HIE ISOLDE Cavity Developments Walter Venturini Delsolaro On
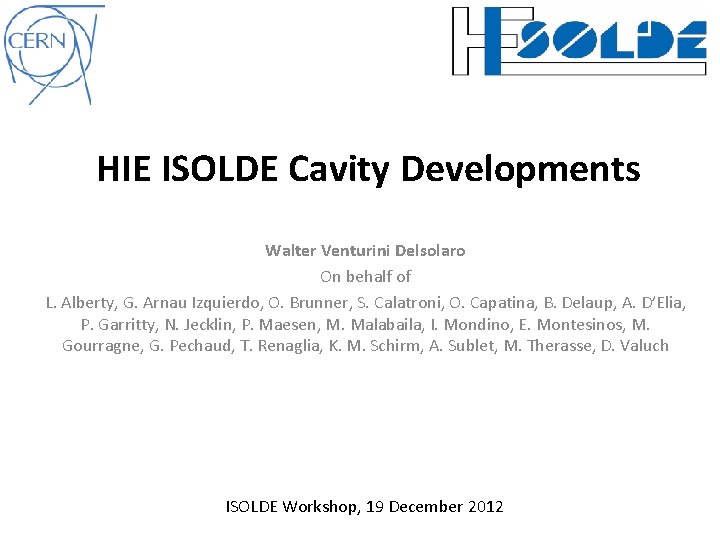
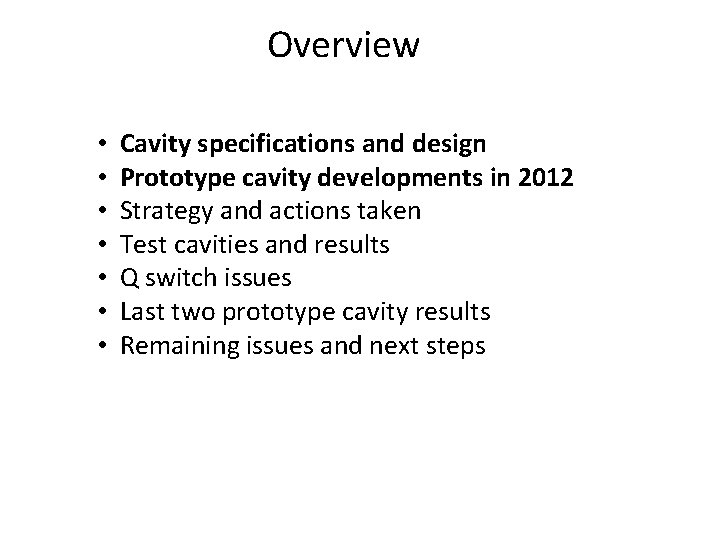
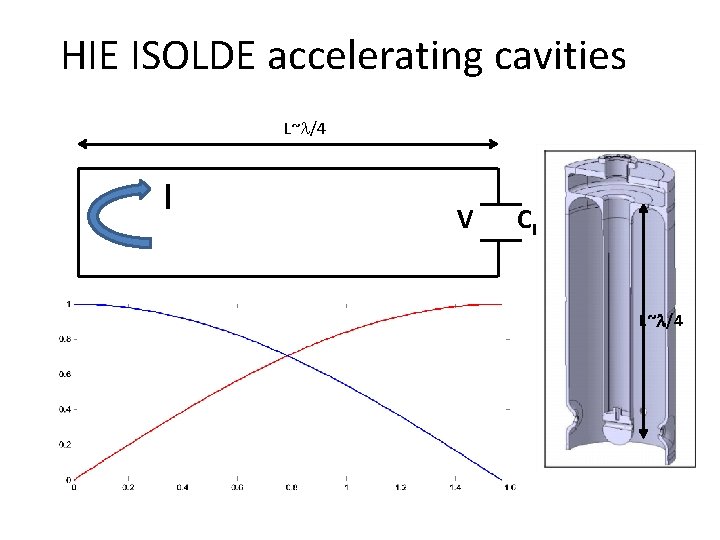
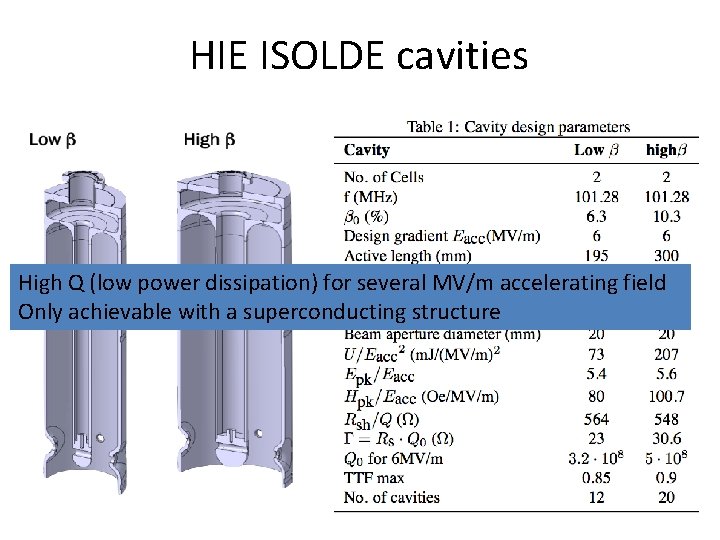
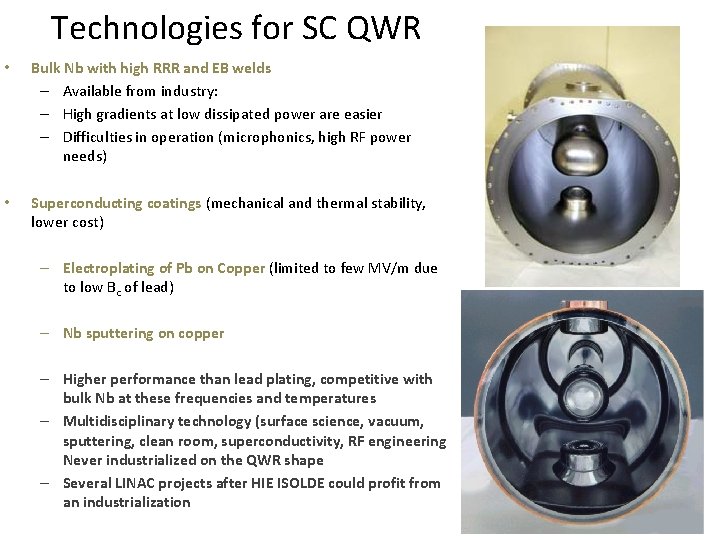
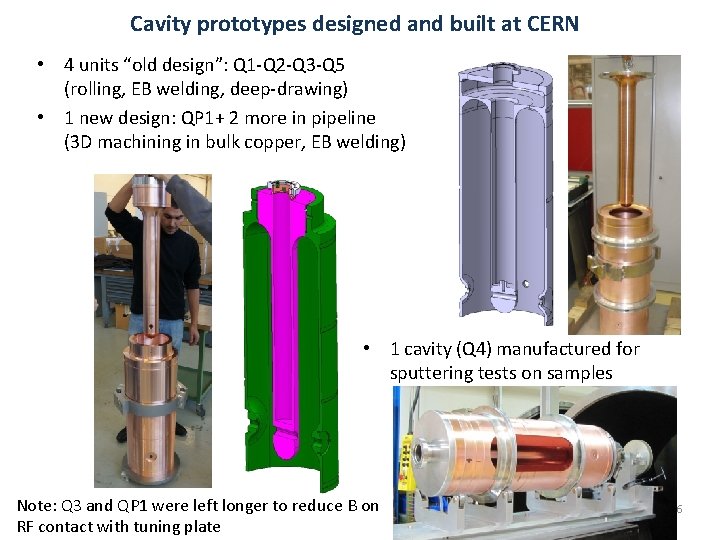
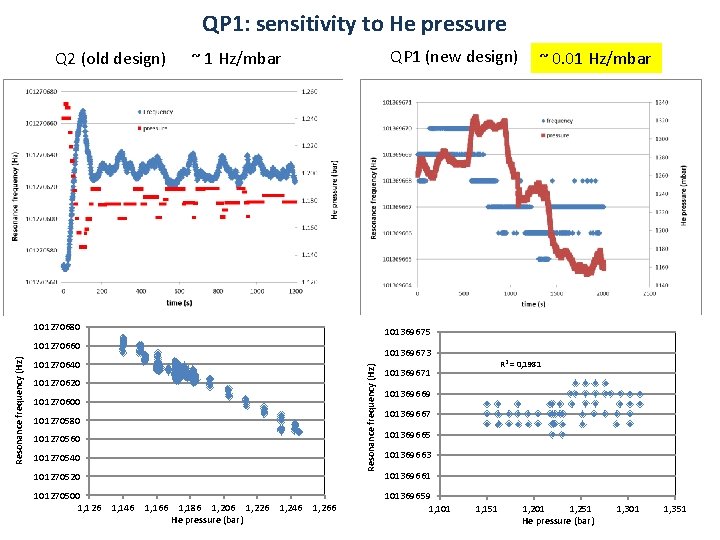
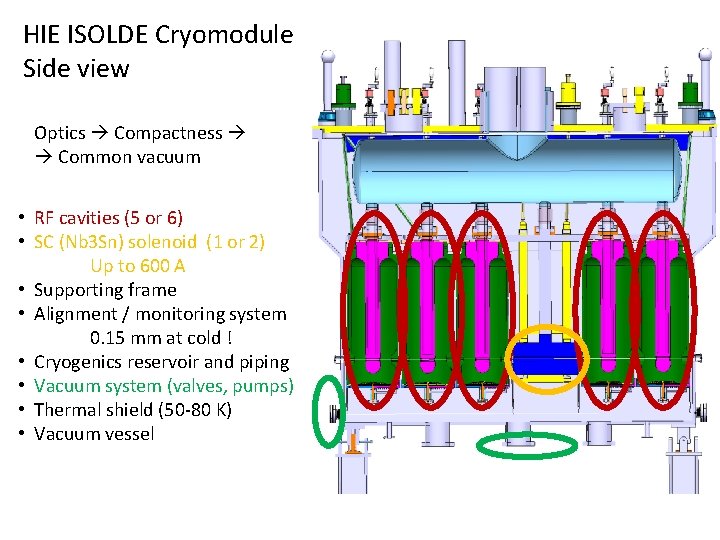
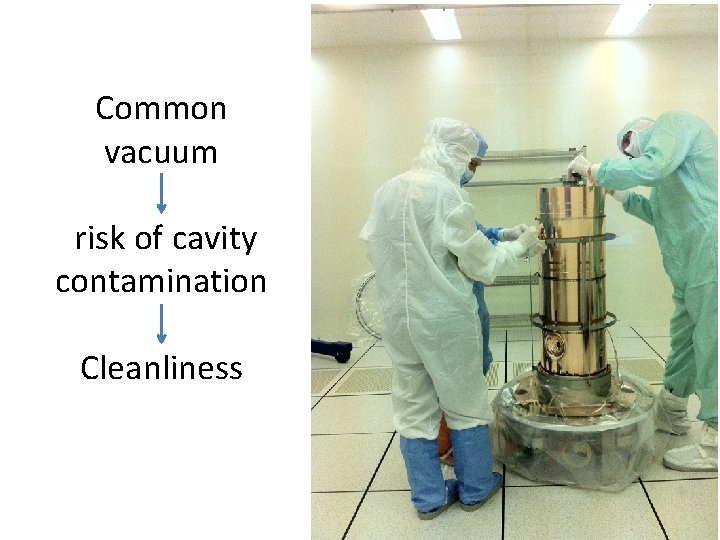
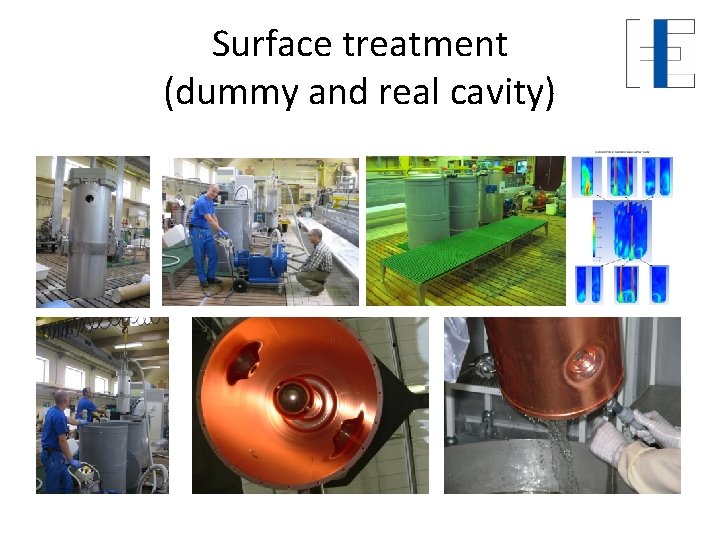
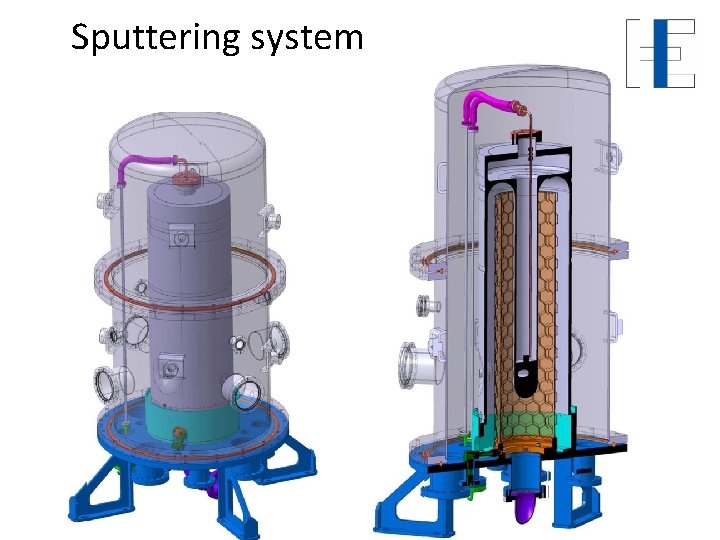
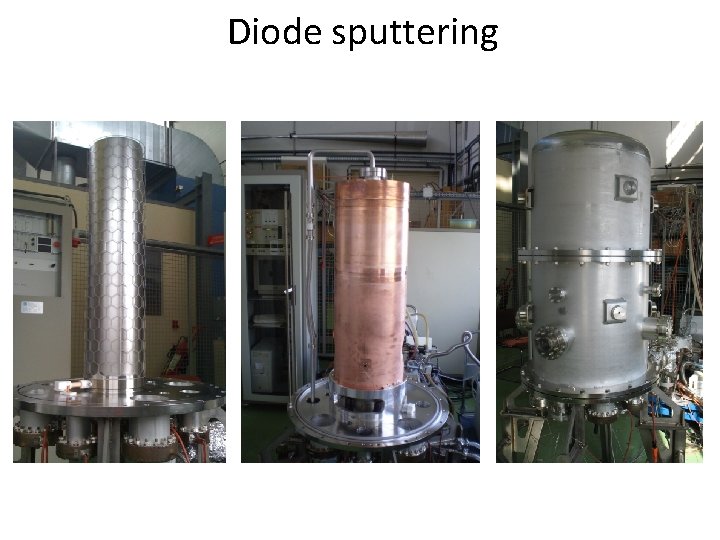
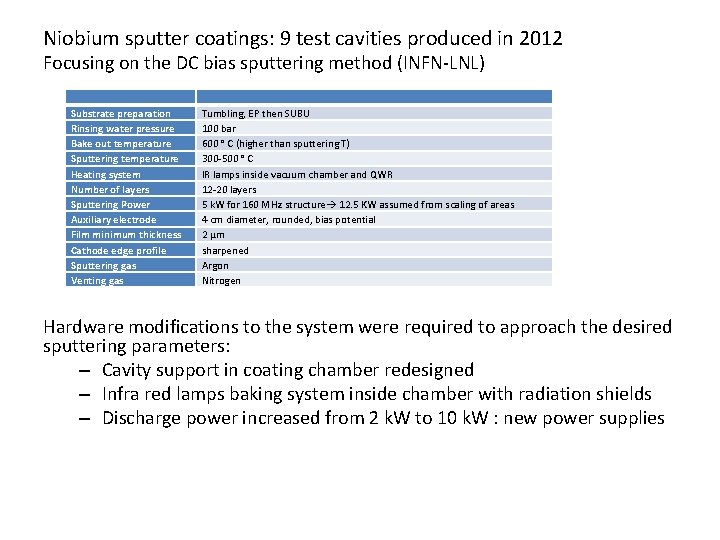
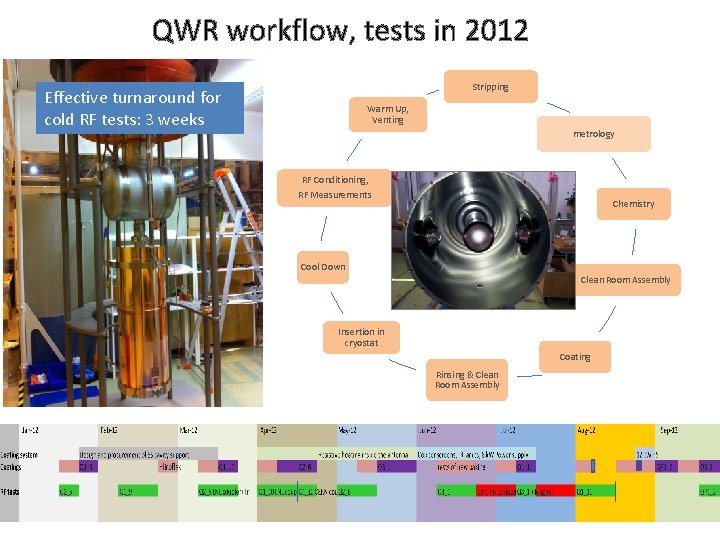
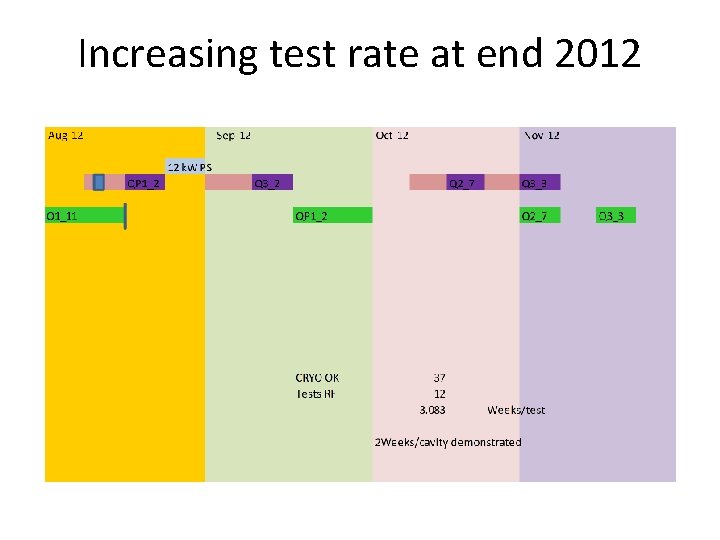
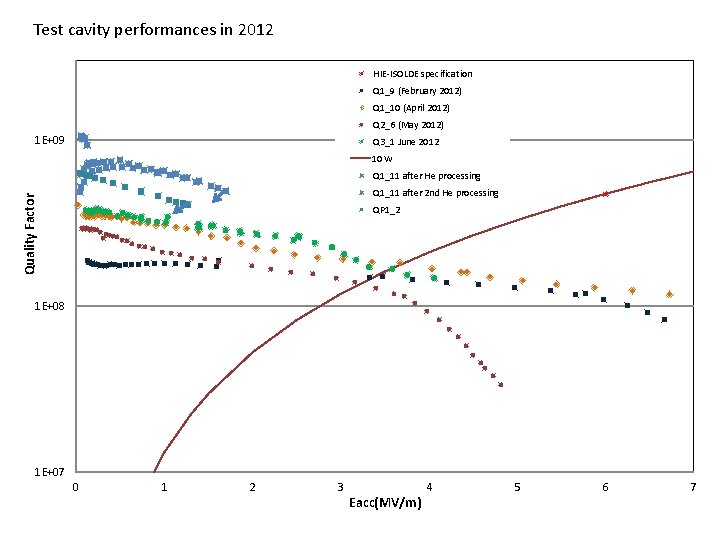
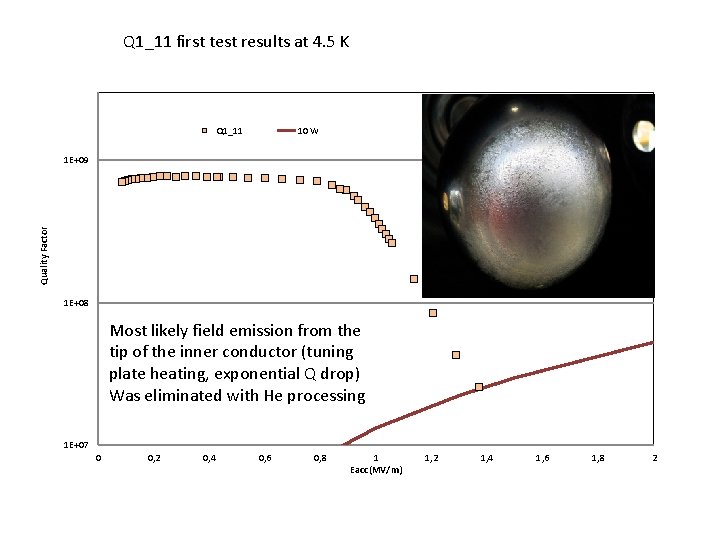
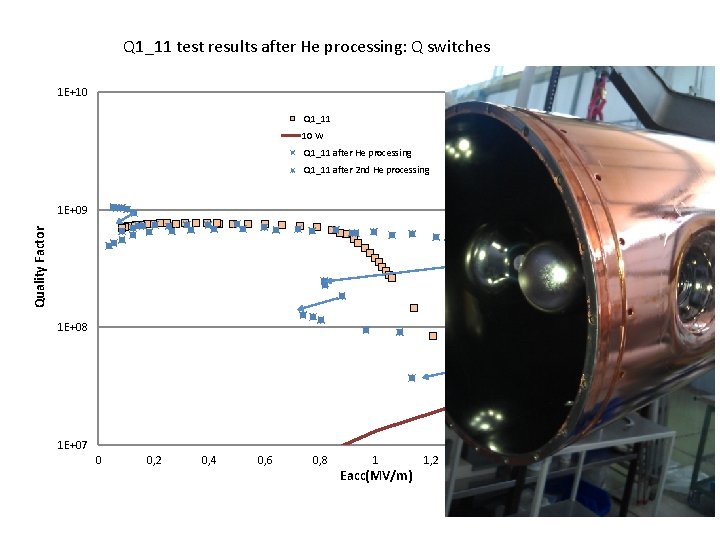
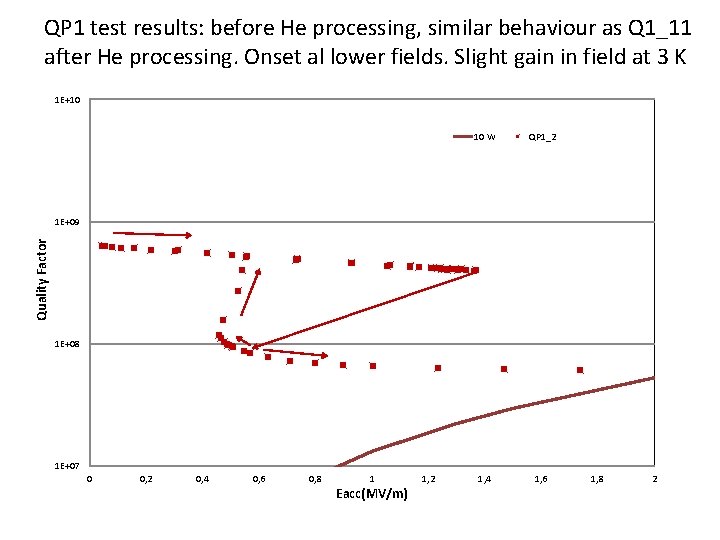
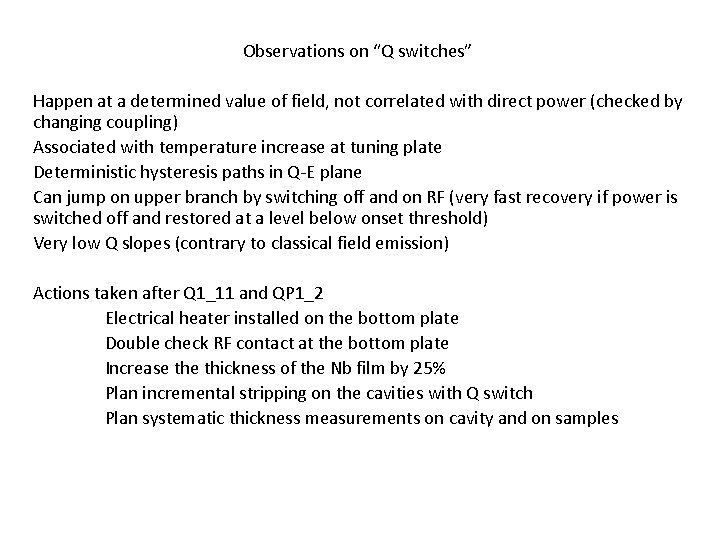
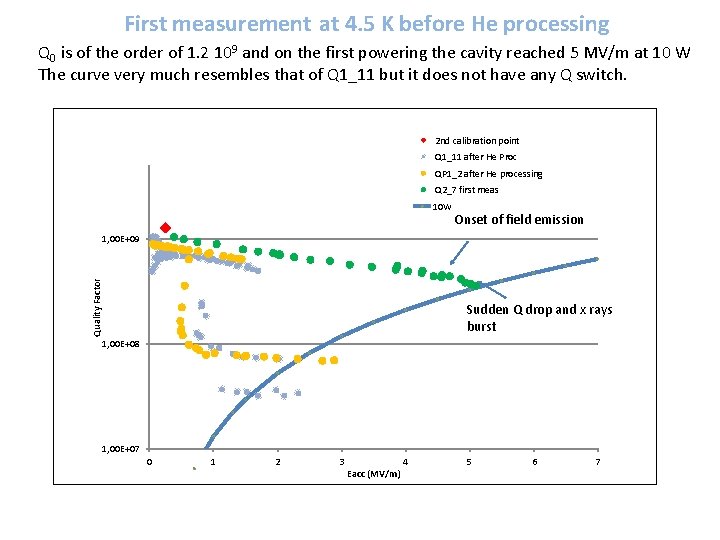
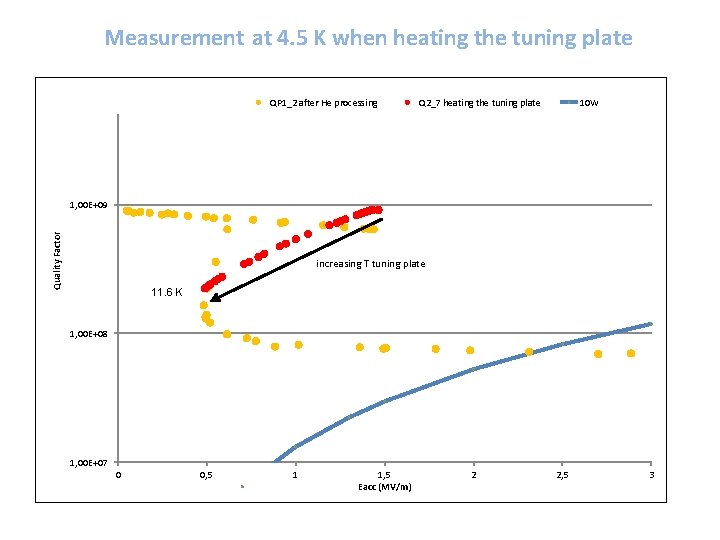
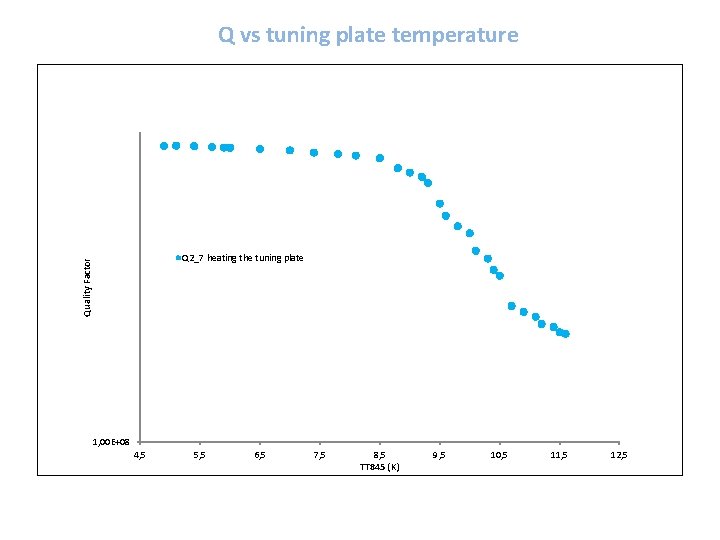
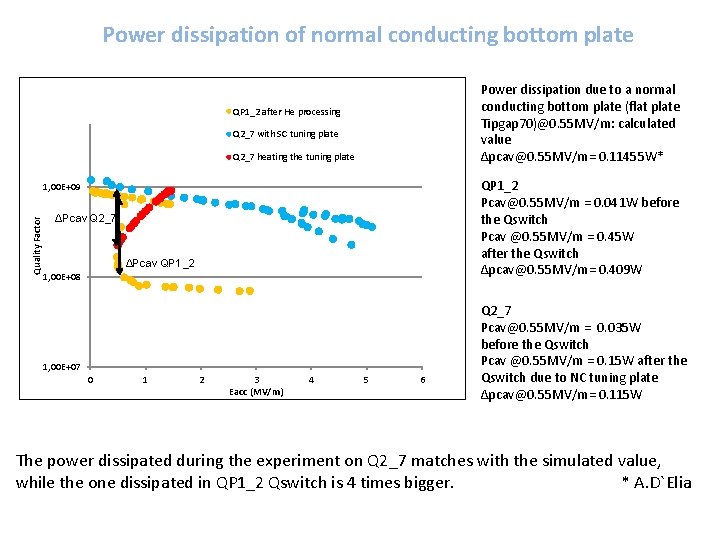
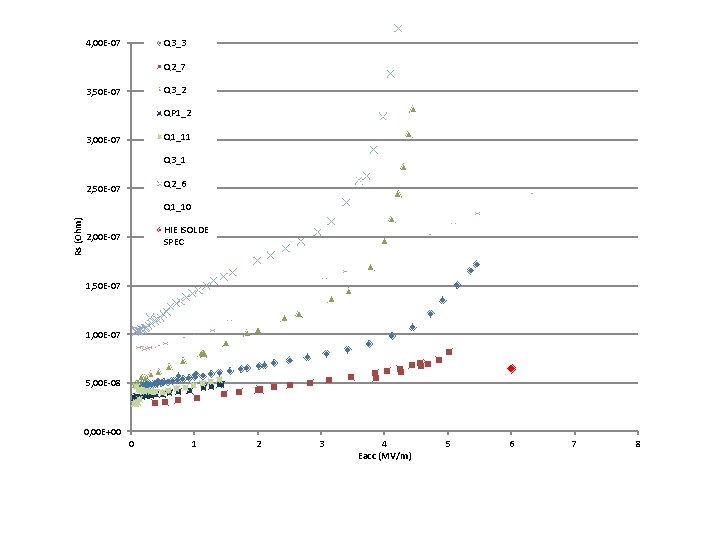
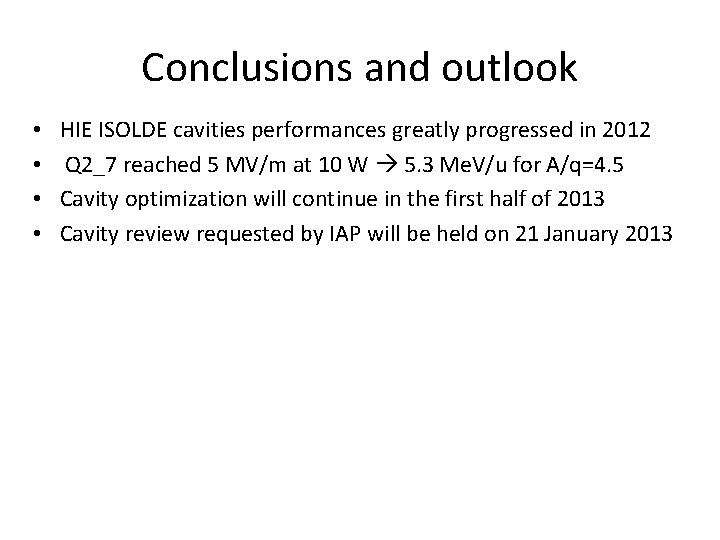
- Slides: 26
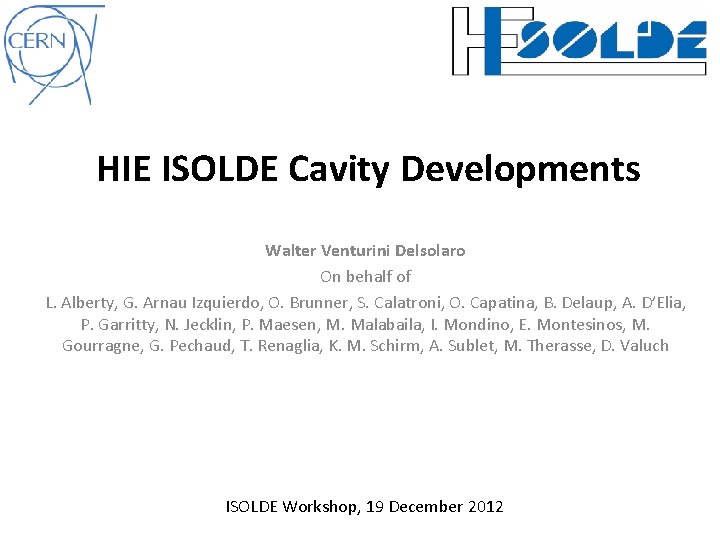
