Chapter 6 Process Selection and Facility Layout Mc
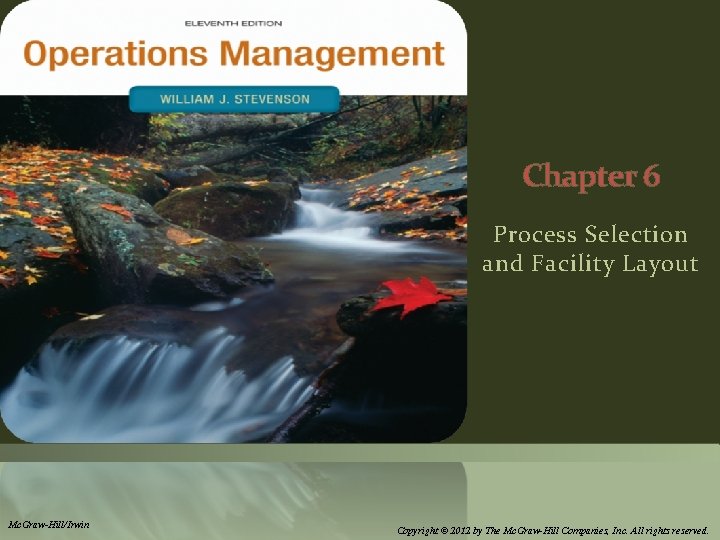
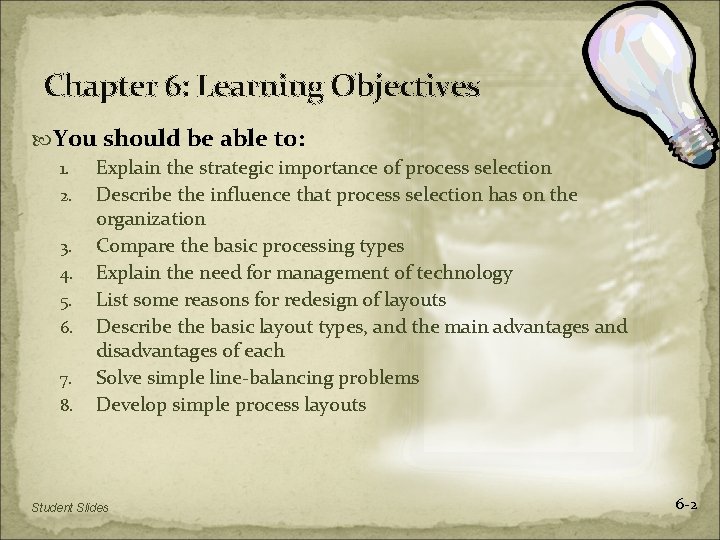
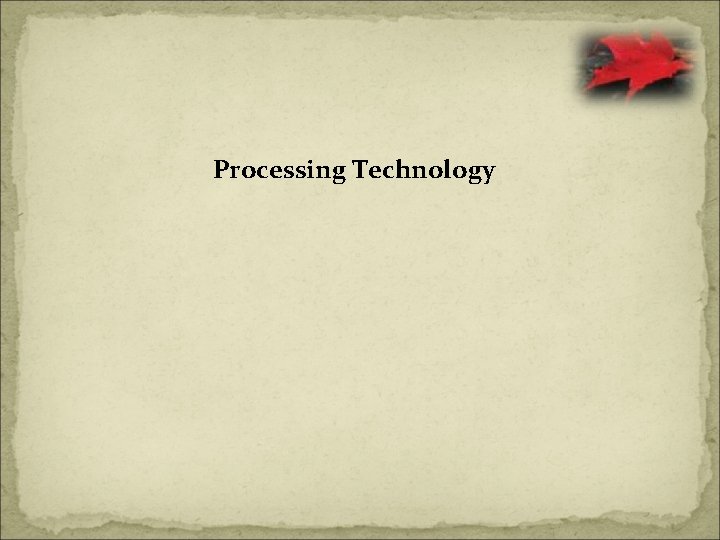
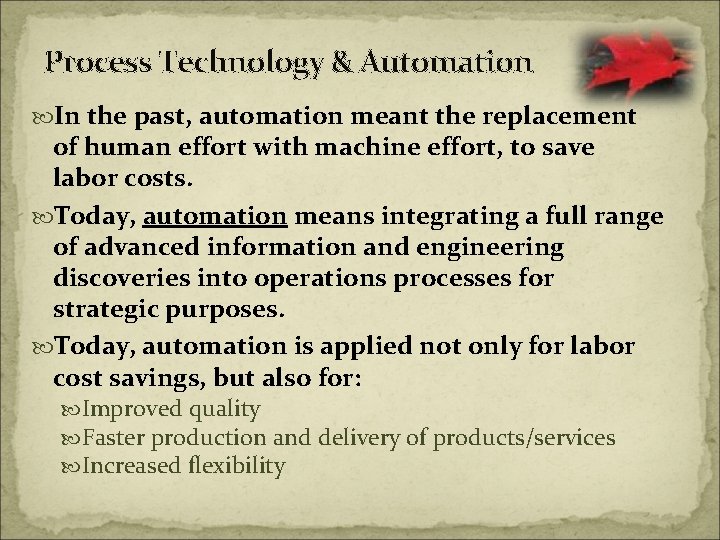
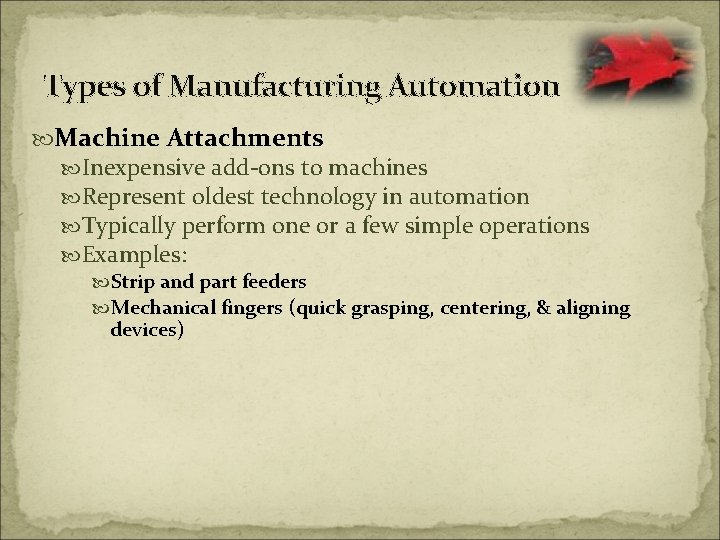
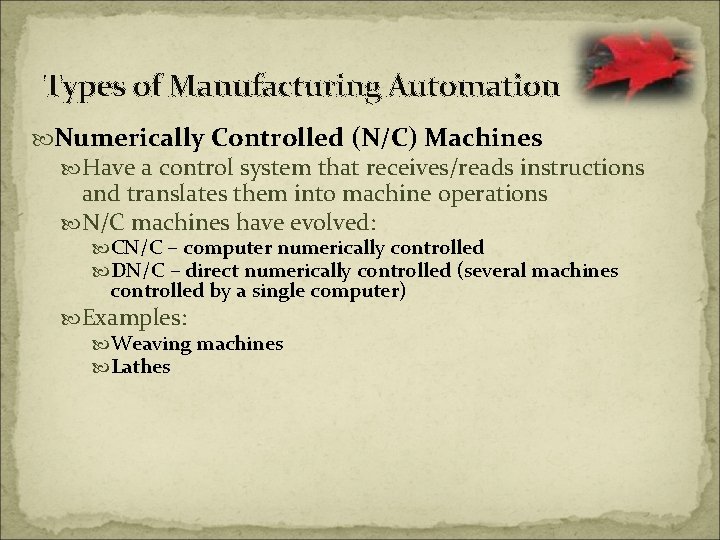
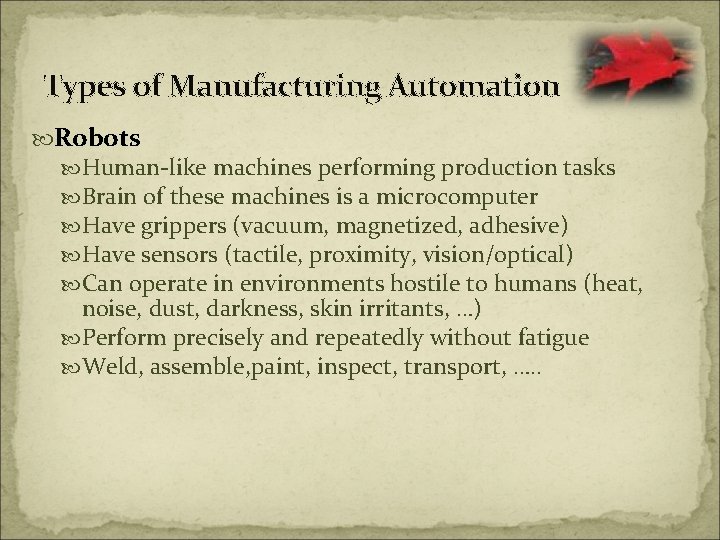
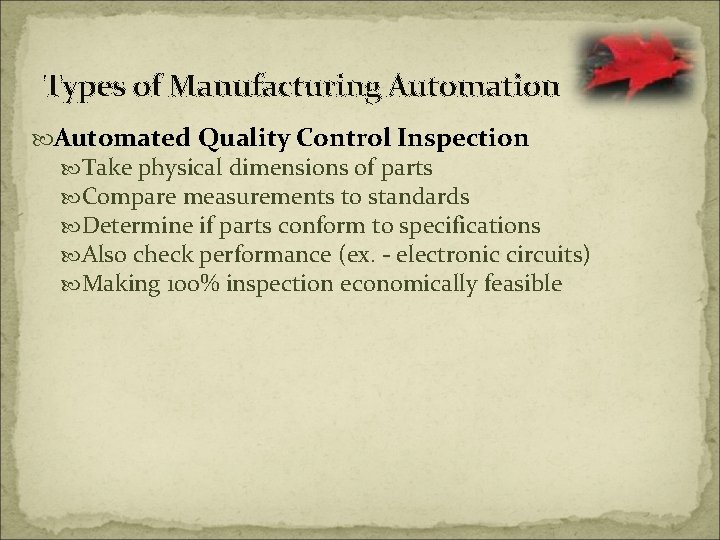
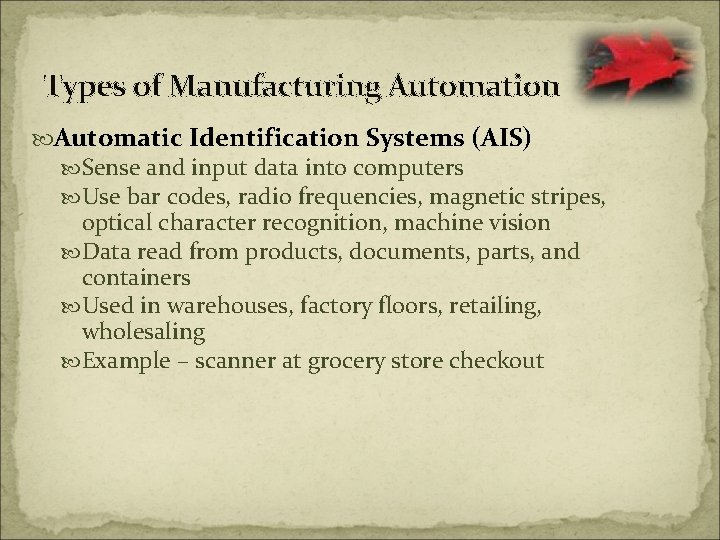

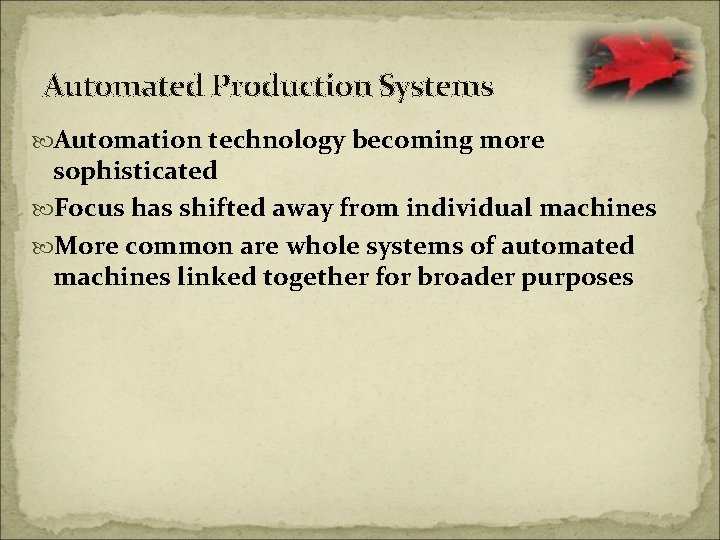
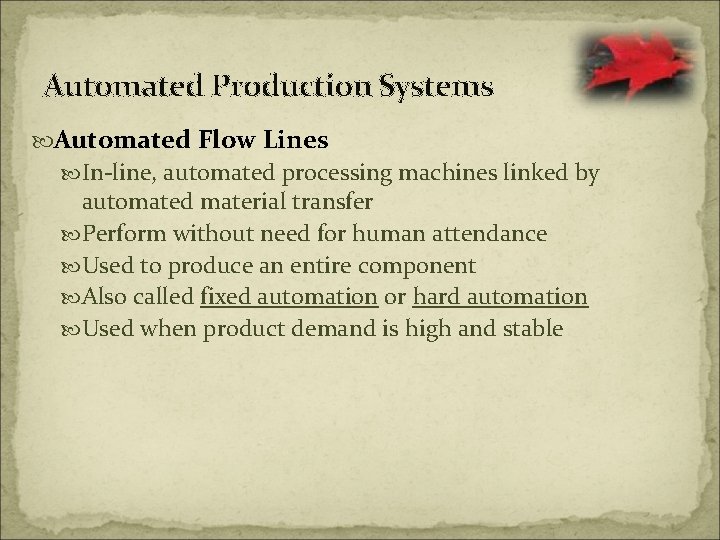
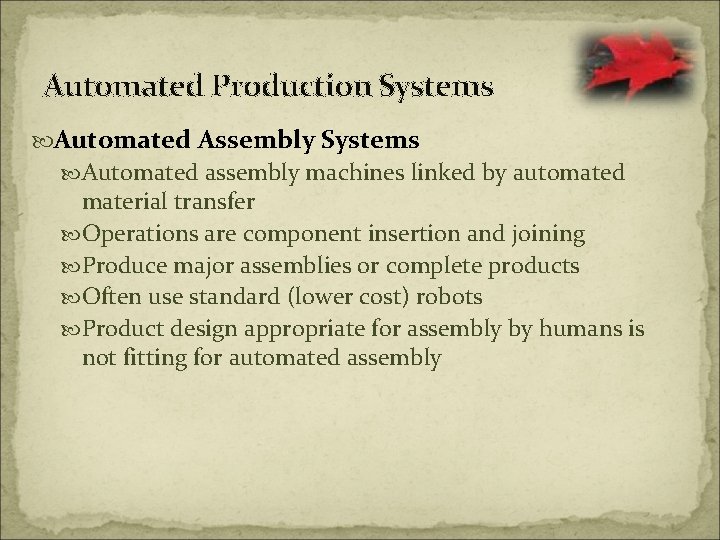
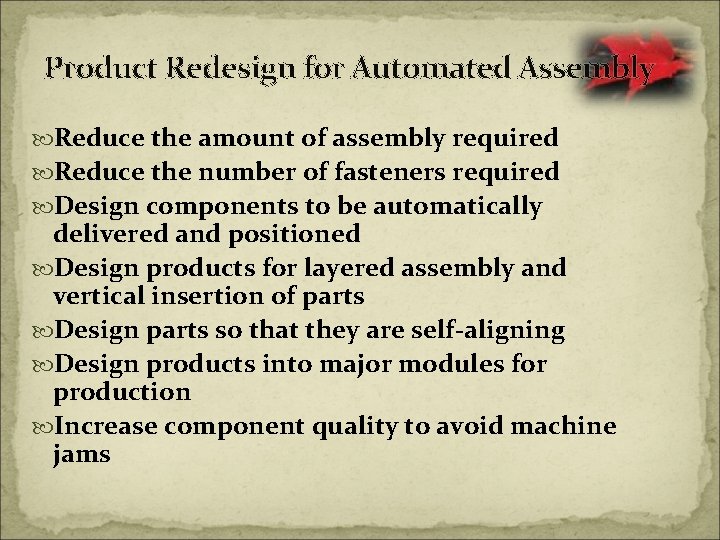
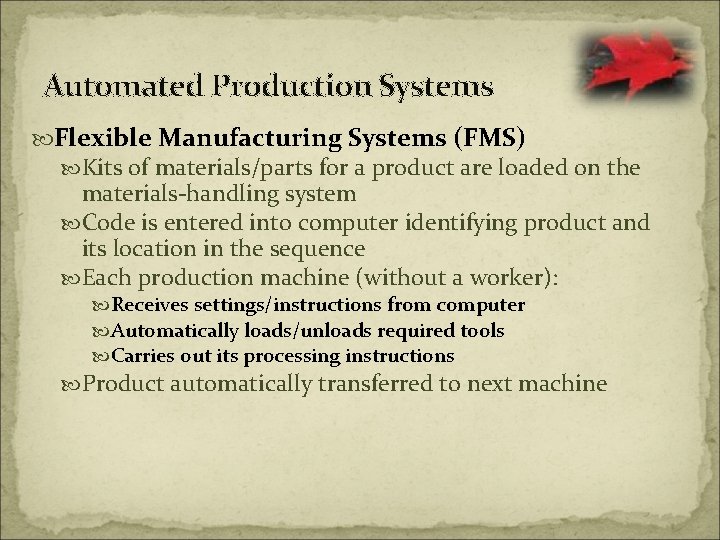
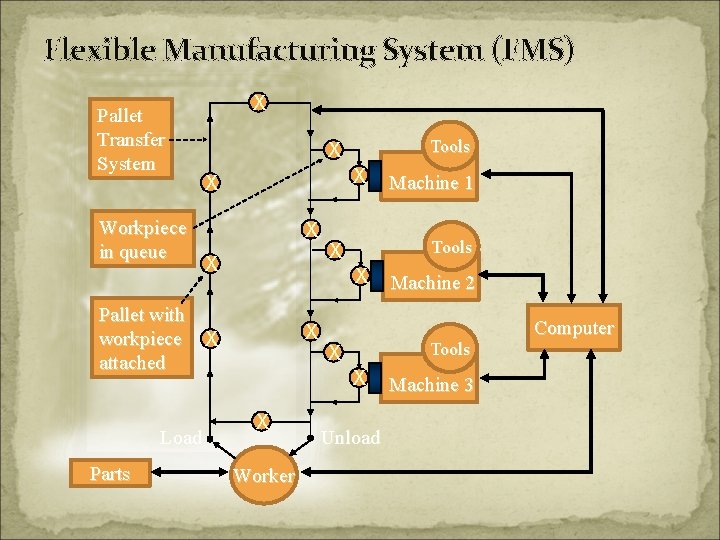
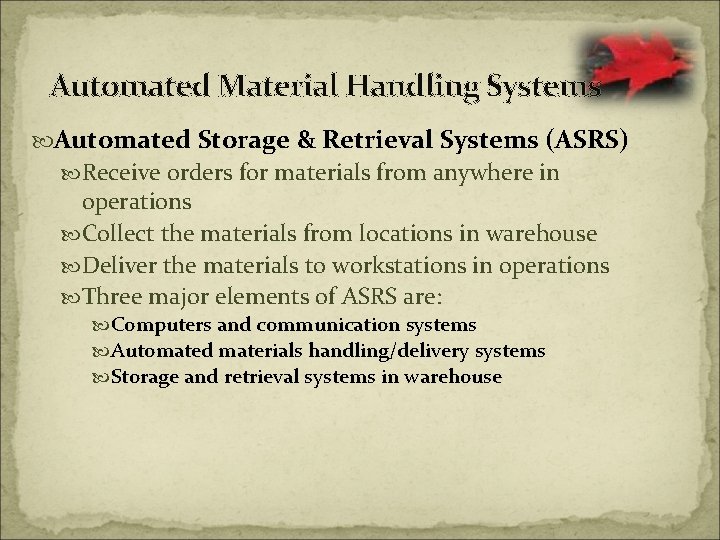
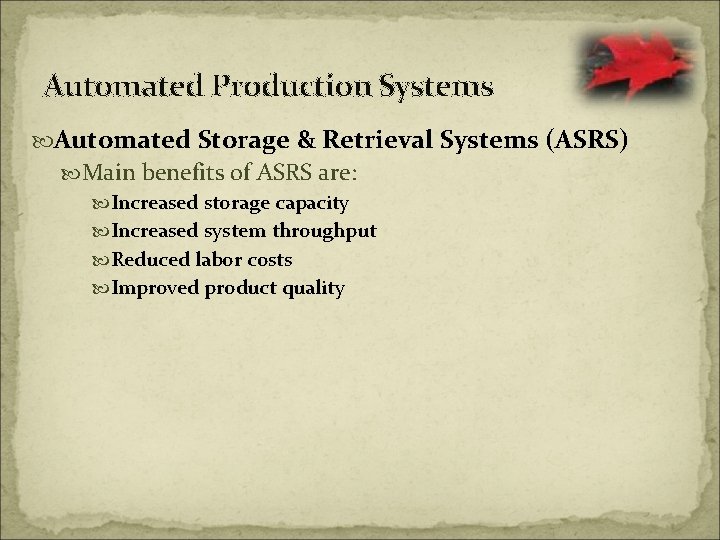

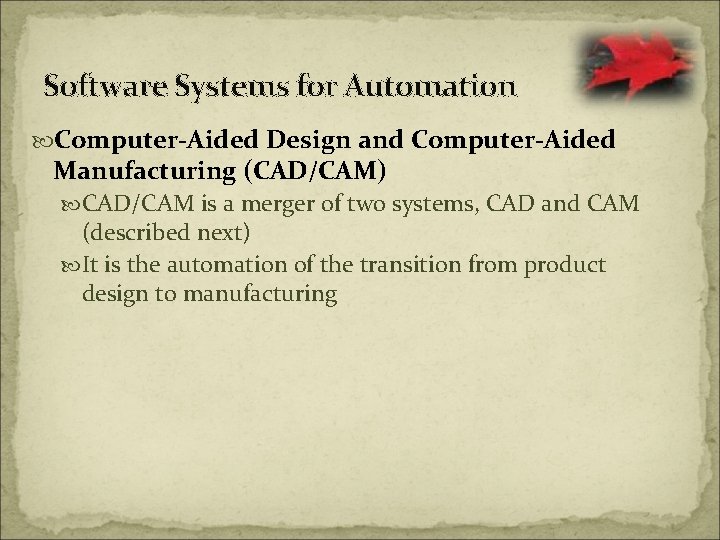
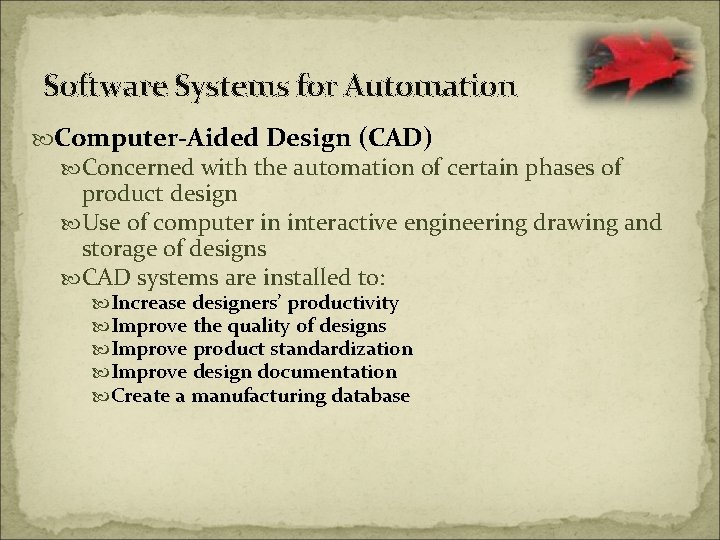
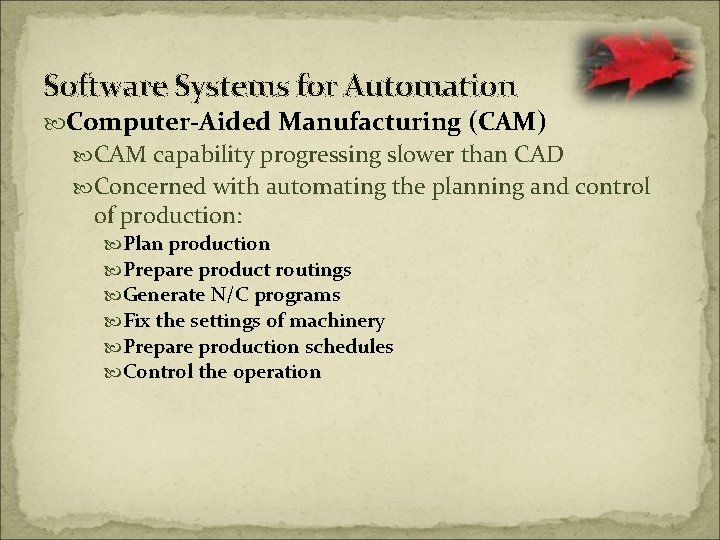
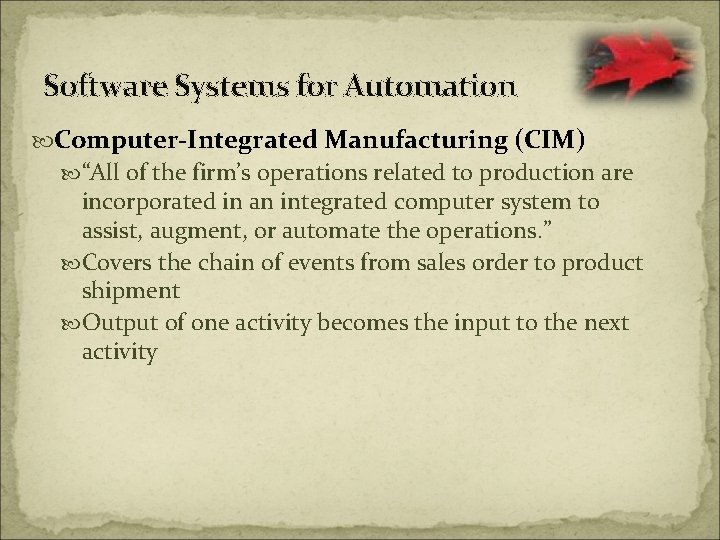
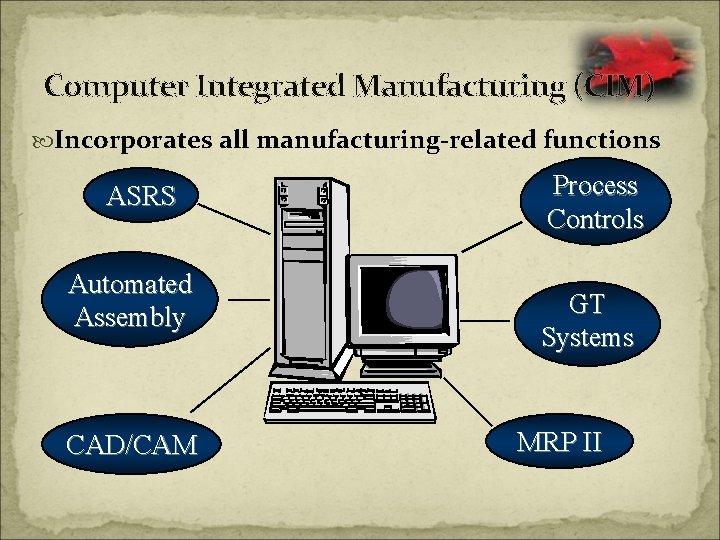
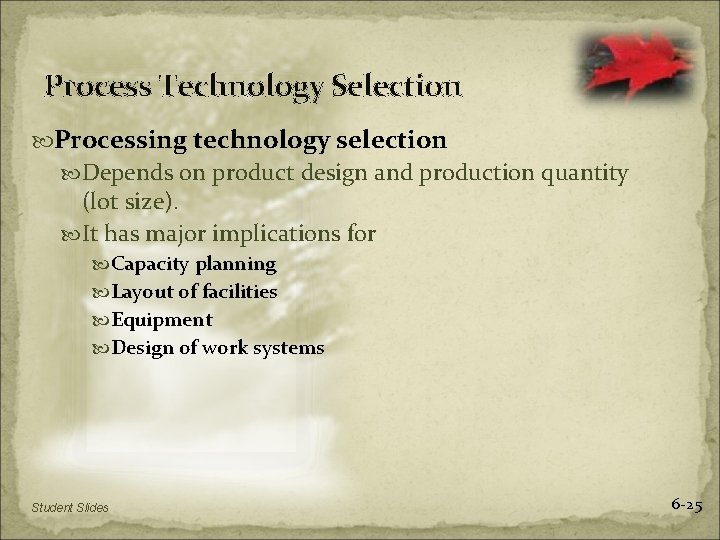
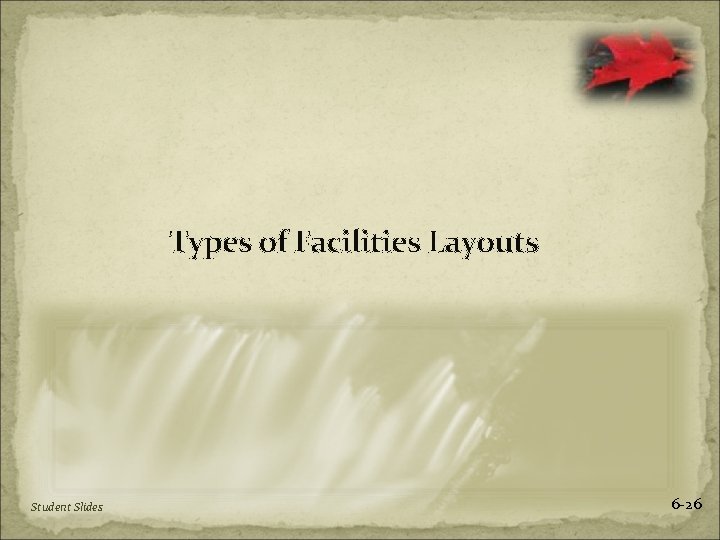
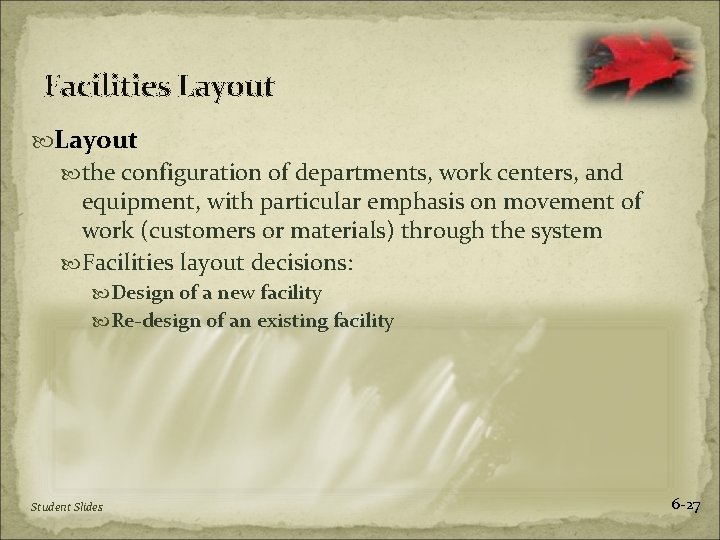
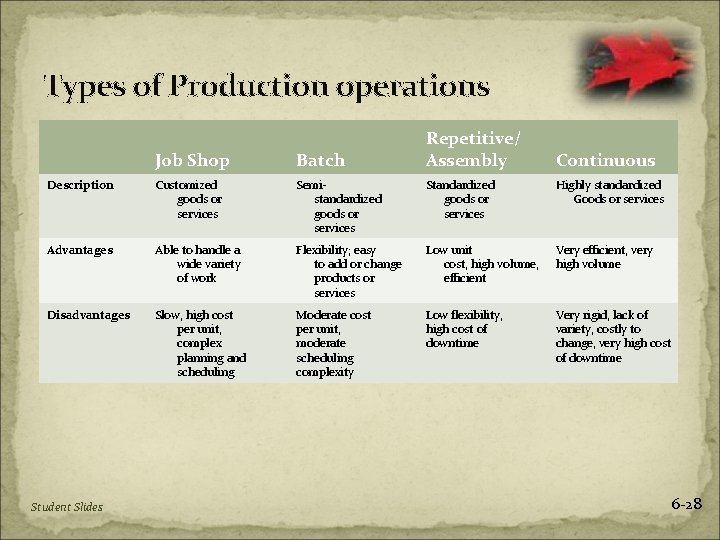
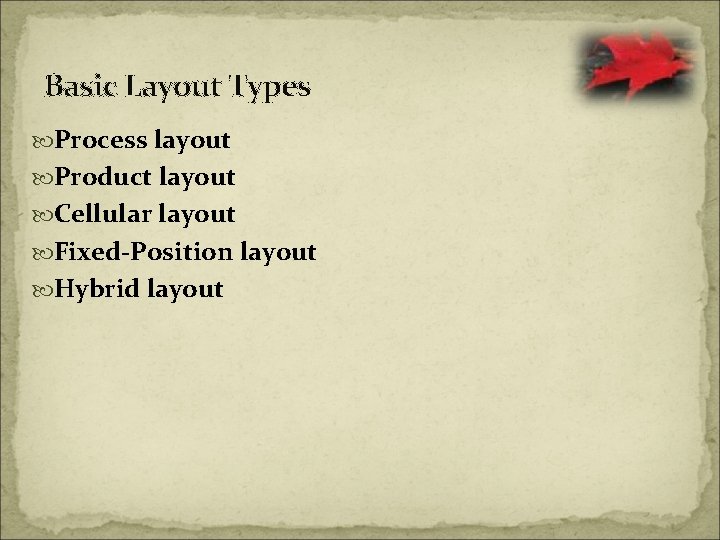
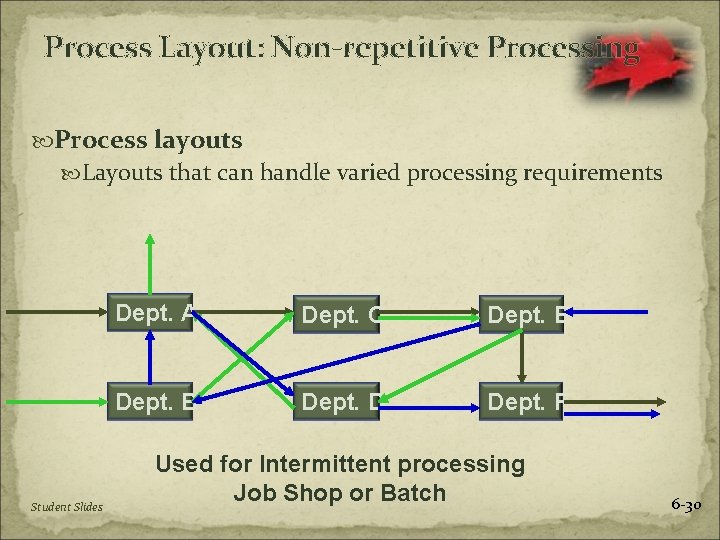
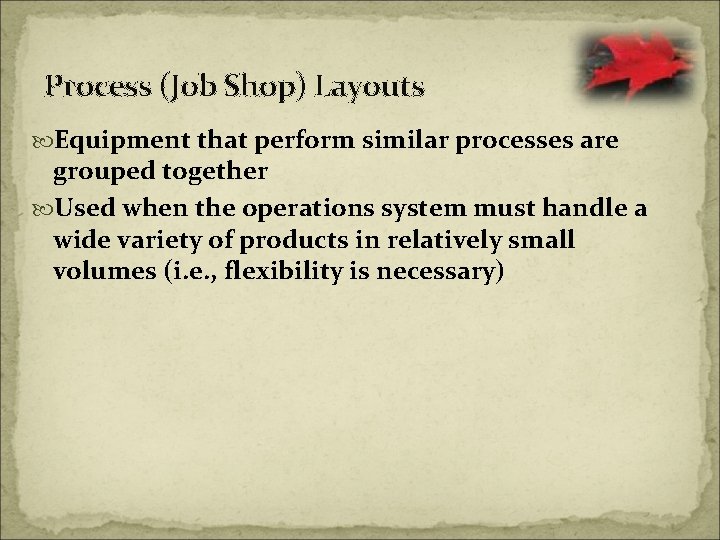
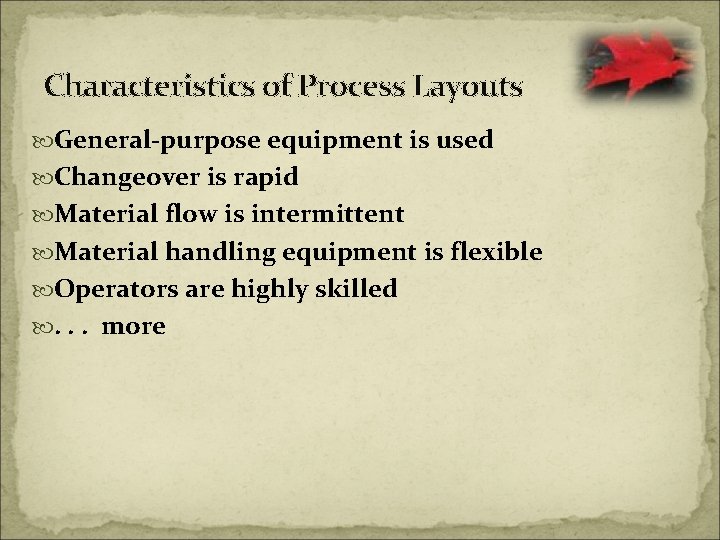
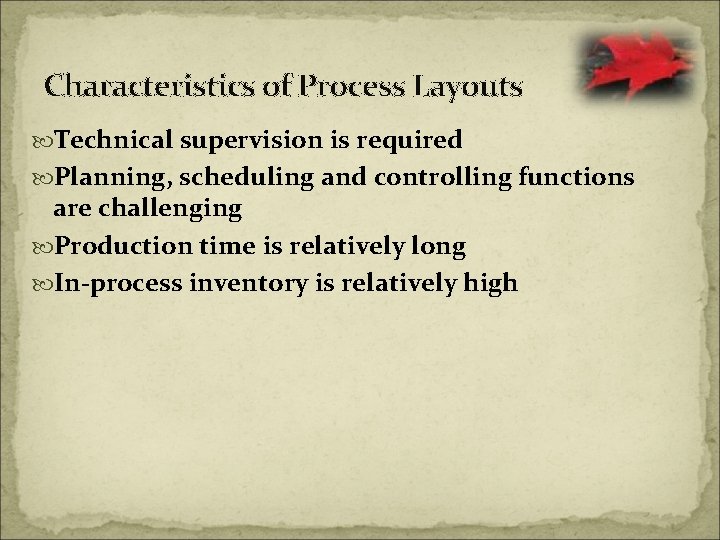
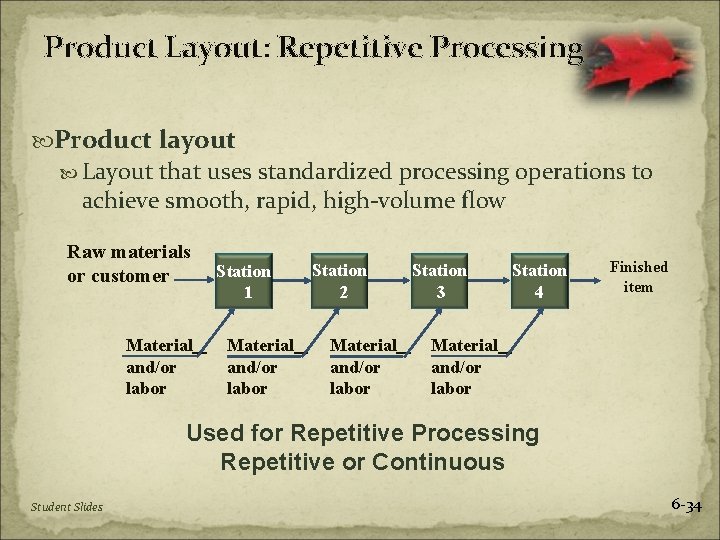
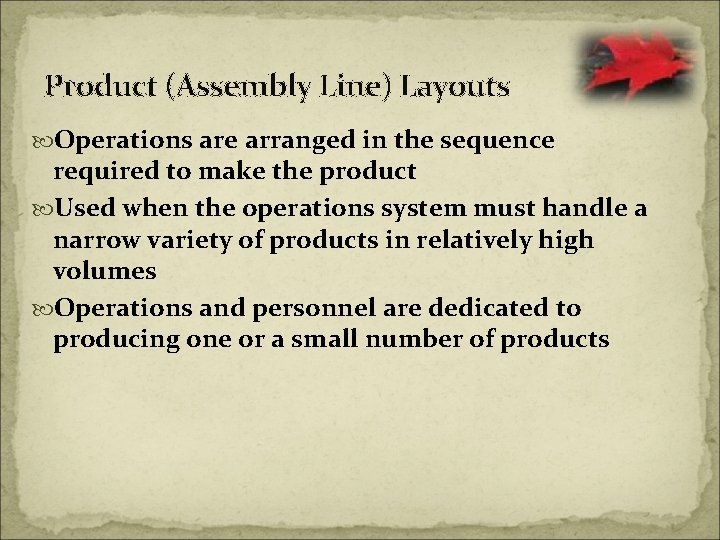
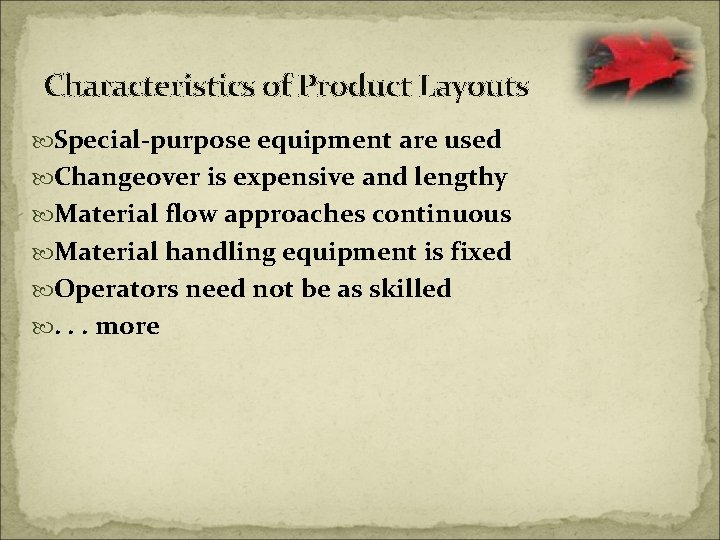
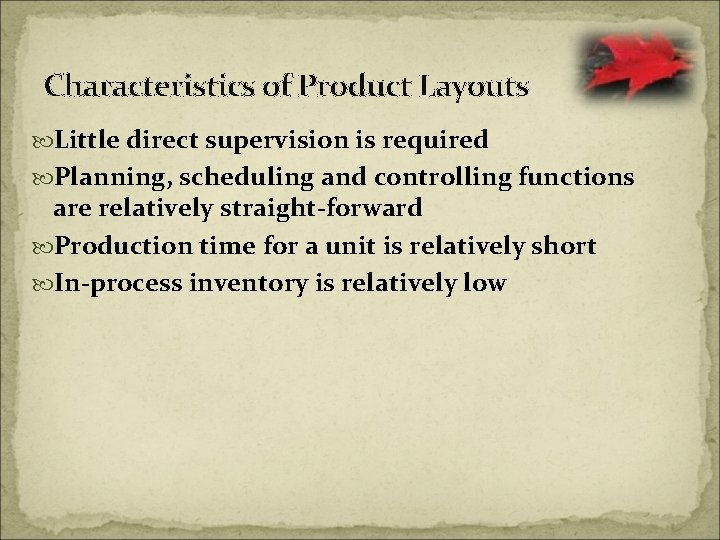
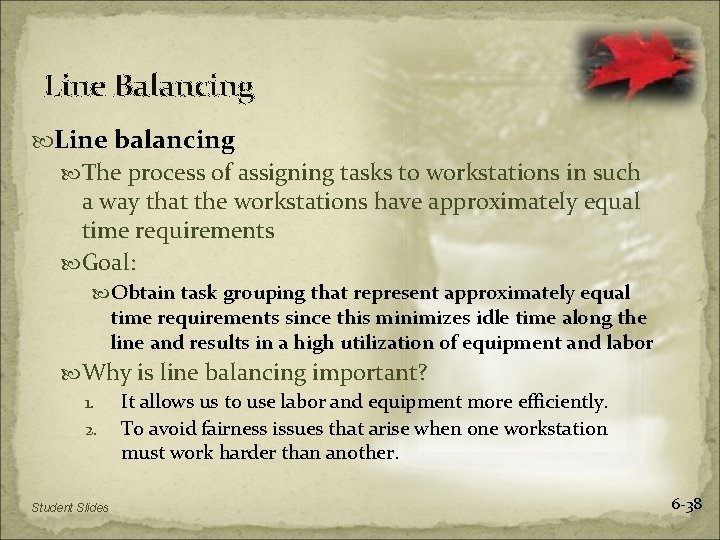
