PLASTK EKL VERME Dzce niversitesi Makina Mhendislii MM
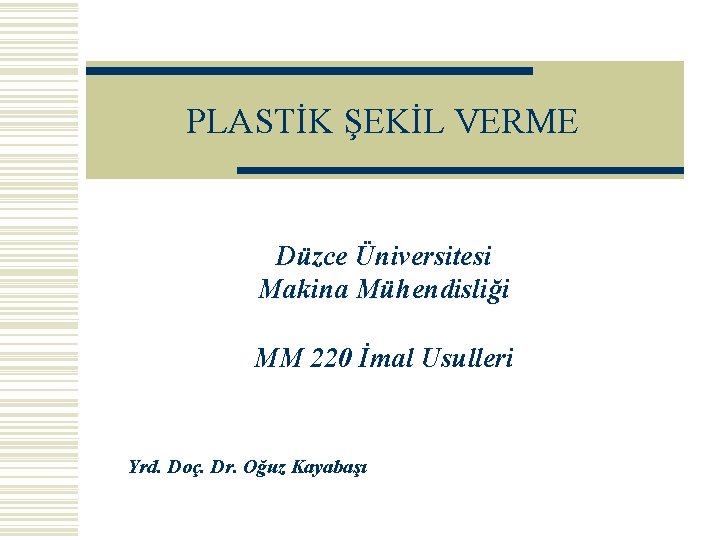
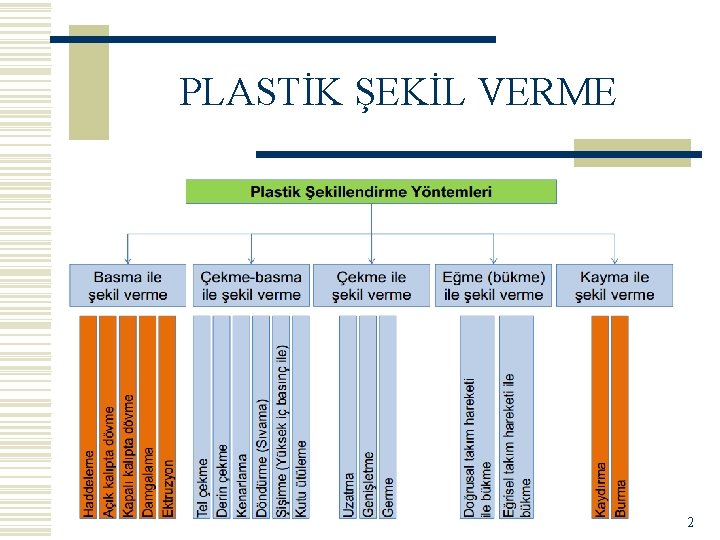
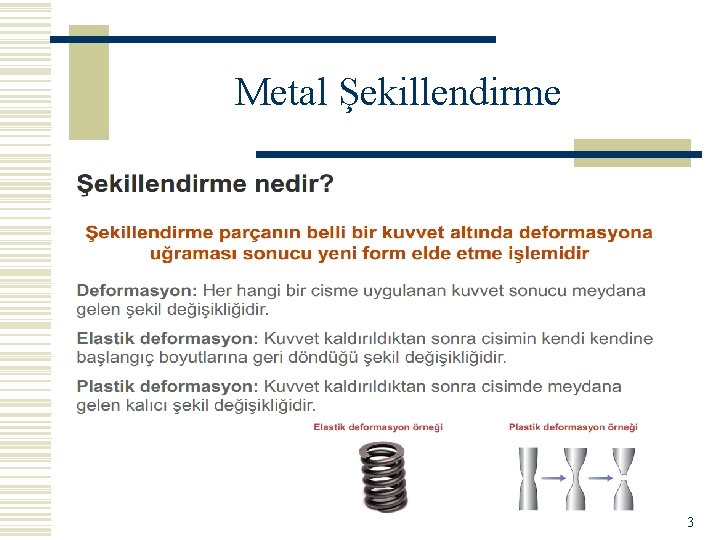
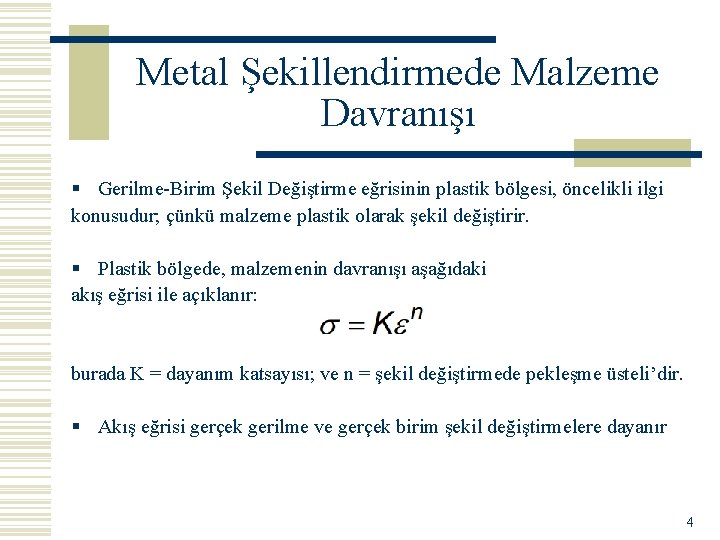
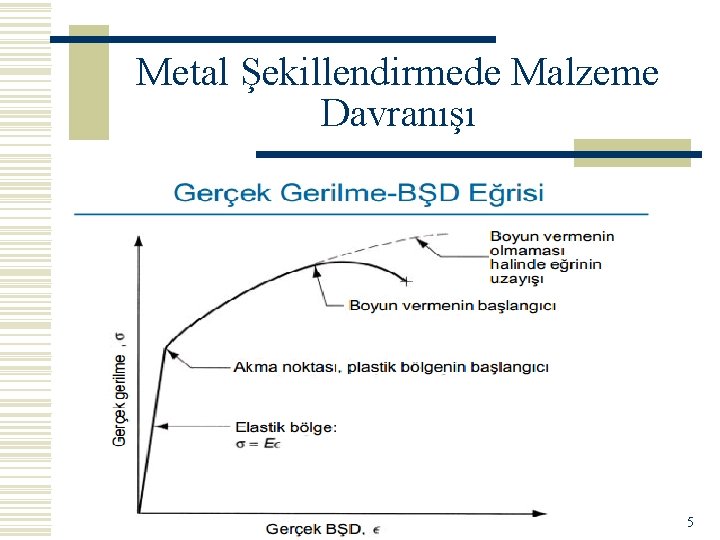
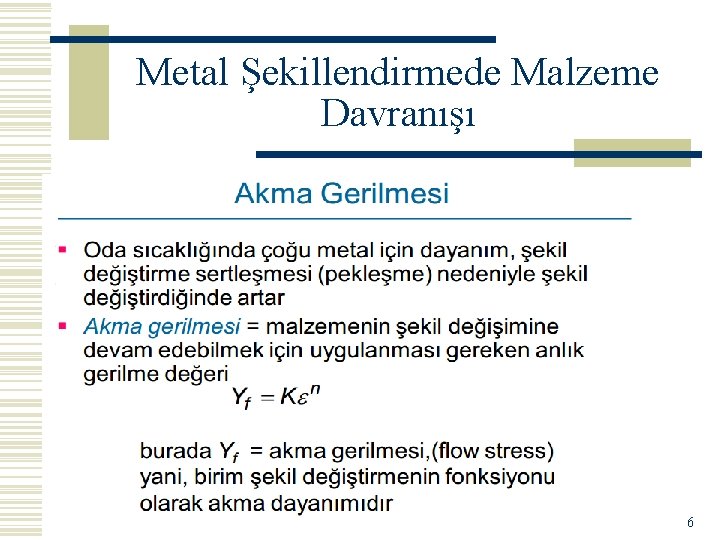
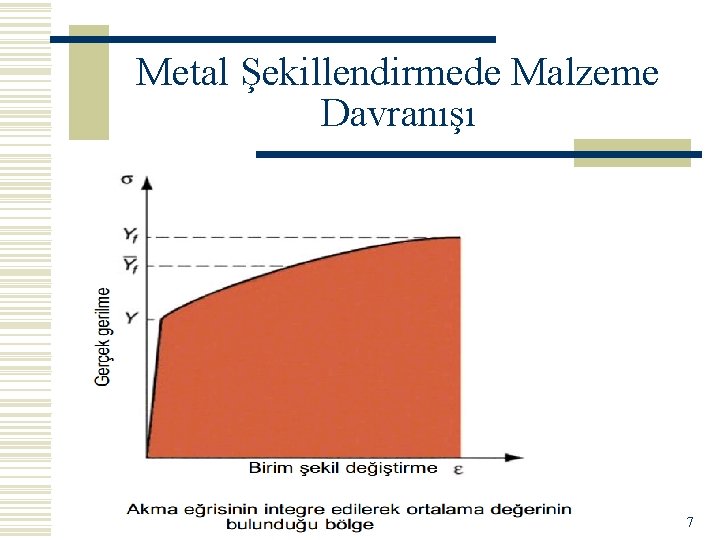
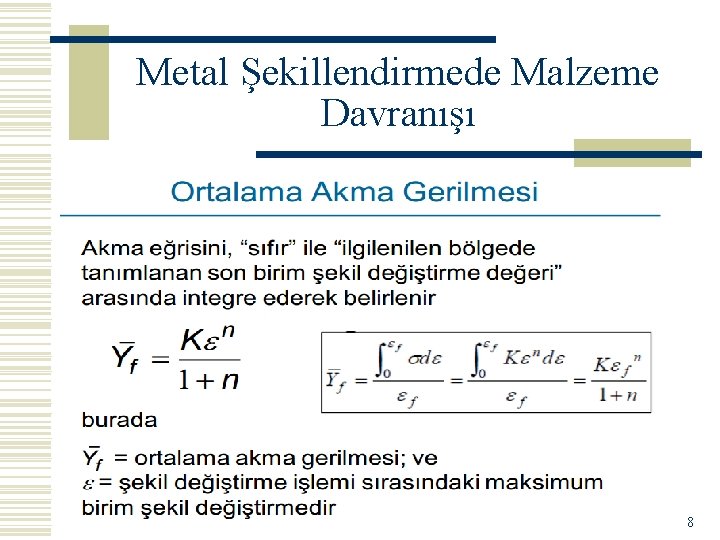
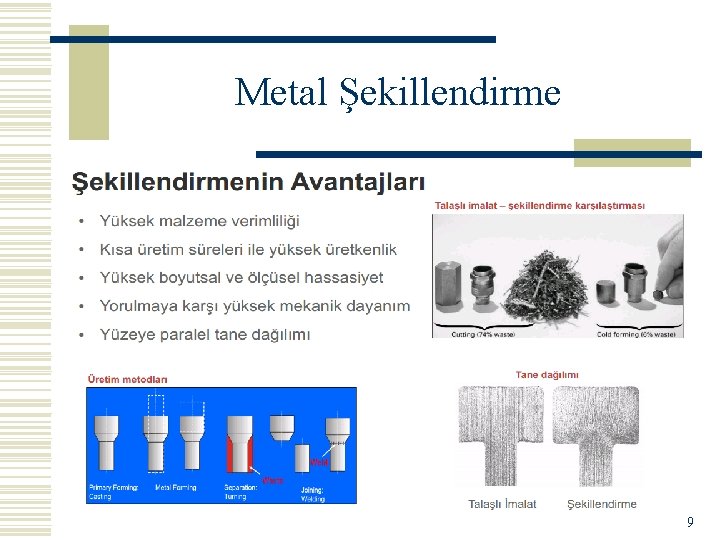
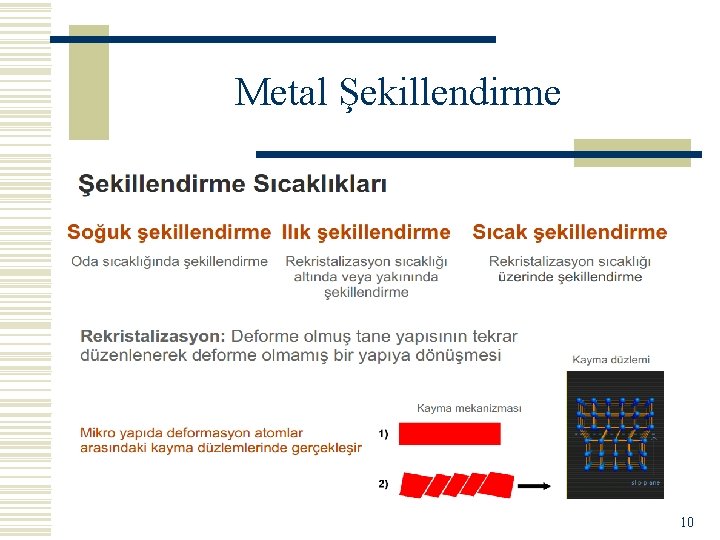
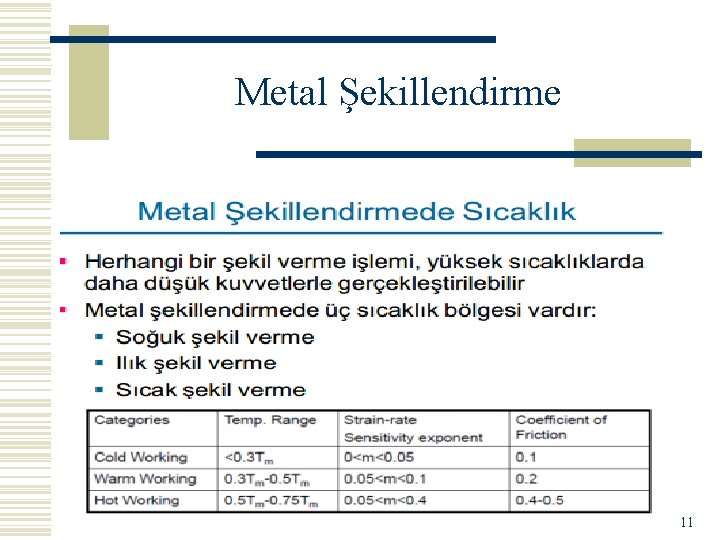
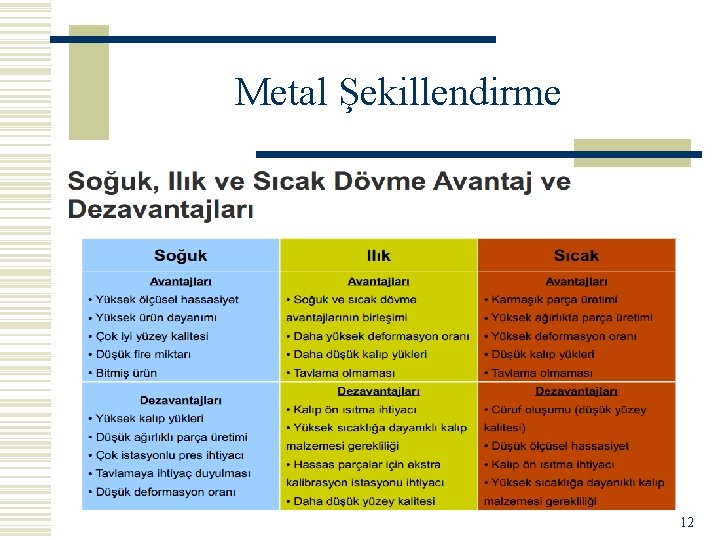
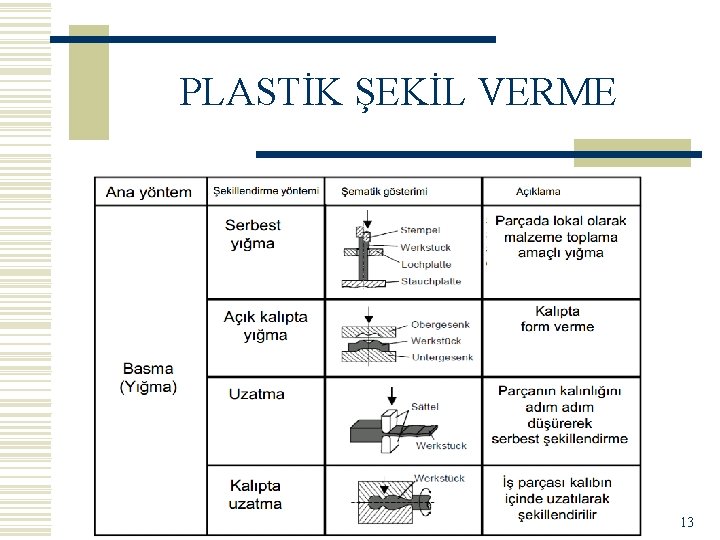
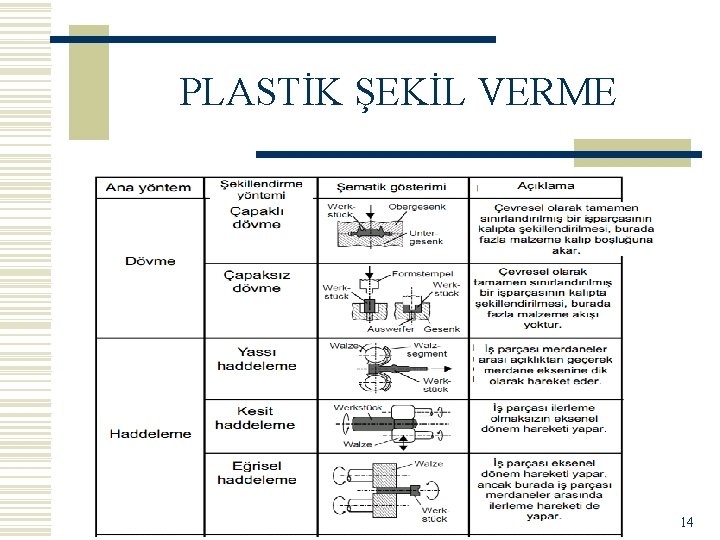
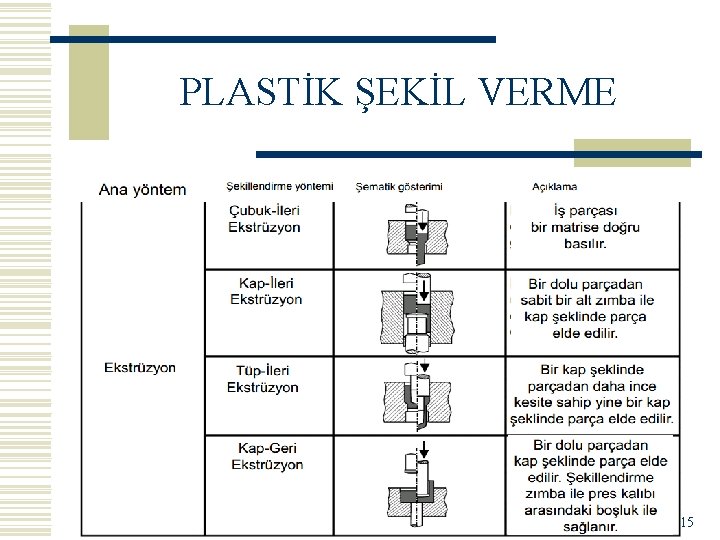
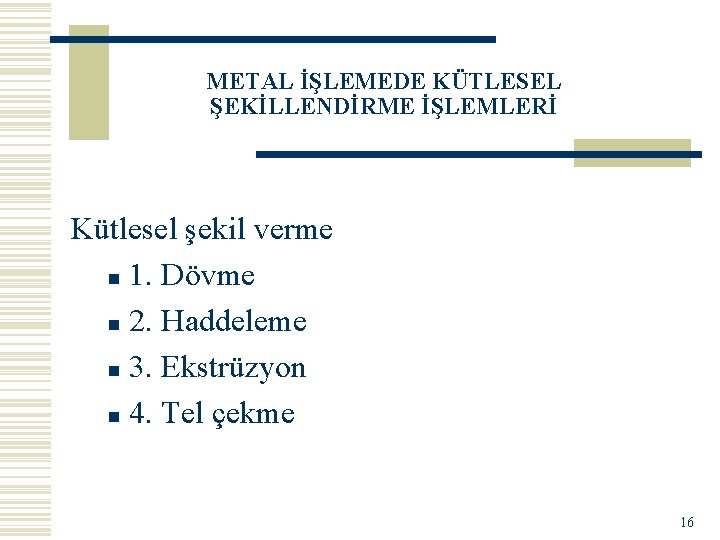
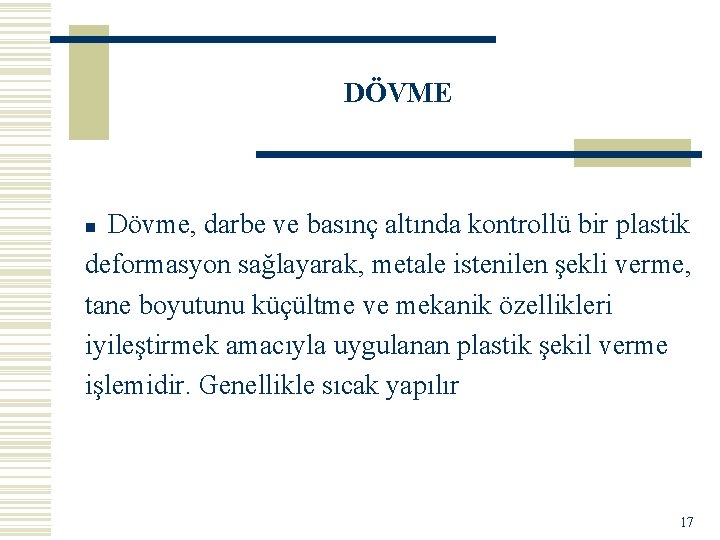
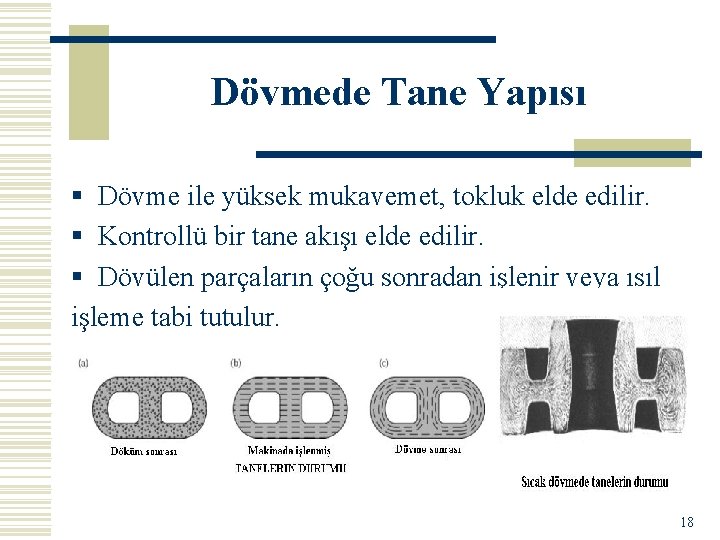
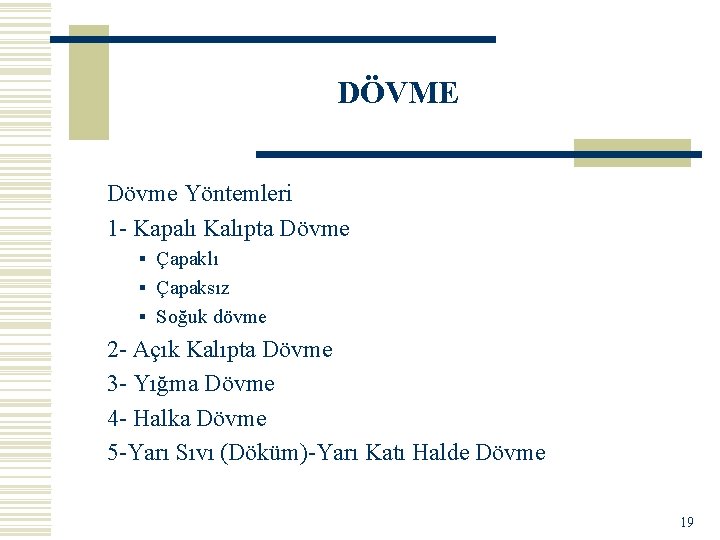
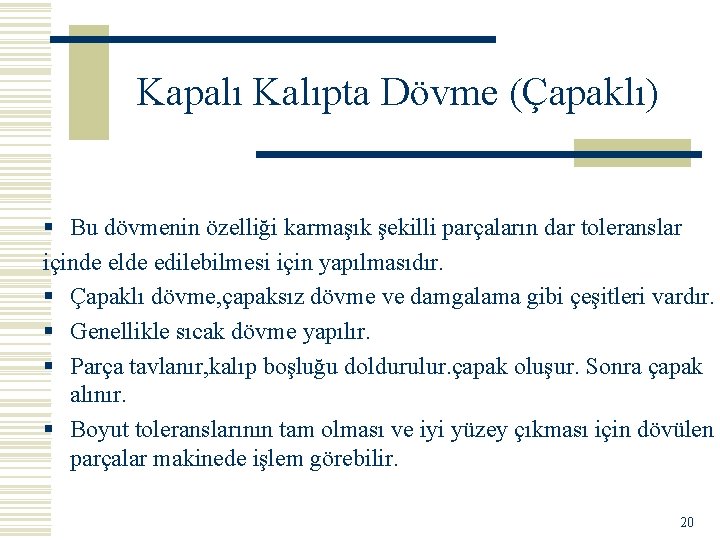
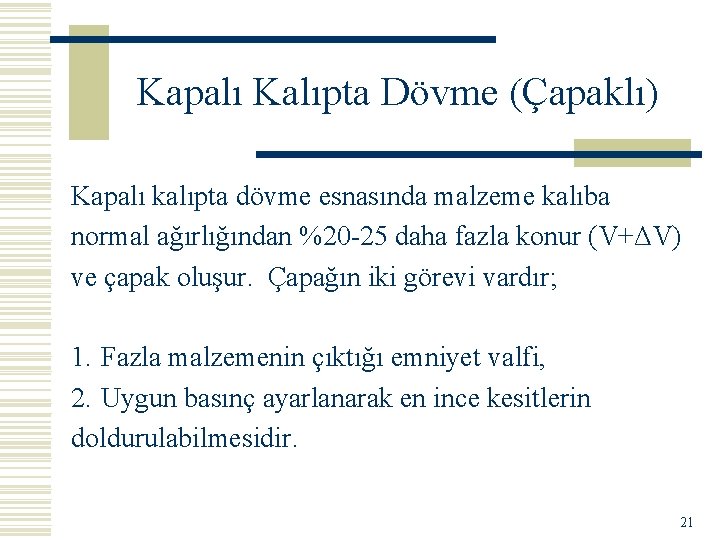
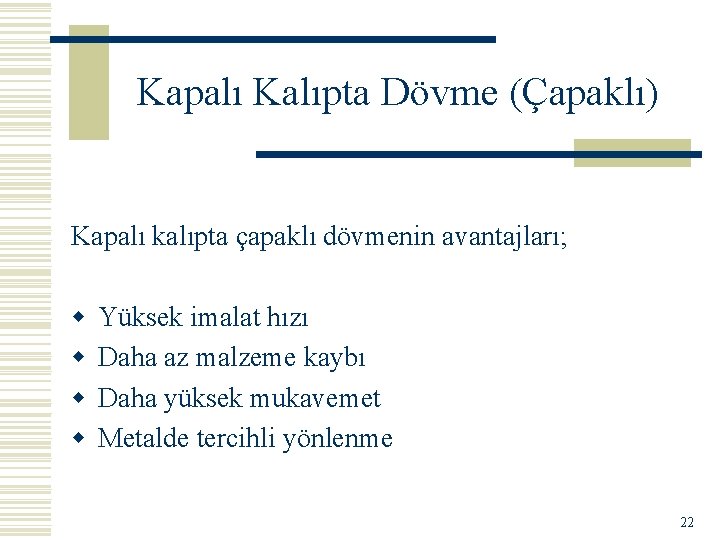
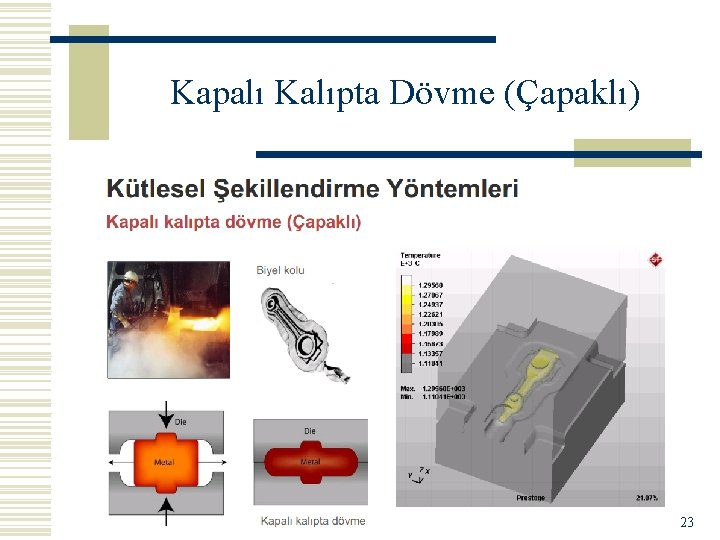
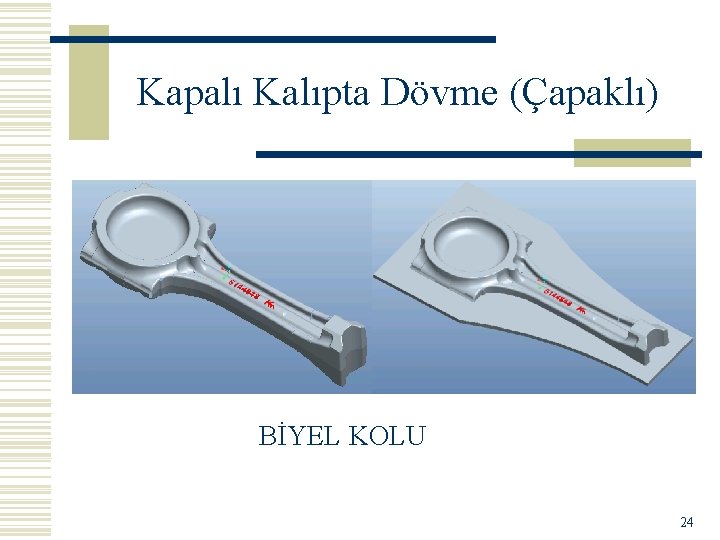
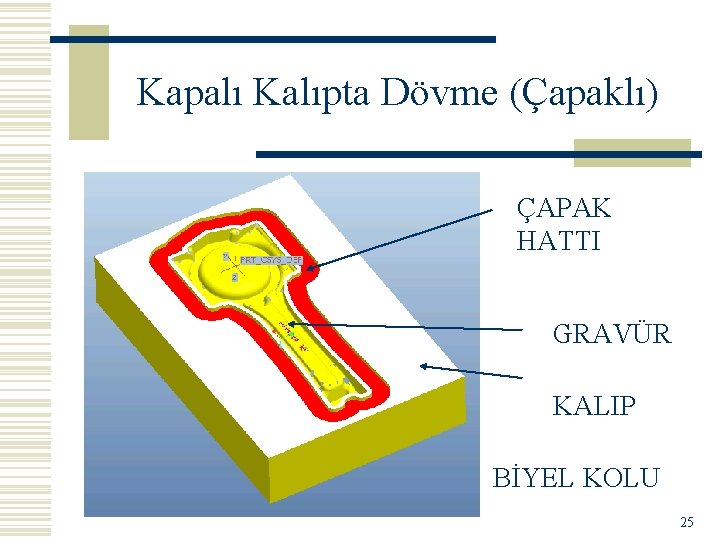
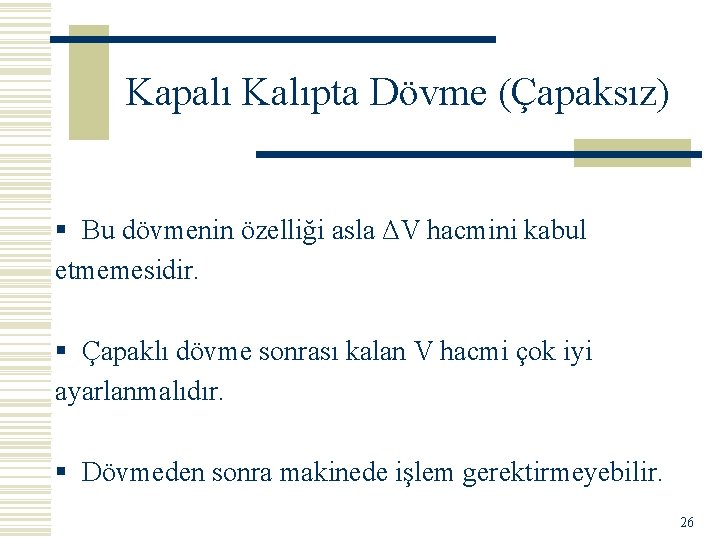
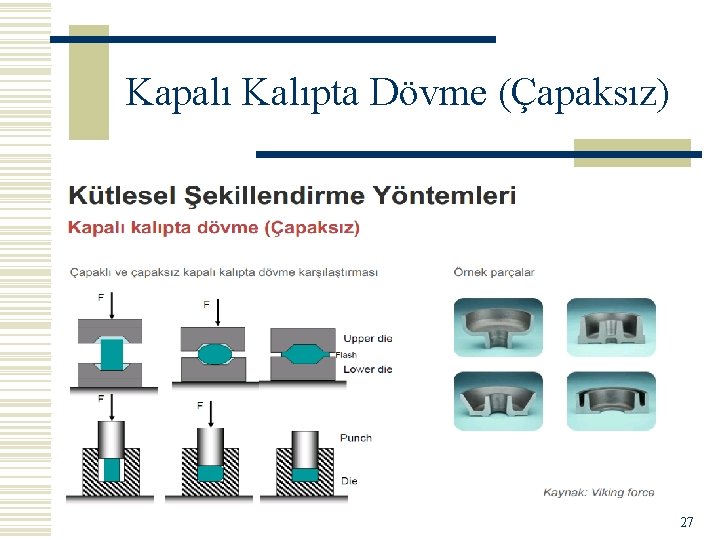
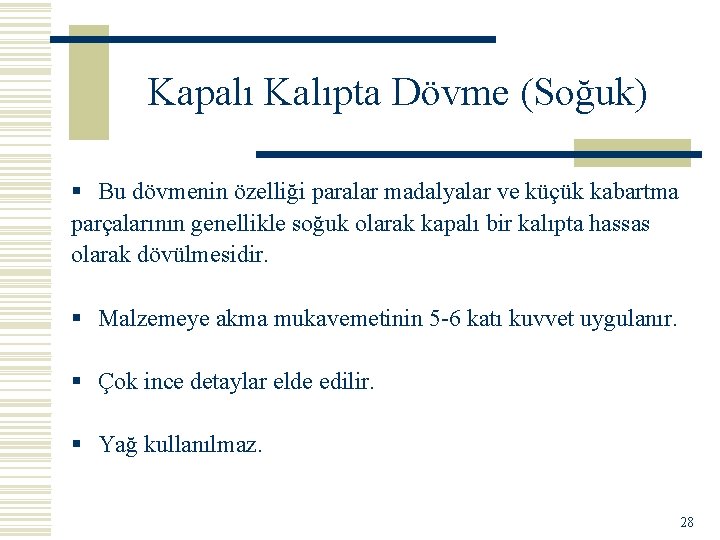
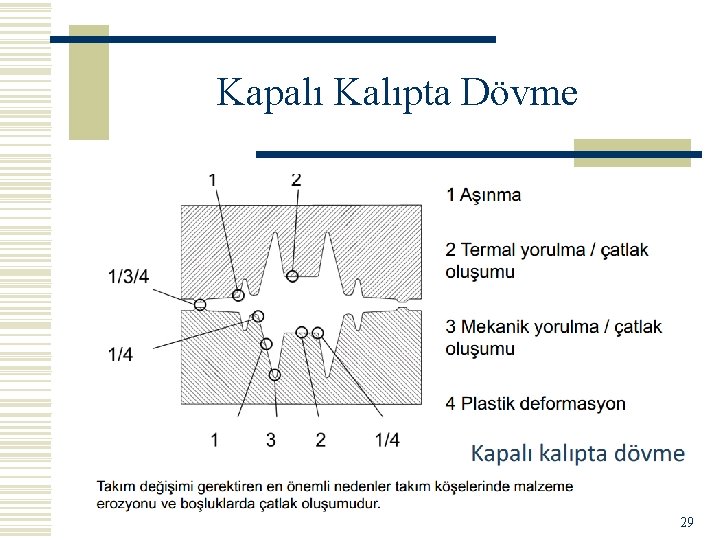
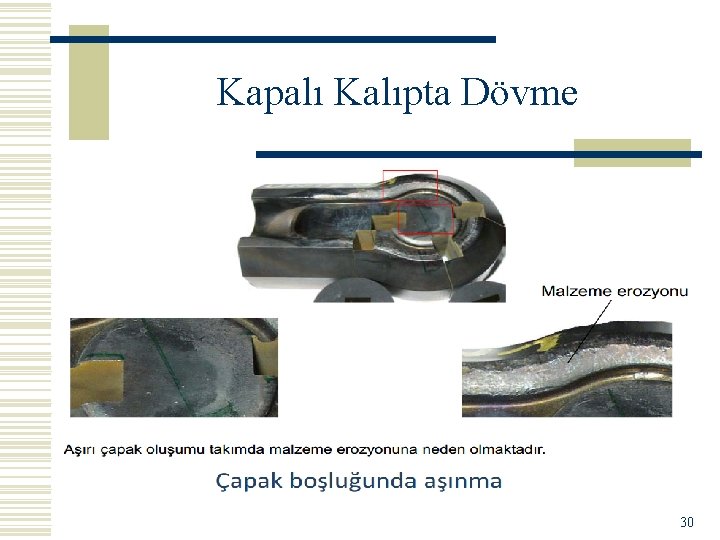
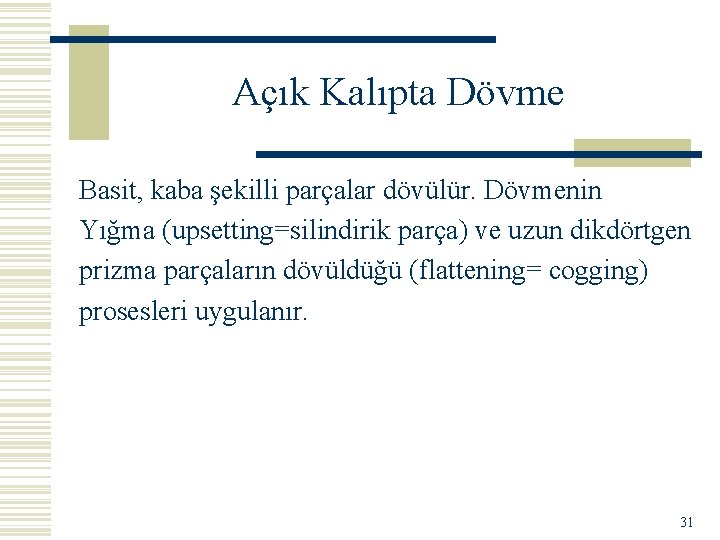
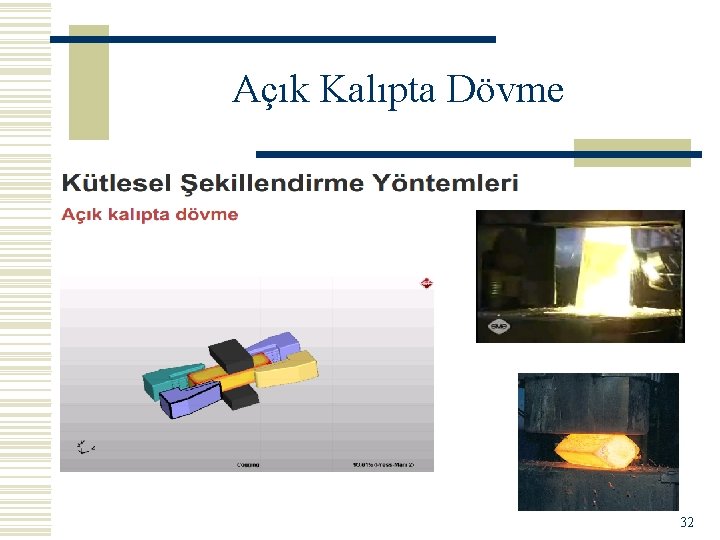
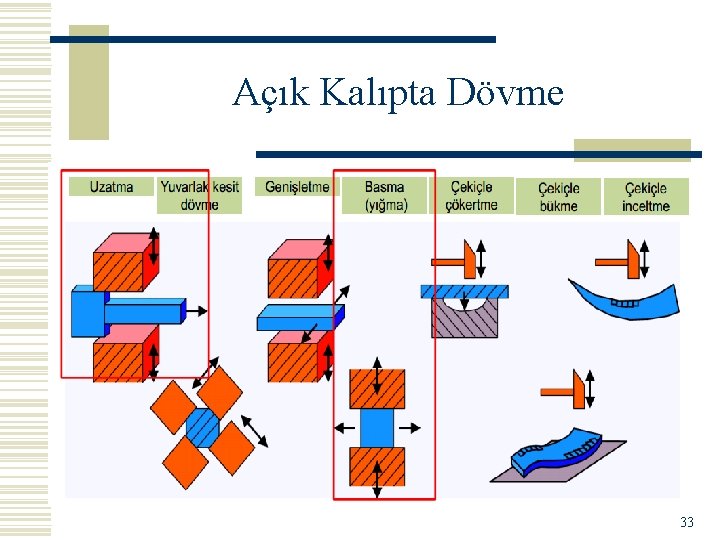
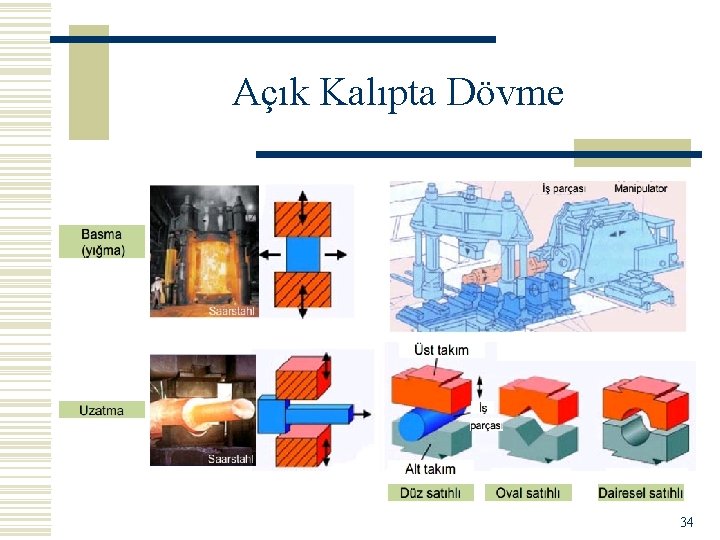
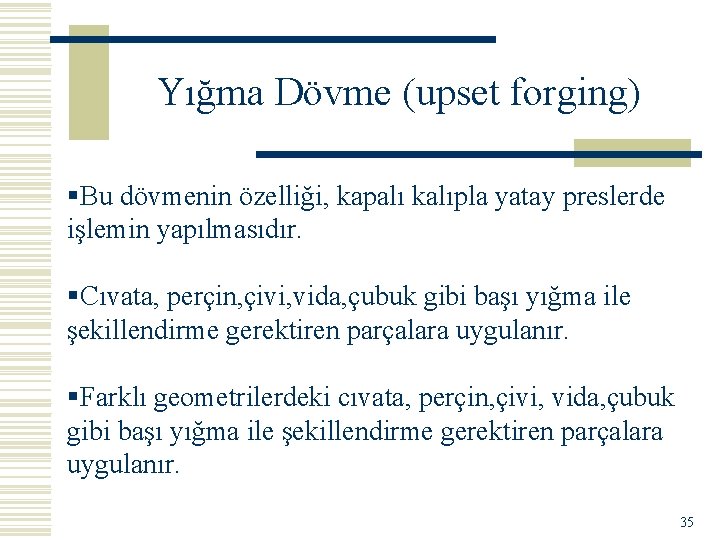
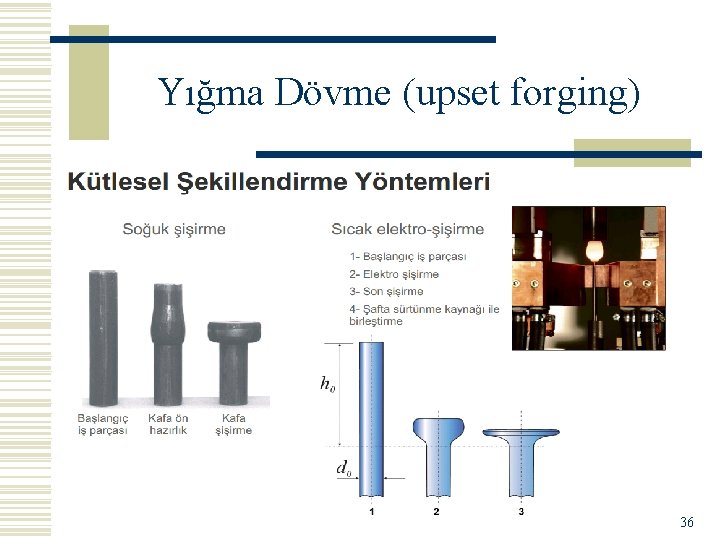
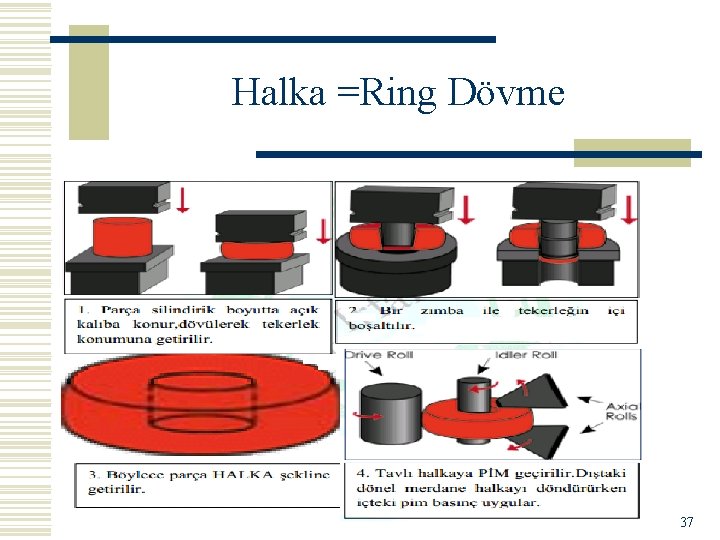
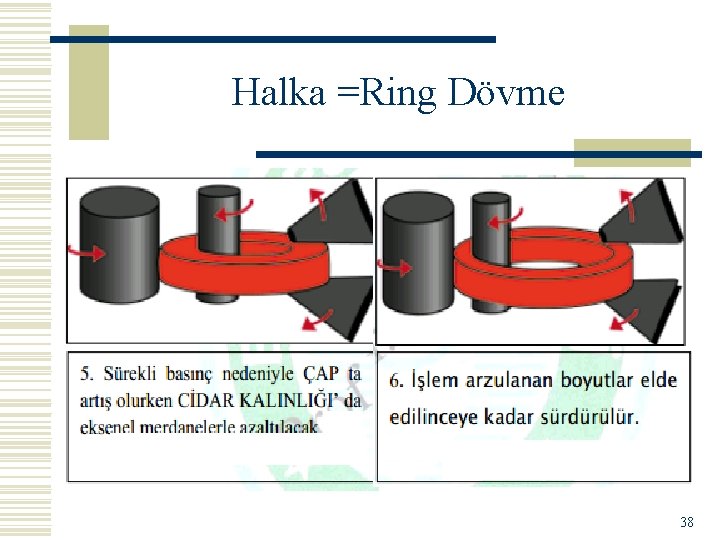
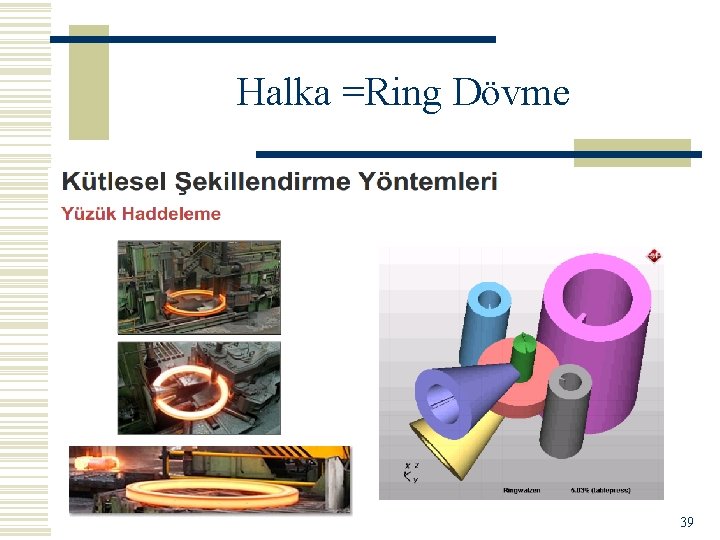
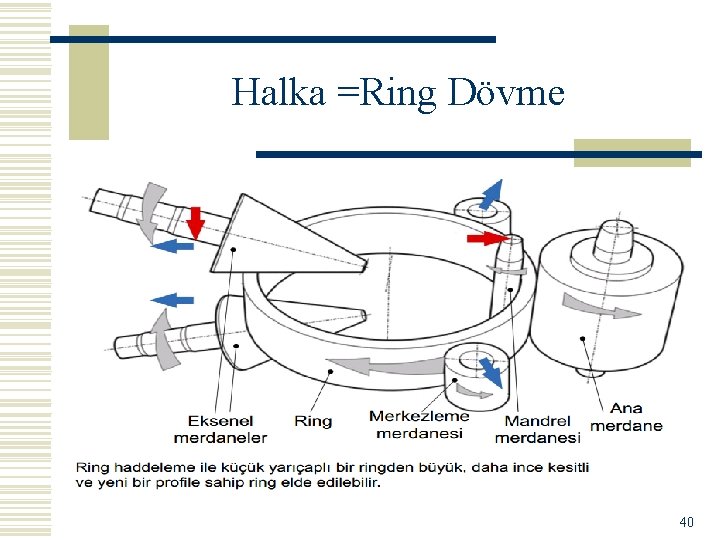
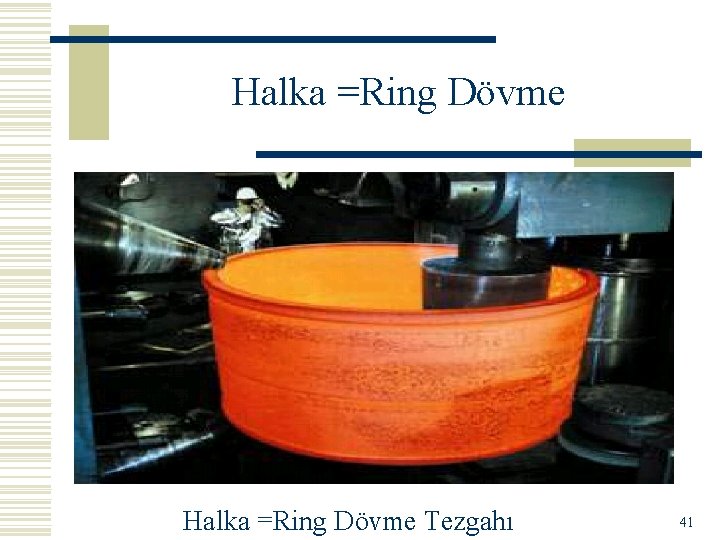

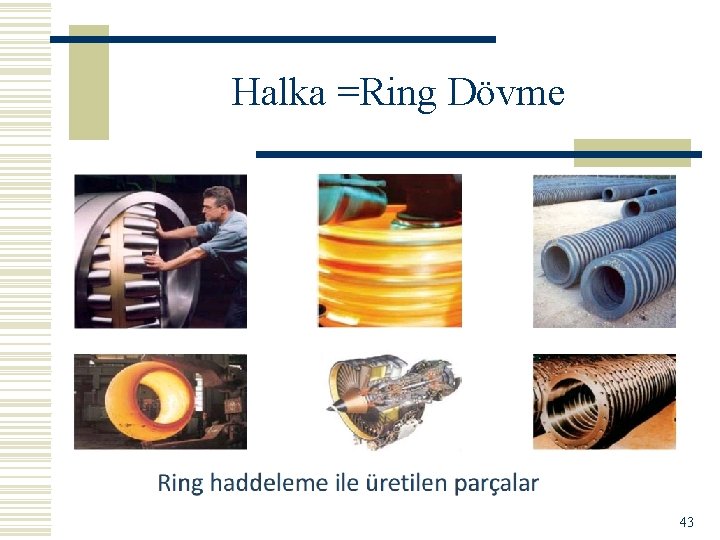
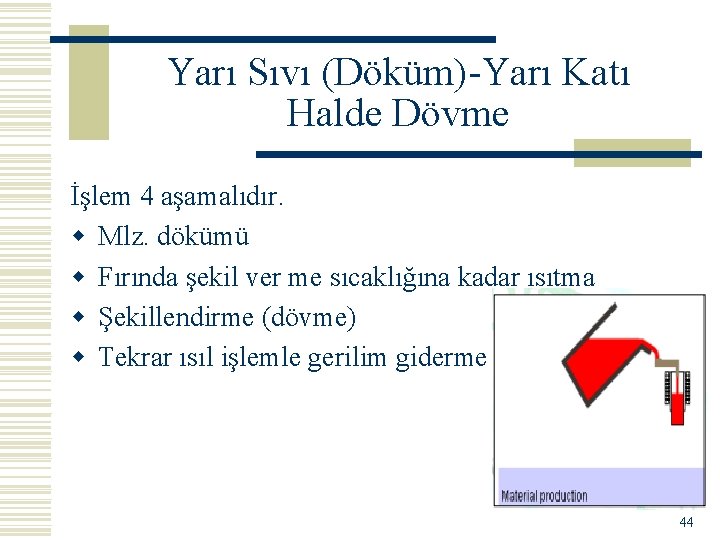
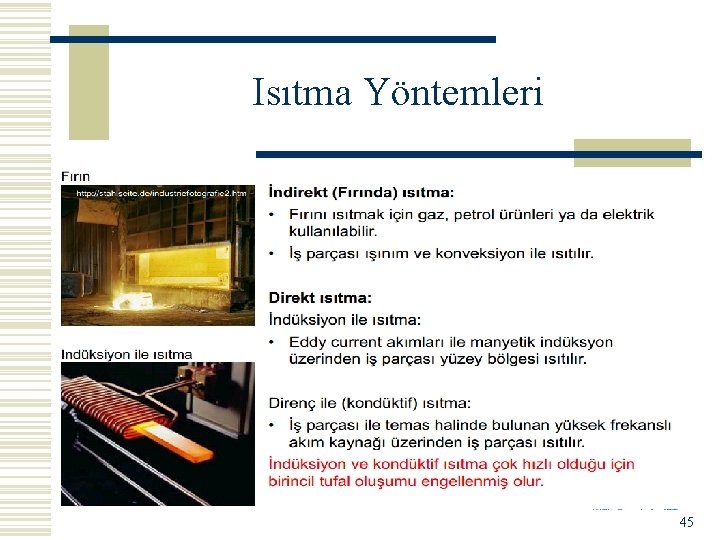
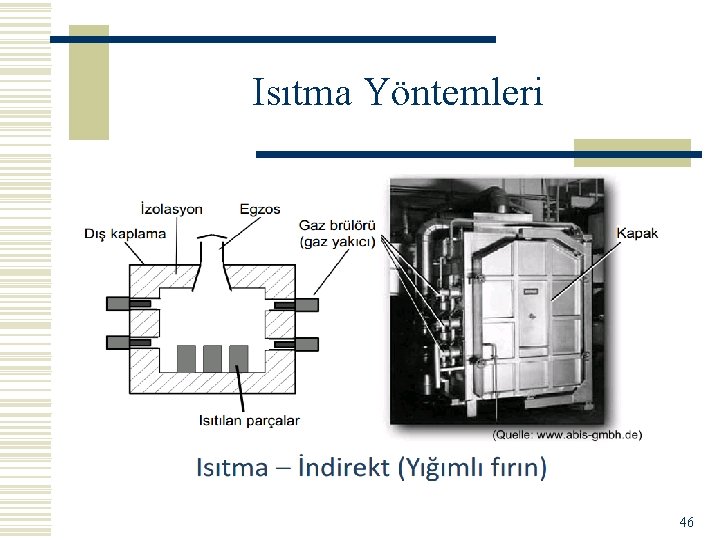
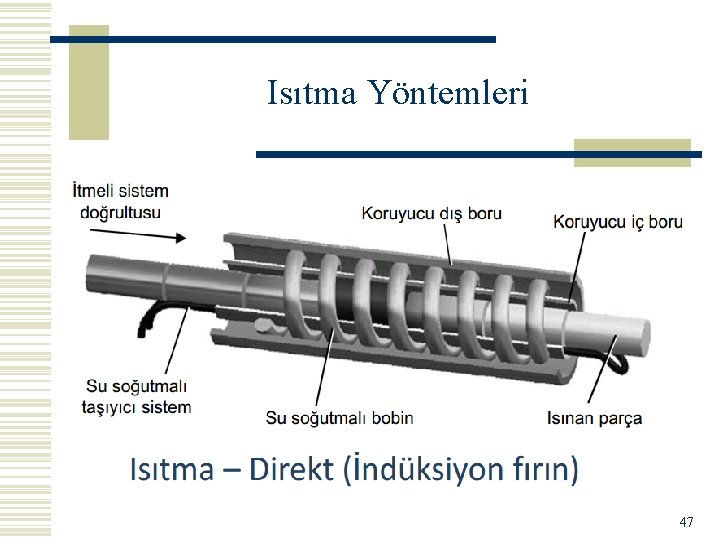

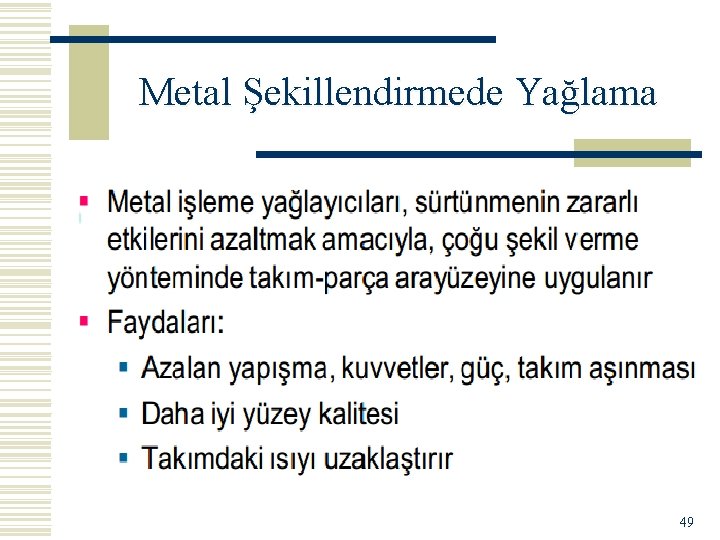
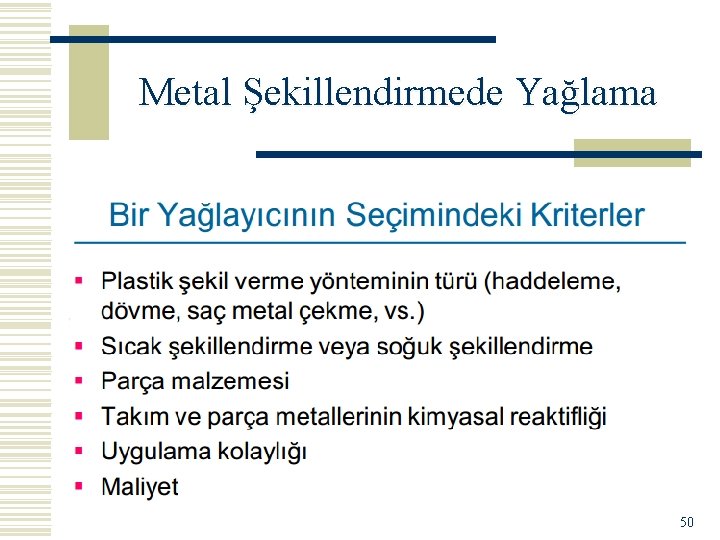
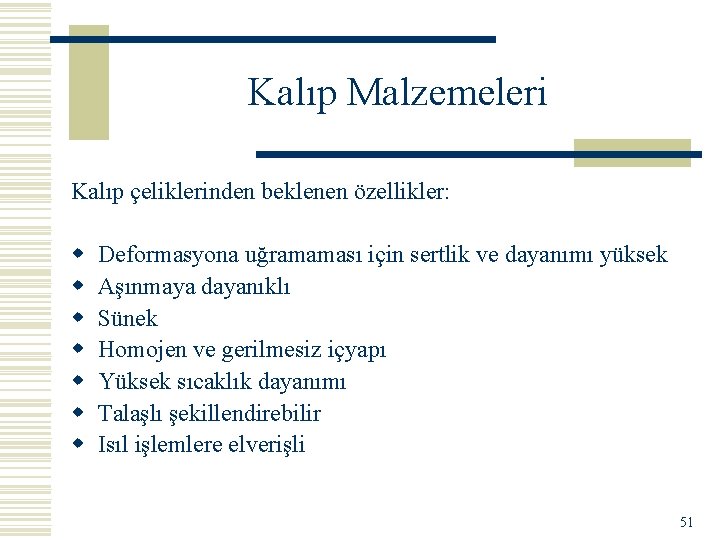
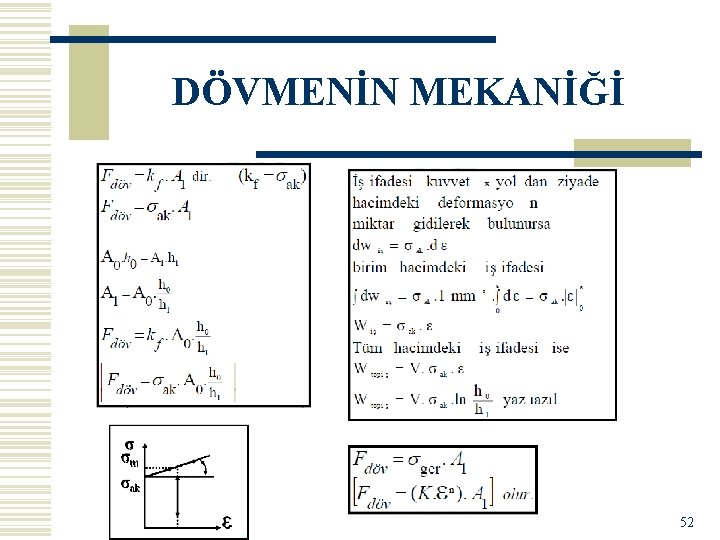

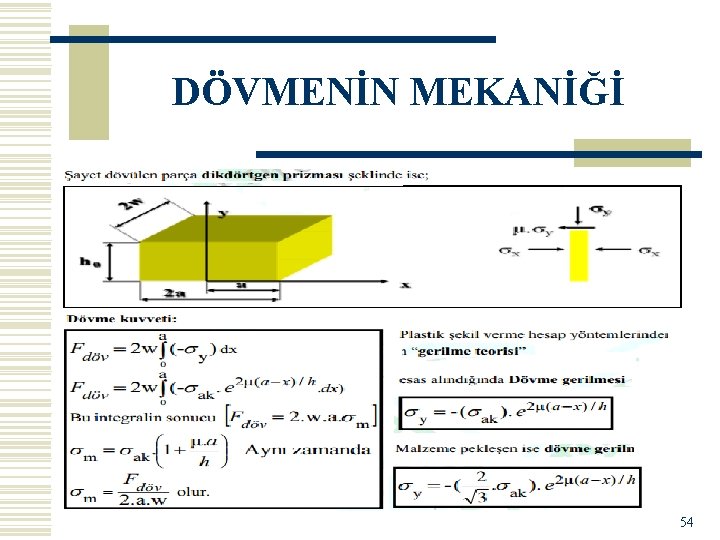
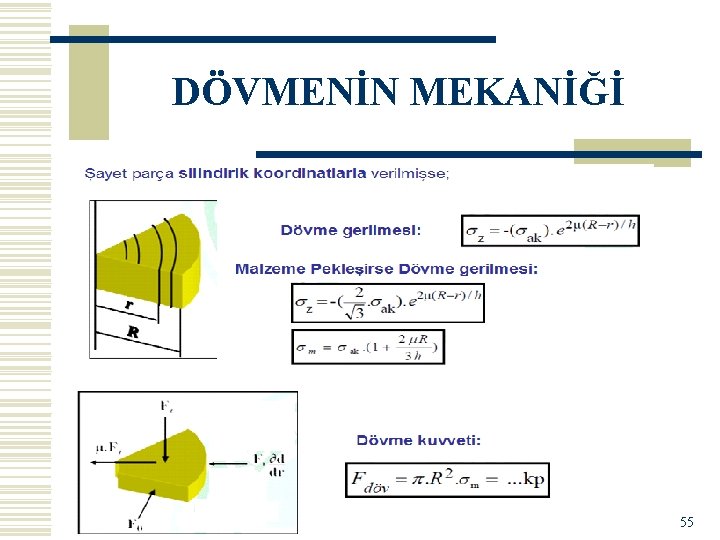
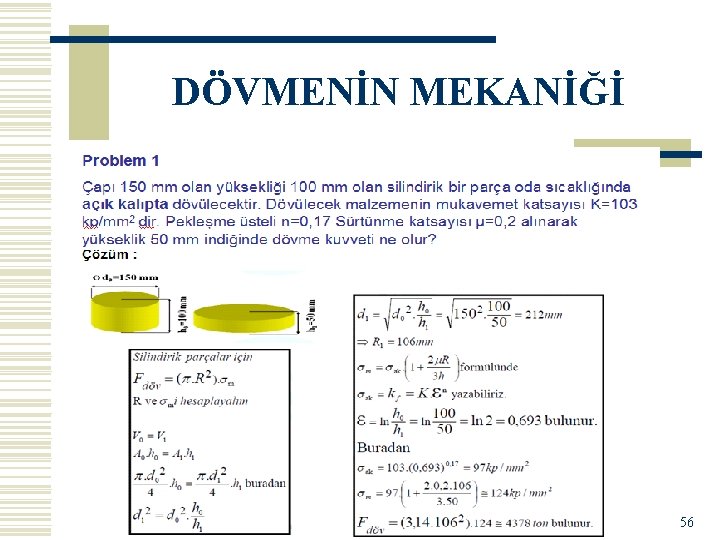
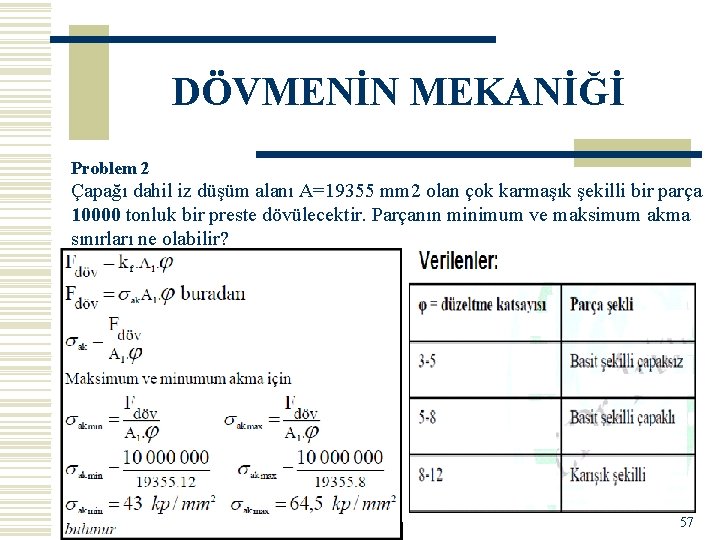
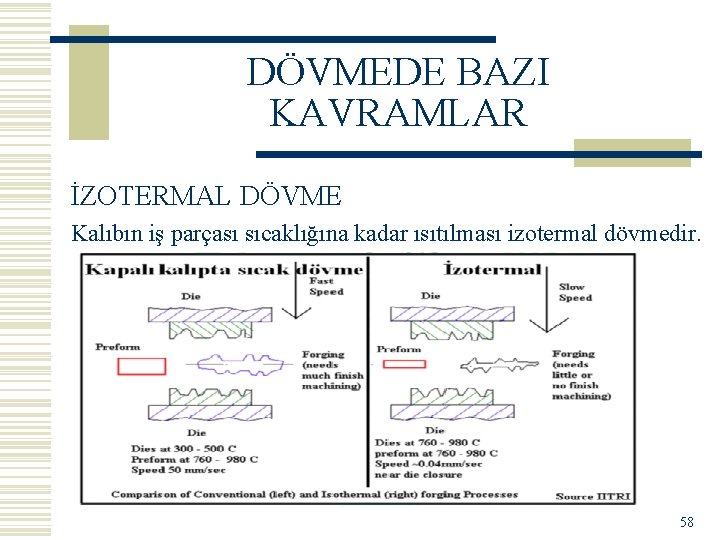
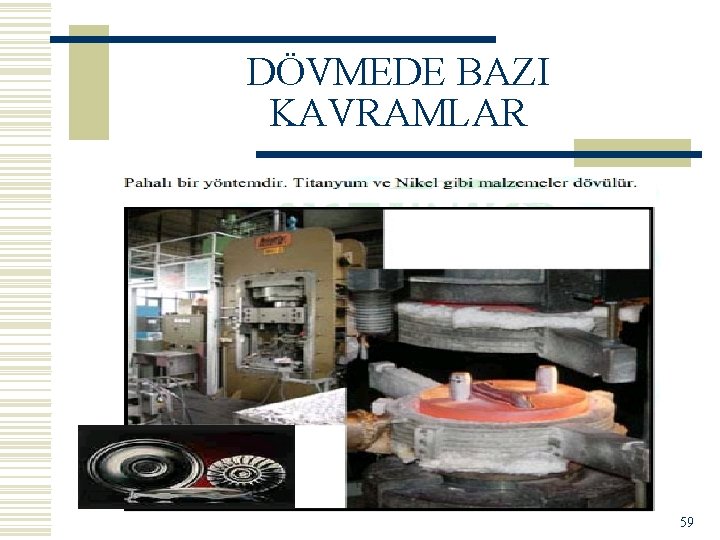
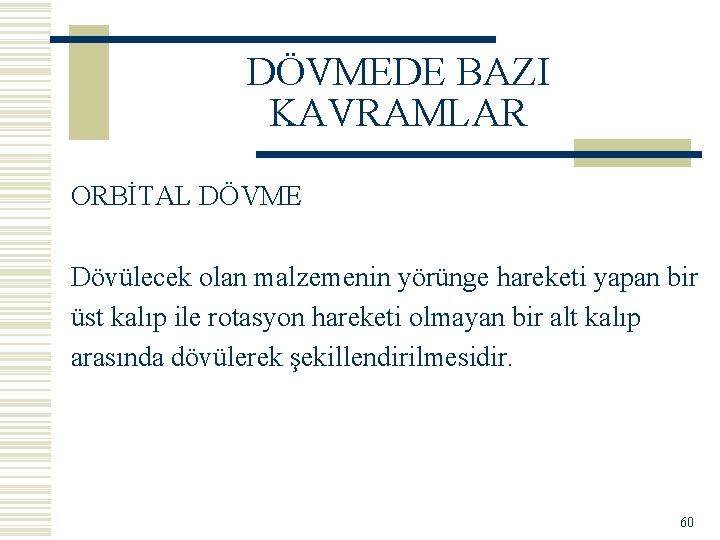
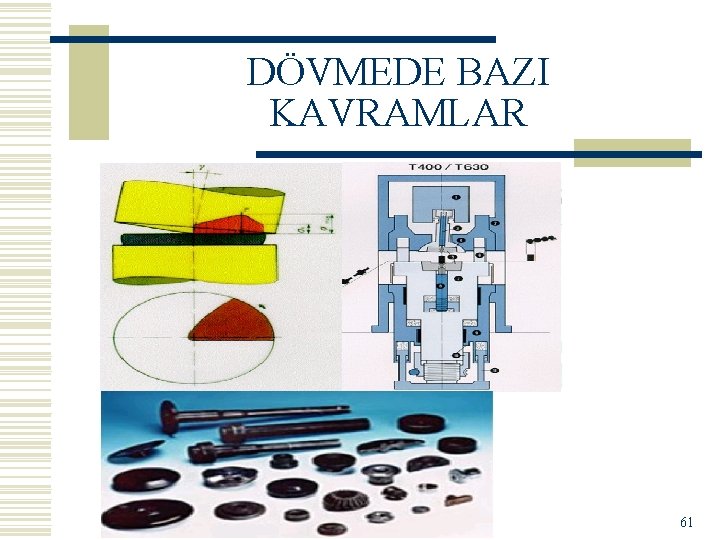
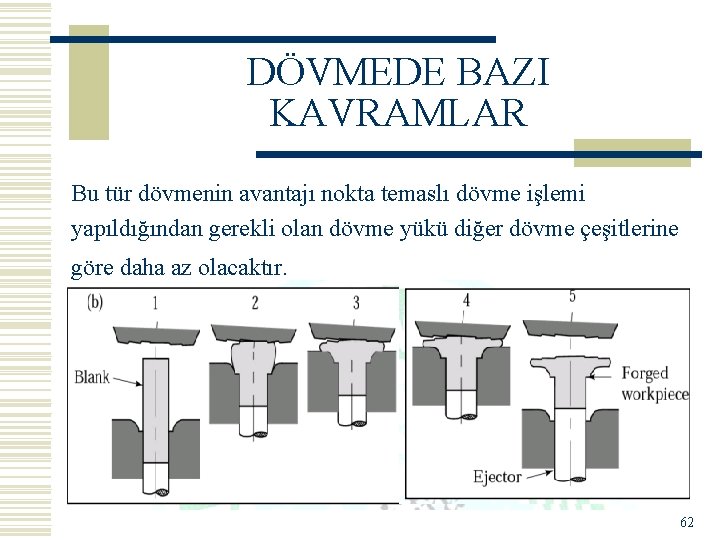
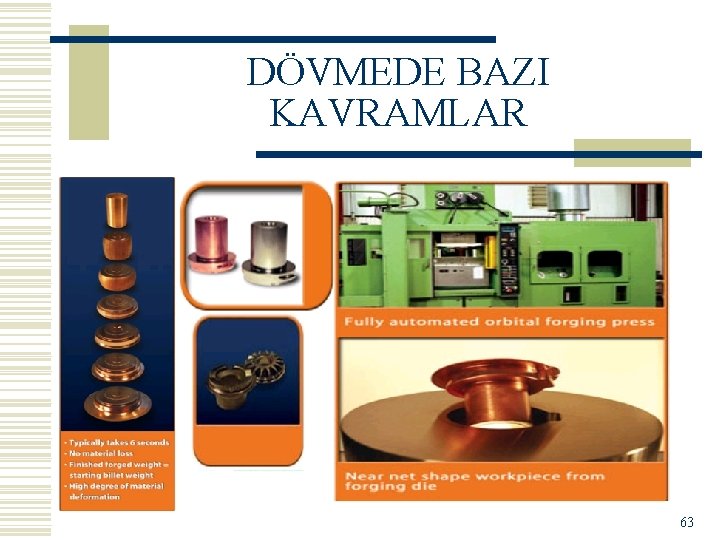
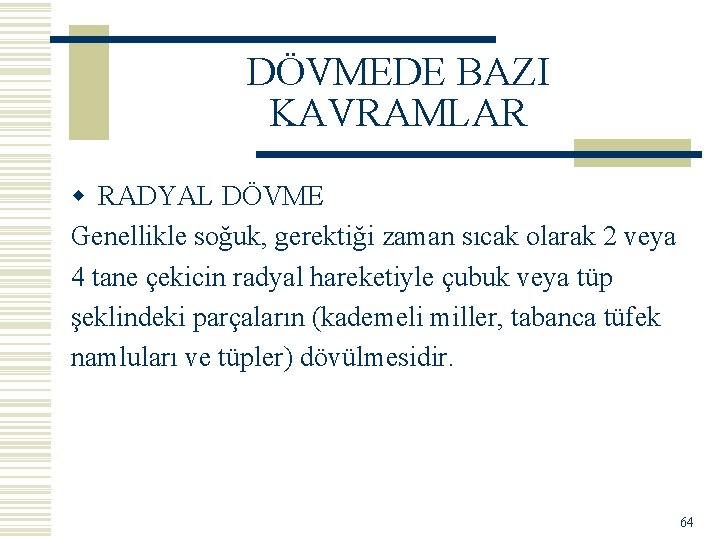

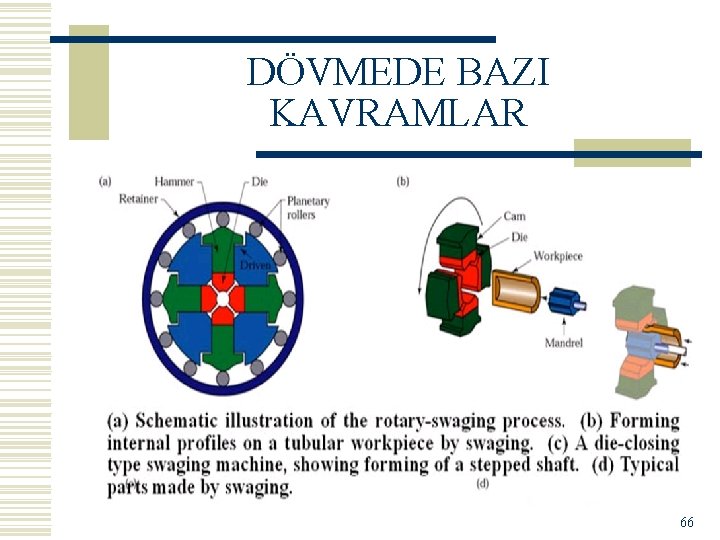
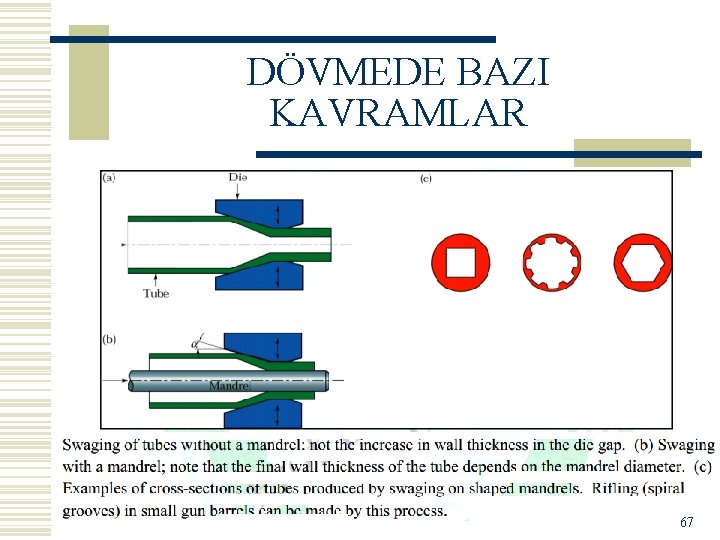
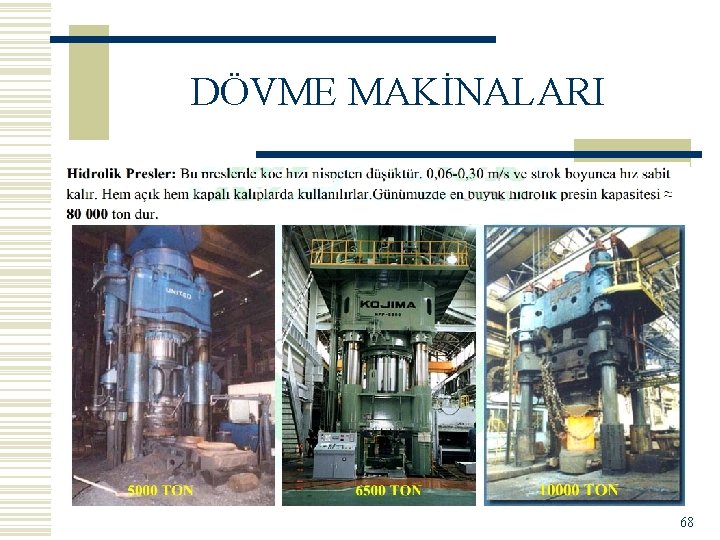
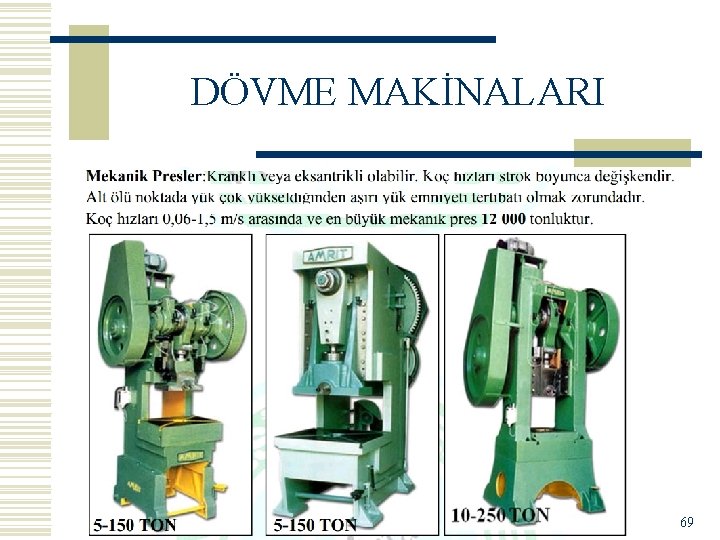
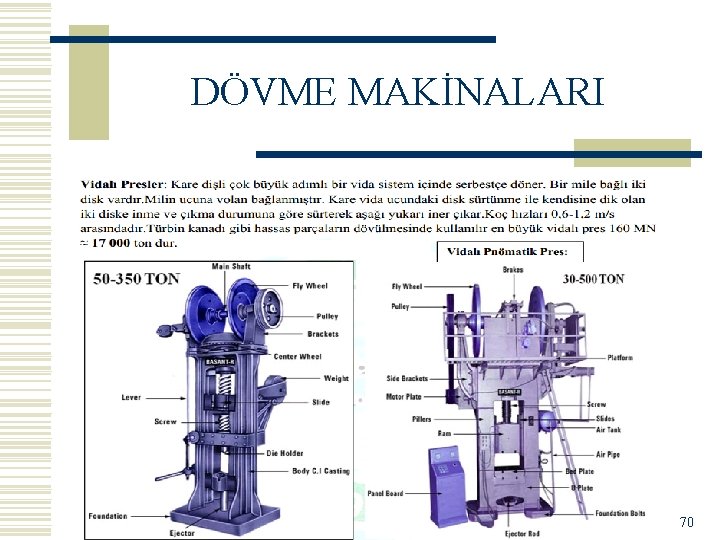
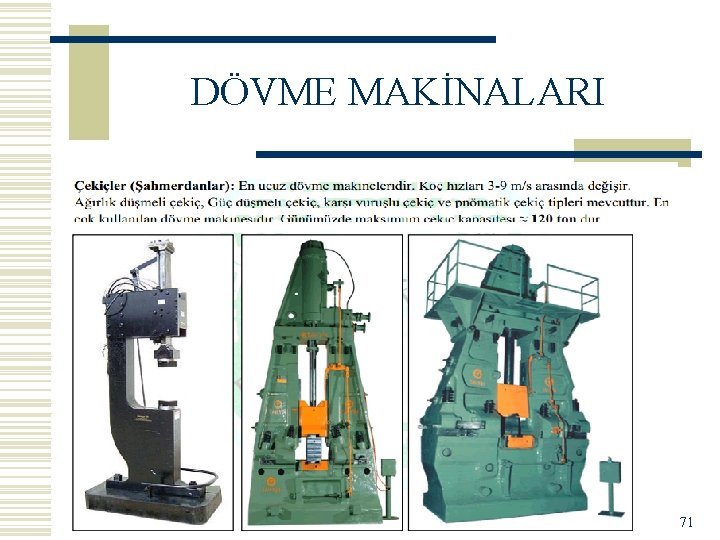
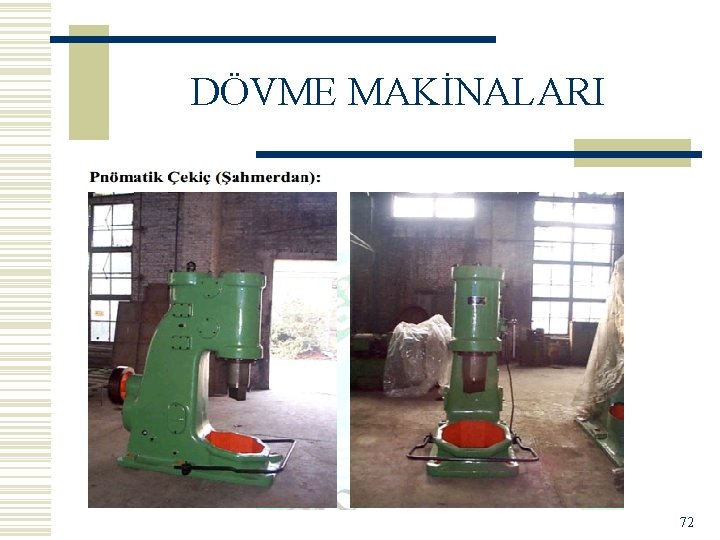
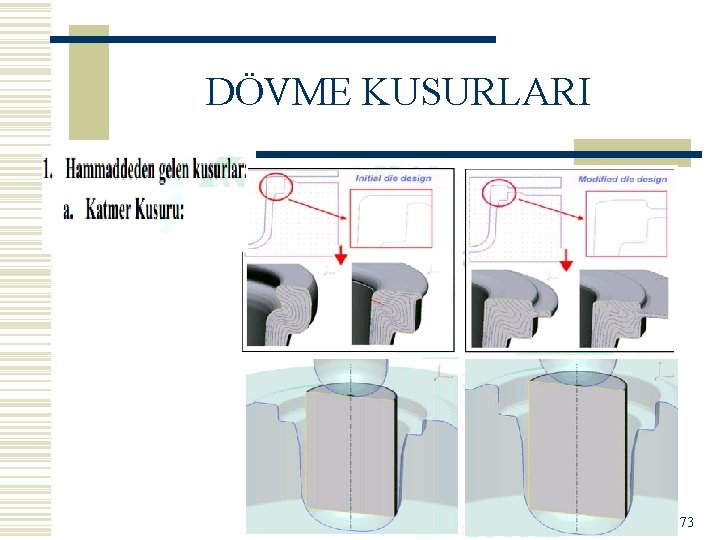
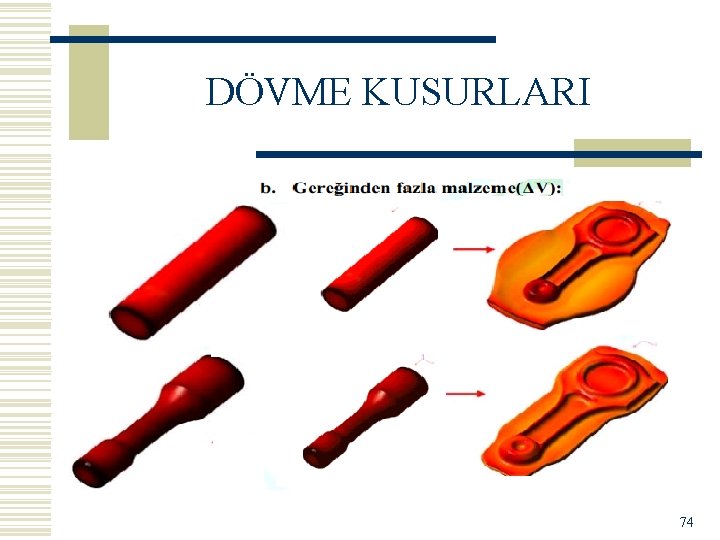
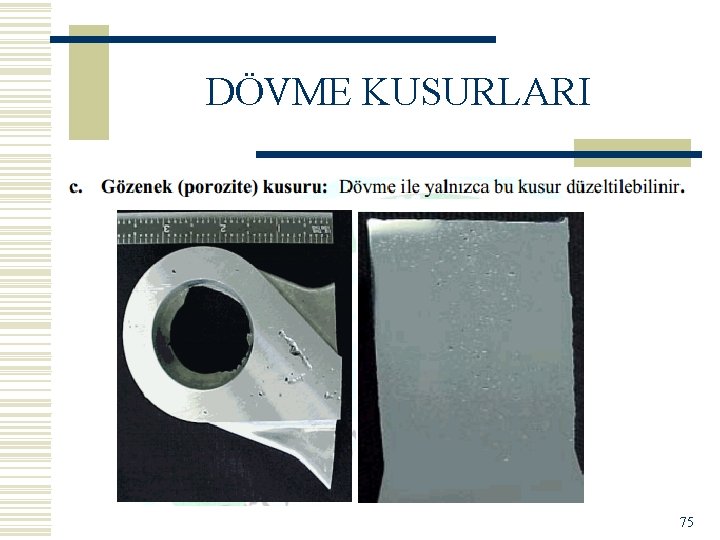
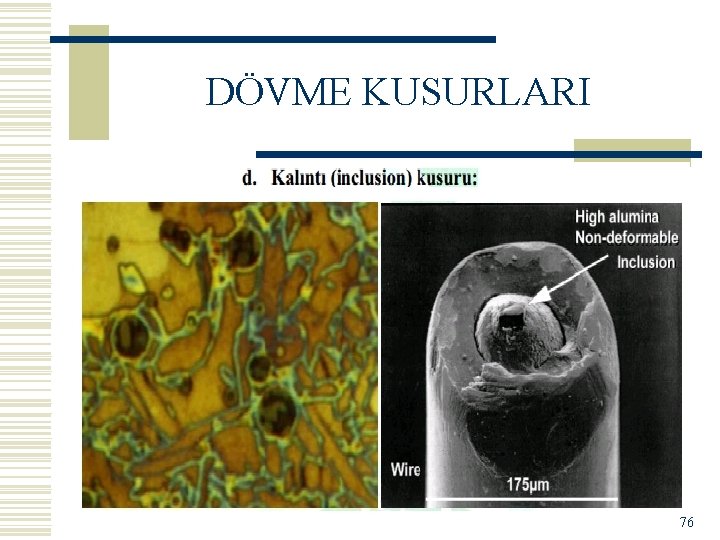
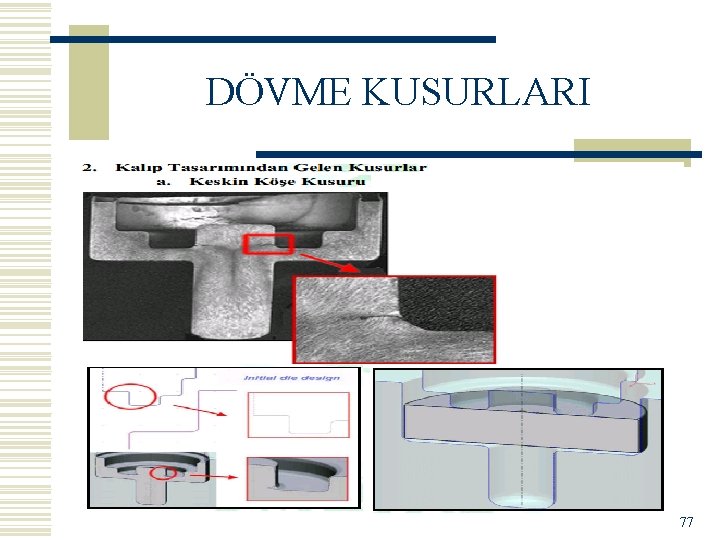
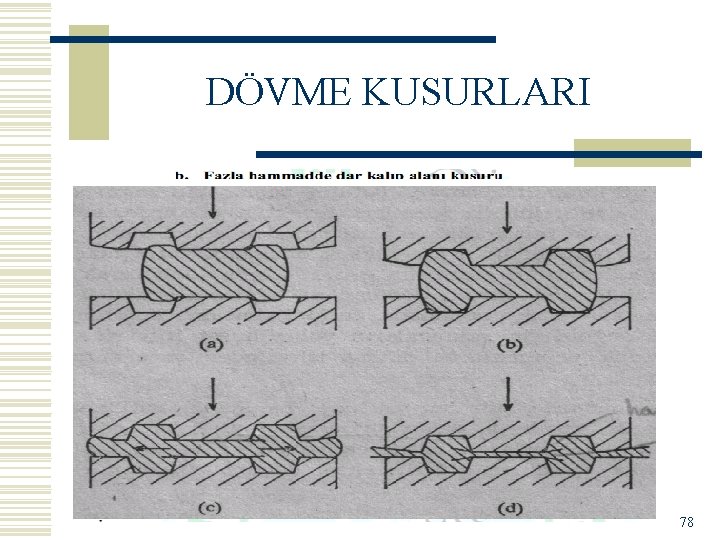
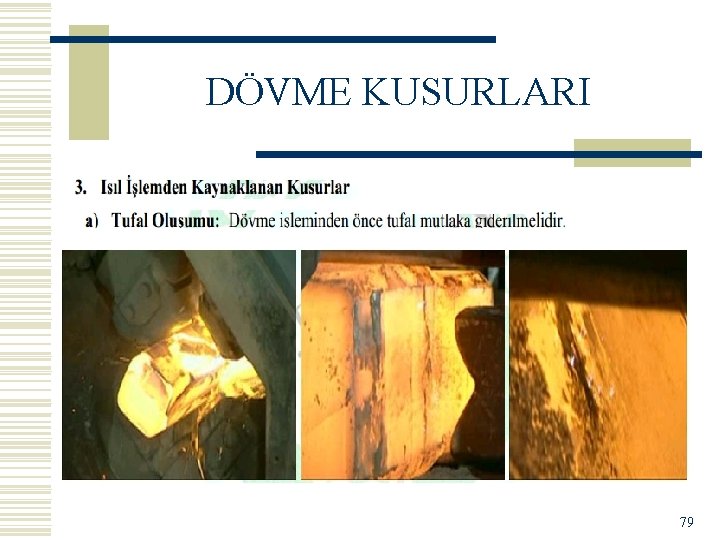
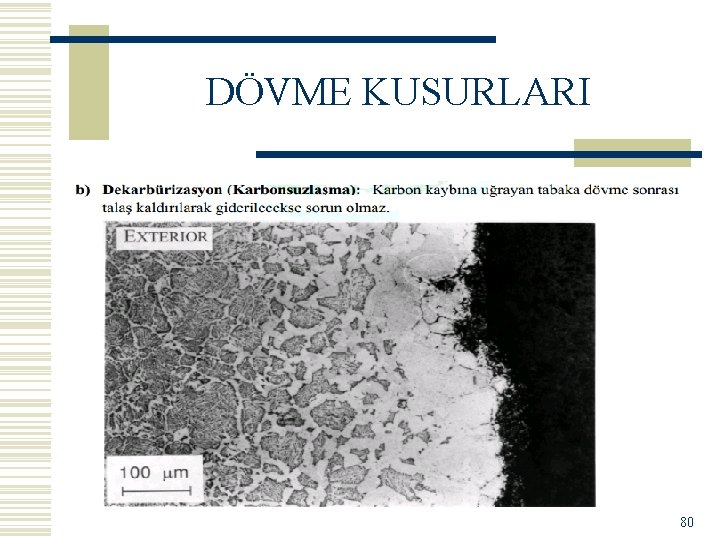
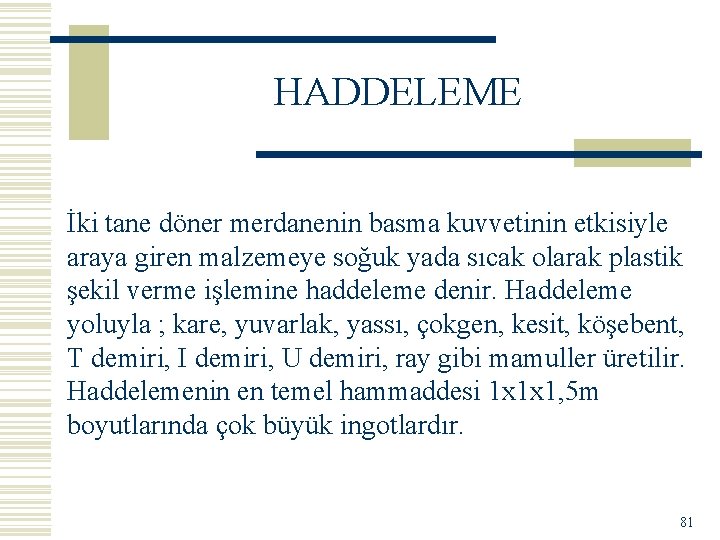
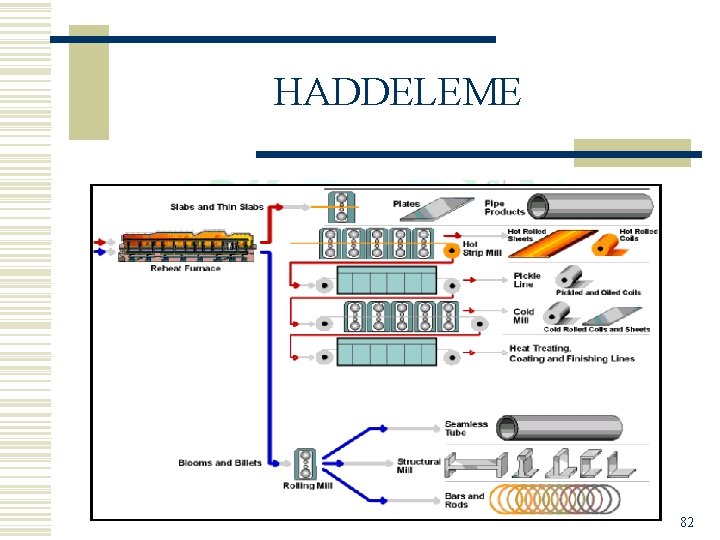
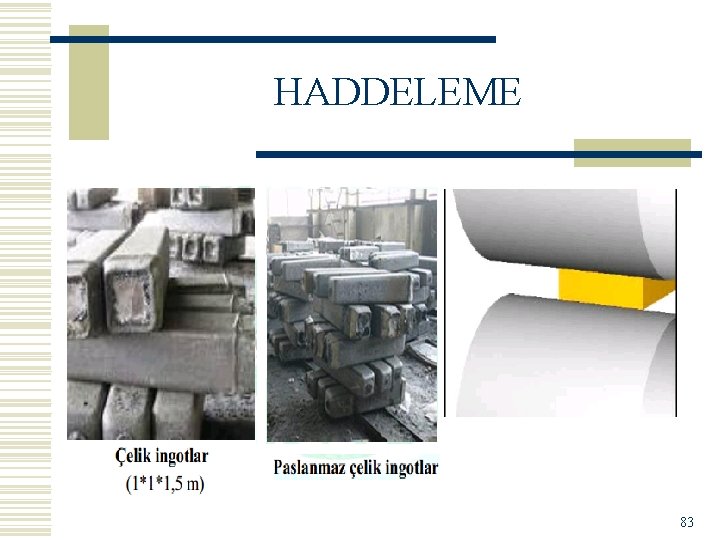
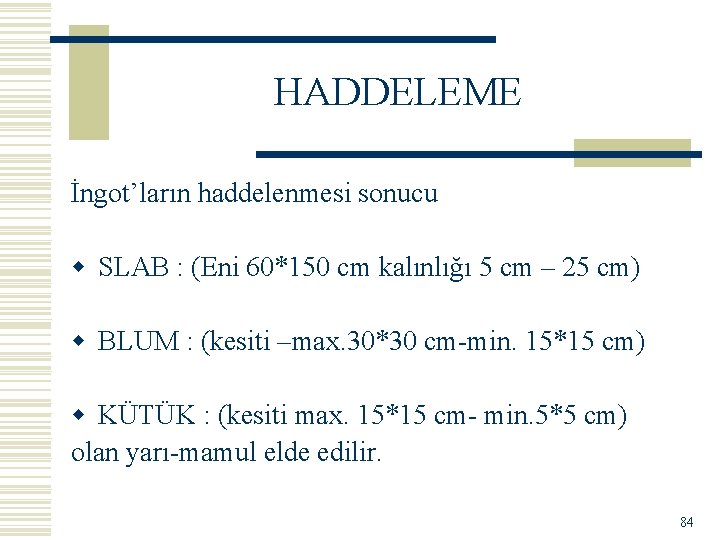
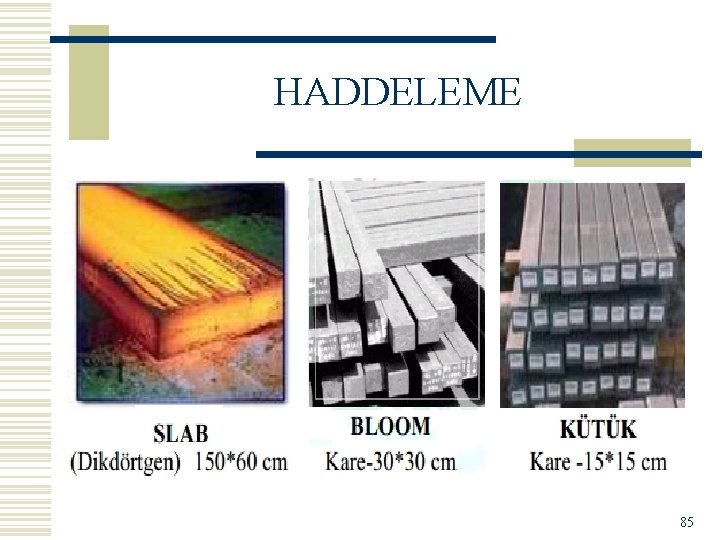
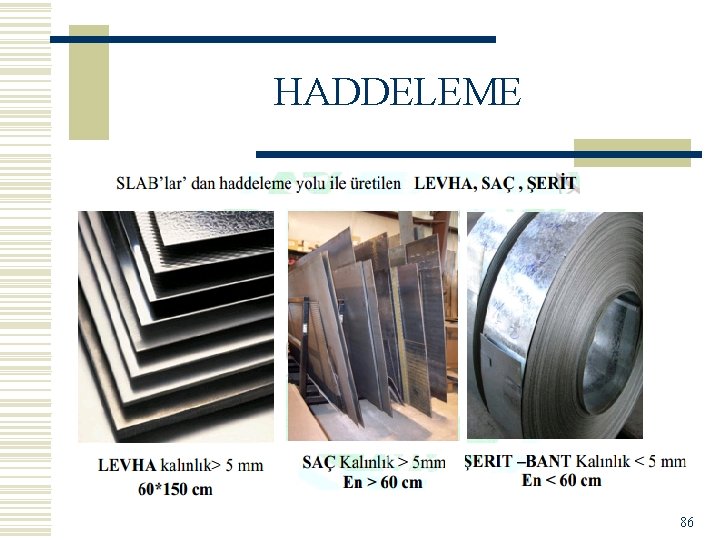
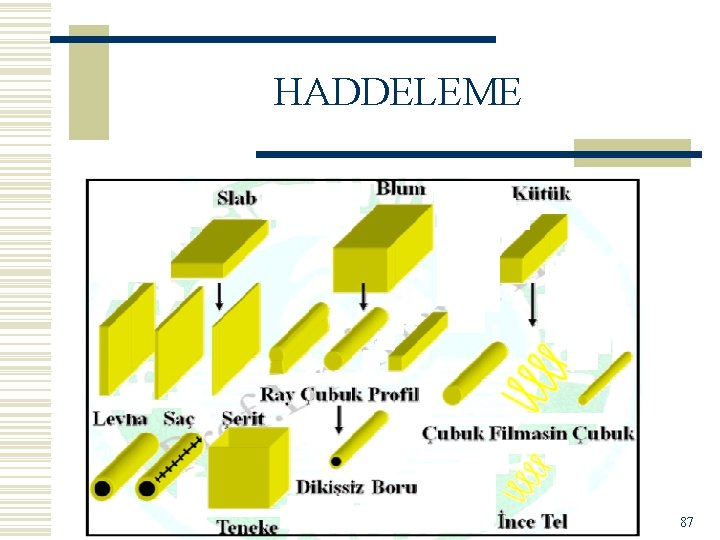
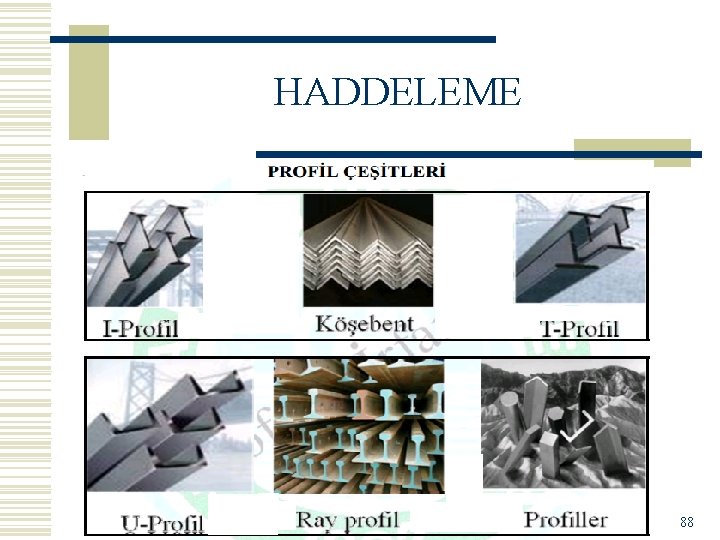
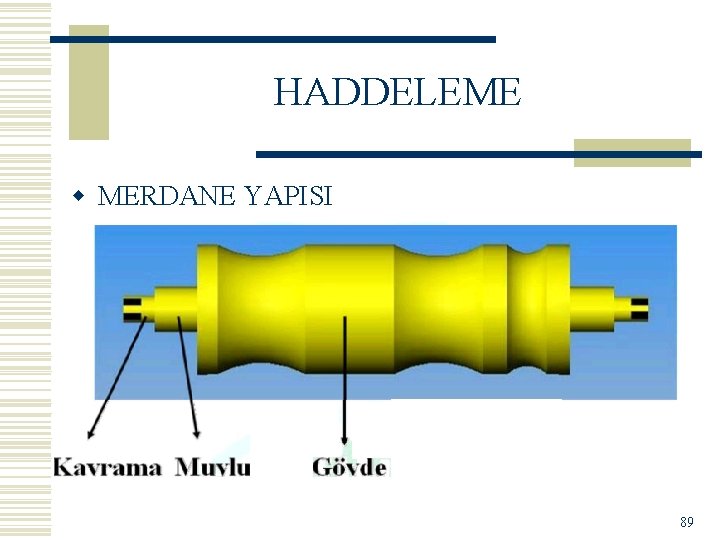
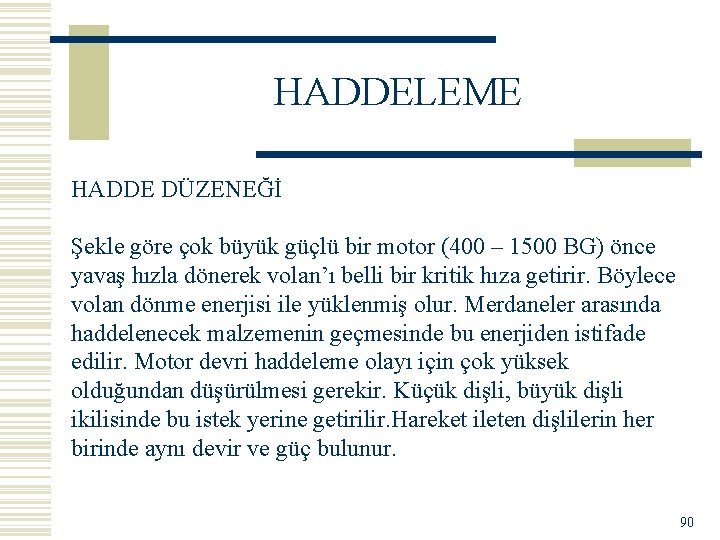
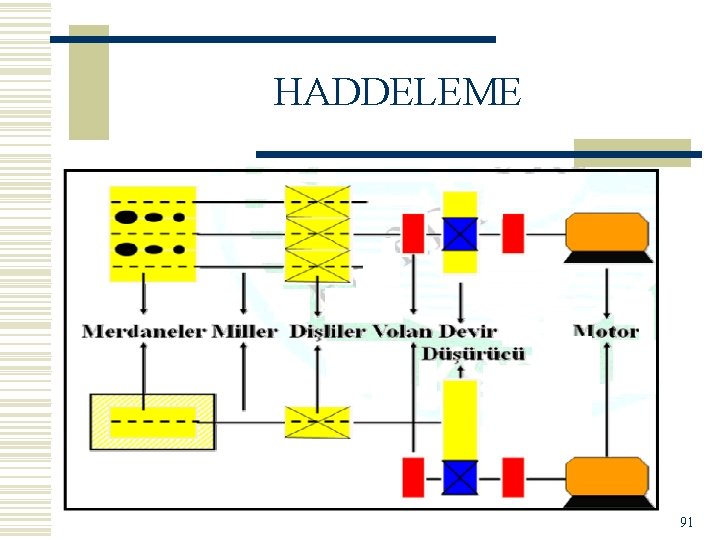
