Ford Material Planning Logistic Supply Chain Management Global
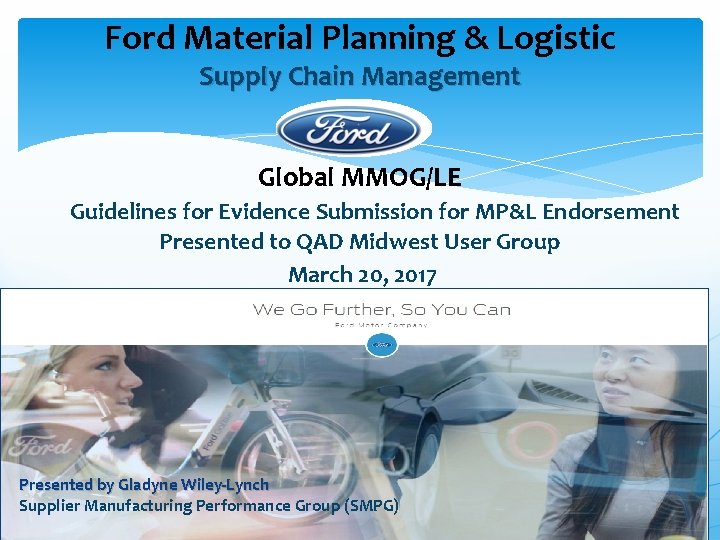
Ford Material Planning & Logistic Supply Chain Management Global MMOG/LE Guidelines for Evidence Submission for MP&L Endorsement Presented to QAD Midwest User Group March 20, 2017 Presented by Gladyne Wiley-Lynch Supplier Manufacturing Performance Group (SMPG)
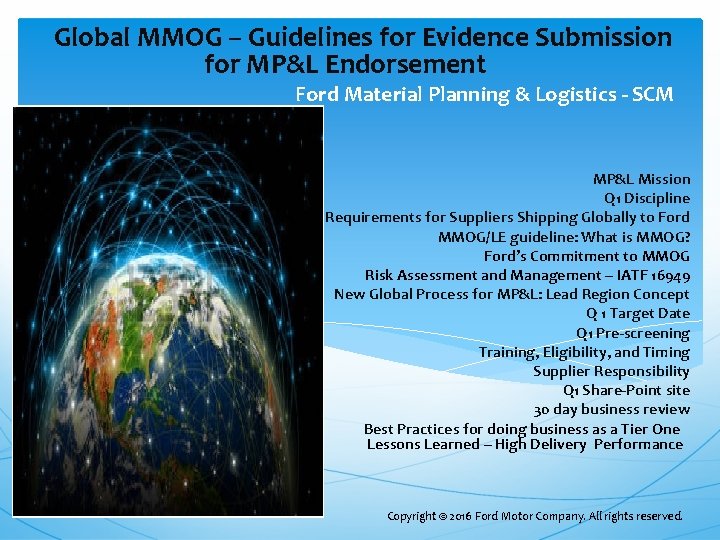
Global MMOG – Guidelines for Evidence Submission for MP&L Endorsement Ford Material Planning & Logistics - SCM MP&L Mission Q 1 Discipline Q 1 Requirements for Suppliers Shipping Globally to Ford MMOG/LE guideline: What is MMOG? Ford’s Commitment to MMOG Risk Assessment and Management – IATF 16949 New Global Process for MP&L: Lead Region Concept Q 1 Target Date Q 1 Pre-screening Training, Eligibility, and Timing Supplier Responsibility Q 1 Share-Point site 30 day business review Best Practices for doing business as a Tier One Lessons Learned – High Delivery Performance Copyright © 2016 Ford Motor Company. All rights reserved.
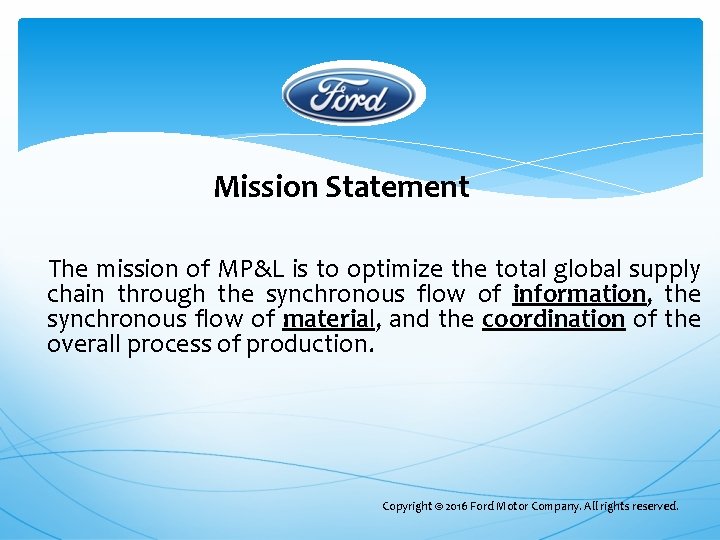
Mission Statement The mission of MP&L is to optimize the total global supply chain through the synchronous flow of information, the synchronous flow of material, and the coordination of the overall process of production. Copyright © 2016 Ford Motor Company. All rights reserved.
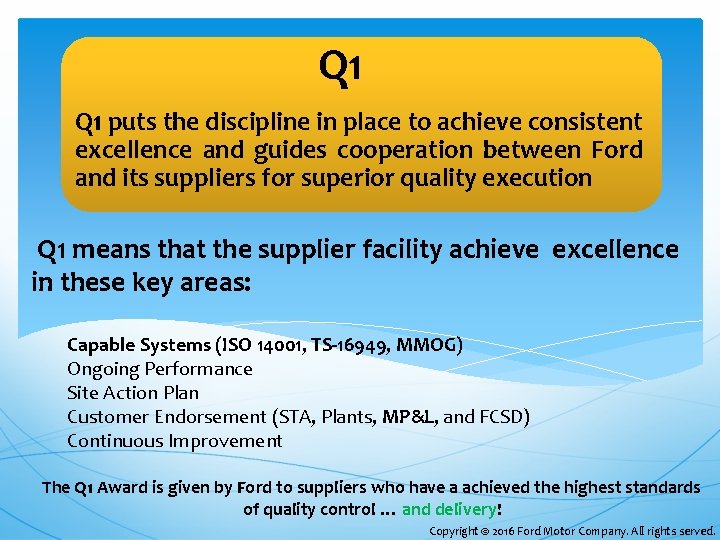
Q 1 puts the discipline in place to achieve consistent excellence and guides cooperation between Ford and its suppliers for superior quality execution Q 1 means that the supplier facility achieve excellence in these key areas: Capable Systems (ISO 14001, TS-16949, MMOG) Ongoing Performance Site Action Plan Customer Endorsement (STA, Plants, MP&L, and FCSD) Continuous Improvement The Q 1 Award is given by Ford to suppliers who have a achieved the highest standards of quality control … and delivery! Copyright © 2016 Ford Motor Company. All rights served.
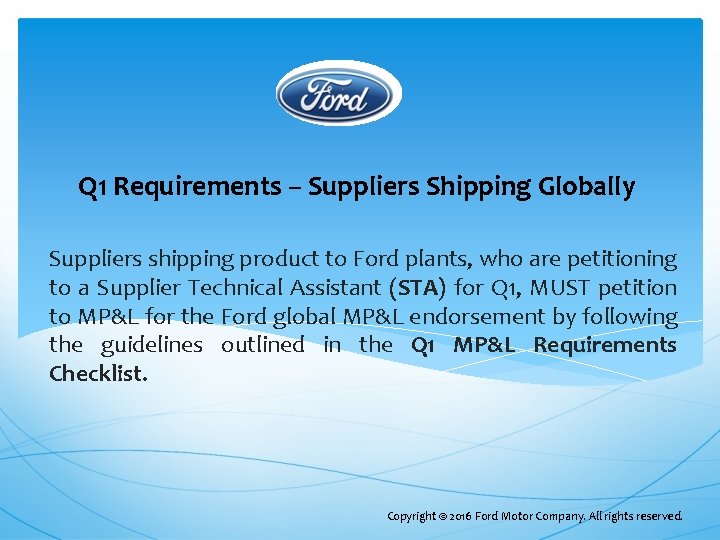
Q 1 Requirements – Suppliers Shipping Globally Suppliers shipping product to Ford plants, who are petitioning to a Supplier Technical Assistant (STA) for Q 1, MUST petition to MP&L for the Ford global MP&L endorsement by following the guidelines outlined in the Q 1 MP&L Requirements Checklist. Copyright © 2016 Ford Motor Company. All rights reserved.
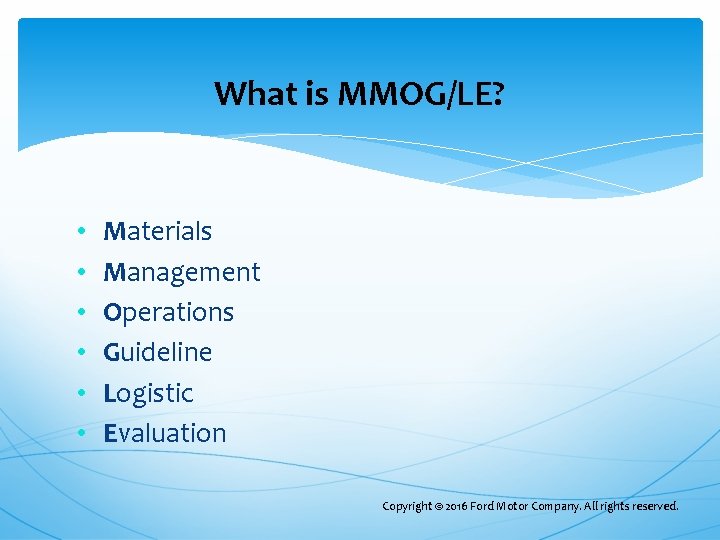
What is MMOG/LE? • • • Materials Management Operations Guideline Logistic Evaluation Copyright © 2016 Ford Motor Company. All rights reserved.
