ASQ Supply Chain Synchronization kkensingerstonecrossgroup com 260 410
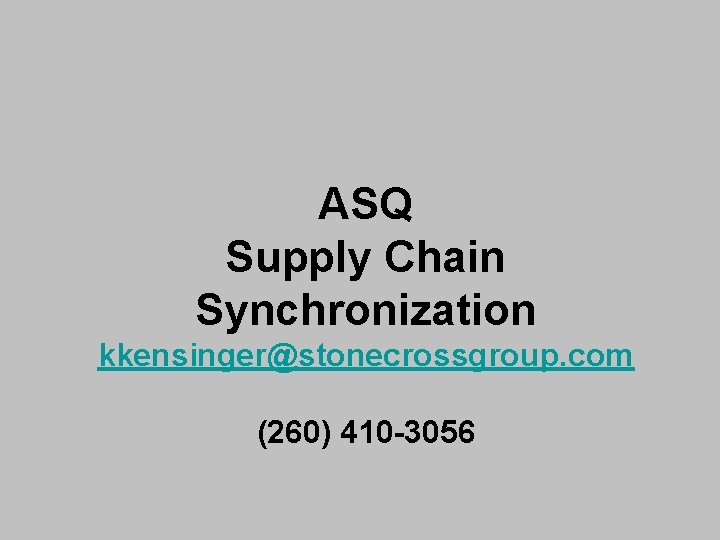
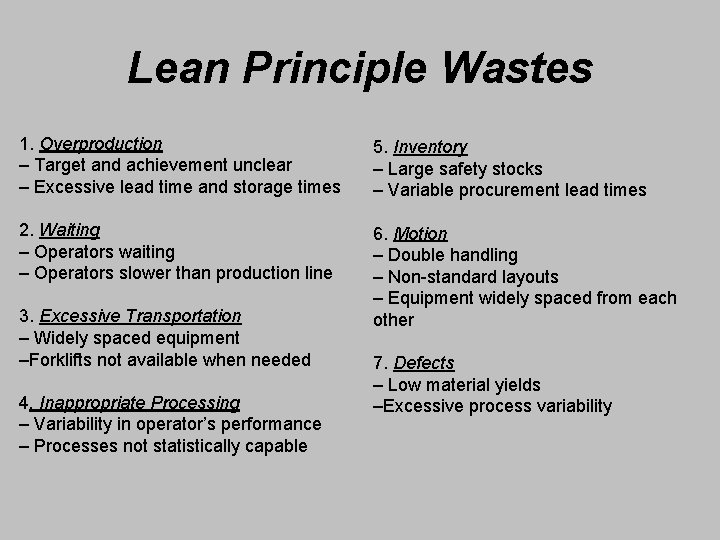
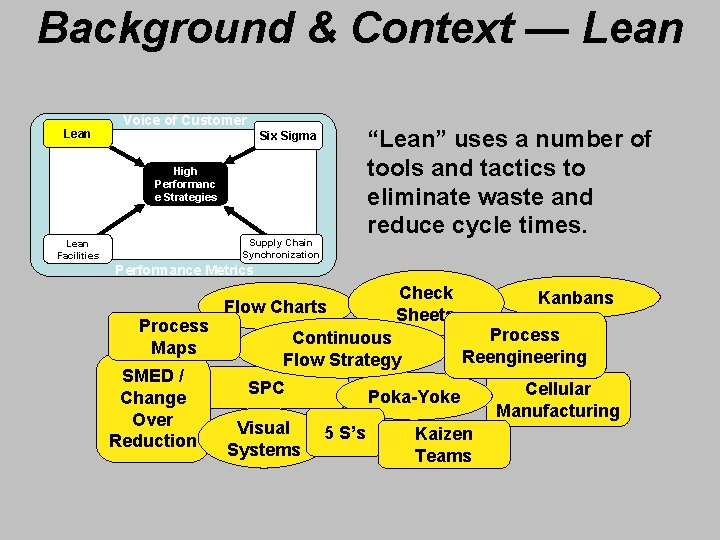
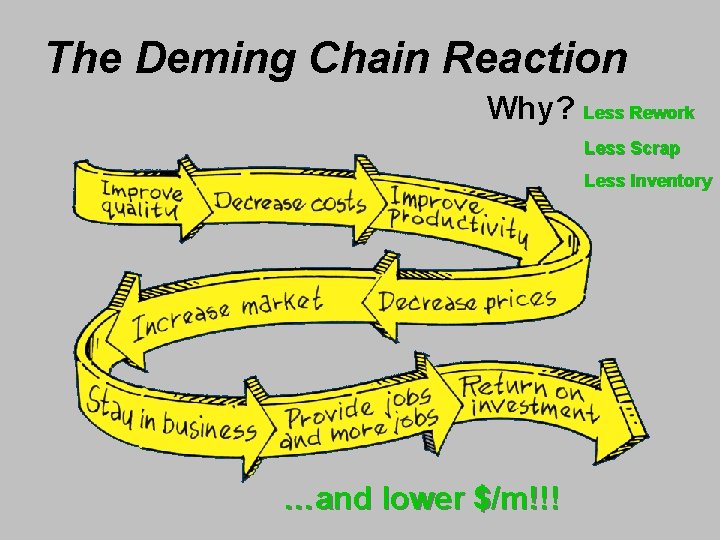
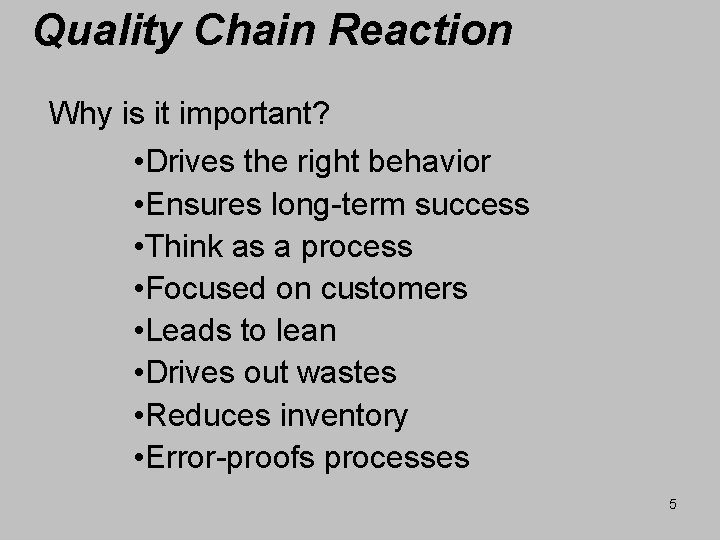
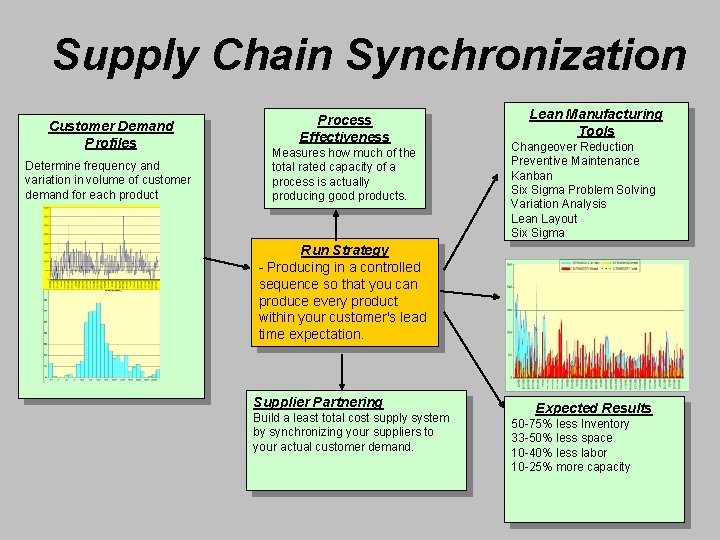
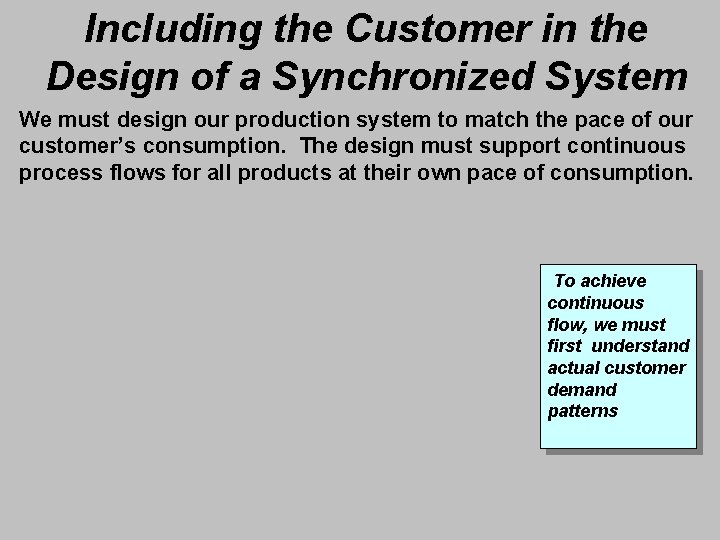
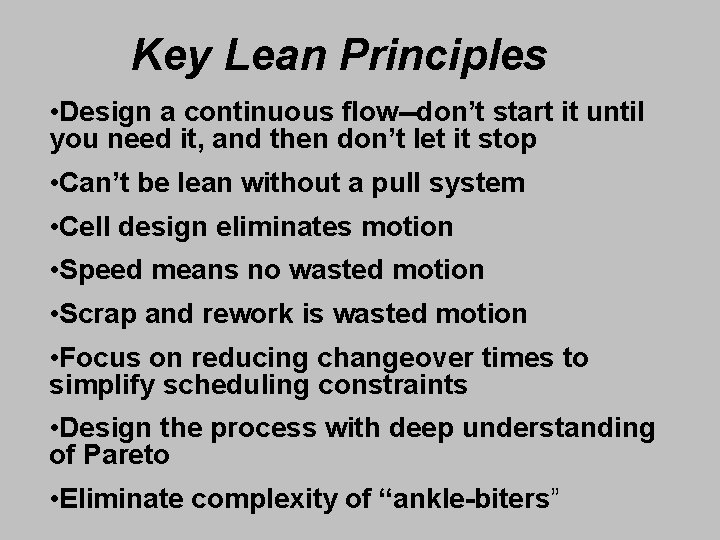
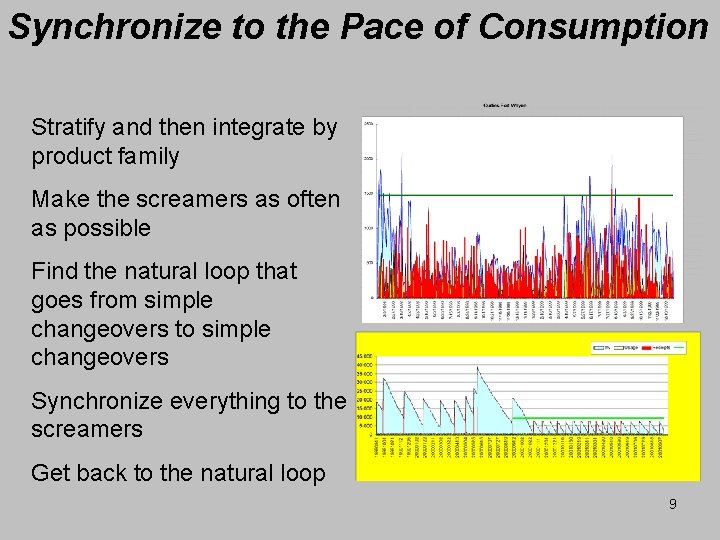
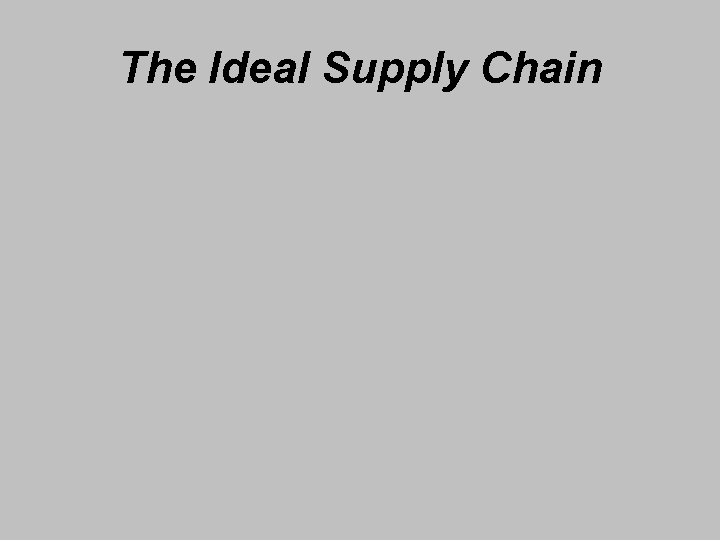
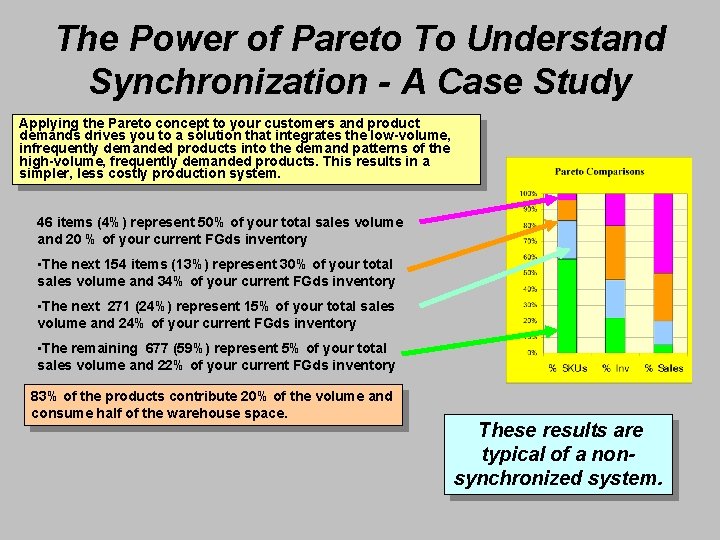
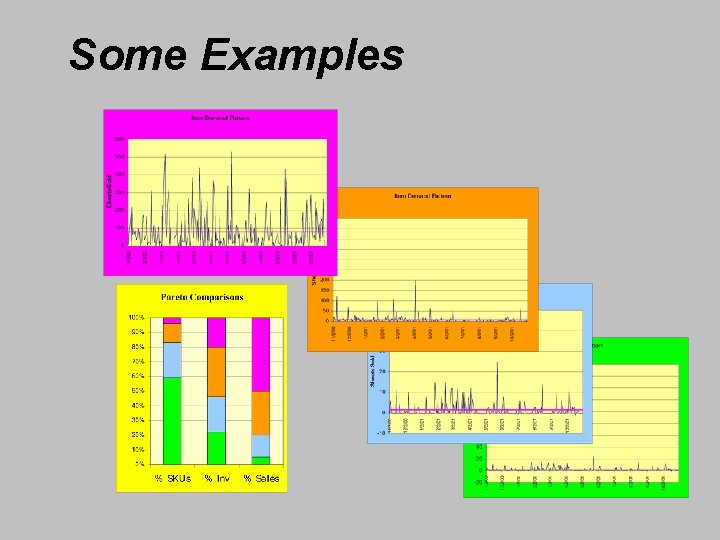
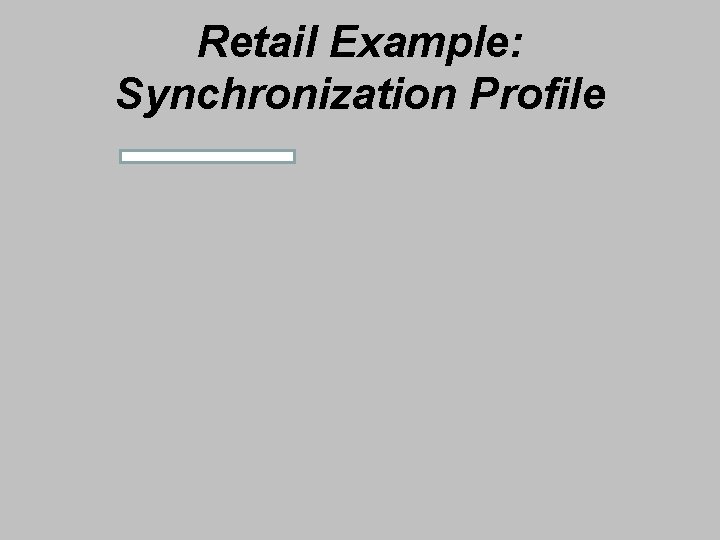
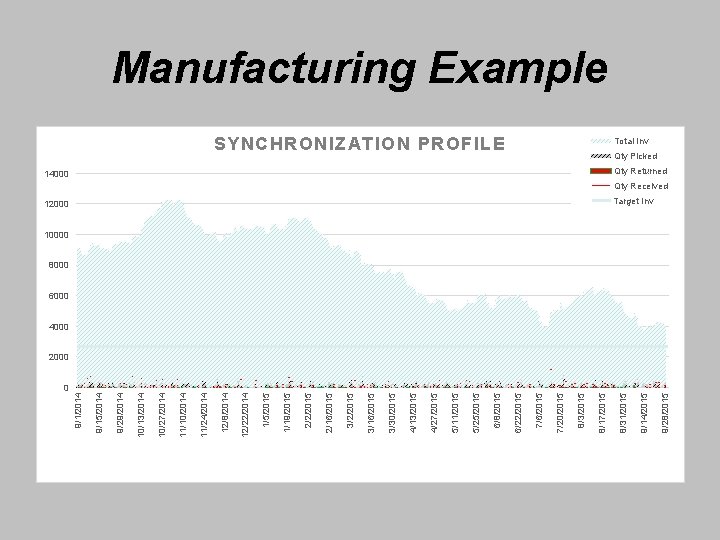