HIE ISOLDE Cavity Developments Walter Venturini Delsolaro On behalf of L. Alberty, G. Arnau Izquierdo, O. Brunner, S. Calatroni, O. Capatina, B. Delaup, A. D’Elia, P. Garritty, N. Jecklin, P. Maesen, M. Malabaila, I. Mondino, E. Montesinos, M. Gourragne, G. Pechaud, T. Renaglia, K. M. Schirm, A. Sublet, M. Therasse, D. Valuch ISOLDE Workshop, 19 December 2012
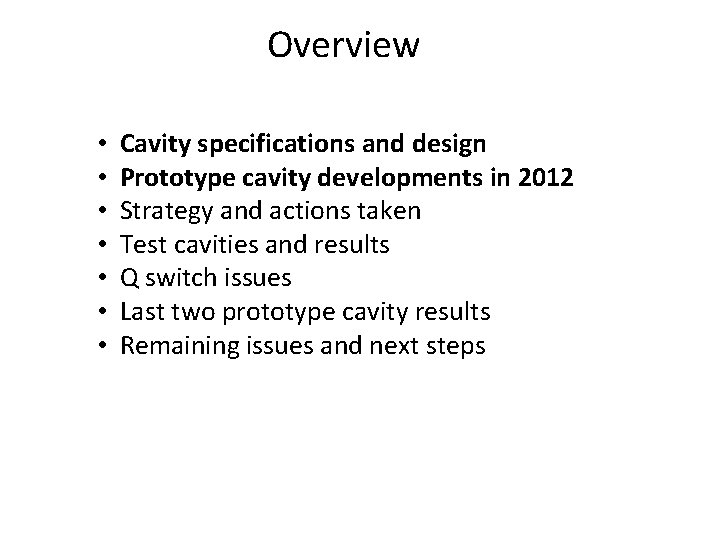
Overview • • Cavity specifications and design Prototype cavity developments in 2012 Strategy and actions taken Test cavities and results Q switch issues Last two prototype cavity results Remaining issues and next steps
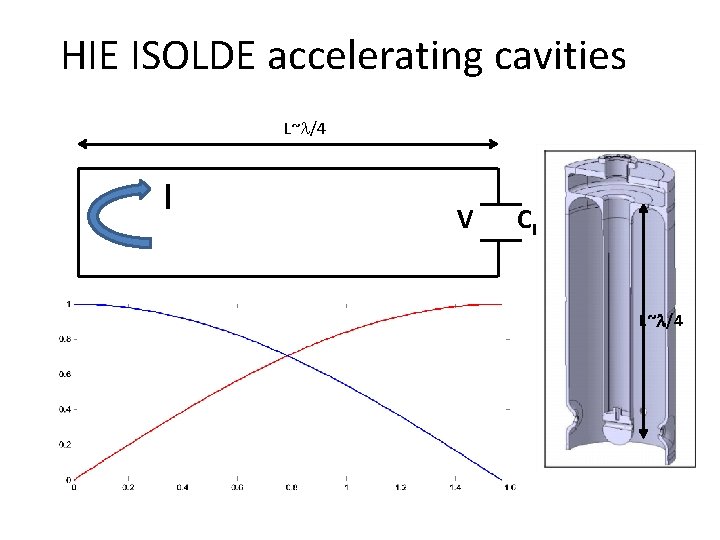
HIE ISOLDE accelerating cavities L~ /4 I V CL L~ /4
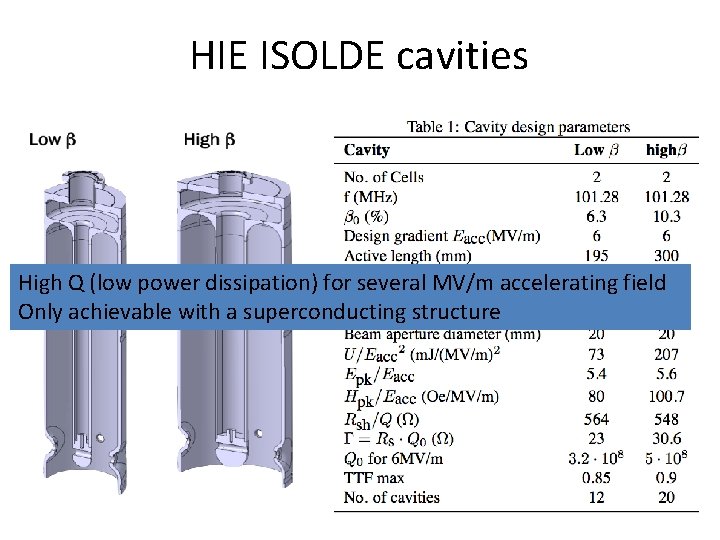
HIE ISOLDE cavities High Q (low power dissipation) for several MV/m accelerating field Only achievable with a superconducting structure
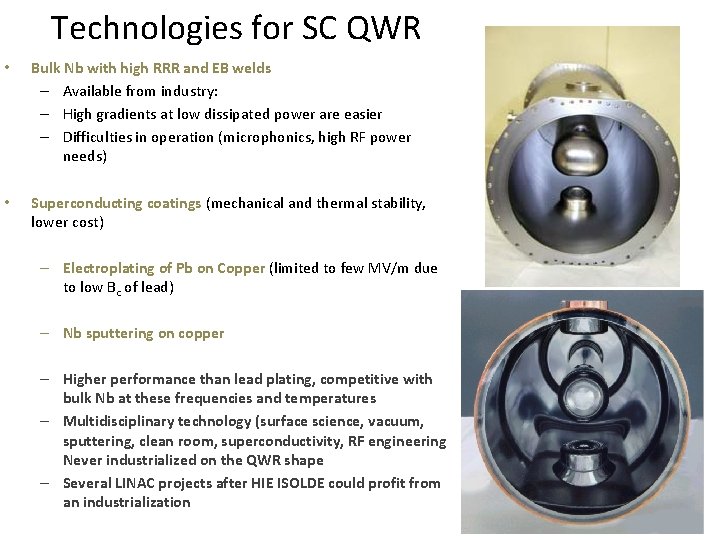
Technologies for SC QWR • Bulk Nb with high RRR and EB welds – Available from industry: – High gradients at low dissipated power are easier – Difficulties in operation (microphonics, high RF power needs) • Superconducting coatings (mechanical and thermal stability, lower cost) – Electroplating of Pb on Copper (limited to few MV/m due to low Bc of lead) – Nb sputtering on copper – Higher performance than lead plating, competitive