The AWE Family Includes Joyal A Division of
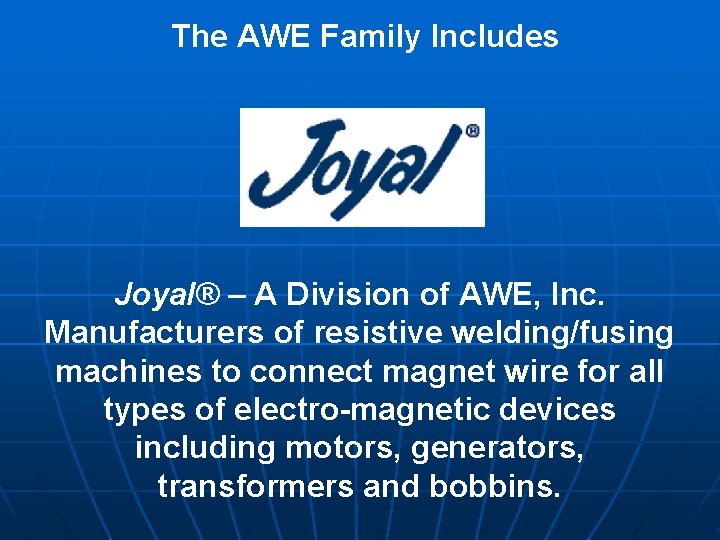
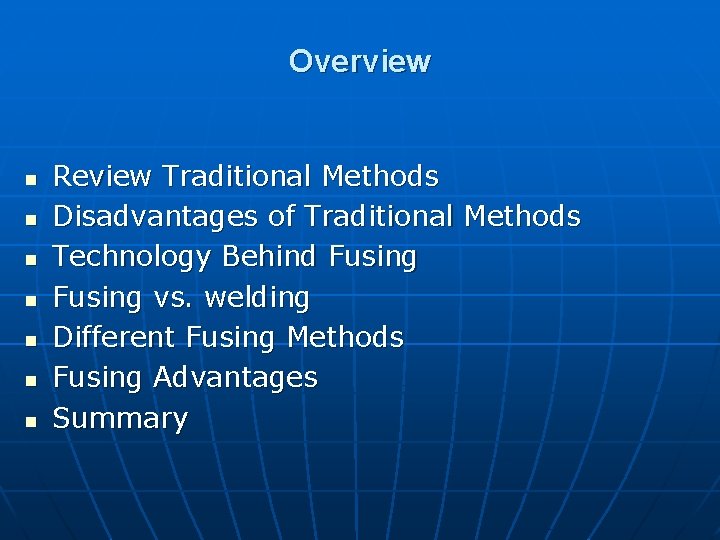
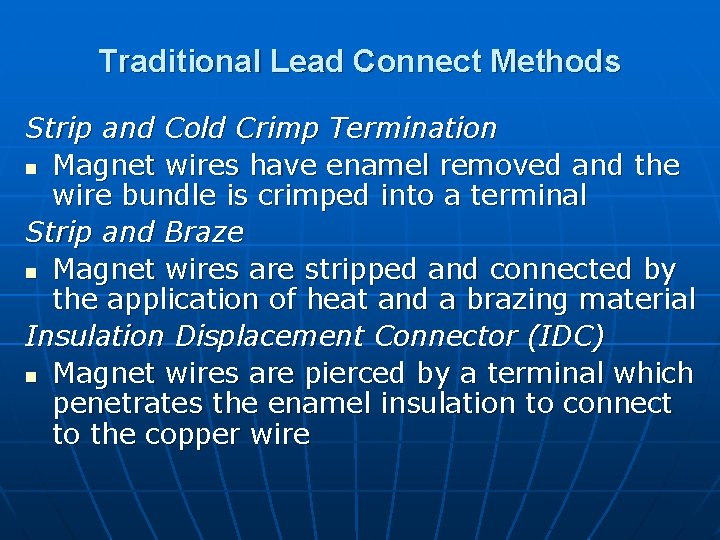
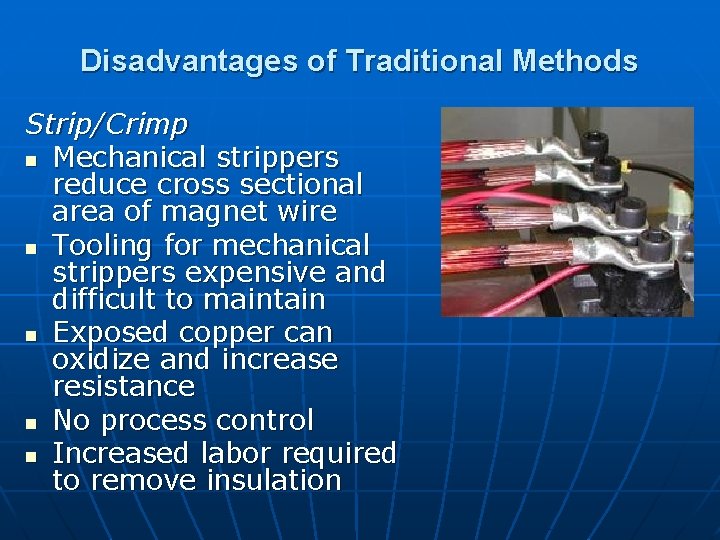
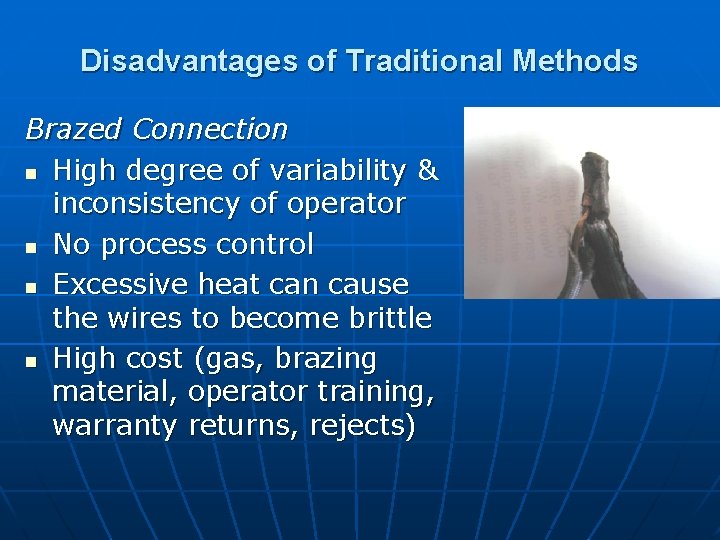
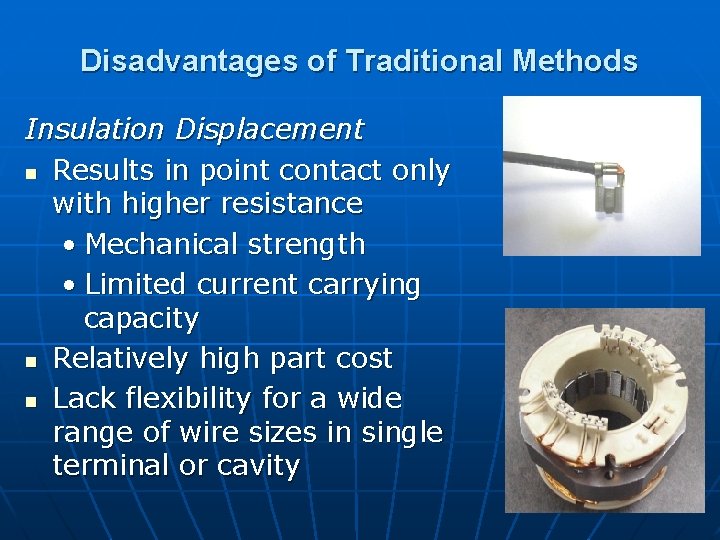
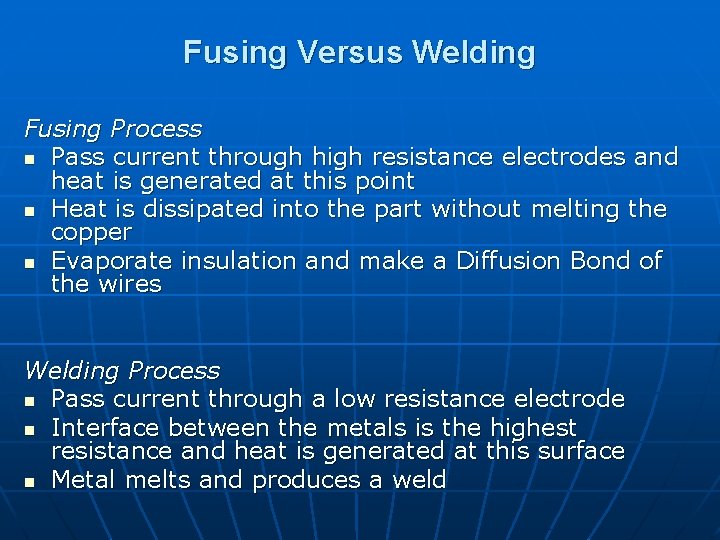
