Voxtel SPADSi PM ROIC and Multichannel TDC Technologies
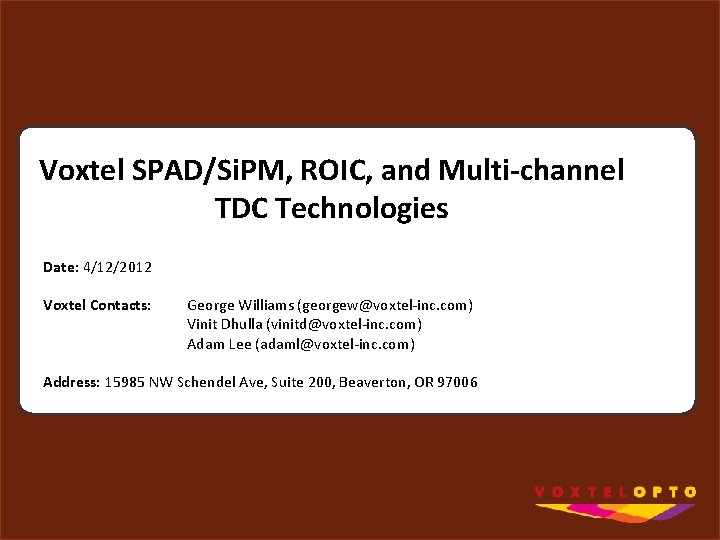
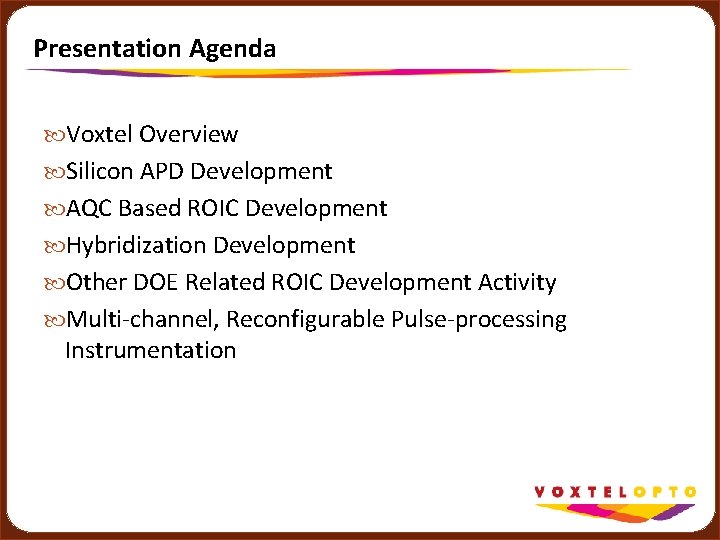
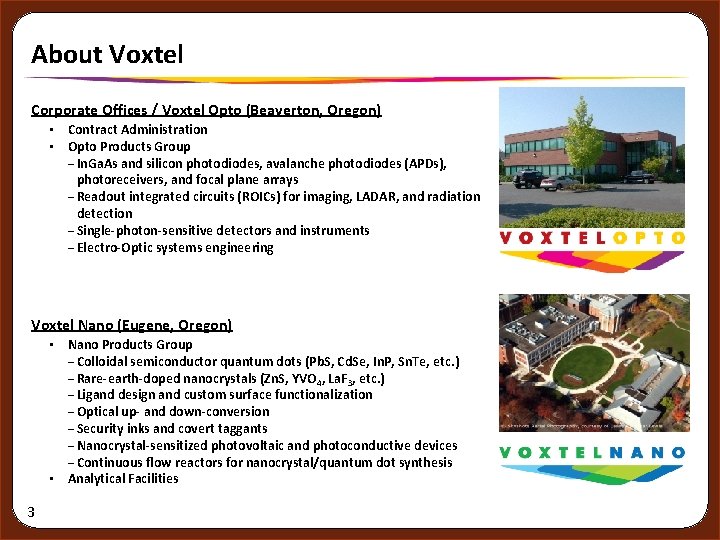
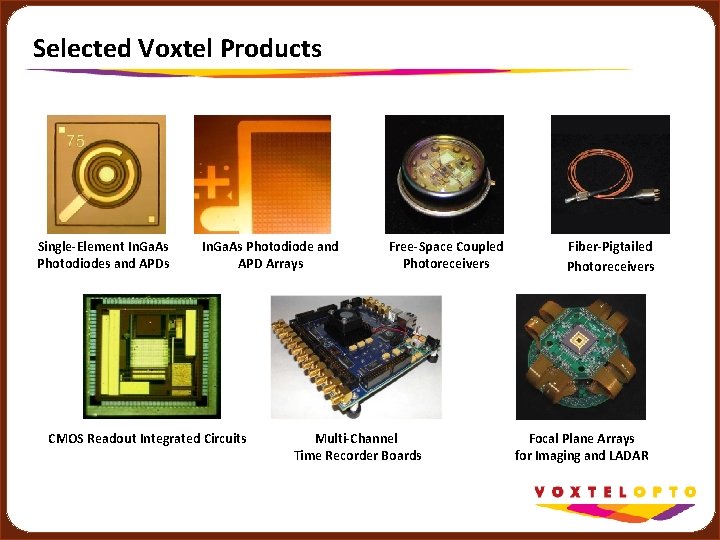
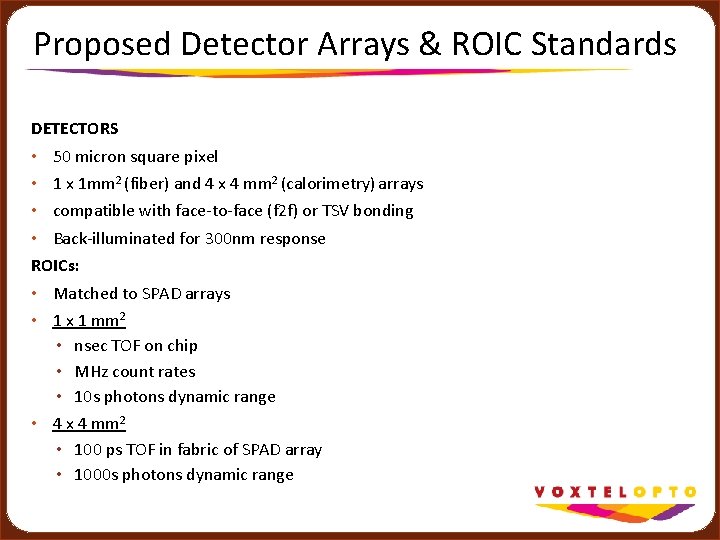
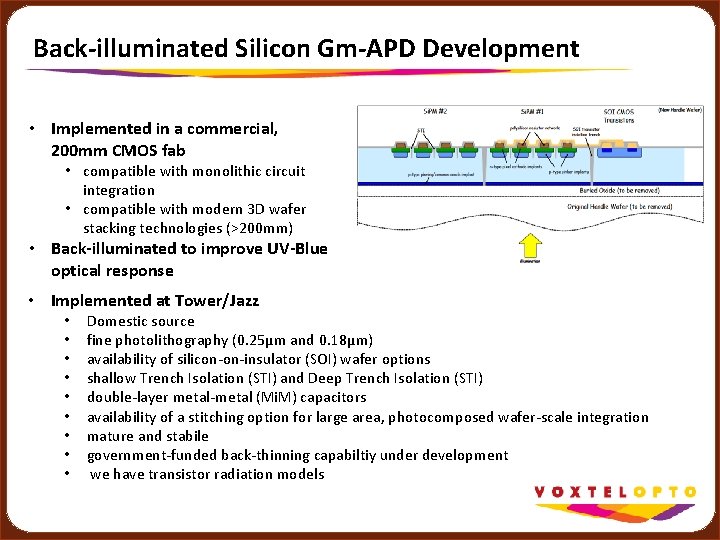
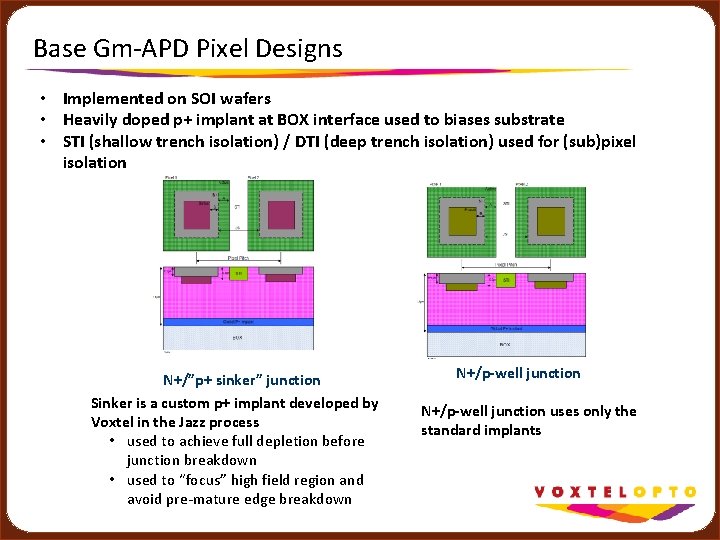
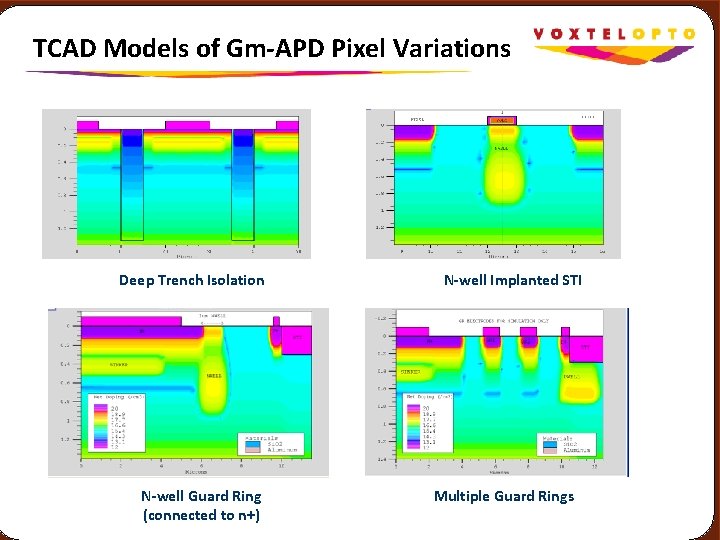
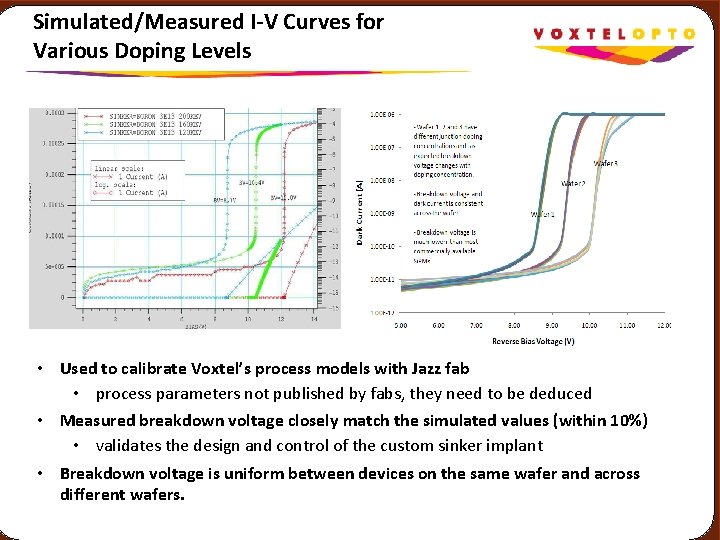
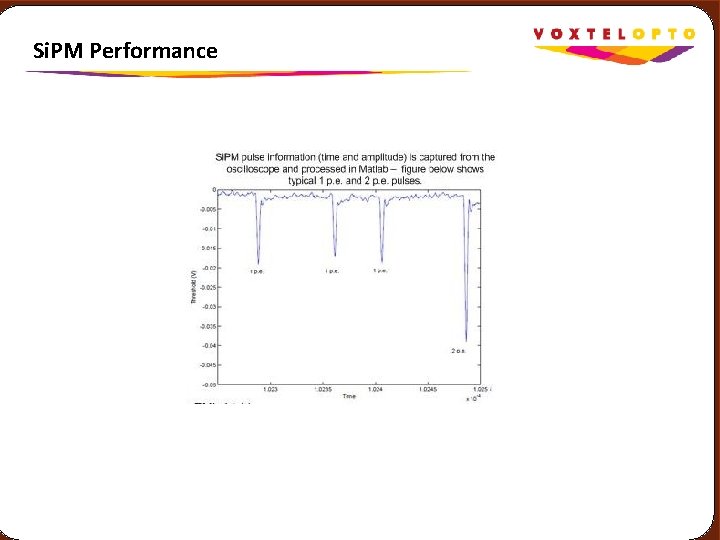
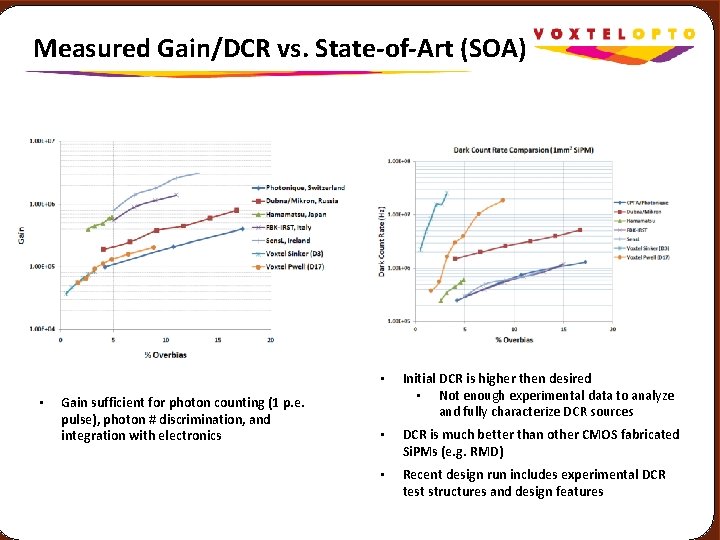
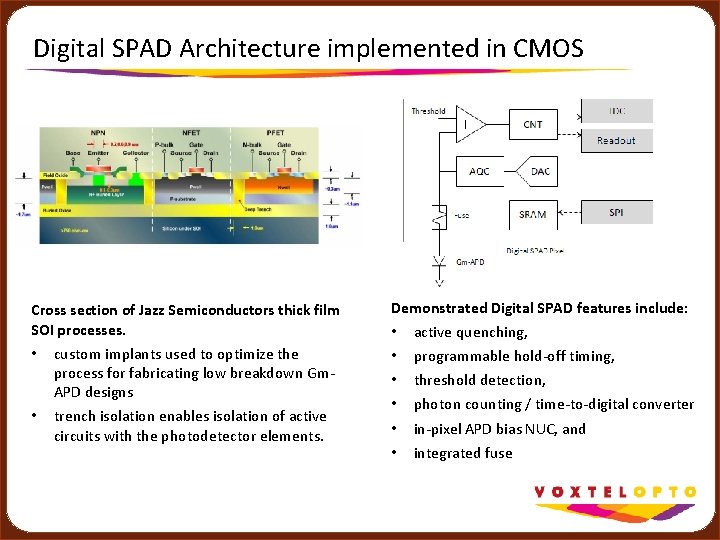
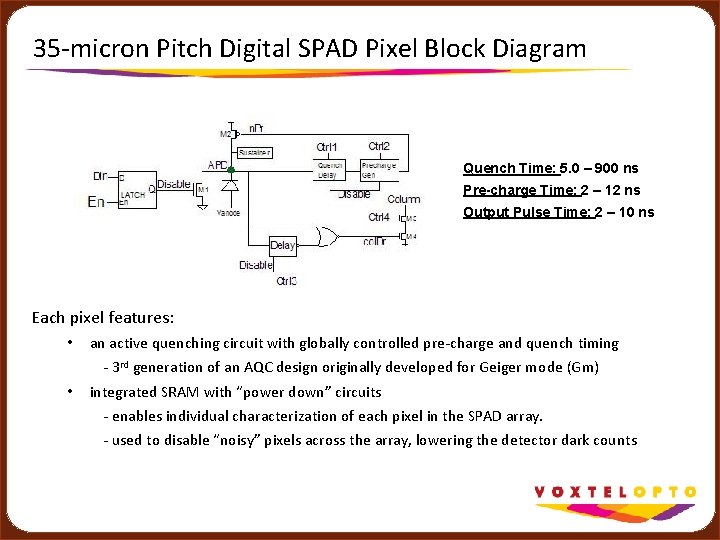
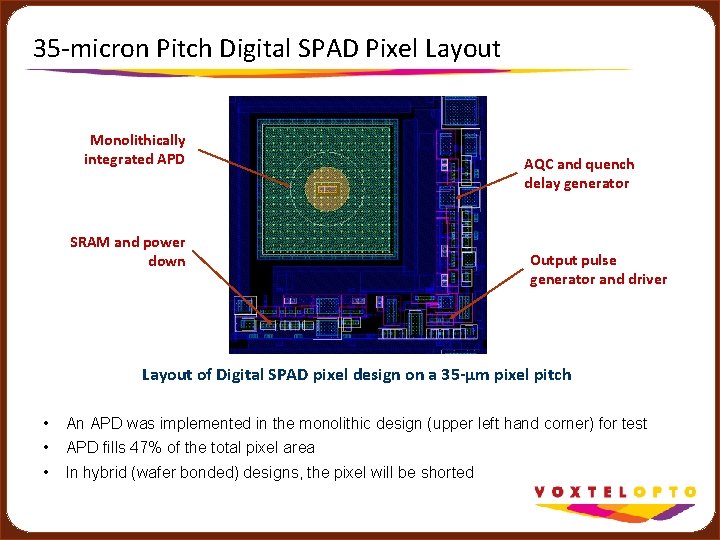
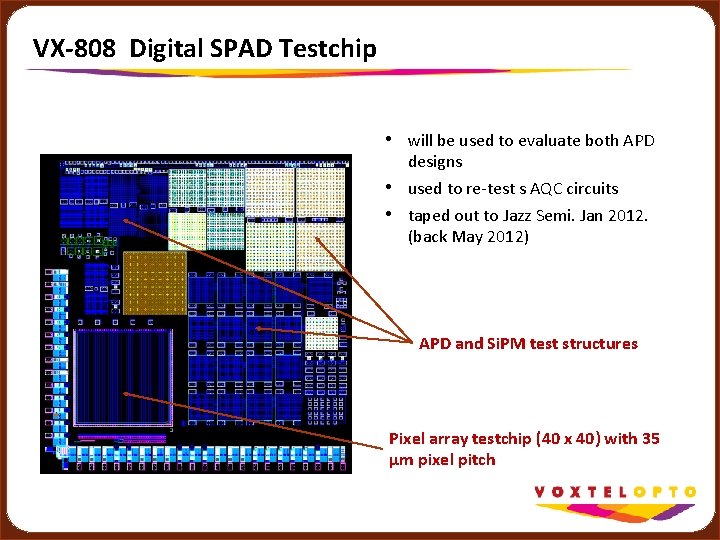
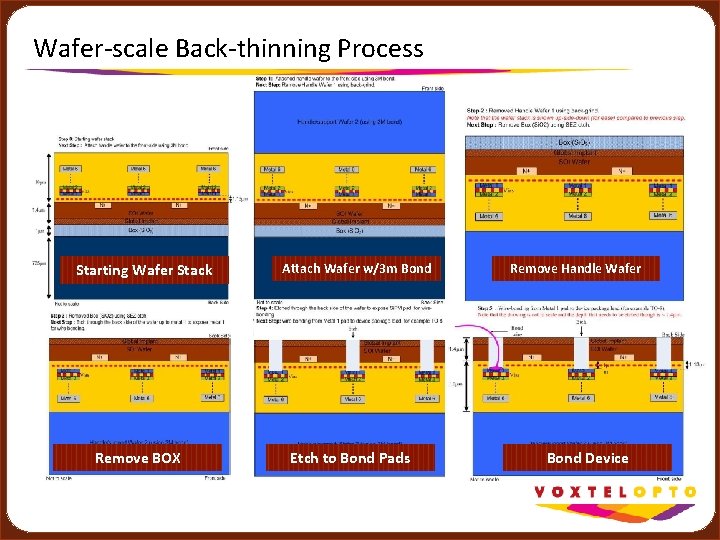
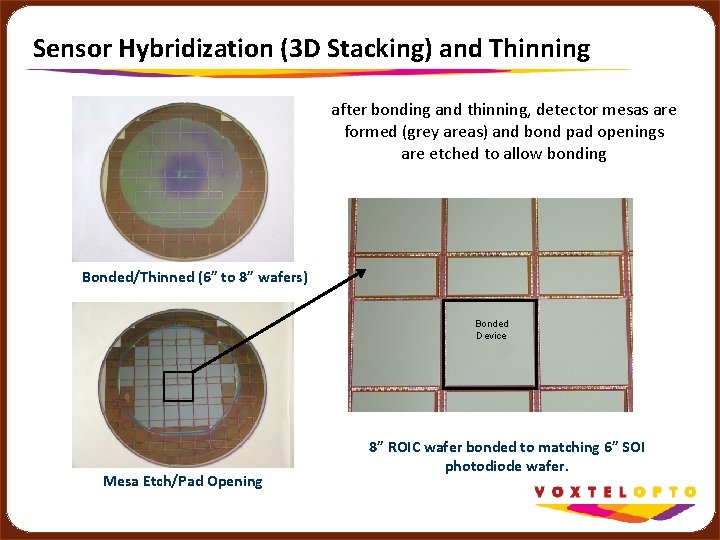
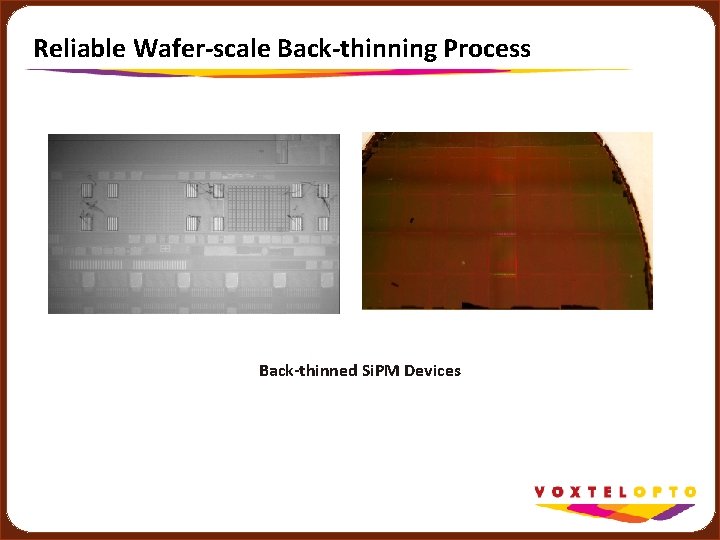
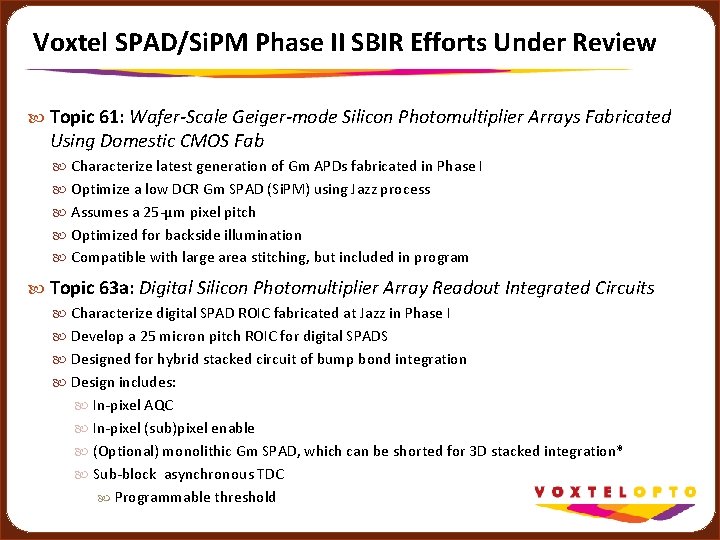
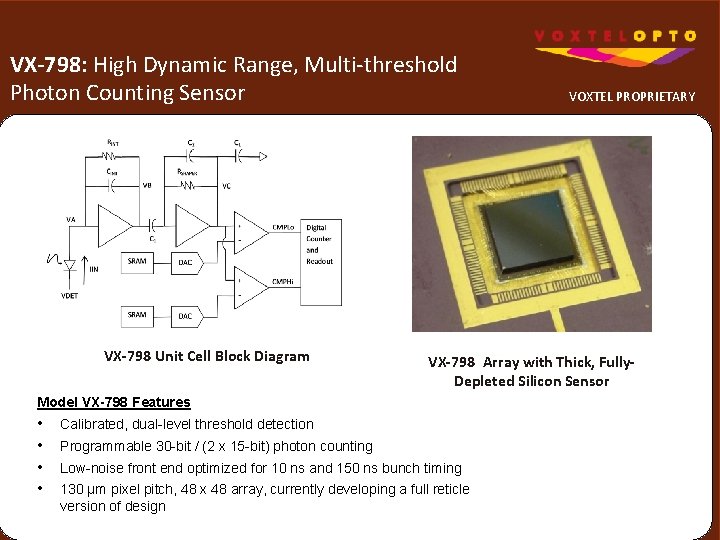
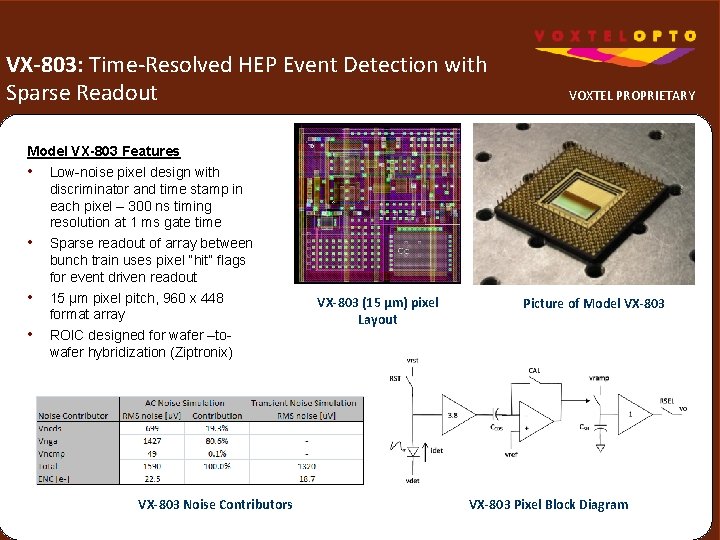
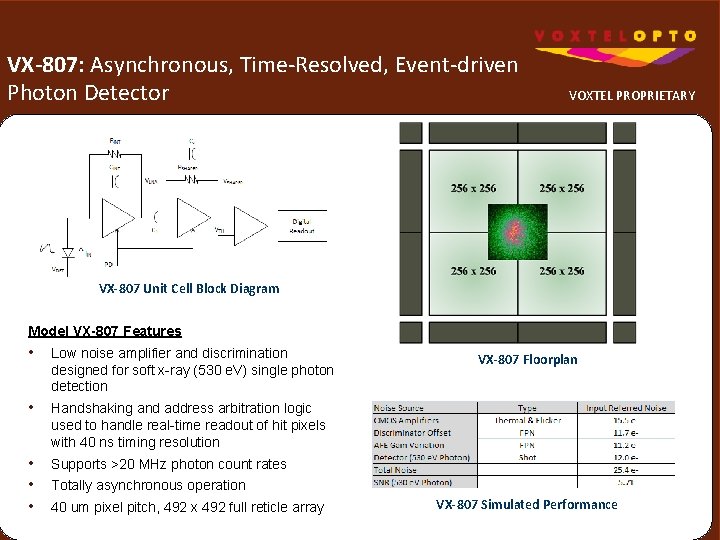
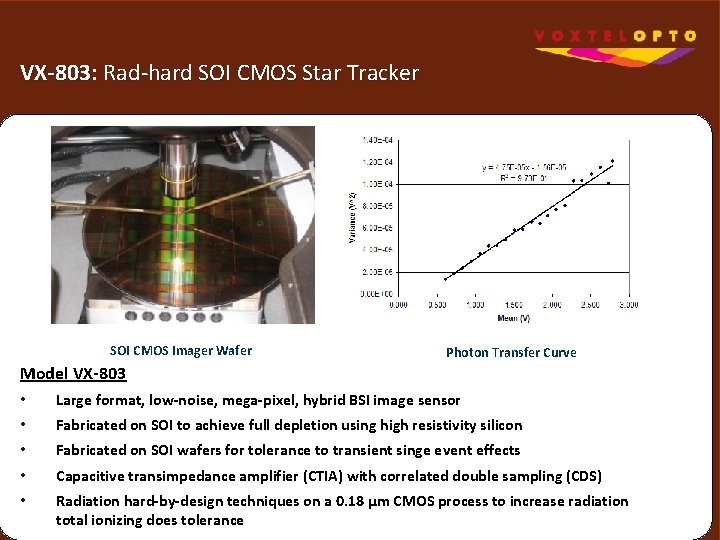

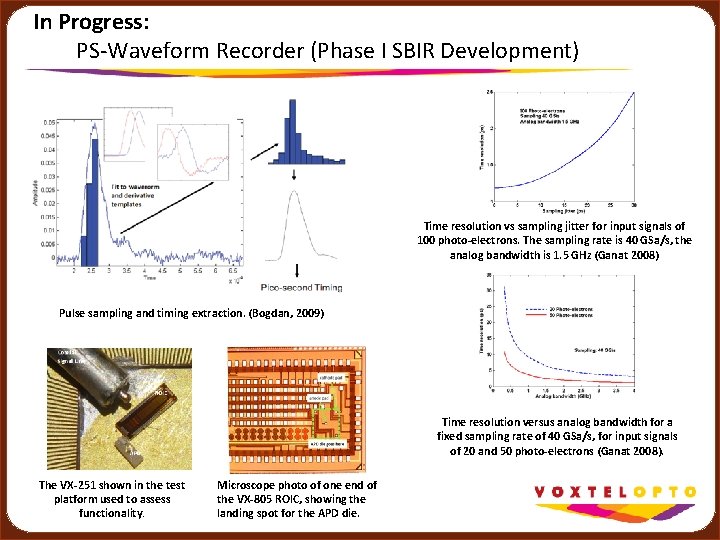
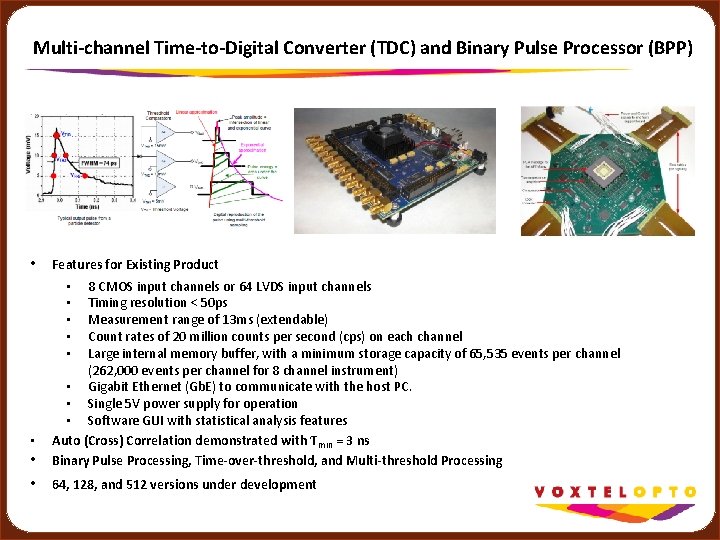

