CONFORMAL COAT APPLICATION TECHNIQUES Conformal Coating Application Techniques
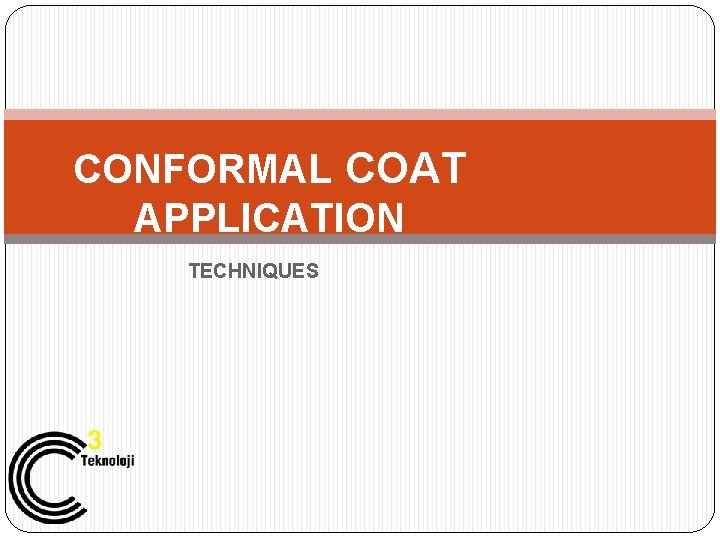
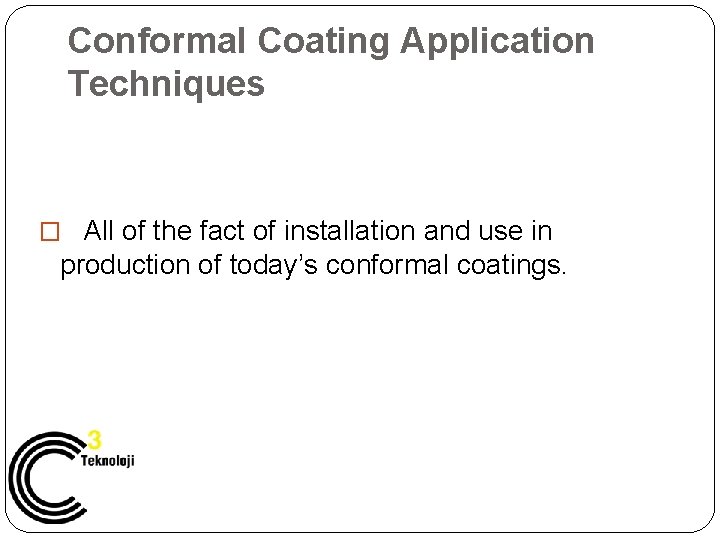
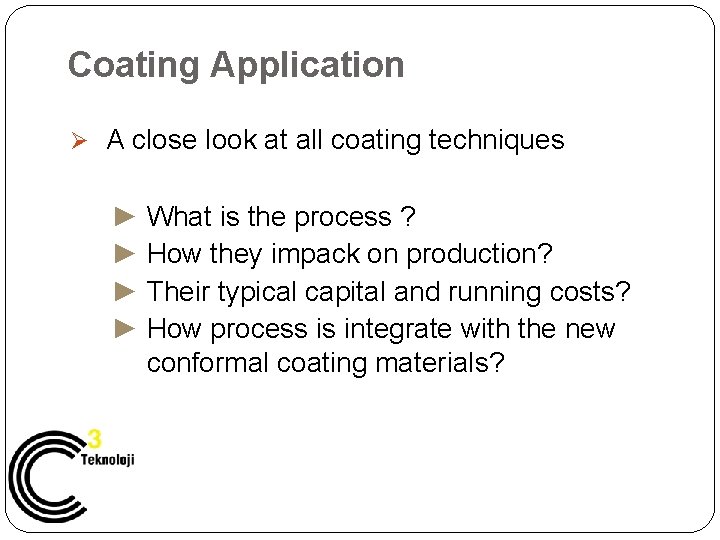
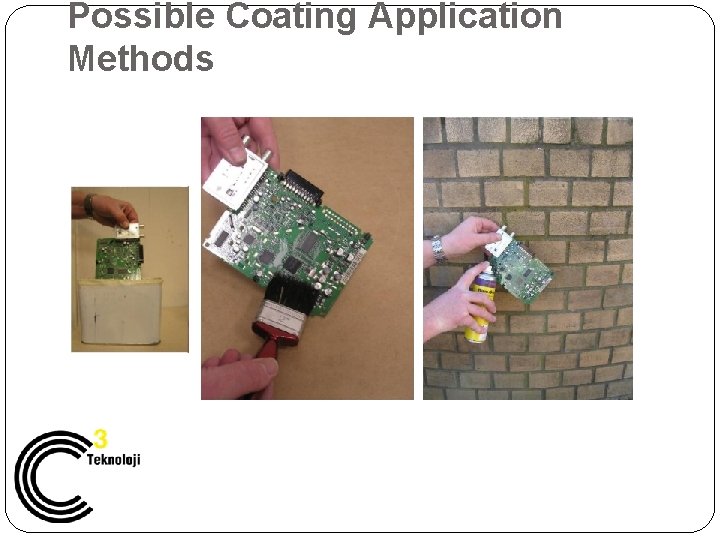
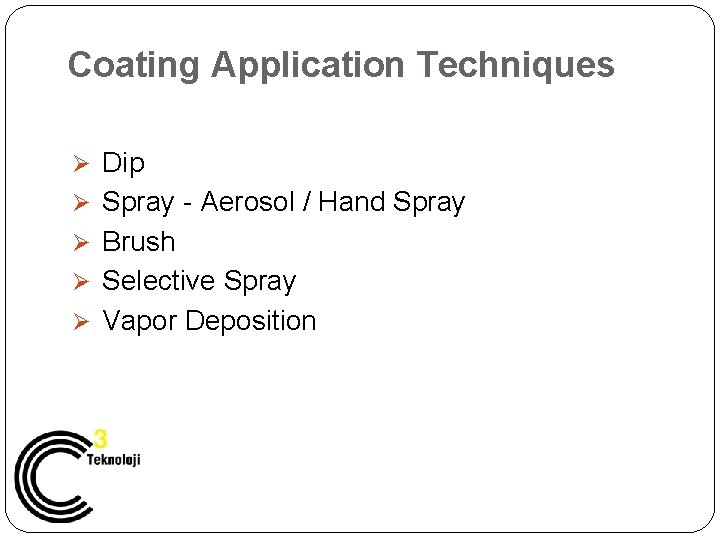
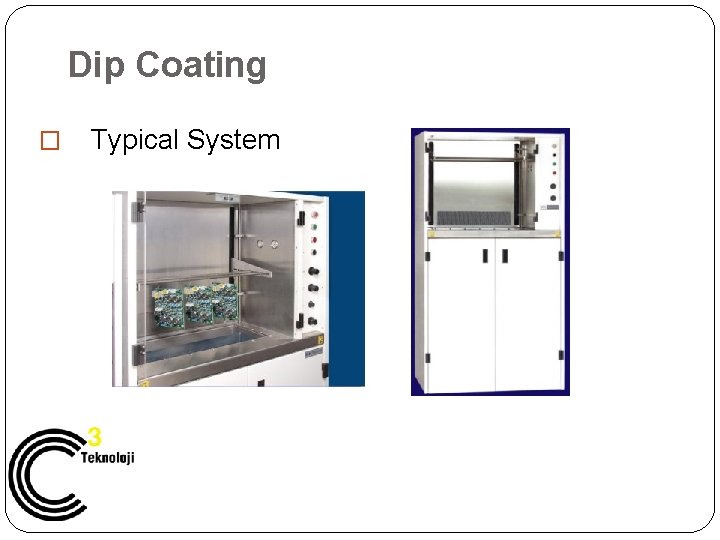
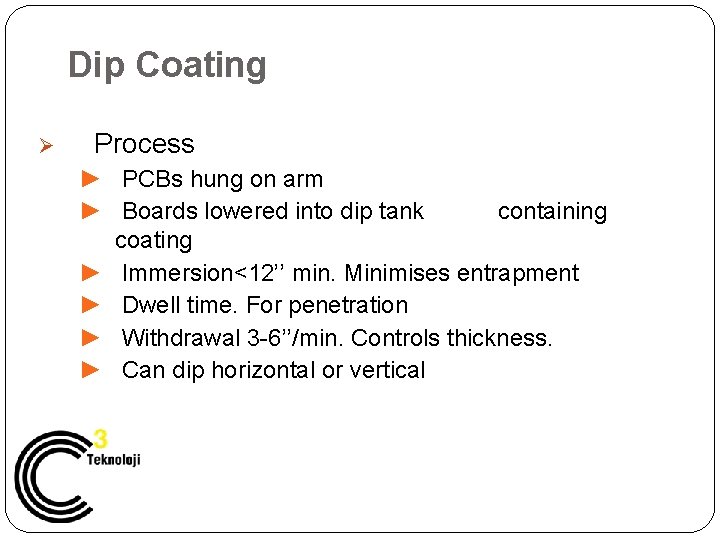
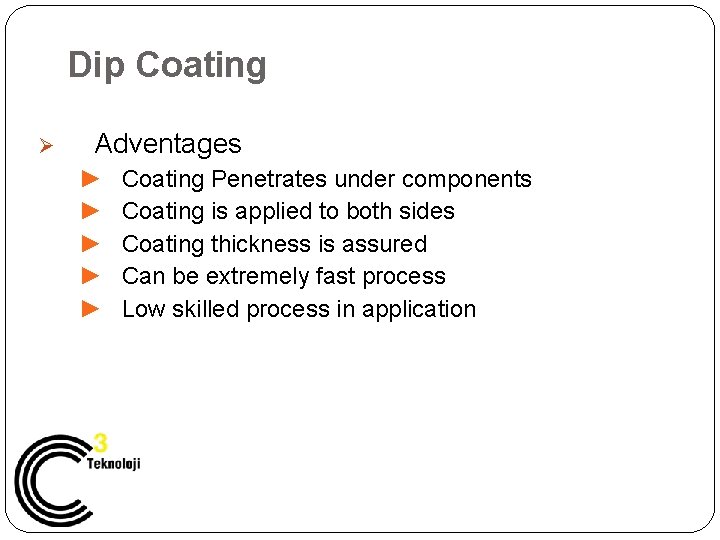
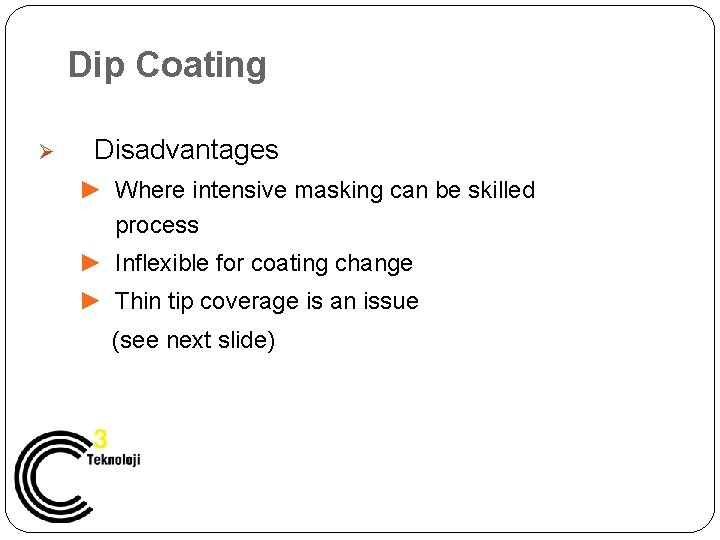
