Logistics Management LSM 730 Lecture 30 Dr Khurrum
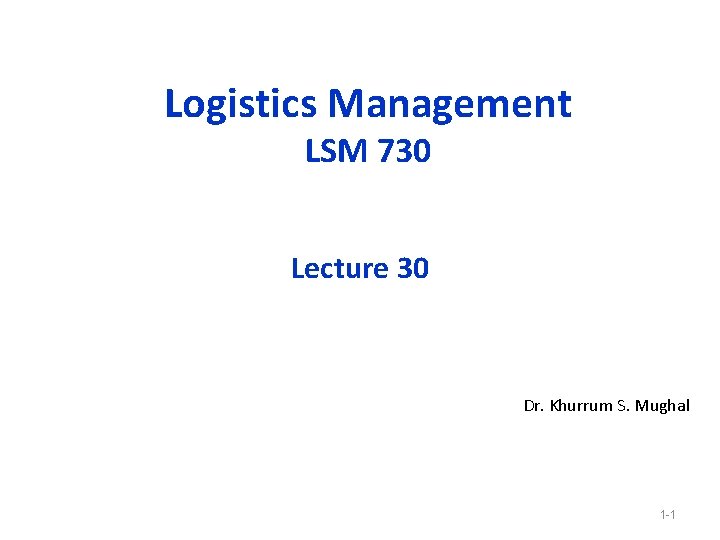
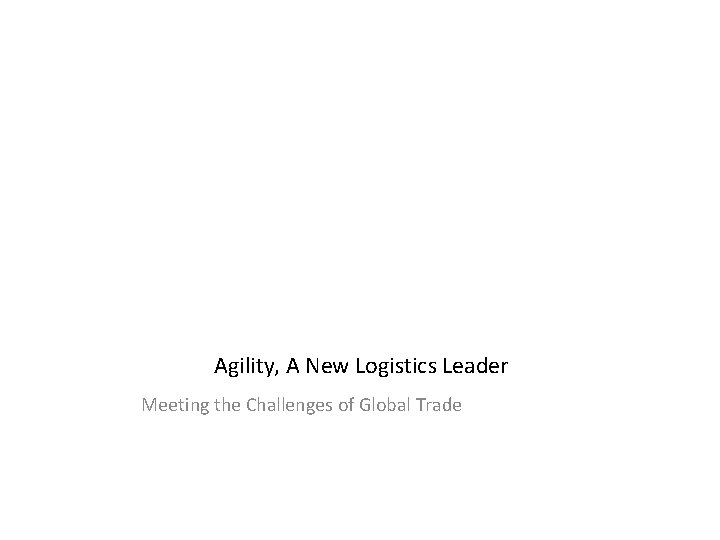
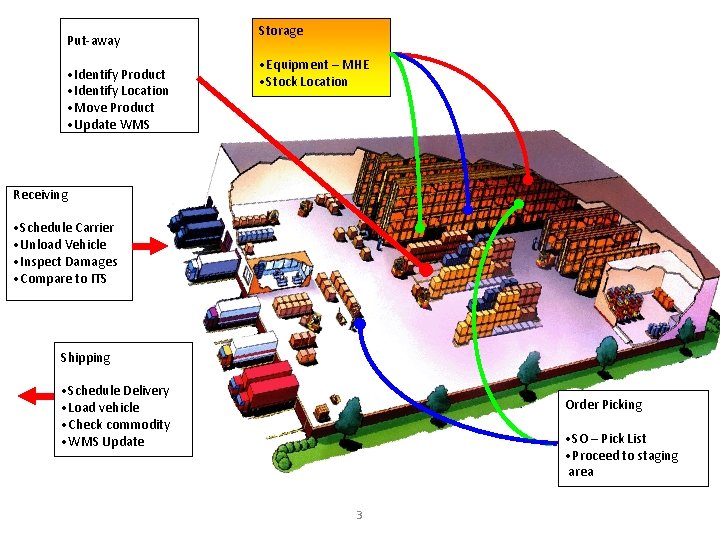
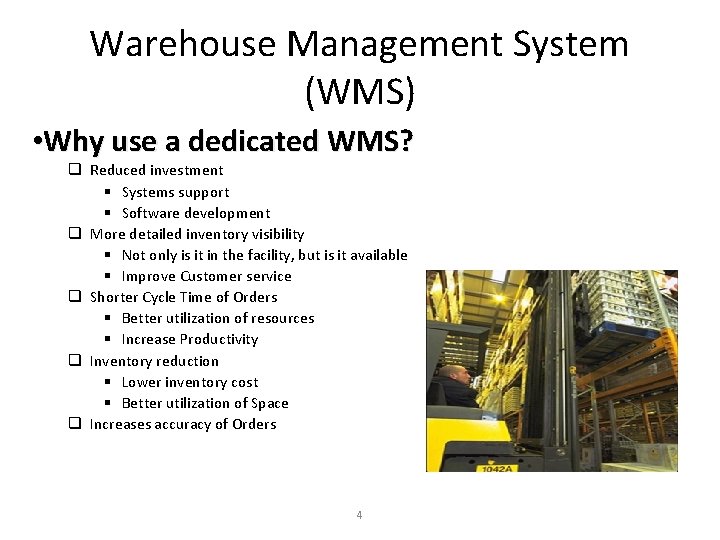
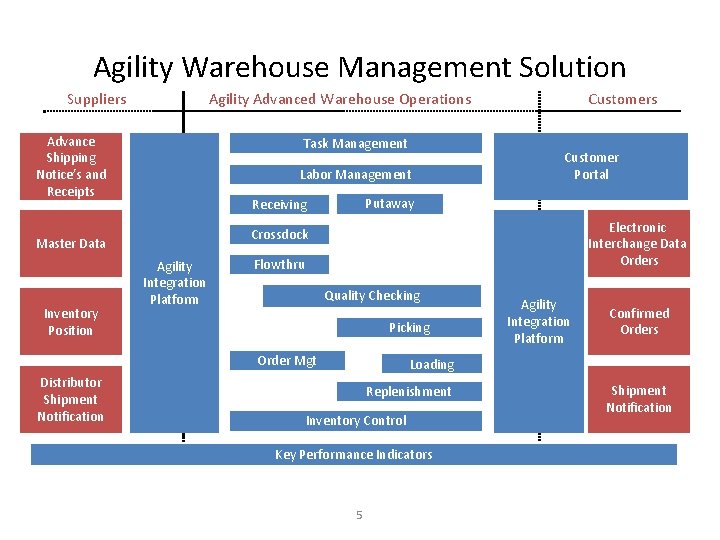
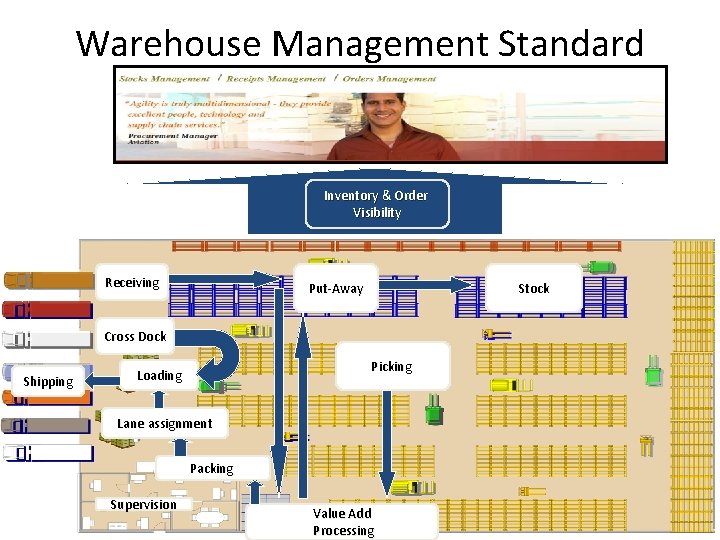
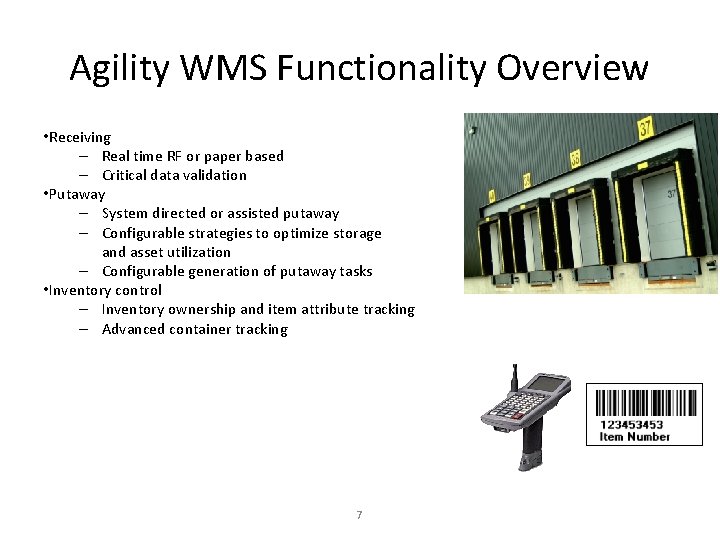
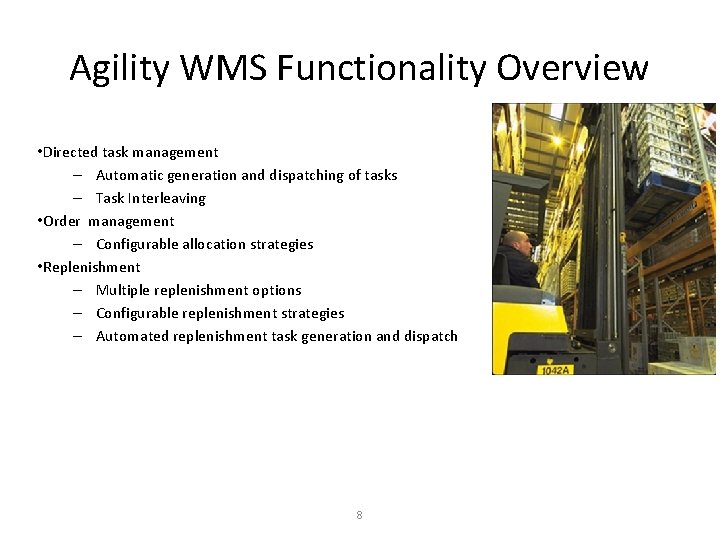
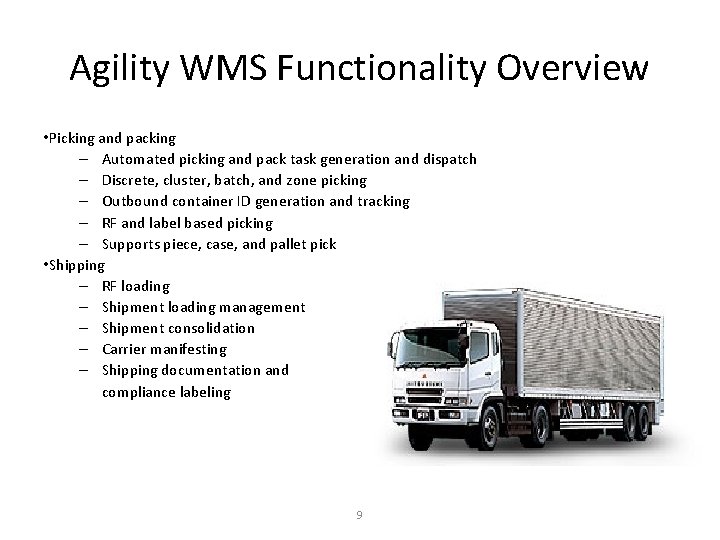
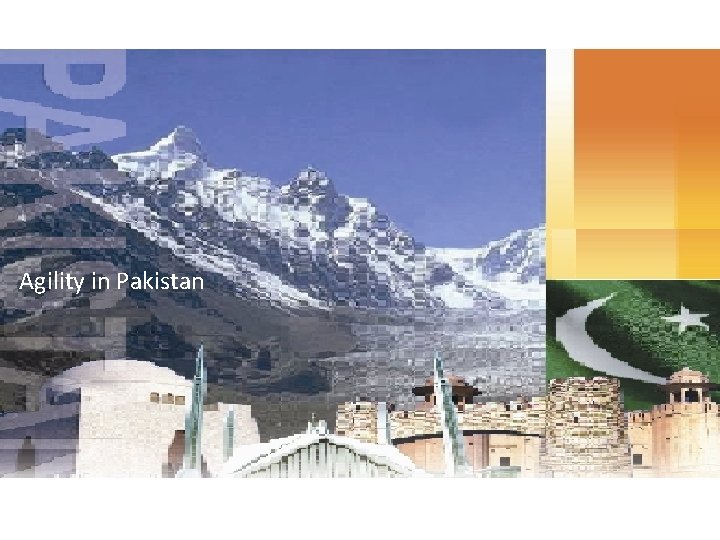
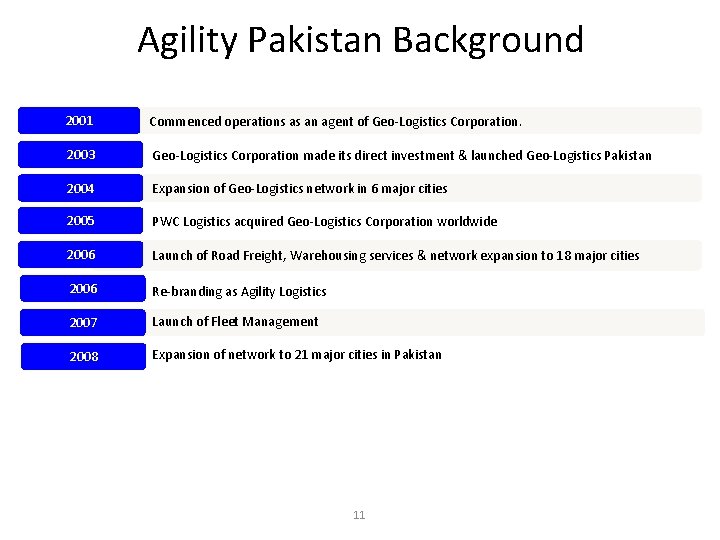
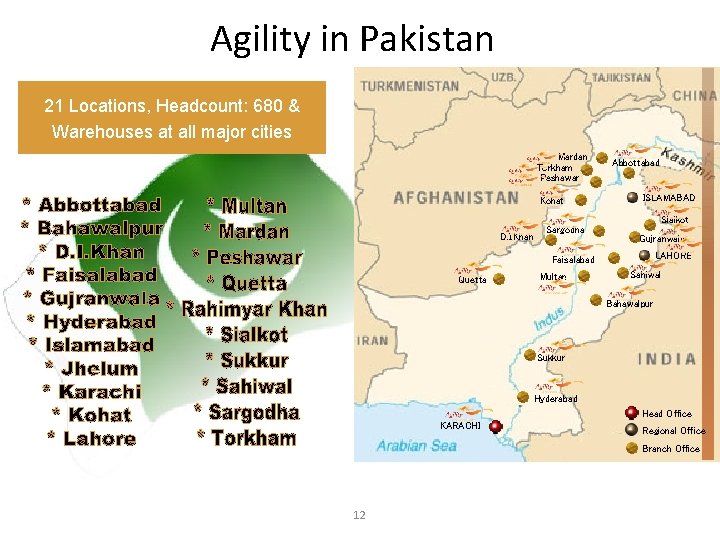
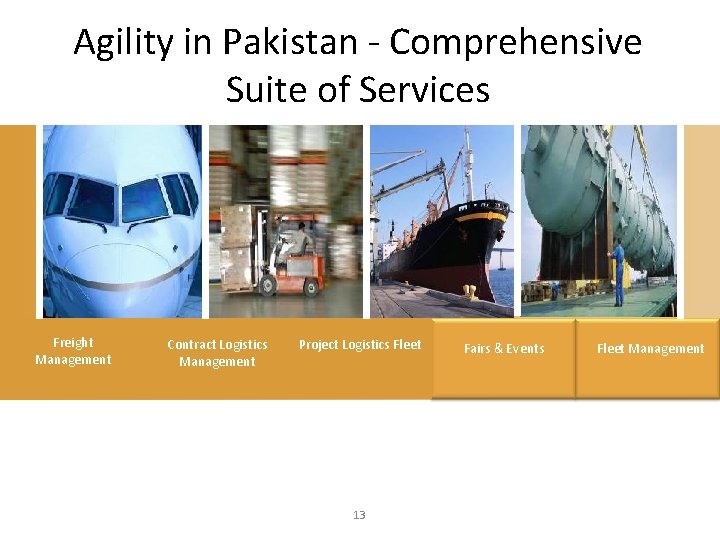
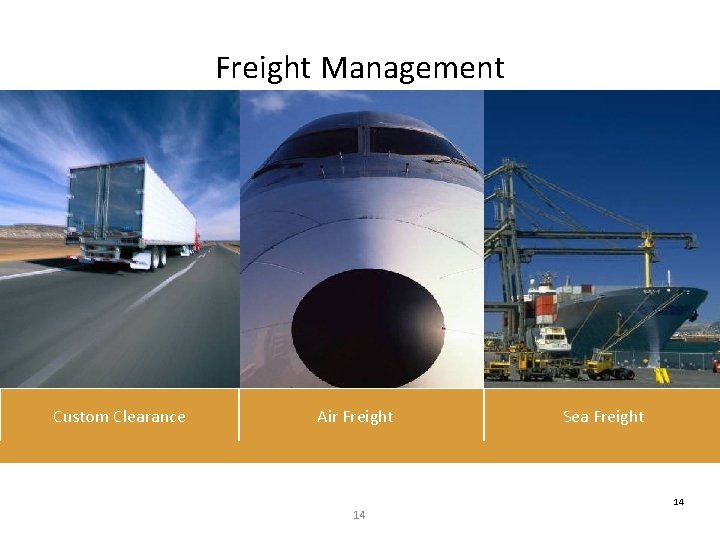
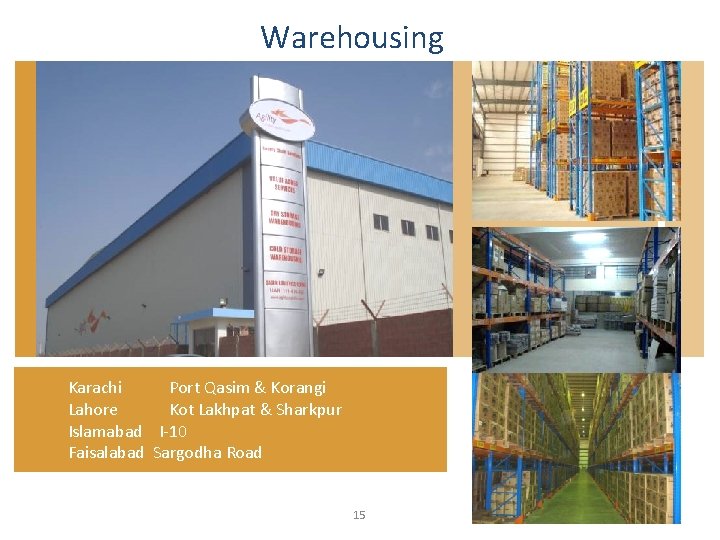
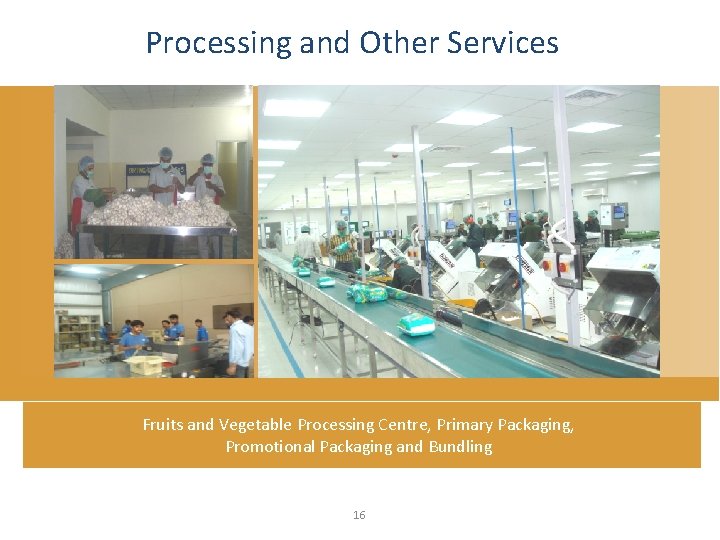
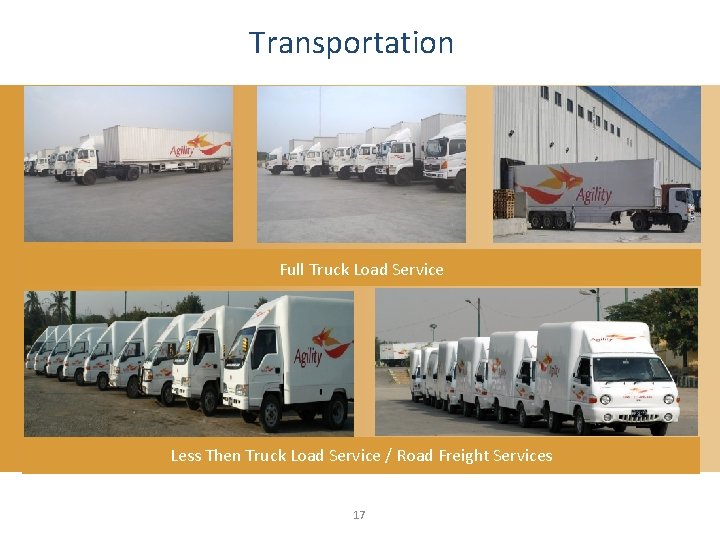
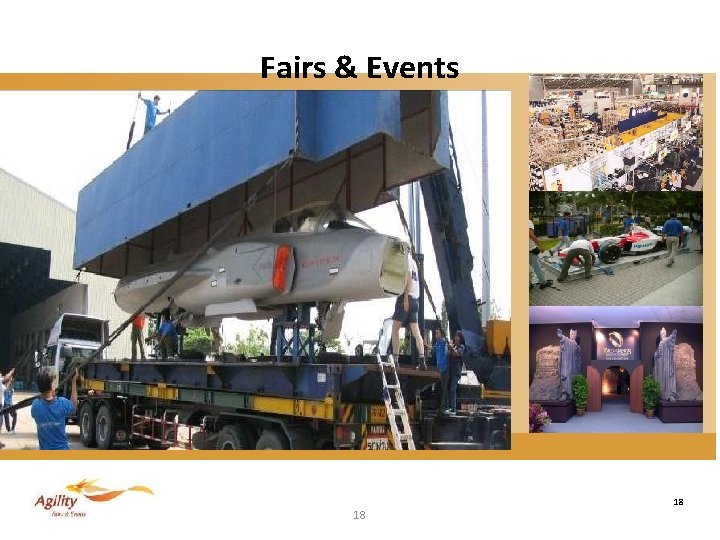
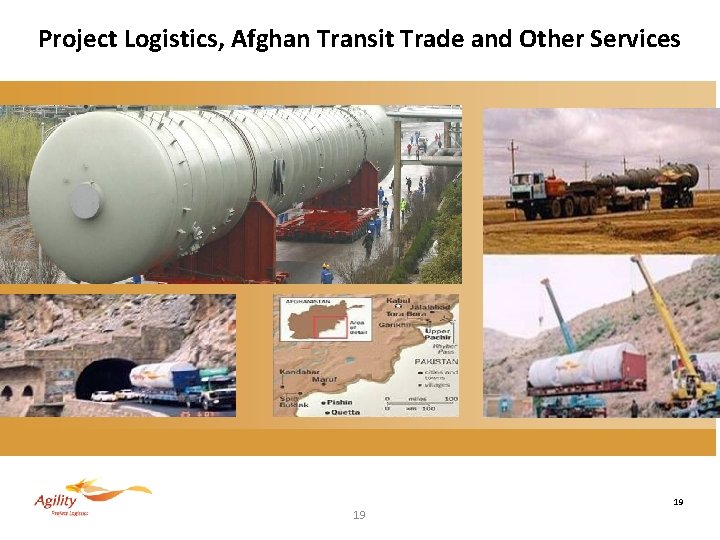
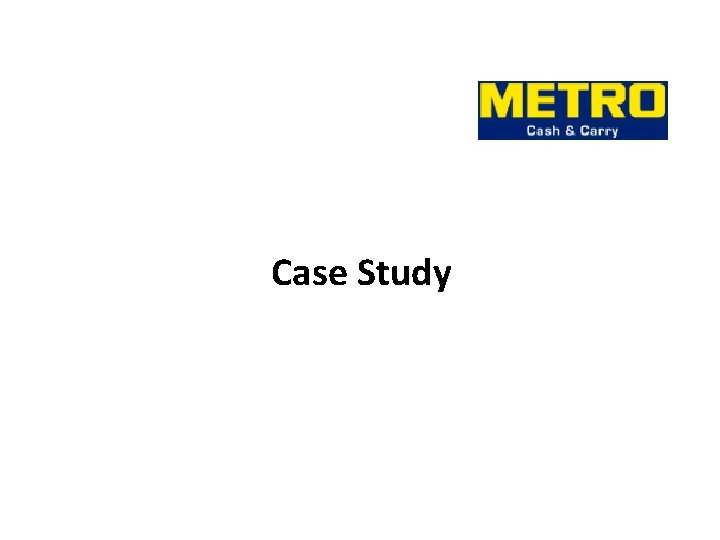
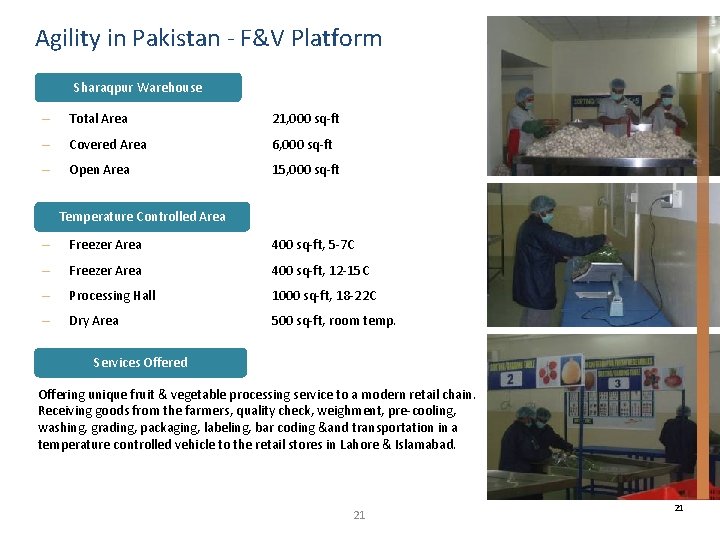
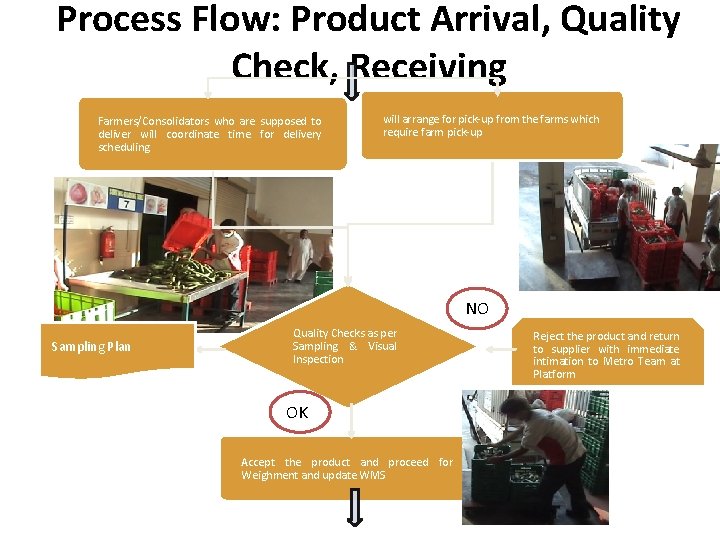
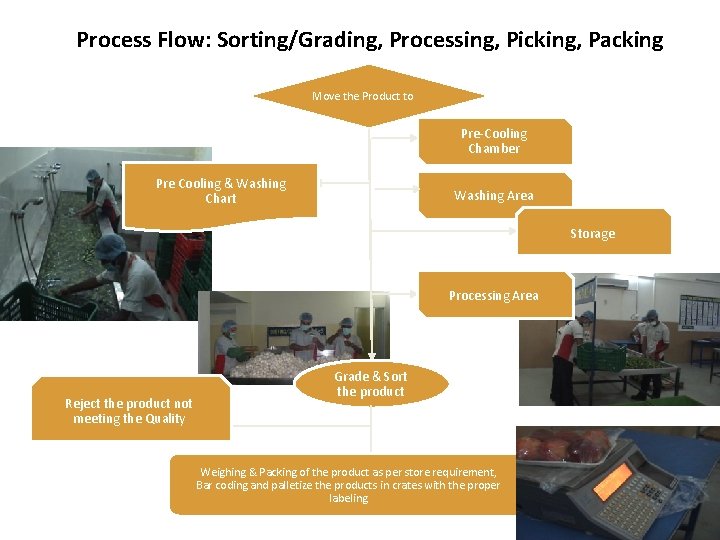
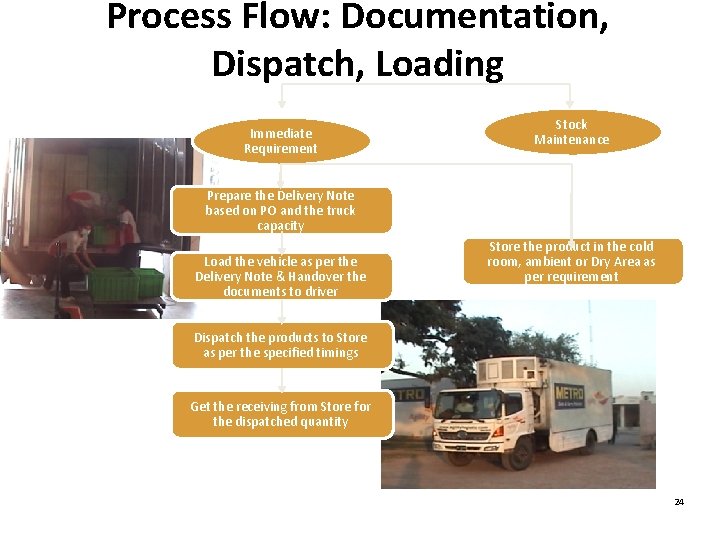
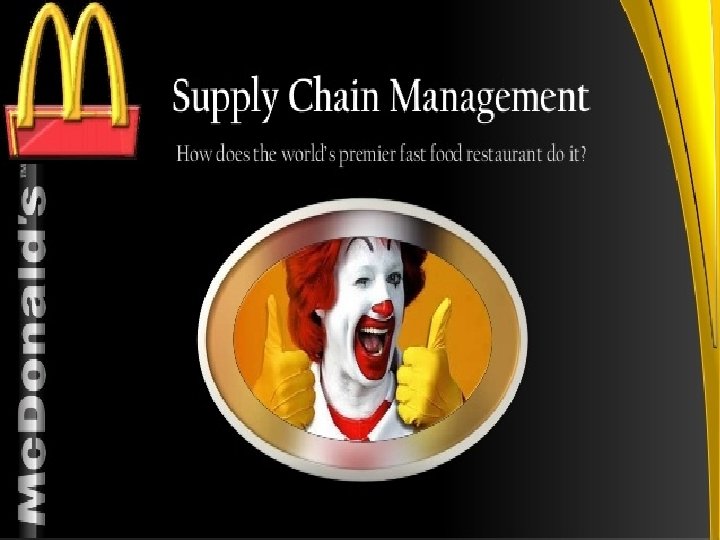
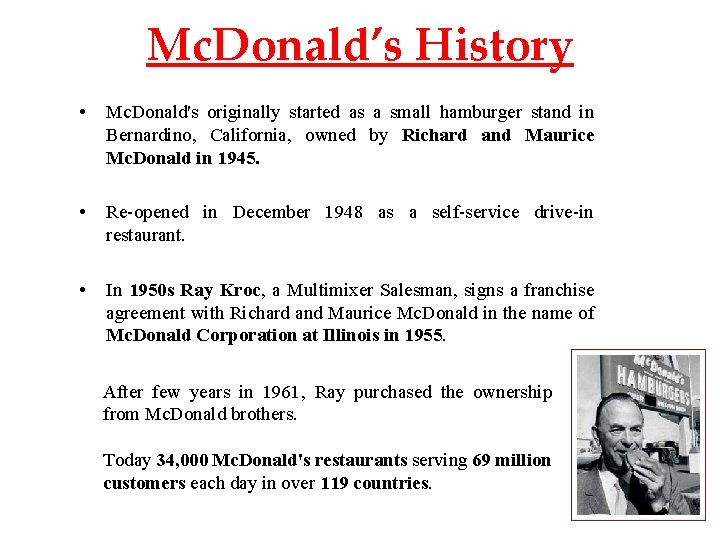
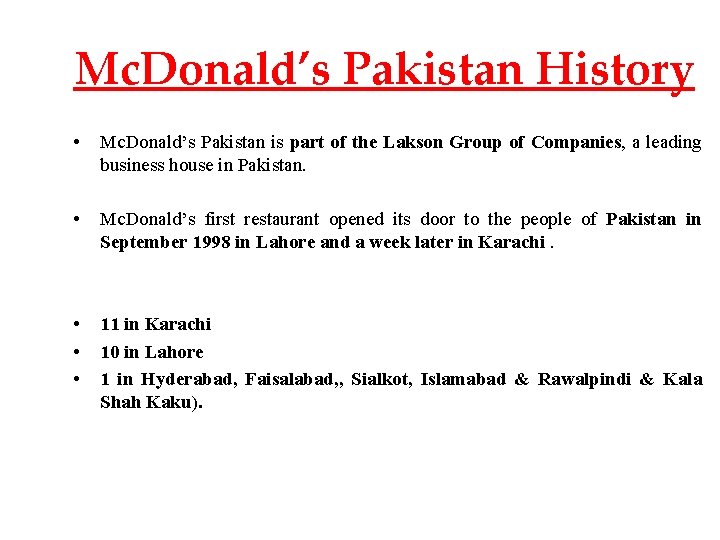
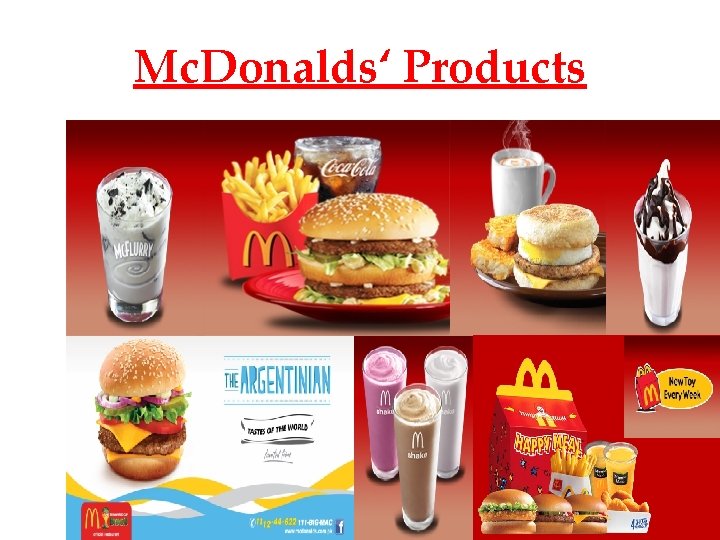
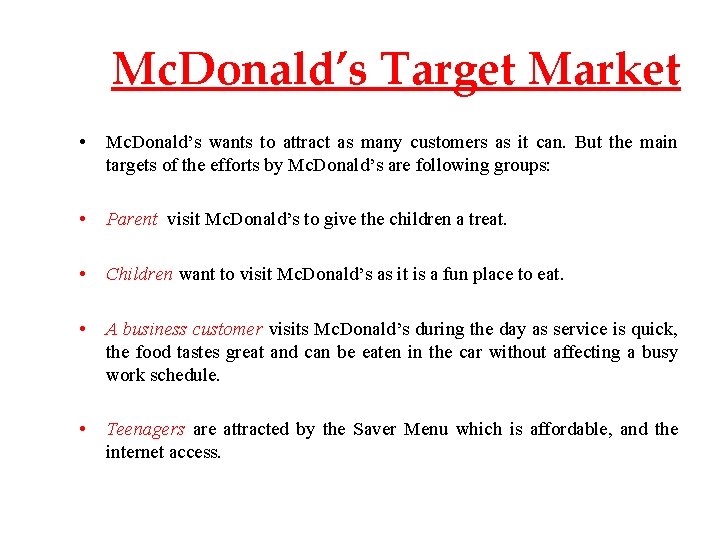
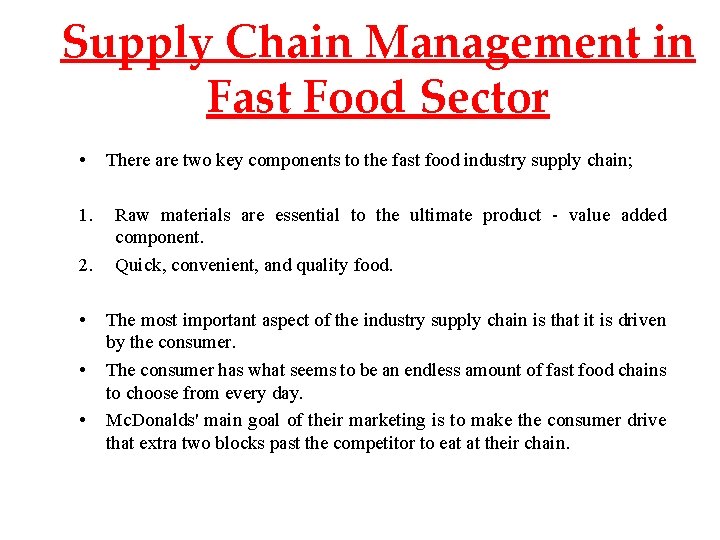
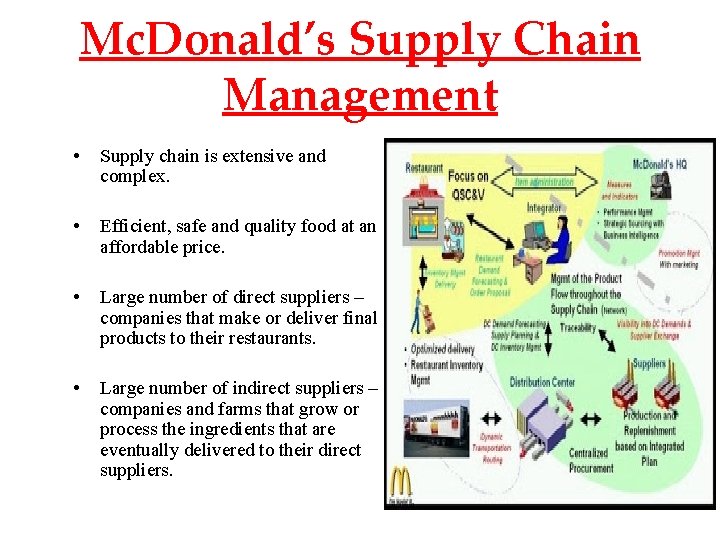
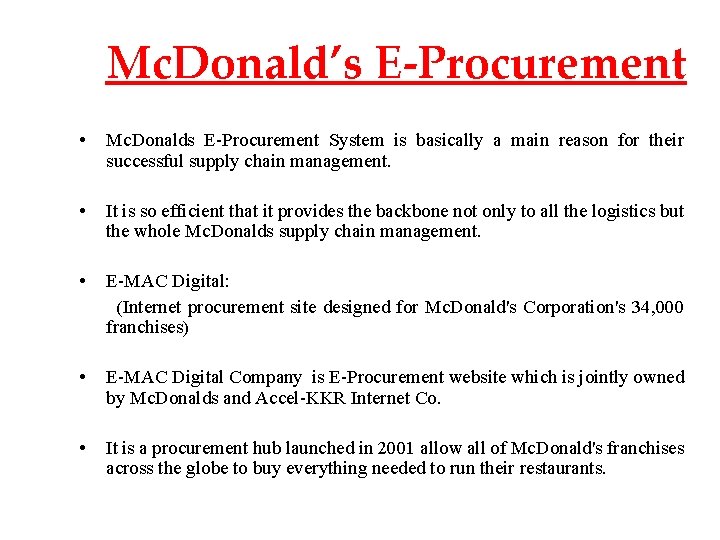
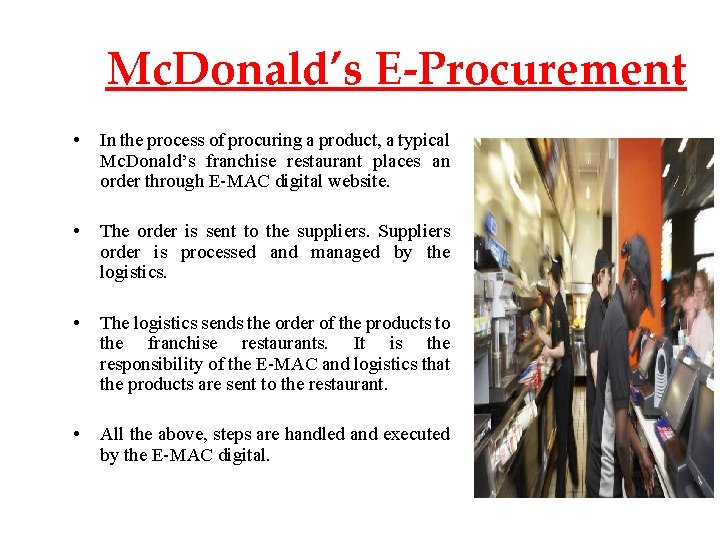
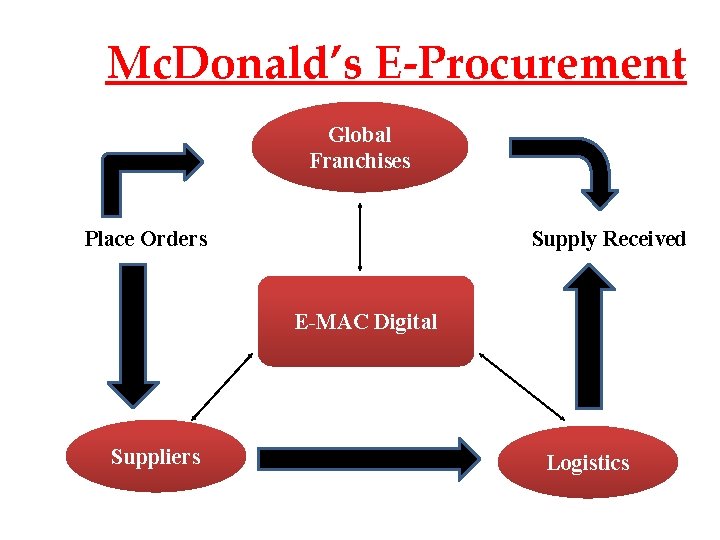
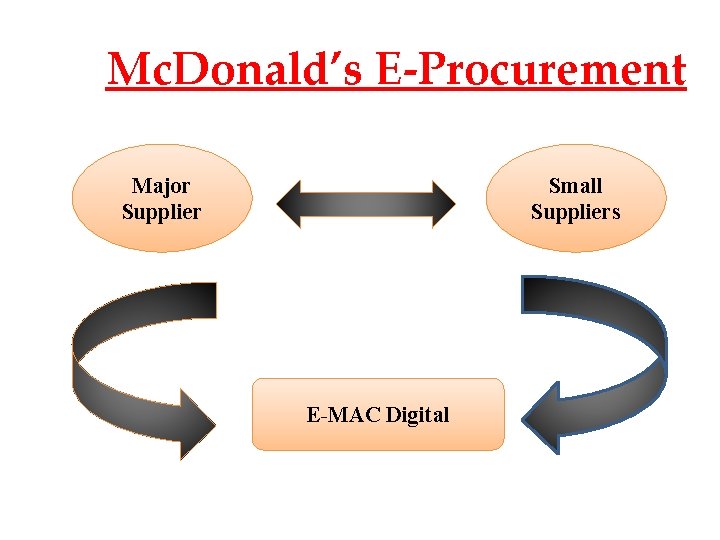
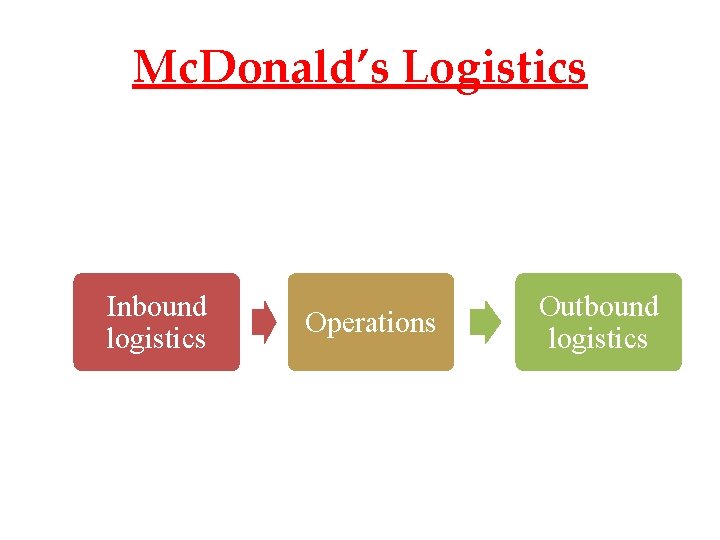
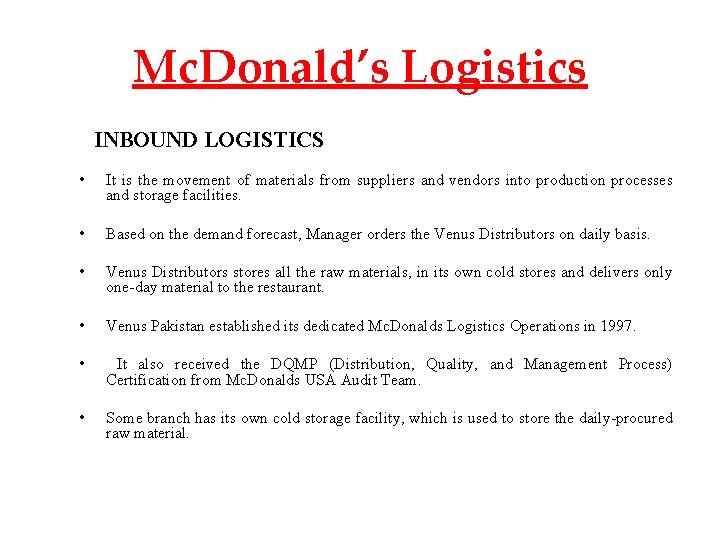
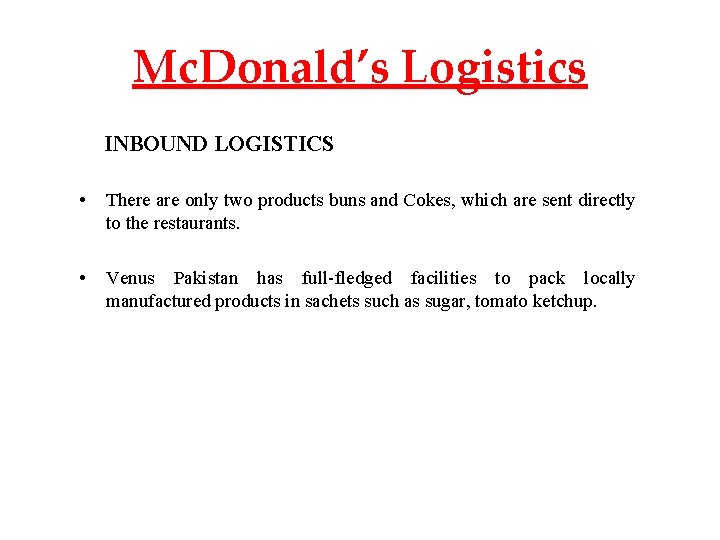
