NATCOR Stochastic Modelling Course Inventory Control Part 1
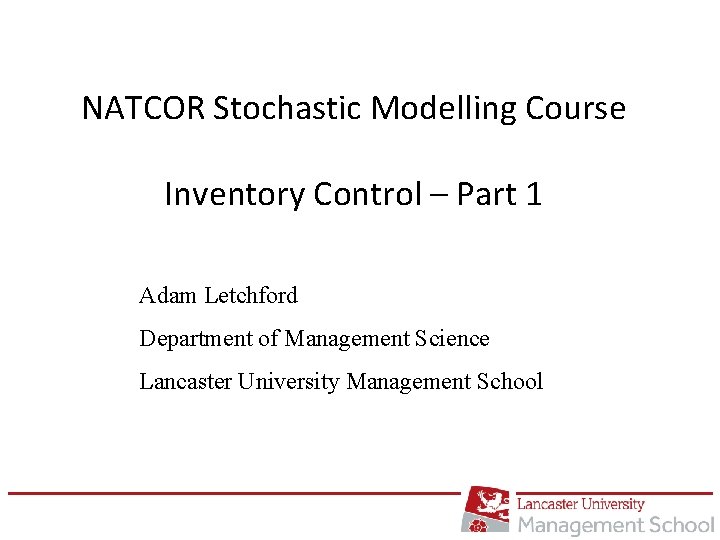
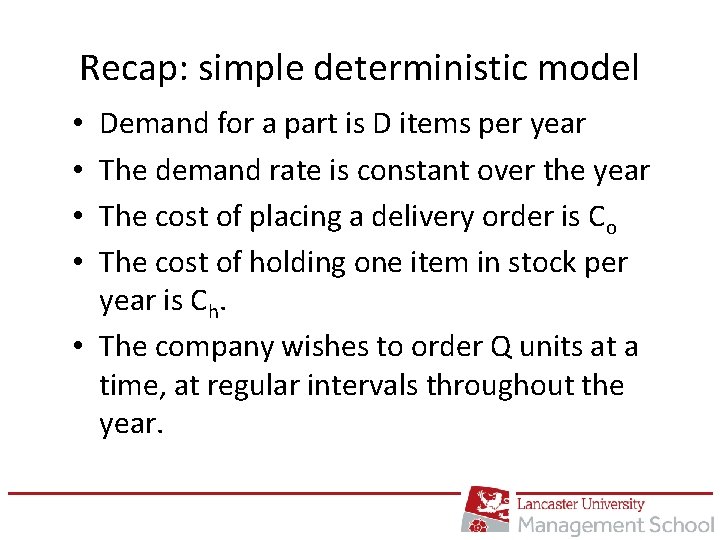
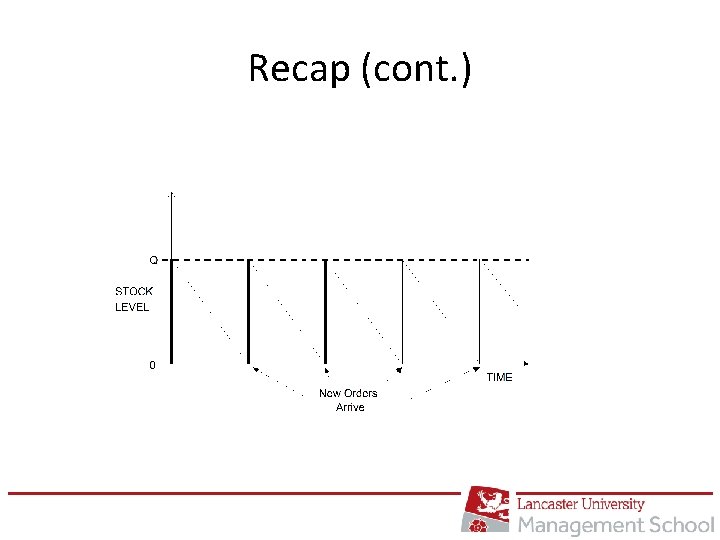
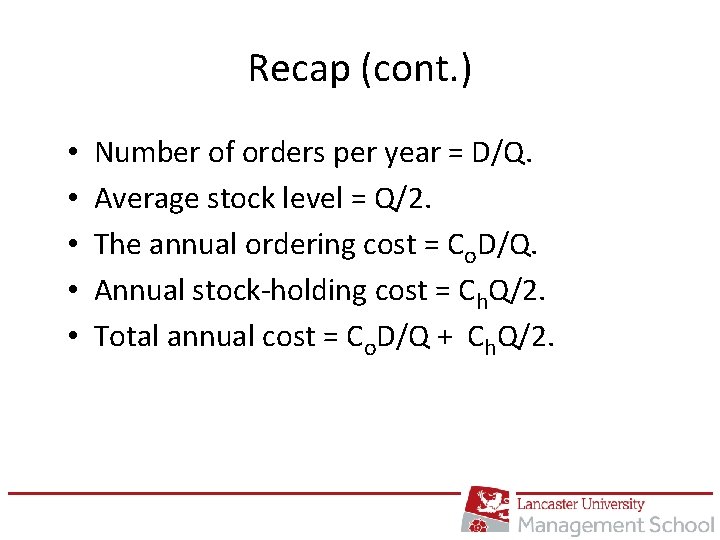
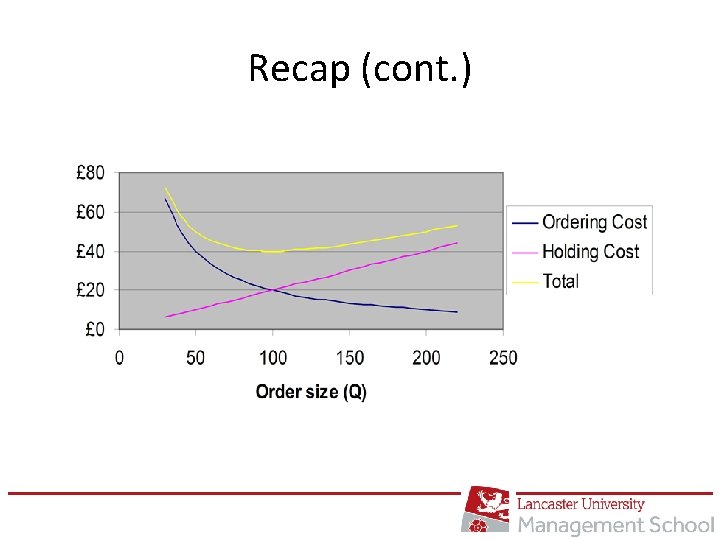
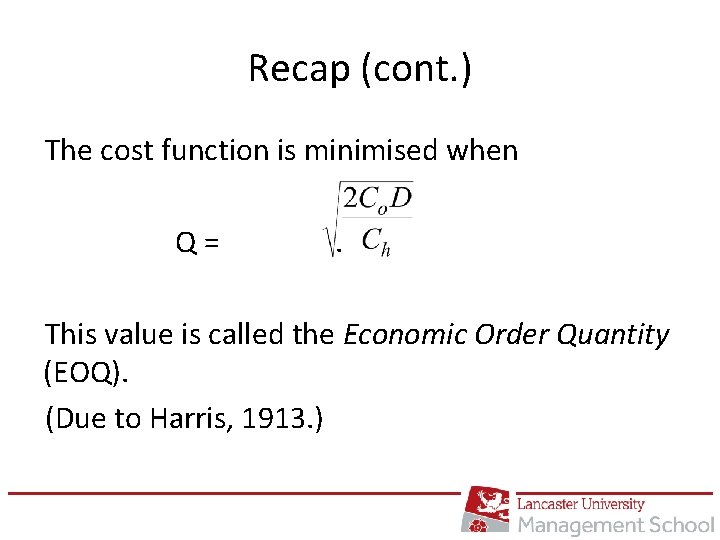
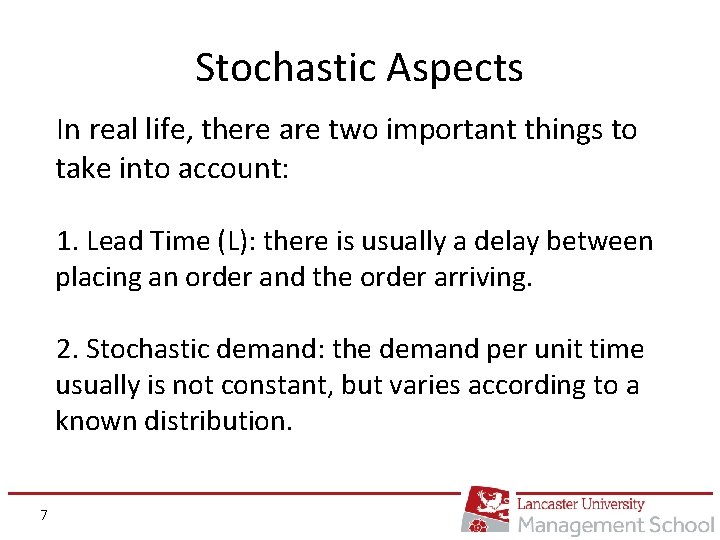
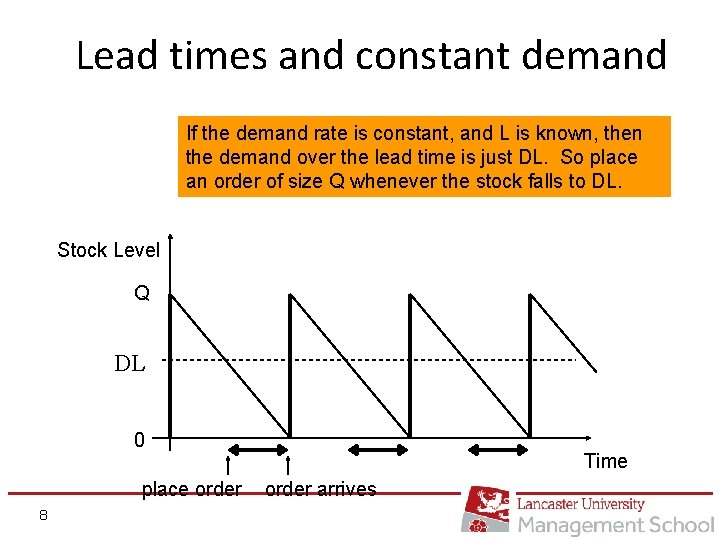
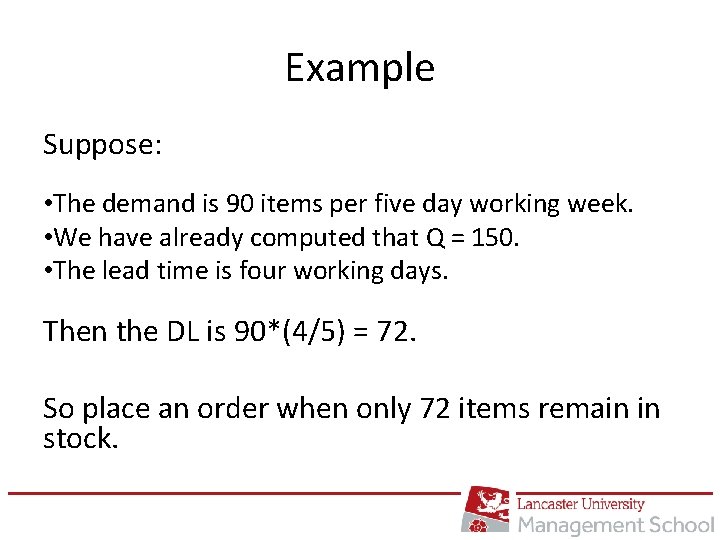
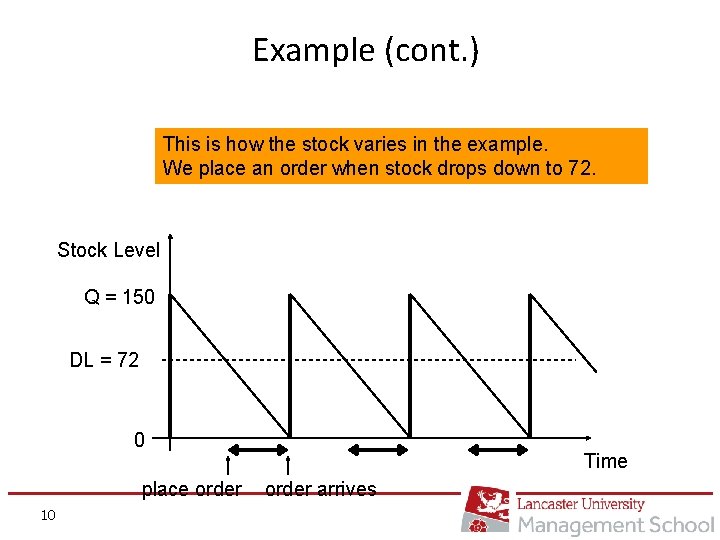
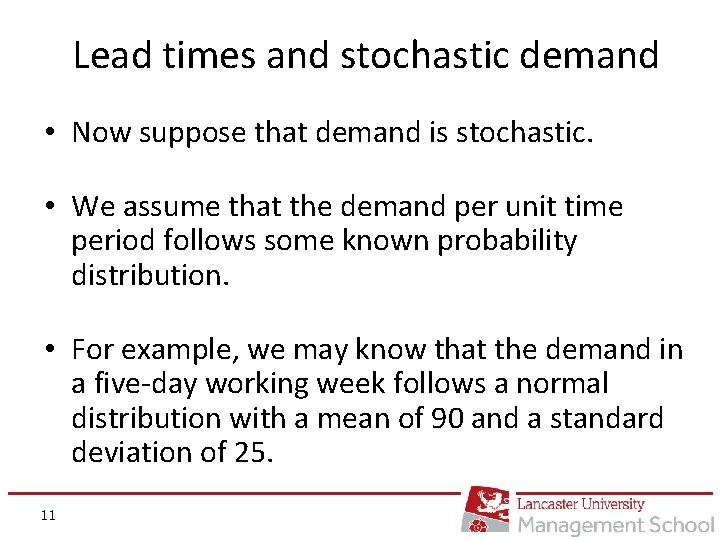
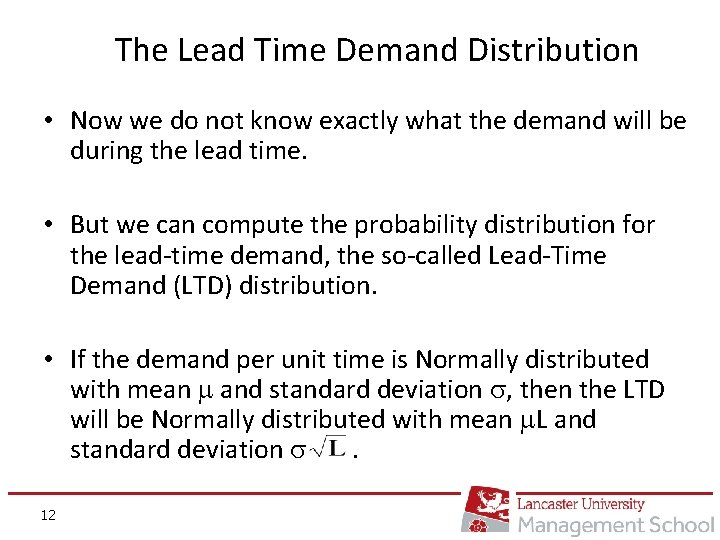
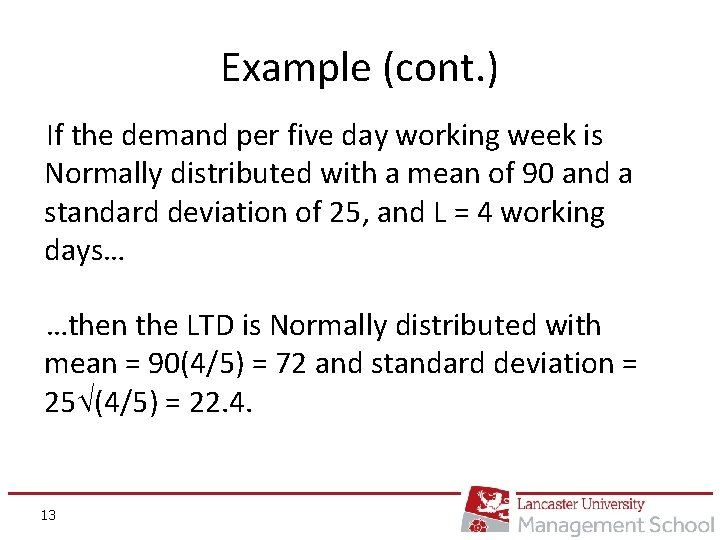
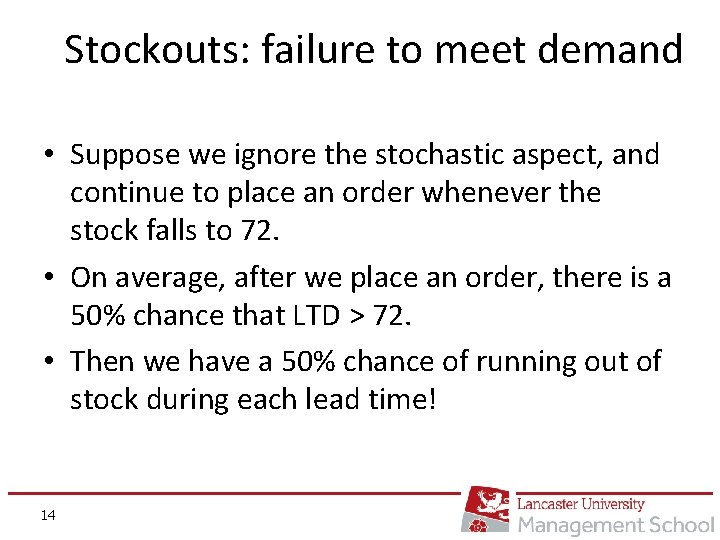
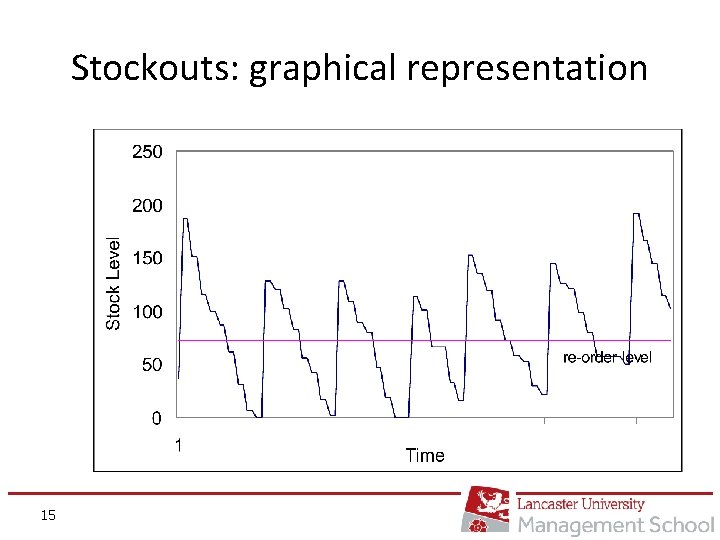
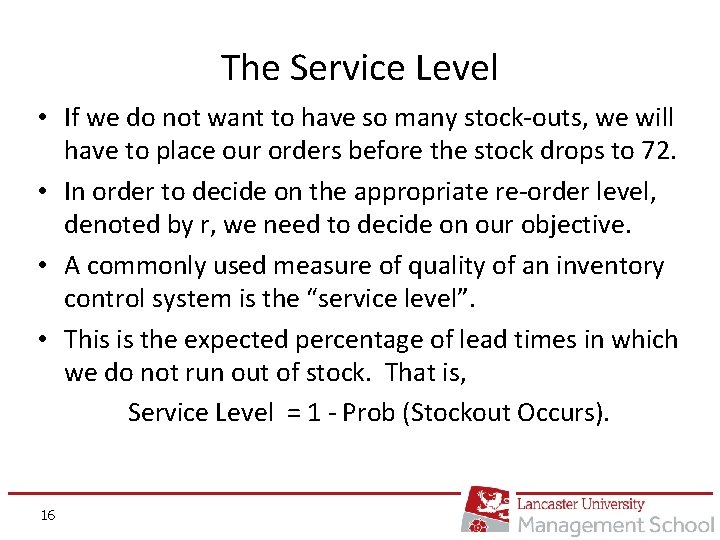
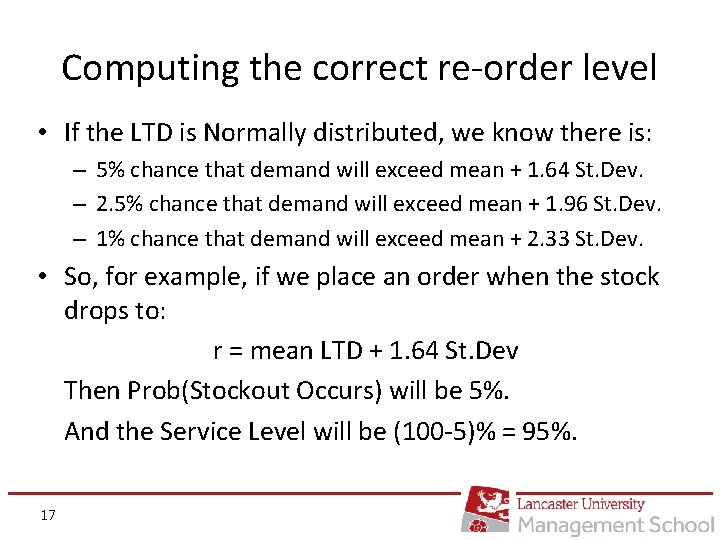
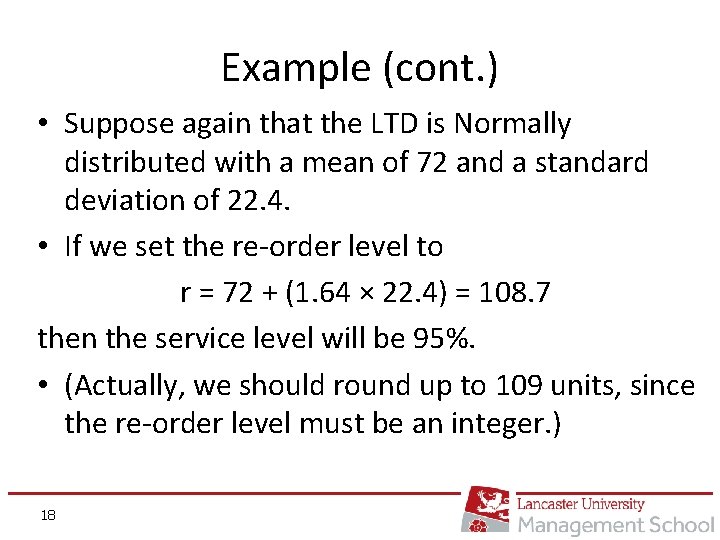
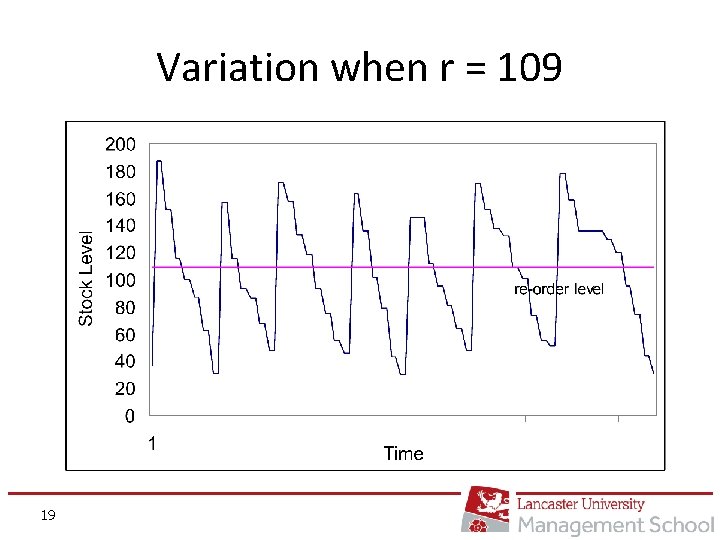
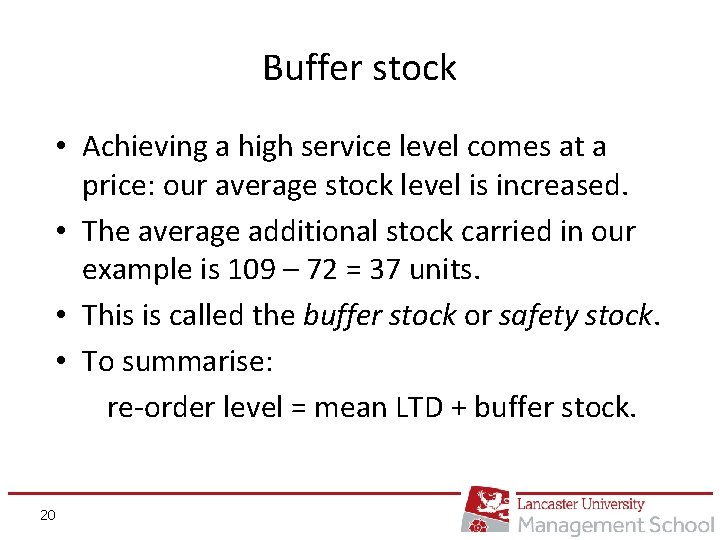
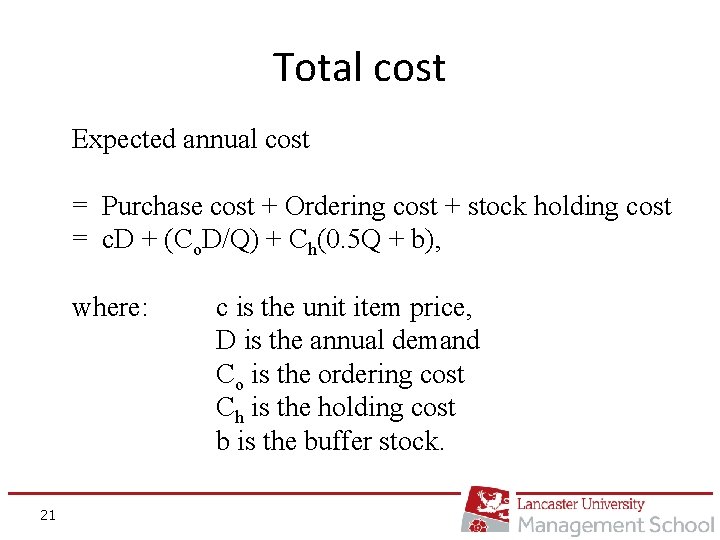
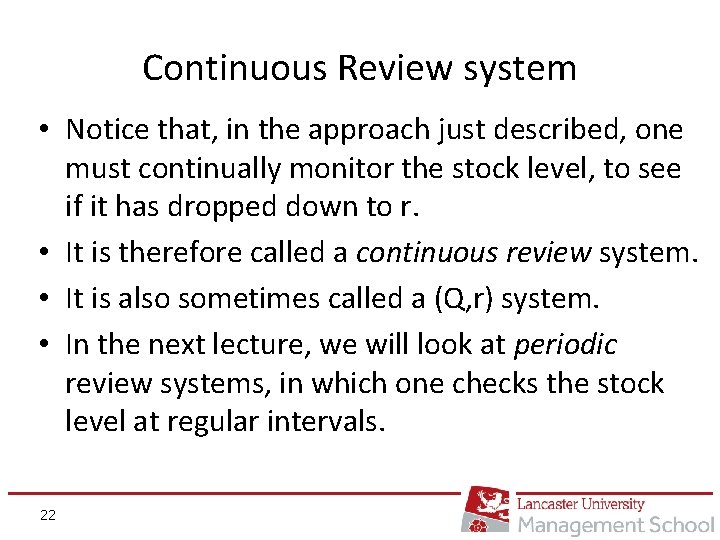
