JITLean Operations Good production systems require that managers

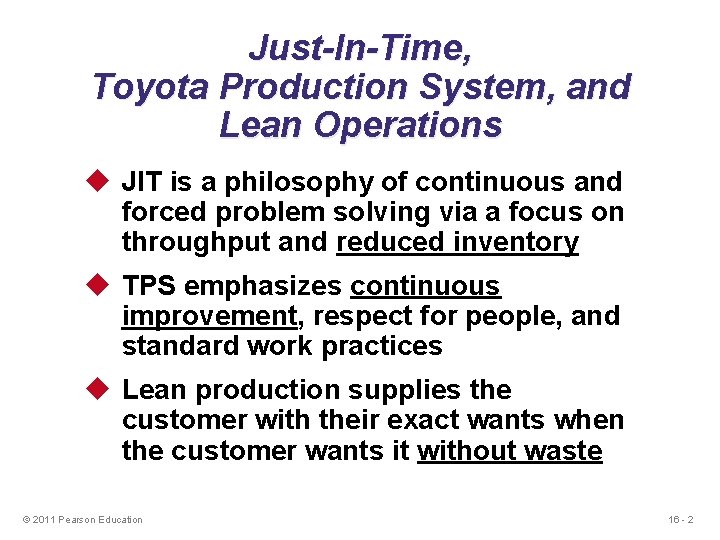
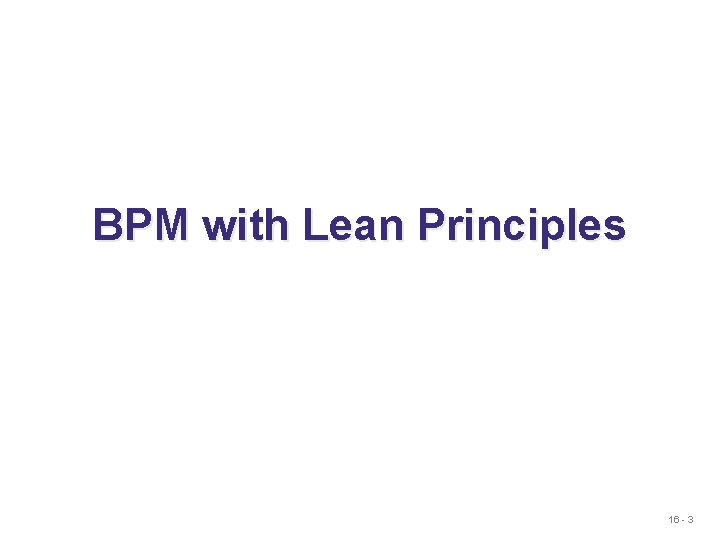
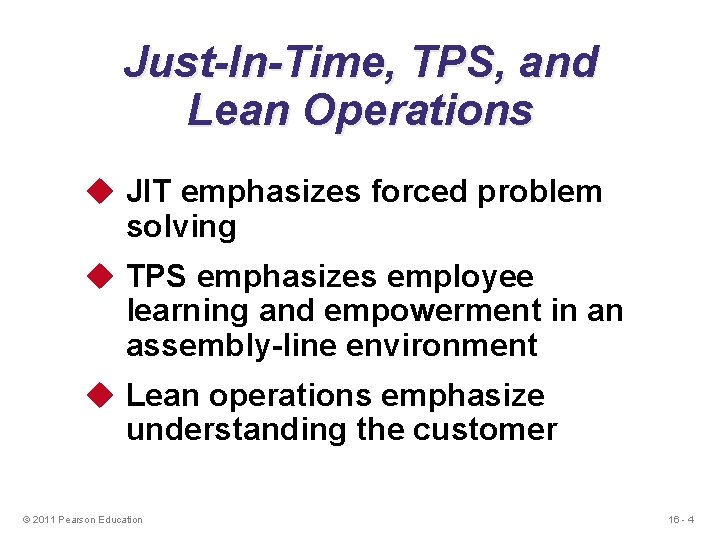
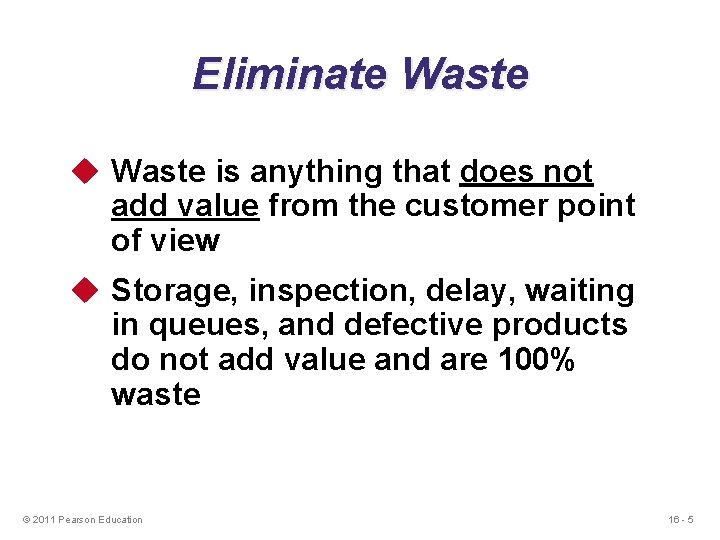
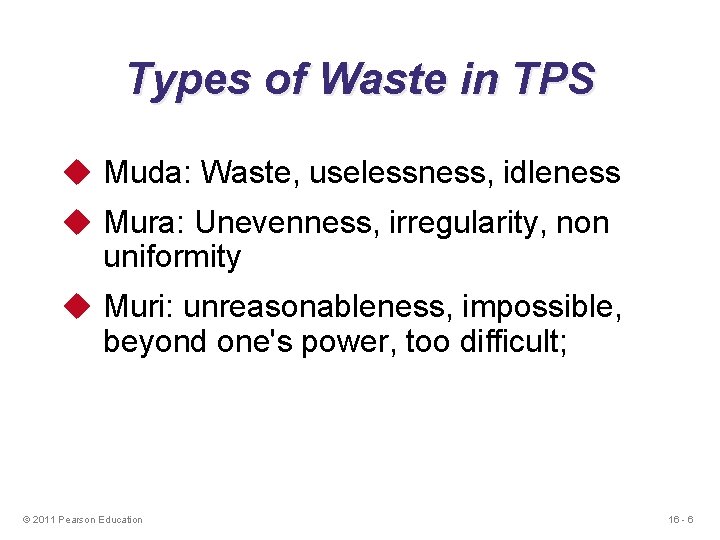
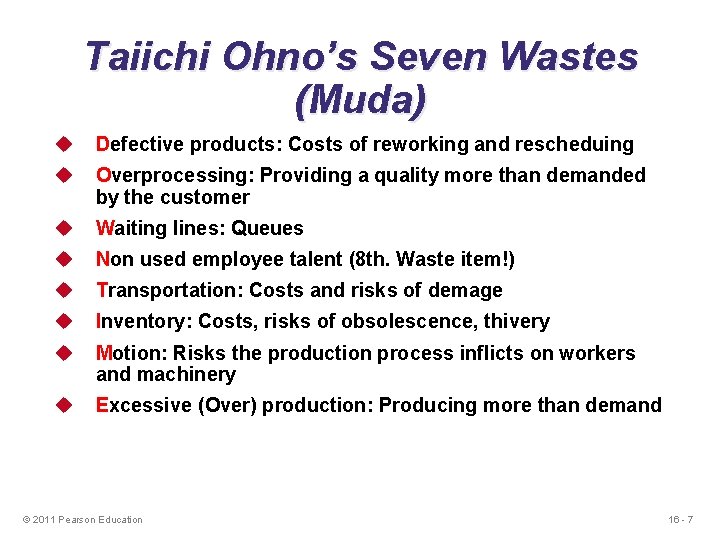
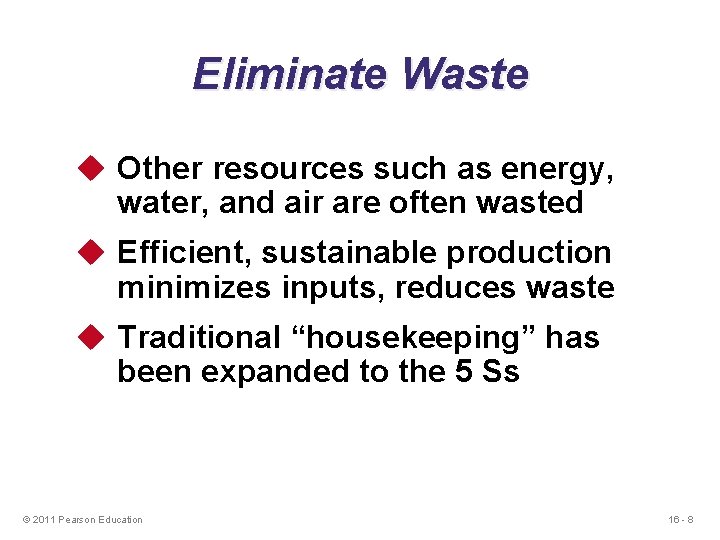
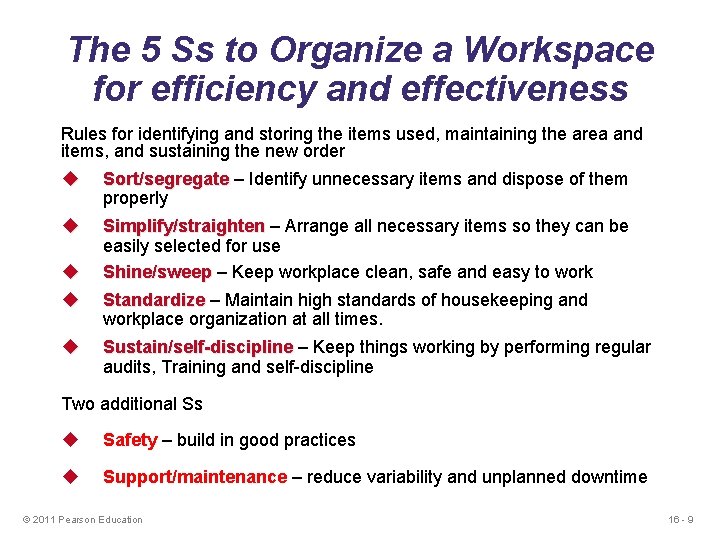
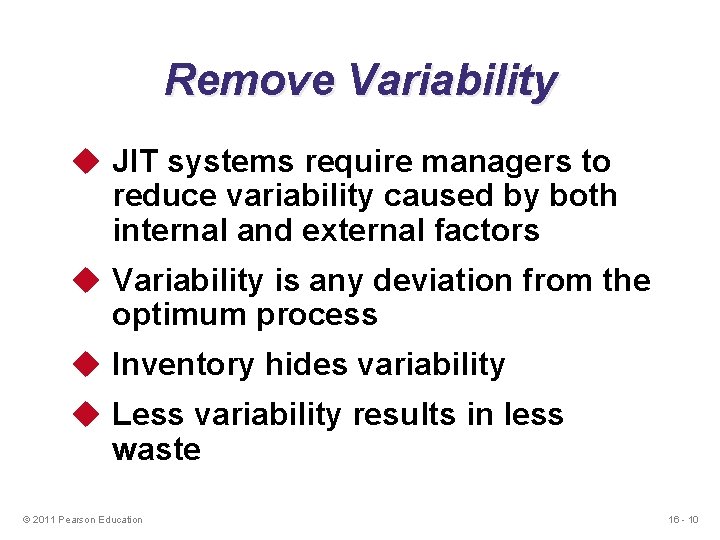
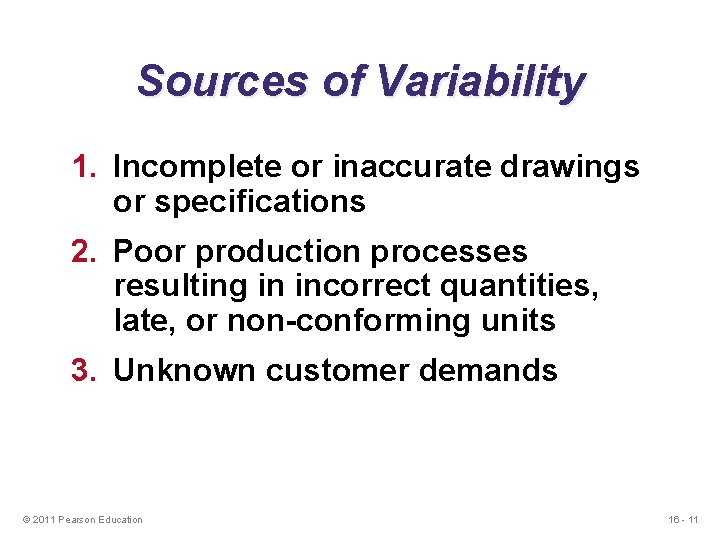
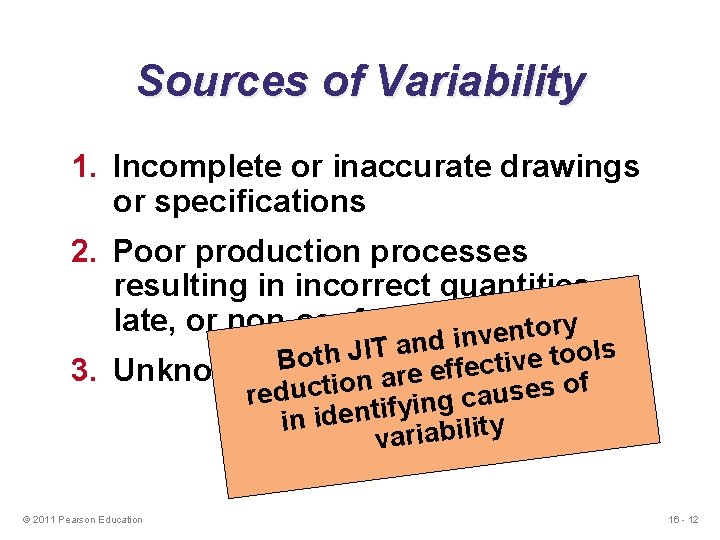
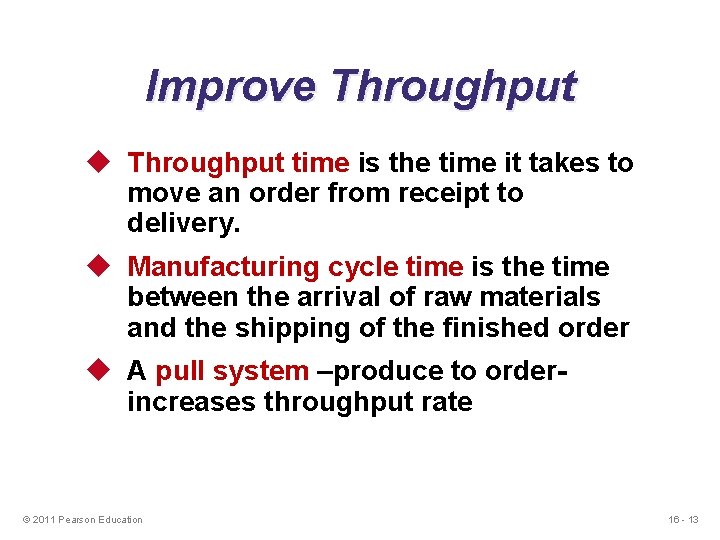
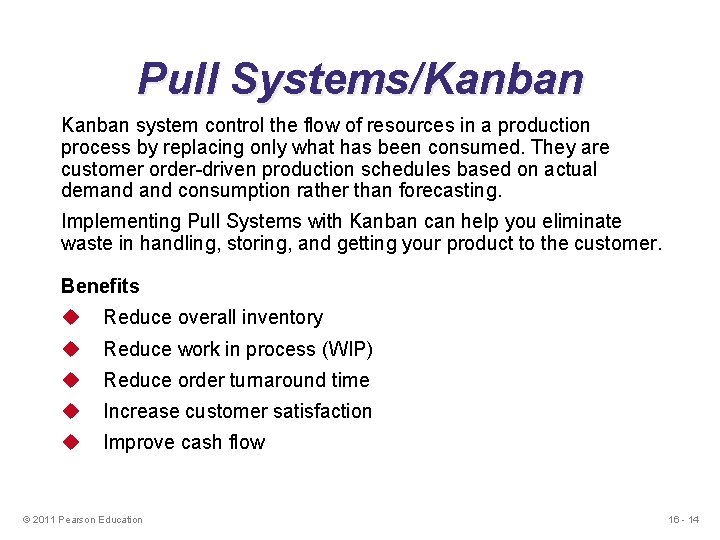
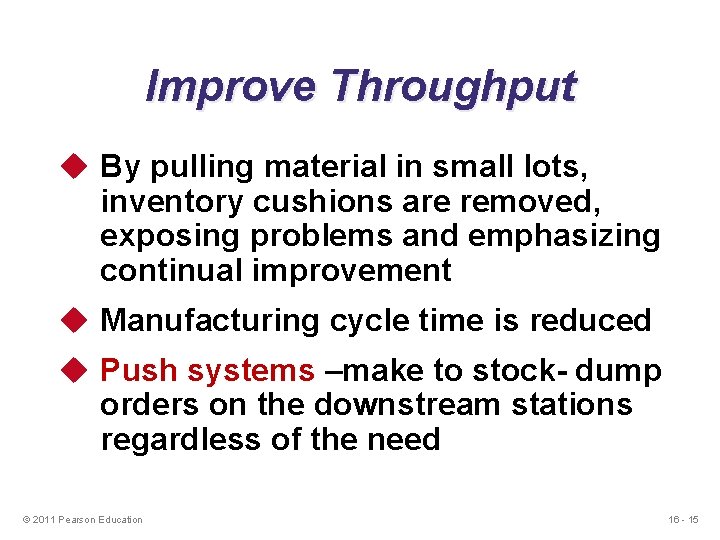
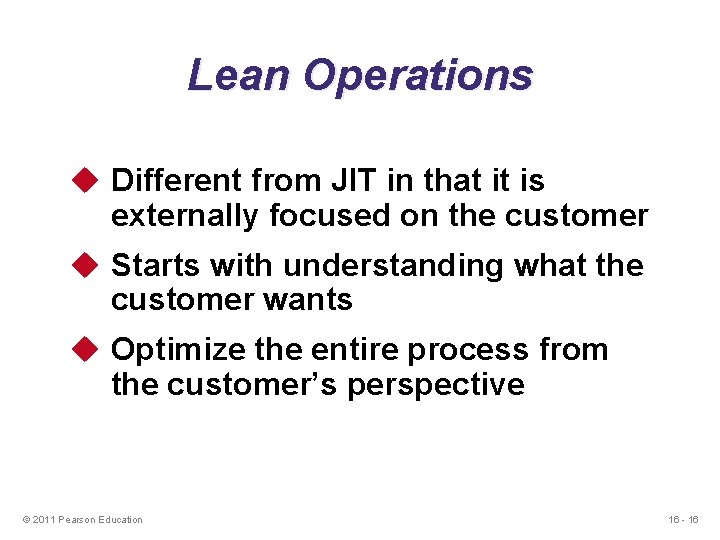
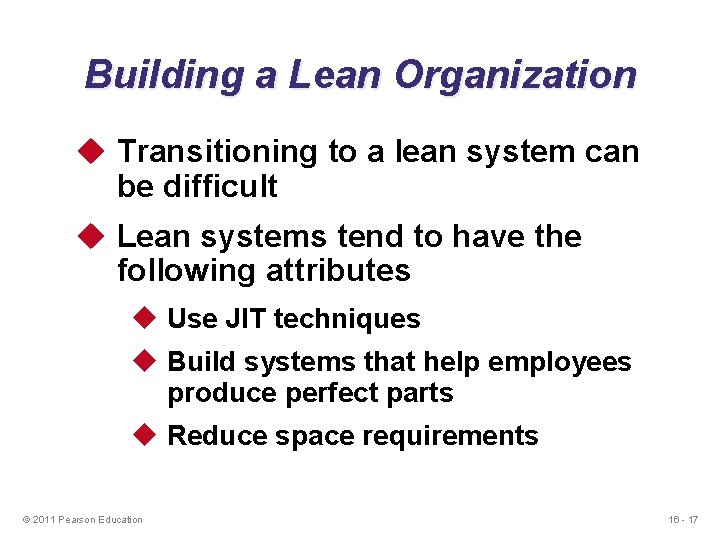
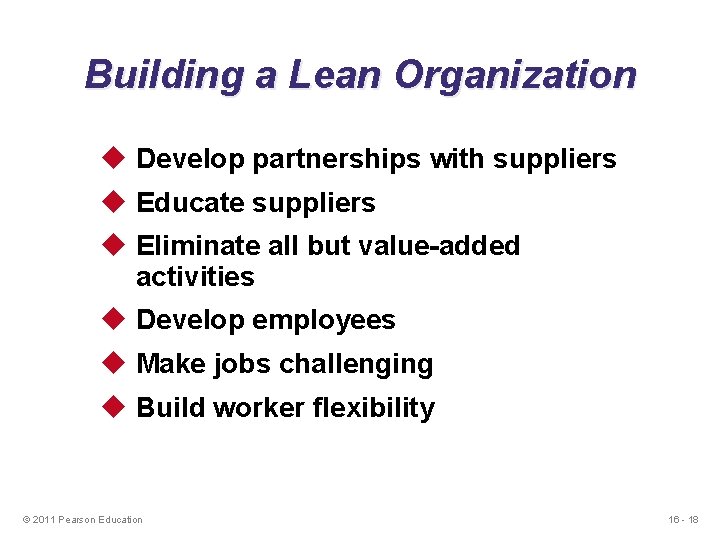
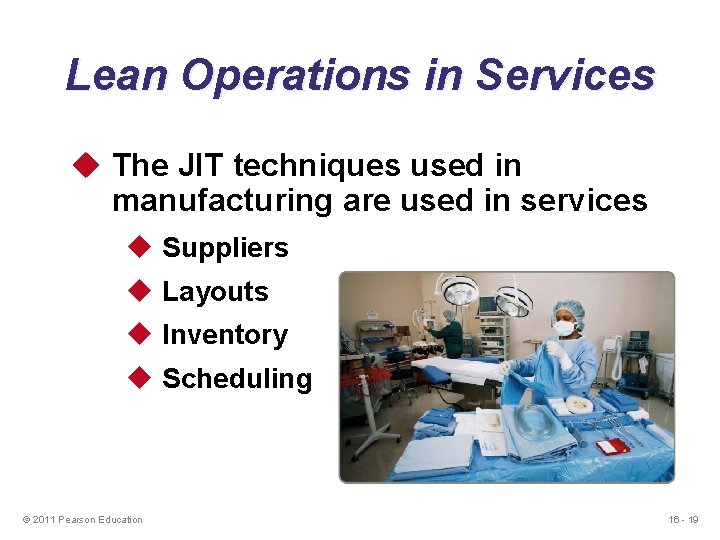
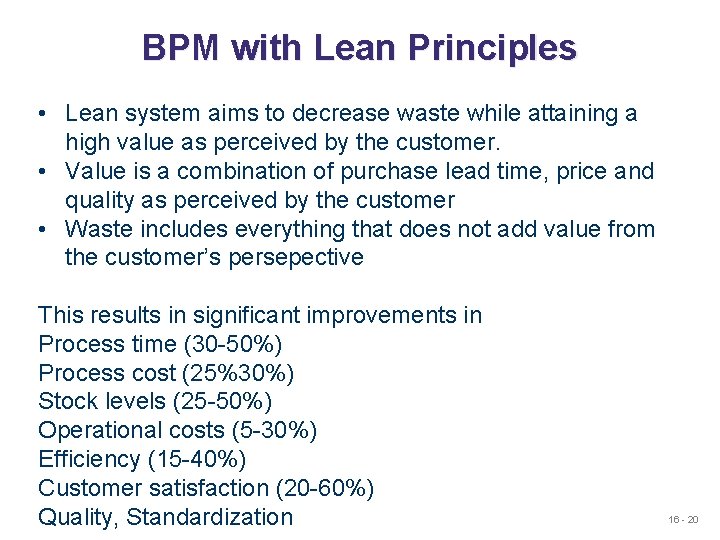
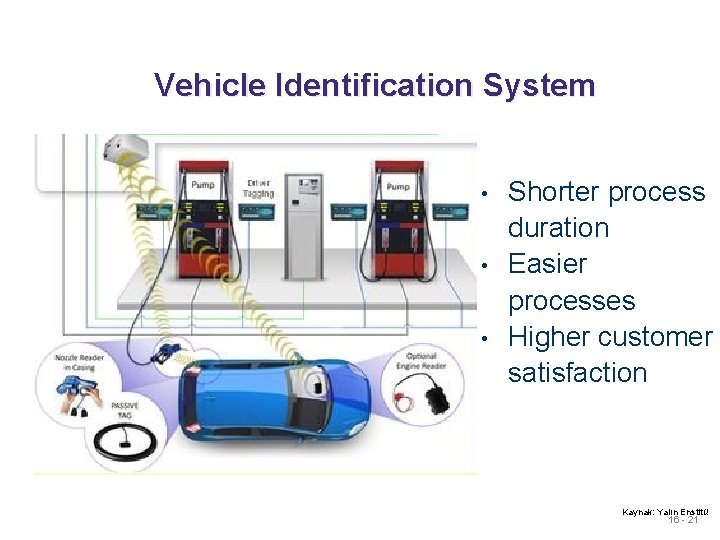
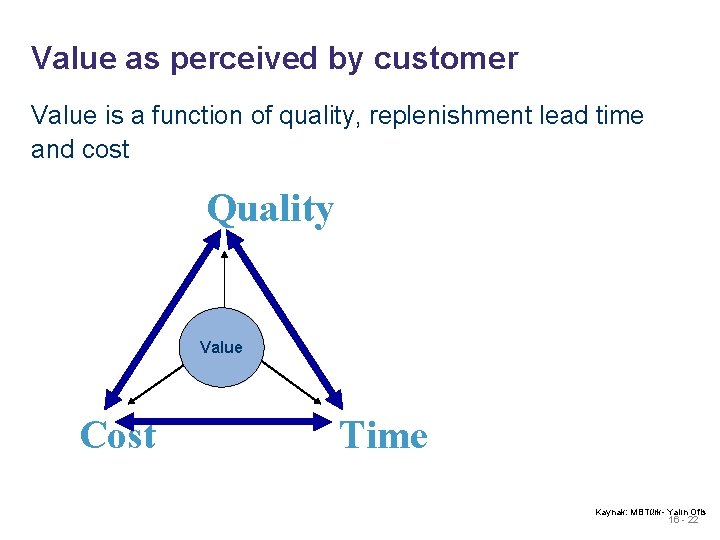
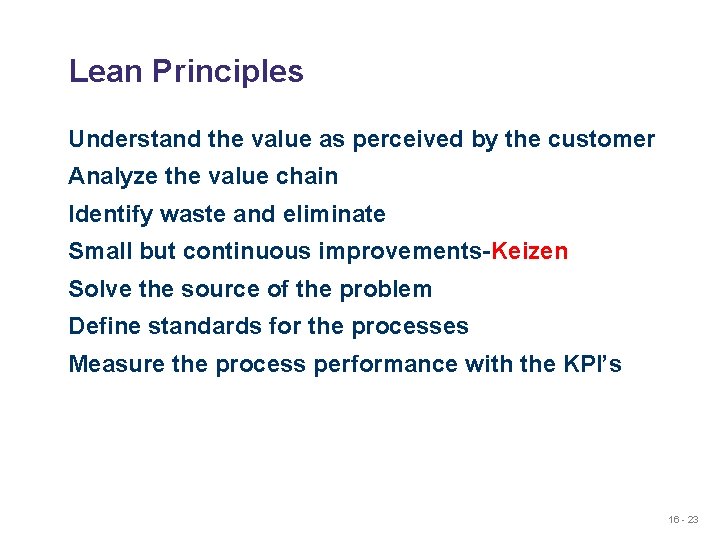
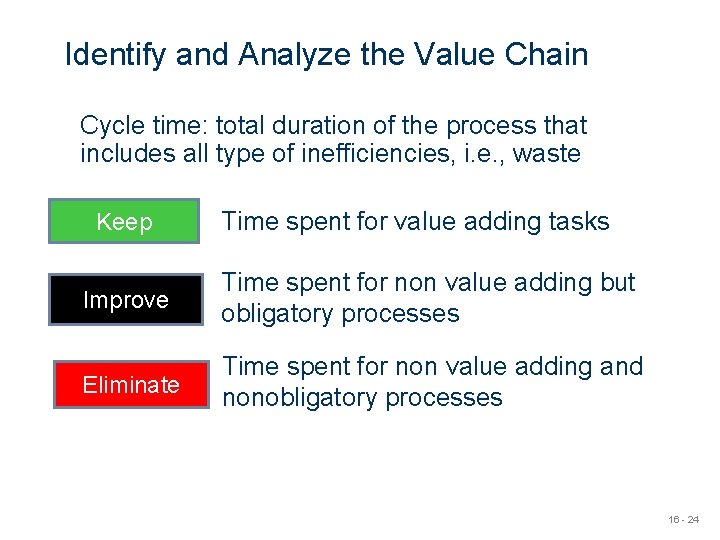
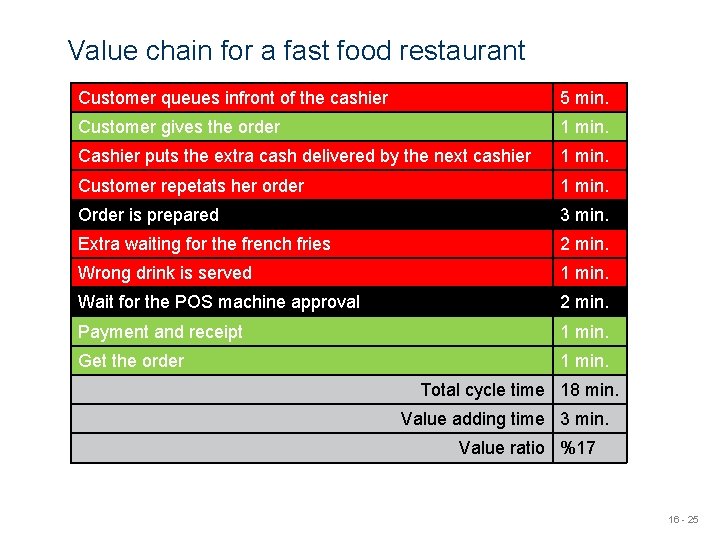
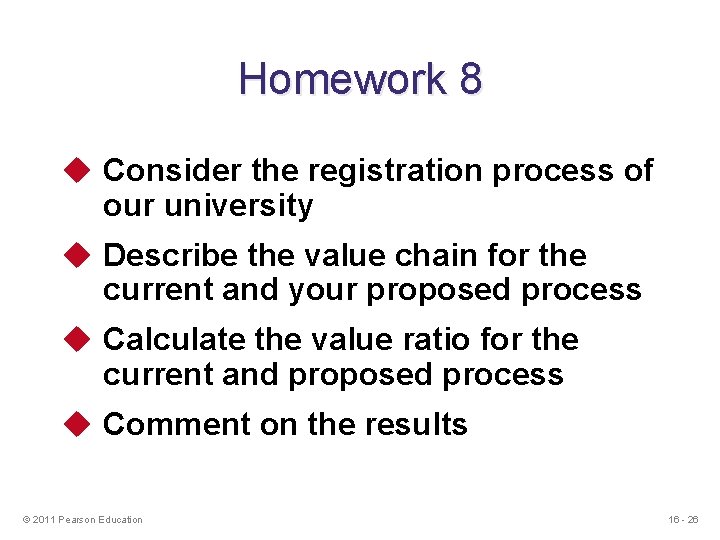
- Slides: 26

JIT/Lean Operations Good production systems require that managers address three issues that are pervasive and fundamental to operations management: u eliminate waste, u remove variability, and u improve throughput © 2011 Pearson Education 16 - 1
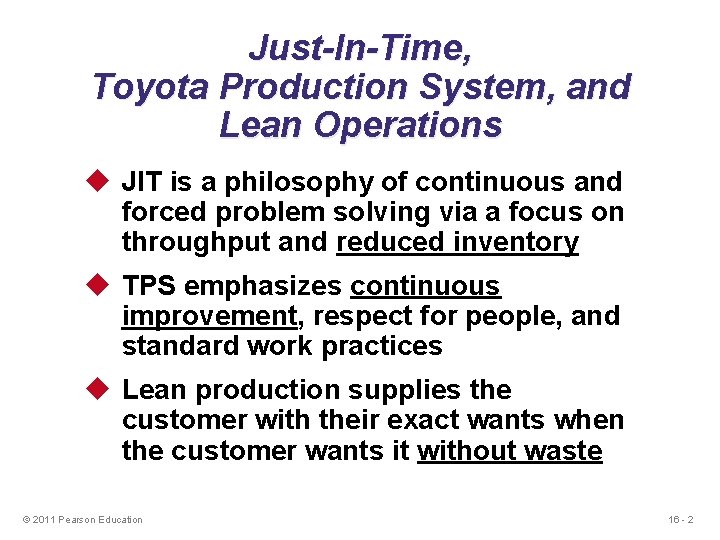