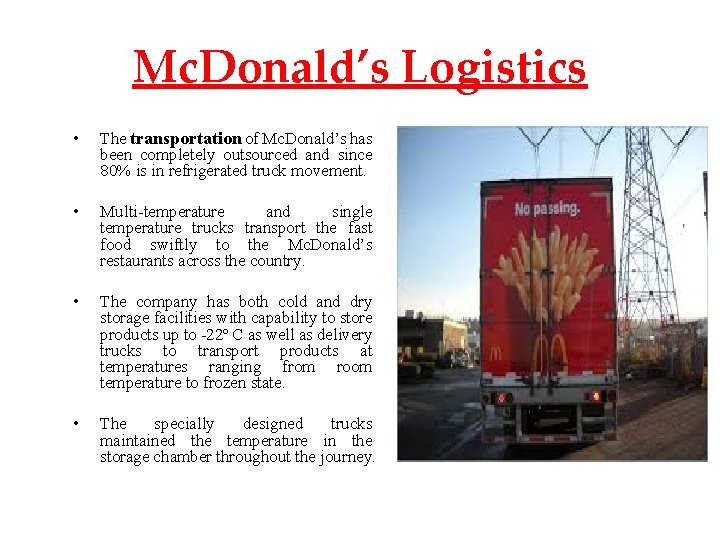
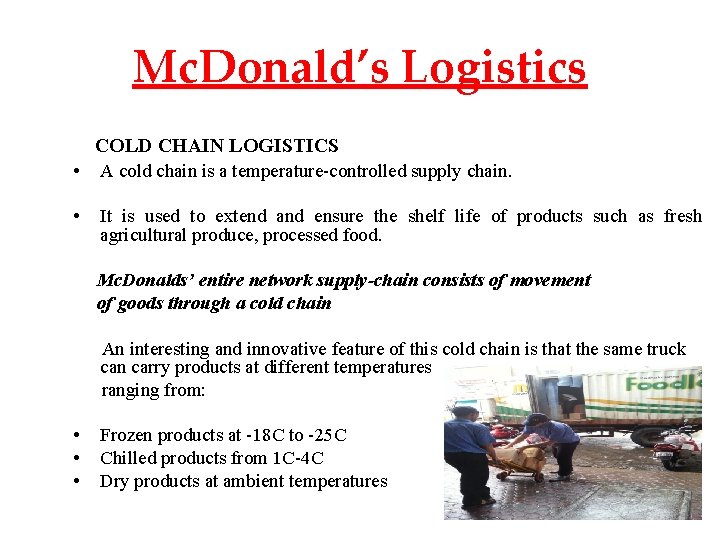
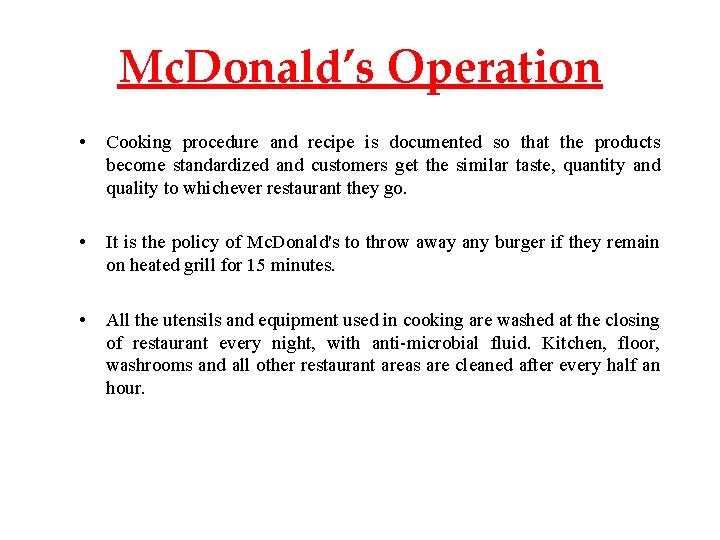
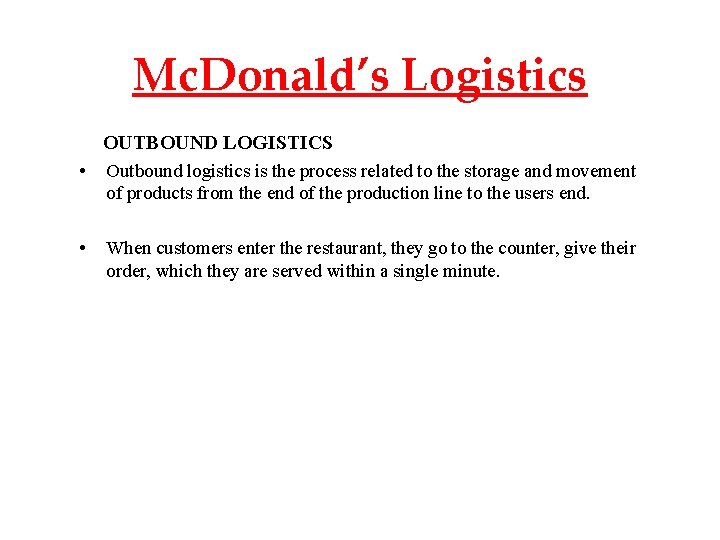
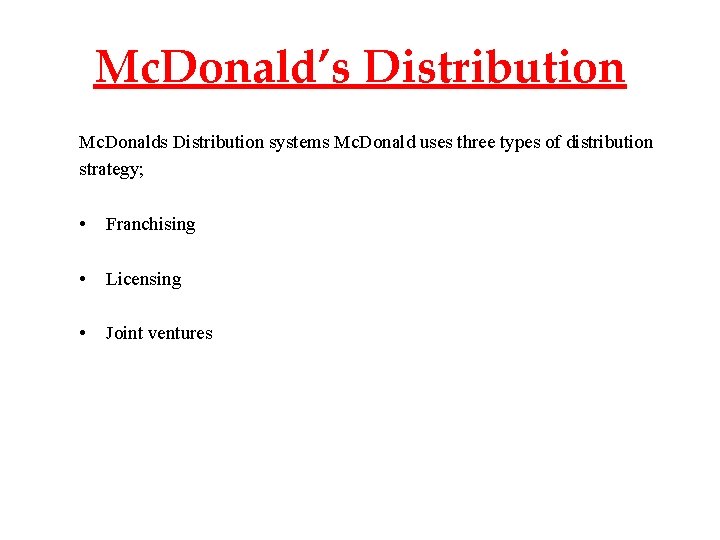
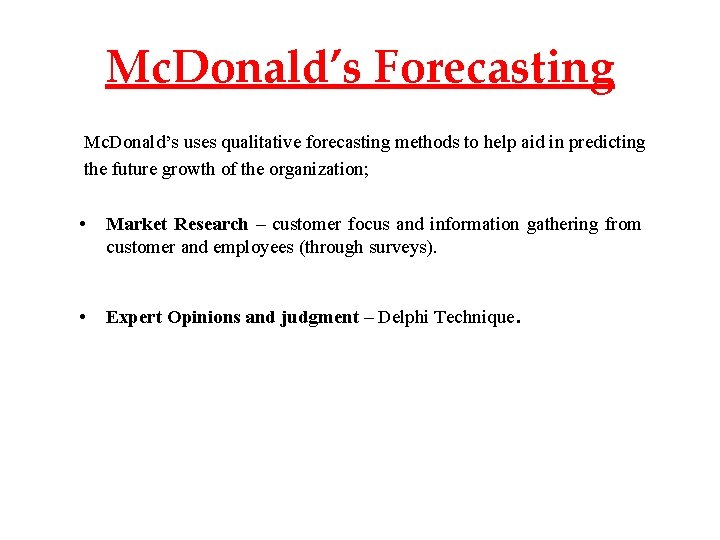
- Slides: 44
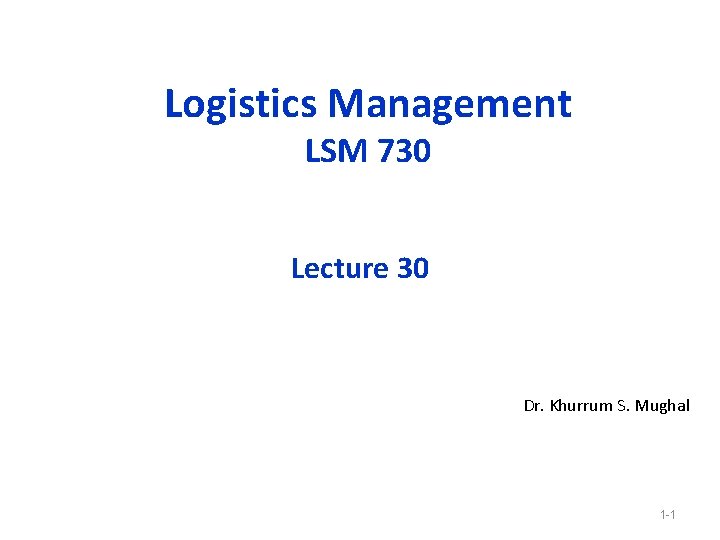
Logistics Management LSM 730 Lecture 30 Dr. Khurrum S. Mughal 1 -1
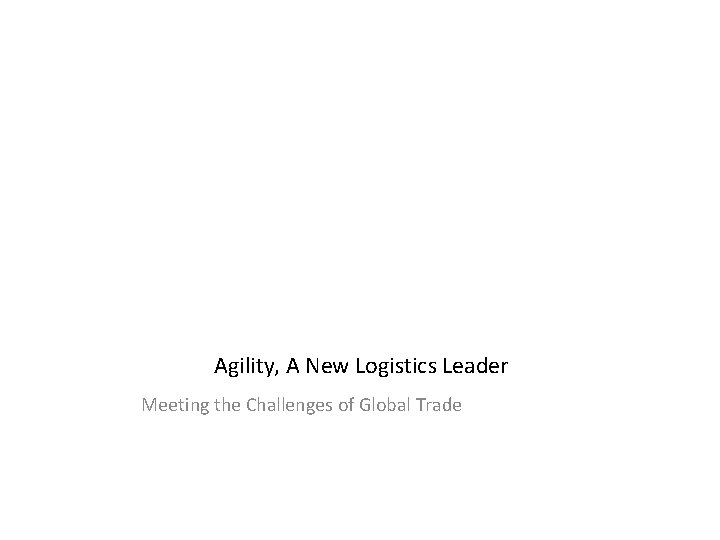
Efficient Supply Chain Services and Introduction of Agility Logistics Agility, A New Logistics Leader Meeting the Challenges of Global Trade
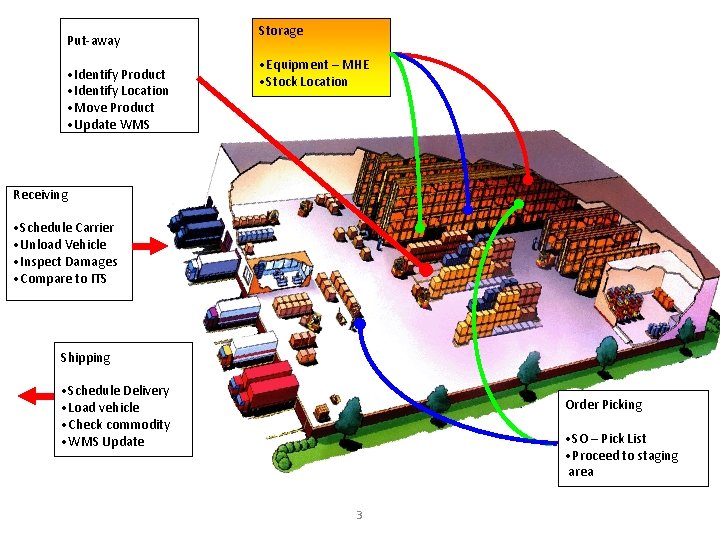
Put-away • Identify Product • Identify Location • Move Product • Update WMS Storage • Equipment – MHE • Stock Location Receiving • Schedule Carrier • Unload Vehicle • Inspect Damages • Compare to ITS Shipping • Schedule Delivery • Load vehicle • Check commodity • WMS Update Order Picking • SO – Pick List • Proceed to staging area 3
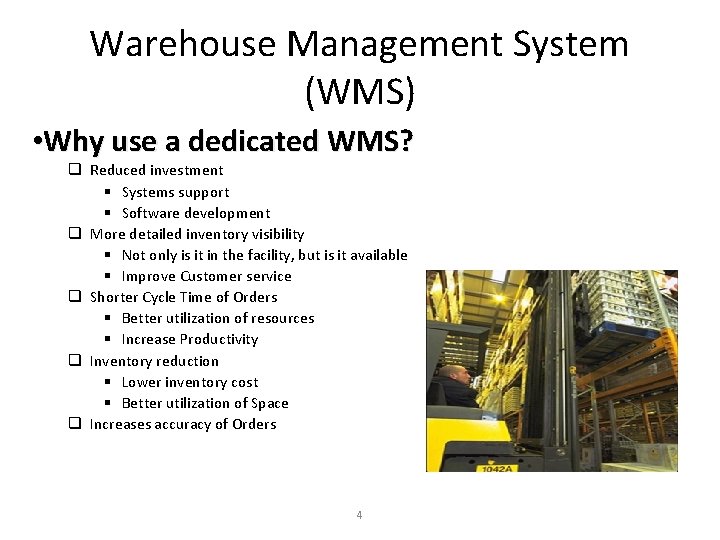
Warehouse Management System (WMS) • Why use a dedicated WMS? q Reduced investment § Systems support § Software development q More detailed inventory visibility § Not only is it in the facility, but is it available § Improve Customer service q Shorter Cycle Time of Orders § Better utilization of resources § Increase Productivity q Inventory reduction § Lower inventory cost § Better utilization of Space q Increases accuracy of Orders 4
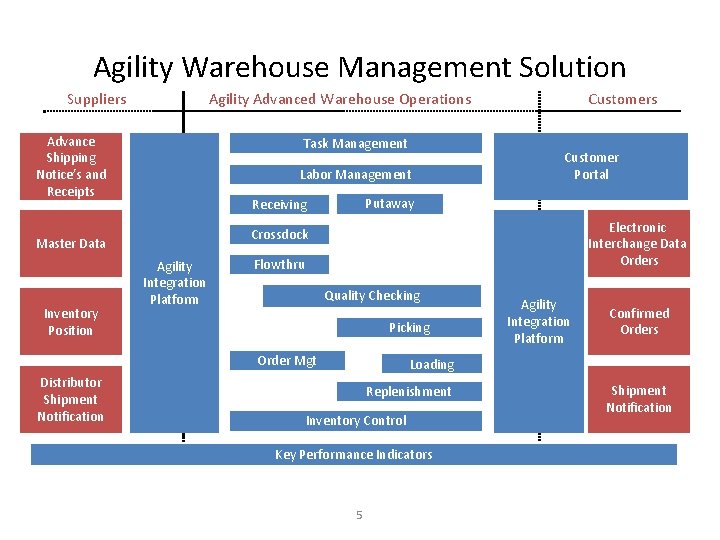
