CHAPTER 10 Polymeric Materials 1 Plastics are large
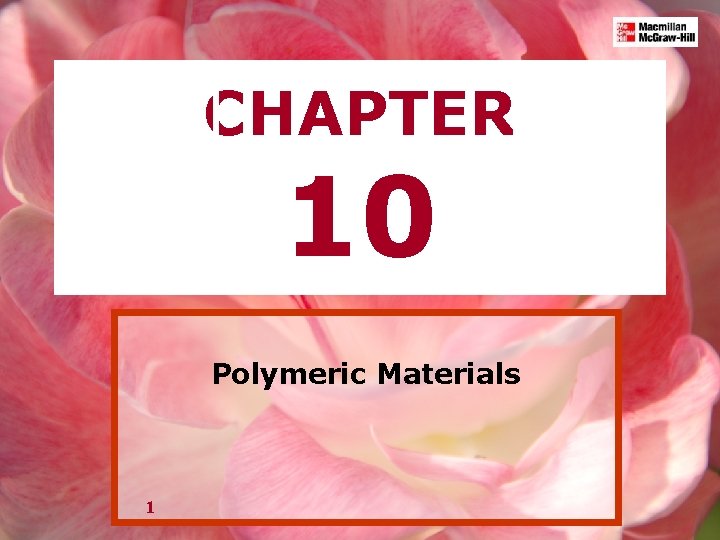
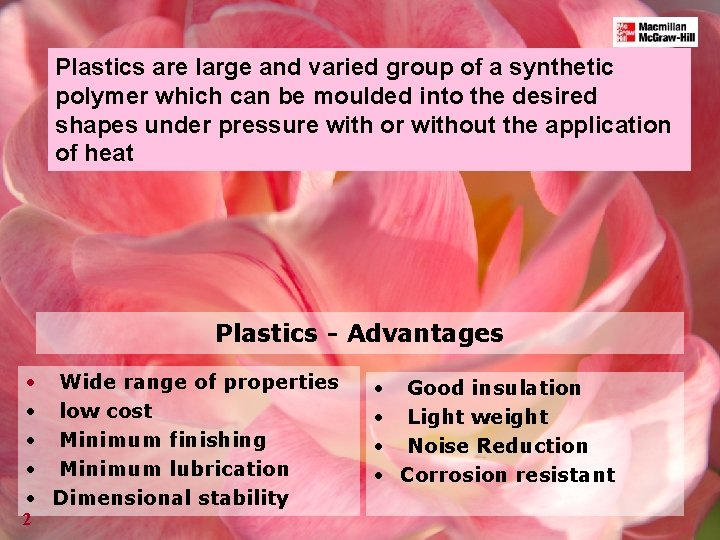

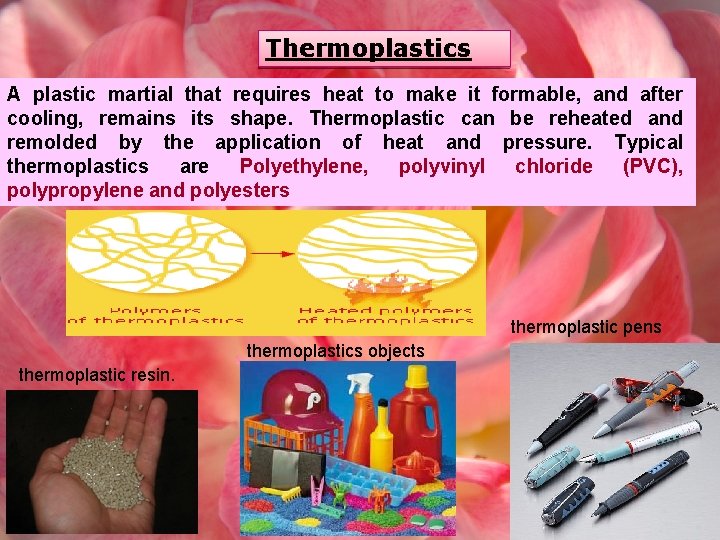

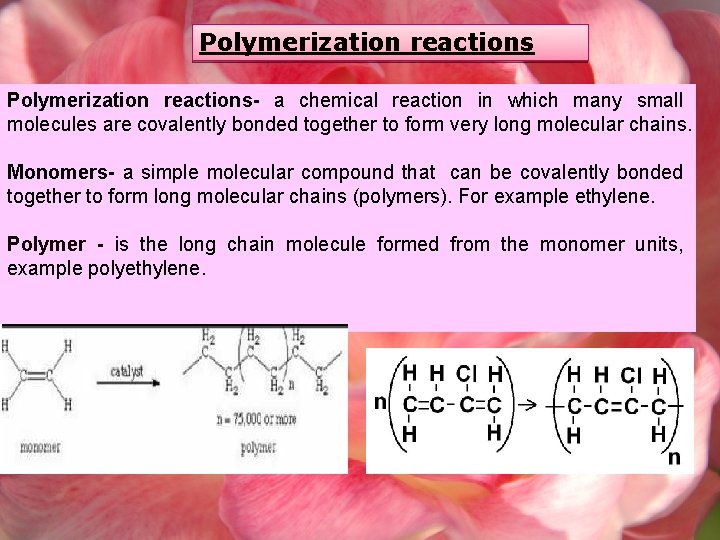
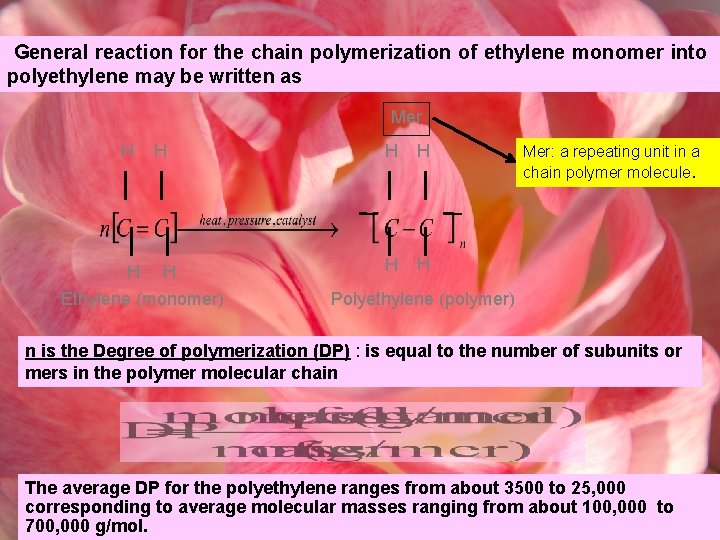
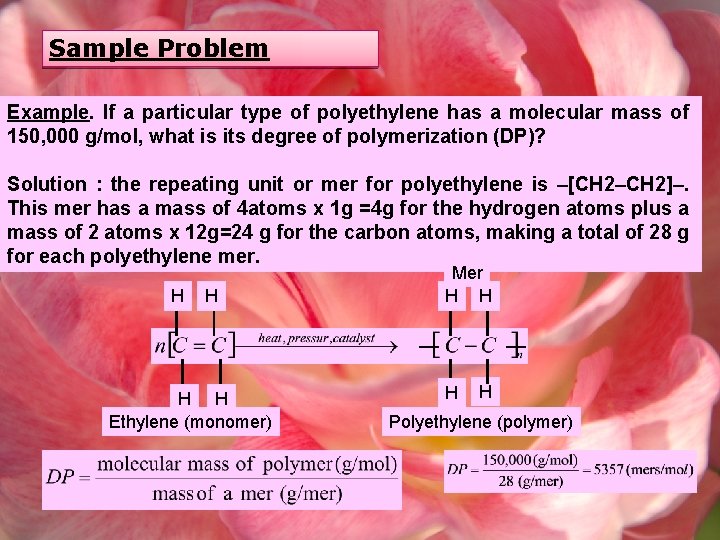
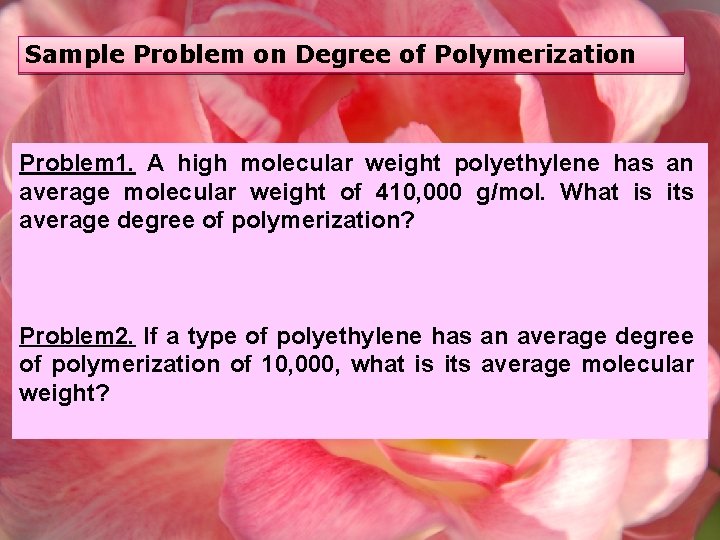
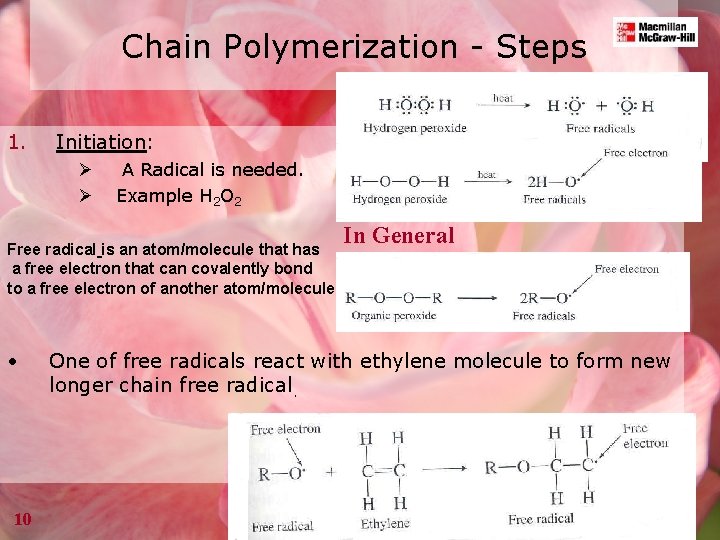
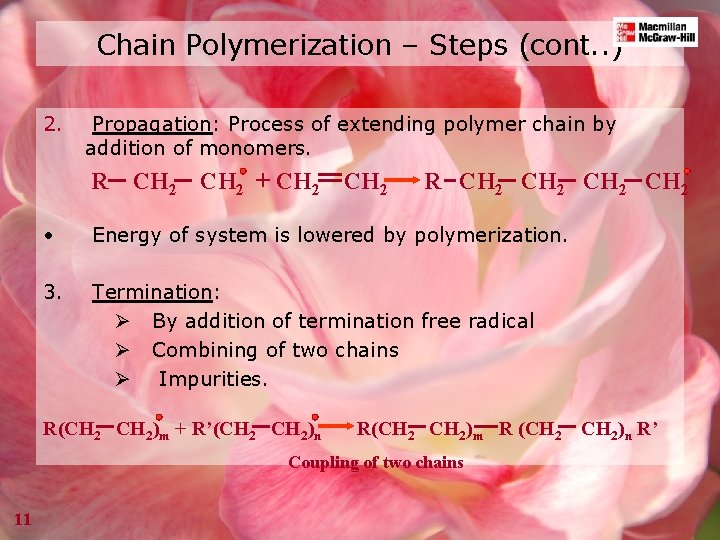
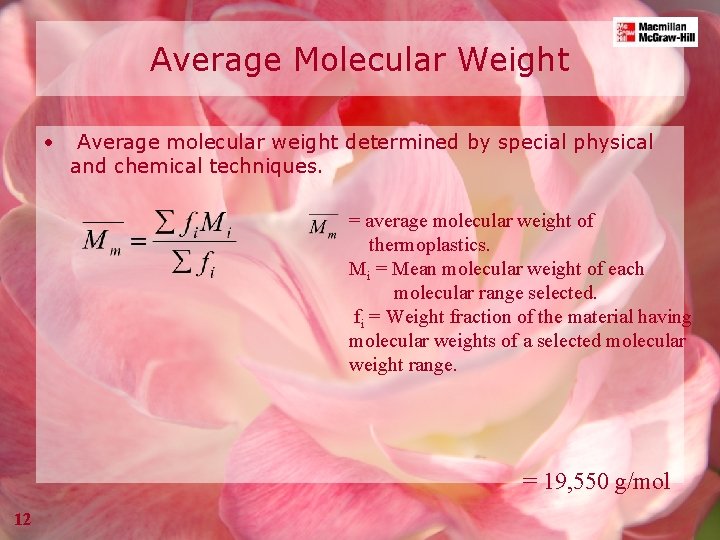
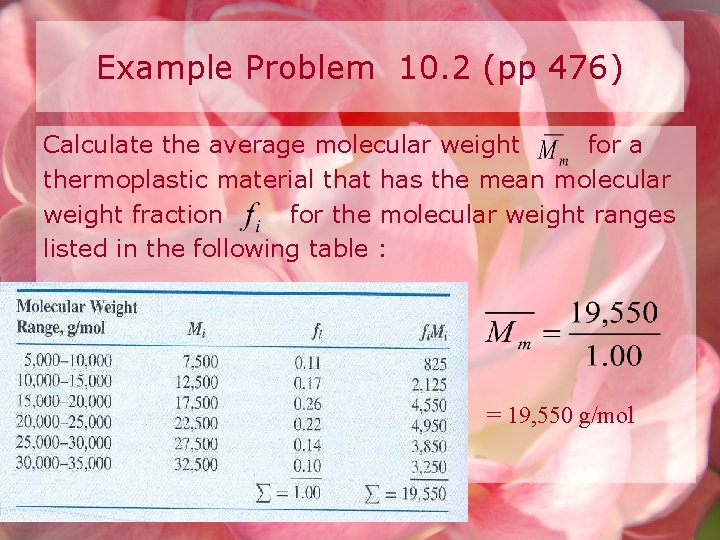
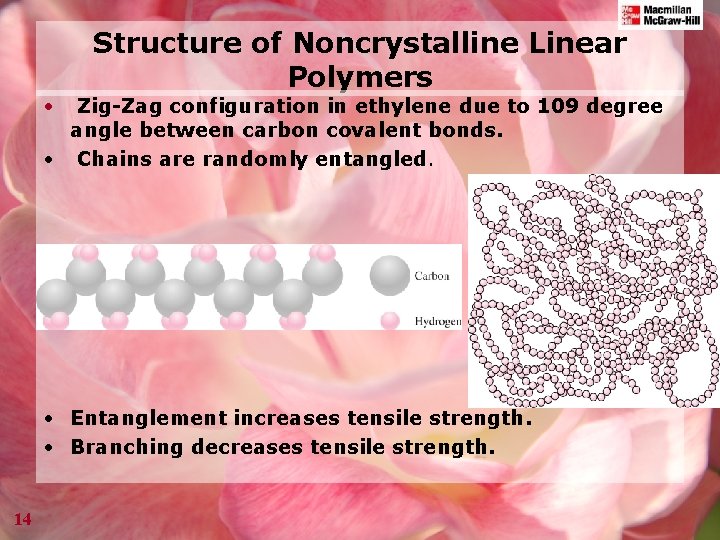
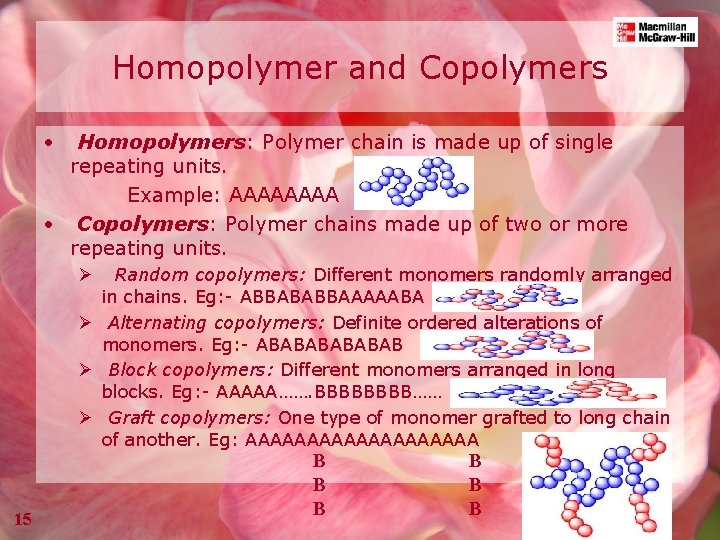
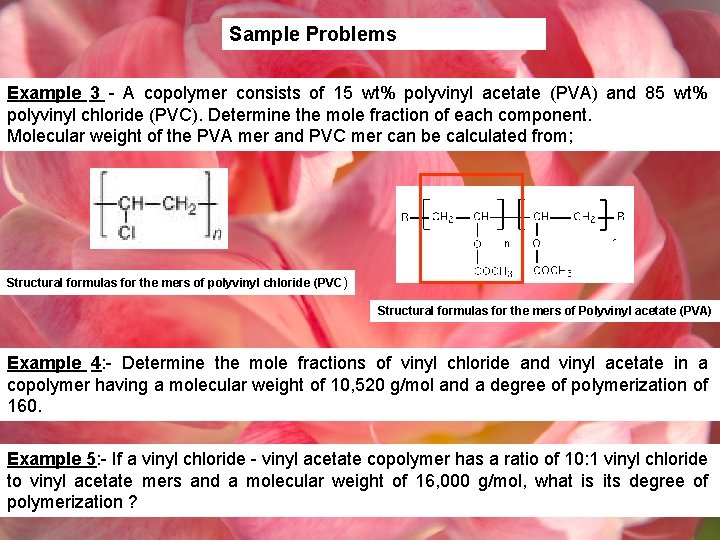

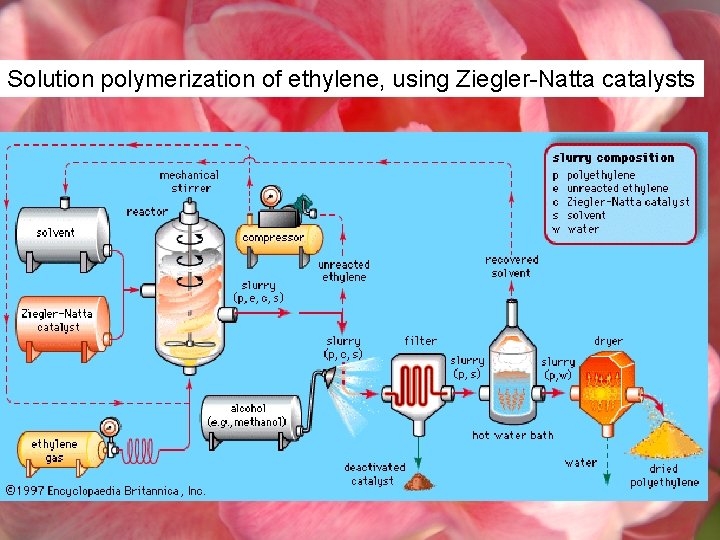
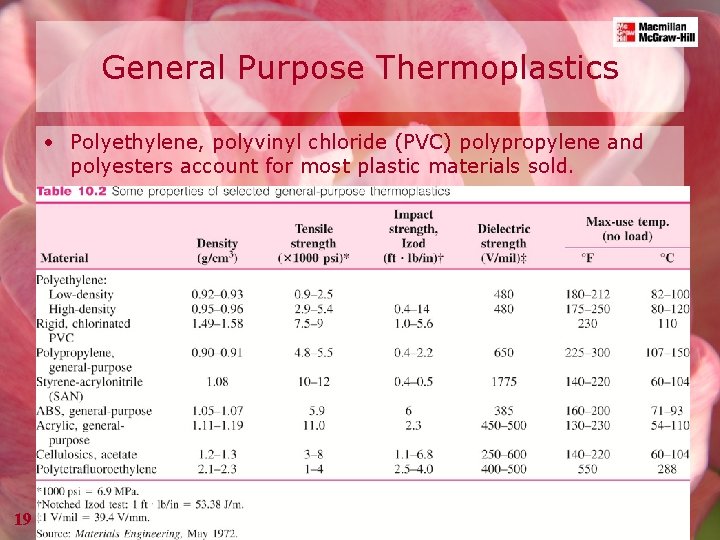
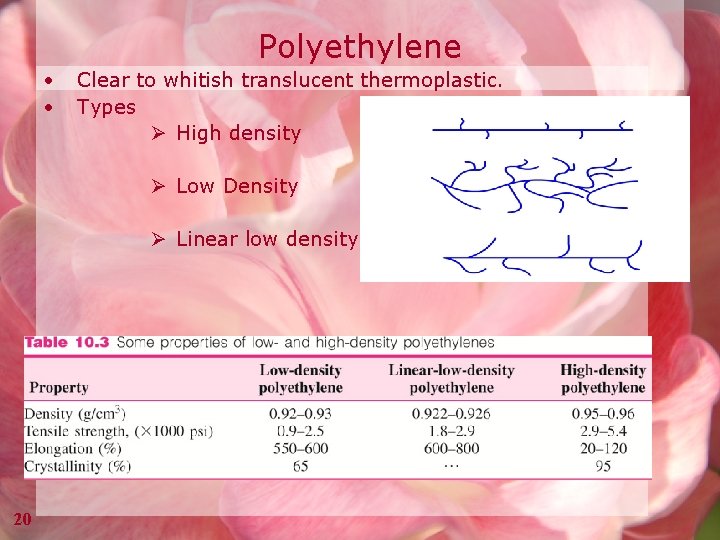
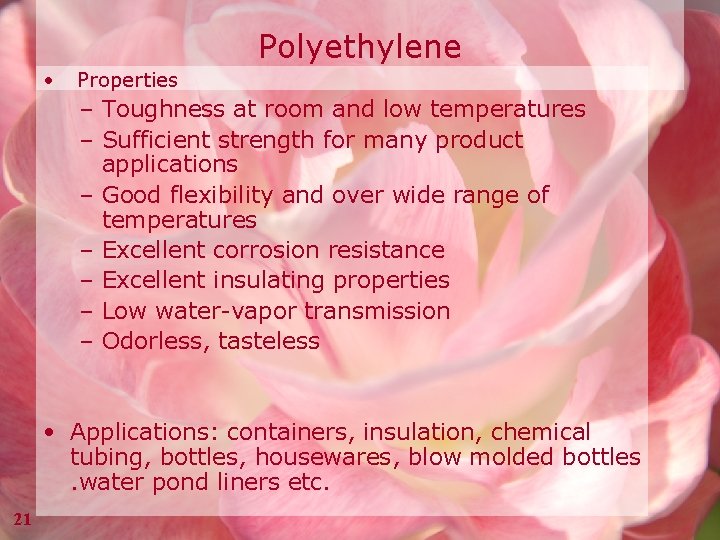
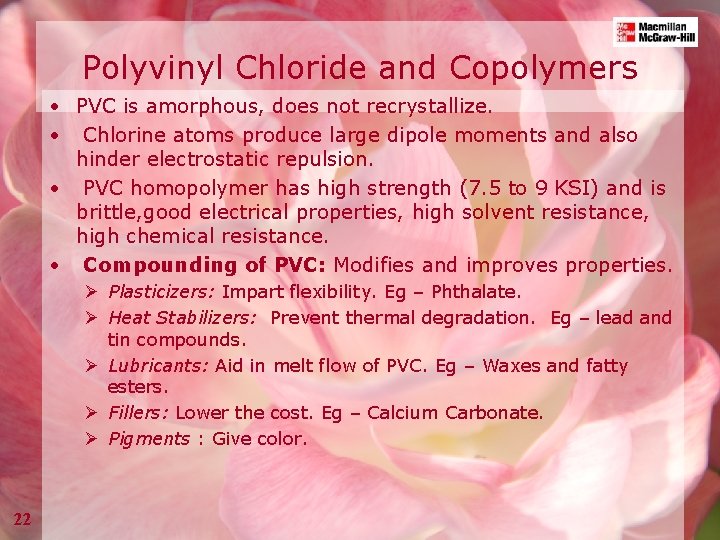
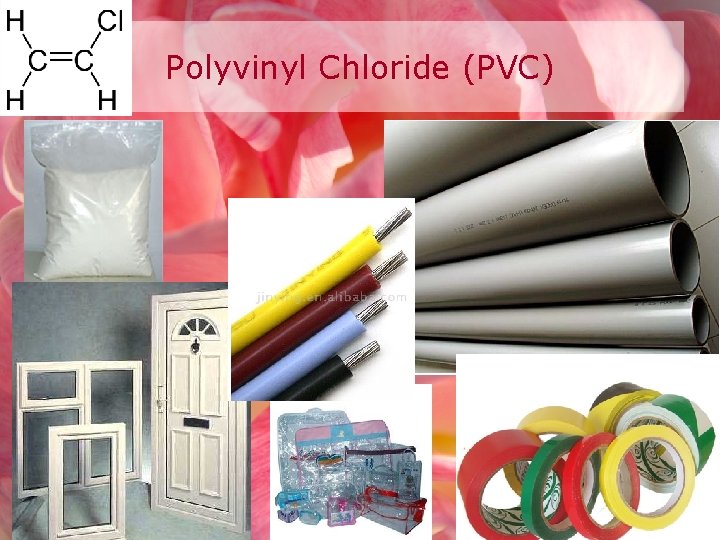
