GEAR DESIGN Part IV Cont GEAR FORMS Prof
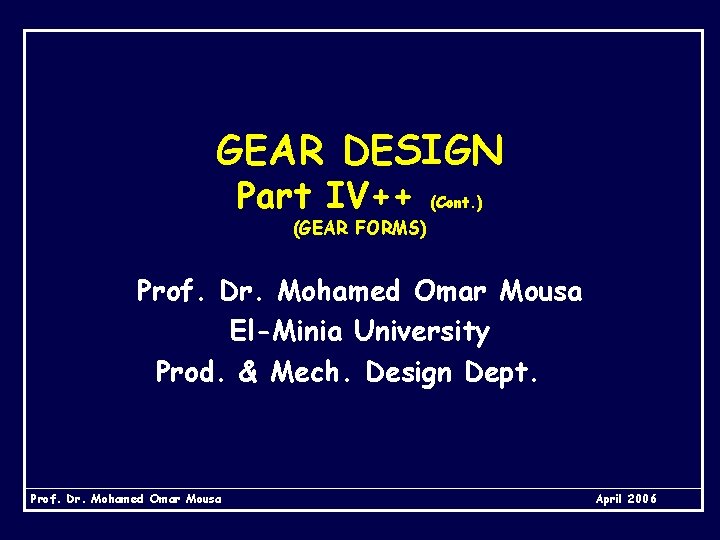
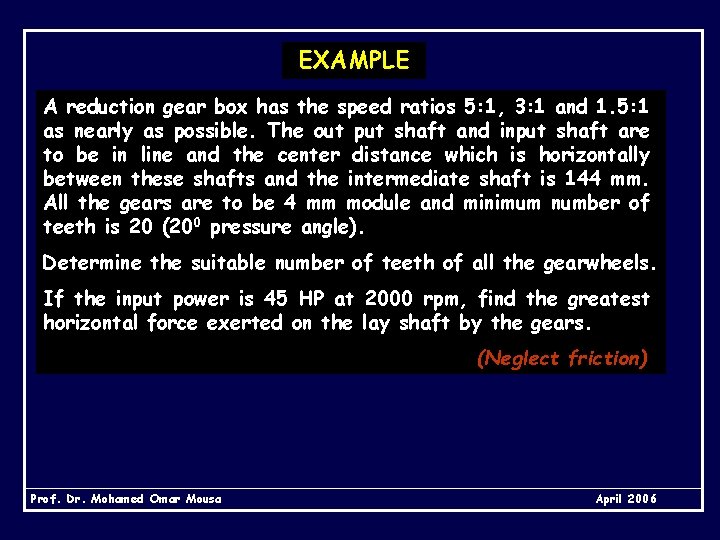
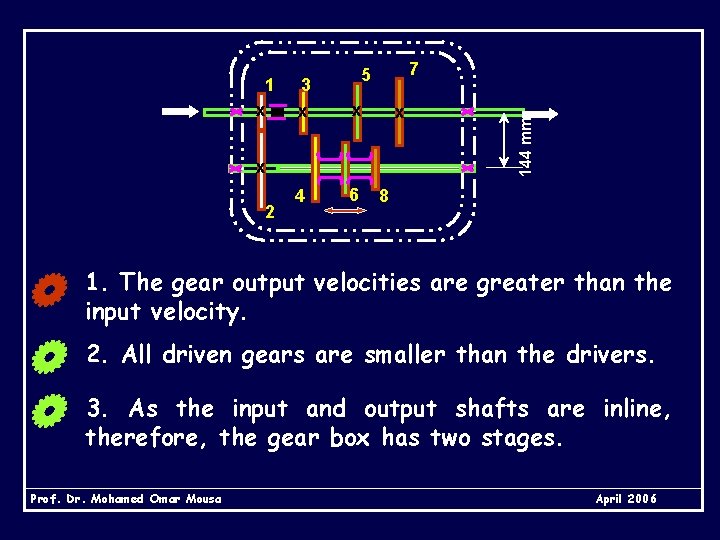
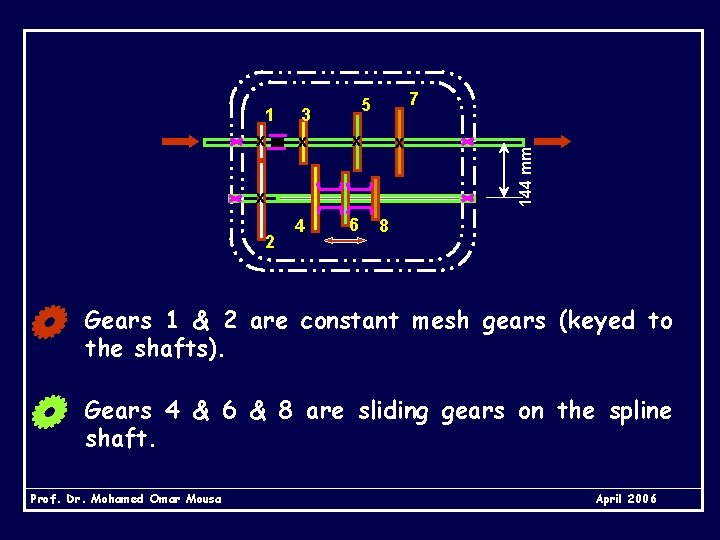
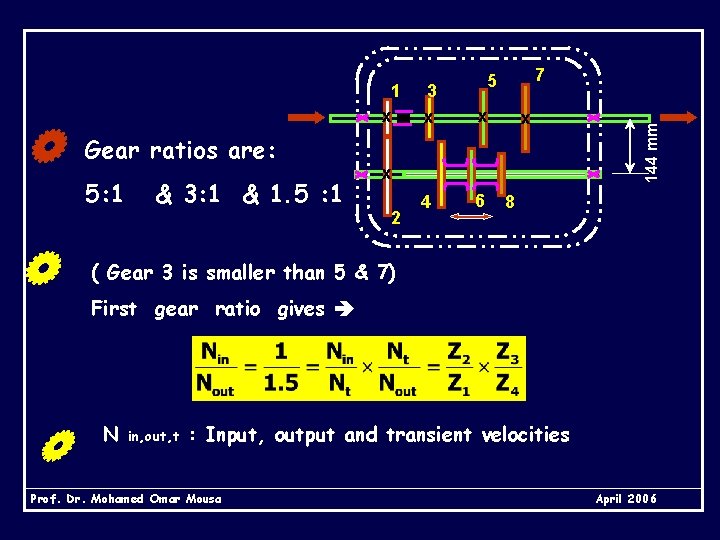
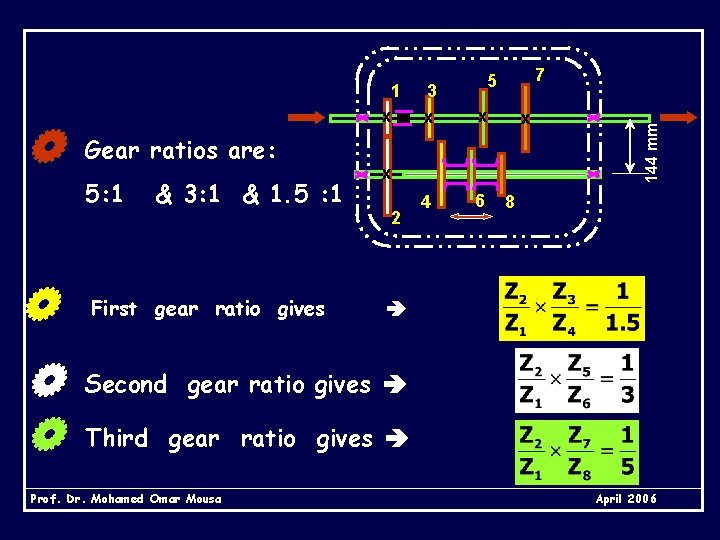
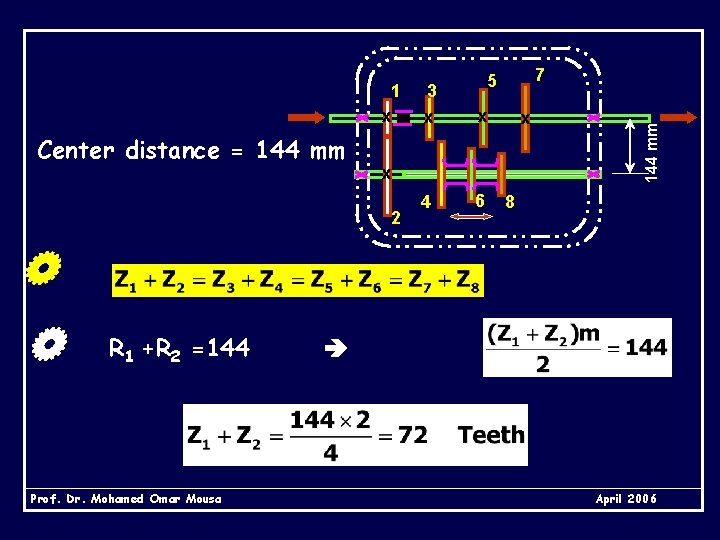
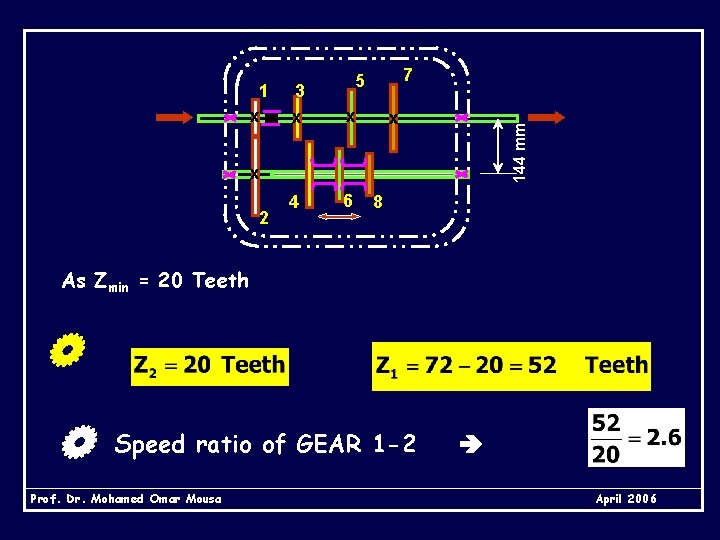
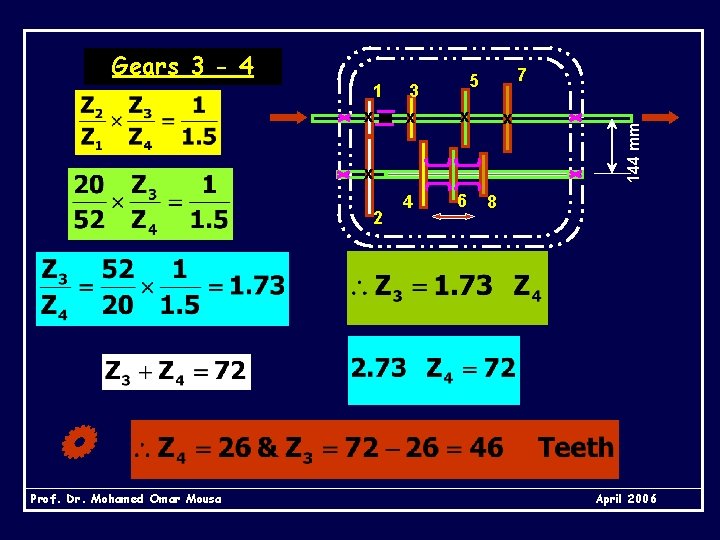
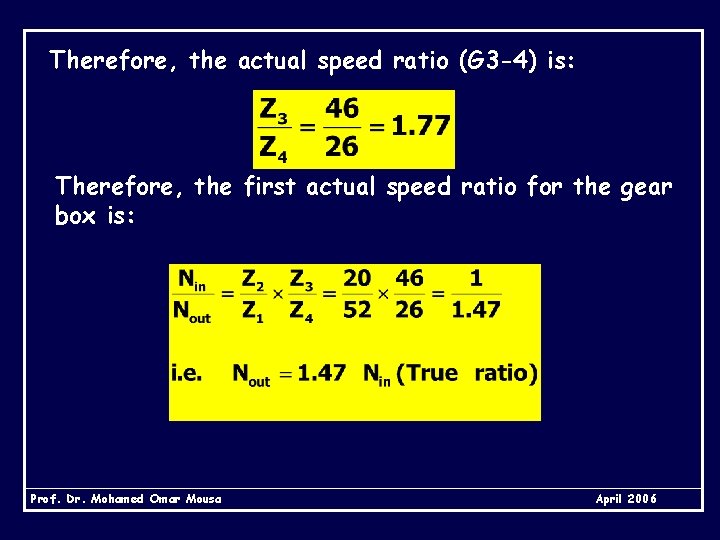
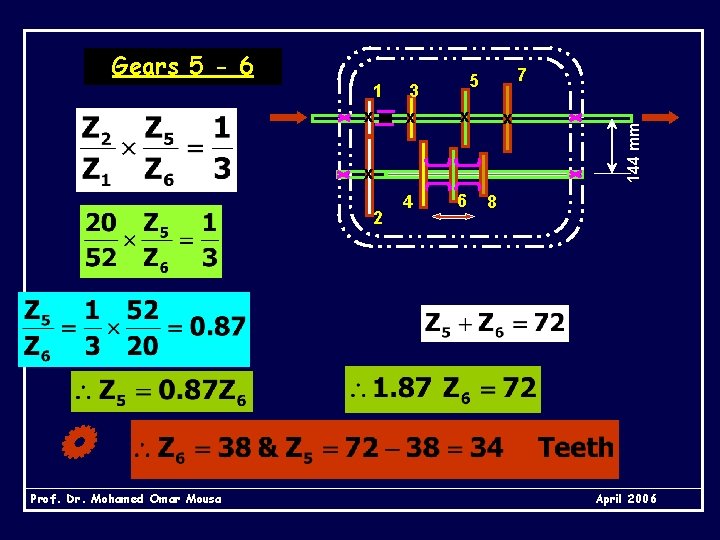
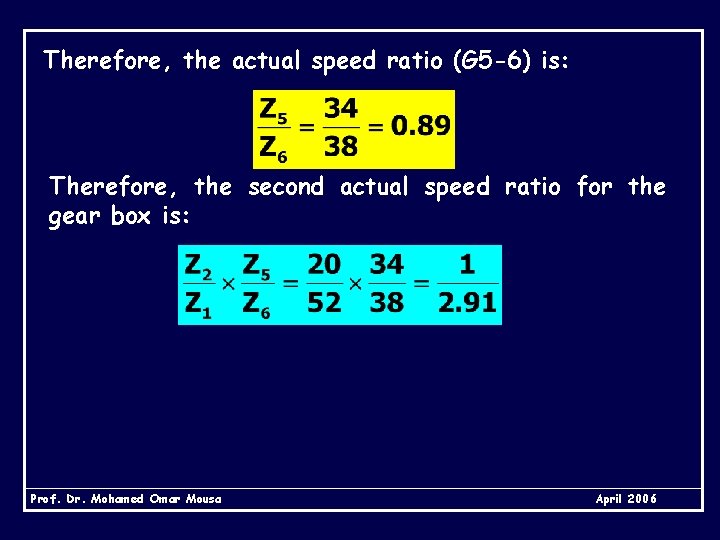
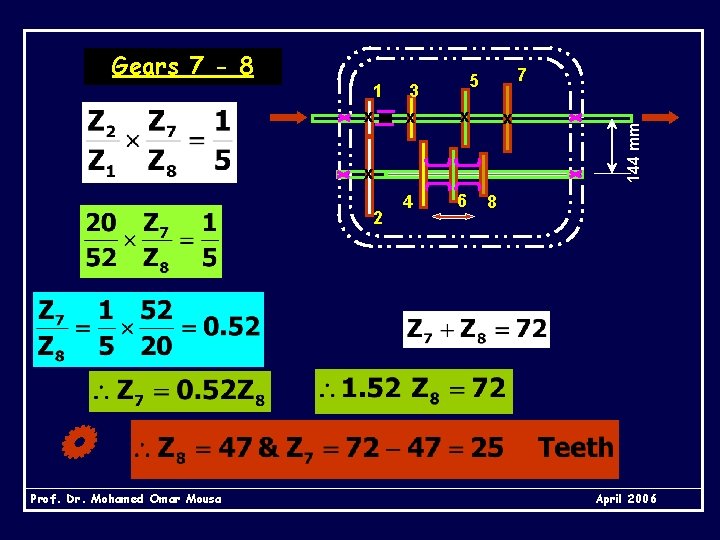
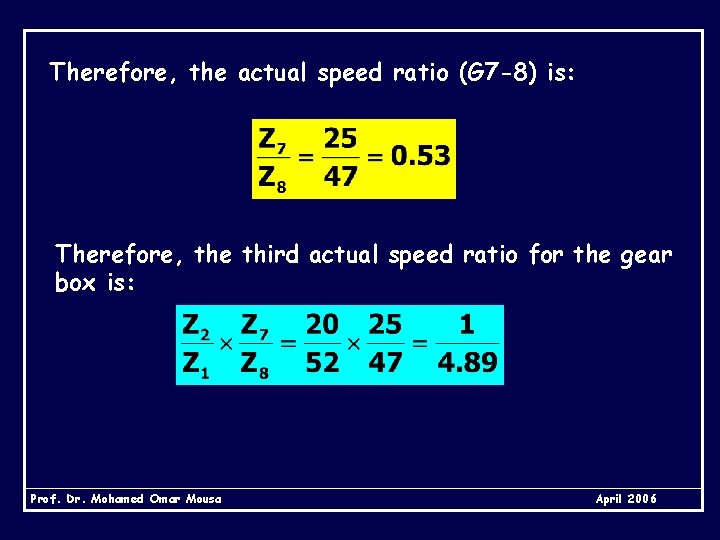
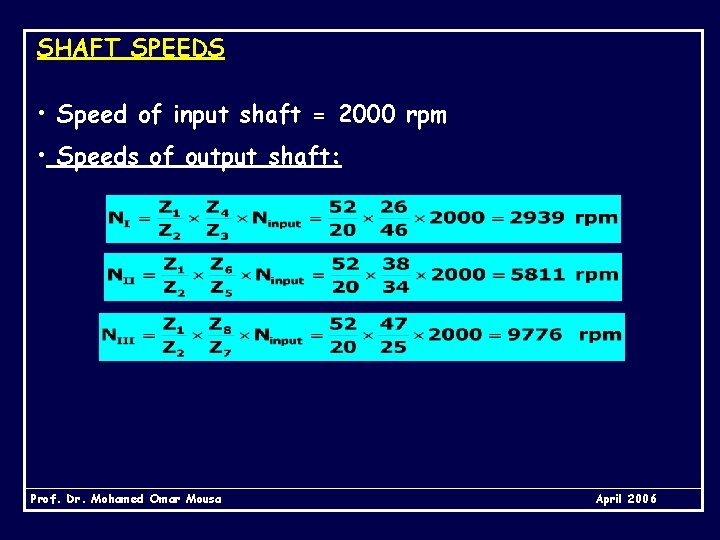
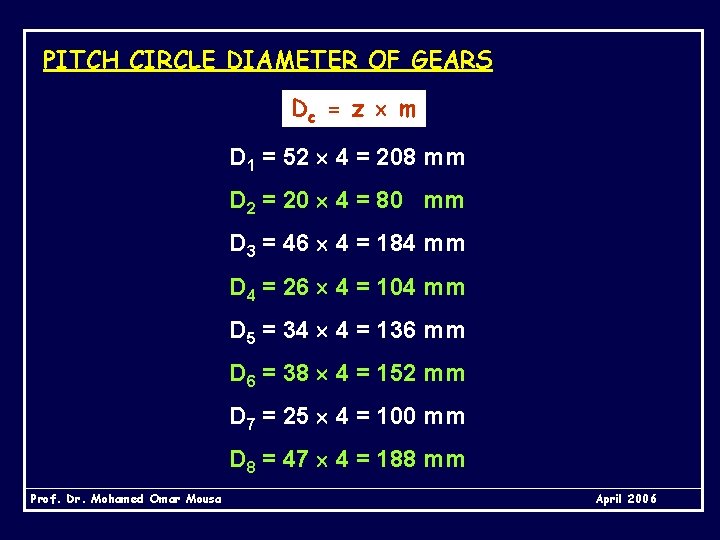
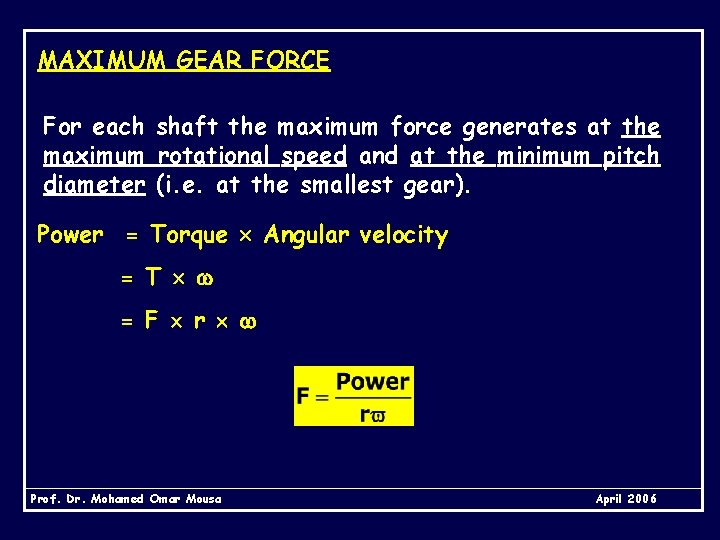
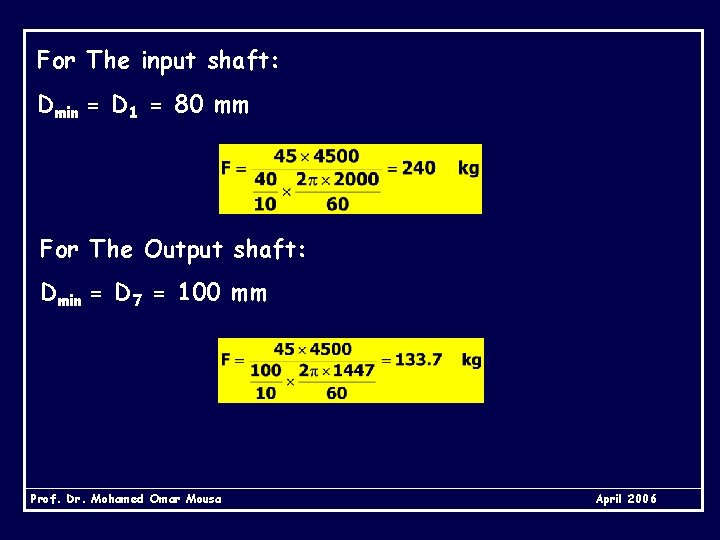