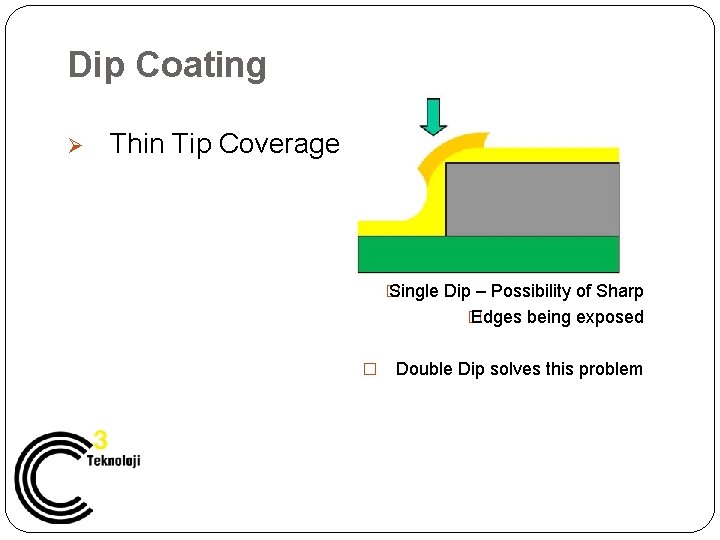
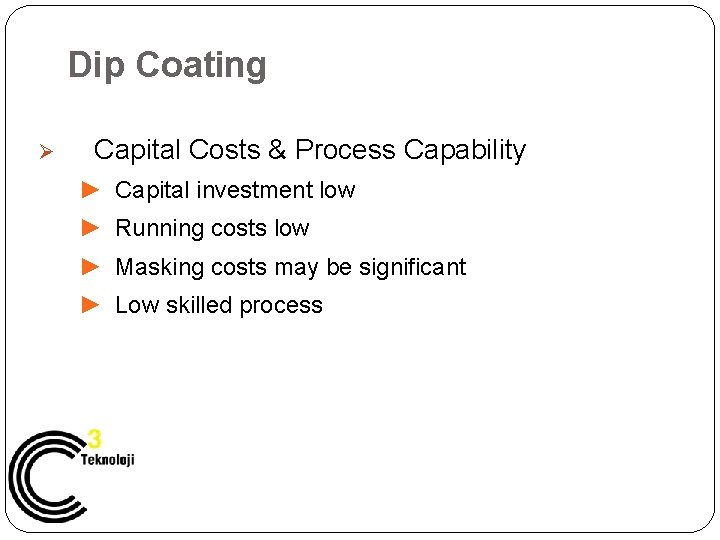
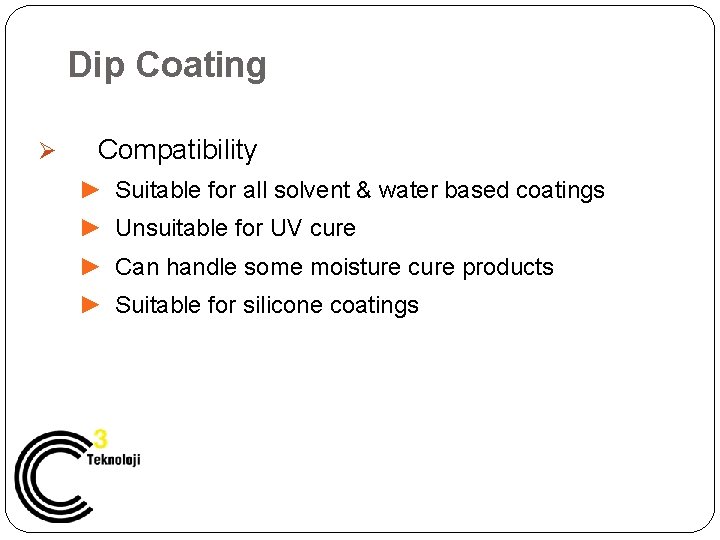
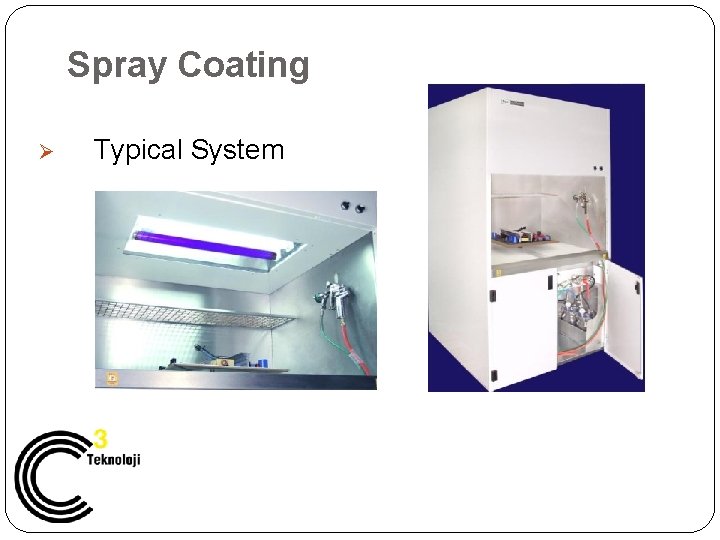
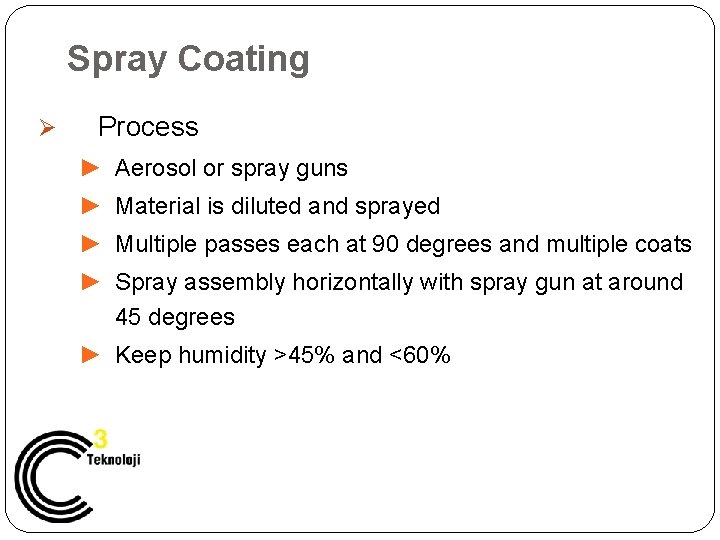
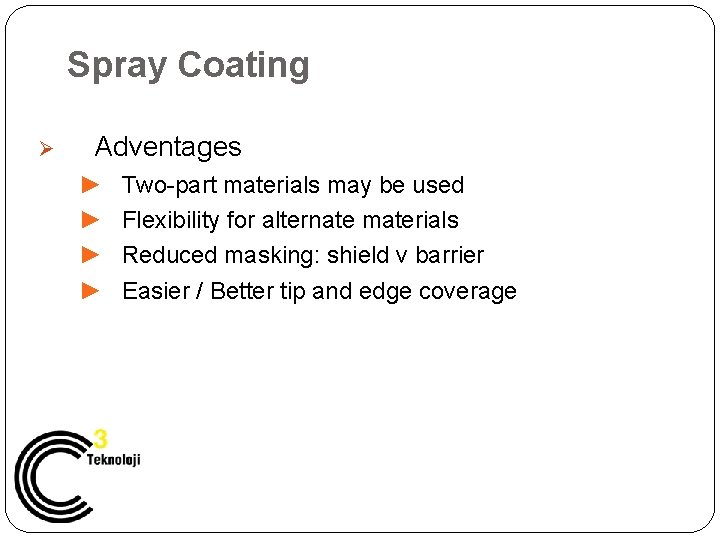
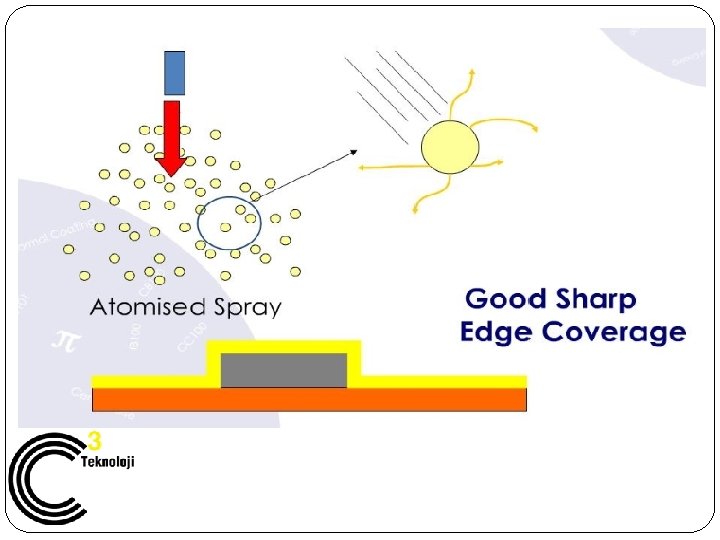
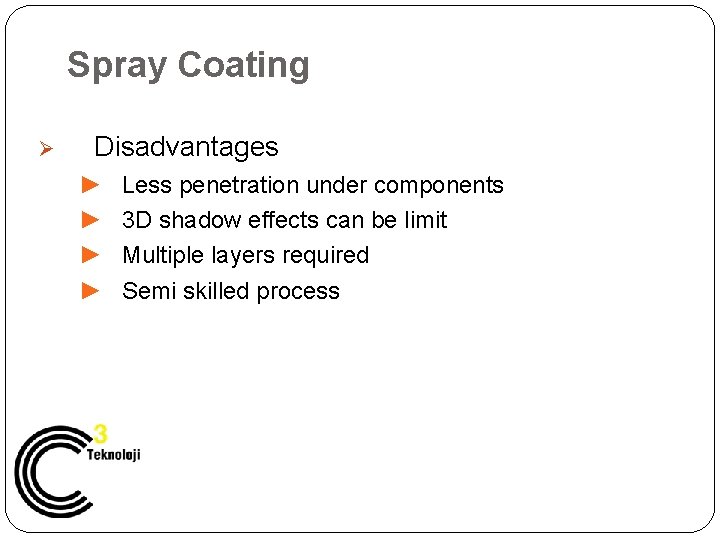
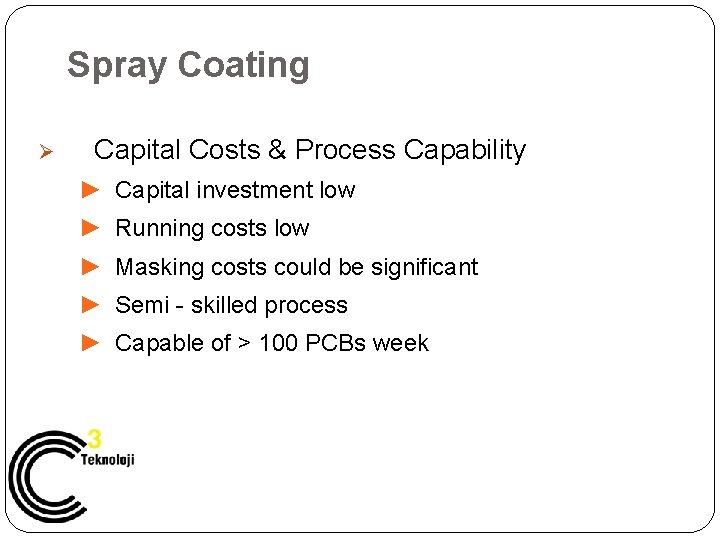
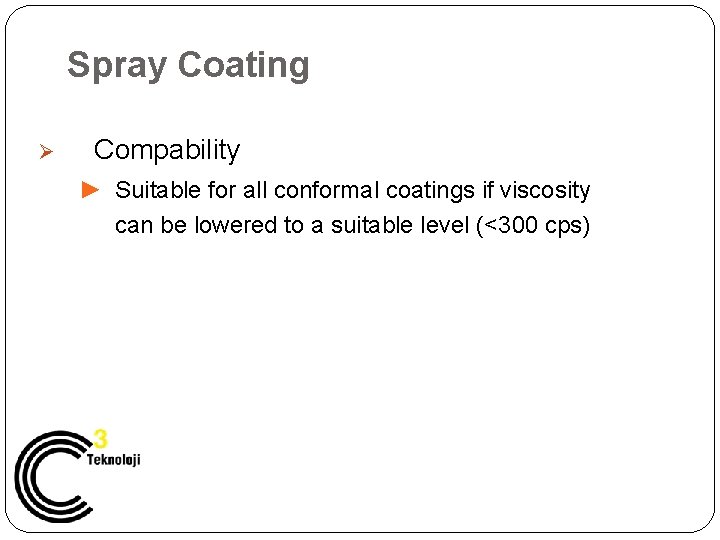
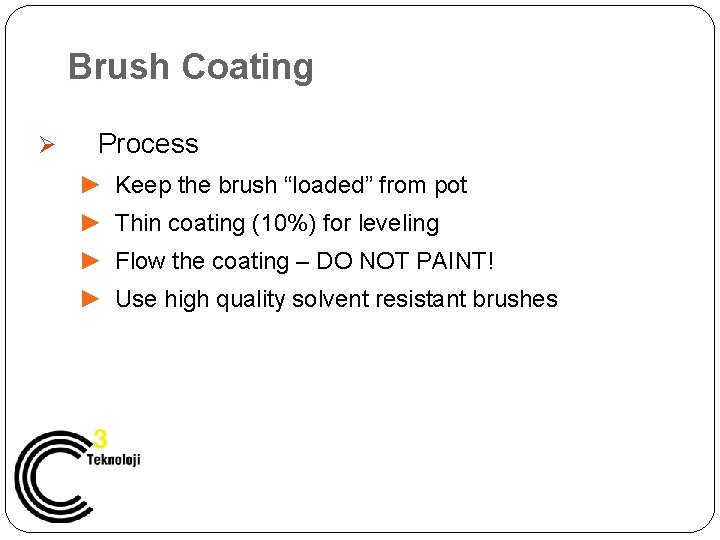
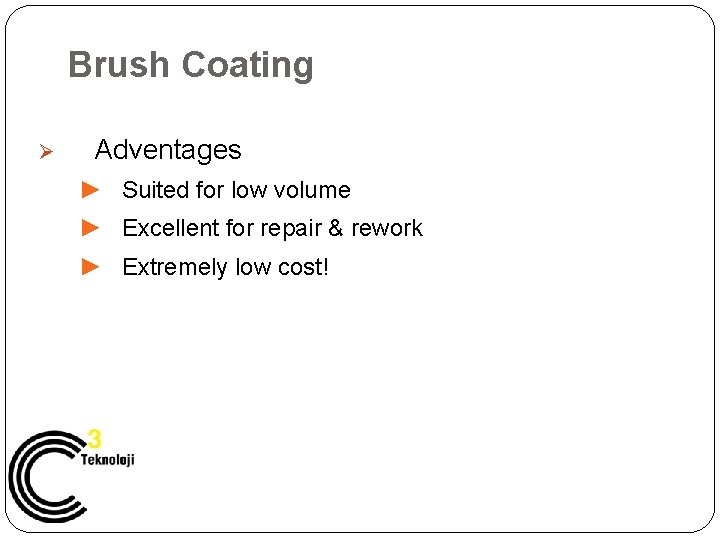
