Emrah T SAK March 2013 European Requalification System
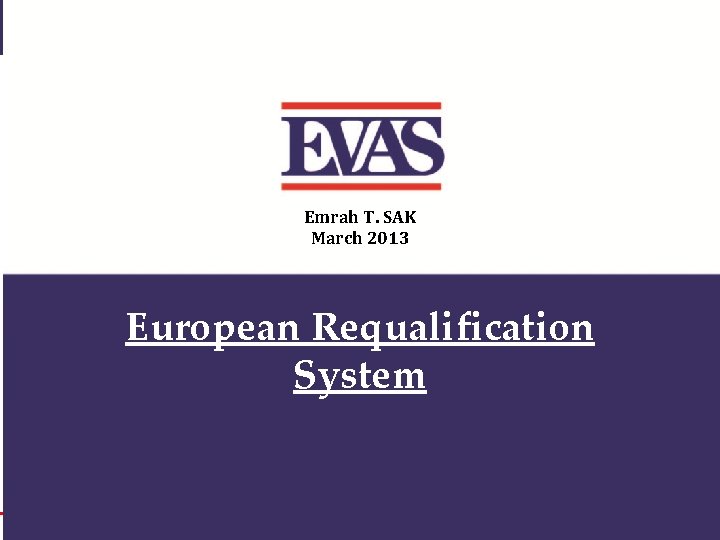
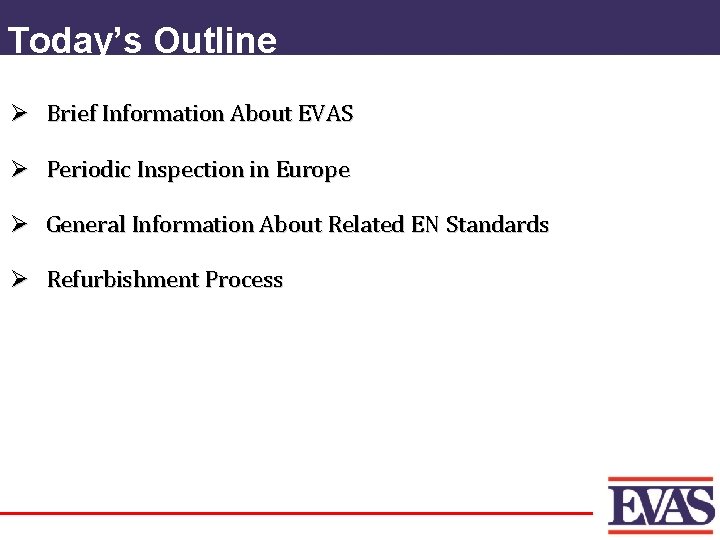
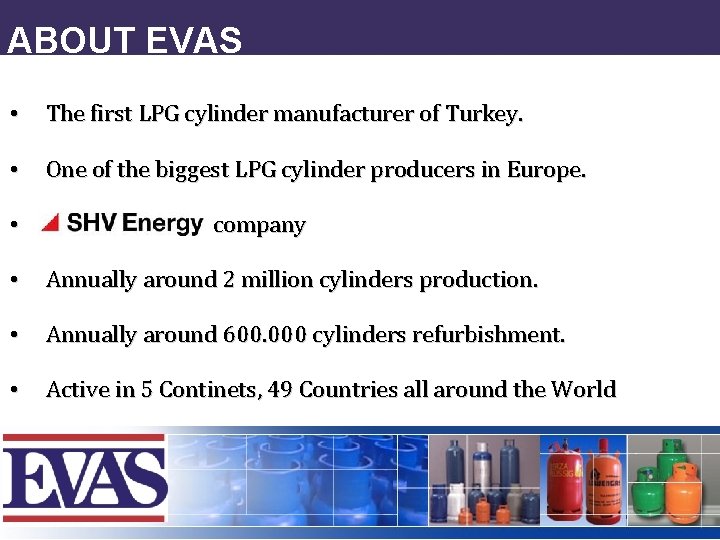
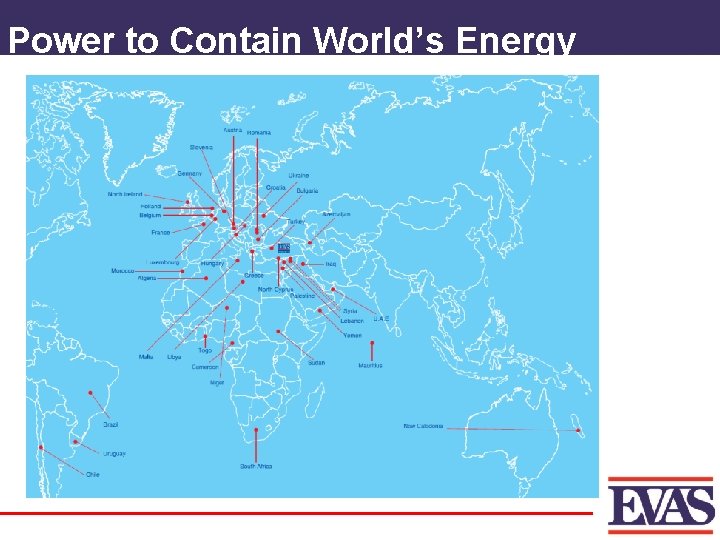
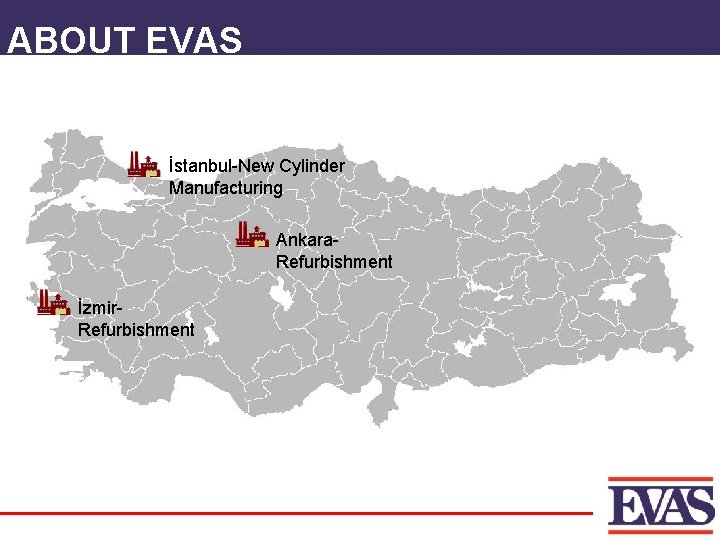
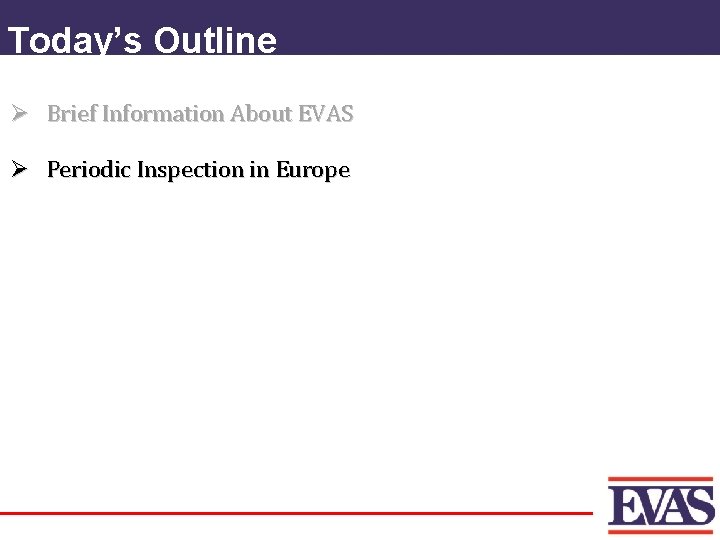
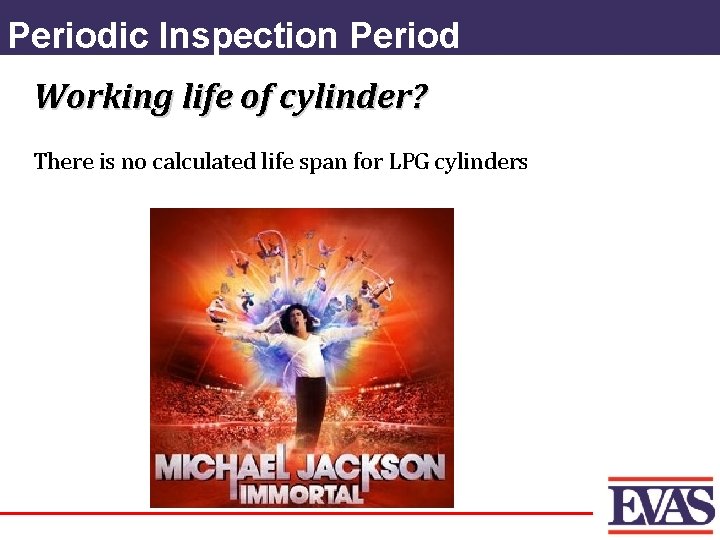
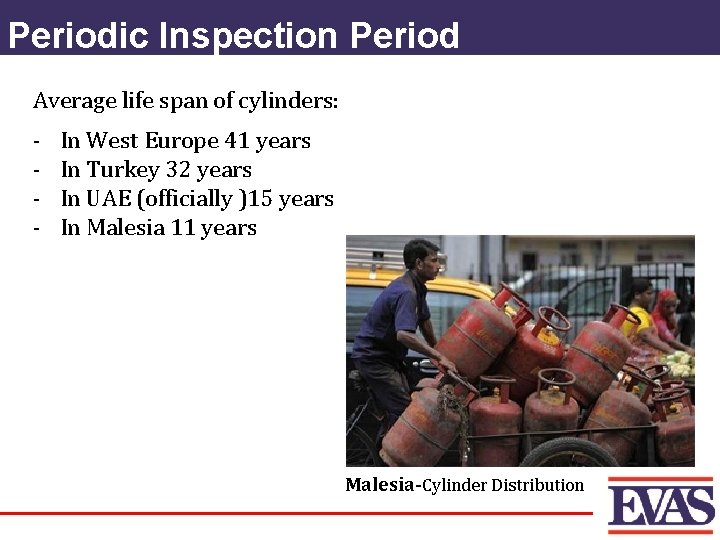
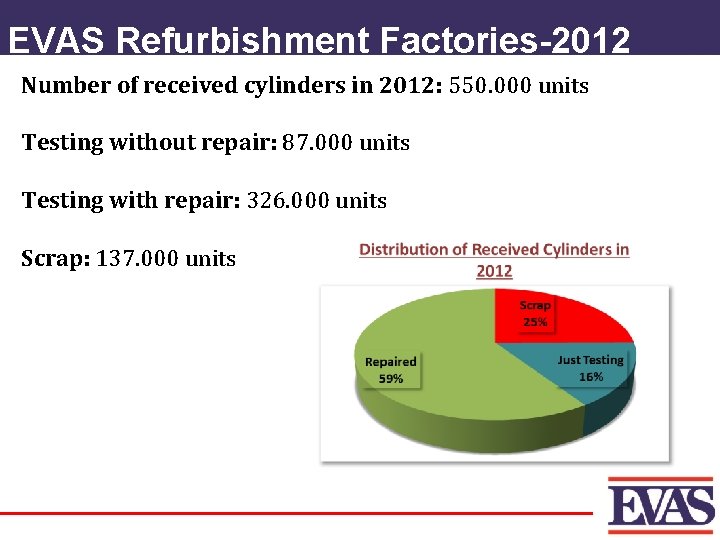
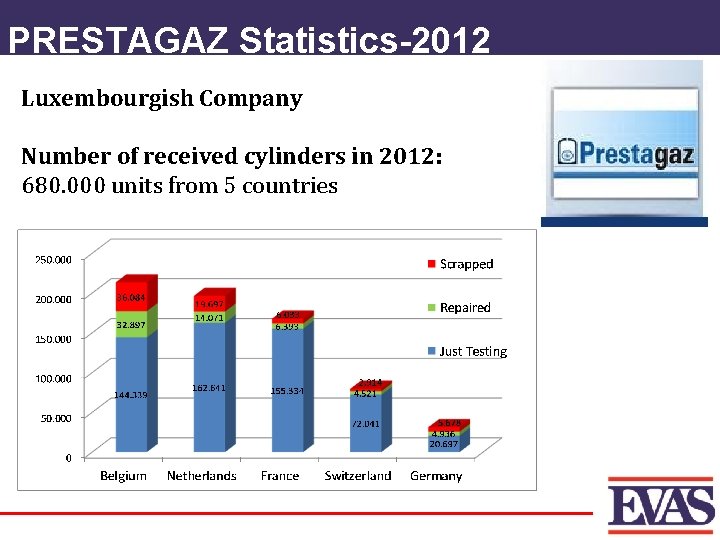
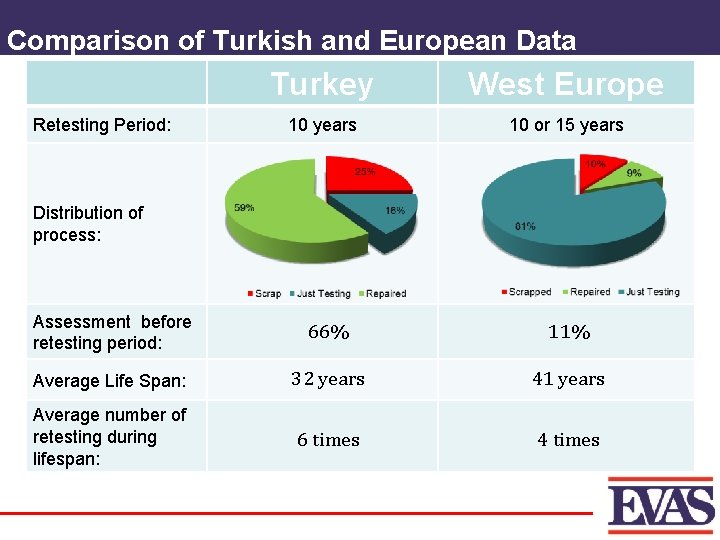
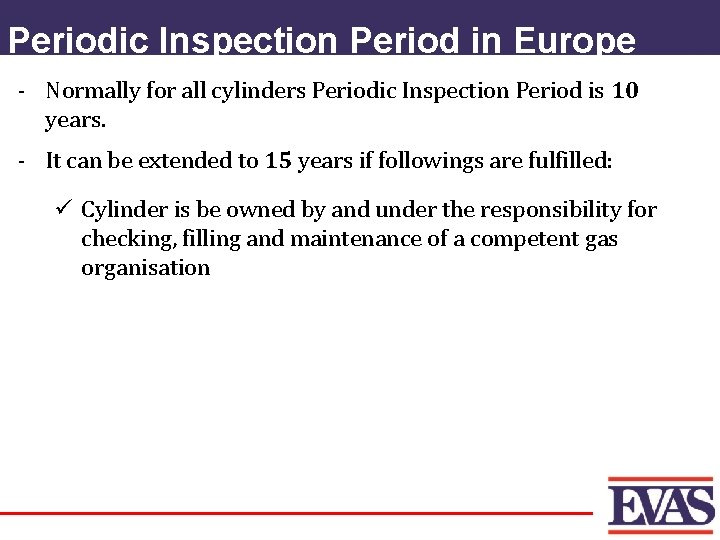
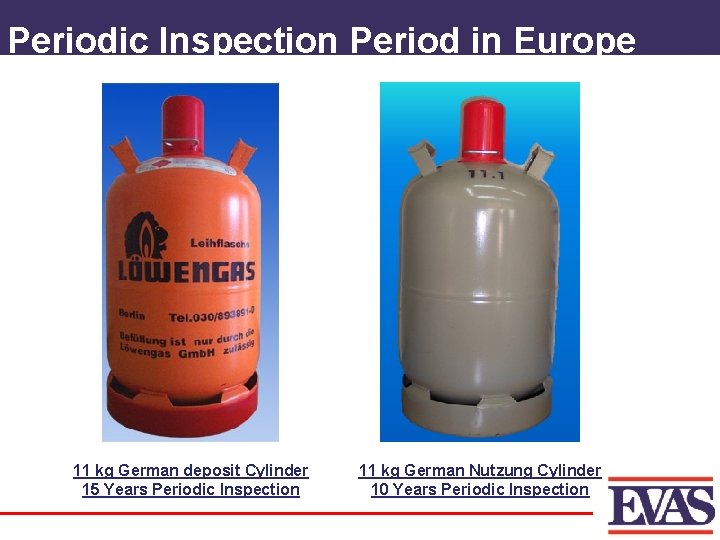
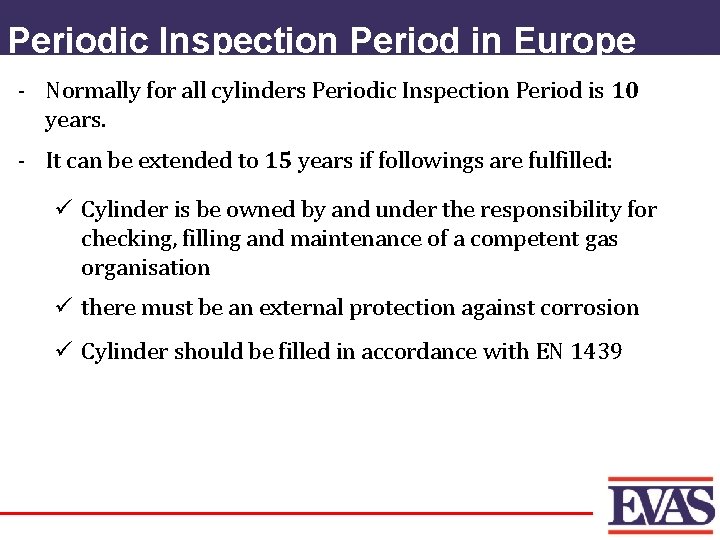
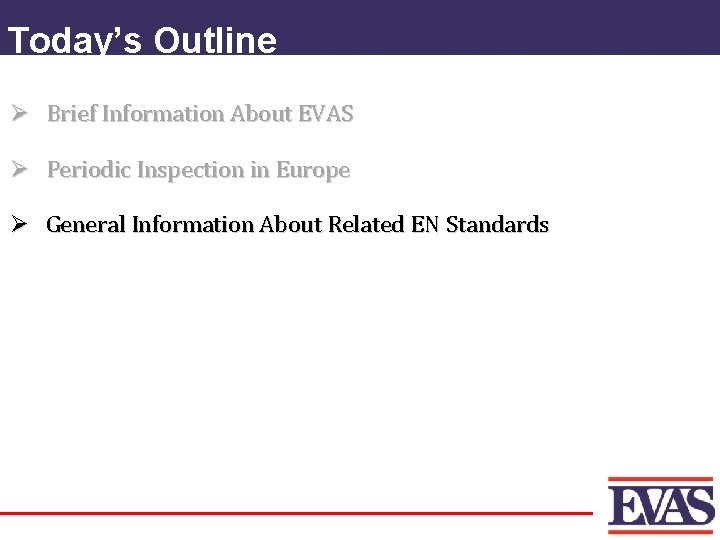
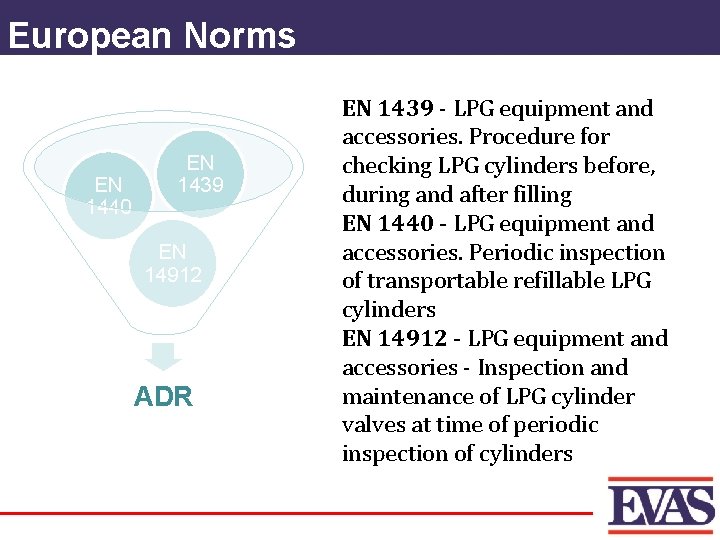
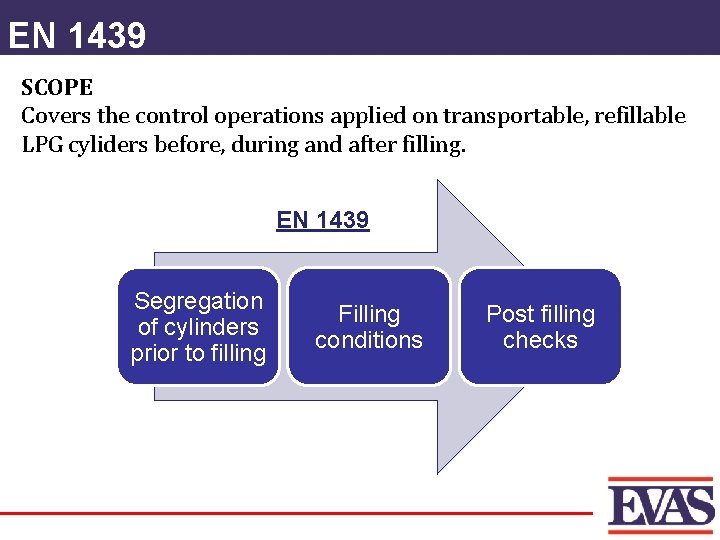
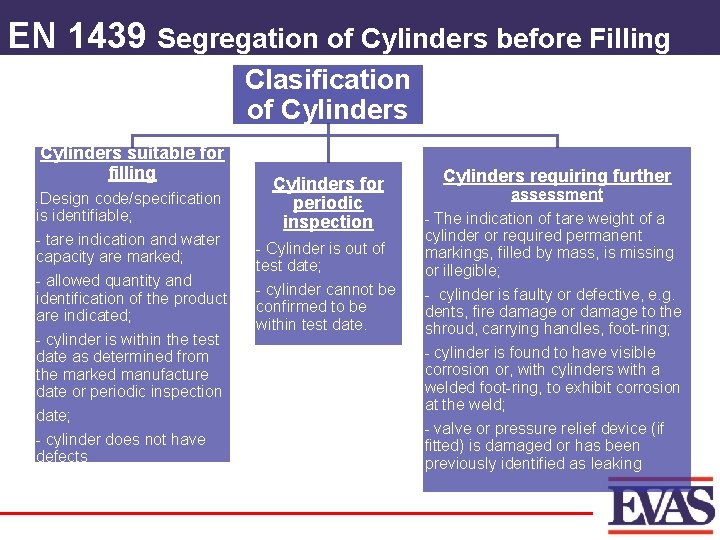
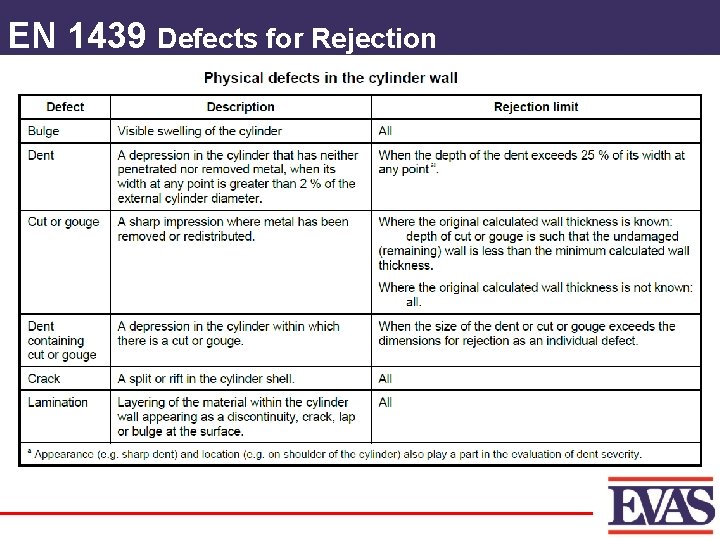
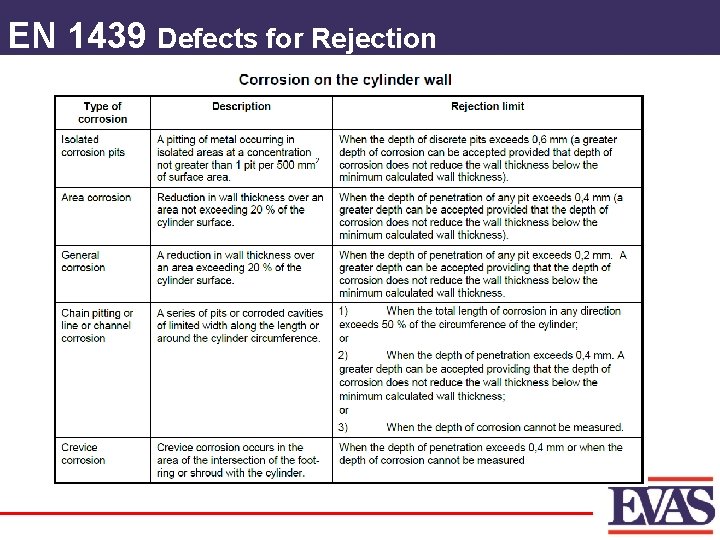
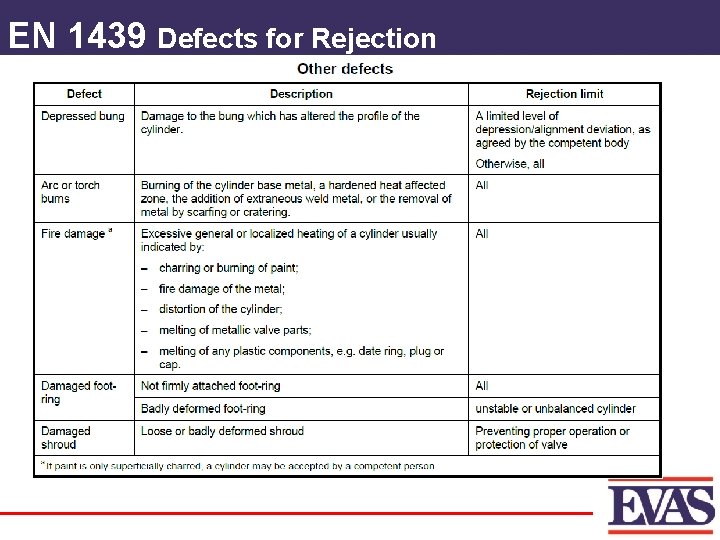
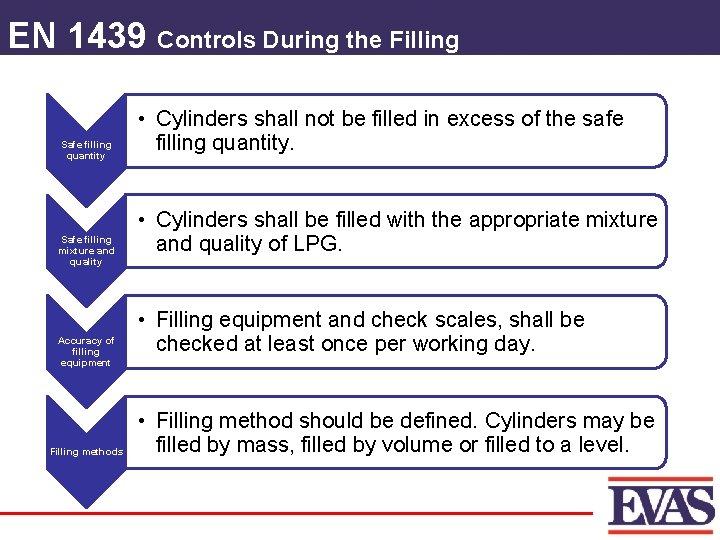
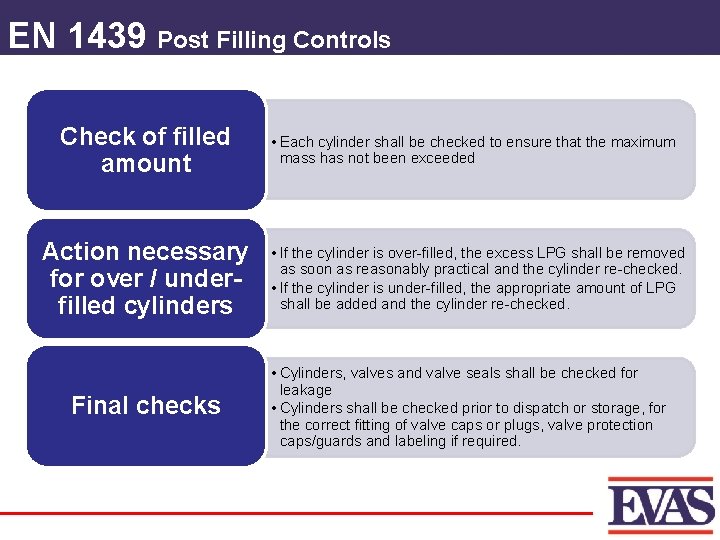
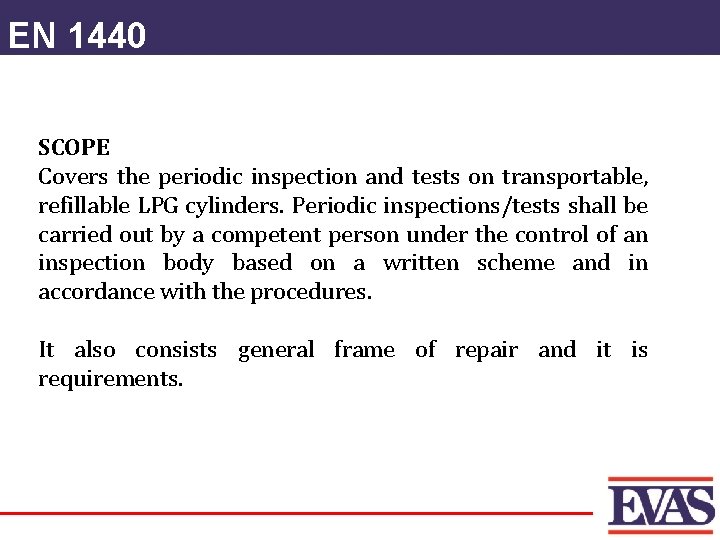
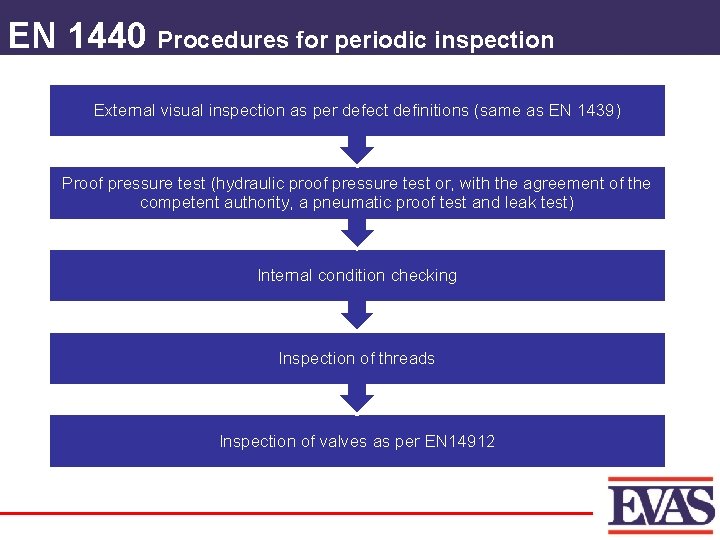
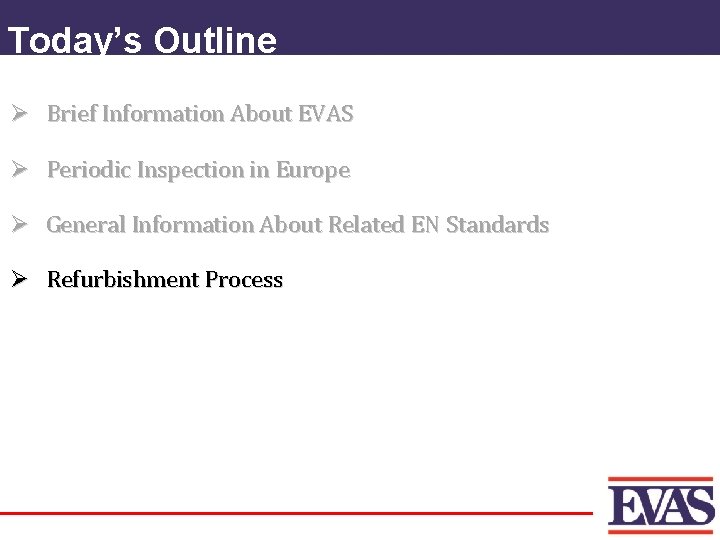
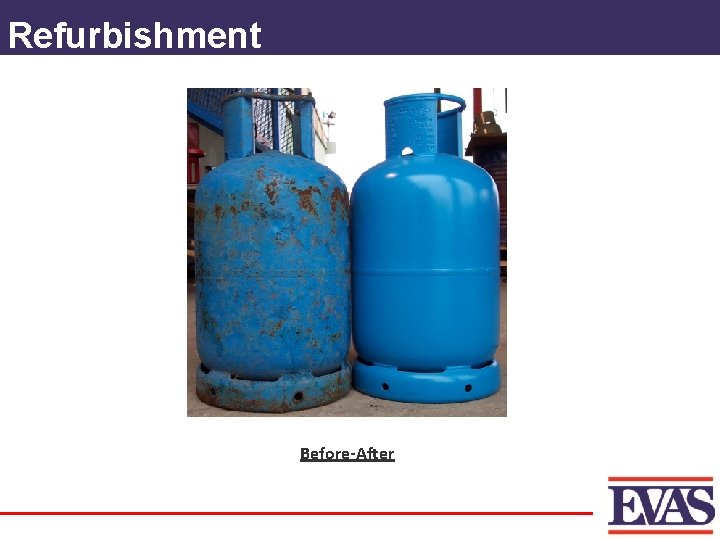
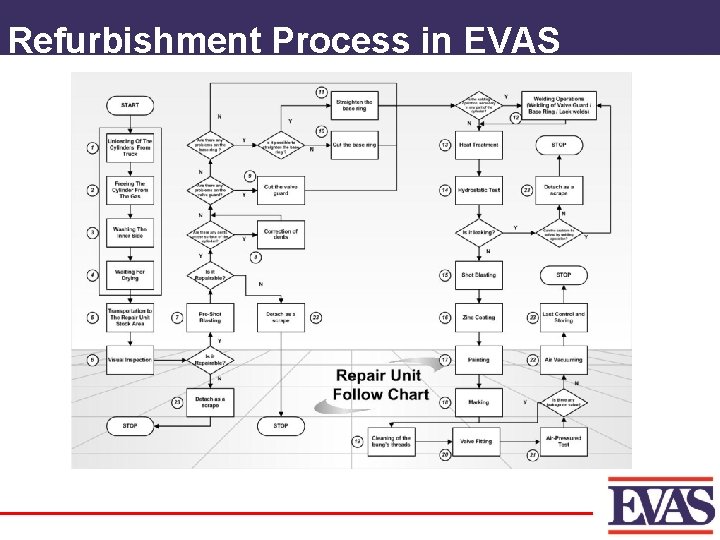