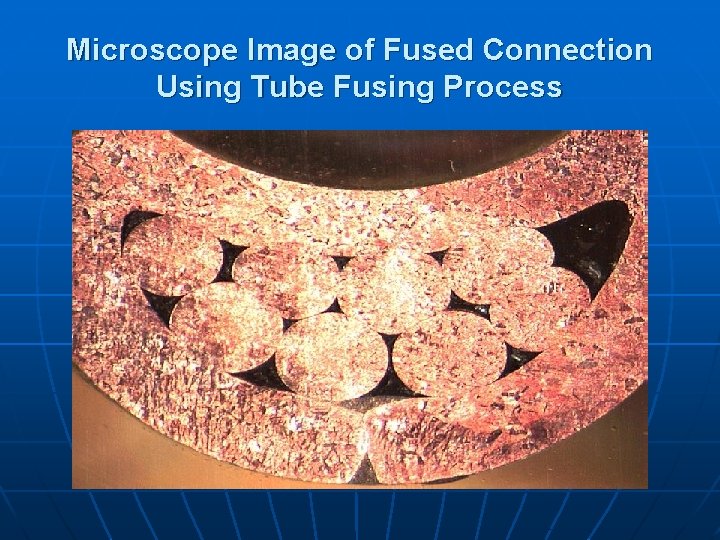
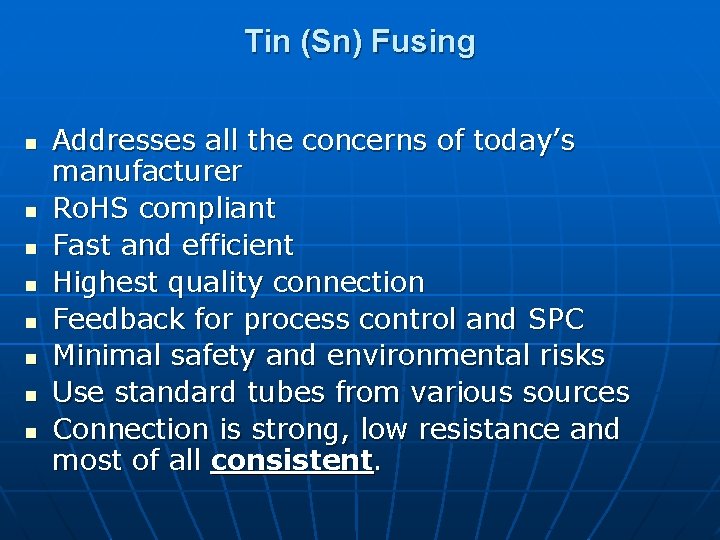
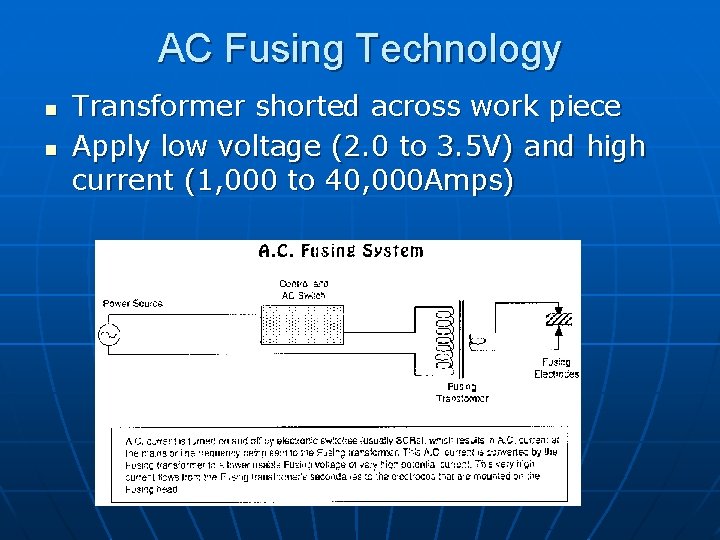
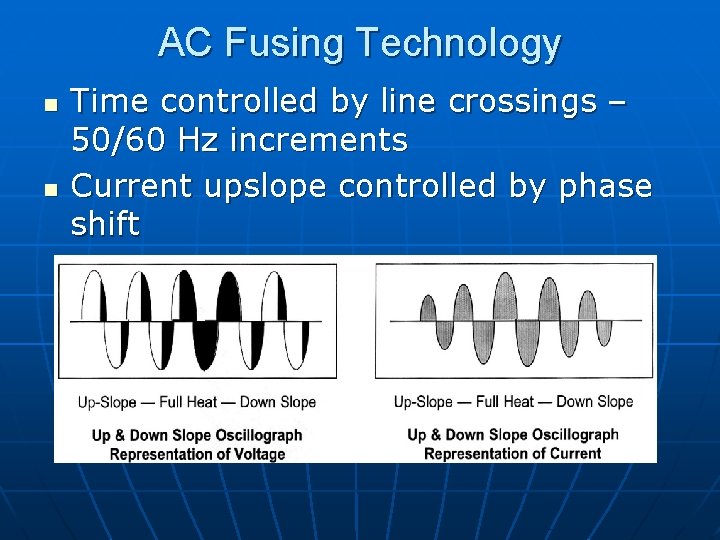
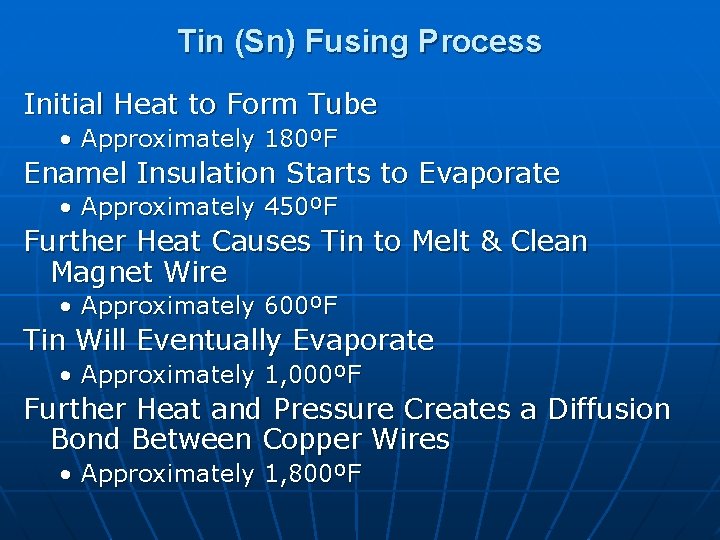
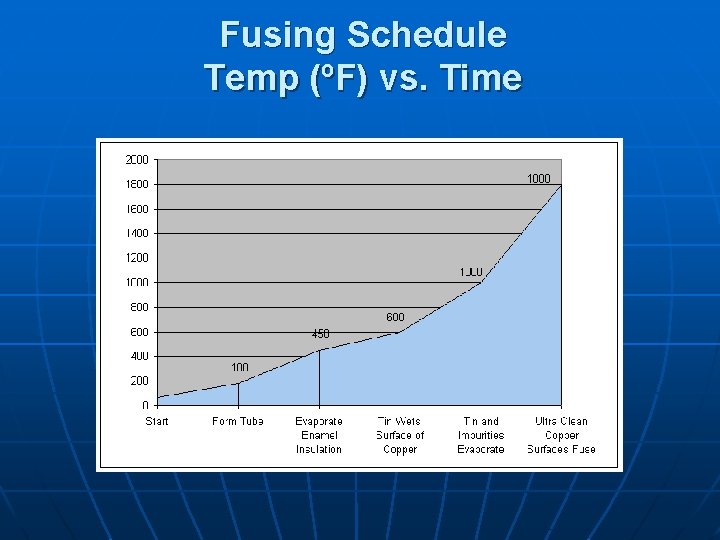
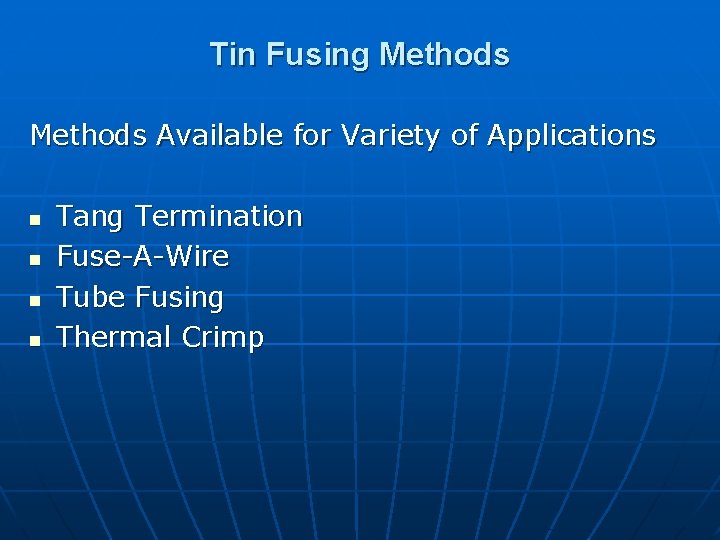
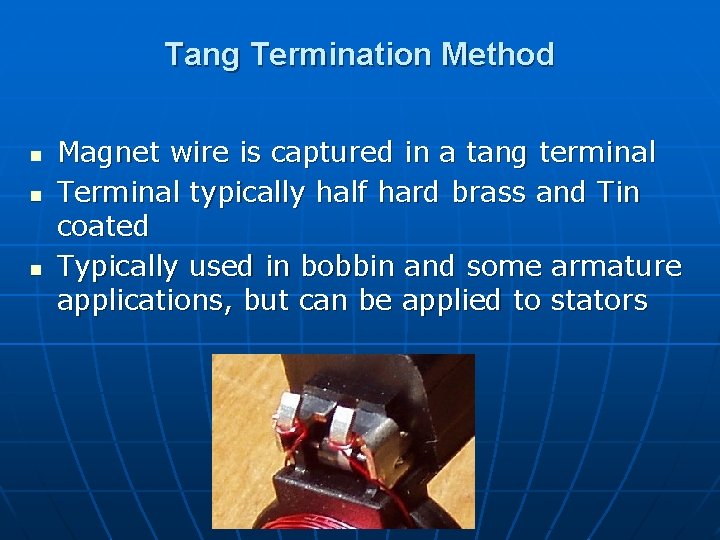