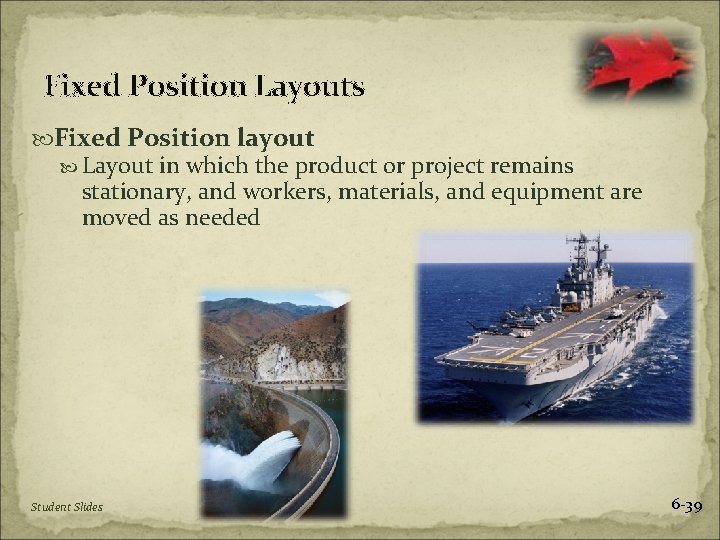
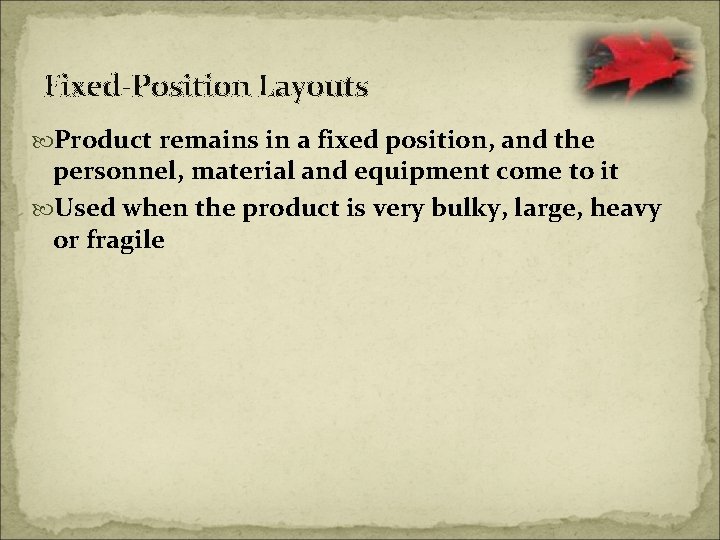
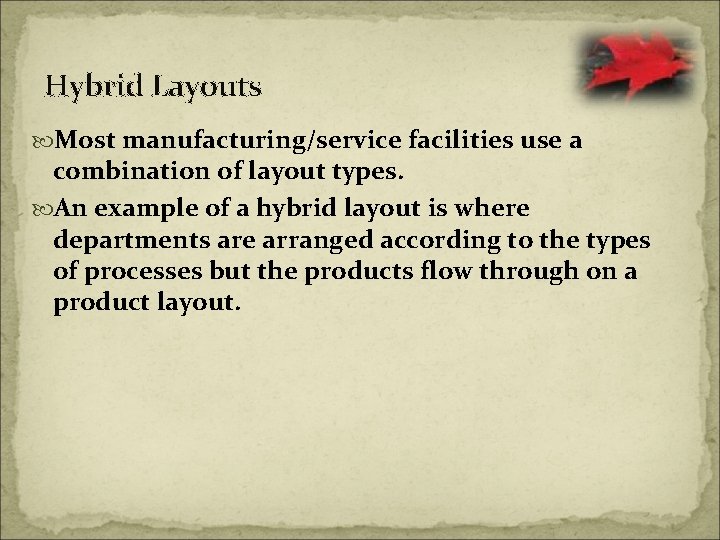
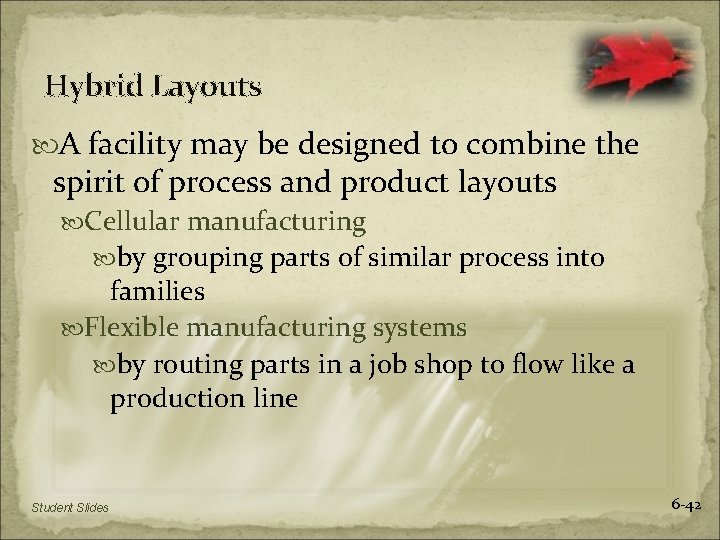
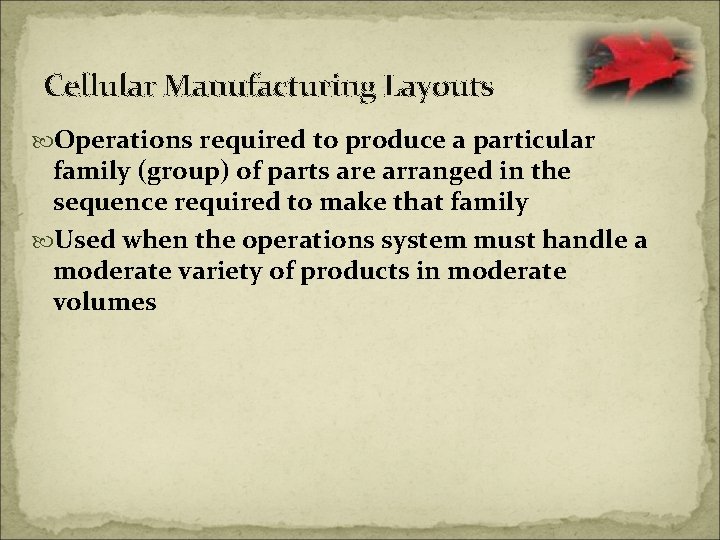

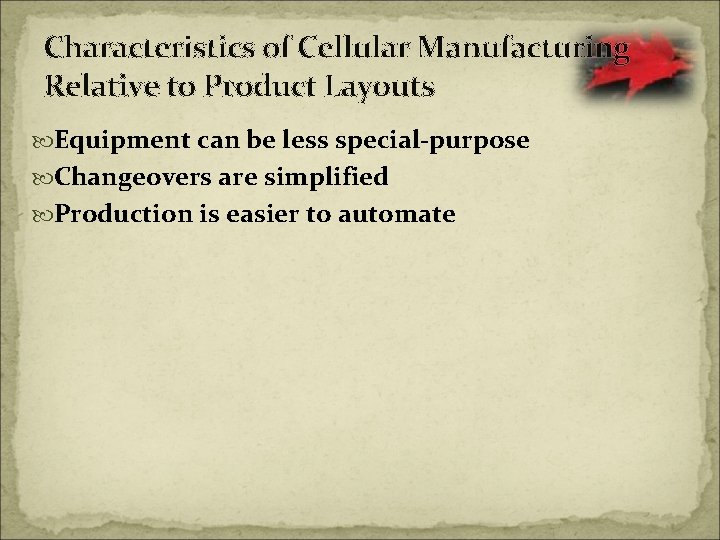
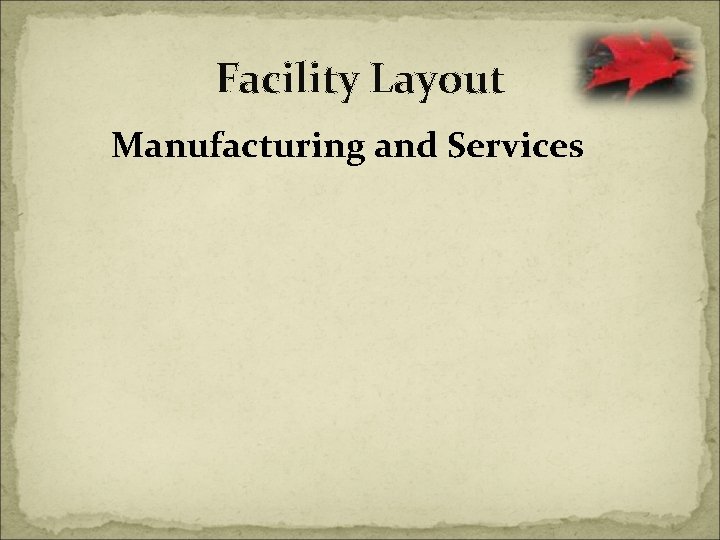
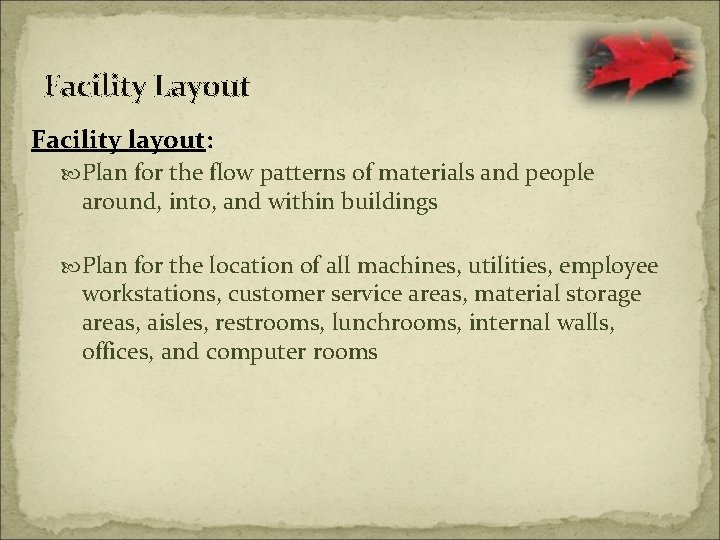
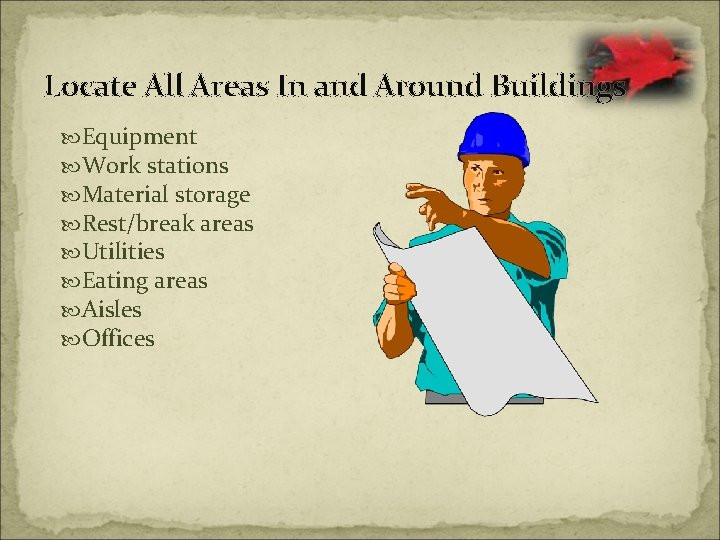
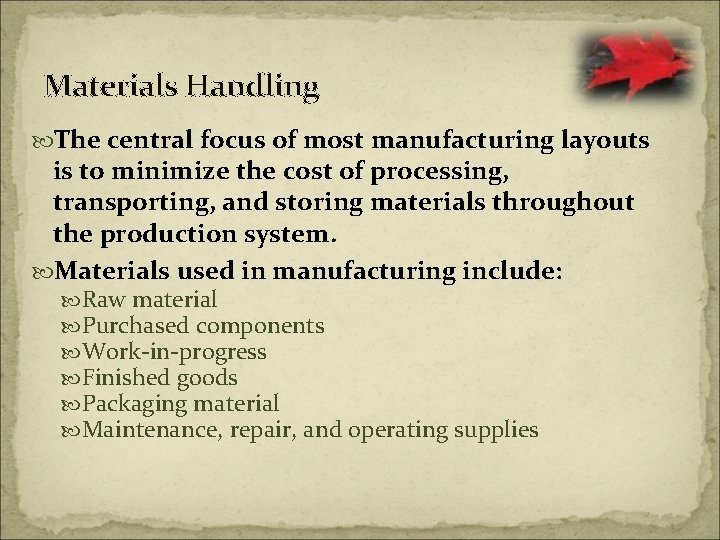

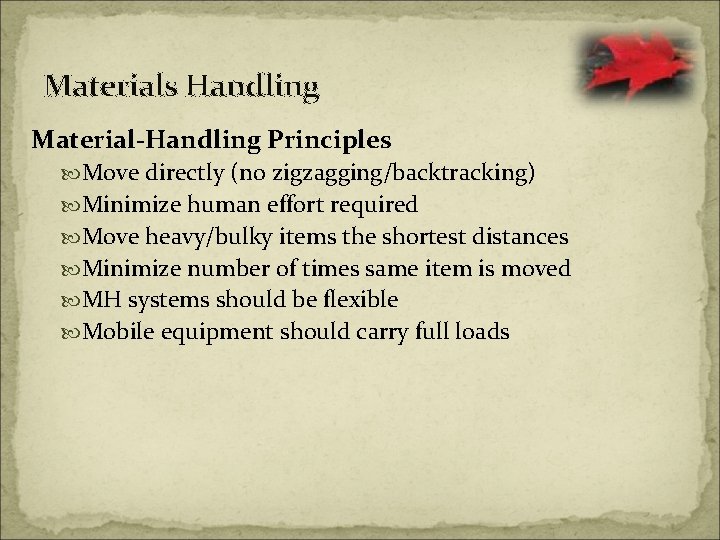
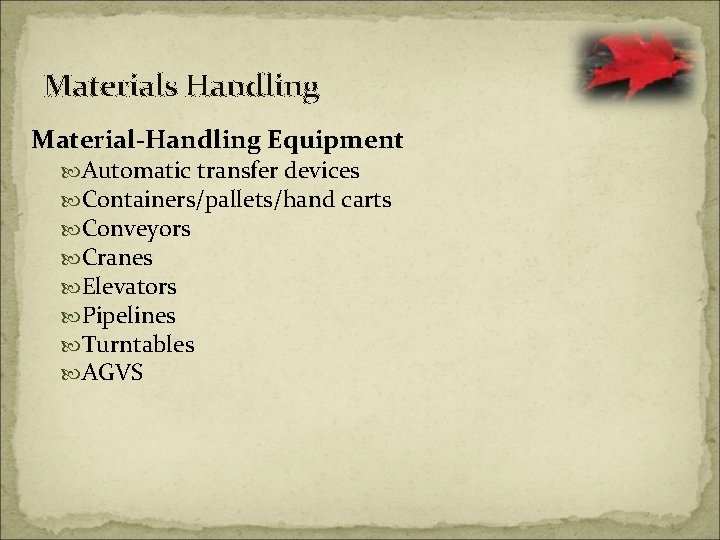
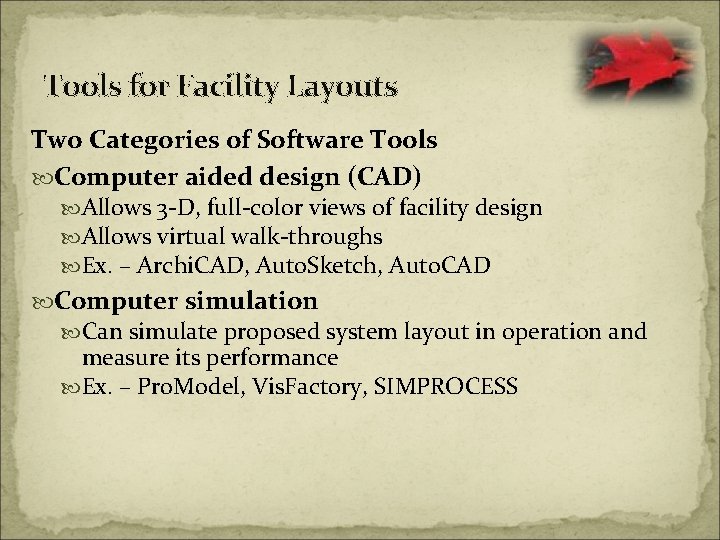
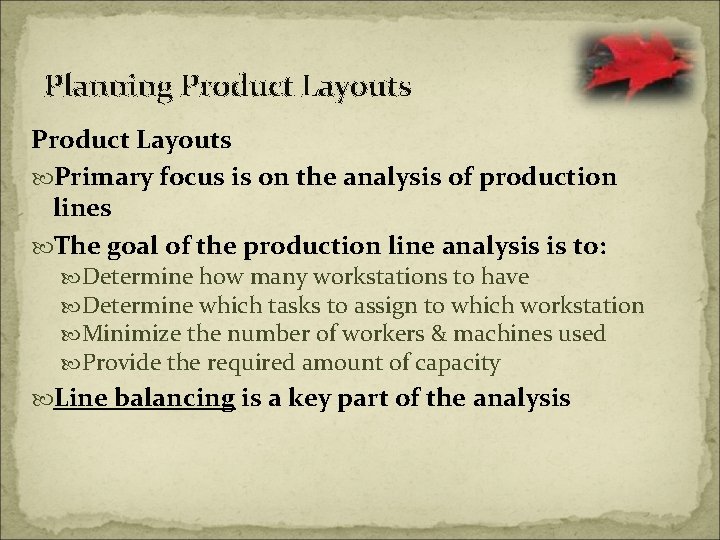
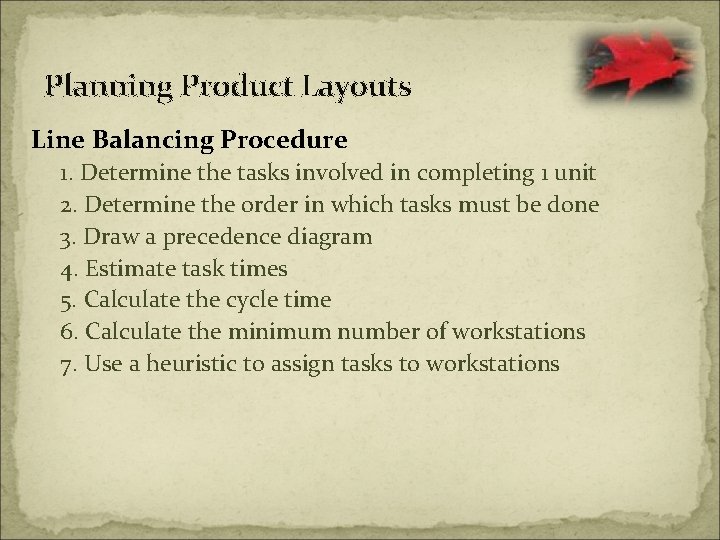
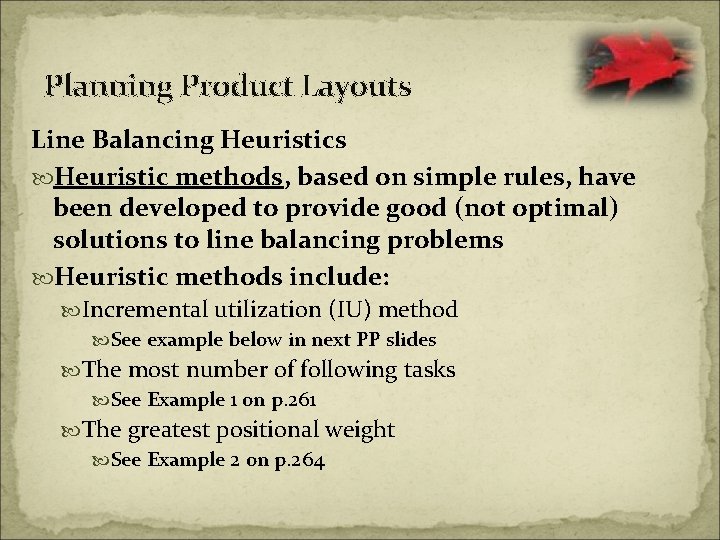
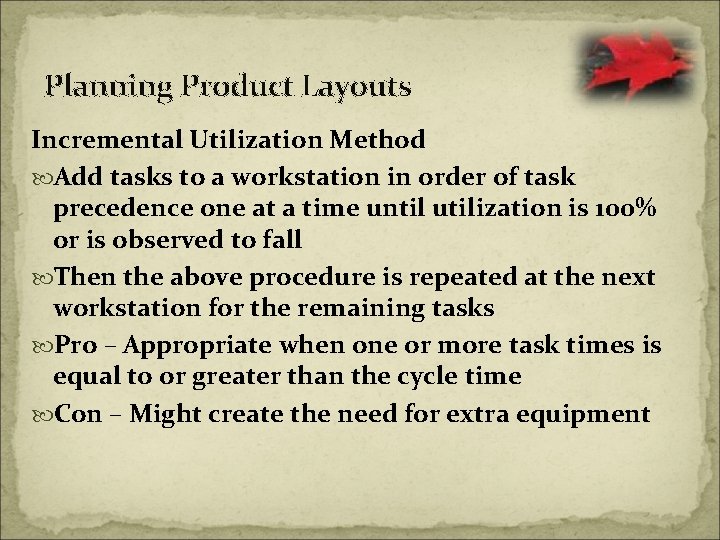
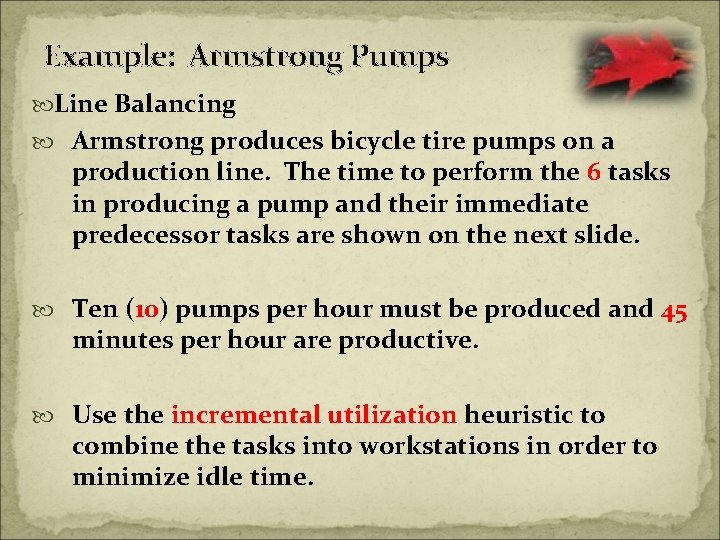
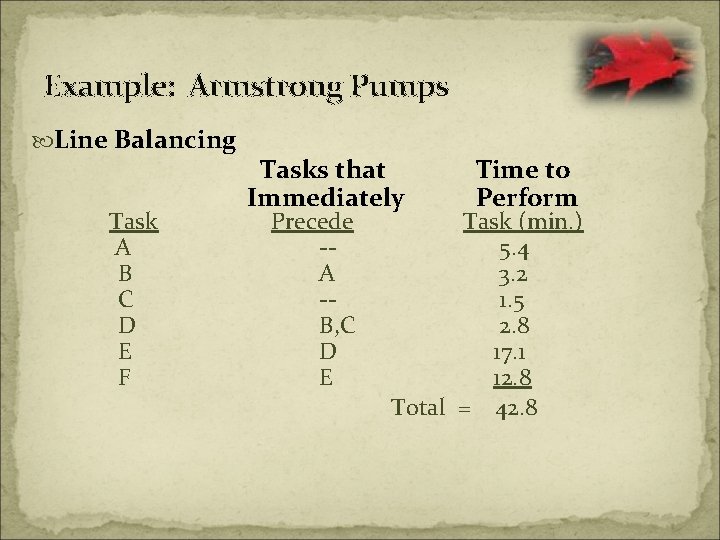
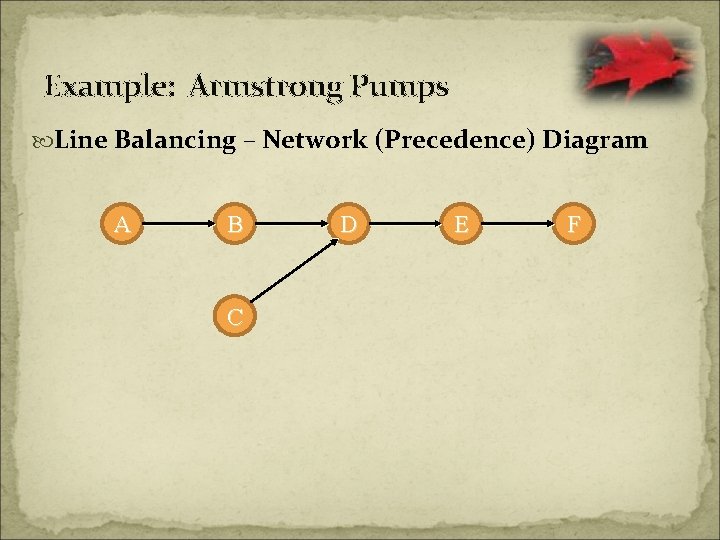
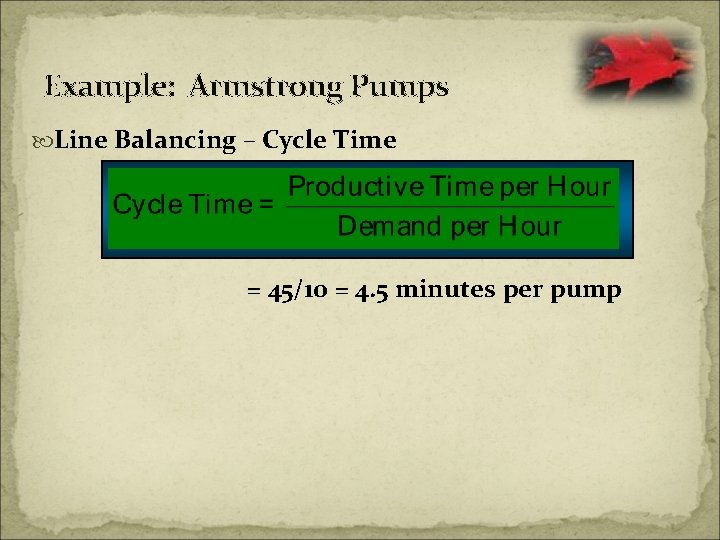
![Example: Armstrong Pumps Line Balancing – Minimum Number of Workstations = [(42. 8)(10)]/45 = Example: Armstrong Pumps Line Balancing – Minimum Number of Workstations = [(42. 8)(10)]/45 =](https://slidetodoc.com/presentation_image_h2/c15633ff1de86f8f4254fb2602aba75b/image-62.jpg)
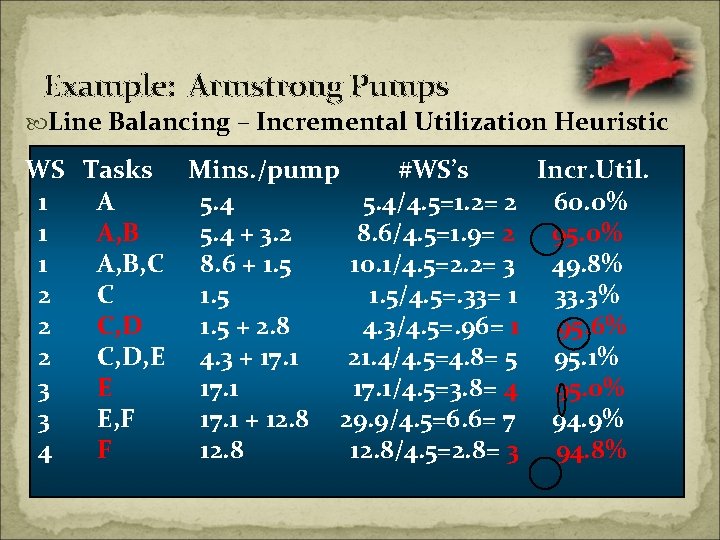
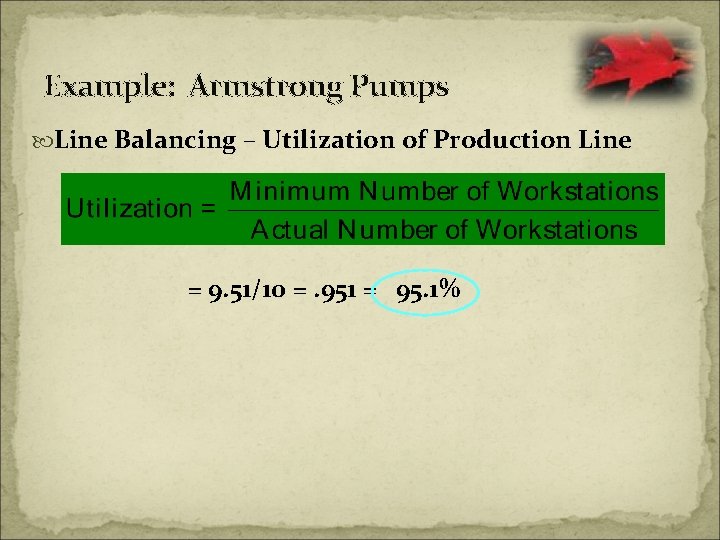
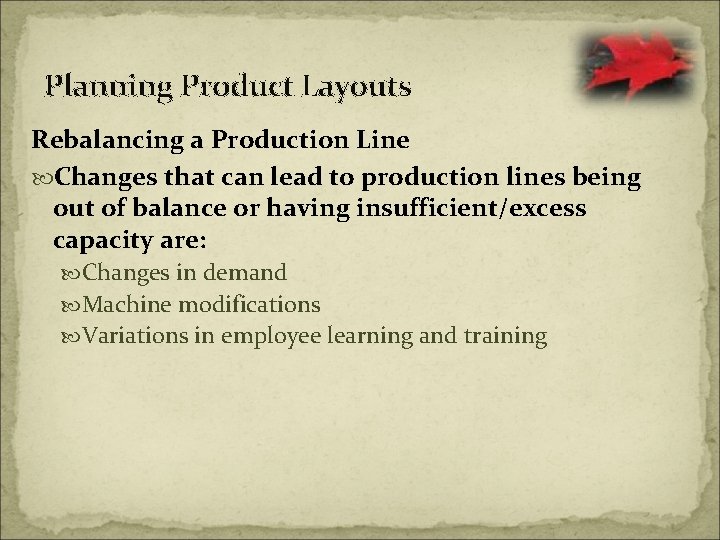
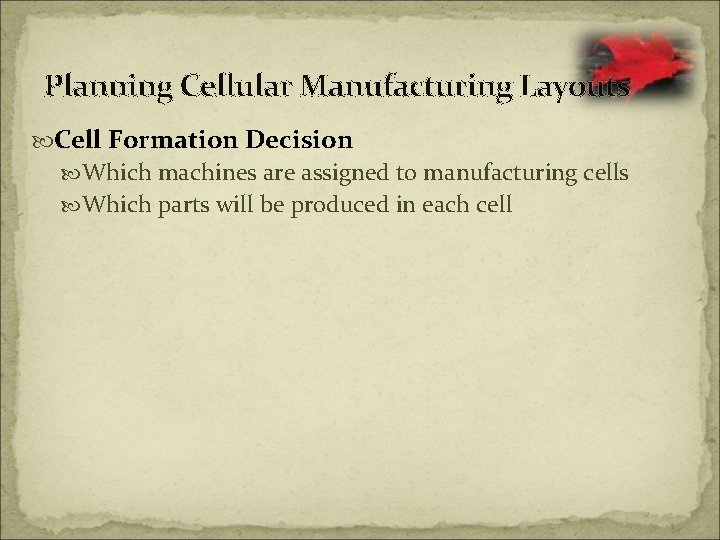
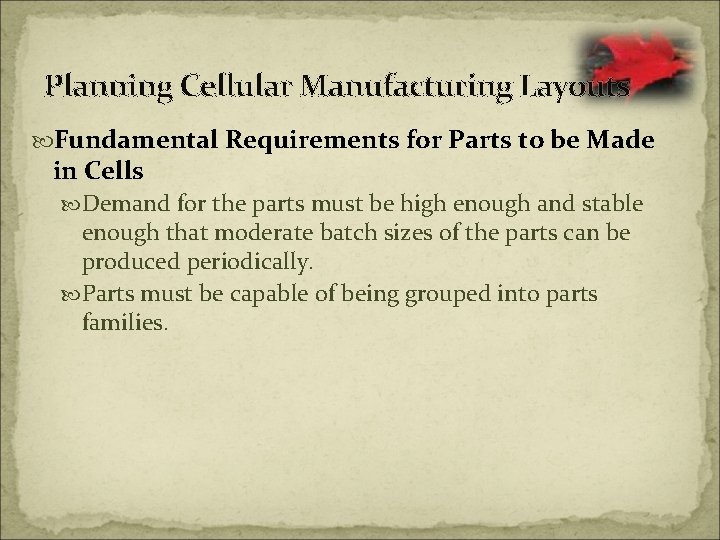
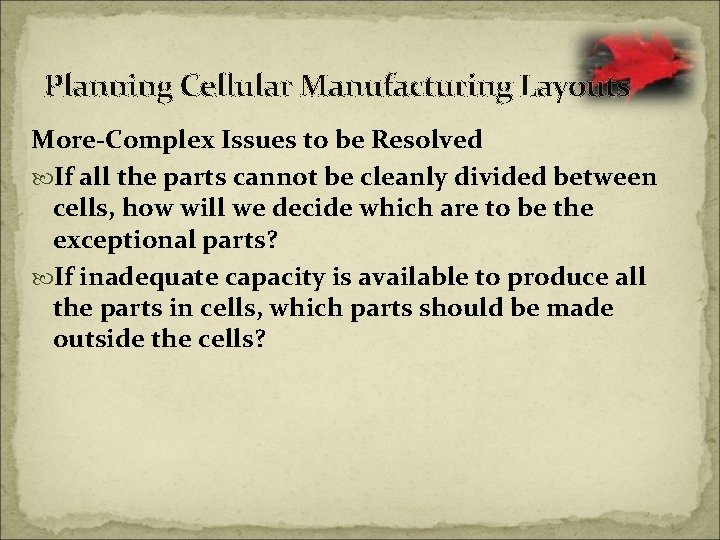
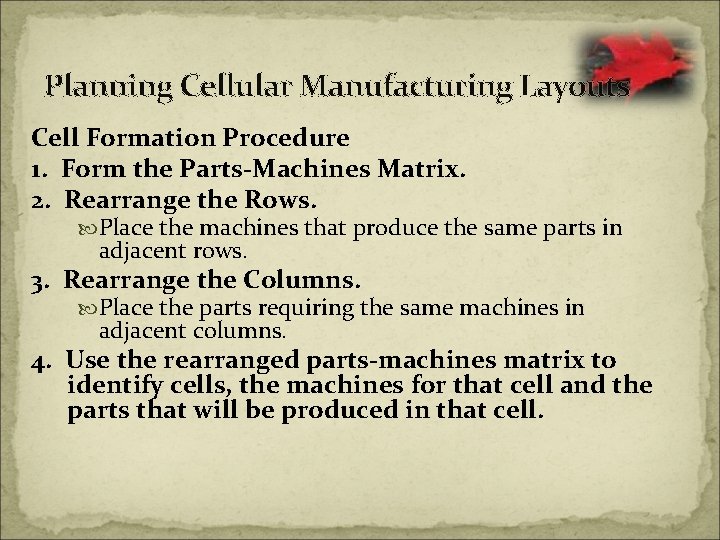
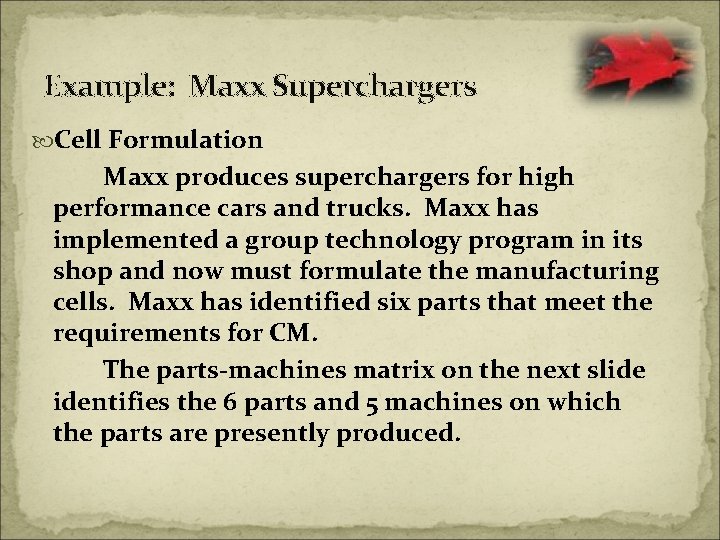
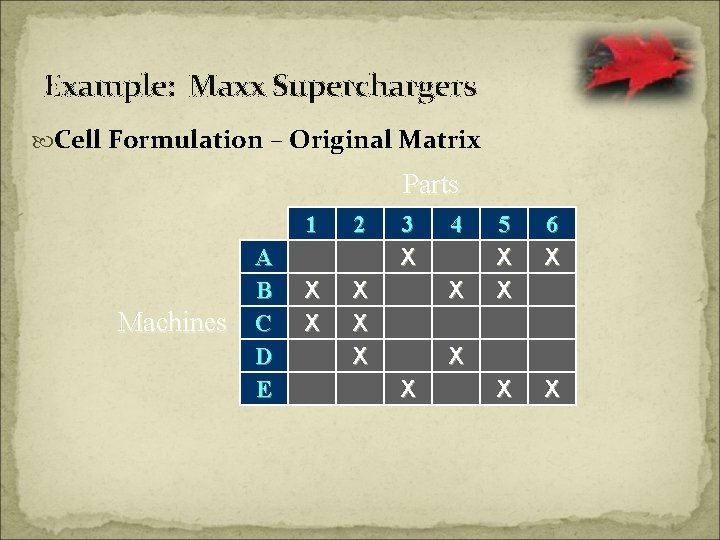
