Operations Management Performance Modeling 1 Operations Strategy 2
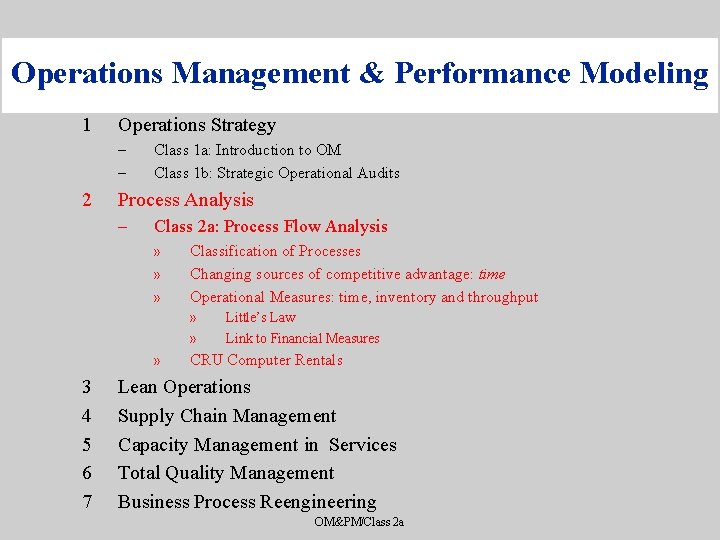
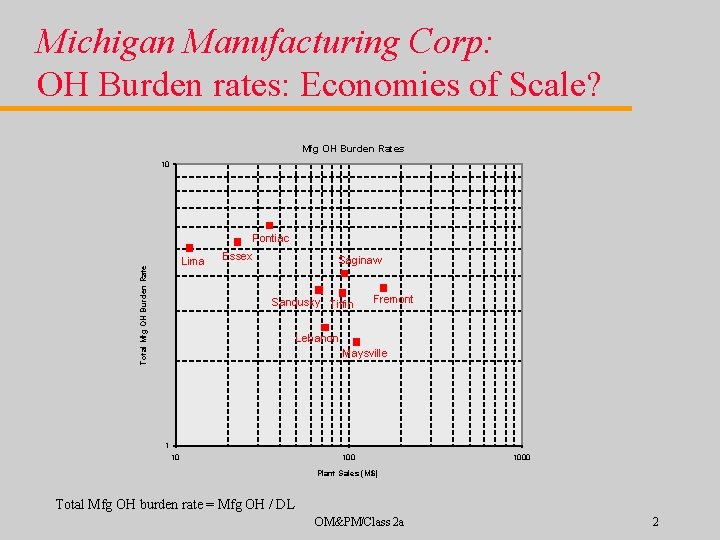
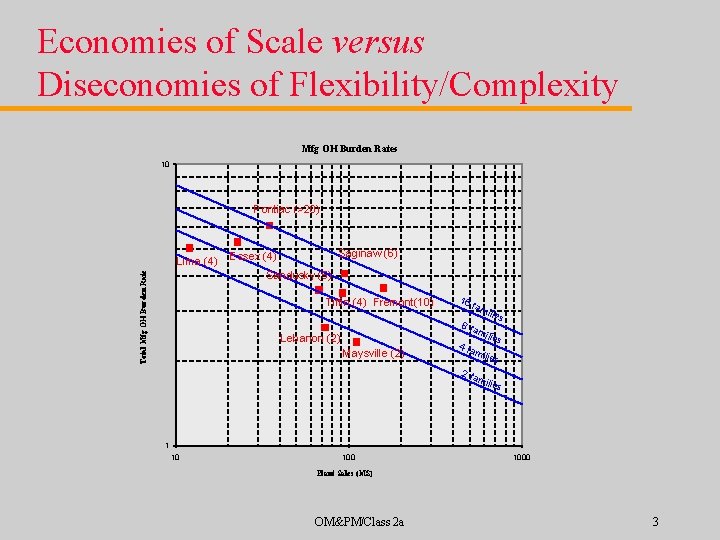
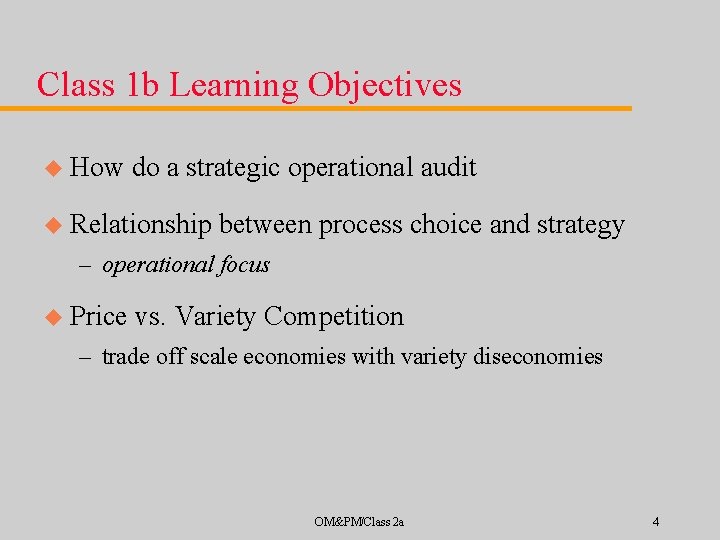
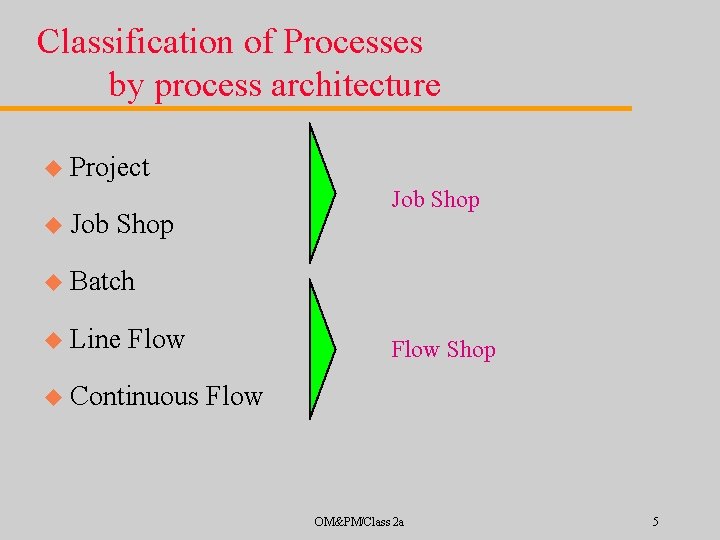
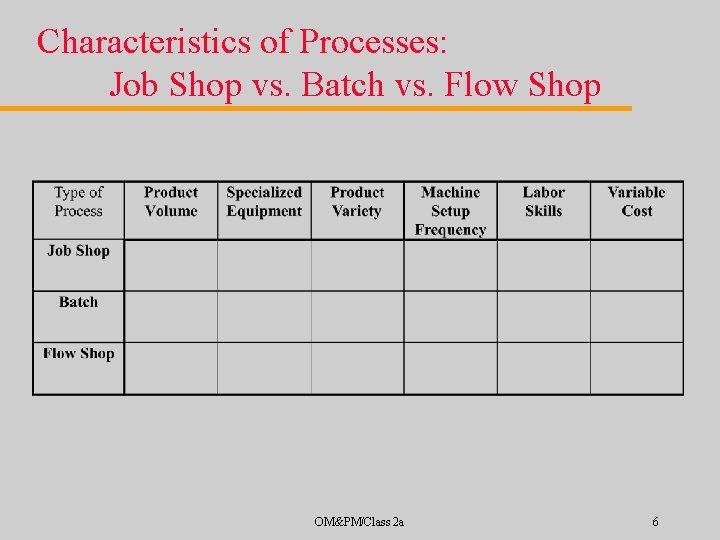
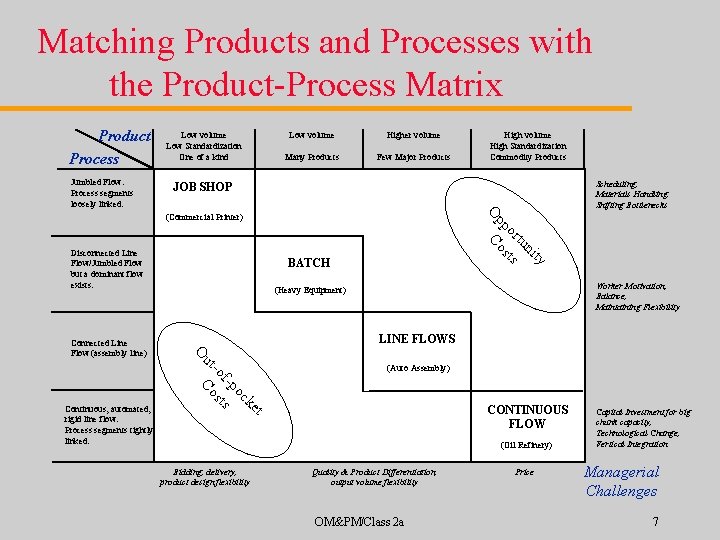
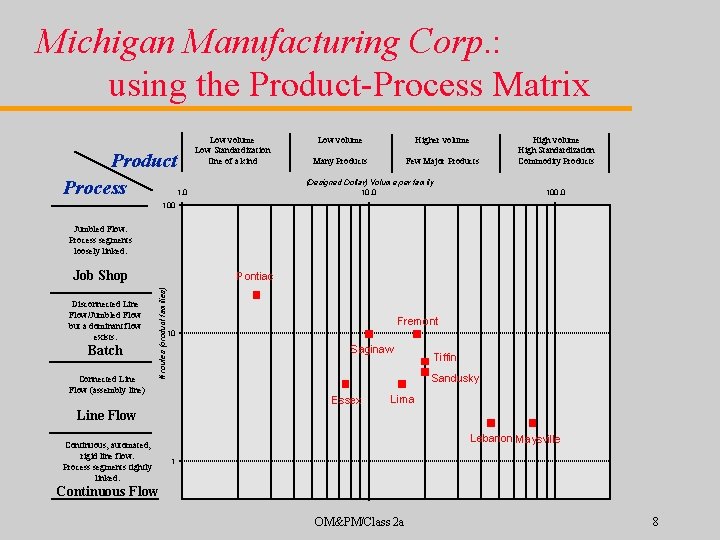
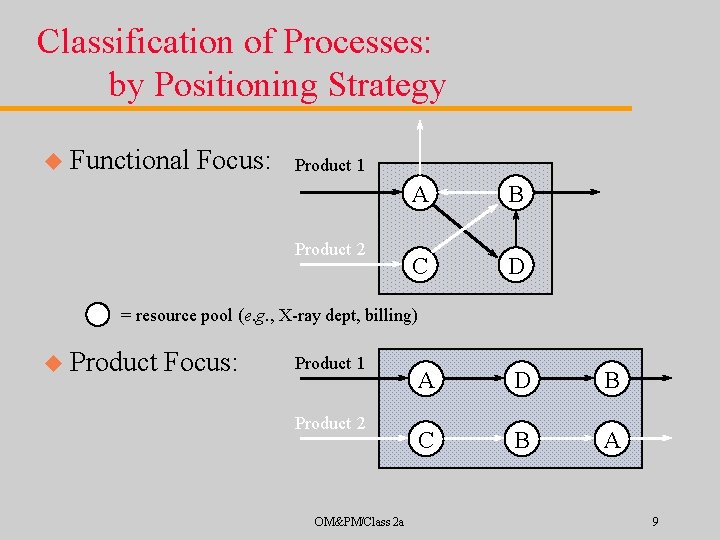
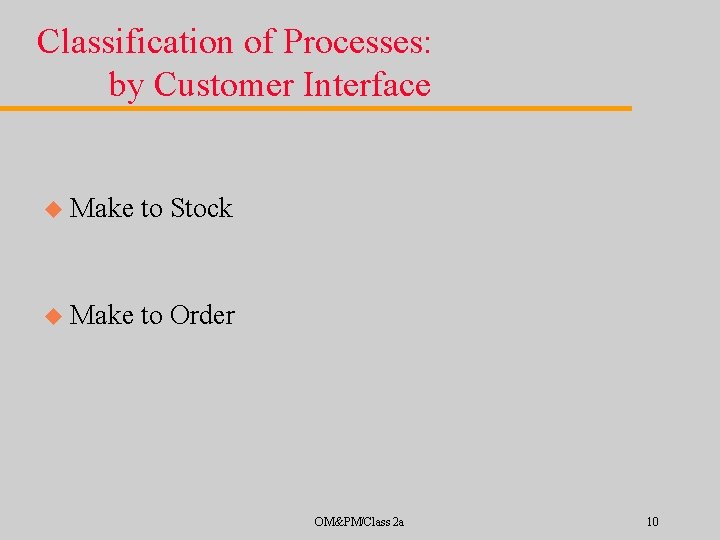
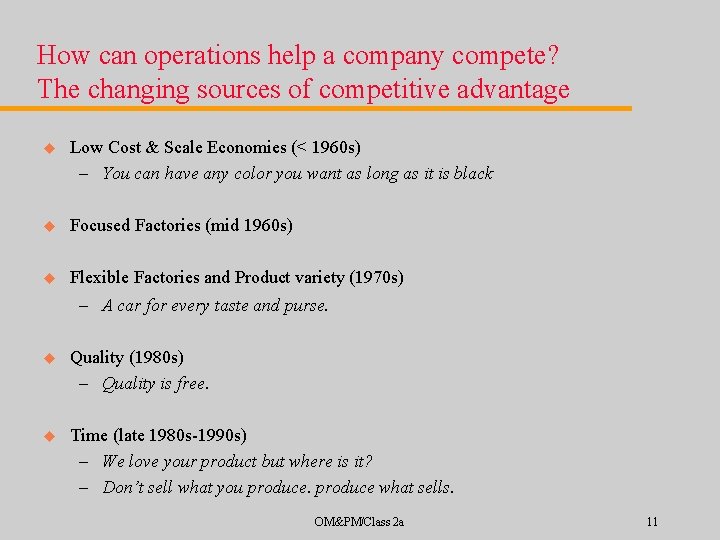
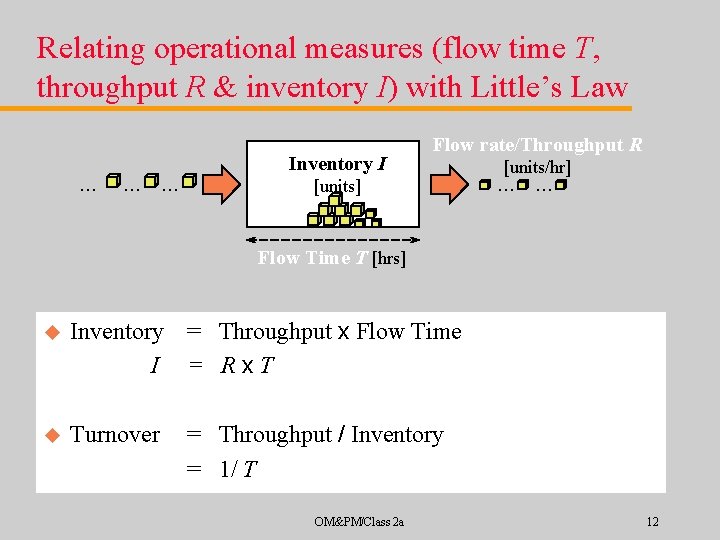
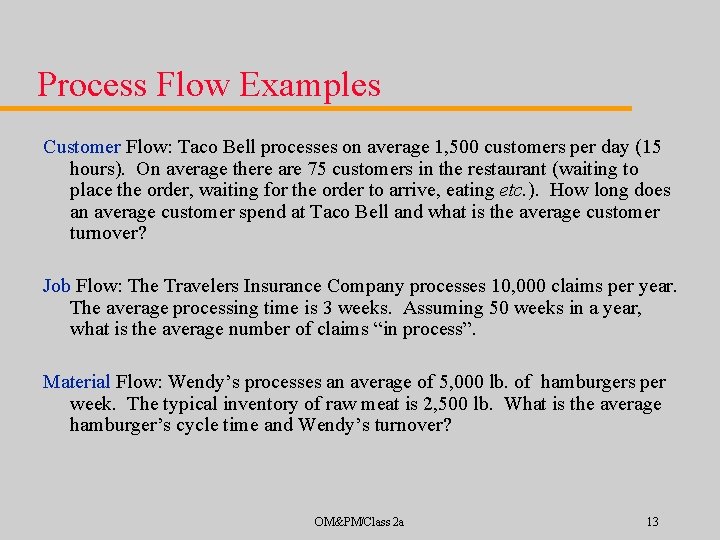
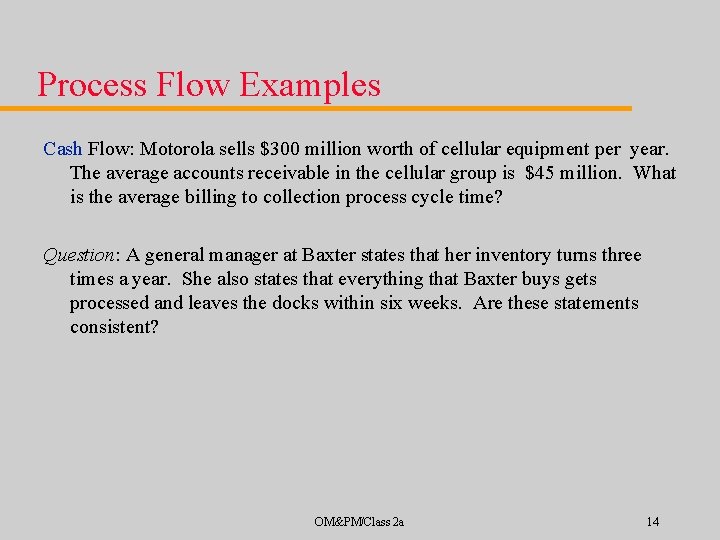
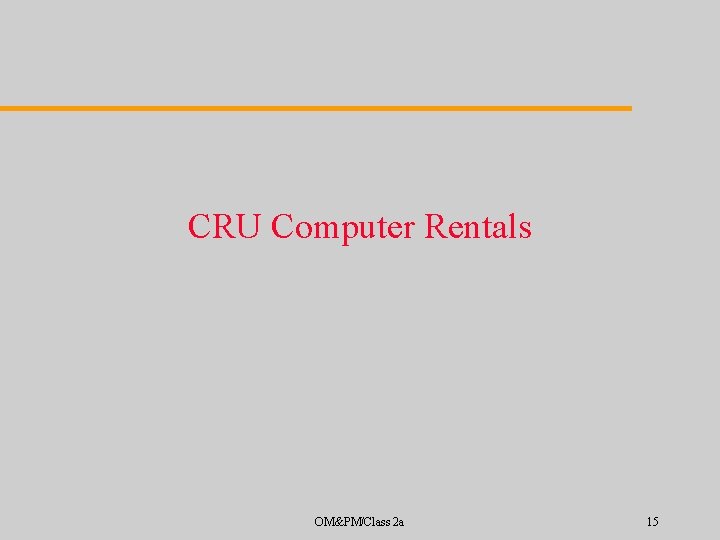
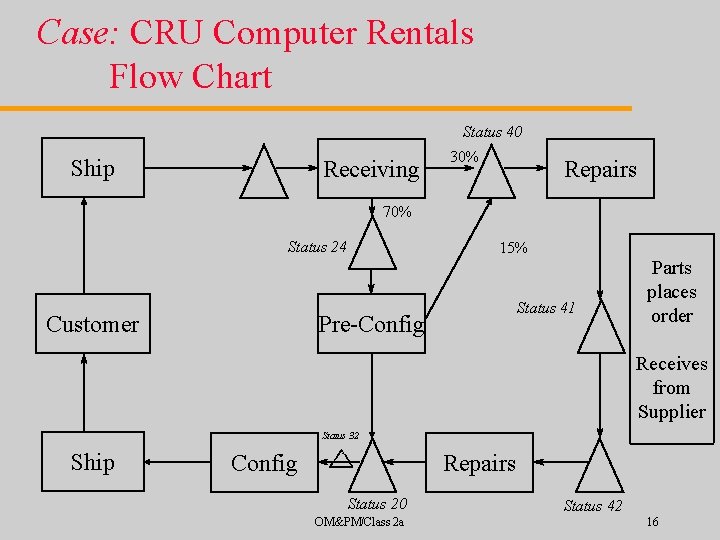
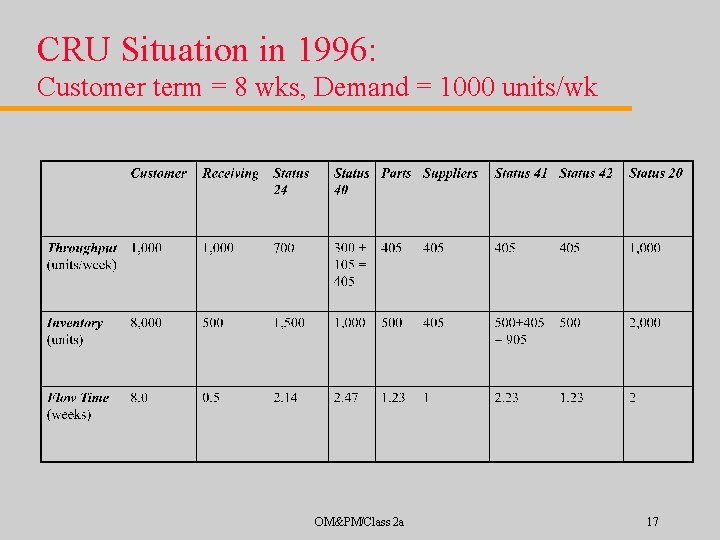
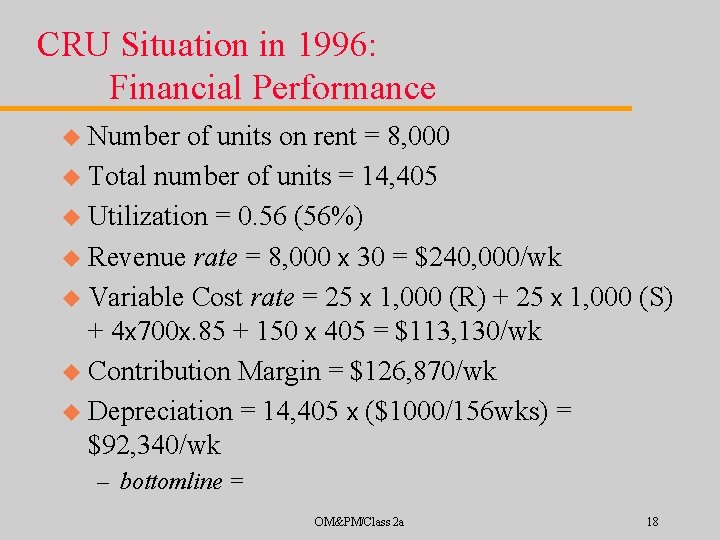
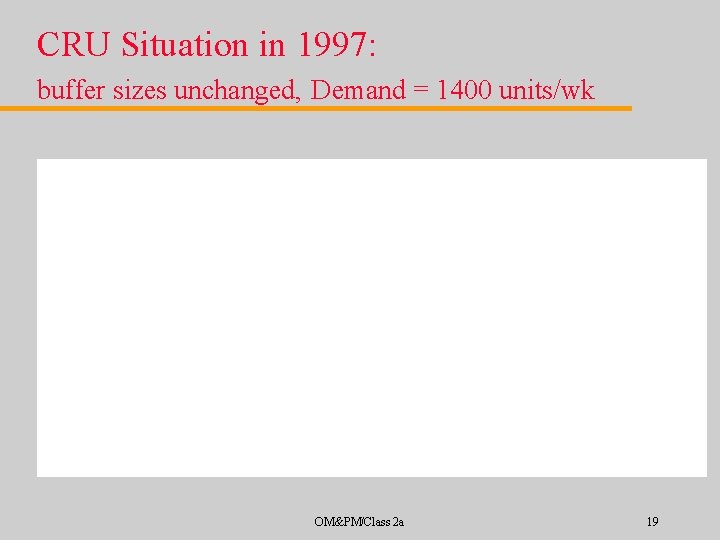
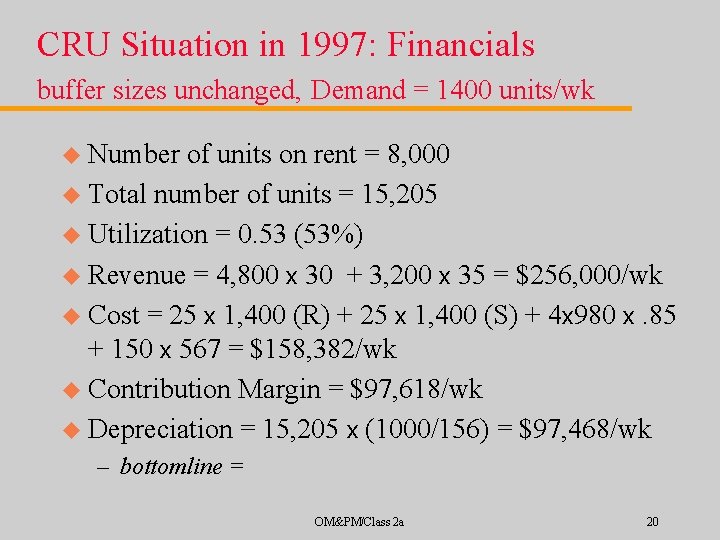
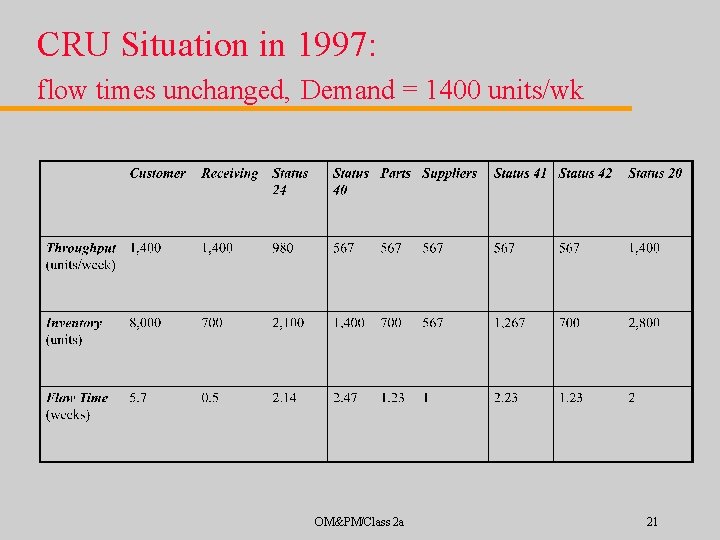
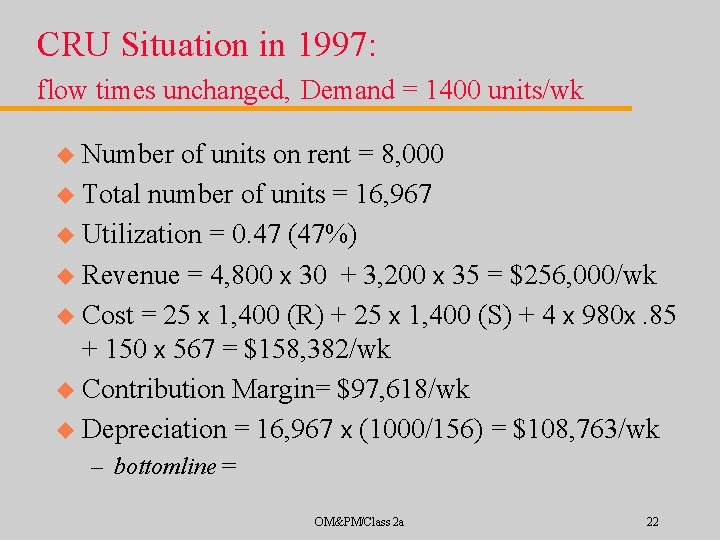
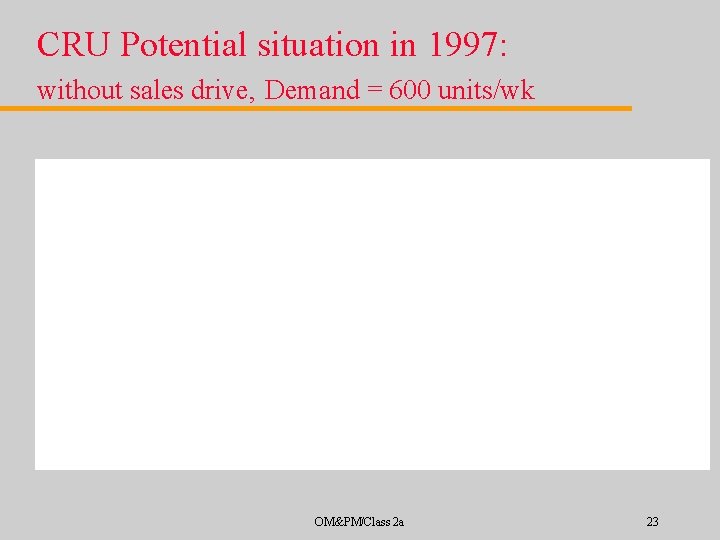
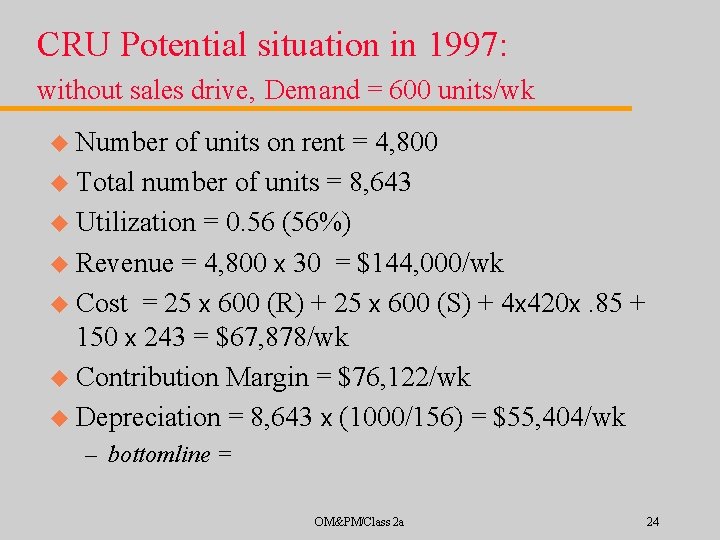
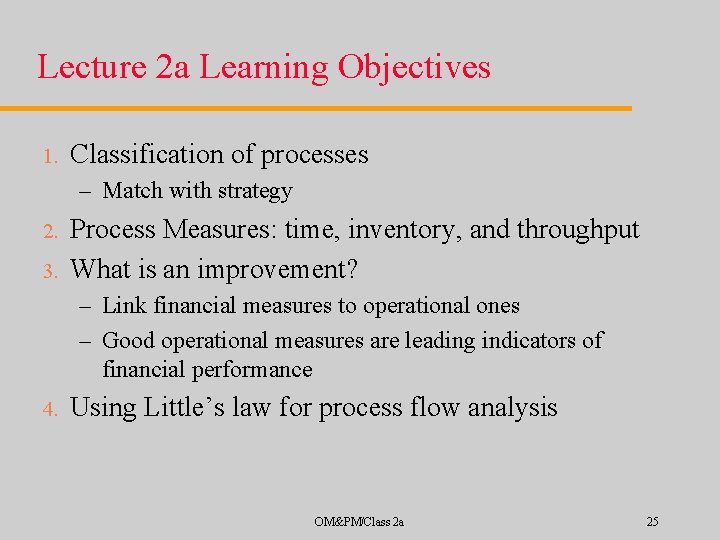
- Slides: 25
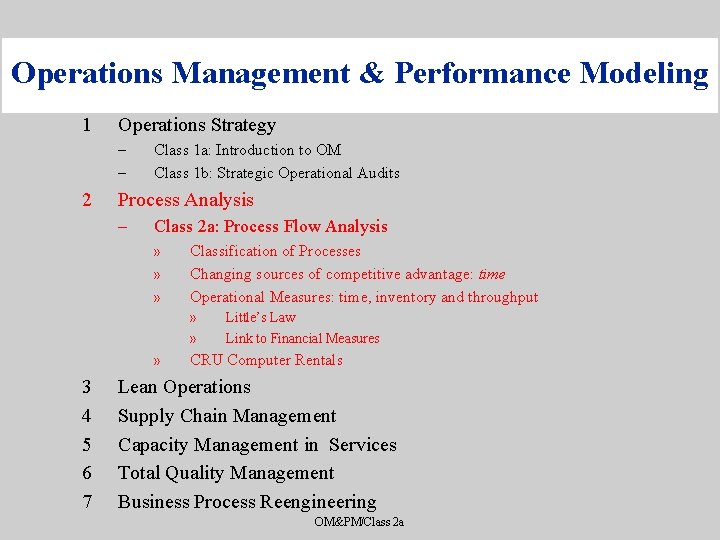
Operations Management & Performance Modeling 1 Operations Strategy – – 2 Class 1 a: Introduction to OM Class 1 b: Strategic Operational Audits Process Analysis – Class 2 a: Process Flow Analysis » » » Classification of Processes Changing sources of competitive