IMPLEMENTING CONTINUOUS QUALITY IMPROVEMENT IN AN AUSTRALIAN PRIVATE

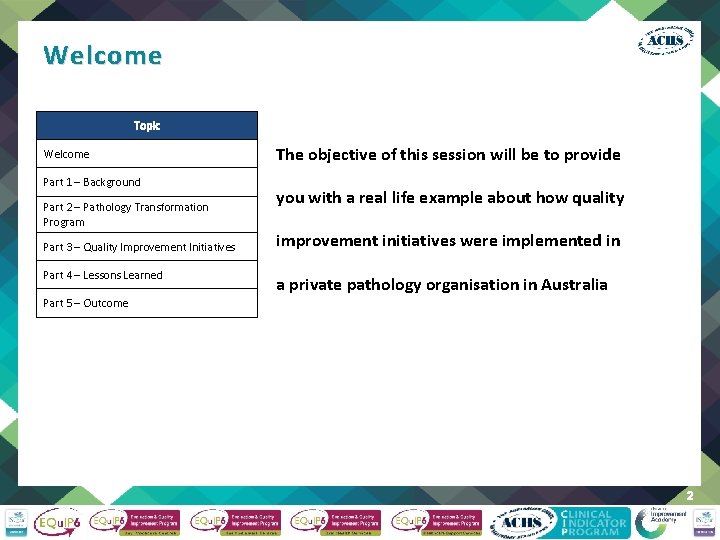
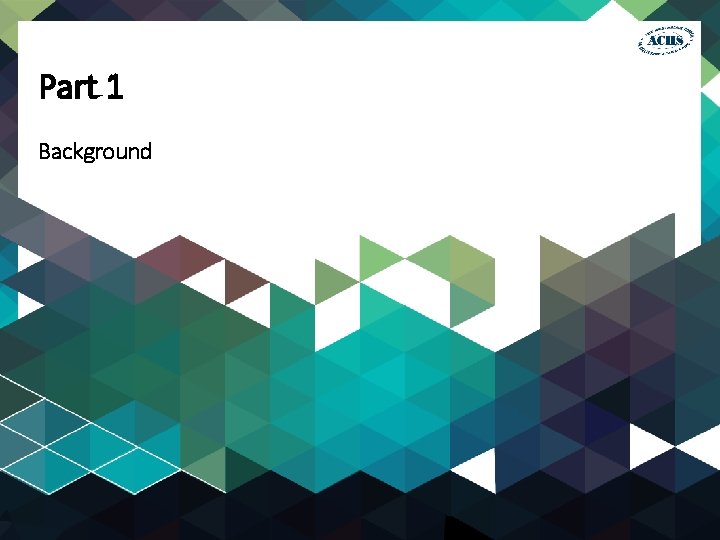
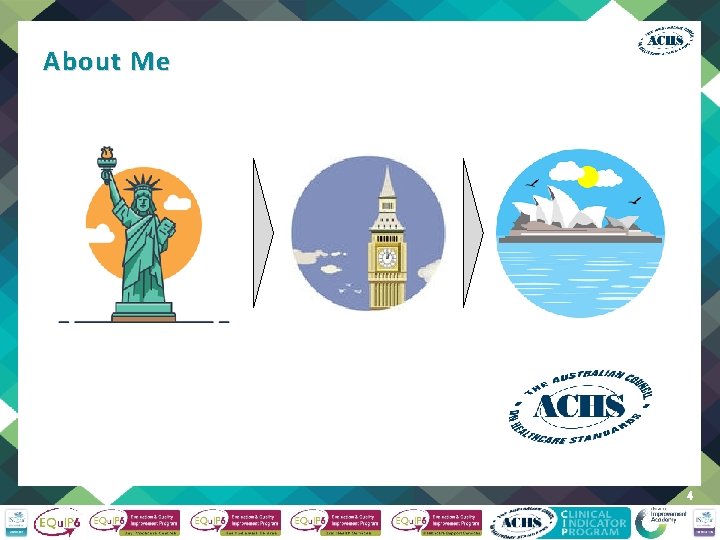
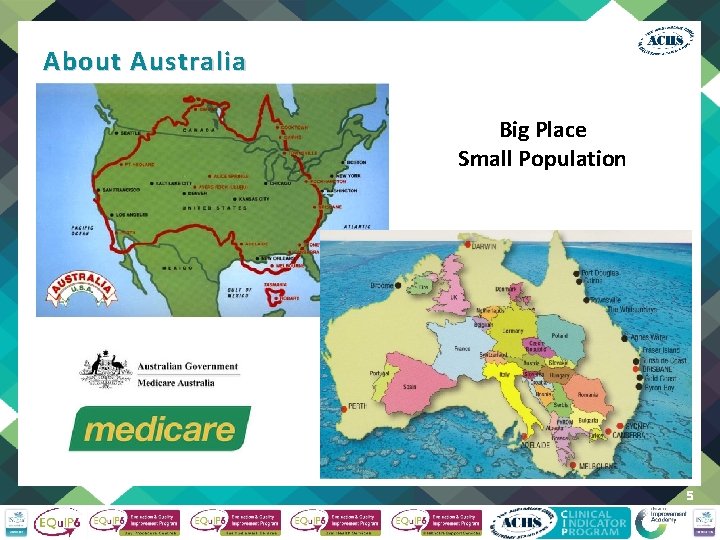
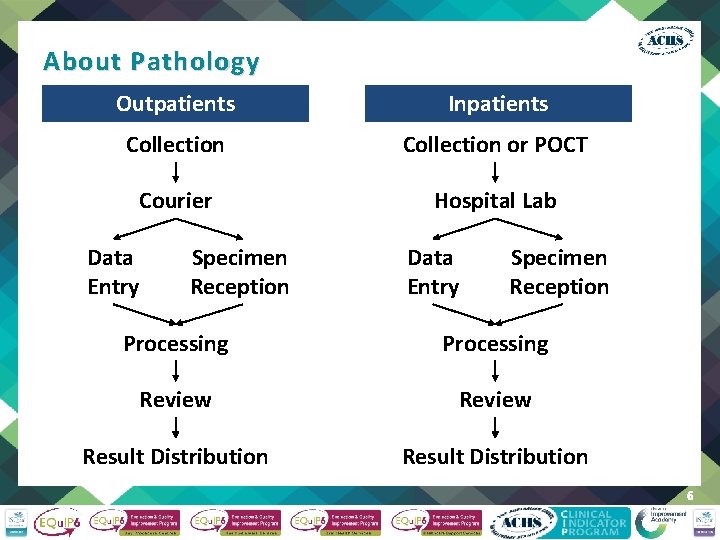
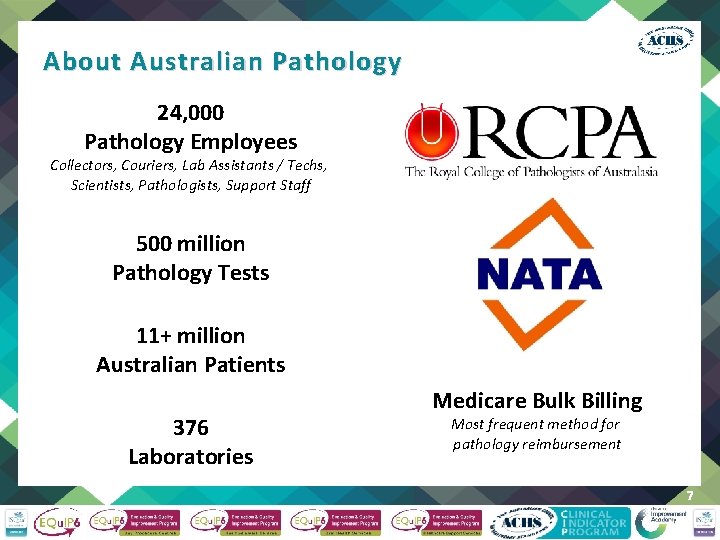
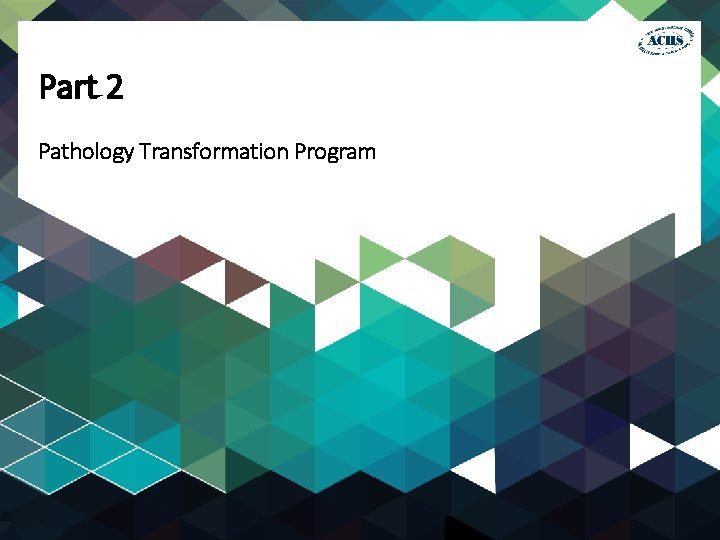
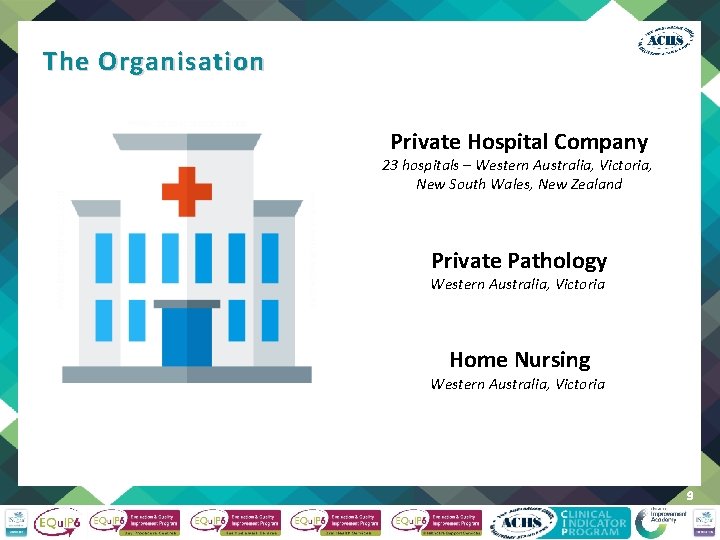
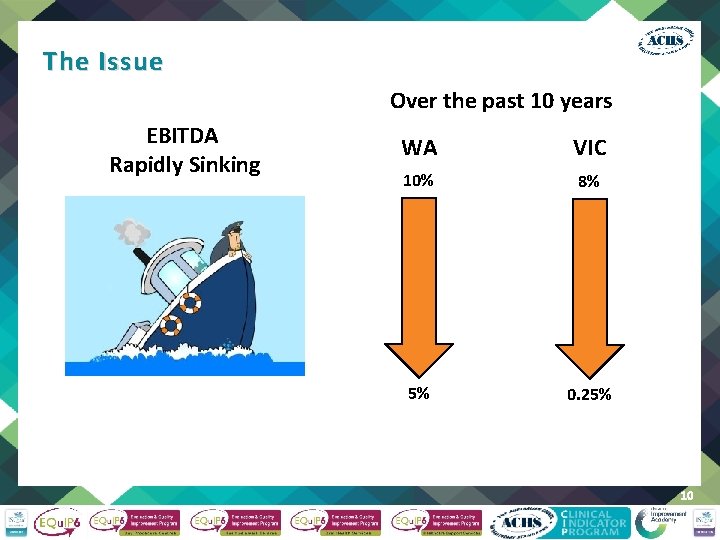
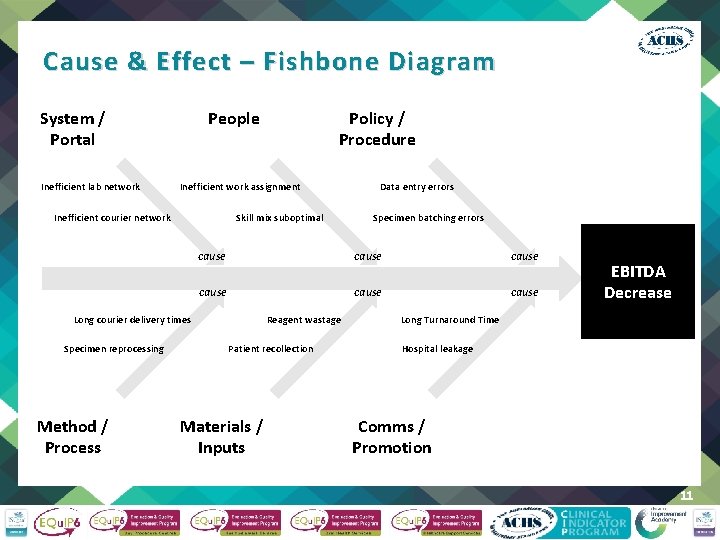
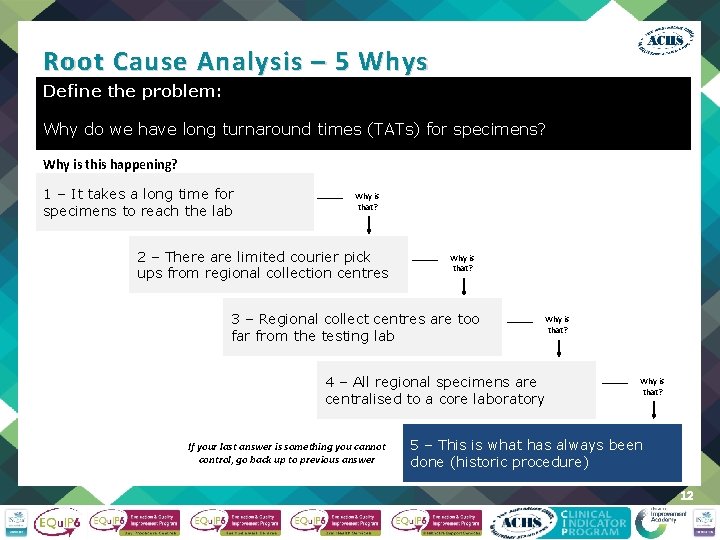
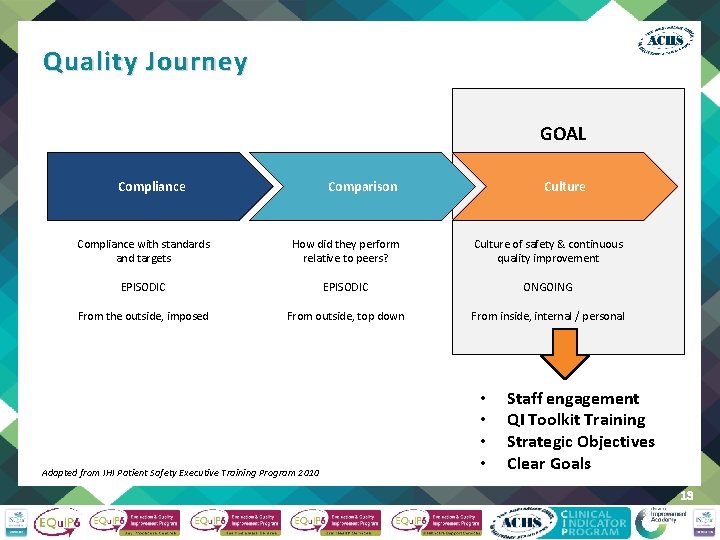
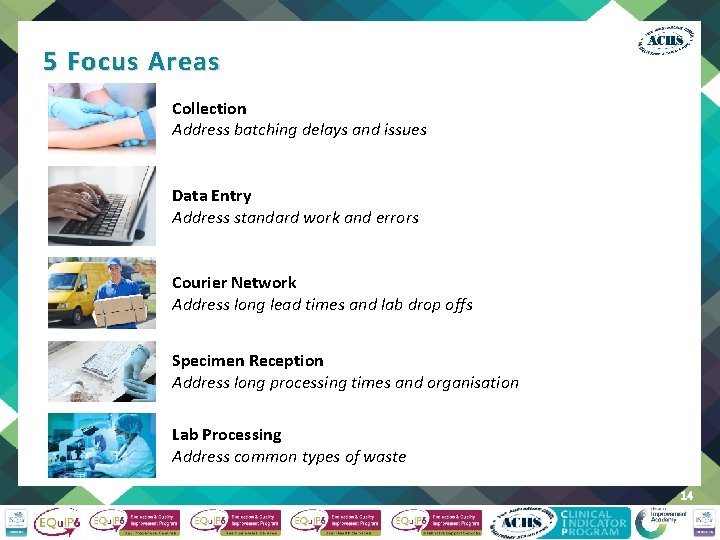
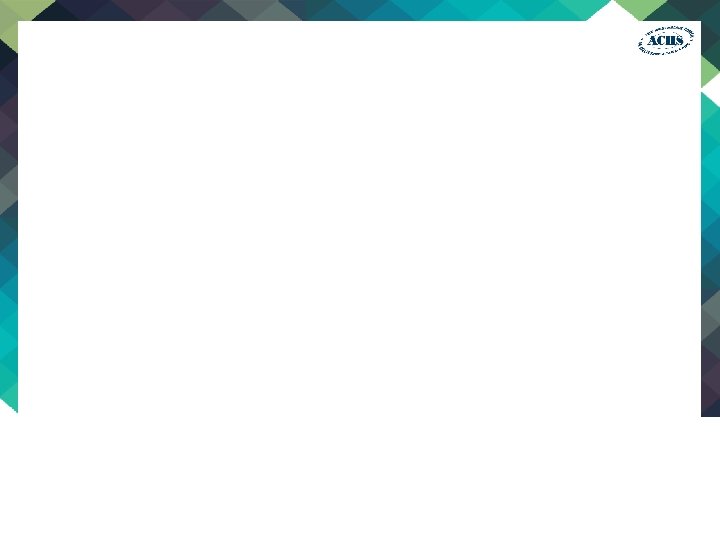
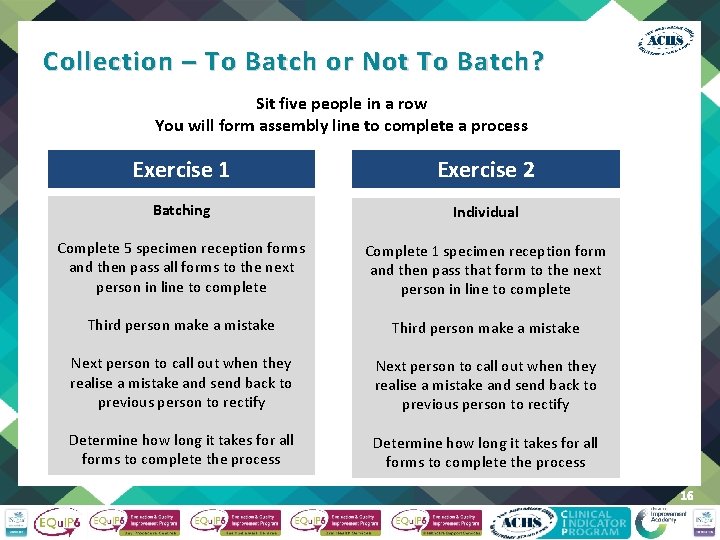
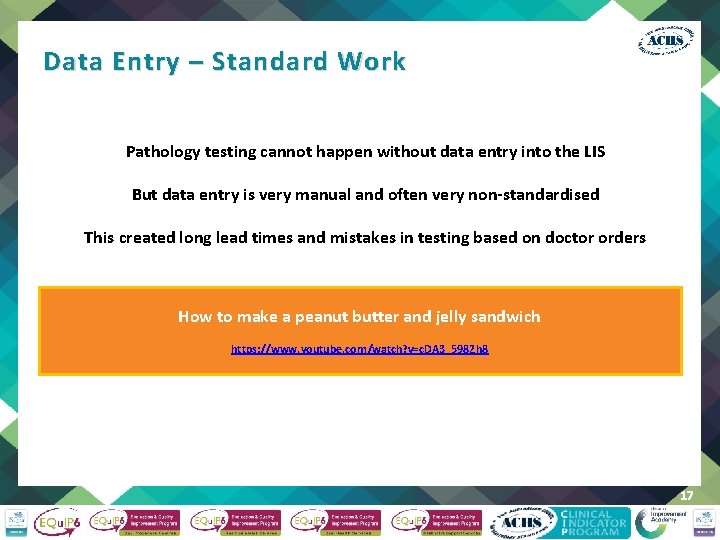
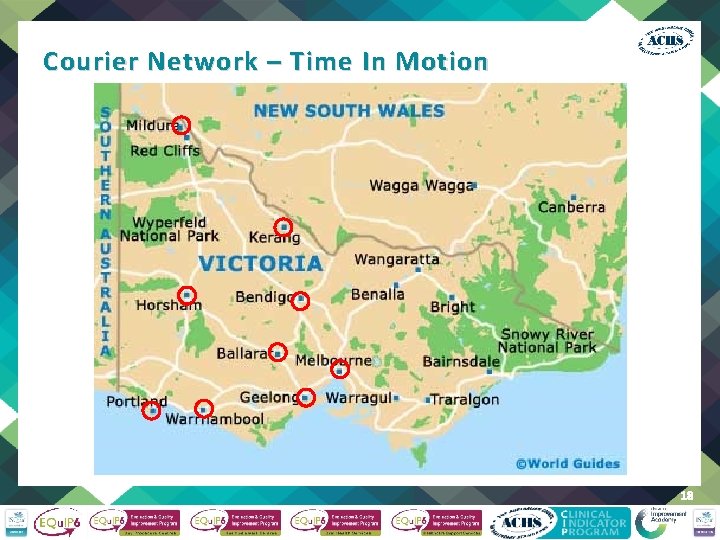
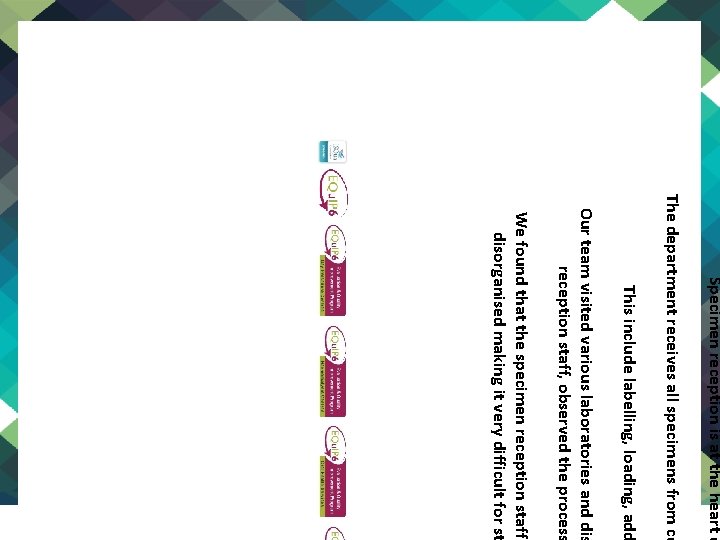
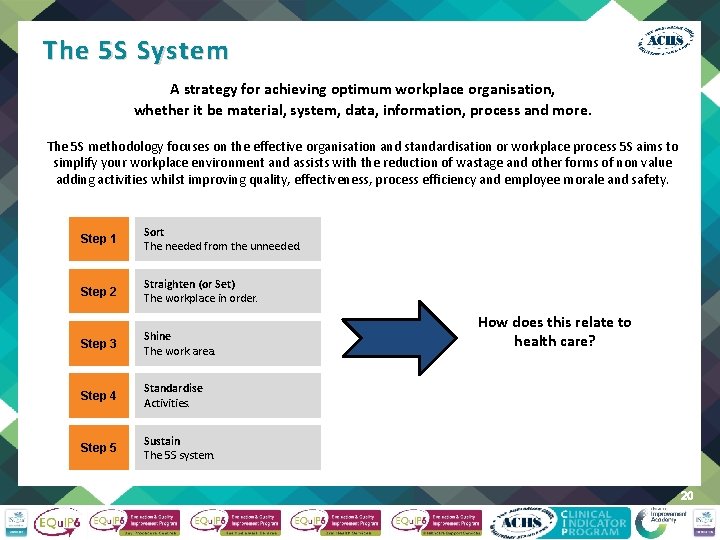
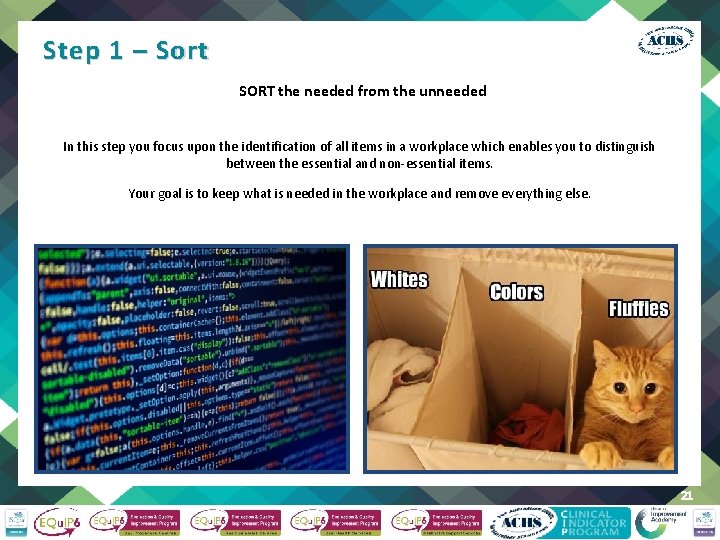
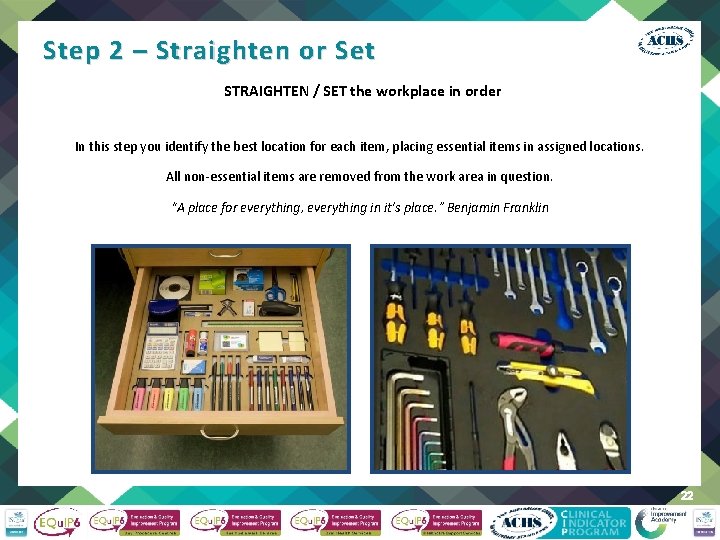
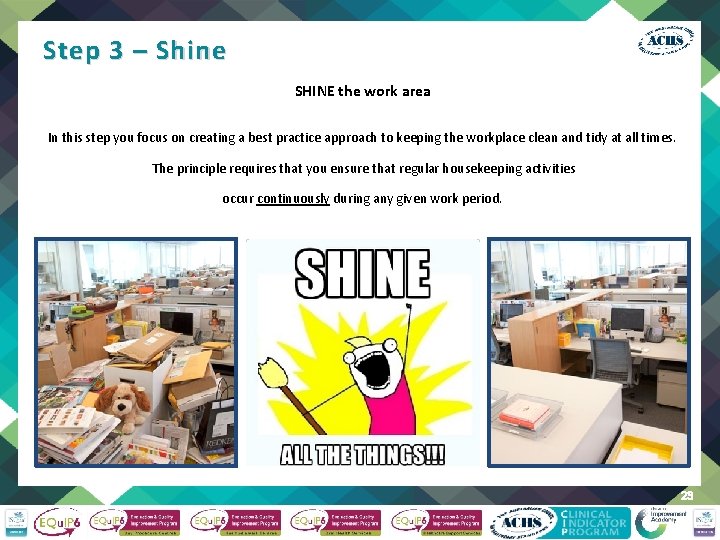
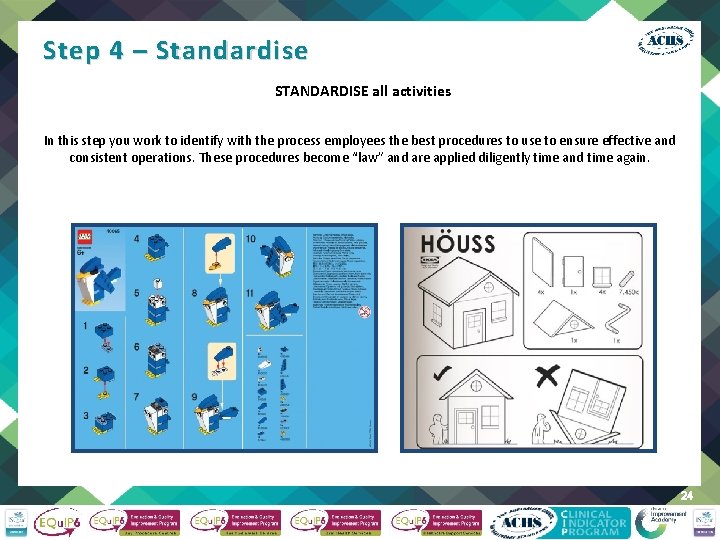
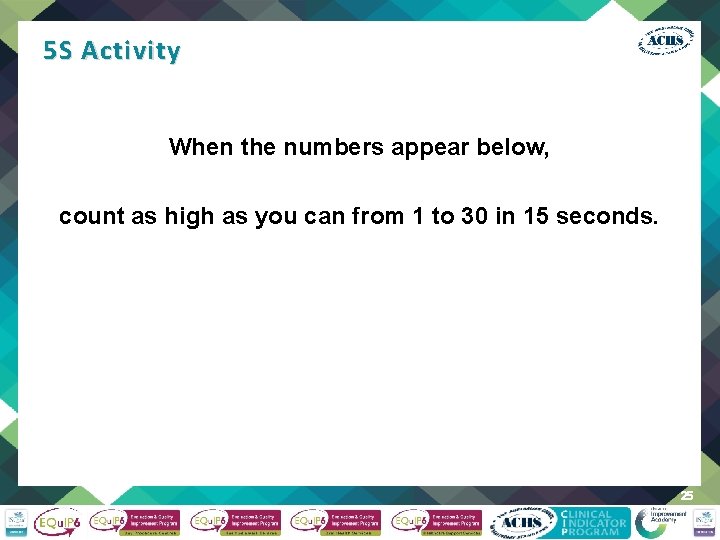
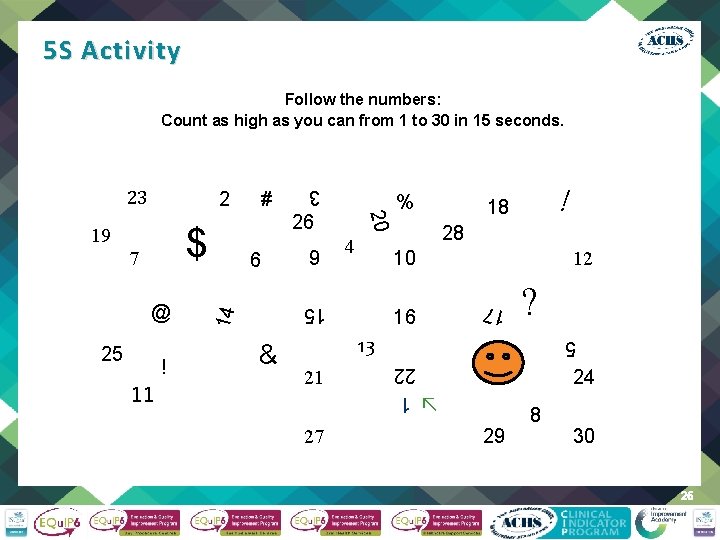
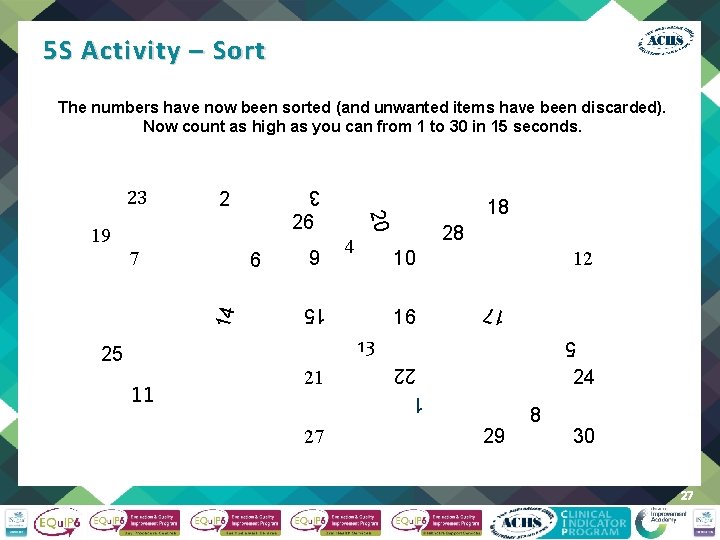
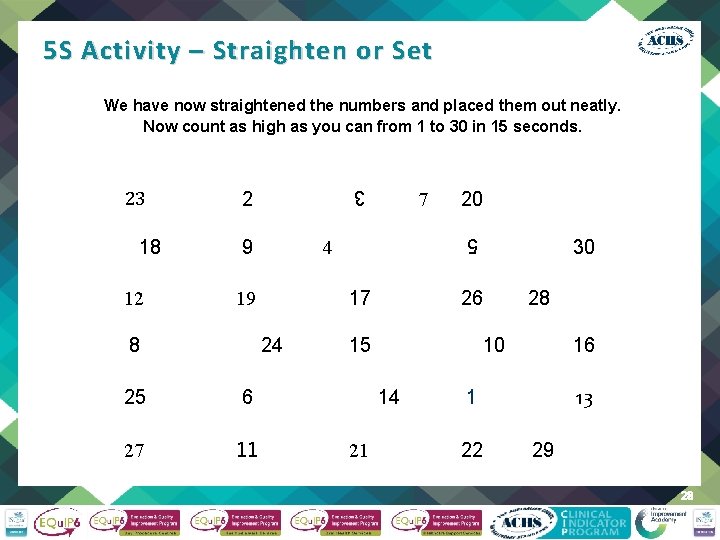
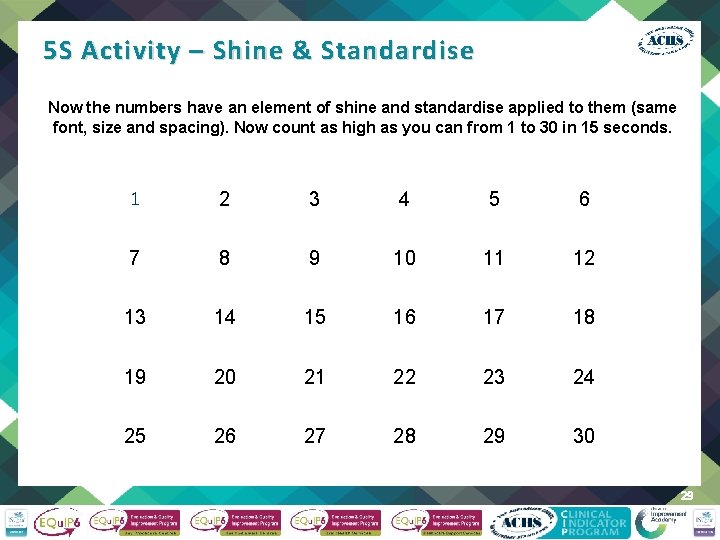
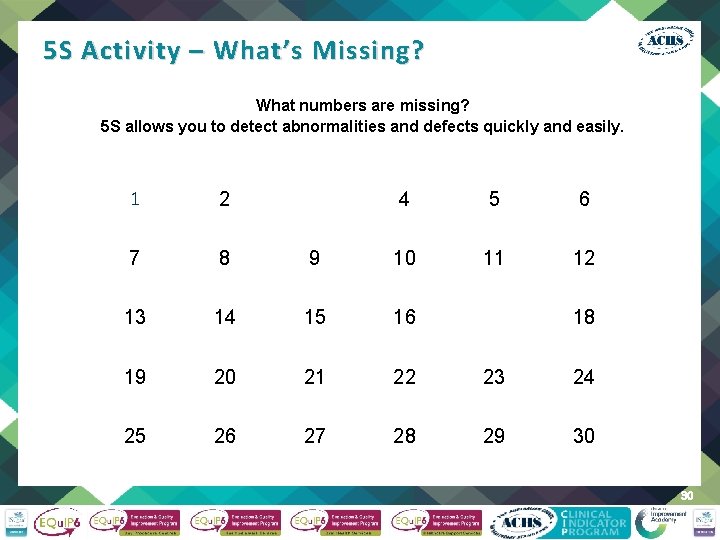
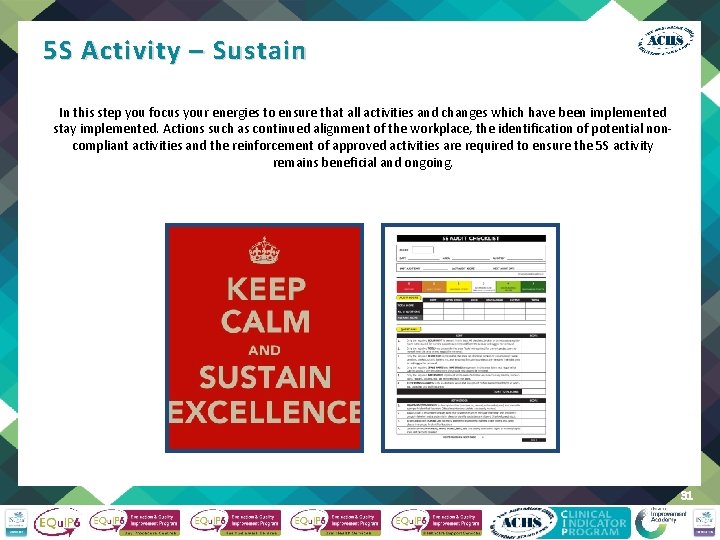
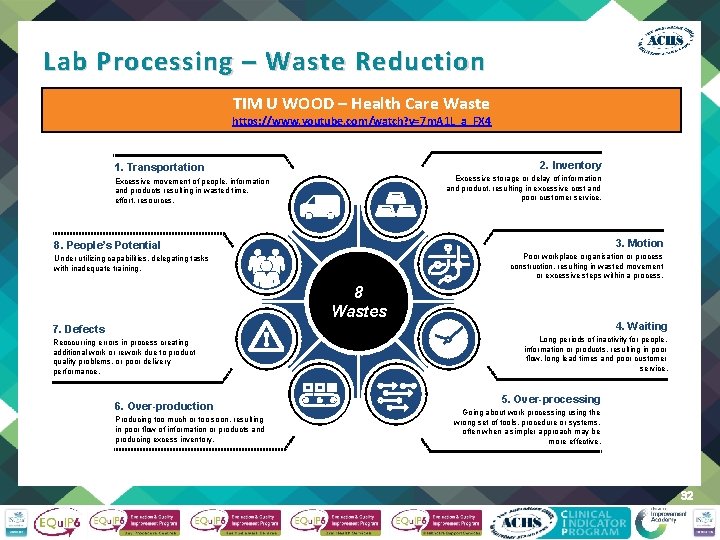
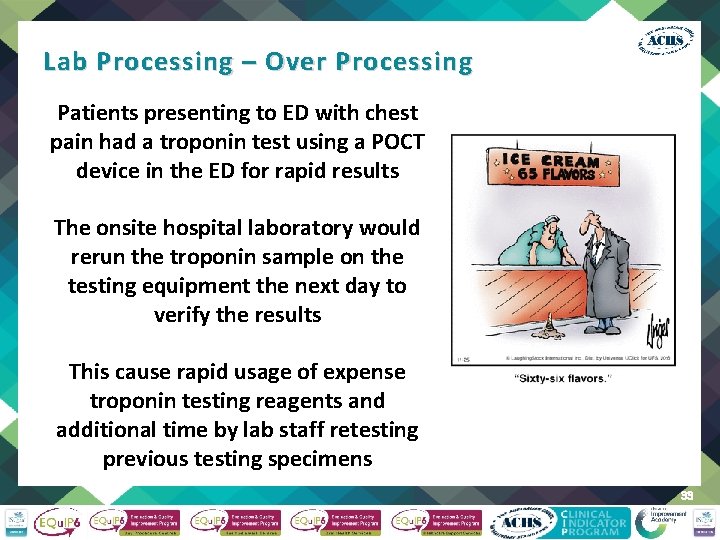
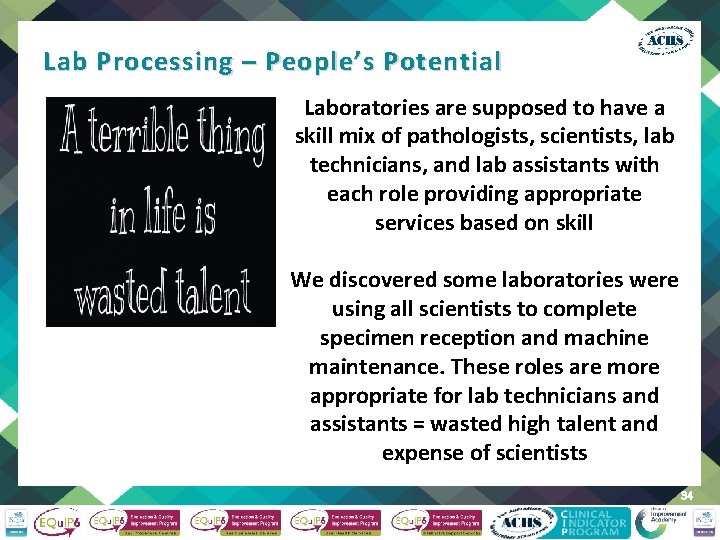
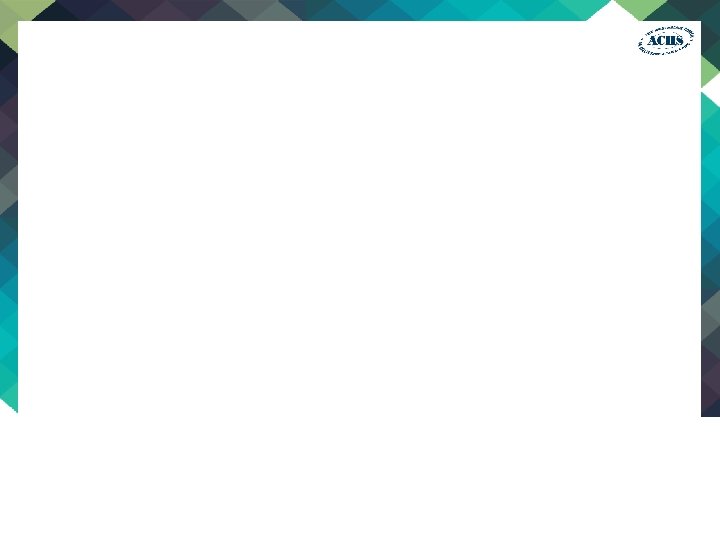
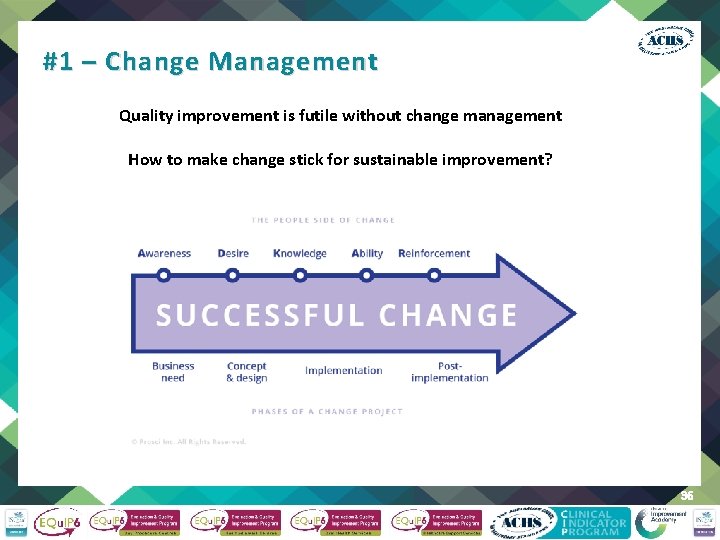
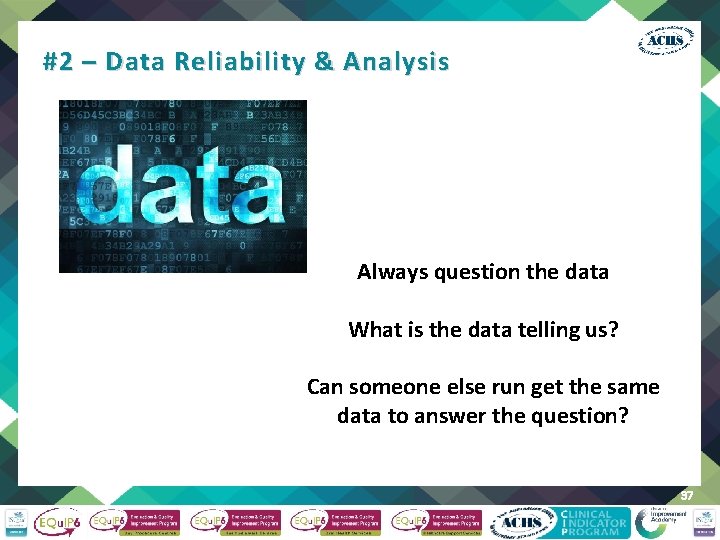
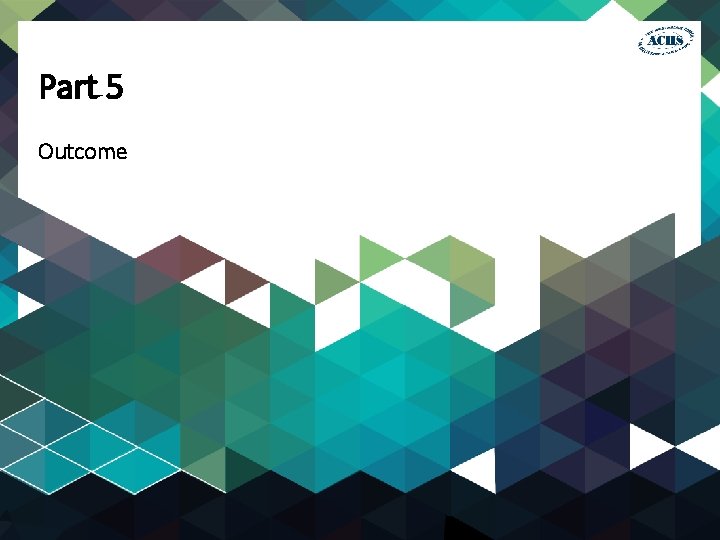
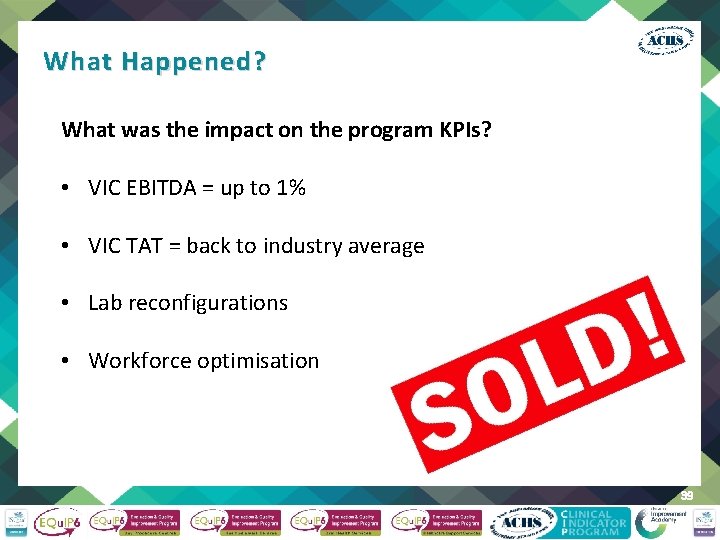
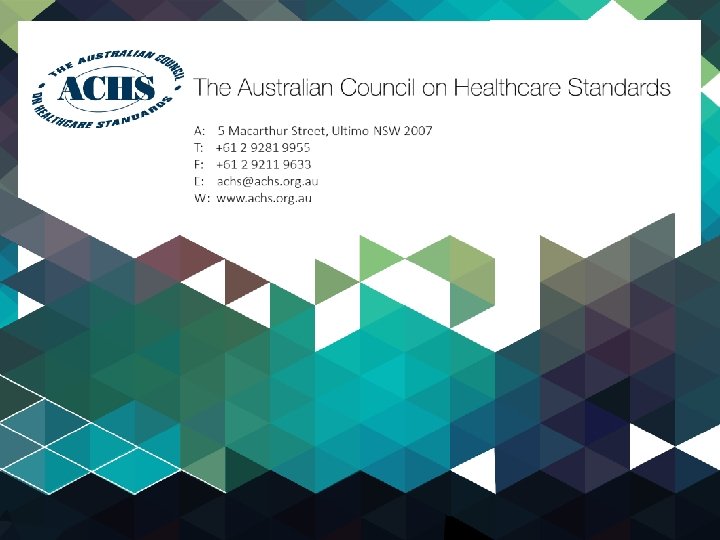
- Slides: 40

IMPLEMENTING CONTINUOUS QUALITY IMPROVEMENT IN AN AUSTRALIAN PRIVATE PATHOLOGY ORGANISATION MIDDLE EAST FORUM ON QUALITY & SAFETY IN HEALTH CARE 25 MARCH 2018