Agility Warehouse Management Solution Suppliers Agility Advanced Warehouse Operations Advance Shipping Notice’s and Receipts Task Management Labor Management Electronic Interchange Data Orders Crossdock Agility Integration Platform Flowthru Quality Checking Picking Order Mgt Distributor Shipment Notification Customer Portal Putaway Receiving Master Data Inventory Position Customers Agility Integration Platform Confirmed Orders Loading Replenishment Inventory Control Key Performance Indicators 5 Shipment Notification
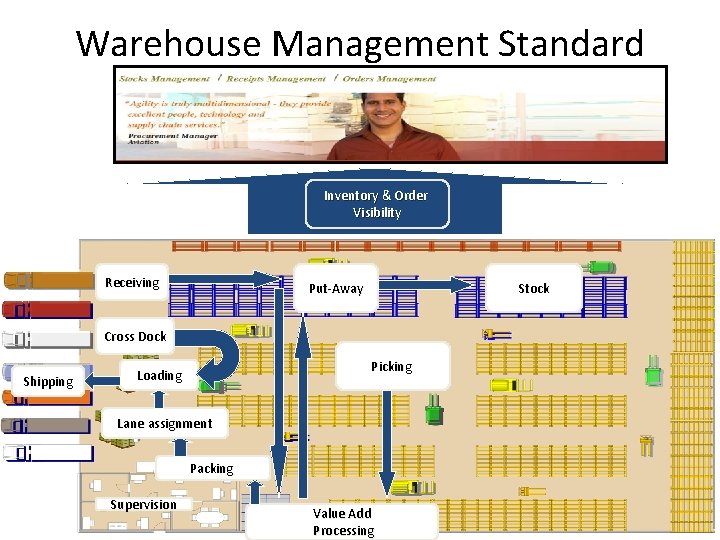
Warehouse Management Standard Process Inventory & Order Visibility Receiving Put-Away Stock Cross Dock Shipping Picking Loading Lane assignment Packing Supervision Value Add 6 Processing
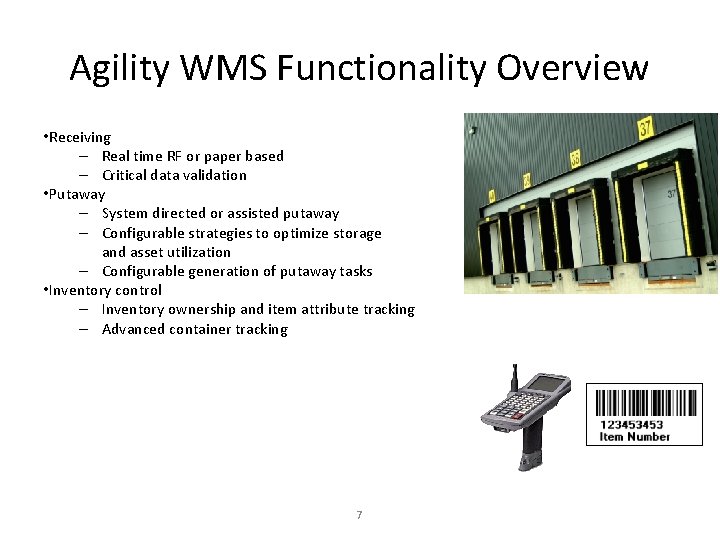
Agility WMS Functionality Overview • Receiving – Real time RF or paper based – Critical data validation • Putaway – System directed or assisted putaway – Configurable strategies to optimize storage and asset utilization – Configurable generation of putaway tasks • Inventory control – Inventory ownership and item attribute tracking – Advanced container tracking 7
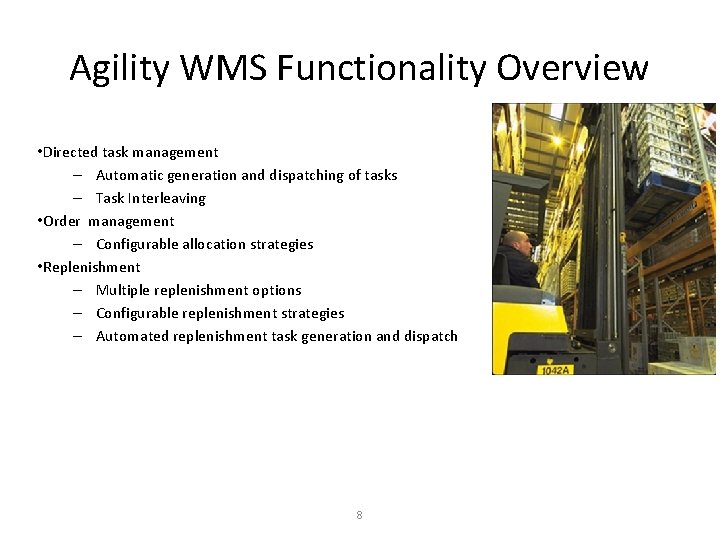
Agility WMS Functionality Overview • Directed task management – Automatic generation and dispatching of tasks – Task Interleaving • Order management – Configurable allocation strategies • Replenishment – Multiple replenishment options – Configurable replenishment strategies – Automated replenishment task generation and dispatch 8
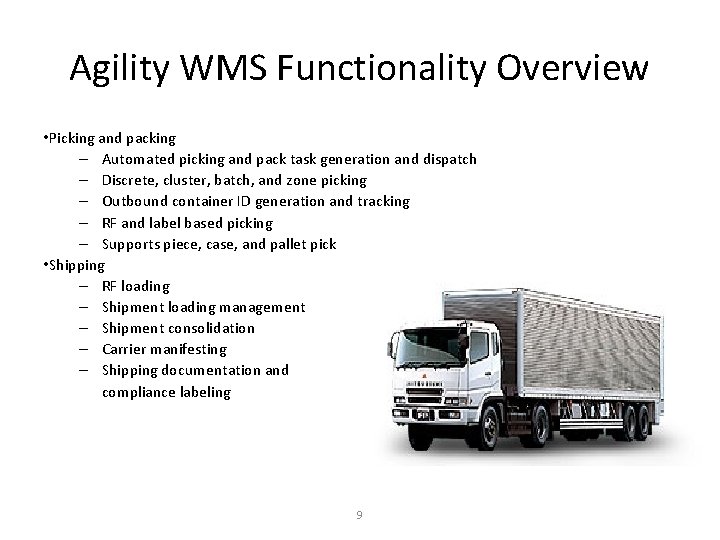
Agility WMS Functionality Overview • Picking and packing – Automated picking and pack task generation and dispatch – Discrete, cluster, batch, and zone picking – Outbound container ID generation and tracking – RF and label based picking – Supports piece, case, and pallet pick • Shipping – RF loading – Shipment loading management – Shipment consolidation – Carrier manifesting – Shipping documentation and compliance labeling 9
