APATS Presentation From Reacting to Learning From Reacting
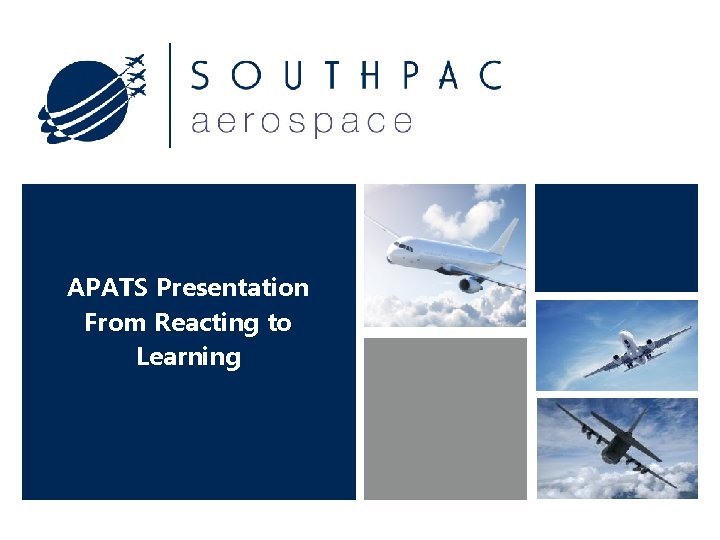
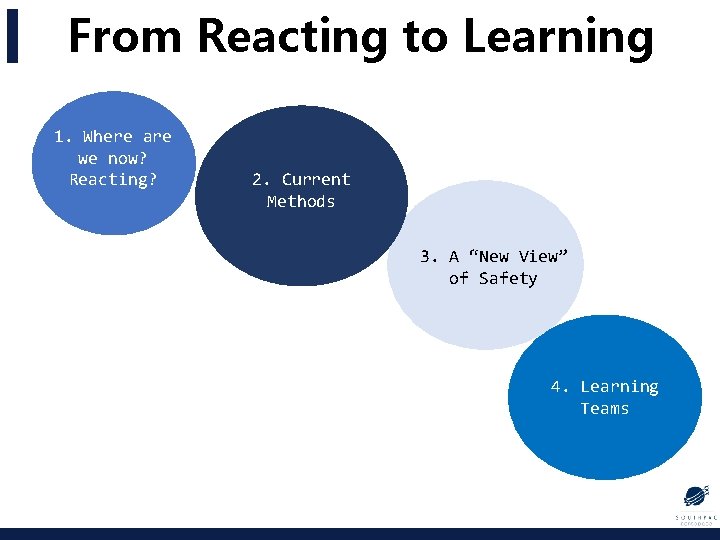
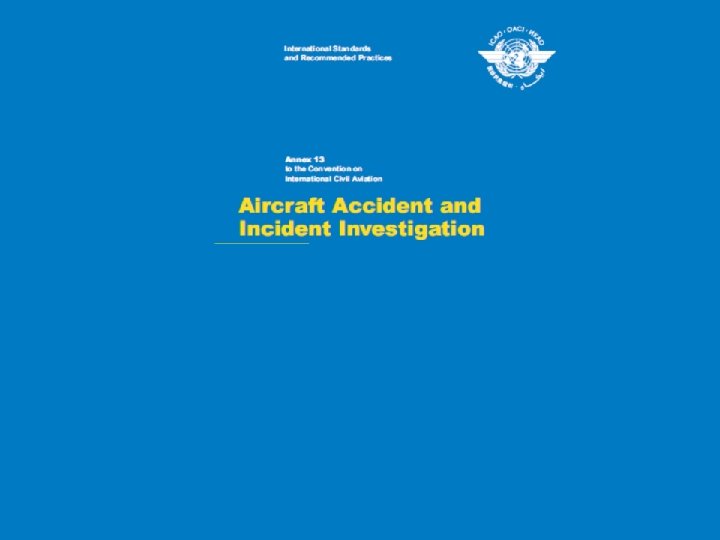
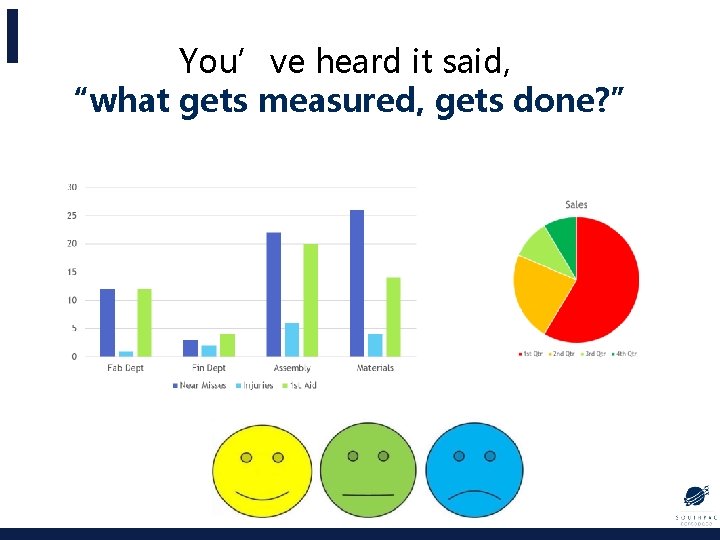
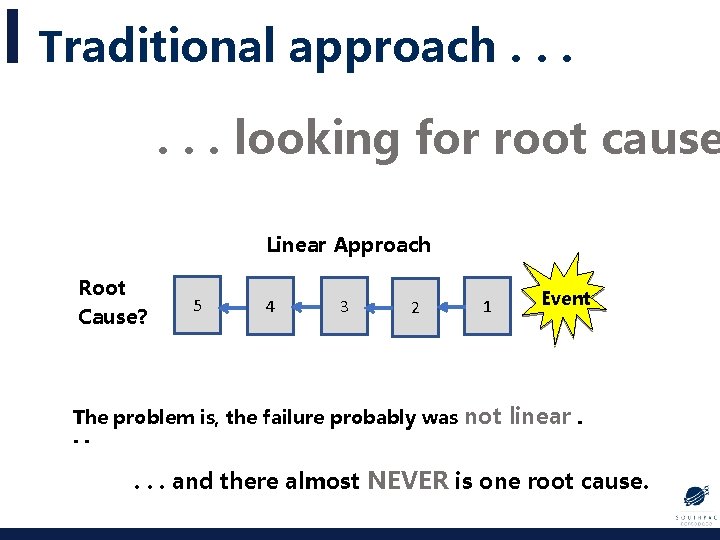
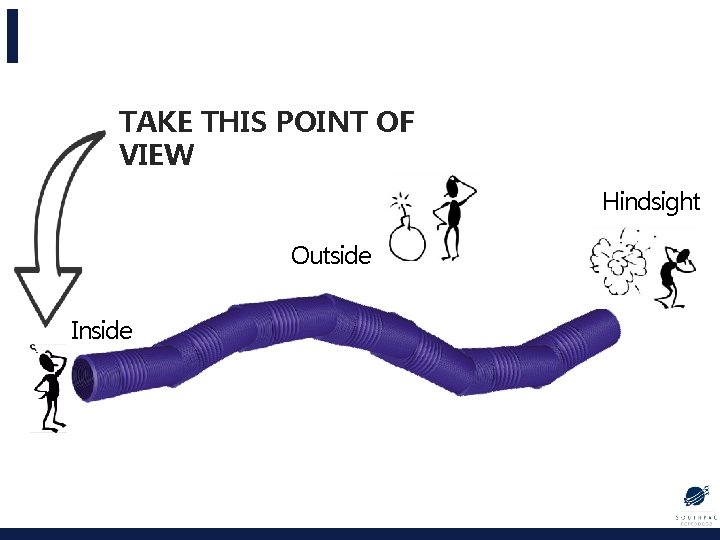
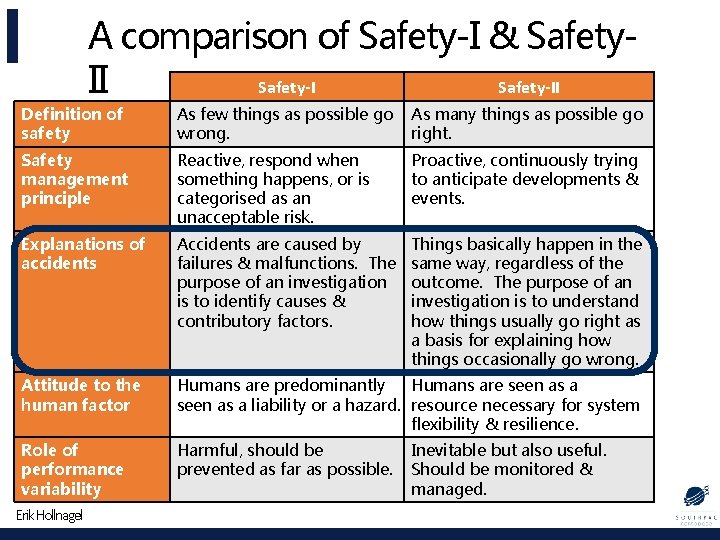
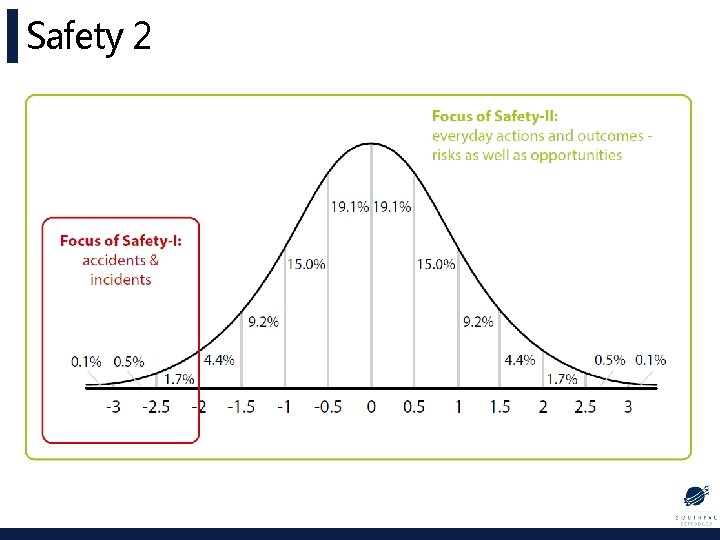
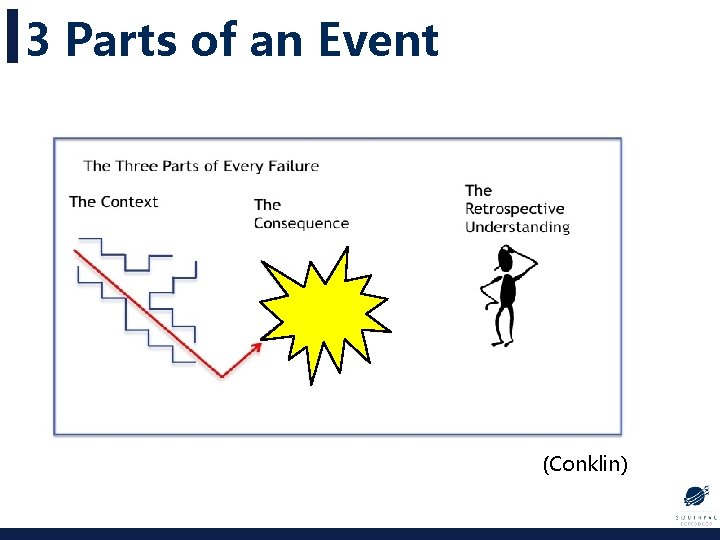
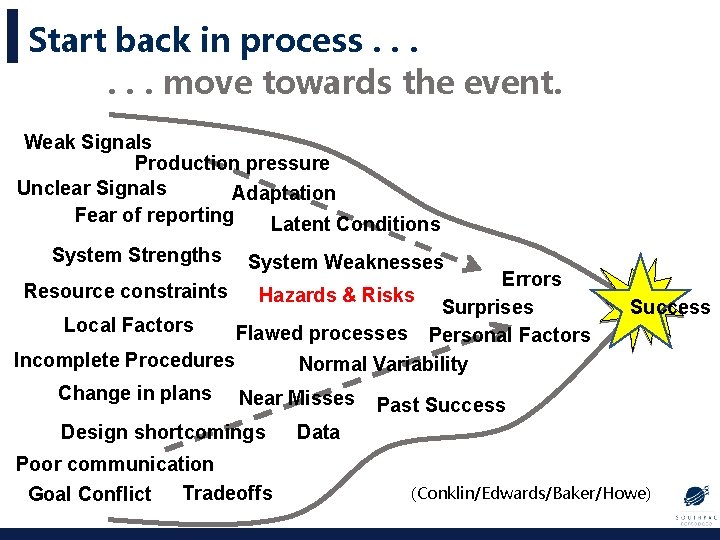
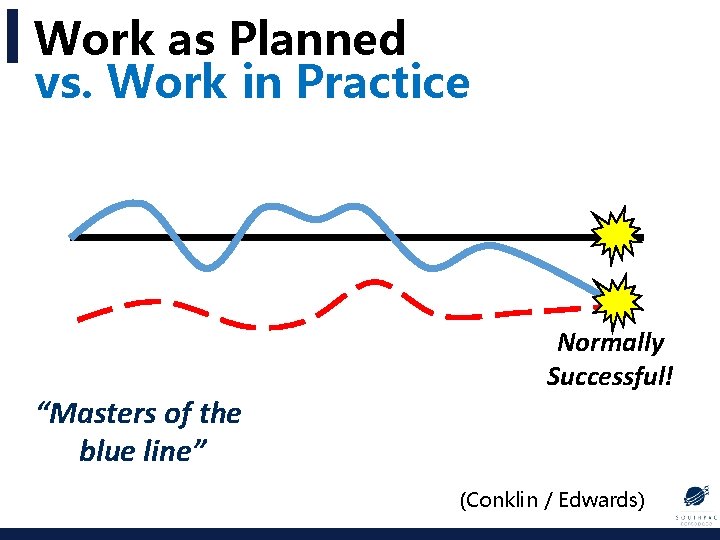
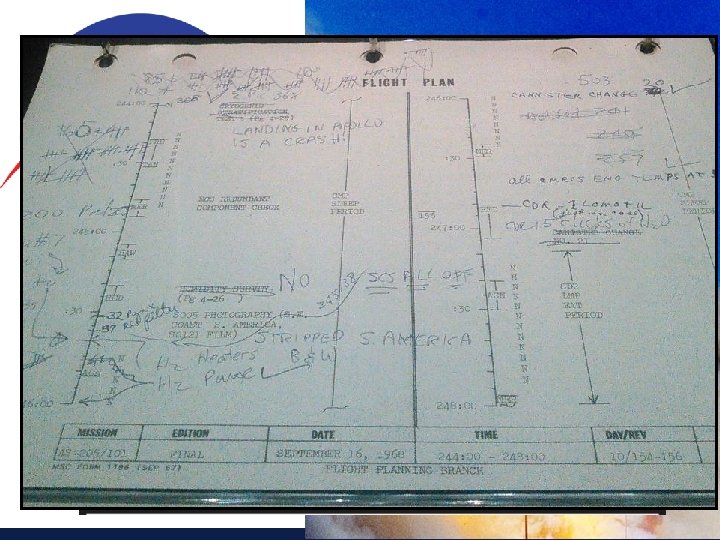