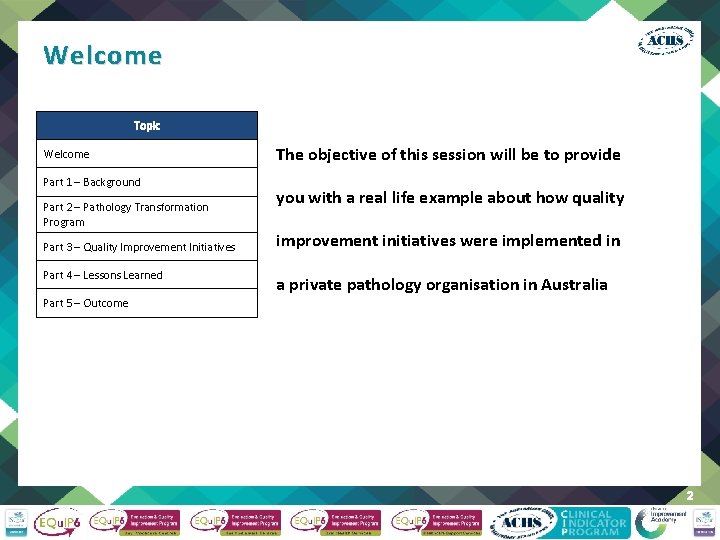
Welcome Topic Welcome Part 1 – Background Part 2 – Pathology Transformation Program Part 3 – Quality Improvement Initiatives Part 4 – Lessons Learned The objective of this session will be to provide you with a real life example about how quality improvement initiatives were implemented in a private pathology organisation in Australia Part 5 – Outcome 2
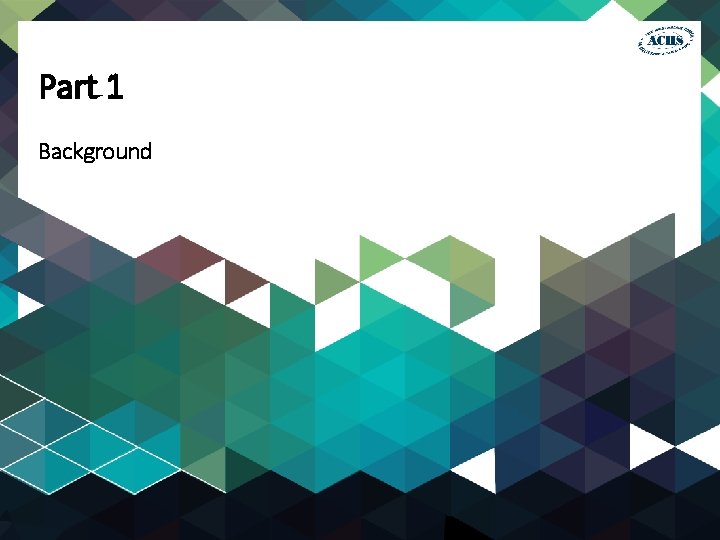
Part 1 Background
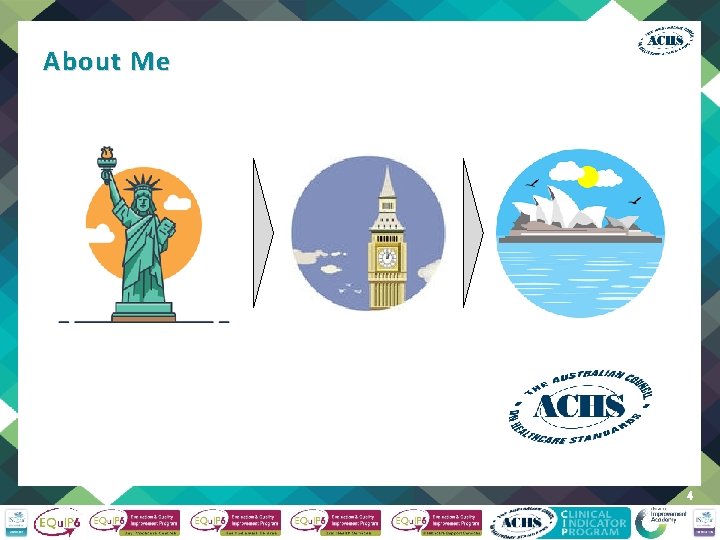
About Me 4
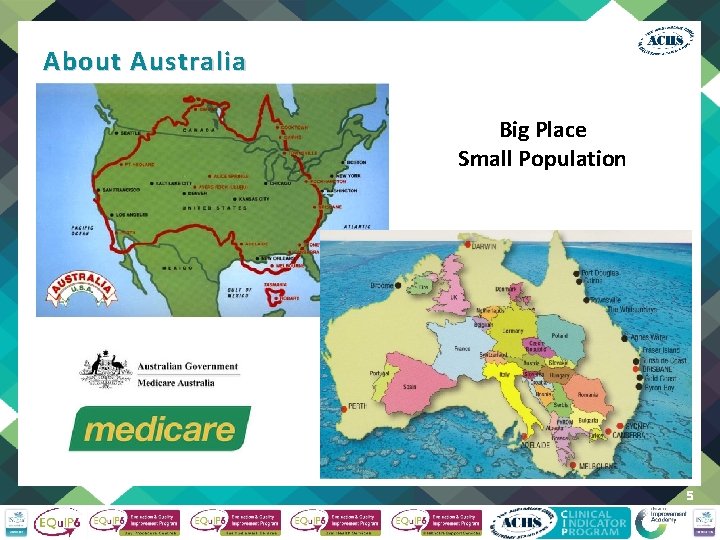
About Australia Big Place Small Population 5
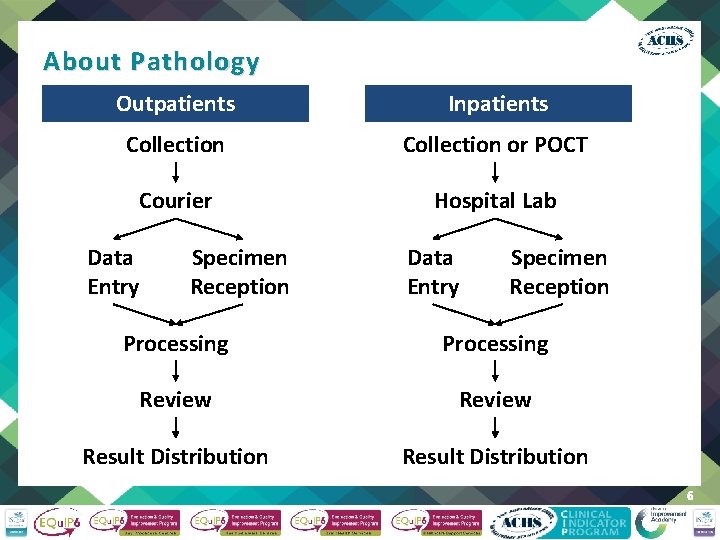
About Pathology Outpatients Inpatients Collection or POCT Courier Hospital Lab Data Entry Specimen Reception Processing Review Result Distribution 6
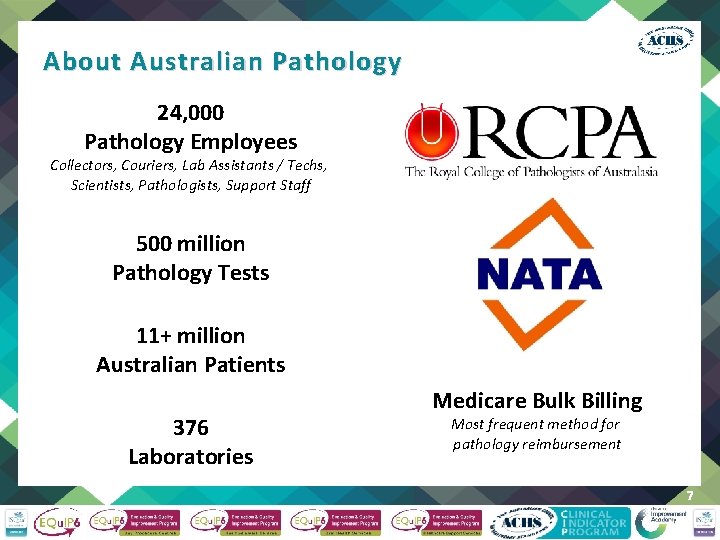
About Australian Pathology 24, 000 Pathology Employees Collectors, Couriers, Lab Assistants / Techs, Scientists, Pathologists, Support Staff 500 million Pathology Tests 11+ million Australian Patients 376 Laboratories Medicare Bulk Billing Most frequent method for pathology reimbursement 7
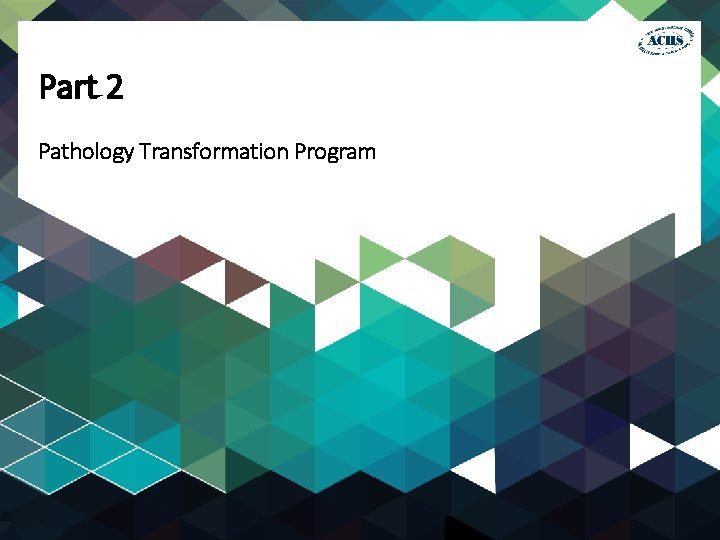
Part 2 Pathology Transformation Program
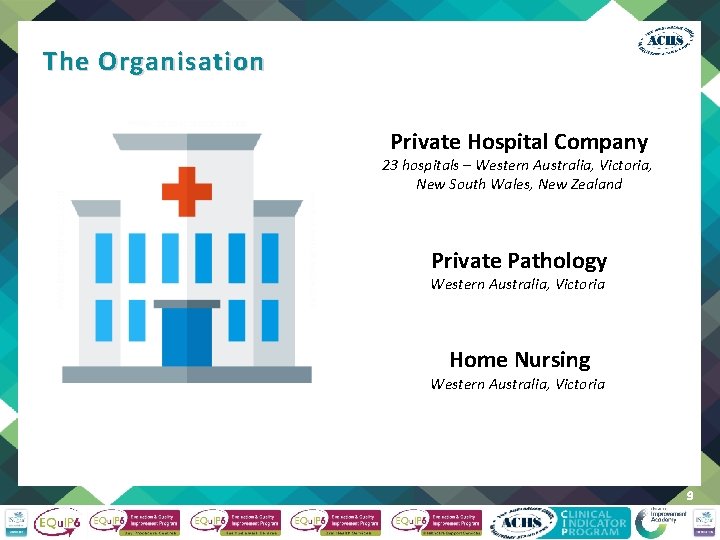
The Organisation Private Hospital Company 23 hospitals – Western Australia, Victoria, New South Wales, New Zealand Private Pathology Western Australia, Victoria Home Nursing Western Australia, Victoria 9
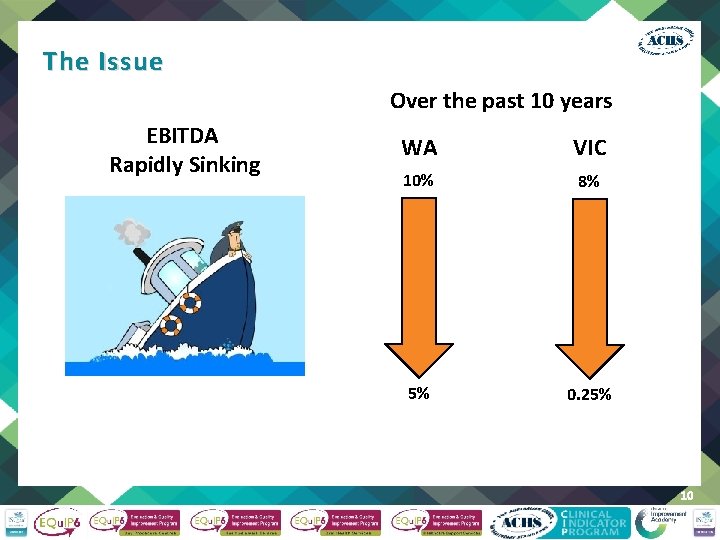
The Issue Over the past 10 years EBITDA Rapidly Sinking WA VIC 10% 8% 5% 0. 25% 10
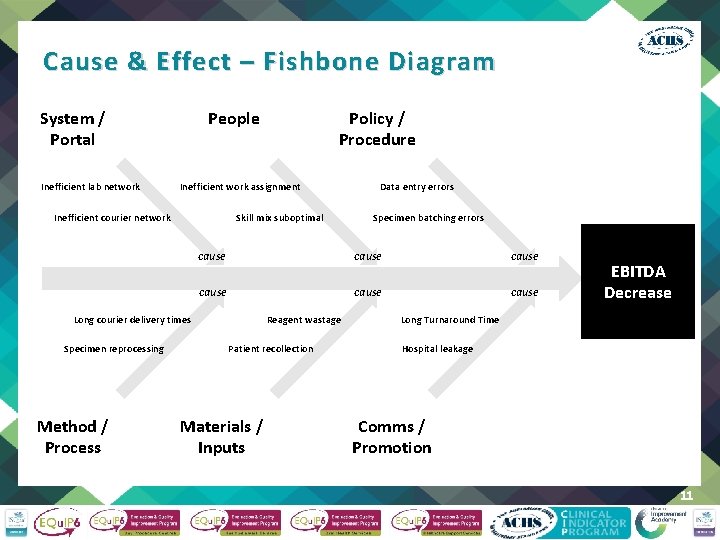
Cause & Effect – Fishbone Diagram System / Portal Inefficient lab network People Inefficient work assignment Inefficient courier network Skill mix suboptimal Method / Process Data entry errors Specimen batching errors cause cause Long courier delivery times Specimen reprocessing Policy / Procedure Reagent wastage Patient recollection Materials / Inputs EBITDA Decrease Long Turnaround Time Hospital leakage Comms / Promotion 11