Just-In-Time, Toyota Production System, and Lean Operations u JIT is a philosophy of continuous and forced problem solving via a focus on throughput and reduced inventory u TPS emphasizes continuous improvement, respect for people, and standard work practices u Lean production supplies the customer with their exact wants when the customer wants it without waste © 2011 Pearson Education 16 - 2
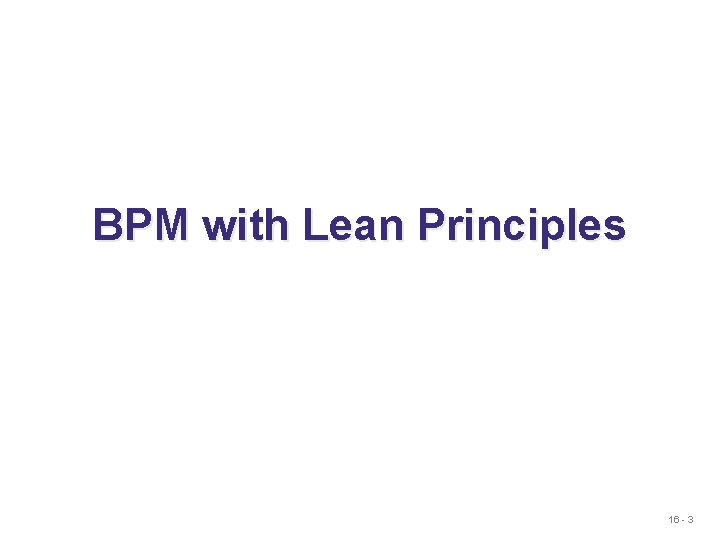
BPM with Lean Principles 16 - 3
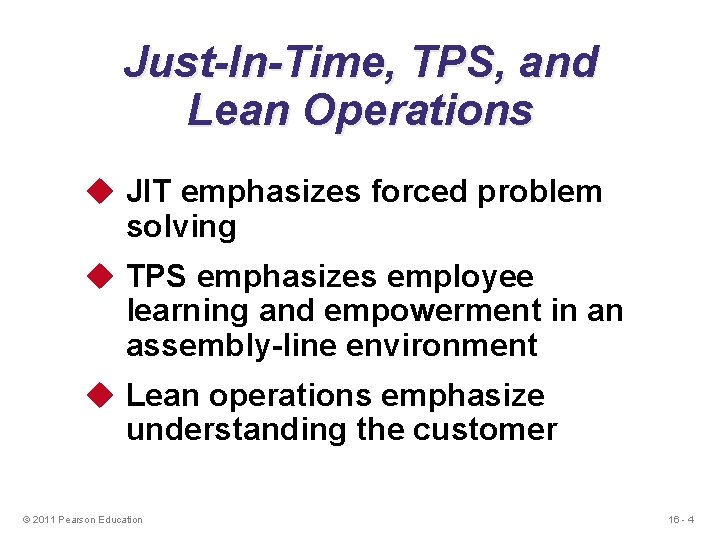
Just-In-Time, TPS, and Lean Operations u JIT emphasizes forced problem solving u TPS emphasizes employee learning and empowerment in an assembly-line environment u Lean operations emphasize understanding the customer © 2011 Pearson Education 16 - 4
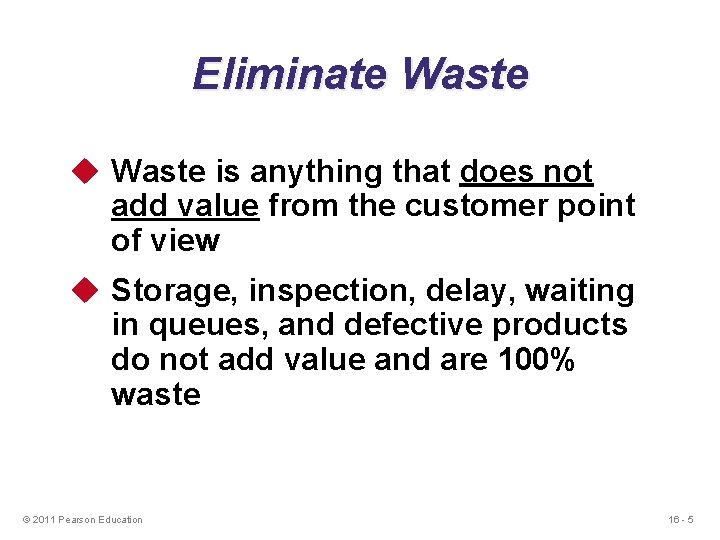
Eliminate Waste u Waste is anything that does not add value from the customer point of view u Storage, inspection, delay, waiting in queues, and defective products do not add value and are 100% waste © 2011 Pearson Education 16 - 5
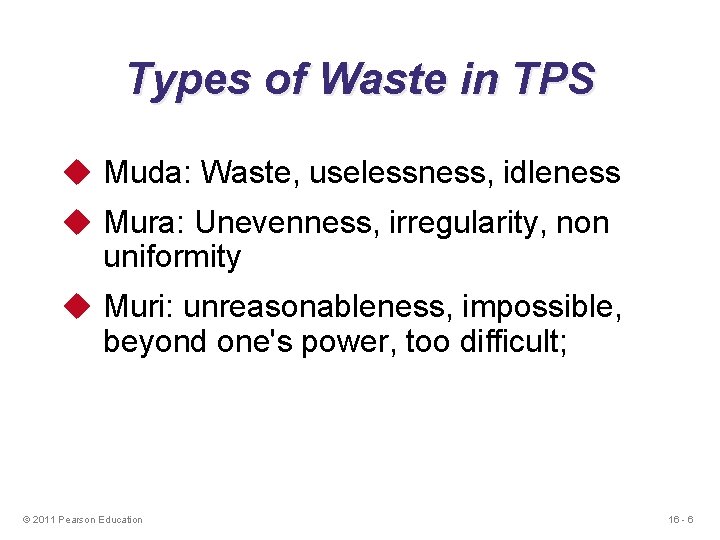
Types of Waste in TPS u Muda: Waste, uselessness, idleness u Mura: Unevenness, irregularity, non uniformity u Muri: unreasonableness, impossible, beyond one's power, too difficult; © 2011 Pearson Education 16 - 6
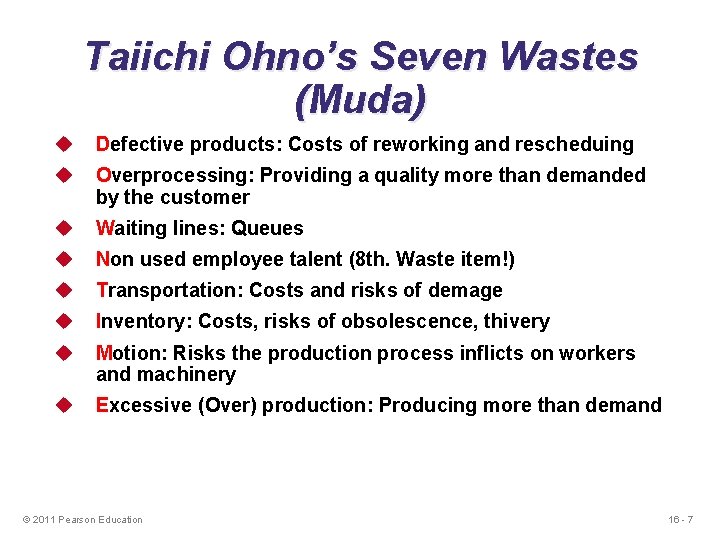