- Slides: 22
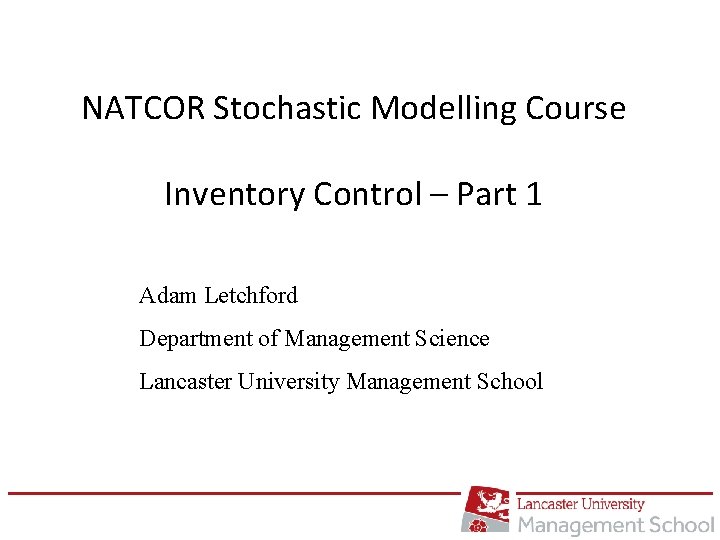
NATCOR Stochastic Modelling Course Inventory Control – Part 1 Adam Letchford Department of Management Science Lancaster University Management School
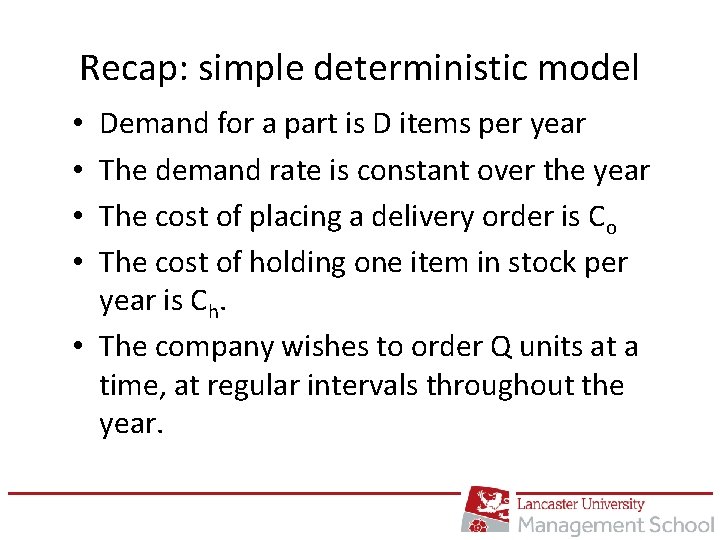
Recap: simple deterministic model Demand for a part is D items per year The demand rate is constant over the year The cost of placing a delivery order is Co The cost of holding one item in stock per year is Ch. • The company wishes to order Q units at a time, at regular intervals throughout the year. • •
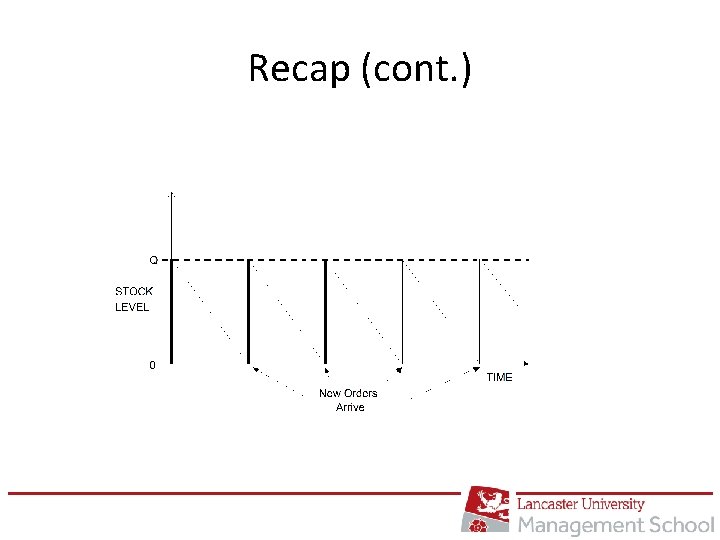
Recap (cont. )
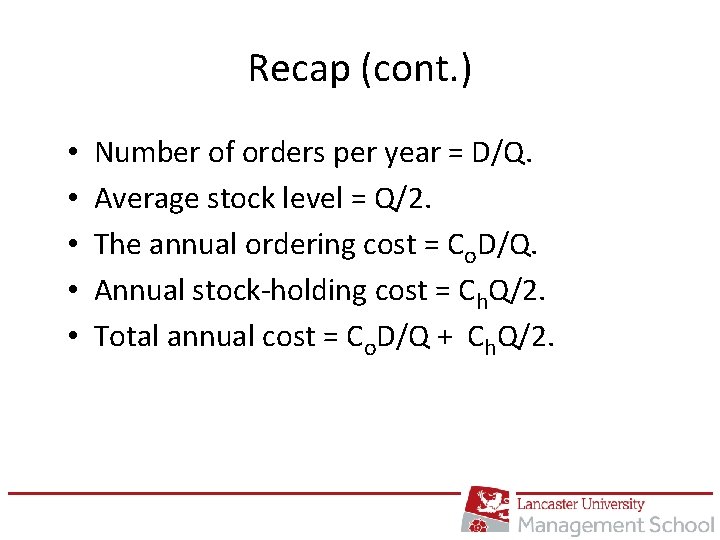
Recap (cont. ) • • • Number of orders per year = D/Q. Average stock level = Q/2. The annual ordering cost = Co. D/Q. Annual stock-holding cost = Ch. Q/2. Total annual cost = Co. D/Q + Ch. Q/2.
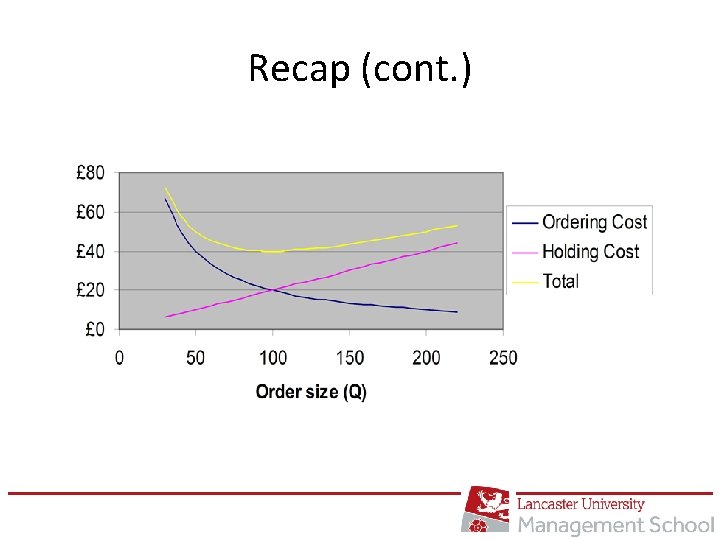
Recap (cont. )
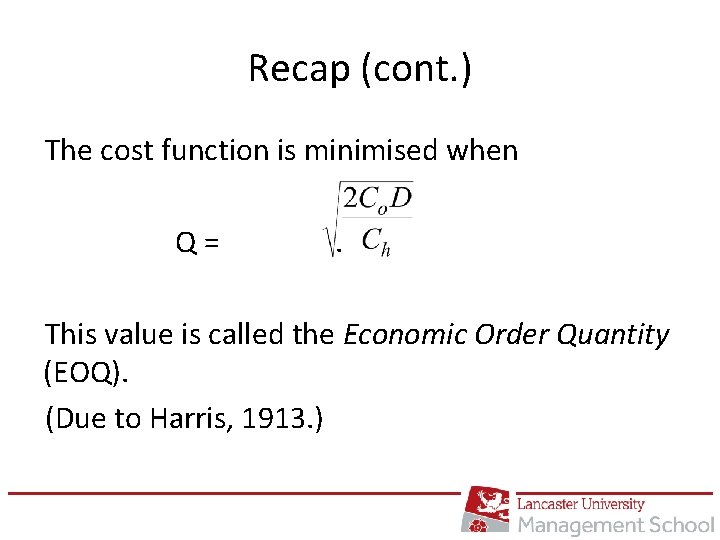