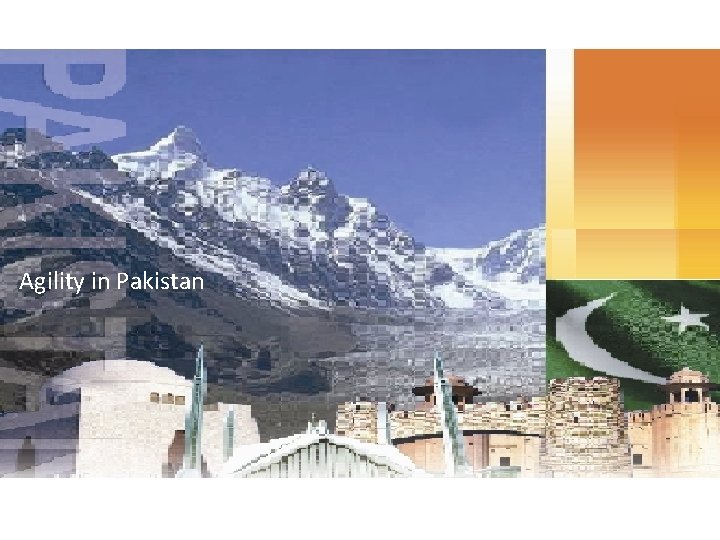
The Agility Advantage Agility in Pakistan
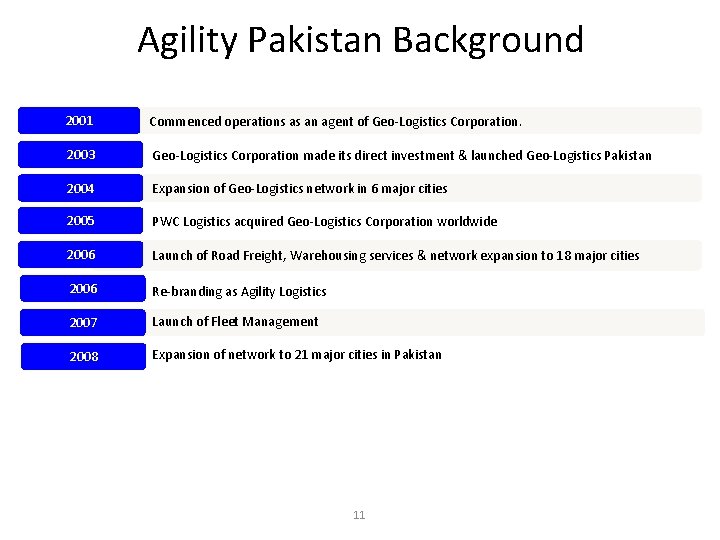
Agility Pakistan Background 2001 Commenced operations as an agent of Geo-Logistics Corporation. 2003 Geo-Logistics Corporation made its direct investment & launched Geo-Logistics Pakistan 2004 Expansion of Geo-Logistics network in 6 major cities 2005 PWC Logistics acquired Geo-Logistics Corporation worldwide 2006 Launch of Road Freight, Warehousing services & network expansion to 18 major cities 2006 Re-branding as Agility Logistics 2007 Launch of Fleet Management 2008 Expansion of network to 21 major cities in Pakistan 11
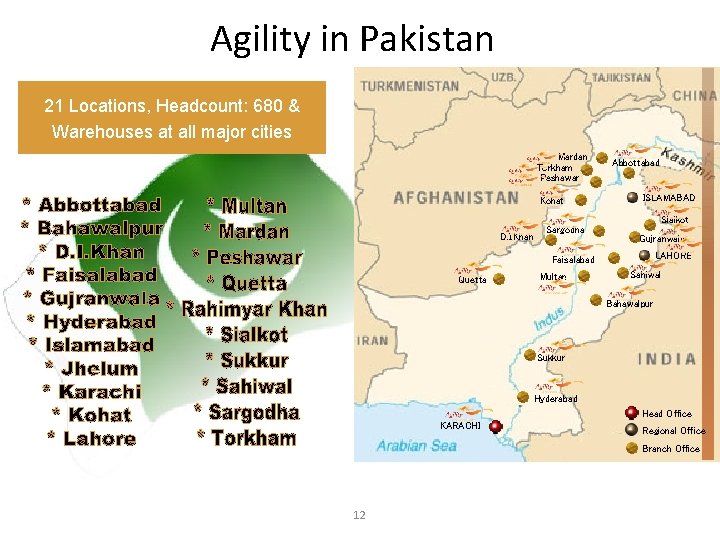
Agility in Pakistan 21 Locations, Headcount: 680 & Warehouses at all major cities Mardan Torkham Peshawar Kohat D. I. Khan Sargodha Abbottabad ISLAMABAD Sialkot Gujranwala LAHORE Faisalabad Quetta Multan Sahiwal Bahawalpur Sukkur Hyderabad Head Office KARACHI Regional Office Branch Office 12
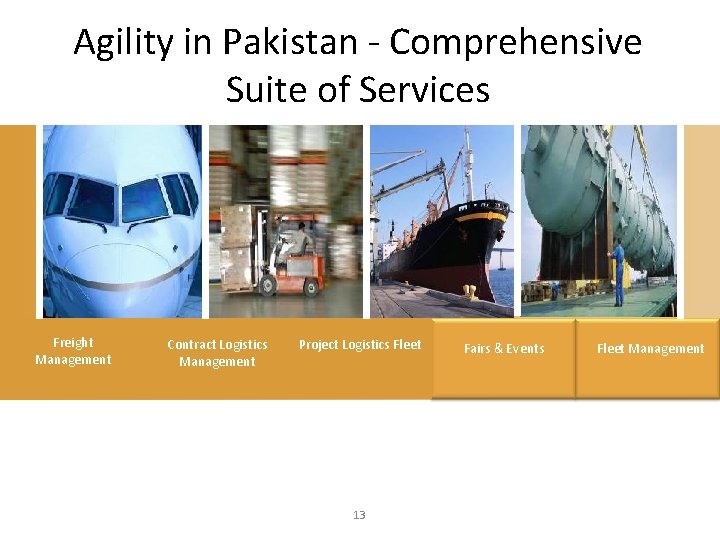
Agility in Pakistan - Comprehensive Suite of Services Freight Management Contract Logistics Management Project Logistics Fleet 13 Fairs & Events Fleet Management
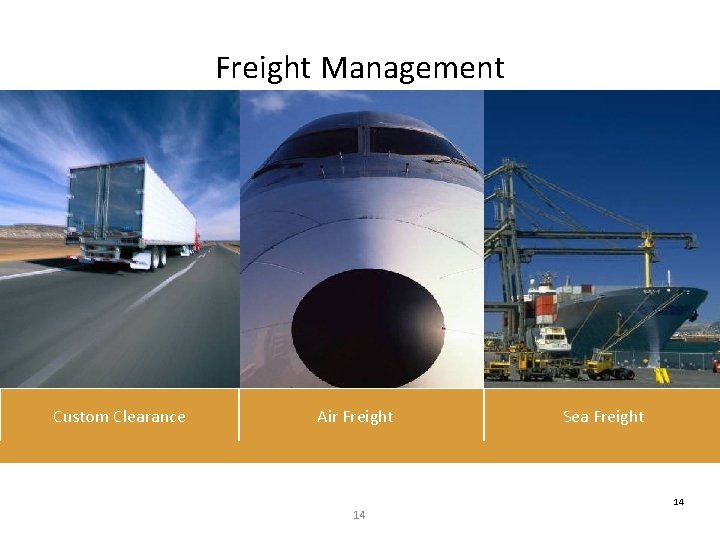
Freight Management Custom Clearance Air Freight 14 Sea Freight 14
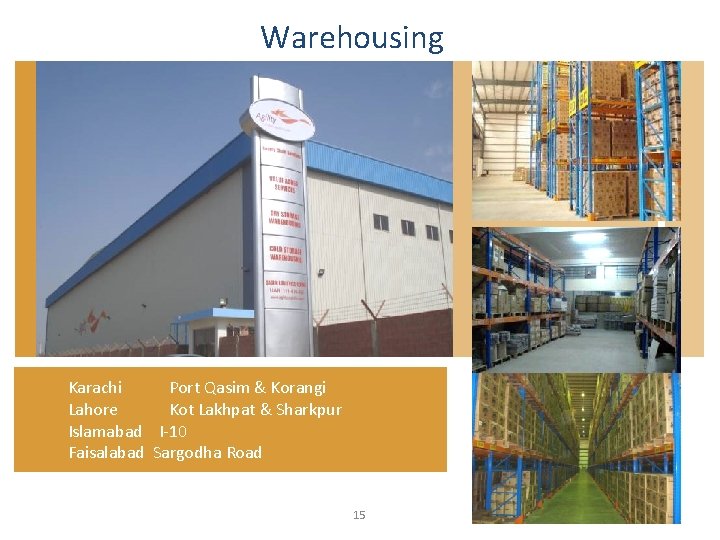
Warehousing Karachi Port Qasim & Korangi Lahore Kot Lakhpat & Sharkpur Islamabad I-10 Faisalabad Sargodha Road 15