Taiichi Ohno’s Seven Wastes (Muda) u Defective products: Costs of reworking and rescheduing u Overprocessing: Providing a quality more than demanded by the customer u Waiting lines: Queues u Non used employee talent (8 th. Waste item!) u Transportation: Costs and risks of demage u Inventory: Costs, risks of obsolescence, thivery u Motion: Risks the production process inflicts on workers and machinery u Excessive (Over) production: Producing more than demand © 2011 Pearson Education 16 - 7
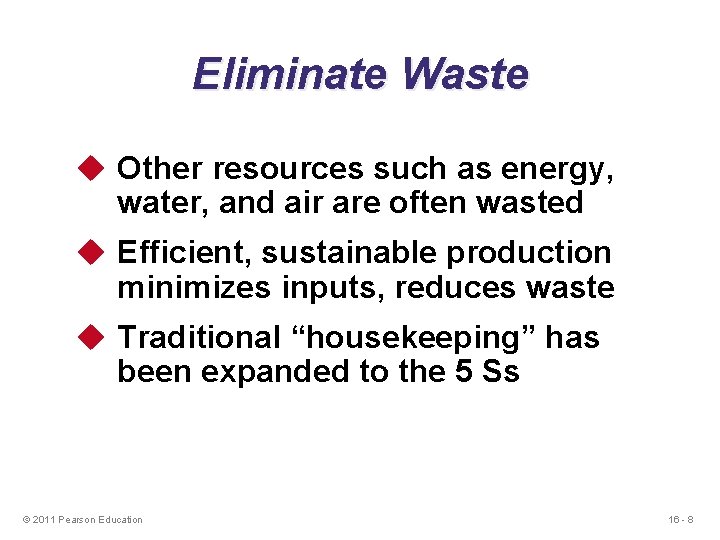
Eliminate Waste u Other resources such as energy, water, and air are often wasted u Efficient, sustainable production minimizes inputs, reduces waste u Traditional “housekeeping” has been expanded to the 5 Ss © 2011 Pearson Education 16 - 8
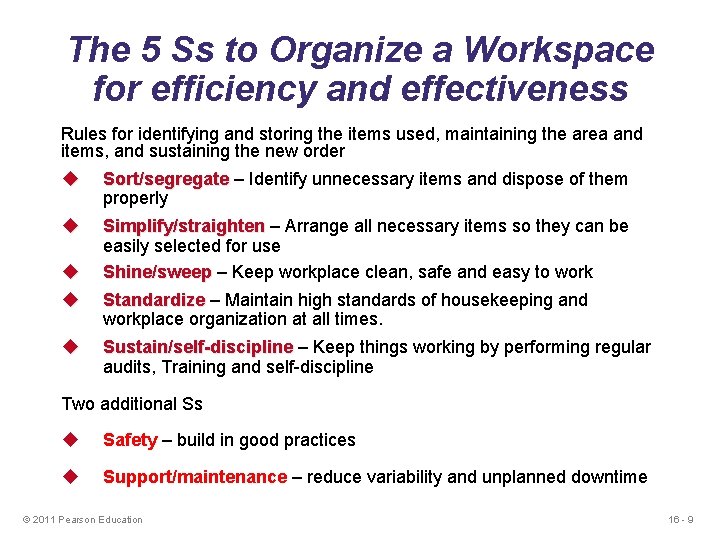
The 5 Ss to Organize a Workspace for efficiency and effectiveness Rules for identifying and storing the items used, maintaining the area and items, and sustaining the new order u Sort/segregate – Identify unnecessary items and dispose of them properly u Simplify/straighten – Arrange all necessary items so they can be easily selected for use Shine/sweep – Keep workplace clean, safe and easy to work u u u Standardize – Maintain high standards of housekeeping and workplace organization at all times. Sustain/self-discipline – Keep things working by performing regular audits, Training and self-discipline Two additional Ss u Safety – build in good practices u Support/maintenance – reduce variability and unplanned downtime © 2011 Pearson Education 16 - 9