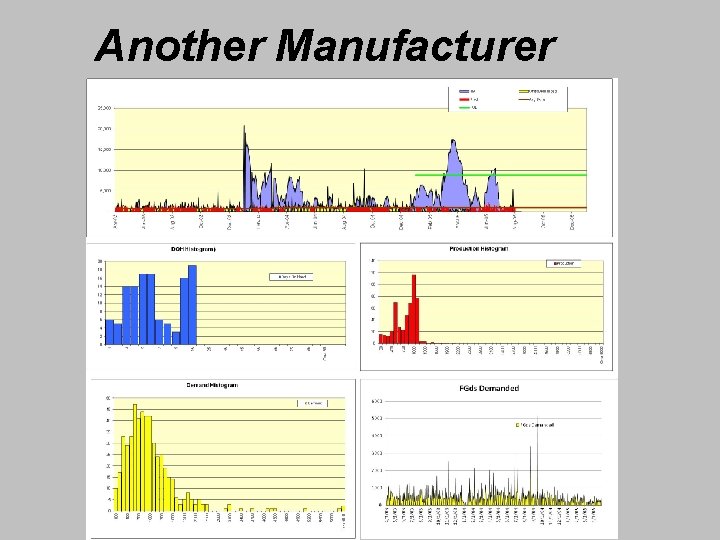
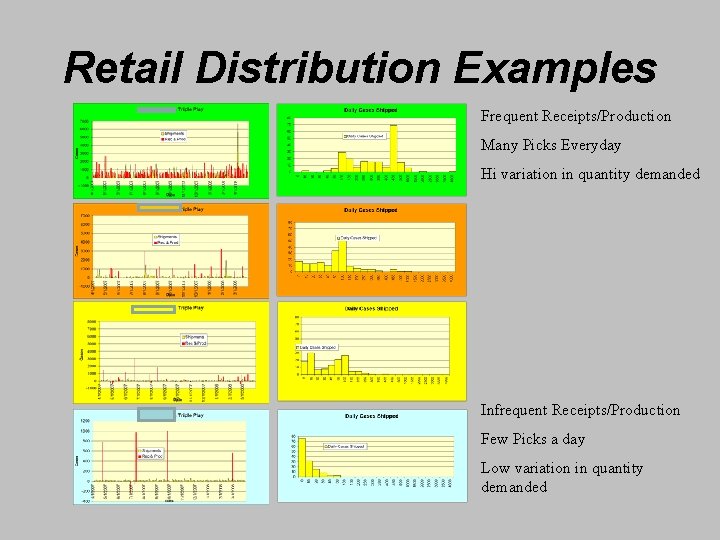
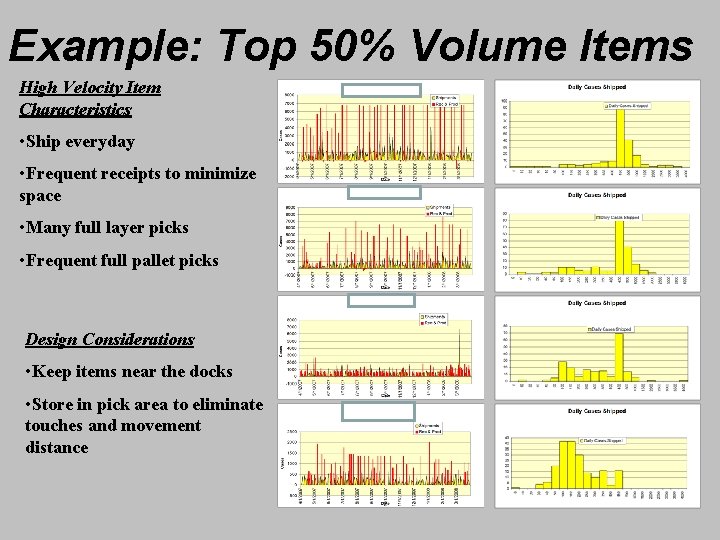
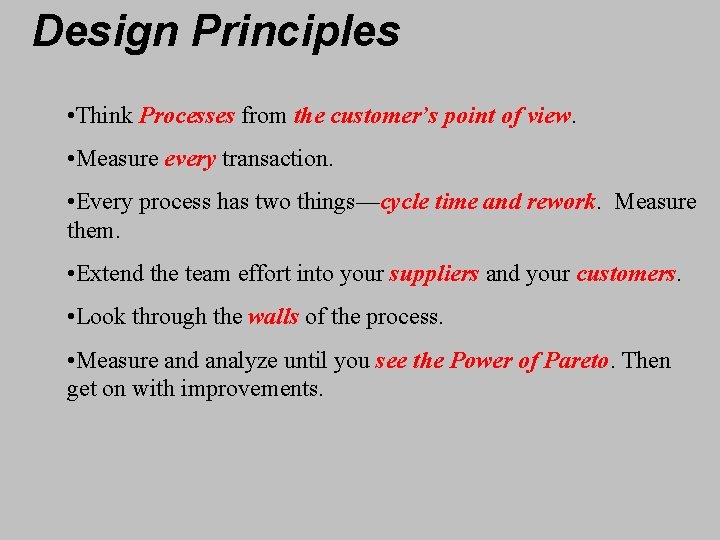
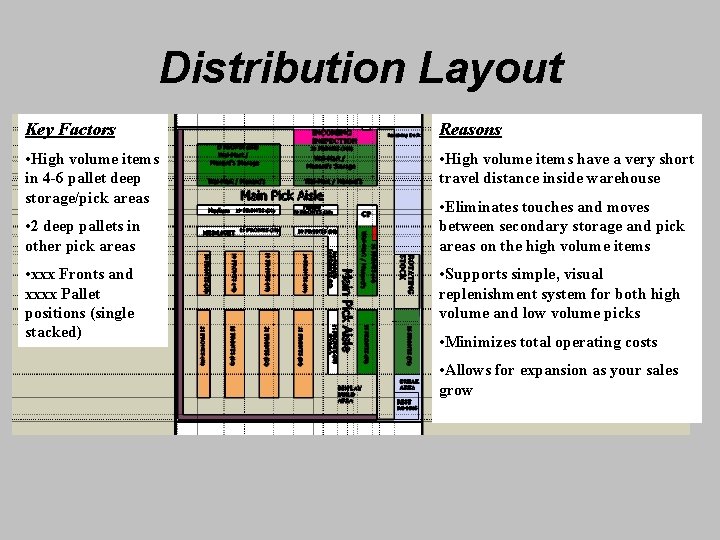

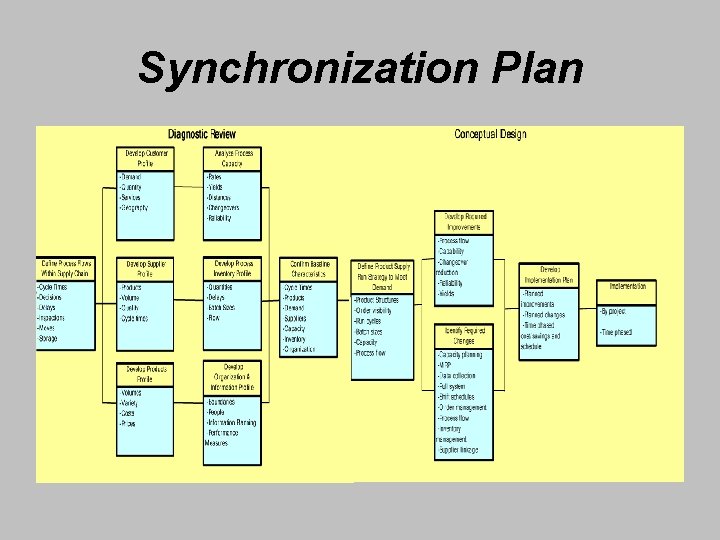
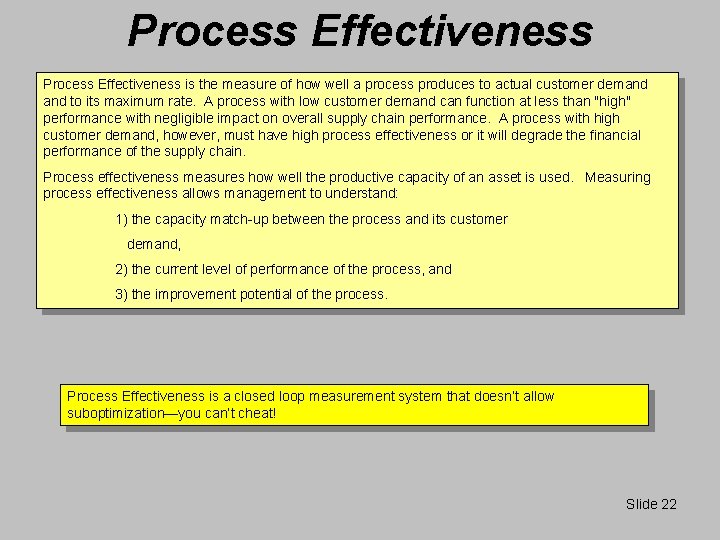
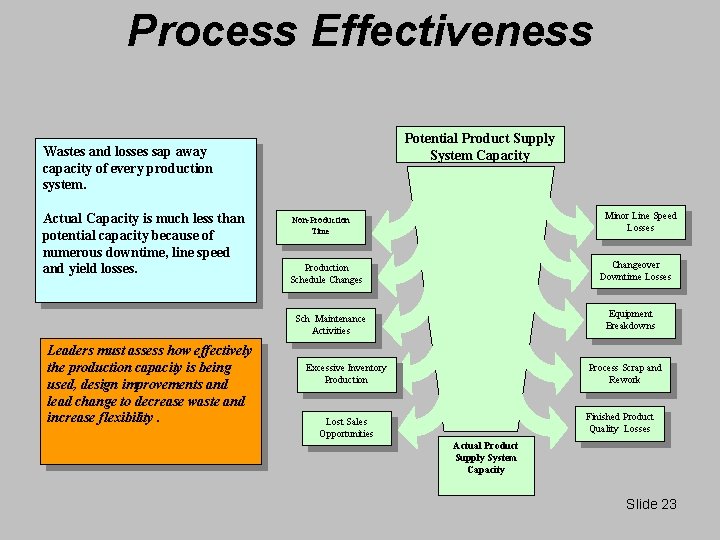
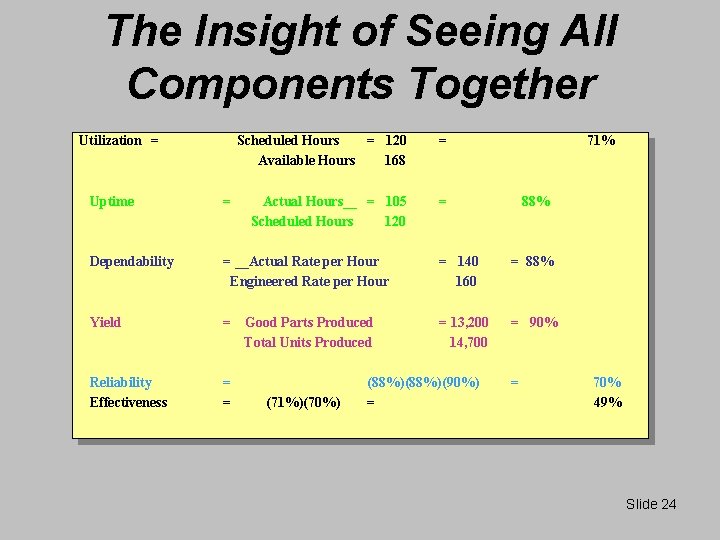
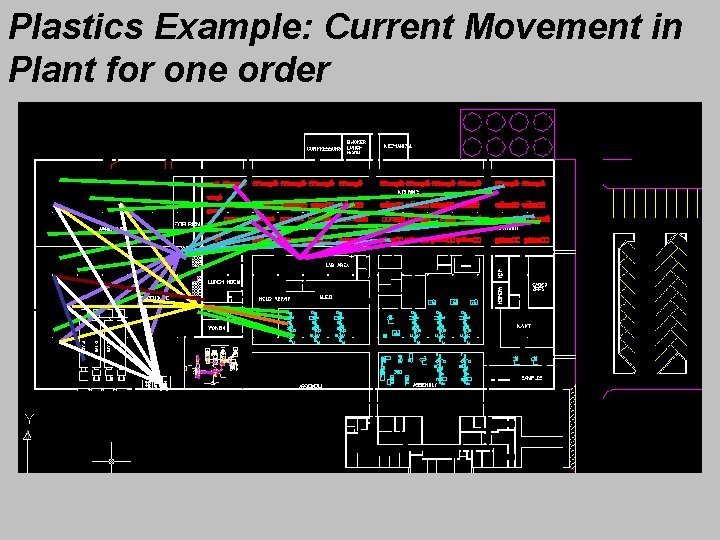
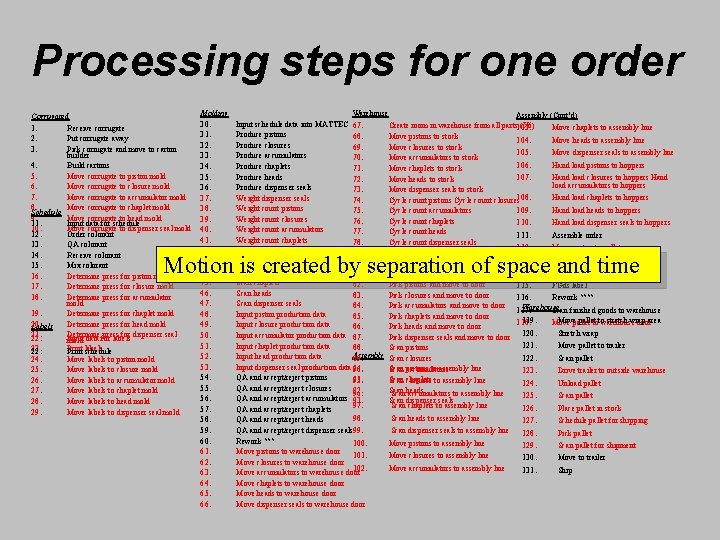
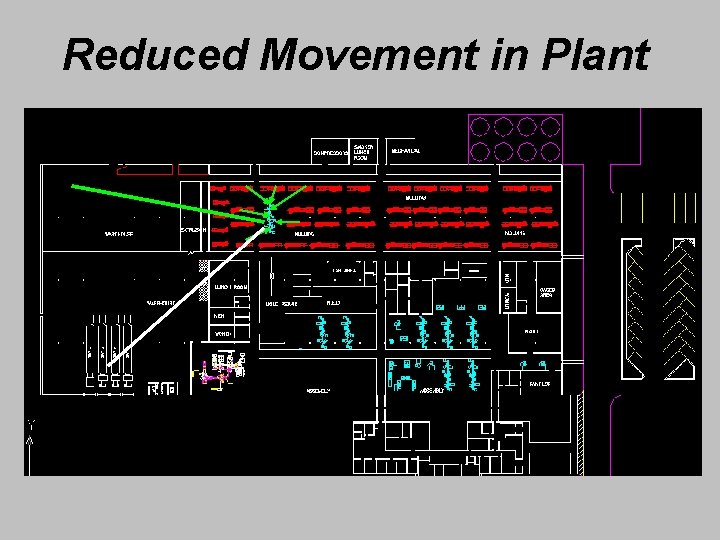
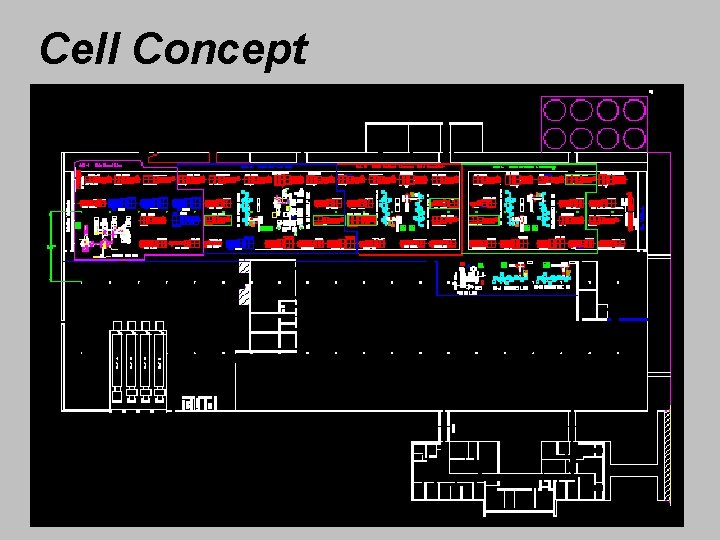
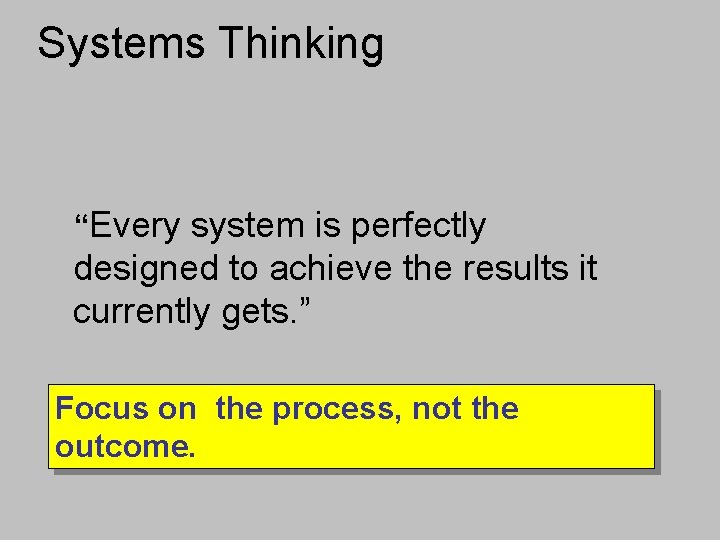
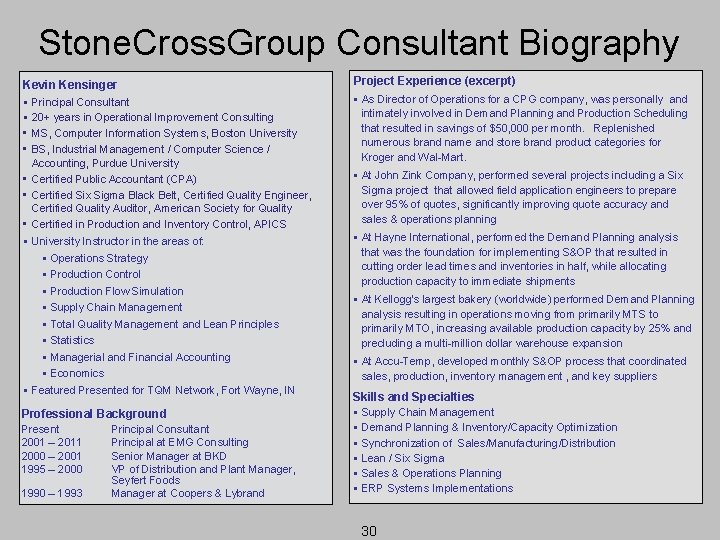
- Slides: 30
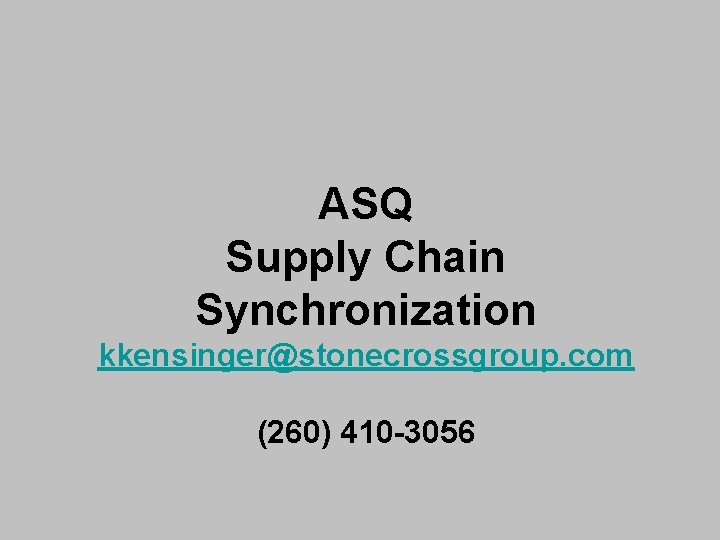