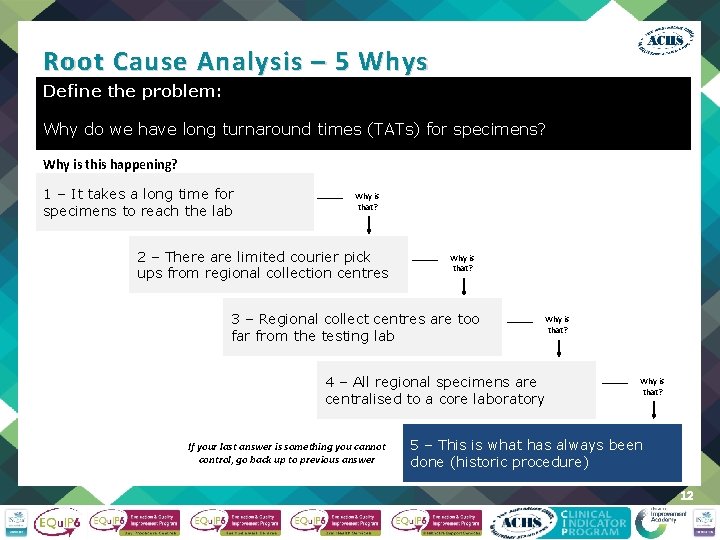
Root Cause Analysis – 5 Whys Define the problem: Why do we have long turnaround times (TATs) for specimens? Why is this happening? 1 – It takes a long time for specimens to reach the lab Why is that? 2 – There are limited courier pick ups from regional collection centres Why is that? 3 – Regional collect centres are too far from the testing lab Why is that? 4 – All regional specimens are centralised to a core laboratory If your last answer is something you cannot control, go back up to previous answer Why is that? 5 – This is what has always been done (historic procedure) 12
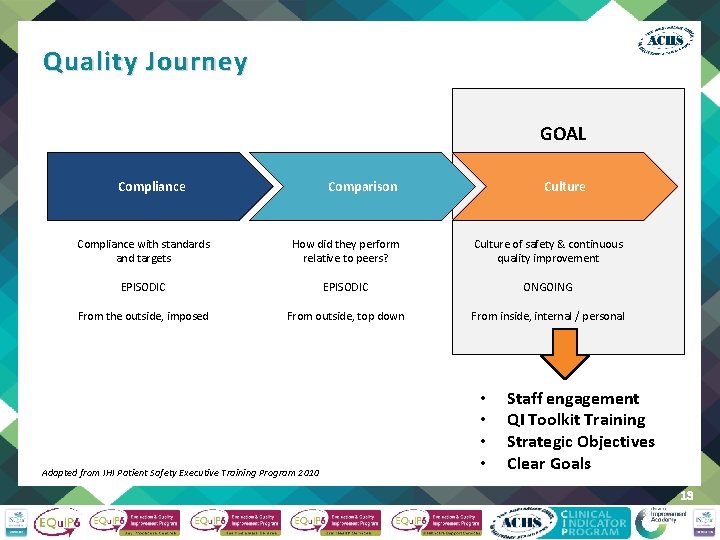
Quality Journey GOAL Compliance Comparison Culture Compliance with standards and targets How did they perform relative to peers? Culture of safety & continuous quality improvement EPISODIC ONGOING From the outside, imposed From outside, top down From inside, internal / personal Adapted from IHI Patient Safety Executive Training Program 2010 • • Staff engagement QI Toolkit Training Strategic Objectives Clear Goals 13
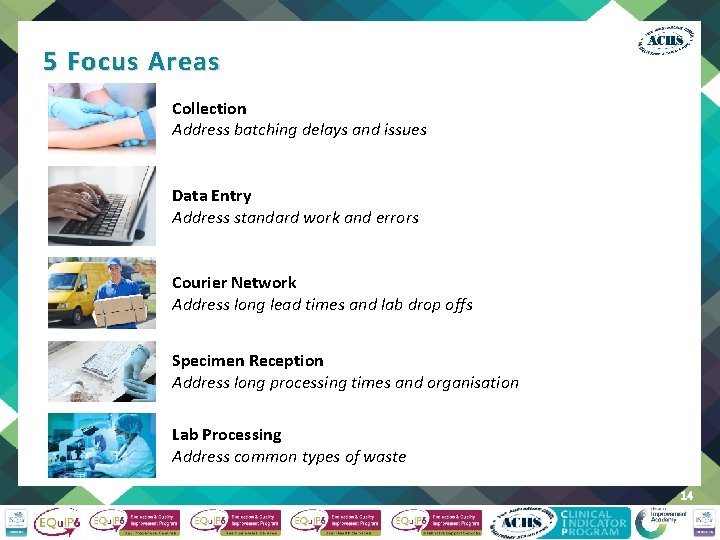
5 Focus Areas Collection Address batching delays and issues Data Entry Address standard work and errors Courier Network Address long lead times and lab drop offs Specimen Reception Address long processing times and organisation Lab Processing Address common types of waste 14
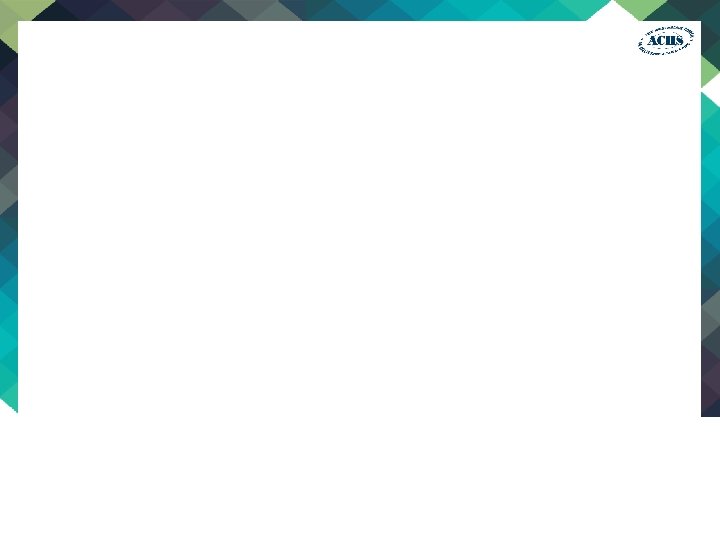
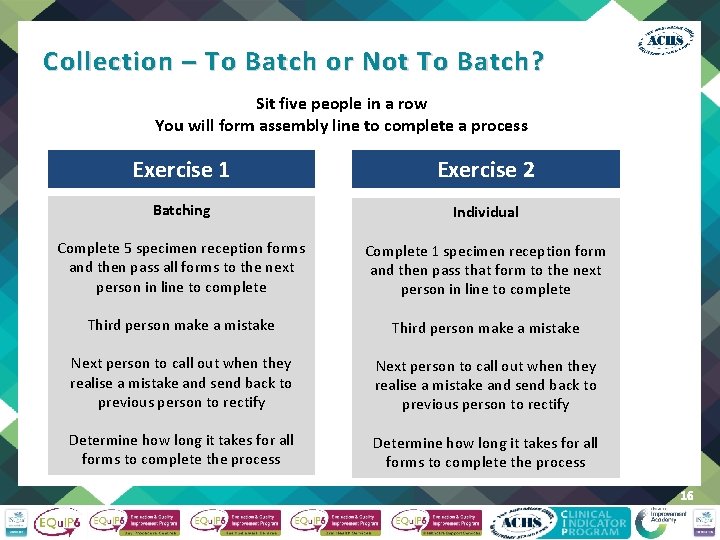