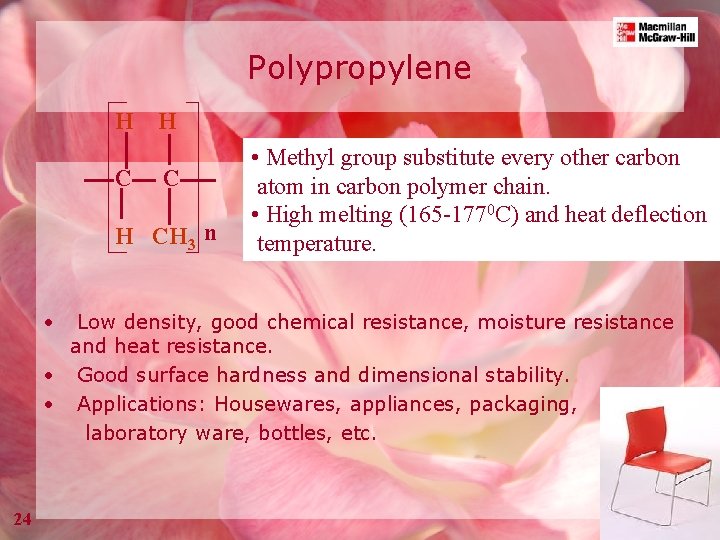
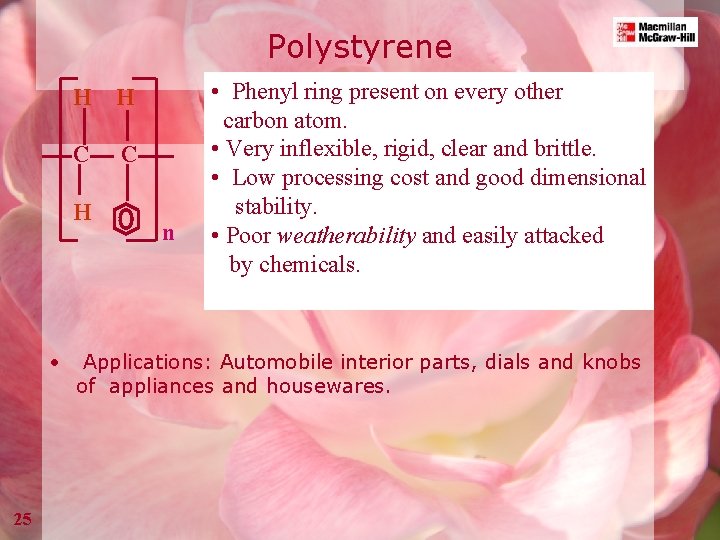
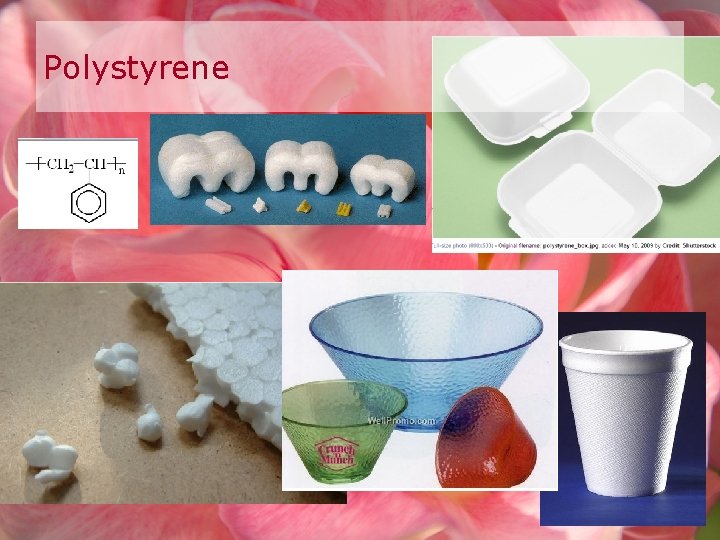
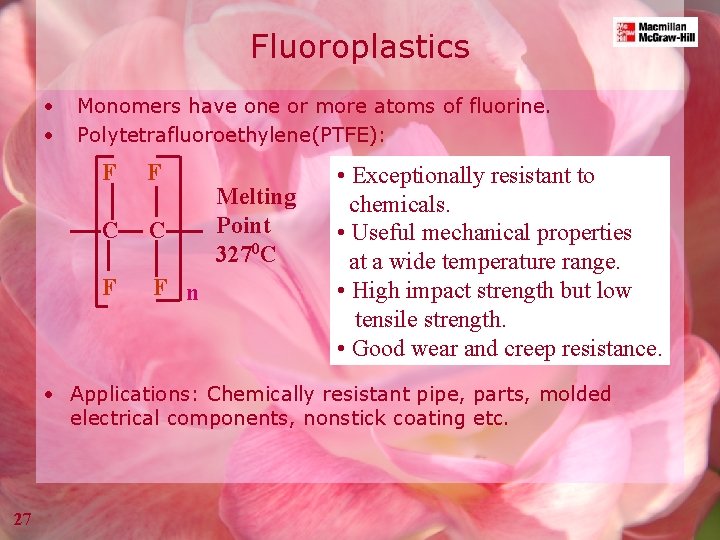
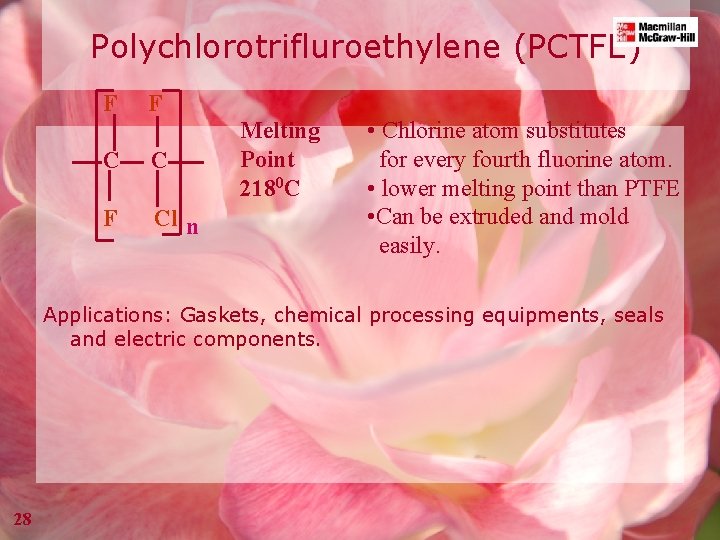
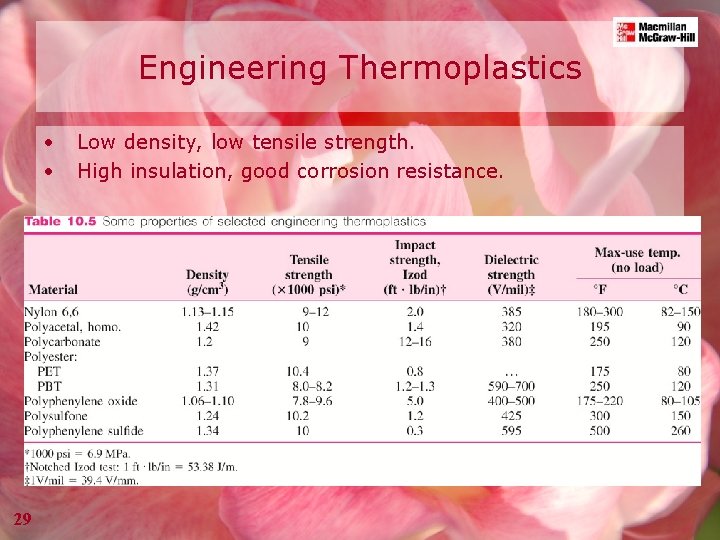
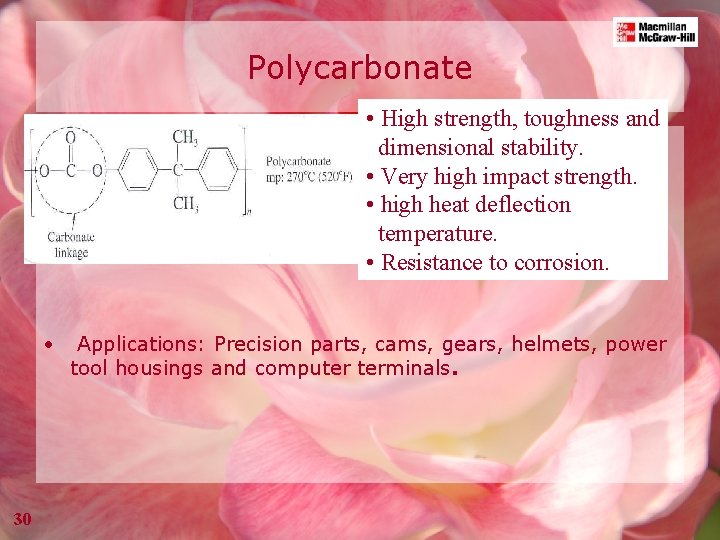
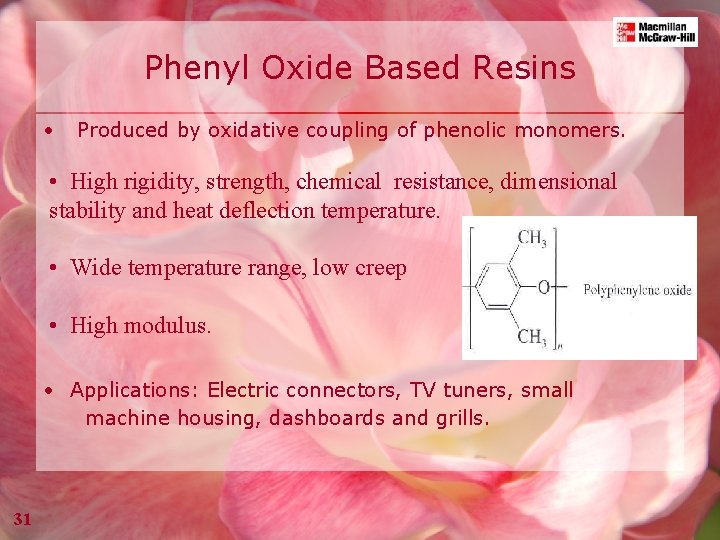

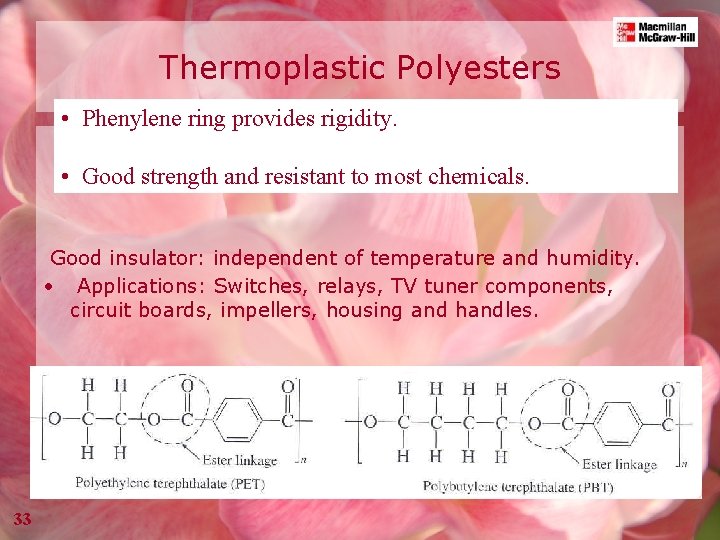
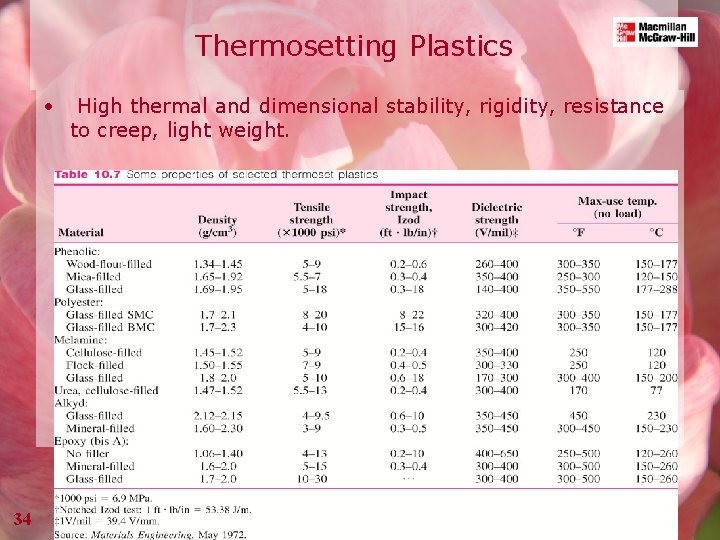
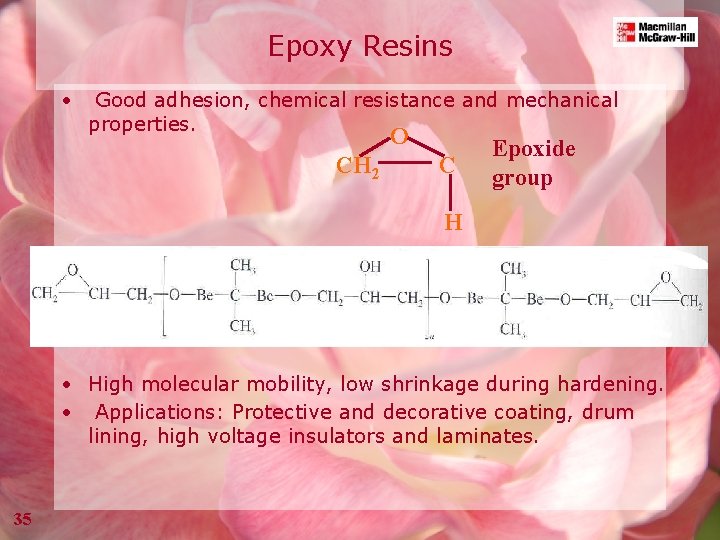
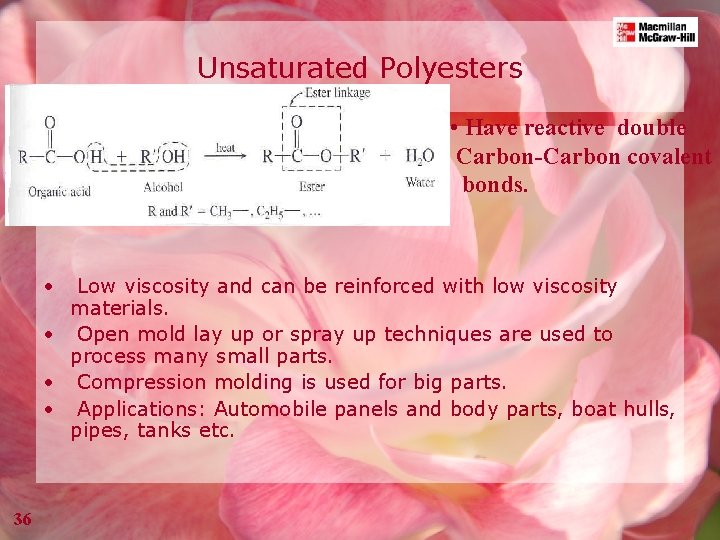
- Slides: 36
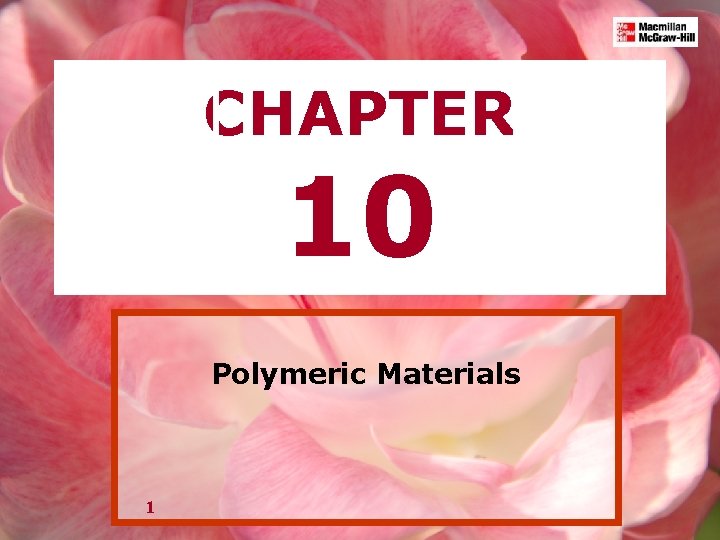
CHAPTER 10 Polymeric Materials 1
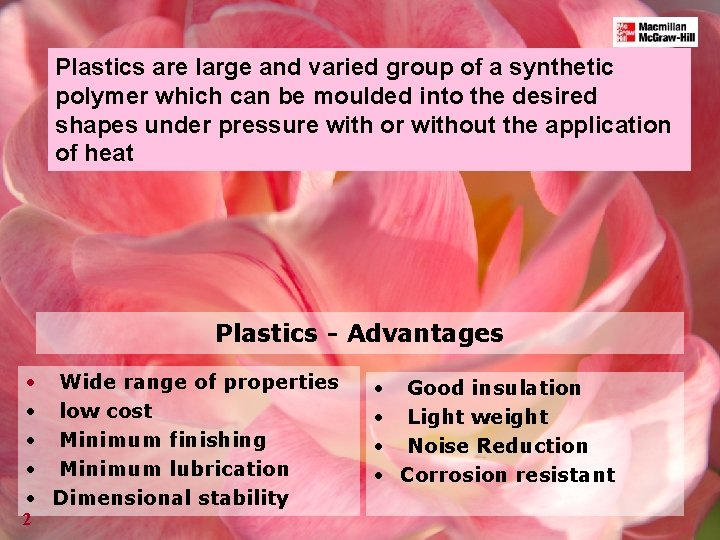
Plastics are large and group a synthetic Polymeric material is avaried material thatofcontains many polymer which can be moulded desired are chemically bonded parts or unitsinto thatthe themselves shapes pressure or without the application bonded