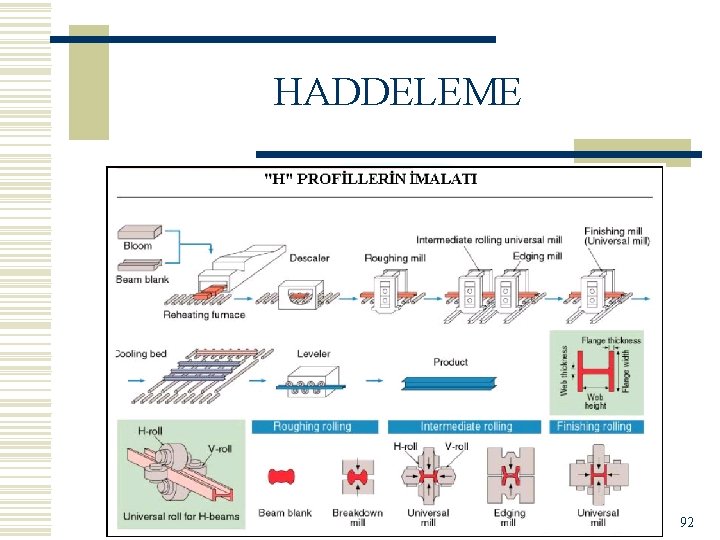
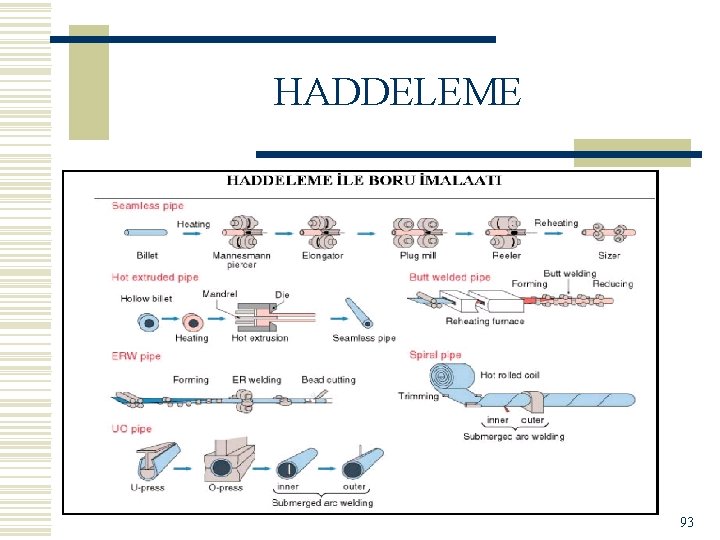
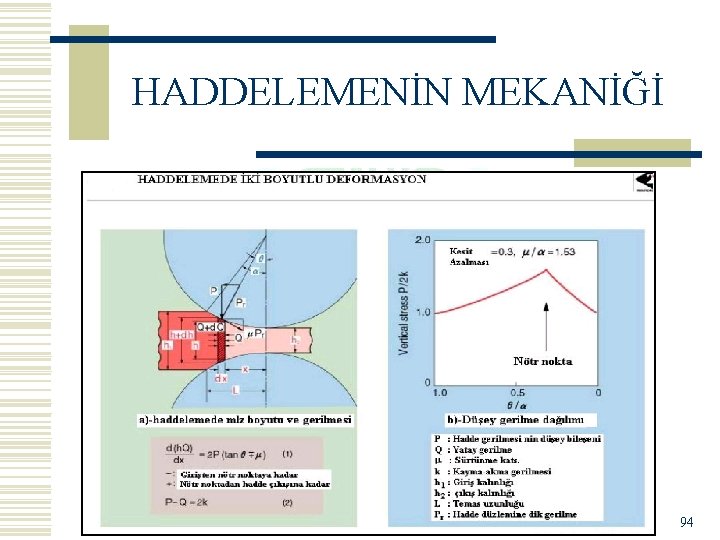
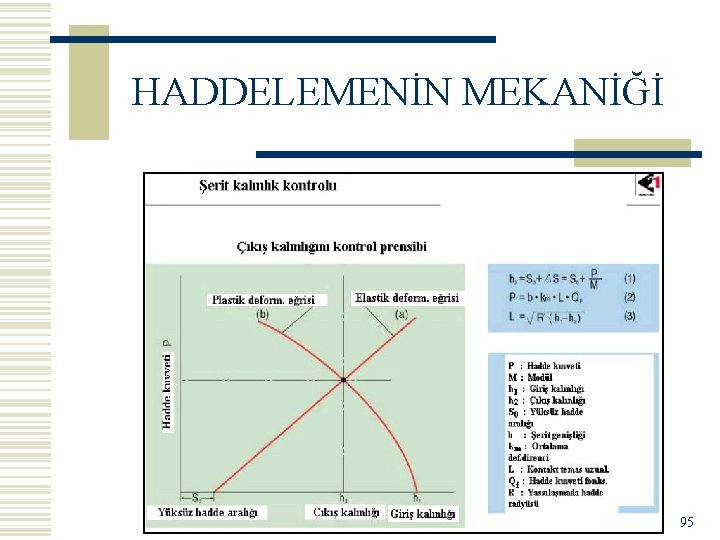

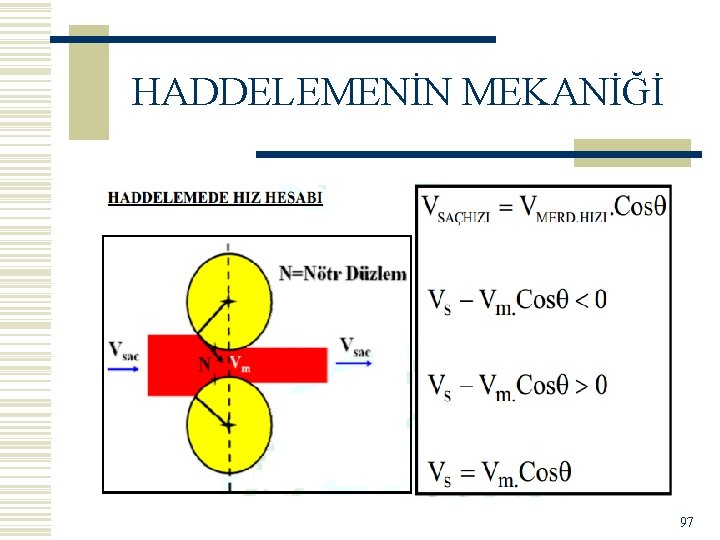
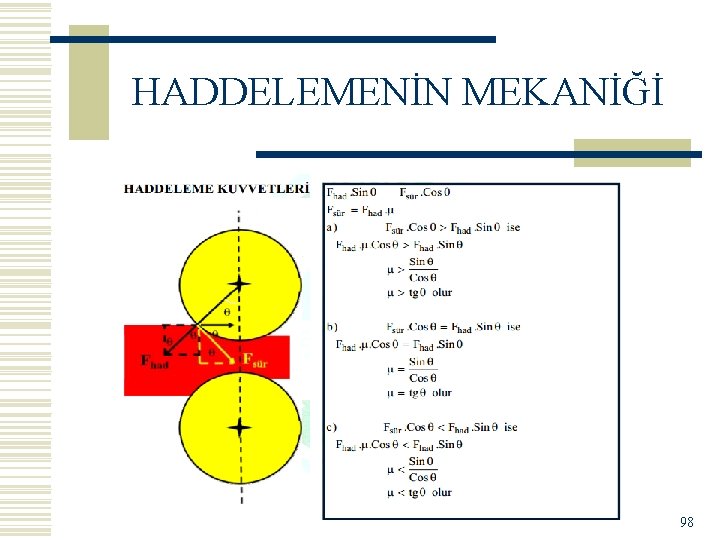
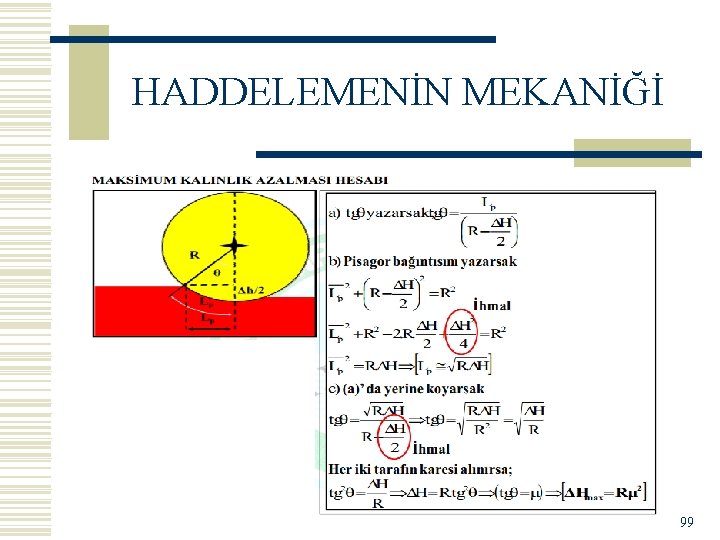
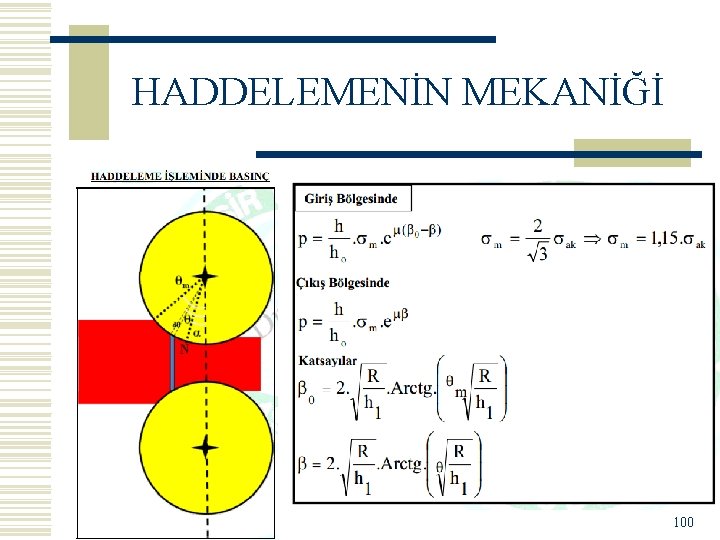
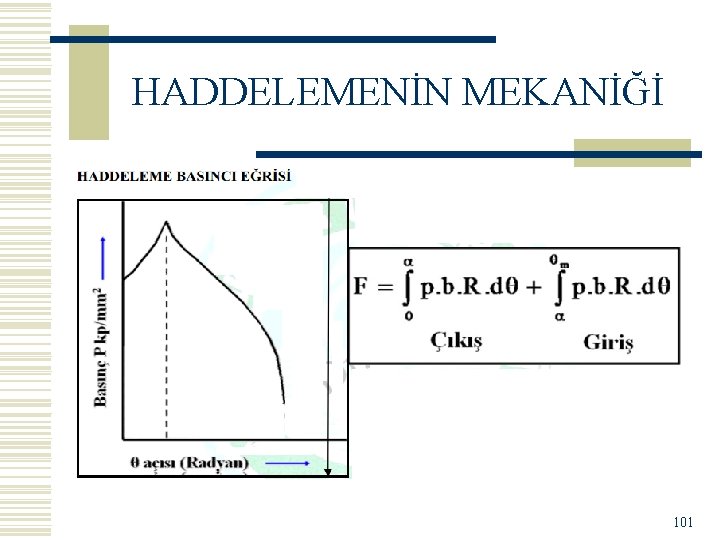
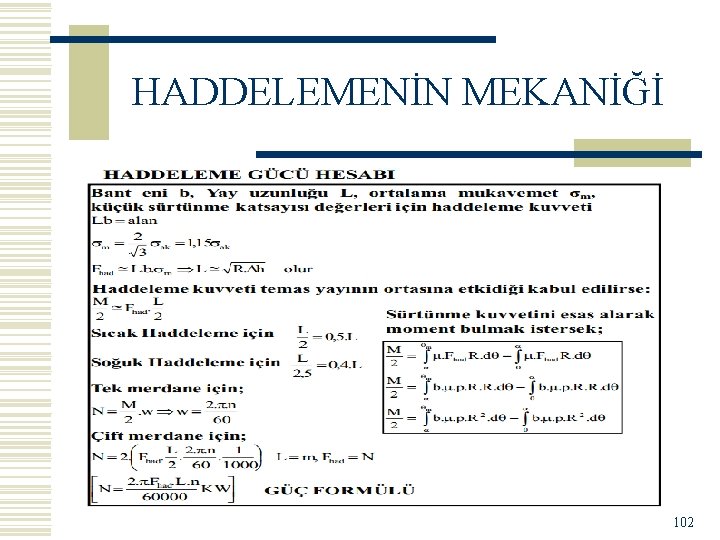
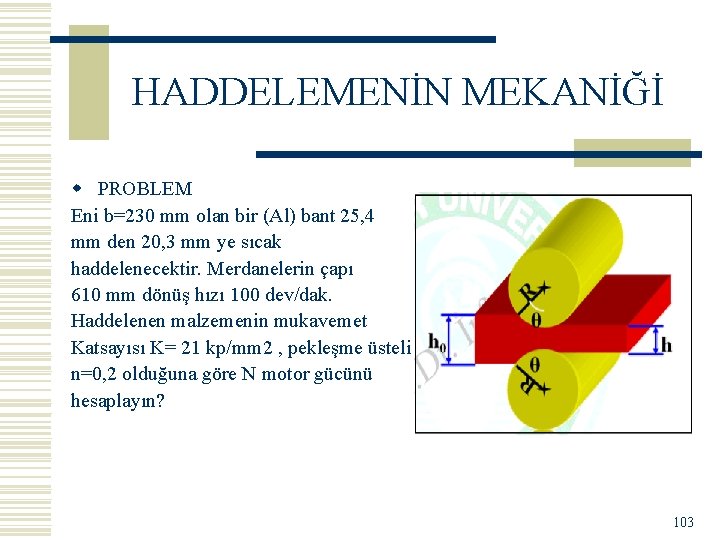
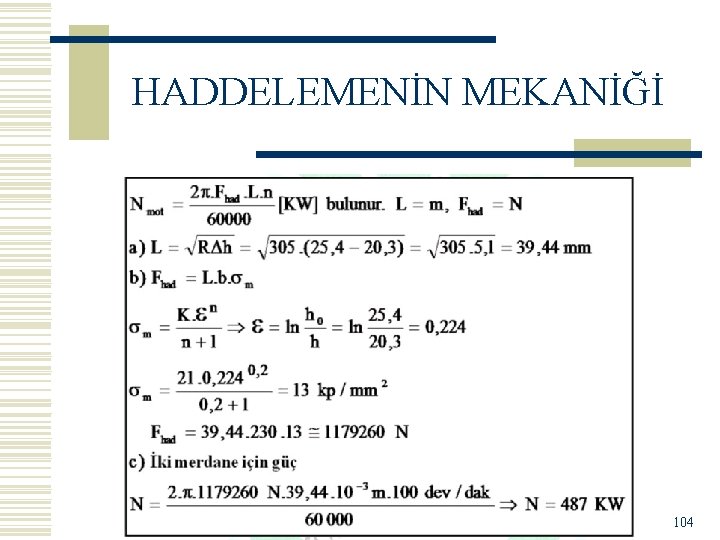
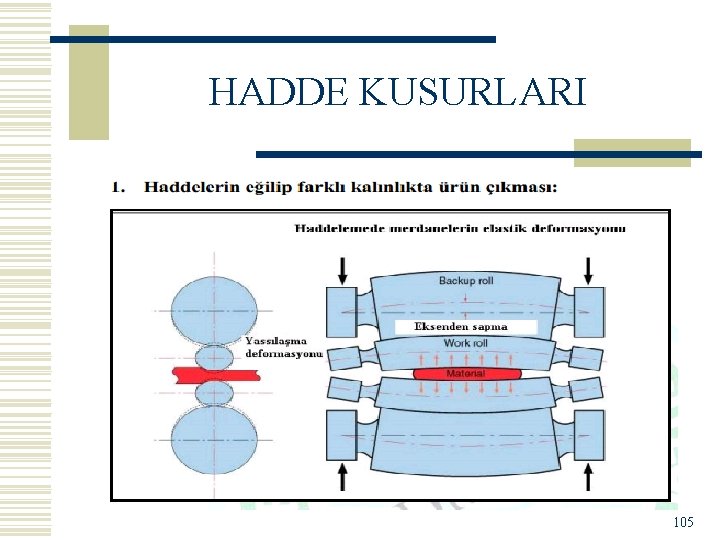
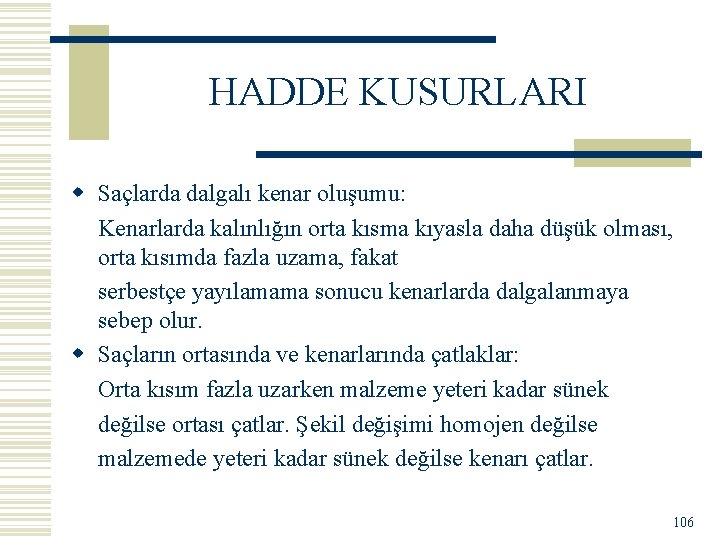
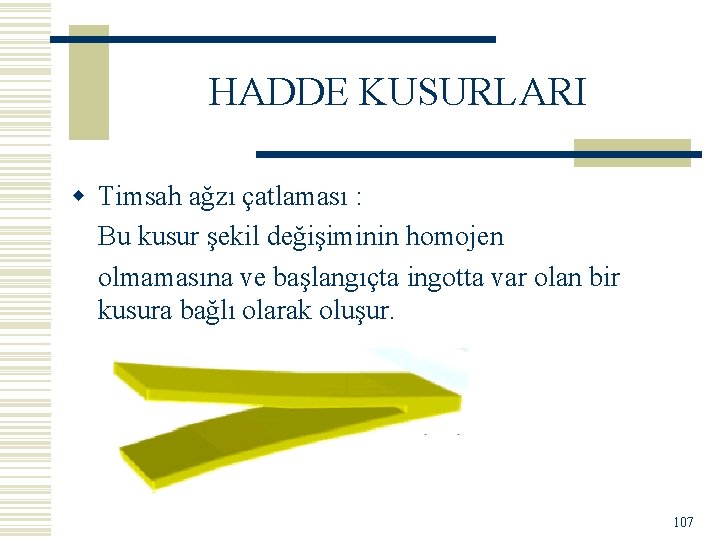
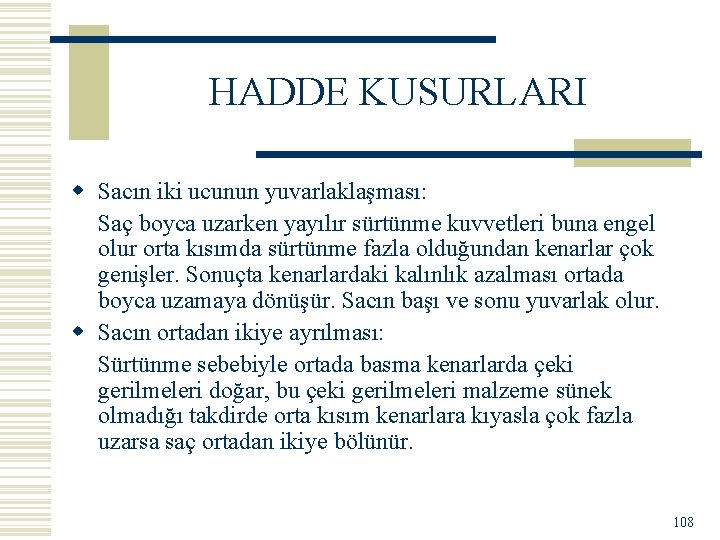
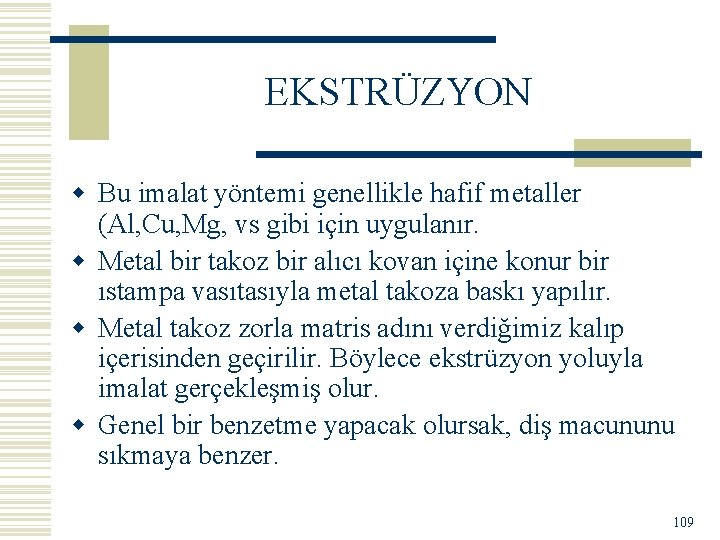
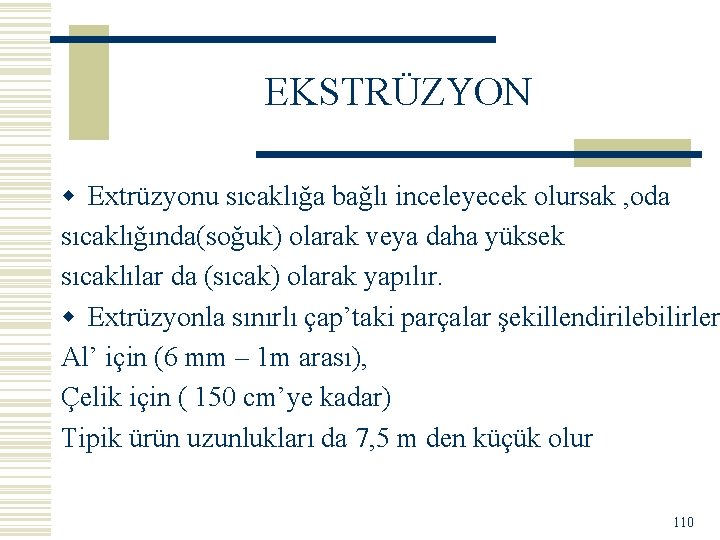
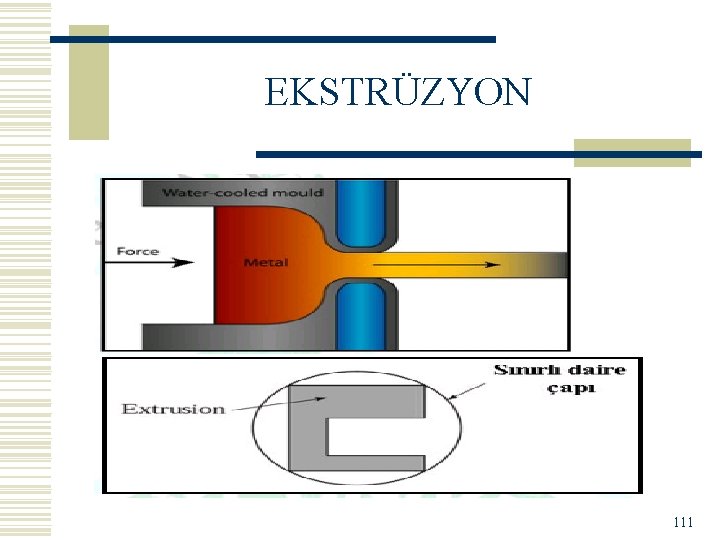
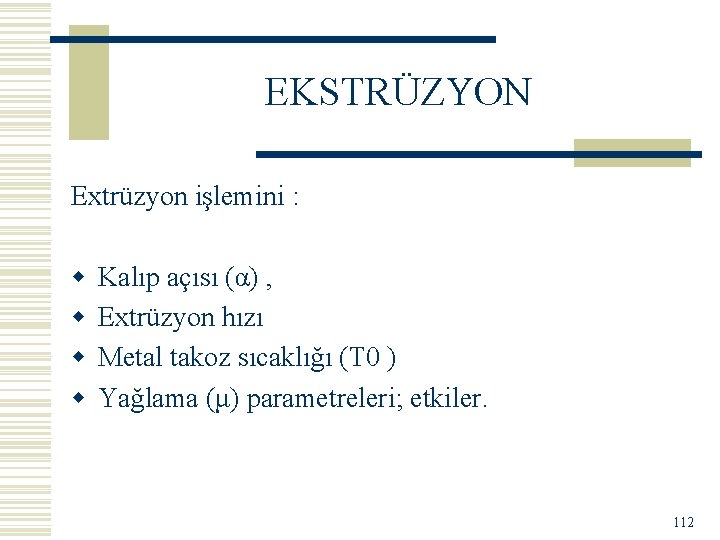
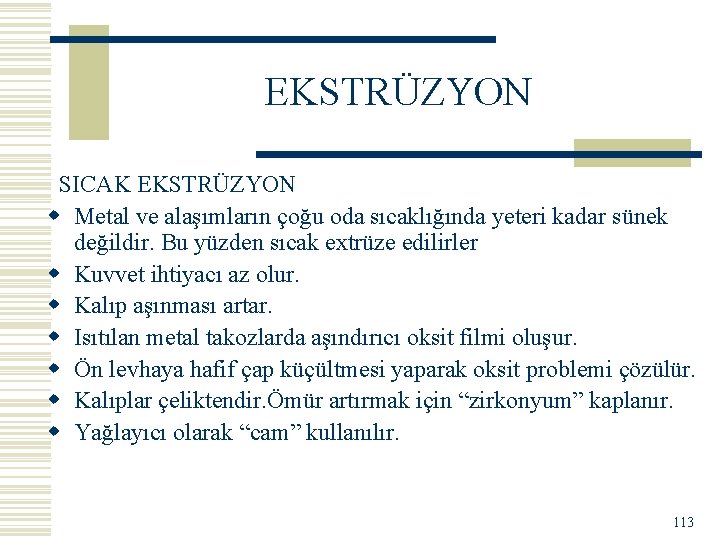
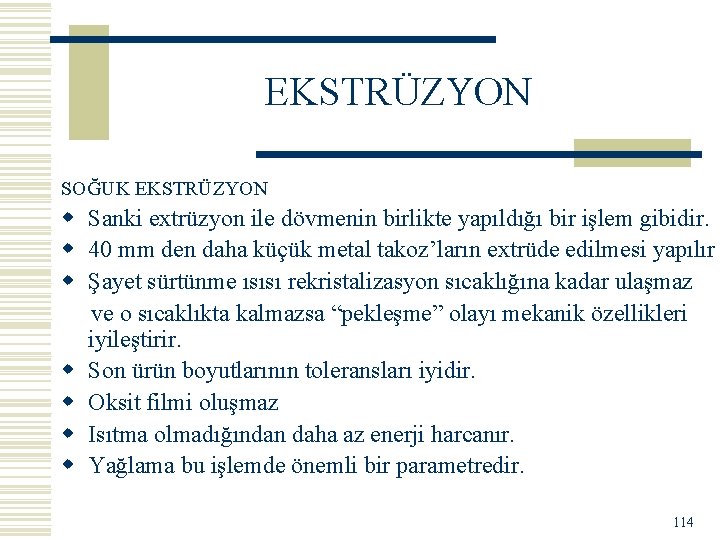
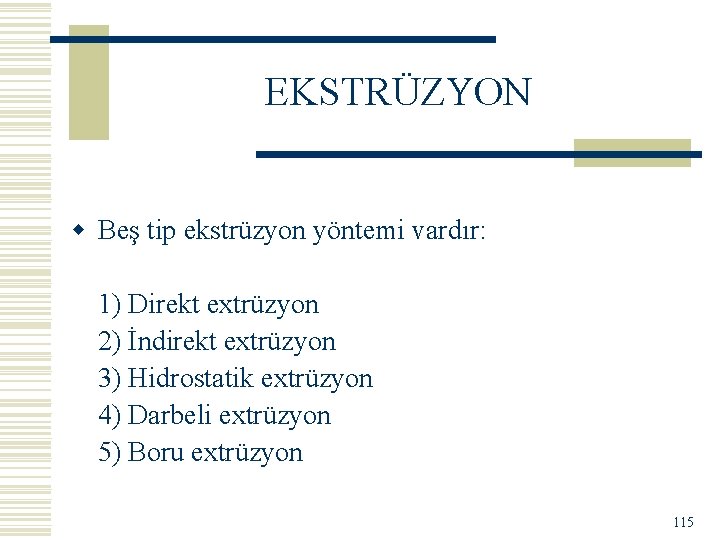
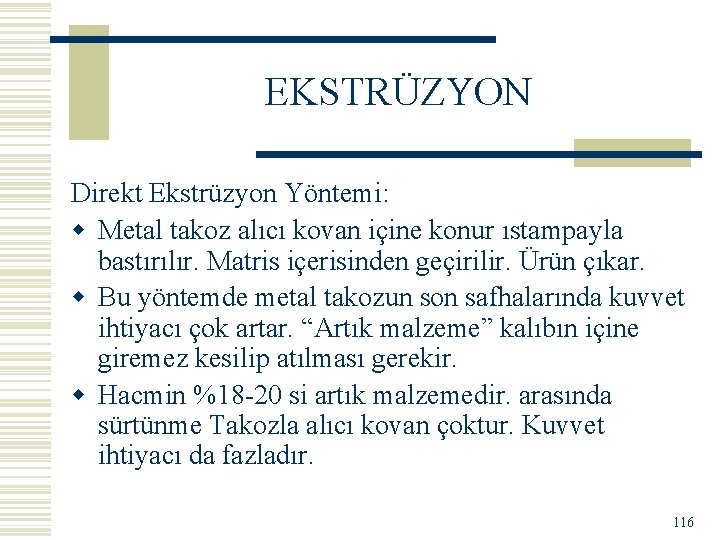
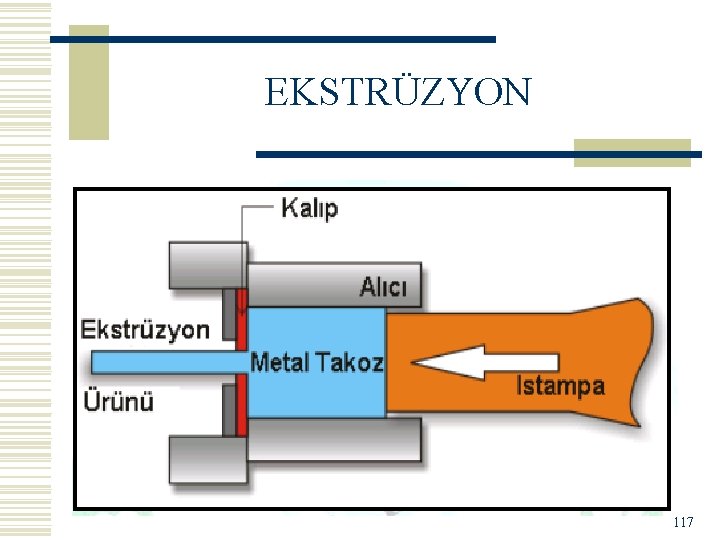
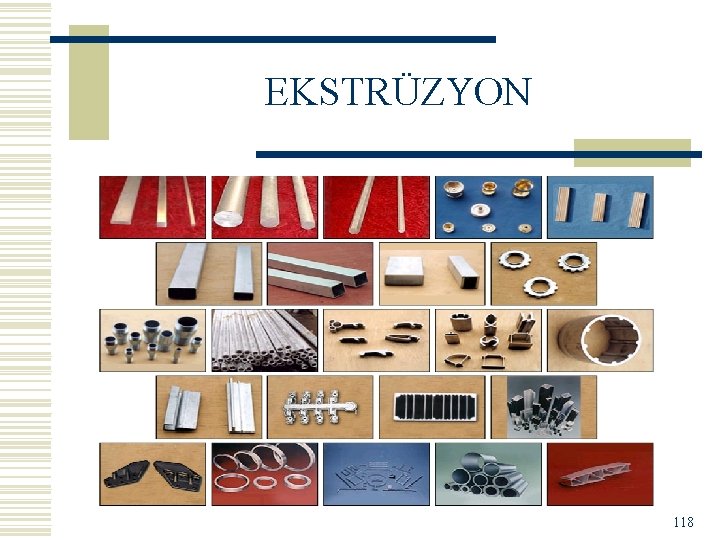
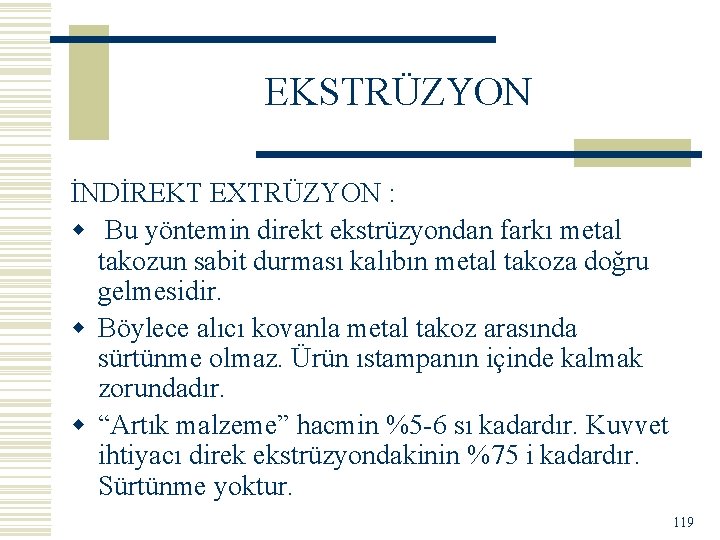
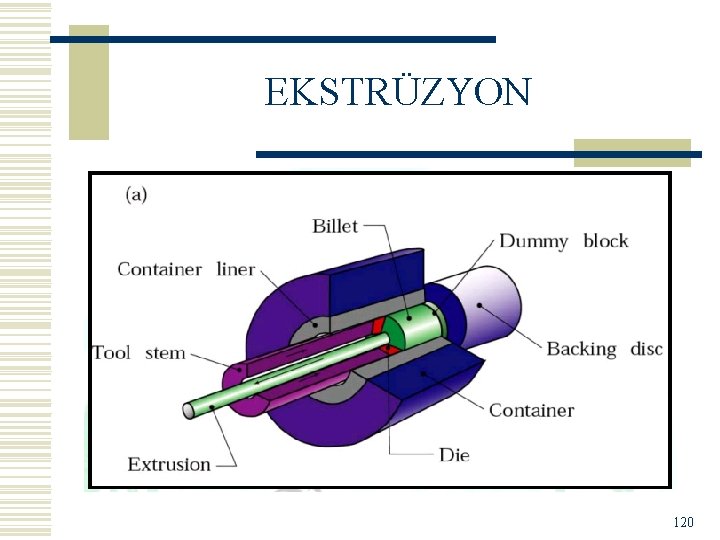
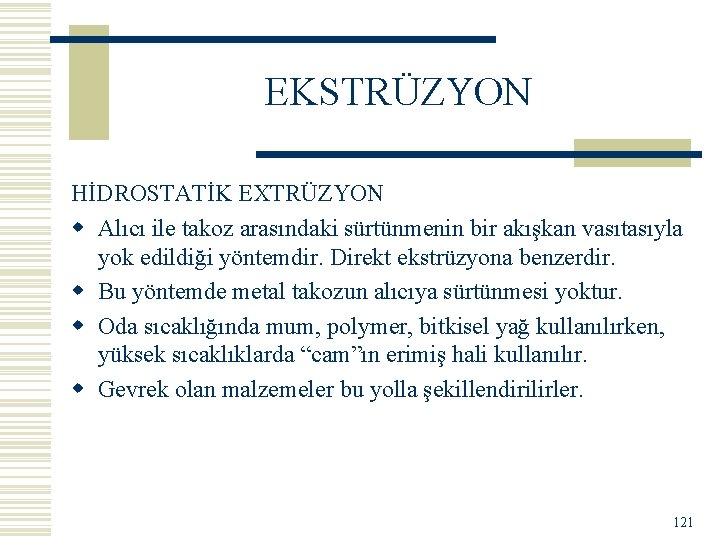
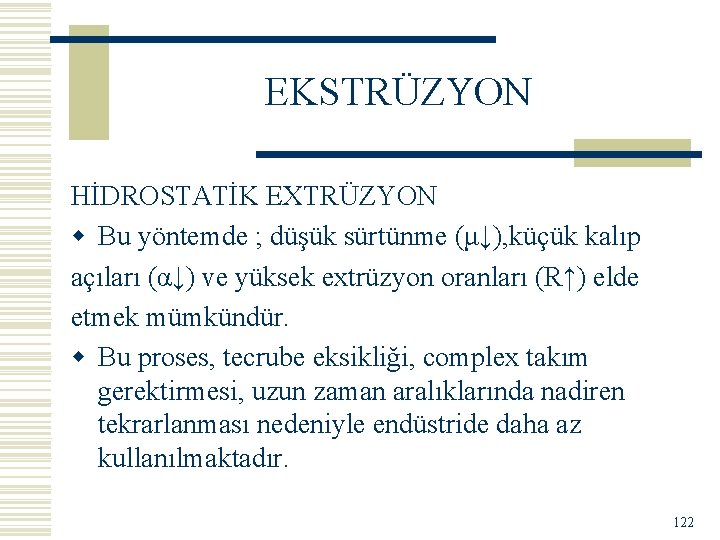
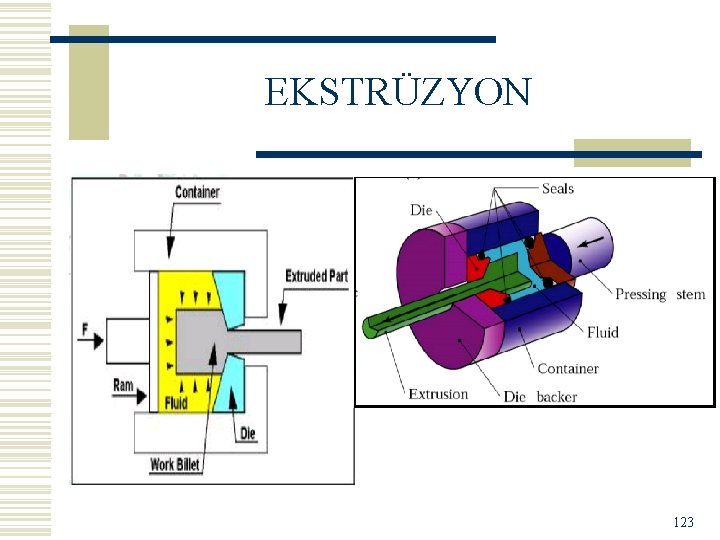
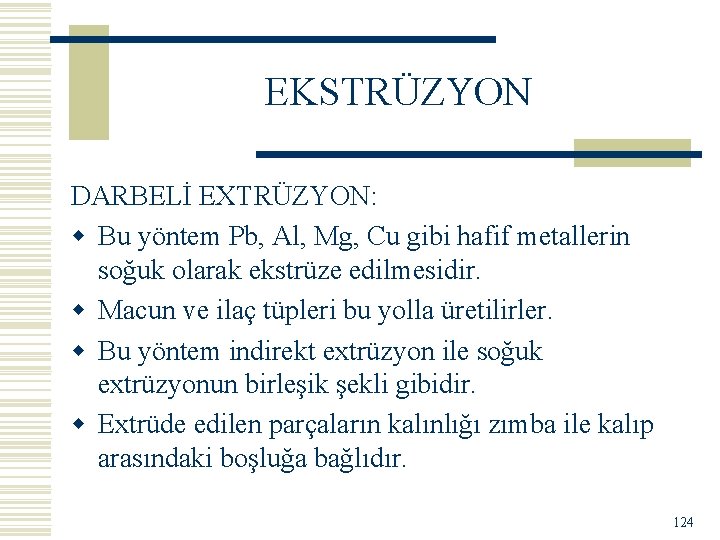
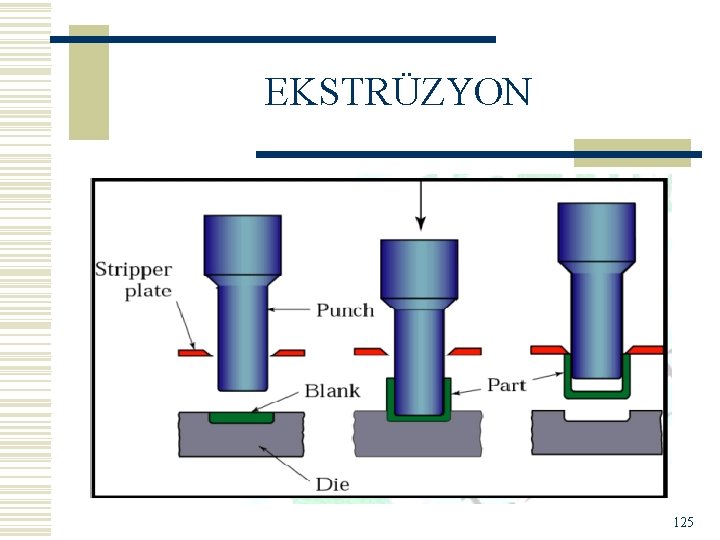

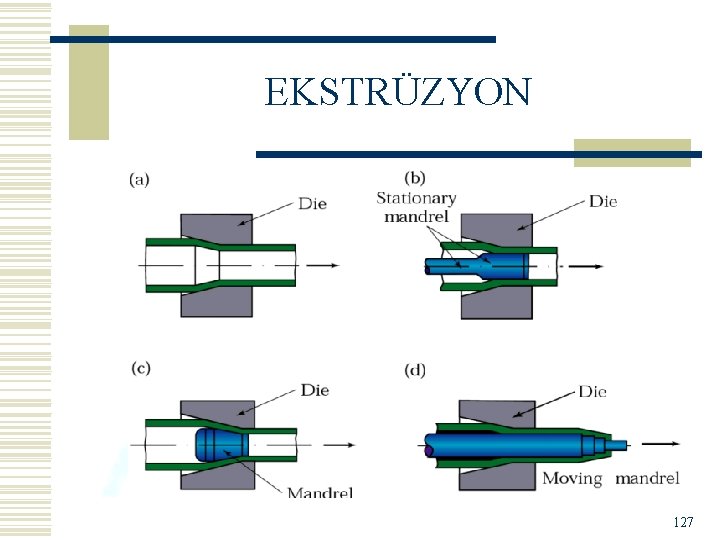
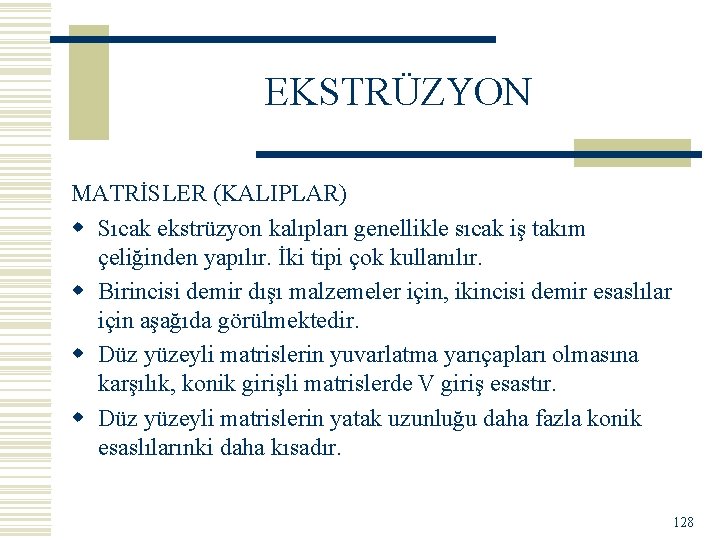
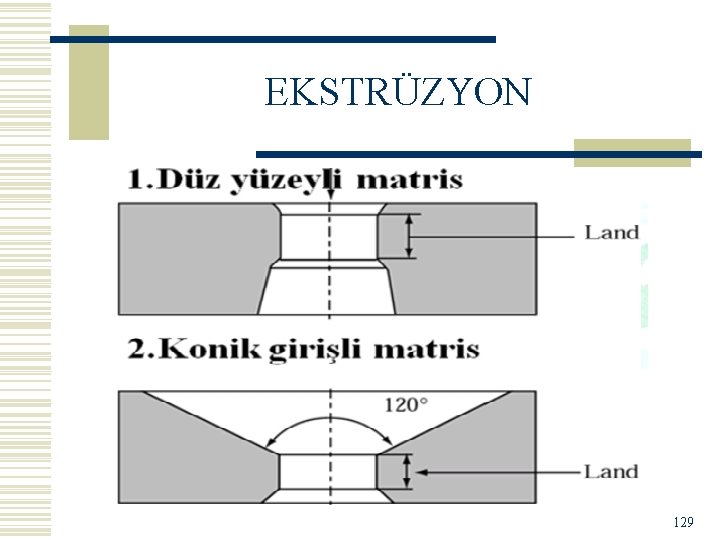
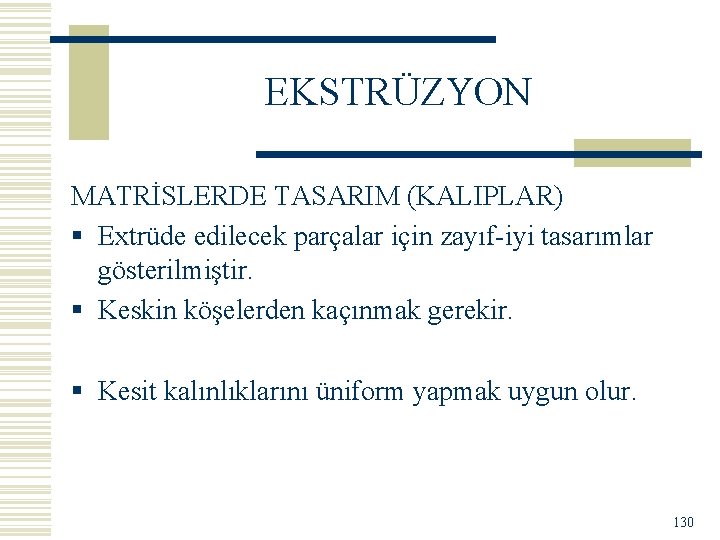
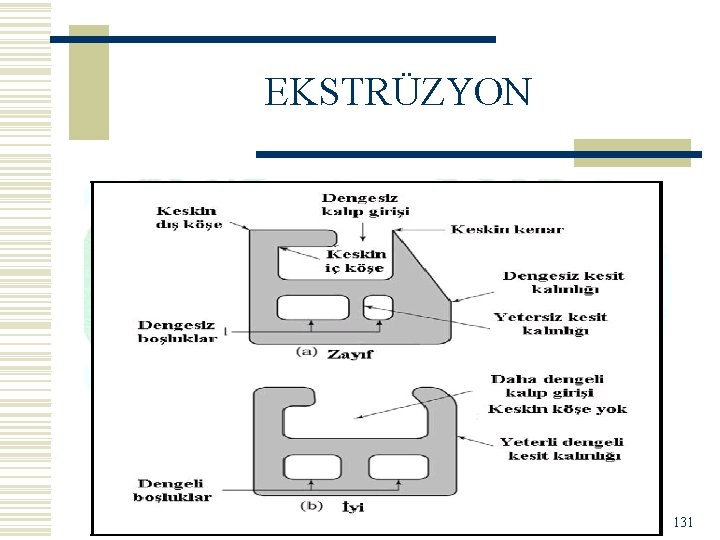
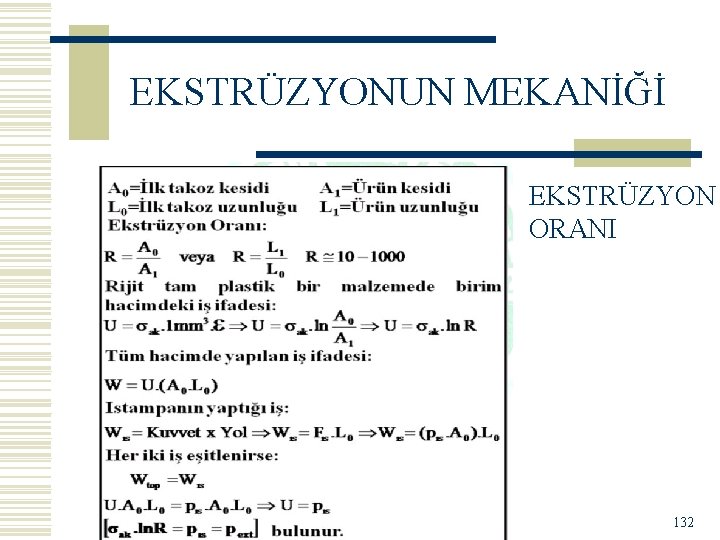
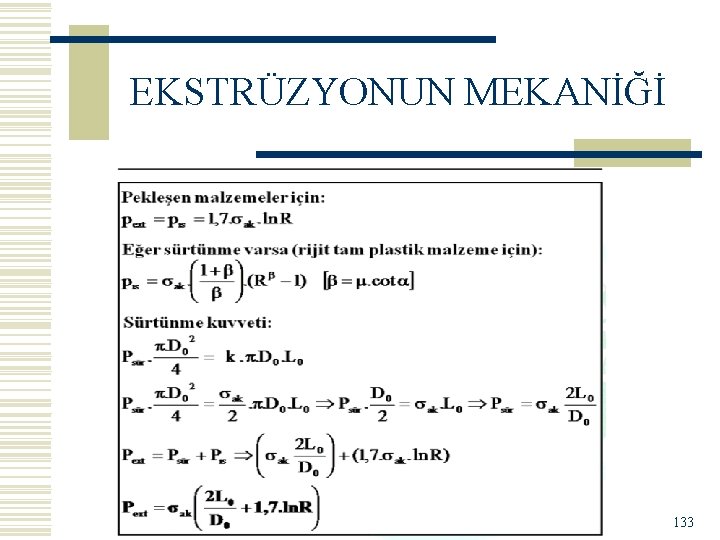
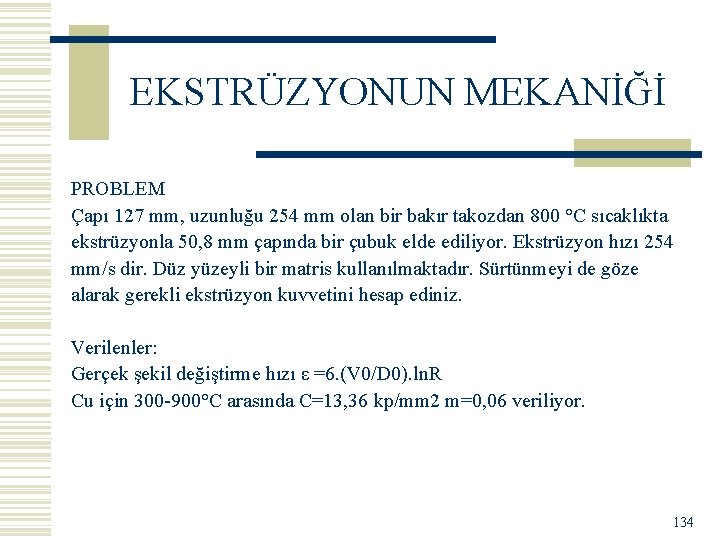
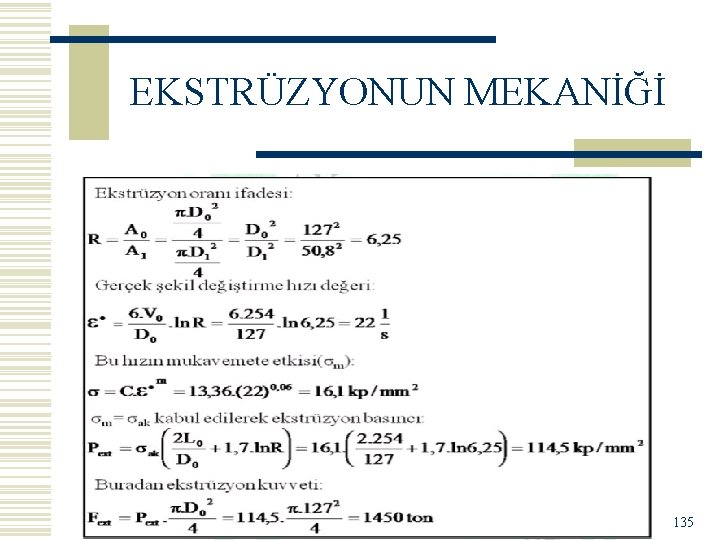
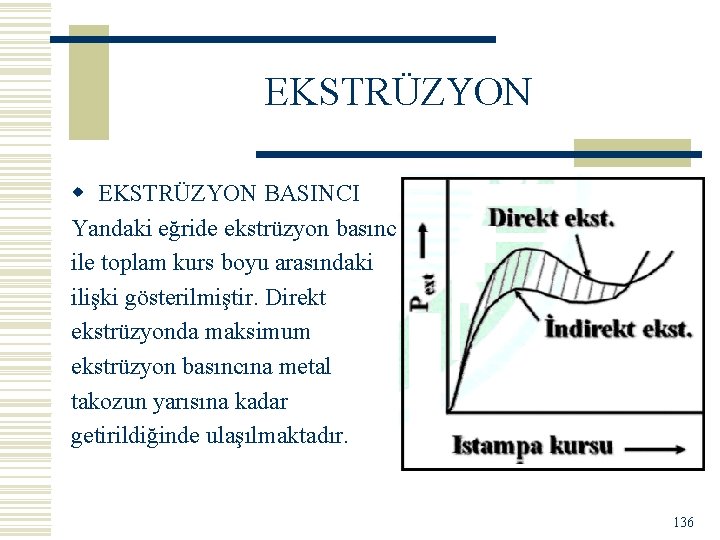
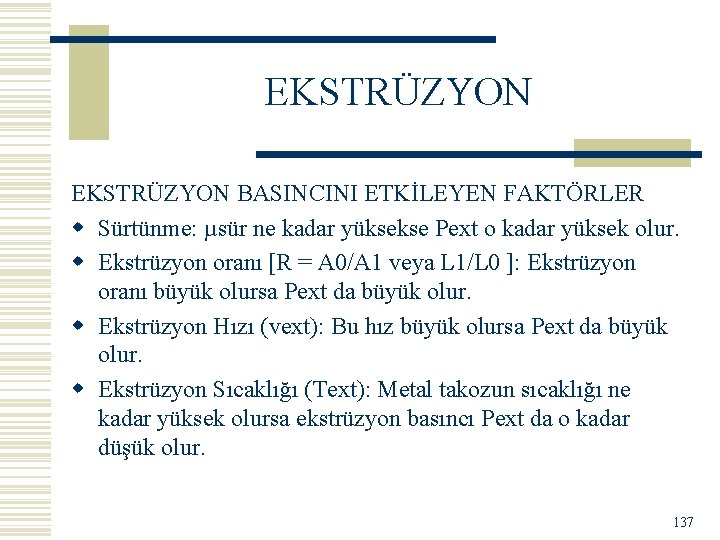
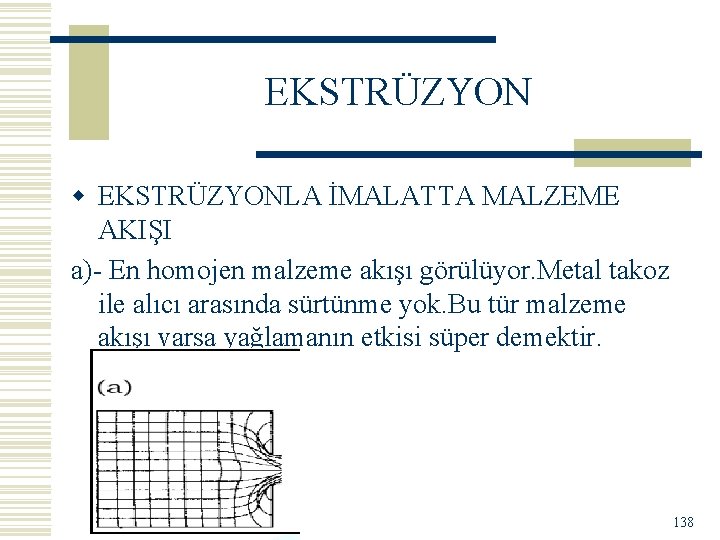
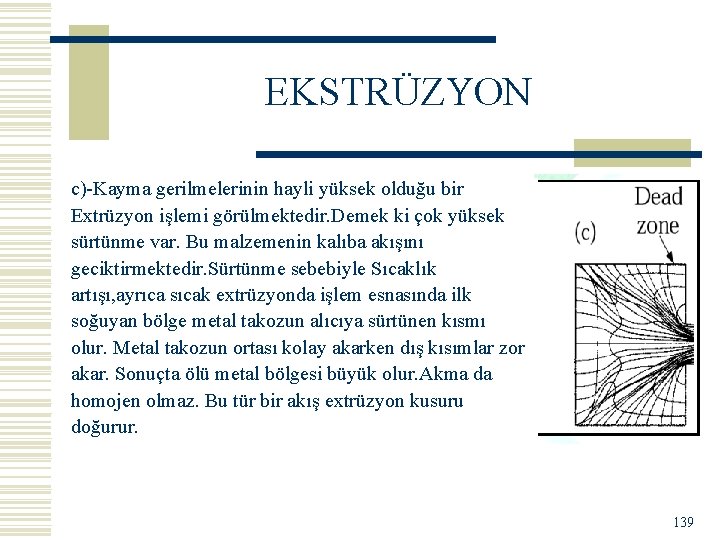
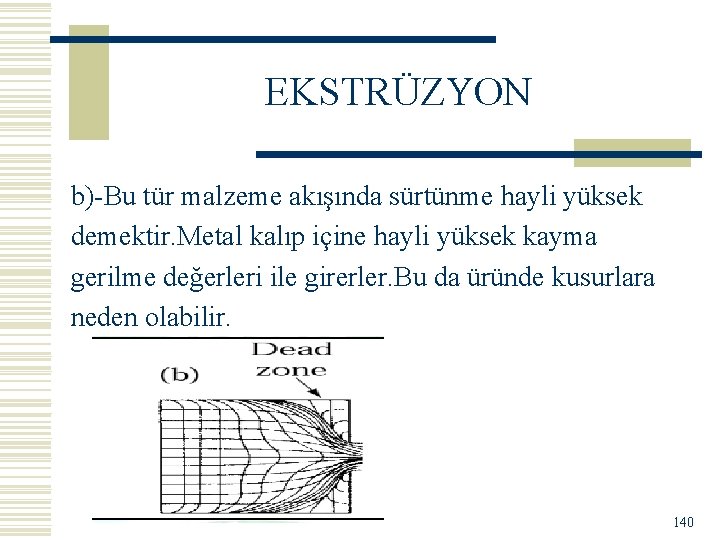
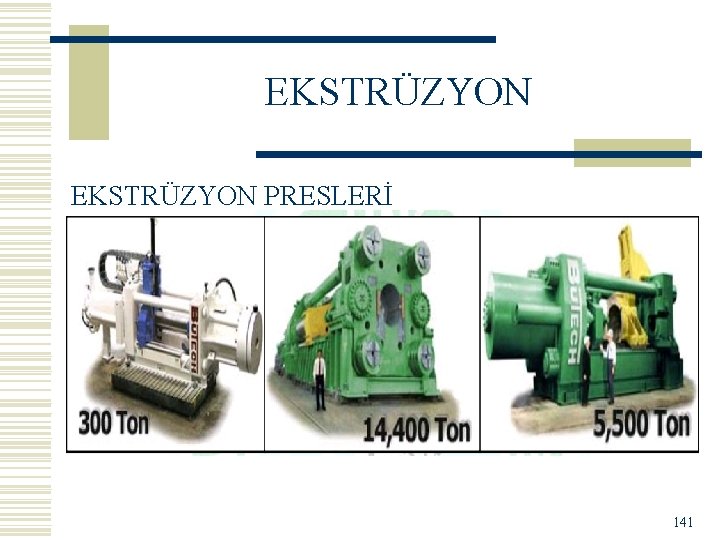
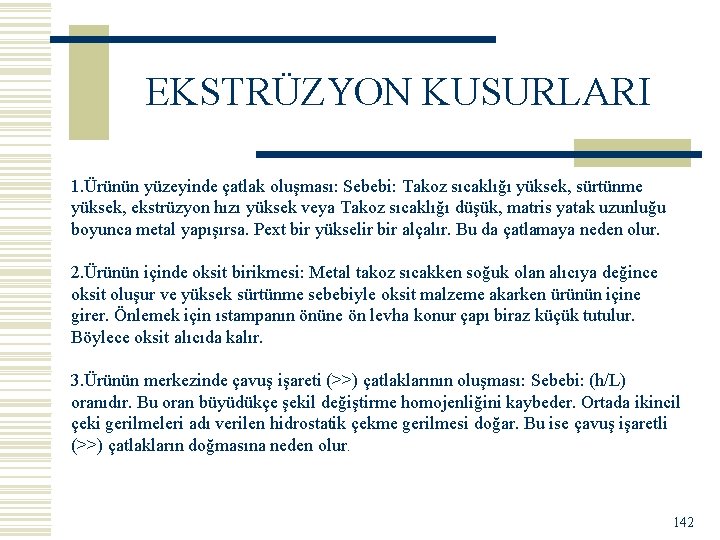
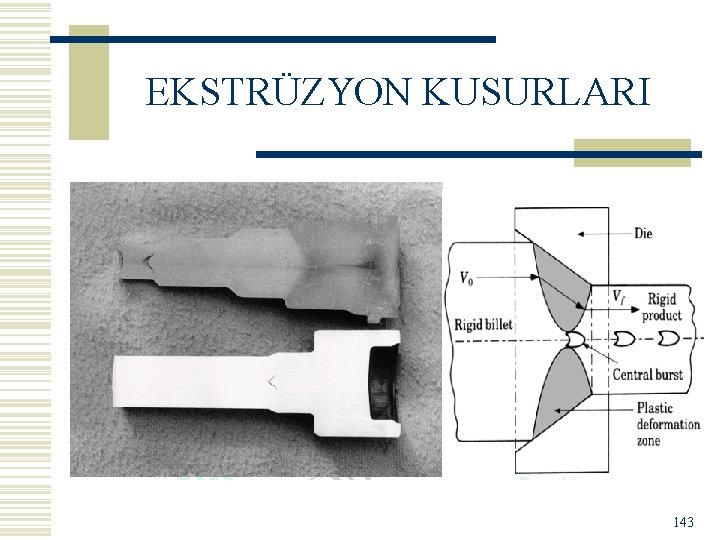
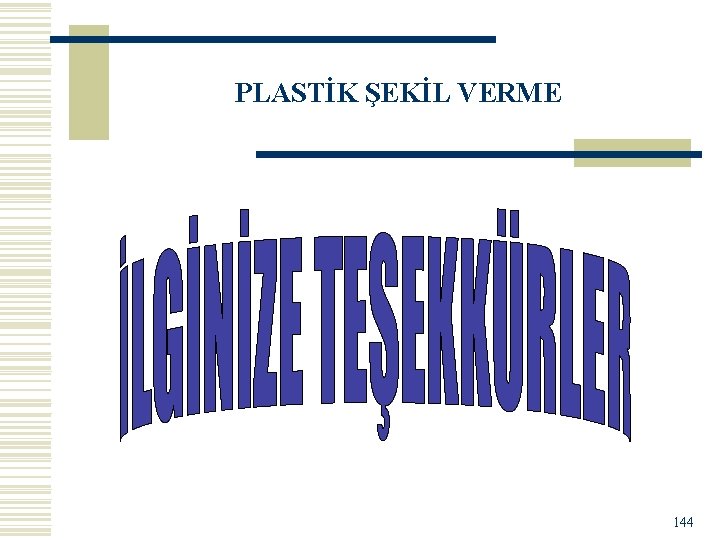
- Slides: 144
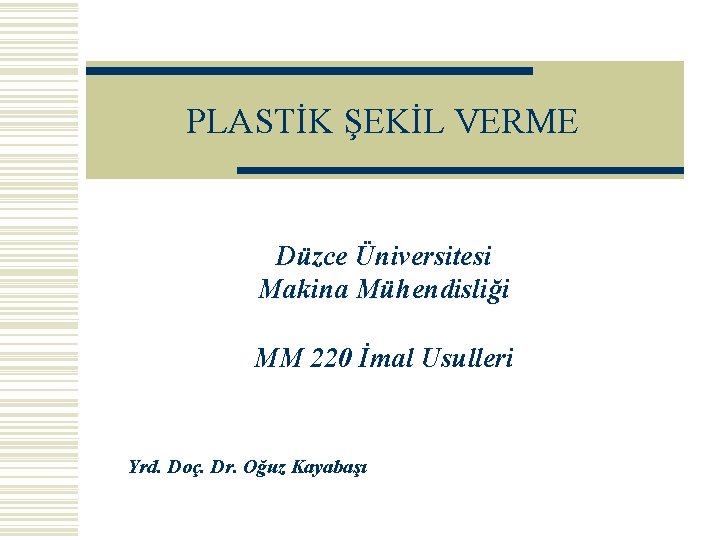
PLASTİK ŞEKİL VERME Düzce Üniversitesi Makina Mühendisliği MM 220 İmal Usulleri Yrd. Doç. Dr. Oğuz Kayabaşı
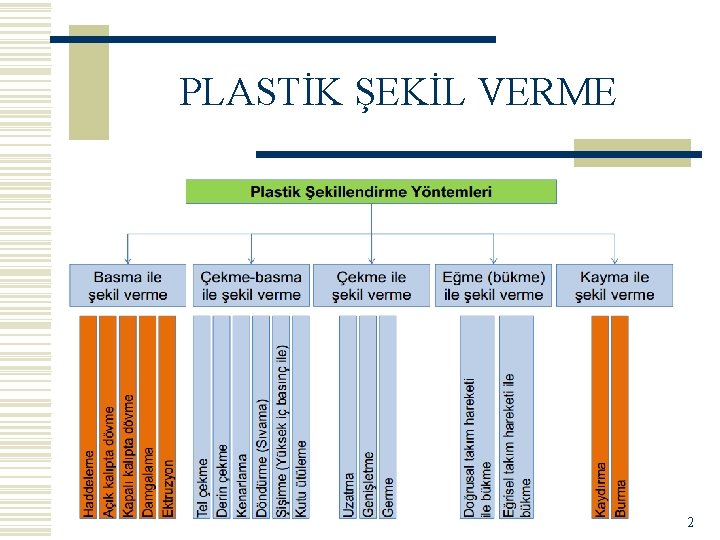
PLASTİK ŞEKİL VERME 2
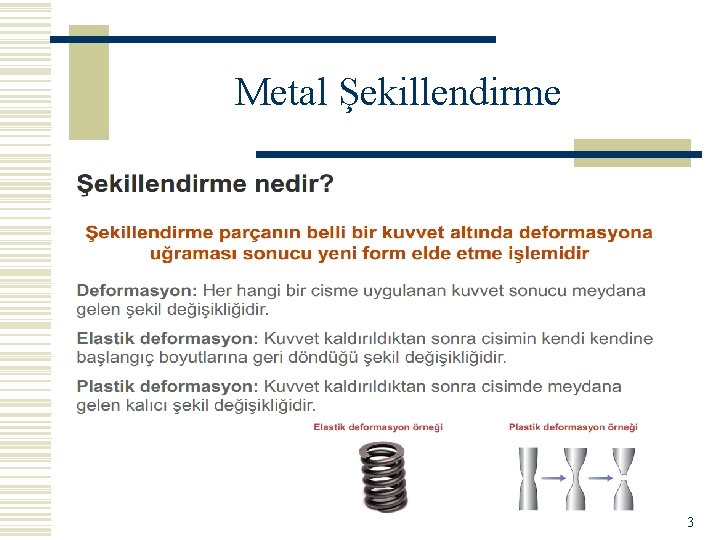
Metal Şekillendirme 3
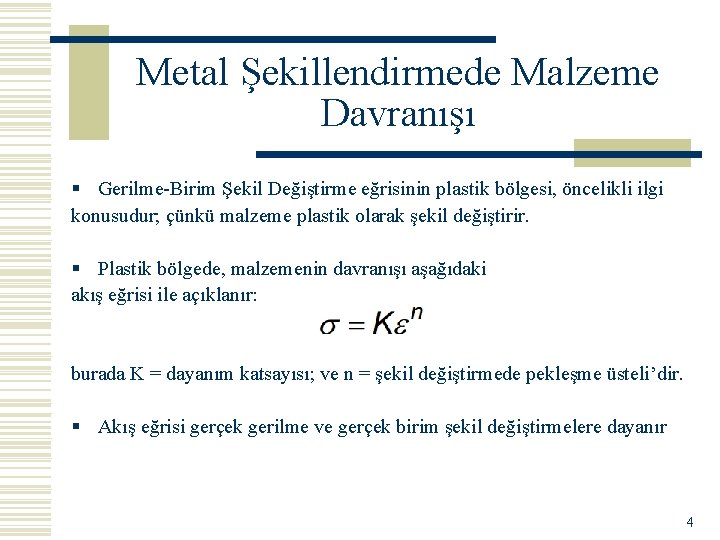
Metal Şekillendirmede Malzeme Davranışı § Gerilme-Birim Şekil Değiştirme eğrisinin plastik bölgesi, öncelikli ilgi konusudur; çünkü malzeme plastik olarak şekil değiştirir. § Plastik bölgede, malzemenin davranışı aşağıdaki akış eğrisi ile açıklanır: burada K = dayanım katsayısı; ve n = şekil değiştirmede pekleşme üsteli’dir. § Akış eğrisi gerçek gerilme ve gerçek birim şekil değiştirmelere dayanır 4
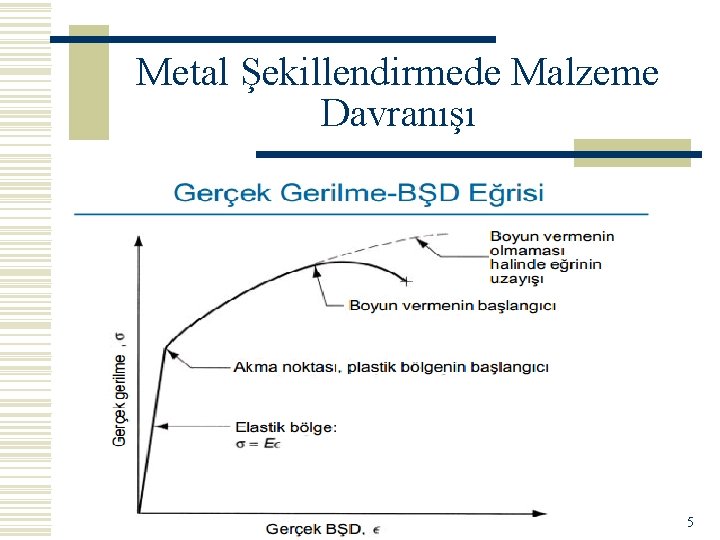
Metal Şekillendirmede Malzeme Davranışı 5
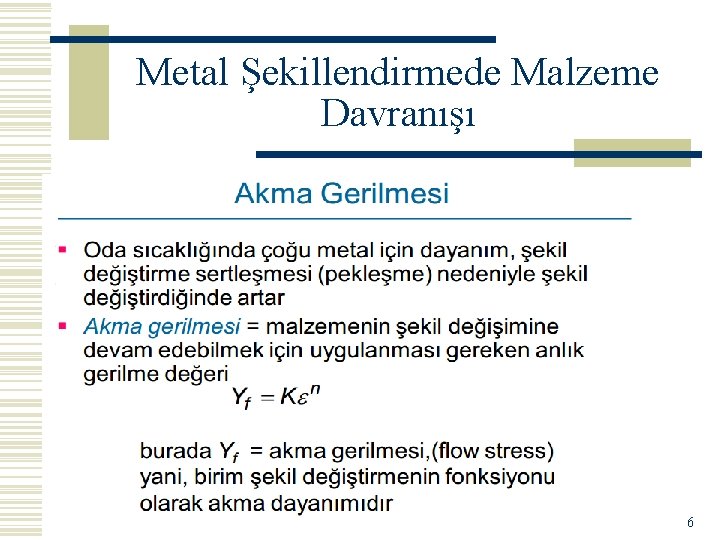
Metal Şekillendirmede Malzeme Davranışı 6
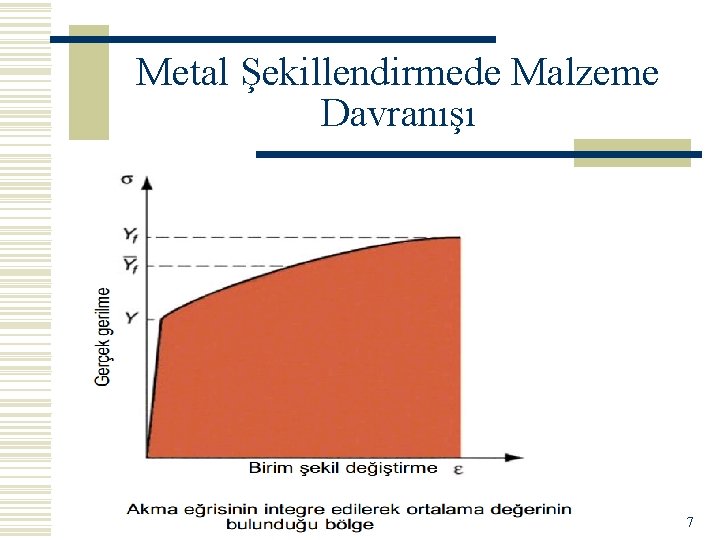
Metal Şekillendirmede Malzeme Davranışı 7
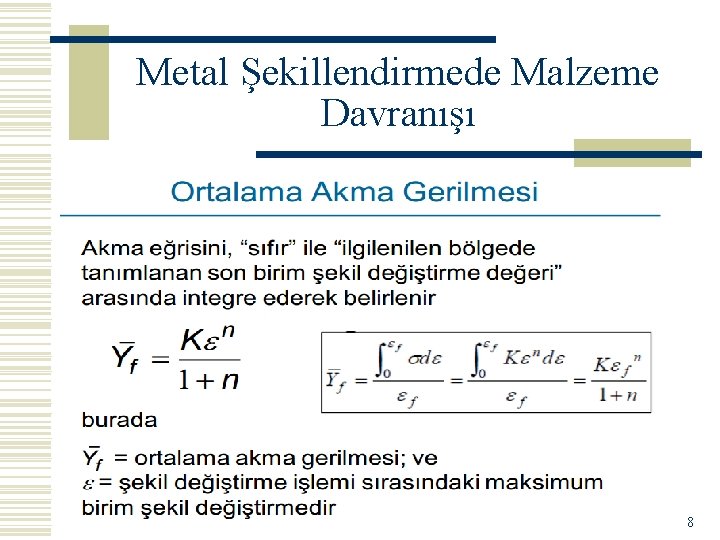
Metal Şekillendirmede Malzeme Davranışı 8
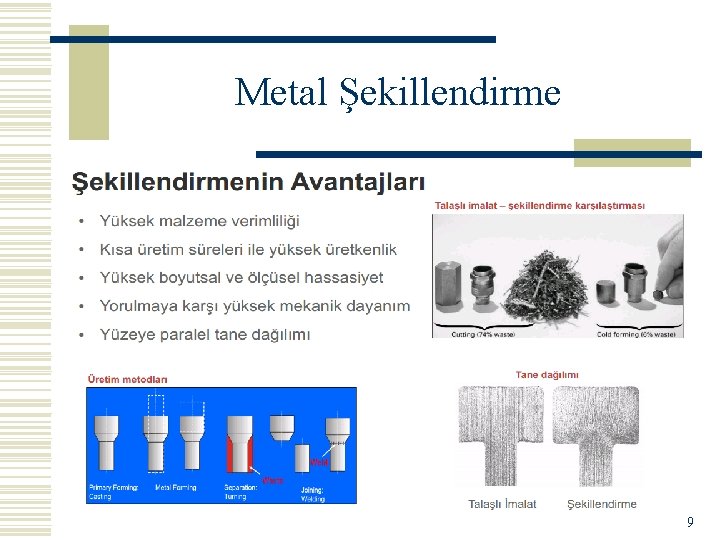
Metal Şekillendirme 9
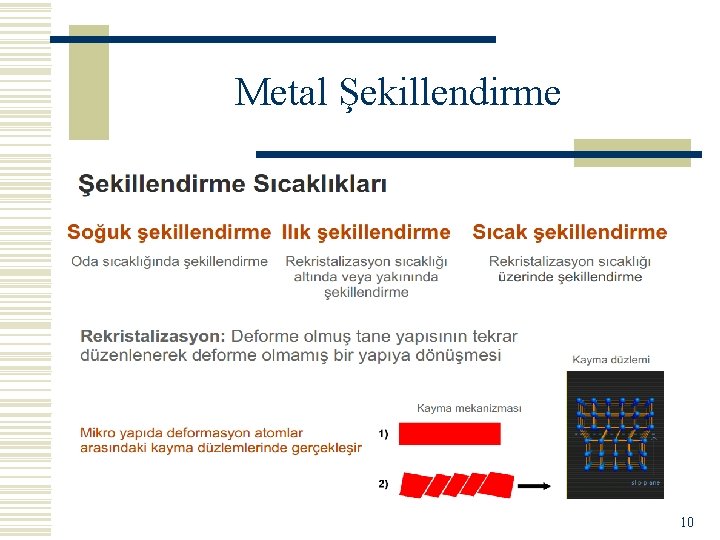
Metal Şekillendirme 10
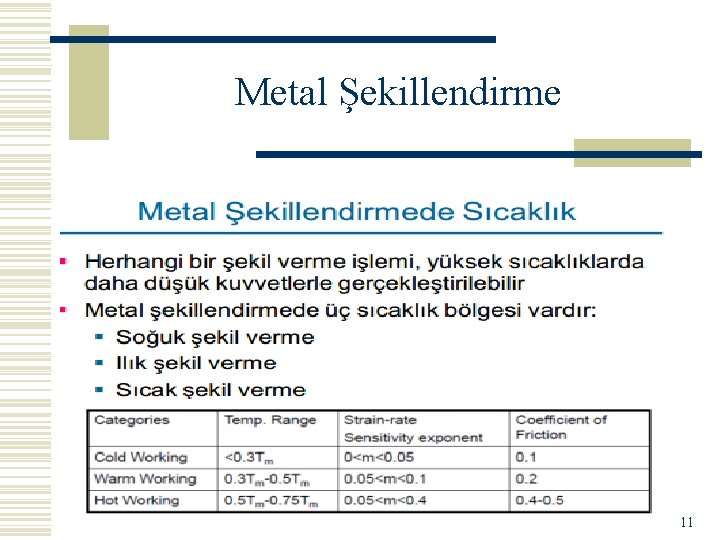
Metal Şekillendirme 11
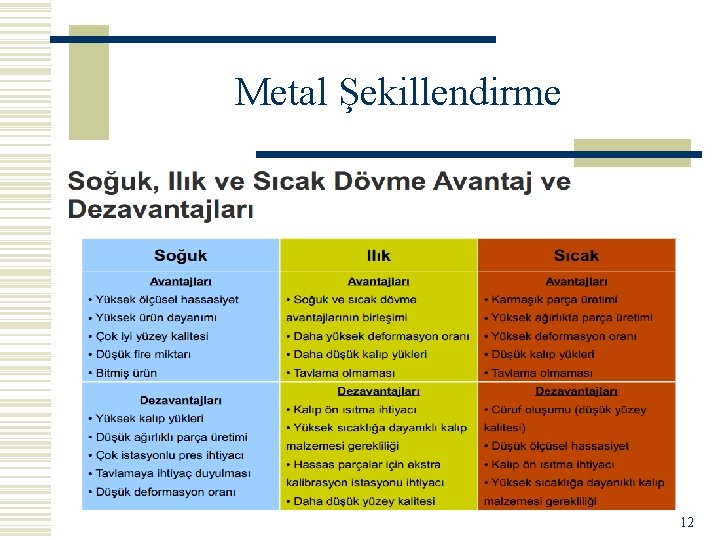
Metal Şekillendirme 12
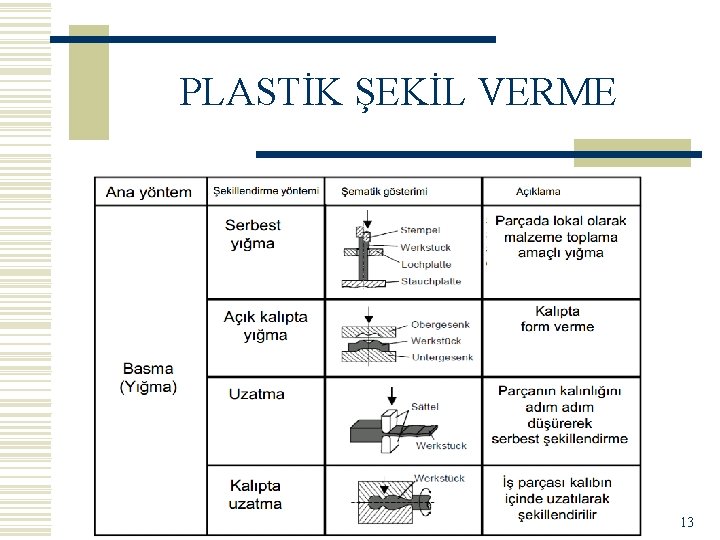
PLASTİK ŞEKİL VERME 13
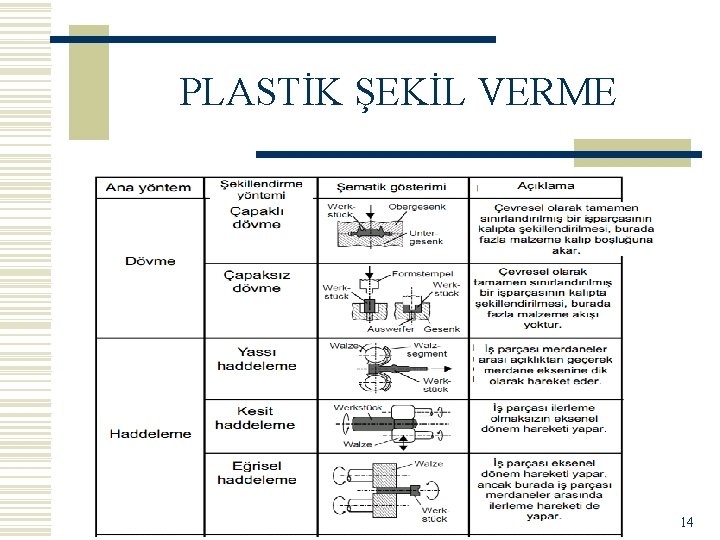
PLASTİK ŞEKİL VERME 14
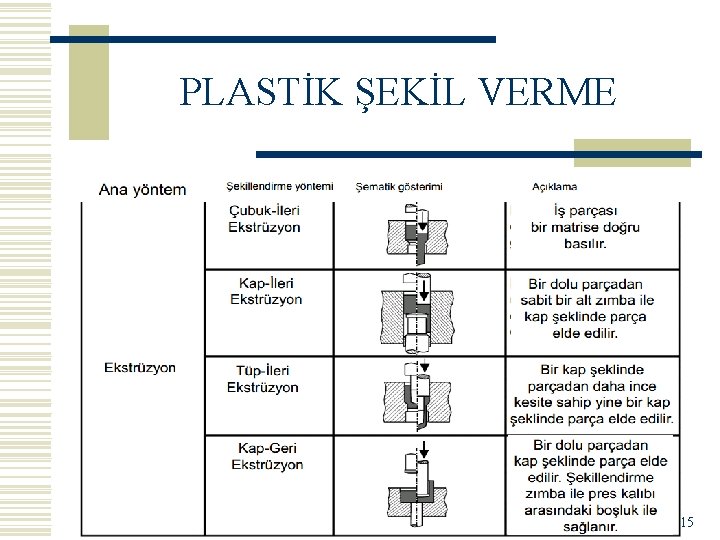
PLASTİK ŞEKİL VERME 15
