Manufacturing Processes Chap 35 Metrology Metrology Definition The
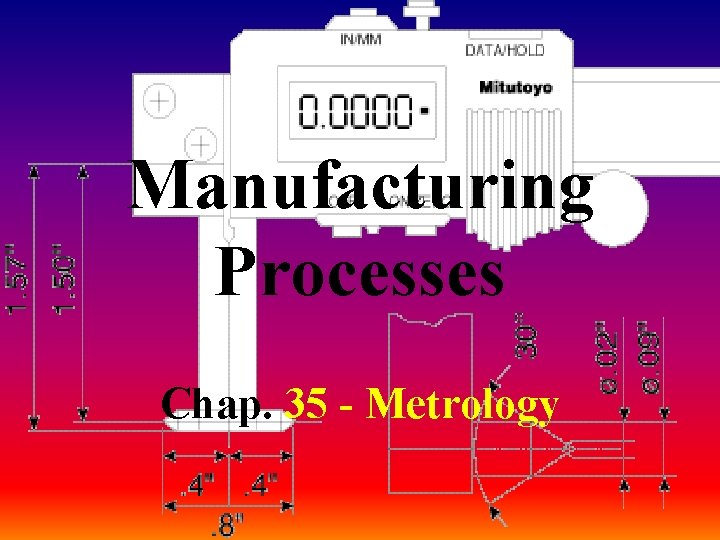
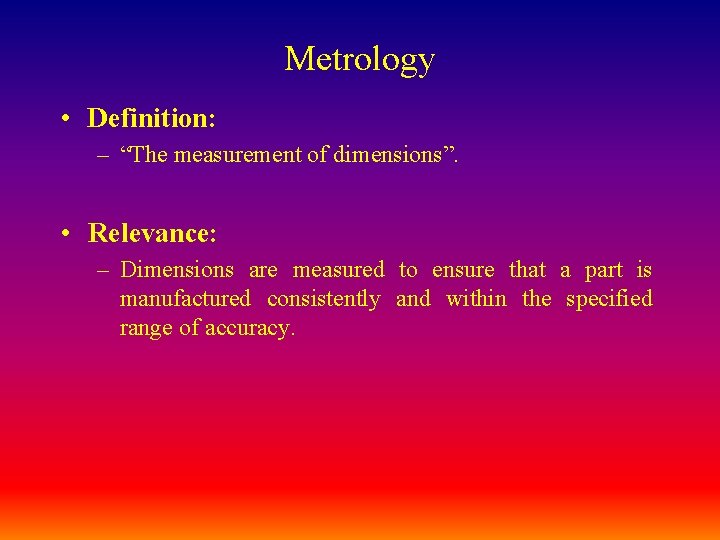
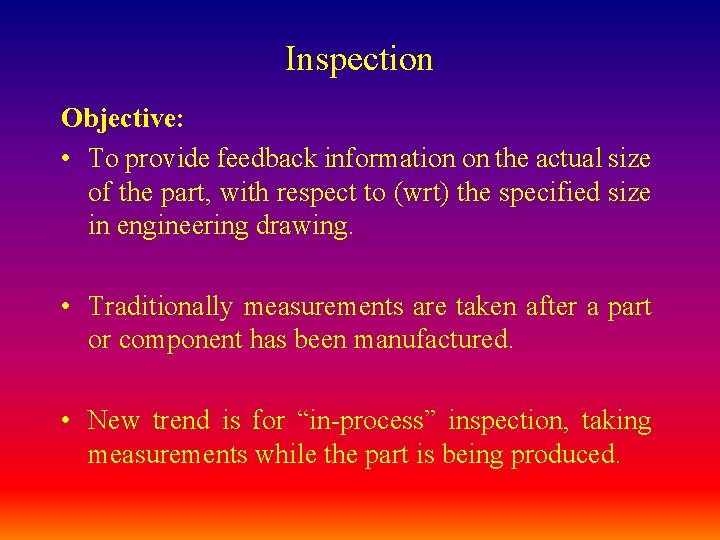
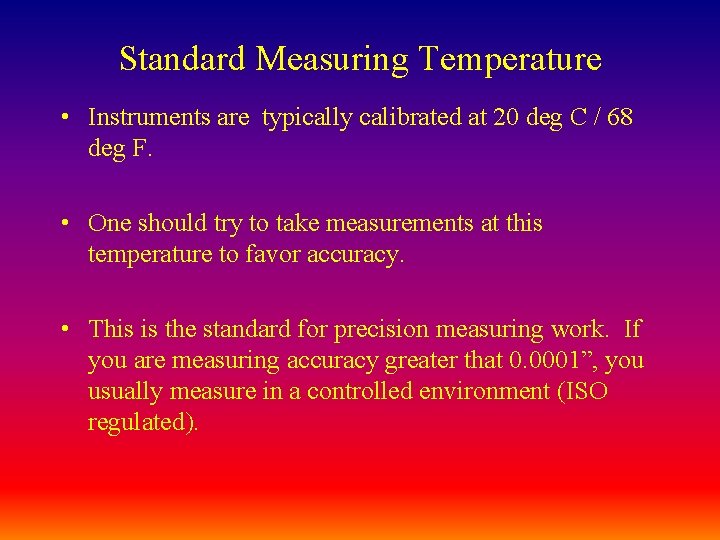
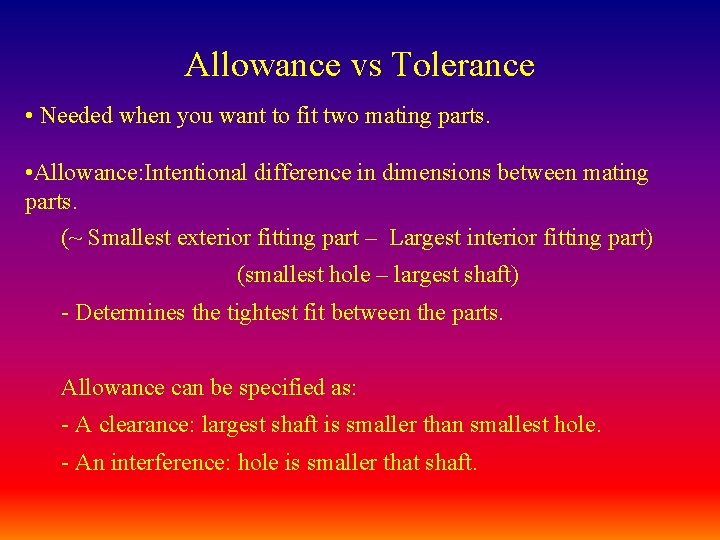
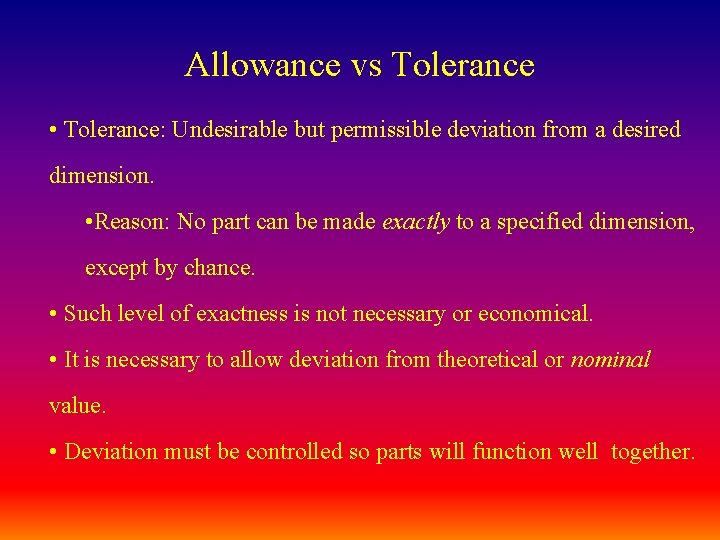
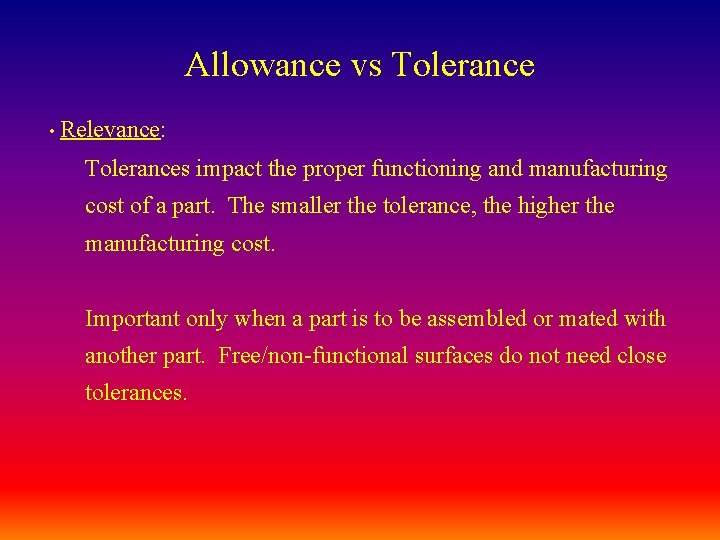
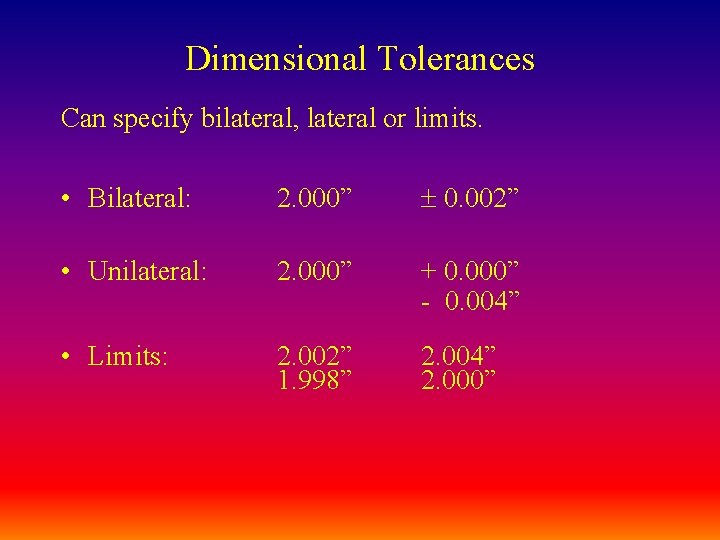
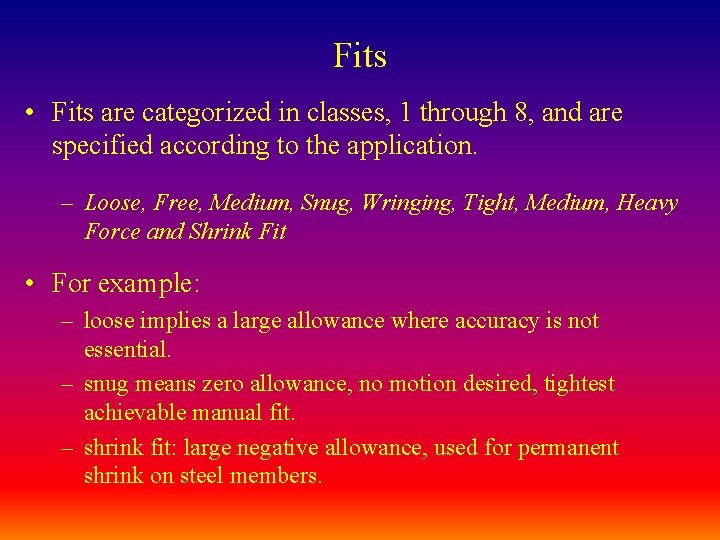
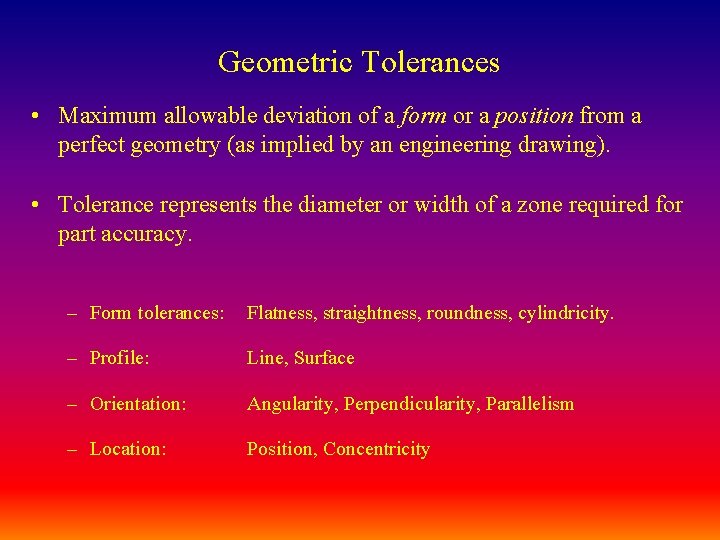
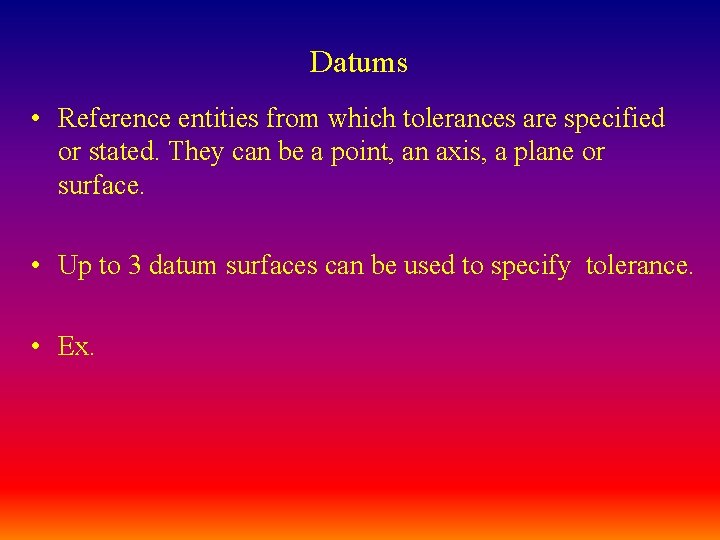
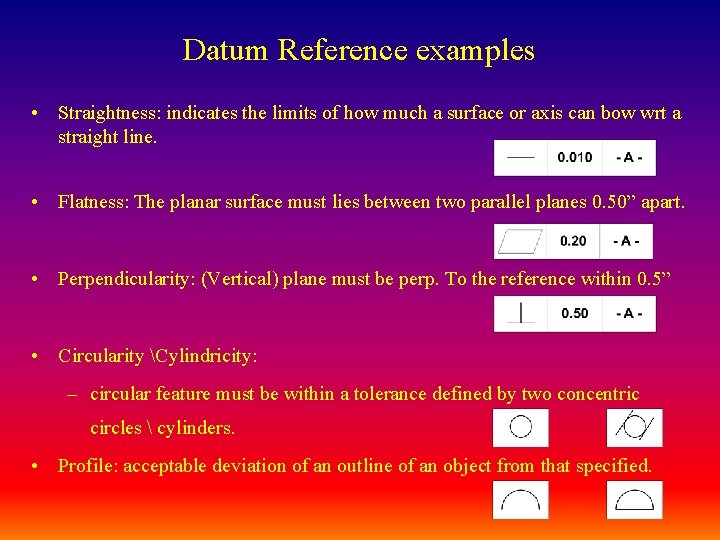