Recap (cont. ) The cost function is minimised when Q= . This value is called the Economic Order Quantity (EOQ). (Due to Harris, 1913. )
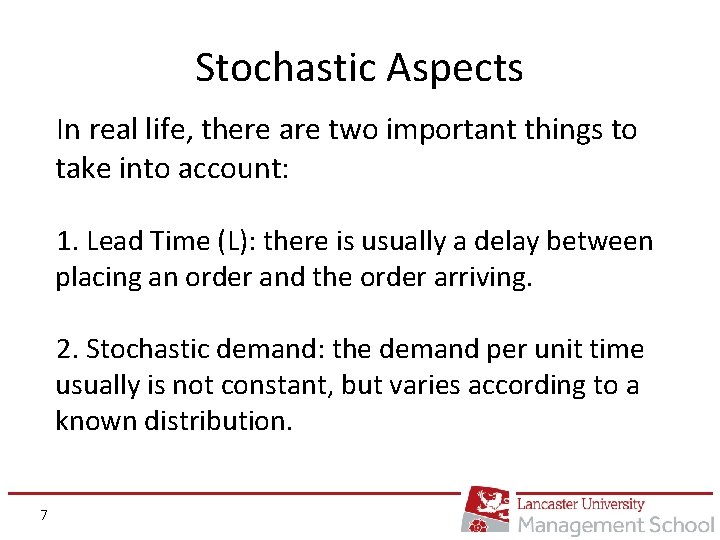
Stochastic Aspects In real life, there are two important things to take into account: 1. Lead Time (L): there is usually a delay between placing an order and the order arriving. 2. Stochastic demand: the demand per unit time usually is not constant, but varies according to a known distribution. 7
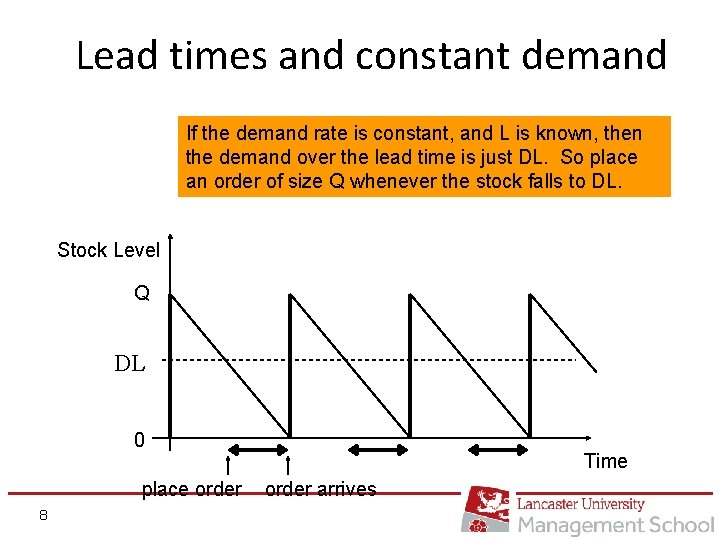
Lead times and constant demand If the demand rate is constant, and L is known, then the demand over the lead time is just DL. So place an order of size Q whenever the stock falls to DL. Stock Level Q DL 0 place order 8 Time order arrives
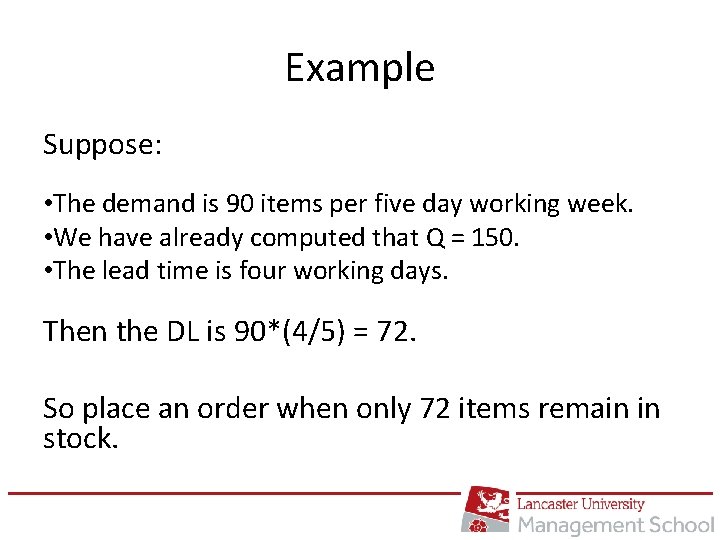
Example Suppose: • The demand is 90 items per five day working week. • We have already computed that Q = 150. • The lead time is four working days. Then the DL is 90*(4/5) = 72. So place an order when only 72 items remain in stock.