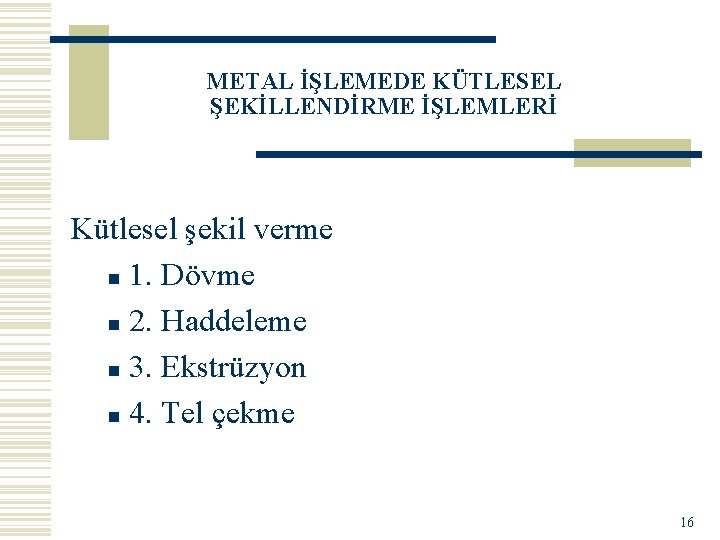
METAL İŞLEMEDE KÜTLESEL ŞEKİLLENDİRME İŞLEMLERİ Kütlesel şekil verme n 1. Dövme n 2. Haddeleme n 3. Ekstrüzyon n 4. Tel çekme 16
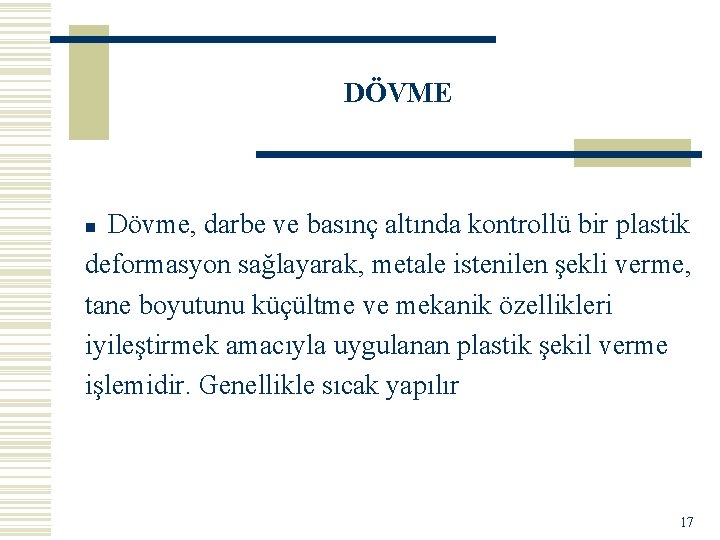
DÖVME Dövme, darbe ve basınç altında kontrollü bir plastik deformasyon sağlayarak, metale istenilen şekli verme, tane boyutunu küçültme ve mekanik özellikleri iyileştirmek amacıyla uygulanan plastik şekil verme işlemidir. Genellikle sıcak yapılır n 17
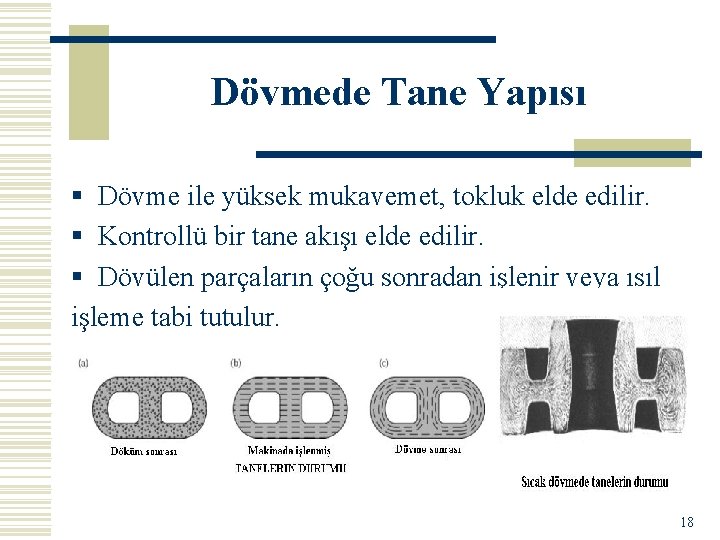
Dövmede Tane Yapısı § Dövme ile yüksek mukavemet, tokluk elde edilir. § Kontrollü bir tane akışı elde edilir. § Dövülen parçaların çoğu sonradan işlenir veya ısıl işleme tabi tutulur. 18
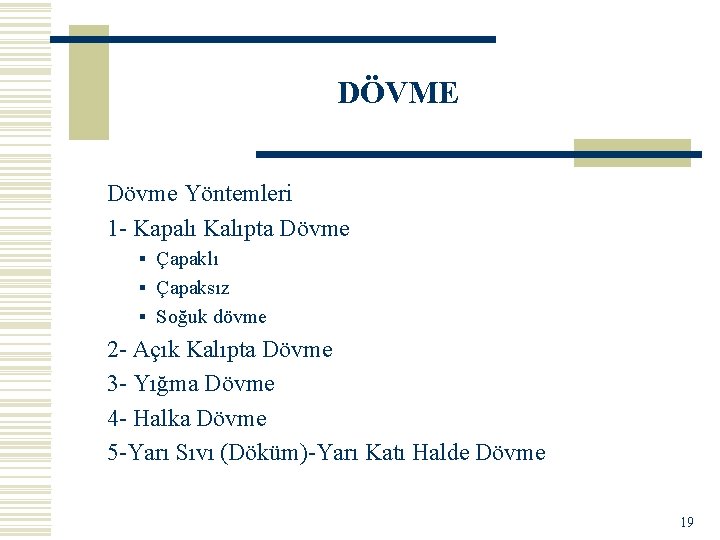
DÖVME Dövme Yöntemleri 1 - Kapalı Kalıpta Dövme § Çapaklı § Çapaksız § Soğuk dövme 2 - Açık Kalıpta Dövme 3 - Yığma Dövme 4 - Halka Dövme 5 -Yarı Sıvı (Döküm)-Yarı Katı Halde Dövme 19
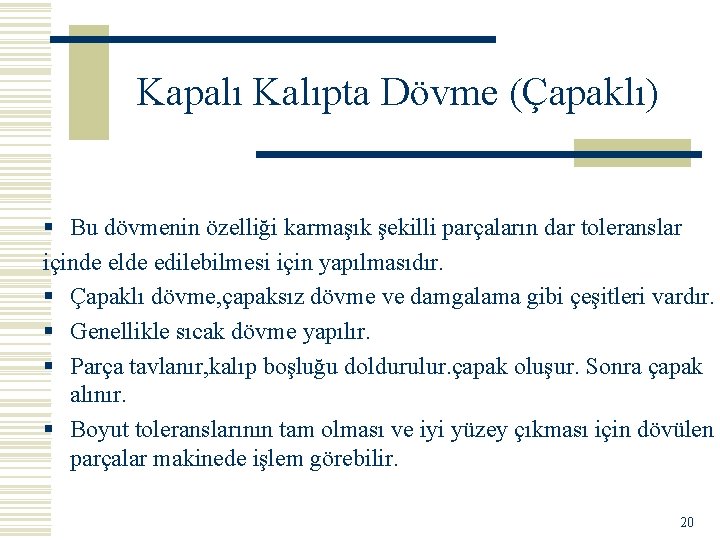
Kapalı Kalıpta Dövme (Çapaklı) § Bu dövmenin özelliği karmaşık şekilli parçaların dar toleranslar içinde elde edilebilmesi için yapılmasıdır. § Çapaklı dövme, çapaksız dövme ve damgalama gibi çeşitleri vardır. § Genellikle sıcak dövme yapılır. § Parça tavlanır, kalıp boşluğu doldurulur. çapak oluşur. Sonra çapak alınır. § Boyut toleranslarının tam olması ve iyi yüzey çıkması için dövülen parçalar makinede işlem görebilir. 20
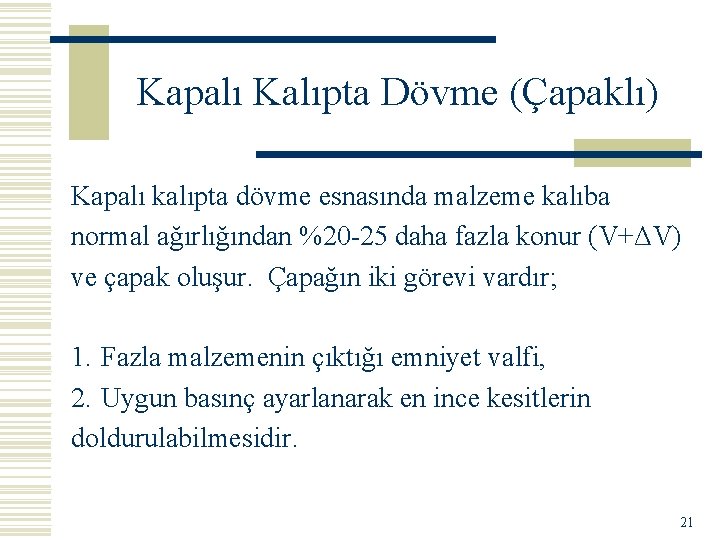
Kapalı Kalıpta Dövme (Çapaklı) Kapalı kalıpta dövme esnasında malzeme kalıba normal ağırlığından %20 -25 daha fazla konur (V+ΔV) ve çapak oluşur. Çapağın iki görevi vardır; 1. Fazla malzemenin çıktığı emniyet valfi, 2. Uygun basınç ayarlanarak en ince kesitlerin doldurulabilmesidir. 21
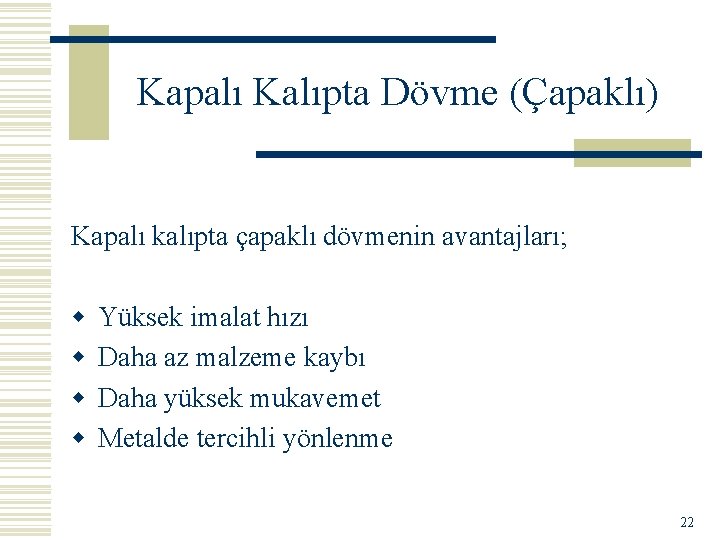
Kapalı Kalıpta Dövme (Çapaklı) Kapalı kalıpta çapaklı dövmenin avantajları; w w Yüksek imalat hızı Daha az malzeme kaybı Daha yüksek mukavemet Metalde tercihli yönlenme 22
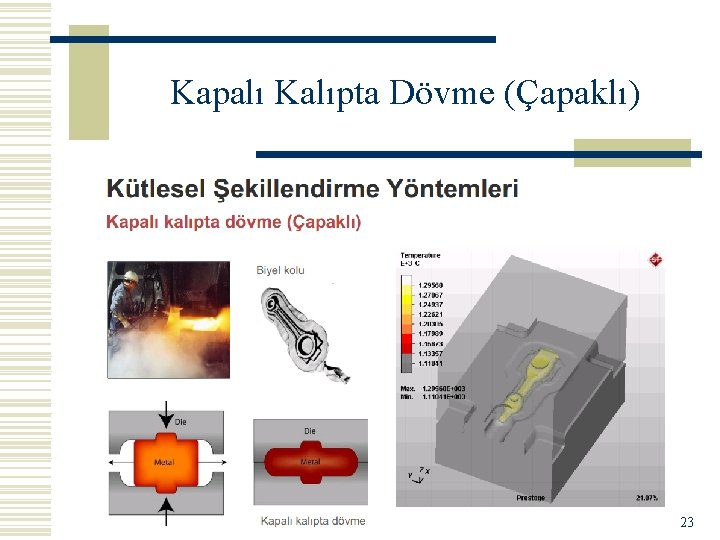
Kapalı Kalıpta Dövme (Çapaklı) 23
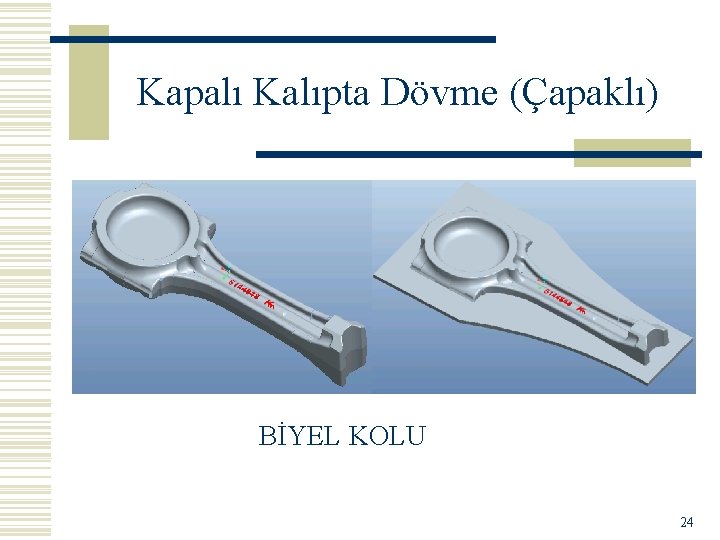
Kapalı Kalıpta Dövme (Çapaklı) BİYEL KOLU 24
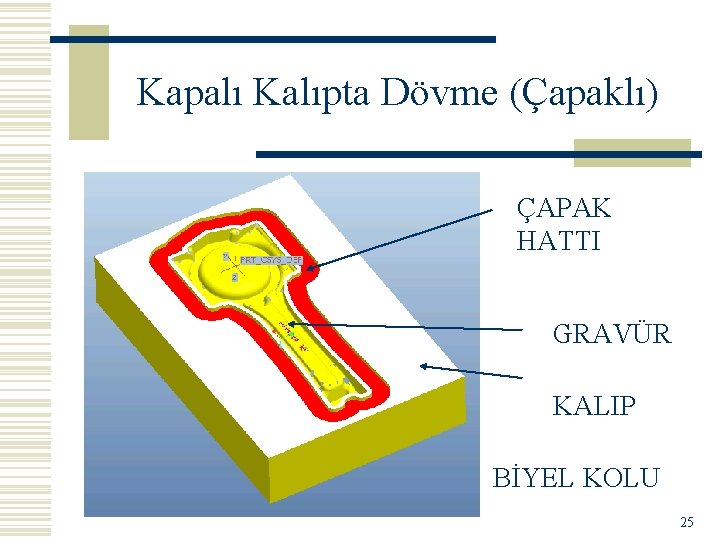
Kapalı Kalıpta Dövme (Çapaklı) ÇAPAK HATTI GRAVÜR KALIP BİYEL KOLU 25
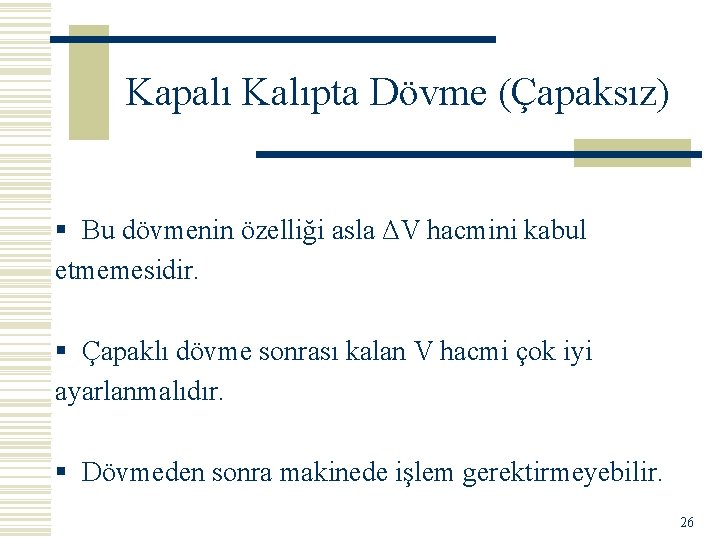
Kapalı Kalıpta Dövme (Çapaksız) § Bu dövmenin özelliği asla ΔV hacmini kabul etmemesidir. § Çapaklı dövme sonrası kalan V hacmi çok iyi ayarlanmalıdır. § Dövmeden sonra makinede işlem gerektirmeyebilir. 26
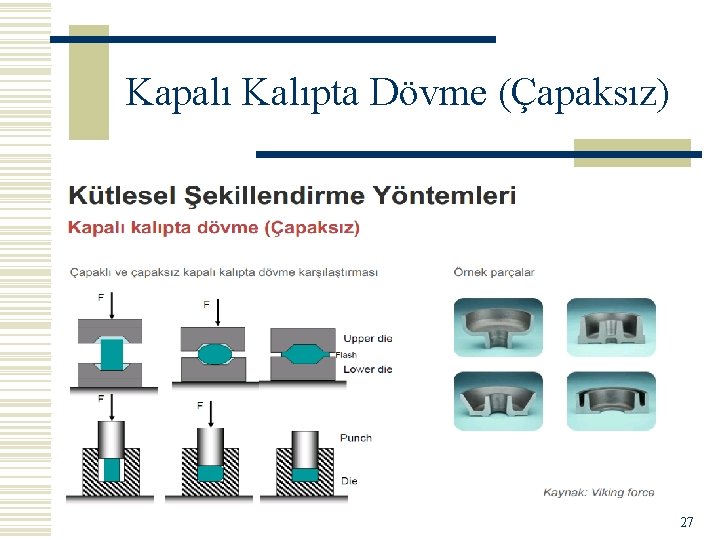
Kapalı Kalıpta Dövme (Çapaksız) 27
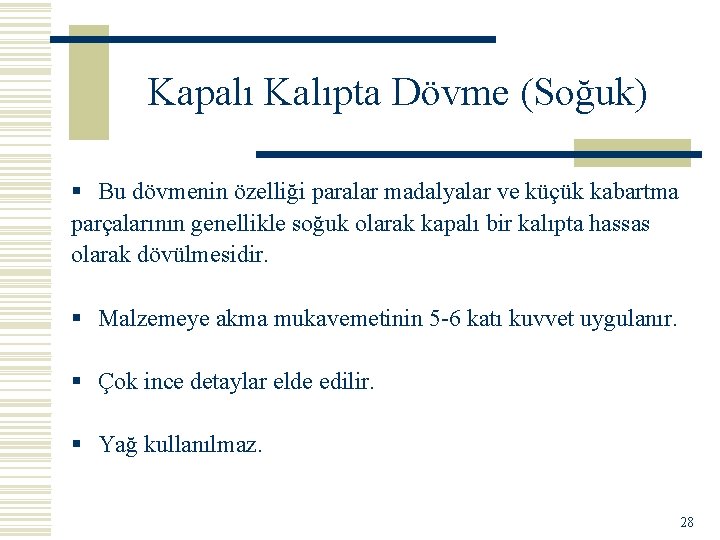
Kapalı Kalıpta Dövme (Soğuk) § Bu dövmenin özelliği paralar madalyalar ve küçük kabartma parçalarının genellikle soğuk olarak kapalı bir kalıpta hassas olarak dövülmesidir. § Malzemeye akma mukavemetinin 5 -6 katı kuvvet uygulanır. § Çok ince detaylar elde edilir. § Yağ kullanılmaz. 28
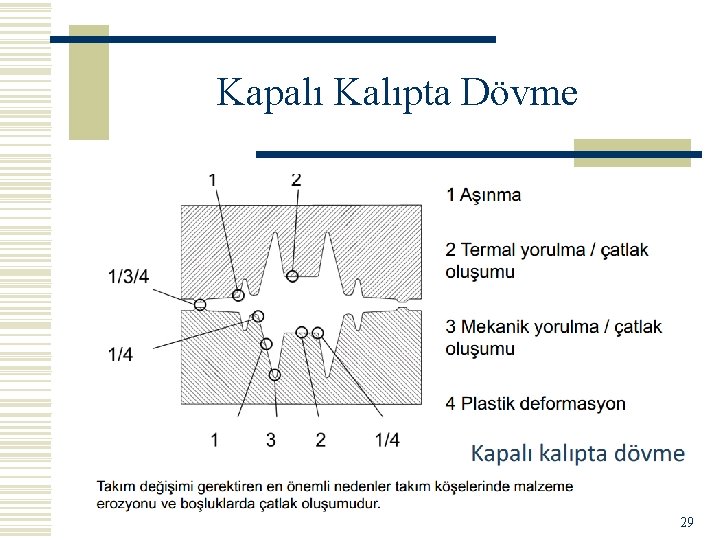
Kapalı Kalıpta Dövme 29
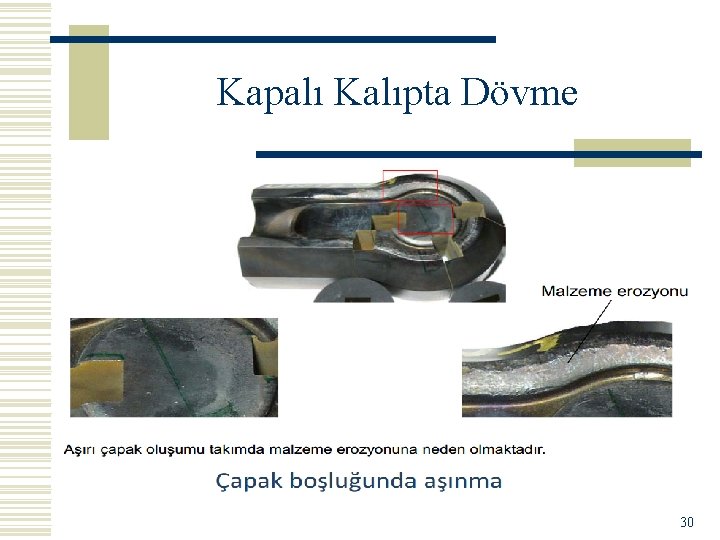
Kapalı Kalıpta Dövme 30
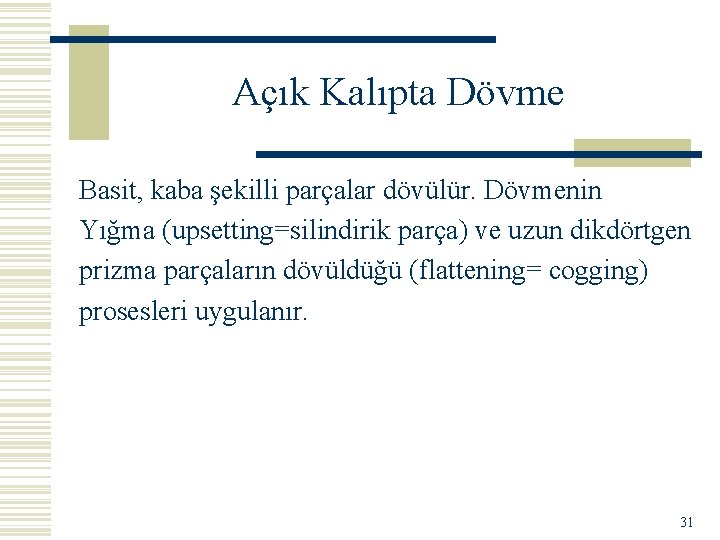
Açık Kalıpta Dövme Basit, kaba şekilli parçalar dövülür. Dövmenin Yığma (upsetting=silindirik parça) ve uzun dikdörtgen prizma parçaların dövüldüğü (flattening= cogging) prosesleri uygulanır. 31
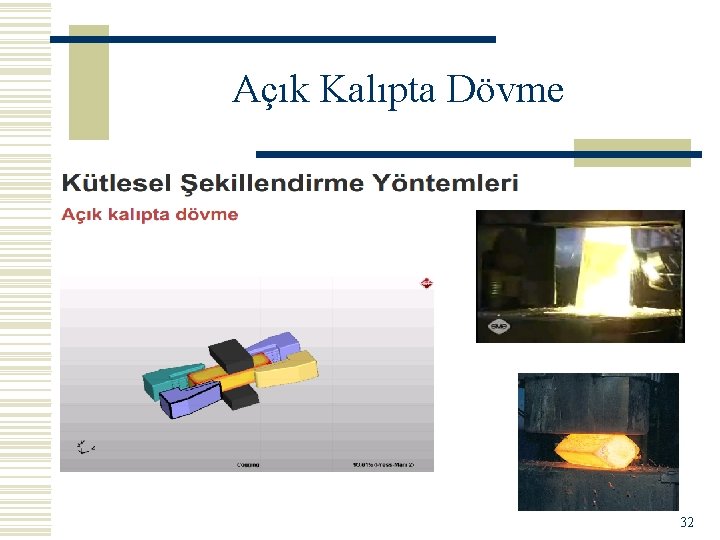
Açık Kalıpta Dövme 32
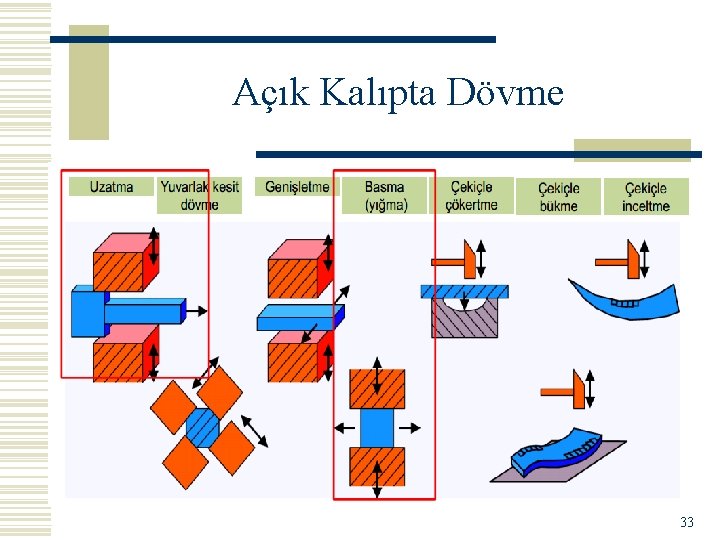
Açık Kalıpta Dövme 33
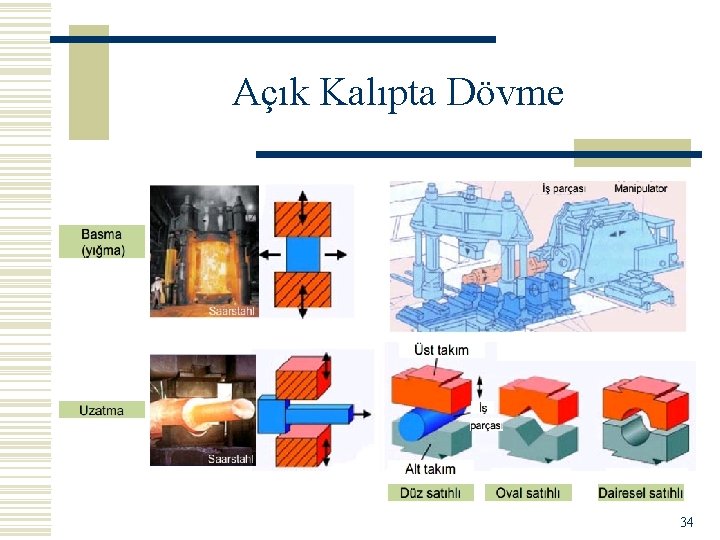
Açık Kalıpta Dövme 34
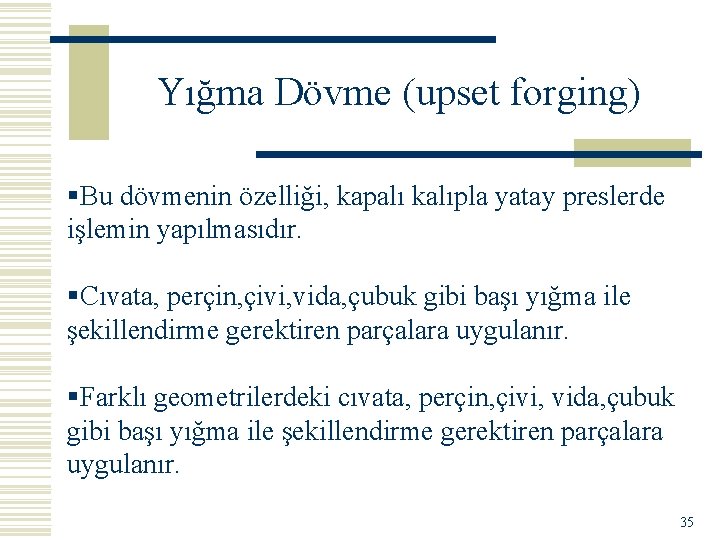