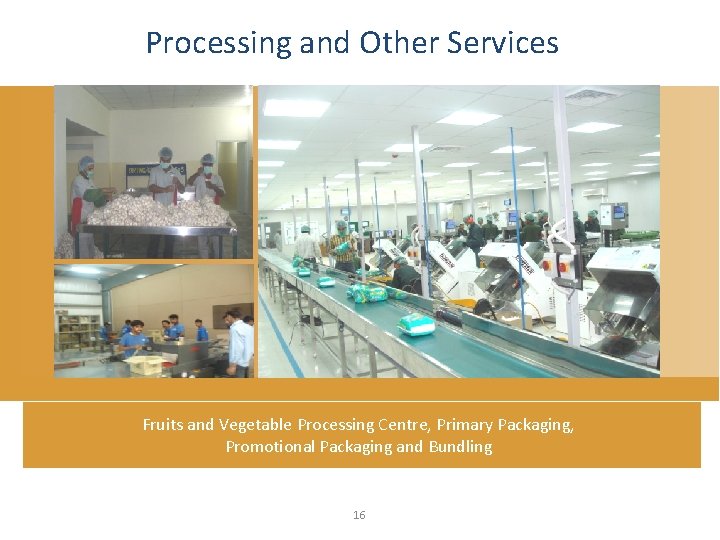
Processing and Other Services Fruits and Vegetable Processing Centre, Primary Packaging, Promotional Packaging and Bundling 16
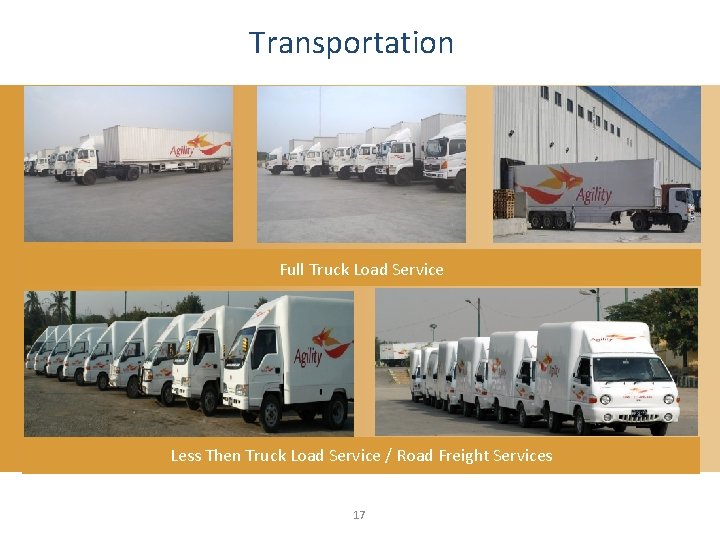
Transportation Full Truck Load Service Less Then Truck Load Service / Road Freight Services 17
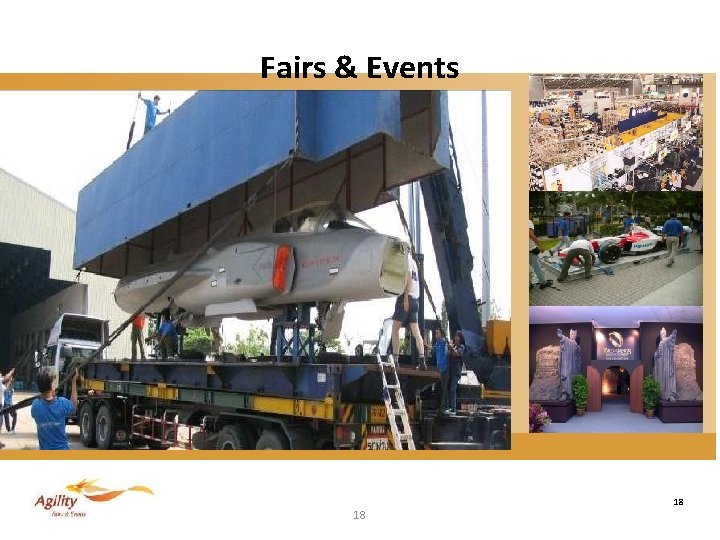
Fairs & Events 18 18
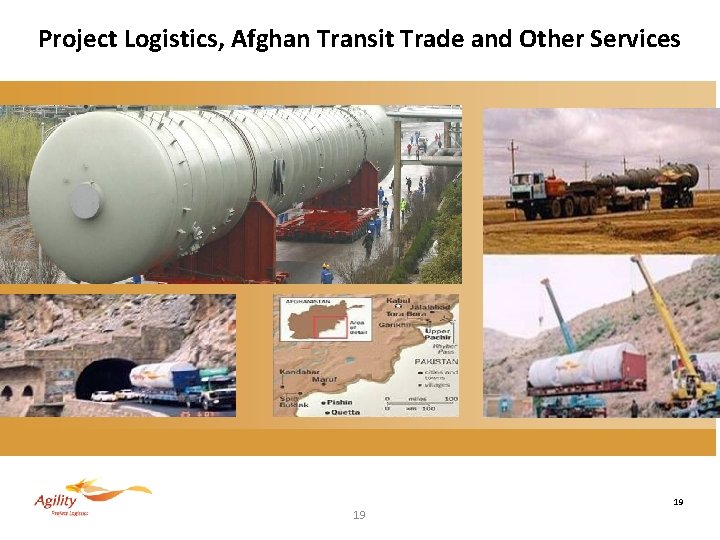
Project Logistics, Afghan Transit Trade and Other Services 19 19
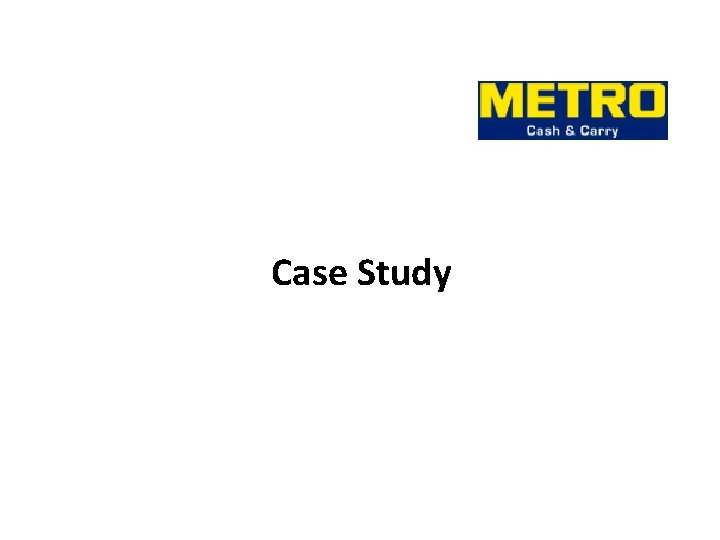
Case Study Platform for METRO Pakistan
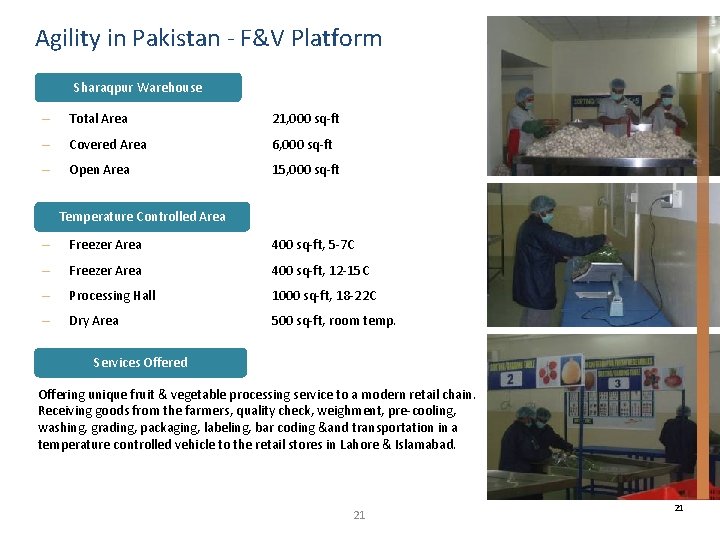
Agility in Pakistan - F&V Platform Sharaqpur Warehouse – Total Area 21, 000 sq-ft – Covered Area 6, 000 sq-ft – Open Area 15, 000 sq-ft Temperature Controlled Area – Freezer Area 400 sq-ft, 5 -7 C – Freezer Area 400 sq-ft, 12 -15 C – Processing Hall 1000 sq-ft, 18 -22 C – Dry Area 500 sq-ft, room temp. Services Offered Offering unique fruit & vegetable processing service to a modern retail chain. Receiving goods from the farmers, quality check, weighment, pre-cooling, washing, grading, packaging, labeling, bar coding &and transportation in a temperature controlled vehicle to the retail stores in Lahore & Islamabad. 21 21
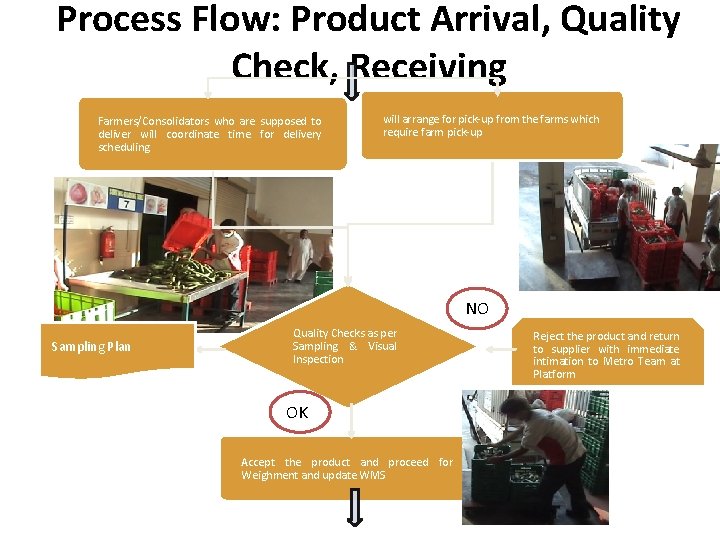
Process Flow: Product Arrival, Quality Check, Receiving Farmers/Consolidators who are supposed to deliver will coordinate time for delivery scheduling will arrange for pick-up from the farms which require farm pick-up NO Sampling Plan Quality Checks as per Sampling & Visual Inspection OK Accept the product and proceed for Weighment and update WMS Reject the product and return to supplier with immediate intimation to Metro Team at Platform