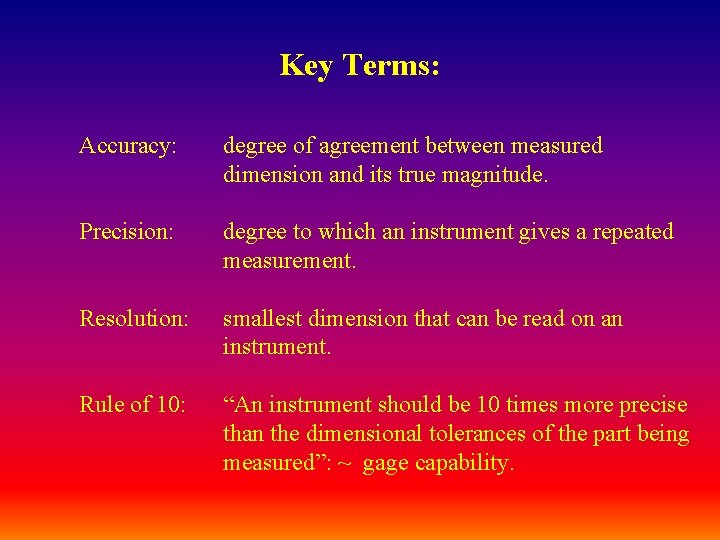
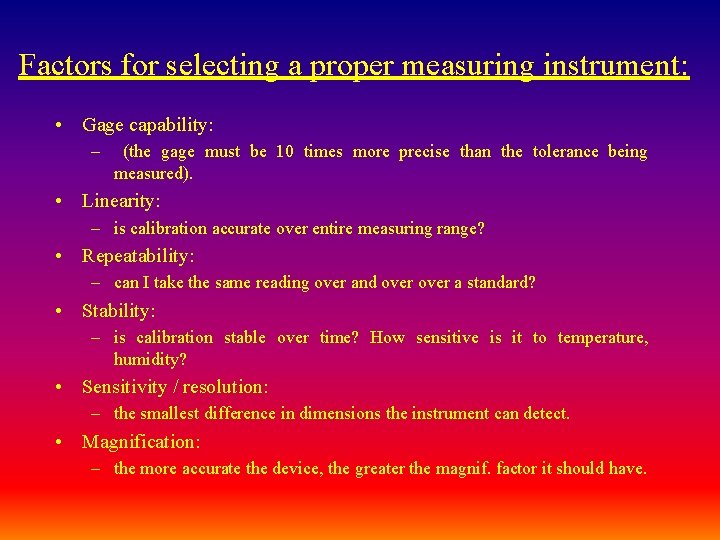
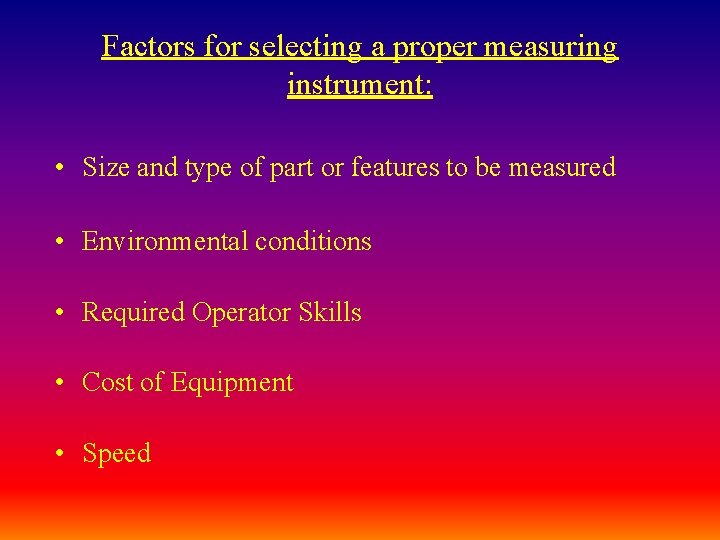
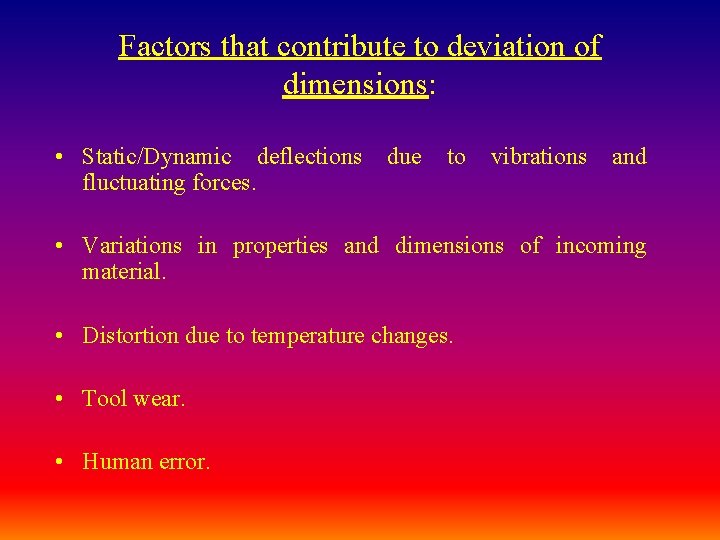
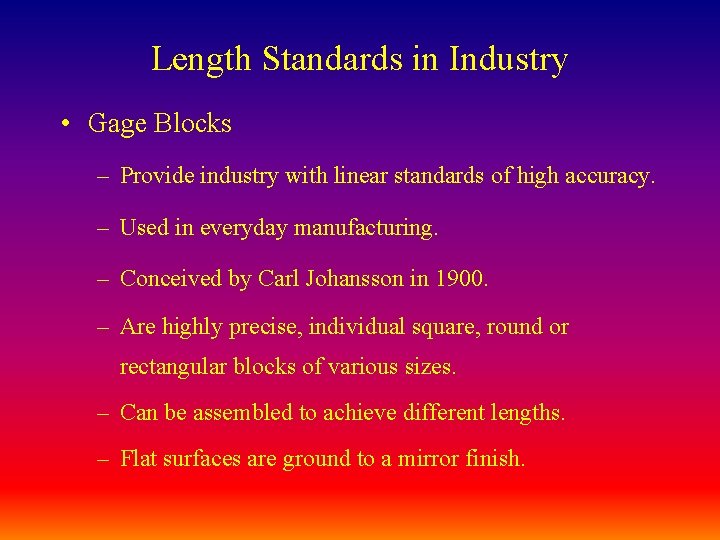
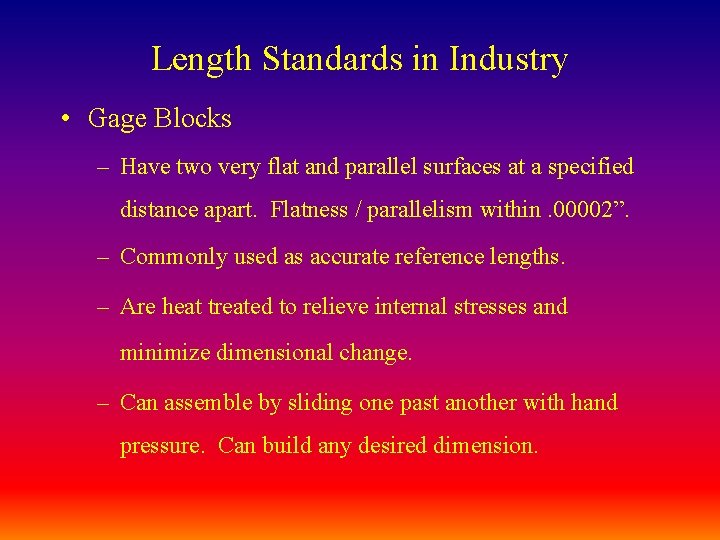
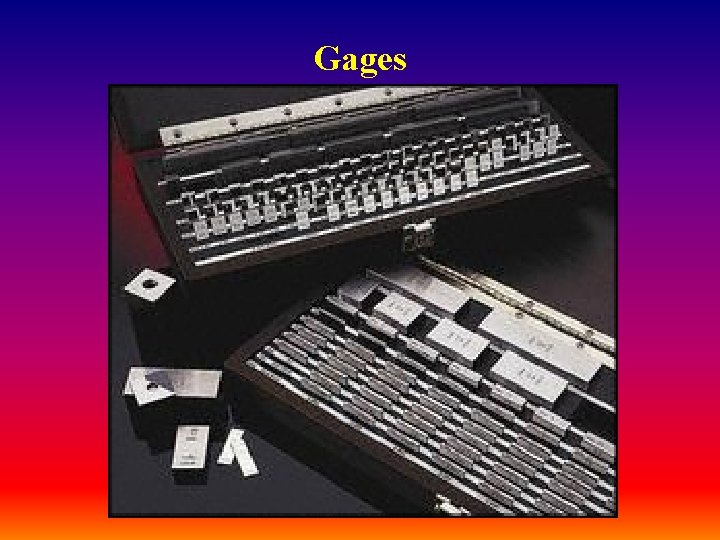
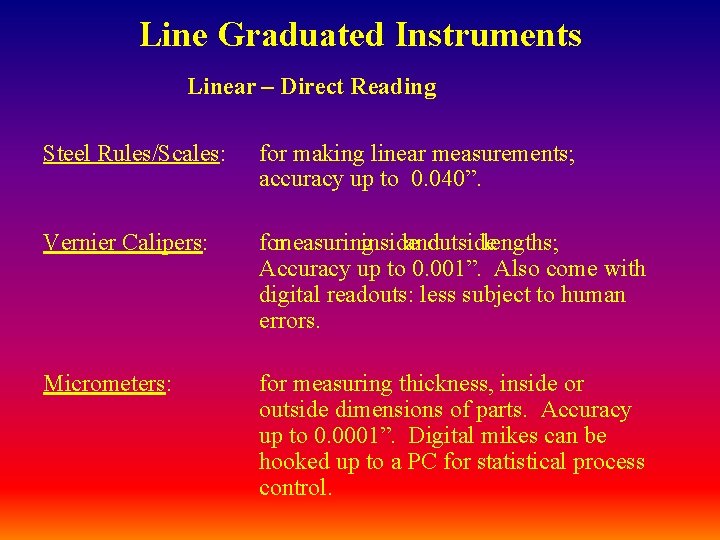
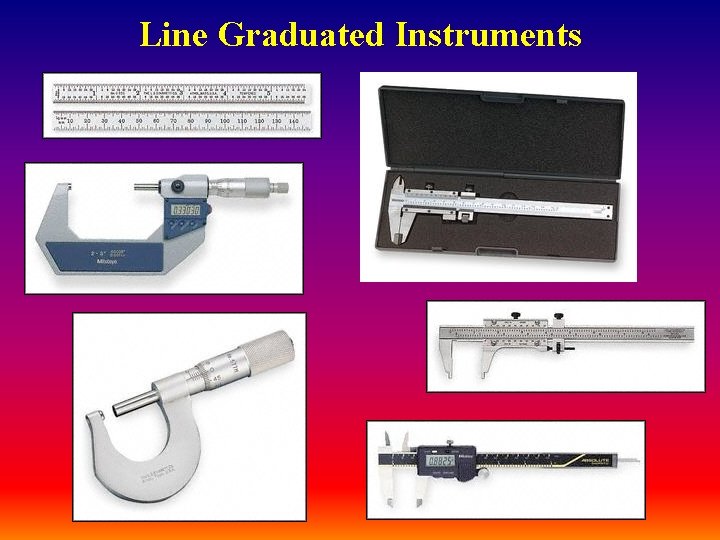
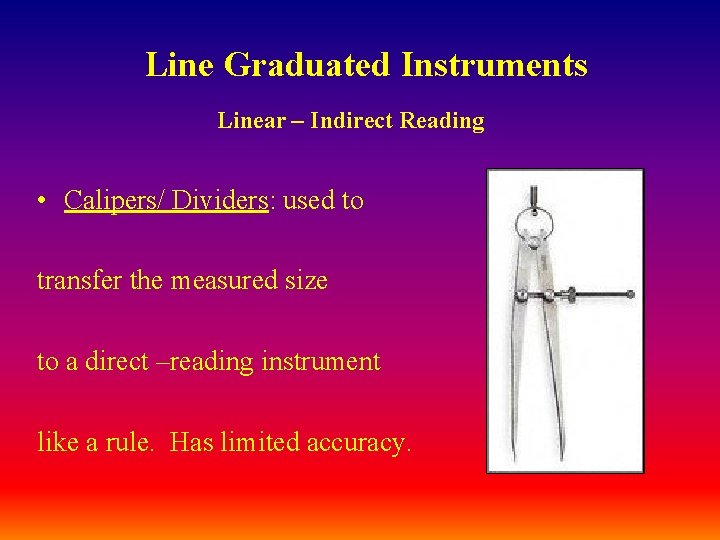
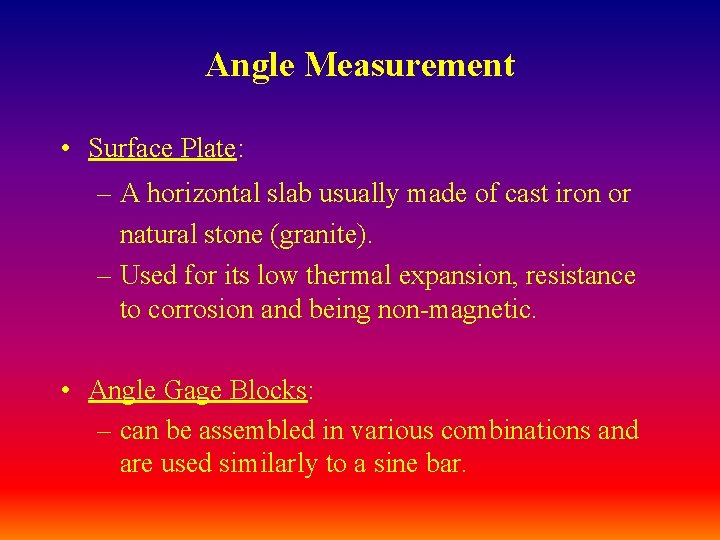
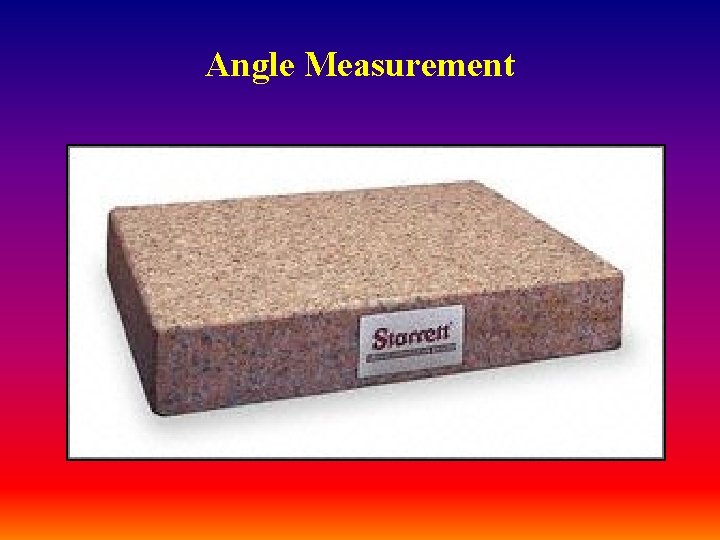
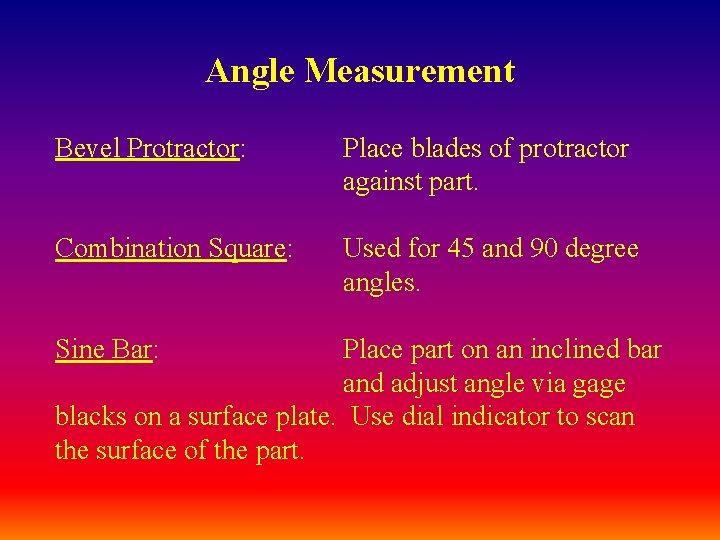