Yığma Dövme (upset forging) §Bu dövmenin özelliği, kapalı kalıpla yatay preslerde işlemin yapılmasıdır. §Cıvata, perçin, çivi, vida, çubuk gibi başı yığma ile şekillendirme gerektiren parçalara uygulanır. §Farklı geometrilerdeki cıvata, perçin, çivi, vida, çubuk gibi başı yığma ile şekillendirme gerektiren parçalara uygulanır. 35
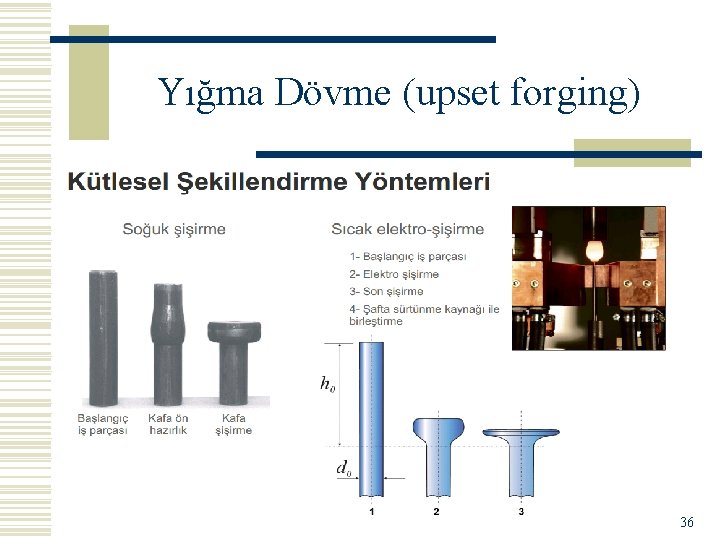
Yığma Dövme (upset forging) 36
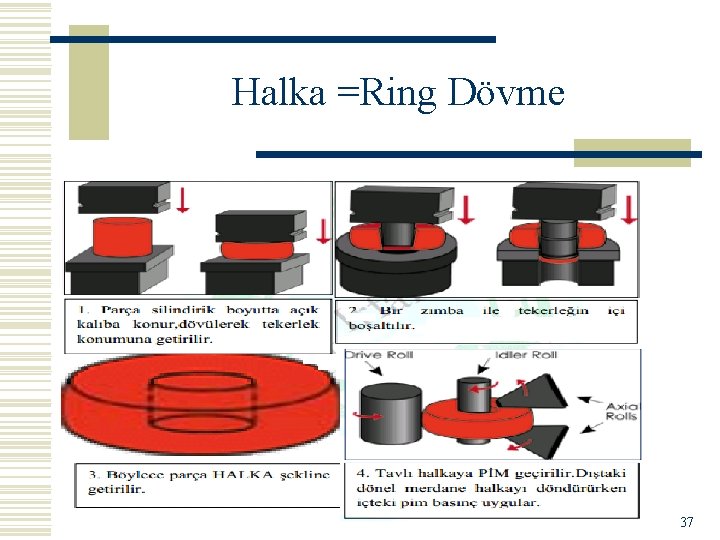
Halka =Ring Dövme 37
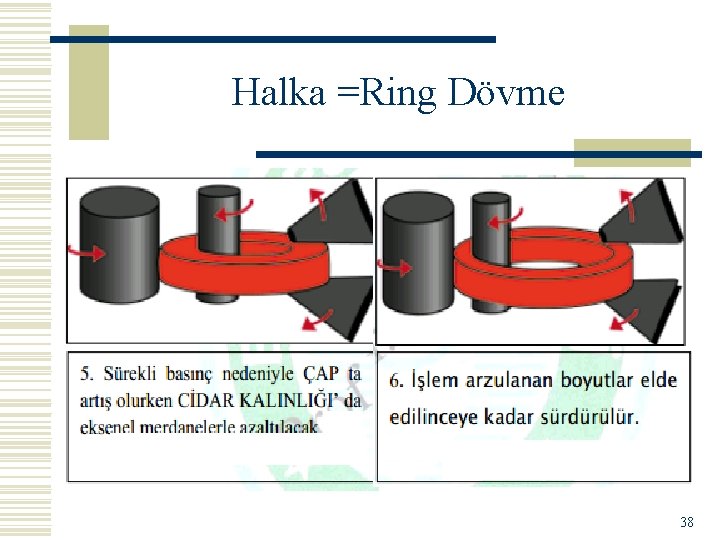
Halka =Ring Dövme 38
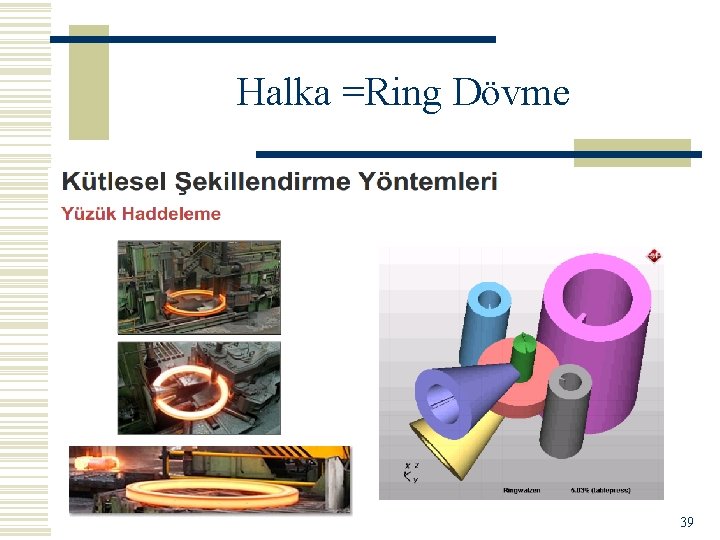
Halka =Ring Dövme 39
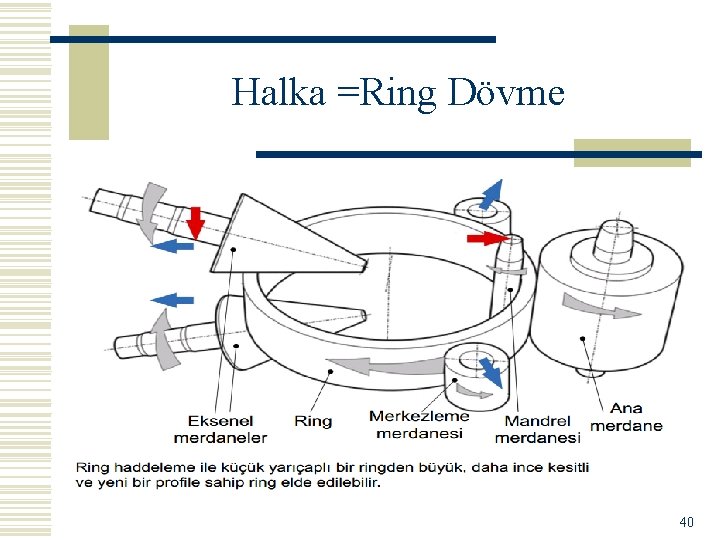
Halka =Ring Dövme 40
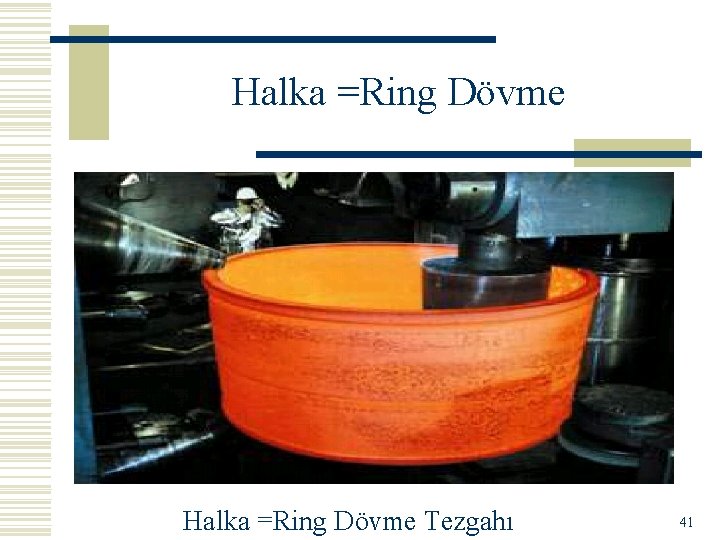
Halka =Ring Dövme Tezgahı 41

Halka =Ring Dövme 42
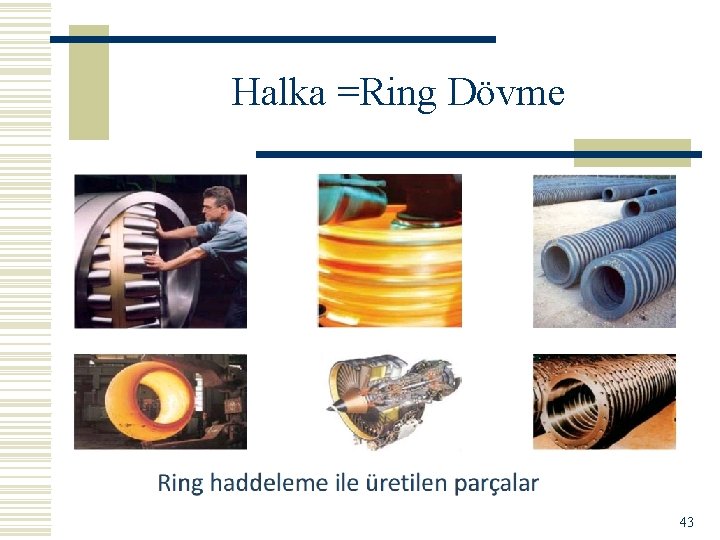
Halka =Ring Dövme 43
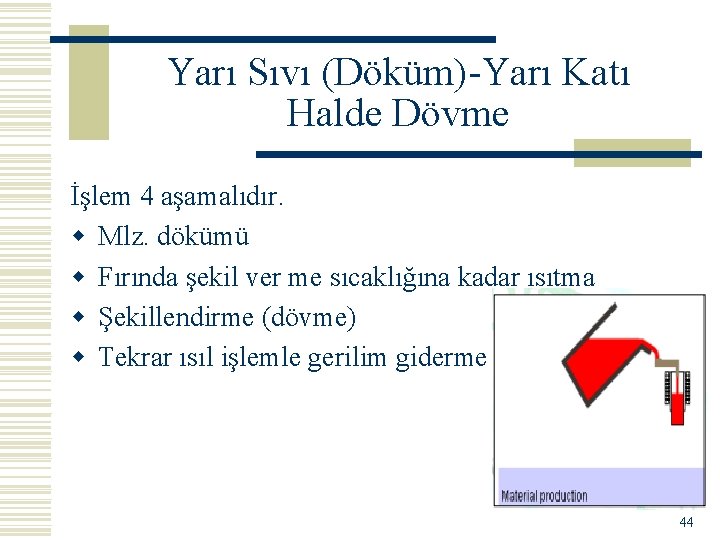
Yarı Sıvı (Döküm)-Yarı Katı Halde Dövme İşlem 4 aşamalıdır. w Mlz. dökümü w Fırında şekil ver me sıcaklığına kadar ısıtma w Şekillendirme (dövme) w Tekrar ısıl işlemle gerilim giderme 44
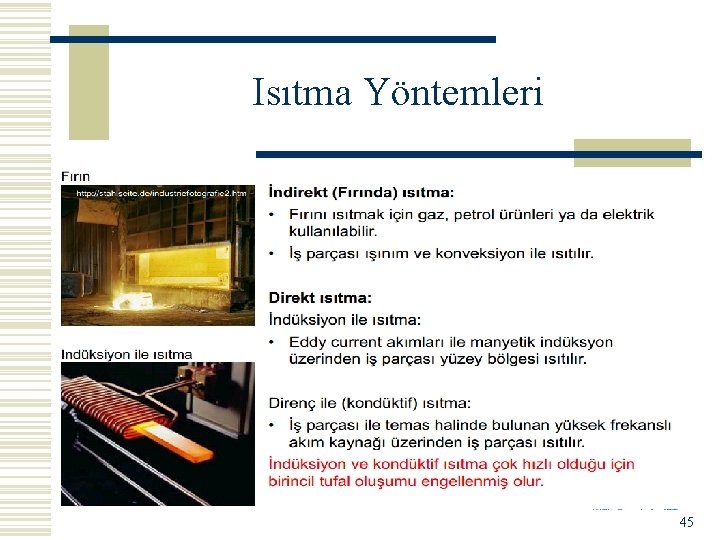
Isıtma Yöntemleri 45
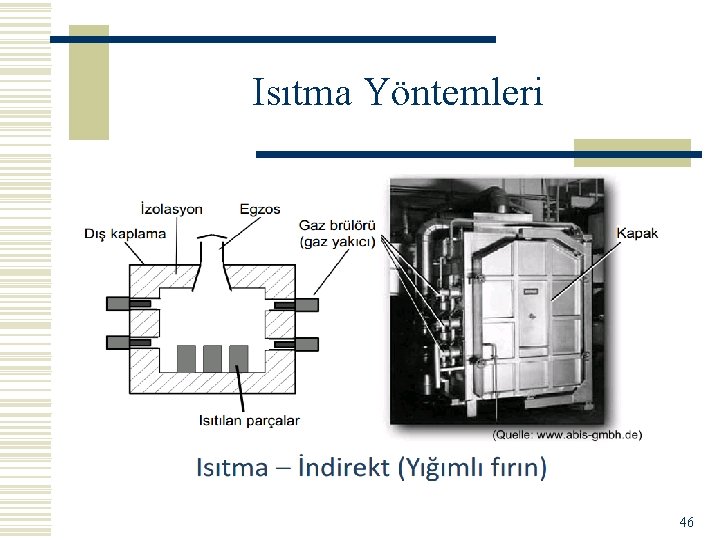
Isıtma Yöntemleri 46
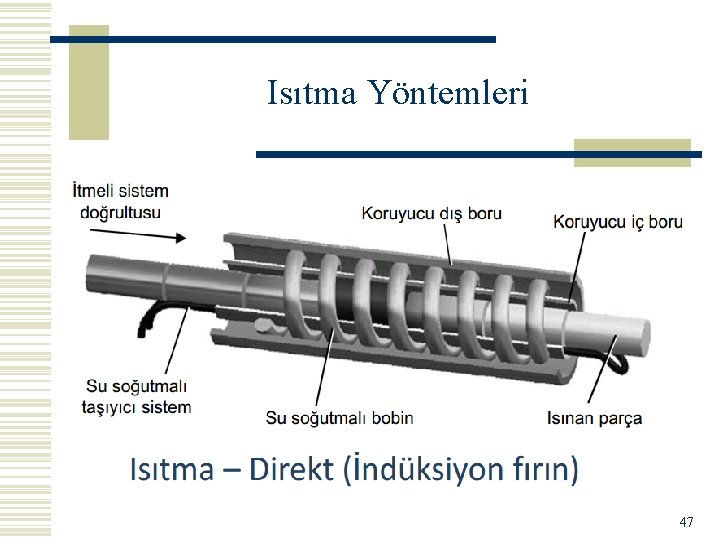
Isıtma Yöntemleri 47

Isıtma Yöntemleri 48
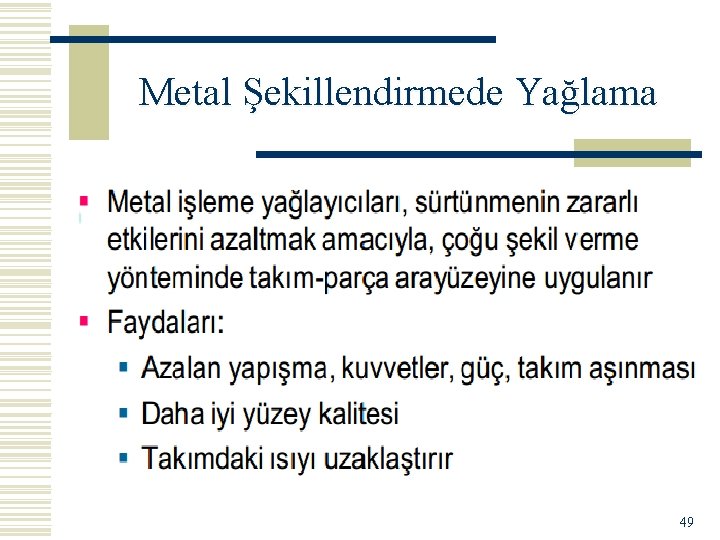
Metal Şekillendirmede Yağlama 49
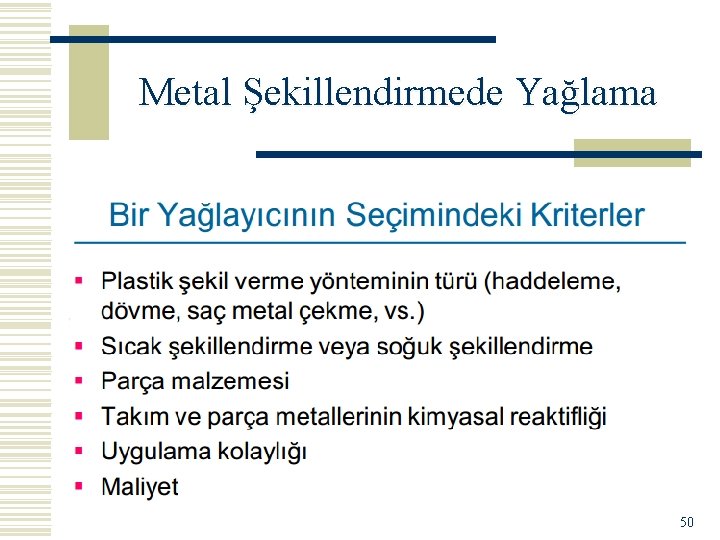
Metal Şekillendirmede Yağlama 50
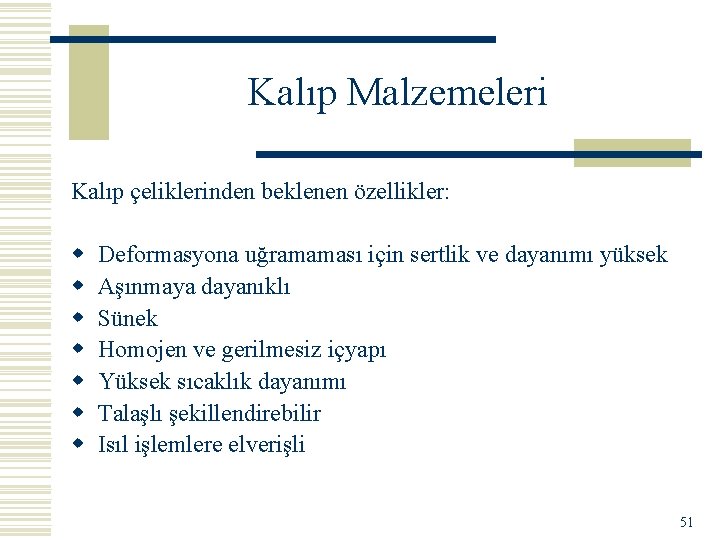
Kalıp Malzemeleri Kalıp çeliklerinden beklenen özellikler: w w w w Deformasyona uğramaması için sertlik ve dayanımı yüksek Aşınmaya dayanıklı Sünek Homojen ve gerilmesiz içyapı Yüksek sıcaklık dayanımı Talaşlı şekillendirebilir Isıl işlemlere elverişli 51
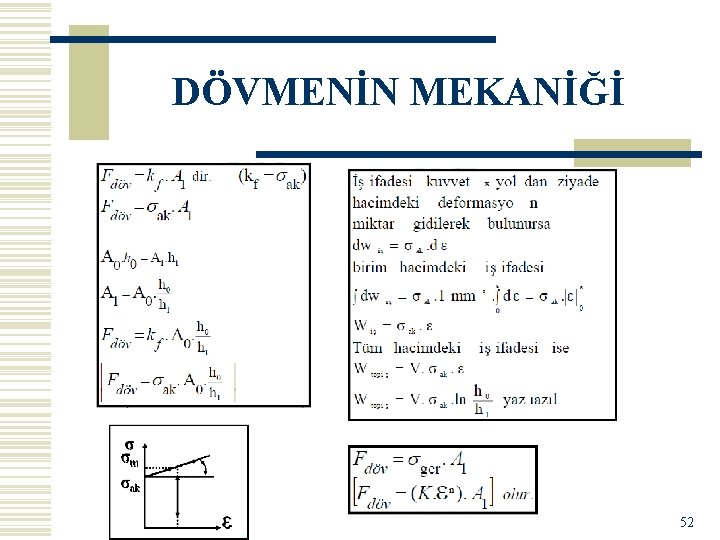
DÖVMENİN MEKANİĞİ 52

DÖVMENİN MEKANİĞİ Toplam dövme işi 53
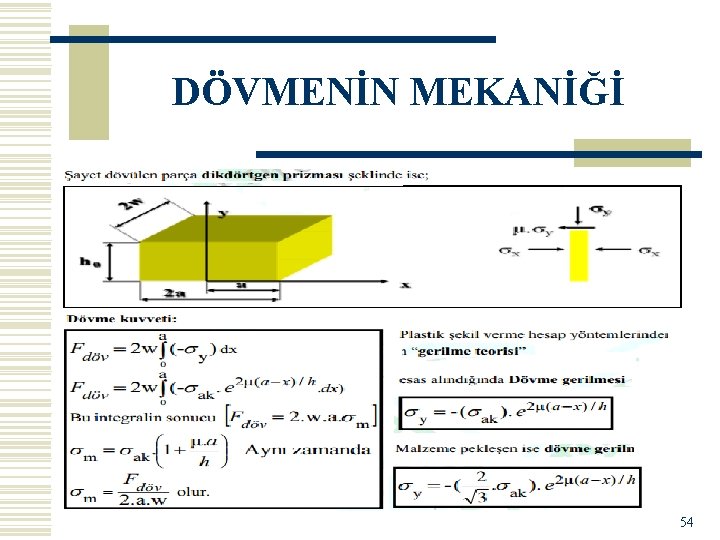
DÖVMENİN MEKANİĞİ 54
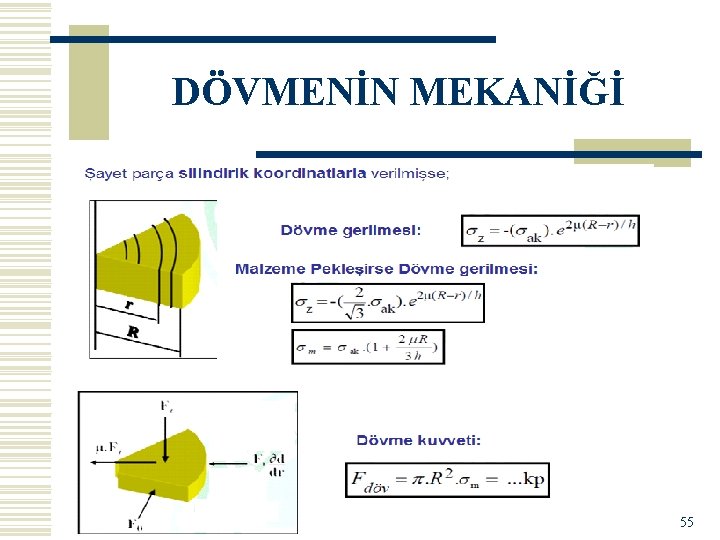
DÖVMENİN MEKANİĞİ 55
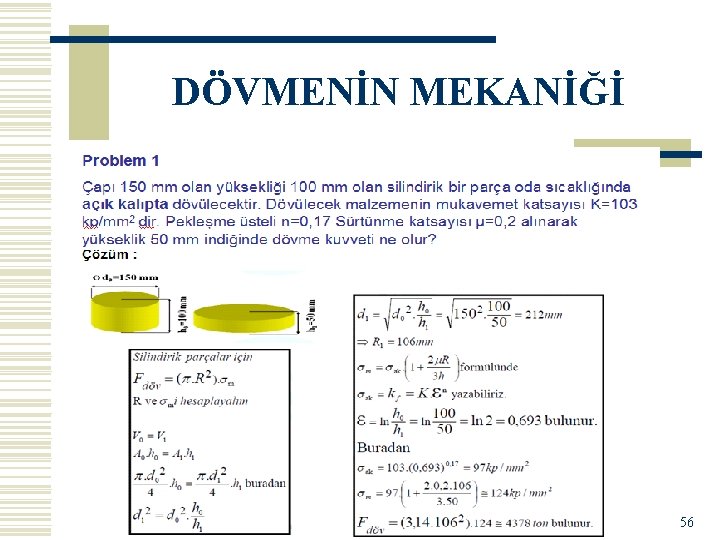
DÖVMENİN MEKANİĞİ 56
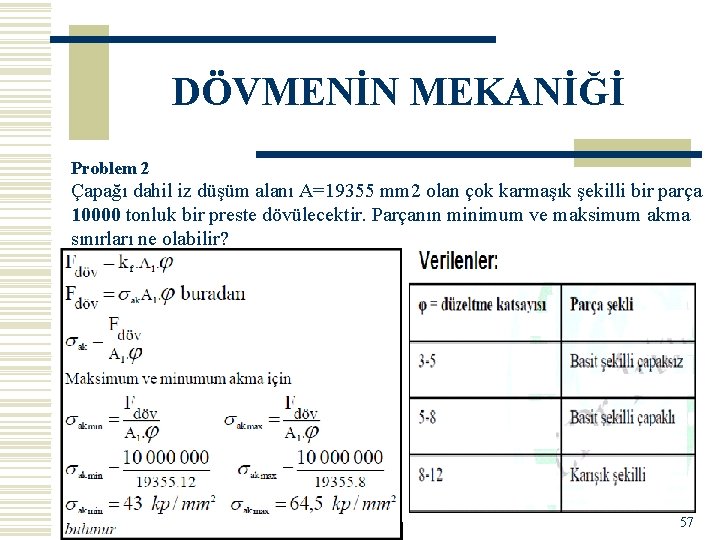
DÖVMENİN MEKANİĞİ Problem 2 Çapağı dahil iz düşüm alanı A=19355 mm 2 olan çok karmaşık şekilli bir parça 10000 tonluk bir preste dövülecektir. Parçanın minimum ve maksimum akma sınırları ne olabilir? 57
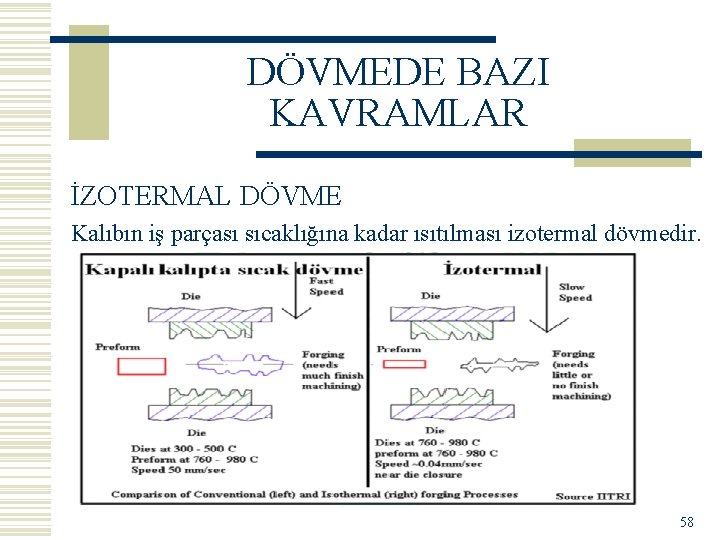
DÖVMEDE BAZI KAVRAMLAR İZOTERMAL DÖVME Kalıbın iş parçası sıcaklığına kadar ısıtılması izotermal dövmedir. 58
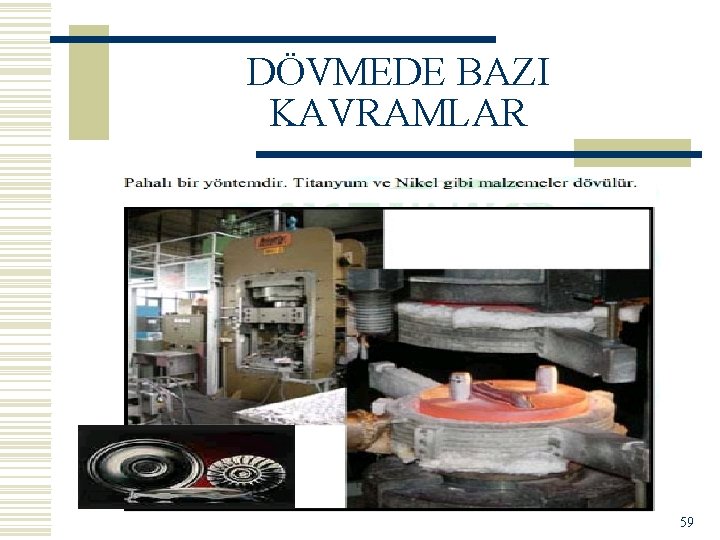
DÖVMEDE BAZI KAVRAMLAR 59
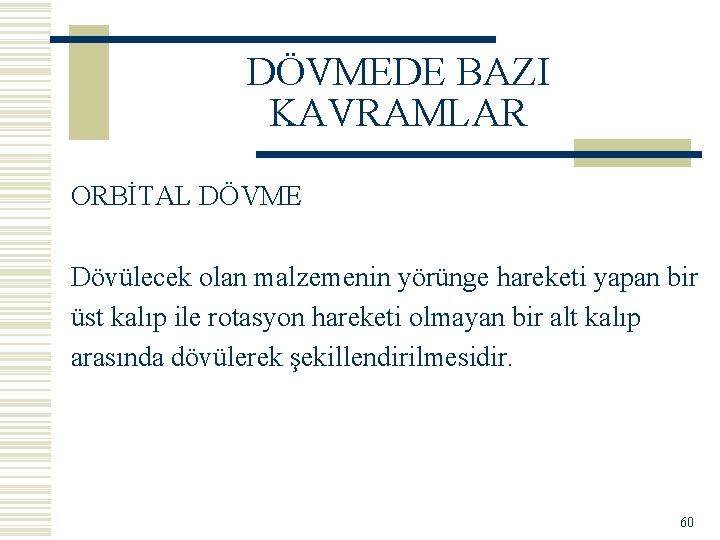
DÖVMEDE BAZI KAVRAMLAR ORBİTAL DÖVME Dövülecek olan malzemenin yörünge hareketi yapan bir üst kalıp ile rotasyon hareketi olmayan bir alt kalıp arasında dövülerek şekillendirilmesidir. 60
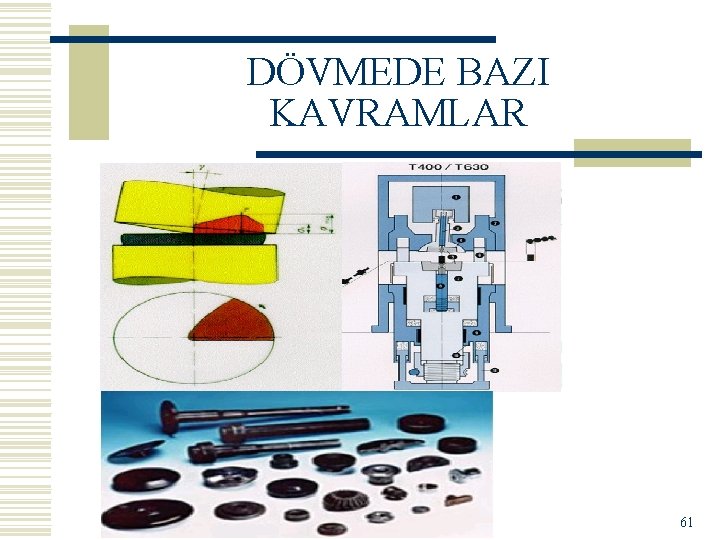
DÖVMEDE BAZI KAVRAMLAR 61
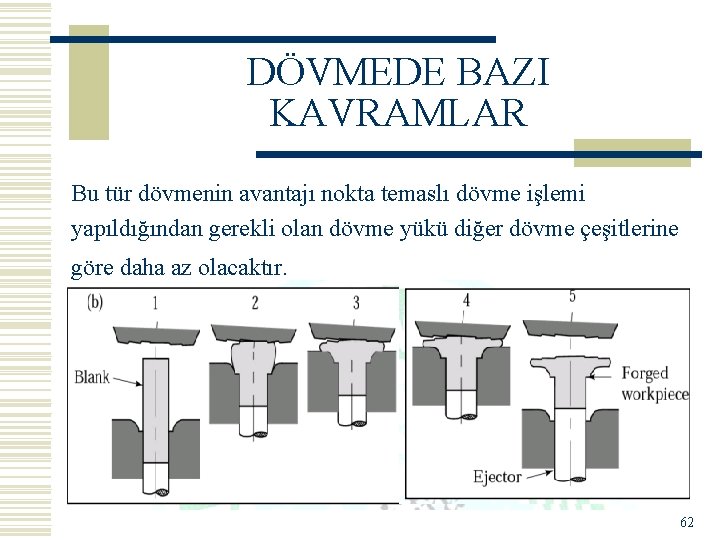
DÖVMEDE BAZI KAVRAMLAR Bu tür dövmenin avantajı nokta temaslı dövme işlemi yapıldığından gerekli olan dövme yükü diğer dövme çeşitlerine göre daha az olacaktır. 62
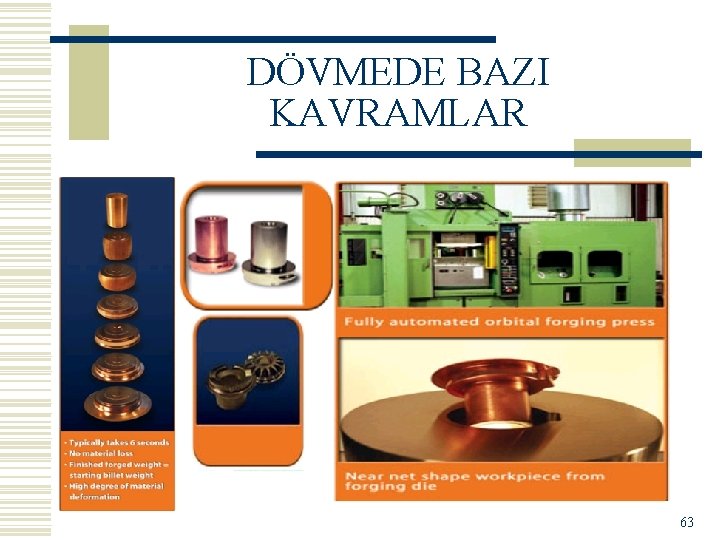
DÖVMEDE BAZI KAVRAMLAR 63
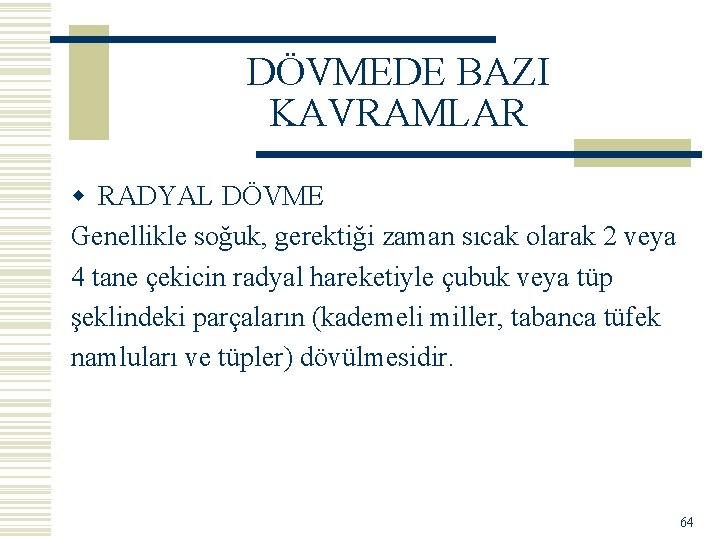
DÖVMEDE BAZI KAVRAMLAR w RADYAL DÖVME Genellikle soğuk, gerektiği zaman sıcak olarak 2 veya 4 tane çekicin radyal hareketiyle çubuk veya tüp şeklindeki parçaların (kademeli miller, tabanca tüfek namluları ve tüpler) dövülmesidir. 64

DÖVMEDE BAZI KAVRAMLAR 65
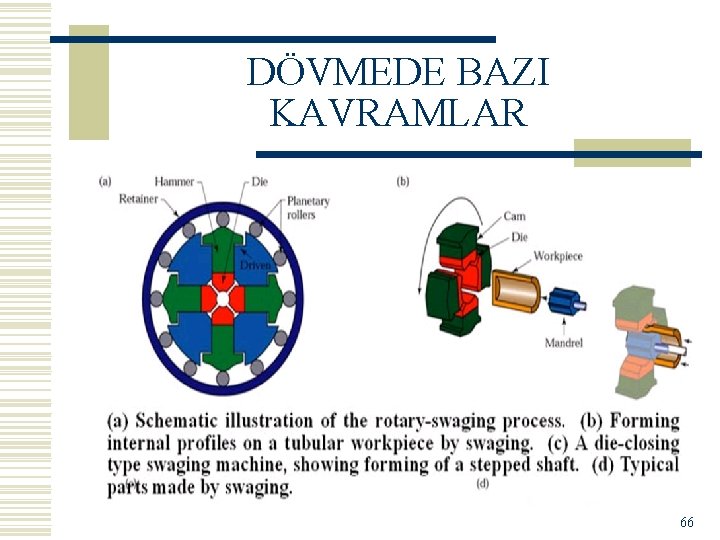
DÖVMEDE BAZI KAVRAMLAR 66
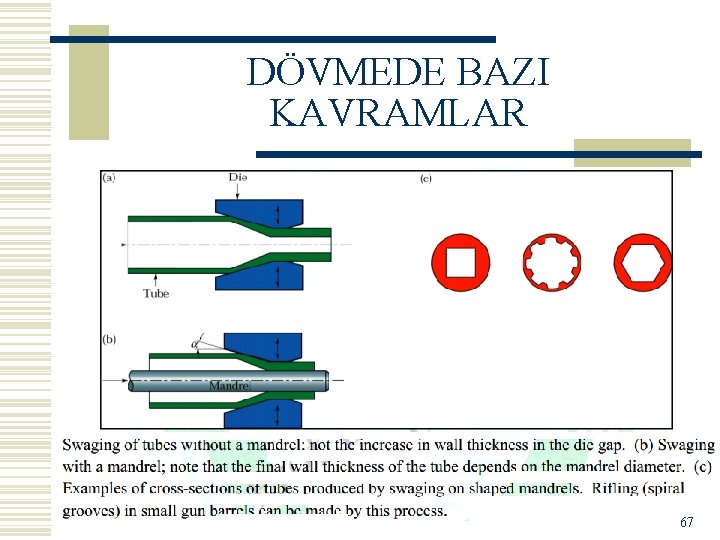
DÖVMEDE BAZI KAVRAMLAR 67
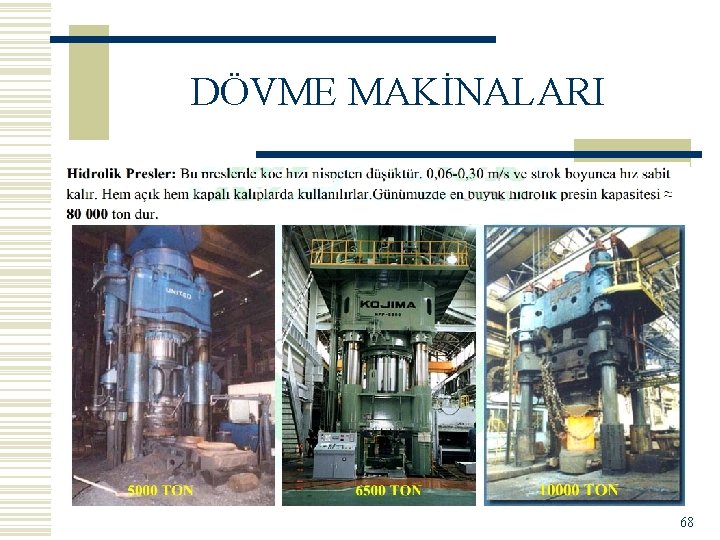
DÖVME MAKİNALARI 68
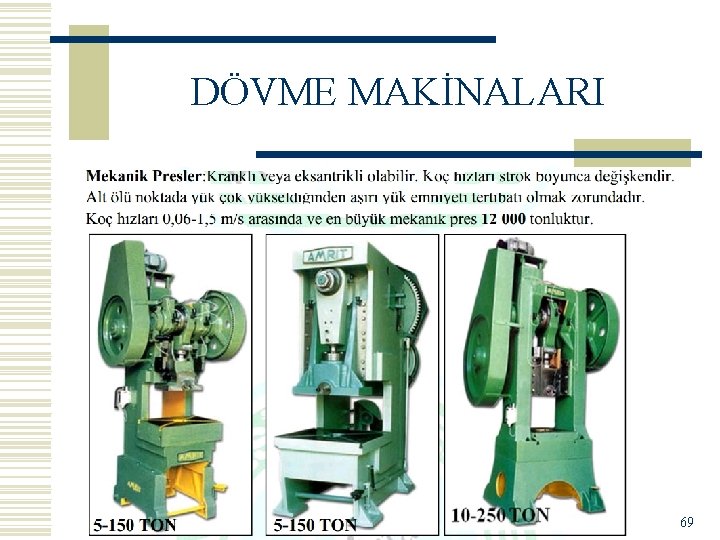
DÖVME MAKİNALARI 69
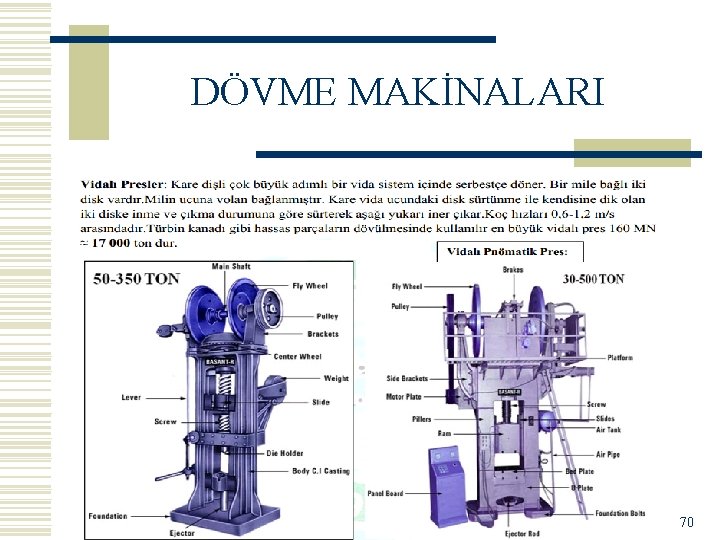
DÖVME MAKİNALARI 70
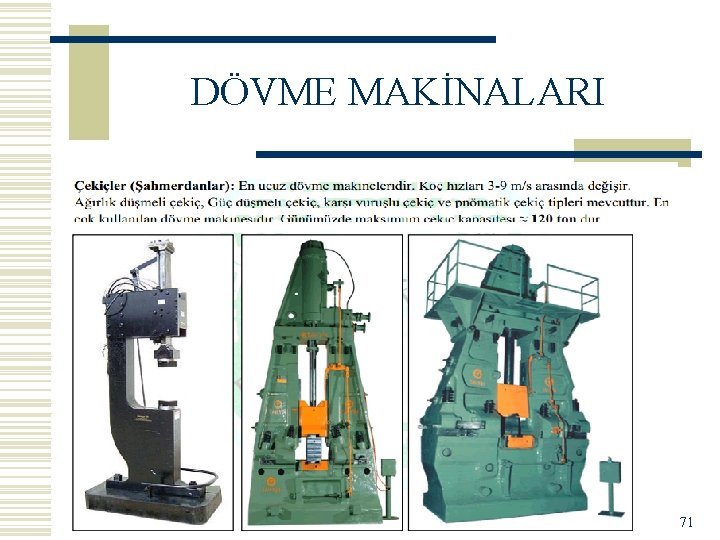
DÖVME MAKİNALARI 71
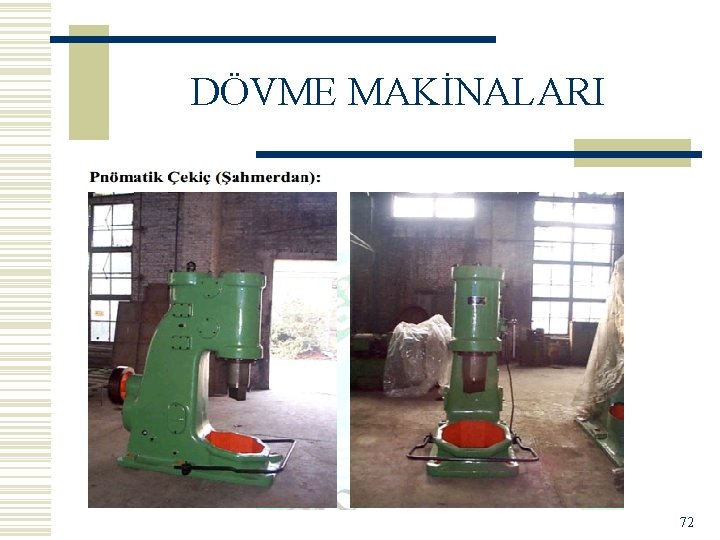
DÖVME MAKİNALARI 72
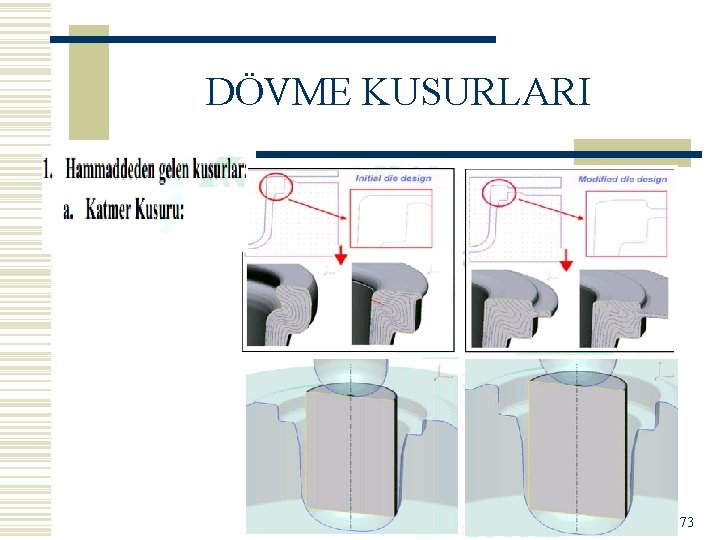
