Large Scale Metrology Instruments Part 1 Tevfik Ekinci
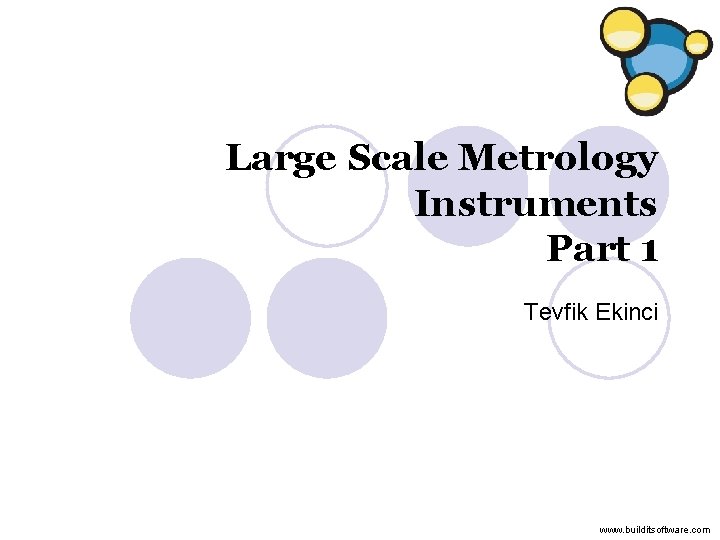
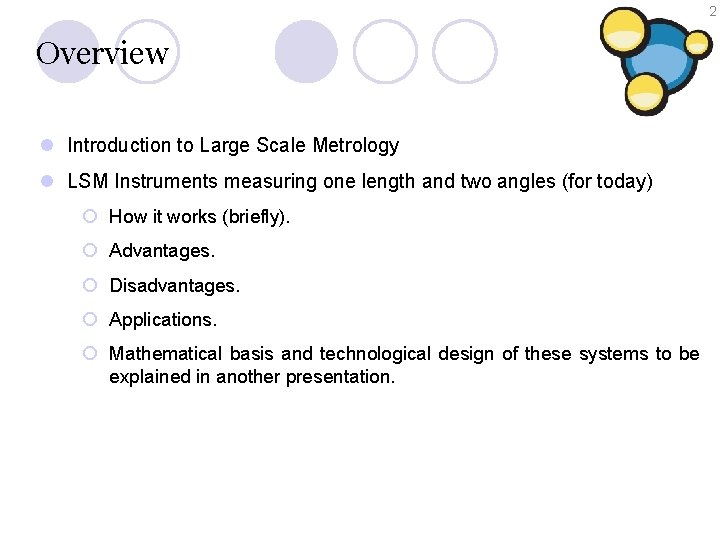
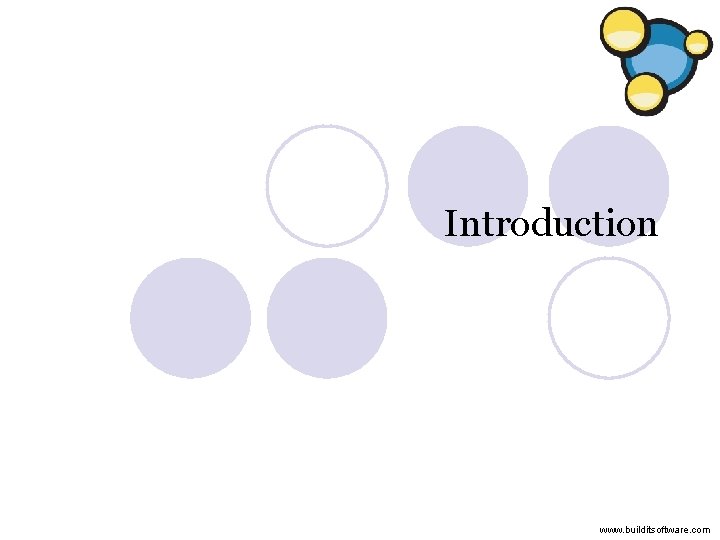
![WHAT IS LARGE SCALE METROLOGY? Metrology of freeform shaped parts [Savio, 2007] The field WHAT IS LARGE SCALE METROLOGY? Metrology of freeform shaped parts [Savio, 2007] The field](https://slidetodoc.com/presentation_image/102245766866fc96f877691adca2ebfe/image-4.jpg)
![5 APPLICATION EXAMPLES Metrology of freeform shaped parts [Savio, 2007] 5 APPLICATION EXAMPLES Metrology of freeform shaped parts [Savio, 2007]](https://slidetodoc.com/presentation_image/102245766866fc96f877691adca2ebfe/image-5.jpg)
![WHY FRAMELESS METROLOGY? Large Scale Metrology In Aerospace Assembly [Muelaner, 2008] Assembly may account WHY FRAMELESS METROLOGY? Large Scale Metrology In Aerospace Assembly [Muelaner, 2008] Assembly may account](https://slidetodoc.com/presentation_image/102245766866fc96f877691adca2ebfe/image-6.jpg)
![WHY AEROSPACE? Users in 3 D Metrology [Kyle, 2010] www. builditsoftware. com WHY AEROSPACE? Users in 3 D Metrology [Kyle, 2010] www. builditsoftware. com](https://slidetodoc.com/presentation_image/102245766866fc96f877691adca2ebfe/image-7.jpg)
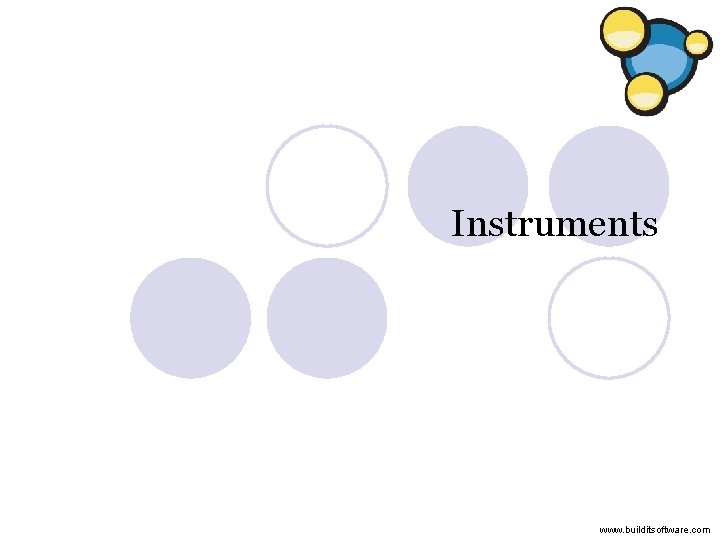
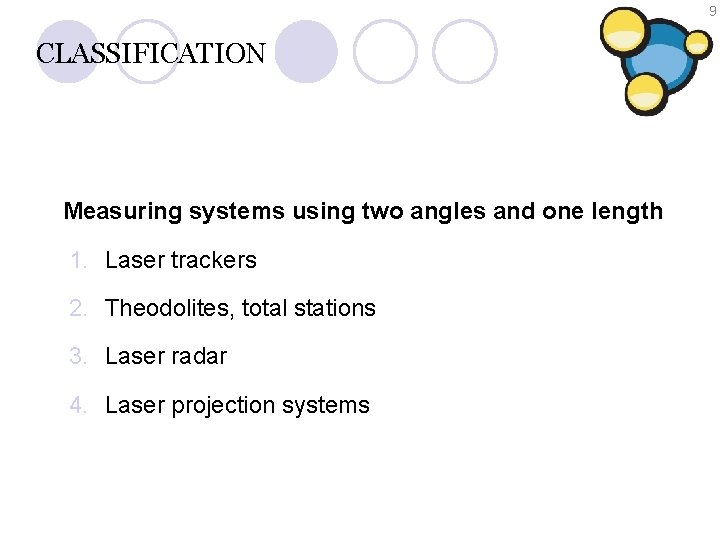
![10 Laser Tracker: How does it work? Laser Tracker [Muelaner, 2008] Laser-based spherical coordinate 10 Laser Tracker: How does it work? Laser Tracker [Muelaner, 2008] Laser-based spherical coordinate](https://slidetodoc.com/presentation_image/102245766866fc96f877691adca2ebfe/image-10.jpg)