Collection – To Batch or Not To Batch? Sit five people in a row You will form assembly line to complete a process Exercise 1 Exercise 2 Batching Individual Complete 5 specimen reception forms and then pass all forms to the next person in line to complete Complete 1 specimen reception form and then pass that form to the next person in line to complete Third person make a mistake Next person to call out when they realise a mistake and send back to previous person to rectify Determine how long it takes for all forms to complete the process 16
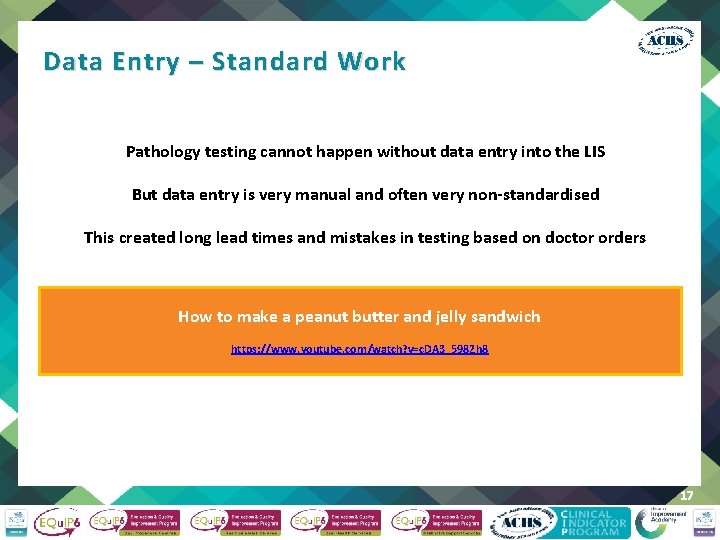
Data Entry – Standard Work Pathology testing cannot happen without data entry into the LIS But data entry is very manual and often very non-standardised This created long lead times and mistakes in testing based on doctor orders How to make a peanut butter and jelly sandwich https: //www. youtube. com/watch? v=c. DA 3_5982 h 8 17
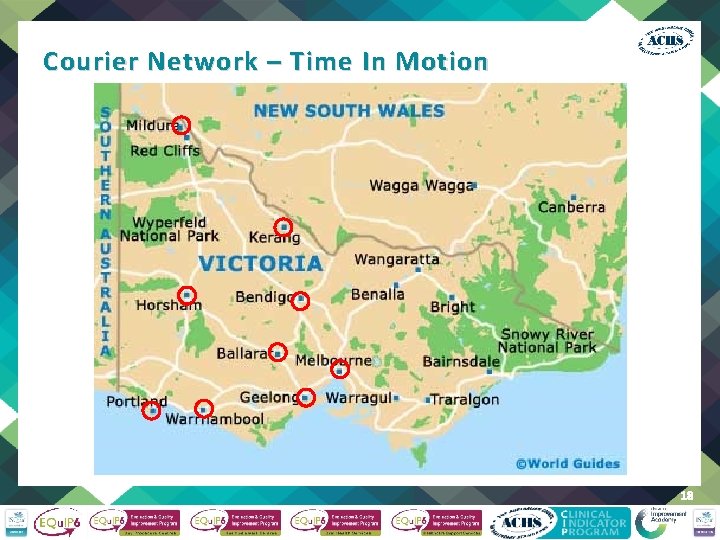
Courier Network – Time In Motion 18
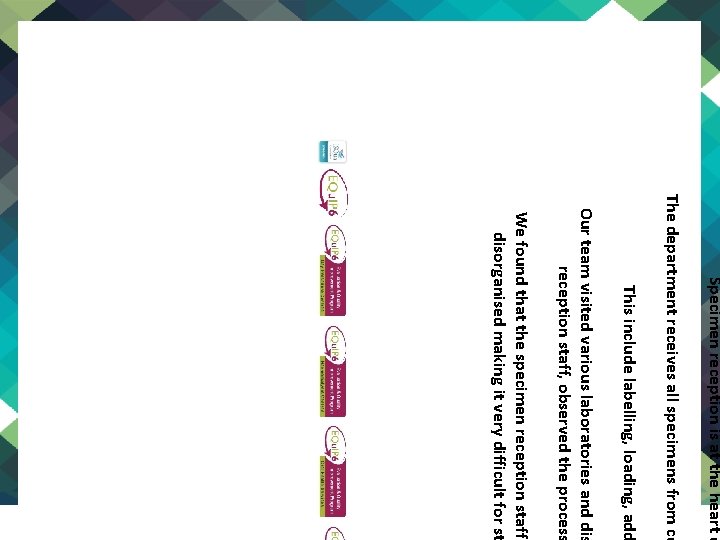
Specimen reception is at the heart o The department receives all specimens from co This include labelling, loading, add Our team visited various laboratories and dis reception staff, observed the process We found that the specimen reception staff disorganised making it very difficult for st
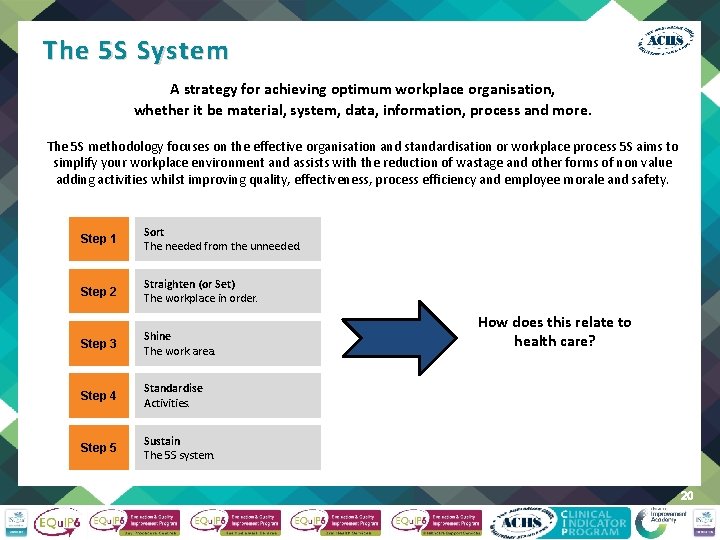
The 5 S System A strategy for achieving optimum workplace organisation, whether it be material, system, data, information, process and more. The 5 S methodology focuses on the effective organisation and standardisation or workplace process 5 S aims to simplify your workplace environment and assists with the reduction of wastage and other forms of non value adding activities whilst improving quality, effectiveness, process efficiency and employee morale and safety. Step 1 Sort The needed from the unneeded. Step 2 Straighten (or Set) The workplace in order. Step 3 Shine The work area. Step 4 Standardise Activities. Step 5 Sustain The 5 S system. How does this relate to health care? 20