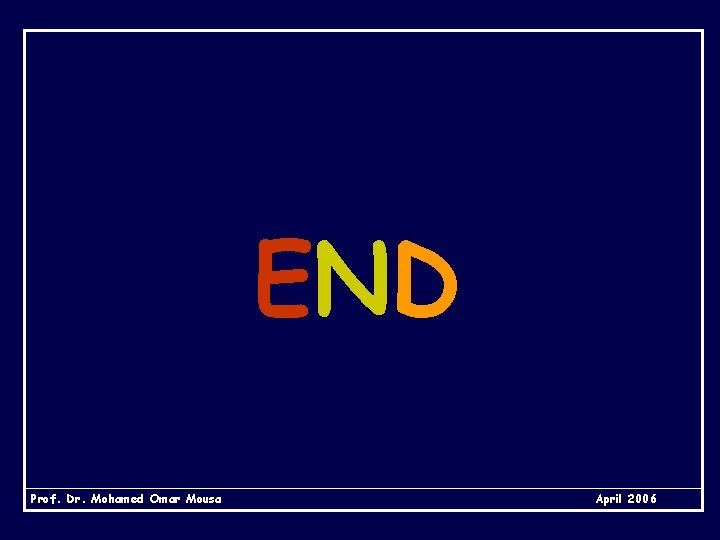
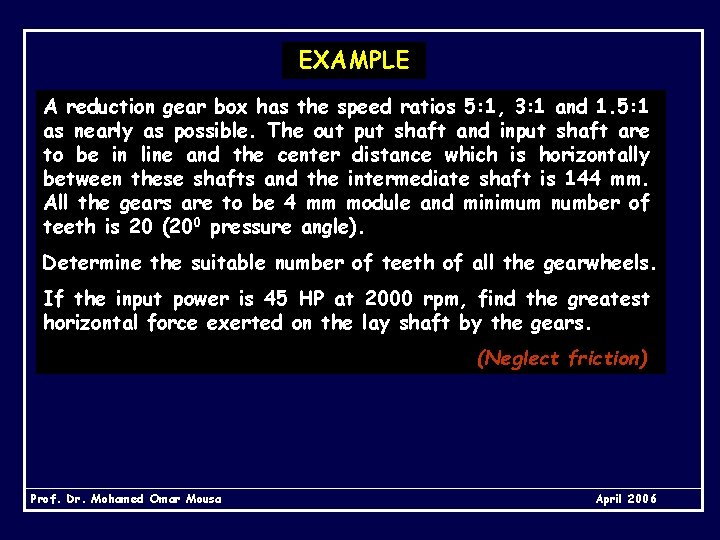
- Slides: 20
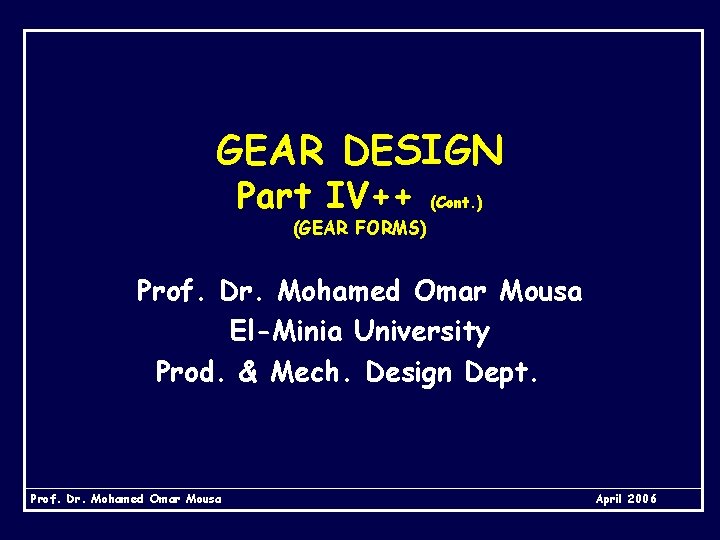
GEAR DESIGN Part IV++ (Cont. ) (GEAR FORMS) Prof. Dr. Mohamed Omar Mousa El-Minia University Prod. & Mech. Design Dept. Prof. Dr. Mohamed Omar Mousa April 2006
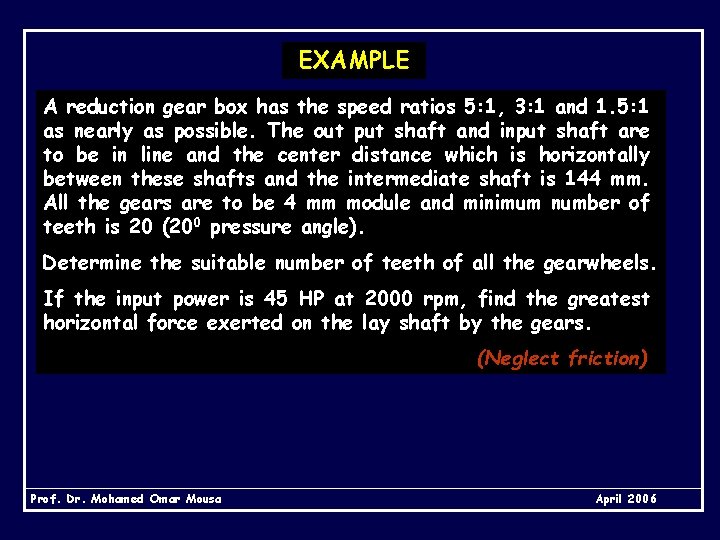
EXAMPLE A reduction gear box has the speed ratios 5: 1, 3: 1 and 1. 5: 1 as nearly as possible. The out put shaft and input shaft are to be in line and the center distance which is horizontally between these shafts and the intermediate shaft is 144 mm. All the gears are to be 4 mm module and minimum number of teeth is 20 (200 pressure angle). Determine the suitable number of teeth of all the