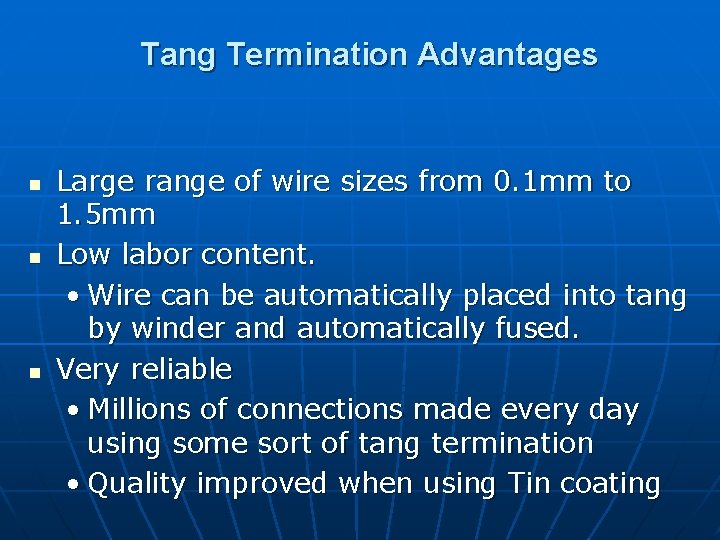
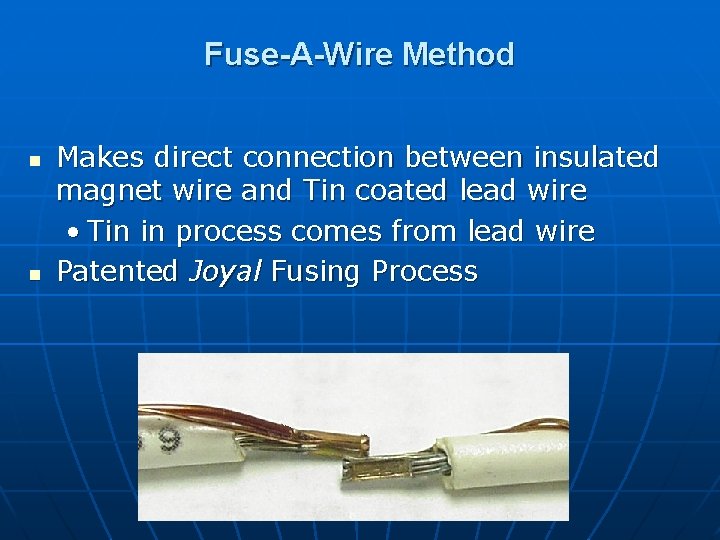
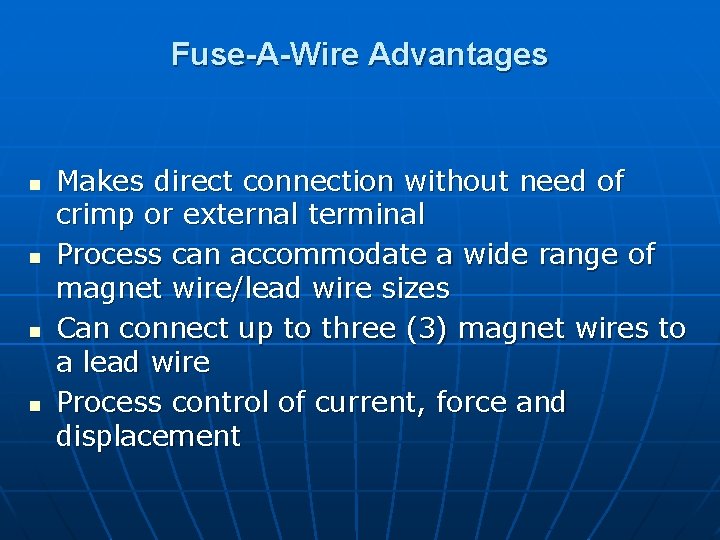
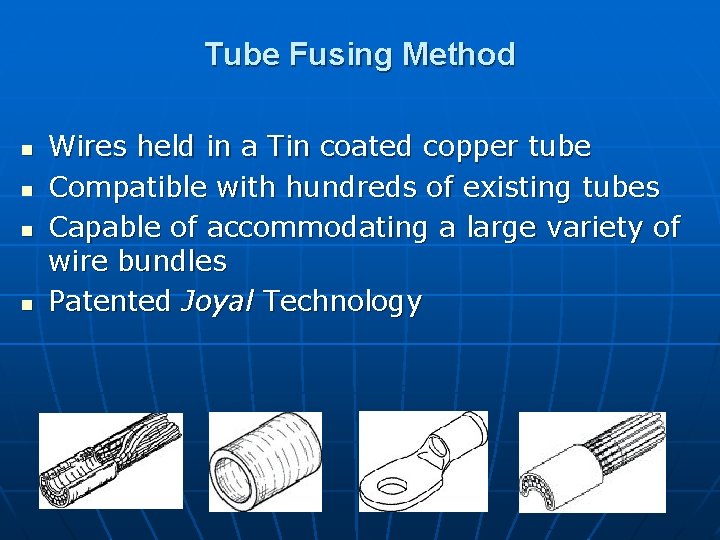
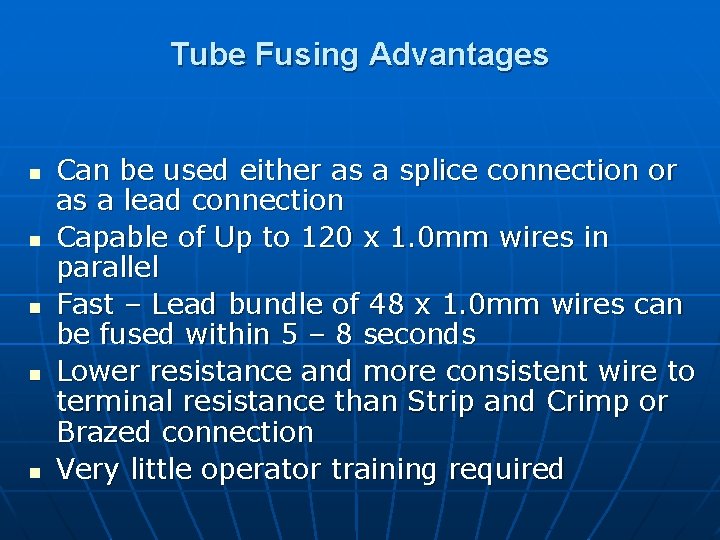
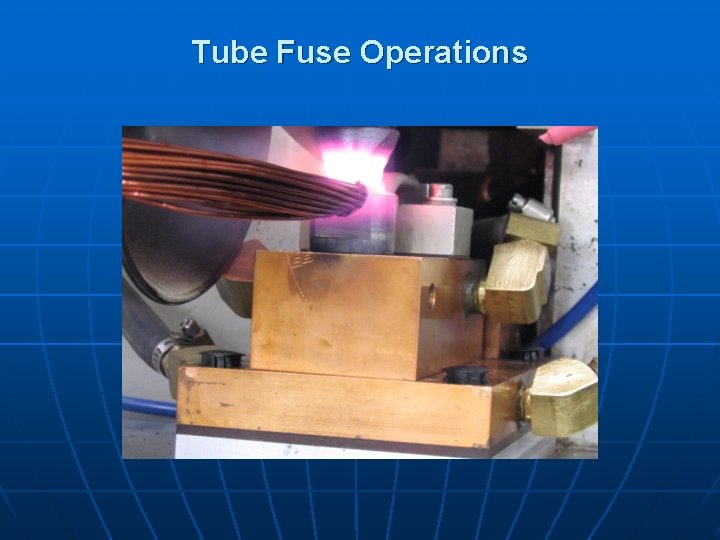

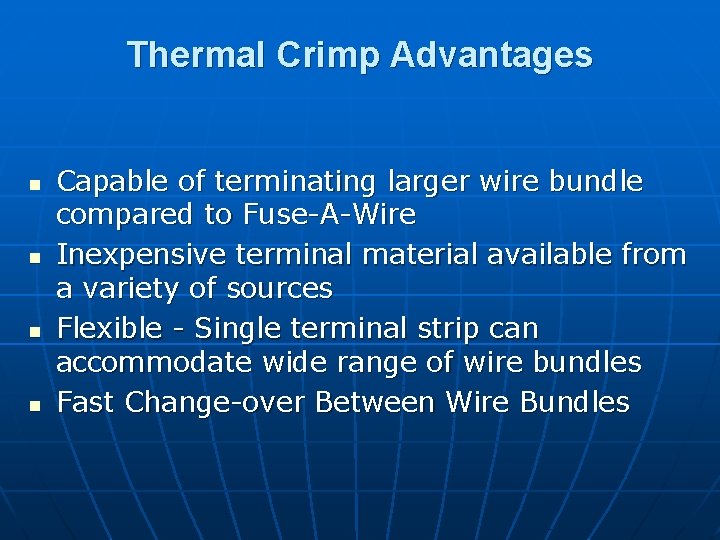
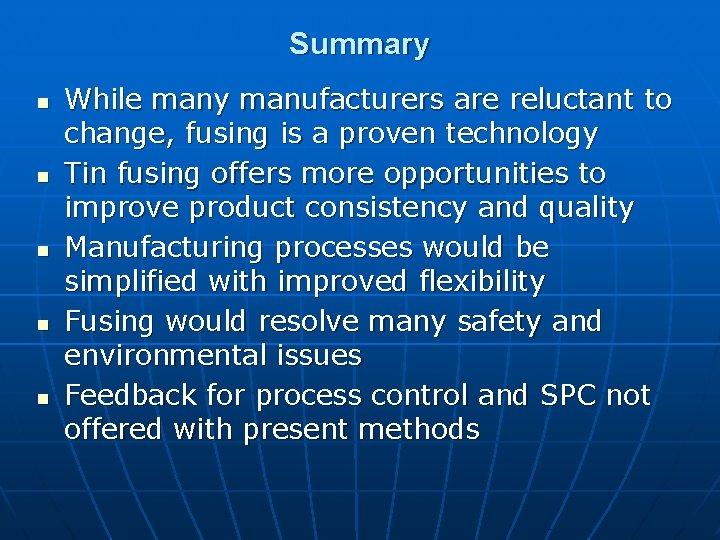
