LCLSII Cavity Performance Dan Gonnella LCLSII HE Cryomodule
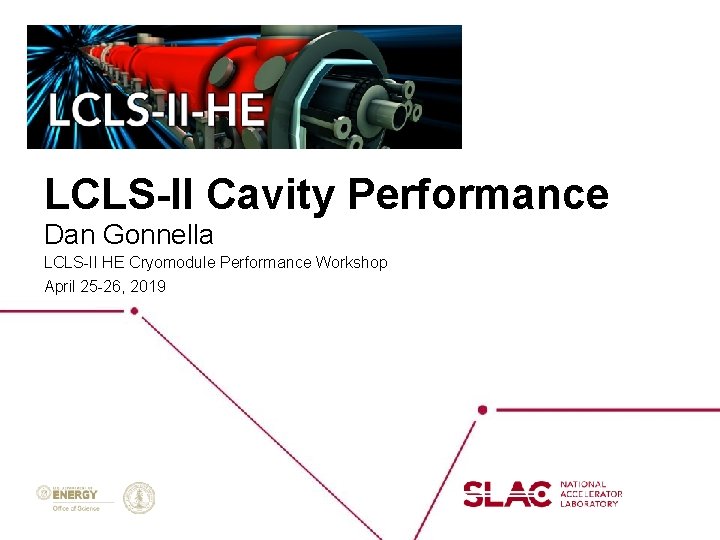
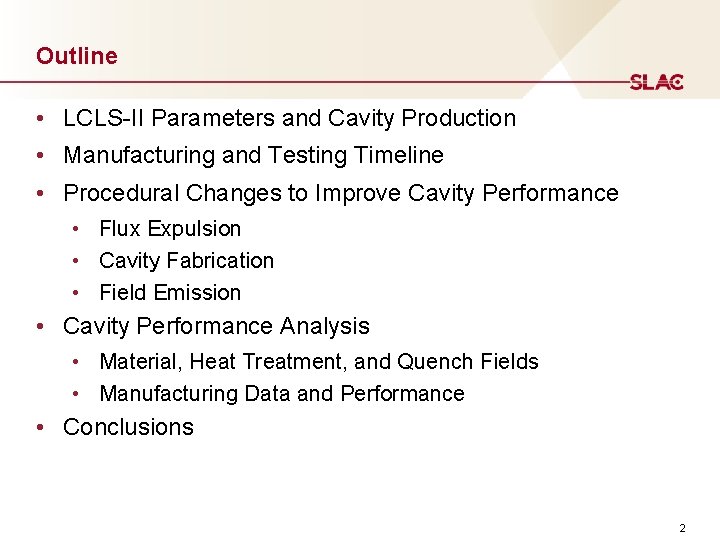
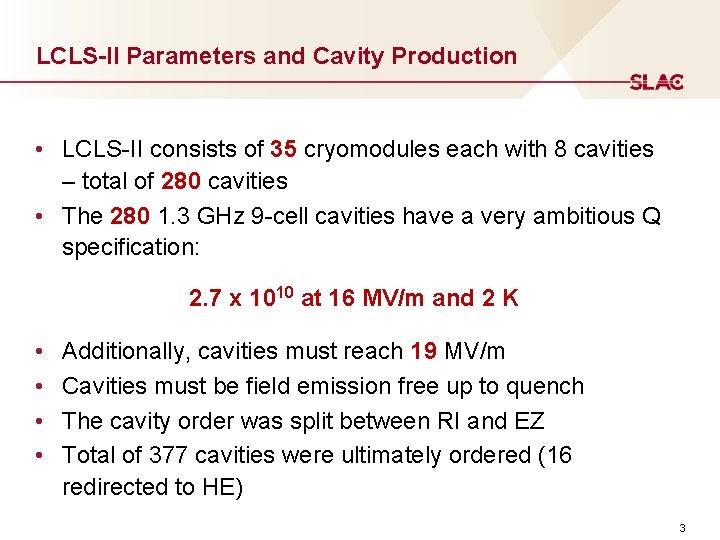
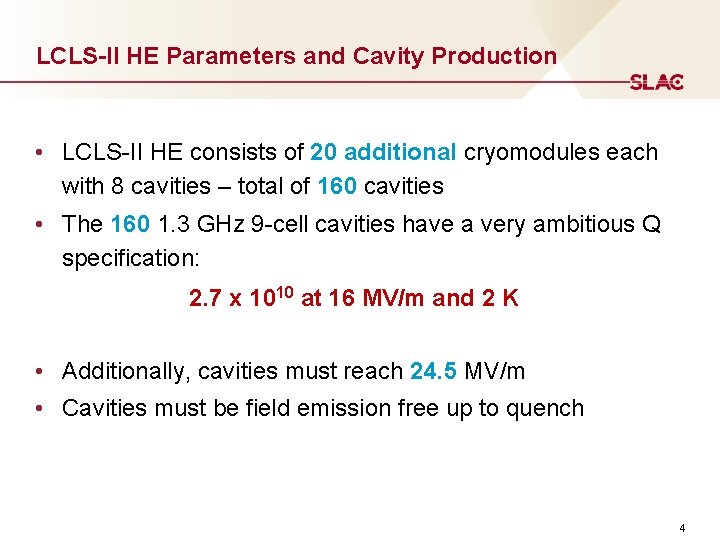
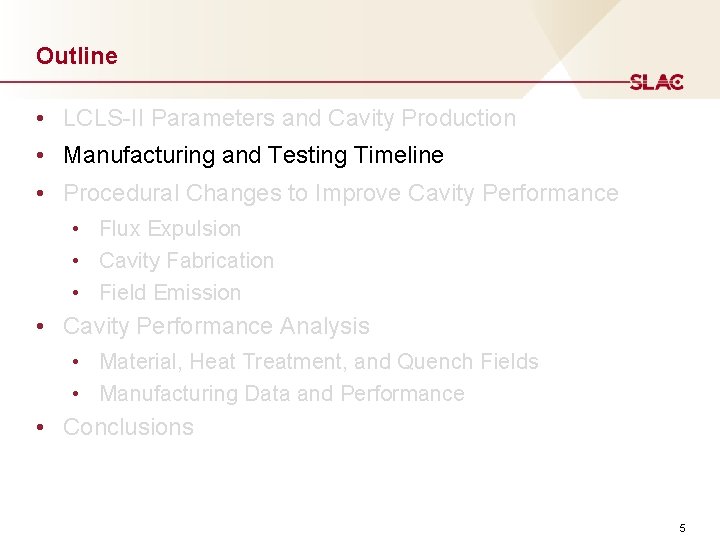
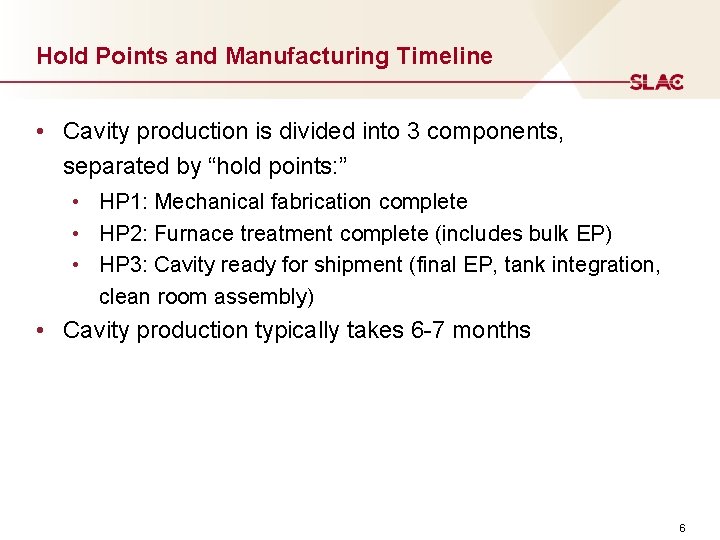
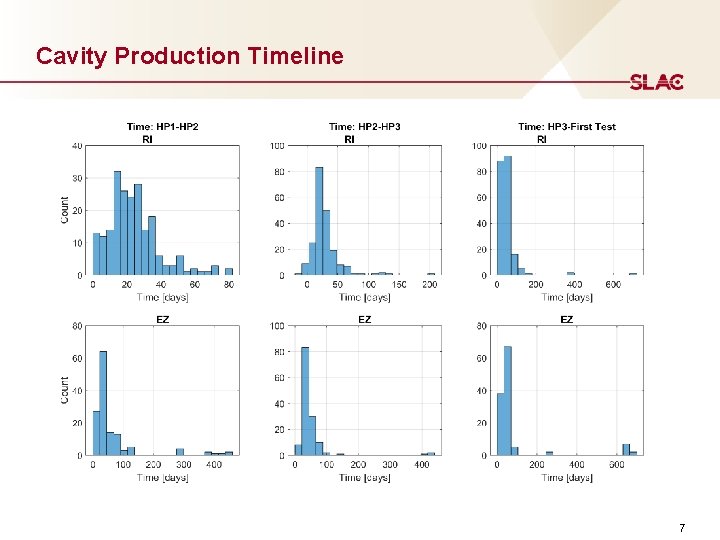
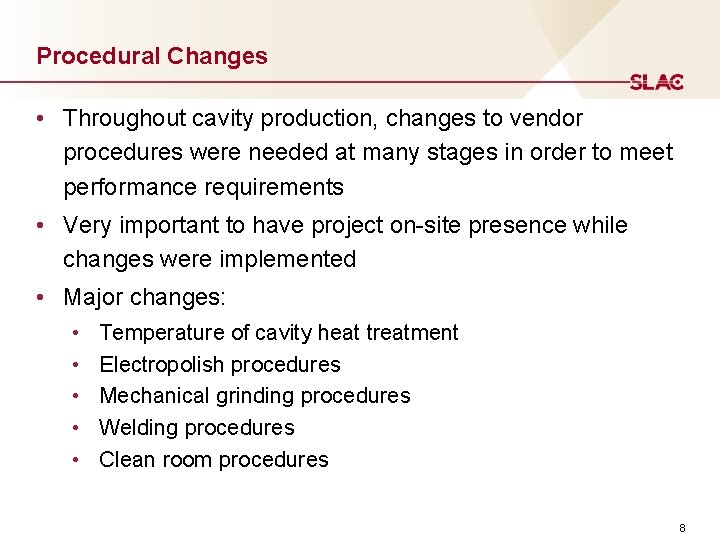
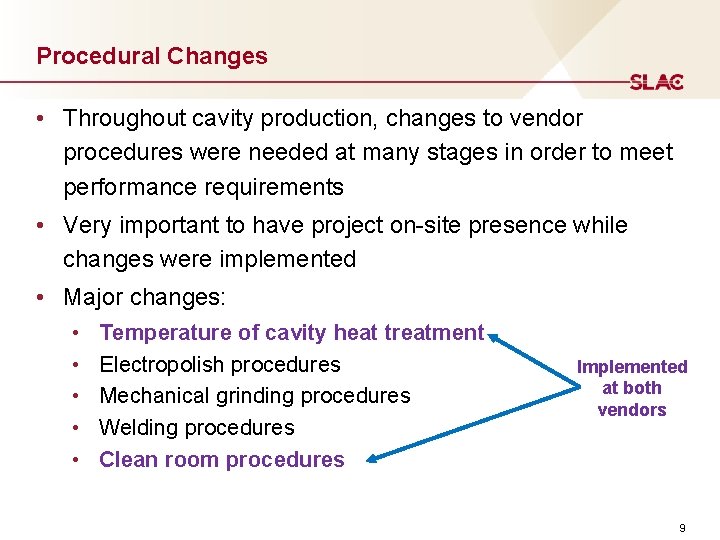
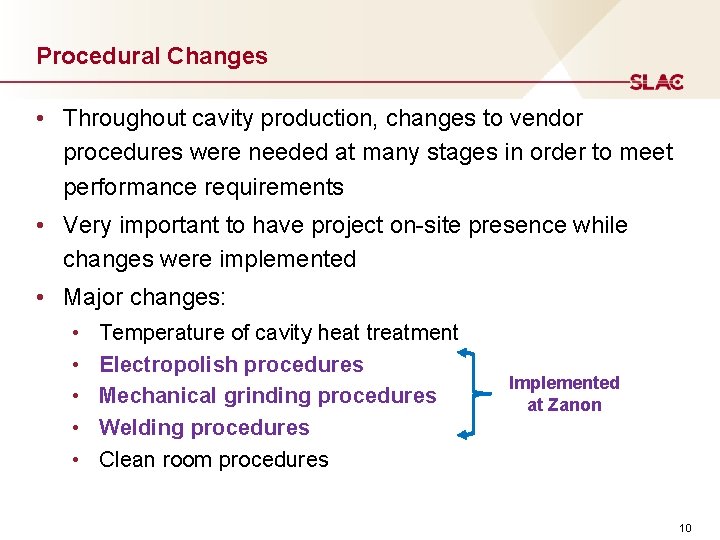
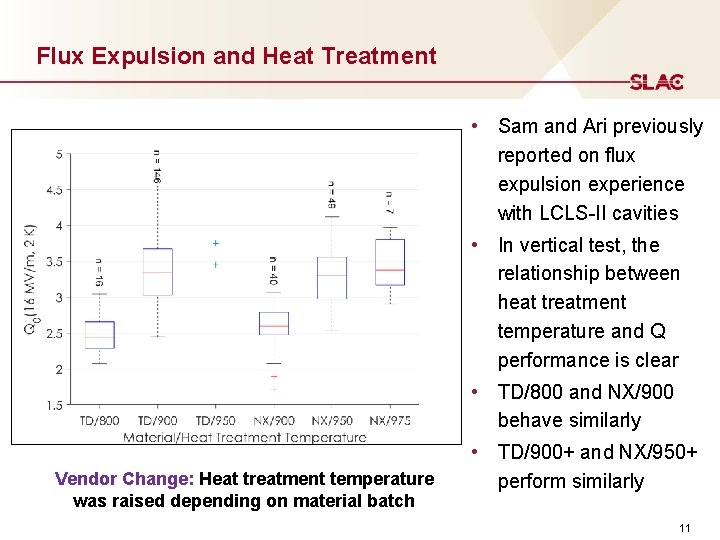
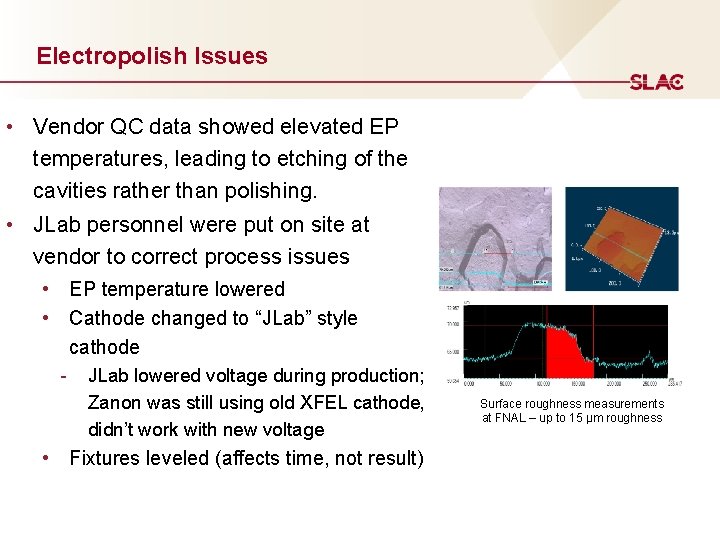
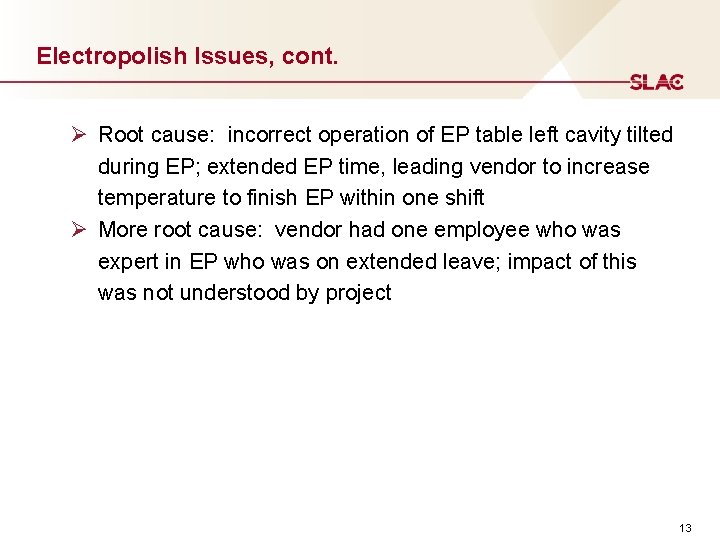
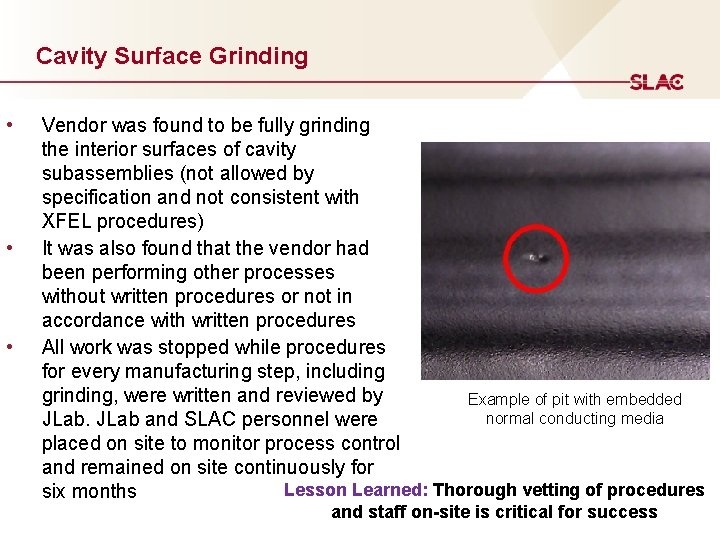
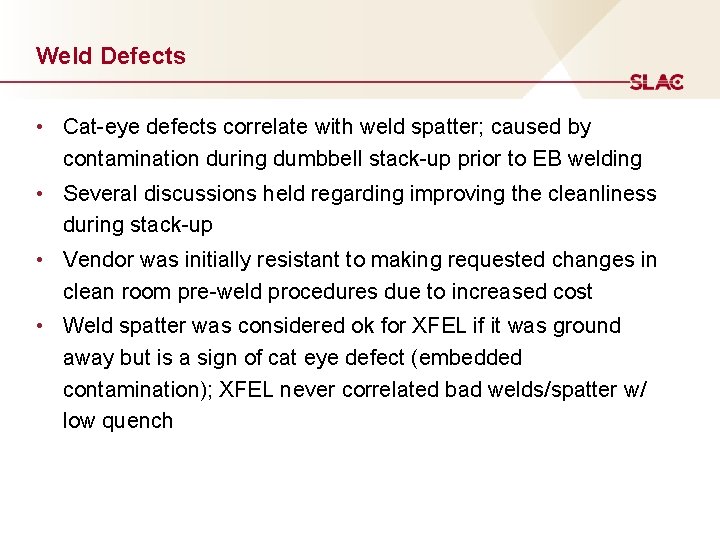
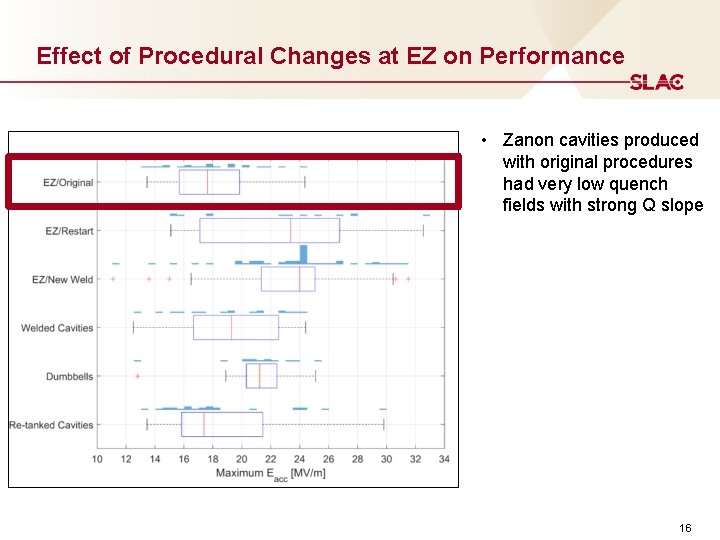
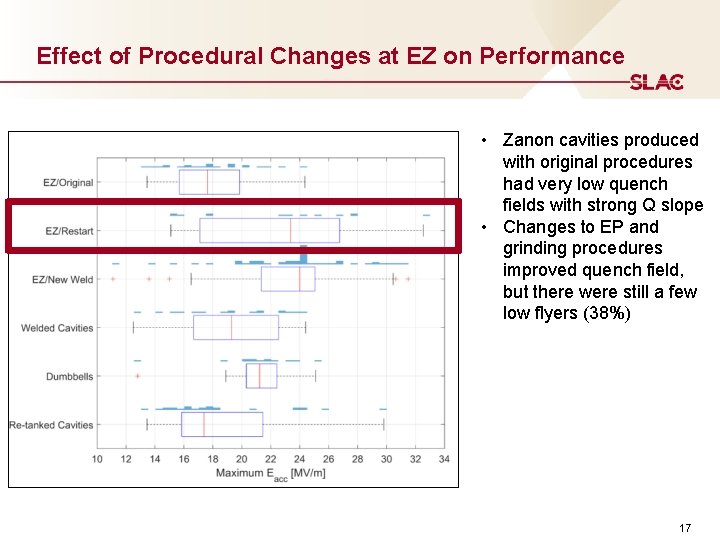
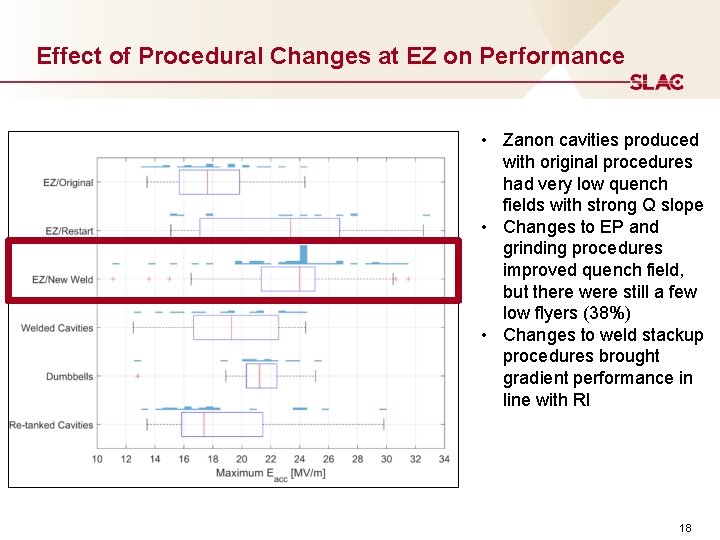
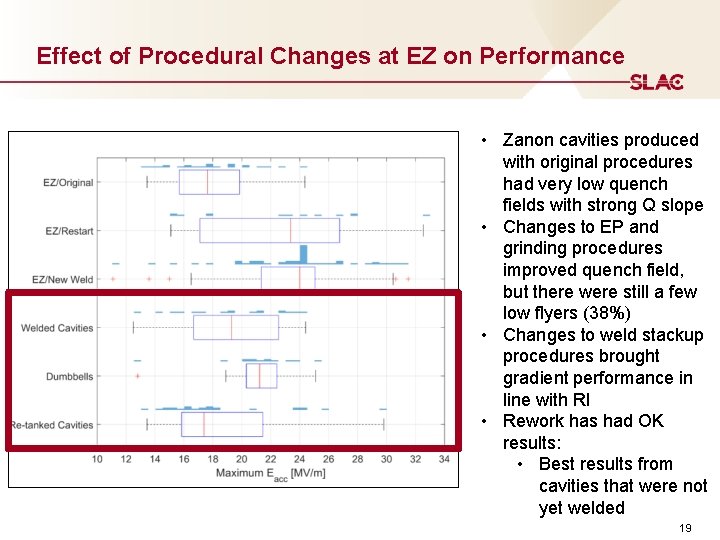
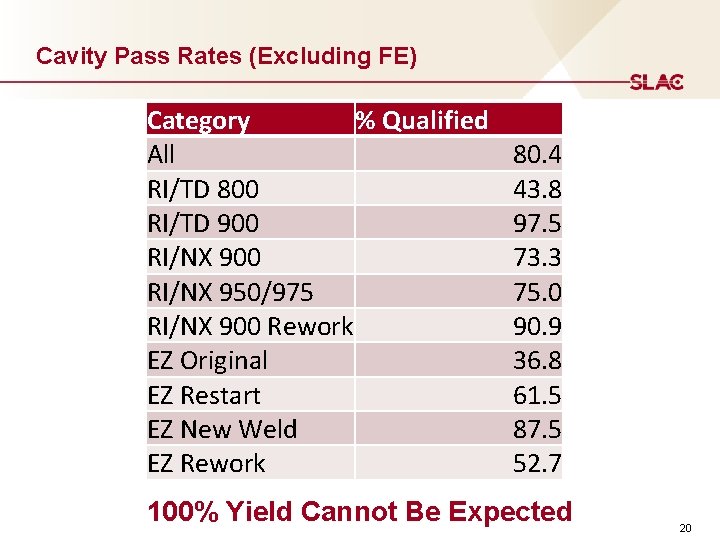
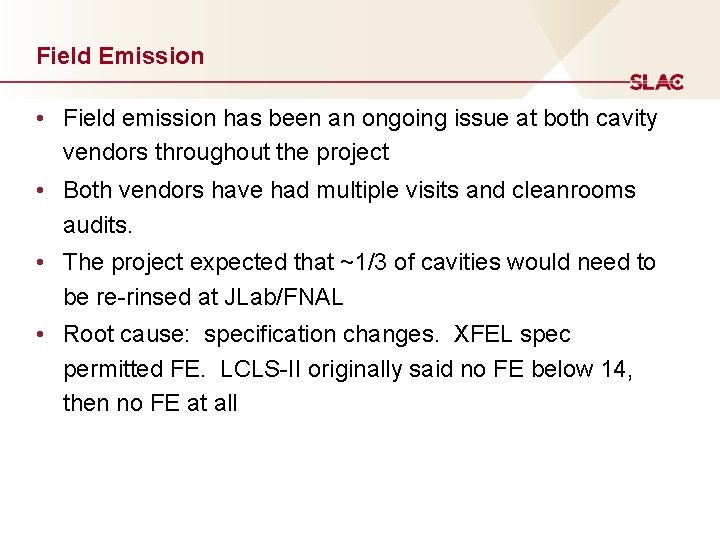
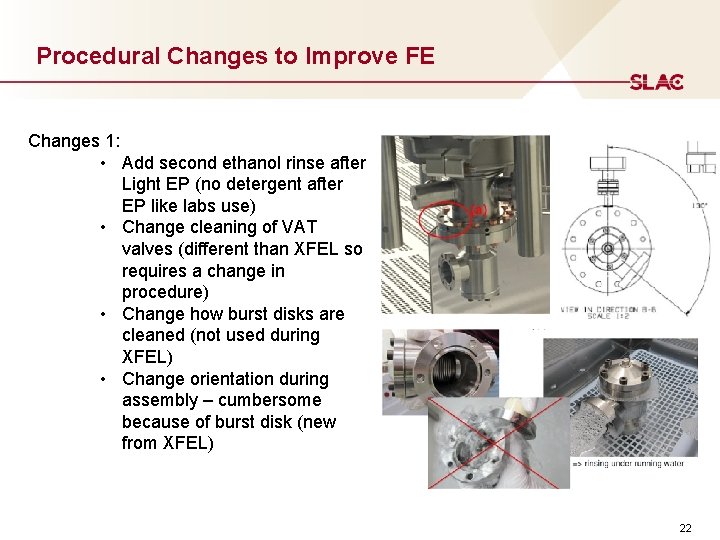
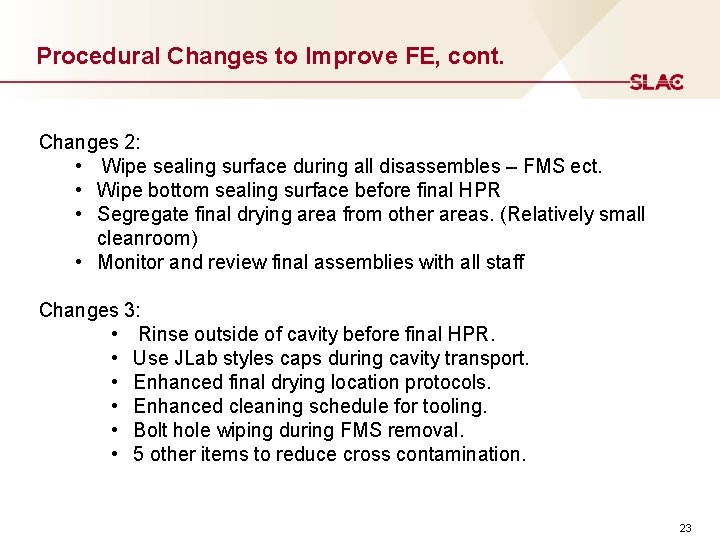
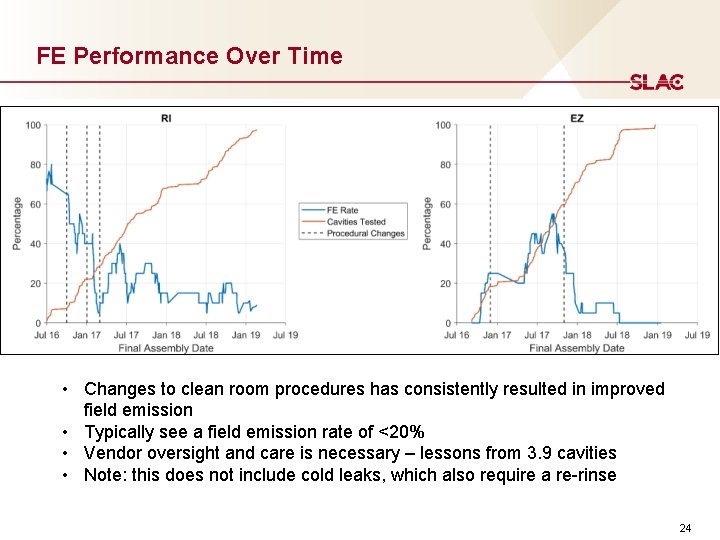
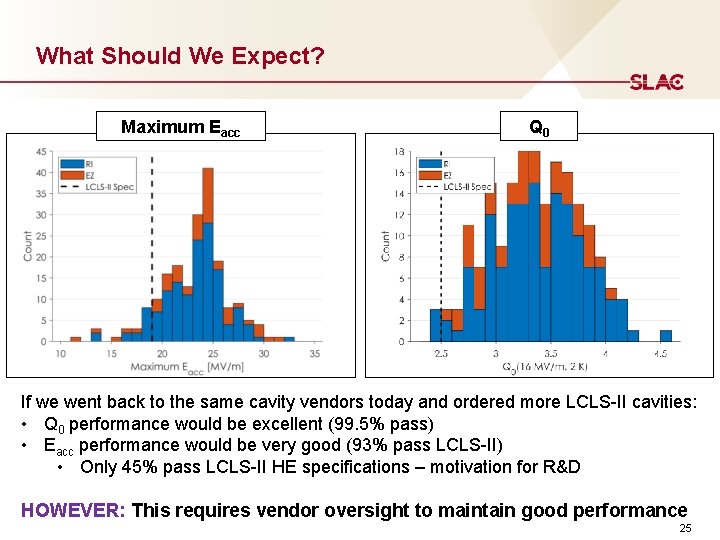
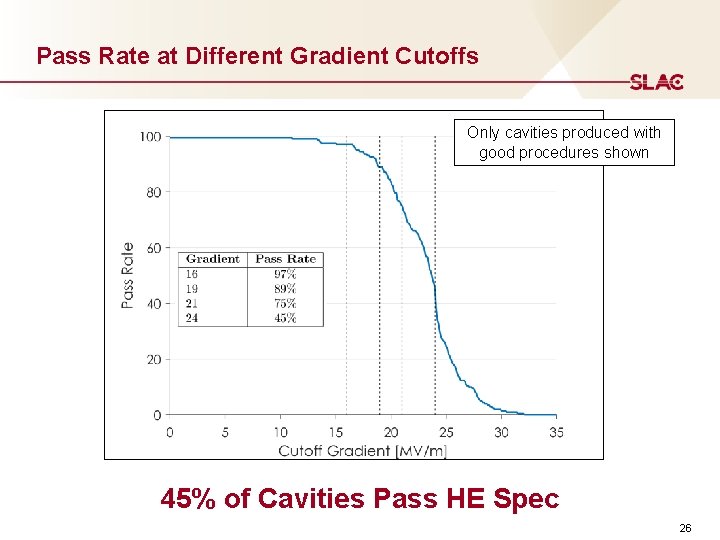
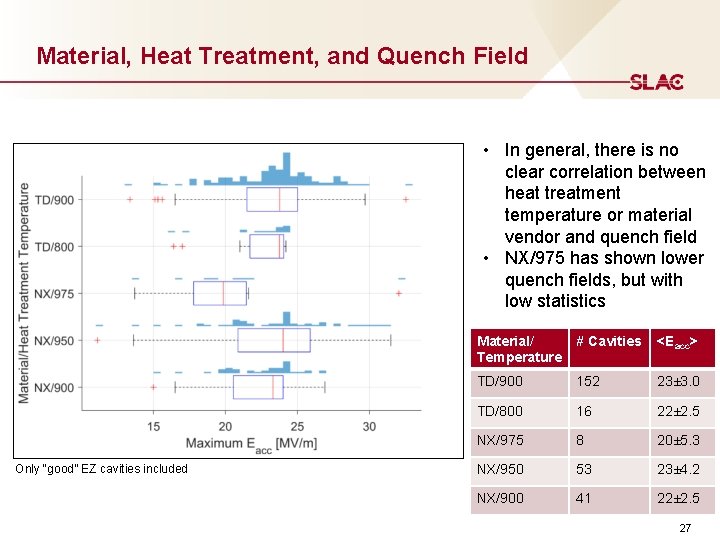
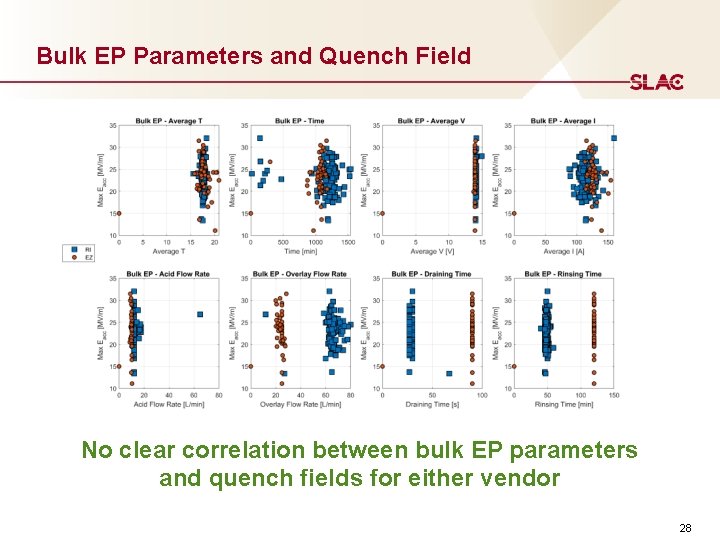
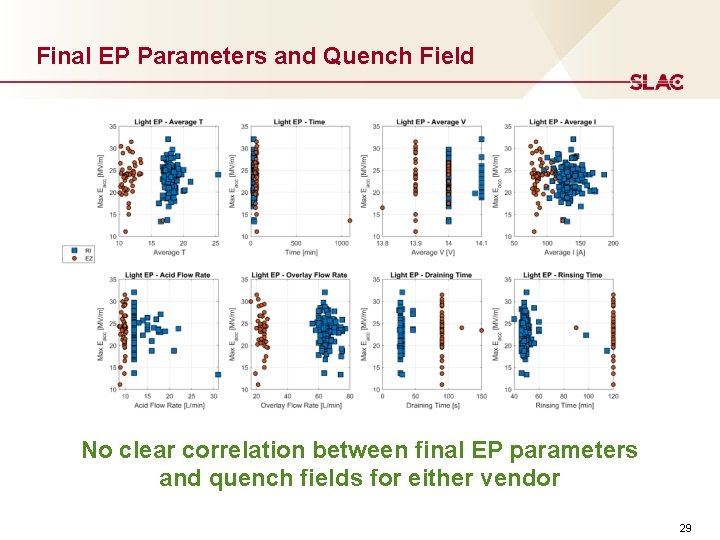
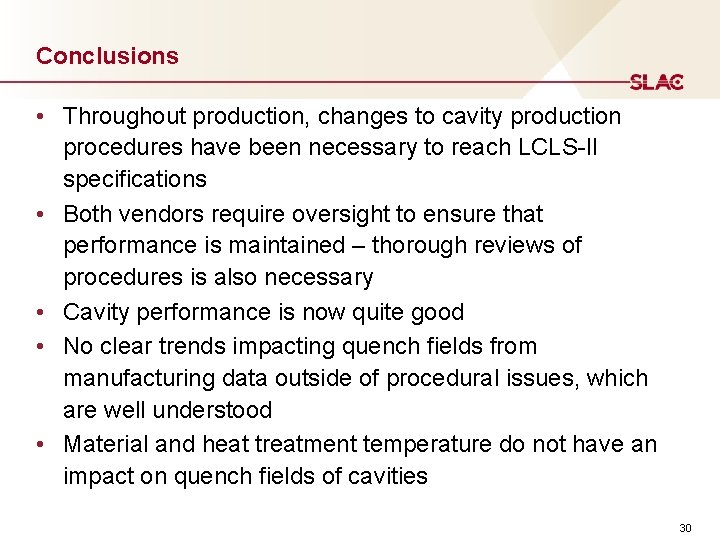
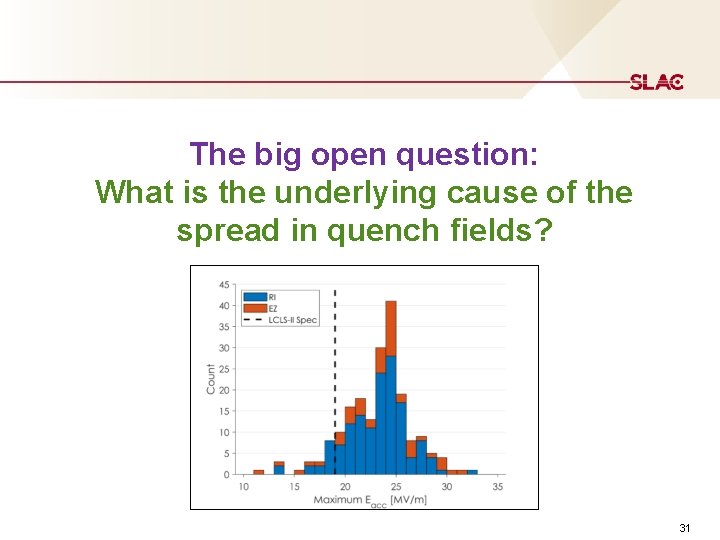
- Slides: 31
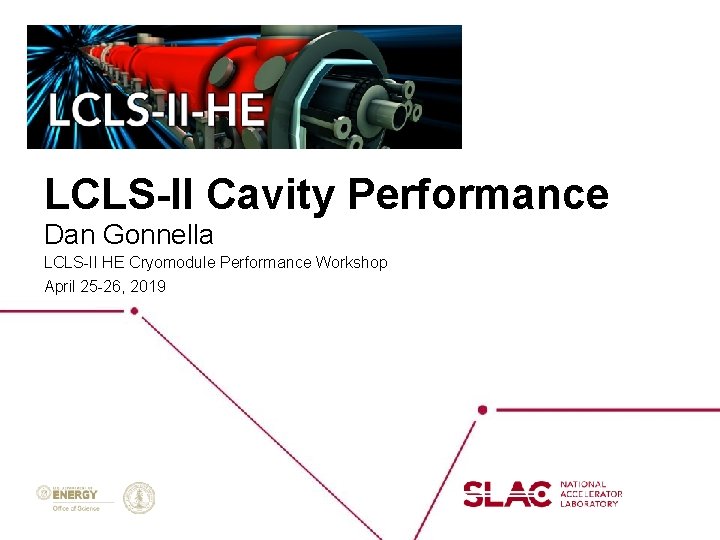
LCLS-II Cavity Performance Dan Gonnella LCLS-II HE Cryomodule Performance Workshop April 25 -26, 2019
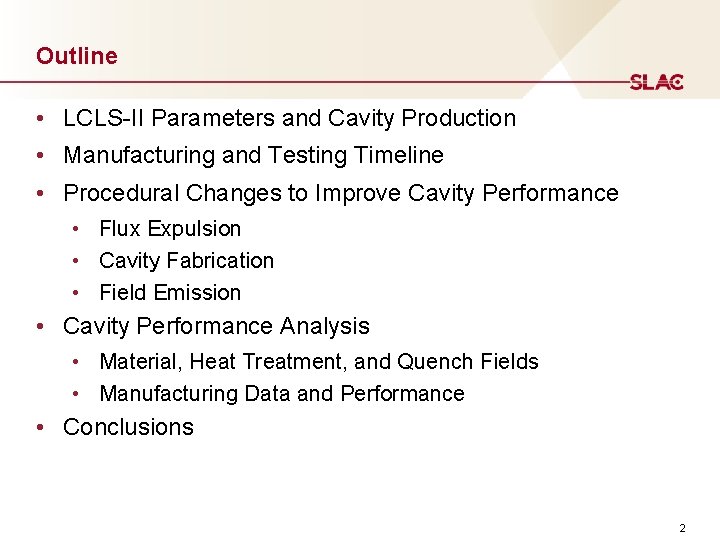
Outline • LCLS-II Parameters and Cavity Production • Manufacturing and Testing Timeline • Procedural Changes to Improve Cavity Performance • Flux Expulsion • Cavity Fabrication • Field Emission • Cavity Performance Analysis • Material, Heat Treatment, and Quench Fields • Manufacturing Data and Performance • Conclusions 2