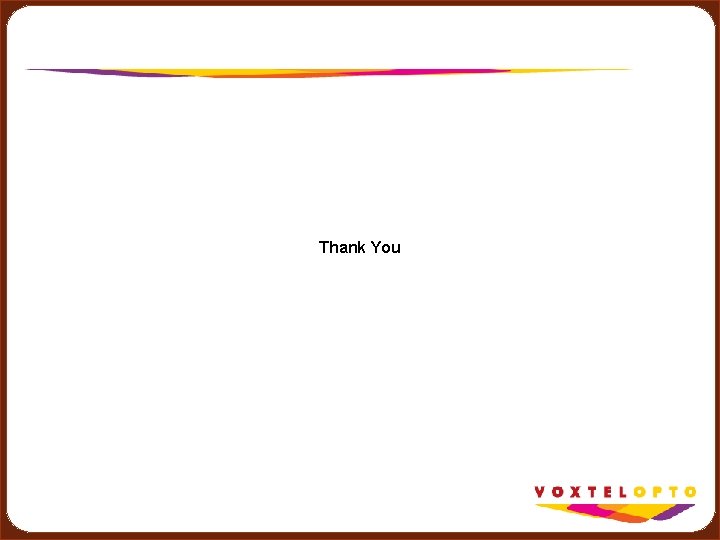
- Slides: 28
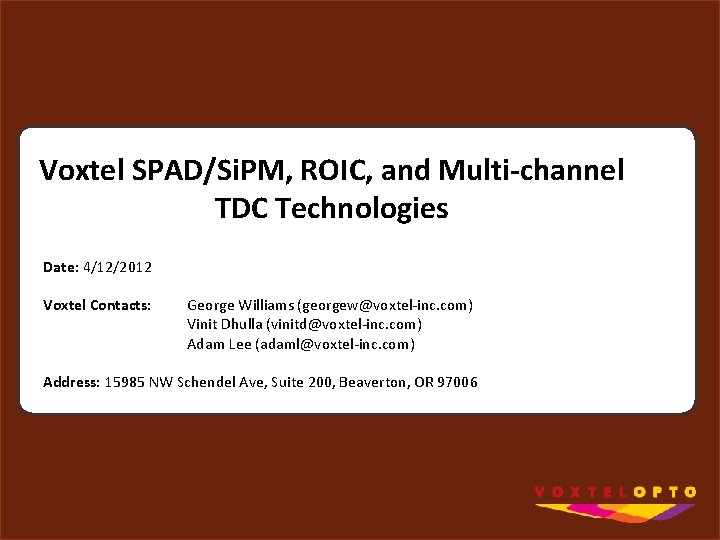
Voxtel SPAD/Si. PM, ROIC, and Multi-channel TDC Technologies Date: 4/12/2012 Voxtel Contacts: George Williams (georgew@voxtel-inc. com) Vinit Dhulla (vinitd@voxtel-inc. com) Adam Lee (adaml@voxtel-inc. com) Address: 15985 NW Schendel Ave, Suite 200, Beaverton, OR 97006
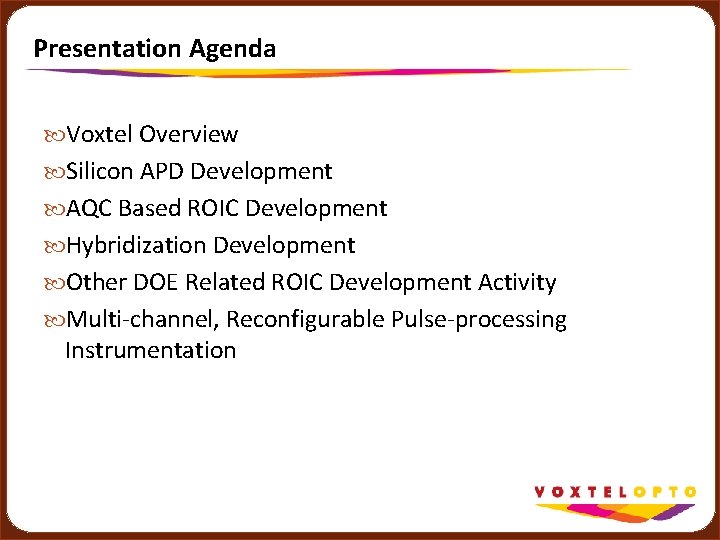
Presentation Agenda Voxtel Overview Silicon APD Development AQC Based ROIC Development Hybridization Development Other DOE Related ROIC Development Activity Multi-channel, Reconfigurable Pulse-processing Instrumentation
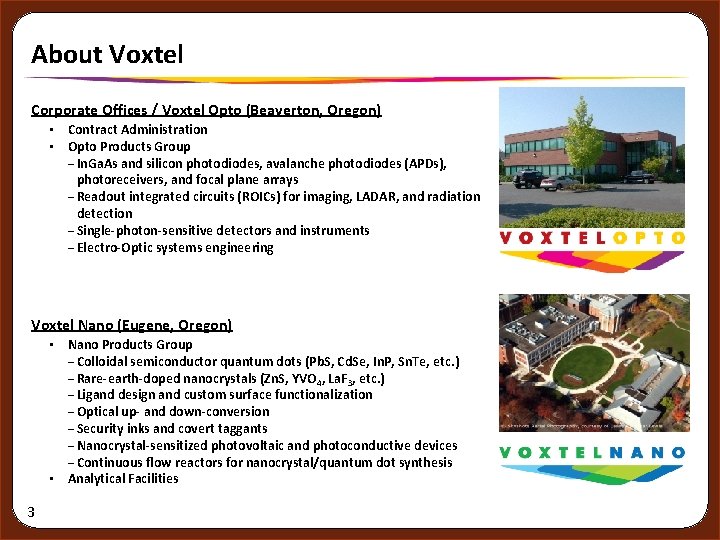
About Voxtel Corporate Offices / Voxtel Opto (Beaverton, Oregon) • Contract Administration • Opto Products Group − In. Ga. As and silicon photodiodes, avalanche photodiodes (APDs), photoreceivers, and focal plane arrays − Readout integrated circuits (ROICs) for imaging, LADAR, and radiation detection − Single-photon-sensitive detectors and instruments − Electro-Optic systems