Motorola RFID Solutions Get Ready Get Set GO
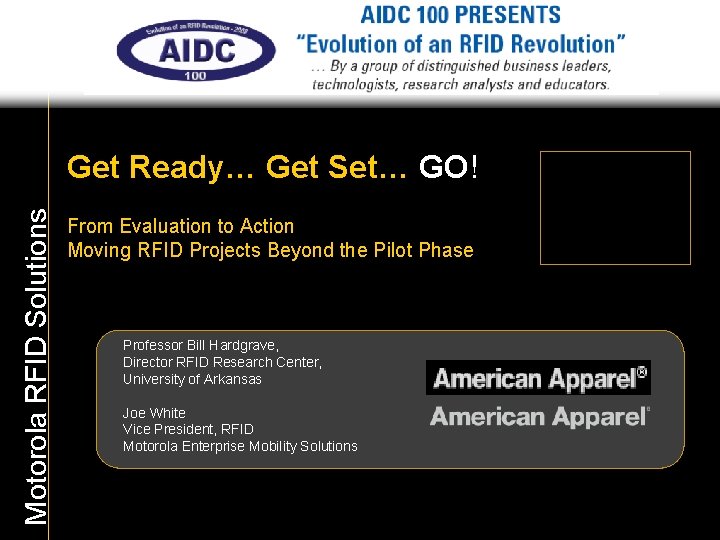
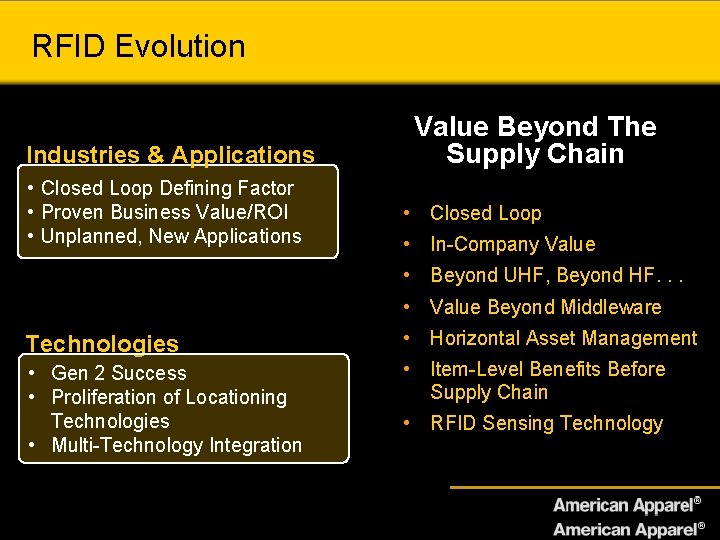
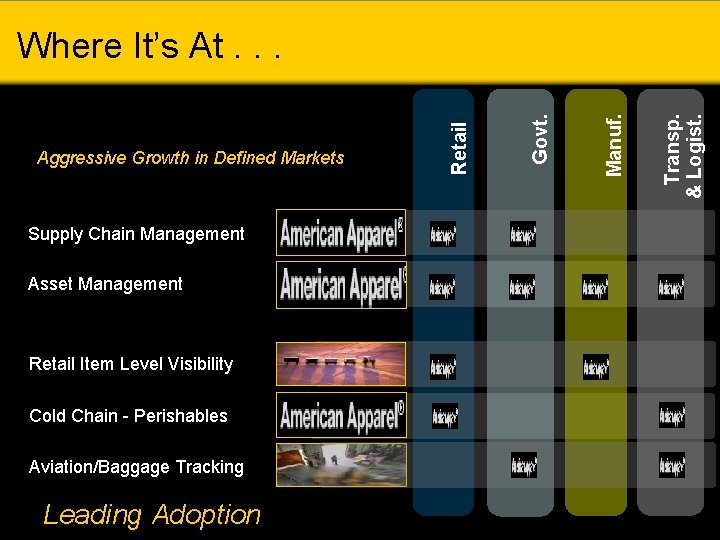
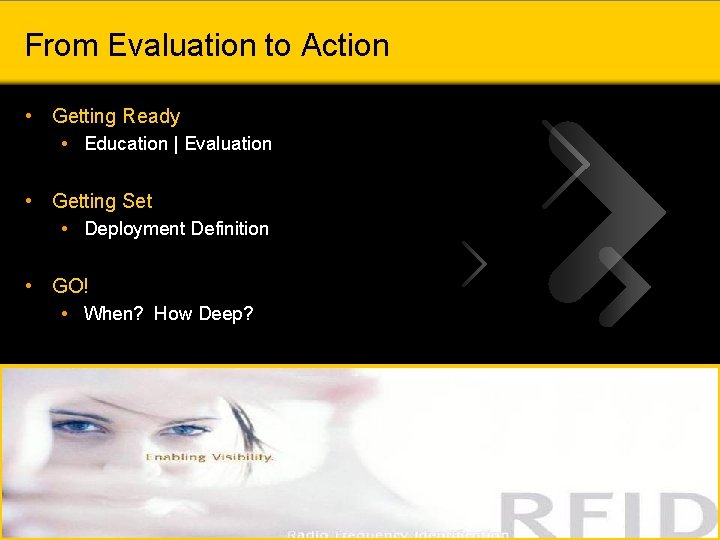

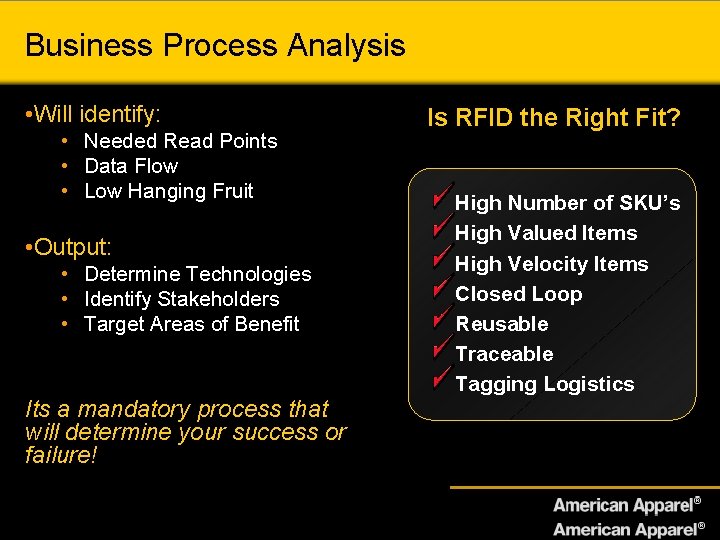
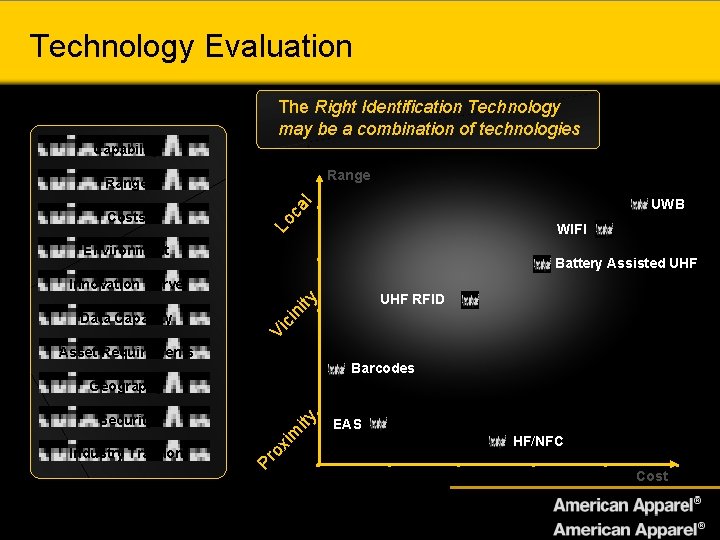
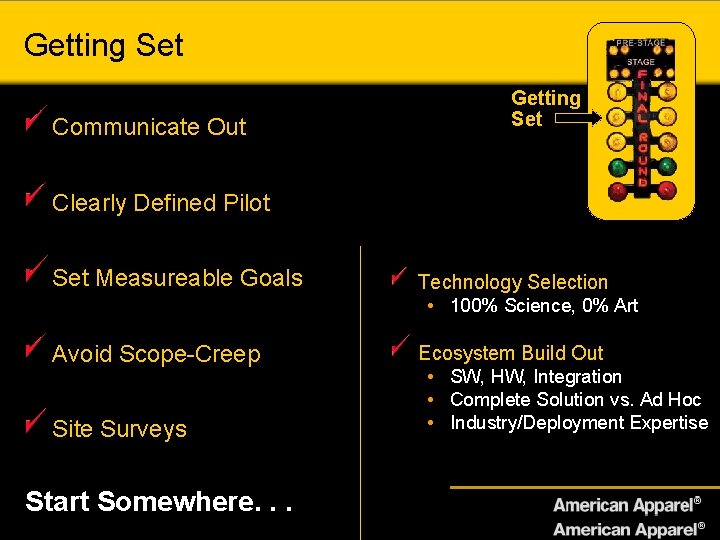
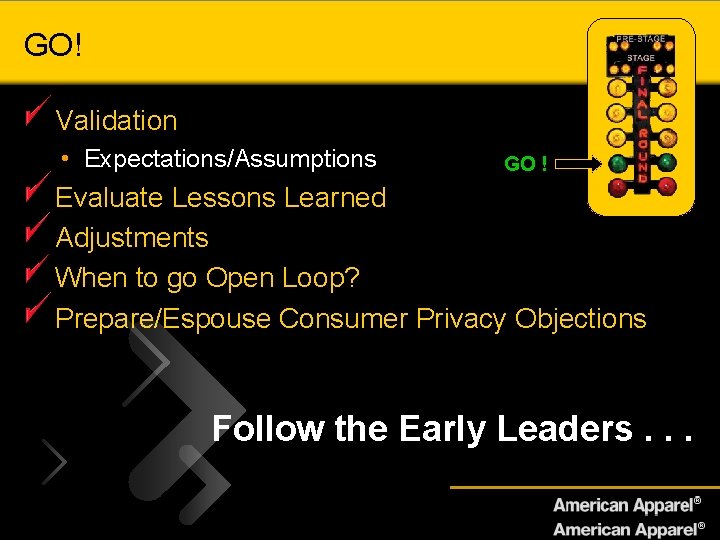
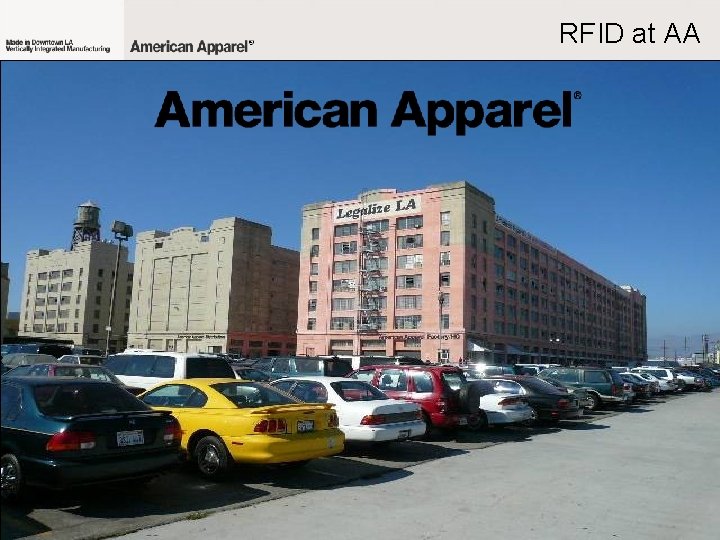
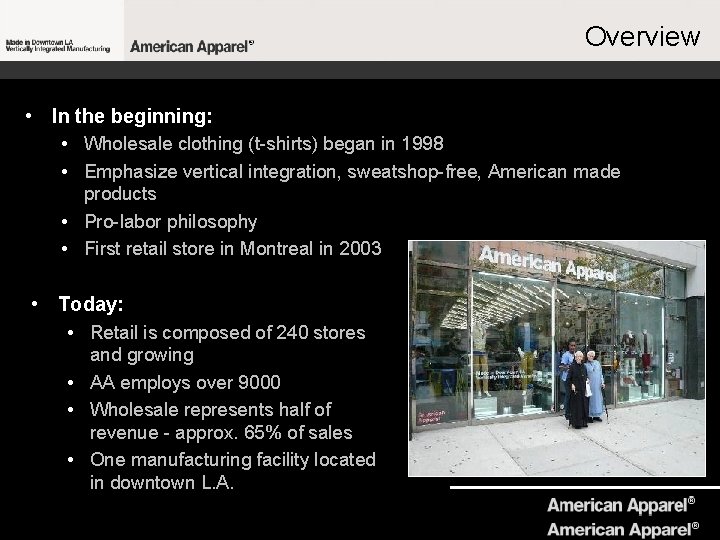
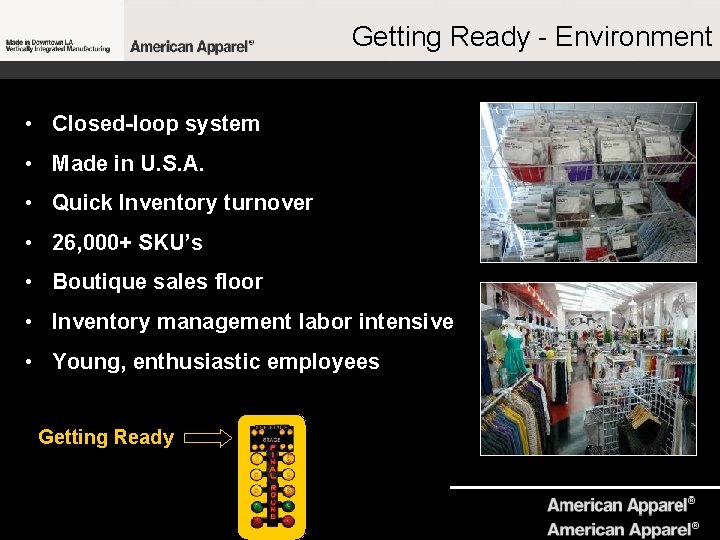
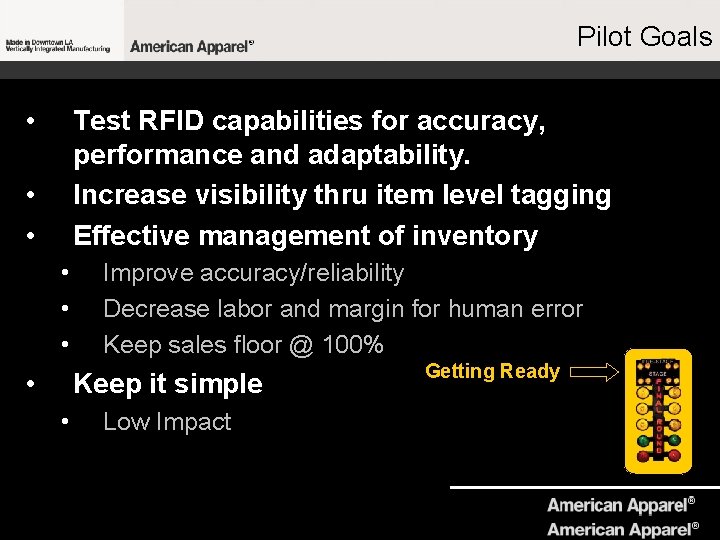