ASQ Supply Chain Synchronization kkensinger@stonecrossgroup. com (260) 410 -3056
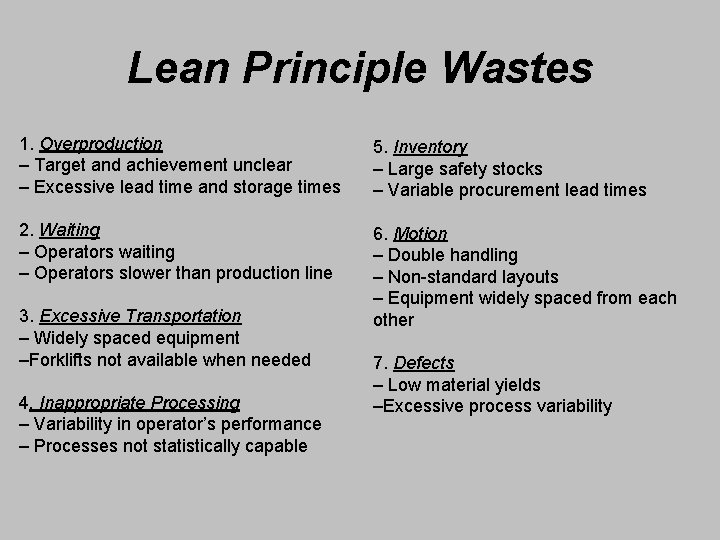
Lean Principle Wastes 1. Overproduction – Target and achievement unclear – Excessive lead time and storage times 5. Inventory – Large safety stocks – Variable procurement lead times 2. Waiting – Operators waiting – Operators slower than production line 6. Motion – Double handling – Non-standard layouts – Equipment widely spaced from each other 3. Excessive Transportation – Widely spaced equipment –Forklifts not available when needed 4. Inappropriate Processing – Variability in operator’s performance – Processes not statistically capable 7. Defects – Low material yields –Excessive process variability
