Two Dimensional Steady State Heat Conduction P M

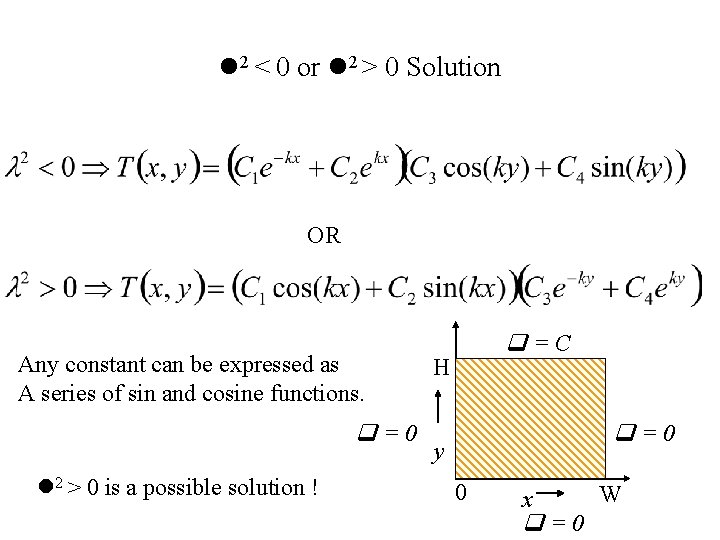
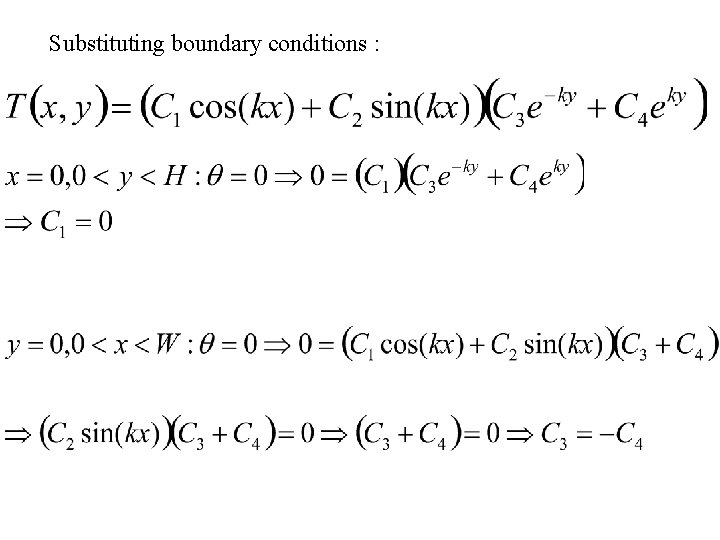
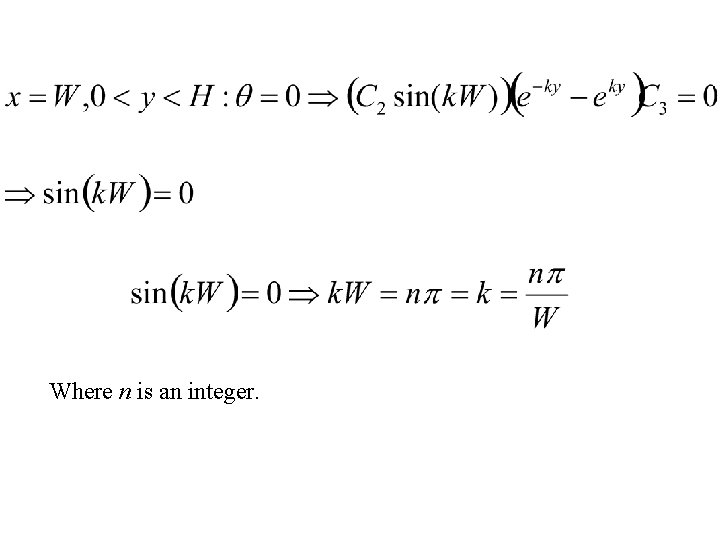
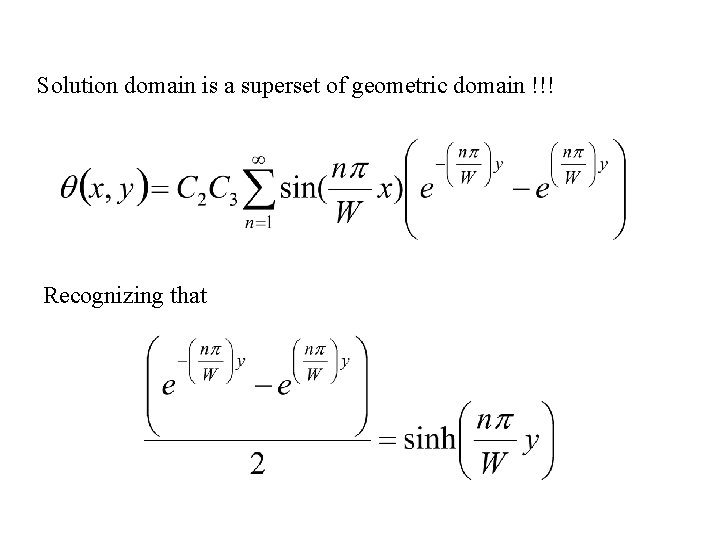
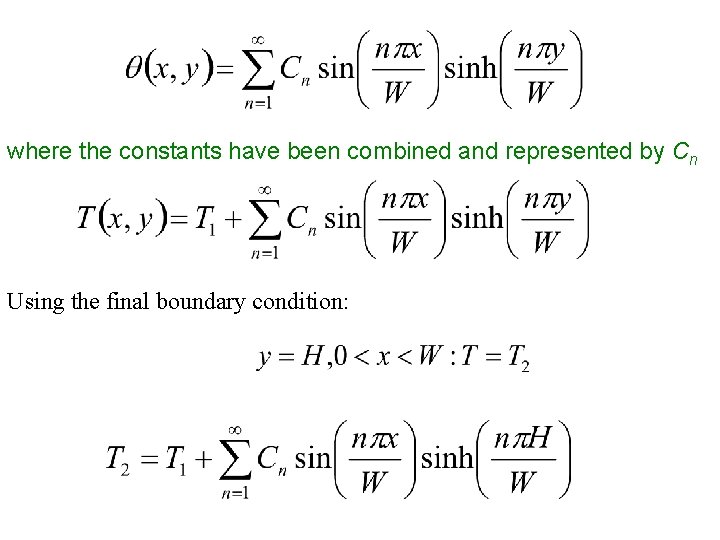
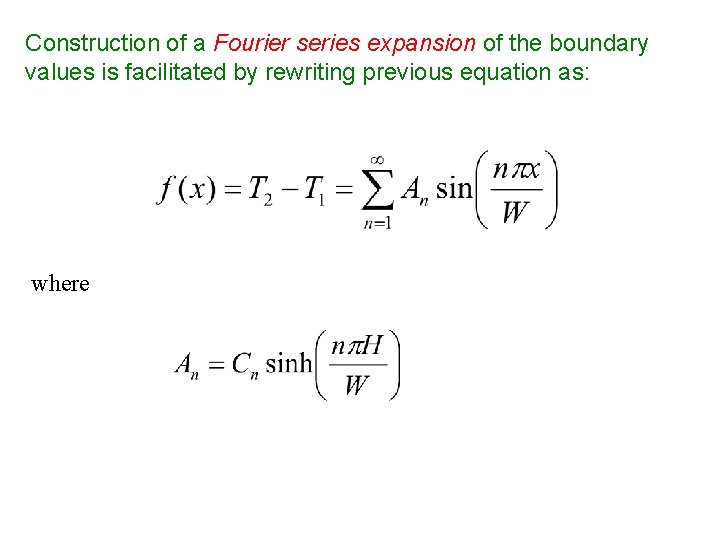
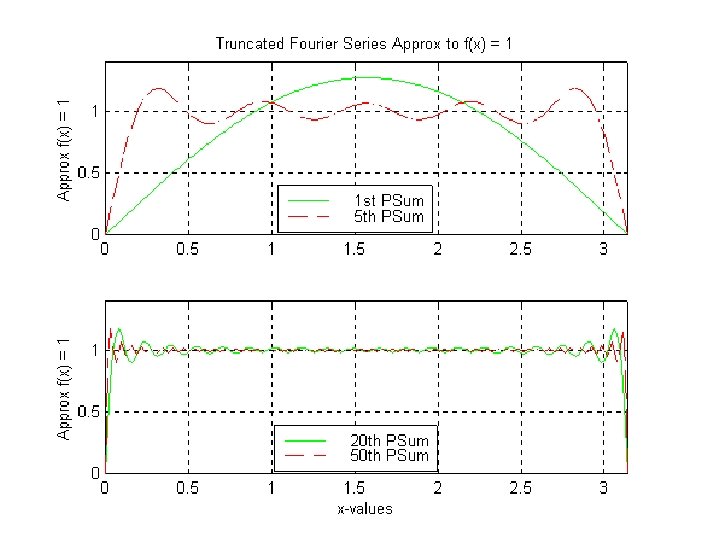
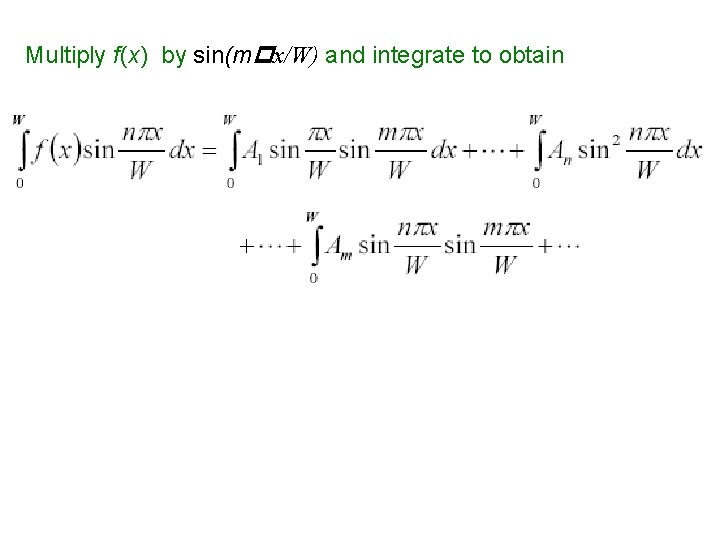
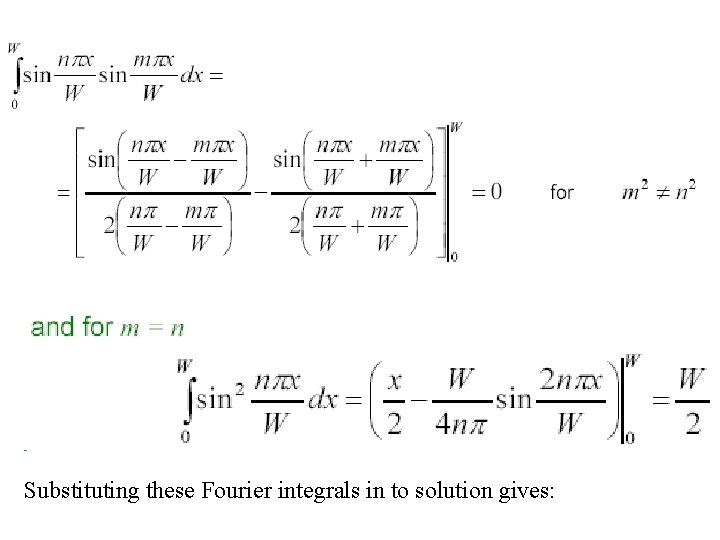
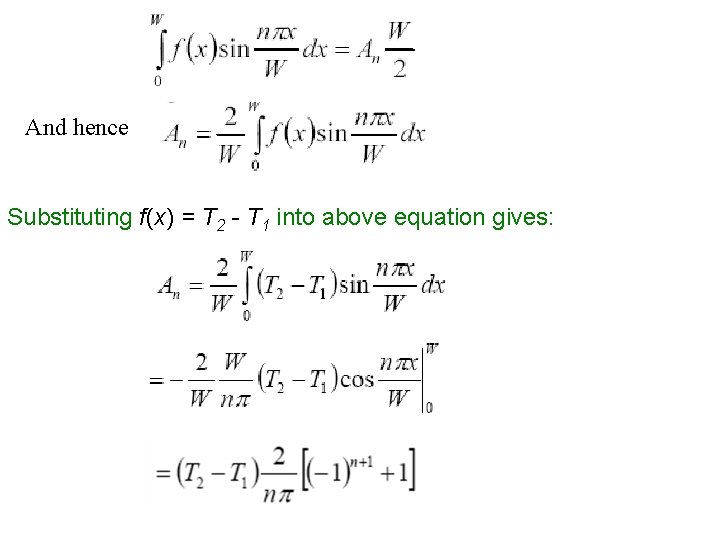
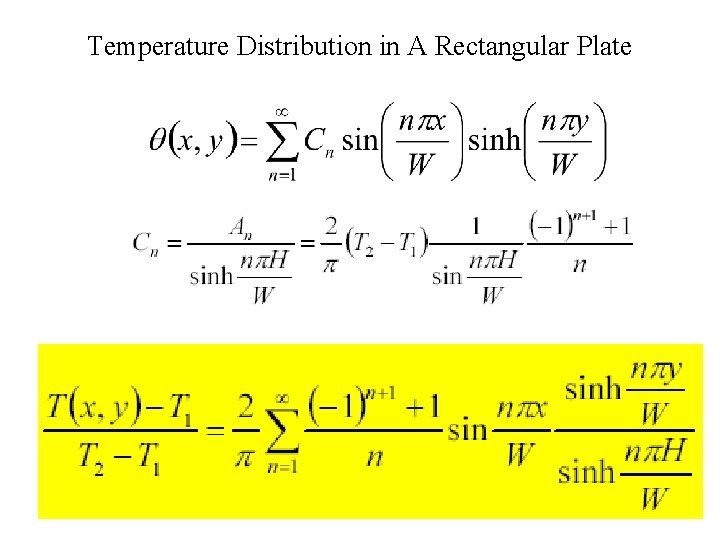
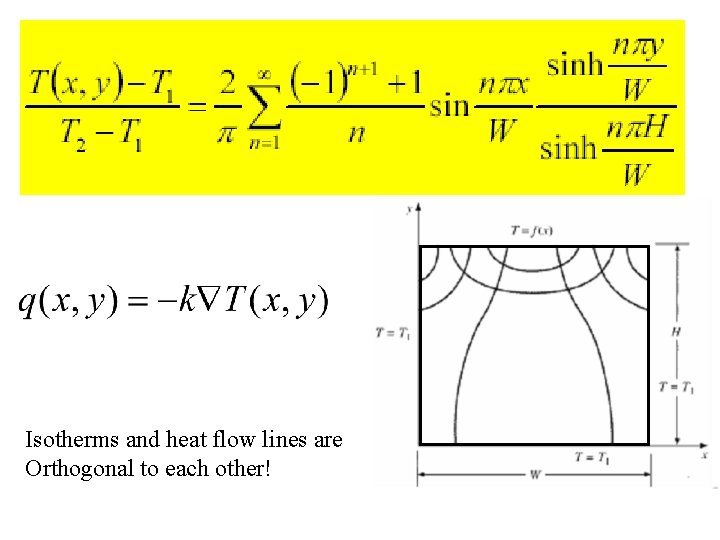