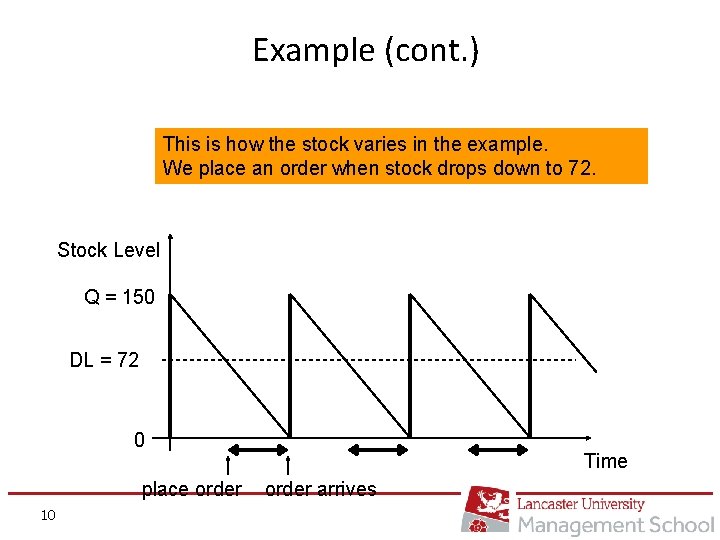
Example (cont. ) This is how the stock varies in the example. We place an order when stock drops down to 72. Stock Level Q = 150 DL = 72 0 place order 10 Time order arrives
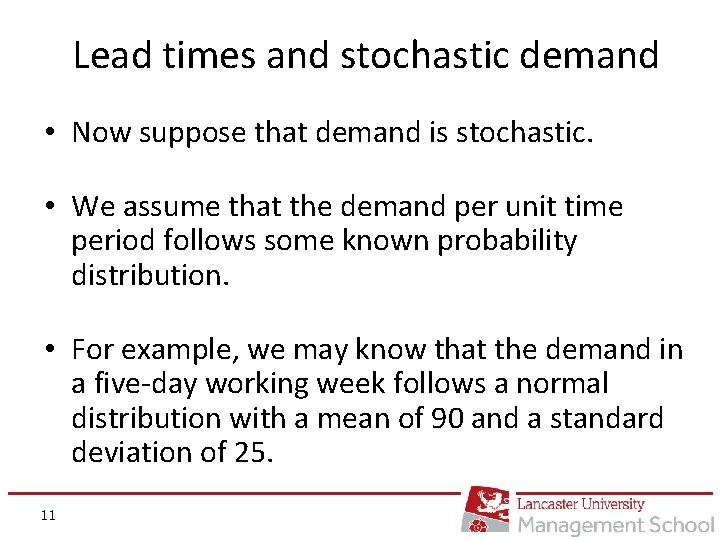
Lead times and stochastic demand • Now suppose that demand is stochastic. • We assume that the demand per unit time period follows some known probability distribution. • For example, we may know that the demand in a five-day working week follows a normal distribution with a mean of 90 and a standard deviation of 25. 11
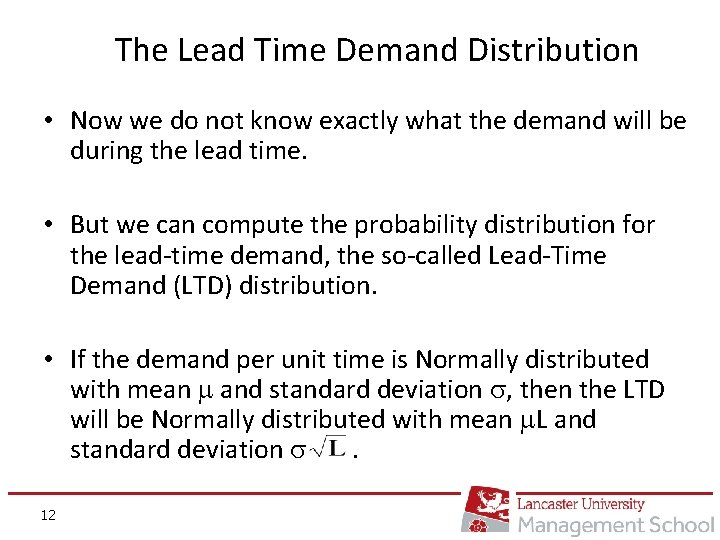
The Lead Time Demand Distribution • Now we do not know exactly what the demand will be during the lead time. • But we can compute the probability distribution for the lead-time demand, the so-called Lead-Time Demand (LTD) distribution. • If the demand per unit time is Normally distributed with mean and standard deviation , then the LTD will be Normally distributed with mean L and standard deviation . 12