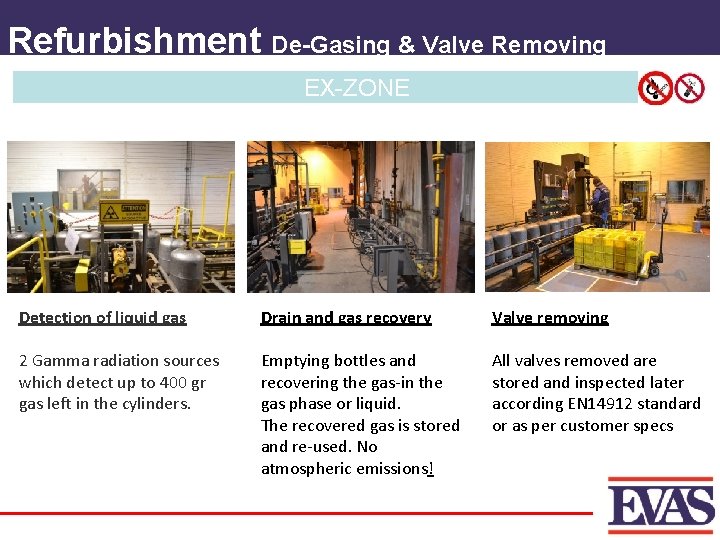
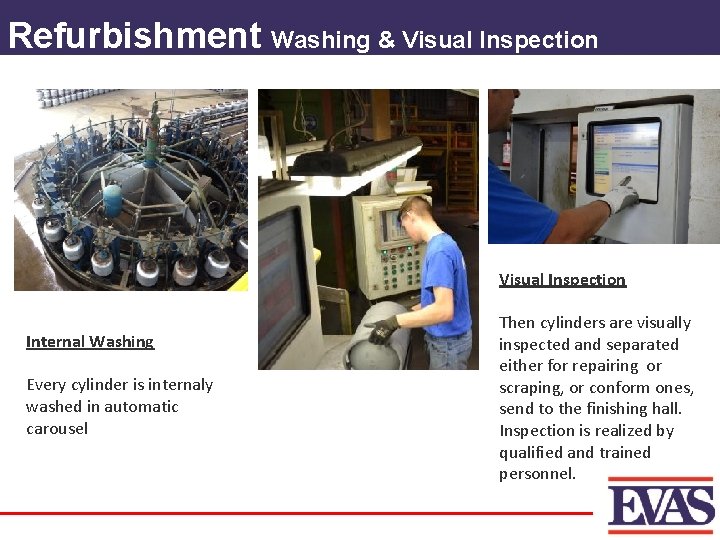
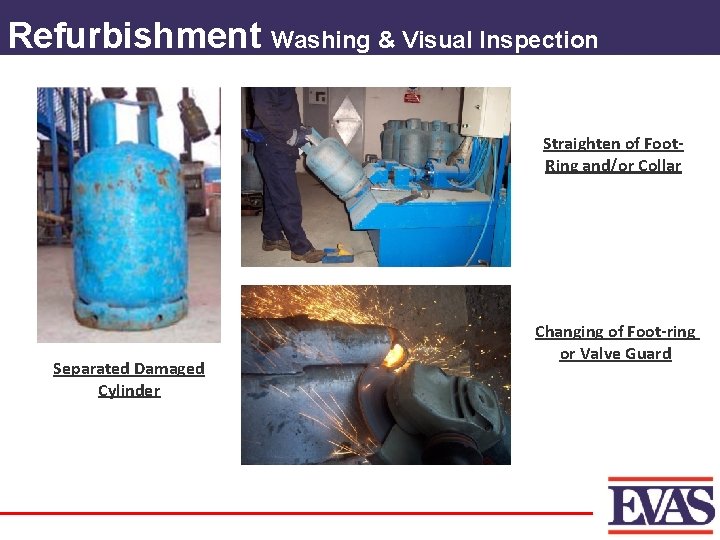
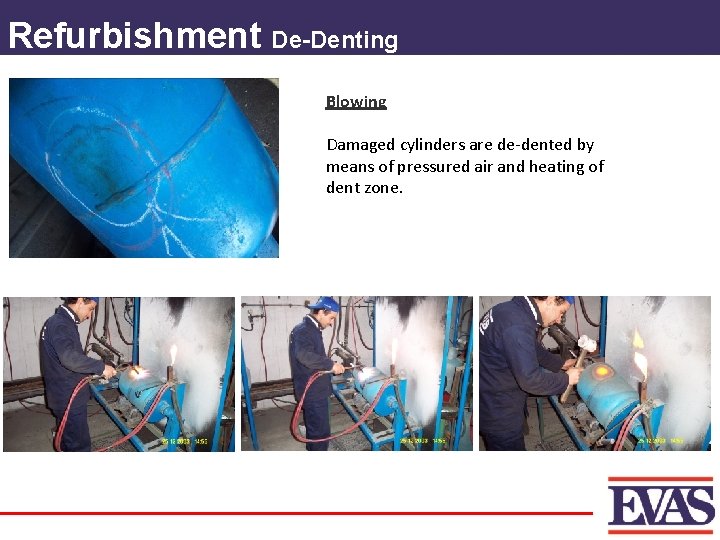
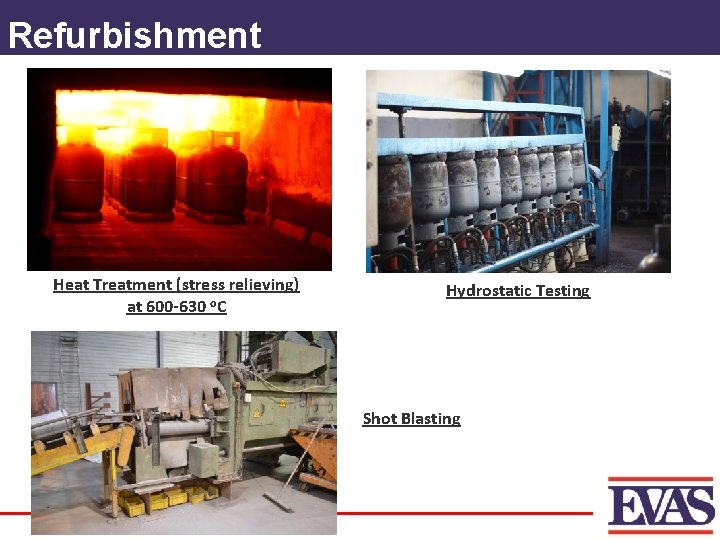
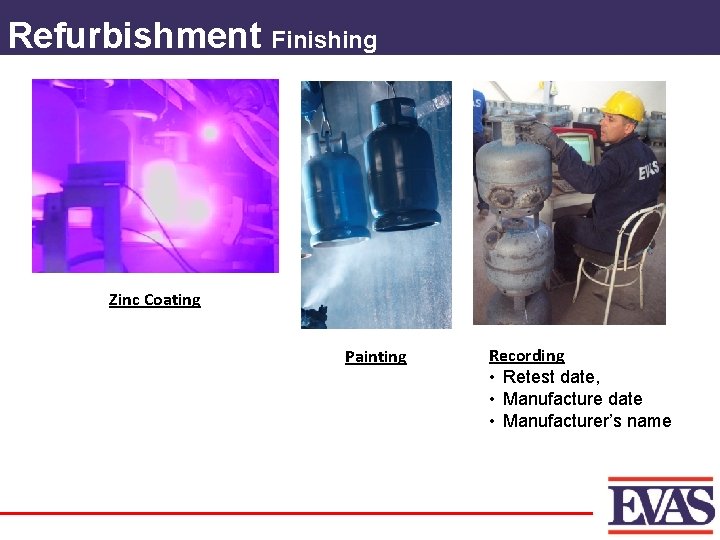
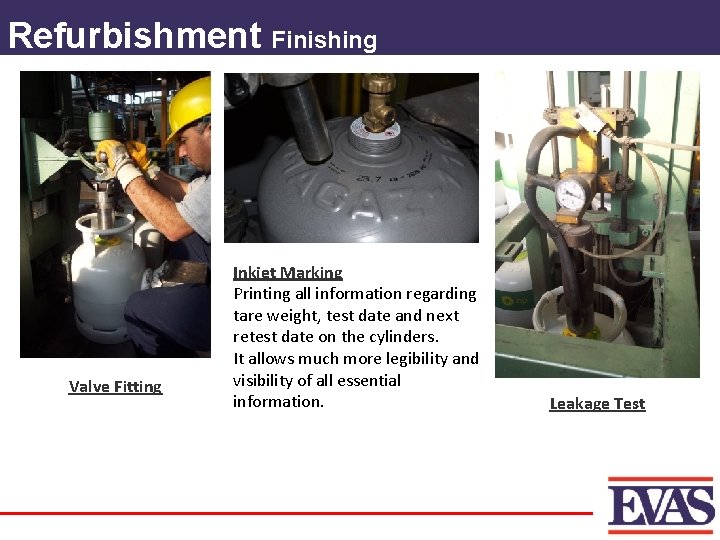
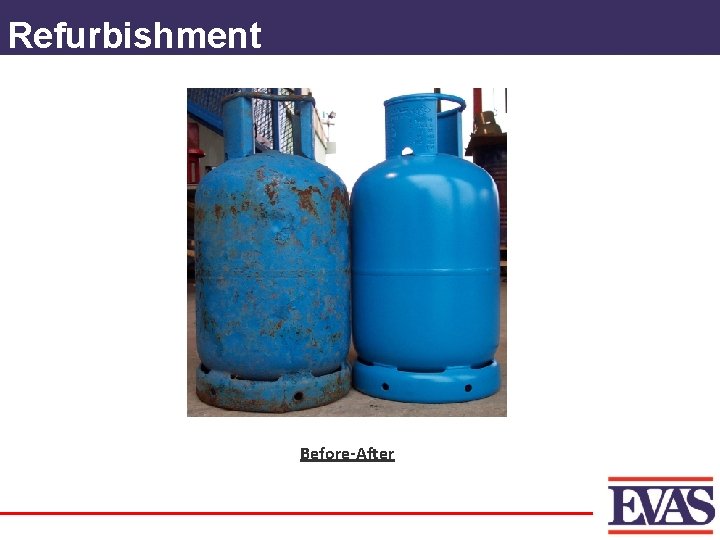
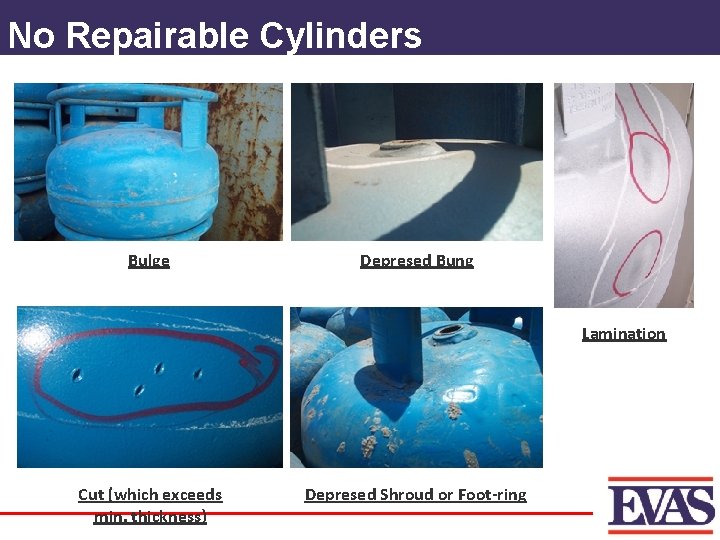
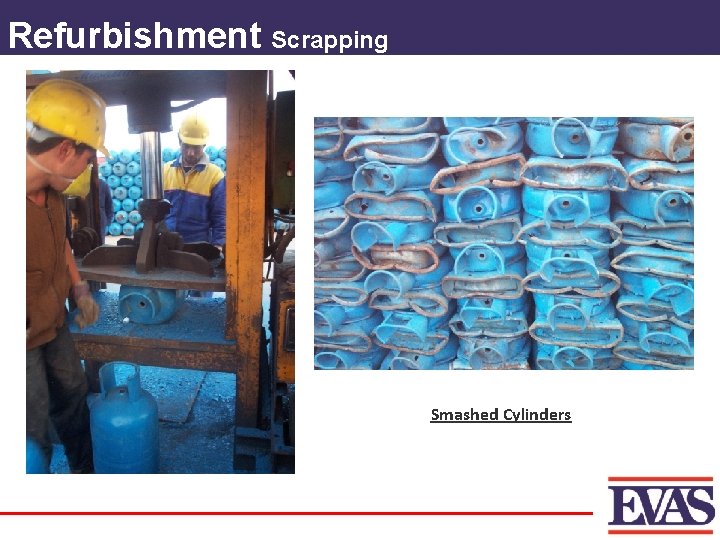
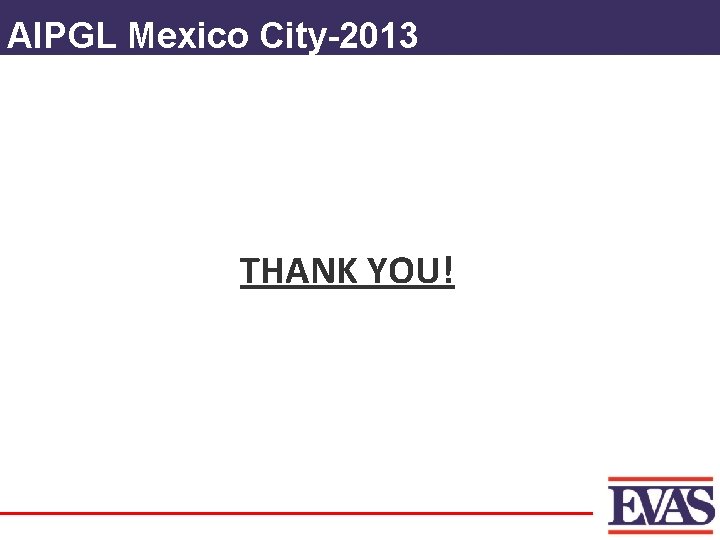
- Slides: 39
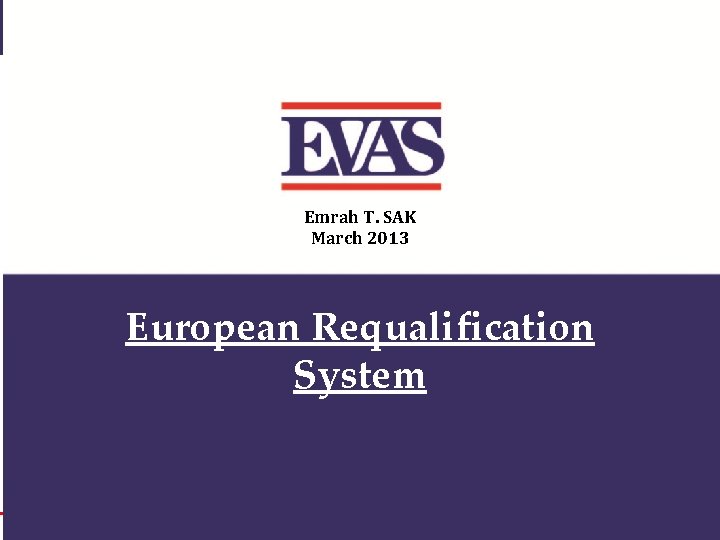
Emrah T. SAK March 2013 European Requalification System
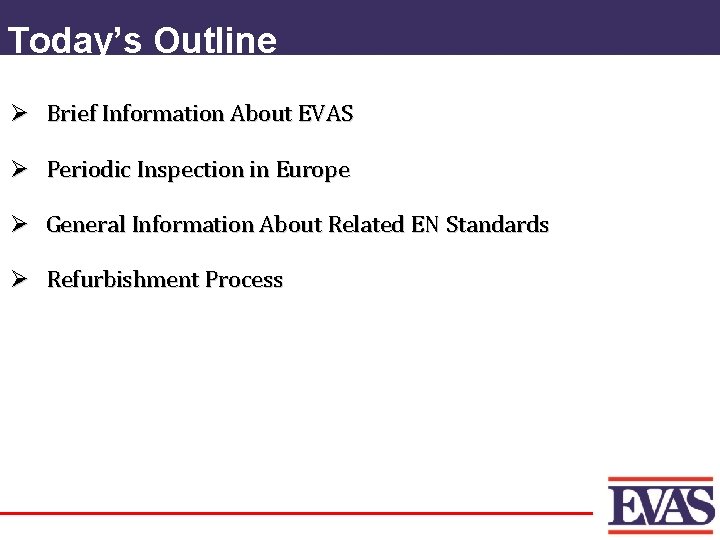
Today’s Outline Ø Brief Information About EVAS Ø Periodic Inspection in Europe Ø General Information About Related EN Standards Ø Refurbishment Process
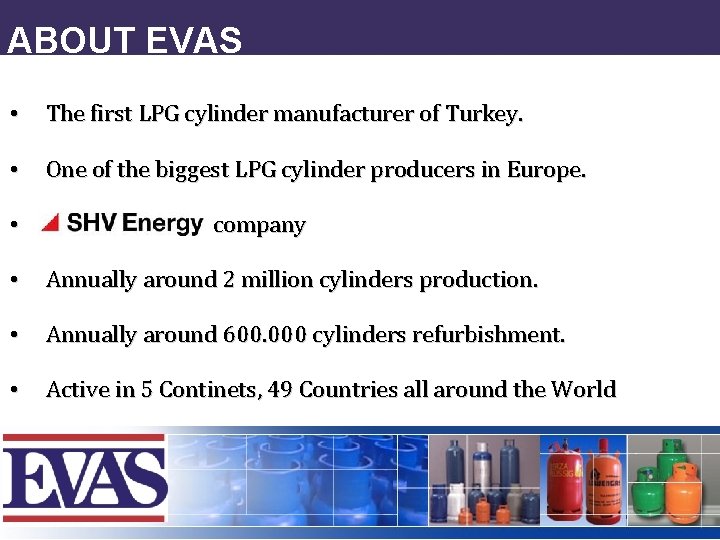
ABOUT EVAS • The first LPG cylinder manufacturer of Turkey. • One of the biggest LPG cylinder producers in Europe. • SHV ENERGY • Annually around 2 million cylinders production. • Annually around 600. 000 cylinders refurbishment. • Active in 5 Continets, 49 Countries all around the World company
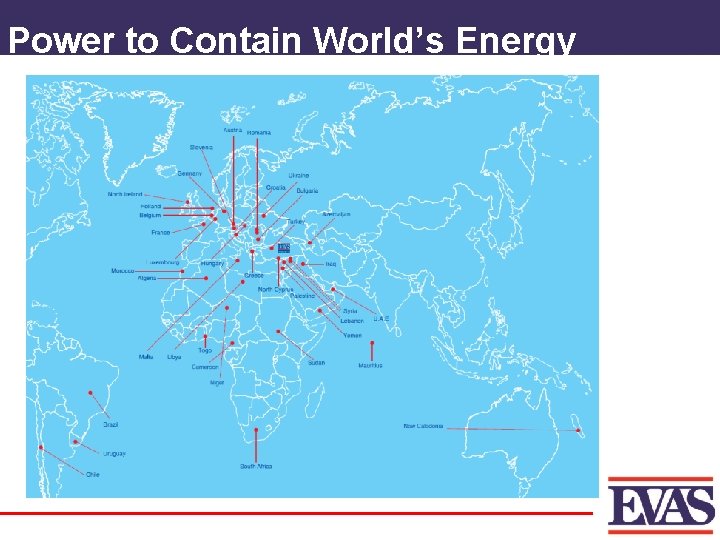
Power to Contain World’s Energy
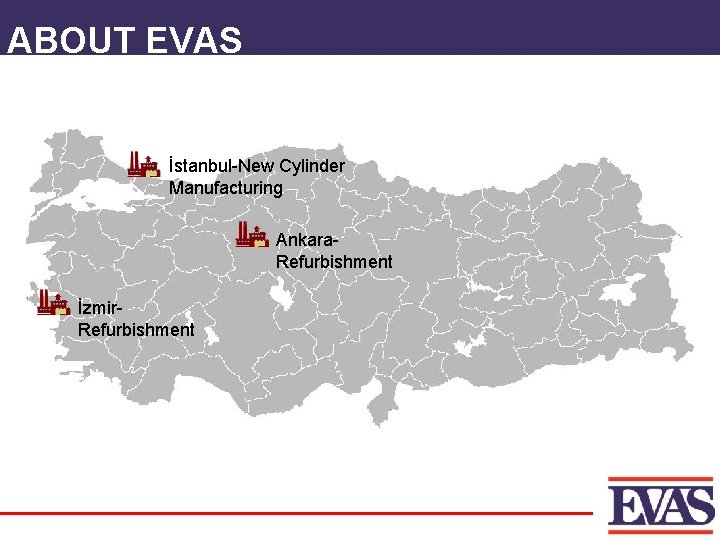