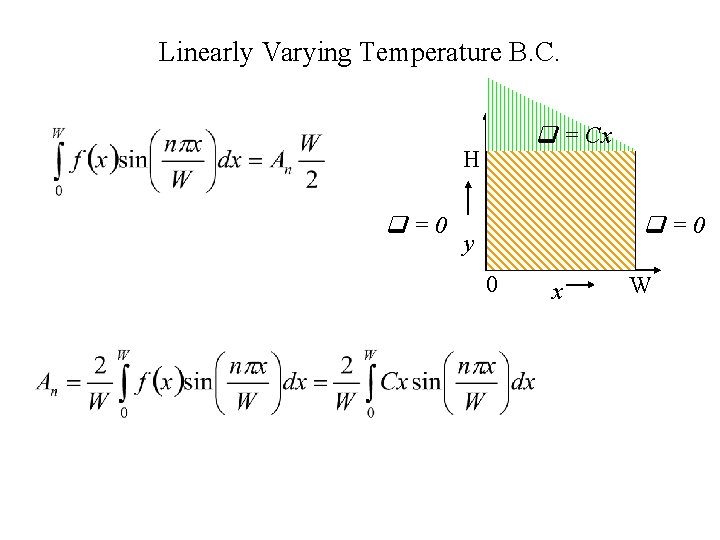
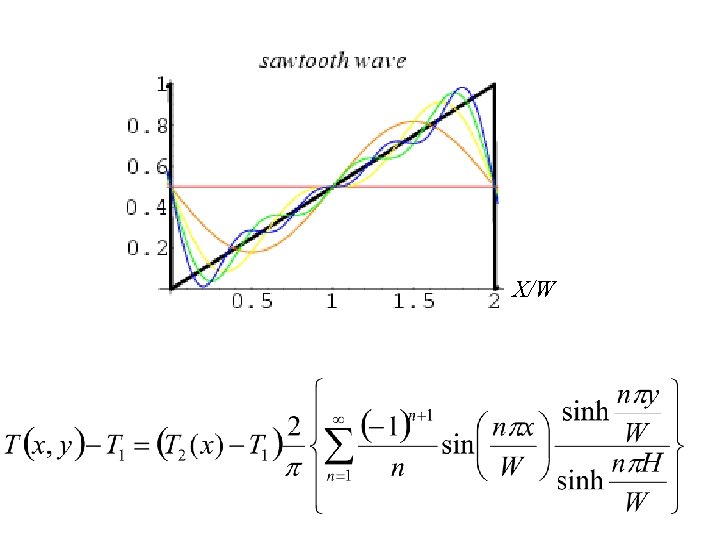
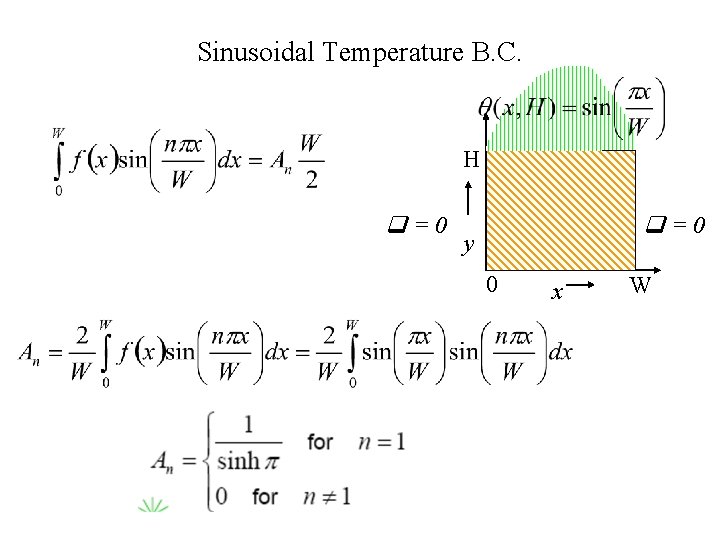
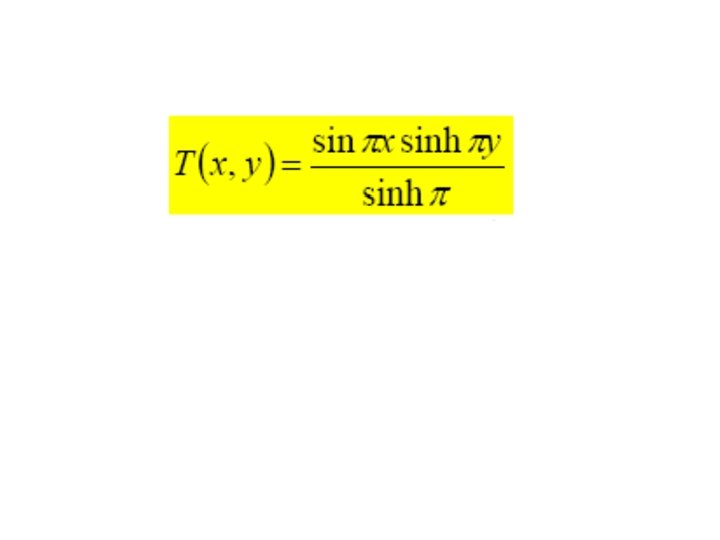
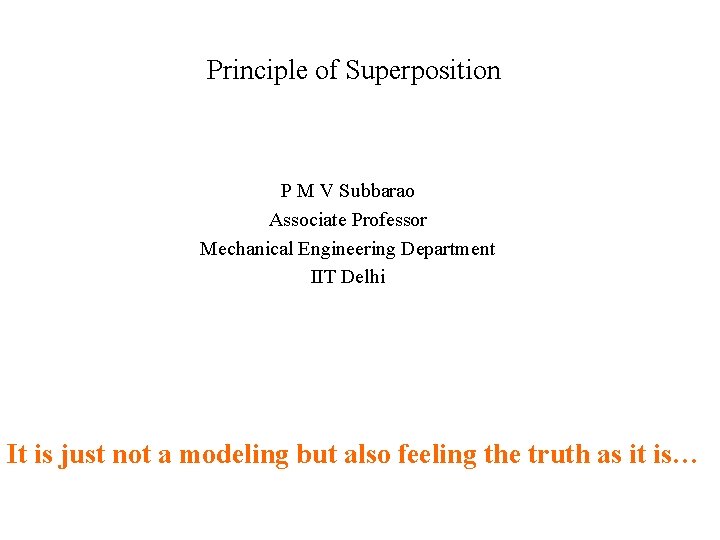
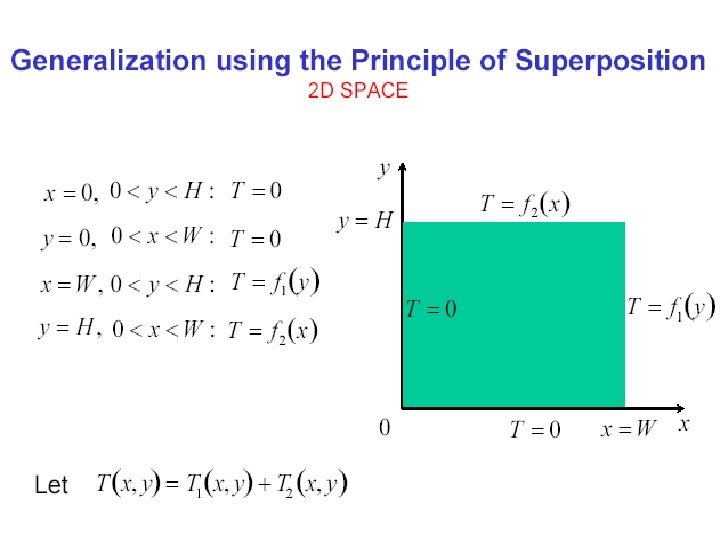
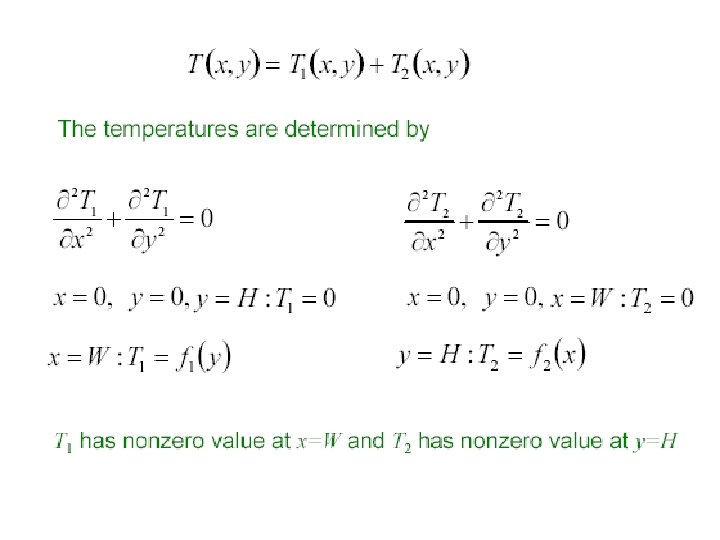
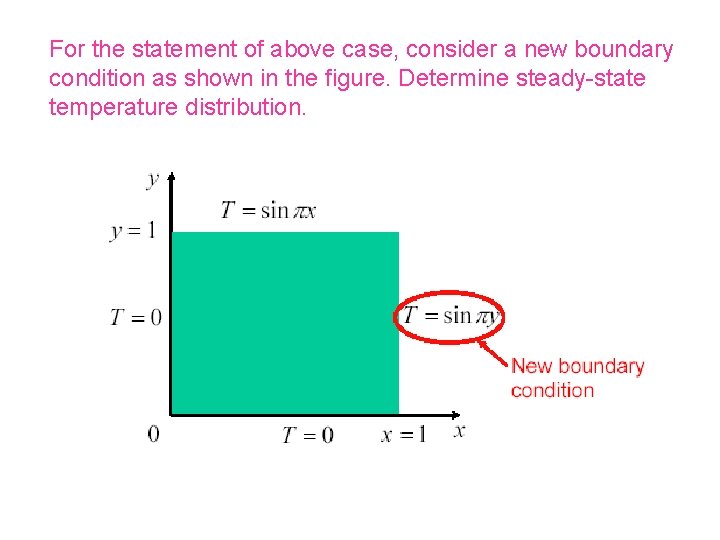
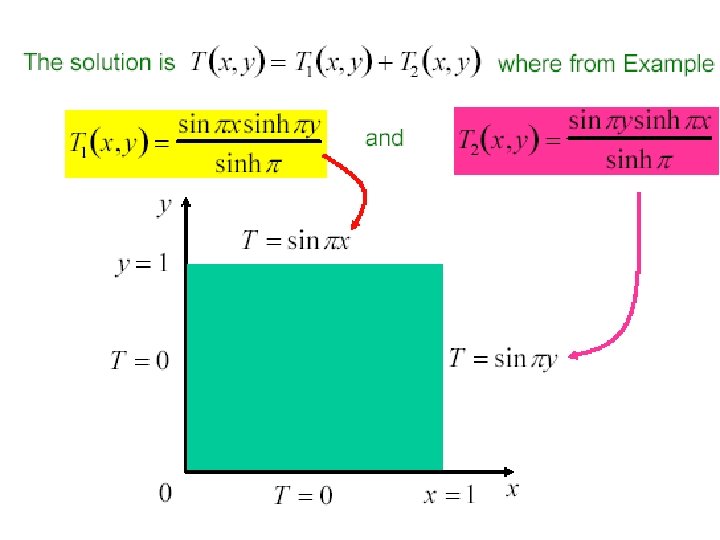
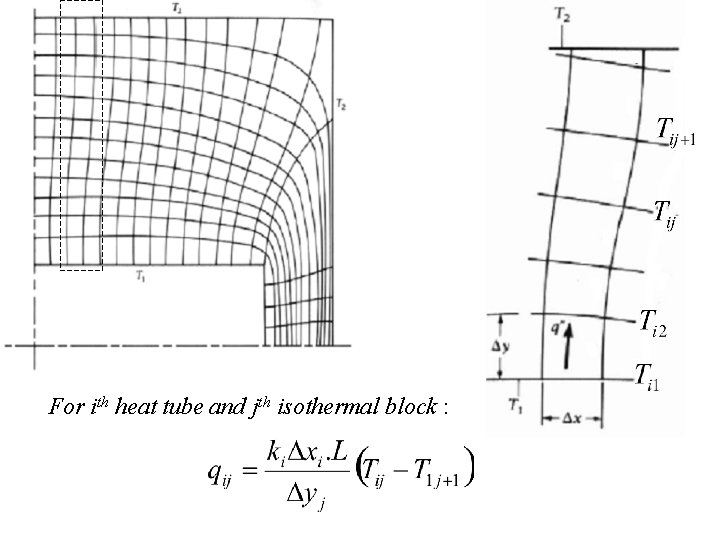
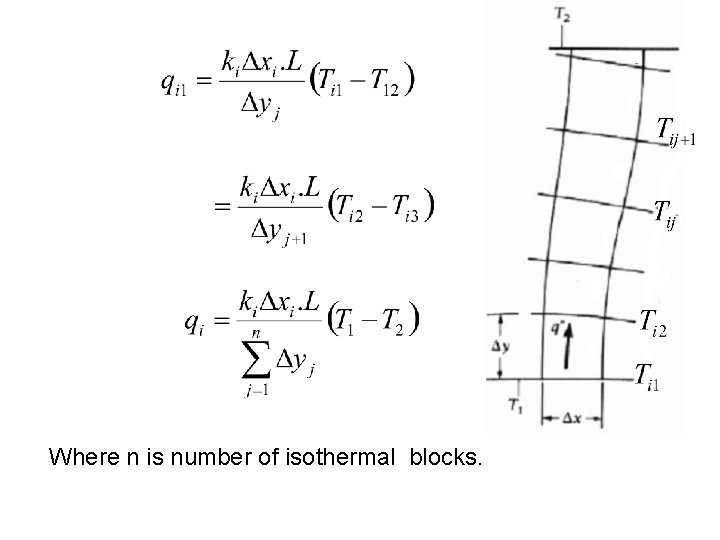
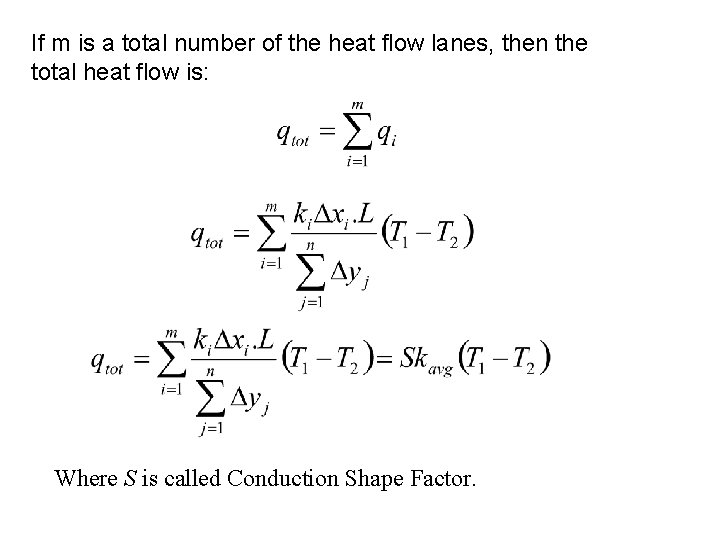
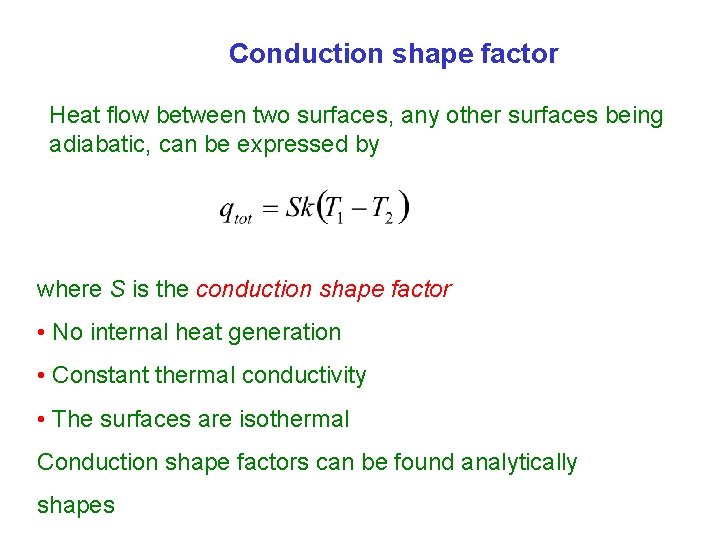
