Quality level Continuous Improvement Check Act Do Plan
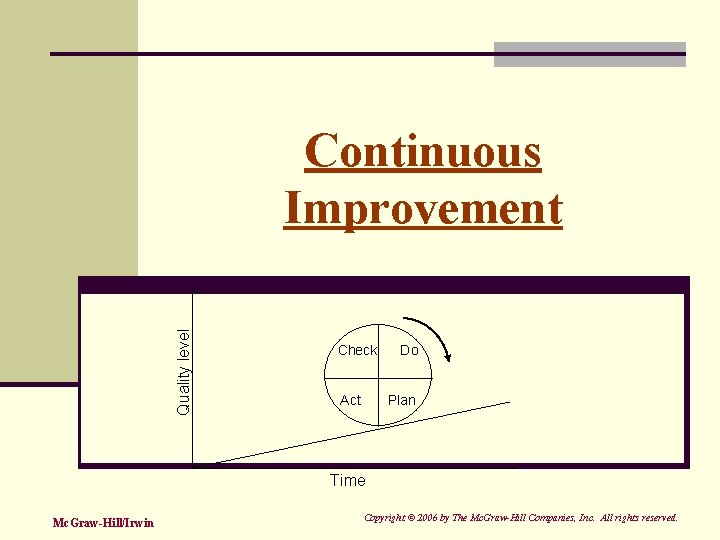
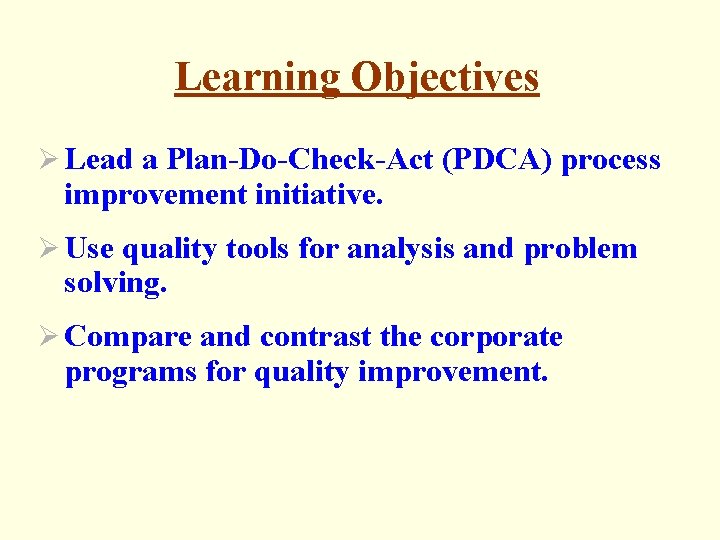
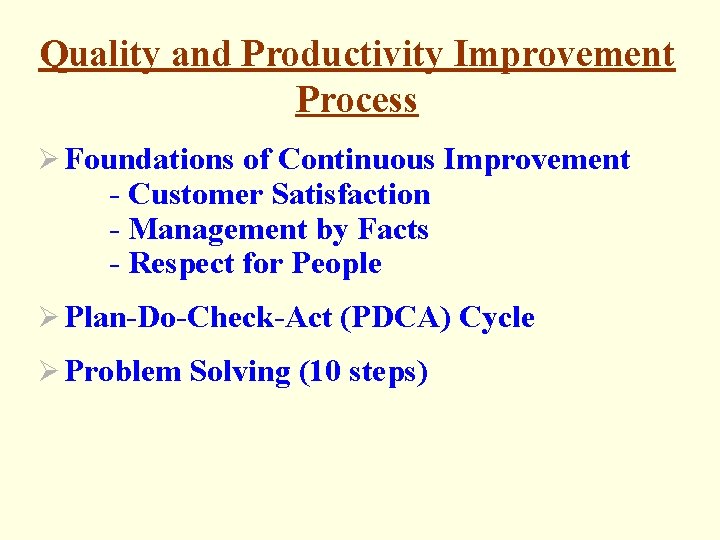
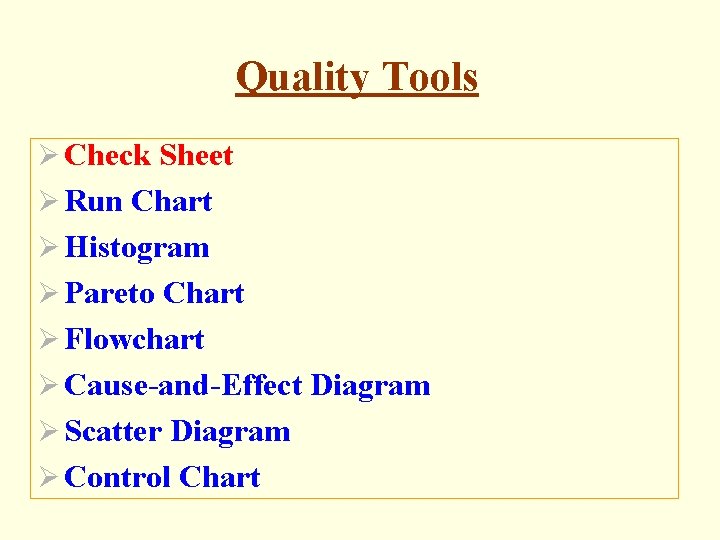
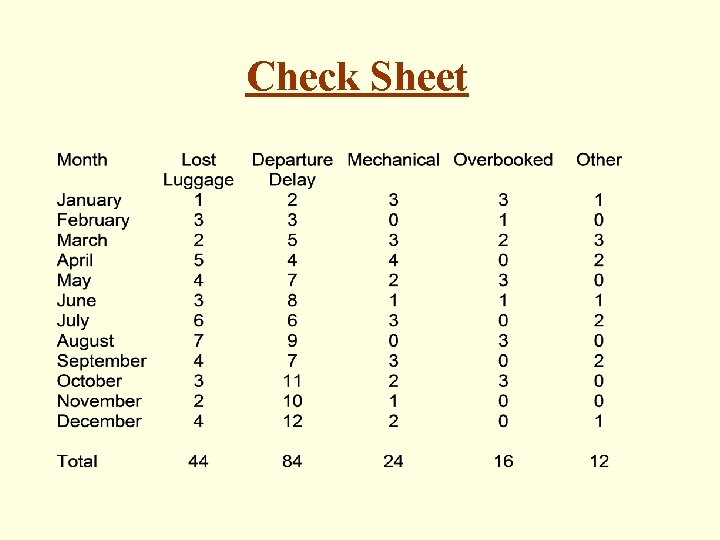
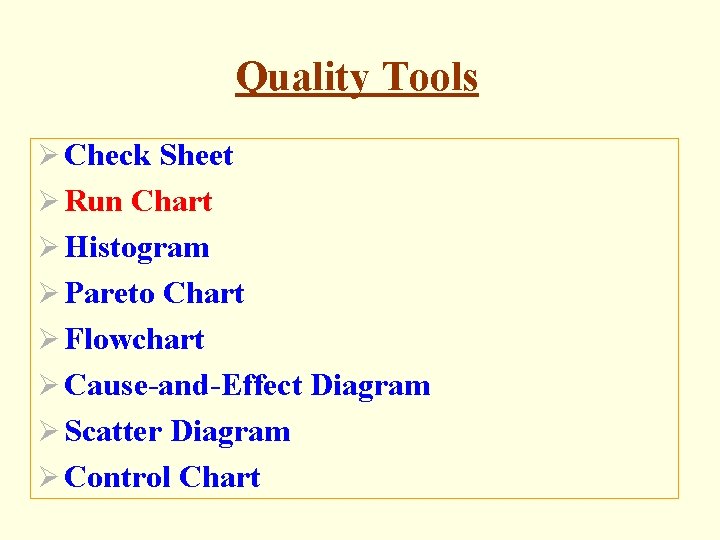