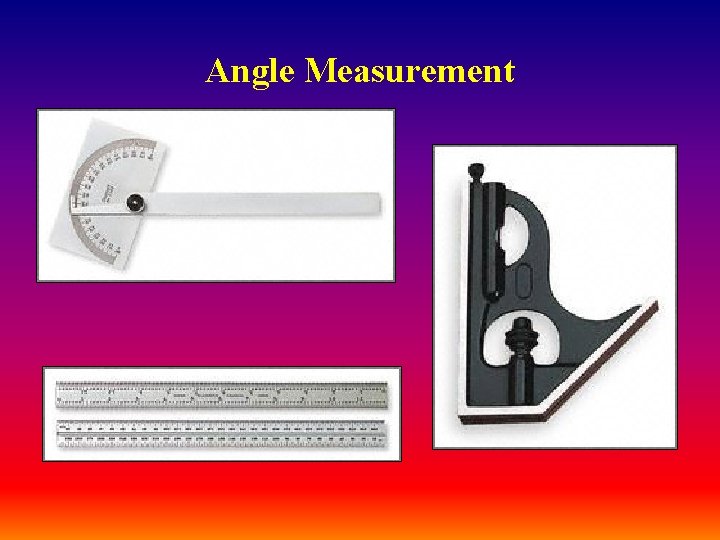

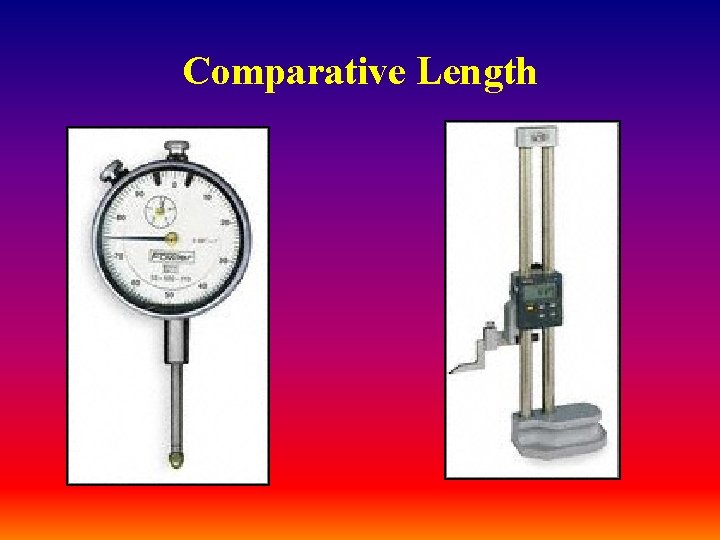
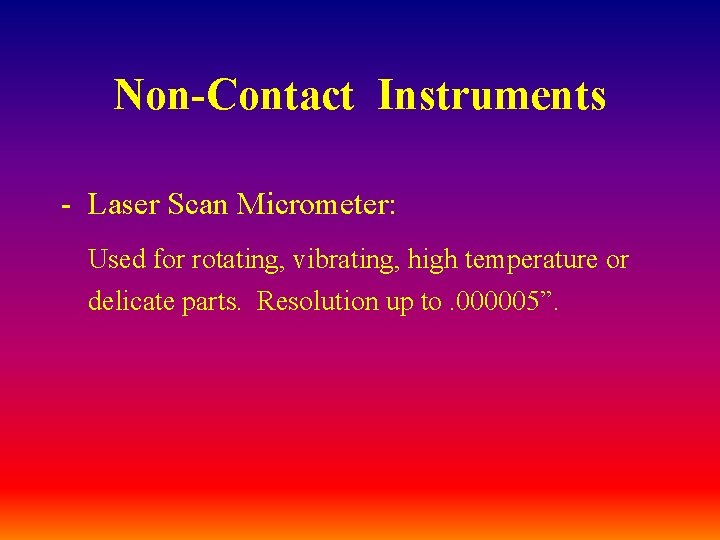
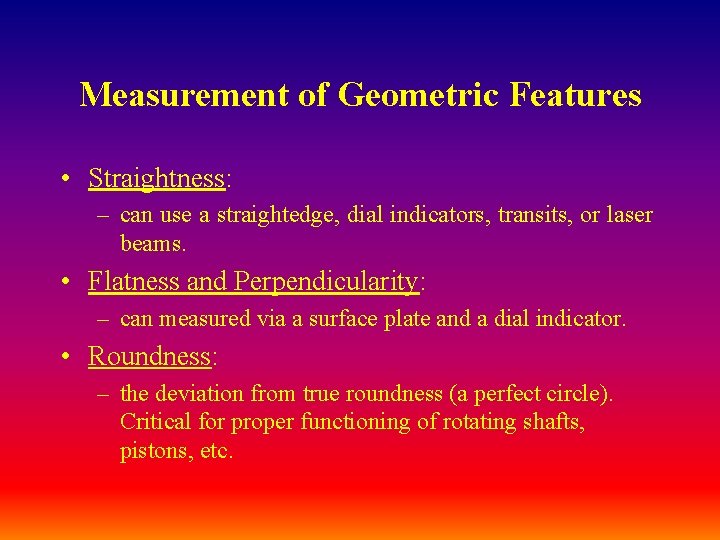
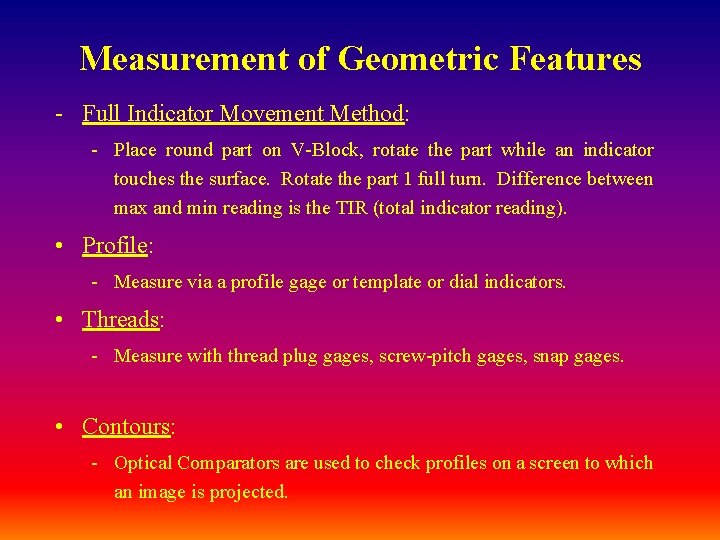
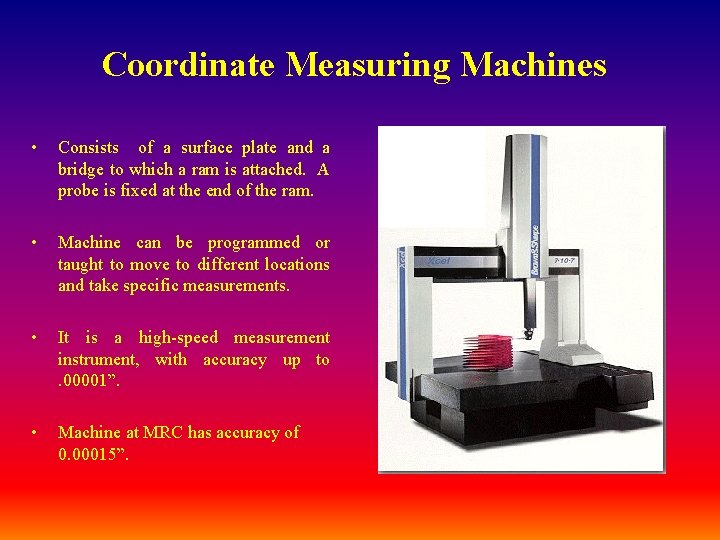
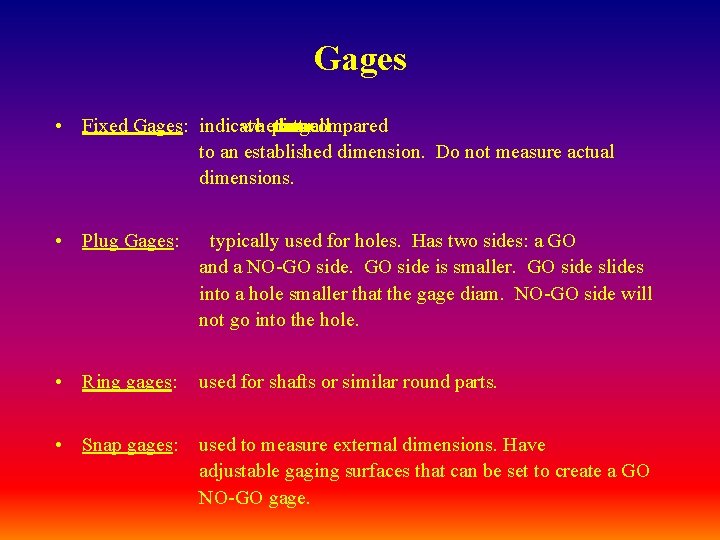
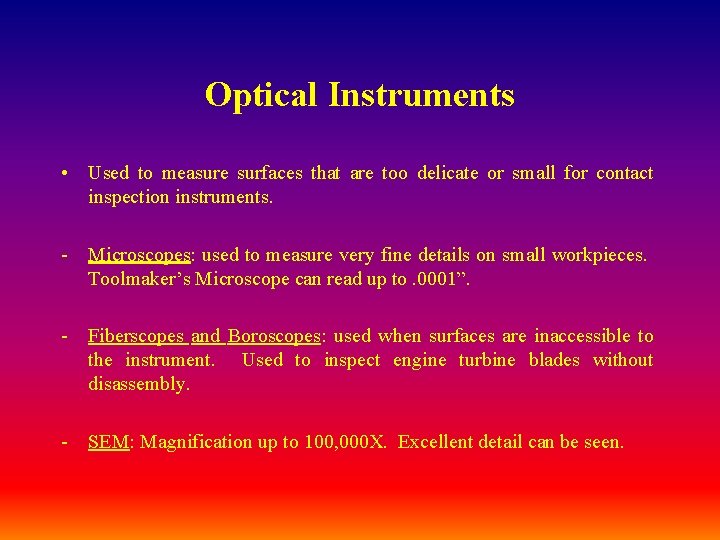
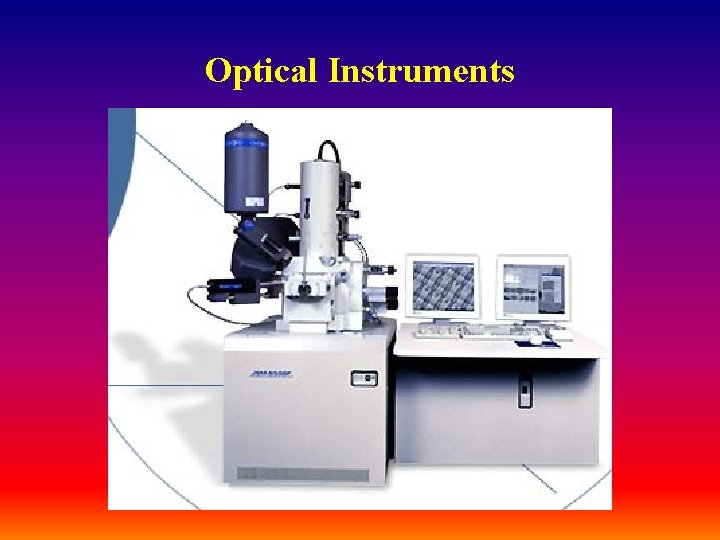
- Slides: 35
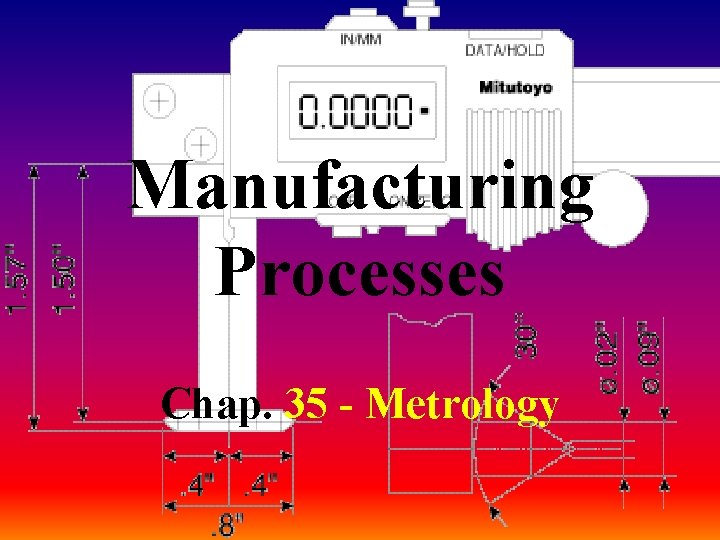
Manufacturing Processes Chap. 35 - Metrology
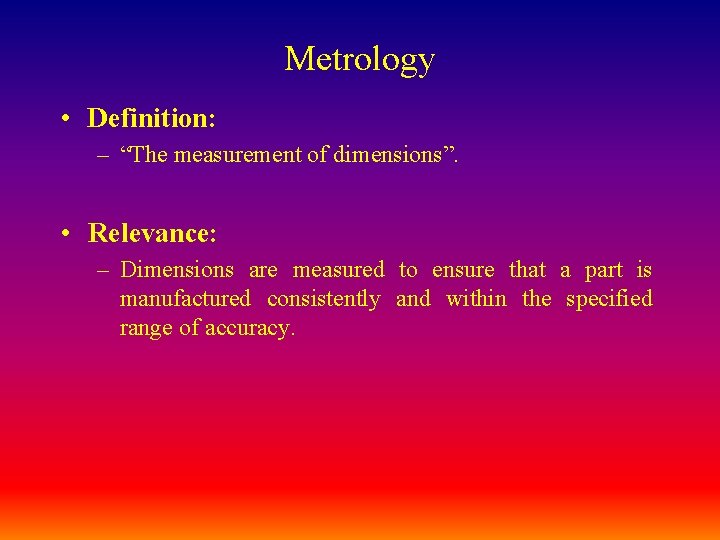