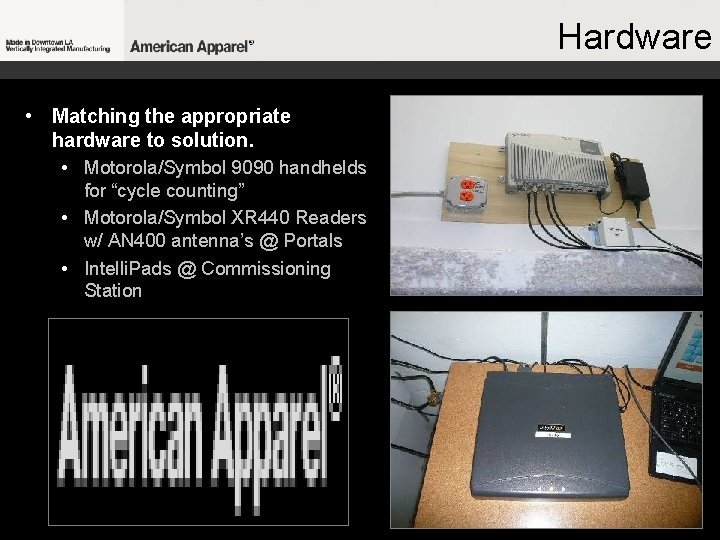
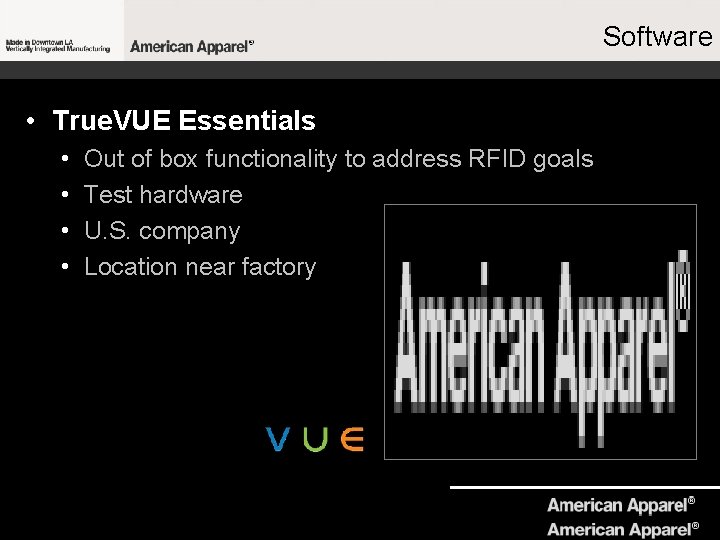
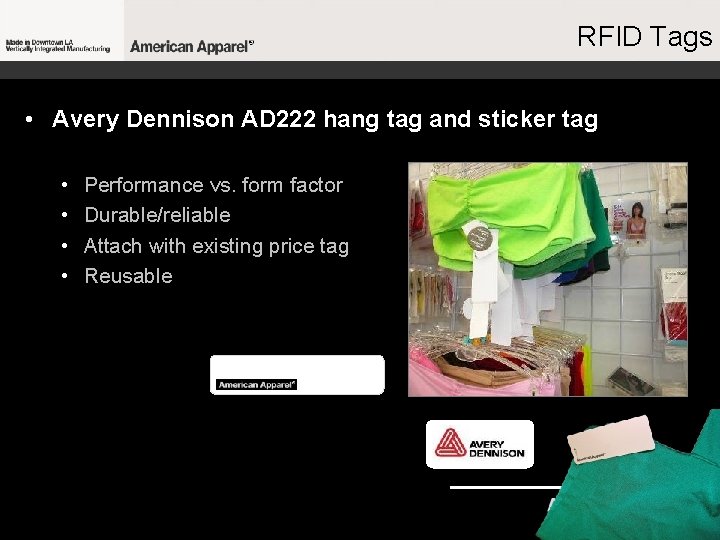
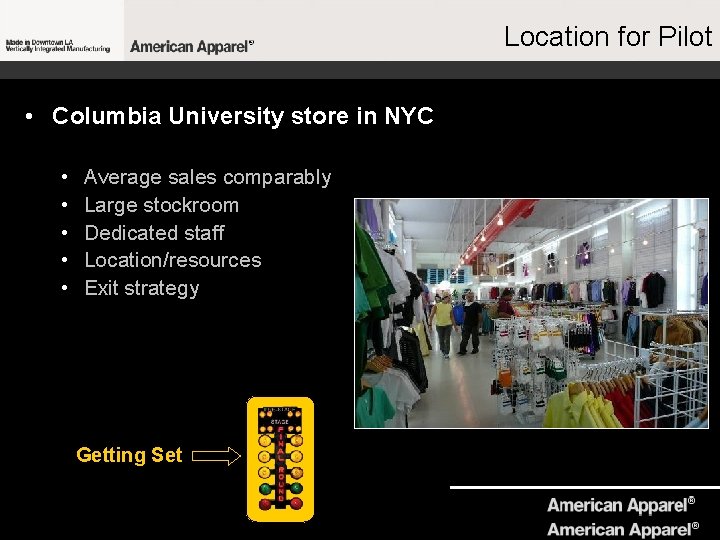
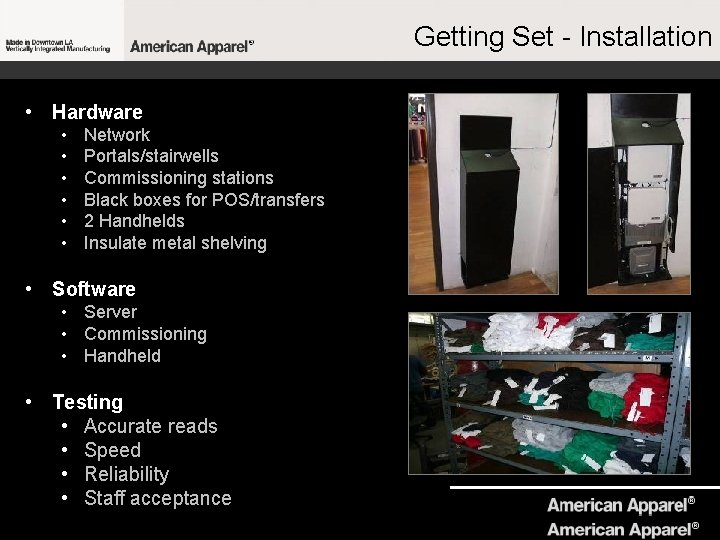
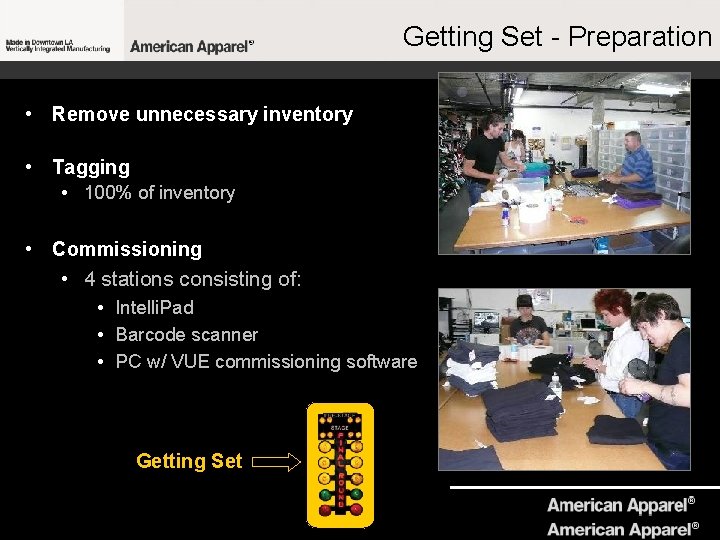
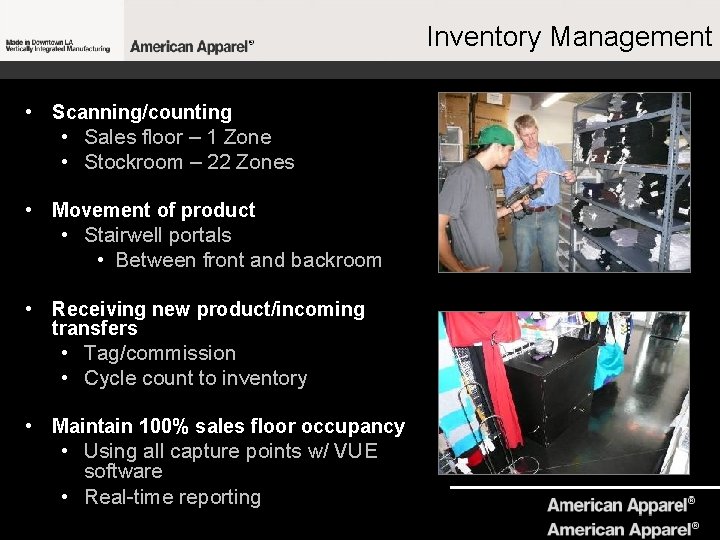
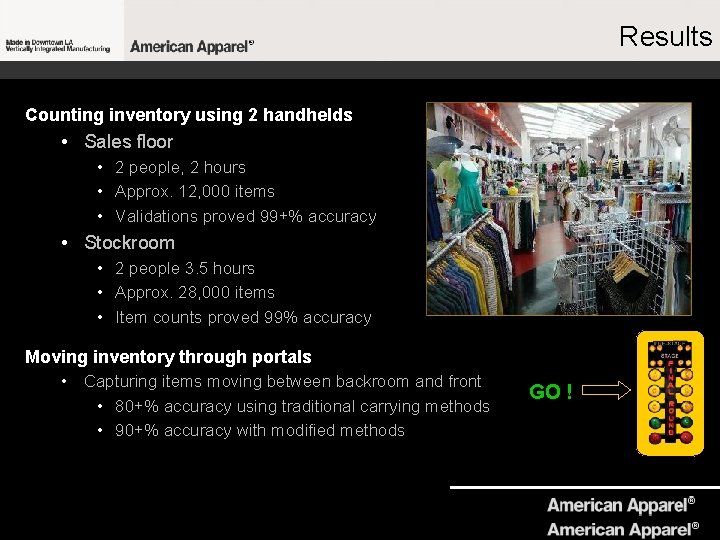
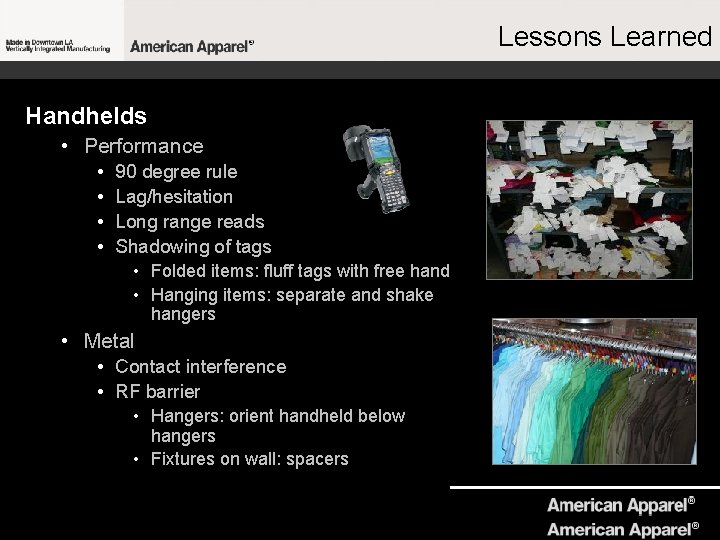
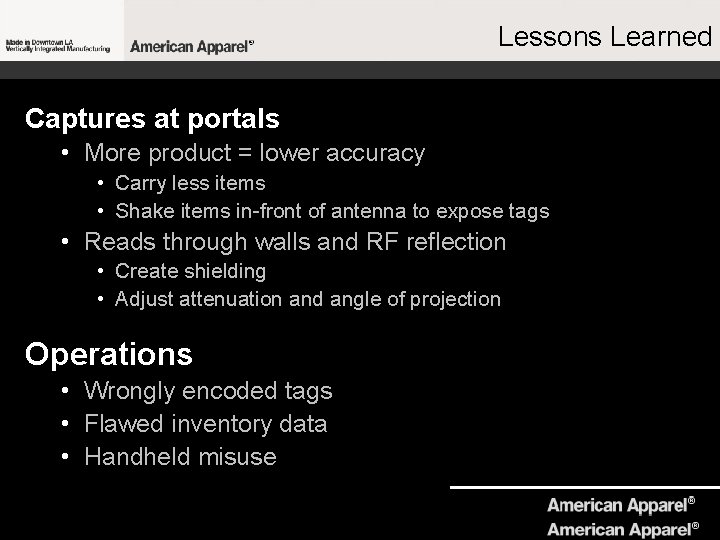
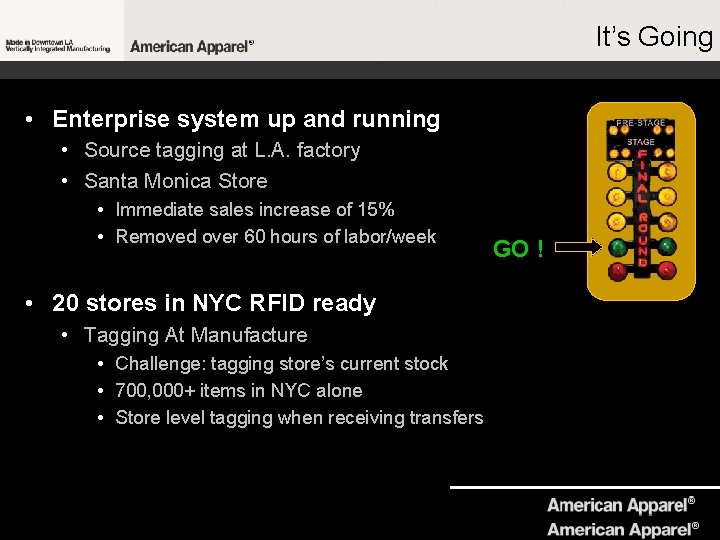
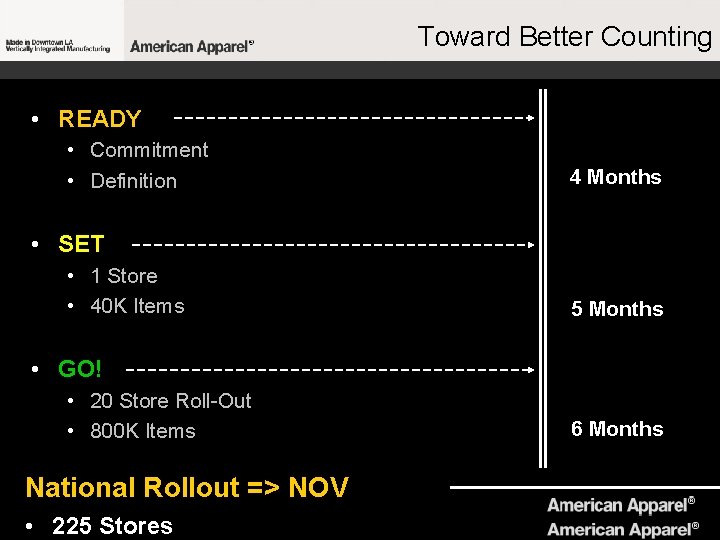
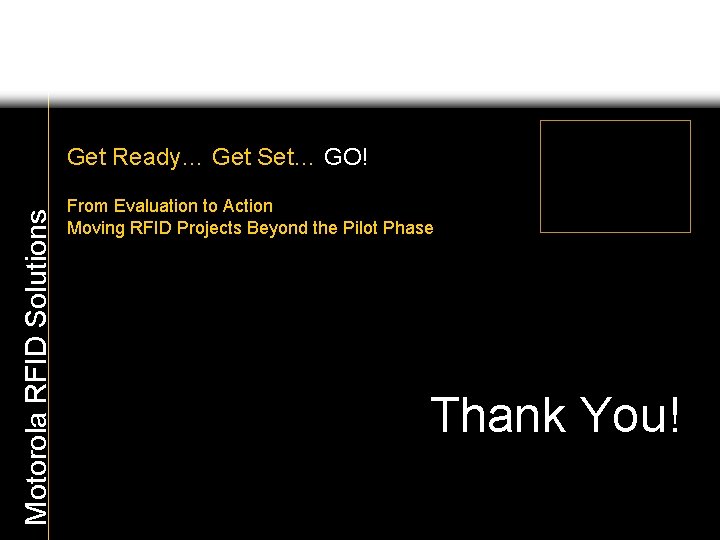
- Slides: 26