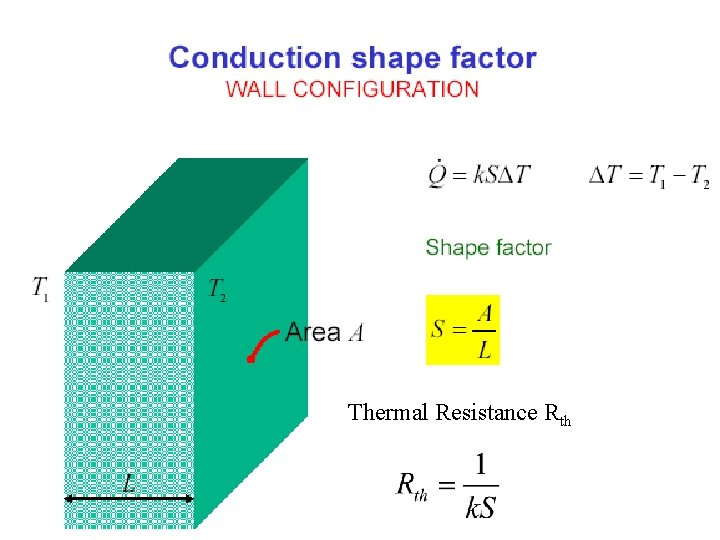
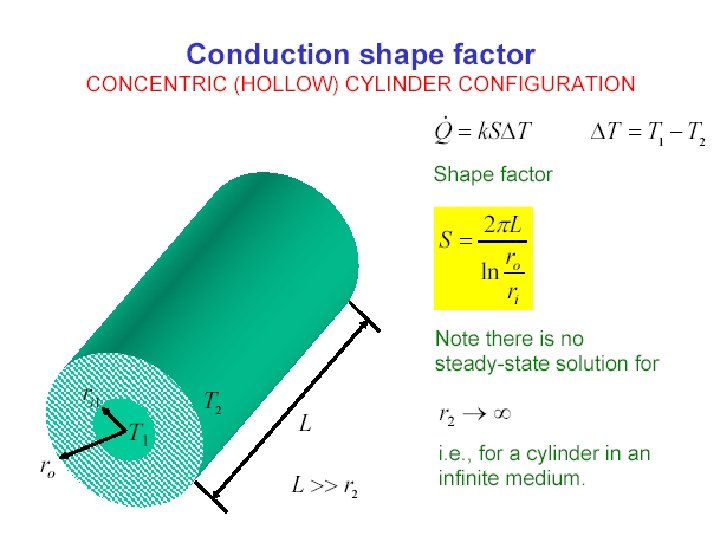
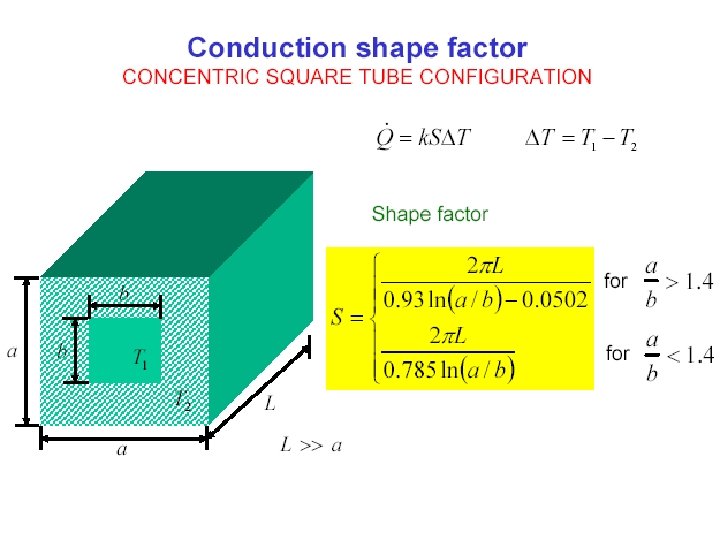
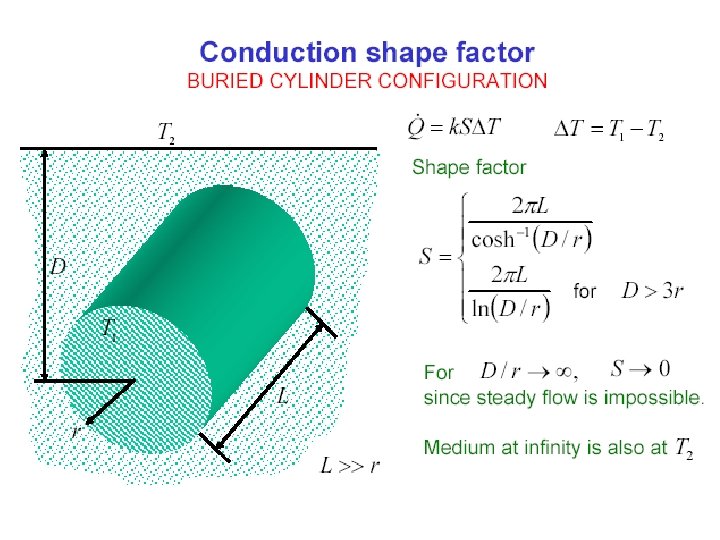
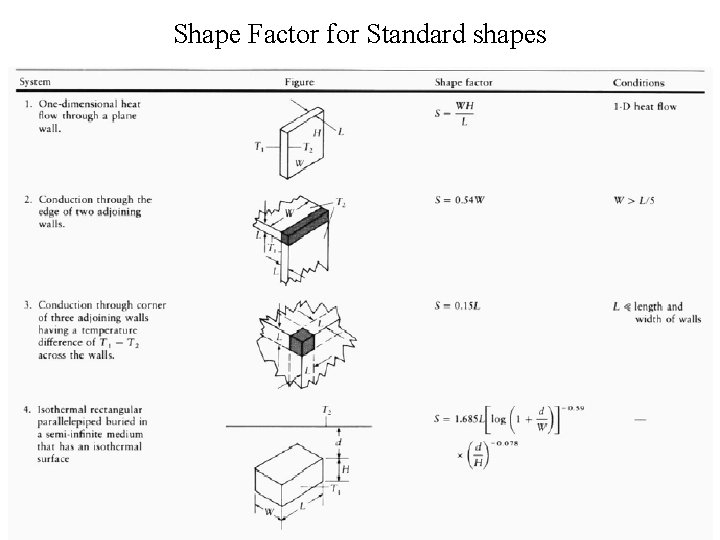
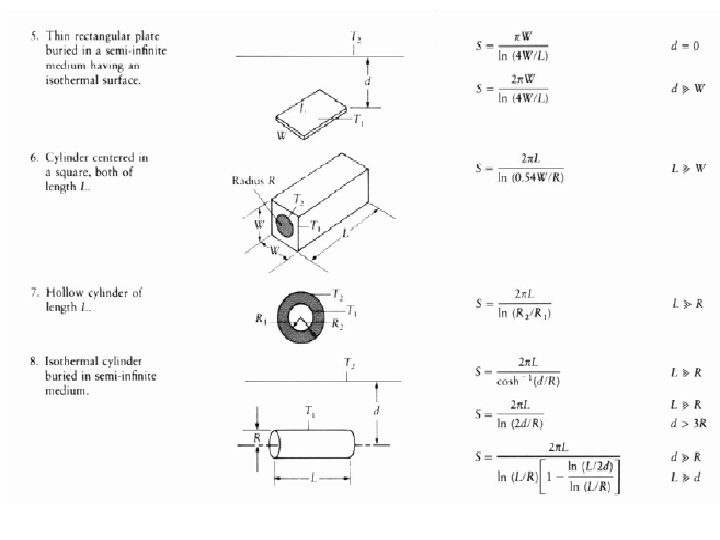
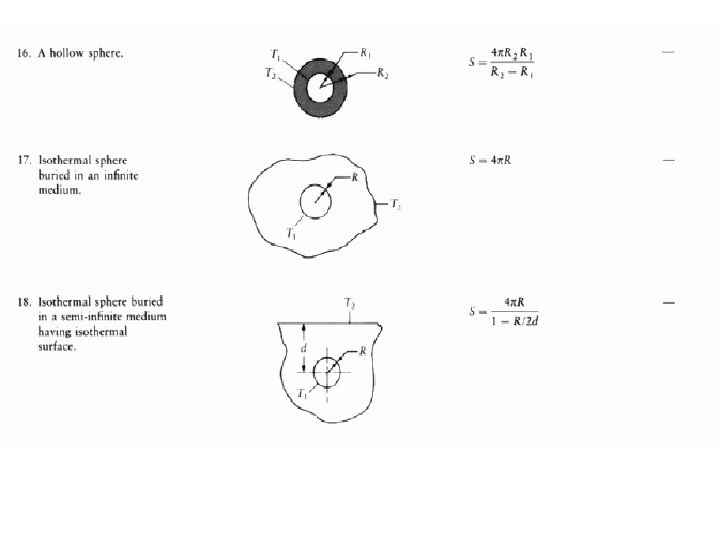
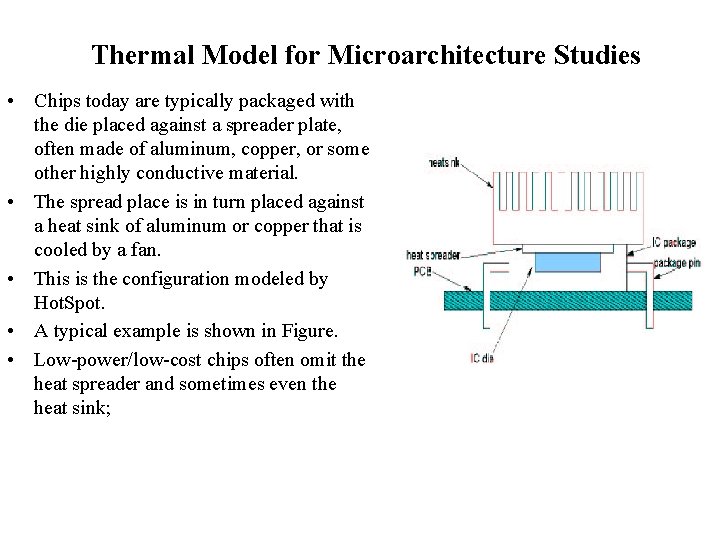
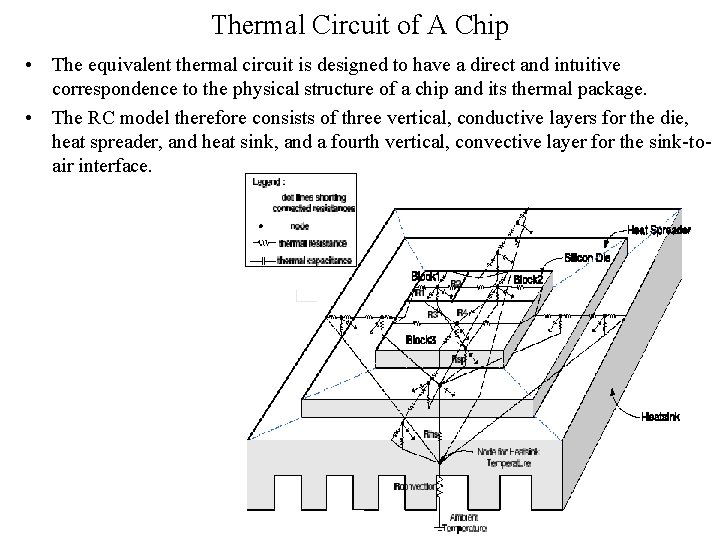
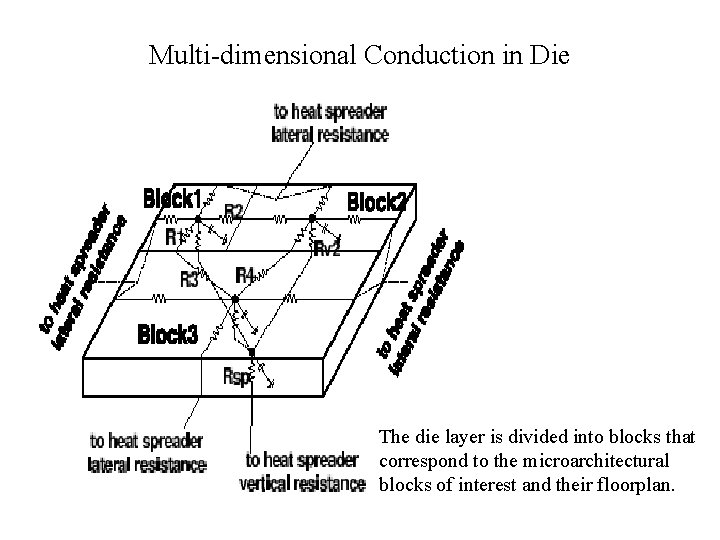
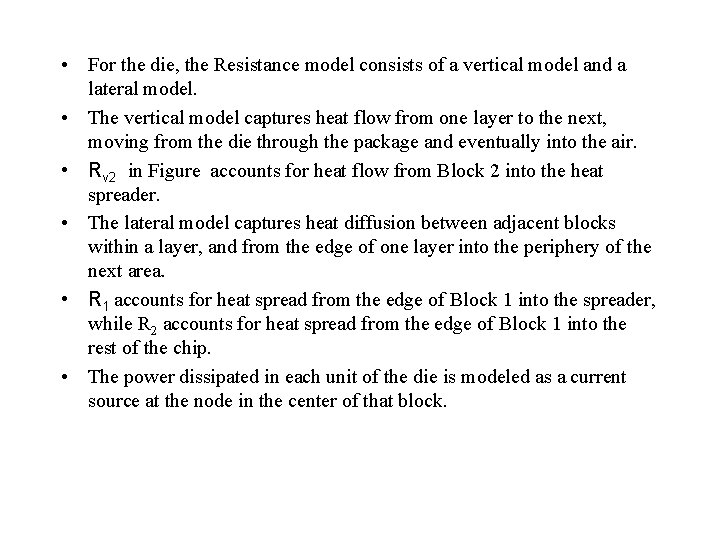
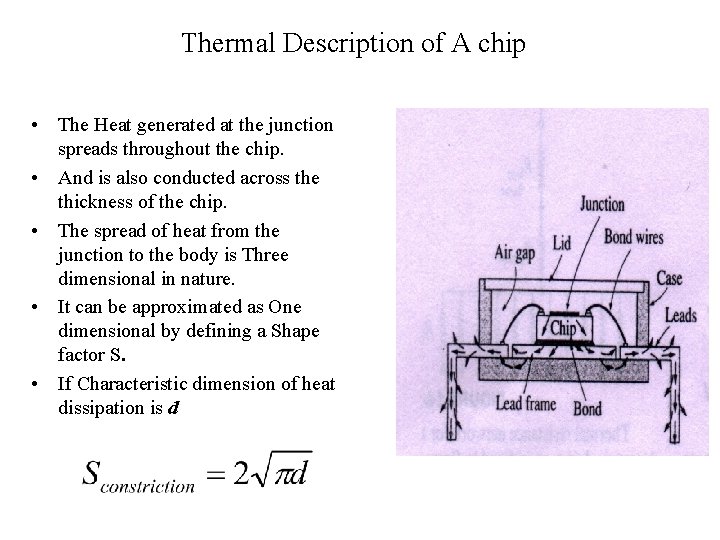
- Slides: 38

