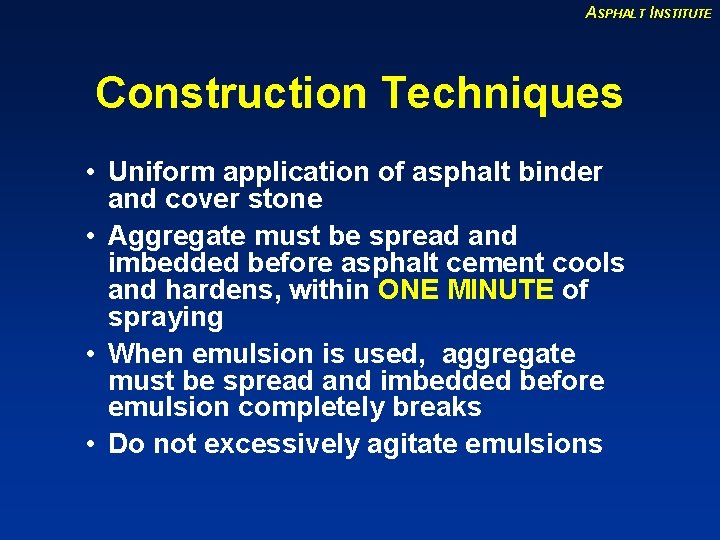
ASPHALT INSTITUTE Construction Techniques • Uniform application of asphalt binder and cover stone • Aggregate must be spread and imbedded before asphalt cement cools and hardens, within ONE MINUTE of spraying • When emulsion is used, aggregate must be spread and imbedded before emulsion completely breaks • Do not excessively agitate emulsions

ASPHALT INSTITUTE First and last piece of equipment on the job!
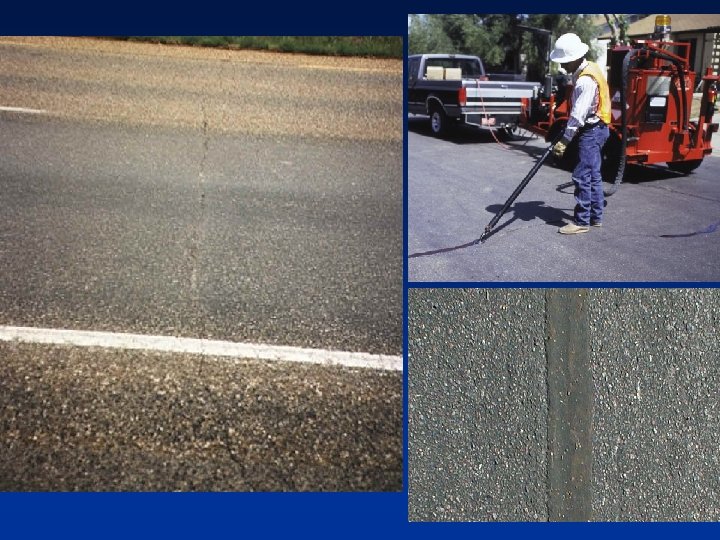

ASPHALT INSTITUTE Temperature/Ambient Conditions • Surface temperature is critical, should exceed 70°F • During cool weather, allow time for surface to warm