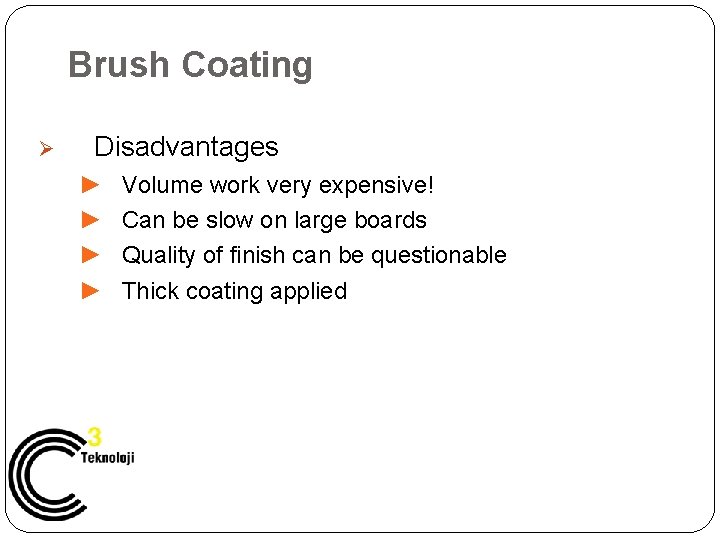
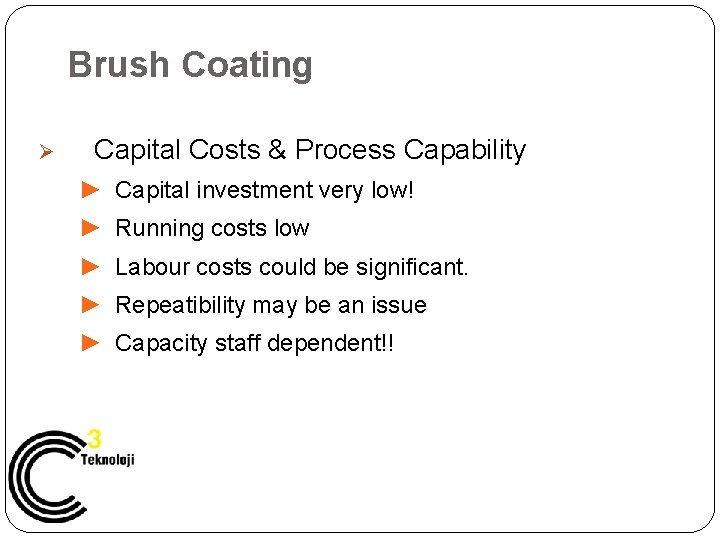
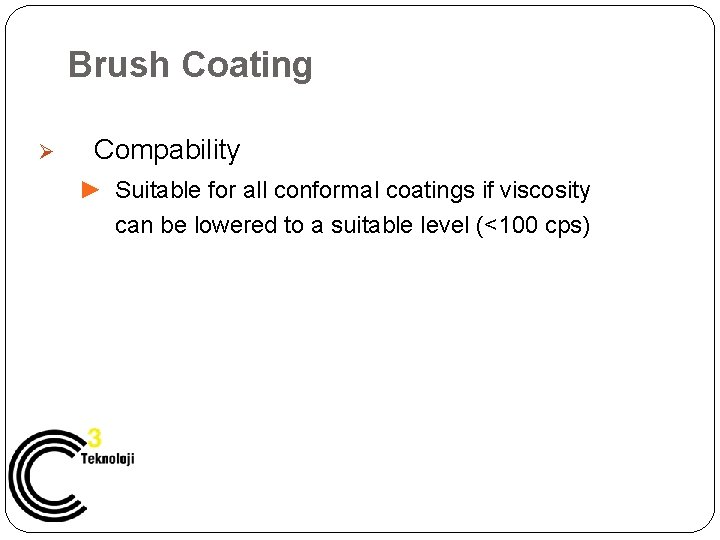
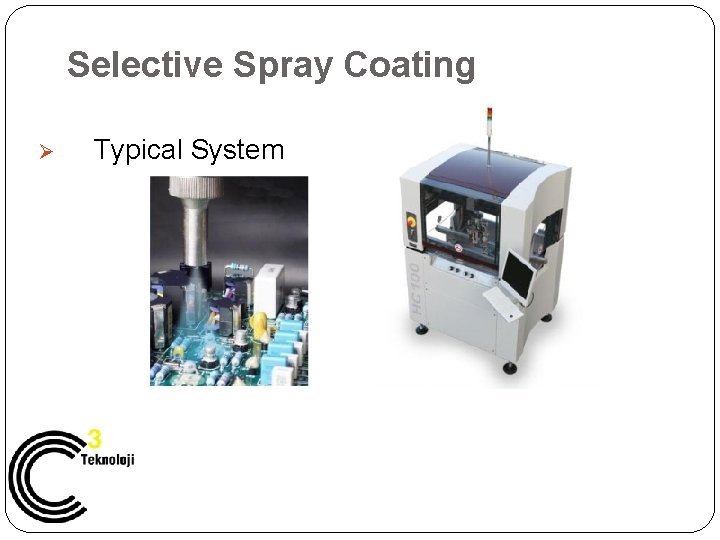
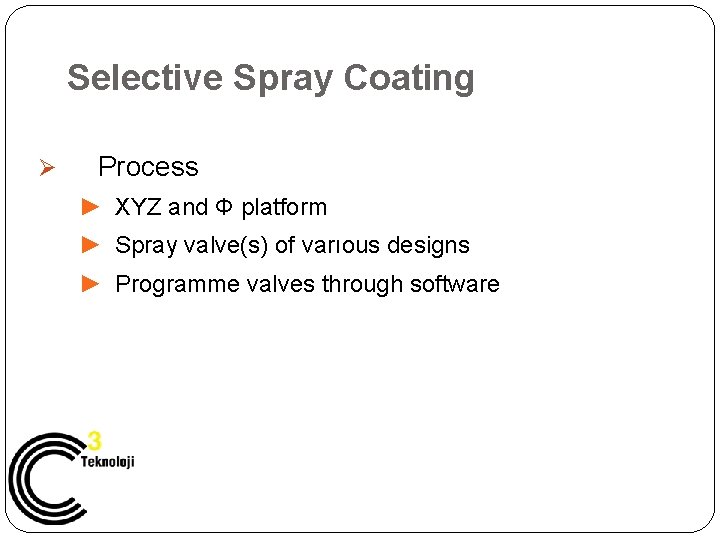
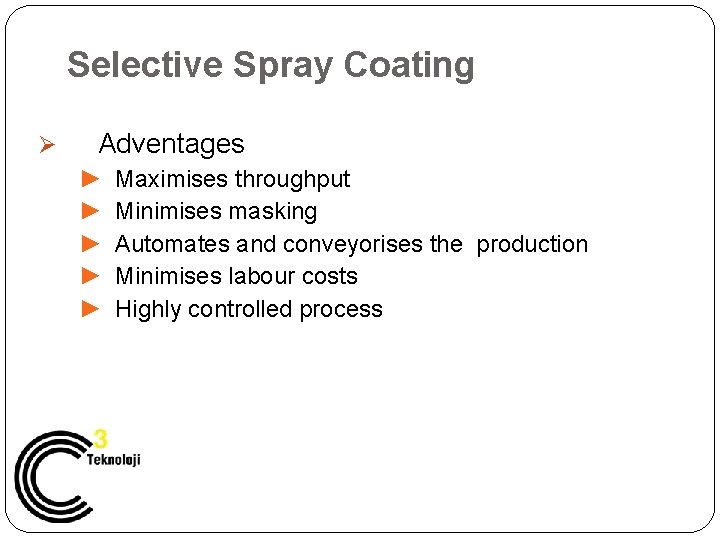
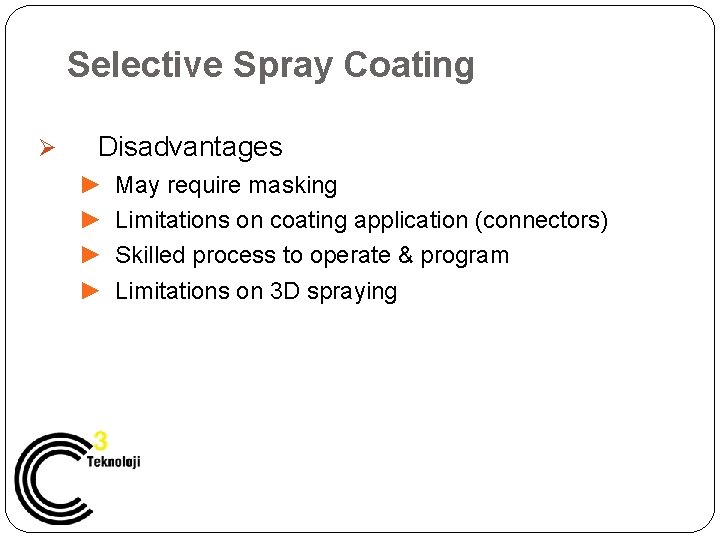
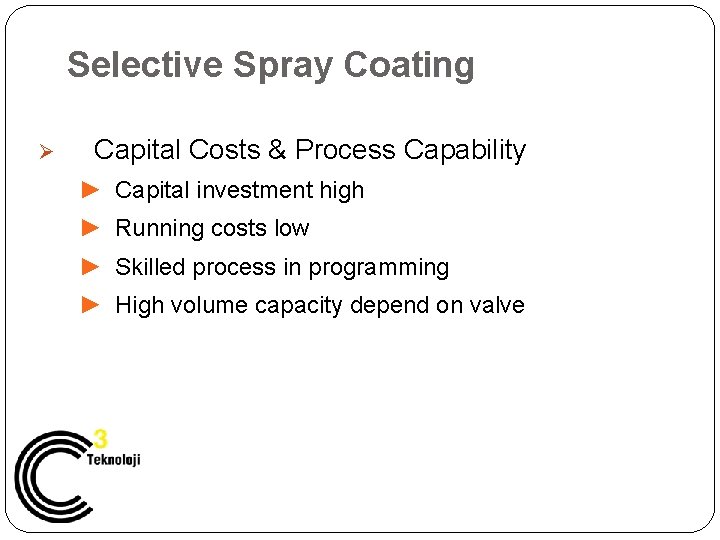
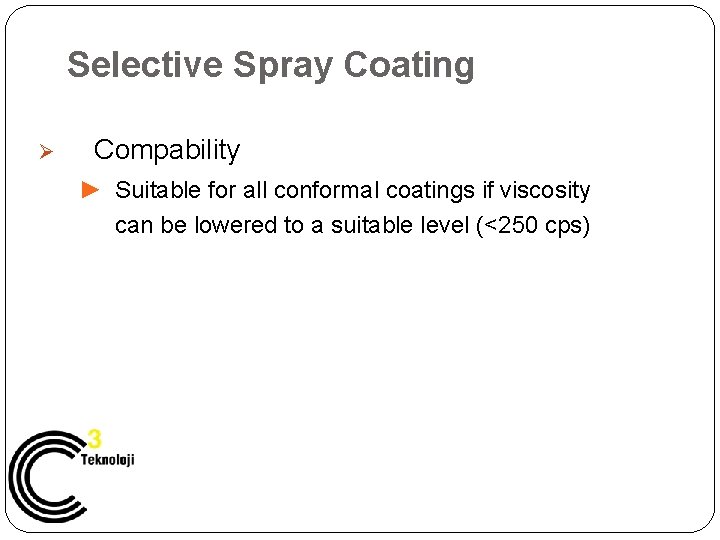
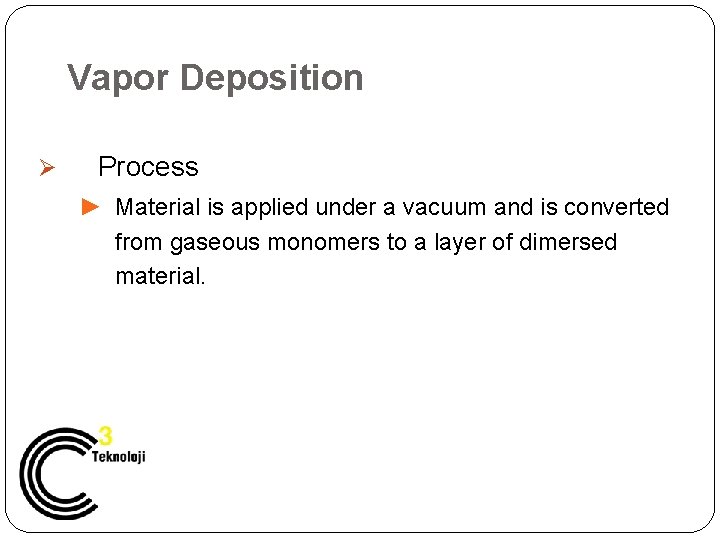
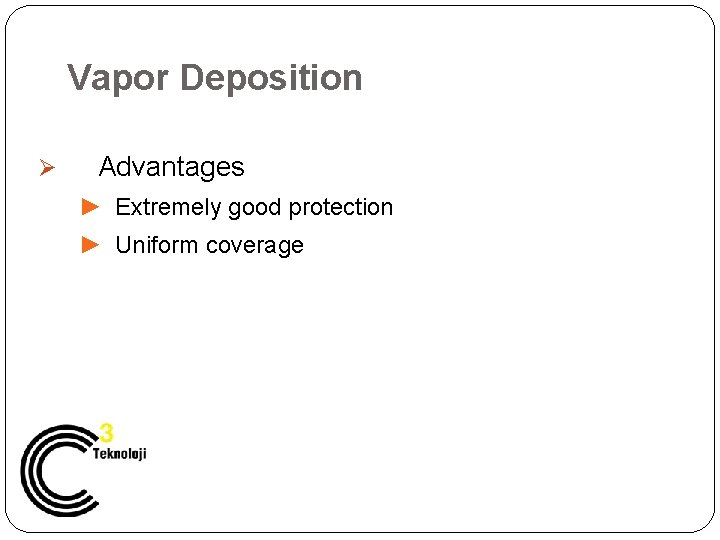