gearwheels. If the input power is 45 HP at 2000 rpm, find the greatest horizontal force exerted on the lay shaft by the gears. (Neglect friction) Prof. Dr. Mohamed Omar Mousa April 2006
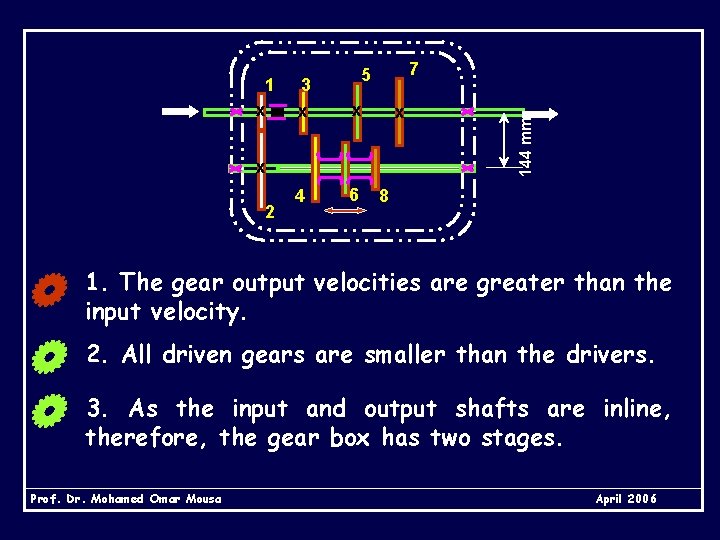
3 x x 4 6 x x 2 144 mm 1 x 7 5 8 1. The gear output velocities are greater than the input velocity. 2. All driven gears are smaller than the drivers. 3. As the input and output shafts are inline, therefore, the gear box has two stages. Prof. Dr. Mohamed Omar Mousa April 2006
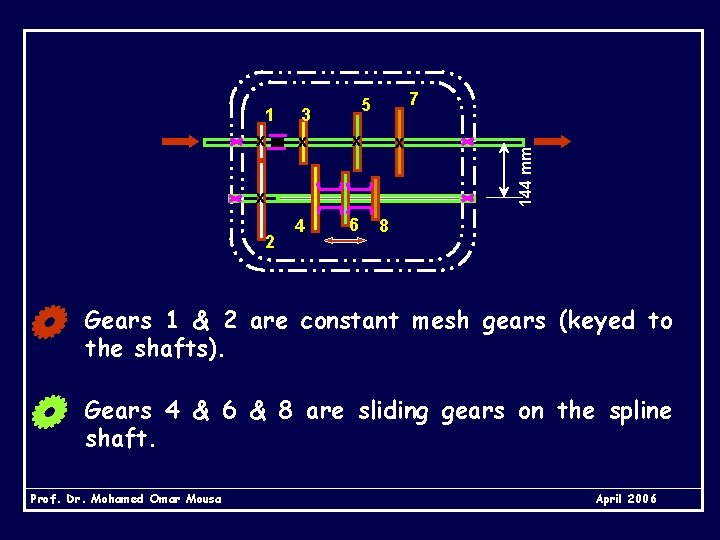
3 x x 4 6 x x 2 144 mm 1 x 7 5 8 Gears 1 & 2 are constant mesh gears (keyed to the shafts). Gears 4 & 6 & 8 are sliding gears on the spline shaft. Prof. Dr. Mohamed Omar Mousa April 2006
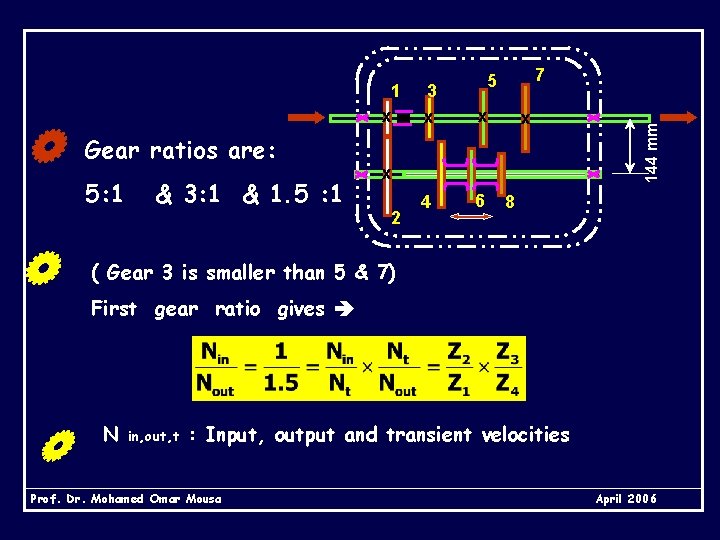