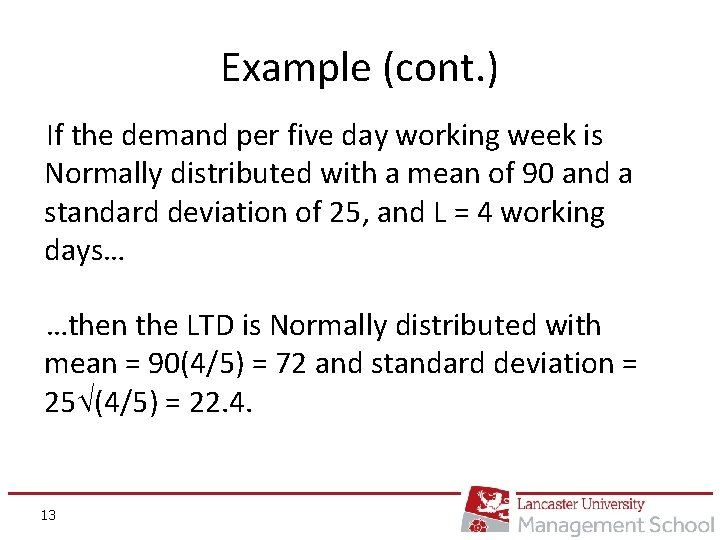
Example (cont. ) If the demand per five day working week is Normally distributed with a mean of 90 and a standard deviation of 25, and L = 4 working days… …then the LTD is Normally distributed with mean = 90(4/5) = 72 and standard deviation = 25 (4/5) = 22. 4. 13
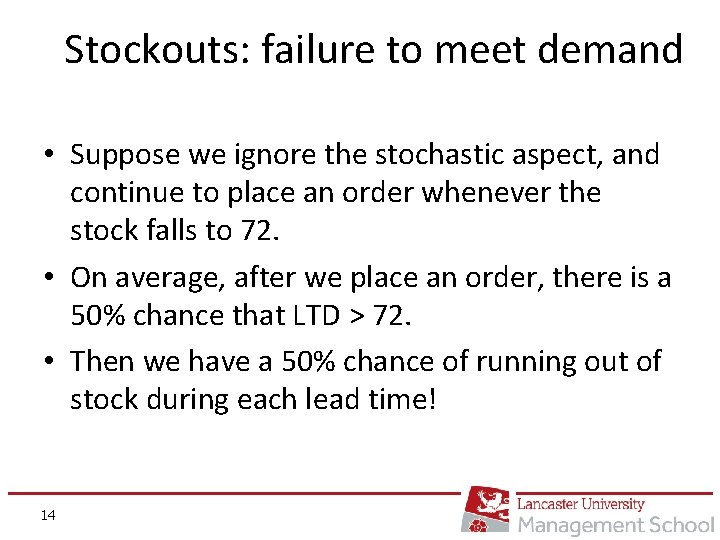
Stockouts: failure to meet demand • Suppose we ignore the stochastic aspect, and continue to place an order whenever the stock falls to 72. • On average, after we place an order, there is a 50% chance that LTD > 72. • Then we have a 50% chance of running out of stock during each lead time! 14
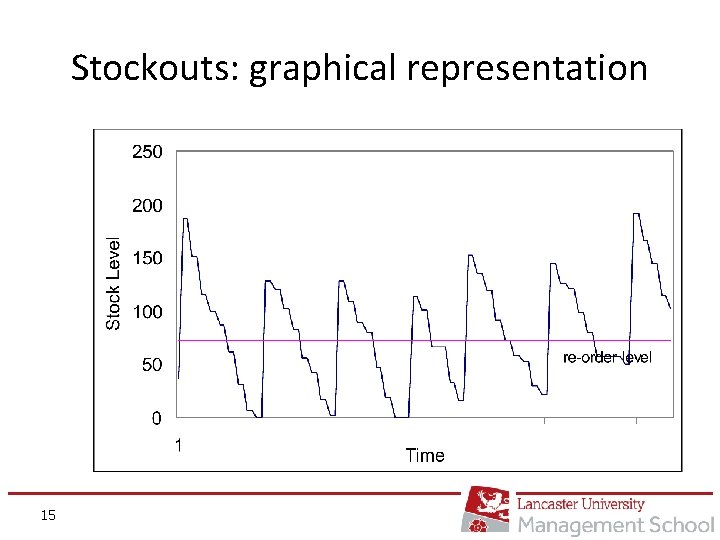
Stockouts: graphical representation 15
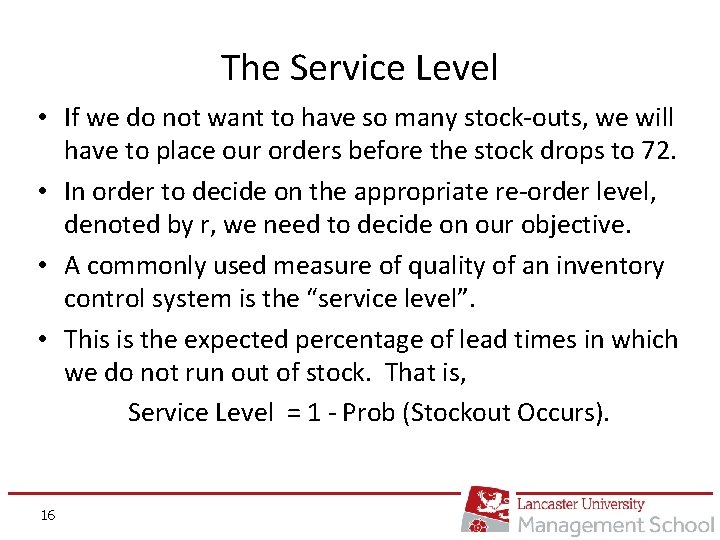