with bulk Nb at these frequencies and temperatures – Multidisciplinary technology (surface science, vacuum, sputtering, clean room, superconductivity, RF engineering Never industrialized on the QWR shape – Several LINAC projects after HIE ISOLDE could profit from an industrialization
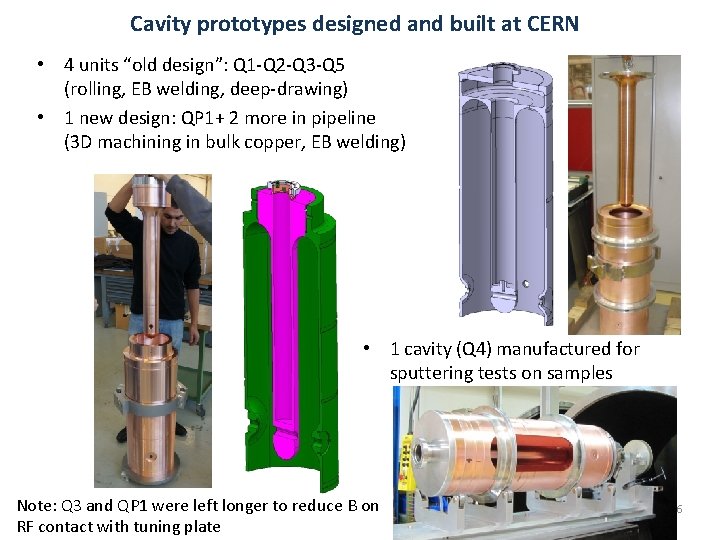
Cavity prototypes designed and built at CERN • 4 units “old design”: Q 1 -Q 2 -Q 3 -Q 5 (rolling, EB welding, deep-drawing) • 1 new design: QP 1+ 2 more in pipeline (3 D machining in bulk copper, EB welding) • 1 cavity (Q 4) manufactured for sputtering tests on samples Note: Q 3 and QP 1 were left longer to reduce B on RF contact with tuning plate 6
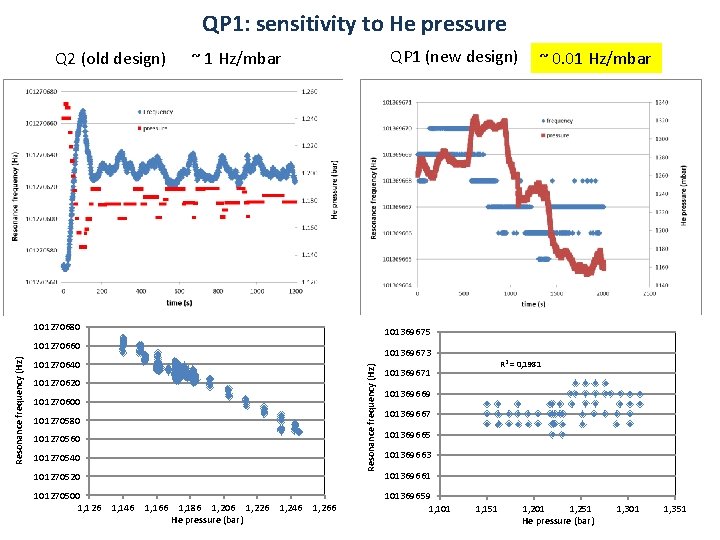
QP 1: sensitivity to He pressure Q 2 (old design) QP 1 (new design) ~ 1 Hz/mbar ~ 0. 01 Hz/mbar R 2 = 0, 9137 101270680 101369675 101369673 101270640 Resonance frequency (Hz) 101270660 101270620 101270600 101270580 101270560 101270540 101270520 101270500 1, 126 1, 146 1, 166 1, 186 1, 206 1, 226 He pressure (bar) 1, 246 1, 266 R 2 = 0, 1981 101369671 101369669 101369667 101369665 101369663 101369661 101369659 1, 101 1, 151 1, 201 1, 251 He pressure (bar) 1, 301 1, 351
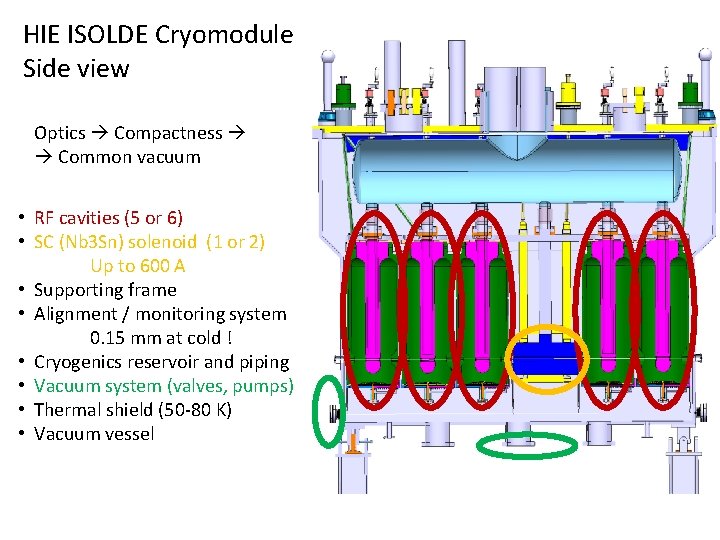