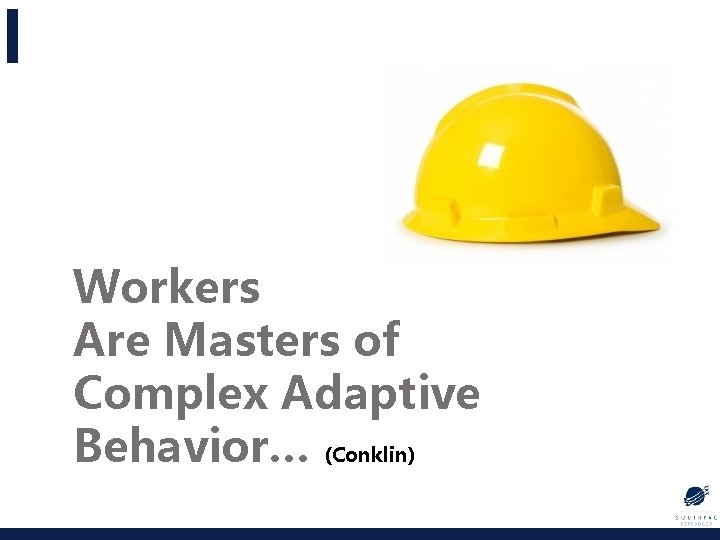
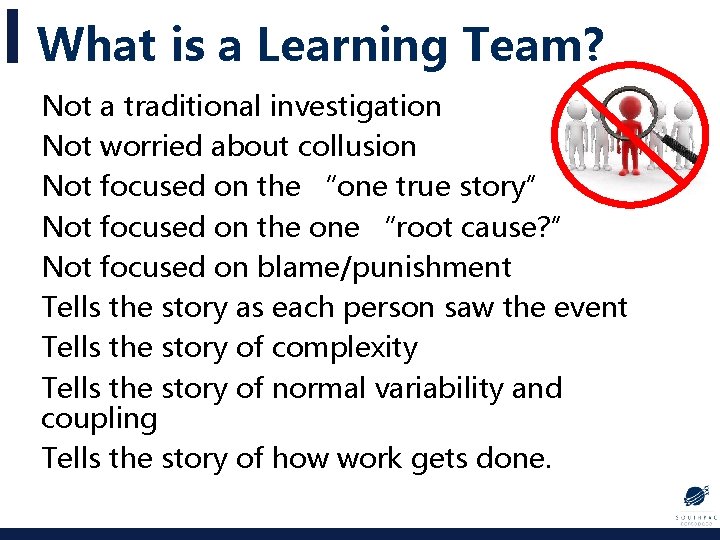
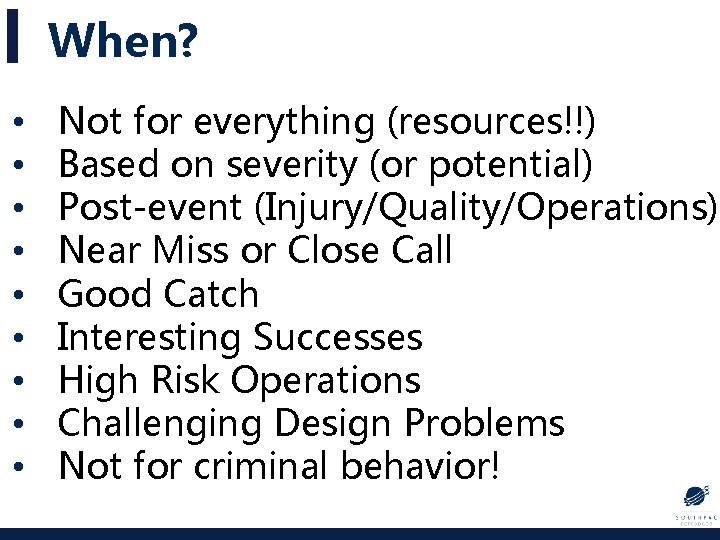
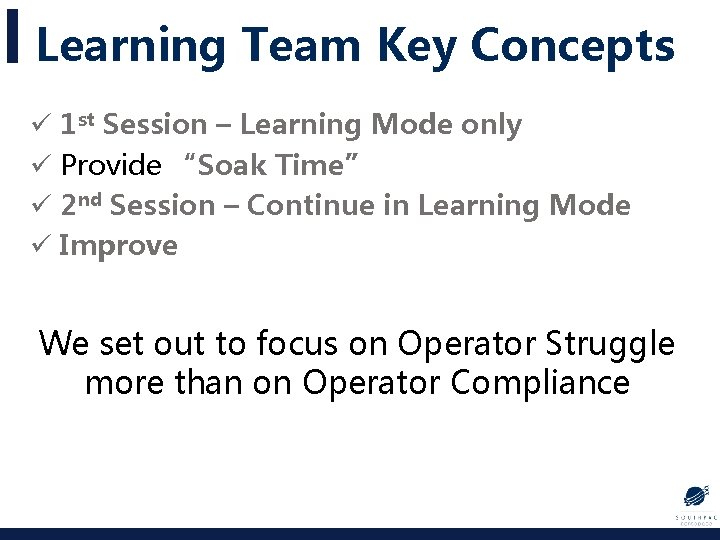
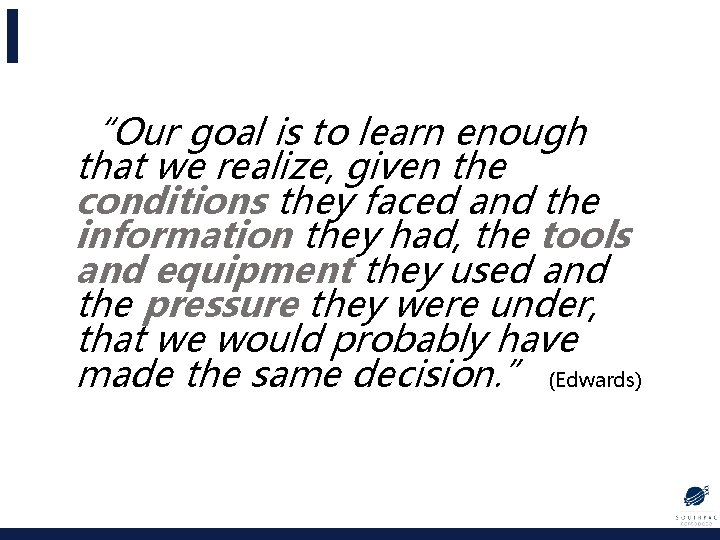
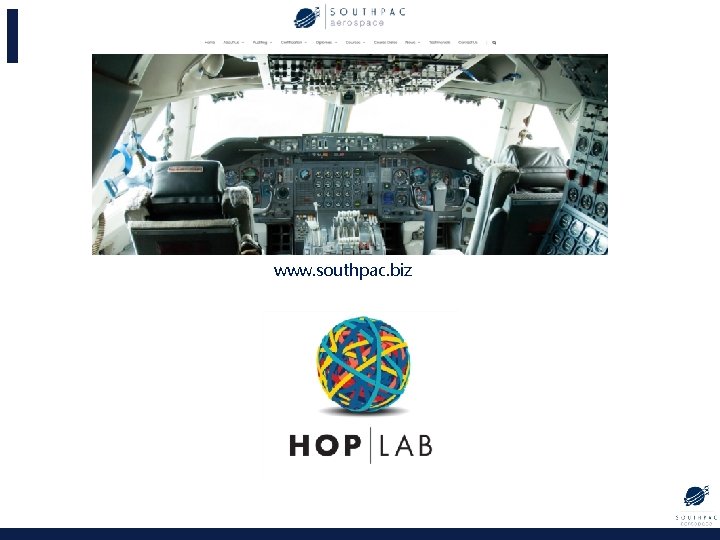
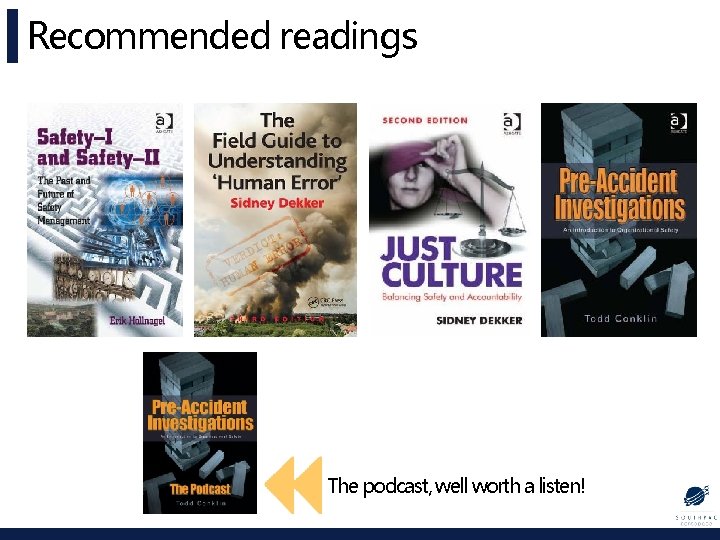
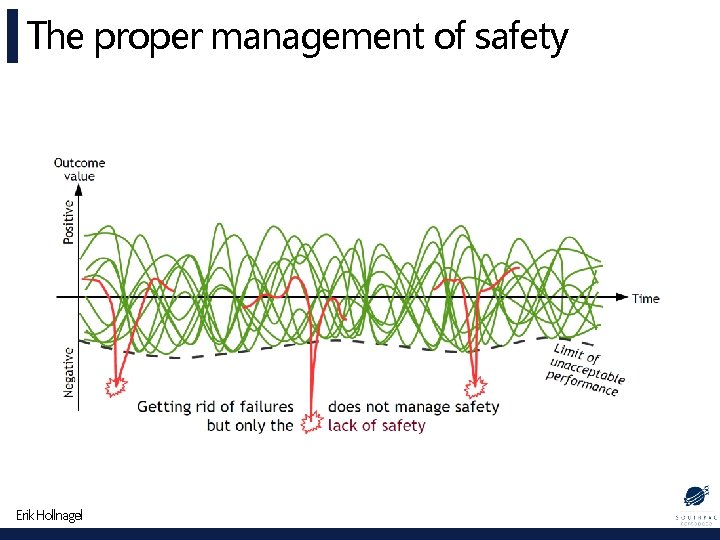
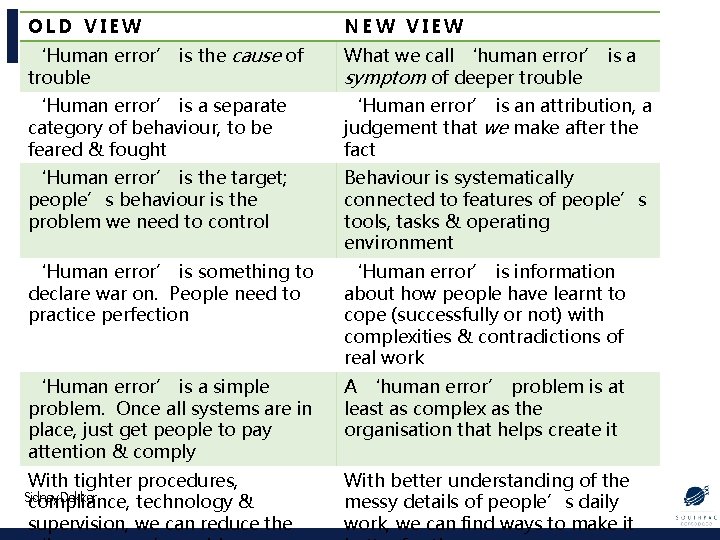
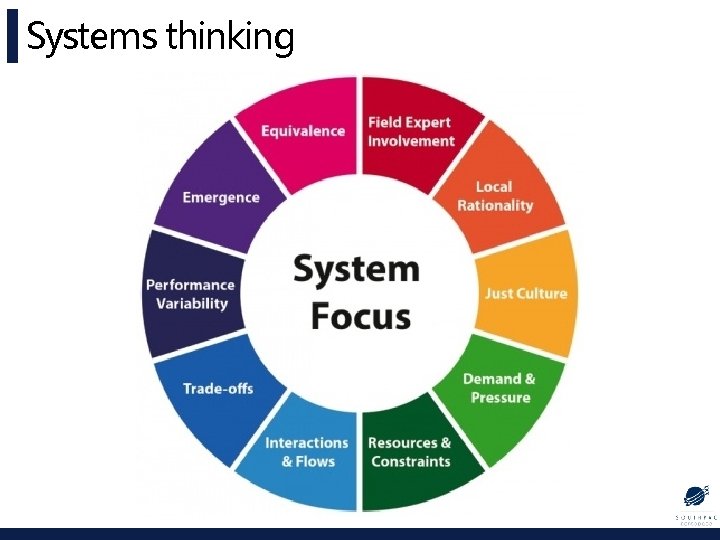
- Slides: 22
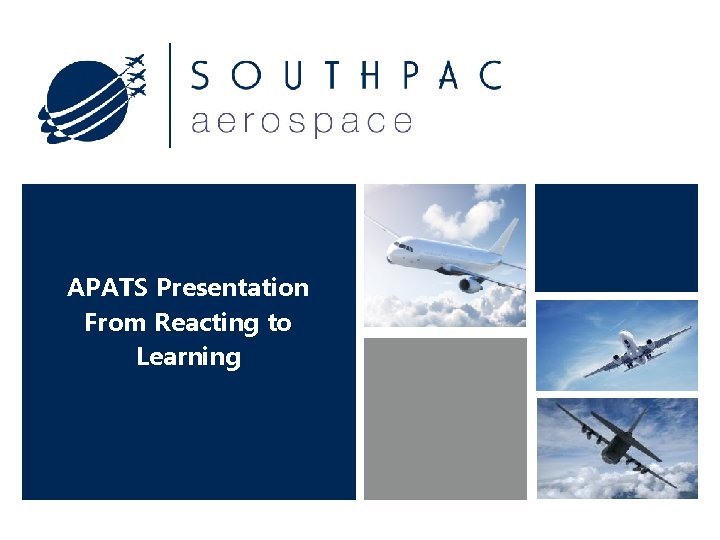
APATS Presentation From Reacting to Learning
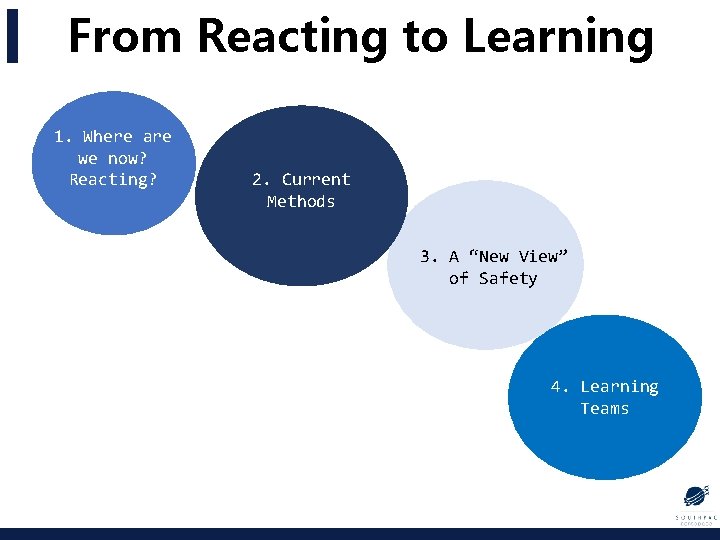
