GEAR DESIGN Part III Prof Dr Mohamed Omar
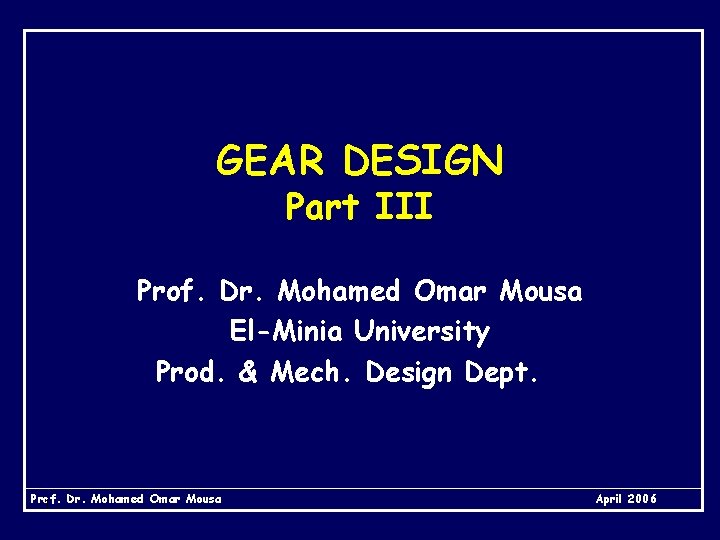
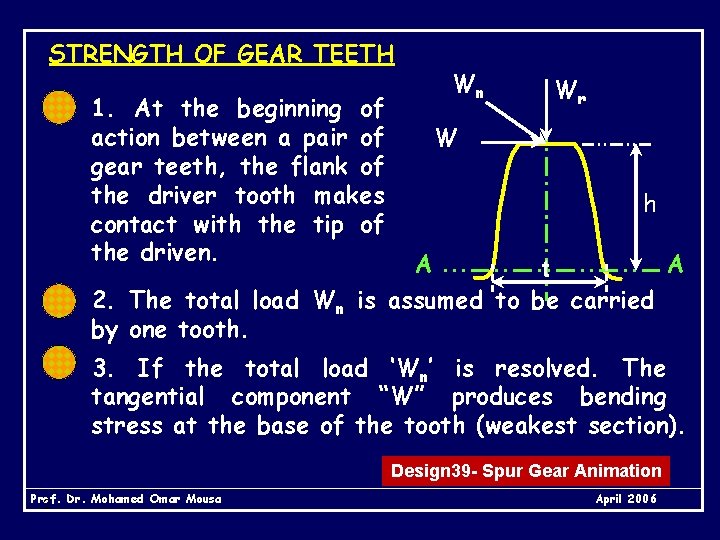
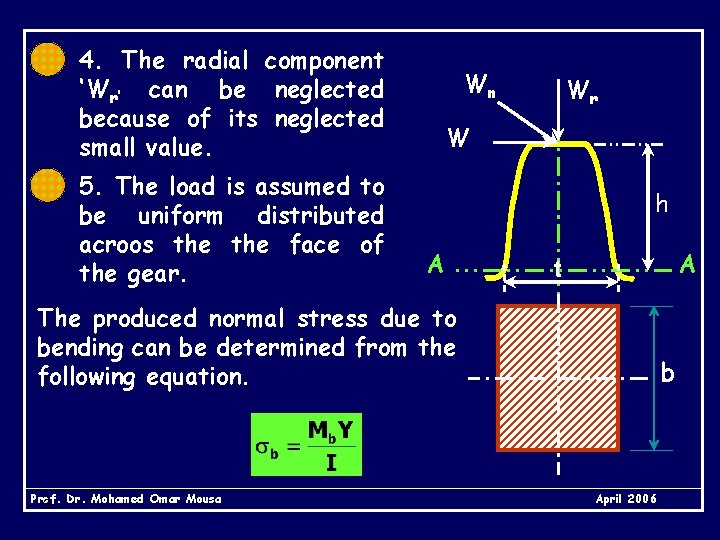
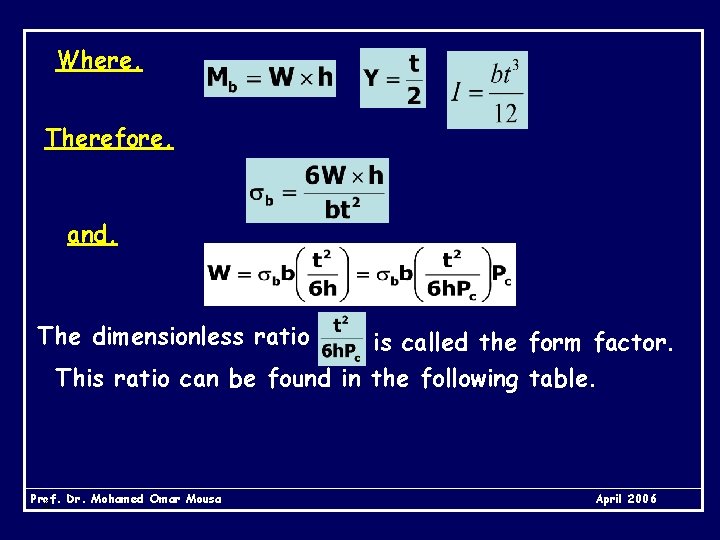
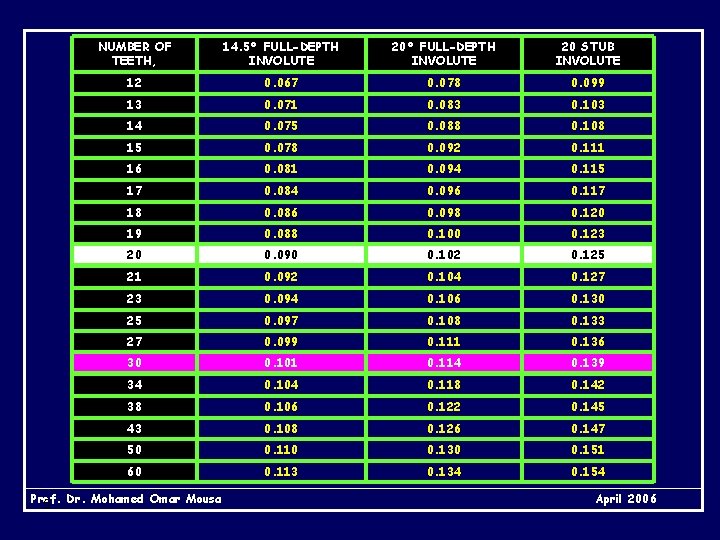
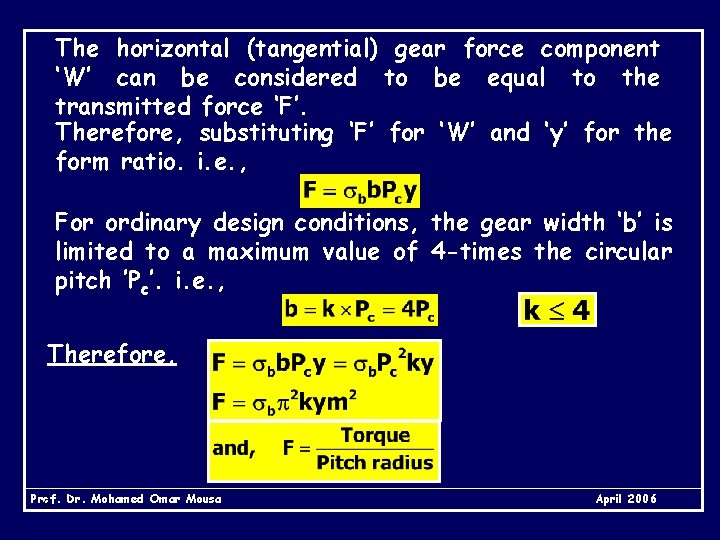
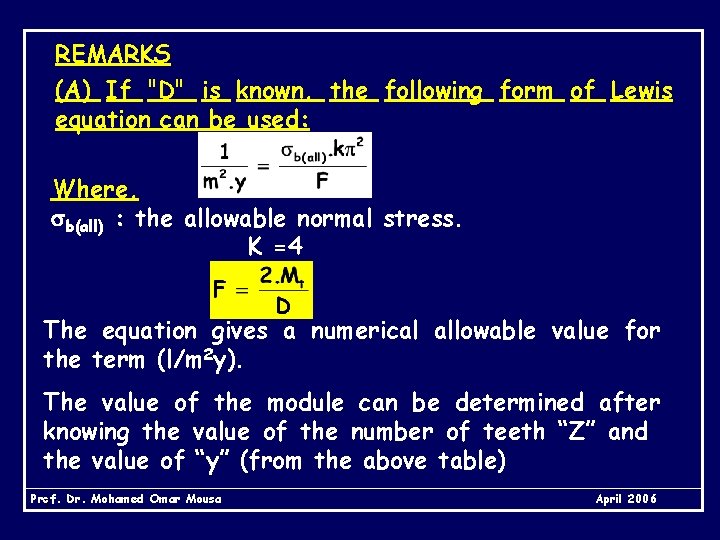
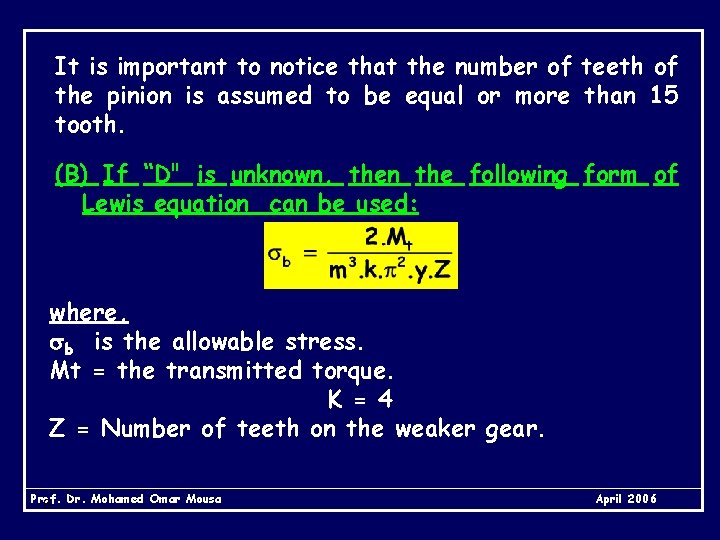
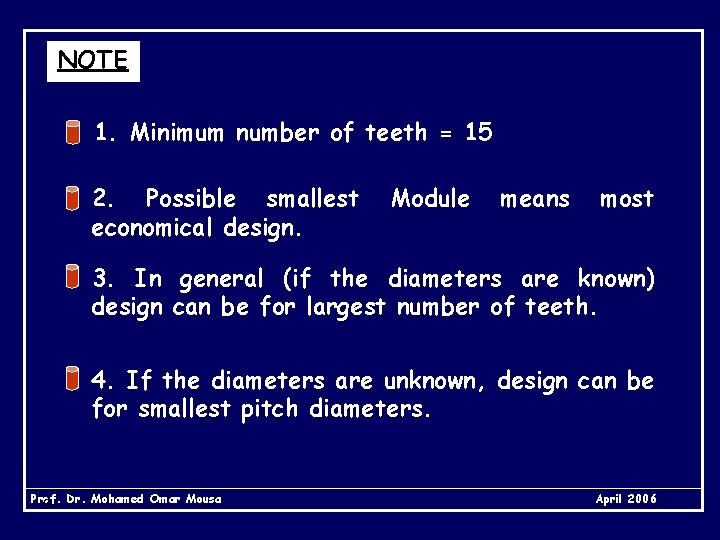
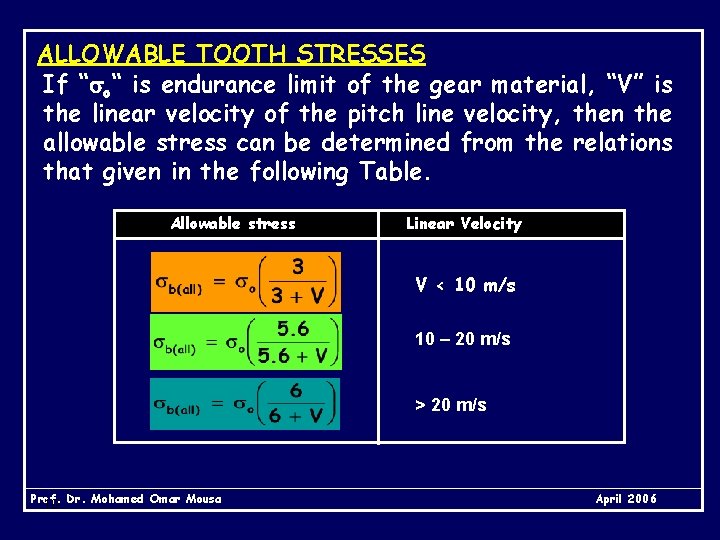
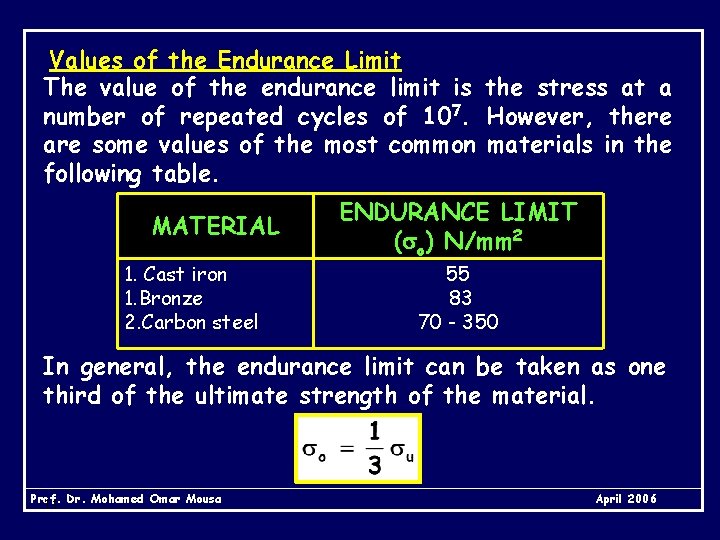
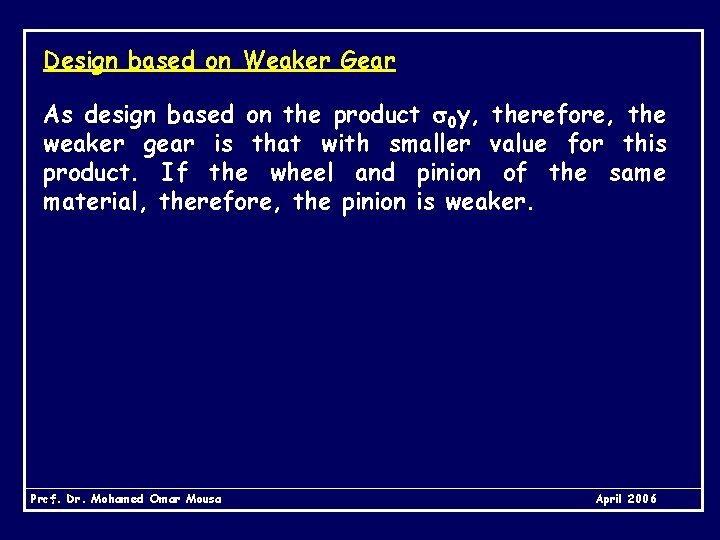
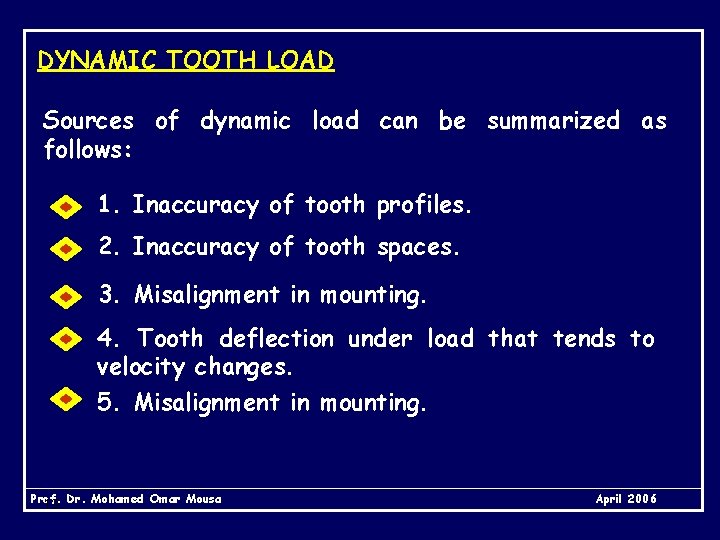
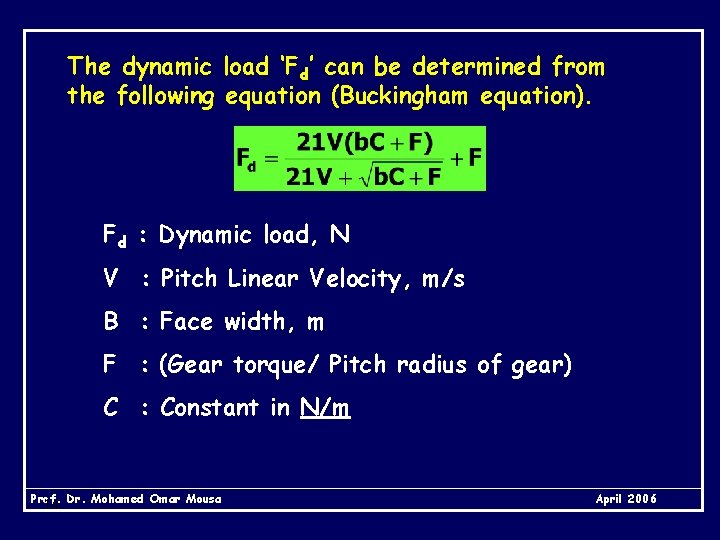
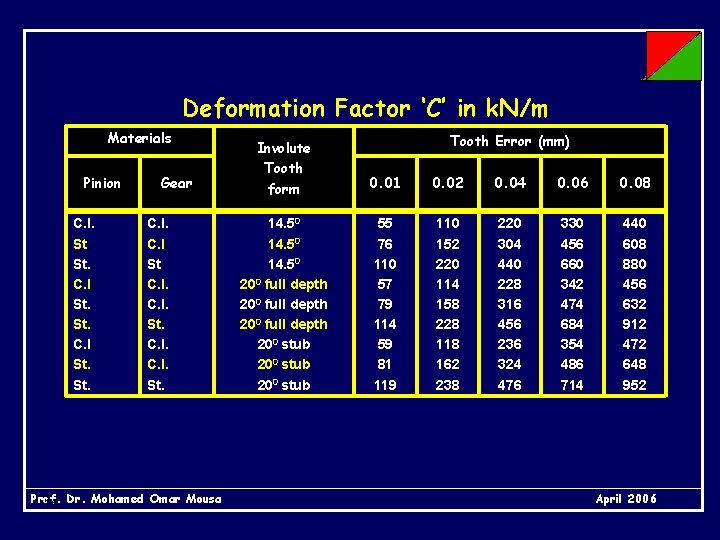
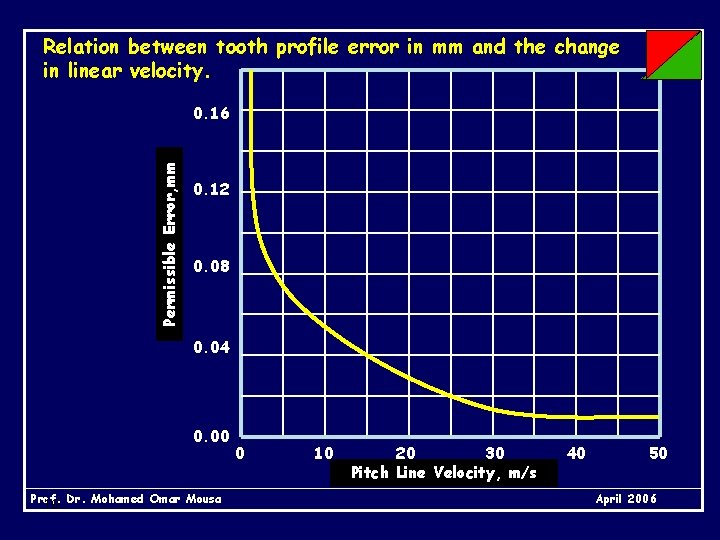
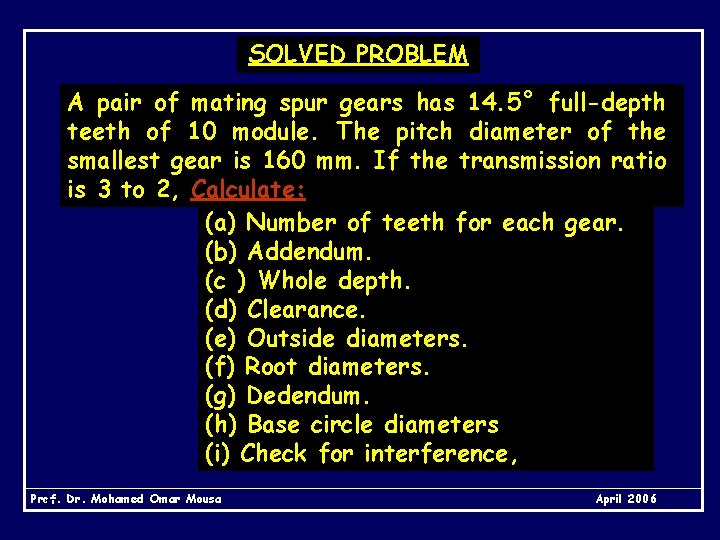
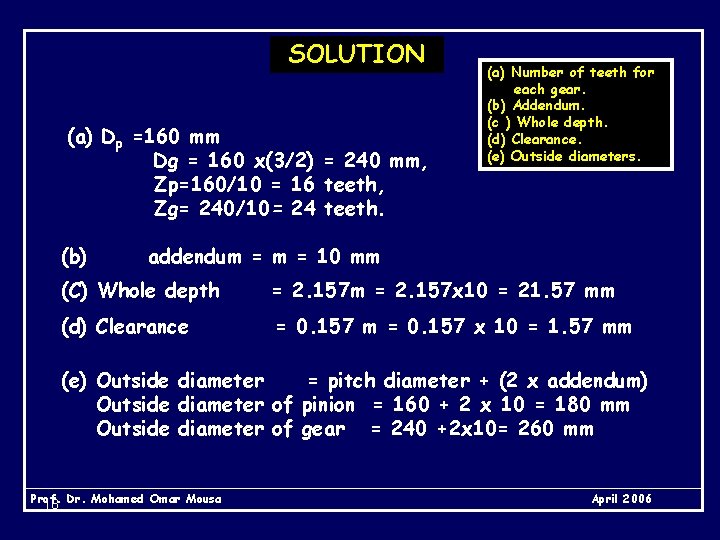
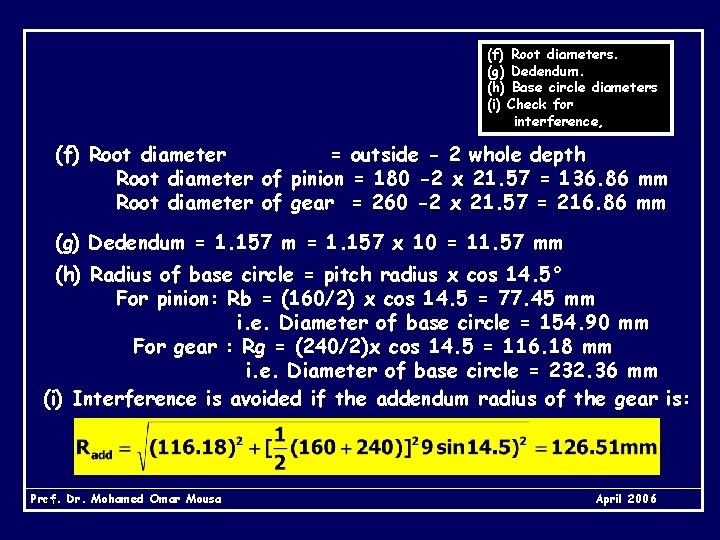
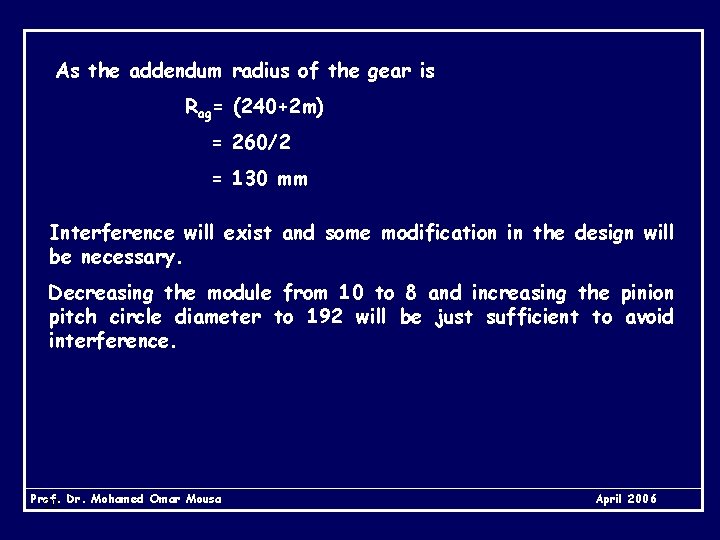
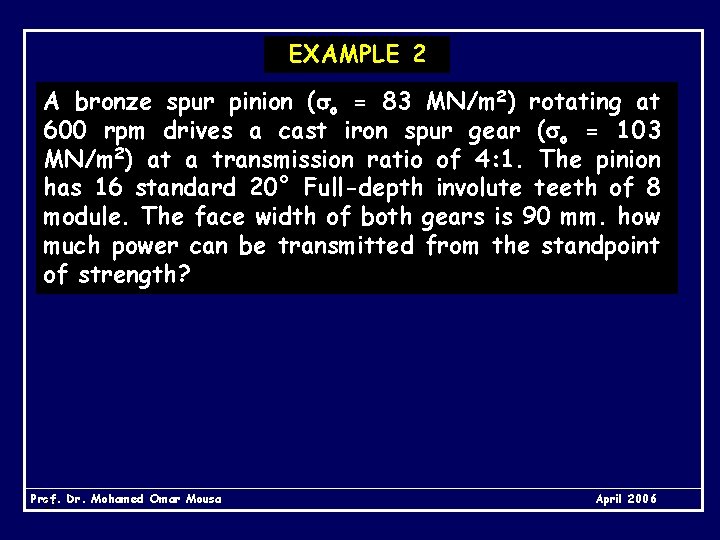
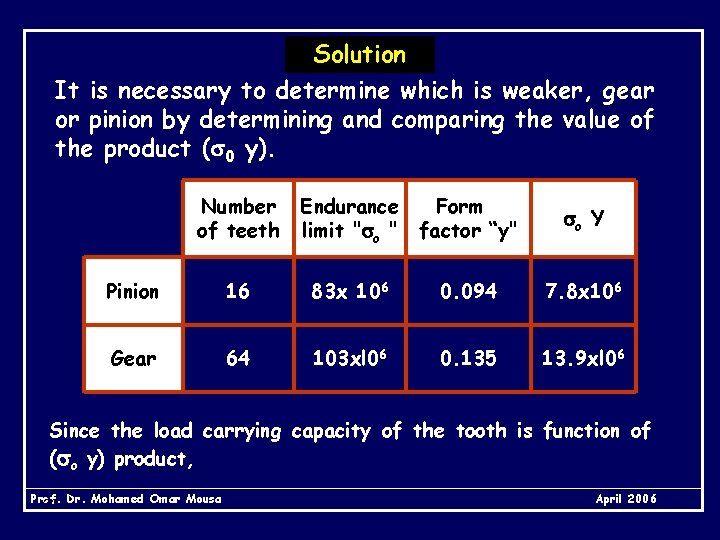
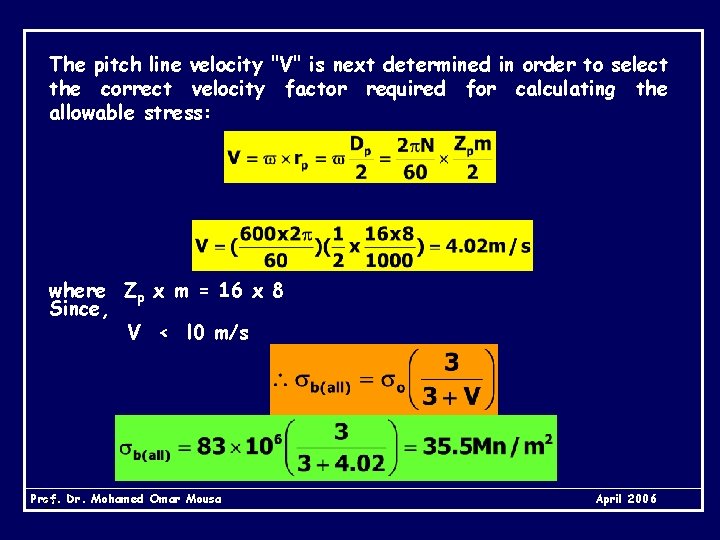
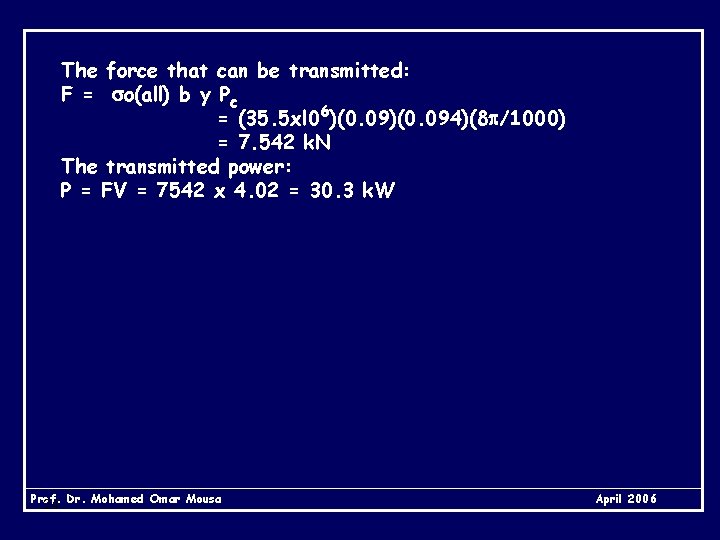
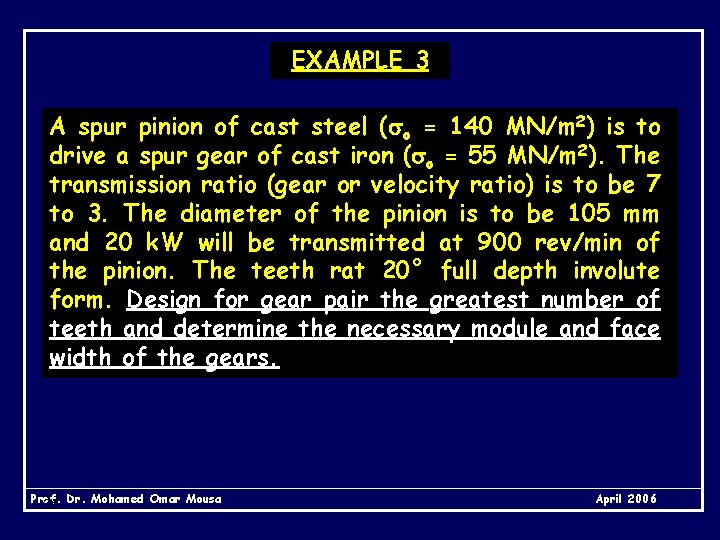
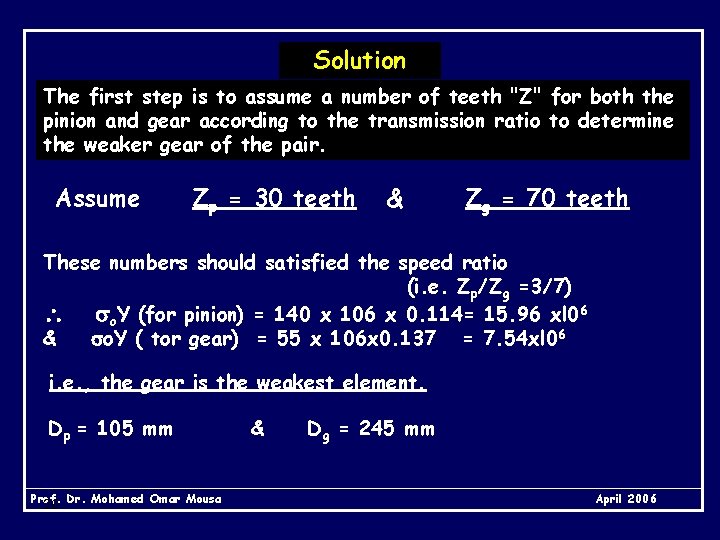
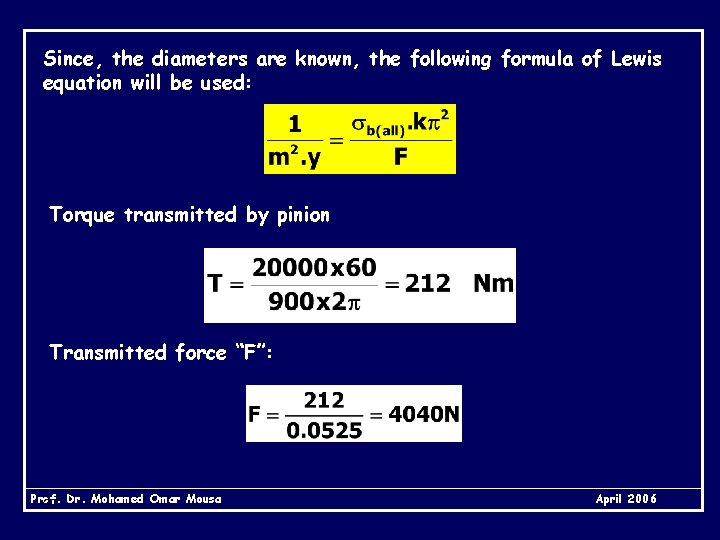
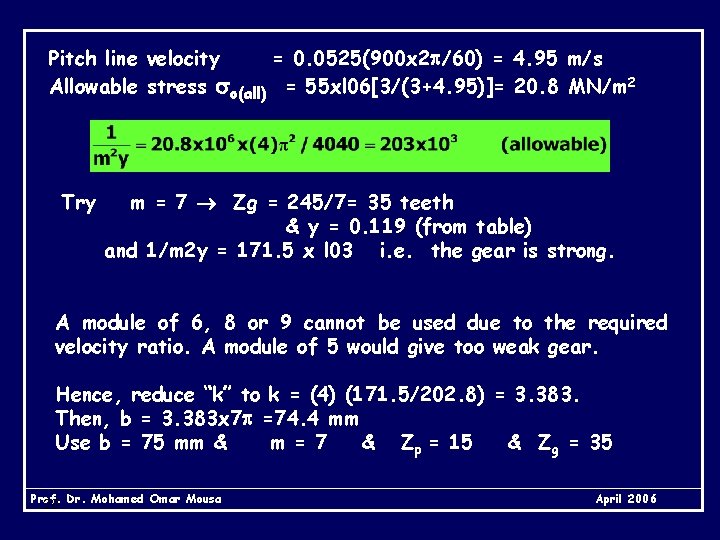
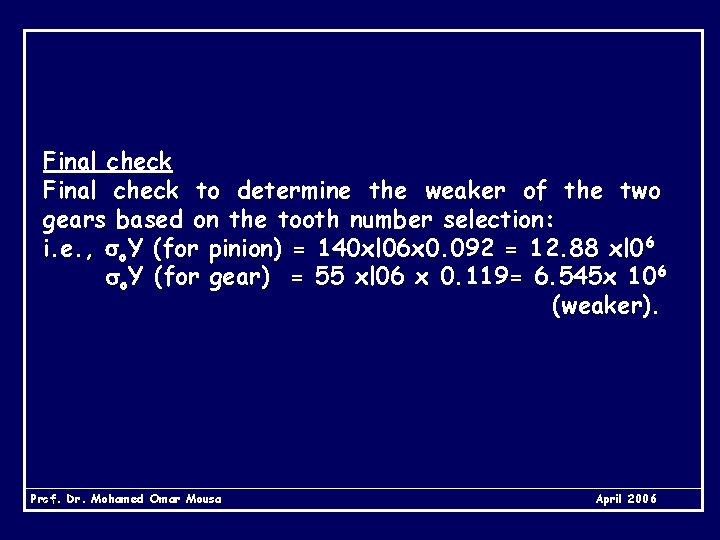
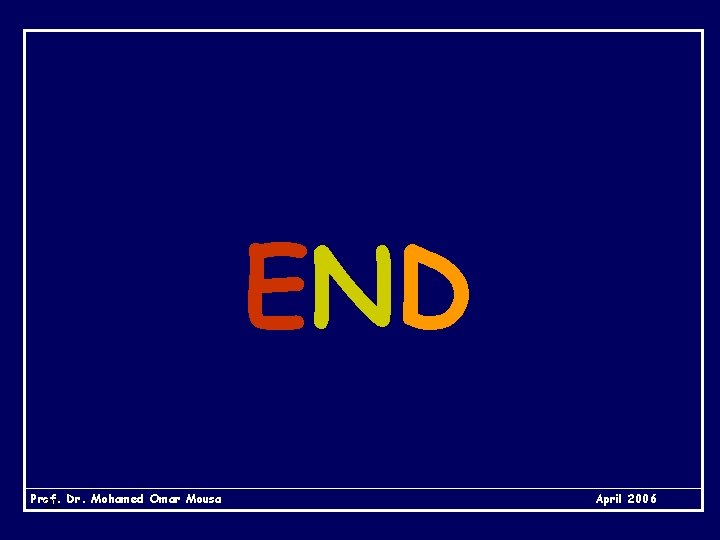
- Slides: 30
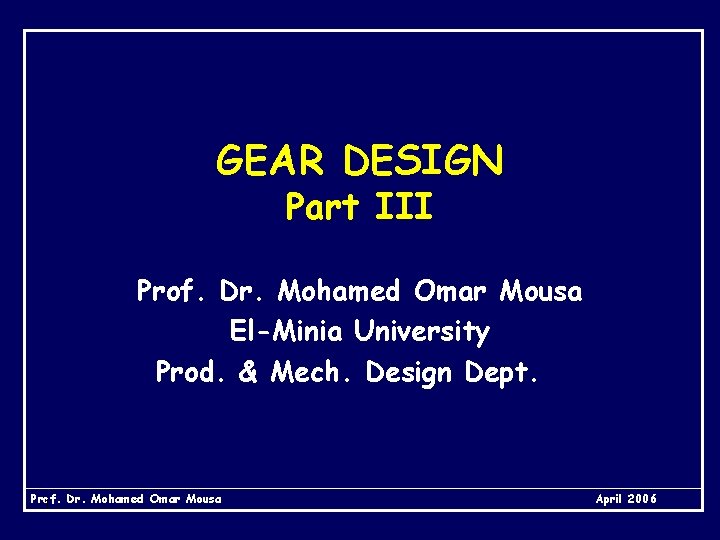
GEAR DESIGN Part III Prof. Dr. Mohamed Omar Mousa El-Minia University Prod. & Mech. Design Dept. Prof. 1 Dr. Mohamed Omar Mousa April 2006
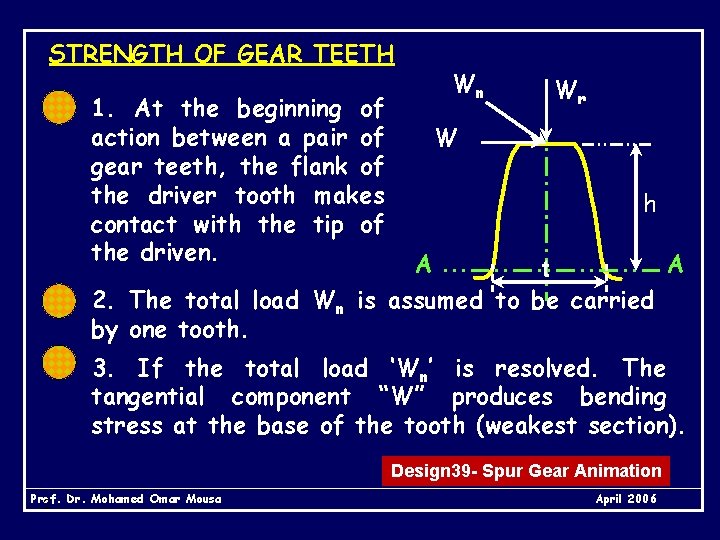