The Service Level • If we do not want to have so many stock-outs, we will have to place our orders before the stock drops to 72. • In order to decide on the appropriate re-order level, denoted by r, we need to decide on our objective. • A commonly used measure of quality of an inventory control system is the “service level”. • This is the expected percentage of lead times in which we do not run out of stock. That is, Service Level = 1 - Prob (Stockout Occurs). 16
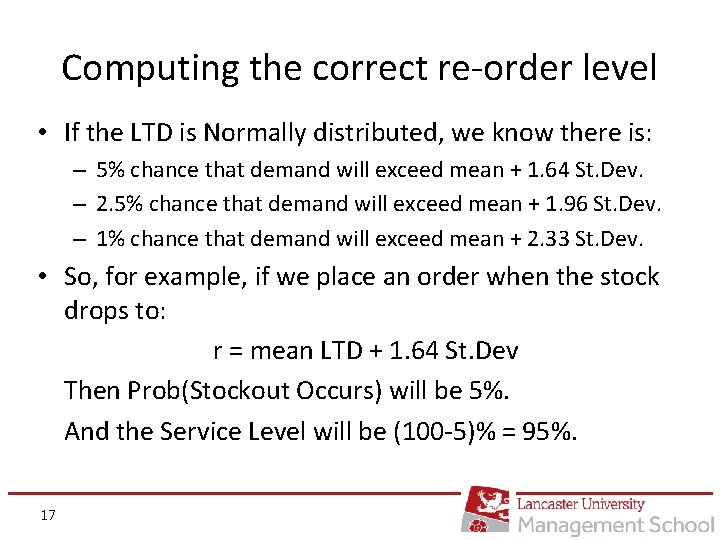
Computing the correct re-order level • If the LTD is Normally distributed, we know there is: – 5% chance that demand will exceed mean + 1. 64 St. Dev. – 2. 5% chance that demand will exceed mean + 1. 96 St. Dev. – 1% chance that demand will exceed mean + 2. 33 St. Dev. • So, for example, if we place an order when the stock drops to: r = mean LTD + 1. 64 St. Dev Then Prob(Stockout Occurs) will be 5%. And the Service Level will be (100 -5)% = 95%. 17
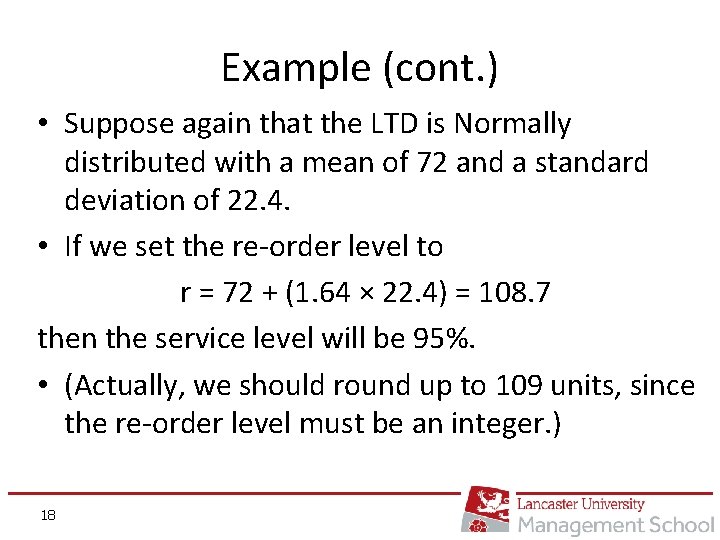