From Reacting to Learning 1. Where are we now? Reacting? 2. Current Methods 3. A “New View” of Safety 4. Learning Teams
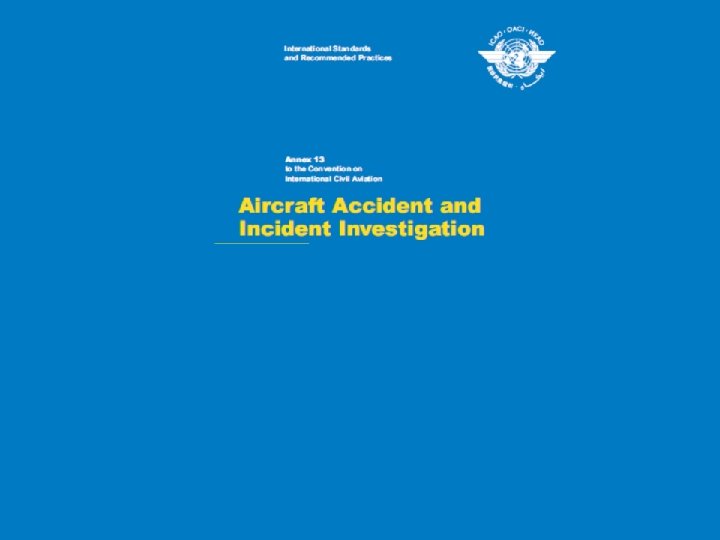
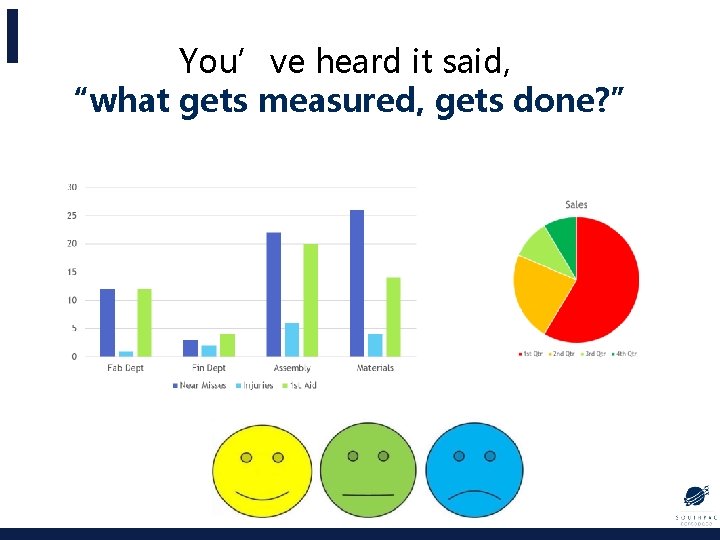
You’ve heard it said, “what gets measured, gets done? ”
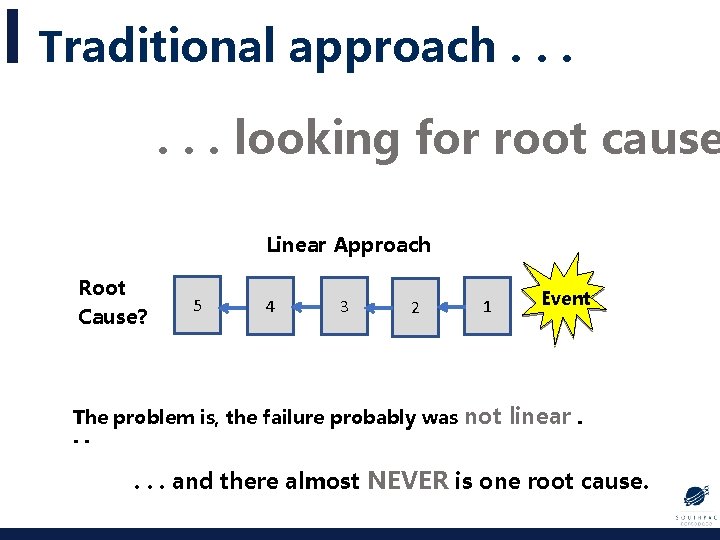
Traditional approach. . . looking for root cause Linear Approach Root Cause? 5 4 3 2 1 Event The problem is, the failure probably was not linear. . . and there almost NEVER is one root cause.
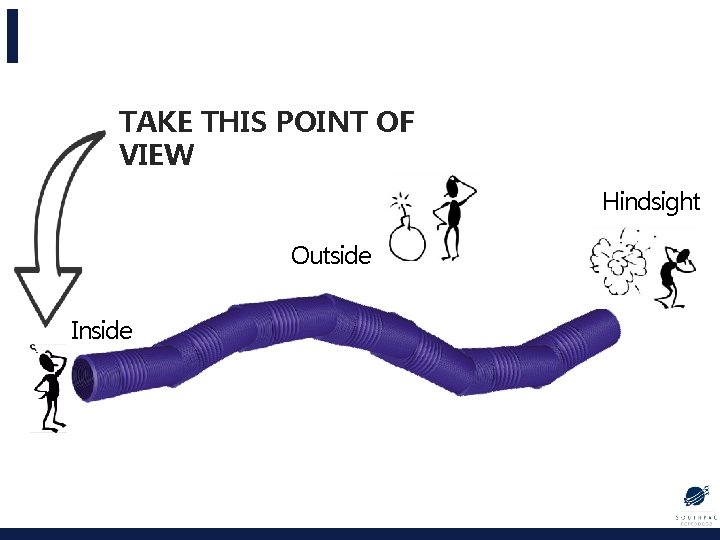