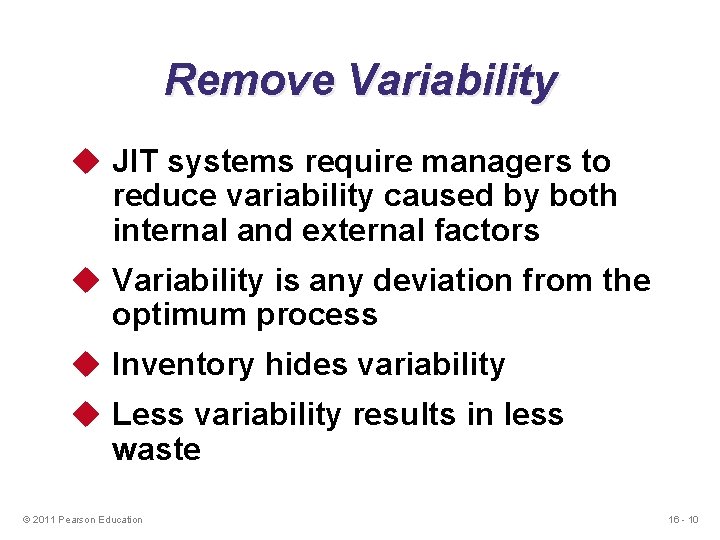
Remove Variability u JIT systems require managers to reduce variability caused by both internal and external factors u Variability is any deviation from the optimum process u Inventory hides variability u Less variability results in less waste © 2011 Pearson Education 16 - 10
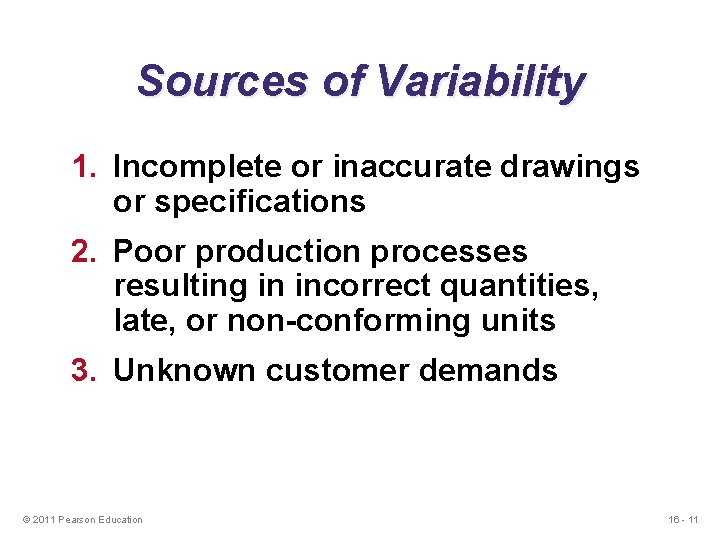
Sources of Variability 1. Incomplete or inaccurate drawings or specifications 2. Poor production processes resulting in incorrect quantities, late, or non-conforming units 3. Unknown customer demands © 2011 Pearson Education 16 - 11
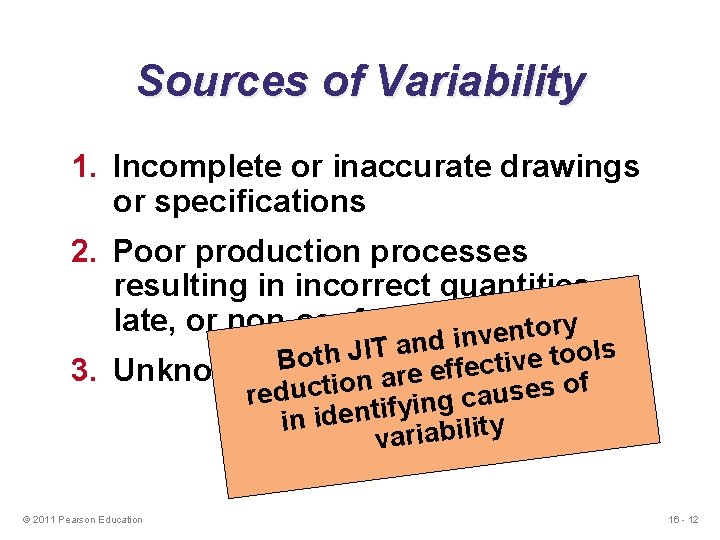
Sources of Variability 1. Incomplete or inaccurate drawings or specifications 2. Poor production processes resulting in incorrect quantities, late, or non-conformingnvunits entory i d n a T s I l o o t th J o e B v i ect f f 3. Unknown customer demands e e r a n o i of t c s e u s d u e r a c g n i y f i t n e in id y t i l i b a i r a v © 2011 Pearson Education 16 - 12
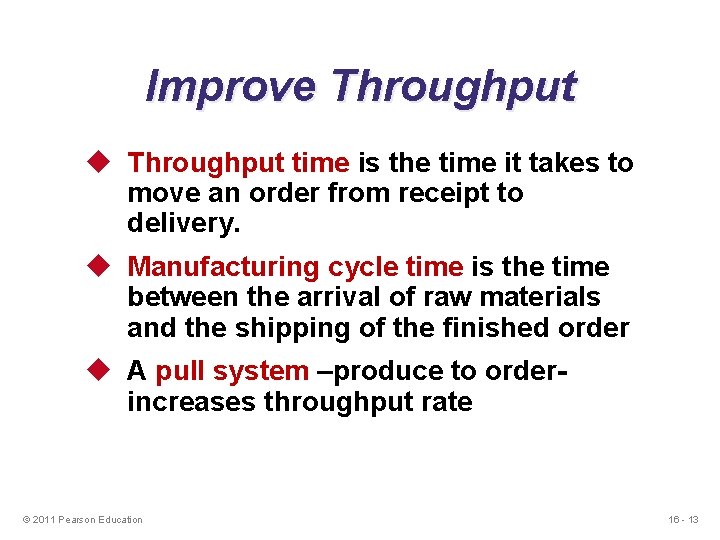
Improve Throughput u Throughput time is the time it takes to move an order from receipt to delivery. u Manufacturing cycle time is the time between the arrival of raw materials and the shipping of the finished order u A pull system –produce to orderincreases throughput rate © 2011 Pearson Education 16 - 13