Gear ratios are: 5: 1 & 3: 1 & 1. 5 : 1 3 x x 4 6 x x 2 144 mm 1 x 7 5 8 ( Gear 3 is smaller than 5 & 7) First gear ratio gives N in, out, t : Input, output and transient velocities Prof. Dr. Mohamed Omar Mousa April 2006
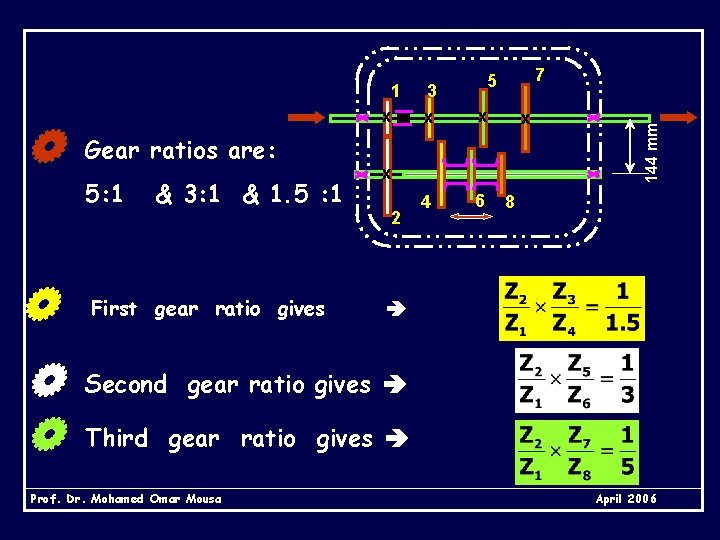
Gear ratios are: 5: 1 & 3: 1 & 1. 5 : 1 First gear ratio gives 3 x x 4 6 x x 2 144 mm 1 x 7 5 8 Second gear ratio gives Third gear ratio gives Prof. Dr. Mohamed Omar Mousa April 2006
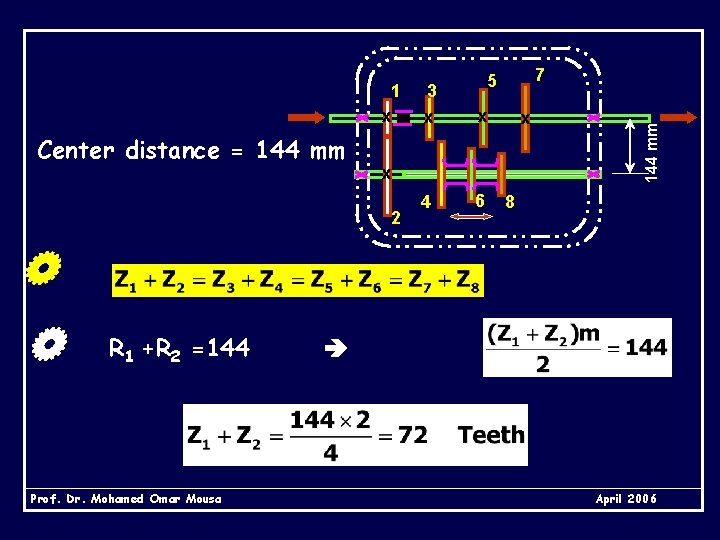
Center distance = 144 mm Prof. Dr. Mohamed Omar Mousa x 4 6 x x 2 R 1 +R 2 =144 3 x 144 mm 1 x 7 5 8 April 2006
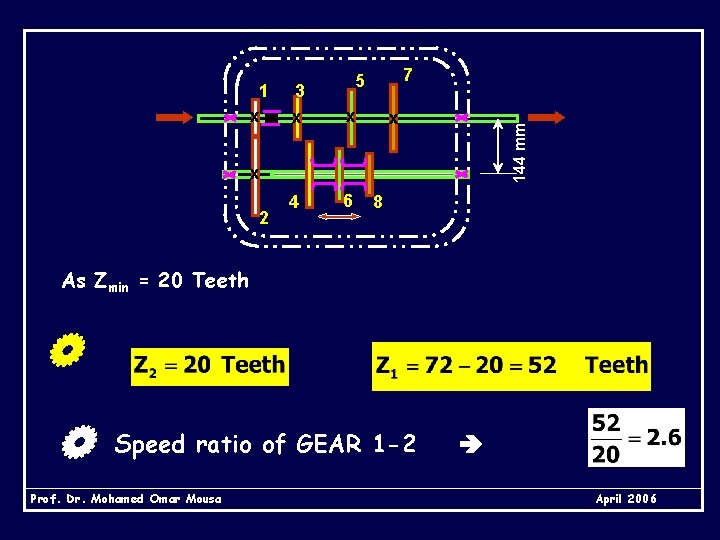
3 x x 4 6 x 144 mm 1 x 7 5 x 2 8 As Zmin = 20 Teeth Speed ratio of GEAR 1 -2 Prof. Dr. Mohamed Omar Mousa April 2006