Two Dimensional Steady State Heat Conduction P M V Subbarao Associate Professor Mechanical Engineering Department IIT Delhi It is just not a modeling but also feeling the truth as it is…
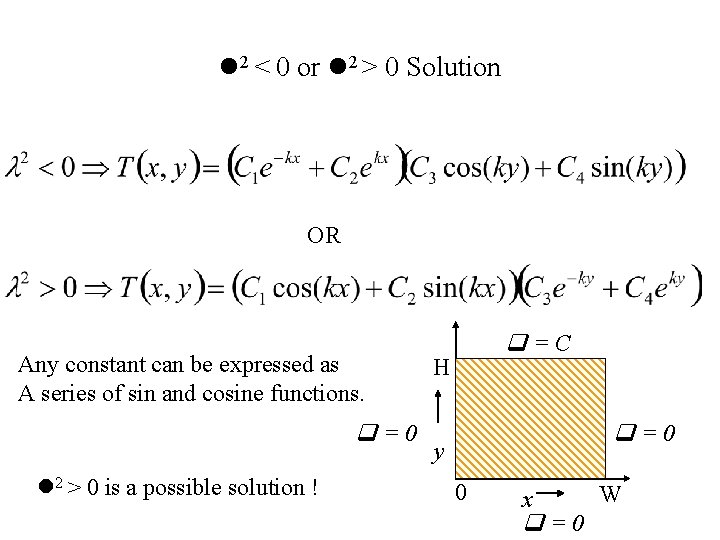
l 2 < 0 or l 2 > 0 Solution OR Any constant can be expressed as A series of sin and cosine functions. q=0 l 2 > 0 is a possible solution ! q=C H q=0 y 0 x q=0 W
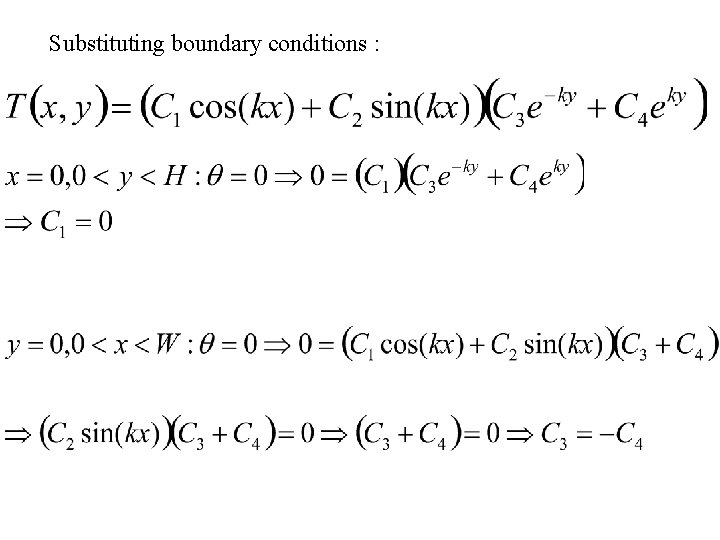
Substituting boundary conditions :
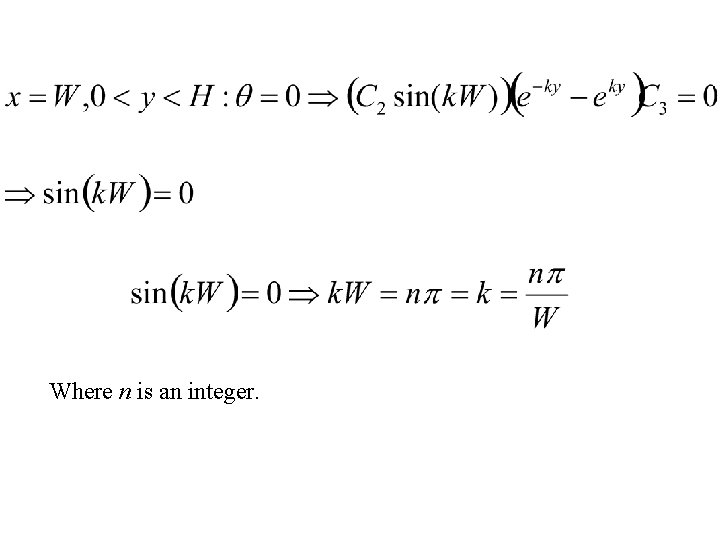
Where n is an integer.