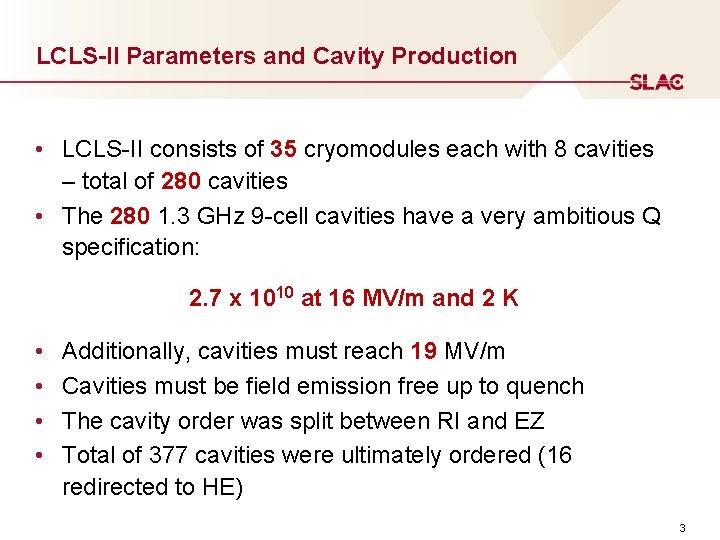
LCLS-II Parameters and Cavity Production • LCLS-II consists of 35 cryomodules each with 8 cavities – total of 280 cavities • The 280 1. 3 GHz 9 -cell cavities have a very ambitious Q specification: 2. 7 x 1010 at 16 MV/m and 2 K • • Additionally, cavities must reach 19 MV/m Cavities must be field emission free up to quench The cavity order was split between RI and EZ Total of 377 cavities were ultimately ordered (16 redirected to HE) 3
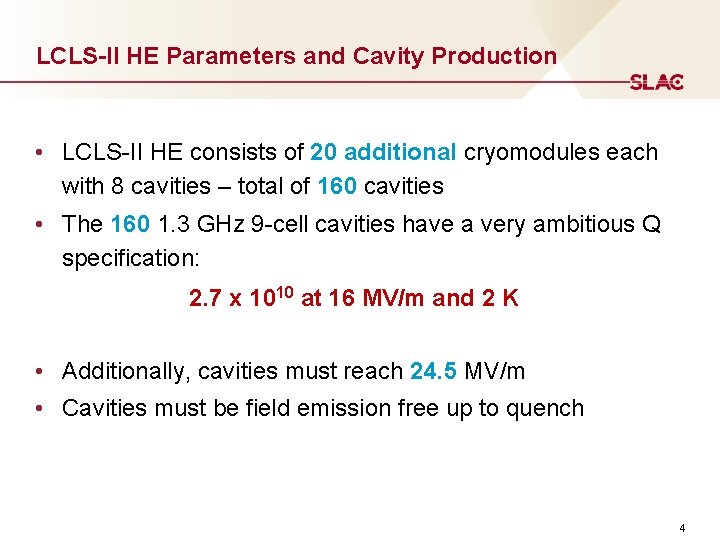
LCLS-II HE Parameters and Cavity Production • LCLS-II HE consists of 20 additional cryomodules each with 8 cavities – total of 160 cavities • The 160 1. 3 GHz 9 -cell cavities have a very ambitious Q specification: 2. 7 x 1010 at 16 MV/m and 2 K • Additionally, cavities must reach 24. 5 MV/m • Cavities must be field emission free up to quench 4
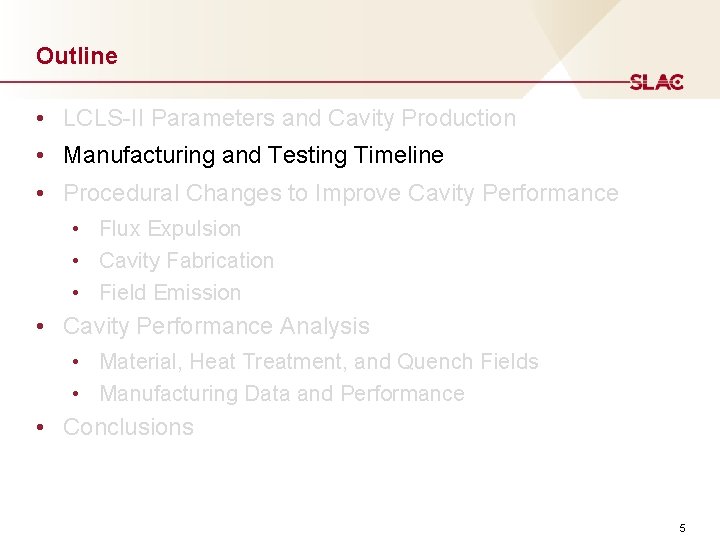
Outline • LCLS-II Parameters and Cavity Production • Manufacturing and Testing Timeline • Procedural Changes to Improve Cavity Performance • Flux Expulsion • Cavity Fabrication • Field Emission • Cavity Performance Analysis • Material, Heat Treatment, and Quench Fields • Manufacturing Data and Performance • Conclusions 5
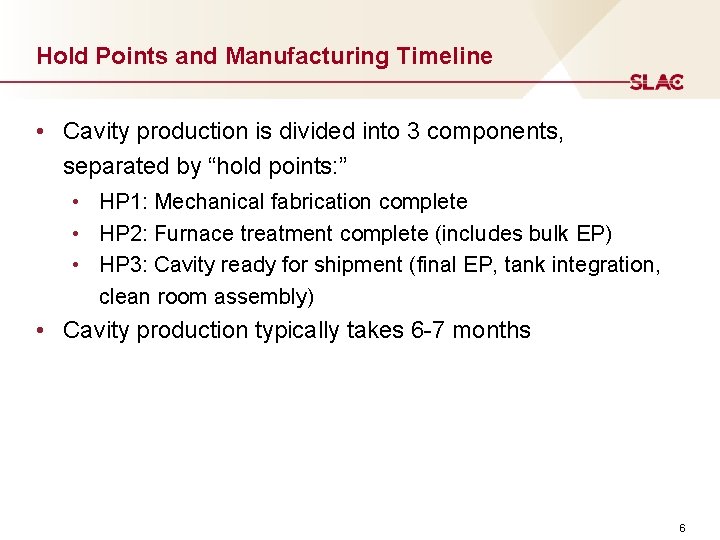
Hold Points and Manufacturing Timeline • Cavity production is divided into 3 components, separated by “hold points: ” • HP 1: Mechanical fabrication complete • HP 2: Furnace treatment complete (includes bulk EP) • HP 3: Cavity ready for shipment (final EP, tank integration, clean room assembly) • Cavity production typically takes 6 -7 months 6