Metrology • Definition: – “The measurement of dimensions”. • Relevance: – Dimensions are measured to ensure that a part is manufactured consistently and within the specified range of accuracy.
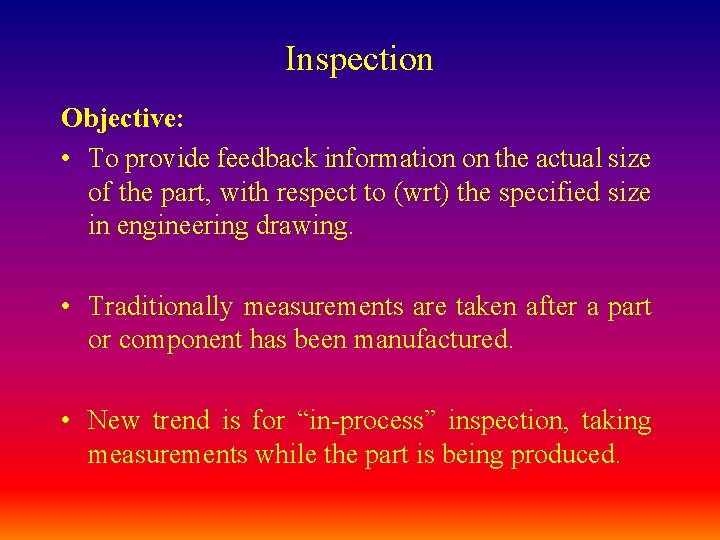
Inspection Objective: • To provide feedback information on the actual size of the part, with respect to (wrt) the specified size in engineering drawing. • Traditionally measurements are taken after a part or component has been manufactured. • New trend is for “in-process” inspection, taking measurements while the part is being produced.
