Interconnect and Packaging Lecture 8 Clock Meshes and
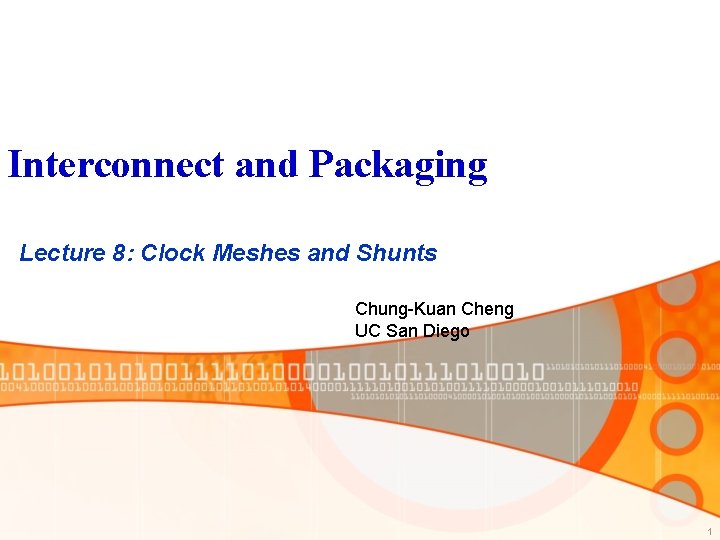
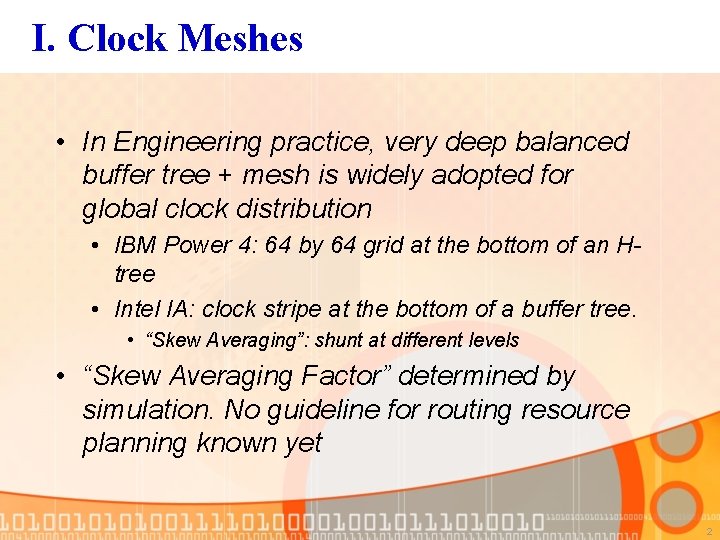
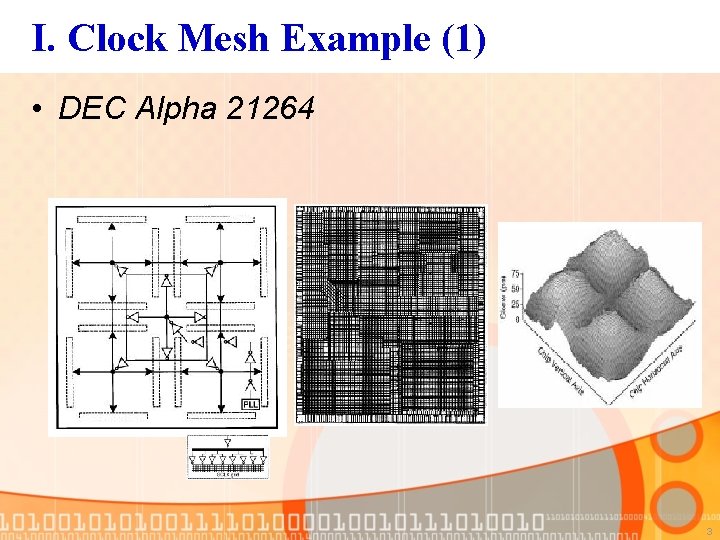
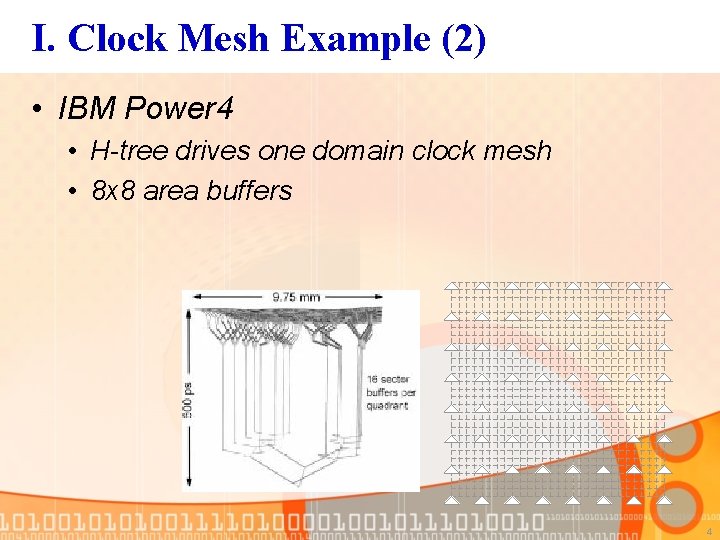
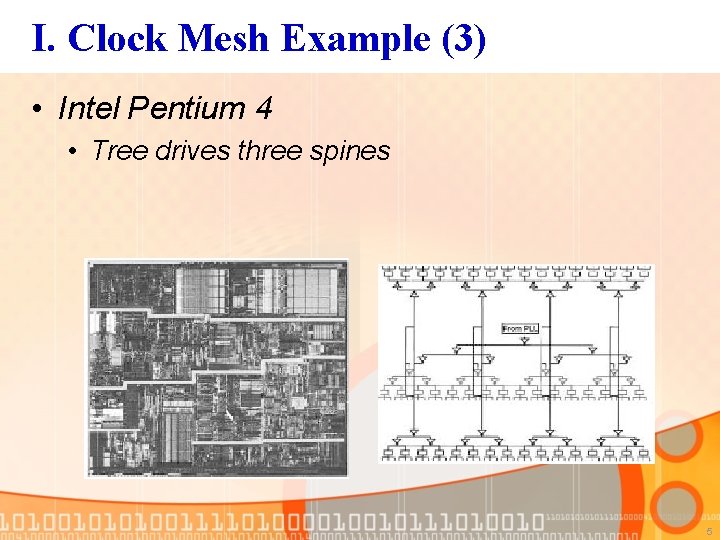
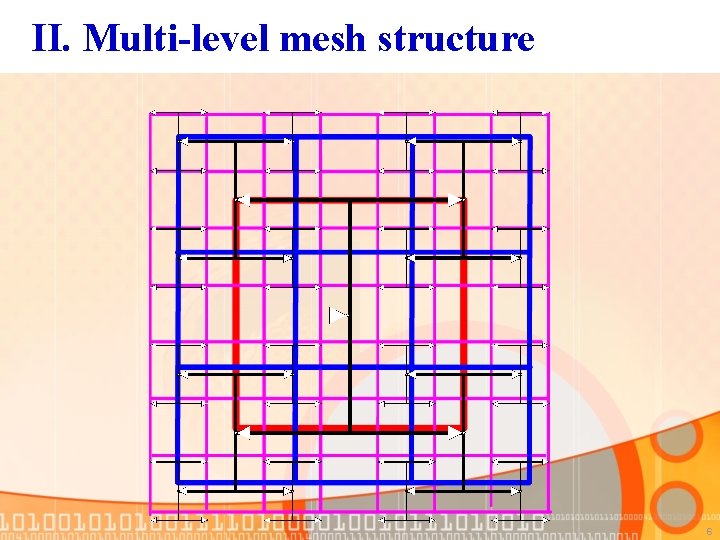
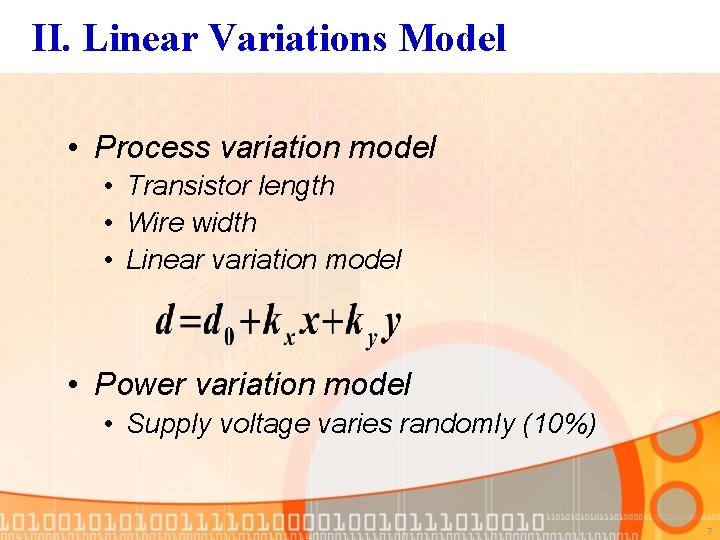
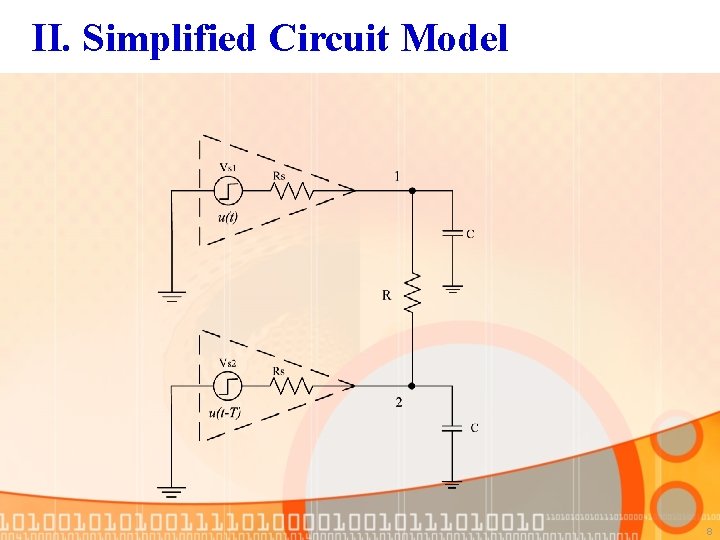
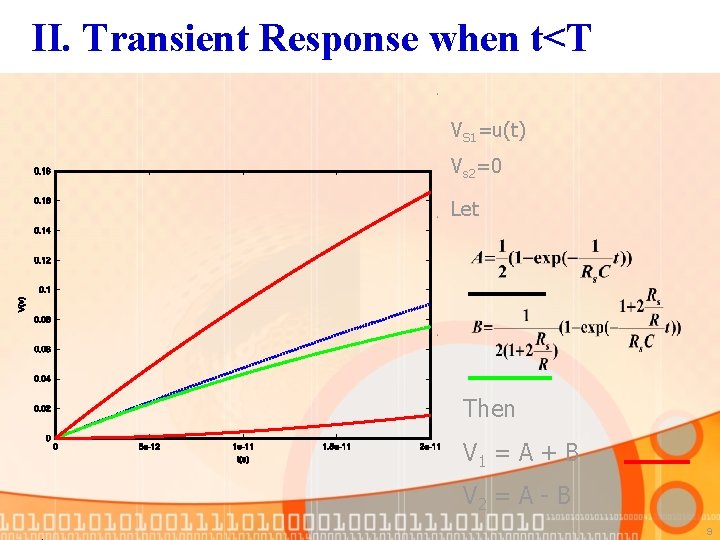
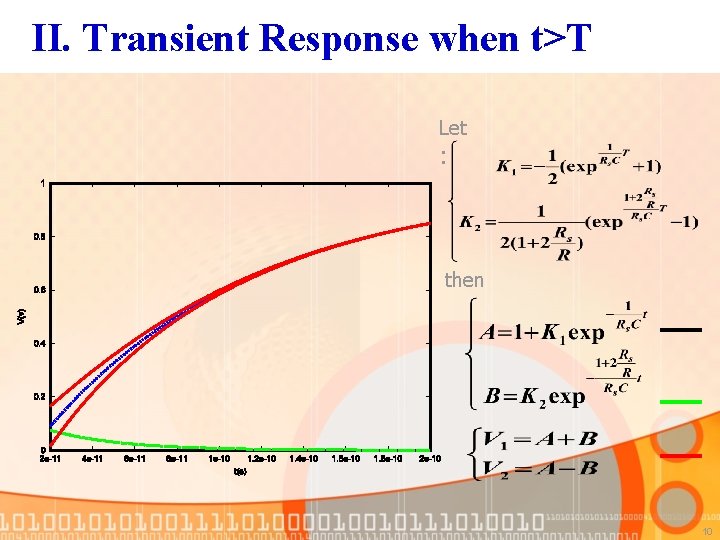
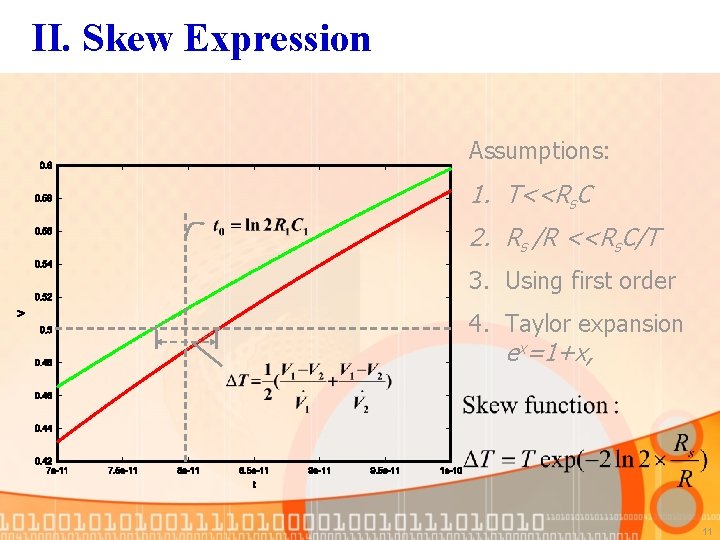
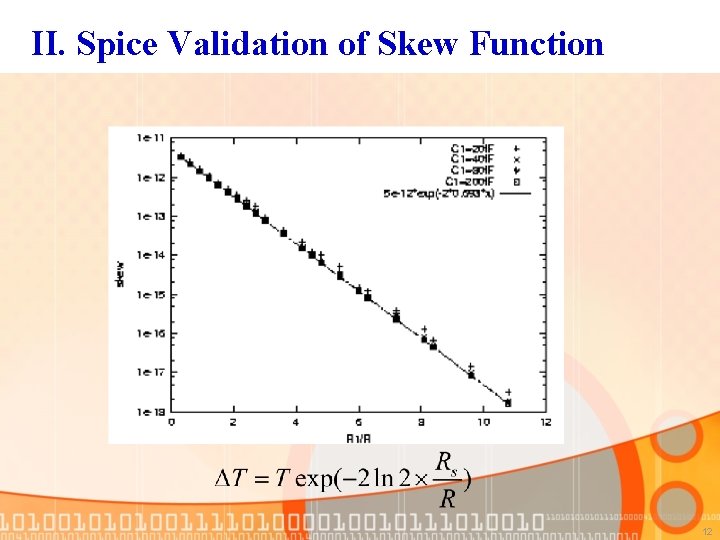
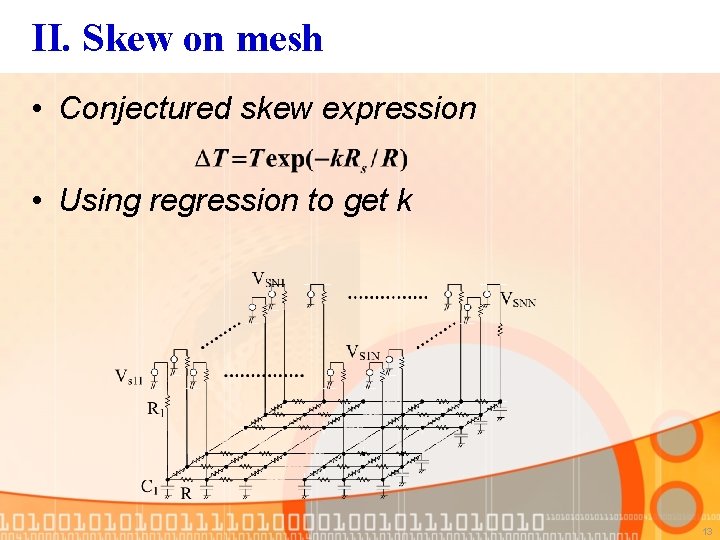
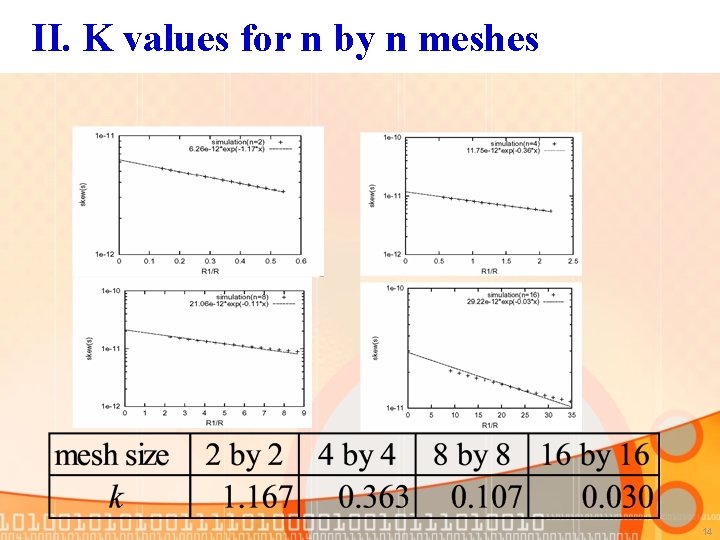
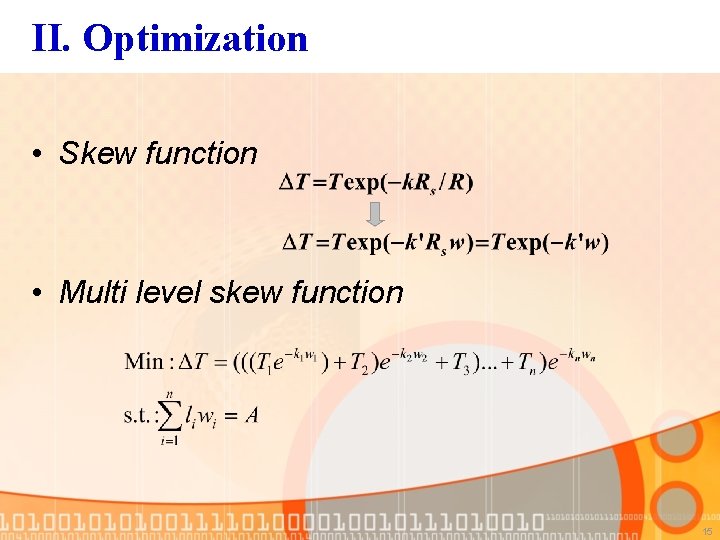