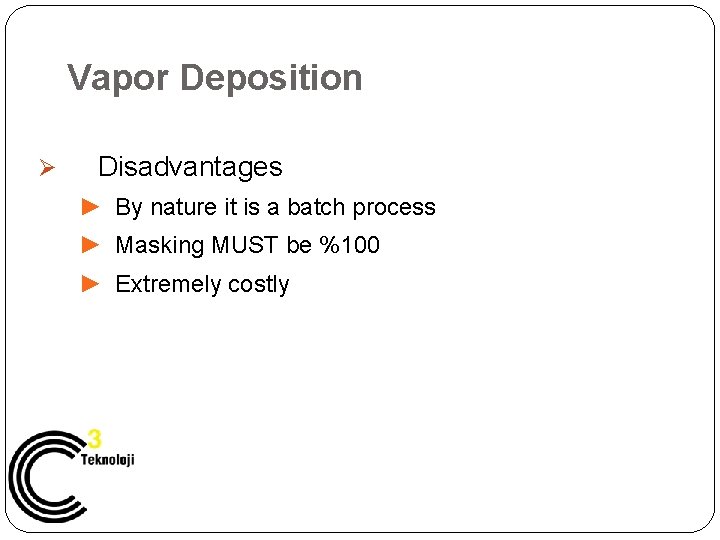
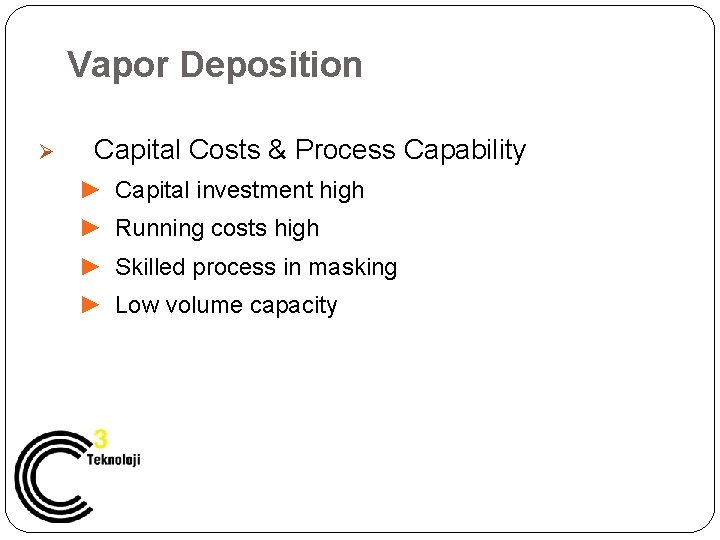
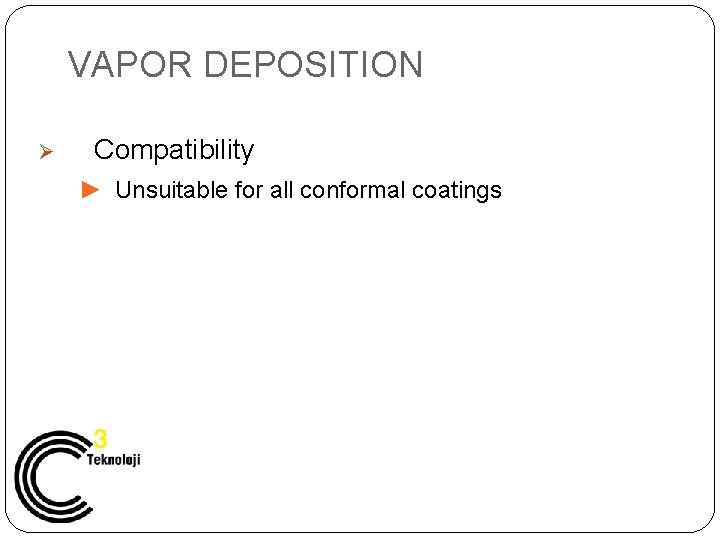
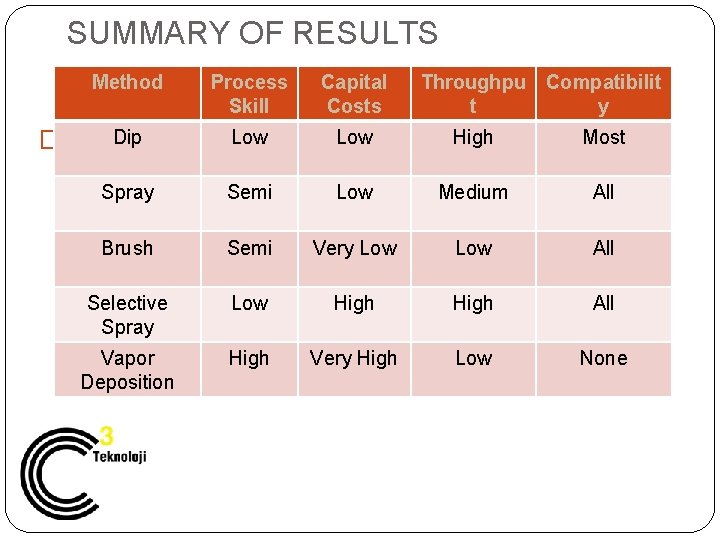
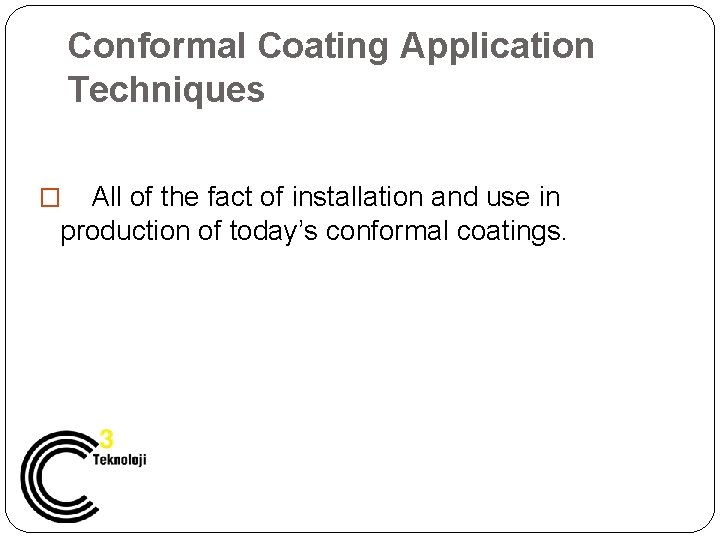
- Slides: 37
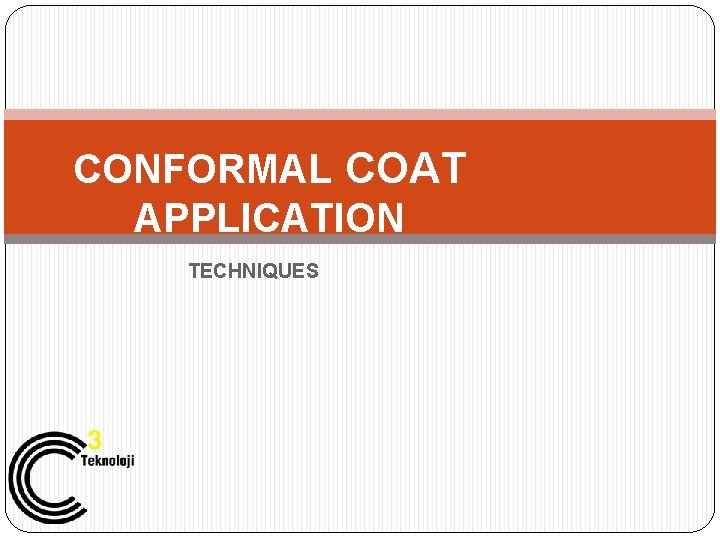
CONFORMAL COAT APPLICATION TECHNIQUES
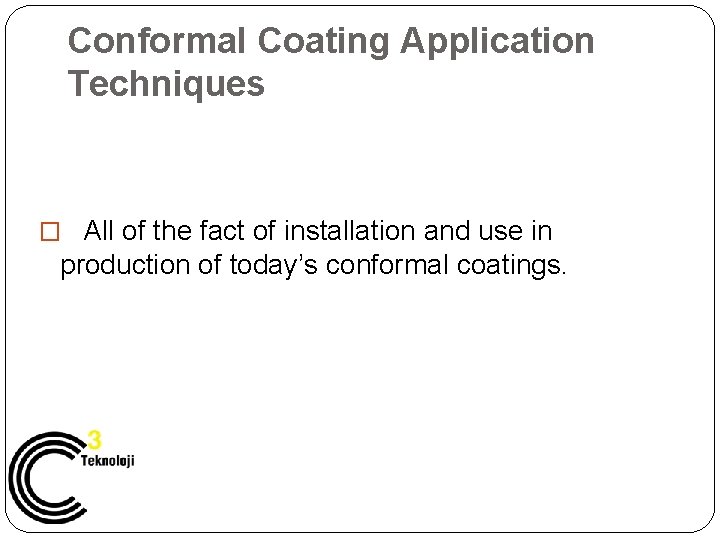
Conformal Coating Application Techniques � All of the fact of installation and use in production of today’s conformal coatings.