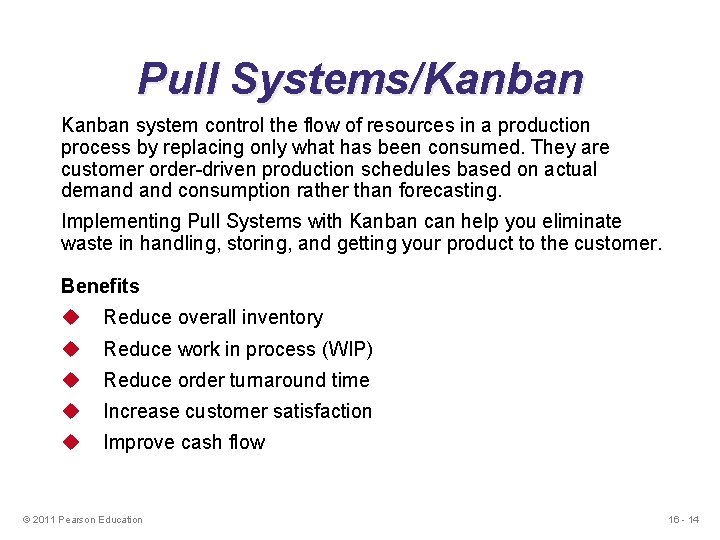
Pull Systems/Kanban system control the flow of resources in a production process by replacing only what has been consumed. They are customer order-driven production schedules based on actual demand consumption rather than forecasting. Implementing Pull Systems with Kanban can help you eliminate waste in handling, storing, and getting your product to the customer. Benefits u Reduce overall inventory u Reduce work in process (WIP) u Reduce order turnaround time u Increase customer satisfaction u Improve cash flow © 2011 Pearson Education 16 - 14
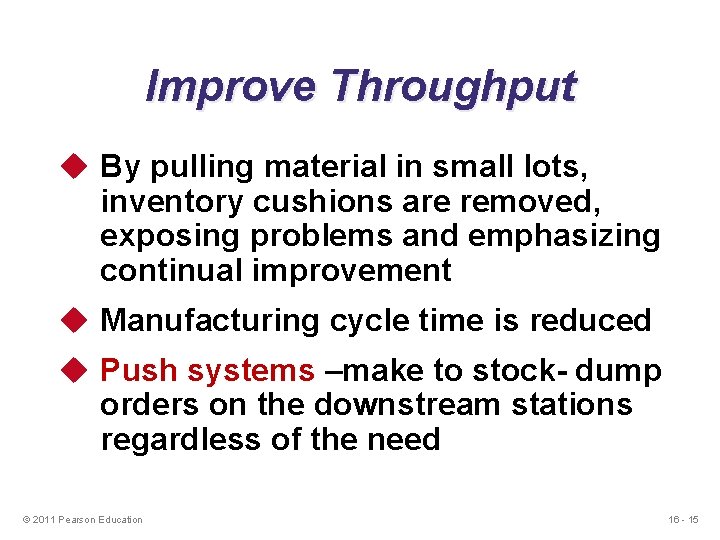
Improve Throughput u By pulling material in small lots, inventory cushions are removed, exposing problems and emphasizing continual improvement u Manufacturing cycle time is reduced u Push systems –make to stock- dump orders on the downstream stations regardless of the need © 2011 Pearson Education 16 - 15
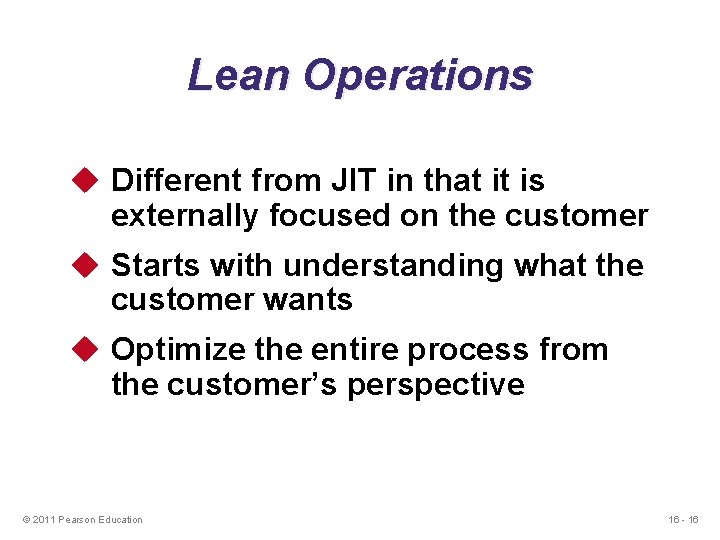
Lean Operations u Different from JIT in that it is externally focused on the customer u Starts with understanding what the customer wants u Optimize the entire process from the customer’s perspective © 2011 Pearson Education 16 - 16
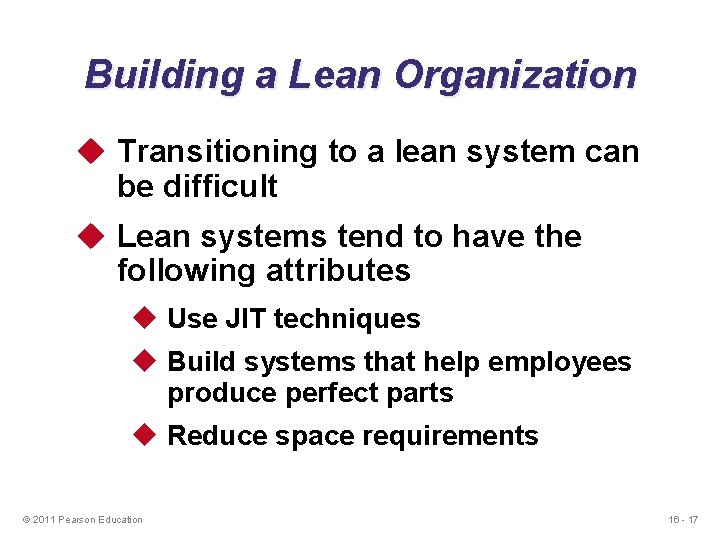