ABOUT EVAS İstanbul-New Cylinder Manufacturing Ankara. Refurbishment İzmir. Refurbishment
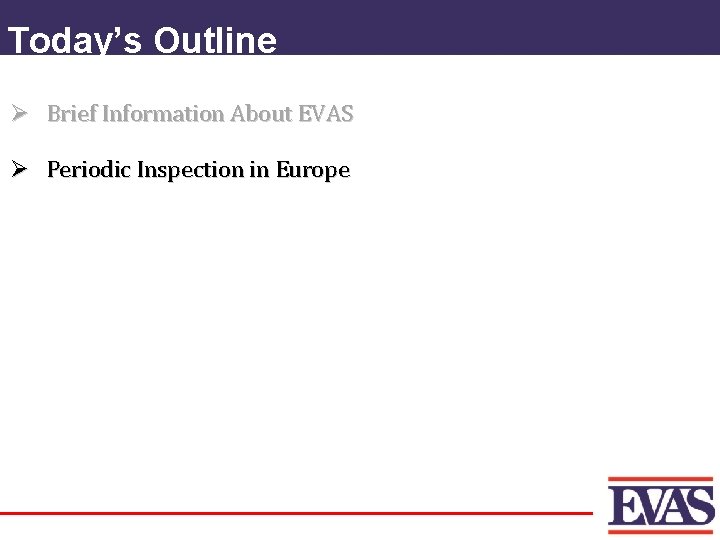
Today’s Outline Ø Brief Information About EVAS Ø Periodic Inspection in Europe
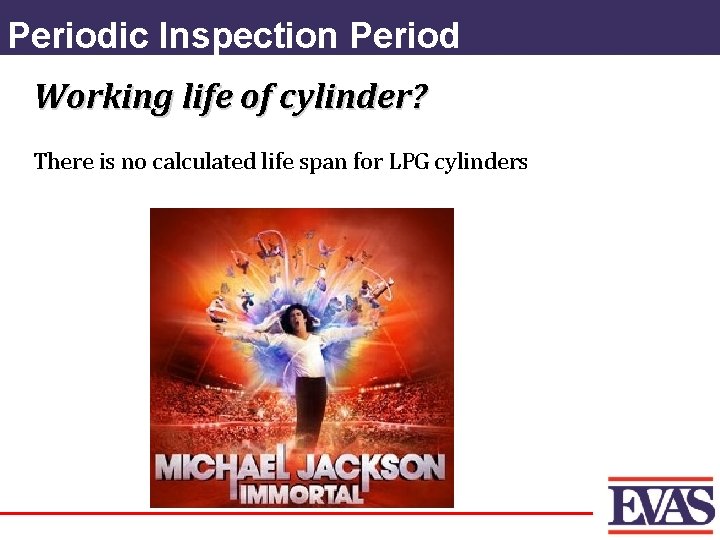
Periodic Inspection Period Working life of cylinder? There is no calculated life span for LPG cylinders
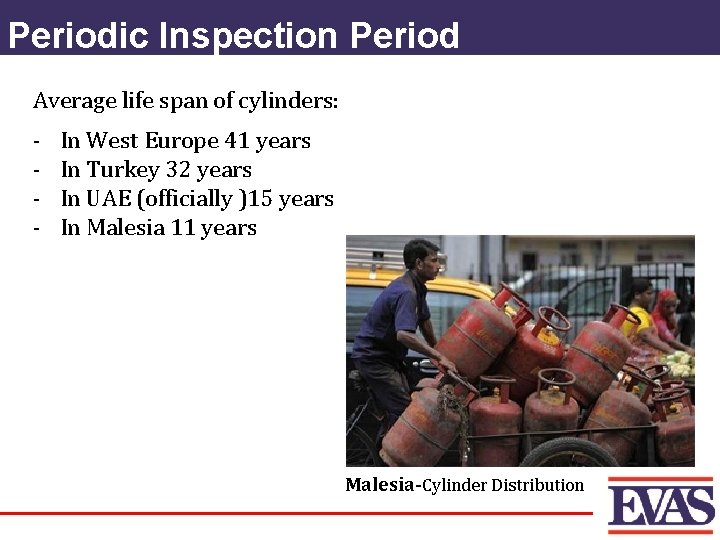
Periodic Inspection Period Average life span of cylinders: - In West Europe 41 years In Turkey 32 years In UAE (officially )15 years In Malesia 11 years Malesia-Cylinder Distribution
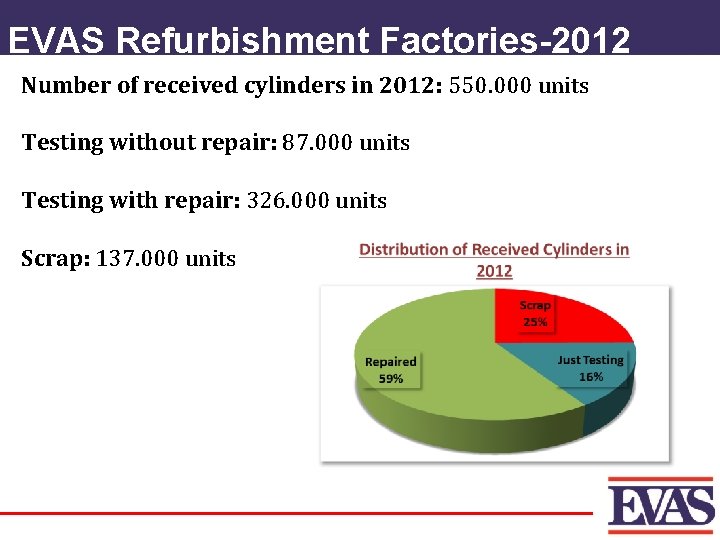
EVAS Refurbishment Factories-2012 Number of received cylinders in 2012: 550. 000 units Testing without repair: 87. 000 units Testing with repair: 326. 000 units Scrap: 137. 000 units
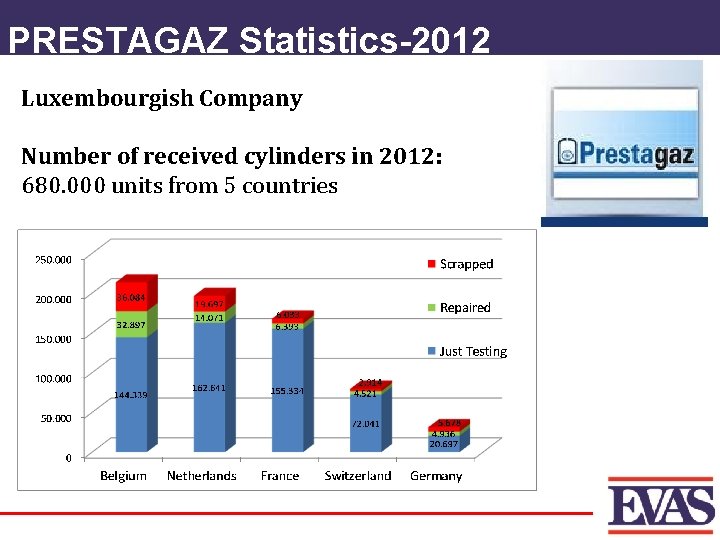
PRESTAGAZ Statistics-2012 Luxembourgish Company Number of received cylinders in 2012: 680. 000 units from 5 countries
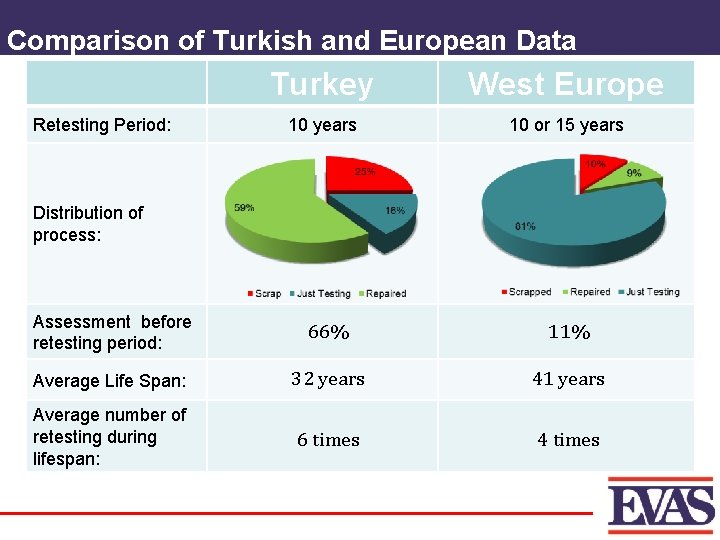
Comparison of Turkish and European Data Retesting Period: Turkey West Europe 10 years 10 or 15 years Distribution of process: Assessment before retesting period: 66% 11% Average Life Span: 32 years 41 years Average number of retesting during lifespan: 6 times 4 times