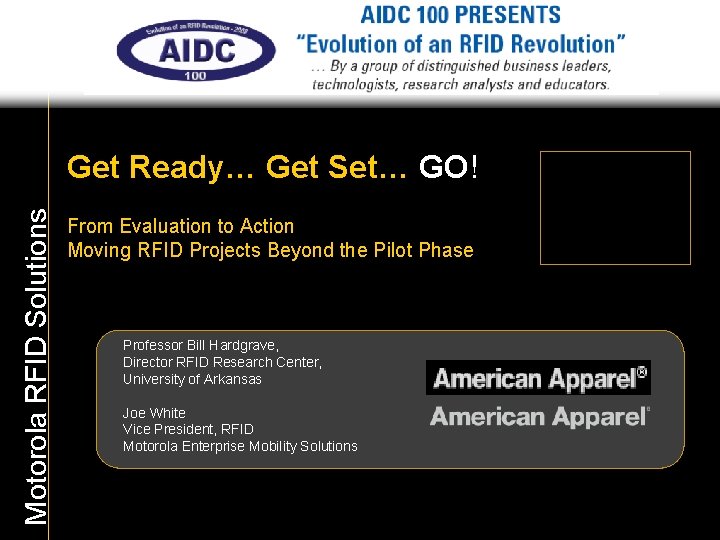
Motorola RFID Solutions Get Ready… Get Set… GO! From Evaluation to Action Moving RFID Projects Beyond the Pilot Phase Professor Bill Hardgrave, Director RFID Research Center, University of Arkansas Joe White Vice President, RFID Motorola Enterprise Mobility Solutions
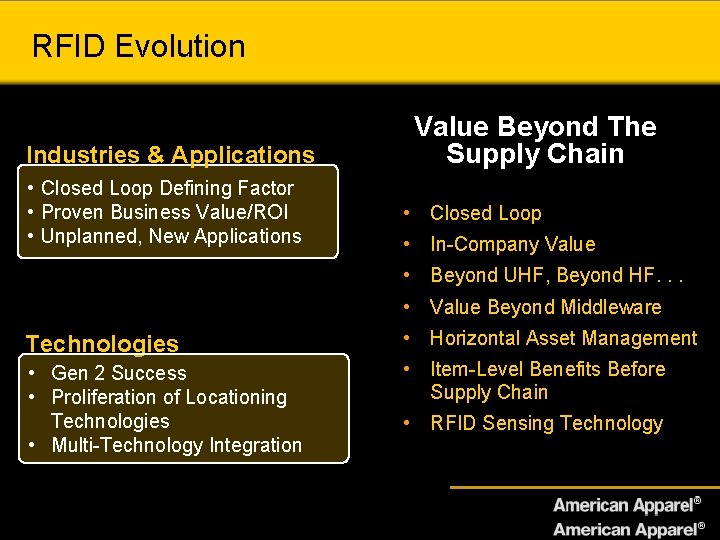
RFID Evolution Industries & Applications • Closed Loop Defining Factor • Proven Business Value/ROI • Unplanned, New Applications Value Beyond The Supply Chain • Closed Loop • In-Company Value • Beyond