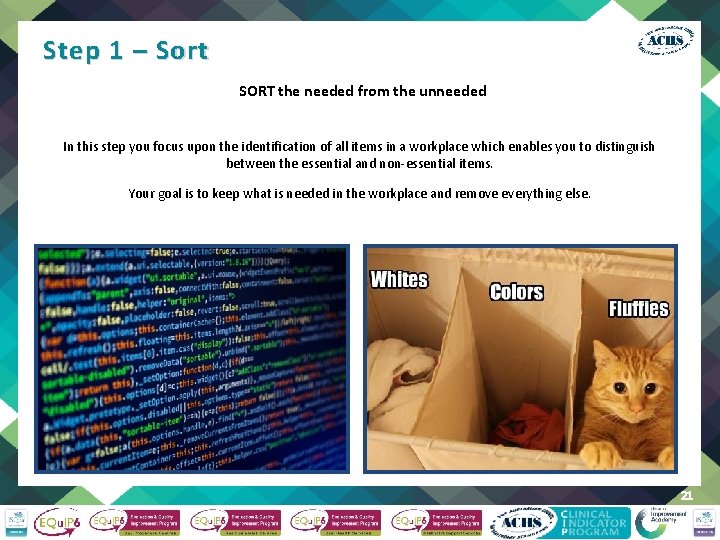
Step 1 – Sort SORT the needed from the unneeded In this step you focus upon the identification of all items in a workplace which enables you to distinguish between the essential and non-essential items. Your goal is to keep what is needed in the workplace and remove everything else. 21
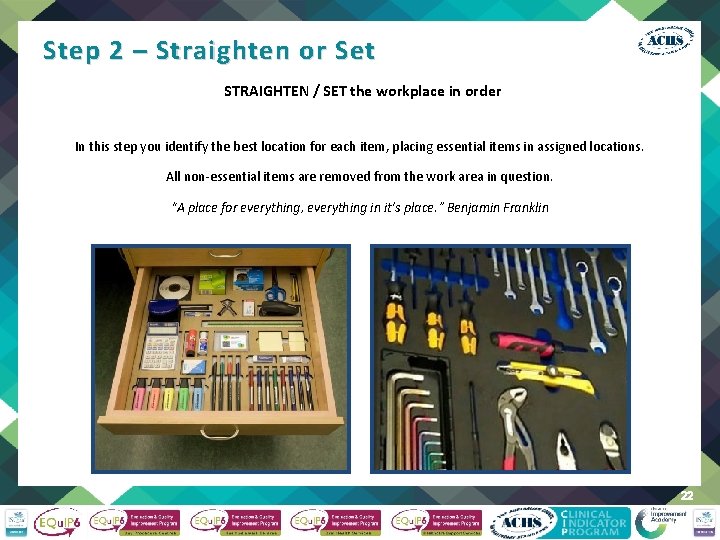
Step 2 – Straighten or Set STRAIGHTEN / SET the workplace in order In this step you identify the best location for each item, placing essential items in assigned locations. All non-essential items are removed from the work area in question. “A place for everything, everything in it’s place. ” Benjamin Franklin 22
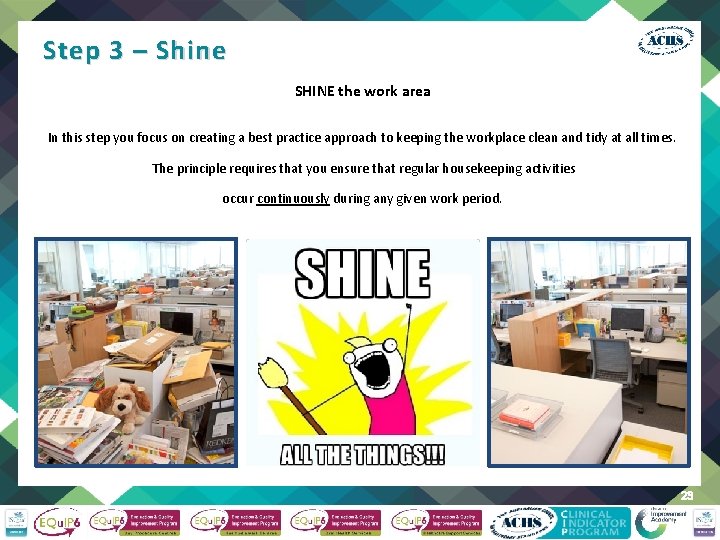
Step 3 – Shine SHINE the work area In this step you focus on creating a best practice approach to keeping the workplace clean and tidy at all times. The principle requires that you ensure that regular housekeeping activities occur continuously during any given work period. 23
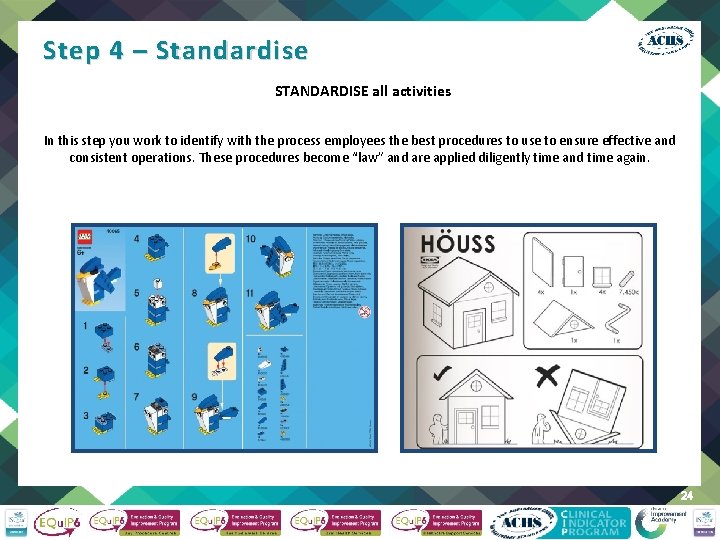
Step 4 – Standardise STANDARDISE all activities In this step you work to identify with the process employees the best procedures to use to ensure effective and consistent operations. These procedures become “law” and are applied diligently time and time again. 24
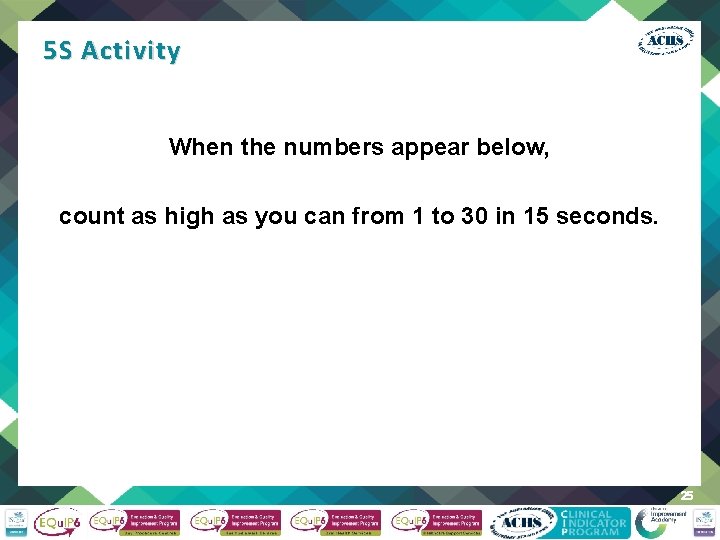
5 S Activity When the numbers appear below, count as high as you can from 1 to 30 in 15 seconds. 25
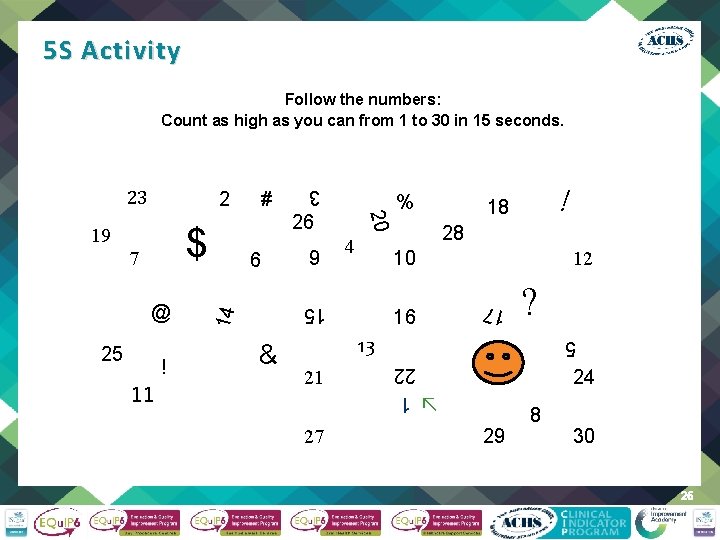
5 S Activity Follow the numbers: Count as high as you can from 1 to 30 in 15 seconds. 11 14 & 28 10 16 12 ? 13 21 27 ↘ 1 22 ! ! 18 5 25 9 15 @ 6 4 % 17 7 20 26 $ 19 # 3 2 23 24 29 8 30 26
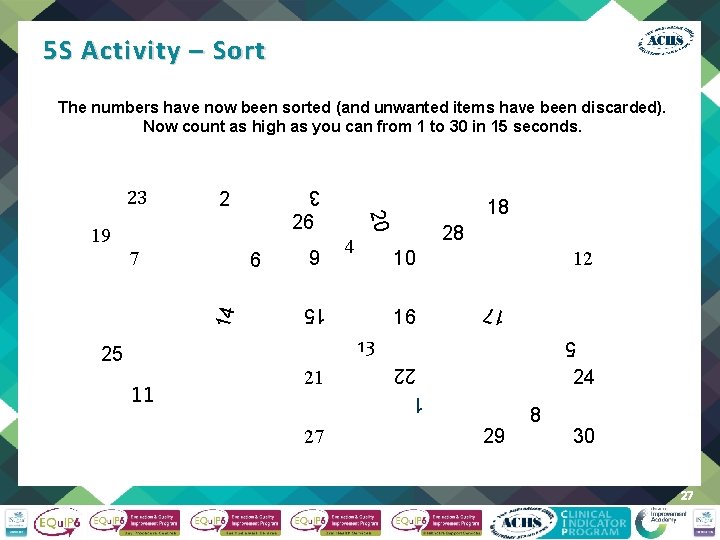