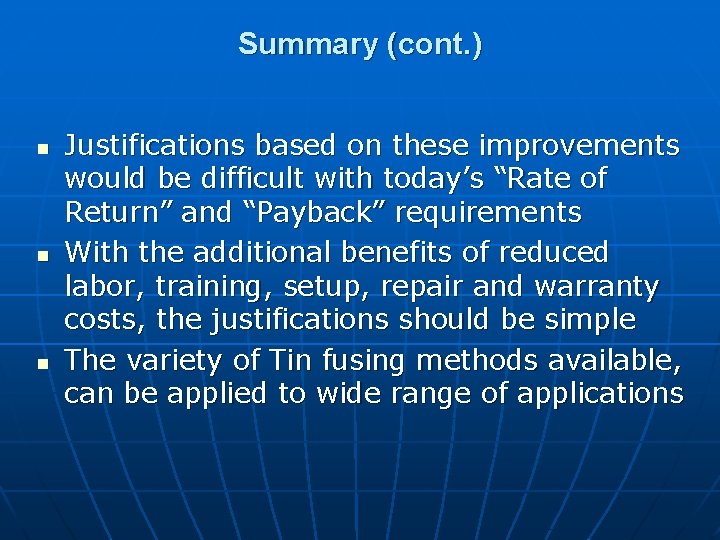
- Slides: 25
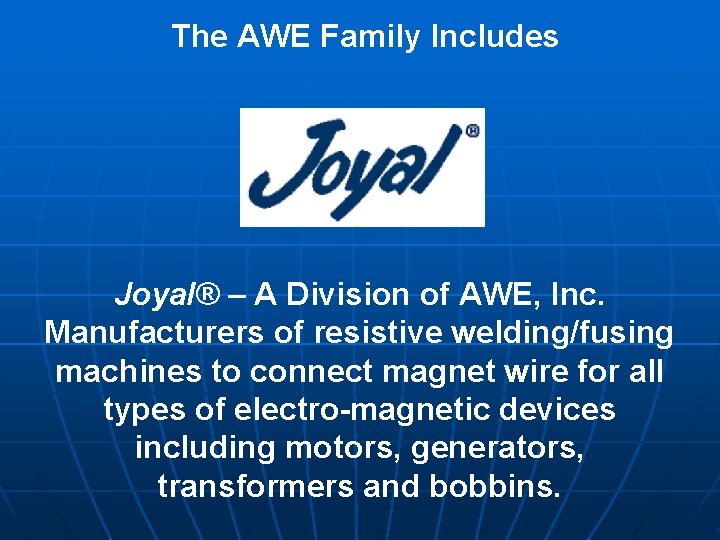
The AWE Family Includes Joyal® – A Division of AWE, Inc. Manufacturers of resistive welding/fusing machines to connect magnet wire for all types of electro-magnetic devices including motors, generators, transformers and bobbins.