under together to formwith a solid of heat Plastics - Advantages • Wide range of properties • low cost • Minimum finishing • Minimum lubrication • Dimensional stability 2 • Good insulation • Light weight • Noise Reduction • Corrosion resistant

2 Types of Plastics
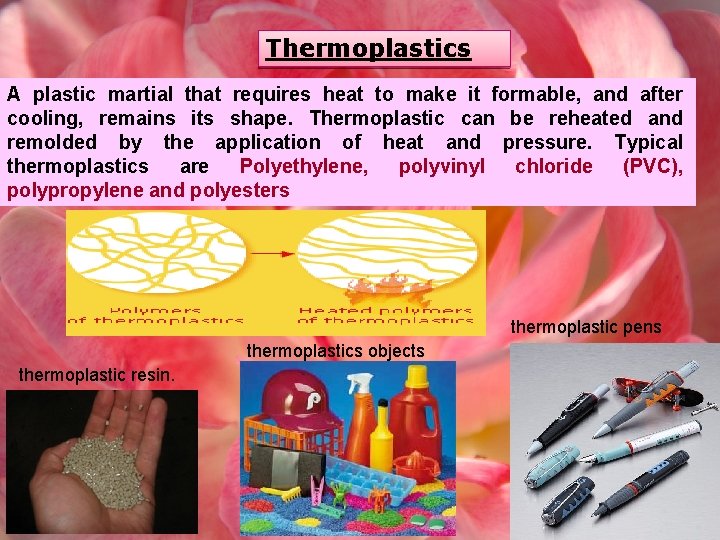
Thermoplastics A plastic martial that requires heat to make it formable, and after cooling, remains its shape. Thermoplastic can be reheated and remolded by the application of heat and pressure. Typical thermoplastics are Polyethylene, polyvinyl chloride (PVC), polypropylene and polyesters thermoplastic pens thermoplastics objects thermoplastic resin.

Thermosetting plastics Usually formed into a permanent shape by heat and pressure during which time a chemical reaction takes place that bonds the atoms together to form a rigid solid. Ø Some thermosetting