5 S Activity – Sort The numbers have now been sorted (and unwanted items have been discarded). Now count as high as you can from 1 to 30 in 15 seconds. 3 2 14 6 9 4 28 10 15 7 20 26 19 18 16 12 17 23 13 27 1 22 11 21 5 25 24 29 8 30 27
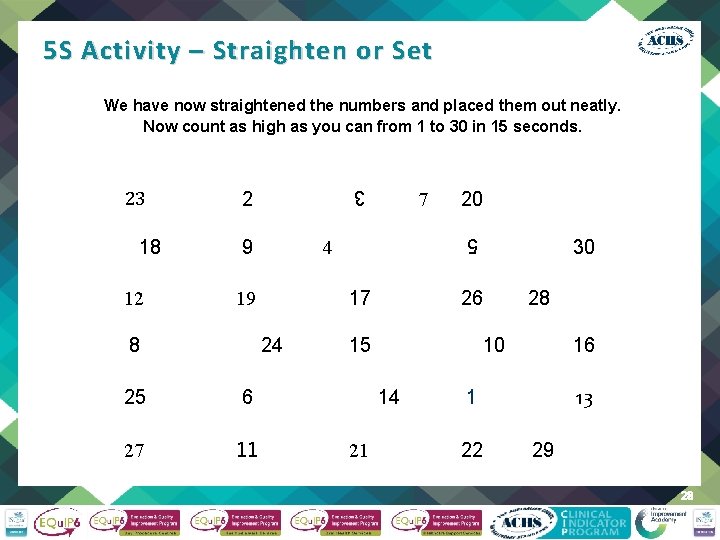
5 S Activity – Straighten or Set We have now straightened the numbers and placed them out neatly. Now count as high as you can from 1 to 30 in 15 seconds. 12 2 9 4 17 19 8 24 25 6 27 11 7 20 5 18 3 23 26 15 28 10 14 21 30 16 13 1 22 29 28
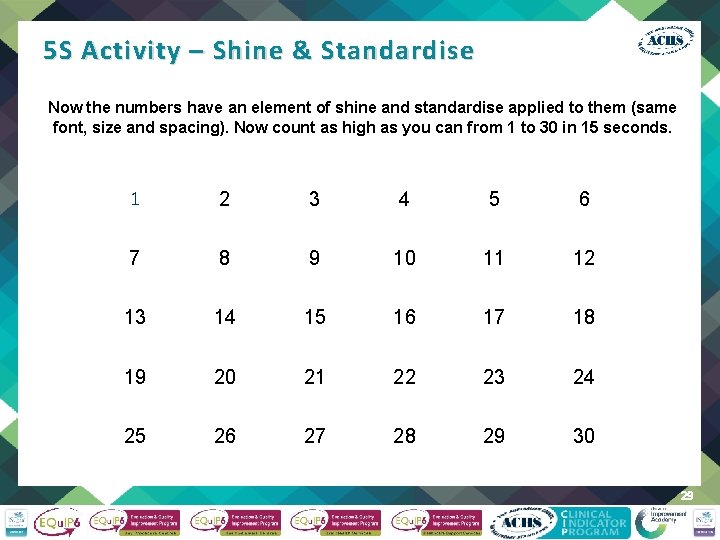
5 S Activity – Shine & Standardise Now the numbers have an element of shine and standardise applied to them (same font, size and spacing). Now count as high as you can from 1 to 30 in 15 seconds. 1 2 3 4 5 6 7 8 9 10 11 12 13 14 15 16 17 18 19 20 21 22 23 24 25 26 27 28 29 30 29
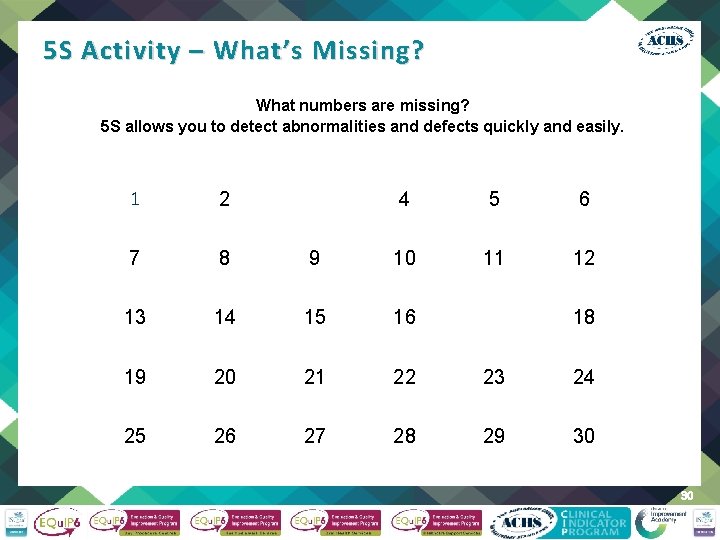
5 S Activity – What’s Missing? What numbers are missing? 5 S allows you to detect abnormalities and defects quickly and easily. 1 2 7 8 13 4 5 6 9 10 11 12 14 15 16 19 20 21 22 23 24 25 26 27 28 29 30 18 30
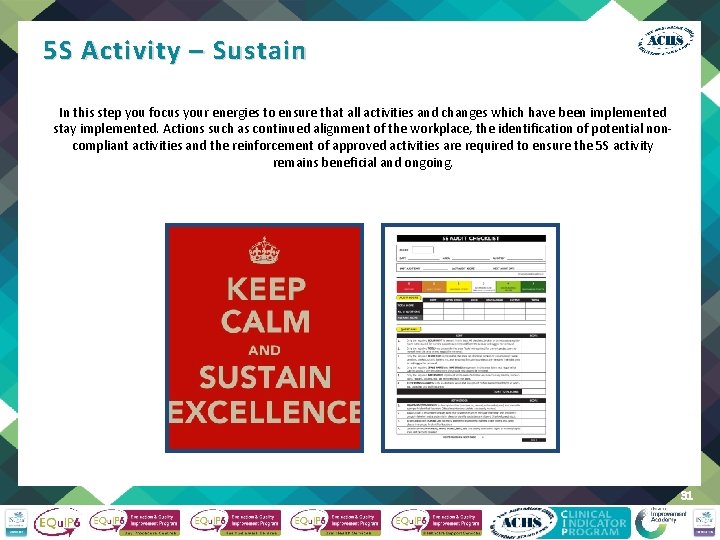
5 S Activity – Sustain In this step you focus your energies to ensure that all activities and changes which have been implemented stay implemented. Actions such as continued alignment of the workplace, the identification of potential noncompliant activities and the reinforcement of approved activities are required to ensure the 5 S activity remains beneficial and ongoing. 31
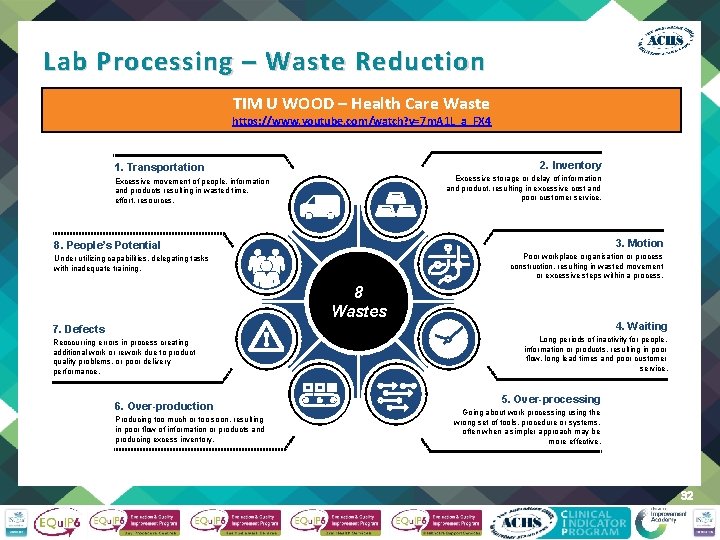
Lab Processing – Waste Reduction TIM U WOOD – Health Care Waste https: //www. youtube. com/watch? v=7 m. A 1 L_a_FX 4 2. Inventory 1. Transportation Excessive movement of people, information and products resulting in wasted time, effort, resources. 1 2 Excessive storage or delay of information and product, resulting in excessive cost and poor customer service. 