advantage: time Operational Measures: time, inventory and throughput » » » 3 4 5 6 7 Little’s Law Link to Financial Measures CRU Computer Rentals Lean Operations Supply Chain Management Capacity Management in Services Total Quality Management Business Process Reengineering OM&PM/Class 2 a
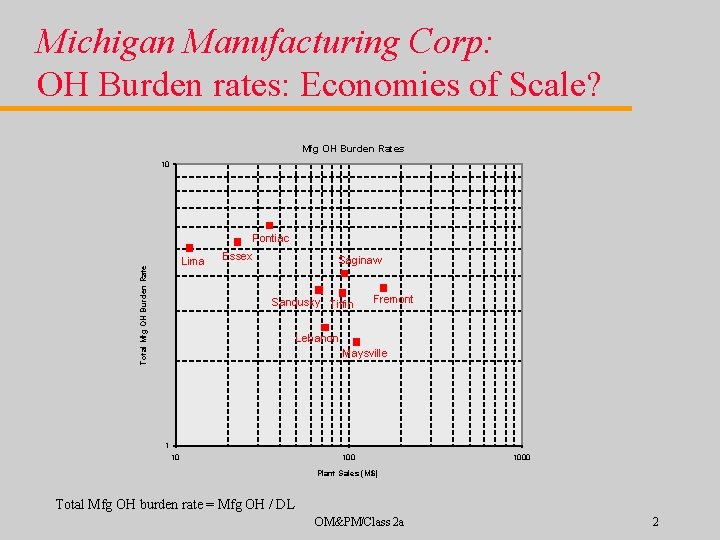
Michigan Manufacturing Corp: OH Burden rates: Economies of Scale? Mfg OH Burden Rates 10 Pontiac Total Mfg OH Burden Rate Lima Essex Saginaw Sandusky Tiffin Fremont Lebanon Maysville 1 10 1000 Plant Sales (M$) Total Mfg OH burden rate = Mfg OH / DL OM&PM/Class 2 a 2
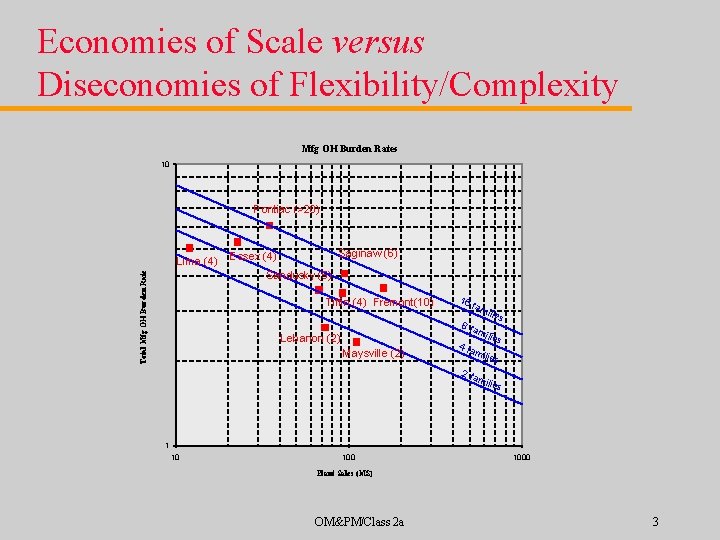
Economies of Scale versus Diseconomies of Flexibility/Complexity Mfg OH Burden Rates 10 Pontiac (>20) Lima (4) Saginaw (6) Essex (4) Total Mfg OH Burden Rate Sandusky (5) Tiffin (4) Fremont(10) 16 fam 8 fa Lebanon (2) Maysville (2) ilies mili es 4 fa mili es 2 fa mili es 1 10 1000 Plant Sales (M$) OM&PM/Class 2 a 3
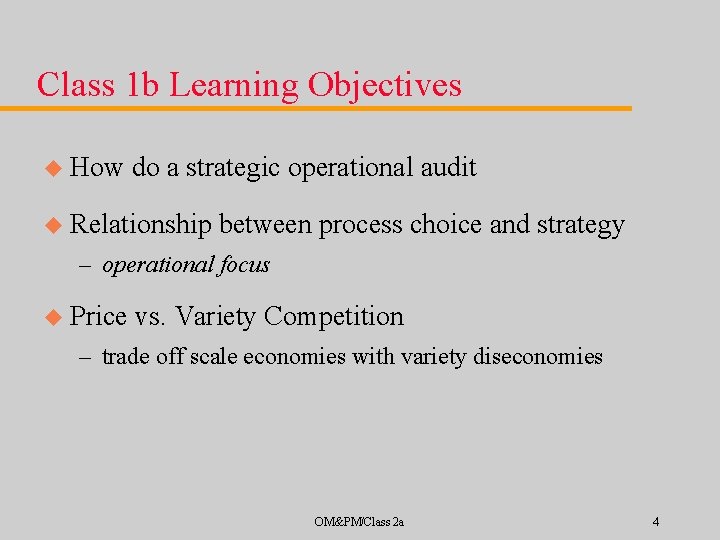
Class 1 b Learning Objectives u How do a strategic operational audit u Relationship between process choice and strategy – operational focus u Price vs. Variety Competition – trade off scale economies with variety diseconomies OM&PM/Class 2 a 4
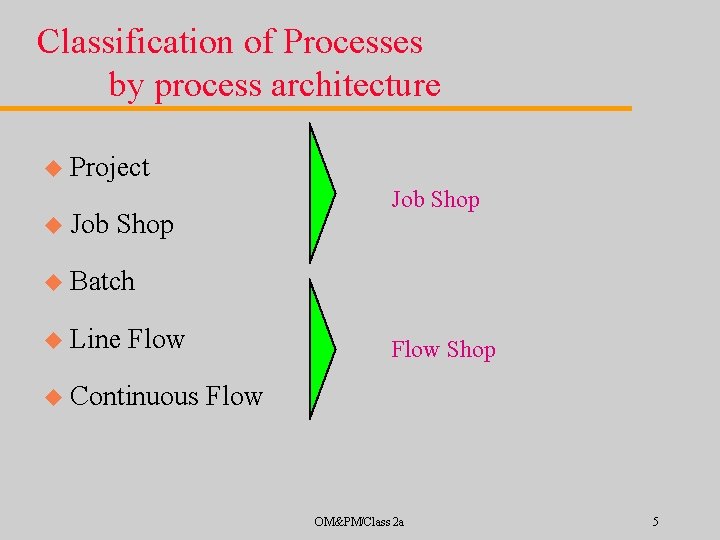
Classification of Processes by process architecture u Project u Job Shop u Batch u Line Flow u Continuous Flow Shop Flow OM&PM/Class 2 a 5
