2010 ASHRAE Rocky Mountain Chapter VFD Fundamentals April
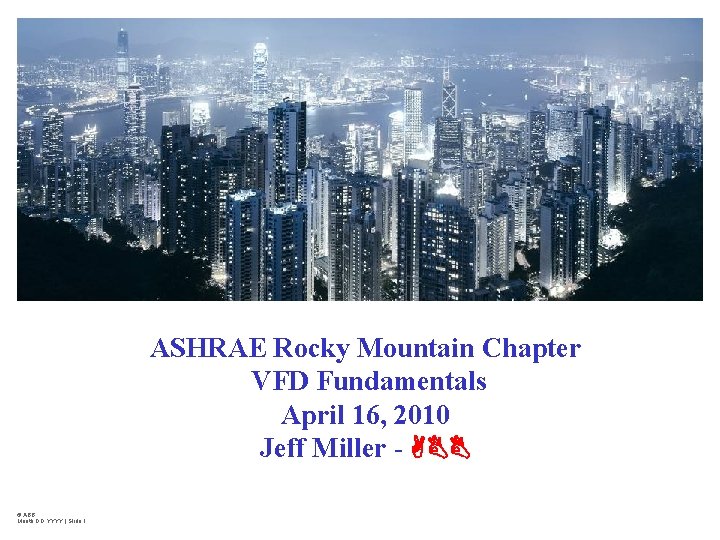
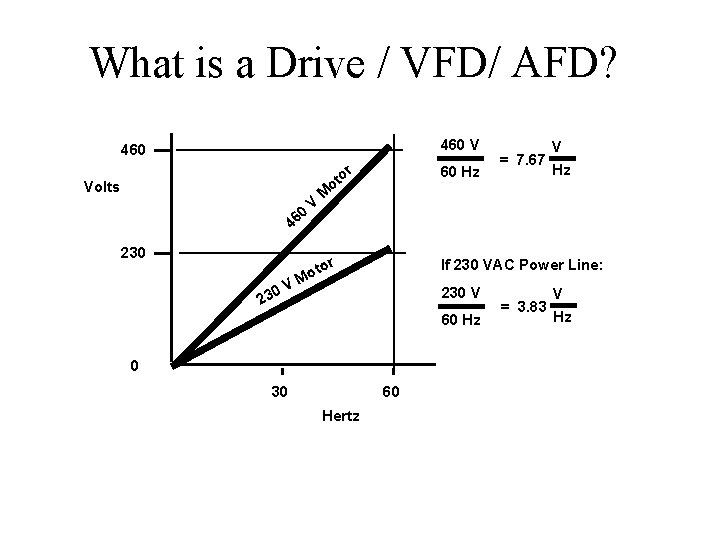
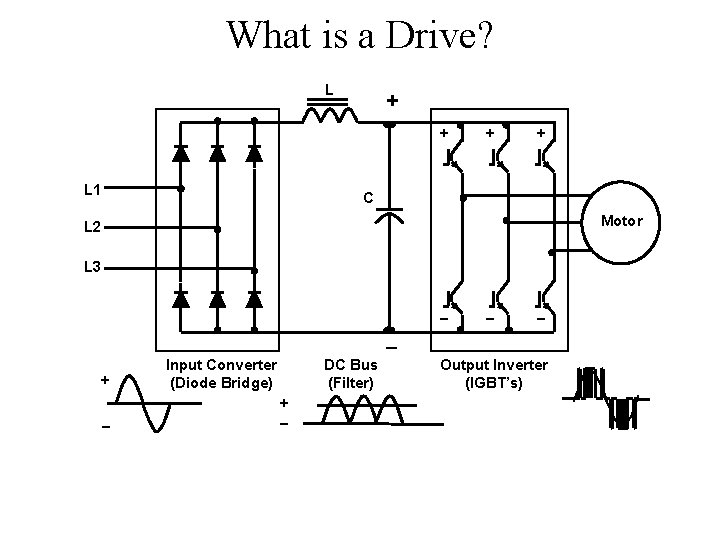
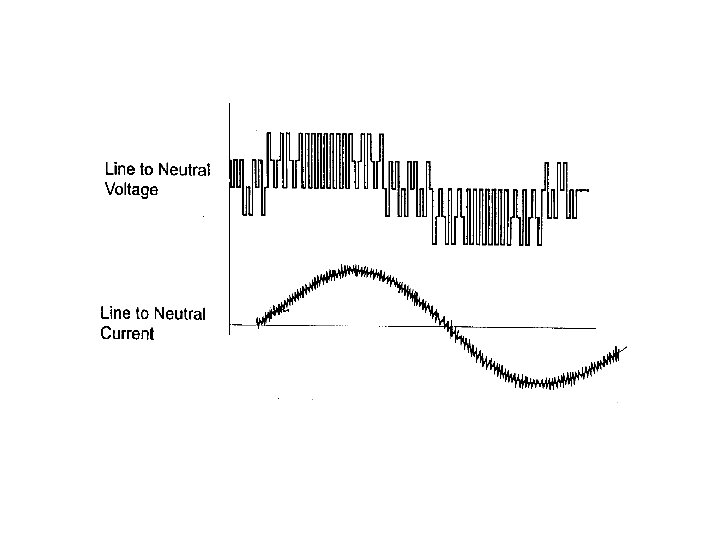
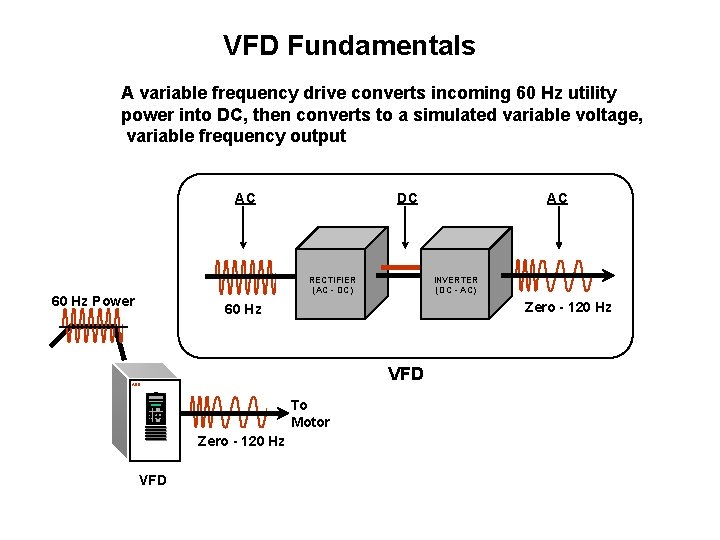
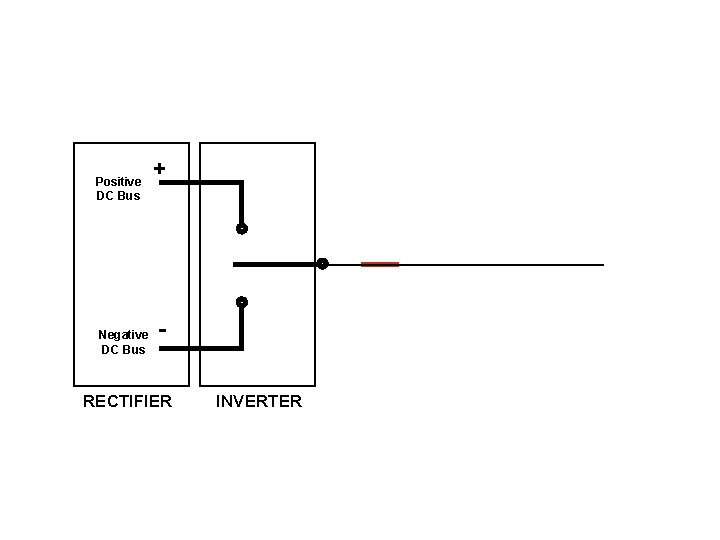
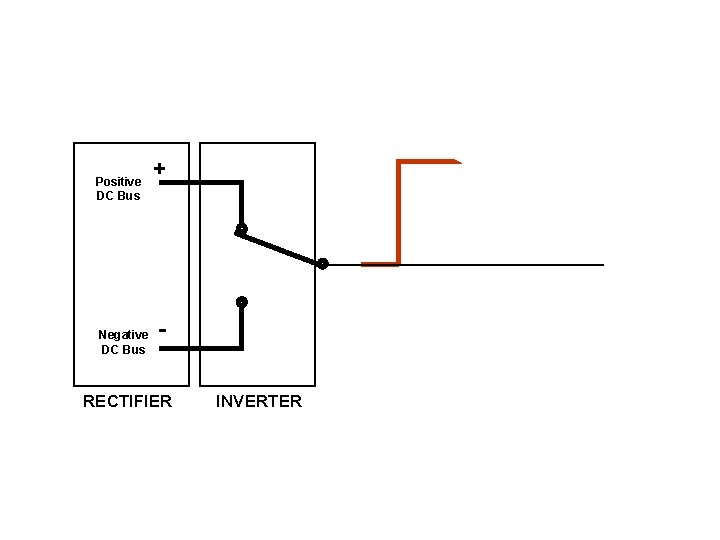
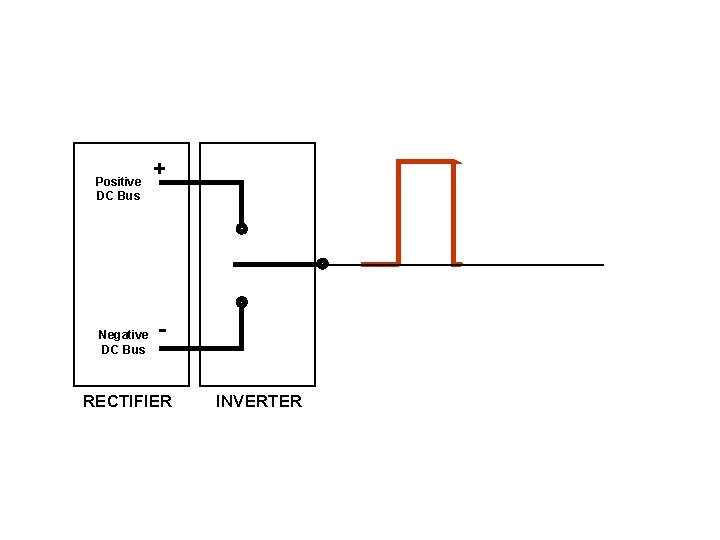
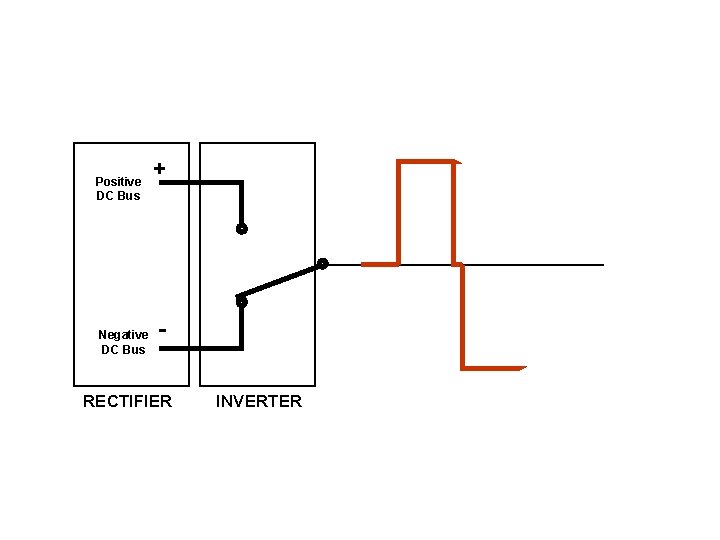
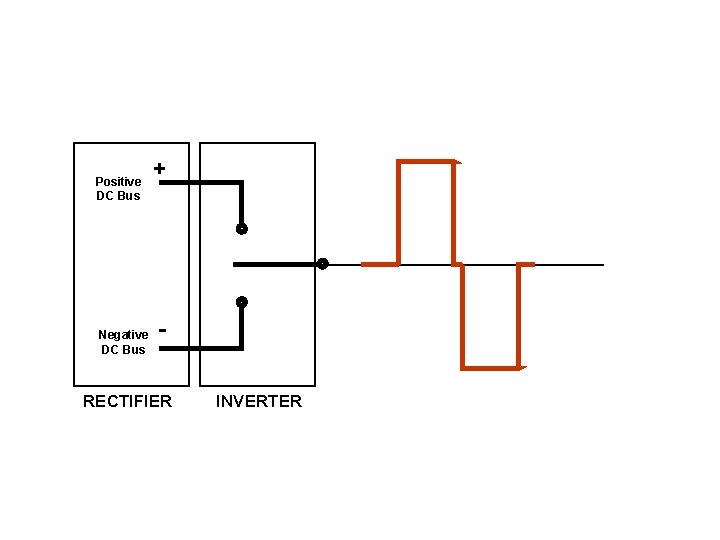

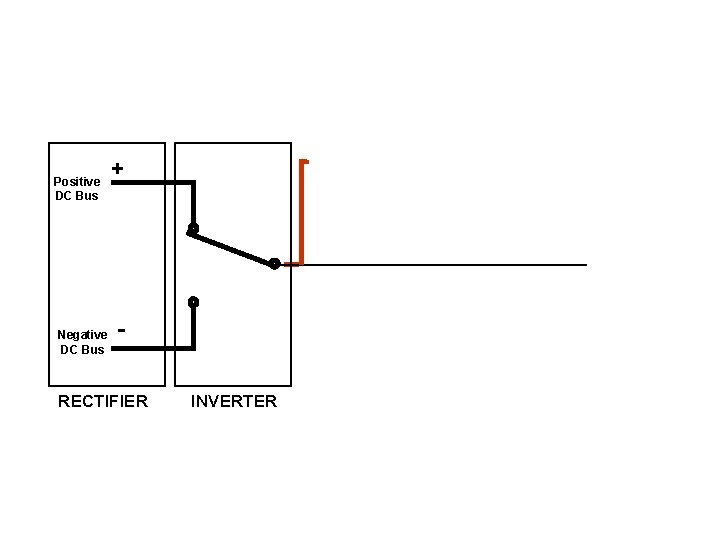
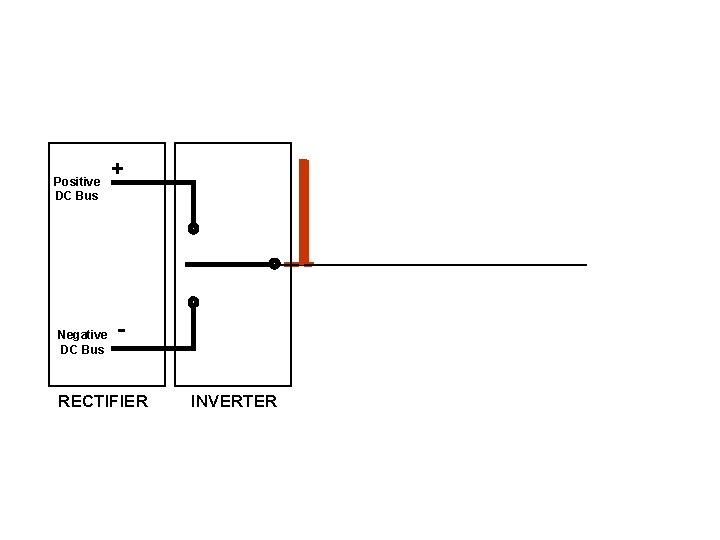
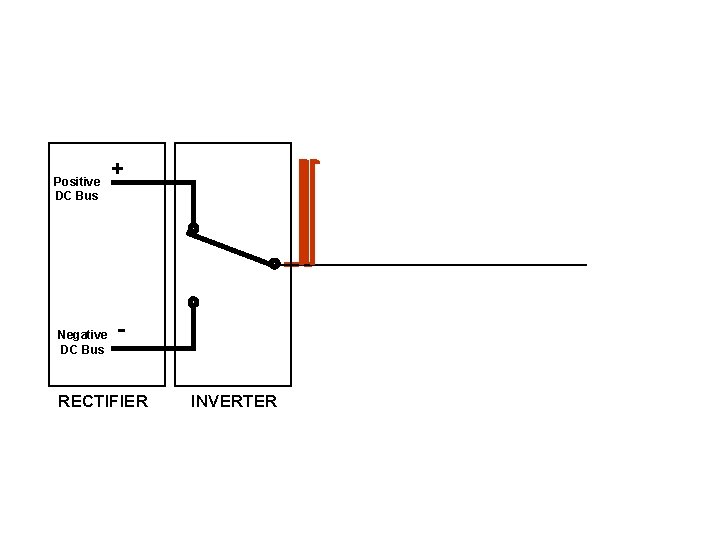
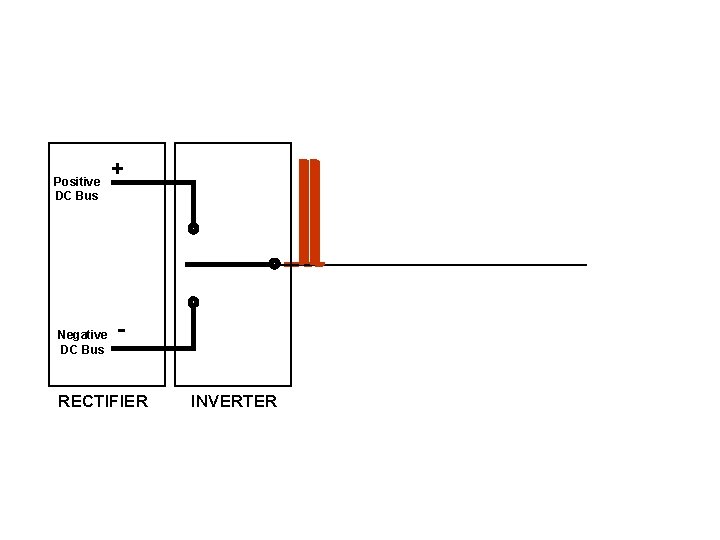
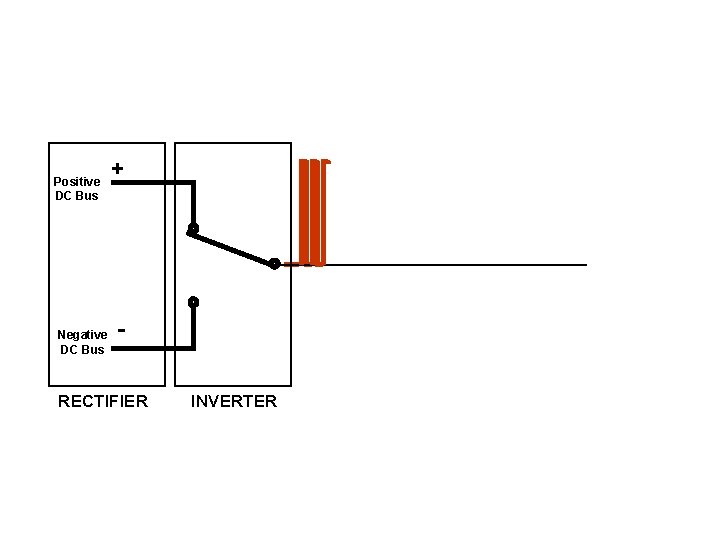
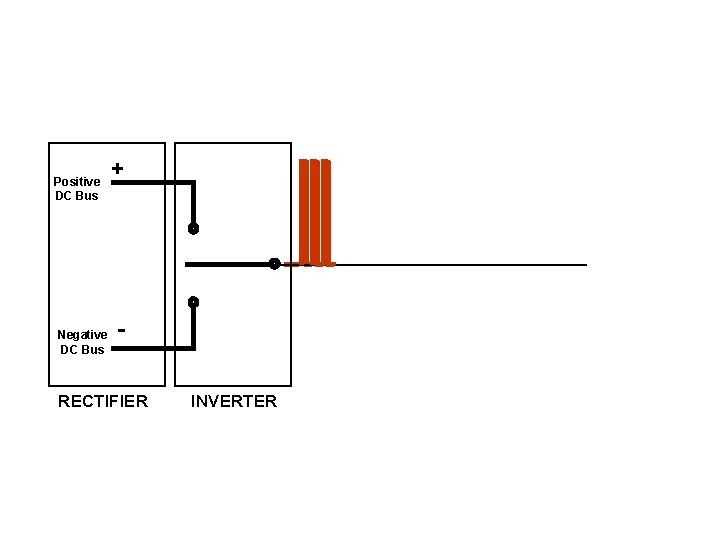
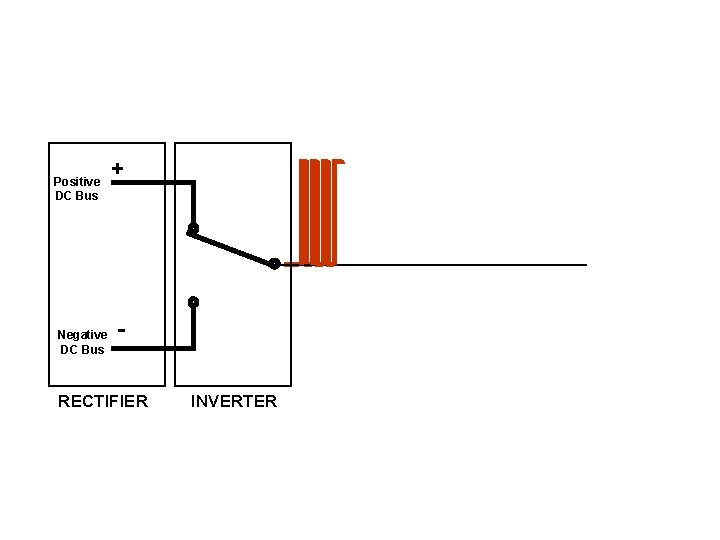
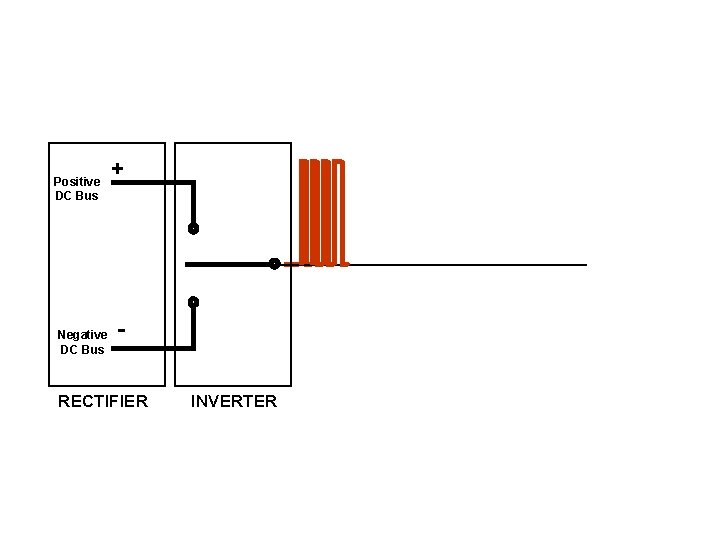
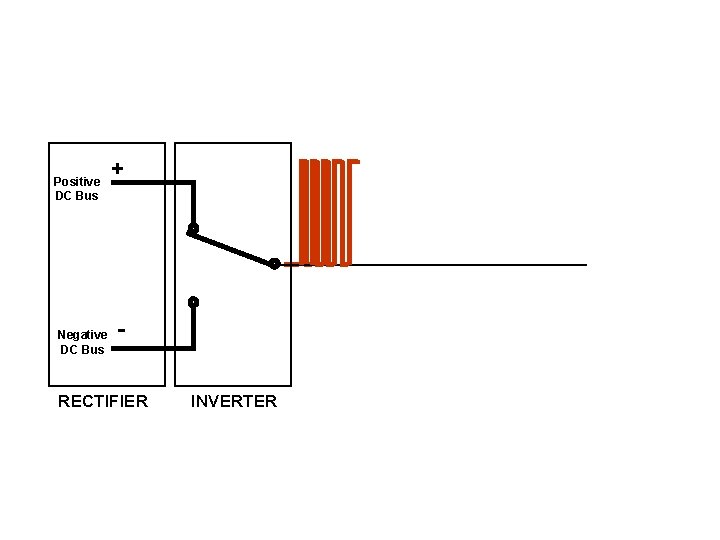
