Marques Fulford Jamie Rosin Jon Olsten Team 3
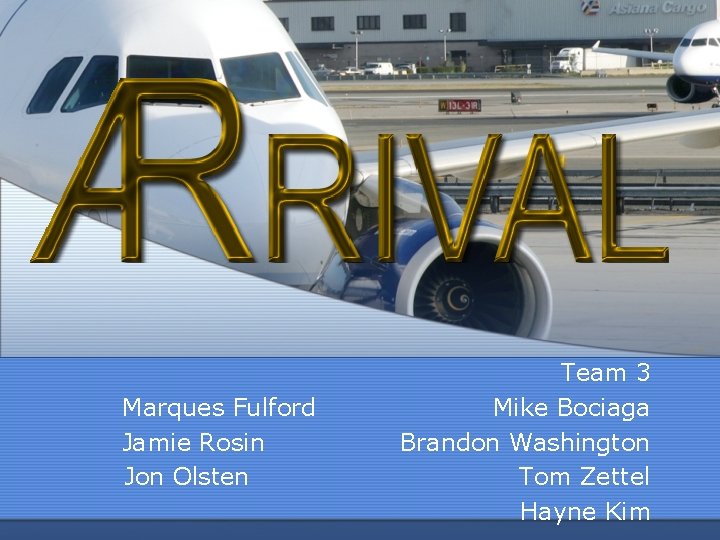
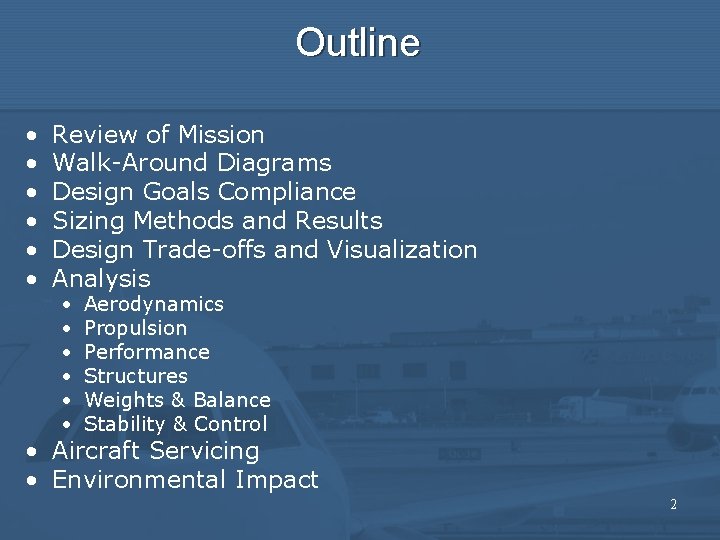
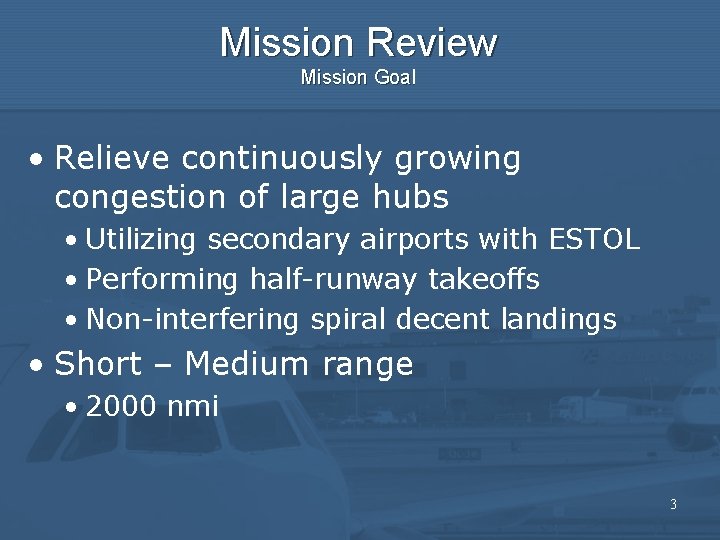

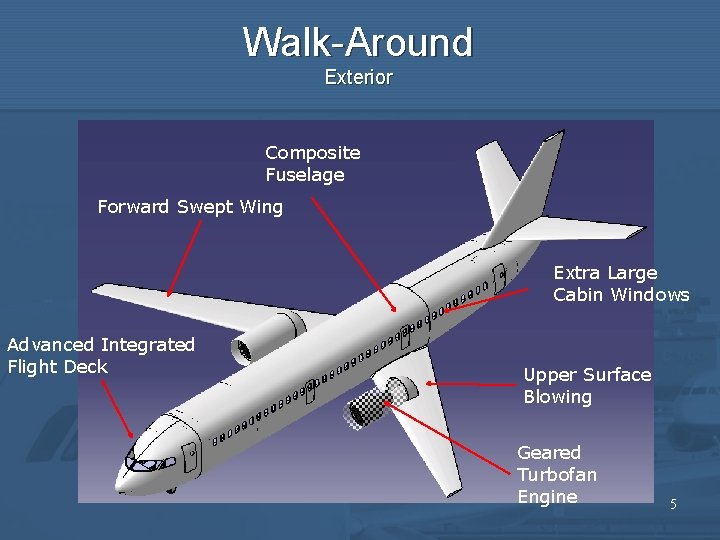
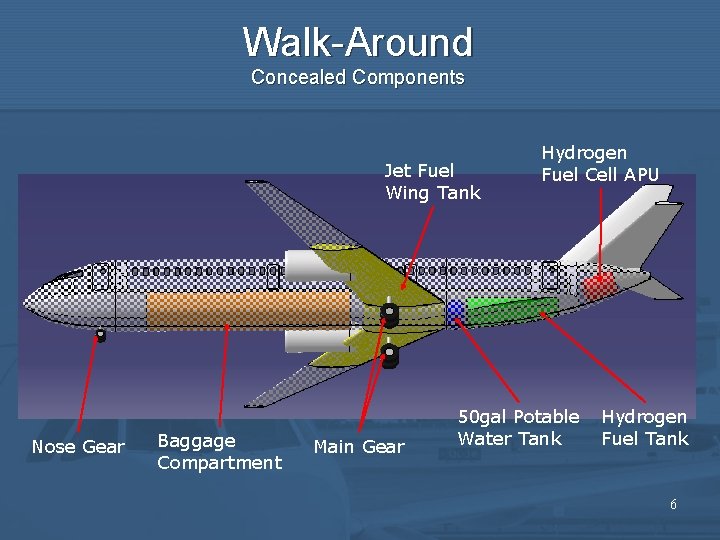
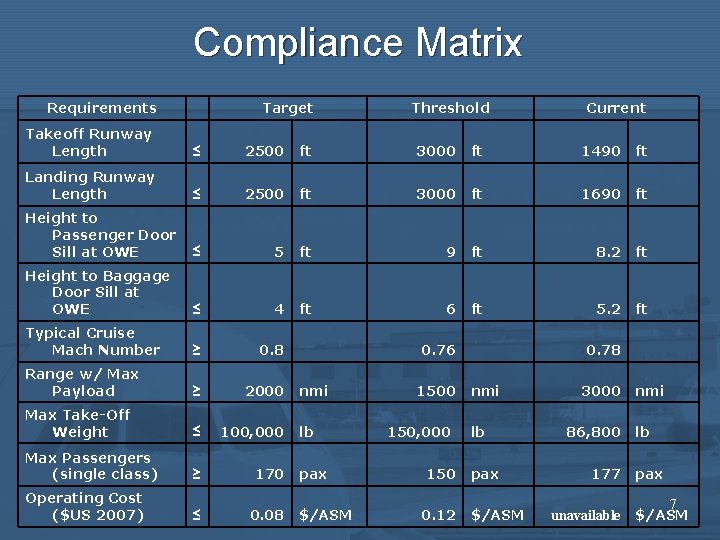
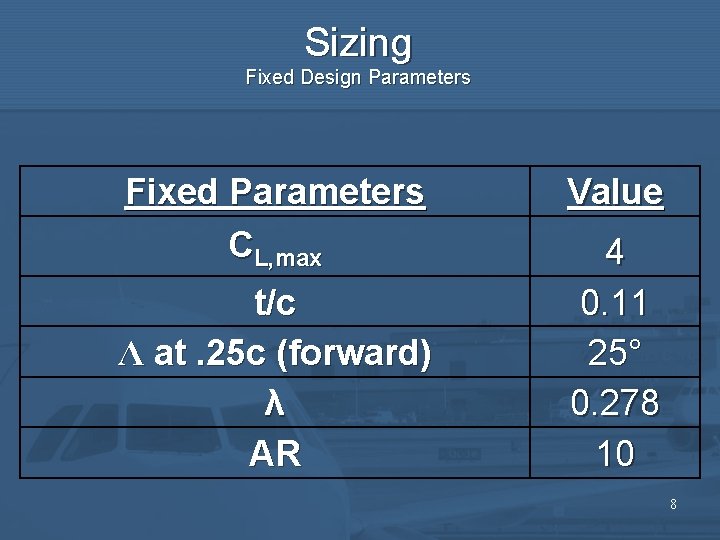
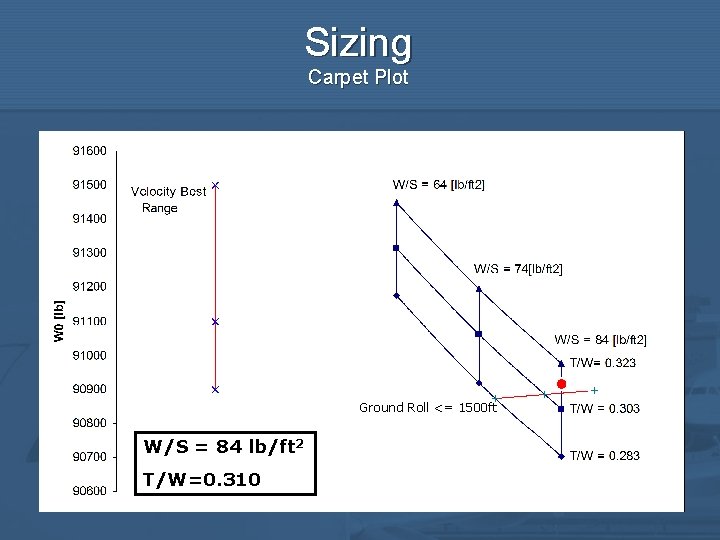
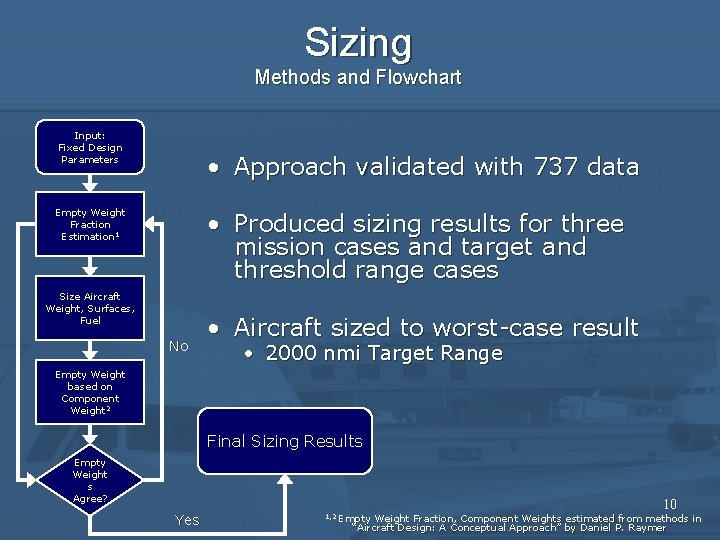
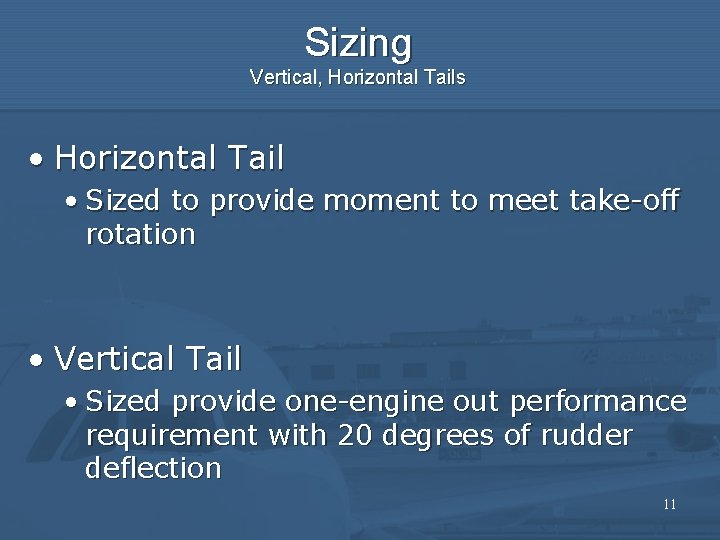
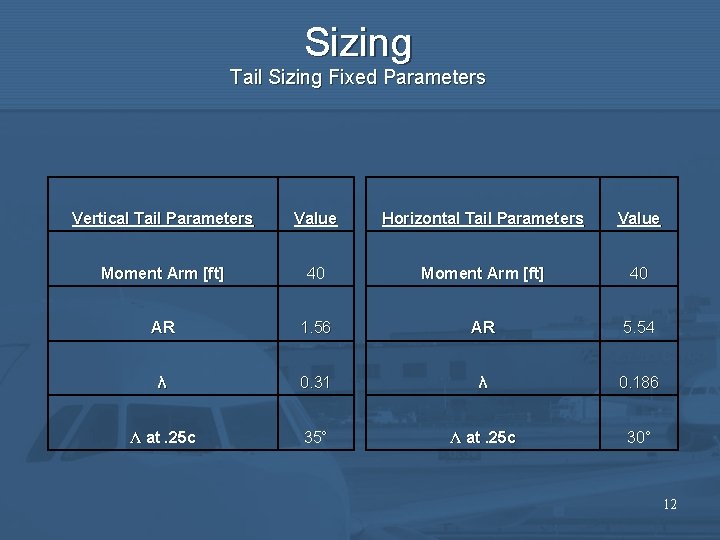
![Sizing Results Weights Value TOGW [lbs] 86, 800 We [lbs] 35, 000 Gross Landing Sizing Results Weights Value TOGW [lbs] 86, 800 We [lbs] 35, 000 Gross Landing](https://slidetodoc.com/presentation_image/851a9c76048945dedeef9c205b3aed55/image-13.jpg)
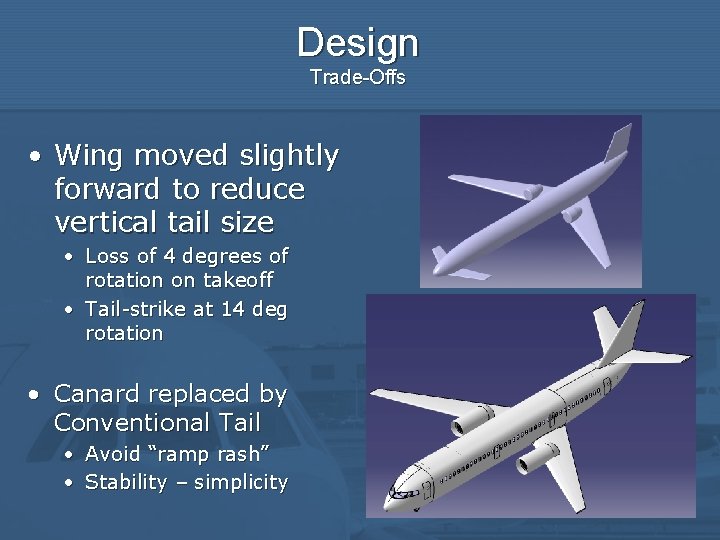
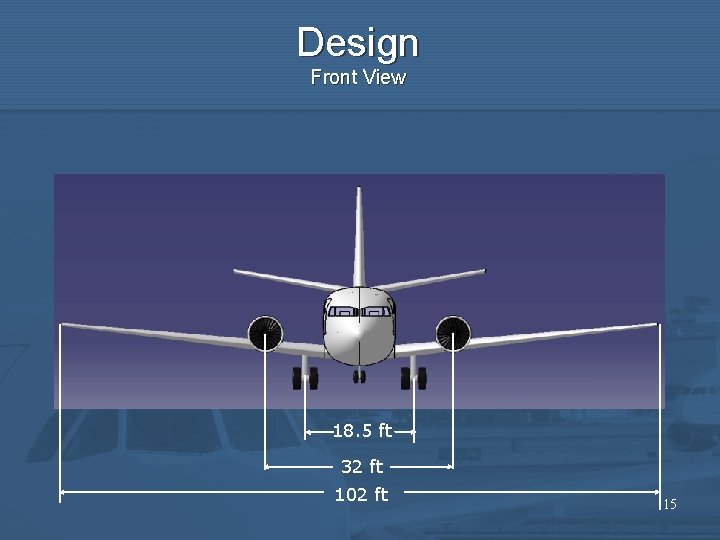
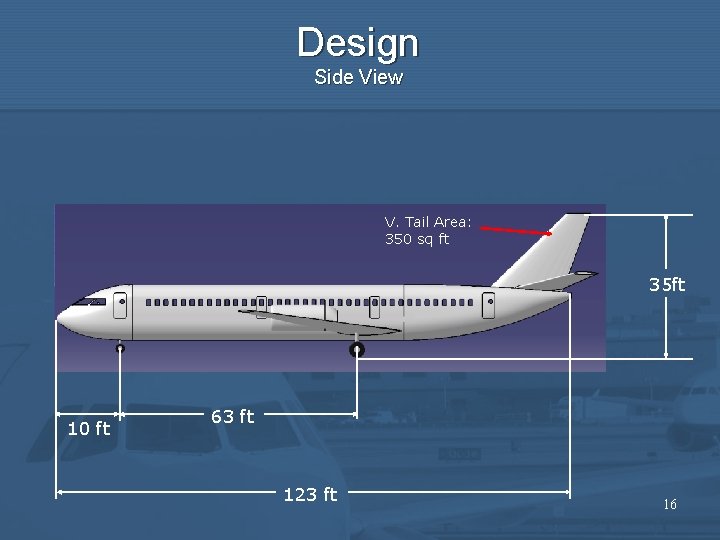
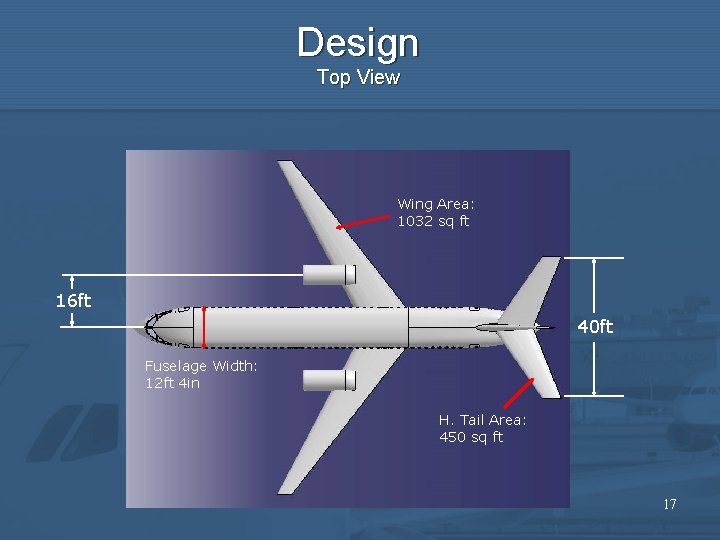
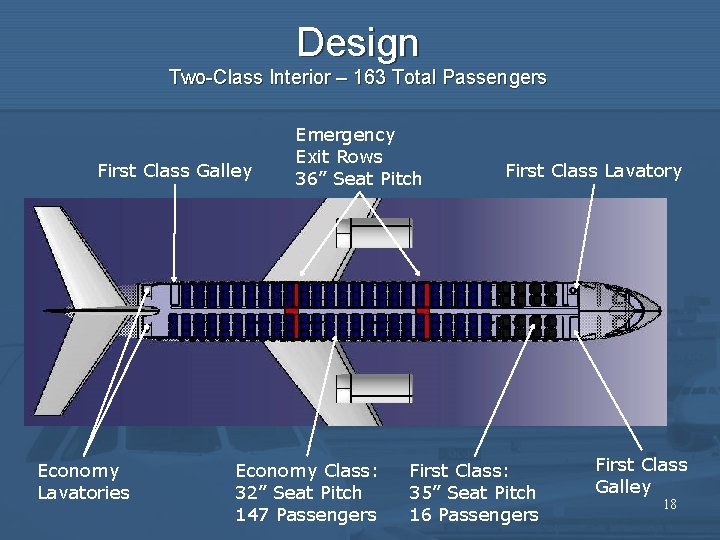
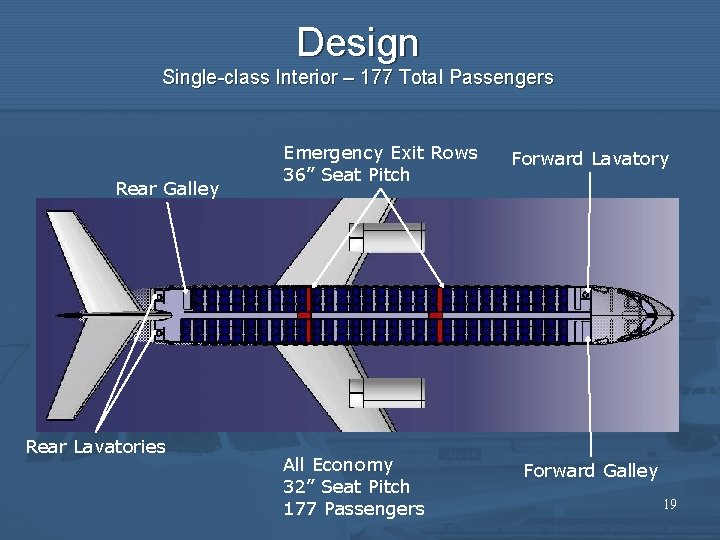
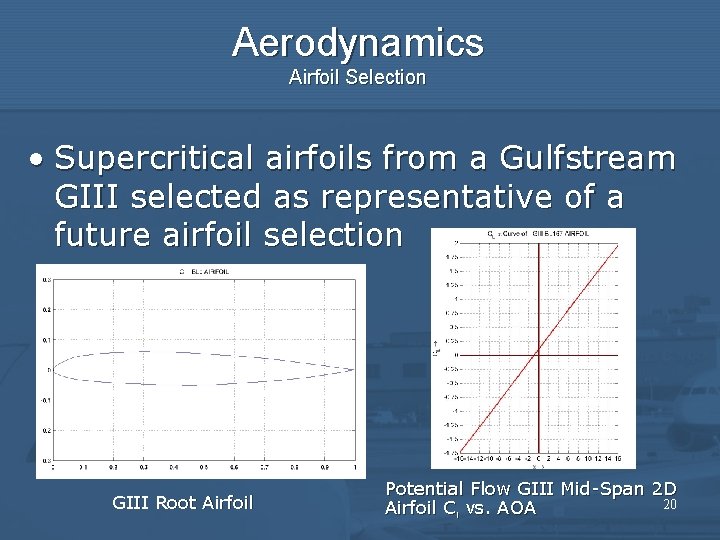
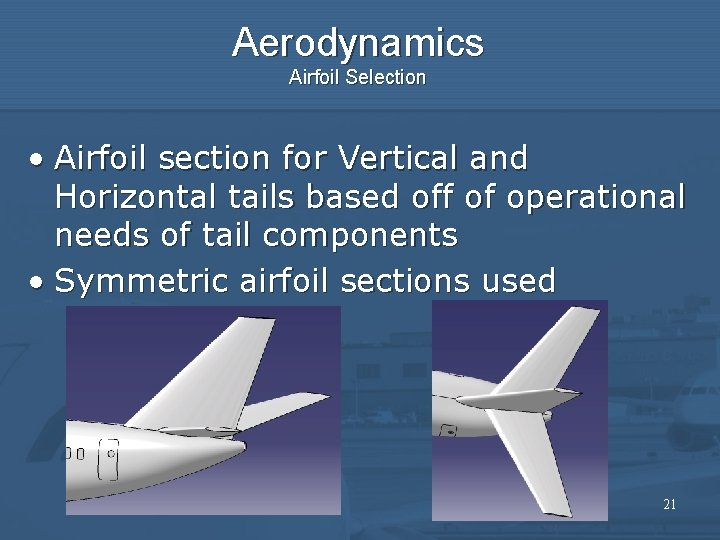
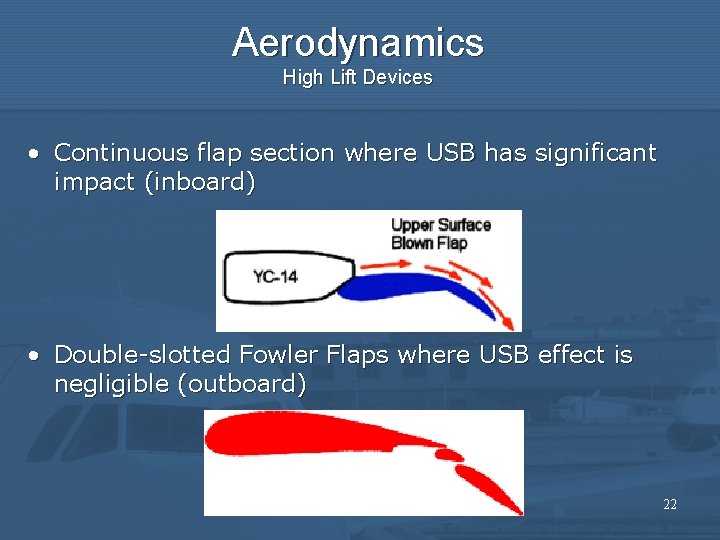
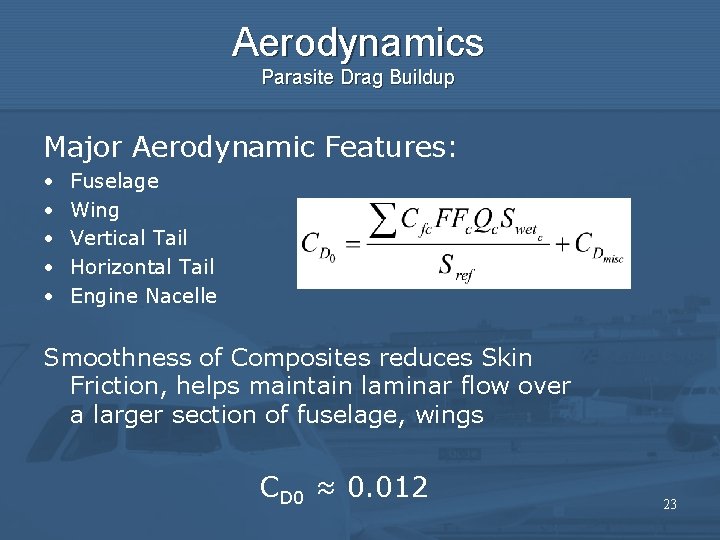
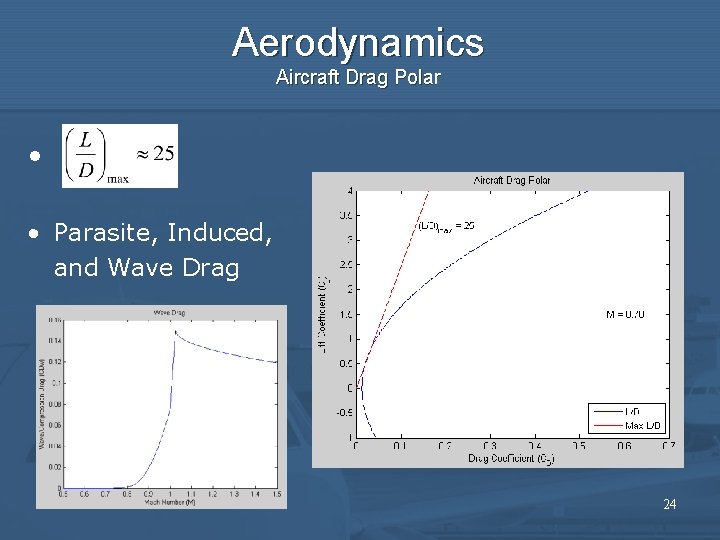
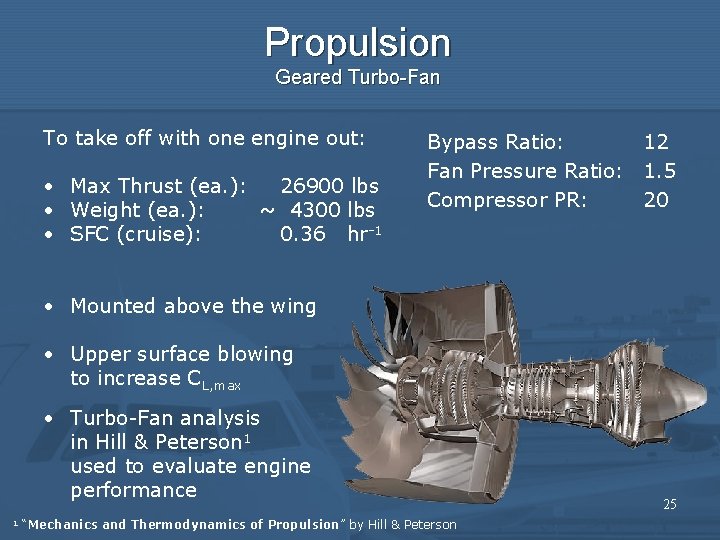
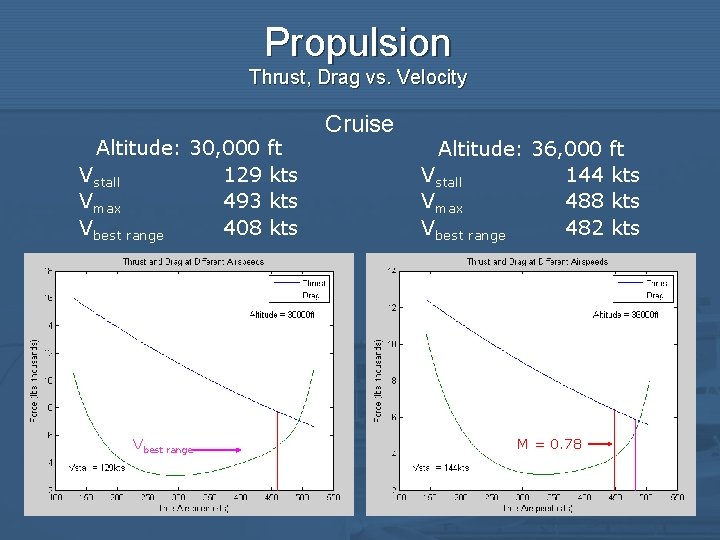
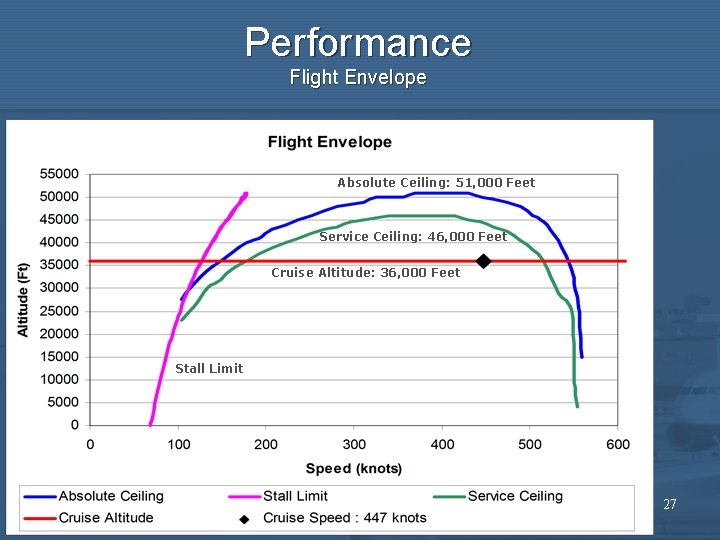
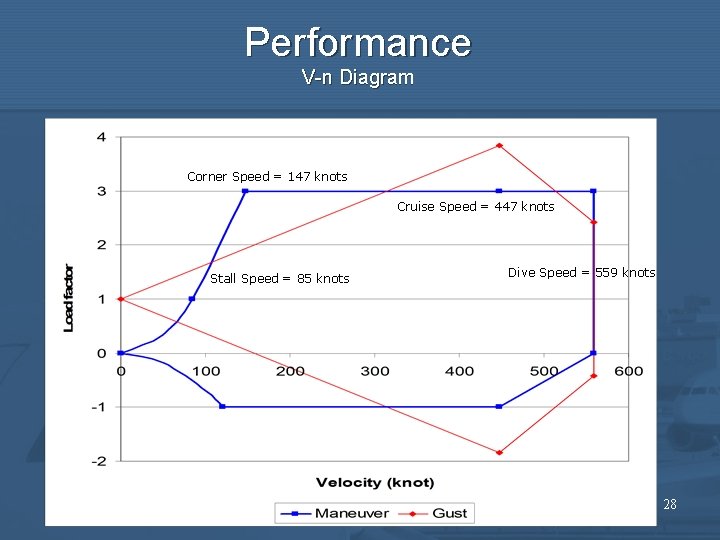
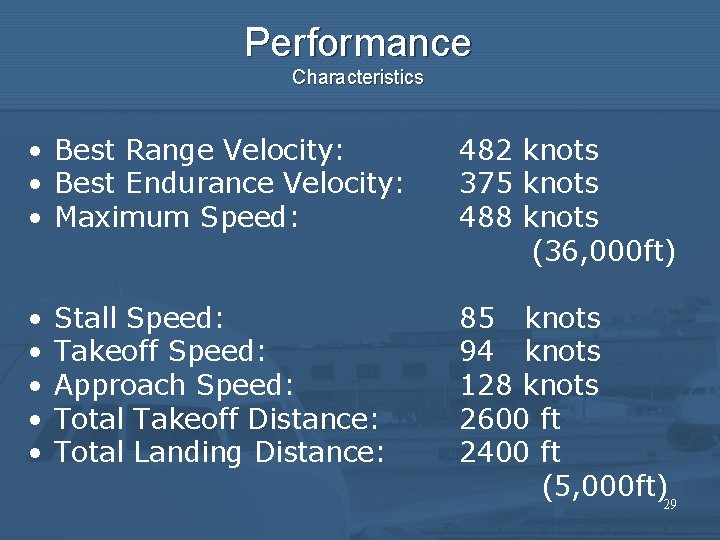
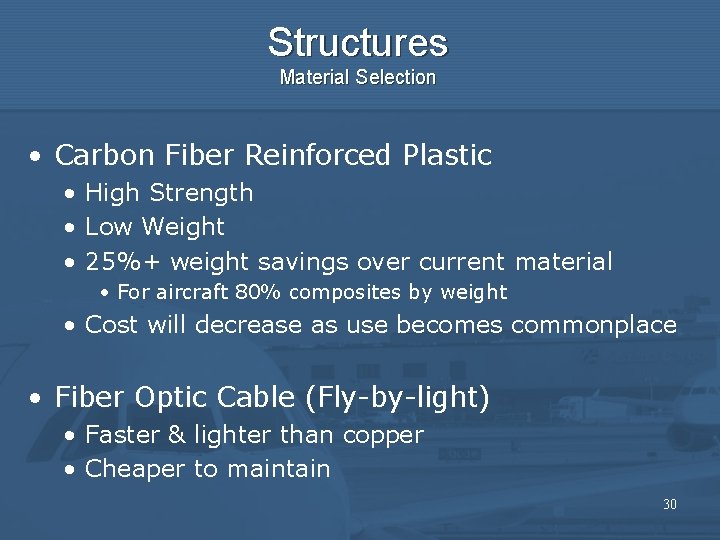
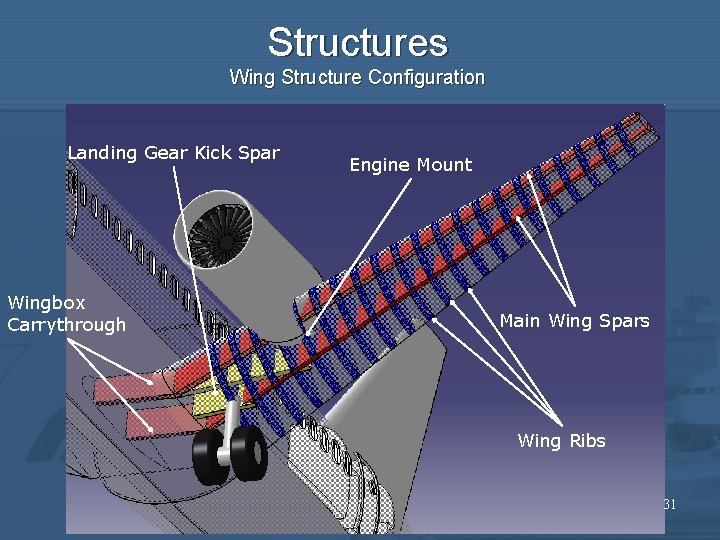
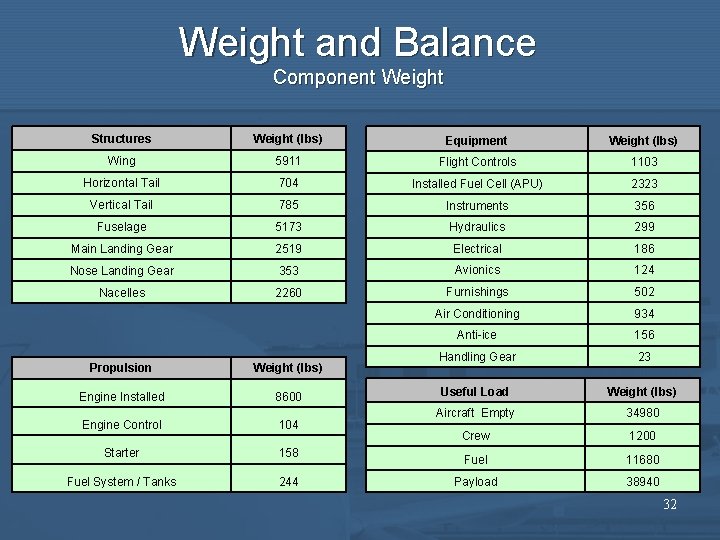
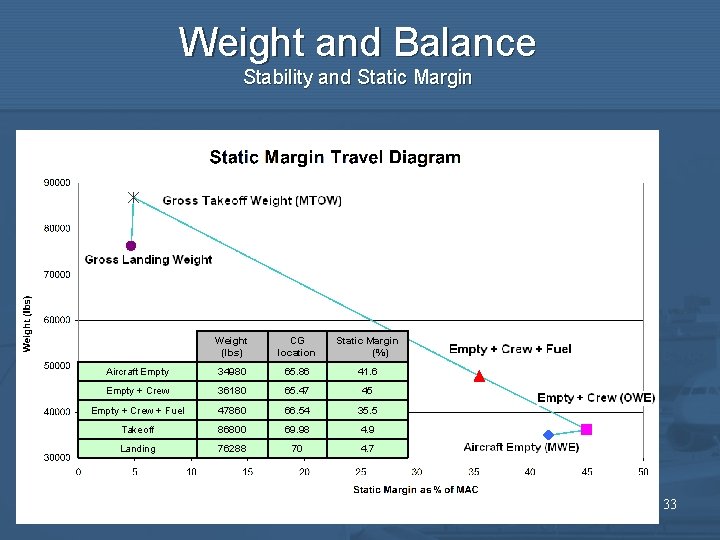
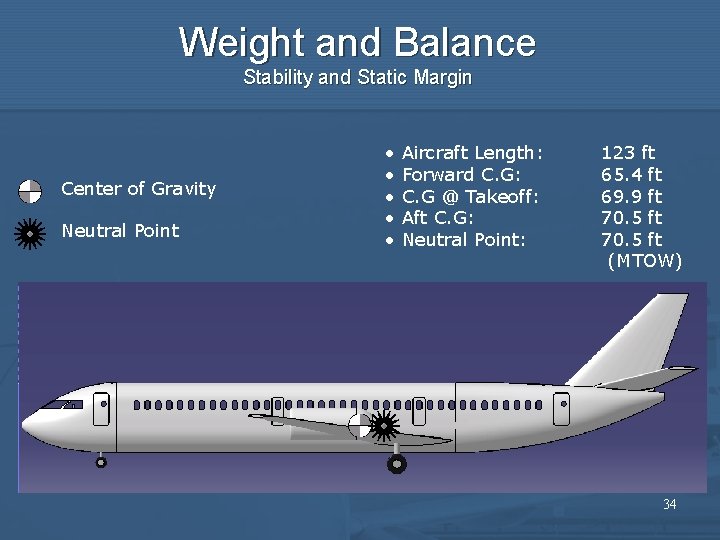
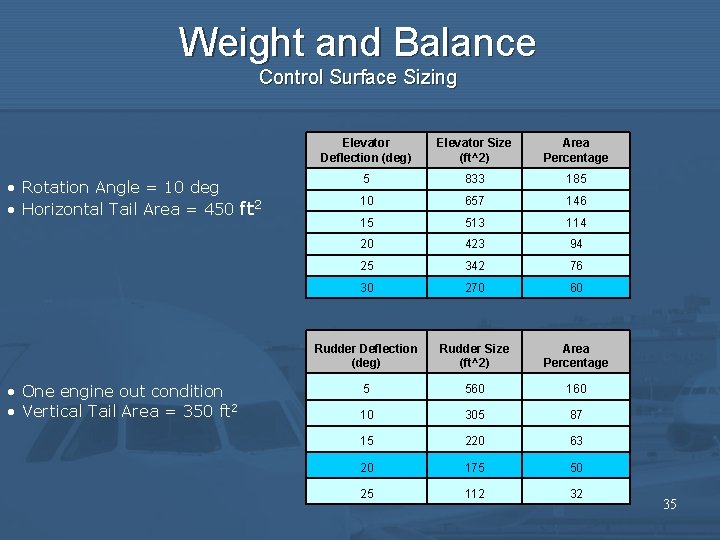
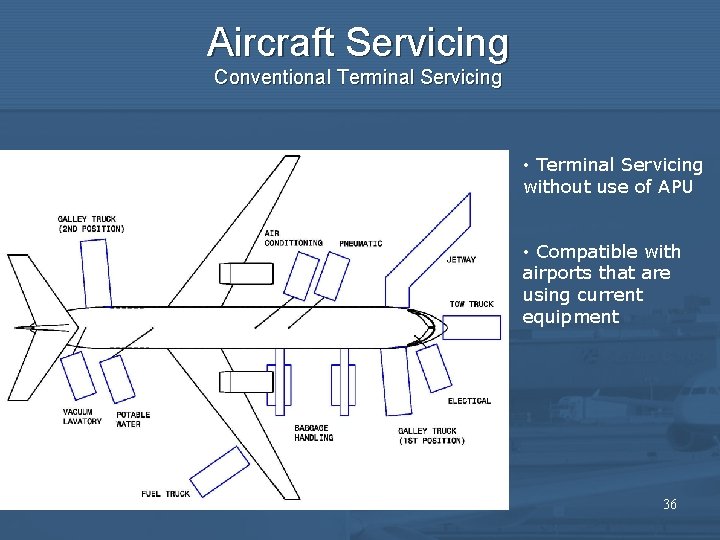