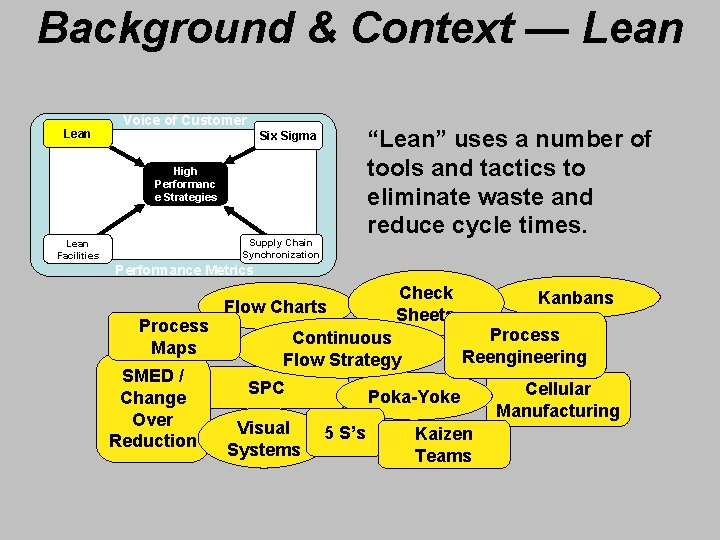
Background & Context — Lean Voice of Customer “Lean” uses a number of tools and tactics to eliminate waste and reduce cycle times. Six Sigma High Performanc e Strategies Supply Chain Synchronization Lean Facilities Performance Metrics Process Maps SMED / Change Over Reduction Flow Charts Check Sheets Process Reengineering Continuous Flow Strategy SPC Visual Systems Kanbans Poka-Yoke 5 S’s Kaizen Teams Cellular Manufacturing
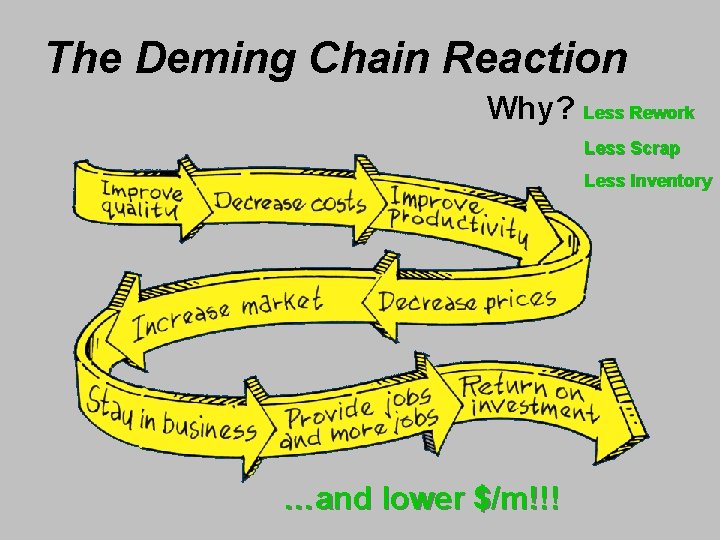
The Deming Chain Reaction Why? Less Rework Less Scrap Less Inventory …and lower $/m!!!