STRENGTH OF GEAR TEETH 1. At the beginning of action between a pair of gear teeth, the flank of the driver tooth makes contact with the tip of the driven. Wn Wr W h A A t 2. The total load Wn is assumed to be carried by one tooth. 3. If the total load ‘Wn’ is resolved. The tangential component “W” produces bending stress at the base of the tooth (weakest section). Design 39 - Spur Gear Animation Prof. 2 Dr. Mohamed Omar Mousa April 2006
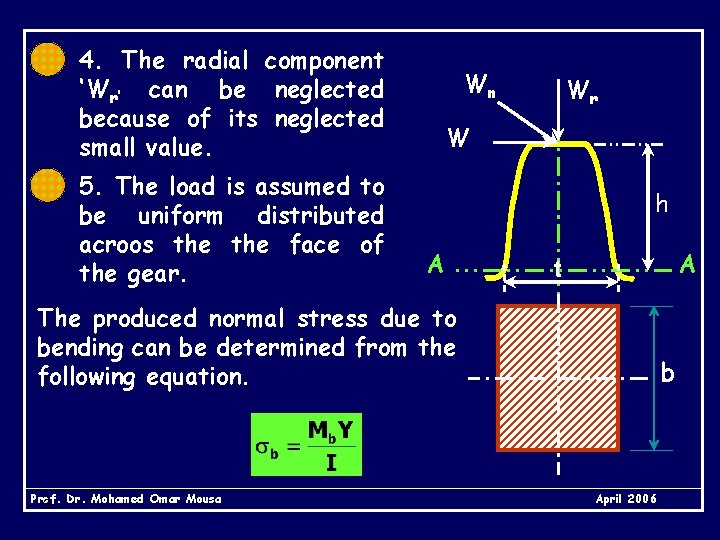
4. The radial component ‘Wr’ can be neglected because of its neglected small value. 5. The load is assumed to be uniform distributed acroos the face of the gear. Wn Wr W h A A t The produced normal stress due to bending can be determined from the following equation. Prof. 3 Dr. Mohamed Omar Mousa b April 2006
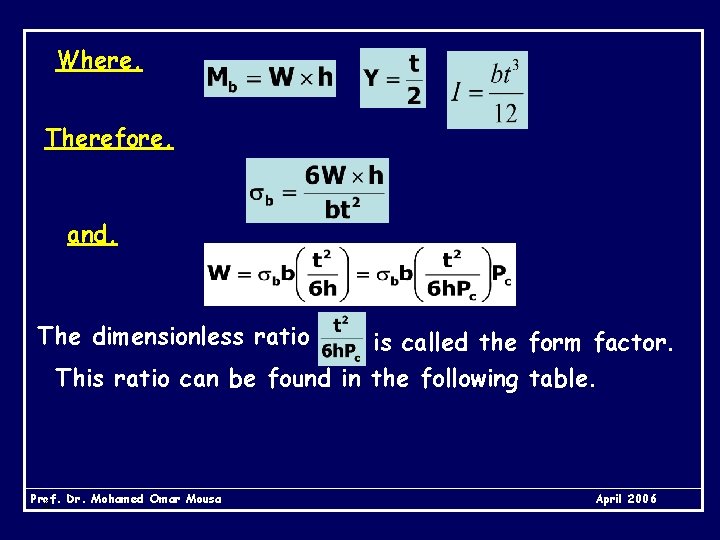
Where, Therefore, and, The dimensionless ratio is called the form factor. This ratio can be found in the following table. Prof. 4 Dr. Mohamed Omar Mousa April 2006
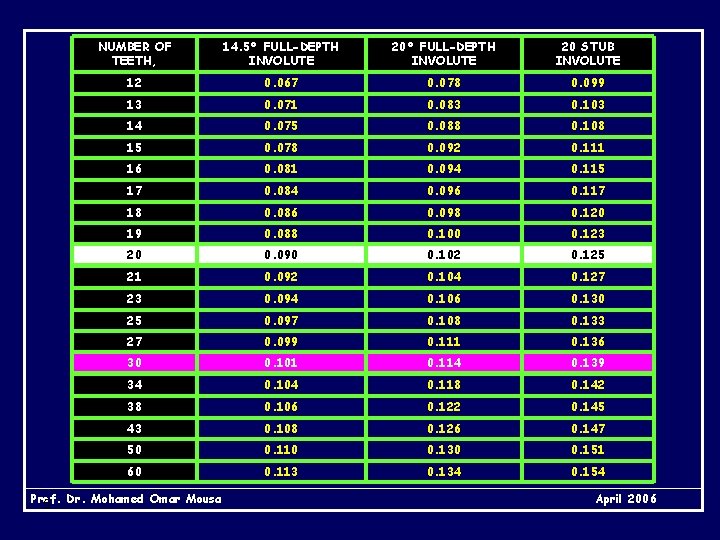
NUMBER OF TEETH, 14. 5° FULL-DEPTH INVOLUTE 20 STUB INVOLUTE 12 0. 067 0. 078 0. 099 13 0. 071 0. 083 0. 103 14 0. 075 0. 088 0. 108 15 0. 078 0. 092 0. 111 16 0. 081 0. 094 0. 115 17 0. 084 0. 096 0. 117 18 0. 086 0. 098 0. 120 19 0. 088 0. 100 0. 123 20 0. 090 0. 102 0. 125 21 0. 092 0. 104 0. 127 23 0. 094 0. 106 0. 130 25 0. 097 0. 108 0. 133 27 0. 099 0. 111 0. 136 30 0. 101 0. 114 0. 139 34 0. 104 0. 118 0. 142 38 0. 106 0. 122 0. 145 43 0. 108 0. 126 0. 147 50 0. 110 0. 130 0. 151 60 0. 113 0. 134 0. 154 Prof. 5 Dr. Mohamed Omar Mousa April 2006
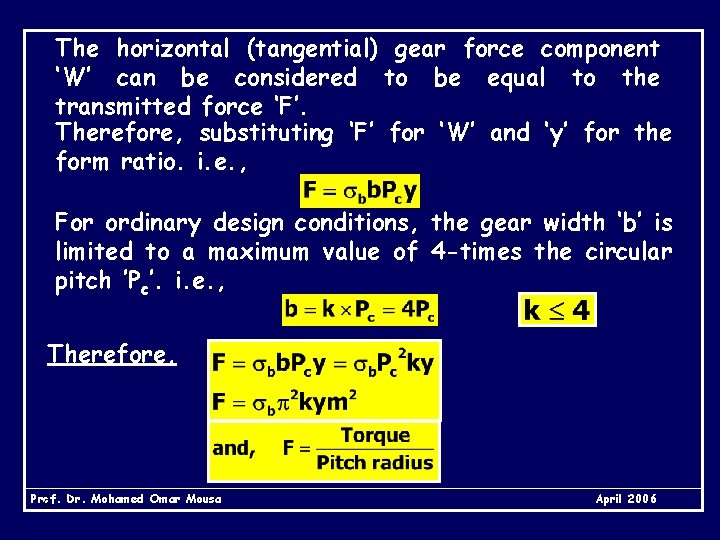
The horizontal (tangential) gear force component ‘W’ can be considered to be equal to the transmitted force ‘F’. Therefore, substituting ‘F’ for ‘W’ and ‘y’ for the form ratio. i. e. , For ordinary design conditions, the gear width ‘b’ is limited to a maximum value of 4 -times the circular pitch ’Pc’. i. e. , Therefore, Prof. 6 Dr. Mohamed Omar Mousa April 2006