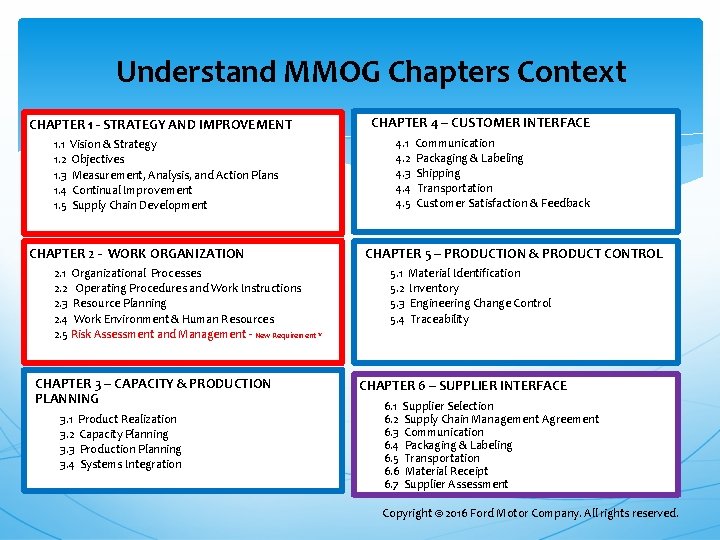
Understand MMOG Chapters Context CHAPTER 1 - STRATEGY AND IMPROVEMENT 1. 1 Vision & Strategy 1. 2 Objectives 1. 3 Measurement, Analysis, and Action Plans 1. 4 Continual Improvement 1. 5 Supply Chain Development CHAPTER 2 - WORK ORGANIZATION 4. 1 Communication 4. 2 Packaging & Labeling 4. 3 Shipping 4. 4 Transportation 4. 5 Customer Satisfaction & Feedback CHAPTER 5 – PRODUCTION & PRODUCT CONTROL 2. 1 Organizational Processes 2. 2 Operating Procedures and Work Instructions 2. 3 Resource Planning 2. 4 Work Environment & Human Resources 2. 5 Risk Assessment and Management - New Requirement * CHAPTER 3 – CAPACITY & PRODUCTION PLANNING 3. 1 Product Realization 3. 2 Capacity Planning 3. 3 Production Planning 3. 4 Systems Integration CHAPTER 4 – CUSTOMER INTERFACE 5. 1 Material Identification 5. 2 Inventory 5. 3 Engineering Change Control 5. 4 Traceability CHAPTER 6 – SUPPLIER INTERFACE 6. 1 Supplier Selection 6. 2 Supply Chain Management Agreement 6. 3 Communication 6. 4 Packaging & Labeling 6. 5 Transportation 6. 6 Material Receipt 6. 7 Supplier Assessment Copyright © 2016 Ford Motor Company. All rights reserved.
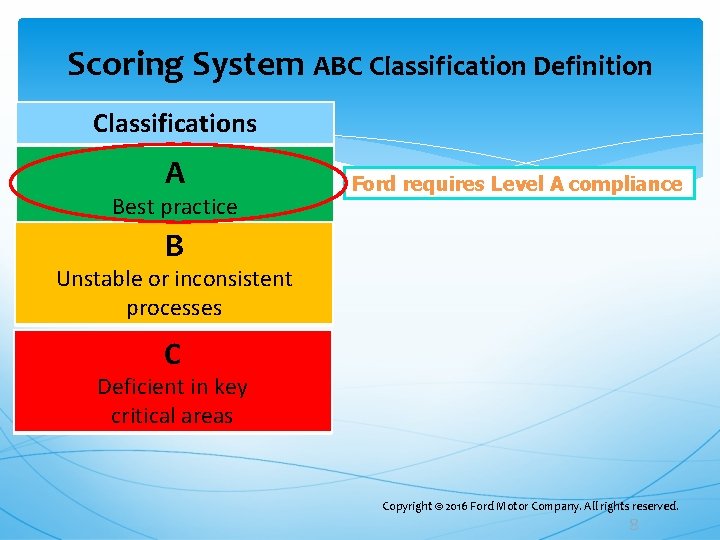
Scoring System ABC Classification Definition Classifications A Ford requires Level A compliance Best practice B Unstable or inconsistent processes C Deficient in key critical areas Copyright © 2016 Ford Motor Company. All rights reserved. 8
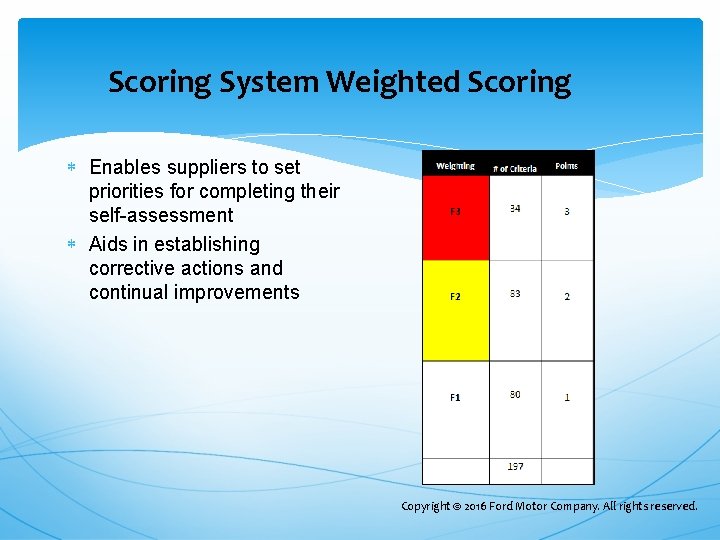
Scoring System Weighted Scoring Enables suppliers to set priorities for completing their self-assessment Aids in establishing corrective actions and continual improvements Copyright © 2016 Ford Motor Company. All rights reserved.
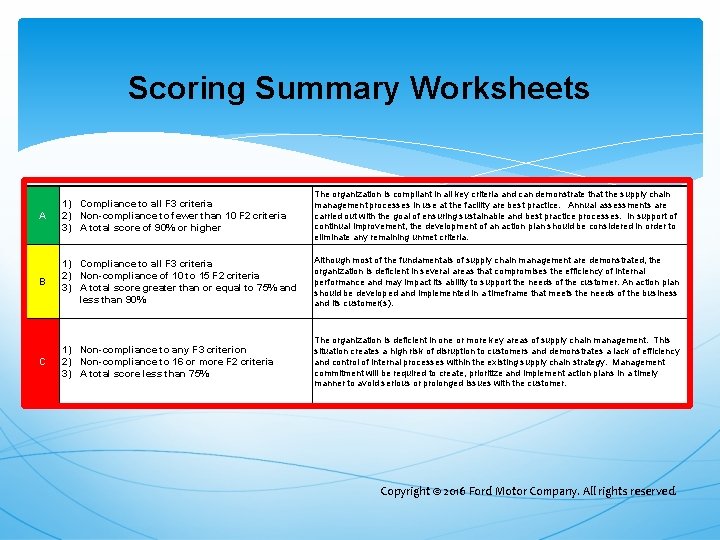
Scoring Summary Worksheets A 1) Compliance to all F 3 criteria 2) Non-compliance to fewer than 10 F 2 criteria 3) A total score of 90% or higher The organization is compliant in all key criteria and can demonstrate that the supply chain management processes in use at the facility are best practice. Annual assessments are carried out with the goal of ensuring sustainable and best practice processes. In support of continual improvement, the development of an action plan should be considered in order to eliminate any remaining unmet criteria. B 1) Compliance to all F 3 criteria 2) Non-compliance of 10 to 15 F 2 criteria 3) A total score greater than or equal to 75% and less than 90% Although most of the fundamentals of supply chain management are demonstrated, the organization is deficient in several areas that compromises the efficiency of internal performance and may impact its ability to support the needs of the customer. An action plan should be developed and implemented in a timeframe that meets the needs of the business and its customer(s). C 1) Non-compliance to any F 3 criterion 2) Non-compliance to 16 or more F 2 criteria 3) A total score less than 75% The organization is deficient in one or more key areas of supply chain management. This situation creates a high risk of disruption to customers and demonstrates a lack of efficiency and control of internal processes within the existing supply chain strategy. Management commitment will be required to create, prioritize and implement action plans in a timely manner to avoid serious or prolonged issues with the customer. Copyright © 2016 Ford Motor Company. All rights reserved.
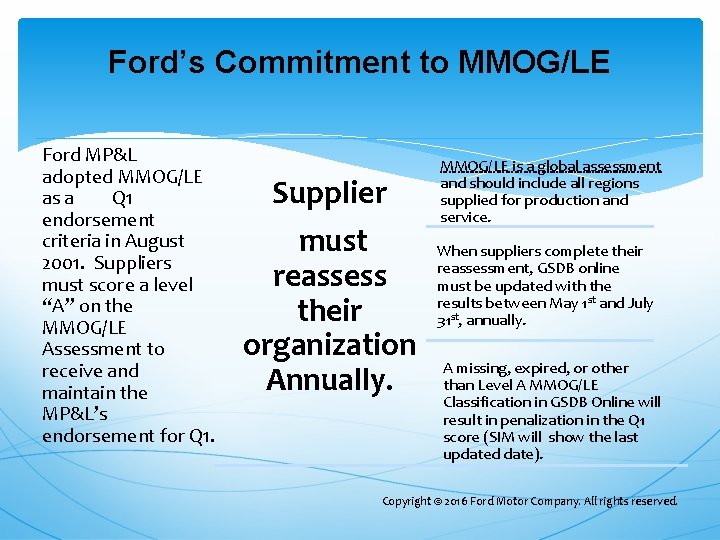
Ford’s Commitment to MMOG/LE Ford MP&L adopted MMOG/LE as a Q 1 endorsement criteria in August 2001. Suppliers must score a level “A” on the MMOG/LE Assessment to receive and maintain the MP&L’s endorsement for Q 1. Supplier must reassess their organization Annually. MMOG/LE is a global assessment and should include all regions supplied for production and service. When suppliers complete their reassessment, GSDB online must be updated with the results between May 1 st and July 31 st, annually. A missing, expired, or other than Level A MMOG/LE Classification in GSDB Online will result in penalization in the Q 1 score (SIM will show the last updated date). Copyright © 2016 Ford Motor Company. All rights reserved.
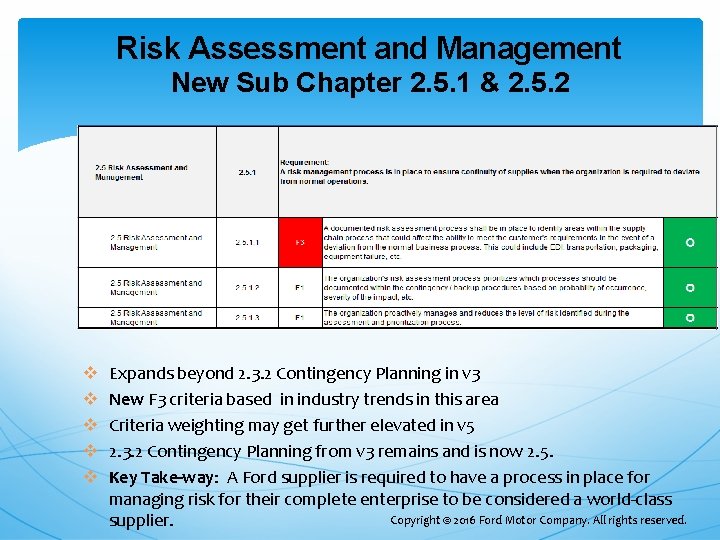
Risk Assessment and Management New Sub Chapter 2. 5. 1 & 2. 5. 2 v v v Expands beyond 2. 3. 2 Contingency Planning in v 3 New F 3 criteria based in industry trends in this area Criteria weighting may get further elevated in v 5 2. 3. 2 Contingency Planning from v 3 remains and is now 2. 5. Key Take-way: A Ford supplier is required to have a process in place for managing risk for their complete enterprise to be considered a world-class Copyright © 2016 Ford Motor Company. All rights reserved. supplier.