DÖVME KUSURLARI 73
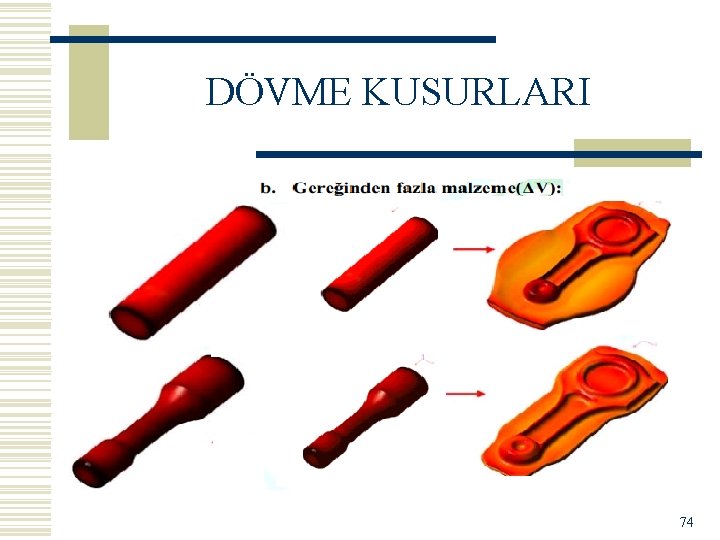
DÖVME KUSURLARI 74
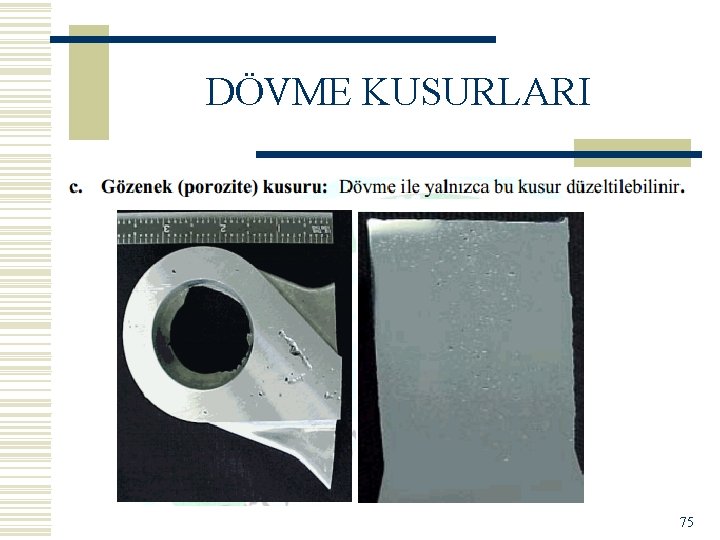
DÖVME KUSURLARI 75
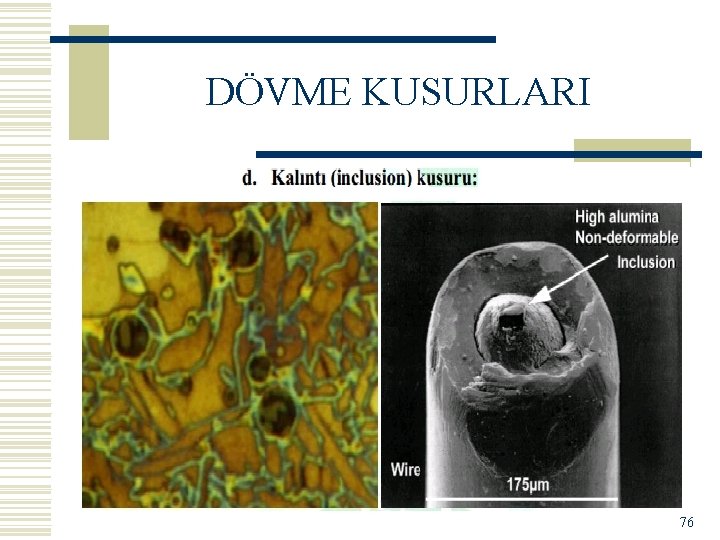
DÖVME KUSURLARI 76
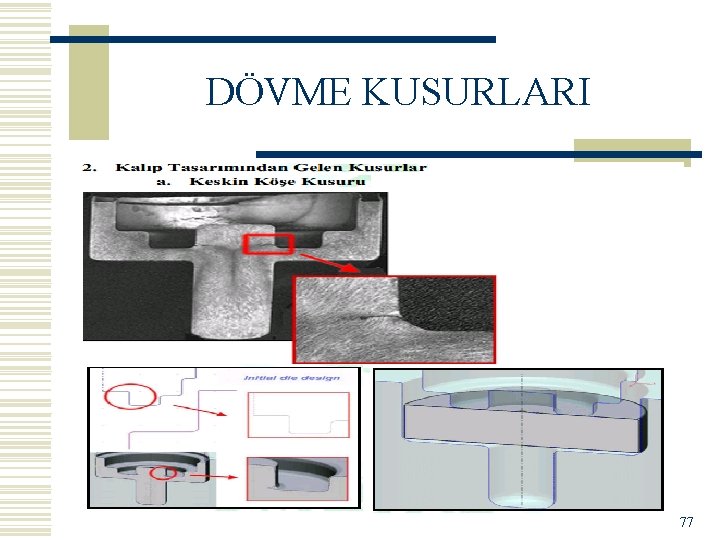
DÖVME KUSURLARI 77
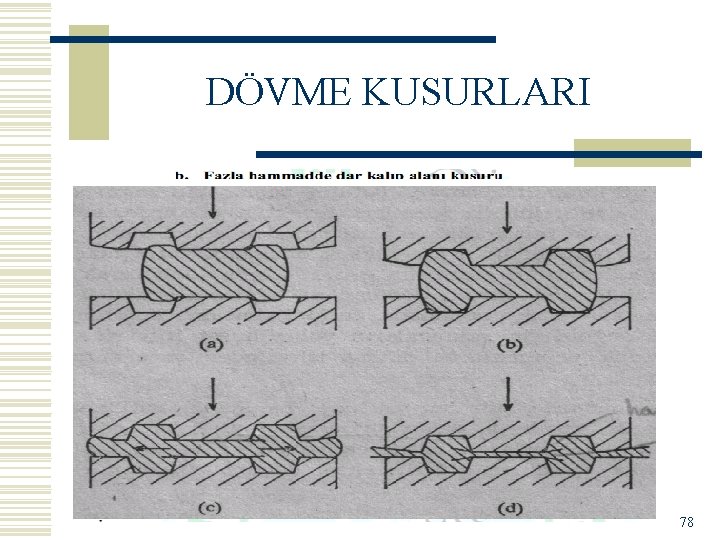
DÖVME KUSURLARI 78
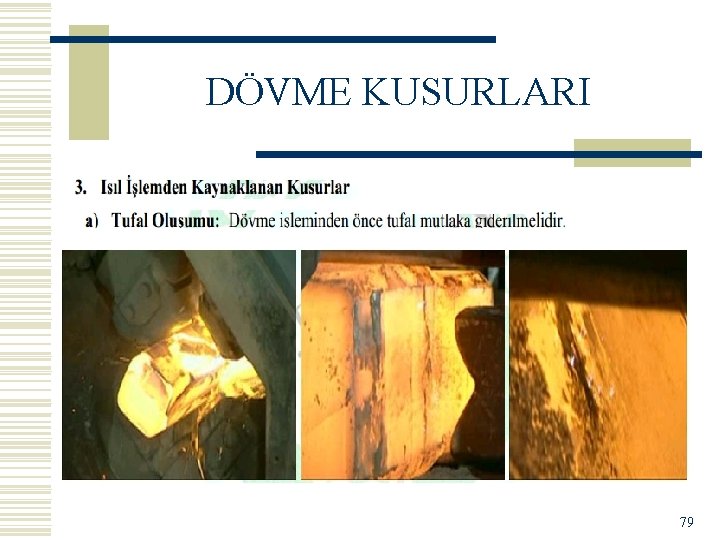
DÖVME KUSURLARI 79
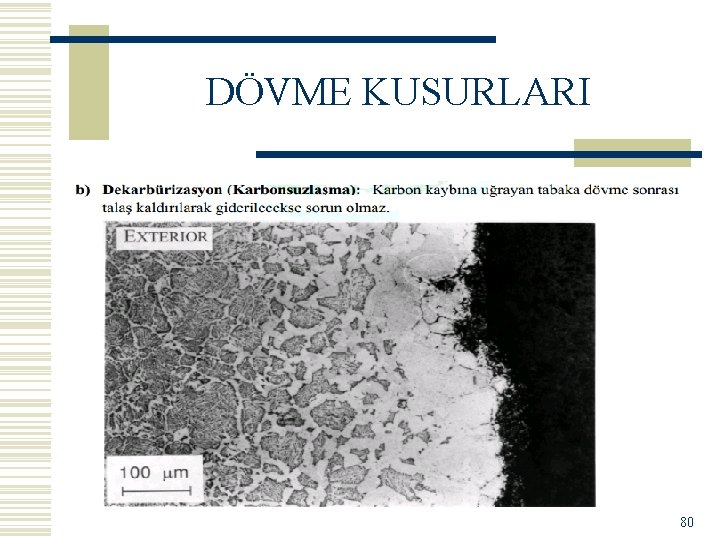
DÖVME KUSURLARI 80
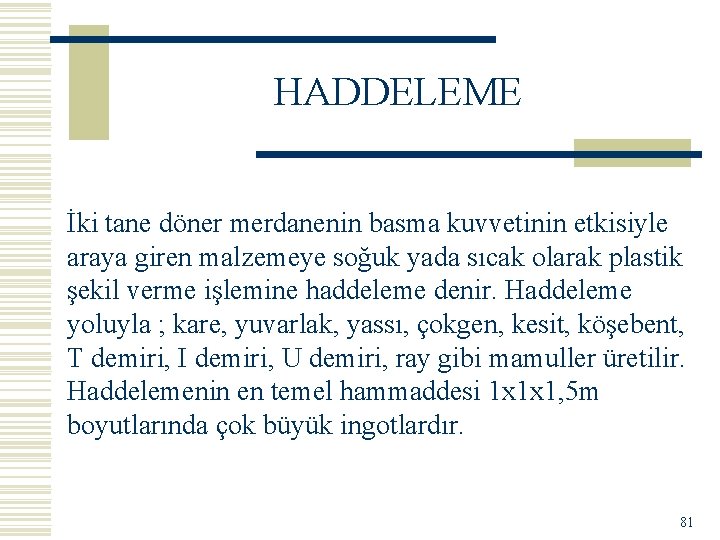
HADDELEME İki tane döner merdanenin basma kuvvetinin etkisiyle araya giren malzemeye soğuk yada sıcak olarak plastik şekil verme işlemine haddeleme denir. Haddeleme yoluyla ; kare, yuvarlak, yassı, çokgen, kesit, köşebent, T demiri, I demiri, U demiri, ray gibi mamuller üretilir. Haddelemenin en temel hammaddesi 1 x 1 x 1, 5 m boyutlarında çok büyük ingotlardır. 81
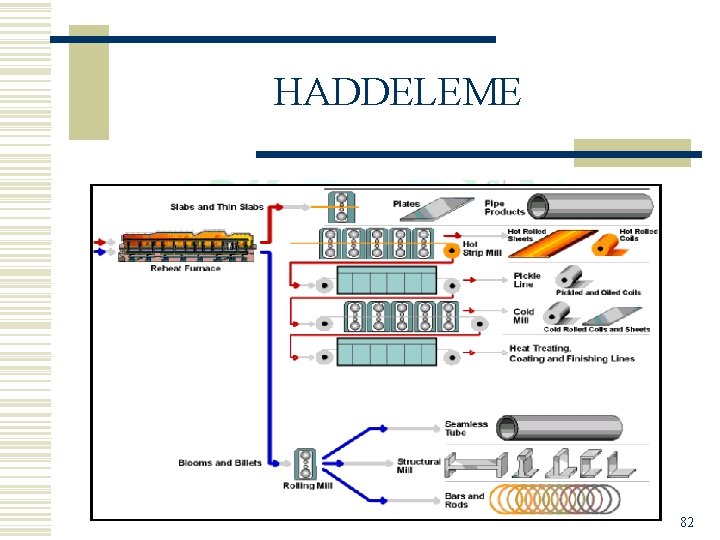
HADDELEME 82
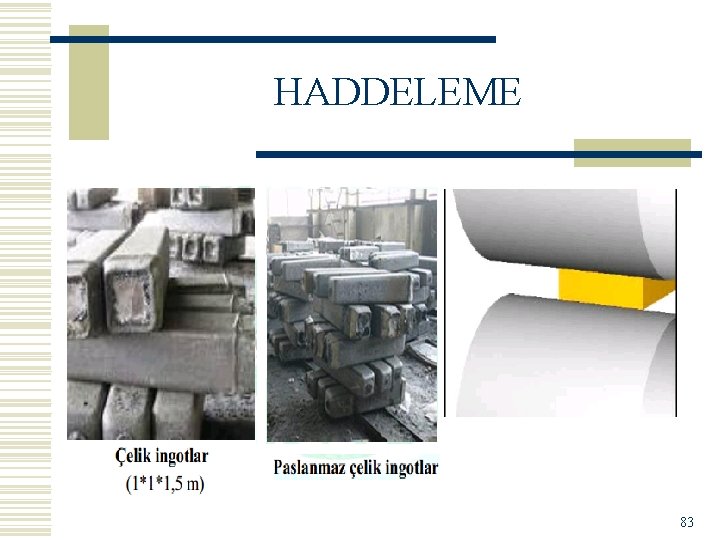
HADDELEME 83
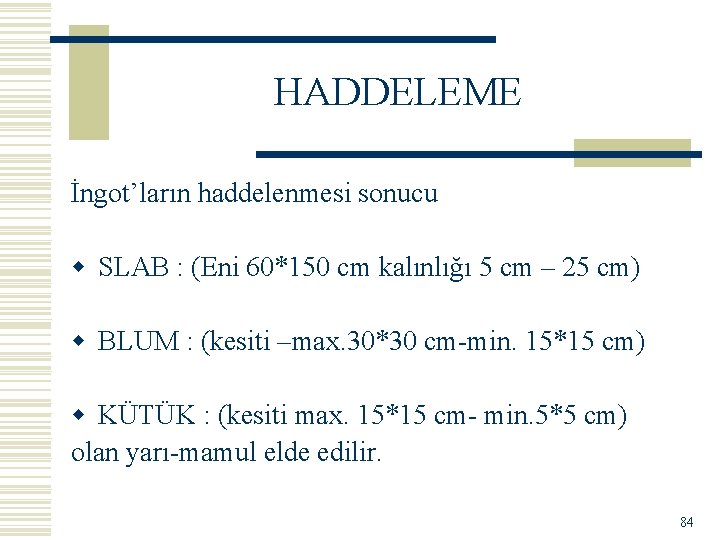
HADDELEME İngot’ların haddelenmesi sonucu w SLAB : (Eni 60*150 cm kalınlığı 5 cm – 25 cm) w BLUM : (kesiti –max. 30*30 cm-min. 15*15 cm) w KÜTÜK : (kesiti max. 15*15 cm- min. 5*5 cm) olan yarı-mamul elde edilir. 84
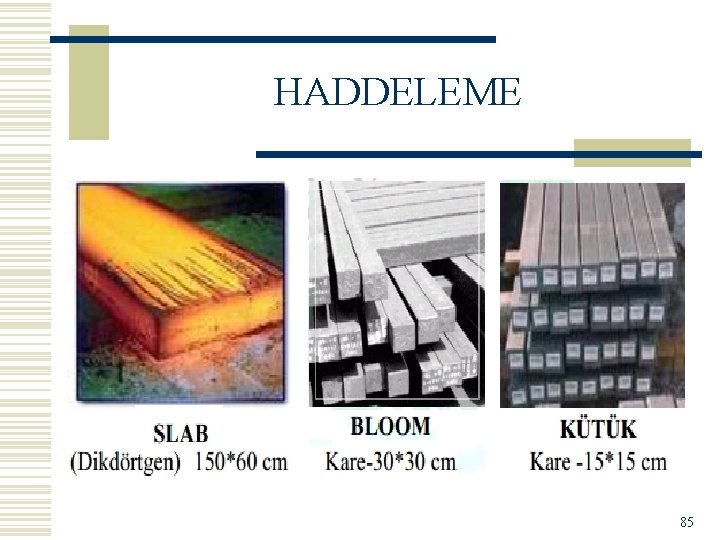
HADDELEME 85
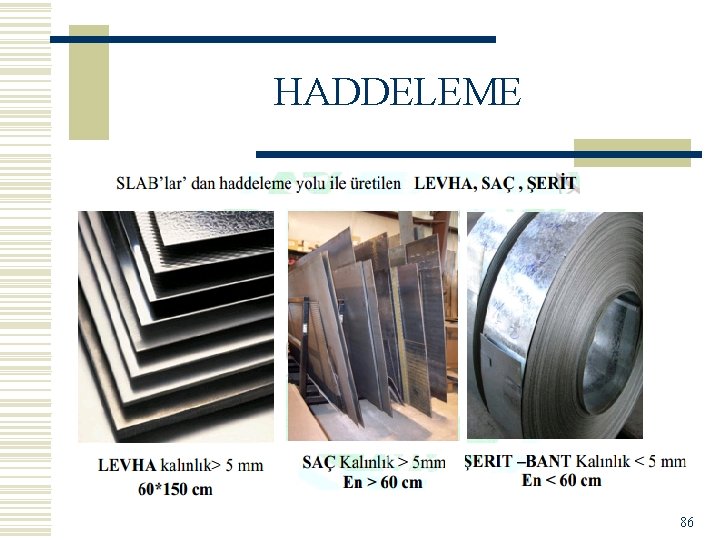
HADDELEME 86
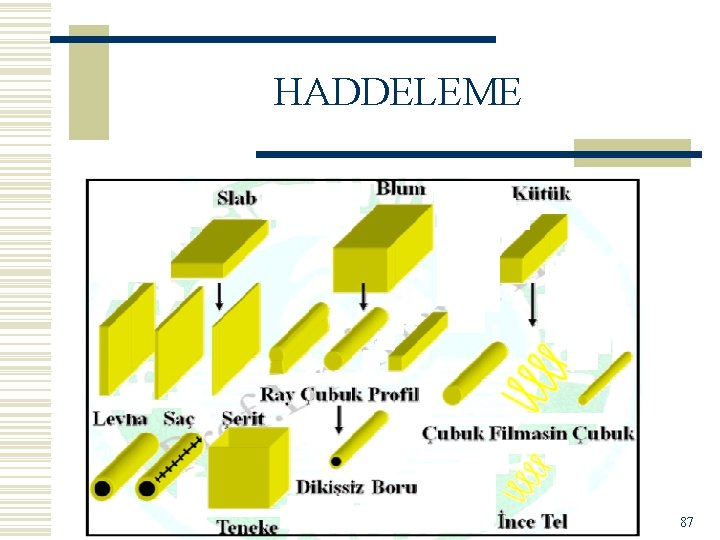
HADDELEME 87
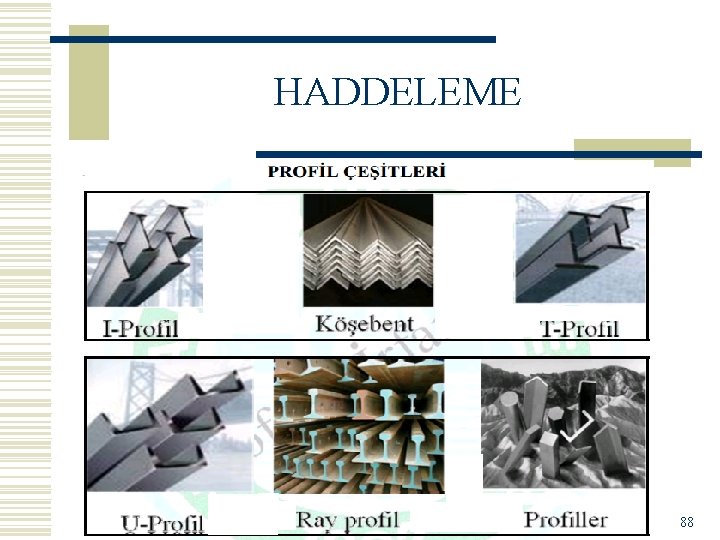
HADDELEME 88
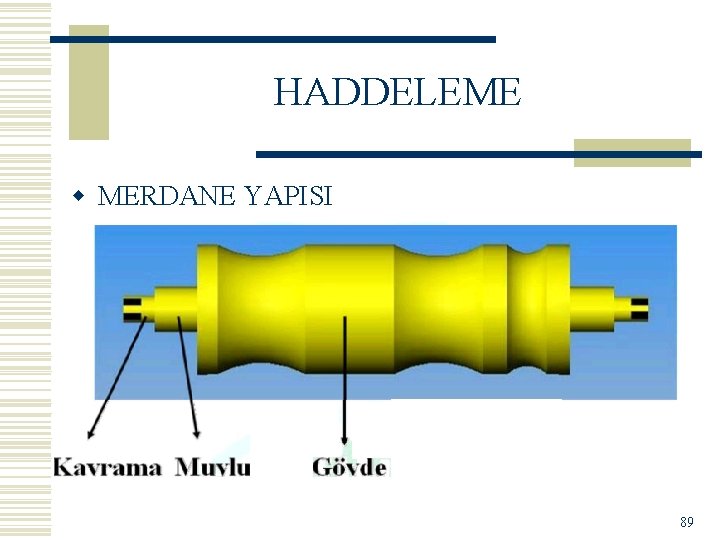
HADDELEME w MERDANE YAPISI 89
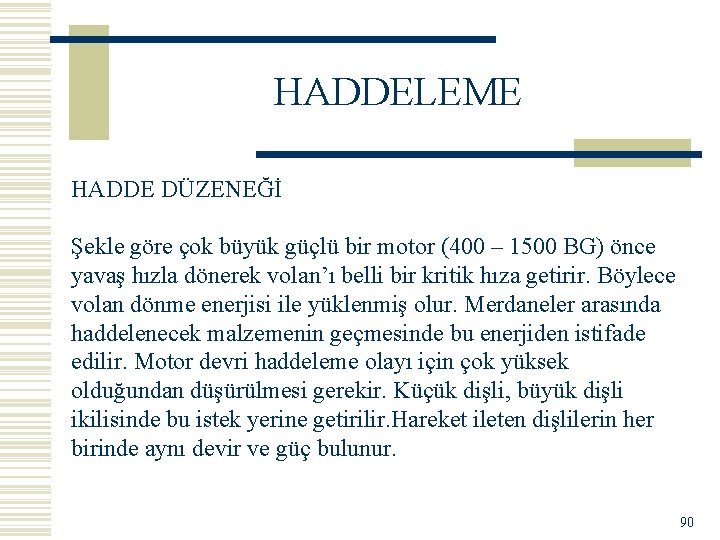
HADDELEME HADDE DÜZENEĞİ Şekle göre çok büyük güçlü bir motor (400 – 1500 BG) önce yavaş hızla dönerek volan’ı belli bir kritik hıza getirir. Böylece volan dönme enerjisi ile yüklenmiş olur. Merdaneler arasında haddelenecek malzemenin geçmesinde bu enerjiden istifade edilir. Motor devri haddeleme olayı için çok yüksek olduğundan düşürülmesi gerekir. Küçük dişli, büyük dişli ikilisinde bu istek yerine getirilir. Hareket ileten dişlilerin her birinde aynı devir ve güç bulunur. 90
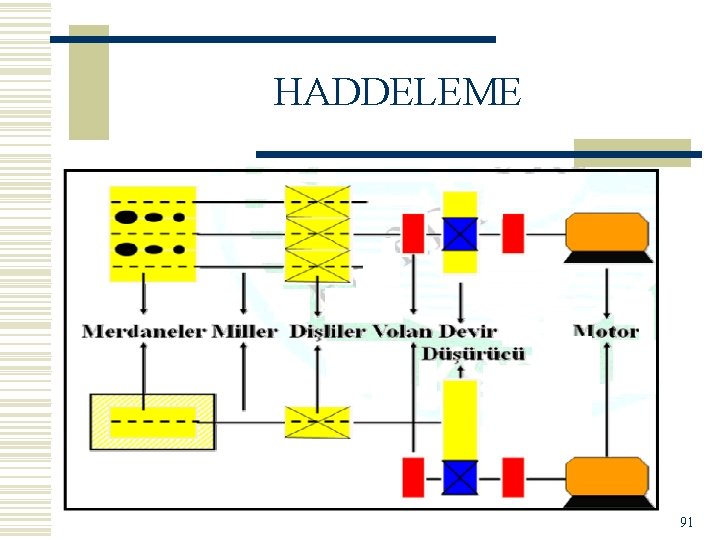
HADDELEME 91
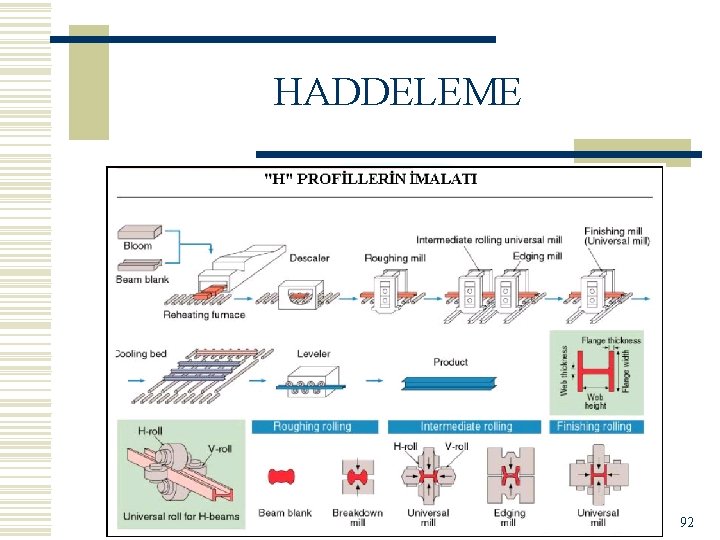
HADDELEME 92
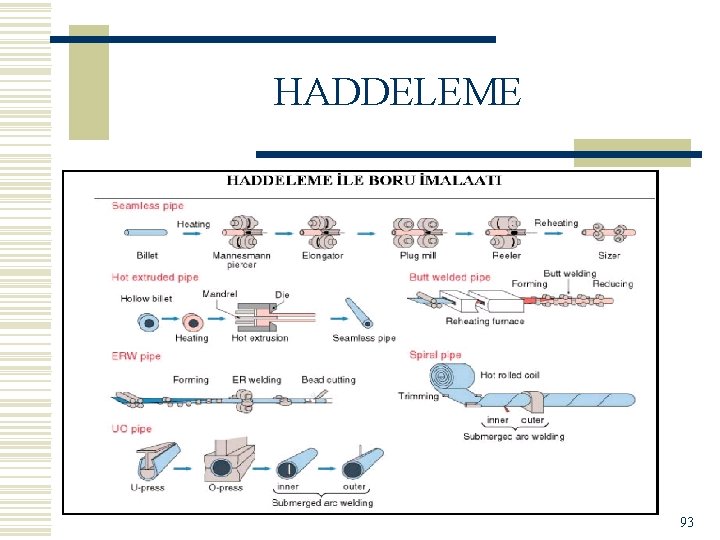
HADDELEME 93
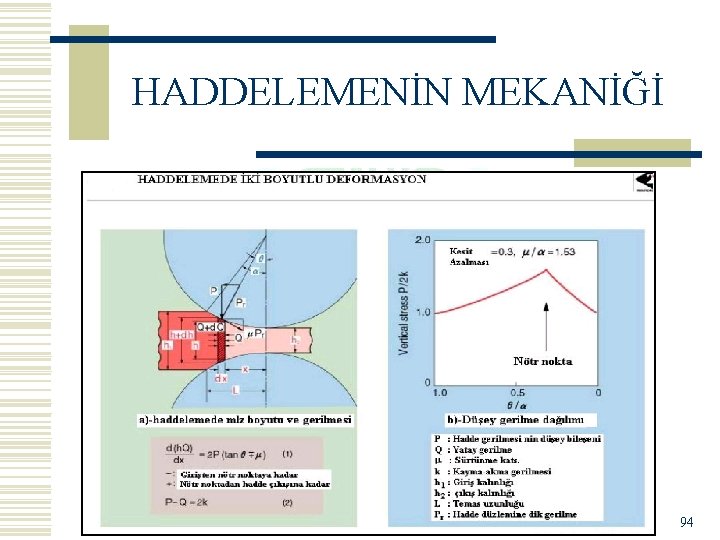
HADDELEMENİN MEKANİĞİ 94
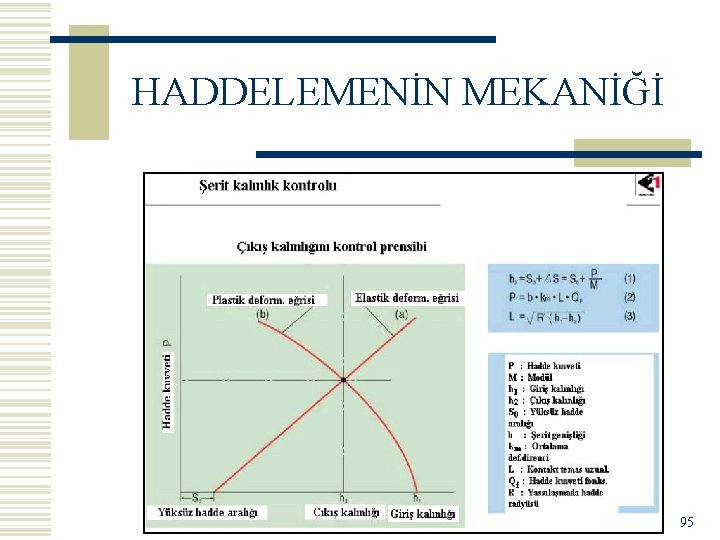
HADDELEMENİN MEKANİĞİ 95

HADDELEMENİN MEKANİĞİ 96
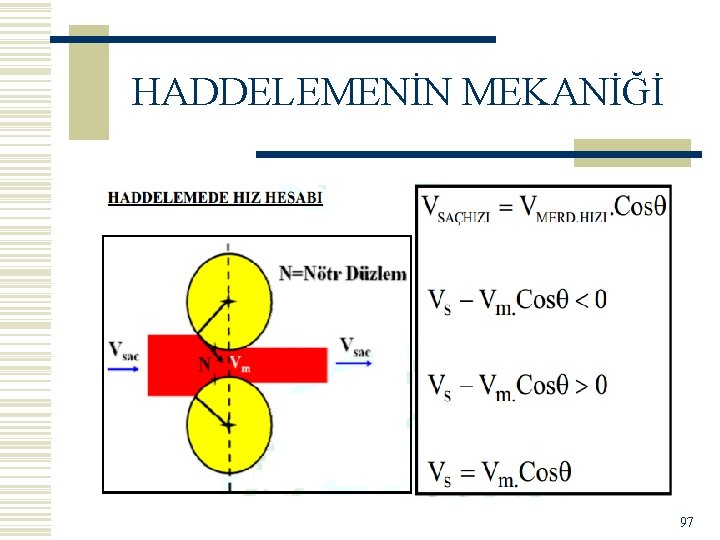
HADDELEMENİN MEKANİĞİ 97
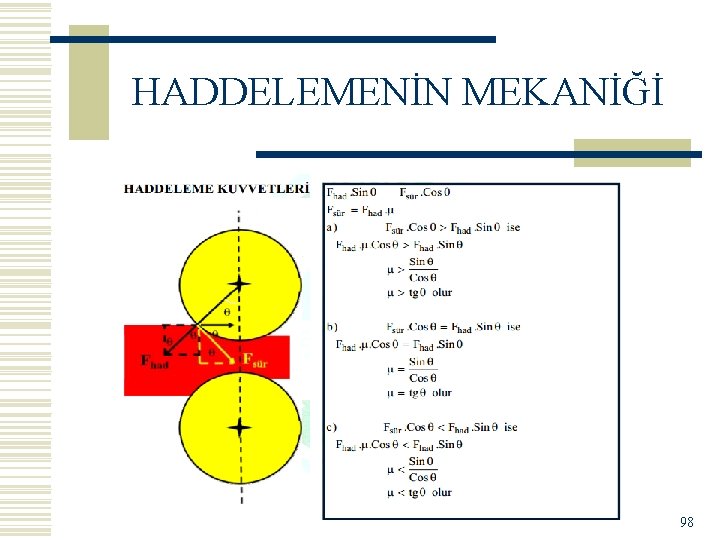
HADDELEMENİN MEKANİĞİ 98
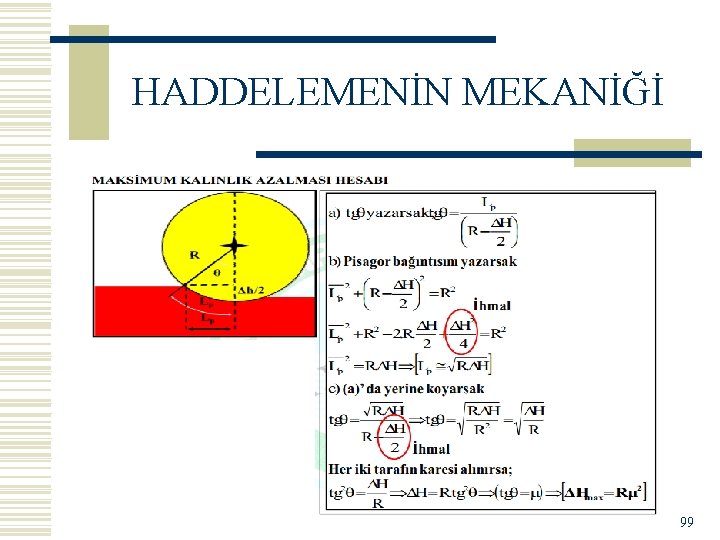
HADDELEMENİN MEKANİĞİ 99
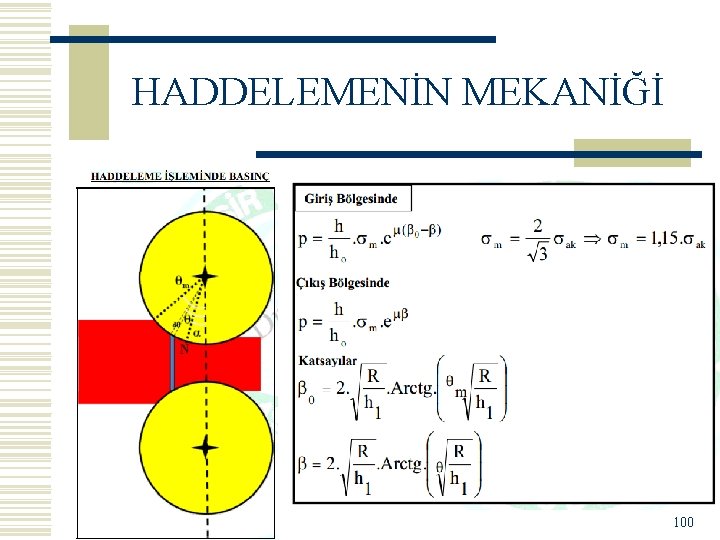
HADDELEMENİN MEKANİĞİ 100
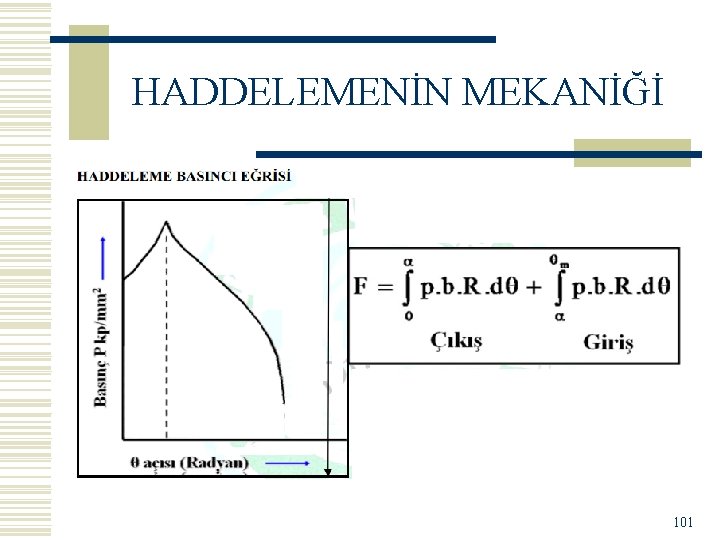
HADDELEMENİN MEKANİĞİ 101
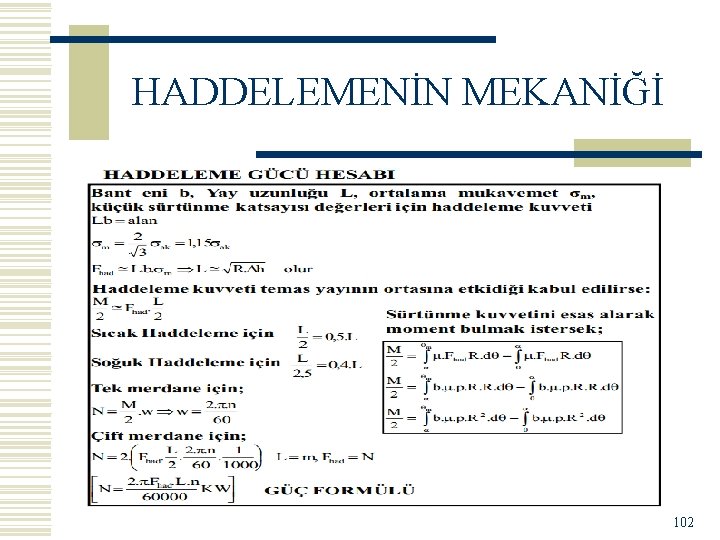
HADDELEMENİN MEKANİĞİ 102
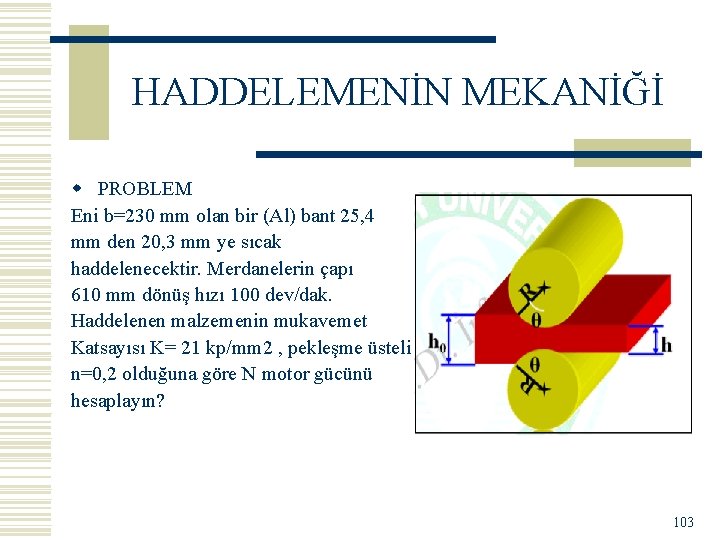
HADDELEMENİN MEKANİĞİ w PROBLEM Eni b=230 mm olan bir (Al) bant 25, 4 mm den 20, 3 mm ye sıcak haddelenecektir. Merdanelerin çapı 610 mm dönüş hızı 100 dev/dak. Haddelenen malzemenin mukavemet Katsayısı K= 21 kp/mm 2 , pekleşme üsteli n=0, 2 olduğuna göre N motor gücünü hesaplayın? 103
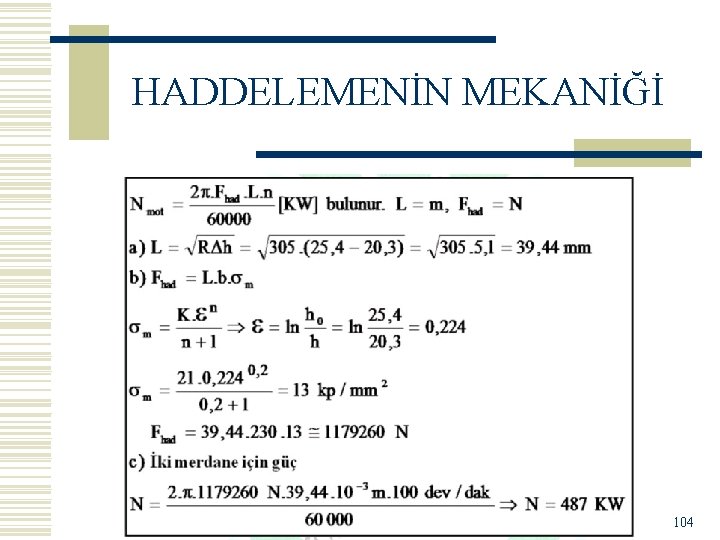
HADDELEMENİN MEKANİĞİ 104
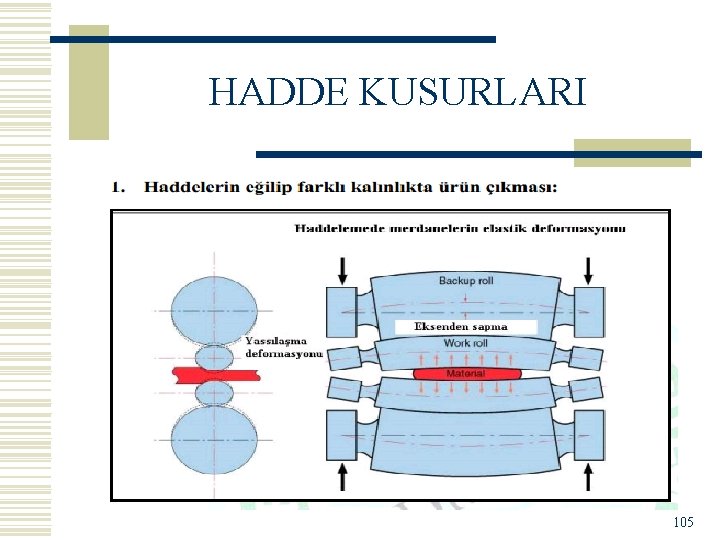
HADDE KUSURLARI 105
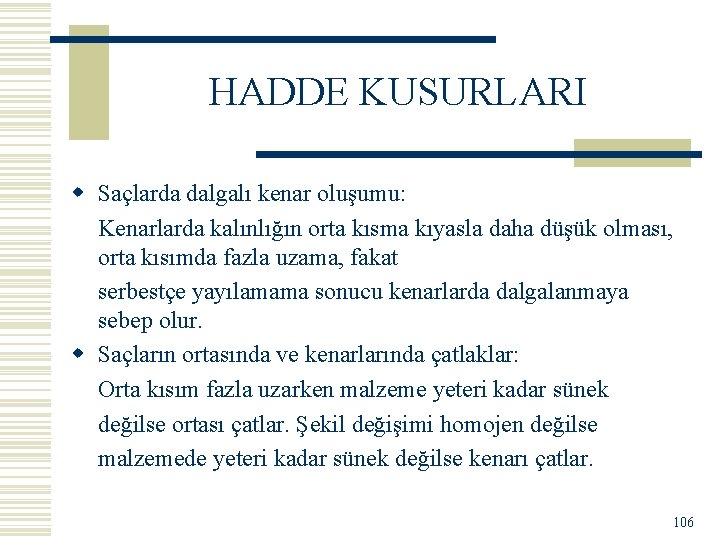
HADDE KUSURLARI w Saçlarda dalgalı kenar oluşumu: Kenarlarda kalınlığın orta kısma kıyasla daha düşük olması, orta kısımda fazla uzama, fakat serbestçe yayılamama sonucu kenarlarda dalgalanmaya sebep olur. w Saçların ortasında ve kenarlarında çatlaklar: Orta kısım fazla uzarken malzeme yeteri kadar sünek değilse ortası çatlar. Şekil değişimi homojen değilse malzemede yeteri kadar sünek değilse kenarı çatlar. 106