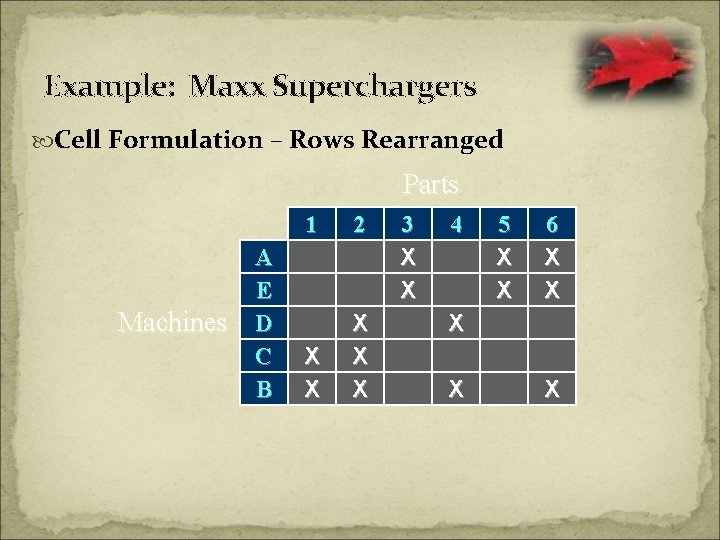
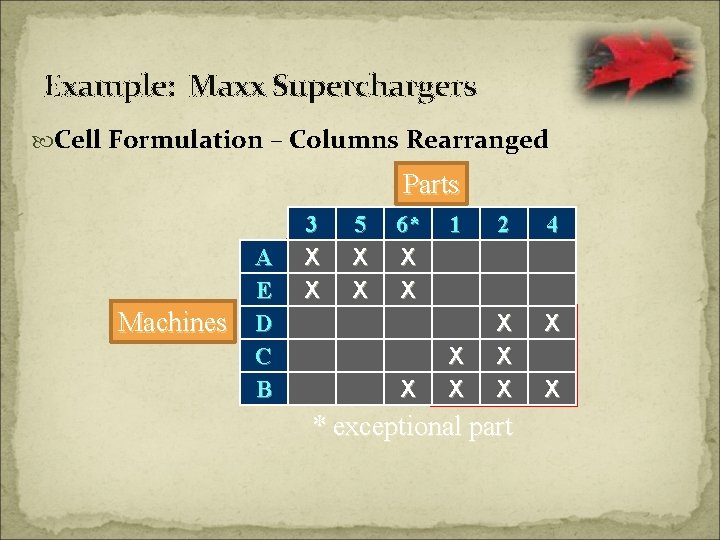
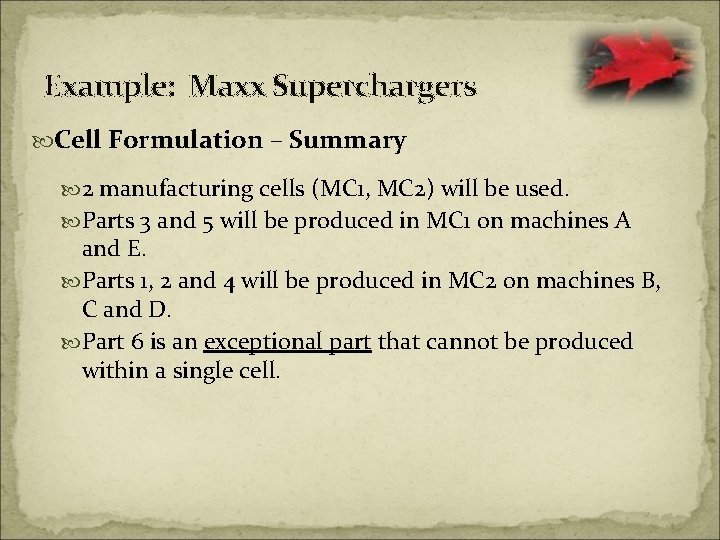
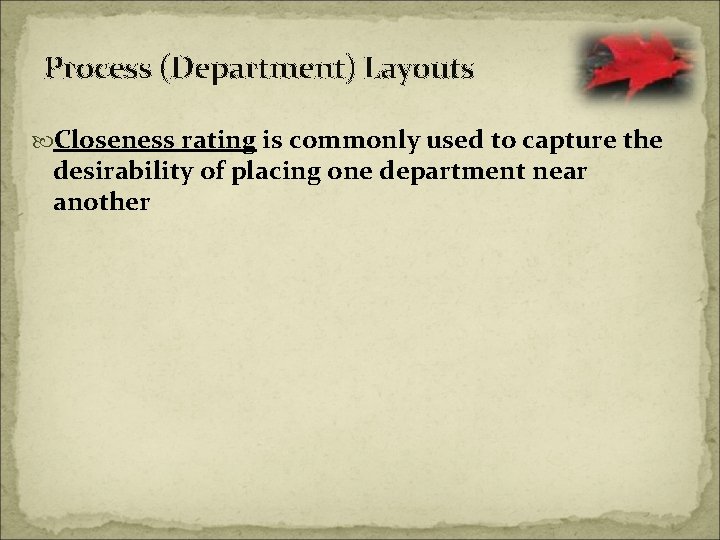
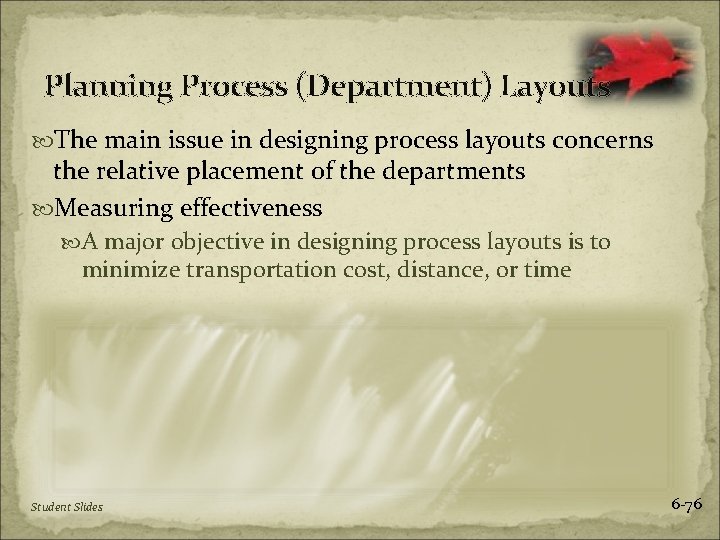
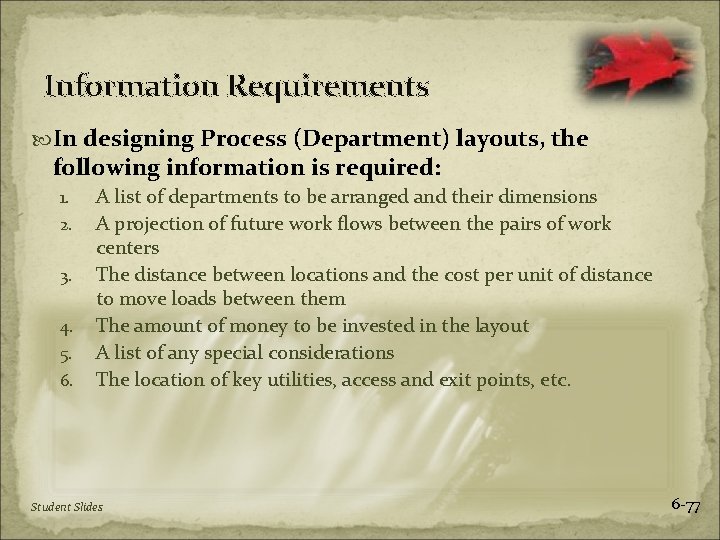
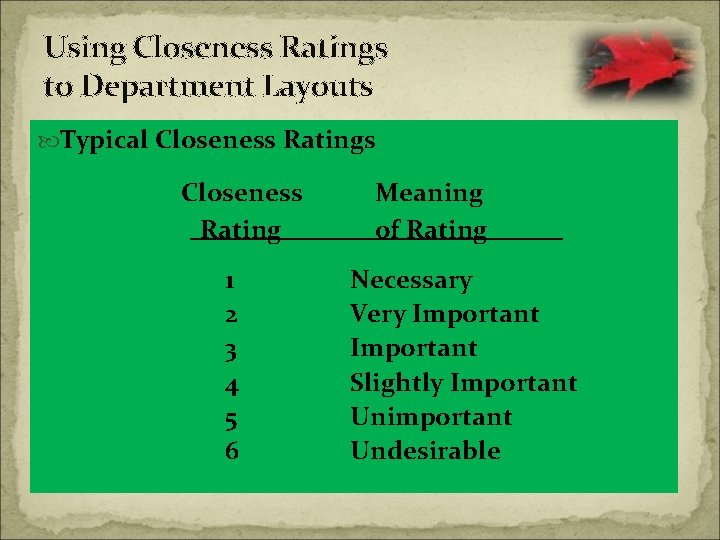
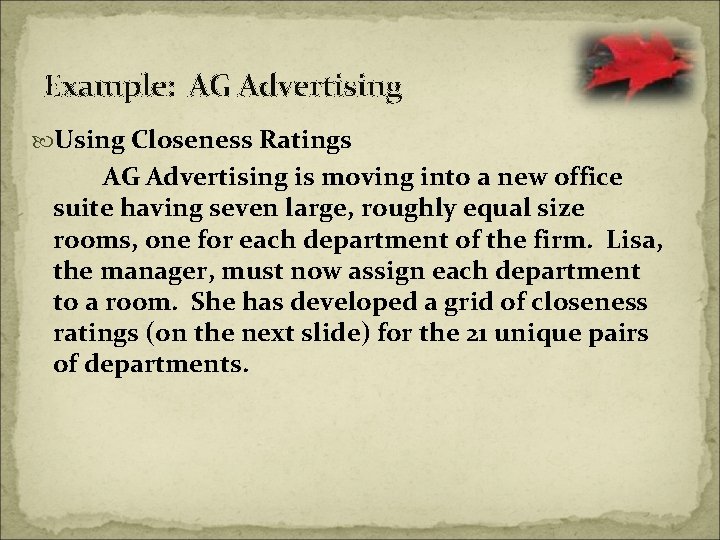
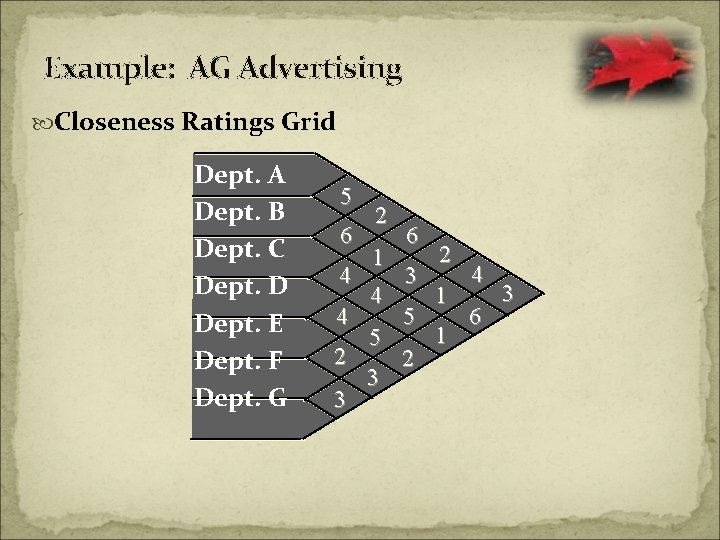
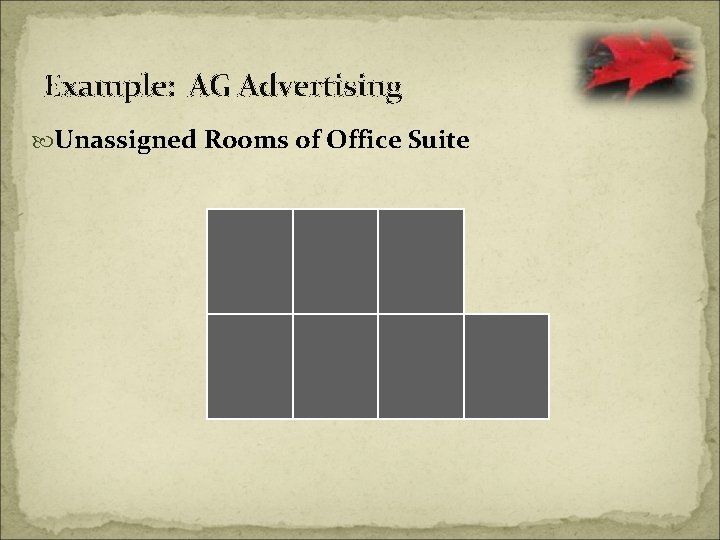
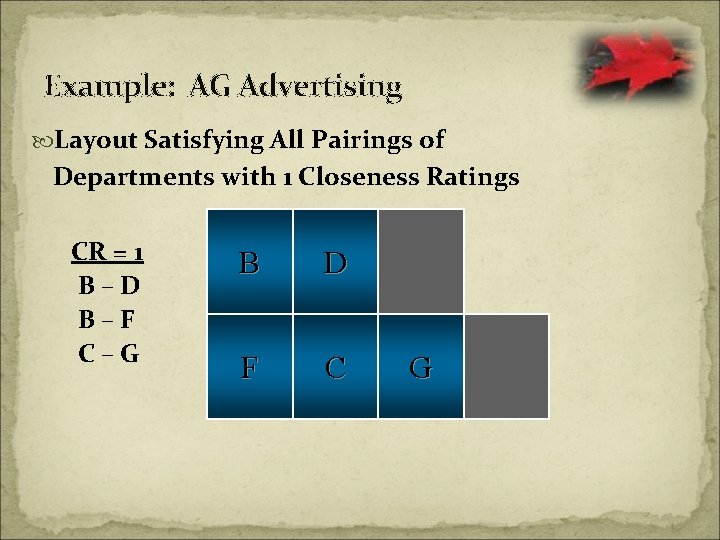
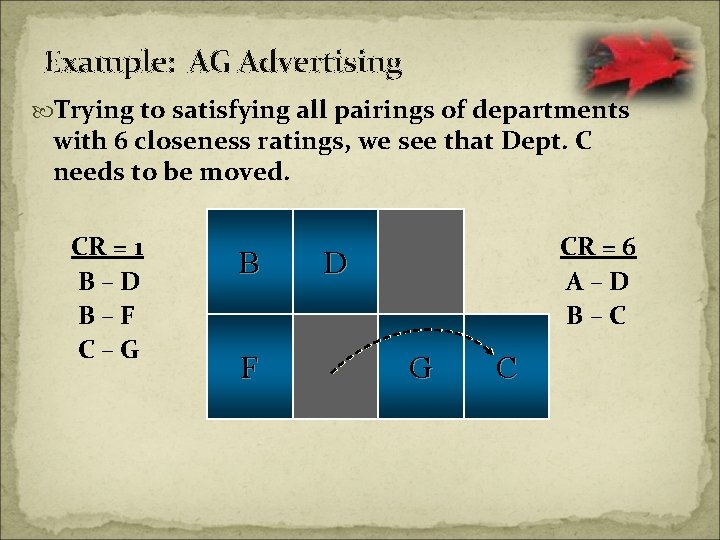
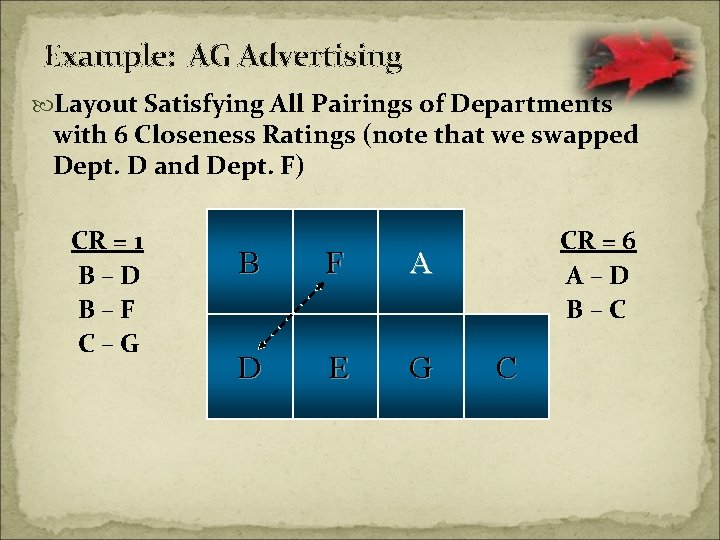
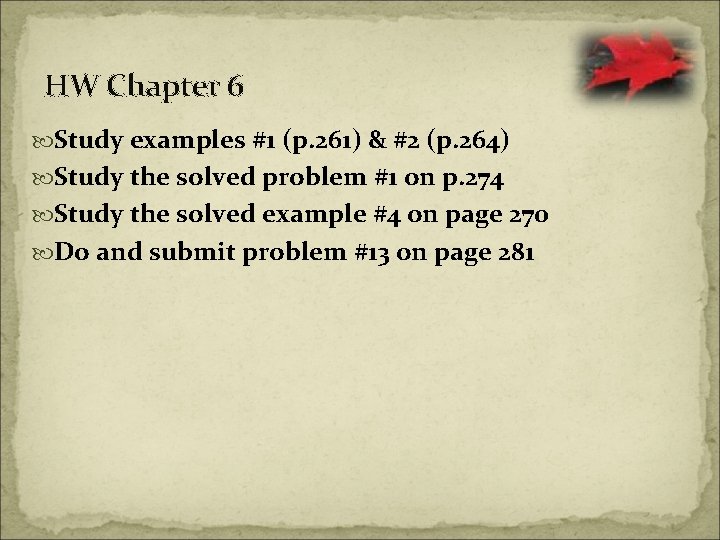
- Slides: 85
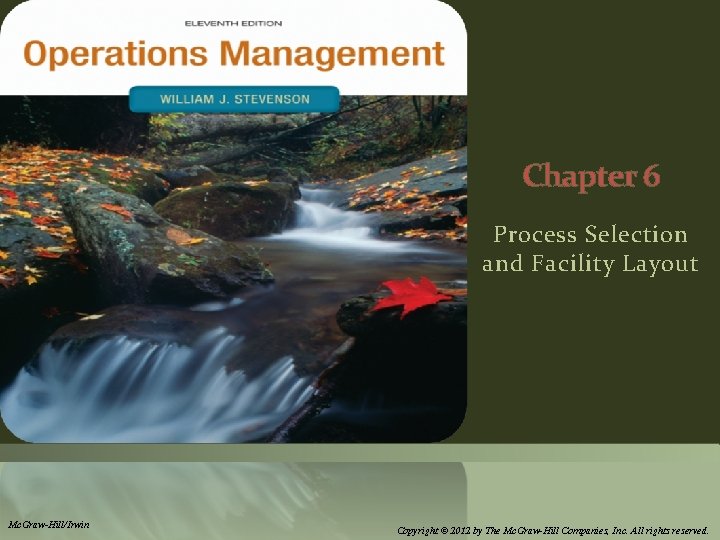
Chapter 6 Process Selection and Facility Layout Mc. Graw-Hill/Irwin Copyright © 2012 by The Mc. Graw-Hill Companies, Inc. All rights reserved.
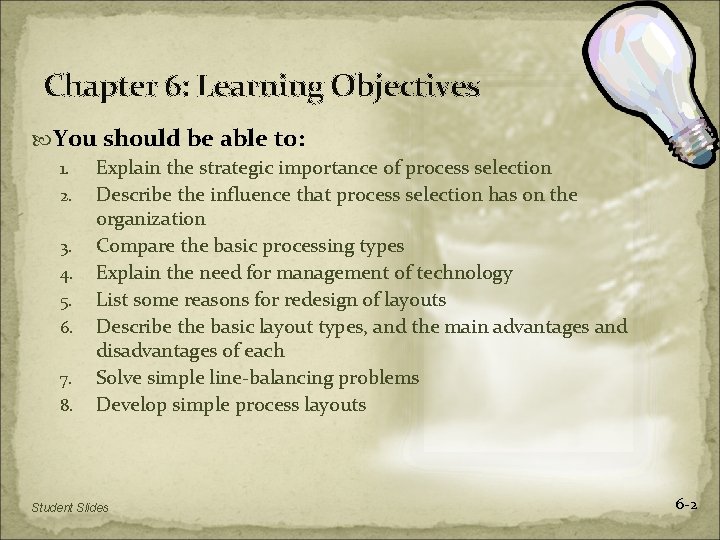
Chapter 6: Learning Objectives You should be able to: 1. Explain the strategic importance of process selection 2. Describe the influence that process selection has on the organization 3. Compare the basic processing types 4. Explain the need for management of technology 5. List some reasons for redesign of layouts 6. Describe the basic layout types, and the main advantages and disadvantages of each 7. Solve simple line-balancing problems 8. Develop simple process layouts Student Slides 6 -2
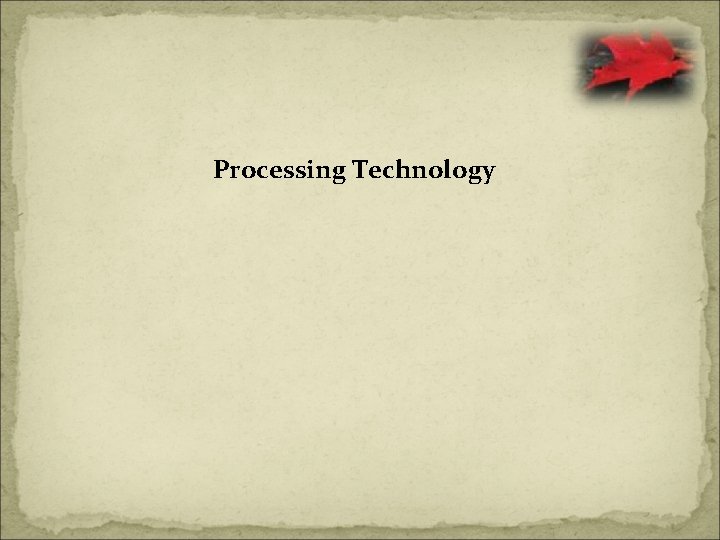
Processing Technology
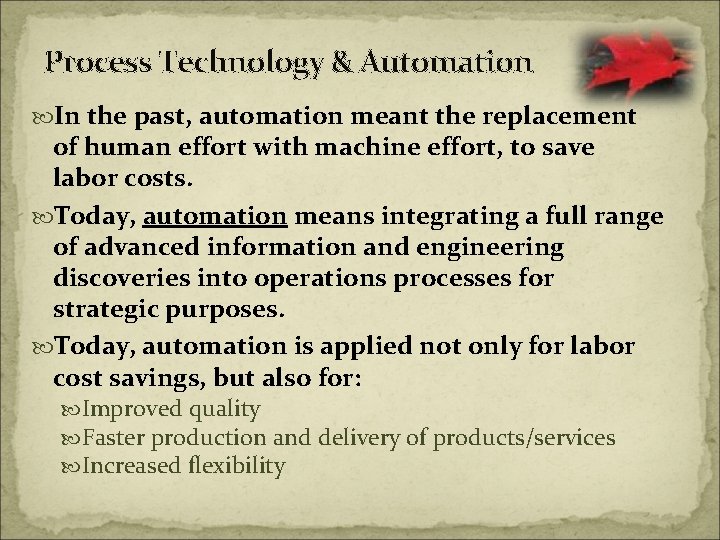