HIE ISOLDE Cryomodule Side view Optics Compactness Common vacuum • RF cavities (5 or 6) • SC (Nb 3 Sn) solenoid (1 or 2) Up to 600 A • Supporting frame • Alignment / monitoring system 0. 15 mm at cold ! • Cryogenics reservoir and piping • Vacuum system (valves, pumps) • Thermal shield (50 -80 K) • Vacuum vessel
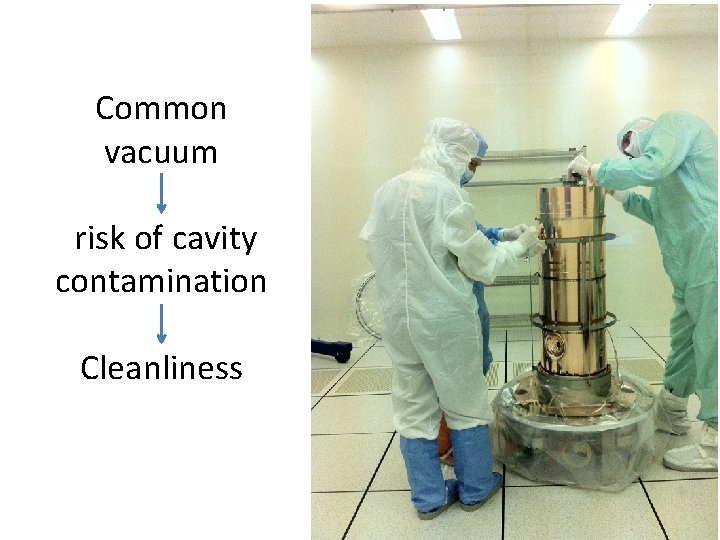
Common vacuum risk of cavity contamination Cleanliness
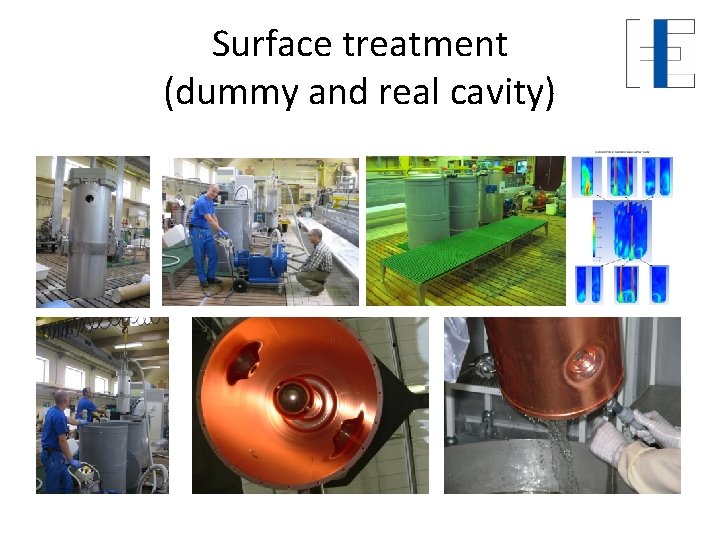
Surface treatment (dummy and real cavity)
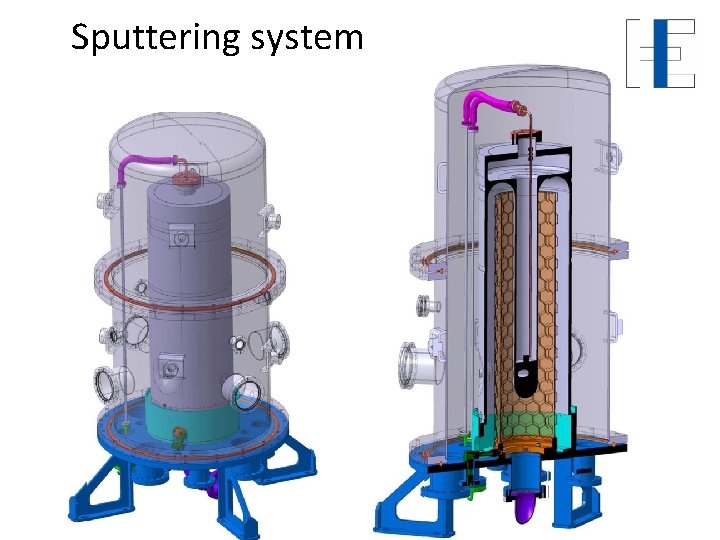
Sputtering system
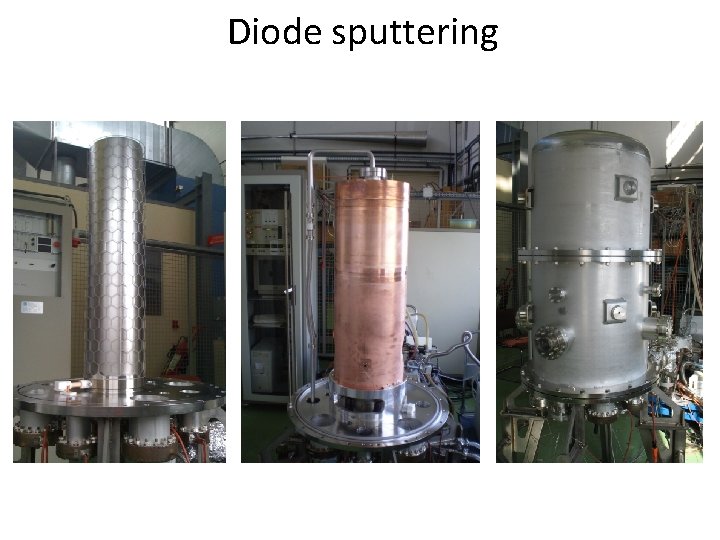
Diode sputtering
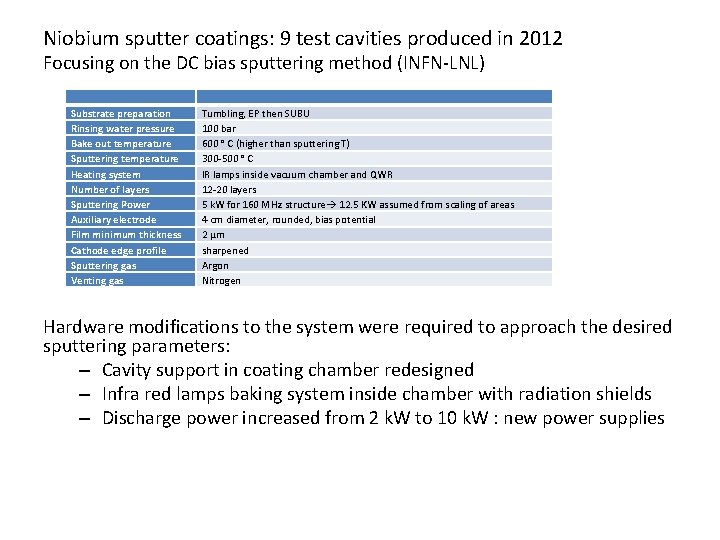
Niobium sputter coatings: 9 test cavities produced in 2012 Focusing on the DC bias sputtering method (INFN-LNL) Substrate preparation Rinsing water pressure Bake out temperature Sputtering temperature Heating system Number of layers Sputtering Power Auxiliary electrode Film minimum thickness Cathode edge profile Sputtering gas Venting gas Tumbling, EP then SUBU 100 bar 600 ᵒ C (higher than sputtering T) 300 -500 ᵒ C IR lamps inside vacuum chamber and QWR 12 -20 layers 5 k. W for 160 MHz structure 12. 