before allowing work to begin • Do not apply when the surface is wet or when the threat of rain is imminent • Control traffic speed during first 24 hrs. (max. 20 mph) • During hot weather, allow seal to “set” overnight before opening to traffic
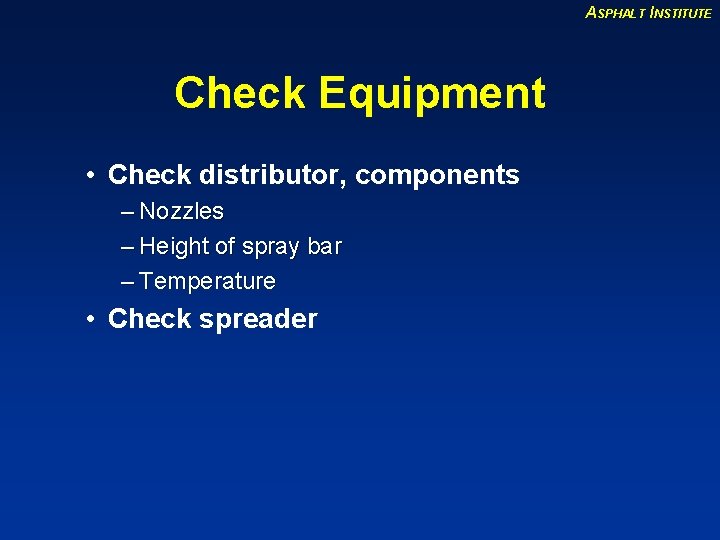
ASPHALT INSTITUTE Check Equipment • Check distributor, components – Nozzles – Height of spray bar – Temperature • Check spreader
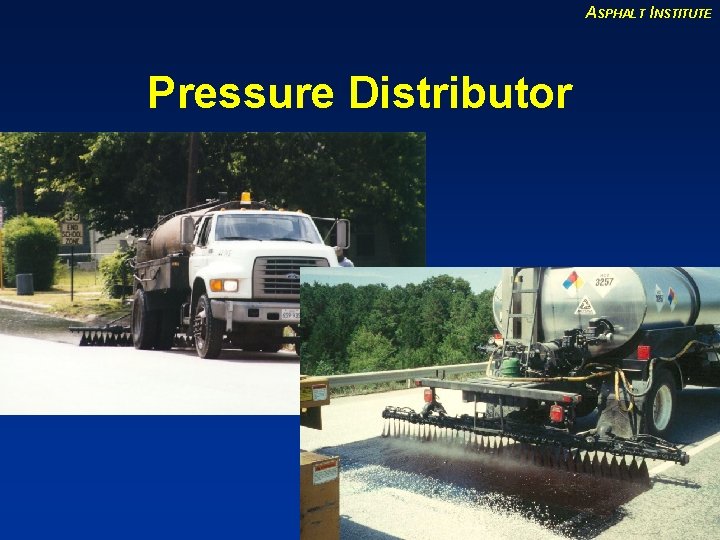
ASPHALT INSTITUTE Pressure Distributor
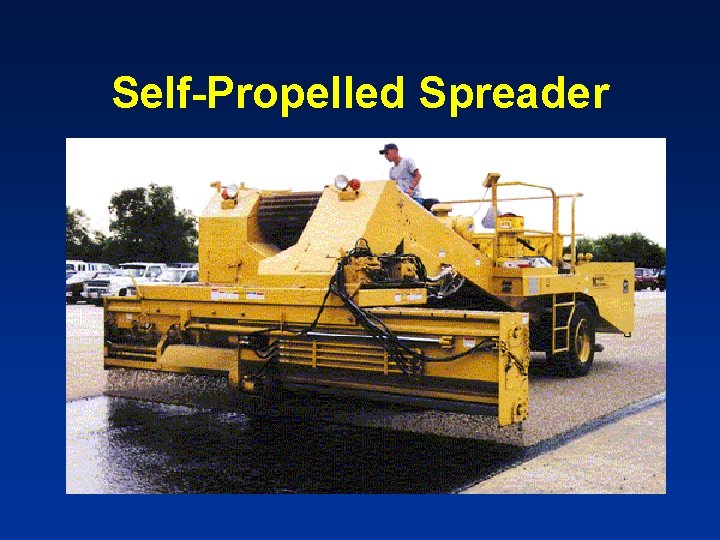
Self-Propelled Spreader