![11 Laser Tracker: How does it work? Laser Tracker [Muelaner, 2008] Sensors detect the 11 Laser Tracker: How does it work? Laser Tracker [Muelaner, 2008] Sensors detect the](https://slidetodoc.com/presentation_image/102245766866fc96f877691adca2ebfe/image-11.jpg)
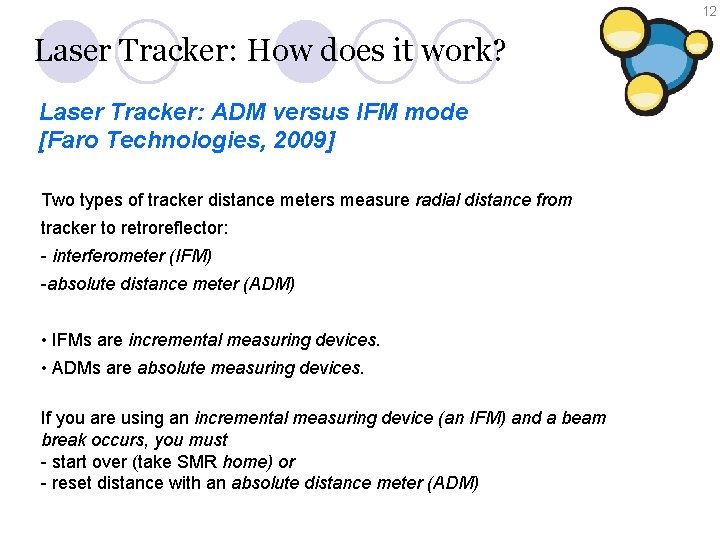
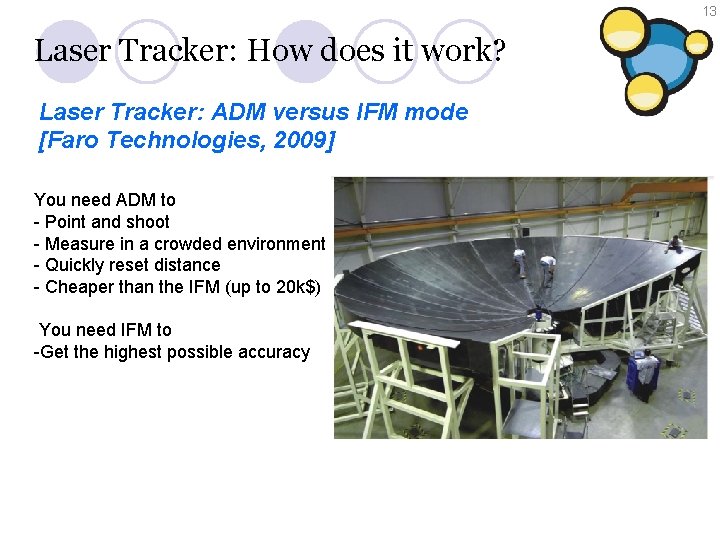
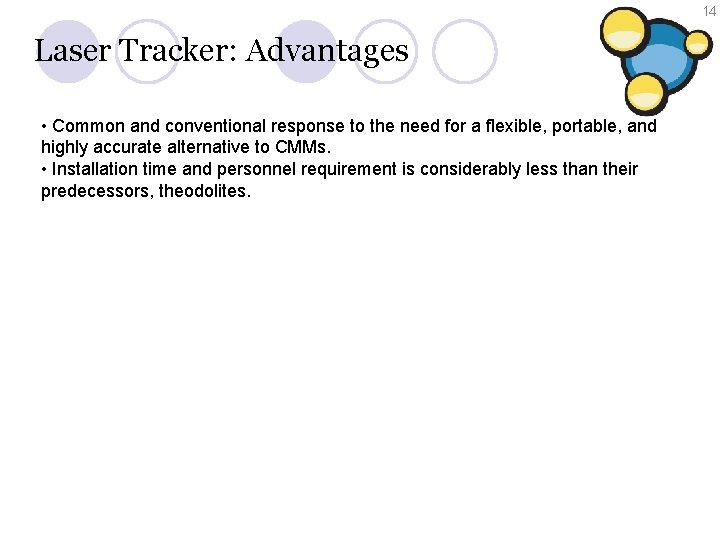
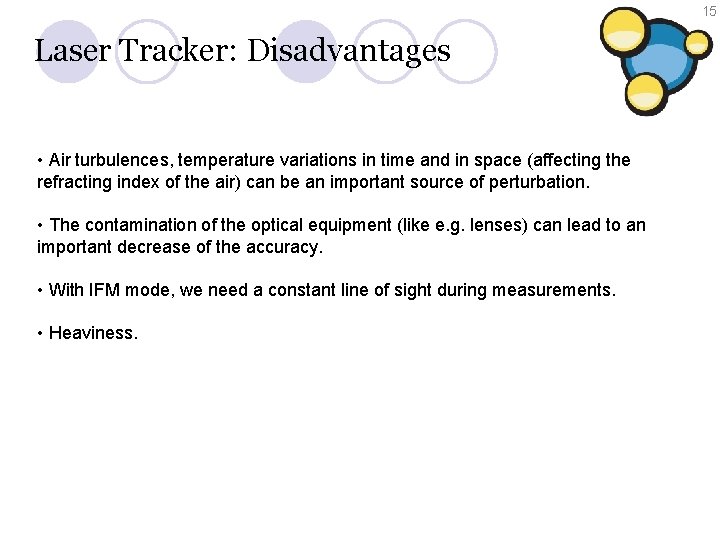
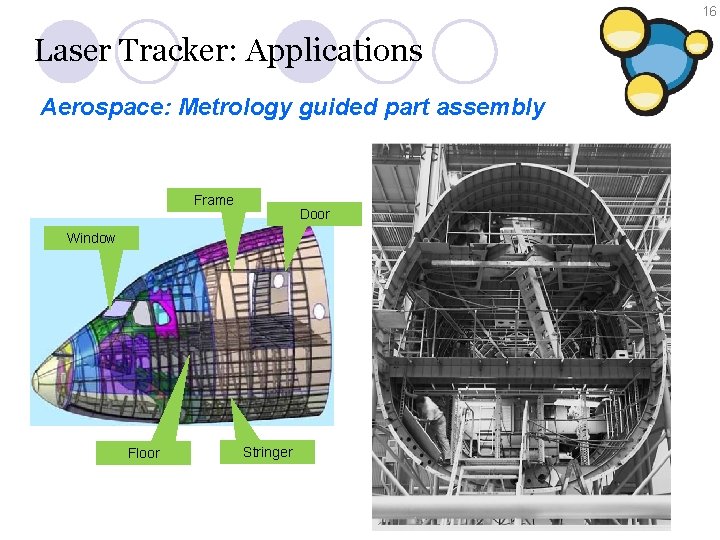
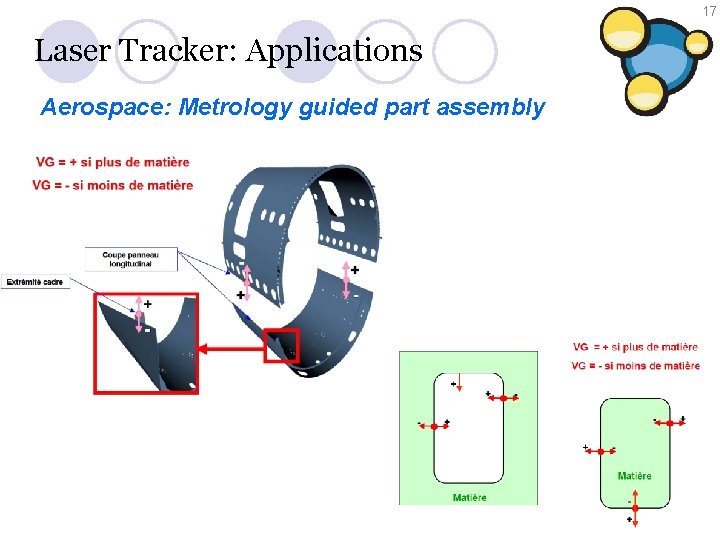
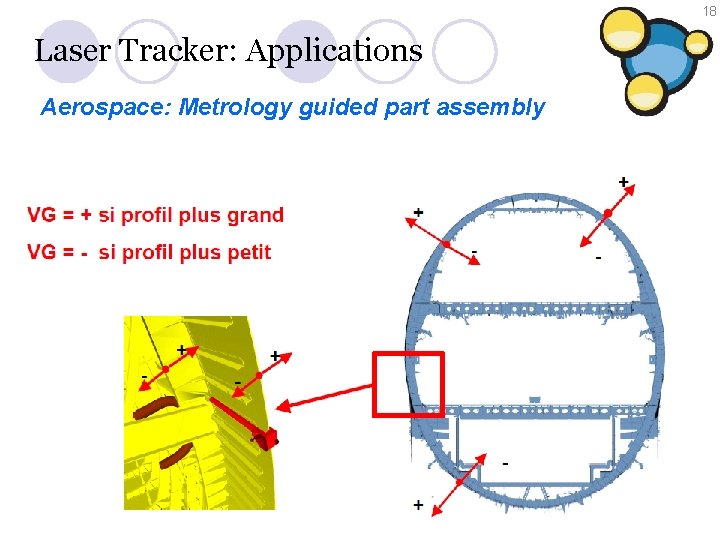
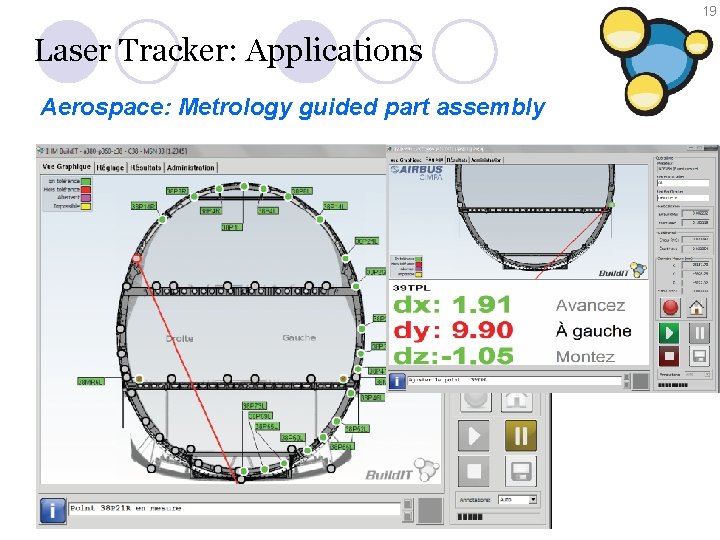
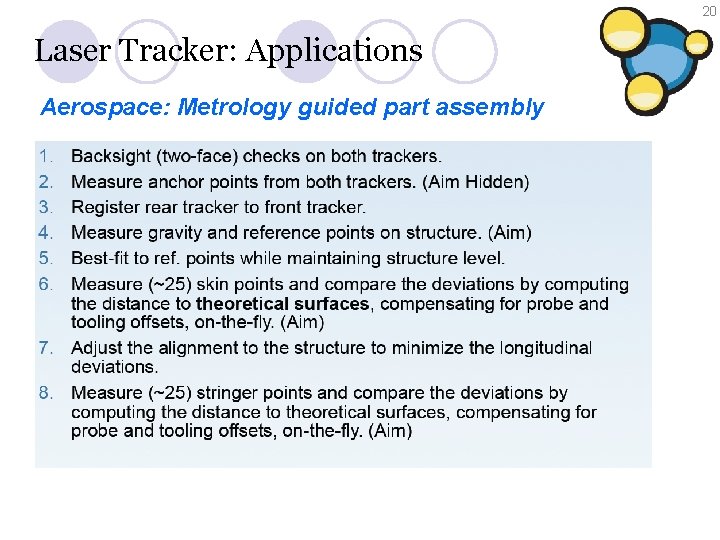
![21 Laser Tracker: Applications Aerospace: Metrology guided jig assembly [Airbus, Airbus 380] 21 Laser Tracker: Applications Aerospace: Metrology guided jig assembly [Airbus, Airbus 380]](https://slidetodoc.com/presentation_image/102245766866fc96f877691adca2ebfe/image-21.jpg)
![22 Laser Tracker: Applications Aerospace: Metrology guided jig assembly [Airbus, Airbus 380] 22 Laser Tracker: Applications Aerospace: Metrology guided jig assembly [Airbus, Airbus 380]](https://slidetodoc.com/presentation_image/102245766866fc96f877691adca2ebfe/image-22.jpg)
![23 Laser Tracker: Applications Aerospace: Metrology guided jig assembly [Airbus, Airbus 380] 23 Laser Tracker: Applications Aerospace: Metrology guided jig assembly [Airbus, Airbus 380]](https://slidetodoc.com/presentation_image/102245766866fc96f877691adca2ebfe/image-23.jpg)
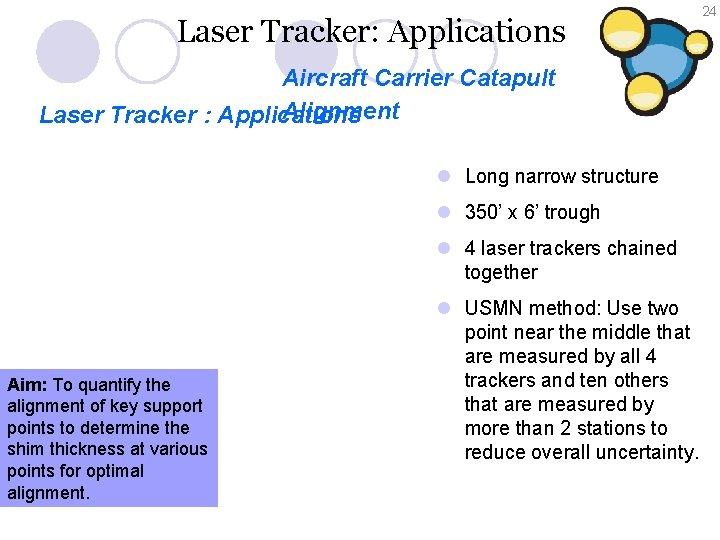
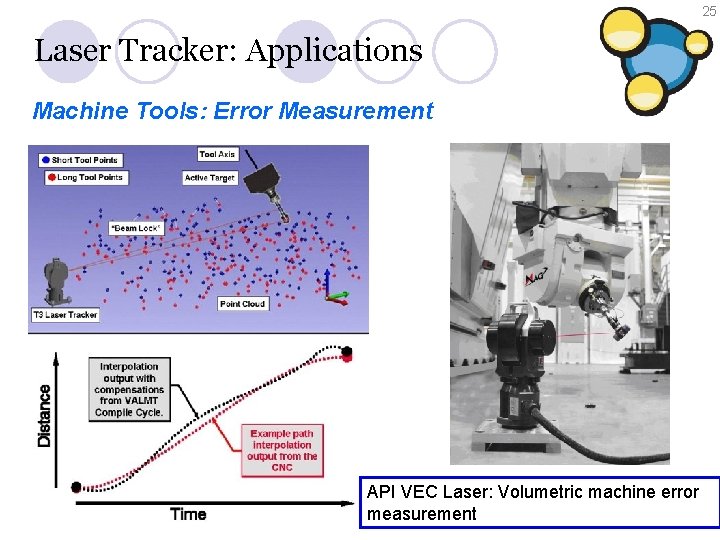
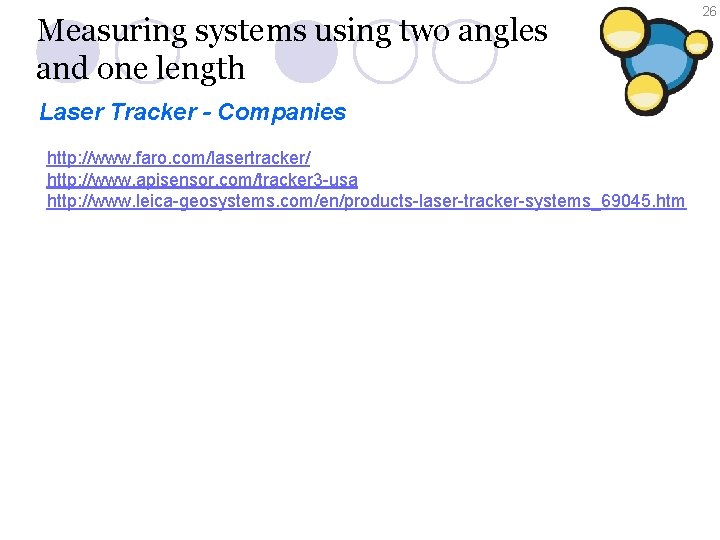