5 KW assumed from scaling of areas 4 cm diameter, rounded, bias potential 2 µm sharpened Argon Nitrogen Hardware modifications to the system were required to approach the desired sputtering parameters: – Cavity support in coating chamber redesigned – Infra red lamps baking system inside chamber with radiation shields – Discharge power increased from 2 k. W to 10 k. W : new power supplies
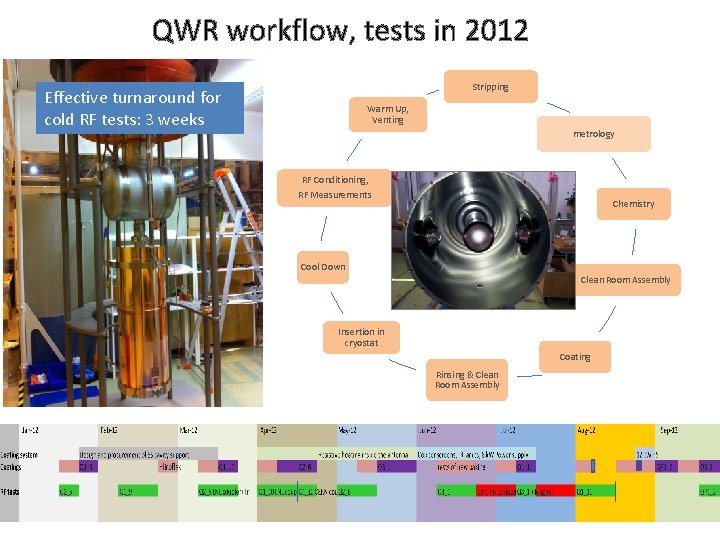
QWR workflow, tests in 2012 Stripping Effective turnaround for cold RF tests: 3 weeks Warm Up, Venting metrology RF Conditioning, RF Measurements Chemistry Cool Down Clean Room Assembly Insertion in cryostat Coating Rinsing & Clean Room Assembly
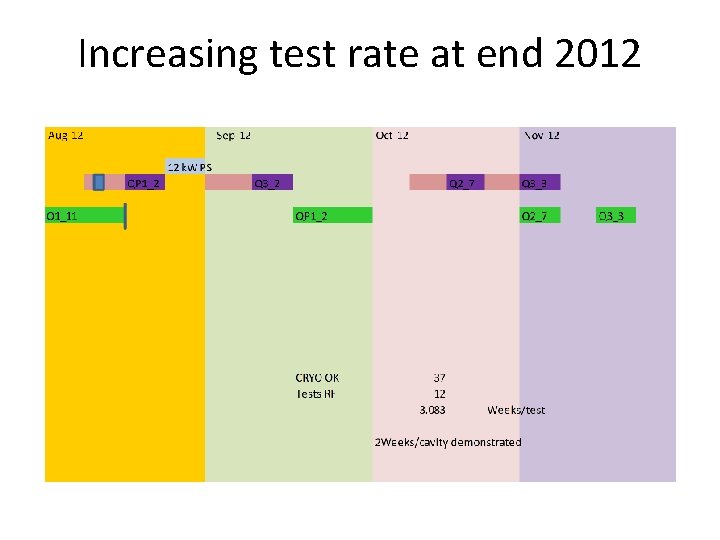
Increasing test rate at end 2012
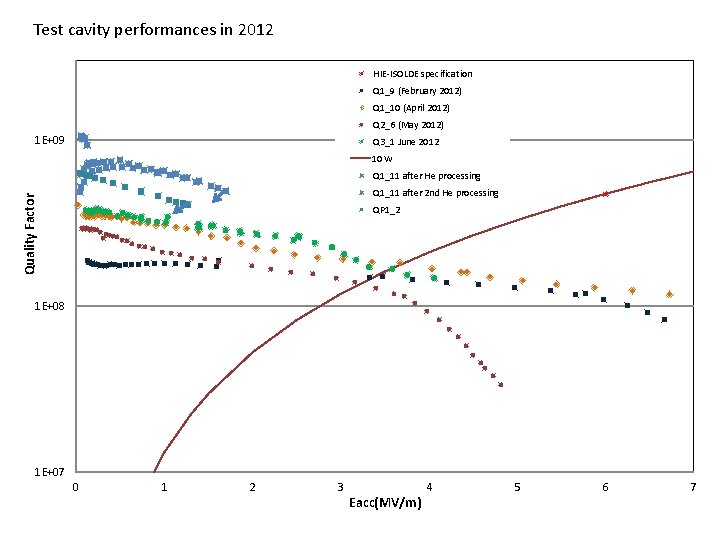
Eacc(MV/m) Quality Factor
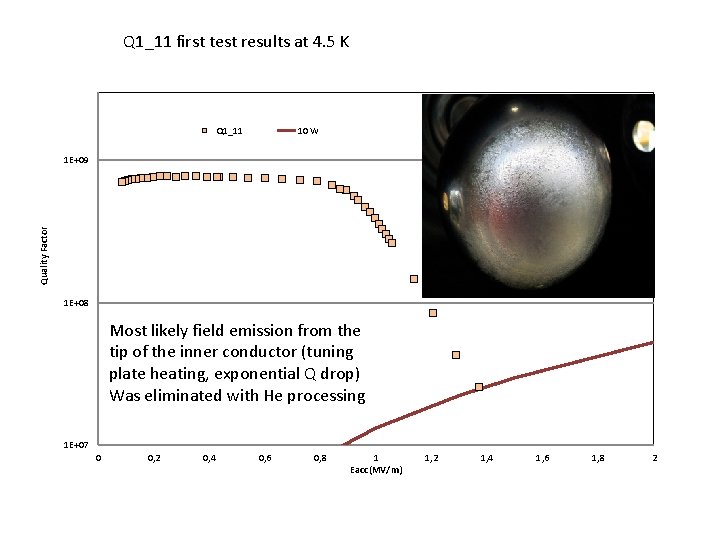
Q 1_11 first test results at 4. 5 K Q 1_11 10 W Quality Factor 1 E+09 1 E+08 Most likely field emission from the tip of the inner conductor (tuning plate heating, exponential Q drop) Was eliminated with He processing 1 E+07 0 0, 2 0, 4 0, 6 0, 8 1 Eacc(MV/m) 1, 2 1, 4 1, 6 1, 8 2
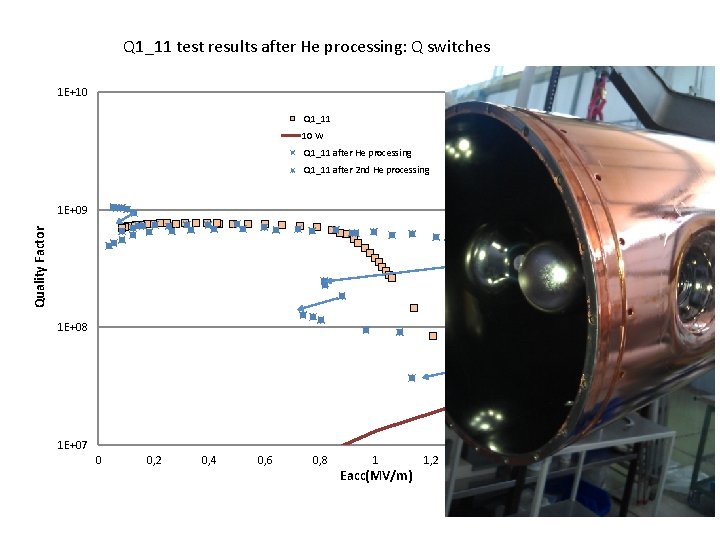
Q 1_11 test results after He processing: Q switches 1 E+10 Q 1_11 10 W Q 1_11 after He processing Q 1_11 after 2 nd He processing Quality Factor 1 E+09 1 E+08 1 E+07 0 0, 2 0, 4 0, 6 0, 8 1 Eacc(MV/m) 1, 2 1, 4 1, 6 1, 8 2