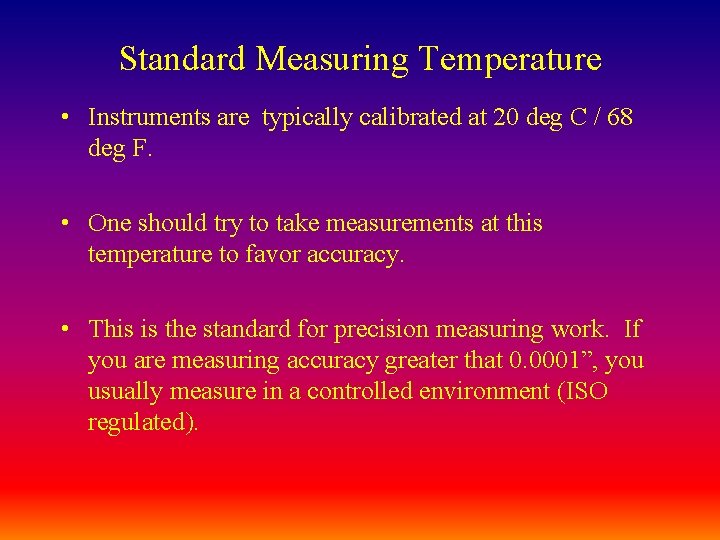
Standard Measuring Temperature • Instruments are typically calibrated at 20 deg C / 68 deg F. • One should try to take measurements at this temperature to favor accuracy. • This is the standard for precision measuring work. If you are measuring accuracy greater that 0. 0001”, you usually measure in a controlled environment (ISO regulated).
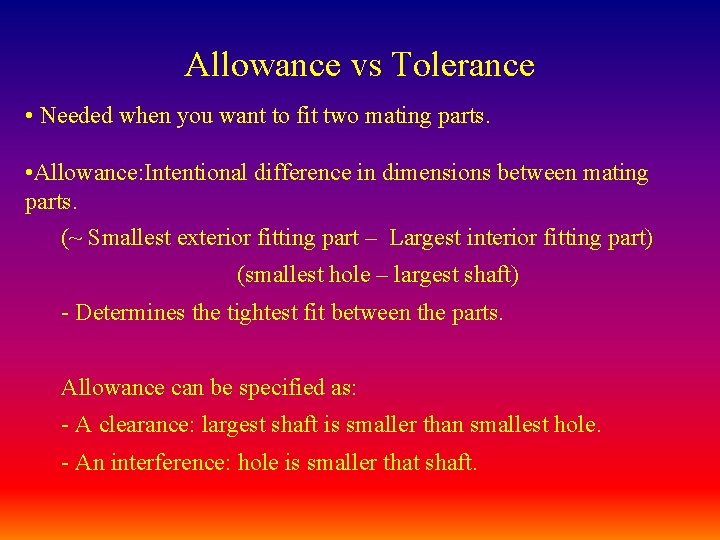
Allowance vs Tolerance • Needed when you want to fit two mating parts. • Allowance: Intentional difference in dimensions between mating parts. (~ Smallest exterior fitting part – Largest interior fitting part) (smallest hole – largest shaft) - Determines the tightest fit between the parts. Allowance can be specified as: - A clearance: largest shaft is smaller than smallest hole. - An interference: hole is smaller that shaft.
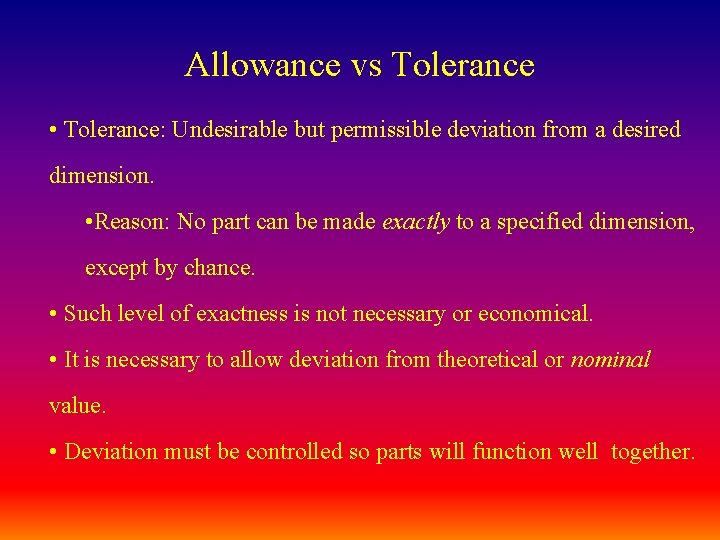
Allowance vs Tolerance • Tolerance: Undesirable but permissible deviation from a desired dimension. • Reason: No part can be made exactly to a specified dimension, except by chance. • Such level of exactness is not necessary or economical. • It is necessary to allow deviation from theoretical or nominal value. • Deviation must be controlled so parts will function well together.
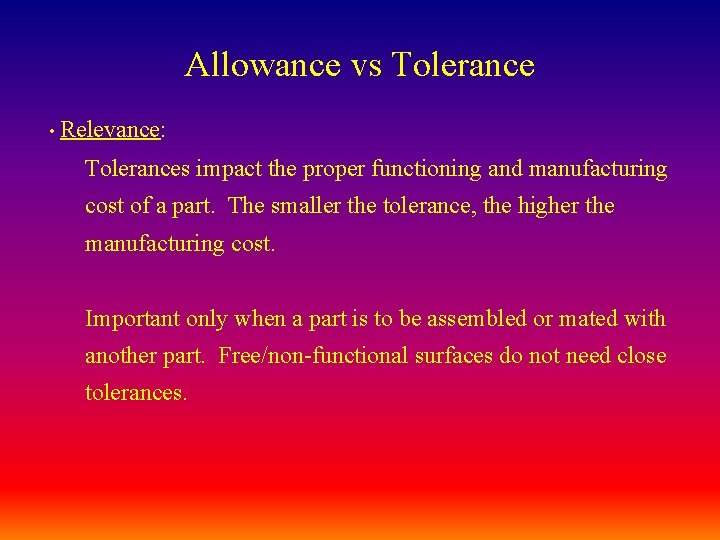
Allowance vs Tolerance • Relevance: Tolerances impact the proper functioning and manufacturing cost of a part. The smaller the tolerance, the higher the manufacturing cost. Important only when a part is to be assembled or mated with another part. Free/non-functional surfaces do not need close tolerances.
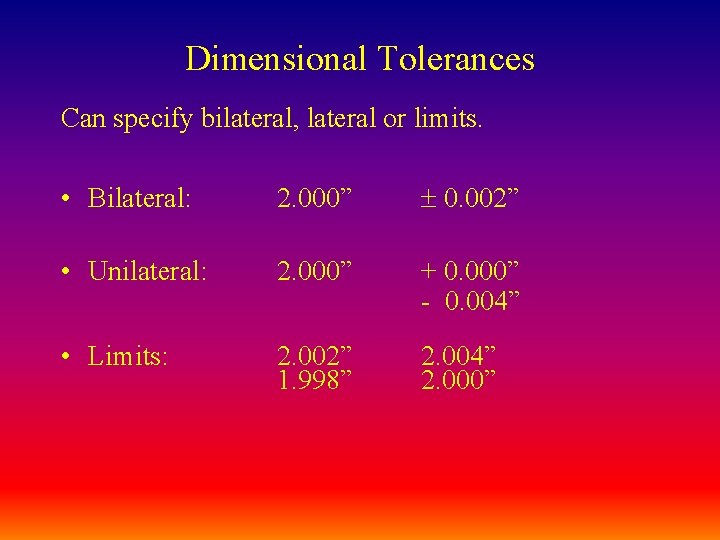
Dimensional Tolerances Can specify bilateral, lateral or limits. • Bilateral: 2. 000” 0. 002” • Unilateral: 2. 000” + 0. 000” - 0. 004” • Limits: 2. 002” 1. 998” 2. 004” 2. 000”
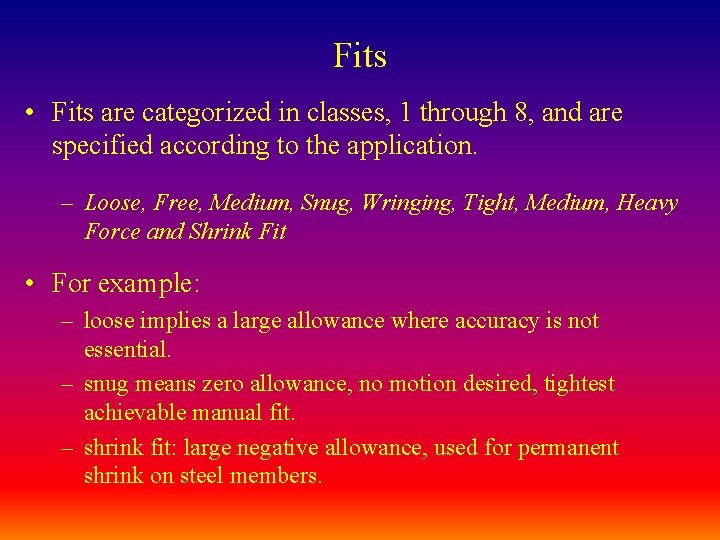
Fits • Fits are categorized in classes, 1 through 8, and are specified according to the application. – Loose, Free, Medium, Snug, Wringing, Tight, Medium, Heavy Force and Shrink Fit • For example: – loose implies a large allowance where accuracy is not essential. – snug means zero allowance, no motion desired, tightest achievable manual fit. – shrink fit: large negative allowance, used for permanent shrink on steel members.
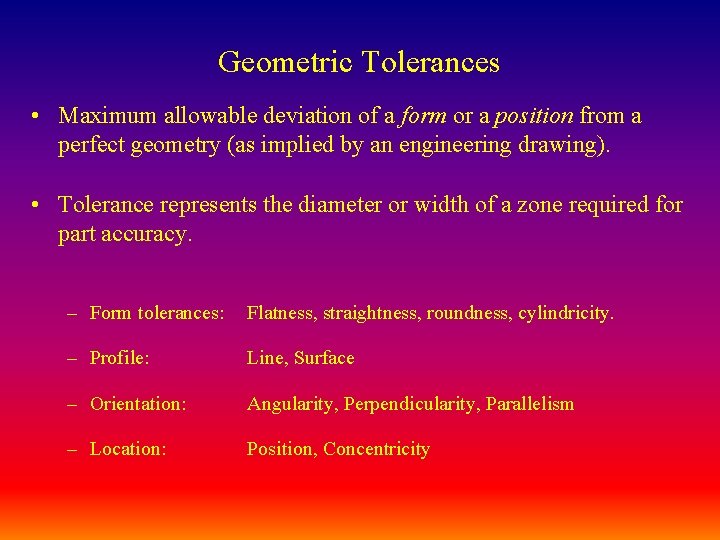
Geometric Tolerances • Maximum allowable deviation of a form or a position from a perfect geometry (as implied by an engineering drawing). • Tolerance represents the diameter or width of a zone required for part accuracy. – Form tolerances: Flatness, straightness, roundness, cylindricity. – Profile: Line, Surface – Orientation: Angularity, Perpendicularity, Parallelism – Location: Position, Concentricity
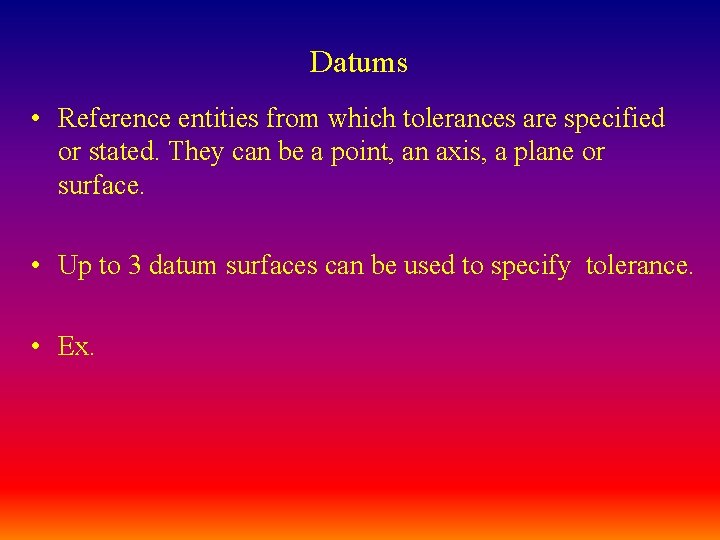
Datums • Reference entities from which tolerances are specified or stated. They can be a point, an axis, a plane or surface. • Up to 3 datum surfaces can be used to specify tolerance. • Ex.