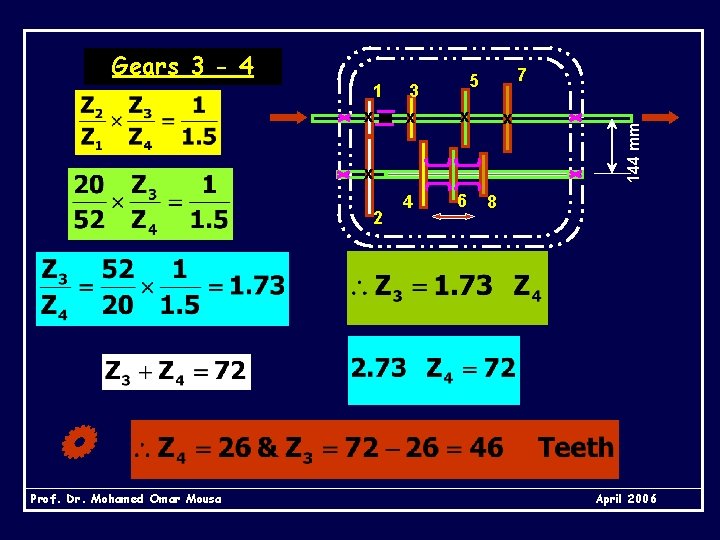
1 x 7 5 3 x x 4 6 x x 2 Prof. Dr. Mohamed Omar Mousa 144 mm Gears 3 - 4 8 April 2006
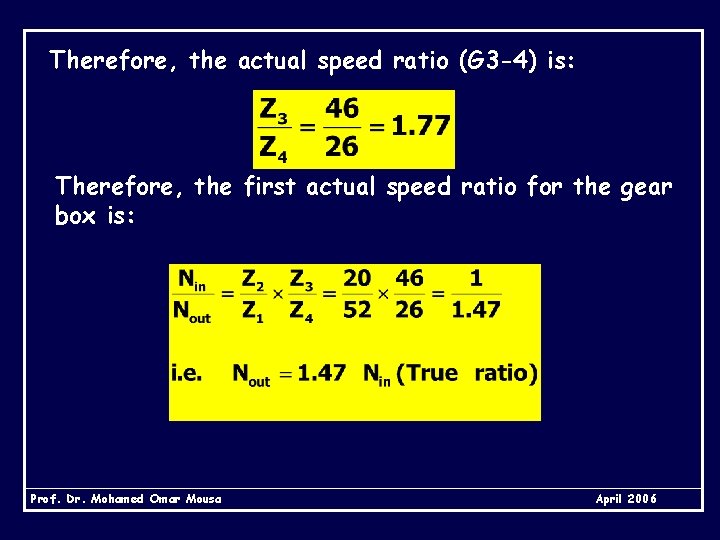
Therefore, the actual speed ratio (G 3 -4) is: Therefore, the first actual speed ratio for the gear box is: Prof. Dr. Mohamed Omar Mousa April 2006
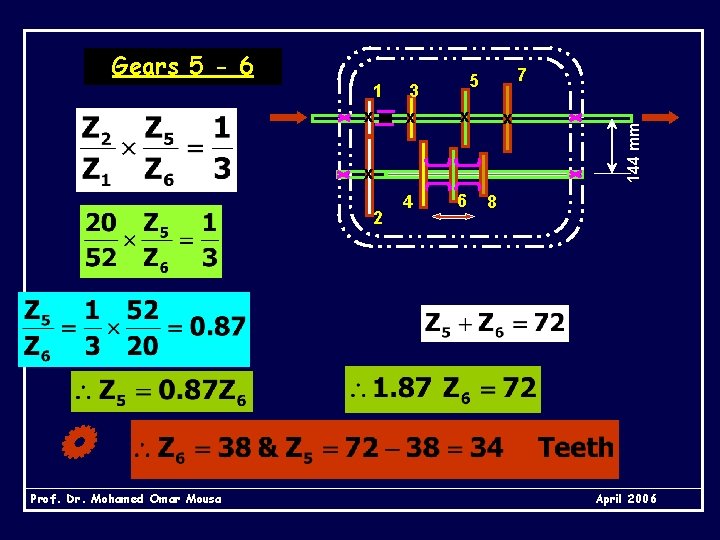
1 x 7 5 3 x x 4 6 x x 2 Prof. Dr. Mohamed Omar Mousa 144 mm Gears 5 - 6 8 April 2006
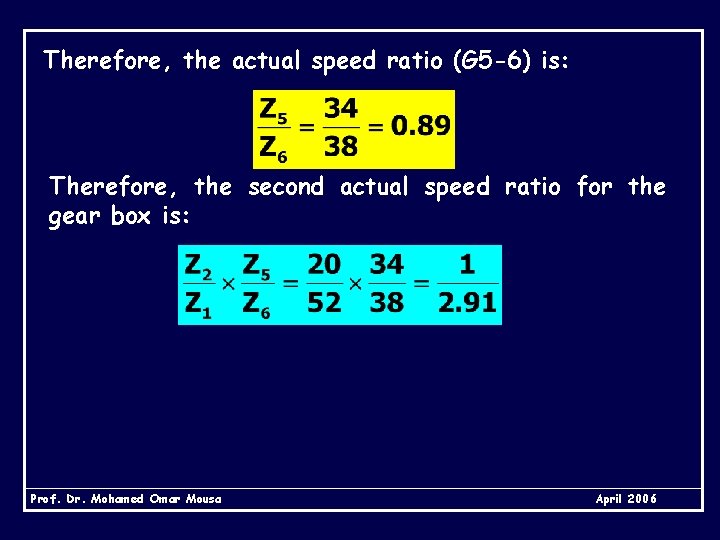
Therefore, the actual speed ratio (G 5 -6) is: Therefore, the second actual speed ratio for the gear box is: Prof. Dr. Mohamed Omar Mousa April 2006
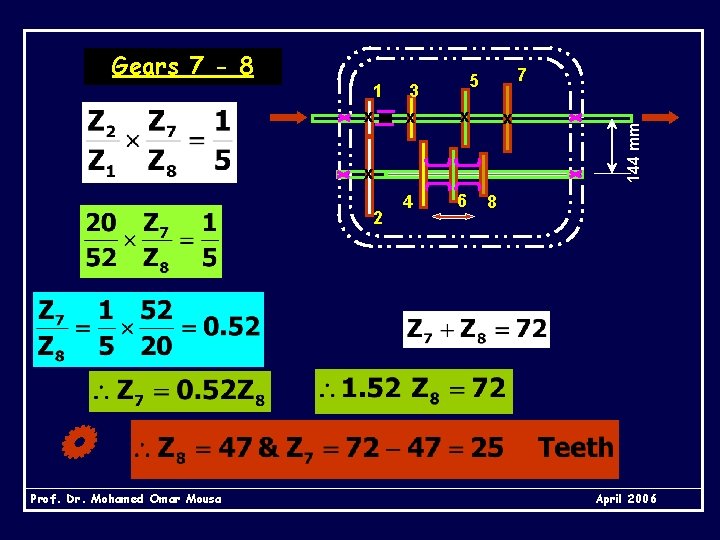
1 x 7 5 3 x x 4 6 x x 2 Prof. Dr. Mohamed Omar Mousa 144 mm Gears 7 - 8 8 April 2006