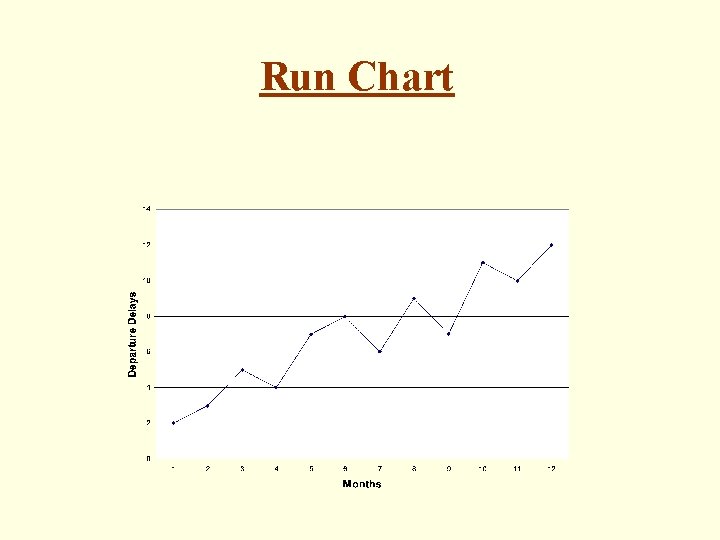
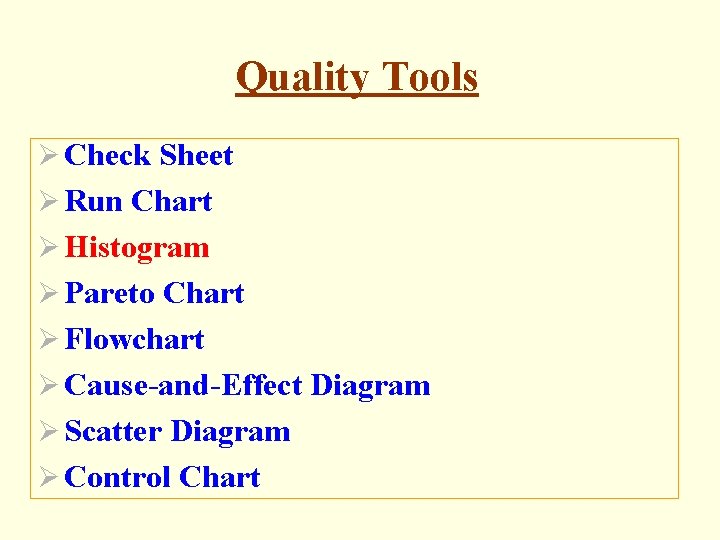
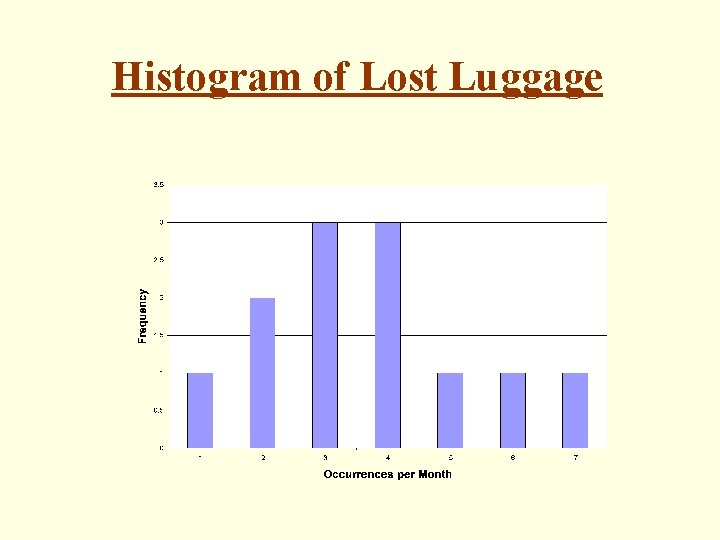
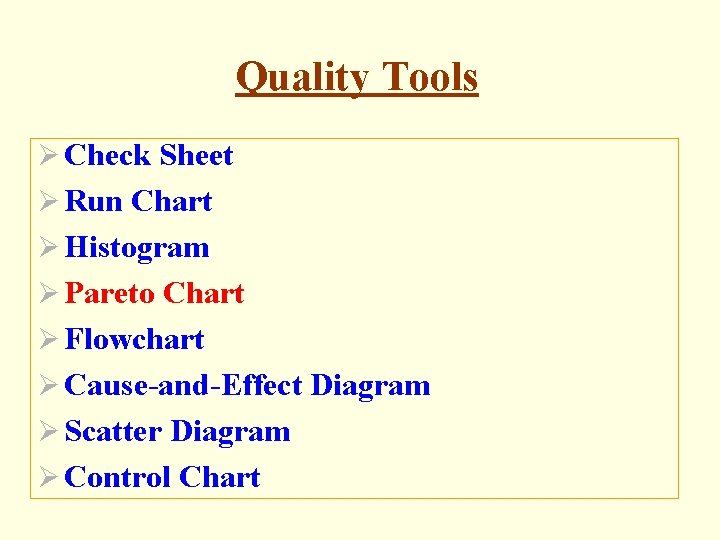
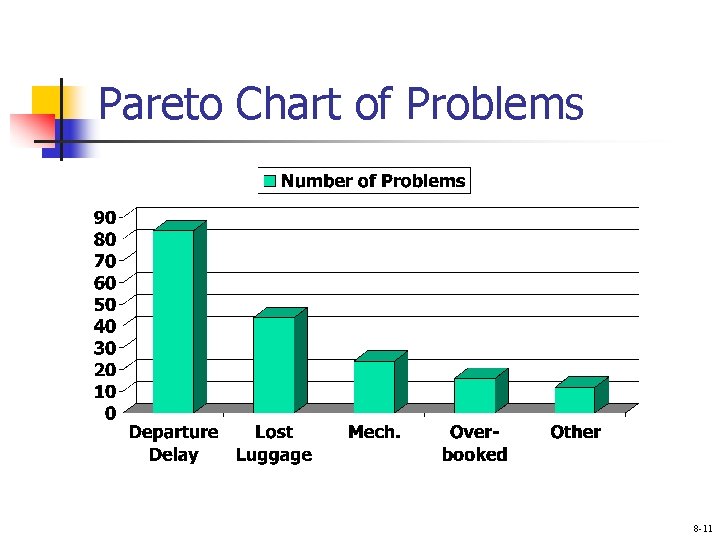
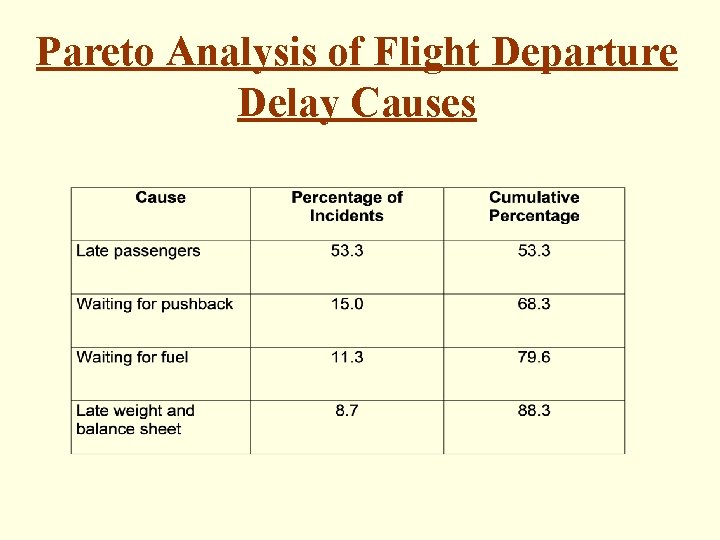
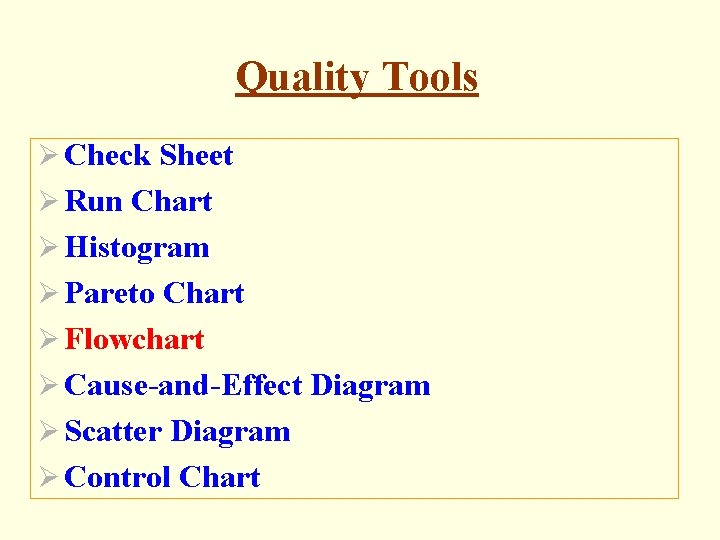