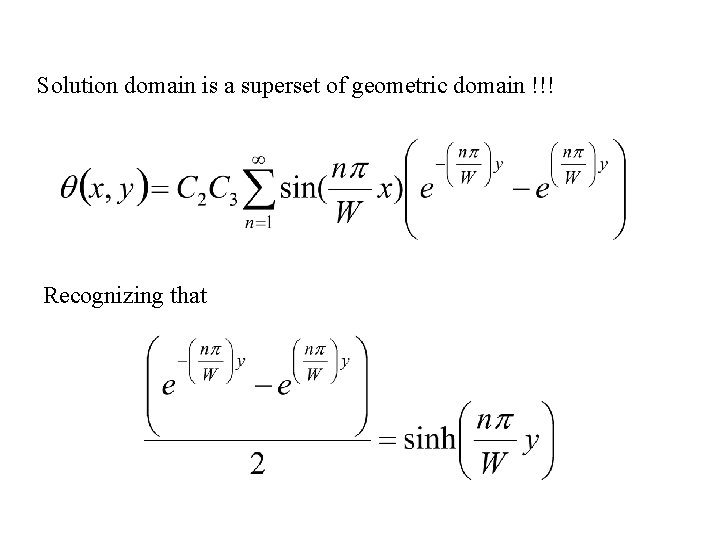
Solution domain is a superset of geometric domain !!! Recognizing that
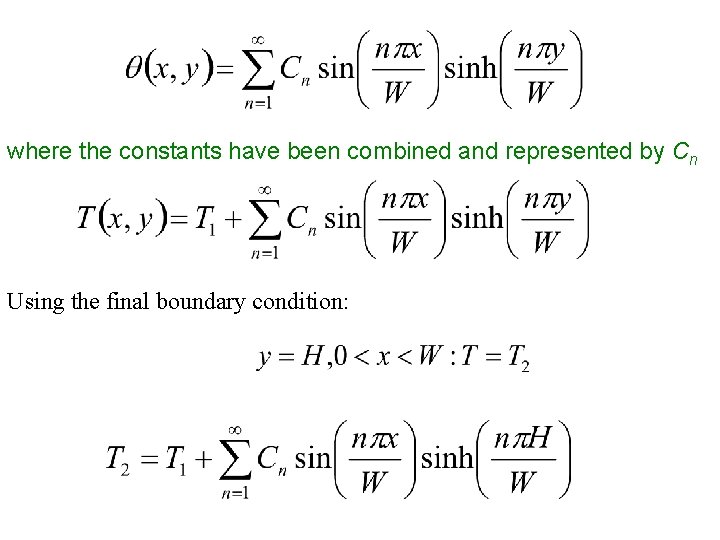
where the constants have been combined and represented by Cn Using the final boundary condition:
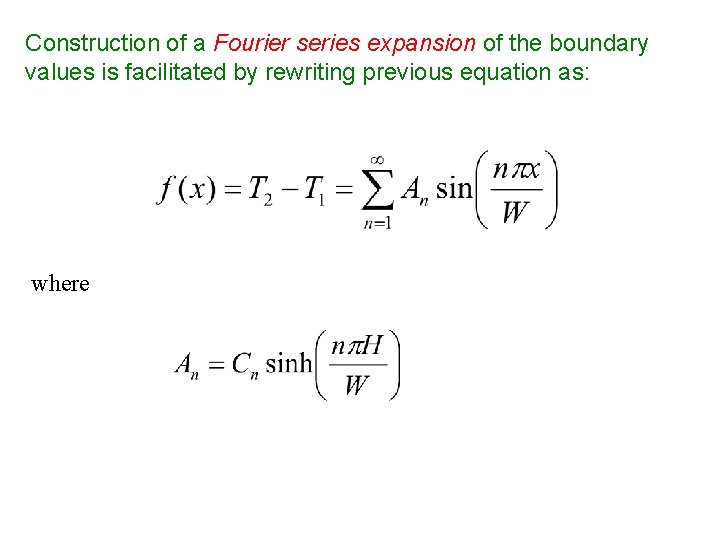
Construction of a Fourier series expansion of the boundary values is facilitated by rewriting previous equation as: where
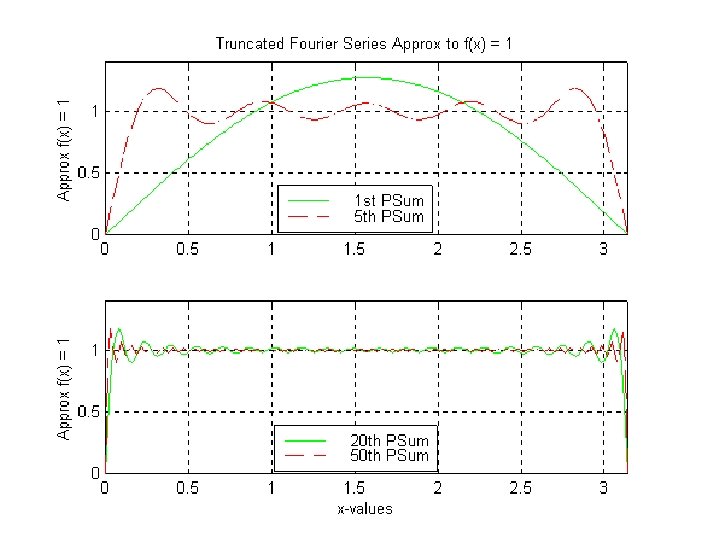
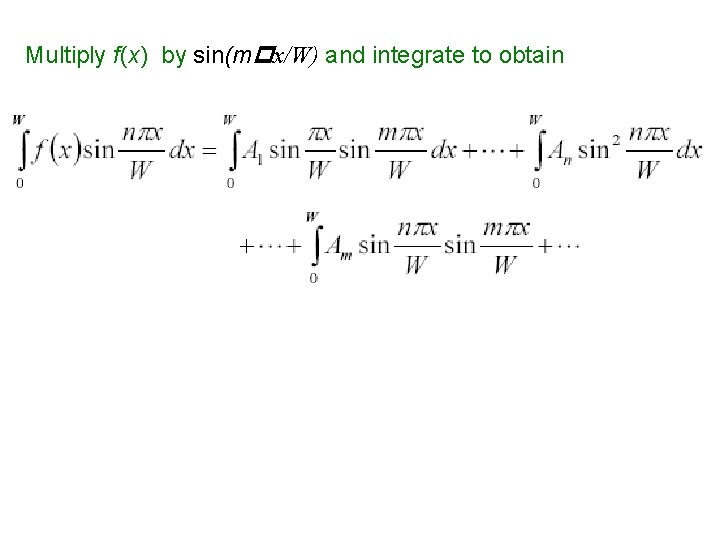
Multiply f(x) by sin(mpx/W) and integrate to obtain
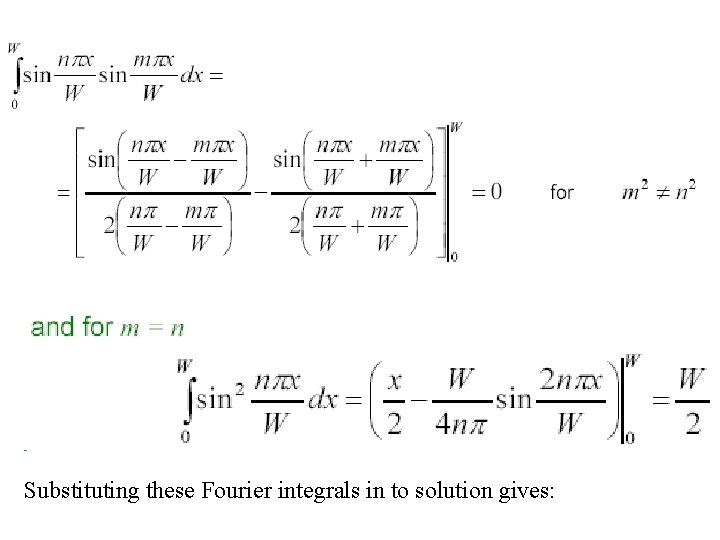
Substituting these Fourier integrals in to solution gives:
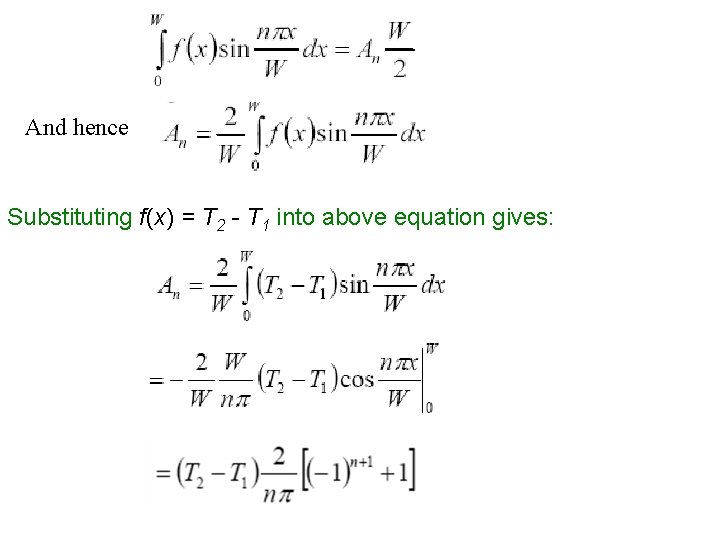
And hence Substituting f(x) = T 2 - T 1 into above equation gives:
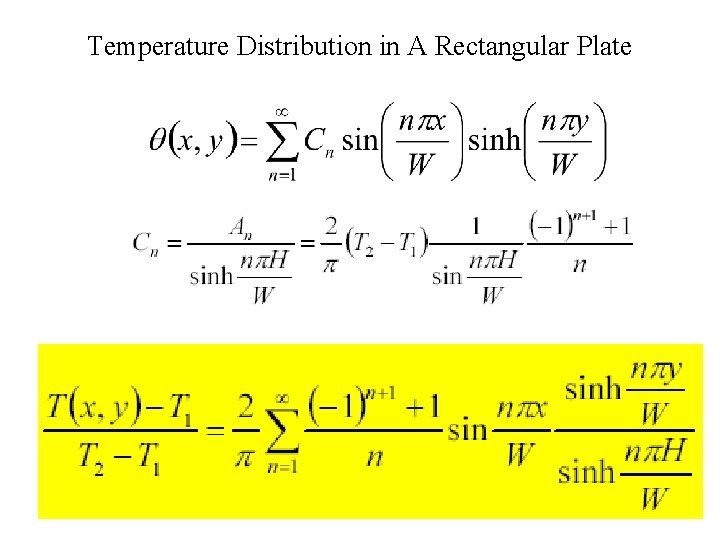
Temperature Distribution in A Rectangular Plate
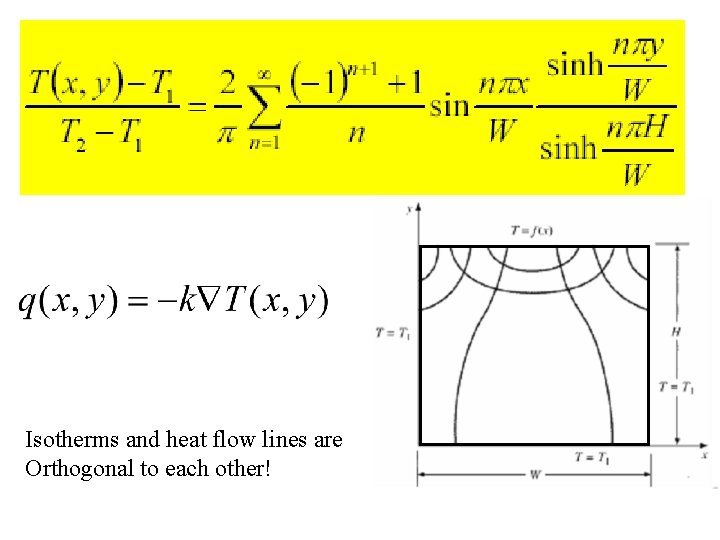
Isotherms and heat flow lines are Orthogonal to each other!