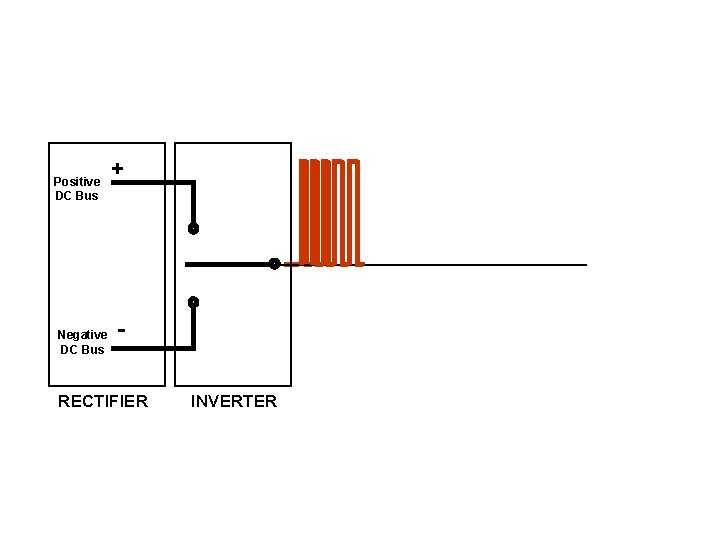
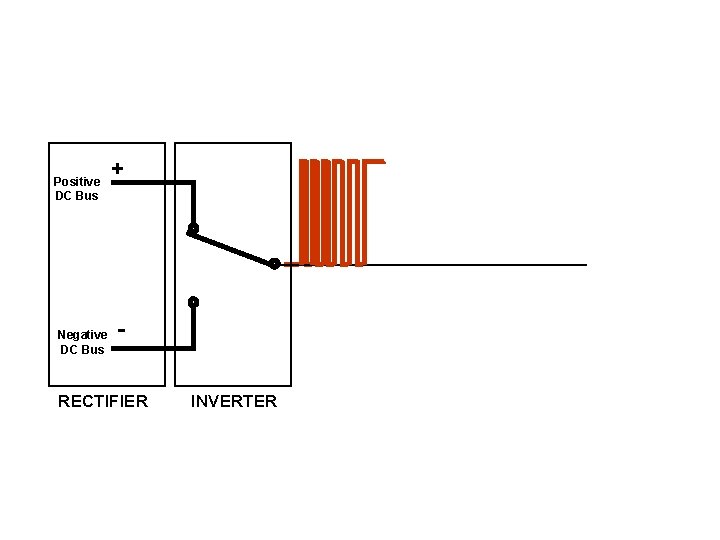
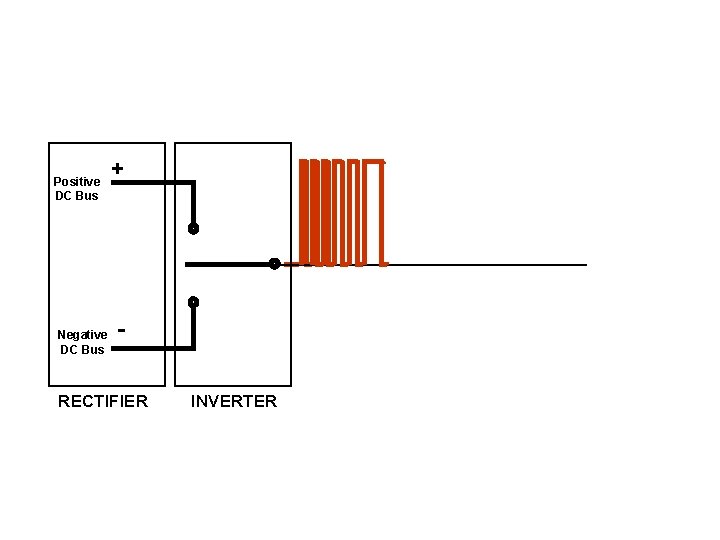
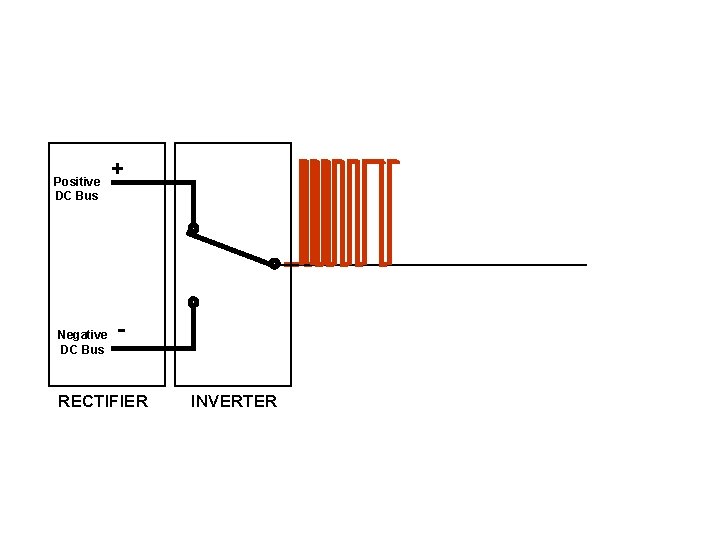
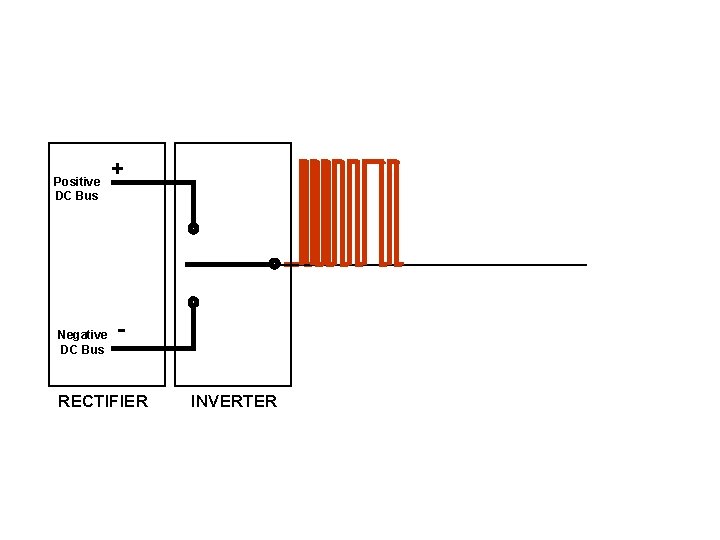
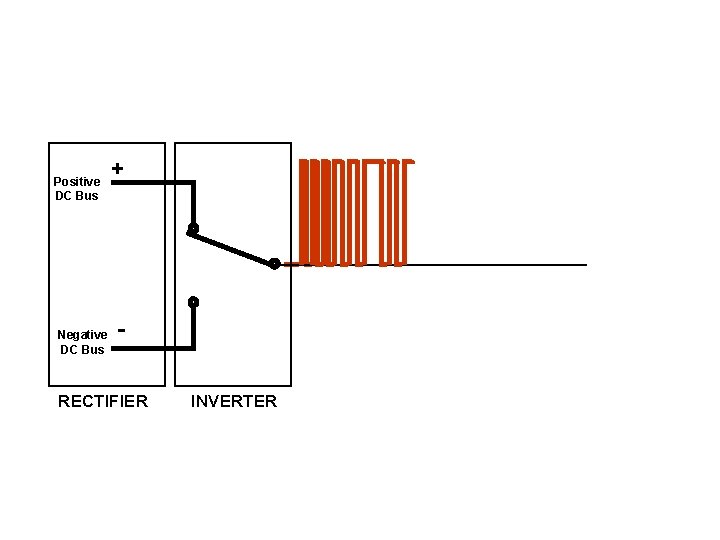
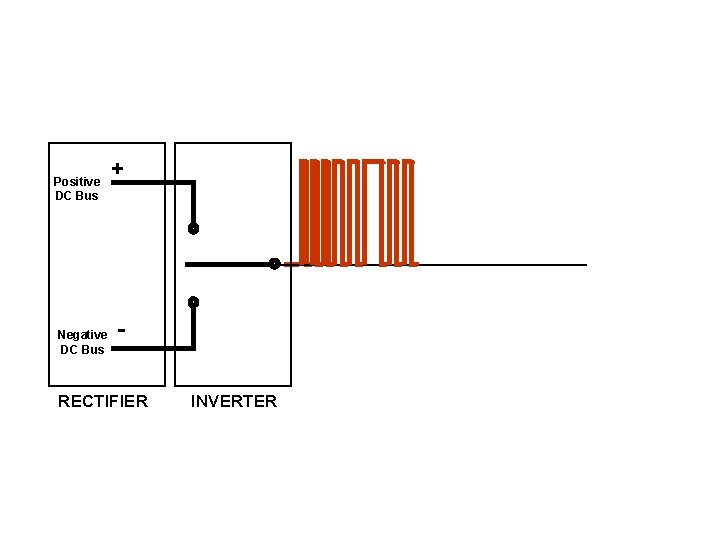
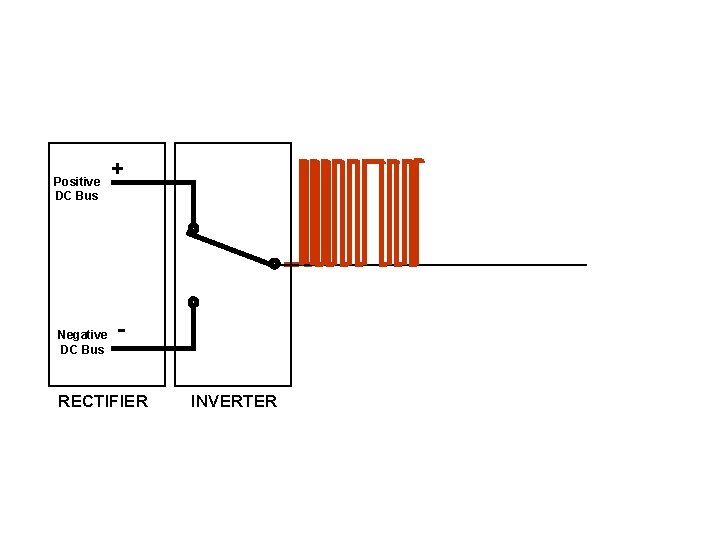
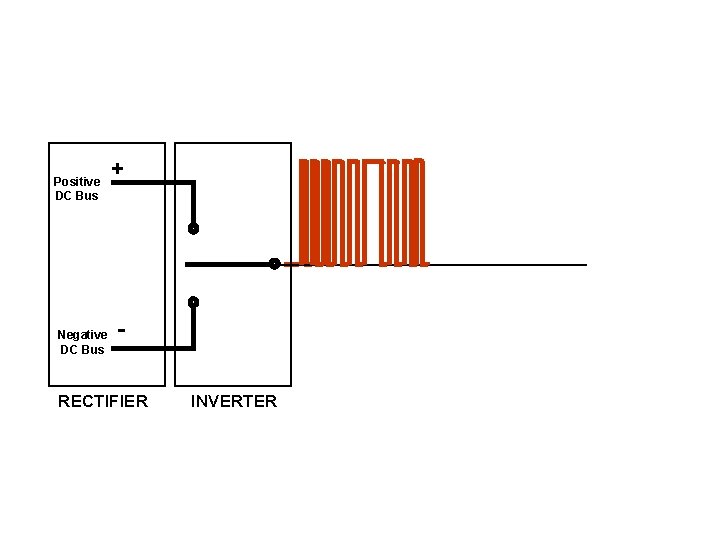
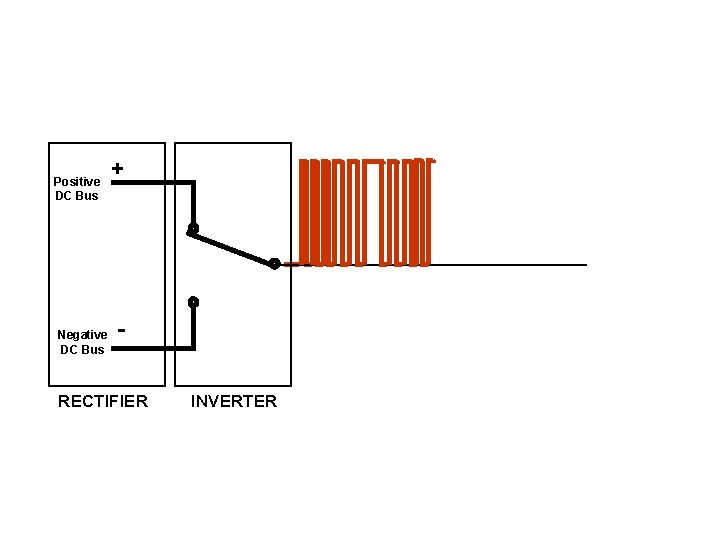
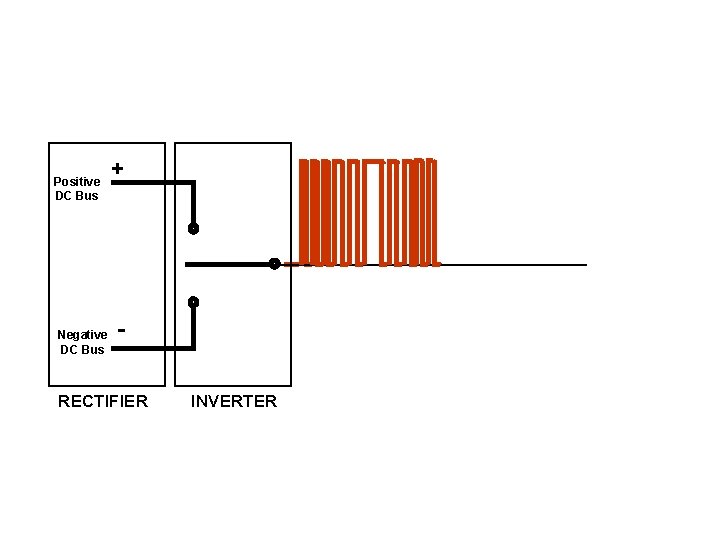
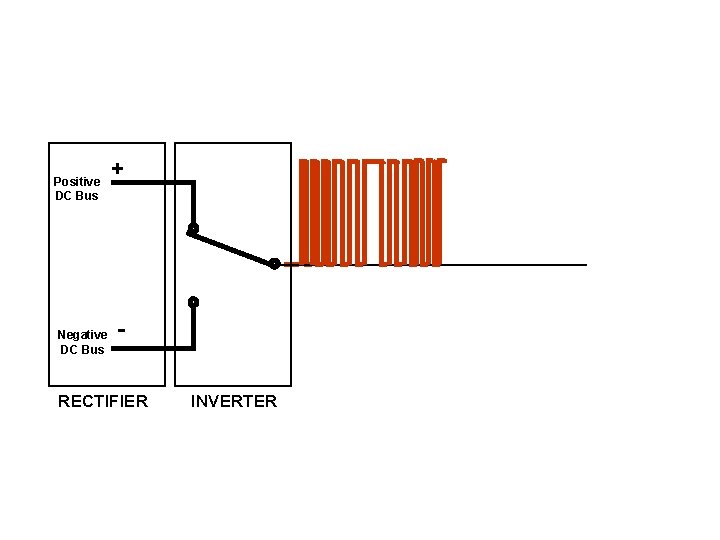
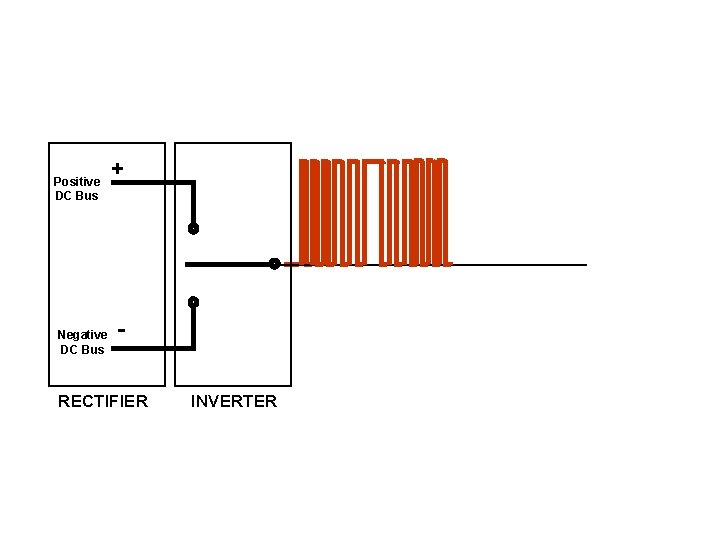
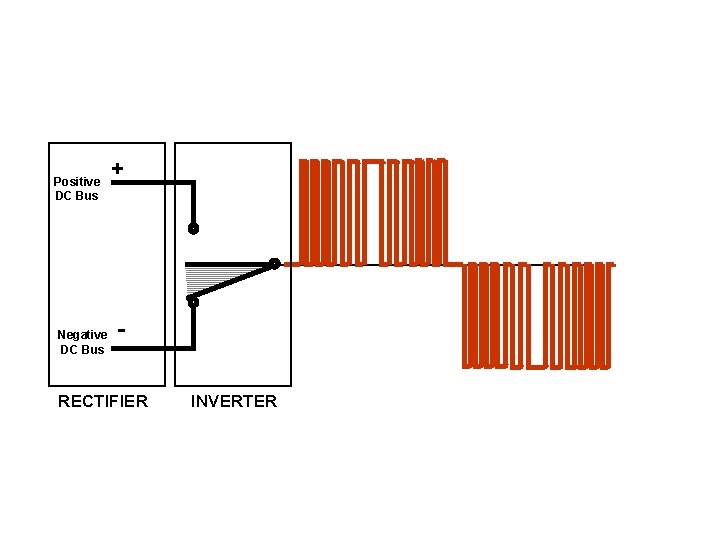
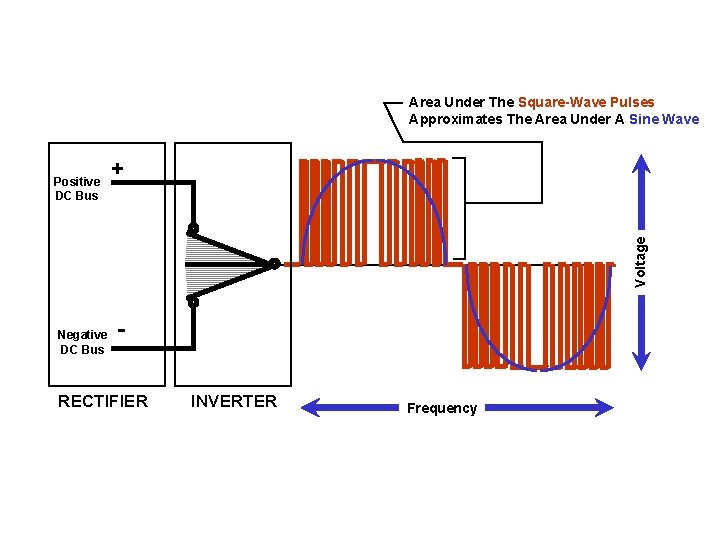
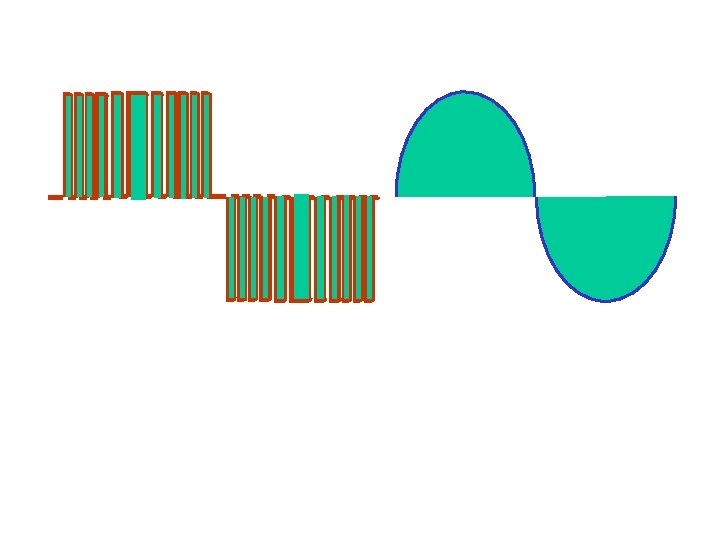
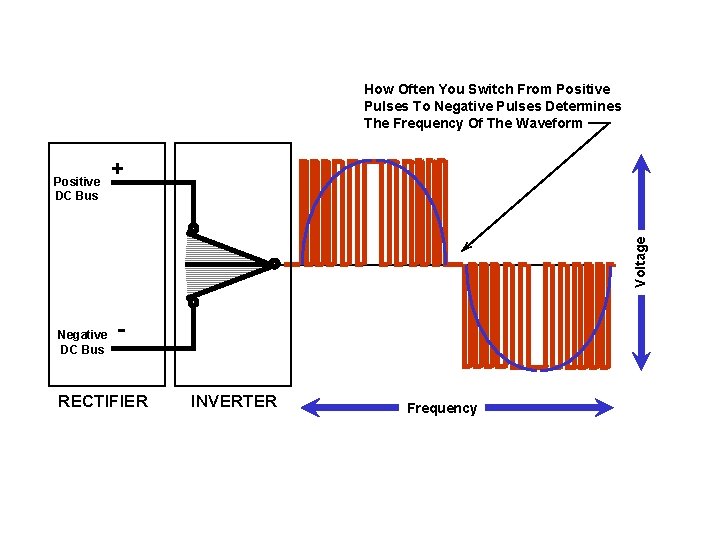
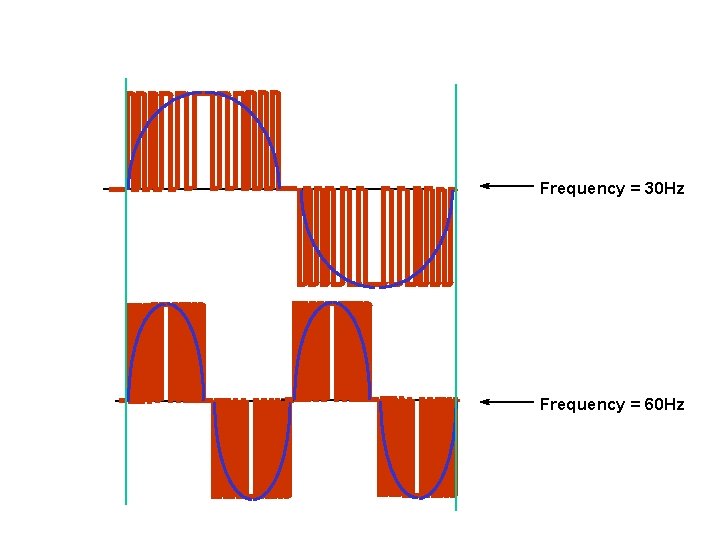
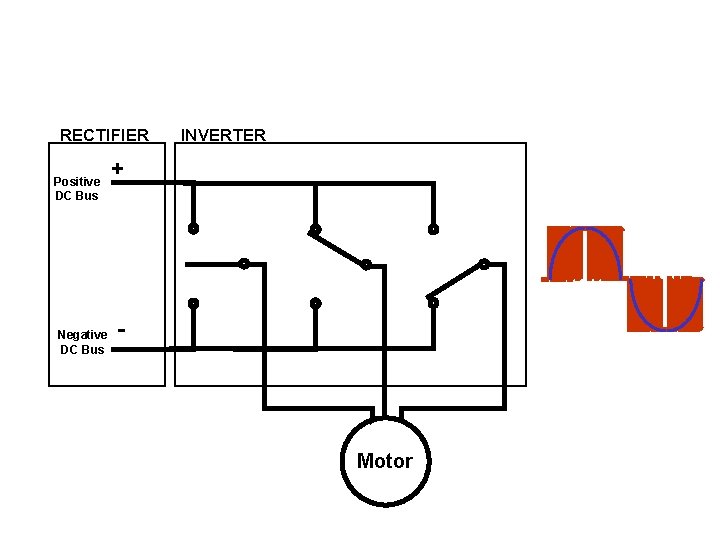
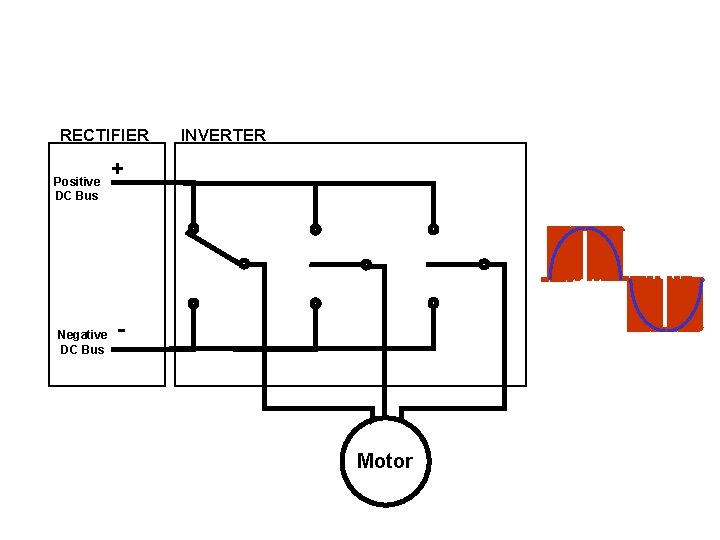
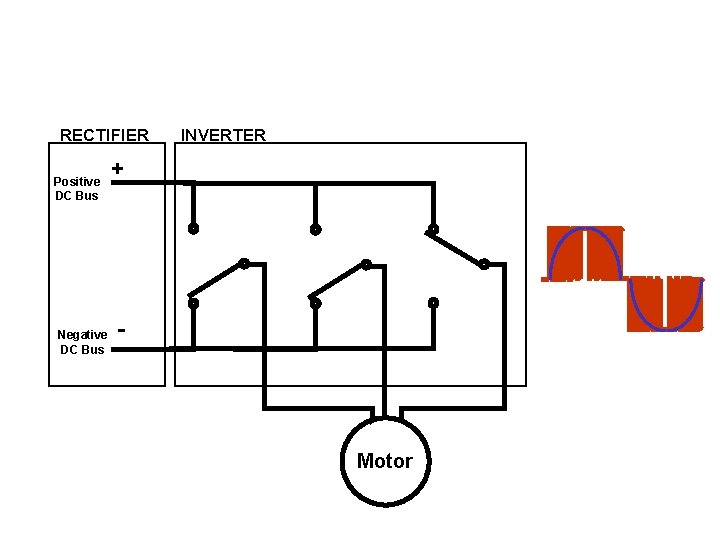