Example (cont. ) • Suppose again that the LTD is Normally distributed with a mean of 72 and a standard deviation of 22. 4. • If we set the re-order level to r = 72 + (1. 64 × 22. 4) = 108. 7 then the service level will be 95%. • (Actually, we should round up to 109 units, since the re-order level must be an integer. ) 18
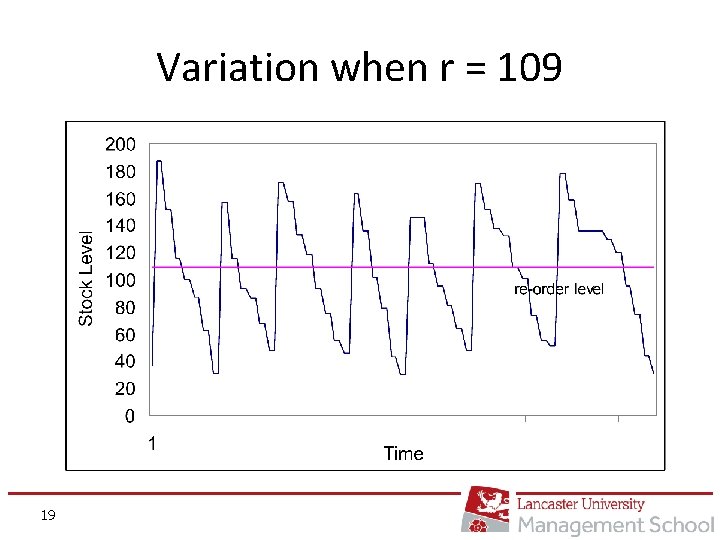
Variation when r = 109 19
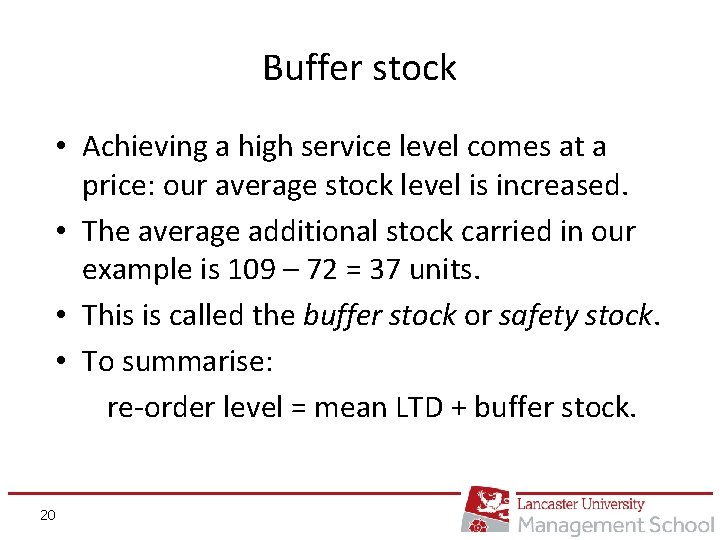
Buffer stock • Achieving a high service level comes at a price: our average stock level is increased. • The average additional stock carried in our example is 109 – 72 = 37 units. • This is called the buffer stock or safety stock. • To summarise: re-order level = mean LTD + buffer stock. 20
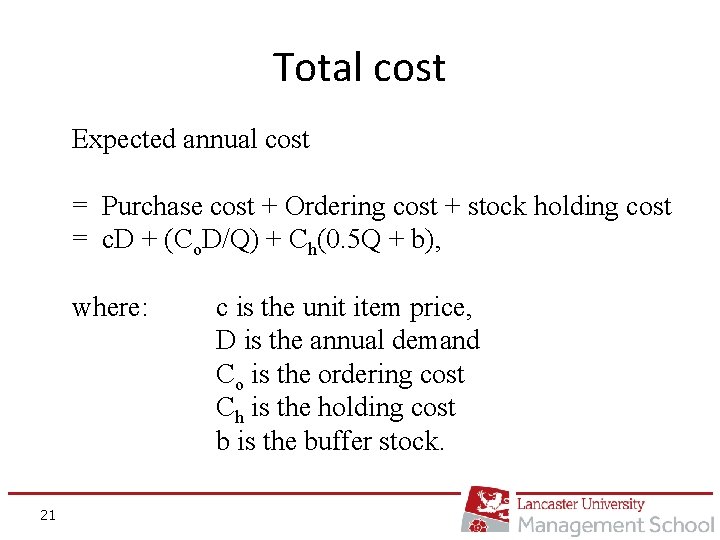
Total cost Expected annual cost = Purchase cost + Ordering cost + stock holding cost = c. D + (Co. D/Q) + Ch(0. 5 Q + b), where: 21 c is the unit item price, D is the annual demand Co is the ordering cost Ch is the holding cost b is the buffer stock.
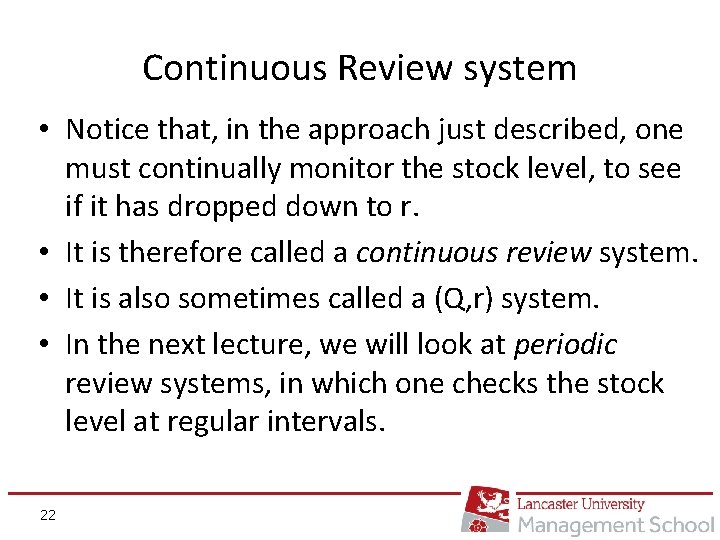
Continuous Review system • Notice that, in the approach just described, one must continually monitor the stock level, to see if it has dropped down to r. • It is therefore called a continuous review system. • It is also sometimes called a (Q, r) system. • In the next lecture, we will look at periodic review systems, in which one checks the stock level at regular intervals. 22
Inventory modeling
Deterministic and stochastic inventory models
A first course in stochastic processes
Thecb course inventory
Stochastic rounding
Stochastic programming
Stochastic process model
Divbar
Put call parity formula
Stochastic vs dynamic
Stochastic matrix
Stochastic regressors
Non stochastic theory of aging
Stochastic process introduction
Stochastic progressive photon mapping
Agent a chapter 2
Discrete variable
Logistic regression stochastic gradient descent
Stochastic process modeling
Stochastic process
Stochastic process
Stochastic process
Stochastic process