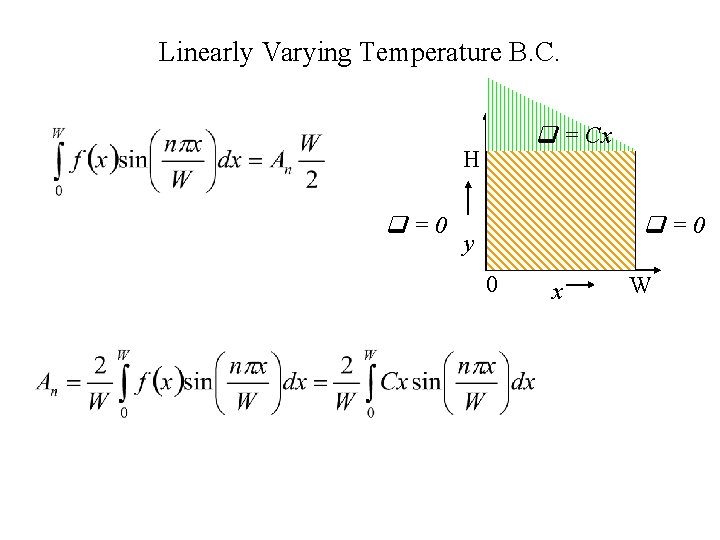
Linearly Varying Temperature B. C. q = Cx H q=0 y 0 x W
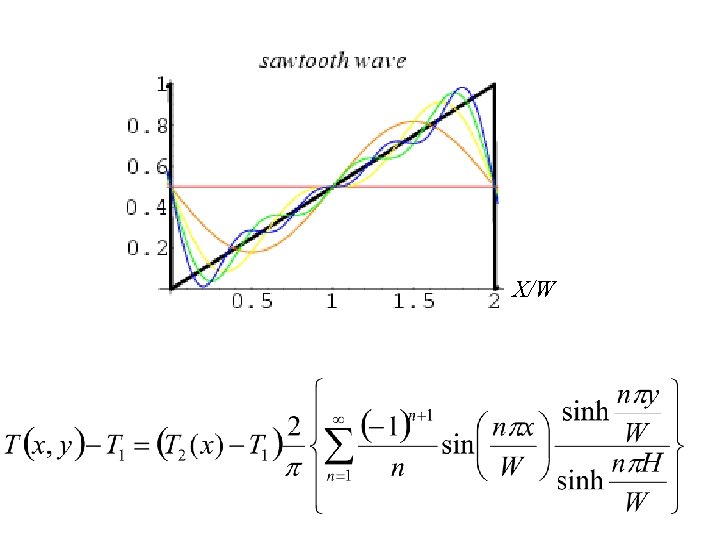
X/W
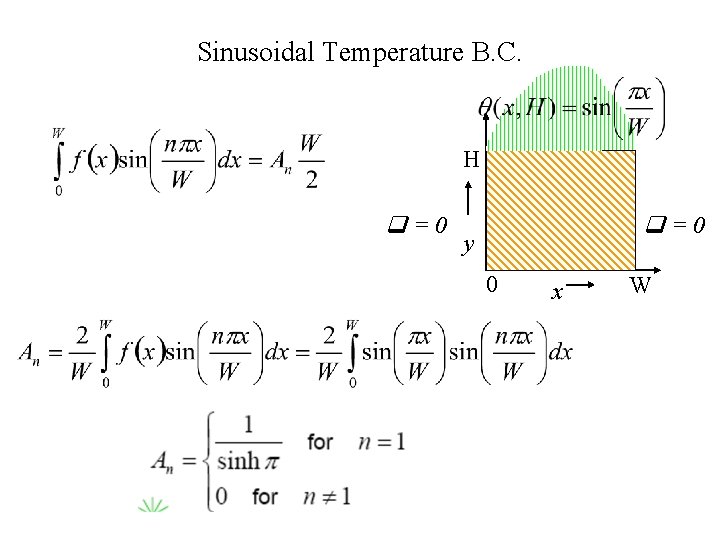
Sinusoidal Temperature B. C. q = Cx H q=0 y 0 x W
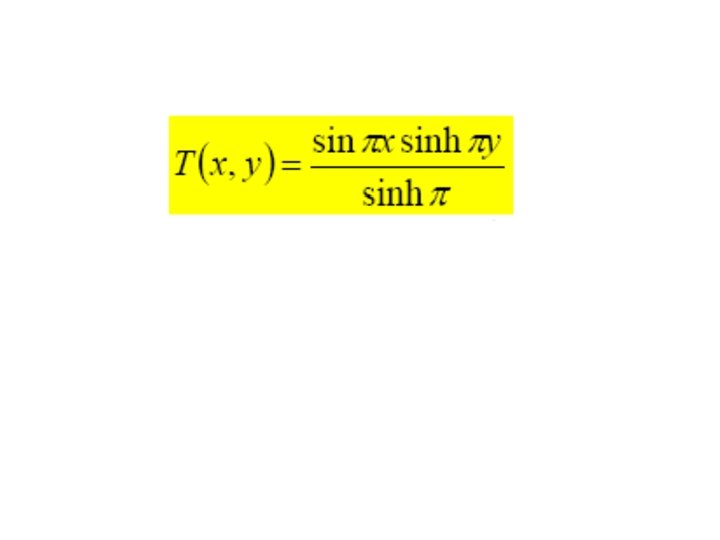
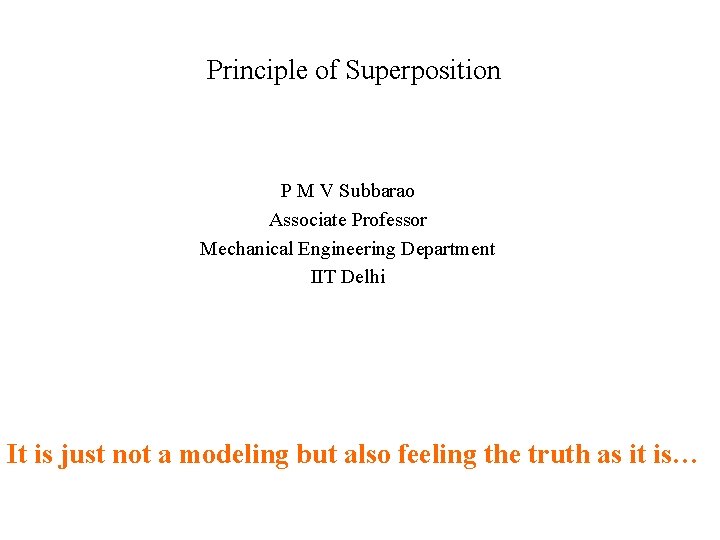
Principle of Superposition P M V Subbarao Associate Professor Mechanical Engineering Department IIT Delhi It is just not a modeling but also feeling the truth as it is…
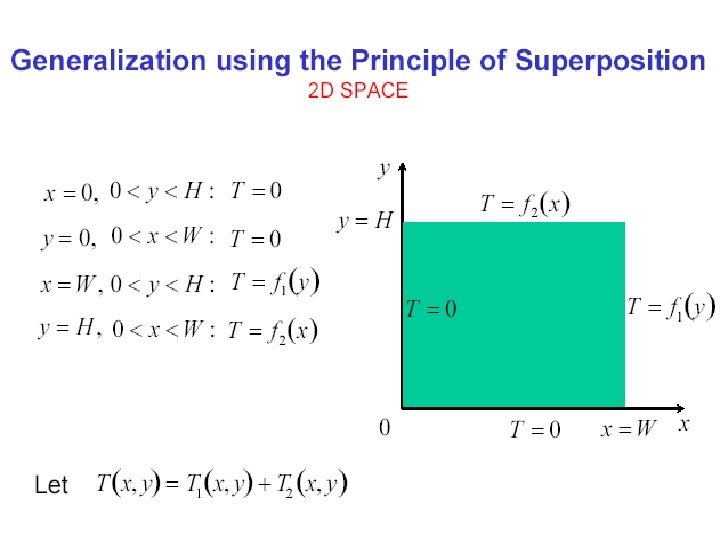
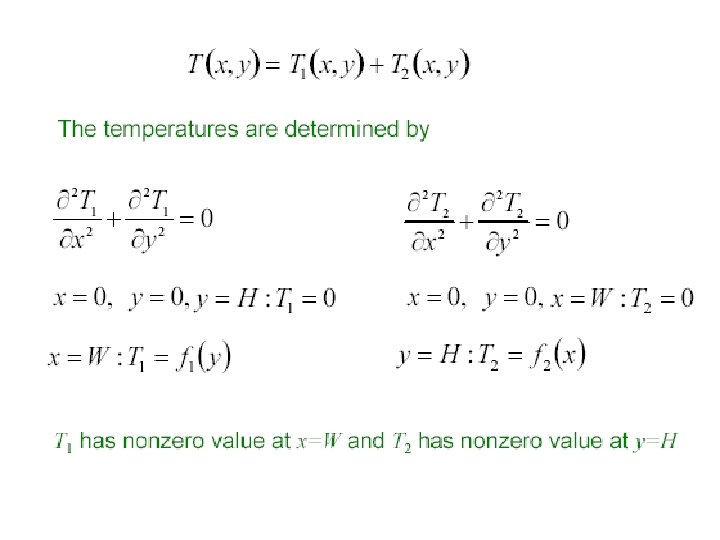
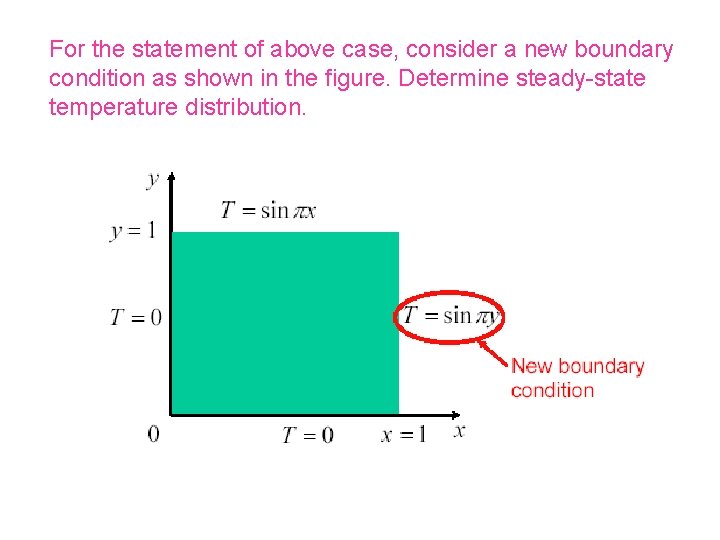
For the statement of above case, consider a new boundary condition as shown in the figure. Determine steady-state temperature distribution.