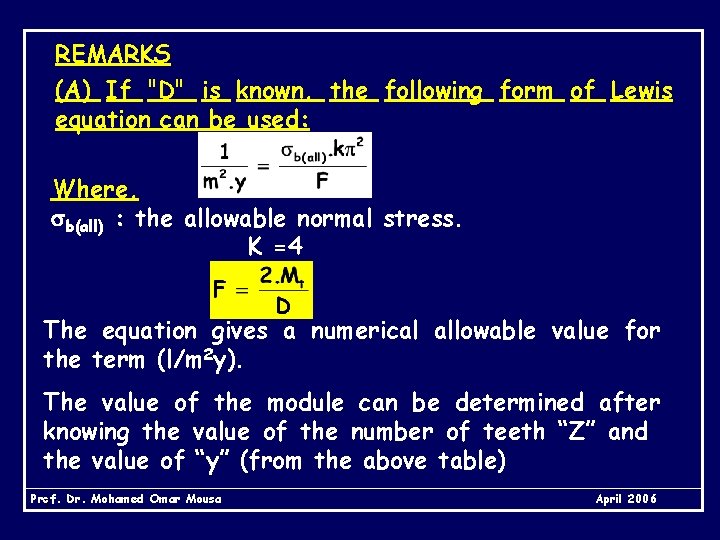
REMARKS (A) If "D" is known, the following form of Lewis equation can be used: Where, b(all) : the allowable normal stress. K =4 The equation gives a numerical allowable value for the term (l/m 2 y). The value of the module can be determined after knowing the value of the number of teeth “Z” and the value of “y” (from the above table) Prof. 7 Dr. Mohamed Omar Mousa April 2006
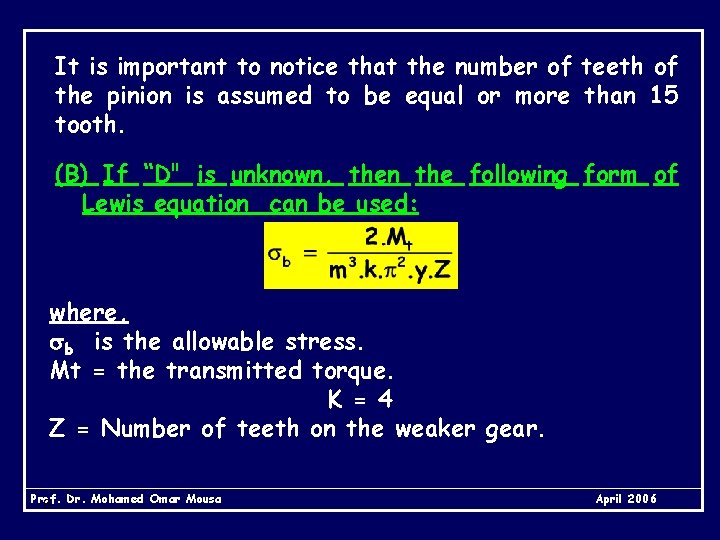
It is important to notice that the number of teeth of the pinion is assumed to be equal or more than 15 tooth. (B) If “D" is unknown, then the following form of Lewis equation can be used: where, b is the allowable stress. Mt = the transmitted torque. K = 4 Z = Number of teeth on the weaker gear. Prof. 8 Dr. Mohamed Omar Mousa April 2006
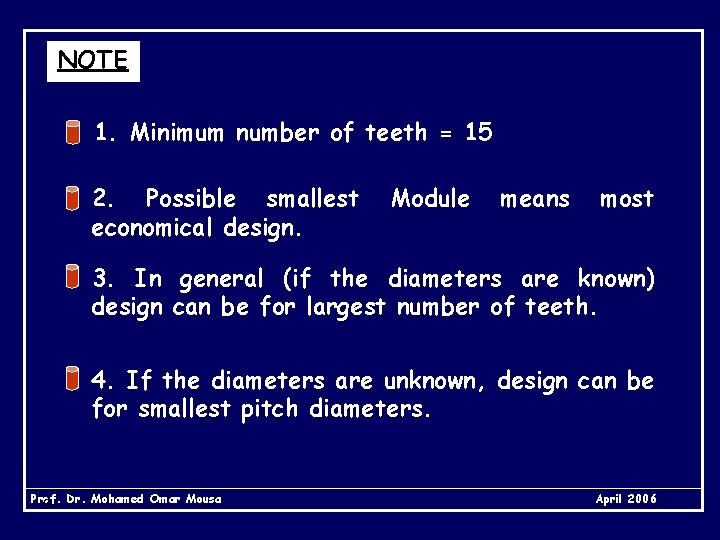
NOTE 1. Minimum number of teeth = 15 2. Possible smallest economical design. Module means most 3. In general (if the diameters are known) design can be for largest number of teeth. 4. If the diameters are unknown, design can be for smallest pitch diameters. Prof. 9 Dr. Mohamed Omar Mousa April 2006
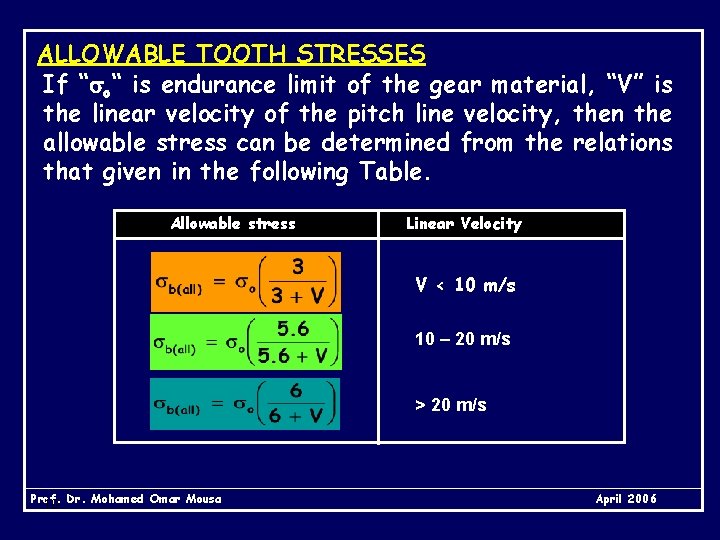
ALLOWABLE TOOTH STRESSES If “ o“ is endurance limit of the gear material, “V” is the linear velocity of the pitch line velocity, then the allowable stress can be determined from the relations that given in the following Table. Allowable stress Linear Velocity V < 10 m/s 10 – 20 m/s > 20 m/s Prof. 10 Dr. Mohamed Omar Mousa April 2006