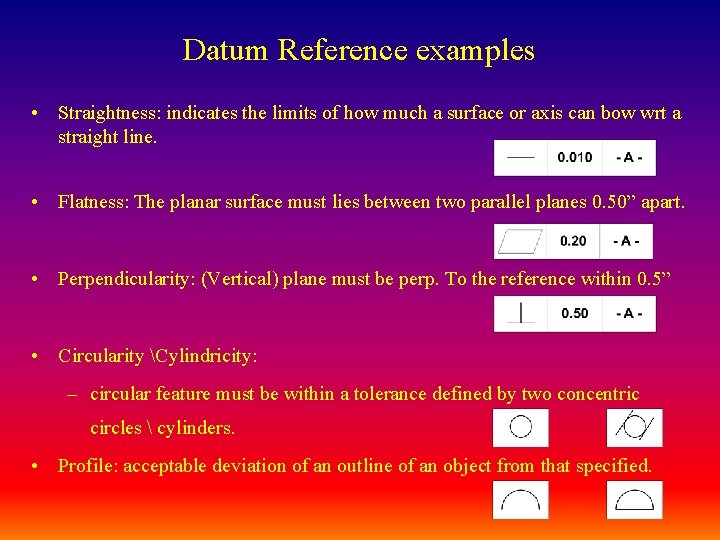
Datum Reference examples • Straightness: indicates the limits of how much a surface or axis can bow wrt a straight line. • Flatness: The planar surface must lies between two parallel planes 0. 50” apart. • Perpendicularity: (Vertical) plane must be perp. To the reference within 0. 5” • Circularity Cylindricity: – circular feature must be within a tolerance defined by two concentric circles cylinders. • Profile: acceptable deviation of an outline of an object from that specified.
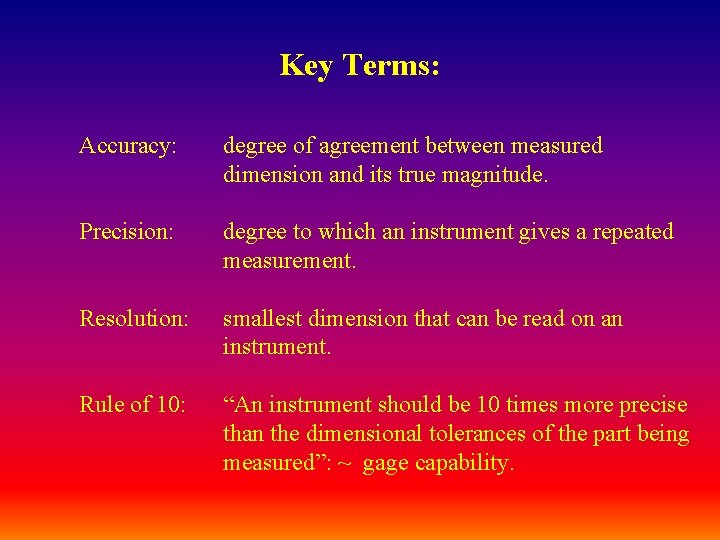
Key Terms: Accuracy: degree of agreement between measured dimension and its true magnitude. Precision: degree to which an instrument gives a repeated measurement. Resolution: smallest dimension that can be read on an instrument. Rule of 10: “An instrument should be 10 times more precise than the dimensional tolerances of the part being measured”: ~ gage capability.
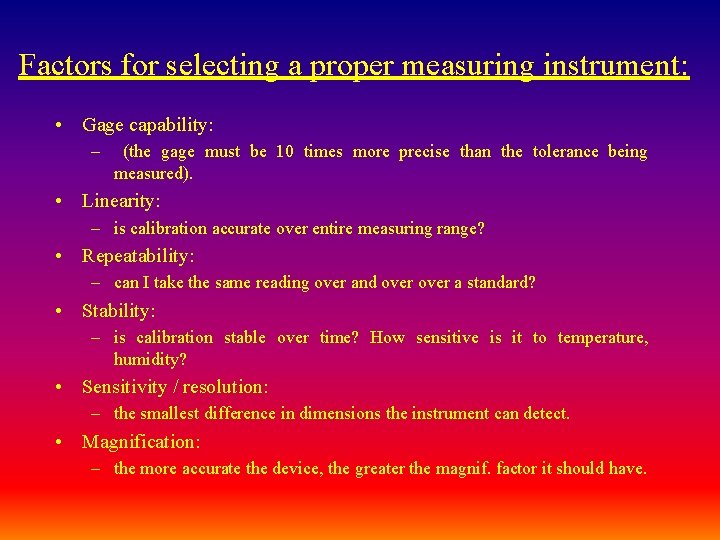
Factors for selecting a proper measuring instrument: • Gage capability: – (the gage must be 10 times more precise than the tolerance being measured). • Linearity: – is calibration accurate over entire measuring range? • Repeatability: – can I take the same reading over and over a standard? • Stability: – is calibration stable over time? How sensitive is it to temperature, humidity? • Sensitivity / resolution: – the smallest difference in dimensions the instrument can detect. • Magnification: – the more accurate the device, the greater the magnif. factor it should have.
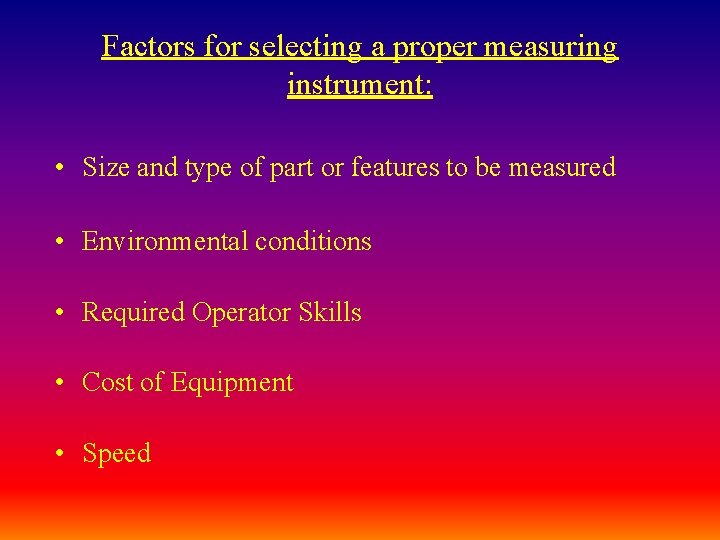
Factors for selecting a proper measuring instrument: • Size and type of part or features to be measured • Environmental conditions • Required Operator Skills • Cost of Equipment • Speed
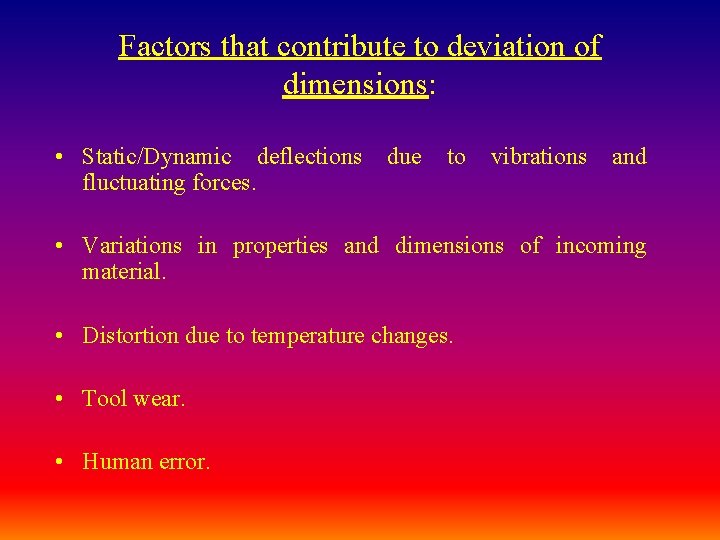
Factors that contribute to deviation of dimensions: • Static/Dynamic deflections fluctuating forces. due to vibrations and • Variations in properties and dimensions of incoming material. • Distortion due to temperature changes. • Tool wear. • Human error.
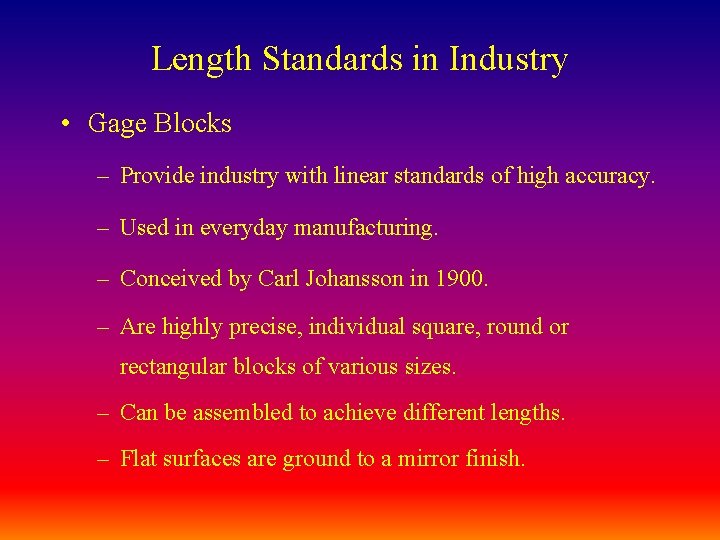
Length Standards in Industry • Gage Blocks – Provide industry with linear standards of high accuracy. – Used in everyday manufacturing. – Conceived by Carl Johansson in 1900. – Are highly precise, individual square, round or rectangular blocks of various sizes. – Can be assembled to achieve different lengths. – Flat surfaces are ground to a mirror finish.
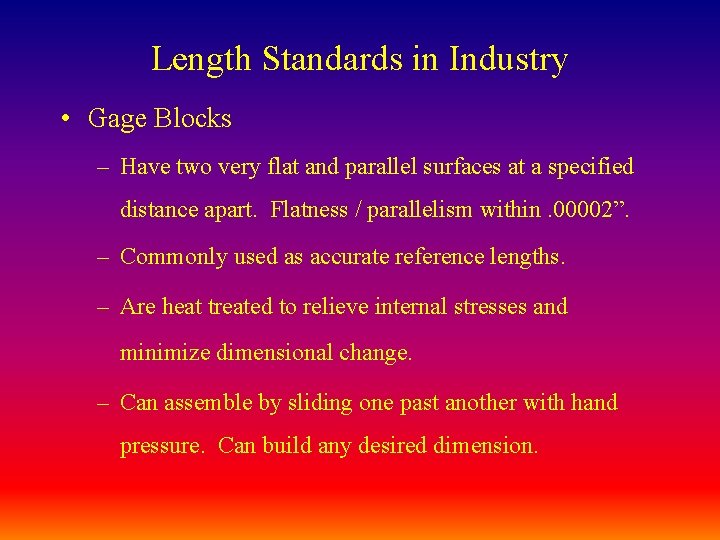
Length Standards in Industry • Gage Blocks – Have two very flat and parallel surfaces at a specified distance apart. Flatness / parallelism within. 00002”. – Commonly used as accurate reference lengths. – Are heat treated to relieve internal stresses and minimize dimensional change. – Can assemble by sliding one past another with hand pressure. Can build any desired dimension.