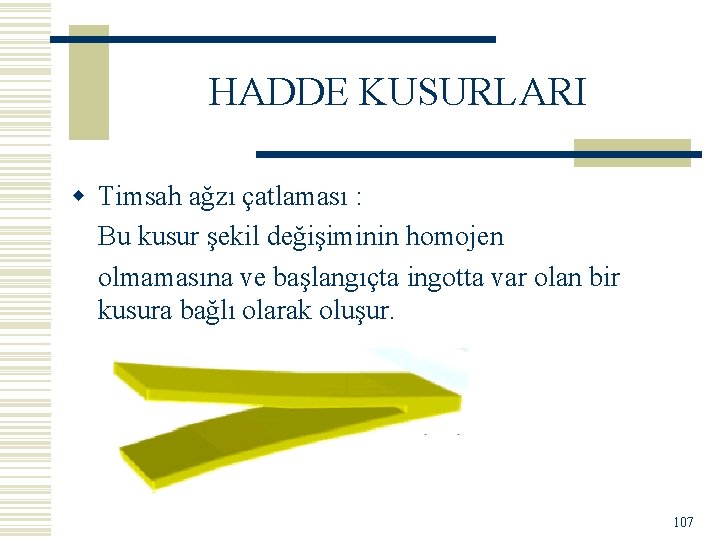
HADDE KUSURLARI w Timsah ağzı çatlaması : Bu kusur şekil değişiminin homojen olmamasına ve başlangıçta ingotta var olan bir kusura bağlı olarak oluşur. 107
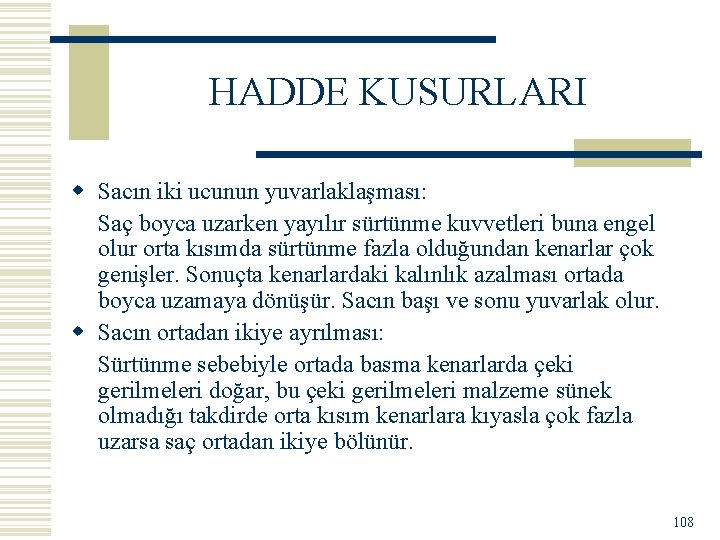
HADDE KUSURLARI w Sacın iki ucunun yuvarlaklaşması: Saç boyca uzarken yayılır sürtünme kuvvetleri buna engel olur orta kısımda sürtünme fazla olduğundan kenarlar çok genişler. Sonuçta kenarlardaki kalınlık azalması ortada boyca uzamaya dönüşür. Sacın başı ve sonu yuvarlak olur. w Sacın ortadan ikiye ayrılması: Sürtünme sebebiyle ortada basma kenarlarda çeki gerilmeleri doğar, bu çeki gerilmeleri malzeme sünek olmadığı takdirde orta kısım kenarlara kıyasla çok fazla uzarsa saç ortadan ikiye bölünür. 108
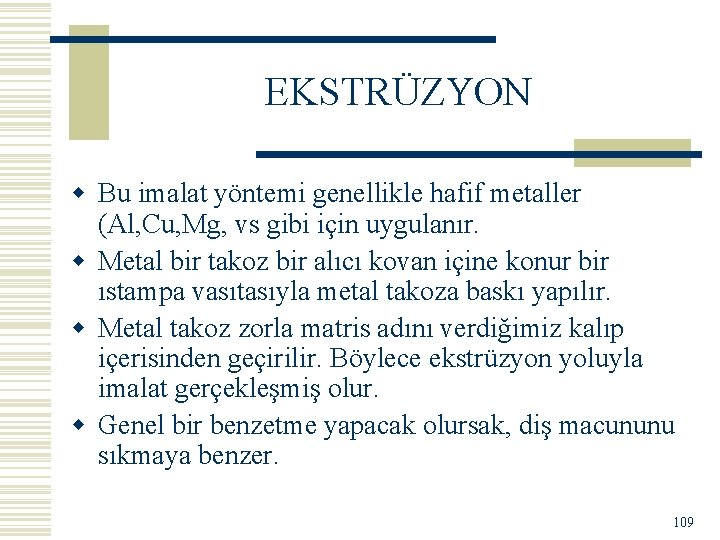
EKSTRÜZYON w Bu imalat yöntemi genellikle hafif metaller (Al, Cu, Mg, vs gibi için uygulanır. w Metal bir takoz bir alıcı kovan içine konur bir ıstampa vasıtasıyla metal takoza baskı yapılır. w Metal takoz zorla matris adını verdiğimiz kalıp içerisinden geçirilir. Böylece ekstrüzyon yoluyla imalat gerçekleşmiş olur. w Genel bir benzetme yapacak olursak, diş macununu sıkmaya benzer. 109
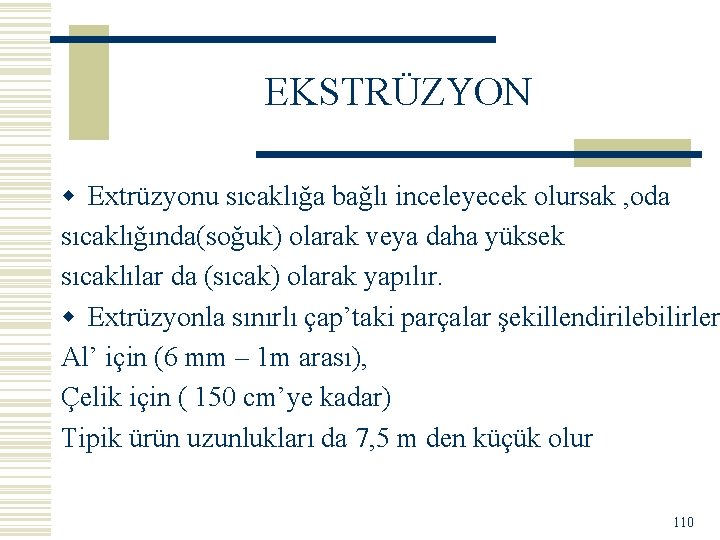
EKSTRÜZYON w Extrüzyonu sıcaklığa bağlı inceleyecek olursak , oda sıcaklığında(soğuk) olarak veya daha yüksek sıcaklılar da (sıcak) olarak yapılır. w Extrüzyonla sınırlı çap’taki parçalar şekillendirilebilirler Al’ için (6 mm – 1 m arası), Çelik için ( 150 cm’ye kadar) Tipik ürün uzunlukları da 7, 5 m den küçük olur 110
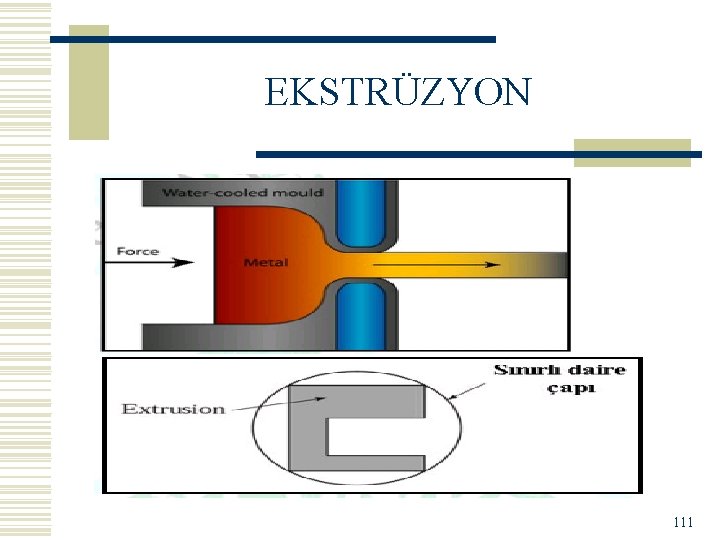
EKSTRÜZYON 111
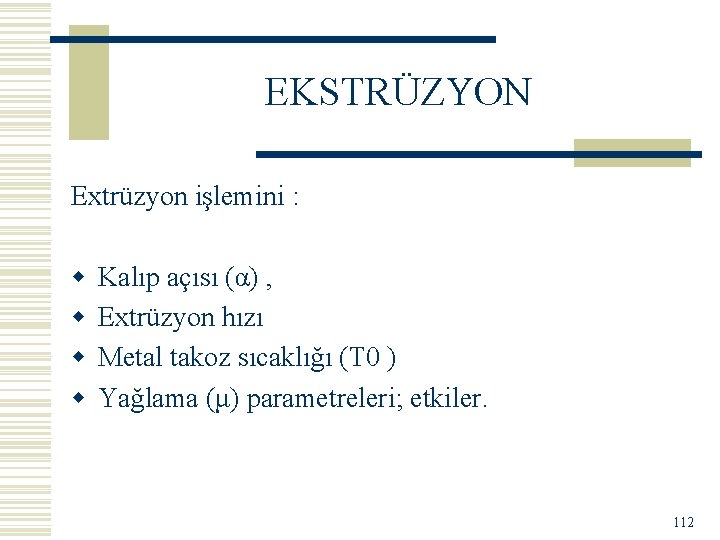
EKSTRÜZYON Extrüzyon işlemini : w w Kalıp açısı (α) , Extrüzyon hızı Metal takoz sıcaklığı (T 0 ) Yağlama (μ) parametreleri; etkiler. 112
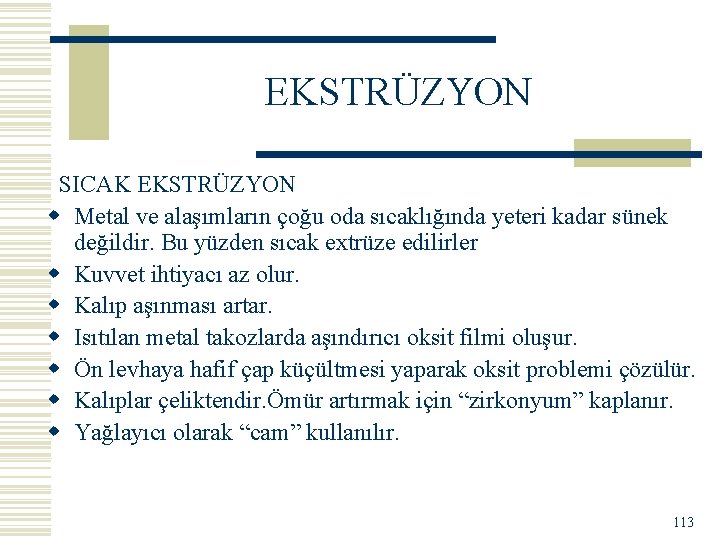
EKSTRÜZYON SICAK EKSTRÜZYON w Metal ve alaşımların çoğu oda sıcaklığında yeteri kadar sünek değildir. Bu yüzden sıcak extrüze edilirler w Kuvvet ihtiyacı az olur. w Kalıp aşınması artar. w Isıtılan metal takozlarda aşındırıcı oksit filmi oluşur. w Ön levhaya hafif çap küçültmesi yaparak oksit problemi çözülür. w Kalıplar çeliktendir. Ömür artırmak için “zirkonyum” kaplanır. w Yağlayıcı olarak “cam” kullanılır. 113
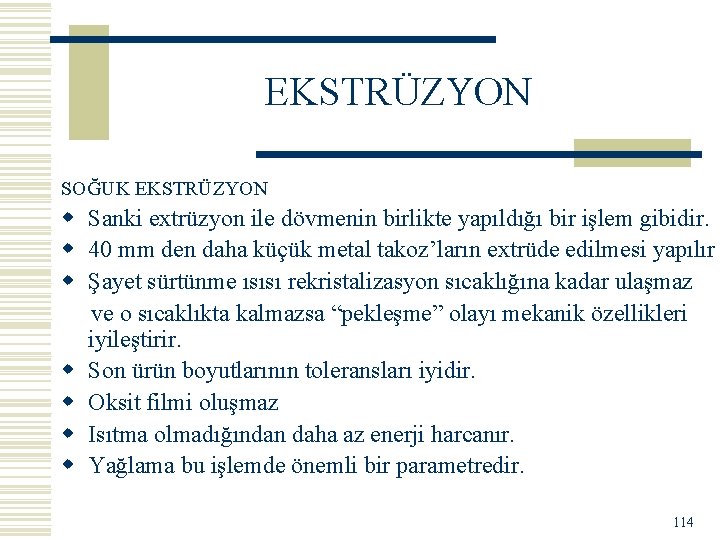
EKSTRÜZYON SOĞUK EKSTRÜZYON w Sanki extrüzyon ile dövmenin birlikte yapıldığı bir işlem gibidir. w 40 mm den daha küçük metal takoz’ların extrüde edilmesi yapılır w Şayet sürtünme ısısı rekristalizasyon sıcaklığına kadar ulaşmaz ve o sıcaklıkta kalmazsa “pekleşme” olayı mekanik özellikleri iyileştirir. w Son ürün boyutlarının toleransları iyidir. w Oksit filmi oluşmaz w Isıtma olmadığından daha az enerji harcanır. w Yağlama bu işlemde önemli bir parametredir. 114
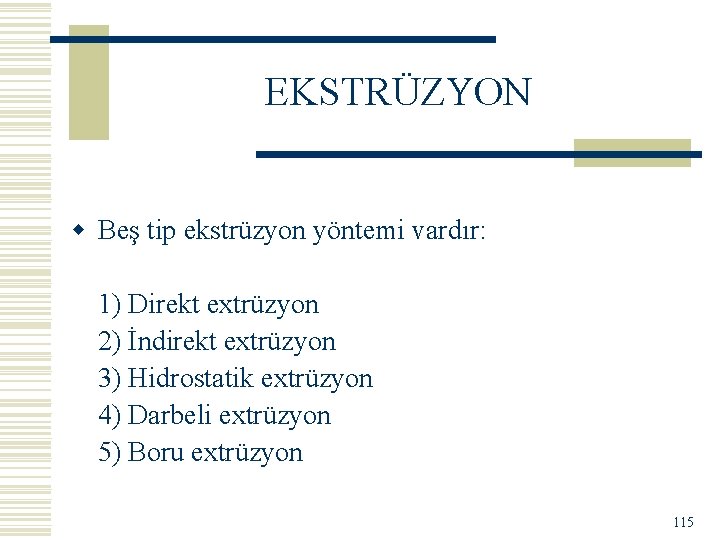
EKSTRÜZYON w Beş tip ekstrüzyon yöntemi vardır: 1) Direkt extrüzyon 2) İndirekt extrüzyon 3) Hidrostatik extrüzyon 4) Darbeli extrüzyon 5) Boru extrüzyon 115
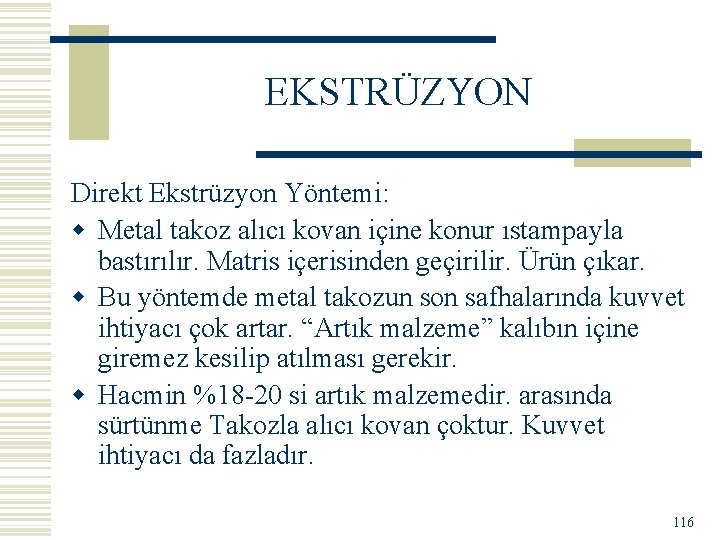
EKSTRÜZYON Direkt Ekstrüzyon Yöntemi: w Metal takoz alıcı kovan içine konur ıstampayla bastırılır. Matris içerisinden geçirilir. Ürün çıkar. w Bu yöntemde metal takozun son safhalarında kuvvet ihtiyacı çok artar. “Artık malzeme” kalıbın içine giremez kesilip atılması gerekir. w Hacmin %18 -20 si artık malzemedir. arasında sürtünme Takozla alıcı kovan çoktur. Kuvvet ihtiyacı da fazladır. 116
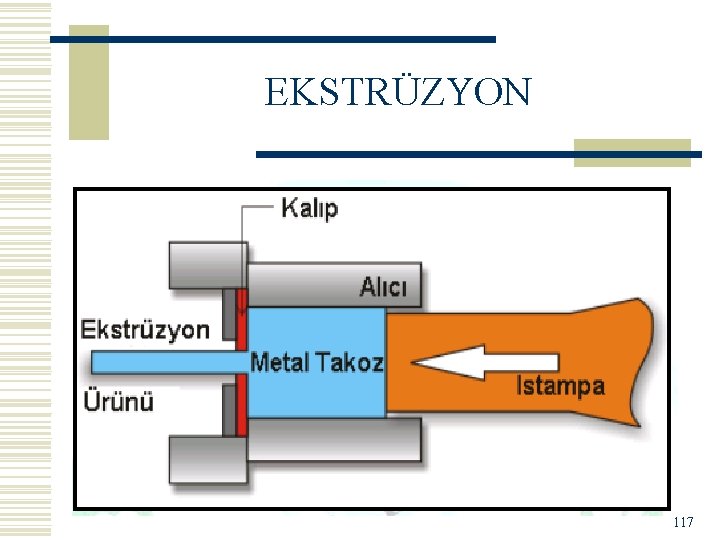
EKSTRÜZYON 117
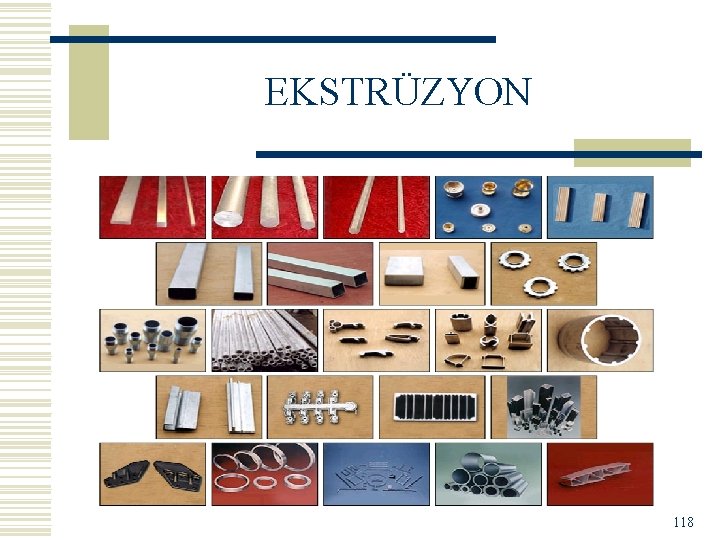
EKSTRÜZYON 118
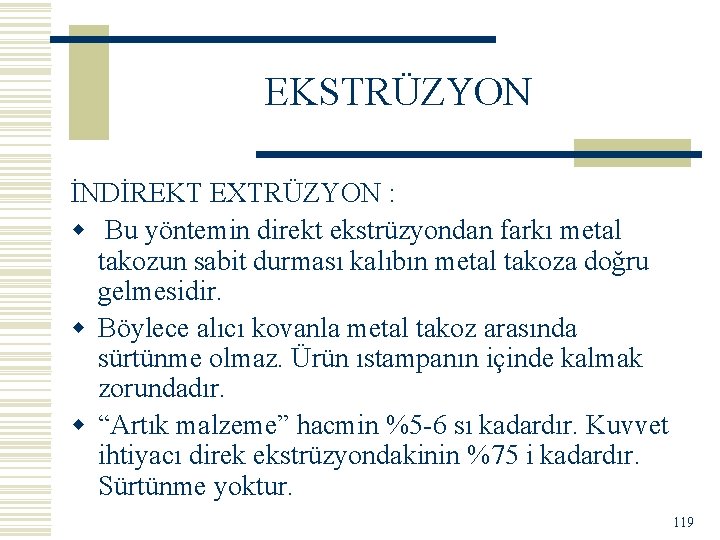