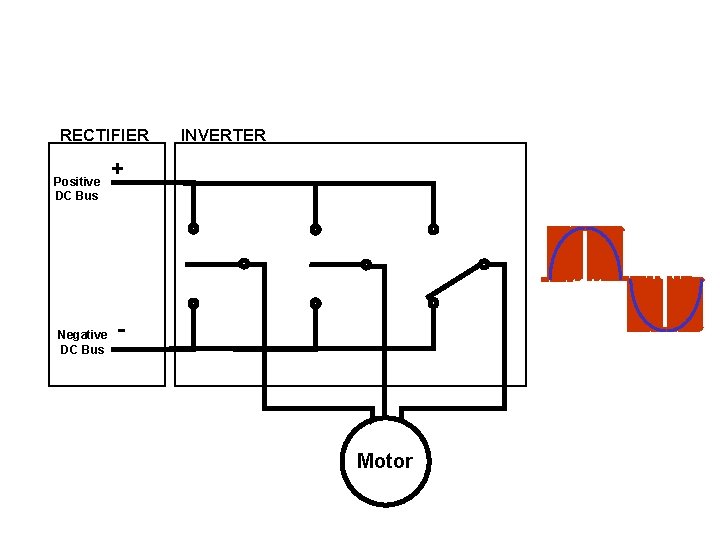
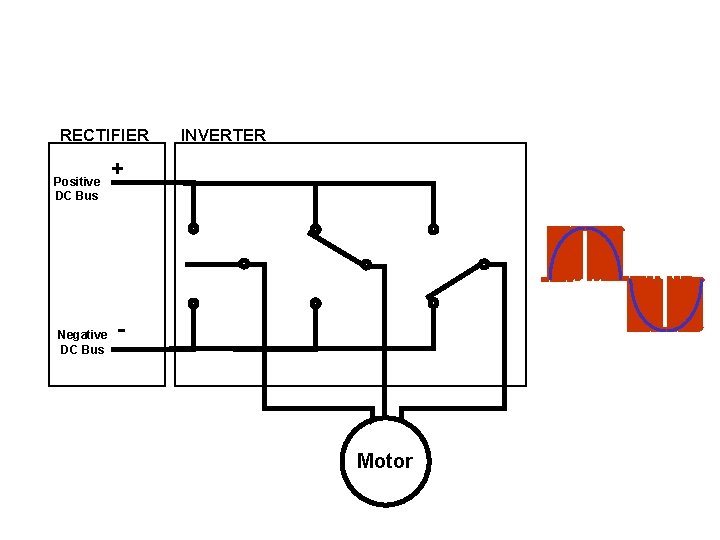
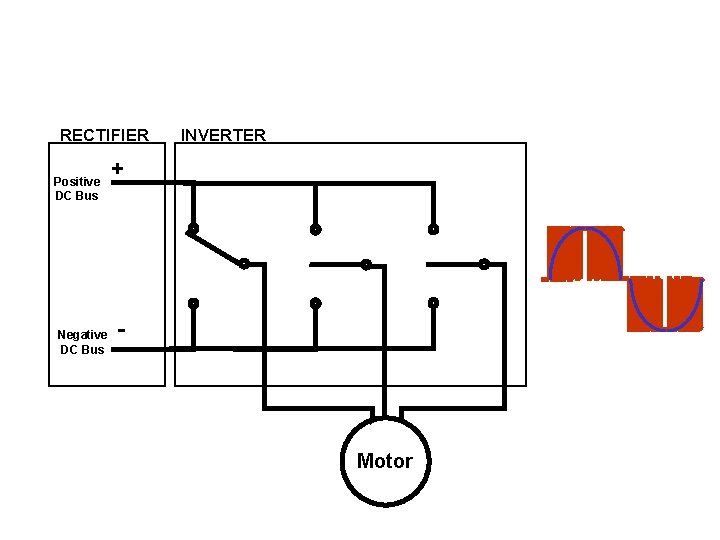
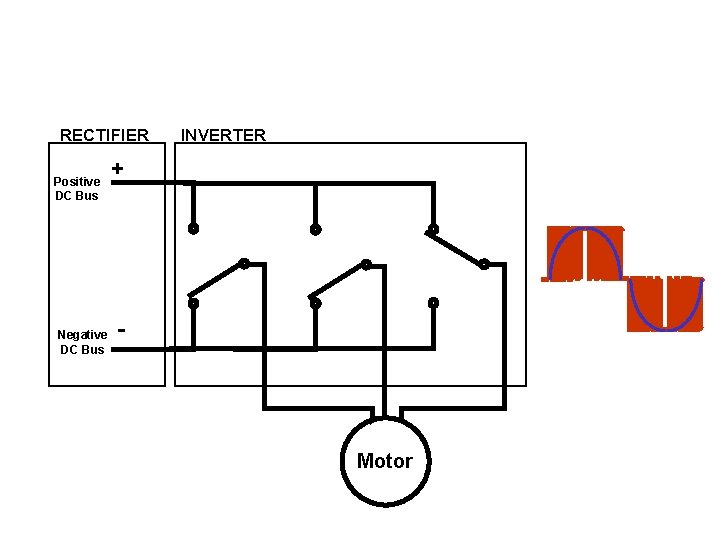
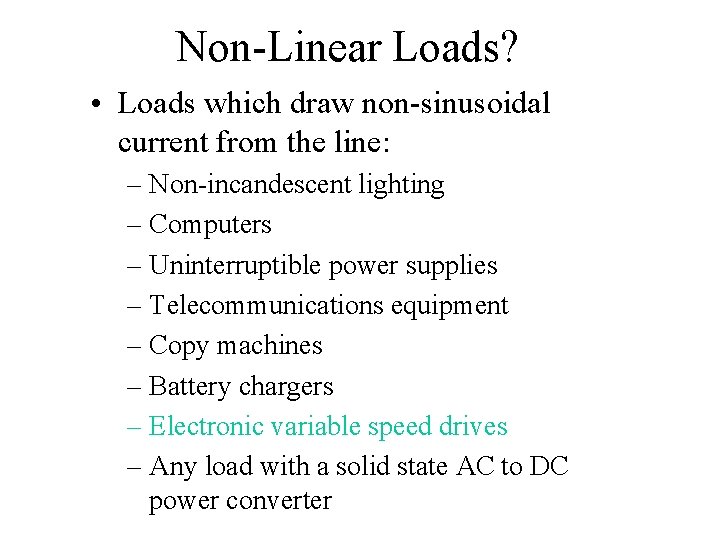
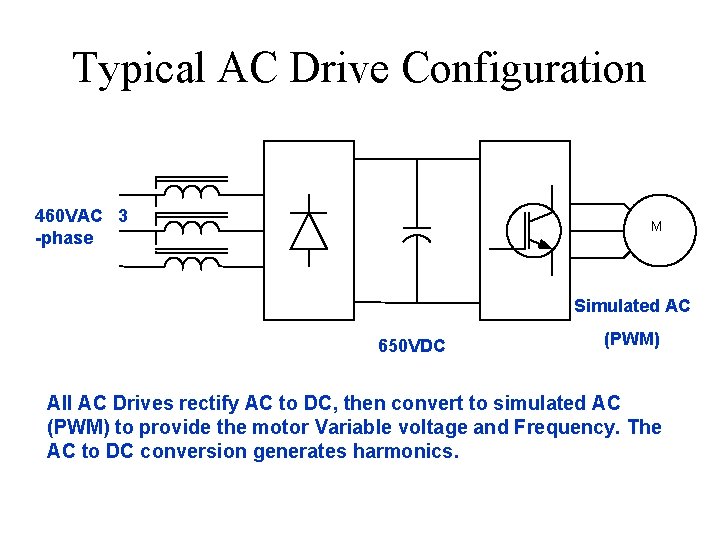
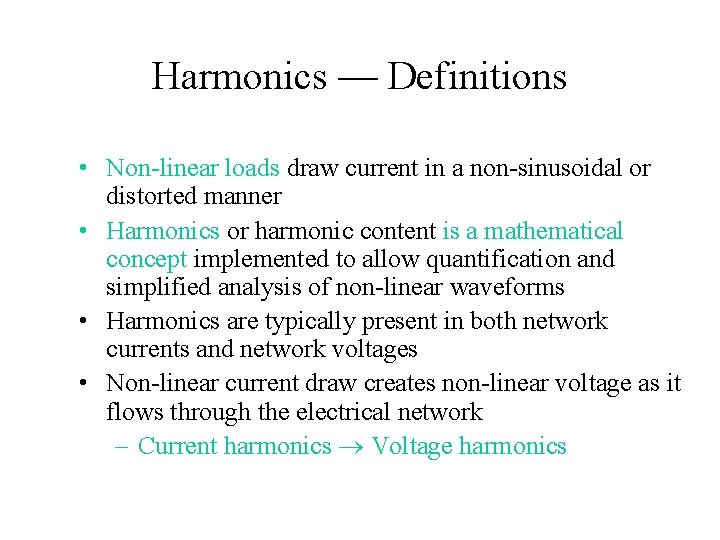
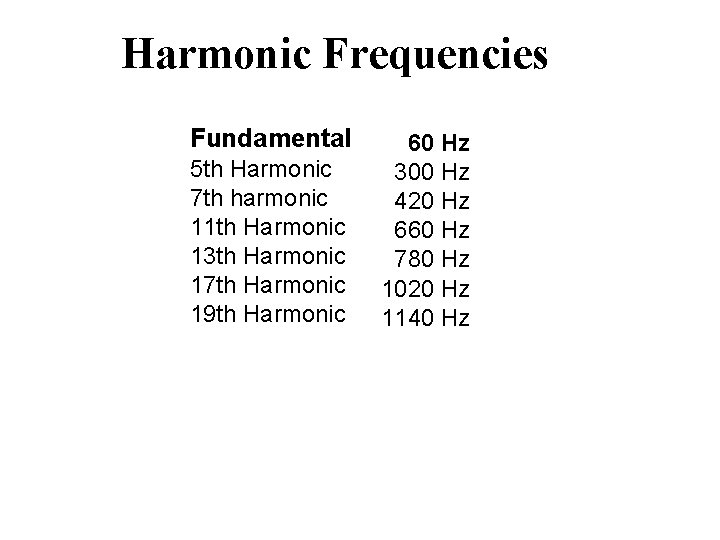
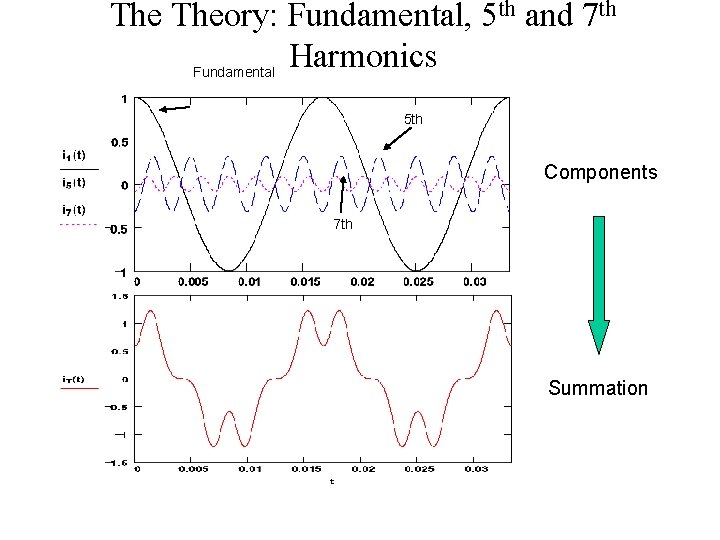
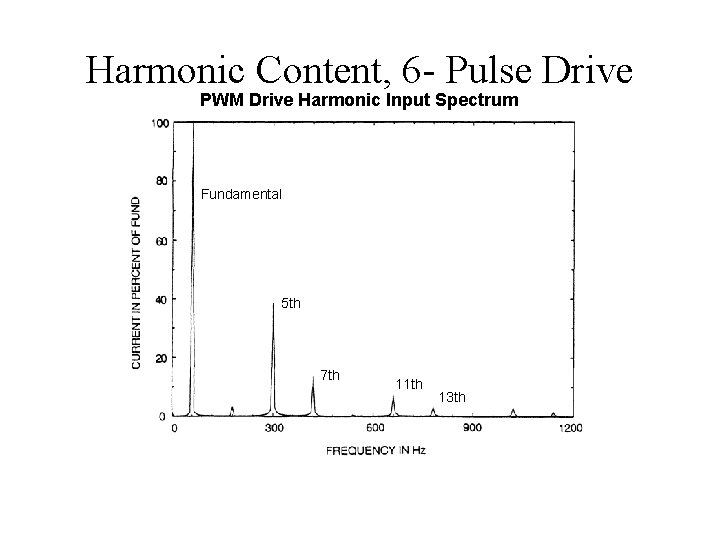
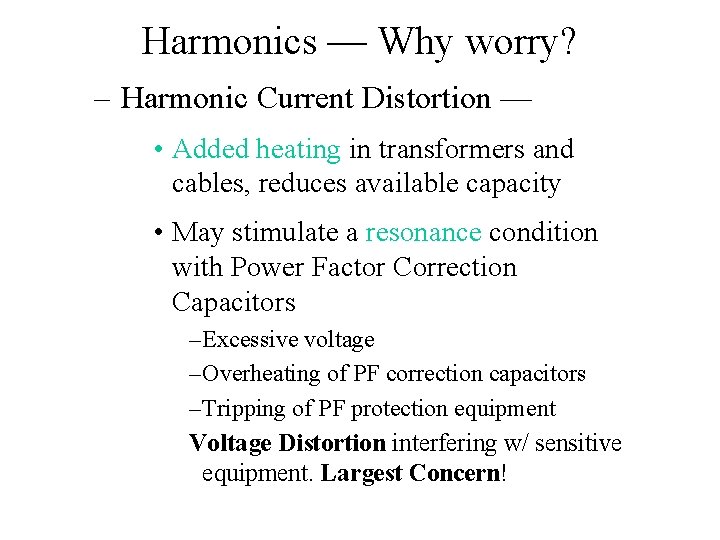
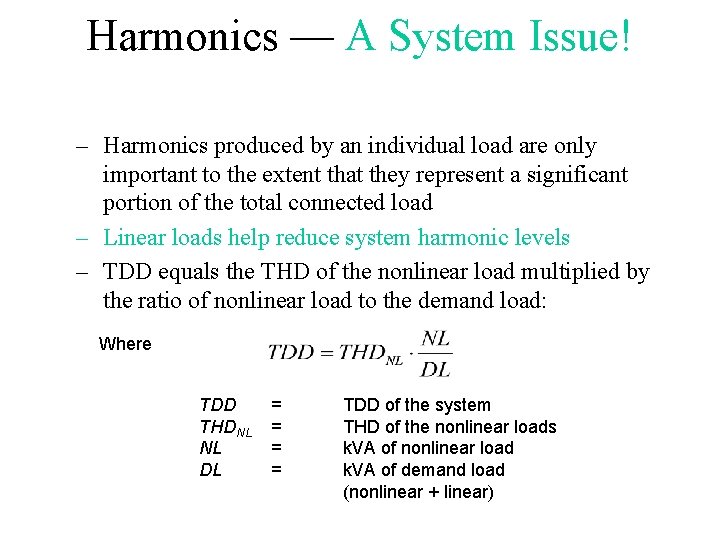
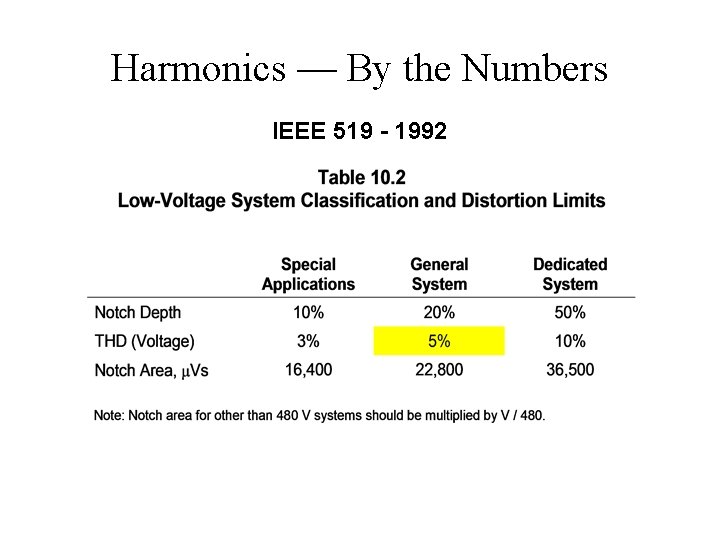
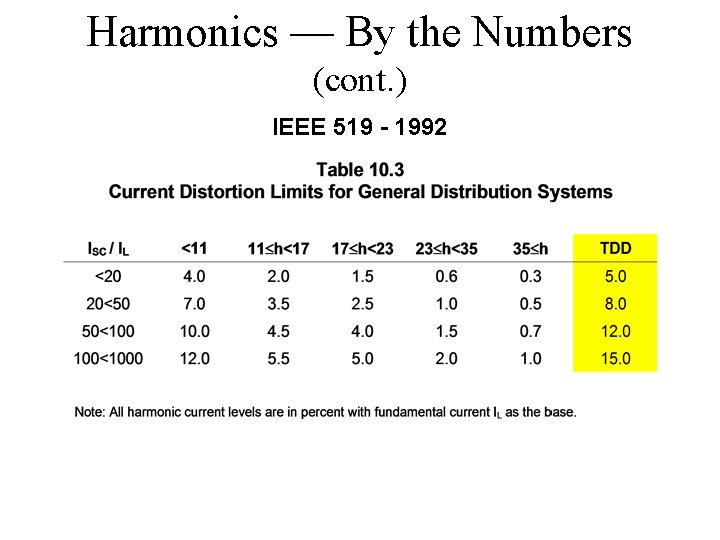
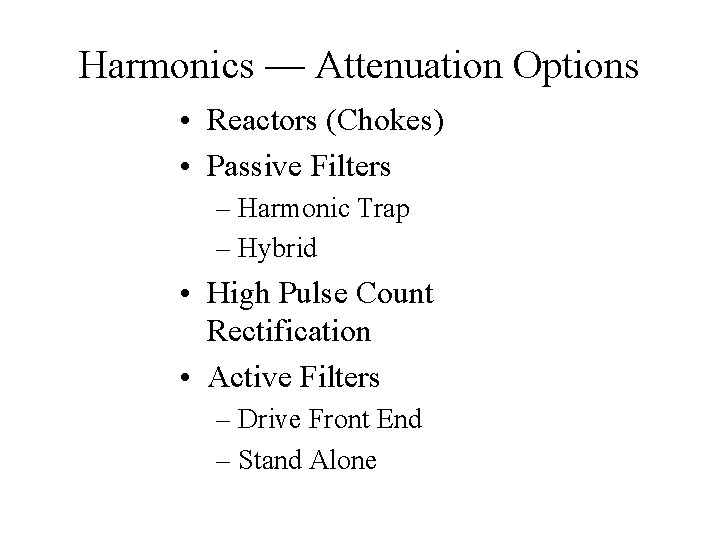
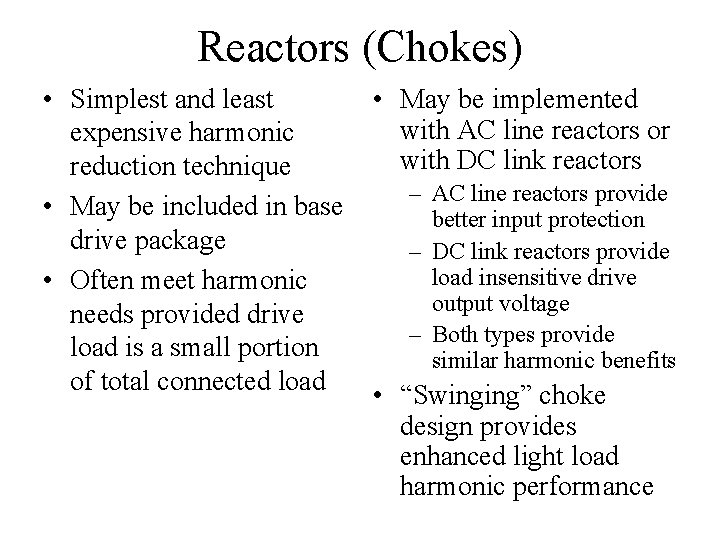
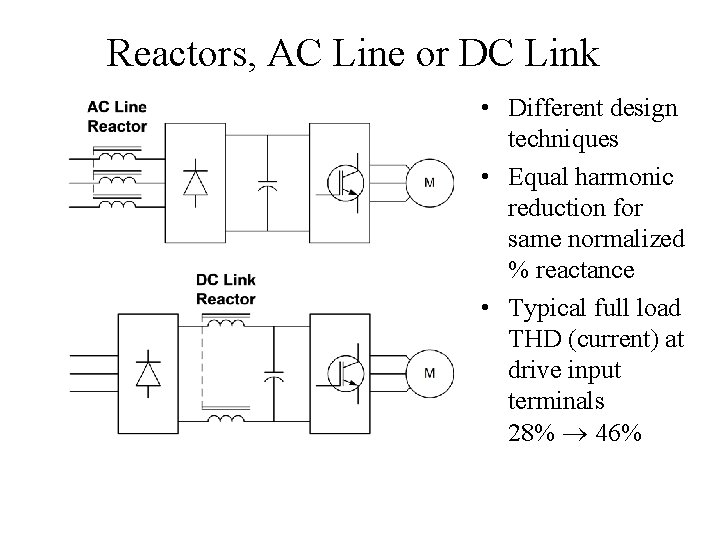
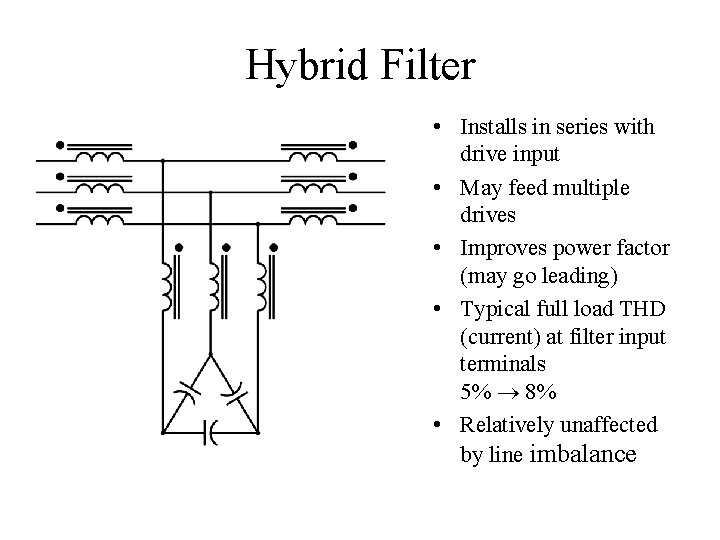
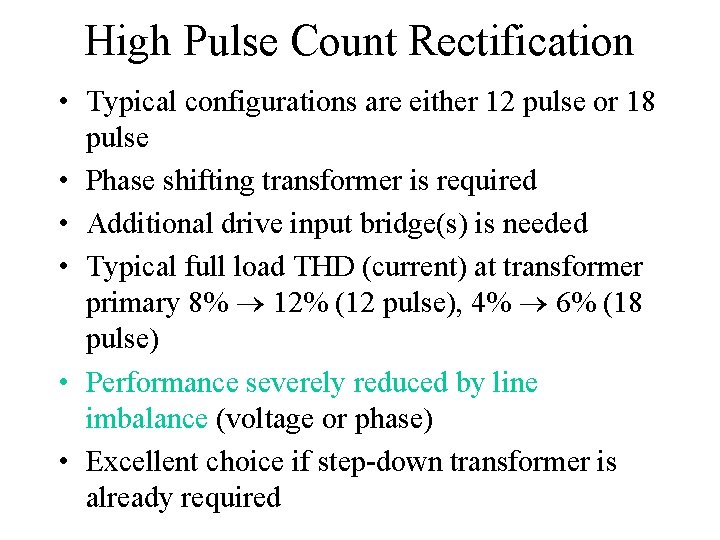
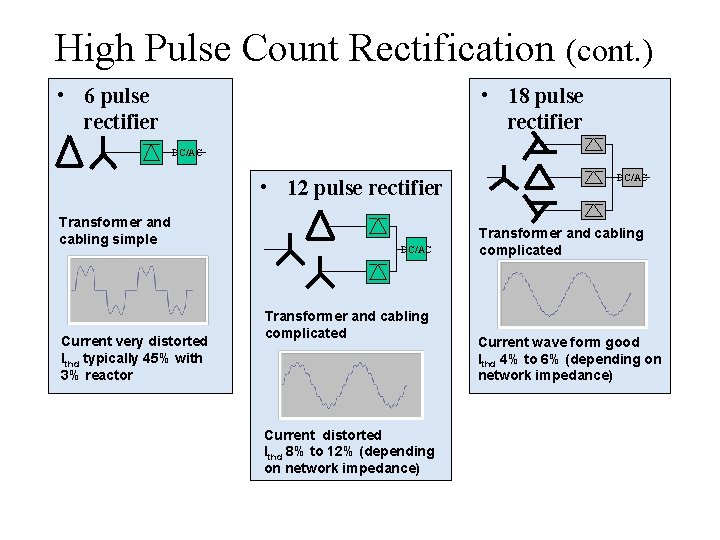
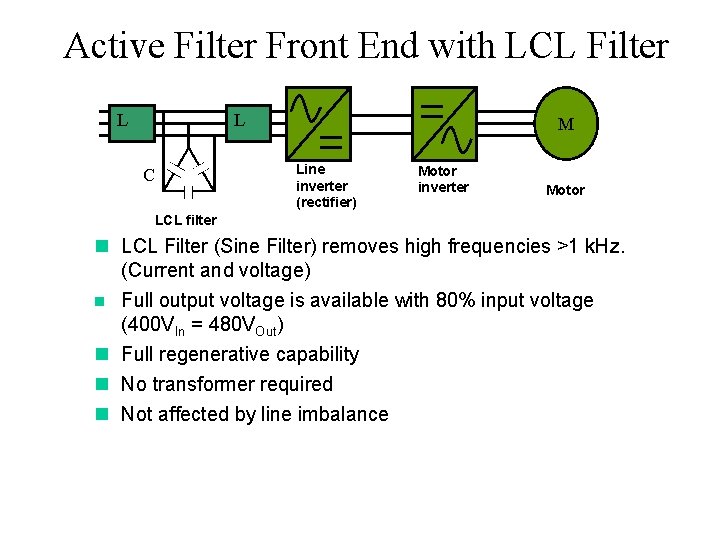