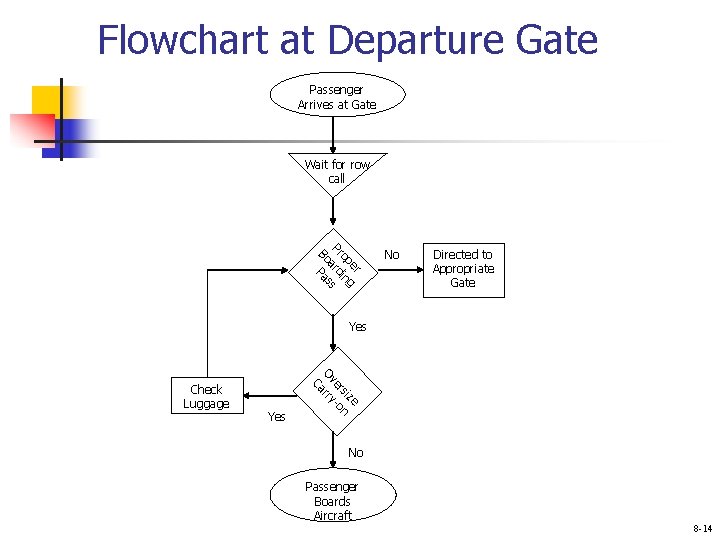
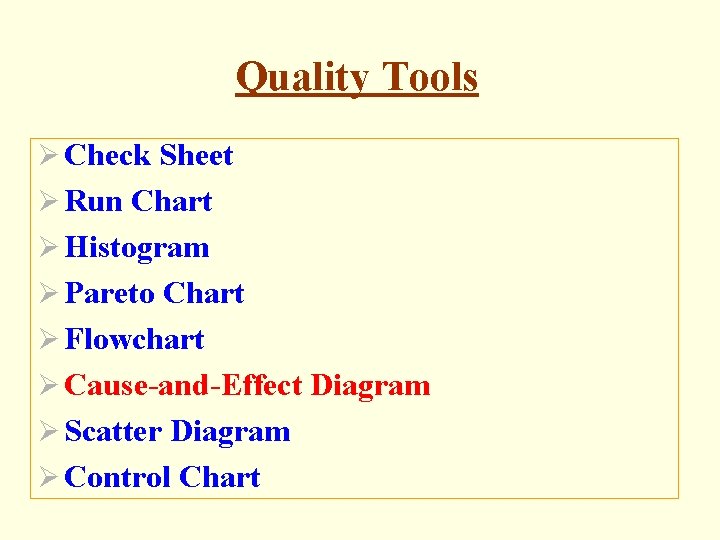
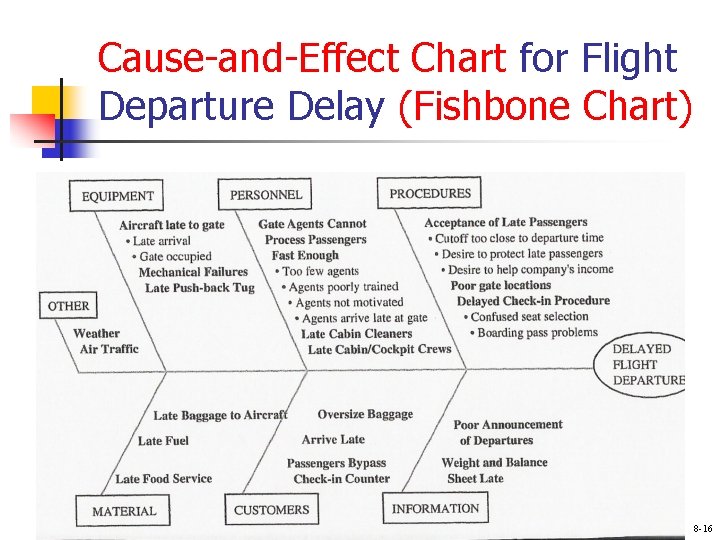
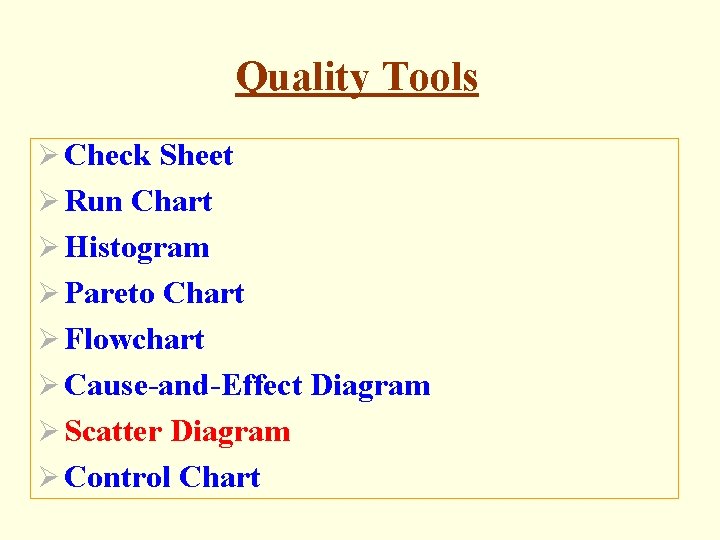
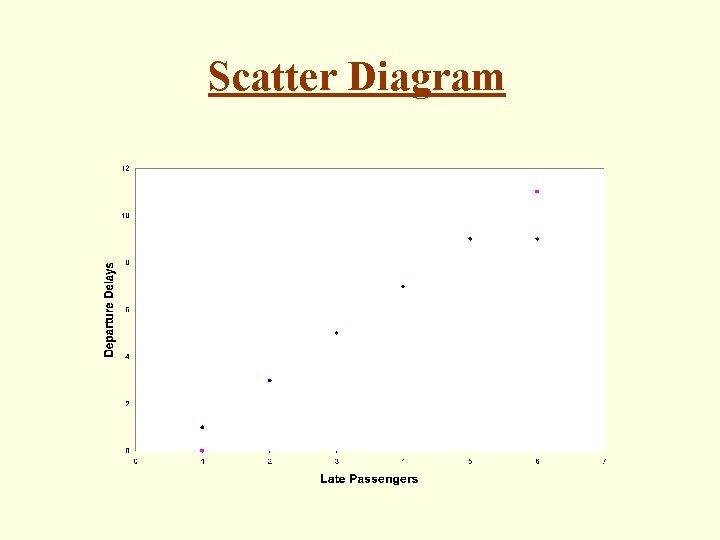
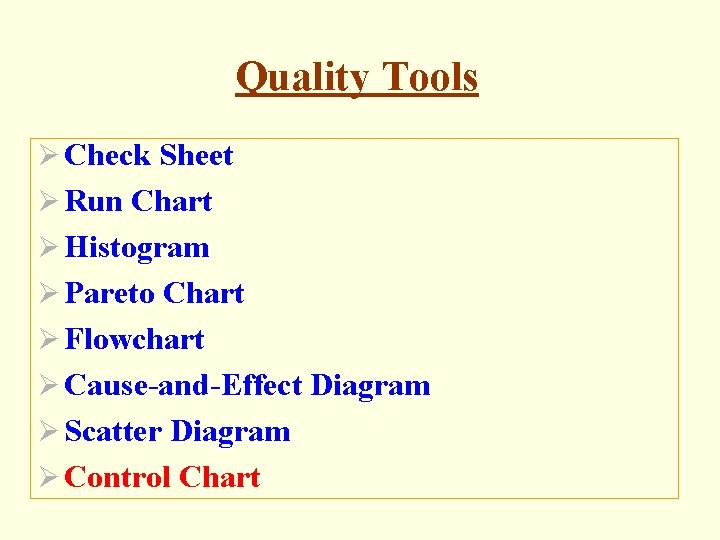
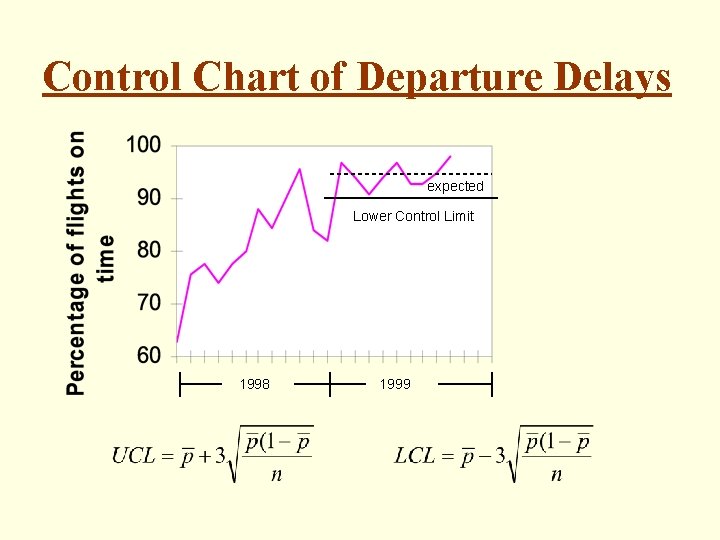
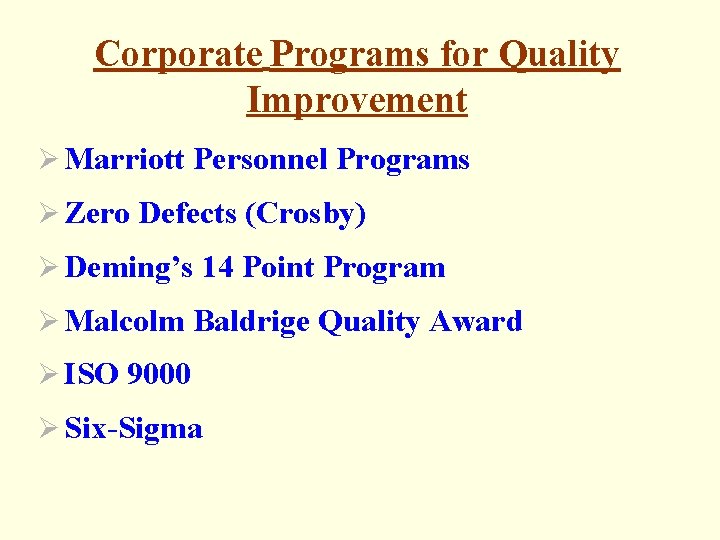