engineering Voxtel Nano (Eugene, Oregon) • Nano Products Group − Colloidal semiconductor quantum dots (Pb. S, Cd. Se, In. P, Sn. Te, etc. ) − Rare-earth-doped nanocrystals (Zn. S, YVO 4, La. F 3, etc. ) − Ligand design and custom surface functionalization − Optical up- and down-conversion − Security inks and covert taggants − Nanocrystal-sensitized photovoltaic and photoconductive devices − Continuous flow reactors for nanocrystal/quantum dot synthesis • Analytical Facilities 3
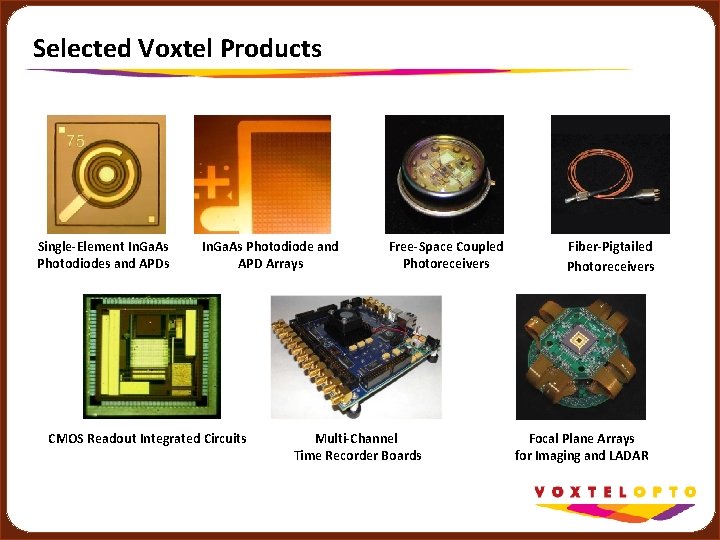
Selected Voxtel Products Single-Element In. Ga. As Photodiodes and APDs In. Ga. As Photodiode and APD Arrays CMOS Readout Integrated Circuits Free-Space Coupled Photoreceivers Multi-Channel Time Recorder Boards Fiber-Pigtailed Photoreceivers Focal Plane Arrays for Imaging and LADAR
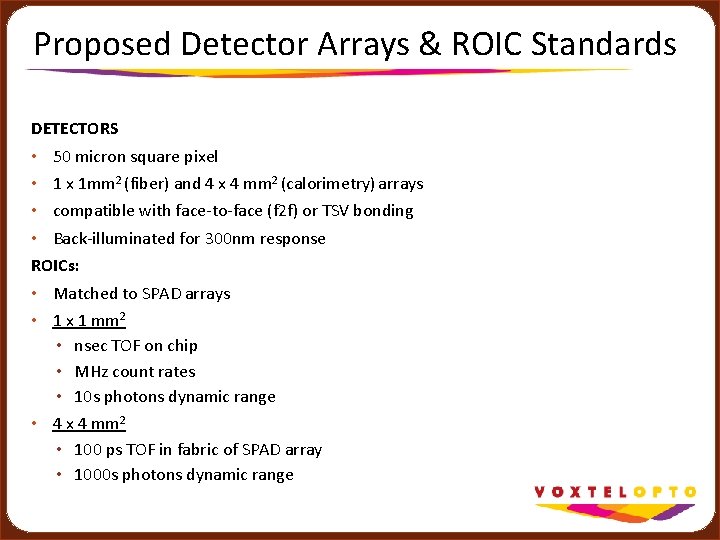
Proposed Detector Arrays & ROIC Standards DETECTORS • 50 micron square pixel • 1 x 1 mm 2 (fiber) and 4 x 4 mm 2 (calorimetry) arrays • compatible with face-to-face (f 2 f) or TSV bonding • Back-illuminated for 300 nm response