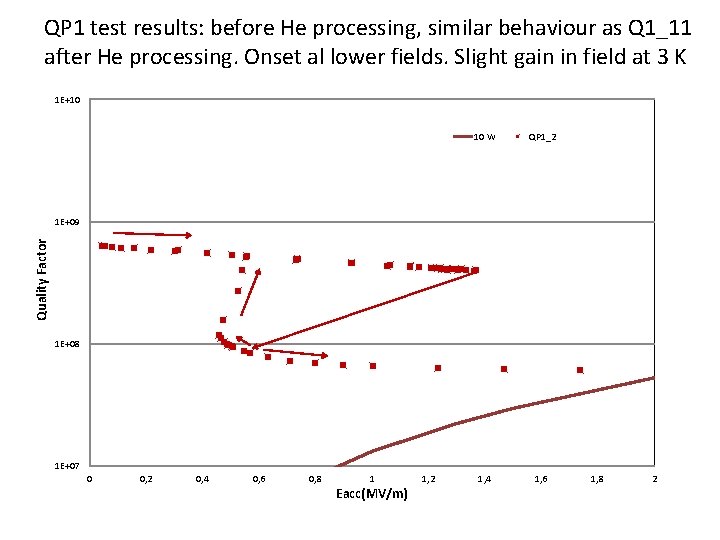
QP 1 test results: before He processing, similar behaviour as Q 1_11 after He processing. Onset al lower fields. Slight gain in field at 3 K 1 E+10 10 W QP 1_2 1, 4 1, 6 Quality Factor 1 E+09 1 E+08 1 E+07 0 0, 2 0, 4 0, 6 0, 8 1 Eacc(MV/m) 1, 2 1, 8 2
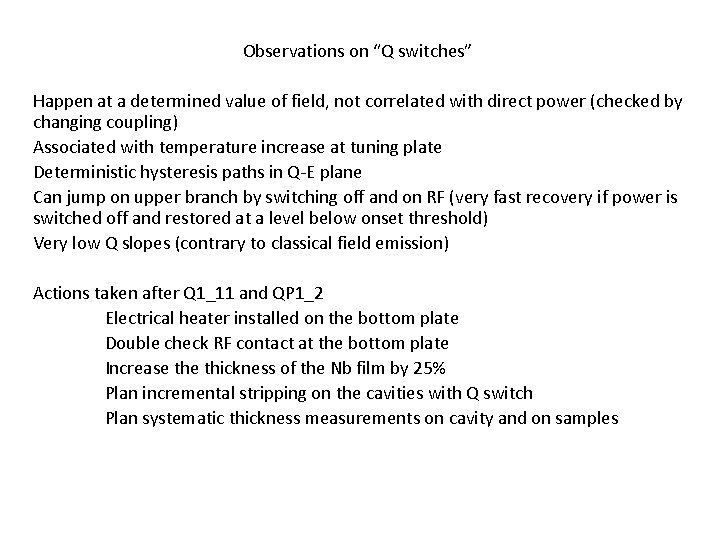
Observations on “Q switches” Happen at a determined value of field, not correlated with direct power (checked by changing coupling) Associated with temperature increase at tuning plate Deterministic hysteresis paths in Q-E plane Can jump on upper branch by switching off and on RF (very fast recovery if power is switched off and restored at a level below onset threshold) Very low Q slopes (contrary to classical field emission) Actions taken after Q 1_11 and QP 1_2 Electrical heater installed on the bottom plate Double check RF contact at the bottom plate Increase thickness of the Nb film by 25% Plan incremental stripping on the cavities with Q switch Plan systematic thickness measurements on cavity and on samples
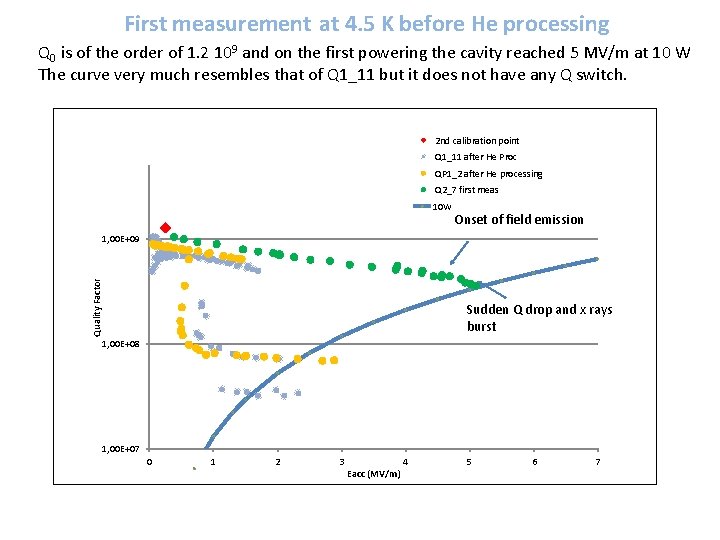
First measurement at 4. 5 K before He processing Q 0 is of the order of 1. 2 109 and on the first powering the cavity reached 5 MV/m at 10 W The curve very much resembles that of Q 1_11 but it does not have any Q switch. 