Process Technology & Automation In the past, automation meant the replacement of human effort with machine effort, to save labor costs. Today, automation means integrating a full range of advanced information and engineering discoveries into operations processes for strategic purposes. Today, automation is applied not only for labor cost savings, but also for: Improved quality Faster production and delivery of products/services Increased flexibility
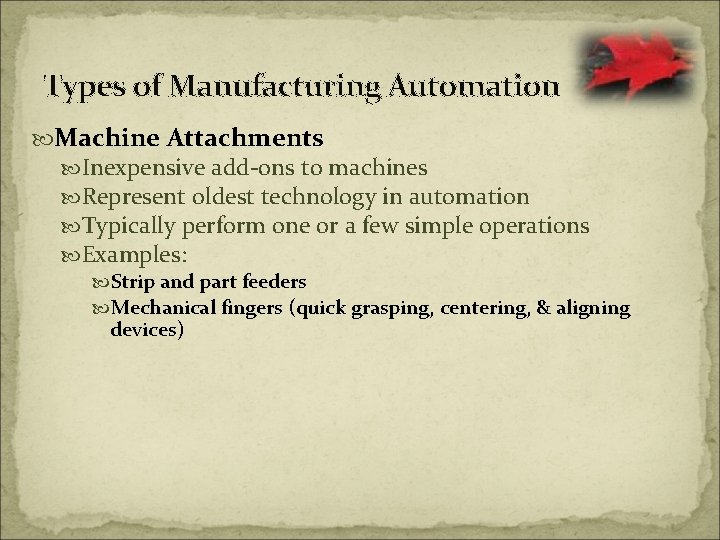
Types of Manufacturing Automation Machine Attachments Inexpensive add-ons to machines Represent oldest technology in automation Typically perform one or a few simple operations Examples: Strip and part feeders Mechanical fingers (quick grasping, centering, & aligning devices)
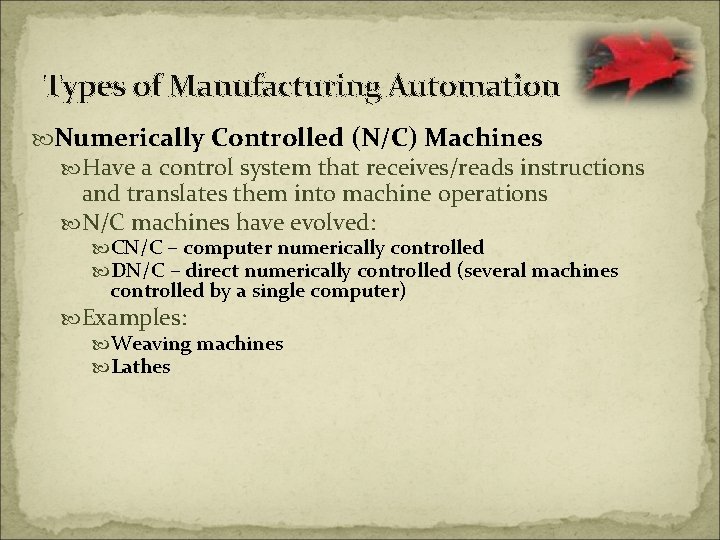
Types of Manufacturing Automation Numerically Controlled (N/C) Machines Have a control system that receives/reads instructions and translates them into machine operations N/C machines have evolved: CN/C – computer numerically controlled DN/C – direct numerically controlled (several machines controlled by a single computer) Examples: Weaving machines Lathes
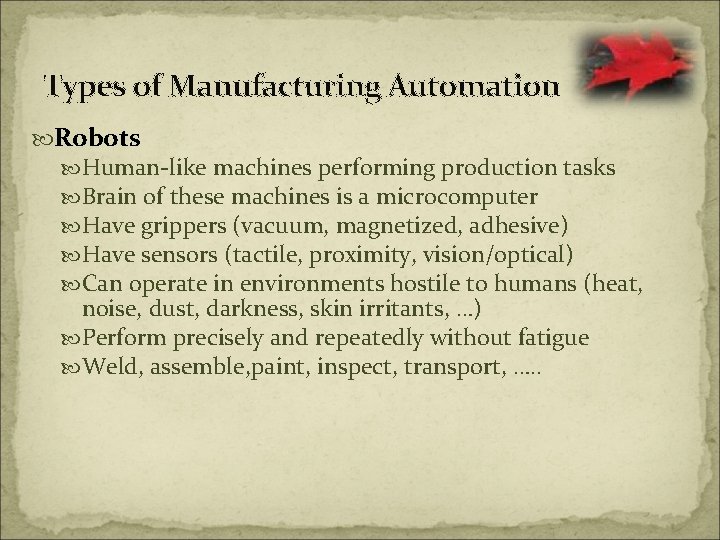
Types of Manufacturing Automation Robots Human-like machines performing production tasks Brain of these machines is a microcomputer Have grippers (vacuum, magnetized, adhesive) Have sensors (tactile, proximity, vision/optical) Can operate in environments hostile to humans (heat, noise, dust, darkness, skin irritants, …) Perform precisely and repeatedly without fatigue Weld, assemble, paint, inspect, transport, …. .