![27 Total Station: How does it work? Theodolite-Total station [Leica, 2010] Evolution: Theodolite measures 27 Total Station: How does it work? Theodolite-Total station [Leica, 2010] Evolution: Theodolite measures](https://slidetodoc.com/presentation_image/102245766866fc96f877691adca2ebfe/image-27.jpg)
![28 Total Station: How does it work? Theodolite-Total station [Leica, 2010] l Triangulation: Knowns: 28 Total Station: How does it work? Theodolite-Total station [Leica, 2010] l Triangulation: Knowns:](https://slidetodoc.com/presentation_image/102245766866fc96f877691adca2ebfe/image-28.jpg)
![29 Total Station: How does it work? Total station – Accuracy [Leica, 2010] 29 Total Station: How does it work? Total station – Accuracy [Leica, 2010]](https://slidetodoc.com/presentation_image/102245766866fc96f877691adca2ebfe/image-29.jpg)
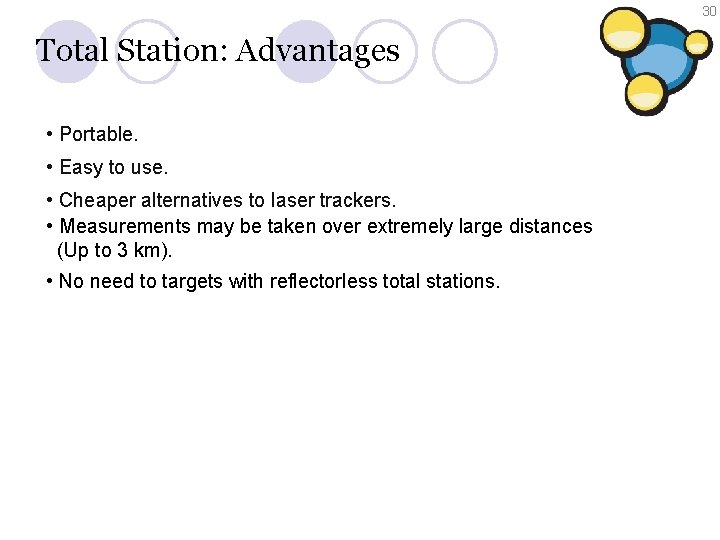
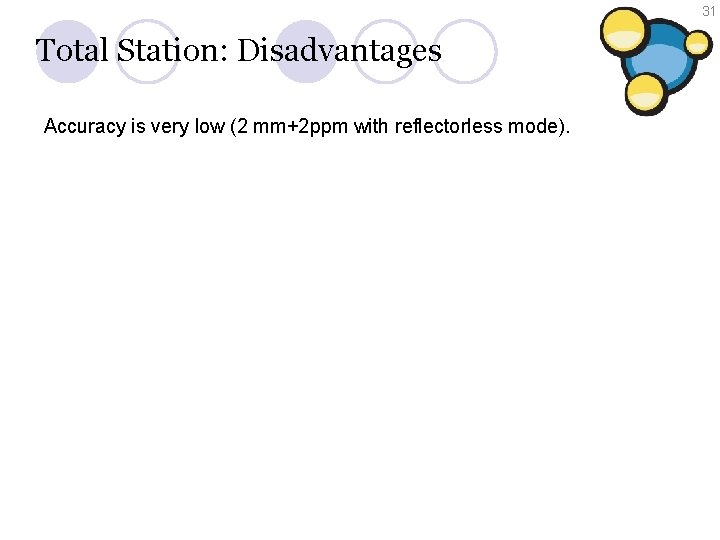
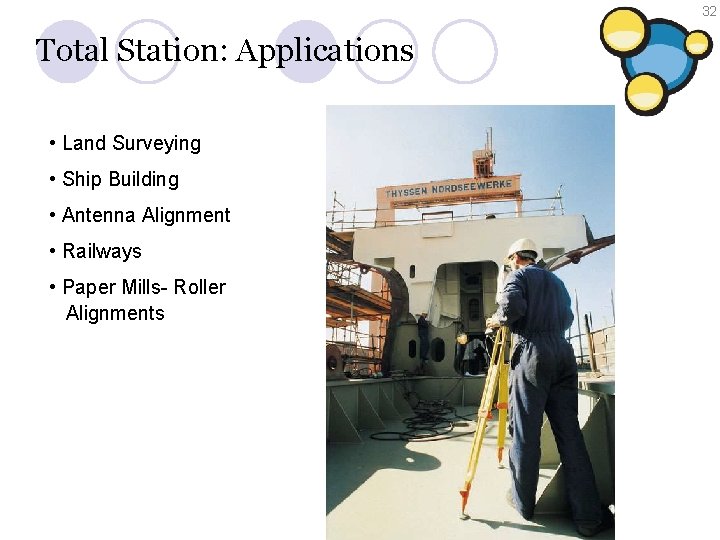
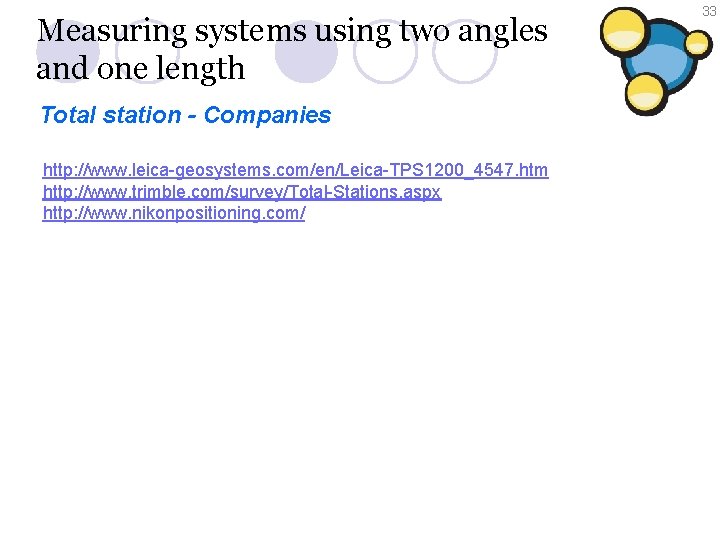
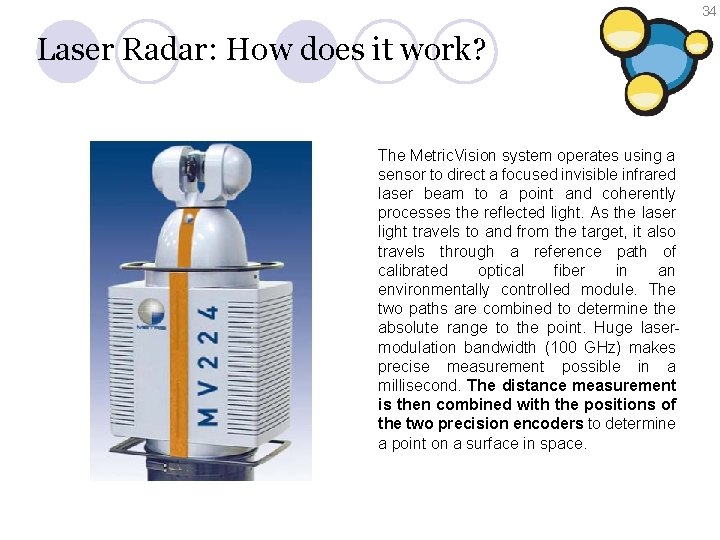
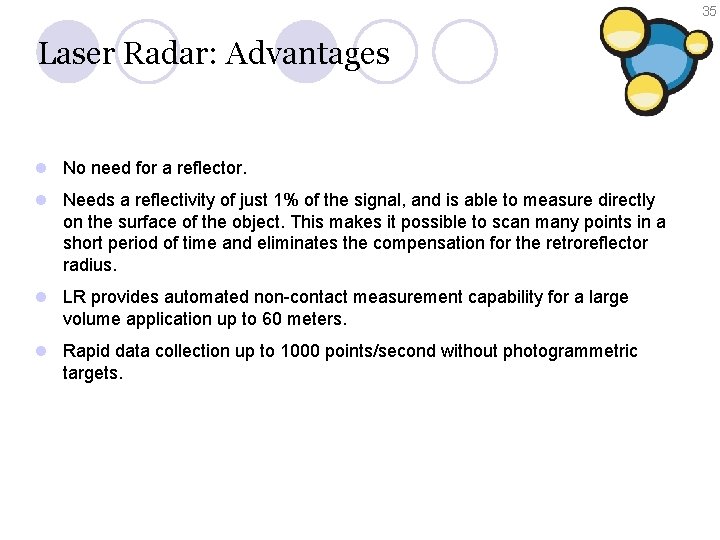
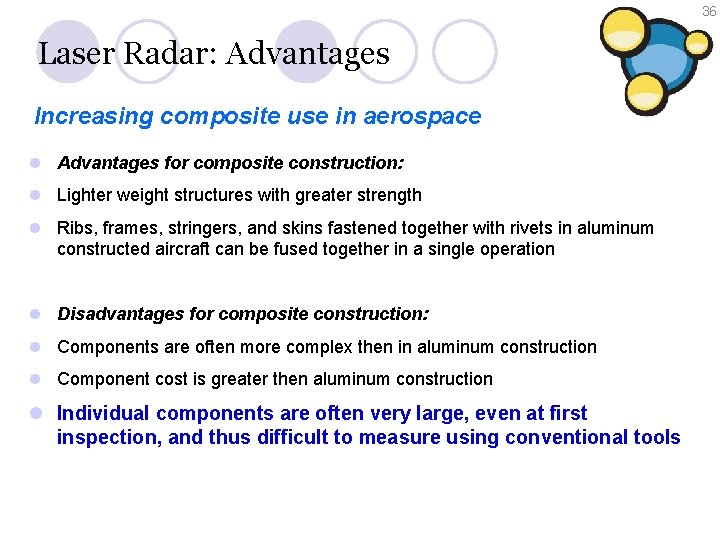
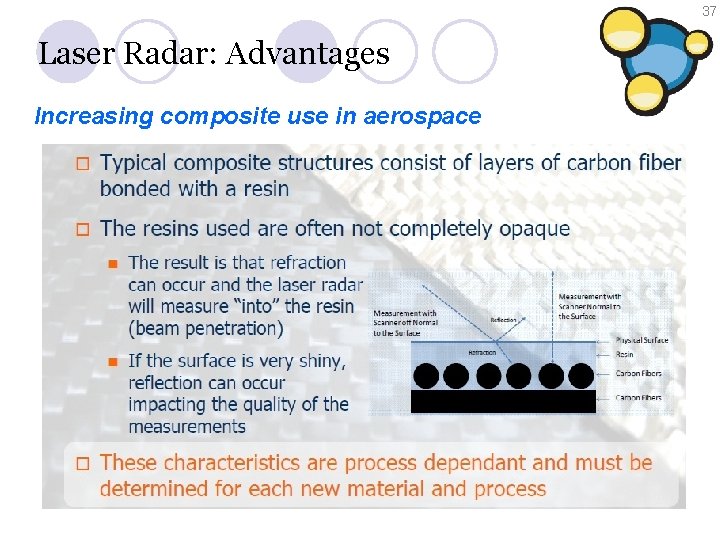
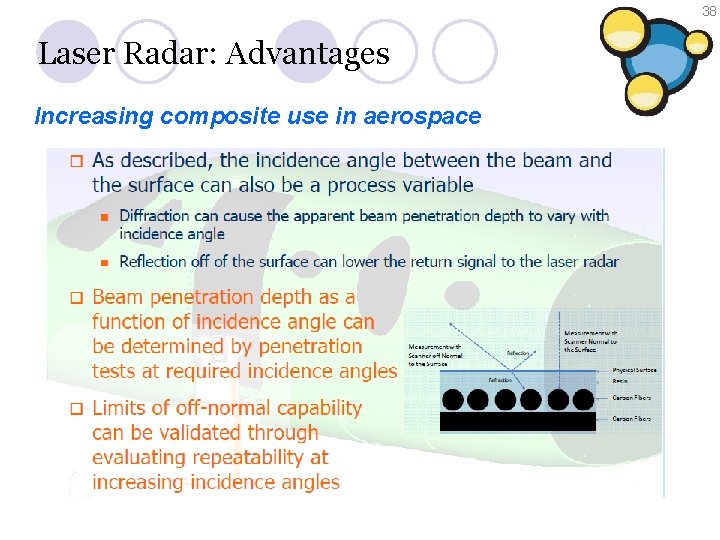
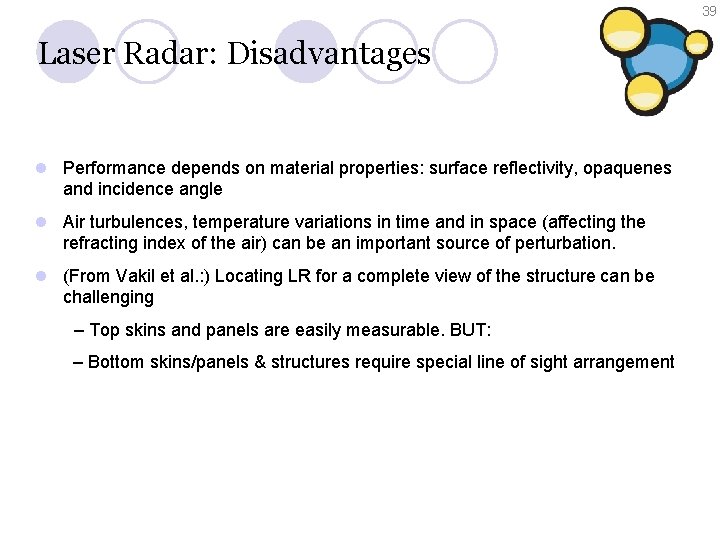
![40 Laser Radar: Applications Aircraft Fuselage Measurement [Lazar, 2007] 40 Laser Radar: Applications Aircraft Fuselage Measurement [Lazar, 2007]](https://slidetodoc.com/presentation_image/102245766866fc96f877691adca2ebfe/image-40.jpg)
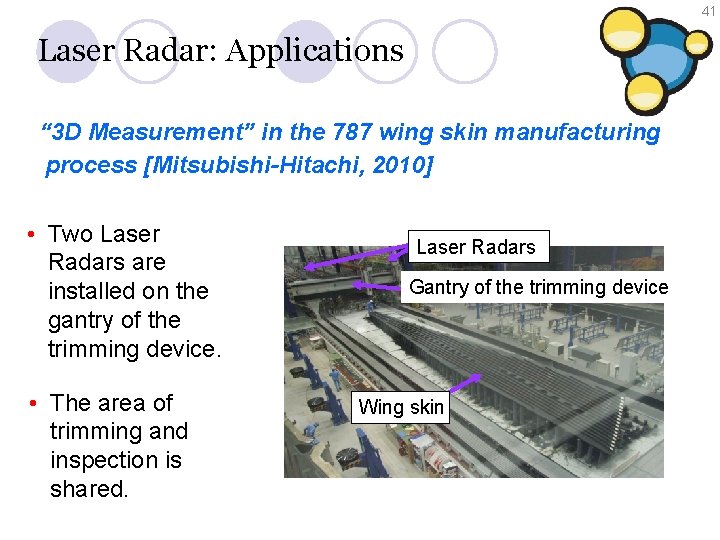
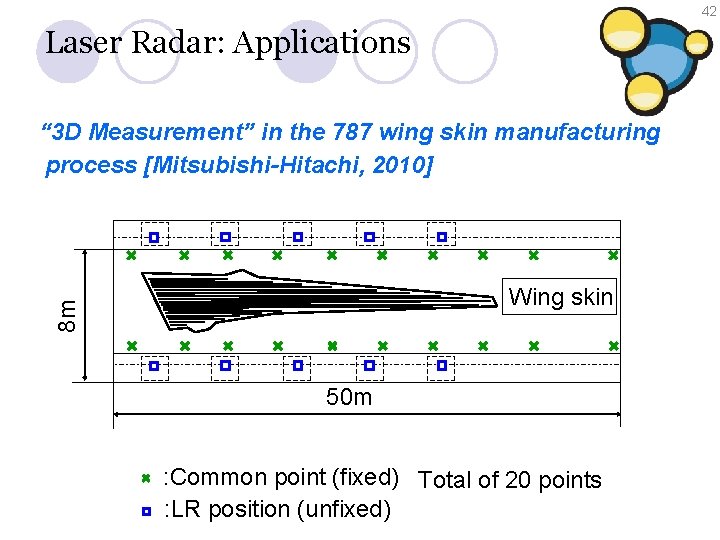