EKSTRÜZYON İNDİREKT EXTRÜZYON : w Bu yöntemin direkt ekstrüzyondan farkı metal takozun sabit durması kalıbın metal takoza doğru gelmesidir. w Böylece alıcı kovanla metal takoz arasında sürtünme olmaz. Ürün ıstampanın içinde kalmak zorundadır. w “Artık malzeme” hacmin %5 -6 sı kadardır. Kuvvet ihtiyacı direk ekstrüzyondakinin %75 i kadardır. Sürtünme yoktur. 119
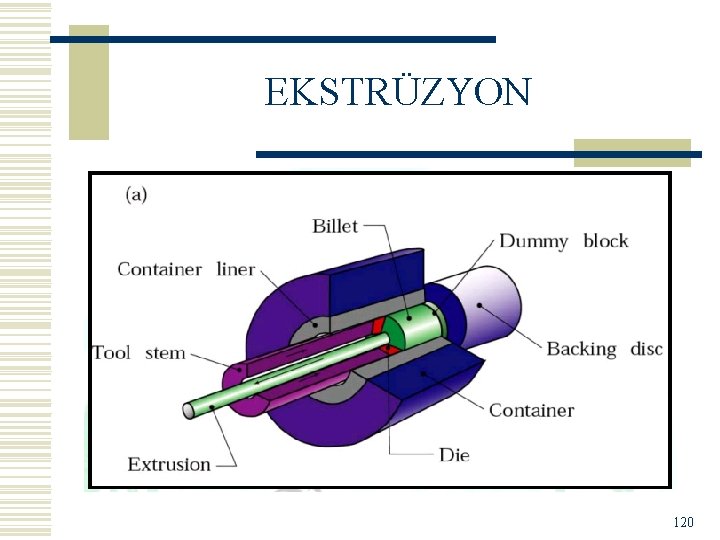
EKSTRÜZYON 120
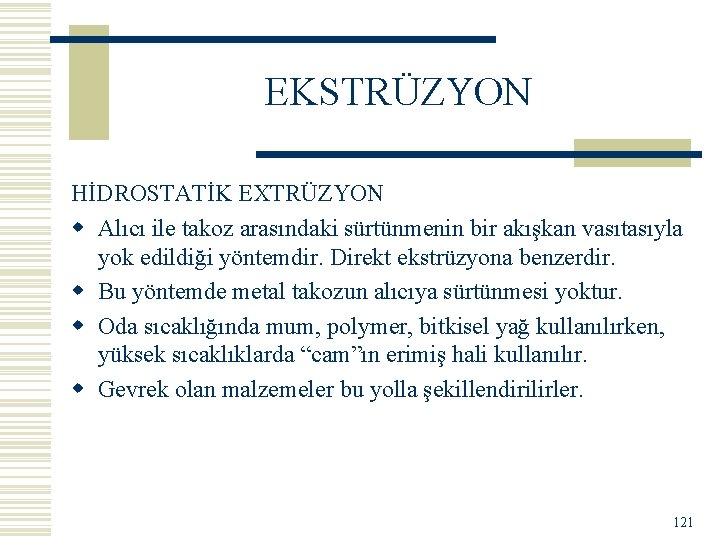
EKSTRÜZYON HİDROSTATİK EXTRÜZYON w Alıcı ile takoz arasındaki sürtünmenin bir akışkan vasıtasıyla yok edildiği yöntemdir. Direkt ekstrüzyona benzerdir. w Bu yöntemde metal takozun alıcıya sürtünmesi yoktur. w Oda sıcaklığında mum, polymer, bitkisel yağ kullanılırken, yüksek sıcaklıklarda “cam”ın erimiş hali kullanılır. w Gevrek olan malzemeler bu yolla şekillendirilirler. 121
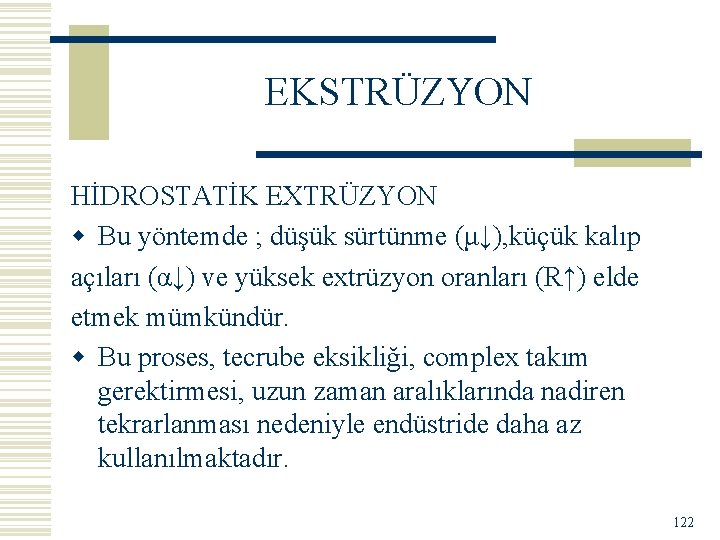
EKSTRÜZYON HİDROSTATİK EXTRÜZYON w Bu yöntemde ; düşük sürtünme (μ↓), küçük kalıp açıları (α↓) ve yüksek extrüzyon oranları (R↑) elde etmek mümkündür. w Bu proses, tecrube eksikliği, complex takım gerektirmesi, uzun zaman aralıklarında nadiren tekrarlanması nedeniyle endüstride daha az kullanılmaktadır. 122
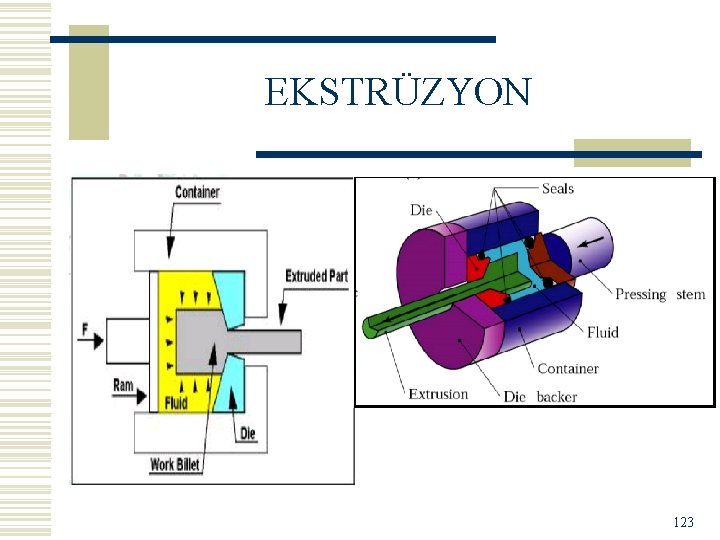
EKSTRÜZYON 123
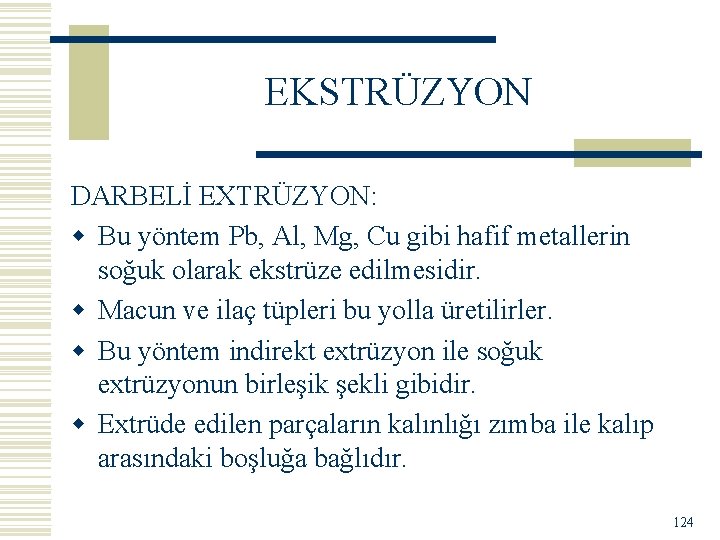
EKSTRÜZYON DARBELİ EXTRÜZYON: w Bu yöntem Pb, Al, Mg, Cu gibi hafif metallerin soğuk olarak ekstrüze edilmesidir. w Macun ve ilaç tüpleri bu yolla üretilirler. w Bu yöntem indirekt extrüzyon ile soğuk extrüzyonun birleşik şekli gibidir. w Extrüde edilen parçaların kalınlığı zımba ile kalıp arasındaki boşluğa bağlıdır. 124
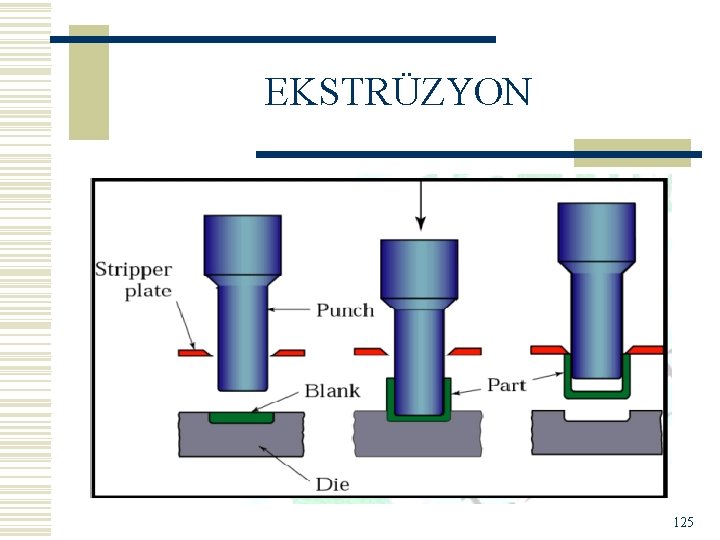
EKSTRÜZYON 125

EKSTRÜZYON BORU EXTRÜZYON : w Bu yöntemde dikişsiz borular ekstrüzyonla üretilirler. w Silindirik takozlar dolu veya deliklidir. w Direkt ekstrüzyonda hem dolu hem delikli takoz kullanılırken indirekt ekstrüzyonda yanlızca delikli takozdan boru üretilir. w Istampaya bağlı bir mandrel kullanılır. 126
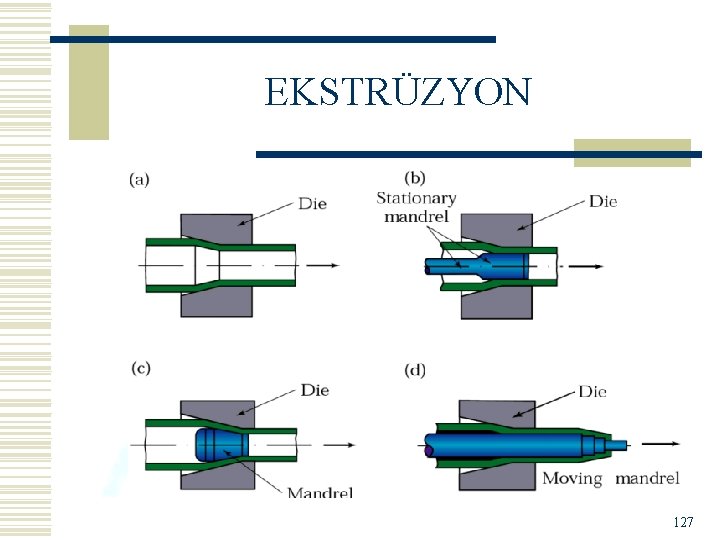
EKSTRÜZYON 127
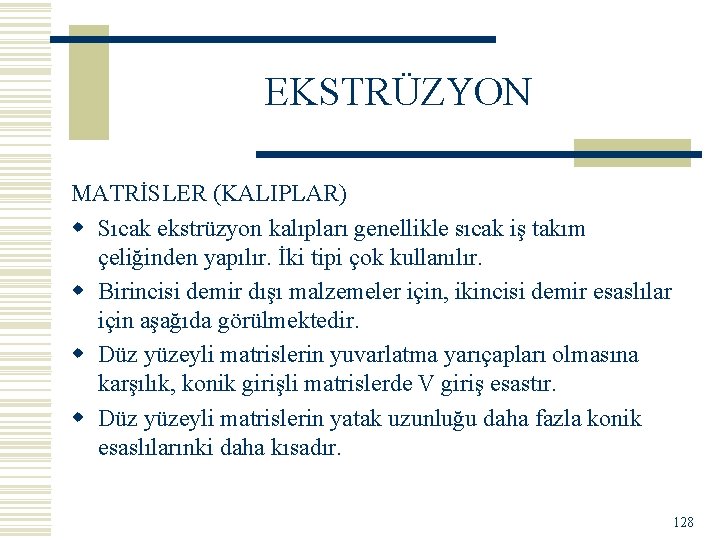
EKSTRÜZYON MATRİSLER (KALIPLAR) w Sıcak ekstrüzyon kalıpları genellikle sıcak iş takım çeliğinden yapılır. İki tipi çok kullanılır. w Birincisi demir dışı malzemeler için, ikincisi demir esaslılar için aşağıda görülmektedir. w Düz yüzeyli matrislerin yuvarlatma yarıçapları olmasına karşılık, konik girişli matrislerde V giriş esastır. w Düz yüzeyli matrislerin yatak uzunluğu daha fazla konik esaslılarınki daha kısadır. 128
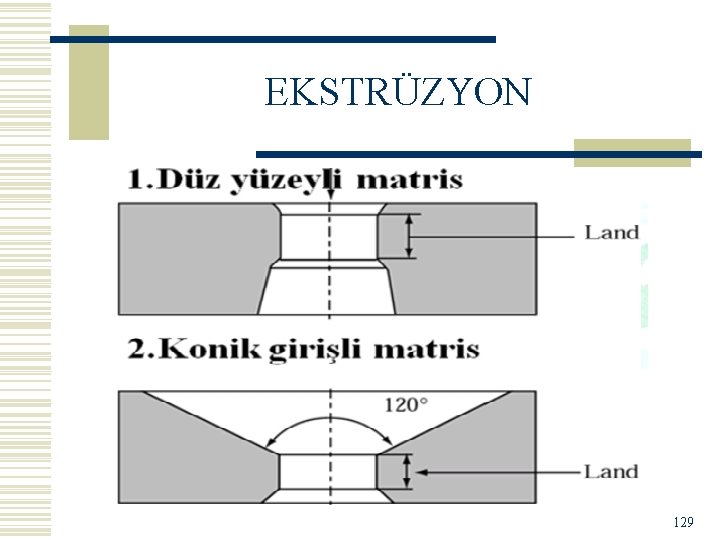
EKSTRÜZYON 129
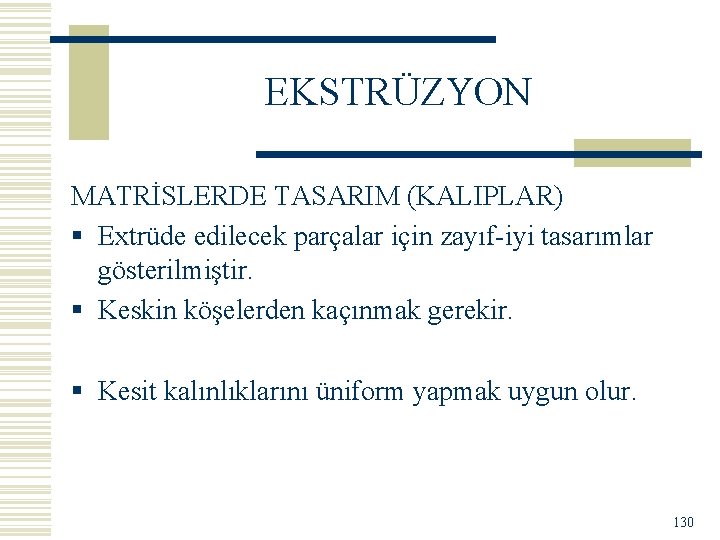
EKSTRÜZYON MATRİSLERDE TASARIM (KALIPLAR) § Extrüde edilecek parçalar için zayıf-iyi tasarımlar gösterilmiştir. § Keskin köşelerden kaçınmak gerekir. § Kesit kalınlıklarını üniform yapmak uygun olur. 130
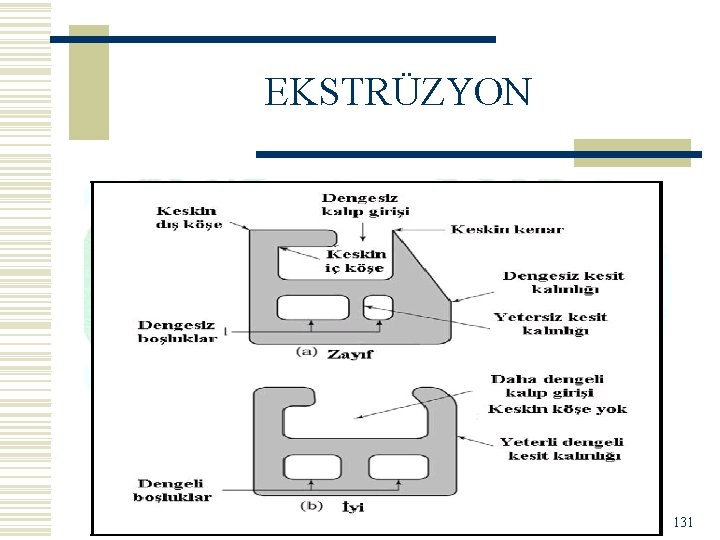
EKSTRÜZYON 131
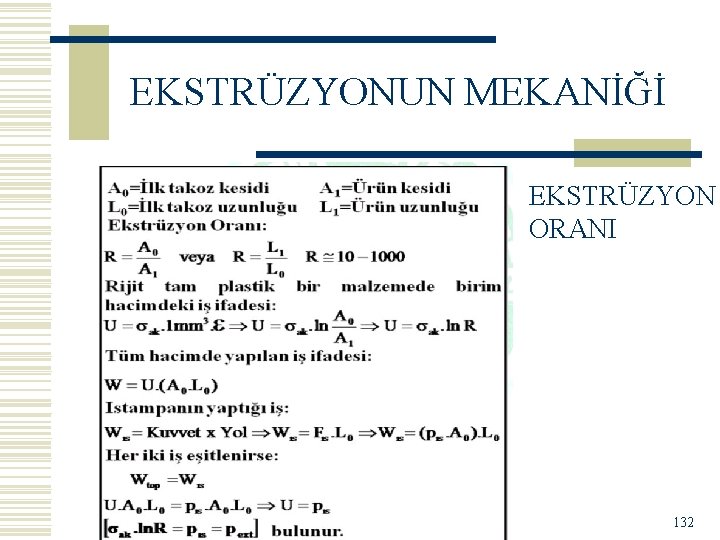
EKSTRÜZYONUN MEKANİĞİ EKSTRÜZYON ORANI 132
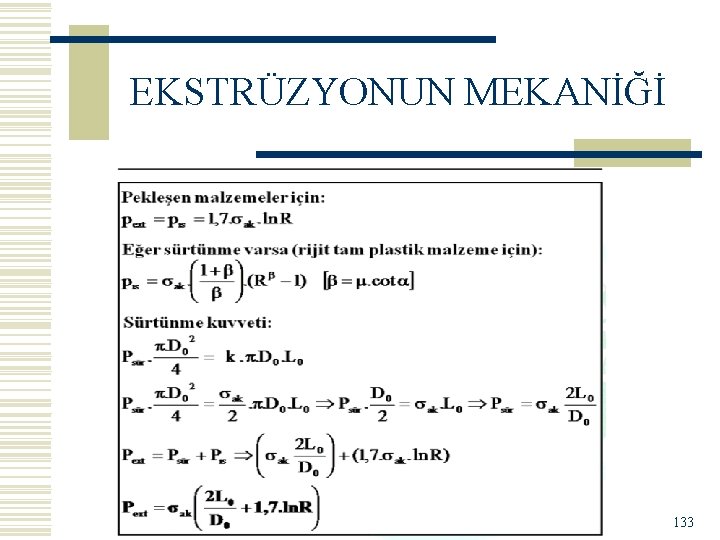
EKSTRÜZYONUN MEKANİĞİ 133
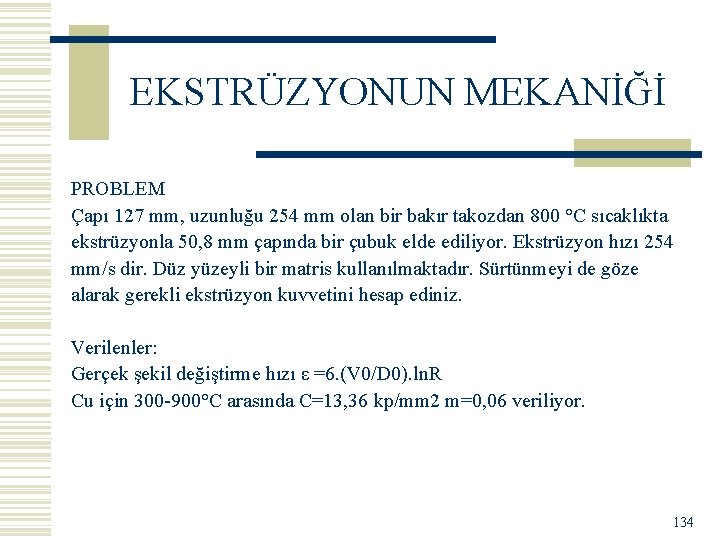
EKSTRÜZYONUN MEKANİĞİ PROBLEM Çapı 127 mm, uzunluğu 254 mm olan bir bakır takozdan 800 °C sıcaklıkta ekstrüzyonla 50, 8 mm çapında bir çubuk elde ediliyor. Ekstrüzyon hızı 254 mm/s dir. Düz yüzeyli bir matris kullanılmaktadır. Sürtünmeyi de göze alarak gerekli ekstrüzyon kuvvetini hesap ediniz. Verilenler: Gerçek şekil değiştirme hızı ε =6. (V 0/D 0). ln. R Cu için 300 -900°C arasında C=13, 36 kp/mm 2 m=0, 06 veriliyor. 134
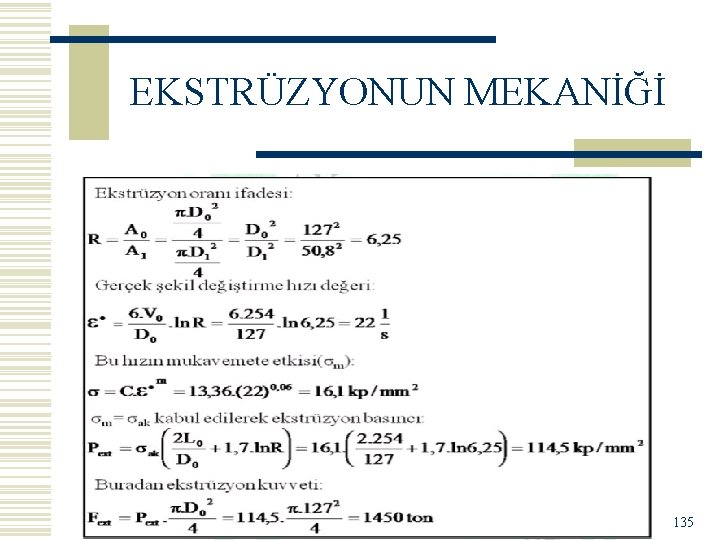
EKSTRÜZYONUN MEKANİĞİ 135
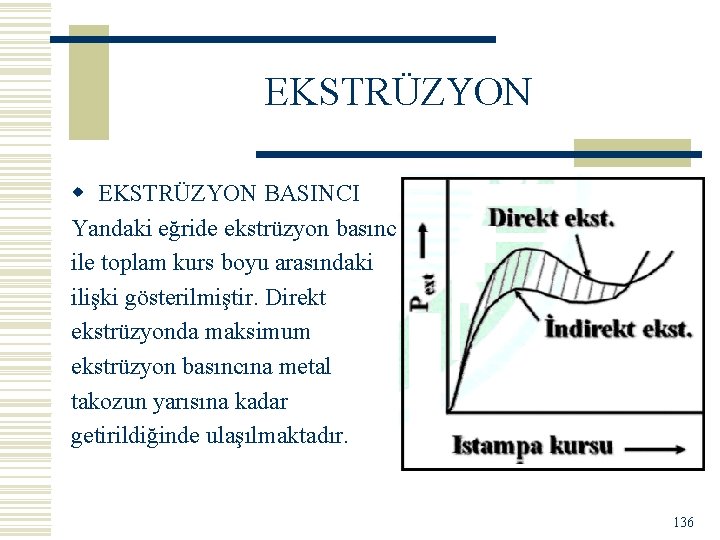