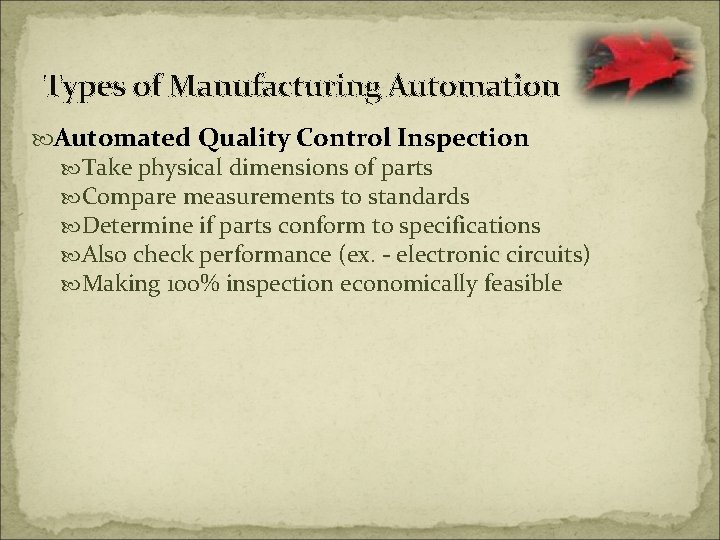
Types of Manufacturing Automation Automated Quality Control Inspection Take physical dimensions of parts Compare measurements to standards Determine if parts conform to specifications Also check performance (ex. - electronic circuits) Making 100% inspection economically feasible
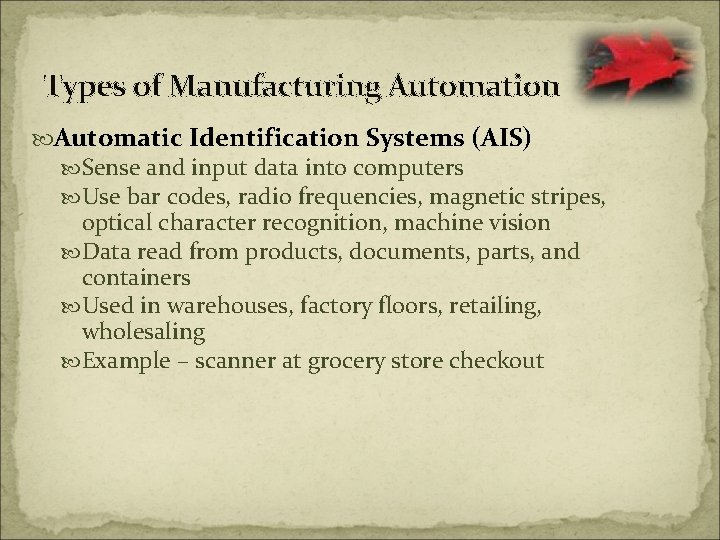
Types of Manufacturing Automation Automatic Identification Systems (AIS) Sense and input data into computers Use bar codes, radio frequencies, magnetic stripes, optical character recognition, machine vision Data read from products, documents, parts, and containers Used in warehouses, factory floors, retailing, wholesaling Example – scanner at grocery store checkout

Types of Manufacturing Automation Automated Process Controls Use sensors to obtain measures of performance Compare measures to standards Might use “expert system” to determine if/what process adjustment is necessary If necessary, change settings of process Long used in chemical processing, petroleum refining, paper production
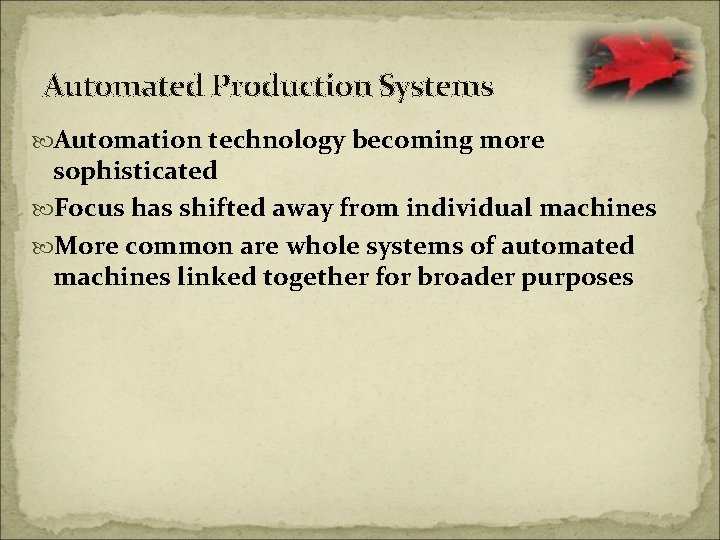
Automated Production Systems Automation technology becoming more sophisticated Focus has shifted away from individual machines More common are whole systems of automated machines linked together for broader purposes
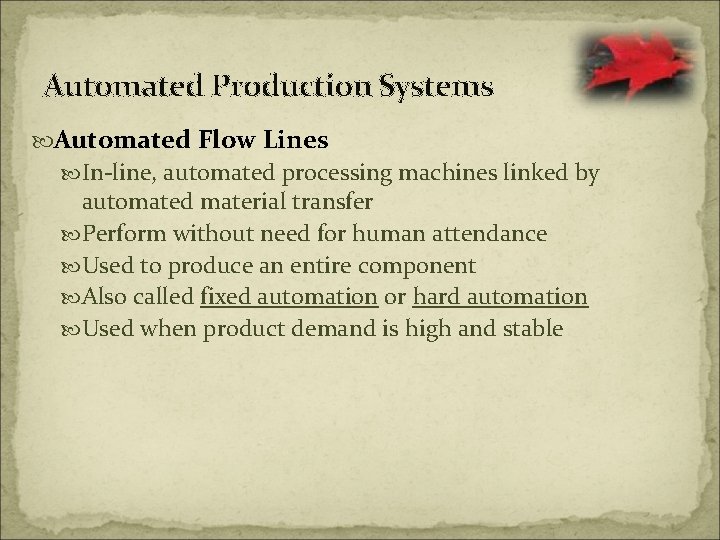
Automated Production Systems Automated Flow Lines In-line, automated processing machines linked by automated material transfer Perform without need for human attendance Used to produce an entire component Also called fixed automation or hard automation Used when product demand is high and stable
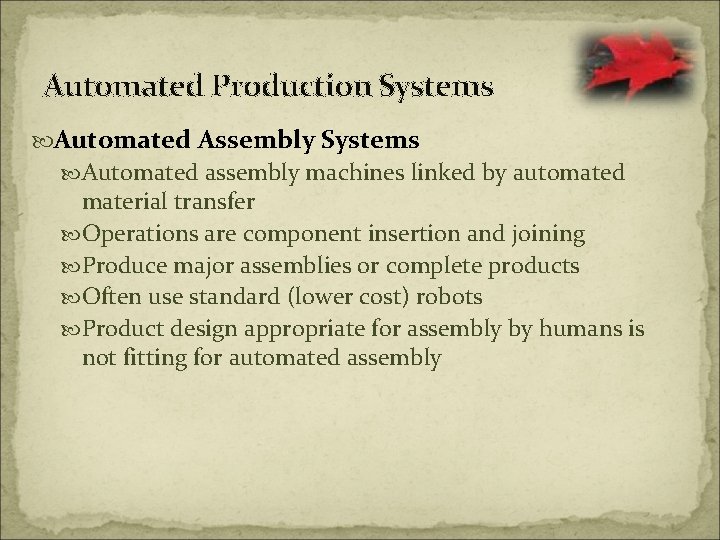
Automated Production Systems Automated Assembly Systems Automated assembly machines linked by automated material transfer Operations are component insertion and joining Produce major assemblies or complete products Often use standard (lower cost) robots Product design appropriate for assembly by humans is not fitting for automated assembly
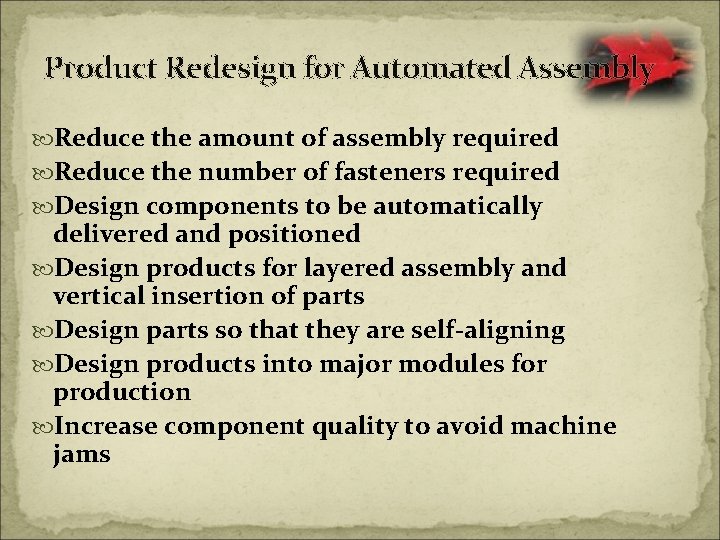
Product Redesign for Automated Assembly Reduce the amount of assembly required Reduce the number of fasteners required Design components to be automatically delivered and positioned Design products for layered assembly and vertical insertion of parts Design parts so that they are self-aligning Design products into major modules for production Increase component quality to avoid machine jams
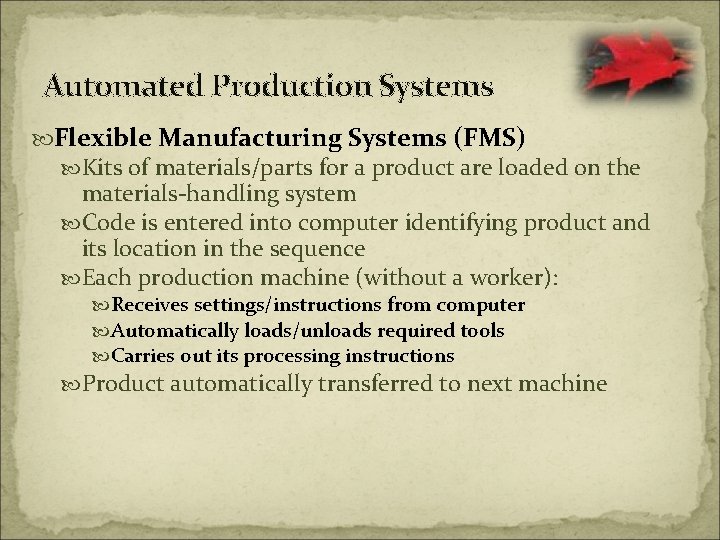
Automated Production Systems Flexible Manufacturing Systems (FMS) Kits of materials/parts for a product are loaded on the materials-handling system Code is entered into computer identifying product and its location in the sequence Each production machine (without a worker): Receives settings/instructions from computer Automatically loads/unloads required tools Carries out its processing instructions Product automatically transferred to next machine
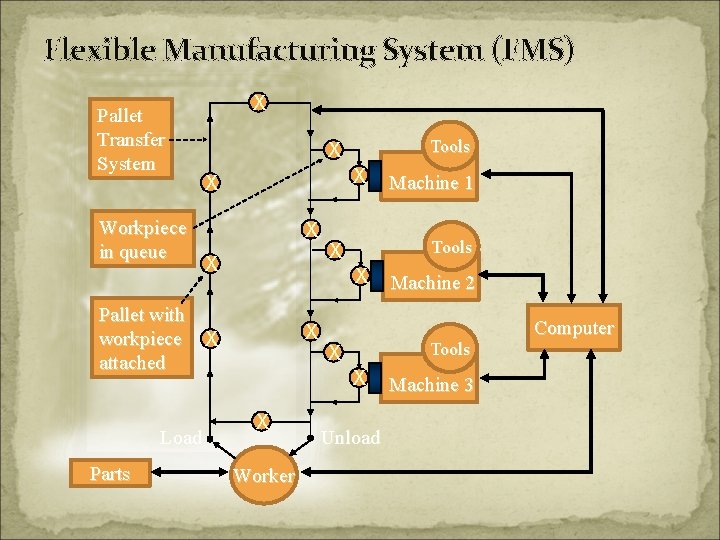
Flexible Manufacturing System (FMS) Pallet Transfer System Workpiece in queue X X X Parts X Worker Machine 2 Tools X X X Machine 1 Tools X X Pallet with workpiece X attached Load Tools X Unload Machine 3 Computer
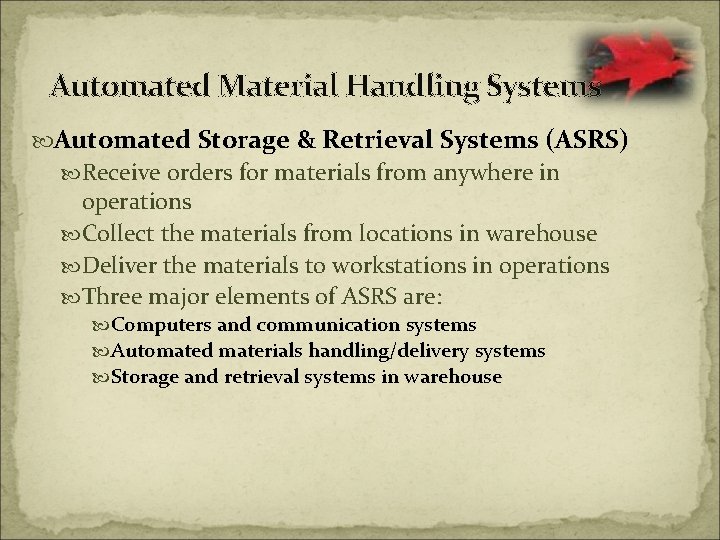
Automated Material Handling Systems Automated Storage & Retrieval Systems (ASRS) Receive orders for materials from anywhere in operations Collect the materials from locations in warehouse Deliver the materials to workstations in operations Three major elements of ASRS are: Computers and communication systems Automated materials handling/delivery systems Storage and retrieval systems in warehouse
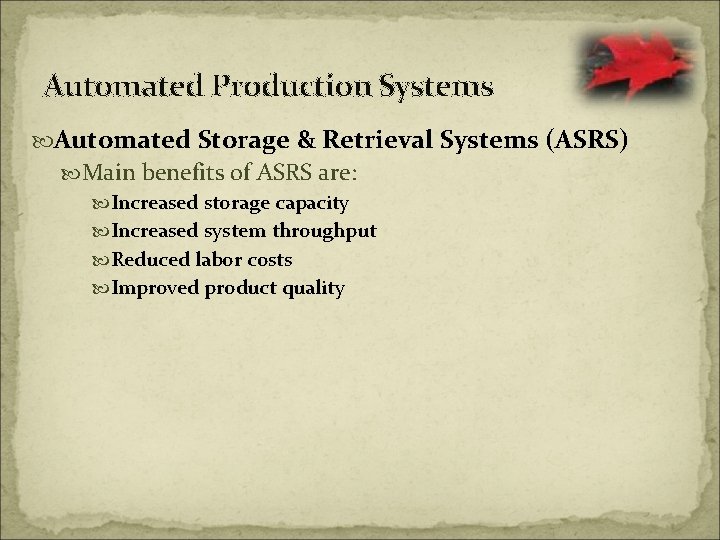
Automated Production Systems Automated Storage & Retrieval Systems (ASRS) Main benefits of ASRS are: Increased storage capacity Increased system throughput Reduced labor costs Improved product quality

Software Systems for Automation Three “complex” computer-based systems Computer-Aided Design and Computer-Aided Manufacturing (CAD/CAM) Computer-Integrated Manufacturing (CIM) Enterprise Resource Planning (ERP)
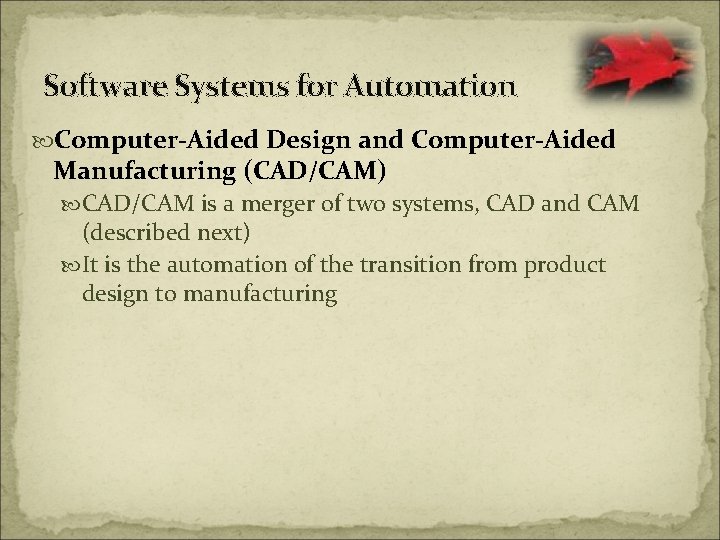
Software Systems for Automation Computer-Aided Design and Computer-Aided Manufacturing (CAD/CAM) CAD/CAM is a merger of two systems, CAD and CAM (described next) It is the automation of the transition from product design to manufacturing
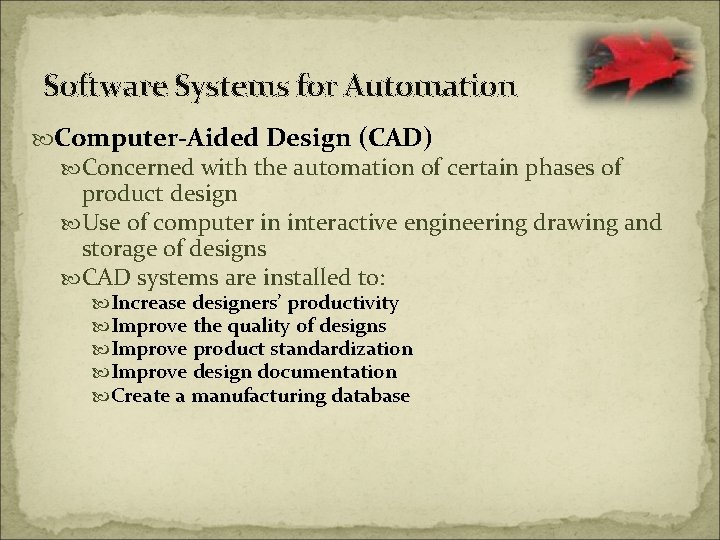
Software Systems for Automation Computer-Aided Design (CAD) Concerned with the automation of certain phases of product design Use of computer in interactive engineering drawing and storage of designs CAD systems are installed to: Increase designers’ productivity Improve the quality of designs Improve product standardization Improve design documentation Create a manufacturing database
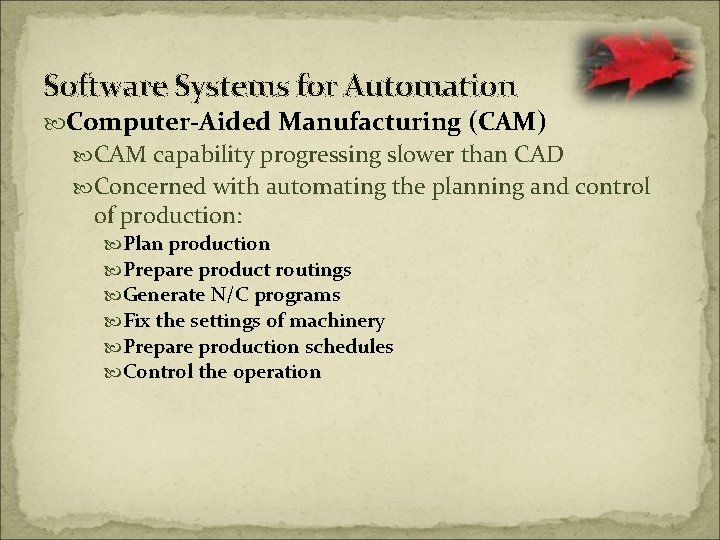
Software Systems for Automation Computer-Aided Manufacturing (CAM) CAM capability progressing slower than CAD Concerned with automating the planning and control of production: Plan production Prepare product routings Generate N/C programs Fix the settings of machinery Prepare production schedules Control the operation
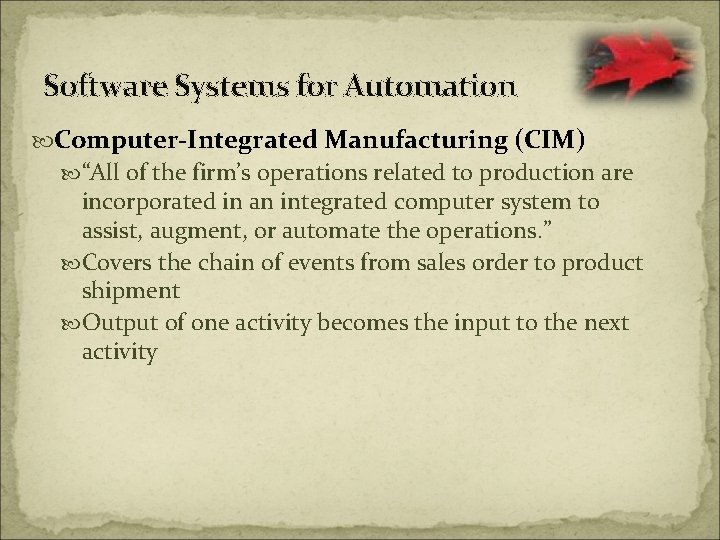
Software Systems for Automation Computer-Integrated Manufacturing (CIM) “All of the firm’s operations related to production are incorporated in an integrated computer system to assist, augment, or automate the operations. ” Covers the chain of events from sales order to product shipment Output of one activity becomes the input to the next activity