UHF, Beyond HF. . . • Value Beyond Middleware Technologies • Horizontal Asset Management • Gen 2 Success • Proliferation of Locationing Technologies • Multi-Technology Integration • Item-Level Benefits Before Supply Chain • RFID Sensing Technology
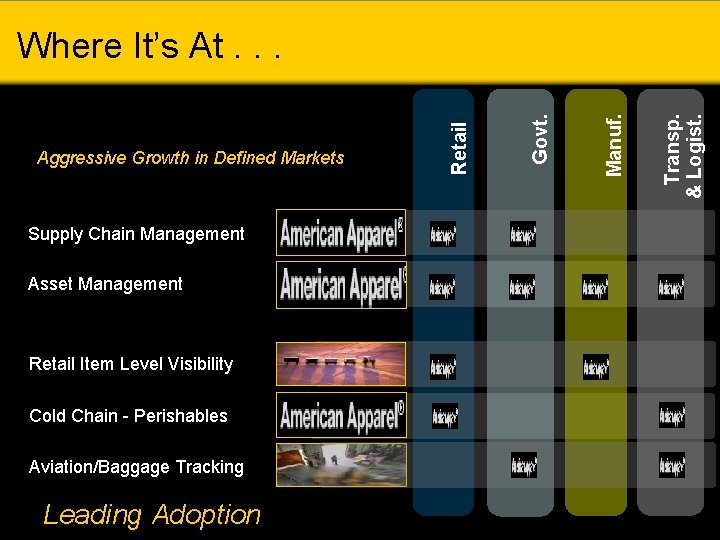
Supply Chain Management Asset Management 2009 and Beyond Retail Item Level Visibility Cold Chain - Perishables Aviation/Baggage Tracking Leading Adoption Manuf. Transp. & Logist. Here and Now Govt. Aggressive Growth in Defined Markets Retail Where It’s At. . .