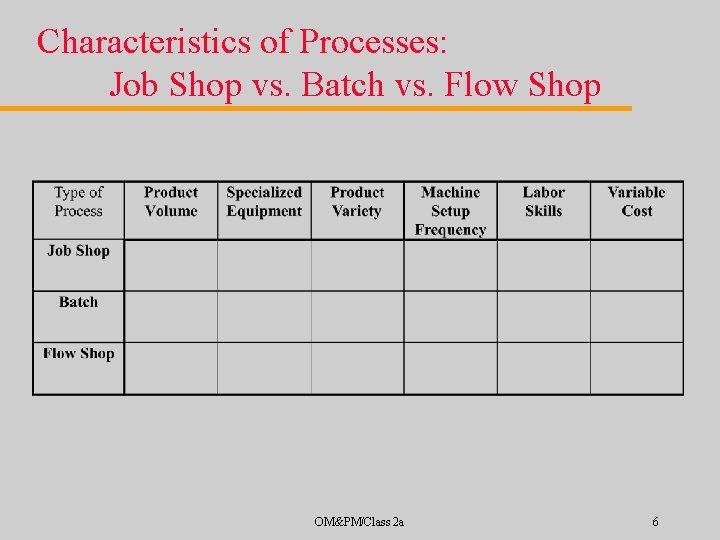
Characteristics of Processes: Job Shop vs. Batch vs. Flow Shop OM&PM/Class 2 a 6
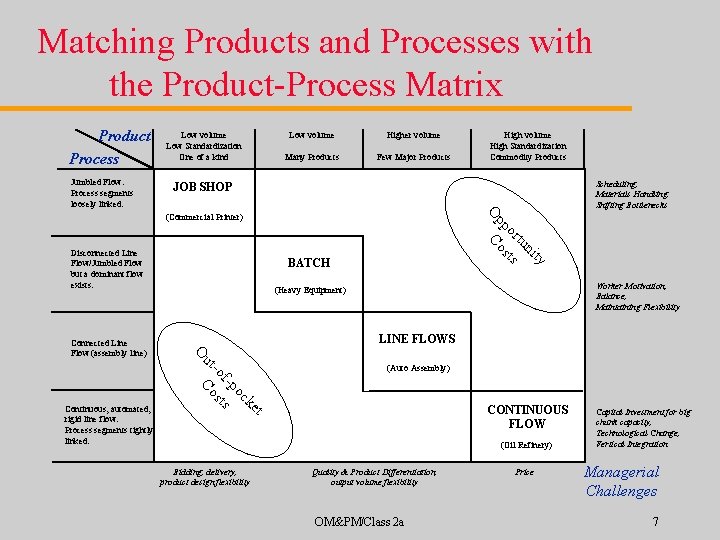
Matching Products and Processes with the Product-Process Matrix Product Process Jumbled Flow. Process segments loosely linked. Low volume Low Standardization One of a kind Low volume Higher volume Many Products Few Major Products Scheduling, Materials Handling, Shifting Bottlenecks JOB SHOP Disconnected Line Flow/Jumbled Flow but a dominant flow exists. BATCH Worker Motivation, Balance, Maintaining Flexibility (Heavy Equipment) LINE FLOWS O (Auto Assembly) CONTINUOUS FLOW t ke oc f-p s -o st ut Co Continuous, automated, rigid line flow. Process segments tightly linked. ty ni tu or ts pp Cos O (Commercial Printer) Connected Line Flow (assembly line) High volume High Standardization Commodity Products (Oil Refinery) Bidding, delivery, product design flexibility Quality & Product Differentiation, output volume flexibility OM&PM/Class 2 a Price Capital Investment for big chunk capacity, Technological Change, Vertical Integration Managerial Challenges 7
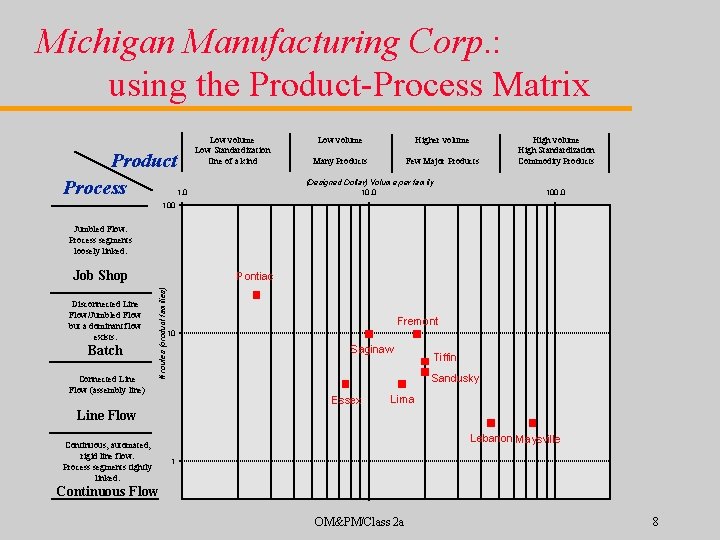