ASPHALT INSTITUTE Rollers • For single seal coats/one course surface treatments, use pneumatic (rubber tire) rollers • Only consider light (low pli) steel-wheel rollers for second course of double seal/two course surface treatment – rubber-coated steel-wheel rollers – “combi” roller (steel drum plus pneumatic tires), operated w/pneumatic in front
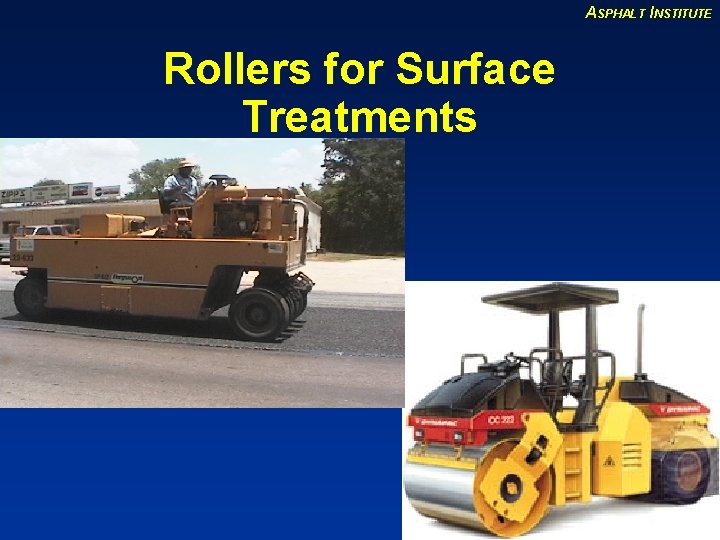
ASPHALT INSTITUTE Rollers for Surface Treatments
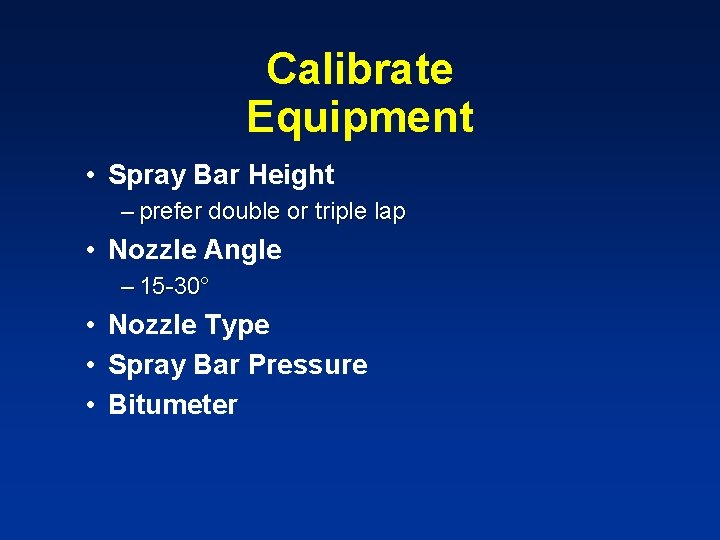
Calibrate Equipment • Spray Bar Height – prefer double or triple lap • Nozzle Angle – 15 -30° • Nozzle Type • Spray Bar Pressure • Bitumeter
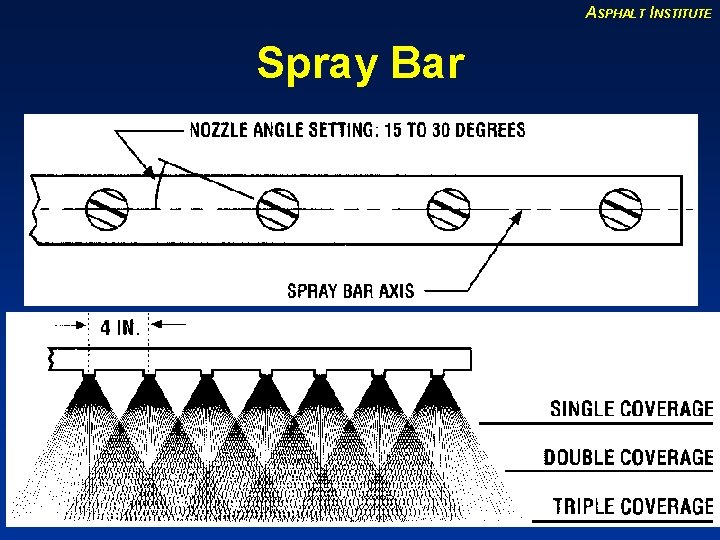
ASPHALT INSTITUTE Spray Bar
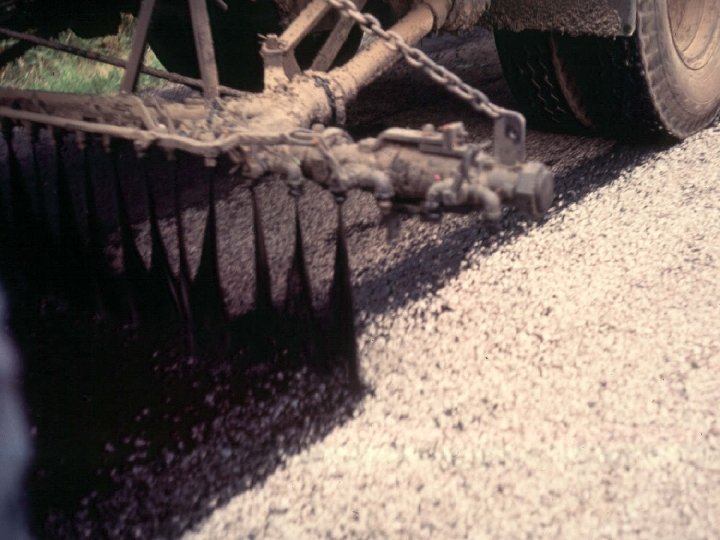