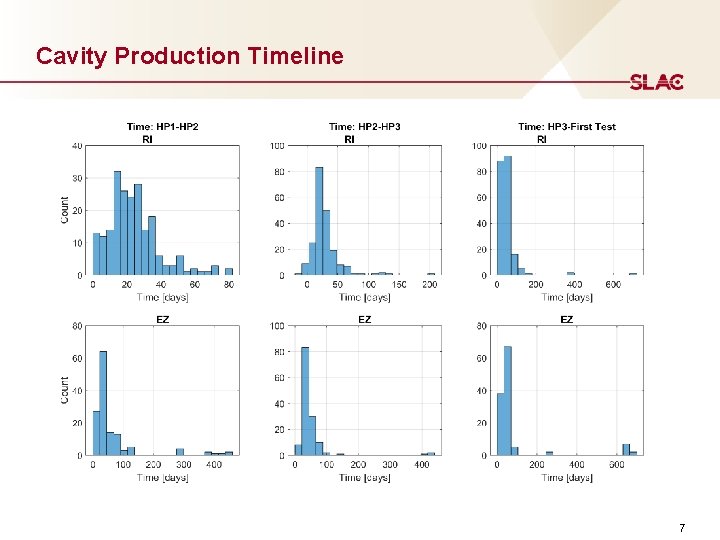
Cavity Production Timeline 7
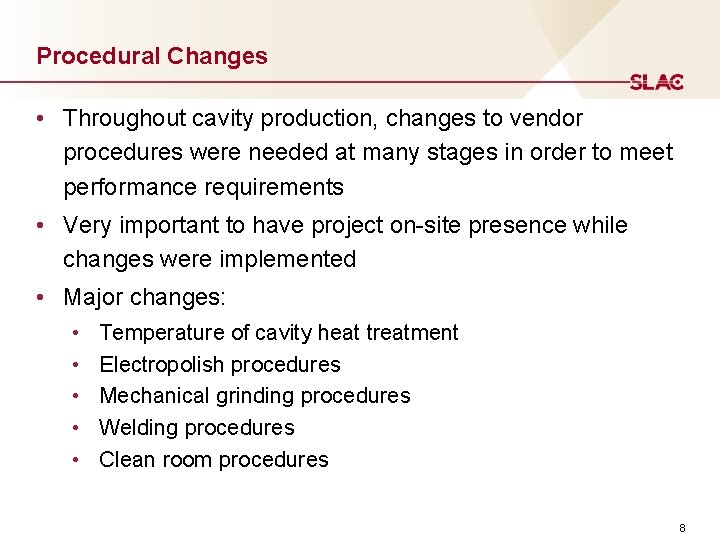
Procedural Changes • Throughout cavity production, changes to vendor procedures were needed at many stages in order to meet performance requirements • Very important to have project on-site presence while changes were implemented • Major changes: • • • Temperature of cavity heat treatment Electropolish procedures Mechanical grinding procedures Welding procedures Clean room procedures 8
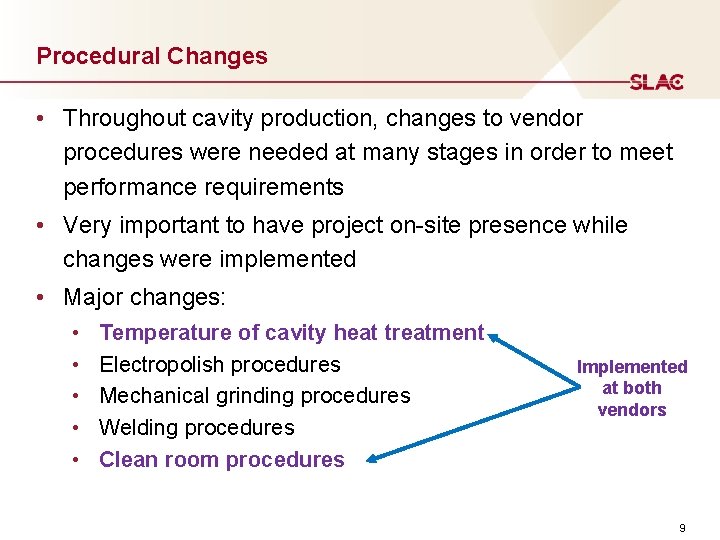
Procedural Changes • Throughout cavity production, changes to vendor procedures were needed at many stages in order to meet performance requirements • Very important to have project on-site presence while changes were implemented • Major changes: • • • Temperature of cavity heat treatment Electropolish procedures Mechanical grinding procedures Welding procedures Clean room procedures Implemented at both vendors 9
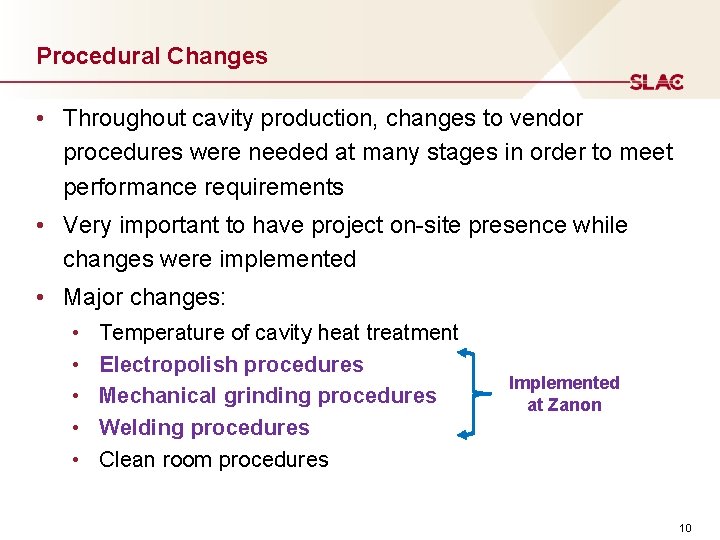
Procedural Changes • Throughout cavity production, changes to vendor procedures were needed at many stages in order to meet performance requirements • Very important to have project on-site presence while changes were implemented • Major changes: • • • Temperature of cavity heat treatment Electropolish procedures Mechanical grinding procedures Welding procedures Clean room procedures Implemented at Zanon 10
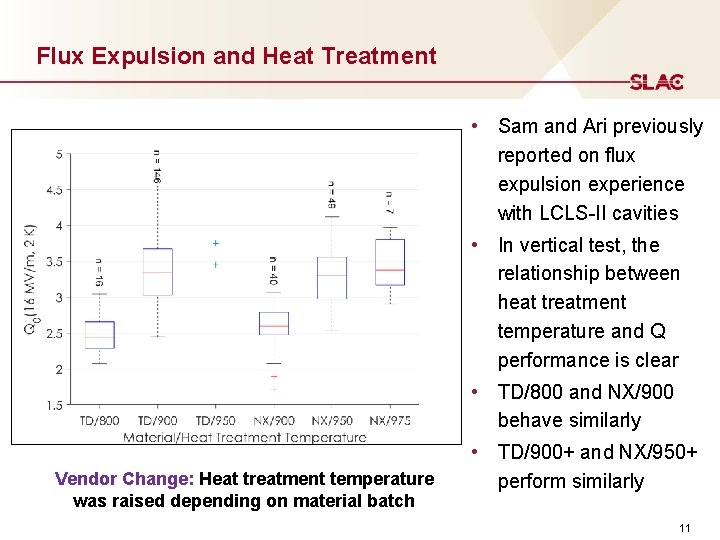
Flux Expulsion and Heat Treatment • Sam and Ari previously reported on flux expulsion experience with LCLS-II cavities • In vertical test, the relationship between heat treatment temperature and Q performance is clear • TD/800 and NX/900 behave similarly Vendor Change: Heat treatment temperature was raised depending on material batch • TD/900+ and NX/950+ perform similarly 11