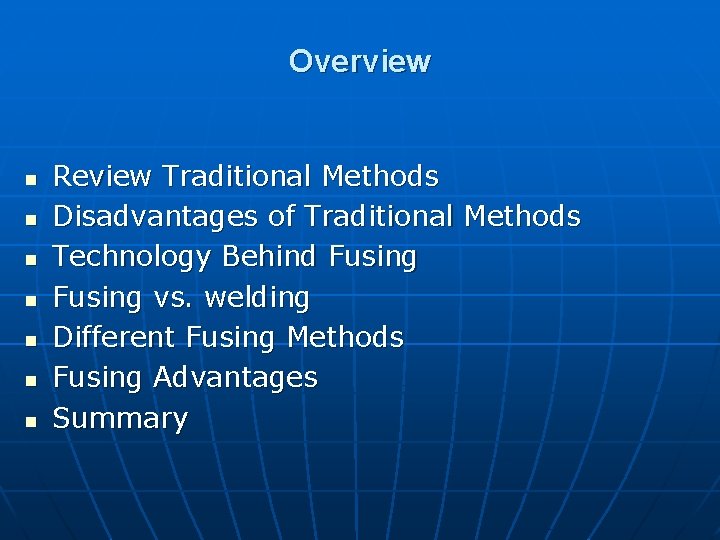
Overview n n n n Review Traditional Methods Disadvantages of Traditional Methods Technology Behind Fusing vs. welding Different Fusing Methods Fusing Advantages Summary
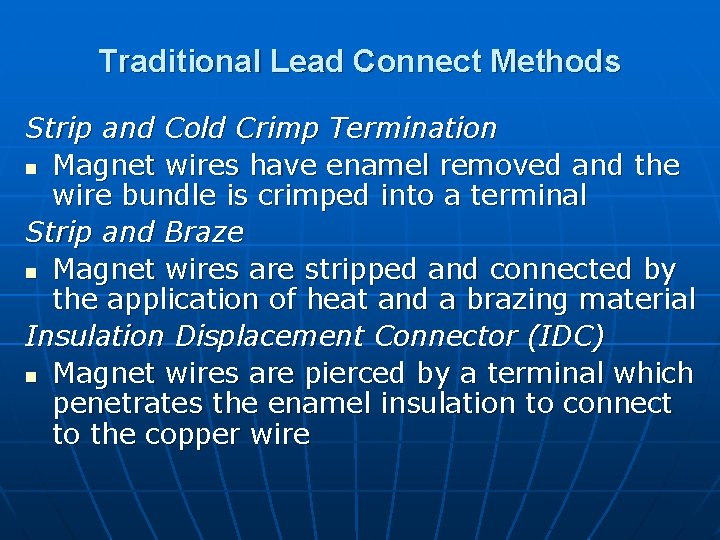
Traditional Lead Connect Methods Strip and Cold Crimp Termination n Magnet wires have enamel removed and the wire bundle is crimped into a terminal Strip and Braze n Magnet wires are stripped and connected by the application of heat and a brazing material Insulation Displacement Connector (IDC) n Magnet wires are pierced by a terminal which penetrates the enamel insulation to connect to the copper wire
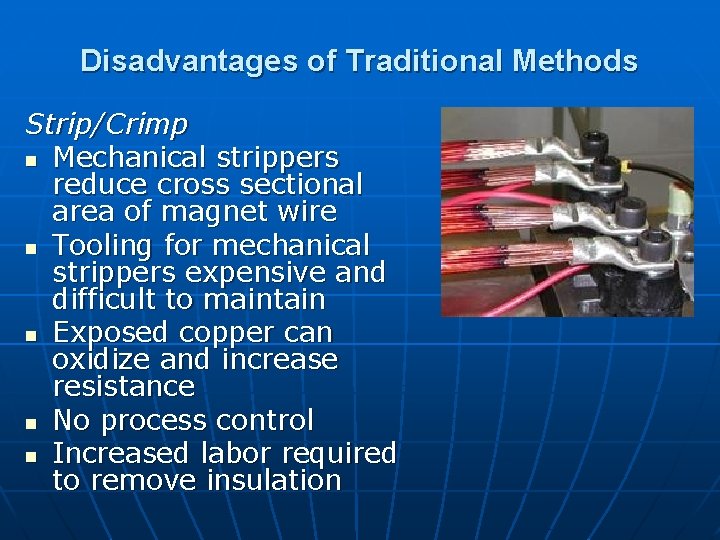
Disadvantages of Traditional Methods Strip/Crimp n Mechanical strippers reduce cross sectional area of magnet wire n Tooling for mechanical strippers expensive and difficult to maintain n Exposed copper can oxidize and increase resistance n No process control n Increased labor required to remove insulation
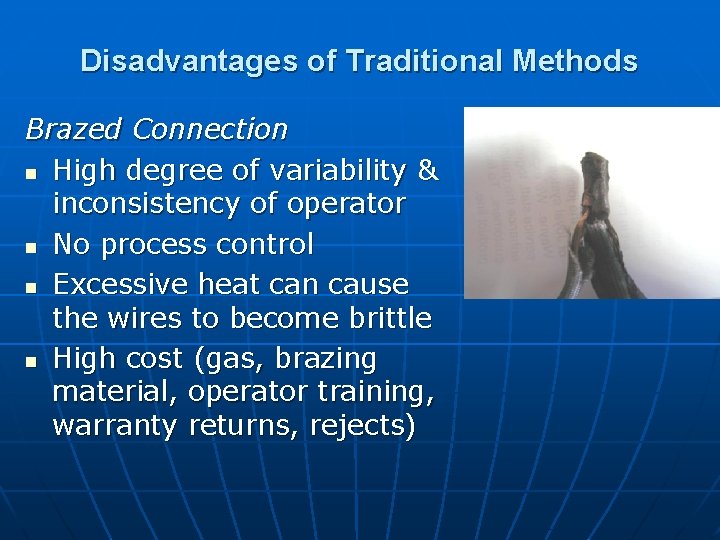
Disadvantages of Traditional Methods Brazed Connection n High degree of variability & inconsistency of operator n No process control n Excessive heat can cause the wires to become brittle n High cost (gas, brazing material, operator training, warranty returns, rejects)
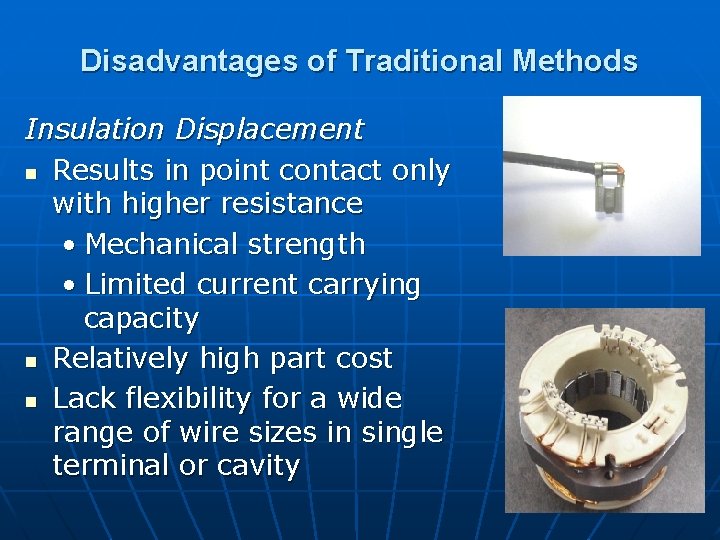
Disadvantages of Traditional Methods Insulation Displacement n Results in point contact only with higher resistance • Mechanical strength • Limited current carrying capacity n Relatively high part cost n Lack flexibility for a wide range of wire sizes in single terminal or cavity
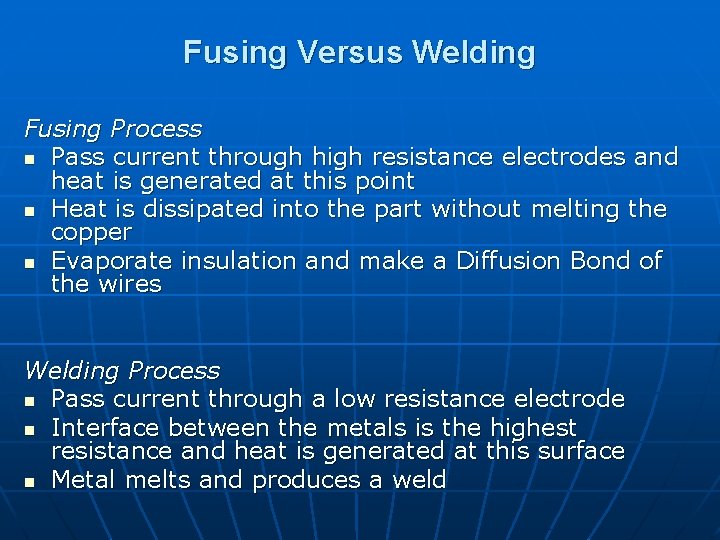
Fusing Versus Welding Fusing Process n Pass current through high resistance electrodes and heat is generated at this point n Heat is dissipated into the part without melting the copper n Evaporate insulation and make a Diffusion Bond of the wires Welding Process n Pass current through a low resistance electrode n Interface between the metals is the highest resistance and heat is generated at this surface n Metal melts and produces a weld
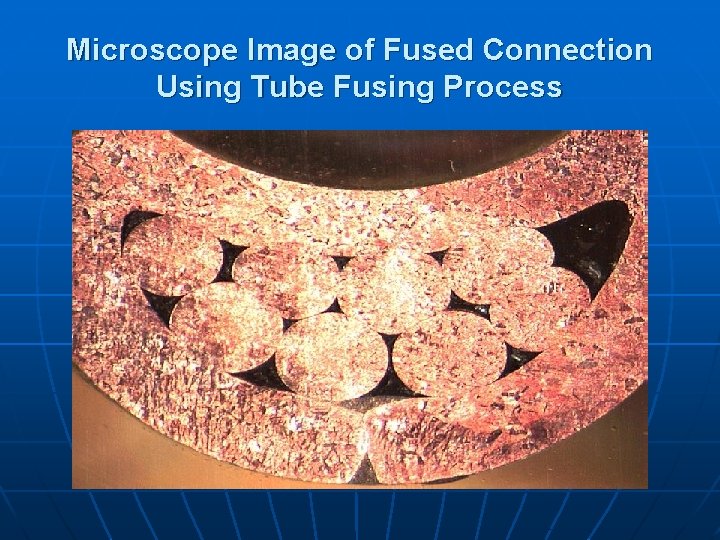
Microscope Image of Fused Connection Using Tube Fusing Process
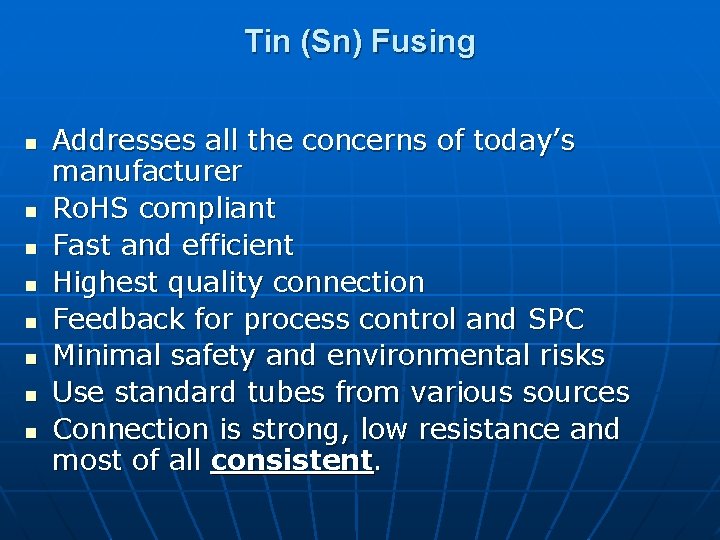
Tin (Sn) Fusing n n n n Addresses all the concerns of today’s manufacturer Ro. HS compliant Fast and efficient Highest quality connection Feedback for process control and SPC Minimal safety and environmental risks Use standard tubes from various sources Connection is strong, low resistance and most of all consistent.
