CMS Pixel Detector Manifold Design April 24 2012
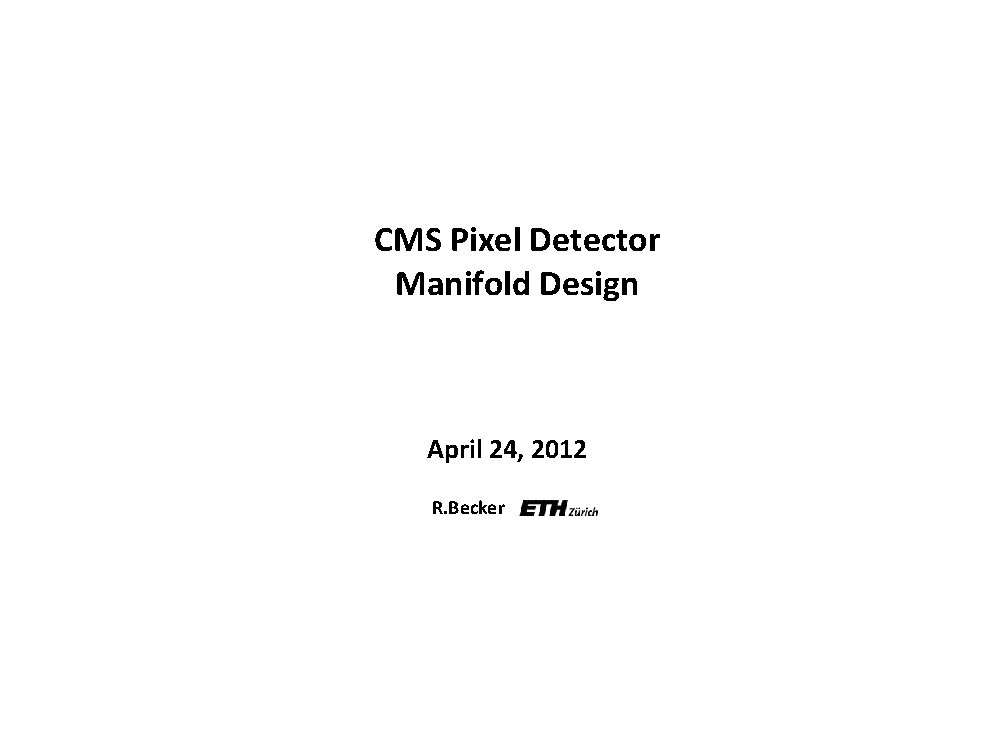
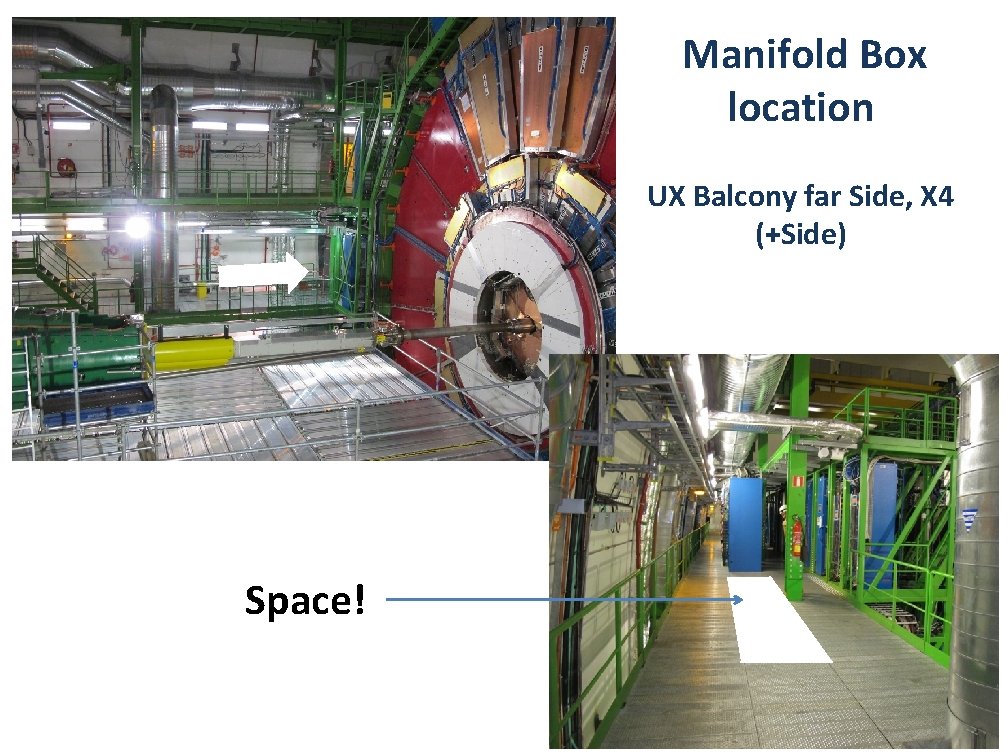
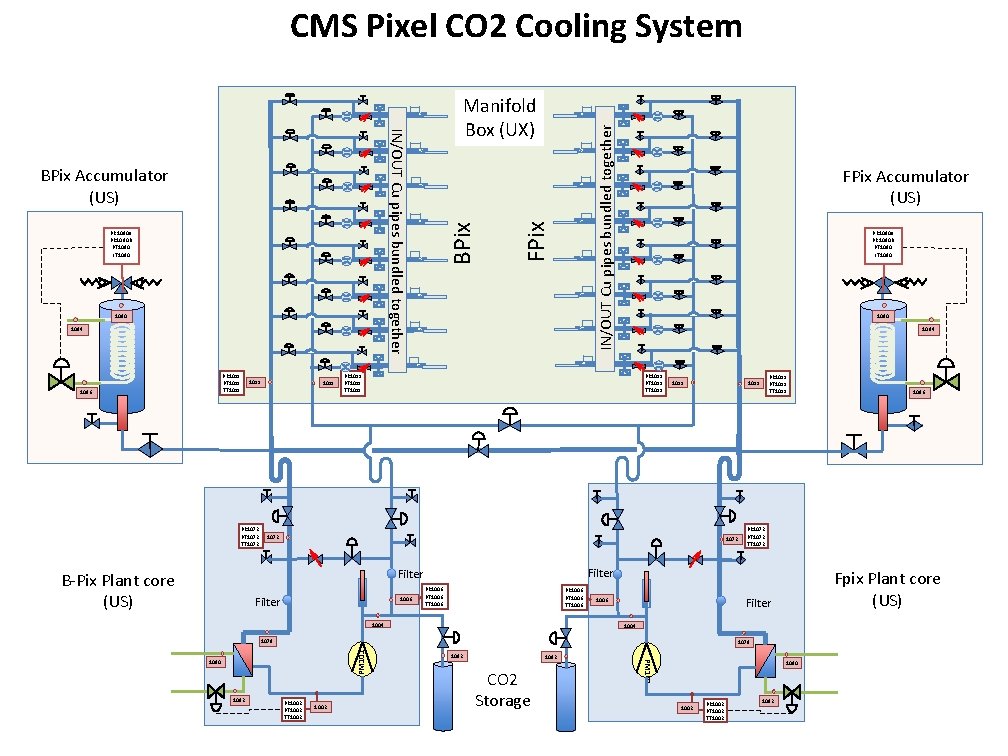
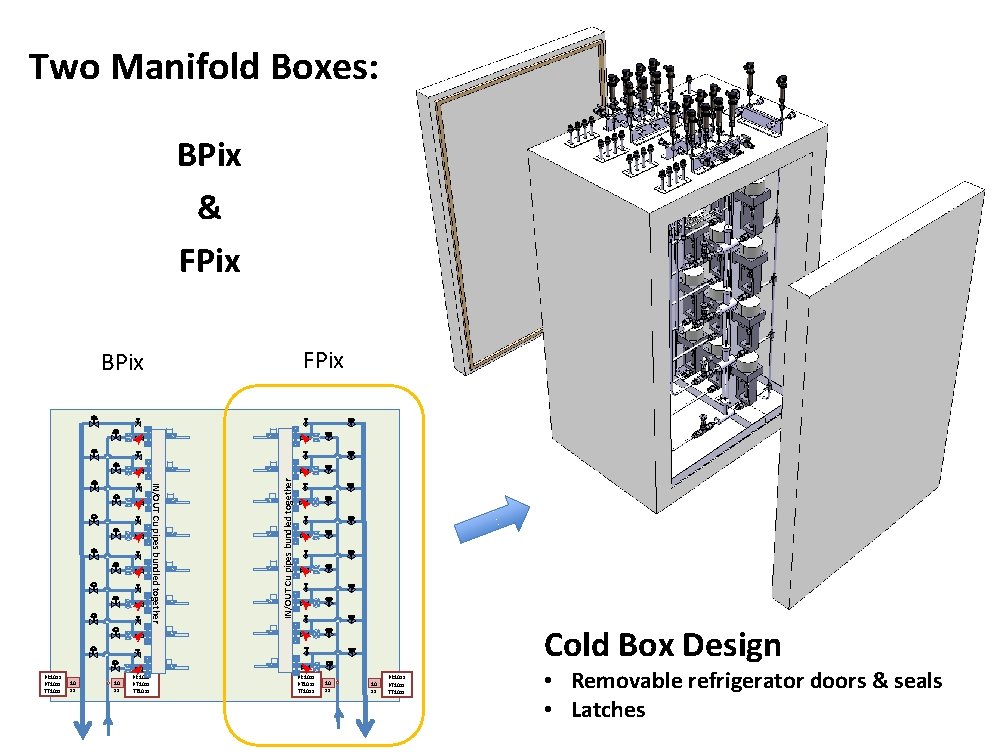
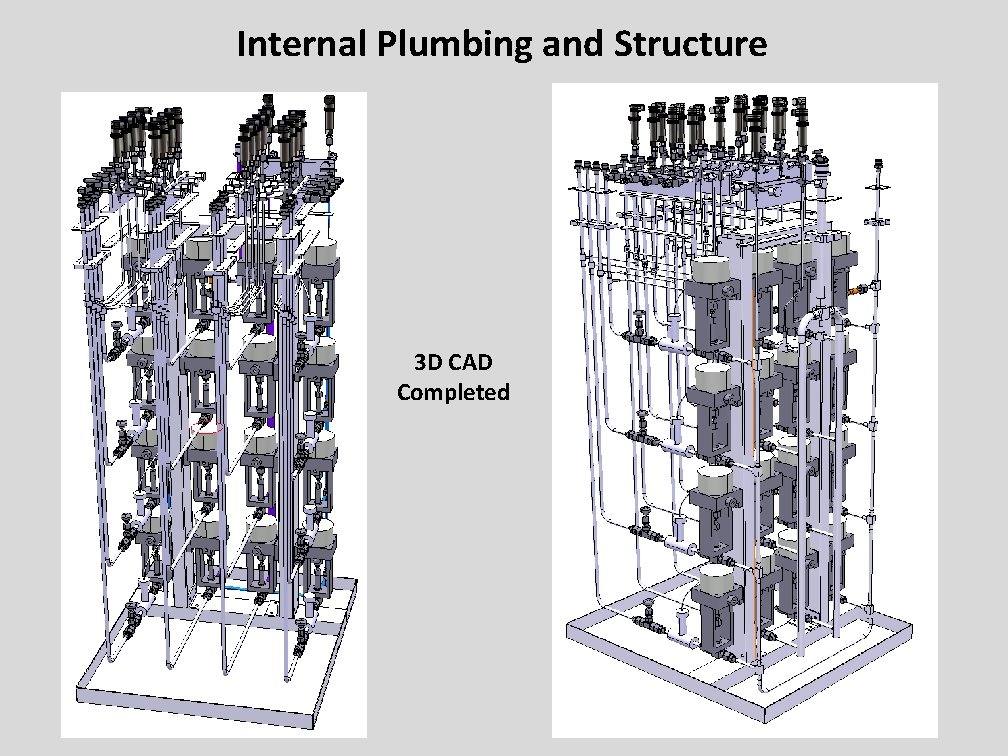
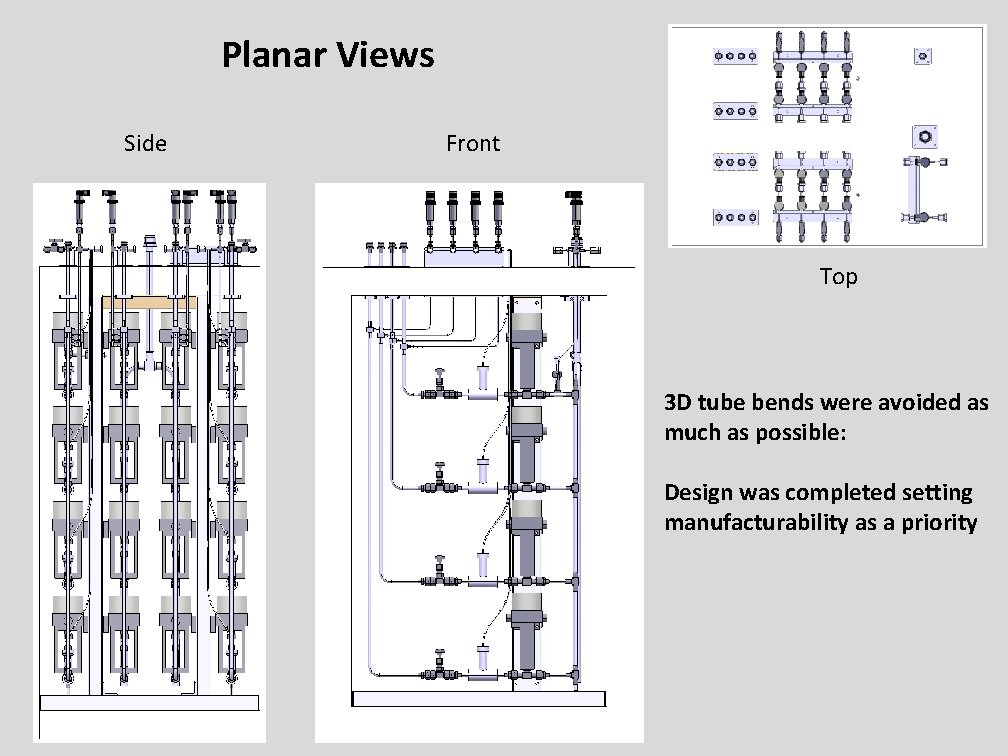
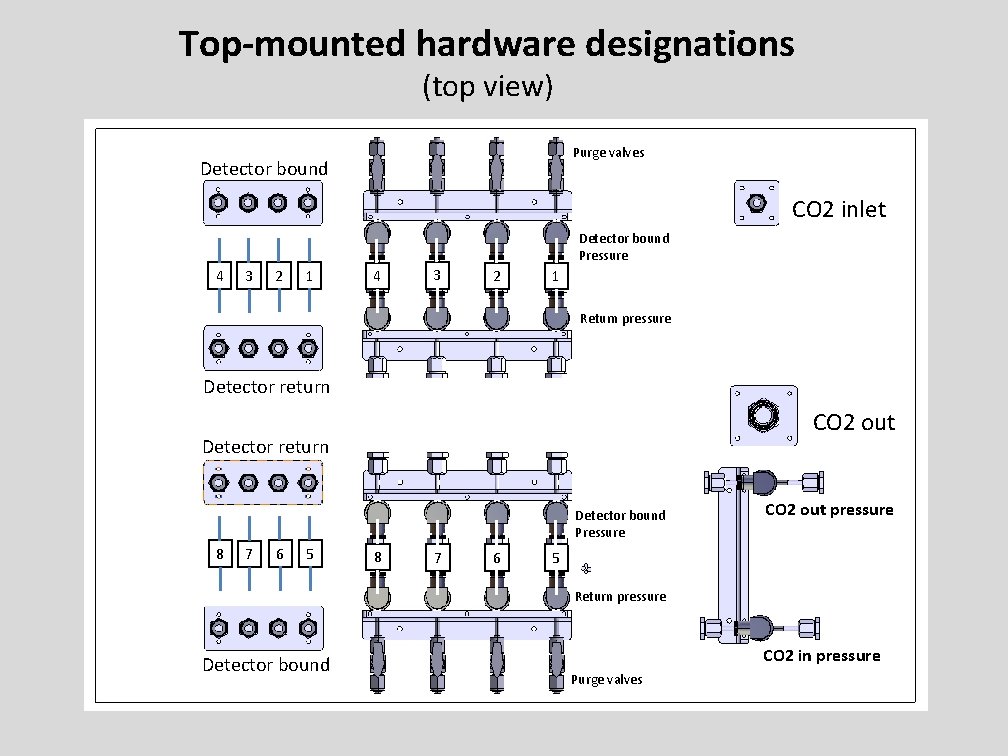