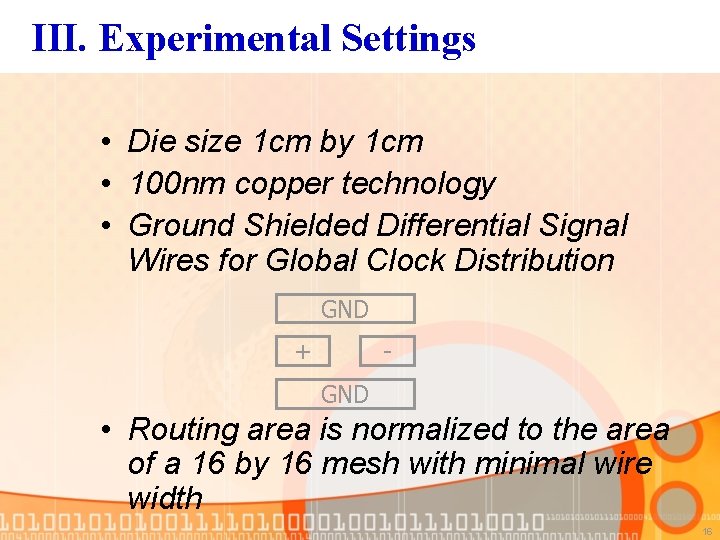
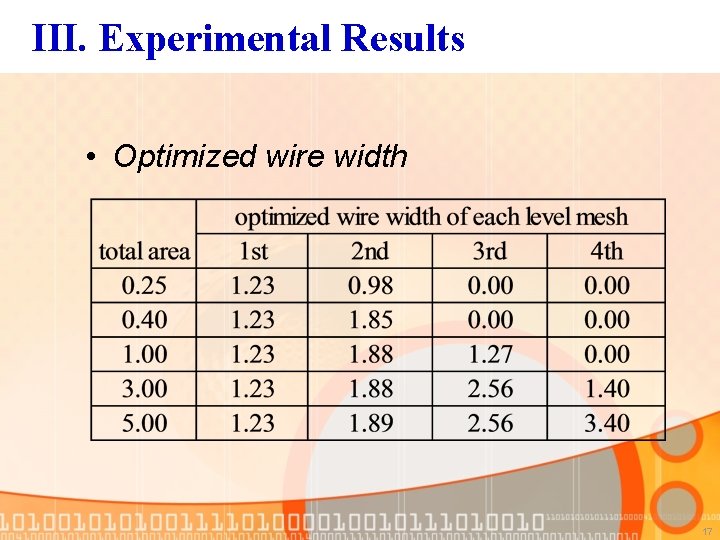
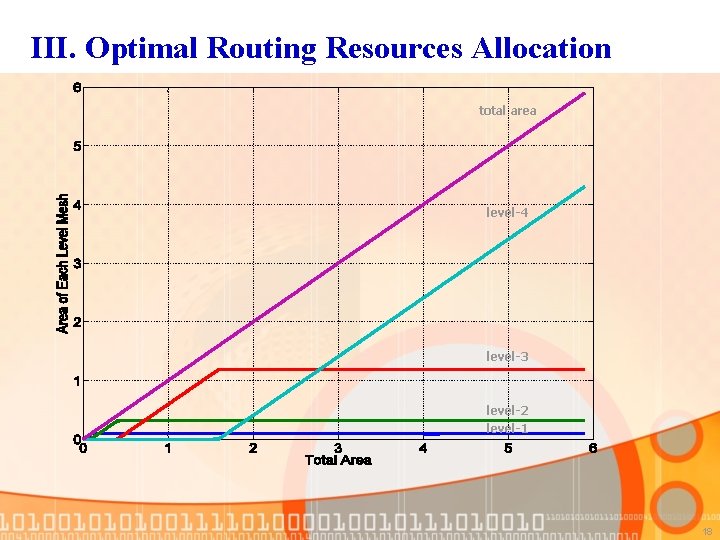
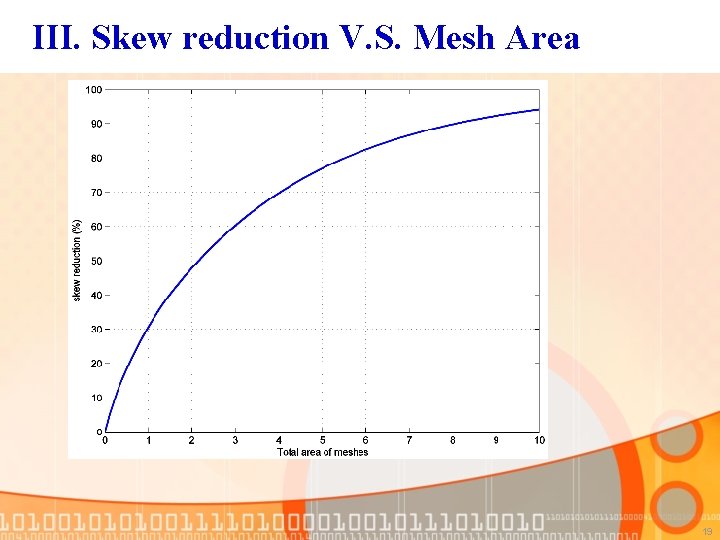
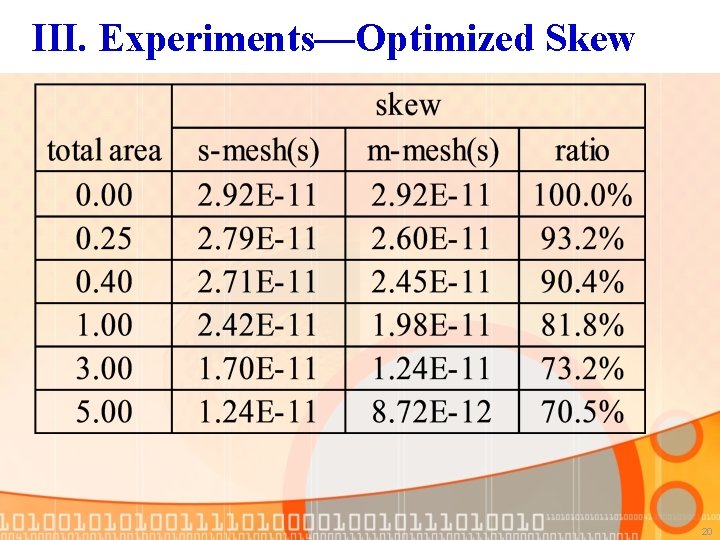
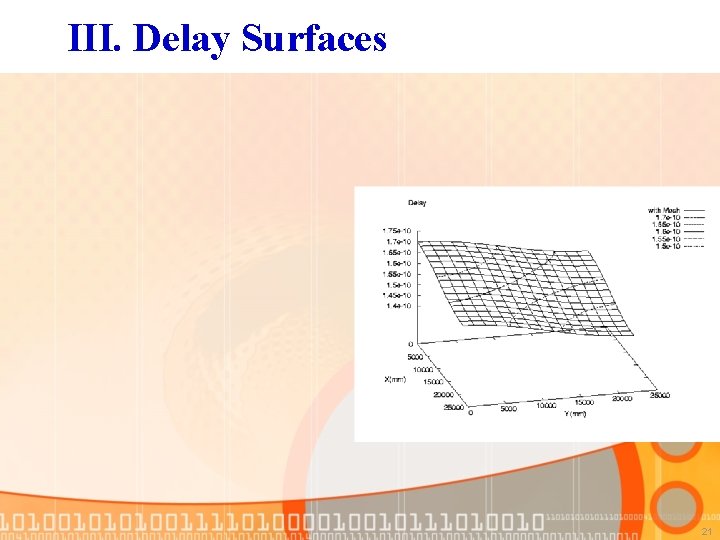
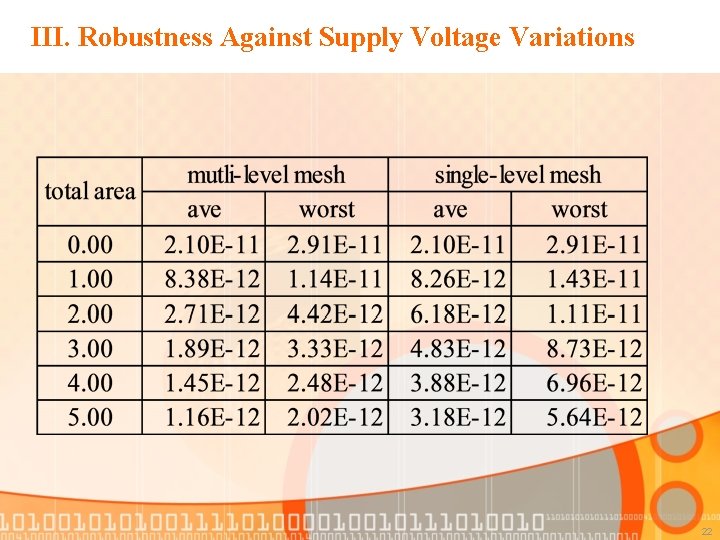
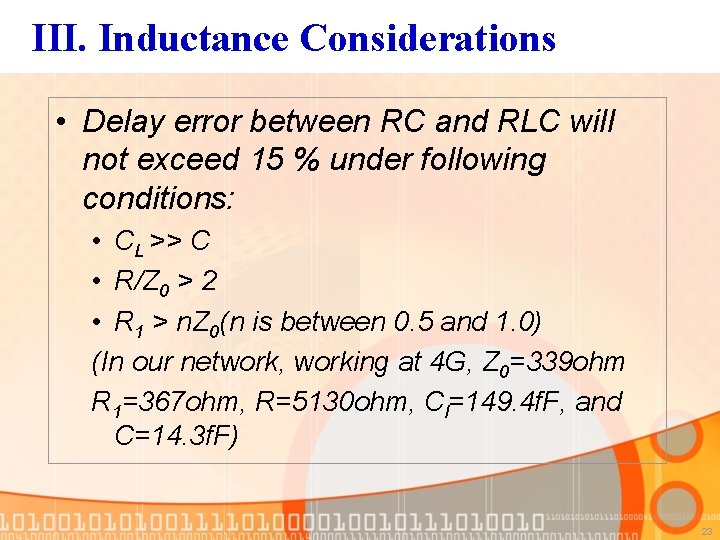
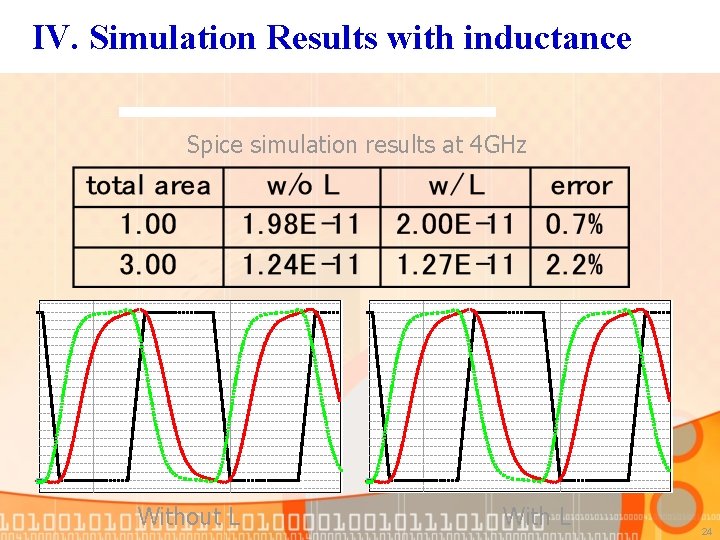
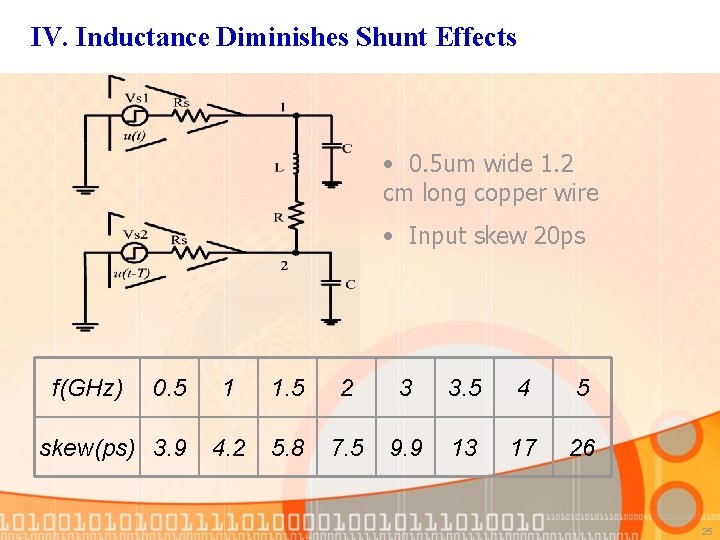
- Slides: 25
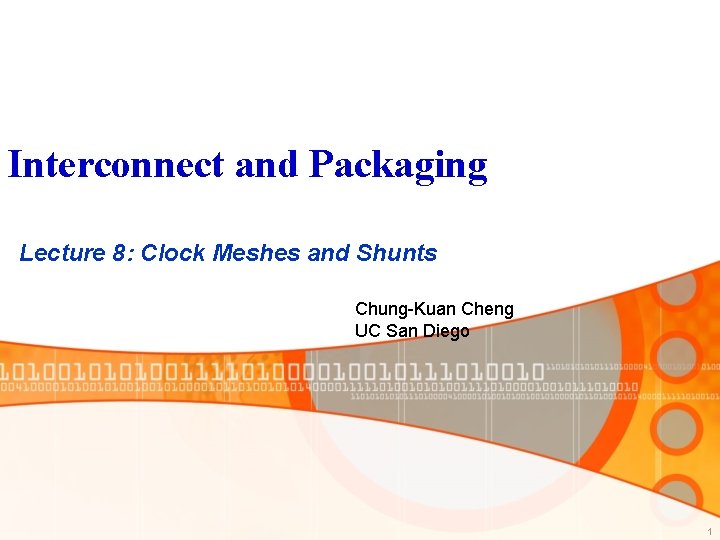
Interconnect and Packaging Lecture 8: Clock Meshes and Shunts Chung-Kuan Cheng UC San Diego 1
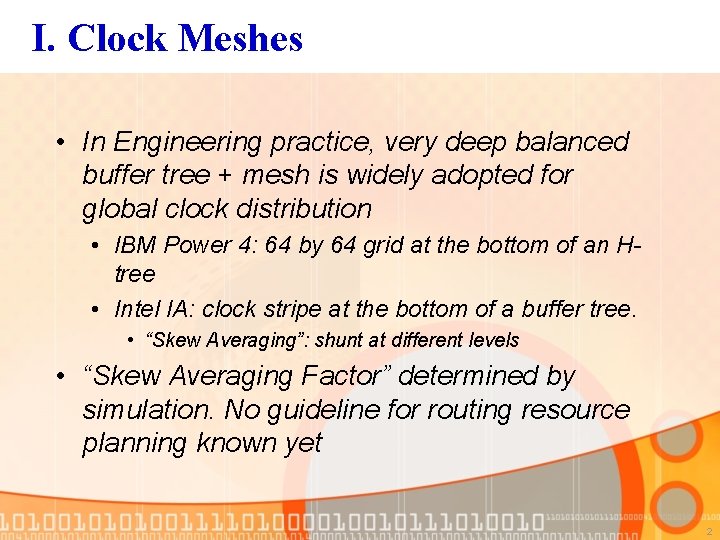