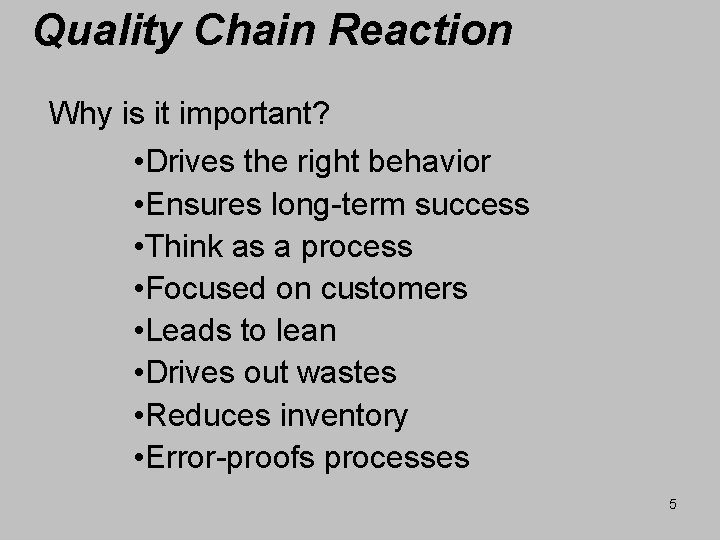
Quality Chain Reaction Why is it important? • Drives the right behavior • Ensures long-term success • Think as a process • Focused on customers • Leads to lean • Drives out wastes • Reduces inventory • Error-proofs processes 5
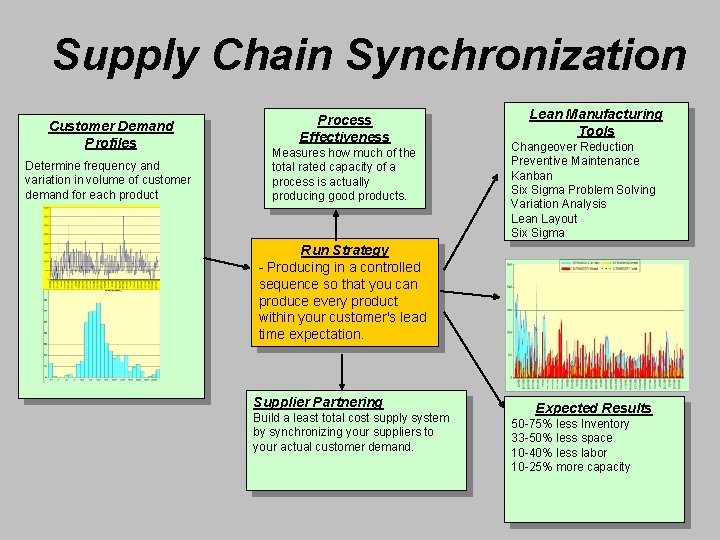
Supply Chain Synchronization Customer Demand Profiles Determine frequency and variation in volume of customer demand for each product Process Effectiveness Measures how much of the total rated capacity of a process is actually producing good products. Lean Manufacturing Tools Changeover Reduction Preventive Maintenance Kanban Six Sigma Problem Solving Variation Analysis Lean Layout Six Sigma Run Strategy - Producing in a controlled sequence so that you can produce every product within your customer's lead time expectation. Supplier Partnering Build a least total cost supply system by synchronizing your suppliers to your actual customer demand. Expected Results 50 -75% less Inventory 33 -50% less space 10 -40% less labor 10 -25% more capacity
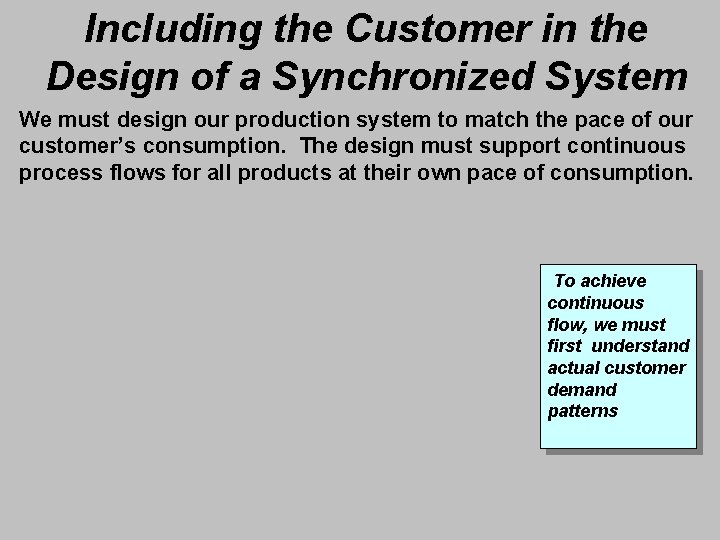
Including the Customer in the Design of a Synchronized System We must design our production system to match the pace of our customer’s consumption. The design must support continuous process flows for all products at their own pace of consumption. To achieve continuous flow, we must first understand actual customer demand patterns
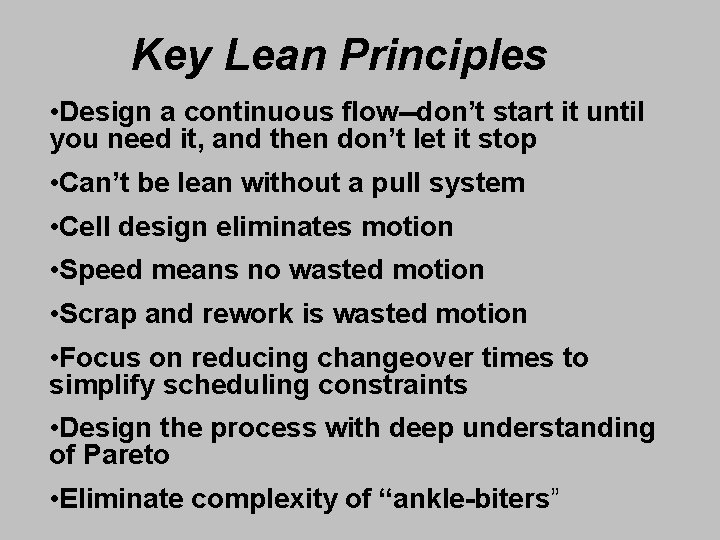
Key Lean Principles • Design a continuous flow--don’t start it until you need it, and then don’t let it stop • Can’t be lean without a pull system • Cell design eliminates motion • Speed means no wasted motion • Scrap and rework is wasted motion • Focus on reducing changeover times to simplify scheduling constraints • Design the process with deep understanding of Pareto • Eliminate complexity of “ankle-biters”
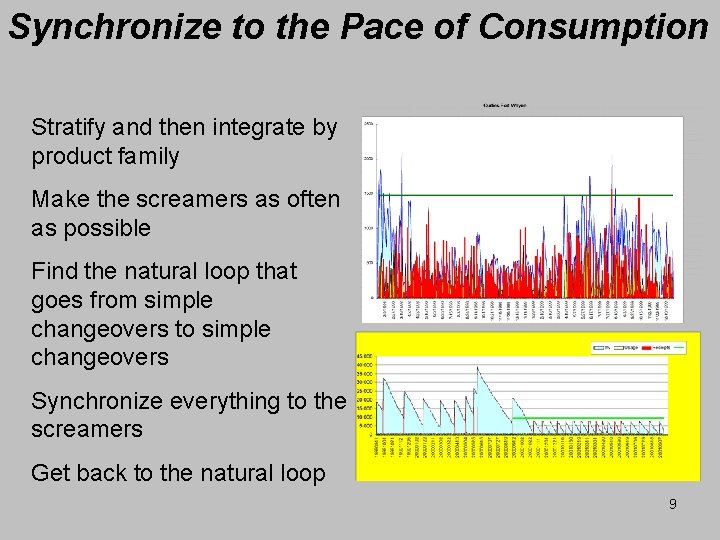
Synchronize to the Pace of Consumption Stratify and then integrate by product family Make the screamers as often as possible Find the natural loop that goes from simple changeovers to simple changeovers Synchronize everything to the screamers Get back to the natural loop 9
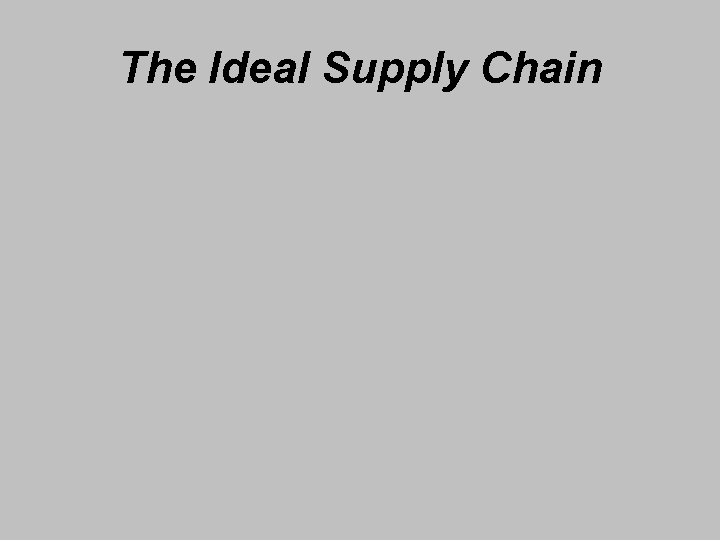
The Ideal Supply Chain
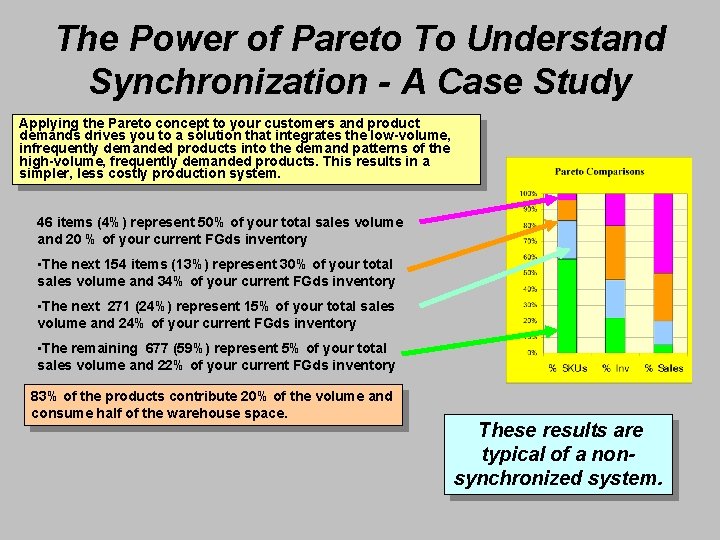
The Power of Pareto To Understand Synchronization - A Case Study Applying the Pareto concept to your customers and product demands drives you to a solution that integrates the low-volume, infrequently demanded products into the demand patterns of the high-volume, frequently demanded products. This results in a simpler, less costly production system. 46 items (4%) represent 50% of your total sales volume and 20 % of your current FGds inventory • The next 154 items (13%) represent 30% of your total sales volume and 34% of your current FGds inventory • The next 271 (24%) represent 15% of your total sales volume and 24% of your current FGds inventory • The remaining 677 (59%) represent 5% of your total sales volume and 22% of your current FGds inventory 83% of the products contribute 20% of the volume and consume half of the warehouse space. These results are typical of a nonsynchronized system.