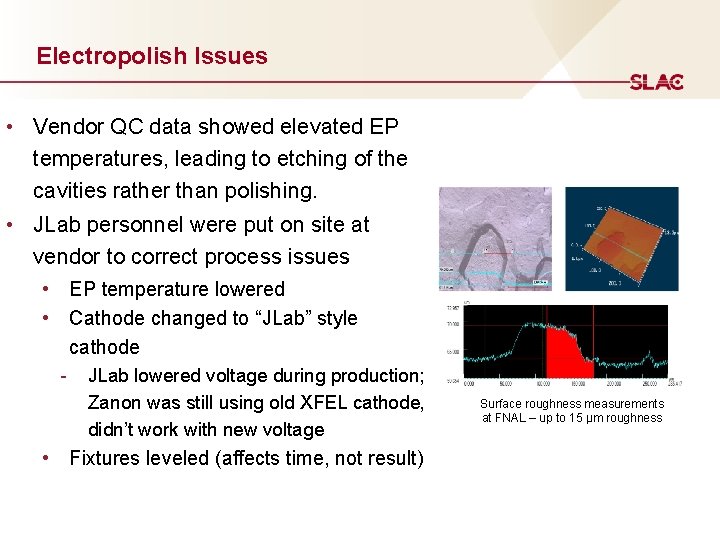
Electropolish Issues • Vendor QC data showed elevated EP temperatures, leading to etching of the cavities rather than polishing. • JLab personnel were put on site at vendor to correct process issues • EP temperature lowered • Cathode changed to “JLab” style cathode - JLab lowered voltage during production; Zanon was still using old XFEL cathode, didn’t work with new voltage • Fixtures leveled (affects time, not result) Surface roughness measurements at FNAL – up to 15 μm roughness
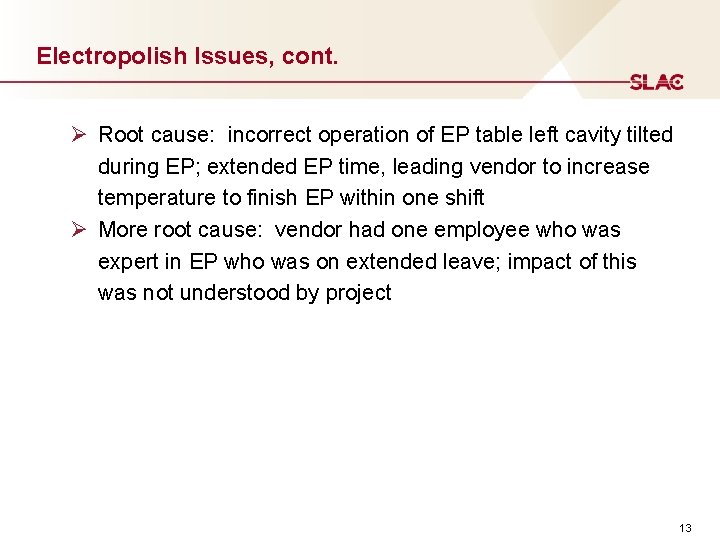
Electropolish Issues, cont. Ø Root cause: incorrect operation of EP table left cavity tilted during EP; extended EP time, leading vendor to increase temperature to finish EP within one shift Ø More root cause: vendor had one employee who was expert in EP who was on extended leave; impact of this was not understood by project 13
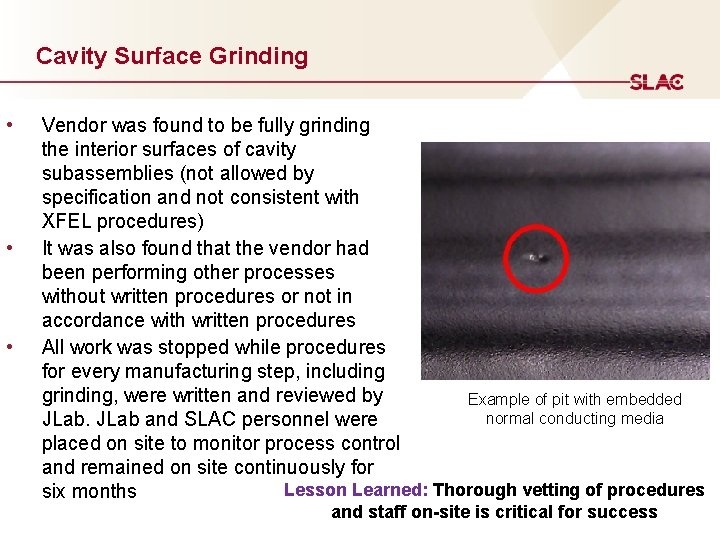
Cavity Surface Grinding • • • Vendor was found to be fully grinding the interior surfaces of cavity subassemblies (not allowed by specification and not consistent with XFEL procedures) It was also found that the vendor had been performing other processes without written procedures or not in accordance with written procedures All work was stopped while procedures for every manufacturing step, including grinding, were written and reviewed by Example of pit with embedded normal conducting media JLab and SLAC personnel were placed on site to monitor process control and remained on site continuously for Lesson Learned: Thorough vetting of procedures six months and staff on-site is critical for success