ROICs: • Matched to SPAD arrays • 1 x 1 mm 2 • nsec TOF on chip • MHz count rates • 10 s photons dynamic range • 4 x 4 mm 2 • 100 ps TOF in fabric of SPAD array • 1000 s photons dynamic range
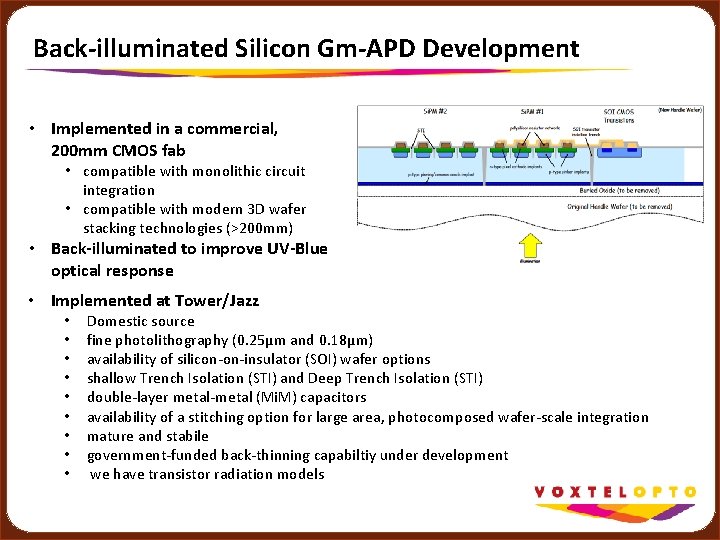
Back-illuminated Silicon Gm-APD Development • Implemented in a commercial, 200 mm CMOS fab • compatible with monolithic circuit integration • compatible with modern 3 D wafer stacking technologies (>200 mm) • Back-illuminated to improve UV-Blue optical response • Implemented at Tower/Jazz • • • Domestic source fine photolithography (0. 25µm and 0. 18µm) availability of silicon-on-insulator (SOI) wafer options shallow Trench Isolation (STI) and Deep Trench Isolation (STI) double-layer metal-metal (Mi. M) capacitors availability of a stitching option for large area, photocomposed wafer-scale integration mature and stabile government-funded back-thinning capabiltiy under development we have transistor radiation models
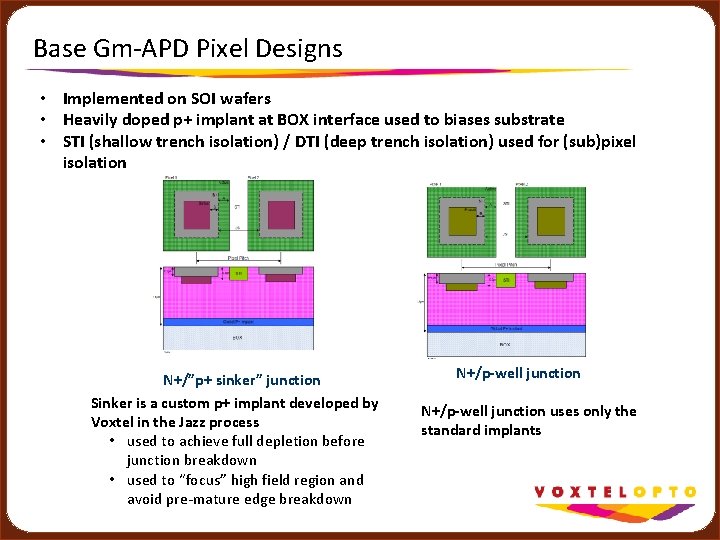