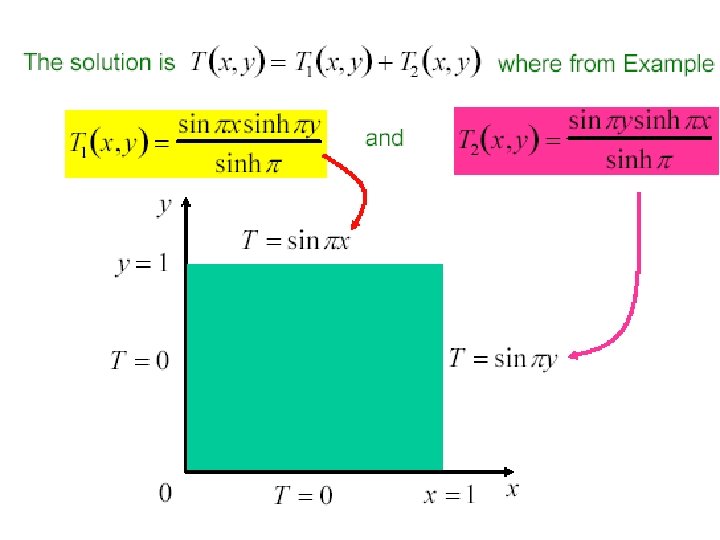
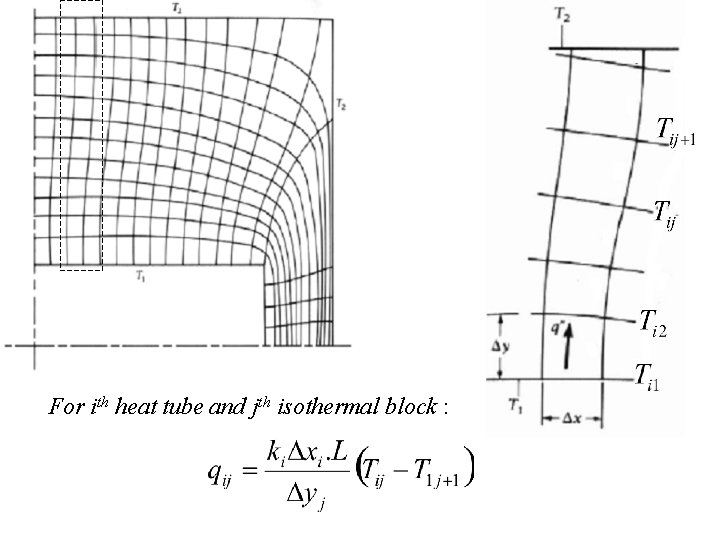
For ith heat tube and jth isothermal block :
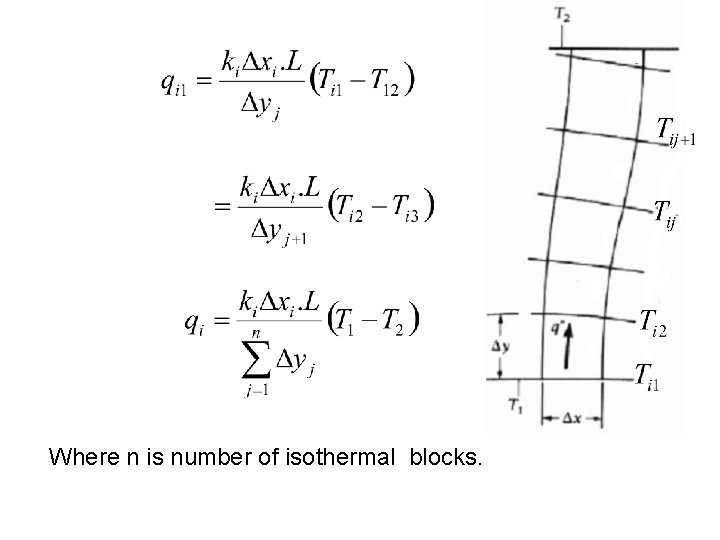
Where n is number of isothermal blocks.
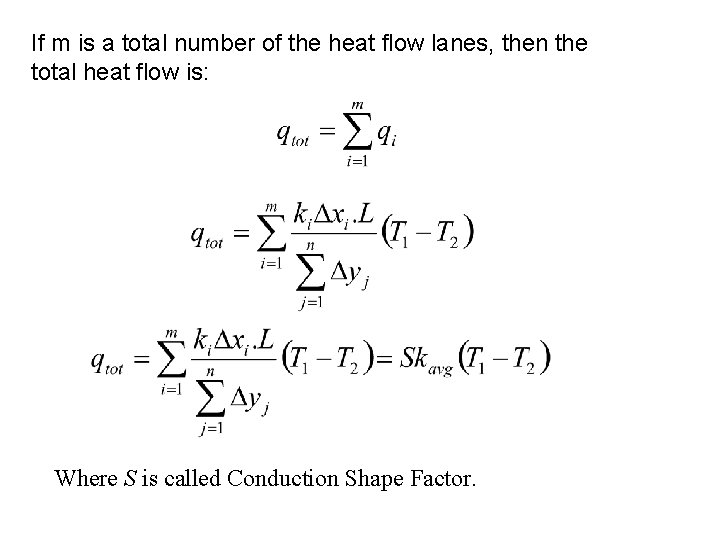
If m is a total number of the heat flow lanes, then the total heat flow is: Where S is called Conduction Shape Factor.
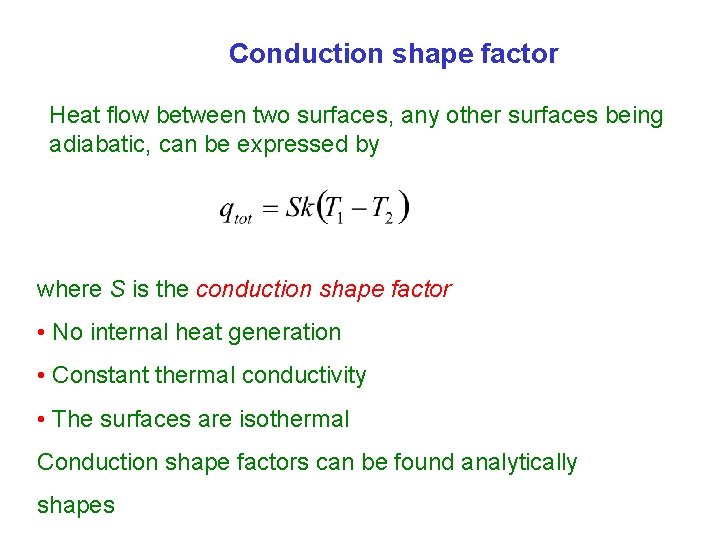
Conduction shape factor Heat flow between two surfaces, any other surfaces being adiabatic, can be expressed by where S is the conduction shape factor • No internal heat generation • Constant thermal conductivity • The surfaces are isothermal Conduction shape factors can be found analytically shapes
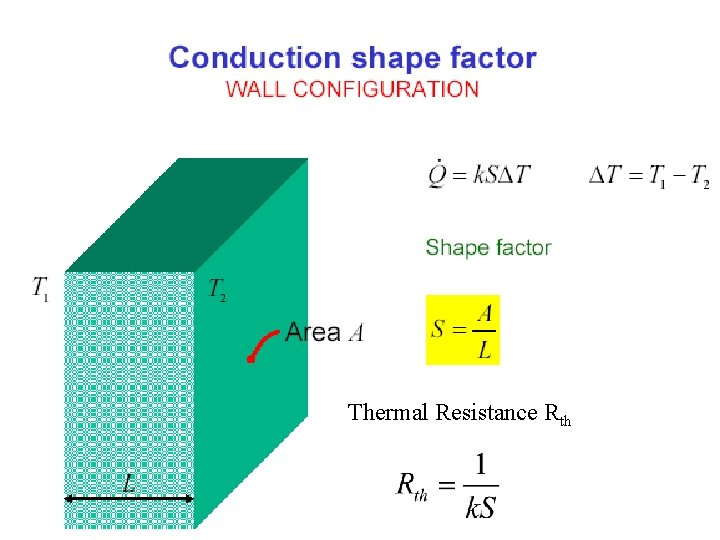
Thermal Resistance Rth
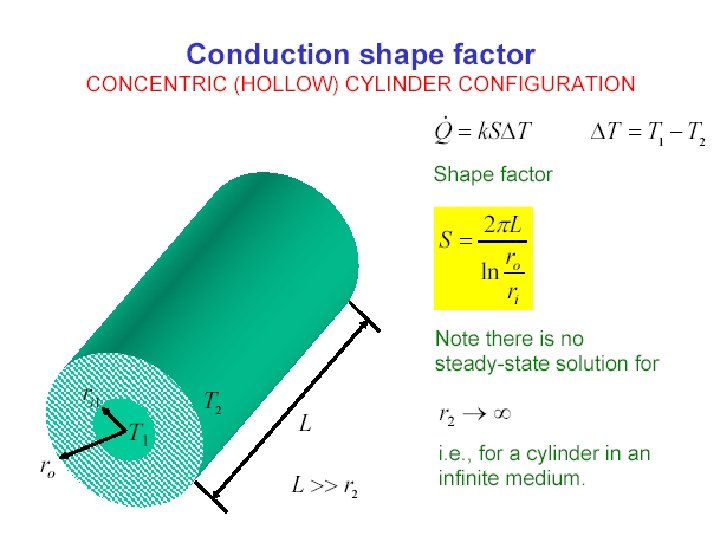
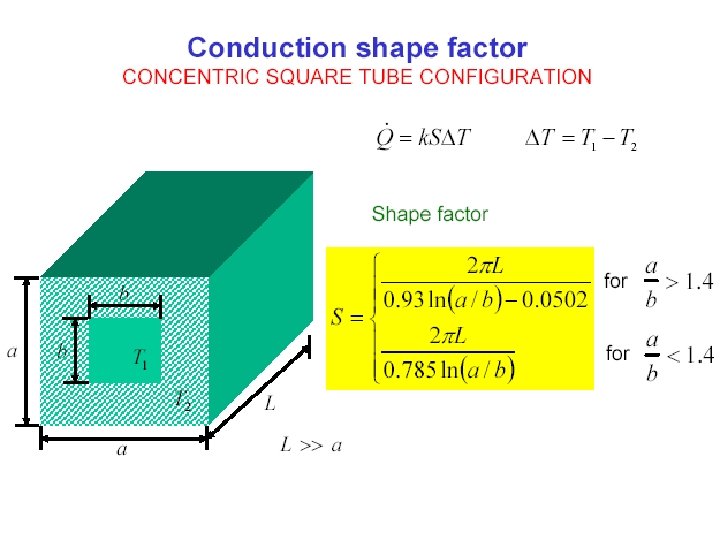
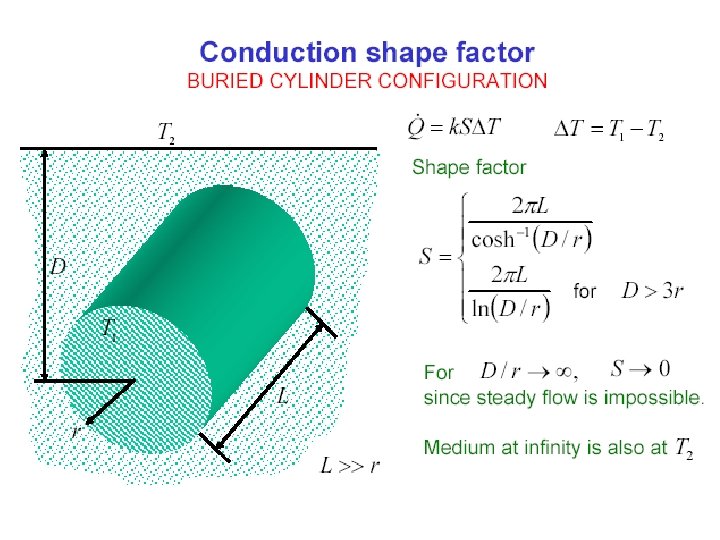
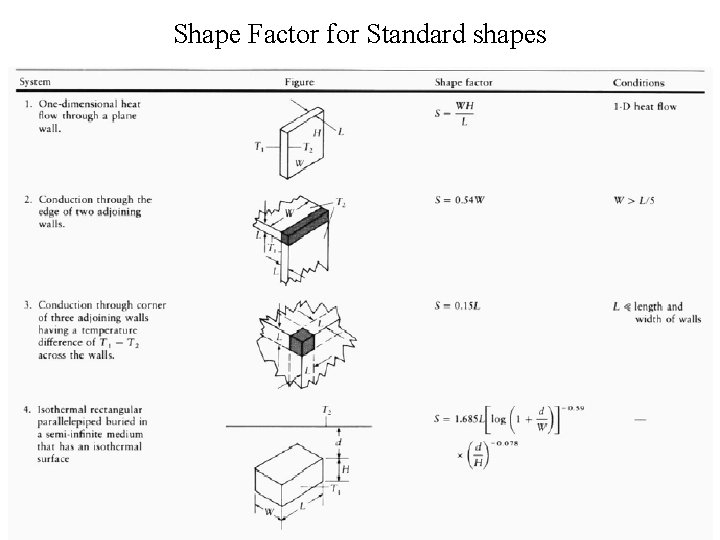
Shape Factor for Standard shapes
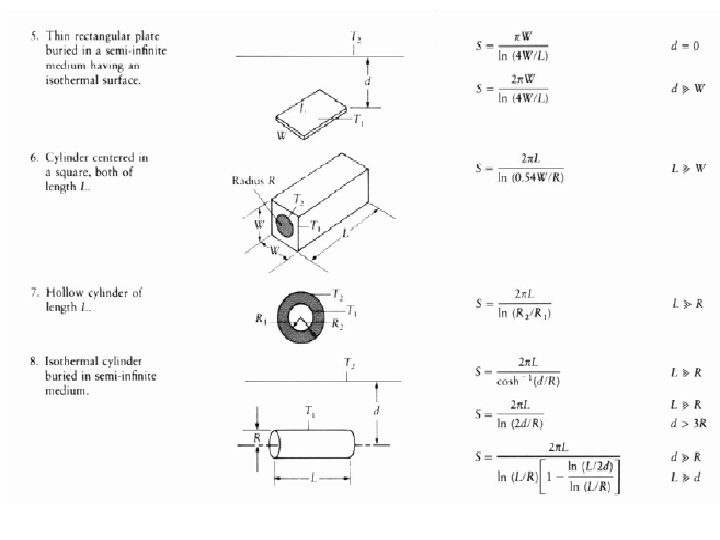
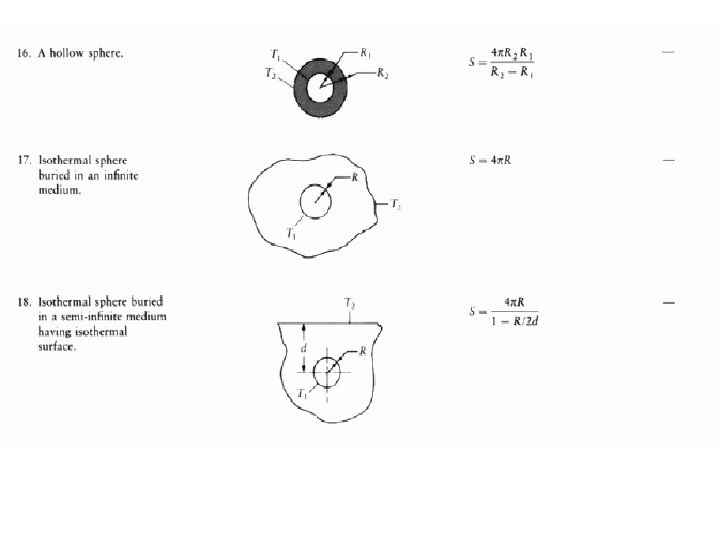
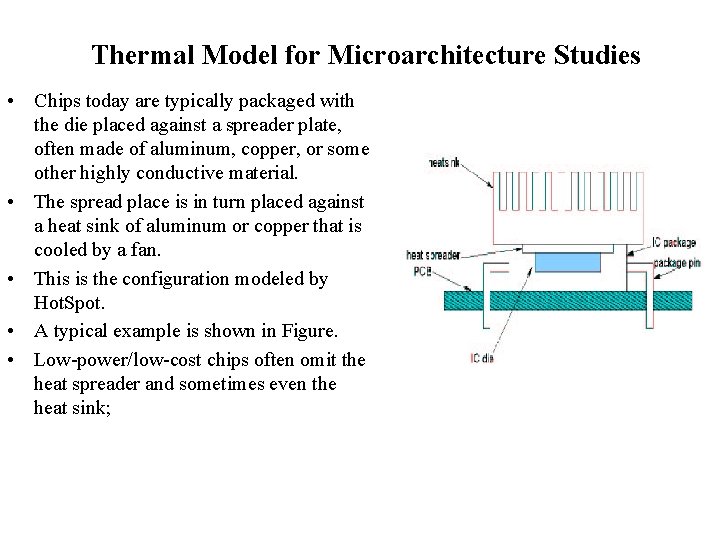
Thermal Model for Microarchitecture Studies • Chips today are typically packaged with the die placed against a spreader plate, often made of aluminum, copper, or some other highly conductive material. • The spread place is in turn placed against a heat sink of aluminum or copper that is cooled by a fan. • This is the configuration modeled by Hot. Spot. • A typical example is shown in Figure. • Low-power/low-cost chips often omit the heat spreader and sometimes even the heat sink;
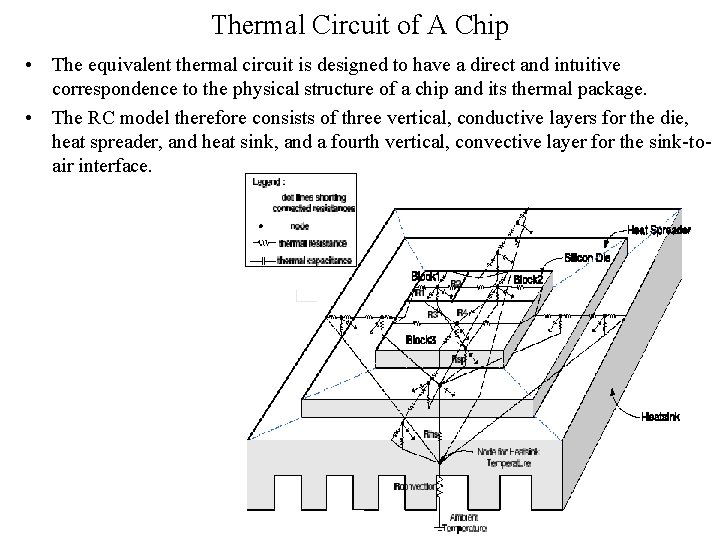
Thermal Circuit of A Chip • The equivalent thermal circuit is designed to have a direct and intuitive correspondence to the physical structure of a chip and its thermal package. • The RC model therefore consists of three vertical, conductive layers for the die, heat spreader, and heat sink, and a fourth vertical, convective layer for the sink-toair interface.
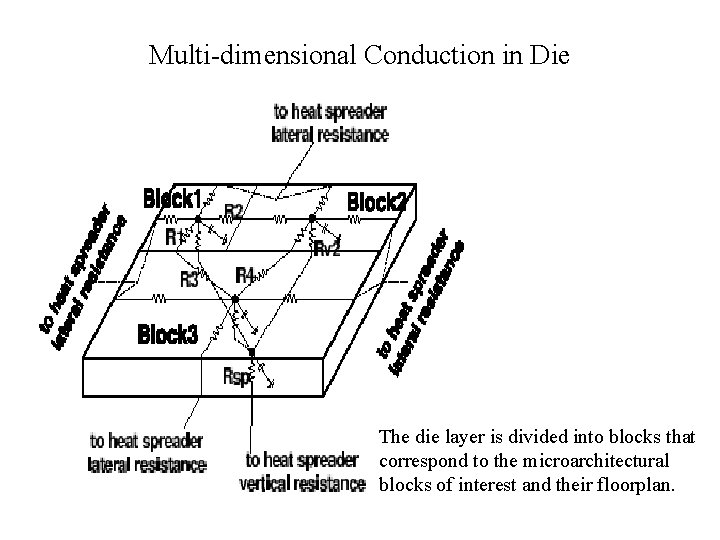
Multi-dimensional Conduction in Die The die layer is divided into blocks that correspond to the microarchitectural blocks of interest and their floorplan.
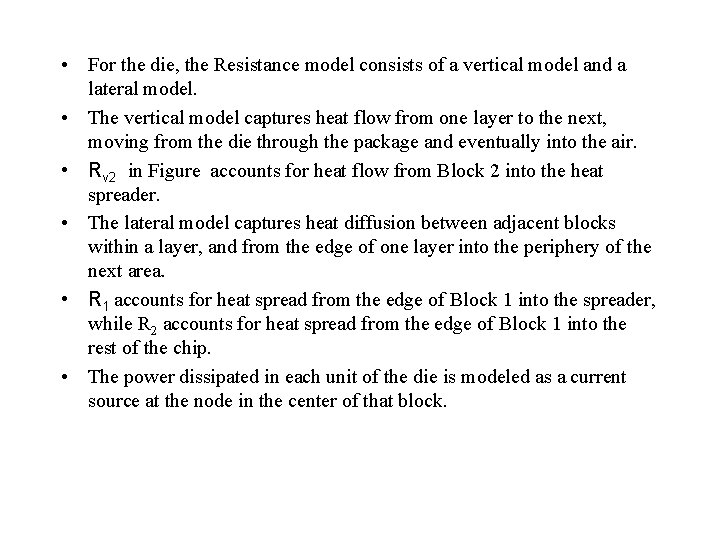