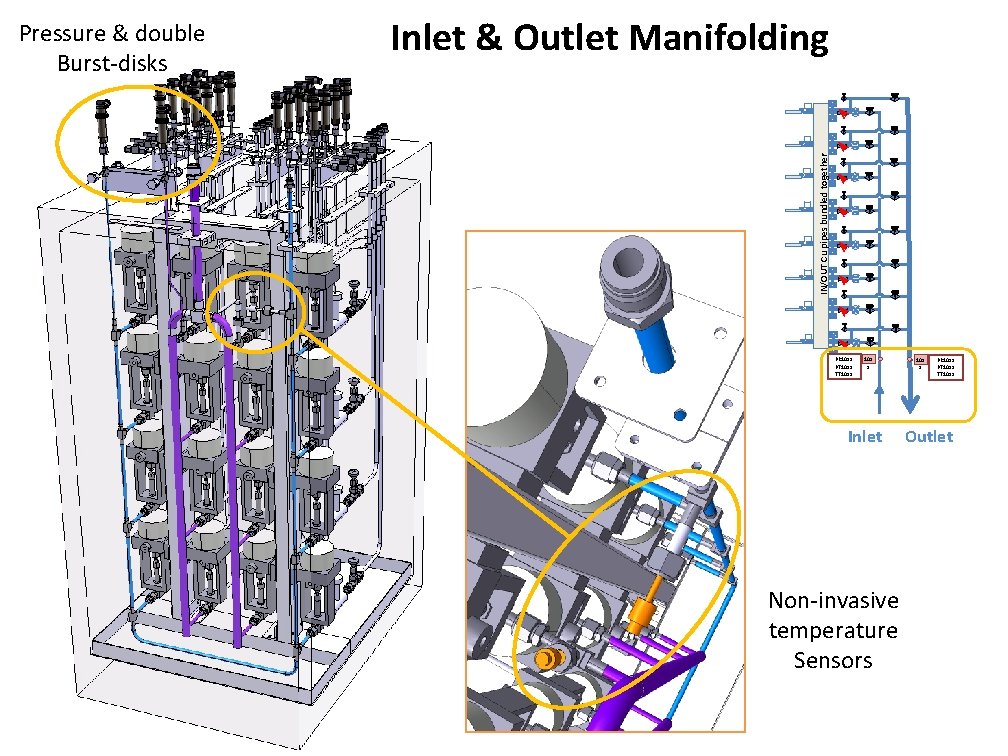
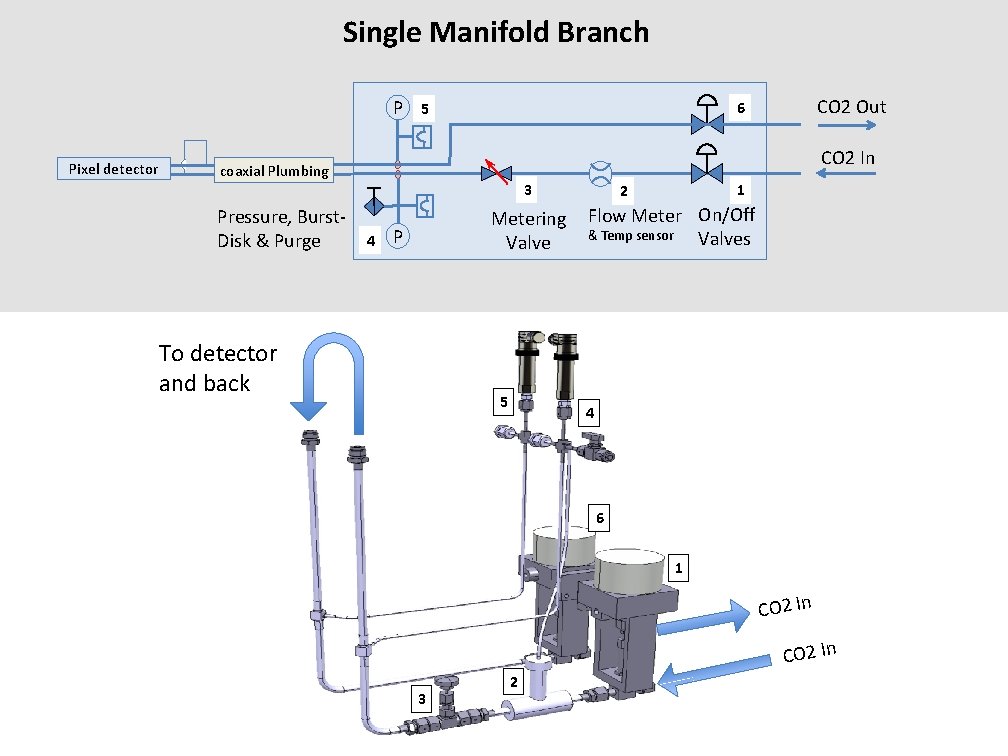
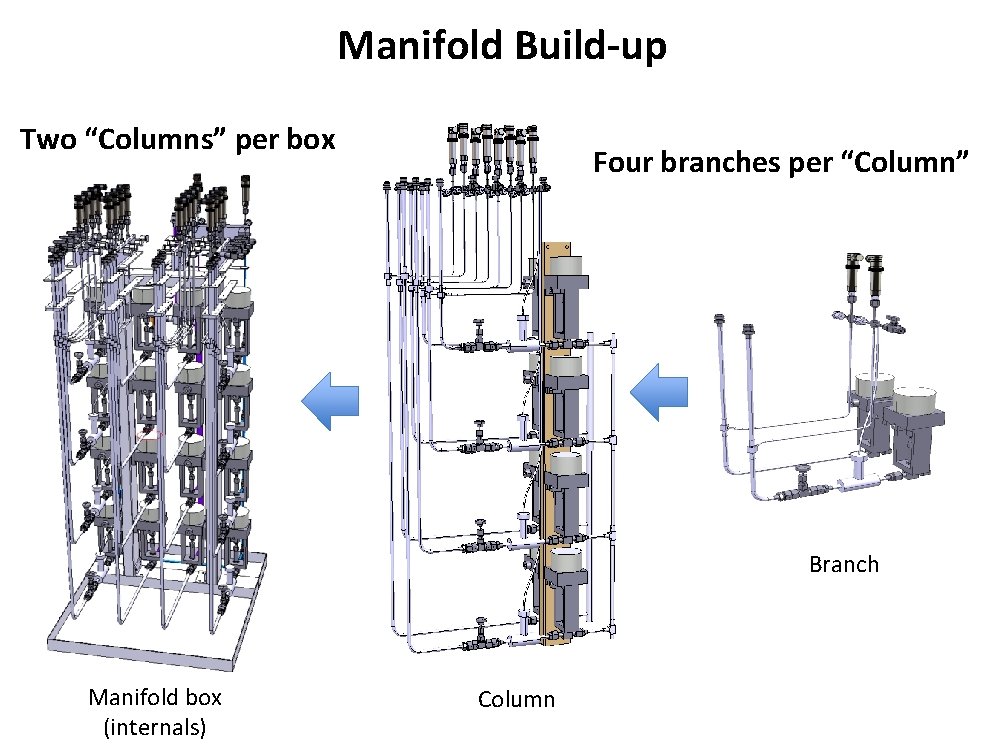
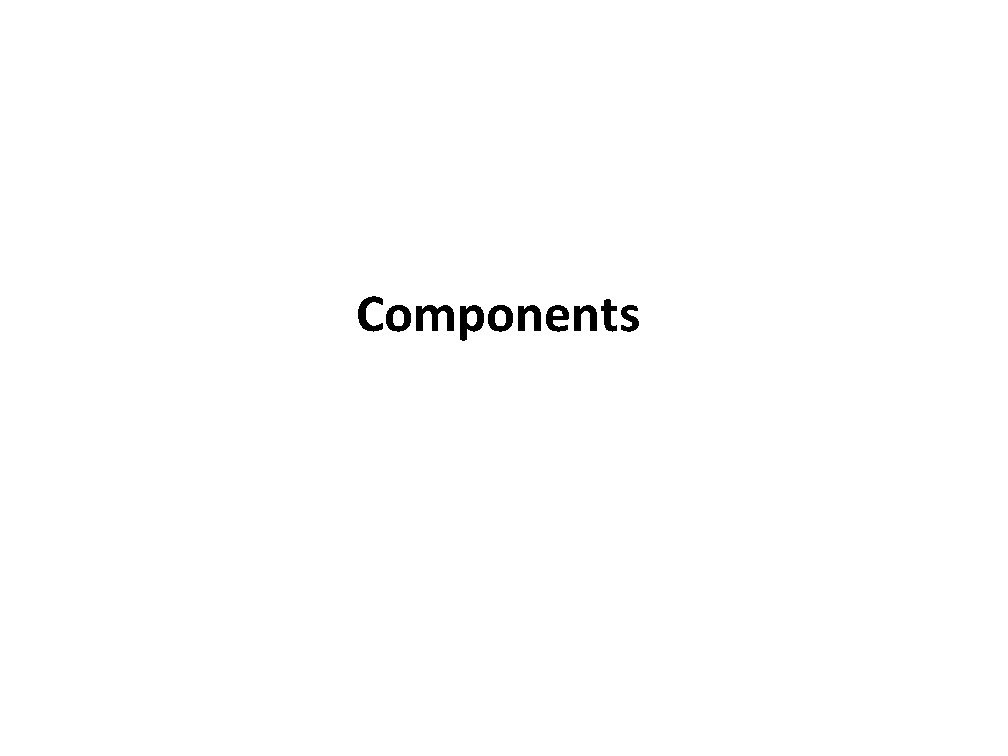
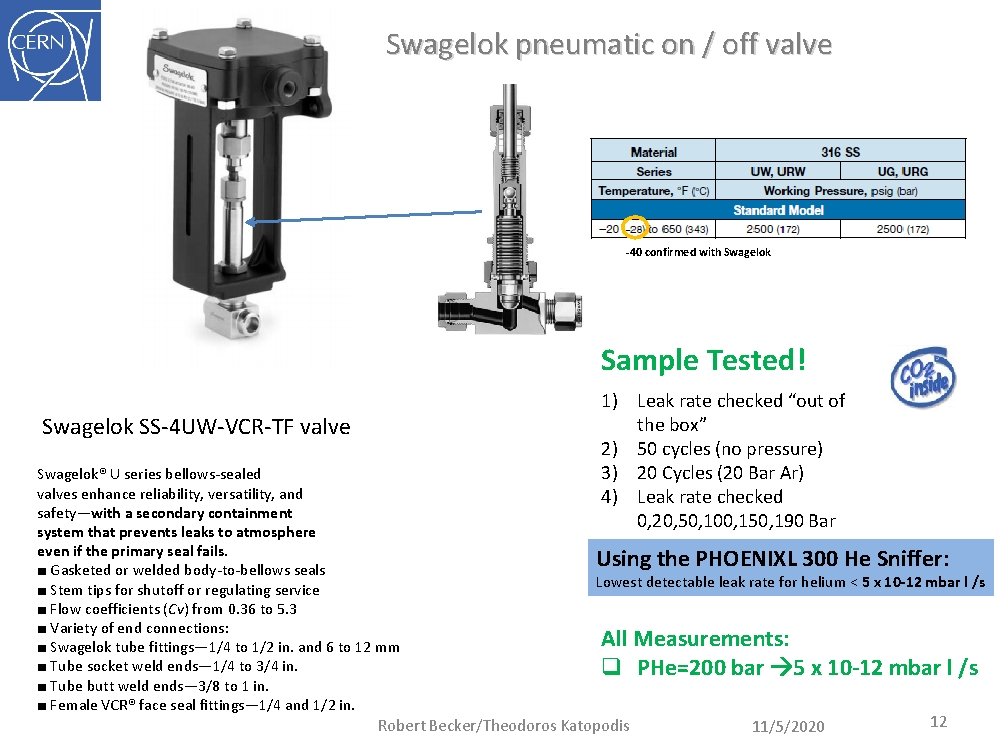
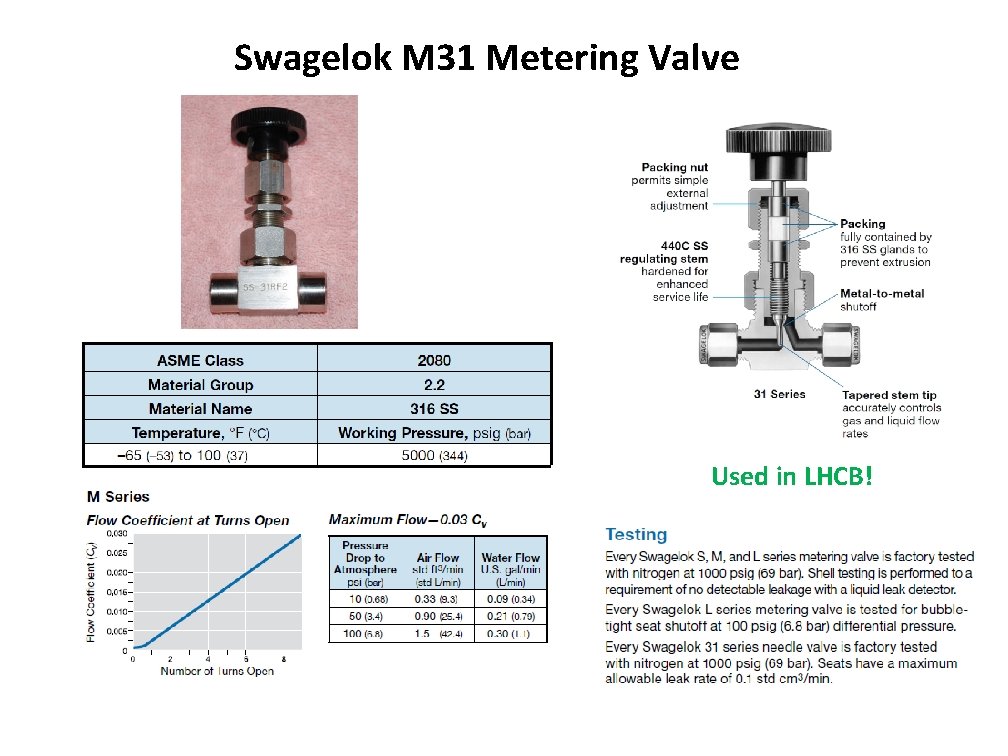
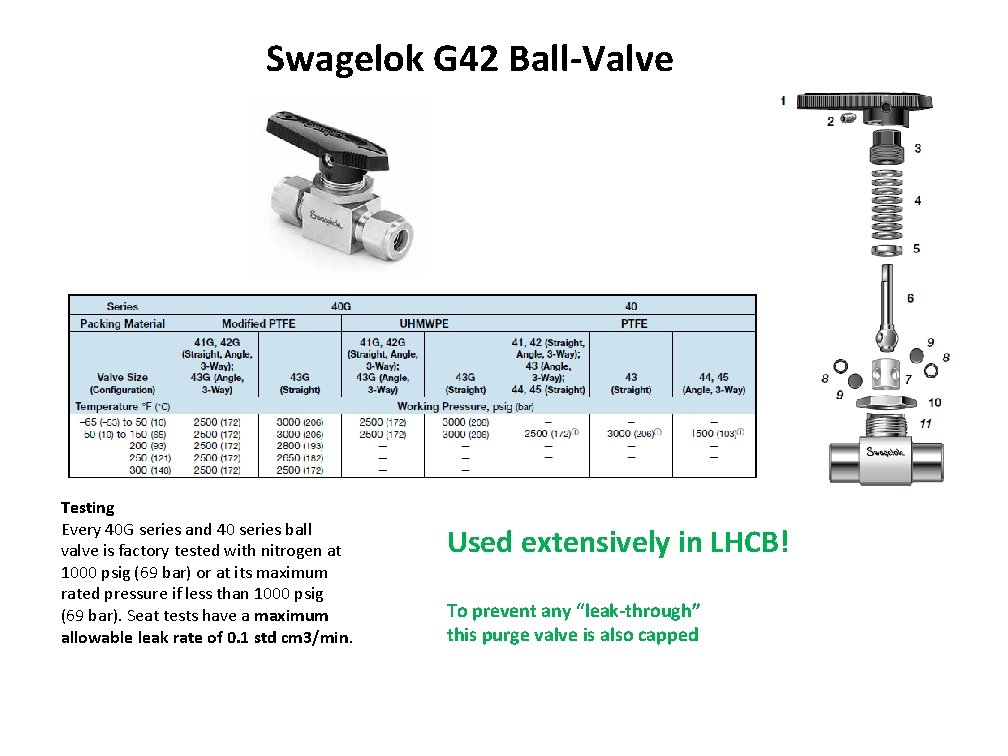
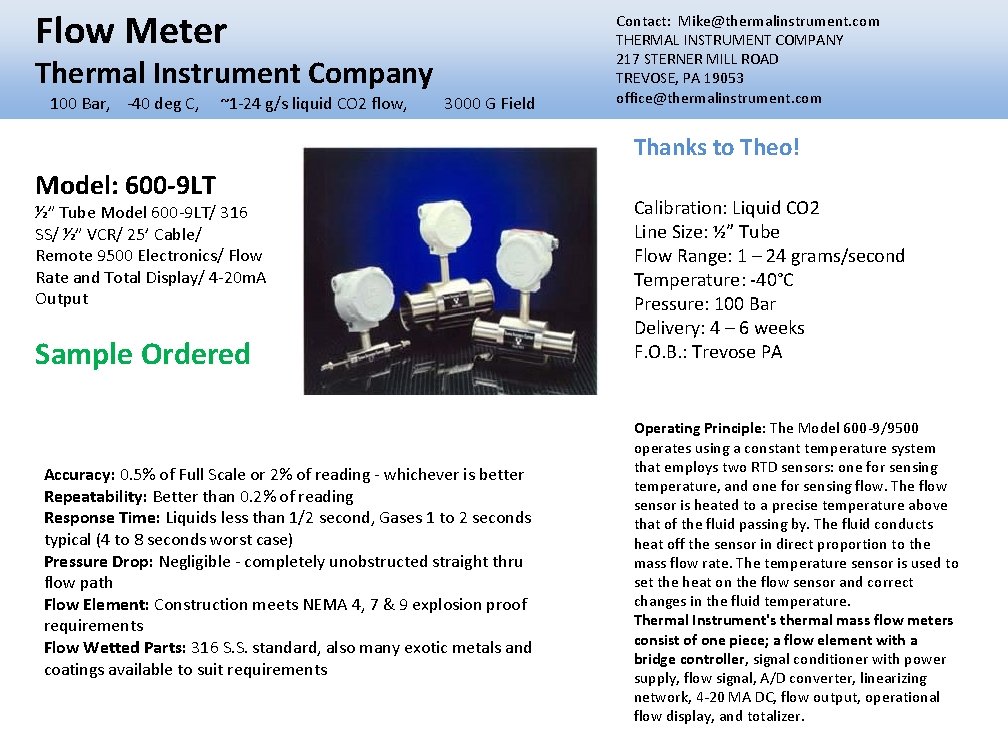