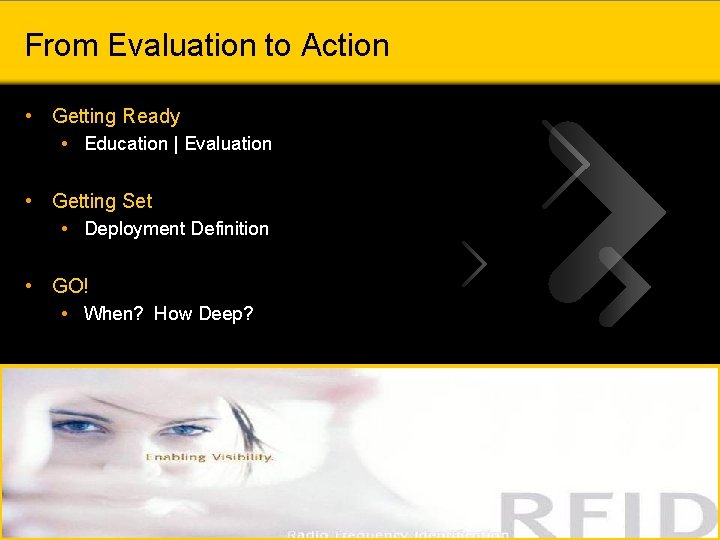
From Evaluation to Action • Getting Ready • Education | Evaluation • Getting Set • Deployment Definition • GO! • When? How Deep?

Getting Ready Education Technology Evaluation Management/Stakeholder Buy-In • Data Ownership Business Process Analysis At The End of The Day, A Better Way To Count! The Technology Works! • Validating the Application, Not the Technology • Buying Solutions / Solution Sets, Not a Product
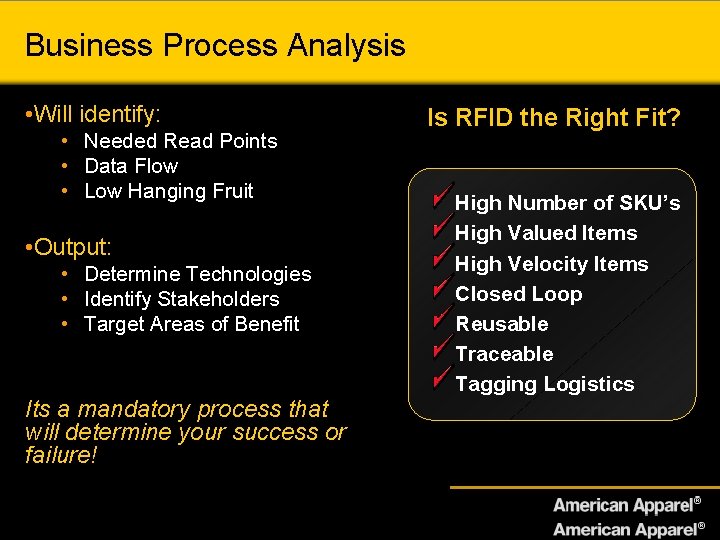
Business Process Analysis • Will identify: • Needed Read Points • Data Flow • Low Hanging Fruit • Output: • Determine Technologies • Identify Stakeholders • Target Areas of Benefit Its a mandatory process that will determine your success or failure! Is RFID the Right Fit? High Number of SKU’s High Valued Items High Velocity Items Closed Loop Reusable Traceable Tagging Logistics
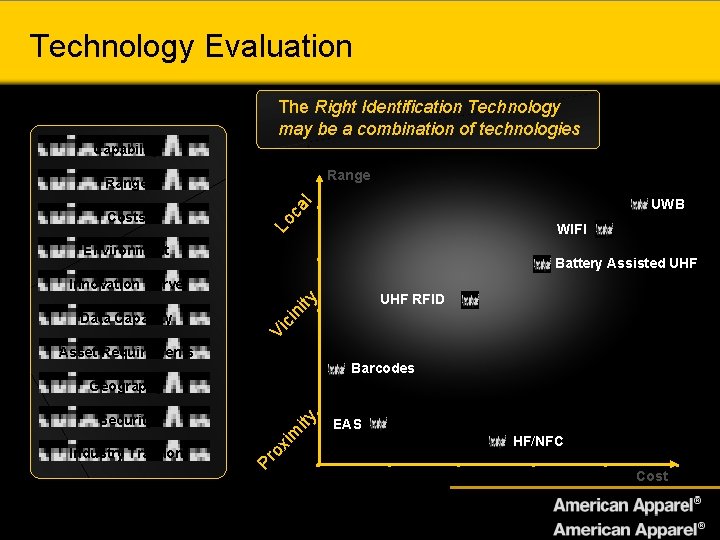
Technology Evaluation The Right Identification Technology may be a combination of technologies Capability Range UWB Lo Costs ca l Range WIFI Environment Battery Assisted UHF Innovation Curve ci Vi Data Capacity ni ty UHF RFID Asset Requirements Barcodes Geography Pr Industry Traction ox im ity Security EAS HF/NFC Cost
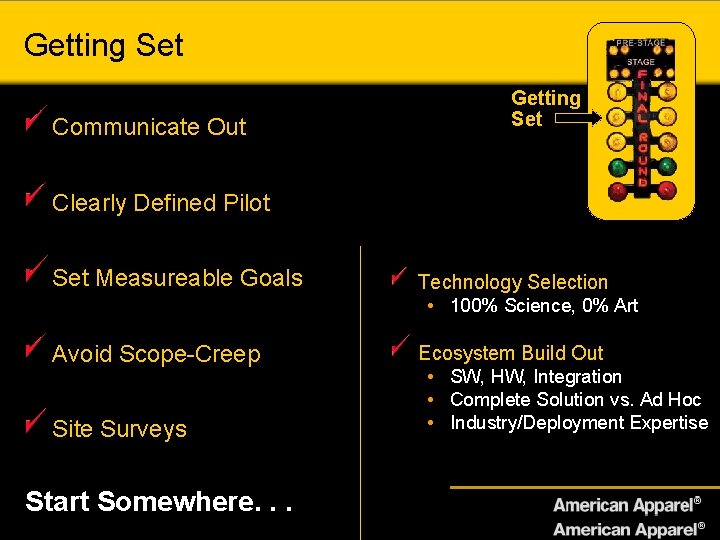
Getting Set Communicate Out Getting Set Clearly Defined Pilot Set Measureable Goals Technology Selection • 100% Science, 0% Art Avoid Scope-Creep Ecosystem Build Out • SW, HW, Integration • Complete Solution vs. Ad Hoc • Industry/Deployment Expertise Site Surveys Start Somewhere. . .
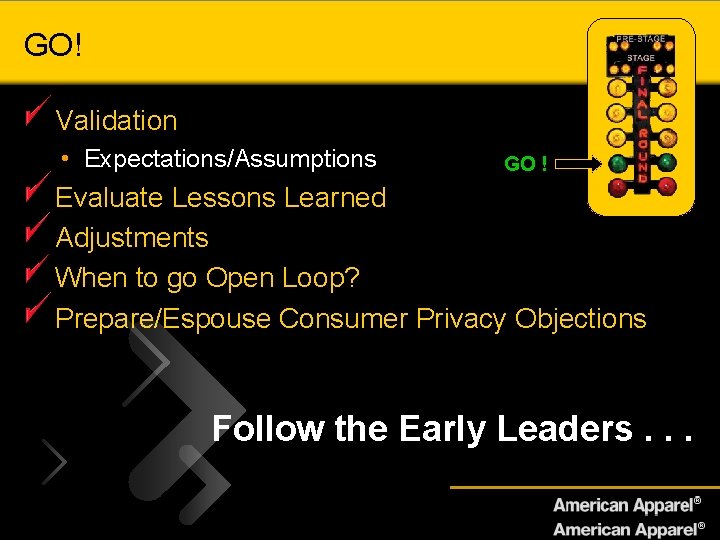
GO! Validation • Expectations/Assumptions GO ! Evaluate Lessons Learned Adjustments When to go Open Loop? Prepare/Espouse Consumer Privacy Objections Follow the Early Leaders. . .