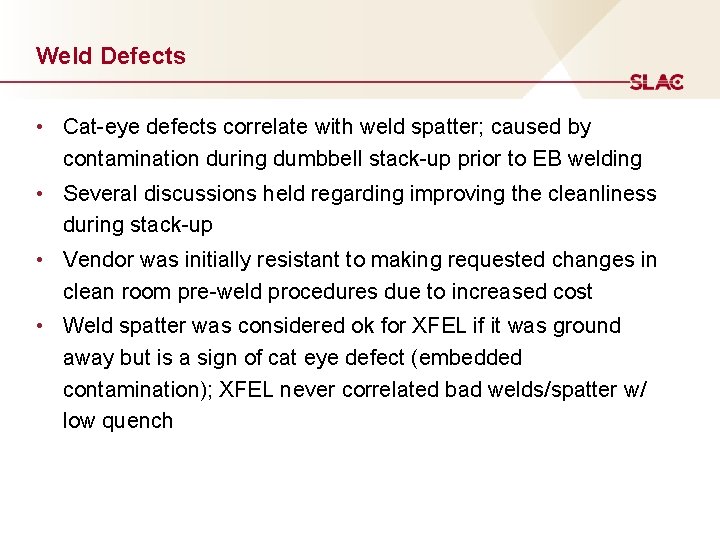
Weld Defects • Cat-eye defects correlate with weld spatter; caused by contamination during dumbbell stack-up prior to EB welding • Several discussions held regarding improving the cleanliness during stack-up • Vendor was initially resistant to making requested changes in clean room pre-weld procedures due to increased cost • Weld spatter was considered ok for XFEL if it was ground away but is a sign of cat eye defect (embedded contamination); XFEL never correlated bad welds/spatter w/ low quench
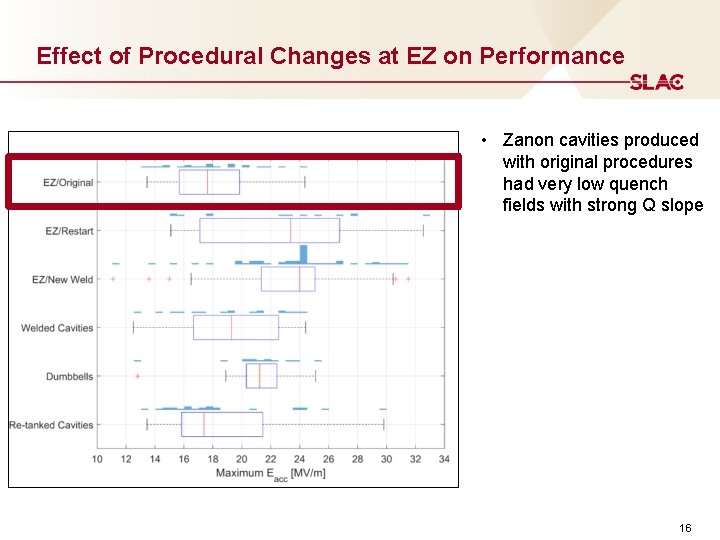
Effect of Procedural Changes at EZ on Performance • Zanon cavities produced with original procedures had very low quench fields with strong Q slope 16
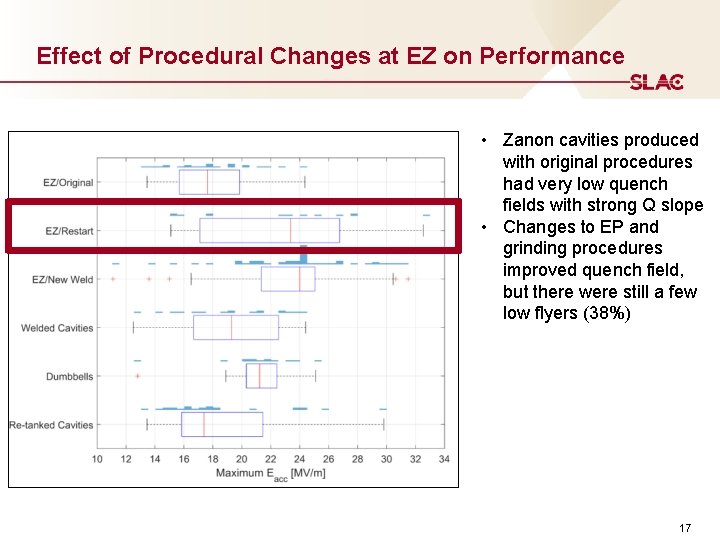
Effect of Procedural Changes at EZ on Performance • Zanon cavities produced with original procedures had very low quench fields with strong Q slope • Changes to EP and grinding procedures improved quench field, but there were still a few low flyers (38%) 17
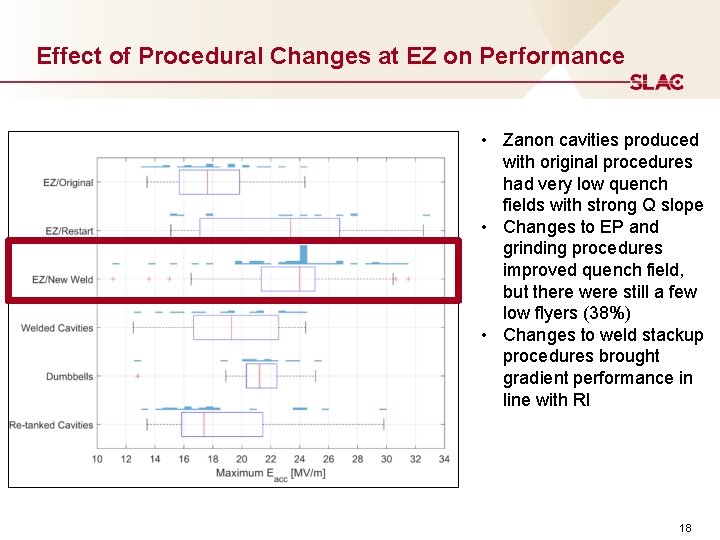
Effect of Procedural Changes at EZ on Performance • Zanon cavities produced with original procedures had very low quench fields with strong Q slope • Changes to EP and grinding procedures improved quench field, but there were still a few low flyers (38%) • Changes to weld stackup procedures brought gradient performance in line with RI 18
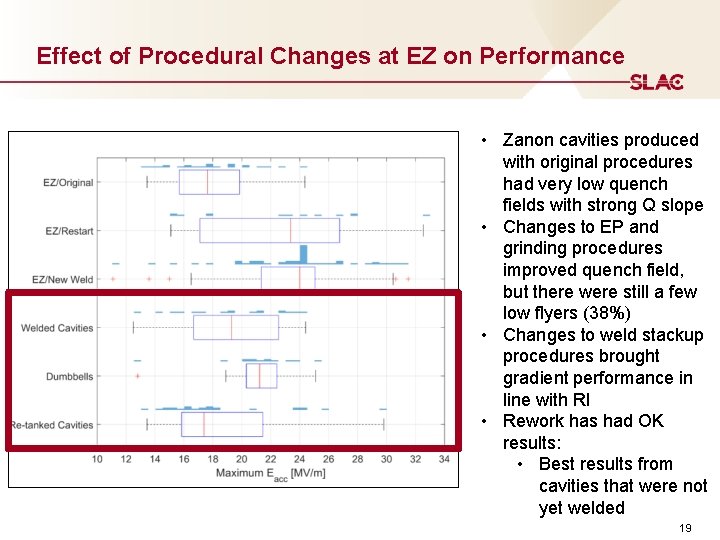