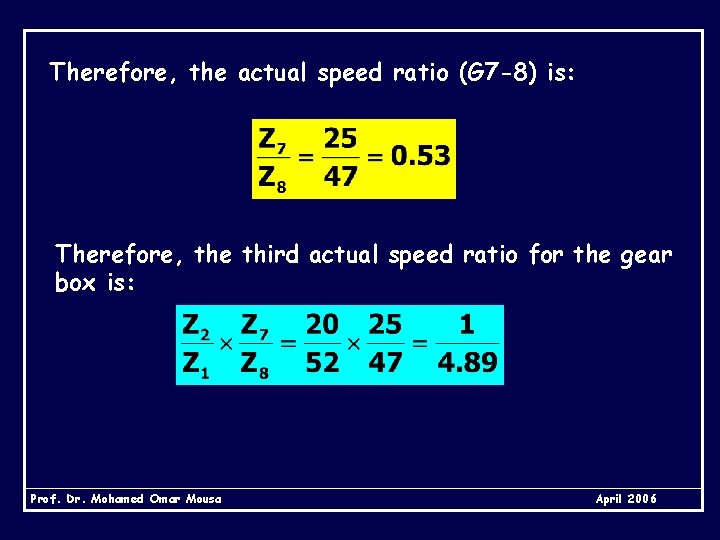
Therefore, the actual speed ratio (G 7 -8) is: Therefore, the third actual speed ratio for the gear box is: Prof. Dr. Mohamed Omar Mousa April 2006
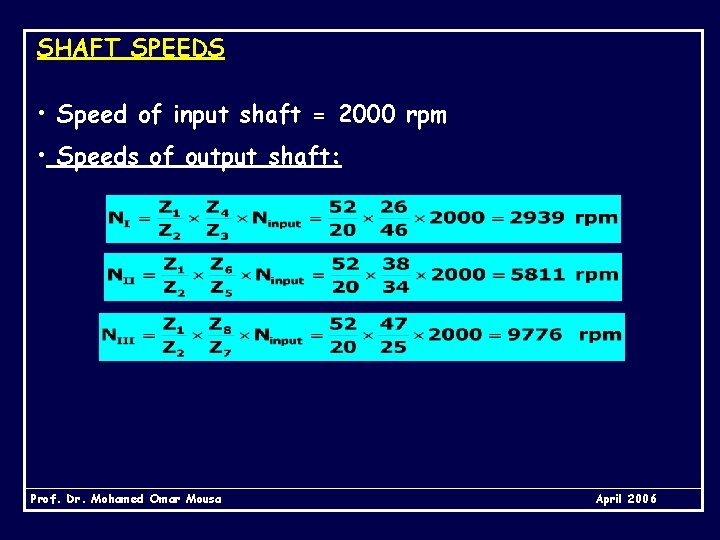
SHAFT SPEEDS • Speed of input shaft = 2000 rpm • Speeds of output shaft: Prof. Dr. Mohamed Omar Mousa April 2006
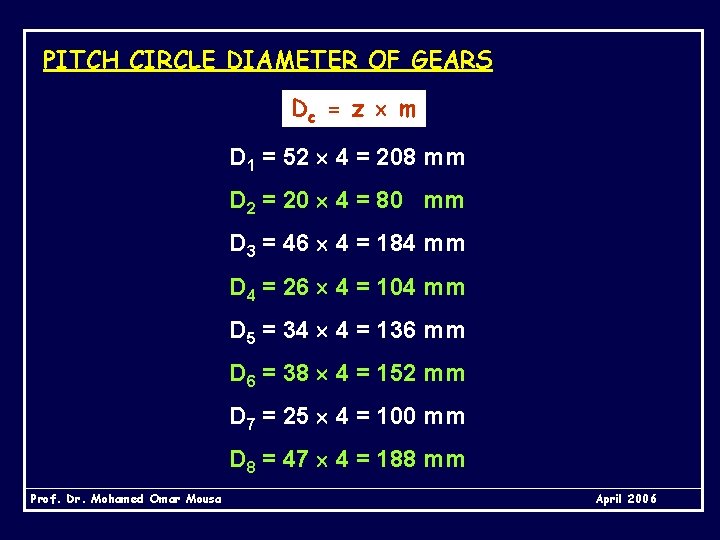
PITCH CIRCLE DIAMETER OF GEARS Dc = z m D 1 = 52 4 = 208 mm D 2 = 20 4 = 80 mm D 3 = 46 4 = 184 mm D 4 = 26 4 = 104 mm D 5 = 34 4 = 136 mm D 6 = 38 4 = 152 mm D 7 = 25 4 = 100 mm D 8 = 47 4 = 188 mm Prof. Dr. Mohamed Omar Mousa April 2006
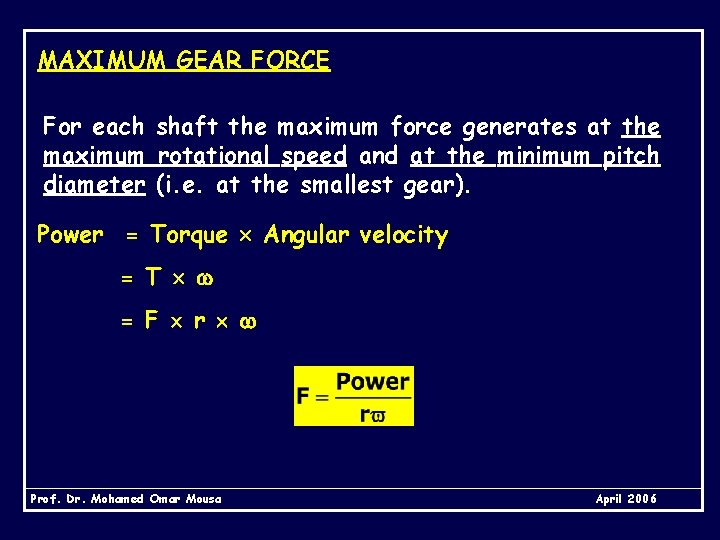