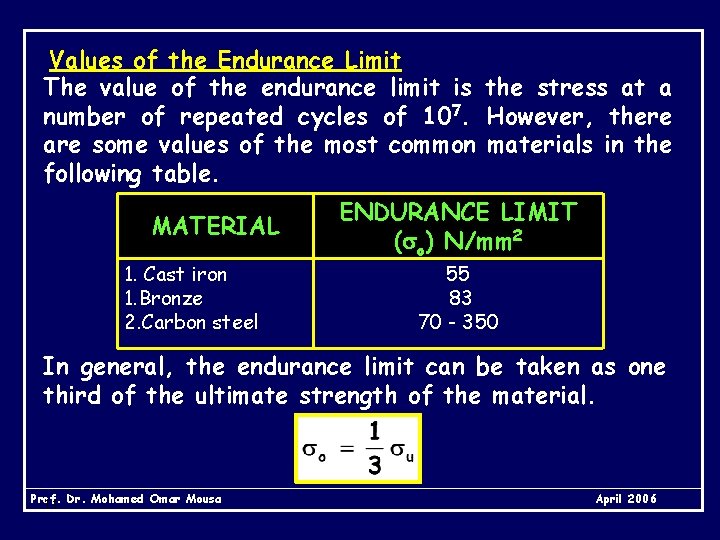
Values of the Endurance Limit The value of the endurance limit is the stress at a number of repeated cycles of 107. However, there are some values of the most common materials in the following table. MATERIAL 1. Cast iron 1. Bronze 2. Carbon steel ENDURANCE LIMIT ( o) N/mm 2 55 83 70 - 350 In general, the endurance limit can be taken as one third of the ultimate strength of the material. Prof. 11 Dr. Mohamed Omar Mousa April 2006
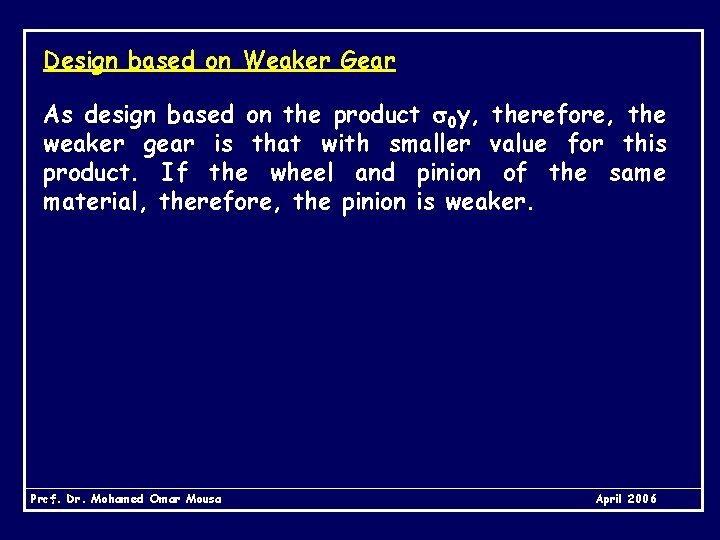
Design based on Weaker Gear As design based on the product 0 y, therefore, the weaker gear is that with smaller value for this product. If the wheel and pinion of the same material, therefore, the pinion is weaker. Prof. 12 Dr. Mohamed Omar Mousa April 2006
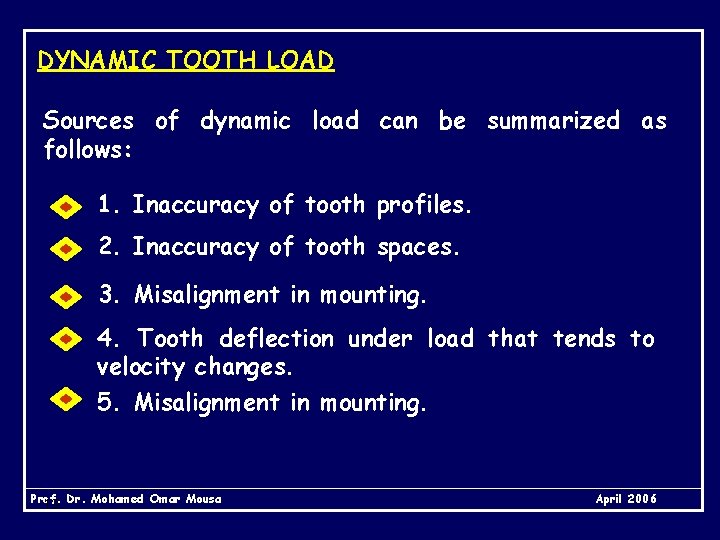
DYNAMIC TOOTH LOAD Sources of dynamic load can be summarized as follows: 1. Inaccuracy of tooth profiles. 2. Inaccuracy of tooth spaces. 3. Misalignment in mounting. 4. Tooth deflection under load that tends to velocity changes. 5. Misalignment in mounting. Prof. 13 Dr. Mohamed Omar Mousa April 2006
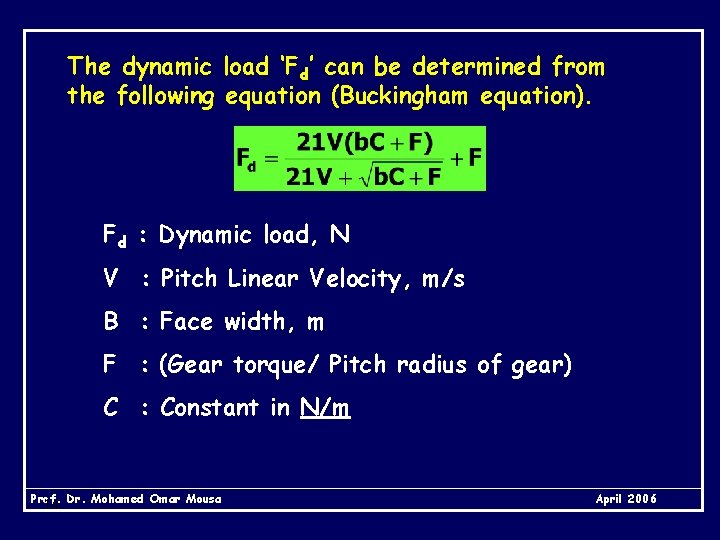
The dynamic load ‘Fd’ can be determined from the following equation (Buckingham equation). Fd : Dynamic load, N V : Pitch Linear Velocity, m/s B : Face width, m F : (Gear torque/ Pitch radius of gear) C : Constant in N/m Prof. 14 Dr. Mohamed Omar Mousa April 2006
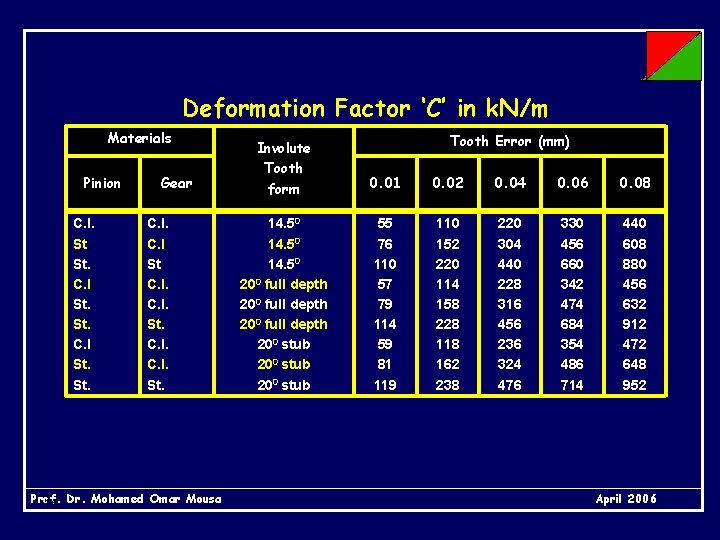