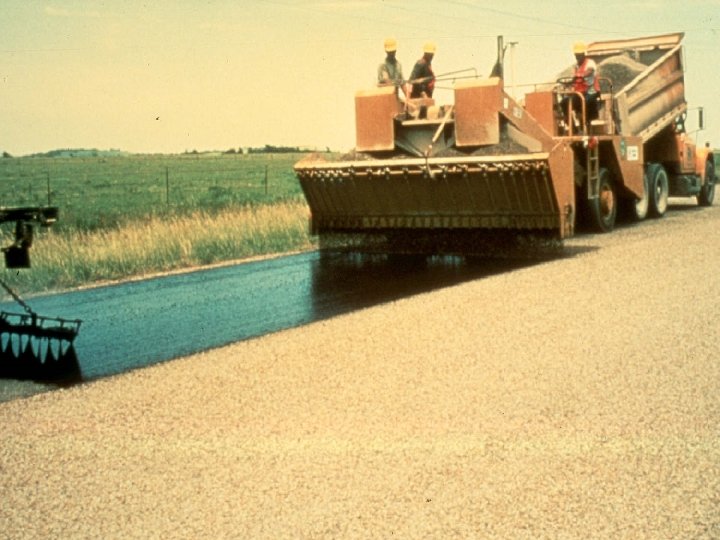
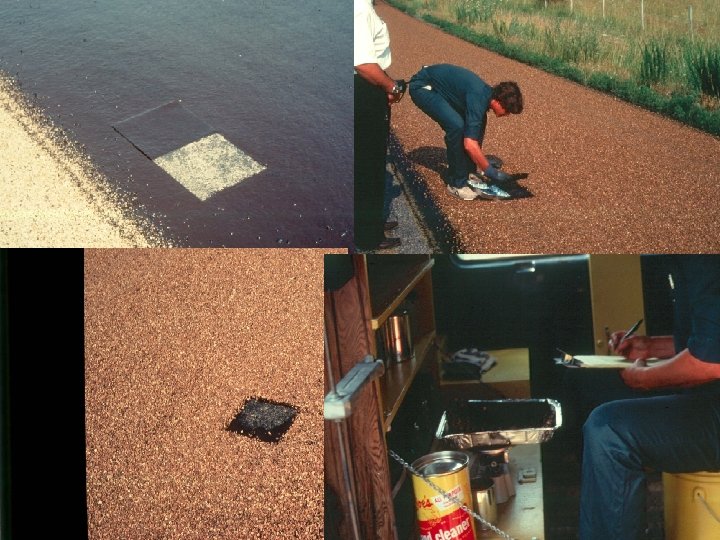
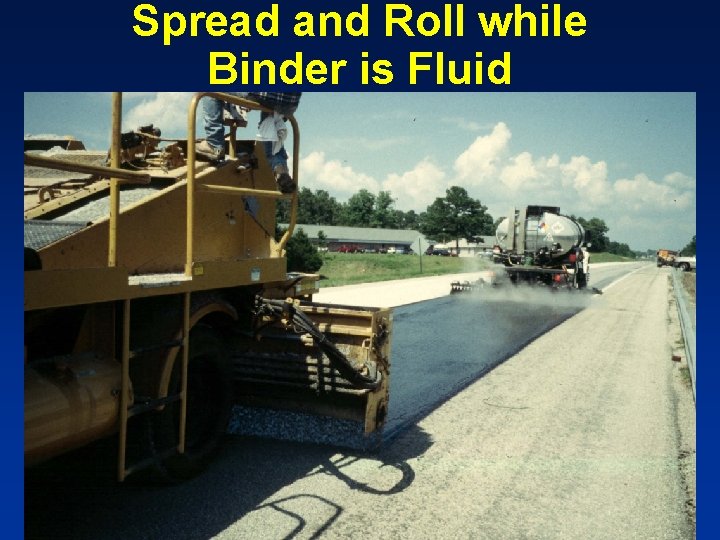
Spread and Roll while Binder is Fluid
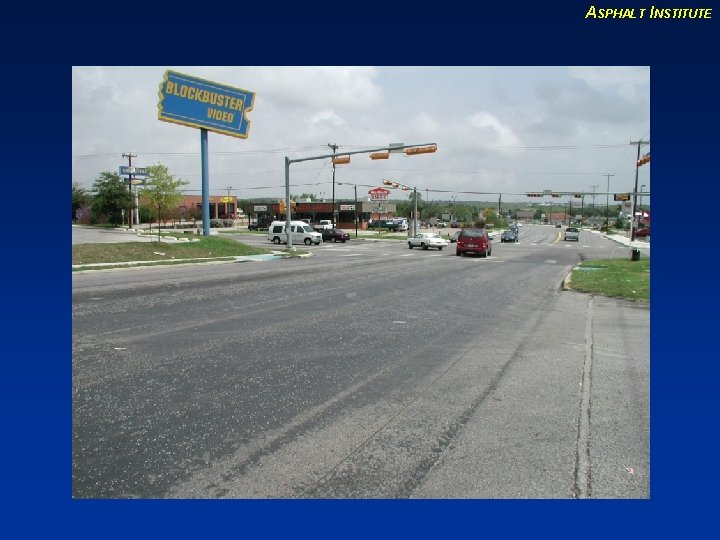
ASPHALT INSTITUTE
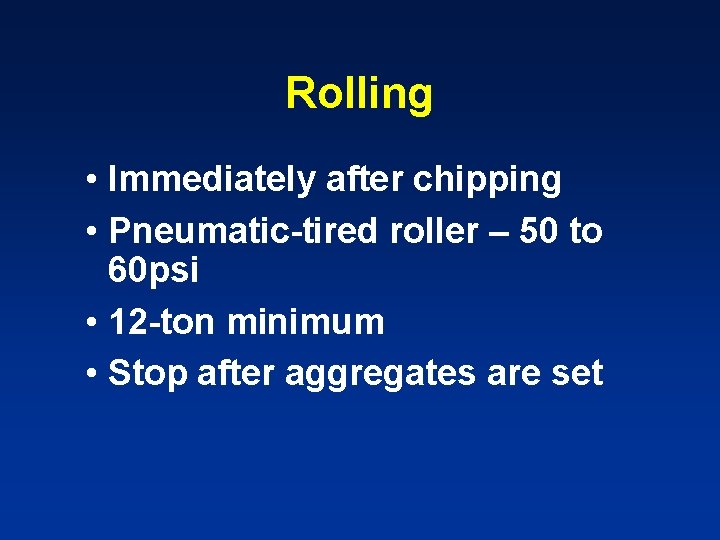
Rolling • Immediately after chipping • Pneumatic-tired roller – 50 to 60 psi • 12 -ton minimum • Stop after aggregates are set
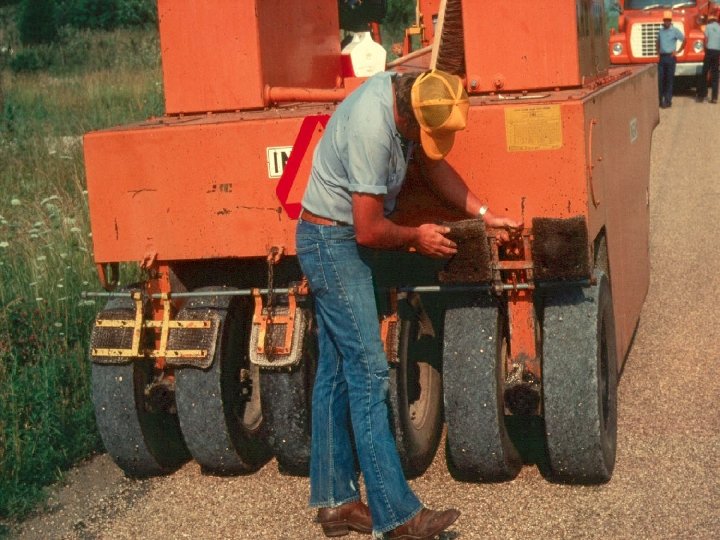
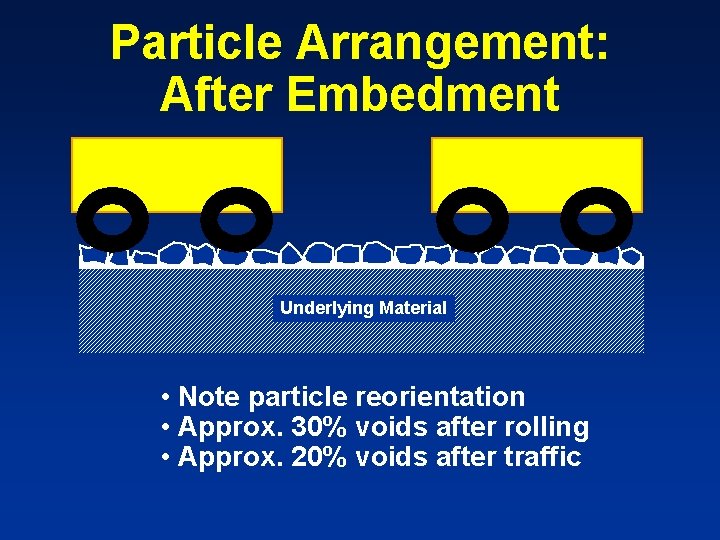
Particle Arrangement: After Embedment Underlying Material • Note particle reorientation • Approx. 30% voids after rolling • Approx. 20% voids after traffic
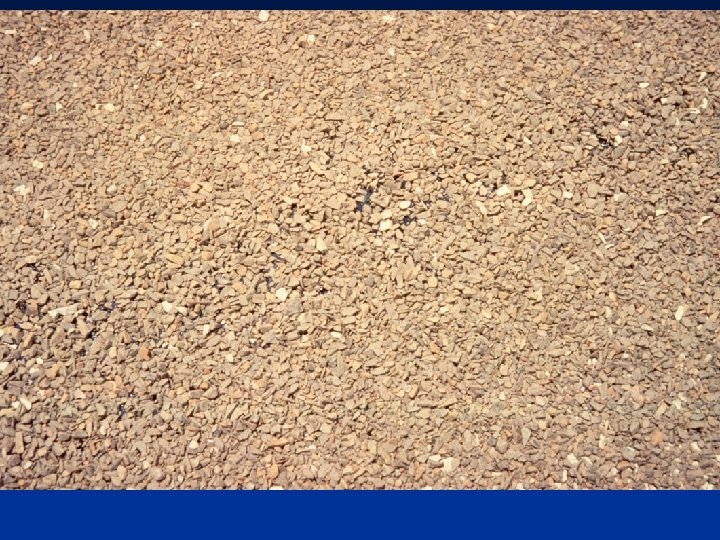