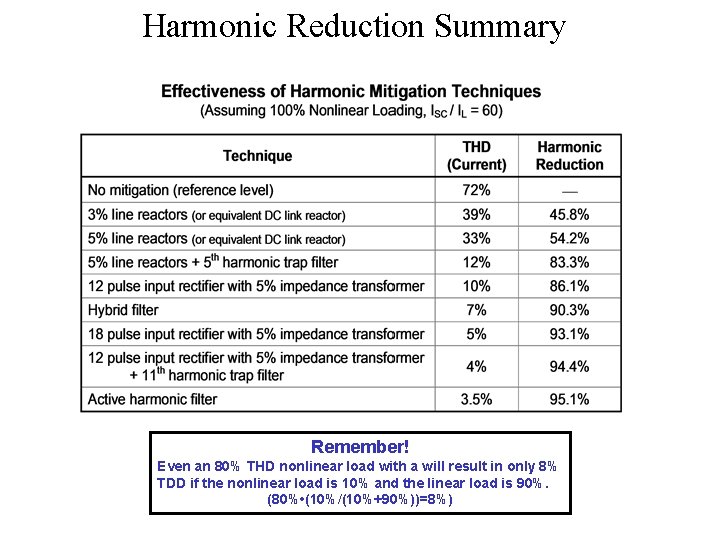
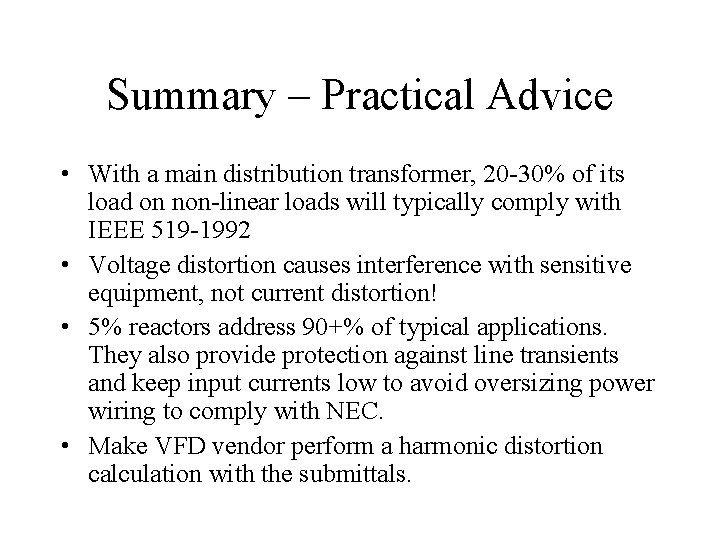
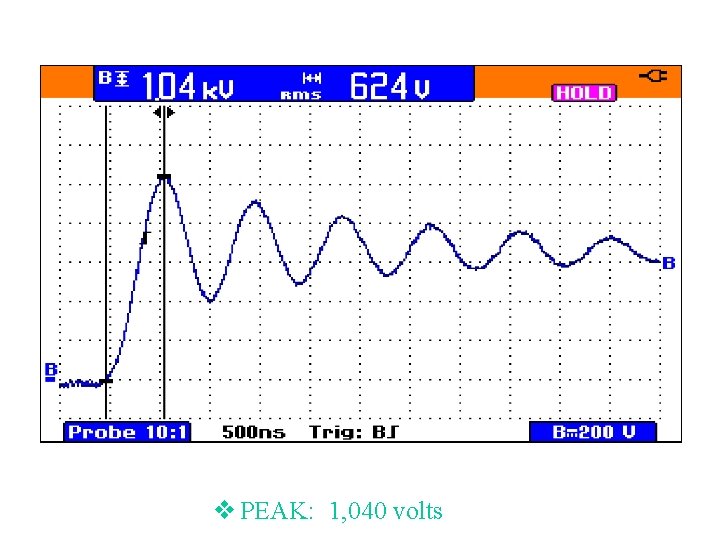
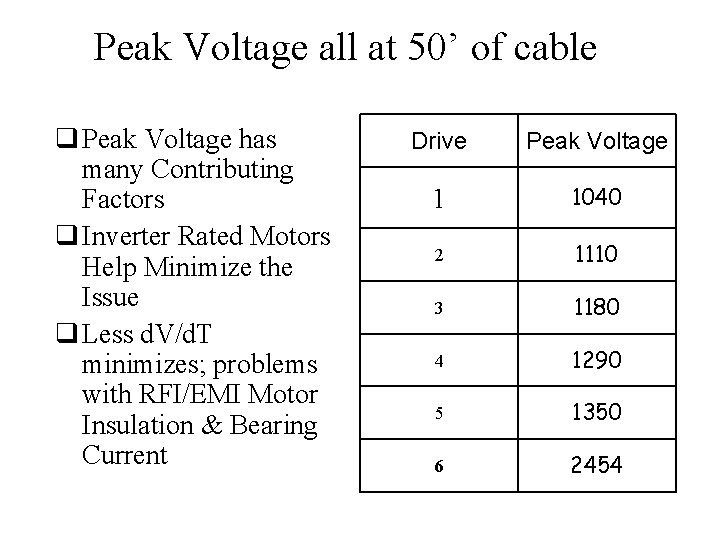
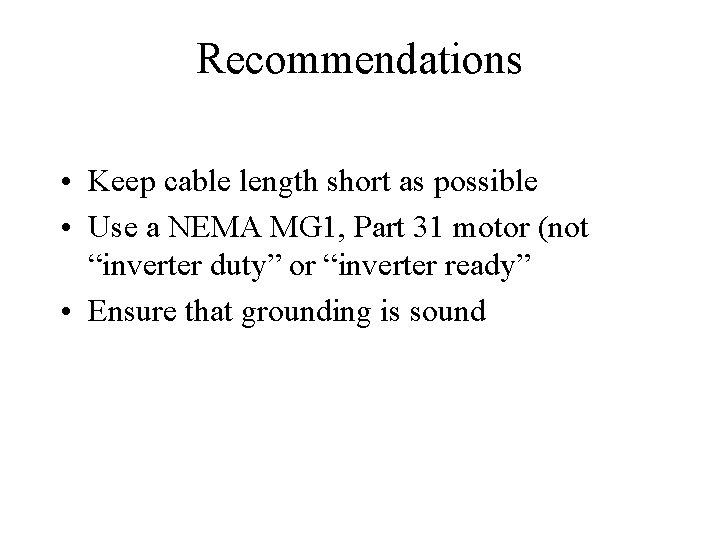
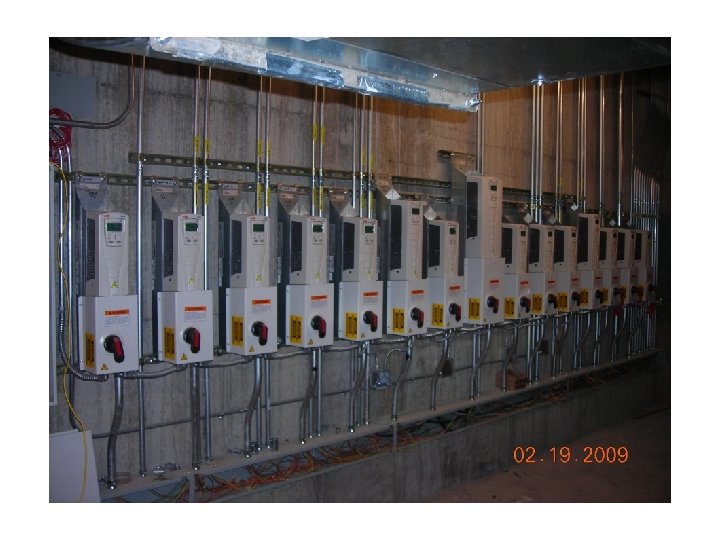
- Slides: 68
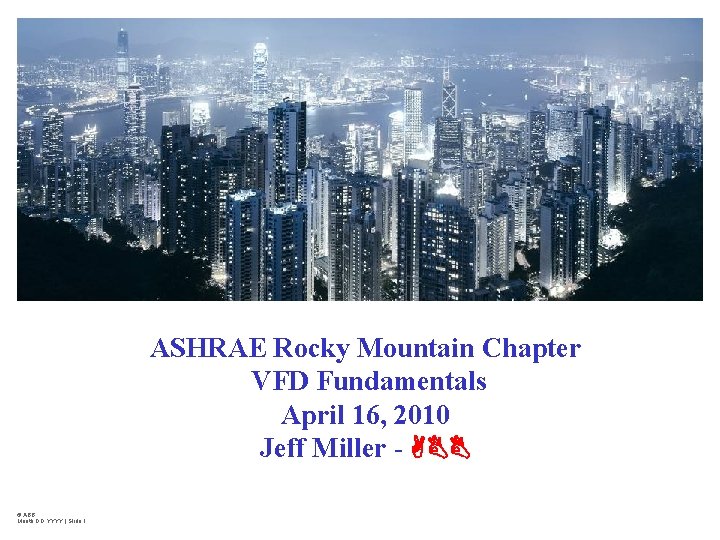
2010 ASHRAE Rocky Mountain Chapter VFD Fundamentals April 16, 2010 Jeff Miller - ABB © ABB Month DD, YYYY | Slide 1
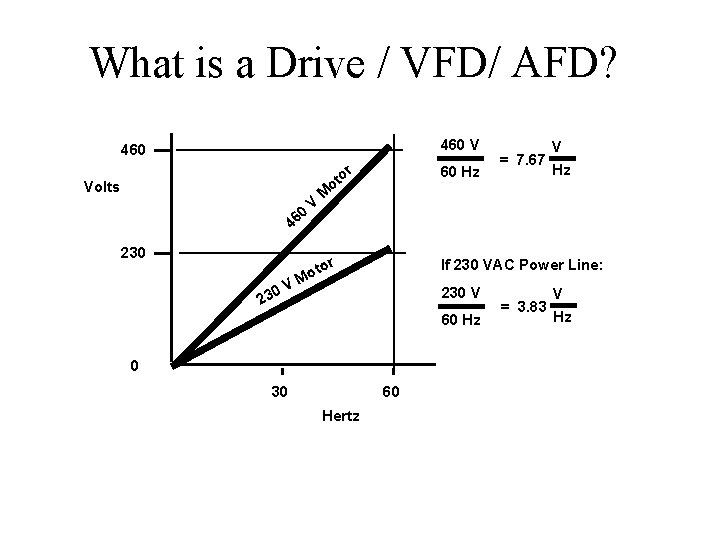
What is a Drive / VFD/ AFD? 460 V 460 or Volts 0 46 230 V 60 Hz ot M r 0 23 V 230 V 60 Hz 0 60 Hertz Hz If 230 VAC Power Line: to Mo 30 = 7. 67 V = 3. 83 V Hz
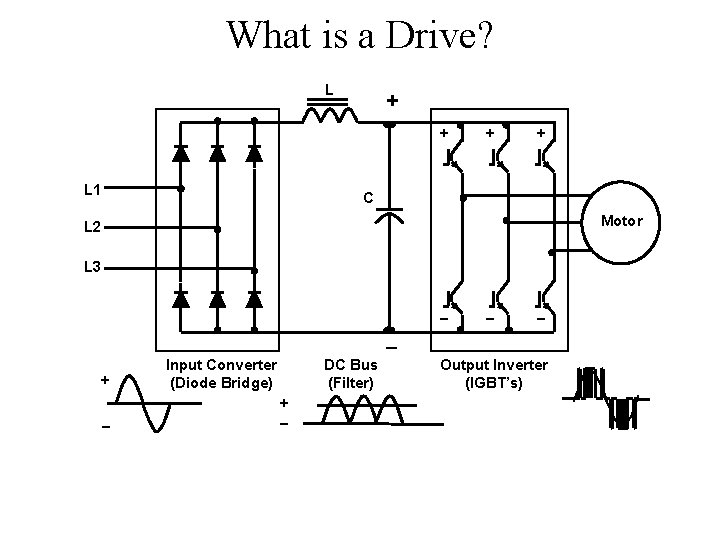
What is a Drive? L + + L 1 + + C Motor L 2 L 3 _ _ + _ Input Converter (Diode Bridge) DC Bus (Filter) + _ Output Inverter (IGBT’s)
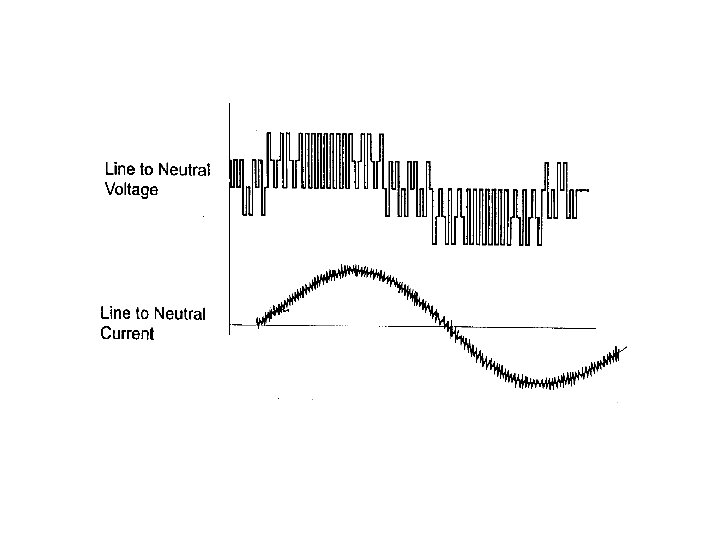
What is a Drive?