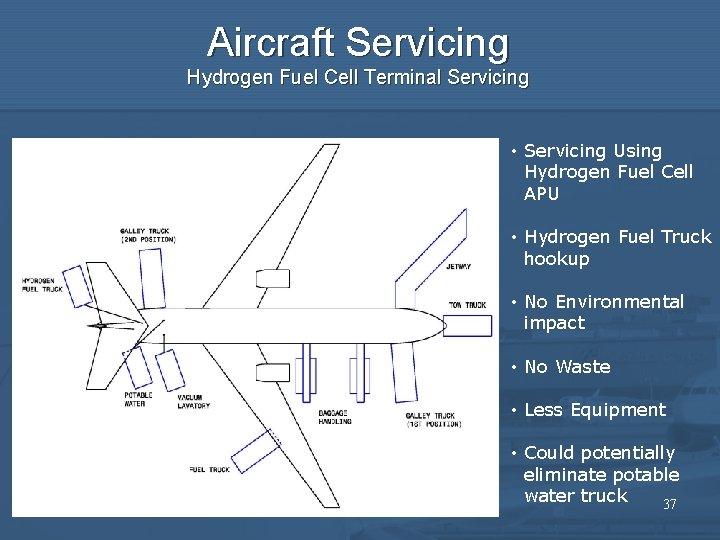
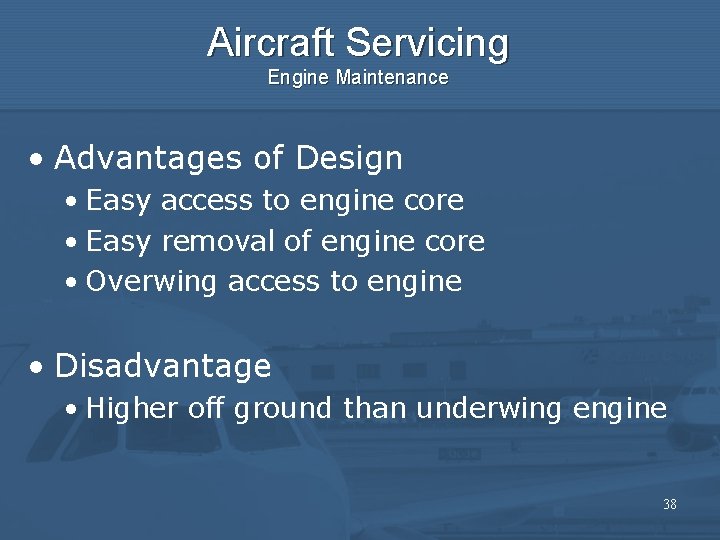
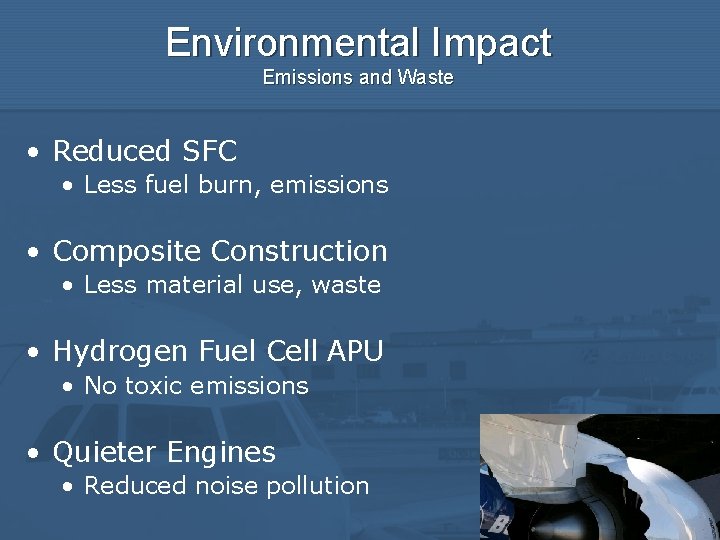
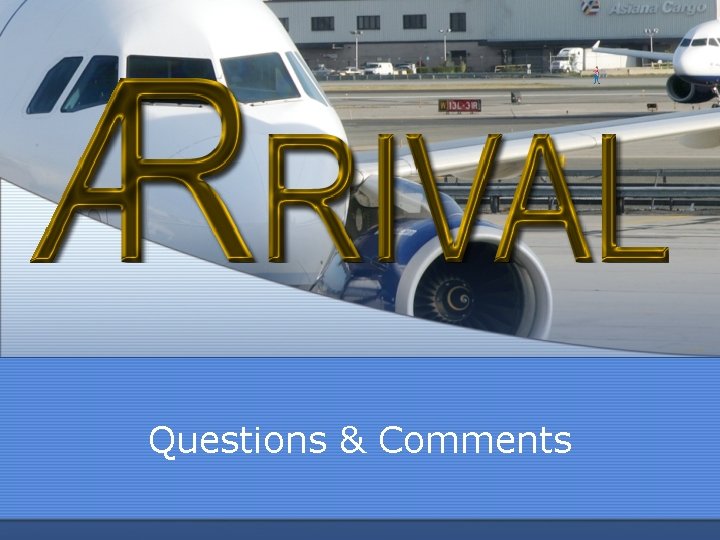
- Slides: 40
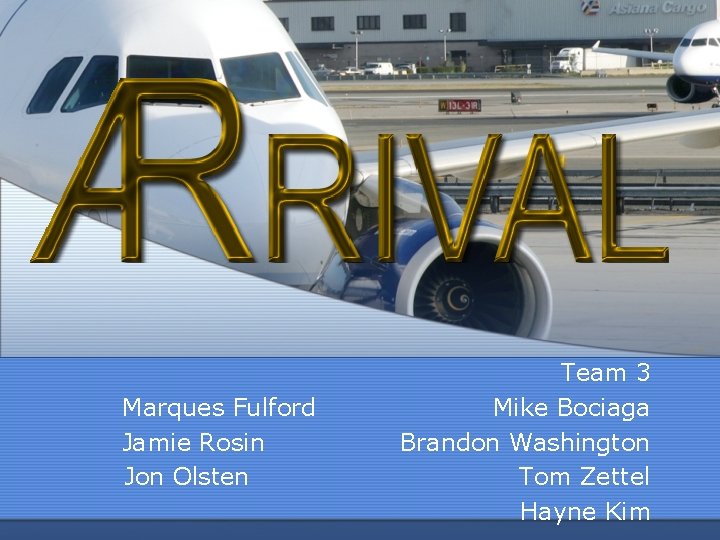
Marques Fulford Jamie Rosin Jon Olsten Team 3 Mike Bociaga Brandon Washington Tom Zettel Hayne Kim
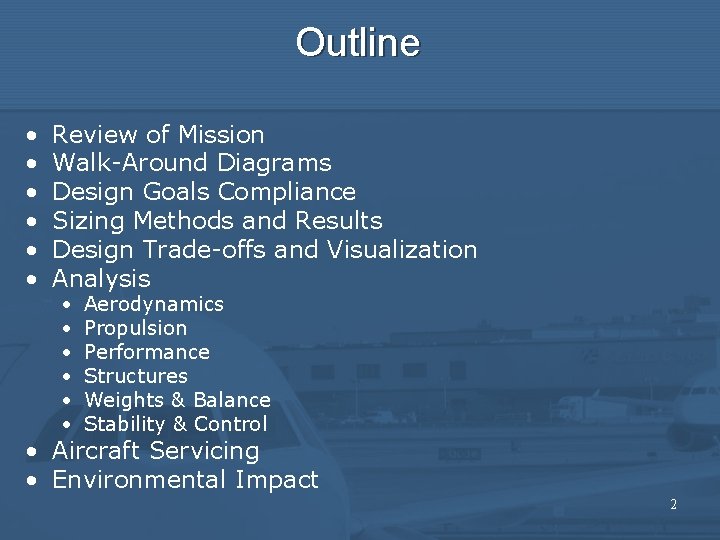
Outline • • • Review of Mission Walk-Around Diagrams Design Goals Compliance Sizing Methods and Results Design Trade-offs and Visualization Analysis • • • Aerodynamics Propulsion Performance Structures Weights & Balance Stability & Control • Aircraft Servicing • Environmental Impact 2
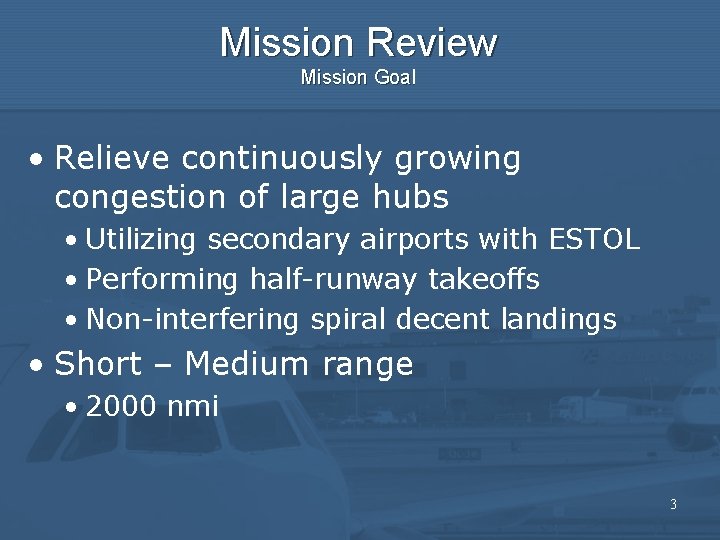
Mission Review Mission Goal • Relieve continuously growing congestion of large hubs • Utilizing secondary airports with ESTOL • Performing half-runway takeoffs • Non-interfering spiral decent landings • Short – Medium range • 2000 nmi 3

Mission Review Use-case Scenarios • Gary Chicago to Dallas Love Field • 693 nmi • New York La. Guardia to Miami International • 935 nmi • Charlotte International to Essex County, NJ • 460 nmi • Round trip without refueling 4
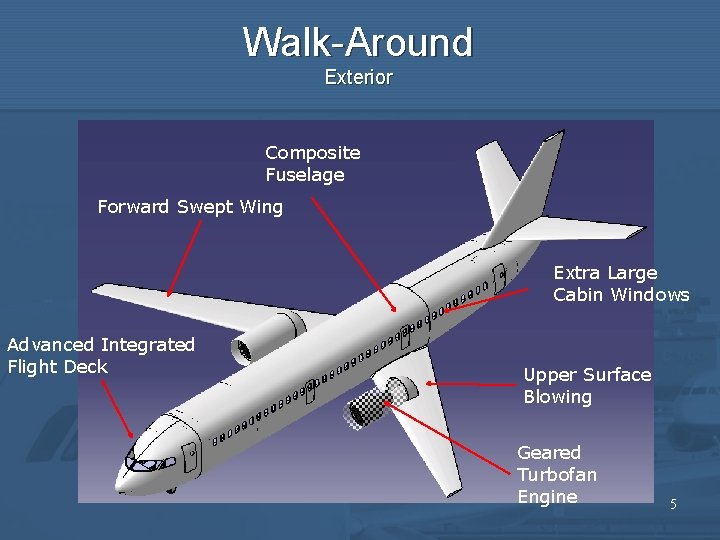
Walk-Around Exterior Composite Fuselage Forward Swept Wing Extra Large Cabin Windows Advanced Integrated Flight Deck Upper Surface Blowing Geared Turbofan Engine 5
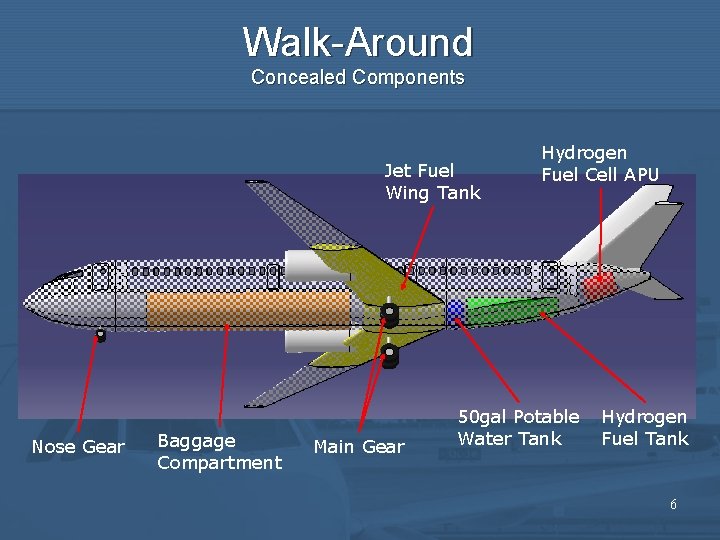
Walk-Around Concealed Components Jet Fuel Wing Tank Nose Gear Baggage Compartment Main Gear Hydrogen Fuel Cell APU 50 gal Potable Water Tank Hydrogen Fuel Tank 6
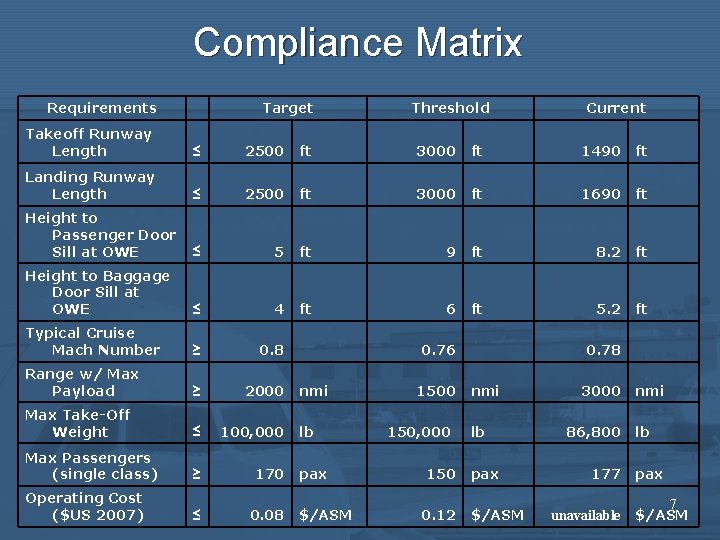