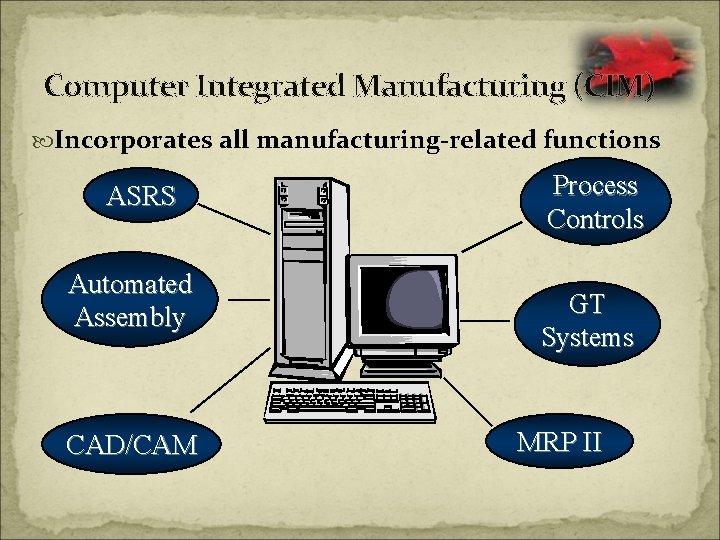
Computer Integrated Manufacturing (CIM) Incorporates all manufacturing-related functions ASRS Automated Assembly CAD/CAM Process Controls GT Systems MRP II
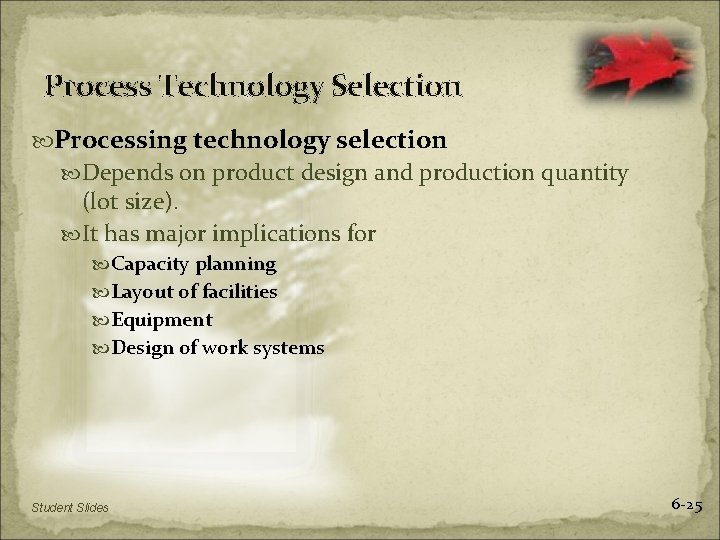
Process Technology Selection Processing technology selection Depends on product design and production quantity (lot size). It has major implications for Capacity planning Layout of facilities Equipment Design of work systems Student Slides 6 -25
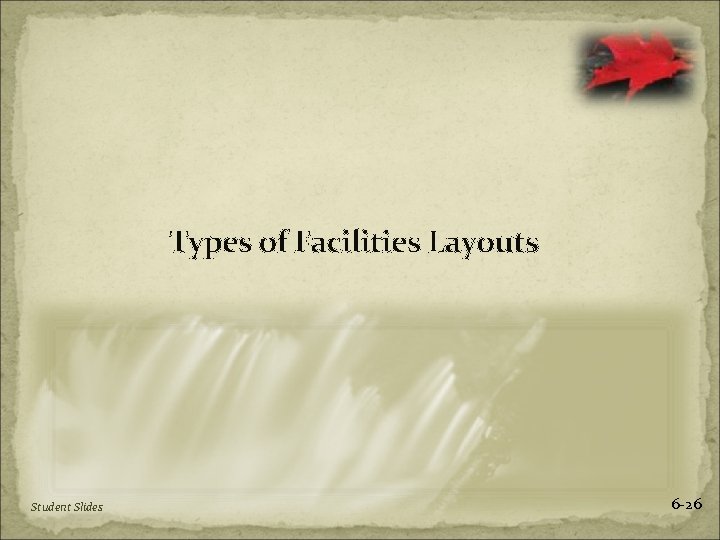
Types of Facilities Layouts Student Slides 6 -26
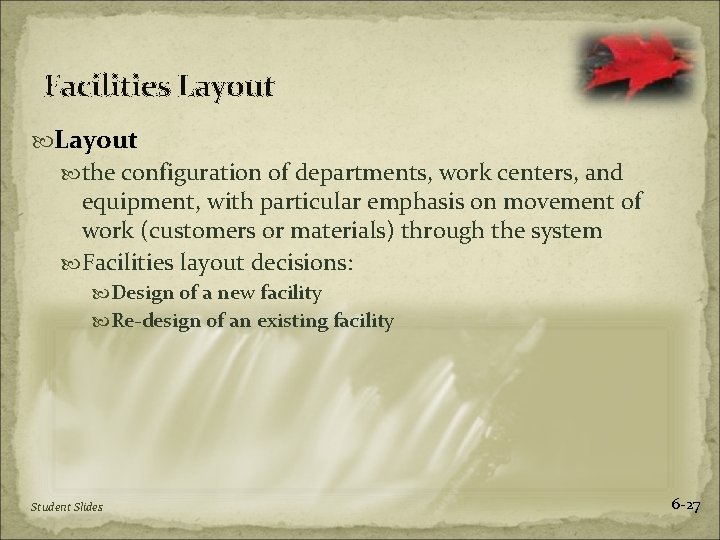
Facilities Layout the configuration of departments, work centers, and equipment, with particular emphasis on movement of work (customers or materials) through the system Facilities layout decisions: Design of a new facility Re-design of an existing facility Student Slides 6 -27
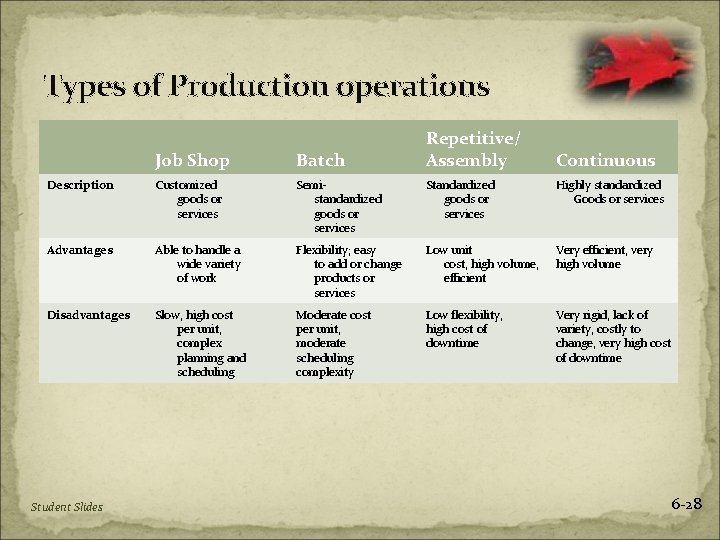
Types of Production operations Repetitive/ Assembly Job Shop Batch Description Customized goods or services Semistandardized goods or services Standardized goods or services Highly standardized Goods or services Advantages Able to handle a wide variety of work Flexibility; easy to add or change products or services Low unit cost, high volume, efficient Very efficient, very high volume Disadvantages Slow, high cost per unit, complex planning and scheduling Moderate cost per unit, moderate scheduling complexity Low flexibility, high cost of downtime Very rigid, lack of variety, costly to change, very high cost of downtime Student Slides Continuous 6 -28
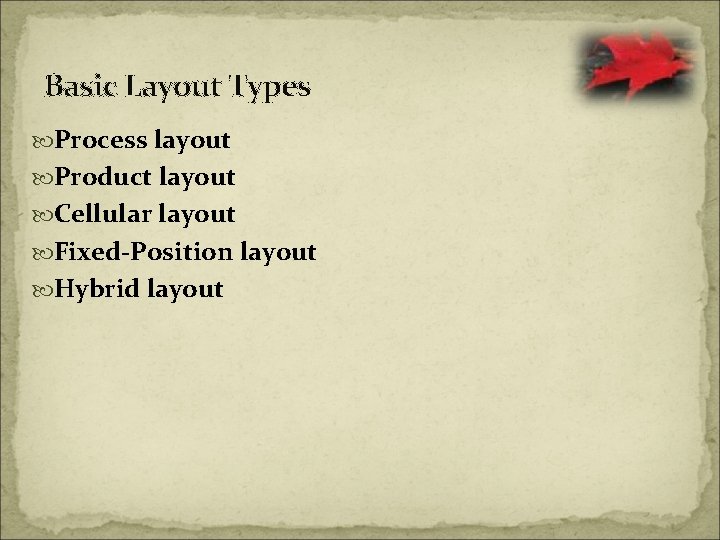
Basic Layout Types Process layout Product layout Cellular layout Fixed-Position layout Hybrid layout
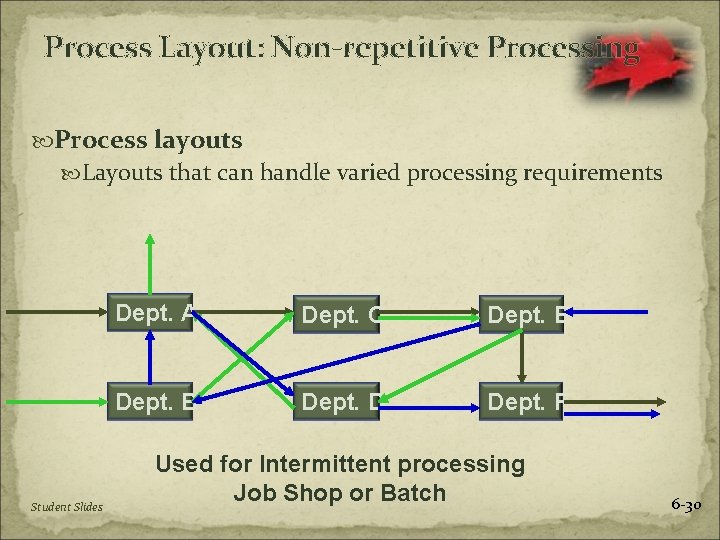
Process Layout: Non-repetitive Processing Process layouts Layouts that can handle varied processing requirements Student Slides Dept. A Dept. C Dept. E Dept. B Dept. D Dept. F Used for Intermittent processing Job Shop or Batch 6 -30
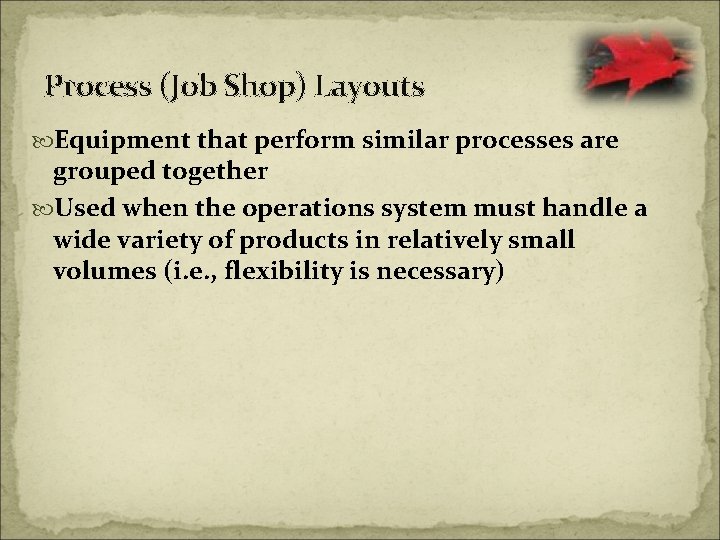
Process (Job Shop) Layouts Equipment that perform similar processes are grouped together Used when the operations system must handle a wide variety of products in relatively small volumes (i. e. , flexibility is necessary)
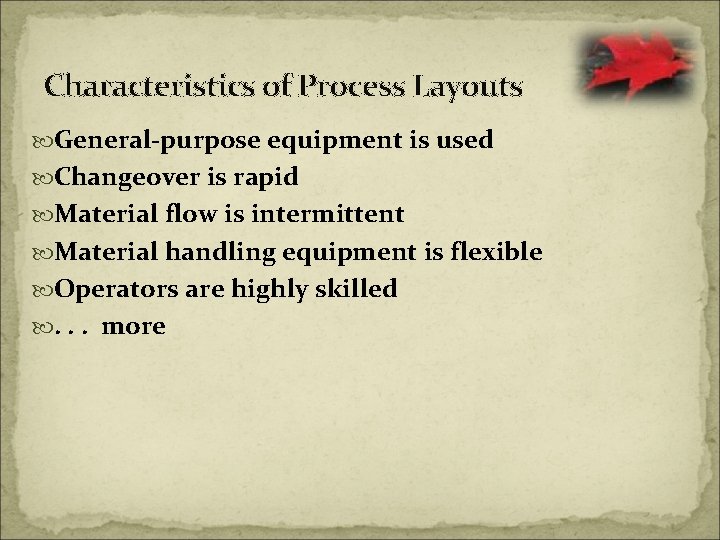
Characteristics of Process Layouts General-purpose equipment is used Changeover is rapid Material flow is intermittent Material handling equipment is flexible Operators are highly skilled . . . more
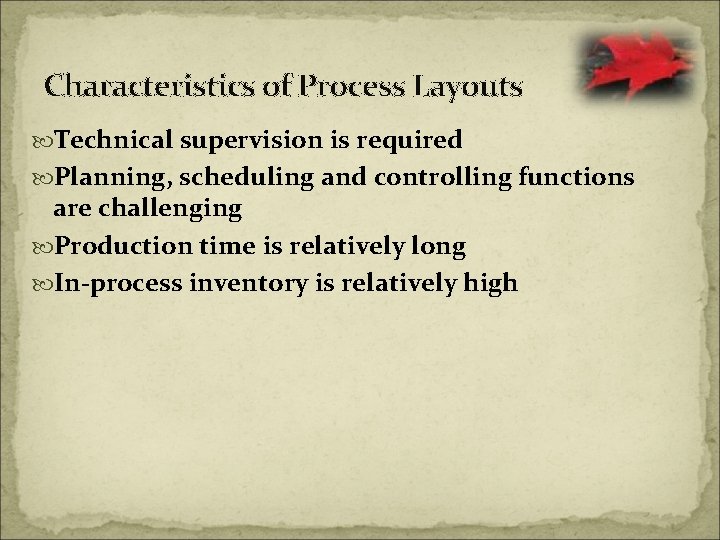
Characteristics of Process Layouts Technical supervision is required Planning, scheduling and controlling functions are challenging Production time is relatively long In-process inventory is relatively high
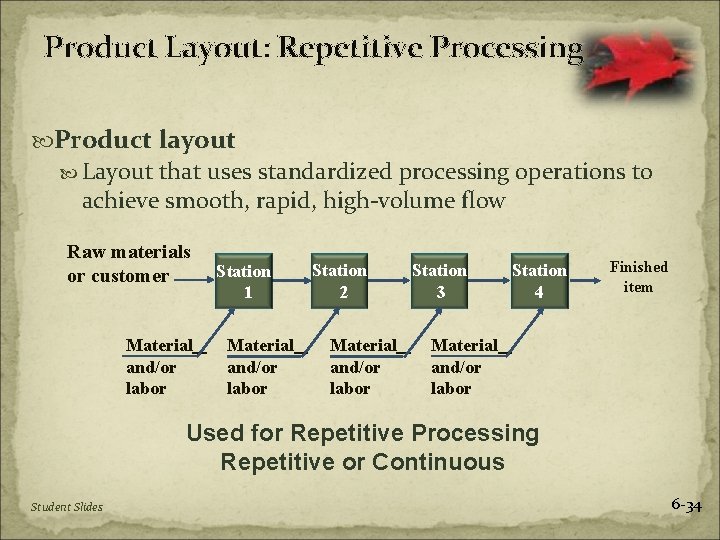
Product Layout: Repetitive Processing Product layout Layout that uses standardized processing operations to achieve smooth, rapid, high-volume flow Raw materials or customer Material and/or labor Station 1 Material and/or labor Station 2 Material and/or labor Station 3 Station 4 Finished item Material and/or labor Used for Repetitive Processing Repetitive or Continuous Student Slides 6 -34
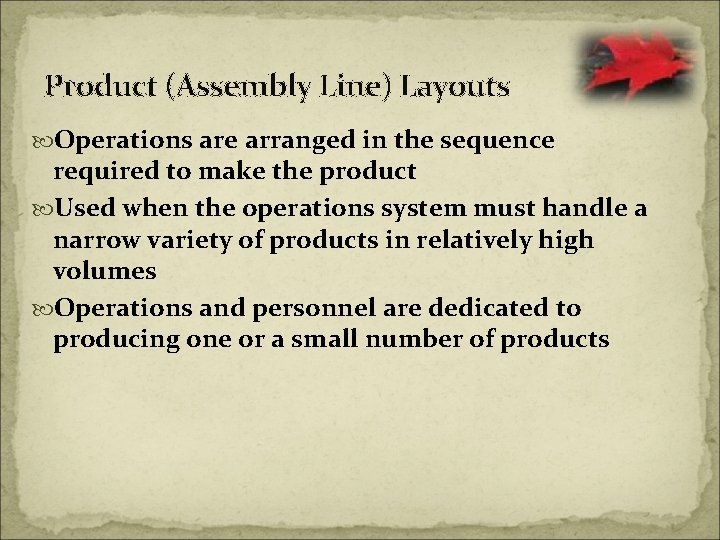
Product (Assembly Line) Layouts Operations are arranged in the sequence required to make the product Used when the operations system must handle a narrow variety of products in relatively high volumes Operations and personnel are dedicated to producing one or a small number of products
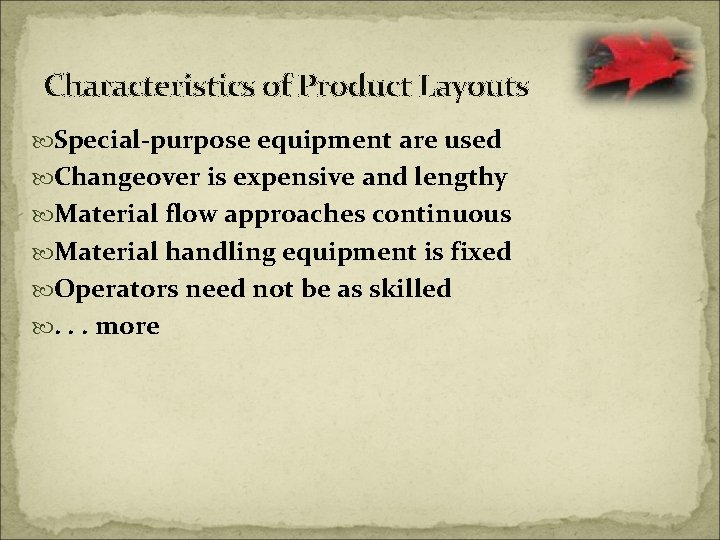
Characteristics of Product Layouts Special-purpose equipment are used Changeover is expensive and lengthy Material flow approaches continuous Material handling equipment is fixed Operators need not be as skilled . . . more
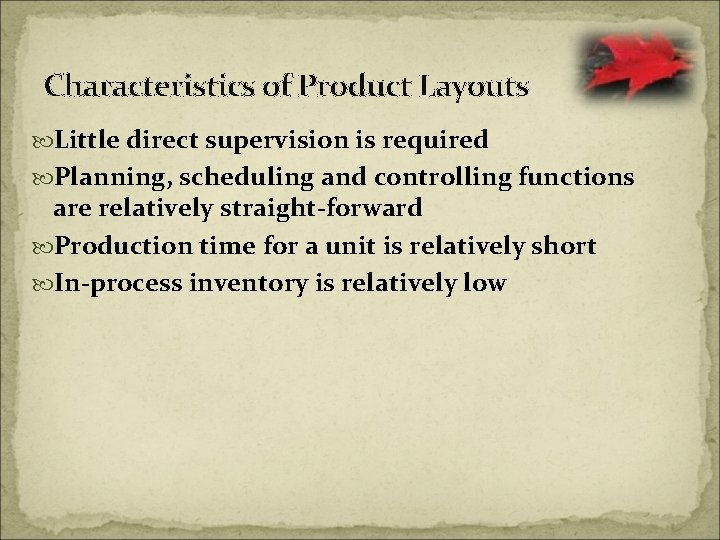
Characteristics of Product Layouts Little direct supervision is required Planning, scheduling and controlling functions are relatively straight-forward Production time for a unit is relatively short In-process inventory is relatively low
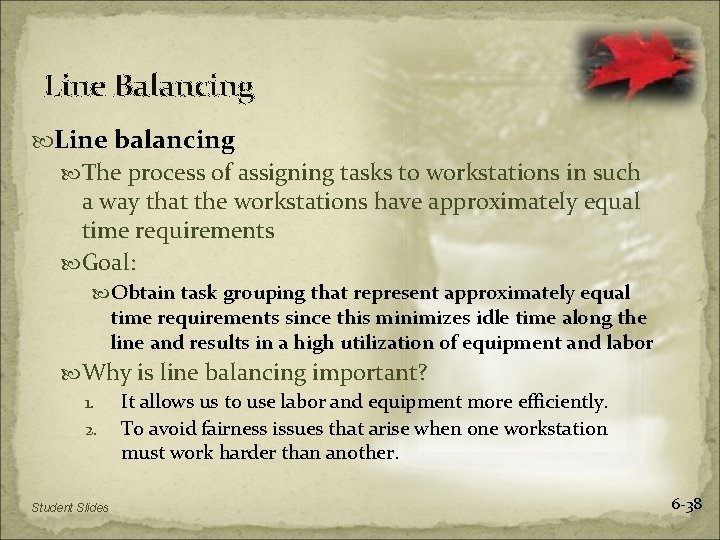
Line Balancing Line balancing The process of assigning tasks to workstations in such a way that the workstations have approximately equal time requirements Goal: Obtain task grouping that represent approximately equal time requirements since this minimizes idle time along the line and results in a high utilization of equipment and labor Why is line balancing important? 1. It allows us to use labor and equipment more efficiently. 2. To avoid fairness issues that arise when one workstation must work harder than another. Student Slides 6 -38
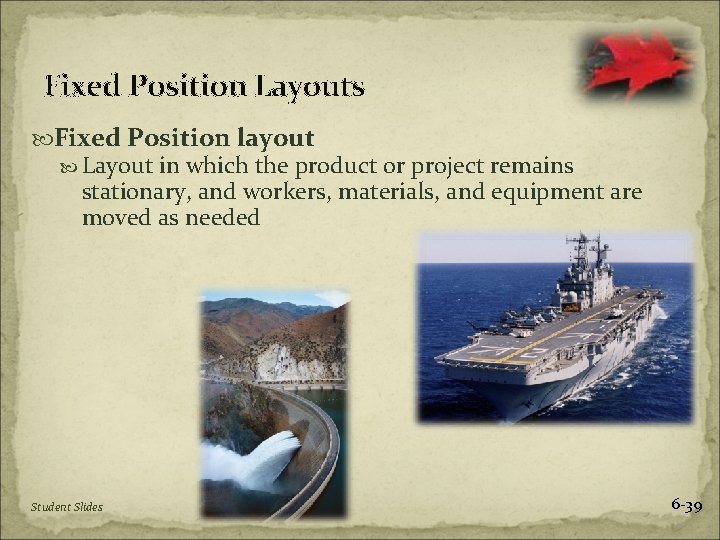
Fixed Position Layouts Fixed Position layout Layout in which the product or project remains stationary, and workers, materials, and equipment are moved as needed Student Slides 6 -39
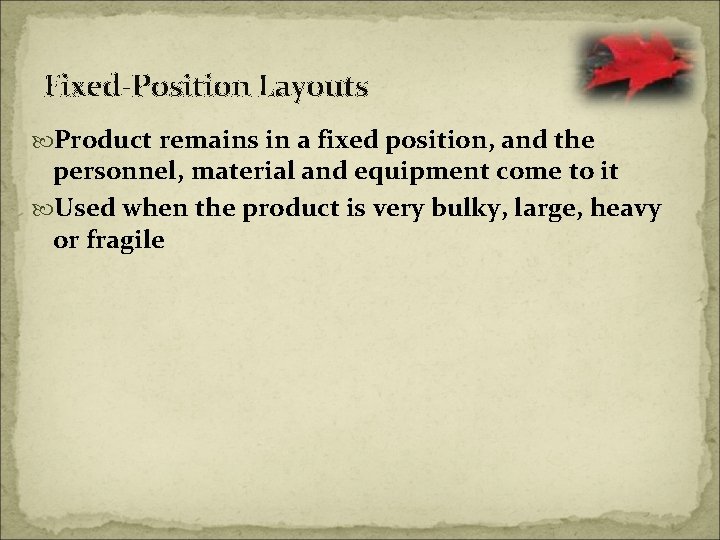
Fixed-Position Layouts Product remains in a fixed position, and the personnel, material and equipment come to it Used when the product is very bulky, large, heavy or fragile
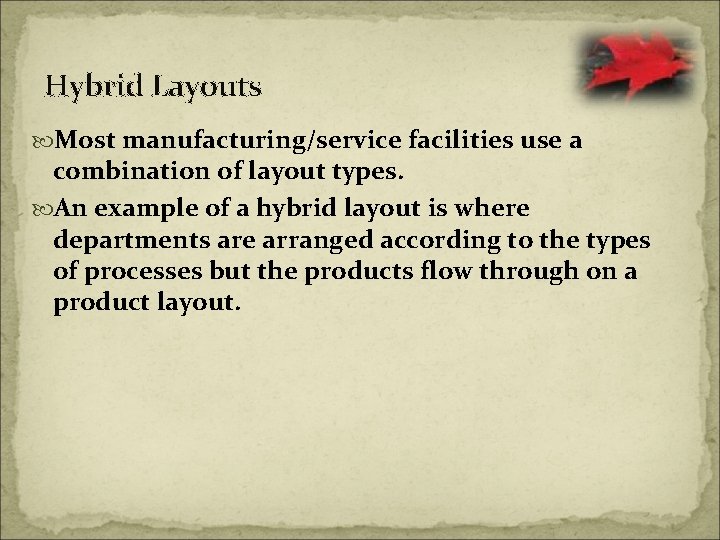
Hybrid Layouts Most manufacturing/service facilities use a combination of layout types. An example of a hybrid layout is where departments are arranged according to the types of processes but the products flow through on a product layout.