TAKE THIS POINT OF VIEW Hindsight Outside Inside
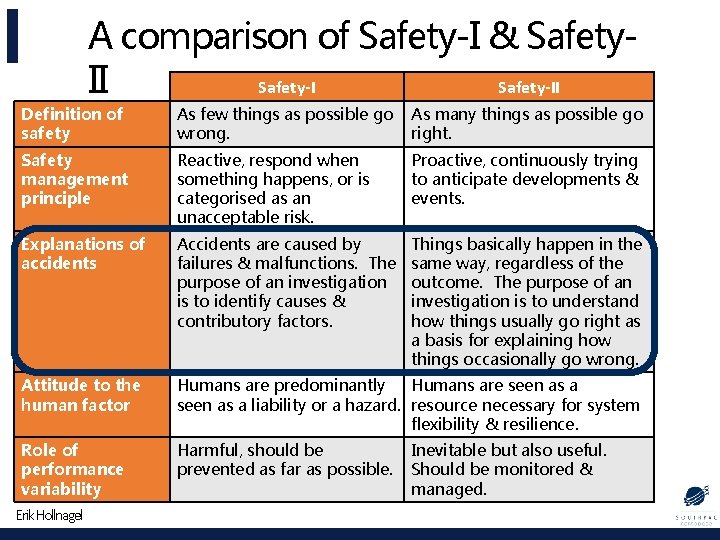
A comparison of Safety-I & Safety. II Safety-II Definition of safety As few things as possible go wrong. As many things as possible go right. Safety management principle Reactive, respond when something happens, or is categorised as an unacceptable risk. Proactive, continuously trying to anticipate developments & events. Explanations of accidents Accidents are caused by failures & malfunctions. The purpose of an investigation is to identify causes & contributory factors. Things basically happen in the same way, regardless of the outcome. The purpose of an investigation is to understand how things usually go right as a basis for explaining how things occasionally go wrong. Attitude to the human factor Humans are predominantly Humans are seen as a liability or a hazard. resource necessary for system flexibility & resilience. Role of performance variability Harmful, should be prevented as far as possible. Erik Hollnagel Inevitable but also useful. Should be monitored & managed.