Compliance Matrix Requirements Target Takeoff Runway Length ≤ 2500 ft 3000 ft 1490 ft Landing Runway Length ≤ 2500 ft 3000 ft 1690 ft Height to Passenger Door ≤ Sill at OWE 5 ft 9 ft 8. 2 ft Height to Baggage Door Sill at OWE ≤ 4 ft 6 ft 5. 2 ft Typical Cruise Mach Number ≥ 0. 8 Range w/ Max Payload ≥ 2000 Max Take-Off Weight ≤ 100, 000 Max Passengers (single class) ≥ 170 Operating Cost ($US 2007) ≤ 0. 08 nmi lb pax $/ASM Threshold 0. 76 1500 150, 000 150 0. 12 nmi lb pax $/ASM Current 0. 78 3000 86, 800 177 unavailable nmi lb pax 7 $/ASM
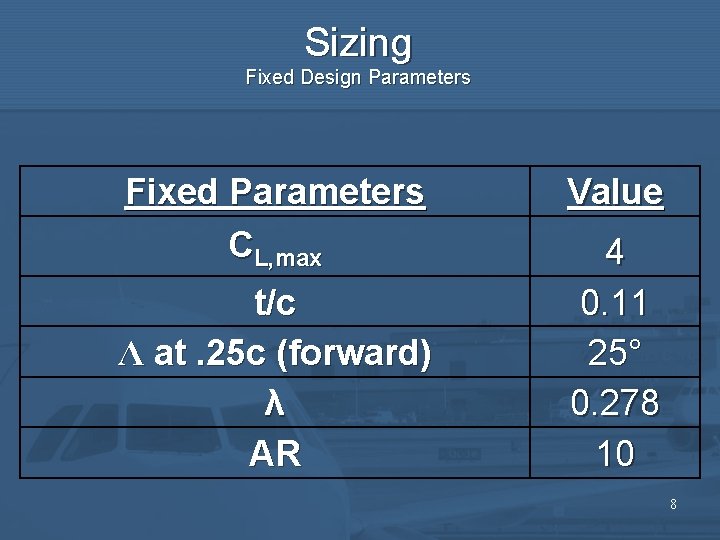
Sizing Fixed Design Parameters Fixed Parameters CL, max t/c Λ at. 25 c (forward) λ AR Value 4 0. 11 25° 0. 278 10 8
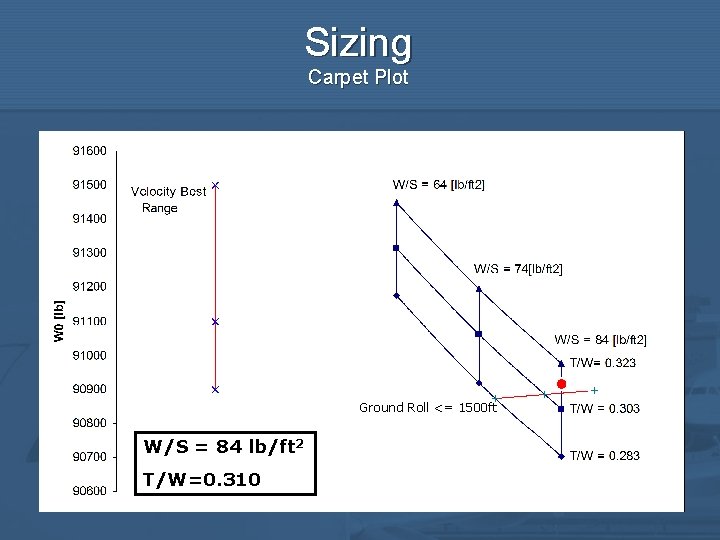
Sizing Carpet Plot Ground Roll <= 1500 ft W/S = 84 lb/ft 2 T/W=0. 310 9
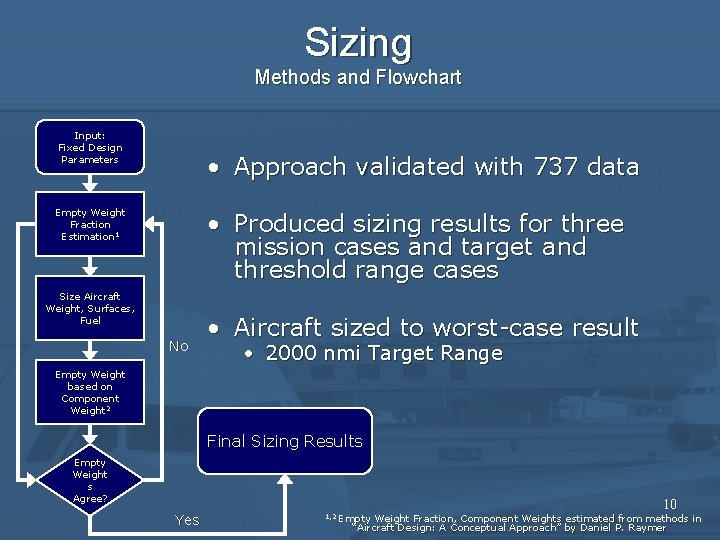
Sizing Methods and Flowchart Input: Fixed Design Parameters • Approach validated with 737 data Empty Weight Fraction Estimation 1 • Produced sizing results for three mission cases and target and threshold range cases Size Aircraft Weight, Surfaces, Fuel No • Aircraft sized to worst-case result • 2000 nmi Target Range Empty Weight based on Component Weight 2 Final Sizing Results Empty Weight s Agree? Yes 10 1, 2 Empty Weight Fraction, Component Weights estimated from methods in “Aircraft Design: A Conceptual Approach” by Daniel P. Raymer
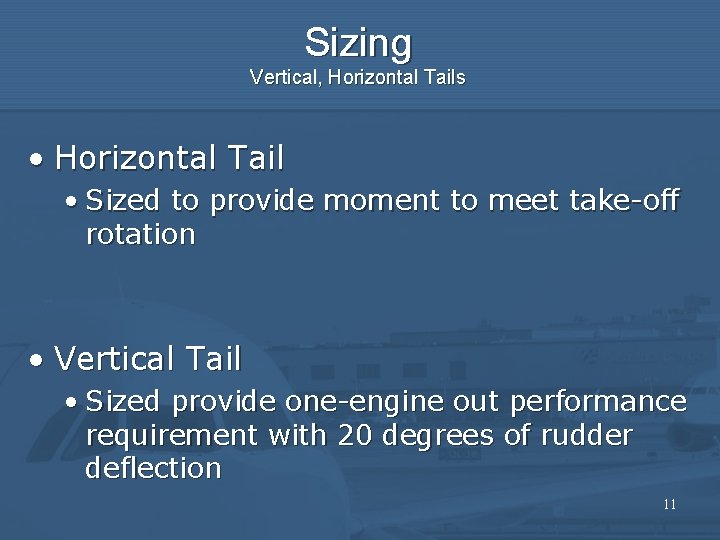
Sizing Vertical, Horizontal Tails • Horizontal Tail • Sized to provide moment to meet take-off rotation • Vertical Tail • Sized provide one-engine out performance requirement with 20 degrees of rudder deflection 11
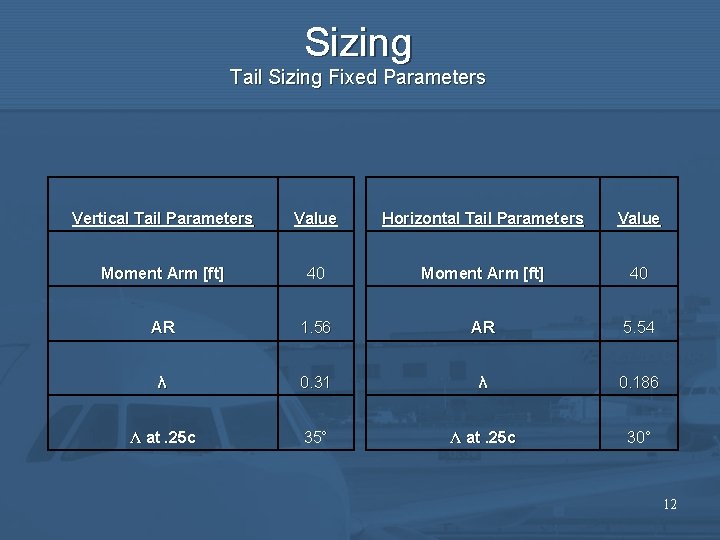