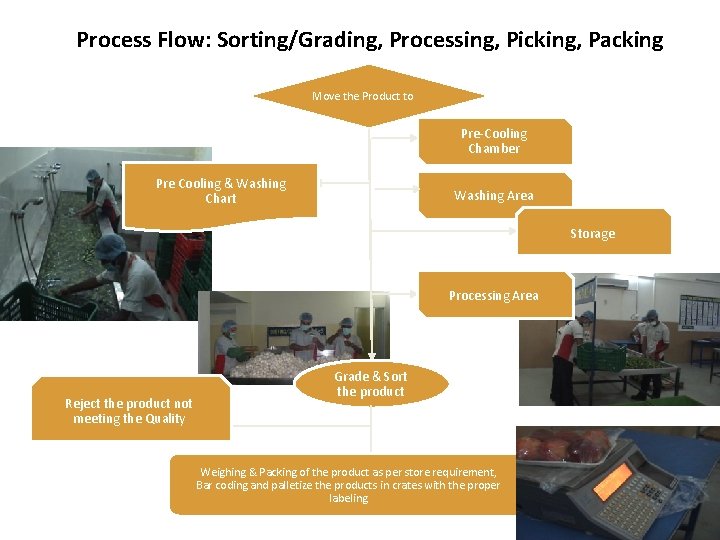
Process Flow: Sorting/Grading, Processing, Picking, Packing Move the Product to Pre-Cooling Chamber Pre Cooling & Washing Chart Washing Area Storage Processing Area Reject the product not meeting the Quality Grade & Sort the product Weighing & Packing of the product as per store requirement, Bar coding and palletize the products in crates with the proper labeling
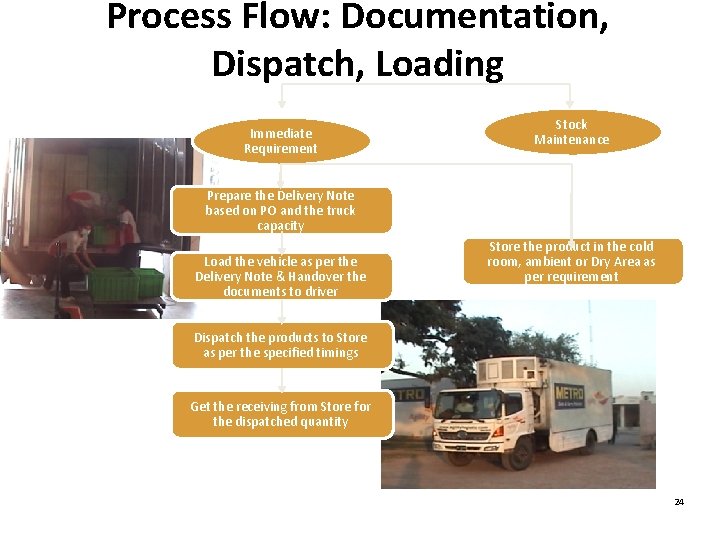
Process Flow: Documentation, Dispatch, Loading Immediate Requirement Stock Maintenance Prepare the Delivery Note based on PO and the truck capacity Load the vehicle as per the Delivery Note & Handover the documents to driver Store the product in the cold room, ambient or Dry Area as per requirement Dispatch the products to Store as per the specified timings Get the receiving from Store for the dispatched quantity 24
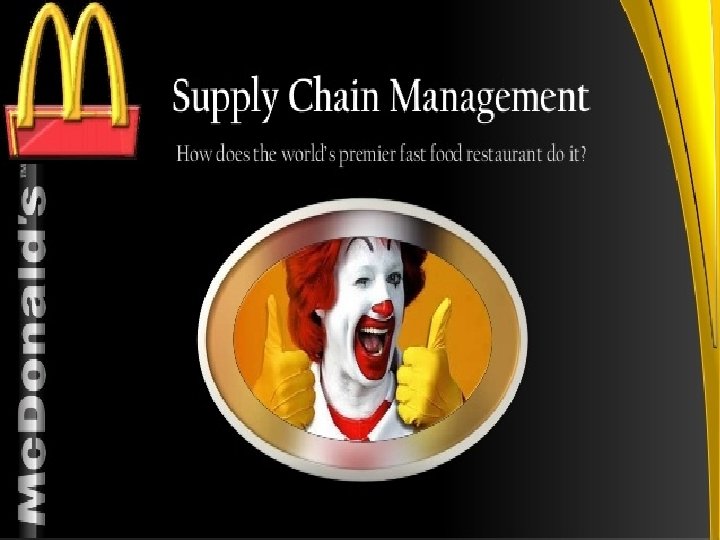
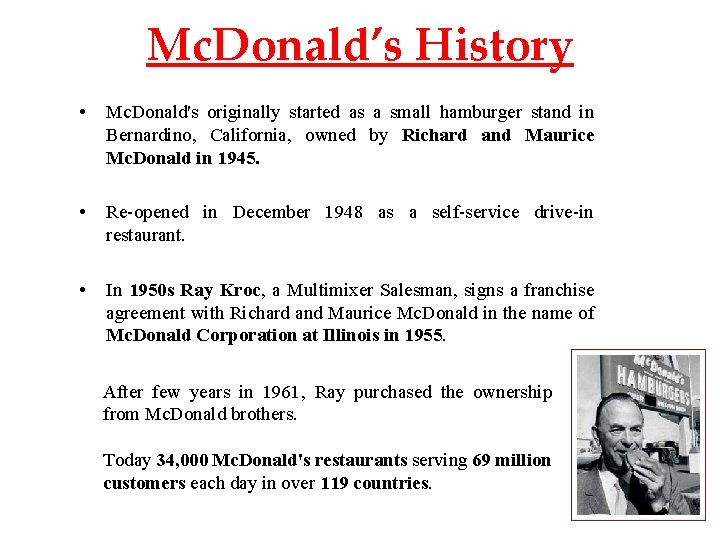
Mc. Donald’s History • Mc. Donald's originally started as a small hamburger stand in Bernardino, California, owned by Richard and Maurice Mc. Donald in 1945. • Re-opened in December 1948 as a self-service drive-in restaurant. • In 1950 s Ray Kroc, a Multimixer Salesman, signs a franchise agreement with Richard and Maurice Mc. Donald in the name of Mc. Donald Corporation at Illinois in 1955. After few years in 1961, Ray purchased the ownership from Mc. Donald brothers. Today 34, 000 Mc. Donald's restaurants serving 69 million customers each day in over 119 countries.