![43 Laser Radar: Applications Antenna Measurement [Fratena, 2010] Comparison between photogrammetry and laser radar 43 Laser Radar: Applications Antenna Measurement [Fratena, 2010] Comparison between photogrammetry and laser radar](https://slidetodoc.com/presentation_image/102245766866fc96f877691adca2ebfe/image-43.jpg)
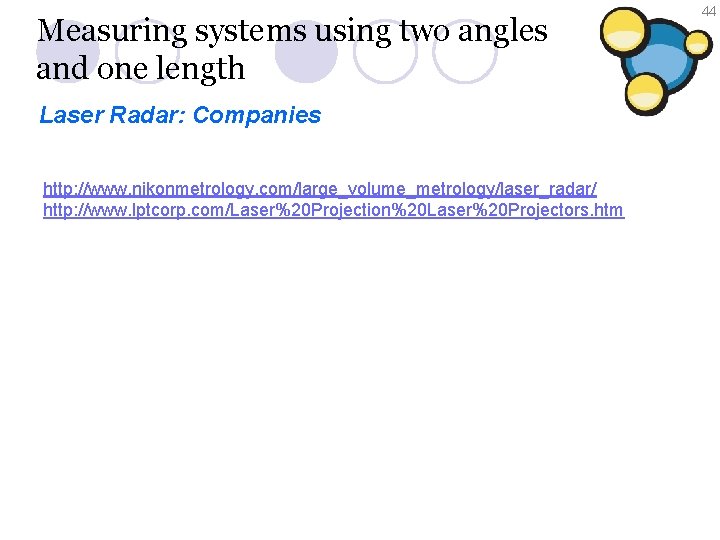
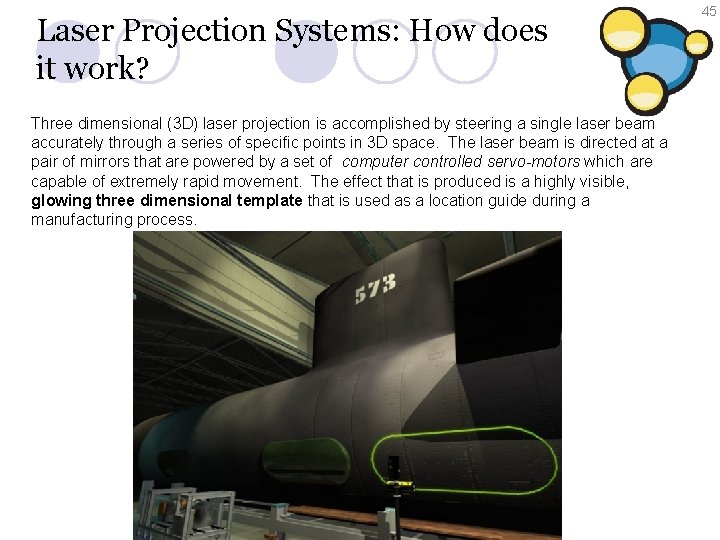
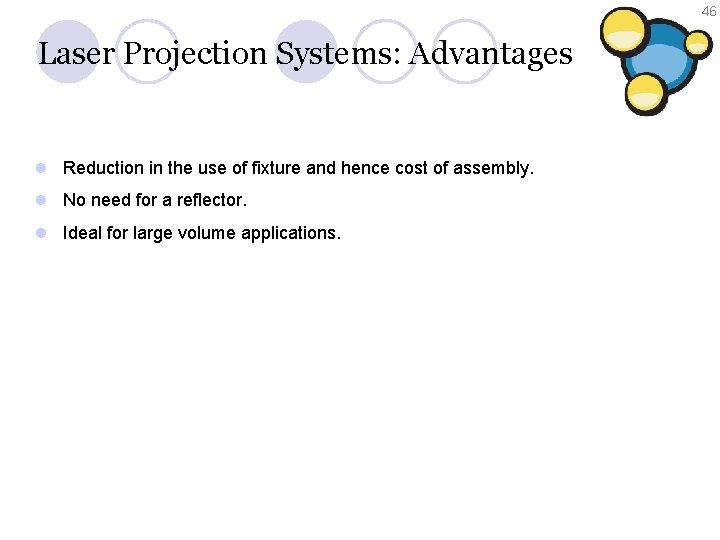
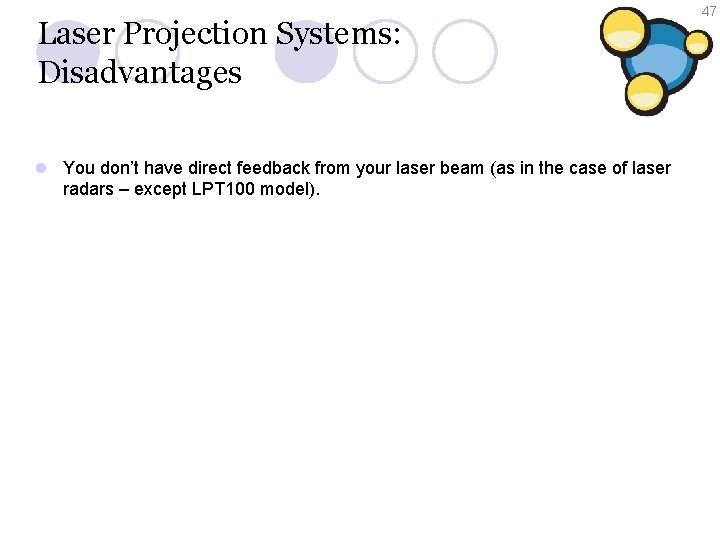
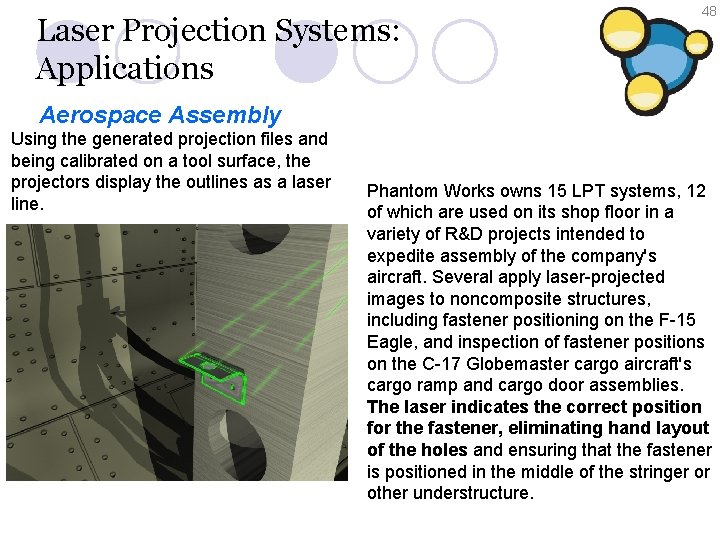
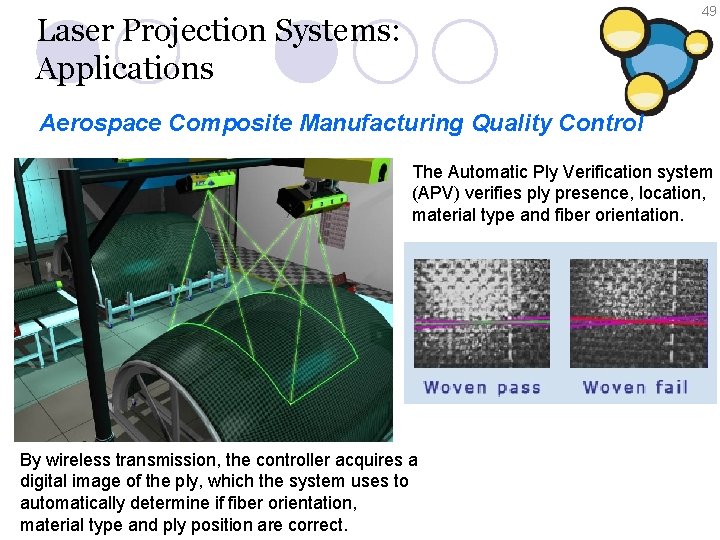
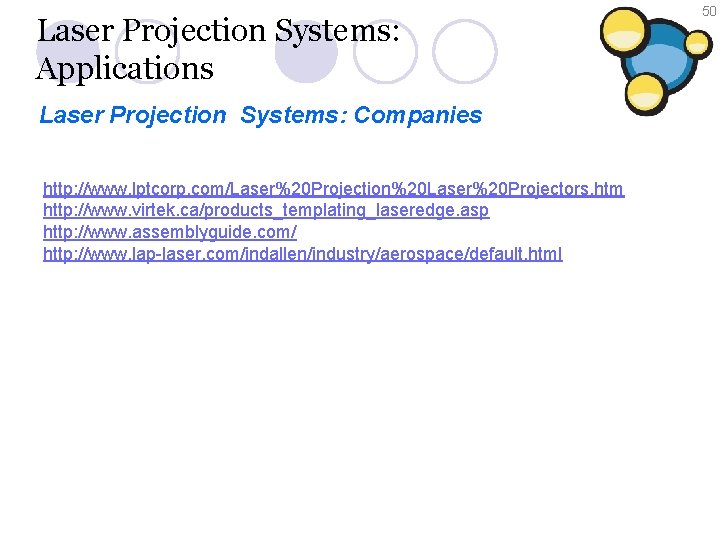
![51 CLASSIFICATION Requirements of a LSM system [Galetto, 2010] IGPS concerns the minimum number 51 CLASSIFICATION Requirements of a LSM system [Galetto, 2010] IGPS concerns the minimum number](https://slidetodoc.com/presentation_image/102245766866fc96f877691adca2ebfe/image-51.jpg)
![52 SYSTEM COMPARISON Large Volume Measurement Systems [Muelaner, 2008] The measurement of a 3 52 SYSTEM COMPARISON Large Volume Measurement Systems [Muelaner, 2008] The measurement of a 3](https://slidetodoc.com/presentation_image/102245766866fc96f877691adca2ebfe/image-52.jpg)
- Slides: 52
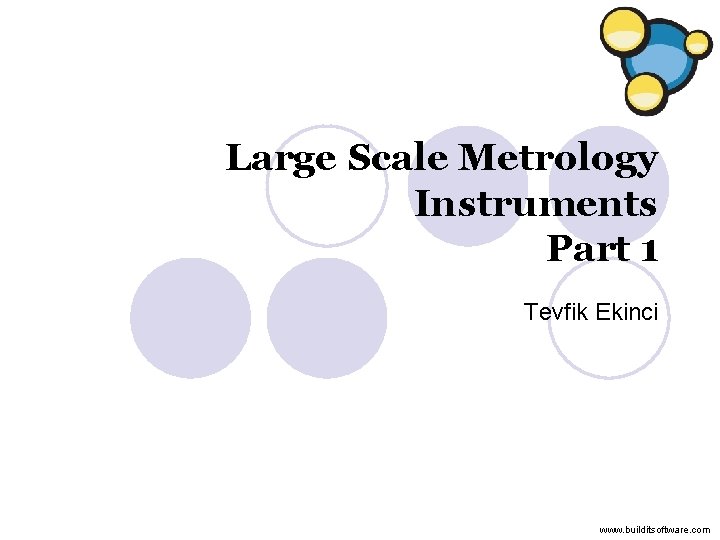
Large Scale Metrology Instruments Part 1 Tevfik Ekinci www. builditsoftware. com
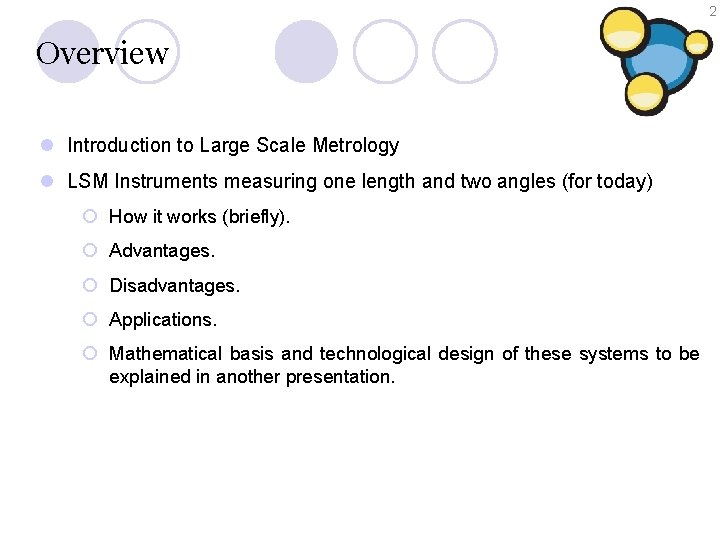
2 Overview l Introduction to Large Scale Metrology l LSM Instruments measuring one length and two angles (for today) ¡ How it works (briefly). ¡ Advantages. ¡ Disadvantages. ¡ Applications. ¡ Mathematical basis and technological design of these systems to be explained in another presentation.