Building a Lean Organization u Transitioning to a lean system can be difficult u Lean systems tend to have the following attributes u Use JIT techniques u Build systems that help employees produce perfect parts u Reduce space requirements © 2011 Pearson Education 16 - 17
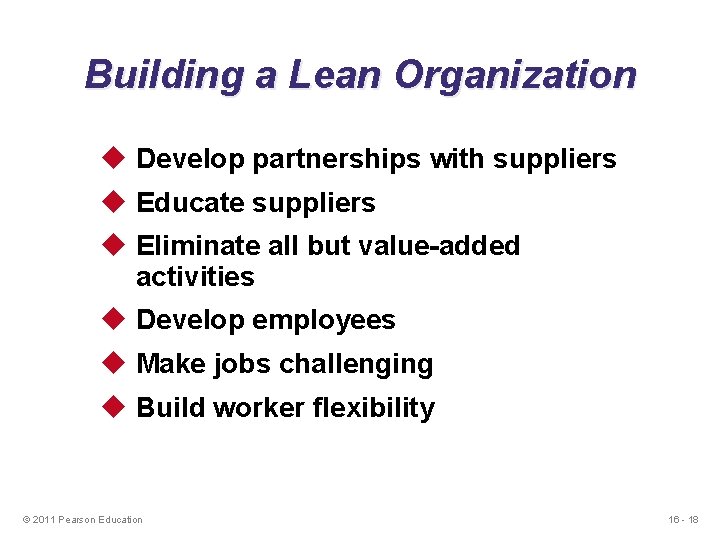
Building a Lean Organization u Develop partnerships with suppliers u Educate suppliers u Eliminate all but value-added activities u Develop employees u Make jobs challenging u Build worker flexibility © 2011 Pearson Education 16 - 18
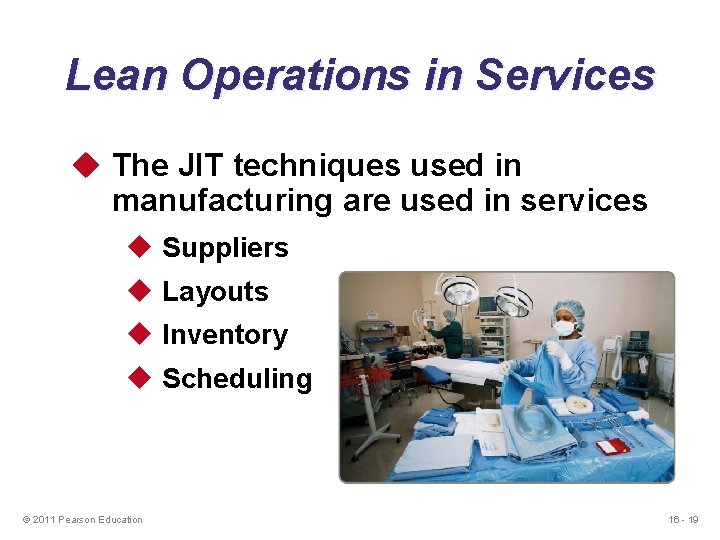
Lean Operations in Services u The JIT techniques used in manufacturing are used in services u Suppliers u Layouts u Inventory u Scheduling © 2011 Pearson Education 16 - 19
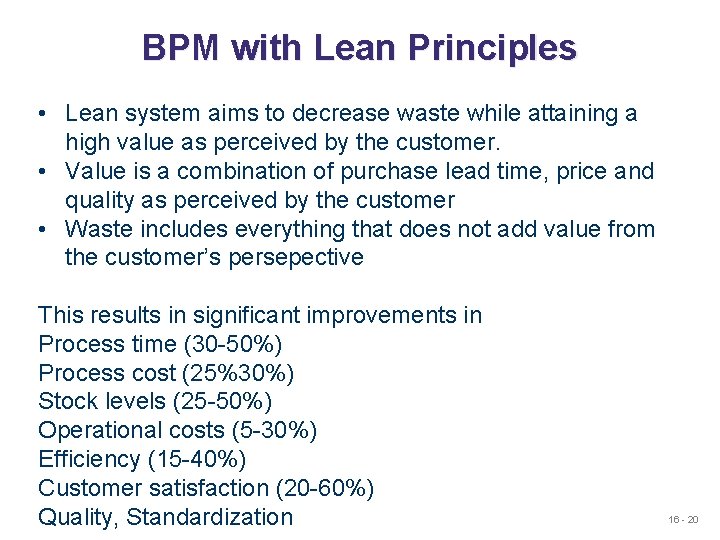
BPM with Lean Principles • Lean system aims to decrease waste while attaining a high value as perceived by the customer. • Value is a combination of purchase lead time, price and quality as perceived by the customer • Waste includes everything that does not add value from the customer’s persepective This results in significant improvements in Process time (30 -50%) Process cost (25%30%) Stock levels (25 -50%) Operational costs (5 -30%) Efficiency (15 -40%) Customer satisfaction (20 -60%) Quality, Standardization 16 - 20
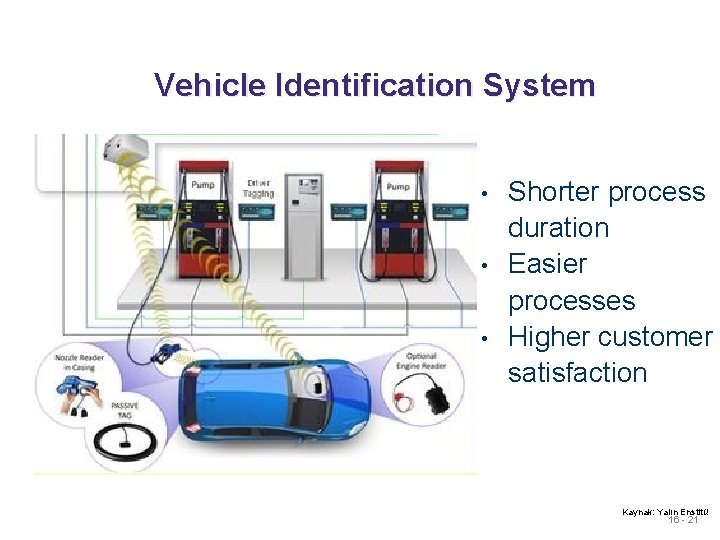