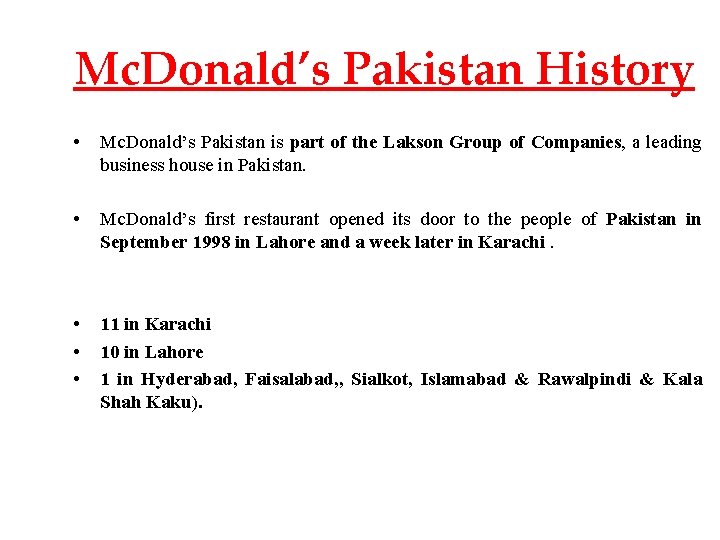
Mc. Donald’s Pakistan History • Mc. Donald’s Pakistan is part of the Lakson Group of Companies, a leading business house in Pakistan. • Mc. Donald’s first restaurant opened its door to the people of Pakistan in September 1998 in Lahore and a week later in Karachi. • • • 11 in Karachi 10 in Lahore 1 in Hyderabad, Faisalabad, , Sialkot, Islamabad & Rawalpindi & Kala Shah Kaku).
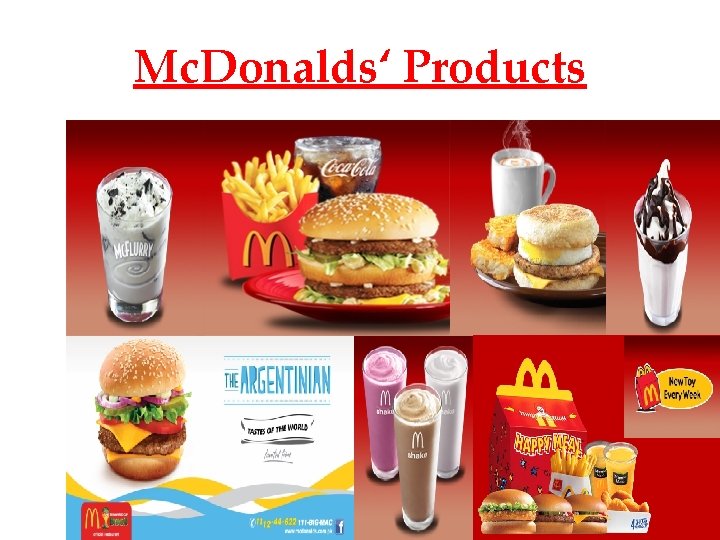
Mc. Donalds‘ Products
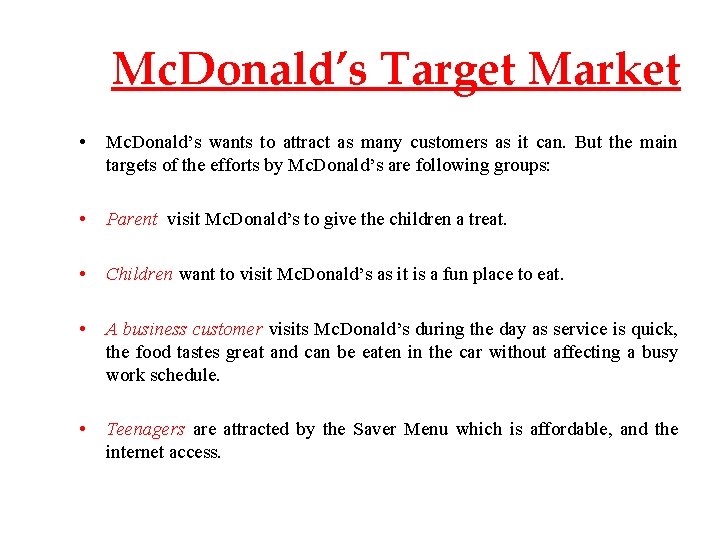
Mc. Donald’s Target Market • Mc. Donald’s wants to attract as many customers as it can. But the main targets of the efforts by Mc. Donald’s are following groups: • Parent visit Mc. Donald’s to give the children a treat. • Children want to visit Mc. Donald’s as it is a fun place to eat. • A business customer visits Mc. Donald’s during the day as service is quick, the food tastes great and can be eaten in the car without affecting a busy work schedule. • Teenagers are attracted by the Saver Menu which is affordable, and the internet access.
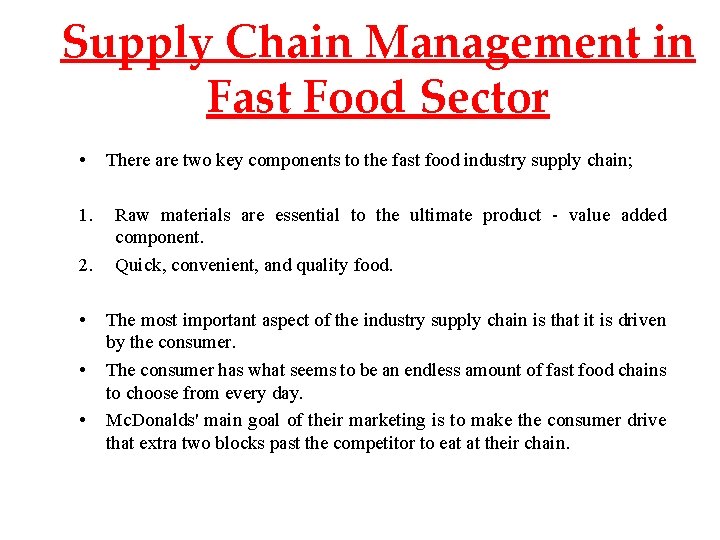
Supply Chain Management in Fast Food Sector • 1. 2. • • • There are two key components to the fast food industry supply chain; Raw materials are essential to the ultimate product - value added component. Quick, convenient, and quality food. The most important aspect of the industry supply chain is that it is driven by the consumer. The consumer has what seems to be an endless amount of fast food chains to choose from every day. Mc. Donalds' main goal of their marketing is to make the consumer drive that extra two blocks past the competitor to eat at their chain.
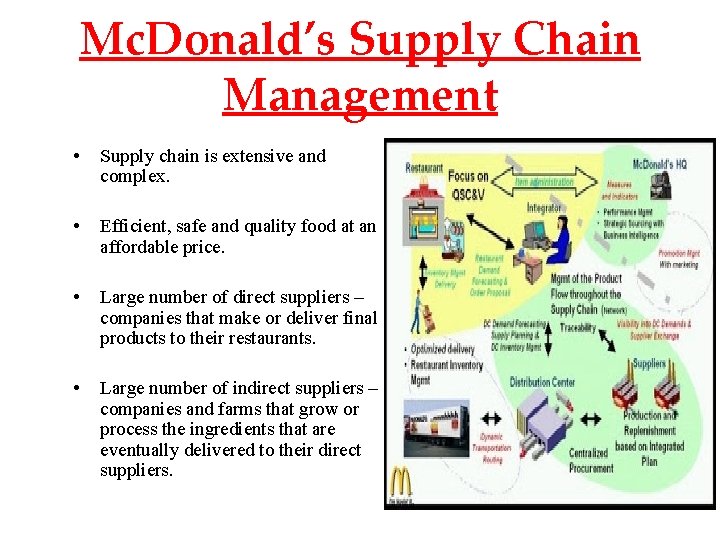
Mc. Donald’s Supply Chain Management • Supply chain is extensive and complex. • Efficient, safe and quality food at an affordable price. • Large number of direct suppliers – companies that make or deliver final products to their restaurants. • Large number of indirect suppliers – companies and farms that grow or process the ingredients that are eventually delivered to their direct suppliers.
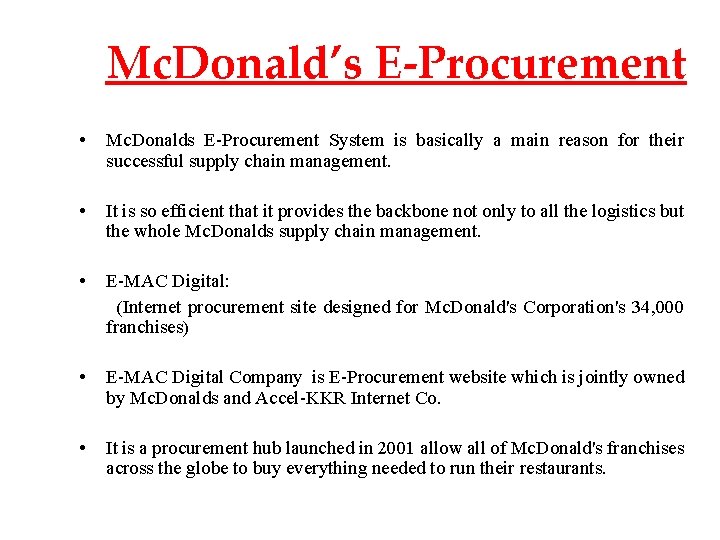
Mc. Donald’s E-Procurement • Mc. Donalds E-Procurement System is basically a main reason for their successful supply chain management. • It is so efficient that it provides the backbone not only to all the logistics but the whole Mc. Donalds supply chain management. • E-MAC Digital: (Internet procurement site designed for Mc. Donald's Corporation's 34, 000 franchises) • E-MAC Digital Company is E-Procurement website which is jointly owned by Mc. Donalds and Accel-KKR Internet Co. • It is a procurement hub launched in 2001 allow all of Mc. Donald's franchises across the globe to buy everything needed to run their restaurants.
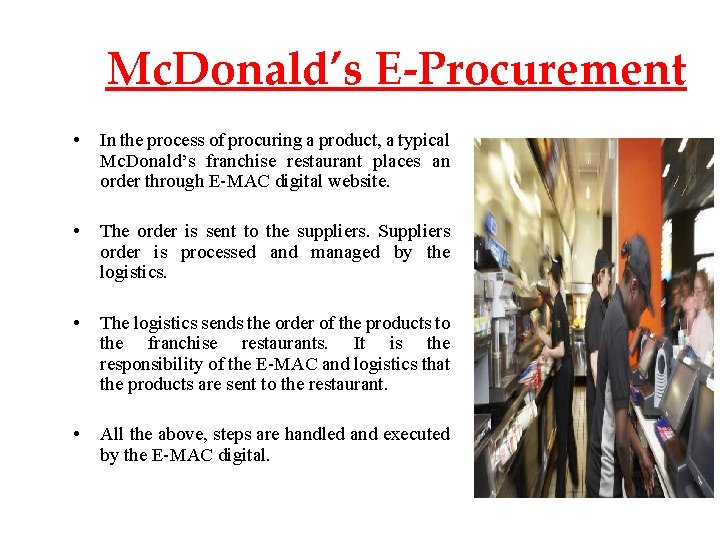
Mc. Donald’s E-Procurement • In the process of procuring a product, a typical Mc. Donald’s franchise restaurant places an order through E-MAC digital website. • The order is sent to the suppliers. Suppliers order is processed and managed by the logistics. • The logistics sends the order of the products to the franchise restaurants. It is the responsibility of the E-MAC and logistics that the products are sent to the restaurant. • All the above, steps are handled and executed by the E-MAC digital.