Deformation Factor ‘C’ in k. N/m Materials Pinion C. I. St. St. C. I. St. Gear C. I. St. Prof. 15 Dr. Mohamed Omar Mousa Tooth Error (mm) Involute Tooth form 0. 01 0. 02 0. 04 0. 06 0. 08 14. 50 200 full depth 200 stub 55 76 110 57 79 114 59 81 119 110 152 220 114 158 228 118 162 238 220 304 440 228 316 456 236 324 476 330 456 660 342 474 684 354 486 714 440 608 880 456 632 912 472 648 952 April 2006
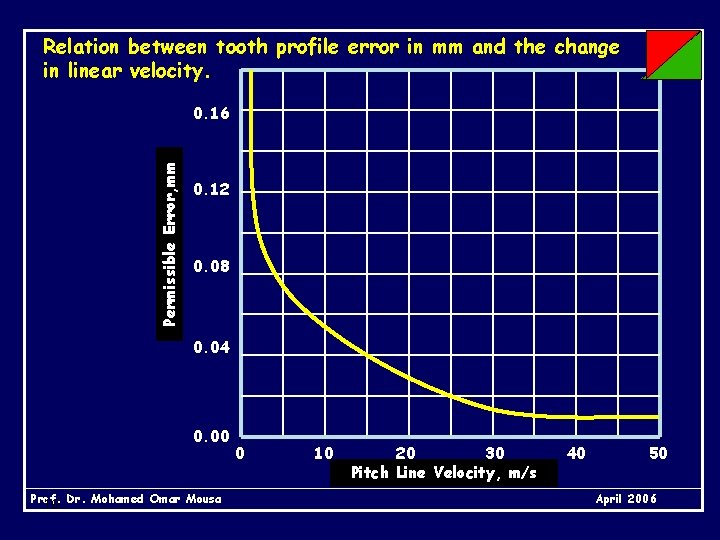
Relation between tooth profile error in mm and the change in linear velocity. Permissible Error, mm 0. 16 0. 12 0. 08 0. 04 0. 00 Prof. 16 Dr. Mohamed Omar Mousa 0 10 20 30 Pitch Line Velocity, m/s 40 50 April 2006
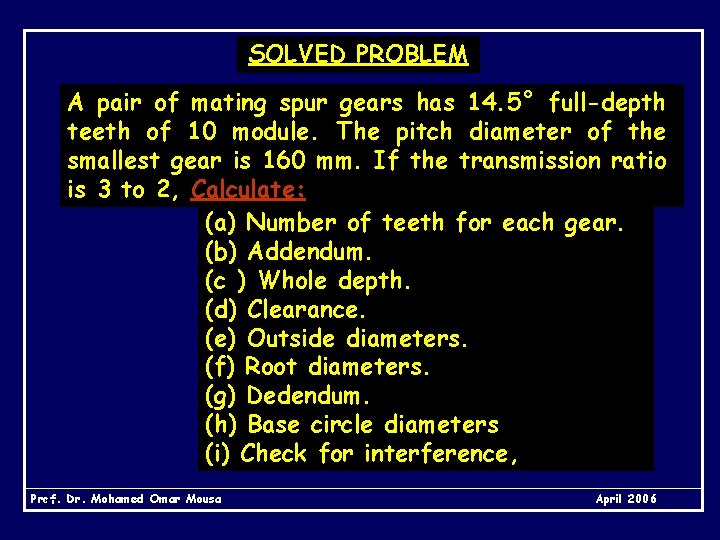
SOLVED PROBLEM A pair of mating spur gears has 14. 5° full-depth teeth of 10 module. The pitch diameter of the smallest gear is 160 mm. If the transmission ratio is 3 to 2, Calculate: (a) Number of teeth for each gear. (b) Addendum. (c ) Whole depth. (d) Clearance. (e) Outside diameters. (f) Root diameters. (g) Dedendum. (h) Base circle diameters (i) Check for interference, Prof. 17 Dr. Mohamed Omar Mousa April 2006
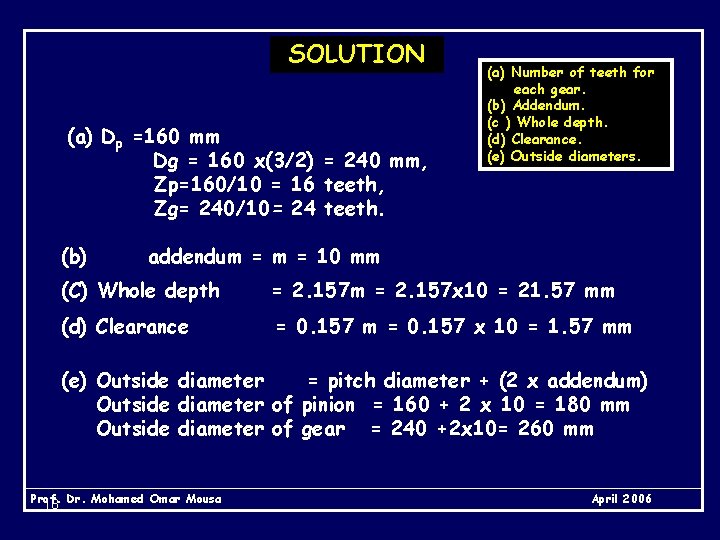
SOLUTION (a) Dp =160 mm Dg = 160 x(3/2) = 240 mm, Zp=160/10 = 16 teeth, Zg= 240/10= 24 teeth. (b) (a) Number of teeth for each gear. (b) Addendum. (c ) Whole depth. (d) Clearance. (e) Outside diameters. addendum = 10 mm (C) Whole depth = 2. 157 m = 2. 157 x 10 = 21. 57 mm (d) Clearance = 0. 157 m = 0. 157 x 10 = 1. 57 mm (e) Outside diameter = pitch diameter + (2 x addendum) Outside diameter of pinion = 160 + 2 x 10 = 180 mm Outside diameter of gear = 240 +2 x 10= 260 mm Prof. 18 Dr. Mohamed Omar Mousa April 2006
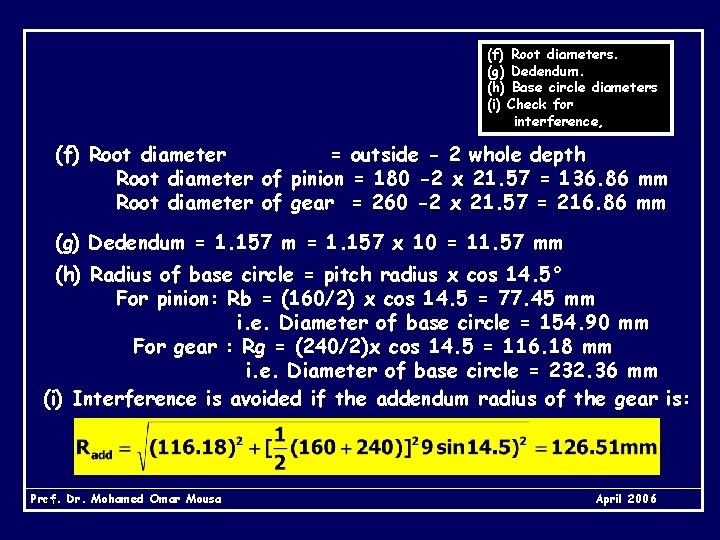