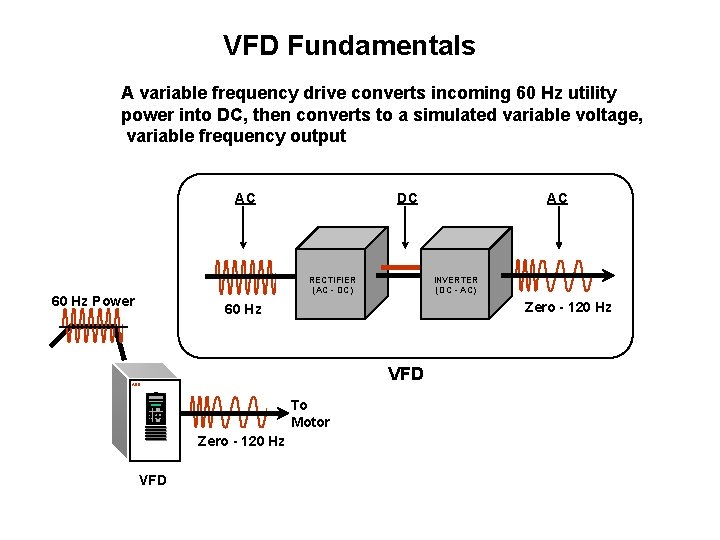
VFD Fundamentals A variable frequency drive converts incoming 60 Hz utility power into DC, then converts to a simulated variable voltage, variable frequency output AC DC RECTIFIER (AC - DC) 60 Hz Power INVERTER (DC - AC) Zero - 120 Hz 60 Hz VFD ABB To Motor Zero - 120 Hz Electrical Energy VFD AC
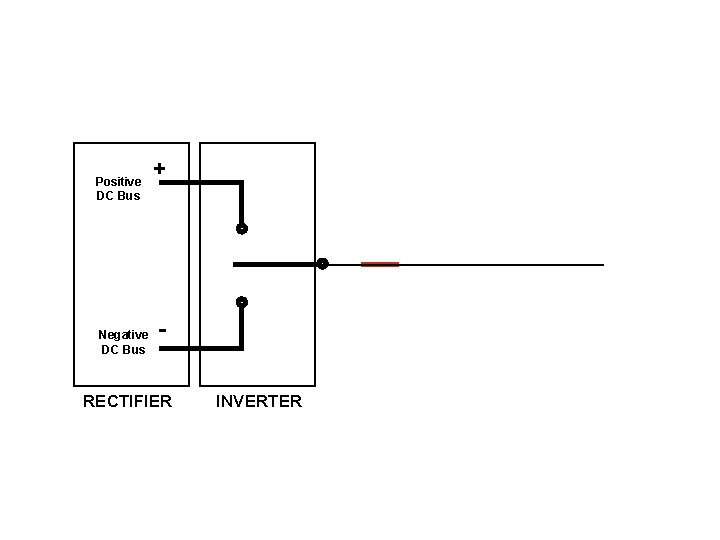
Positive DC Bus Negative DC Bus + - RECTIFIER INVERTER
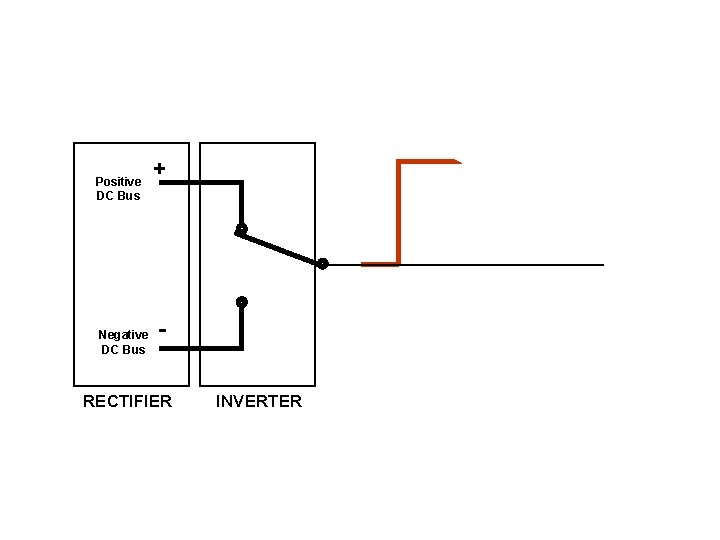
Positive DC Bus Negative DC Bus + - RECTIFIER INVERTER
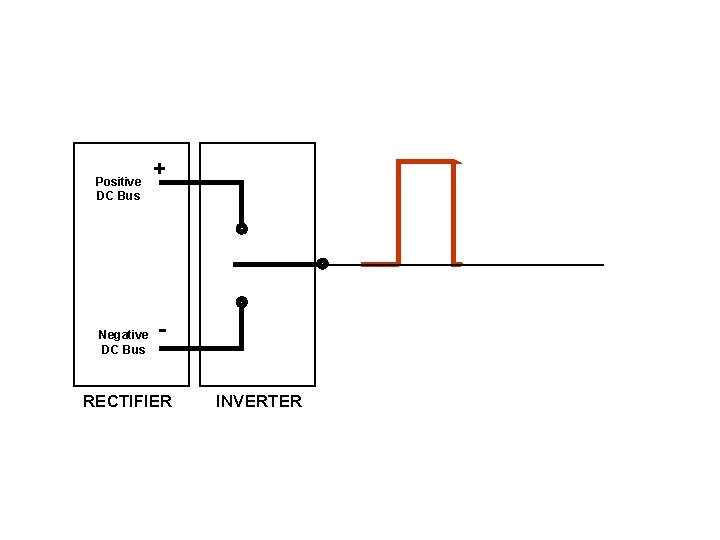
Positive DC Bus Negative DC Bus + - RECTIFIER INVERTER
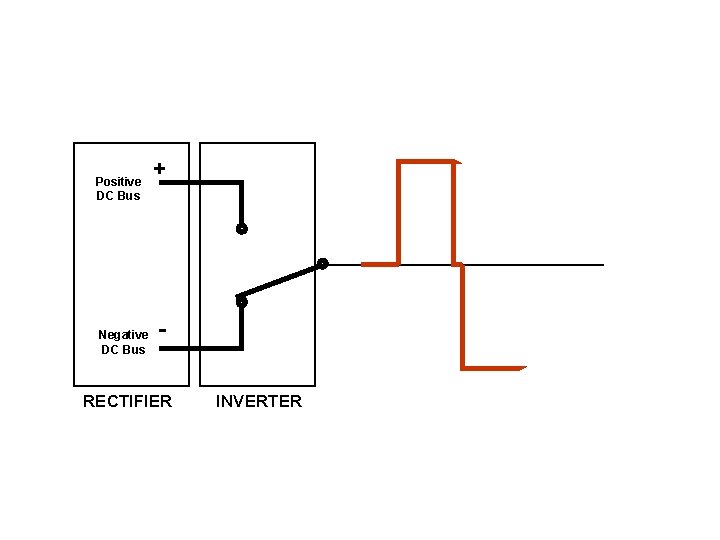
Positive DC Bus Negative DC Bus + - RECTIFIER INVERTER
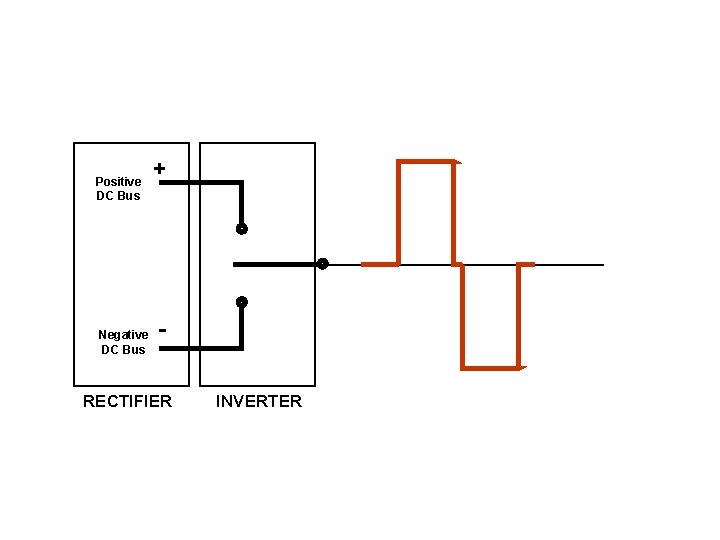
Positive DC Bus Negative DC Bus + - RECTIFIER INVERTER

Positive DC Bus Negative DC Bus + - RECTIFIER INVERTER
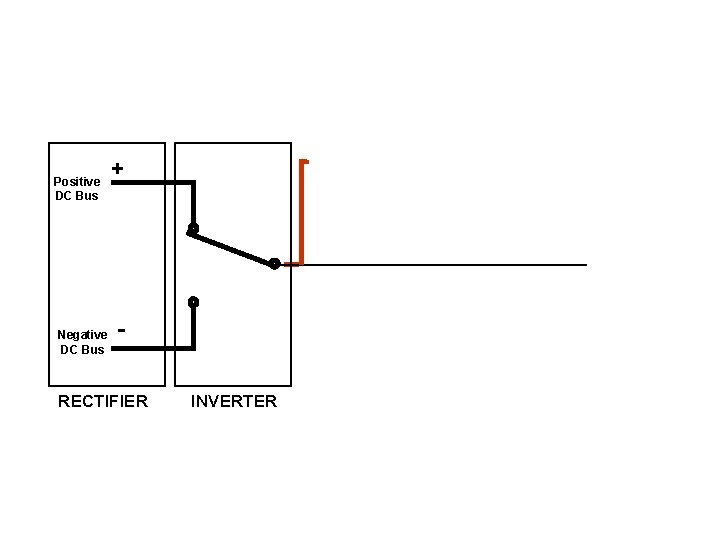
Positive DC Bus Negative DC Bus + - RECTIFIER INVERTER
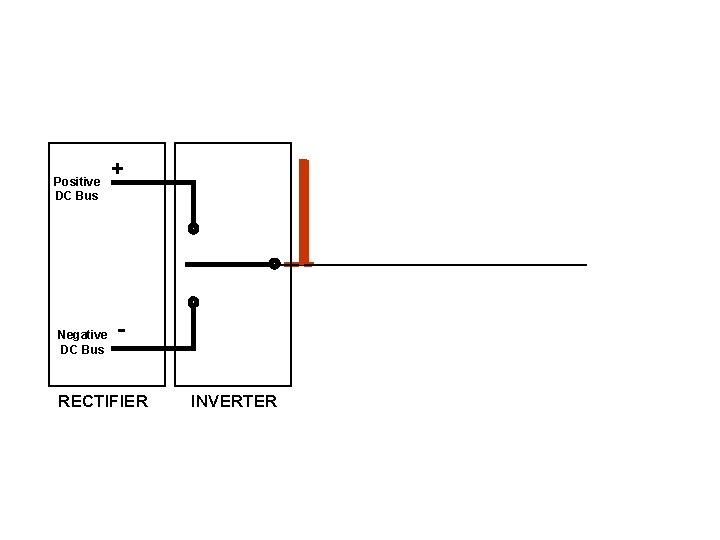
Positive DC Bus Negative DC Bus + - RECTIFIER INVERTER
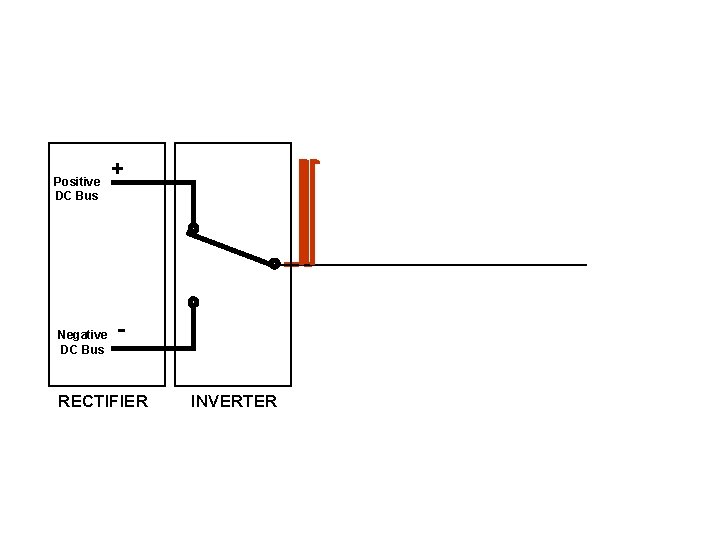
Positive DC Bus Negative DC Bus + - RECTIFIER INVERTER
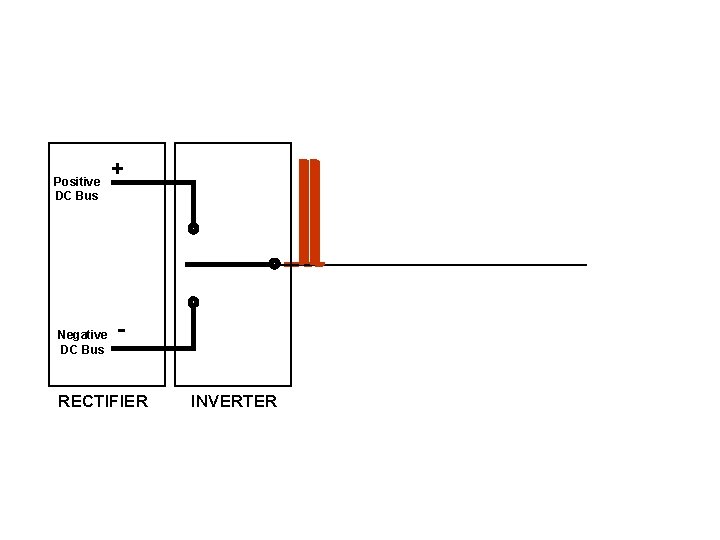
Positive DC Bus Negative DC Bus + - RECTIFIER INVERTER
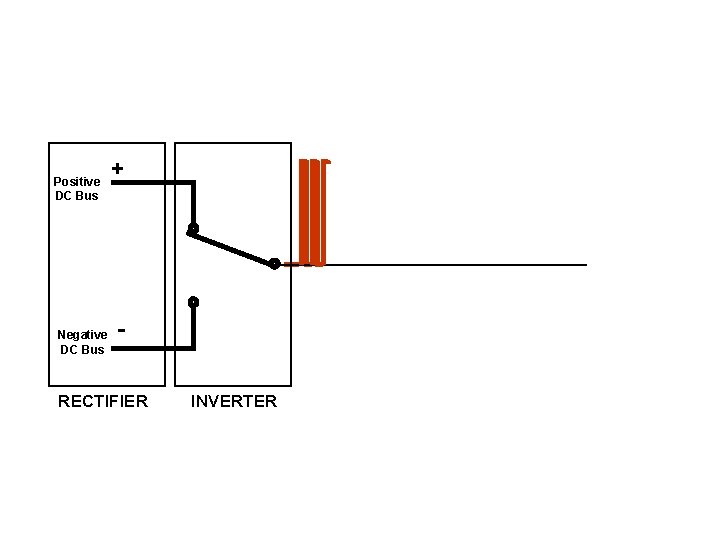
Positive DC Bus Negative DC Bus + - RECTIFIER INVERTER
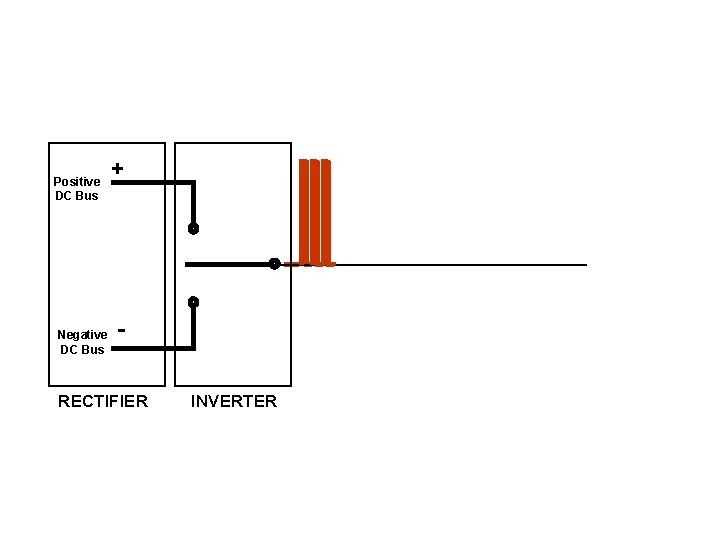
Positive DC Bus Negative DC Bus + - RECTIFIER INVERTER
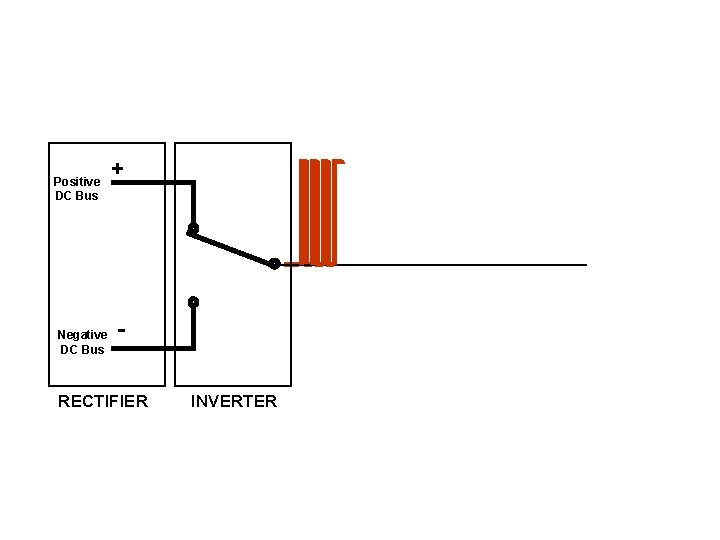
Positive DC Bus Negative DC Bus + - RECTIFIER INVERTER
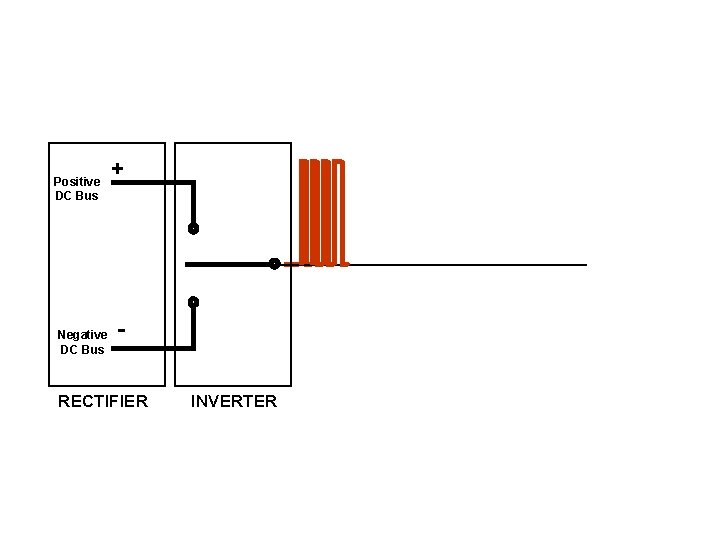
Positive DC Bus Negative DC Bus + - RECTIFIER INVERTER
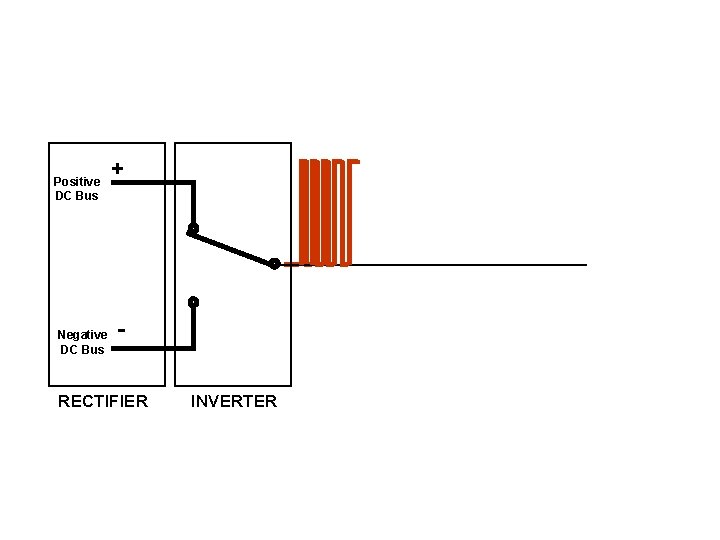
Positive DC Bus Negative DC Bus + - RECTIFIER INVERTER
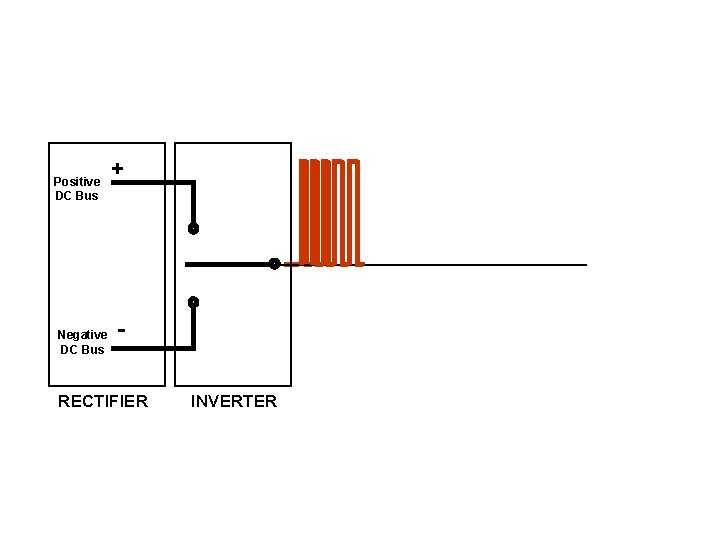
Positive DC Bus Negative DC Bus + - RECTIFIER INVERTER
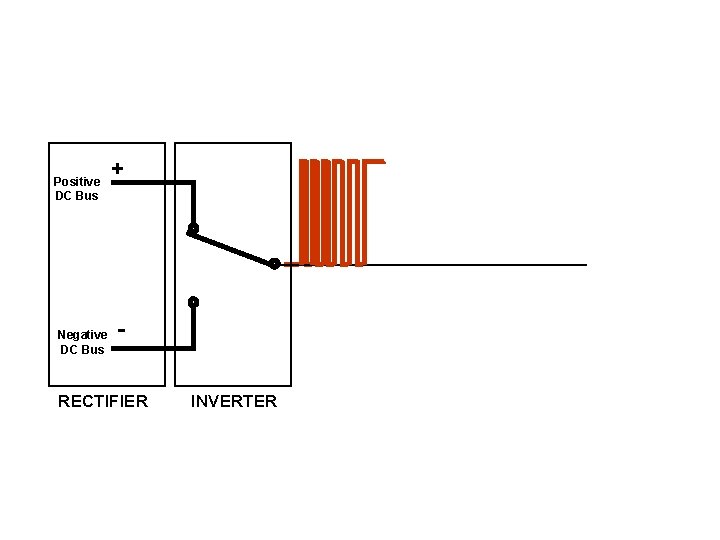
Positive DC Bus Negative DC Bus + - RECTIFIER INVERTER
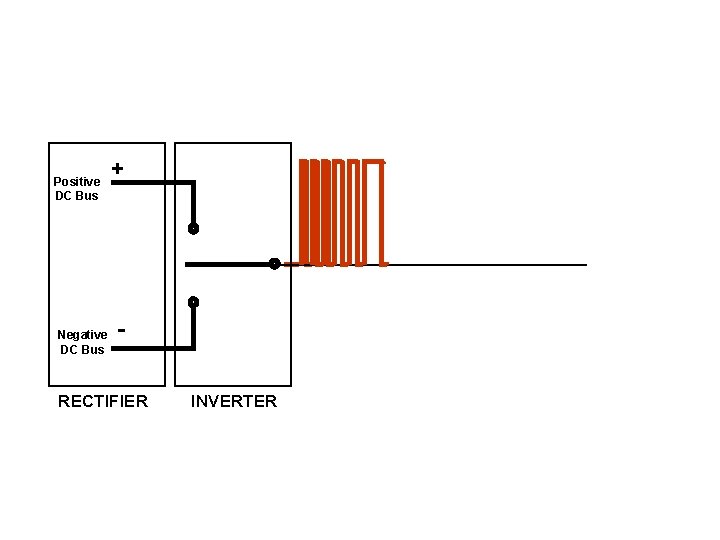
Positive DC Bus Negative DC Bus + - RECTIFIER INVERTER
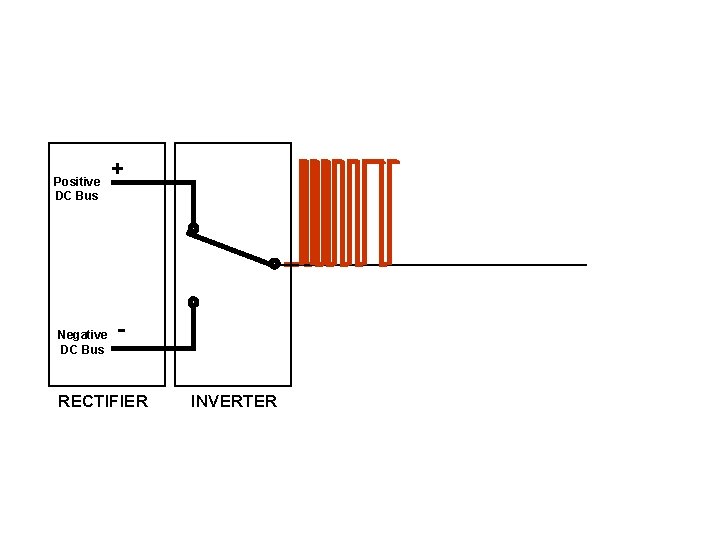
Positive DC Bus Negative DC Bus + - RECTIFIER INVERTER