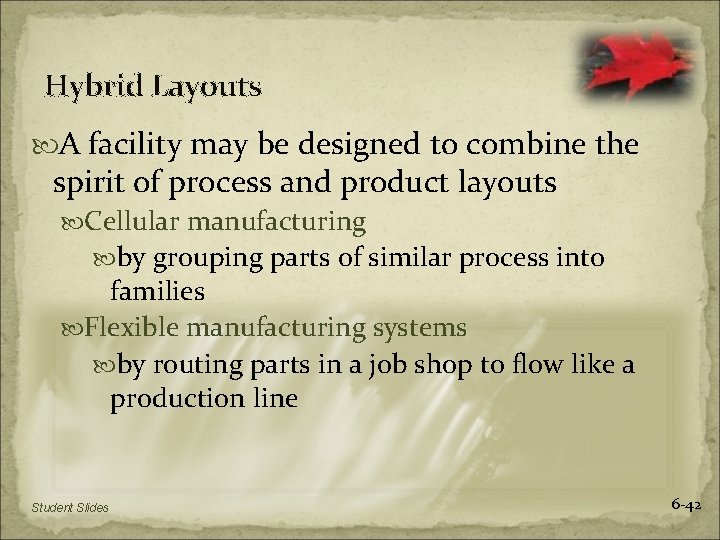
Hybrid Layouts A facility may be designed to combine the spirit of process and product layouts Cellular manufacturing by grouping parts of similar process into families Flexible manufacturing systems by routing parts in a job shop to flow like a production line Student Slides 6 -42
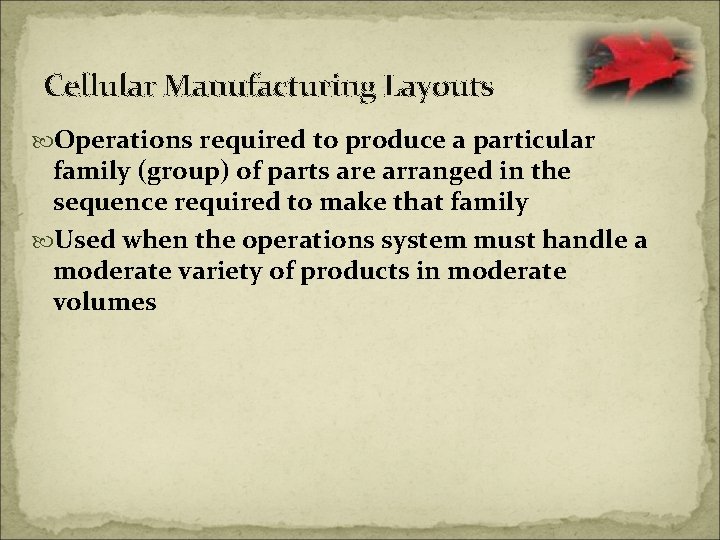
Cellular Manufacturing Layouts Operations required to produce a particular family (group) of parts are arranged in the sequence required to make that family Used when the operations system must handle a moderate variety of products in moderate volumes

Characteristics of Cellular Manufacturing Relative to Process Layouts Equipment can be less general-purpose Material handling costs are reduced Training periods for operators are shortened In-process inventory is lower Parts can be made faster and shipped more quickly
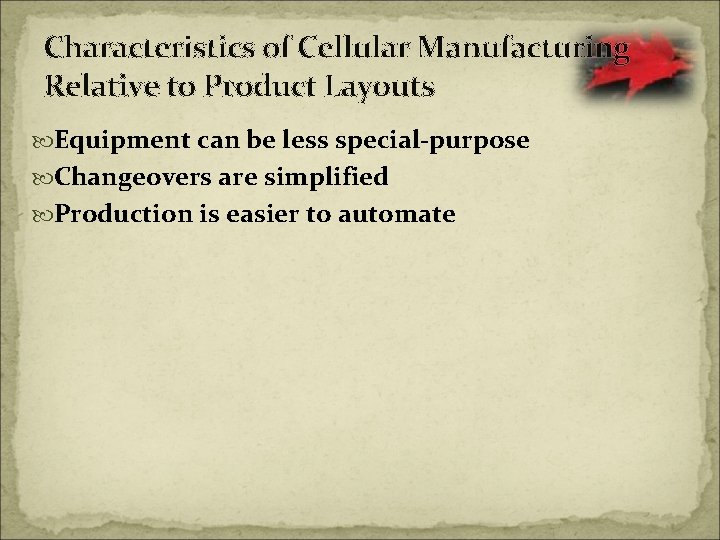
Characteristics of Cellular Manufacturing Relative to Product Layouts Equipment can be less special-purpose Changeovers are simplified Production is easier to automate
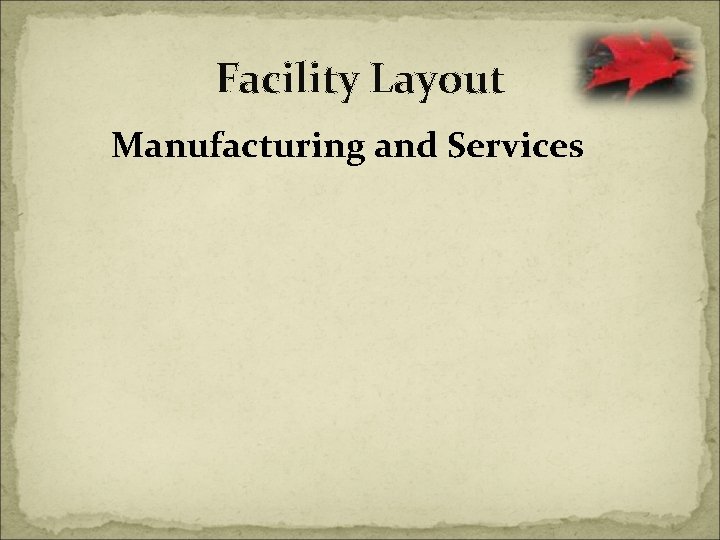
Facility Layout Manufacturing and Services
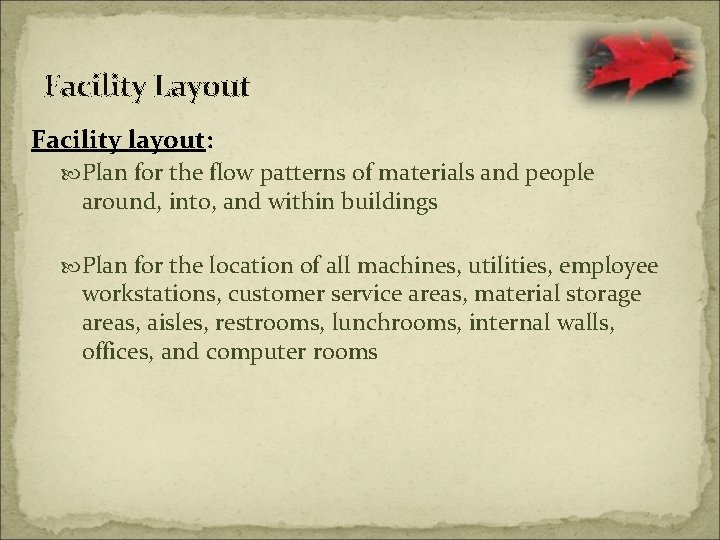
Facility Layout Facility layout: Plan for the flow patterns of materials and people around, into, and within buildings Plan for the location of all machines, utilities, employee workstations, customer service areas, material storage areas, aisles, restrooms, lunchrooms, internal walls, offices, and computer rooms
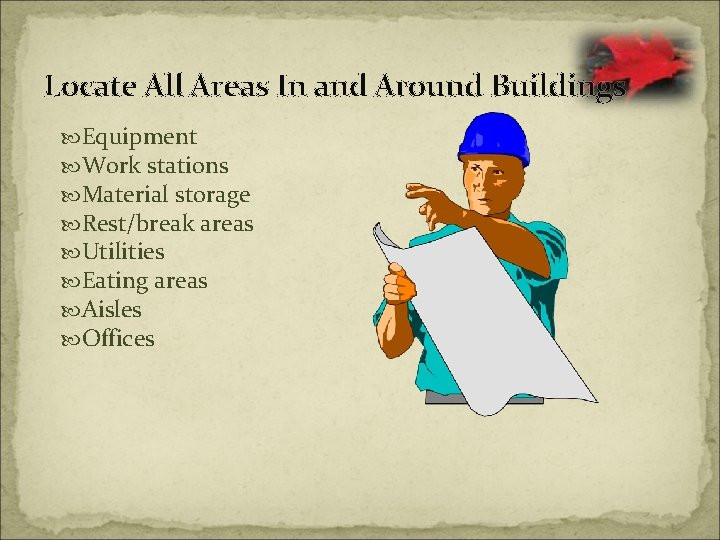
Locate All Areas In and Around Buildings Equipment Work stations Material storage Rest/break areas Utilities Eating areas Aisles Offices
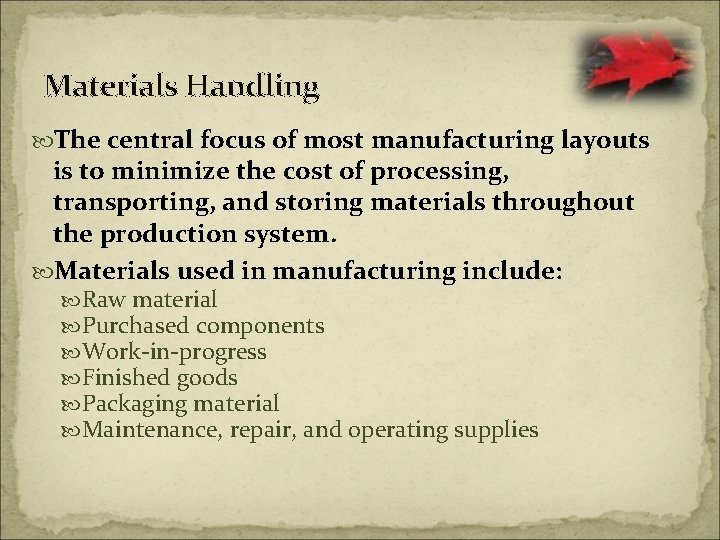
Materials Handling The central focus of most manufacturing layouts is to minimize the cost of processing, transporting, and storing materials throughout the production system. Materials used in manufacturing include: Raw material Purchased components Work-in-progress Finished goods Packaging material Maintenance, repair, and operating supplies

Materials Handling A materials-handling system is the entire network of transportation that: Receives material Stores material in inventories Moves material between processing points Deposits the finished products into vehicles for delivery to customers
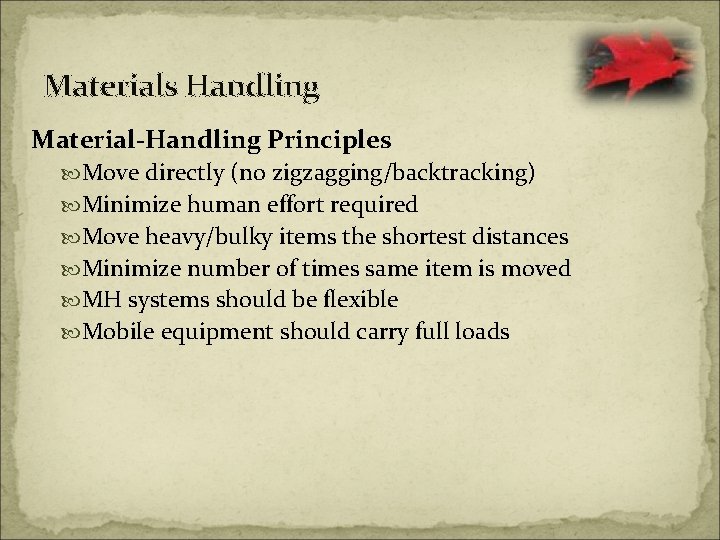
Materials Handling Material-Handling Principles Move directly (no zigzagging/backtracking) Minimize human effort required Move heavy/bulky items the shortest distances Minimize number of times same item is moved MH systems should be flexible Mobile equipment should carry full loads
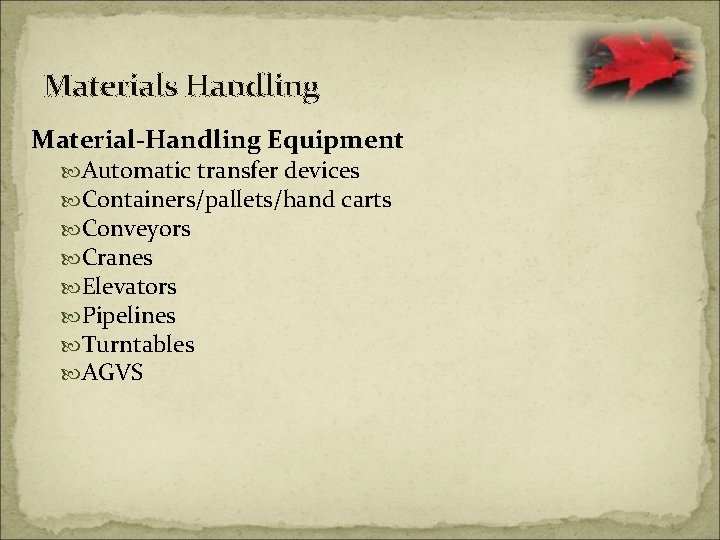
Materials Handling Material-Handling Equipment Automatic transfer devices Containers/pallets/hand carts Conveyors Cranes Elevators Pipelines Turntables AGVS
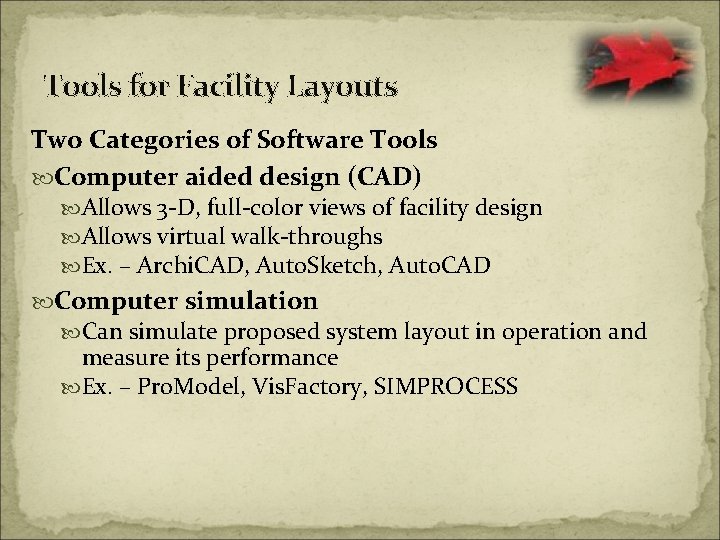
Tools for Facility Layouts Two Categories of Software Tools Computer aided design (CAD) Allows 3 -D, full-color views of facility design Allows virtual walk-throughs Ex. – Archi. CAD, Auto. Sketch, Auto. CAD Computer simulation Can simulate proposed system layout in operation and measure its performance Ex. – Pro. Model, Vis. Factory, SIMPROCESS
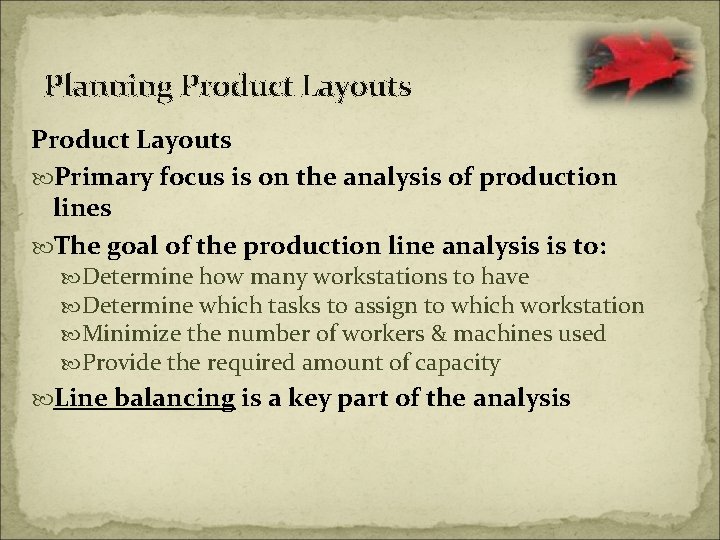
Planning Product Layouts Primary focus is on the analysis of production lines The goal of the production line analysis is to: Determine how many workstations to have Determine which tasks to assign to which workstation Minimize the number of workers & machines used Provide the required amount of capacity Line balancing is a key part of the analysis
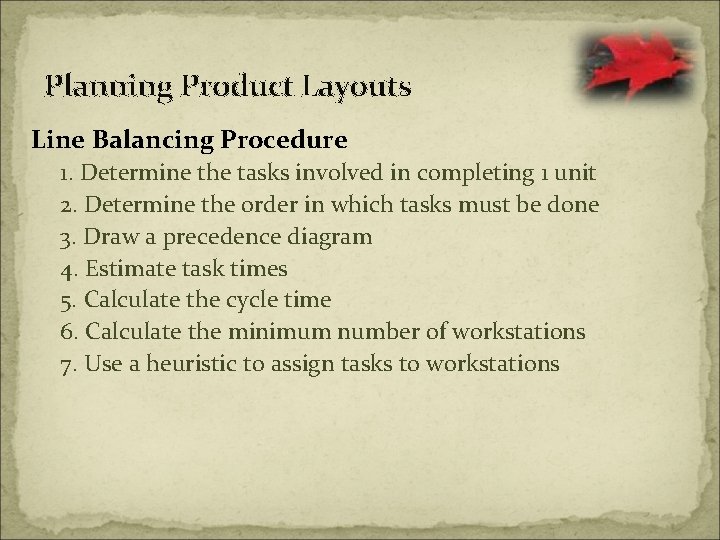
Planning Product Layouts Line Balancing Procedure 1. Determine the tasks involved in completing 1 unit 2. Determine the order in which tasks must be done 3. Draw a precedence diagram 4. Estimate task times 5. Calculate the cycle time 6. Calculate the minimum number of workstations 7. Use a heuristic to assign tasks to workstations
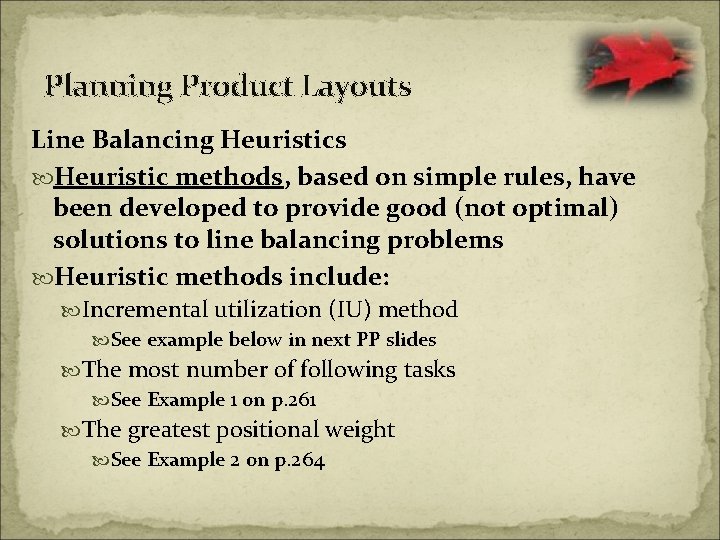
Planning Product Layouts Line Balancing Heuristics Heuristic methods, based on simple rules, have been developed to provide good (not optimal) solutions to line balancing problems Heuristic methods include: Incremental utilization (IU) method See example below in next PP slides The most number of following tasks See Example 1 on p. 261 The greatest positional weight See Example 2 on p. 264
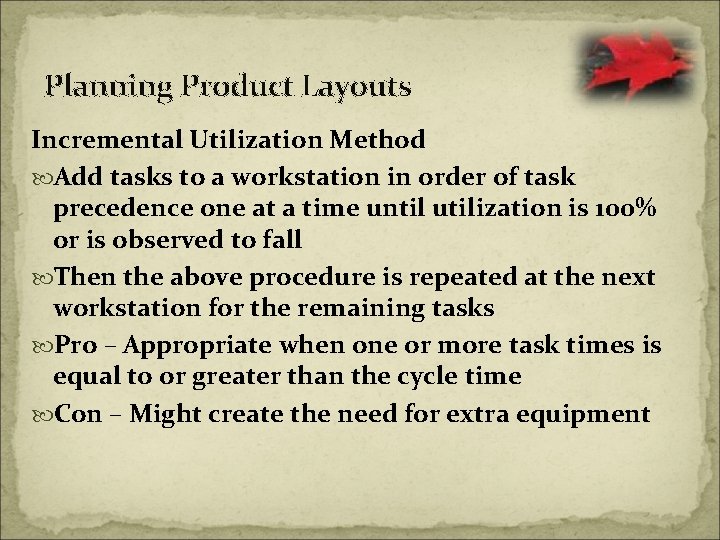
Planning Product Layouts Incremental Utilization Method Add tasks to a workstation in order of task precedence one at a time until utilization is 100% or is observed to fall Then the above procedure is repeated at the next workstation for the remaining tasks Pro – Appropriate when one or more task times is equal to or greater than the cycle time Con – Might create the need for extra equipment
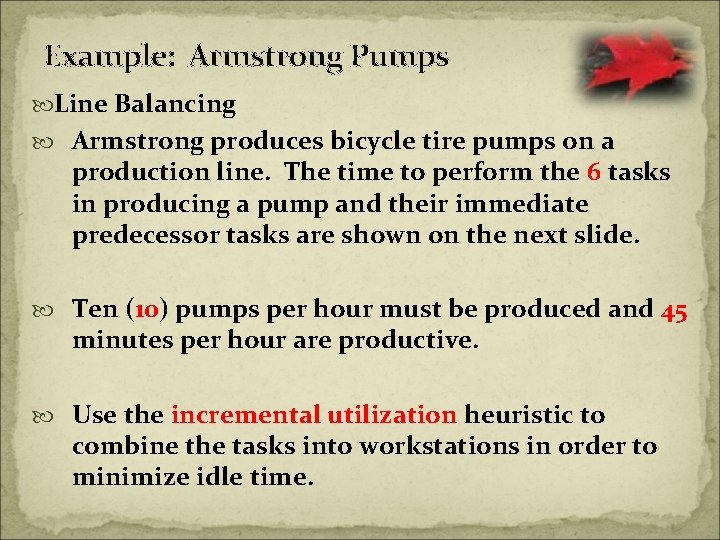
Example: Armstrong Pumps Line Balancing Armstrong produces bicycle tire pumps on a production line. The time to perform the 6 tasks in producing a pump and their immediate predecessor tasks are shown on the next slide. Ten (10) pumps per hour must be produced and 45 minutes per hour are productive. Use the incremental utilization heuristic to combine the tasks into workstations in order to minimize idle time.
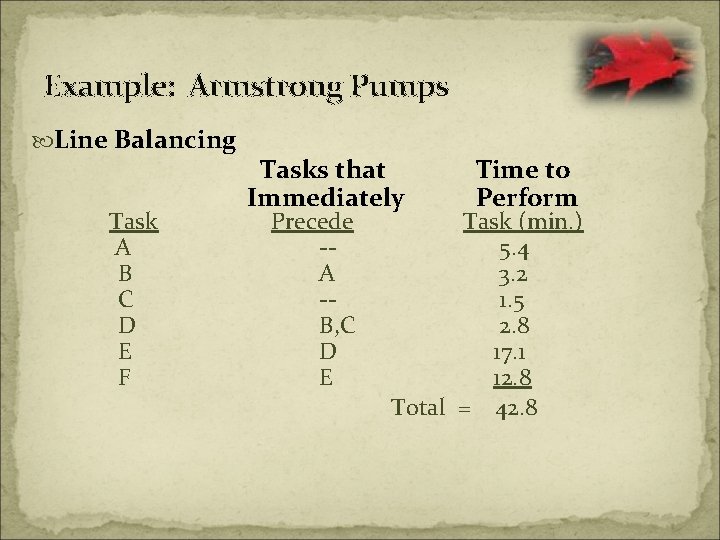
Example: Armstrong Pumps Line Balancing Task A B C D E F Tasks that Immediately Precede -A -B, C D E Time to Perform Task (min. ) 5. 4 3. 2 1. 5 2. 8 17. 1 12. 8 Total = 42. 8
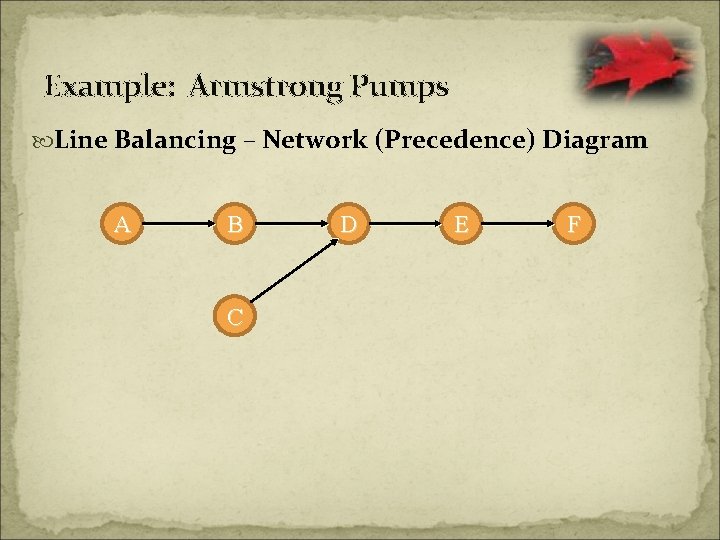
Example: Armstrong Pumps Line Balancing – Network (Precedence) Diagram A B C D E F
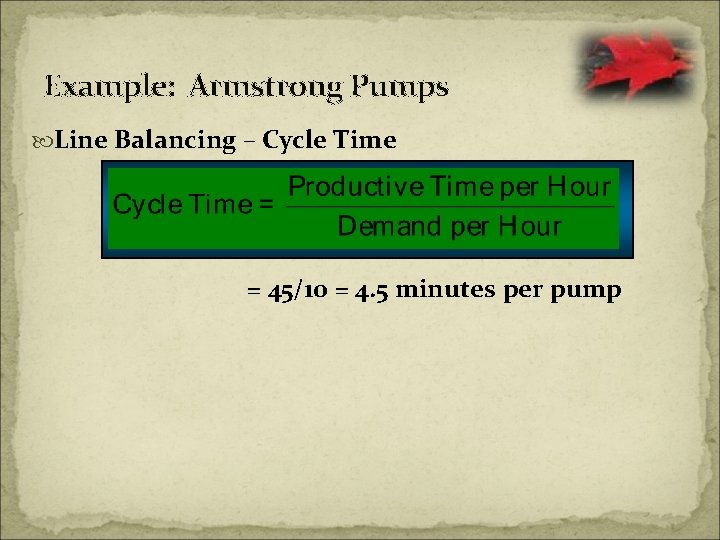
Example: Armstrong Pumps Line Balancing – Cycle Time = 45/10 = 4. 5 minutes per pump
![Example Armstrong Pumps Line Balancing Minimum Number of Workstations 42 81045 Example: Armstrong Pumps Line Balancing – Minimum Number of Workstations = [(42. 8)(10)]/45 =](https://slidetodoc.com/presentation_image_h2/c15633ff1de86f8f4254fb2602aba75b/image-62.jpg)
Example: Armstrong Pumps Line Balancing – Minimum Number of Workstations = [(42. 8)(10)]/45 = 9. 51 workstations
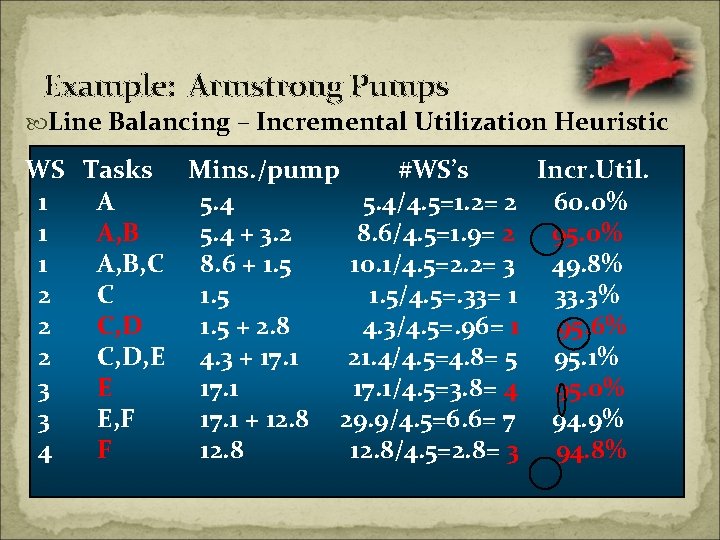
Example: Armstrong Pumps Line Balancing – Incremental Utilization Heuristic WS Tasks Mins. /pump #WS’s Incr. Util. 1 A 5. 4/4. 5=1. 2= 2 60. 0% 1 A, B 5. 4 + 3. 2 8. 6/4. 5=1. 9= 2 95. 0% 1 A, B, C 8. 6 + 1. 5 10. 1/4. 5=2. 2= 3 49. 8% 2 C 1. 5/4. 5=. 33= 1 33. 3% 2 C, D 1. 5 + 2. 8 4. 3/4. 5=. 96= 1 95. 6% 2 C, D, E 4. 3 + 17. 1 21. 4/4. 5=4. 8= 5 95. 1% 3 E 17. 1/4. 5=3. 8= 4 95. 0% 3 E, F 17. 1 + 12. 8 29. 9/4. 5=6. 6= 7 94. 9% 4 F 12. 8/4. 5=2. 8= 3 94. 8%
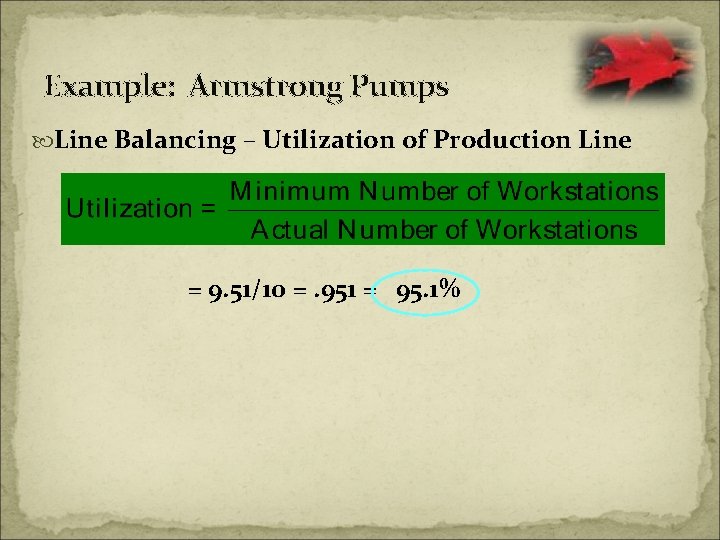
Example: Armstrong Pumps Line Balancing – Utilization of Production Line = 9. 51/10 =. 951 = 95. 1%
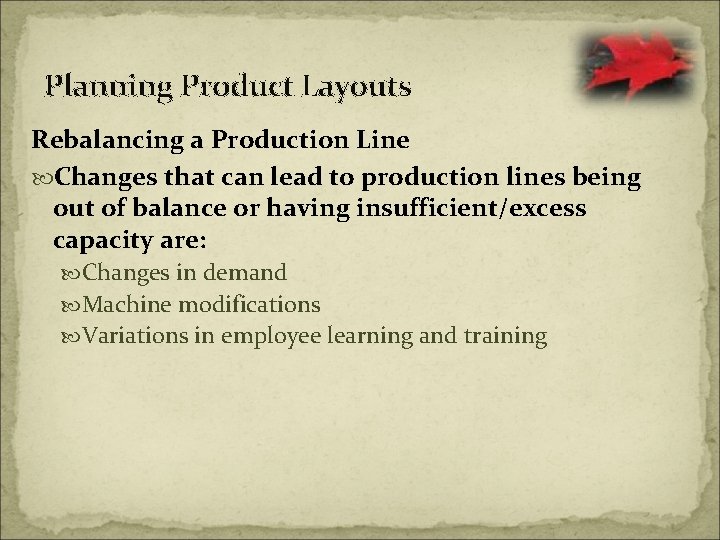
Planning Product Layouts Rebalancing a Production Line Changes that can lead to production lines being out of balance or having insufficient/excess capacity are: Changes in demand Machine modifications Variations in employee learning and training
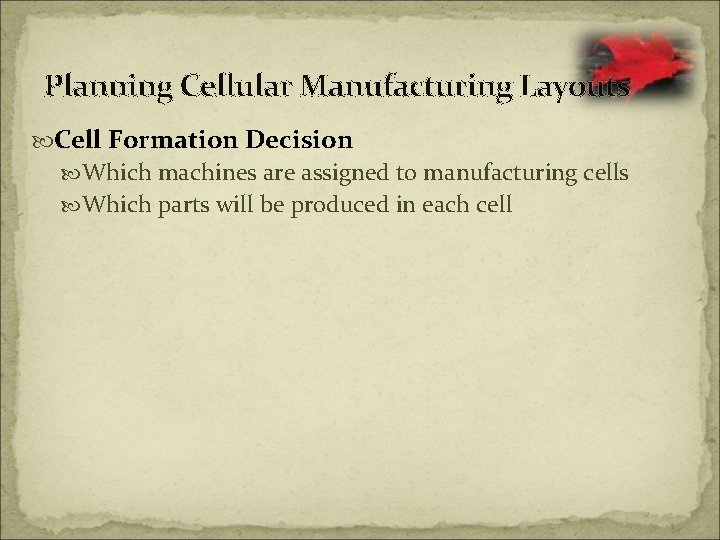
Planning Cellular Manufacturing Layouts Cell Formation Decision Which machines are assigned to manufacturing cells Which parts will be produced in each cell
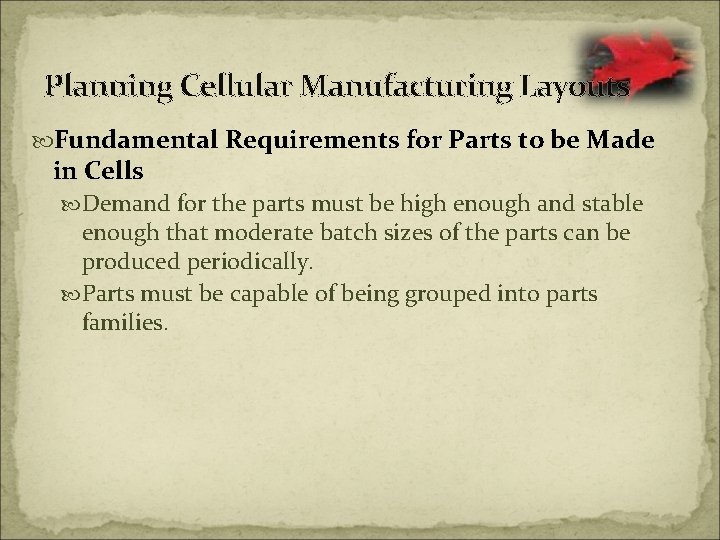
Planning Cellular Manufacturing Layouts Fundamental Requirements for Parts to be Made in Cells Demand for the parts must be high enough and stable enough that moderate batch sizes of the parts can be produced periodically. Parts must be capable of being grouped into parts families.
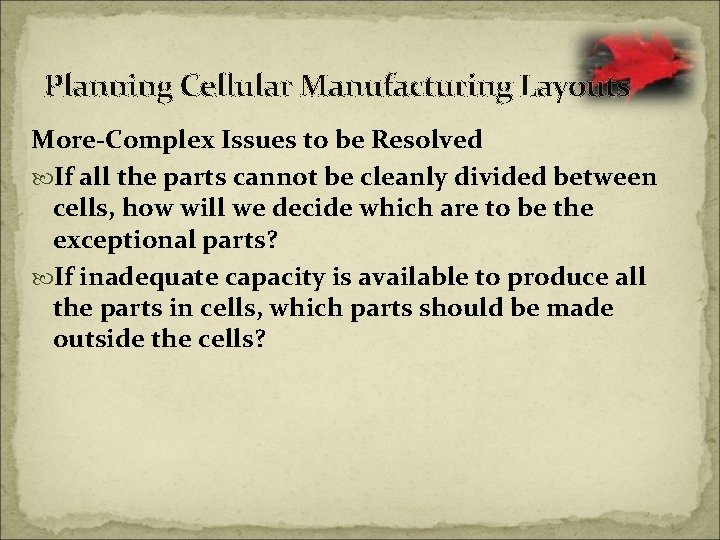
Planning Cellular Manufacturing Layouts More-Complex Issues to be Resolved If all the parts cannot be cleanly divided between cells, how will we decide which are to be the exceptional parts? If inadequate capacity is available to produce all the parts in cells, which parts should be made outside the cells?