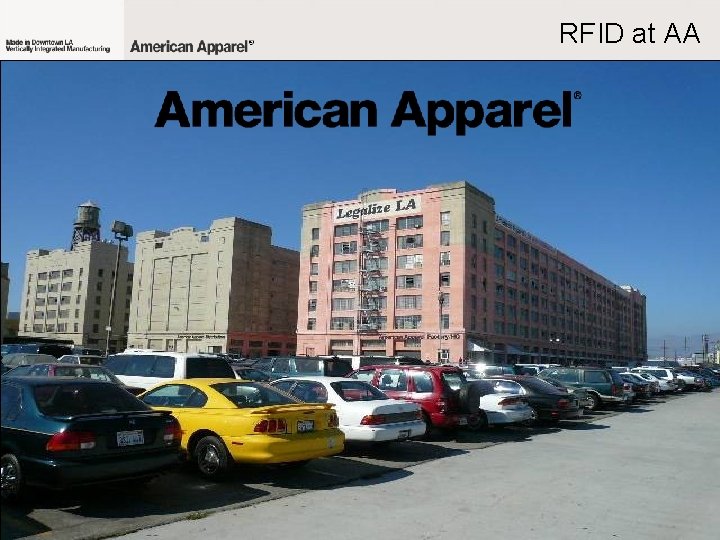
RFID at AA
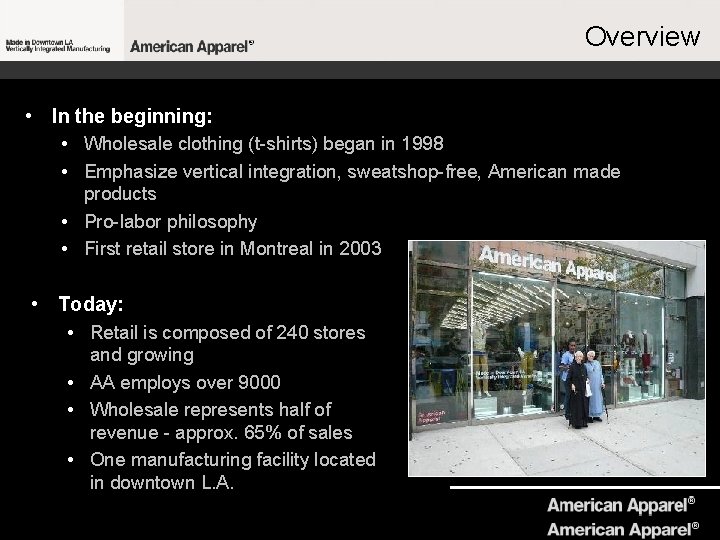
Overview • In the beginning: • Wholesale clothing (t-shirts) began in 1998 • Emphasize vertical integration, sweatshop-free, American made products • Pro-labor philosophy • First retail store in Montreal in 2003 • Today: • Retail is composed of 240 stores and growing • AA employs over 9000 • Wholesale represents half of revenue - approx. 65% of sales • One manufacturing facility located in downtown L. A.
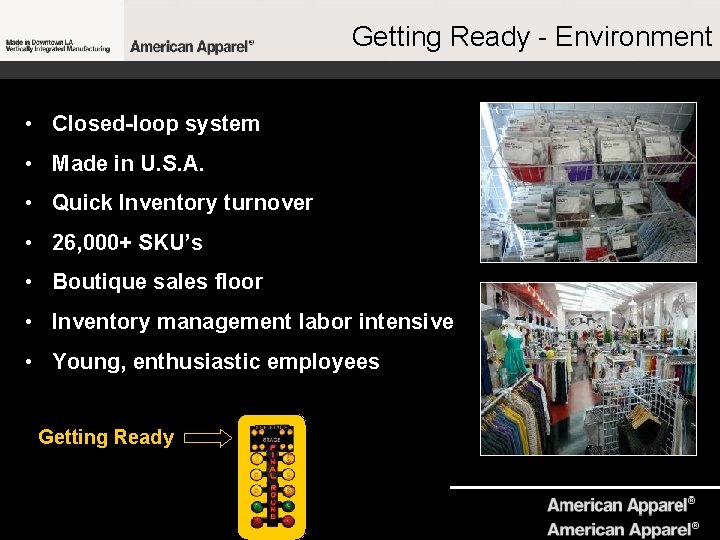
Getting Ready - Environment • Closed-loop system • Made in U. S. A. • Quick Inventory turnover • 26, 000+ SKU’s • Boutique sales floor • Inventory management labor intensive • Young, enthusiastic employees Getting Ready
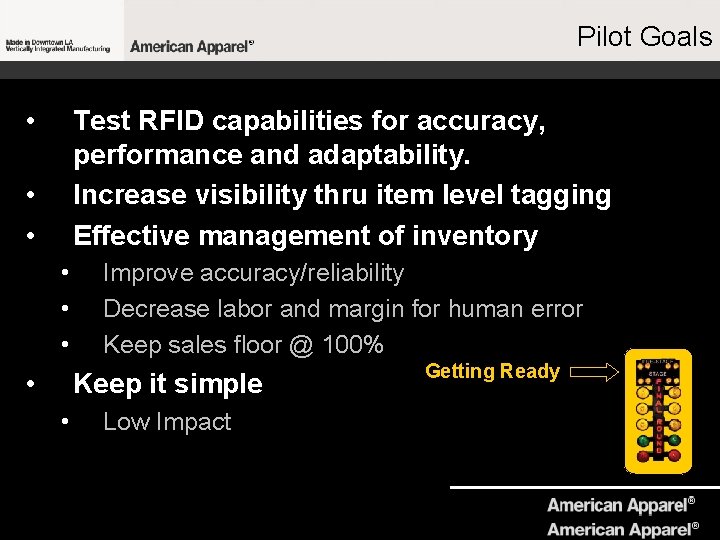
Pilot Goals • Test RFID capabilities for accuracy, performance and adaptability. Increase visibility thru item level tagging Effective management of inventory • • • Improve accuracy/reliability Decrease labor and margin for human error Keep sales floor @ 100% Keep it simple • Low Impact Getting Ready
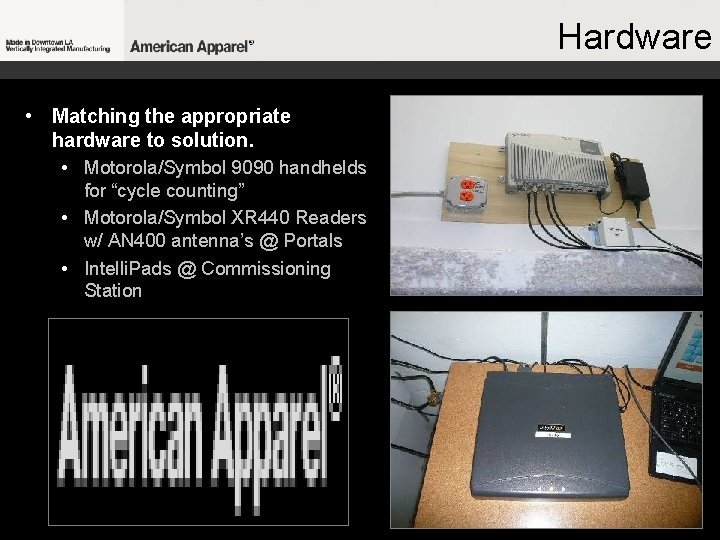
Hardware • Matching the appropriate hardware to solution. • Motorola/Symbol 9090 handhelds for “cycle counting” • Motorola/Symbol XR 440 Readers w/ AN 400 antenna’s @ Portals • Intelli. Pads @ Commissioning Station
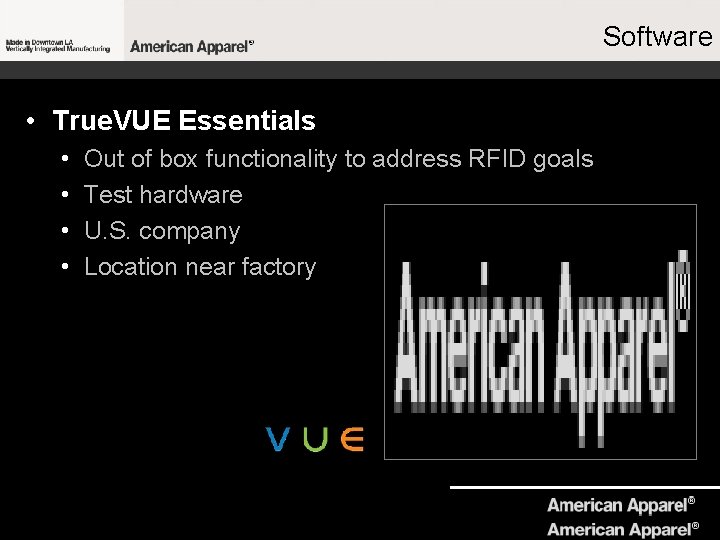
Software • True. VUE Essentials • • Out of box functionality to address RFID goals Test hardware U. S. company Location near factory
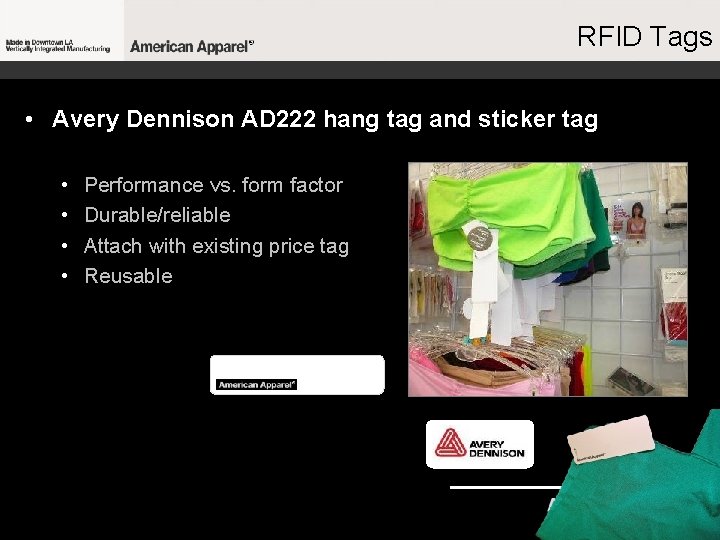
RFID Tags • Avery Dennison AD 222 hang tag and sticker tag • • Performance vs. form factor Durable/reliable Attach with existing price tag Reusable