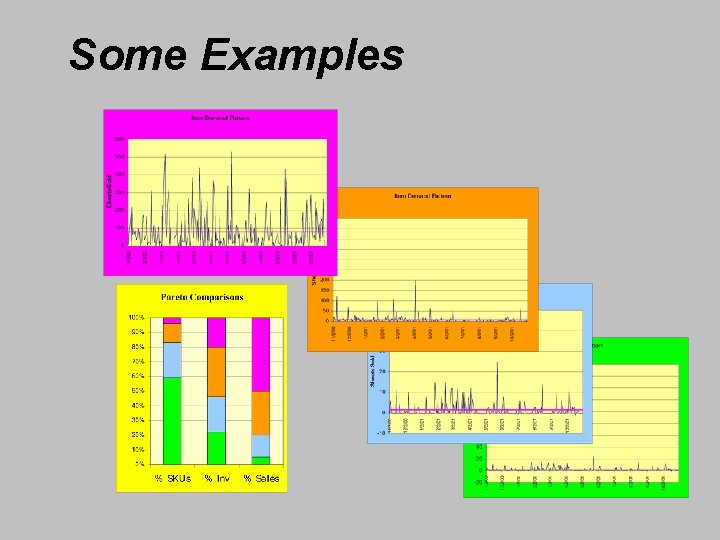
Some Examples
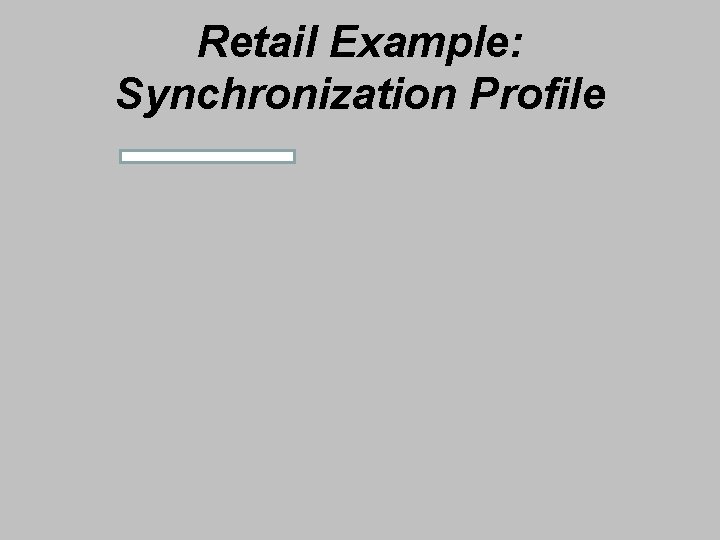
Retail Example: Synchronization Profile
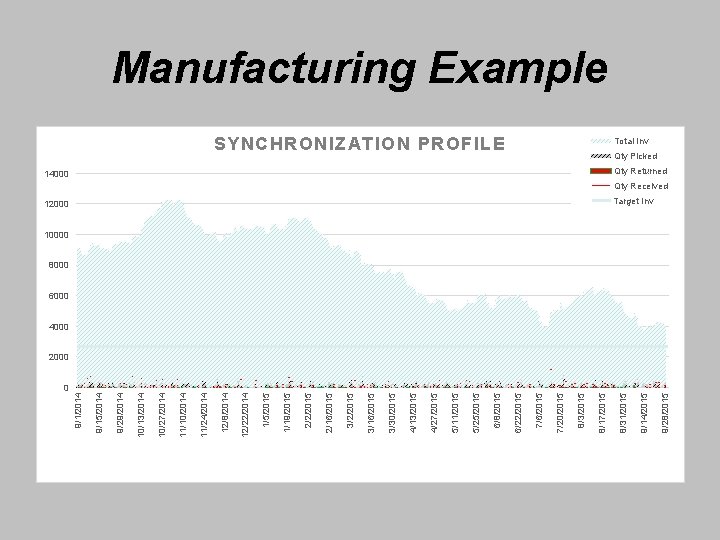
9/28/2015 9/14/2015 SYNCHRONIZATION PROFILE 8/31/2015 8/17/2015 8/3/2015 7/20/2015 7/6/2015 6/22/2015 6/8/2015 5/25/2015 5/11/2015 4/27/2015 4/13/2015 3/30/2015 3/16/2015 3/2/2015 2/16/2015 2/2/2015 1/19/2015 1/5/2015 12/22/2014 12/8/2014 11/24/2014 11/10/2014 10/27/2014 10/13/2014 9/29/2014 9/15/2014 9/1/2014 Manufacturing Example Total Inv Qty Picked 14000 Qty Returned 12000 Target Inv Qty Received 10000 8000 6000 4000 2000 0
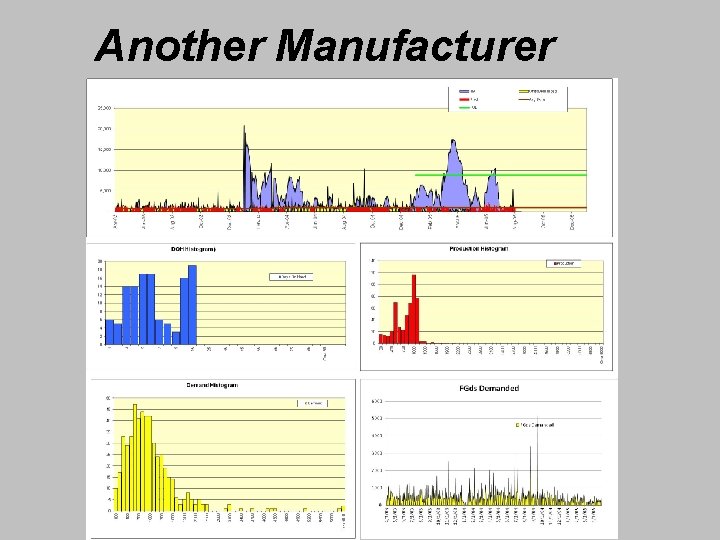
Another Manufacturer
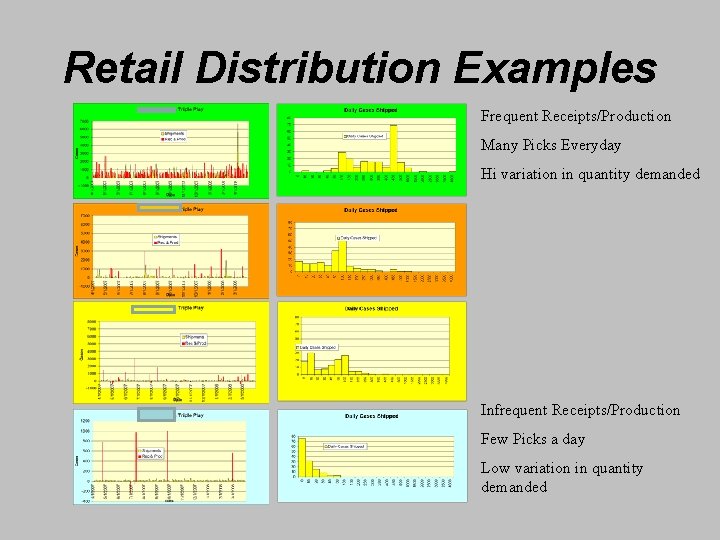
Retail Distribution Examples Frequent Receipts/Production Many Picks Everyday Hi variation in quantity demanded Infrequent Receipts/Production Few Picks a day Low variation in quantity demanded
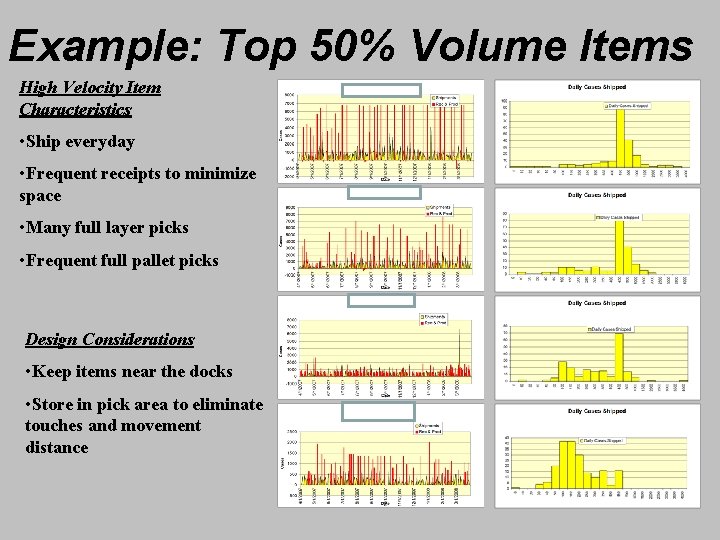
Example: Top 50% Volume Items High Velocity Item Characteristics • Ship everyday • Frequent receipts to minimize space • Many full layer picks • Frequent full pallet picks Design Considerations • Keep items near the docks • Store in pick area to eliminate touches and movement distance
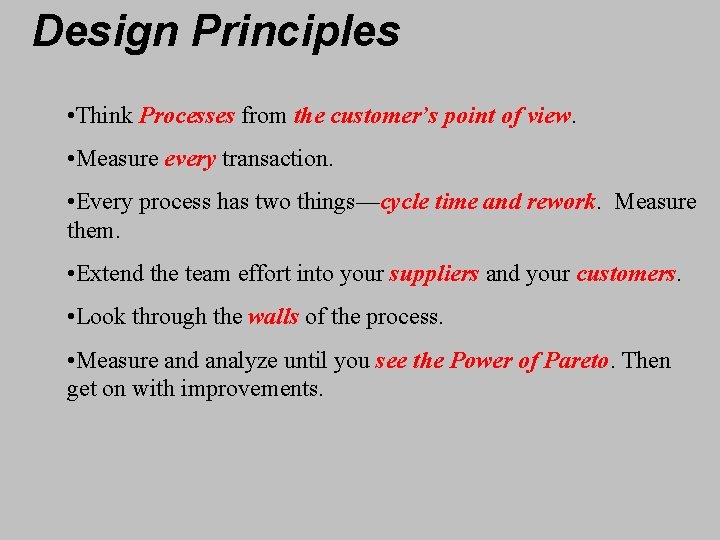
Design Principles • Think Processes from the customer’s point of view. • Measure every transaction. • Every process has two things—cycle time and rework. Measure them. • Extend the team effort into your suppliers and your customers. • Look through the walls of the process. • Measure and analyze until you see the Power of Pareto. Then get on with improvements.
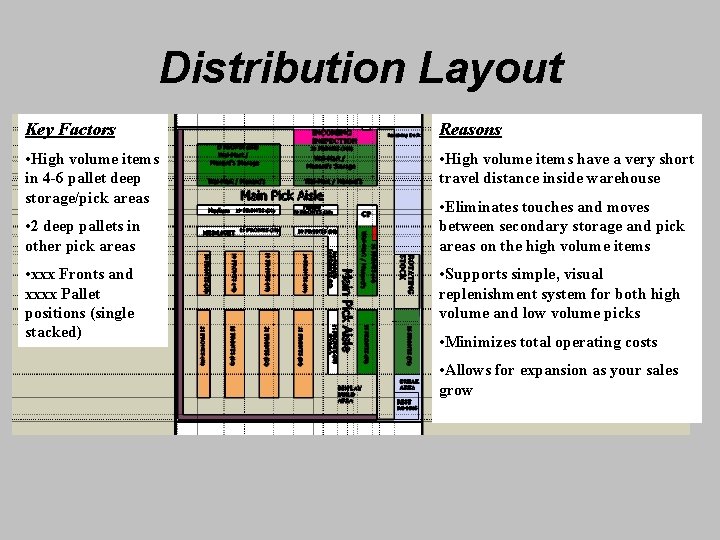
Distribution Layout Key Factors Reasons • High volume items in 4 -6 pallet deep storage/pick areas • High volume items have a very short travel distance inside warehouse • 2 deep pallets in other pick areas • xxx Fronts and xxxx Pallet positions (single stacked) • Eliminates touches and moves between secondary storage and pick areas on the high volume items • Supports simple, visual replenishment system for both high volume and low volume picks • Minimizes total operating costs • Allows for expansion as your sales grow

Data Analysis— Four SKUs involve half of the movements and touches. Only 34 SKUs involve 95% of all movements and touches. Location of these items can significant impact total operating costs. Designs that reduce touches, move distances, and shipping preparation time for the high velocity items will reduce total operating costs.