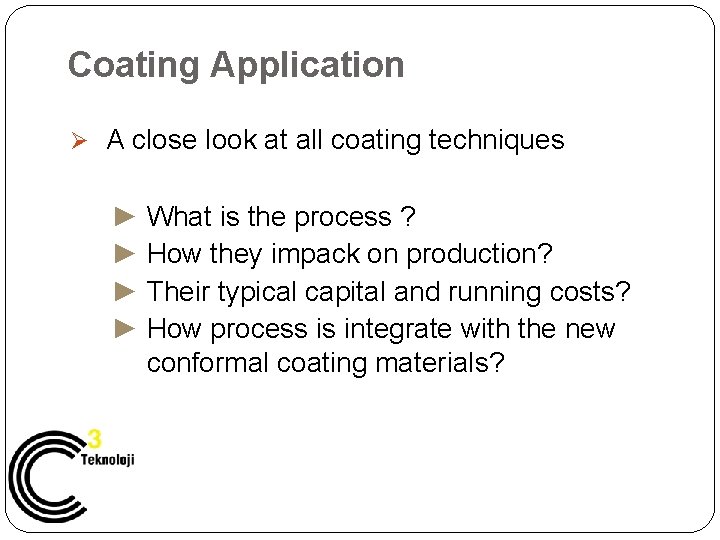
Coating Application Ø A close look at all coating techniques ► What is the process ? ► How they impack on production? ► Their typical capital and running costs? ► How process is integrate with the new conformal coating materials?
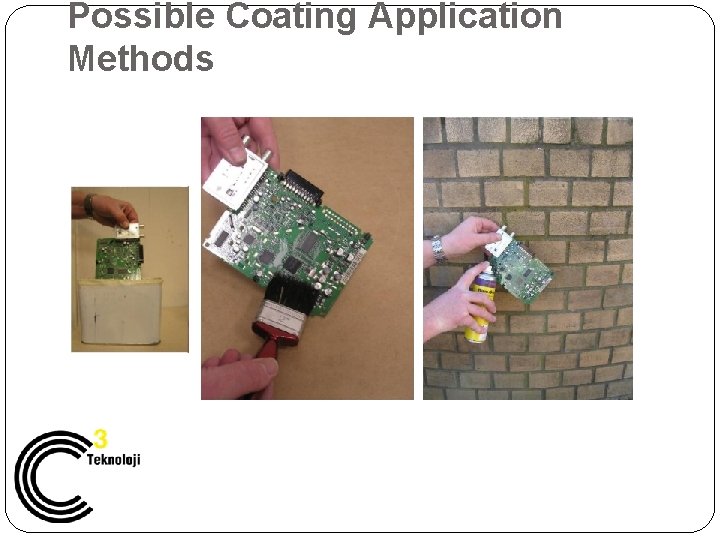
Possible Coating Application Methods
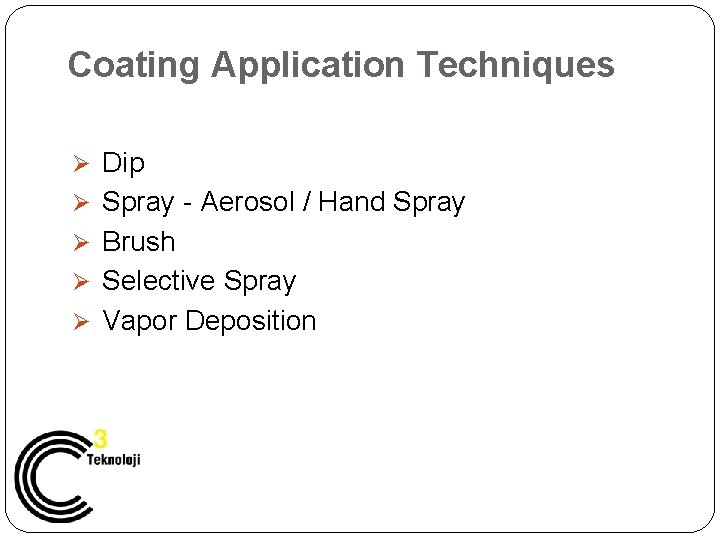
Coating Application Techniques Ø Dip Ø Spray - Aerosol / Hand Spray Ø Brush Ø Selective Spray Ø Vapor Deposition
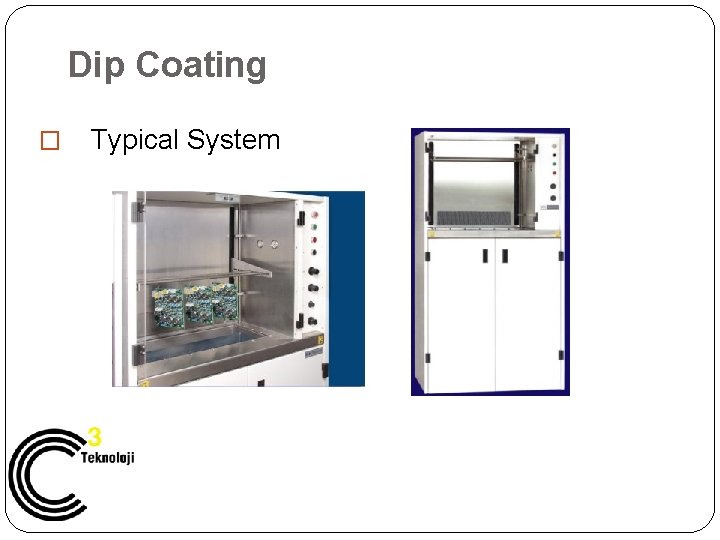
Dip Coating � Typical System
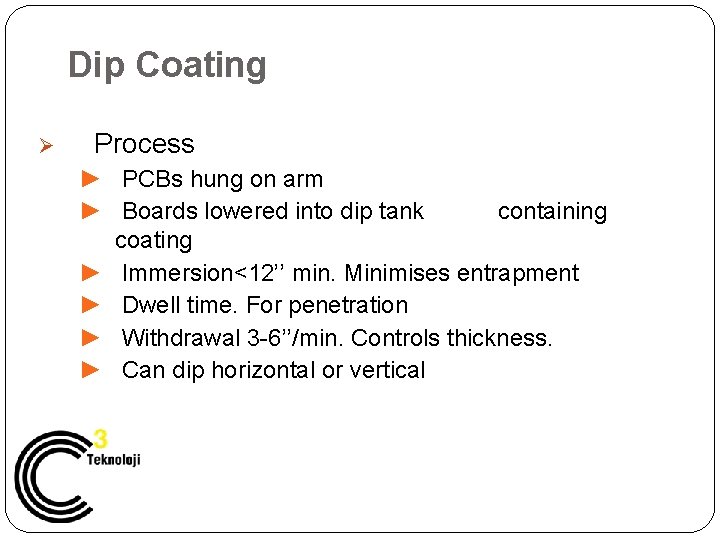
Dip Coating Ø Process ► PCBs hung on arm ► Boards lowered into dip tank containing coating ► Immersion<12’’ min. Minimises entrapment ► Dwell time. For penetration ► Withdrawal 3 -6’’/min. Controls thickness. ► Can dip horizontal or vertical
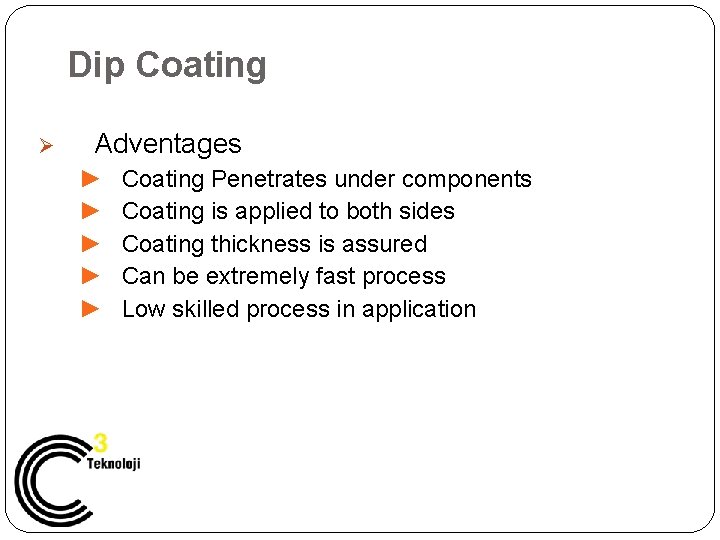
Dip Coating Ø Adventages ► ► ► Coating Penetrates under components Coating is applied to both sides Coating thickness is assured Can be extremely fast process Low skilled process in application
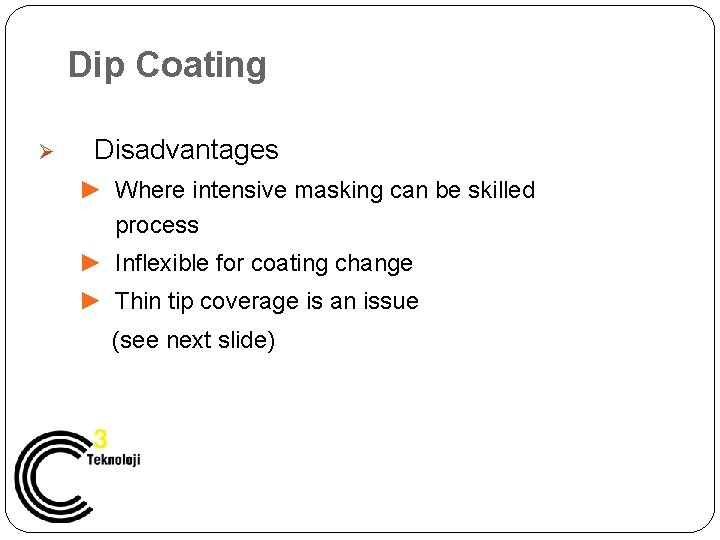
Dip Coating Ø Disadvantages ► Where intensive masking can be skilled process ► Inflexible for coating change ► Thin tip coverage is an issue (see next slide)
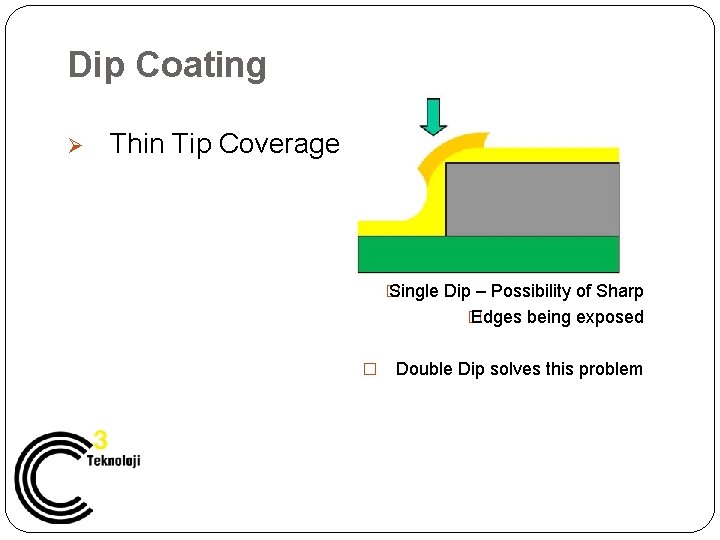
Dip Coating Ø Thin Tip Coverage � Single Dip – Possibility of Sharp � Edges being exposed � Double Dip solves this problem
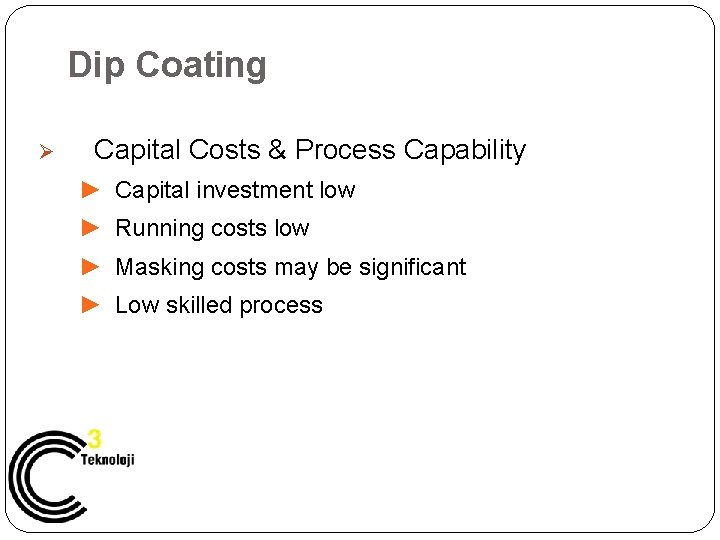
Dip Coating Ø Capital Costs & Process Capability ► Capital investment low ► Running costs low ► Masking costs may be significant ► Low skilled process
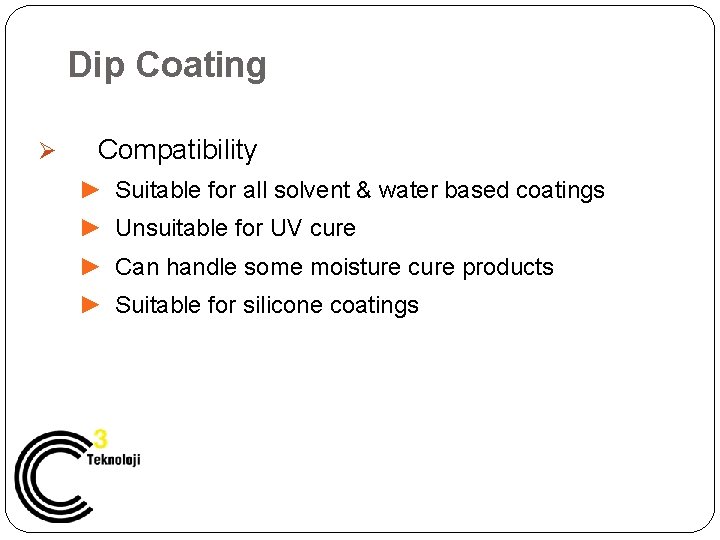