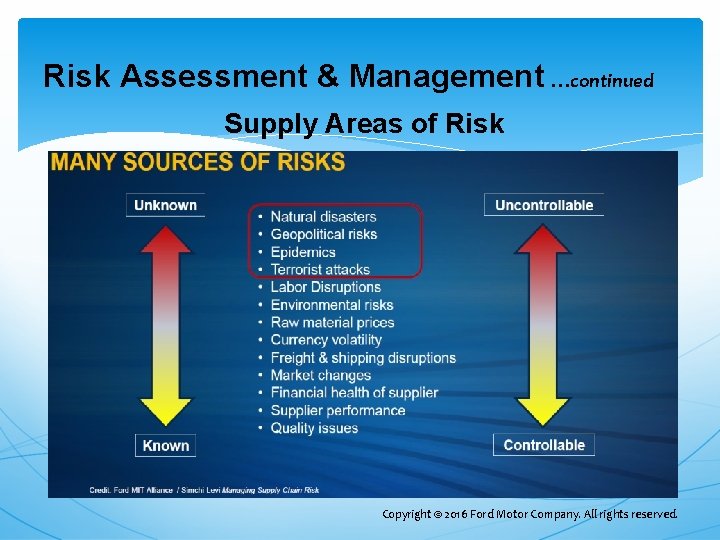
Risk Assessment & Management …continued Supply Areas of Risk Copyright © 2016 Ford Motor Company. All rights reserved.
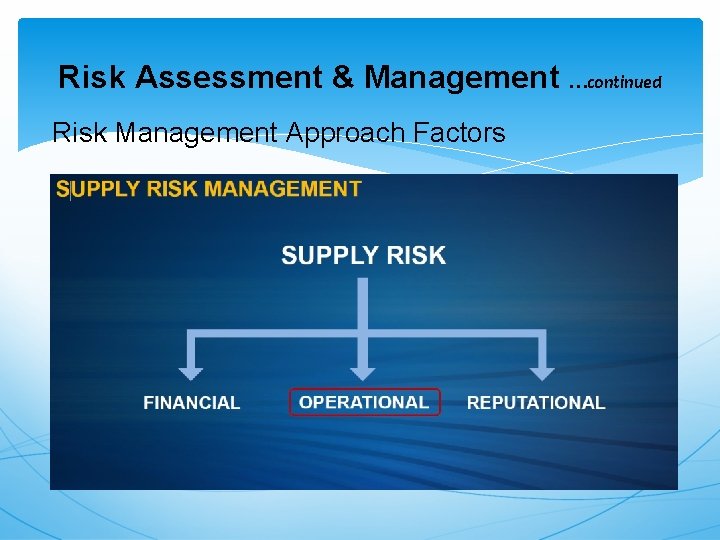
Risk Assessment & Management …continued Risk Management Approach Factors
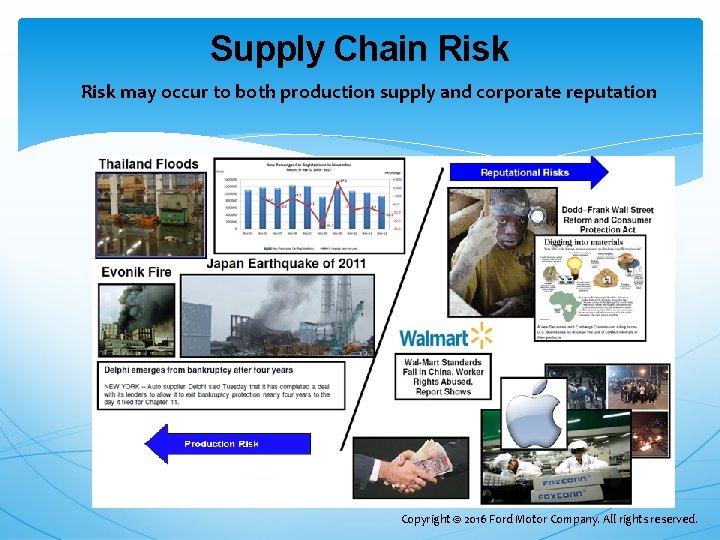
Supply Chain Risk may occur to both production supply and corporate reputation Copyright © 2016 Ford Motor Company. All rights reserved.
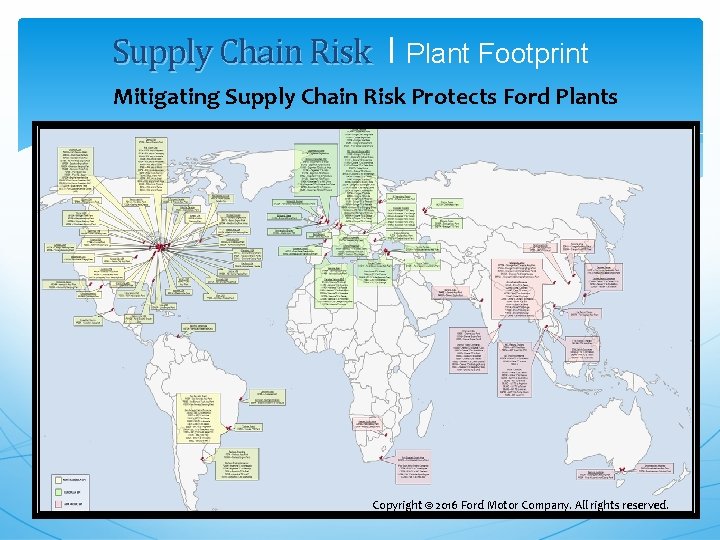
Supply Chain Risk l Plant Footprint Mitigating Supply Chain Risk Protects Ford Plants Copyright © 2016 Ford Motor Company. All rights reserved.
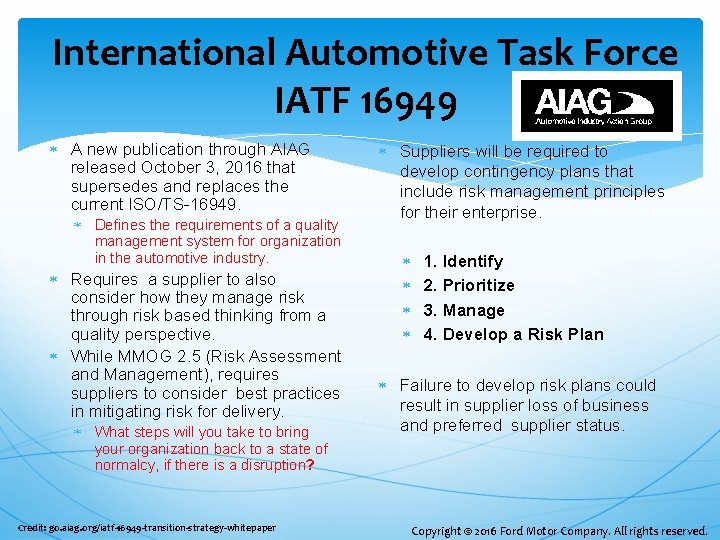
International Automotive Task Force IATF 16949 A new publication through AIAG released October 3, 2016 that supersedes and replaces the current ISO/TS-16949. Defines the requirements of a quality management system for organization in the automotive industry. Requires a supplier to also consider how they manage risk through risk based thinking from a quality perspective. While MMOG 2. 5 (Risk Assessment and Management), requires suppliers to consider best practices in mitigating risk for delivery. What steps will you take to bring your organization back to a state of normalcy, if there is a disruption? Credit: go. aiag. org/iatf-16949 -transition-strategy-whitepaper Suppliers will be required to develop contingency plans that include risk management principles for their enterprise. 1. Identify 2. Prioritize 3. Manage 4. Develop a Risk Plan Failure to develop risk plans could result in supplier loss of business and preferred supplier status. Copyright © 2016 Ford Motor Company. All rights reserved.
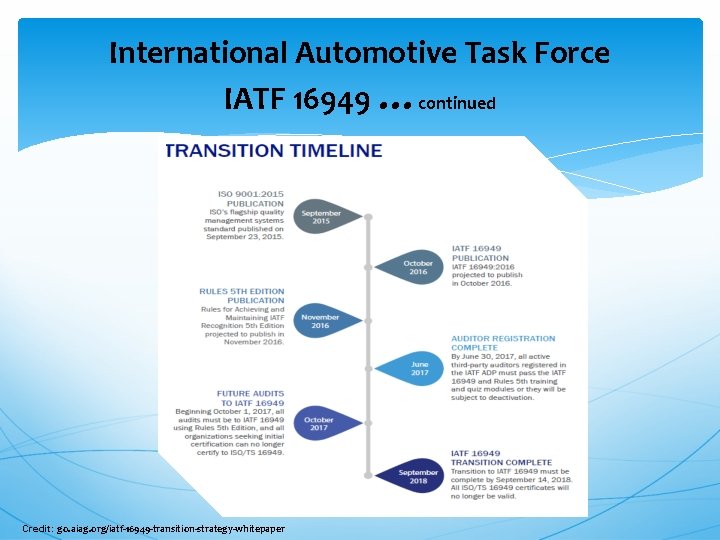
International Automotive Task Force IATF 16949 …continued Credit: go. aiag. org/iatf-16949 -transition-strategy-whitepaper
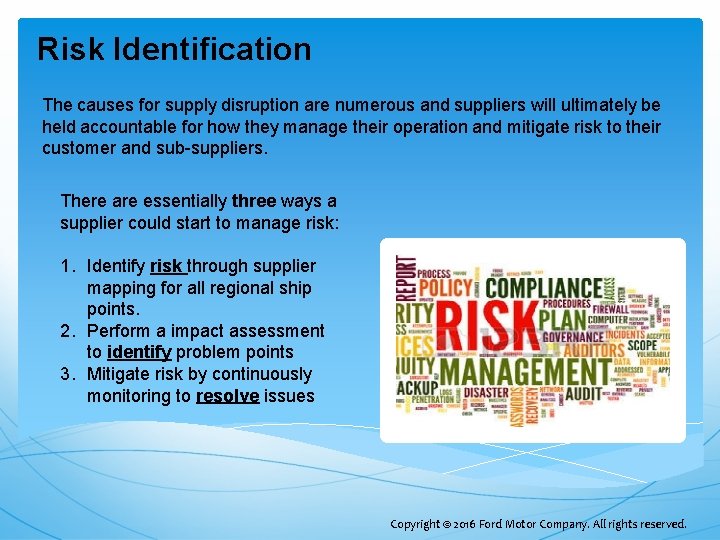
Risk Identification The causes for supply disruption are numerous and suppliers will ultimately be held accountable for how they manage their operation and mitigate risk to their customer and sub-suppliers. There are essentially three ways a supplier could start to manage risk: 1. Identify risk through supplier mapping for all regional ship points. 2. Perform a impact assessment to identify problem points 3. Mitigate risk by continuously monitoring to resolve issues Copyright © 2016 Ford Motor Company. All rights reserved.