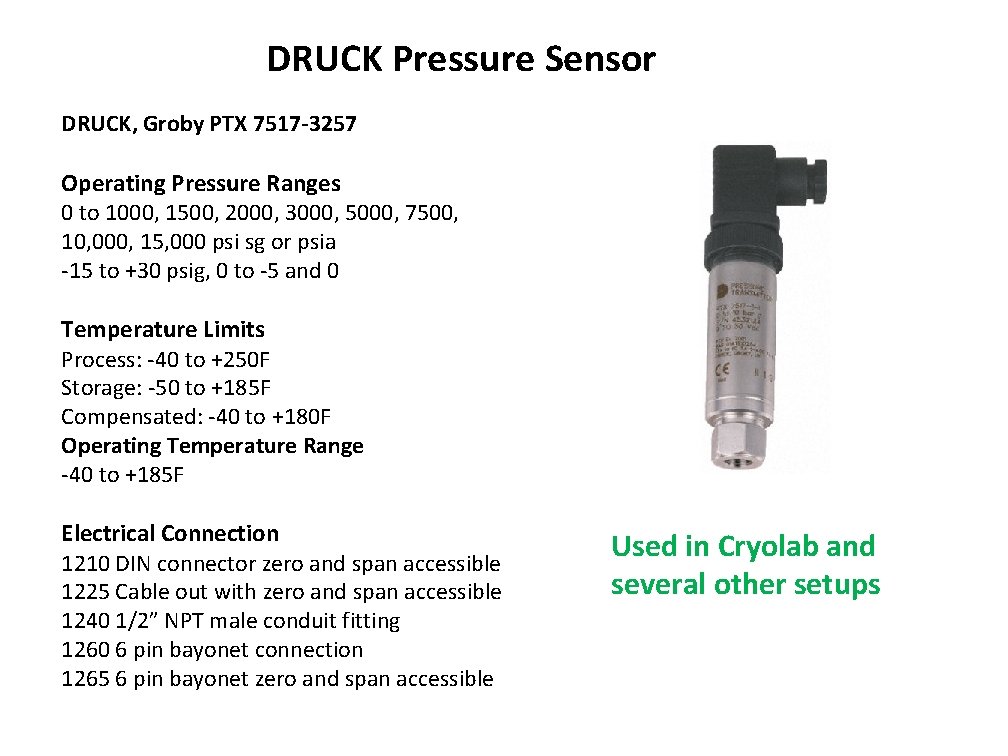
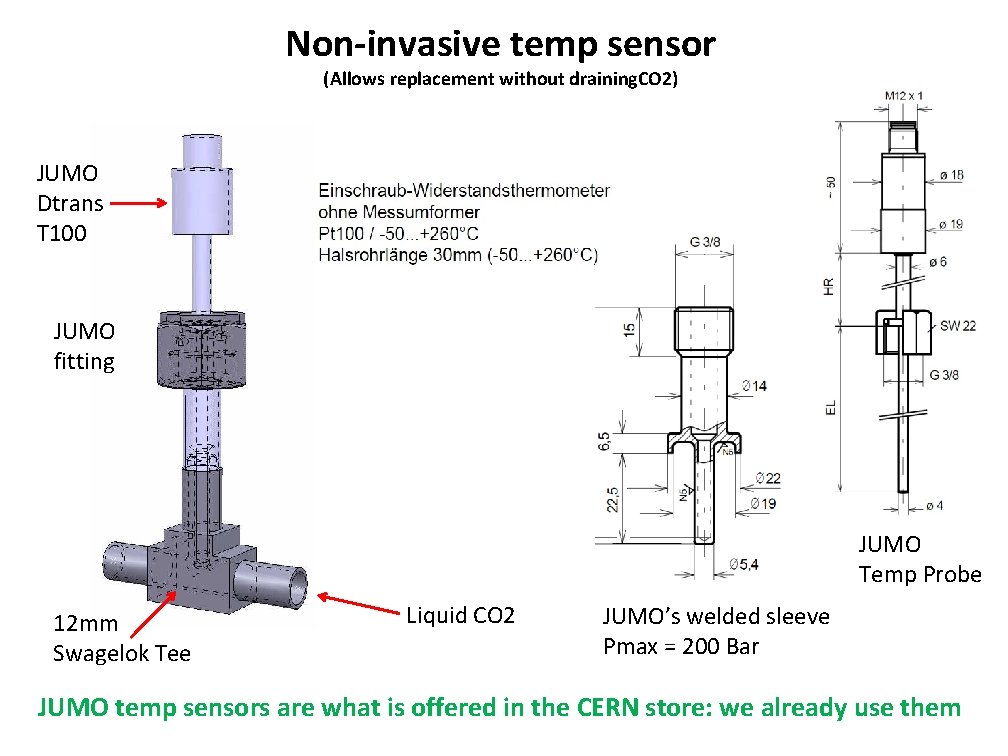
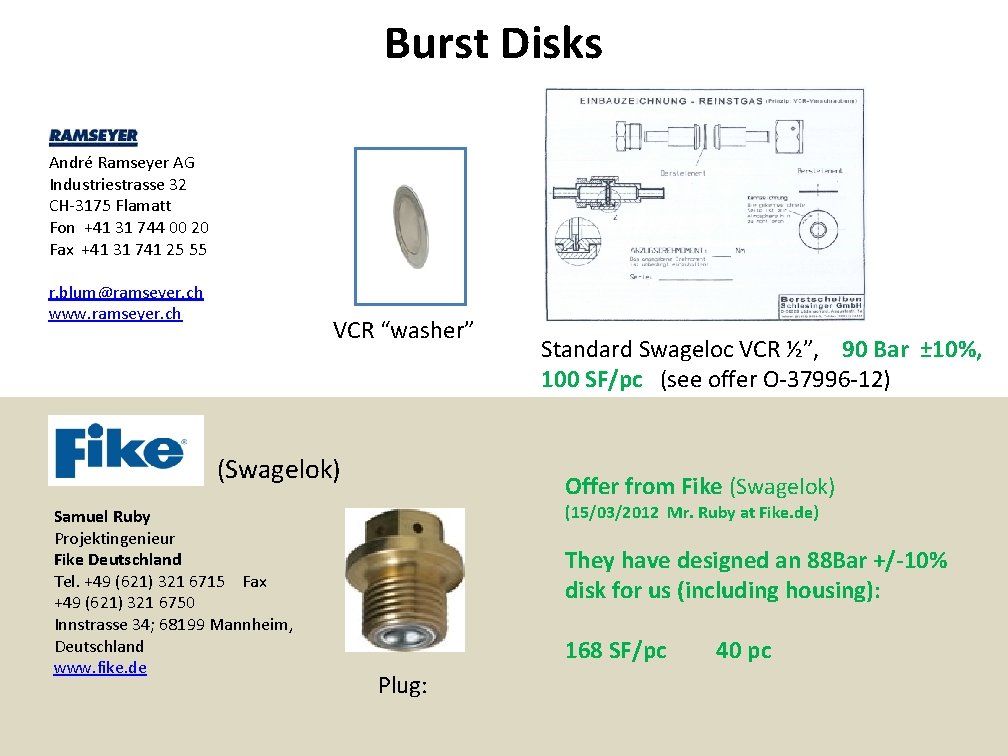
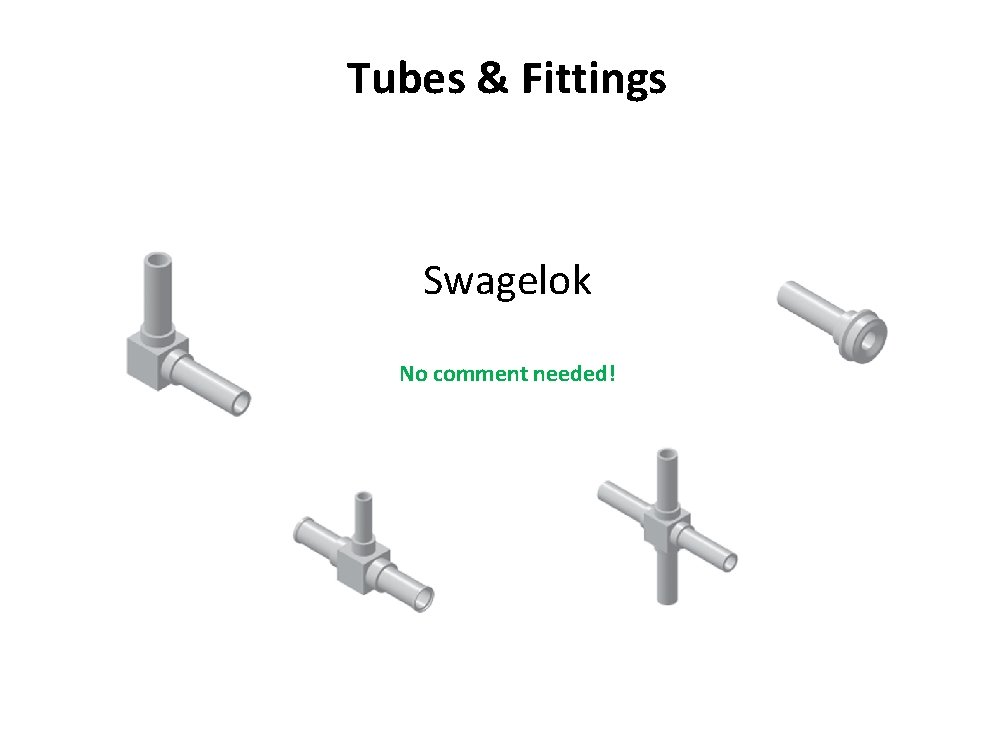
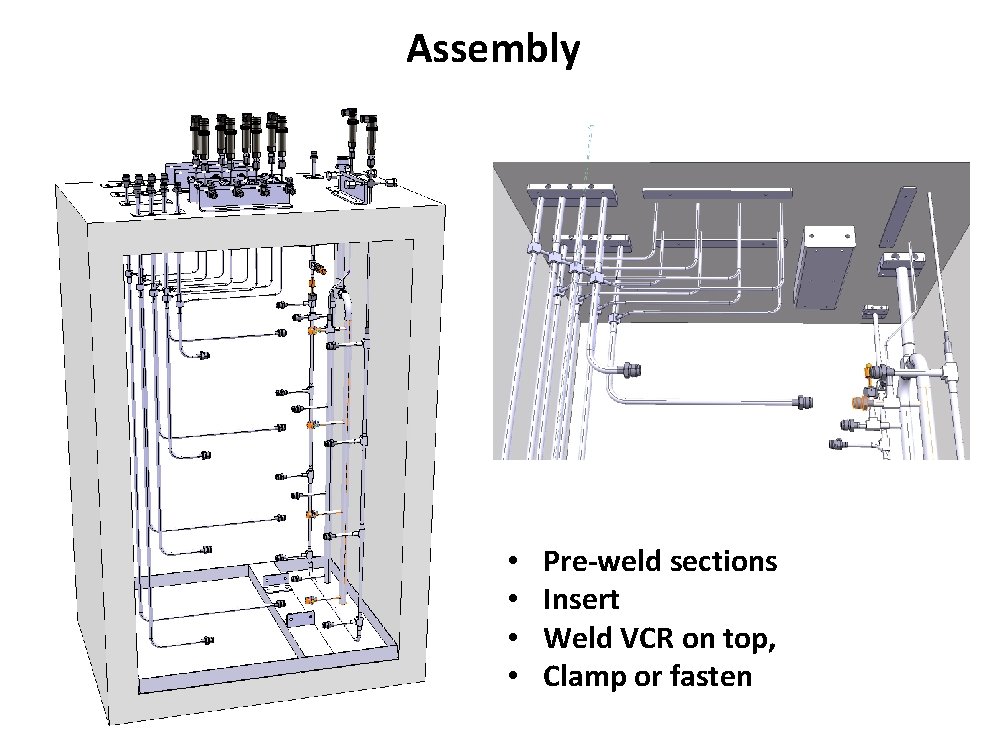
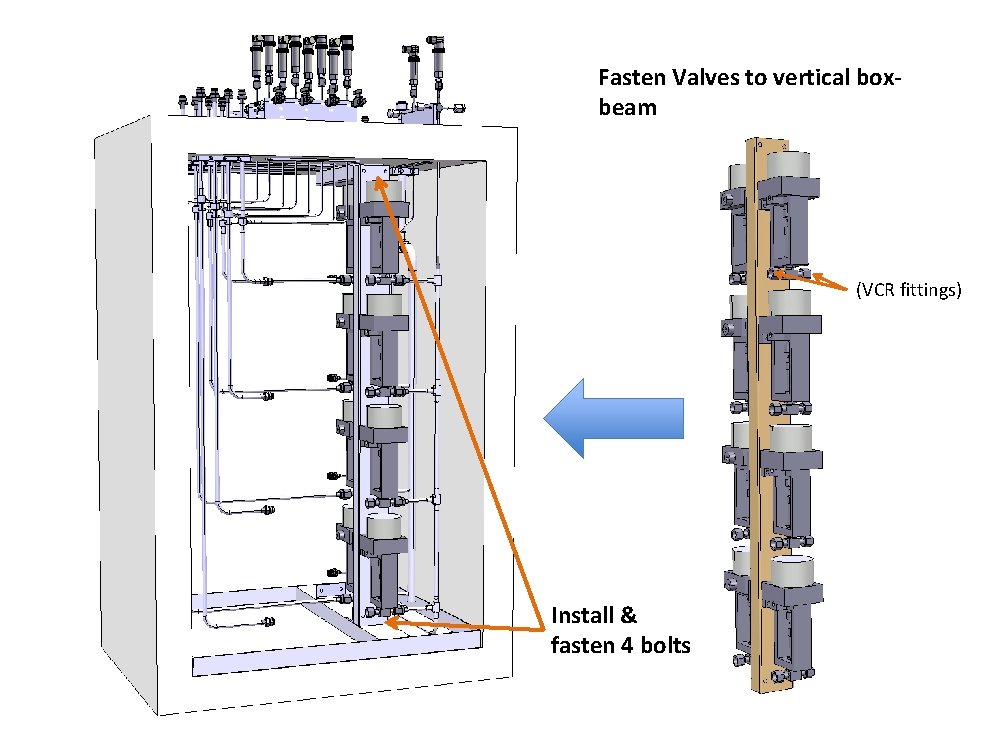
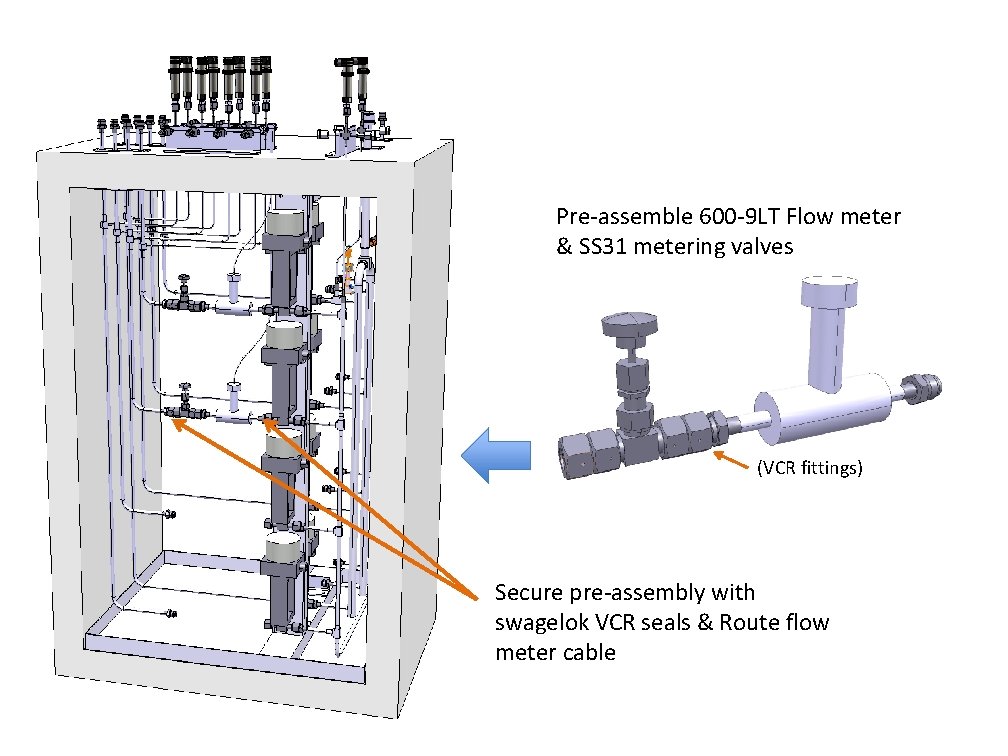
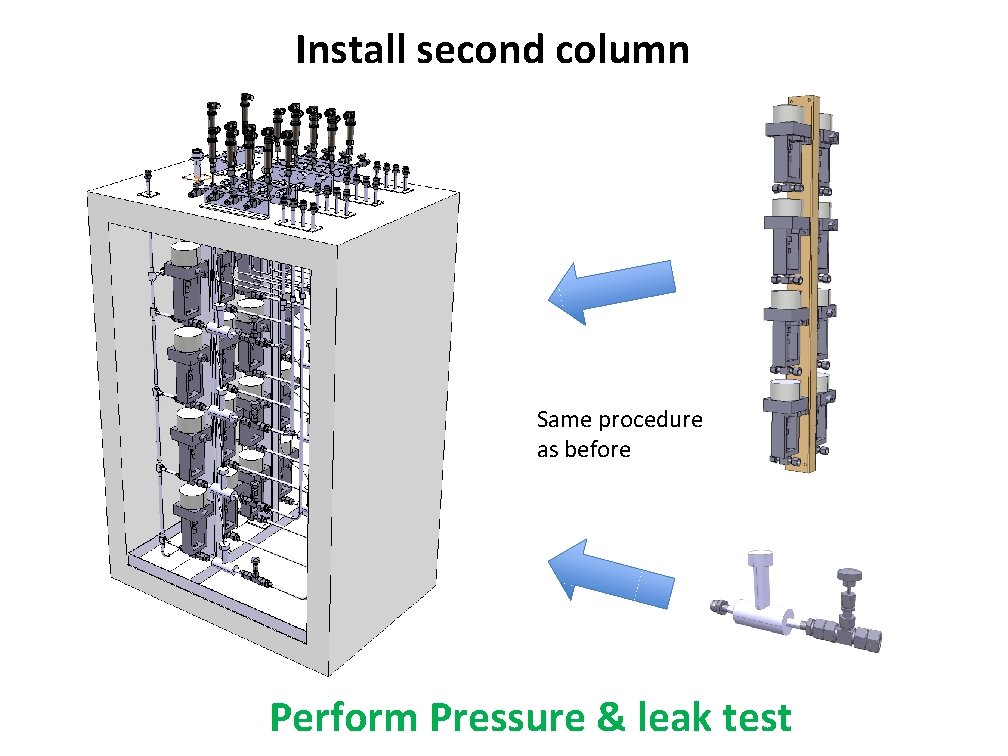