I. Clock Meshes • In Engineering practice, very deep balanced buffer tree + mesh is widely adopted for global clock distribution • IBM Power 4: 64 by 64 grid at the bottom of an Htree • Intel IA: clock stripe at the bottom of a buffer tree. • “Skew Averaging”: shunt at different levels • “Skew Averaging Factor” determined by simulation. No guideline for routing resource planning known yet 2
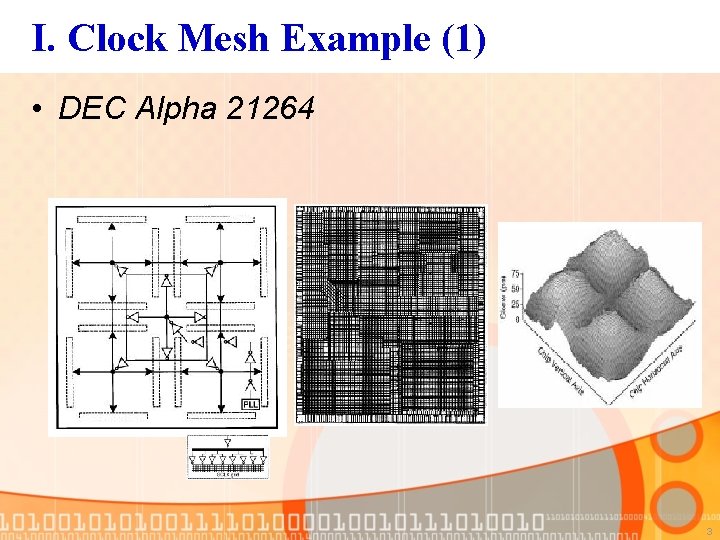
I. Clock Mesh Example (1) • DEC Alpha 21264 3
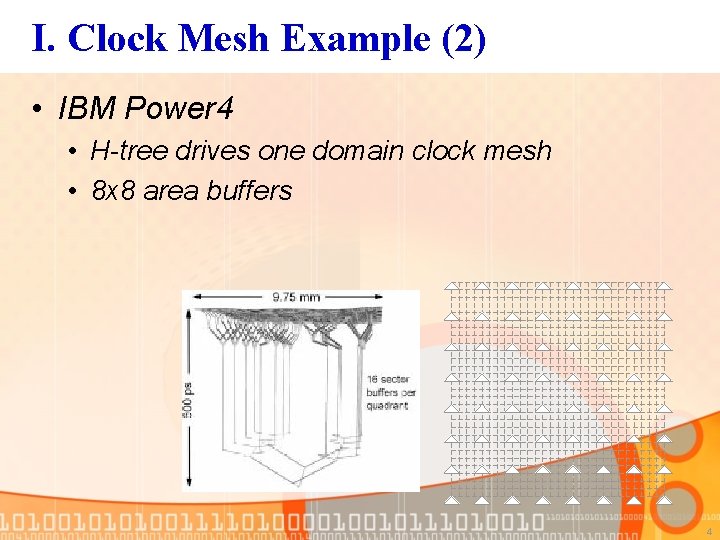
I. Clock Mesh Example (2) • IBM Power 4 • H-tree drives one domain clock mesh • 8 x 8 area buffers 4
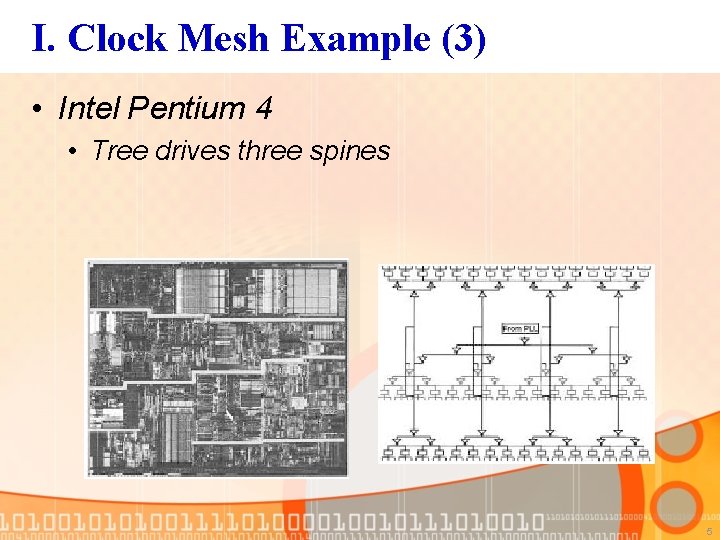
I. Clock Mesh Example (3) • Intel Pentium 4 • Tree drives three spines 5