Michigan Manufacturing Corp. : using the Product-Process Matrix Product Process Low volume Low Standardization One of a kind Low volume Higher volume Many Products Few Major Products (Designed Dollar) Volume per family 10. 0 1. 0 High volume High Standardization Commodity Products 100. 0 100 Jumbled Flow. Process segments loosely linked. Job Shop Batch Connected Line Flow (assembly line) # routes (product families) Disconnected Line Flow/Jumbled Flow but a dominant flow exists. Pontiac Fremont 10 Saginaw Tiffin Sandusky Essex Lima Line Flow Continuous, automated, rigid line flow. Process segments tightly linked. Lebanon Maysville 1 Continuous Flow OM&PM/Class 2 a 8
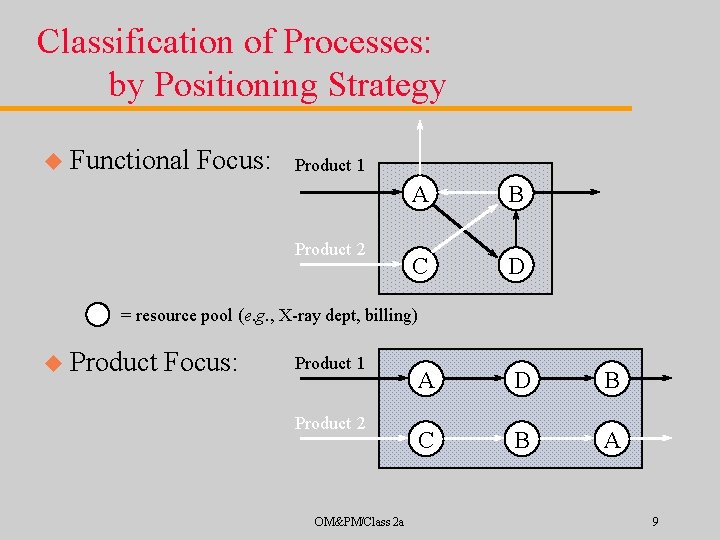
Classification of Processes: by Positioning Strategy u Functional Focus: Product 1 Product 2 A B C D = resource pool (e. g. , X-ray dept, billing) u Product Focus: Product 1 Product 2 OM&PM/Class 2 a A D B C B A 9
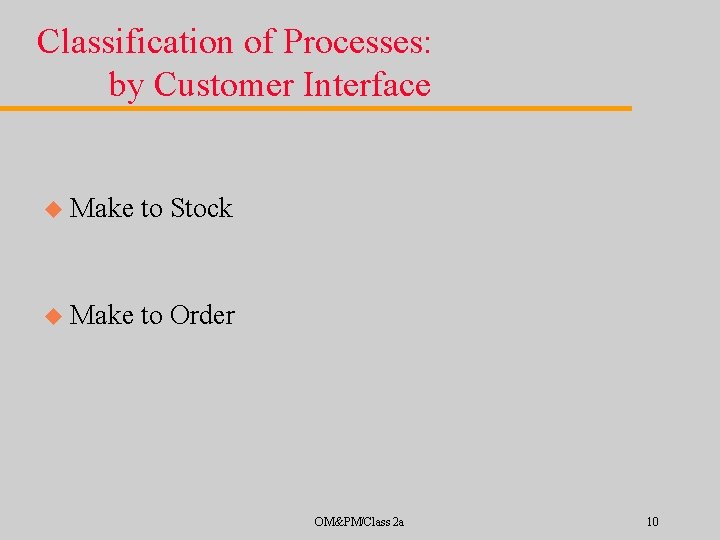
Classification of Processes: by Customer Interface u Make to Stock u Make to Order OM&PM/Class 2 a 10
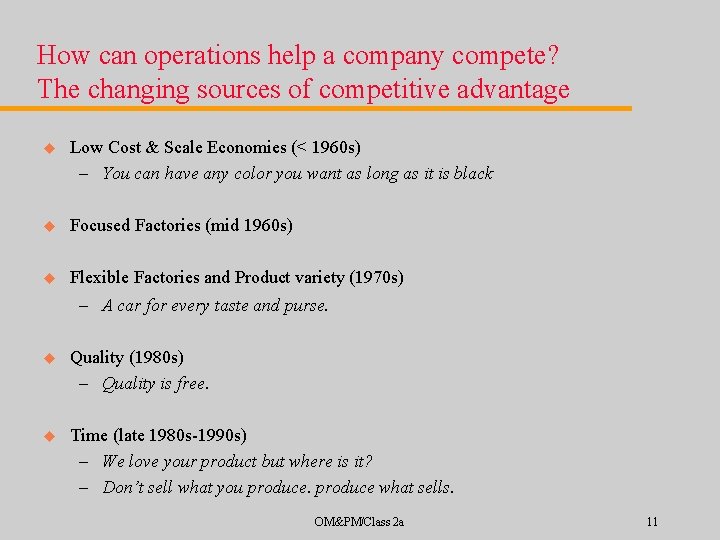
How can operations help a company compete? The changing sources of competitive advantage u Low Cost & Scale Economies (< 1960 s) – You can have any color you want as long as it is black u Focused Factories (mid 1960 s) u Flexible Factories and Product variety (1970 s) – A car for every taste and purse. u Quality (1980 s) – Quality is free. u Time (late 1980 s-1990 s) – We love your product but where is it? – Don’t sell what you produce what sells. OM&PM/Class 2 a 11
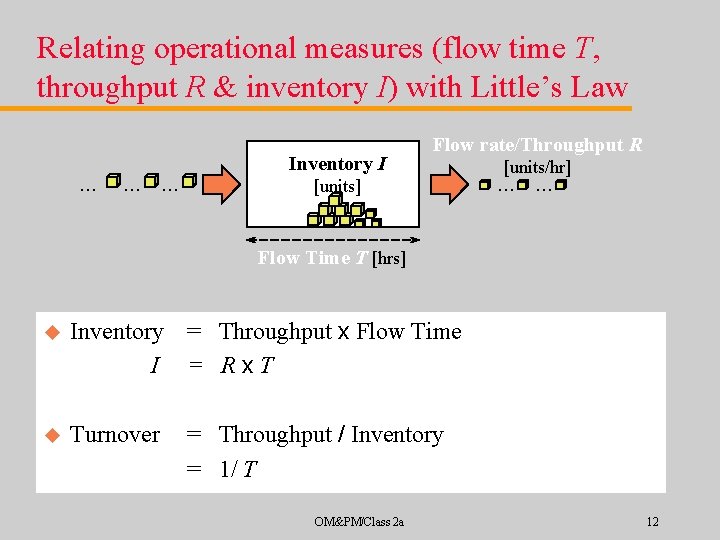