Effect of Procedural Changes at EZ on Performance • Zanon cavities produced with original procedures had very low quench fields with strong Q slope • Changes to EP and grinding procedures improved quench field, but there were still a few low flyers (38%) • Changes to weld stackup procedures brought gradient performance in line with RI • Rework has had OK results: • Best results from cavities that were not yet welded 19
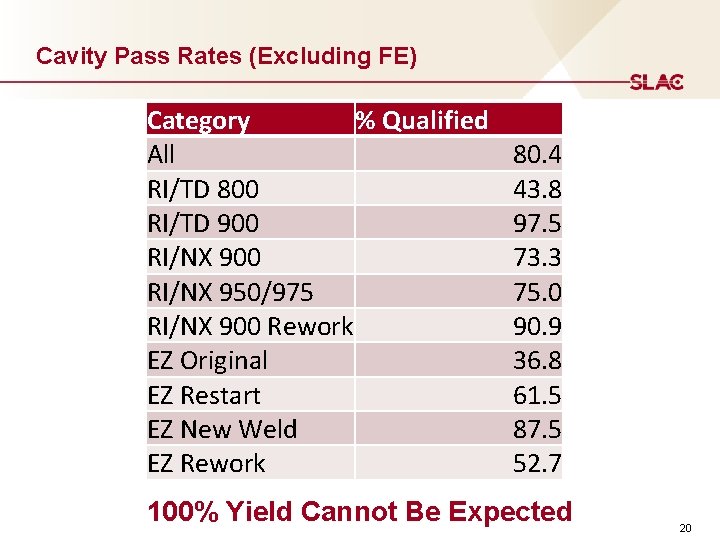
Cavity Pass Rates (Excluding FE) Category % Qualified All RI/TD 800 RI/TD 900 RI/NX 950/975 RI/NX 900 Rework EZ Original EZ Restart EZ New Weld EZ Rework 80. 4 43. 8 97. 5 73. 3 75. 0 90. 9 36. 8 61. 5 87. 5 52. 7 100% Yield Cannot Be Expected 20
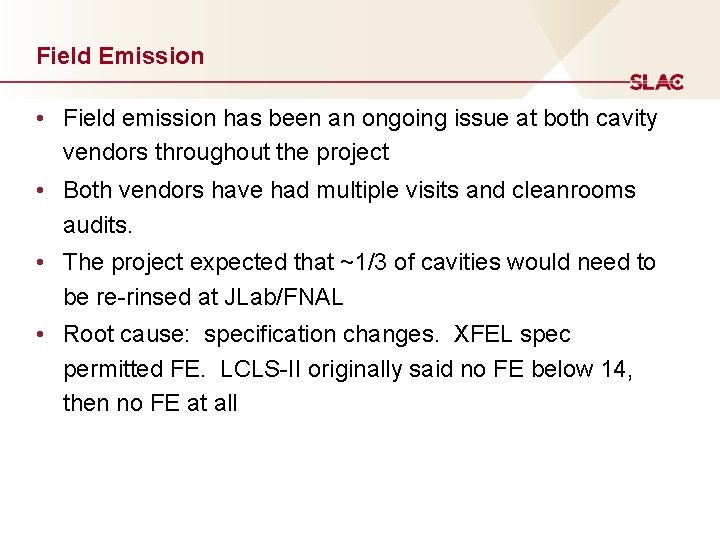
Field Emission • Field emission has been an ongoing issue at both cavity vendors throughout the project • Both vendors have had multiple visits and cleanrooms audits. • The project expected that ~1/3 of cavities would need to be re-rinsed at JLab/FNAL • Root cause: specification changes. XFEL spec permitted FE. LCLS-II originally said no FE below 14, then no FE at all
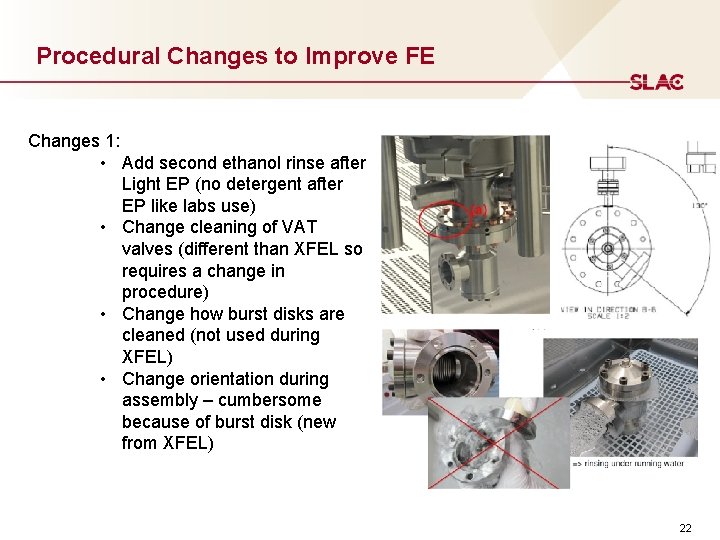
Procedural Changes to Improve FE Changes 1: • Add second ethanol rinse after Light EP (no detergent after EP like labs use) • Change cleaning of VAT valves (different than XFEL so requires a change in procedure) • Change how burst disks are cleaned (not used during XFEL) • Change orientation during assembly – cumbersome because of burst disk (new from XFEL) 22
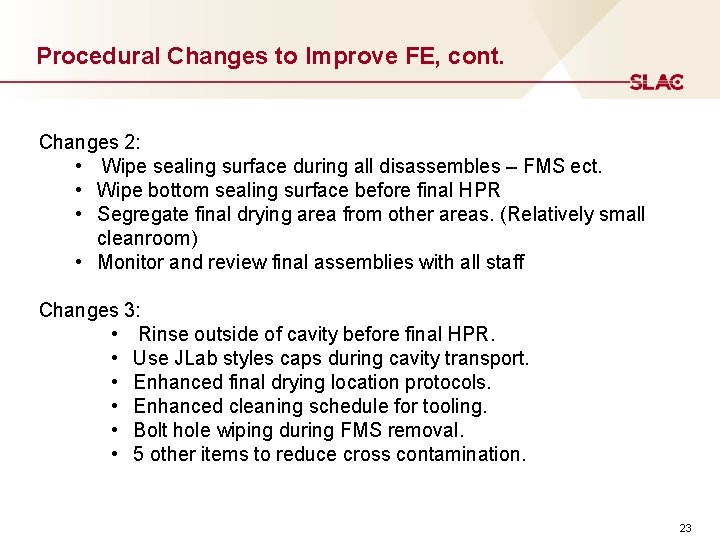
Procedural Changes to Improve FE, cont. Changes 2: • Wipe sealing surface during all disassembles – FMS ect. • Wipe bottom sealing surface before final HPR • Segregate final drying area from other areas. (Relatively small cleanroom) • Monitor and review final assemblies with all