(f) Root diameters. (g) Dedendum. (h) Base circle diameters (i) Check for interference, (f) Root diameter = outside - 2 whole depth Root diameter of pinion = 180 -2 x 21. 57 = 136. 86 mm Root diameter of gear = 260 -2 x 21. 57 = 216. 86 mm (g) Dedendum = 1. 157 x 10 = 11. 57 mm (h) Radius of base circle = pitch radius x cos 14. 5° For pinion: Rb = (160/2) x cos 14. 5 = 77. 45 mm i. e. Diameter of base circle = 154. 90 mm For gear : Rg = (240/2)x cos 14. 5 = 116. 18 mm i. e. Diameter of base circle = 232. 36 mm (i) Interference is avoided if the addendum radius of the gear is: Prof. 19 Dr. Mohamed Omar Mousa April 2006
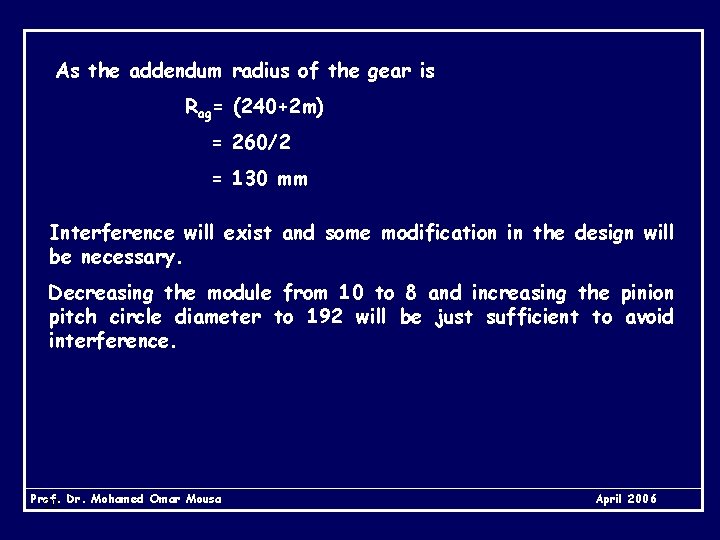
As the addendum radius of the gear is Rag= (240+2 m) = 260/2 = 130 mm Interference will exist and some modification in the design will be necessary. Decreasing the module from 10 to 8 and increasing the pinion pitch circle diameter to 192 will be just sufficient to avoid interference. Prof. 20 Dr. Mohamed Omar Mousa April 2006
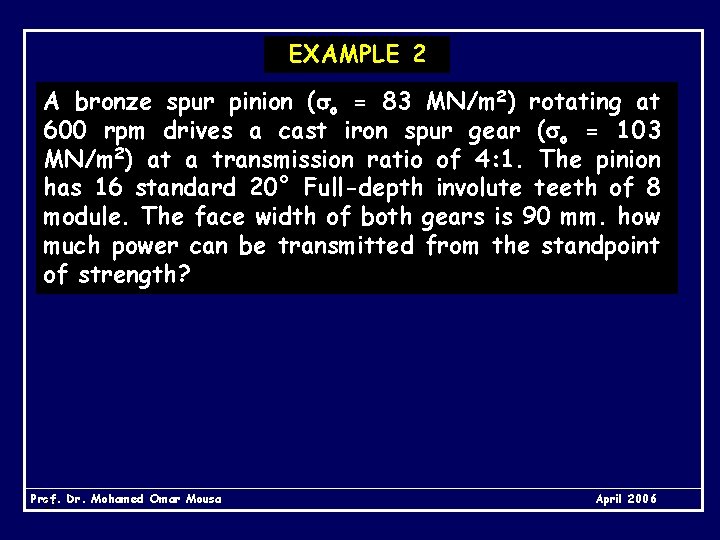
EXAMPLE 2 A bronze spur pinion ( o = 83 MN/m 2) rotating at 600 rpm drives a cast iron spur gear ( o = 103 MN/m 2) at a transmission ratio of 4: 1. The pinion has 16 standard 20° Full-depth involute teeth of 8 module. The face width of both gears is 90 mm. how much power can be transmitted from the standpoint of strength? Prof. 21 Dr. Mohamed Omar Mousa April 2006
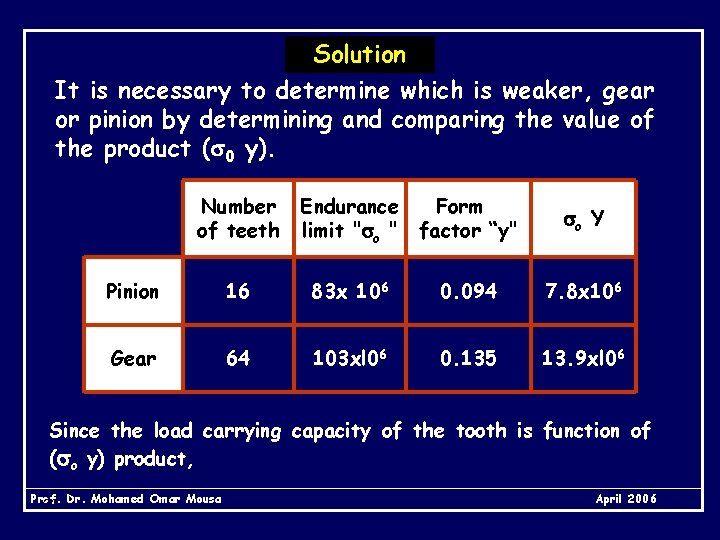
Solution It is necessary to determine which is weaker, gear or pinion by determining and comparing the value of the product ( 0 y). Number of teeth Endurance limit " o " Form factor “y" o Y Pinion 16 83 x 106 0. 094 7. 8 x 106 Gear 64 103 xl 06 0. 135 13. 9 xl 06 Since the load carrying capacity of the tooth is function of ( o y) product, Prof. 22 Dr. Mohamed Omar Mousa April 2006