Sizing Tail Sizing Fixed Parameters Vertical Tail Parameters Value Horizontal Tail Parameters Value Moment Arm [ft] 40 AR 1. 56 AR 5. 54 λ 0. 31 λ 0. 186 Λ at. 25 c 35° Λ at. 25 c 30° 12
![Sizing Results Weights Value TOGW lbs 86 800 We lbs 35 000 Gross Landing Sizing Results Weights Value TOGW [lbs] 86, 800 We [lbs] 35, 000 Gross Landing](https://slidetodoc.com/presentation_image/851a9c76048945dedeef9c205b3aed55/image-13.jpg)
Sizing Results Weights Value TOGW [lbs] 86, 800 We [lbs] 35, 000 Gross Landing Weight [lbs] 76, 350 We/Wo 0. 403 Fuel Weight [lbs] 11, 680 Aircraft Dimensions Wingspan [ft] Wing Area [sq. ft] Value 102 1, 032 Wing Mean Aero. Chord [ft] 11 Vertical Tail Height [ft] 23 Vertical Tail Area [sq. ft] 350 Horizontal Tail Span [ft] 66 Horizontal Tail Area [sq. ft] 450 Fuselage Length [ft] 123 13
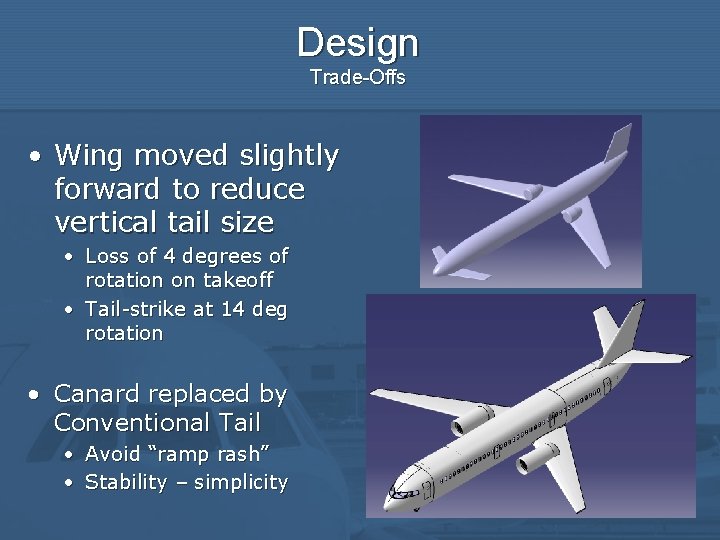
Design Trade-Offs • Wing moved slightly forward to reduce vertical tail size • Loss of 4 degrees of rotation on takeoff • Tail-strike at 14 deg rotation • Canard replaced by Conventional Tail • Avoid “ramp rash” • Stability – simplicity 14
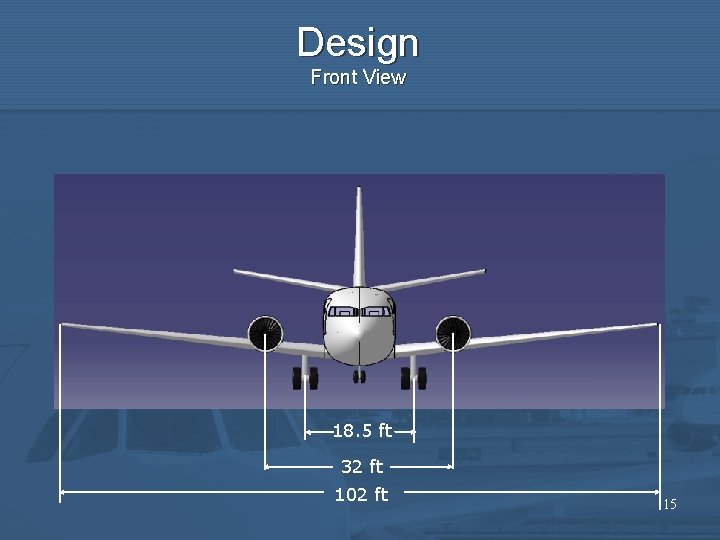
Design Front View 18. 5 ft 32 ft 102 ft 15
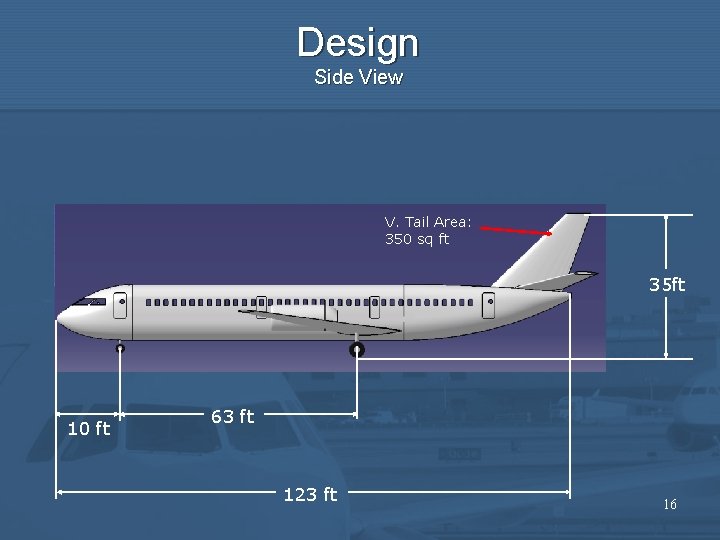
Design Side View V. Tail Area: 350 sq ft 35 ft 10 ft 63 ft 123 ft 16
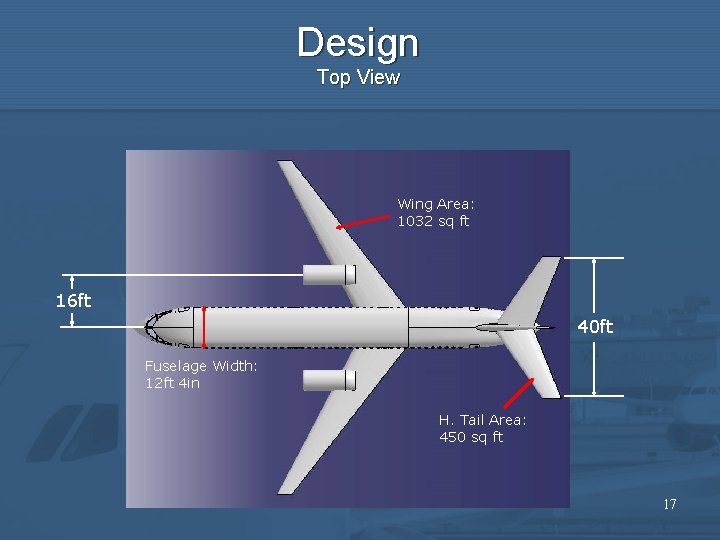
Design Top View Wing Area: 1032 sq ft 16 ft 40 ft Fuselage Width: 12 ft 4 in H. Tail Area: 450 sq ft 17
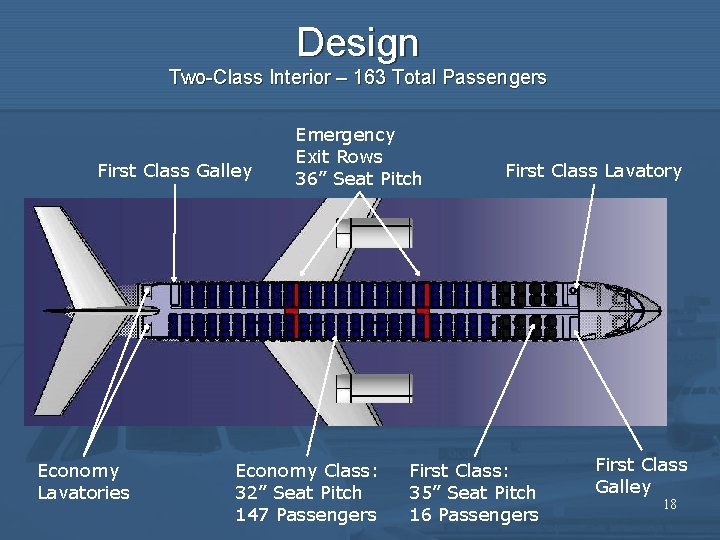
Design Two-Class Interior – 163 Total Passengers First Class Galley Economy Lavatories Emergency Exit Rows 36” Seat Pitch Economy Class: 32” Seat Pitch 147 Passengers First Class Lavatory First Class: 35” Seat Pitch 16 Passengers First Class Galley 18
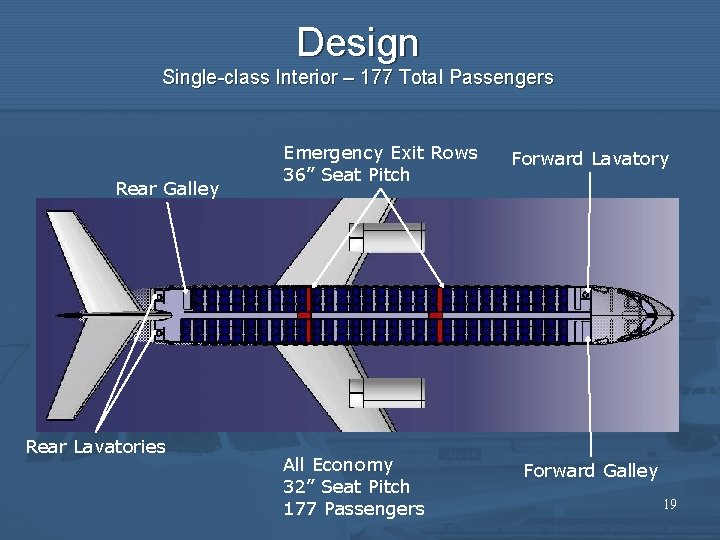