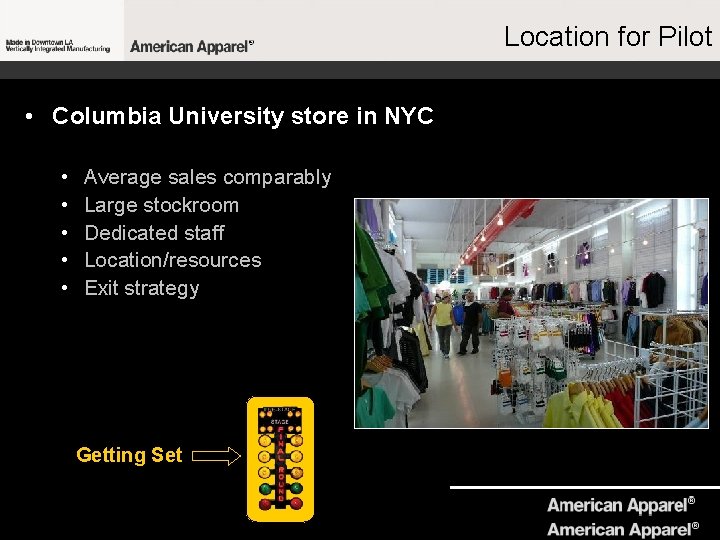
Location for Pilot • Columbia University store in NYC • • • Average sales comparably Large stockroom Dedicated staff Location/resources Exit strategy Getting Set
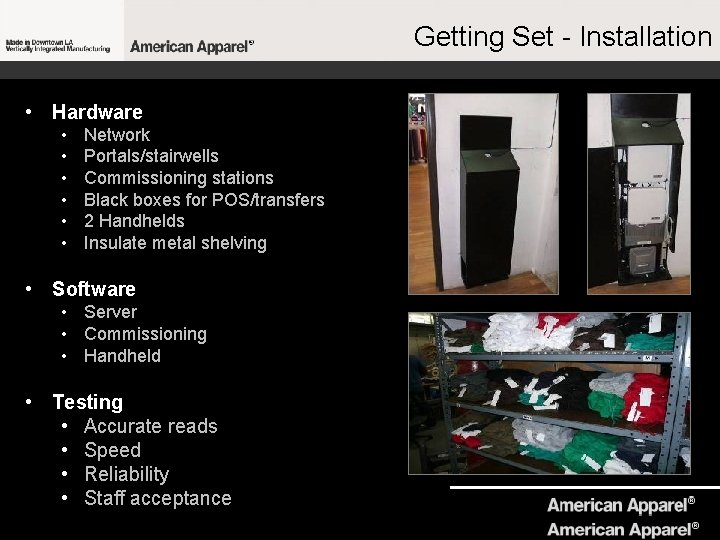
Getting Set - Installation • Hardware • • • Network Portals/stairwells Commissioning stations Black boxes for POS/transfers 2 Handhelds Insulate metal shelving • Software • Server • Commissioning • Handheld • Testing • Accurate reads • Speed • Reliability • Staff acceptance
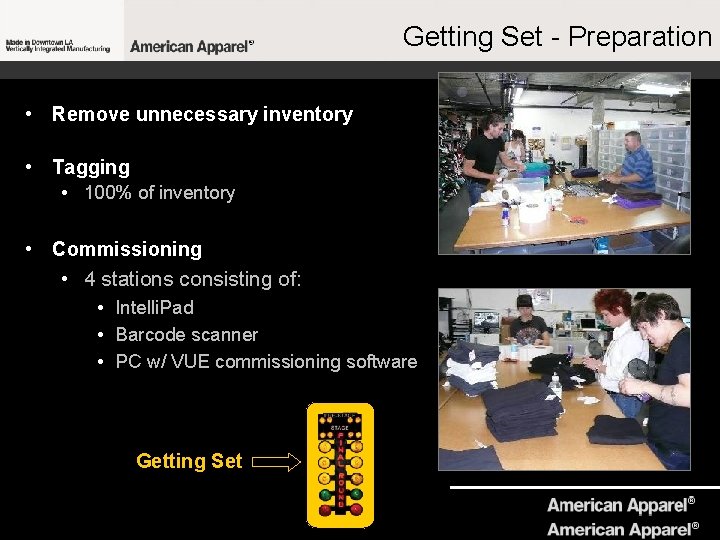
Getting Set - Preparation • Remove unnecessary inventory • Tagging • 100% of inventory • Commissioning • 4 stations consisting of: • Intelli. Pad • Barcode scanner • PC w/ VUE commissioning software Getting Set
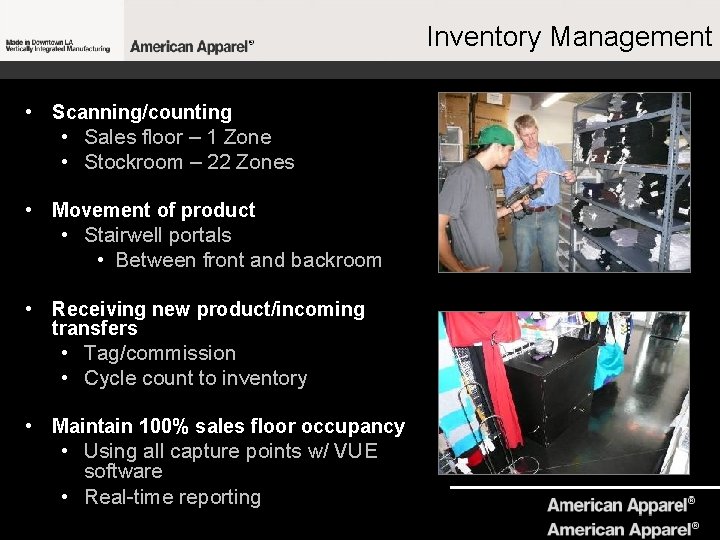
Inventory Management • Scanning/counting • Sales floor – 1 Zone • Stockroom – 22 Zones • Movement of product • Stairwell portals • Between front and backroom • Receiving new product/incoming transfers • Tag/commission • Cycle count to inventory • Maintain 100% sales floor occupancy • Using all capture points w/ VUE software • Real-time reporting
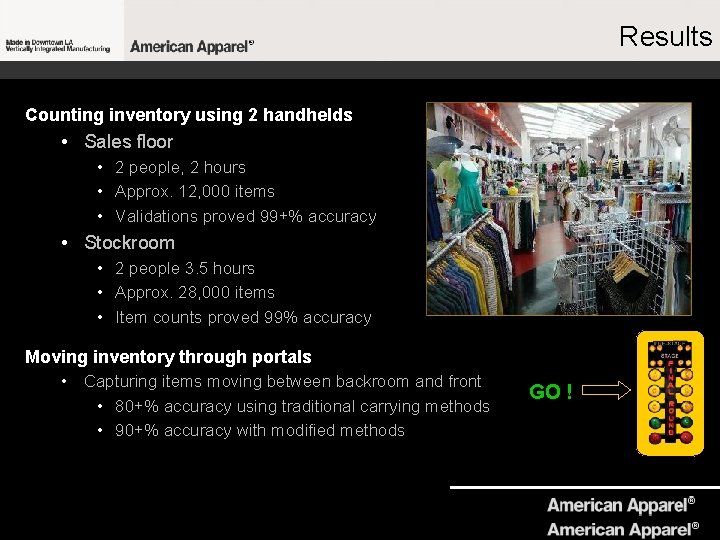
Results Counting inventory using 2 handhelds • Sales floor • 2 people, 2 hours • Approx. 12, 000 items • Validations proved 99+% accuracy • Stockroom • 2 people 3. 5 hours • Approx. 28, 000 items • Item counts proved 99% accuracy Moving inventory through portals • Capturing items moving between backroom and front • 80+% accuracy using traditional carrying methods • 90+% accuracy with modified methods GO !