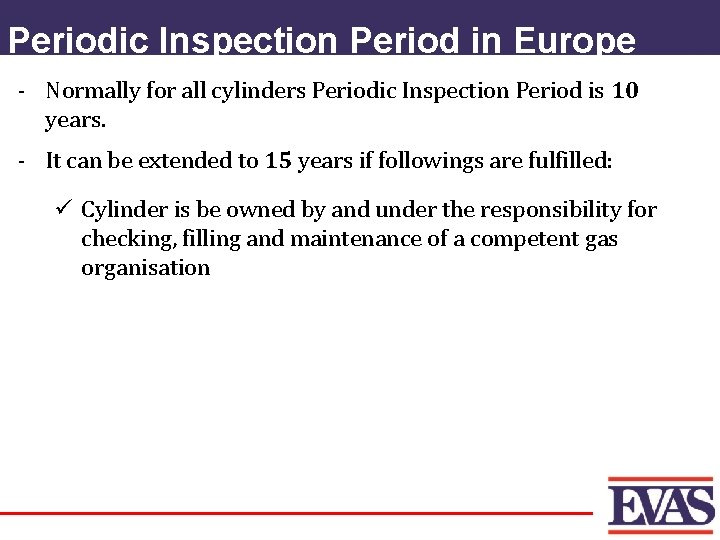
Periodic Inspection Period in Europe - Normally for all cylinders Periodic Inspection Period is 10 years. - It can be extended to 15 years if followings are fulfilled: ü Cylinder is be owned by and under the responsibility for checking, filling and maintenance of a competent gas organisation
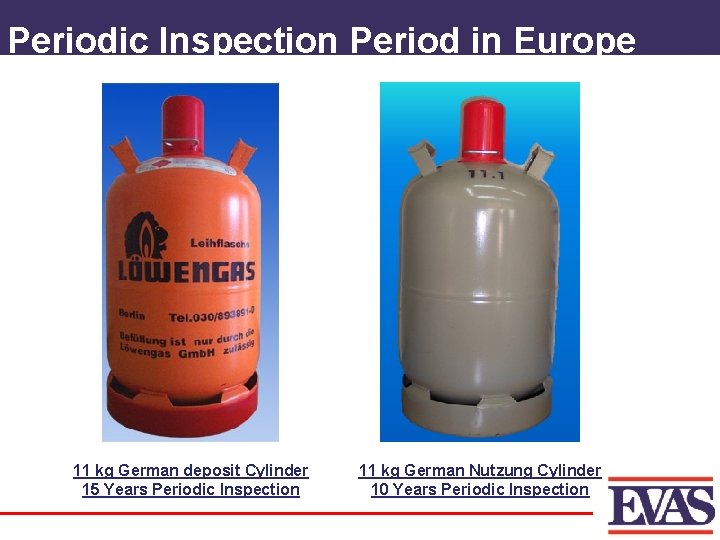
Periodic Inspection Period in Europe 11 kg German deposit Cylinder 15 Years Periodic Inspection 11 kg German Nutzung Cylinder 10 Years Periodic Inspection
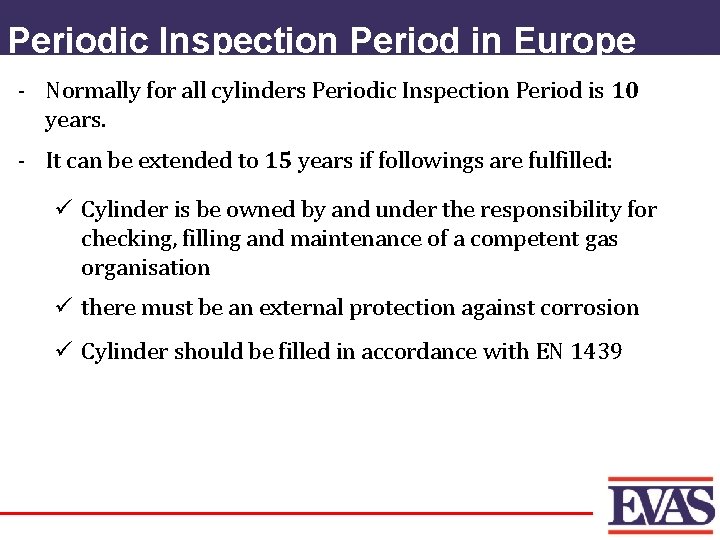
Periodic Inspection Period in Europe - Normally for all cylinders Periodic Inspection Period is 10 years. - It can be extended to 15 years if followings are fulfilled: ü Cylinder is be owned by and under the responsibility for checking, filling and maintenance of a competent gas organisation ü there must be an external protection against corrosion ü Cylinder should be filled in accordance with EN 1439
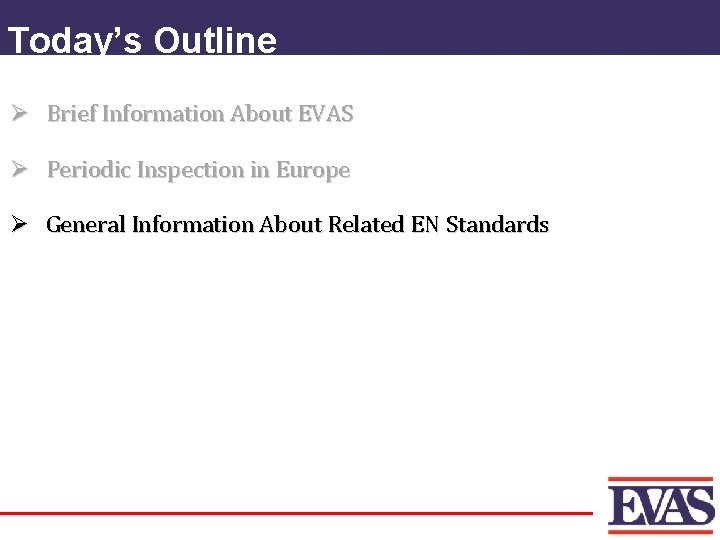
Today’s Outline Ø Brief Information About EVAS Ø Periodic Inspection in Europe Ø General Information About Related EN Standards
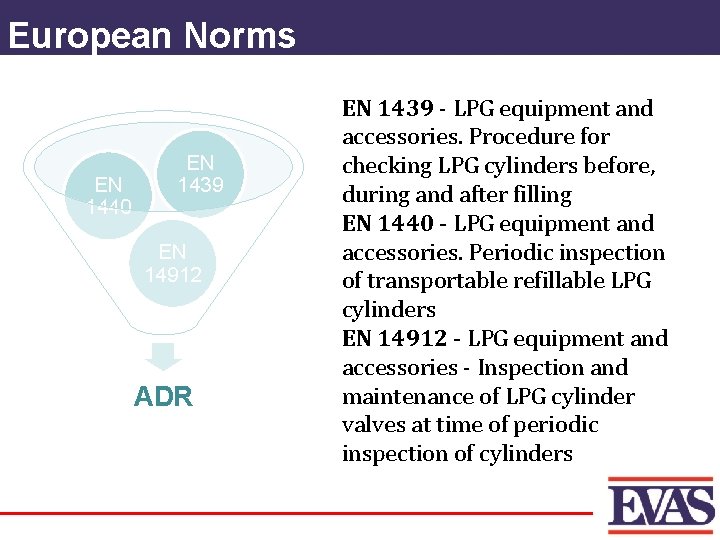