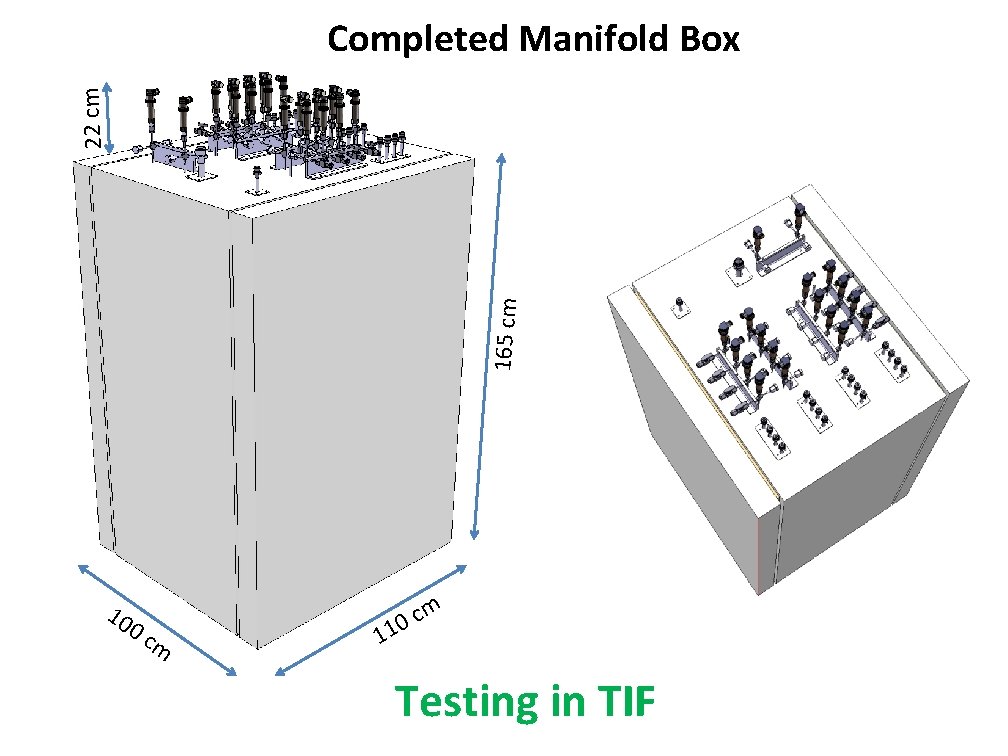
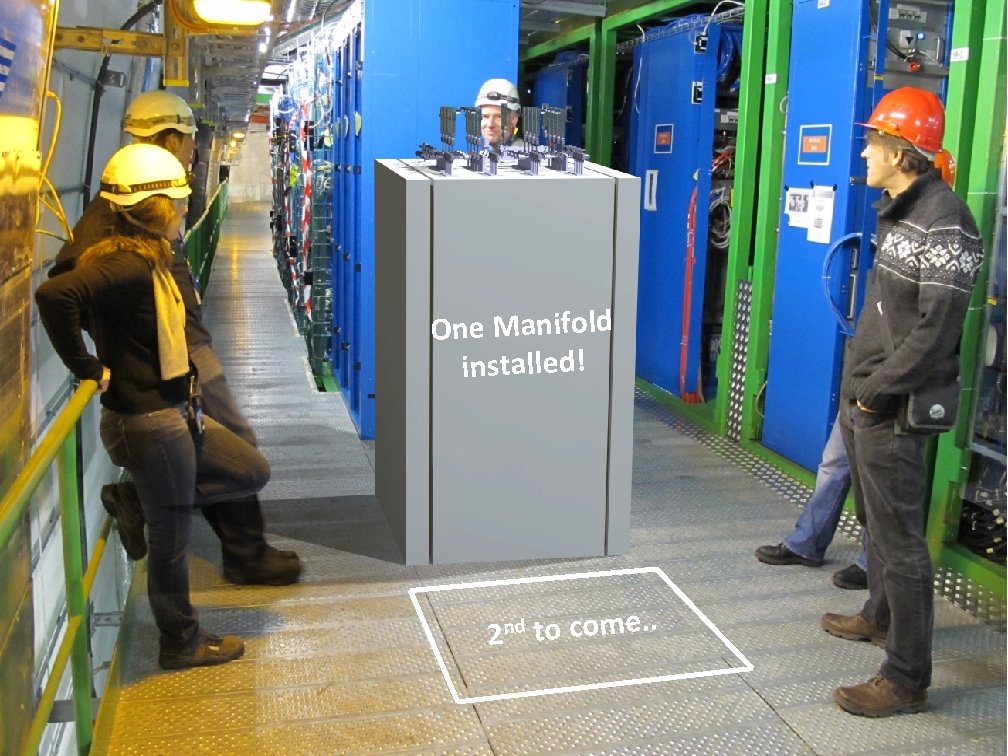
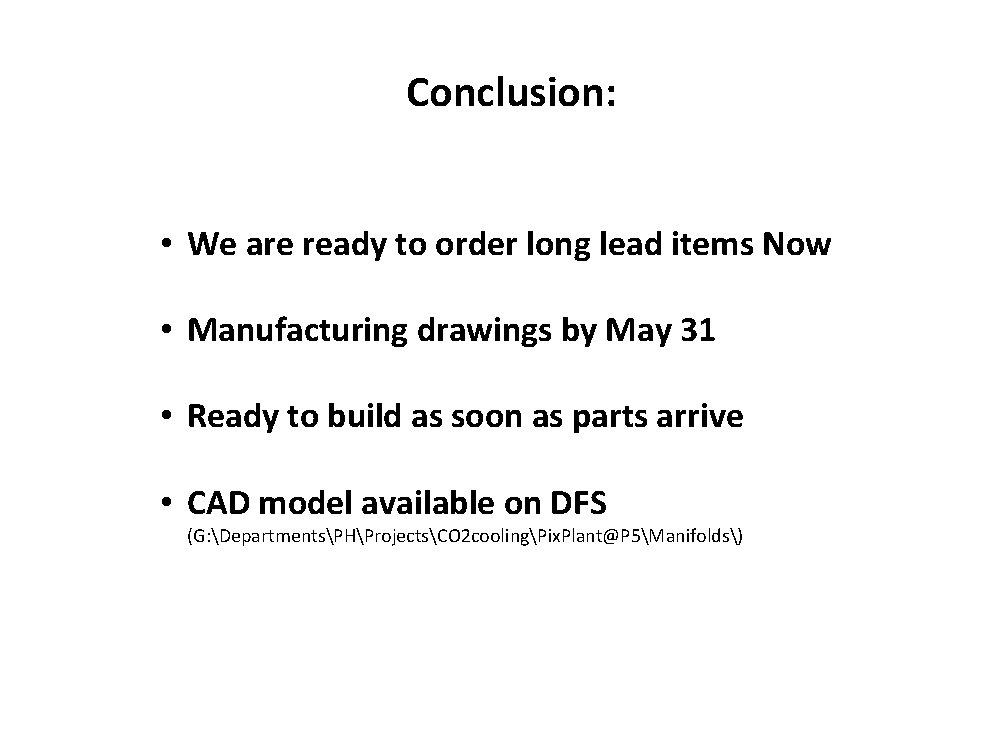
- Slides: 26
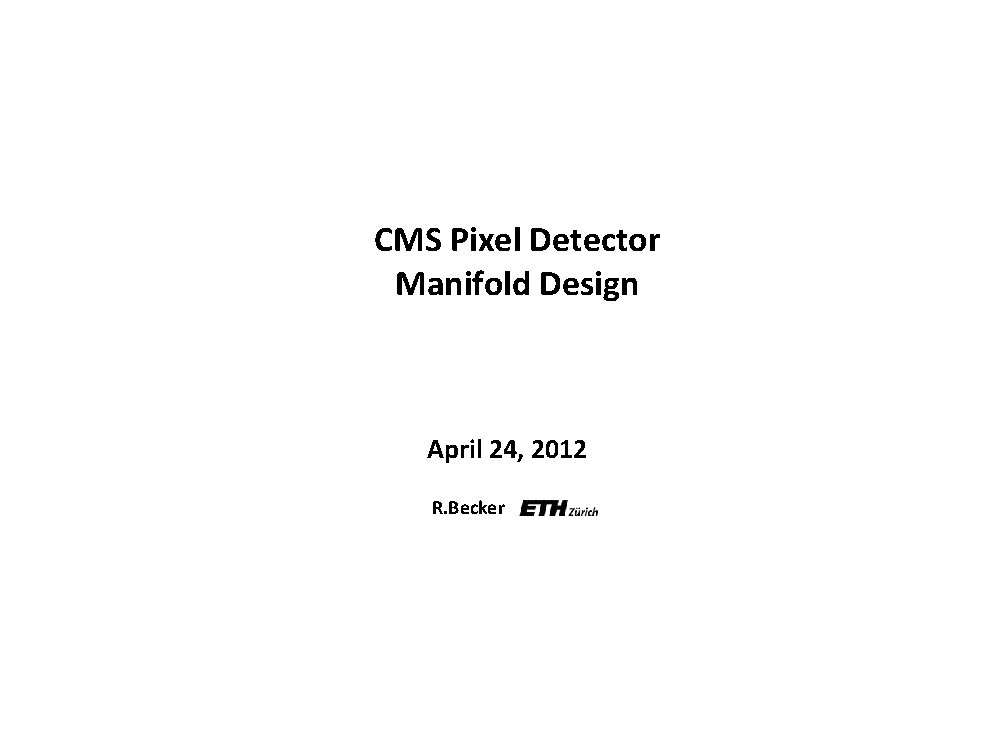
CMS Pixel Detector Manifold Design April 24, 2012 R. Becker
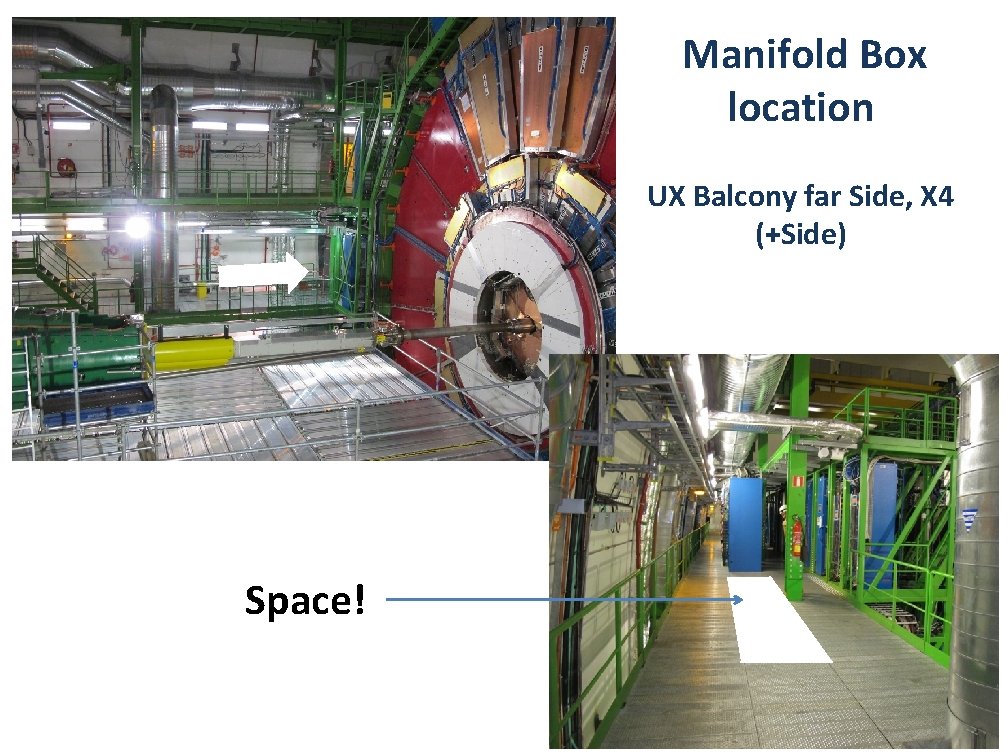
Manifold Box location UX Balcony far Side, X 4 (+Side) Space!