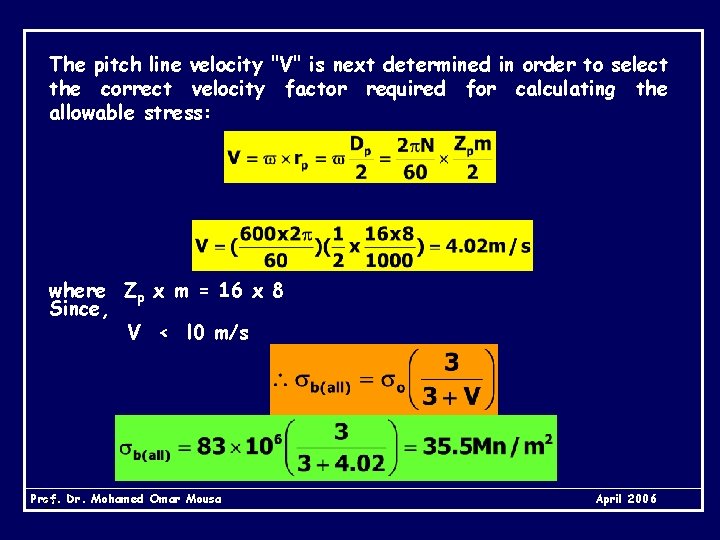
The pitch line velocity "V" is next determined in order to select the correct velocity factor required for calculating the allowable stress: where Zp x m = 16 x 8 Since, V < l 0 m/s Prof. 23 Dr. Mohamed Omar Mousa April 2006
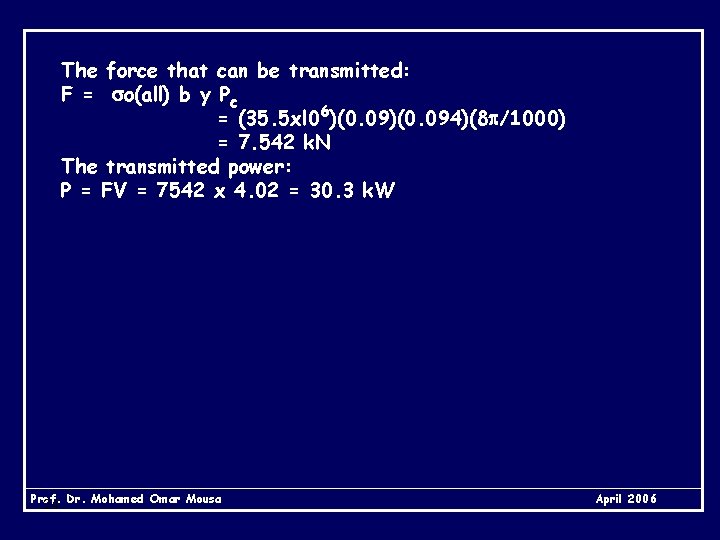
The force that can be transmitted: F = o(all) b y Pc = (35. 5 xl 06)(0. 094)(8 /1000) = 7. 542 k. N The transmitted power: P = FV = 7542 x 4. 02 = 30. 3 k. W Prof. 24 Dr. Mohamed Omar Mousa April 2006
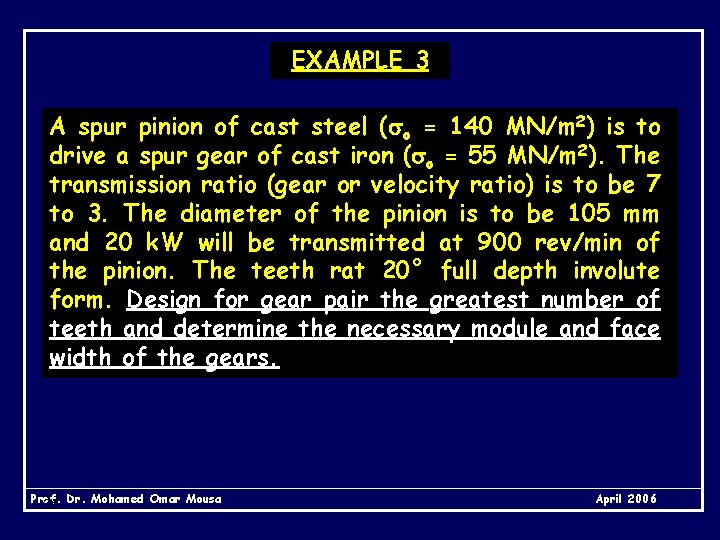
EXAMPLE 3 A spur pinion of cast steel ( o = 140 MN/m 2) is to drive a spur gear of cast iron ( o = 55 MN/m 2). The transmission ratio (gear or velocity ratio) is to be 7 to 3. The diameter of the pinion is to be 105 mm and 20 k. W will be transmitted at 900 rev/min of the pinion. The teeth rat 20° full depth involute form. Design for gear pair the greatest number of teeth and determine the necessary module and face width of the gears. Prof. 25 Dr. Mohamed Omar Mousa April 2006
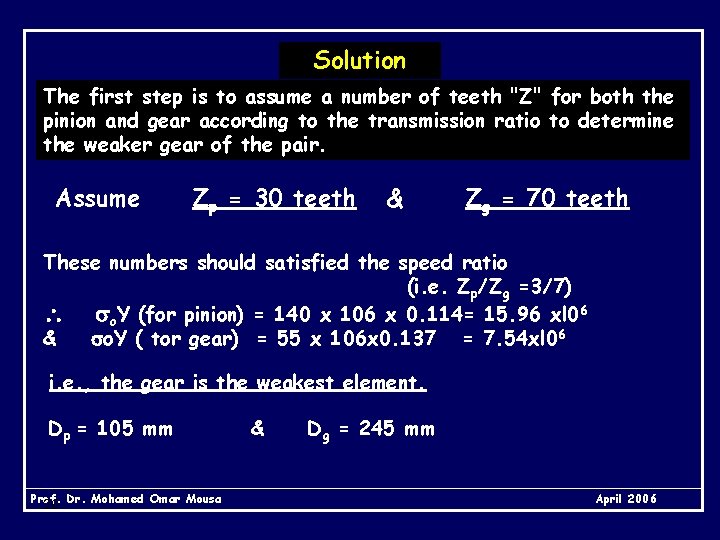
Solution The first step is to assume a number of teeth "Z" for both the pinion and gear according to the transmission ratio to determine the weaker gear of the pair. Assume Zp = 30 teeth & Zg = 70 teeth These numbers should satisfied the speed ratio (i. e. Zp/Zg =3/7) o. Y (for pinion) = 140 x 106 x 0. 114= 15. 96 xl 06 & o. Y ( tor gear) = 55 x 106 x 0. 137 = 7. 54 xl 06 i. e. , the gear is the weakest element. Dp = 105 mm Prof. 26 Dr. Mohamed Omar Mousa & Dg = 245 mm April 2006
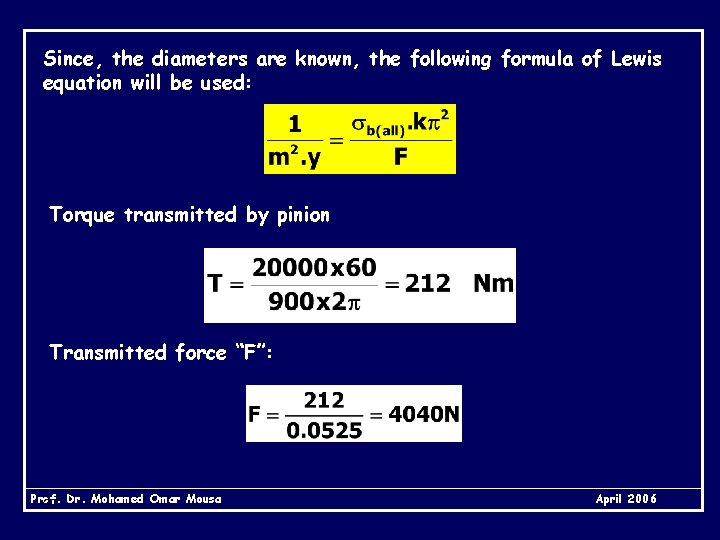