Relating operational measures (flow time T, throughput R & inventory I) with Little’s Law. . Inventory I Flow rate/Throughput R [units] [units/hr] . . . Flow Time T [hrs] u Inventory = Throughput x Flow Time I = Rx. T u Turnover = Throughput / Inventory = 1/ T OM&PM/Class 2 a 12
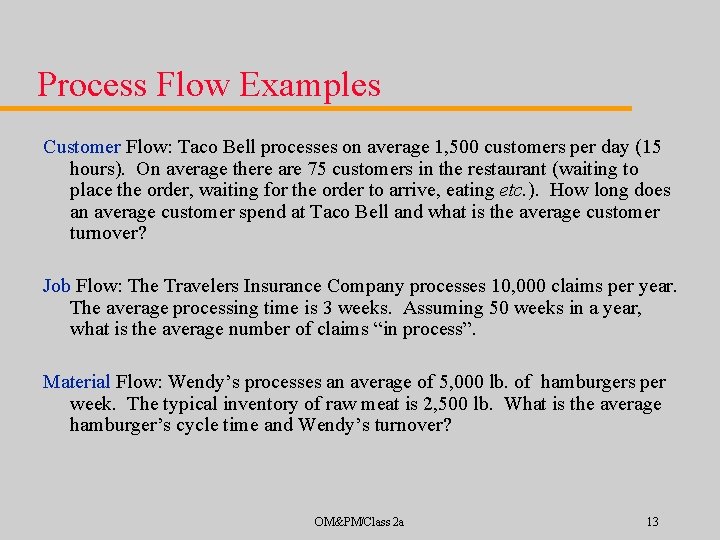
Process Flow Examples Customer Flow: Taco Bell processes on average 1, 500 customers per day (15 hours). On average there are 75 customers in the restaurant (waiting to place the order, waiting for the order to arrive, eating etc. ). How long does an average customer spend at Taco Bell and what is the average customer turnover? Job Flow: The Travelers Insurance Company processes 10, 000 claims per year. The average processing time is 3 weeks. Assuming 50 weeks in a year, what is the average number of claims “in process”. Material Flow: Wendy’s processes an average of 5, 000 lb. of hamburgers per week. The typical inventory of raw meat is 2, 500 lb. What is the average hamburger’s cycle time and Wendy’s turnover? OM&PM/Class 2 a 13
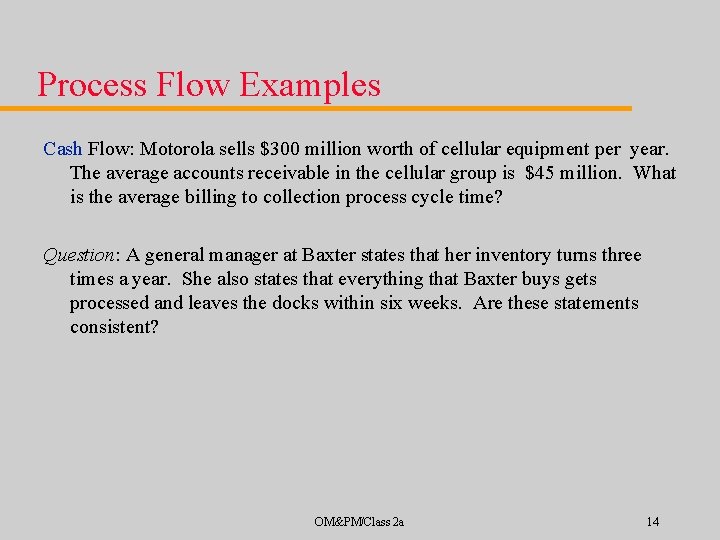
Process Flow Examples Cash Flow: Motorola sells $300 million worth of cellular equipment per year. The average accounts receivable in the cellular group is $45 million. What is the average billing to collection process cycle time? Question: A general manager at Baxter states that her inventory turns three times a year. She also states that everything that Baxter buys gets processed and leaves the docks within six weeks. Are these statements consistent? OM&PM/Class 2 a 14