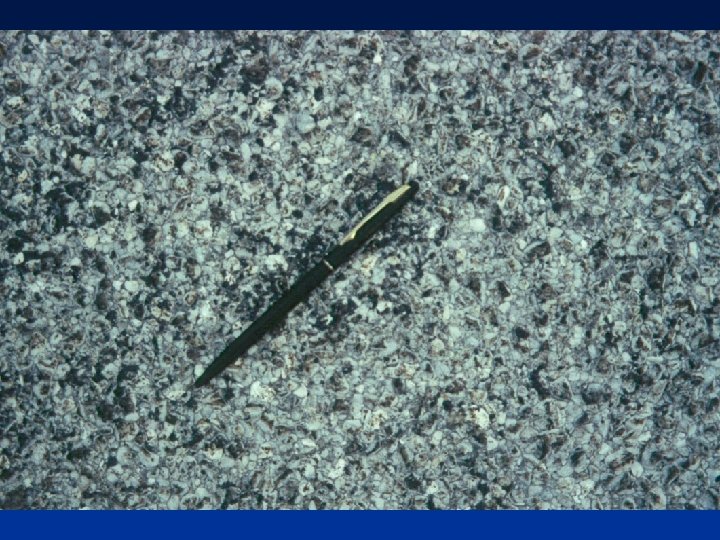
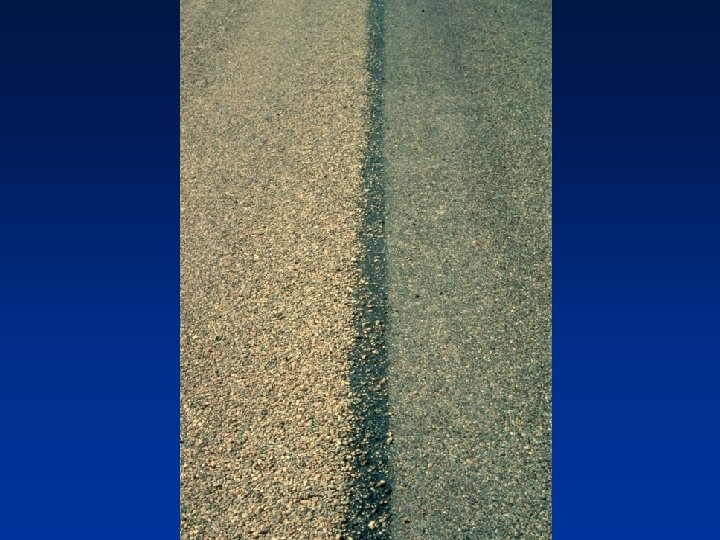
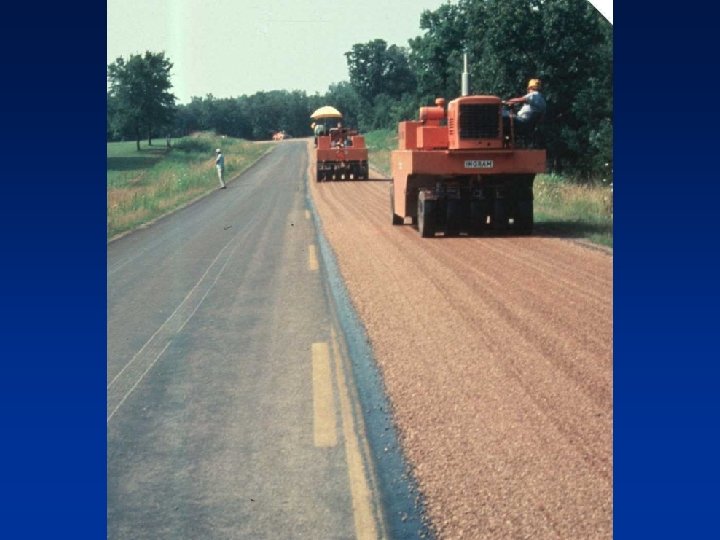
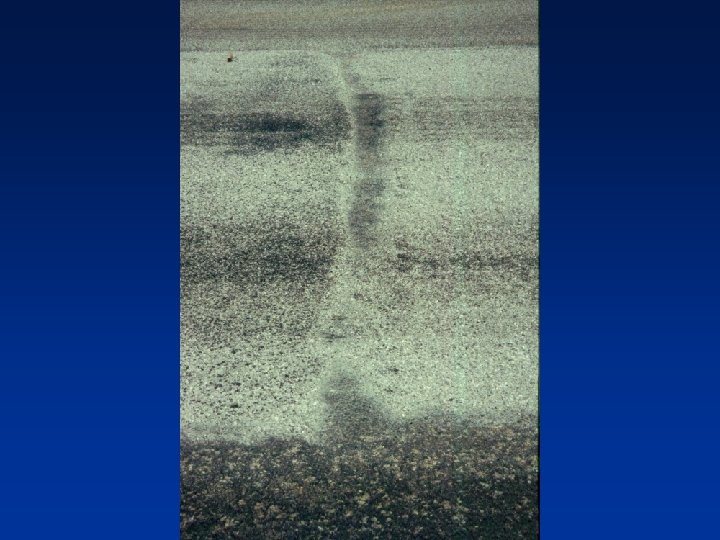
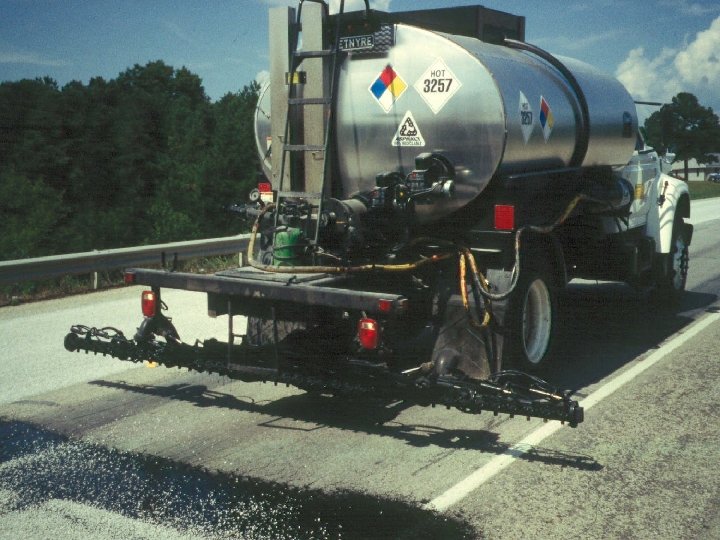
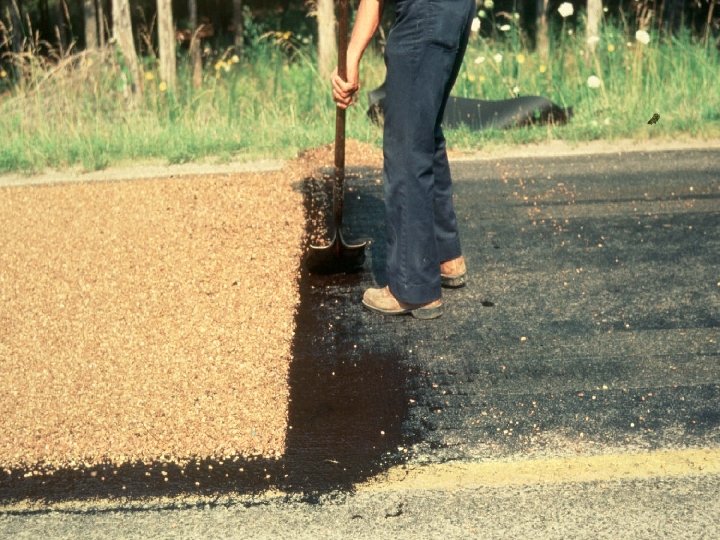
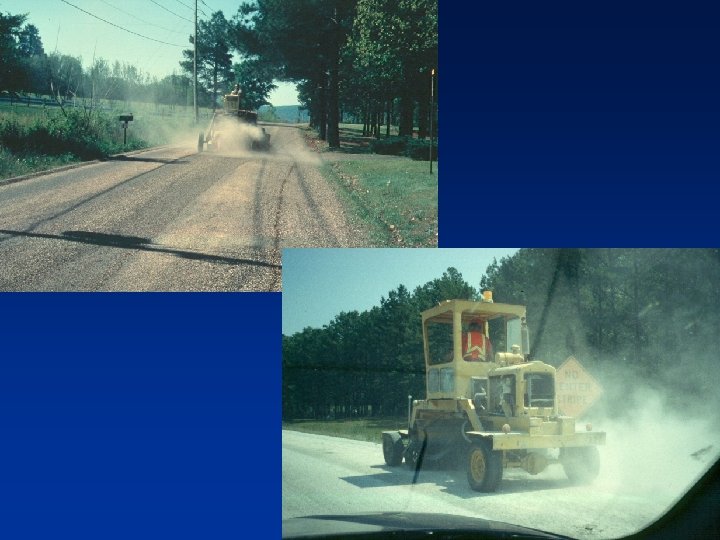
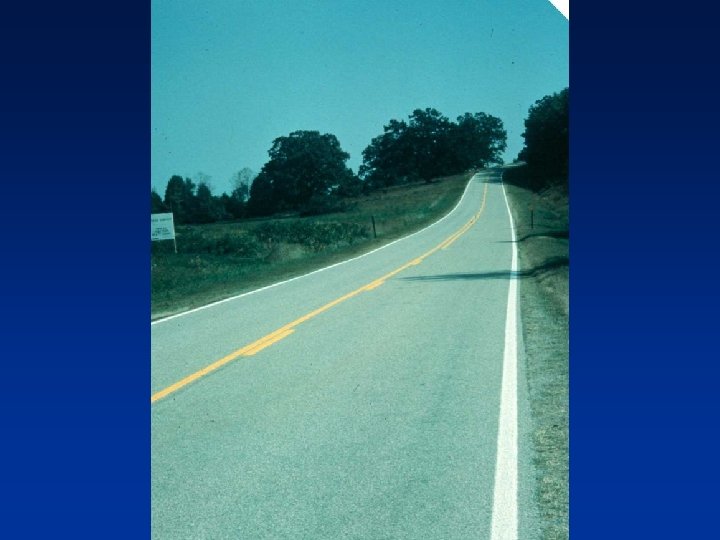
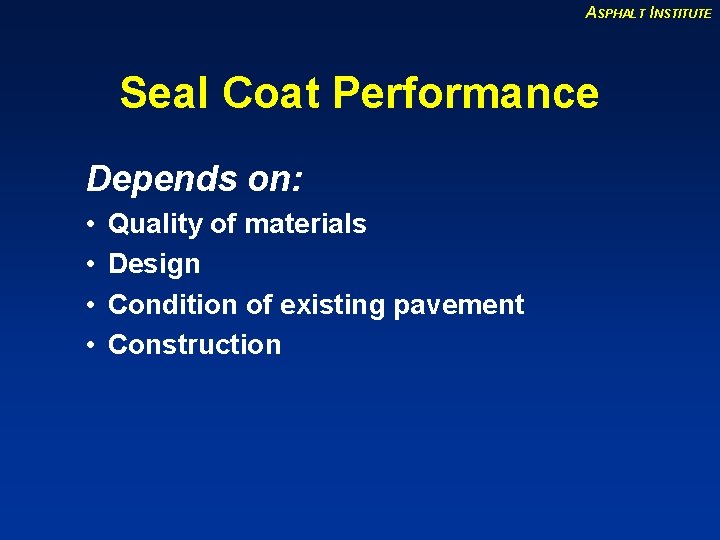
ASPHALT INSTITUTE Seal Coat Performance Depends on: • • Quality of materials Design Condition of existing pavement Construction
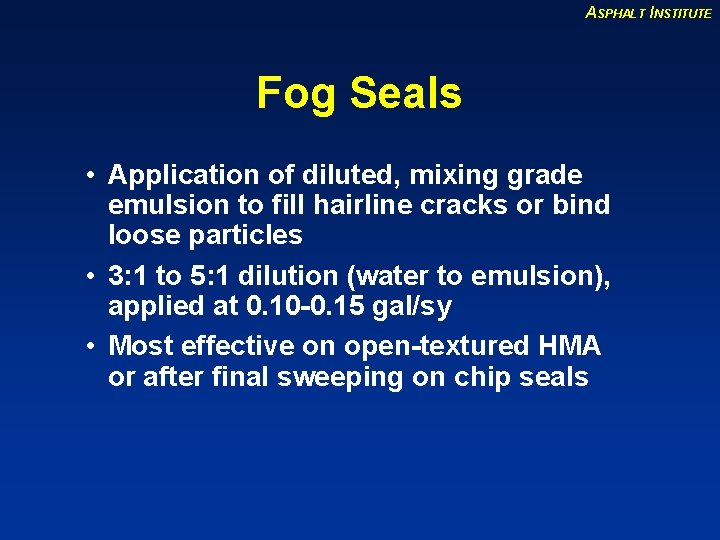
ASPHALT INSTITUTE Fog Seals • Application of diluted, mixing grade emulsion to fill hairline cracks or bind loose particles • 3: 1 to 5: 1 dilution (water to emulsion), applied at 0. 