Dip Coating Ø Compatibility ► Suitable for all solvent & water based coatings ► Unsuitable for UV cure ► Can handle some moisture cure products ► Suitable for silicone coatings
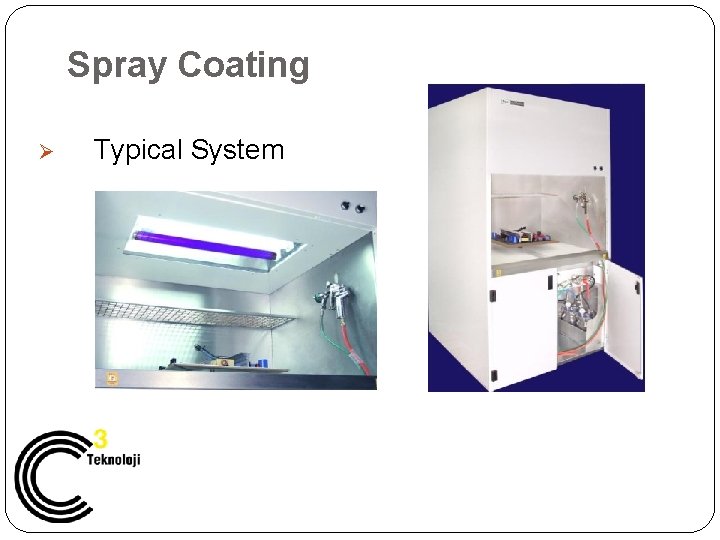
Spray Coating Ø Typical System
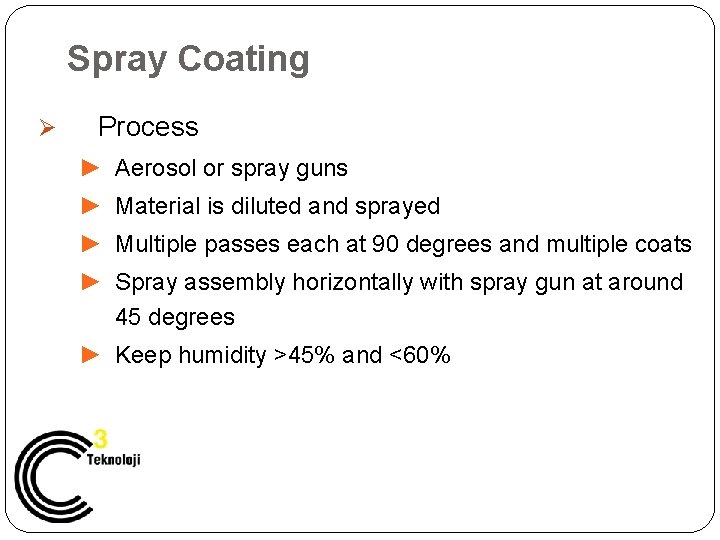
Spray Coating Ø Process ► Aerosol or spray guns ► Material is diluted and sprayed ► Multiple passes each at 90 degrees and multiple coats ► Spray assembly horizontally with spray gun at around 45 degrees ► Keep humidity >45% and <60%
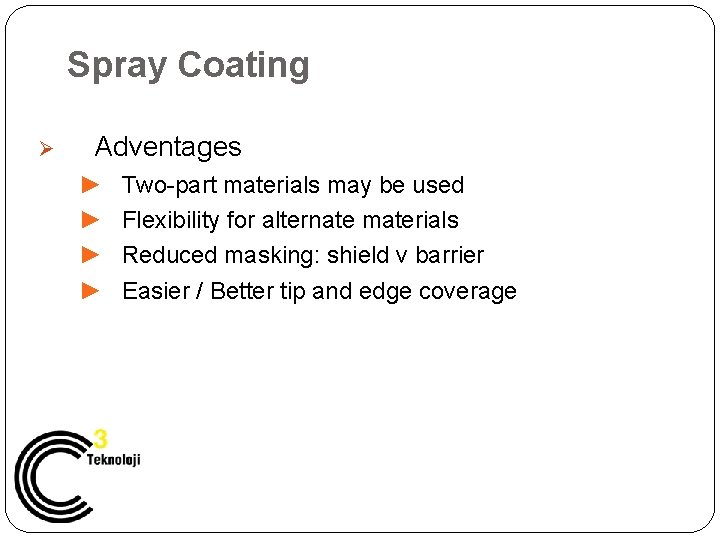
Spray Coating Ø Adventages ► ► Two-part materials may be used Flexibility for alternate materials Reduced masking: shield v barrier Easier / Better tip and edge coverage
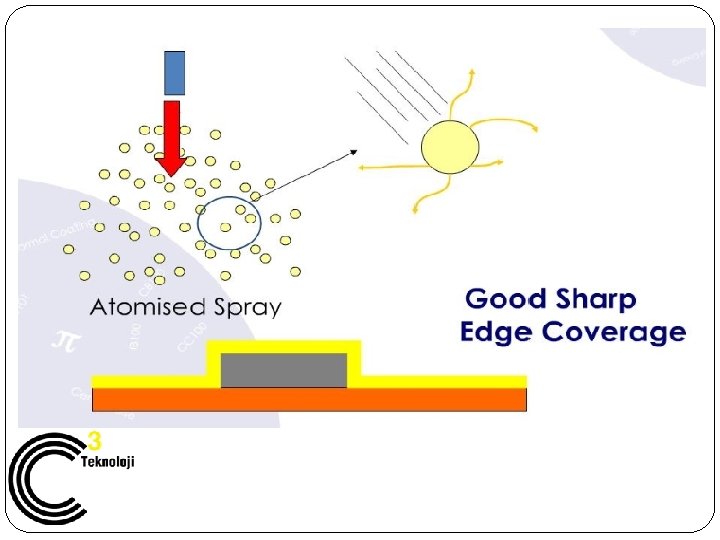
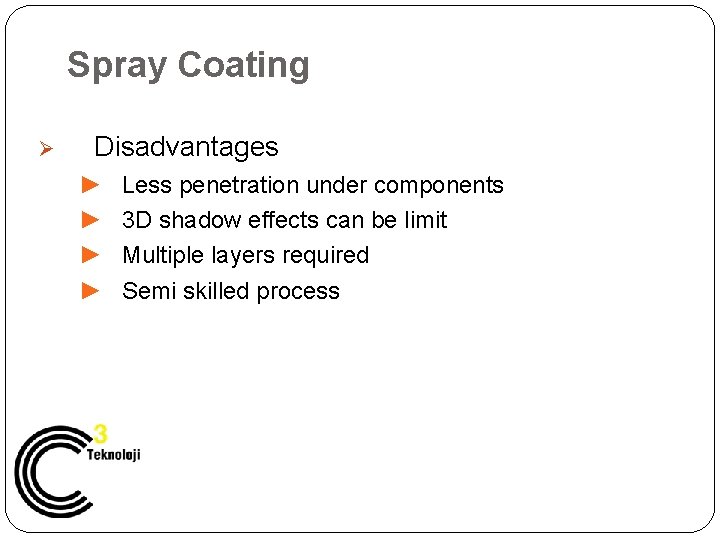
Spray Coating Ø Disadvantages ► ► Less penetration under components 3 D shadow effects can be limit Multiple layers required Semi skilled process
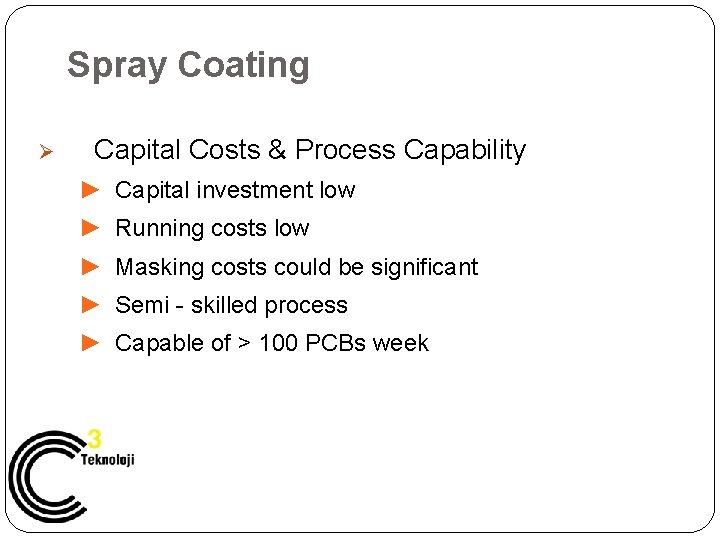
Spray Coating Ø Capital Costs & Process Capability ► Capital investment low ► Running costs low ► Masking costs could be significant ► Semi - skilled process ► Capable of > 100 PCBs week
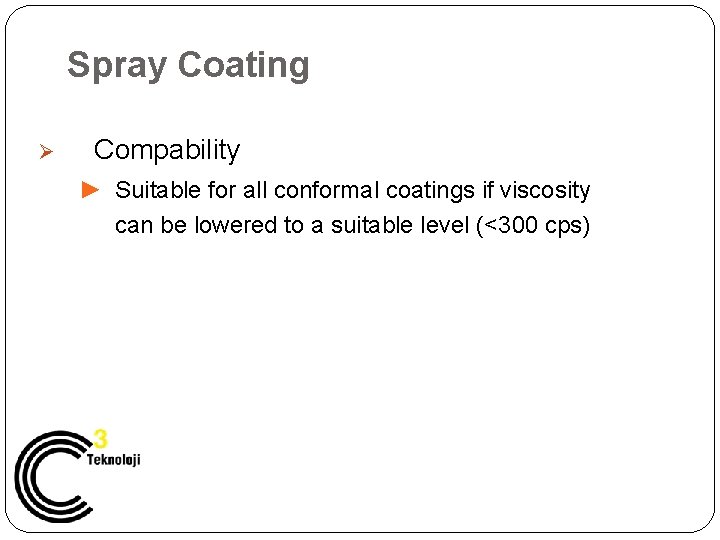
Spray Coating Ø Compability ► Suitable for all conformal coatings if viscosity can be lowered to a suitable level (<300 cps)
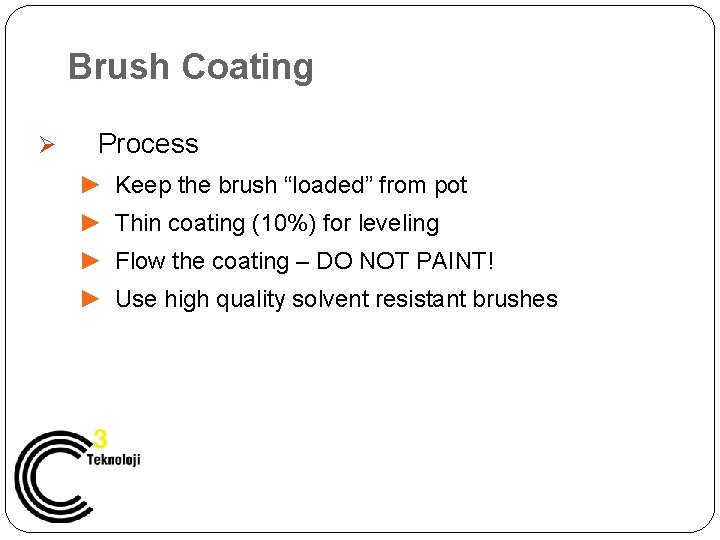
Brush Coating Ø Process ► Keep the brush “loaded” from pot ► Thin coating (10%) for leveling ► Flow the coating – DO NOT PAINT! ► Use high quality solvent resistant brushes
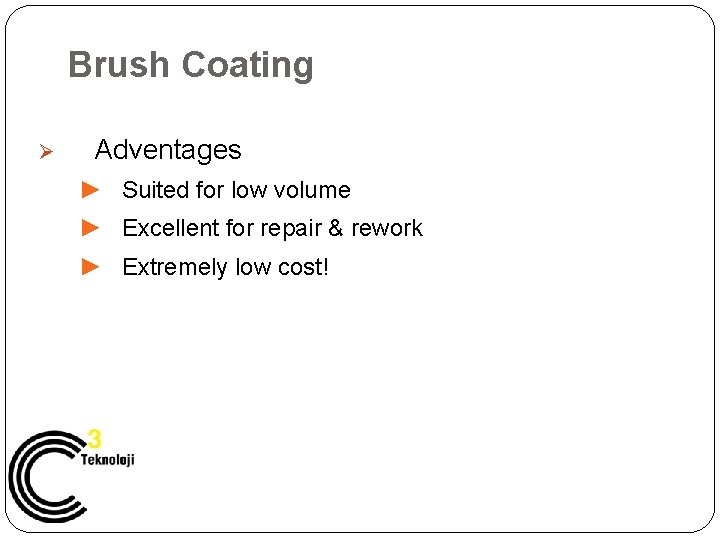
Brush Coating Ø Adventages ► Suited for low volume ► Excellent for repair & rework ► Extremely low cost!