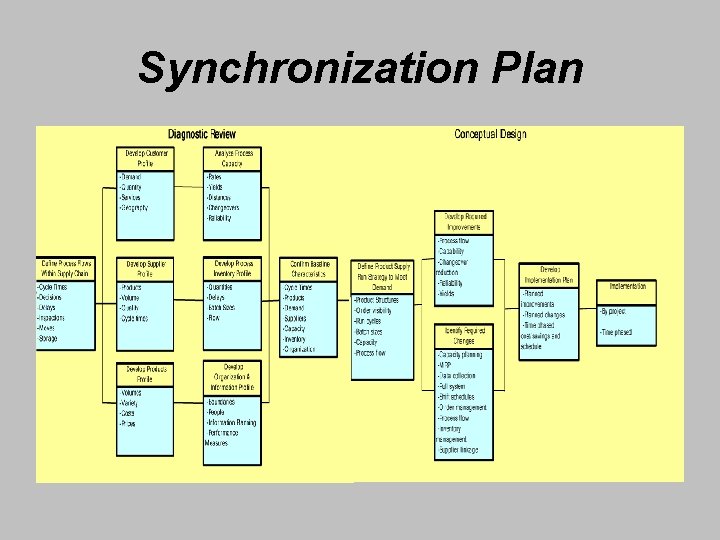
Synchronization Plan
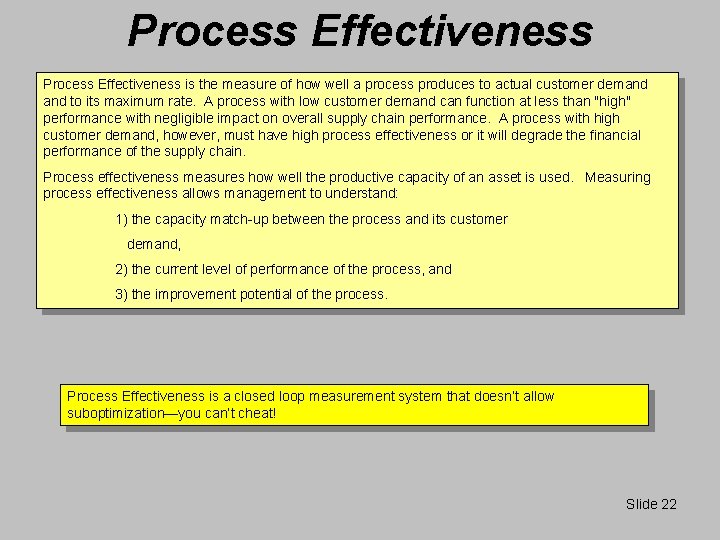
Process Effectiveness is the measure of how well a process produces to actual customer demand to its maximum rate. A process with low customer demand can function at less than "high" performance with negligible impact on overall supply chain performance. A process with high customer demand, however, must have high process effectiveness or it will degrade the financial performance of the supply chain. Process effectiveness measures how well the productive capacity of an asset is used. Measuring process effectiveness allows management to understand: 1) the capacity match-up between the process and its customer demand, 2) the current level of performance of the process, and 3) the improvement potential of the process. Process Effectiveness is a closed loop measurement system that doesn’t allow suboptimization—you can’t cheat! Slide 22
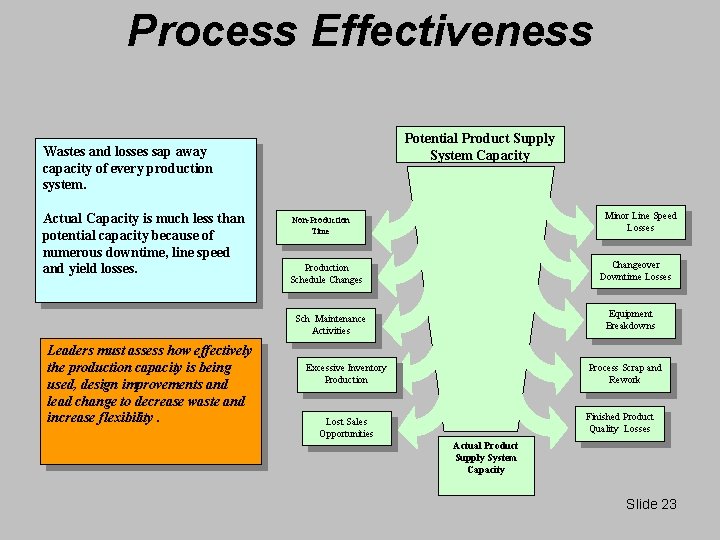
Process Effectiveness Potential Product Supply System Capacity Wastes and losses sap away capacity of every production system. Actual Capacity is much less than potential capacity because of numerous downtime, line speed and yield losses. Minor Line Speed Losses Non-Production Time Changeover Downtime Losses Production Schedule Changes Equipment Breakdowns Sch Maintenance Activities Leaders must assess how effectively the production capacity is being used, design improvements and lead change to decrease waste and increase flexibility. Excessive Inventory Production Process Scrap and Rework Finished Product Quality Losses Lost Sales Opportunities Actual Product Supply System Capacity Slide 23
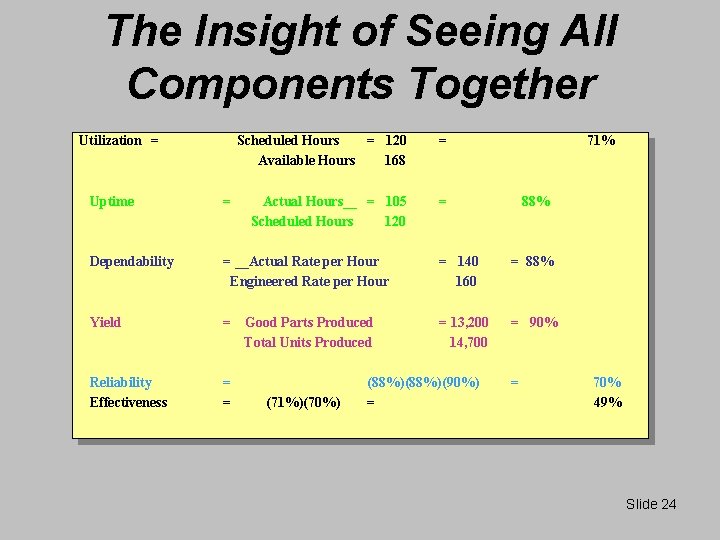
The Insight of Seeing All Components Together Utilization = Scheduled Hours = 120 Available Hours 168 = Actual Hours__ = 105 Scheduled Hours 120 = 71% Uptime = Dependability = __Actual Rate per Hour Engineered Rate per Hour = 140 160 = 88% Yield = = 13, 200 14, 700 = 90% Reliability Effectiveness = = Good Parts Produced Total Units Produced (71%)(70%) (88%)(90%) = 88% = 70% 49% Slide 24
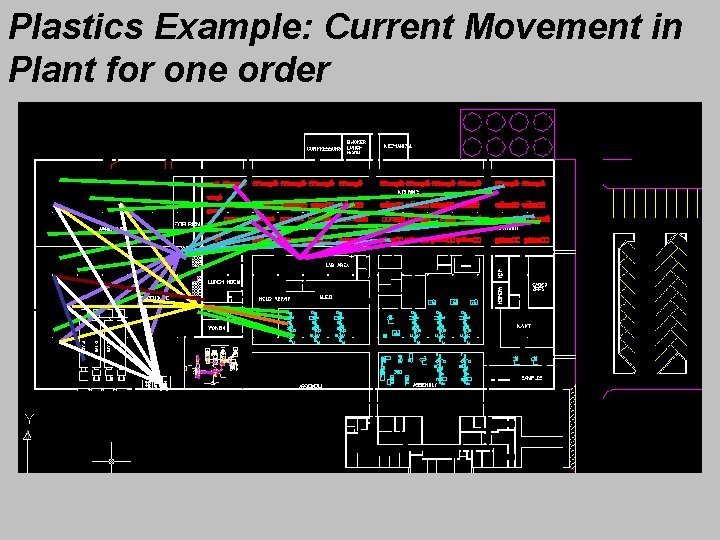
Plastics Example: Current Movement in Plant for one order
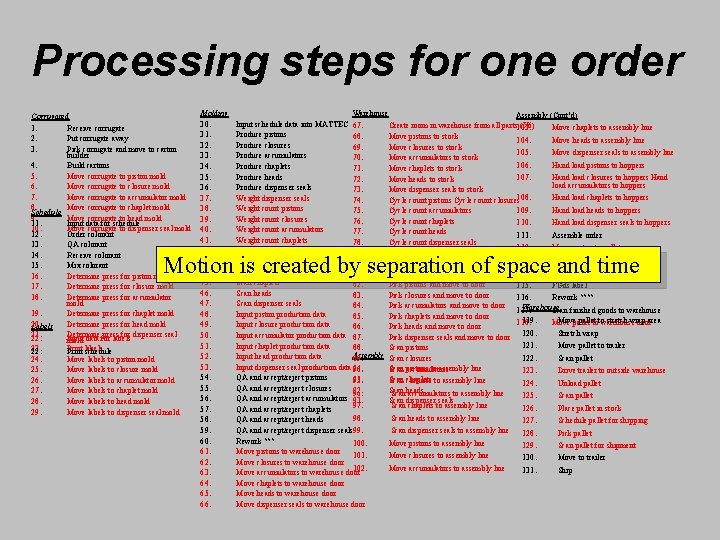
Processing steps for one order Corrugated 1. Receive corrugate 2. Put corrugate away 3. Pick corrugate and move to carton builder 4. Build cartons 5. Move corrugate to piston mold 6. Move corrugate to closure mold 7. Move corrugate to accumulator mold 8. Move corrugate to chaplet mold Schedule 9. Move corrugate to head mold 11. Input data for schedule 10. Move corrugate to dispenser seal mold 12. Order colorant 13. QA colorant 14. Receive colorant 15. Mix colorant 16. Determine press for piston mold 17. Determine press for closure mold 18. Determine press for accumulator mold 19. Determine press for chaplet mold 20. Determine press for head mold Labels 21. Determine press for dispenser seal 22. Input mold data for labels 23. Print labels 22. Print schedule 24. Move labels to piston mold 25. Move labels to closure mold 26. Move labels to accumulator mold 27. Move labels to chaplet mold 28. Move labels to head mold 29. Move labels to dispenser seal mold Molding 30. 31. 32. 33. 34. 35. 36. 37. 38. 39. 40. 41. 42. 43. 44. 45. 46. 47. 48. 49. 50. 51. 52. 53. 54. 55. 56. 57. 58. 59. 60. 61. 62. 63. 64. 65. 66. Warehouse Assembly (Cont’d) Input schedule data into MATTEC 67. Create room in warehouse from all parts 103. (X 6) Move chaplets to assembly line Produce pistons 68. Move pistons to stock 104. Move heads to assembly line Produce closures 69. Move closures to stock 105. Move dispenser seals to assembly line Produce accumulators 70. Move accumulators to stock 106. Hand load pistons to hoppers Produce chaplets 71. Move chaplets to stock Produce heads 107. Hand load closures to hoppers Hand 72. Move heads to stock load accumulators to hoppers Produce dispenser seals 73. Move dispenser seals to stock 108. Hand load chaplets to hoppers Weight dispenser seals 74. Cycle count pistons Cycle count closures Weight count pistons 109. Hand load heads to hoppers 75. Cycle count accumulators Weight count closures 76. Cycle count chaplets 110. Hand load dispenser seals to hoppers Weight count accumulators 77. Cycle count heads 111. Assemble order Weight count chaplets 78. Cycle count dispenser seals 112. Move carton to pallet Weight count heads Scan pistons 79. Relocate ? ? (many times X 6) 113. QA accept/reject Scan closures 80. Schedule order Scan accumulators 114. Printe 81. Input Pick Request Scan chaplets 82. Pick pistons and move to door 115. FGds label Scan heads 83. Pick closures and move to door 116. Rework ? ? Scan dispenser seals 84. Pick accumulators and move to door Warehouse 117. Scan finished goods to warehouse Input piston production data 85. Pick chaplets and move to door 119. Movepallettotowarehouse stretch wrap 118. Move doorarea Input closure production data 86. Pick heads and move to door 120. Stretch wrap Input accumulator production data 87. Pick dispenser seals and move to door 121. Move pallet to trailer Input chaplet production data 88. Scan pistons Assembly Input head production data 122. Scan pallet 89. Scan closures Input dispenser seal production data 90. 