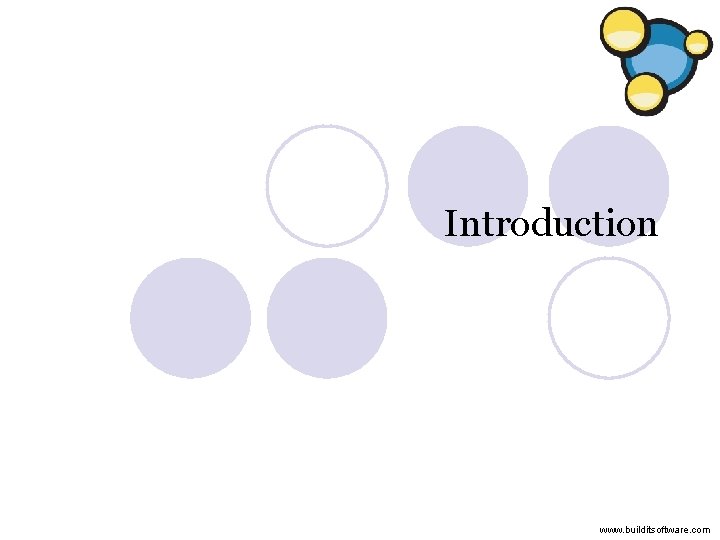
Introduction www. builditsoftware. com
![WHAT IS LARGE SCALE METROLOGY Metrology of freeform shaped parts Savio 2007 The field WHAT IS LARGE SCALE METROLOGY? Metrology of freeform shaped parts [Savio, 2007] The field](https://slidetodoc.com/presentation_image/102245766866fc96f877691adca2ebfe/image-4.jpg)
WHAT IS LARGE SCALE METROLOGY? Metrology of freeform shaped parts [Savio, 2007] The field of large-scale metrology can be defined as the metrology of large machines and structures. The boundaries of this field are laboratory measurements at one end and surveying at the other. Neither boundary is well defined and will generally be confined to the metrology of objects in which the linear dimensions range from tens to hundreds of meters 4
![5 APPLICATION EXAMPLES Metrology of freeform shaped parts Savio 2007 5 APPLICATION EXAMPLES Metrology of freeform shaped parts [Savio, 2007]](https://slidetodoc.com/presentation_image/102245766866fc96f877691adca2ebfe/image-5.jpg)
5 APPLICATION EXAMPLES Metrology of freeform shaped parts [Savio, 2007]
![WHY FRAMELESS METROLOGY Large Scale Metrology In Aerospace Assembly Muelaner 2008 Assembly may account WHY FRAMELESS METROLOGY? Large Scale Metrology In Aerospace Assembly [Muelaner, 2008] Assembly may account](https://slidetodoc.com/presentation_image/102245766866fc96f877691adca2ebfe/image-6.jpg)
WHY FRAMELESS METROLOGY? Large Scale Metrology In Aerospace Assembly [Muelaner, 2008] Assembly may account for as much as 40% of the total cost of manufacturing an airframe due largely to the labour and quality issues inherent to drilling thousands of holes per aircraft (Bullen 1997). Approximately 5% of the total manufacturing cost of an aircraft (Rooks 2005) or 10% of the airframe (Burley et al, 1999) is related to the use of fixed tooling. Large scale frameless metrology systems such as laser and vision based technologies have the potential to overcome many problems in aerospace assembly by enabling flexible automation systems. www. builditsoftware. com
![WHY AEROSPACE Users in 3 D Metrology Kyle 2010 www builditsoftware com WHY AEROSPACE? Users in 3 D Metrology [Kyle, 2010] www. builditsoftware. com](https://slidetodoc.com/presentation_image/102245766866fc96f877691adca2ebfe/image-7.jpg)
WHY AEROSPACE? Users in 3 D Metrology [Kyle, 2010] www. builditsoftware. com
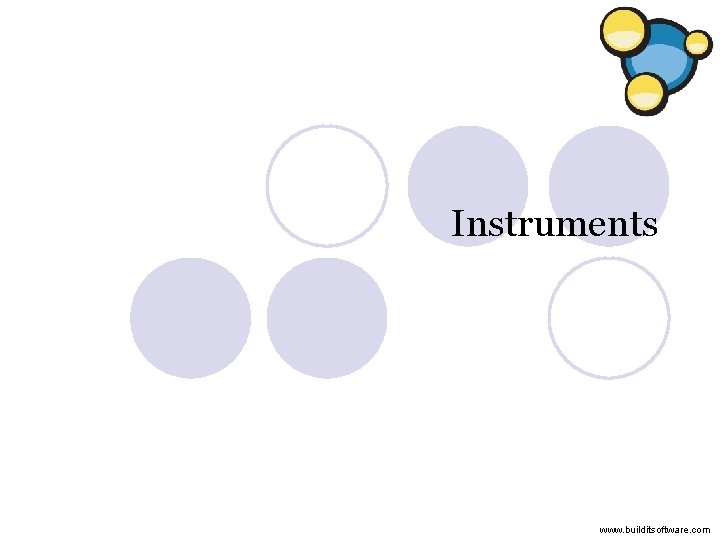
Instruments www. builditsoftware. com
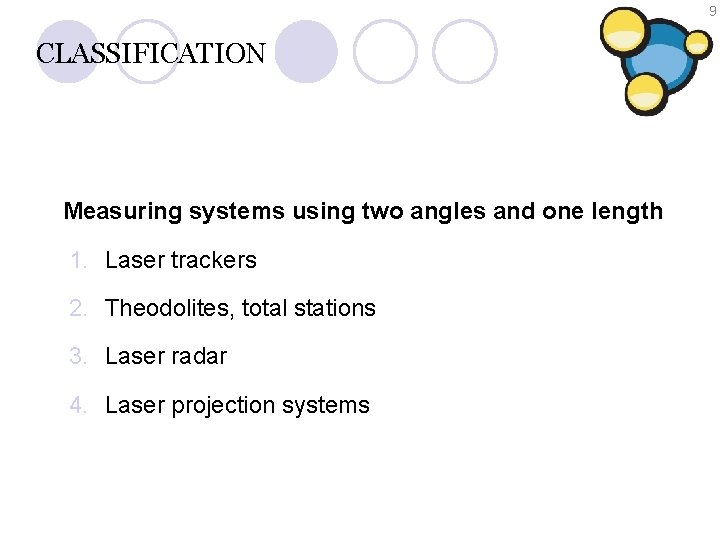
9 CLASSIFICATION Measuring systems using two angles and one length 1. Laser trackers 2. Theodolites, total stations 3. Laser radar 4. Laser projection systems
![10 Laser Tracker How does it work Laser Tracker Muelaner 2008 Laserbased spherical coordinate 10 Laser Tracker: How does it work? Laser Tracker [Muelaner, 2008] Laser-based spherical coordinate](https://slidetodoc.com/presentation_image/102245766866fc96f877691adca2ebfe/image-10.jpg)
10 Laser Tracker: How does it work? Laser Tracker [Muelaner, 2008] Laser-based spherical coordinate measurement systems combine a laser distance measurement with two angle measurements to give coordinate measurements in 3 dimensions. The main body of the instrument emits a laser from a gimbaled head; in the case of a laser tracker a spherically mounted retroreflector (SMR) is then used to reflect the laser back to the unit allowing the distance to be measured.
![11 Laser Tracker How does it work Laser Tracker Muelaner 2008 Sensors detect the 11 Laser Tracker: How does it work? Laser Tracker [Muelaner, 2008] Sensors detect the](https://slidetodoc.com/presentation_image/102245766866fc96f877691adca2ebfe/image-11.jpg)
11 Laser Tracker: How does it work? Laser Tracker [Muelaner, 2008] Sensors detect the position of the returned laser and provide feedback to sensors in the gimbal in order to track the reflector so that as the reflector moves so does the gimbaled head; keeping the laser aimed at the reflector. Encoders in the gimbal measure the azimuth and elevation angle to the reflector. In this way the laser tracker is able to measure the coordinates to the center of the SMR. The SMR has a known calibrated radius and so can be used as a probe with which objects can be measured.
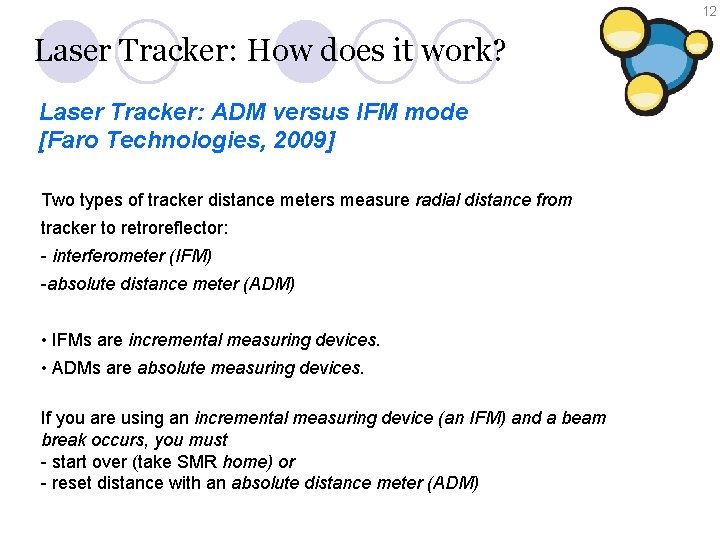
12 Laser Tracker: How does it work? Laser Tracker: ADM versus IFM mode [Faro Technologies, 2009] Two types of tracker distance meters measure radial distance from tracker to retroreflector: - interferometer (IFM) -absolute distance meter (ADM) • IFMs are incremental measuring devices. • ADMs are absolute measuring devices. If you are using an incremental measuring device (an IFM) and a beam break occurs, you must - start over (take SMR home) or - reset distance with an absolute distance meter (ADM)
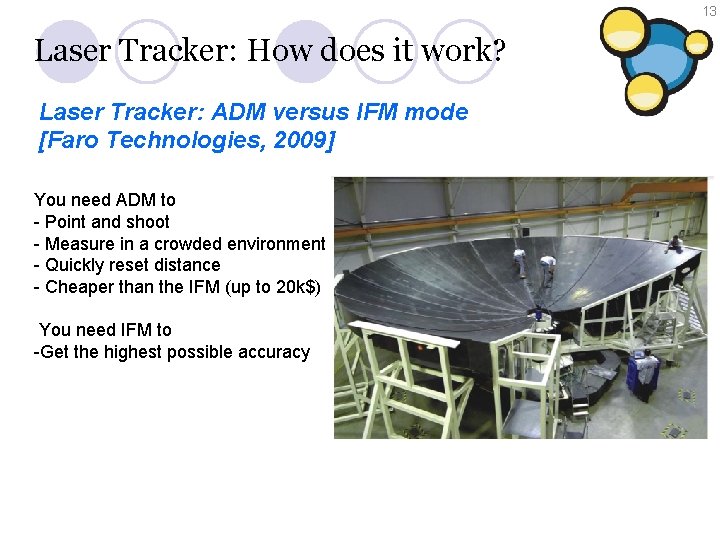
13 Laser Tracker: How does it work? Laser Tracker: ADM versus IFM mode [Faro Technologies, 2009] You need ADM to - Point and shoot - Measure in a crowded environment - Quickly reset distance - Cheaper than the IFM (up to 20 k$) You need IFM to -Get the highest possible accuracy
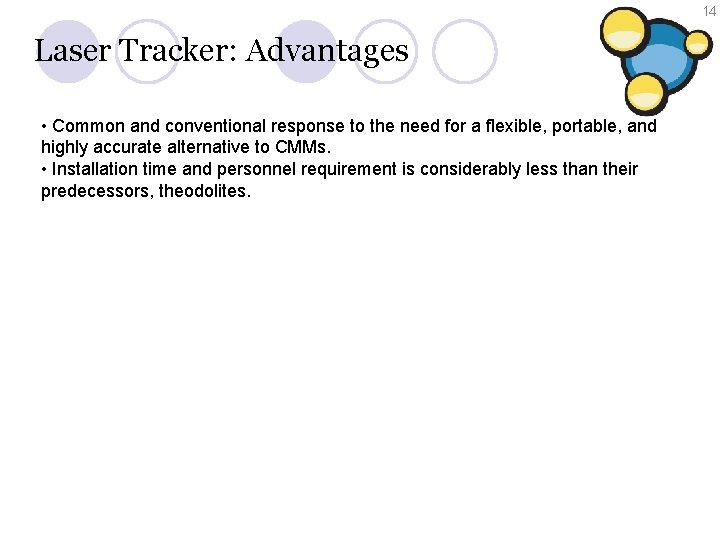
14 Laser Tracker: Advantages • Common and conventional response to the need for a flexible, portable, and highly accurate alternative to CMMs. • Installation time and personnel requirement is considerably less than their predecessors, theodolites.
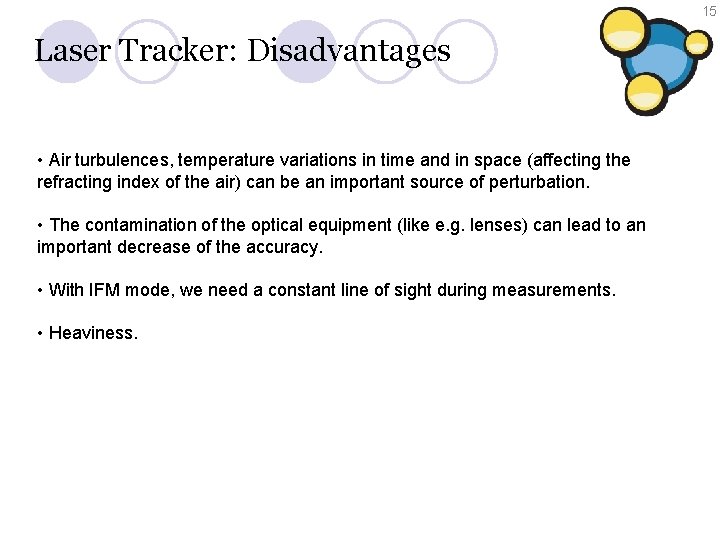
15 Laser Tracker: Disadvantages • Air turbulences, temperature variations in time and in space (affecting the refracting index of the air) can be an important source of perturbation. • The contamination of the optical equipment (like e. g. lenses) can lead to an important decrease of the accuracy. • With IFM mode, we need a constant line of sight during measurements. • Heaviness.