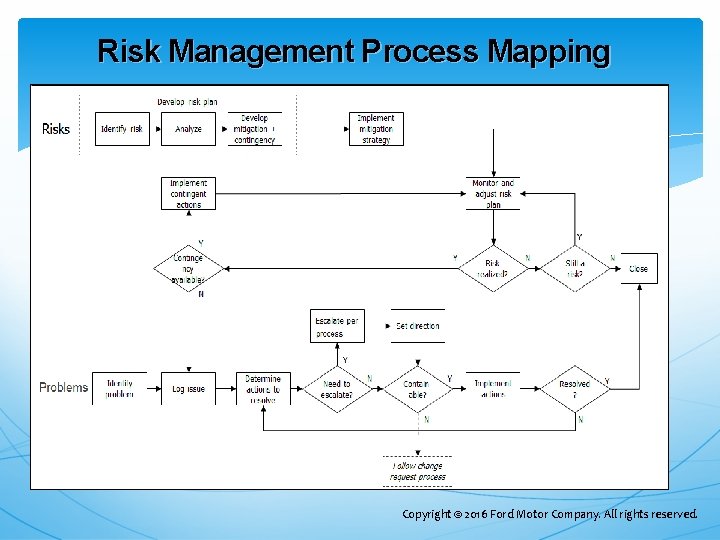
Risk Management Process Mapping Copyright © 2016 Ford Motor Company. All rights reserved.
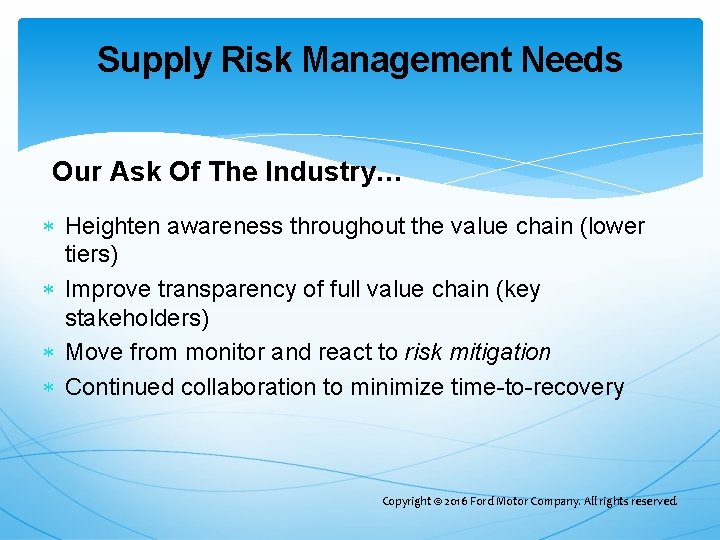
Supply Risk Management Needs Our Ask Of The Industry… Heighten awareness throughout the value chain (lower tiers) Improve transparency of full value chain (key stakeholders) Move from monitor and react to risk mitigation Continued collaboration to minimize time-to-recovery Copyright © 2016 Ford Motor Company. All rights reserved.
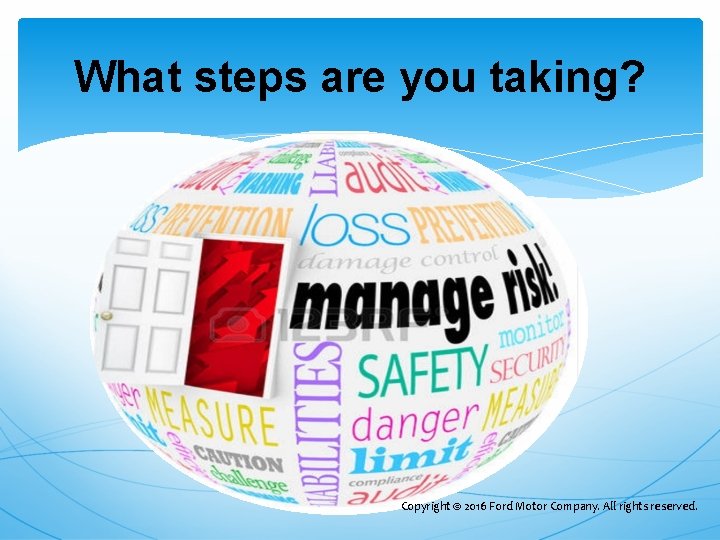
What steps are you taking? Copyright © 2016 Ford Motor Company. All rights reserved.
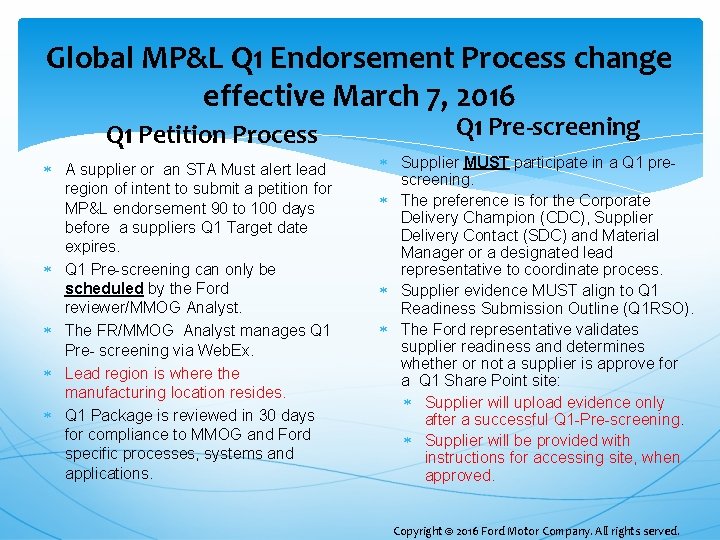
Global MP&L Q 1 Endorsement Process change effective March 7, 2016 Q 1 Petition Process A supplier or an STA Must alert lead region of intent to submit a petition for MP&L endorsement 90 to 100 days before a suppliers Q 1 Target date expires. Q 1 Pre-screening can only be scheduled by the Ford reviewer/MMOG Analyst. The FR/MMOG Analyst manages Q 1 Pre- screening via Web. Ex. Lead region is where the manufacturing location resides. Q 1 Package is reviewed in 30 days for compliance to MMOG and Ford specific processes, systems and applications. Q 1 Pre-screening Supplier MUST participate in a Q 1 prescreening. The preference is for the Corporate Delivery Champion (CDC), Supplier Delivery Contact (SDC) and Material Manager or a designated lead representative to coordinate process. Supplier evidence MUST align to Q 1 Readiness Submission Outline (Q 1 RSO). The Ford representative validates supplier readiness and determines whether or not a supplier is approve for a Q 1 Share Point site: Supplier will upload evidence only after a successful Q 1 -Pre-screening. Supplier will be provided with instructions for accessing site, when approved. Copyright © 2016 Ford Motor Company. All rights served.
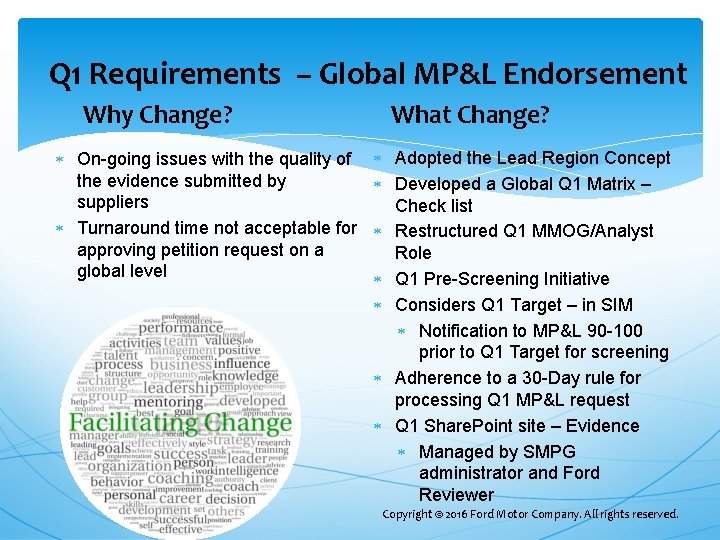
Q 1 Requirements – Global MP&L Endorsement What Change? Why Change? Adopted the Lead Region Concept Developed a Global Q 1 Matrix – Check list Restructured Q 1 MMOG/Analyst Role Q 1 Pre-Screening Initiative Considers Q 1 Target – in SIM Notification to MP&L 90 -100 prior to Q 1 Target for screening Adherence to a 30 -Day rule for processing Q 1 MP&L request Q 1 Share. Point site – Evidence Managed by SMPG administrator and Ford Reviewer Copyright © 2016 Ford Motor Company. All rights reserved. On-going issues with the quality of the evidence submitted by suppliers Turnaround time not acceptable for approving petition request on a global level
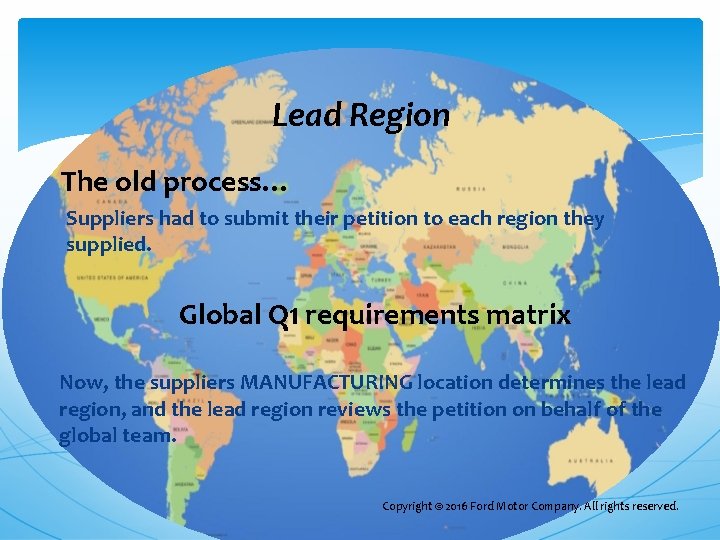
Lead Region The old process… Suppliers had to submit their petition to each region they supplied. Global Q 1 requirements matrix Now, the suppliers MANUFACTURING location determines the lead region, and the lead region reviews the petition on behalf of the global team. Copyright © 2016 Ford Motor Company. All rights reserved.