MAXIMUM GEAR FORCE For each shaft the maximum force generates at the maximum rotational speed and at the minimum pitch diameter (i. e. at the smallest gear). Power = Torque Angular velocity = T = F r Prof. Dr. Mohamed Omar Mousa April 2006
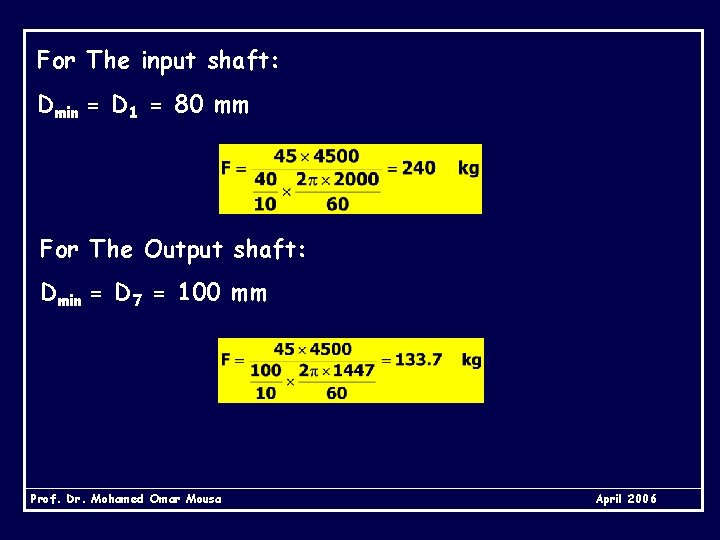
For The input shaft: Dmin = D 1 = 80 mm For The Output shaft: Dmin = D 7 = 100 mm Prof. Dr. Mohamed Omar Mousa April 2006
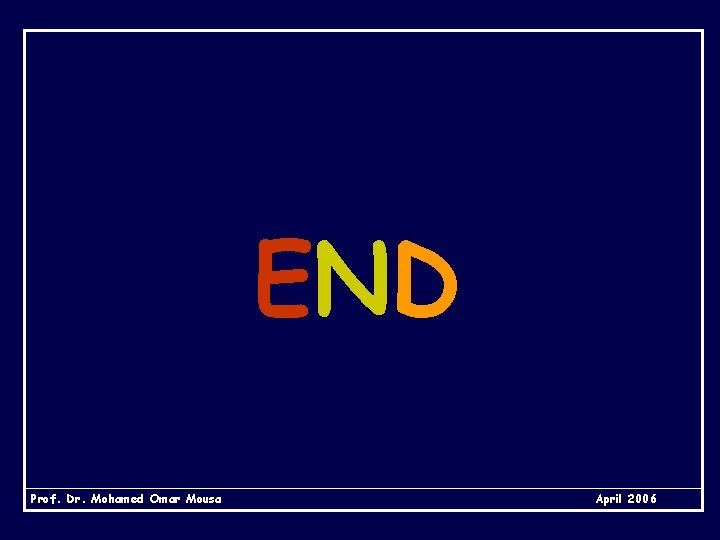
EN D Prof. Dr. Mohamed Omar Mousa April 2006
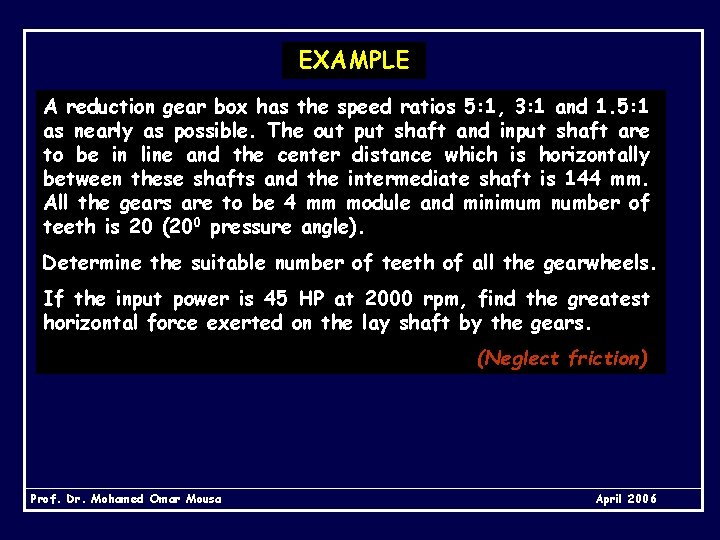
EXAMPLE A reduction gear box has the speed ratios 5: 1, 3: 1 and 1. 5: 1 as nearly as possible. The out put shaft and input shaft are to be in line and the center distance which is horizontally between these shafts and the intermediate shaft is 144 mm. All the gears are to be 4 mm module and minimum number of teeth is 20 (200 pressure angle). Determine the suitable number of teeth of all the gearwheels. If the input power is 45 HP at 2000 rpm, find the greatest horizontal force exerted on the lay shaft by the gears. (Neglect friction) Prof. Dr. Mohamed Omar Mousa April 2006
Cont or cont'd
Cont or cont'd
External and internal gear pump
Definition of gear ratio
Why are related forms more agreeable than unrelated forms?
Had contracted form
Why are related forms more agreeable than unrelated forms
Why are related forms more agreeable than unrelated forms?
Strong and weak forms
Part 4 forms of energy continued
Pneumatic shock absorber design
Tredgold approximation
Intermodal cont
Objective of un
Local winds
Cont'n air
Plusnet data
Un cont
301 cont
Celtic cont
Cont'n air