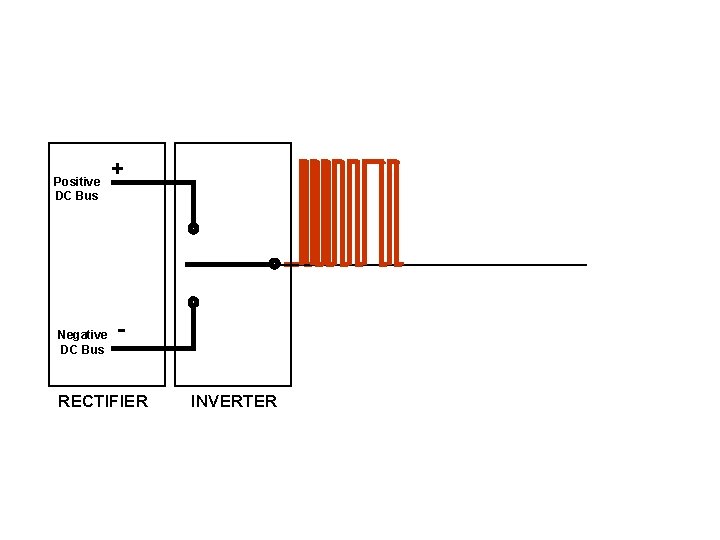
Positive DC Bus Negative DC Bus + - RECTIFIER INVERTER
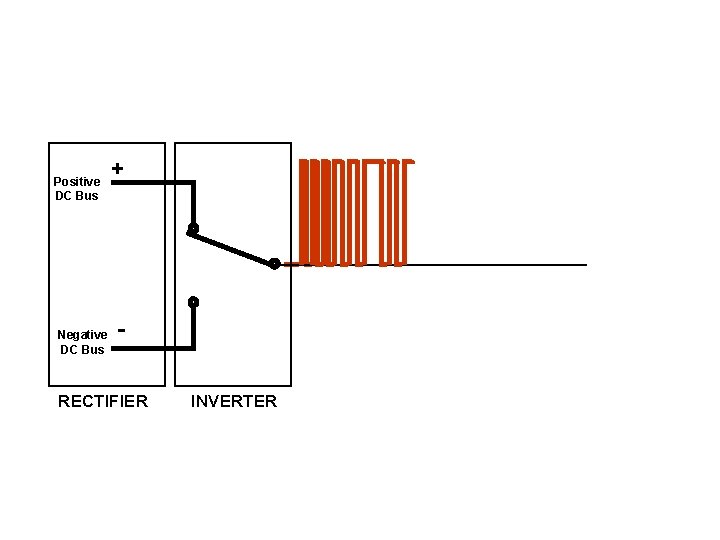
Positive DC Bus Negative DC Bus + - RECTIFIER INVERTER
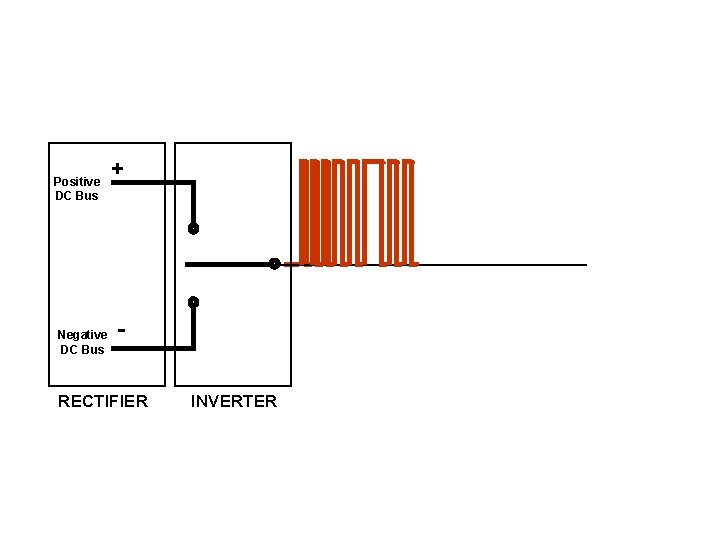
Positive DC Bus Negative DC Bus + - RECTIFIER INVERTER
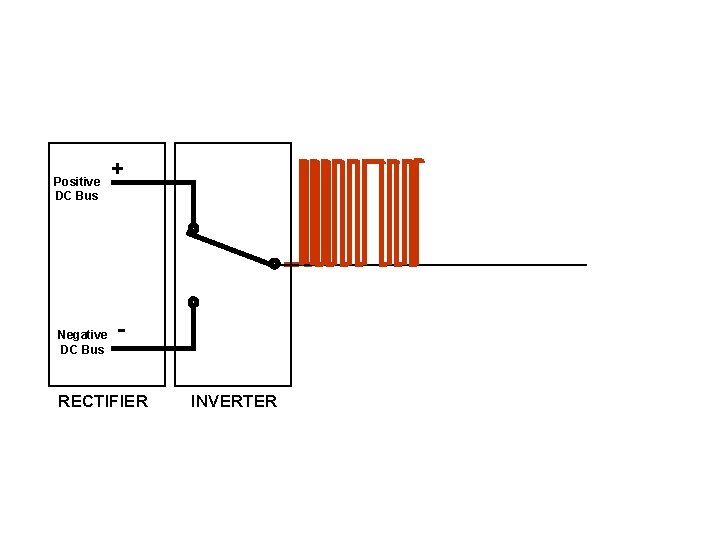
Positive DC Bus Negative DC Bus + - RECTIFIER INVERTER
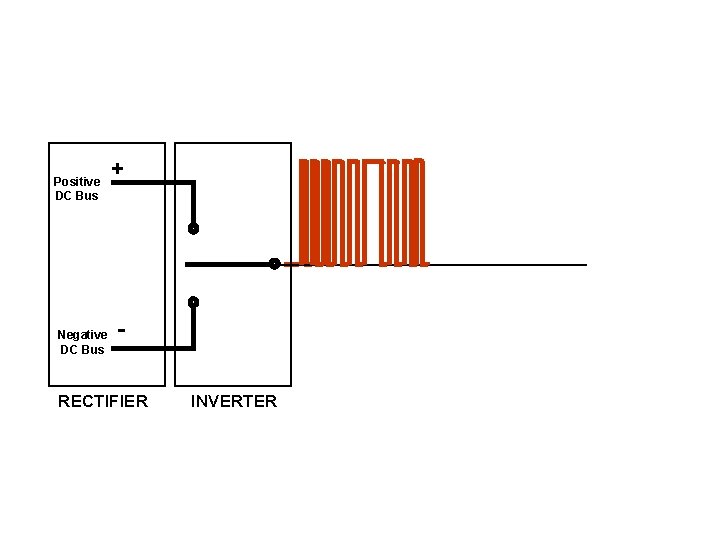
Positive DC Bus Negative DC Bus + - RECTIFIER INVERTER
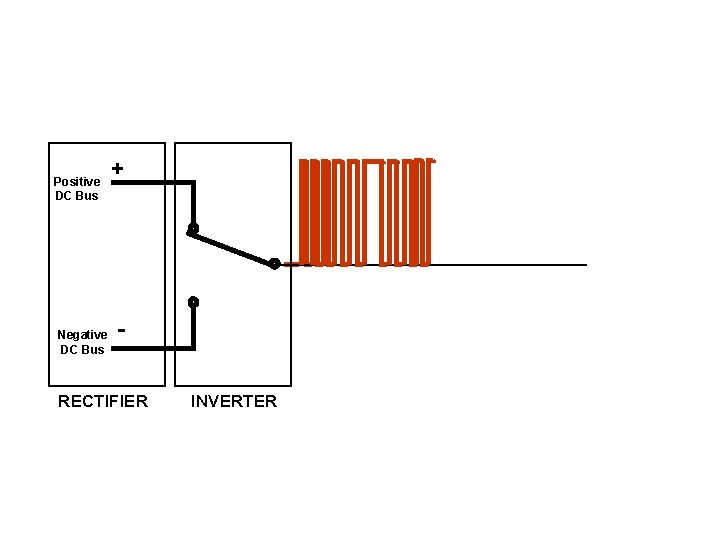
Positive DC Bus Negative DC Bus + - RECTIFIER INVERTER
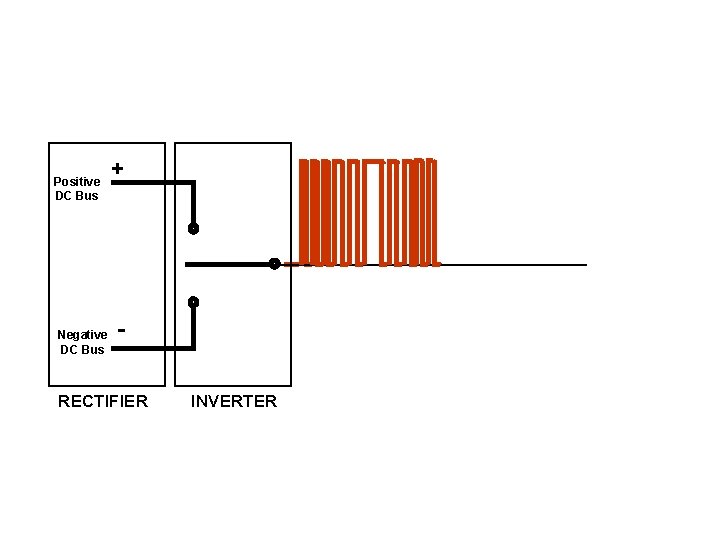
Positive DC Bus Negative DC Bus + - RECTIFIER INVERTER
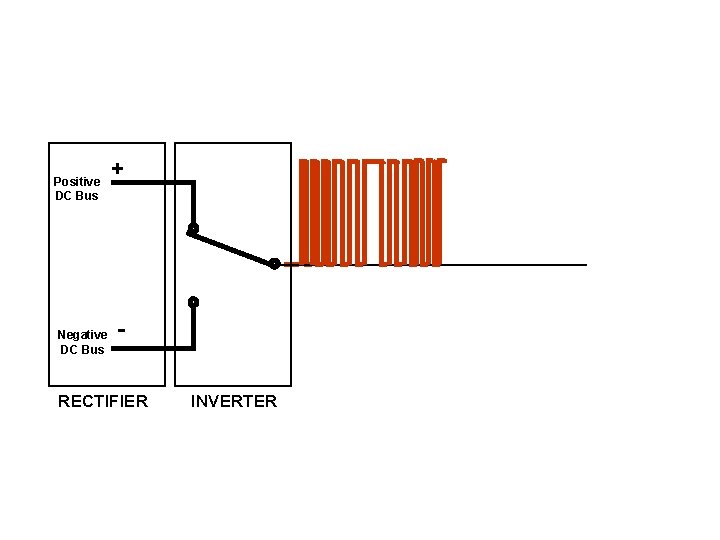
Positive DC Bus Negative DC Bus + - RECTIFIER INVERTER
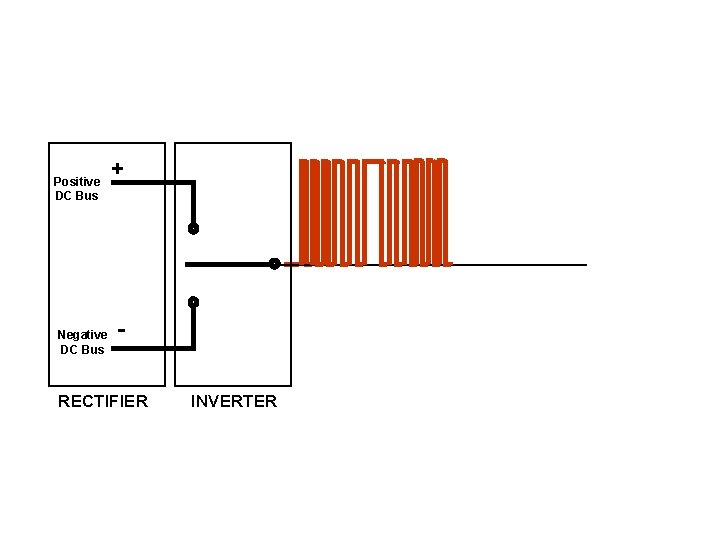
Positive DC Bus Negative DC Bus + - RECTIFIER INVERTER
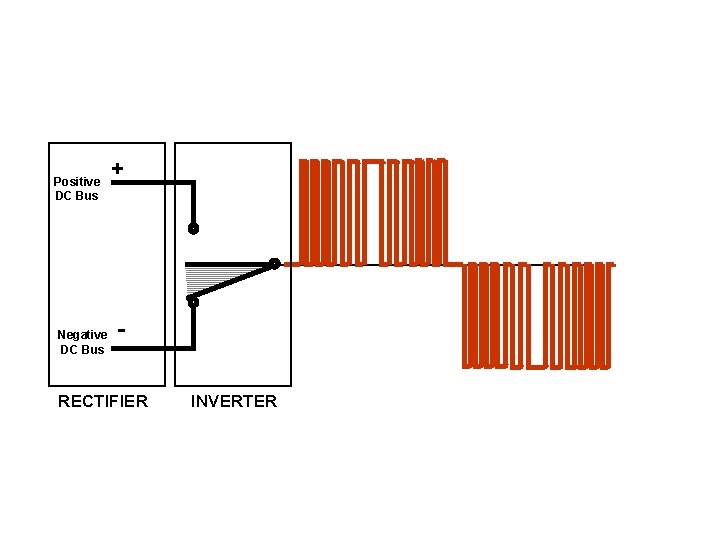
Positive DC Bus Negative DC Bus + - RECTIFIER INVERTER
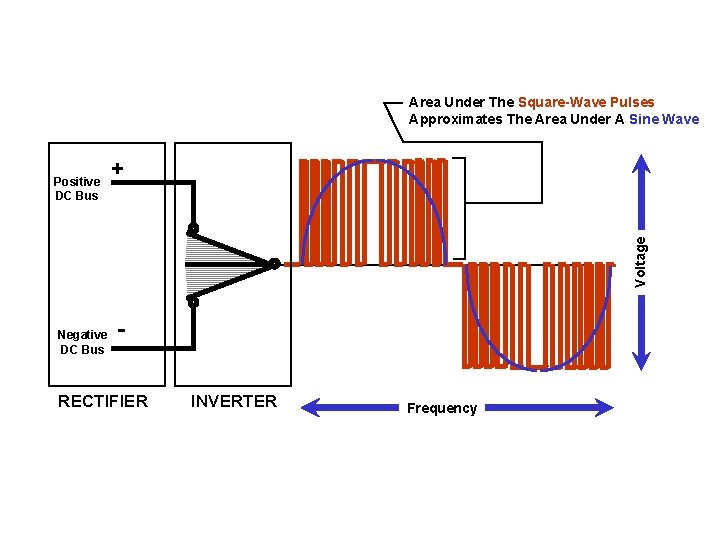
Area Under The Square-Wave Pulses Approximates The Area Under A Sine Wave + Voltage Positive DC Bus Negative DC Bus - RECTIFIER INVERTER Frequency
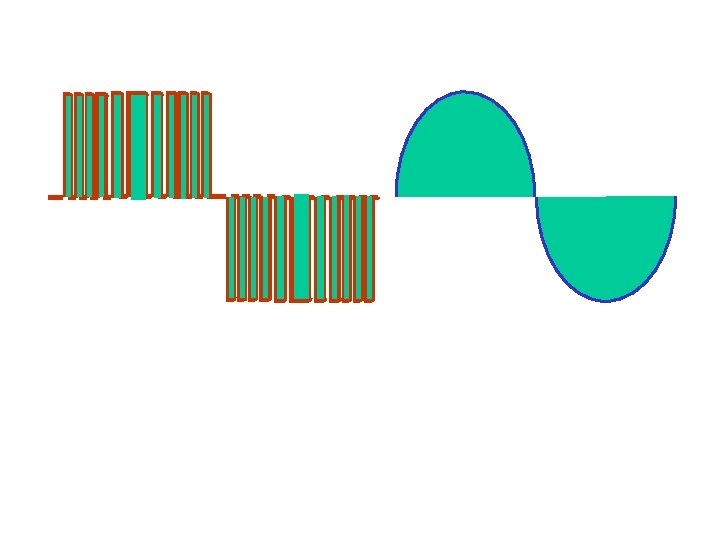
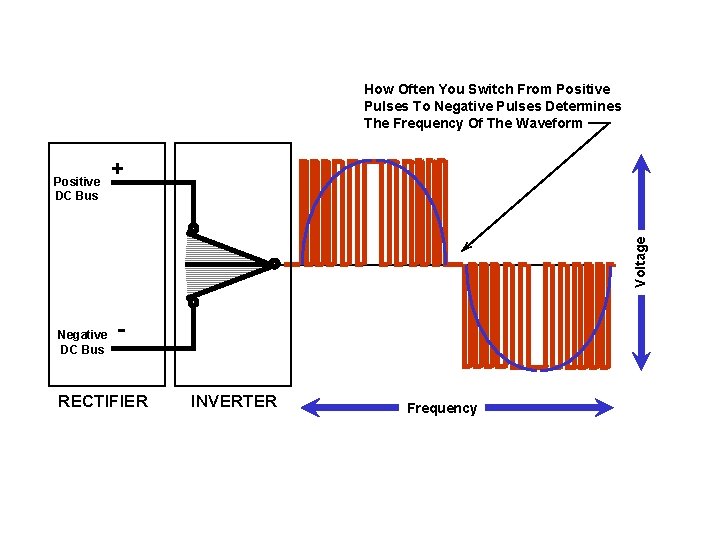
How Often You Switch From Positive Pulses To Negative Pulses Determines The Frequency Of The Waveform + Voltage Positive DC Bus Negative DC Bus - RECTIFIER INVERTER Frequency
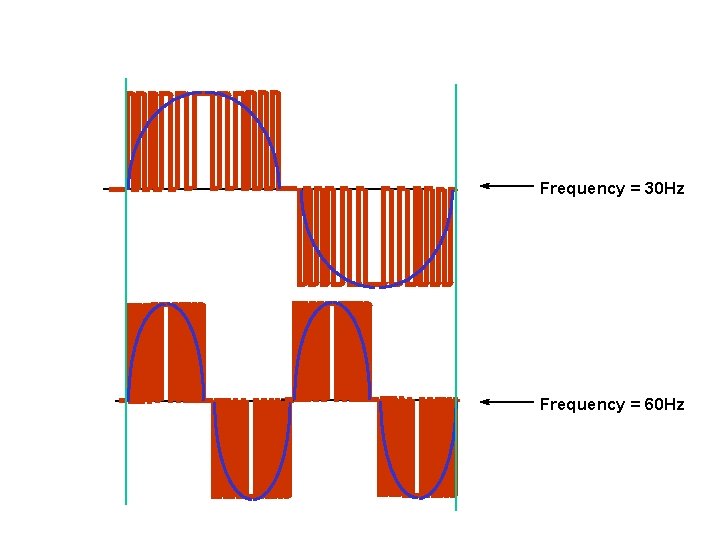
Frequency = 30 Hz Frequency = 60 Hz
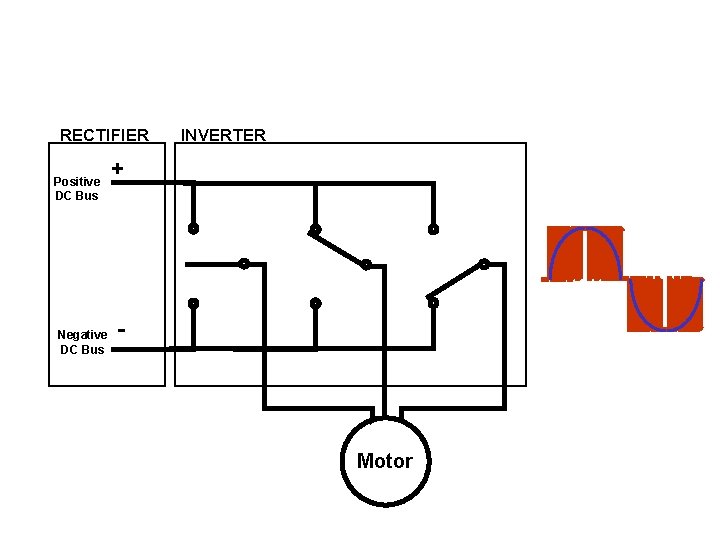
RECTIFIER Positive DC Bus Negative DC Bus INVERTER + - Motor
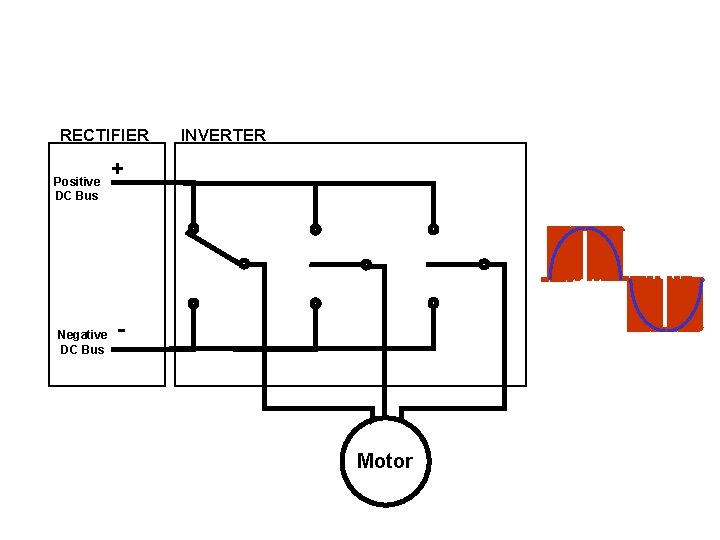
RECTIFIER Positive DC Bus Negative DC Bus INVERTER + - Motor
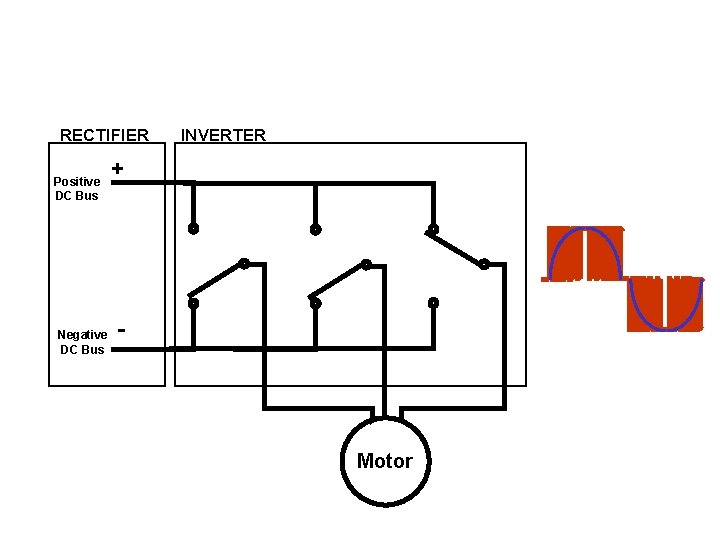
RECTIFIER Positive DC Bus Negative DC Bus INVERTER + - Motor
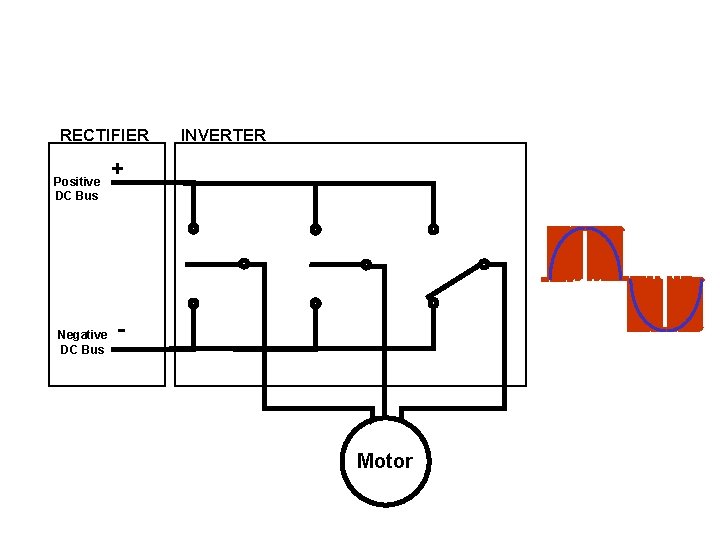
RECTIFIER Positive DC Bus Negative DC Bus INVERTER + - Motor
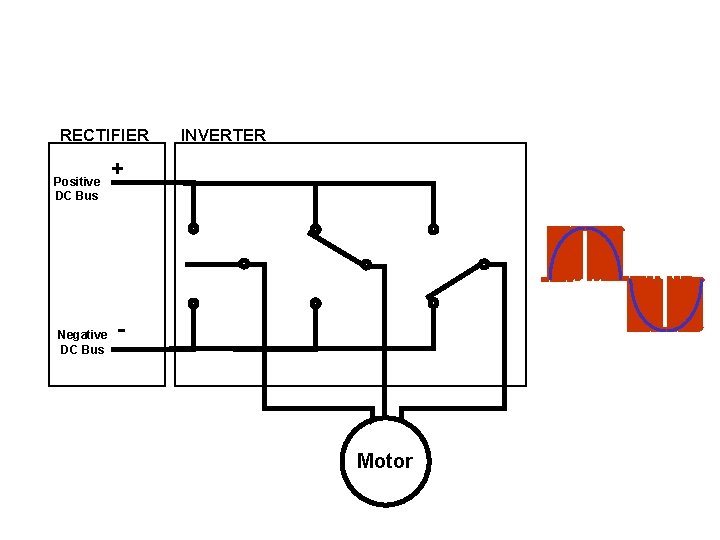
RECTIFIER Positive DC Bus Negative DC Bus INVERTER + - Motor
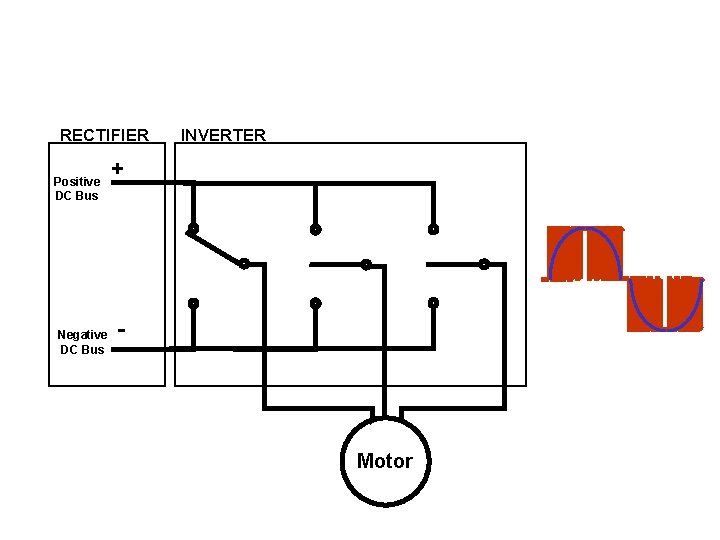
RECTIFIER Positive DC Bus Negative DC Bus INVERTER + - Motor