reactions take place at room temperature without the use of heat and pressure. Ø Thermosetting plastic cannot be remelted after they are set or cured and upon heating to a high temperature, they degrade or decompose. CAN NOT BE RECYCLED. Ø Typical thermosetting plastics are phenolics, unsaturated polyesters and epoxies. The linear chains are crosslinked strongly chemically bonded. This prevents a thermosetting plastic object from being melted and reformed
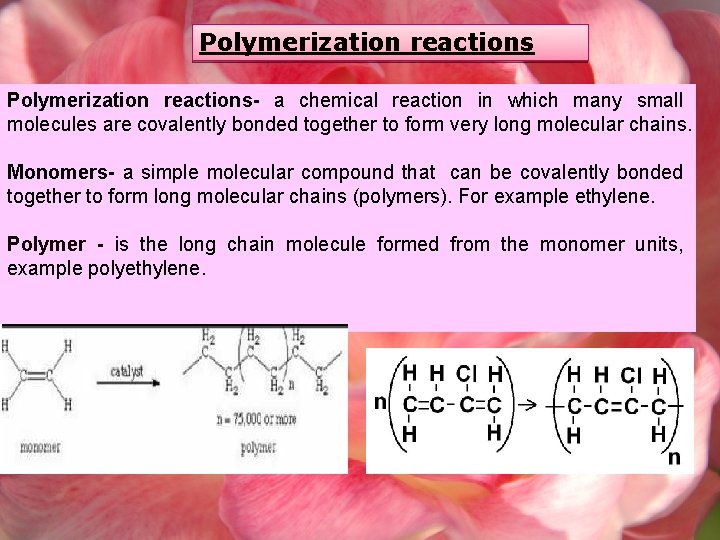
Polymerization reactions- a chemical reaction in which many small molecules are covalently bonded together to form very long molecular chains. Monomers- a simple molecular compound that can be covalently bonded together to form long molecular chains (polymers). For example ethylene. Polymer - is the long chain molecule formed from the monomer units, example polyethylene.