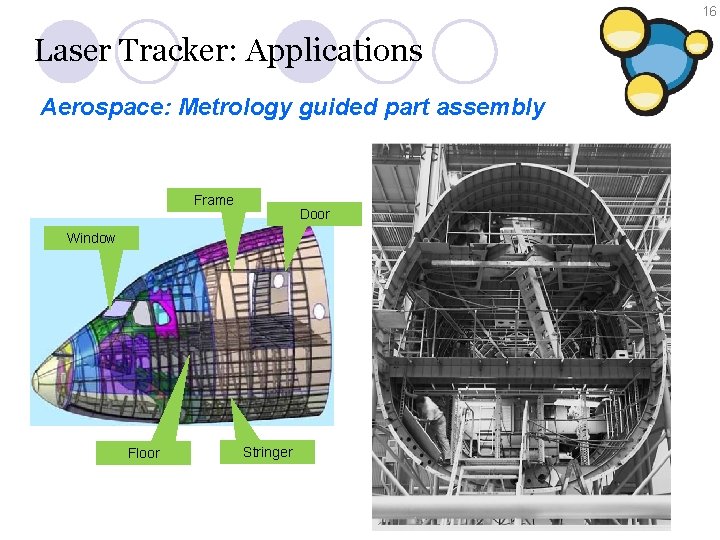
16 Laser Tracker: Applications Aerospace: Metrology guided part assembly Frame Door Window Floor Stringer
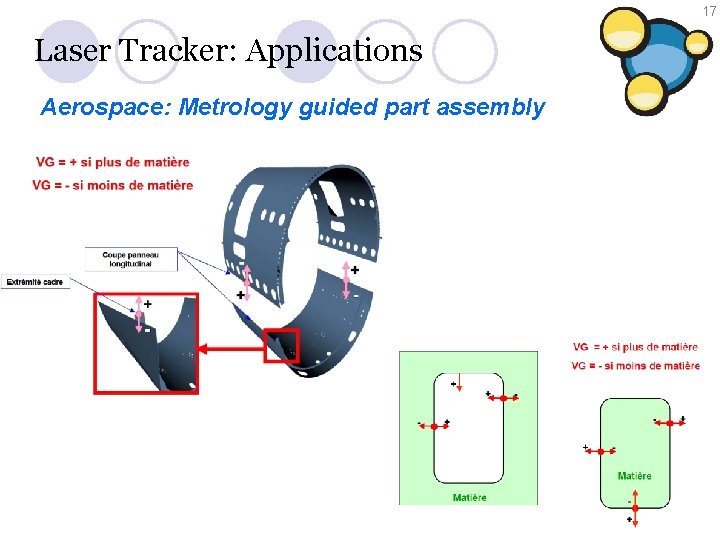
17 Laser Tracker: Applications Aerospace: Metrology guided part assembly Used especially for tooling applications.
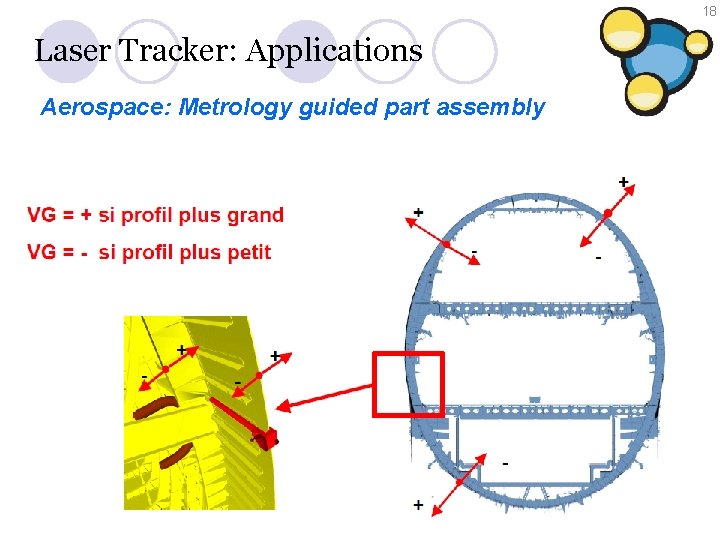
18 Laser Tracker: Applications Aerospace: Metrology guided part assembly Used especially for tooling applications.
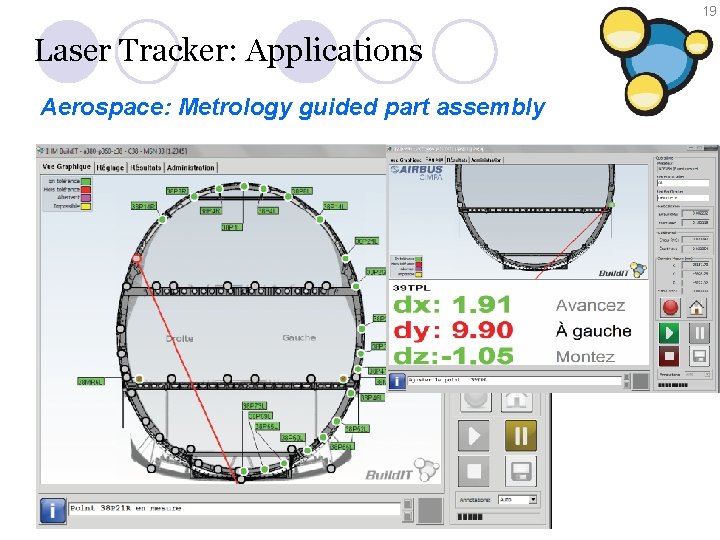
19 Laser Tracker: Applications Aerospace: Metrology guided part assembly Used especially for tooling applications.
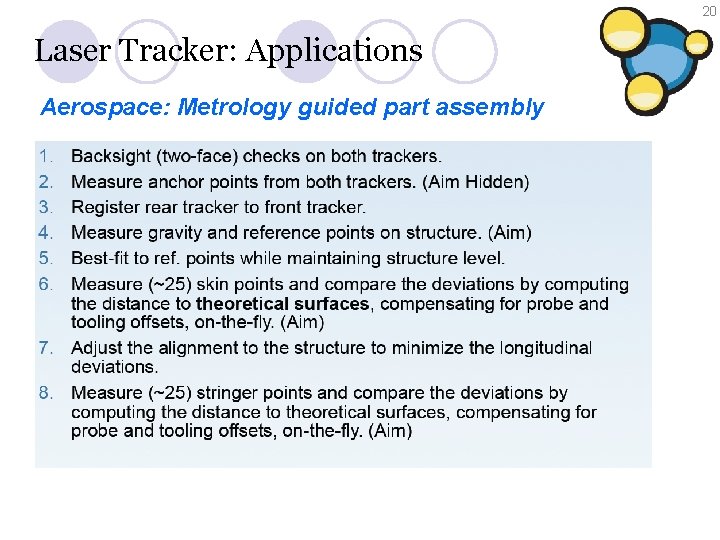
20 Laser Tracker: Applications Aerospace: Metrology guided part assembly Used especially for tooling applications.
![21 Laser Tracker Applications Aerospace Metrology guided jig assembly Airbus Airbus 380 21 Laser Tracker: Applications Aerospace: Metrology guided jig assembly [Airbus, Airbus 380]](https://slidetodoc.com/presentation_image/102245766866fc96f877691adca2ebfe/image-21.jpg)
21 Laser Tracker: Applications Aerospace: Metrology guided jig assembly [Airbus, Airbus 380]
![22 Laser Tracker Applications Aerospace Metrology guided jig assembly Airbus Airbus 380 22 Laser Tracker: Applications Aerospace: Metrology guided jig assembly [Airbus, Airbus 380]](https://slidetodoc.com/presentation_image/102245766866fc96f877691adca2ebfe/image-22.jpg)
22 Laser Tracker: Applications Aerospace: Metrology guided jig assembly [Airbus, Airbus 380]
![23 Laser Tracker Applications Aerospace Metrology guided jig assembly Airbus Airbus 380 23 Laser Tracker: Applications Aerospace: Metrology guided jig assembly [Airbus, Airbus 380]](https://slidetodoc.com/presentation_image/102245766866fc96f877691adca2ebfe/image-23.jpg)
23 Laser Tracker: Applications Aerospace: Metrology guided jig assembly [Airbus, Airbus 380]
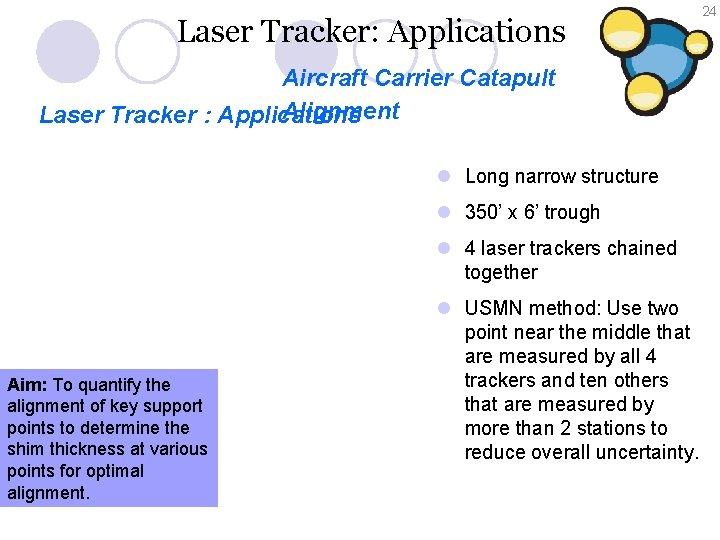
Laser Tracker: Applications 24 Aircraft Carrier Catapult Alignment Laser Tracker : Applications l Long narrow structure l 350’ x 6’ trough l 4 laser trackers chained together Aim: To quantify the alignment of key support points to determine the shim thickness at various points for optimal alignment. l USMN method: Use two point near the middle that are measured by all 4 trackers and ten others that are measured by more than 2 stations to reduce overall uncertainty.
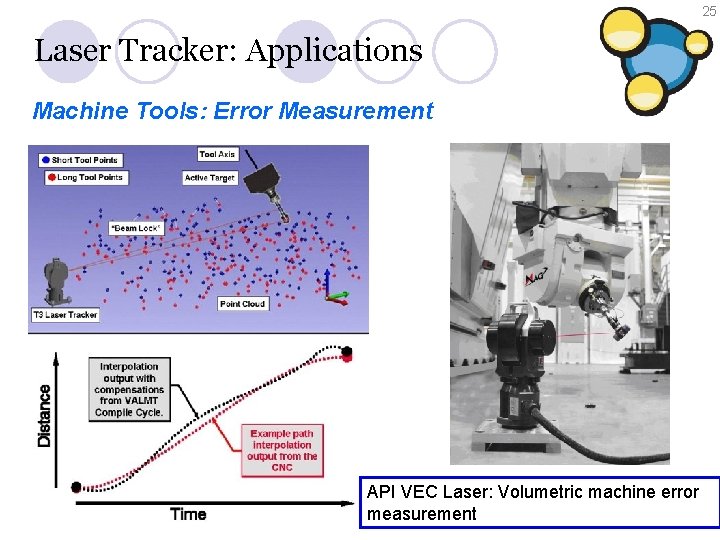
25 Laser Tracker: Applications Machine Tools: Error Measurement API VEC Laser: Volumetric machine error measurement
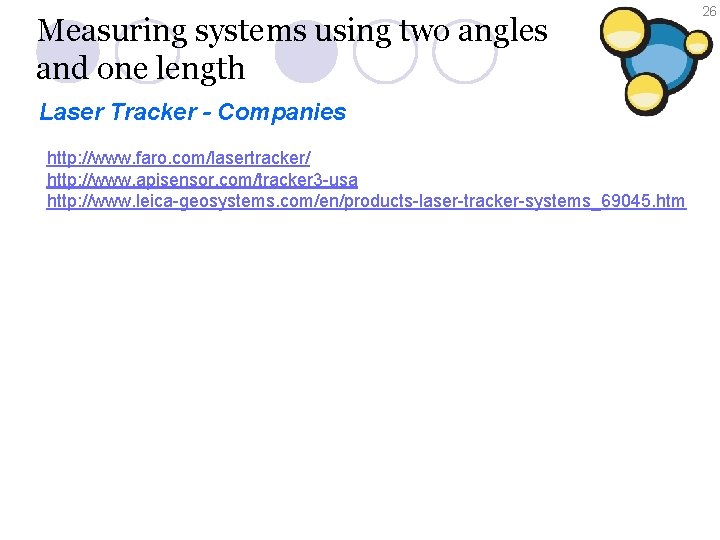
Measuring systems using two angles and one length Laser Tracker - Companies http: //www. faro. com/lasertracker/ http: //www. apisensor. com/tracker 3 -usa http: //www. leica-geosystems. com/en/products-laser-tracker-systems_69045. htm 26
![27 Total Station How does it work TheodoliteTotal station Leica 2010 Evolution Theodolite measures 27 Total Station: How does it work? Theodolite-Total station [Leica, 2010] Evolution: Theodolite measures](https://slidetodoc.com/presentation_image/102245766866fc96f877691adca2ebfe/image-27.jpg)
27 Total Station: How does it work? Theodolite-Total station [Leica, 2010] Evolution: Theodolite measures only azimuth and elevation angles. Total station measures both angles along with distance.
![28 Total Station How does it work TheodoliteTotal station Leica 2010 l Triangulation Knowns 28 Total Station: How does it work? Theodolite-Total station [Leica, 2010] l Triangulation: Knowns:](https://slidetodoc.com/presentation_image/102245766866fc96f877691adca2ebfe/image-28.jpg)
28 Total Station: How does it work? Theodolite-Total station [Leica, 2010] l Triangulation: Knowns: Distance AB, angles BAP and ABP. By Sinus theorem, we find the position of P. (Theodolite –capable of measuring only angles- is positioned in 2 positions with a known distance between them).
![29 Total Station How does it work Total station Accuracy Leica 2010 29 Total Station: How does it work? Total station – Accuracy [Leica, 2010]](https://slidetodoc.com/presentation_image/102245766866fc96f877691adca2ebfe/image-29.jpg)
29 Total Station: How does it work? Total station – Accuracy [Leica, 2010]
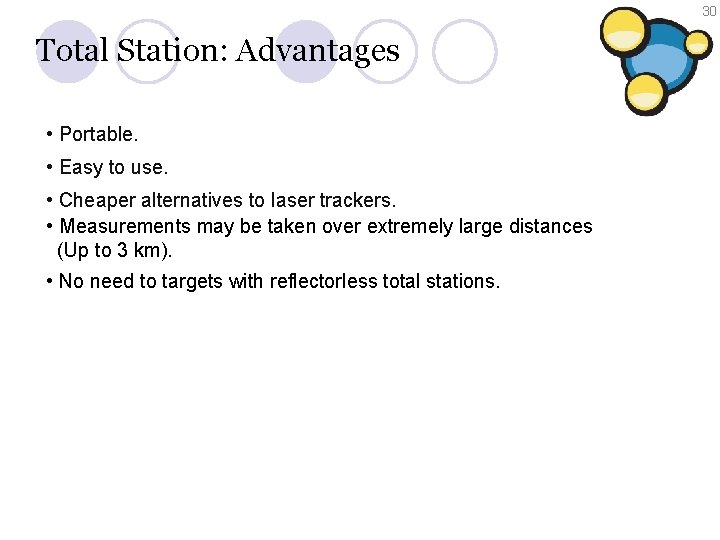
30 Total Station: Advantages • Portable. • Easy to use. • Cheaper alternatives to laser trackers. • Measurements may be taken over extremely large distances (Up to 3 km). • No need to targets with reflectorless total stations.