staff Changes 3: • Rinse outside of cavity before final HPR. • Use JLab styles caps during cavity transport. • Enhanced final drying location protocols. • Enhanced cleaning schedule for tooling. • Bolt hole wiping during FMS removal. • 5 other items to reduce cross contamination. 23
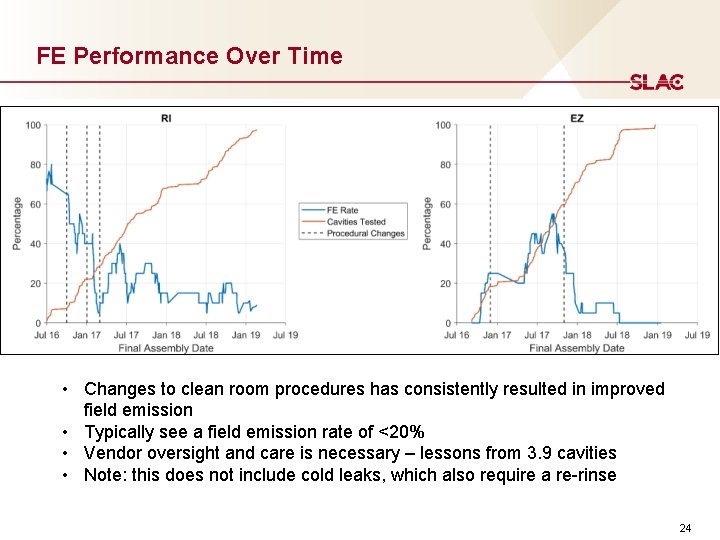
FE Performance Over Time • Changes to clean room procedures has consistently resulted in improved field emission • Typically see a field emission rate of <20% • Vendor oversight and care is necessary – lessons from 3. 9 cavities • Note: this does not include cold leaks, which also require a re-rinse 24
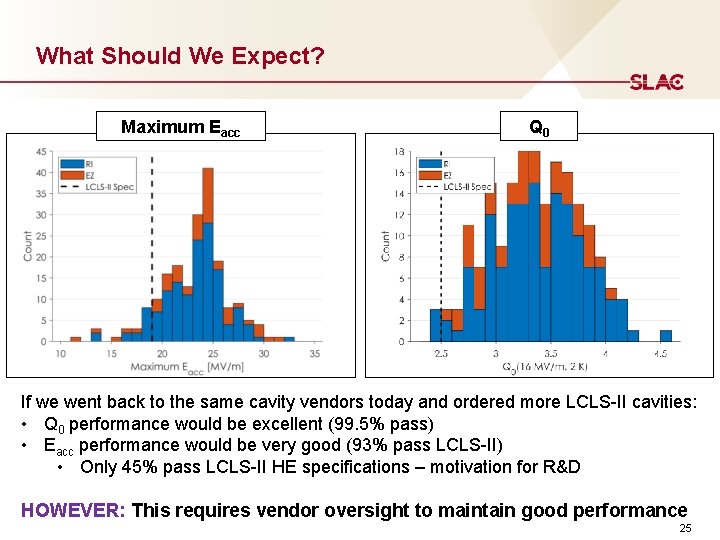
What Should We Expect? Maximum Eacc Q 0 If we went back to the same cavity vendors today and ordered more LCLS-II cavities: • Q 0 performance would be excellent (99. 5% pass) • Eacc performance would be very good (93% pass LCLS-II) • Only 45% pass LCLS-II HE specifications – motivation for R&D HOWEVER: This requires vendor oversight to maintain good performance 25
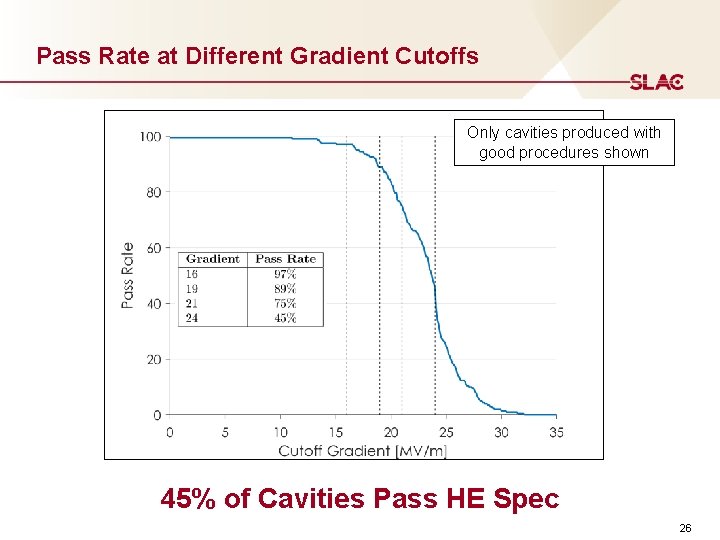
Pass Rate at Different Gradient Cutoffs Only cavities produced with good procedures shown 45% of Cavities Pass HE Spec 26
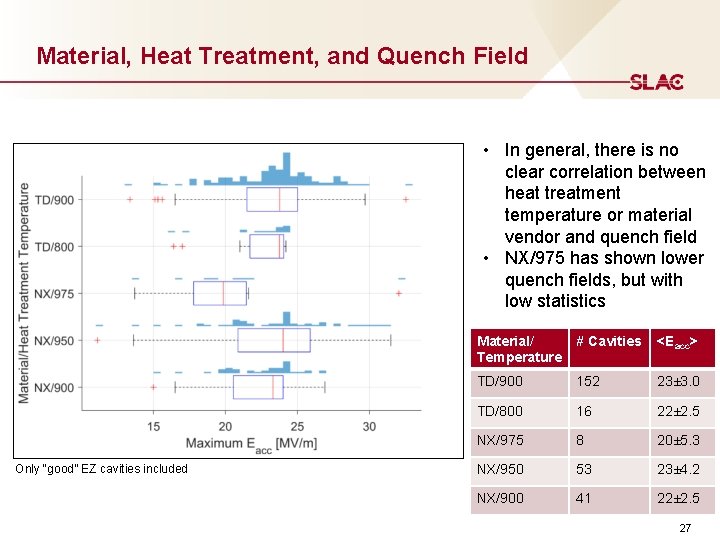
Material, Heat Treatment, and Quench Field • In general, there is no clear correlation between heat treatment temperature or material vendor and quench field • NX/975 has shown lower quench fields, but with low statistics Only “good” EZ cavities included Material/ Temperature # Cavities <Eacc> TD/900 152 23± 3. 0 TD/800 16 22± 2. 5 NX/975 8 20± 5. 3 NX/950 53 23± 4. 2 NX/900 41 22± 2. 5 27
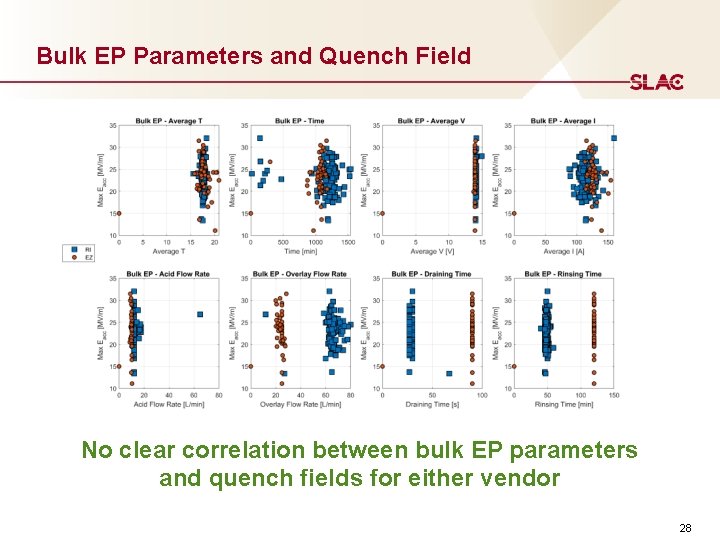