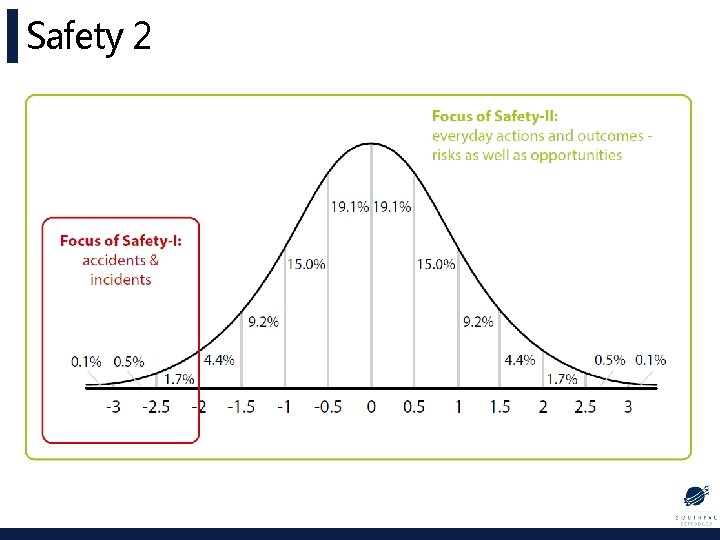
Safety 2
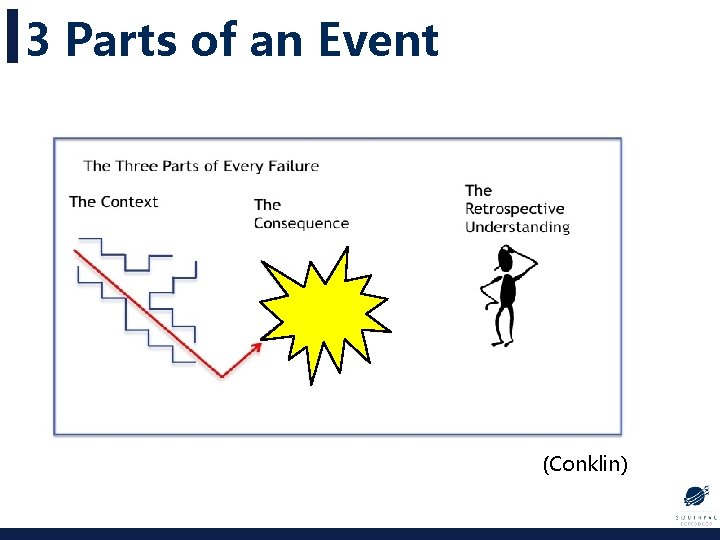
3 Parts of an Event (Conklin)
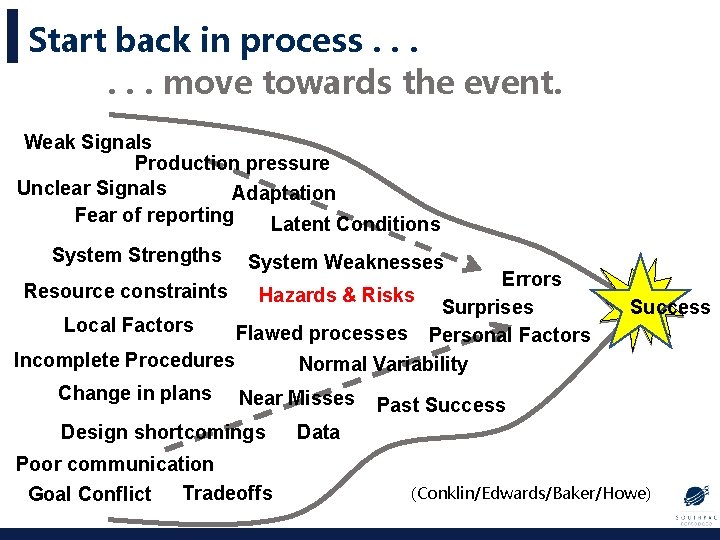
Start back in process. . . move towards the event. Weak Signals Production pressure Unclear Signals Adaptation Fear of reporting Latent Conditions System Strengths System Weaknesses Errors Hazards & Risks Surprises Local Factors Flawed processes Personal Factors Incomplete Procedures Normal Variability Change in plans Near Misses Past Success Data Design shortcomings Resource constraints Poor communication Goal Conflict Tradeoffs Event Success (Conklin/Edwards/Baker/Howe)
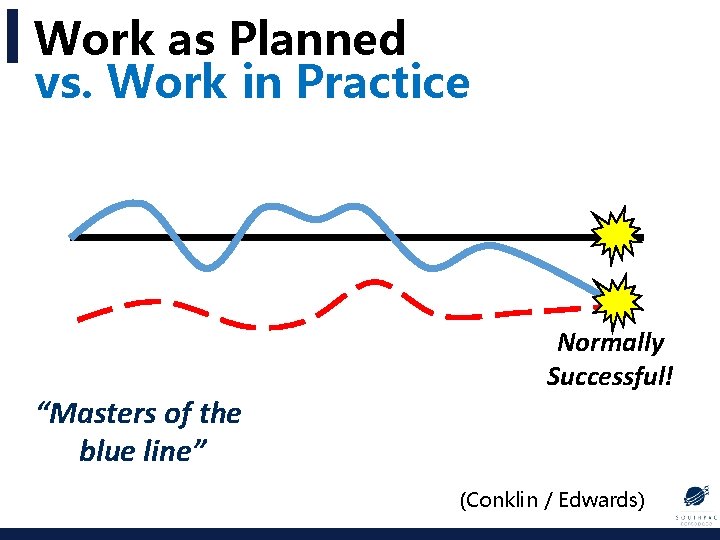
Work as Planned vs. Work in Practice “Masters of the blue line” Normally Successful! (Conklin / Edwards)
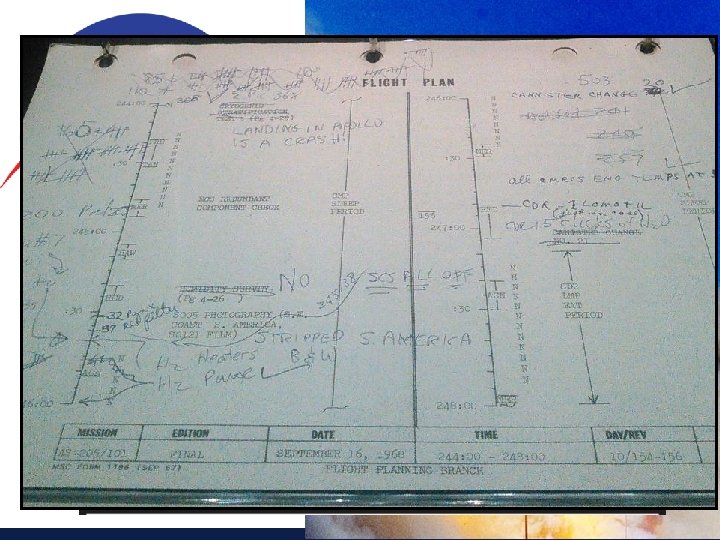
Apollo 7 Saturn IB Rocket
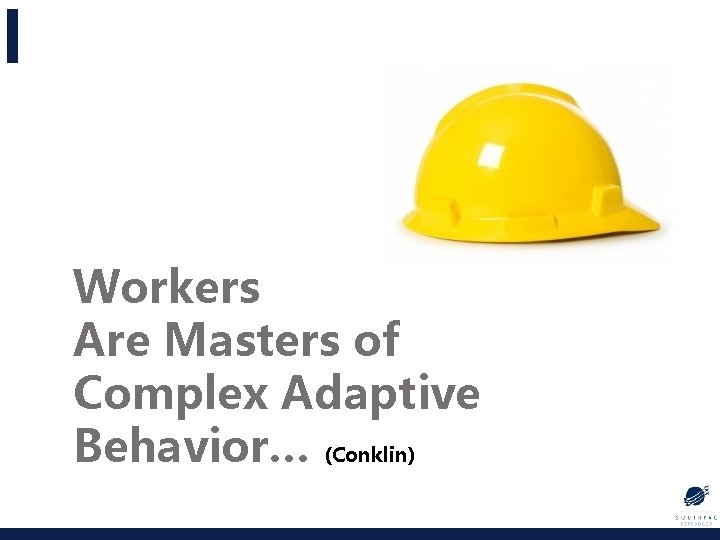
Workers Are Masters of Complex Adaptive Behavior… (Conklin)
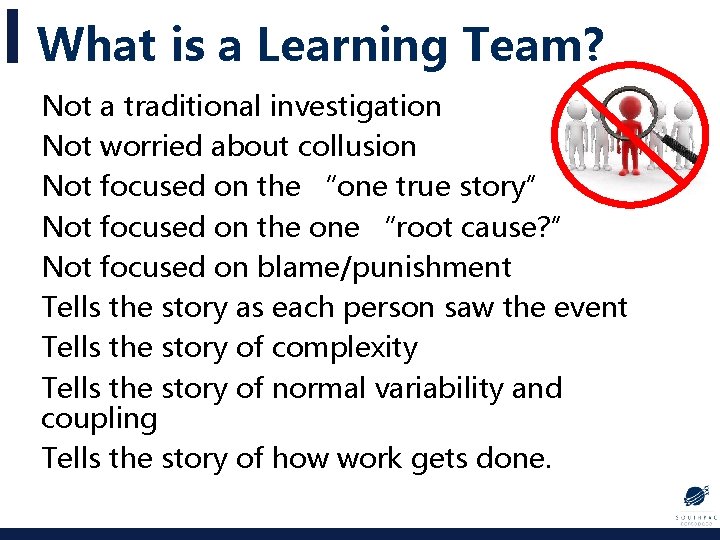