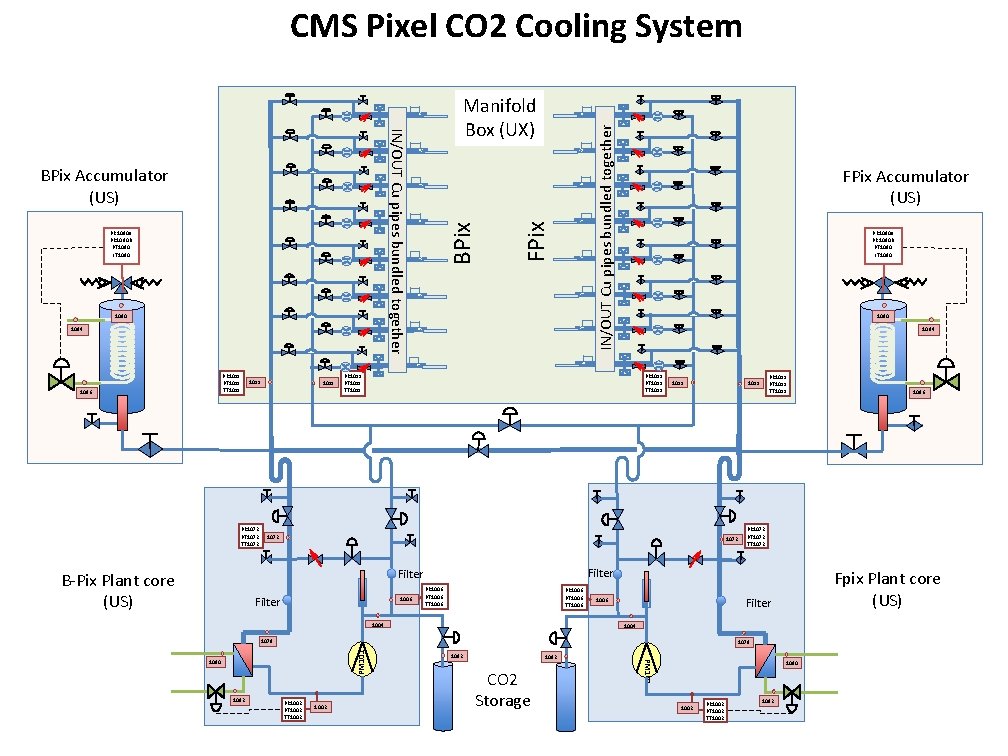
CMS Pixel CO 2 Cooling System 1080 1094 PR 10 xx PT 10 xx TT 10 xx 1096 10 xx PR 1072 PT 1072 TT 1072 10 xx IN/OUT Cu pipes bundled together PR 1080 a PR 1080 b PT 1080 LT 1080 FPix BPix Accumulator (US) BPix IN/OUT Cu pipes bundled together Manifold Box (UX) PR 1080 a PR 1080 b PT 1080 LT 1080 1094 PR 10 xx PT 10 xx TT 10 xx 1072 Filter 1006 PR 1006 PT 1006 TT 1006 Fpix Plant core (US) Filter 1006 1004 1078 1090 PR 1002 PT 1002 TT 1002 1082 CO 2 Storage PM 101 1078 1082 1090 1002 PR 1002 PT 1002 TT 1002 1096 PR 1072 PT 1072 TT 1072 Filter PR 1006 PT 1006 TT 1006 1004 1092 PR 10 xx PT 10 xx TT 10 xx 1072 Filter B-Pix Plant core (US) FPix Accumulator (US) 1092
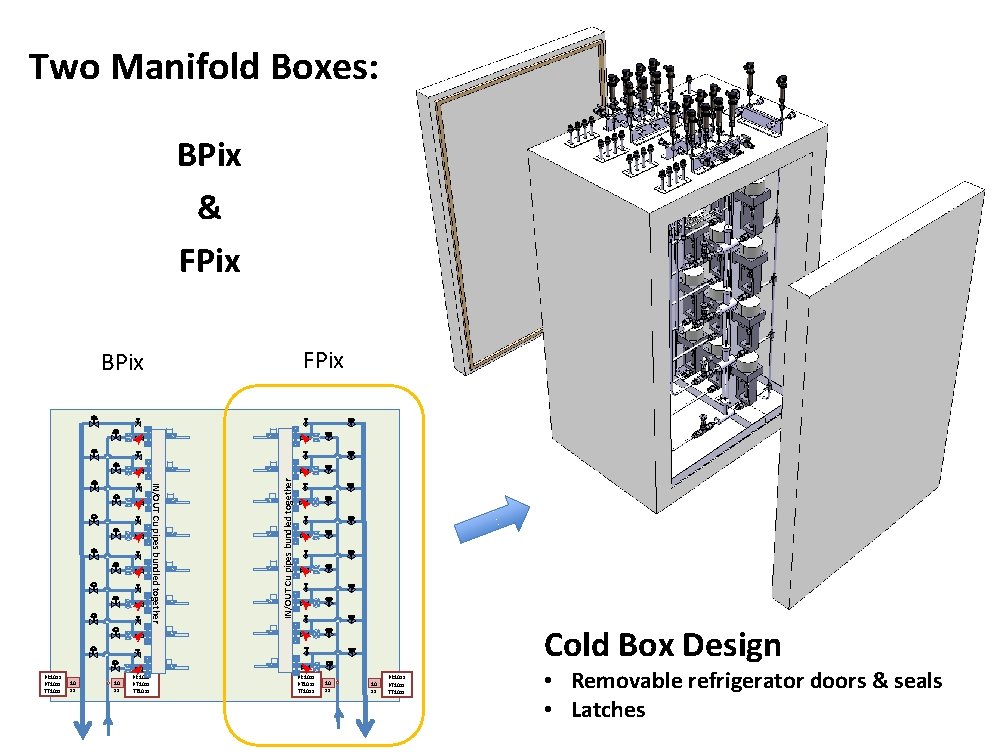
Two Manifold Boxes: BPix & FPix IN/OUT Cu pipes bundled together BPix Outlet PR 10 xx PT 10 xx TT 10 xx 10 xx PR 10 xx PT 10 xx TT 10 xx Cold Box Design • Removable refrigerator doors & seals • Latches
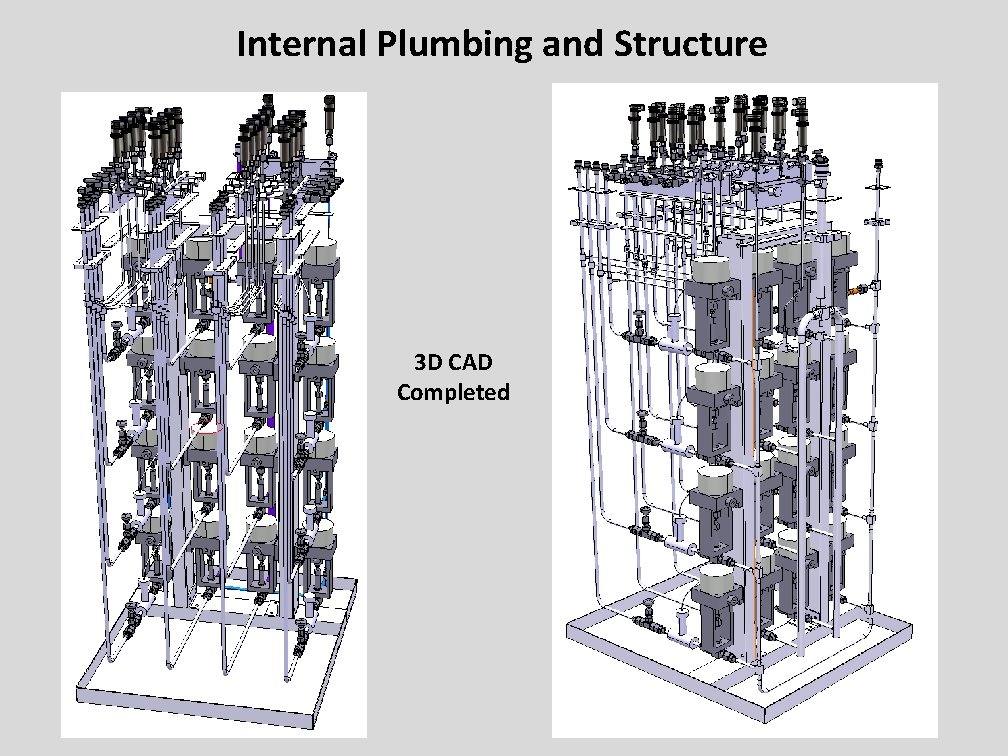
Internal Plumbing and Structure 3 D CAD Completed
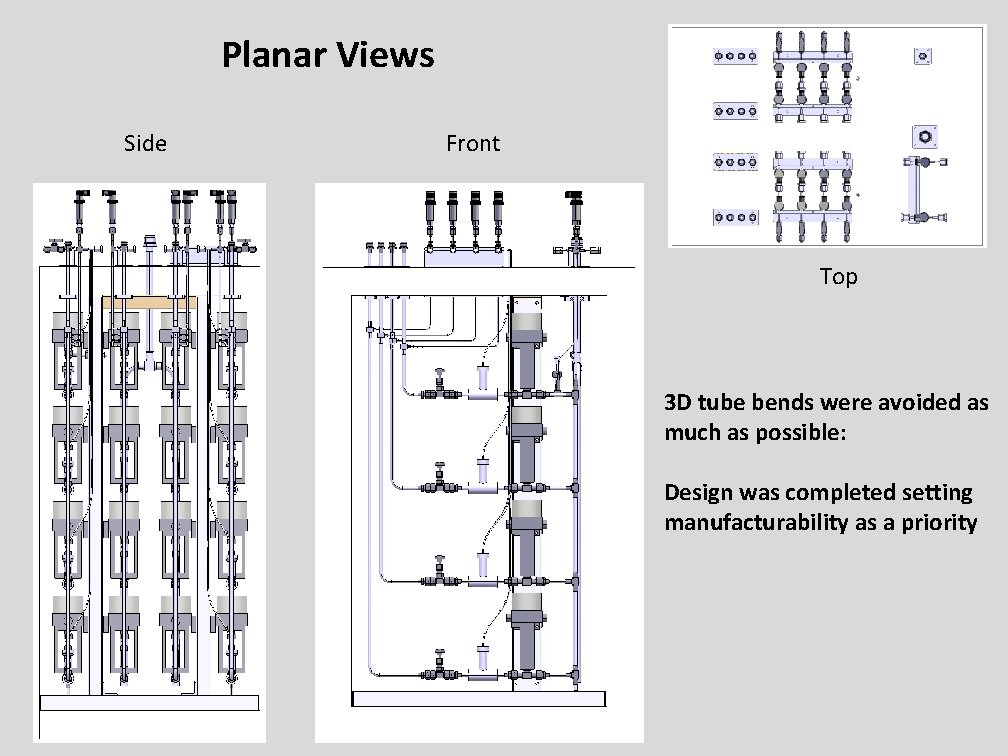
Planar Views Side Front Top 3 D tube bends were avoided as much as possible: Design was completed setting manufacturability as a priority
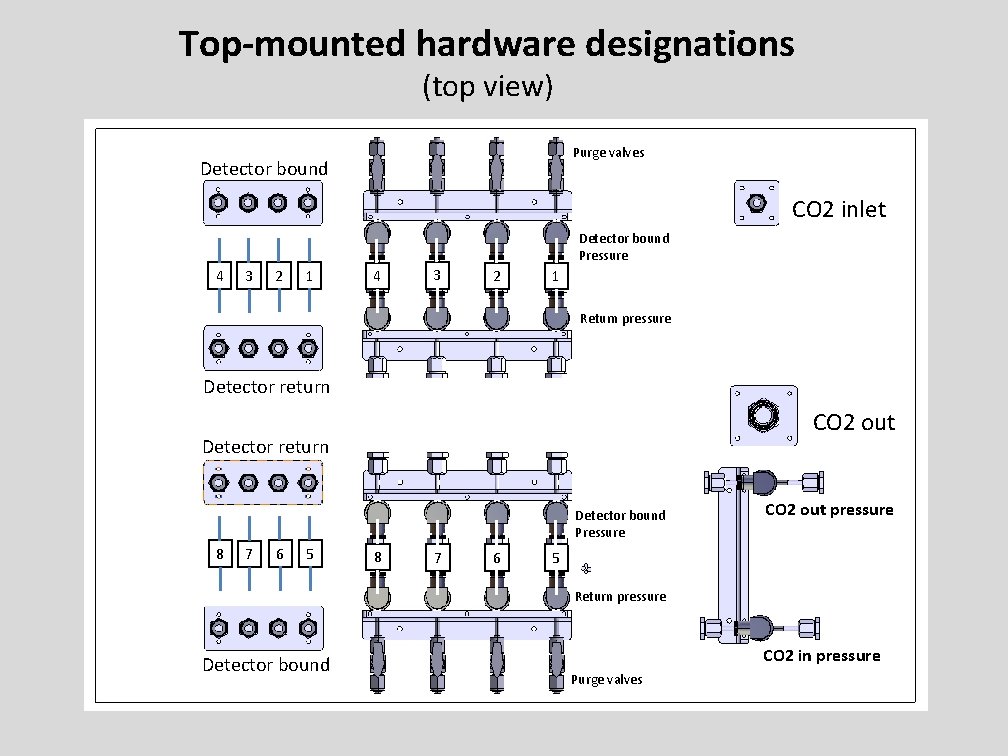
Top-mounted hardware designations (top view) Purge valves Detector bound CO 2 inlet Detector bound Pressure 4 3 2 1 Return pressure Detector return CO 2 out Detector return Detector bound Pressure 8 7 6 5 8 7 6 CO 2 out pressure 5 Return pressure Detector bound CO 2 in pressure Purge valves
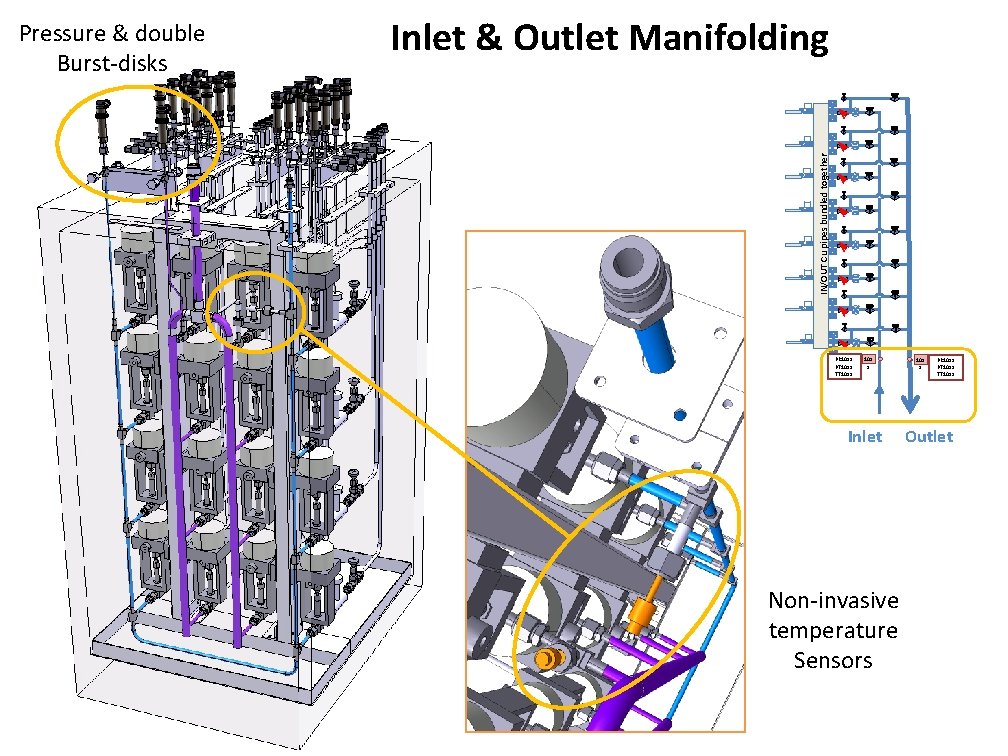