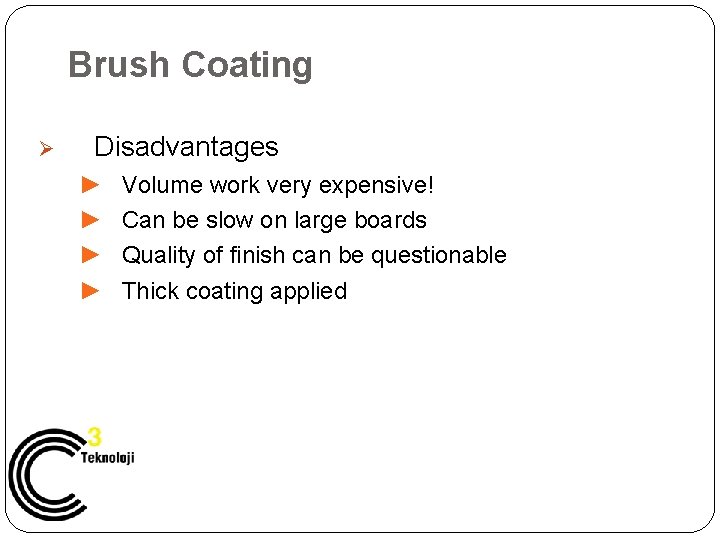
Brush Coating Ø Disadvantages ► ► Volume work very expensive! Can be slow on large boards Quality of finish can be questionable Thick coating applied
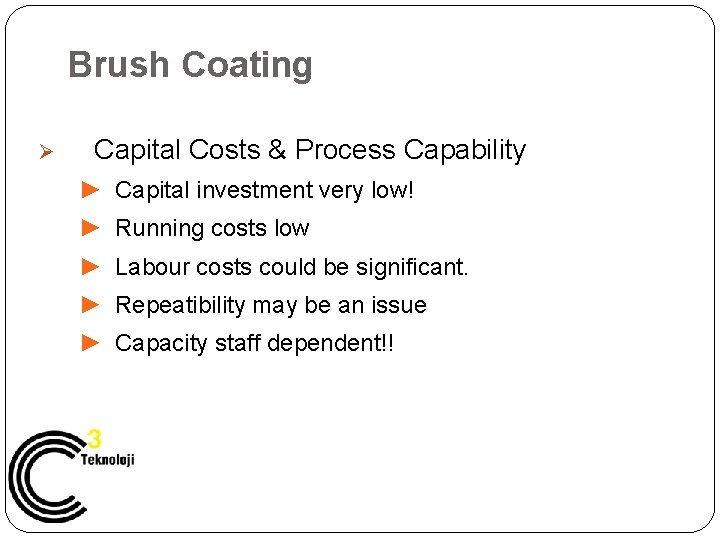
Brush Coating Ø Capital Costs & Process Capability ► Capital investment very low! ► Running costs low ► Labour costs could be significant. ► Repeatibility may be an issue ► Capacity staff dependent!!
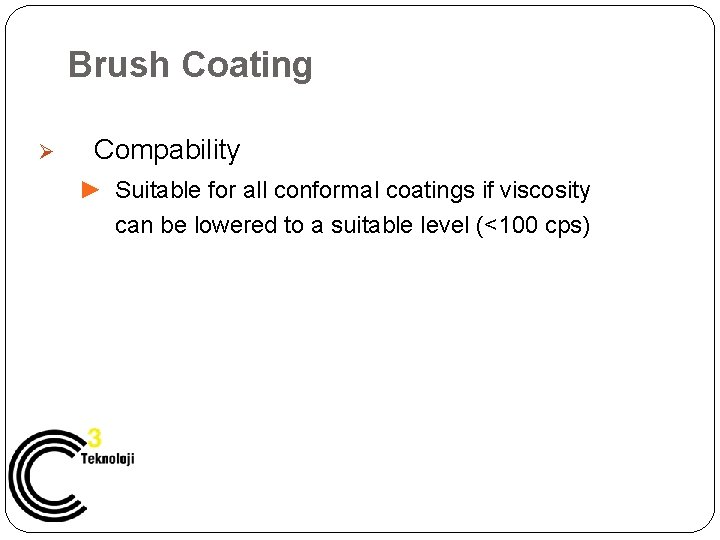
Brush Coating Ø Compability ► Suitable for all conformal coatings if viscosity can be lowered to a suitable level (<100 cps)
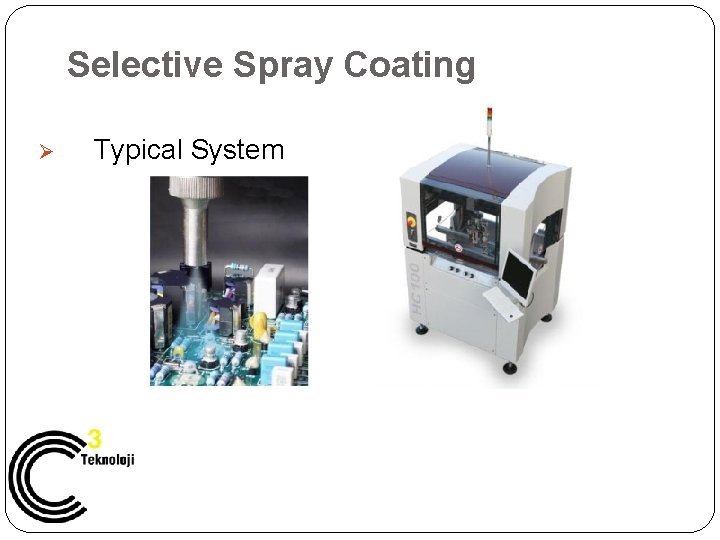
Selective Spray Coating Ø Typical System
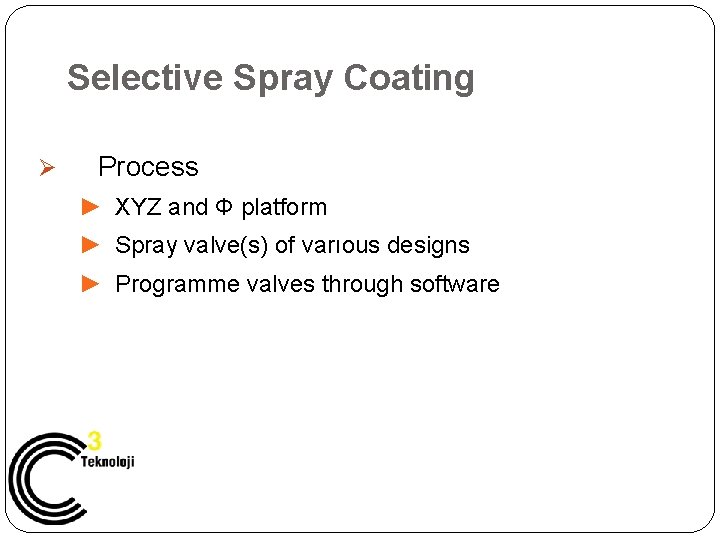
Selective Spray Coating Ø Process ► XYZ and Φ platform ► Spray valve(s) of varıous designs ► Programme valves through software
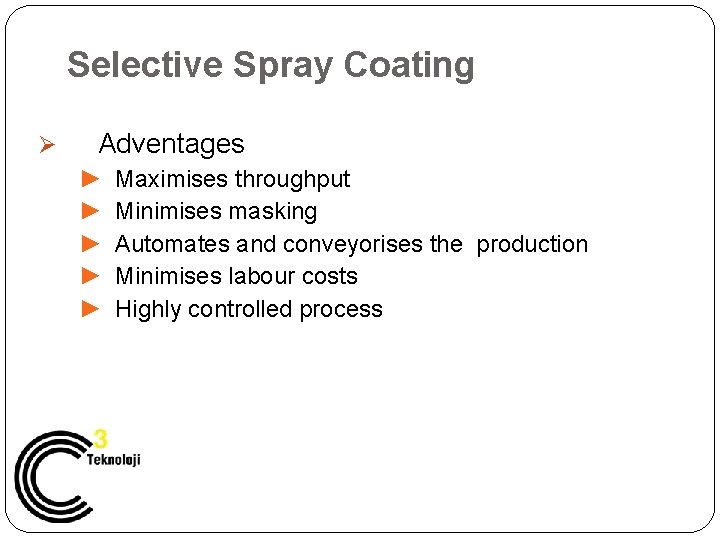
Selective Spray Coating Ø Adventages ► ► ► Maximises throughput Minimises masking Automates and conveyorises the production Minimises labour costs Highly controlled process
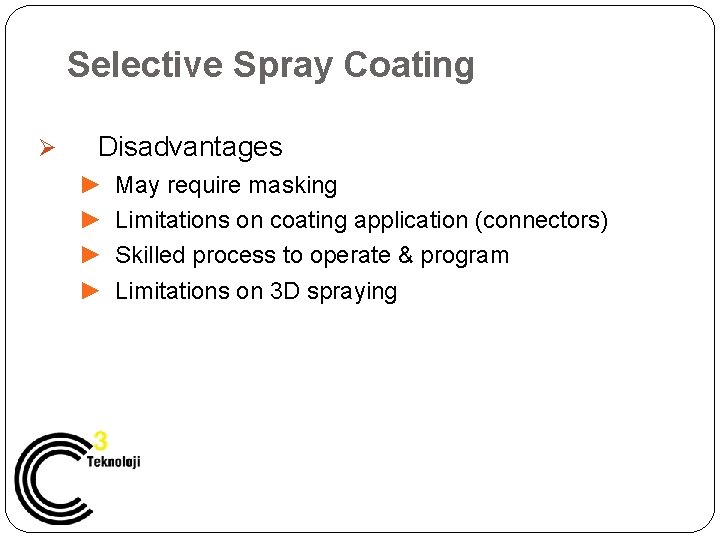
Selective Spray Coating Ø Disadvantages ► ► May require masking Limitations on coating application (connectors) Skilled process to operate & program Limitations on 3 D spraying
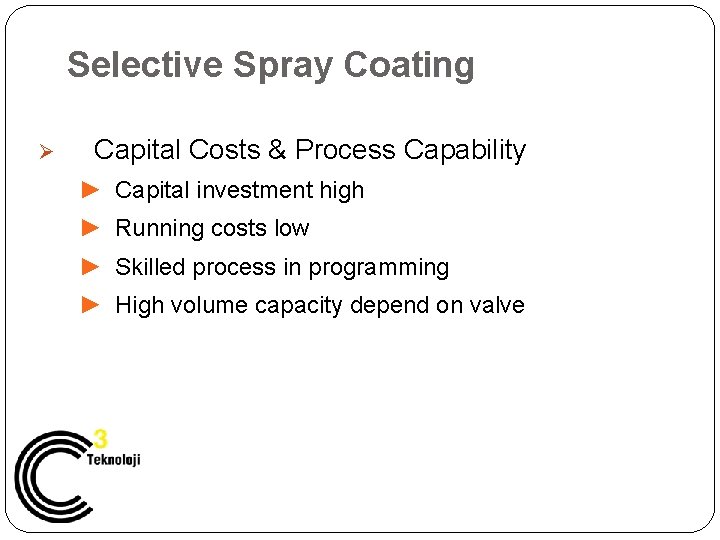
Selective Spray Coating Ø Capital Costs & Process Capability ► Capital investment high ► Running costs low ► Skilled process in programming ► High volume capacity depend on valve
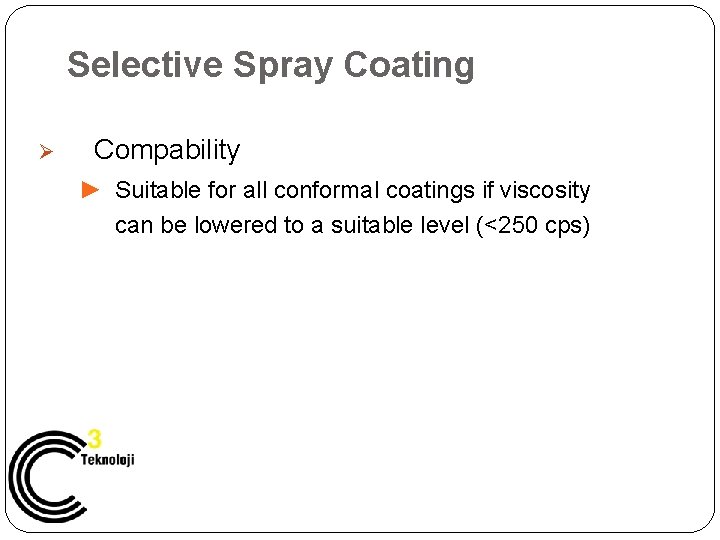
Selective Spray Coating Ø Compability ► Suitable for all conformal coatings if viscosity can be lowered to a suitable level (<250 cps)
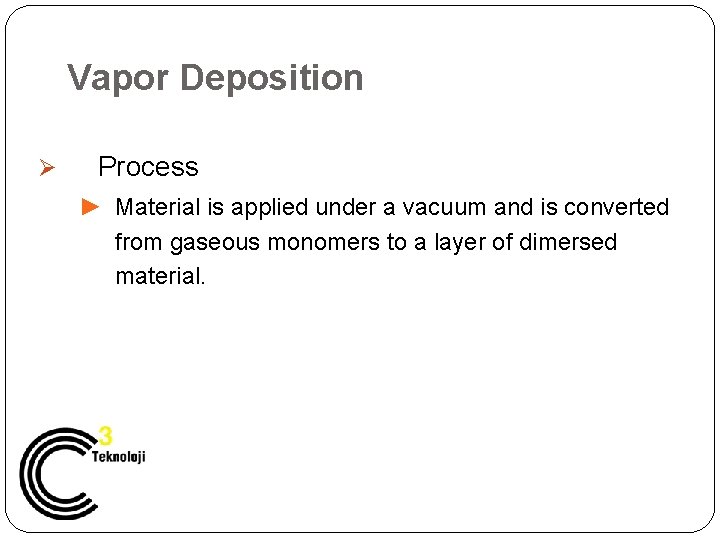
Vapor Deposition Ø Process ► Material is applied under a vacuum and is converted from gaseous monomers to a layer of dimersed material.