Base Gm-APD Pixel Designs • Implemented on SOI wafers • Heavily doped p+ implant at BOX interface used to biases substrate • STI (shallow trench isolation) / DTI (deep trench isolation) used for (sub)pixel isolation N+/”p+ sinker” junction Sinker is a custom p+ implant developed by Voxtel in the Jazz process • used to achieve full depletion before junction breakdown • used to “focus” high field region and avoid pre-mature edge breakdown N+/p-well junction uses only the standard implants
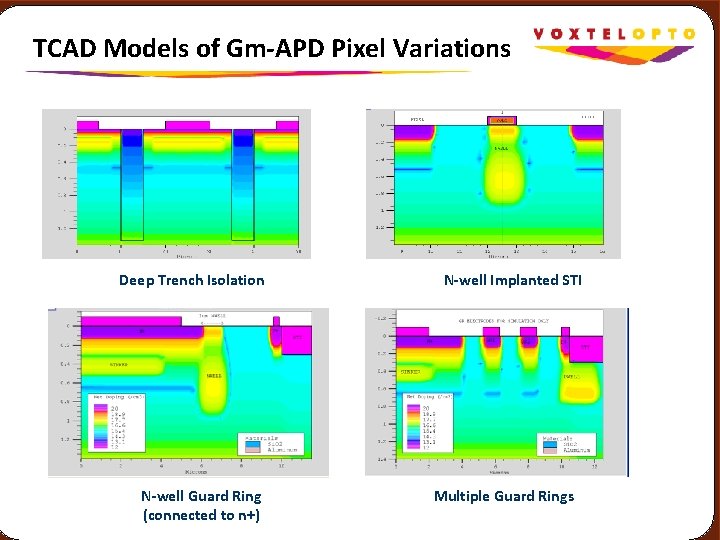
TCAD Models of Gm-APD Pixel Variations Deep Trench Isolation N-well Guard Ring (connected to n+) N-well Implanted STI Multiple Guard Rings
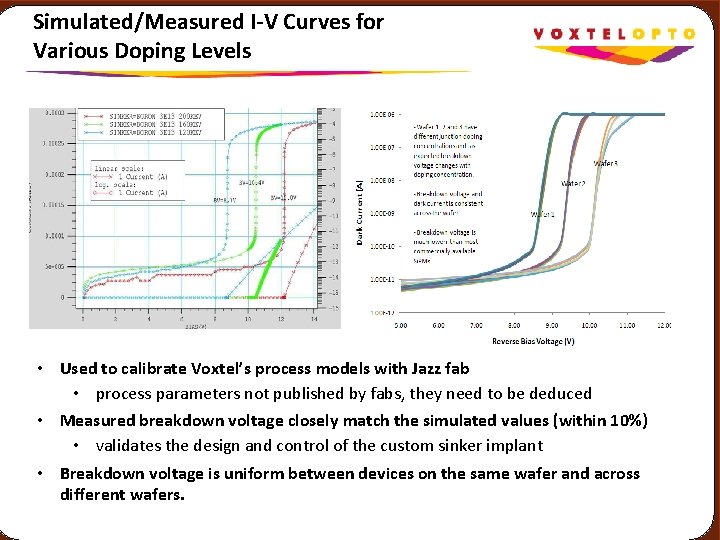
Simulated/Measured I-V Curves for Various Doping Levels • Used to calibrate Voxtel’s process models with Jazz fab • process parameters not published by fabs, they need to be deduced • Measured breakdown voltage closely match the simulated values (within 10%) • validates the design and control of the custom sinker implant • Breakdown voltage is uniform between devices on the same wafer and across different wafers.