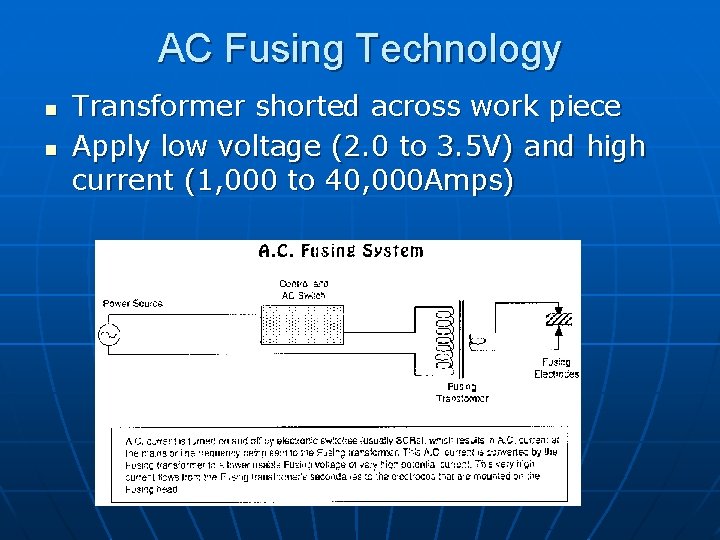
AC Fusing Technology n n Transformer shorted across work piece Apply low voltage (2. 0 to 3. 5 V) and high current (1, 000 to 40, 000 Amps)
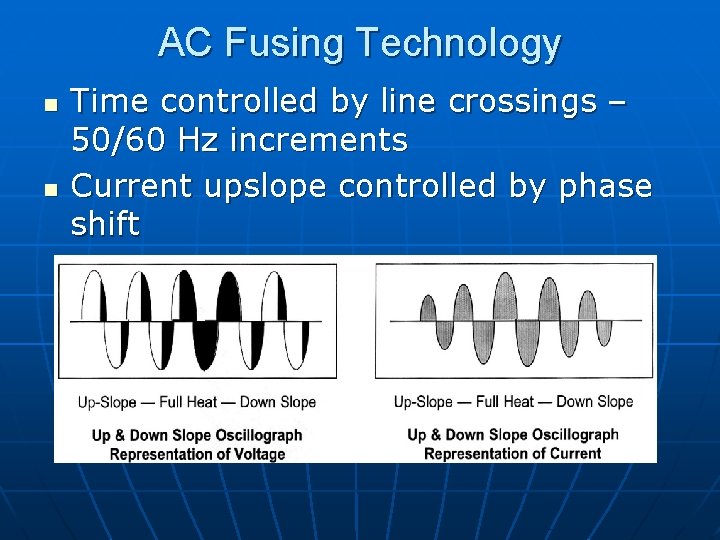
AC Fusing Technology n n Time controlled by line crossings – 50/60 Hz increments Current upslope controlled by phase shift
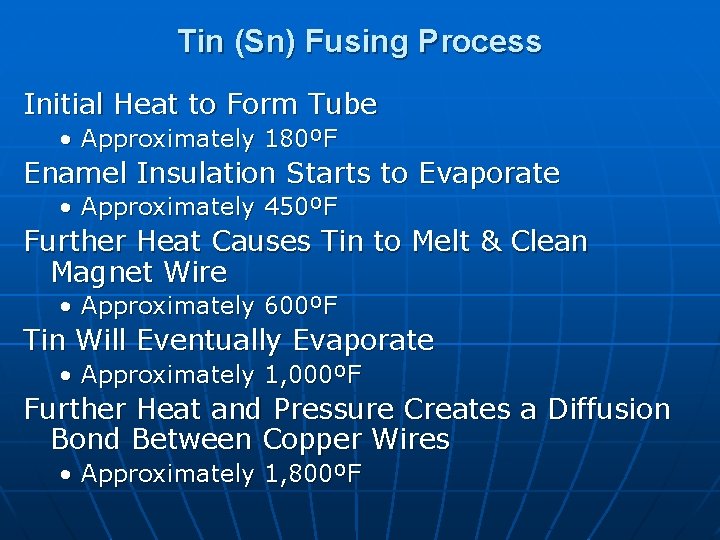
Tin (Sn) Fusing Process Initial Heat to Form Tube • Approximately 180ºF Enamel Insulation Starts to Evaporate • Approximately 450ºF Further Heat Causes Tin to Melt & Clean Magnet Wire • Approximately 600ºF Tin Will Eventually Evaporate • Approximately 1, 000ºF Further Heat and Pressure Creates a Diffusion Bond Between Copper Wires • Approximately 1, 800ºF
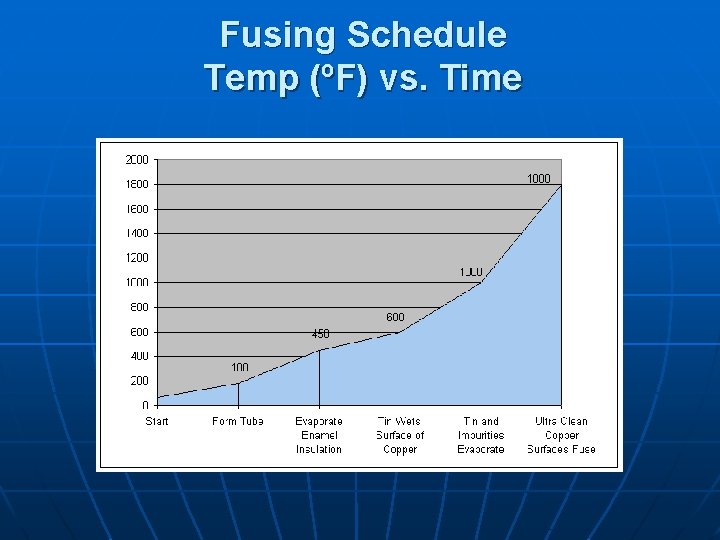
Fusing Schedule Temp (ºF) vs. Time
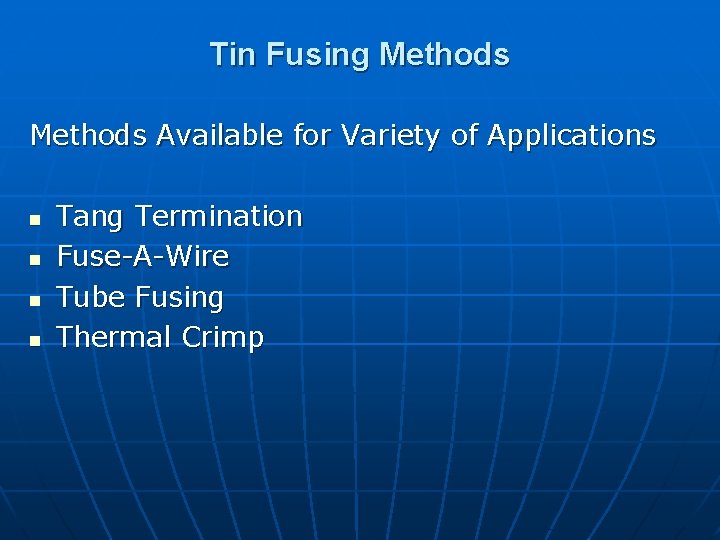
Tin Fusing Methods Available for Variety of Applications n n Tang Termination Fuse-A-Wire Tube Fusing Thermal Crimp
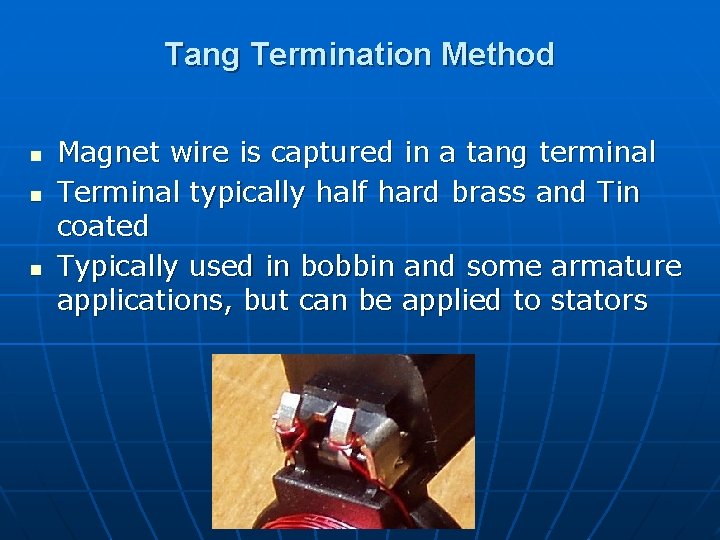
Tang Termination Method n n n Magnet wire is captured in a tang terminal Terminal typically half hard brass and Tin coated Typically used in bobbin and some armature applications, but can be applied to stators
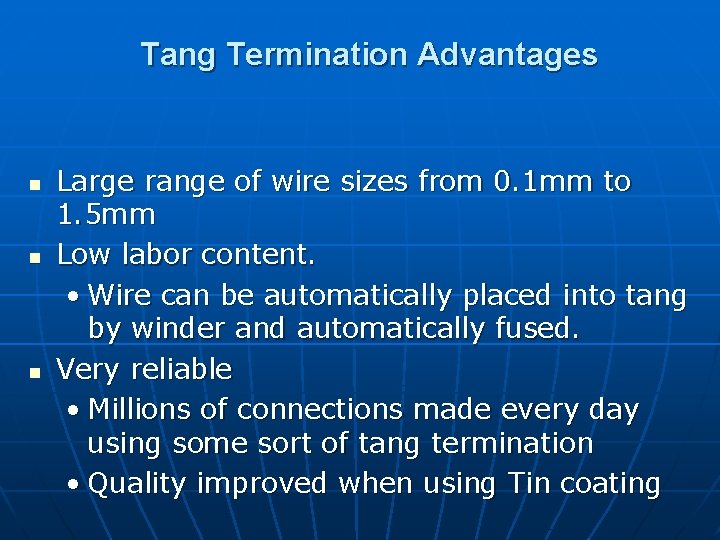
Tang Termination Advantages n n n Large range of wire sizes from 0. 1 mm to 1. 5 mm Low labor content. • Wire can be automatically placed into tang by winder and automatically fused. Very reliable • Millions of connections made every day using some sort of tang termination • Quality improved when using Tin coating