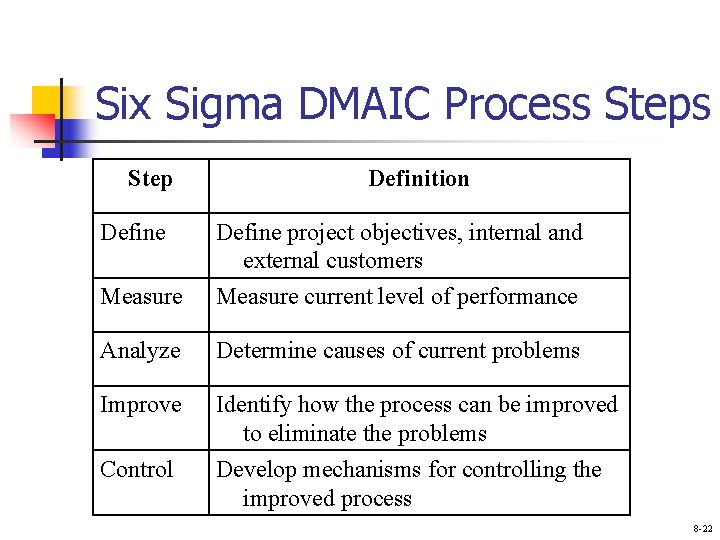
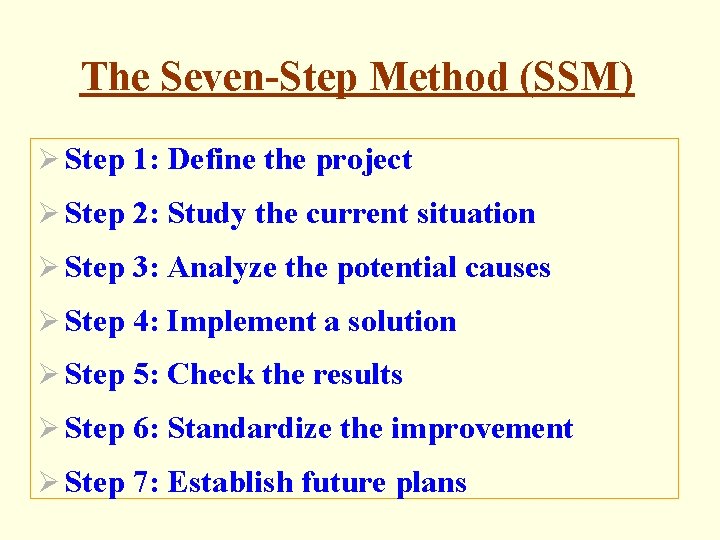
- Slides: 23
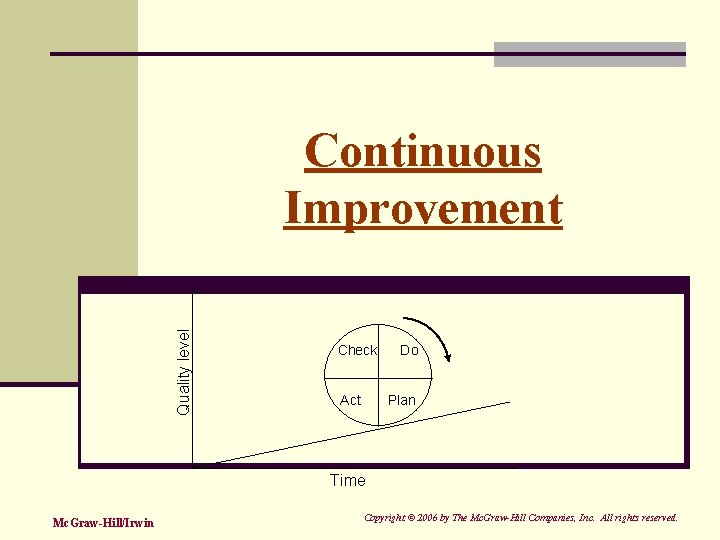
Quality level Continuous Improvement Check Act Do Plan Time Mc. Graw-Hill/Irwin Copyright © 2006 by The Mc. Graw-Hill Companies, Inc. All rights reserved.