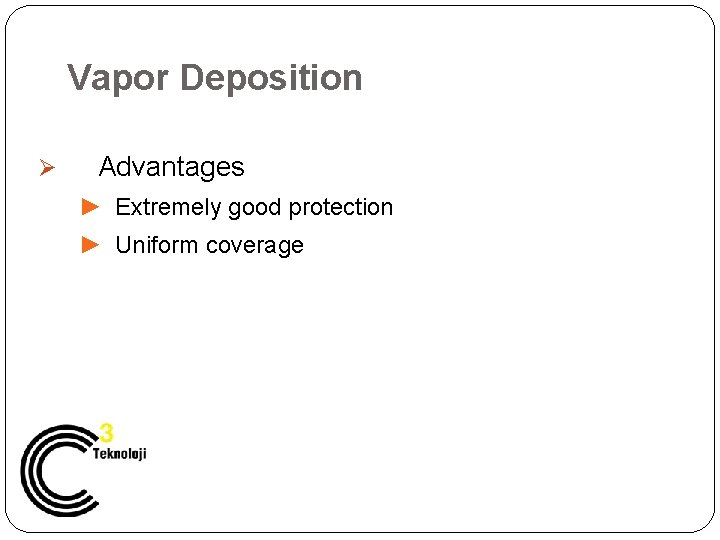
Vapor Deposition Ø Advantages ► Extremely good protection ► Uniform coverage
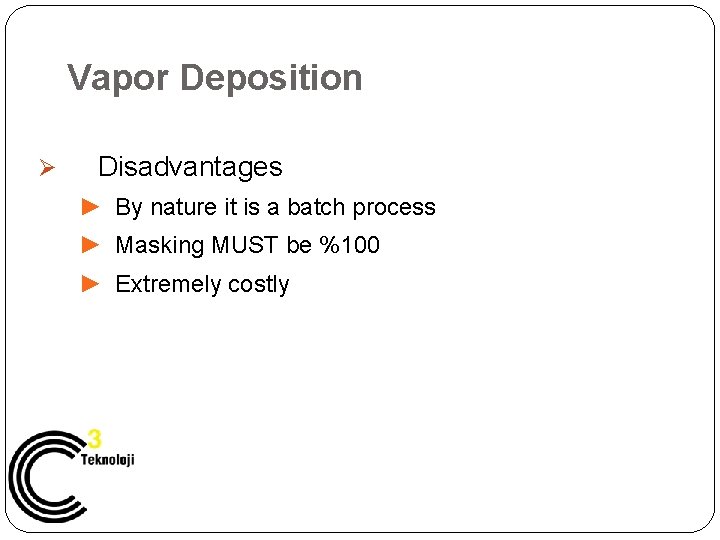
Vapor Deposition Ø Disadvantages ► By nature it is a batch process ► Masking MUST be %100 ► Extremely costly
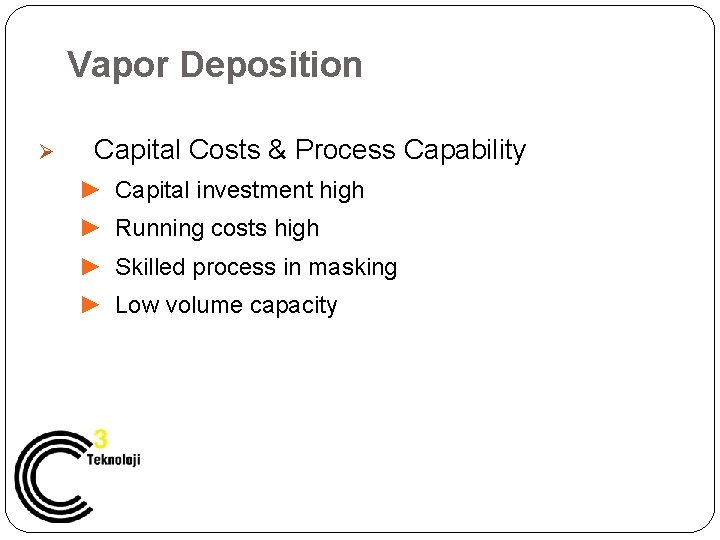
Vapor Deposition Ø Capital Costs & Process Capability ► Capital investment high ► Running costs high ► Skilled process in masking ► Low volume capacity
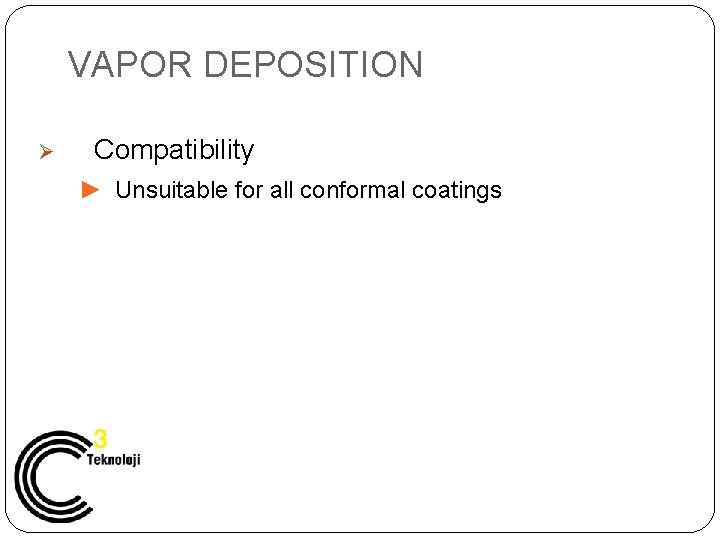
VAPOR DEPOSITION Ø Compatibility ► Unsuitable for all conformal coatings
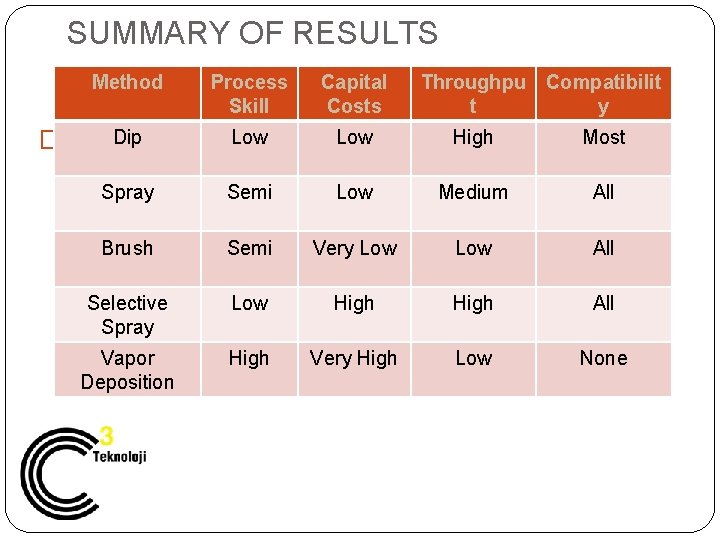
SUMMARY OF RESULTS � Method Process Skill Capital Costs Throughpu t Compatibilit y Dip Low High Most Spray Semi Low Medium All Brush Semi Very Low All Selective Spray Low High All Vapor Deposition High Very High Low None
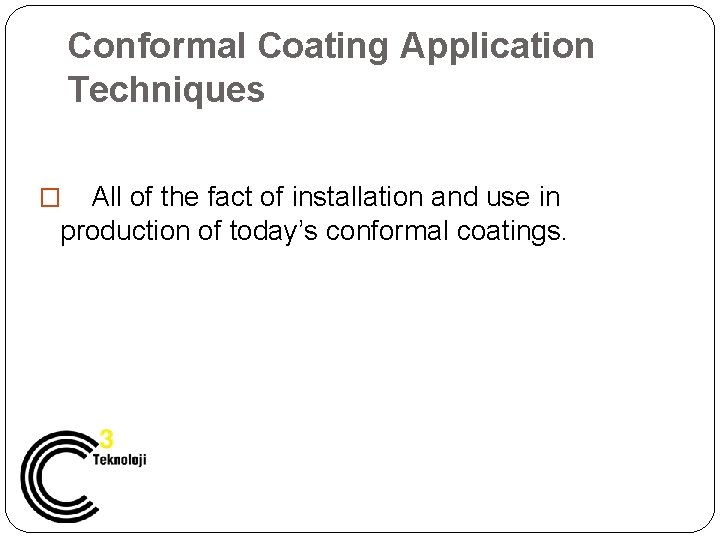
Conformal Coating Application Techniques All of the fact of installation and use in production of today’s conformal coatings. �
Conformal coating standards
Coating application specialist
2d conformal transformation
Substrate conformal imprint lithography
What is a conformal projection
Pvd vs cvd
Tablet opaquant
Stripe
Spin coating thickness equation
Bfb boiler coating
Rubber coated u bolts
Plural component spray coatings
Define tablet coating
Sugar-coated tablets examples
Ftg software
Balinit futura nano coating
Spraylat copper conductive coating
Apex metal oxide coating
Slideshare
Escp corp
Edible coating definition
Dursan coating
Which part of the neuron serves as the protective coating?
Hvaf coating
Lithography
Advantages of enteric coated tablets
Photoresist coating
Automated spray coating systems
Powder coating kildare
Powder coating twin screw extruder
Brandwerende verf voor staal
Architectural metal coating
Optical coating stress
Coating plasma innovation
Zinc hazards
Naval coating
Gpc company abu dhabi
Ivd coating wiki