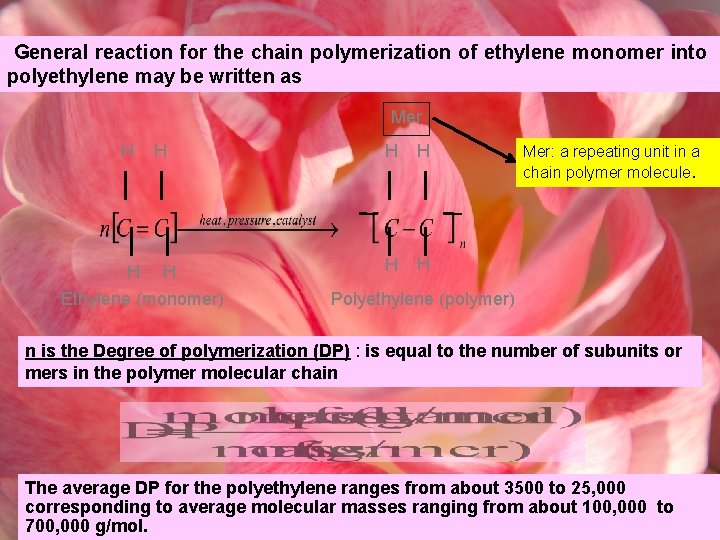
General reaction for the chain polymerization of ethylene monomer into polyethylene may be written as Mer H H Ethylene (monomer) H H Mer: a repeating unit in a chain polymer molecule. Polyethylene (polymer) n is the Degree of polymerization (DP) : is equal to the number of subunits or mers in the polymer molecular chain The average DP for the polyethylene ranges from about 3500 to 25, 000 corresponding to average molecular masses ranging from about 100, 000 to 700, 000 g/mol.
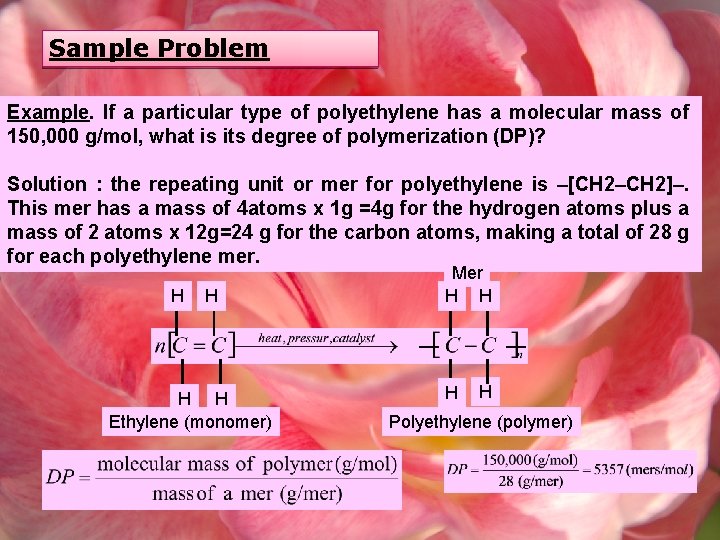
Sample Problem Example. If a particular type of polyethylene has a molecular mass of 150, 000 g/mol, what is its degree of polymerization (DP)? Solution : the repeating unit or mer for polyethylene is –[CH 2–CH 2]–. This mer has a mass of 4 atoms x 1 g =4 g for the hydrogen atoms plus a mass of 2 atoms x 12 g=24 g for the carbon atoms, making a total of 28 g for each polyethylene mer. H H Ethylene (monomer) Mer H H Polyethylene (polymer)
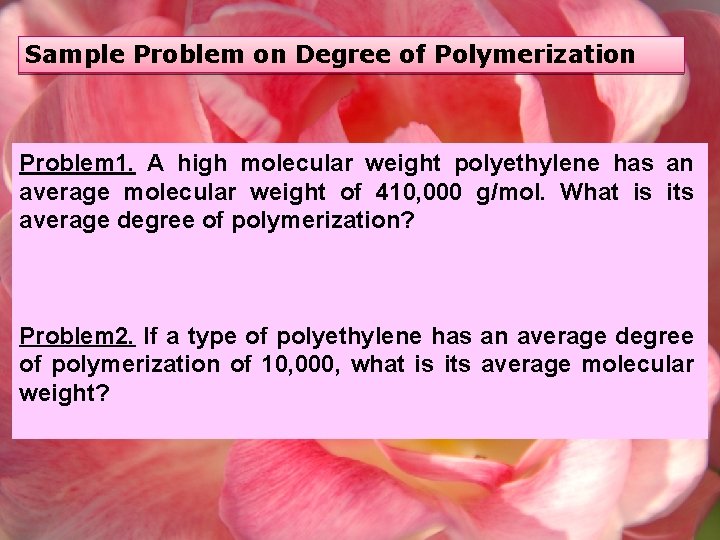
Sample Problem on Degree of Polymerization Problem 1. A high molecular weight polyethylene has an average molecular weight of 410, 000 g/mol. What is its average degree of polymerization? Problem 2. If a type of polyethylene has an average degree of polymerization of 10, 000, what is its average molecular weight?
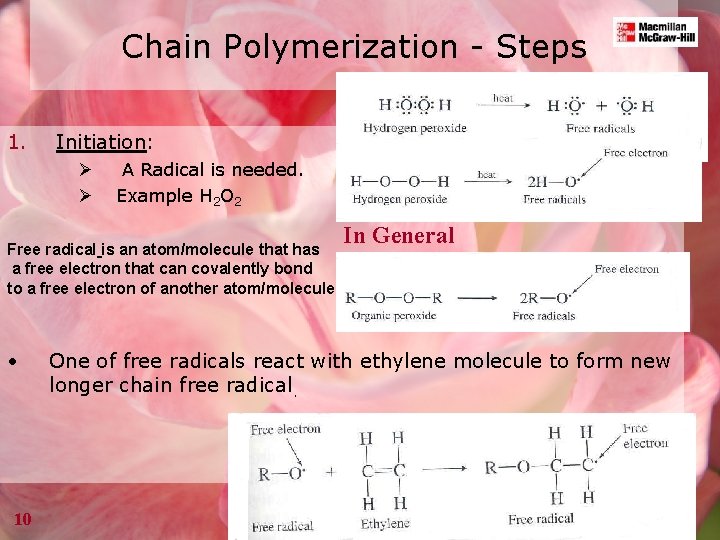
Chain Polymerization - Steps 1. Initiation: Ø Ø A Radical is needed. Example H 2 O 2 Free radical is an atom/molecule that has a free electron that can covalently bond to a free electron of another atom/molecule • 10 In General One of free radicals react with ethylene molecule to form new longer chain free radical.
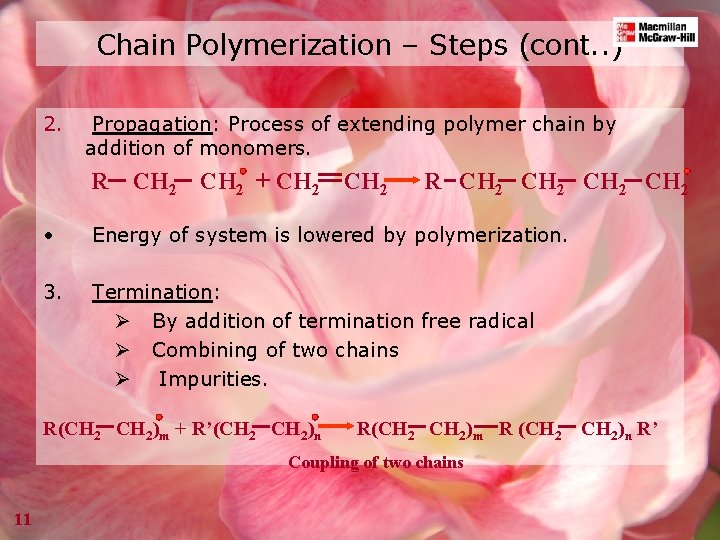
Chain Polymerization – Steps (cont. . ) 2. Propagation: Process of extending polymer chain by addition of monomers. R CH 2 + CH 2 R CH 2 • Energy of system is lowered by polymerization. 3. Termination: Ø By addition of termination free radical Ø Combining of two chains Ø Impurities. R(CH 2)m + R’(CH 2)n R(CH 2)m R (CH 2 Coupling of two chains 11 CH 2)n R’
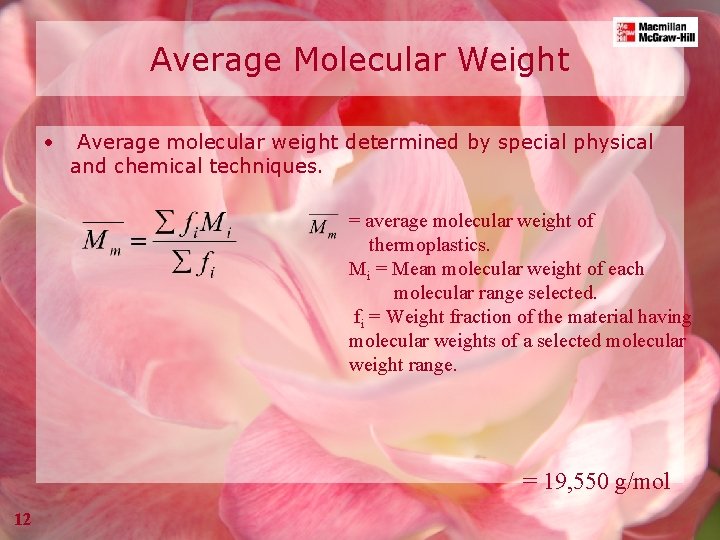
Average Molecular Weight • Average molecular weight determined by special physical and chemical techniques. = average molecular weight of thermoplastics. Mi = Mean molecular weight of each molecular range selected. fi = Weight fraction of the material having molecular weights of a selected molecular weight range. = 19, 550 g/mol 12
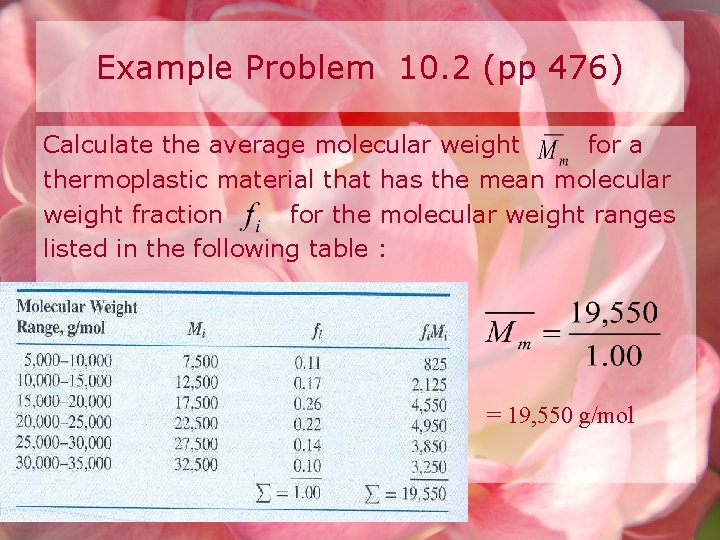
Example Problem 10. 2 (pp 476) Calculate the average molecular weight for a thermoplastic material that has the mean molecular weight fraction for the molecular weight ranges listed in the following table : = 19, 550 g/mol