• For the die, the Resistance model consists of a vertical model and a lateral model. • The vertical model captures heat flow from one layer to the next, moving from the die through the package and eventually into the air. • Rv 2 in Figure accounts for heat flow from Block 2 into the heat spreader. • The lateral model captures heat diffusion between adjacent blocks within a layer, and from the edge of one layer into the periphery of the next area. • R 1 accounts for heat spread from the edge of Block 1 into the spreader, while R 2 accounts for heat spread from the edge of Block 1 into the rest of the chip. • The power dissipated in each unit of the die is modeled as a current source at the node in the center of that block.
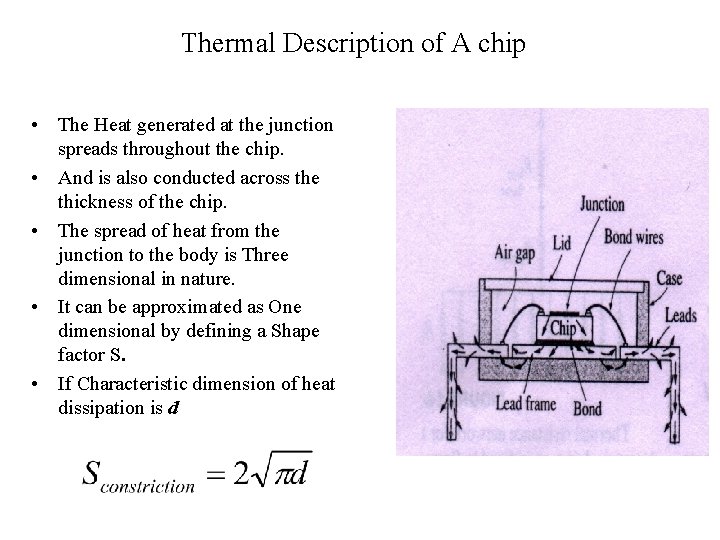
Thermal Description of A chip • The Heat generated at the junction spreads throughout the chip. • And is also conducted across the thickness of the chip. • The spread of heat from the junction to the body is Three dimensional in nature. • It can be approximated as One dimensional by defining a Shape factor S. • If Characteristic dimension of heat dissipation is d
One dimensional steady state heat conduction
Critical radius of insulation for cylinder
A circular motion is one dimensional
Steady state heat
Difference between linear and radial heat conduction
Energy transfer
Transient heat transfer in industry
Types of heat transfer
What is heat transfer conduction convection and radiation
Convection examples
Examples of radiation
Mechanisms of heat loss in newborn
โจทย์ heat transfer พร้อมเฉลย
Fourier's law heat transfer
Radiation travels in straight lines
Radiation examples
Linear heat conduction experiment
Transfer heat
What is thermal radiation
How does heat energy flow
Lumped system analysis
Conduction, convection radiation diagram
Spherical heat equation
Heat conduction expert
Tcola
Heat transfer electrical analogy
Steady state thermal analysis
In time domain analysis, finite steady state error is
Sinusoidal steady state
Tingkat pengangguran alamiah adalah
Steady state kondition
Michaelis menten steady state
Steady flow process in thermodynamics
The impulse signal imitate the
In a normal operations/steady state eoc activation level,
Steady state error
Sinusoidal steady state analysis of coupled circuits
Steady state vs equilibrium
What is steady-state thermal analysis?