3. Motion 8. People’s Potential Under utilizing capabilities, delegating tasks with inadequate training. 8 3 Poor workplace organisation or process construction, resulting in wasted movement or excessive steps within a process. 8 Wastes 7. Defects Reoccurring errors in process creating additional work or rework due to product quality problems, or poor delivery performance. 7 6. Over-production Producing too much or too soon, resulting in poor flow of information or products and producing excess inventory. 4 6 5 4. Waiting Long periods of inactivity for people, information or products, resulting in poor flow, long lead times and poor customer service. 5. Over-processing Going about work processing using the wrong set of tools, procedure or systems, often when a simpler approach may be more effective. 32
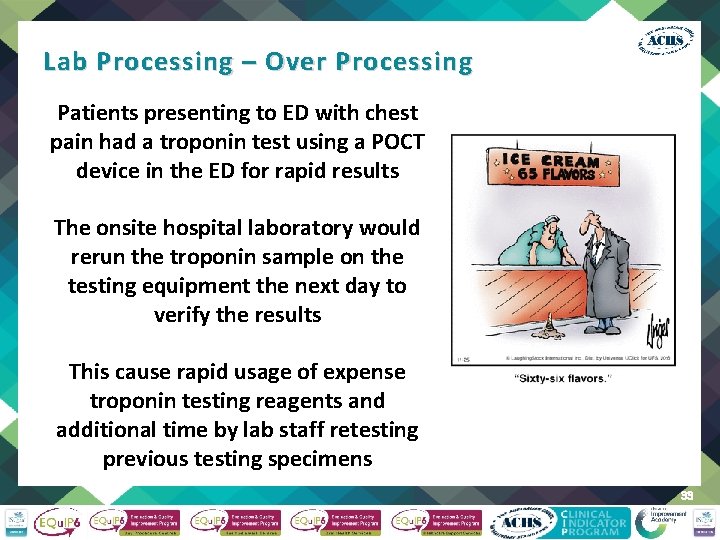
Lab Processing – Over Processing Patients presenting to ED with chest pain had a troponin test using a POCT device in the ED for rapid results The onsite hospital laboratory would rerun the troponin sample on the testing equipment the next day to verify the results This cause rapid usage of expense troponin testing reagents and additional time by lab staff retesting previous testing specimens 33
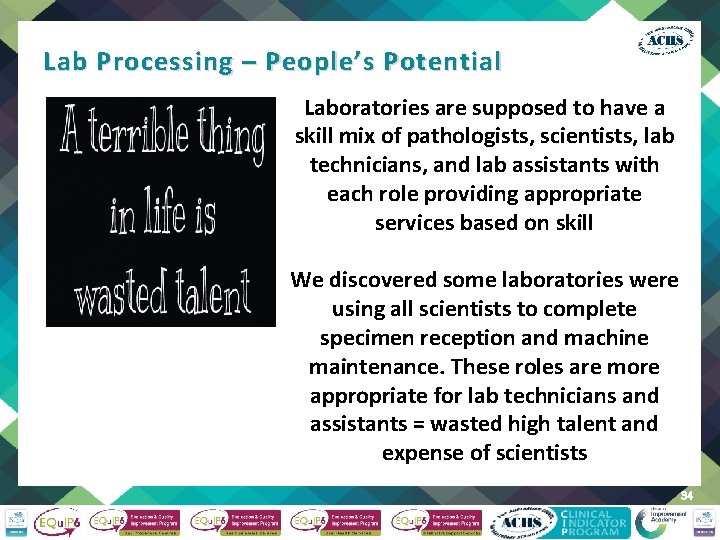
Lab Processing – People’s Potential Laboratories are supposed to have a skill mix of pathologists, scientists, lab technicians, and lab assistants with each role providing appropriate services based on skill We discovered some laboratories were using all scientists to complete specimen reception and machine maintenance. These roles are more appropriate for lab technicians and assistants = wasted high talent and expense of scientists 34
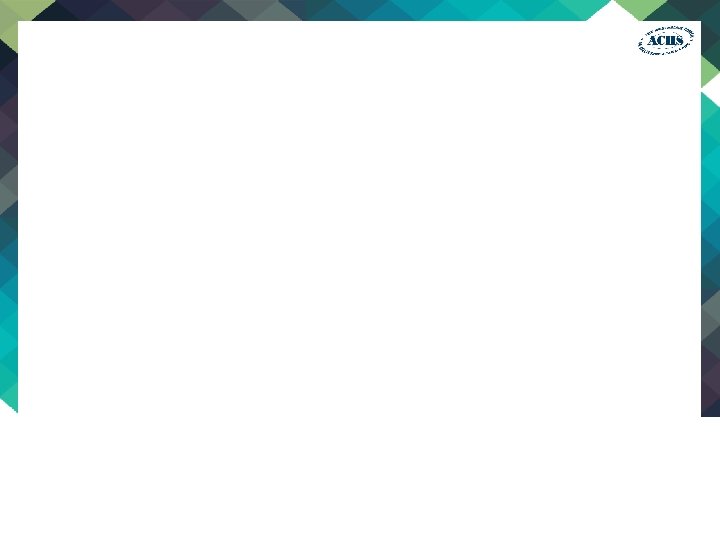