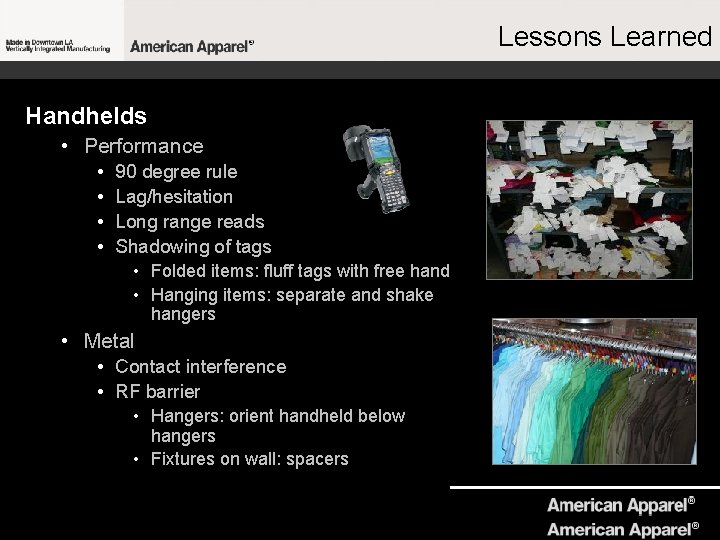
Lessons Learned Handhelds • Performance • • 90 degree rule Lag/hesitation Long range reads Shadowing of tags • Folded items: fluff tags with free hand • Hanging items: separate and shake hangers • Metal • Contact interference • RF barrier • Hangers: orient handheld below hangers • Fixtures on wall: spacers
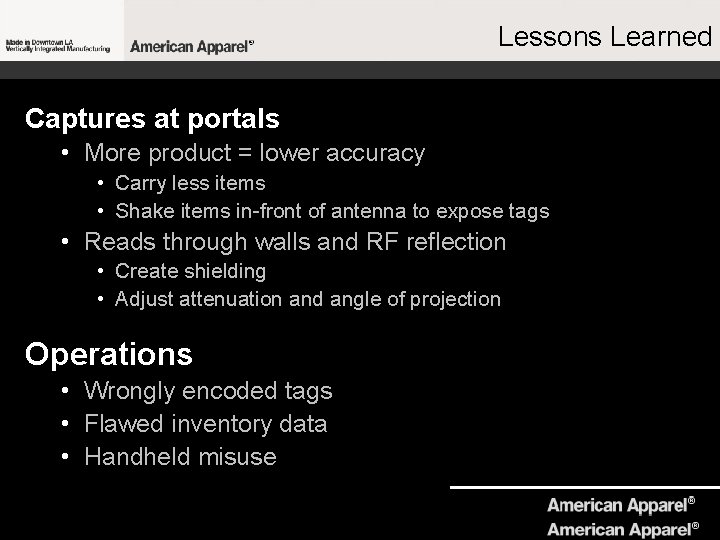
Lessons Learned Captures at portals • More product = lower accuracy • Carry less items • Shake items in-front of antenna to expose tags • Reads through walls and RF reflection • Create shielding • Adjust attenuation and angle of projection Operations • Wrongly encoded tags • Flawed inventory data • Handheld misuse
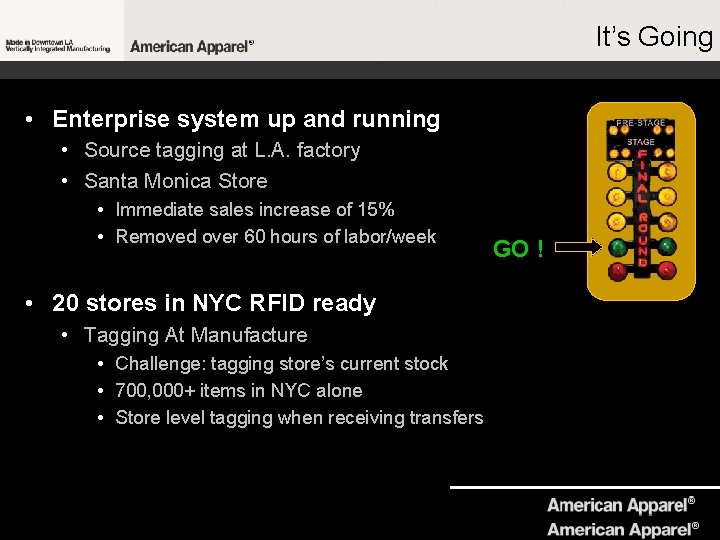
It’s Going • Enterprise system up and running • Source tagging at L. A. factory • Santa Monica Store • Immediate sales increase of 15% • Removed over 60 hours of labor/week • 20 stores in NYC RFID ready • Tagging At Manufacture • Challenge: tagging store’s current stock • 700, 000+ items in NYC alone • Store level tagging when receiving transfers GO !
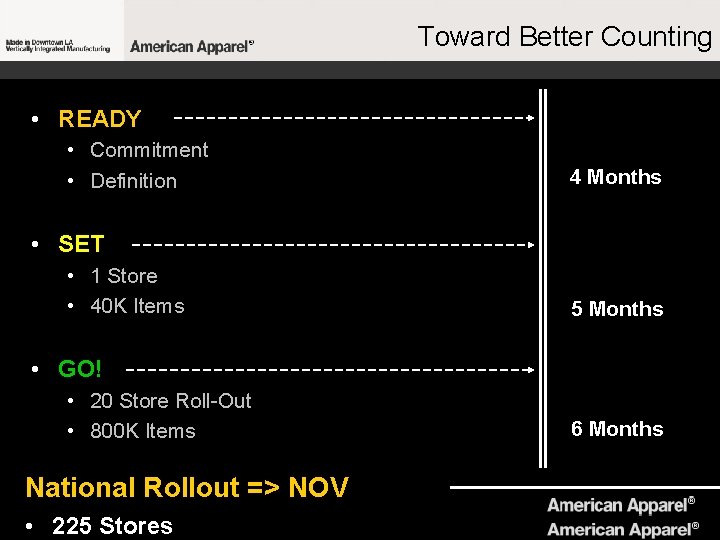
Toward Better Counting • READY • Commitment • Definition 4 Months • SET • 1 Store • 40 K Items 5 Months • GO! • 20 Store Roll-Out • 800 K Items National Rollout => NOV • 225 Stores 6 Months
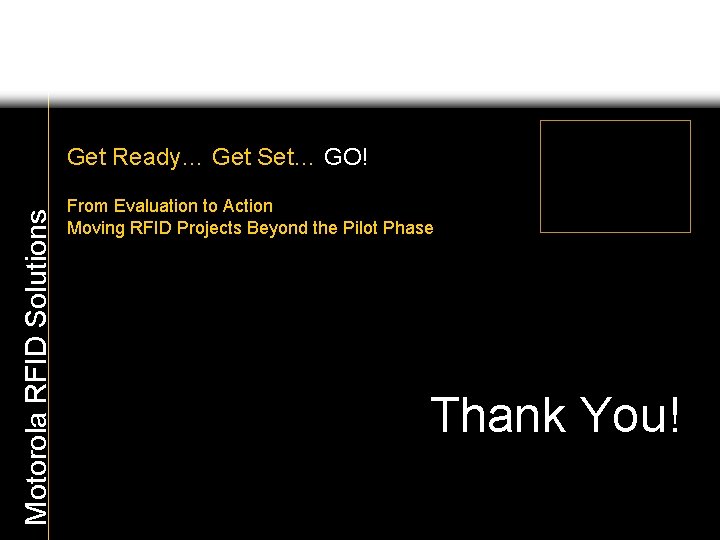
Motorola RFID Solutions Get Ready… Get Set… GO! From Evaluation to Action Moving RFID Projects Beyond the Pilot Phase Thank You!
Stay ready to keep from getting ready
Get on get in get off
Motorola ready to go
Ready, get set, kahoot!
Chapter 3 introduction
Motorola 68000 assembler
Motorola 68000 instruction set
Motorola internship
Total set awareness set consideration set
Training set validation set test set
One direction one thing
Ready set go transition inventory
Go maths
Belcher elementary
Ready set go
Ready set bingo
Hybrid cloud ready
Get ready for invalsi soluzioni
When god says get ready
Get ready
Vocabulary lesson 7
Please get ready
Let's look at the menu and see what we want to eat.
Ready
Motorola xt 400
Rfid antenna
Baile trunking