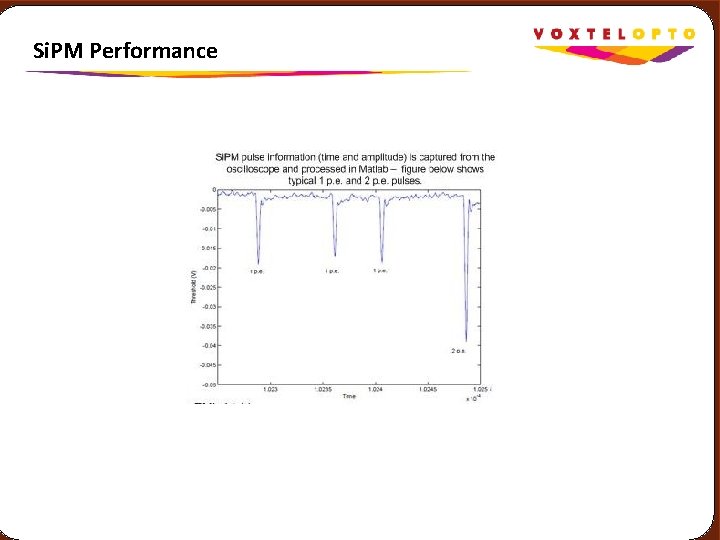
Si. PM Performance
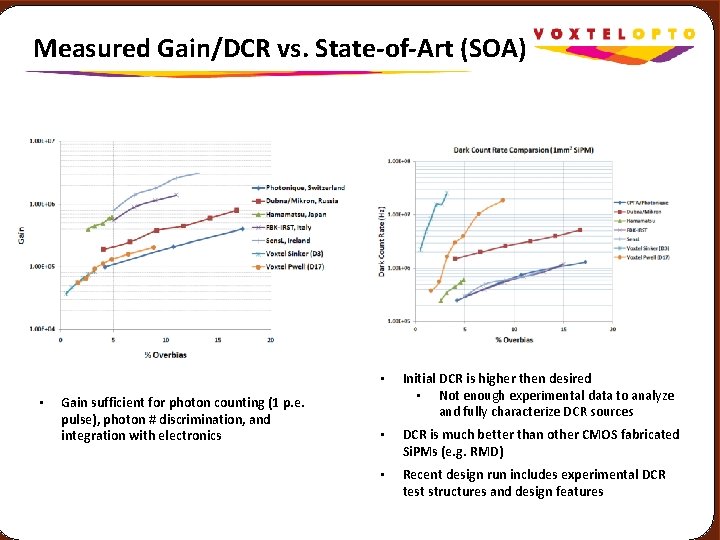
Measured Gain/DCR vs. State-of-Art (SOA) • Gain sufficient for photon counting (1 p. e. pulse), photon # discrimination, and integration with electronics • Initial DCR is higher then desired • Not enough experimental data to analyze and fully characterize DCR sources • DCR is much better than other CMOS fabricated Si. PMs (e. g. RMD) • Recent design run includes experimental DCR test structures and design features
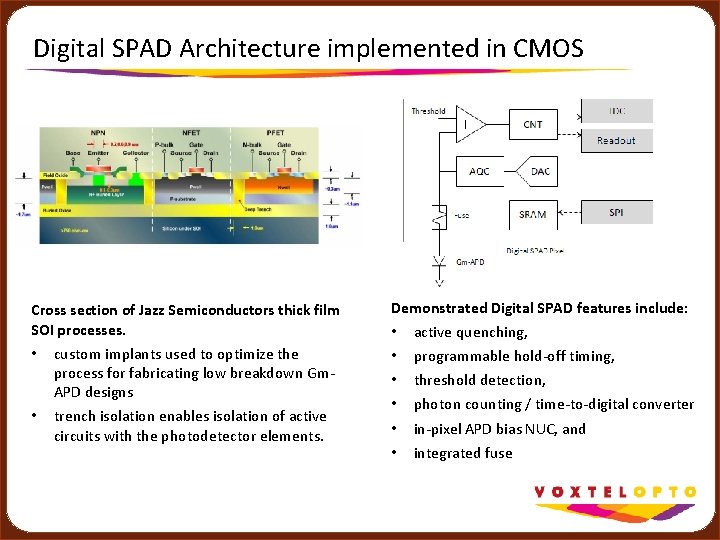
Digital SPAD Architecture implemented in CMOS Cross section of Jazz Semiconductors thick film SOI processes. • custom implants used to optimize the process for fabricating low breakdown Gm. APD designs • trench isolation enables isolation of active circuits with the photodetector elements. Demonstrated Digital SPAD features include: • • • active quenching, programmable hold-off timing, threshold detection, photon counting / time-to-digital converter in-pixel APD bias NUC, and integrated fuse
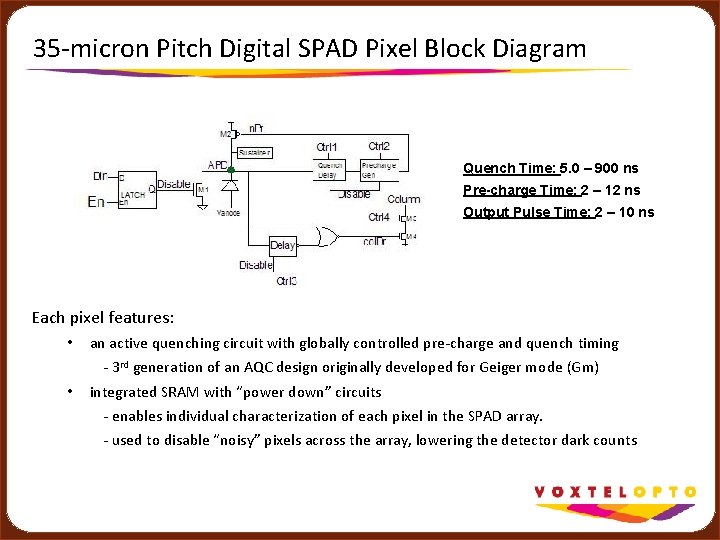
35 -micron Pitch Digital SPAD Pixel Block Diagram Quench Time: 5. 0 – 900 ns Pre-charge Time: 2 – 12 ns Output Pulse Time: 2 – 10 ns Each pixel features: • an active quenching circuit with globally controlled pre-charge and quench timing - 3 rd generation of an AQC design originally developed for Geiger mode (Gm) • integrated SRAM with “power down” circuits - enables individual characterization of each pixel in the SPAD array. - used to disable “noisy” pixels across the array, lowering the detector dark counts
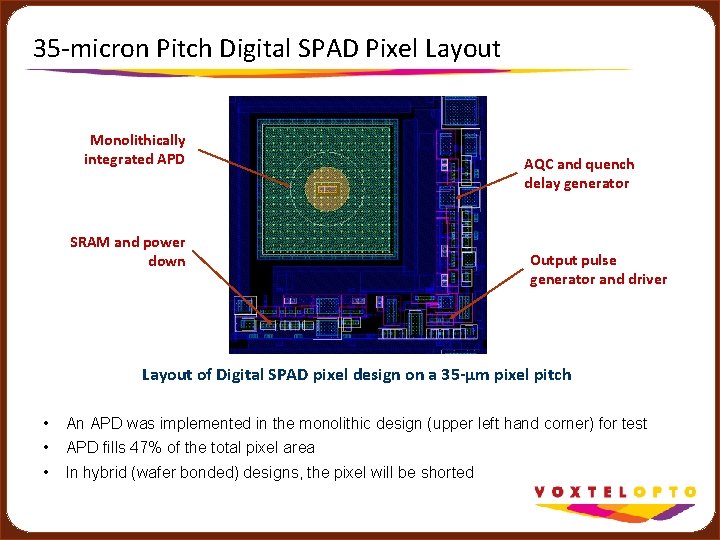
35 -micron Pitch Digital SPAD Pixel Layout Monolithically integrated APD SRAM and power down AQC and quench delay generator Output pulse generator and driver Layout of Digital SPAD pixel design on a 35 -µm pixel pitch • An APD was implemented in the monolithic design (upper left hand corner) for test • APD fills 47% of the total pixel area • In hybrid (wafer bonded) designs, the pixel will be shorted
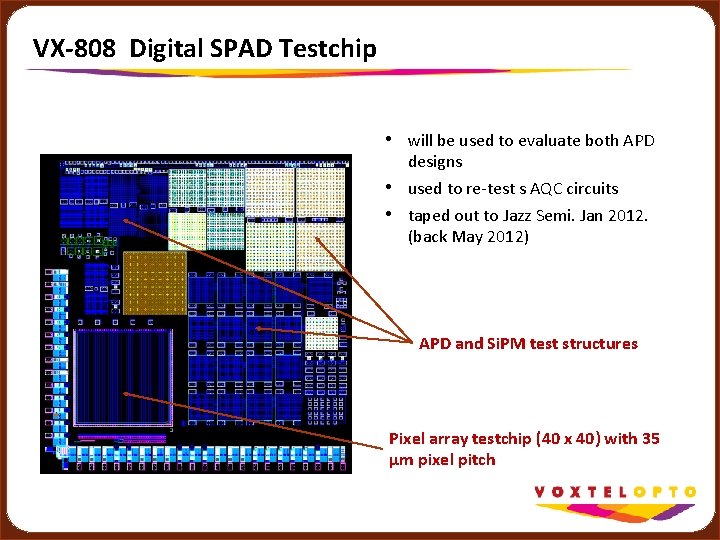
VX-808 Digital SPAD Testchip • will be used to evaluate both APD designs • used to re-test s AQC circuits • taped out to Jazz Semi. Jan 2012. (back May 2012) APD and Si. PM test structures Pixel array testchip (40 x 40) with 35 µm pixel pitch
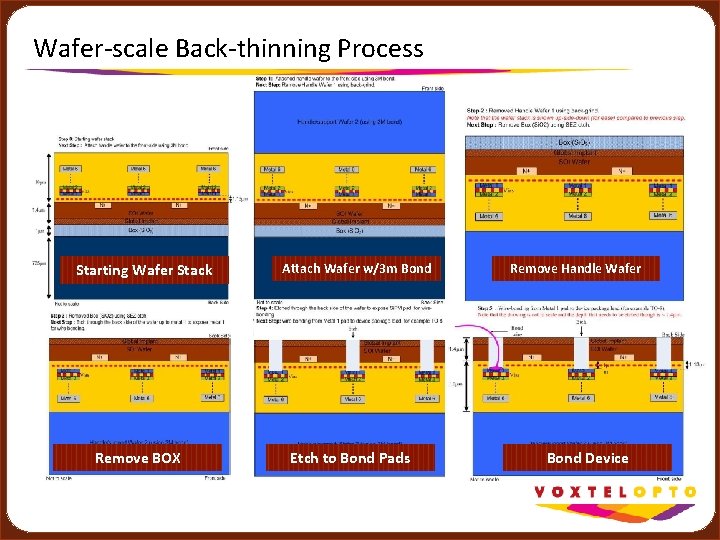
Wafer-scale Back-thinning Process Starting Wafer Stack Remove BOX Attach Wafer w/3 m Bond Etch to Bond Pads Remove Handle Wafer Bond Device
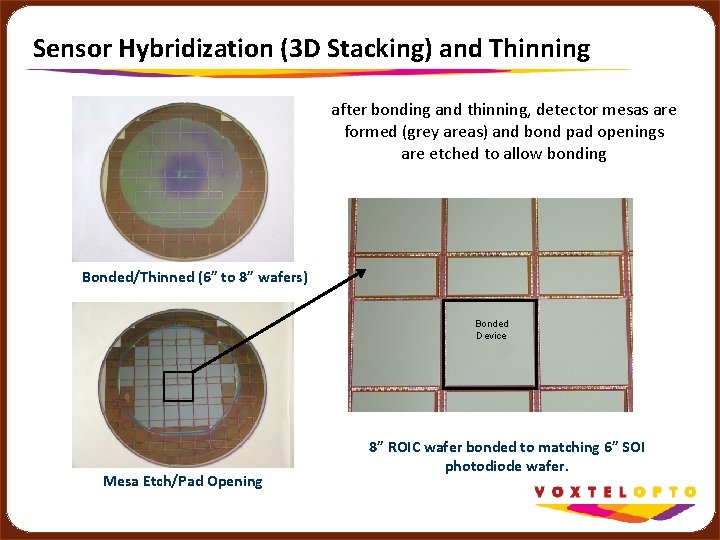
Sensor Hybridization (3 D Stacking) and Thinning after bonding and thinning, detector mesas are formed (grey areas) and bond pad openings are etched to allow bonding Bonded/Thinned (6” to 8” wafers) Bonded Device Mesa Etch/Pad Opening 8” ROIC wafer bonded to matching 6” SOI photodiode wafer.