Since, the diameters are known, the following formula of Lewis equation will be used: Torque transmitted by pinion Transmitted force “F”: Prof. 27 Dr. Mohamed Omar Mousa April 2006
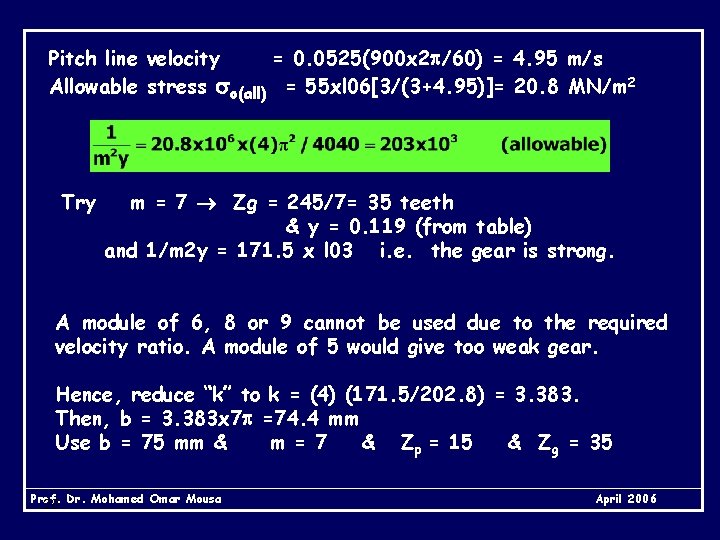
Pitch line velocity = 0. 0525(900 x 2 /60) = 4. 95 m/s Allowable stress o(all) = 55 xl 06[3/(3+4. 95)]= 20. 8 MN/m 2 Try m = 7 Zg = 245/7= 35 teeth & y = 0. 119 (from table) and 1/m 2 y = 171. 5 x l 03 i. e. the gear is strong. A module of 6, 8 or 9 cannot be used due to the required velocity ratio. A module of 5 would give too weak gear. Hence, reduce “k” to k = (4) (171. 5/202. 8) = 3. 383. Then, b = 3. 383 x 7 =74. 4 mm Use b = 75 mm & m = 7 & Zp = 15 & Zg = 35 Prof. 28 Dr. Mohamed Omar Mousa April 2006
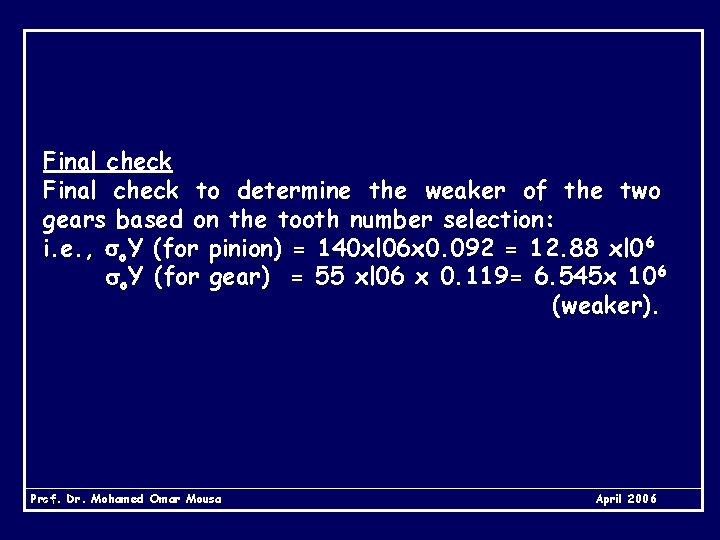
Final check to determine the weaker of the two gears based on the tooth number selection: i. e. , o. Y (for pinion) = 140 xl 06 x 0. 092 = 12. 88 xl 06 o. Y (for gear) = 55 xl 06 x 0. 119= 6. 545 x 106 (weaker). Prof. 29 Dr. Mohamed Omar Mousa April 2006
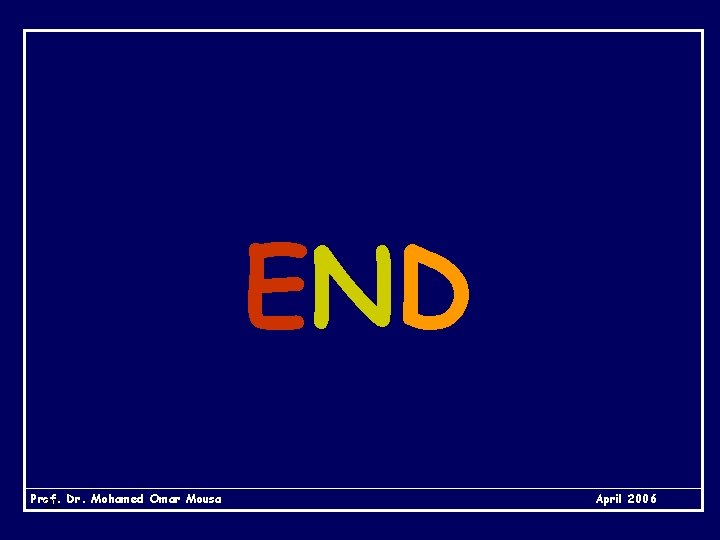
EN D Prof. 30 Dr. Mohamed Omar Mousa April 2006
Yahye mohamed omar
Mannaar helsinki
Internal external gear
Driver gears
Mohamed samir design
Mohamed samir design
Hamlet act iii scene ii
Va professional standards board
Shock absorber design calculation
Gear design
Riham mohamed aly
Mohamed dahoui
Dr elsayed mohamed
Mohamed kossentini
Mohamed homayed death
Mohamed computer technology
Mohamed el merouani
Hopital mohamed seghir nekkache
Dr mohamed bashar shala
Dr nasser mohamed
Dr mohamed eldeib
Power rating
Bouhicha
Abdelrahman mohamed
Dr mohamed bashar shala
Dr alboushi
Mohamed salah
Zofinopril
Mohamed akel
Mohamed akel
Mohamed zahran nyu