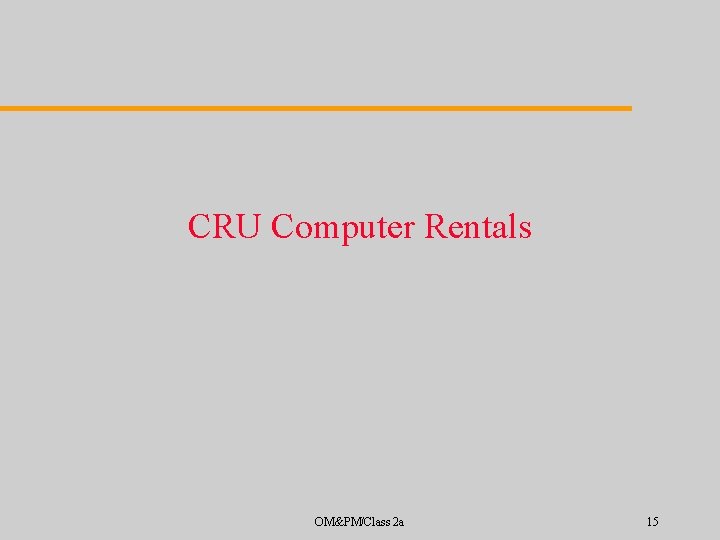
CRU Computer Rentals OM&PM/Class 2 a 15
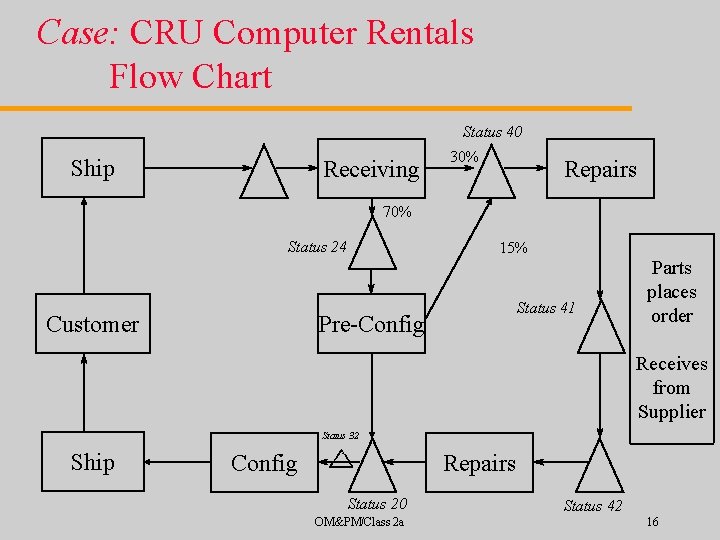
Case: CRU Computer Rentals Flow Chart Status 40 Ship Receiving 30% Repairs 70% Status 24 Customer 15% Status 41 Pre-Config Parts places order Receives from Supplier Status 32 Ship Config Repairs Status 20 OM&PM/Class 2 a Status 42 16
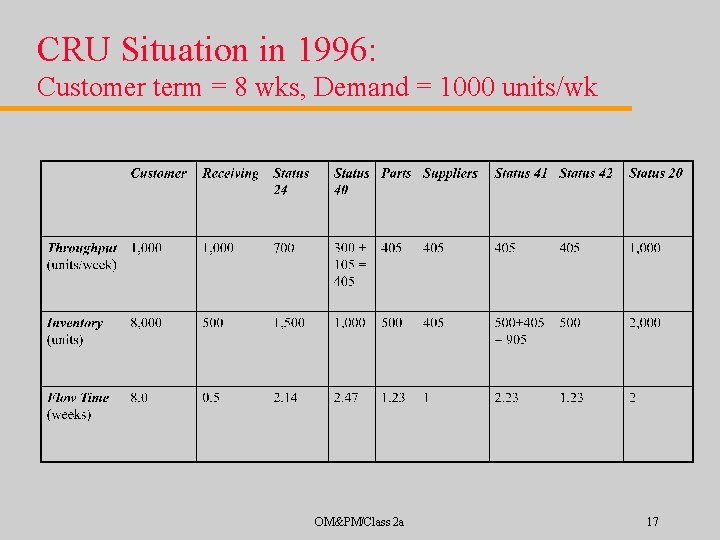
CRU Situation in 1996: Customer term = 8 wks, Demand = 1000 units/wk OM&PM/Class 2 a 17
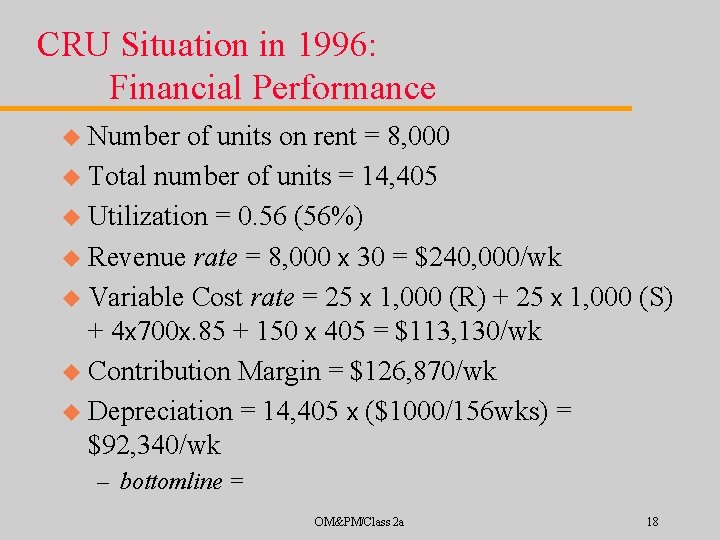
CRU Situation in 1996: Financial Performance u Number of units on rent = 8, 000 u Total number of units = 14, 405 u Utilization = 0. 56 (56%) u Revenue rate = 8, 000 x 30 = $240, 000/wk u Variable Cost rate = 25 x 1, 000 (R) + 25 x 1, 000 (S) + 4 x 700 x. 85 + 150 x 405 = $113, 130/wk u Contribution Margin = $126, 870/wk u Depreciation = 14, 405 x ($1000/156 wks) = $92, 340/wk – bottomline = OM&PM/Class 2 a 18
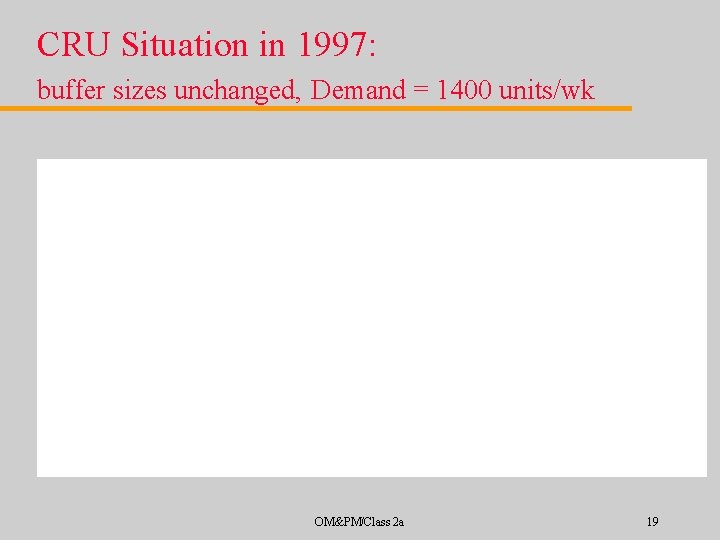
CRU Situation in 1997: buffer sizes unchanged, Demand = 1400 units/wk OM&PM/Class 2 a 19
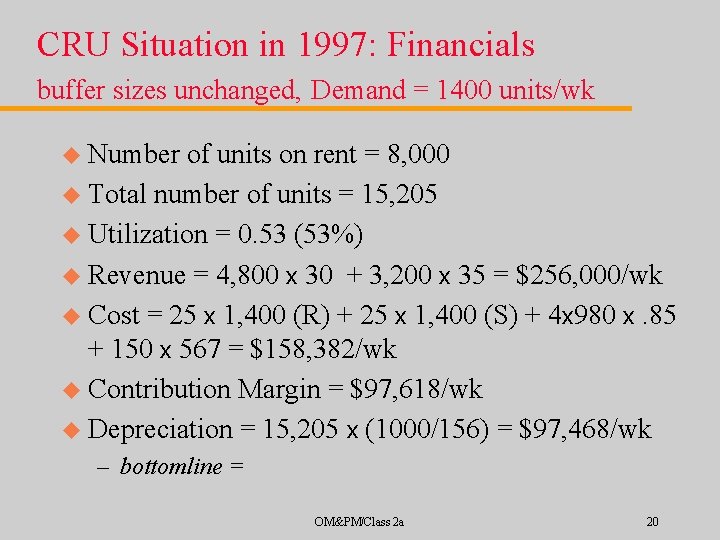