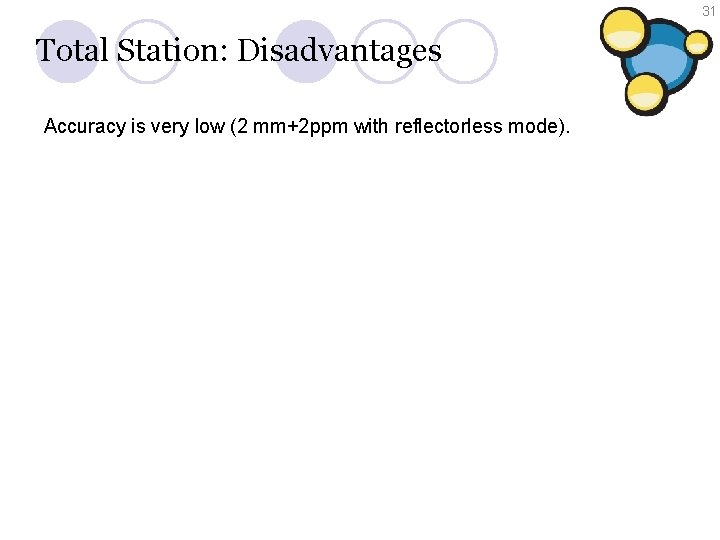
31 Total Station: Disadvantages Accuracy is very low (2 mm+2 ppm with reflectorless mode).
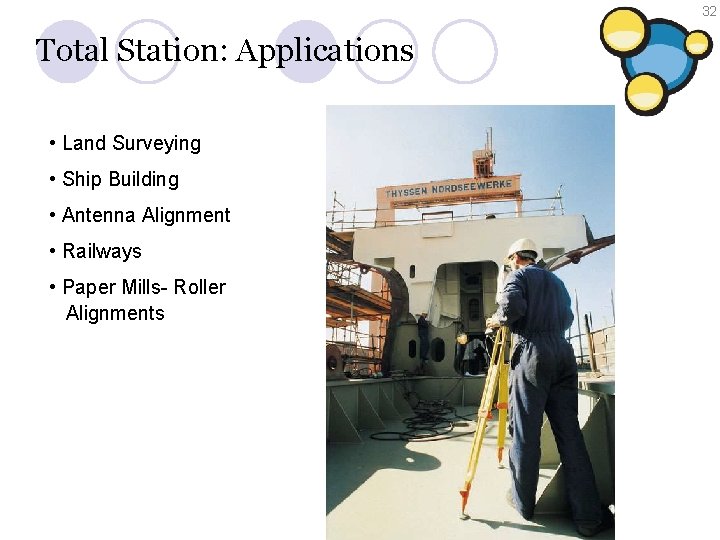
32 Total Station: Applications • Land Surveying • Ship Building • Antenna Alignment • Railways • Paper Mills- Roller Alignments
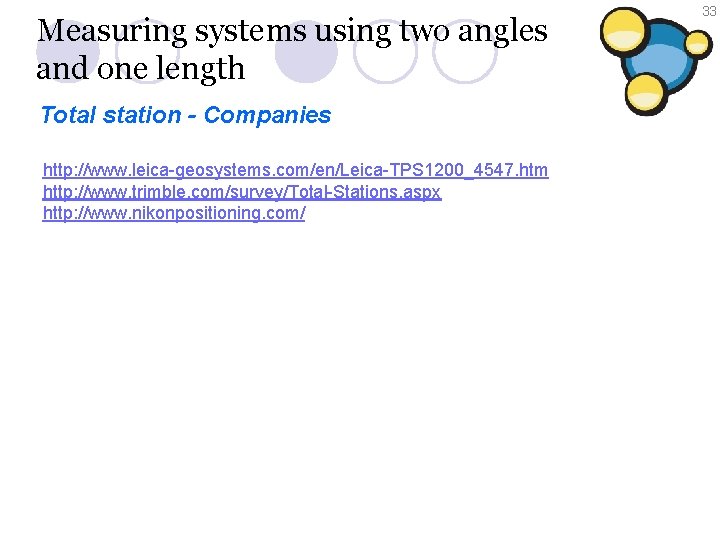
Measuring systems using two angles and one length Total station - Companies http: //www. leica-geosystems. com/en/Leica-TPS 1200_4547. htm http: //www. trimble. com/survey/Total-Stations. aspx http: //www. nikonpositioning. com/ 33
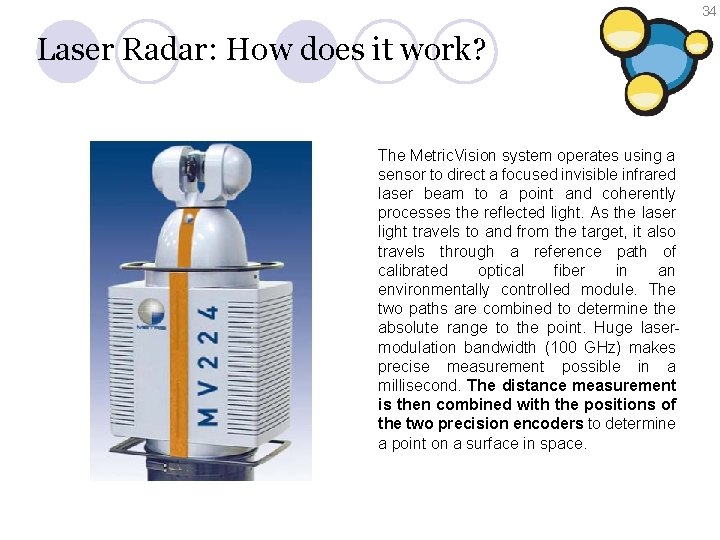
34 Laser Radar: How does it work? The Metric. Vision system operates using a sensor to direct a focused invisible infrared laser beam to a point and coherently processes the reflected light. As the laser light travels to and from the target, it also travels through a reference path of calibrated optical fiber in an environmentally controlled module. The two paths are combined to determine the absolute range to the point. Huge lasermodulation bandwidth (100 GHz) makes precise measurement possible in a millisecond. The distance measurement is then combined with the positions of the two precision encoders to determine a point on a surface in space.
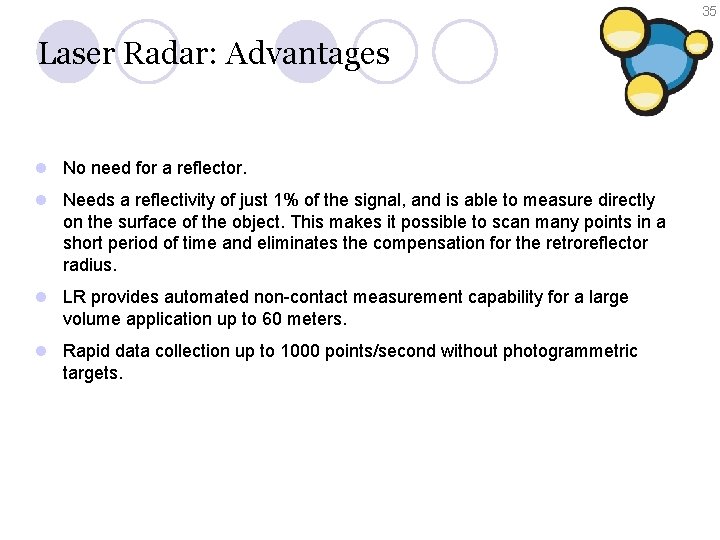
35 Laser Radar: Advantages l No need for a reflector. l Needs a reflectivity of just 1% of the signal, and is able to measure directly on the surface of the object. This makes it possible to scan many points in a short period of time and eliminates the compensation for the retroreflector radius. l LR provides automated non-contact measurement capability for a large volume application up to 60 meters. l Rapid data collection up to 1000 points/second without photogrammetric targets.
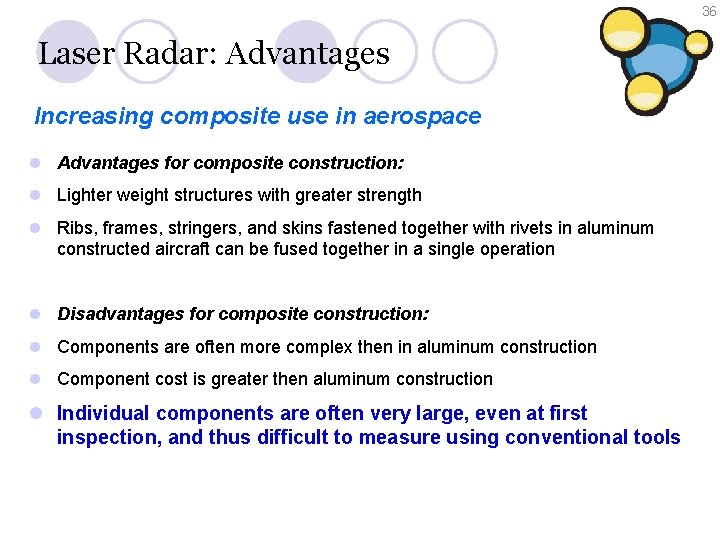
36 Laser Radar: Advantages Increasing composite use in aerospace l Advantages for composite construction: l Lighter weight structures with greater strength l Ribs, frames, stringers, and skins fastened together with rivets in aluminum constructed aircraft can be fused together in a single operation l Disadvantages for composite construction: l Components are often more complex then in aluminum construction l Component cost is greater then aluminum construction l Individual components are often very large, even at first inspection, and thus difficult to measure using conventional tools
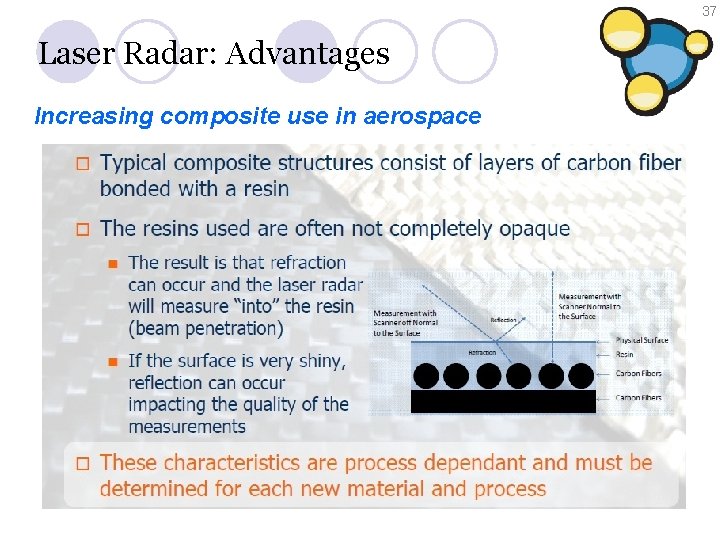
37 Laser Radar: Advantages Increasing composite use in aerospace
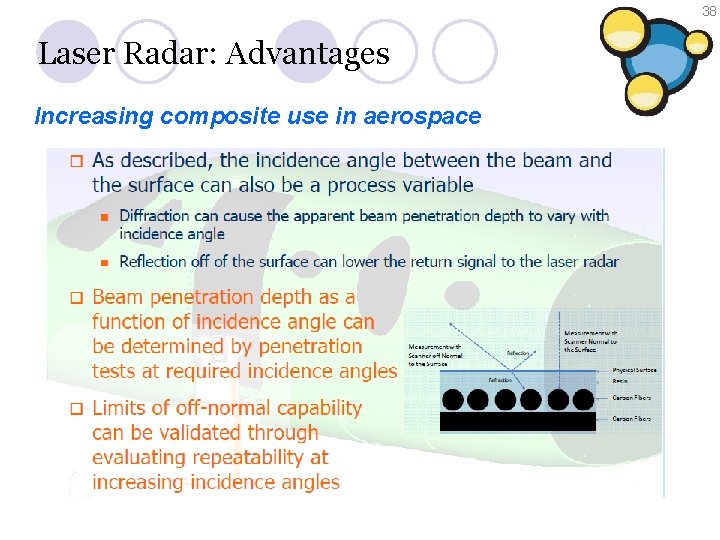
38 Laser Radar: Advantages Increasing composite use in aerospace
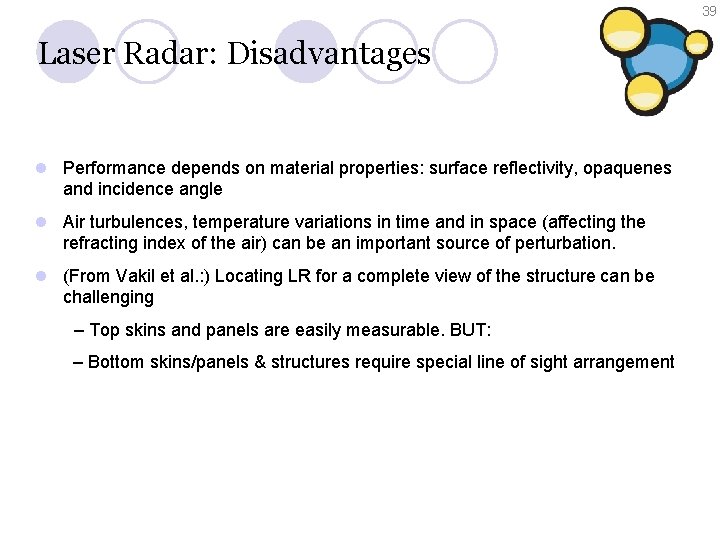
39 Laser Radar: Disadvantages l Performance depends on material properties: surface reflectivity, opaquenes and incidence angle l Air turbulences, temperature variations in time and in space (affecting the refracting index of the air) can be an important source of perturbation. l (From Vakil et al. : ) Locating LR for a complete view of the structure can be challenging – Top skins and panels are easily measurable. BUT: – Bottom skins/panels & structures require special line of sight arrangement
![40 Laser Radar Applications Aircraft Fuselage Measurement Lazar 2007 40 Laser Radar: Applications Aircraft Fuselage Measurement [Lazar, 2007]](https://slidetodoc.com/presentation_image/102245766866fc96f877691adca2ebfe/image-40.jpg)
40 Laser Radar: Applications Aircraft Fuselage Measurement [Lazar, 2007]
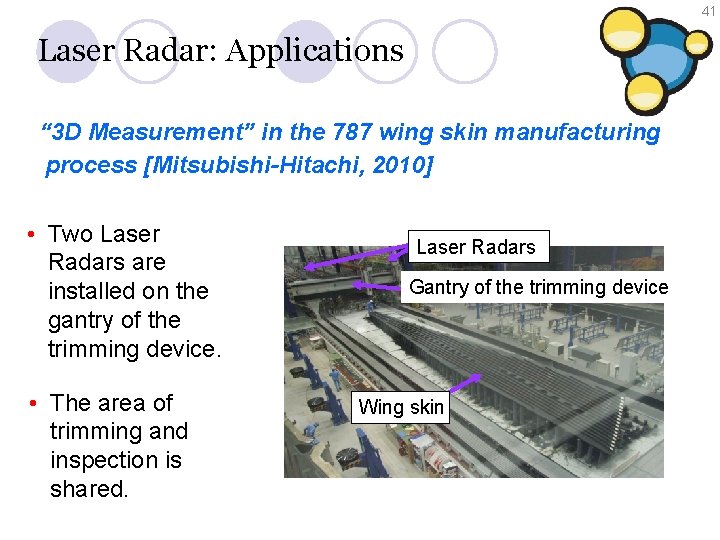
41 Laser Radar: Applications “ 3 D Measurement” in the 787 wing skin manufacturing process [Mitsubishi-Hitachi, 2010] • Two Laser Radars are installed on the gantry of the trimming device. • The area of trimming and inspection is shared. Laser Radars Gantry of the trimming device Wing skin
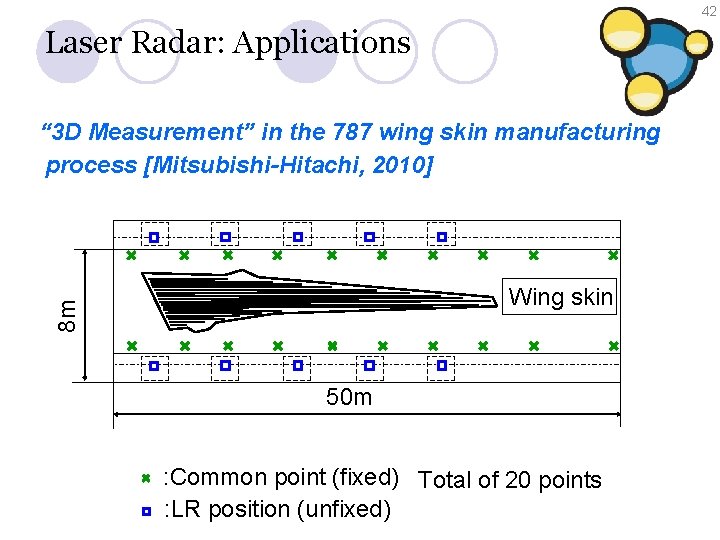
42 Laser Radar: Applications “ 3 D Measurement” in the 787 wing skin manufacturing process [Mitsubishi-Hitachi, 2010] 8 m Wing skin 50 m : Common point (fixed) Total of 20 points : LR position (unfixed)
![43 Laser Radar Applications Antenna Measurement Fratena 2010 Comparison between photogrammetry and laser radar 43 Laser Radar: Applications Antenna Measurement [Fratena, 2010] Comparison between photogrammetry and laser radar](https://slidetodoc.com/presentation_image/102245766866fc96f877691adca2ebfe/image-43.jpg)
43 Laser Radar: Applications Antenna Measurement [Fratena, 2010] Comparison between photogrammetry and laser radar
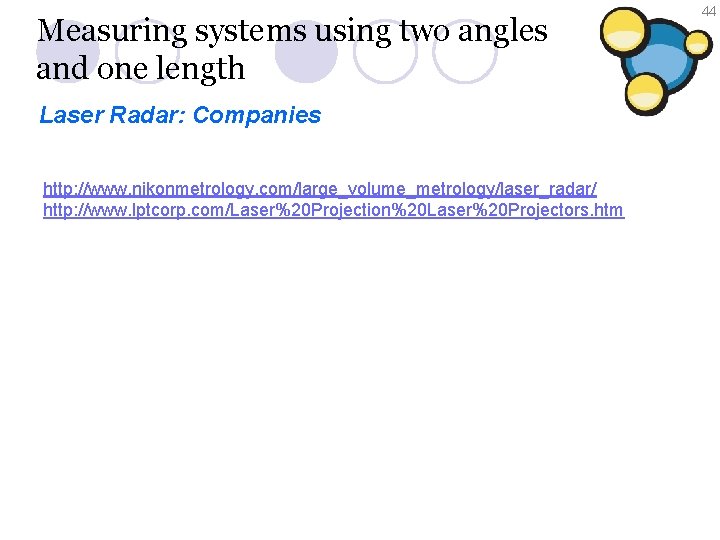
Measuring systems using two angles and one length Laser Radar: Companies http: //www. nikonmetrology. com/large_volume_metrology/laser_radar/ http: //www. lptcorp. com/Laser%20 Projection%20 Laser%20 Projectors. htm 44
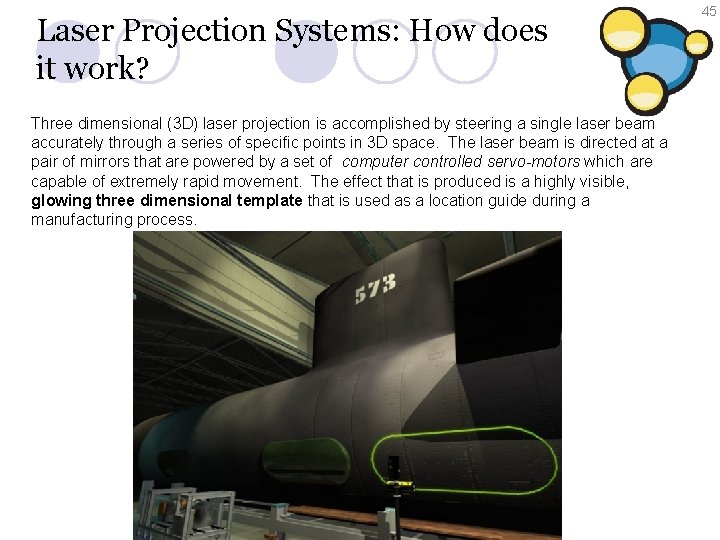