European Norms EN 1440 EN 1439 EN 14912 ADR EN 1439 - LPG equipment and accessories. Procedure for checking LPG cylinders before, during and after filling EN 1440 - LPG equipment and accessories. Periodic inspection of transportable refillable LPG cylinders EN 14912 - LPG equipment and accessories - Inspection and maintenance of LPG cylinder valves at time of periodic inspection of cylinders
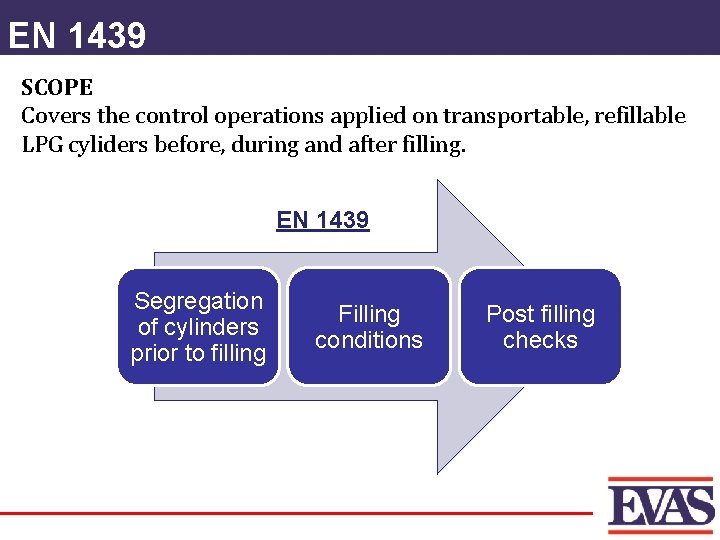
EN 1439 SCOPE Covers the control operations applied on transportable, refillable LPG cyliders before, during and after filling. EN 1439 Segregation of cylinders prior to filling Filling conditions Post filling checks
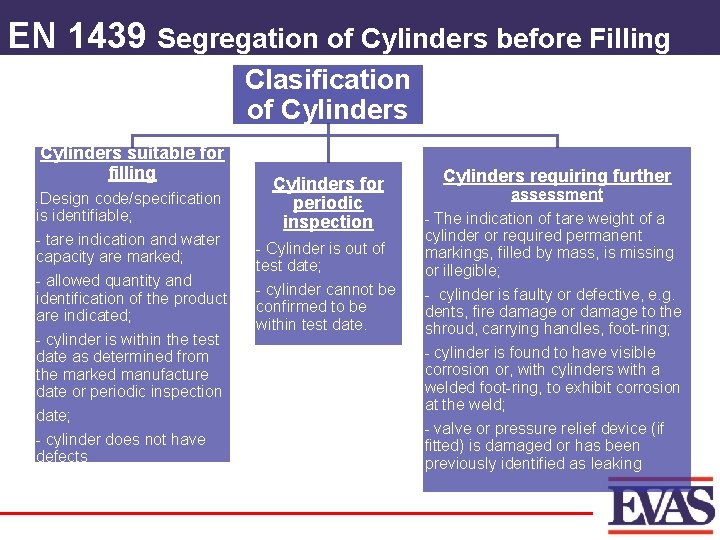
EN 1439 Segregation of Cylinders before Filling Clasification of Cylinders suitable for filling Design code/specification is identifiable; - tare indication and water capacity are marked; - allowed quantity and identification of the product are indicated; - cylinder is within the test date as determined from the marked manufacture date or periodic inspection date; - cylinder does not have defects - Cylinders for periodic inspection - Cylinder is out of test date; - cylinder cannot be confirmed to be within test date. Cylinders