Inlet & Outlet Manifolding IN/OUT Cu pipes bundled together Pressure & double Burst-disks PR 10 xx PT 10 xx TT 10 xx 10 x x Inlet Non-invasive temperature Sensors 10 x x PR 10 xx PT 10 xx TT 10 xx Outlet
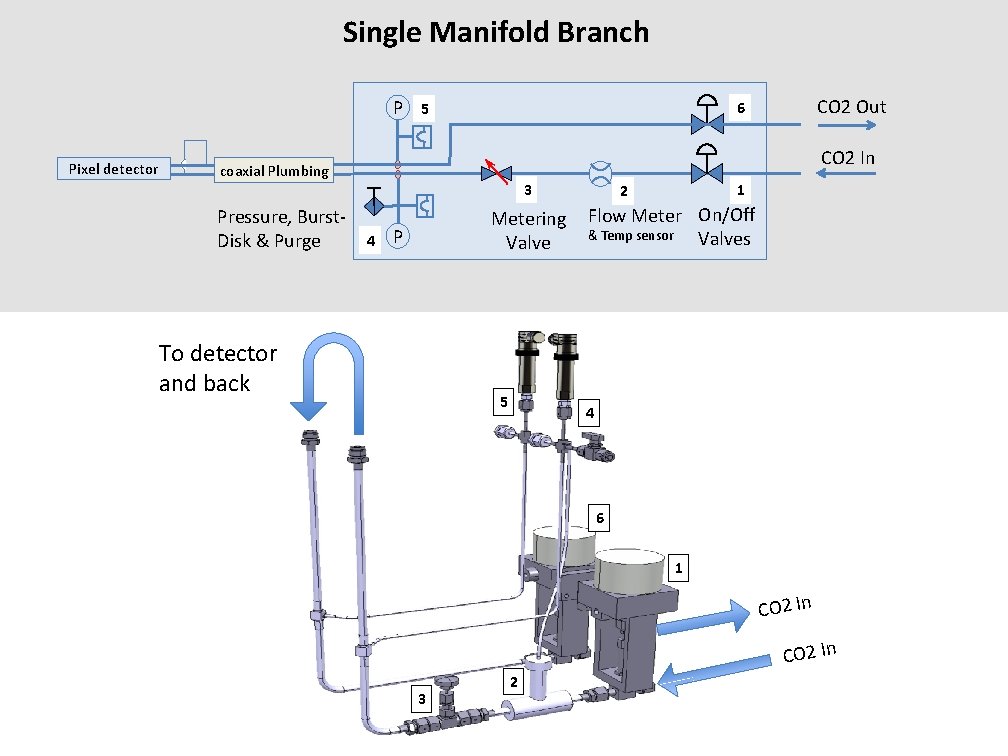
Single Manifold Branch P Pixel detector CO 2 In coaxial Plumbing Pressure, Burst. Disk & Purge CO 2 Out 6 5 3 4 1 2 Metering Flow Meter On/Off & Temp sensor Valves Valve P To detector and back 5 4 6 1 CO 2 In 3 2
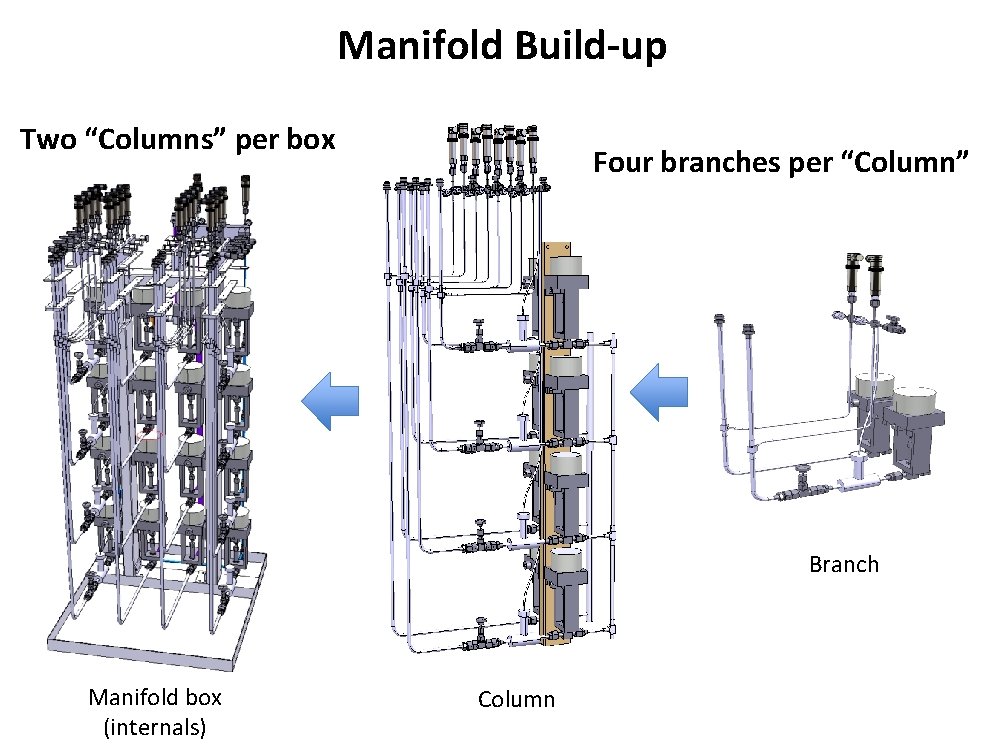
Manifold Build-up Two “Columns” per box Four branches per “Column” Branch Manifold box (internals) Column
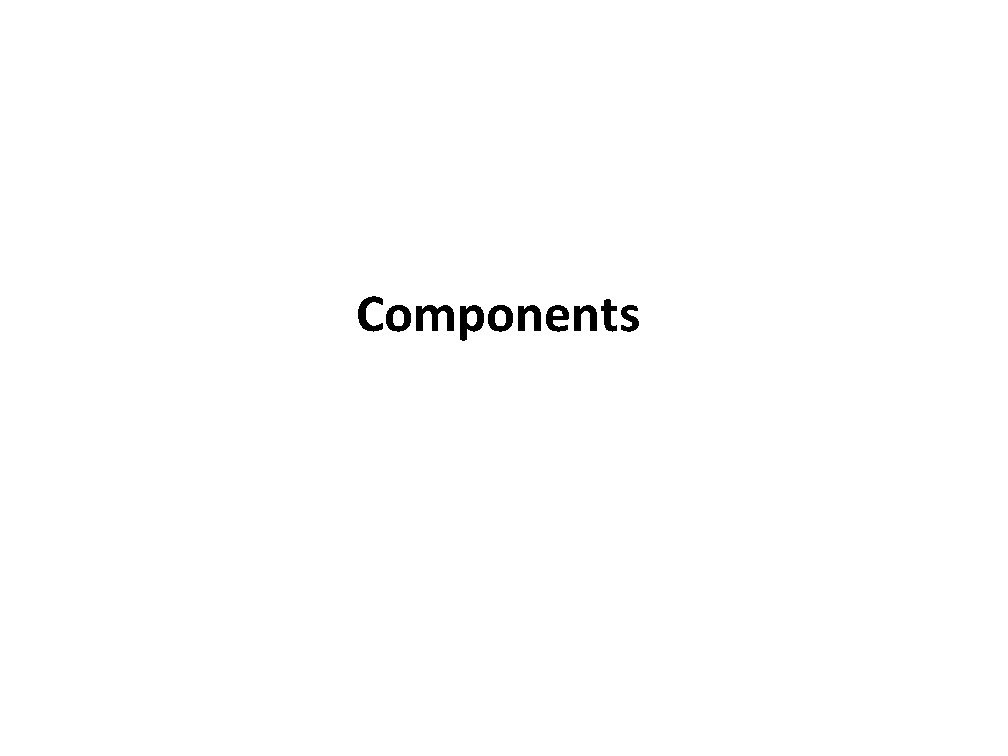
Components
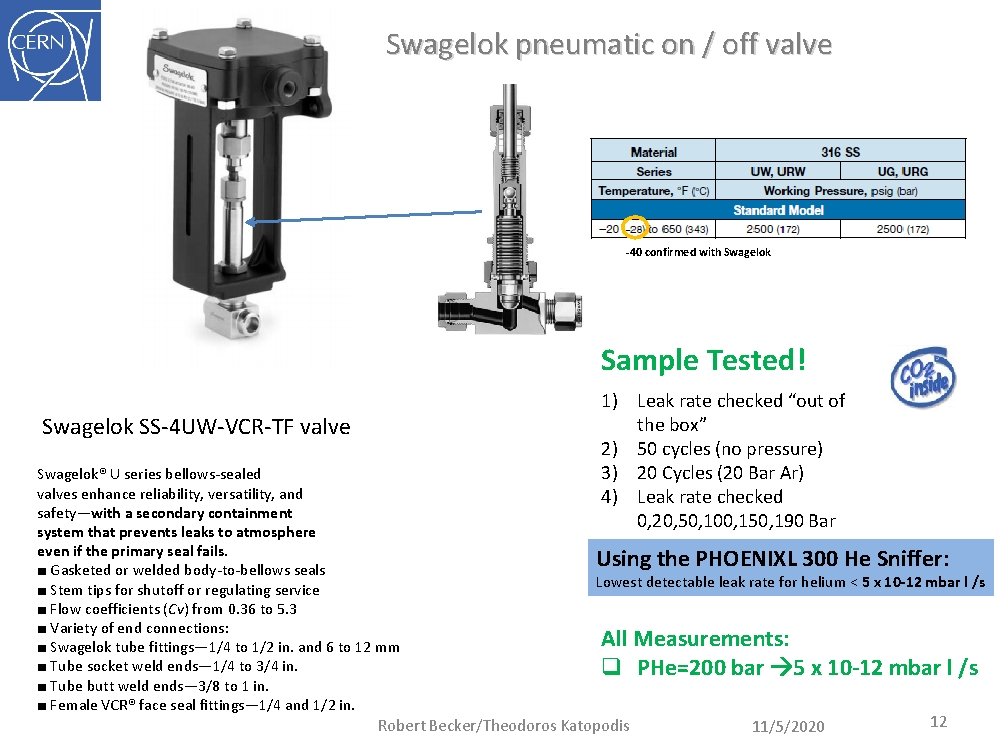
Swagelok pneumatic on / off valve -40 confirmed with Swagelok Sample Tested! Swagelok SS-4 UW-VCR-TF valve Swagelok® U series bellows-sealed valves enhance reliability, versatility, and safety—with a secondary containment system that prevents leaks to atmosphere even if the primary seal fails. ■ Gasketed or welded body-to-bellows seals ■ Stem tips for shutoff or regulating service ■ Flow coefficients (Cv) from 0. 36 to 5. 3 ■ Variety of end connections: ■ Swagelok tube fittings— 1/4 to 1/2 in. and 6 to 12 mm ■ Tube socket weld ends— 1/4 to 3/4 in. ■ Tube butt weld ends— 3/8 to 1 in. ■ Female VCR® face seal fittings— 1/4 and 1/2 in. 1) Leak rate checked “out of the box” 2) 50 cycles (no pressure) 3) 20 Cycles (20 Bar Ar) 4) Leak rate checked 0, 20, 50, 100, 150, 190 Bar Using the PHOENIXL 300 He Sniffer: Lowest detectable leak rate for helium < 5 x 10 -12 mbar l /s All Measurements: q PHe=200 bar 5 x 10 -12 mbar l /s Robert Becker/Theodoros Katopodis 11/5/2020 12
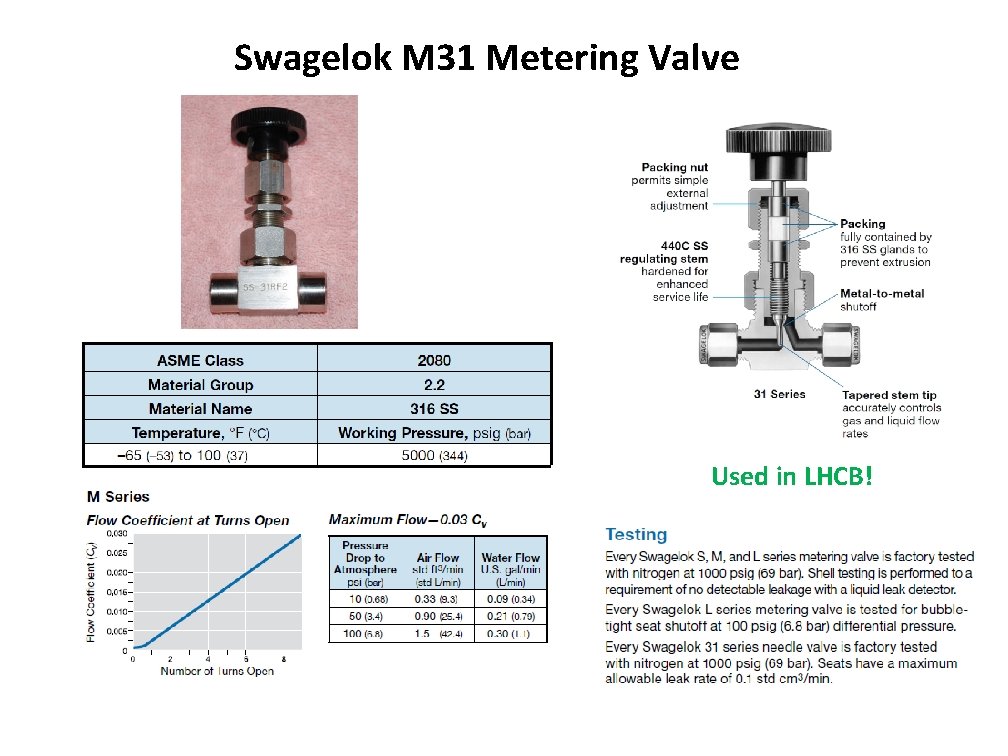
Swagelok M 31 Metering Valve Used in LHCB!