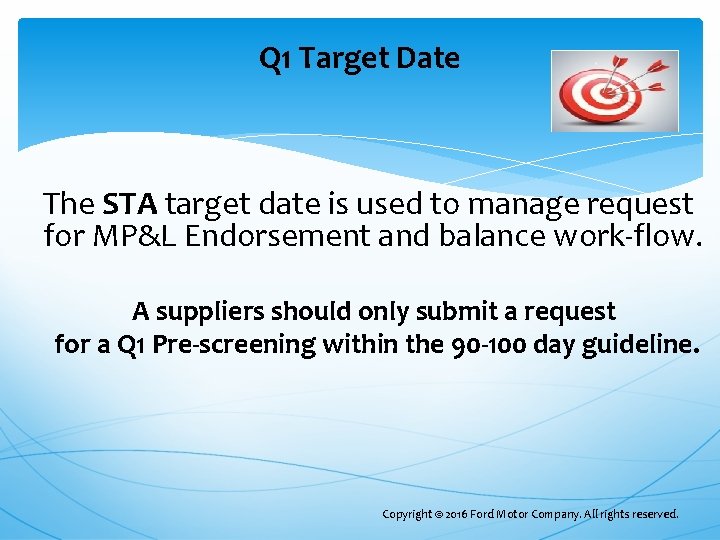
Q 1 Target Date The STA target date is used to manage request for MP&L Endorsement and balance work-flow. A suppliers should only submit a request for a Q 1 Pre-screening within the 90 -100 day guideline. Copyright © 2016 Ford Motor Company. All rights reserved.
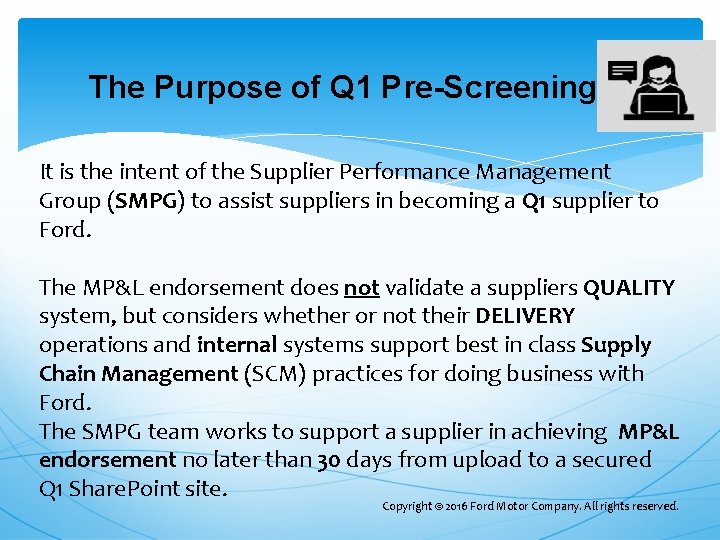
The Purpose of Q 1 Pre-Screening It is the intent of the Supplier Performance Management Group (SMPG) to assist suppliers in becoming a Q 1 supplier to Ford. The MP&L endorsement does not validate a suppliers QUALITY system, but considers whether or not their DELIVERY operations and internal systems support best in class Supply Chain Management (SCM) practices for doing business with Ford. The SMPG team works to support a supplier in achieving MP&L endorsement no later than 30 days from upload to a secured Q 1 Share. Point site. Copyright © 2016 Ford Motor Company. All rights reserved.
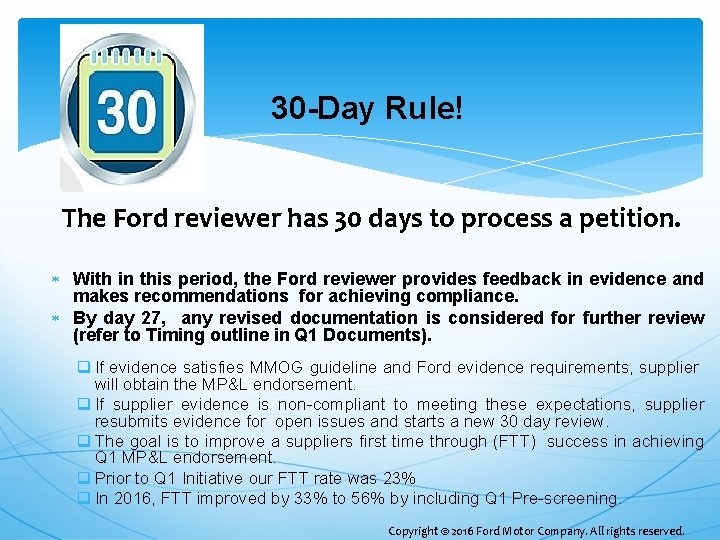
30 -Day Rule! The Ford reviewer has 30 days to process a petition. With in this period, the Ford reviewer provides feedback in evidence and makes recommendations for achieving compliance. By day 27, any revised documentation is considered for further review (refer to Timing outline in Q 1 Documents). q If evidence satisfies MMOG guideline and Ford evidence requirements, supplier will obtain the MP&L endorsement. q If supplier evidence is non-compliant to meeting these expectations, supplier resubmits evidence for open issues and starts a new 30 day review. q The goal is to improve a suppliers first time through (FTT) success in achieving Q 1 MP&L endorsement. q Prior to Q 1 Initiative our FTT rate was 23% q In 2016, FTT improved by 33% to 56% by including Q 1 Pre-screening. Copyright © 2016 Ford Motor Company. All rights reserved.
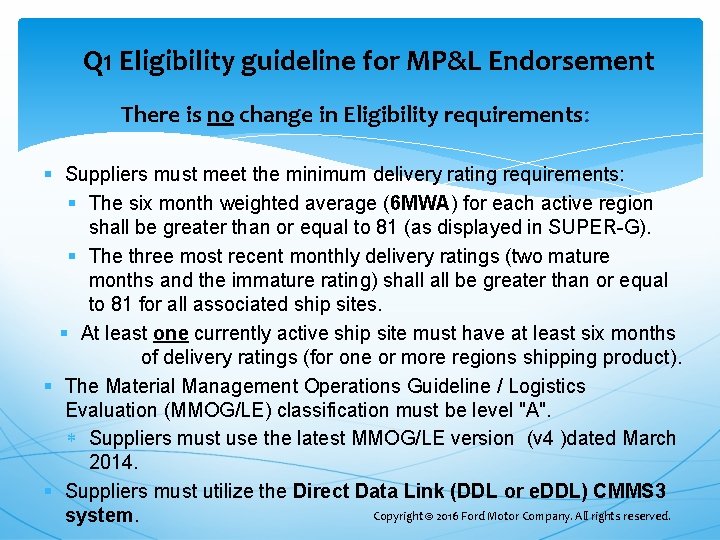
Q 1 Eligibility guideline for MP&L Endorsement There is no change in Eligibility requirements: § Suppliers must meet the minimum delivery rating requirements: § The six month weighted average (6 MWA) for each active region shall be greater than or equal to 81 (as displayed in SUPER-G). § The three most recent monthly delivery ratings (two mature months and the immature rating) shall be greater than or equal to 81 for all associated ship sites. § At least one currently active ship site must have at least six months of delivery ratings (for one or more regions shipping product). § The Material Management Operations Guideline / Logistics Evaluation (MMOG/LE) classification must be level "A". Suppliers must use the latest MMOG/LE version (v 4 )dated March 2014. § Suppliers must utilize the Direct Data Link (DDL or e. DDL) CMMS 3 Copyright © 2016 Ford Motor Company. All rights reserved. system.
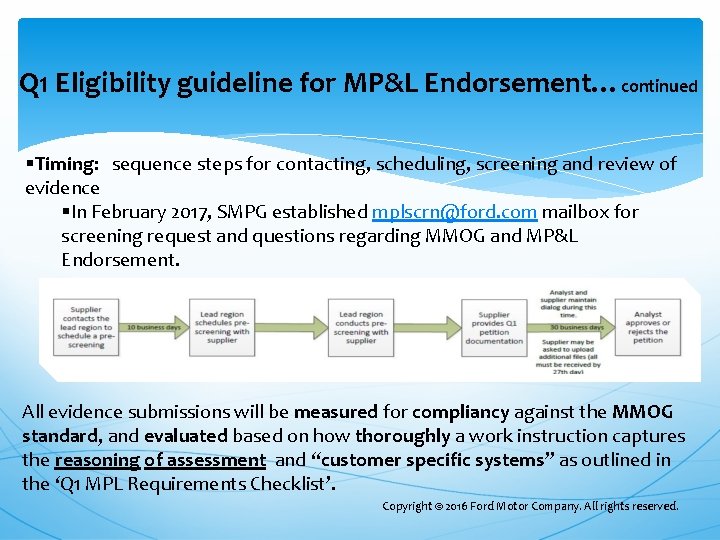
Q 1 Eligibility guideline for MP&L Endorsement…continued §Timing: sequence steps for contacting, scheduling, screening and review of evidence §In February 2017, SMPG established mplscrn@ford. com mailbox for screening request and questions regarding MMOG and MP&L Endorsement. All evidence submissions will be measured for compliancy against the MMOG standard, and evaluated based on how thoroughly a work instruction captures the reasoning of assessment and “customer specific systems” as outlined in the ‘Q 1 MPL Requirements Checklist’. Copyright © 2016 Ford Motor Company. All rights reserved.
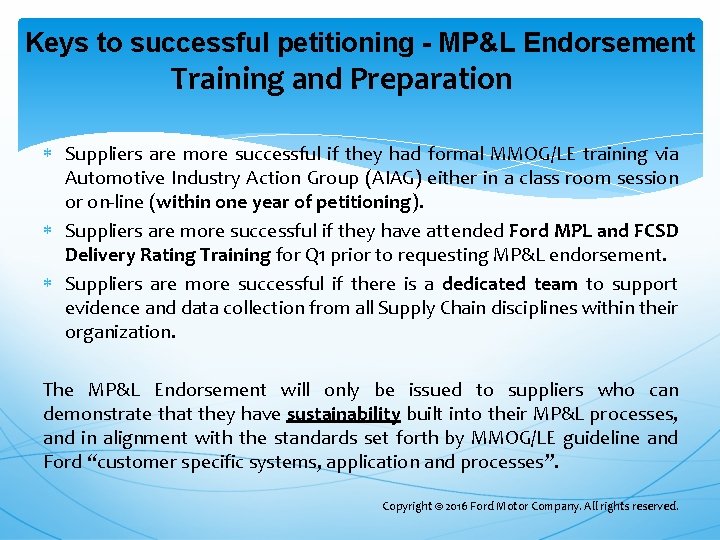
Keys to successful petitioning - MP&L Endorsement Training and Preparation Suppliers are more successful if they had formal MMOG/LE training via Automotive Industry Action Group (AIAG) either in a class room session or on-line (within one year of petitioning). Suppliers are more successful if they have attended Ford MPL and FCSD Delivery Rating Training for Q 1 prior to requesting MP&L endorsement. Suppliers are more successful if there is a dedicated team to support evidence and data collection from all Supply Chain disciplines within their organization. The MP&L Endorsement will only be issued to suppliers who can demonstrate that they have sustainability built into their MP&L processes, and in alignment with the standards set forth by MMOG/LE guideline and Ford “customer specific systems, application and processes”. Copyright © 2016 Ford Motor Company. All rights reserved.