Design Single-class Interior – 177 Total Passengers Rear Galley Rear Lavatories Emergency Exit Rows 36” Seat Pitch All Economy 32” Seat Pitch 177 Passengers Forward Lavatory Forward Galley 19
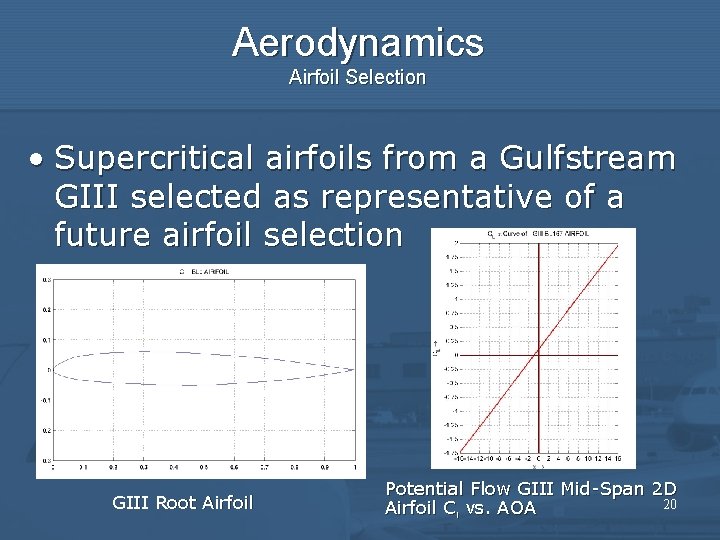
Aerodynamics Airfoil Selection • Supercritical airfoils from a Gulfstream GIII selected as representative of a future airfoil selection GIII Root Airfoil Potential Flow GIII Mid-Span 2 D 20 Airfoil Cl vs. AOA
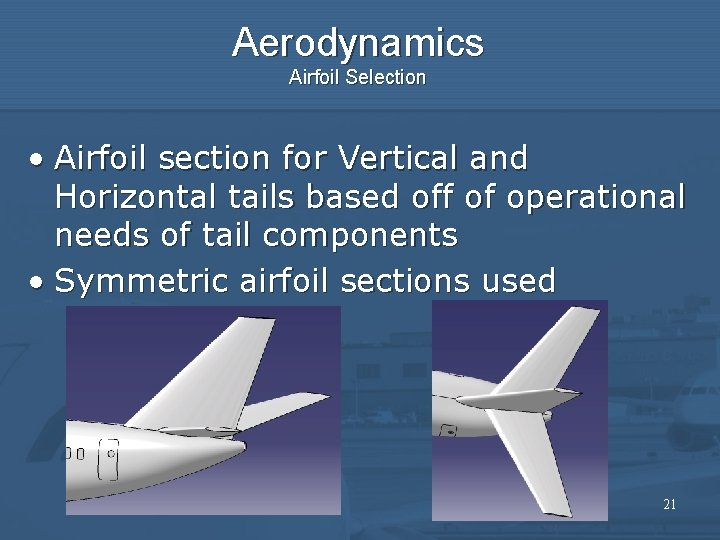
Aerodynamics Airfoil Selection • Airfoil section for Vertical and Horizontal tails based off of operational needs of tail components • Symmetric airfoil sections used 21
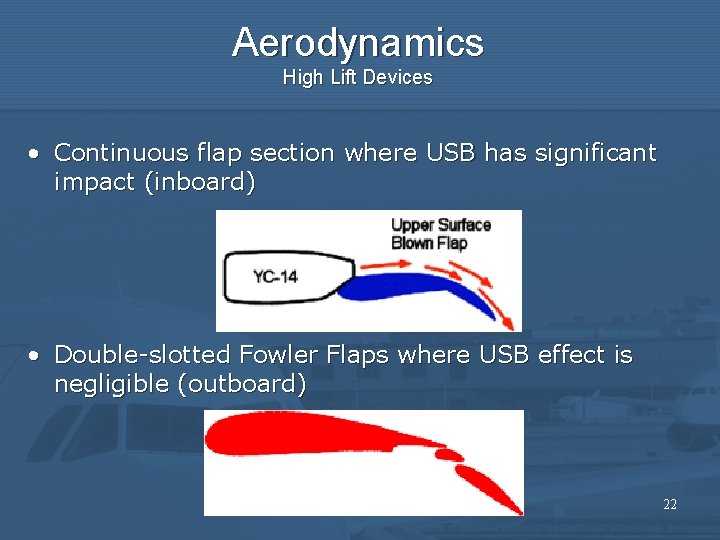
Aerodynamics High Lift Devices • Continuous flap section where USB has significant impact (inboard) • Double-slotted Fowler Flaps where USB effect is negligible (outboard) 22
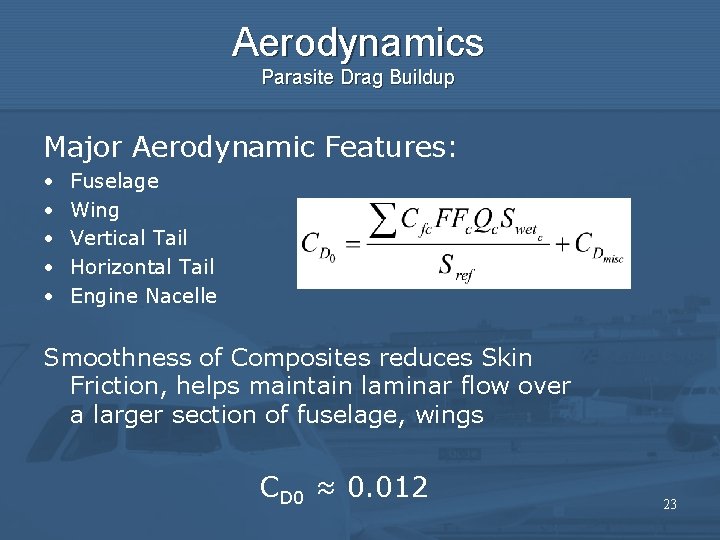
Aerodynamics Parasite Drag Buildup Major Aerodynamic Features: • • • Fuselage Wing Vertical Tail Horizontal Tail Engine Nacelle Smoothness of Composites reduces Skin Friction, helps maintain laminar flow over a larger section of fuselage, wings CD 0 ≈ 0. 012 23
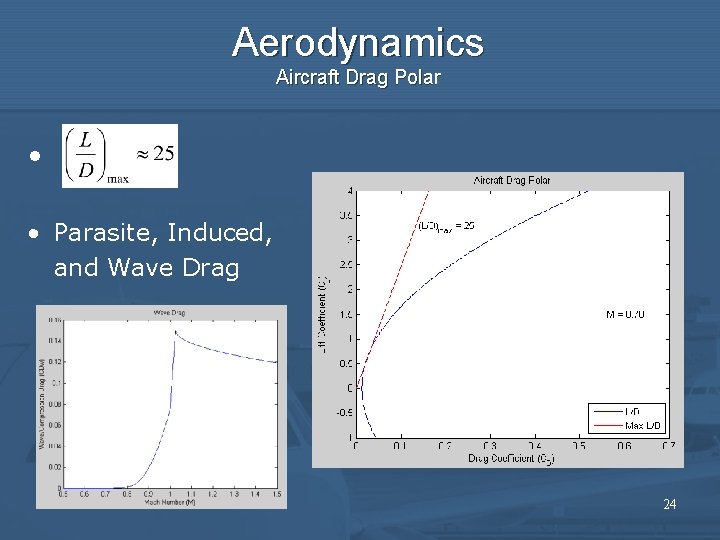
Aerodynamics Aircraft Drag Polar • • Parasite, Induced, and Wave Drag 24
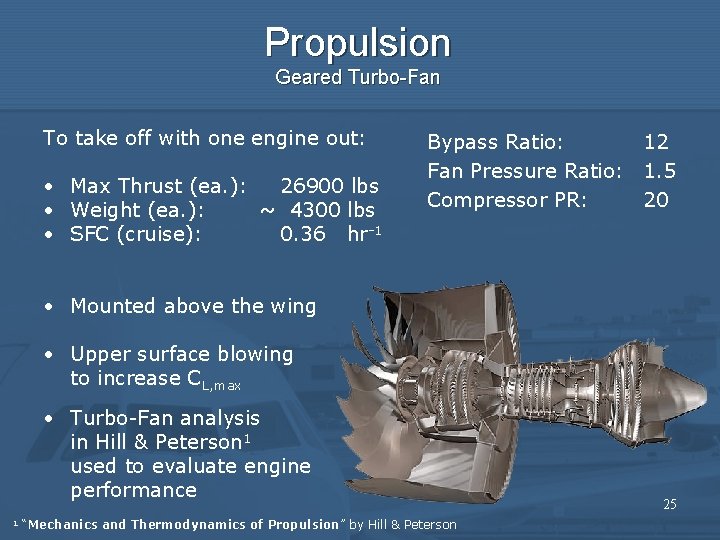
Propulsion Geared Turbo-Fan To take off with one engine out: • Max Thrust (ea. ): 26900 lbs • Weight (ea. ): ~ 4300 lbs • SFC (cruise): 0. 36 hr-1 Bypass Ratio: 12 Fan Pressure Ratio: 1. 5 Compressor PR: 20 • Mounted above the wing • Upper surface blowing to increase CL, max • Turbo-Fan analysis in Hill & Peterson 1 used to evaluate engine performance 1 “Mechanics and Thermodynamics of Propulsion” by Hill & Peterson 25