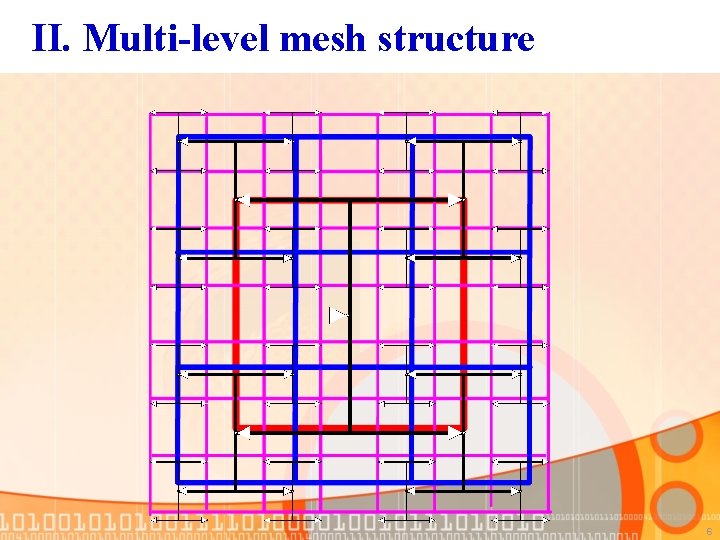
II. Multi-level mesh structure 6
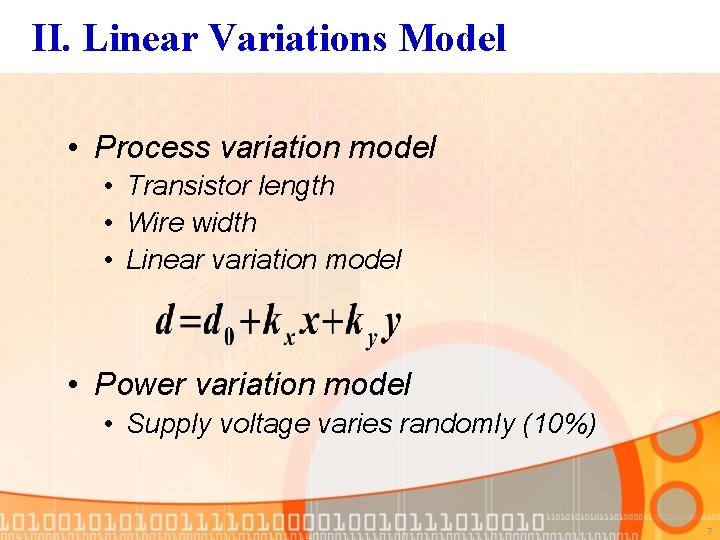
II. Linear Variations Model • Process variation model • Transistor length • Wire width • Linear variation model • Power variation model • Supply voltage varies randomly (10%) 7
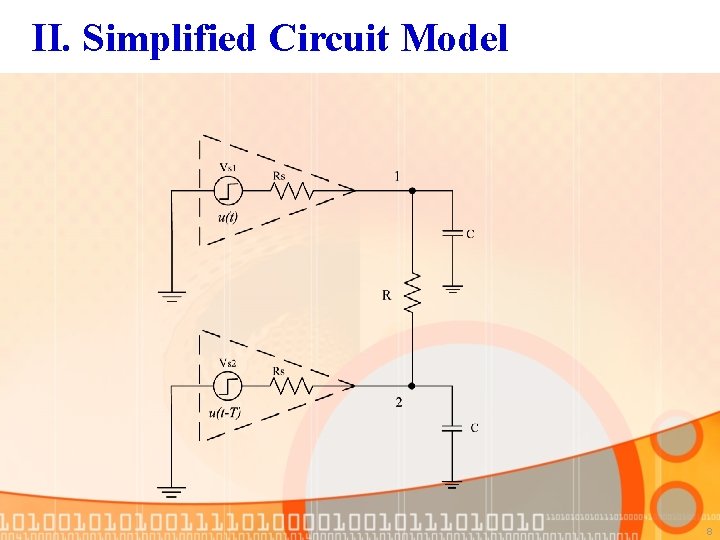
II. Simplified Circuit Model 8
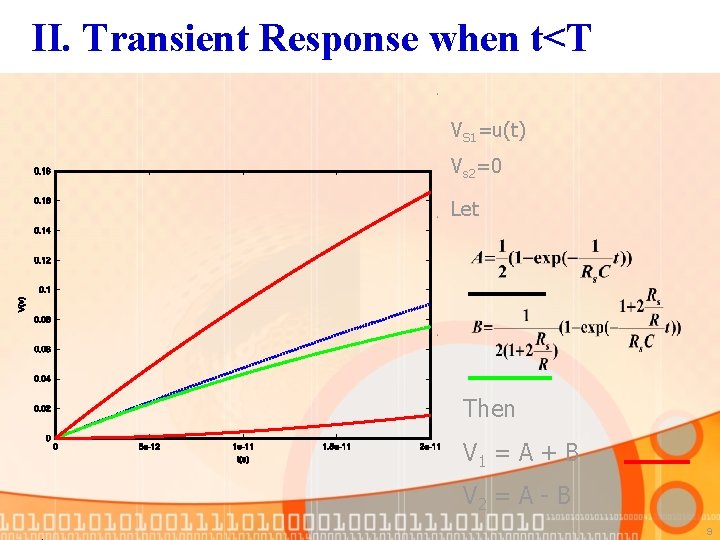
II. Transient Response when t<T VS 1=u(t) Vs 2=0 Let Then V 1 = A + B V 2 = A - B 9
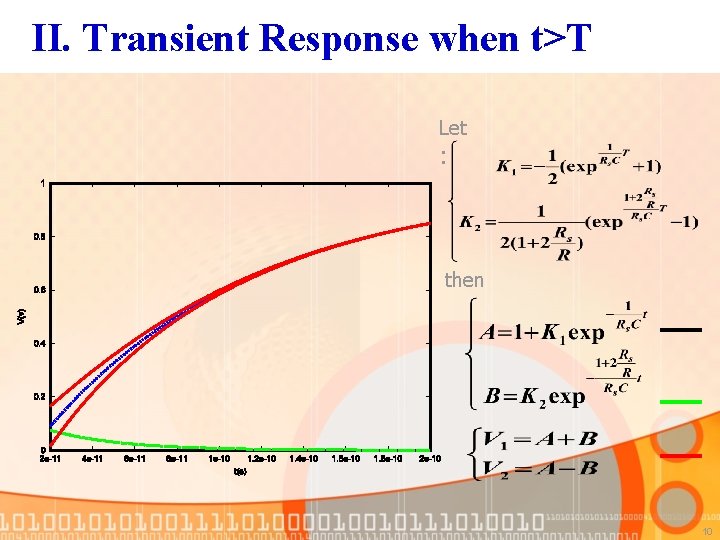
II. Transient Response when t>T Let : then 10
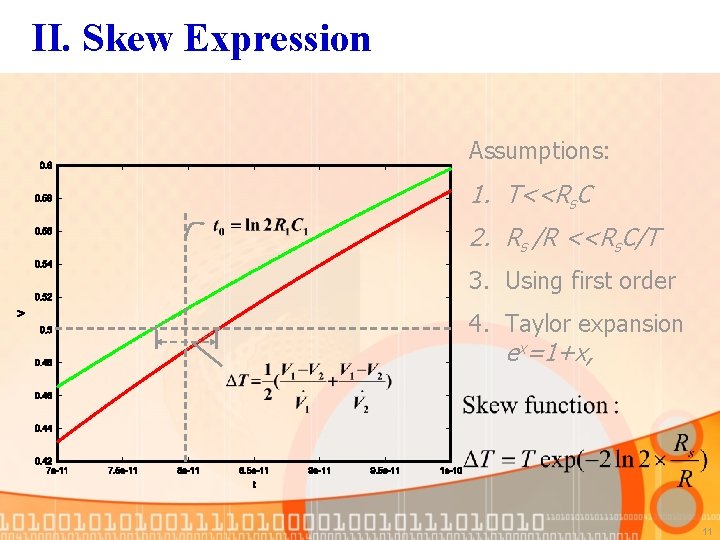