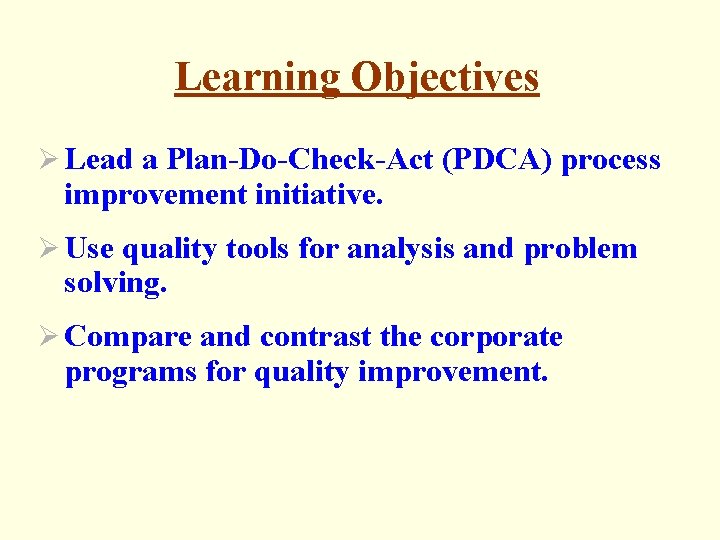
Learning Objectives Ø Lead a Plan-Do-Check-Act (PDCA) process improvement initiative. Ø Use quality tools for analysis and problem solving. Ø Compare and contrast the corporate programs for quality improvement.
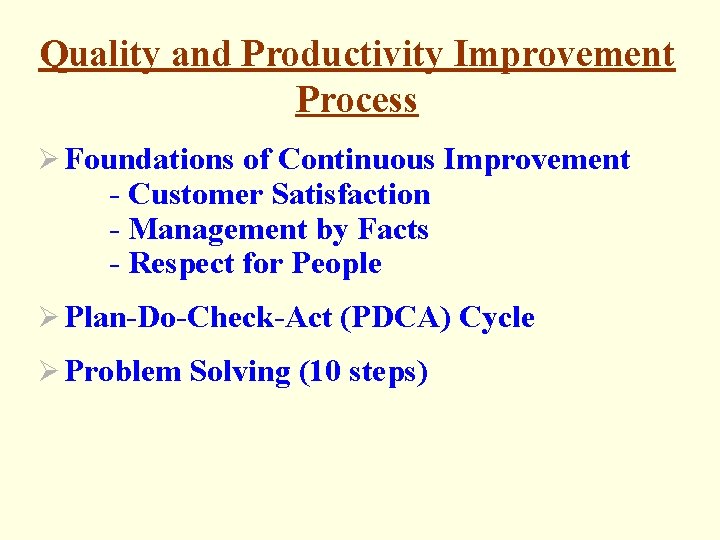
Quality and Productivity Improvement Process Ø Foundations of Continuous Improvement - Customer Satisfaction - Management by Facts - Respect for People Ø Plan-Do-Check-Act (PDCA) Cycle Ø Problem Solving (10 steps)
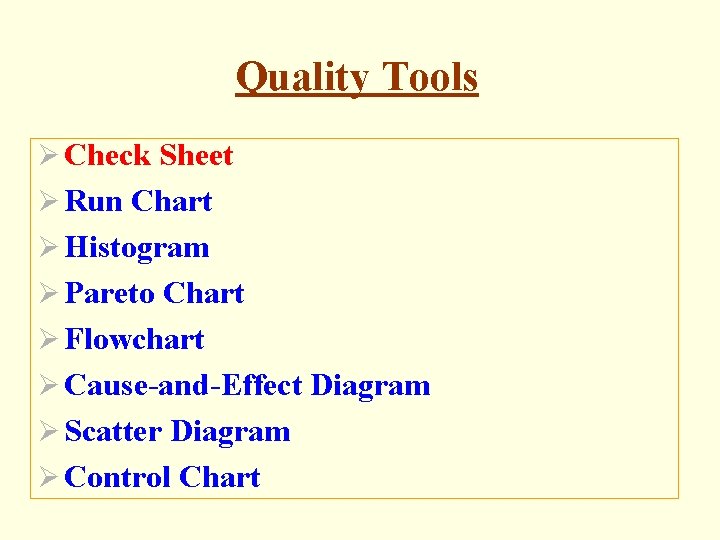
Quality Tools Ø Check Sheet Ø Run Chart Ø Histogram Ø Pareto Chart Ø Flowchart Ø Cause-and-Effect Diagram Ø Scatter Diagram Ø Control Chart
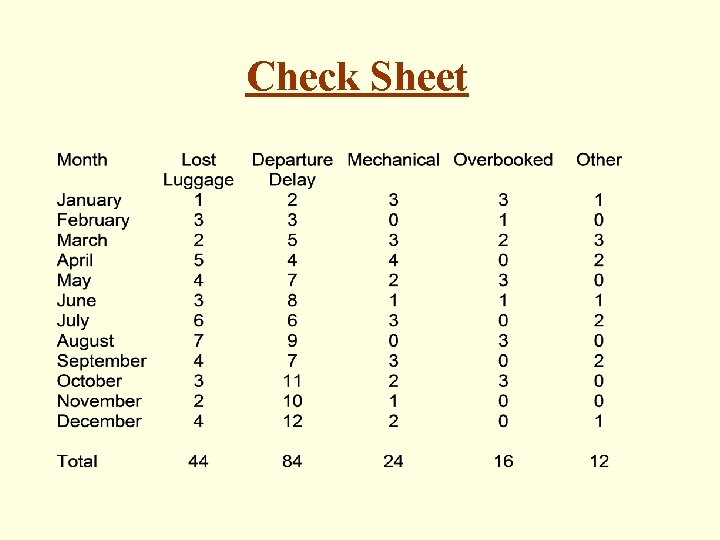
Check Sheet
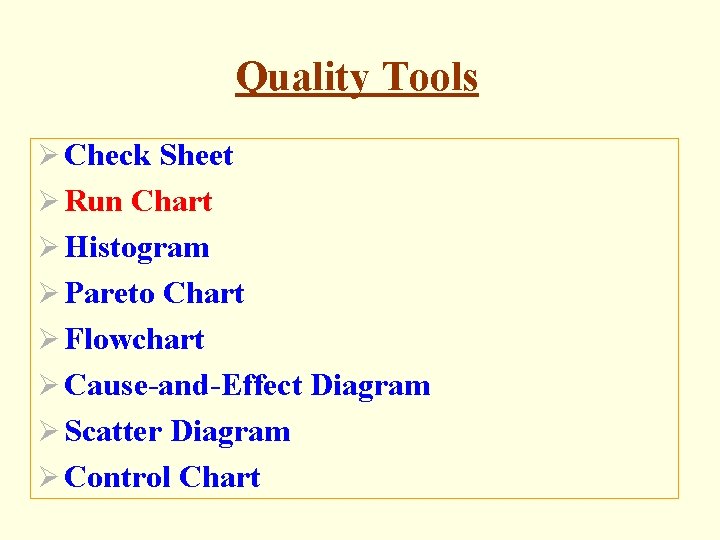
Quality Tools Ø Check Sheet Ø Run Chart Ø Histogram Ø Pareto Chart Ø Flowchart Ø Cause-and-Effect Diagram Ø Scatter Diagram Ø Control Chart
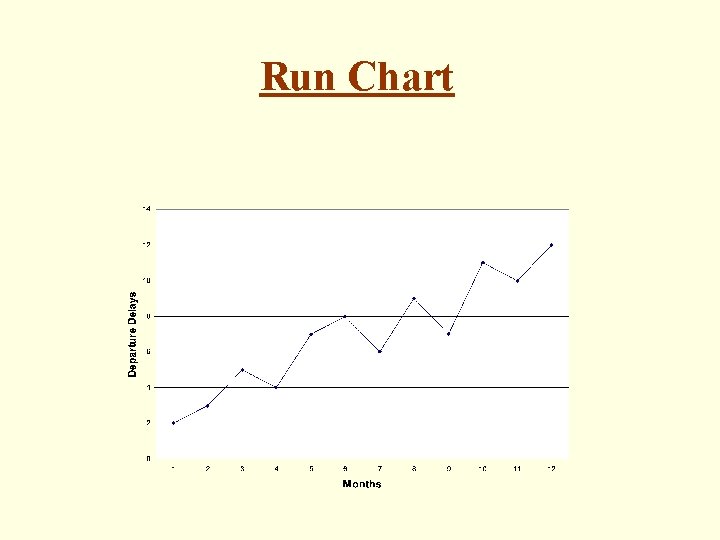
Run Chart
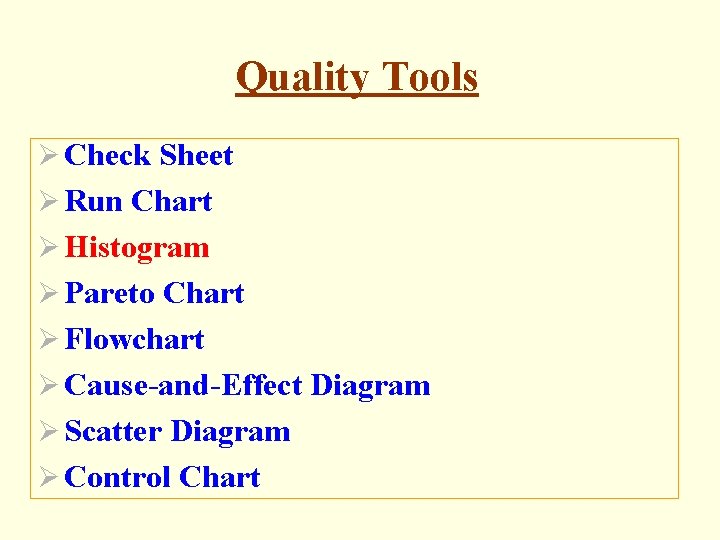
Quality Tools Ø Check Sheet Ø Run Chart Ø Histogram Ø Pareto Chart Ø Flowchart Ø Cause-and-Effect Diagram Ø Scatter Diagram Ø Control Chart