Vehicle Identification System • • • Shorter process duration Easier processes Higher customer satisfaction Kaynak: Yalın Enstitü 16 - 21
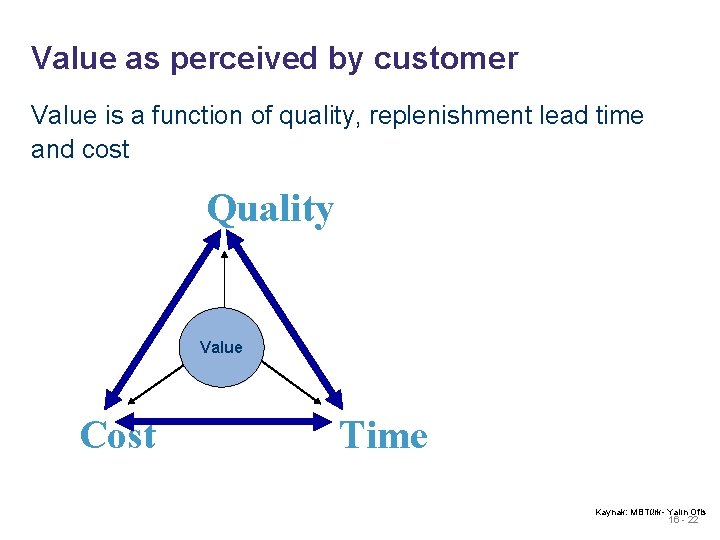
Value as perceived by customer Value is a function of quality, replenishment lead time and cost Quality Value Cost Time Kaynak: MBTürk- Yalın Ofis 16 - 22
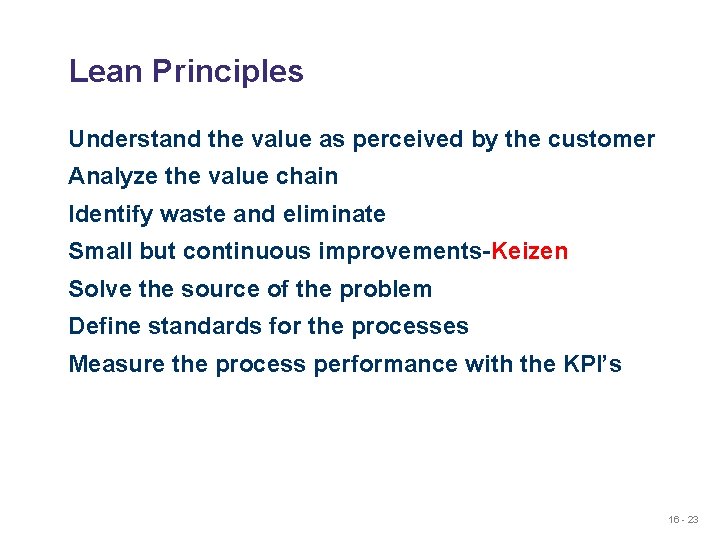
Lean Principles Understand the value as perceived by the customer Analyze the value chain Identify waste and eliminate Small but continuous improvements-Keizen Solve the source of the problem Define standards for the processes Measure the process performance with the KPI’s 16 - 23
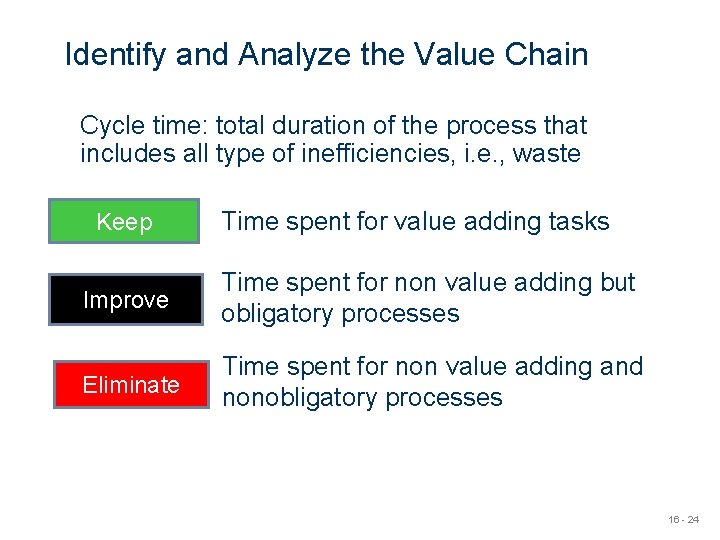
Identify and Analyze the Value Chain Cycle time: total duration of the process that includes all type of inefficiencies, i. e. , waste Keep Time spent for value adding tasks Improve Time spent for non value adding but obligatory processes Eliminate Time spent for non value adding and nonobligatory processes 16 - 24
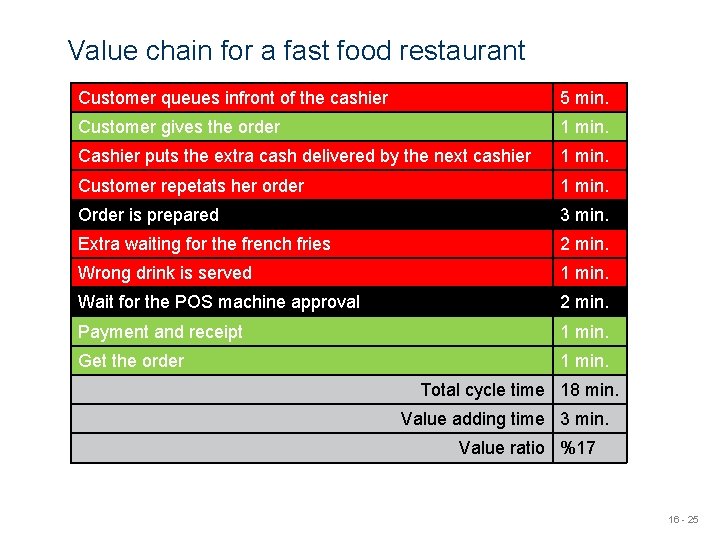
Value chain for a fast food restaurant Customer queues infront of the cashier 5 min. Customer gives the order 1 min. Cashier puts the extra cash delivered by the next cashier 1 min. Customer repetats her order 1 min. Order is prepared 3 min. Extra waiting for the french fries 2 min. Wrong drink is served 1 min. Wait for the POS machine approval 2 min. Payment and receipt 1 min. Get the order 1 min. Total cycle time 18 min. Value adding time 3 min. Value ratio %17 16 - 25