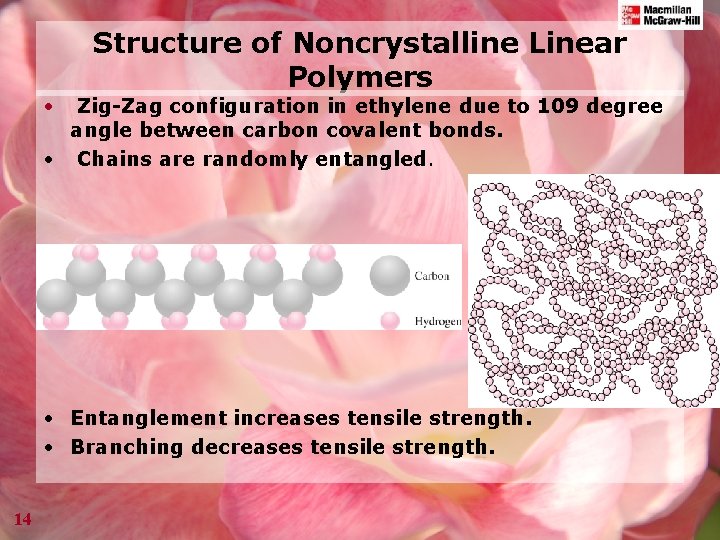
Structure of Noncrystalline Linear Polymers • Zig-Zag configuration in ethylene due to 109 degree angle between carbon covalent bonds. • Chains are randomly entangled. • Entanglement increases tensile strength. • Branching decreases tensile strength. 14
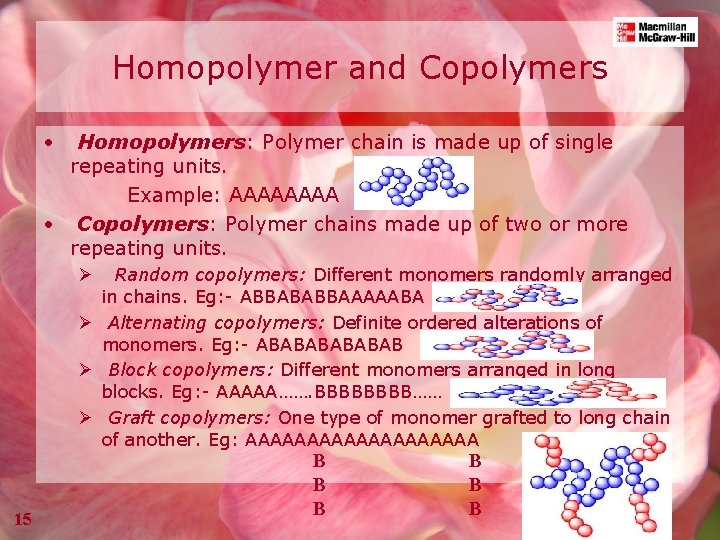
Homopolymer and Copolymers • Homopolymers: Polymer chain is made up of single repeating units. Example: AAAA • Copolymers: Polymer chains made up of two or more repeating units. Random copolymers: Different monomers randomly arranged in chains. Eg: - ABBABABBAAAAABA Ø Alternating copolymers: Definite ordered alterations of monomers. Eg: - ABABAB Ø Block copolymers: Different monomers arranged in long blocks. Eg: - AAAAA……. BBBB…… Ø Graft copolymers: One type of monomer grafted to long chain of another. Eg: AAAAAAAAAA Ø 15 B B B
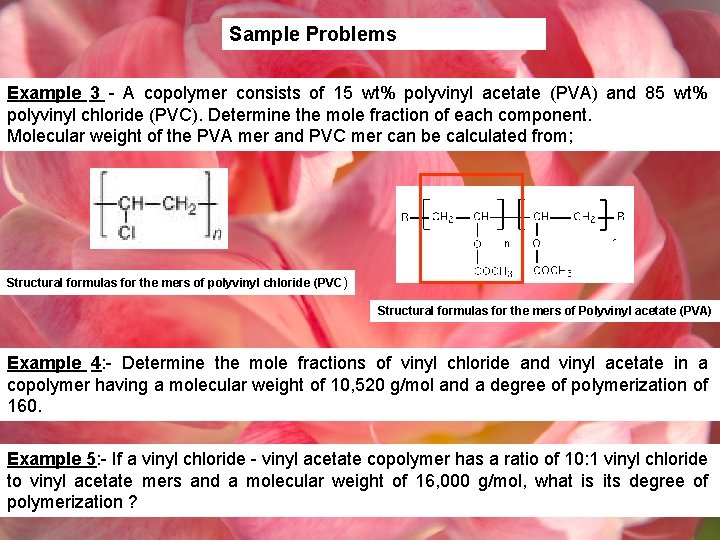
Sample Problems Example 3 - A copolymer consists of 15 wt% polyvinyl acetate (PVA) and 85 wt% polyvinyl chloride (PVC). Determine the mole fraction of each component. Molecular weight of the PVA mer and PVC mer can be calculated from; Structural formulas for the mers of polyvinyl chloride (PVC ) Structural formulas for the mers of Polyvinyl acetate (PVA) Example 4: - Determine the mole fractions of vinyl chloride and vinyl acetate in a copolymer having a molecular weight of 10, 520 g/mol and a degree of polymerization of 160. Example 5: - If a vinyl chloride - vinyl acetate copolymer has a ratio of 10: 1 vinyl chloride to vinyl acetate mers and a molecular weight of 16, 000 g/mol, what is its degree of polymerization ?

Industrial Polymerization Raw Materials: Natural gas, Petroleum and coal Granules, pellets, Polymerization powders or liquids. • Bulk polymerization : Monomer and activator mixed in a reactor and heated and cooled as desired • Solution polymerization: Monomer dissolved in non-reactive solvent and catalyst. • Suspension polymerization: monomer and catalyst suspended in water. • Emulsion polymerization: Monomer and catalyst suspended in water along with emulsifier. 17
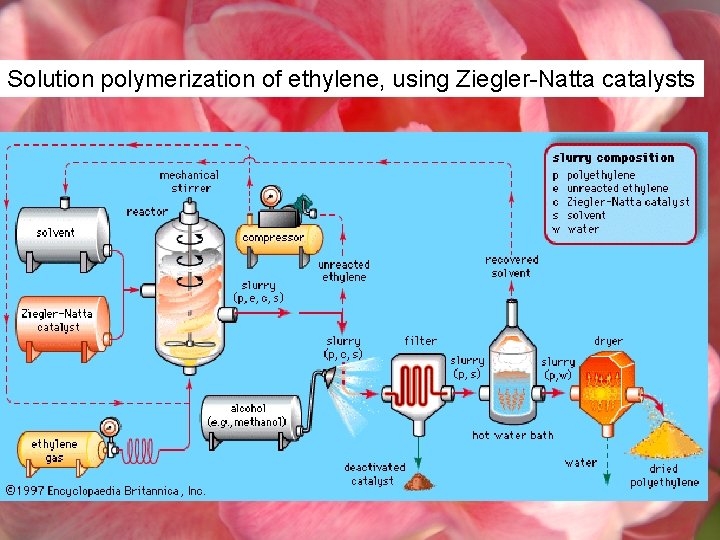
Solution polymerization of ethylene, using Ziegler-Natta catalysts
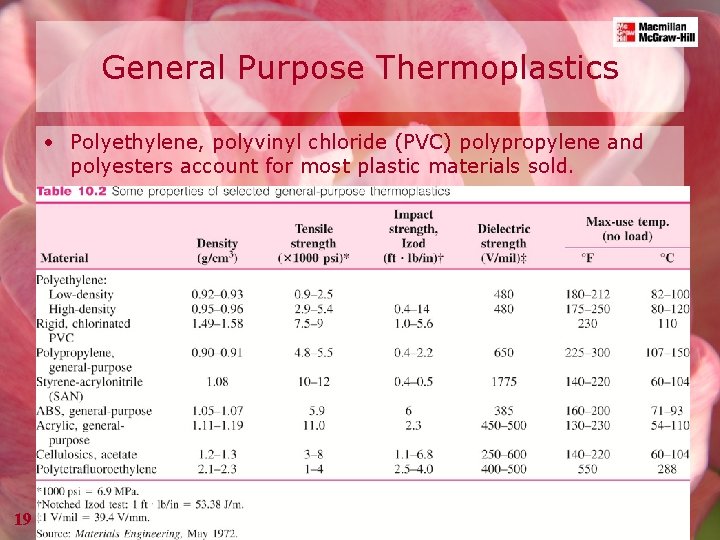
General Purpose Thermoplastics • Polyethylene, polyvinyl chloride (PVC) polypropylene and polyesters account for most plastic materials sold. 19
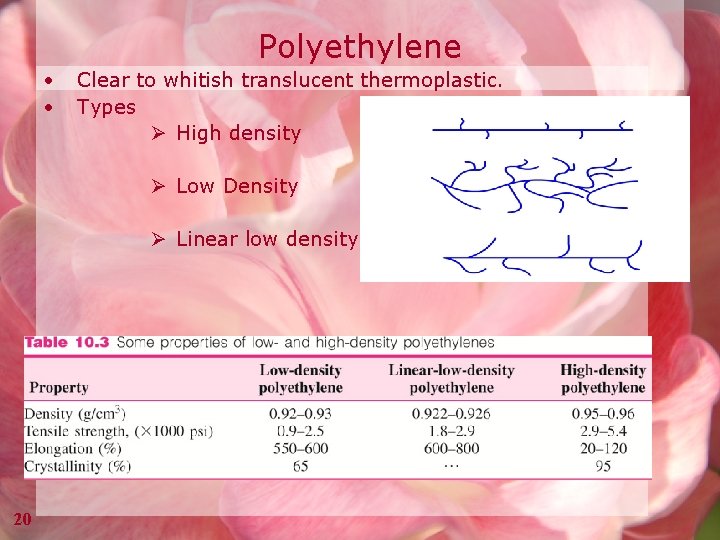
Polyethylene • • Clear to whitish translucent thermoplastic. Types Ø High density Ø Low Density Ø Linear low density 20
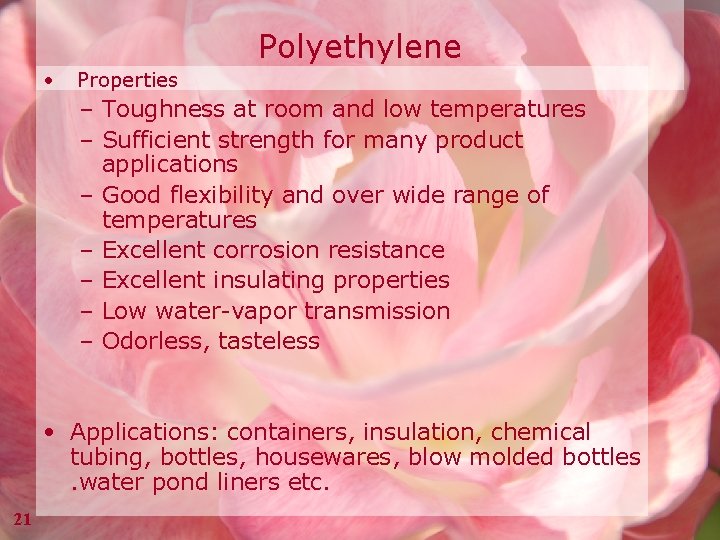