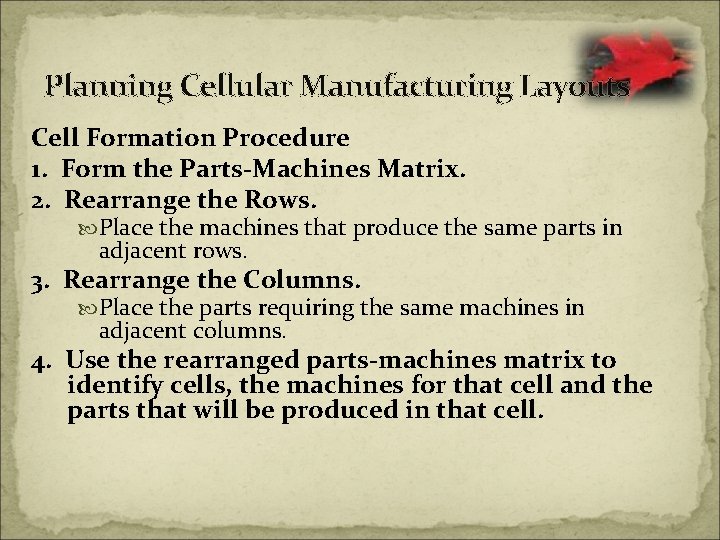
Planning Cellular Manufacturing Layouts Cell Formation Procedure 1. Form the Parts-Machines Matrix. 2. Rearrange the Rows. Place the machines that produce the same parts in adjacent rows. 3. Rearrange the Columns. Place the parts requiring the same machines in adjacent columns. 4. Use the rearranged parts-machines matrix to identify cells, the machines for that cell and the parts that will be produced in that cell.
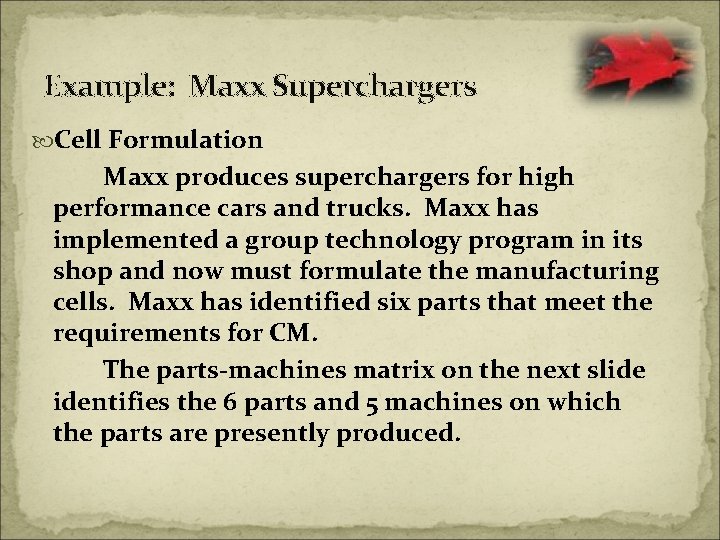
Example: Maxx Superchargers Cell Formulation Maxx produces superchargers for high performance cars and trucks. Maxx has implemented a group technology program in its shop and now must formulate the manufacturing cells. Maxx has identified six parts that meet the requirements for CM. The parts-machines matrix on the next slide identifies the 6 parts and 5 machines on which the parts are presently produced.
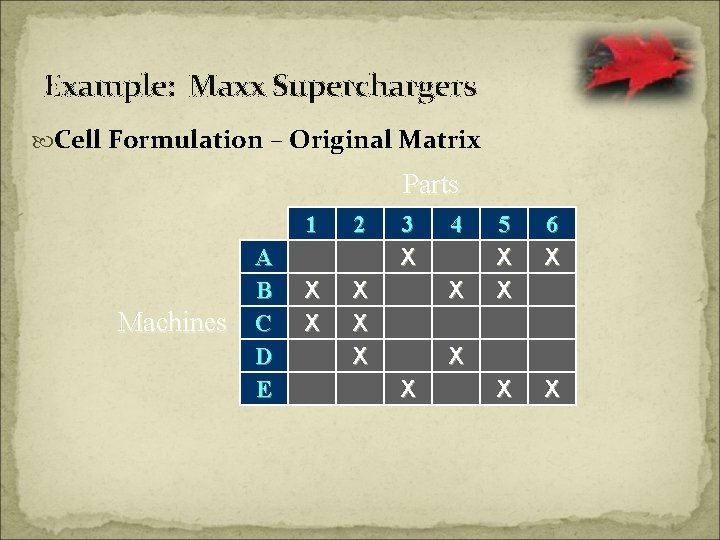
Example: Maxx Superchargers Cell Formulation – Original Matrix Parts Machines A B C D E 1 2 X X X 3 X 4 X 5 X X 6 X X X
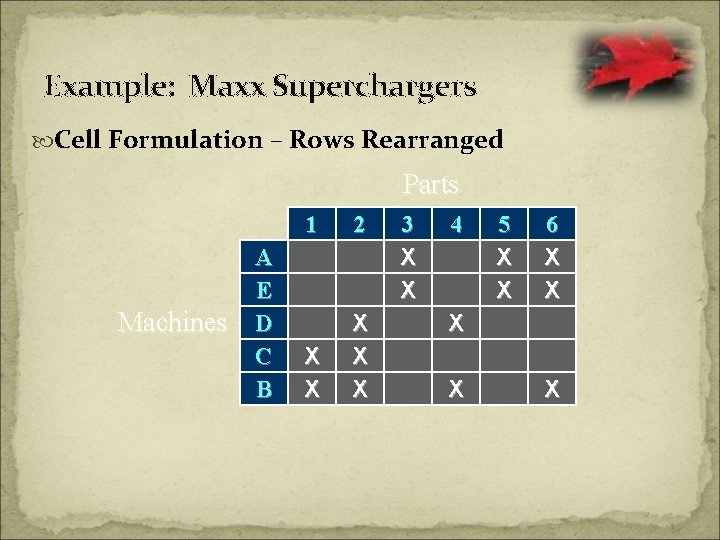
Example: Maxx Superchargers Cell Formulation – Rows Rearranged Parts Machines A E D C B 1 2 X X X 3 X X 4 5 X X 6 X X X
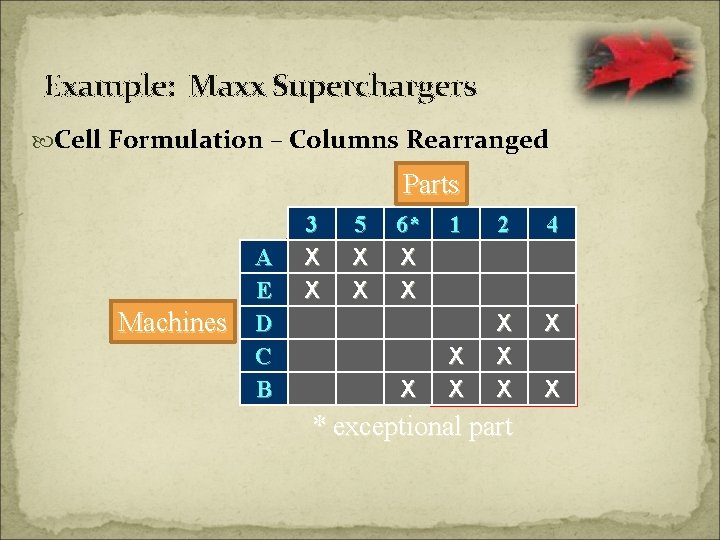
Example: Maxx Superchargers Cell Formulation – Columns Rearranged Parts Machines A E D C B 3 X X 5 X X 6* X X X 1 2 4 X X X * exceptional part X
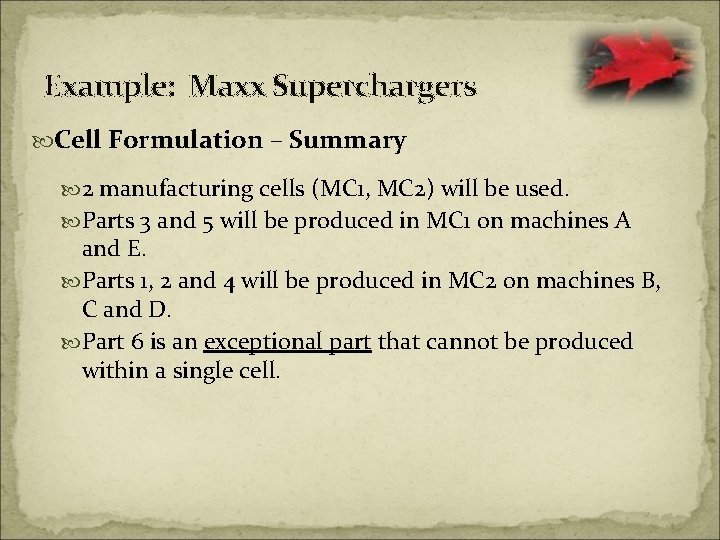
Example: Maxx Superchargers Cell Formulation – Summary 2 manufacturing cells (MC 1, MC 2) will be used. Parts 3 and 5 will be produced in MC 1 on machines A and E. Parts 1, 2 and 4 will be produced in MC 2 on machines B, C and D. Part 6 is an exceptional part that cannot be produced within a single cell.
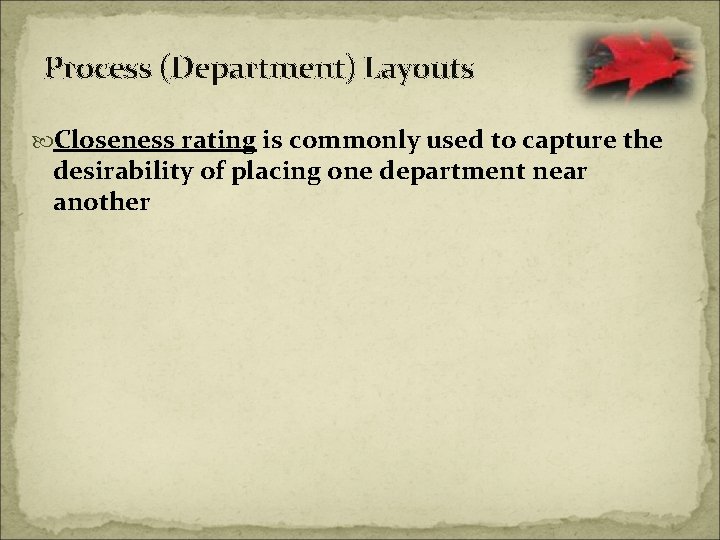
Process (Department) Layouts Closeness rating is commonly used to capture the desirability of placing one department near another
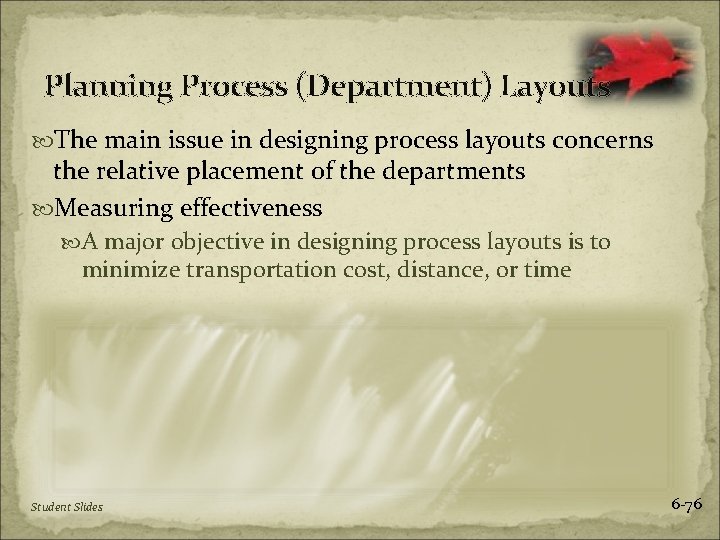
Planning Process (Department) Layouts The main issue in designing process layouts concerns the relative placement of the departments Measuring effectiveness A major objective in designing process layouts is to minimize transportation cost, distance, or time Student Slides 6 -76
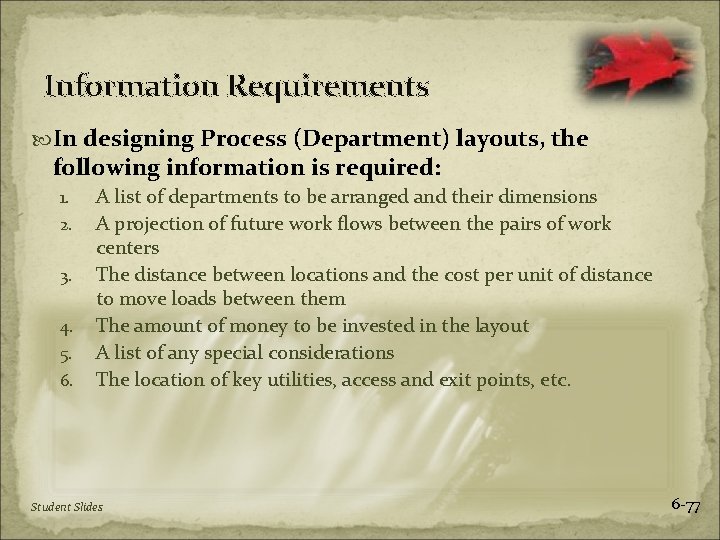
Information Requirements In designing Process (Department) layouts, the following information is required: 1. 2. 3. 4. 5. 6. A list of departments to be arranged and their dimensions A projection of future work flows between the pairs of work centers The distance between locations and the cost per unit of distance to move loads between them The amount of money to be invested in the layout A list of any special considerations The location of key utilities, access and exit points, etc. Student Slides 6 -77
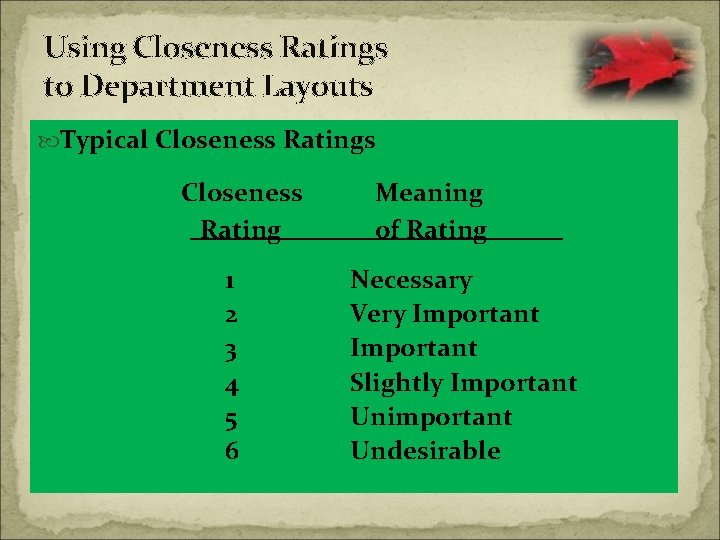
Using Closeness Ratings to Department Layouts Typical Closeness Ratings Closeness Rating 1 2 3 4 5 6 Meaning of Rating Necessary Very Important Slightly Important Unimportant Undesirable
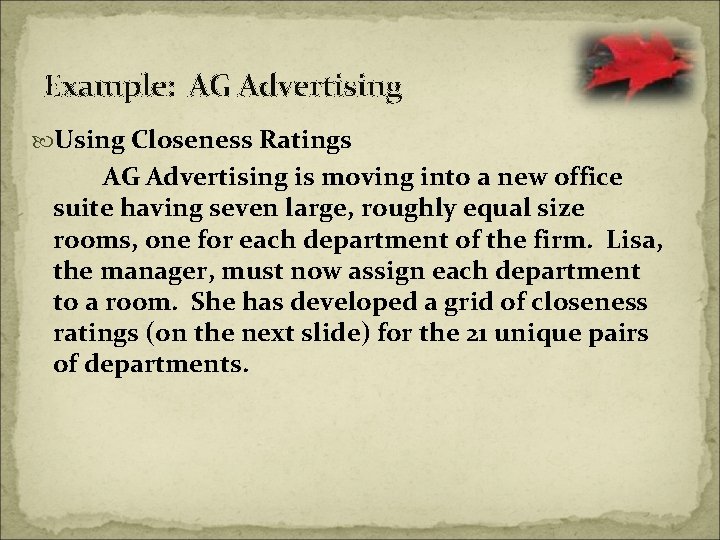
Example: AG Advertising Using Closeness Ratings AG Advertising is moving into a new office suite having seven large, roughly equal size rooms, one for each department of the firm. Lisa, the manager, must now assign each department to a room. She has developed a grid of closeness ratings (on the next slide) for the 21 unique pairs of departments.
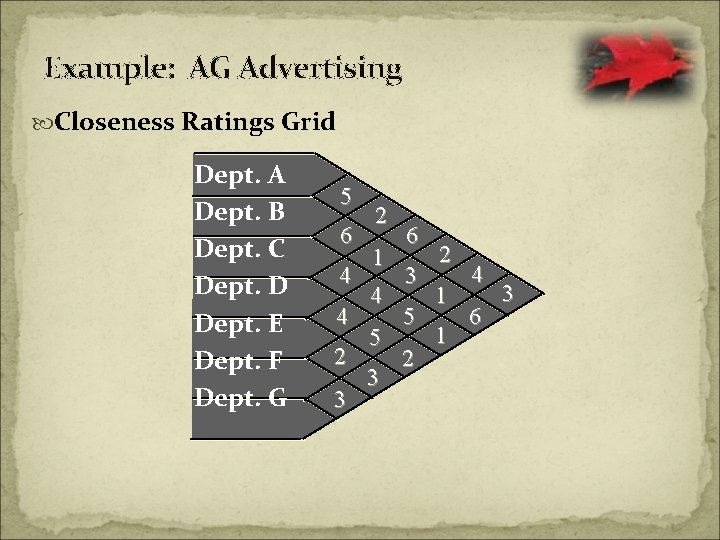
Example: AG Advertising Closeness Ratings Grid Dept. A Dept. B Dept. C Dept. D Dept. E Dept. F Dept. G 5 6 4 4 2 3 2 1 4 5 3 6 3 5 2 2 1 1 4 6 3
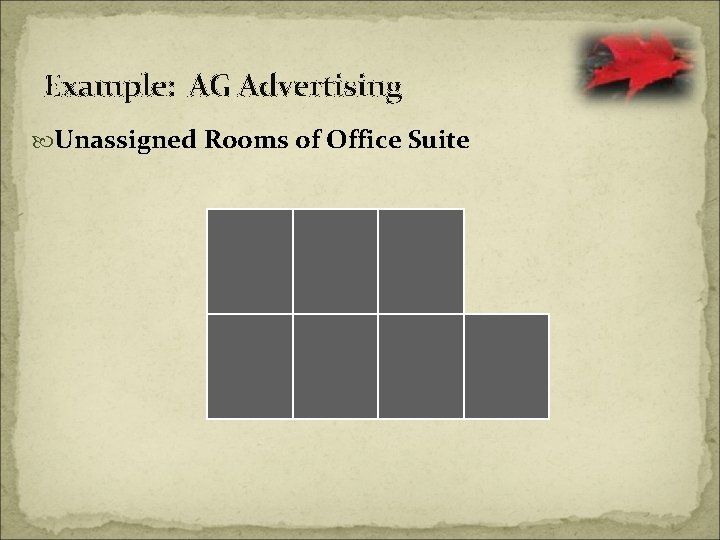
Example: AG Advertising Unassigned Rooms of Office Suite
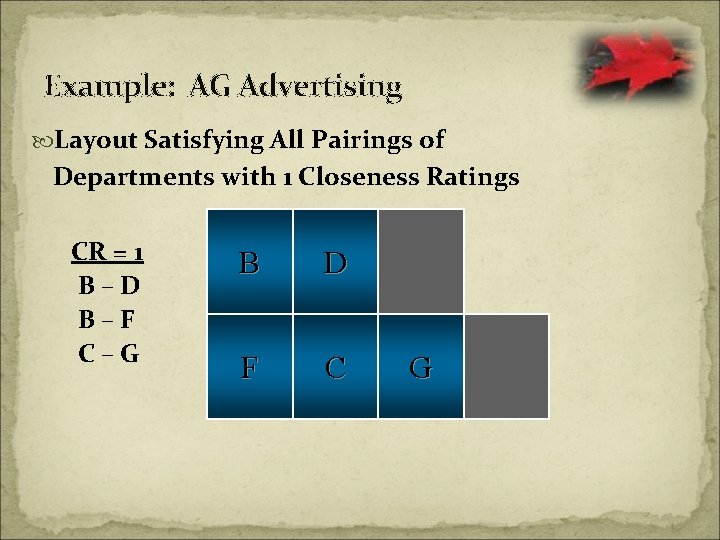
Example: AG Advertising Layout Satisfying All Pairings of Departments with 1 Closeness Ratings CR = 1 B–D B–F C–G B D F C G
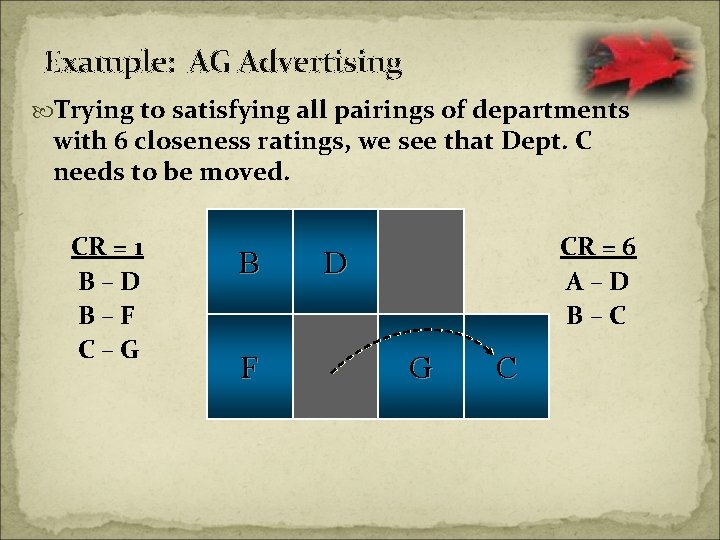
Example: AG Advertising Trying to satisfying all pairings of departments with 6 closeness ratings, we see that Dept. C needs to be moved. CR = 1 B–D B–F C–G B F CR = 6 A–D B–C D G C
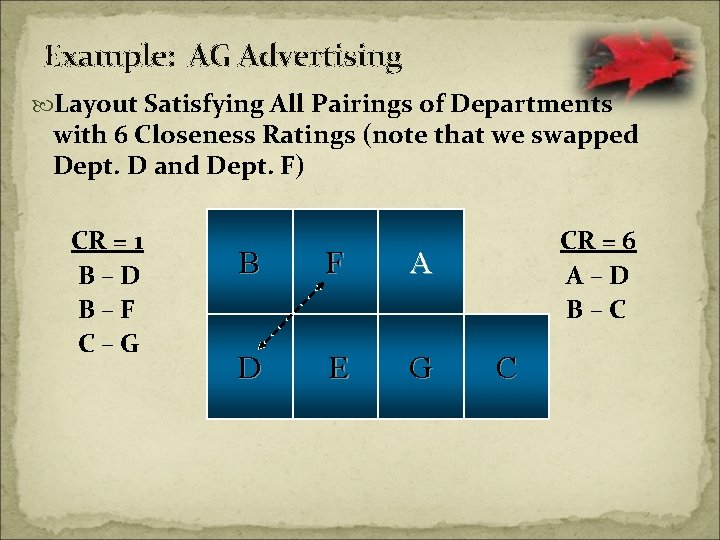
Example: AG Advertising Layout Satisfying All Pairings of Departments with 6 Closeness Ratings (note that we swapped Dept. D and Dept. F) CR = 1 B–D B–F C–G B F A D E G CR = 6 A–D B–C C
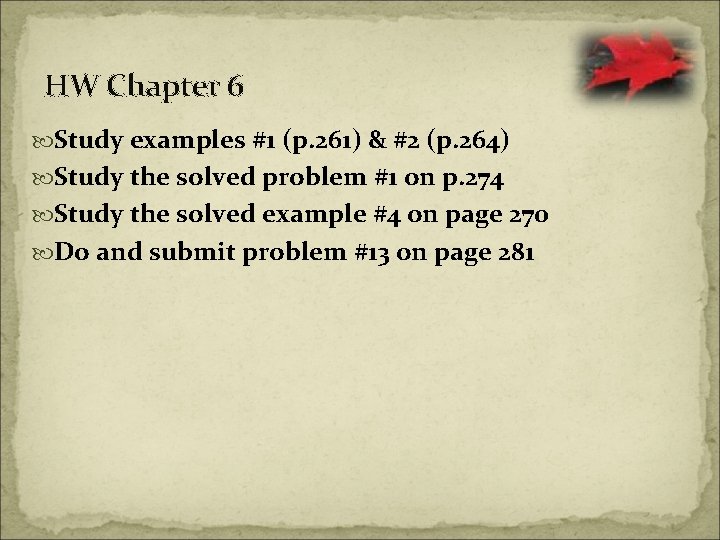
HW Chapter 6 Study examples #1 (p. 261) & #2 (p. 264) Study the solved problem #1 on p. 274 Study the solved example #4 on page 270 Do and submit problem #13 on page 281
Process selection and facility layout pdf
Process selection and facility layout
Importance of process selection and facility layout
Process selection and facility layout
Importance of process selection and facility layout
Process selection and facility layout
Perencanaan lokasi dan tata letak perusahaan
What are the objective of plant layout
Process oriented plant layout
Aeioux layout
Meaning of facility layout
Aldep layout
Objectives of facility layout
Aldep layout
Product vs process layout
Facilities layout
Two way selection and multiway selection
Multiway selection
Mass selection and pure line selection
Supporting facility example
Chapter 8 the international market selection process
Balancing selection vs stabilizing selection
Similarities
K selected
Natural selection vs artificial selection
Difference between continuous and discontinuous variation
Disruptive selevtion
Clumped dispersion
Natural selection vs artificial selection
Denominator layout
Language
Smil head layout root-layout
Fixed vs fluid layout
Define facility planning
Recruitment selection and placement
Process selection and capacity planning
Product and process design in operations management
How will you make the selection of product design
Product design in operations management
Product design and process selection
A-c-m-e-e model of training
Recruitment selection and induction process
Process selection and capacity planning
Identifying and selecting systems development projects
Resourcing strategy
Process selection in operations management
Selection of welding process
Talent aquisition meaning
Instruksi dikerjakan secara sekuensial berurutan
Selection process in staffing
Selection ratio
Product selection process
Selection and placement
Ocps zoning map
What is scientific selection
Process selection charts
Crm decision matrix
Process selection in operations management
Market selection
Channel member selection
Strategic selection process
Discuss the various steps involved in portfolio development
Project selection process
Product selection in operations management
Chapter 6 employee testing and selection ppt
Selection and storage of meats chapter 13
Process memory layout
Process-oriented layout example
Product-oriented layout example
Process oriented layout example
Process-oriented layout example
Hybrid layout examples
Fixed position layout design
Tipe layout
Process oriented layout example
Job shop vs flow shop
Future of facilities management
Child care facility rules and regulations exam
Global facility for disaster reduction and recovery
Software and systems integration facility
Neal road recycling and waste facility
Aub egov
Sport event and facility management
Chapter one the selection of a research approach
Chapter 15 section 1 darwins theory of natural selection
The selection chapter 18