What is a Learning Team? Not a traditional investigation Not worried about collusion Not focused on the “one true story” Not focused on the one “root cause? ” Not focused on blame/punishment Tells the story as each person saw the event Tells the story of complexity Tells the story of normal variability and coupling Tells the story of how work gets done.
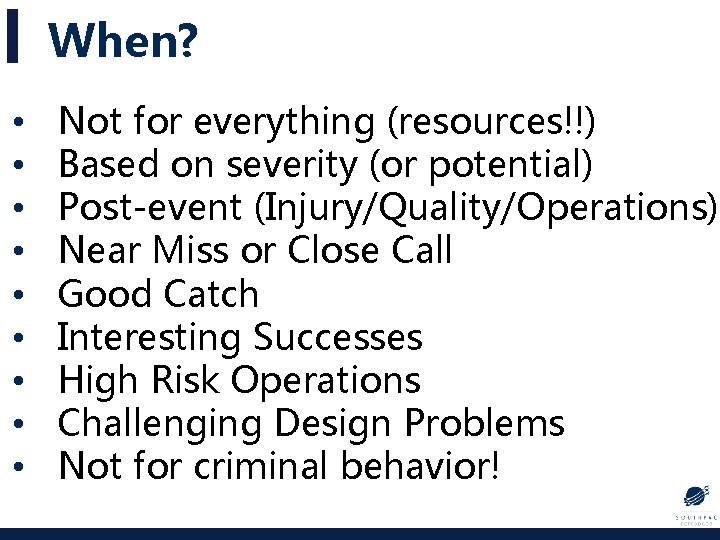
When? • • • Not for everything (resources!!) Based on severity (or potential) Post-event (Injury/Quality/Operations) Near Miss or Close Call Good Catch Interesting Successes High Risk Operations Challenging Design Problems Not for criminal behavior!
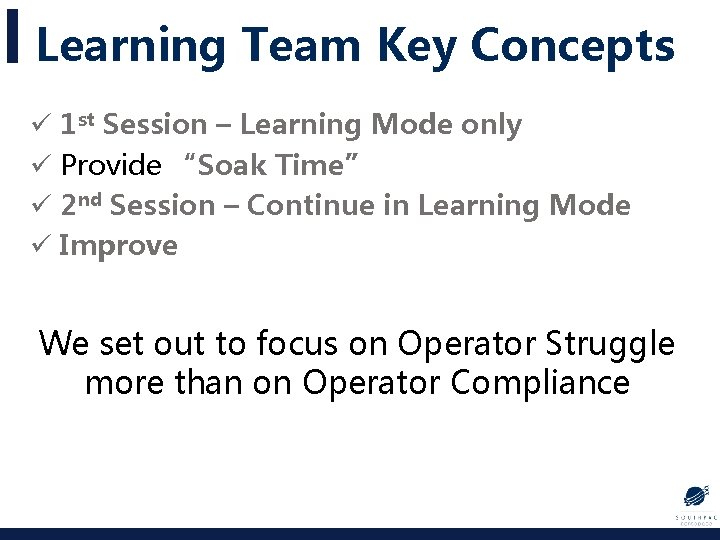
Learning Team Key Concepts ü 1 st Session – Learning Mode only ü Provide “Soak Time” ü 2 nd Session – Continue in Learning Mode ü Improve We set out to focus on Operator Struggle more than on Operator Compliance
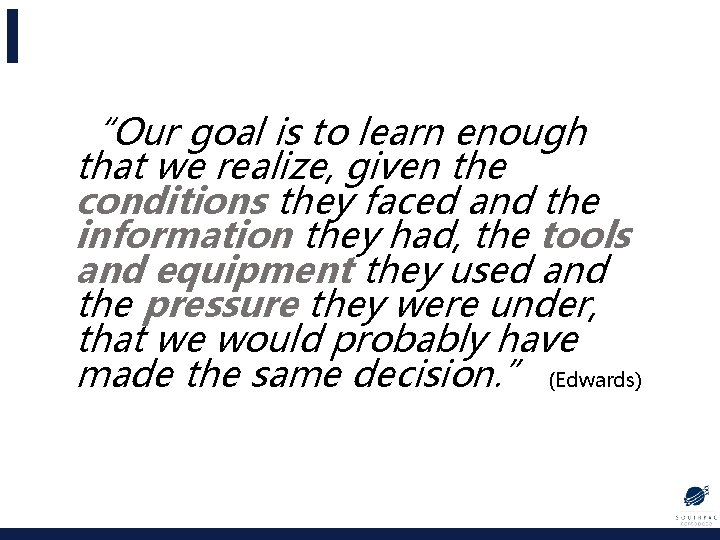
“Our goal is to learn enough that we realize, given the conditions they faced and the information they had, the tools and equipment they used and the pressure they were under, that we would probably have made the same decision. ” (Edwards)
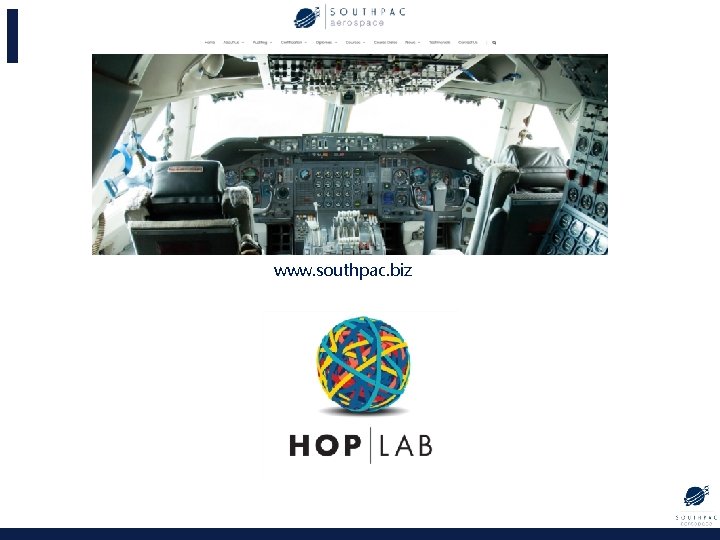
www. southpac. biz
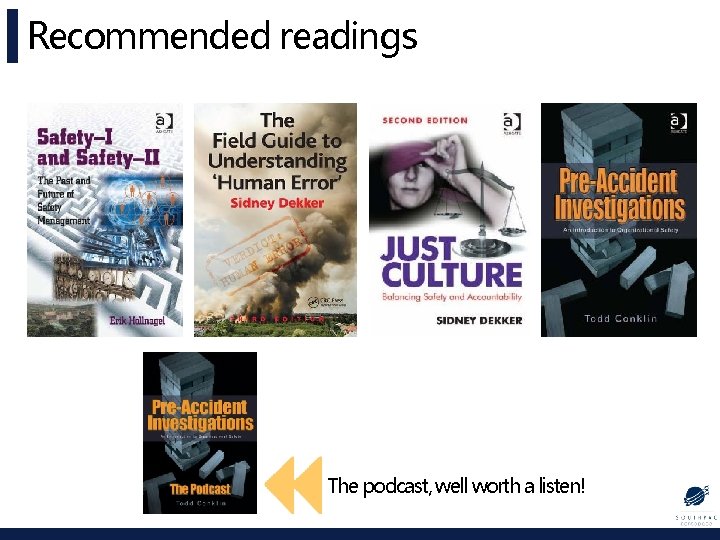
Recommended readings The podcast, well worth a listen!