10 -0. 15 gal/sy • Most effective on open-textured HMA or after final sweeping on chip seals
Asphalt pavement design example
Cbr method of pavement design
Alabama asphalt pavement association
Asphalt pavement thickness design
Quiet pavement
Flexible pavement thickness
Pavement structural design
Base subbase subgrade
Flexible pavement and rigid pavement
Flexible pavement vs rigid pavement
Sog oil seal manufacturer
Alan seals weather
Stop clubbing baby seals punctuation
Seven seals of revelation
Signs and seals of the covenant
Heritage park seals
Characteristics of marine mammals
Ppc mechanical seals
7 sealed scroll
What are the 7 bowls
Pei easter seals ambassadors
Easter seals project action
Fasteners gaskets seals and sealants
Harp seals life cycle
Caribbean cleaners national geographic
Red seals sso
Fips 140-1 seals
Chapter 8 fasteners gaskets seals and sealants
Cci pipeline systems
Automotive bearings and seals
Asphalt base layer
Colas liquid asphalt
Fred smith asphalt plant
Mixed asphalt shingle suppliers
Contained rock asphalt mat
404 asphalt
Rowe asphalt paving
Core
What is this sing
Asphalt rolling pattern
S&b asphalt
Recycled asphalt colorado springs
Pete's absolute asphalt
China nonionic asphalt emulsifier
Capa asphalt
Determann asphalt
Warmmix
Bulldosing
Contraction joint in rigid pavement
Hrs types
Functional evaluation of pavement
Pavement bondi junction
Aashto flexible pavement design example
Pavement design jkr
320
Report illegal parking birmingham
Definition of desert
Interlocking cement concrete pavement
Faulting in rigid pavement
Karst definition geography
Aashto flexible pavement design calculator
Semi flexible pavement
Guide and international signs
Carol ann duffy before you were mine
Jointed plain concrete pavement
Jpcp pavement
Pavement
Cost comparison of flexible and rigid pavement
Objectives of pavement design