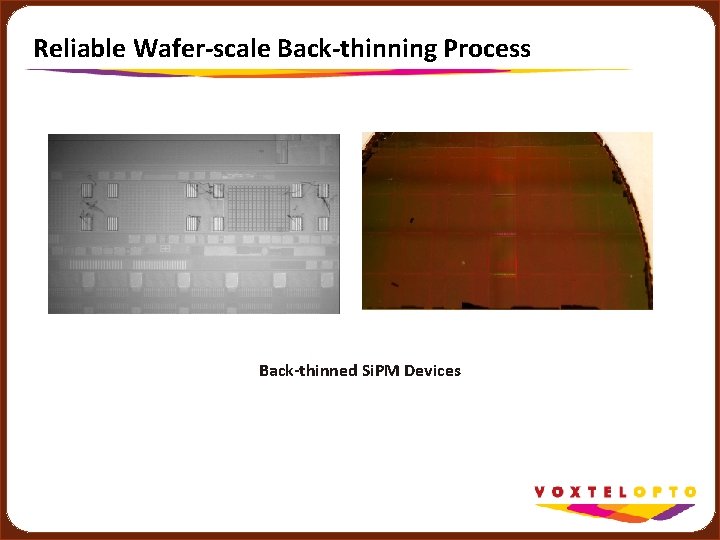
Reliable Wafer-scale Back-thinning Process Back-thinned Si. PM Devices
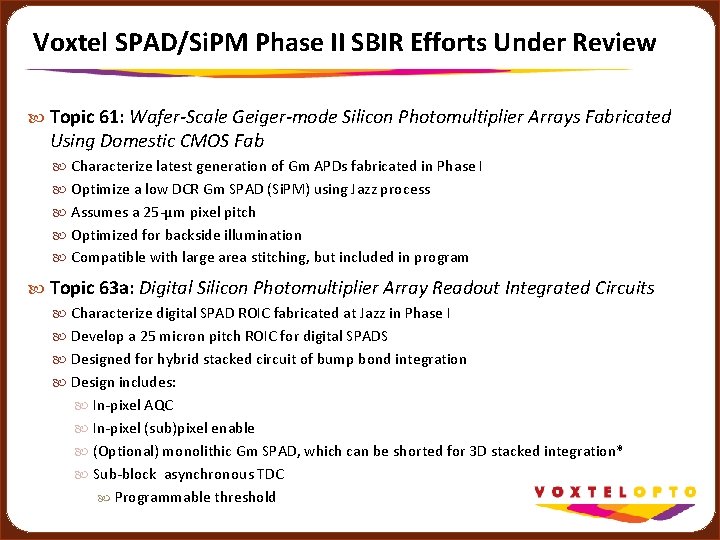
Voxtel SPAD/Si. PM Phase II SBIR Efforts Under Review Topic 61: Wafer-Scale Geiger-mode Silicon Photomultiplier Arrays Fabricated Using Domestic CMOS Fab Characterize latest generation of Gm APDs fabricated in Phase I Optimize a low DCR Gm SPAD (Si. PM) using Jazz process Assumes a 25 -µm pixel pitch Optimized for backside illumination Compatible with large area stitching, but included in program Topic 63 a: Digital Silicon Photomultiplier Array Readout Integrated Circuits Characterize digital SPAD ROIC fabricated at Jazz in Phase I Develop a 25 micron pitch ROIC for digital SPADS Designed for hybrid stacked circuit of bump bond integration Design includes: In-pixel AQC In-pixel (sub)pixel enable (Optional) monolithic Gm SPAD, which can be shorted for 3 D stacked integration* Sub-block asynchronous TDC Programmable threshold
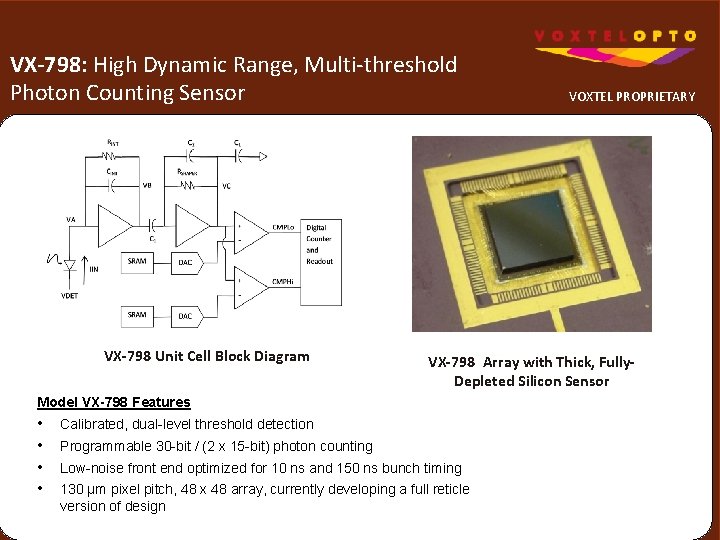
VX-798: High Dynamic Range, Multi-threshold Photon Counting Sensor VX-798 Unit Cell Block Diagram VX-798 Array with Thick, Fully. Depleted Silicon Sensor Model VX-798 Features • • VOXTEL PROPRIETARY Calibrated, dual-level threshold detection Programmable 30 -bit / (2 x 15 -bit) photon counting Low-noise front end optimized for 10 ns and 150 ns bunch timing 130 µm pixel pitch, 48 x 48 array, currently developing a full reticle version of design
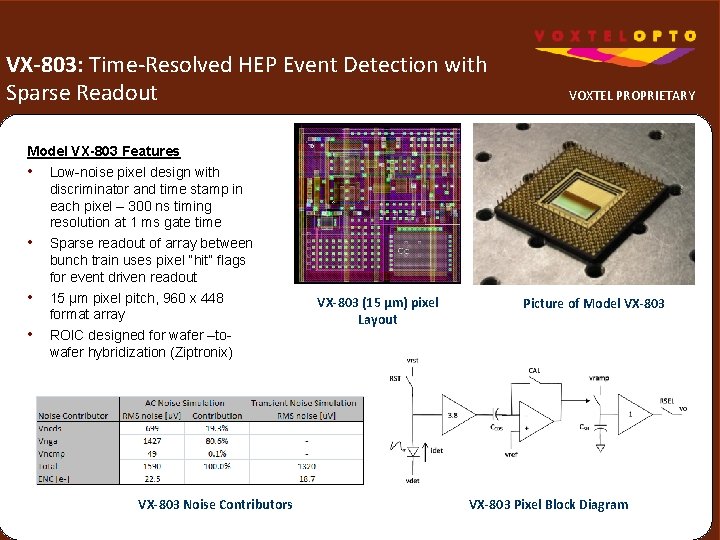
VX-803: Time-Resolved HEP Event Detection with Sparse Readout Model VX-803 Features • Low-noise pixel design with discriminator and time stamp in each pixel – 300 ns timing resolution at 1 ms gate time • Sparse readout of array between bunch train uses pixel “hit” flags for event driven readout • 15 µm pixel pitch, 960 x 448 format array • ROIC designed for wafer –towafer hybridization (Ziptronix) VX-803 Noise Contributors VX-803 (15 µm) pixel Layout VOXTEL PROPRIETARY Picture of Model VX-803 Pixel Block Diagram
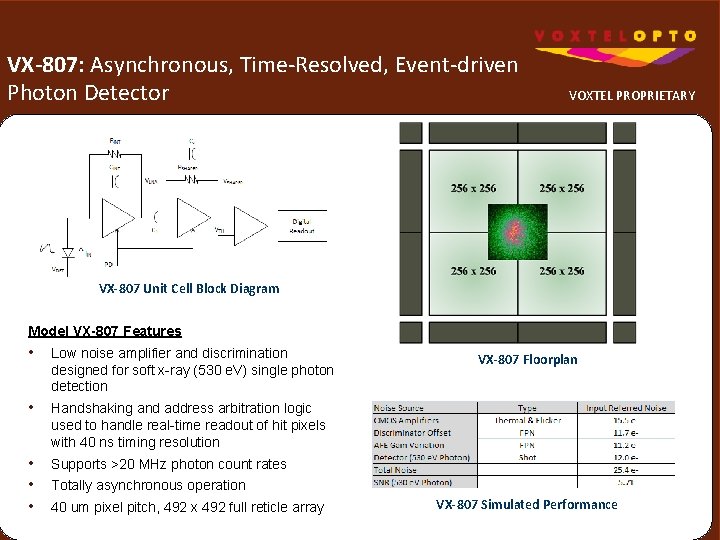
VX-807: Asynchronous, Time-Resolved, Event-driven Photon Detector VOXTEL PROPRIETARY VX-807 Unit Cell Block Diagram Model VX-807 Features • Low noise amplifier and discrimination designed for soft x-ray (530 e. V) single photon detection • Handshaking and address arbitration logic used to handle real-time readout of hit pixels with 40 ns timing resolution • • • Supports >20 MHz photon count rates VX-807 Floorplan Totally asynchronous operation 40 um pixel pitch, 492 x 492 full reticle array VX-807 Simulated Performance
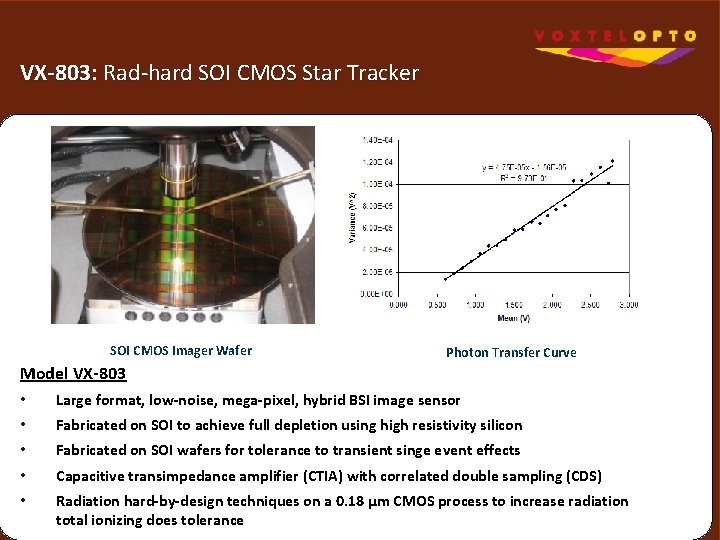
VX-803: R VX-803: ad-hard SOI CMOS Star Tracker SOI CMOS Imager Wafer Photon Transfer Curve Model VX-803 • Large format, low-noise, mega-pixel, hybrid BSI image sensor • Fabricated on SOI to achieve full depletion using high resistivity silicon • Fabricated on SOI wafers for tolerance to transient singe event effects • Capacitive transimpedance amplifier (CTIA) with correlated double sampling (CDS) • Radiation hard-by-design techniques on a 0. 18 µm CMOS process to increase radiation total ionizing does tolerance