CRU Situation in 1997: Financials buffer sizes unchanged, Demand = 1400 units/wk u Number of units on rent = 8, 000 u Total number of units = 15, 205 u Utilization = 0. 53 (53%) u Revenue = 4, 800 x 30 + 3, 200 x 35 = $256, 000/wk u Cost = 25 x 1, 400 (R) + 25 x 1, 400 (S) + 4 x 980 x. 85 + 150 x 567 = $158, 382/wk u Contribution Margin = $97, 618/wk u Depreciation = 15, 205 x (1000/156) = $97, 468/wk – bottomline = OM&PM/Class 2 a 20
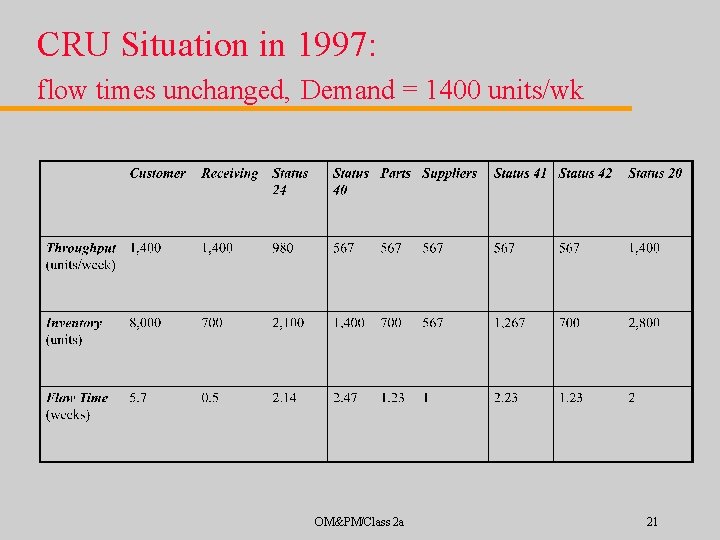
CRU Situation in 1997: flow times unchanged, Demand = 1400 units/wk OM&PM/Class 2 a 21
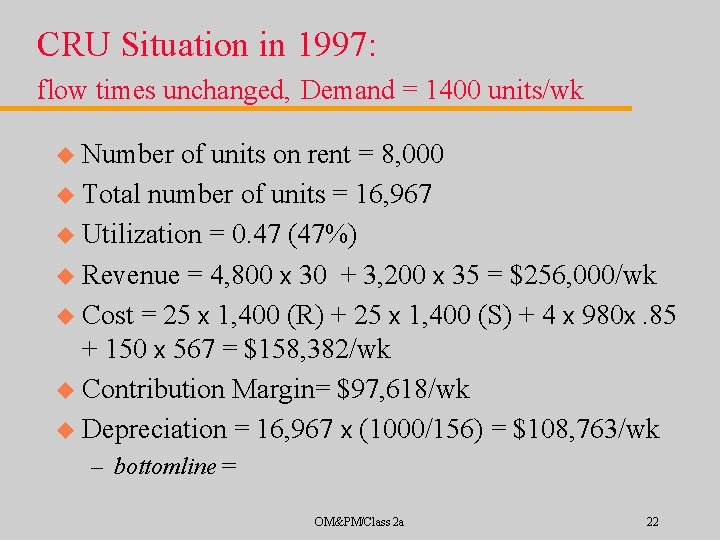
CRU Situation in 1997: flow times unchanged, Demand = 1400 units/wk u Number of units on rent = 8, 000 u Total number of units = 16, 967 u Utilization = 0. 47 (47%) u Revenue = 4, 800 x 30 + 3, 200 x 35 = $256, 000/wk u Cost = 25 x 1, 400 (R) + 25 x 1, 400 (S) + 4 x 980 x. 85 + 150 x 567 = $158, 382/wk u Contribution Margin= $97, 618/wk u Depreciation = 16, 967 x (1000/156) = $108, 763/wk – bottomline = OM&PM/Class 2 a 22
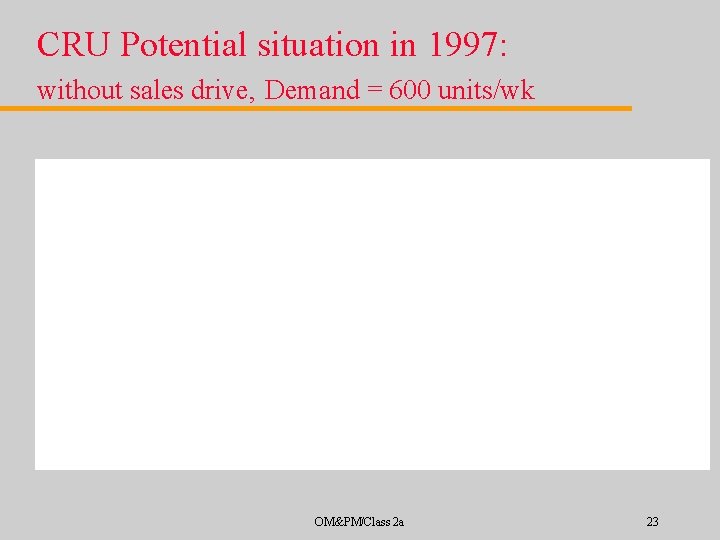
CRU Potential situation in 1997: without sales drive, Demand = 600 units/wk OM&PM/Class 2 a 23
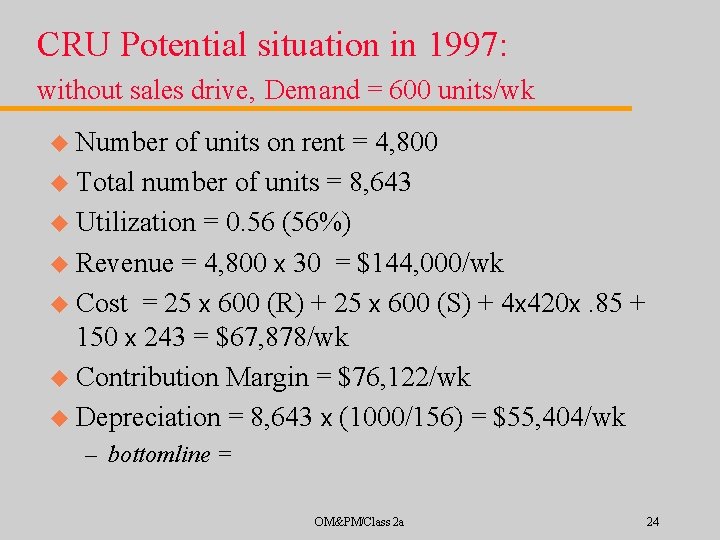
CRU Potential situation in 1997: without sales drive, Demand = 600 units/wk u Number of units on rent = 4, 800 u Total number of units = 8, 643 u Utilization = 0. 56 (56%) u Revenue = 4, 800 x 30 = $144, 000/wk u Cost = 25 x 600 (R) + 25 x 600 (S) + 4 x 420 x. 85 + 150 x 243 = $67, 878/wk u Contribution Margin = $76, 122/wk u Depreciation = 8, 643 x (1000/156) = $55, 404/wk – bottomline = OM&PM/Class 2 a 24