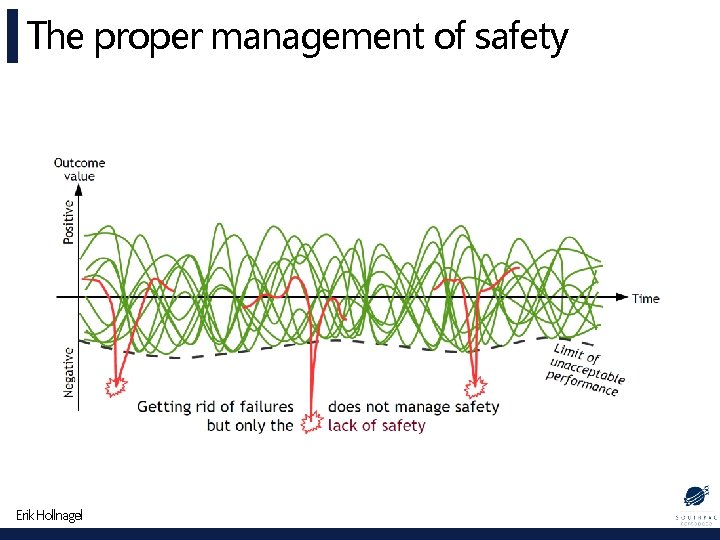
The proper management of safety Erik Hollnagel
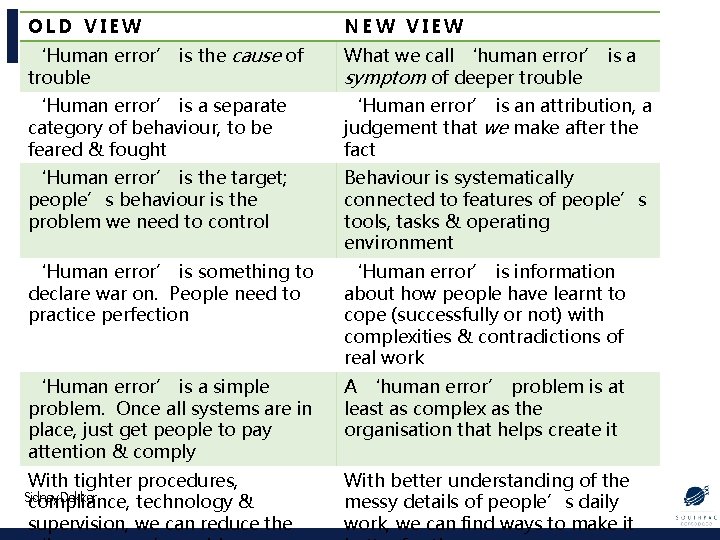
OLD VIEW NEW VIEW ‘Human error’ is the cause of trouble What we call ‘human error’ is a symptom of deeper trouble ‘Human error’ is a separate category of behaviour, to be feared & fought ‘Human error’ is an attribution, a judgement that we make after the fact ‘Human error’ is the target; people’s behaviour is the problem we need to control Behaviour is systematically connected to features of people’s tools, tasks & operating environment ‘Human error’ is something to declare war on. People need to practice perfection ‘Human error’ is information about how people have learnt to cope (successfully or not) with complexities & contradictions of real work ‘Human error’ is a simple problem. Once all systems are in place, just get people to pay attention & comply A ‘human error’ problem is at least as complex as the organisation that helps create it With tighter procedures, Sidney Dekker compliance, technology & supervision, we can reduce the With better understanding of the messy details of people’s daily work, we can find ways to make it
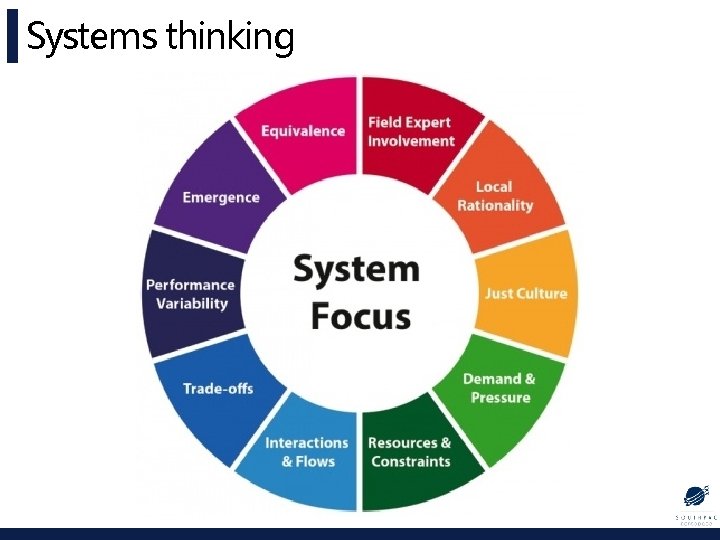
Systems thinking
Lithium and oxygen word equation
First law analysis of combustion process
Magnesium reacting with nitric acid equation
Reacting masses questions
Reacting masses and volumes
Chemical name for sodium carbonate
Magnesium reacting with oxygen
Alkali metals reacting with water
React to indirect fire while mounted
How to react to indirect fire
Reaction of copper with air
Alkali metals reacting with water
Alkali metals reacting with water
Cuadro comparativo de e-learning
Diameters of fetal head
Vertex presentation and cephalic presentation
Learning and development strategy presentation
Comp 6321 concordia
"deep reinforcement learning"
Concept learning task in machine learning
Analytical learning in machine learning
Nonassociative learning example
Remarks on lazy and eager learning