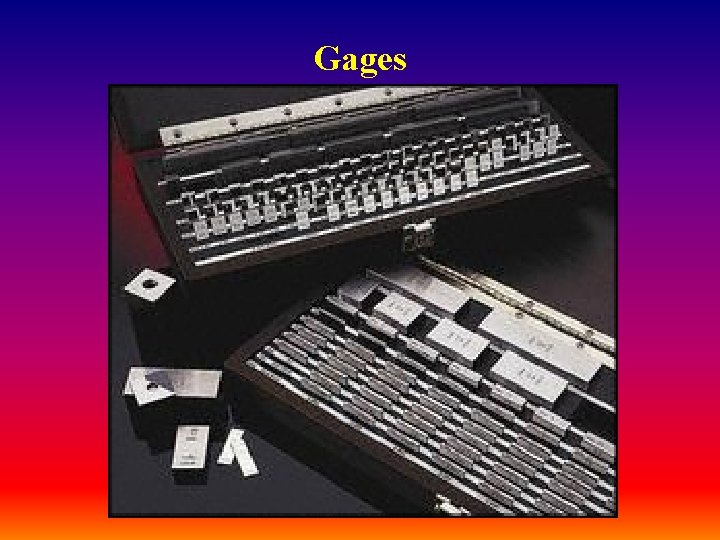
Gages
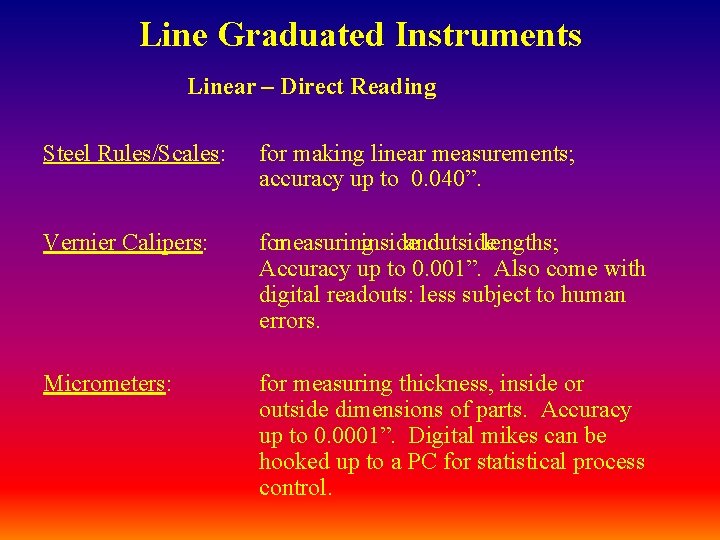
Line Graduated Instruments Linear – Direct Reading Steel Rules/Scales: for making linear measurements; accuracy up to 0. 040”. Vernier Calipers: for measuring inside and outside lengths; Accuracy up to 0. 001”. Also come with digital readouts: less subject to human errors. Micrometers: for measuring thickness, inside or outside dimensions of parts. Accuracy up to 0. 0001”. Digital mikes can be hooked up to a PC for statistical process control.
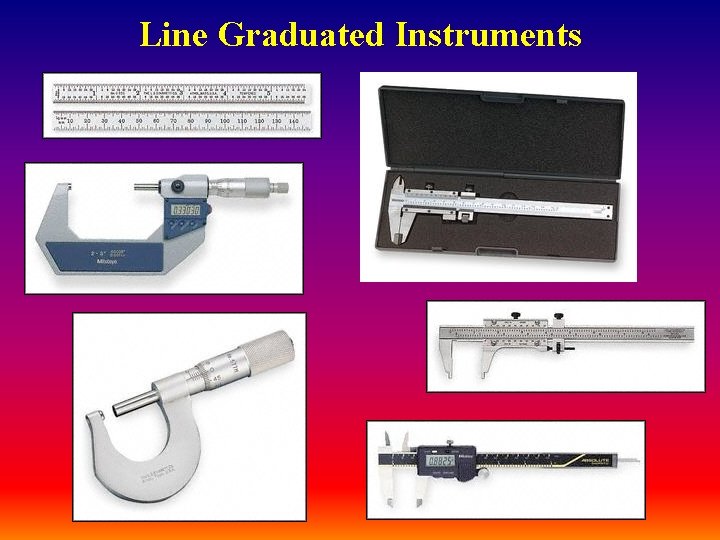
Line Graduated Instruments
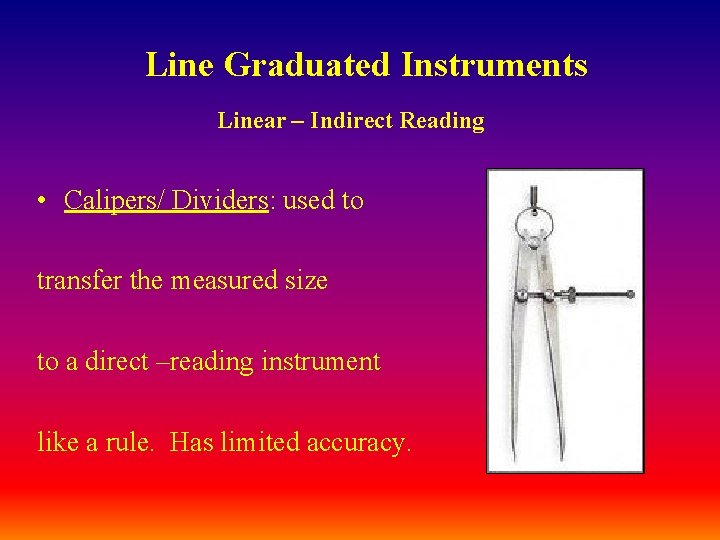
Line Graduated Instruments Linear – Indirect Reading • Calipers/ Dividers: used to transfer the measured size to a direct –reading instrument like a rule. Has limited accuracy.
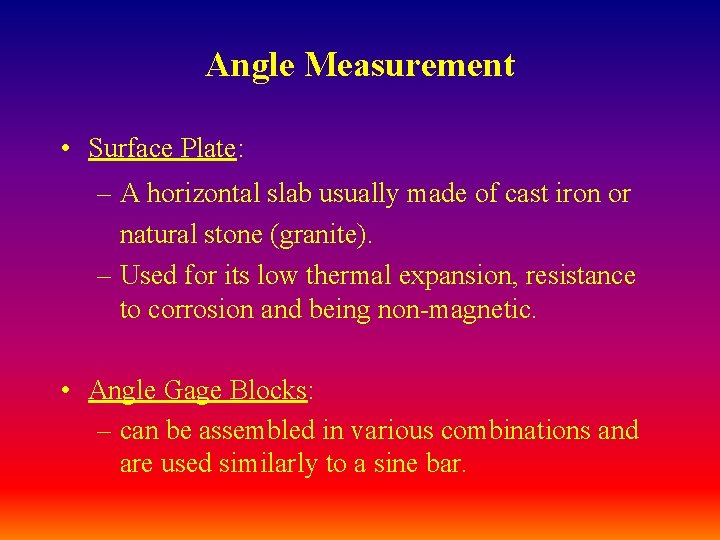
Angle Measurement • Surface Plate: – A horizontal slab usually made of cast iron or natural stone (granite). – Used for its low thermal expansion, resistance to corrosion and being non-magnetic. • Angle Gage Blocks: – can be assembled in various combinations and are used similarly to a sine bar.
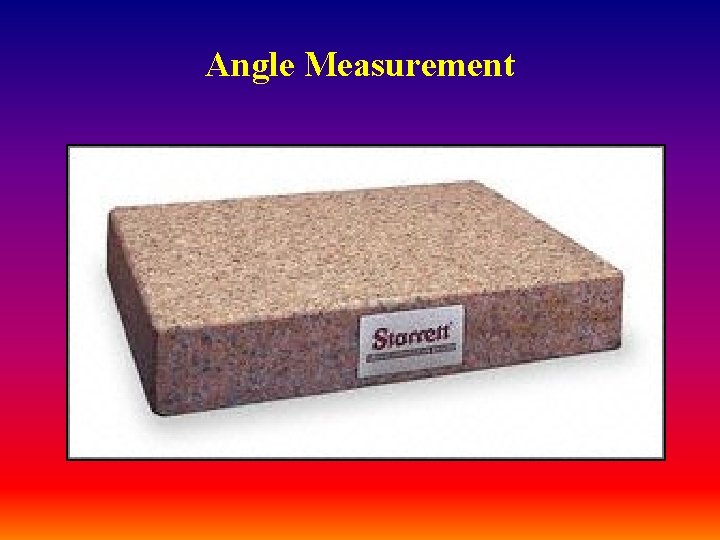
Angle Measurement
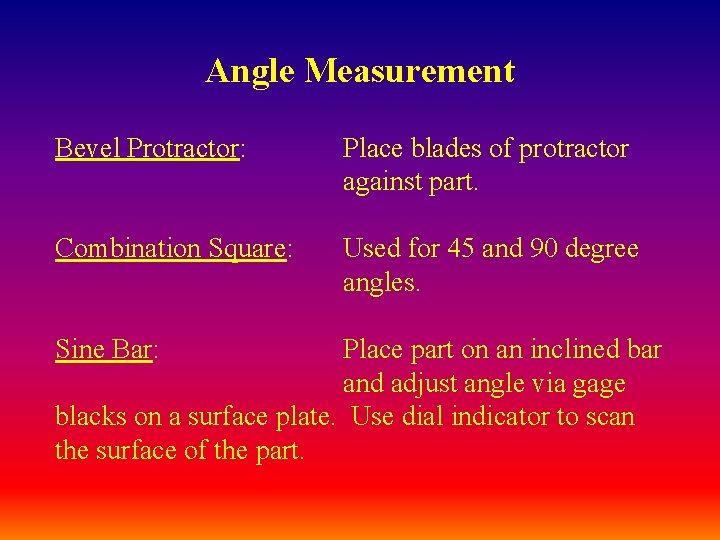
Angle Measurement Bevel Protractor: Place blades of protractor against part. Combination Square: Used for 45 and 90 degree angles. Sine Bar: Place part on an inclined bar and adjust angle via gage blacks on a surface plate. Use dial indicator to scan the surface of the part.
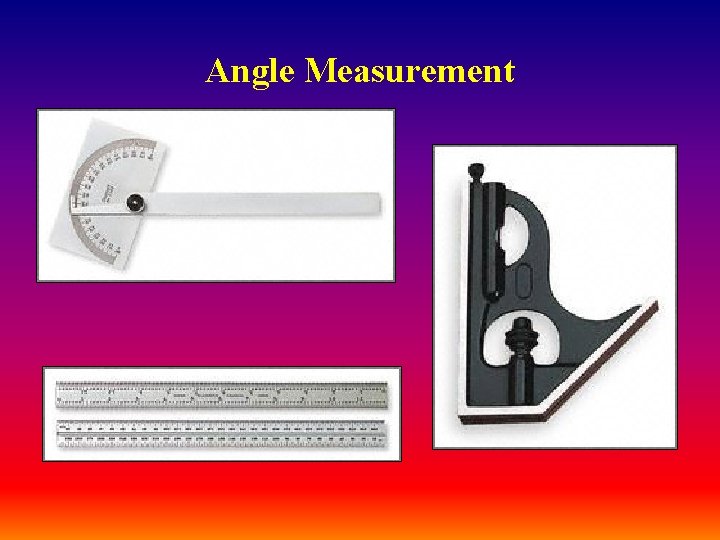
Angle Measurement

Comparative Length - Dial Indicators: mechanical device that converts linear displacement of a pointer to a rotation of an indicator on a circular dial. Accuracy up to. 00004”. - Electronic Gages: senses motion of contact pointer through changes in resistance of a strain gage. - Advantages: ease of operation, rapid response, digital readout, reduced possibility of human error.