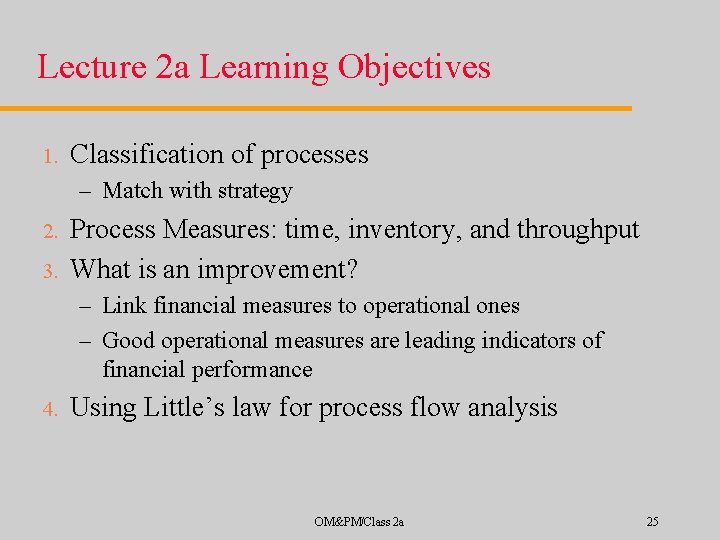
Lecture 2 a Learning Objectives 1. Classification of processes – Match with strategy 2. 3. Process Measures: time, inventory, and throughput What is an improvement? – Link financial measures to operational ones – Good operational measures are leading indicators of financial performance 4. Using Little’s law for process flow analysis OM&PM/Class 2 a 25
Model and role modeling theory
Relational modeling vs dimensional modeling
Behaviorally anchored rating scale
Performance levels
Performance modeling
Repetitive process in operations management
Location analysis in operations management
Layout strategy
Layout strategy in operations management
Process strategy operations management
Hamburger chart
Location strategy in operations management
Location strategy in operations management
Service process matrix
Layout strategy in operations management
Network performance management system
Operations and quality management
Chapter 12 inventory management
What is tqm
Management science the art of modeling with spreadsheets
Jcids manual
Performance evaluation for decentralized operations
Turning great strategy into great performance
Strategic intent
Operations strategy in global environment
Operations strategy as a competitive weapon