requiring further assessment - The indication of tare weight of a cylinder or required permanent markings, filled by mass, is missing or illegible; - cylinder is faulty or defective, e. g. dents, fire damage or damage to the shroud, carrying handles, foot-ring; - cylinder is found to have visible corrosion or, with cylinders with a welded foot-ring, to exhibit corrosion at the weld; - valve or pressure relief device (if fitted) is damaged or has been previously identified as leaking
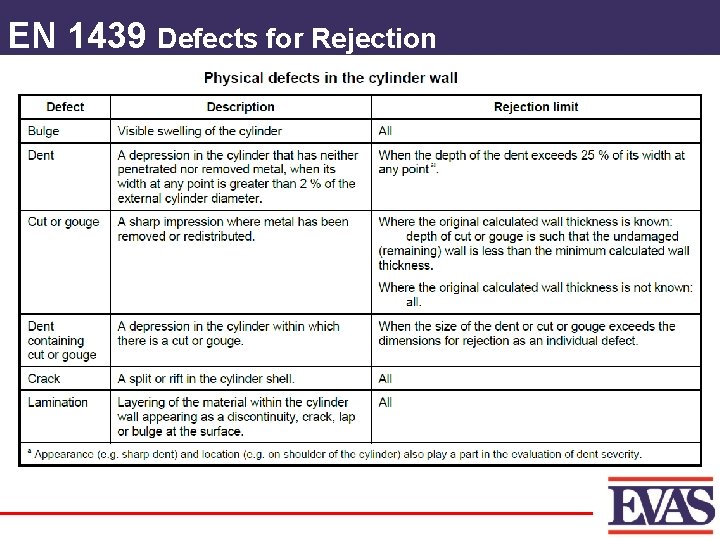
EN 1439 Defects for Rejection
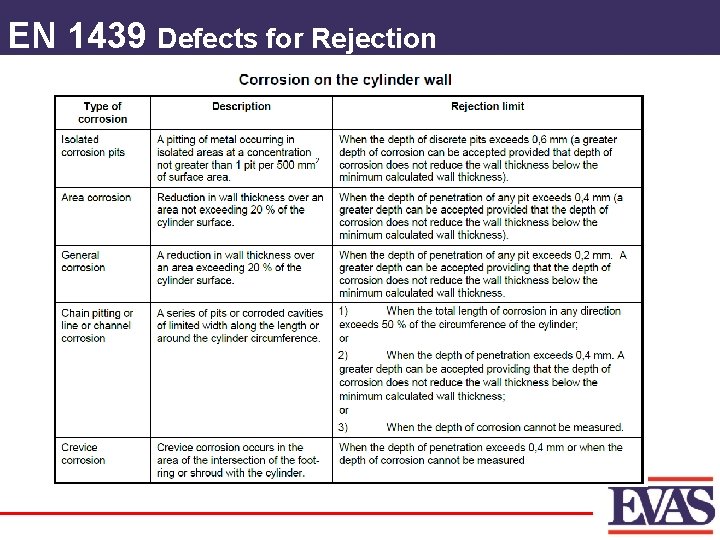
EN 1439 Defects for Rejection
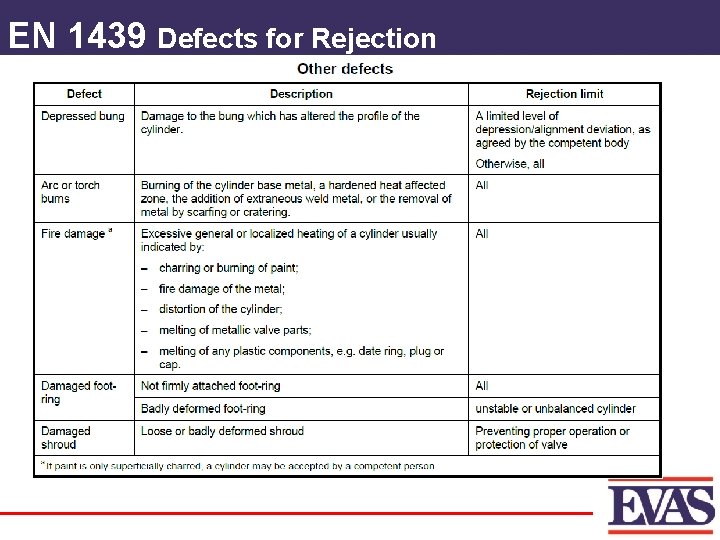
EN 1439 Defects for Rejection
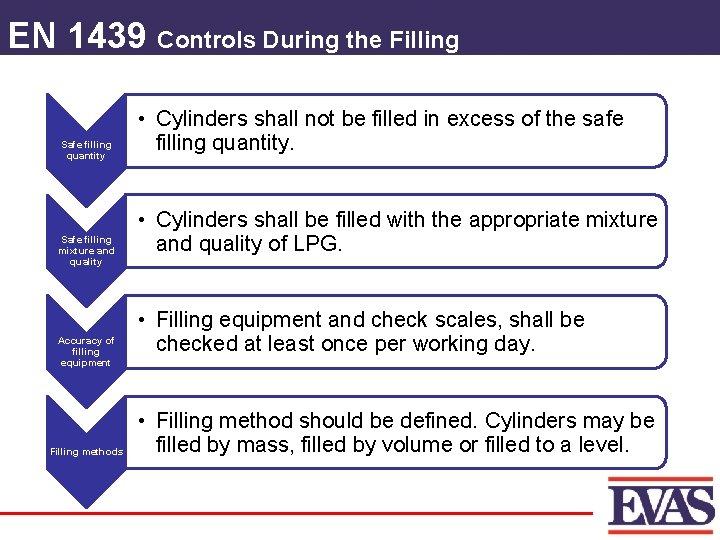
EN 1439 Controls During the Filling Safe filling quantity Safe filling mixture and quality Accuracy of filling equipment Filling methods • Cylinders shall not be filled in excess of the safe filling quantity. • Cylinders shall be filled with the appropriate mixture and quality of LPG. • Filling equipment and check scales, shall be checked at least once per working day. • Filling method should be defined. Cylinders may be filled by mass, filled by volume or filled to a level.