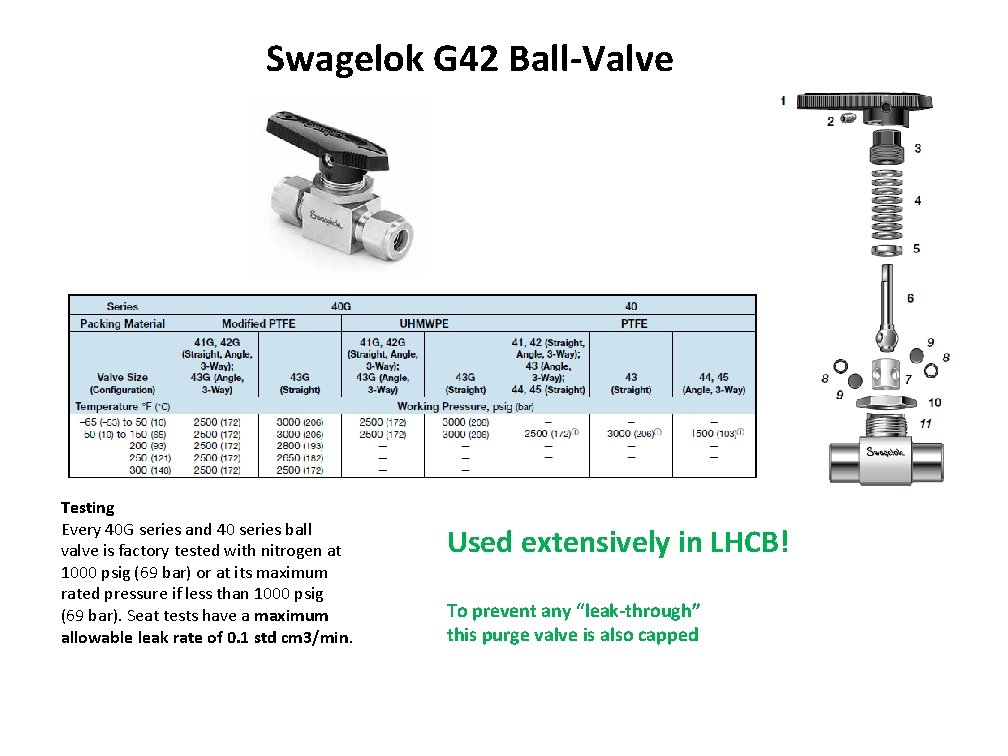
Swagelok G 42 Ball-Valve Testing Every 40 G series and 40 series ball valve is factory tested with nitrogen at 1000 psig (69 bar) or at its maximum rated pressure if less than 1000 psig (69 bar). Seat tests have a maximum allowable leak rate of 0. 1 std cm 3/min. Used extensively in LHCB! To prevent any “leak-through” this purge valve is also capped
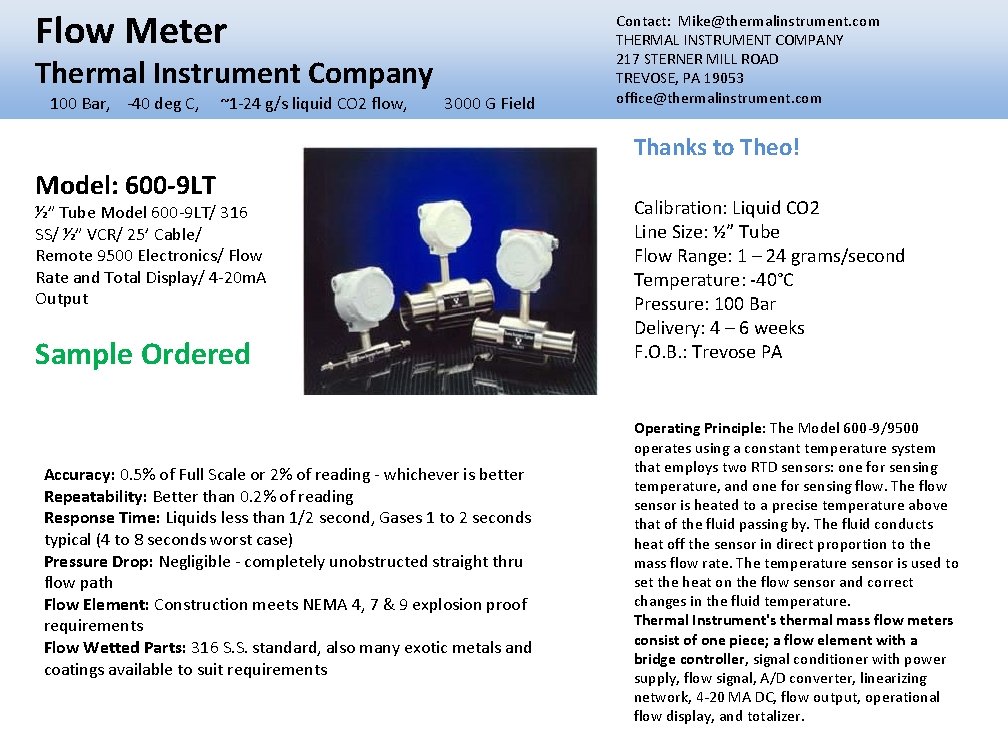
Flow Meter Thermal Instrument Company 100 Bar, -40 deg C, ~1 -24 g/s liquid CO 2 flow, 3000 G Field Contact: Mike@thermalinstrument. com THERMAL INSTRUMENT COMPANY 217 STERNER MILL ROAD TREVOSE, PA 19053 office@thermalinstrument. com Thanks to Theo! Model: 600 -9 LT ½” Tube Model 600 -9 LT/ 316 SS/ ½” VCR/ 25’ Cable/ Remote 9500 Electronics/ Flow Rate and Total Display/ 4 -20 m. A Output Sample Ordered Accuracy: 0. 5% of Full Scale or 2% of reading - whichever is better Repeatability: Better than 0. 2% of reading Response Time: Liquids less than 1/2 second, Gases 1 to 2 seconds typical (4 to 8 seconds worst case) Pressure Drop: Negligible - completely unobstructed straight thru flow path Flow Element: Construction meets NEMA 4, 7 & 9 explosion proof requirements Flow Wetted Parts: 316 S. S. standard, also many exotic metals and coatings available to suit requirements Calibration: Liquid CO 2 Line Size: ½” Tube Flow Range: 1 – 24 grams/second Temperature: -40°C Pressure: 100 Bar Delivery: 4 – 6 weeks F. O. B. : Trevose PA Operating Principle: The Model 600 -9/9500 operates using a constant temperature system that employs two RTD sensors: one for sensing temperature, and one for sensing flow. The flow sensor is heated to a precise temperature above that of the fluid passing by. The fluid conducts heat off the sensor in direct proportion to the mass flow rate. The temperature sensor is used to set the heat on the flow sensor and correct changes in the fluid temperature. Thermal Instrument's thermal mass flow meters consist of one piece; a flow element with a bridge controller, signal conditioner with power supply, flow signal, A/D converter, linearizing network, 4 -20 MA DC, flow output, operational flow display, and totalizer.
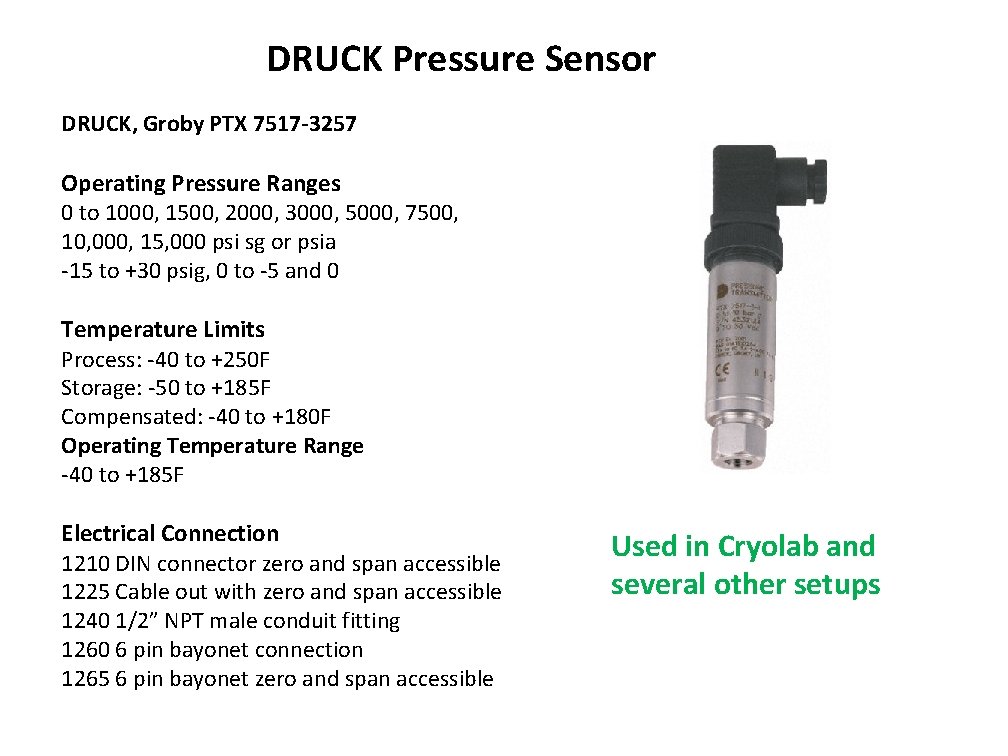
DRUCK Pressure Sensor DRUCK, Groby PTX 7517 -3257 Operating Pressure Ranges 0 to 1000, 1500, 2000, 3000, 5000, 7500, 10, 000, 15, 000 psi sg or psia -15 to +30 psig, 0 to -5 and 0 Temperature Limits Process: -40 to +250 F Storage: -50 to +185 F Compensated: -40 to +180 F Operating Temperature Range -40 to +185 F Electrical Connection 1210 DIN connector zero and span accessible 1225 Cable out with zero and span accessible 1240 1/2” NPT male conduit fitting 1260 6 pin bayonet connection 1265 6 pin bayonet zero and span accessible Used in Cryolab and several other setups
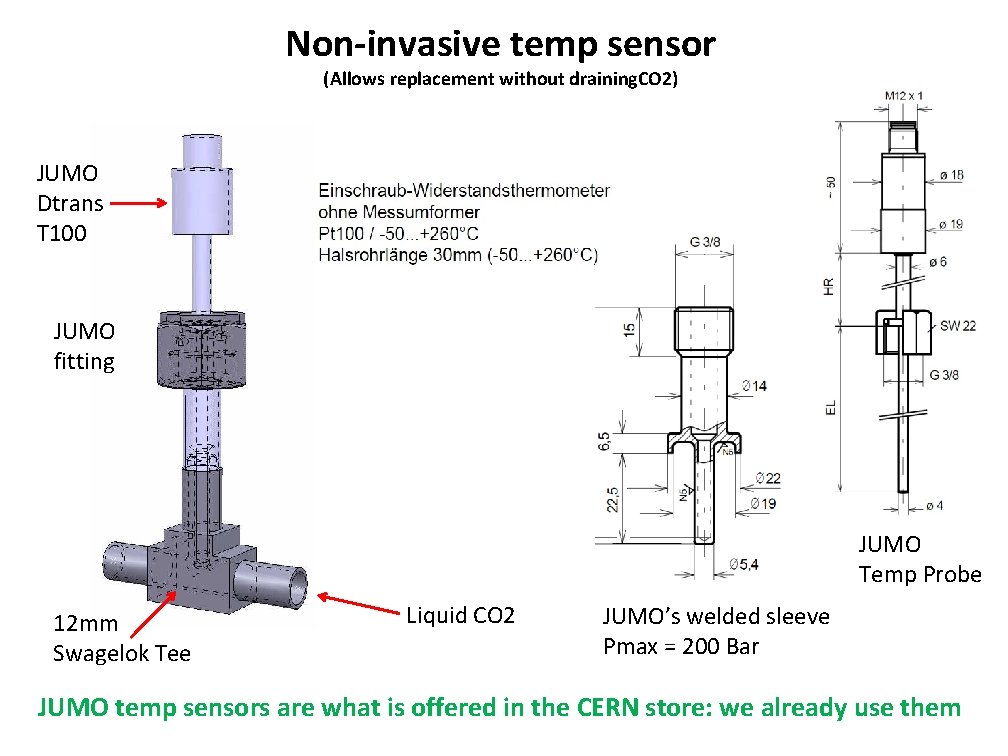
Non-invasive temp sensor (Allows replacement without draining. CO 2) JUMO Dtrans T 100 JUMO fitting JUMO Temp Probe 12 mm Swagelok Tee Liquid CO 2 JUMO’s welded sleeve Pmax = 200 Bar JUMO temp sensors are what is offered in the CERN store: we already use them
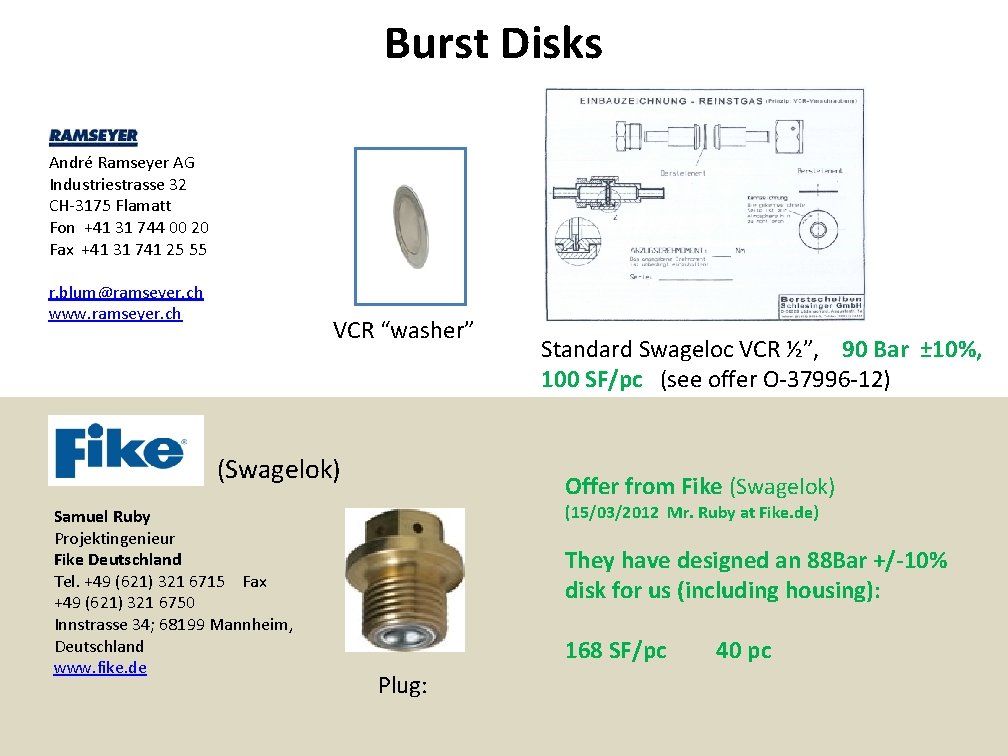
Burst Disks André Ramseyer AG Industriestrasse 32 CH-3175 Flamatt Fon +41 31 744 00 20 Fax +41 31 741 25 55 r. blum@ramseyer. ch www. ramseyer. ch VCR “washer” (Swagelok) Samuel Ruby Projektingenieur Fike Deutschland Tel. +49 (621) 321 6715 Fax +49 (621) 321 6750 Innstrasse 34; 68199 Mannheim, Deutschland www. fike. de Standard Swageloc VCR ½”, 90 Bar ± 10%, 100 SF/pc (see offer O-37996 -12) Offer from Fike (Swagelok) (15/03/2012 Mr. Ruby at Fike. de) They have designed an 88 Bar +/-10% disk for us (including housing): 168 SF/pc Plug: 40 pc
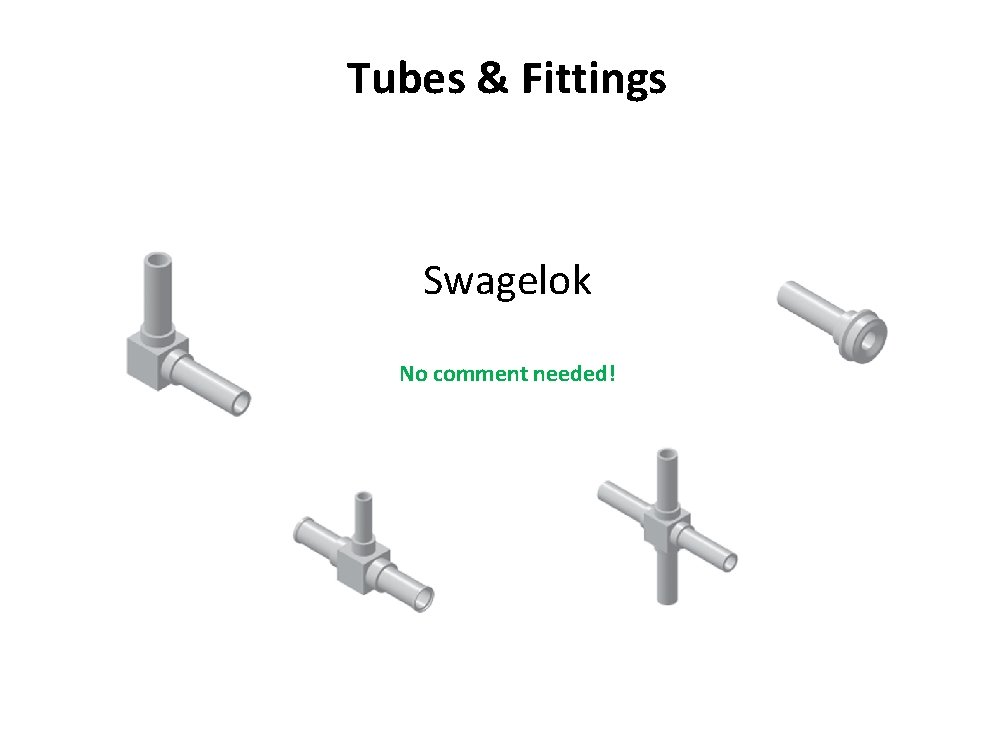
Tubes & Fittings Swagelok No comment needed!