Polyethylene • Properties – Toughness at room and low temperatures – Sufficient strength for many product applications – Good flexibility and over wide range of temperatures – Excellent corrosion resistance – Excellent insulating properties – Low water-vapor transmission – Odorless, tasteless • Applications: containers, insulation, chemical tubing, bottles, housewares, blow molded bottles. water pond liners etc. 21
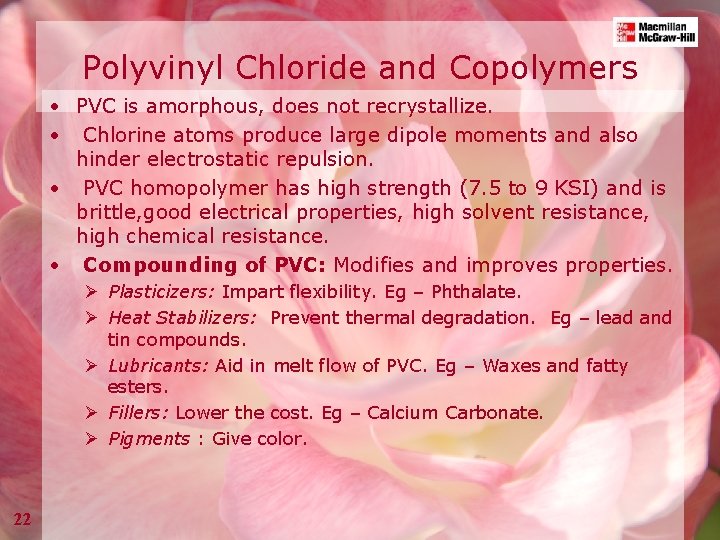
Polyvinyl Chloride and Copolymers • PVC is amorphous, does not recrystallize. • Chlorine atoms produce large dipole moments and also hinder electrostatic repulsion. • PVC homopolymer has high strength (7. 5 to 9 KSI) and is brittle, good electrical properties, high solvent resistance, high chemical resistance. • Compounding of PVC: Modifies and improves properties. Ø Plasticizers: Impart flexibility. Eg – Phthalate. Ø Heat Stabilizers: Prevent thermal degradation. Eg – lead and tin compounds. Ø Lubricants: Aid in melt flow of PVC. Eg – Waxes and fatty esters. Ø Fillers: Lower the cost. Eg – Calcium Carbonate. Ø Pigments : Give color. 22
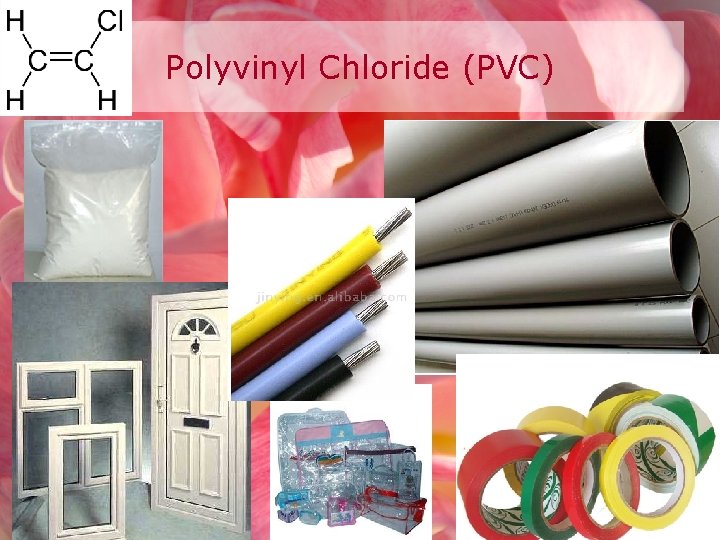
Polyvinyl Chloride (PVC)
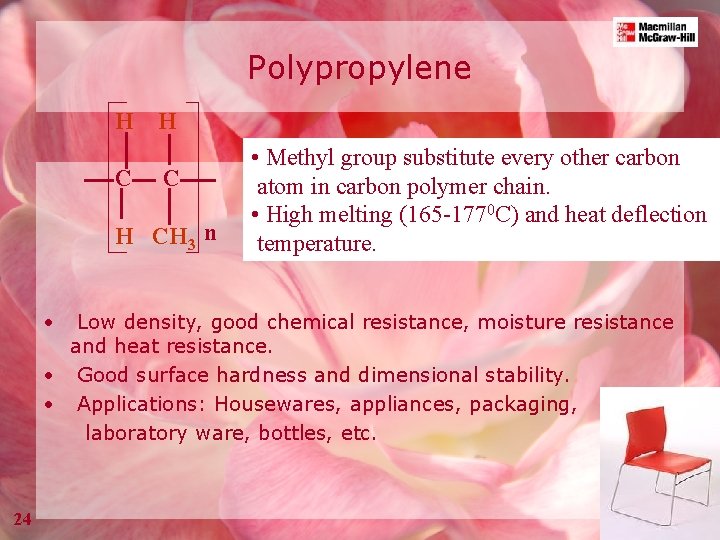
Polypropylene H H C C H CH 3 n • • Methyl group substitute every other carbon atom in carbon polymer chain. • High melting (165 -1770 C) and heat deflection temperature. Low density, good chemical resistance, moisture resistance and heat resistance. • Good surface hardness and dimensional stability. • Applications: Housewares, appliances, packaging, laboratory ware, bottles, etc. 24
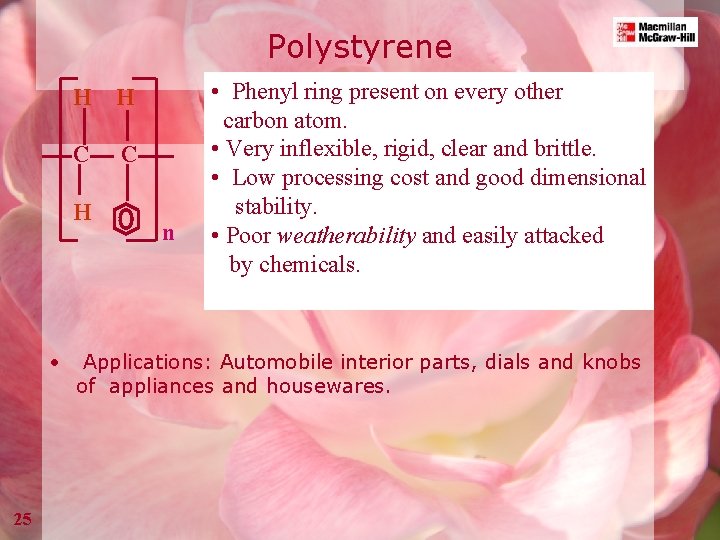
Polystyrene H H C C H • 25 n • Phenyl ring present on every other carbon atom. • Very inflexible, rigid, clear and brittle. • Low processing cost and good dimensional stability. • Poor weatherability and easily attacked by chemicals. Applications: Automobile interior parts, dials and knobs of appliances and housewares.
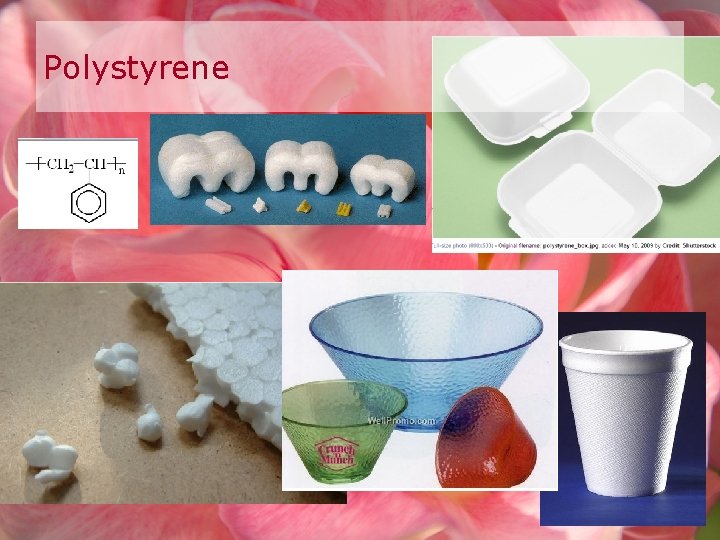
Polystyrene
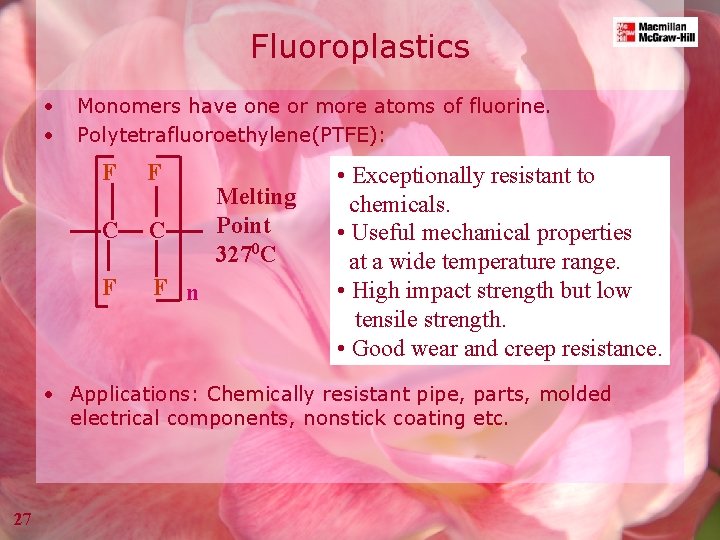
Fluoroplastics • • Monomers have one or more atoms of fluorine. Polytetrafluoroethylene(PTFE): F F C C F F n Melting Point 3270 C • Exceptionally resistant to chemicals. • Useful mechanical properties at a wide temperature range. • High impact strength but low tensile strength. • Good wear and creep resistance. • Applications: Chemically resistant pipe, parts, molded electrical components, nonstick coating etc. 27
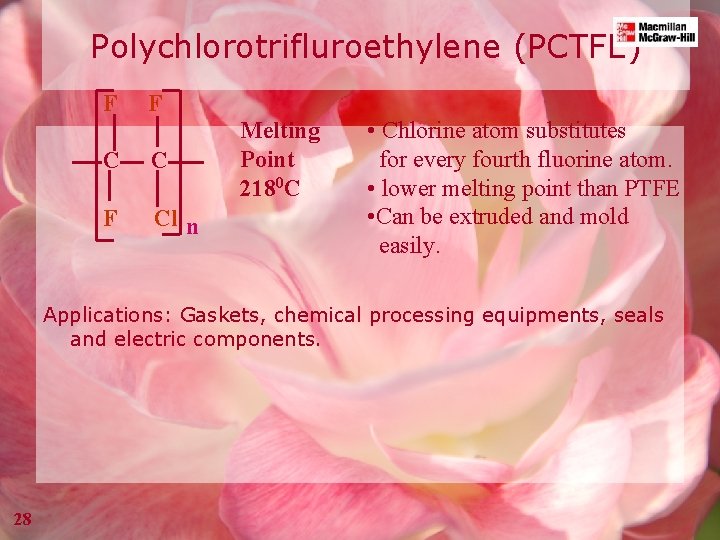
Polychlorotrifluroethylene (PCTFE) F F C C F Cl n Melting Point 2180 C • Chlorine atom substitutes for every fourth fluorine atom. • lower melting point than PTFE • Can be extruded and mold easily. Applications: Gaskets, chemical processing equipments, seals and electric components. 28
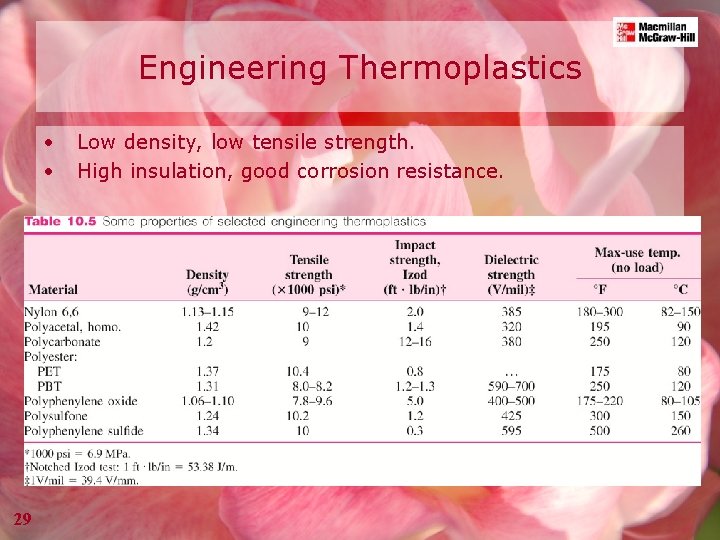
Engineering Thermoplastics • • 29 Low density, low tensile strength. High insulation, good corrosion resistance.