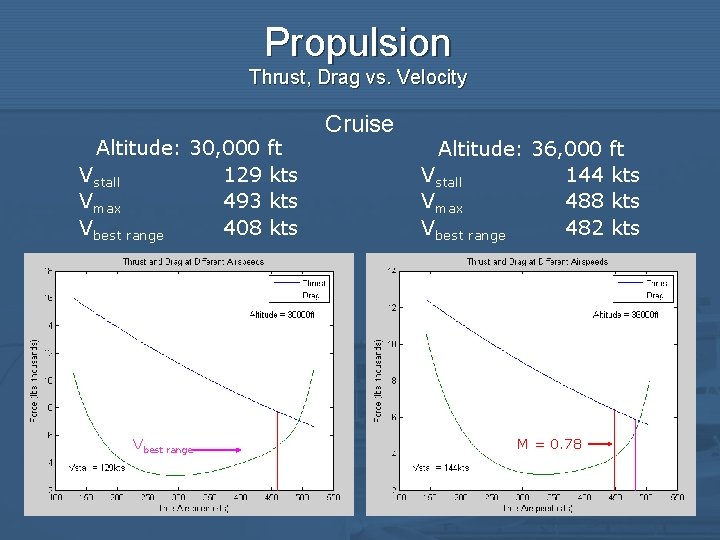
Propulsion Thrust, Drag vs. Velocity Altitude: 30, 000 ft Vstall 129 kts Vmax 493 kts Vbest range 408 kts Vbest range Cruise Altitude: 36, 000 ft Vstall 144 kts Vmax 488 kts Vbest range 482 kts M = 0. 78 26
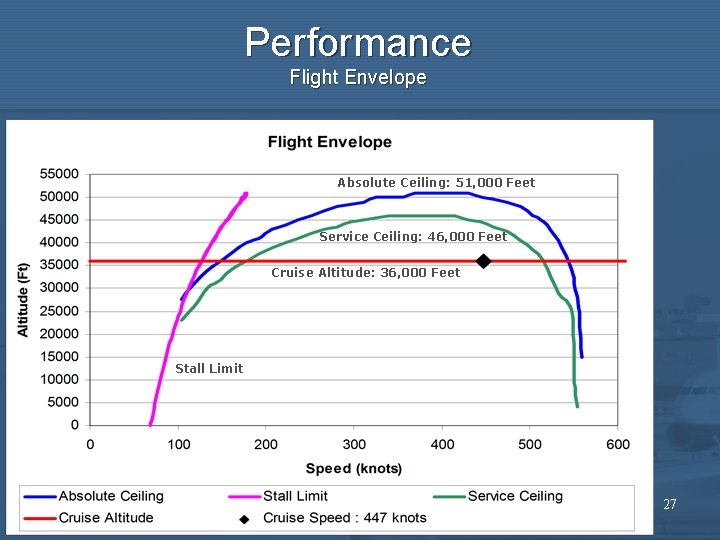
Performance Flight Envelope Absolute Ceiling: 51, 000 Feet Service Ceiling: 46, 000 Feet Cruise Altitude: 36, 000 Feet Stall Limit 27
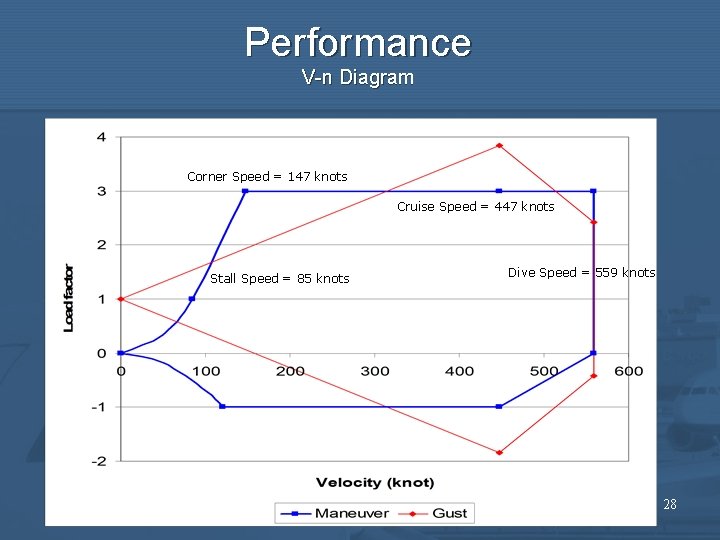
Performance V-n Diagram • Corner Speed = 147 knots • • Stall Speed = 85 knots Cruise Speed = 447 knots • Dive Speed = 559 knots 28
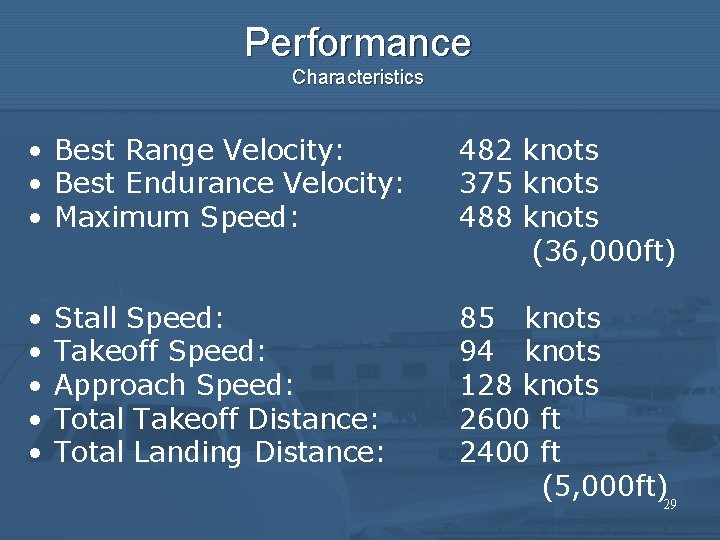
Performance Characteristics • Best Range Velocity: • Best Endurance Velocity: • Maximum Speed: 482 knots 375 knots 488 knots (36, 000 ft) • • • 85 knots 94 knots 128 knots 2600 ft 2400 ft (5, 000 ft)29 Stall Speed: Takeoff Speed: Approach Speed: Total Takeoff Distance: Total Landing Distance:
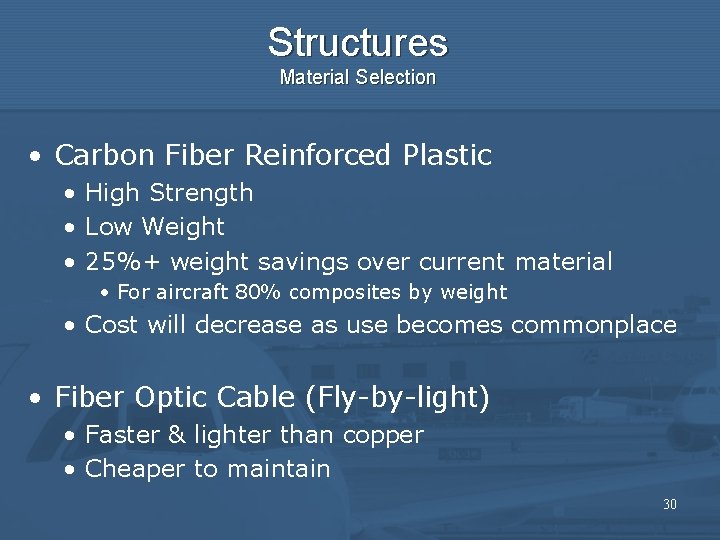
Structures Material Selection • Carbon Fiber Reinforced Plastic • High Strength • Low Weight • 25%+ weight savings over current material • For aircraft 80% composites by weight • Cost will decrease as use becomes commonplace • Fiber Optic Cable (Fly-by-light) • Faster & lighter than copper • Cheaper to maintain 30
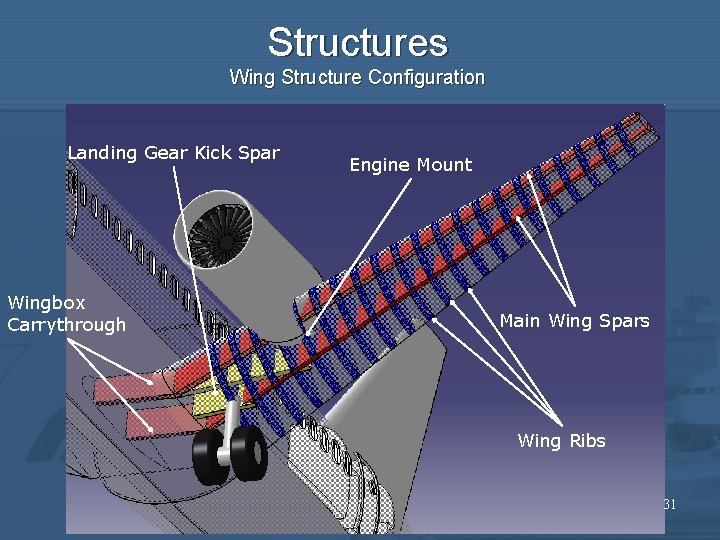
Structures Wing Structure Configuration Landing Gear Kick Spar Wingbox Carrythrough Engine Mount Main Wing Spars Wing Ribs 31
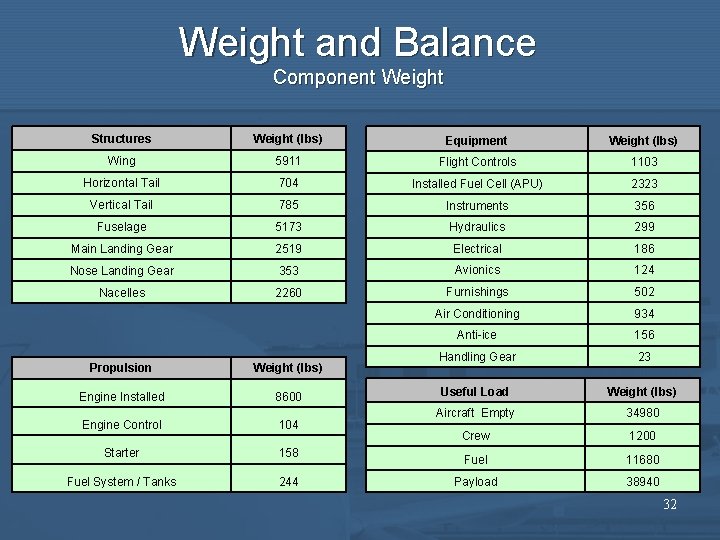