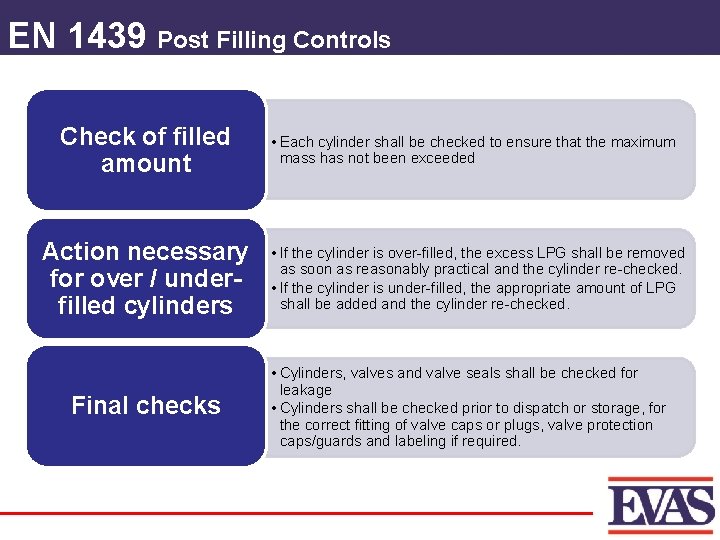
EN 1439 Post Filling Controls Check of filled amount Action necessary for over / underfilled cylinders Final checks • Each cylinder shall be checked to ensure that the maximum mass has not been exceeded • If the cylinder is over-filled, the excess LPG shall be removed as soon as reasonably practical and the cylinder re-checked. • If the cylinder is under-filled, the appropriate amount of LPG shall be added and the cylinder re-checked. • Cylinders, valves and valve seals shall be checked for leakage • Cylinders shall be checked prior to dispatch or storage, for the correct fitting of valve caps or plugs, valve protection caps/guards and labeling if required.
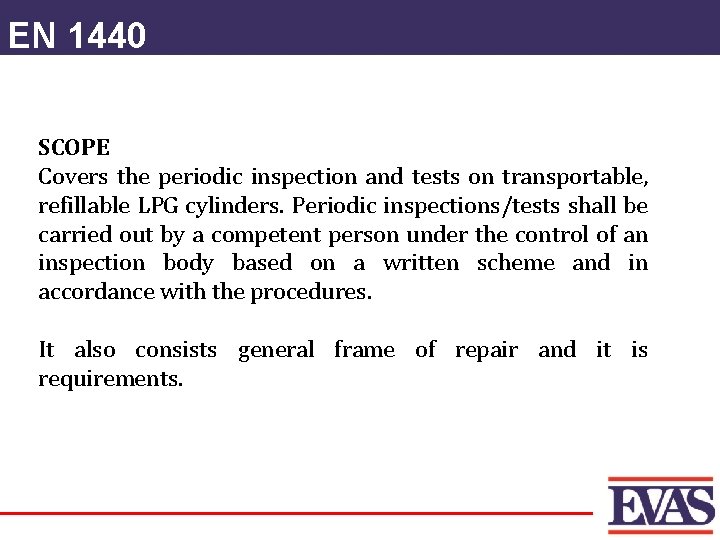
EN 1440 SCOPE Covers the periodic inspection and tests on transportable, refillable LPG cylinders. Periodic inspections/tests shall be carried out by a competent person under the control of an inspection body based on a written scheme and in accordance with the procedures. It also consists general frame of repair and it is requirements.
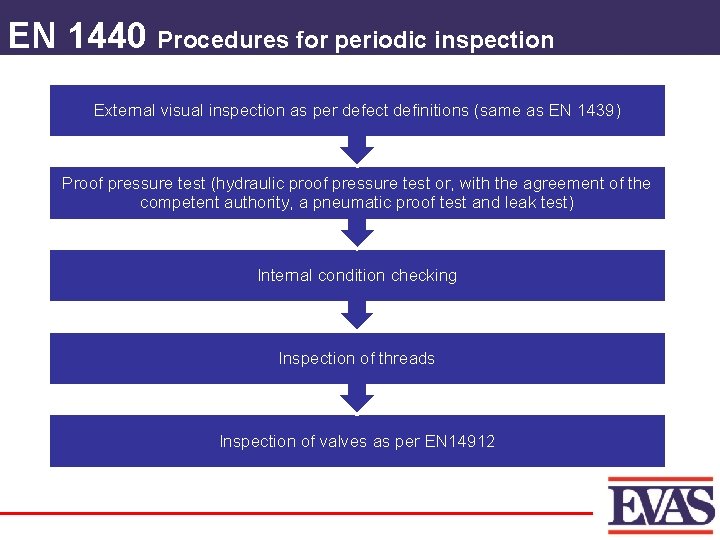
EN 1440 Procedures for periodic inspection External visual inspection as per defect definitions (same as EN 1439) Proof pressure test (hydraulic proof pressure test or, with the agreement of the competent authority, a pneumatic proof test and leak test) Internal condition checking Inspection of threads Inspection of valves as per EN 14912
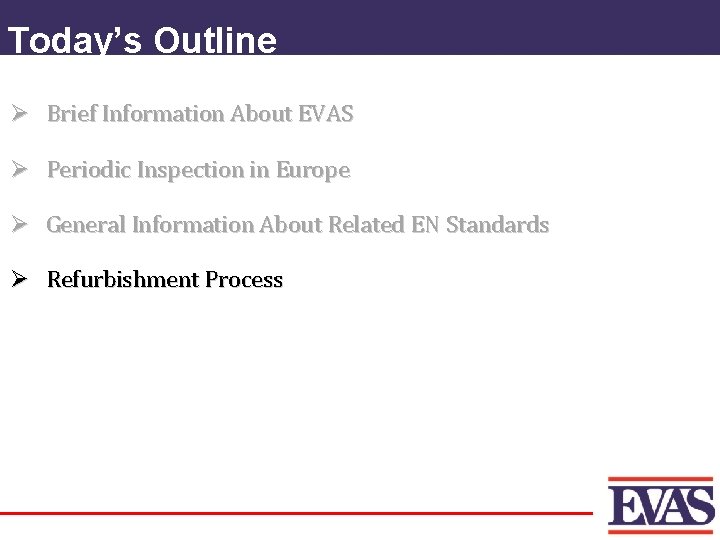
Today’s Outline Ø Brief Information About EVAS Ø Periodic Inspection in Europe Ø General Information About Related EN Standards Ø Refurbishment Process
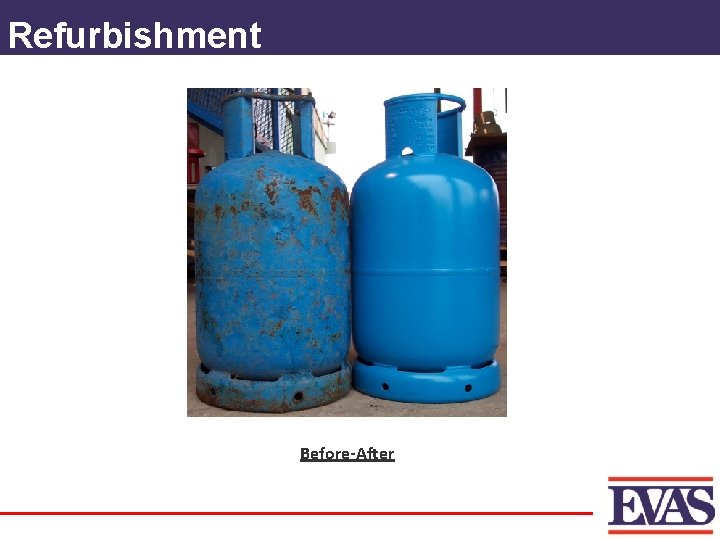
Refurbishment Before-After
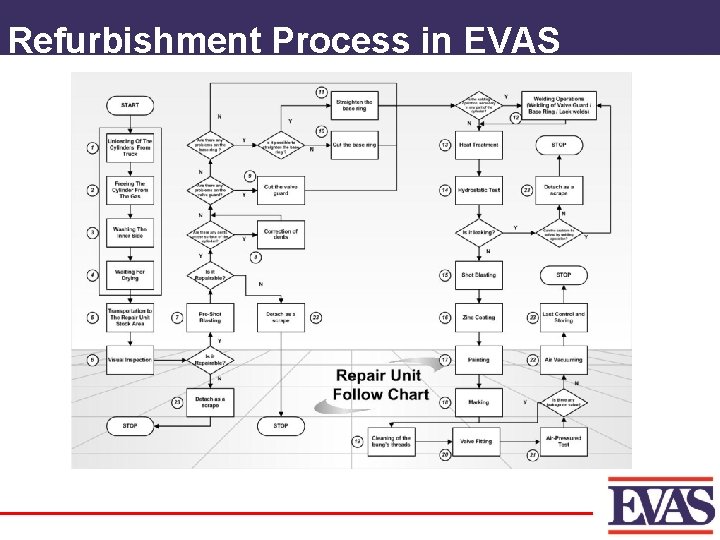
Refurbishment Process in EVAS
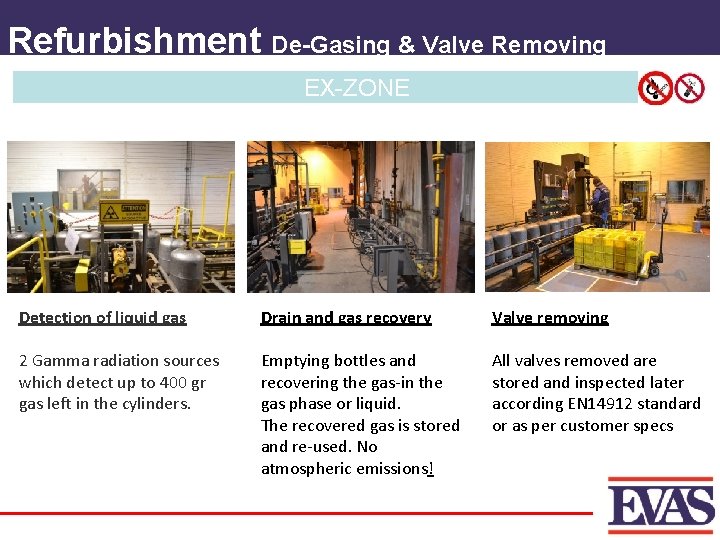
Refurbishment De-Gasing & Valve Removing EX-ZONE Detection of liquid gas Drain and gas recovery Valve removing 2 Gamma radiation sources which detect up to 400 gr gas left in the cylinders. Emptying bottles and recovering the gas-in the gas phase or liquid. The recovered gas is stored and re-used. No atmospheric emissions! All valves removed are stored and inspected later according EN 14912 standard or as per customer specs
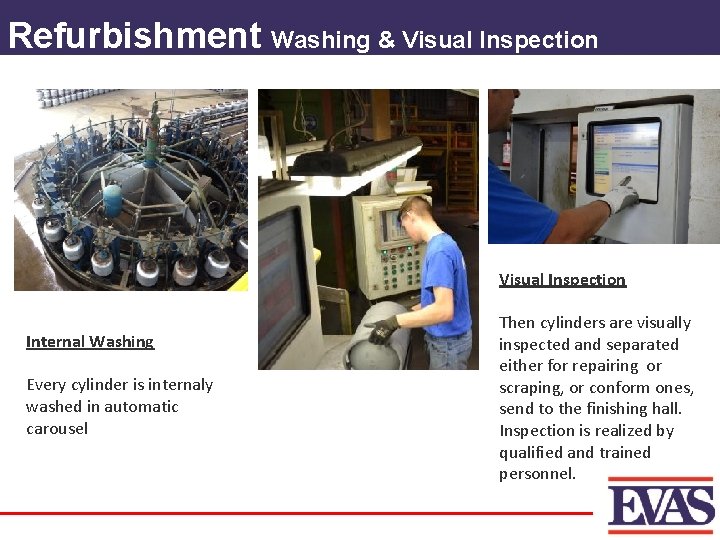
Refurbishment Washing & Visual Inspection Internal Washing Every cylinder is internaly washed in automatic carousel Then cylinders are visually inspected and separated either for repairing or scraping, or conform ones, send to the finishing hall. Inspection is realized by qualified and trained personnel.