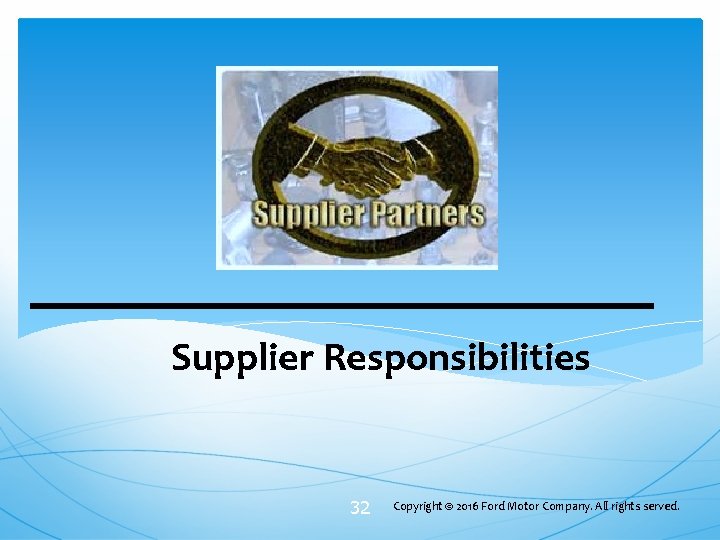
Supplier Responsibilities 32 Copyright © 2016 Ford Motor Company. All rights served.
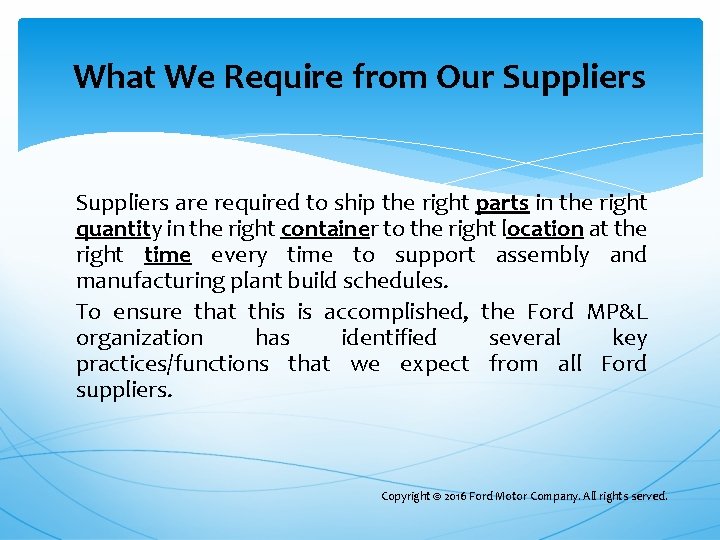
What We Require from Our Suppliers are required to ship the right parts in the right quantity in the right container to the right location at the right time every time to support assembly and manufacturing plant build schedules. To ensure that this is accomplished, the Ford MP&L organization has identified several key practices/functions that we expect from all Ford suppliers. Copyright © 2016 Ford Motor Company. All rights served.
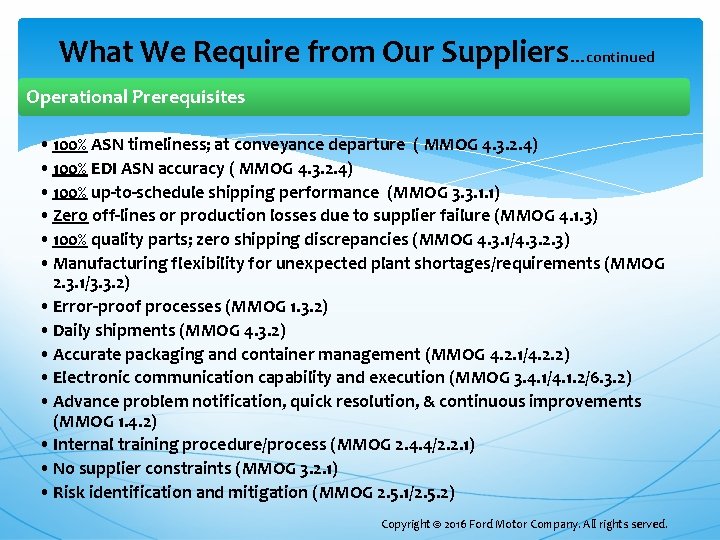
What We Require from Our Suppliers…continued Operational Prerequisites • 100% ASN timeliness; at conveyance departure ( MMOG 4. 3. 2. 4) • 100% EDI ASN accuracy ( MMOG 4. 3. 2. 4) • 100% up-to-schedule shipping performance (MMOG 3. 3. 1. 1) • Zero off-lines or production losses due to supplier failure (MMOG 4. 1. 3) • 100% quality parts; zero shipping discrepancies (MMOG 4. 3. 1/4. 3. 2. 3) • Manufacturing flexibility for unexpected plant shortages/requirements (MMOG 2. 3. 1/3. 3. 2) • Error-proof processes (MMOG 1. 3. 2) • Daily shipments (MMOG 4. 3. 2) • Accurate packaging and container management (MMOG 4. 2. 1/4. 2. 2) • Electronic communication capability and execution (MMOG 3. 4. 1/4. 1. 2/6. 3. 2) • Advance problem notification, quick resolution, & continuous improvements (MMOG 1. 4. 2) • Internal training procedure/process (MMOG 2. 4. 4/2. 2. 1) • No supplier constraints (MMOG 3. 2. 1) • Risk identification and mitigation (MMOG 2. 5. 1/2. 5. 2) Copyright © 2016 Ford Motor Company. All rights served.
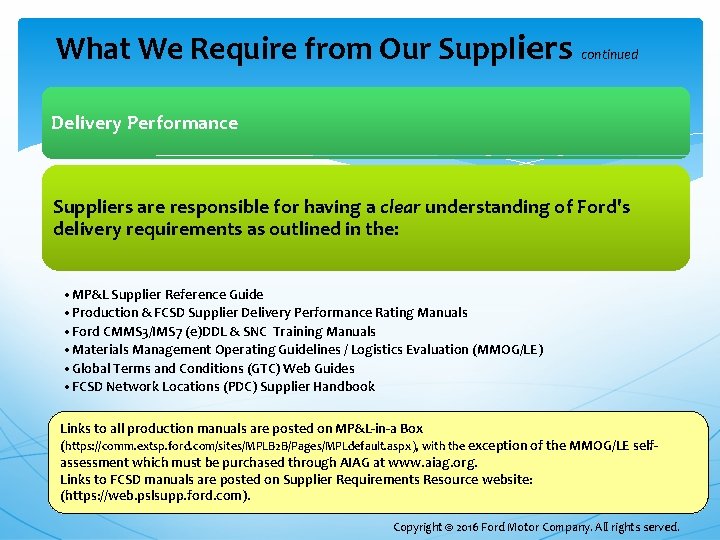
What We Require from Our Suppliers continued Delivery Performance Suppliers are responsible for having a clear understanding of Ford's delivery requirements as outlined in the: • MP&L Supplier Reference Guide • Production & FCSD Supplier Delivery Performance Rating Manuals • Ford CMMS 3/IMS 7 (e)DDL & SNC Training Manuals • Materials Management Operating Guidelines / Logistics Evaluation (MMOG/LE) • Global Terms and Conditions (GTC) Web Guides • FCSD Network Locations (PDC) Supplier Handbook Links to all production manuals are posted on MP&L-in-a Box (https: //comm. extsp. ford. com/sites/MPLB 2 B/Pages/MPLdefault. aspx), with the exception of the MMOG/LE selfassessment which must be purchased through AIAG at www. aiag. org. Links to FCSD manuals are posted on Supplier Requirements Resource website: (https: //web. pslsupp. ford. com). Copyright © 2016 Ford Motor Company. All rights served.
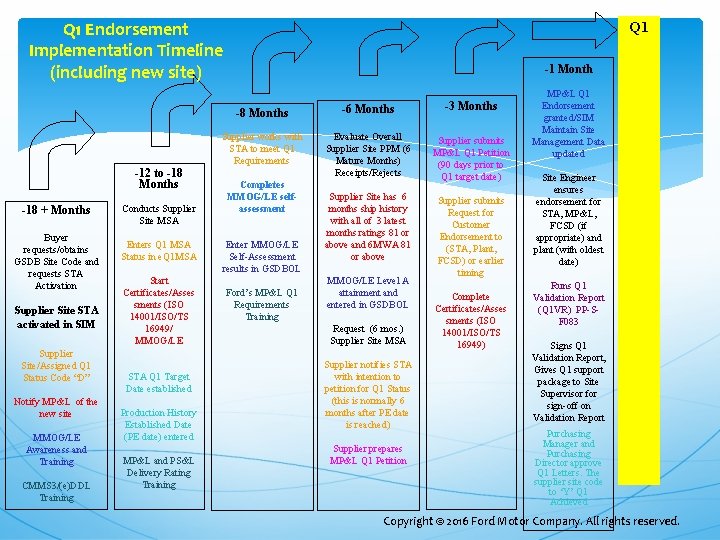
Q 1 Endorsement Implementation Timeline (including new site) -12 to -18 Months -18 + Months Buyer requests/obtains GSDB Site Code and requests STA Activation Supplier Site STA activated in SIM Supplier Site/Assigned Q 1 Status Code “D” Notify MP&L of the new site MMOG/LE Awareness and Training CMMS 3/(e)DDL Training Conducts Supplier Site MSA Enters Q 1 MSA Status in e. Q 1 MSA Start Certificates/Asses sments (ISO 14001/ISO/TS 16949/ MMOG/LE STA Q 1 Target Date established Production History Established Date (PE date) entered MP&L and PS&L Delivery Rating Training Q 1 -1 Month -8 Months -6 Months -3 Months Supplier works with STA to meet Q 1 Requirements Evaluate Overall Supplier Site PPM (6 Mature Months) Receipts/Rejects Supplier submits MP&L Q 1 Petition (90 days prior to Q 1 target date) Supplier Site has 6 months ship history with all of 3 latest months ratings 81 or above and 6 MWA 81 or above Supplier submits Request for Customer Endorsement to (STA, Plant, FCSD) or earlier timing Completes MMOG/LE selfassessment Enter MMOG/LE Self-Assessment results in GSDBOL Ford’s MP&L Q 1 Requirements Training MMOG/LE Level A attainment and entered in GSDBOL Request (6 mos. ) Supplier Site MSA Supplier notifies STA with intention to petition for Q 1 Status (this is normally 6 months after PE date is reached) Supplier prepares MP&L Q 1 Petition Complete Certificates/Asses sments (ISO 14001/ISO/TS 16949) MP&L Q 1 Endorsement granted/SIM Maintain Site Management Data updated Site Engineer ensures endorsement for STA, MP&L, FCSD (if appropriate) and plant (with oldest date) Runs Q 1 Validation Report (Q 1 VR) PP-SF 083 Signs Q 1 Validation Report, Gives Q 1 support package to Site Supervisor for sign-off on Validation Report Purchasing Manager and Purchasing Director approve Q 1 Letters. The supplier site code to ‘Y’ Q 1 Achieved Copyright © 2016 Ford Motor Company. All rights reserved.