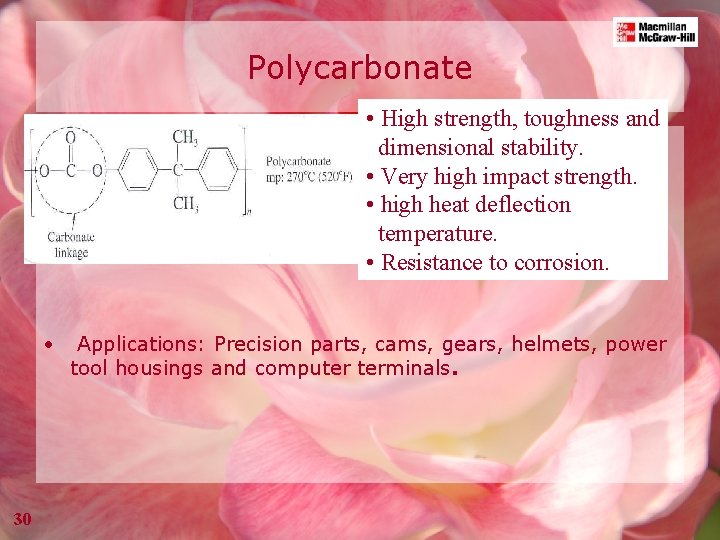
Polycarbonate • High strength, toughness and dimensional stability. • Very high impact strength. • high heat deflection temperature. • Resistance to corrosion. • 30 Applications: Precision parts, cams, gears, helmets, power tool housings and computer terminals.
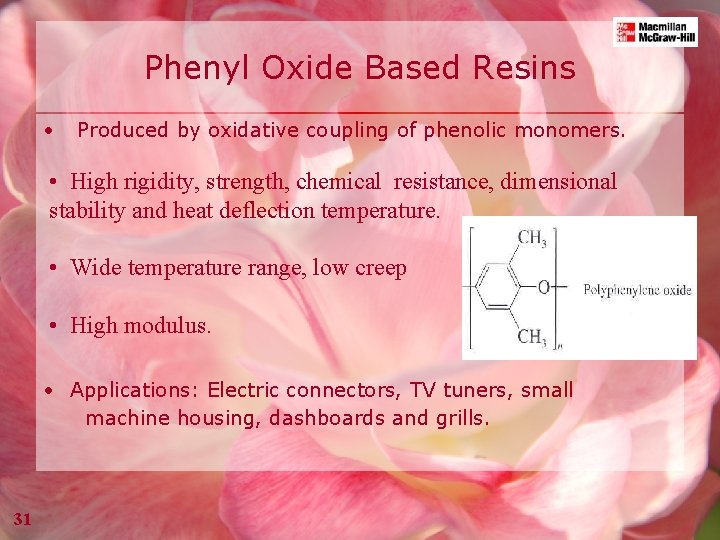
Phenyl Oxide Based Resins • Produced by oxidative coupling of phenolic monomers. • High rigidity, strength, chemical resistance, dimensional stability and heat deflection temperature. • Wide temperature range, low creep • High modulus. • Applications: Electric connectors, TV tuners, small machine housing, dashboards and grills. 31

Acetals • Strongest (68. 9 Mpa) and stiffest (2820 Mpa) thermoplastics. H C H Polyoxymethylene mp: 1750 C O n 2 Types • Homopolymers • Copolymers • Excellent long term load carrying capacity and dimensional stability. • Homopolymer is harder and rigid than copolymer. • Low wear and friction but flammable. • Applications: Fuel systems, seat belts, window handles of automobiles, couplings, impellers, gears and housing. 32
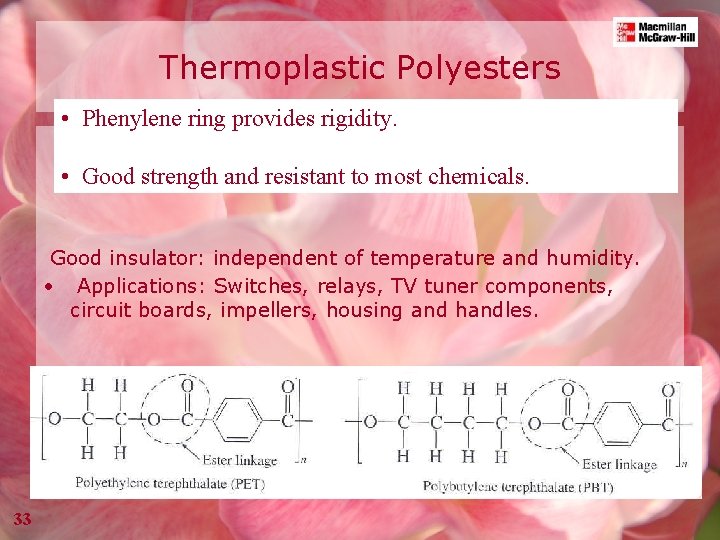
Thermoplastic Polyesters • Phenylene ring provides rigidity. • Good strength and resistant to most chemicals. Good insulator: independent of temperature and humidity. • Applications: Switches, relays, TV tuner components, circuit boards, impellers, housing and handles. 33
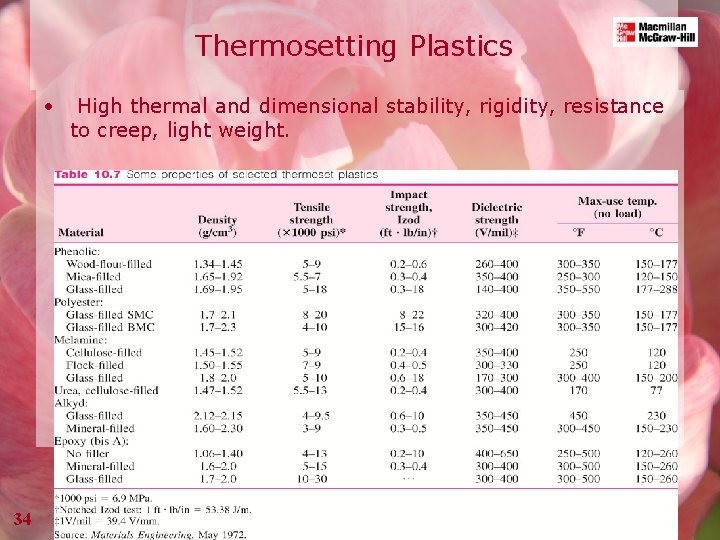
Thermosetting Plastics • 34 High thermal and dimensional stability, rigidity, resistance to creep, light weight.
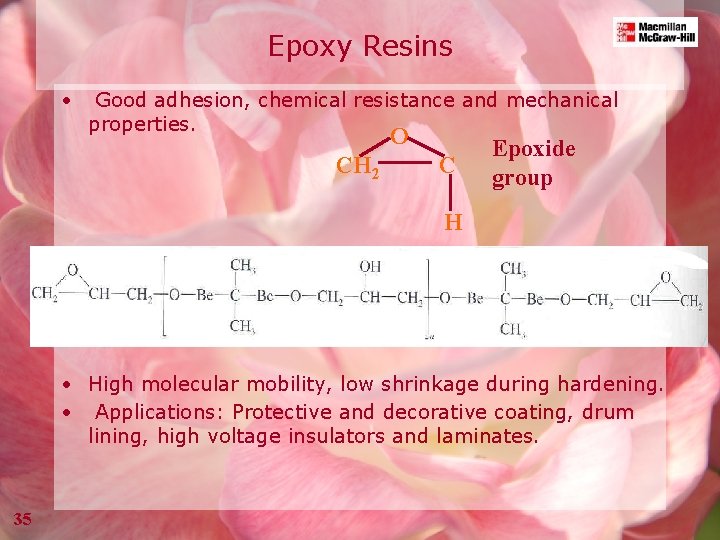
Epoxy Resins • Good adhesion, chemical resistance and mechanical properties. O CH 2 C Epoxide group H • High molecular mobility, low shrinkage during hardening. • Applications: Protective and decorative coating, drum lining, high voltage insulators and laminates. 35
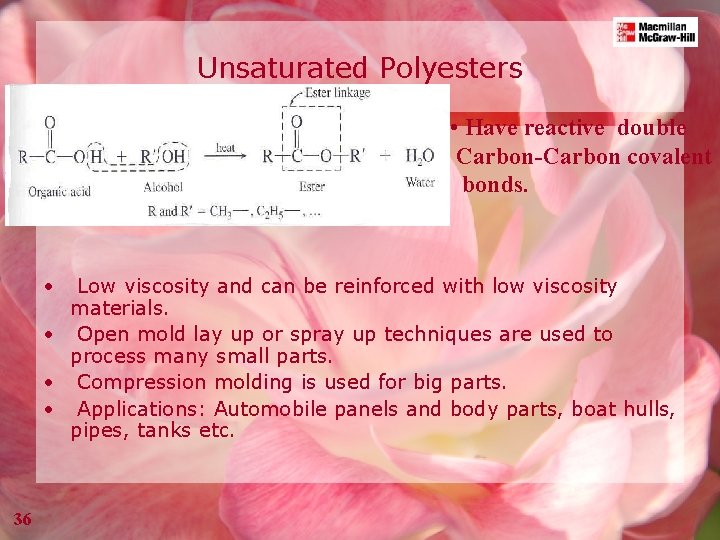
Unsaturated Polyesters • Have reactive double Carbon-Carbon covalent bonds. • Low viscosity and can be reinforced with low viscosity materials. • Open mold lay up or spray up techniques are used to process many small parts. • Compression molding is used for big parts. • Applications: Automobile panels and body parts, boat hulls, pipes, tanks etc. 36
Antigentest åre
Polymer in dentistry
Silicones and phosphazenes notes
Gene interaction example
Yonyu plastics co. ltd
Balcan plastics
American plastic distributors
Shaping processes
Plastics can be shaped into
Snap fit joint
Century mold and tool
Pmmai
Properties of plastic
Plasticscore
Moldflow plastic insight
Types of commodity plastics
Why do different polymers have different properties
Distribuzione formosa plastics
Thermoplastic and thermosetting
Renato moretto
Applications of plastics
Plastics engineering consulting
Burbank plastics
Calendering process
Tap plastics santa rosa
Injection molding indiana
Skip swanson
Sert plastics
"curbell plastics"
Maico plastics
Shaping processes for plastics
Na plastics
Plastics tax
Sohner plastics
Ghs pictograms
Go noodle cant stop the feeling
Useful materials harmful materials