Bulk EP Parameters and Quench Field No clear correlation between bulk EP parameters and quench fields for either vendor 28
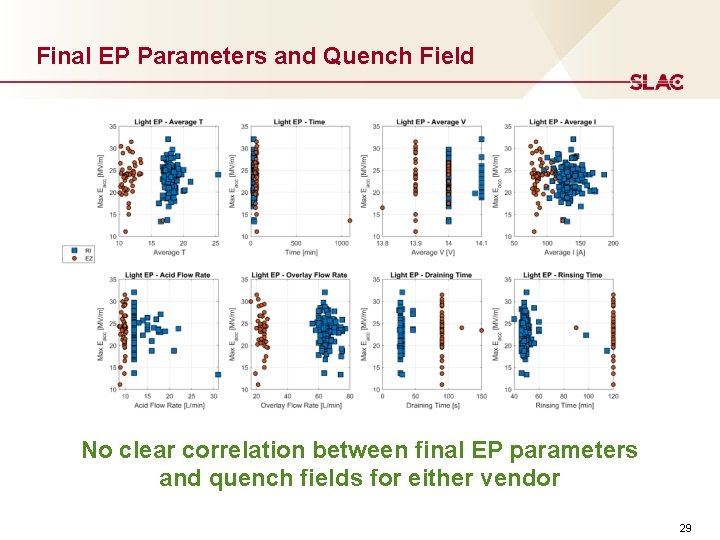
Final EP Parameters and Quench Field No clear correlation between final EP parameters and quench fields for either vendor 29
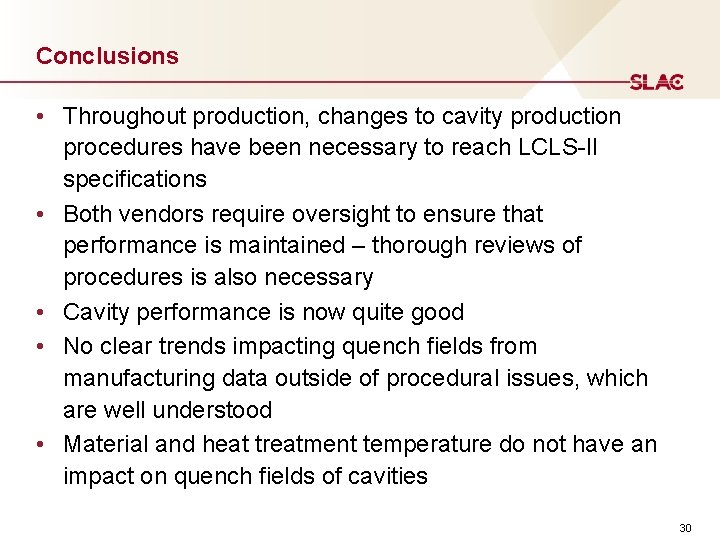
Conclusions • Throughout production, changes to cavity production procedures have been necessary to reach LCLS-II specifications • Both vendors require oversight to ensure that performance is maintained – thorough reviews of procedures is also necessary • Cavity performance is now quite good • No clear trends impacting quench fields from manufacturing data outside of procedural issues, which are well understood • Material and heat treatment temperature do not have an impact on quench fields of cavities 30
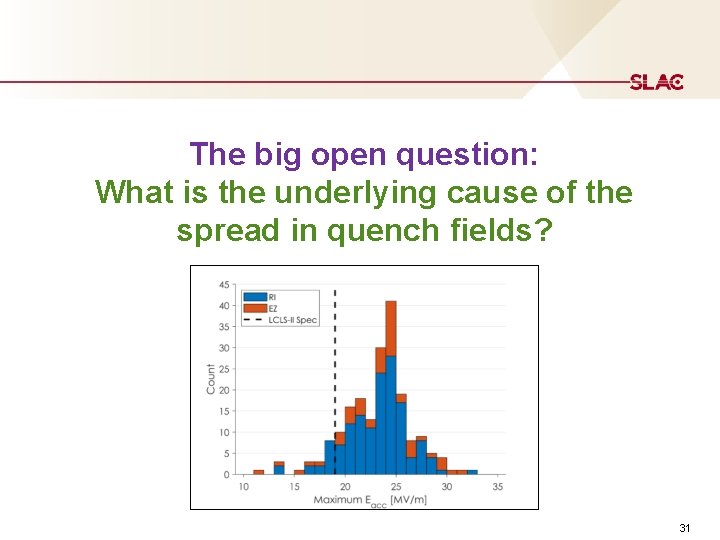
The big open question: What is the underlying cause of the spread in quench fields? 31
Orbital body
Thoracic cavity and abdominal cavity
Mental anatomical term
Peritoneal cavity vs abdominal cavity
Omental foramen
Chapter 11 performance appraisal - (pdf)
Performance levels
Jcids manual 2018
Equazione di boltzmann
Nine regions of the abdominopelvic cavity
Muscularis externa
Thorax cavity
Finesse of a cavity
Die cavity tablet
Upper molar canals
How do sponges differ from other animals
Infected dentin vs affected dentin
Oblique plane
Portuguese man of war characteristics
Isthmus area of class 2 cavity
Palatine aponeurosis
Salpingopharyngeus
Nasal septum venous drainage
Seno paranasal
Cavity of sphenoid bone
Superior meatus nose
Pharynx and oral cavity
Amalgam vs inlay
Heel block in mould
Finesse of a cavity
Pig thoracic cavity diagram
Black 1 cavity