II. Skew Expression Assumptions: 1. T<<Rs. C 2. Rs /R <<Rs. C/T 3. Using first order 4. Taylor expansion ex=1+x, 11
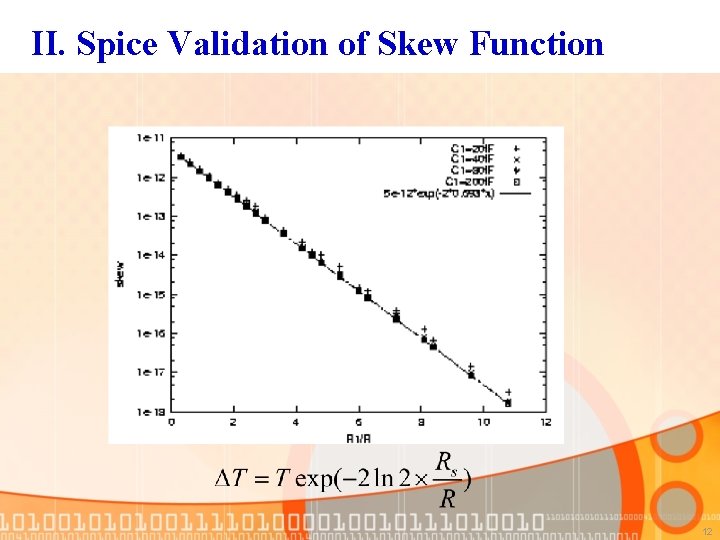
II. Spice Validation of Skew Function 12
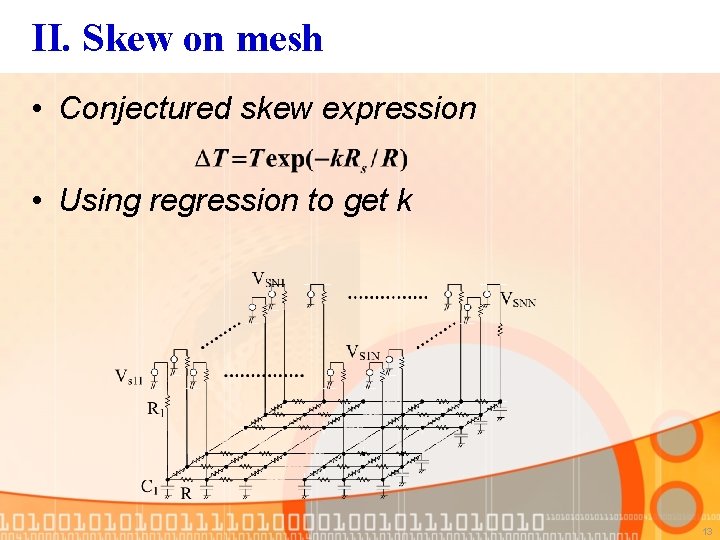
II. Skew on mesh • Conjectured skew expression • Using regression to get k 13
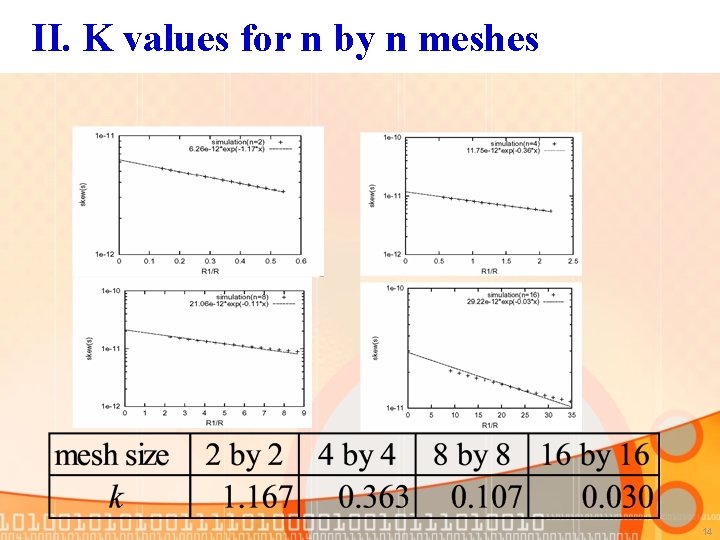
II. K values for n by n meshes 14
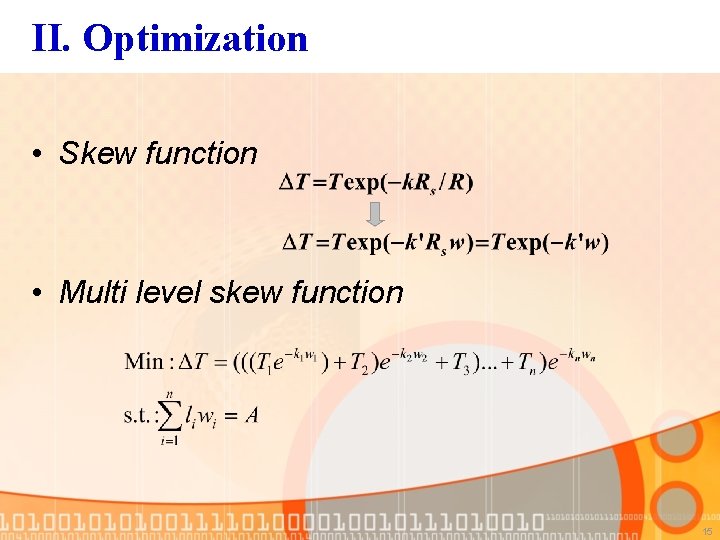
II. Optimization • Skew function • Multi level skew function 15
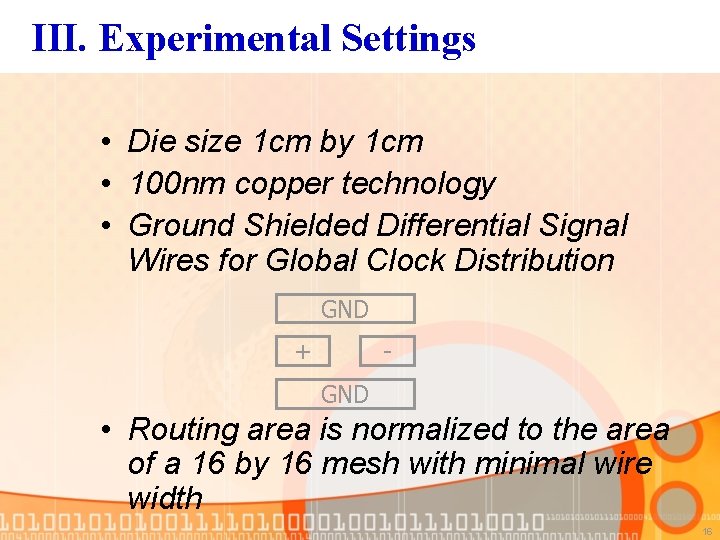
III. Experimental Settings • Die size 1 cm by 1 cm • 100 nm copper technology • Ground Shielded Differential Signal Wires for Global Clock Distribution GND + GND • Routing area is normalized to the area of a 16 by 16 mesh with minimal wire width 16