2 nd calibration point Q 1_11 after He Proc QP 1_2 after He processing Q 2_7 first meas 10 W Onset of field emission Quality Factor 1, 00 E+09 Sudden Q drop and x rays burst 1, 00 E+08 1, 00 E+07 0 1 2 3 Eacc (MV/m) 4 5 6 7
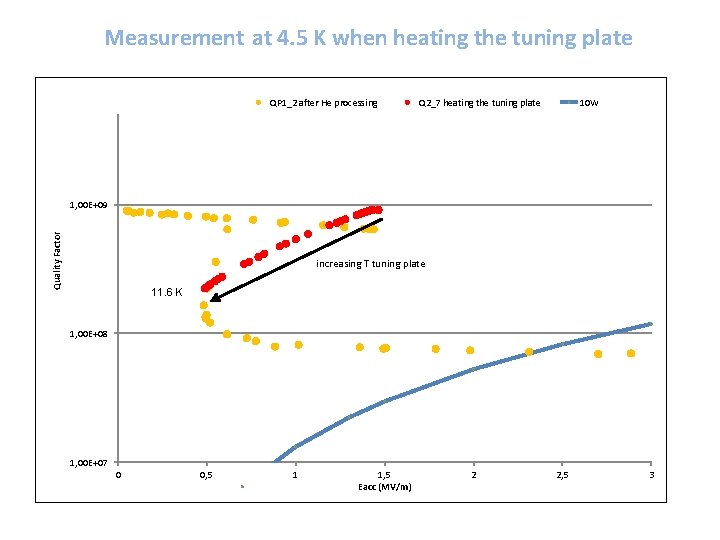
Measurement at 4. 5 K when heating the tuning plate QP 1_2 after He processing Q 2_7 heating the tuning plate 10 W Quality Factor 1, 00 E+09 increasing T tuning plate 11. 6 K 1, 00 E+08 1, 00 E+07 0 0, 5 1 1, 5 Eacc (MV/m) 2 2, 5 3
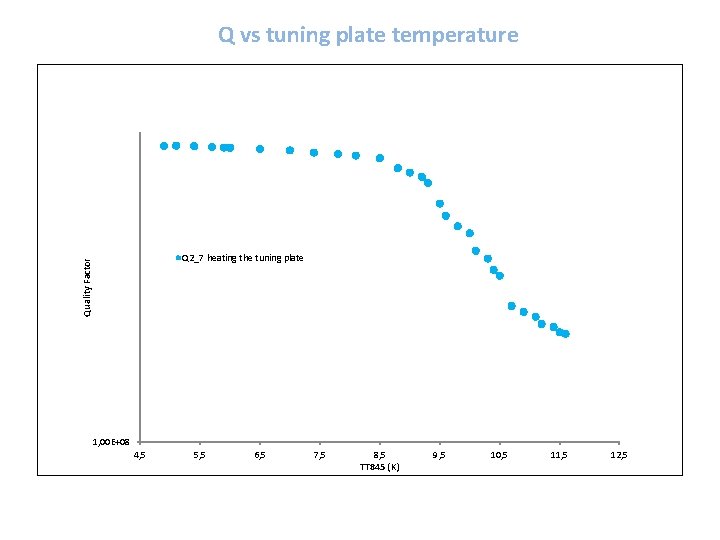
Q vs tuning plate temperature Quality Factor Q 2_7 heating the tuning plate 1, 00 E+08 4, 5 5, 5 6, 5 7, 5 8, 5 TT 845 (K) 9, 5 10, 5 11, 5 12, 5
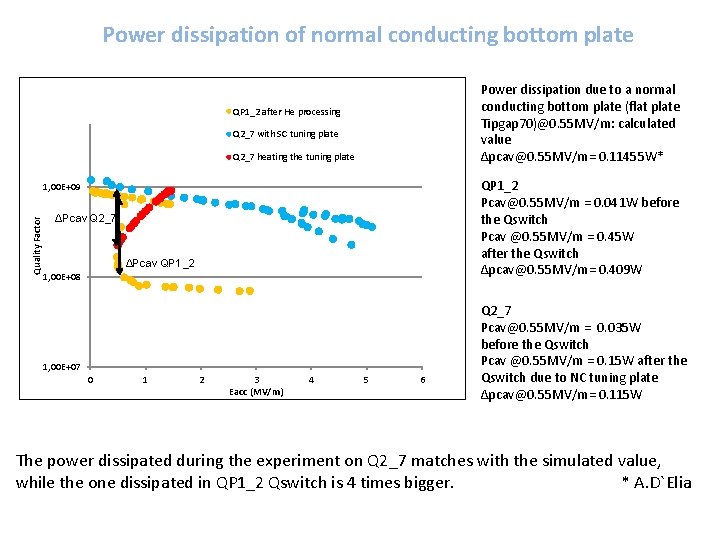
Power dissipation of normal conducting bottom plate Power dissipation due to a normal conducting bottom plate (flat plate Tipgap 70)@0. 55 MV/m: calculated value Δpcav@0. 55 MV/m= 0. 11455 W* QP 1_2 after He processing Q 2_7 with SC tuning plate Q 2_7 heating the tuning plate QP 1_2 Pcav@0. 55 MV/m = 0. 041 W before the Qswitch Pcav @0. 55 MV/m = 0. 45 W after the Qswitch Δpcav@0. 55 MV/m= 0. 409 W Quality Factor 1, 00 E+09 ΔPcav Q 2_7 ΔPcav QP 1_2 1, 00 E+08 1, 00 E+07 0 1 2 3 Eacc (MV/m) 4 5 6 Q 2_7 Pcav@0. 