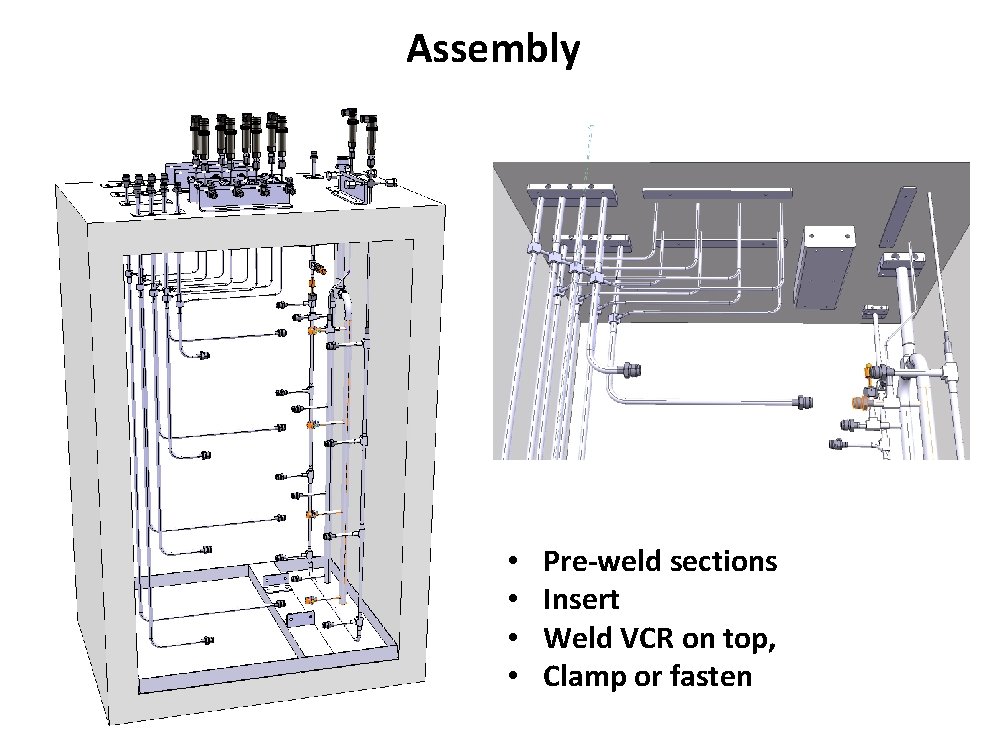
Assembly • • Pre-weld sections Insert Weld VCR on top, Clamp or fasten
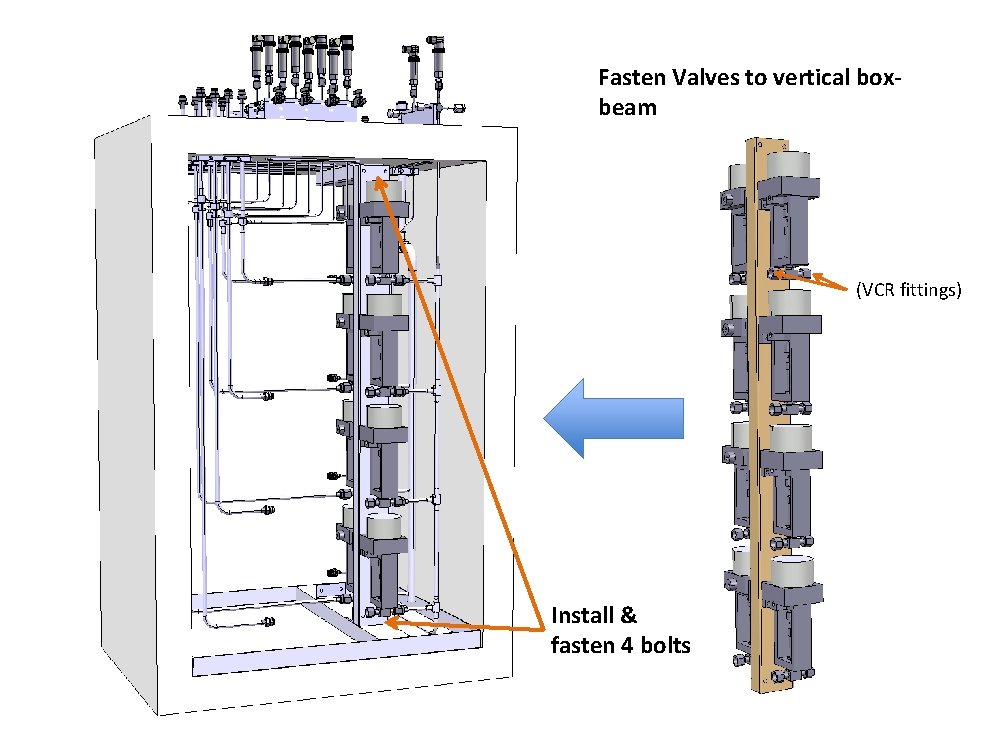
Fasten Valves to vertical boxbeam (VCR fittings) Install & fasten 4 bolts
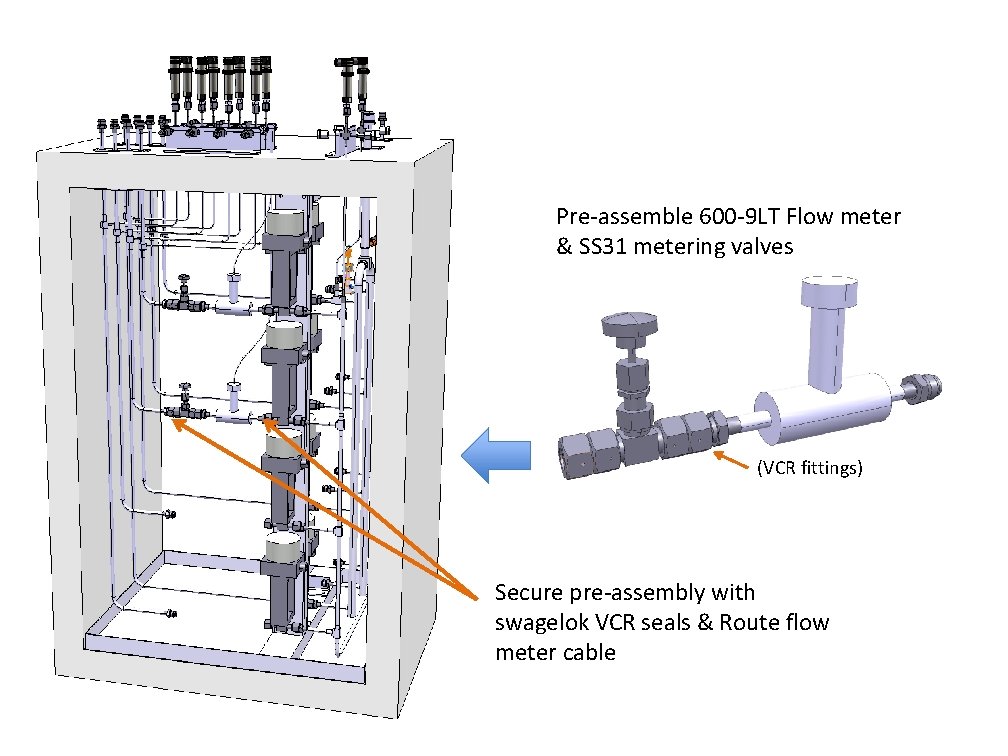
Pre-assemble 600 -9 LT Flow meter & SS 31 metering valves (VCR fittings) Secure pre-assembly with swagelok VCR seals & Route flow meter cable
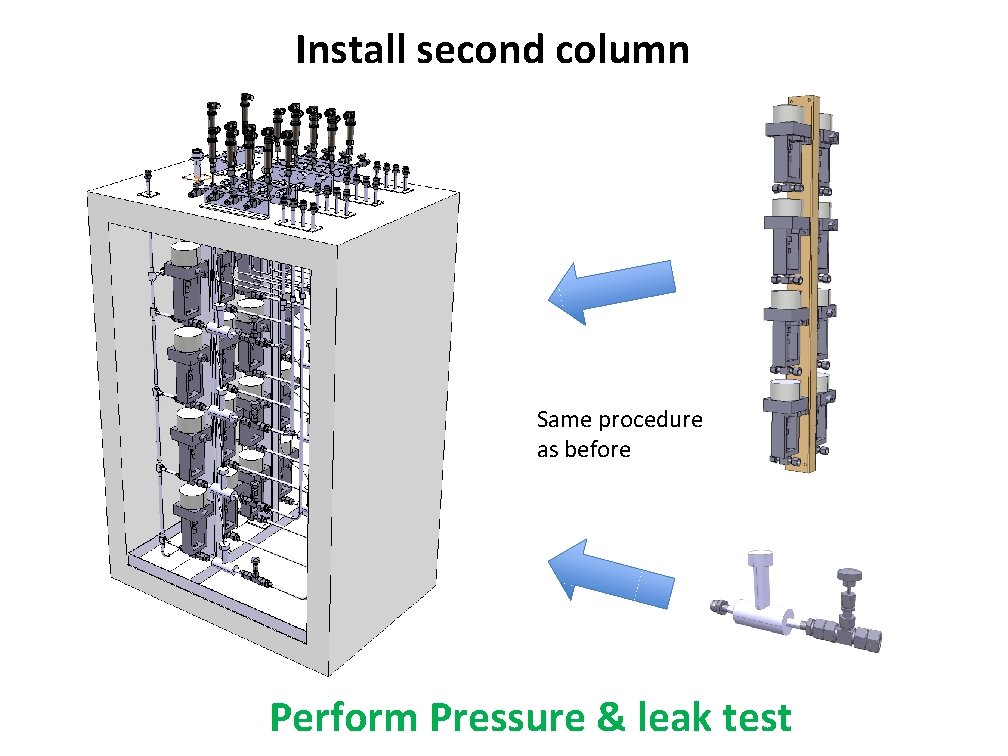
Install second column Same procedure as before Perform Pressure & leak test
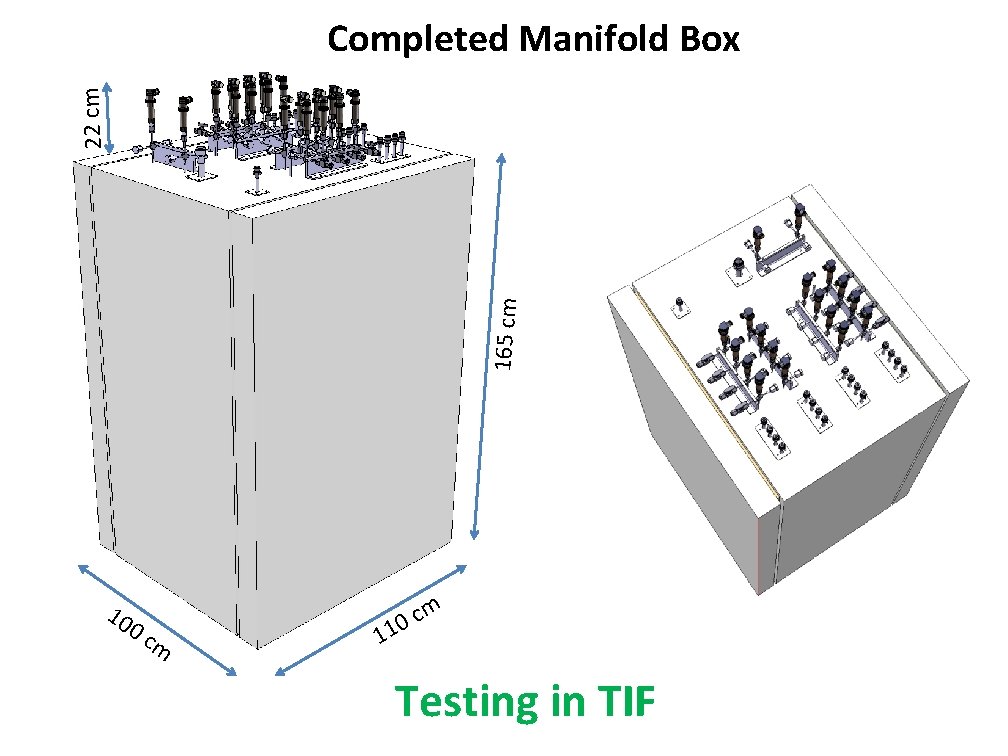
165 cm 22 cm Completed Manifold Box 10 0 c m m c 0 11 Testing in TIF
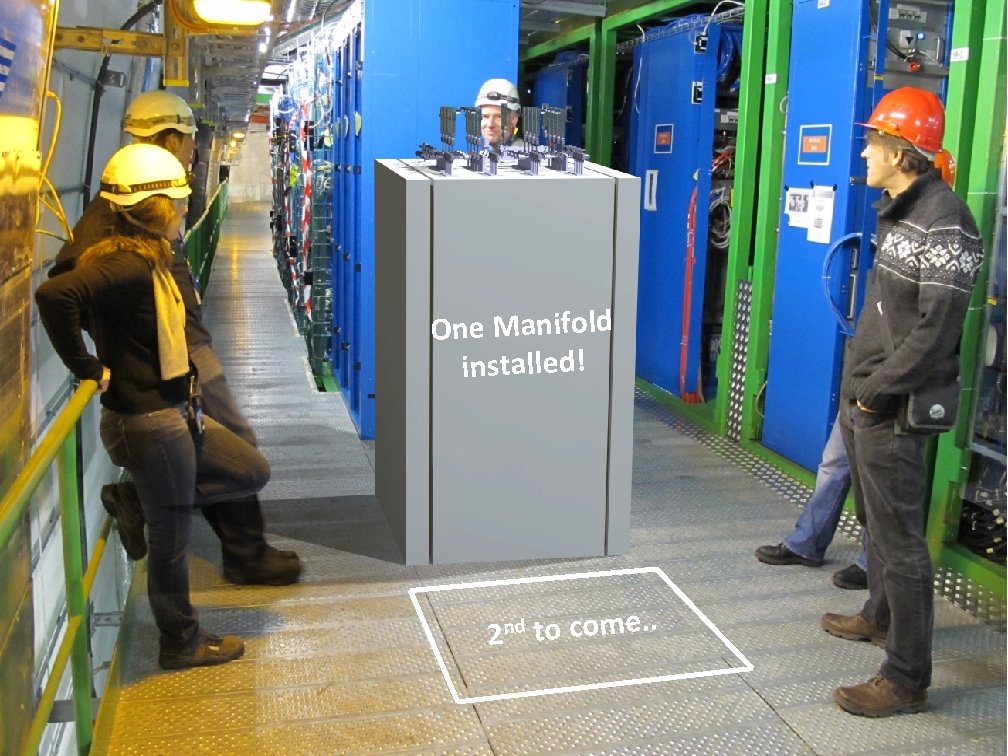
One Manifold installed! . . e m o c o t 2 nd
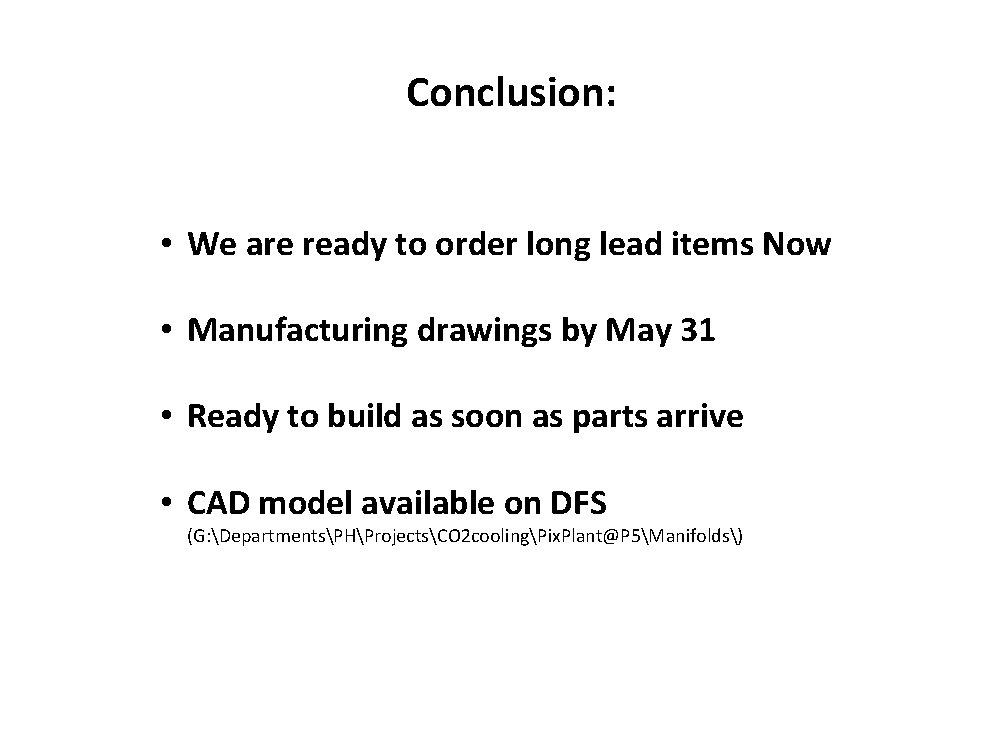
Conclusion: • We are ready to order long lead items Now • Manufacturing drawings by May 31 • Ready to build as soon as parts arrive • CAD model available on DFS (G: DepartmentsPHProjectsCO 2 coolingPix. Plant@P 5Manifolds)
Cms detector
Intake manifold design theory
Head loss formula
Chronological tabulation is based on
Specular manifold sampling
Steam tracing manifold
Testing the manifold hypothesis
Collision manifold
As the load on an engine increases the manifold
A typical map compares the vacuum in the intake manifold to
One dimensional manifold
One dimensional manifold
Manifold clustering
Tri tech medical
Manifold gis tutorial
Ethereum series seriesblock
Multiport fuel injection system
Cms database design
Pixel coordinates
Graphic text
Basic relationships between pixels
Pixel gsi
Pixelrnn
Purity index
Pixel pilot
M adjacency in image processing
Pixel aspect ratio