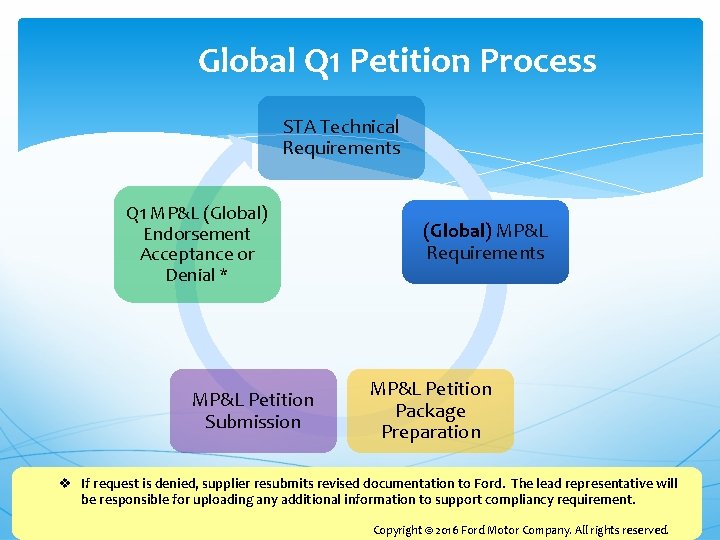
Global Q 1 Petition Process STA Technical Requirements Q 1 MP&L (Global) Endorsement Acceptance or Denial * MP&L Petition Submission (Global) MP&L Requirements MP&L Petition Package Preparation v If request is denied, supplier resubmits revised documentation to Ford. The lead representative will be responsible for uploading any additional information to support compliancy requirement. 37 Copyright © 2016 Ford Motor Company. All rights reserved.
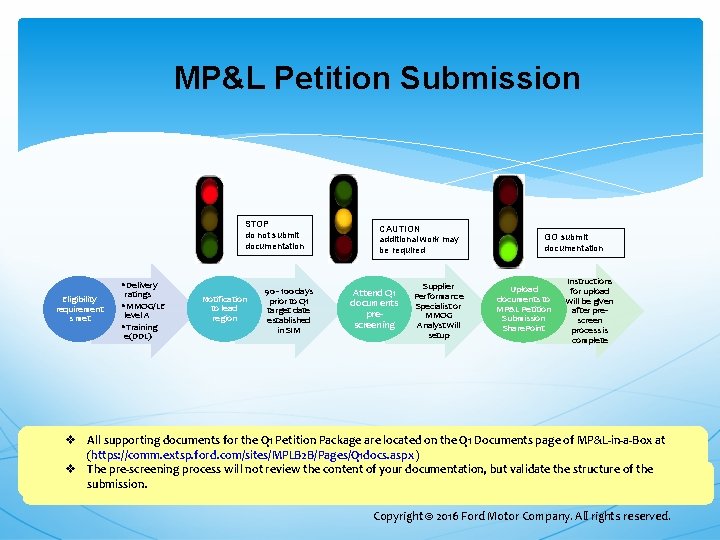
MP&L Petition Submission STOP do not submit documentation • Delivery Eligibility requirement s met ratings • MMOG/LE level A • Training e(DDL) Notification to lead region 90 - 100 days prior to Q 1 target date established in SIM CAUTION additional work may be required Attend Q 1 documents prescreening Supplier Performance Specialist or MMOG Analyst will setup GO submit documentation Upload documents to MP&L Petition Submission Share. Point Instructions for upload will be given after prescreen process is complete v All supporting documents for the Q 1 Petition Package are located on the Q 1 Documents page of MP&L-in-a-Box at (https: //comm. extsp. ford. com/sites/MPLB 2 B/Pages/Q 1 docs. aspx) v v The pre-screening process will not review the content of your documentation, but validate the structure of the All supporting documents for the Q 1 Petition Package are located on the Q 1 Documents page of MP&L-in-a-Box at submission. (https: //comm. extsp. ford. com/sites/MPLB 2 B/Pages/Q 1 docs. aspx) Copyright © 2016 Ford Motor Company. All rights reserved.
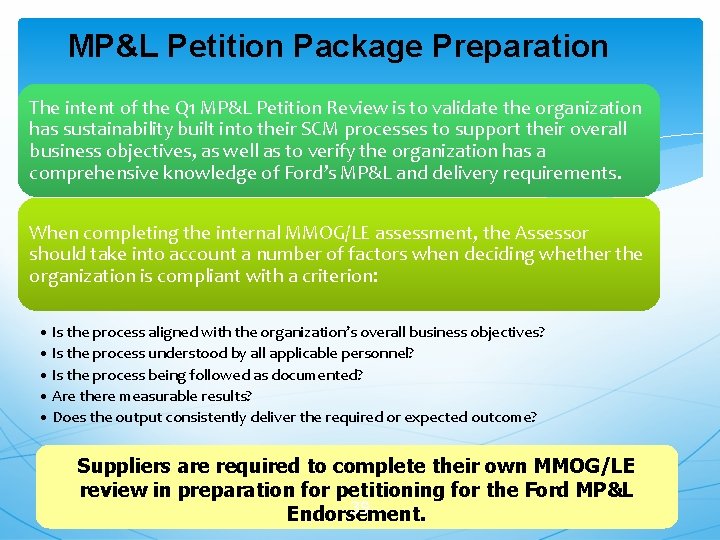
MP&L Petition Package Preparation The intent of the Q 1 MP&L Petition Review is to validate the organization has sustainability built into their SCM processes to support their overall business objectives, as well as to verify the organization has a comprehensive knowledge of Ford’s MP&L and delivery requirements. When completing the internal MMOG/LE assessment, the Assessor should take into account a number of factors when deciding whether the organization is compliant with a criterion: • Is the process aligned with the organization’s overall business objectives? • Is the process understood by all applicable personnel? • Is the process being followed as documented? • Are there measurable results? • Does the output consistently deliver the required or expected outcome? Suppliers are required to complete their own MMOG/LE review in preparation for petitioning for the Ford MP&L 39 Endorsement.
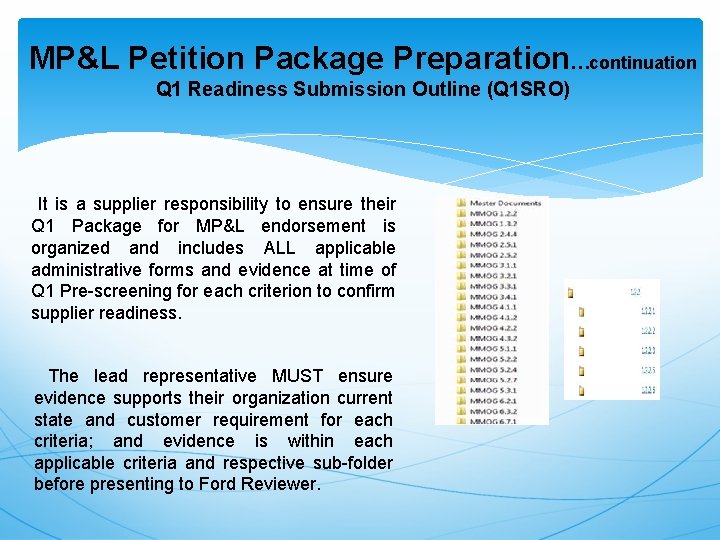
MP&L Petition Package Preparation…continuation Q 1 Readiness Submission Outline (Q 1 SRO) It is a supplier responsibility to ensure their Q 1 Package for MP&L endorsement is organized and includes ALL applicable administrative forms and evidence at time of Q 1 Pre-screening for each criterion to confirm supplier readiness. The lead representative MUST ensure evidence supports their organization current state and customer requirement for each criteria; and evidence is within each applicable criteria and respective sub-folder before presenting to Ford Reviewer.
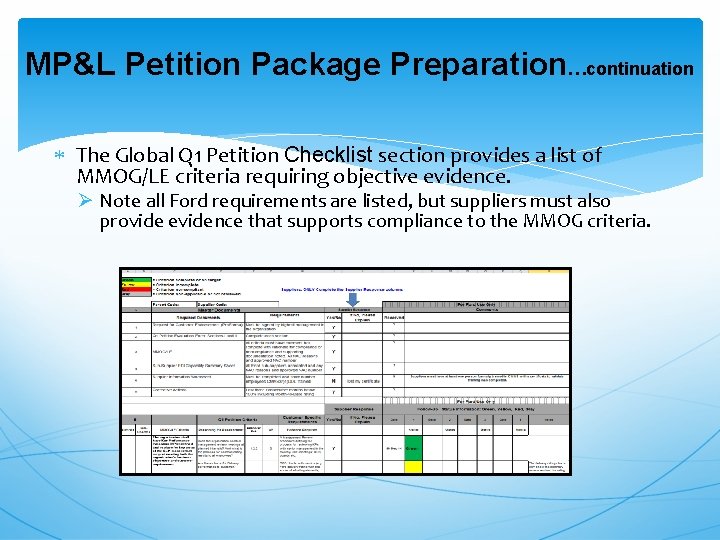
MP&L Petition Package Preparation…continuation The Global Q 1 Petition Checklist section provides a list of MMOG/LE criteria requiring objective evidence. Ø Note all Ford requirements are listed, but suppliers must also provide evidence that supports compliance to the MMOG criteria.
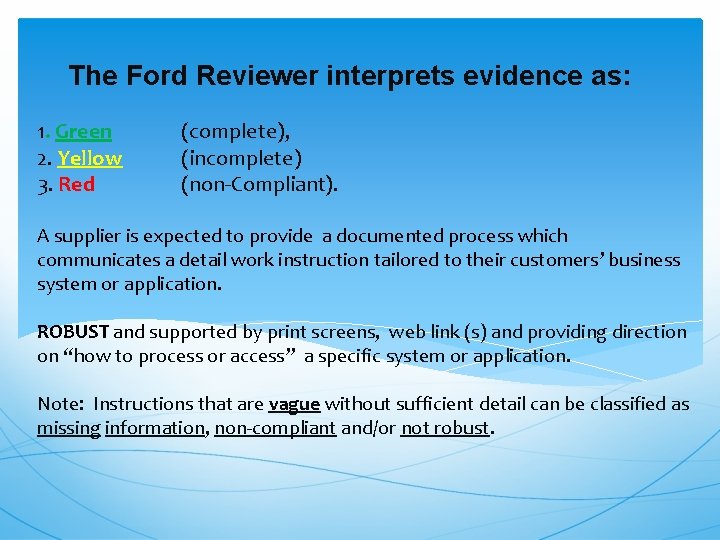
The Ford Reviewer interprets evidence as: 1. Green 2. Yellow 3. Red (complete), (incomplete) (non-Compliant). A supplier is expected to provide a documented process which communicates a detail work instruction tailored to their customers’ business system or application. ROBUST and supported by print screens, web link (s) and providing direction on “how to process or access” a specific system or application. Note: Instructions that are vague without sufficient detail can be classified as missing information, non-compliant and/or not robust.