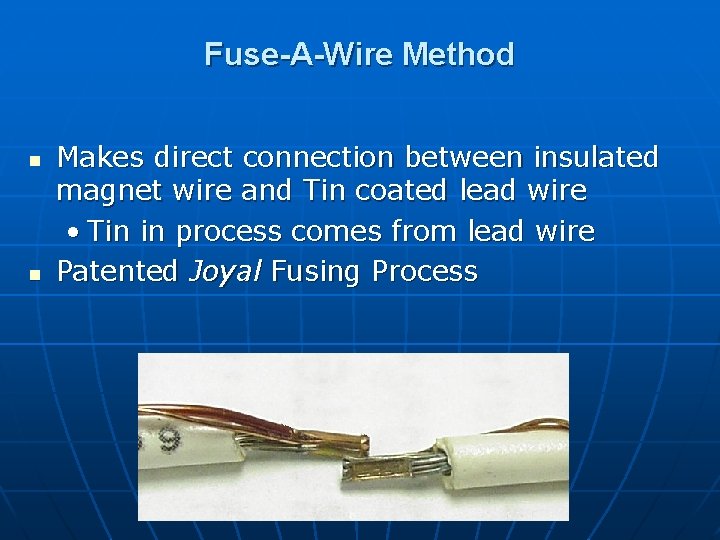
Fuse-A-Wire Method n n Makes direct connection between insulated magnet wire and Tin coated lead wire • Tin in process comes from lead wire Patented Joyal Fusing Process
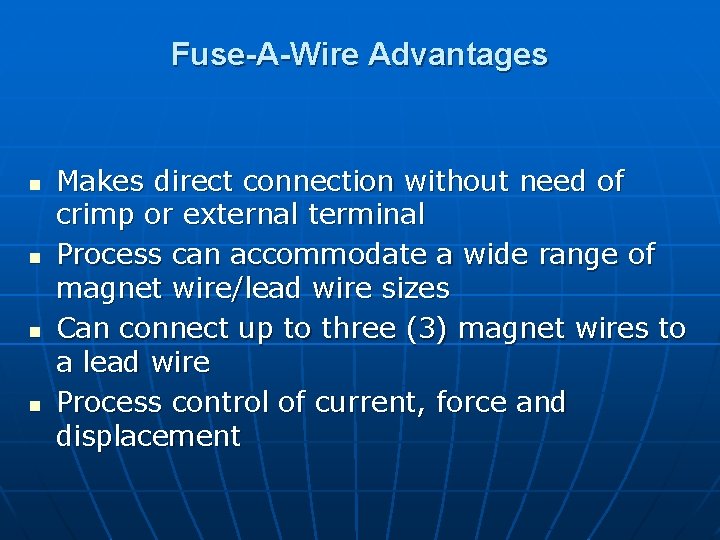
Fuse-A-Wire Advantages n n Makes direct connection without need of crimp or external terminal Process can accommodate a wide range of magnet wire/lead wire sizes Can connect up to three (3) magnet wires to a lead wire Process control of current, force and displacement
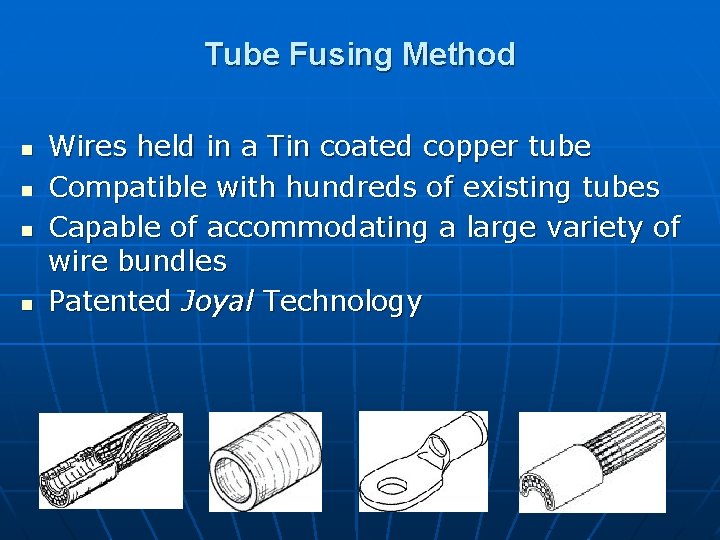
Tube Fusing Method n n Wires held in a Tin coated copper tube Compatible with hundreds of existing tubes Capable of accommodating a large variety of wire bundles Patented Joyal Technology
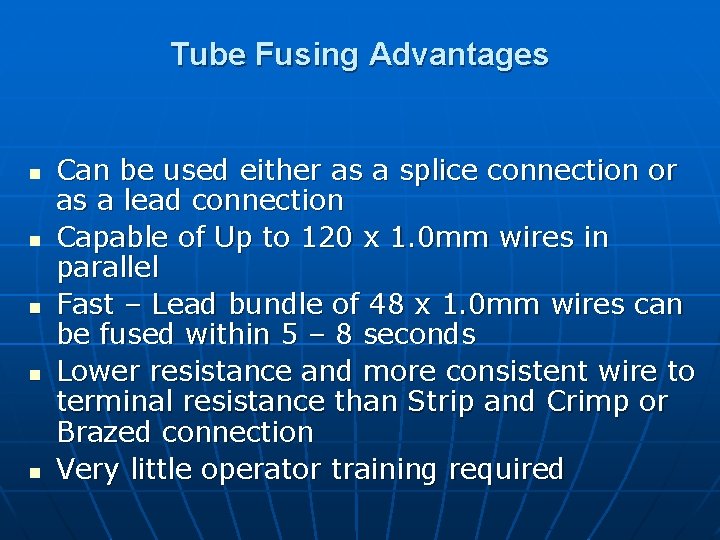
Tube Fusing Advantages n n n Can be used either as a splice connection or as a lead connection Capable of Up to 120 x 1. 0 mm wires in parallel Fast – Lead bundle of 48 x 1. 0 mm wires can be fused within 5 – 8 seconds Lower resistance and more consistent wire to terminal resistance than Strip and Crimp or Brazed connection Very little operator training required
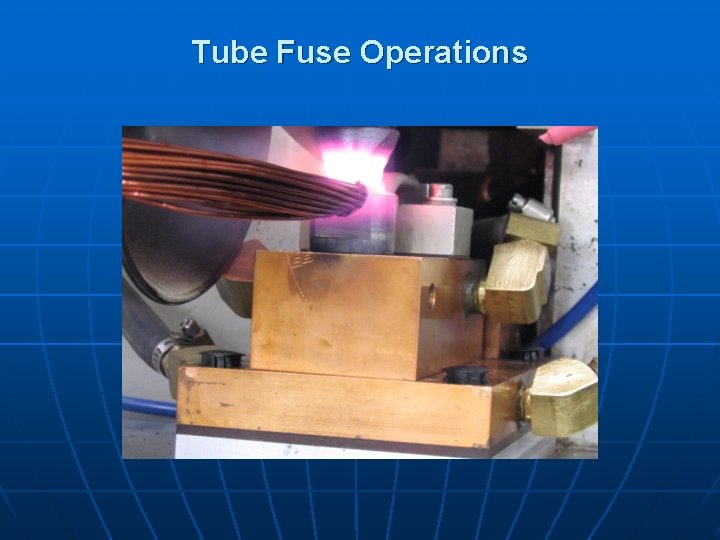
Tube Fuse Operations

Thermal Crimp Method n n n Connection captured in a Tin coated copper terminal Terminal automatically made from flat strip Patented Castechnology
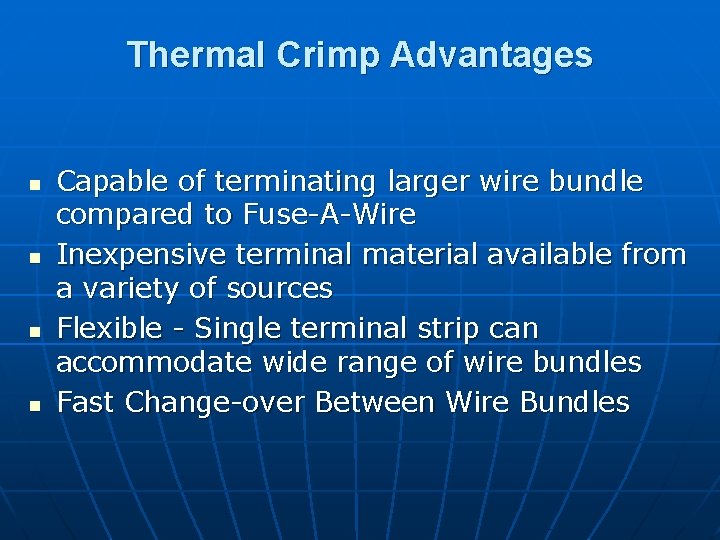
Thermal Crimp Advantages n n Capable of terminating larger wire bundle compared to Fuse-A-Wire Inexpensive terminal material available from a variety of sources Flexible - Single terminal strip can accommodate wide range of wire bundles Fast Change-over Between Wire Bundles