Weight and Balance Component Weight Structures Weight (lbs) Equipment Weight (lbs) Wing 5911 Flight Controls 1103 Horizontal Tail 704 Installed Fuel Cell (APU) 2323 Vertical Tail 785 Instruments 356 Fuselage 5173 Hydraulics 299 Main Landing Gear 2519 Electrical 186 Nose Landing Gear 353 Avionics 124 Nacelles 2260 Furnishings 502 Air Conditioning 934 Anti-ice 156 Handling Gear 23 Useful Load Weight (lbs) Aircraft Empty 34980 Crew 1200 Fuel 11680 Payload 38940 Propulsion Weight (lbs) Engine Installed 8600 Engine Control 104 Starter 158 Fuel System / Tanks 244 32
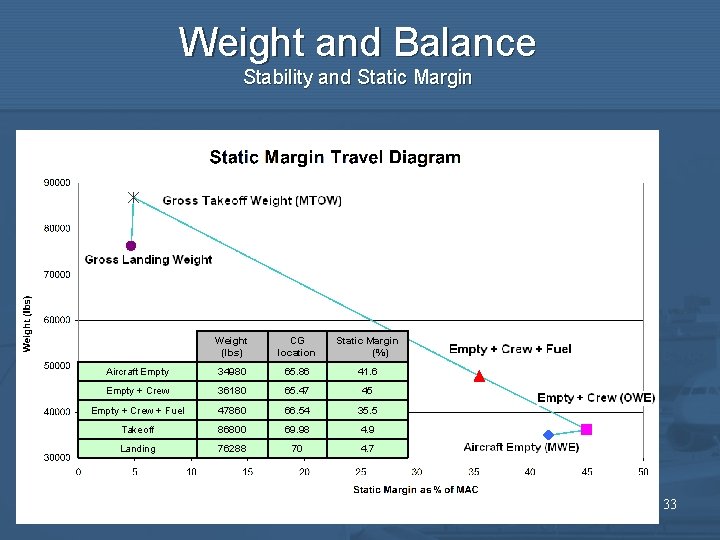
Weight and Balance Stability and Static Margin Weight (lbs) CG location Static Margin (%) Aircraft Empty 34980 65. 86 41. 6 Empty + Crew 36180 65. 47 45 Empty + Crew + Fuel 47860 66. 54 35. 5 Takeoff 86800 69. 98 4. 9 Landing 76288 70 4. 7 33
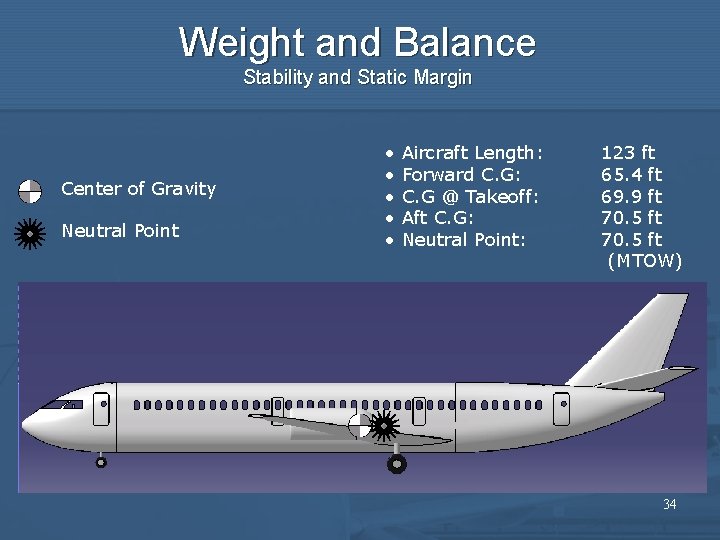
Weight and Balance Stability and Static Margin Center of Gravity Neutral Point • • • Aircraft Length: Forward C. G: C. G @ Takeoff: Aft C. G: Neutral Point: 123 ft 65. 4 ft 69. 9 ft 70. 5 ft (MTOW) 34
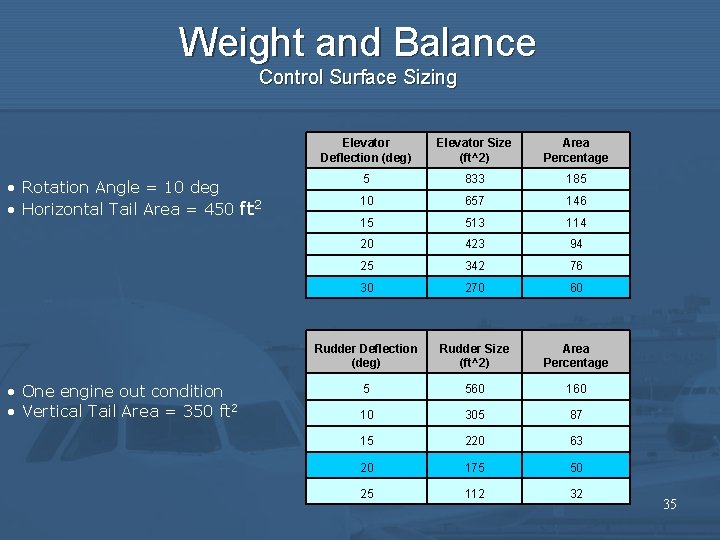
Weight and Balance Control Surface Sizing • Rotation Angle = 10 deg • Horizontal Tail Area = 450 ft 2 • One engine out condition • Vertical Tail Area = 350 ft 2 Elevator Deflection (deg) Elevator Size (ft^2) Area Percentage 5 833 185 10 657 146 15 513 114 20 423 94 25 342 76 30 270 60 Rudder Deflection (deg) Rudder Size (ft^2) Area Percentage 5 560 10 305 87 15 220 63 20 175 50 25 112 32 35
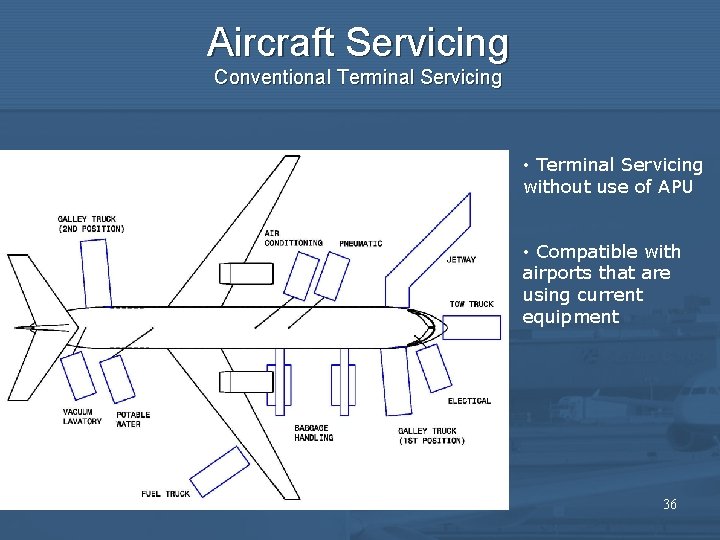
Aircraft Servicing Conventional Terminal Servicing • Terminal Servicing without use of APU • Compatible with airports that are using current equipment 36
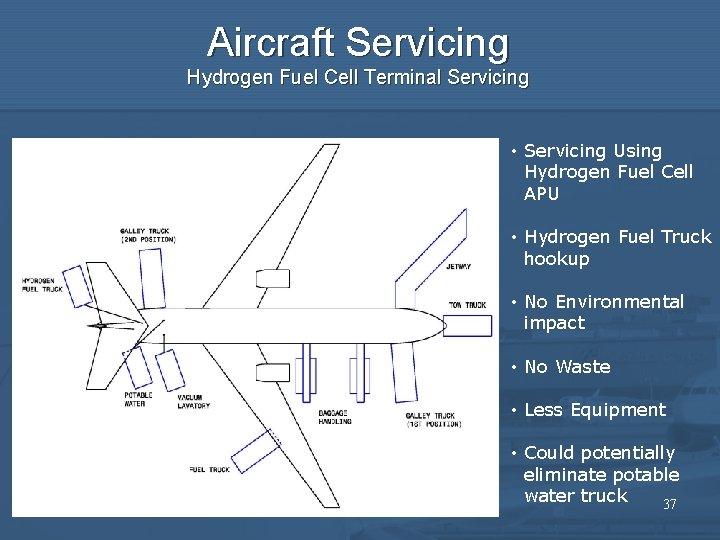