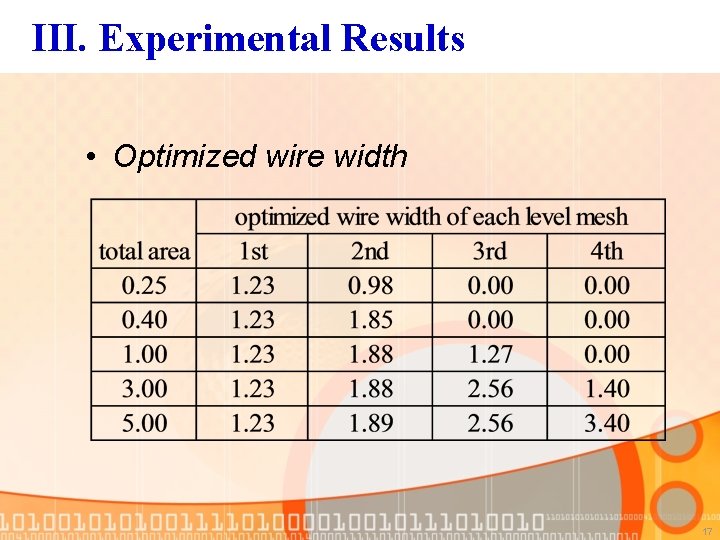
III. Experimental Results • Optimized wire width 17
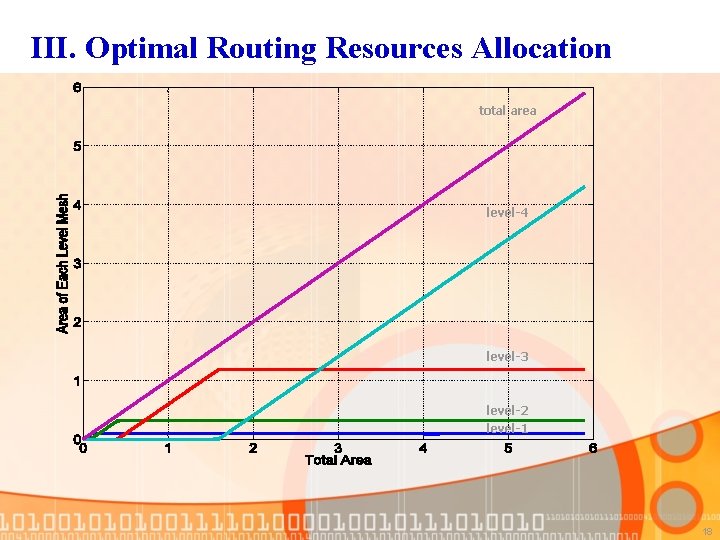
III. Optimal Routing Resources Allocation total area level-4 level-3 level-2 level-1 18
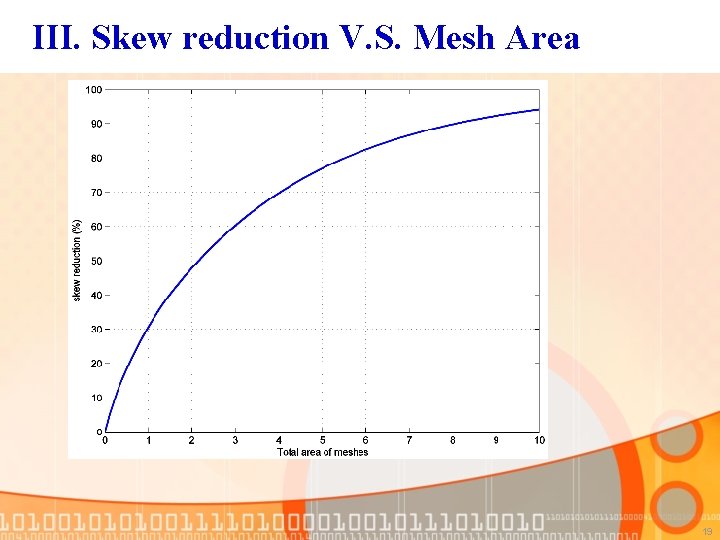
III. Skew reduction V. S. Mesh Area 19
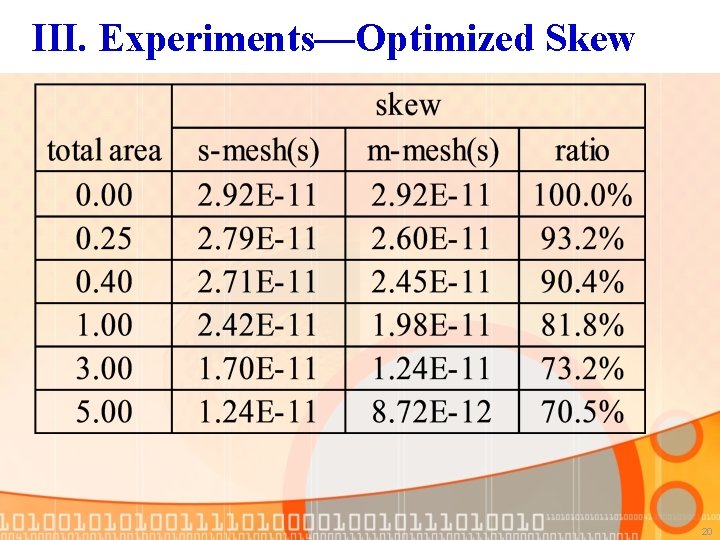
III. Experiments—Optimized Skew 20
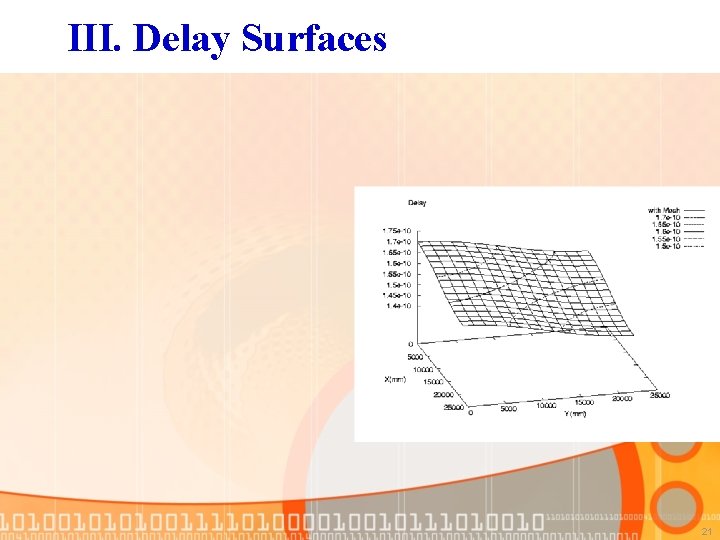
III. Delay Surfaces 21
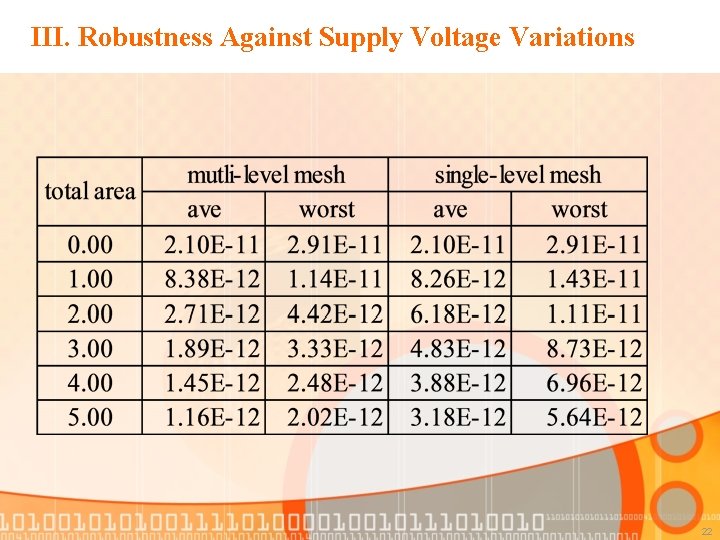
III. Robustness Against Supply Voltage Variations 22
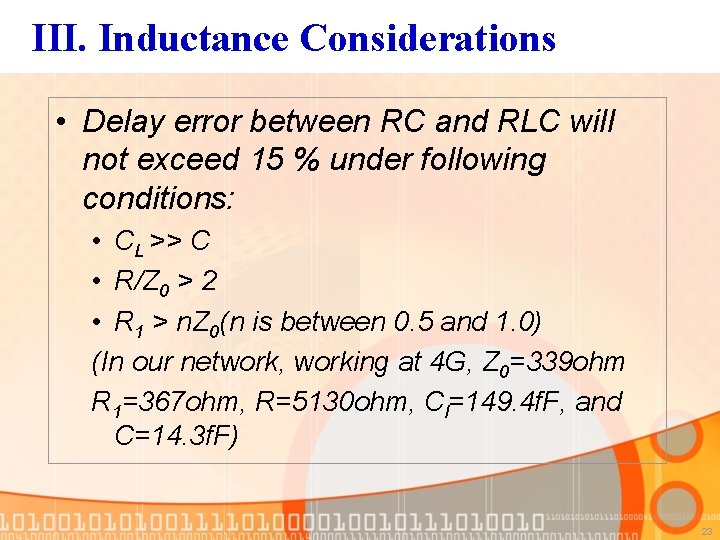