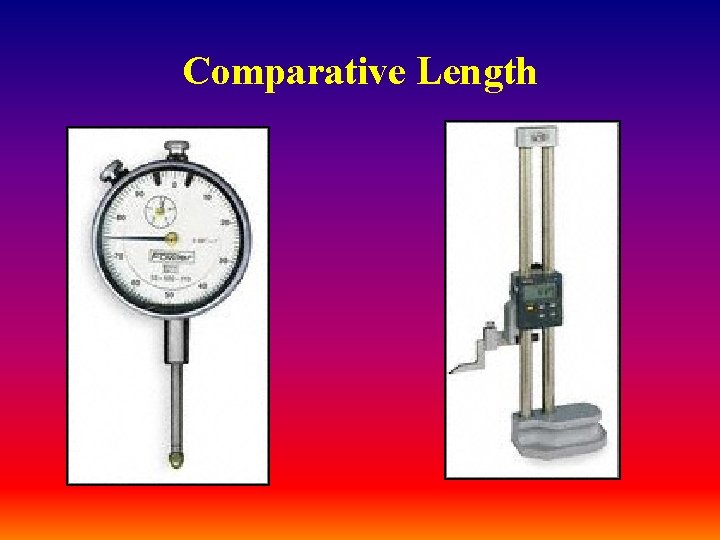
Comparative Length
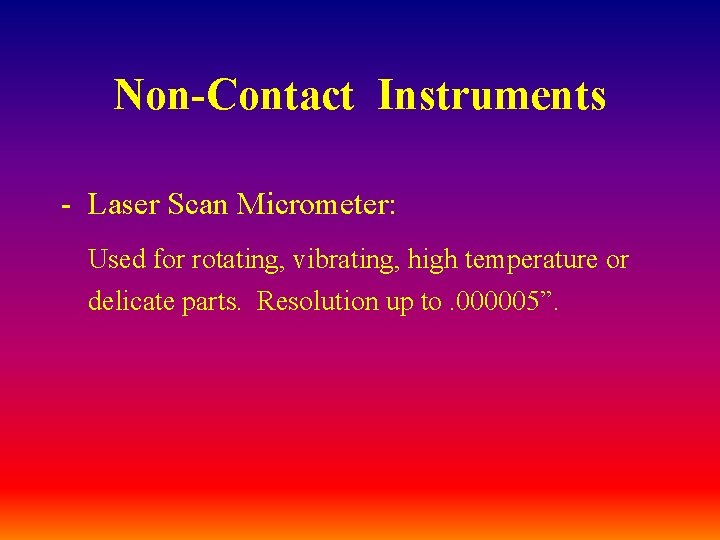
Non-Contact Instruments - Laser Scan Micrometer: Used for rotating, vibrating, high temperature or delicate parts. Resolution up to. 000005”.
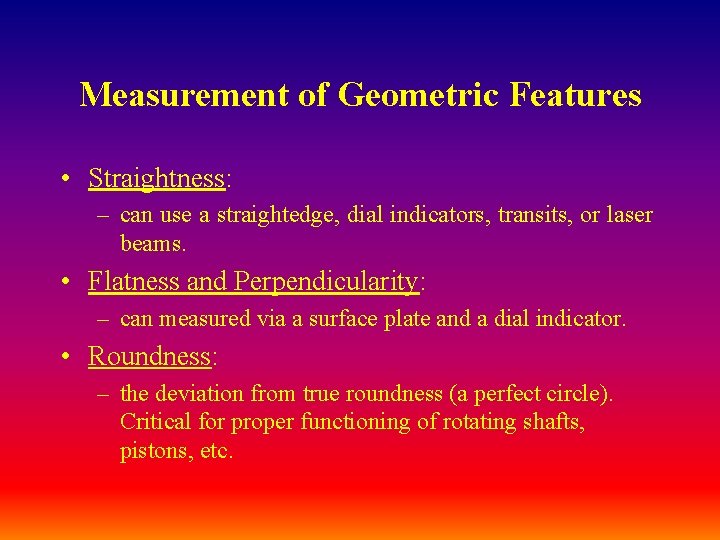
Measurement of Geometric Features • Straightness: – can use a straightedge, dial indicators, transits, or laser beams. • Flatness and Perpendicularity: – can measured via a surface plate and a dial indicator. • Roundness: – the deviation from true roundness (a perfect circle). Critical for proper functioning of rotating shafts, pistons, etc.
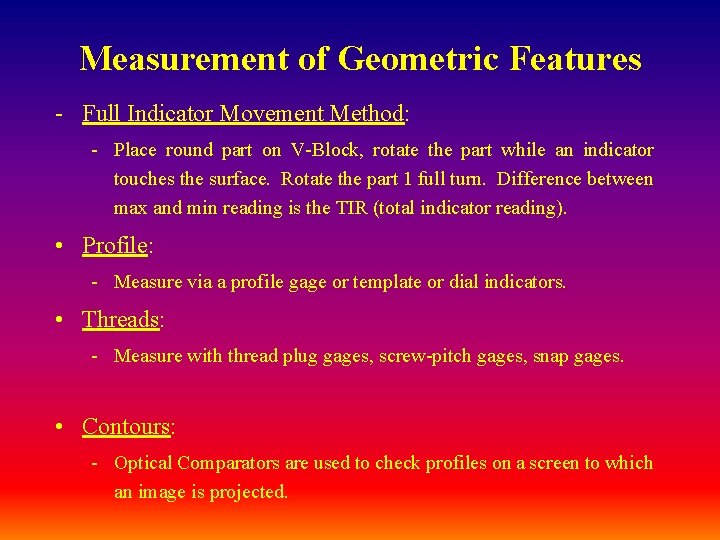
Measurement of Geometric Features - Full Indicator Movement Method: - Place round part on V-Block, rotate the part while an indicator touches the surface. Rotate the part 1 full turn. Difference between max and min reading is the TIR (total indicator reading). • Profile: - Measure via a profile gage or template or dial indicators. • Threads: - Measure with thread plug gages, screw-pitch gages, snap gages. • Contours: - Optical Comparators are used to check profiles on a screen to which an image is projected.
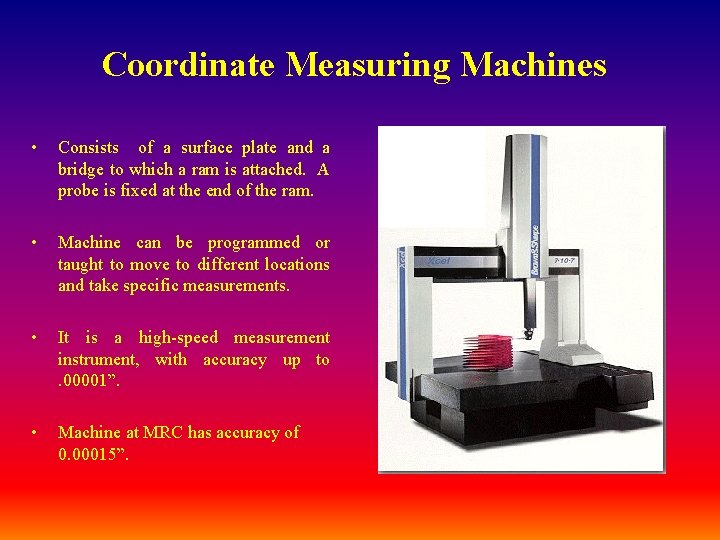
Coordinate Measuring Machines • Consists of a surface plate and a bridge to which a ram is attached. A probe is fixed at the end of the ram. • Machine can be programmed or taught to move to different locations and take specific measurements. • It is a high-speed measurement instrument, with accuracy up to. 00001”. • Machine at MRC has accuracy of 0. 00015”.
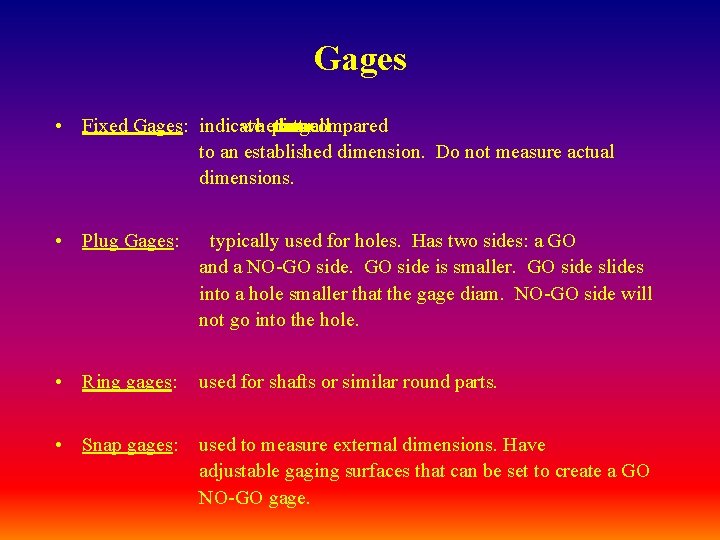
Gages • Fixed Gages: indicate whether part too large is asmall to orcompared to an established dimension. Do not measure actual dimensions. • Plug Gages: typically used for holes. Has two sides: a GO and a NO-GO side is smaller. GO side slides into a hole smaller that the gage diam. NO-GO side will not go into the hole. • Ring gages: used for shafts or similar round parts. • Snap gages: used to measure external dimensions. Have adjustable gaging surfaces that can be set to create a GO NO-GO gage.
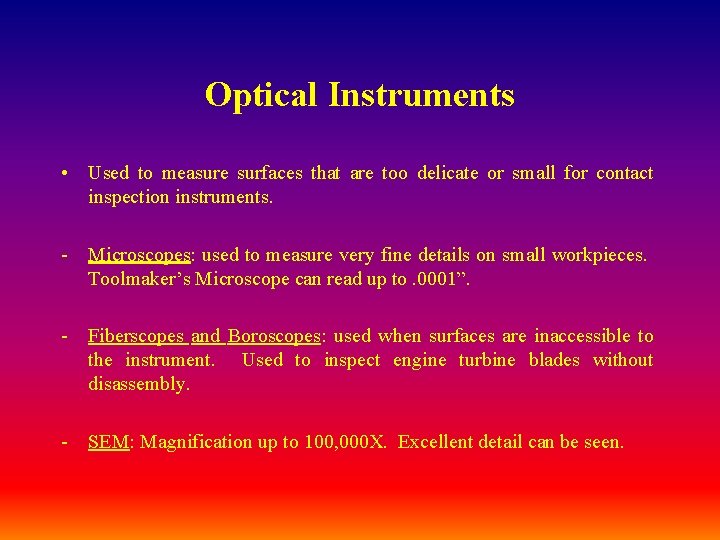
Optical Instruments • Used to measure surfaces that are too delicate or small for contact inspection instruments. - Microscopes: used to measure very fine details on small workpieces. Toolmaker’s Microscope can read up to. 0001”. - Fiberscopes and Boroscopes: used when surfaces are inaccessible to the instrument. Used to inspect engine turbine blades without disassembly. - SEM: Magnification up to 100, 000 X. Excellent detail can be seen.
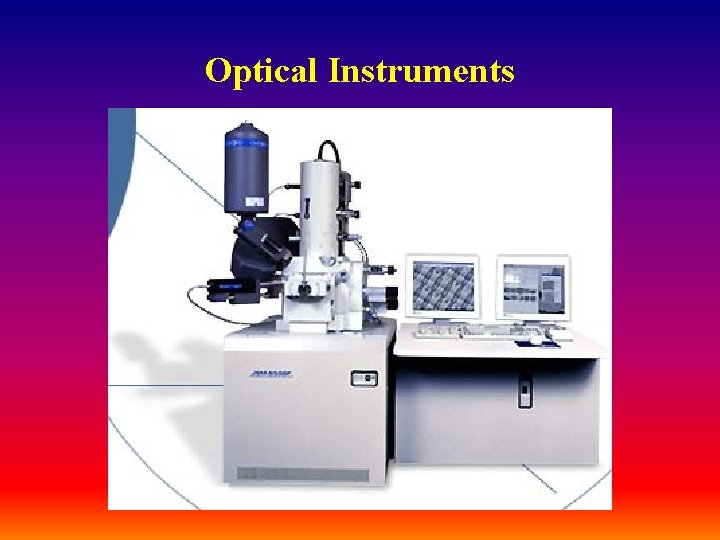
Optical Instruments
Chap chap slide
Manufacturing cost vs non manufacturing cost
Job costing vs. process costing
Commited cost
Manufacturing cost vs non manufacturing cost
Additively
Manufacturing process for engineering materials
Manufacturing process classification
List of manufacturing processes
Composite manufacturing process
Nontraditional manufacturing processes
Traditional manufacturing processes
Industrial revolution transition
Nature of manufacturing process
Concurrent in os
Interchangeability definition in metrology
Windbreaker chapter 1
Passion chap 6
Bank run chap 11
Durbin chap
Riddles of spices with answer
Kstn chap 18
Characteristics of extended family
The origin of species manga cap 24
Anything that can satisfy needs and wants
The origin of species 22 manga
Mad dog tkam
Matthew 5
Child development chapter 1
Rivalry 1 chap 6
System engineer chap 1
Chap tree
Kstn chap 7
I was in that state when a chap easily turns nasty analysis
The origin of species manga 24
Passion chap 9