Laser Projection Systems: How does it work? Three dimensional (3 D) laser projection is accomplished by steering a single laser beam accurately through a series of specific points in 3 D space. The laser beam is directed at a pair of mirrors that are powered by a set of computer controlled servo-motors which are capable of extremely rapid movement. The effect that is produced is a highly visible, glowing three dimensional template that is used as a location guide during a manufacturing process. 45
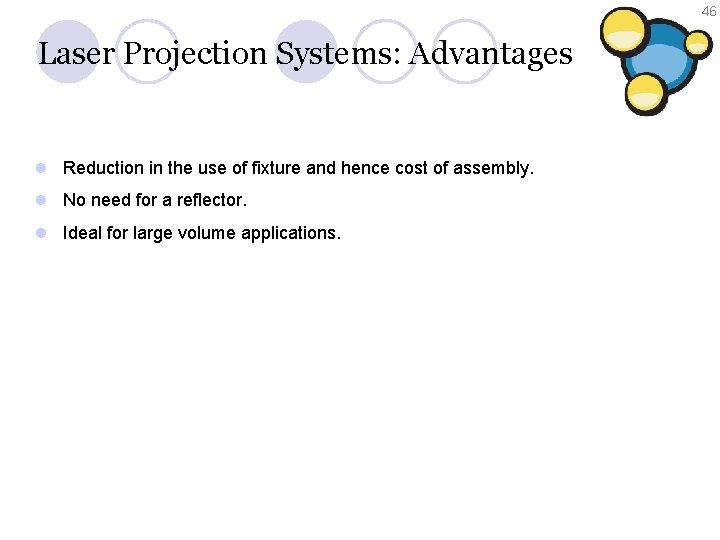
46 Laser Projection Systems: Advantages l Reduction in the use of fixture and hence cost of assembly. l No need for a reflector. l Ideal for large volume applications.
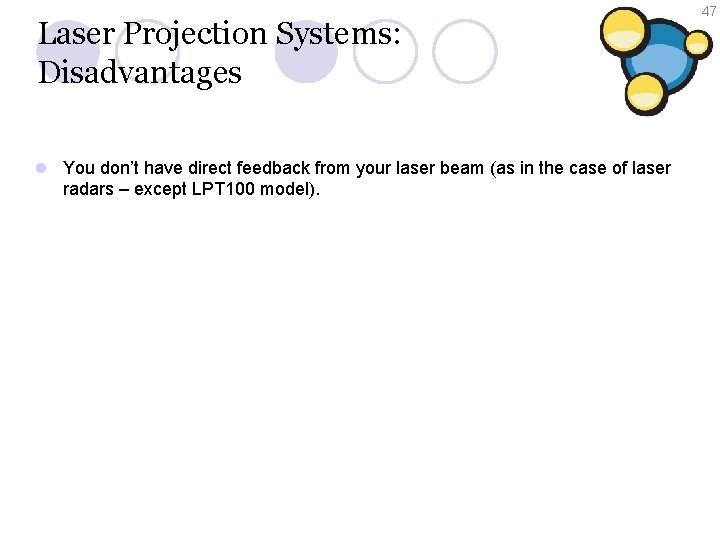
Laser Projection Systems: Disadvantages l You don’t have direct feedback from your laser beam (as in the case of laser radars – except LPT 100 model). 47
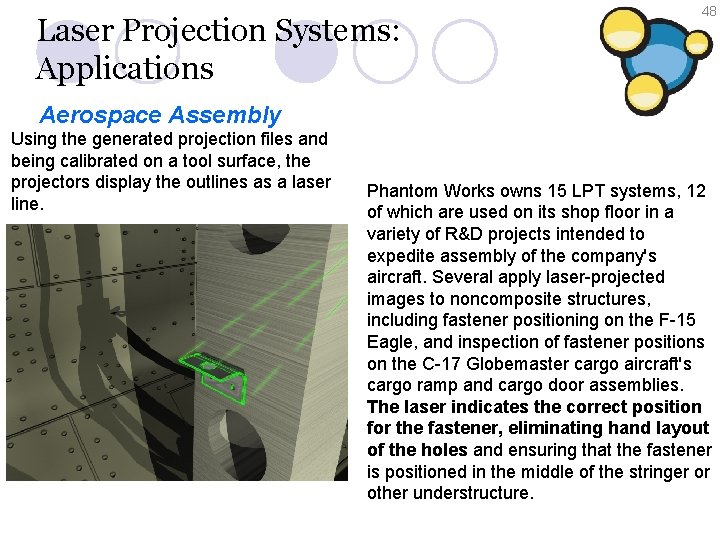
Laser Projection Systems: Applications 48 Aerospace Assembly Using the generated projection files and being calibrated on a tool surface, the projectors display the outlines as a laser line. Phantom Works owns 15 LPT systems, 12 of which are used on its shop floor in a variety of R&D projects intended to expedite assembly of the company's aircraft. Several apply laser-projected images to noncomposite structures, including fastener positioning on the F-15 Eagle, and inspection of fastener positions on the C-17 Globemaster cargo aircraft's cargo ramp and cargo door assemblies. The laser indicates the correct position for the fastener, eliminating hand layout of the holes and ensuring that the fastener is positioned in the middle of the stringer or other understructure.
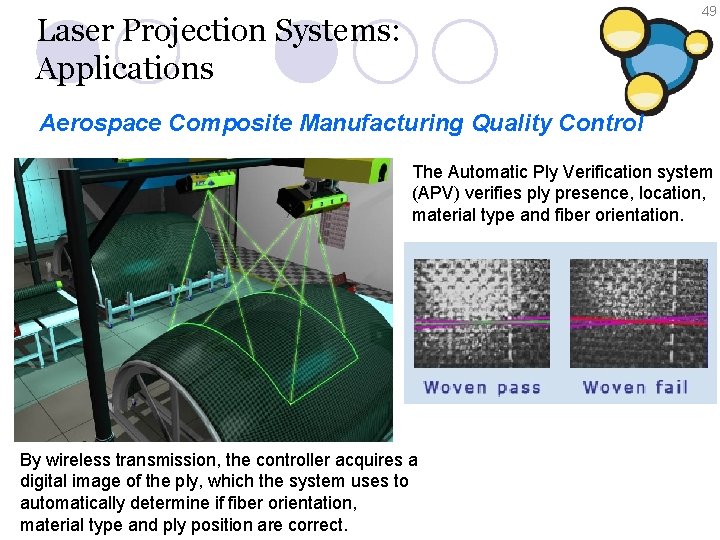
49 Laser Projection Systems: Applications Aerospace Composite Manufacturing Quality Control The Automatic Ply Verification system (APV) verifies ply presence, location, material type and fiber orientation. By wireless transmission, the controller acquires a digital image of the ply, which the system uses to automatically determine if fiber orientation, material type and ply position are correct.
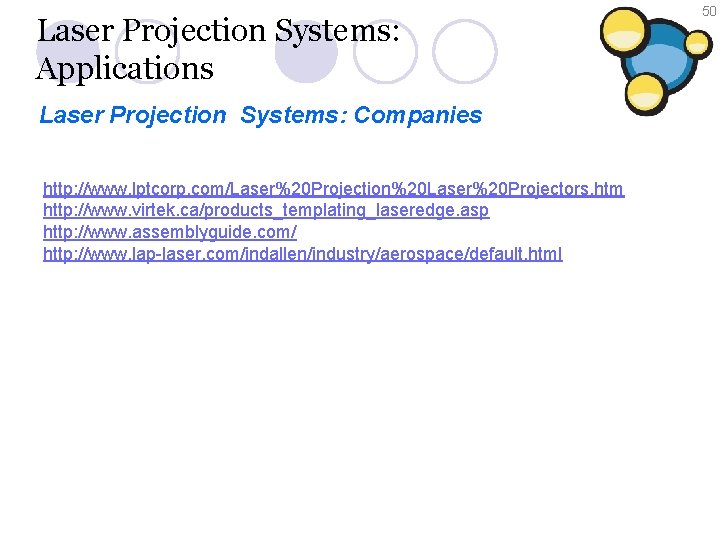
Laser Projection Systems: Applications Laser Projection Systems: Companies http: //www. lptcorp. com/Laser%20 Projection%20 Laser%20 Projectors. htm http: //www. virtek. ca/products_templating_laseredge. asp http: //www. assemblyguide. com/ http: //www. lap-laser. com/indallen/industry/aerospace/default. html 50
![51 CLASSIFICATION Requirements of a LSM system Galetto 2010 IGPS concerns the minimum number 51 CLASSIFICATION Requirements of a LSM system [Galetto, 2010] IGPS concerns the minimum number](https://slidetodoc.com/presentation_image/102245766866fc96f877691adca2ebfe/image-51.jpg)
51 CLASSIFICATION Requirements of a LSM system [Galetto, 2010] IGPS concerns the minimum number of sensors necessary: 3 units.
![52 SYSTEM COMPARISON Large Volume Measurement Systems Muelaner 2008 The measurement of a 3 52 SYSTEM COMPARISON Large Volume Measurement Systems [Muelaner, 2008] The measurement of a 3](https://slidetodoc.com/presentation_image/102245766866fc96f877691adca2ebfe/image-52.jpg)
52 SYSTEM COMPARISON Large Volume Measurement Systems [Muelaner, 2008] The measurement of a 3 m part at a range of 4 m.
Sosyalbilgiler biz
Mehmet behzat ekinci
Zelal ekinci
Dr zelal ekinci
Small scale or large scale
Large scale map definition
Map scale ratio
Large scale vs small scale map
Geography skills handbook
1474
Hüseyin tevfik paşa
Mehmet tevfik dorak
Mehmet dorak
Tevfik dorak
Bandaging material elasticon
What are passive instruments
Pressure measuring devices
The anatomy of a large scale hypertextual web search engine
The anatomy of a large scale hypertextual web search engine
Large rotating air mass
Bench scale fermentation
Large scale chart definition
Ultra large scale
Large scale global investment
Automatic wrappers for large scale web extraction
Berk atikoglu
Large scale fading in wireless communication
Large-scale cluster management at google with borg
Large scale interventions
Large scale entry example
Distbelief
A comparison of approaches to large-scale data analysis
How do maps help focus the reader's attention
Pregel: a system for large-scale graph processing
Large scale systems
The anatomy of a large scale hypertextual web search engine
The anatomy of a large-scale hypertextual web search engine
Large scale manufacturing of semisolids
Market entry modes for international businesses chapter 7
Small scale maps
Perchloron
Oag: toward linking large-scale heterogeneous entity graphs
Large scale classification
Large-scale philanthropy
Aser
Part of large intestine
Single view metrology
Saudi standards, metrology and quality organization
Toshiba 1b japanasia
Reliability in metrology
Legal metrology department delhi
International metrology organization headquarters
Metrology