III. Inductance Considerations • Delay error between RC and RLC will not exceed 15 % under following conditions: • CL >> C • R/Z 0 > 2 • R 1 > n. Z 0(n is between 0. 5 and 1. 0) (In our network, working at 4 G, Z 0=339 ohm R 1=367 ohm, R=5130 ohm, Cl=149. 4 f. F, and C=14. 3 f. F) 23
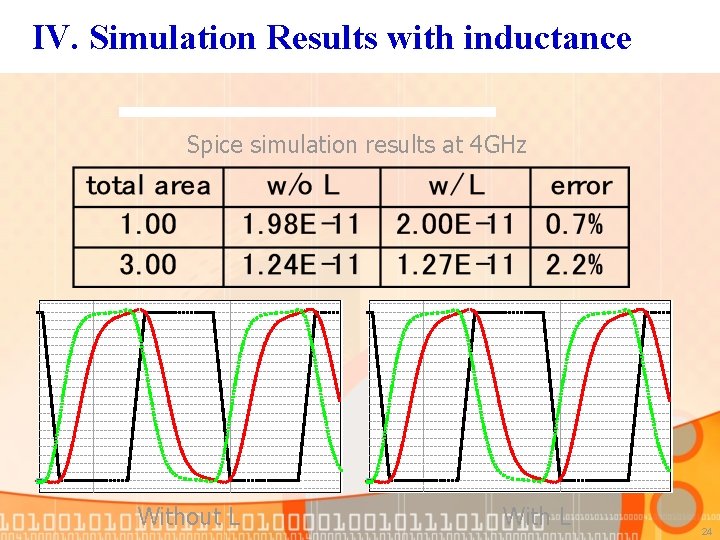
IV. Simulation Results with inductance Spice simulation results at 4 GHz Without L With L 24
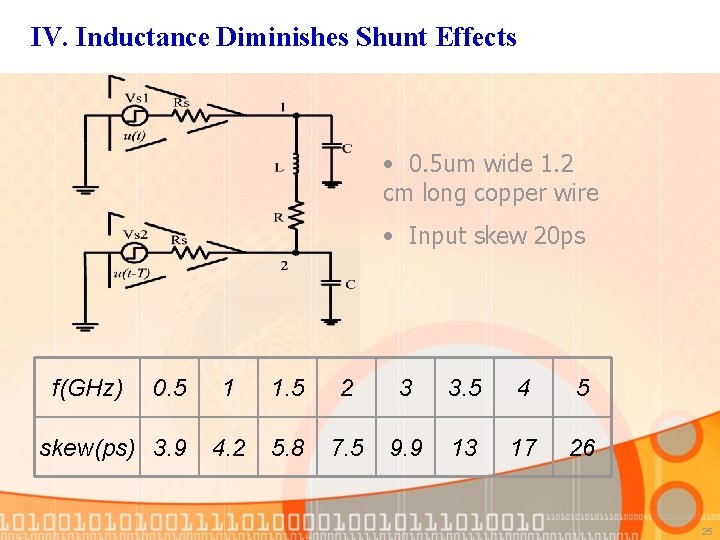
IV. Inductance Diminishes Shunt Effects • 0. 5 um wide 1. 2 cm long copper wire • Input skew 20 ps f(GHz) 0. 5 skew(ps) 3. 9 1 1. 5 2 3 3. 5 4. 2 5. 8 7. 5 9. 9 13 17 26 25
Fast exact and approximate geodesics on meshes
Brc global standard for packaging and packaging materials
Steve tattum
Progressive meshes
Hoppes construction
Texture mapping progressive meshes
Fast clock to slow clock synchronization
60 seconds make a minute
01:640:244 lecture notes - lecture 15: plat, idah, farad
Sip interconnect
Virtual protocol interconnect
Optical interconnect
Optical interconnect solutions
Butterfly network topology
Programmable interconnect
Rating vs. billing
Cross building interconnect
Quick path interconnect
Wishbone fpga
Chet mehta
Dolphin interconnect
Open systems interconnect
High frequency interconnect
Interconnect scaling
Interconnect
Dspx simulation suite