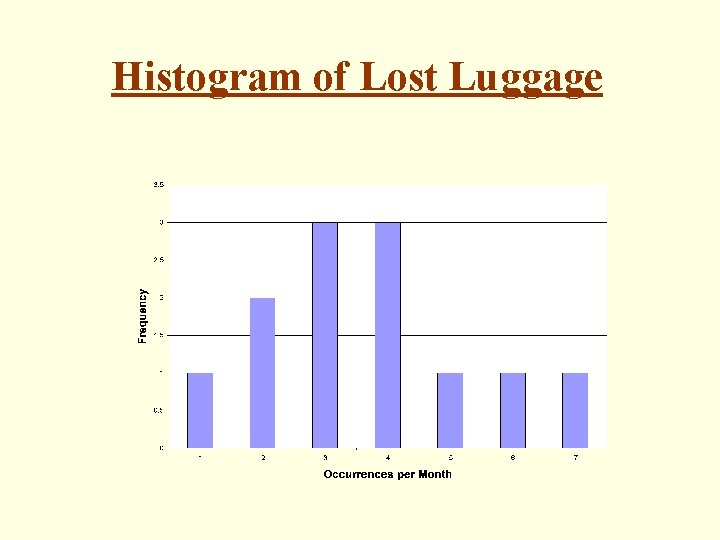
Histogram of Lost Luggage
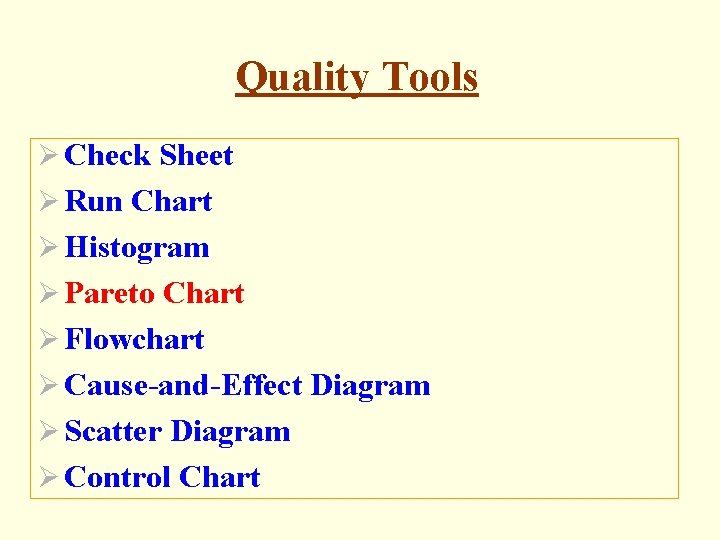
Quality Tools Ø Check Sheet Ø Run Chart Ø Histogram Ø Pareto Chart Ø Flowchart Ø Cause-and-Effect Diagram Ø Scatter Diagram Ø Control Chart
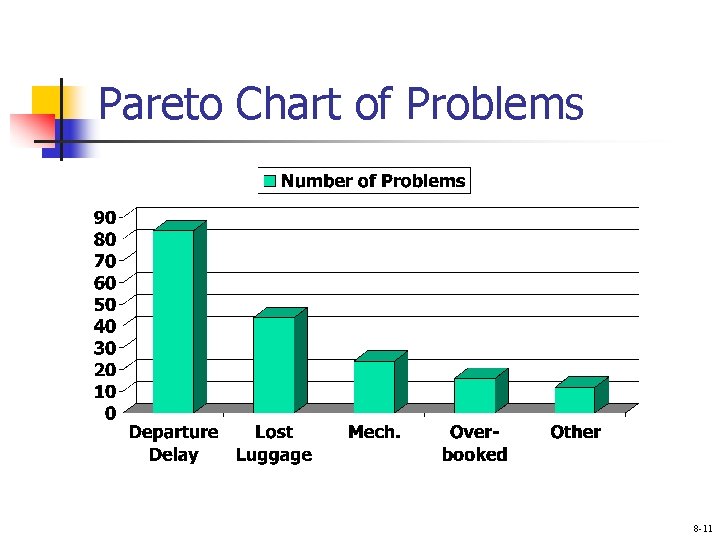
Pareto Chart of Problems 8 -11
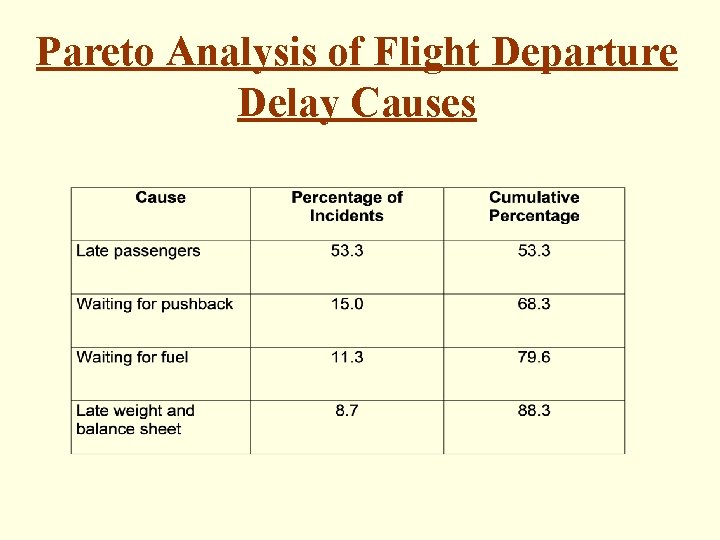
Pareto Analysis of Flight Departure Delay Causes
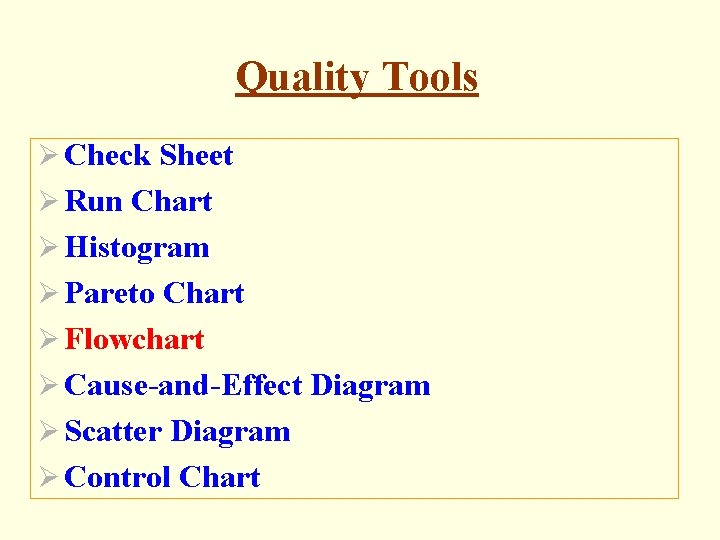
Quality Tools Ø Check Sheet Ø Run Chart Ø Histogram Ø Pareto Chart Ø Flowchart Ø Cause-and-Effect Diagram Ø Scatter Diagram Ø Control Chart
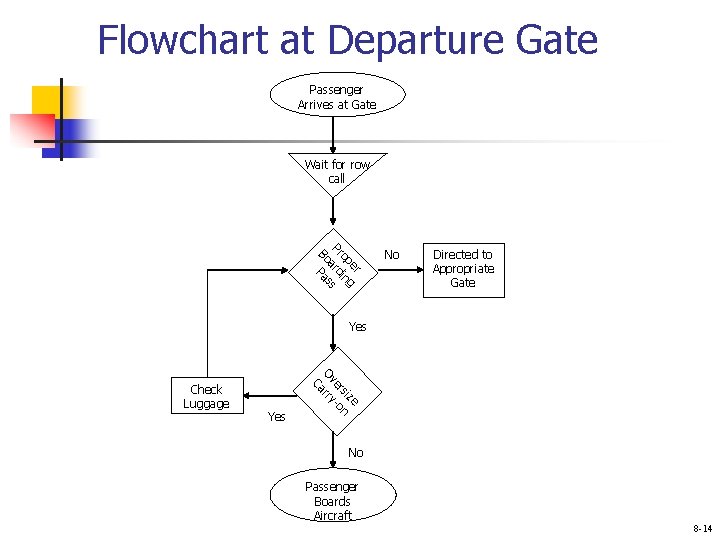
Flowchart at Departure Gate Passenger Arrives at Gate Wait for row call er g op in Pr ard s s Bo Pa No Directed to Appropriate Gate Yes e siz n er -o Ov arry C Check Luggage No Passenger Boards Aircraft 8 -14
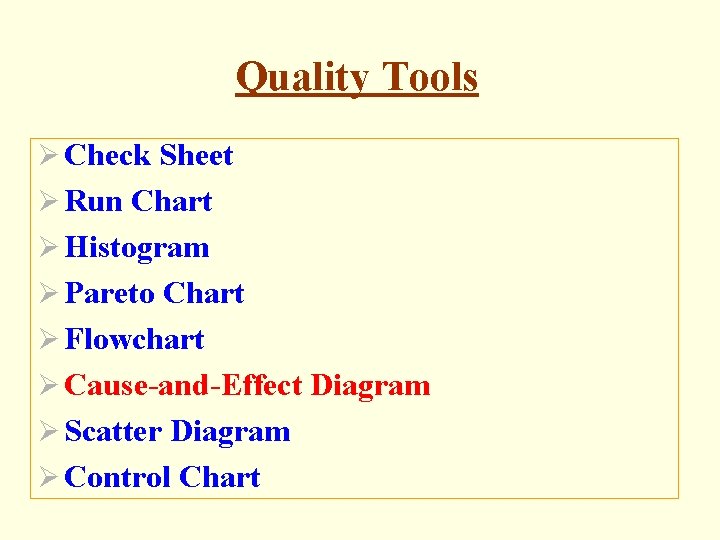
Quality Tools Ø Check Sheet Ø Run Chart Ø Histogram Ø Pareto Chart Ø Flowchart Ø Cause-and-Effect Diagram Ø Scatter Diagram Ø Control Chart
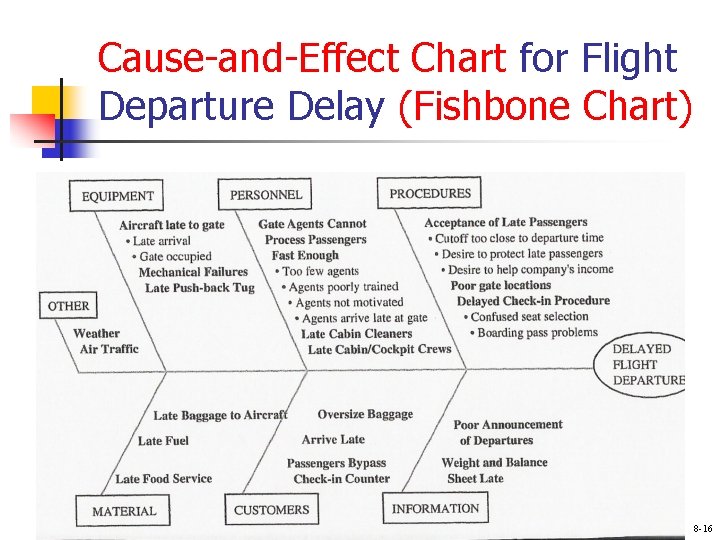