94. pistons to assembly line Scan accumulators 123. Drive trailer to outside warehouse QA and accept/reject pistons 91. Scan chaplets 95. closures to assembly line 124. Unload pallet QA and accept/reject closures 92. Scan 96. Scanheads accumulators to assembly line 125. Scan pallet QA and accept/reject accumulators 93. Scan dispenser seals 97. Scan chaplets to assembly line 126. Place pallet in stock QA and accept/reject chaplets 98. Scan heads to assembly line QA and accept/reject heads 127. Schedule pallet for shipping Motion is created by separation of space and time QA and accept/reject dispenser seals 99. Rework ? ? ? 100. Move pistons to warehouse door 101. Move closures to warehouse door 102. Move accumulators to warehouse door Move chaplets to warehouse door Move heads to warehouse door Move dispenser seals to warehouse door Scan dispenser seals to assembly line Move pistons to assembly line Move closures to assembly line Move accumulators to assembly line 128. 129. 130. 131. Pick pallet Scan pallet for shipment Move to trailer Ship
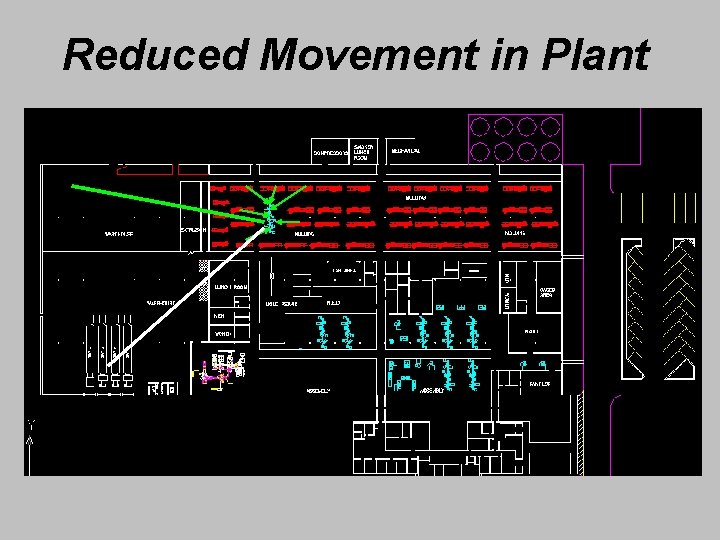
Reduced Movement in Plant
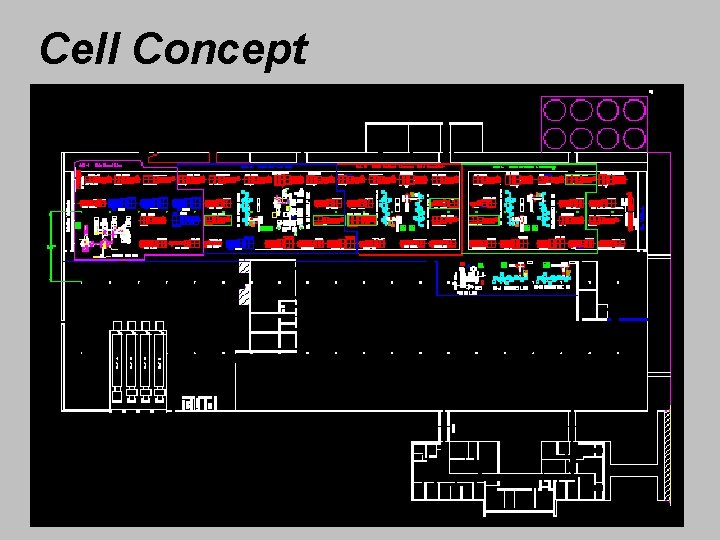
Cell Concept
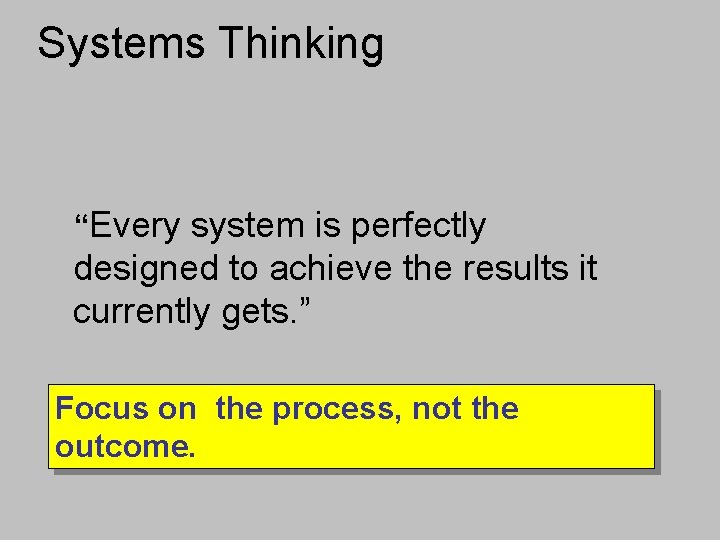
Systems Thinking “Every system is perfectly designed to achieve the results it currently gets. ” Focus on the process, not the outcome.
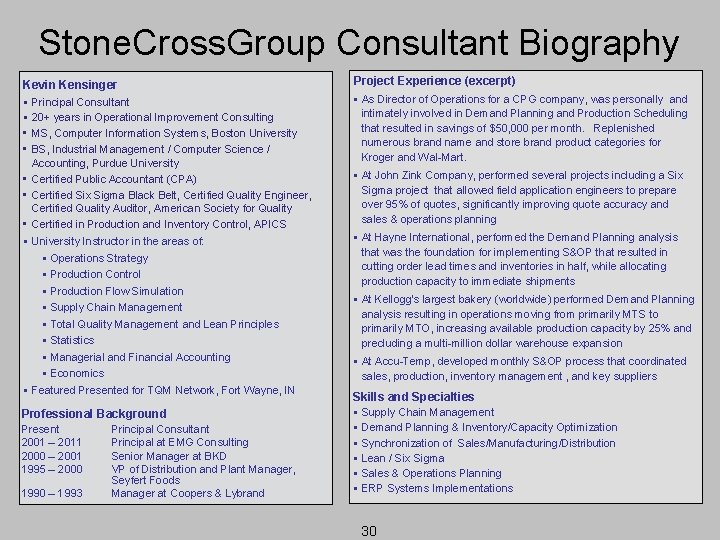
Stone. Cross. Group Consultant Biography Kevin Kensinger Project Experience (excerpt) § Principal Consultant § As Director of Operations for a CPG company, was personally and § 20+ years in Operational Improvement Consulting • MS, Computer Information Systems, Boston University • BS, Industrial Management / Computer Science / Accounting, Purdue University • Certified Public Accountant (CPA) • Certified Six Sigma Black Belt, Certified Quality Engineer, Certified Quality Auditor, American Society for Quality • Certified in Production and Inventory Control, APICS § University Instructor in the areas of: § Operations Strategy § Production Control § Production Flow Simulation § Supply Chain Management § Total Quality Management and Lean Principles § Statistics § Managerial and Financial Accounting § Economics § Featured Presented for TQM Network, Fort Wayne, IN intimately involved in Demand Planning and Production Scheduling that resulted in savings of $50, 000 per month. Replenished numerous brand name and store brand product categories for Kroger and Wal-Mart. § At John Zink Company, performed several projects including a Six Sigma project that allowed field application engineers to prepare over 95% of quotes, significantly improving quote accuracy and sales & operations planning § At Hayne International, performed the Demand Planning analysis that was the foundation for implementing S&OP that resulted in cutting order lead times and inventories in half, while allocating production capacity to immediate shipments § At Kellogg’s largest bakery (worldwide) performed Demand Planning analysis resulting in operations moving from primarily MTS to primarily MTO, increasing available production capacity by 25% and precluding a multi-million dollar warehouse expansion § At Accu-Temp, developed monthly S&OP process that coordinated sales, production, inventory management , and key suppliers Skills and Specialties Professional Background § Supply Chain Management Present 2001 – 2011 2000 – 2001 1995 – 2000 § Demand Planning & Inventory/Capacity Optimization 1990 – 1993 Principal Consultant Principal at EMG Consulting Senior Manager at BKD VP of Distribution and Plant Manager, Seyfert Foods Manager at Coopers & Lybrand § Synchronization of Sales/Manufacturing/Distribution § Lean / Six Sigma § Sales & Operations Planning § ERP Systems Implementations 30
Supply chain synchronization
Bài thơ mẹ đi làm từ sáng sớm
Cơm
Matching supply with demand
What is logistics management
Eltonian pyramid
Asq certified calibration technician
Certified biomedical auditor
Asq 9100
Asq skjema
Cqe recertification
Asq world conference
Operations management chapter 10 quality control solutions
Asq se 2 scoring interpretation
Asq sampling plan
Asq quality tools
Asq reliability
Aci asq
Ages and stages questionnaire calculator
Asq cba
410/18
Si-410
The bradley family owns 410 acres
Inverted indexing
Svsd 410
Gmayag
Cse 410
What is cross projection sketch
6-12/410
Ved yöntemi nedir
Ethics entertainment