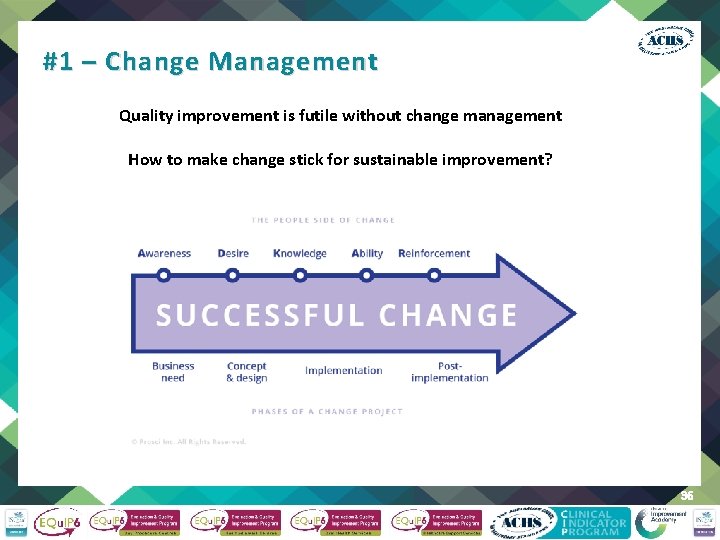
#1 – Change Management Quality improvement is futile without change management How to make change stick for sustainable improvement? 36
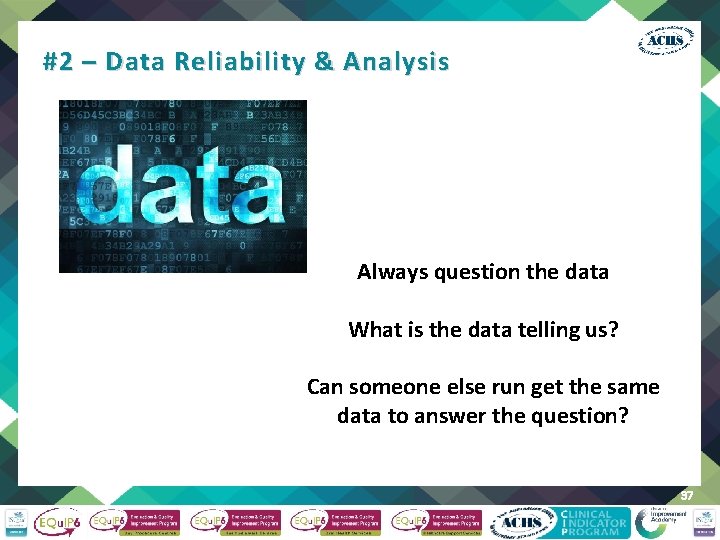
#2 – Data Reliability & Analysis Always question the data What is the data telling us? Can someone else run get the same data to answer the question? 37
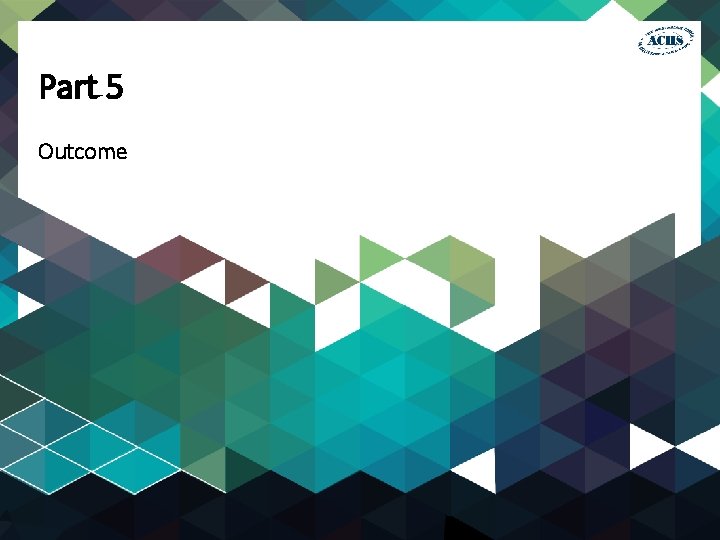
Part 5 Outcome
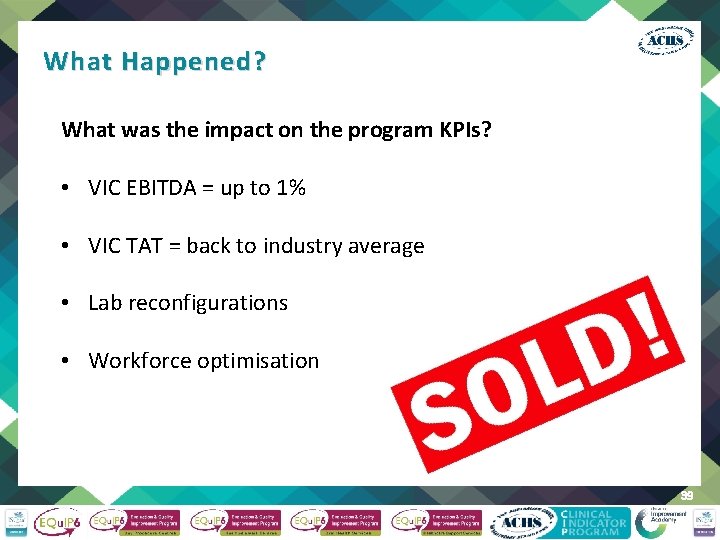
What Happened? What was the impact on the program KPIs? • VIC EBITDA = up to 1% • VIC TAT = back to industry average • Lab reconfigurations • Workforce optimisation 39
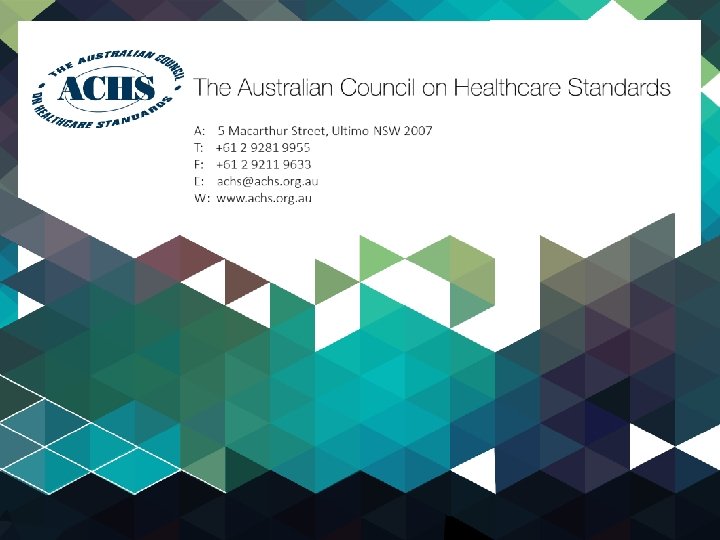
Quality assurance cycle in nursing
Compliance vs quality
Define continuous quality improvement
Define continuous quality improvement
Cqi action plan template
Future continuous present continuous
Present simple present continuous past simple
Jhm irb
Qsen standards
Quality improvement paradigm
Pocqi ppt
Efmd quality improvement system
Indiana perinatal quality improvement collaborative
Tea quality improvement
Quality improvement
Sus qi
Quality improvement nurse
Quality improvement
Juran 10 steps to quality improvement
Swot analysis for quality
Malnutrition quality improvement initiative
Quality improvement
Data driven quality improvement
Rapid cycle quality improvement
Quality is free
Jrotc continuous improvement plan ideas
Continuous improvement
Florida continuous improvement model
Corrective action board
Cip 1
Continuous improvement check sheet
8 step improvement
Continuous improvement roadmap
Bsbmgt516 facilitate continuous improvement
Continuous improvement documentation
Egra arata tool
Just do it kaizen
Objectives of orientation
Suzuki kaizen
Hrd program implementation and evaluation
Implementing strategies management and operations issues