EKSTRÜZYON w EKSTRÜZYON BASINCI Yandaki eğride ekstrüzyon basıncı ile toplam kurs boyu arasındaki ilişki gösterilmiştir. Direkt ekstrüzyonda maksimum ekstrüzyon basıncına metal takozun yarısına kadar getirildiğinde ulaşılmaktadır. 136
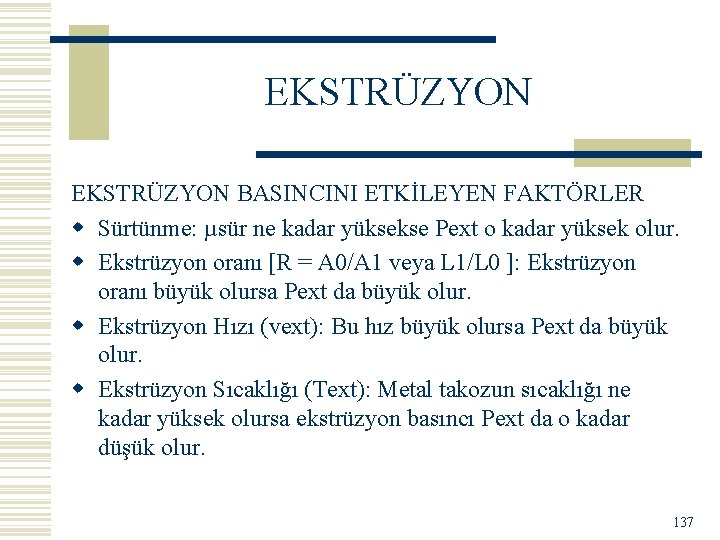
EKSTRÜZYON BASINCINI ETKİLEYEN FAKTÖRLER w Sürtünme: µsür ne kadar yüksekse Pext o kadar yüksek olur. w Ekstrüzyon oranı [R = A 0/A 1 veya L 1/L 0 ]: Ekstrüzyon oranı büyük olursa Pext da büyük olur. w Ekstrüzyon Hızı (vext): Bu hız büyük olursa Pext da büyük olur. w Ekstrüzyon Sıcaklığı (Text): Metal takozun sıcaklığı ne kadar yüksek olursa ekstrüzyon basıncı Pext da o kadar düşük olur. 137
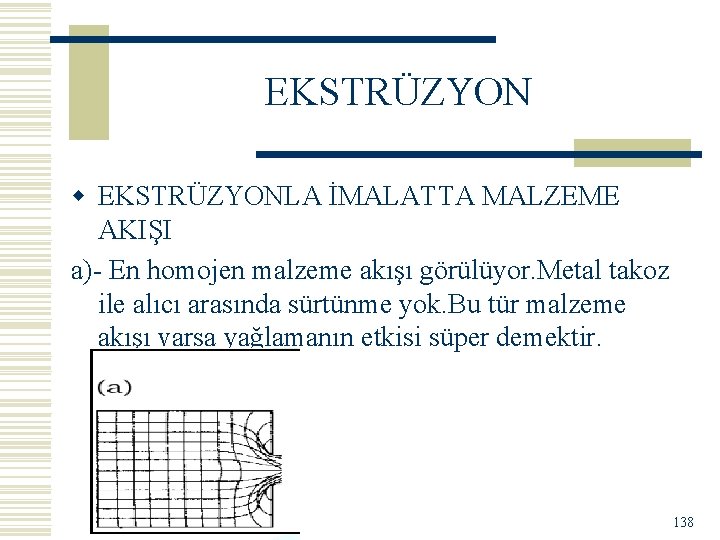
EKSTRÜZYON w EKSTRÜZYONLA İMALATTA MALZEME AKIŞI a)- En homojen malzeme akışı görülüyor. Metal takoz ile alıcı arasında sürtünme yok. Bu tür malzeme akışı varsa yağlamanın etkisi süper demektir. 138
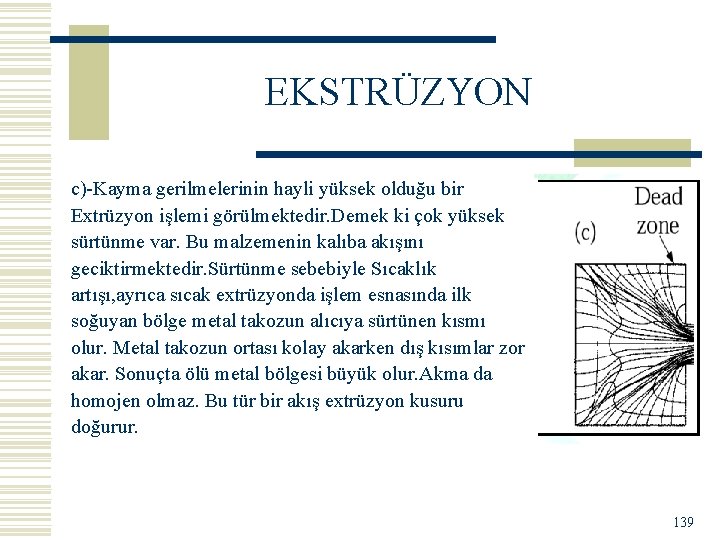
EKSTRÜZYON c)-Kayma gerilmelerinin hayli yüksek olduğu bir Extrüzyon işlemi görülmektedir. Demek ki çok yüksek sürtünme var. Bu malzemenin kalıba akışını geciktirmektedir. Sürtünme sebebiyle Sıcaklık artışı, ayrıca sıcak extrüzyonda işlem esnasında ilk soğuyan bölge metal takozun alıcıya sürtünen kısmı olur. Metal takozun ortası kolay akarken dış kısımlar zor akar. Sonuçta ölü metal bölgesi büyük olur. Akma da homojen olmaz. Bu tür bir akış extrüzyon kusuru doğurur. 139
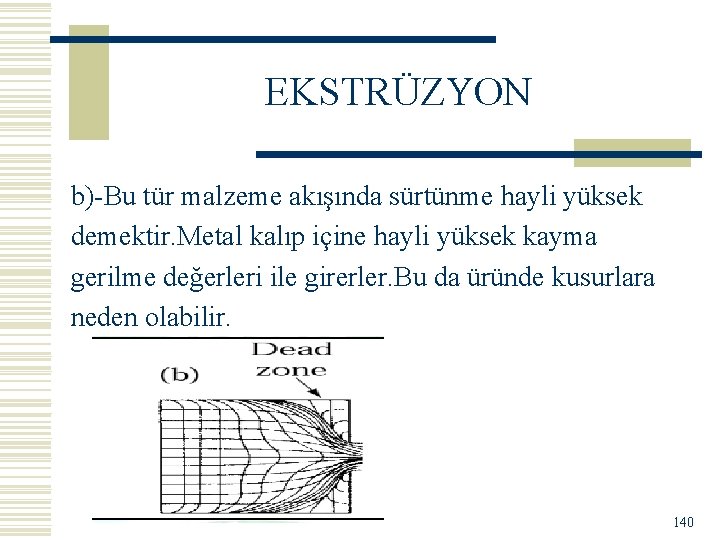
EKSTRÜZYON b)-Bu tür malzeme akışında sürtünme hayli yüksek demektir. Metal kalıp içine hayli yüksek kayma gerilme değerleri ile girerler. Bu da üründe kusurlara neden olabilir. 140
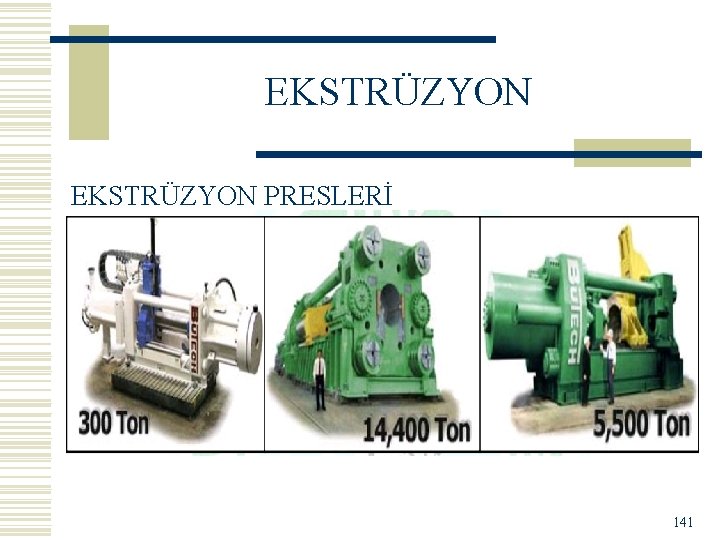
EKSTRÜZYON PRESLERİ 141
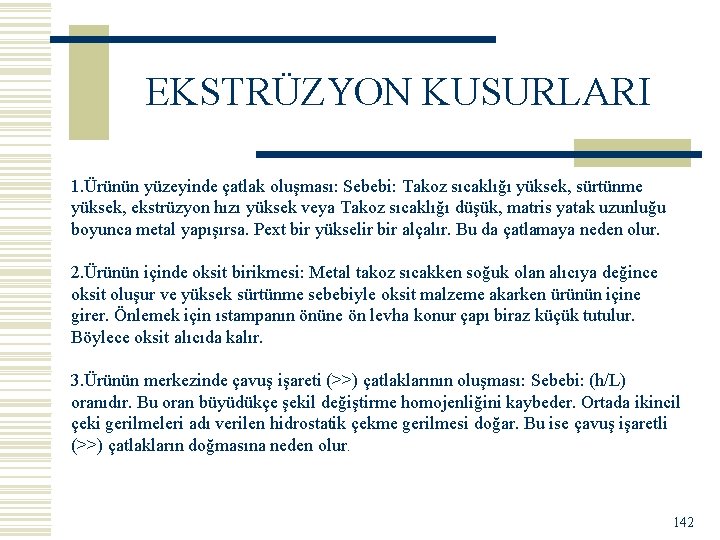
EKSTRÜZYON KUSURLARI 1. Ürünün yüzeyinde çatlak oluşması: Sebebi: Takoz sıcaklığı yüksek, sürtünme yüksek, ekstrüzyon hızı yüksek veya Takoz sıcaklığı düşük, matris yatak uzunluğu boyunca metal yapışırsa. Pext bir yükselir bir alçalır. Bu da çatlamaya neden olur. 2. Ürünün içinde oksit birikmesi: Metal takoz sıcakken soğuk olan alıcıya değince oksit oluşur ve yüksek sürtünme sebebiyle oksit malzeme akarken ürünün içine girer. Önlemek için ıstampanın önüne ön levha konur çapı biraz küçük tutulur. Böylece oksit alıcıda kalır. 3. Ürünün merkezinde çavuş işareti (>>) çatlaklarının oluşması: Sebebi: (h/L) oranıdır. Bu oran büyüdükçe şekil değiştirme homojenliğini kaybeder. Ortada ikincil çeki gerilmeleri adı verilen hidrostatik çekme gerilmesi doğar. Bu ise çavuş işaretli (>>) çatlakların doğmasına neden olur. 142
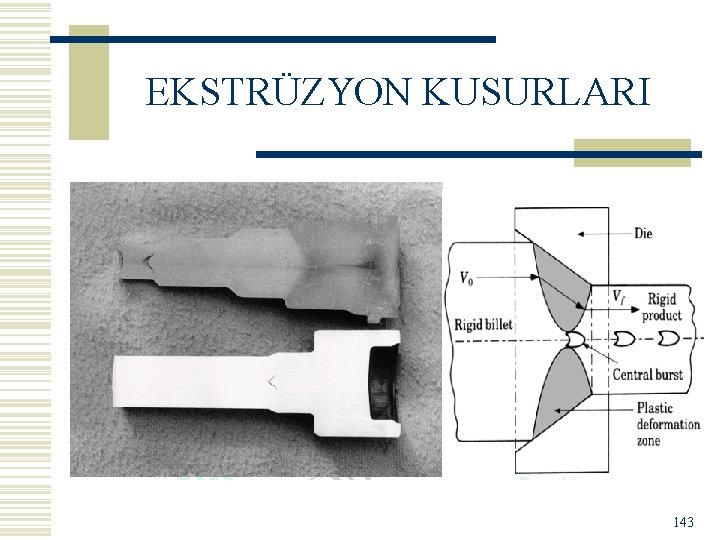
EKSTRÜZYON KUSURLARI 143
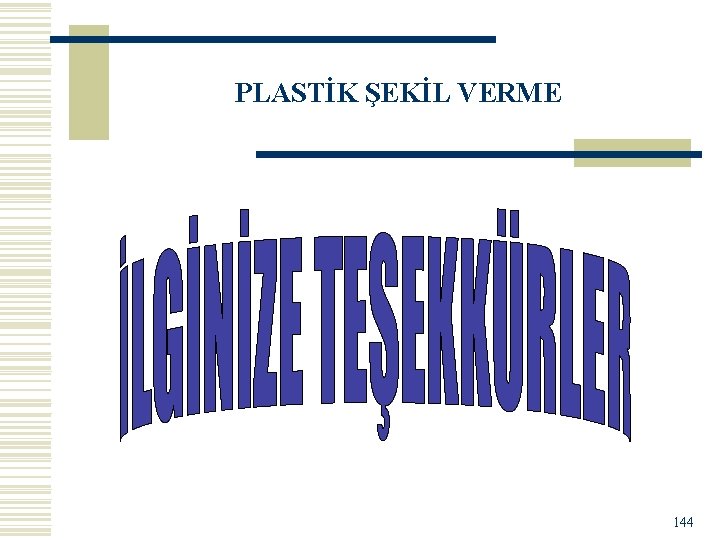
PLASTİK ŞEKİL VERME 144
Energikartläggningsstöd
Ekl hämeen piiri
Ankara niversitesi
Izole ventrikülomegali
Ankara niversitesi
Anadolu ?niversitesi
Ankara niversitesi
Ankara niversitesi
Ankara niversitesi
Nurdan bilgin makina dinamiği
Karin makina
Deu makina
Temren makina
Sa paghahanda ng lupa ang unang
Botsal
Paletli akış ölçer
Makina
Cts makina
Yapım işlerinde kdv tevkifatı
Makinat frezuese
Protokol hediye
Planaria reprodução
Solunum pigmenti
Verme
Hola, david! ¿por qué querías verme con tanta urgencia?
Eliftir doksan bin kelamın başı nazım türü
Enfermedad causada por ascaris lumbricoides
Nematódeos reprodução
Salik verme
Soluk alıp verme mekanizması
Nicel karar verme yöntemleri
Değer verme basamağı
Taşınır tüketime verme
Etik karar verme modeli basamakları
Ascaridase
Oxiuros
Mordeu
Salik verme
Risklere cevap verme yöntemleri
Ao primeiro verme que roeu
Taşınır tüketime verme
Verme oxiúrus fotos
Kilo verme sayı sekansı
Abc modeli örnekleri
Ascaris lumbricoides ciclo
Solenocitos