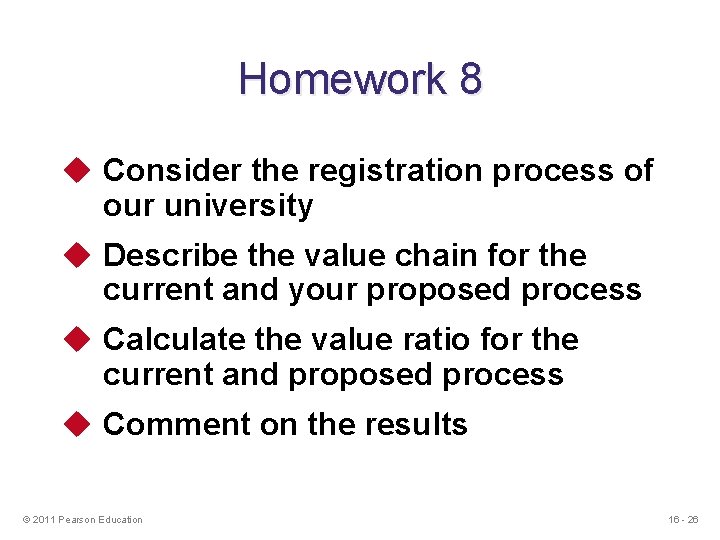
Homework 8 u Consider the registration process of our university u Describe the value chain for the current and your proposed process u Calculate the value ratio for the current and proposed process u Comment on the results © 2011 Pearson Education 16 - 26
Production post production pre production
Phân độ lown ngoại tâm thu
Block nhĩ thất cấp 1
Thể thơ truyền thống
Thơ thất ngôn tứ tuyệt đường luật
Chiến lược kinh doanh quốc tế của walmart
Tìm vết của mặt phẳng
Con hãy đưa tay khi thấy người vấp ngã
Tôn thất thuyết là ai
Gây tê cơ vuông thắt lưng
Sau thất bại ở hồ điển triệt
The process of recruiting and retaining capable employees
Why good managers make bad ethical choices
Good thoughts, good words, good deeds meaning
Hello good afternoon teacher
Buenas tardes good afternoon
You are good you are good when theres nothing good in me
Buenas tardes
Production management definition
Chapter 13 production and business operations
Toyota operations management
Examples of operation management
Product and process design in operations management
Surface finishing operations in production technology
Restaurant kitchen production systems
Terrestrial food production systems
Food production system example