VX-819: 2 D-Array Event-driven Ripple Waveform Sampling VX-819 Pixel Block Diagram VX-819 Pixel Layout Model VX-819 • Programmable pulse detection circuit • 40 samples in 55 um pixel VOXTEL PROPRIETARY • Programmable sample rate ( 1 ns minimum) • Used with curve fitting to achieve 50 -ps timing resolution
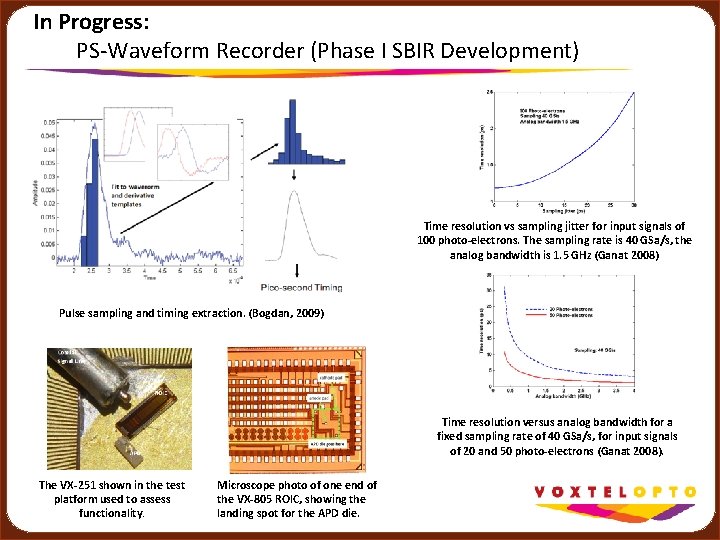
In Progress: PS-Waveform Recorder (Phase I SBIR Development) Time resolution vs sampling jitter for input signals of 100 photo-electrons. The sampling rate is 40 GSa/s, the analog bandwidth is 1. 5 GHz (Ganat 2008) Pulse sampling and timing extraction. (Bogdan, 2009) Time resolution versus analog bandwidth for a fixed sampling rate of 40 GSa/s, for input signals of 20 and 50 photo-electrons (Ganat 2008). The VX-251 shown in the test platform used to assess functionality. Microscope photo of one end of the VX-805 ROIC, showing the landing spot for the APD die.
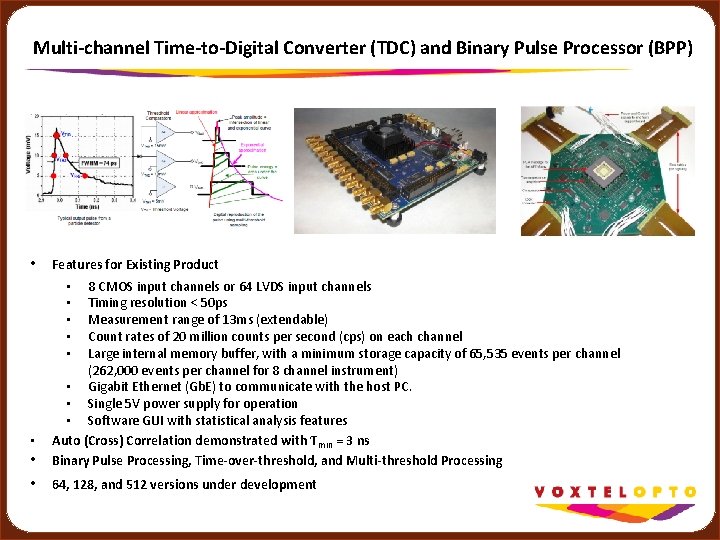
Multi-channel Time-to-Digital Converter (TDC) and Binary Pulse Processor (BPP) • Features for Existing Product • 8 CMOS input channels or 64 LVDS input channels Timing resolution < 50 ps Measurement range of 13 ms (extendable) Count rates of 20 million counts per second (cps) on each channel Large internal memory buffer, with a minimum storage capacity of 65, 535 events per channel (262, 000 events per channel for 8 channel instrument) • Gigabit Ethernet (Gb. E) to communicate with the host PC. • Single 5 V power supply for operation • Software GUI with statistical analysis features Auto (Cross) Correlation demonstrated with Ƭmin = 3 ns Binary Pulse Processing, Time-over-threshold, and Multi-threshold Processing • 64, 128, and 512 versions under development • • •

High channel Count, Re-configurable Multi-Purpose Pulseprocessing Platform Planned Features • Easily reconfigurable pulse-processing platform with multiple daughter boards to meet different application needs • Application-specific, pluggable front-end modules – time-stamping (analog and digital inputs), analog to digital conversion, auto and cross-correlation • Up to 1000 channels • High timing resolution (tens of pico-seconds to sub-ns, depending on the channel count and application) • Data transfer rates of up to 400 MB/s • Variable measurement times, depending on the application • Ability to time-stamp positive and negative edges • Ability to measure really short pulses (<1 ns) • Minimum dead-time between pulses (<3 ns) • High input pulse count rates (> 250 MHz) • User friendly software GUI
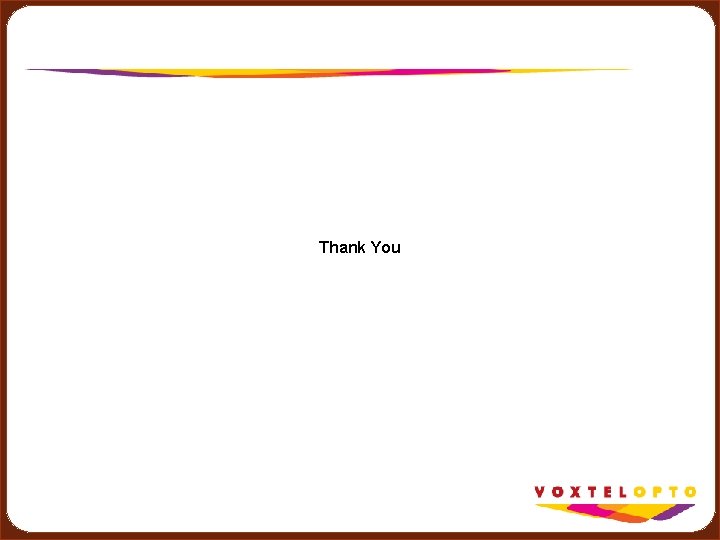
Thank You
Voxtel apd
How does the ranking of roic by industry typically go?
Noplat formula
Roic formula
Mckinsey approach value based management
How to calculate noplat
Flir roic
Data acquisition system شرح
Multichannel multipoint distribution service
Ausstellungsstrasse 80
Multichannel distribution system
Multichannel publishing
Multichannel fundraising
Multichannel publishing cms
A multi channel retailer sells merchandise
Single channel marketing definition
Bufferedserial
Multichannel adalah
Multichannel publishing
Multichannel conflict
Merchandise assortment planning ppt
Manual gsk 980 t-d b en español
Tdc mdcps
Tdc systems integration
Strutture logiche preformate
Tdc fpga
Honeywell tdc 2000
Tdc switch
Batch controller