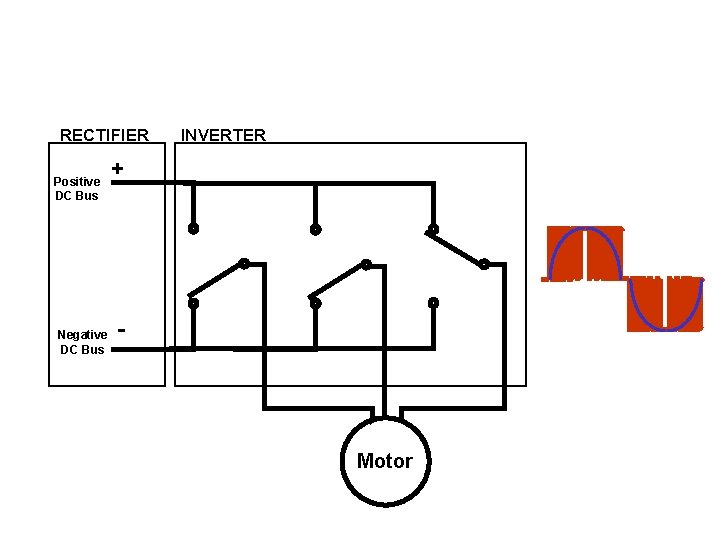
RECTIFIER Positive DC Bus Negative DC Bus INVERTER + - Motor
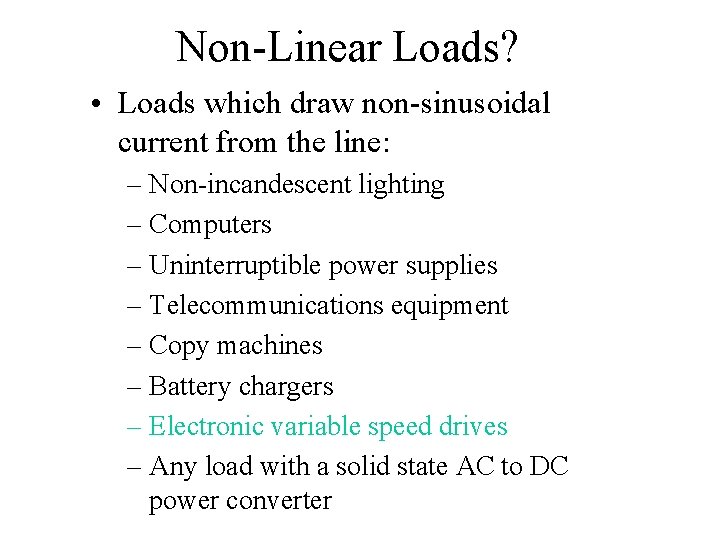
Non-Linear Loads? • Loads which draw non-sinusoidal current from the line: – Non-incandescent lighting – Computers – Uninterruptible power supplies – Telecommunications equipment – Copy machines – Battery chargers – Electronic variable speed drives – Any load with a solid state AC to DC power converter
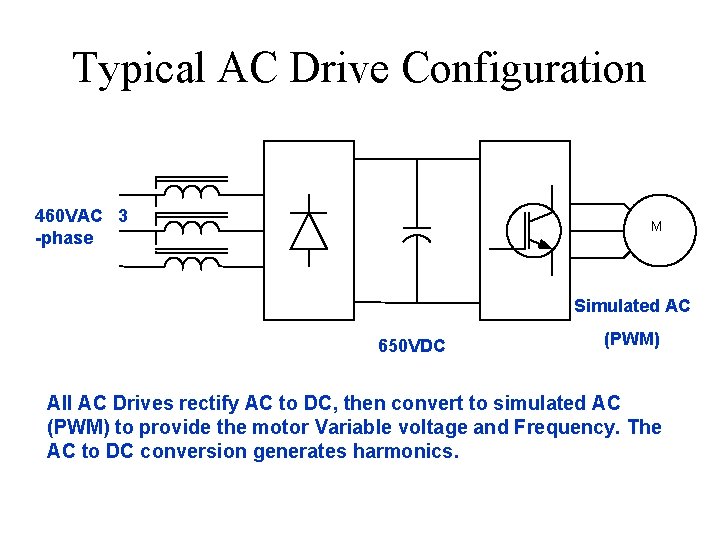
Typical AC Drive Configuration 460 VAC 3 -phase M Simulated AC 650 VDC (PWM) All AC Drives rectify AC to DC, then convert to simulated AC (PWM) to provide the motor Variable voltage and Frequency. The AC to DC conversion generates harmonics.
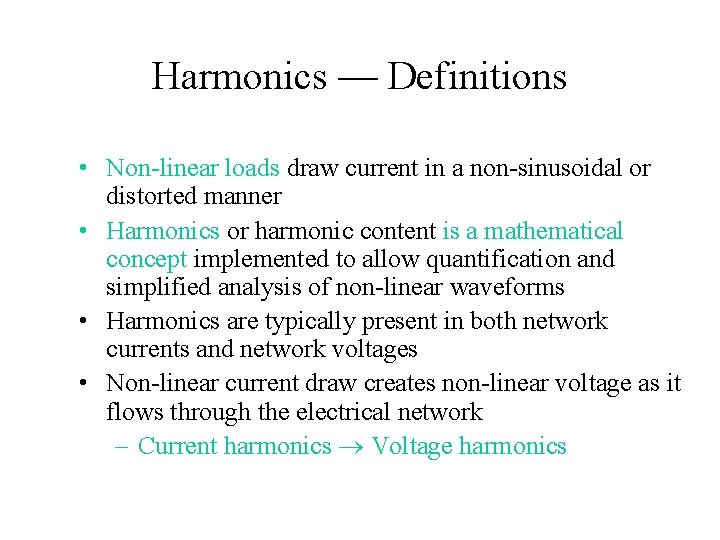
Harmonics — Definitions • Non-linear loads draw current in a non-sinusoidal or distorted manner • Harmonics or harmonic content is a mathematical concept implemented to allow quantification and simplified analysis of non-linear waveforms • Harmonics are typically present in both network currents and network voltages • Non-linear current draw creates non-linear voltage as it flows through the electrical network – Current harmonics Voltage harmonics
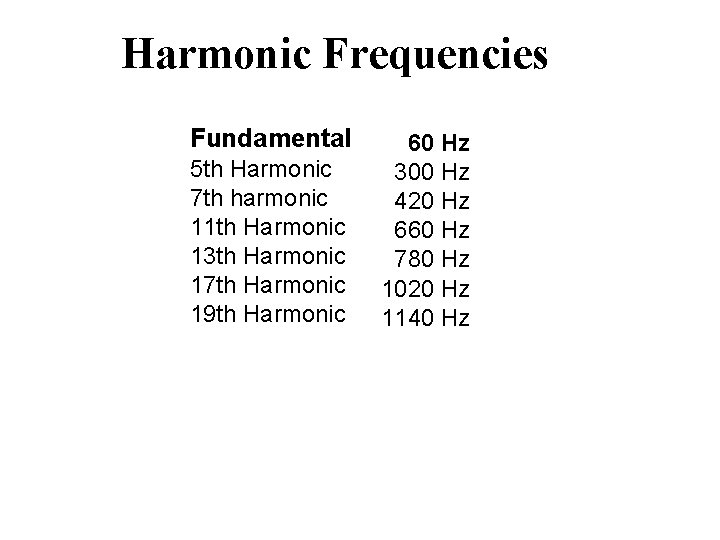
Harmonic Frequencies Fundamental 5 th Harmonic 7 th harmonic 11 th Harmonic 13 th Harmonic 17 th Harmonic 19 th Harmonic 60 Hz 300 Hz 420 Hz 660 Hz 780 Hz 1020 Hz 1140 Hz
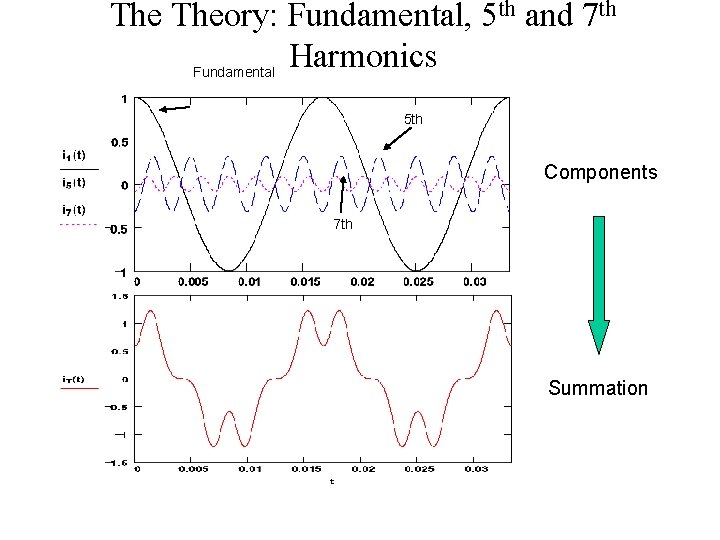
The Theory: Fundamental, 5 th and 7 th Harmonics Fundamental 5 th Components 7 th Summation
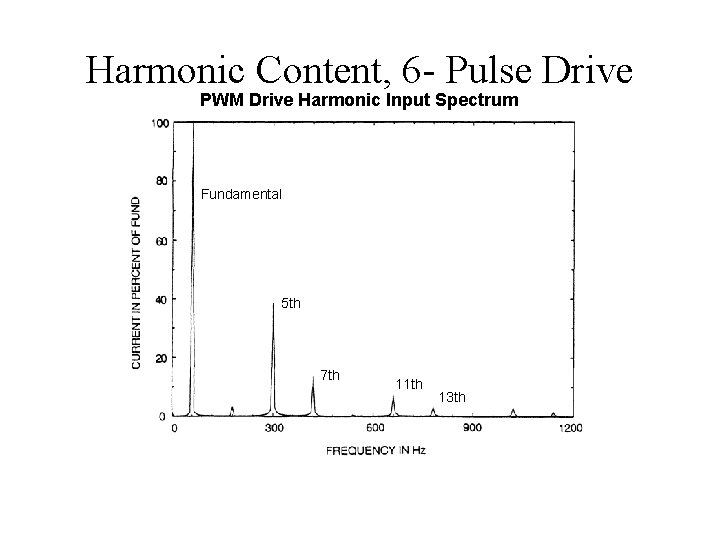
Harmonic Content, 6 - Pulse Drive PWM Drive Harmonic Input Spectrum Fundamental 5 th 7 th 11 th 13 th
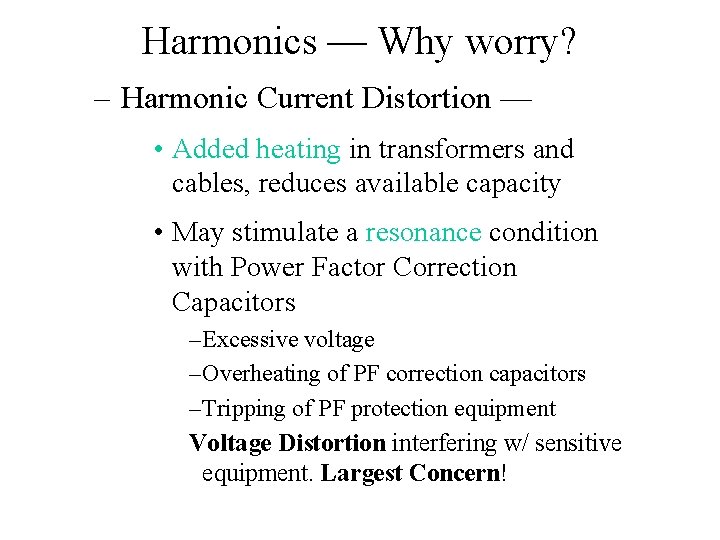
Harmonics — Why worry? – Harmonic Current Distortion — • Added heating in transformers and cables, reduces available capacity • May stimulate a resonance condition with Power Factor Correction Capacitors – Excessive voltage – Overheating of PF correction capacitors – Tripping of PF protection equipment Voltage Distortion interfering w/ sensitive equipment. Largest Concern!