55 MV/m = 0. 035 W before the Qswitch Pcav @0. 55 MV/m = 0. 15 W after the Qswitch due to NC tuning plate Δpcav@0. 55 MV/m= 0. 115 W The power dissipated during the experiment on Q 2_7 matches with the simulated value, while the one dissipated in QP 1_2 Qswitch is 4 times bigger. * A. D`Elia
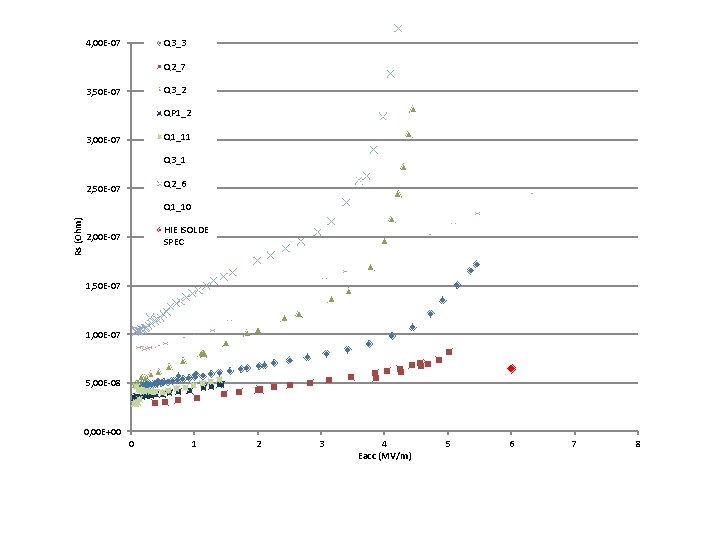
4, 00 E-07 Q 3_3 Q 2_7 Q 3_2 3, 50 E-07 QP 1_2 Q 1_11 3, 00 E-07 Q 3_1 Q 2_6 2, 50 E-07 Rs (Ohm) Q 1_10 HIE ISOLDE SPEC 2, 00 E-07 1, 50 E-07 1, 00 E-07 5, 00 E-08 0, 00 E+00 0 1 2 3 4 Eacc (MV/m) 5 6 7 8
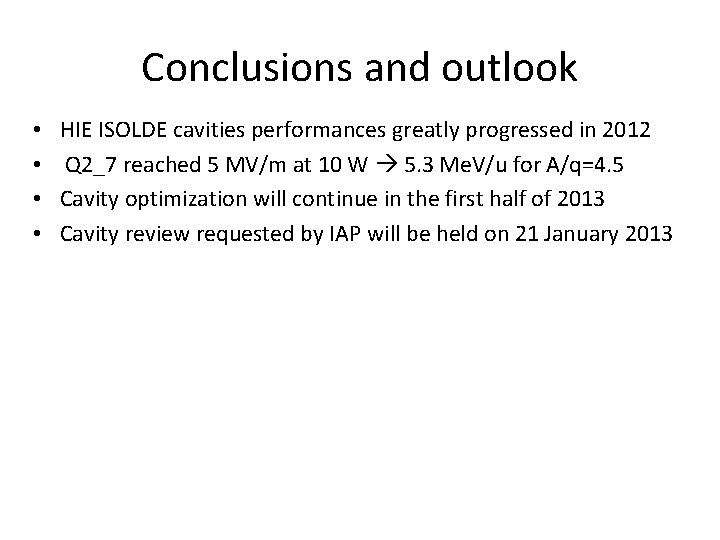
Conclusions and outlook • • HIE ISOLDE cavities performances greatly progressed in 2012 Q 2_7 reached 5 MV/m at 10 W 5. 3 Me. V/u for A/q=4. 5 Cavity optimization will continue in the first half of 2013 Cavity review requested by IAP will be held on 21 January 2013
Orbital body
Walter venturini
Walter venturini
Walter venturini
Marco venturini studio 3
Gilberto venturini
Gilberto venturini
Mental anatomical term
Ligaments of stomach
Gastric veins
Vertebral cavity
Phys. rev. c
Isolde yield database
Isolde
@isolde
Sps ikg
Isolde frank
Isolde reveal
Maria jg
Isolde k
Offshorekrane / bohrinselkrane
Isolde
Isolde workshop
Terminology services
Perinatal asphyxia
Simone hié
Roshini jayasankar