Cause-and-Effect Chart for Flight Departure Delay (Fishbone Chart) 8 -16
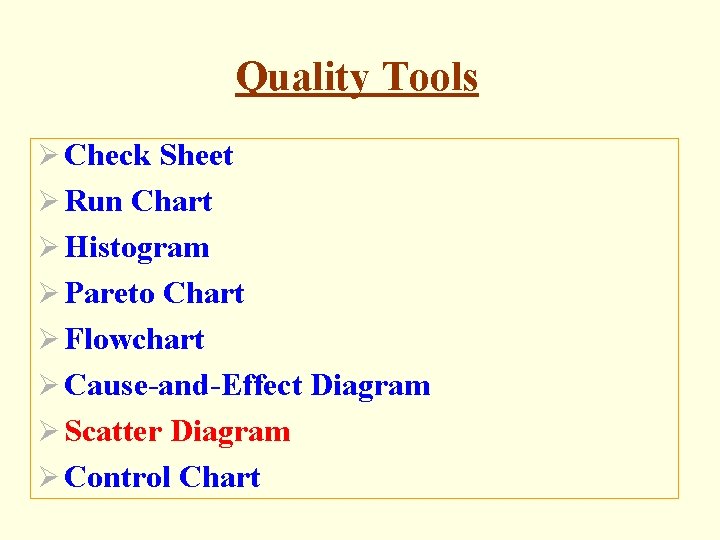
Quality Tools Ø Check Sheet Ø Run Chart Ø Histogram Ø Pareto Chart Ø Flowchart Ø Cause-and-Effect Diagram Ø Scatter Diagram Ø Control Chart
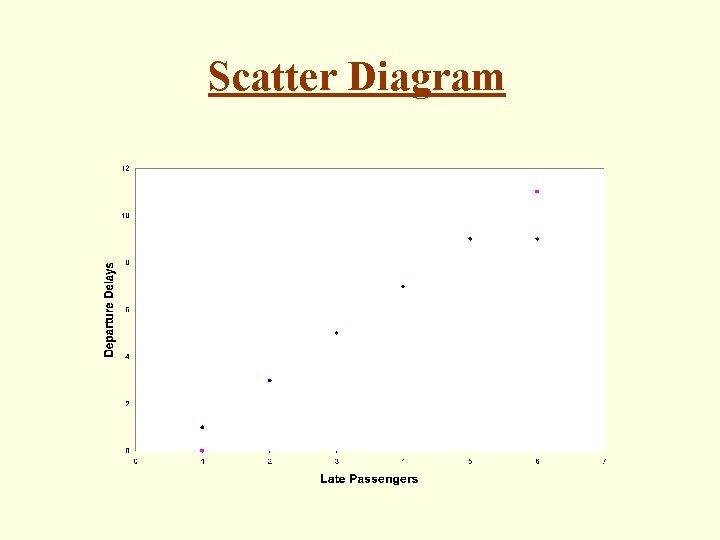
Scatter Diagram
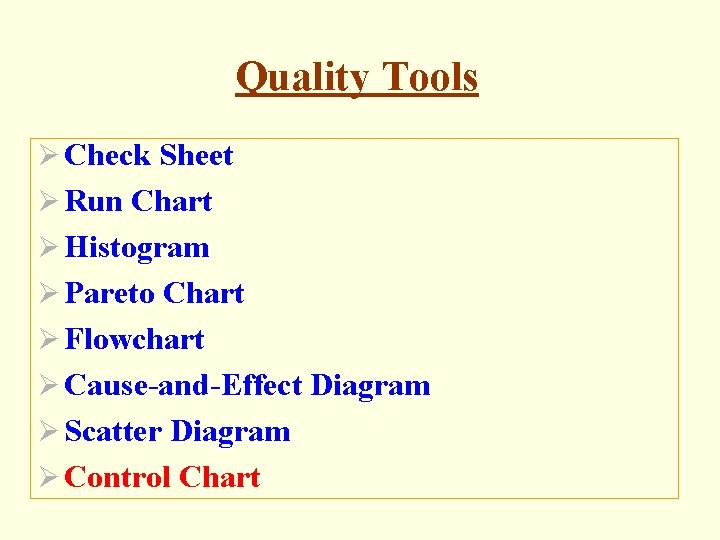
Quality Tools Ø Check Sheet Ø Run Chart Ø Histogram Ø Pareto Chart Ø Flowchart Ø Cause-and-Effect Diagram Ø Scatter Diagram Ø Control Chart
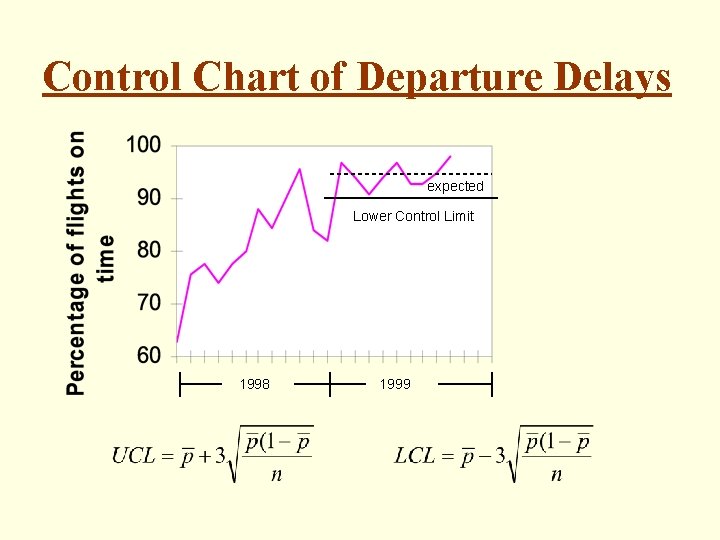
Control Chart of Departure Delays expected Lower Control Limit 1998 1999
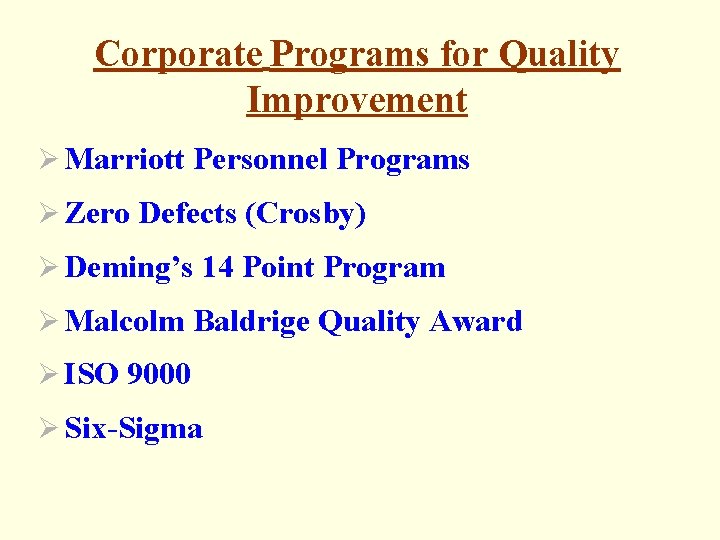
Corporate Programs for Quality Improvement Ø Marriott Personnel Programs Ø Zero Defects (Crosby) Ø Deming’s 14 Point Program Ø Malcolm Baldrige Quality Award Ø ISO 9000 Ø Six-Sigma
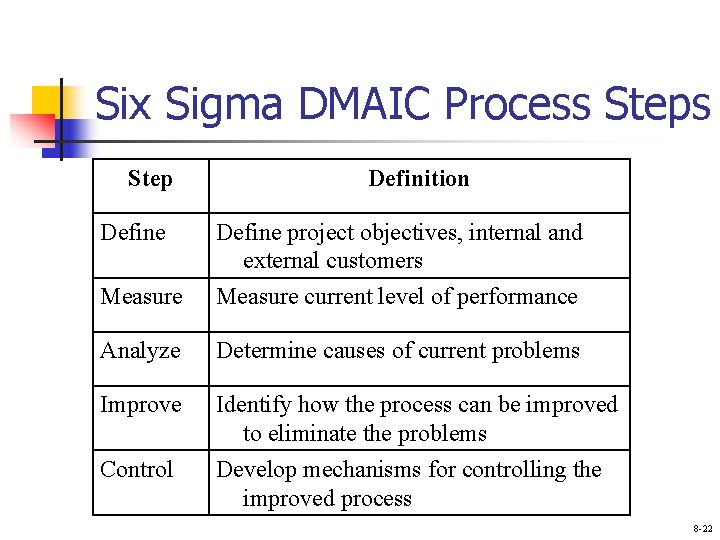
Six Sigma DMAIC Process Step Define Definition Measure Define project objectives, internal and external customers Measure current level of performance Analyze Determine causes of current problems Improve Identify how the process can be improved to eliminate the problems Develop mechanisms for controlling the improved process Control 8 -22