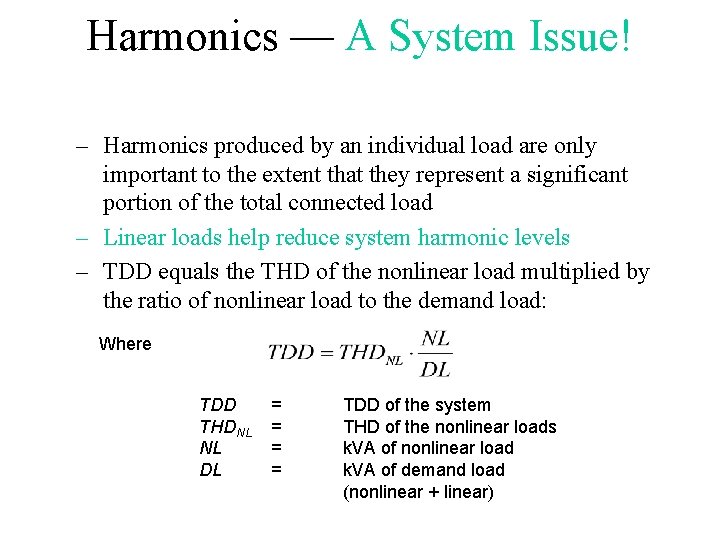
Harmonics — A System Issue! – Harmonics produced by an individual load are only important to the extent that they represent a significant portion of the total connected load – Linear loads help reduce system harmonic levels – TDD equals the THD of the nonlinear load multiplied by the ratio of nonlinear load to the demand load: Where TDD THDNL NL DL = = TDD of the system THD of the nonlinear loads k. VA of nonlinear load k. VA of demand load (nonlinear + linear)
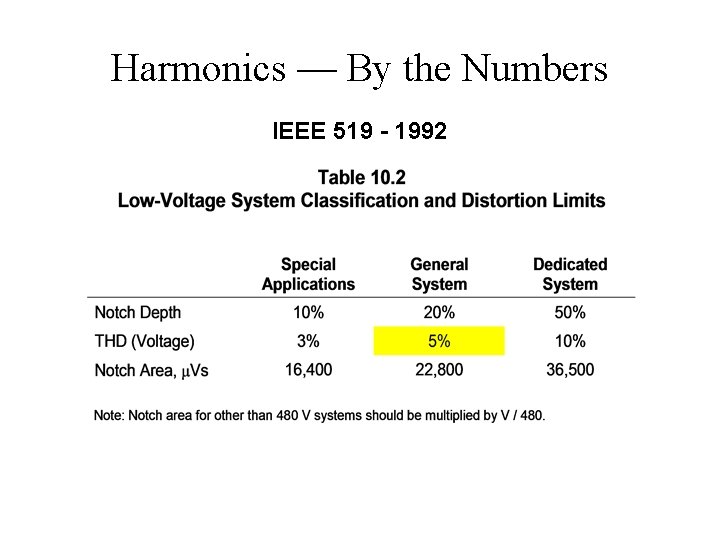
Harmonics — By the Numbers IEEE 519 - 1992
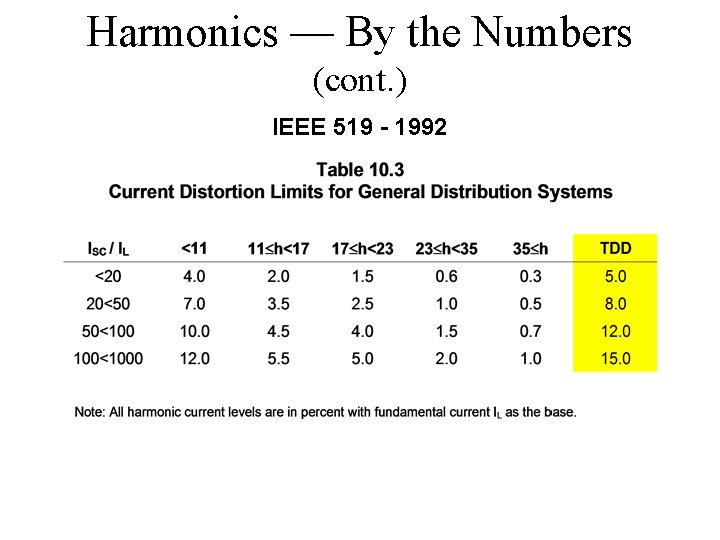
Harmonics — By the Numbers (cont. ) IEEE 519 - 1992
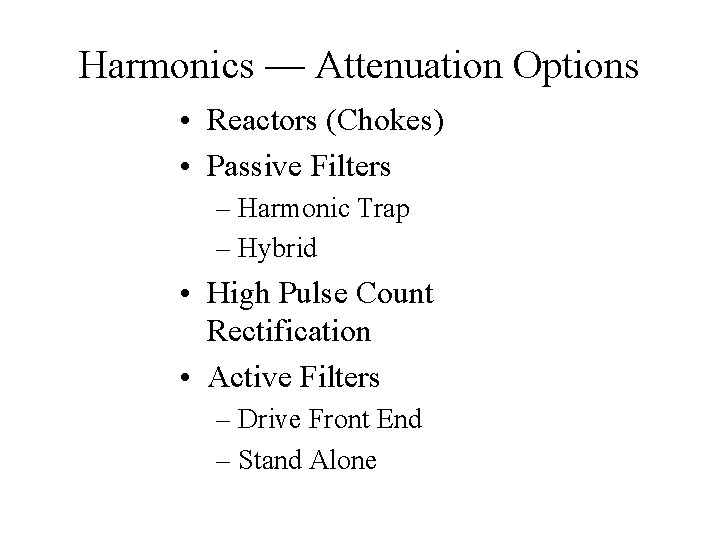
Harmonics — Attenuation Options • Reactors (Chokes) • Passive Filters – Harmonic Trap – Hybrid • High Pulse Count Rectification • Active Filters – Drive Front End – Stand Alone
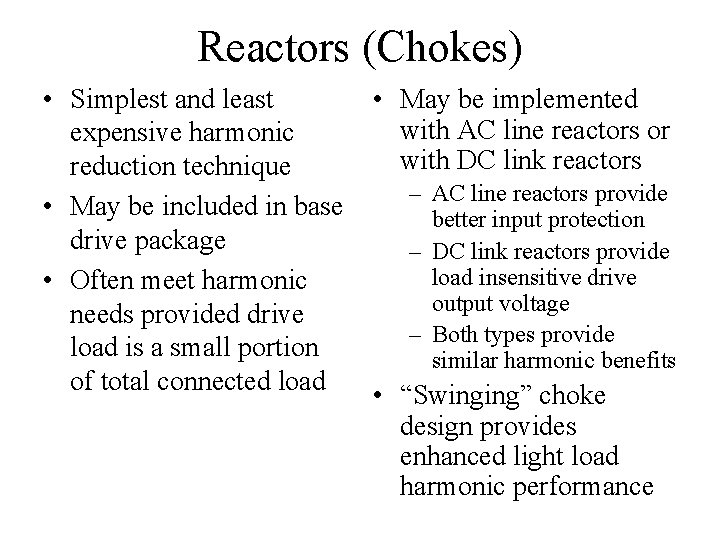
Reactors (Chokes) • Simplest and least expensive harmonic reduction technique • May be included in base drive package • Often meet harmonic needs provided drive load is a small portion of total connected load • May be implemented with AC line reactors or with DC link reactors – AC line reactors provide better input protection – DC link reactors provide load insensitive drive output voltage – Both types provide similar harmonic benefits • “Swinging” choke design provides enhanced light load harmonic performance
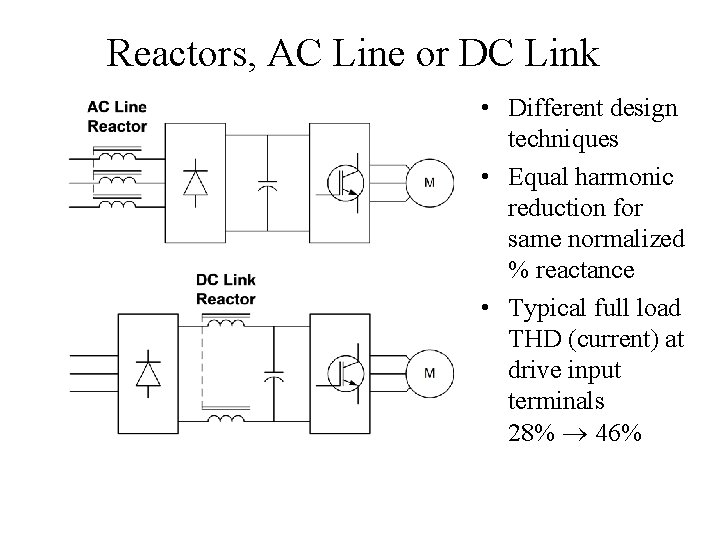
Reactors, AC Line or DC Link • Different design techniques • Equal harmonic reduction for same normalized % reactance • Typical full load THD (current) at drive input terminals 28% 46%
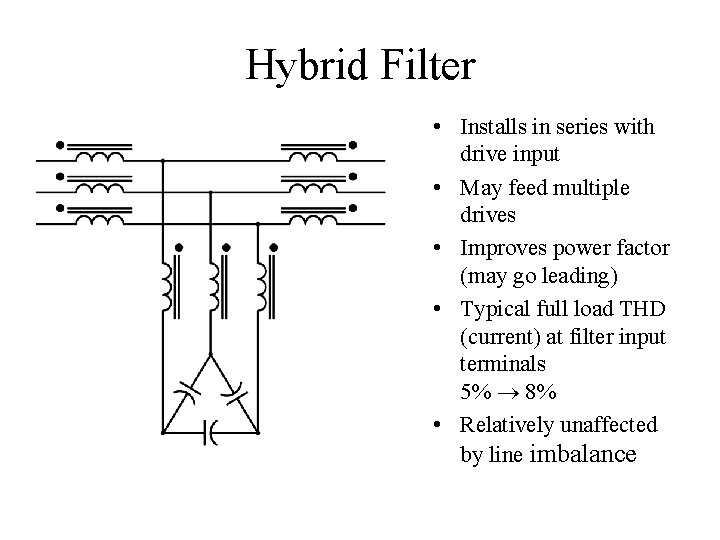
Hybrid Filter • Installs in series with drive input • May feed multiple drives • Improves power factor (may go leading) • Typical full load THD (current) at filter input terminals 5% 8% • Relatively unaffected by line imbalance
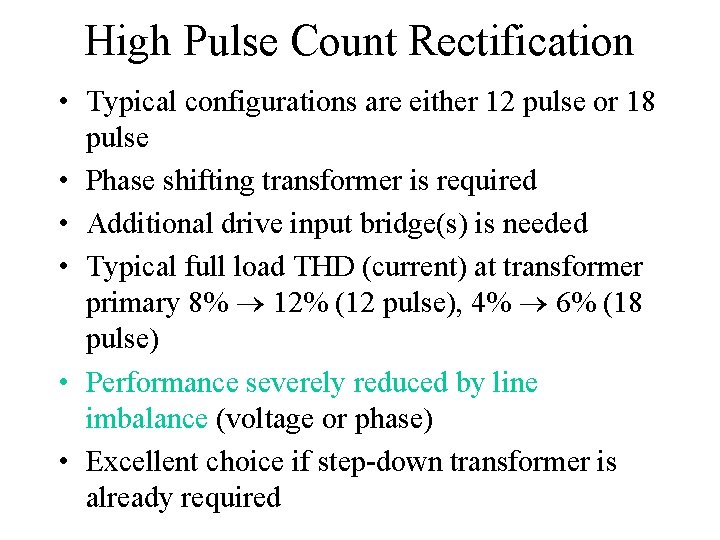
High Pulse Count Rectification • Typical configurations are either 12 pulse or 18 pulse • Phase shifting transformer is required • Additional drive input bridge(s) is needed • Typical full load THD (current) at transformer primary 8% 12% (12 pulse), 4% 6% (18 pulse) • Performance severely reduced by line imbalance (voltage or phase) • Excellent choice if step-down transformer is already required
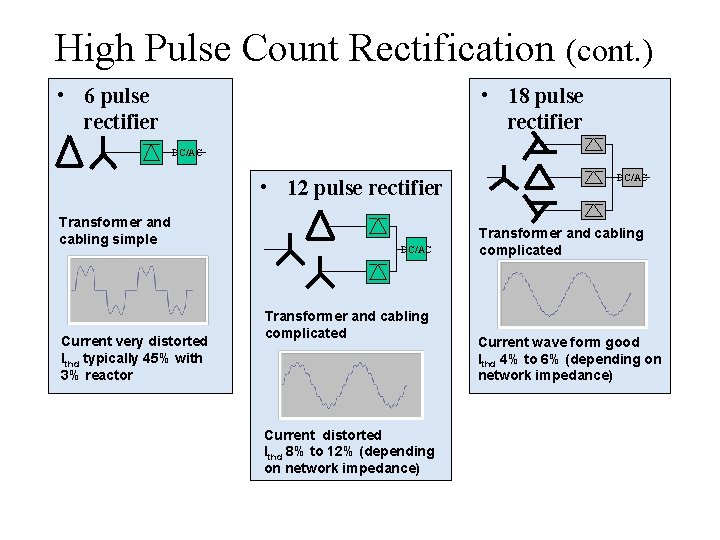
High Pulse Count Rectification (cont. ) • 6 pulse rectifier • 18 pulse rectifier DC/AC • 12 pulse rectifier Transformer and cabling simple Current very distorted Ithd typically 45% with 3% reactor DC/AC Transformer and cabling complicated Current distorted Ithd 8% to 12% (depending on network impedance) DC/AC Transformer and cabling complicated Current wave form good Ithd 4% to 6% (depending on network impedance)
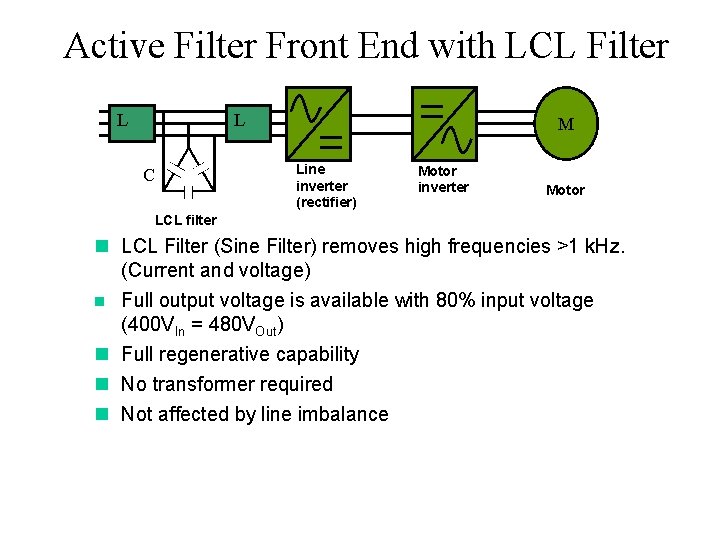
Active Filter Front End with LCL Filter L L M Line inverter (rectifier) C Motor inverter Motor LCL filter n LCL Filter (Sine Filter) removes high frequencies >1 k. Hz. (Current and voltage) n Full output voltage is available with 80% input voltage (400 VIn = 480 VOut) n Full regenerative capability n No transformer required n Not affected by line imbalance
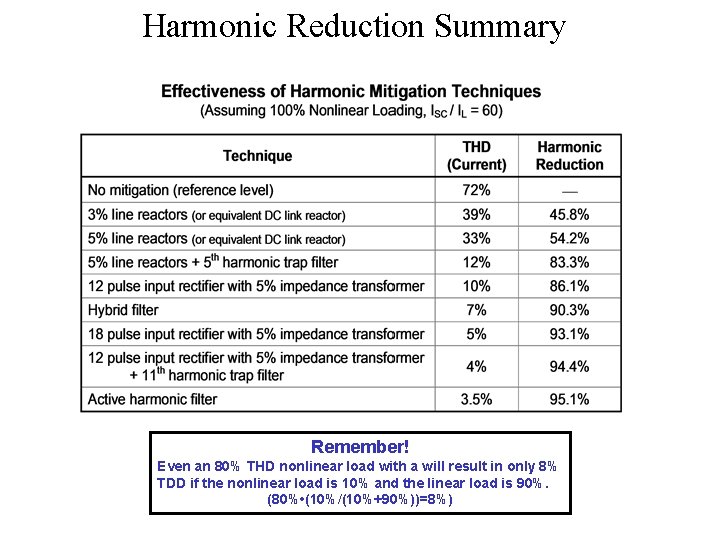
Harmonic Reduction Summary Remember! Even an 80% THD nonlinear load with a will result in only 8% TDD if the nonlinear load is 10% and the linear load is 90%. (80% • (10%/(10%+90%))=8%)
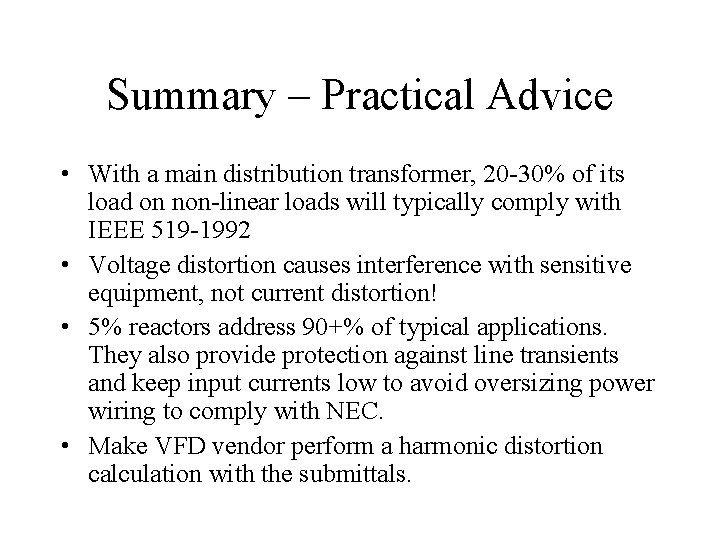
Summary – Practical Advice • With a main distribution transformer, 20 -30% of its load on non-linear loads will typically comply with IEEE 519 -1992 • Voltage distortion causes interference with sensitive equipment, not current distortion! • 5% reactors address 90+% of typical applications. They also provide protection against line transients and keep input currents low to avoid oversizing power wiring to comply with NEC. • Make VFD vendor perform a harmonic distortion calculation with the submittals.
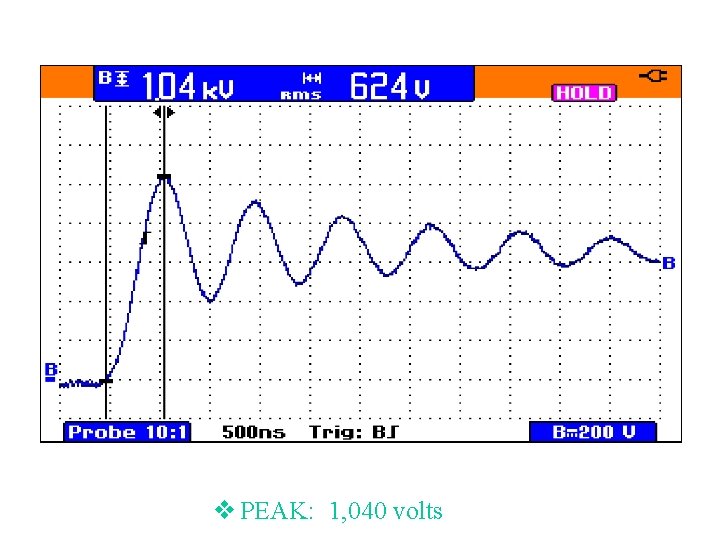
v PEAK: 1, 040 volts
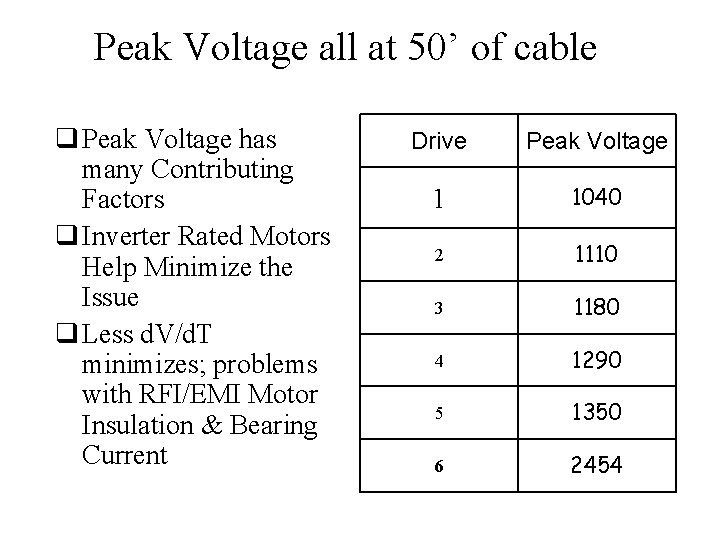
Peak Voltage all at 50’ of cable q Peak Voltage has many Contributing Factors q Inverter Rated Motors Help Minimize the Issue q Less d. V/d. T minimizes; problems with RFI/EMI Motor Insulation & Bearing Current Drive Peak Voltage 1 1040 2 1110 3 1180 4 1290 5 1350 6 2454
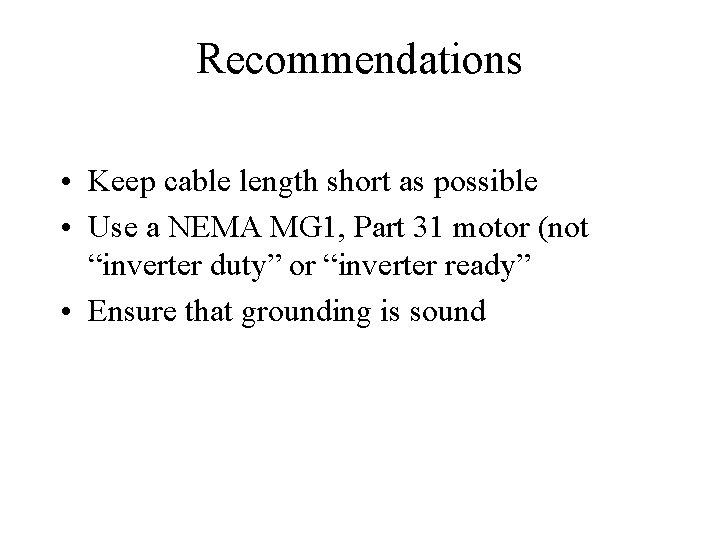
Recommendations • Keep cable length short as possible • Use a NEMA MG 1, Part 31 motor (not “inverter duty” or “inverter ready” • Ensure that grounding is sound
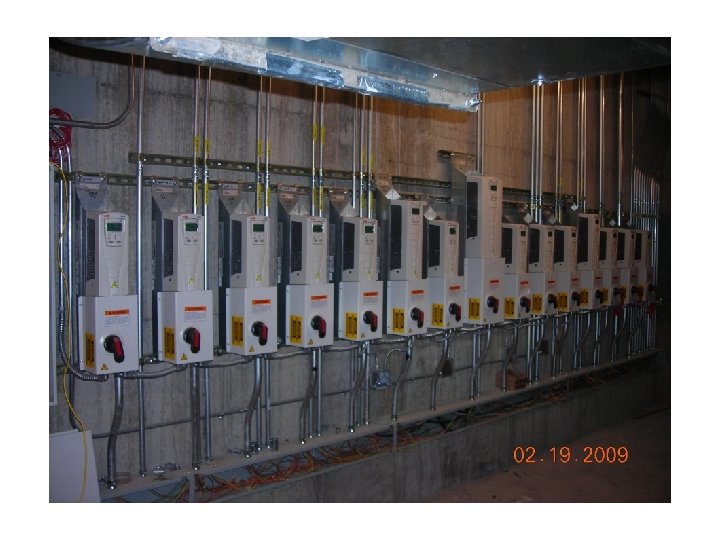
Rocky mountain ashrae
Rocky mountain ashrae
Vfd fundamentals
Rocky mountain health plans dualcare plus
Rocky mountain outfitters
Rocky mountain tissue bank
Pacific region
Rocky mountain water environment association
Rickettsia microbiology pdf
Rocky
Liquid cooled vfd
Yaskawa vfd training
Vfd scalar vs vector
Liquid cooled vfd
Iec 61131-3
Ls vfd
Unitronics vfd
Kaic calculator
Ashrae standard 15 refrigerant monitor
Ashrae standard 202 pdf
Ashrae standard 180
Transfer function method cooling load
Ashrae 188 water management plan
Ashrae 52
Ashrae tac
Ashrae certification
Ashrae 52
Effective temperature in climatology
Ashrae
Ashrae
Www.ashrae.org membership
Rocky geyer
Rocky planet surface
The stolen child yeats
Come away o human child song
Rocky mountains south america
Rocky slowly got up from the mat
Rocky slowly got up from the mat
Rocky soil in new england colonies
Strike slip fault
Rocky davis incision
Which colonial region contained rocky soil and cold climate
Chapter 13 lesson 1 physical geography of eastern europe
Rocky bay family services
Rocky or metallic
Incision rocky davis
A group of rocky rapids
Rocky shore adaptations
Rocky davis incision
Solid, rocky surface
Rocky crust
The brittle, rocky outer layer of earth
Gobi taklamakan desert
Kintch
Rocky slowly got up from the mat
Rocky vs terminator
Erosional work of sea waves
Rocky, stony or metallic debris
Rocky shores food web
Rockey davis incision
Chitons adaptations
A rocky leftover planetesimal orbiting the sun is
What are landforms
Rocky neck campground map
A section of the nile river with rapids and rocky terrain
Alvarado skoru
Rocky shores animals
Rocky lemus
Listen carefully 507-728-3437