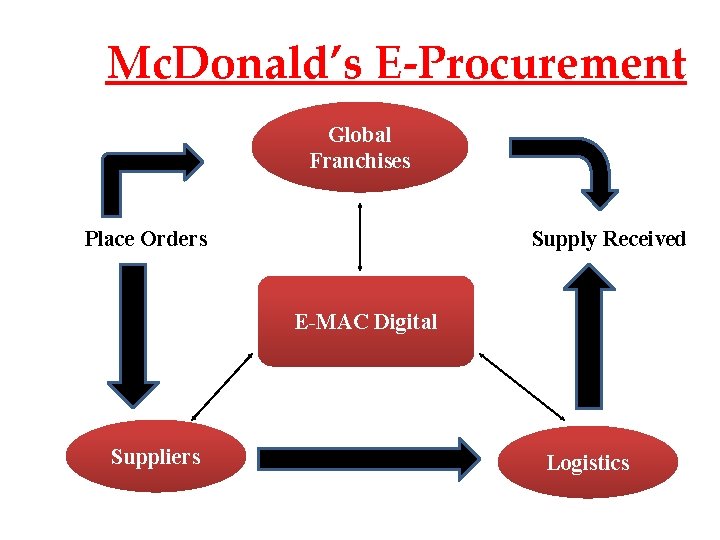
Mc. Donald’s E-Procurement Global Franchises Place Orders Supply Received E-MAC Digital Suppliers Logistics
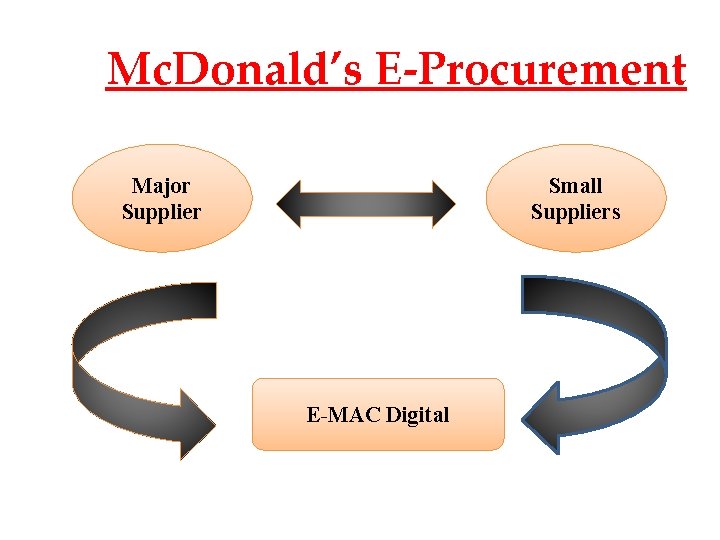
Mc. Donald’s E-Procurement Major Supplier Small Suppliers E-MAC Digital
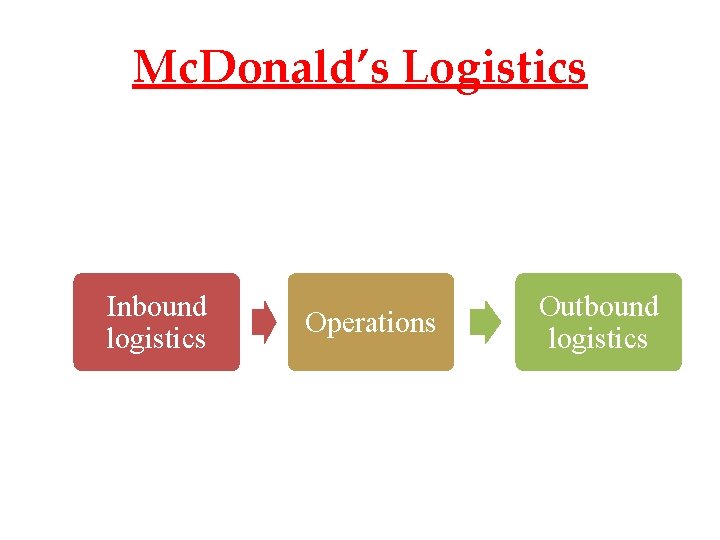
Mc. Donald’s Logistics Inbound logistics Operations Outbound logistics
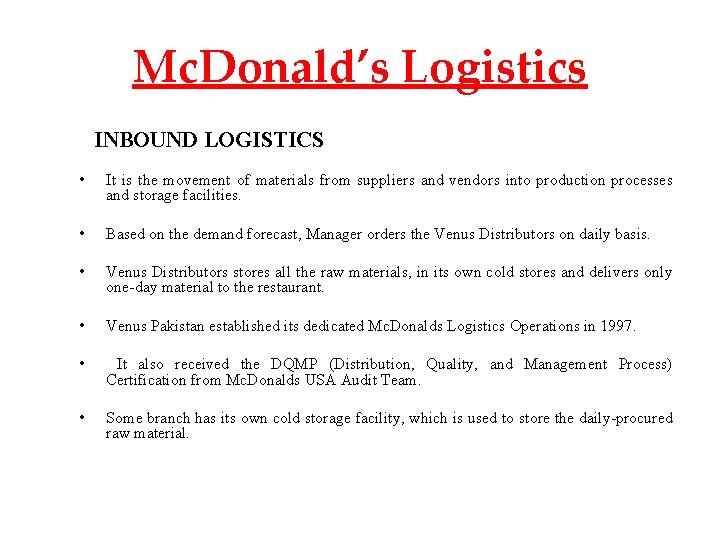
Mc. Donald’s Logistics INBOUND LOGISTICS • It is the movement of materials from suppliers and vendors into production processes and storage facilities. • Based on the demand forecast, Manager orders the Venus Distributors on daily basis. • Venus Distributors stores all the raw materials, in its own cold stores and delivers only one-day material to the restaurant. • Venus Pakistan established its dedicated Mc. Donalds Logistics Operations in 1997. • It also received the DQMP (Distribution, Quality, and Management Process) Certification from Mc. Donalds USA Audit Team. • Some branch has its own cold storage facility, which is used to store the daily-procured raw material.
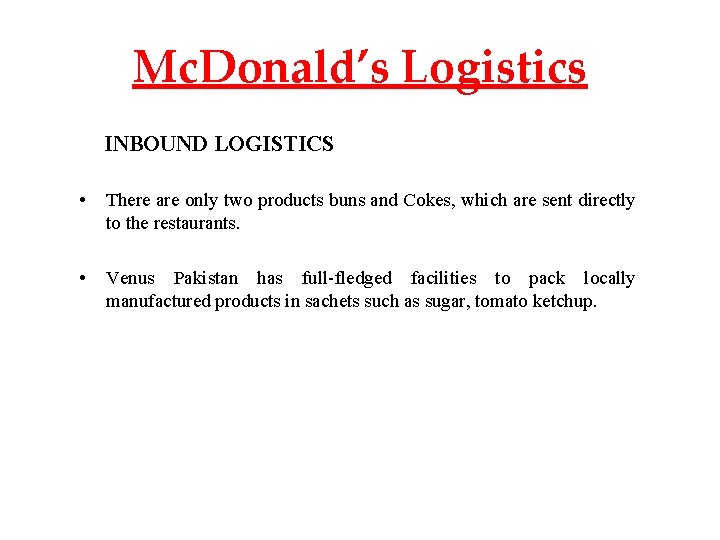
Mc. Donald’s Logistics INBOUND LOGISTICS • There are only two products buns and Cokes, which are sent directly to the restaurants. • Venus Pakistan has full-fledged facilities to pack locally manufactured products in sachets such as sugar, tomato ketchup.
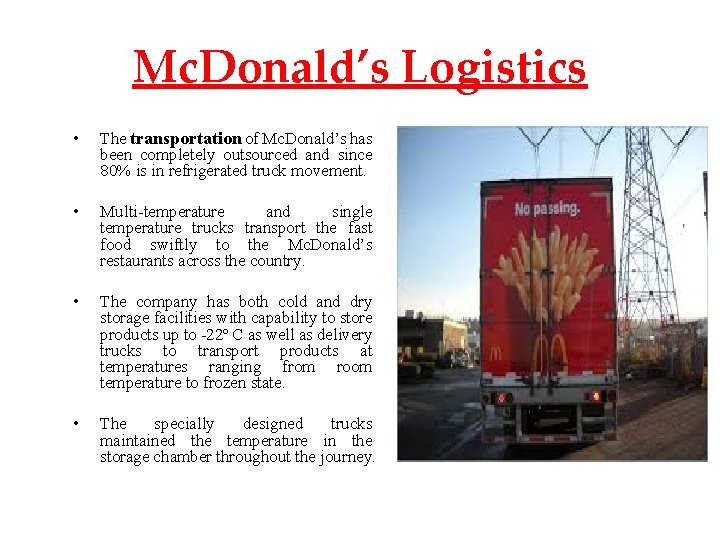
Mc. Donald’s Logistics • The transportation of Mc. Donald’s has been completely outsourced and since 80% is in refrigerated truck movement. • Multi-temperature and single temperature trucks transport the fast food swiftly to the Mc. Donald’s restaurants across the country. • The company has both cold and dry storage facilities with capability to store products up to -22º C as well as delivery trucks to transport products at temperatures ranging from room temperature to frozen state. • The specially designed trucks maintained the temperature in the storage chamber throughout the journey.
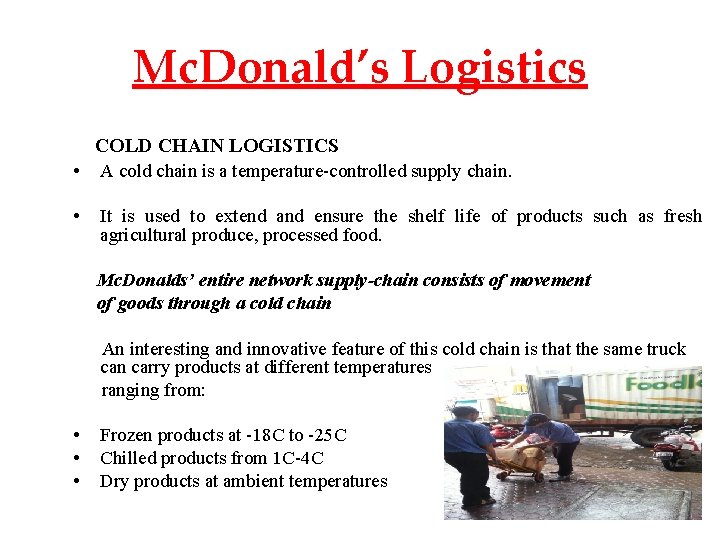
Mc. Donald’s Logistics COLD CHAIN LOGISTICS • A cold chain is a temperature-controlled supply chain. • It is used to extend and ensure the shelf life of products such as fresh agricultural produce, processed food. Mc. Donalds’ entire network supply-chain consists of movement of goods through a cold chain An interesting and innovative feature of this cold chain is that the same truck can carry products at different temperatures ranging from: • • • Frozen products at -18 C to -25 C Chilled products from 1 C-4 C Dry products at ambient temperatures
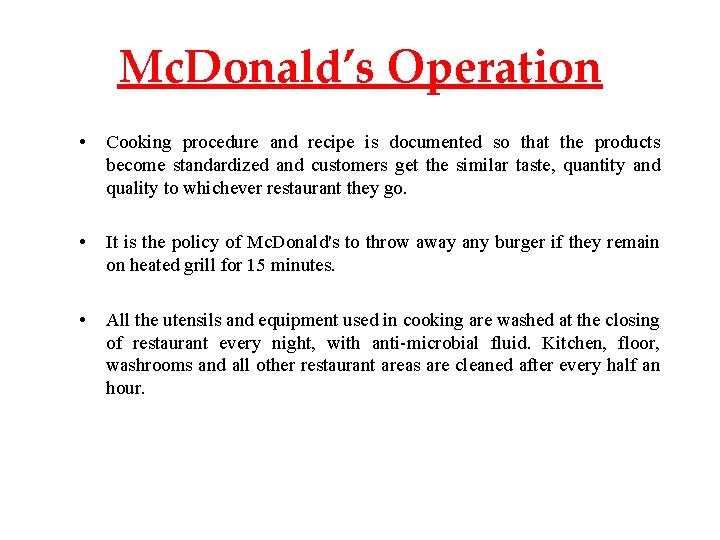
Mc. Donald’s Operation • Cooking procedure and recipe is documented so that the products become standardized and customers get the similar taste, quantity and quality to whichever restaurant they go. • It is the policy of Mc. Donald's to throw away any burger if they remain on heated grill for 15 minutes. • All the utensils and equipment used in cooking are washed at the closing of restaurant every night, with anti-microbial fluid. Kitchen, floor, washrooms and all other restaurant areas are cleaned after every half an hour.
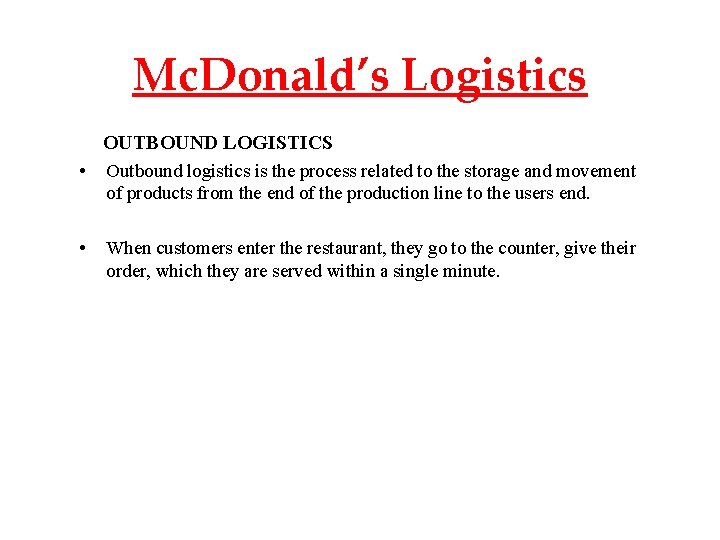
Mc. Donald’s Logistics OUTBOUND LOGISTICS • Outbound logistics is the process related to the storage and movement of products from the end of the production line to the users end. • When customers enter the restaurant, they go to the counter, give their order, which they are served within a single minute.
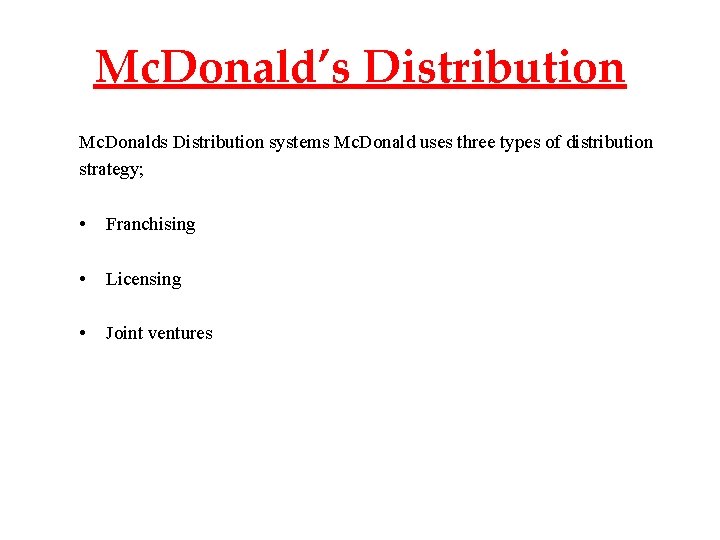
Mc. Donald’s Distribution Mc. Donalds Distribution systems Mc. Donald uses three types of distribution strategy; • Franchising • Licensing • Joint ventures
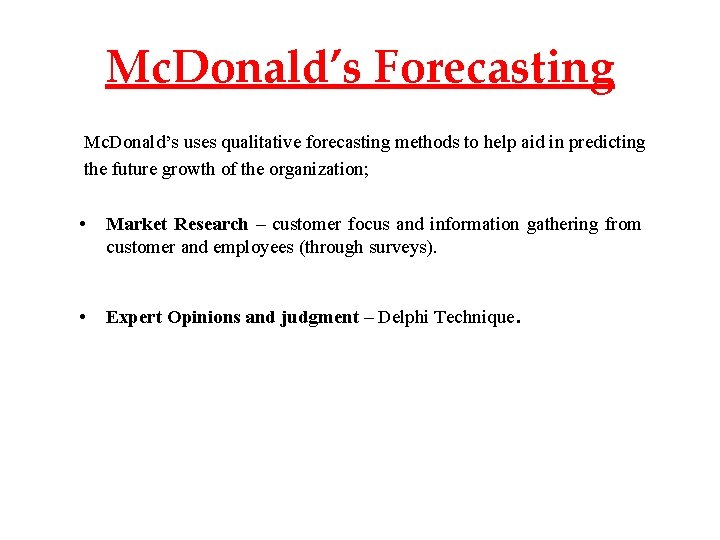
Mc. Donald’s Forecasting Mc. Donald’s uses qualitative forecasting methods to help aid in predicting the future growth of the organization; • Market Research – customer focus and information gathering from customer and employees (through surveys). • Expert Opinions and judgment – Delphi Technique .
Ieee 730
Trimble sps 930
649 en yakın yüzlüğe yuvarlama
Ars 28-730
730-170
Arlon 25fr
Lsm groups
Lsm groups
Zhuozhen cai
Lsm linux
Stage lsm
Noah land surface model
Cara mendirikan lsm
Ptrace protection with yama lsm (non-broker)
01:640:244 lecture notes - lecture 15: plat, idah, farad
Us army logistics management college
Army logistics management college
Performance cycle uncertainty
Sinotrans air huawei
Introduction to operations and supply chain management
Council of logistics management (clm)
Objectives of logistics management
Objectives of logistics management
Family planning logistics management information system
What is crm in supply chain management
Objectives of logistics management
What is logistics management
Logistics and channel management
Ford cmms system
Triangle logistics management
Role of logistics management
Components of physical distribution
What is logistics
Integrated logistics management
Global logistics and supply chain management
Project procurement management lecture notes
Strategic management lecture
4 ps of project management
Project management lecture notes doc
Financial management lecture
Public sector accounting lecture notes in uganda
Om 306
Performance management lecture
Management fifteenth edition
Human resources management chapter 1