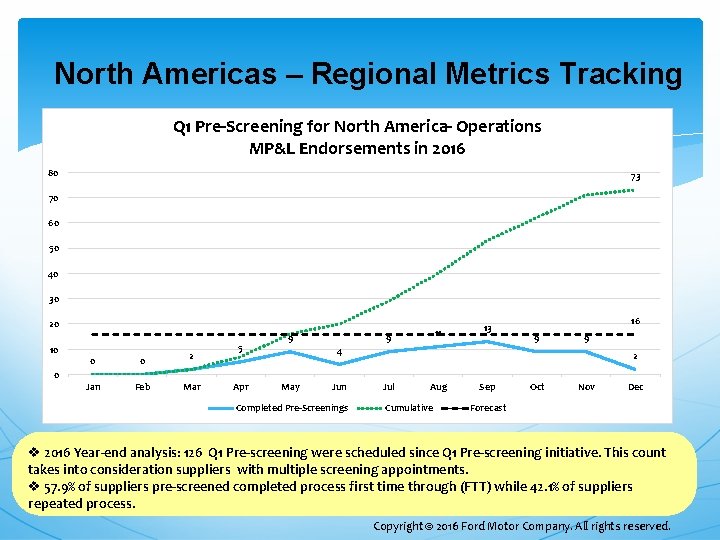
North Americas – Regional Metrics Tracking Q 1 Pre-Screening for North America- Operations MP&L Endorsements in 2016 80 73 70 60 50 40 30 20 10 0 0 Jan Feb 2 5 9 11 9 13 16 9 9 4 2 0 Mar Apr May Jun Completed Pre-Screenings Jul Aug Cumulative Sep Oct Nov Dec Forecast v 2016 Year-end analysis: 126 Q 1 Pre-screening were scheduled since Q 1 Pre-screening initiative. This count takes into consideration suppliers with multiple screening appointments. v 57. 9% of suppliers pre-screened completed process first time through (FTT) while 42. 1% of suppliers repeated process. Copyright © 2016 Ford Motor Company. All rights reserved.
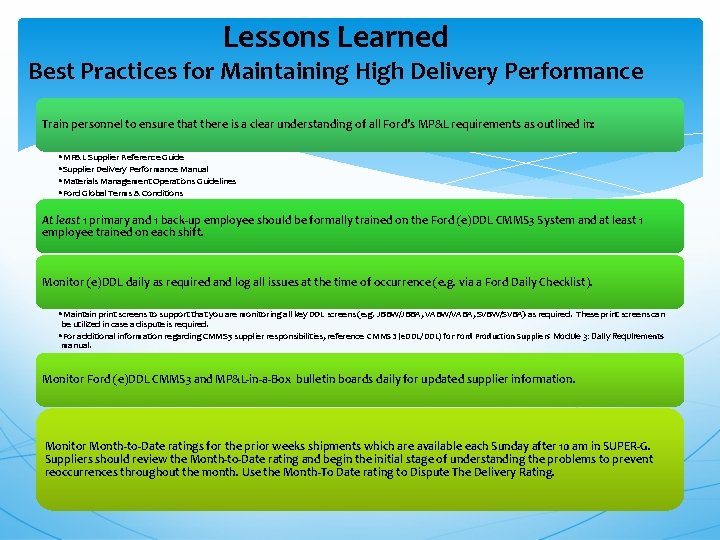
Lessons Learned Best Practices for Maintaining High Delivery Performance Train personnel to ensure that there is a clear understanding of all Ford’s MP&L requirements as outlined in: • MP&L Supplier Reference Guide • Supplier Delivery Performance Manual • Materials Management Operations Guidelines • Ford Global Terms & Conditions At least 1 primary and 1 back-up employee should be formally trained on the Ford (e)DDL CMMS 3 System and at least 1 employee trained on each shift. Monitor (e)DDL daily as required and log all issues at the time of occurrence (e. g. via a Ford Daily Checklist). • Maintain print screens to support that you are monitoring all key DDL screens (e. g. JBBW/JBBA, VABW/VABA, SVBW/SVBA) as required. These print screens can be utilized in case a dispute is required. • For additional information regarding CMMS 3 supplier responsibilities, reference CMMS 3 (e. DDL/DDL) for Ford Production Suppliers Module 3: Daily Requirements manual. Monitor Ford (e)DDL CMMS 3 and MP&L-in-a-Box bulletin boards daily for updated supplier information. Monitor Month-to-Date ratings for the prior weeks shipments which are available each Sunday after 10 am in SUPER-G. Suppliers should review the Month-to-Date rating and begin the initial stage of understanding the problems to prevent reoccurrences throughout the month. Use the Month-To Date rating to Dispute The Delivery Rating.
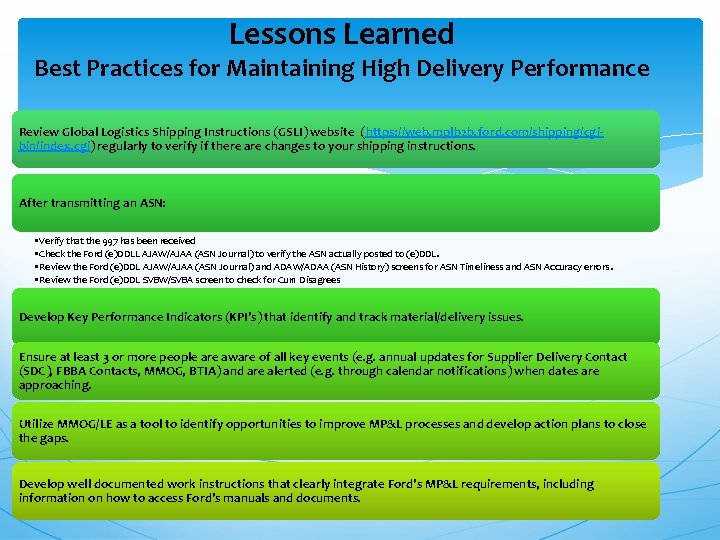
Lessons Learned Best Practices for Maintaining High Delivery Performance Review Global Logistics Shipping Instructions (GSLI) website (https: //web. mplb 2 b. ford. com/shipping/cgibin/index. cgi) regularly to verify if there are changes to your shipping instructions. After transmitting an ASN: • Verify that the 997 has been received • Check the Ford (e)DDLL AJAW/AJAA (ASN Journal) to verify the ASN actually posted to (e)DDL. • Review the Ford (e)DDL AJAW/AJAA (ASN Journal) and ADAW/ADAA (ASN History) screens for ASN Timeliness and ASN Accuracy errors. • Review the Ford (e)DDL SVBW/SVBA screen to check for Cum Disagrees Develop Key Performance Indicators (KPI’s) that identify and track material/delivery issues. Ensure at least 3 or more people are aware of all key events (e. g. annual updates for Supplier Delivery Contact (SDC), FBBA Contacts, MMOG, BTIA) and are alerted (e. g. through calendar notifications) when dates are approaching. Utilize MMOG/LE as a tool to identify opportunities to improve MP&L processes and develop action plans to close the gaps. Develop well documented work instructions that clearly integrate Ford’s MP&L requirements, including information on how to access Ford’s manuals and documents.
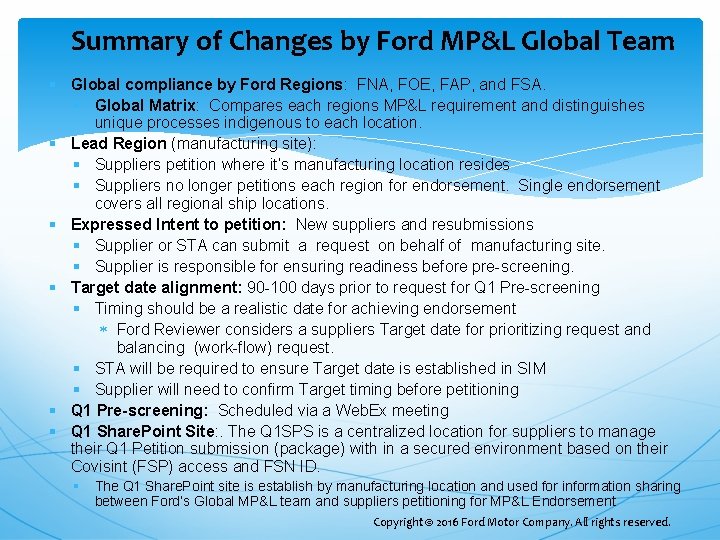
Summary of Changes by Ford MP&L Global Team § Global compliance by Ford Regions: FNA, FOE, FAP, and FSA. § Global Matrix: Compares each regions MP&L requirement and distinguishes unique processes indigenous to each location. § Lead Region (manufacturing site): § Suppliers petition where it’s manufacturing location resides § Suppliers no longer petitions each region for endorsement. Single endorsement covers all regional ship locations. § Expressed Intent to petition: New suppliers and resubmissions § Supplier or STA can submit a request on behalf of manufacturing site. § Supplier is responsible for ensuring readiness before pre-screening. § Target date alignment: 90 -100 days prior to request for Q 1 Pre-screening § Timing should be a realistic date for achieving endorsement Ford Reviewer considers a suppliers Target date for prioritizing request and balancing (work-flow) request. § STA will be required to ensure Target date is established in SIM § Supplier will need to confirm Target timing before petitioning § Q 1 Pre-screening: Scheduled via a Web. Ex meeting § Q 1 Share. Point Site: . The Q 1 SPS is a centralized location for suppliers to manage their Q 1 Petition submission (package) with in a secured environment based on their Covisint (FSP) access and FSN ID. § The Q 1 Share. Point site is establish by manufacturing location and used for information sharing between Ford’s Global MP&L team and suppliers petitioning for MP&L Endorsement Copyright © 2016 Ford Motor Company. All rights reserved.
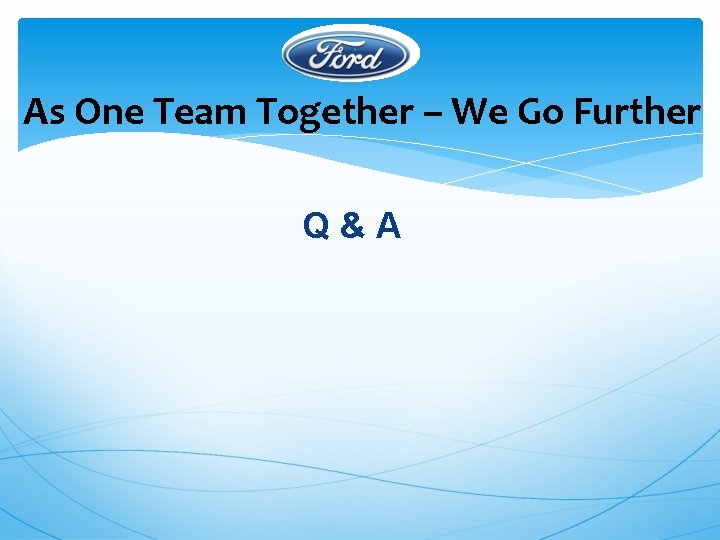
As One Team Together – We Go Further Q & A
- Slides: 47