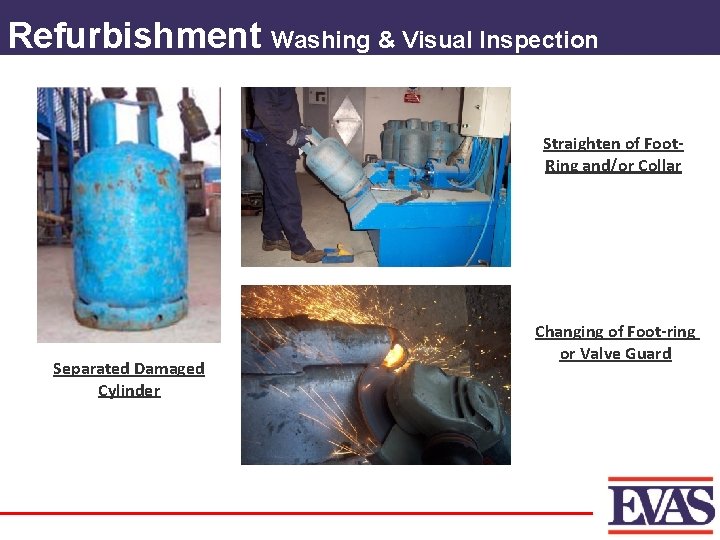
Refurbishment Washing & Visual Inspection Straighten of Foot. Ring and/or Collar Separated Damaged Cylinder Changing of Foot-ring or Valve Guard
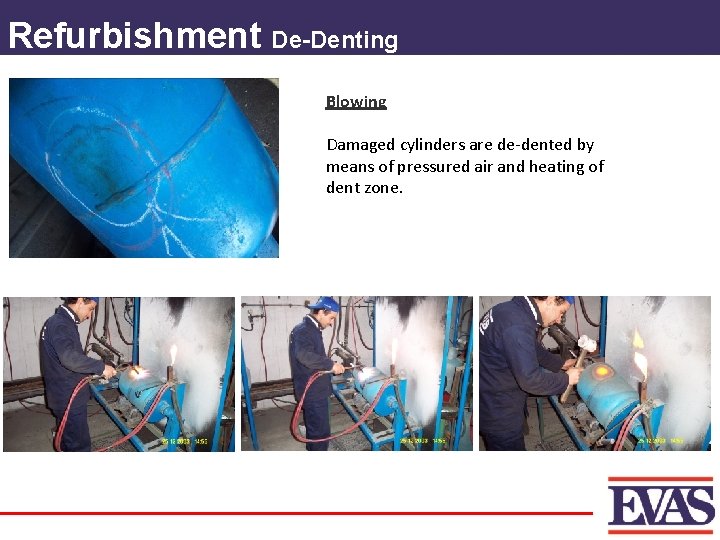
Refurbishment De-Denting Blowing Damaged cylinders are de-dented by means of pressured air and heating of dent zone.
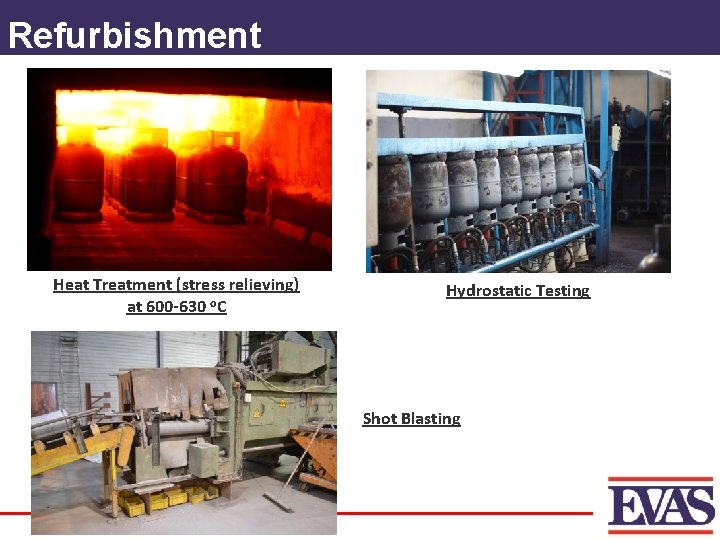
Refurbishment Heat Treatment (stress relieving) at 600 -630 o. C Hydrostatic Testing Shot Blasting
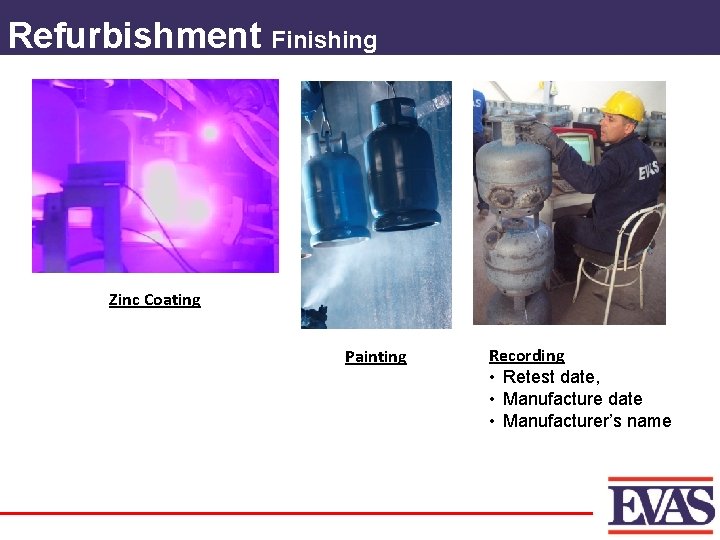
Refurbishment Finishing Zinc Coating Painting Recording • Retest date, • Manufacture date • Manufacturer’s name
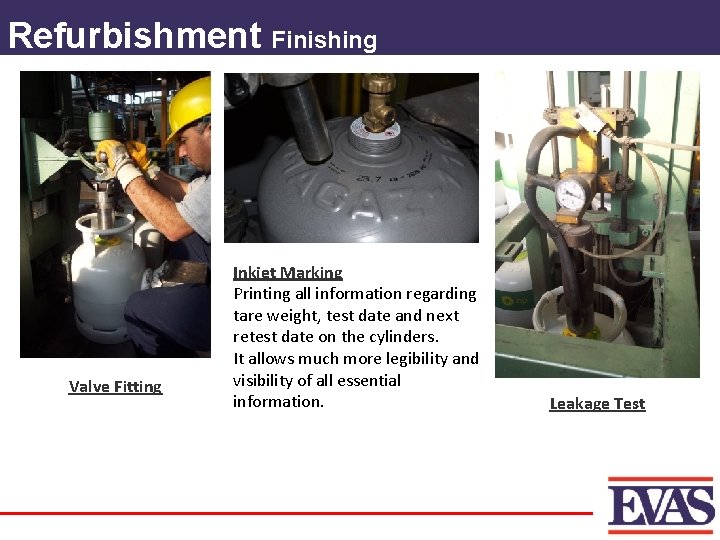
Refurbishment Finishing Valve Fitting Inkjet Marking Printing all information regarding tare weight, test date and next retest date on the cylinders. It allows much more legibility and visibility of all essential information. Leakage Test
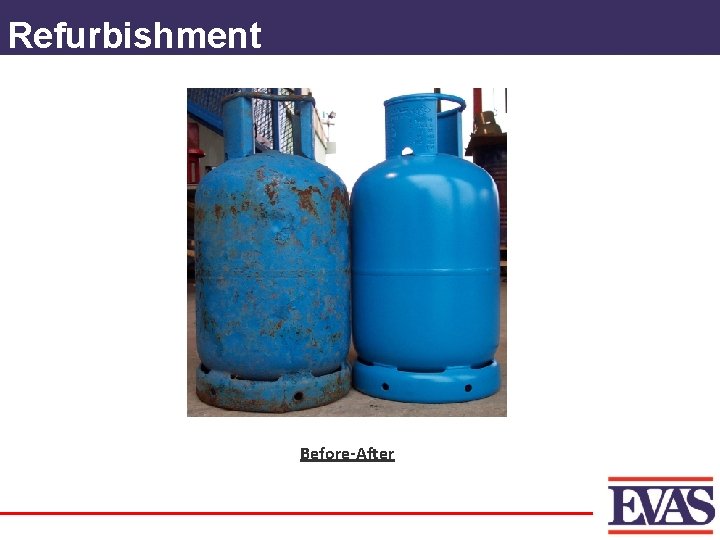
Refurbishment Before-After
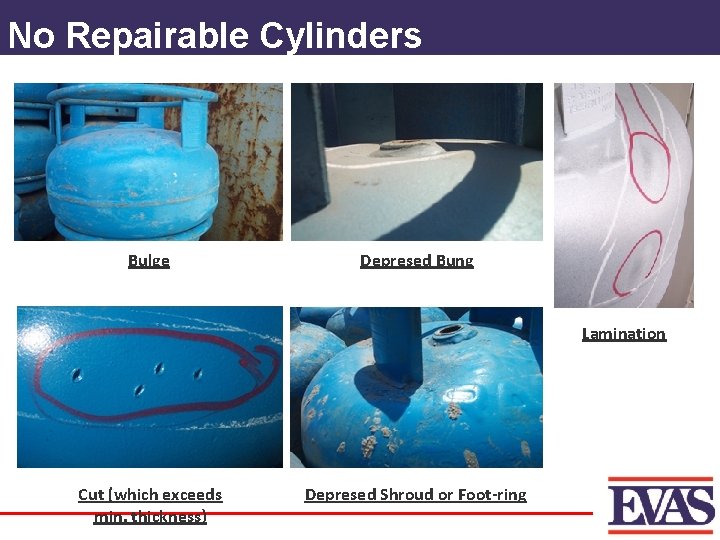
No Repairable Cylinders Bulge Depresed Bung Lamination Cut (which exceeds min. thickness) Depresed Shroud or Foot-ring
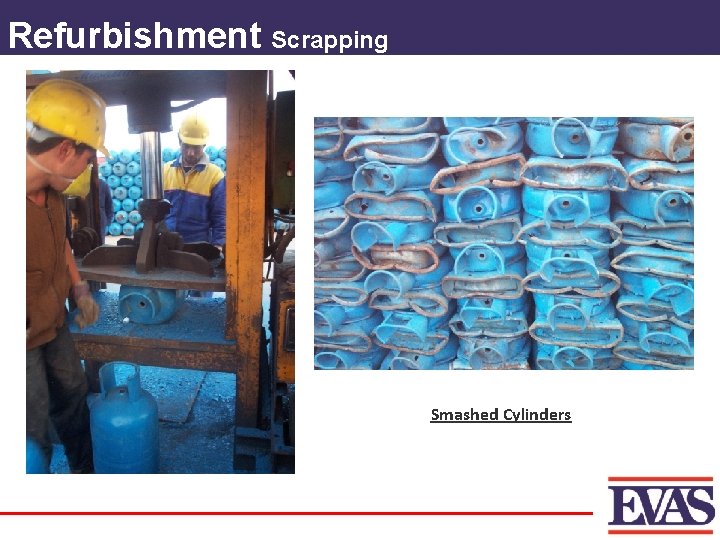
Refurbishment Scrapping Smashed Cylinders
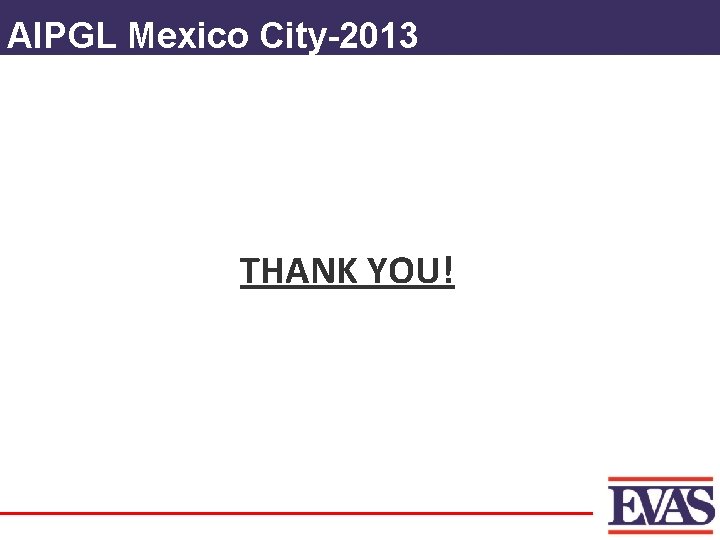
AIPGL Mexico City-2013 THANK YOU!
Selisih kurs masuk akun apa
Dot cylinder requalification
Anthem of poland
Writing to learn
What is ngo?
Emrah taylan
Emrah şefik abamor
Emrah kutlu
Emrah sazak
Emrah has
Bertil emrah oder cv
Sahinny
Emrah tiras
Emrah taylan
Sak etap bab 24 tentang pajak
Iq skalası
Tkt testi örneği
Jinekolog ne demek
Sak 13-5
Sak etap bab 23
Sak beyin bt
Kerangka konseptual sak
Sinektik tekniği örnekleri
Sak entitas privat ppt
Kerangka dasar sak umum
Sak etap bab 15 tentang aset tetap
Ruang lingkup sak emkm
Contoh penerapan retrospektif
Iapi ppl
Bunga kontraktual adalah
Maszkaronizm
Monopolar bipolar koter farkı
Central european pipeline system
Feudal pyramid of power
European plate observing system
European statistical system committee
European collateral management system
European manorial system
European credit transfer and accumulation system
European collateral management system