Aircraft Servicing Hydrogen Fuel Cell Terminal Servicing • Servicing Using Hydrogen Fuel Cell APU • Hydrogen Fuel Truck hookup • No Environmental impact • No Waste • Less Equipment • Could potentially eliminate potable water truck 37
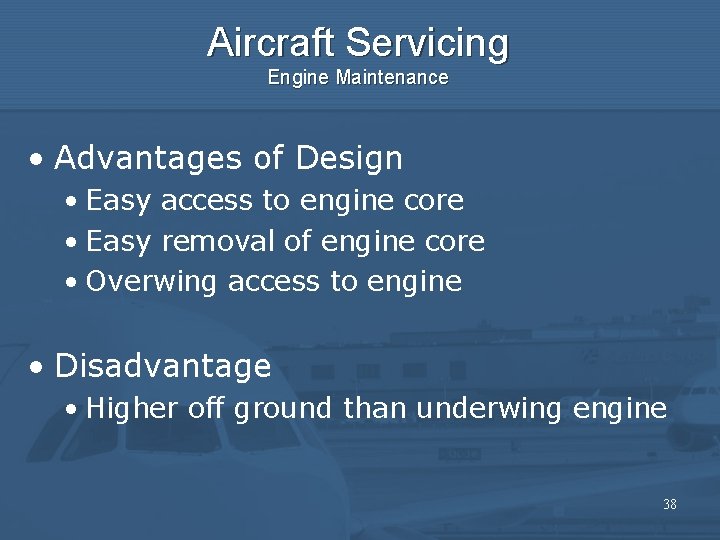
Aircraft Servicing Engine Maintenance • Advantages of Design • Easy access to engine core • Easy removal of engine core • Overwing access to engine • Disadvantage • Higher off ground than underwing engine 38
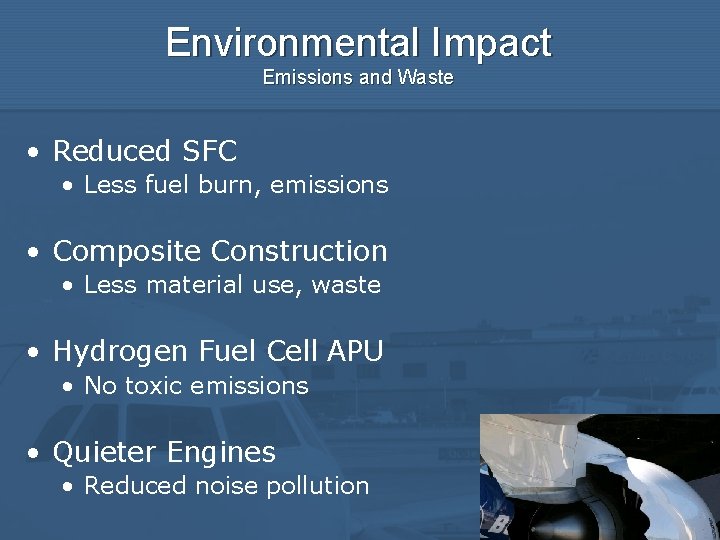
Environmental Impact Emissions and Waste • Reduced SFC • Less fuel burn, emissions • Composite Construction • Less material use, waste • Hydrogen Fuel Cell APU • No toxic emissions • Quieter Engines • Reduced noise pollution 39
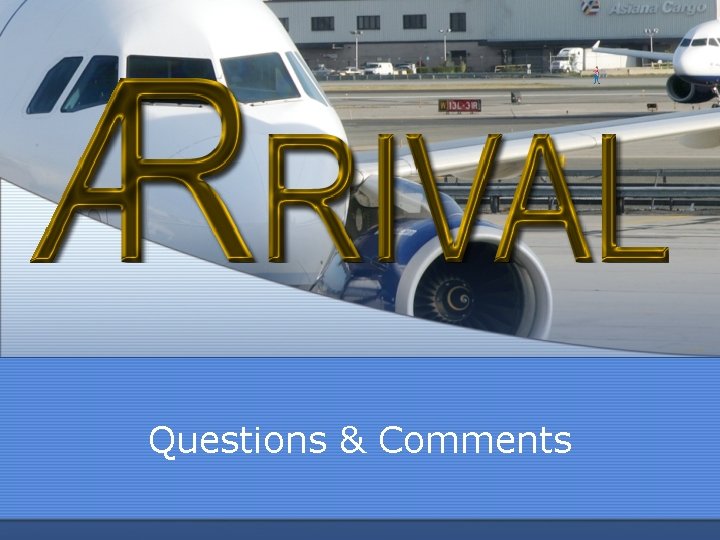
Questions & Comments
Jamie rosin
Eventbreit
Martyn fulford
Martyn poliakoff parkinson's
Harald haradra
Pere marquès graells
Philip marques
Logo des marques automobiles
Nabila sardar
Calendario escolar aina moll
Alfredo marques gubern
Wgep
Anna maria marques cintra
Direito de preempção
Alfredo marques gubern
Groupe lvmh entreprises
Cómicos na farsa de inês pereira
Adriana marques rossetto
Tarde llegaste marquez a volver arrepentido
Prof pedro marques
Indice de subjectivité
The white team cheers for the blue team, just like
Going native project management
Team spirit becomes team infatuation
Jamie picus
Jamie young wikipedia
Ma huateng leadership style
Ama collegiate conference
Jamie caine
Jamie sullivan traffic
Jamie knopf
Jamie wallace bp
La catrina episodio 4
Cory markham
Jamie lee curtis klinefelter
Jamie buchenauer
Jamie wiebe
Jamie rentoul
How did queen elizabeths dad die
Radiohead just youtube
Mhc evolution