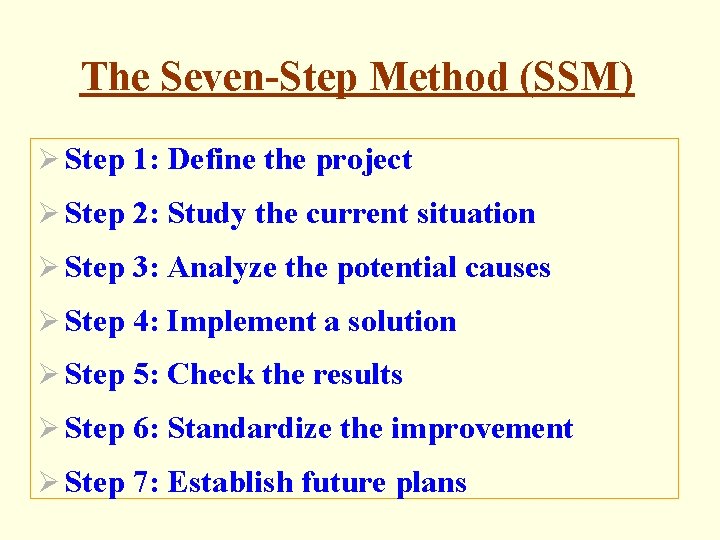
The Seven-Step Method (SSM) Ø Step 1: Define the project Ø Step 2: Study the current situation Ø Step 3: Analyze the potential causes Ø Step 4: Implement a solution Ø Step 5: Check the results Ø Step 6: Standardize the improvement Ø Step 7: Establish future plans
Define continuous quality improvement
Continuous improvement check sheet
Ana quality assurance model
Quality improvement vs quality assurance
Define continuous quality improvement
Cqi action plan template
Jrotc continuous improvement plan
Plan do check act ppt
Plan do check act
Present continuous vs past continuous
Present continuous past continuous future continuous
Jhm irb
Qsen patient centered care examples
Quality improvement paradigm
Point of care quality improvement
Efmd quality improvement system
Indiana perinatal quality improvement collaborative
Tea quality improvement
Quality improvement
Sustainability in quality improvement
Quality improvement nurse
Quality improvement
Juran 10 steps to quality improvement
Swot analysis quality improvement