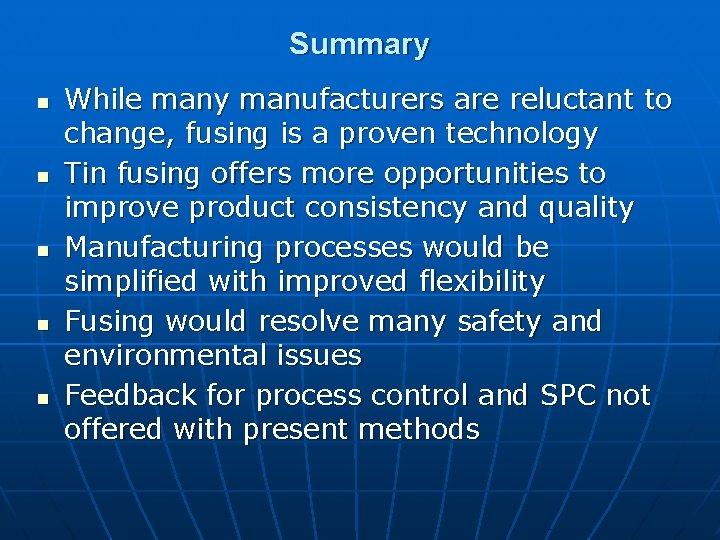
Summary n n n While many manufacturers are reluctant to change, fusing is a proven technology Tin fusing offers more opportunities to improve product consistency and quality Manufacturing processes would be simplified with improved flexibility Fusing would resolve many safety and environmental issues Feedback for process control and SPC not offered with present methods
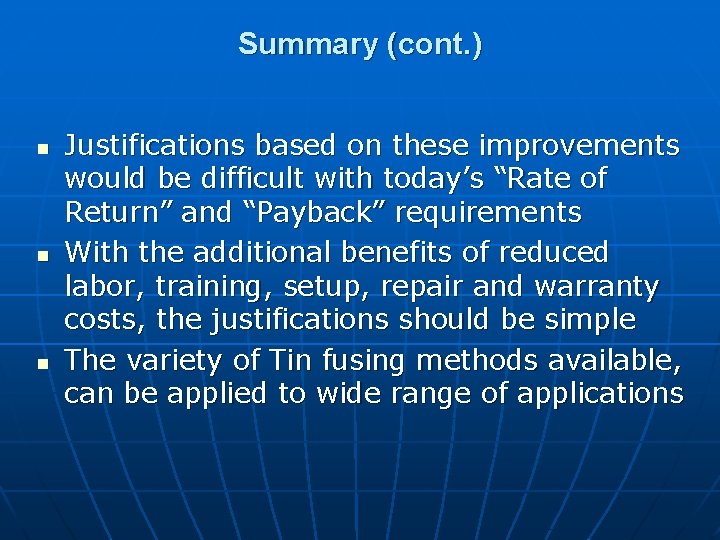
Summary (cont. ) n n n Justifications based on these improvements would be difficult with today’s “Rate of Return” and “Payback” requirements With the additional benefits of reduced labor, training, setup, repair and warranty costs, the justifications should be simple The variety of Tin fusing methods available, can be applied to wide range of applications
Red algae classification
Wonder and awe gift of the holy spirit
Use awe to allocate memory
Eggs hearse sized hay lee
Awe suffix
Ron had a course introduction
The world on the turtle's back to support social customs
Thick awe loved hoot he
Carb bond
Includes the individual and the family community is
Synthetic dicision
Parts of long division
Shnthetic division
369 times 2
Long division family
Tia chieu sa te
Một số thể thơ truyền thống
Thế nào là hệ số cao nhất
Sơ đồ cơ thể người
Lp html
Số nguyên tố là số gì
Tư thế ngồi viết
đặc điểm cơ thể của người tối cổ
Cách giải mật thư tọa độ
Các châu lục và đại dương trên thế giới
Thang điểm glasgow